Эпоксидная смола: характеристика и сфера применения
0 votes
+
Голос за!
—
Голос против!
Эпоксидная смола – материал, знакомый практически каждому человеку, находящемуся в сознательном возрасте. Появившись на строительном рынке в пятидесятые годы прошлого столетия, она заняла заслуженное место на многих строительных площадках, что обусловлено ее универсальными потребительскими характеристиками. Сфера применения синтетического олигомера, которым является эпоксидная смола, достаточно широка и включает судостроительство, отрасли промышленного производства и домашнего хозяйства. Развитие современных технологий и постоянная разработка новых составов способствует постоянному расширению этого списка, а, соответственно, и возможностей применения эпоксидных смол. Несмотря на это, данный материал никогда не используется в чистом виде и приобретает свои ценные свойства только после смешения с отвердителем, что способствует окончанию реакций полимеризации.
Содержание
- Эпоксидный состав: соотношение смолы и отвердителя
- Основные разновидности эпоксидной смолы
- Эпоксидная смола ЭД-20: краткая характеристика
- Преимущества эпоксидных смол
- Сфера применения эпоксидной смолы: основные направления использования
- Эпоксидный клей: краткая характеристика
- Приготовление больших объемов эпоксидной смолы своими руками
- Изготовление объемного изделия из эпоксидной смолы: рекомендации мастеров
Эпоксидный состав: соотношение смолы и отвердителя
Востребованная практически во всех отраслях промышленности эпоксидная смола, с точки зрения химического строения, представляет собой синтетическое олигомерное соединение, которое используется в комплексе с отвердителями, способствующими завершению процессов полимеризации.
В процессе комбинации различных видов эпоксидных смол и отвердителей образуются разнообразные вещества, обладающие порой противоположными свойствами. Одни из них могут быть твердыми и жесткими, прочность которых превышает прочность стали, а другие, напротив, будут мягкими, по консистенции напоминающими резину. В зависимости от исходных компонентов эпоксидной смеси, отверждение эпоксидной смолы может происходить в условиях большого температурного диапазона: от -10 до +200 градусов, а сам материал также делится на две разновидности: смолу горячего и холодного отверждения, что определяется, в основном, видом используемого отвердителя.
Эпоксидная смола в комплексе с отвердителем холодного отверждения используется в бытовых целях, в условиях небольших производств и в случаях, когда термическая обработка не допустима.
Если эпоксидная смола используется для изготовления изделий, которые изначально должны быть устойчивы к воздействию высоких температур, механических нагрузок и агрессивных химических веществ, она дополняется отвердителем горячего отверждения. Это обусловлено тем, что использование отвердителей горячего отверждения способствует образованию более плотной молекулярной решетки, что легло в основе производства эпоксидных систем, отверждение которых реализуется в условиях высокой влажности или в морской воде.
Отвердитель для эпоксидной смолы выполняет функцию полимеризующего компонента. В качестве отвердителя могут использоваться третичные амины и их аналоги и фенолы. Соотношение эпоксидной смолы и отвердителя может быть остаточно вариабельным и напрямую определяется составом исходных компонентов. Будучи реактопластом, эпоксидная смола вступает в необратимую реакцию полимеризации с отвердителем, что способствует получению прочного вещества, не растворимого в воде и под действием высоких температур.
В процессе смешения компонентов важно соблюдать необходимые пропорции, актуальные для того или иного вида смолы, так как избыток или недостаток отвердителя оказывает негативное влияние на качество готового полимера, снижая его прочность, устойчивость к воздействию влаги, температуры и агрессивной химии. Соотношение компонентов в современных эпоксидных составах – 1:2 или 1:1.
Важно!
Один из распространенных мифов об эпоксидной смоле гласит, что в случае превышения используемой нормы отвердителя, отверждение смолы происходит значительно быстрее. Чтобы развенчать его, отметим, что превышение количества отвердителя не оказывает влияния на скорость полимеризации материала. Единственно возможным способом ускорения полимеризации смолы является повышение температуры реагирующей смеси. Доказано, что повышение температуры на 10 градусов способствует ускорению процесса застывания в 2-3 раза. Данное свойство легло в основу производства компаундов, в структуре которых содержатся ускорители отверждения. Также разработаны эпоксидные составы, застывание которых происходит при более низких температурах.
Таким образом, основными и единственными факторами, влияющими на скорость отверждения, являются температура смеси и тип отвердителя.
Основные разновидности эпоксидной смолы
Различают несколько видов смол эпоксидной природы, каждый из которых включает в себя несколько подвидов.- Эпоксидно-диановые смолы – собирательное понятие, включающее несколько подвидов смол эпоксидной природы – материалы с маркировкой ЭД-20 и ЭД-22.
- Эпоксидная смола ЭД-20 – наиболее часто используемая разновидность жидких смол, обладающая универсальными эксплуатационными характеристиками. Широко используется как в промышленности, так и в быту в составе заливочных и пропиточных компаундов, а также в процессе производства герметиков и клеевых составов. Может использоваться в качестве связующего материала для производства армированного пластика и защитных покрытий.
- Эпоксидная смола ЭД-22 – еще один представитель жидких смол эпоксидной природы, характеризующийся относительно низкой вязкостью и склонностью к кристаллизации в процессе хранения. Как и ЭД-20, обладает универсальными эксплуатационными свойствами.
- Эпоксидная смола ЭД-16 – материал, обладающий высокой вязкостью, вследствие чего он используется только в процессе производства стеклопластика в качестве связующего вещества;
- Эпоксидные смолы ЭД-10 и ЭД-8 – твердые вещества, использующиеся в электро- и радиотехнике.
- Эпоксидно-диановые смолы для лакокрасочных материалов – группа смол эпоксидной природы, включающая марки Э-40 и Э-40р, которые используются для изготовления лаков, красок, шпаклевок и покрытий, демонстрирующих устойчивость к повышенному воздействию химических веществ и агрессивных факторов внешней среды. Эпоксидная смола Э-41, также как и предыдущие марки, используется в составе заливочных композиций, шпаклевок, эмалей и клеевых составов.
- Эпоксидно-модифицированные смолы марки ЭПОФОМ – материалы, которые используются для производства эпоксидных компаундов, применяющихся в качестве защитных покрытий при обустройстве наливных полов и ремонте трубопровода.
Группа эпоксидно-модифицированных смол включает марки ЭПОФОМ-1,2,3. Они являются сырьем для производства материалов, выполняющих функцию защитных покрытий, основная функция которых заключается в предотвращении бетонных и металлических конструкций. Защищает строительные объекты от воздействия химически агрессивных веществ.
Эпоксидные смолы специального назначения – группа материалов, использующихся для производства композиций, обладающих особыми физико-механическими и технологическими характеристиками и эксплуатируемых в экстремальных условиях, а также изделий, используемых в различных областях промышленности и находящихся под воздействием агрессивных факторов внешней среды. Наиболее известными смолами группы специального назначения являются:
- Смола ЭХД (хлорсодержащая), используемая в качестве основы в процессе производства герметиков, клеевых составов, и связующего компонента для угле- и стеклопластика, характеризующегося механической устойчивостью, пониженной горючестью и влагостойкостью;
- Смола УП-637, в составе которой присутствует резорцин, является основным материалом, используемым в качестве основы для производства пропиточных и заливочных компаундов.
Еще одна разновидность марки УП-631 является структурным компонентом негорючих компаундов для заливки и пропитки.
Эпоксидная смола ЭД-20: краткая характеристика
С точки зрения химического строения, эпоксидная смола ЭД-20 представляет собой олигомерное соединение, основу которого составляет диглицидиловый эфир дифенилолпропана. В качестве отвердителя для эпоксидно-диановой смолы данной марки могут использоваться разнообразные биоорганические вещества – фенолформальдегидные смолы, ангидриды поликарбоновых кислот, ароматические и алифатические амины, полиамиды и другие вещества. В зависимости от используемого отвердителя, технические и эксплуатационные характеристики смолы ЭД-20 варьируются в широких пределах.
С учетом этого определяется и сфера ее применения, также характеризующаяся многогранностью:
- Эпоксидная смола марки ЭД-20 – одна из немногих разновидностей смол эпоксидной природы, которая может применяться в промышленном производстве и в составе композиционных материалов, например, заливочных и пропиточных компаундов, и в чистом виде;
- ЭД-20 используется для производства эпоксидного клея и герметика;
- Выполняет функцию связующего компонента в процессе производства армированного пластика и защитных покрытий.
Важно! Будучи абсолютно не взрывоопасной, смола ЭД-20 не горит в открытом огне. В составе материала присутствует летучие вещества – эпихлоргидрин и толуол, которые относятся ко второму классу опасности по степени воздействия на организм человека.
Преимущества эпоксидных смол
- Устойчивость к воздействию абразивных веществ, а, соответственно, и износу;
- Прочность клеевого соединения в случае использования клеевых составов на основе эпоксидной смолы;
- Оптимальные физико-механические характеристики;
- После отверждения эпоксидная смола характеризуется минимальной влагопроницаемостью;
- Минимальная усадка в процессе и после отверждения.
Сфера применения эпоксидной смолы: основные направления использования
Впервые использование эпоксидной смолы началось в 50-е годы прошлого столетия – в те времена смола заняла заслуженное место во многих отраслях промышленности. С тех пор характер ее использования претерпел немало изменений, однако основные области ее использования остались без изменений:
- Стекловолокно и эпоксидная смола – неизменное направление использования последней. В качестве пропиточного состава для стеклонити и стеклоткани, а также склеивания деталей эпоксидная смола используется во многих инженерно-технических отраслях – радиоэлектронике, электротехнике, авиационной и автомобильной промышленности, корабле- и машиностроении, а также в процессе производства стеклопластика, и мастерских, практикующих ремонт кузовных элементов автомобиля и лодочных корпусов;
- Эпоксидная смола, применение которой также многогранно, как и ее свойства, может использоваться в качестве гидроизоляционных покрытий для пола, бассейна и стен подвальных помещений;
- Включение в состав химически устойчивых покрытий – использование эпоксидной смолы лежит в основе производства красок и материалов, предназначенных для внутренней и наружной отделки зданий, например, пропиток, повышающих прочность и влагостойкость пористых материалов – дерева, бетона и других;
- Прозрачная эпоксидная смола, предназначенная для заливки в формы, после отверждения подвергается механической обработке посредством резки и шлифовки.
Обработанные элементы могут использоваться в электронной промышленности, домашнее хозяйстве, дизайнерских работах и даже ювелирном искусстве.
Важно! Украшения из натуральных материалов сейчас на пике популярности. Используя ювелирную эпоксидную смолу, представляющую собой пластичную массу, вы сможете изготовить изделия, полностью имитирующие стекло. Чтобы сделать украшения из эпоксидной смолы более привлекательными, в смолу заливают природные материалы – сухие цветы, листья, шишки или даже насекомых.
Эпоксидный клей: краткая характеристика
Многогранные свойства эпоксидной смолы проявляются, когда она используется в качестве клея, демонстрирующего все прелести используемого сырья. Эпоксидный клей является универсальным составом для склеивания материалов, характеризующихся непористой поверхностью: алюминия, фаянса, керамики, твердых пород древесины, таких как дуб, тик, эвкалипт и др. С одинаковой популярностью используется и в обувных мастерских, и в авиастроении. Это обусловлено высокой адгезией и прочностью образуемого соединения. Различают два типа клеевых составов на основе эпоксидной смолы: эластичные и жесткие.
Важно! Если вы планируете проведение работ в бытовых условиях, специалисты рекомендуют отдавать предпочтение клеевым составам, не требующим точного соблюдения соотношения смолы и отвердителя. Комплект таких составов дополнен отвердителем холодного типа.
Для приготовления эпоксидного клея смолу необходимо смешать с небольшим количеством отвердителя (несколько граммов) при комнатной температуре. В основном эпоксидную смолу и отвердитель берут в пропорции 1: 10, однако допускается превышение нормы отвердителя, способствующее изменению соотношения до 1: 5. Компоненты состава смешиваются вручную.
Приготовление больших объемов эпоксидной смолы своими руками
Для эпоксидной смолы характерен ряд специфических свойств, незнание которых может привести к проблемам в процессе изготовления больших объемов эпоксидного состава. Важно знать, что в процессе работы с большим количеством эпоксидного материала выделяется тепло, и если смола не предназначена для смешивания с отвердителем в больших количествах, сразу после соединения компонентов, она подвергается полимеризации и затвердеванию, становясь непригодной к использованию. В худшем случае смесь вскипает с выделением едкого дыма и подвергается самовозгоранию, что объясняется лавинообразным разогреванием смолы, в процессе которого ускоряется реакция полимеризации и происходит интенсивное теплообразование.
Важно! Приобретая эпоксидную смолу и отвердитель, уточните у специалиста, для каких целей она предназначена. Из специального состава, предназначенного для приготовления больших объемов смеси, вы получите чистую, прозрачную, равномерно застывшую отливку, характеризующуюся отсутствием воздушных пузырей.
Технология приготовления больших объемов эпоксидной смолы, например, нескольких килограммов смеси, отличается от замешивания небольшого количества эпоксидного клея. Рассмотрим этот процесс более подробно.
- Зачастую при длительном хранении смолы, она становится более вязкой, а также мутнеет и кристаллизуется. Чтобы устранить эти явления, перед добавлением отвердителя и пластификатора нагрейте смолу на водяной бане, что позволит уменьшить ее вязкость. Для этого емкость со смолой опустите в воду и нагрейте до температуры 50-60 градусов;
Важно! В процессе нагревания смолы помните, что увеличение температуры на 10 градусов способствует ускорению процесса полимеризации в 2-3 раза. Вследствие этого, важно следить за температурой смолы, так как в случае закипания она приобретет мутно-белый оттенок и вспенится, став непригодной к использованию.
Важно! Зачастую неопытные мастера для повышения вязкости смолы используют растворитель, однако даже небольшая его концентрация (не более 5-7 %) приведет к выраженному снижению прочностных характеристик и теплостойкости изделия.
Кроме того, в процессе эксплуатации изделия часто происходит «выпотевание» растворителя из полимера, что также ухудшает качество материала.
- Полностью исключите наличие воды в эпоксидной смоле и отвердителе. При попадании воды эпоксидная смола становится мутной, теряя свои свойства. Однако развитие современных технологий позволяет выпускать водоразбавляемые эпоксидные составы, которые разводятся дистиллированной водой;
- Приготовление эпоксидного состава начинают с добавления пластификатора. Если вы используете ДБФ, смолу с пластификатором медленно нагрейте, а при использовании ДЭГ-1 просто перемешайте состав, используя строительный миксер или насадку на дрель. Пропорция используемого пластификатора и смолы определяется требуемой пластичностью смеси, однако в большинстве случаев доля пластификатора в составе смеси не превышает 5-10 %;
- Перед тем, как в смесь смолы и пластификатора добавить отвердитель, остудите ее до 30 градусов, что позволит предотвратить ее закипание.
После этого добавьте в смесь отвердитель, исходя из соотношения 1: 10. Иногда допускается изменение пропорций от 1:5 до 1:20. Чтобы добиться равномерного растворения отвердителя в смоле, необходимо постоянно перемешивать состав, в противном случае, при неравномерном распределении отвердителя, он останется несвязанным и будет выпотевать. Чтобы добиться приготовления однородной смеси, медленно и постепенно наливайте отвердитель тонкой струйкой, постоянно перемешивая состав.
Важно! Даже кратковременное повышение концентрации отвердителя приведет к вскипанию смолы – она приобретет матово-белый оттенок, покроется пеной и станет непригодной к использованию. Старайтесь избегать передозировки отвердителя, так как в некоторых случаях может произойти моментальное затвердевание смолы.
Изготовление объемного изделия из эпоксидной смолы: рекомендации мастеров
- Объемное изделие из эпоксидной смолы должно быть прозрачным, без пузырьков воздуха.
Отверждение материала должно быть равномерным, как в толще, так и на поверхности изделия. Если толщина готового изделия превышает 2 мм, смолу необходимо наносить слоями, после того, как произойдет первичная полимеризация предыдущего слоя.
- Также эпоксидную смолу можно заливать в формы. Чтобы после полимеризации смолы готовое изделия можно было легко извлечь из формы, ее необходимо смазать техническим вазелином. Чтобы придать изделию цвет, используют порошковый краситель.
- После того, как вы завершили работу, изделие необходимо выдержать при температуре немного выше комнатной. По истечении 2-3 часов после первичной полимеризации изделие прогревают в жарочном шкафу, что позволит ускорить процесс полимеризации до 5-6 часов. При комнатной температуре процесс полимеризации длится 7 дней.
- В последующем изделие, отлитое из эпоксидной смолы, подлежит механической обработке – резке и шлифованию.
Важно! Эпоксидная смола отечественного производства в большинстве случаев непригодна для изготовления объемных изделий, что определяется ее неравномерным отверждением в толще изделия.
Эпоксидная смола: характеристика и сфера применения
0 votes
+
Голос за!
—
Голос против!
Эпоксидная смола – материал, знакомый практически каждому человеку, находящемуся в сознательном возрасте. Появившись на строительном рынке в пятидесятые годы прошлого столетия, она заняла заслуженное место на многих строительных площадках, что обусловлено ее универсальными потребительскими характеристиками. Сфера применения синтетического олигомера, которым является эпоксидная смола, достаточно широка и включает судостроительство, отрасли промышленного производства и домашнего хозяйства. Развитие современных технологий и постоянная разработка новых составов способствует постоянному расширению этого списка, а, соответственно, и возможностей применения эпоксидных смол. Несмотря на это, данный материал никогда не используется в чистом виде и приобретает свои ценные свойства только после смешения с отвердителем, что способствует окончанию реакций полимеризации. В связи с востребованностью эпоксидной смолы на современных строительных площадках, а также в сфере домашнего хозяйства и творчества, в настоящей статье мы рассмотрим технические характеристики данного материала и субстанции, в составе которых используется эпоксидная смола.
Содержание
- Эпоксидный состав: соотношение смолы и отвердителя
- Основные разновидности эпоксидной смолы
- Эпоксидная смола ЭД-20: краткая характеристика
- Преимущества эпоксидных смол
- Сфера применения эпоксидной смолы: основные направления использования
- Эпоксидный клей: краткая характеристика
- Приготовление больших объемов эпоксидной смолы своими руками
- Изготовление объемного изделия из эпоксидной смолы: рекомендации мастеров
Эпоксидный состав: соотношение смолы и отвердителя
Востребованная практически во всех отраслях промышленности эпоксидная смола, с точки зрения химического строения, представляет собой синтетическое олигомерное соединение, которое используется в комплексе с отвердителями, способствующими завершению процессов полимеризации. Именно эти процессы, после завершения которых, эпоксидная смола готова к использованию, определяют ее технические и эксплуатационные характеристики. С учетом этого, можно прийти к выводу, что эпоксидная смола не может использоваться в чистом виде.
В процессе комбинации различных видов эпоксидных смол и отвердителей образуются разнообразные вещества, обладающие порой противоположными свойствами. Одни из них могут быть твердыми и жесткими, прочность которых превышает прочность стали, а другие, напротив, будут мягкими, по консистенции напоминающими резину. В зависимости от исходных компонентов эпоксидной смеси, отверждение эпоксидной смолы может происходить в условиях большого температурного диапазона: от -10 до +200 градусов, а сам материал также делится на две разновидности: смолу горячего и холодного отверждения, что определяется, в основном, видом используемого отвердителя.
Эпоксидная смола в комплексе с отвердителем холодного отверждения используется в бытовых целях, в условиях небольших производств и в случаях, когда термическая обработка не допустима.
Если эпоксидная смола используется для изготовления изделий, которые изначально должны быть устойчивы к воздействию высоких температур, механических нагрузок и агрессивных химических веществ, она дополняется отвердителем горячего отверждения. Это обусловлено тем, что использование отвердителей горячего отверждения способствует образованию более плотной молекулярной решетки, что легло в основе производства эпоксидных систем, отверждение которых реализуется в условиях высокой влажности или в морской воде.
Отвердитель для эпоксидной смолы выполняет функцию полимеризующего компонента. В качестве отвердителя могут использоваться третичные амины и их аналоги и фенолы. Соотношение эпоксидной смолы и отвердителя может быть остаточно вариабельным и напрямую определяется составом исходных компонентов. Будучи реактопластом, эпоксидная смола вступает в необратимую реакцию полимеризации с отвердителем, что способствует получению прочного вещества, не растворимого в воде и под действием высоких температур.
В процессе смешения компонентов важно соблюдать необходимые пропорции, актуальные для того или иного вида смолы, так как избыток или недостаток отвердителя оказывает негативное влияние на качество готового полимера, снижая его прочность, устойчивость к воздействию влаги, температуры и агрессивной химии. Соотношение компонентов в современных эпоксидных составах – 1:2 или 1:1.
Важно! Один из распространенных мифов об эпоксидной смоле гласит, что в случае превышения используемой нормы отвердителя, отверждение смолы происходит значительно быстрее. Чтобы развенчать его, отметим, что превышение количества отвердителя не оказывает влияния на скорость полимеризации материала. Единственно возможным способом ускорения полимеризации смолы является повышение температуры реагирующей смеси. Доказано, что повышение температуры на 10 градусов способствует ускорению процесса застывания в 2-3 раза. Данное свойство легло в основу производства компаундов, в структуре которых содержатся ускорители отверждения.
Также разработаны эпоксидные составы, застывание которых происходит при более низких температурах.
Таким образом, основными и единственными факторами, влияющими на скорость отверждения, являются температура смеси и тип отвердителя.
Основные разновидности эпоксидной смолы
Различают несколько видов смол эпоксидной природы, каждый из которых включает в себя несколько подвидов.
- Эпоксидно-диановые смолы – собирательное понятие, включающее несколько подвидов смол эпоксидной природы – материалы с маркировкой ЭД-20 и ЭД-22.
- Эпоксидная смола ЭД-20 – наиболее часто используемая разновидность жидких смол, обладающая универсальными эксплуатационными характеристиками. Широко используется как в промышленности, так и в быту в составе заливочных и пропиточных компаундов, а также в процессе производства герметиков и клеевых составов. Может использоваться в качестве связующего материала для производства армированного пластика и защитных покрытий.
- Эпоксидная смола ЭД-22 – еще один представитель жидких смол эпоксидной природы, характеризующийся относительно низкой вязкостью и склонностью к кристаллизации в процессе хранения. Как и ЭД-20, обладает универсальными эксплуатационными свойствами.
- Эпоксидная смола ЭД-16 – материал, обладающий высокой вязкостью, вследствие чего он используется только в процессе производства стеклопластика в качестве связующего вещества;
- Эпоксидные смолы ЭД-10 и ЭД-8 – твердые вещества, использующиеся в электро- и радиотехнике.
- Эпоксидно-диановые смолы для лакокрасочных материалов – группа смол эпоксидной природы, включающая марки Э-40 и Э-40р, которые используются для изготовления лаков, красок, шпаклевок и покрытий, демонстрирующих устойчивость к повышенному воздействию химических веществ и агрессивных факторов внешней среды. Эпоксидная смола Э-41, также как и предыдущие марки, используется в составе заливочных композиций, шпаклевок, эмалей и клеевых составов.
- Эпоксидно-модифицированные смолы марки ЭПОФОМ – материалы, которые используются для производства эпоксидных компаундов, применяющихся в качестве защитных покрытий при обустройстве наливных полов и ремонте трубопровода.
Группа эпоксидно-модифицированных смол включает марки ЭПОФОМ-1,2,3. Они являются сырьем для производства материалов, выполняющих функцию защитных покрытий, основная функция которых заключается в предотвращении бетонных и металлических конструкций. Защищает строительные объекты от воздействия химически агрессивных веществ.
