Булатная сталь. Секреты совершенного оружия.
Булат — сталь с предельно высоким содержанием углерода, обычно около 2%, иногда больше. Несмотря настоль высокое содержание С, что дает булату превосходную твердость до 70 HRC, он также обладает и феноменальной упругостью. Благодаря этим двум, казалось бы несовместимым свойствам — максимальной твердости и пластичности, клинок из булата сломать не удастся. Его можно согнуть, правда с большим трудом, что сопоставимо с попыткой согнуть рессору, но при достижении предельной нагрузки, булат не сломается, а всего-лишь согнется. Но потом, после правки он полностью сохранит все свои поистине потрясающие качества.
Изготавливается булатная сталь методом плавки в виде небольших слитков, размером с хоккейную шайбу. Слитки эти называются «вуц». Если поверхность булата отшлифовать и протравить — то проявится тот самый, характерный булатный рисунок.
Классический литой булат изготавливался в Индии, в настоящее время практически не делается.
Первое упоминание о булате относится к временам Александра Македонского. Географически булат распространялся по путям распространения ислама. На Руси булат также называется «хоролугом».
Булат, в отличии от легированных сталей, делается из двух компонентов — железа и древесного угля, либо графита.
Технология получения литого булата таит в себе много нюансов и знаний на уровне интуиции кузнеца. В двух словах эта технология следующая (на самом деле об изготовлении булата написаны целые научные работы):
- губчатое железо проковывается молотом
- железо смешивается с древесным углем, помещается в тигель
- тигель нагревается до температуры 1200 градусов
- после этого тигель очень медленно охлаждаетя и получается вуц — небольшой слиток булата.
И далее, из слитков булата ковался тот самый пресловутый булатный нож, клинки и сабли. Здесь тоже имеется тысячи тонкостей, секретов и заморочек. Так, например, если заготовку клинка из булата нагреть свыше 850 градусов, то она при дальнейшей ковке раскрошится как стекло. Аналогично обстоит и с последующей закалкой — все эти тонкости передавались от мастера к мастеру и в настоящее время большинство секретов утеряно.
Узор булата имеет поверхностное строение, образуется во время падения температуры отливки и представляет собой светлые линии цементитной сетки высаженного углерода по границам зерен аустенита. И чем темнее фон и светлее линии — тем булат дороже.
Несмотря на проводимые работы в области исследования и получения булата, до сих пор изготовление индийского булата имеет очень много белых пятен и в случае разгадки может быть запатентовано.
Найти видео с процессом и технологией производства ножа из булатной стали дело неблагодарное, поскольку те кузнецы, которые владеют секретами литого булата навряд ли ими поделятся с широкой общественностью), поэтому этот ролик — скорее носит информационный характер о булате.
плюсы и минусы для ножей, характеристики клинка из булата
На чтение 8 мин. Просмотров 16k. Опубликовано Обновлено
Булатная сталь (вуц, табан, хорасан, фаранд) была известна уже несколько тысяч лет назад. Этот материал отличается сложным технологическим процессом производства, при котором необходимо в точности соблюдать химический состав сплава и обеспечить уникальную технологию обработки. Всё это позволяет получить материал с отличными эксплуатационными характеристиками, которые не потеряли своей актуальности и сегодня, несмотря на обилие разнообразных сплавов и использование широкого спектра легирующих элементов.
Заготовка клинка из булатной стали.Историческая справка
Мечи и ножи из булата фигурируют в сказках и реальных исторических справках многих стран.
Булатный нож всегда стоил дороже обычного, поскольку давал в бою реальное преимущество.
Немного о древнем булате
Булатная сталь — отличный выбор для ножей. Она представляет собой сплав железа и углерода без дополнительных легирующих добавок. Но высокое содержание углерода (почти как у чугуна) даёт возможность после термообработки получить твёрдость вплоть до 64 HRC.
Ещё один нюанс — булатный клинок после травления отличается характерным красивым рисунком. Именно поэтому древний булат в Индии, которая является родиной этого сплава, называли индийской узорчатой сталью — в древние времена она стоила целое состояние.
