- МЕТАЛЛОВ МЕХАНИЧЕСКИЕ СВОЙСТВА
Когда на металлический образец действует сила или система сил, он реагирует на это, изменяя свою форму (деформируется). Различные характеристики, которыми определяются поведение и конечное состояние металлического образца в зависимости от вида и интенсивности сил, называются механическими свойствами металла. Интенсивность силы, действующей на образец, называется напряжением и измеряется как полная сила, отнесенная к площади, на которую она действует. Под деформацией понимается относительное изменение размеров образца, вызванное приложенными напряжениями.
УПРУГАЯ И ПЛАСТИЧЕСКАЯ ДЕФОРМАЦИЯ, РАЗРУШЕНИЕ
Если напряжение, приложенное к металлическому образцу, не слишком велико, то его деформация оказывается упругой — стоит снять напряжение, как его форма восстанавливается. Некоторые металлические конструкции намеренно проектируют так, чтобы они упруго деформировались. Так, от пружин обычно требуется довольно большая упругая деформация. В других случаях упругую деформацию сводят к минимуму. Мосты, балки, механизмы, приборы делают по возможности более жесткими. Упругая деформация металлического образца пропорциональна силе или сумме сил, действующих на него. Это выражается законом Гука, согласно которому напряжение равно упругой деформации, умноженной на постоянный коэффициент пропорциональности, называемый модулем упругости: s = eY, где s — напряжение, e — упругая деформация, а Y — модуль упругости (модуль Юнга). Модули упругости ряда металлов представлены в табл. 1.
Рис. 1. ДИАГРАММЫ РАСТЯЖЕНИЯ для двух металлов с разной пластичностью: сравнительно хрупкого (штриховая линия) и более пластичного (сплошная линия). Пределы текучести обоих металлов почти совпадают. Более хрупкий металл разрушается по достижении своего предела прочности при растяжении, а более пластичный — пройдя через свой предел прочности.
Типичные значения величин, характеризующих прочность на растяжение ряда металлов и сплавов, представлены в табл. 2. Нетрудно видеть, что эти значения для одного и того же материала могут сильно различаться в зависимости от обработки.
Сжатие. Упругие и пластические свойства при сжатии обычно весьма сходны с тем, что наблюдается при растяжении (рис. 2). Кривая соотношения между условным напряжением и условной деформацией при сжатии проходит выше соответствующей кривой для растяжения только потому, что при сжатии поперечное сечение образца не уменьшается, а увеличивается. Если же по осям графика откладывать истинное напряжение и истинную деформацию, то кривые практически совпадают, хотя при растяжении разрушение происходит раньше.
Рис. 2. ДИАГРАММЫ РАСТЯЖЕНИЯ И СЖАТИЯ.
Кривая условного напряжения для сжатия проходит выше, чем для растяжения, только потому, что при сжатии поперечное сечение увеличивается, а не уменьшается.
Твердость. Твердость материала — это его способность сопротивляться пластической деформации. Поскольку испытания на растяжение требуют дорогостоящего оборудования и больших затрат времени, часто прибегают к более простым испытаниям на твердость. При испытаниях по методам Бринелля и Роквелла в поверхность металла при заданных нагрузке и скорости нагружения вдавливают «индентор» (наконечник, имеющий форму шара или пирамиды). Затем измеряют (часто это делается автоматически) размер отпечатка, и по нему определяют показатель (число) твердости. Чем меньше отпечаток, тем больше твердость. Твердость и предел текучести — это в какой-то мере сравнимые характеристики: обычно при увеличении одной из них увеличивается и другая. Может сложиться впечатление, что в металлических материалах всегда желательны максимальные предел текучести и твердость. На самом деле это не так, и не только по экономическим соображениям (процессы упрочнения требуют дополнительных затрат). Во-первых, материалам необходимо придавать форму различных изделий, а это обычно осуществляется с применением процессов (прокатки, штамповки, прессования), в которых важную роль играет пластическая деформация. Даже при обработке на металлорежущем станке очень существенна пластическая деформация. Если твердость материала слишком велика, то для придания ему нужной формы требуются слишком большие силы, вследствие чего режущие инструменты быстро изнашиваются. Такого рода трудности можно уменьшить, обрабатывая металлы при повышенной температуре, когда они становятся мягче. Если же горячая обработка невозможна, то используется отжиг металла (медленные нагрев и охлаждение). Во-вторых, по мере того как металлический материал становится тверже, он обычно теряет пластичность. Иначе говоря, материал становится хрупким, если его предел текучести столь велик, что пластическая деформация не происходит вплоть до тех напряжений, которые сразу же вызывают разрушение. Конструктору обычно приходится выбирать какие-то промежуточные уровни твердости и пластичности.
См. также РАЗРУШЕНИЯ МЕХАНИЗМЫ. Усталость, несомненно, является самой распространенной причиной выхода конструкций из строя в условиях эксплуатации. Особенно подвержены этому детали машин, работающие в условиях циклического нагружения. В авиастроении усталость оказывается очень важной проблемой из-за вибрации. Во избежание усталостного разрушения приходится часто проверять и заменять детали самолетов и вертолетов.
Ползучесть. Ползучестью (или крипом) называется медленное нарастание пластической деформации металла под действием постоянной нагрузки. С появлением воздушно-реактивных двигателей, газовых турбин и ракет стали приобретать все более важное значение свойства материалов при повышенных температурах. Во многих областях техники дальнейшее развитие сдерживается ограничениями, связанными с высокотемпературными механическими свойствами материалов. При нормальных температурах пластическая деформация устанавливается почти мгновенно, как только прикладывается соответствующее напряжение, и в дальнейшем мало увеличивается. При повышенных же температурах металлы не только становятся мягче, но и деформируются так, что деформация продолжает нарастать со временем. Такая зависящая от времени деформация, или ползучесть, может ограничивать срок службы конструкций, которые должны длительное время работать при повышенных температурах. Чем больше напряжения и чем выше температура, тем больше скорость ползучести. Типичные кривые ползучести представлены на рис. 3. После начальной стадии быстрой (неустановившейся) ползучести эта скорость уменьшается и становится почти постоянной. Перед разрушением скорость ползучести вновь увеличивается. Температура, при которой ползучесть становится критической, неодинакова для разных металлов. Предметом забот телефонных компаний является ползучесть подвесных кабелей в свинцовой оболочке, работающих при обычных температурах окружающей среды; в то же время некоторые специальные сплавы могут работать при 800° С, не обнаруживая чрезмерной ползучести.
Рис. 3. ТИПИЧНЫЕ КРИВЫЕ ПОЛЗУЧЕСТИ. После стадии быстрой неустановившейся ползучести скорость ползучести уменьшается и становится почти постоянной, а затем наступает стадия ускоренной ползучести, которая завершается разрушением.
Срок службы деталей в условиях ползучести может определяться либо предельно допустимой деформацией, либо разрушением, и конструктор должен всегда иметь в виду эти два возможных варианта. Пригодность материалов для изготовления изделий, рассчитанных на длительную работу при повышенных температурах, например лопаток турбин, трудно оценить заранее. Испытания за время, равное предполагаемому сроку службы, зачастую практически невозможны, а результаты кратковременных (ускоренных) испытаний не так просто экстраполировать на более длительные сроки, поскольку может измениться характер разрушения. Хотя механические свойства жаропрочных сплавов постоянно улучшаются, перед металлофизиками и материаловедами всегда будет стоять задача создания материалов, способных выдерживать еще более высокие температуры.
См. также МЕТАЛЛОВЕДЕНИЕ ФИЗИЧЕСКОЕ.
КРИСТАЛЛИЧЕСКАЯ СТРУКТУРА
Выше речь шла об общих закономерностях поведения металлов под действием механических нагрузок. Чтобы лучше понять соответствующие явления, нужно рассмотреть атомное строение металлов. Все твердые металлы — кристаллические вещества. Они состоят из кристаллов, или зерен, расположение атомов в которых соответствует правильной трехмерной решетке. Кристаллическую структуру металла можно представить как состоящую из атомных плоскостей, или слоев. Когда прикладывается напряжение сдвига (сила, заставляющая две соседние плоскости металлического образца скользить друг по другу в противоположных направлениях), один слой атомов может сдвинуться на целое межатомное расстояние. Такой сдвиг скажется на форме поверхности, но не на кристаллической структуре. Если один слой сдвинется на много межатомных расстояний, то на поверхности образуется «ступенька». Хотя отдельные атомы слишком малы, чтобы их можно было увидеть под микроскопом, ступеньки, образовавшиеся за счет скольжения, хорошо видны под микроскопом и названы линиями скольжения. Обычные металлические предметы, встречающиеся нам ежедневно, являются поликристаллическими, т.е. состоят из большого числа кристаллов, в каждом из которых своя ориентация атомных плоскостей. Деформация обычного поликристаллического металла имеет с деформацией монокристалла то общее, что она происходит за счет скольжения по атомным плоскостям в каждом кристалле. Заметное же скольжение целых кристаллов по их границам наблюдается только в условиях ползучести при повышенных температурах. Средний размер одного кристалла, или зерна, может составлять от нескольких тысячных до нескольких десятых долей сантиметра. Желательна более мелкая зернистость, так как механические характеристики мелкозернистого металла лучше, чем у крупнозернистого. Кроме того, мелкозернистые металлы менее хрупки.
Скольжение и дислокации. Процессы скольжения удалось подробнее исследовать на монокристаллах металлов, выращенных в лаборатории. При этом выяснилось не только то, что скольжение происходит в некоторых определенных направлениях и обычно по вполне определенным плоскостям, но и то, что монокристаллы деформируются при очень малых напряжениях. Переход монокристаллов в состояние текучести начинается для алюминия при 1, а для железа — при 15-25 МПа. Теоретически же этот переход в обоих случаях должен происходить при напряжениях ок. 10 000 МПа. Такое расхождение между экспериментальными данными и теоретическими расчетами на протяжении многих лет оставалось важной проблемой. В 1934 Тейлор, Полани и Орован предложили объяснение, основанное на представлении о дефектах кристаллической структуры. Они высказали предположение, что при скольжении сначала происходит смещение в какой-то точке атомной плоскости, которое затем распространяется по кристаллу. Граница между сдвинувшейся и несдвинувшейся областями (рис. 4) представляет собой линейный дефект кристаллической структуры, названный дислокацией (на рисунке эта линия уходит в кристалл перпендикулярно плоскости рисунка). Когда к кристаллу прикладывается напряжение сдвига, дислокация движется, вызывая скольжение по плоскости, в которой она находится. После того как дислокации образовались, они очень легко движутся по кристаллу, чем и объясняется «мягкость» монокристаллов.
Рис. 4. КРИСТАЛЛИЧЕСКАЯ РЕШЕТКА. а — напряжение сдвига прилагается в направлении стрелок; слева образуется дислокация (б), обведенная кружком, которая движется вправо (в), после чего снова восстанавливается равновесие (г).
В кристаллах металлов обычно имеется множество дислокаций (общая длина дислокаций в одном кубическом сантиметре отожженного металлического кристалла может составлять более 10 км). Но в 1952 научные сотрудники лабораторий корпорации «Белл телефон», испытывая на изгиб очень тонкие нитевидные кристаллы («усы») олова, обнаружили, к своему удивлению, что изгибная прочность таких кристаллов близка к теоретическому значению для совершенных кристаллов. Позднее были обнаружены чрезвычайно прочные нитевидные кристаллы и многих других металлов. Как предполагают, столь высокая прочность обусловлена тем, что в таких кристаллах либо вообще нет дислокаций, либо имеется одна, идущая по всей длине кристалла.