Эпоксидные смолы специального назначения – группа материалов, использующихся для производства композиций, обладающих особыми физико-механическими и технологическими характеристиками и эксплуатируемых в экстремальных условиях, а также изделий, используемых в различных областях промышленности и находящихся под воздействием агрессивных факторов внешней среды. Наиболее известными смолами группы специального назначения являются:
- Смола ЭХД (хлорсодержащая), используемая в качестве основы в процессе производства герметиков, клеевых составов, и связующего компонента для угле- и стеклопластика, характеризующегося механической устойчивостью, пониженной горючестью и влагостойкостью;
- Смола УП-637, в составе которой присутствует резорцин, является основным материалом, используемым в качестве основы для производства пропиточных и заливочных компаундов.
Еще одна разновидность марки УП-631 является структурным компонентом негорючих компаундов для заливки и пропитки.
Эпоксидная смола ЭД-20: краткая характеристика
С точки зрения химического строения, эпоксидная смола ЭД-20 представляет собой олигомерное соединение, основу которого составляет диглицидиловый эфир дифенилолпропана. В качестве отвердителя для эпоксидно-диановой смолы данной марки могут использоваться разнообразные биоорганические вещества – фенолформальдегидные смолы, ангидриды поликарбоновых кислот, ароматические и алифатические амины, полиамиды и другие вещества. В зависимости от используемого отвердителя, технические и эксплуатационные характеристики смолы ЭД-20 варьируются в широких пределах.
С учетом этого определяется и сфера ее применения, также характеризующаяся многогранностью:
- Эпоксидная смола марки ЭД-20 – одна из немногих разновидностей смол эпоксидной природы, которая может применяться в промышленном производстве и в составе композиционных материалов, например, заливочных и пропиточных компаундов, и в чистом виде;
- ЭД-20 используется для производства эпоксидного клея и герметика;
- Выполняет функцию связующего компонента в процессе производства армированного пластика и защитных покрытий.
Важно! Будучи абсолютно не взрывоопасной, смола ЭД-20 не горит в открытом огне. В составе материала присутствует летучие вещества – эпихлоргидрин и толуол, которые относятся ко второму классу опасности по степени воздействия на организм человека.
Преимущества эпоксидных смол
- Устойчивость к воздействию абразивных веществ, а, соответственно, и износу;
- Прочность клеевого соединения в случае использования клеевых составов на основе эпоксидной смолы;
- Оптимальные физико-механические характеристики;
- После отверждения эпоксидная смола характеризуется минимальной влагопроницаемостью;
- Минимальная усадка в процессе и после отверждения.
Сфера применения эпоксидной смолы: основные направления использования
Впервые использование эпоксидной смолы началось в 50-е годы прошлого столетия – в те времена смола заняла заслуженное место во многих отраслях промышленности. С тех пор характер ее использования претерпел немало изменений, однако основные области ее использования остались без изменений:
- Стекловолокно и эпоксидная смола – неизменное направление использования последней. В качестве пропиточного состава для стеклонити и стеклоткани, а также склеивания деталей эпоксидная смола используется во многих инженерно-технических отраслях – радиоэлектронике, электротехнике, авиационной и автомобильной промышленности, корабле- и машиностроении, а также в процессе производства стеклопластика, и мастерских, практикующих ремонт кузовных элементов автомобиля и лодочных корпусов;
- Эпоксидная смола, применение которой также многогранно, как и ее свойства, может использоваться в качестве гидроизоляционных покрытий для пола, бассейна и стен подвальных помещений;
- Включение в состав химически устойчивых покрытий – использование эпоксидной смолы лежит в основе производства красок и материалов, предназначенных для внутренней и наружной отделки зданий, например, пропиток, повышающих прочность и влагостойкость пористых материалов – дерева, бетона и других;
- Прозрачная эпоксидная смола, предназначенная для заливки в формы, после отверждения подвергается механической обработке посредством резки и шлифовки.
Обработанные элементы могут использоваться в электронной промышленности, домашнее хозяйстве, дизайнерских работах и даже ювелирном искусстве.
Важно! Украшения из натуральных материалов сейчас на пике популярности. Используя ювелирную эпоксидную смолу, представляющую собой пластичную массу, вы сможете изготовить изделия, полностью имитирующие стекло. Чтобы сделать украшения из эпоксидной смолы более привлекательными, в смолу заливают природные материалы – сухие цветы, листья, шишки или даже насекомых.
Эпоксидный клей: краткая характеристика
Многогранные свойства эпоксидной смолы проявляются, когда она используется в качестве клея, демонстрирующего все прелести используемого сырья. Эпоксидный клей является универсальным составом для склеивания материалов, характеризующихся непористой поверхностью: алюминия, фаянса, керамики, твердых пород древесины, таких как дуб, тик, эвкалипт и др. С одинаковой популярностью используется и в обувных мастерских, и в авиастроении. Это обусловлено высокой адгезией и прочностью образуемого соединения. Различают два типа клеевых составов на основе эпоксидной смолы: эластичные и жесткие.
Важно! Если вы планируете проведение работ в бытовых условиях, специалисты рекомендуют отдавать предпочтение клеевым составам, не требующим точного соблюдения соотношения смолы и отвердителя. Комплект таких составов дополнен отвердителем холодного типа.
Для приготовления эпоксидного клея смолу необходимо смешать с небольшим количеством отвердителя (несколько граммов) при комнатной температуре. В основном эпоксидную смолу и отвердитель берут в пропорции 1: 10, однако допускается превышение нормы отвердителя, способствующее изменению соотношения до 1: 5. Компоненты состава смешиваются вручную.
Приготовление больших объемов эпоксидной смолы своими руками
Для эпоксидной смолы характерен ряд специфических свойств, незнание которых может привести к проблемам в процессе изготовления больших объемов эпоксидного состава. Важно знать, что в процессе работы с большим количеством эпоксидного материала выделяется тепло, и если смола не предназначена для смешивания с отвердителем в больших количествах, сразу после соединения компонентов, она подвергается полимеризации и затвердеванию, становясь непригодной к использованию. В худшем случае смесь вскипает с выделением едкого дыма и подвергается самовозгоранию, что объясняется лавинообразным разогреванием смолы, в процессе которого ускоряется реакция полимеризации и происходит интенсивное теплообразование.
Важно! Приобретая эпоксидную смолу и отвердитель, уточните у специалиста, для каких целей она предназначена. Из специального состава, предназначенного для приготовления больших объемов смеси, вы получите чистую, прозрачную, равномерно застывшую отливку, характеризующуюся отсутствием воздушных пузырей.
Технология приготовления больших объемов эпоксидной смолы, например, нескольких килограммов смеси, отличается от замешивания небольшого количества эпоксидного клея. Рассмотрим этот процесс более подробно.
- Зачастую при длительном хранении смолы, она становится более вязкой, а также мутнеет и кристаллизуется. Чтобы устранить эти явления, перед добавлением отвердителя и пластификатора нагрейте смолу на водяной бане, что позволит уменьшить ее вязкость. Для этого емкость со смолой опустите в воду и нагрейте до температуры 50-60 градусов;
Важно! В процессе нагревания смолы помните, что увеличение температуры на 10 градусов способствует ускорению процесса полимеризации в 2-3 раза. Вследствие этого, важно следить за температурой смолы, так как в случае закипания она приобретет мутно-белый оттенок и вспенится, став непригодной к использованию.
Важно! Зачастую неопытные мастера для повышения вязкости смолы используют растворитель, однако даже небольшая его концентрация (не более 5-7 %) приведет к выраженному снижению прочностных характеристик и теплостойкости изделия.
Кроме того, в процессе эксплуатации изделия часто происходит «выпотевание» растворителя из полимера, что также ухудшает качество материала.
- Полностью исключите наличие воды в эпоксидной смоле и отвердителе. При попадании воды эпоксидная смола становится мутной, теряя свои свойства. Однако развитие современных технологий позволяет выпускать водоразбавляемые эпоксидные составы, которые разводятся дистиллированной водой;
- Приготовление эпоксидного состава начинают с добавления пластификатора. Если вы используете ДБФ, смолу с пластификатором медленно нагрейте, а при использовании ДЭГ-1 просто перемешайте состав, используя строительный миксер или насадку на дрель. Пропорция используемого пластификатора и смолы определяется требуемой пластичностью смеси, однако в большинстве случаев доля пластификатора в составе смеси не превышает 5-10 %;
- Перед тем, как в смесь смолы и пластификатора добавить отвердитель, остудите ее до 30 градусов, что позволит предотвратить ее закипание.
После этого добавьте в смесь отвердитель, исходя из соотношения 1: 10. Иногда допускается изменение пропорций от 1:5 до 1:20. Чтобы добиться равномерного растворения отвердителя в смоле, необходимо постоянно перемешивать состав, в противном случае, при неравномерном распределении отвердителя, он останется несвязанным и будет выпотевать. Чтобы добиться приготовления однородной смеси, медленно и постепенно наливайте отвердитель тонкой струйкой, постоянно перемешивая состав.
Важно! Даже кратковременное повышение концентрации отвердителя приведет к вскипанию смолы – она приобретет матово-белый оттенок, покроется пеной и станет непригодной к использованию. Старайтесь избегать передозировки отвердителя, так как в некоторых случаях может произойти моментальное затвердевание смолы.
Изготовление объемного изделия из эпоксидной смолы: рекомендации мастеров
- Объемное изделие из эпоксидной смолы должно быть прозрачным, без пузырьков воздуха.
Отверждение материала должно быть равномерным, как в толще, так и на поверхности изделия. Если толщина готового изделия превышает 2 мм, смолу необходимо наносить слоями, после того, как произойдет первичная полимеризация предыдущего слоя.
- Также эпоксидную смолу можно заливать в формы. Чтобы после полимеризации смолы готовое изделия можно было легко извлечь из формы, ее необходимо смазать техническим вазелином. Чтобы придать изделию цвет, используют порошковый краситель.
- После того, как вы завершили работу, изделие необходимо выдержать при температуре немного выше комнатной. По истечении 2-3 часов после первичной полимеризации изделие прогревают в жарочном шкафу, что позволит ускорить процесс полимеризации до 5-6 часов. При комнатной температуре процесс полимеризации длится 7 дней.
- В последующем изделие, отлитое из эпоксидной смолы, подлежит механической обработке – резке и шлифованию.
Важно! Эпоксидная смола отечественного производства в большинстве случаев непригодна для изготовления объемных изделий, что определяется ее неравномерным отверждением в толще изделия.
Эпоксидная смола: характеристика и сфера применения
0 votes
+
Голос за!
—
Голос против!
Эпоксидная смола – материал, знакомый практически каждому человеку, находящемуся в сознательном возрасте. Появившись на строительном рынке в пятидесятые годы прошлого столетия, она заняла заслуженное место на многих строительных площадках, что обусловлено ее универсальными потребительскими характеристиками. Сфера применения синтетического олигомера, которым является эпоксидная смола, достаточно широка и включает судостроительство, отрасли промышленного производства и домашнего хозяйства. Развитие современных технологий и постоянная разработка новых составов способствует постоянному расширению этого списка, а, соответственно, и возможностей применения эпоксидных смол. Несмотря на это, данный материал никогда не используется в чистом виде и приобретает свои ценные свойства только после смешения с отвердителем, что способствует окончанию реакций полимеризации. В связи с востребованностью эпоксидной смолы на современных строительных площадках, а также в сфере домашнего хозяйства и творчества, в настоящей статье мы рассмотрим технические характеристики данного материала и субстанции, в составе которых используется эпоксидная смола.
Содержание
- Эпоксидный состав: соотношение смолы и отвердителя
- Основные разновидности эпоксидной смолы
- Эпоксидная смола ЭД-20: краткая характеристика
- Преимущества эпоксидных смол
- Сфера применения эпоксидной смолы: основные направления использования
- Эпоксидный клей: краткая характеристика
- Приготовление больших объемов эпоксидной смолы своими руками
- Изготовление объемного изделия из эпоксидной смолы: рекомендации мастеров
Эпоксидный состав: соотношение смолы и отвердителя
Востребованная практически во всех отраслях промышленности эпоксидная смола, с точки зрения химического строения, представляет собой синтетическое олигомерное соединение, которое используется в комплексе с отвердителями, способствующими завершению процессов полимеризации. Именно эти процессы, после завершения которых, эпоксидная смола готова к использованию, определяют ее технические и эксплуатационные характеристики. С учетом этого, можно прийти к выводу, что эпоксидная смола не может использоваться в чистом виде.
В процессе комбинации различных видов эпоксидных смол и отвердителей образуются разнообразные вещества, обладающие порой противоположными свойствами. Одни из них могут быть твердыми и жесткими, прочность которых превышает прочность стали, а другие, напротив, будут мягкими, по консистенции напоминающими резину. В зависимости от исходных компонентов эпоксидной смеси, отверждение эпоксидной смолы может происходить в условиях большого температурного диапазона: от -10 до +200 градусов, а сам материал также делится на две разновидности: смолу горячего и холодного отверждения, что определяется, в основном, видом используемого отвердителя.
Эпоксидная смола в комплексе с отвердителем холодного отверждения используется в бытовых целях, в условиях небольших производств и в случаях, когда термическая обработка не допустима.
Если эпоксидная смола используется для изготовления изделий, которые изначально должны быть устойчивы к воздействию высоких температур, механических нагрузок и агрессивных химических веществ, она дополняется отвердителем горячего отверждения. Это обусловлено тем, что использование отвердителей горячего отверждения способствует образованию более плотной молекулярной решетки, что легло в основе производства эпоксидных систем, отверждение которых реализуется в условиях высокой влажности или в морской воде.
Отвердитель для эпоксидной смолы выполняет функцию полимеризующего компонента. В качестве отвердителя могут использоваться третичные амины и их аналоги и фенолы. Соотношение эпоксидной смолы и отвердителя может быть остаточно вариабельным и напрямую определяется составом исходных компонентов. Будучи реактопластом, эпоксидная смола вступает в необратимую реакцию полимеризации с отвердителем, что способствует получению прочного вещества, не растворимого в воде и под действием высоких температур.
В процессе смешения компонентов важно соблюдать необходимые пропорции, актуальные для того или иного вида смолы, так как избыток или недостаток отвердителя оказывает негативное влияние на качество готового полимера, снижая его прочность, устойчивость к воздействию влаги, температуры и агрессивной химии. Соотношение компонентов в современных эпоксидных составах – 1:2 или 1:1.
Важно! Один из распространенных мифов об эпоксидной смоле гласит, что в случае превышения используемой нормы отвердителя, отверждение смолы происходит значительно быстрее. Чтобы развенчать его, отметим, что превышение количества отвердителя не оказывает влияния на скорость полимеризации материала. Единственно возможным способом ускорения полимеризации смолы является повышение температуры реагирующей смеси. Доказано, что повышение температуры на 10 градусов способствует ускорению процесса застывания в 2-3 раза. Данное свойство легло в основу производства компаундов, в структуре которых содержатся ускорители отверждения.
Также разработаны эпоксидные составы, застывание которых происходит при более низких температурах.
Таким образом, основными и единственными факторами, влияющими на скорость отверждения, являются температура смеси и тип отвердителя.
Основные разновидности эпоксидной смолы
Различают несколько видов смол эпоксидной природы, каждый из которых включает в себя несколько подвидов.
- Эпоксидно-диановые смолы – собирательное понятие, включающее несколько подвидов смол эпоксидной природы – материалы с маркировкой ЭД-20 и ЭД-22.
- Эпоксидная смола ЭД-20 – наиболее часто используемая разновидность жидких смол, обладающая универсальными эксплуатационными характеристиками. Широко используется как в промышленности, так и в быту в составе заливочных и пропиточных компаундов, а также в процессе производства герметиков и клеевых составов. Может использоваться в качестве связующего материала для производства армированного пластика и защитных покрытий.
- Эпоксидная смола ЭД-22 – еще один представитель жидких смол эпоксидной природы, характеризующийся относительно низкой вязкостью и склонностью к кристаллизации в процессе хранения. Как и ЭД-20, обладает универсальными эксплуатационными свойствами.
- Эпоксидная смола ЭД-16 – материал, обладающий высокой вязкостью, вследствие чего он используется только в процессе производства стеклопластика в качестве связующего вещества;
- Эпоксидные смолы ЭД-10 и ЭД-8 – твердые вещества, использующиеся в электро- и радиотехнике.
- Эпоксидно-диановые смолы для лакокрасочных материалов – группа смол эпоксидной природы, включающая марки Э-40 и Э-40р, которые используются для изготовления лаков, красок, шпаклевок и покрытий, демонстрирующих устойчивость к повышенному воздействию химических веществ и агрессивных факторов внешней среды. Эпоксидная смола Э-41, также как и предыдущие марки, используется в составе заливочных композиций, шпаклевок, эмалей и клеевых составов.
- Эпоксидно-модифицированные смолы марки ЭПОФОМ – материалы, которые используются для производства эпоксидных компаундов, применяющихся в качестве защитных покрытий при обустройстве наливных полов и ремонте трубопровода.
Группа эпоксидно-модифицированных смол включает марки ЭПОФОМ-1,2,3. Они являются сырьем для производства материалов, выполняющих функцию защитных покрытий, основная функция которых заключается в предотвращении бетонных и металлических конструкций. Защищает строительные объекты от воздействия химически агрессивных веществ.
Эпоксидные смолы специального назначения – группа материалов, использующихся для производства композиций, обладающих особыми физико-механическими и технологическими характеристиками и эксплуатируемых в экстремальных условиях, а также изделий, используемых в различных областях промышленности и находящихся под воздействием агрессивных факторов внешней среды. Наиболее известными смолами группы специального назначения являются:
- Смола ЭХД (хлорсодержащая), используемая в качестве основы в процессе производства герметиков, клеевых составов, и связующего компонента для угле- и стеклопластика, характеризующегося механической устойчивостью, пониженной горючестью и влагостойкостью;
- Смола УП-637, в составе которой присутствует резорцин, является основным материалом, используемым в качестве основы для производства пропиточных и заливочных компаундов.
Еще одна разновидность марки УП-631 является структурным компонентом негорючих компаундов для заливки и пропитки.
Эпоксидная смола ЭД-20: краткая характеристика
С точки зрения химического строения, эпоксидная смола ЭД-20 представляет собой олигомерное соединение, основу которого составляет диглицидиловый эфир дифенилолпропана. В качестве отвердителя для эпоксидно-диановой смолы данной марки могут использоваться разнообразные биоорганические вещества – фенолформальдегидные смолы, ангидриды поликарбоновых кислот, ароматические и алифатические амины, полиамиды и другие вещества. В зависимости от используемого отвердителя, технические и эксплуатационные характеристики смолы ЭД-20 варьируются в широких пределах.
С учетом этого определяется и сфера ее применения, также характеризующаяся многогранностью:
- Эпоксидная смола марки ЭД-20 – одна из немногих разновидностей смол эпоксидной природы, которая может применяться в промышленном производстве и в составе композиционных материалов, например, заливочных и пропиточных компаундов, и в чистом виде;
- ЭД-20 используется для производства эпоксидного клея и герметика;
- Выполняет функцию связующего компонента в процессе производства армированного пластика и защитных покрытий.
Важно! Будучи абсолютно не взрывоопасной, смола ЭД-20 не горит в открытом огне. В составе материала присутствует летучие вещества – эпихлоргидрин и толуол, которые относятся ко второму классу опасности по степени воздействия на организм человека.
Преимущества эпоксидных смол
- Устойчивость к воздействию абразивных веществ, а, соответственно, и износу;
- Прочность клеевого соединения в случае использования клеевых составов на основе эпоксидной смолы;
- Оптимальные физико-механические характеристики;
- После отверждения эпоксидная смола характеризуется минимальной влагопроницаемостью;
- Минимальная усадка в процессе и после отверждения.
Сфера применения эпоксидной смолы: основные направления использования
Впервые использование эпоксидной смолы началось в 50-е годы прошлого столетия – в те времена смола заняла заслуженное место во многих отраслях промышленности. С тех пор характер ее использования претерпел немало изменений, однако основные области ее использования остались без изменений:
- Стекловолокно и эпоксидная смола – неизменное направление использования последней. В качестве пропиточного состава для стеклонити и стеклоткани, а также склеивания деталей эпоксидная смола используется во многих инженерно-технических отраслях – радиоэлектронике, электротехнике, авиационной и автомобильной промышленности, корабле- и машиностроении, а также в процессе производства стеклопластика, и мастерских, практикующих ремонт кузовных элементов автомобиля и лодочных корпусов;
- Эпоксидная смола, применение которой также многогранно, как и ее свойства, может использоваться в качестве гидроизоляционных покрытий для пола, бассейна и стен подвальных помещений;
- Включение в состав химически устойчивых покрытий – использование эпоксидной смолы лежит в основе производства красок и материалов, предназначенных для внутренней и наружной отделки зданий, например, пропиток, повышающих прочность и влагостойкость пористых материалов – дерева, бетона и других;
- Прозрачная эпоксидная смола, предназначенная для заливки в формы, после отверждения подвергается механической обработке посредством резки и шлифовки.
Обработанные элементы могут использоваться в электронной промышленности, домашнее хозяйстве, дизайнерских работах и даже ювелирном искусстве.
Важно! Украшения из натуральных материалов сейчас на пике популярности. Используя ювелирную эпоксидную смолу, представляющую собой пластичную массу, вы сможете изготовить изделия, полностью имитирующие стекло. Чтобы сделать украшения из эпоксидной смолы более привлекательными, в смолу заливают природные материалы – сухие цветы, листья, шишки или даже насекомых.
Эпоксидный клей: краткая характеристика
Многогранные свойства эпоксидной смолы проявляются, когда она используется в качестве клея, демонстрирующего все прелести используемого сырья. Эпоксидный клей является универсальным составом для склеивания материалов, характеризующихся непористой поверхностью: алюминия, фаянса, керамики, твердых пород древесины, таких как дуб, тик, эвкалипт и др. С одинаковой популярностью используется и в обувных мастерских, и в авиастроении. Это обусловлено высокой адгезией и прочностью образуемого соединения. Различают два типа клеевых составов на основе эпоксидной смолы: эластичные и жесткие.
Важно! Если вы планируете проведение работ в бытовых условиях, специалисты рекомендуют отдавать предпочтение клеевым составам, не требующим точного соблюдения соотношения смолы и отвердителя. Комплект таких составов дополнен отвердителем холодного типа.
Для приготовления эпоксидного клея смолу необходимо смешать с небольшим количеством отвердителя (несколько граммов) при комнатной температуре. В основном эпоксидную смолу и отвердитель берут в пропорции 1: 10, однако допускается превышение нормы отвердителя, способствующее изменению соотношения до 1: 5. Компоненты состава смешиваются вручную.
Приготовление больших объемов эпоксидной смолы своими руками
Для эпоксидной смолы характерен ряд специфических свойств, незнание которых может привести к проблемам в процессе изготовления больших объемов эпоксидного состава. Важно знать, что в процессе работы с большим количеством эпоксидного материала выделяется тепло, и если смола не предназначена для смешивания с отвердителем в больших количествах, сразу после соединения компонентов, она подвергается полимеризации и затвердеванию, становясь непригодной к использованию. В худшем случае смесь вскипает с выделением едкого дыма и подвергается самовозгоранию, что объясняется лавинообразным разогреванием смолы, в процессе которого ускоряется реакция полимеризации и происходит интенсивное теплообразование.
Важно! Приобретая эпоксидную смолу и отвердитель, уточните у специалиста, для каких целей она предназначена. Из специального состава, предназначенного для приготовления больших объемов смеси, вы получите чистую, прозрачную, равномерно застывшую отливку, характеризующуюся отсутствием воздушных пузырей.