Мастера хранили секрет булата внутри касты, но после пришествия в Сирию Тимура захваченные мастера со своим секретами переехали в Самарканд.
Именно там древние технологии производства высококачественного булата были окончательно утеряны.
Булатная сталь П.П. Аносова
Восстановить техпроцесс производства стали с аналогичными характеристиками старались многие специалисты. Это наконец удалось Павлу Петровичу Аносову.
Горный начальник Златоустовских заводов активно интересовался, что такое булат и как его можно производить своими силами. Целенаправленное исследование этого вопроса дало результат в 1837 году.
Булатная сталь Аносова.Аносов разработал несколько технологий, в том числе и плавку обсечков в горшочках из глины в высокотемпературных печах.
Возвращение легенды
Открытый секрет производства булатной стали в начале 20 века опять был утрачен. Очередной виток интереса к технологии начался уже в советский период.
Повторить подвиг Аносова смог Златоустовский металлург Сергей Баранов. Серия пробных плавок позволила добиться желаемого результата, что подтвердило соответствующее заключение РАН.
Современный булат
Сейчас существует множество сталей, свойства которых превосходят булат. Но этот материал до сих пор используется и является примером приготовления высококачественной стали без применения современных измерительных приборов.
Сейчас производство булата ведётся по чётким технологическим процессам, что позволяет гарантированно получить твёрдый, вязкий, ковкий сплав с уникальным рисунком на каждом изделии.
Отличие тигельного булата от литого
Сейчас булат изготавливают по нескольким технологиям — материалы в целом идентичны, но имеют и ряд отличий:
- При производстве тигельного сплава железную руду, древесный уголь и специальный флюс нагревают в спецтиглях — плавку выполняют в древесных печах (по сравнению с газовыми или электрическим они обеспечивают не такую высокую температуру). Технология требует затрат, но так делают клинки для коллекционеров.
- Товары из литого булата проще, их можно встретить на распродажах в Москве. Сырьём для стали является не железная руда, а специальные марки низкоуглеродистых сталей. Отличить такой булат просто — рисунок на стали не такой выраженный, но по свойствам ножи практически не отличаются.
Конечно, цена литого материала в разы ниже.
Клинок из булатной стали.Что представляет собой булат и его характеристики
Свойства булата определяются содержанием углерода в сплаве — его примерно 2% , так что сталь сохраняет упругость и твёрдость. Но свои особенные свойства материал получает именно из-за температуры плавки — если сырьё перегреть, то такая сталь не получится.
Техпроцесс производства сварного булата, то есть дамаска, сложнее, но дешевле по себестоимости. При производстве ножа необходимо соединить пакеты металла (желательно с разным содержанием углерода) между собой кузнечной сваркой, что позволяет получить не монолитную, а многослойную структуру.
Плюсы
Основными преимуществами булата считают:
отличные режущие свойствам;
высокая стойкость к ударным, изгибающим нагрузкам;
высокая твёрдость и износостойкость;
заточив нож, можно долго им пользоваться — булат хорошо держит заточку.
Минусы
Всё в нашем мире не идеально:
дорогой материал;
заточить сложно из-за твёрдости стали;
ржавеет ли булат? — Да. Сопротивляемость коррозии низкая.
Фактически булатные клинки больше интересуют коллекционеров, поскольку среди современных сталей есть более технологичные варианты и при этом более доступные.
Основные виды ножей и сфера применения
Булат используется при изготовлении ножей следующих типов:
- цельнометаллические,
- с фиксированным клинком,
- складные.
Что касается сферы применения, то модели можно разделить на ножики для охоты, рыбалки и туристов, военные. Отдельно стоят метательные модели и коллекционное оружие.
Ножи для коллекционеров могут быть очень дорогими — для их изготовления используют ценную древесину, драгоценные камни, металлы, натуральный рог, не говоря уже о ручной работе над каждым ножом.
На что обратить внимание при выборе
Чтобы остаться полностью удовлетворённым от покупки ножа из булата необходимо обратить внимание на:
- Хаотичный рисунок на тёмном фоне — линии и точки должны быть чёткими и крупными, но не симметричными. Ровные и симметричные линии — это характеристика более дешёвой дамасской стали.