Температурные эффекты. Влияние повышенных температур можно объяснить, исходя из представлений о дислокациях и зеренной структуре. Многочисленные дислокации в кристаллах деформационно-упрочненного металла искажают кристаллическую решетку и увеличивают энергию кристалла. Когда же металл нагревается, атомы становятся подвижными и перестраиваются в новые, более совершенные кристаллы, содержащие меньше дислокаций. С такой рекристаллизацией и связано разупрочнение, которое наблюдается при отжиге металлов.
ЛИТЕРАТУРА
Бернштейн М.Л., Займовский В.А. Механические свойства металлов. М., 1979 Уайэтт О.Г., Дью-Хьюз Д. Металлы, керамики, полимеры. М., 1979 Павлов П.А. Механические состояния и прочность материалов. Л., 1980 Соболев Н.Д., Богданович К.П. Механические свойства материалов и основы физики прочности. М., 1985 Жуковец И.И. Механические испытания металлов. М., 1986 Бобылев А.В. Механические и технологические свойства металлов. М., 1987
Энциклопедия Кольера. — Открытое общество. 2000.
- ЧАН-ЧАН
- РАЗРУШЕНИЯ МЕХАНИЗМЫ
Смотреть что такое «МЕТАЛЛОВ МЕХАНИЧЕСКИЕ СВОЙСТВА» в других словарях:
Механические свойства материалов — Механические свойства материалов, такие как прочность, сопротивление разрушению, твёрдость и др. являются во многих случаях определяющими для принятия решения о применении материала. Методы проверки механических свойств Следует отметить следующие … Википедия
МЕХАНИЧЕСКИЕ СВОЙСТВА — материалов реакция материала на приложенные механич. нагрузки. Осн. характеристиками механич. свойств являются напряжения и деформации. Напряжения характеристики сил, к рые относят к единице сечения образца материала или изделия, конструкции из… … Физическая энциклопедия
Механические свойства — материалов, такие как прочность, сопротивление разрушению, твёрдость и др. являются во многих случаях определяющими для принятия решения о применении материала. Методы проверки механических свойств Следует отметить следующие основные методы… … Википедия
Механические свойства материалов — совокупность показателей, характеризующих сопротивление материала воз действующей на него нагрузке, его способность деформироваться при этом, а также особенности его поведения в процессе разрушения. В соответствии с этим М. с. м. измеряют … Большая советская энциклопедия
МЕХАНИЧЕСКИЕ СВОЙСТВА — материалов, определяют их поведение под действием мех. нагрузки. Основные М. с. твердых тел деформационные (жесткость, пластичность, ползучесть, твердость, предельные деформации при разрушении e), прочностные (предел прочности s, долговечность,… … Химическая энциклопедия
ГОСТ Р ИСО 898-5-2009: Механические свойства крепежных изделий из углеродистой и легированной стали. Часть 5. Установочные винты и аналогичные резьбовые крепежные изделия, не подвергаемые растягивающим напряжениям — Терминология ГОСТ Р ИСО 898 5 2009: Механические свойства крепежных изделий из углеродистой и легированной стали. Часть 5. Установочные винты и аналогичные резьбовые крепежные изделия, не подвергаемые растягивающим напряжениям оригинал документа … Словарь-справочник терминов нормативно-технической документации
Физико-механические свойства платиновых металлов — Металл Атомная масса, г Плотность при 20°С, г/см3 Температура плавления, °С Удельное электрическое сопротивление, Ом ·м Отражательная способность, % … Химический справочник
МЕТАЛЛОВ ИСПЫТАНИЯ — Цель испытания материалов состоит в том, чтобы оценить качество материала, определить его механические и эксплуатационные характеристики и выявить причины потери прочности. Химические методы. Химические испытания обычно состоят в том, что… … Энциклопедия Кольера
свойства металлов — [properties of metals] характеристики металлов и сплавов, а также изделий (полуфабрикатов) из них, преимущественно определяется их атомно кристаллическим строением, химическим составом, количеством и свойствами отдельных фазовых составляющих, их… … Энциклопедический словарь по металлургии
МЕТАЛЛОВ ОБРАБОТКА ДАВЛЕНИЕМ — формование металлических материалов механическими средствами без снятия стружки. Наряду с формообразованием обработка давлением может улучшать качество и механические свойства металла. Обработка металлов давлением производится либо в горячем… … Энциклопедия Кольера
МЕТАЛЛОВ МЕХАНИЧЕСКИЕ СВОЙСТВА. Когда на металлический образец действует сила или система сил, он реагирует на это, изменяя свою форму (деформируется). Различные характеристики, которыми определяются поведение и конечное состояние металлического образца в зависимости от вида и интенсивности сил, называются механическими свойствами металла.
Интенсивность силы, действующей на образец, называется напряжением и измеряется как полная сила, отнесенная к площади, на которую она действует. Под деформацией понимается относительное изменение размеров образца, вызванное приложенными напряжениями.
УПРУГАЯ И ПЛАСТИЧЕСКАЯ ДЕФОРМАЦИЯ, РАЗРУШЕНИЕ
Если напряжение, приложенное к металлическому образцу, не слишком велико, то его деформация оказывается упругой – стоит снять напряжение, как его форма восстанавливается. Некоторые металлические конструкции намеренно проектируют так, чтобы они упруго деформировались. Так, от пружин обычно требуется довольно большая упругая деформация. В других случаях упругую деформацию сводят к минимуму. Мосты, балки, механизмы, приборы делают по возможности более жесткими. Упругая деформация металлического образца пропорциональна силе или сумме сил, действующих на него. Это выражается законом Гука, согласно которому напряжение равно упругой деформации, умноженной на постоянный коэффициент пропорциональности, называемый модулем упругости: s = eY, где s – напряжение, e – упругая деформация, а Y – модуль упругости (модуль Юнга). Модули упругости ряда металлов представлены в табл. 1.
Таблица 1 | ||||||
Металл | Вольфрам | Железо (сталь) | Медь | Алюминий | Магний | Свинец |
Модуль Юнга, 105 МПа | 3,5 | 2,0 | 1,1 | 0,70 | 0,45 | 0,18 |
Пользуясь данными этой таблицы, можно вычислить, например, силу, необходимую для того, чтобы растянуть стальной стержень квадратного поперечного сечения со стороной 1 см на 0,1% его длины:
F = YґAґDL/L = 200 000 МПа ґ 1 см2ґ0,001 = 20 000 Н (= 20 кН)
Когда к металлическому образцу прикладываются напряжения, превышающие его предел упругости, они вызывают пластическую (необратимую) деформацию, приводящую к необратимому изменению его формы. Более высокие напряжения могут вызвать разрушение материала.
Важнейшим критерием при выборе металлического материала, от которого требуется высокая упругость, является предел текучести. У самых лучших пружинных сталей практически такой же модуль упругости, как и у самых дешевых строительных, но пружинные стали способны выдерживать гораздо большие напряжения, а следовательно, и гораздо большие упругие деформации без пластической деформации, поскольку у них выше предел текучести.
Пластические свойства металлического материала (в отличие от упругих) можно изменять путем сплавления и термообработки. Так, предел текучести железа подобными методами можно повысить в 50 раз. Чистое железо переходит в состояние текучести уже при напряжениях порядка 40 МПа, тогда как предел текучести сталей, содержащих 0,5% углерода и несколько процентов хрома и никеля, после нагревания до 950° С и закалки может достигать 2000 МПа.
Когда металлический материал нагружен с превышением предела текучести, он продолжает деформироваться пластически, но в процессе деформирования становится более твердым, так что для дальнейшего увеличения деформации требуется все больше повышать напряжение. Такое явление называется деформационным или механическим упрочнением (а также наклепом). Его можно продемонстрировать, скручивая или многократно перегибая металлическую проволоку. Деформационное упрочнение металлических изделий часто осуществляется на заводах. Листовую латунь, медную проволоку, алюминиевые стержни можно холодной прокаткой или холодным волочением довести до уровня твердости, который требуется от окончательной продукции.
Растяжение.
Соотношение между напряжением и деформацией для материалов часто исследуют, проводя испытания на растяжение, и при этом получают диаграмму растяжения – график, по горизонтальной оси которого откладывается деформация, а по вертикальной – напряжение (рис. 1). Хотя при растяжении поперечное сечение образца уменьшается (а длина увеличивается), напряжение обычно вычисляют, относя силу к исходной площади поперечного сечения, а не к уменьшенной, которая давала бы истинное напряжение. При малых деформациях это не имеет особого значения, но при больших может приводить к заметной разнице. На рис. 1 представлены кривые деформация – напряжение для двух материалов с неодинаковой пластичностью. (Пластичность – это способность материала удлиняться без разрушения, но и без возврата к первоначальной форме после снятия нагрузки.) Начальный линейный участок как той, так и другой кривой заканчивается в точке предела текучести, где начинается пластическое течение. Для менее пластичного материала высшая точка диаграммы, его предел прочности на растяжение, соответствует разрушению. Для более пластичного материала предел прочности на растяжение достигается тогда, когда скорость уменьшения поперечного сечения при деформировании становится больше скорости деформационного упрочнения. На этой стадии в ходе испытания начинается образование «шейки» (локальное ускоренное уменьшение поперечного сечения). Хотя способность образца выдерживать нагрузку уменьшается, материал в шейке продолжает упрочняться. Испытание заканчивается разрывом шейки.
Типичные значения величин, характеризующих прочность на растяжение ряда металлов и сплавов, представлены в табл. 2. Нетрудно видеть, что эти значения для одного и того же материала могут сильно различаться в зависимости от обработки.
Таблица 2 | ||||
Металлы и сплавы | Состояние | Предел текучести, МПа | Предел прочности на растяжение, МПа | Удлинение, % |
Малоуглеродистая сталь (0,2% С) | Горячекатанная | 300 | 450 | 35 |
Среднеуглеродистая сталь (0,4% С, 0,5% Mn) | Упрочненная и отпущенная | 450 | 700 | 21 |
Высокопрочная сталь (0,4% С, 1,0% Mn, 1,5% Si, 2,0% Cr, 0,5% Мo) | Упрочненная и отпущенная | 1750 | 2300 | 11 |
Серый чугун | После литья | – | 175–300 | 0,4 |
Алюминий технически чистый | Отожженный | 35 | 90 | 45 |
Алюминий технически чистый | Деформационно-упрочненный | 150 | 170 | 15 |
Алюминиевый сплав (4,5% Cu, 1,5% Mg, 0,6% Mn) | Упрочненный старением | 360 | 500 | 13 |
Латунь листовая (70% Cu, 30% Zn) | Полностью отожженная | 80 | 300 | 66 |
Латунь листовая (70% Cu, 30% Zn) | Деформационно-упрочненная | 500 | 530 | 8 |
Вольфрам, проволока | Тянутая до диаметра 0,63 мм | 2200 | 2300 | 2,5 |
Свинец | После литья | 0,006 | 12 | 30 |
Сжатие.
Упругие и пластические свойства при сжатии обычно весьма сходны с тем, что наблюдается при растяжении (рис. 2). Кривая соотношения между условным напряжением и условной деформацией при сжатии проходит выше соответствующей кривой для растяжения только потому, что при сжатии поперечное сечение образца не уменьшается, а увеличивается. Если же по осям графика откладывать истинное напряжение и истинную деформацию, то кривые практически совпадают, хотя при растяжении разрушение происходит раньше.
Твердость.
Твердость материала – это его способность сопротивляться пластической деформации. Поскольку испытания на растяжение требуют дорогостоящего оборудования и больших затрат времени, часто прибегают к более простым испытаниям на твердость. При испытаниях по методам Бринелля и Роквелла в поверхность металла при заданных нагрузке и скорости нагружения вдавливают «индентор» (наконечник, имеющий форму шара или пирамиды). Затем измеряют (часто это делается автоматически) размер отпечатка, и по нему определяют показатель (число) твердости. Чем меньше отпечаток, тем больше твердость. Твердость и предел текучести – это в какой-то мере сравнимые характеристики: обычно при увеличении одной из них увеличивается и другая.