Технология приготовления больших объемов эпоксидной смолы, например, нескольких килограммов смеси, отличается от замешивания небольшого количества эпоксидного клея. Рассмотрим этот процесс более подробно.
- Зачастую при длительном хранении смолы, она становится более вязкой, а также мутнеет и кристаллизуется. Чтобы устранить эти явления, перед добавлением отвердителя и пластификатора нагрейте смолу на водяной бане, что позволит уменьшить ее вязкость. Для этого емкость со смолой опустите в воду и нагрейте до температуры 50-60 градусов;
Важно! В процессе нагревания смолы помните, что увеличение температуры на 10 градусов способствует ускорению процесса полимеризации в 2-3 раза. Вследствие этого, важно следить за температурой смолы, так как в случае закипания она приобретет мутно-белый оттенок и вспенится, став непригодной к использованию.
Важно! Зачастую неопытные мастера для повышения вязкости смолы используют растворитель, однако даже небольшая его концентрация (не более 5-7 %) приведет к выраженному снижению прочностных характеристик и теплостойкости изделия.
Кроме того, в процессе эксплуатации изделия часто происходит «выпотевание» растворителя из полимера, что также ухудшает качество материала.
- Полностью исключите наличие воды в эпоксидной смоле и отвердителе. При попадании воды эпоксидная смола становится мутной, теряя свои свойства. Однако развитие современных технологий позволяет выпускать водоразбавляемые эпоксидные составы, которые разводятся дистиллированной водой;
- Приготовление эпоксидного состава начинают с добавления пластификатора. Если вы используете ДБФ, смолу с пластификатором медленно нагрейте, а при использовании ДЭГ-1 просто перемешайте состав, используя строительный миксер или насадку на дрель. Пропорция используемого пластификатора и смолы определяется требуемой пластичностью смеси, однако в большинстве случаев доля пластификатора в составе смеси не превышает 5-10 %;
- Перед тем, как в смесь смолы и пластификатора добавить отвердитель, остудите ее до 30 градусов, что позволит предотвратить ее закипание.
После этого добавьте в смесь отвердитель, исходя из соотношения 1: 10. Иногда допускается изменение пропорций от 1:5 до 1:20. Чтобы добиться равномерного растворения отвердителя в смоле, необходимо постоянно перемешивать состав, в противном случае, при неравномерном распределении отвердителя, он останется несвязанным и будет выпотевать. Чтобы добиться приготовления однородной смеси, медленно и постепенно наливайте отвердитель тонкой струйкой, постоянно перемешивая состав.
Важно! Даже кратковременное повышение концентрации отвердителя приведет к вскипанию смолы – она приобретет матово-белый оттенок, покроется пеной и станет непригодной к использованию. Старайтесь избегать передозировки отвердителя, так как в некоторых случаях может произойти моментальное затвердевание смолы.
Изготовление объемного изделия из эпоксидной смолы: рекомендации мастеров
- Объемное изделие из эпоксидной смолы должно быть прозрачным, без пузырьков воздуха.
Отверждение материала должно быть равномерным, как в толще, так и на поверхности изделия. Если толщина готового изделия превышает 2 мм, смолу необходимо наносить слоями, после того, как произойдет первичная полимеризация предыдущего слоя.
- Также эпоксидную смолу можно заливать в формы. Чтобы после полимеризации смолы готовое изделия можно было легко извлечь из формы, ее необходимо смазать техническим вазелином. Чтобы придать изделию цвет, используют порошковый краситель.
- После того, как вы завершили работу, изделие необходимо выдержать при температуре немного выше комнатной. По истечении 2-3 часов после первичной полимеризации изделие прогревают в жарочном шкафу, что позволит ускорить процесс полимеризации до 5-6 часов. При комнатной температуре процесс полимеризации длится 7 дней.
- В последующем изделие, отлитое из эпоксидной смолы, подлежит механической обработке – резке и шлифованию.
Важно! Эпоксидная смола отечественного производства в большинстве случаев непригодна для изготовления объемных изделий, что определяется ее неравномерным отверждением в толще изделия.
Эпоксидная смола: виды, характеристики, применение
В былые времена эпоксидная смола использовалась преимущественно в промышленности, где данный состав применялся для склеивания различных поверхностей. Причем уже тогда «эпоксидка» считалась достойной альтернативой шурупам, гвоздям, сварке и прочим средствам соединения деталей.
В наше время эпоксидная смола обрела еще большую популярность, и сегодня используется повсеместно, в том числе и в частном строительстве, где ею покрывают столешницы и деревянные подоконники, применяют для герметизации швов и используют для изготовления наливных полов.
Давайте поближе познакомимся с этим удивительным материалом и, возможно, он не раз придет вам на помощь в процессе строительства.
Содержание статьи
Характеристика эпоксидной смолы
Эпоксидная смола является синтетическим олигомерным соединением, которое при контакте с отвердителем образует прочный полимер. При этом данный полимер имеет удивительные адгезивные способности, благодаря которым склеивает практически любые материалы – кожу, дерево, стекло, металл и т.д.
Важно! Не поддается «эпоксидке» лишь оргстекло, полиэтилен, капрон и прочие эластичные материалы, не имеющие пор.
По сути, эпоксидная смола представляет собой сильнейший двухкомпонентный клей на синтетической основе, который внешне напоминает смолу. Ее цвет может варьироваться от белого до темно-оранжевого, хотя чаще всего приходится работать с желтой прозрачной жидкостью, похожей на жидкий мед или древесную смолу.
Эпоксидная смола и эпоксидный клей
Стоит сказать, что многие путают понятие эпоксидного клея и эпоксидной смолы. Смола представляет собой синтетический полимер, коих в природе насчитывается огромное множество. Но чтобы эта субстанция приносила пользу, ее необходимо смешать с отвердителем. В качестве отвердителя могут применяться третичные амины или различные фенольные соединения.
От выбора конкретных компонентов зависит конечный продукт, который мы желаем получить. Это может быть смола, по твердости не уступающая металлу, а может быть смола, напоминающая резину. Да и по цвету они могут серьезно отличаться.
Эпоксидный клей – это один из вариантов соединения синтетического полимера с отвердителем. Он создан в одном варианте и изначально использовался только для склеивания деталей. Сегодня же эпоксидный клей применяют во многих сферах производства и в быту.
Выпускается данный продукт в тубах 30-70 мл, а также в строительных шприцах, флаконах, строительных ведрах и даже в промышленных бочках (от 15 до 19 кг). Большие объемы эпоксидного клея, как правило, применяются для изготовления наливных полов.
Технические характеристики эпоксидного клея
- Расход клея составляет 1,0-1,1 кг на 1 м² поверхности.
- Температура, при которой эксплуатируется такой клей, варьируется от -20°C до +120°C.
- Не подходит для склеивания посуды (т.
к. может вызвать отравление).
- Класс опасности – 3. Состав считается малоопасным, однако в процессе нанесения важно беречь дыхательные пути и кожные покровы. Попадание клея на кожу вызывает ожоги!
- Хранить клей можно, только если не нарушена герметичная упаковка. Срок хранения не должен превышать 3 лет.
Важно! Клей отлично отталкивает воду и может использоваться для соединения изделий, работающих в условиях повышенной влажности.
Различия эпоксидной смолы и эпоксидного клея
Здесь мы наблюдаем ключевые различия между описываемыми материалами:
- Время застывания. Эпоксидная смола застывает медленно, до 24 часов, и на этом этапе проходит несколько состояний. Их можно использовать для придания «эпоксидке» различной формы. Клей же схватывается за несколько минут, а до окончательной кристаллизации проходит не более 3 часов.
- Цвет. Даже после застывания смола долгое время остается прозрачной, в то время как клей мутнеет и приобретает желтоватый оттенок.
- Сфера использования. Эпоксидный клей используется при строительных работах и в быту, для соединения различных элементов, создания наливных полов и мозаики. Смола также может использоваться для этих целей, но помимо этого применяется для создания декоративных изделий.
- Смешивание. Смолу нужно смешивать, а значит, импровизируя, можно получать тот или иной результат. В отличие от нее, клей – это готовый продукт, который годится исключительно для использования по назначению.
Сфера применения эпоксидной смолы
Создатель полимерного материала, швейцарский химик и изобретатель П.Кастан, даже представить не мог, что спустя 90 лет его детище не только не потеряет свою актуальность, но и получит небывалое распространение в самых разных сферах:
1) Машиностроение – изготовление штампов и оснастки, рессор, специальных емкостей и даже подшипников;
2) Судостороение – изготовление корпусов плавающих суден, емкостей для хранения топлива и гребных винтов;
3) Авиа- и ракетостроение – обшивка лопастей вертолета и крыльев самолета. Изготовление баков и газовых емкостей;
4) Радиотехника – используется для изоляции электрических кабелей и проводов, для заливки трансформаторов;
5) Строительство – заливка популярных в наши дни наливных полов, изготовление трубопроводов, создание лакокрасочных материалов, а также нанесение разметки на асфальтированные дороги.
Кроме того, эпоксидная смола входит в состав плиточного клея, шпаклевок и других строительных смесей, для повышения адгезии (сцепления смесей с поверхностями).
6) Применение в быту – подходит для склеивания разорвавшихся труб, кожи и металлических изделий, ремонта техники и мебели.
7) Декоративное использование — эпоксидную смолу широко используют любители мастерить необычные изделия своими руками, начиная от декоративных украшений, а заканчивая ювелирными изделиями. Более того, «эпоксидку» можно заливать в различные формы, получая необычные и невероятно красивые изделия!
Итак, можно сделать вывод о том, что эпоксидная смола и эпоксидный клей – один и тот же продукт. Просто когда нам необходимо склеить определенные предметы или залить пол, проще использовать готовый продукт – эпоксидный клей. Если же мы решили заняться декорированием помещения или изготавливать красивую бижутерию, понадобится более универсальная в этом плане эпоксидная смола.
Важно! Эпоксидный клей бывает трех видов: моментально застывающий (не более 2 минут), застывающий в течение 10 минут, а также обычный, схватывающийся в течение получаса.
Из известных марок такого клея стоит обратить внимание на следующие: «Момент», «ЭДП», «Контакт», «Секунда», а также «Холодная сварка» и «Класс».
Если говорить об эпоксидных смолах, то наибольшую популярность получили полимерные материалы марок ЭД-16, ЭД-20, а также «Экованна», «Леонардо» и «EPS2106».
Как пользоваться эпоксидной смолой
Для приготовления «эпоксидки» понадобится соединить смолу с отвердителем. Продаются они, обычно, вместе, причем на обоих флаконах можно отыскать пропорции, в которых смешиваются материалы.
В зависимости от того, какую смолу вы желаете получить, пропорции могут быть: 10:1, 10:4 или же 10:6 (первой указывается смола, второй – отвердитель). Если на упаковке не указаны пропорции, используйте для расчетов мерные стаканчики.
Важно в точности соблюдать пропорции смешивания смолы с отвердителем. Повышая количество отвердителя, вы делаете состав менее прочным, а при недостатке этого компонента, смолянистая масса будет слишком липкой.
Для смешивания удобно использовать также шприц. Им можно набрать определенное количество смолы, заполнить ею емкость, а затем туда же добавить отвердитель.
Помните! Заливаться должен именно отвердитель в смолу, а не наоборот.
Отвердитель следует добавлять медленно, в противном случае он может разбрызгаться. После добавления приступайте к перемешиванию. Делать это также нужно медленно, ведь быстрое перемешивание приведет к образованию внутри состава пузырьков с воздухом.
Кстати, если консистенция смолы жидкая, пузырьки самостоятельно выйдут на поверхность. Если же консистенция смеси густая, пузырьки могут остаться. Густая консистенция плоха еще и тем, что в случае заливки определенных форм, смола не сможет проникнуть во все щели и рельеф получится неявным.
Далее нужно дать составу застыть до определенной консистенции, и применять по назначению.
Стадии застывания «эпоксидки»
— Первые 30 минут смесь остается жидкой и легко может проникнуть в самые мельчайшие поры. Если вы заливает определенную форму, и желаете, чтобы на ее поверхности проявились все рытвинки и углубления, наполняйте форму в этот период, пока оно отличается хорошей текучестью.
— С течением времени смола густеет и становится менее текучей. В этот период ею легче управлять, а потому смолу такой консистенции используют для заливки полов, столешниц, или любых других плоских поверхностей.
Важно! Когда слой эпоксидной смолы застывает, он притягивает к себе пыль, и это может испортить всю авторскую задумку. Поэтому производить работы с «эпоксидкой» нужно в чистом помещении, удалив предварительно всю пыль.
Если же изделие небольшое, заранее придумайте коробку, которой сможете накрыть изделие до его полного застывания.
— Став еще гуще, состав уже не подходит для создания рельефных форм. Зато на данной стадии сильнее проявляются адгезивные свойства материала. Это значит, смола становится идеальным материалом для склеивания предметов.
— В определенный момент загустевшая смола приобретает свойства подобные резине. Она перестает прилипать к рукам, но при этом остается достаточно эластичной, чтобы вы смогли придать ей необходимую форму. Если вы поместите данный материал в определенную форму и хорошо зажмете его на несколько часов, эпоксидная смола затвердеет в нужном вам положении.
— Полностью затвердев, смола превращается в прочный пластик, который не так просто поцарапать.
Нужно сказать, что указать точное время каждого из этапов застывания невозможно. У каждого состава оно будет своим, а потому устанавливать его следует самостоятельно, практическим путем.
Важно! При отсутствии специальной формы, подходящей для заливки эпоксидной смолы, можно использовать форму из любого материала, предварительно смазав ее поверхность растительным маслом. Но будьте осторожны! Каждый состав «эпоксидки» реагирует на масло по-разному.
Температурный режим при застывании «эпоксидки»
На скорость кристаллизации, а значит, и затвердевание эпоксидной смолы, влияет температура. Если подогреть состав буквально на 10ºC, этот процесс ускорится в 3 раза!
Кстати, в подавляющем большинстве случае в быту применяются отвердители холодного типа, которые нет необходимости подогревать. Однако в некоторых случаях есть необходимость в применении отвердителей горячего типа. Они позволяют получить прочнейшие изделия, выдерживающие высокие температуры и большие нагрузки. Просто застывание в нагретом состоянии приводит к формированию более густой сетки молекул, в результате чего изделие становится прочнее.
Расход эпоксидной смолы
Очевидно, что на расход данного материала во много влияет качество заливаемой поверхности, в частности, ее шероховатость, пористость и склонность к впитыванию других веществ.
Обычно вопрос расхода «эпоксидки» волнует тех, кто решил залить наливной пол. И здесь, опять же, большое значение имеют требования, предъявляемые к полу. Если вы хотите, чтобы бетонный пол перестал пылить, хватит и 100 г на 1 кв.м. поверхности. Когда же необходимо получить идеально ровное, прочное и даже армированное покрытие, расход может увеличиваться до 3-3,5 кг смолы на квадратный метр пола.
Применение «эпоксидки» для изготовления наливных полов
Это один из наиболее популярных способов применения рассматриваемого материала. Он прост в использовании и позволяет получить гладкий, блестящий, бесшовный полиуретановый пол, который прослужит вам долгие годы.
Тонкослойный и толстослойный заливной пол
Важно понимать, что ваш пол может быть как тонкослойным, так и толстослойным.
1. Тонкослойный пол представляет собой пленку на поверхности, толщиной не более 1 мм, которую можно нанести на пол обычным валиком. С этим может справиться даже непрофессионал.
В результате вы получите гладкую матовую или глянцевую, прозрачную либо цветную поверхность, которая выгодно выделит помещение. Правда, даже учитывая твердость застывшей смолы, такой пол подвержен царапинам и склонен к истиранию, особенно если заливать им часто используемые помещения — кухонные полы или полы в коридоре. А учитывая, что данный слой, скорее, относится к защитному, при необходимости им можно покрывать кирпичные, бетонные или деревянные стены.
2. Толстослойный заливной пол представляет собой пленку толщиной от 3 до 10 мм. Благодаря имеющейся толщине, в материал можно добавлять не только различные красители, но и наполнители, в т.ч. кварцевую крошку, мелкие речные камешки, медную или алюминиевую стружку и т.д. Этот пол подойдет для любых жилых помещений с интенсивной пропускной способностью, например, для ванной комнаты, спальни, кухни, гостиной или даже гаража.
Такой слой довольно сложно повредить, он не царапается и не трескается. Кроме того, выбирая смолу с частиками кварца, вы получает идеально ровный пол, по которому не будут скользить ноги!
Важно лишь понимать, что залить двухкомпонентный толстослойный пол без определенных навыков и подходящего инструмента проблематично.
Вы можете испортить материал. Такую работу стоит доверить профессионалам.
Технология изготовления наливного пола
Итак давайте подробнее рассмотрим процесс изготовления наливного пола
Расчет количества материала
Эпоксидная смола в больших объемах может показаться вам дорогой, а потому нужно рассчитать точное количество материала, чтобы не переплачивать. Для этого просто посчитайте площадь поверхности, которую планируете заливать, после чего умножьте полученное число на толщину слоя, которую желаете получить. Останется лишь перевести полученный объем в литры и можно приобретать материал.
Этап 1. Подготовка поверхности
Лучше всего формировать такой пол на основании из бетона. Древесина будет впитывать смолу и вам может понадобиться больше материала. При этом с пола необходимо удалить старую краску и заделать все щели. А чтобы смола лучше держалась, поверхность пола желательно обработать наждачной бумагой или вибрационной шлифтмашинкой.
Перед тем, как приступить к заливке, поверхность стоит обезжирить, вымыв ее с мыльным раствором и оставив сохнуть на сутки.
Важно! Если вы совсем недавно залили бетонный пол, должно пройти не менее месяца, прежде чем можно делать наливные полы. Повышенная влажность поверхности рискует испортить все ваши старания.
Перед нанесением смолы пол следует прогрунтовать специальной эпоксидной грунтовкой. Наносить ее можно в один или в два слоя, но с обязательным высыханием каждого из слоев не менее 12 часов.
Этап 2. Смешивание эпоксидной смолы
В ведро следует вылить смолу, а затем добавить отвердитель. Взяв строительный миксер, компоненты нужно медленно перемешивать на протяжении 5-7 минут. Важно не спешить, чтобы состав не разбрызгался, и в нем не появились пузырьки. При желании к составу можно добавить подходящий по цвету краситель.
Этап 3. Заливка первого слоя
Как только состав будет готов, кистью нанесите смолу по углам и кромке пола. После этого вылейте жидкую массу на центр, и при помощи валика распределите по всей поверхности. У вас должен получиться слой примерно в 5 мм толщиной.
Этап 4. Нанесение рисунка (при необходимости)
Как только пройдет 72 часа, и первый слой высохнет, можно наносить рисунок.
Этап 5. Заливка второго слоя
После можно наносить финишный слой эпоксидной смолы. К слову, чтобы создать особый наливной пол с различными декоративными элементами, можно использовать несколько слоев.
Вред для здоровья
Работать с «эпоксидкой» нужно осторожно. Особенно это касается смолы, ведь в процессе разведения капли могут попадать на кожу, вызывая ожоги. Для работы с таким составом нужно использовать перчатки.
Важно! Если капли эпоксидной смолы попали на кожу, удалите их при помощи спирта, а затем помойте руки с мылом.
Если же «эпоксидка» попала в глаза или на слизистые оболочки, немедленно обратитесь к врачу!
Более того, начиная от процесса смешивания, и до полного отвердевания смолы, из состава выделяются ядовитые соединения, которые могут вызывать отравление. Поэтому работать с рассматриваемой смолой нужно в помещении, которое хорошо проветривается или имеет вытяжку. Если же работы происходят в гараже или другом помещении, которое плохо вентилируется, желательно находится в респираторе. Зато после застывания данная смола становится абсолютно безопасной!
Советы по использованию эпоксидной смолы
- Используйте полиэтилен в работе. Учитывая, что «эпоксидка» не склеивается с полиэтиленом, перед началом работы застелите все ответственные поверхности полиэтиленовой пленкой. Это убережет вас от попадания на них капель лака. В противном случае убрать загрязнения будет проблематично.
- Не используйте бумагу. Использовать бумагу для защиты поверхностей, не лучший вариант.
Смола пропитывает бумагу и проникает сквозь нее.
- Работайте в сухом помещении. Нормальному застыванию «эпоксидки» может помешать попадание на состав воды. Даже работа во влажном помещении может привести к ухудшению застывания.
- Температура должна быть более 22ºC. Помешать застыванию способна и низкая температура в помещении. Для нормального процесса температура воздуха должна быть более 22ºC.
- Для ускорения застывания используйте батарею. Чтобы нанесенный состав застыл быстрее, небольшое изделие можно положить на теплую батарею отопления. Важно лишь, чтобы смола не слишком сильно нагрелась, и в ней не начали образовываться пузырьки.
- Используйте трубочку. Пузырек воздуха, который находится близко к поверхности, можно убрать, если подуть на него через трубочку.
- Для придания разных цветов можно использовать краску из фломастера или чернил гелевых ручек. Для декорирования поверхностей используется эпоксидная смола разных цветов и оттенков.
Добиваются этого добавлением в состав специальных тонеров. Правда, стоимость их довольно высока, поэтому находчивые обыватели придумали добавлять в «эпоксидку» краску из фломастеров или чернила из гелевых ручек.
- При обнаружении крупинок и хлопьев положите банку на батарею. Если после хранения эпоксидной смолы в холодном помещении вы обнаружили появление в составе крупинок и хлопьев, достаточно поставить банку с лаком на батарею. Разогреть состав до 50-60ºC, он станет однородным.
- Для работы на солнце используйте материал, имеющий ультрафиолетовый фильтр. При изготовлении декоративных изделий важно, чтобы эпоксидная смола не желтела под воздействием солнечных лучей. Для этого изначально покупайте материал, имеющий ультрафиолетовый фильтр.
Теперь вы знаете, как можно использовать эпоксидную смолу в строительстве и декорировании помещений. Дерзайте, проявляйте фантазию и удивляйте окружающих изделиями из «эпоксидки»!
youtube.com/embed/ZVz_XUoMXg8″ frameborder=»0″ allowfullscreen=»allowfullscreen»/>Эпоксидная смола ЭД-20 – свойства, технические характеристики, инструкция по применению
Эпоксидные смолы – универсальный олигомерный материал, применяющийся для производства компаундов, композитов, а также для заливки различных поверхностей и изготовления клея, герметика. Благодаря уникальному сочетанию полезных свойств эпоксидка пригодится и в промышленности, и в быту. Из всего многообразия продуктов выделяется эпоксидная смола ЭД-20 – недорогое средство высокого качества.
Содержание:
- Свойства смолы ЭД-20 и применение
- Технические параметры
- Аналоги материала org/ListItem»> ЭД-8
- ЭД-16
- ЭД-22
- Э-40
- Инструкция по использованию ЭД-20
- Подготовка смолы
- Использование пластификатора
- Пластификатор ДБФ
- Пластификаторы ДЭГ 1 и ТЭГ 1
- Использование отвердителя org/ListItem»> ПЭПА, ТЭТА и ДЭТА
- ЭТАЛ 45М
- Жизнеспособность эпоксидки
- Разное качество склеивания
- Упаковка, хранение и транспортировка
- Безопасность ЭД-20
Свойства смолы ЭД-20 и применение
Эпоксидно-диановая смола ЭД-20 – прозрачная вязкая жидкость желтого, коричневатого цвета без механических примесей, включений. Она представляет собой плавкий реакционноспособный продукт на основе дифенилолпропана и эпихлоргидрина. Производитель смолы данной марки – ФКП Завод им. Свердлова, также ее выпускает ряд иных компаний. Средняя массовая доля эпоксидных групп в смоле равна 20%, отсюда и обозначение материала.
