Механические свойства стали
Без сомнения наиболее важными свойствами сталей, благодаря которым они находят такое широкое применение, являются их механические свойства. Эти свойства включают комбинацию очень высокой прочности со способностью к значительному изменению формы, например, пластическому прогибу, перед окончательным разрушением. Чтобы характеризовать прочность и пластичность (меру пластического прогиба) сталей и других металлов разработаны различные методы испытаний.
Прочность сталей
Механические свойства сталей, как и других металлических материалов, чаще всего определяются с помощью испытания на растяжение. Испытание на растяжение заключается в приложении растягивающего усилия к образцу – чаще всего, в виде стержня – и измерении изменения длины образца при увеличении прилагаемого усилия (рисунок 1). Образец вырезают из интересующего материала или изделия. Результат испытания представляет собой диаграмму растяжения — график, на котором по вертикали откладывается
Рисунок 1 – Диаграмма напряжение-деформация
при испытании образца на растяжение
При малых деформациях стержень ведет себя упруго – он «отпружинивает» обратно к своей исходной длине, если приложенные напряжения снимают. При напряжении выше величины, которую называют пределом текучести, стержень начинает деформироваться пластически. Это значит, что после снятия прилагаемых напряжений стержень уже не возвращается к своей исходной длине, а получает необратимое удлинение. Путем растяжения стержня до разрушения находят максимальное напряжение на диаграмме растяжения. Это максимальное напряжение называют прочностью при растяжении или временным сопротивлением растяжению материала, из которого был изготовлен образец.
Пластичность сталей
Если при простом испытании на изгиб металл разрушается только после большого пластического прогиба, то его считают пластичным. Если такого прогиба нет совсем или он незначительный – материал называют хрупким. Хорошая пластичность металла проявляется при испытании на растяжение высокой величиной удлинения образца и/или его сужения. Удлинение выражает в процентах увеличение длины образца после разрушения к его исходной длине (см. рисунок 1). Аналогично сужение выражает в процентах уменьшение площади образца по сравнению с его исходной площадью (рисунок 2).
Рисунок 2 – Диаграмма растяжения для хрупкого и пластичного металлов
Чаще всего механические свойства сталей в целом оценивают по трем показателям: пределу прочности, пределу текучести и удлинению. Пределы прочности и пластичности обычно выражают в мегапаскалях (МПа), удлинение – в процентах (%). Практически всегда с увеличением прочности металла или сплава его пластичность снижается.
Твердость сталей
При испытаниях на твердость механические свойства сталей оценивают путем внедрения в него при заданном усилии твердого материала, так называемого индентора (рисунок 3). Часто такой индентор изготавливают из алмаза. В результате испытания в материале образуется отпечаток – по его размерам судят от твердости стали: в испытании по Роквеллу — по глубине отпечатка, в испытаниях по Бриннелю и Викерсу – по его ширине.
Рисунок 3 – Схема испытания на твердость и его основные характеристики
Соотношение прочности и твердости сталей
В закаленных и отпущенных сталях наблюдается хорошая корреляция между пределом прочности и твердостью – по твердости можно оценивать прочность и наоборот. Для термически упрочненных сталей твердость 45 HRC и выше является обычным делом. Твердость 45 HRC соответствует прочности при растяжении 1480 МПа. Если сравнить это с самыми прочными промышленными сплавами алюминия, меди и титана, которые грубо имеют прочность соответственно 570, 1220 и 1350 МПа, то станет ясно, что сталь прочнее всех этих материалов.
Вязкость сталей
Важным механическим свойством стали является ее вязкость. Обычно термин вязкость применяют, как меру способности металла разрушаться нехрупко.
Характер разрушения – хрупкий или пластичный – хорошо рассматривать на примере ферритных сталей. Все металлы с объемноцентрированной кубической атомной решеткой – как и ферритные стали – имеют один общий недостаток. Они разрушаются хрупко при низких температурах, тогда как при достаточно высоких температурах разрушаются нормально – пластически. Температура перехода от пластического разрушения к хрупкому называется температурой вязко-хрупкого перехода. Она определяется как температура, ниже которой происходит хрупкое разрушение. Температуру хрупкого перехода можно в принципе определять испытанием на растяжение, но при одноосном растяжении ее величина значительно ниже, чем та, которую наблюдают в сложных стальных деталях. Опыт показал, что испытания на ударную вязкость по методу Шарпи намного лучше согласуются с опытными данными по хрупкому разрушению сложных деталей. Схема метода испытания на ударную вязкость по Шарпи показана на рисунке 4.
Рисунок 4 – Схема ударного испытания по методу Шарпи
Усталость сталей
Усталостное разрушение – это тип разрушения, который происходит в металлических деталях, которые подвергаются циклическим нагрузкам.
Рассмотрим ось на колесах, на которую «давит» довольно тяжелый груз. Это груз вызывает изгиб в центре в точке посередине между колесами, как показано схематически на рисунке 5.