Может сложиться впечатление, что в металлических материалах всегда желательны максимальные предел текучести и твердость. На самом деле это не так, и не только по экономическим соображениям (процессы упрочнения требуют дополнительных затрат).
Во-первых, материалам необходимо придавать форму различных изделий, а это обычно осуществляется с применением процессов (прокатки, штамповки, прессования), в которых важную роль играет пластическая деформация. Даже при обработке на металлорежущем станке очень существенна пластическая деформация. Если твердость материала слишком велика, то для придания ему нужной формы требуются слишком большие силы, вследствие чего режущие инструменты быстро изнашиваются. Такого рода трудности можно уменьшить, обрабатывая металлы при повышенной температуре, когда они становятся мягче. Если же горячая обработка невозможна, то используется отжиг металла (медленные нагрев и охлаждение).
Во-вторых, по мере того как металлический материал становится тверже, он обычно теряет пластичность. Иначе говоря, материал становится хрупким, если его предел текучести столь велик, что пластическая деформация не происходит вплоть до тех напряжений, которые сразу же вызывают разрушение. Конструктору обычно приходится выбирать какие-то промежуточные уровни твердости и пластичности.
Ударная вязкость и хрупкость.
Вязкость противоположна хрупкости. Это способность материала сопротивляться разрушению, поглощая энергию удара. Например, стекло хрупкое, потому что оно не способно поглощать энергию за счет пластической деформации. При столь же резком ударе по листу мягкого алюминия не возникают большие напряжения, так как алюминий способен к пластической деформации, поглощающей энергию удара.
Существует много разных методов испытания металлов на ударную вязкость. При использовании метода Шарпи призматический образец металла с надрезом подставляют под удар отведенного маятника. Работу, затраченную на разрушение образца, определяют по расстоянию, на которое маятник отклоняется после удара. Такие испытания показывают, что стали и многие металлы ведут себя как хрупкие при пониженных температурах, но как вязкие – при повышенных. Переход от хрупкого поведения к вязкому часто происходит в довольно узком температурном диапазоне, среднюю точку которого называют температурой хрупко-вязкого перехода. Другие испытания на ударную вязкость тоже указывают на наличие такого перехода, но измеренная температура перехода изменяется от испытания к испытанию в зависимости от глубины надреза, размеров и формы образца, а также от метода и скорости ударного нагружения. Поскольку ни в одном из видов испытаний не воспроизводится весь диапазон рабочих условий, испытания на ударную вязкость ценны лишь тем, что позволяют сравнивать разные материалы. Тем не менее они дали много важной информации о влиянии сплавления, технологии изготовления и термообработки на склонность к хрупкому разрушению. Температура перехода для сталей, измеренная по методу Шарпи с V-образным надрезом, может достигать +90° С, но соответствующими легирующими присадками и термообработкой ее можно понизить до -130° С.
Хрупкое разрушение стали было причиной многочисленных аварий, таких, как неожиданные прорывы трубопроводов, взрывы сосудов давления и складских резервуаров, обвалы мостов. Среди самых известных примеров – большое количество морских судов типа «Либерти», обшивка которых неожиданно расходилась во время плавания. Как показало расследование, выход из строя судов «Либерти» был обусловлен, в частности, неправильной технологией сварки, оставлявшей внутренние напряжения, плохим контролем за составом сварного шва и дефектами конструкции. Сведения, полученные в результате лабораторных испытаний, позволили существенно уменьшить вероятность таких аварий. Температура хрупко-вязкого перехода некоторых материалов, например вольфрама, кремния и хрома, в обычных условиях значительно выше комнатной. Такие материалы обычно считаются хрупкими, и придавать им нужную форму за счет пластической деформации можно только при нагреве. В то же время медь, алюминий, свинец, никель, некоторые марки нержавеющих сталей и другие металлы и сплавы вообще не становятся хрупкими при понижении температуры. Хотя многое уже известно о хрупком разрушении, это явление нельзя еще считать полностью изученным.
Усталость.
Усталостью называется разрушение конструкции под действием циклических нагрузок. Когда деталь изгибается то в одну, то в другую сторону, ее поверхности поочередно подвергаются то сжатию, то растяжению. При достаточно большом числе циклов нагружения разрушение могут вызывать напряжения, значительно более низкие, чем те, при которых происходит разрушение в случае однократного нагружения. Знакопеременные напряжения вызывают локализованные пластическую деформацию и деформационное упрочнение материала, в результате чего с течением времени возникают малые трещины. Концентрация напряжений вблизи концов таких трещин заставляет их расти. Сначала трещины растут медленно, но по мере уменьшения поперечного сечения, на которое приходится нагрузка, напряжения у концов трещин увеличиваются. При этом трещины растут все быстрее и, наконец, мгновенно распространяются на все сечение детали. См. также РАЗРУШЕНИЯ МЕХАНИЗМЫ.
Усталость, несомненно, является самой распространенной причиной выхода конструкций из строя в условиях эксплуатации. Особенно подвержены этому детали машин, работающие в условиях циклического нагружения. В авиастроении усталость оказывается очень важной проблемой из-за вибрации. Во избежание усталостного разрушения приходится часто проверять и заменять детали самолетов и вертолетов.
Ползучесть.
Ползучестью (или крипом) называется медленное нарастание пластической деформации металла под действием постоянной нагрузки. С появлением воздушно-реактивных двигателей, газовых турбин и ракет стали приобретать все более важное значение свойства материалов при повышенных температурах. Во многих областях техники дальнейшее развитие сдерживается ограничениями, связанными с высокотемпературными механическими свойствами материалов.
При нормальных температурах пластическая деформация устанавливается почти мгновенно, как только прикладывается соответствующее напряжение, и в дальнейшем мало увеличивается. При повышенных же температурах металлы не только становятся мягче, но и деформируются так, что деформация продолжает нарастать со временем. Такая зависящая от времени деформация, или ползучесть, может ограничивать срок службы конструкций, которые должны длительное время работать при повышенных температурах.
Чем больше напряжения и чем выше температура, тем больше скорость ползучести. Типичные кривые ползучести представлены на рис. 3. После начальной стадии быстрой (неустановившейся) ползучести эта скорость уменьшается и становится почти постоянной. Перед разрушением скорость ползучести вновь увеличивается. Температура, при которой ползучесть становится критической, неодинакова для разных металлов. Предметом забот телефонных компаний является ползучесть подвесных кабелей в свинцовой оболочке, работающих при обычных температурах окружающей среды; в то же время некоторые специальные сплавы могут работать при 800° С, не обнаруживая чрезмерной ползучести.
Срок службы деталей в условиях ползучести может определяться либо предельно допустимой деформацией, либо разрушением, и конструктор должен всегда иметь в виду эти два возможных варианта. Пригодность материалов для изготовления изделий, рассчитанных на длительную работу при повышенных температурах, например лопаток турбин, трудно оценить заранее. Испытания за время, равное предполагаемому сроку службы, зачастую практически невозможны, а результаты кратковременных (ускоренных) испытаний не так просто экстраполировать на более длительные сроки, поскольку может измениться характер разрушения. Хотя механические свойства жаропрочных сплавов постоянно улучшаются, перед металлофизиками и материаловедами всегда будет стоять задача создания материалов, способных выдерживать еще более высокие температуры. См. также МЕТАЛЛОВЕДЕНИЕ ФИЗИЧЕСКОЕ.
КРИСТАЛЛИЧЕСКАЯ СТРУКТУРА
Выше речь шла об общих закономерностях поведения металлов под действием механических нагрузок. Чтобы лучше понять соответствующие явления, нужно рассмотреть атомное строение металлов. Все твердые металлы – кристаллические вещества. Они состоят из кристаллов, или зерен, расположение атомов в которых соответствует правильной трехмерной решетке. Кристаллическую структуру металла можно представить как состоящую из атомных плоскостей, или слоев. Когда прикладывается напряжение сдвига (сила, заставляющая две соседние плоскости металлического образца скользить друг по другу в противоположных направлениях), один слой атомов может сдвинуться на целое межатомное расстояние. Такой сдвиг скажется на форме поверхности, но не на кристаллической структуре. Если один слой сдвинется на много межатомных расстояний, то на поверхности образуется «ступенька». Хотя отдельные атомы слишком малы, чтобы их можно было увидеть под микроскопом, ступеньки, образовавшиеся за счет скольжения, хорошо видны под микроскопом и названы линиями скольжения.
Обычные металлические предметы, встречающиеся нам ежедневно, являются поликристаллическими, т.е. состоят из большого числа кристаллов, в каждом из которых своя ориентация атомных плоскостей. Деформация обычного поликристаллического металла имеет с деформацией монокристалла то общее, что она происходит за счет скольжения по атомным плоскостям в каждом кристалле. Заметное же скольжение целых кристаллов по их границам наблюдается только в условиях ползучести при повышенных температурах. Средний размер одного кристалла, или зерна, может составлять от нескольких тысячных до нескольких десятых долей сантиметра. Желательна более мелкая зернистость, так как механические характеристики мелкозернистого металла лучше, чем у крупнозернистого. Кроме того, мелкозернистые металлы менее хрупки.
Скольжение и дислокации.
Процессы скольжения удалось подробнее исследовать на монокристаллах металлов, выращенных в лаборатории. При этом выяснилось не только то, что скольжение происходит в некоторых определенных направлениях и обычно по вполне определенным плоскостям, но и то, что монокристаллы деформируются при очень малых напряжениях. Переход монокристаллов в состояние текучести начинается для алюминия при 1, а для железа – при 15–25 МПа. Теоретически же этот переход в обоих случаях должен происходить при напряжениях ок. 10 000 МПа. Такое расхождение между экспериментальными данными и теоретическими расчетами на протяжении многих лет оставалось важной проблемой. В 1934 Тейлор, Полани и Орован предложили объяснение, основанное на представлении о дефектах кристаллической структуры. Они высказали предположение, что при скольжении сначала происходит смещение в какой-то точке атомной плоскости, которое затем распространяется по кристаллу. Граница между сдвинувшейся и несдвинувшейся областями (рис. 4) представляет собой линейный дефект кристаллической структуры, названный дислокацией (на рисунке эта линия уходит в кристалл перпендикулярно плоскости рисунка). Когда к кристаллу прикладывается напряжение сдвига, дислокация движется, вызывая скольжение по плоскости, в которой она находится. После того как дислокации образовались, они очень легко движутся по кристаллу, чем и объясняется «мягкость» монокристаллов.
В кристаллах металлов обычно имеется множество дислокаций (общая длина дислокаций в одном кубическом сантиметре отожженного металлического кристалла может составлять более 10 км). Но в 1952 научные сотрудники лабораторий корпорации «Белл телефон», испытывая на изгиб очень тонкие нитевидные кристаллы («усы») олова, обнаружили, к своему удивлению, что изгибная прочность таких кристаллов близка к теоретическому значению для совершенных кристаллов. Позднее были обнаружены чрезвычайно прочные нитевидные кристаллы и многих других металлов. Как предполагают, столь высокая прочность обусловлена тем, что в таких кристаллах либо вообще нет дислокаций, либо имеется одна, идущая по всей длине кристалла.
Температурные эффекты.
Влияние повышенных температур можно объяснить, исходя из представлений о дислокациях и зеренной структуре. Многочисленные дислокации в кристаллах деформационно-упрочненного металла искажают кристаллическую решетку и увеличивают энергию кристалла. Когда же металл нагревается, атомы становятся подвижными и перестраиваются в новые, более совершенные кристаллы, содержащие меньше дислокаций. С такой рекристаллизацией и связано разупрочнение, которое наблюдается при отжиге металлов.