ЭД-20 комбинируется с разными отвердителями, в некоторых случаях требуется добавление пластификаторов (для уменьшения жесткости готового изделия). Отверждение возможно холодным и горячим способом (при комнатной или повышенной температуре), для этого процесса не требуется прессовое и термическое оборудование. Свойства ЭД-20 таковы:
- высокая плотность, беспористость готового продукта;
- отличная твердость, стойкость к механическому повреждению, агрессивной среде, влиянию влаги;
- термостойкость;
- диэлектрические и противокоррозионные способности;
- хорошая адгезия с пластиком, металлом, стеклом, керамикой, деревом, кевларом, углеволокном и многими другими материалами;
- легкость в работе;
- малая усадка, низкий удельный вес.
Эпоксидка имеет широкое применение в разных сферах народного хозяйства. Ее используют для ремонта электротехники, компьютеров, радиоэлектроники, деталей и корпусов яхт, лодок, катеров, для производства мебели – столов, стульев.
При помощи ЭД-20 делают красивые столешницы, галантерею, изделия для ванной. Материал хорошо подходит для строительства, машиностроения, авиационной промышленности, приборостроения. Его использование для покрытия стен, создания наливных полов помогает в самых смелых дизайнерских решениях.
ЭД-20 входит в состав различных лакокрасочных материалов – грунтовок, пропиточных лаков, эмалей, заливочных смесей. На основе эпоксидки делают армированный пластик, стеклопластик, стекловолокно.
к содержанию ↑
Технические параметры
Время желатинизации эпоксидки составляет 8 часов, а период полного отверждения равен 24 часам. В описании высшего сорта материала указаны следующие технические характеристики:
- плотность при холодном отверждении – 1110–1230 кг м3, при горячем отверждении – 1200–1270;
- массовая доля ионов хлора – 0,001%, омыляемого хлора – 0,3%;
- массовая доля гидроксильных групп – 1,7%, летучих веществ – 0,2%;
- вязкость динамическая – 13–20 ПА/секунду;
- температурный режим для размягчения – до 60 градусов.
к содержанию ↑
Аналоги материала
По входящим в состав компонентам, свойствам и применению есть ряд аналогичных эпоксидных смол из групп ЭД, ТЭГ, КДА. При необходимости ими можно заменить ЭД-20. Ниже приведены самые известные смолы.
ЭД-8
Эпоксидка ЭД-8 производится согласно ГОСТ 10587-84. Она представляет собой растворимый плавкий олигомерный продукт из тех же веществ, что и ЭД-20 (дифенилолпропан и эпихлоргидрин). Смола широко применяется в авиационной, судостроительной, машиностроительной промышленности, при изготовлении лакокрасочных материалов, на стройке, в ремонте техники, электроники. Эпоксидка служит и как связующий компонент для армированного пластика.
По физико-химическим показателям ЭД-8 также мало отличается от ЭД-20. Содержание ионов хлора и омыляемого хлора аналогичное, зато гидроксильные группы в массе не обнаруживаются. Вязкость и температура размягчения такие же. Основное отличие – в массовой доле эпоксидных групп (8%) и времени желатинизации (3 часа).
к содержанию ↑
ЭД-16
Эпоксидная смола ЭД-16 имеет те же свойства и применение, но включает иное число эпоксидных групп – около 16%. Вязкость продукта меньше, чем у ЭД-20, следовательно, желатинизация происходит быстрее (примерно 4 часа). Средство отличается высокими прочностными показателями клеевого шва, но в нем более высокое количество хлора.
к содержанию ↑
ЭД-22
Еще одна эпоксидка на основе эпихлоргидрина и дифенилолпропана, доля эпоксидных групп – 22%. Смола ЭД-22 среди особенностей имеет более высокое время желатинизации – 18 часов, при этом динамическая вязкость составляет 8–12 ПА/секунду.
Э-40
Технология изготовления эпоксидки Э-40 несколько отличается от создания материалов марки ЭД. Продукт получают путем конденсации эпихлоргидрина и дифенилолпропана в щелочной среде с добавлением растворителя толуола. Средство можно переводить в неплавкое состояние путем применения отвердителей – поликарбоновых кислот, их ангидридов, полиаминов.
Сфера применения материала – приготовление эмалей, обладающих высокими защитными свойствами, а также создание лаков и шпаклевок. Кроме того, Э-40 выступает как полуфабрикат для изготовления других эпоксидных смол, клеев и компаундов для заливки. Смола обладает высокой пластичностью, влагостойкостью, в полимеризованном виде не реагирует на действие умеренно агрессивных кислот, щелочей.
к содержанию ↑
Инструкция по использованию ЭД-20
Результат смешивания смолы и отвердителя будет сильно зависеть от их пропорции, условий окружающей среды, качества подготовки тары и ряда индивидуальных факторов. Инструкция по применению не всегда пошаговая, в ней обычно указываются лишь точные соотношения компонентов и основные требования к процессу полимеризации. Рекомендуется вначале купить указанный производителем жидкий отвердитель (если он не идет в комплекте) и смешать его со смолой в самых минимальных дозировках. Это позволит увидеть результат и сделать выводы о правильности пропорций.
Смешивание смолы в небольших объемах трудностей не представляет. Для этой цели идеально подходит технология холодного отверждения, когда все работы проводятся при комнатных температурах. Перед смешиванием эпоксидки в большом объеме придется подготовить посуду для нагревания смолы, так как применяется способ горячего отверждения. Эпоксидку греют на водяной бане до температуры 50–55 градусов, после чего производят дальнейшие работы в ускоренном режиме.
Важно учесть, что после добавления отвердителя реакция полимеризации является необратимой, остановить ее невозможно, есть шанс лишь немного замедлить снижением температуры окружающей среды. Неправильно выполненные действия приведут к порче порции эпоксидки, поэтому все расчеты должны быть произведены заранее.
к содержанию ↑
Подготовка смолы
Для холодного отверждения никакой особенной подготовки материала не требуется. Для горячего способа и ускорения пропитки (заливки) рекомендуется нагревать отмерянную порцию средства. Для этого устанавливают водяную баню, располагают на ней емкость с эпоксидной смолой. Важно следить, чтобы ни капли воды не проникло в массу, это испортит ее. Также нельзя перегревать материал, реакция пойдет слишком быстро, а доведение до кипения приведет смолу в негодность. Оптимальным будет нагрев до 55 градусов или меньше. Можно и вовсе опустить емкость с материалом в посуду с горячей водой, дать постоять без кипячения воды. Периодически перемешивать массу для равномерности нагрева.
При хранении или превышении срока годности эпоксидка способна кристаллизоваться. Надо убедиться, что в ней нет кристаллов, мутностей, в противном случае ее подогревают до +40 градусов с интенсивным перемешиванием. Это поможет вернуть материалу прозрачность.
к содержанию ↑
Использование пластификатора
Добавление ряда компонентов поможет пластифицировать эпоксидную смолу. Зачем это нужно? Если изделие в будущем должно выдерживать высокие ударные или иные механические нагрузки, усилие на излом с использованием рычага, его упругость надо повысить. Добавление специальных пластификаторов позволяет частично гасить такие нагрузки. Также их введение рекомендуется для усиления эластичности швов, если эпоксидка будет применяться для склеивания и заливки.
к содержанию ↑
Пластификатор ДБФ
Дибутилфталат, или ДБФ – самый популярный пластификатор для эпоксидки, его добавляют в малом количестве – до 2–5% от общего объема. Средство способно защитить изделия от растрескивания при морозах, ударах. Особенно показано вводить ДБФ при использовании отвердителей ПЭПА и ТЭТА. Если же используется отвердитель Этал 45М, добавления пластификатора не требуется. Недостатком ДБФ можно назвать сложное соединение со смолой, поэтому приходится применять долгое перемешивание с нагревом.
к содержанию ↑
Пластификаторы ДЭГ 1 и ТЭГ 1
Диэтиленгликоль, или ДЭГ 1, сам по себе является эпоксидкой, при этом годится для разбавления основной массы в качестве пластификатора. Рабочая концентрация для ЭД-20 составляет 3–10% – чем больше средства добавлено, тем более смола будет напоминать резину. ДЭГ-1 легко соединяется с эпоксидкой, его намного проще применять, если неважна бесцветность. Из-за оранжевого оттенка данный пластификатор подходит не в каждом случае.
ТЭГ 1 по свойствам и применению схож с ДЭГ 1, но чуть более вязкий по консистенции, имеет коричневый или желтый цвет. Основное отличие в составе – вместо диэтиленгликоля в ТЭГ 1 присутствует триэтиленгликоль.
к содержанию ↑
Использование отвердителя
Отвердитель – полноценный участник химической реакции полимеризации эпоксидной смолы. Он вводится в массу после добавления пластификаторов. Для снижения риска закипания эпоксидки ее температура в момент смешивания с отвердителем должна составлять не более 30–40 градусов.
Обычно вводят 1 часть отвердителя на 10 частей смолы, но пропорции будут зависеть от потребностей, типа готового изделия. В ряде случаев достаточно соотношения 20:1, а иногда, напротив, требуется 5:1. Отвердитель добавляют в основную массу очень медленно, поскольку запуск тепловой реакции может вызвать перегрев и порчу смолы. Быстрое вливание обычно вызывает лавинообразный процесс, когда масса перегревается и мгновенно застывает. К тем же последствиям могут привести слишком большое количество отвердителя, высокая начальная температура эпоксидки.
к содержанию ↑
ПЭПА, ТЭТА и ДЭТА
Полиэтиленполиамин, или ПЭПА, – недорогой и очень популярный отвердитель, он работает при комнатной или пониженной температуре, не требует нагревания исходной массы. ПЭПА не снижает своих свойств даже при повышенной влажности. Он имеет желтый, коричневый цвет, иногда чуть зеленоватый, в его основе – этиленовые амины. Оптимальное количество для добавления в эпоксидку – 13,7%, важно войти в диапазон 10–15%.
Триэтилентетрамин ТЭТА – еще один известный традиционный отвердитель, позволяет готовить смолу при температурах +15…+25 градусов. К минусам можно отнести едкий запах, токсичность вещества. Оно требует строжайшего соблюдения пропорций (для ПЭПА это не так важно).
Отвердитель ДЭТА относится к этой же группе веществ для холодной полимеризации эпоксидных смол. Отличительной чертой является схватывание из воздуха влаги и углерода, поэтому хранить его надо плотно закрытым. Средство отверждает смолы за 1,5 часа.
к содержанию ↑
ЭТАЛ 45М
Этот универсальный отвердитель обладает «заданной пластичностью», поэтому не требует введения пластификаторов. Его консистенция близка к самой смоле ЭД-20, перемешивание будет легким. Температурная реакция от добавления Этал 45М менее бурная, к тому же он не токсичен, не вызывает аллергии, без неприятного запаха.
к содержанию ↑
Жизнеспособность эпоксидки
Временем жизни называют промежуток времени, в который сохраняется жидкое или вязкое состояние массы после введения отвердителя. В этот период эпоксидка пригодна к работе. У разных смол жизнеспособность различная, как и у отвердителей. Обычно этот показатель составляет 30–60 минут.
При добавлении ПЭПА в ЭД-20 время жизни равно 30–50 минут и зависит от температуры, количества отвердителя. Полная полимеризация длится от 24 часов до нескольких суток. Для Этал 45М жизнеспособность в 3 раза больше, а полная полимеризация такая же, что удобно для мастера.
к содержанию ↑
Разное качество склеивания
Качество эпоксидки может различаться в зависимости от марки отвердителя, пластификатора. Чем более дорогие и эффективные добавки применяются, тем больше готовое изделие будет соответствовать требованиям. Поэтому не стоит экономить и покупать самые дешевые наполнители.
Упаковка, хранение и транспортировка
Эпоксидную смолу упаковывают в тару по 50–220 кг (барабаны), а также в канистры, пластиковые емкости от 0,5 кг и более. Транспортируют средство на крытом транспорте. Допускается хранение материала при температуре +15…+40 градусов, плотно закрытым, вдали от солнечных лучей. Нельзя хранить его рядом с кислотами и окислителями.
Безопасность ЭД-20
Работы с данным средством должны проводиться в хорошо проветриваемом помещении или при наличии качественной вентиляции. Для защиты следует применять респиратор, очки, перчатки, плотную одежду или фартук. ЭД-20 не взрывоопасна, но при попадании в огонь горит.
Степень опасности смолы характерна для веществ 2-го класса воздействия на организм человека. При попадании на кожу часто возникают аллергические реакции, дерматиты. Пораженное место надо обмыть с мылом, протереть спиртом, после смазать вазелином, касторовым маслом.
инструкция по применению, характеристики, пропорции
Содержание
Основные характеристики смолы ЭД-20
Особенности применения эпоксидной смолы ЭД-20
Смолы эпоксидного типа продолжают оставаться самым востребованным материалом для изготовления композитов, компаундных термопластических смесей и клеевых составов различного назначения. Также «эпоксидка» довольно широко применяется в качестве основы для производства герметиков и уплотнителей. ЭД-20 – одна из самых популярных марок эпоксидной смолы. Это универсальное средство, подходящее как для промышленного, так и для бытового использования.
Смола разводится с помощью отвердителей. Когда необходимо получить материал пониженной жесткости, то в приготавливаемый состав дополнительно вводят пластифицирующие компоненты. Процесс отвердевания в домашних условиях не требует наличия никакого специального оборудования. Изготовление рабочей смеси осуществляется двумя способами: холодным и горячим.
Основные технические характеристики ЭД-20:
- Цвет: желтая или желтая с коричневым оттенком прозрачная жидкость.
- Концентрация эпоксидных групп (среднее значение): 20%.
- Химически активный состав: на основе эпихлоргидрина и дифенилопропана.
- Ионы хлора: 0,001 – обычный хлор; 0,3 – омыляемый хлор.
- Вещества гидроксильных групп: 1,7%.
- Летучие соединения: 0,2%.
- Консистенция: вязкий однородный продукт без посторонних включений и механических примесей.
- Значение динамической вязкости: 16,5±3,5 ПА/сек.
- Показатель плотности при отвердевании холодным методом: 1170±60 кг/м³.
- Показатель плотности при отвердевании горячим методом: 1235±35 кг/м³.
- Температура для проведения размягчения: не более 60°C.
- Время первичного затвердевания: около 8-ми часов.
- Время полного затвердевания: около суток.
- При длительном хранении продукт может кристаллизоваться.
Преимущества и область применения
Популярность материала объясняется его достоинствами:
- Высокая степень плотности.
- Незначительная усадка и показатели удельного веса.
- Влаго/водостойкость.
- Устойчивость к высокоагрессивным жидким и газовым химическим средам.
- Отличные показатели твердости. Вместе с хорошей плотностью это делает «эпоксидку» устойчивой к различным механическим воздействиям.
- Высокая коррозионная стойкость.
- Биоинертность. Плесень/грибок не поражает эпоксидные покрытия.
- Термическая стойкость.
- Нечувствительность к перепадам температуры.
- Смола является диэлектриком.
- Отличная адгезия с различными рабочими основаниями: металл, дерево, стекло, керамика, углеволокно, разные виды пластика и др.
- Простота применения.
- Долговечность.
- Экологическая безопасность. В процессе эксплуатации застывшая эпоксидная смола не выделяет в окружающую среду вредные вещества.
Эксплуатационные характеристики эпоксидной смолы позволяют использовать ее очень широко. Наверное, проще назвать сферы, где она не востребована. Во-первых, на основе смолы производятся сотни различных марок ЛКМ, грунтовок, клеевых и гермент-смесей, которые используются для работы с самыми разными материалами.
Во-вторых, «эпоксидка» остается лучшим диэлектрическим и клеевым средством в сфере производства и ремонта всевозможной электротехники. В-третьих, на основе смолы изготавливают высокопрочный стеклопластик, армопластик, стекловолокно и т.п. Наконец, нельзя пройти мимо особопрочного эпоксидного клея, который повсеместно применяется на различных видах производства и в быту.
Особенности применения
Свойства рабочей смеси зависят от температуры среды, вида и количества введенного отвердителя. Точные пропорции всегда указаны на этикетке с товаром или в прилагаемой к нему инструкции. В остальном следует придерживаться общих правил использования эпоксидных смол.
Холодный способ предполагает добавление отвердителя в условиях комнатной температуры – без какой-либо специальной подготовки компонентов. Это оптимальный вариант для приготовления малого объема смеси. Для разведения смолы в достаточно большом объеме придется прибегнуть к горячему способу.
В быту горячее отвердевание часто проводят на водяной бане: емкость со смолой помещают в емкость большего диаметра, заполненную водой примерно на треть. Водяная баня нагревается на огне или просто ставится в посуду с горячей водой. Перегревать смолу и, тем более, доводить ее до состояния кипения нельзя. Оптимальная температура подогрева: 52,5±2,5°C. Для равномерного прогревания эпоксидный состав следует помешивать.
Необходимо помнить, что после введения отвердителя полимеризацию нельзя будет обратить вспять или замедлить на длительное время. Можно будет только немного пролонгировать процесс затвердевания путем понижения температуры. Поэтому нужно все подготовить к работе, не ошибиться с количеством рабочей смеси и пропорцией разведения. Для подстраховки рекомендуется провести пробное смешивание минимального количества эпоксидной смолы ЭД-20 с отвердителем и посмотреть, как быстро произойдет полимеризация, и каким получится материал после схватывания.
Использование отвердителя имеет свои нюансы. Для минимизации риска закипания смолы она должна быть прогрета не более чем до 40°C. Принудительный нагрев ведется до более высокой температуры для того, чтобы «эпоксидка» не остыла сразу. Чаще всего разведение делают в пропорции 1:10 (агент для отвердевания:эпоксидная смола), но она может быть и другой – 1:5 или 1:20 – здесь все зависит от требований к качеству склеивания/обработки рабочих оснований. В любом случае отвердитель вводят медленно – чтобы запущенная тепловая реакция не испортила смолу по причине перегрева. Быстрое введение приводит к моментальному перегреванию и практически мгновенному твердению смолы. Такой же эффект способны вызвать превышение дозировки отвердителя или слишком высокая температура эпоксидного материала.
Что касается жизнеспособности полученного по всем правилам состава, то она зависит от компонента, отвечающего за полимеризацию. Например, ЭД-20 в комбинации с отвердителем ПЭПА «живет» в среднем 40 минут, а полностью полимеризация завершается через сутки. Повысить жизнеспособность примерно до двух часов можно с помощью отвердителя Этал 45М – при этом срок окончательной полимеризации тоже составит сутки.
ЭД-20 желательно хранить при постоянной температуре не ниже 15°C и не выше 40°C в плотно закрытой таре. В помещения не должны проникать лучи солнца. Складирование вблизи кислот или других веществ с окисляющими свойствами запрещено.
Типы, применение, свойства и химическая структура
Что такое реактопласт?
Что такое реактопласт?
Термореактивная смола или термореактивная смола представляет собой полимер, который отверждается или принимает твердую форму с использованием таких методов отверждения, как тепло или излучение.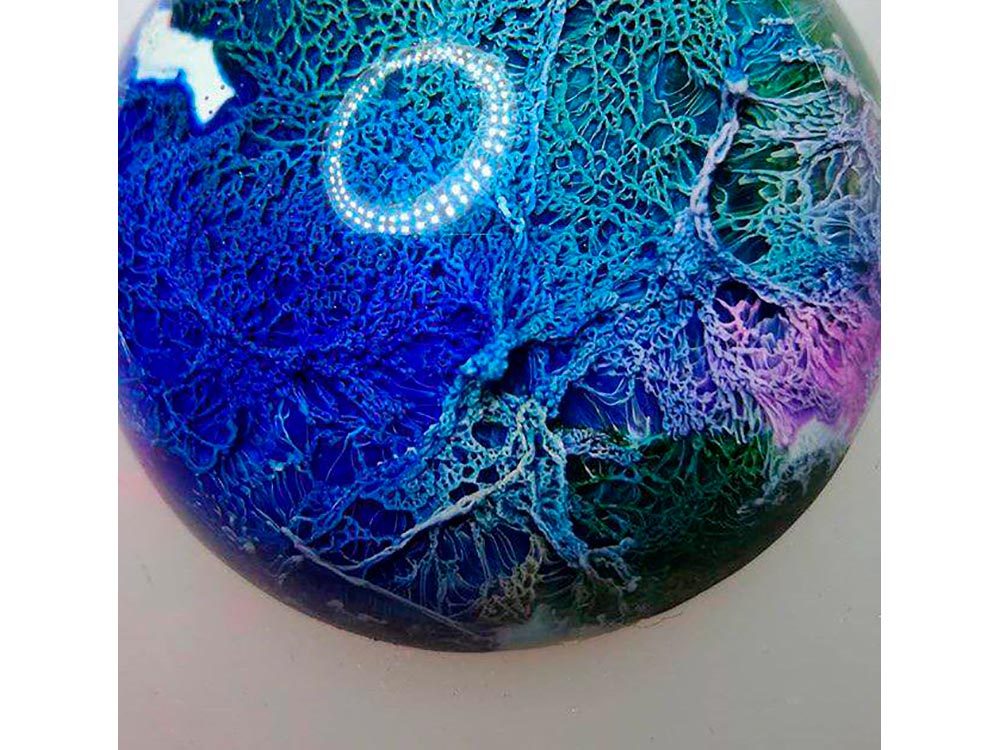
При нагревании, в отличие от термопластов, реактопласты остаются твердыми до тех пор, пока температура не достигнет точки, при которой реактопласты начинают разлагаться.
Фенольные смолы, аминосмолы, полиэфирные смолы, силиконовые смолы, эпоксидные смолы и полиуретаны (полиэфиры, виниловые эфиры, эпоксидные смолы, бисмалеимиды, цианатные эфиры, полиимиды и фенольные смолы) являются несколькими примерами термореактивных смол.
Среди них эпоксиды или эпоксидные смолы являются одними из наиболее распространенных и широко используемых термореактивных материалов сегодня в конструкционных и специальных композитных материалах. Благодаря своей высокой прочности и жесткости (из-за высокой степени сшивки) эпоксидные термореактивные смолы могут быть адаптированы практически для любого применения.
Но что делает эпоксидную смолу универсальной смолой для этих применений? Давайте узнаем об этом подробнее…
Что делает эпоксидную смолу универсальной?
Что делает эпоксидную смолу универсальной?
Термин «эпоксидная смола», «эпоксидная смола» или «эпоксид» (Европа), α-эпоксидная смола, 1,2-эпоксидная смола и т.
Следовательно, наличие этой функциональной группы определяет молекулу как эпоксидную, где молекулярная основа может широко варьироваться, что приводит к различным классам эпоксидных смол. И они успешны, потому что предлагают разнообразие молекулярной структуры, которую можно получить с помощью одного и того же химического метода.
Кроме того, эпоксидные смолы можно комбинировать с различными отвердителями и модификаторами для достижения свойств, необходимых для конкретного применения.
Учебное пособие по часам: как выбрать лучший отвердитель для эпоксидных систем
Эпоксидные смолы обычно образуются реакцией соединений, содержащих не менее двух активных атомов водорода (полифенольные соединения, диамины, аминофенолы, гетероциклические имиды и амиды, алифатические диолы и т.