Рисунок 5 – Смена сжимающих и растягивающих напряжения
на поверхности вращающейся оси
Этот изгиб заставляет металл растягиваться в точке Т и сжиматься в точке С. Другими словами это означает, что в точке Т металл подвергается растягивающим напряжениям, а в точке С – сжимающим. Поэтому, поскольку ось вращается каждая точка посередине оси подвергается циклическим напряжениям – растягивающим, когда она находится внизу и сжимающим, когда вверху.
В хорошо спроектированной оси максимальные растягивающие напряжения будут далеко ниже предела текучести и все деформации, которые происходят на поверхности металла во время вращения, будут в упругой области, как это показано в нижней части рисунка 5.
Однако, если на поверхности металла есть маленькая царапина, то в этом месте поверхности возникает так называемая концентрация напряжений. Если величина напряжений в этой точке будет превышать предел текучести, то здесь может зародиться трещина. Каждый раз, когда ось делает оборот, эта трещина будет расти, пока не станет достаточно большой, чтобы привести к разрушению оси. Этот процесс называют усталостным разрушением или усталостью сталей. Способность стали сопротивляться циклическим напряжениях называют усталостной прочностью или циклической прочностью. Усталостные разрушения происходят в металлических деталях, которые подвергаются циклическим напряжениям, таких как вращающиеся детали, клапаны, пружины, а также вибрирующие детали, такие как самолетные крылья.
Источник: John D. Verhoeven, Steel Metallurgy for Non-Metallurgists, 2007
steel-guide.ru
Прочностная характеристика — сталь — Большая Энциклопедия Нефти и Газа, статья, страница 1
Прочностная характеристика — сталь
Cтраница 1
Прочностные характеристики стали, термически обработанной на сг0 2 75 кГ / ммг по данным [40], не изменяются под влиянием длительных ( до 10000 час. Для стали, термически обработанной на cr0i2: 65 кГ / мм2, длительные выдержки при 500 — 550 не дают разупрочнения. Ударная вязкость при 20 под влиянием длительных выдержек при 450 — 550 в нагруженном и ненагруженном состояниях испытывает только небольшие изменения, что позволяет считать сталь нечувствительной к тепловой хрупкости. [1]
Прочностные характеристики сталей повышенной и высокой прочности предопределяют значительную экономию металла и широкое их использование в массовом строительстве. [2]
Сравнение прочностных характеристик стали после ВТМО и обычной закалки при одной температуре отпуска не отражает реального повышения прочности, поскольку в результате ВТМО сталь имеет повышенную пластичность, а как известно, надежность работы любой детали в машине определяется в значительной степени способностью материала детали сопротивляться внезапным перегрузкам, которые зависят от пластичности материала. [3]
Повышение прочностных характеристик стали для сварных труб позволяет уменьшить толщину стенки и тем самым повысить экономическую эффективность производства. [4]
Благодаря улучшению прочностной характеристики стали в процессе обработки этот метод позволяет применять в качестве исходного материала для заготовки горячекатаную сталь вместо холоднотянутой, что дает дополнительную экономию от стоимости материала. [5]
Некоторое ухудшение прочностных характеристик стали ХН70ВМТЮ может быть объяснено химическими взаимодействиями стали, содержащей молибден, со стеклосмазкой с повышенным содержанием окиси бора. [7]
Температура также ограничивается прочностными характеристиками сталей, применяемых для изготовления лопаток и дисков турбин. [8]
НТМО еще больше повышает прочностные характеристики стали
: о 2700 — 3000 Мн / мг. НТМО используют только для сталей с широкой зоной устойчивого аустенита. [9]Максимальная твердость, определяющая прочностные характеристики стали и ее конструктивную прочность, получаемые при закалке, обусловлена содержанием углерода в стали. Однако максимальная твердость, которая может быть достигнута при закалке изделий, имеющих большие размеры, чем образцы, зависит также от массы этих изделий, часто не позволяющей получить в структуре 100 % мартенсита. [10]
На рис. 4.4 представлены прочностные характеристики стали ШХ15 в зависимости от твердости. HRC, которая получается в результате отпуска стали при 250 С. [12]
В оснс классификации положена прочностные характеристики стали труб, , воиетричеокие раэиери-попервчного сечения, максимальная стрела прогиба и длина арки. При разработке классификации учтено развитие упругопластическ / а. [13]
Кратковременное азотирование не влияет на прочностные характеристики стали, однако показатели пластичности и величина ударной вязкости существенно снижаются. [14]
Страницы: 1 2 3 4
www.ngpedia.ru
Характеристики прочности
Предел пропорциональности:
. (2.21)
Наибольшее напряжение, до которого справедлив закон Гука.
Предел текучести:
. (2.22)
Наименьшее напряжение, при котором деформация образца происходит при постоянном растягивающем усилии.
Предел прочности (временное сопротивление):
. (2.23)
Наибольшее напряжение, отмеченное в процессе испытания.
