Предел прочности стали при сжатии и растяжении
Прочность металлических конструкций – один из важнейших параметров, определяющих их надежность и безопасность. Издревле вопросы прочности решались опытным путем — если какое-либо изделие ломалось — то следующее делали толще и массивнее. С 17 века ученые начали планомерное исследование проблемы, прочностные параметры материалов и конструкций из них можно рассчитать заранее, на этапе проектирования. Металлурги разработали добавки, влияющие на прочность стальных сплавов.
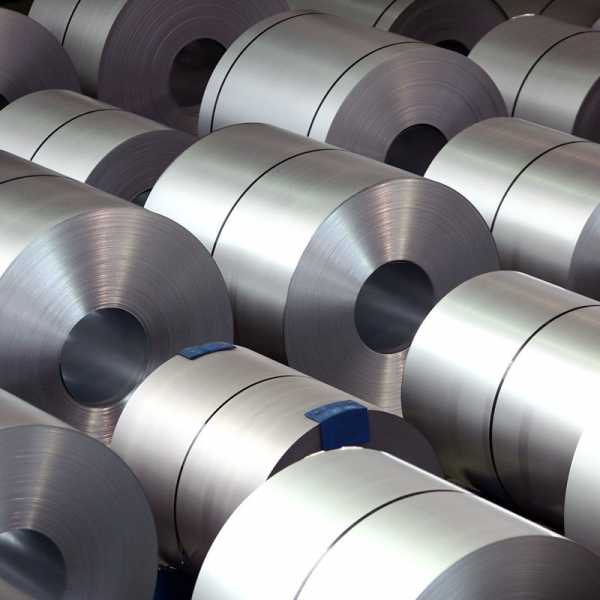
Предел прочности
Предел прочности — это максимальное значение напряжений, испытываемых материалом до того, как он начнет разрушаться. Его физический смысл определяет усилие растяжения, которое нужно приложить к стрежневидному образцу определенного сечения, чтобы разорвать его.
Каким образом производится испытание на прочность
Прочностные испытания на сопротивление разрыву проводятся на специальных испытательных стендах. В них неподвижно закрепляется один конец испытываемого образца, а к другому присоединяют крепление привода, электромеханического или гидравлического. Этот привод создает плавно увеличивающее усилие, действующее на разрыв образца, или же на его изгиб или скручивание.
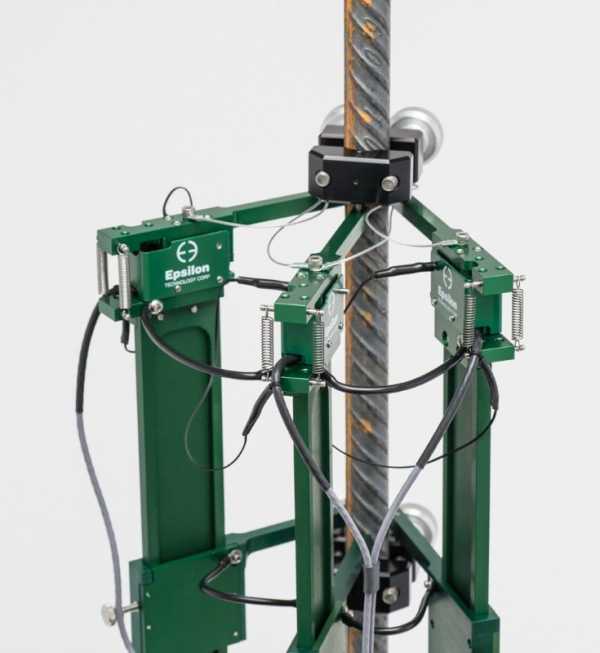
Испытание на разрыв
Электронная система контроля фиксирует усилие растяжения и относительное удлинение, и другие виды деформации образца.
Виды пределов прочности
Предел прочности — один из главных механических параметров стали, равно как и любого другого конструкционного материала.
Эта величина используется при прочностных расчетах деталей и конструкций, судя по ней, решают, применим ли данный материал в конкретной сфере или нужно подбирать более прочный.
Различают следующие виды предела прочности при:
- сжатии — определяет способность материала сопротивляться давлению внешней силы;
- изгибе — влияет на гибкость деталей;
- кручении – показывает, насколько материал пригоден для нагруженных приводных валов, передающих крутящий момент;
- растяжении.
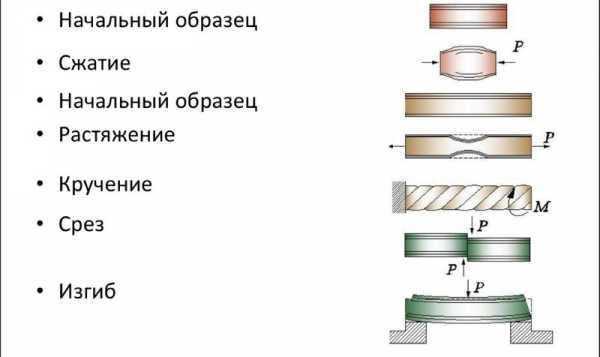
Виды испытаний прочности материалов
Научное название параметра, используемое в стандартах и других официальных документах — временное сопротивление разрыву.
Предел прочности стали
На сегодняшний день сталь все еще является наиболее применяемым конструкционным материалом, понемногу уступая свои позиции различным пластмассам и композитным материалам. От корректного расчета пределов прочности металла зависит его долговечность, надежность и безопасность в эксплуатации.
Предел прочности стали зависит от ее марки и изменяется в пределах от 300 Мпа у обычной низкоуглеродистой конструкционной стали до 900 Мпа у специальных высоколегированных марок.
На значение параметра влияют:
- химический состав сплава;
- термические процедуры, способствующие упрочнению материалов: закалка, отпуск, отжиг и т.д.
Некоторые примеси снижают прочность, и от них стараются избавляться на этапе отливки и проката, другие, наоборот, повышают. Их специально добавляют в состав сплава.
Условный предел текучести
Кроме предела прочности, в инженерных расчетах широко применяется связанное с ним понятие-предел текучести, обозначаемый σт. Он равен величине напряжения сопротивления разрыву, которое необходимо создать в материале, для того, чтобы деформация продолжала расти без наращивания нагрузки. Это состояние материала непосредственно предшествует его разрушению.
На микроуровне при таких напряжениях начинают рваться межатомные связи в кристаллической решетке, а на оставшиеся связи увеличивается удельная нагрузка.
Общие сведения и характеристики сталей
С точки зрения конструктора, наибольшую важность для сплавов, работающих в обычных условиях, имеют физико-механические параметры стали. В отдельных случаях, когда изделию предстоит работать в условиях экстремально высоких или низких температур, высокого давления, повышенной влажности, под воздействием агрессивных сред — не меньшую важность приобретают и химические свойства стали. Как физико-механические, так и химические свойства сплавов во многом определяются их химическим составом.
Влияние содержание углерода на свойства сталей
По мере увеличения процентной доли углерода происходит снижение пластичности вещества с одновременным ростом прочности и твердости. Этот эффект наблюдается до приблизительно 1% доли, далее начинается снижение прочностных характеристик.
Повышение доли углерода также повышает порог хладоемкости, это используется при создании морозоустойчивых и криогенных марок.
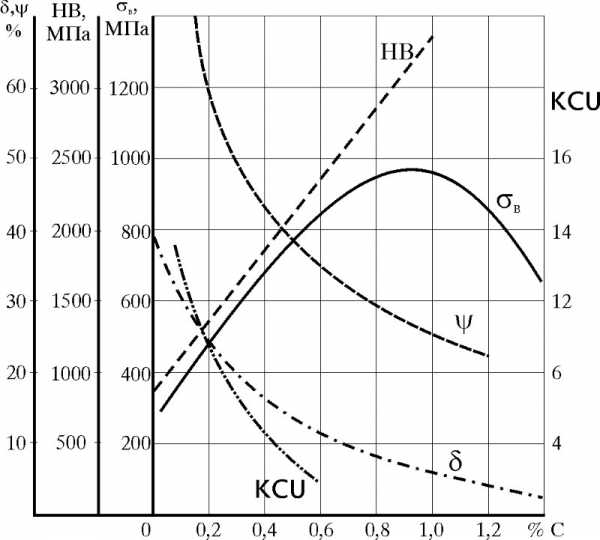
Влияние углерода на механические свойства стали
Рост содержания С приводит к ухудшению литейных свойств, отрицательно влияет на способность материала к механической обработке.
Добавки марганца и кремния
Mn содержится в большинстве марок стали. Его применяют для вытеснения из расплава кислорода и серы. Рост содержания Mn до определенного предела (2%) улучшает такие параметры обрабатываемости, как ковкость и свариваемость. После этого предела дальнейшее увеличение содержания ведет к образованию трещин при термообработке.
Влияние кремния на свойства сталей
Si применяется в роли раскислителя, используемого при выплавке стальных сплавов и определяет тип стали. В спокойных высокоуглеродистых марках должно содержаться не более 0,6% кремния. Для полуспокойных марок этот предел еще ниже — 0,1 %.
При производстве ферритов кремний увеличивает их прочностные параметры, не понижая пластичности. Этот эффект сохраняется до порогового содержания в 0,4%.
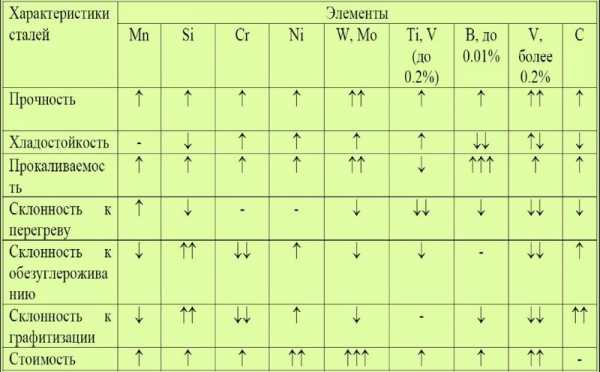
Влияние легирующих добавок на свойства стали
В сочетании с Mn или Mo кремний способствует росту закаливаемости, а вместе с Сг и Ni повышает коррозионную устойчивость сплавов.