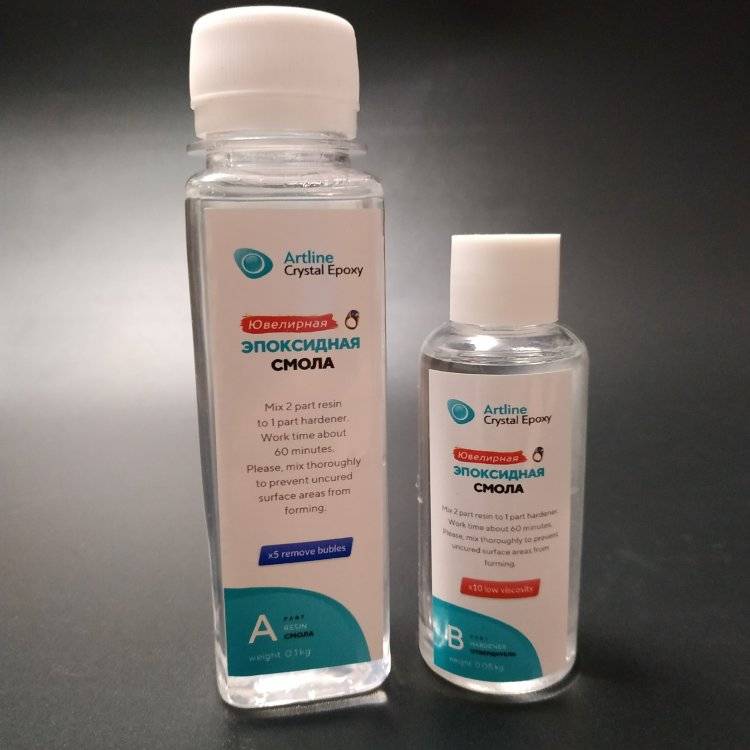
Синтез диглицидилового эфира бисфенола А (ДГЭБА), наиболее широко используемого мономера эпоксидной смолы:
Синтез эпоксидного мономера из бисфенола А и эпихлоргидрина
Оксирановая группа эпоксидного мономера реагирует с различными отвердителями, такими как алифатические амины, ароматические амины, фенолы, тиолы, полиамиды, амидоамины, ангидриды, тиолы, кислоты и другие подходящие соединения, раскрывающие цикл; формирование жестких термореактивных изделий. Отвержденные эпоксидные смолы являются хрупкими по своей природе из-за высокой степени сшивки, и они способствуют ослаблению ударной вязкости эпоксидной смолы и других соответствующих свойств.
Следовательно, модификация эпоксидных мономеров необходима для улучшения их гибкости и ударной вязкости, а также термических свойств.
Три основных класса эпоксидных смол, используемых в композитах :
- Фенольные глицидиловые эфиры
- Ароматические глицидиламины и
- Циклоалифатические соединения
Фенольные глицидиловые эфиры
Образуются в результате реакции конденсации эпихлоргидрина с фенольной группой.

Изменение соотношения эпихлоргидрина и BPA во время производства может привести к образованию высокомолекулярных смол. Эта HMW увеличивает вязкость, и, следовательно, эти смолы являются твердыми при комнатной температуре. Другие разновидности этого класса включают гидрированные эпоксидные смолы на основе бисфенола-А, бромированные смолы, полученные из тетрабромбисфенола-А, диглицидиловый эфир бисфенола-F, диглицидиловый эфир бисфенола-Н, диглицидиловый эфир бисфенола-S и т. д. Бромированные смолы являются антипиренами. и в основном используются в электротехнике. Кроме того, DGEBH демонстрирует многообещающую устойчивость к атмосферным воздействиям, а DGEBS используется для получения термостойкой эпоксидной смолы.
Новолаки фенола и крезола представляют собой еще два типа ароматических глицидиловых эфиров. Они производятся путем объединения фенола или крезола с формальдегидом, образуя полифенол. Этот полифенол впоследствии реагирует с эпихлоргидрином с образованием эпоксидной смолы с высокой функциональностью и высокой Tg отверждения.
Ароматические глицидиламины
Они образуются реакцией эпихлоргидрина с амином, с ароматическими аминами, пригодными для применения при высоких температурах. Наиболее важной смолой этого класса является тетраглицидилметилендианилин (ТГМДА). 9Смолы 0020 TGDMA обладают превосходными механическими свойствами и высокими температурами стеклования и подходят для передовых композитных аэрокосмических приложений.
TGPAP — триглицидил-п-аминофенол — еще один тип глицидиламина. Он обладает низкой вязкостью при комнатной температуре и поэтому обычно смешивается с другими эпоксидными смолами для изменения текучести или липкости состава без потери Tg.
Другие коммерческие глицидиламины включают диглицидиланилин, тетраглицидилмета-ксилолдиамин. Основным недостатком этого класса является стоимость, которая может быть выше по сравнению со смолами Bis-A.
Циклоалифатические соединения
Циклоалифатические эпоксидные смолыпредназначены для применений, требующих устойчивости к высоким температурам, хороших характеристик электроизоляции и устойчивости к ультрафиолетовому излучению. Они содержат эпоксидное кольцо, которое находится внутри кольцевой структуры. Составы циклоалифатических эпоксидных смол
используются для изготовления многих конструкционных компонентов, армированных волокном. Составы, включающие эти смолы, могут иметь высокие температуры стеклования в диапазоне 200°C.
Важной и широко используемой циклоалифатической эпоксидной смолой является диглицидиловый эфир гексагидрофталевой кислоты и 3,4-эпоксициклогексилметил-3′,4′-эпоксициклогексана.
Диглицидиловый эфир гексагидрофталевой кислоты
Основные свойства эпоксидных смол
Основные свойства эпоксидных смол
Ниже мы перечисляем основные свойства эпоксидных смол.
- Высокая прочность
- Низкая усадка
- Отличная адгезия к различным основаниям
- Эффективная электрическая изоляция
- Химическая стойкость и устойчивость к растворителям и
- Низкая стоимость и низкая токсичность
Эпоксидные смолы легко отверждаются и совместимы с большинством оснований. Они имеют тенденцию легко смачивать поверхности, что делает их особенно подходящими для композитных приложений. Эпоксидная смола также используется для модификации некоторых полимеров, таких как полиуретан или ненасыщенные полиэфиры, для улучшения их физических и химических свойств.
Для термореактивных эпоксидных смол:
- Прочность на растяжение от 90 до 120 МПа
- Модуль упругости при растяжении от 3100 до 3800 МПа
- Температуры стеклования (Tg) в диапазоне от 150 до 220 °C
Помимо перечисленных выше свойств, эпоксидные смолы имеют два основных недостатка: их хрупкость и чувствительность к влаге .

Эпоксидные композиты: добавки для повышения эффективности
Эпоксидные композиты: добавки для повышения эффективности
Наполнители также играют важную роль в рецептурах эпоксидных смол. Армирующие волокна, такие как стекло, графит и полиарамид, улучшают механические свойства до такой степени, что эпоксидные смолы можно использовать во многих конструкционных применениях. Другие неармирующие наполнители включают:- Порошки металлов для улучшения электрической и теплопроводности
- Глинозем для теплопроводности
- Силикагель для снижения затрат и повышения прочности
- Слюда – электрическое сопротивление
- Тальк и карбонат кальция – снижение затрат
- Угольный и графитовый порошки для повышения смазывающей способности
При компаундировании наполненных систем необходимо учитывать некоторые важные факторы, в том числе:
- Объемная доля наполнителя
- Характеристики частиц (размер, доля, площадь поверхности…)
- Соотношение сторон наполнителя
- Прочность и модуль наполнителя
- Адгезия наполнителя к смоле
- Вязкость базовой смолы
- Прочность базового повода
Эпоксидные композиты , армированные наночастицами, также вызвали значительный интерес в промышленности за последние десятилетия.
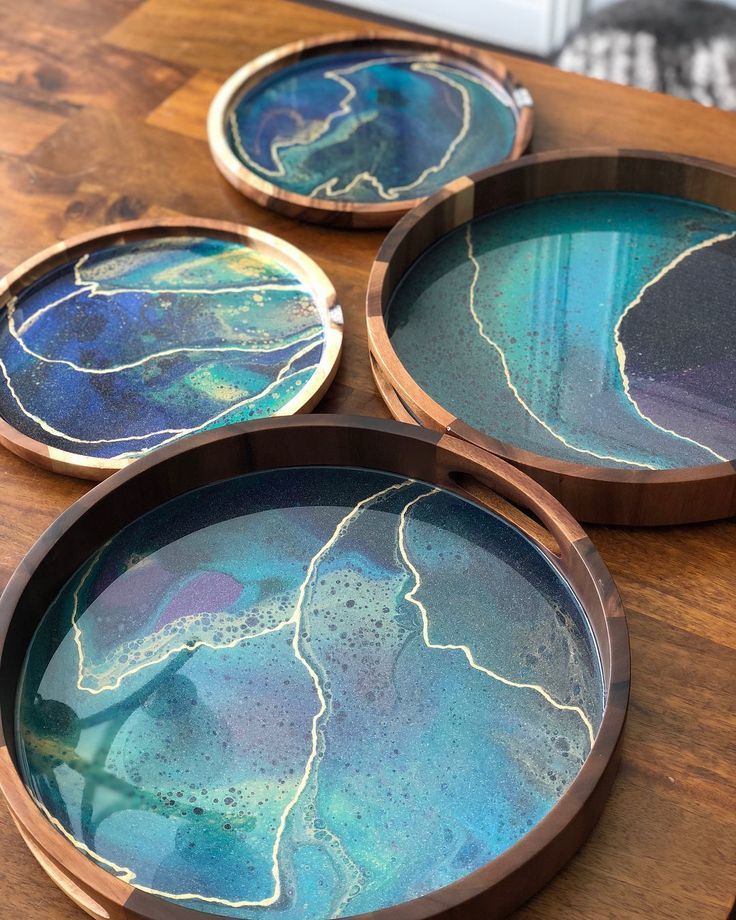
Основной целью армирующих смесей эпоксидных смол является достижение желаемых свойств при сохранении низких затрат. Увеличение содержания наполнителя обычно увеличивает вязкость и затрудняет обработку. Удельный вес обычно увеличивается, хотя некоторые наполнители, такие как полое стекло или фенольные микрошарики, создают синтактические пены со значительно меньшей плотностью.
Другими важными модификаторами, используемыми в рецептурах эпоксидных смол, являются:
Добавки к каучуку – Они используются для повышения гибкости, сопротивления усталости, трещиностойкости, ударной вязкости эпоксидных смол. Жидкие каучуки, наиболее часто используемые в эпоксидных композитах, представляют собой сополимер бутадиена и акрилонитрила с концевыми карбоксильными группами (CTBN). Однако содержание акрилонитрила в каучуке является важным фактором при использовании модификатора каучука. По мере увеличения содержания нитрила в каучуке его растворимость увеличивается, и в конечном итоге размер частиц в отвержденной матрице уменьшается. Нереакционноспособные каучуки не используются в эпоксидных композитах.
Добавки для термопластов – Используются для повышения трещиностойкости эпоксидных смол. В эпоксидных смолах могут растворяться только ТП с относительно низкой молекулярной массой. Обычно используемыми термопластами являются фенокси, полиэфирблокамиды, ПВБ, полисульфон, полиэфирсульфон, полиимид, полиэфиримид, нейлон.
По сравнению с каучуками термопласты являются более эффективными упрочнителями в высокосшитых матрицах и не влияют на Tg и модуль.
Однако высокие нагрузки TP приводят к увеличению чувствительности к растворителям и снижению сопротивления ползучести и усталости.
Огнезащитные составы – добавляются в эпоксидные смолы для придания огнестойкости. Присутствие галогенов и образующих уголь ароматических соединений в эпоксидной смоле на основе отвердителя снижает воспламеняемость.
Цвета и красители . С эпоксидными смолами можно использовать широкий спектр красителей, таких как неорганические пигменты, кроме хромовой зелени, натуральные охры, белила на основе сульфида цинка и т. д., а также органические пигменты, такие как углеродная сажа.
Эпоксидные смолы и полиэфирные смолы
Эпоксидные смолы в сравнении с полиэфирными смолами
Эпоксидная смола | Полиэстер |
|
![]() |
В целом, эпоксидные смолы имеют преимущества перед сложными полиэфирами и виниловыми эфирами в пяти основных областях:
- Улучшенные адгезионные свойства (способность приклеиваться к арматуре или заполнителю)
- Превосходные механические свойства (особенно прочность и жесткость)
- Повышенная устойчивость к усталости и микротрещинам
- Снижение деградации от проникновения воды (ухудшение свойств из-за проникновения воды)
- Повышенная устойчивость к осмосу (деградация поверхности из-за водопроницаемости)
Переработка и эпоксидные системы на биологической основе
Переработка и эпоксидные системы на биологической основе
Как обсуждалось выше, термореактивные эпоксидные композиты представляют собой материалы с высокими эксплуатационными характеристиками, которые широко применяются в промышленности.
Есть несколько новых разработок в области термореактивных эпоксидных смол, которые в некоторой степени могут быть переработаны, но их коммерческое значение еще не полностью использовано.
Кроме того, достижения в области систем термореактивных смол на биологической основе привлекли значительное внимание, учитывая их экологические преимущества. Некоторые из термореактивных материалов из биологического сырья включают:
- На основе натуральных масел (соевых, льняных, касторовых…)
- На основе изосорбида
- Эпоксидные системы на основе фурана
- Фенольные и полифенольные эпоксидные смолы
- Эпоксидированный натуральный каучук
- Эпоксидные производные лигнина
- Смолы на основе канифоли
Найти подходящую эпоксидную смолу
Ознакомьтесь с широким ассортиментом эпоксидных смол, доступных сегодня на рынке, проанализируйте технические характеристики каждого продукта, получите техническую помощь или запросите образцы.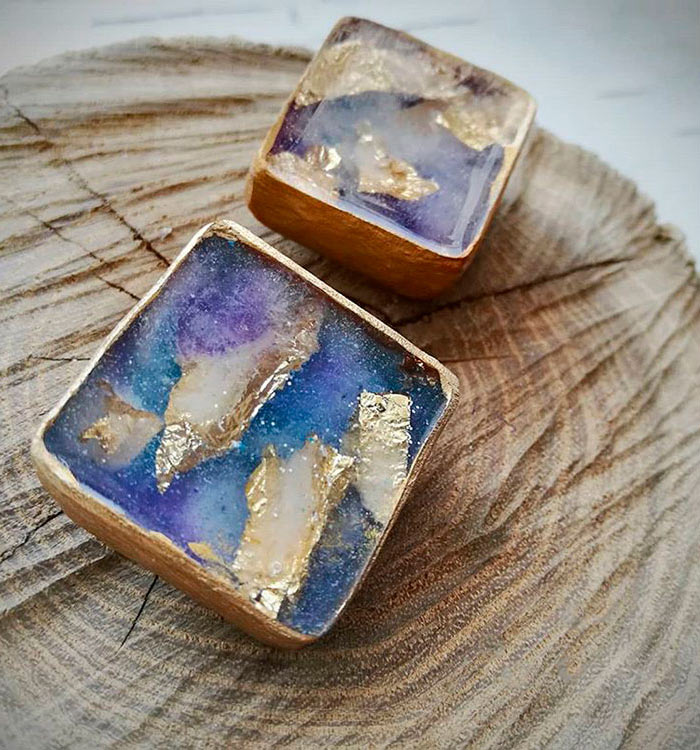
Сравните физические свойства эпоксидной смолы — Эпоксидная смола WEST SYSTEM
Мы сравниваем физические свойства эпоксидной смолы WEST SYSTEM с использованием научных тестов ASTM. При лабораторном сравнении физических свойств эпоксидных смол образцы для испытаний отверждаются при комнатной температуре в течение двух недель, если не указано иное. В таблице ниже перечислены типичные значения физических свойств. Их не следует рассматривать как спецификации. Чистые образцы эпоксидной смолы (т.е. , не содержащий наполнителей или армирующих волокон) использовали для испытаний.
ЭПОКСИД ФИЗИЧЕСКИЕ СВОЙСТВА | 105 Эпоксидная смола/205 Быстродействующий отвердитель | 105 Эпоксидная смола/ 206 Медленный отвердитель | 105 Эпоксидная смола/207 Специальный прозрачный отвердитель | 105 Эпоксидная смола/209Сверхмедленный отвердитель | Загущенный эпоксидный клей Six10 | 650-32 G/flex Упрочненная эпоксидная смола |
Соотношение смеси по весу* | См.![]() | См. техпаспорт | См. техпаспорт | См. техпаспорт | См. техпаспорт | См. техпаспорт |
Вязкость смеси при 72°F (сПз) | 975 | 725 | 760 | 650 | гель | 15 000 |
Жизнеспособность 100 г при 72°F (мин.) | 12 | 21,5 | 22 | 45 | 42 | 45 |
Удельный вес отвержденной смолы | 1,18 | 1,18 | 1,15 | 1,16 | 1,18 | 1.11 |
Твердость через 2 недели (по Шору D) | 83 | 83 | 84,4 | 82 | 80,6 | 75 |
Предел сжатия за 2 недели (PSI) | 11 418 | 11 500 | 11 043 | 11 960 | 9 693 | 5 268 |
Прочность на растяжение (PSI) | 7 846 | 7 320 | 6 748 | 7 280 | 6 438 | 3 440 |
Удлинение при растяжении (%) | 3,4 | 4,5 | 3,8 | 3,6 | 7,9 | 32,7 |
Модуль упругости при растяжении (PSI) | 4.![]() | 4.60E+05 | 4.40E+05 | 3.98E+05 | 3.71E+05 | 1.44E+05 |
Прочность на изгиб (PSI) | 14 112 | 11 810 | 11 324 | 12 459 | 11 320 | 5 192 |
Модуль упругости при изгибе (PSI) | 4.61E+05 | 4.50E+05 | 4.12E+05 | 3.97E+05 | 3.51E+05 | 1.56E+05 |
Температура теплового прогиба (°F) | 118 | 123 | 117 | 117 | 127 | 127 |
Начало Tg по ДСК (°F) | 129 | 126 | 116 | 122 | 127 | 138 |
Предельная Tg по ДСК (°F) | 142 | 139 | 116 | 130 | 133 | 154 |
* Фактическое соотношение, выдаваемое калиброванными мининасосами WEST SYSTEM® 300.
Характеристики эпоксидных смол WEST SYSTEM
WEST SYSTEM Эпоксидная смола и отвердители являются основными компонентами двухкомпонентной морской эпоксидной смолы, первоначально разработанной специально для использования в судостроении. Наша эпоксидная смола и добавки созданы для обеспечения максимальных физических свойств и в то же время максимально удобны в использовании. Продукты WEST SYSTEM предназначены для смешивания на месте в специальных рецептурах, необходимых для различных работ. Строители и ремонтники могут выбирать из ряда отвердителей и добавок, чтобы адаптировать характеристики обработки эпоксидной смеси и физические свойства отвержденной эпоксидной смолы в соответствии с рабочими условиями и требованиями их конкретного покрытия или склеивания.
Эпоксидные смолы WEST SYSTEM при отверждении образуют твердый пластик с превосходными механическими свойствами. При добавлении небольшого количества наполнителя к смеси смолы и отвердителя эпоксидная смола на основе смолы WEST SYSTEM 105 становится очень прочным клеем, заполняющим зазоры. Соединения, скрепленные этими эпоксидными смесями, часто прочнее окружающих их волокон. Другие комбинации эпоксидной смолы WEST SYSTEM и наполнителей дают смеси, которые можно использовать для обтекания и скругления. Эпоксидная смола WEST SYSTEM является превосходным средством для передачи нагрузок от древесного волокна к металлам. Он будет служить эффективным интерфейсом для распределения точечной нагрузки на большую площадь поверхности, чем это было бы возможно в противном случае. Эпоксидные материалы WEST SYSTEM предназначены для склеивания стекловолокна, арамида (Kevlar™), графита и других синтетических волокон в конструкционных и армирующих материалах.
Успех любого эпоксидного композита частично зависит от способности эпоксидной смолы защищать подложку от влаги. В то время как ни одна эпоксидная смола не образует абсолютный барьер для паров влаги, всего два слоя эпоксидной смолы WEST SYSTEM препятствуют прохождению паров влаги до такой степени, что содержание влаги в покрытии, инкапсулированном эпоксидной смолой, остается стабильным. Эпоксидная смола контролирует колебания содержания влаги, улучшая механические свойства и стабильность размеров. При использовании для герметизации древесины эпоксидная смола ограничивает как влажность, так и кислород, что делает невозможным выживание грибков сухой гнили.
A WEST SYSTEM Эпоксидный влагозащитный слой также создает стабильную основу для краски и лака. Деревянные поверхности, защищенные эпоксидными покрытиями WEST SYSTEM, не могут пропитаться водой. Краска прилипает лучше, с меньшим растрескиванием и отслаиванием, чем на подложках без эпоксидного покрытия.
Эпоксидная смола склеивается при комнатной температуре с небольшим усилием смыкания, поэтому требуется небольшое количество специальных инструментов и форм. В результате накладные расходы на проект могут быть значительно сокращены, а производство деталей с эпоксидной смолой становится более гибким.
Наши знания об эпоксидных композитах растут с каждым днем испытаний. Текущие данные о продуктах публикуются в наших практических руководствах, журнале Epoxyworks Magazine и здесь, на нашем веб-сайте. Наш технический персонал всегда готов ответить на любые ваши вопросы.
— все, что вам нужно знать об эпоксидной смоле
Этот пост может содержать партнерские ссылки. Мы можем получать небольшую комиссию от покупок, сделанных через них, без каких-либо дополнительных затрат для вас.
Искусство использования смолы для украшения или покрытия мебели стало тенденцией во всем мире. Все больше и больше людей во всем мире хотят научиться использовать эпоксидную смолу для своих собственных проектов. Здесь вы сможете узнать все тонкости различных смол, чтобы добиться наилучшего результата для своего дизайнерского проекта.
Содержание
- 1 Что такое смола?
- 1.1 Свойства эпоксидной смолы, на которые следует обращать внимание в различных марках
- 2 Для чего используется смола?
- 3 Что следует учитывать при покупке эпоксидных смол
- 4 Какая эпоксидная смола лучше всего подходит для вашего проекта?
- 4.
1 Casting Resins (Low Viscosity)
- 4.2 Laminating Resins (High Viscosity)
- 4.
- 5 What You Should Know About Resin Viscosities
- 5.1 Layer Density
- 5.2 Processing Time
- 5.3 Curing Time
- 6 Характеристики эпоксидной смолы
- 6.1 Преимущества эпоксидных смол
- 6.2 Потенциальные недостатки использования эпоксидной смолы
- 7 Считается ли эпоксидная смола токсичной?
- 8 Как раскрасить свою прозрачную эпоксидную смолу
- 8.1 Подходящее средство раскраски смолы
- 8.2 Выбор вашего продукта
- 8.3. Другие способы раскрасить вашу смолу
- 9 Часто задаваемые вопросы об использовании эпокс. Покрыть древесину эпоксидной смолой?
- 9.2 Как удалить смолу с определенных частей?
- 9.3 Есть ли у вас пищевая смола?
- 9.4 Что означает смола?
- 9.5 Можно ли дополнительно обрабатывать уже отвержденную смолу?
- 9.
6 Водонепроницаемы ли покрытия из смолы?
- 9.7 Что означает термин «жизнеспособность»?
- 9.8 Как предотвратить образование пузырьков в смоле?
Что такое смола?
При рассмотрении определения эпоксидной смолы полезно отметить, что сам термин происходит от соединения, известного как эпоксид. Эпоксиды известны своими свойствами клея, поскольку 9Эпоксидные смолы 0032 часто используются в качестве сильных клеев или покрытий.
При смешивании жидкой смолы с соответствующим отвердителем происходит химическая реакция. Этот химический процесс происходит при смешивании двухкомпонентных компонентов эпоксидной смолы, которые затем излучают тепло до тех пор, пока жидкость не затвердеет и не превратится в твердое состояние.