Содержание статьи:
Металлы и их сплавы являются одним из самых распространенных материалов для изготовления изделий различных видов. Но так как каждый из типов имеет определенные свойства – перед применением их следует детально изучить.
Зачем нужно знать механические свойства металлов
Основные виды чистых металлов
Металлы относятся к химическим элементам и веществам, которые характеризуются высоким показателем теплопроводности, в большинстве своем имеют жесткость. Под воздействием высоких температур повышается пластичность, обладают ковкостью. Эти характеристики материалов позволяют осуществлять их обработку различными способами.
Металлические материалы и их сплавы характеризуются рядом показателей: химическими, механическими, физическими и эксплуатационными. В совокупности они дают возможность определить фактические характеристики в полном объеме. Выделить наиболее важные из них невозможно. Но для решения определенных задач большее внимание уделяется конкретной группе свойств.
Механические свойства металлов необходимо знать для решения следующих вопросов:
- производство изделия с определенными качествами;
- выбор оптимального процесса обработки заготовки;
- влияние механических характеристик металлических материалов на эксплуатационные свойства продукта.
Для определения конкретных механических свойств применяются различные методы. Испытания металлов и сплавов проводятся с помощью специальных приборов. Это делается в лабораторных условиях. Для достижения точных результатов рекомендуется использовать результаты исследований государственных метрологических организаций.
Механические свойства определяют показатель сопротивляемости того или иного материала на внешние силовые воздействия. Для каждого параметра существует определенные числовые показатели.
Твердость
Методика проверки металлов на твердость
При воздействии внешних факторов на металлические изделия происходит их деформация – пластическая или упругая. Твердость описывает сопротивление этим факторам, характеризует степень сохранения изначальной формы и свойств материала, изделия.
В зависимости от желаемых результатов проверка материала на твердость осуществляется тремя методами:
- статический. На специальный индикатор, расположенный на поверхности металла, прикладывают механическую силу. Это делается постепенно и одновременно с этим фиксируется степень деформации;
- динамический. Воздействие происходит для фиксации упругой отдачи или формирования отпечатка с определенной конфигурацией;
- кинетический. Схож со статическим. Разница заключается в непрерывном воздействии для построения диаграммы изменения характеристик образца.
Измерение твердости зависит от выбранного метода — Бринелля (НВ), Роквелла (шкалы А, В и С) или Виккерса (НV). Все зависит от степени воздействия на материал, с помощью которых можно определить поверхностную, проекционную или объемную твердость.
Шкала Мосса применяется для вычисления показателя твердости редко. Ее суть состоит в вычислении характеристиках объекта методом царапания его поверхности.
Вязкость и хрупкость
Описание показателя вязкости
Эти характеристики указывают на возможность металла оказывать сопротивление при воздействии ударных нагрузок. Показателем является скорость деформации, т.е. изменение изначальной конфигурации заготовки при внешнем воздействии.
Знание показателя вязкости и хрупкости необходимо для расчета поглощаемой энергии воздействия, которая приводит к деформации металлического образца. В зависимости от необходимых данных различают следующие методы измерения и виды вязкости металлов:
- статическая. Происходит медленное воздействие на материал до момента его разрушения;
- циклическая. Образец подвергают многократным нагрузкам с одинаковым или изменяющимся показателем силы. При этом основной величиной циклической вязкости является количество работы, необходимой для разрушения образца;
- ударная. Для ее расчета применяют маятниковый копер. Заготовку крепят на нижнем основании, маятник с рубящим конусом находится в верхней точке. После его опускания происходит взаимодействие металла и рубящей части. Степень деформации характеризуется вязкостью образца.
В зависимости от системы измерения существуют различные показатели вязкости:
- СИ — м²/с;
- СГС – стокс (СТ) или сантистокс (сСт)
Помимо метода испытания необходимо учитывать другие механические свойства металлов – температура на его поверхности и в структуре, влажность в помещении и т.д.
Хрупкость является обратным показателем вязкости. Она определяет, насколько быстро металл или сплав будет разрушаться под воздействием внешней силы.
Напряжение
Виды напряжений
Напряжением называется возникновение внутренних сил с различными векторами направленности при внешнем воздействии. Эта величина может быть внутренняя или поверхностная. Является обязательным для расчета при изготовлении несущих стальных конструкций или элементов оборудования, подвергающихся постоянным нагрузкам.
Главным условием для измерения этого показателя является равномерная нагрузка, действующая в определенном направлении. При этом возникает напряженное состояние образца, который подвергается воздействию уравновешенных сил. Помимо этого, воздействие может быть односекторным или много векторным.
Существуют следующие виды напряжения материалов и их сплавов:
- остаточное. Формируется уже после окончания воздействия внешних факторов. К ним относятся не только механические силы, но и быстрый нагрев или охлаждение образца;
- временные. Возникают только при внешних нагрузках. После их прекращения изделие приобретает изначальные характеристики;
- внутреннее. Чаще всего происходит в результате неравномерного нагрева заготовок.
Напряжение является отношением силы воздействия на площадь, на которую она прилагается.
Кроме прямого давления на поверхность может наблюдаться касательное. Расчет этого параметра требует более сложных методик.
Выносливость и усталость
Пример деформации из-за усталости металла
При длительном приложении внешних сил в структуре образца выявляются деформации и дефекты. Они приводят к потере прочности образца и как следствие – к его разрушению. Это называется усталостью металла. Выносливость является обратной характеристикой.
Такое явление наступает в результате появления последовательных напряжений (внутренних или поверхностных) за определенный промежуток времени. Если структура не подвергается изменению – говорят о хорошем показателе выносливости. В противном случае происходит деформация.
В зависимости от точности расчета выполняют следующие испытания образца на выносливость для того, чтобы узнать механические свойства металлов:
- чистый изгиб. Деталь закрепляется на концах и происходит ее вращение, в результате чего она деформируется;
- поперечный изгиб. Дополнительно выполняется вращение образца;
- изгиб в одной плоскости;
- поперечный и продольный изгиб в одной плоскости;
- неравномерное кручение с повторением цикла.
Эти испытания позволяют определить показатель выносливости и рассчитать время наступления усталости детали.
Для проведения испытаний необходимо руководствоваться принятыми методиками, которые изложены в ГОСТ-1497-84. Особое внимание уделяется отклонению свойств металла от нормы.
Ползучесть
Пример дефекта, возникшего из-за ползучести
Этот показатель определяет степень непрерывной пластической деформации при постоянном воздействии внешних и внутренних факторов. Вычисление этого параметра необходимы для определения жаропрочности металлов и их сплавов.
Для определения ползучести образец нагревают до определенной температуры. После этого наблюдают степень изменения его конфигурации с учетом приложенного напряжения. В зависимости от термического воздействия различают два вида испытаний на ползучесть:
- низкотемпературное. Степень нагрева образца не превышает 0,4 от температуры его плавления;
- высокотемпературная. Коэффициент нагрева больше 0,4 температуры нагрева.
Для проведения испытаний используют стандартные образцы прямоугольной или цилиндрической формы. При этом степень погрешности измерения не должна превышать 0,002 мм. В результате испытаний формируется кривая, характеризующая процесс ползучести.
В видеоматериале показан пример работы маятникового копера:
Механические свойства характеризуют способность материалов сопротивляться действию внешних сил. К основным механическим свойствам относятся прочность, твердость, ударная вязкость, упругость, пластичность, хрупкость и др.
Прочность — это способность материала сопротивляться разрушающему воздействию внешних сил.
Твердость — это способность материала сопротивляться внедрению в него другого, более твердого тела под действием нагрузки.
Вязкостью называется свойство материала сопротивляться разрушению под действием динамических нагрузок.
Упругость — это свойство материалов восстанавливать свои размеры и форму после прекращения действия нагрузки.
Пластичностью называется способность материалов изменять свои размеры и форму под действием внешних сил, не разрушаясь при этом.
Хрупкость — это свойство материалов разрушаться под действием внешних сил без остаточных деформаций.
При статических испытаниях на растяжение определяют величины, характеризующие прочность, пластичность и упругость материала. Испытания производятся на цилиндрических (или плоских) образцах с определенным соотношением между длиной l0 и диаметром d0. Образец растягивается под действием приложенной силы Р (рис. 1, а) до разрушения. Внешняя нагрузка вызывает в образце напряжение и деформацию. Напряжение σ — это отношение силы Р к площади поперечного сечения F0, МПа:
σ = P/F0,
Деформация характеризует изменение размеров образца под действием нагрузки, %:
ε = [(l1—l0)/l0] · 100,
где l1 — длина растянутого образца.
Деформация может быть упругой (исчезающей после снятия нагрузки) и пластической (остающейся после снятия нагрузки).
При испытаниях стоится диаграмма растяжения, представляющая собой зависимость напряжения от деформации. На рис. 1 приведена такая диаграмма для низкоуглеродистой стали. После проведения испытаний определяются следующие характеристики механических свойств.
Предел упругости σу — это максимальное напряжение при котором в образце не возникают пластические деформации.
Предел текучести σт — это напряжение, соответствующее площадке текучести на диаграмме растяжения (рис. 1). Если на диаграмме нет площадки текучести (что наблюдается для хрупких материалов), то определяют условный предел текучести σ0,2 — напряжение, вызывающее пластическую деформацию, равную 0,2 %. Предел прочности (или временное сопротивление) σв — это напряжение, отвечающее максимальной нагрузке, которую выдерживает образец при испытании.
Относительное удлинение после разрыва δ — отношение приращения длины образца при растяжении к начальной длине l0, %:
δ = [(lk—l0)/l0]·100,
где lк — длина образца после разрыва.
Рис. 1. Статические испытания на растяжение: а – схема испытания;
б – диаграмма растяжения
Относительным сужением после разрыва ψ называется уменьшение площади поперечного сечения образца, отнесенное к начальному сечению образца, %:
ψ = [(F0—Fk)/F0]·100,
где Fк — площадь поперечного сечения образца в месте разрыва. Относительное удлинение и относительное сужение характеризуют пластичность материала.
Твердость металлов измеряется путем вдавливания в испытуемый образец твердого наконечника различной формы.
Метод Бринелля основан на вдавливании в поверхность металла стального закаленного шарика под действием определенной нагрузки. После снятия нагрузки в образце остается отпечаток. Число твердости по Бринеллю НВ определяется отношением нагрузки, действующей на шарик, к площади поверхности полученного отпечатка.
Метод Роквелла основан на вдавливании в испытуемый образец закаленного стального шарика диаметром 1,588 мм (шкала В) или алмазного конуса с углом при вершине 120° (шкалы А и С). Вдавливание производится под действием двух нагрузок — предварительной равной 100 Н и окончательной равной 600, 1000. 1500 Н для шкал А, В и С соответственно. Число твердости по Роквеллу HRA, HRB и HRC определяется по разности глубин вдавливания.
В методе Виккерса применяют вдавливание алмазной четырехгранной пирамиды с углом при вершине 136°. Число твердости по Виккерсу HV определяется отношением приложенной нагрузки к площади поверхности отпечатка.
Ударная вязкость определяется работой A, затраченной на разрушение образца, отнесенной к площади его поперечною сечения F; Дж/м2:
KC=A/F
Испытания проводятся ударом специального маятникового копра. Для испытания применяется стандартный надрезанный образец, устанавливаемый на опорах копра. Маятник определенной массы наносит удар по стороне противоположной надрезу.
К физическим свойствам материалов относится плотность, температура плавления, электропроводность, теплопроводность, магнитные свойства, коэффициент температурного расширения и др.
Плотностью называется отношение массы однородного материала к единице его объема.