- Звон монолитного булата чистый и продолжительный. Если клинок не цельный (слои, флуктуации различного вида) звук будет низким и коротким.
- Ответственный производитель всегда указывает назначение клинка — размеры и параметр должны соответствовать. Охотничий клинок длиннее, рыбацкий и туристический короче, со складной конструкцией.
- Сборка должна быть качественной без зазоров, заусенец и пр.
- Документация — гарантийный талон, сертификат (подтверждение, что этот нож — нехолодное оружие).
- Футляр/чехол.
Особенности заточки
Булатная сталь исключительно прочная, так что в домашних условиях заточить её непросто. Лучше доверить её профи. Такие клинки точатся алмазными брусками, можно использовать твёрдый камень.
Правила использования и ухода
- Поскольку такой нож может ржаветь, то после использования сталь нужно очистить, промыть водой и вытереть насухо ветошью.
- Хранится такое металлоизделие в тёплом, сухом месте, исключая образование конденсата.
- Лучше использовать кожаный чехол. Для длительного хранения клинок лучше покрыть слоем рыбьего жира, парафина.
- При появлении ржавчины нужно сразу убрать налёт — применяется керосин, но агрессивные средства запрещены. Можно использовать и мелкую наждачку, но после обработки придётся протравить нож, поскольку рисунок потускнеет.
Заключение
Несмотря на высокую стоимость и сложности в уходе владельцы булатных ножей оставляют только самые восторженные отзывы. При покупке стоит отдавать предпочтение только проверенным производителям и магазинам, поскольку на рынке огромное количество поддельной продукции.
НожиVanadis 10 — шведская порошковая сталь от Böhler
СледующаяИзготовление ножейКак сделать нож из цепи своими руками
Что такое булатная сталь?
Мало кто знает, но булатная сталь, выплавляющаяся в Индии еще 2500 лет назад, до сих пор остается самым загадочным из всех созданных человеком металлов. Этот удивительный сплав раздражает своим существованием опытных сталеваров и искренне радует счастливых обладателей клинков из булата.
Интернет-магазин «Ножи 74» предлагает выгодно купить булатные ножи Златоустовского производства с гарантией и оперативной доставкой по регионам России.
Свойства булата
По своей сути булат является твердым чугуном из-за большого содержания углерода, но при этом удивительным образом гнется, сохраняет высокую вязкость и обладает ковкостью на уровне низкоуглеродистых марок стали.
Булатная сталь полностью «игнорирует» каноны ножестроения, в которых четко указано, что твердость и вязкость являются разнонаправленными характеристиками клинка. Твердый нож способен долго сохранять острый рез, но может легко выкрошиться или треснуть от сильного удара. Вязкая сталь клинка обеспечивает его стойкость к динамическим нагрузкам, но быстро тупится. Поэтому производители ножевой продукции всегда ищут компромисс между этими двумя показателями и в зависимости от функционального назначения ножа применяют различные марки стали и способы дальнейшей термообработки.
Булатные ножи не требуют поиска оптимального сочетания упругости и твердости. Они от природы обладают способностью беспроблемно справляться с огромными ударными нагрузками и нагрузками на изгиб и при этом не тупятся, обеспечивая быстрый, легкий и острейший рез.
История булатной стали
Недалеко от индийского Пешавара расположен провинциальный городок Чарсада, который раньше назывался Пукхалавати, или на персидский манер – «пулад». Именно здесь тысячелетия назад процветало производство уникальной тигельной стали – булата. Уникальной ее делали не только поверхностный узор и необычный естественный цвет в широкой гамме серых, бурых и черных оттенков, но и немыслимое сочетание физико-технических свойств.
Как ни удивительно это звучит, но в XVII веке секрет производства качественного булата был полностью утерян. В начале XIX века за восстановление рецепта булатной стали взялись английские металлурги, которые вывезли из Индии оставшиеся слитки оригинального булата и привлекли для изысканий ученого с мировым именем – Майкла Фарадея. Эти попытки не увенчались успехом, но стимулировали поиск секрета булата в других странах.