Обычно при смешивании смолы и отвердителя используется соотношение 1 к 1 или 1 к 2. Таким образом, более простое определение эпоксидной смолы может относиться к соединению или материалу, полученному путем смешивания двух взаимодополняющих компонентов.
Свойства эпоксидной смолы различных марок, на которые следует обращать внимание
Существует большое количество различных видов смол, каждый из которых обладает собственным набором свойств, которые могут подходить для различных применений и проектов. Каждый тип смолы будет отличаться в зависимости от того, сколько времени требуется для отверждения, толщины слоя, термостойкости, а также прочности готового продукта. Эти характеристики следует учитывать при принятии решения о том, какая смола лучше всего подойдет для вашего конкретного проекта. Основные свойства смолы, которые могут различаться в зависимости от продукта:
- ВИСКАЗИТЕЛЬНОСТЬ (ПЛЮЧИВА)
- Максимальная толщина слоя для каждого листа
- Длина процесса отверждения
- Приливчивости DISTIAL Product 43 .
- Уплотнительный грунт для строительства зданий.
- Ремонт старых зданий.
- Крепление каменных ковров или дорожек.
- УФ-смолу можно использовать для быстрого ремонта и ремонта.
- Смола также может использоваться для фиксации или склеивания деталей.
- Герметизация столешниц и рабочих мест на кухне для предотвращения порезов.
- Использование кусочков дерева и смолы для изготовления разделочных досок.
- Ювелирные изделия могут быть изготовлены из смолы или отлиты из нее.
- Произведения искусства и декоративные предметы, такие как статуи, статуэтки, модели и формы.
- Мебель из долговечной смолы.
- Декоративные полимерные полы.
- Использование смолы в качестве водонепроницаемого герметика, например, для полов в гараже .
- Строительство аквариумов и террариумов.
- Смола в качестве верхнего слоя при строительстве лодки.
- Самодельные кайтборды или доски для серфинга.
- Литья любых типов форм.
- Создание украшений.
- Литые элементы в моделировании.
- Мебель, особенно столы из смолы.
- Ремонт трещин или отверстий в древесине.
- Полимерные полы для жилых помещений и гаражей.
- Искусство смолы , когда вы отливаете изображение из смолы.
- Декоративные предметы, такие как смоляные жеоды или безделушки.
- Завершающий штрих к вашим картинам или произведениям искусства.
- Некоторые виды ювелирных изделий из смолы.
- Герметизация или покрытие поверхностей, таких как столешницы и столы.
- Вы можете добиться определенных особых эффектов, добавляя краситель к этому типу смолы.
- Вы можете создавать больше слоев быстрее, так как несколько слоев могут быть добавлены друг к другу за более короткие промежутки времени.
- Пузыри чаще образуются в некоторых ситуациях, когда вентиляция затруднена.
- При воздействии УФ-излучения может появиться желтый цвет.
- Более длительное время обработки позволяет выполнять более тщательную и кропотливую работу, где у вас будет достаточно времени для смешивания различных цветов в собственном темпе.
.
- При укладке нескольких слоев прозрачной смолы друг на друга переход от одного слоя к другому менее заметен.
- Для заливки нескольких слоев вам потребуются дополнительные инструменты, такие как шпатели и миски для смешивания.
- Для добавления дополнительных слоев требуется больше времени из-за более медленного высыхания
- Короткое время обработки примерно от 20 до 60 минут должно быть полностью отверждено в течение 24 часов.
- Более длительное время обработки до 12 часов потребует времени отверждения до одной недели.
- Устойчив к кислотам и коррозии, что делает его хорошим выбором для стойких к порезам покрытий на столешницах и других рабочих поверхностях.
- Чрезвычайно прочный и прочный.
- Маловероятно, что он сломается от удара.
- Переход от жидкого состояния к твердому во время процесса отверждения означает очень небольшую усадку.
- Умеренная плотность около 1,2 грамма на кубический сантиметр.
- Хорошая устойчивость к ультрафиолетовому излучению.
- Отличное сцепление с большинством материалов, например, с деревом.
- Высокая термостойкость.
- Практически полное отсутствие растрескивания самой смолы, если она подготовлена должным образом.
- Устойчив к атмосферным воздействиям, что означает, что его можно использовать как внутри, так и снаружи помещений.
Важно иметь хорошее представление о том, чем могут отличаться различные типы смолы, чтобы вы могли быть уверены, что у вас есть подходящие инструменты и материалы для вашего проекта.
![]()
Для чего используется смола?
Те, кто хочет узнать, как использовать эпоксидную смолу, будут рады узнать, что этот материал является одним из самых универсальных с точки зрения его использования. Эту смолу можно использовать в коммерческих и промышленных целях, а также для любого количества творческих проектов «сделай сам». Следующий список применений смолы ни в коем случае не является исчерпывающим, так как существует много других способов использования этого многогранного материала:
На что следует обратить внимание при покупке эпоксидных смол
Многие люди, заинтересованные в обучении использованию эпоксидной смолы, могут оттолкнуться, обнаружив высокую стоимость необходимых продуктов и материалов. Эту смолу можно купить у большинства специалистов и в магазинах для рукоделия, хотя в Интернете можно найти более широкий выбор продуктов и ресурсов.
Именно состав продукта, а также его общая прочность и долговечность могут объясняться высокой стоимостью смолы. Тем не менее, именно на этот продукт стоит потратиться. Вместо этого может возникнуть соблазн выбрать более дешевые смолы, но они очень часто имеют гораздо более низкое качество, что может быть заметно в готовом продукте.
Некоторые более дешевые продукты могут также содержать токсичные растворители, которые выделяются в процессе отверждения и могут быть опасны для здоровья. Другие низкокачественные продукты не являются полностью прозрачными, как это должно быть в случае с прозрачной эпоксидной смолой, а вместо этого имеют несколько желтоватый цвет.
Совет: если вы планируете использовать эпоксидные смолы для проекта «сделай сам», лучше потратить больше на продукты самого высокого качества, так как именно так вы можете гарантировать успешные результаты для вашего готового изделия.
![]()
Какая эпоксидная смола лучше всего подходит для вашего проекта?
Каждая отдельная эпоксидная смесь имеет свой собственный набор свойств, поэтому перед началом работы пользователям обязательно нужно прочитать все инструкции по конкретному продукту. Для разных проектов потребуются разные типы смолы, поэтому важно знать, какие характеристики смолы лучше всего подходят для вашей идеи. Смолы для литья и смолы для ламинирования сильно различаются по своей вязкости, которая указывает на то, насколько хорошо жидкость может проникать в отливку.
Литейные смолы (низкая вязкость)
Смолы с низкой вязкостью относятся к особенно жидким и текучим жидкостям, что делает их более текучими и более легкими для заливки. Водоподобная консистенция литейных смол делает их идеальными для литья форм или для проектов, требующих постоянного потока жидкости, таких как речные столы.
Текучесть смолы этого типа означает, однако, что она отверждается медленнее. Таким образом, пользователи должны планировать заранее, чтобы интервалы между кастингами были достаточно длинными. Смола с низкой вязкостью имеет тенденцию затвердевать в течение периода от 12 до 24 часов, в течение которых процесс химической реакции протекает намного медленнее. В результате во время этого процесса выделяется очень мало тепла, что делает этот тип смолы идеальным для более толстых слоев и больших количеств, используемых за одну операцию обработки.
Литейная смола лучше всего подходит для:
Смолы для ламинирования (высокой вязкости)
Смола для ламинирования лучше всего подходит в качестве покрытия для поверхностей из-за ее высокой вязкости, что означает ее густую медовую текстуру. Несмотря на то, что густая консистенция и медленно растекающийся характер этой смолы делают ее идеальной для покрытия поверхностей, ламинирование смолы также является подходящим выбором для создания произведений искусства из смолы или жеод из смолы.
Плотность этого продукта означает, что необходимо строго соблюдать максимальную толщину каждого слоя. Рекомендуемую толщину слоя обычно можно найти в инструкциях производителя, хотя рекомендуется создавать слой толщиной не более 1–2 см.
Смола для ламинирования лучше всего подходит для:
Что следует знать о вязкости смол
Текучесть и текучесть жидкой смолы являются ключевой частью любого проекта смолы, так как это будет влиять на используемые материалы, толщину каждого слоя смолы, продолжительность времени обработки, а также продолжительность смола затвердевает.
Совет: Как правило, всю необходимую информацию об использовании смолы можно найти на упаковке продукта. Информация производителя всегда должна четко указывать, сколько смолы можно использовать в рамках одного процесса.
Плотность слоя
В процессе отверждения смола нагревается и медленно затвердевает. Обычно рекомендуются более тонкие слои, чтобы предотвратить перегрев смолы. Также легче удалить пузырьки воздуха из тонких слоев смолы, так как они способны подниматься вверх и выходить с поверхности.
Таким образом, использование смолы с низкой вязкостью, такой как литьевая смола, позволит вам наливать более толстые и плотные слои из-за ее водянистой консистенции. Смола с низкой вязкостью также выделяет меньше тепла в процессе отверждения, что является еще одной причиной, по которой вы можете отливать более толстые слои с помощью этого типа смолы. Пузырьки воздуха можно легко удалить, осторожно продув участок горячим феном или горелкой.
Смолу высокой вязкости, напротив, нельзя наливать слоями толщиной более 1–2 см. Из-за плотности этого типа смолы очень трудно удалить пузырьки воздуха, а это означает, что более тонкий слой облегчит этот процесс. Эта смола также известна как смола для ламинирования, так как ее густая консистенция делает ее идеальной для покрытия различных поверхностей.
Время обработки
Время обработки также часто называют временем жизнеспособности смолы или открытым временем смолы. Это период времени, в течение которого смола может обрабатываться до того, как она затвердеет. Жизнеспособность начинается с момента смешивания двухкомпонентных компонентов эпоксидной смолы и заканчивается, когда смола начинает схватываться и затвердевать. Перед выбором типа смолы следует взвесить плюсы и минусы как короткого, так и длительного времени обработки.
Короткое время обработки
Плюсы
Минусы
Длительное время обработки
Профессионалы
Минусы
Время отверждения
Время отверждения смолы относится к периоду времени, после которого смола становится полностью твердой и прочной. Этот период, как правило, напрямую связан со временем обработки смолы, поскольку смола с коротким временем обработки, вероятно, будет полностью отверждена после относительно короткого промежутка времени.
Время обработки различных продуктов
Характеристики эпоксидной смолы
Этот материал с годами стал настолько популярным благодаря множеству применений. Многие преимущества этого универсального продукта значительно перевешивают его недостатки, что делает его отличным материалом для выполнения любого количества проектов «сделай сам».
Преимущества эпоксидных смол
Несмотря на длительный и сложный процесс заливки смолы, конечный продукт, который получается после полного отверждения смолы, будет обладать следующими свойствами: .
Вы можете ожидать наилучших свойств и преимуществ от изделий из смолы более высокого качества. Было обнаружено, что высококачественные смолы почти или полностью воспламеняются в жидком состоянии.
Возможные недостатки использования эпоксидной смолы
Как и в случае со многими продуктами, использование эпоксидной смолы имеет некоторые недостатки:
- Требуемые материалы могут быть довольно дорогими.
- Смола может быть не полностью устойчивой к кислотам высокой концентрации.
- Смола в жидком состоянии может вызвать аллергическую реакцию у некоторых пользователей при контакте с кожей.
- После отверждения смолы ее очень трудно удалить.
Является ли эпоксидная смола токсичной?
Хотя смола не считается особенно опасной, необработанные компоненты двухкомпонентной эпоксидной смолы могут вызвать раздражение кожи или аллергическую реакцию у некоторых пользователей. Чтобы этого не произошло, рекомендуется носить защитные перчатки и очки, чтобы предотвратить контакт кожи или любой другой части тела со смолой. Фильтрующая дыхательная маска также может быть полезна, чтобы избежать вдыхания токсичных паров.
Маловероятно, что вы столкнетесь с какими-либо серьезными проблемами, связанными со здоровьем и безопасностью, при работе со смолой, если вы будете следовать некоторым основным правилам защиты. При работе с цветной или прозрачной эпоксидной смолой обязательно соблюдайте следующие меры безопасности:
- Носите защитные очки, полностью закрывающие глаза.
- Надевайте защитные нитриловые перчатки.
- Носите старую одежду с длинными рукавами и штанинами, чтобы максимально прикрыть тело. Вы также можете носить защитный костюм для этой цели.
- В качестве рабочего места используйте хорошо проветриваемое помещение.
- Защитите себя от вредных паров, надев маску со встроенным фильтром.
- Убедитесь, что вы не наливаете слишком много эпоксидной смолы в ванночку для смешивания при перемешивании жидкой смолы и отвердителя, так как это может привести к выплескиванию смеси.
Как окрасить прозрачную эпоксидную смолу
После смешивания жидкой смолы и отвердителя вы получите полностью прозрачное вещество (хотя продукты более низкого качества могут привести к желтоватому веществу). вместо). Есть несколько способов, которыми вы можете добавить цвет к своей смоле, в зависимости от желаемого эффекта.
Подходящие средства для окрашивания смолы
Если вы решили использовать краску для окрашивания смолы, вы не должны использовать краски на водной основе. Это связано с тем, что вода в этих красках может препятствовать правильному отверждению смолы, а также некоторым другим нежелательным эффектам. Вы также можете добавить цвет к смоле , используя:
- Порошковые цветные пигменты
- Алкогольные чернила
- Жидкие цветные концентраты
- Краски для аэрографа
Выбор продукта
При окрашивании смолы лучше всего выбирать продукты максимально возможного качества, так как низкокачественные пигменты с большей вероятностью выцветают со временем. Вы можете гарантировать яркий и стойкий пигмент смолы, когда покупаете продукт, соответствующий стандартам качества.
Другие способы окрашивания смолы
Еще один способ придать цвет смоле — покрасить ее после отверждения. Окрашивание изделия из смолы может быть затруднено, так как лучше всего использовать автомобильную краску высшего качества. Таким образом, этот метод, как правило, используется для более специальных проектов, таких как аквариум или террариум.
Часто задаваемые вопросы об использовании эпоксидных смол
Можно ли герметизировать древесину эпоксидной смолой?
Древесина является одним из самых популярных материалов для использования смолы, так как смола эффективно изолирует гибкую пористую поверхность, характерную для большинства пород дерева, предотвращая таким образом попадание влаги. Древесину и смолу можно использовать по-разному, например:
- Добавление защитного покрытия к частям лодки.
- Герметизация и защита столешниц.
- Герметизация и покрытие любых деревянных поверхностей.
Как удалить смолу с определенных частей?
Эпоксидная смола известна своими адгезионными свойствами и отличной устойчивостью к большим нагрузкам и ударам. Однако долговечность этого материала означает, что его еще труднее удалить после отверждения. Хотя удаление смолы физическими средствами может оказаться почти невозможным, его можно удалить, вернув смолу в жидкое состояние, чтобы ее можно было соскрести.
Для этого необходимо нанести на целевую область растворитель под названием ацетон и оставить на один час в хорошо проветриваемом помещении. Это должно привести к тому, что смола станет немного мягче. Теперь, когда область размягчилась, предварительно нагрейте тепловую пушку до 200 градусов по Цельсию и пройдитесь по смоле, пока она не станет жидкой и ее можно будет соскрести. Когда вы нагреваете смолу, вы должны следить за тем, чтобы это делалось очень осторожно и медленно, чтобы не повредить или не сжечь любую другую часть изделия.
В процессе нагревания твердой смолы до жидкого состояния могут выделяться токсичные пары. Таким образом, вы должны убедиться, что вы носите соответствующую дыхательную маску, чтобы защитить себя от вдыхания любых опасных паров.
Вы получаете пищевую смолу?
После того, как кусок смолы полностью затвердеет, взаимодействие с пищевыми продуктами абсолютно безопасно. Однако процесс отверждения некоторых смол может занять до нескольких недель, прежде чем они полностью затвердеют. Некоторые производители смол предпочитают сертифицировать свои продукты как безопасные для использования с пищевыми продуктами, хотя это случается редко из-за высоких затрат на это.
Что означает смола?
Слово «смола» стало общим термином в мире современного искусства для всех без исключения видов смолы. Это слово особенно популярно в английском и немецком языках как синоним, в частности, смолы на основе эпоксидной смолы.
Можно ли дополнительно обрабатывать уже отвержденную смолу?
Когда кусок смолы полностью отвержден, он становится очень твердым и прочным. Таким образом, ваш отвержденный кусок смолы может быть дополнительно обработан следующим образом, что может быть достигнуто вручную или с помощью машины:
- Шлифовка
- Полировка
- Сверление
Водонепроницаемы ли покрытия из смолы?
Смола представляет собой очень прочный материал после отверждения, поэтому она полностью водонепроницаема и устойчива к атмосферным воздействиям. Этот материал станет восприимчивым к воздействию воды только в том случае, если он сломается или треснет, что маловероятно из-за прочности смолы.
Что означает термин «жизнеспособность»?
Жизнеспособность относится к максимальному количеству времени, необходимому для обработки смолы до полного отверждения. Продолжительность жизнеспособности смолы зависит от следующего:
- Марка и тип используемой смолы.
- Количество смолы, которое можно переработать за одну операцию.
- Внешние факторы, такие как температура окружающей среды и поверхность, на которой вы создаете свое произведение.
- Температура смешанной смолы .
В течение жизнеспособности смесь смол претерпевает ряд изменений. Консистенция жидкости изменится от очень тонкой до очень густой, после чего наступит момент, когда смола больше не может быть обработана, так как она полностью затвердела.
Поскольку время обработки может различаться в зависимости от типа смолы, важно смешать точное количество смолы, которое вы, вероятно, сможете обработать, не подвергаясь стрессу. Смешивание слишком большого количества смолы может привести к тому, что время обработки закончится до того, как вы сможете пройти через всю смесь, что приведет к потерям.
Как предотвратить образование пузырей в смоле?
Пузырьки образуются естественным образом, когда вы заливаете жидкую смолу в отливку или форму. Во избежание образования пузырьков в смеси смолы обратите внимание на следующее:
- Не встряхивайте контейнеры с компонентами смолы и отвердителя перед смешиванием.
- Держите руку ровно, когда смешиваете два компонента.
- Заранее подогрейте контейнеры со смолой и отвердителем, добавив их в ванну с теплой водой.
- Иногда в процессе отливки в смолу попадают пузырьки воздуха. Этого можно избежать, предварительно покрыв объект тонким слоем смолы.
- В более сложных случаях пузырьки воздуха можно удалить с помощью вакуумного насоса или горячего фена.
Эпоксидная смола — одно из самых полезных веществ для творчества, ремесел и проектов «сделай сам».
Эта смола обеспечивает прочное покрытие, которое можно использовать для улучшения различных поверхностей и создания красивых эффектов. Для всех, кто заинтересован в использовании эпоксидной смолы, приведенное выше руководство должно научить вас всему, что вам нужно знать.
Общие химические и физические свойства эпоксидных пластиков – Nils Malmgren AB
Эпоксидная смола определяется как молекула с более чем одной эпоксидной группой, которая может быть отверждена до пригодного для использования пластика. Эпоксидная группа, которую также называют глицидильной группой, благодаря своему характерному внешнему виду дала название эпоксидной смоле.
Эпоксидная группа
То, что вы видите, это атом кислорода снаружи углеродной цепи. Эпи означает «снаружи», а вторая часть слова происходит от кислорода.
Есть два варианта написания: эпоксидная смола и эпоксидная смола. Первый возникает из-за связи кислорода с углеродной цепью, называемой оксидом. Эпоксидная смола производится из простых основных химических веществ, которые легко доступны.
С помощью химических формул последняя стадия выхода выглядит следующим образом:
Бисфенол А + эпихлоргидрин
Диглицидиловый эфир бисфенола А (ДГЭБА) эпоксидная смола
Варьируя соотношение между бисфенолом А и эпихлоргидрином, получают различные молекулярные массы для готовой эпоксидной смолы. Самая низкая молекулярная масса, которую может иметь эпоксидная смола типа DGEBA, составляет 340, но если два элемента вместе могут образовывать разные молекулярные массы при взаимодействии, эпоксидная смола будет содержать смесь эпоксидных молекул различной длины. Поэтому речь идет не о молекулярной массе эпоксидных смол, а скорее об их средней молекулярной массе.
Эпоксидная смола со средней молекулярной массой более 700 называется высокомолекулярной, а эпоксидная смола со средней молекулярной массой менее 700 — низкомолекулярной. Эпоксидные смолы могут быть аллергенами, и именно молекулярная масса определяет, насколько велик риск. Чем выше молекулярная масса, тем ниже вероятность аллергии.
В формуле эпоксидной смолы после скобки стоит буква «н». Если n=0, то есть то, что находится внутри брекета, не существует, тогда мы имеем самую короткую молекулу эпоксидной смолы с молекулярной массой 340. Она имеет самую высокую реакционную способность и, таким образом, также представляет наибольший риск аллергии. При n=1 молекулярная масса равна 624, при n=2 – 9.08 и т. д.
При каждом увеличении n на 1 молекулярная масса увеличивается на 284. В низкомолекулярной эпоксидной смоле со средней молекулярной массой 380 распределение составляет примерно 88% n=0, 10% n=1 и 2% n=2. Чистая эпоксидная смола с n=2 не является аллергеном, но если мы посмотрим на коммерческую эпоксидную смолу с молекулярной массой 1080, то распределение составит примерно 20% n=0, 15% n=1, 15% n=2. и 50% n=3, 4 и 5. Это означает, что даже высокомолекулярная эпоксидная смола может быть аллергеном.
Низкомолекулярная эпоксидная смола со средней молекулярной массой 380 является жидкой при комнатной температуре, тогда как эпоксидная смола со средней молекулярной массой 1000 является твердой при комнатной температуре. Молекулярная масса определяет, для чего можно использовать эпоксидную смолу.
Низкомолекулярные эпоксидные смолы можно обрабатывать без растворителей, которые испаряются и поэтому используются для литья, толстых покрытий, клеев для заполнения зазоров и т. д. , что ограничивает использование красок и лаков.
Для превращения эпоксидной смолы в эпоксидный пластик требуется реакция с подходящим веществом. Такое вещество в данном контексте называется отвердителем.
Примерами групп веществ, которые действуют как отвердители эпоксидных смол, являются: амины, амиды, ангидриды кислот, имидазолы, комплексы трехфтористого бора, фенолы, меркаптаны и оксиды металлов.
Для отверждения при комнатной температуре в основном используют амины и амиды и в некоторой степени меркаптаны. Другим типам отвердителей обычно требуется температура выше +150°C для реакции с эпоксидной смолой. С этого момента далее будут описаны только амины и амидные отвердители.
Амины — это вещества, близкие к аммиаку ( NH 3 ). В зависимости от того, сколько атомов водорода замещено алкильными группами, возникают первичные амины NH 2 -R , вторичные амины NH-R 1 или третичные амины N-R 2 . Общее количество аминогрупп определяет, является ли амин моноамином ( NH 2 -R ), диамином ( NH 2 -R-NH 2 ) или полиамином ( NH 2 -R-NH-R-NH-R-NH 2 ).
Кроме того, амины делятся на алифатические, то есть с прямой углеродной цепью, циклоалифатические с кольцеобразной углеродной цепью и, наконец, ароматические, в которых аминогруппа связана с бензольным кольцом.
В качестве отвердителя для эпоксидной смолы в основном используются диамины и полиамины.
Первичная аминогруппа NH 2 содержит, как видно, два атома водорода и один атом азота. Именно водород составляет реактивную часть, а реакция происходит с кислородом в эпоксидной группе.