Азот и кислород в сплаве
Эти самые распространенные в земной атмосфере газы вредно влияют на прочностные свойства. Образуемые ими соединения в виде включений в кристаллическую структуру существенно снижают прочностные параметры и пластичность.
Легирующие добавки в составе сплавов
Это вещества, намеренно добавляемые в расплав для улучшения свойств сплава и доведения его параметров до требуемых. Одни из них добавляются в больших количествах (более процента), другие — в очень малых. Наиболее часто применяю следующие легирующие добавки:
- Хром. Применяется для повышения прокаливаемости и твердости. Доля – 0,8-0,2%.
- Бор. Улучшает хладноломкость и радиационную стойкость. Доля – 0,003%.
- Титан. Добавляется для улучшения структуры Cr-Mn сплавов. Доля – 0,1%.
- Молибден. Повышает прочностные характеристики и коррозионную стойкость, снижает хрупкость. Доля – 0,15-0,45%.
- Ванадий. Улучшает прочностные параметры и упругость. Доля – 0,1-0,3%.
- Никель. Способствует росту прочностных характеристик и прокаливаемости, однако при этом ведет к увеличению хрупкости. Этот эффект компенсируют одновременным добавлением молибдена.
Металлурги используют и более сложные комбинации легирующих добавок, добиваясь получения уникальных сочетаний физико-механических свойств стали. Стоимость таких марок в несколько раз (а то и десятков раз) превышает стоимость обычных низкоуглеродистых сталей. Применяются они для особо ответственных конструкций и узлов.
Если вы нашли ошибку, пожалуйста, выделите фрагмент текста и нажмите Ctrl+Enter.
stankiexpert.ru
Прочностная характеристика — сталь — Большая Энциклопедия Нефти и Газа, статья, страница 1
Прочностная характеристика — сталь
Cтраница 1
Прочностные характеристики стали, термически обработанной на сг0 2 75 кГ / ммг по данным [40], не изменяются под влиянием длительных ( до 10000 час. Для стали, термически обработанной на cr0i2: 65 кГ / мм2, длительные выдержки при 500 — 550 не дают разупрочнения. Ударная вязкость при 20 под влиянием длительных выдержек при 450 — 550 в нагруженном и ненагруженном состояниях испытывает только небольшие изменения, что позволяет считать сталь нечувствительной к тепловой хрупкости. [1]
Прочностные характеристики сталей повышенной и высокой прочности предопределяют значительную экономию металла и широкое их использование в массовом строительстве. [2]
Сравнение прочностных характеристик стали после ВТМО и обычной закалки при одной температуре отпуска не отражает реального повышения прочности, поскольку в результате ВТМО сталь имеет повышенную пластичность, а как известно, надежность работы любой детали в машине определяется в значительной степени способностью материала детали сопротивляться внезапным перегрузкам, которые зависят от пластичности материала. [3]
Повышение прочностных характеристик стали для сварных труб позволяет уменьшить толщину стенки и тем самым повысить экономическую эффективность производства. [4]
Благодаря улучшению прочностной характеристики стали в процессе обработки этот метод позволяет применять в качестве исходного материала для заготовки горячекатаную сталь вместо холоднотянутой, что дает дополнительную экономию от стоимости материала. [5]
Некоторое ухудшение прочностных характеристик стали ХН70ВМТЮ может быть объяснено химическими взаимодействиями стали, содержащей молибден, со стеклосмазкой с повышенным содержанием окиси бора. [7]
Температура также ограничивается прочностными характеристиками сталей, применяемых для изготовления лопаток и дисков турбин. [8]
НТМО еще больше повышает прочностные характеристики стали: о 2700 — 3000 Мн / мг. НТМО используют только для сталей с широкой зоной устойчивого аустенита. [9]
Максимальная твердость, определяющая прочностные характеристики стали и ее конструктивную прочность, получаемые при закалке, обусловлена содержанием углерода в стали. Однако максимальная твердость, которая может быть достигнута при закалке изделий, имеющих большие размеры, чем образцы, зависит также от массы этих изделий, часто не позволяющей получить в структуре 100 % мартенсита. [10]
На рис. 4.4 представлены прочностные характеристики стали ШХ15 в зависимости от твердости. HRC, которая получается в результате отпуска стали при 250 С. [12]
В оснс классификации положена прочностные характеристики стали труб, , воиетричеокие раэиери-попервчного сечения, максимальная стрела прогиба и длина арки. При разработке классификации учтено развитие упругопластическ / а. [13]
Кратковременное азотирование не влияет на прочностные характеристики стали, однако показатели пластичности и величина ударной вязкости существенно снижаются. [14]
Страницы: 1 2 3 4
www.ngpedia.ru
Упругие и прочностные характеристики материалов
Диаграммы напряжений
На сегодняшний день существует несколько методик испытания образцов материалов. При этом одним из самых простых и показательных являются испытания на растяжение (на разрыв), позволяющие определить предел пропорциональности, предел текучести, модуль упругости и другие важные характеристики материала. Так как важнейшей характеристикой напряженного состояния материала является деформация, то определение значения деформации при известных размерах образца и действующих на образец нагрузок позволяет установить вышеуказанные характеристики материала.
Тут может возникнуть вопрос: почему нельзя просто определить сопротивление материала? Дело в том, что абсолютно упругие материалы, разрушающиеся только после преодоления некоторого предела — сопротивления, существуют только в теории. В реальности большинство материалов обладают как упругими так и пластическими свойствами, что это за свойства, рассмотрим ниже на примере металлов.
Испытания металлов на растяжение проводятся согласно ГОСТ 1497-84. Для этого используются стандартные образцы. Методика испытаний выглядит приблизительно так: к образцу прикладывается статическая нагрузка, определяется абсолютное удлинение образца Δl, затем нагрузка увеличивается на некоторое шаговое значение и снова определяется абсолютное удлинение образца и так далее. На основании полученных данных строится график зависимости удлинений от нагрузки. Этот график называется диаграммой напряжений.
Рисунок 318.1. Диаграмма напряжений для стального образца.
На данной диаграмме мы видим 5 характерных точек:
1. Предел пропорциональности Рп (точка А)
Нормальные напряжения в поперечном сечении образца при достижении предела пропорциональности будут равны:
σп = Рп/Fo
(318.2.1)Предел пропорциональности ограничивает участок упругих деформаций на диаграмме. На этом участке деформации прямо пропорциональны напряжениям, что выражается законом Гука:
Рп = kΔl (318.2.2)
где k — коэффициент жесткости:
k = EF/l (318.2.3)
где l — длина образца, F — площадь сечения, Е — модуль Юнга.
Модули упругости
Главными характеристиками упругих свойств материалов являются модуль Юнга Е (модуль упругости первого рода, модуль упругости при растяжении), модуль упругости второго рода G (модуль упругости при сдвиге) и коэффициент Пуассона μ (коэффициент поперечной деформации).
Модуль Юнга Е показывает отношение нормальных напряжений к относительным деформациям в пределах пропорциональности
Модуль Юнга также определяется опытным путем при испытании стандартных образцов на растяжение. Так как нормальные напряжения в материале равны силе, деленной на начальную площадь сечения:
σ = Р/Fо (318.3.1), (317.2)
а относительное удлинение ε — отношению абсолютной деформации к начальной длине
εпр = Δl/lo (318.3.2)
то модуль Юнга согласно закону Гука можно выразить так
Е = σ/εпр = Plo/FoΔl = tgα (318.3.3)
Рисунок 318.2. Диаграммы напряжений некоторых сплавов металлов
Коэффициент Пуассона μ показывает отношение поперечных деформаций к продольным
Под воздействием нагрузок не только увеличивается длина образца, но и уменьшается площадь рассматриваемого поперечного сечения (если предположить, что объем материала в области упругих деформаций остается постоянным, то значит увеличение длины образца приводит к уменьшению площади сечения). Для образца, имеющего круглое сечение, изменение площади сечения можно выразить так:
εпоп = Δd/do (318.3.4)
Тогда коэффициент Пуассона можно выразить следующим уравнением:μ = εпоп/εпр (318.3.5)
Модуль сдвига G показывает отношение касательных напряжений т к углу сдвига
Модуль сдвига G может быть определен опытным путем при испытании образцов на кручение.
При угловых деформациях рассматриваемое сечение перемещается не линейно, а под некоторым углом — углом сдвига γ к начальному сечению. Так как касательные напряжения равны силе, деленной на площадь в плоскости которой действует сила:
т = Р/F (318.3.6)
а тангенс угла наклона можно выразить отношением абсолютной деформации Δl к расстоянию h от места фиксации абсолютной деформации до точки, относительно которой осуществлялся поворот:
tgγ = Δl/h (318.3.7)
то при малых значениях угла сдвига модуль сдвига можно выразить следующим уравнением:
G = т/γ = Ph/FΔl (318.3.8)
Модуль Юнга, модуль сдвига и коэффициент Пуассона связаны между собой следующим отношением:
Е = 2(1 + μ)G (318.3.9)
Значения постоянных Е, G и µ приводятся в таблице 318.1
Таблица 318.1. Ориентировочные значения упругих характеристик некоторых материалов
Примечание: Модули упругости являются постоянными величинами, однако технологии изготовления различных строительных материалов меняются и более точные значения модулей упругости следует уточнять по действующим в настоящий момент нормативным документам. Модули упругости бетона зависят от класса бетона и потому здесь не приводятся.
Упругие характеристики определяются для различных материалов в пределах упругих деформаций, ограниченных на диаграмме напряжений точкой А. Между тем на диаграмме напряжений можно выделить еще несколько точек:
2. Предел упругости Ру
Нормальные напряжения в поперечном сечении образца при достижении предела упругости будут равны:σу = Ру/Fo (318.2.4)
Предел упругости ограничивает участок на котором появляющиеся пластические деформации находятся в пределах некоторой малой величины, нормированной техническими условиями (например 0,001%; 0,01% и т. д.). Иногда предел упругости обозначается соответственно допуску σ0.001, σ0.01 и т.д.