Свою вторую жизнь булат приобрел за 4000 тысячи километров от Туманного Альбиона, в российском городе Златоуст. Именно здесь творил свои великие дела ученый-металлург Павел Петрович Аносов, который в 1841 году создал легендарный Златоустовский булат и организовал производство булатных сабель и шашек.
Следующее вехи в истории булатной стали связаны с именем златоустовского производителя-кузнеца Сергея Баранова, который совсем недавно, в 2006 году, создал уникальные пластины булата. Это научное открытие имело настолько значимый вес, что в 2010 году булат Баранова рассматривался как реальный соискатель на получение Нобелевской премии по физике.
Достоинства современного Златоустовского булата
К достоинствам булатных клинков, изготовленных в Златоусте, следует отнести:
- неограниченный эксплуатационный ресурс;
- внешняя эстетика;
- идеальные режуще-рубящие свойства;
- высокая прочность и гибкость;
- способность сохранять острый рез после многократного использования;
- устойчивость к негативным средам и легкость ухода;
- доступная цена.
На нашем сайте в тематическом разделе «Булатные ножи» представлен широкий ассортимент высококачественных кованых ножевых изделий из Златоустовского булата на любой вкус и кошелек, начиная с кухонно-разделочных моделей и заканчивая тактическими клинками.
Чем булат отличается от дамаска
«Все куплю», – сказало злато.
«Все возьму», – сказал булат.
Наверняка вам встречались оба термина – и булат, и дамаск. Но, возможно, у вас еще нет четкого представления о том, чем одна «узорчатая сталь» отличается от другой.
Разбираемся в терминологии
В общем, здесь все не так сложно, как может показаться. Общим у этих материалов является наличие узора, но технологии их изготовления различаются радикально. Легендарный индийский булат – это, к сожалению, утраченная технология: когда-то она передавалась изустно и так тщательно скрывалась, что полностью утерялась несколько веков назад. Производство булата было недешевым, а уже в XVII веке начали появляться доступные и достаточно качественные промышленные стали, поэтому спрос на булат упал, а затем и вовсе сошел на нет. Все, что мы знаем о нем (частично благодаря истории, частично благодаря экспериментам русского металлурга Павла Петровича Аносова), укладывается в пару фраз – булат был исключительно прочным, резучим и, конечно, легендарно красивым. На Руси булат часто назывался харалугом (хоролугом), или харалужной (хоролужной)* сталью, хотя в сказках мы частенько встречаем и сам термин «булат».
* Можно встретить как одно, так и другое написание. Возможно, правильнее будет вариант, вынесенный за скобки, так как, во-первых, именно он встречается в древних источниках, в том же «Слове о полку Игореве», во-вторых, он сохраняет букву «а» в общетюркском корне «хара»/«кара» («черный»).
Кстати, о сказках и былинах. Булатным клинкам в них приписываются чуть ли не магические свойства, но думать, что это какой-то несуществующий, сказочный металл – неправильно. На самом деле булат был просто лучшим вариантом для своего времени. Практические тесты даже лучших образцов, доживших до наших дней, показывают свойства, близкие к обычным недорогим углеродистым сталям современного изготовления. Однако в Средние века основную массу клинков делали из столь низкокачественного сырья, что даже такие свойства казались современникам мистическими и волшебными.
В свое время Аносову в первой половине XIX века удалось создать сплав, полностью отвечающий всем характеристикам булата. Хотя, конечно, достоверно мы не можем знать о том, насколько технология и состав, открытые нашим металлургом, сходны с «оригиналом». Дело в том, что технологий производства булата и в древности существовало несколько: воссоздал ли Аносов одну из них или придумал собственную, доподлинно неизвестно.
Булат клинка турецкой сабли – то, что мы и называем историческим булатом
И вот теперь мы подходим собственно к разъяснению. Исторически существовало две главных технологии получения узорчатой стали. Одна из них подразумевала литье, другая – сварку и проковку нескольких видов сталей между собой; первая оставила за собой название булата, а вторая стала называться дамаском.