С несколько упрощенными химическими формулами это выглядит так:
Первичный амин + эпоксидная группа дает Вторичная аминогруппа
В первой фазе реакции один из атомов водорода амина реагирует с кислородом эпоксидной группы, вызывая образование гидроксильная группа (ОН – ) одновременно с первичным амином восстанавливается до вторичного амина. Реакция продолжается:
Вторичный амин реагирует с еще одной эпоксидной группой, и реакция завершается.
Молекула эпоксидной смолы обычно содержит две эпоксидные группы, а один первичный диамин имеет четыре реакционноспособных атома водорода. Схема эпоксидного пластика выглядит следующим образом:
Молекула эпоксидного пластика, конечно же, в действительности трехмерна.
Примеры аминов, которые используются в качестве отвердителей для эпоксидных смол
Алифатические амины
- Диэтилентриамин
- Триэтилентетрамин
- Аминоэтилпиперазин
- Триметилгексаметилендиамин
Циклоалифатические амины
- Изофорондиамин
- Диаминодициклогексилметан
Ароматические амины
- Диаминодифенилметан
- м-фенилендиамин
Обычно амины предварительно реагируют с определенной частью эпоксидной смолы. Целью этого является получение отвердителя, который является менее текучим, чем чистый амин, и имеет несколько более высокую реакционную способность.
Этот тип отвердителя называется аддуктом амина, и его реакция в основном аналогична показанной ранее.
Следующей большой группой отвердителей являются амиды или, точнее, полиаминоамиды. Амид образуется при взаимодействии полиамина с жирной кислотой.
Это относится ко всем полиамидам, даже к нейлону. Изменяя соотношение между жирной кислотой и амином, можно решить, будет ли полиамид с концевыми кислотами (типа нейлона) или с концевыми аминогруппами, то есть какие концевые группы будут у полиамида. В качестве отвердителей эпоксидных смол можно использовать только полиамиды с концевыми аминогруппами. В качестве жирной кислоты чаще всего используют талловую жирную кислоту, линолевую кислоту или олеин. Жирные кислоты используют либо мономер (одна карбоксильная группа), либо димер (две карбоксильные группы). В качестве полиаминов используют диэтилентриамин, триэтилентетрамин и тетраэтиленпентамин. Водород в амидной группе ( CONH ) не является реакционноспособным, а скорее представляет собой водород в первичных аминогруппах на концах полиамида и вторичных аминогруппах, полученных из полиамина, которые вступают в реакцию с эпоксидной смолой так же, как описано ранее.
Как аддукты аминов, так и полиамиды можно сделать водорастворимыми. Такие растворы способны эмульгировать низкомолекулярную эпоксидную смолу, что, в свою очередь, дает возможность производить водорастворимые эпоксидные краски.
Реакция между эпоксидной смолой и отвердителем представляет собой необратимое полиприсоединение, т.е. не образуются побочные продукты, а эпоксидный пластик не может разлагаться на эпоксидную смолу и отвердитель. Реакция экзотермическая, что означает выделение тепла. В зависимости от типа используемого отвердителя можно добиться очень больших различий в скорости реакции. Это имеет большое практическое значение при работе с эпоксидной смолой. Время, за которое израсходуется смесь эпоксидной смолы и отвердителя, называется жизнеспособность . В зависимости от реакционной способности смеси срок жизнеспособности может варьироваться от нескольких секунд до нескольких лет.
Жизнеспособность можно определить несколькими способами.
Один из методов заключается в закалке эпоксидной смолы и отвердителя до +20°C. После этого в пластиковой чашке смешивают 100 граммов. Время до достижения температуры смеси +50°С принимается за жизнеспособность смеси. Для систем с низкой реакционной способностью (длительный срок жизнеспособности) чаще всего выбирают измерение вязкости или консистенции, а также измерение времени до удвоения исходной вязкости.
Оба эти метода неприменимы для водных эмульгированных или водных дисперсных систем. В этом случае вместо этого проводят тест укладки и измеряют время до снижения блеска.
Большинство химических реакций следуют закону Аррениуса, согласно которому скорость реакции удваивается на каждую десятую градуса повышения температуры. Это означает, что при +30°C реакция протекает в два раза быстрее, чем при +20°C.
Чем больше количество смешивается, тем больше выделяется экзотермического тепла. У этого тепла недостаточно времени, чтобы рассеяться через поверхность сосуда для смеси, поэтому вместо этого оно нагревает смесь. По мере повышения температуры скорость реакции также увеличивается, что означает, что жизнеспособность тем короче, чем больше смешивается количество.
Пример жизнеспособности для 100 и 500 граммов одной и той же смеси эпоксидной смолы/отвердителя
Жизнеспособность эпоксидной системы, следовательно, предоставляет пользователю определенную информацию о рабочем времени после смешивания, но необходимо учитывать количество смешанного материала. , и начальная температура материала. Время отверждения эпоксидной смолы определяется как время от нанесения эпоксидной смолы до достижения формованным эпоксидным пластиком своих окончательных свойств, касающихся прочности и химической стойкости.
Для эпоксидной смолы, наносимой тонкими слоями, экзотермический нагрев не приведет к значительному повышению температуры в слое, вместо этого эпоксидная смола быстро принимает температуру подложки. Реакция между эпоксидной смолой и отвердителем вначале идет относительно быстро из-за большого количества реактивных молекул и из-за того, что подвижность молекул высока, пока вязкость низкая.
По мере образования полных молекул эпоксидной смолы количество реактивных молекул уменьшается одновременно с увеличением вязкости. Скорость реакции постепенно замедляется.
Как правило, эпоксидной смоле, отвержденной при комнатной температуре, требуется около 7 дней при +20°C для достижения максимальных свойств, но уже через 24 часа можно достичь 70–80% окончательных свойств.
Закон Аррениуса естественно применяется, даже если реакция протекает при постоянной температуре. Это означает, что если субстрат находится при температуре +10°C, для достижения окончательных свойств требуется около 14 дней.
Пример процесса отверждения эпоксидной смолы при постоянной температуре.
Основные характеристики эпоксидного пластика
В настоящее время более 50 различных веществ соответствуют определению эпоксидной смолы. Если еще добавить, что существует несколько сотен различных отвердителей, то легко понять, что свойства эпоксидного пластика можно модифицировать для удовлетворения самых разных требований. Тем не менее, некоторые основные свойства всегда присутствуют.
Адгезия
Одним из наиболее характерных свойств эпоксидного пластика является способность прилипать к большинству поверхностей. Причиной этого является наличие полярных гидроксильных групп и эфирных связей. Незначительная усадка также означает, что контакт между эпоксидным пластиком и подложкой не нарушается напряжениями. Поверхностное натяжение эпоксидного пластика чаще всего ниже критической поверхностной энергии для большинства материалов. Это одно из условий достижения адгезии.
Механическая прочность
Никакой другой твердый пластик не обладает такой высокой механической прочностью, как правильно подобранный эпоксидный пластик. Опять же, благодаря минимальной усадке удается избежать встроенных напряжений. Прочность на растяжение может превышать 80 МПа.
Химическая стойкость
Благодаря возможности варьирования свойств эпоксидных пластиков можно сделать эпоксидный пластик устойчивым к большинству химических веществ. В целом эпоксидный пластик очень устойчив к щелочам, что важно при поверхностной обработке бетона.
Диффузионная плотность
Эпоксидная смола обычно имеет относительно высокое сопротивление паропроницанию, но с помощью специальной технологии эпоксидный пластик можно сделать открытым для диффузии. Эпоксидная смола, открытая для диффузии, может быть нанесена, например, на влажный бетон и обеспечивает адгезию выше, чем прочность бетона на растяжение.
Водонепроницаемость
Эпоксидные пластики считаются водонепроницаемыми и часто используются для защиты от воды.
Электрическая изоляция
Эпоксидные пластмассы являются превосходными электрическими изоляторами. Объемное удельное сопротивление обычно составляет 10 15 Ом·см. Это в сочетании с высокой влагостойкостью и химической стойкостью делает эпоксидную смолу пригодной как для изготовления электронных компонентов, так и для заливки трансформаторов.
Усадка
Эпоксидные пластики имеют очень небольшую усадку при отверждении. Это связано с тем, что молекула эпоксидной смолы имеет довольно небольшую переориентацию в процессе отверждения по сравнению, например, с полиэфиром и метилметакрилатом.
Термостойкость
По термостойкости эпоксидный пластик, затвердевший при комнатной температуре, очень мало отличается от термоотверждаемого. Часто теплостойкость указывается с помощью HDT (температура теплового отклонения) или Tg (температура стеклования).
При HDT механическая прочность быстро снижается. Эпоксидная смола, отвержденная при комнатной температуре, редко достигает HDT выше 70°C, в то время как температура затвердевания при нагревании может достигать 250°C.
Поддающийся модификации
Возможно, главным свойством эпоксидной смолы является почти неограниченная способность изменять окончательные свойства эпоксидного пластика для удовлетворения особых требований. В первую очередь на свойства пластика влияет отвердитель, но, как будет показано в следующей главе, на эпоксидные продукты влияет множество других веществ.
Светостойкость
Эпоксидные пластики на основе ароматических эпоксидных смол чувствительны к свету в УФ-диапазоне. Прямое облучение ультрафиолетом быстро вызывает пожелтение. Даже обычный солнечный свет содержит достаточно ультрафиолетового излучения, чтобы произошло пожелтение. Наиболее стойкими являются алифатические эпоксидные смолы с ангидридным или аминным отвердителем.
Модификация эпоксидных смол
Вязкость при 25°С немодифицированной низкомолекулярной эпоксидной смолы типа ДГЭБА около 10 Па·с, при 20°С около 24 Па·с и при 15°С около 68 Па·с с.
Легко понять, что немодифицированную эпоксидную смолу не всегда можно использовать на открытом воздухе или при низкой температуре. Таким образом, первой причиной модификации является снижение вязкости до подходящей рабочей консистенции. Здесь доступно несколько вариантов.
Во-первых, у нас есть нереакционноспособные разбавители , которые относятся к таким веществам, которые можно смешивать с эпоксидной смолой, но которые не участвуют в реакции между эпоксидной смолой и отвердителем. Сюда входят обычные растворители, такие как ксилол, толуол, гликолевые эфиры, кетоны, низшие спирты и т. д.
Другие нереакционноспособные разбавители включают большое количество веществ с достаточно низким давлением паров, чтобы они не испарялись из затвердевшего пластика при нормальных условиях. Их примерами являются бензиловый спирт и кумароновые смолы. Вещества, химически не связанные в молекуле эпоксидного пластика, следует представлять себе отложившимися между молекулярными цепями пластика.
В эту группу входят «обычные» растворители, оказывающие самое сильное влияние на вязкость, но часто влекущие за собой опасный путь.
Эпоксидная смола обладает очень высокой способностью удерживать растворители, т.е. способностью удерживать растворители. Это означает, что пройдет много времени, прежде чем растворитель испарится. В слое толщиной 1 мм остатки растворителя можно обнаружить через несколько месяцев при комнатной температуре.
Повреждение, которое может быть вызвано растворителями, обычно проявляется образованием пузырей либо из-за сильного нагрева, либо из-за осмоса, когда в бетоне появляется влага. Еще одна причина, по которой следует избегать растворителей, — эффект усадки, который может привести к отслоению слоев от слабой подложки.
Разбавители, которые при нормальных условиях не испаряются, влияют на свойства эпоксидного пластика не только на снижение вязкости, но иным образом. Положительными изменениями могут быть гибкость, улучшенная стойкость к воде и растворам солей из-за гидрофобизации, повышенная реакционная способность, частично из-за лучшей подвижности эпоксидной смолы и молекулы отвердителя при более низкой вязкости, а частично из-за каталитического действия гидроксильных групп в например, бензиловый спирт.
Отрицательными изменениями являются снижение теплостойкости и увеличение теплового расширения.
При более высоких температурах летучесть некоторых из этих веществ может быть значительной. Это может привести к усадке с растрескиванием и последующему снижению адгезии. Еще одним аспектом, который иногда необходимо учитывать, является совместимость с битумом. Меньшая часть нереакционноспособных разбавителей не просачивается в битум.
Кроме того, многие разбавители этой группы представляют собой сложные эфиры, которые могут омыляться при контакте с бетоном под воздействием воды.
Реактивный разбавитель (разбавители)
Эти вещества обладают, как следует из названия, способностью вступать в реакцию с эпоксидной смолой или отвердителем, таким образом связывая молекулу пластика.
Наиболее часто используемые типы содержат одну или несколько эпоксидных групп. Существует очень большая группа таких веществ, которые все могут придать конечному пластику разные свойства.
Отличительной чертой этих веществ является то, что они не могут мигрировать, испаряться или экстрагироваться из эпоксидного пластика. Термостойкость несколько снижается по сравнению с немодифицированной эпоксидной смолой, но совсем не так сильно, как в случае нереакционноспособного разбавителя. Ценным свойством реактивного разбавителя является то, что он снижает поверхностное натяжение эпоксидной смолы, что, в свою очередь, может улучшить смачивающие свойства и, следовательно, адгезию. В зависимости от состава реактивного разбавителя могут быть затронуты как гибкость, так и химическая стойкость.
Другими веществами, используемыми для модификации свойств эпоксидного пластика, являются, например, высокомолекулярные изоцианаты, которые через отвердитель могут реагировать с эпоксидной смолой. В результате получается пластик с эластичными свойствами резины, которые сохраняются примерно до -40°C.
Такая модификация изменяет основные свойства эпоксидного пластика.
Термостойкость и химическая стойкость снижаются с повышением эластичности. В то же время вязкость увеличивается, потому что изоцианаты сами по себе очень вязкие. Это означает, что необходима дальнейшая модификация для снижения вязкости.
Следующая группа модифицирующих веществ – пигменты и наполнители. Пигмент
используется для окрашивания эпоксидного материала, а наполнитель для повышения механической прочности и снижения затрат.
В качестве пигментов чаще всего используются оксиды металлов, такие как диоксид титана, оксид железа и оксид хрома.
Как правило, наполнителями являются тонкоизмельченные минералы и кварцевый песок. Важно, чтобы и пигменты, и наполнители были правильно диспергированы в эпоксидном связующем.
В дополнение к перечисленным модифицирующим веществам существует ряд вспомогательных веществ, влияющих на такие параметры, как реология, т. е. консистенция, текучесть, пузырьки воздуха и адгезия.
Легко понять, что эпоксидный продукт имеет относительно сложный состав, в котором входящие в состав компоненты должны взаимодействовать для получения ожидаемых результатов.
Свойства эпоксидных смол для ремонта и восстановления конструкций
🕑 Время чтения: 1 минута
Синтетические смолы, такие как эпоксидные, полиэфирные, акриловые, полиуретановые и подобные им смолы, широко используются в гражданском строительстве. Синтетические смолы используются для:
- Заполнение трещин, образовавшихся в элементах бетонных конструкций
- Ремонт бетонных конструкций, подвергшихся эрозии
- Аварийный ремонт мостов
- Ремонт акведуков
- Исправление колонн и балок, подвергшихся химической эрозии
Эпоксидная смола обладает широким спектром свойств при отверждении с помощью различных типов отвердителей.
Состав:
- Характеристики эпоксидной смолы
- Base Resin
- Epoxy Curatives
- Epoxy Modifiers
- Rubber Additives
- Diluents
- Flame Retardants
- Unreactive Fillers
- Pigments and Dyes
Основными характеристиками эпоксидных смол, благодаря которым они широко используются в гражданском строительстве, являются:
- Свойство высокой адгезионной прочности почти ко всем материалам
- Низкая вероятность усадки во время отверждения
- Повышенная стабильность размеров
- Естественные свойства заполнения зазоров
- Термореактивные свойства — не плавится
- Повышенная устойчивость к химическим веществам и различным условиям окружающей среды
- Может полимеризоваться даже во влажных условиях. Например Подводная конструкция
- Простота применения
Эпоксидная смола — это общий термин, который представляет собой название соединений, описывающих различные классы термореактивных полимеров. Здесь первичное сшивание происходит с реакцией эпоксидной группы.
Наиболее важным сырьем, которое используется в производстве эпоксидной смолы, является эпихлоргидрин. Диглицидиловый эфир бисфенола-А или ДГЭБА является основной эпоксидной смолой, которая используется в строительной промышленности.
ДГЭБА в стандартной форме представляет собой продукт конденсации бисфенола-А и эпихлоргидрина.
В зависимости от количества избытка эпихлоргидрина по отношению к бисфенолу-А, который используется в производственном процессе, молекулярная масса эпоксидной смолы будет варьироваться от низкой до высокой. Из-за своей высокой вязкости основная смола этого типа не подходит для многих применений.
Следовательно, модификация базовой смолы необходима для достижения требуемой скорости отверждения и других механических и химических свойств в дополнение к более низкой вязкости.
Это отвердители, которые называются отвердителями . Отвердители в сочетании с эпоксидной смолой превращают ее из жидкой в затвердевшую массу.
Среди множества соединений наиболее часто используемыми отвердителями являются алифатические и ароматические амины и полиамиды. Эти соединения представляют собой отверждающие композиции, активные при комнатной температуре, что облегчает применение в строительстве.
Вот некоторые из примеров, подпадающих под это разделение:
- Ароматические амины, включая диаминодифенилсульфон (ДДС) и диметиланилин (ДМА)
- Амин/фенолформальдегид, такой как формальдегид мочевины и формальдегид меламина
- Триэтилентетрамин (ТЭТА) и диэтилентриамин (ДЭТА)
- Ангидрид, подобный фталевому ангидриду и надиметилангидриду (NMA)
- Некоторые каталитические агенты, такие как третичные амины и комплекс трехфтористого бора.
Для изменения определенных физических и химических свойств смолы используются модификаторы. Общие категории эпоксидных модификаторов:
- Каучуки
- Разбавители
- Термопласты
- Огнезащитные составы
- Пигменты и красители
- Наполнители
Добавки к каучукам представляют собой модификаторы эпоксидных смол, которые используются для улучшения следующих свойств смолы:
- Сопротивление усталости
- Гибкость
- Трещиностойкость
- Поглощение энергии или свойство ударной вязкости
- Гибкость
Добавки к каучуку представляют собой полимеры, которые можно использовать либо в жидком, либо в твердом виде, либо в виде сыпучих компонентов.
Разбавители Разбавители представляют собой модификаторы, используемые для снижения вязкости эпоксидных смол. Следовательно, это улучшит эксплуатационные характеристики эпоксидной смолы. Поэтому его делят на реактивный и нереактивный.
Реакционноспособные разбавители имеют более низкую молекулярную массу глицидиловых эфиров с низкой вязкостью. Это поможет уменьшить плотность поперечных связей эпоксидной системы.
Нереакционноспособные разбавители, такие как толуол, ксилол и другие типы ароматических углеводородов, значительно снижают вязкость смол с низким молекулярным весом. Дибутилепталат, используемый с жидкой смолой, является популярным нереакционноспособным разбавителем.
Антипиреновые свойства эпоксидной смолы можно получить с помощью антипиренов. Антипирены добавляются в эпоксидную смолу в качестве наполнителя. Было обнаружено, что полимерная система с большим количеством углерода и водорода легко воспламеняется по своей природе. Присутствие галогенов в эпоксидной смоле на основе отвердителя поможет снизить воспламеняемость.
Нереактивные наполнители Нереакционноспособные наполнители широко используются и могут быть классифицированы как минералы, металлы, углерод, волокна, стекло и другие разнообразные органические вещества. Их можно использовать в различных физических формах, в том числе в виде порошков, пульпы, хлопьев, сфер, микрошариков, усов и коротких волокон.
Для окрашивания эпоксидной смолы можно использовать самые разные пигменты и красители. Они могут быть органическими или неорганическими по своей природе. Нерастворимые частицы, представляющие собой дисперсию смолы, образуют пигменты. Красители представляют собой растворимые органические молекулы. Из-за ограничения температуры красители не подходят для применения в эпоксидных композитах. Подробнее: Инъекционная эпоксидная смола для ремонта трещин в бетоне Инъекционная заливка трещин в конструкциях на основе эпоксидной смолы Способ заполнения трещин в бетонных конструкциях
Получение и свойства лигнин-эпоксидной смолы :: Биоресурсы
Инь, К., Ян, В., Сунь, К., и Ди, М. (2012). «Приготовление и свойства композита лигнин-эпоксидная смола», BioRes.
Abstract
Сшитый биомасса-полимерный композит с содержанием лигнина до 60% был приготовлен путем смешивания лигнина с эпоксидной смолой и полиамином с использованием процесса горячего прессования. Особенности реакции отверждения лигнина с эпоксидной смолой изучали с помощью ДСК и ИК-Фурье анализа. Влияние температуры формования и давления формования на механические свойства и микроструктуру композита лигнин/эпоксидная смола также изучалось с помощью анализов SEM, DMA и TG. Результаты показали, что эпоксидная смола может быть отверждена лигнином, а температура отверждения смесей может быть снижена за счет введения полиаминового отвердителя. Свойства композита, такие как прочность на изгиб, ударная вязкость, температура стеклования и термическая стабильность, очевидно, находились под влиянием процесса формования. Между лигнином и эпоксидной смолой образовалась хорошая межфазная комбинация. Повышение температуры и давления формования оказалось полезным для достижения лучшего межфазного сочетания композита, а степень вязкого разрушения была увеличена на поверхности разрушения композита.
Скачать PDF
Полный текст статьи
Получение и свойства композита лигнин-эпоксидная смола
Цюаньфу Инь, Вэйцзюнь Ян, Чэнцзюнь Сун и Минвэй Ди*
Сшитый биомасса-полимерный композит с содержанием лигнина до 60% был получен путем смешивания лигнина с эпоксидной смолой и полиамином с использованием процесса горячего прессования. Особенности реакции отверждения лигнина с эпоксидной смолой изучали с помощью ДСК и ИК-Фурье анализа. Влияние температуры формования и давления формования на механические свойства и микроструктуру композита лигнин/эпоксидная смола также изучалось с помощью анализов SEM, DMA и TG. Результаты показали, что эпоксидная смола может быть отверждена лигнином, а температура отверждения смесей может быть снижена за счет введения полиаминового отвердителя. Свойства композита, такие как прочность на изгиб, ударная вязкость, температура стеклования и термическая стабильность, очевидно, находились под влиянием процесса формования. Между лигнином и эпоксидной смолой образовалась хорошая межфазная комбинация. Повышение температуры и давления формования оказалось полезным для достижения лучшего межфазного сочетания композита, а степень вязкого разрушения была увеличена на поверхности разрушения композита.
Ключевые слова: лигнин; Эпоксидная смола; Композиты; Механические свойства; микроструктура; Процесс формования
Контактная информация: Ключевая лаборатория биоматериаловедения и технологии (Министерство образования), Северо-Восточный университет лесного хозяйства, Харбин 150040 Китай;
* Ответственный автор, [email protected]
ВВЕДЕНИЕ
Лигнин считается одним из наиболее перспективных органических ресурсов будущего, поскольку он является возобновляемым и уступает только целлюлозе среди встречающихся в природе полимеров. Общепризнанно, что наиболее важными химическими функциональными группами в структуре молекулы лигнина являются ароматические, гидроксильные, метоксильные, карбонильные и карбоксильные группы (Wang и др. . 2010 г.; Юань и Хуан, 2011). Таким образом, лигнин может быть использован в качестве органического сырья на биологической основе для синтеза и модификации полимерных композитов. Лигнин имеет несколько преимуществ, таких как достаточное количество источников, низкая стоимость, биоразлагаемость и возобновляемость. Поэтому его разработка и применение представляли интерес для многих исследователей (Bhat et al. . 2009; Feldman et al. . 1991; Funaoka 1999; Gonzalez et al. . 2009; Ibrahim et al. et al. 90aka). и др. . 1997 год; Стюарт 2008). Однако в прошлом большинство исследований проводилось с жидким лигнином, используемым для частичной замены фенолов, участвующих в синтезе полимерных материалов (Mansouri et al , 2011; Park et al , 2008). Кроме того, в молекулярный состав лигнина заложена высокая реакционная способность полифенольных структур, что выгодно для использования лигнина в качестве добавки для удешевления производства композиционных материалов или в качестве модификаторов для улучшения характеристик композиционного материала за счет смешивание с другими полимерами (Путо и др.