Напряжение в момент разрыва:
. (2.24)
Определяемое таким образом напряжение при разрыве весьма условно и не может быть использовано в качестве характеристики механических свойств стали. Условность состоит в том, что получено оно делением силы в момент разрыва на первоначальную площадь поперечного сечения образца, а не на действительную его площадь при разрыве, которая значительно меньше начальной вследствие образования шейки.
Характеристики пластичности
Напомним, что пластичность – это способность материала деформироваться без разрушения. Характеристики пластичности – деформационные, поэтому определяются по данным измерения образца после разрушения:
∆ℓос = ℓ1 — ℓ0 – остаточное удлинение,
–площадь шейки.
Относительное удлинение после разрыва:
. (2.25)
Эта характеристика зависит не только от материала, но и от соотношения размеров образца. Именно поэтому стандартные образцы имеют фиксированное отношение ℓ0 = 5d0 или ℓ0 = 10d0 и величина δ всегда приводится с индексом – δ5 или δ10, причём δ5 > δ10.
Относительное сужение после разрыва:
. (2.26)
Удельная работа деформации:
. (2.27)
где А – работа, затраченная на разрушение образца; находится как площадь, ограниченная диаграммой растяжения и осью абсцисс (площадь фигуры OABCDKLMR). Удельная работа деформации характеризует способность материала сопротивляться ударному действию нагрузки.
Из всех полученных при испытании механических характеристик основными характеристиками прочности являются предел текучести σт и предел прочности σпч, а основными характеристиками пластичности – относительное удлинение δ и относительное сужение ψ после разрыва.
Разгрузка и повторное нагружение
При описании диаграммы растяжения было указано, что в точке К испытание остановили и произвели разгрузку образца. Процесс разгрузки описывался прямой KN (рис.2.16), параллельной прямолинейному участку OA диаграммы. Это означает, что удлинение образца ∆ℓ′П, полученное до начала разгрузки, полностью не исчезает. Исчезнувшая часть удлинения на диаграмме изображается отрезком NQ, оставшаяся – отрезком ОN. Следовательно, полное удлинение образца за пределом упругости состоит из двух частей – упругой и остаточной (пластической):
∆ℓ′П = ∆ℓ′уп + ∆ℓ′ос.
Так будет вплоть до разрыва образца. После разрыва упругая составляющая полного удлинения (отрезок ∆ℓуп) исчезает. Остаточное удлинение изображается отрезком ∆ℓос. Если же прекратить нагружение и разгрузить образец в пределах участка OB, то процесс разгрузки изобразится линией, совпадающей с линией нагрузки – деформация чисто упругая.
При повторном нагружении образца длиною ℓ0 + ∆ℓ′ос линия нагружения практически совпадает с линией разгрузки NK. Предел пропорциональности повысился и стал равным тому напряжению, от которого производилась разгрузка. Далее прямая NK перешла в кривую KL без площадки текучести. Часть диаграммы, расположенная левее линии NK, оказалась отрезанной, т.е. начало координат переместилось в точку N. Таким образом, в результате вытяжки за предел текучести, образец изменил свои механические свойства:
1). повысился предел пропорциональности;
2). исчезла площадка текучести;
3). уменьшилось относительное удлинение после разрыва.
Такое изменение свойств называется наклёпом.
При наклёпе повышаются упругие свойства и понижается пластичность. В некоторых случаях (например, при механической обработке) явление наклёпа нежелательно и его устраняют термообработкой. В других случаях его создают искусственно для улучшения упругости деталей или конструкций (обработка дробью рессор или вытяжка тросов грузоподъёмных машин).
studfiles.net
Основные механические свойства стали. Работа стали на растяжение
Главнейшими показателями механических свойств стали являются прочность, упругость и пластичность, характеризуемые напряжениями и удлинениями.
Прочность определяется сопротивляемостью материала внешним воздействиям.
Упругость — это свойство материала восстанавливать свою первоначальную форму после снятия внешних нагрузок.
Пластичность — это свойство материала не возвращаться в свое первоначальное состояние после снятия внешних нагрузок, т. е. свойство получать остаточные деформации.
Зависимость между напряжениями и деформациями для различных материалов устанавливается опытным путем. Наиболее простым и надежным испытанием является испытание образцов на растяжение, которым и определяется прочность стали, а также ее упругие и пластические свойства.
«Проектирование стальных конструкций»,
К.К.Муханов
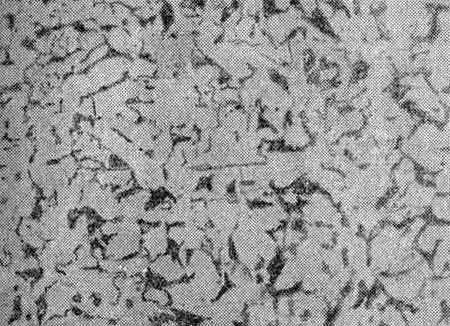
Малоуглеродистая сталь представляет собой однородное кристаллическое тело, состоящее из мелких кристаллов феррита, образующих зерна (Fe — чистое железо), и перлита (смесь цементита Fe3C с ферритом), расположенного главным образом по стыкам ферритных зерен и образующего как бы «сетку» или вкрапления между зернами. Структура стали Ст. 3 (микрошлиф Х 80) Перлит значительно тверже феррита и более хрупок….