Итак:
- Литой булат – это узорчатая сталь в привычном нам историческом понимании, полученная литейными и кузнечными методами.
- Сварной булат (или дамаск) – это узорчатая сталь, полученная преимущественно кузнечными методами.
Высококачественное оружие изготавливалось из специальных «булатных» слитков, называемых вутц. Именно красоту булатного узора связывали с его великолепными свойствами. Но вутц был дорог и сложен в производстве, что подстегнуло поиски технологий создания узорчатых клинков альтернативными средствами. То, что ныне называется дамаском, начали производить специально, складывая и проковывая несколько слоев заготовок из разных видов стали. Новый материал по прочности не уступал булату, а внешне получался куда красивее, чем литой булат.
Теперь чуть подробнее о типах булата и видах дамаска – такое деление мы сделаем из-за того, что классифицируем материалы по разным принципам: касательно булата расскажем про легирующие элементы в его составе, а касательно дамаска – еще и про несколько технологий.
Типы литого булата: высокоуглеродистый и нержавеющий сплавы
Еще одно важное замечание о булате и дамаске, которое стоит сделать прямо сейчас. По своему химическому составу они больше всего напоминают привычные нам высокоуглеродистые стали, но с очень неоднородным составом, а именно это означает как повышенную прочность и резучесть, так и подверженность ржавлению. Углеродка и нержавейка, как мы знаем, это не просто две разных по своему составу стали. Отличие довольно зыбкое – все дело в том, есть ли в материале легирующие элементы, повышающие коррозионную стойкость стали, и в каком количестве.
Так вот, в норме булат соответствует тому, что мы называем углеродистой сталью, однако измененный химический состав (добавление значительного количества хрома – от 14 % и более) при сохранении физической структуры дает нам так называемый нержавеющий булат. Он сохраняет свойства прочности и твердости, присущие обычному литому булату, а изделия из него почти так же хорошо поддаются заточке. Но стоит изделие из него, как, впрочем, и любое, скованное вручную, баснословно дорого.
Слева – обычный литой булат с высоким содержанием углерода; справа – нержавеющий состав с обычной технологией литья булата
Восемь видов сварного булата (дамаска)
С дамаском все куда интереснее: существует как минимум восемь разновидностей сварного булата, он же – дамаск. Прежде чем мы перейдем к ним, стоит сделать небольшое примечание.
В принципе, возможно создать и нержавеющий дамаск. Для этого нужно собрать пакет легированной нужными присадками стали и начать сваривать его в вакууме, накладывая слоями и расковывая, а затем снова повторяя этот цикл. Технически это довольно сложно, однако современные технологии успешно справляются с задачей, примером чему служат поварские ножи с узорчатыми нержавеющими обкладками.
Кухонный нож Kanetsugu из ассортимента Tojiro с обкладками из узорчатой стали
«Дикий» дамаск
Это тот самый дамаск, который получается, если мастер не пользуется особыми инструментами и технологиями, то есть если процесс проистекает естественным образом. Листы стали с различным химическим составом складываются между собой, свариваются и расковываются; затем рубятся пополам, снова складываются, и все действия повторяются. В результате получается слоистая сталь. Если ее ковка не имеет четкого плана, то узор получается неупорядоченным, или «диким».
«Дикий» и простой дамаск – два подвида техники, которая не имеет характерных черт, а представляет собой обычное наложение друг на друга слоев с последующей расковкой в свободном стиле
Штемпельный дамаск
При изготовлении этого вида узорчатой стали кузнец использует инструмент, называемый штемпелем: благодаря ему на поверхности слоистой пластины дамаска появляется красивый узор, не очень напоминающий узор на простом дамаске. В зависимости от узора штемпеля он может напоминать лестницу, годичные слои на срезе дерева, поверхность воды под дождем и комбинацию этих узоров.
Штемпельный дамаск производят с помощью специального инструмента – штемпеля
Мозаичный дамаск
Мозаичные дамаски часто отличаются не только технологией проковки, но и самим составом – пакет собирают на манер мозаики из заготовок стали разной формы и состава так, чтобы в результате наложения и расковки получался такой вот характерный узор.