Это свойство важно при использовании материалов в авиационной и ракетной технике, где создаваемые конструкции должны быть легкими и прочными.
Температура плавления — это такая температура, при которой металл переходит из твердого состояния в жидкое. Чем ниже температура плавления металла, тем легче протекают процессы его плавления, сварки и тем они дешевле.
Электропроводностью называется способность материала хорошо и без потерь на выделение тепла проводить электрический ток. Хорошей электропроводностью обладают металлы и их сплавы, особенно медь и алюминий. Большинство неметаллических материалов не способны проводить электрический ток, что также является важным свойством, используемом в электроизоляционных материалах.
Теплопроводность — это способность материала переносить теплоту от более нагретых частей тел к менее нагретым. Хорошей теплопроводностью характеризуются металлические материалы.
Магнитными свойствами т.е. способностью хорошо намагничиваться обладают только железо, никель, кобальт и их сплавы.
Коэффициенты линейного и объемного расширения характеризуют способность материала расширяться при нагревании. Это свойство важно учитывать при строительстве мостов, прокладке железнодорожных и трамвайных путей и т.д.
Химические свойства характеризуют склонность материалов к взаимодействию с различными веществами и связаны со способностью материалов противостоять вредному действию этих веществ. Способность металлов и сплавов сопротивляться действию различных агрессивных сред называется коррозионной стойкостью, а аналогичная способность неметаллических материалов — химической стойкостью.
К эксплуатационным (служебным) свойствам относятся жаростойкость, жаропрочность, износостойкость, радиационная стойкость, коррозионная и химическая стойкость и др.
Жаростойкость характеризует способность металлического материала сопротивляться окислению в газовой среде при высокой температуре.
Жаропрочность характеризует способность материала сохранять механические свойства при высокой температуре.
Износостойкость — это способность материала сопротивляться разрушению его поверхностных слоев при трении.
Радиационная стойкость характеризует способность материала сопротивляться действию ядерного облучения.
Технологические свойства определяют способность материалов подвергаться различным видом обработки. Литейные свойства характеризуются способностью металлов и сплавов в расплавленном состоянии хорошо заполнять полость литейной формы и точно воспроизводить ее очертания (жидкотекучестъю), величиной уменьшения объема при затвердевании (усадкой), склонностью к образованию трещин и пор, склонностью к поглощению газов в расплавленном состоянии. Ковкость — это способность металлов и сплавов подвергаться различным видам обработки давлением без разрушения. Свариваемость определяется способностью материалов образовывать прочные сварные соединения. Обрабатываемость резанием определяется способностью материалов поддаваться обработке режущим инструментом.
Теория сплавов
Металлическим сплавом называется материал, полученный сплавлением двух или более металлов или металлов с неметаллами, обладающий металлическими свойствами. Вещества, которые образуют сплав называются компонентами.
Фазой называют однородную часть сплава, характеризующуюся определенными составом и строением и отделенную от других частей сплава поверхностью раздела. Под структурой понимают форму размер и характер взаимного расположения фаз в металлах и сплавах. Структурными составляющими называют обособленные части сплава, имеющие одинаковое строение с присущими им характерными особенностями.
Виды сплавов по структуре. По характеру взаимодействия компонентов все сплавы подразделяются на три основных типа: механические смеси, химические соединения и твердые растворы.
Механическая смесь двух компонентов А и В образуется, если они не способны к взаимодействию или взаимному растворению. Каждый компонент при этом кристаллизуется в свою кристаллическую решетку. Структура механических смесей неоднородная, состоящая из отдельных зерен компонента А и компонента В. Свойства механических смесей зависят от количественного соотношения компонентов: чем больше в сплаве данного компонента, тем ближе к его свойствам свойства смеси.
Химическое соединение образуется когда компоненты сплава А и В вступают в химическое взаимодействие. При этом при этом соотношение чисел атомов в соединении соответствует его химической формуле АmВn . Химическое соединение имеет свою кристаллическую решетку, которая отличается от кристаллических решеток компонентов. Химические соединения имеют однородную структуру, состоящую из одинаковых по составу и свойствам зерен.
При образовании твердого раствора атомы одного компонента входят в кристаллическую решетку другого. Твердые растворы замещения образуются в результате частичного замещения атомов кристаллической решетки одного компонента атомами второго (рис. 6, б).
Твердые растворы внедрения образуются когда атомы растворенного компонента внедряются в кристаллическую решетку компонента -растворителя (рис. 6, в). Твердый раствор имеет однородную структуру, одну кристаллическую решетку. В отличие от химического соединения твердый раствор существует не при строго определенном соотношении компонентов, а в интервале концентраций. Обозначают твердые растворы строчными буквами греческого алфавита: α, β, γ, δ и т. д.
Диаграмма состояния
Диаграмма состояния показывает строение сплава в зависимости от соотношения компонентов и от температуры. Она строится экспериментально по кривым охлаждения сплавов (рис. 8). В отличие от чистых металлов сплавы кристаллизуются не при постоянной температуре, а в интервале температур. Поэтому на кривых охлаждения сплавов имеется две критические точки. В верхней критической точке, называемой точкой ликвидус (tл), начинается кристаллизация. В нижней критической точке, которая называется точкой солидус (tc), кристаллизация завершается. Кривая охлаждения механической смеси (рис. 8, а) отличается от кривой охлаждения твердого раствора (рис. 8, б) наличием горизонтального участка. На этом участке происходит кристаллизация эвтектики.
Эвтектикой называют механическую смесь двух фаз, одновременно кристаллизовавшихся из жидкого сплава. Эвтектика имеет определенный химический состав и образуется при постоянной температуре.
Диаграмму состояния строят в координатах температура-концентрация. Линии диаграммы разграничивают области одинаковых фазовых состояний. Вид диаграммы зависит от того, как взаимодействуют между собой компоненты. Для построения диаграммы состояния используют большое количество кривых охлаждения для сплавов различных концентраций. При построении диаграммы критические точки переносятся с кривых охлаждения на диаграмму и соединяются линией. В получившихся на диаграмме областях записывают фазы или структурные составляющие. Линия диаграммы состояния на которой при охлаждении начинается кристаллизация сплава называется линией ликвидус, а линия на которой кристаллизация завершается — линией солидус.
Виды диаграмм состояния
Диаграмма состояния сплавов, образующих механические смеси (рис. 9), характеризуется отсутствием растворения компонентов в твердом состоянии. Поэтому в этом сплаве возможно образование трех фаз: жидкого сплава Ж, кристаллов А и кристаллов В. Линия АСВ диаграммы является линией ликвидус: на участке АС при охлаждении начинается кристаллизация компонента А, а на участке СD — компонента В. Линия DСВ является линией солидус, на ней завершается кристаллизация А или В и при постоянной температуре происходит кристаллизация эвтектики Э. Сплавы концентрация которых соответствует точке С диаграммы называются эвтектическими, их структура представляет собой чистую эвтектику.
Сплавы, расположенные на диаграмме левее эвтектического, называются доэвтектическими, их структура состоит из зерен А и эвтектики. Те сплавы которые на диаграмме расположены правее эвтектического, называются заэвтектическими, их структура представляет собой зерна В, окруженные эвтектикой.
Диаграмма состояния сплавов с неограниченной растворимостью компонентов в твердом состоянии изображена на рис. 10. Для этого сплава возможно образование двух фаз: жидкого сплава и твердого раствора а. На диаграмме имеется всего две линии, верхняя является линией ликвидус, а нижняя — линией солидус.
Диаграмма состояния сплавов с ограниченной растворимостью компонентов в твердом состоянии показана на рис 11. В этом сплаве могут существовать три фазы — жидкий сплав, твердый раствор α компонента В в компоненте А и твердый раствор β компонента А в компоненте В. Данная диаграмма содержит в себе элементы двух предыдущих. Линия АСВ является линией ликвидус, линия АDСЕВ — линией солидус. Здесь также образуется эвтектика, имеются эвтектический, доэвтектический и заэвтектический сплавы. По линиям FD и EG происходит выделение вторичных кристаллов αIIи βII(вследствие уменьшения растворимости с понижением температуры). Процесс выделения вторичных кристаллов из твердой фазы называется вторичной кристаллизацией.
Диаграмма состояния сплавов, образующих химическое соединение (рис. 12) характеризуется наличием вертикальной линии, соответствующей соотношением компонентов в химическом соединении АmВn. Эта линия делит диаграмму на две части, которые можно рассматривать как самостоятельные диаграммы сплавов, образуемых одним из компонентов с химическим соединением. На рис. 12 изображена диаграмма для случая, когда каждый из компонентов образует с химическим соединением механическую смесь.
Основные механические свойства
Основные механические свойства металлов представлены прочностью, твердостью, пластичностью, ударной вязкостью, износоусточивостью и ползучестью. Прочность металлов представляет собой их устойчивость к деформации и разрушению под воздействием растягивания, сжимания, скручивания, изгибания и срезания. Нагрузки при этом делятся на внешние и внутренние, а также на статические и динамические.
Внешние нагрузки представлены весом, давлением и т.д., тогда как внутренние нагрузки представлены нагреванием, охлаждением, изменением структуры металла и т.д.
Твердостью металлов называют коэффициент их сопротивления проникновению в них более твердого тела. Упругостью – способность к восстановлению первоначальной формы после окончания действия какой-либо внешней нагрузки. Пластичностью – способность к изменению формы без разрушения и под действием определенной нагрузки, а также сохранение формы после снятия нагрузки. Ударная вязкость представляет собой сопротивление металлов к воздействию ударных нагрузок, измеряемых в Джоулях на метр квадратный. Ползучесть – медленную и непрерывную пластическую деформацию под воздействием постоянных нагрузок (особенно при повышенной температуре). Усталость – постепенные разрушения при большом количестве повторно-переменной нагрузки, тогда как выносливость – свойство к выдерживанию данной нагрузки.
Дополнительные механические свойства
Основными механическими свойствами металлов являются: временное сопротивление (предел прочности при условном напряжении), истинное сопротивление разрыву (предел прочности при действительном напряжении), физический предел текучести (деформация при минимальном напряжении) и условный предел текучести (напряжение, в условиях которого остаточное удлинение участка образца составляет 0,2%).
Механические свойства металлов определяют в процессе статических, динамических и повторно-переменных испытаний.
Также к механическим свойствам металлов относят: условный предел пропорциональности (напряжение, в условиях которого отклонение от линейной зависимости достигает 50%-ного увеличения величины), предел упругости (напряжение, соответствующее остаточной деформации), относительное удлинение после разрыва (приращение длины образца к изначальной расчетной длине) и относительное сужение после разрыва.
Основные свойства металлов и сплавов
Подробности- Подробности
- Опубликовано 27.05.2012 13:19
- Просмотров: 57882
Чтобы машина работала долго и надежно в различных условиях, необходимо ее детали изготовлять из материалов, имеющих определенные физические, механические, технологические и химические свойства.
Физические свойства. К этим свойствам относятся: цвет, удельный вес, теплопроводность, электропроводность, температура плавления, расширение при нагревании.
Цвет металла или сплава является одним из признаков, позволяющих судить о его свойствах. При нагреве по цвету поверхности металла можно примерно определить, до какой температуры он нагрет, что особо важно для сварщиков. Однако некоторые металлы (алюминий) при нагреве не меняют цвета.
Поверхность окисленного металла имеет иной цвет, чем не окисленного.
Удельный вес — вес одного кубического сантиметра вещества, выраженный в граммах. Например, углеродистая сталь имеет удельный вес, равный 7,8 г/см. В авто- и авиастроении вес деталей является одной из важнейших характеристик, поскольку конструкции должны быть не только прочными, но и легкими. Чем больше удельный вес металла, тем более тяжелым (при равном объеме) получается изделие.