3. Предел текучести Рт
σт = Рт/Fo (318.2.5)
Ограничивает участок диаграммы на котором деформация увеличивается без значительного увеличения нагрузки (состояние текучести). При этом по всему объему образца происходит частичный разрыв внутренних связей, что и проводит к значительным пластическим деформациям. Материал образца полностью не разрушается, но его начальные геометрические размеры претерпевают необратимые изменения. На отшлифованной поверхности образцов наблюдаются фигуры текучести — линии сдвигов (открытые профессором В. Д. Черновым). Для различных металлов углы наклона этих линий различны, но находятся в пределах 40-50
На диаграммах напряжений отмечен нижний предел текучести. Именно этот предел для большинства материалов принимается за нормативное сопротивление материала.
Некоторые материалы не имеют выраженной площадки текучести. Для них за условный предел текучести σ0.2 принимается напряжение, при котором остаточное удлинение образца достигает значения ε ≈0,2%.
4. Предел прочности Рмакс (временное сопротивление)
Нормальные напряжения в поперечном сечении образца при достижении предела прочности будут равны:
σв = Рмакс/Fo (318.2.6)
После преодоления верхнего предела текучести (на диаграммах напряжения не показан) материал снова начинает сопротивляться нагрузкам. При максимальном усилии Рмакс начинается полное разрушение внутренних связей материала. При этом пластические деформации концентрируются в одном месте, образуя в образце так называемую шейку.
Напряжение при максимальной нагрузке называется пределом прочности или временным сопротивлением материала.
В таблицах 318.2 — 318.5 приведены ориентировочные величины пределов прочности для некоторых материалов:
Таблица 318.2 Ориентировочные пределы прочности на сжатие (временные сопротивления) некоторых строительных материалов.
Примечание: Для металлов и сплавов значение пределов прочности следует определять согласно нормативных документов. Значение временных сопротивлений для некоторых марок стали можно посмотреть здесь.
Таблица 318.3. Ориентировочные пределы прочности (временные сопротивления) для некоторых пластмасс
Таблица 318.4. Ориентировочные пределы прочности для некоторых волокон
Таблица 318.5. Ориентировочные пределы прочности для некоторых древесных пород
5. Разрушение материала Рр
Если посмотреть на диаграмму напряжений, то создается впечатление, что разрушение материала наступает при уменьшении нагрузки. Такое впечатление создается потому, что в результате образования «шейки» значительно изменяется площадь сечения образца в районе «шейки». Если построить диаграмму напряжений для образца из малоуглеродистой стали в зависимости от изменяющейся площади сечения, то будет видно, что напряжения в рассматриваемом сечении увеличиваются до некоторого предела:
Рисунок 318.3. Диаграмма напряжений: 2 — по отношению к начальной площади поперечного сечения, 1 — по отношению к изменяющейся площади сечения в районе шейки.
Тем не менее более правильным является рассмотрение прочностных характеристик материала по отношению к площади первоначального сечения, так как расчетами на прочность изменение первоначальной геометрической формы редко предусматривается.
Одной из механических характеристик металлов является относительное изменение ψ площади поперечного сечения в районе шейки, выражаемое в процентах:
ψ = 100(Fo — F)/Fo (318.2.7)
где Fo — начальная площадь поперечного сечения образца (площадь поперечного сечения до деформации), F — площадь поперечного сечения в районе «шейки». Чем больше значение ψ, тем более ярко выражены пластические свойства материала. Чем меньше значение ψ, тем больше хрупкость материала.
Если сложить разорванные части образца и измерить его удлинение, то выяснится, что оно меньше удлинения на диаграмме (на длину отрезка NL), так как после разрыва упругие деформации исчезают и остаются только пластические. Величина пластической деформации (удлинения) также является важной характеристикой механических свойств материала.
За пределами упругости, вплоть до разрушения, полная деформация состоит из упругой и пластической составляющих. Если довести материал до напряжений, превышающих предел текучести (на рис. 318.1 некоторая точка между пределом текучести и пределом прочности), и затем разгрузить его, то в образце останутся пластические деформации, но при повторном загружении через некоторое время предел упругости станет выше, так как в данном случае изменение геометрической формы образца в результате пластических деформаций становится как бы результатом действия внутренних связей, а изменившаяся геометрическая форма, становится начальной. Этот процесс загрузки и разгрузки материала можно повторять несколько раз, при этом прочностные свойства материала будут увеличиваться:
Рисунок 318.4. Диаграмма напряжений при наклепе (наклонные прямые соответствуют разгрузкам и повторным загружениям)
Такое изменение прочностных свойств материала, получаемое путем повторяющихся статических загружений, называется наклепом. Тем не менее при повышении прочности металла путем наклепа уменьшаются его пластические свойства, а хрупкость увеличивается, поэтому полезным как правило считается относительно небольшой наклеп.
Работа деформации
Прочность материала тем выше, чем больше внутренние силы взаимодействия частиц материала. Поэтому величина сопротивления удлинению, отнесенная к единице объема материала, может служить характеристикой его прочности. В этом случае предел прочности не является исчерпывающей характеристикой прочностных свойств данного материала, так как он характеризует только поперечные сечения. При разрыве разрушаются взаимосвязи по всей площади сечения, а при сдвигах, которые происходят при всякой пластической деформации, разрушаются только местные взаимосвязи. На разрушение этих связей затрачивается определенная работа внутренних сил взаимодействия, которая равна работе внешних сил, затрачиваемой на перемещения:
А = РΔl/2 (318.4.1)
где 1/2 — результат статического действия нагрузки, возрастающей от 0 до Р в момент ее приложения (среднее значение (0 + Р)/2)
При упругой деформации работа сил определяется площадью треугольника ОАВ (см. рис. 318.1). Полная работа, затраченная на деформацию образца и его разрушение:
А = ηРмаксΔlмакс (318.4.2)
где η — коэффициент полноты диаграммы, равный отношению площади всей диаграммы, ограниченной кривой АМ и прямыми ОА, MN и ON, к площади прямоугольника со сторонами 0Рмакс (по оси Р) и Δlмакс (пунктир на рис. 318.1). При этом надо вычесть работу, определяемую площадью треугольника MNL (относящуюся к упругим деформациям).
Работа, затрачиваемая на пластические деформации и разрушение образца, является одной из важных характеристик материала, определяющих степень его хрупкости.
Деформация сжатия
Деформации сжатия подобны деформациям растяжения: сначала происходят упругие деформации, к которым за пределом упругости добавляются пластические. Характер деформации и разрушения при сжатии показан на рис. 318.5:
Рисунок 318.5
а — для пластических материалов; б — для хрупких материалов ; в — для дерева вдоль волокон, г — для дерева поперек волокон.
Испытания на сжатие менее удобны для определения механических свойств пластических материалов из-за трудности фиксирования момента разрушения. Методы механических испытаний металлов регламентируются ГОСТ 25.503-97. При испытании на сжатие формы образца и его размеры могут быть различными. Ориентировочные значения пределов прочности для различных материалов приведены в таблицах 318.2 — 318.5.
Если материал находится под нагрузкой при постоянном напряжении, то к практически мгновенной упругой деформации постепенно прибавляется добавочная упругая деформация. При полном снятии нагрузки упругая деформация уменьшается пропорционально уменьшающимся напряжениям, а добавочная упругая деформация исчезает медленнее.
Образовавшаяся добавочная упругая деформация при постоянном напряжении, которая исчезает не сразу после разгрузки, называется упругим последействием.
Влияние температуры на изменение механических свойств материалов
Твердое состояние — не единственное агрегатное состояние вещества. Твердые тела существуют только в определенном интервале температур и давлений. Повышение температуры приводит к фазовому переходу из твердого состояния в жидкое, а сам процесс перехода называется плавлением. Температуры плавления, как и другие физические характеристики материалов, зависят от множества факторов и также определяются опытным путем.
Таблица 318.6. Температуры плавления некоторых веществ
Примечание: В таблице приведены температуры плавления при атмосферном давлении (кроме гелия).
Упругие и прочностные характеристики материалов, приведенные в таблицах 318.1-318.5, определяются как правило при температуре +20оС. ГОСТом 25.503-97 допускается проводить испытания металлических образцов в диапазоне температур от +10 до +35оС.
При изменении температуры изменяется потенциальная энергия тела, а значит, изменяется и значение внутренних сил взаимодействия. Поэтому механические свойства материалов зависят не только от абсолютной величины температуры, но и от продолжительности ее действия. Для большинства материалов при нагреве прочностные характеристики (σп, σт и σв) уменьшаются, при этом пластичность материала увеличивается. При снижении температуры прочностные характеристики увеличиваются, но при этом повышается хрупкость. При нагреве уменьшается модуль Юнга Е, а коэффициент Пуассона увеличивается. При снижении температуры происходит обратный процесс.
Рисунок 318.6. Влияние температуры на механические характеристики углеродистой стали.
При нагревании цветных металлов и сплавов из них прочность их сразу падает и при температуре, близкой к 600° С, практически теряется. Исключение составляет алюмотермический хром, предел прочности которого с увеличением температуры увеличивается и при температуре равной 1100° С достигает максимума σв1100 = 2σв20.
Характеристики пластичности меди, медных сплавов и магния с ростом температуры уменьшаются, а алюминия — увеличиваются. При нагреве пластмасс и резины их предел прочности резко снижается, а при охлаждении эти материалы становятся очень хрупкими.
Влияние радиоактивного облучения на изменение механических свойств
Радиоактивное облучение по-разному влияет на различные материалы. Облучение материалов неорганического происхождения по своему влиянию на механические характеристики и характеристики пластичности подобно понижению температуры: с увеличением дозы радиоактивного облучения увеличивается предел прочности и особенно предел текучести, а характеристики пластичности снижаются.
Облучение пластмасс также приводит к увеличению хрупкости, причем на предел прочности этих материалов облучение оказывает различное влияние: на некоторых пластмассах оно почти не сказывается (полиэтилен), у других вызывает значительное понижение предела прочности (катамен), а в третьих — повышение предела прочности (селектрон).
doctorlom.com
Основные характеристики малоуглеродистой стали, стали обычной прочности, стали повышенной прочности, стали высокой прочности.
Металлические конструкции, включая сварку.