Мозаика на поверхности этого вида дамаска – «заслуга» не технологии, а правильной подборки пакета стали
Мозаичный порошковый дамаск
Один из самых сложных видов дамаска; технология, которая редко практикуется в России.
Чтобы создать такой клинок, как на фото, требуется подготовить клише с определенным прорезным узором из стали. Затем клише засыпается порошковой сталью, которая при травлении будет контрастировать с основой, и под действием высоких температур и давления превращается в монолит. Теперь из этого слитка можно по обычной технологии расковывать клинок, сваривая или чередуя узорчатые слои между собой.
Порошковый мозаичный дамаск – явление, редкое в России
Крученый дамаск
Крученый дамаск, он же турецкий, создается с помощью закручивания заготовки из нескольких сваренных между собой стержней вокруг себя. Рисунок будет зависеть от количества и состава сталей в исходном пакете, угла закручивания и глубины взрезки. Как и по мозаичной технологии, из полученной «скрутки» далее можно по обычной технологии расковывать клинок, сваривая или чередуя узорчатые слои между собой.
Крученый дамаск (он же турецкий) получает характерный узор, когда кузнец в процессе расковки скручивает заготовку несколько раз
Мозаичный торцевой дамаск
Техника изготовления такого вида дамаска несколько отличается от прочих. На лопатку из однородной стали накладывается узорчатая мозаика из деталей различной формы и разных сталей. Затем заготовка проваривается под вакуумным прессом. Таким образом, ни сворачиваний, не кручения при его изготовлении не используют. Когда готов полностью прокованный блок, с него срезают пластины, служившие ранее основой для сборки мозаики.
Боковые обкладки такого дамаска – это срезы с готового прокованного блока
Волокнистый дамаск
Еще один зарубежный способ ковки дамаска. Состав его ничем не отличается от стандартного, и начало расковывания – тоже. Но примерно на середине процесса кузнец разворачивает заготовку на 90 градусов и начинает расковывать ее снова. Именно так получаются характерные «короткие» (по сравнению с обычными) разводы.
Короткие «волокна» этого вида дамаска – результат особой техники, когда кузнец поворачивает наполовину прокованную заготовку и начинает все сначала
Многорядный дамаск
Это вид, скорее, не материала, а уже готового изделия, то есть клинка. Полосы дамаска разной выделки (мозаичного, крученого и пр.) кладут рядом и проковывают между собой с целью создать зрительно эффектную комбинацию узоров. Состав и техника изготовления этих полос зачастую различаются: ближе к режущей кромке помещают прочный и резучий вид дамаска, а ближе к обуху – прочный и вязкий вид с особенно красивыми узорами.
Многорядным правильнее называть сам клинок, а не дамаск
Немного о технологиях изготовления булата и дамаска
Готового, единственно правильного «рецепта» пакета стали для изготовления литого булата и сварного дамаска нет, и носить это название могут очень многие узорчатые стали, собранные с помощью технологий литья и ковки. Однако несколько характерных черт у булатных сплавов все-таки есть.
Вот, пожалуй, самое минимальное, что нужно знать тому, кто собрался приобретать булатный (литой или сварной) клинок.
что такое булат и откуда он появился
Немного о древнем булате
Булатная сталь представляет собой сплав железа и углерода, причем содержание последнего очень высоко, и практически приближено к составу его в чугуне. После специфической термообработки твердость этого сплава достигает 64 HRC, а травленая его поверхность имеет характерный и очень красивый рисунок.
Однако, если сравнивать булатный сплав и простую высокоуглеродистую сталь, то можно проследить ту же закономерность, что и при сравнении алмаза и угля: состав один, а свойства разные. Технология производства булата крайне сложна и не лежит на поверхности.
Данные археологический исследований позволяют считать, что ещё 2,5 тысячи лет назад Индийские кузнецы умели изготавливать оружие из особенного металла. Индийская узорчатая сталь стоила целое состояние, а мастера касты кузнецов строго хранили свои секреты. Клинки из неё опытные мастера выковывали на протяжении нескольких лет, используя достаточно небольшие молоточки, вместо стандартного молота кузнецы.