Теплопроводность — способность металла проводить тепло — измеряется количеством тепла, которое проходит по металлическому стержню сечением в 1 см2 за 1 мин. Чем больше теплопроводность, тем труднее нагреть кромки свариваемой детали до нужной температуры.
Температура плавления — температура, при которой металл переходит из твердого состояния в жидкое. Чистые металлы плавятся при одной постоянной температуре, а сплавы — в интервале температур.
Расширение металлов при нагревании является важной характеристикой. Поскольку при сварке происходит местный нагрев (нагрев лишь небольшого участка изделия), то изделие в различных частях нагревается до разных температур, что приводит к деформированию (короблению) изделия. Две детали, изготовленные из разных металлов и нагретые до одинаковой температуры, будут расширяться по-разному. Поэтому, если эти детали будут скреплены между собой, то при нагревании могут изогнуться и даже разрушиться.
Усадка — уменьшение объема расплавленного металла при его охлаждении. В процессе усадки металла сварного шва наблюдается коробление детали, появляются трещины или образуются усадочные раковины. Каждый металл имеет свою величину усадки. Чем она больше, тем труднее получить качественное соединение.
Механические свойства. К механическим свойствам металлов и сплавов относятся прочность, твердость, упругость, пластичность, вязкость.
Эти свойства обычно являются решающими показателями, по которым судят о пригодности металла к различным условиям работы.
Прочность — способность металла сопротивляться разрушению при действии на него нагрузки.
Твердость — способность металла сопротивляться внедрению в его поверхность другого более твердого тела.
Упругость — свойство металла восстанавливать свою форму и размеры после прекращения действия нагрузки. Высокой упругостью должна обладать, например, рессоры и пружины, поэтому они изготовляются из специальных сплавов.
Пластичность — способность металла изменять форму и размеры под действием внешней нагрузки и сохранять новую форму и размеры после прекращения действия сил. Пластичность — свойство, обратное упругости. Чем больше пластичность, тем легче металл куется, штампуется, прокатывается.
Вязкость — способность металла оказывать сопротивление быстро возрастающим (ударным) нагрузкам. Вязкость — свойство, обратное хрупкости. Вязкие металлы применяются в тех случаях, когда детали при работе подвергаются ударной нагрузке (детали вагонов, автомобилей и т. п.).
Механические свойства выявляются при воздействии на металл растягивающих, изгибающих или других сил. Механические свойства металлов характеризуются: 1) пределом прочности в кг/мм2; 2) относительным удлинением в %;3) ударной вязкостью в кгм/см2; 4) твердостью; 5) углом загиба. Перечисленные основные свойства металлов определяются следующими испытаниями: 1) на растяжение; 2) на загиб; 3) на твердость; 4) на удар. Все эти испытания производятся на образцах металла при помощи специальных машин.
Испытание на растяжение. Испытанием на растяжение определяют предел прочности и относительное удлинение металла. Пределом прочности называется усилие, которое надо приложить на единицу площади поперечного сечения образца металла, чтобы разорвать его.
Для испытания на растяжение изготовляют образцы, форма и размеры которых установлены ГОСТ 1497-42. На рисунке представлены размеры и форма цилиндрических образцов для испытания на растяжение на специальных разрывных машинах» Головки образца закрепляют в захваты машины, после чего дают нагрузку, растягивающую образец до разрушения. Если величину разрушающего усилия выраженного в килограммах, разделить на число квадратных миллиметров поперечного сечения образца Fo9 то получим величину предела прочности в килограммах на квадратный миллиметр (предел прочности обозначается ов):
Для испытания листового металла изготовляют плоские образцы. На рисунке, в показаны размеры и форма плоских образцов для испытания сварных соединений. Малоуглеродистые стали имеют предел прочности около 40 кг/мм2 стали повышенной прочности и специальные — 150 кг/мм2. Для вычисления относительного удлинения, обозначаемого Ъ, определяют сначала абсолютное удлинение образца. Для этого разорванные части образца плотно прикладывают друг к другу и замеряют расстояние между метками границ расчетной длины (получают размер /). Затем из полученной длины вычитают первоначальную расчетную длину образца /о, остаток делят на первоначальную расчетную длину и умножают на 100.
Относительное удлинение металла есть выраженное в процентах отношение остающегося после разрыва увеличения длины образца К его первоначальной длине.
Относительное удлинение малоуглеродистой стали примерно равно 20%. Относительное удлинение характеризует пластичность металла, оно снижается с повышением предела прочности.
Испытание на твердость. В нашей промышленности для определения твердости металла чаще всего применяется прибор Бринеля или Роквелла. Твердость по Бринелю определяют следующим образом. Твердый стальной шарик диаметром 10,5 или 2,5 мм вдавливается под прессом в испытуемый металл. Затем при помощи бинокулярной трубки измеряют диаметр отпечатка, который получился под шариком на испытуемом металле. По диаметру отпечатка и по соответствующей таблице определяют твердость по Бринелю.
Твердость некоторых сталей в единицах по Бринелю:
Малоуглеродистая сталь……ИВ 120—130
Сталь повышенной прочности …. ИВ 200—300 Твердые закаленные стали…..ИВ 500—600
С увеличением твердости пластичность металла снижается. Испытание на удар. Этим испытанием определяют способность металла противостоять ударным нагрузкам. Испытанием на удар определяют ударную вязкость металла.
Ударная вязкость определяется путем испытания образцов на специальных маятниковых копрах. Для испытания применяются специальные квадратные образцы с надрезом (фиг. 11,е). Чем меньше ударная вязкость, тем более хрупок и тем менее надежен в работе такой металл. Чем выше ударная вязкость, тем металл лучше. Хорошая малоуглеродистая сталь имеет ударную вязкость, равную 10—15 кгм/см2.
Во многих случаях для проверки пластичности металлов или сварных соединений применяют технологические испытания образцов, к которым относятся испытания на угол загиба, на сплющивание, продавливание и др.
Испытания на загиб. Для проведения испытания на загиб образец из металла укладывается на шарнирных опорах и нагрузкой, приложенной посредине, изгибается до появления трещин на выпуклой стороне образца. После этого испытание прекращают и измеряют величину внешнего угла а. Чем больше угол загиба, тем пластичнее металл. Качественная малоуглеродистая сталь дает угол загиба 180°.
Для определения пластичности сварного соединения вырезают такой же плоский образец со сварным швом, расположенным посредине, и со снятым усилением.
Испытанием на сплющивание определяют способность металла деформироваться при сплющивании. Этой пробе обычно подвергают отрезки сварных труб диаметром 22—52 мм со стенками толщиной от 2,5 до 10 мм. Проба заключается в сплющивании образца под прессом до получения просвета между внутренними стенками трубы, равного учетверенной толщине стенки трубы. При этом испытании образец не должен давать трещин.
Технологические свойства. В эту группу свойств входят свариваемость, жидкотекучесть, ковкость, обрабатываемость резанием и другие. Технологические свойства имеют весьма важное значение при производстве тех или иных технологических операций и определяют пригодность металла к обработке тем или иным способом.
Свариваемость — свойство металлов давать доброкачественные соединения при сварке, характеризующиеся отсутствием трещин и других пороков металла в швах и прилегающих зонах, причем иногда металл хорошо сваривается одним методом и неудовлетворительно— другим. Например, дюралюминий удовлетворительно сваривается точечной сваркой и плохо — газовой, чугун хорошо сваривается газовой сваркой с подогревом и плохо — дуговой и т. д.
Жидкотекучесть — способность расплавленных металлов и сплавов заполнять литерную форму.
Ковкость — способность металлов и сплавов изменять свою форму при обработке давлением.
Обрабатываемость резанием — способность металла более или менее легко обрабатываться острым режущим инструментом (резцом, фрезой, ножовкой и т. д.) при различных операциях механической обработки (резание, фрезерование и т. д.).
Химические свойства. Под химическими свойствами металлов подразумевается их способность вступать в соединение с различными веществами и в первую очередь с кислородом. Чем легче металл вступает в соединение с вредными для него элементами, тем легче он разрушается. Разрушение металлов под действием окружающей их среды (воздуха, влаги, растворов солей, кислот, щелочей) называется коррозией. Для достижения высокой коррозионной стойкости изготавливаются специальные стали (нержавеющие, кислотостойкие и т. п.).
Читайте также
Добавить комментарий
Рис. 1 Распределение деформации и толщины |
Напряжение
Деформацию можно определить просто как измеримую деформацию металла.Другими словами, металл должен быть «натянут», чтобы изменить свою форму. Напряжения могут быть положительными (растяжение металла или растяжение) или отрицательными (растяжение металла или сжатие). Напряжения также могут быть постоянными (пластичные) или восстанавливаемыми (упругими). Результат упругого напряжения обычно называют упругим возвратом или упругим восстановлением.
Помните, что каждый тип металла хочет вернуться к своей первоначальной форме, когда он деформирован. Количество металлических пружин зависит от их механических свойств.Когда инженеры ссылаются на области детали, которые являются «высоконапряженными», они обычно ссылаются на области, которые были подвергнуты значительному растяжению или сжатию. На рисунке 1 показано моделируемое изображение растянутой детали. Каждый цвет представляет различный тип и количество напряжения. Некоторые штаммы положительные, а другие отрицательные.
Стресс
Стресс — это просто результат напряжения металла. При воздействии напряжения металл подвергается внутренним изменениям, которые вызывают его отскок или неравномерную деформацию.Захваченные напряжения внутри детали часто приводят к потере плоскостности или других геометрических характеристик. Все порезанные или сформованные детали подвергаются нагрузке.
Распределение растяжения
Рисунок 2 Испытание на растяжение / растяжение |
Распределение растяжения является очень важным механическим свойством. Характеристики распределения металла по растяжению контролируют, сколько площади поверхности растянутого металла постоянно деформируется.Распределение растяжения определяется в первую очередь путем проверки толщины металла, когда он деформируется при растяжении в процессе испытания на растяжение. Чем более равномерное распределение по толщине, тем лучше распределение по растяжению. Распределение растяжения также частично выражается в значении n металла. На рисунке 2 показаны различные результаты распределения растяжений. Красные области образца тестового купона представляют собой области, которые были растянуты.
n Значение
Чтобы понять значение n, иначе называемое показателем рабочего или деформационного упрочнения, необходимо понимать, что каждый раз, когда металл подвергается постоянной деформации, происходит упрочнение.То же самое происходит, когда вы сгибаете вешалку взад-вперед. Когда вы сгибаете вешалку, становится все труднее сгибаться. Также становится сложнее согнуть его в одном месте. Это увеличение прочности является результатом работы или деформационного упрочнения. Однако, если вы продолжите сгибать вешалку в том же месте, она в конечном итоге потерпит неудачу.
Как ни парадоксально, материалы должны подвергаться упрочнению для достижения как хорошей растяжимости, так и распределения растяжения. Как они работают — это ключ.Значение n материала может быть определено в основном как растяжимость металла; однако это также является выражением характеристик распределения материала по растяжению.
Возможно, одно из самых важных механических свойств, которое следует учитывать, если штампованная деталь требует большого растяжения, значение n выражается численно в числах от 0,100 до 0,300 и обычно выполняется с двумя или тремя десятичными знаками. Чем выше число, тем больше растяжимость металла и распределение растяжения.Металлы с более высокой прочностью, такие как пружинная сталь, имеют очень низкие значения n, в то время как металлы, такие как те, которые используются для изготовления масляных поддонов и других глубокоформованных деталей, обычно имеют более высокие значения n.
Значение n металла также является ключевым механическим значением, используемым при создании предельных диаграмм формирования. (Это будет обсуждаться в последующих частях этой серии.)