При опытном изучении образцов на растяжение устанавливается значение предела текучести σт. При этом в образцах развиваются нормальные линейные напряжения, т. е. имеет место одноосное напряженное состояние. В случае сложного напряженного состояния (например, плоского напряженного состояния, когда образец растягивается в двух направлениях, или при совместном действии нормальных и касательных напряжений при изгибе) переход в пластическое состояние,…
Если подвергнуть образец растяжению, последовательно увеличивая нагрузку Р, и производить при этом замеры получающихся удлинений ∆l, то можно построить опытную диаграмму растяжения, откладывая удлинение в функции нагрузки. Для удобства сравнения эту диаграмму выражают в напряжениях и относительных удлинениях: где σ — нормальное напряжение; F — первоначальная площадь сечения образца; ε — относительное удлинение в процентах;…
www.ktovdome.ru
Свойства сталей — Металлы и металлические изделия
Свойства сталей
Сталь наряду с бетонами — главнейший конструкционный материал. Широкому использованию в строительстве сталь обязана высоким физико-механическим показателям, технологичности (возможности получения из нее конструкций различными методами) и большими объемами производства. Ниже рассмотрены основные технические характеристики стали и приведены числовые значения некоторых характеристик сталей различного состава и строения.
Плотность стали — 7850 кг/м , что приблизительно в 3 раза выше плотности каменных материалов (например, обычный тяжелый бетон имеет плотность 2400 ± 50 кг/м).
Прочностные и деформативные свойства стали обычно определяются испытанием стали на растяжение. При этом строится диаграмма «напряжение — деформация». Сталь, как и другие металлы, ведет себя как упругопластичный материал. В начале испытаний деформации у стали пропорциональны напряжениям. Максимальное напряжение, при котором сохраняется эта зависимость, называют пределом пропорциональности ау (при этом напряжении остаточные деформации не должны превышать 0,05 %).
При дальнейшем повышении напряжения начинает проявляться текучесть стали — быстрый рост деформаций при небольшом подъеме напряжений. Напряжение, соответствующее началу течения, называют пределом текучести ат.
Затем наступает некоторое замедление роста деформаций при подъеме напряжений («временное упрочнение»), после чего наступает разрушение образца, называемое временным сопротивлением ав, что является фактическим пределом прочности стали (Rp).
Рис. 7.2. Диаграмма испытания стали (1 — низкоуглеродистой; 2 — высокоуглеродистой) на растяжение
Испытание на растяжение является основным при оценке механических свойств сталей. Модуль упругости стали составляет 2,1 * 105 МПа.
Твердость сталей определяют на твердомерах Бринелля (НВ) или Роквелла (HR) по величине вдавливания индентера (закаленного шарика или алмазной пирамидки) в испытуемую сталь. Твердость вычисляют в МПа с указанием метода испытаний. Твердость поверхности стали можно повышать специальной обработкой (например, цементацией — насыщением поверхностного слоя стали углеродом или закалкой токами высокой частоты).
Ударная вязкость — свойство стали противостоять динамическим (ударным) нагрузкам. Ее значение определяют по величине работы, необходимой для разрушения образца на маятниковом копре. Ударная вязкость зависит от состава стали, наличия легирующих элементов и заметно меняется при изменении температуры. Так, у СтЗ ударная вязкость при +20 °С составляет 0,5… 1 МДж/м2, а при -20 °С – 0,3…0,5 МДж/м2.
Технологические свойства стали показывают ее способность принимать определенные деформации, аналогичные тем, которые стальное изделие будет иметь при дальнейшей обработке или в условиях эксплуатации. Для строительных сталей чаще всего производят пробу на холодный загиб.
При испытании на загиб (рис. 7.3) определяются не усилия для осуществления деформации, а условия (угол загиба, диаметр оправки), при которых возможно протекание деформации без нарушения сплошности образца (т. е. без появления трещин и расслоения). Чем пластичнее сталь, тем меньше диаметр оправки при испытаниях (см. табл. 7.2).
Для стальной проволоки подобные испытания проводятся на установке, позволяющей перегибать проволоку на заданный угол. Мерой пластичности служит число перегибов проволоки до разрушения.
Рис. 7.3. Схема испытаний на загиб: а — исходное положение; 6 — загиб на 180° с оправкой; в — загиб на 180° без оправки
Теплотехнические свойства сталей в малой степени зависят от ее состава.
Теплопроводность стали, как и всех металлов, очень высока и составляет около 70 Вт/(м * К), т. е. в 50…70 раз выше, чем у бетона.
Коэффициент линейного термического расширения стали составляет 10 * 10-6 К-1, т. е. практически равен КЛТР бетона.