Малоуглеродистые стали обычной прочности.
Из группы малоуглеродистых сталей обыкновенного качества, производимых металлургической промышленностью по ГОСТ 380 — 71, с изм., для строительных металлоконструкций применяется сталь марок CT3 и СтЗГпс.
Сталь марки СтЗ производится кипящей, полуспокойной и спокойной. Малоуглеродистые стали хорошо свариваются. В зависимости от назначения сталь поставляется по следующим трем группам:
А — по механическим свойствам;
Б — по химическому составу;
В — по механическим свойствам и химическому составу.
Поскольку для несущих строительных конструкций необходимо обеспечить прочность и свариваемость, а также надлежащее сопротивление хрупкому разрушению и динамическим воздействиям, сталь для этих конструкций заказывается по группе В, т.е. с гарантией механических свойств и химического состава.
Сталь марки СтЗ содержит углерода 0,14 — 0,22 %, марганца в кипящей стали — 0,3 — 0,6 %, в полуспокойной и спокойной — 0,4 — 0,65 %, кремния в кипящей стали от следов — до 0,07 %, в полуспокойной
0,05 — 0,17 %, в спокойной — 0,12 — 0,3 %.
Сталь марки СтЗГпс с повышенным содержанием марганца имеет углерода 0,14 — 0,22 %, марганца 0,8 -1,1, %, кремния до 0,15 %.
В зависимости от вида конструкций и условий их эксплуатации стали, из которой они изготавливаются, предъявляются те или другие требования по ГОСТ 380 — 71 (с изм.).
Углеродистая сталь разделена на шесть категорий. Для всех категорий стали марок ВСтЗ и ВСтЗГпс требуется, чтобы при поставке гарантировались химический состав, временное сопротивление, предел текучести, относительное удлинение, изгиб в холодном состоянии. Требования ударной вязкости для каждой категории различны .
Кипящая сталь изготовляется по 2-й категории — ВСтЗкп2, полуспокойная — по 6-й категории — ВСтЗпс6, спокойная и полуспокойная с повышенным содержанием марганца — по 5-й категории — ВСтЗсп5 и ВСтЗГпс5. Маркировка стали согласно ГОСТ 380 — 71 (с изм.): вначале ставится соответствующее буквенное обозначение группы поставки, затем марки, далее степень раскисления и в конце категория, например обозначение 3СтЗпс6. ГОСТ 23570 — 79 «Прокат из стали углеродистой свариваемой для строительных металлических конструкций» ограничивает содержание азота, мышьяка, устанавливает более строгий контроль механических свойств. В обозначение марки стали по ОСТ 23570 — 79 входят содержание углеродa в сотых долях процента, степень раскисления и при повышенном содержании марганца буква Г. Прокат изготовляют из сталей 18кп, 18пс, 18сп, 18Гпс и 18Гсп. По сравнению с ГОСТ 380 — 71
1.2. (с изм.) несколько повышены прочностные характеристики проката.
Значительная часть проката имеет механические свойства выше установленных ГОСТ 380 — 71 (с изм.). Институтом электросварки имени Е. О. Патона в целях экономии металла прокат из углеродистой стали марок СтЗ, СтЗГпс и низколегированной стали марок 09Г2 и 09Г2С предложено дифференцировать по прочности на 2 группы с минимальными и повышенными показателями прочности, так, для стали ВСтЗ 1-й группы принято б,=250 — 260 МПа, а для 2-й группы б,=280 — 290 МПа (см. рис. 2.3), временное сопротивление отрыву б, повышено на 20— 30 МПа. Прокат из такой стали поставляется по ТУ 14-1-3023-80 «Прокат листовой, широкополосный универсальный и фасонный из углеродистой и низколегированной стали с гарантированным уровнем механических свойств, дифференцированным по группам прочности».
Стали повышенной прочности. Сталь повышенной прочности можно получить как термической обработкой малоуглеродистой стали, так и легированием. Малоуглеродистая термически обработанная сталь марки ВстТ поставляется по ГОСТ 14637 — 79. Эта сталь получается термической обработкой стали СтЗ кипящих, полуспокойных и спокойных плавок. Для металлических конструкций рекомендуются стали полуспокойной и спокойной плавок; стали кипящие как весьма неоднородные не рекомендуются. Сталь марки ВСтТпс имеет предел текучести 295 МПа, временное сопротивление 430 МПа. Показатели ударной вязкости этой стали выше, чем показатели стали СтЗ (0,35 МДж/м’ при температуре — 40’С). Повышенная прочность низколегированных сталей получается введением марганца, кремния, хрома, никеля, меди, ванадия. При этом некоторые марки стали подвергаются термическому упрочнению. Подбор легирующих элементов обеспечивает хорошую свариваемость. Прокат из этих сталей поставляется по ГОСТ 19281 — 73 «Сталь низколегированная сортовая и фасонная», по ГОСТ 19282 — 73 «Сталь низколегированная листовая и широкополосная универсальная» и различным техническим условиям.
В зависимости от нормируемых свойств (химического состава, вре-менного сопротивления, предела текучести, ударной вязкости при раз- ных температурах и после механического старения)’ согласно ГОСТУ
эти стали подразделяются на 15 категорий. Основные марки сталей повышенной прочности приведены в табл. 2.1. За счет более высоких прочностных характеристик применение сталей повышенной прочности. Приводит к экономии металла до 20 — 25 %.
Сталь высокой прочности. Прокат из стали с пределом текучести
440 МПа и временным сопротивлением 590 МПа и выше получают пу- тем легирования и термической обработки (см. табл. 2.1).
При сварке термообработанных сталей вследствие неравномерного нагрева и быстрого охлаждения в разных зонах сварного соединения
1.3. происходят различные структурные превращения. На одних участках образуются закалочные структуры, обладающие повышенной прочностью и хрупкостью (жесткие прослойки), на других металл подвергается высокому отпуску и имеет пониженную прочность и высокую пластичность (мягкие прослойки). Разупрочнение стали в околошовной зоне может достигать 5 — 30%, что необходимо учитывать при проектировании сварных конструкций из термообработанных сталей. Введение в состав стали некоторых карбидообразующих элементов (молибден, ванадий) снижает эффект разупрочнения. Применение сталей высокой прочности приводит к экономии металла на 25 — 30 % по сравнению с конструкциями из малоуглеродистых сталей и особенно целесообразно в большепролетных и тяжело нагруженных конструкциях.
studfiles.net
Прочностные характеристики углеродистых сталей — Энциклопедия по машиностроению XXL
Прочностные характеристики углеродистых сталей [c.27]Прочностные характеристики углеродистой стали (предел прочности, предел текучести и твердость) непрерывно уменьшаются с ростом температуры отпуска выше 300°С, а показатели пластичности (относительное удлинение и сужение) непрерывно повышаются (рис. 201). Ударная вязкость, очень важная характеристика конструкционной стали, начинает интенсивно возрастать при отпуске выше 300°С. Максимальной ударной вязкостью обладает сталь с сорбитной структурой, отпущенная при 600°С. Некоторое снижение ударной вязкости при температурах отпуска выше 600°С можно объяснить тем, что частицы цементита по границам ферритных зерен, растущие за счет растворения частиц внутри а-фазы, становятся слишком грубыми. [c.349]
Под действием легирующих элементов эвтектическая (С) и эвтектоидная 5 точки смещаются не только по температуре, но и по концентрации. При указанных на рис. 52 концентрациях марганца и хрома перлит содержит примерно 0,3 и 0,4% С соответственно вместо 0,83% у углеродистой стали. Таким образом, введение легирующих элементов увеличивает количество карбидов в стали, что в свою очередь повышает твердость и прочностные характеристики легированной стали в сравнении с углеродистой при одинаковом содержании в них углерода. [c.124]
Как известно, в настоящее время большое количество металлических конструкций ферм, опор, высоковольтных передач, каркасов зданий и промышленных сооружений изготовляют из обычной углеродистой стали, ныне для этой цели применяют главным образом кипящую сталь марки Зкп, которая, хотя и имеет достаточно высокие пластические свойства, все же обладает сравнительно низкими прочностными характеристиками. Кипящая сталь имеет малую ударную вязкость цри пониженных температурах. [c.89]
Осредненные прочностные характеристики углеродистых и легированных сталей (при оптимальной термообработке) [c.165]
Для получения высоких прочностных характеристик КПМ используют более сложные технологические процессы, включающие двойное (тройное) прессование, калибровку, горячее прессование, горячую объемную штамповку и т. д. Физико-механические свойства наиболее распространенных углеродистых порошковых сталей различных подгрупп плотности приведены в табл. 7.2. [c.175]
Углеродистые стали широко применяются в машиностроении. Так, например, стали 30 и 35 используются для изготовления деталей, испытывающих небольшие напряжения осей, валиков, шпинделей, тяг, рычагов и т. д. Стали 40 и 45, имеющие более высокие прочностные характеристики, применяются для изготовления коленчатых валов, шатунов, зубчатых колес, маховиков, головок цилиндров, осей прокатных валов и для других нормализуемых, улучшаемых и подвергаемых поверхностной обработке деталей, от которых требуется повышенная прочность. [c.77]
Основными легирующими элементами стали являются хром, никель, молибден, вольфрам, ванадий, титан, алюминий, марганец, кремний, бор. Неизбежными примесями в сталях являются марганец, кремний, фосфор, сера. Легирующие элементы, вводимые в углеродистую сталь, изменяют состав, строение, дисперсность и количество структурных составляющих и фаз. Фазами легированной стали могут быть твердые растворы — легированный феррит и аустенит, специальные карбиды и нитриды, интерметаллиды, неметаллические включения — окислы, сульфиды, нитриды. Как правило, за счет легирования повышаются прочностные характеристики стали (пределы прочности и текучести). [c.66]
В состав низколегированных сталей входят малые добавки таких элементов, как медь, хром, никель, молибден, кремний и марганец, за счет чего и достигается повышение прочности по сравнению с углеродистой сталью. Коммерческой характеристикой низколегированных сталей является не строгий химический состав, а их прочностные свойства. Суммарное содержание легирующих добавок обычно составляет около [c.42]
Способность титана и его сплавов к формоизменению при штамповке и ковке несколько хуже, чем аустенитных нержавеющих и углеродистых сталей. С повышением температуры выше 20 °С прочностные характеристики монотонно снижаются, а пластические вначале немного снижаются, а затем резко возрастают. Титан и его сплавы обладают высокой упругой отдачей, малым диапазоном пластического деформирования (оцениваемого по отношению пониженными значениями равномерного удлинения и сужения, что усложняет процесс формоизменения заготовок. Снижение пластичности происходит в диапазоне 300—400 °С. [c.234]