Значение r
Значение металла r определяется металлургически как коэффициент пластической деформации. Чтобы понять эту концепцию, вы должны четко знать разницу между растяжкой и рисованием.Растяжение — это процесс формования металла, при котором металл подвергается растяжению. Это приводит к увеличению площади поверхности. Такие элементы, как большинство автомобильных капотов и крыльев, изготавливаются с использованием этого процесса.
Вытягивание — это перемещение металла в полость или через пуансон посредством пластического потока или подачи металла. Такие элементы, как большие банки, поддоны для масла и детали глубокой формы, обычно изготавливаются с использованием этого процесса.
Рисунок 3 Коэффициент деформации пластика r Значение |
Значение r металла можно определить просто как способность металла течь.Это также выражается численно с использованием значения от 1 до 2, которое обычно выполняется с двумя десятичными знаками. Чем больше значение r, тем более тягучий металл ( Рис. 3 ).
Значение r металла неодинаково по всему листу. Большинство металлов имеют разные значения r относительно направления прокатки металла. Проверка значения r металла требует испытания на растяжение в трех разных направлениях — с направлением прокатки, против направления прокатки и под углом 45 градусов к направлению прокатки.Результаты теста обычно усредняются и выражаются в виде r-бара или среднего значения r.
Рисунок 4 Серьга, вызванная различием в значении металла |
Различия в коэффициенте пластической деформации приводят к серьге металла при вытягивании. Например, при рисовании круглой оболочки из круглой заготовки, результаты будут иметь почти квадратное дно на фланце чашки. Этот эффект (, рис. 4 ) вызван различными величинами потока металла по отношению к металлу
Топография поверхности
Топография поверхности металла, определяемая просто как обработка поверхности металла, создается в основном во время процесса прокатки металла.Топография поверхности является важной характеристикой металла. При вытягивании металлы часто требуют обработки поверхности, способной удерживать смазку. Топография поверхности определяется с помощью измерительного инструмента, который называется профилометр.
Это завершает обсуждение характеристик листового металла. Следующая статья этой серии будет посвящена резке металла.
Металл , любой из классов веществ, характеризующихся высокой электрической и теплопроводностью, а также пластичностью, пластичностью и высокой отражающей способностью света.
Блок из золота Блок из металлического золота. © Jupiterimages CorporationБританика Викторина
Металлы: факт или вымысел?
Марганец — красновато-коричневый металл.
Приблизительно три четверти всех известных химических элементов составляют металлы. Наиболее распространенными сортами в земной коре являются алюминий, железо, кальций, натрий, калий и магний. Подавляющее большинство металлов содержится в рудах (минеральных веществах), но некоторые из них, такие как медь, золото, платина и серебро, часто находятся в свободном состоянии, потому что они не легко реагируют с другими элементами.
Металлы, как правило, кристаллические твердые вещества. В большинстве случаев они имеют относительно простую кристаллическую структуру, отличающуюся плотной упаковкой атомов и высокой степенью симметрии.Как правило, атомы металлов содержат менее половины полного набора электронов в их внешней оболочке. Из-за этой характеристики металлы, как правило, не образуют соединения друг с другом. Однако они легче соединяются с неметаллами (например, кислородом и серой), которые обычно имеют более половины максимального числа валентных электронов. Металлы сильно различаются по своей химической реактивности. Наиболее реактивными являются литий, калий и радий, в то время как низкореакционноспособными являются золото, серебро, палладий и платина.
Высокая электрическая и теплопроводность простых металлов (т.е. непереходных металлов периодической таблицы) лучше всего объясняется со ссылкой на теорию свободных электронов. Согласно этой концепции, отдельные атомы в таких металлах потеряли свои валентные электроны во всем твердом теле, и эти свободные электроны, которые вызывают проводимость, движутся как группа по всему телу. В случае более сложных металлов (т.е. переходных элементов) проводимость лучше объясняется теорией зон, которая учитывает не только наличие свободных электронов, но также их взаимодействие с так называемыми d электронами.
Получите эксклюзивный доступ к контенту из нашего первого издания 1768 года с вашей подпиской. Подпишитесь сегодняМеханические свойства металлов, такие как твердость, способность противостоять многократным нагрузкам (усталостная прочность), пластичность и пластичность, часто связаны с дефектами или несовершенством их кристаллической структуры. Например, отсутствие слоя атомов в его плотно упакованной структуре позволяет металлу пластически деформироваться и предотвращает его хрупкость.
% PDF-1.6 % 1 0 объектов >>> endobj 2 0 объектов > поток UUID: 46d28c5b-A341-b74c-9060-4eb1c55360dd саман: DocId: INDD: 4077309b-c29e-11e1-90c3-ed17f1a77285 xmp.id:4187c42d-4d58-44dc-8101-9b1cef8b70b9 Доказательство: pdf xmp.iid: 653e3c5f-7a96-4744-a443-2954ca28a6fb саман: DocId: INDD: 4077309b-c29e-11e1-90c3-ed17f1a77285 саман: DocId: INDD: 4077309b-c29e-11e1-90c3-ed17f1a77285 дефолт
— совокупность показателей, характеризующих сопротивление материала действующей на него нагрузке, степень деформации под нагрузкой и его поведение в процессе разрушения. Соответственно, свойства измеряются в напряжениях (обычно в килограммах-силах на кв. Мм [кгс / мм 2 ] или меганьютонах на кв. М [МН / м 2 ]), деформациях (в процентах), удельной деформации и разрушении энергия (обычно в кгс.м / см 2 или мегаджоуля на кв. м [МДж / м 2 ]), а также скорость развития процесса отказа при статической или многократной нагрузке (чаще всего в миллиметрах в секунду или на тысячу циклов нагрузки ). Механические свойства материалов определяются при механических испытаниях образцов различной формы.
Материалы в конструкциях подвергаются самым различным нагрузкам (рис. 1), работают под растяжением, сжатием, изгибом, скручиванием, сдвигом и другими факторами, или они могут подвергаться совместному действию нескольких типов нагрузок, таких как растяжение и изгиб.Условия использования материалов также разнообразны с точки зрения температуры, окружающей среды, скорости приложения нагрузки и характера ее изменения во времени. Соответственно существует множество показателей механических свойств материалов и множество методов механических испытаний. Испытания на растяжение, твердость и ударный изгиб наиболее широко используются для металлов и конструкционных пластиков; Хрупкие конструкционные материалы, такие как керамика и металлокерамика, часто испытывают на сжатие и статическое изгибание. Также важно оценить механические свойства композиционных материалов при испытаниях на сдвиг.
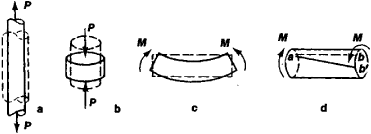
Рисунок 1 . Диаграммы деформации при различных режимах напряжения: (а) растяжение, (б) сжатие, (в) изгиб, (г) скручивание (пунктирная линия указывает на первоначальную форму образцов)
Диаграмма напряжения-деформации . Нагрузка, приложенная к образцу, вызывает его деформацию. Корреляции между нагрузкой и деформацией описываются диаграммой напряжения-деформации (рис. 2). Деформация образца (при растяжении, длина приращения l ) первоначально пропорциональна растущей нагрузке P , а затем в точке n пропорциональность нарушается.Однако для увеличения деформации требуется дальнейшее увеличение нагрузки P . Когда Δ × > Δ или деформация развивается без приложения внешней силы, под постепенно уменьшающейся нагрузкой. Внешний вид диаграммы напряжения-деформации не изменится, если на ординате нанесено напряжение σ = P / F 0 , а на абсциссе нанесено относительное удлинение δ = Δ л / л 0 ( где F 0 и l 0 — начальное поперечное сечение и расчетная длина образца, соответственно).
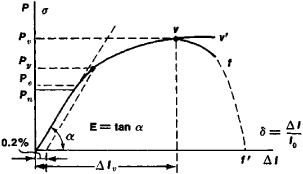
Рисунок 2 . Типичная диаграмма напряжения-деформации при растяжении металлоконструкций
Прочность материалов измеряется напряжениями, характеризующими нагрузку на единицу поперечного сечения образца, σ = P / F 0 (кгс / мм 2 ) , Напряжение σ n = P n / F 0 , при котором пропорциональность увеличения деформации нагрузке нарушается, называется пределом пропорциональности.Для нагрузки P < P n снятие нагрузки с образца приводит к исчезновению деформации, возникшей под действием приложенного усилия. Такая деформация называется упругой. Характер деформации может не измениться, если нагрузка немного превышает P n — как и раньше, она сохранит свой упругий характер. Максимальная нагрузка, которую выдерживает образец без появления остаточной пластической деформации при разгрузке, определяет предел упругости материала: σ e = P e / F 0 .
В неметаллических конструкционных материалах (пластмассах или резине) приложенная нагрузка может вызвать упругую, высокоэластичную или постоянную деформацию. В отличие от упругой деформации, высокоэластичная деформация исчезает со временем, а не сразу после снятия нагрузки. Высокоэластичные армированные полимеры (такие как Fiberglas и угольные пластики) разрушаются при удлинении на 1-3 процента. Высокоэластичная деформация появляется в некоторых армированных полимерах на последних стадиях нагружения. Модуль высокой упругости ниже, чем модуль упругости; поэтому диаграмма напряжения в этом случае имеет тенденцию отклоняться в сторону абсциссы.
Упругие свойства . В упругой области напряжение и деформация взаимосвязаны константой пропорциональности. При расширении σ = E δ, где E — модуль нормальной упругости, который численно равен тангенсу угла наклона прямолинейного отрезка кривой σ = σ (δ) к оси деформации ( Фигура 2). Во время испытания на растяжение цилиндрического или плоского образца — трехосное деформированное состояние (увеличение длины в направлении действия приложенных сил и уменьшение линейных размеров в двух других взаимно перпендикулярных направлениях; δ 1 > 0; δ 2 = 3 <0) соответствует одноосному напряженному состоянию ( 1 > 0; 2 = 0 = 3 = 0).Соотношение между поперечной деформацией и растяжением (коэффициент Пуассона), Jμ = δ 2 / δ 1 , изменяется в очень узком диапазоне в пределах упругости для основных конструкционных материалов (0,27–0,30 для сталей, 0,30–0,33 для алюминиевых сплавов). Коэффициент Пуассона является одной из основных расчетных характеристик. Если известны µ и E , то модуль сдвига G = E / [2 (1 + μ)] и объемный модуль K = E / [3 (l — 2μ)] можно определить по расчету.Тензометры используются для определения E, G и μ.
Стойкость к пластической деформации . Заметная необратимая пластическая деформация, которая не исчезает при снятии нагрузки, появляется в дополнение к неуклонно растущей упругой деформации при нагрузках P> P и . Напряжение, при котором относительная пластическая деформация (или, при растяжении, удлинение) достигает заданного значения (0,2%, согласно ГОСТу), называется произвольным пределом текучести и обозначается как σo.2 = P y / F 0 . На практике точность современных методов тестирования такова, что σ n и σ e определяются с заданными допусками с точки зрения отклонения от пропорциональности (увеличение в кроватке на 25–50 процентов [90 — α]) и величина перманентной деформации (0,003–0,05 процента) соответственно, и мы говорим о произвольных пределах пропорциональности и эластичности. Кривая нагрузки-удлинение конструкционных металлов может иметь максимум (точка v на рисунке 2) или она может быть прерывистой, когда достигается максимальная нагрузка P .Соотношение P v / F 0 = σ v характеризует предел прочности материала на растяжение. Когда максимум на кривой удлинения нагрузки присутствует в области нагрузок, которые лежат слева от v на кривой, образец деформируется равномерно по всей длине l 0 , постепенно уменьшаясь в диаметре, но сохраняя исходный цилиндрической или призматической формы. Металлы упрочняются при пластической деформации; поэтому, несмотря на уменьшение поперечного сечения образца, для дальнейшей деформации необходимо приложить увеличивающуюся нагрузку.Величина 1 , как и произвольная 0,2 , n и e , характеризует сопротивление металлов пластической деформации. На участке диаграммы напряжения-деформации справа от v форма вытянутого образца изменяется: начинается период концентрированной деформации, который выражается в виде «шейки». Уменьшение сечения на шейке «обгоняет» упрочнение металлов. Это объясняет уменьшение внешней нагрузки в сегменте P v -P f .