Температура плавления стали зависит от ее состава и для обычных углеродистых сталей находится в пределах 1500…1300 °С (чугун с содержанием углерода 4,3 % плавится при 1150 °С).
Температуроустойчивость стали связана с тем, что при нагревании в ней происходят полиморфные превращения, приводящие к снижению прочности. Небольшая потеря прочности наблюдается уже при нагреве выше 200 °С; после достижения температуры 500…600 °С обычные стали становятся мягкими и резко теряют прочность. Поэтому стальные конструкции не огнестойки и их необходимо защищать от действия огня, например, оштукатуриванием цементными растворами или созданием теплоизоляционных негорючих покрытий.
Читать далее:
Коррозия металлов и способы защиты от нее
Цветные металлы и сплавы
Соединение стальных конструкций
Стальная арматура
Стальной прокат и стальные конструкции
Термическая обработка стали
Углеродистые и легированные стали
Основы технологии черных металлов
Строение и свойства железоуглеродистых сплавов
Общие сведения о металлах и сплавах
stroy-server.ru
СВОЙСТВА СТАЛЕЙ
Строительные материалы и изделия
Сталь наряду с бетонами — главнейший конструкционный материал. Широкому использованию в строительстве сталь обязана высоким физико-механическим показателям, технологичности (возможности получения из нее конструкций различными методами) и большими объемами производства. Ниже рассмотрены основные технические характеристики стали и приведены численные значения некоторых характеристик сталей различного состава и строения.
ЧР — ТЬютностьстали — 7850 кг/м3, что при-
а, МПа Р и с. 7.2. Диаграмма испытания стали на растяжение: |
близительно в 3 раза выше плотности каменных материалов (например, обычный тяжелый бетон имеет плотность — 2400 ±
± 50 кг/м3).
Прочностные и деформативные свойства стали обычно определяются испытанием стали на растяжение. При этом строится диаграмма «напряжение — деформация».
Сталь, как и другие металлы, ведет себя как упруго-пластичный материал (рис. 7.2). В начале испытаний деформации у стали пропорциональны напряжениям. Максимальное напряжение, при котором сохраняется эта зависимость, называется предел пропорциональности оу (при этом напряжении остаточные деформации не должны превышать 0,05 %).
<ту — предел упругости; еу — упру — *. гая деформация; <тв — временное сопротивление; Rv — предел проч.- . ности |
При дальнейшем повышении напряжения начинает проявляться текучесть стали — быстрый рост деформаций при небольшом подъеме напряжений. Напряжение, соответствующее началу течения, называют предел текучести ат.
Затем наступает некоторое замедление роста деформаций при подъеме напряжений («временное упрочнение»), после чего наступает разрушение образца, называется временным сопротивлением ов, что является фактическим пределом прочности стали (Д,).
Относительное удлинение стали є в момент разрыва характеризует ее пластичность. Оно рассчитывается по формуле: . д
Є = ((/,- k)/h) -100, V.’/. .з;—.,’
где 4 — начальная длина расчетной части образца, мм; /, — длина этой части в момент разрыва образца, мм.
Испытание на растяжение является основным при оценке механических свойств сталей. Модуль упругости стали составляет 2,1 • 105 МПа.
Твердость сталей определяют на твердомерах Бринелля (НВ) или Роквелла (HR) по величине вдавливания индентера (закаленного шарика или алмазной пирамидки) в испытуемую сталь. Твердость вычисляют в МПа с указанием метода испытаний. Твердость поверхности стали можно повышать специальной обработкой (например, цементацией — насыщением поверхностного слоя стали углеродом или закал — укой токами высокой частоты).
У///////////ШШ77Ш////////, 777777777777777777/7/77777777777/ а) б) Рис. 7.3. Схема испытаний на загиб: п,‘ ‘ а — исходное положение; б— загиб на 180° с оправкой; в— загиб на 180° без оправки |
вязкость — свойство стали противостоять динамическим (ударным) нагрузкам. Ее значение определяют по величине работы, необходимой для разрушения образца на маятниковом копре. Ударная вязкость зависит от состава стали, наличия легирующих элементов и заметно меняется при изменении температуры. Так, у СтЗ ударная вязкость при + 20° С составляет 0,5… 1 МДж/м2, а при —20° С — 0,3…0,5 МДж/м2.
Технологические свойства. Технологические испытания стали показывают ее способность принимать определенные деформации, аналогичные тем, которые стальное изделие будет иметь при дальнейшей обработке или в условиях эксплуатации. Для строительных сталей чаще всего производят пробу на холодный загиб.
При испытании на загиб (рис. 7.3) определяются не усилия для осуществления деформации, а условия (угол загиба, диаметр оправки), при которых возможно протекание деформации без нарушения сплошности образца (т. е. без появления трещин и расслоения). Чем пла — стичнее сталь, тем меньше диаметр оправки при испытаниях (см. табл.
7.2).
Для стальной проволоки подобные испытания проводятся на установке, позволяющей перегибать проволоку на заданный угол. Мерой пластичности служит число перегибов проволоки до разрушения.