Сравнение прочностных и весовых характеристик деталей, изготовленных из углеродистой и низколегированной сталей (Wi). Сравнение легированных, низколегированных и углеродистых сталей по прочности и себестоимости (434). [c.545]
Рис. 5. Характер изменения прочностных и пластических характеристик двух марок углеродистой стали | ![]() |
На рис. 118 показана зависимость предела текучести и относительного удлинения от степени деформации для углеродистой стали У10. При достижении общего относительного обжатия в 50 % предел текучести и предел прочности увеличились в два с лишним раза, а относительное удлинение уменьшилось с 30 до 2,5%. Значительное увеличение прочностных характеристик металла и почти полная потеря пластичности, как результат [c.249]
С Мо, W, Nb и Ti тантал образует непрерывный ряд твердых растворов. Сплавы тантала имеют повышенные прочностные характеристики. Как конструкционный материал тантал находит применение в химическом машиностроении. Из него изготавливают теплообменную аппаратуру для получения брома из смеси хлора и брома, для дистилляции соляной и азотной кислот из неочищенного сырья, при получении бромида этилена и хлористого бензола, при регенерации серной кислоты. Из тантала изготавливают нагреватели, работающие в особо агрессивных средах, например, в смеси хромовой и серной кислот, при дистилляции пероксида водорода. В ряде случаев тантал используют для плакировки аппаратуры из углеродистой стали. [c.222]
Требуемые свойства достигаются при последующем от пуске стали На рис 84 показано изменение механических свойств закаленной углеродистой стали 40 при отпуске на разные температуры С повышением температуры отпуска прочностные характеристики непрерывно уменьшаются, а пластичность и вязкость стали увеличиваются По таким [c.155]
Стали, применяемые для индукционной закалки. Существенных ограничений на номенклатуру сталей индукционный нагрев не накладывает. Обычно производят выбор для каждой детали наименее легированной стали, обеспечивающей при учете возможностей индукционной закалки достижение требуемых прочностных характеристик. Широко применяют углеродистые стали с содержанием 0,3—0,5% углерода, низколегированные стали типа 40Х (детали с предварительно улучшенной сердцевиной). [c.611]
Для изучения этой проблемы в ходе диагностирования широкого спектра нефтехимического оборудования, отслужившего 20 — 25 лет, нами были исследованы механические свойства металла более 60 контрольных вырезок из стенок аппаратов и трубопроводов, изготовленных из углеродистых, низко и среднелегированных сталей отечественного и импортного производства. Твердость металла измерялась на заготовках, из которых затем изготавливались образцы для определения прочностных характеристик сталей, что позволило свести к минимуму возможный разброс экспериментальных данных. [c.89]
С повышением прочностных характеристик стали возрастает ее склонность к сероводородному растрескиванию, т. е. высокопрочные низколегированные стали, как правило, в большей степени подвержены этому виду разрушения, чем обычные углеродистые. На рис. 3.6 [50] и 3.7 [54] показано, что с повышением исходных [c.51]
Перед холодной калибровкой поверхность поковки должна быть тщательно очищена от окалины. Глубина поверхностных дефектов на очищенной поковке не должна превышать 0,2 мм для калибровки обычной точности и 0,1 мм для калибровки повышенной точности. Раковины и вмятины большей глубины подлежат зачистке. Поковки из углеродистых сталей с содержанием углерода более 0,2% и поковки из легированных сталей должны быть до калибровки подвергнуты тер-мической обработке (отжигу, нормализации), снижающей прочностные характеристики обрабатываемого металла. [c.568]
Прочностные свойства стали характеризуются временным сопротивлением разрыву и пределом текучести, так как в условиях умеренных температур эти характеристики являются основой выбора допускаемых напряжений. Временное сопротивление разрыву стали зависит от температуры. При повышении температуры до 250—300 °С временное сопротивление углеродистой стали увеличивается, а затем с ростом температуры начинает уменьшаться.— [c.283]
К среднелегированным относятся стали, легированные одним или несколькими элементами при суммарном их содержании 2,5—10 %. Главной и общей характеристикой этих сталей являются механические свойства. Так, временное сопротивление их составляет 588—1960 МПа, что значительно превышает аналогичный показатель обычных углеродистых конструкционных сталей. При высоких прочностных свойствах среднелегированные стали после соответствующей термообработки по пластичности и вязкости не только не уступают, но в ряде случаев и превосходят малоуглеродистую сталь. При этом среднелегированные стали обладают высокой стойкостью против перехода в хрупкое состояние. Поэтому их применяют для работы в условиях ударных и знакопеременных нагрузок, низких и высоких температур, в агрессивных средах. Получение сварных соединений необходимого качества, учитывая особые физикохимические свойства среднелегированных сталей, встречает ряд специфических трудностей. Прежде всего, глав- [c.108]
Современное машиностроение характеризуется возможностью применения различных конструкционных материалов с огромны-м разнообразием прочностных характеристик, что делает возможным разработку конструкций машин с минимальным весом. Низколегированные стали по сравнению с углеродистыми обеспечивают снижение конструктивной металлоемкости в пределах 20—25%. [c.50]
Примечание. Для бронз, у которых кривая изменения расчетной прочностной характеристики при температурах до 250″ С аналогична кривой для углеродистой стали, допускается применять давления, указанные в табл. 2 для углеродистой стали при температурах среды до 250 С. [c.152]
Пр, 1 низком давлении процесс обезуглероживания, очевидно, невозможен. Он будет протекать только на поверхности стали (прн повышенных температурах) благодаря диффузии углерода из ее внутренних слоев с отводом образующегося метана в окружающую среду. При высоких давлениях и температурах обезуглероживание объема стали объясняется резким ростом скорости диффузии водорода в подповерхностные слои металла ( водородная атака ). Поскольку поверхностное обезуглероживание приводит к уменьшению содержания углерода в стали, водородная атака , вызывающая глубинное обезуглероживание, является конкурирующим ироцессом, требующим поставки углерода к внутренним микро- и макрополостям металла. Существенное ухудшение практически всех прочностных характеристик углеродистой стали связано именно с ее внутренним обезуглероживанием при пнтенсивном необратимом водородном охрупчивании и потерей межкристаллитиой прочности. [c.69]
Проектируя морское сооружение из низколегированной стали, конструктор, при заданной прочности мог бы взять меньшую толщину стенок, чем при использовании углеродистой стали. Однако при более высокой скорости коррозии это может привести к ускоренному разрушению конструкции. Таким образом, при проектировании, в принципе, следовало бы предусматривать больший допуск на коррозию низколегированных сталей, чем для углеродистой стали. В то же время при использовании подходящего защитного покрытия более высокие прочностные характеристики низколегированных сталей позволяют добпться общего выигрыша. Катодную защиту в случае низколегированных сталей следует применять с большой осторожностью, поскольку эти сплавы нередко более склонны к водородному охрупчиванию, чем углеродистая сталь. [c.57]
О значительной роли так называемых дефектов кристаллической решетки говорит также тот факт, что очень часто относительно малый объем примесных (дефектньгх) атомов глобально меняет свойства основного материала. Например, добавление нескольких десятых долей процента атомов углерода позволяет существенно повысить прочностные характеристики чистого железа, превращая его в углеродистую сталь — совершенно иной конструкционный материал. Добавка примерно 0,001 % висмута предотвращает переход белого олова в серое, стабилизируя металлическое олово при низких температурах, тогда как добавка 0,1 % алюминия ускоряет этот процесс [88]. [c.194]
Из литературных источников известно, что высокими прочностными характеристиками при повышенных температурах обладают сплавы с интерметаллидными упрочнителями типа TiNi, TiNig, TiFe и др. [7]. В настоящей работе ставилось целью изучить процесс диффузионного насыщения титаном и никелем углеродистой стали и чугуна для получения покрытия с интерметаллидными упрочнителями. [c.74]
Влияние облучения на изменение прочностных свойств нержавею-ш их сталей видно из данных табл. 5.5. Так же как в углеродистых и низколегированных сталях, имеются большие изменения предела текучести. Однако изменения предела прочности и пластичности в результате облучения значительно меньше, чем у углеродистых сталей. Во многих случаях отмечено падение пластичности меньше чем на 50% после облучения интегральным потоком 1 нейтронIсм . Некоторые результаты [33] указывают, что после облучения интегральным потоком 5-10 нейтрон 1см предел текучести нержавеюш ей стали тина 347 при комнатной температуре сравним с величиной предела текучести для меньших потоков, что указывает на достижение насыш ения в изменении этой характеристики. Подобное насыш ение или уменьшение скорости падения пластичности также наблюдается для этой стали. [c.246]
Комплекс механических свойств стали Г13Л отличается высоким уровнем как прочностных характеристик, так и пластических. Это является результатом упрочнения стали в зонах повышенной деформации, вследствие чего растяжение образцов стали происходит практически без образования шейки, но с появлением большого количества надрывов и трещин. Диаграмма растяжения поэтому сильно отличается от таковой для углеродистых сталей. В частности, отсутствует площадка текучести и предел текучести рассчитывается условно по заданной деформации. [c.384]
Сравнение прочностных и весовых характеристик детали, изготовленной из углеродистой и низколегированной сталей (416). Сравнение легированных, низколегированныхи углеродистых сталей по прочности и себестоимости (416). Экономия бронзы при использовании [c.539]