. 2004 г.; Симионеску и др. . 1993). До сих пор не было эффективного и достаточного использования лигнина.
Лигнин ферментативного гидролиза представляет собой новую форму лигнина, которая выделяется из остатков ферментативного гидролиза биомассы. Являясь побочным продуктом производства биомассы, лигнин ферментативного гидролиза обладает большей химической активностью и применимостью, чем лигносульфонат или крафт-лигнин (Jin et al . 2011; Xie et al . 2011 г.; Ченг и Лю 2006). Это связано с тем, что процесс ферментативного гидролиза биомассы осуществляется в относительно мягких условиях; таким образом, многие функциональные группы, такие как фенольный гидроксил и спиртовой гидроксил, хорошо сохранились. Следовательно, ферментативный гидролиз лигнина можно использовать для модификации полимерных материалов путем прямого взаимодействия с формальдегидом, эпихлоргидрином, изоцианатом и т. д.
Процесс подготовки путем смешивания двух или более полимеров считается одним из наиболее многообещающих методов получения новых материалов с хорошими характеристиками по сравнению с их химической модификацией. Сочетание синтетических полимеров с натуральными материалами позволяет снизить затраты и дает преимущества за счет комбинированных свойств. Объединение путем смешивания представляет собой интересный способ преодоления некоторых наиболее важных недостатков полимера, таких как плохие механические свойства и низкая способность к разложению. Смешивание искусственных полимеров с природными полимерами позволяет получить новые полимерные материалы с превосходными характеристиками при одновременном снижении количества используемых химических синтетических полимеров. По сравнению с синтезом или модификацией новых полимерных материалов эти методы могут снизить затраты и сэкономить время (Doherty и др. . 2011). В данном исследовании сшитый биомасса-полимерный композит на основе ферментативного гидролиза лигнина кукурузной соломы с содержанием лигнина до 60% был приготовлен путем смешивания лигнина с термореактивной эпоксидной смолой. Влияние ферментативного гидролиза лигнина на поведение эпоксидной смолы при отверждении изучали с помощью анализа ДСК и FTIR.
Влияние температуры формования и давления формования на механические свойства и микроструктуру композита лигнин/эпоксидная смола также изучалось с помощью анализов СЭМ, ДМА и ТГ.
ЭКСПЕРИМЕНТАЛЬНЫЙ
Материалы
Лигнин кукурузной соломы для ферментативного гидролиза с насыпной плотностью 0,6 г/см 3 был предоставлен компанией Songyuan Laihe Chemicals Co., Ltd., Китай. Перед смешиванием его сушили при 50°С в течение 24 часов в вакуумной печи. Бисфенол, эпоксидная смола с эпоксидным числом 0,51, была предоставлена китайской компанией Nantong Xingchen Synthetic Material Co., Ltd. Отвердитель полиамин с торговой маркой TY-200 был предоставлен китайской компанией Tianjin YanHai Chemical Co., Ltd.
Приготовление композита
В соответствии с массовыми соотношениями, приведенными в таблице 1, лигнин, эпоксидную смолу и полиамин смешивали на двухвалковой мельнице при скорости 20 об/мин и температуре от 20 до 30 °С в течение от 10 до 30 мин. Смешанные материалы удаляли и помещали в форму для горячего прессования при определенной температуре и давлении. Время горячего прессования выбирали в соответствии с толщиной композитных материалов и поддерживали на уровне от 2 до 5 мин/мм. Холодное прессование проводили при определенной температуре после горячего прессования. Наконец, композиты были извлечены из формы и удалены для дальнейшего тестирования.
Таблица 1. Массовые соотношения лигнина, эпоксидной смолы и полиамина
Тесты и анализы
Прочность композита на изгиб была испытана в соответствии с китайским стандартом GB/T 9341-2000 с помощью электронной универсальной испытательной машины CMT-6104, предоставленной китайской компанией Shenzhen Ruigeir Instrument Co., Ltd. Прутки образцов имели размеры 80 мм × 12,7 мм × 4 мм (длина × ширина × толщина) и были подготовлены для испытаний. Испытание проводили при скорости 2 мм мин −1 с пролетом 64 мм. Ударные свойства композита по Изоду с надрезом испытывали в соответствии с китайским стандартом GB/T 1043-93 на машине для испытаний на удар по Шарпи XJJ-50, предоставленной Chengde Experiment Machine Co., Ltd., Китай. Размеры образцов составляли 80 мм × 10 мм × 4 мм (длина × ширина × толщина), а испытание проводили при скорости 3,5 м с −1 на образцах с пролетом 60 мм. Энергия удара составляла 1 Дж. Все измерения проводились в условиях окружающей среды с относительной влажностью около 50%. Для каждого составного состава испытывали не менее пяти образцов.
Система дифференциальной сканирующей калориметрии (ДСК) модели NETZSCH 204, предоставленная немецкой компанией NETZSCH Scientific Instruments Co., Ltd., использовалась для анализа реакции отверждения лигнина с эпоксидной смолой при скорости нагревания 5 °C/мин. Анализ спектра FTIR был получен с помощью инфракрасного спектрографа с преобразованием Фурье Nicolet 560, предоставленного Nicolet Co., Ltd. Каждый спектр был записан в диапазоне частот от 400 до 4000 см -1 с использованием диска из бромида калия (KBr). KBr предварительно сушили в печи, чтобы уменьшить воздействие воды. Микроскопическая структура композита лигнин/эпоксидная смола была проанализирована и охарактеризована с помощью прибора динамического механического анализа (ДМА) DMA 242C и прибора TG 209.- Прибор для термогравиметрического анализа (ТГ) F3, предоставленный NETZSCH Scientific Instruments Co., Ltd. из Германии, и сканирующий электронный микроскоп (СЭМ) QUANTA 200 с рабочим расстоянием около 10 мм при 12,5 кВ, предоставленный FEI Co., Ltd. США. Измерения ДМА проводились в режиме трехточечного изгиба на прямоугольных образцах размерами 50 мм х 10 мм х 2 мм в диапазоне температур от 25 °С до 180 °С со скоростью нагрева 5 °С/мин в токе азота. . Образцы сканировали с фиксированной частотой 2,5 Гц со статической силой 0,2 Н и динамической силой 0,8 Н. Составной образец (размерами 50 мм х 10 мм х 2 мм) для СЭМ исследования погружали в жидкий азот на 5 минут для быстрого замораживания, а затем был немедленно разрушен силой удара.
Поверхность излома была выбрана для исследования с помощью СЭМ. Все образцы СЭМ перед исследованием были покрыты золотом толщиной примерно от 10 до 20 нм.
РЕЗУЛЬТАТЫ И ОБСУЖДЕНИЕ
Реакция отверждения эпоксидной смолы с лигнином
Реакция отверждения эпоксидной смолы является экзотермической. Таким образом, анализ ДСК может определить, отверждена ли эпоксидная смола, в соответствии с изменением температуры в смесях эпоксидных смол. Изменения температуры для смесей лигнин-эпоксидная смола (1:1) и смесей лигнин-эпоксидная смола-полиамин (1:1:0,5) при повышении температуры показаны на рис. 1.
Рис. 1. Кривые ДСК для двух смесей при скорости нагревания 5 °С/мин
На рис. 1 показано, что на кривой ДСК для смесей лигнин-эпоксидная смола наблюдался только один экзотермический пик в диапазоне температур, выбранном для эксперимента, и что температура пика составляла 174,4 °С. Это показывает, что эпоксидная смола может быть отверждена путем ферментативного гидролиза лигнина кукурузной соломы. Одна из причин этого заключается в том, что реакция отверждения катализируется полифенольной структурой лигнина, а другая причина заключается в том, что карбоксильные или гидроксильные группы, содержащиеся в ферментативном гидролизе лигнина, реагируют с эпоксидной смолой, вызывая отверждение эпоксидной смолы. Смеси лигнин-эпоксидная смола имели только один полный экзотермический пик после добавления отвердителя полиамина, а температура пика составляла 10°С.0,7 °С. Это явление приписывали тому факту, что полиамин не мешал отверждению эпоксидной смолы; скорее, это снизило температуру отверждения. Таким образом, смеси лигнина и эпоксидной смолы можно термоформовать при более низких температурах за счет добавления полиаминового отвердителя. Кроме того, в качестве гибкого отвердителя с длинной молекулярной цепью полиамин может компенсировать внутреннюю хрупкость, характерную для отвержденных смесей лигнина и эпоксидной смолы, и, следовательно, характеристики смесей были улучшены.
Спектры FTIR для эпоксидной смолы, смесей лигнин-эпоксидная смола (1:1) и смесей лигнин-эпоксидная смола-полиамин (1:1:0,5) показаны на рис. 2. Анализ спектра FTIR был использован для характеристики сырья и анализировать изменения в структуре эпоксидной смолы в процессе ее отверждения, в основном для наблюдения за введением новых функциональных групп или исчезновением существующих. Из спектра FTIR неотвержденной эпоксидной смолы, представленного на рис. 2, видно, что поглощение валентных колебаний для эпоксидной группы составляет 914 см -1 . FTIR-спектр лигнина характеризовался полосой O-H при 3456 см -1 и интенсивной полосой C-H при 2935 см -1 , которые являются типичными колебаниями метоксильных групп. Поглощение карбонильных групп проявляется в виде полосы при 1727 см -1 . Поглощение колебания C-H ароматического кольца было при 1606 см -1 и 1504 см -1 . Пики при 1224 см -1 и 1121 см -1 соответствуют C-O с ароматическим кольцом и эфирной связью (-O-) при 1030 см -1 .
Рис. 2. Спектры FTIR для эпоксидной смолы, смесей эпоксидной смолы и лигнина и смесей эпоксидной смолы, лигнина и полиамина
После смешивания эпоксидной смолы с лигнином о введении групп в структуру эпоксидной смолы свидетельствовало наличие полос при 3456 см -1 и 1727 см -1 . Пики при 1121 см -1 также были значительно усилены. Кроме того, не наблюдалось поглощения вибрации при растяжении эпоксидной группы при 914 см -1 . После добавления полиаминового отвердителя FTIR-спектр основного пика для смесей лигнин-эпоксидная смола-полиамин не изменился, а пик поглощения для эпоксидной группы при 914 см -1 исчез аналогичным образом.
Результаты анализа ДСК и ИК-Фурье показали, что эпоксидная смола может быть отверждена путем ферментативного гидролиза лигнина кукурузной соломы, и в процессе отверждения может существовать химическая связь между активными группами лигнина и эпоксидными или гидроксильными группами. Это дало возможность сформировать хорошую межфазную комбинацию между лигнином и эпоксидной смолой при приготовлении смесей, что положительно сказалось на свойствах композита лигнин-эпоксидная смола.
Механические свойства
Влияние температуры формования и давления формования на прочность на изгиб и ударную вязкость смесей лигнин-эпоксидная смола-полиамин показано на рис. 3 и 4, соответственно.
Как показано на рис. 3, с повышением температуры формования прочность на изгиб и ударная вязкость композита лигнин/эпоксидная смола сначала увеличиваются, а затем снижаются. Значения прочности на изгиб и ударной вязкости достигли максимальных значений 44,52 МПа и 4,58 кДж/м 9 .1379 2 при температуре формования 130 °С. Причина этого заключается в том, что более высокая температура формования способствовала улучшению текучести эпоксидной смолы, благодаря чему эпоксидная смола более равномерно заполнила пространство между лигнинной мукой, тем самым улучшив сцепление между лигнином и эпоксидной смолой.
Рис. 3. Влияние температуры формования на прочность при изгибе и ударную вязкость смесей лигнинэпоксидной смолы и полиамина
Рис. 4. Влияние давления формования на прочность при изгибе и ударную вязкость смесей лигнин-эпоксидная смола-полиамин
Между тем, с повышением температуры формования степень отверждения эпоксидной смолы увеличивалась, а активность лигнина еще больше повышалась, что улучшало химическую связь между лигнином и эпоксидной смолой, и, следовательно, увеличивалась плотность сшивки композита. Однако чрезмерно высокая температура формования привела к деградации и хрупкости композита, особенно лигнина в составе композита, что негативно повлияло на его механические свойства.
Из рис. 4 видно, что прочность композита на изгиб увеличивалась с увеличением давления формования, так что прочность на изгиб достигала 43,12 МПа, когда давление формования было установлено на уровне 12 МПа. Ударная вязкость композитов сначала увеличивалась, а затем оставалась на стабильном уровне. Это может быть связано с тем, что низкое формовочное давление уменьшало внешнее действующее усилие, что нарушало пропитку эпоксидной смолы лигнином и устраняло остаточный газ внутри композита. С увеличением давления формования пропитывающая способность эпоксидной смолы увеличивалась, а сила молекулярного взаимодействия между лигнином, эпоксидной смолой и полиамином также увеличивалась. В то же время остаточный газ внутри композита легче удалялся из смесей. При дальнейшем увеличении давления формования скорость уплотнения смесей лигнин-эпоксидная смола-полиамин достигла насыщения, что помогло достичь подходящего баланса механических свойств композита.
Анализ прямого доступа к памяти
На рис. 5 показано влияние температуры формования на тангенс угла потерь (tanδ) для композита лигнин/эпоксидная смола. Массовое соотношение компонентов композита W Лигнин :W Эпоксидная смола :W Полиамин составляло 6:2:2, а давление формования устанавливалось на уровне 8 МПа.
DMA является полезным средством выявления микроскопического релаксационного движения полимерных молекул. Хорошо известно, что Пики α на кривых зависимости угла потерь (tan δ ) от температуры тесно связаны со стеклованием. В целом повышение температуры стеклования ( T g ) и уменьшение высоты пика α-перехода можно связать с увеличением плотности сшивки в аморфных полимерах. Из рис. 5 видно, что при температуре формования 130 °C температура смесей увеличивается, а пик tan 9Значение 0269 δ уменьшается с повышением температуры формования, что указывает на увеличение плотности сшивания смесей. Напротив, при дальнейшем повышении температуры формования T g снижается, а пик tan δ увеличивается, показывая, что плотность поперечного сшивания уменьшается.
Можно сделать вывод, что разумное повышение температуры формования будет способствовать увеличению плотности сшивки, а когда температура формования превышает 140 °C, плотность сшивания композита будет снижена из-за разложения лигнина в композит. Этот результат согласуется с тем, что было получено с помощью приведенного выше анализа механических свойств.
На рис. 6 показано влияние давления формования на тангенс угла потерь (tan δ ) для композита лигнин/эпоксидная смола. Массовое соотношение компонентов композита W Лигнин :W Эпоксидная смола :W Полиамин составляло 6:2:2, а температуру формования устанавливали на уровне 120 °C.
Рис. 5. Влияние температуры формования на tanδ композита лигнин-эпоксидная смола
Рис. 6. Влияние давления формования на tanδ композита лигнин-эпоксидная смола
На рисунке 6 показано, что температура смесей увеличивается, а пиковое значение tan δ уменьшается с увеличением давления формования, что указывает на то, что плотность сшивки смесей увеличивается с увеличением давления формования. Причина этого в том, что более высокое давление формования положительно влияет на силы молекулярного взаимодействия между лигнином, эпоксидной смолой и полиамином. В результате также улучшилось межфазное сочетание лигнина, эпоксидной смолы и полиамина. Этот результат также согласуется с результатами, полученными с помощью приведенного выше анализа механических свойств.
Анализ ТГ
На рисунках 7 и 8 показано влияние температуры формования и давления на термическую стабильность композита лигнин-эпоксидная смола, соответственно. Данные ТГ-анализа композита лигнин-эпоксидная смола при различных температурах и давлениях формования также представлены в таблицах 2 и 3 соответственно.
Рис. 7. Влияние температуры формования на термостойкость композита лигнин-эпоксидная смола
Таблица 2. Данные ТГ-анализа композита лигнин-эпоксидная смола при различных температурах формования
Рис. 8. Влияние формовочного давления на термостойкость композита лигнин-эпоксидная смола
Таблица 3. Данные ТГ-анализа композита лигнин-эпоксидная смола при различном давлении формования
Из рис. 7 и табл. 2 видно, что для композита лигнин-эпоксидная смола температуры потери массы при скорости потери массы 50 % увеличивались с повышением температуры формования, а остаточная масса композита показывала тенденция сначала к увеличению, а затем к снижению. Для термической стабильности композита лигнин-эпоксидная смола при изменении давления формования, показанного на рис. 8 и в таблице 3, можно видеть, что как температуры потери массы при скорости потери массы 50%, так и остаточная масса лигнин- Композит на основе эпоксидной смолы увеличивался с увеличением давления формования.
Результаты ТГ-анализа показали, что надлежащая температура формования и давление формования способствуют реакциям отверждения и сшивки эпоксидной смолы. Следовательно, также увеличилась плотность сшивки композита, что повысило термическую стабильность композита лигнин-эпоксидная смола. Эти результаты дополнительно подтвердили данные, полученные с помощью вышеуказанного анализа механических свойств и анализа DMA.
СЭМ-наблюдение
На рис. 9 показана морфология излома композита лигнин-эпоксидная смола, изготовленного в условиях формования 4 МПа/110 °C, 8 МПа/110 °C и 8 МПа/130 °C. Он показывает, что лигнин может быть равномерно распределен в матрице эпоксидной смолы. Также не было очевидно существующей межфазной границы, что объясняет хорошую межфазную комбинацию между лигнином и эпоксидной смолой. Это также является гарантией того, что композит имеет лучшие механические свойства.
Рис. 9. Морфология излома композита лигнин-эпоксидная смола
а) 4 МПа/110 °С; б) 8 МПа/110 °С; в) 8 МПа/130 °С
Однако на степень межфазной комбинации между лигнином и эпоксидной смолой могут явно влиять различные условия формования. В условиях более низких давления формования и температуры формования, как показано на рис. 9а, морфология излома композита лигнин-эпоксидная смола была относительно гладкой и характеризовалась поверхностью излома с определенной степенью хрупкости. Морфология излома композита, прессованного горячим способом при более высоких давлении и температуре формования, стала явно шероховатой, как показано на рис. 9.б и 9в. Специально для композита, прессованного горячим способом при температуре формования 130 °C и давлении формования 8 МПа, поверхность излома, показанная на рис. 9с, имела много следов разрыва, которые демонстрировали явный пластичный излом.
Вязкость эпоксидной смолы была чувствительна к температуре, а вязкость смесей лигнина и эпоксидной смолы снижалась по мере повышения температуры формования. Таким образом, были улучшены текучесть смесей и смачиваемость эпоксидной смолы лигнином, что улучшило диспергируемость лигнина в матрице эпоксидной смолы. Соответственно, межфазная комбинация для композита лигнин-эпоксидная смола была усилена. Между тем, более высокое давление формования способствовало улучшению текучести эпоксидной смолы. Затем лигнин вдавливали в матрицу из эпоксидной смолы под действием механической силы, в результате чего усиливалось механическое зацепление, а также усиливалась межфазная комбинация композита лигнин-эпоксидная смола. Результаты анализа были эффективно подтверждены наблюдением СЭМ.
ВЫВОДЫ
- Эпоксидную смолу можно было отверждать вместе с ферментативным гидролизом лигнина при высокой температуре, но температуру отверждения смесей лигнин-эпоксидная смола можно было снизить за счет введения полиаминового отвердителя. Композит лигнин-эпоксидная смола с содержанием лигнина до 60% был приготовлен путем смешивания лигнина с эпоксидной смолой и полиамином с использованием процесса горячего прессования.
- Прочность на изгиб, ударная вязкость, температура стеклования и термическая стабильность для композита лигнин-эпоксидная смола имеют тенденцию сначала увеличиваться, а затем снижаться с повышением температуры формования. Оптимальные эксплуатационные характеристики композиционных материалов достигаются при температуре формования 130 °С.
- Прочность на изгиб, температура стеклования и термическая стабильность для композита лигнин-эпоксидная смола постепенно улучшались с увеличением давления формования, в то время как ударная вязкость сначала увеличивалась, а затем уменьшалась.
- Между лигнином и эпоксидной смолой была сформирована хорошая межфазная комбинация, и на степень межфазной комбинации непосредственно влиял процесс формования. Повышение температуры и давления формования оказалось полезным для достижения лучшего межфазного сочетания композита, а также увеличилась степень вязкого разрушения на поверхности разрушения композита.
БЛАГОДАРНОСТИ
Рукопись была поддержана Фондом фундаментальных исследований центральных университетов (DL12EB06-02). Авторы глубоко признательны г-же Шуджуань Суй, инженеру Материаловедения и инженерного колледжа Северо-восточного университета лесного хозяйства, за ее большую помощь в настоящей работе.
ССЫЛКИ
Бхат, Р., Халил, Х. П. С. А., и Карим, А. А. (2009). «Изучение антиоксидантного потенциала лигнина, выделенного из черного щелока отходов масличной пальмы», C. R. Biologies 332, 827-831.
Ченг, К.С., и Лю, К.Л. (2006). «Выделение лигнина из остатков стеблей кукурузы путем ферментативного гидролиза и его свойства», Modern Chemical Industry 26, 99-102.
Доэрти, У. О. С., Мусавиоун, П., и Феллоуз, К. М. (2011). «Добавление ценности целлюлозному этанолу: полимеры лигнина», Industrial Crops and Products 33, 259-276.
Фельдман, Д., Баун, Д., Лучиан, К., и Ван, Дж. (1991). «Полисмеси эпокси-лигнина: корреляция между взаимодействием полимеров и температурой отверждения», Journal of Applied Polymer Science 42(5), 1307–1318.
Фунаока, Массачусетс (1999). «Новый тип сетчатого полимера на основе фенольного лигнина со структурно-переменной функцией, состоящей из звеньев 1,1-диарилпропана», Polymer International 47(3), 277-290.
Гонсалес М., Техадо А., Бланко М., Мондрагон И. и Лабиди Дж. (2009). «Отходы сельскохозяйственных пальмовых деревьев в качестве сырья для производства целлюлозы, лигнина и гемицеллюлозы с помощью процесса варки этиленгликоля», Журнал химической инженерии 148, 106-114.
Ибрагим, М.Н.М., Закария, Н., Сипат, К.С., Сулейман, О., и Хашим, Р. (2011). «Химические и термические свойства лигнинов из биомассы масличной пальмы в качестве заменителя фенола в производстве фенолформальдегидной смолы», Углеводный полимер 86(1), 112-119.
Джин, Ю., Руан, X., Ченг, X., и Лу, Q.-F. (2011). «Сжижение лигнина полиэтиленгликолем и глицерином», Bioresource Technology 102, 3581-3583.
Мансури, Н.Э., Юань, К.Л., и Хуанг, Ф.Р. (2011). «Синтез и характеристика эпоксидной смолы на основе крафт-лигнина», BioResources 6(3), 2492-2503.
Нонака Ю., Томита Б. и Хатано Ю. (1997). «Синтез лигнин/эпоксидных смол в водных системах и их свойства», Holzforschung 51(2), 183-187.
Парк, Ю., Доэрти, У. О. С., и Галлей, П. Дж. (2008). «Разработка покрытий и композитов на основе смолы на основе лигнина», Технические культуры и продукты 27, 163-167.
Путо, К., Баумбергер, С., Катала, Б.