Теплотехнические свойства сталей в малой степени зависят от ее состава.
Теплопроводность стали, как и всех металлов, очень высока и составляет около 70 Вт/(м • К).
Коэффициент линейного термического расширения стали составляет
ю-5к.
Температура плавления стали зависит от ее состава и для обычных углеродистых сталей находится в пределах 1500…1300° С (чугун с содержанием углерода 4,3 % плавится при 1150° С).
Температуроустойчивостьстали связана с тем, что при нагревании в ней происходят полиморфные превращения, приводящие к снижению прочности. Небольшая потеря прочности наблюдается уже при нагреве выше 200° С; после достижения температуры 500. ..600° С обычные стали становятся мягкими и резко теряют прочность. Поэтому стальные конструкции не огнестойки и их необходимо защищать от действия огня, например, покрытием цементными растворами.
Лакокрасочные материалы (ЛКМ) используются для получения защитных и декоративных покрытий на изделиях. ЛКМ после нанесения на поверхность отвердевают, образуя непроницаемую пленку, которая прочно сцепляется с основанием. Толщина пленки может составлять …
Геосинтетические материалы — это материалы на основе полимерных волокон, проволоки, пленки, тканей, сеток, сотовых каркасов и т. д. Их применяют в гидротехническом строительстве; при строительстве дорог и аэродромов; сооружении хвостохранилищ, …
Полимербетон отличается от других видов бетона тем, что связующим веществом в нем являются термореактивные смолы (полиэфирные, фенольные, фурановые, карбамидные, реже — полиуретановые и эпоксидные). Термопластичные полимеры также могут быть использованы, …
msd.com.ua
Прочностные характеристики конструктивных материалов, которые должны учитываться при конструировании арматуры
В арматуростроении используется большое число различных материалов: черные и цветные металлы и сплавы, пластмассы, набивочные и прокладочные материалы и т. д. Значительное влияние на свойства этих материалов оказывает технология изготовления деталей (литье, прокат, поковка, сварная конструкция, штамповка и т. д.), и это нужно учитывать при выборе материалов отдельных деталей трубопроводной арматуры.
При определении применимости материала в определенных условиях необходимо учитывать весь комплекс его свойств, принимая во внимание планируемую долговечность конструкции. Из этого комплекса можно выделить основные свойства, которые являются решающими. Например, для деталей, работающих при высоких давлениях на химически нейтральных средах, основным свойством является прочность металла; для арматуры, работающей на агрессивных или коррозионных средах при низких давлениях, важнейшим свойством является коррозионная устойчивость материала в данной среде при соответствующей концентрации и температуре. Прочность металла в последнем случае не имеет решающего значения и во многих случаях при этих условиях применяются пластмассы, имеющие по сравнению с металлами значительно меньшую прочность, но высокую химическую стойкость. Для прокладочных и набивочных материалов решающими свойствами являются упругость и пластичность.
Из материалов с одинаковыми свойствами выбирается более дешевый. Но в любом случае ценовая политика при выборе материала не должна оказывать отрицательное влияние на планируемое качество отдельных деталей и готового изделия.
При выборе конструкционных металлов прежде всего исходят из их прочности и технологических свойств. Прочность металлов оценивается по результатам испытаний образцов на испытательных машинах, главным образом на разрывных. Основной характеристикой прочности хрупких материалов является предел прочности при разрыве σв, т. е. наибольшее напряжение, в кг/мм2, отнесенное к первоначальному поперечному сечению образца, которое он выдерживает при разрыве. Для пластичных материалов помимо предела прочности важное значение имеет (условный) предел текучести σт, т. е. напряжение, в кг/мм2, соответствующее остаточному относительному удлинению в 0,2%.