После покорения Тимуром Сирии, мастера были вывезены в Самарканд, ставший затем центром производства булата. Однако расселившиеся по Средней Азии мастера настолько хорошо хранили свои секреты, что в конечном итоге древние технологии, дающие возможность получить высококачественный булатный вутц были утеряны.
Булатная сталь П.П. Аносова
Раскрытие секрета производства булата стало сложной целью для многих именитых металлургов. Западноевропейские мастера многие десятилетия пытались воссоздать легендарные древние рецепты, то приближаясь к результату, то снова откатываясь назад.
Павел Петрович Аносов, будучи в должности горного начальника Златоустовских заводов, проводил целенаправленные исследования, целью которых было повышение качества продукции, выпускаемой вверенной ему Оружейной фабрикой. В 1828 году он начал многолетние работы, позволяющие получить булатный сплав, которые венчались успехом только в 1837 году.
Помимо классической технологии Аносов разработал и так называемое производство сущность которого «заключается в сплавлении негодных к употреблению железных и стальных обсечков в глиняных горшках (тиглях) при помощи возвышенной температуры воздушных печей».
Возвращение легенды
И снова, уже в начале 20 века эта сложнейшая технология была утрачена. Многолетние исследования Аносова остались только в архивных и музейных записях тех времен. Восстановить технологию стремились многие, сначала советские, а затем и российские металлурги. Ближе всех подойти к разгадке тайны, и получить аносовский булат удалось только Златоустовскому металлургу Сергею Баранову. Для этого потребовались многие года и огромное количество пробных плавок.
Булатная сталь Сергея Баранова на сегодняшний имеет соответствующее заключение РАН, а сам Сергей стал членом-корреспондентом Петровской Академии «Наук и Искусств».
Отличие тигельного булата от литого
Два эти вида стали имеют, как отличия, так и поразительное сходство. Их неодинаковость начинается уже на этапе производства. Тигельный сплав производится в специальных тиглях из железной руды с добавлением древесного угля и специальных флюсов. Плавка проводится в древесных печах, температура в которых гораздо ниже, нежели в газовых или электрических. Это очень затратная во всех отношениях технология, поэтому выполненные из такого металла клинки относятся к разряду коллекционных.
Технология литого булата немного проще, поскольку позволяет использовать вместо железной руды специально подобранные марки низкоуглеродистых сталей. Визуально рисунок, который имеет булатный тигельный клинок более выражен и интенсивен. Однако свойства ножей из этих металлов практически идентичны, а литой сплав более доступен по цене.
Последние
Булат. Структура, свойства и секреты изготовления. :: Книги по металлургии
Что же такое булат?
Нам уже известно, что настоящий булат — это прежде всего литая углеродистая сталь, обладающая специфическими узорами.
Первым подробно описал литой индийский булат или вутц Павел Петрович Аносов [13]. «Булатом называется, — писал П. П. Аносов, — сталь, имеющая узорчатую поверхность: на некоторых булатах узор виден непосредственно после полировки, на других же — не прежде, как поверхность подвергается действию какой-либо слабой кислоты». Легкость проявления рисунка при травлении являлась характерным признаком литого булата.
Кроме того, рисунок должен принадлежать всей массе булатного клинка и быть результатом естественной структуры металла, а не результатом сварки кусков металла раз¬личной твердости, как в дамасской стали. Расположение узоров на булатном клинке отличалось тем, что, повторяясь по форме, каждый из них имел неповторимые штрихи. Поэтому искусственно создать булатный узор практически невозможно. Если узор стирался с поверхности изделия, то последующей шлифовкой, полировкой и травлением его можно было очень хорошо выявить вновь. узор сохранялся даже при перековке сабли в кортик, нож или другое изделие.