Для котлов на давление 100 кгс/см барабаны изготовляются внутренним диаметром 1600 мм из качественной углеродистой стали марки 22К и рассчитываются на внутреннее давление 110—115 кгс/см . В котлах на 140 кгс/см барабаны должны работать при 155 кгс/см . До 1969 г. их изготовляли внутренним диаметром 1800 мм из слаболегированной стали 16ГНМ, в которой, как и в стали марки 22К, повышение прочностных характеристик достигается в основном за счет увеличенного содержания марганца. В дальнейшем по изложенным ниже причинам эти барабаны стали изготовлять преимущественно из стали 16ГНМА внутренним диаметром 1600 мм. [c.120]
Листовая сталь. До начала 30-х годов барабаны и днища котлов на рабочее давление до 22 кПсм изготовлялись клепаными из мягкой углеродистой стали, соответствующей современной марке Ст. 2. Для котлов на рабочее давление 32—34 кГ см , выпуск которых был освоен в конце 20-х годов, применялись импортные барабаны, сначала кованые с закатанными днищами, а затем сварные с приклепанными штампованными днищами. Освоение на ТКЗ производства сварных барабанов (сварка водяным газом) позволило сократить ввоз барабанов из-за границы, а затем и полностью отказаться от него. Кованые и сварные барабаны для котлов на рабочее давление 32—34 кГ1см изготовлялись также из углеродистой стали марок, соответствующих современным маркам стали 15, 20 и 25. Лишь для котлов на рабочее давление 100 кГ см потребовалось применение барабанов из стали с повышенными прочностными характеристиками, в частности с более высоким пределом текучести при рабочей температуре, равной 320° С. В этой связи была разработана и освоена в производстве низколегированная молибденовая сталь 15М, а затем марганцовистая сталь 22К. Для барабанов котлов на рабочее давление 170 и 140 кГ1см разработана марганцово- [c.187]
Углеродистые стали в сварных диафрагмах можно использовать практически до температуры 350° С вследствие ограниченной прокали-ваемости этих сталей в больших сечениях и невысоких прочностных характеристик, влекущих за собой резкое увеличение габаритов диафрагм (а следовательно, и цилиндров) в осевом направлении. Диафрагмы луглеродистых сталей 22к по ГОСТу 5520—69, стали 20 по ГОСТу 1050—60 или из мартеновской стали Ст. 3, спокойной, поставляемой по группе В, т. е. с приемкой по химическому составу и механическим свойствам (ГОСТ 380—71). В зонах высокого и среднего давления турбин АЭС при наличии влажного пара применение углеродистой стали не допускается. [c.372]
Расчетное допускаемое напряжение материала трубы при рабочей температуре 0, определяют умножением номинального допустимого напряжения Одоп на поправочный коэффициент т], учитывающий особенности конструкции и эксплуатации трубопровода. Для трубопроводов и поверхностей нагрева, находящихся под внутренним давлением, г) = 1. Номинальное допускаемое напряжение принимается по наименьшей из величин, определяемых гарантированными прочностными характеристиками металла при рабочих температурах с учетом коэффициентов запаса прочности для элементов, работающих при температурах, не вызывающих ползучесть, — по временному сопротивлению и пределу текучести Для элементов, работающих в условиях ползучести, у которых расчетная температура стенки превышает 425°С для углеродистых и низколегированных марганцовистых сталей, 475 С для низколегированных жаропрочных сталей и 540°С для сталей аустенитного класса, — по временному сопротивлению, пределу текучести и пределу длительной прочности. Расчет на прочность по пределу ползучести Нормами не предусматривается, так как соблюдение необходимого запаса по длительной прочности обеспечивает прочность и по условиям ползучести. В табл. 8-6 приведены значения номинальных допускаемых напряжений для некоторых сталей. [c.148]
Существующий опыт выбора сталей для конструкций высокого давления показывает, что оценка их работоспособности при повы-щенной температуре по прочности и пластичности, определенных при испытаниях металла без учета временнбго фактора, допускается для углеродистой стали при температуре не выше 380 °С, для низколегированной стали при температуре 420…450 °С, для аустенит-ной стали при температуре не выше 525 °С. При более высоких температурах эксплуатации прочностные и пластические характеристики сталей следует оценивать с учетом влияния длительности воздействия статических нагрузок и температур. В этих условиях свойства стали оцениваются исходя из следующих характеристик временного сопротивления предела длительной прочности максимальной пластичности при разрушении. [c.815]
Механические свойства проката и поковок различных сечений приведены в Марочнике на основании опыта машиностроительных заводов и явллются минимальными. В большинстве случаев прокат и поковки из углеродистой стали применяются в термически обработанном состоянии для повышения прочностных характеристик термообработка состоит из нормализации с отпуском или закалки с отпуском в зависимости от требований, предъявляемых к изделиям. [c.11]
В этих условиях микроорганизмы способствуют сдвигу потенциала в сторону электроотрицательных значений более чем на 150 мВ, стимулируя процесс коррозии. В результате биокоррозии элементы конструкции оборудования ГЭС (затворы, напорный трубопровод, камеры гидротурбин, каркас градирен, трубопровод водоподающих и дренажных систем, теплообменная аппаратура), выполненные из углеродистых сталей, имели следующие повреждения отложения толщиной до 15 мм и диаметром до 25 мм, под которыми были язвы глубиной до 3 мм. При большом числе таких повреждений снижались прочностные характеристики конструкций. [c.309]
Теплообменные трубы из сталей Х5М, Х8, 0X13 используют в трубных пучках и секциях аппаратов в тех случаях, когда трубы из углеродистых сталей разрушаются в результате высокотемпературной сернистой коррозии (протекающей со скоростью более 0,4 мм/год, срок службы менее 3 лет) или вследствие низких прочностных характеристик металла. Выбор между перечисленными хромистыми сталями производится на основе анализа конкретных условий эксплуатации и накопленного производственного опыта. [c.147]
Среднелегкрованной называется сталь, в которой суммарное содержание легирующих компонентов составляет от 2,5 до 10% (кроме углерода). Для изготовления сварных конструкций применяют конструкционные среднелегированные стали, соде ржащие до0,5% угл рЬда, среднелегированные жаропрочные стали, содержащие не более 0,25% углерода и до 5% хрома в качестве обязательного легирующего элемента. Главной и общей характеристикой среднелегированных сталей являются механические свойства. Среднелегированные стали имеют временное сопротивление от 600 до 2000 МПа, что значительно превышает временное сопротивление обычных углеродистых конструкционных сталей. При высоких прочностных свойствах среднелегированные стали после термообработки не только не уступают по пластичности и вязкости, но в ряде случаев превосходят такой пластичный материал, как низкоуглеродистая сталь. [c.130]
mash-xxl.info
1.Основные хар-ки малоуглеродистой стали обычной прочности, повышенной прочности, высокой прочности.
Малоуглеродистые стали обычной прочности. Из группы малоугле- родистых сталей обыкновенного качества, производимых металлургиче- ской промышленностью по ГОСТ 380 — 71, с изм., для строительных ме- таллоконструкций применяется сталь марок CT3 и СтЗГпс.
Сталь марки СтЗ производится кипящей, полуспокойной и спокойной. Малоуглероднстые стали хорошо свариваются. В зависимости от назначения сталь поставляется по следующим трем группам:
А — по механическим свойствам; Б — по химическому составу;
В — по механическим свойствам и химическому составу. Поскольку для несущих строительных конструкций необходимо обеспечить прочность и свариваемость, а также надлежащее сопротивление хрупкому разрушению и динамическим воздействиям, сталь для этих конструкций заказывается по группе В, т.е. с гарантией механических свойств и химического состава.
Сталь марки СтЗ содержит углерода 0,14 — 0,22 %, марганца в кипящей стали — 0,3 — 0,6 %, в полуспокойной и спокойной — 0,4 — 0,65 %, кремния в кипящей стали от следов — до 0,07 %, в полуспокойной
0,05 — 0,17 %, в спокойной — 0,12 — 0,3 %. Сталь марки СтЗГпс с повышенным содержанием марганца имеет углерода 0,14 — 0,22 %, марганца 0,8 -1,1, %, кремния до 0,15 %. В зависимости от вида конструкций и условий их эксплуатации стали, из которой они изготавливаются, предъявляются те или другие требования по ГОСТ 380 — 71 (с изм.). Углеродистая сталь разделена на шесть категорий. Для всех категорий стали марок ВСтЗ и ВСтЗГпс требуется, чтобы при.поставке гарантировались химический состав, временное сопротивление, предел текучести, относительное удлинение, изгиб в холодном состоянии. Требования ударной вязкости для каждой категории различны (табл. 2.2).
Кипящая сталь изготовляется по 2-й категории — ВСтЗкп2, полуспо- койная — по 6-й категории — ВСтЗпс6, спокойная и полуспокойная с по- вышенным содержанием марганца — по 5-й категории — ВСтЗсп5 и ВСтЗГпс5. Маркировка стали согласно ГОСТ 380 — 71 (с изм.): вначале ставится соответствующее буквенное обозначение группы поставки, затем марки, далее степень раскисления и в конце категория, например обозначение 3СтЗпс6. ГОСТ 23570 — 79 «Прокат из стали углеродистой свариваемой для строиельных металлических конструкций» ограничивает содержание азота, мышьяка, устанавливает более строгий контроль механических свойств. В обозначение марки стали по ОСТ 23570 — 79 входят содержание углеродa в сотых долях процента, степень раскисления и при повышенном содержании марганца буква Г. Прокат изготовляют из сталей 18кп, 18пс, 18сп, 18Гпс и 18Гсп. По сравнению с ГОСТ 380 — 71
1.2. (с изм.) несколько повышены прочностные характеристики проката.
Значительная часть проката имеет механические свойства выше установленных ГОСТ 380 — 71 (с изм.). Институтом электросварки им. Е. О. Патона в целях экономии металла прокат из углеродистой стали марок СтЗ, СтЗГпс и низколегированной стали марок 09Г2 и 09Г2С предложенодифференцировать по прочности на 2 группы с минимальны- ми и повышенными показателями прочности, так, для стали ВСтЗ 1-й группы принято б,=250 — 260 МПа, а для 2-й группы б,=280 — 290 МПа (см. рис. 2.3), временное сопротивление отрыву б, повышено на 20— 30 МПа. Прокат из такой стали поставляется по ТУ 14-1-3023-80 «Прокат листовой, широкополосный универсальный и фасонный из углеродистой и низколегированной стали с гарантированным уровнем механических свойств, дифференцированным по группам прочности».