Расчет деталей из пластичных материалов обычно производят с учетом предела текучести, так как в машинах, как правило, нельзя допускать значительных остаточных деформаций, которые могли бы вызвать нарушение работы. В связи с этим величина предела текучести при растяжении определяется напряжением, которое вызывает остаточное относительное удлинение в 0,2%. Во многих деталях арматуры такая величина деформации не вызывает опасений за качество работы изделия, и в ряде случаев можно было бы ориентироваться на предел текучести при остаточном относительном удлинении больше 0,2%, например в 0,5%, однако таких данных еще очень мало и при расчете арматуры используют значения предела текучести σт 0 2. Предел пропорциональности σп или наибольшее напряжение, до которого деформация изменяется пропорционально напряжению, используется в основном при расчете на продольную устойчивость. Модуль упругости при растяжении Е кг/мм2, характеризующий жесткость материала, его способность сопротивляться деформациям, входит в формулы во всех расчетах при определении деформаций растяжения, изгиба или сжатия (прогиб стенок деталей, дисков, тарелок и пр.). При определении деформации кручения (пружины) в формулы входит модуль сдвига G кг/мм2. Модуль упругости при растяжении представляет собой условное напряжение в материале, увеличивающее его длину вдвое. Модуль упругости при сдвиге для сталей при температуре t = 20° С обычно равен G ≈ 0,38Е. При растяжении образца из пластичной стали имеет место продольная и поперечная деформации сечения образца, которые характеризуют пластические свойства материала. Пластические свойства оцениваются по величине относительного удлинения при разрыве, величине относительного сужения и ударной вязкости. Относительное удлинение при разрыве δ определяется на образцах, имеющих соотношение длины к диаметру 10:1 — δ10 или 5:1 — δ5, выражается в процентах и представляет собой отношение увеличения длины образца при разрыве к его первоначальной длине. Относительное сужение ψ выражается в процентах и представляет собой отношение уменьшения площади поперечного сечения образца при разрыве к первоначальной площади образца. Ударная вязкость материала ан кг-м/см2 характеризует способность материала сопротивляться динамическим нагрузкам и определяется количеством энергии, затрачиваемой на излом единицы площади сечения образца. Величина ан вычисляется как частное от деления работы в кг-м, затраченной на излом образца, на площадь поперечного сечения образца в см2 в месте излома. Эта характеристика имеет большое значение также для оценки пластических свойств материала. При расчетах на прочность используется также коэффициент Пуассона — υ, который представляет собой отношение относительной поперечной деформации к относительной продольной. Коэффициент Пуассона до предела пропорциональности имеет постоянное значение и равен: для стали υ = 0,25÷0,33, для чугуна υ = 0,23÷0,27, для бронзы υ = 0,32÷0,35, для латуни υ = 0,32÷0,42, для каучука υ = 0,47. При υ = 0,5 объем материала при деформации не изменяется, как это, например, происходит с резиной, при v < 0,5 растяжение вызывает увеличение объема материала, сжатие — уменьшение.
С изменением температуры меняются и свойства материалов. С повышением температуры пластические свойства как правило повышаются, а прочностные характеристики понижаются; и наоборот, при понижении температуры ухудшаются пластические свойства, металлы и другие материалы становятся хрупкими, а прочностные характеристики становятся выше. При высоких температурах в арматуре часто одновременно действуют и высокие давления, вызывающие в деталях значительные напряжения. В этих условиях под действием высоких напряжений и температур в металле непрерывно протекают внутренние процессы, оказывающие существенное влияние на прочность металла и на перераспределение напряжений.
При этом особое влияние на конструкцию оказывает явление ползучести, определяюшее медленную и непрерывную пластическую деформацию металла, которая происходит при постоянном напряжении. Под воздействием высокой температуры в металле одновременно происходят противоположные процессы: с одной стороны происходит упрочнение под воздействием протекающей под напряжением деформации, с другой стороны происходит разупрочнение под воздействием высоких температур. В различные периоды времени эти процессы дают различные результаты, в связи с чем весь процесс ползучести можно разбить на три периода. На рис. 1 показана характерная кривая ползучести. В первый период скорость деформации все время уменьшается и достигает определенной постоянной величины. Во втором периоде сохраняется установившаяся минимальная скорость ползучести. В третьем периоде скорость ползучести возрастает.
Рисунок 1 – Кривая ползучести
При расчете деталей необходимо обеспечить условия, чтобы в течение всего заданного срока службы изделия материал работал в пределах второго периода ползучести. В ряде случаев это условие является необходимым, но недостаточным, так как значительная деформация деталей, даже в пределах второго периода ползучести, может нарушить нормальную работу машины. В этих условиях задаются определенной скоростью ползучести, исходя из наибольшей допустимой величины деформации. При расчете деталей арматуры принимают такой предел ползучести σпл, который вызывает суммарную деформацию в 1% за 100 000 ч работы или 1-10-7 мм/мм ч. Характер графика и значения скоростей ползучести зависят как от свойств сталей, так и от действующей температуры. Скорость ползучести зависит и от напряжения (рис. 2).
Рисунок 2 — Кривые ползучести при разных напряжениях (σ1 ˂ σ2 ˂ σ3 ˂ σ4 ˂ σ5)
Скорость ползу чести металла в установившемся периоде ползучести, в зависимости от напряжения при постоянной температуре, может быть выражена эмпирической зависимостью σпл = А σn, где σпл — скорость равномерной ползучести; σ — напряжение в стали; А — коэффициент; п — показатель степени.
Некоторые данные значений А и n можно взять из справочников по машиностроительным материалам.
Указанные выше механические характеристики не исчерпывают всех свойств металлов. Эксплуатация деталей при высокой температуре показала, что при длительном воздействии высокой температуры и больших напряжений снижается прочность металлов. Большую опасность представляет возможность хрупкого разрушения стали, возникающая в результате длительного совместного действия высокой температуры и высоких напряжений.