Во многих конструкционных материалах сопротивление пластической деформации в упругопластической области практически одинаково при растяжении и сжатии. Значительные различия в этой характеристике при растяжении и сжатии характерны для некоторых металлов и сплавов (например, магниевых сплавов и высокопрочных сталей). Стойкость к пластической деформации оценивается особенно часто (например, при контроле качества продукции или мониторинге условий термообработки) на основе результатов испытаний на твердость, проводимых путем оттиска твердого наконечника в форме сферы (твердость по Бринеллю или Роквеллу) , конус (твердость по Роквеллу) или пирамида (твердость по Виккерсу).Испытания на твердость не требуют нарушения целостности детали и, следовательно, являются наиболее широко используемым средством контроля механических свойств. Твердость по Бринеллю (HB) при вдавливании шарика диаметром D под нагрузкой P характеризует среднее напряжение сжатия, произвольно рассчитанное на единицу поверхности сферической выемки диаметром d :
Характеристики пластичности . Пластичность конструкционных материалов при растяжении оценивается по удлинению δ = ( л f — л 0 ) / л 0 X 100% или сужению ϕ = ( F 0 — F f ) / F 0 X 100 процентов; при сжатии с точки зрения укорочения Δ = ( ч 0 — ч f ) / ч 0 X 100 процентов (где ч 0 и ч f начальная и конечная высота образца); и при скручивании по максимальному углу закручивания θ рабочей части образца в радианах или по относительному сдвигу γ = θ r (где r — радиус образца).Конечная ордината диаграммы напряжения-деформации (точка f на рисунке 2) характеризует сопротивление разрушению S f металла, которое определяется как S f = P f / F f (где F f — фактическая площадь в точке разрыва).
Характеристики отказа . Отказ происходит не мгновенно (в точке и ), а скорее развивается со временем.Начало сбоя может соответствовать некоторой промежуточной точке на сегменте и , и весь процесс заканчивается, когда нагрузка постепенно уменьшается до нуля. Положение точки f на диаграмме напряжения-деформации определяется в основном жесткостью испытательной машины и инерцией измерительной системы. Это делает количество S f в значительной степени произвольным.
После расширения многие конструкционные металлы (стали, в том числе высокопрочные, а также жаропрочные хромоникелевые сплавы и мягкие алюминиевые сплавы) разрушаются после значительной пластической деформации, что приводит к образованию шейки.Поверхность разрушения часто лежит под углом приблизительно 45 ° к направлению растягивающей силы (например, в высокопрочных алюминиевых сплавах). При определенных условиях (например, при испытании холоднокатаных сталей в жидком азоте или водороде и при воздействии растягивающих напряжений и агрессивной среды для металлов, склонных к коррозии под воздействием напряжения) разрушение происходит в участках, перпендикулярных растягивающей силе. (даже перелом), без макропластической деформации.
Прочность материалов, достигаемых в элементах конструкции, зависит не только от механических свойств самого металла, но также от формы и размера детали (эффекты формы и масштаба), упругой энергии, накопленной в нагруженной структуре, характера эффективной нагрузки (статической, динамической или периодически изменяющейся величины), диаграмма приложенных внешних сил (одноосное и двухосное удлинение, удлинение с приложенным изгибом и т. д.), рабочая температура и окружающая среда.Зависимость прочности и пластичности металлов от формы характеризуется чувствительностью к надрезу, которая обычно оценивается из соотношения прочности на растяжение надрезанных и гладких образцов (в цилиндрических образцах надрез обычно вырезается в виде круглого углубления в полосках он прорезан в виде центрального отверстия или боковых углублений). Для многих конструкционных материалов это отношение больше 1 при статической нагрузке из-за значительной локальной пластической деформации на вершине надреза.Чем острее выемка, тем ниже локальная пластическая деформация и тем больше доля ровного разрушения в поперечном сечении трещины. Хорошо развитый равномерный разрыв может быть получен в большинстве конструкционных материалов при комнатной температуре в лабораторных условиях, если образцы с большим поперечным сечением (чем пластичнее материал, тем толще поперечное сечение) подвергаются растяжению или изгибу после узкой специальной щели с в образце была сделана искусственная трещина (рис. 3). Когда широкий, плоский образец
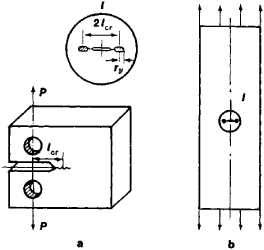
Рисунок 3 .Образец с усталостной трещиной, специально созданной на пике надреза для определения K, c. Испытания на эксцентричное натяжение (а) и осевое натяжение (б).
растянут, пластическая деформация затруднена и ограничена небольшой областью размером 2r y (заштрихованная область на рис. 3, b), которая примыкает к концу трещины. Даже разрушение обычно характерно для эксплуатационных отказов конструктивных элементов.
Такие показатели, как критический коэффициент интенсивности напряжений при плоской деформации K 1c и вязкость разрушения G 1c = K 2 1c / E , которые были предложены американским ученым ГРАММ.Р. Ирвин, как константы для условий хрупкого разрушения, получил широкое применение. Здесь процесс разрушения рассматривается с течением времени, и индексы K 1c (G 1c ) относятся к критическому моменту, когда устойчивое развитие трещины нарушается; трещина становится нестабильной и распространяется самопроизвольно, когда энергия, необходимая для увеличения ее длины, меньше энергии упругой деформации, достигающей вершины трещины из соседних упруго-напряженных зон металла.
Обозначая толщину образца т и размер трещины 2 л кр , мы исходим из следующего требования: л кр ≥ 2,5 (К 1с /σ0,2) 2 ≤ т . Коэффициент интенсивности напряжений K учитывает не только величину нагрузки, но и длину увеличивающейся трещины: K = . ; (; учитывает геометрию трещины и образца) выражается в кгс / мм 3/2 или в мН / м 3/2 .Склонность конструкционных материалов к хрупкому разрушению в рабочих условиях может быть оценена из K 1c или G 1c .
Ударные испытания призматических образцов с надрезом на одной стороне широко используются для оценки качества металла. Здесь делается оценка ударной вязкости (в кг. М / см 2 или МДж / м 2 ) — работа деформации и разрушения образца, произвольно отнесенная к поперечному сечению, образованному надрезом.Испытания на ударную вязкость образцов с усталостной трещиной, искусственно изготовленной на вершине надреза, широко используются. В целом работа разрушения в таких образцах α и удовлетворительно согласуется с такой характеристикой разрушения, как K 1c и еще лучше с соотношением ( K 1c /σ0.2) 2
Зависимость прочности от времени . Прочность пластической деформации и сопротивление разрушению уменьшаются с увеличением времени воздействия нагрузки.В металлах при комнатной температуре это становится особенно заметно при воздействии коррозийного агента (коррозия под нагрузкой) или другого активного агента (эффект Ребиндера). Явление ползучести, то есть увеличение пластической деформации со временем при постоянном напряжении (рис. 4, а), наблюдается при высоких температурах. Прочность металлов на ползучесть оценивается по произвольному пределу ползучести, чаще всего по напряжению, при котором пластическая деформация достигает 0,2 процента за 100 часов, и обозначается как σ0.2/100. Чем выше температура t , тем более выражена ползучесть и тем больше уменьшается прочность металла на разрыв со временем (рис. 4, б). Последнее свойство характеризуется долговременной прочностью, которая представляет собой напряжение, которое вызывает разрыв материала при заданной температуре в течение заданного времени (например, t 100 и t 1000). Температурно-временная зависимость прочности и деформации более выражена для полимеров, чем для металлов. Когда пластмассы нагреваются, наблюдается высокоэластичная обратимая деформация.Начиная с некоторой более высокой температуры, развивается необратимая деформация, связанная с переходом материала в состояние вязкого течения.

Рисунок 4 . Изменение механических свойств конструкционных материалов в зависимости от времени (или числа циклов)
Другое важное механическое свойство материалов — тенденция к релаксации напряжений, то есть к постепенному снижению напряжения в условиях, в которых общее (упругая и пластическая) деформация поддерживает постоянное заданное значение (например, в затянутых болтах) — также связано с ползучестью.Релаксация напряжений обусловлена увеличением доли пластической составляющей в общей деформации и уменьшением ее упругой составляющей.
Если на металл действует нагрузка, которая периодически изменяется в соответствии с каким-либо законом (например, законом синуса), то с увеличением числа циклов нагрузки N прочность металла уменьшается (Рис. 4, c). ) — металлическая «усталость». Для конструкционной стали такое снижение прочности наблюдается до N = (2 — 5) X 10 6 циклов.Соответственно, мы говорим о пределе усталости конструкционной стали, под которым обычно подразумевается амплитуда напряжения ( max — мин ) / 2, ниже которой сталь не разрушается при многократной переменной нагрузке. Когда 37σ мин ǀ = ǀσ макс limit предел усталости обозначается символом σ -1 . Кривые усталости алюминиевых, титановых и магниевых сплавов обычно не имеют горизонтального сегмента; следовательно, усталостная прочность этих сплавов характеризуется ограниченными пределами усталости (соответствует заданному N ).Усталостная прочность также зависит от частоты приложения нагрузки. Сопротивление материалов на низких частотах и при высоких значениях многократного нагружения (медленная или кратковременная усталость) однозначно не связано с пределами усталости. При повторяющихся переменных нагрузках, в отличие от статической нагрузки, всегда проявляется чувствительность к надрезу, то есть предел усталости ниже при наличии надреза, чем для гладкого образца. Для удобства чувствительность надреза при усталости выражается соотношением
K σ = σ R / σ R n
(где R = σ мин / σ макс характеризует асимметрию цикла).В процессе усталости можно выделить период, предшествующий образованию очага усталостного разрушения, а также период, который следует за ним, который иногда очень велик (период развития усталостной трещины). Чем медленнее развивается трещина, тем надежнее материал функционирует в структуре. Скорость развития усталостной трещины дл / дн связана с коэффициентом интенсивности напряжений экспоненциальной функцией дл / дн = cK n .
Термостойкость также отличается. В этом случае напряжения, возникающие в материале, вызваны тем, что по разным причинам (например, из-за формы детали или характера ее крепления) тепловые смещения возникают при циклическом изменении температуры. не может быть реализовано. Сопротивление термической усталости также зависит от многих других свойств материала, таких как коэффициент линейного расширения, температуропроводность, модуль упругости и предел упругости.
СПИСОК ЛИТЕРАТУРЫ
Давиденков Н.Н. Динамические исследования металлов , 2-е изд. Ленинград-Москва, 1936.Ратнер, С. И. Разрушение при повторных загрузках . М., 1959.
Серенсен, С. В., В. П. Когаев, Р. М. Шнейдерович. Несчастная практика и расчеты деталей машин на прошлое , 2-е изд. М., 1963.
Прикладные вопросы виаскости разрушения . М., 1968. (пер. С англ.)
Фридман, ла.Б. Механические свойства металла , 3-е изд. М., 1974.
Методы исследования, контроля и исследований машиностроительных материалов , вып. 2. Под редакцией А. Т. Туманова. Москва, 1974..