Стали повышенной прочности. Сталь повышенной прочности можно получить как термической обработкой малоуглеродистой стали, так и легированием. Малоуглеродистая термически обработанная сталь марки ВстТ поставляется по ГОСТ 14637 — 79. Эта сталь получается термической обработкой стали СтЗ кипящих, полуспокойных и спокойных плавок. Для металлических конструкций рекомендуются стали полуспокойной и спокойной плавок; стали кипящие как весьма неоднородные не рекомендуются. Сталь марки ВСтТпс имеет предел текучести 295 МПа, временное сопротивление 430 МПа. Показатели ударной вязкости этой стали выше, чем показатели стали СтЗ (0,35 МДж/м’ при температуре — 40’С). Повышенная прочность низколегированных сталей получается введением марганца, кремния, хрома, никеля, меди, ванадия. При этом некоторые марки стали подвергаются термическому упрочнению. Подбор легирующих элементов обеспечивает хорошую свариваемость. Прокат из этих сталей поставляется по ГОСТ 19281 — 73 «Сталь низколегированная сортовая и фасонная», по ГОСТ 19282 — 73 «Сталь низколегированная листовая и широкополосная универсальная» и различным техническим условиям.
В зависимости от нормируемых свойств (химического состава, вре- менного сопротивления, предела текучести, ударной вязкости при раз- ных температурах и после механического старения)’ согласно ГОСТУ
эти стали подразделяются на 15 категорий. Основные марки сталей повышенной прочности приведены в табл. 2.1. За счет более высоких прочностных характеристик применение сталей повышенной прочности. Приводит к экономии металла до 20 — 25 %.
Сталь высокой прочности. Прокат из стали с пределом текучести
440 МПа и временным сопротивлением 590 МПа и выше получают пу- тем легирования и термической обработки (см. табл. 2.1).
При сварке термообработанных сталей вследствие неравномерного нагрева и быстрого охлаждения в разных зонах сварного соединения
1.3. происходят различные структурные превращения. На одних участках образуются закалочные структуры, обладающие повышенной прочностью и хрупкостью (жесткие прослойки), на других металл подвергается высокому отпуску и имеет пониженную прочность и высокую пластичность (мягкие прослойки). Разупрочнение стали в околошовной зоне может достигать 5 — 30%, что необходимо учитывать при проектировании сварных конструкций из термообработанных сталей. Введение в состав стали некоторых карбидообразующих элементов (молибден, ванадий) снижает эффект разупрочнения. Применение сталей высокой прочности приводит к экономии металла на 25 — 30 % по сравнению с конструкциями из малоуглеродистых сталей и особенно целесообразно в большепролетных и тяжело нагруженных конструкциях.
Таблица
2.1. Основные марки строительных сталей
и их механическиехарактеристики.
studfiles.net
Удельная прочность металлов: таблица. Механические свойства металлов
Использовать металлы в повседневной жизни начали еще вначале развития человечества. Медь – это первый их представитель. Она доступна в природе и прекрасно обрабатывается. При археологических раскопках часто находят изготовленные из нее предметы домашнего обихода и разные изделия.
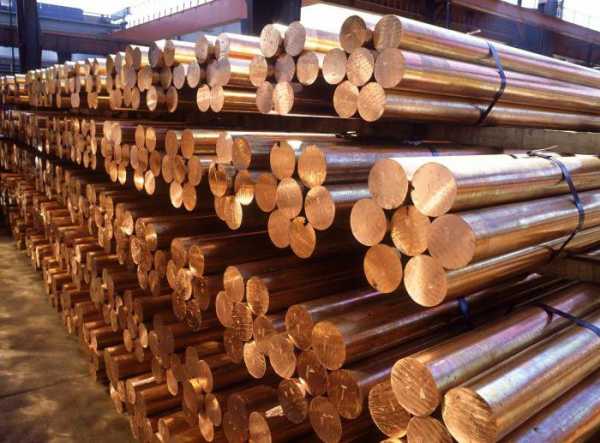
Виды нагрузок
К механическим свойствам металлов и сплавов относятся такие, которые способны оказывать сопротивление действию на них внешних сил или нагрузок. Они могут быть самыми разнообразными и по своему воздействию различают:
- статические, которые неспешно возрастают от нулевого значения до максимума, а затем остаются постоянными или незначительно меняются;
- динамические – возникают вследствие удара и действуют короткий промежуток.
Виды деформации
Деформация – это видоизменение конфигурации твердого тела под воздействием прилагаемых к нему нагрузок (внешних сил). Деформации, после которых материал возвращается в прежнюю форму и сохраняет первоначальные размеры, считают упругими, в противном случае (форма изменилась, материал удлинился) – пластическими или остаточными. Существует несколько видов деформации:
- Сжатие. Уменьшается объем тела в результате действия на него сдавливающих сил. Такую деформацию испытывают фундаменты котлов и машин.
- Растяжение. Увеличивается длина тела, когда к его концам прилагаются силы, направление которых совпадает с его осью. Растяжению подвергаются тросы, приводные ремни.
- Сдвиг или срез. В этом случае силы направлены навстречу друг другу и при определенных условиях наступает срез. Примером служат заклепки и болты стяжки.
- Кручение. Пара сил, противоположно направленных, действует на закрепленное одним концом тело (валы двигателей и станков).
- Изгиб. Изменение кривизны тела при воздействии внешних сил. Такое действие характерно для балок, стрел подъемных кранов, железнодорожных рельсов.
Определение прочности металла
Одно из основных требований, которое предъявляют к металлу, применяемому для производства металлических конструкций и деталей, является прочность. Для ее определения берется образец металла и растягивается на испытательной машине. Эталон становится тоньше, площадь поперечного сечения уменьшается с одновременным увеличением его длины. В определенный момент образец начинает растягиваться лишь в одном месте, образуя «шейку». А через некоторое время происходит разрыв в области самого тонкого места. Так ведут себя исключительно вязкие металлы, хрупкие: твердая сталь и чугун растягиваются незначительно и у них не образуется шейка.
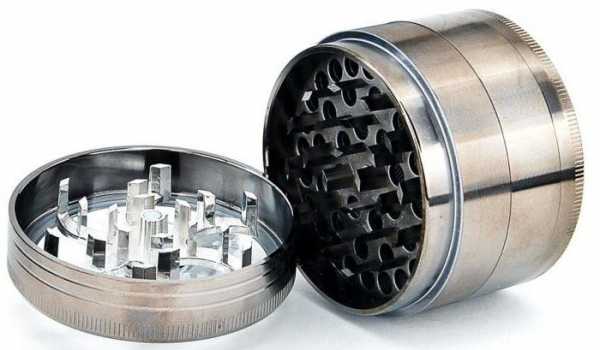
Самые прочные металлы в мире
К высокопрочным металлам можно отнести следующие:
Титан находит применение в медицине, военной промышленности, кораблестроении, авиации.
- Уран. Самый известный и прочный металл в мире, является слабым радиоактивным материалом. Встречается в природе в чистом виде и в соединениях. Он относится к тяжелым металлам, гибкий, ковкий и относительно пластичный. Широко используется в производственных сферах.
- Вольфрам. Расчет прочности металла показывает, что это самый прочный и тугоплавкий металл, не поддающийся химическому воздействию. Хорошо куется, его можно вытянуть в тонкую нить. Используется для нити накаливания.
- Рений. Тугоплавкий, имеет высокую плотность и твердость. Очень прочный, не подвержен перепадам температуры. Находит применение в электронике и технике.
- Осмий. Твердый металл, тугоплавкий, стойкий к механическим повреждениям и агрессивным средам. Применяют в медицине, используют для ракетной техники, электронной аппаратуры.
- Иридий. В природе в свободном виде встречается редко, чаще – в соединениях с осмием. Механической обработке поддается плохо, имеет высокую стойкость к химическим веществам и прочность. Сплавы с металлом: титаном, хромом, вольфрамом, используют для изготовления ювелирных изделий.
- Бериллий. Высокотоксичный металл с относительной плотностью, имеющий светло-серый цвет. Находит применение в черной металлургии, атомной энергетике, лазерной и аэрокосмической технике. Имеет высокую твердость и используется для легирования сплавов.
- Хром. Очень твердый металл с высокой прочностью, бело-голубого цвета, обладает стойкостью к щелочам и кислотам. Прочность металла и сплавов позволяют их использовать для изготовления медицинского и химического оборудования, а также для металлорежущих инструментов.
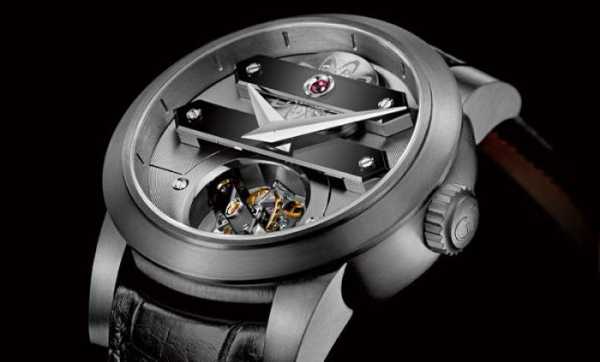
- Тантал. Металл серебристого цвета, имеет высокую твердость, прочность, обладает тугоплавкостью и стойкостью к коррозии, пластичен, легко обрабатывается. Находит применение при создании ядерных реакторов, в металлургии и химической промышленности.
- Рутений. Принадлежит к металлам платиновой группы. Обладает высокой прочностью, твердостью, тугоплавкостью, химической стойкостью. Из него изготовляют контакты, электроды, острые наконечники.
Как определяют свойства металлов?
Для испытания металлов на прочность применяют химические, физические и технологические методы. Твердость определяет, как сопротивляются материалы деформациям. Стойкий металл имеет большую прочность и детали, изготовленные из него, меньше снашиваются. Для определения твердости вдавливают шарик, алмазный конус или пирамидку в металл. Значение твердости устанавливают по диаметру отпечатка или по глубине вдавливания предмета. Более крепкий металл меньше деформируется, и глубина отпечатка будет меньше.