В зависимости от температуры и длительности ее воздействия на металл могут иметь место два вида разрушения сталей: внутрикристаллическое и межкристаллическое. При внутрикристаллическом разрушении происходят значительные деформации зерен. При межкристаллическом разрушении деформации зерен незначительны. В качестве величины, характеризующей длительную прочность материала, принимается предел длительной прочности σдл. Он представляет собой напряжение, которое при данных условиях длительного испытания на прочность приводит образец к разрушению. В арматуростроении, как и в энергетике вообще, принимается в качестве предела длительной прочности напряжение, выдерживаемое образцом в течение 100 000 ч, что обеспечивает непрерывную работу материала при этом напряжении в течение десяти лет и более.
При температуре среды до 550° С предел ползучести обычно меньше предела длительной прочности.
Для оценки условий работы деталей арматуры при высоких температурах необходимо учитывать и явление релаксации, тесно связанное с явлением ползучести. Релаксация – это самопроизвольное снижение напряжений в материале при неизменной величине начальной деформации. Результаты этого явления наиболее отчетливо проявляются, например, в болтах и шпильках фланцевых соединений, работающих при высоких температурах. В этих условиях упругая деформация металла от первоначального затяга переходит в пластическую, затяг болтов и шпилек самопроизвольно снижается и нарушается плотность соединения. Поэтому в таких соединениях возникает необходимость периодически подтягивать гайки. На рис. 3 схематически показана кривая релаксации. К сталям, работающим при высоких температурах, предъявляются определенные требования релаксационной стойкости, т. е. способности сохранять напряженное состояние. Релаксационную стойкость стали оценивают по скорости снижения напряжения со временем.
Рисунок 3 – Кривая релаксации
С течением времени в стали, даже находящейся при нормальной температуре, происходят структурные изменения, которые приводят к так называемому старению стали. Кратковременные нагревы до 200—300° С ускоряют этот процесс. В результате старения снижаются пластические свойства стали и в особенности ударная вязкость. Длительное пребывание стали в интервале температур 400—500° С может вызвать особый вид хрупкости стали, так называемую тепловую хрупкость. К тепловой хрупкости склонны стали, содержащие хром, марганец или никель; присадки молибдена, вольфрама и ванадия снижают склонность стали к тепловой хрупкости. Тепловая хрупкость стали может быть выявлена лишь испытанием на ударную вязкость. При возникновении тепловой хрупкости ударная вязкость снижается вдвое и более. Наиболее опасна тепловая хрупкость для деталей, имеющих острые выточки и резьбы, где создаются кон¬центрации напряжений, например в шпильках и болтах. Эти детали для работы при высоких температурах рекомендуется изготовлять из сталей, не содержащих никеля, так как низколегированные хромоникелевые стали имеют склонность к тепловой хрупкости. При работе некоторых деталей арматуры в струе пара или газа создаются условия для быстрого эрозионного износа. Для таких деталей важно обеспечить эрозионную стойкость материала. Очень сложные условия для работы арматуры создают коррозионные среды. Влияние коррозионного воздействия на металл, особенно от щелочей, не ограничивается уменьшением толщины стенки; коррозия, проникая в глубь металла, снижает его прочностные свойства.
При длительном пребывании паровой арматуры при высоких температурах на поверхности стенок, соприкасающихся с паром, с течением времени образуется окалина. Интенсивность процесса образования окалины зависит от жаростойкости или окалиностойкости металла. С образованием окалины толщина стенок арматуры уменьшается; чтобы компенсировать утонение стенок, дается прибавка на толщину из расчета 0,07—0,17 мм/год, исходя из длительности работы арматуры от 10 до 20 лет.
Под длительным действием высокой температуры происходит также графитизация стали, заключающаяся в том, что в металле выделяется свободный графит в виде сфероидальных зерен. Это приводит к ослаблению структуры металла и снижению его механических свойств. Сложные условия работы материала в трубопроводной арматуре требуют не только квалифицированного выбора марки материала, точного соблюдения технологии изготовления деталей, но и тщательного контроля свойств металла как при изготовлении арматуры, так и в процессе ее эксплуатации.
Пластмассы как конструкционные материалы широко применяются в арматуростроении и имеют большие перспективы для использования их в особенности для арматуры химических производств. В связи с разнообразием методов изготовления пластмасс и свойств исходного материала свойства различных пластмасс сильно отличаются, а их механические характеристики имеют большое разнообразие. На свойства пластмасс большое влияние оказывает температура. Некоторые пластмассы, как, например, винипласт, могут быть использованы в относительно узком интервале температур — до 60° С или несколько выше. В различных пластмассах большое значение имеют специфические свойства, такие, как длительная прочность (винипласт), ползучесть (фторопласт), явление старения (полиэтилен) и др. Многие прочностные характеристики различных пластмасс еще достаточно тщательно не изучены, особенно свойства пластмасс при работе в условиях эксплуатации, и в настоящее время подвергаются дальнейшим исследованиям. Поэтому пока для пластмасс, как и для металлов, обычно используются такие характеристики, как предел прочности на растяжение, на сжатие, на изгиб, на кручение или сдвиг, предел текучести, модуль упругости, относительное удлинение и т. д. с учетом действующей температуры.
admiralzavod.ru