А вот образцы на растяжение испытываются на разрывных машинах с плавно нарастающей при растягивании нагрузкой. Эталон может иметь в сечении круг или квадрат. Для проверки металла противостоять нагрузкам ударного характера проводят испытания на удар. В середине специально изготовленного образца делают надрез и устанавливают его напротив ударного устройства. Разрушение должно происходить там, где слабое место. При испытании металлов на прочность структуру материала исследуют рентгеновскими лучами, ультразвуком и при помощи мощных микроскопов, а также используют травление химическими веществами.
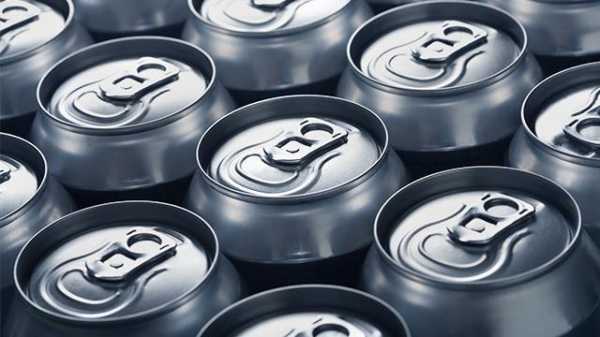
Механические свойства металлов и сплавов
К механическим свойствам материалов из металла относятся следующие:
- Прочность. Она заключается в способности материала оказывать сопротивление разрушению под воздействием сил извне. Вид прочности зависит от того, как действуют внешние силы. Ее разделяют на: сжатие, растяжение, кручение, изгиб, ползучесть, усталость.
- Пластичность. Это способность металлов и их сплавов под воздействием нагрузки менять форму, не подвергаясь разрушению, и сохранять ее после окончания воздействия. Пластичность материала из металла определяют при его растяжении. Чем больше происходит удлинение, при одновременном уменьшении сечения, тем пластичнее металл. Материалы, обладающие хорошей пластичностью, прекрасно обрабатываются давлением: ковке, прессованию. Пластичность характеризуют двумя величинами: относительное сужение и удлинение.
- Твердость. Такое качество металла заключается в способности оказывать сопротивление проникновению в него инородного тела, имеющего более значительную твердость, и не получить при этом остаточных деформаций. Износоустойчивость и прочность – это основные характеристики металлов и сплавов, которые тесно связаны с твердостью. Материалы с такими свойствами находят применение для изготовления инструментов, применяемых для обработки металлов: резцы, напильники, сверла, метчики. Нередко по твердости материала определяют его износоустойчивость. Так твердые стали при эксплуатации изнашиваются меньше, чем более мягкие сорта.
- Ударная вязкость. Особенность сплавов и металлов сопротивляться влиянию нагрузок, сопровождающихся ударом. Это одна из важных характеристик материала, из которого изготовлены детали, испытывающие ударную нагрузку, во время работы машины: оси колес, коленчатые валы.
- Усталость. Это состояние металла, который находится под постоянным воздействием нагрузок. Усталость металлического материала происходит постепенно и может закончиться разрушением изделия. Способность металлов оказывать сопротивление разрушению от усталости называют выносливостью. Это свойство находится в зависимости от природы сплава или металла, состояния поверхности, характера обработки, условий работы.
Классы прочности и их обозначения
Нормативными документами по механическим свойствам крепежных изделий введено понятие класс прочности металла и установлена система обозначения. Каждый класс прочности обозначается двумя цифрами, между которыми ставится точка. Первое число означает предел прочности, уменьшенный в 100 раз. Например, класс прочности 5.6 означат, что предел прочности будет 500. Второе число увеличено в 10 раз – это отношение предела текучести к временному сопротивлению, выраженному в процентах (500х0,6=300), т. е. 30 % составляет минимальный предел текучести от предела прочности на растяжение. Все изделия, используемые для крепежа, классифицируются по назначению применения, форме, используемому материалу, классу прочности и покрытию. По назначению использования они бывают:
- Лемешные. Их используются для сельскохозяйственных машин.
- Мебельные. Применяются в строительстве и мебельном производстве.
- Дорожные. Ими крепят металлоконструкции.
- Машиностроительные. Применяют в машиностроительной промышленности и приборостроении.
Механические свойства крепежных изделий зависят от стали, из которой они изготовлены и качества обработки.
Удельная прочность
Удельная прочность материала (формула ниже) характеризуется отношением предела прочности к плотности металла. Эта величина показывает прочность конструкции при данной его массе. Наибольшую важность она представляет для таких отраслей, как авиастроение, ракетостроение и производство космических аппаратов.
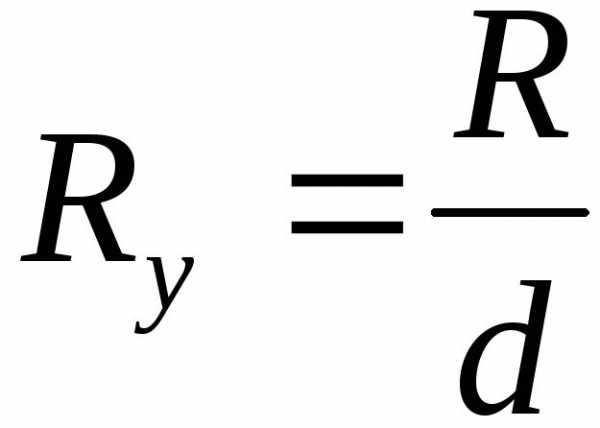
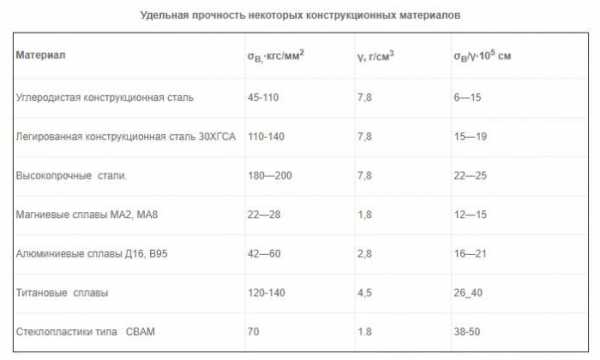
Использование пластичности и прочности металлов
Очень важными свойствами металла являются пластичность и прочность. Эти свойства находятся в прямой зависимости друг от друга. Они не позволяют металлу изменять форму и препятствуют макроскопическому разрушению при воздействии на него внешних и внутренних сил.
Металлы, обладающие высокой пластичностью, под воздействием нагрузки разрушаются постепенно. Вначале у них появляется изгиб и только затем он начинает постепенно разрушаться. Пластичные металлы легко меняют форму, поэтому их широко используют для изготовления кузовов автомобилей. Прочность и пластичность металлов зависит от того, как направлены приложенные к нему силы и в каком направлении проводилась прокатка при изготовлении материала. Установлено, что при прокатке кристаллы металла удлиняются в ее направлении больше, чем в поперечной направленности. У листовой стали прочность и пластичность значительно больше в направлении прокатки. В поперечном же направлении прочность уменьшается на 30 %, а пластичность на 50 %, по толщине листа эти показатели еще ниже. Например, появление излома на стальном листе при сваривании можно объяснить параллельностью оси шва и направления прокатки. По пластичности и прочности материала устанавливают возможность его использования для изготовления различных деталей машин, сооружений, инструментов, приборов.
Нормативное и расчетное сопротивление металла
Одним из основных параметров, которые характеризуют сопротивление металлов воздействиям силы, является нормативное сопротивление. Оно устанавливается по нормам проектирования. Расчетное сопротивление получается в результате деления нормативного на соответствующий коэффициент надежности по данному материалу. В некоторых случаях учитывают еще и коэффициент условий работы конструкций. В вычислениях, имеющих практическое значение, в основном используют расчетное сопротивление металла.
Пути повышения прочности металла
Существует несколько способов повышения прочности металлов и сплавов:
- Создание сплавов и металлов, имеющих бездефектную структуру. Имеются разработки по изготовлению нитевидных кристаллов (усов) в несколько десятков раз превышающих прочность обыкновенных металлов.
- Получение объемного и поверхностного наклепа искусственным путем. При обработке металла давлением (ковка, волочение, прокатка, прессование) образуется объемный наклеп, а накатка и дробеструйная обработка дает поверхностный наклеп.
- Создание легированного металла, используя элементы из таблицы Менделеева.
- Очищение металла, от имеющихся в нем примесей. В результате этого улучшаются его механические свойства, распространение трещин значительно уменьшается.
- Устранение с поверхности деталей шероховатости.
Интересные факты
- Сплавы из титана, удельный вес которых превышает алюминиевые примерно на 70 %, прочнее их в 4 раза, поэтому, по удельной прочности сплавы, содержащие титан, выгоднее использовать для самолетостроения.
- Многие алюминиевые сплавы превышают удельную прочность сталей, содержащих углерод. Сплавы из алюминия имеют высокую пластичность, коррозийную стойкость, прекрасно обрабатываются давлением и резанием.
- У пластмасс удельная прочность выше, чем у металлов. Но из-за недостаточной жесткости, механической прочности, старения, повышенной хрупкости и малой термостойкости ограничены в применении слоистые пластики, текстолиты и гетинаксы, особенно в крупногабаритных конструкциях.
- Установлено, что по выносливости к коррозии и удельной прочности, металлы черные, цветные и многие их сплавы уступают стеклопластикам.
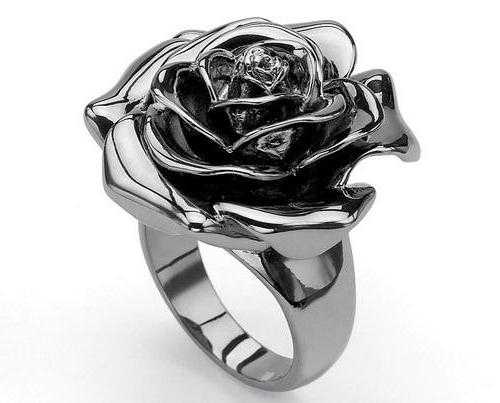
fb.ru