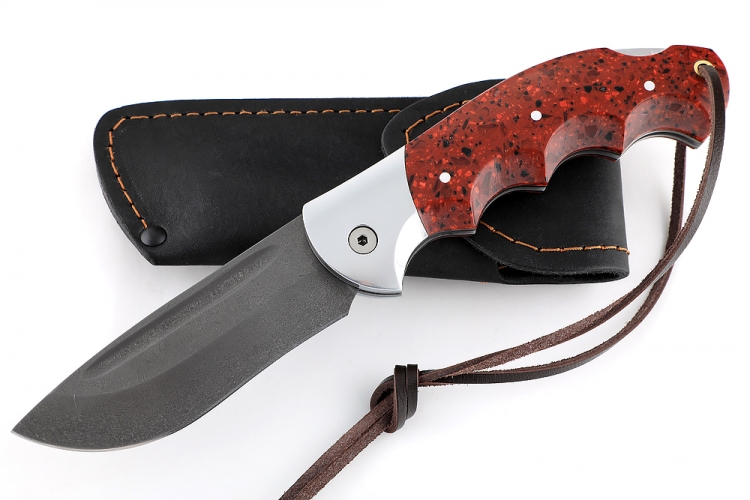
Как мы уже говорили, индийский булат поставлялся на рынки Персии и Сирии в виде разрубленной пополам лепешки литой стали — вутца. Вутц имел диаметр примерно 12,5 см, толщину около 1 см и массу примерно 1 кг. Характерно, что вутц также имел естественный рисунок. Сохранились воспоминания путешественников по Индии, которые видели, как плавят булатную сталь. Они утверждают, что булатные слитки имели своеобразные узоры, не похожие на рисунок на готовых клинках. Очевидно, вутц рубили пополам для того, чтобы покупатель мог рассмотреть строение металла. Чтобы из вутца сделать клинок, необходимо было его правильно проковать, термически обработать и окончательно отделать. Таким образом, качество булатного клинка определялось не только материалом, но и способами его изготовления, термообработки и отделки.

Арабский ученый XII века Едриза сообщает, что в его время индийцы еще славились производством железа, индийской сталью и выковкой знаменитых мечей. В Дамаске из этой стали изготовляли клинки, славу о которых крестоносцы разнесли по всей Европе. К сожалению, в Древней Индии так тщательно прятали секреты выплавки вутца, что в конце концов потеряли их совсем. Уже в XII веке табан, например, не могли делать ни в Индии, ни в Сирии, ни в Персии.
После того как Тимур покорил Сирию и вывез оттуда всех мастеров, искусство изготовления оружия из литого булата переместилось в Самарканд; однако вскоре оно везде пришло в упадок. Потомки вывезенных мастеров, рассеявшись по всему Востоку, окончательно потеряли способы изготовления булатного оружия. В XVI—XVIII веках мало кто в мире знал секрет производства литого булата и изготовления из него холодного оружия. Возможно, что на роди¬не булата в Индии редкие образцы его делали вплоть до XVIII века. Производство окончательно исчезло после нашествия европейцев, которые завезли в страну современные способы производства стали.

Ко времени, когда были установлены научные методы определения структуры, фазового состава и механических свойств металла, в распоряжении металлургов оказались лишь музейные экспонаты булатных изделий. Некоторые из них с годами потеряли свои свойства практически полностью. Другие сохранились относительно хорошо, но владельцы редко соглашаются жертвовать своими сокровищами. Все же некоторые металловедческие исследования булата проделаны были, и мы об этом еще расскажем.
Интересно, что время оказалось самым надежным индикатором для определения настоящей булатной стали. известно, что неоднородный металл больше подвержен коррозии, чем однородный, поэтому полосы дамасской стали ржавели довольно быстро.
До наших дней не дошел ни один меч с полностью сохранившимся цветным узором и первоначальной полировкой. Лучший образец Дамаска (сварочного многослойного булата) — дротик городского исторического музея в Дюссельдорфе — имеет первоначальную политуру, но цвет узора сохранил лишь частично.

Таким образом, на вопрос, что такое булат, можно ответить пока только так: это литая углеродистая сталь, обладающая естественным узором и необыкновенно высокими свойствами.
Какова природа естественного узора на изделиях из литой стали? Почему его характер определял свойства этой стали? Как в древности умудрялись ковать «сверхуглеродистую» сталь, близкую по составу к чугуну? Чем объясняется необыкновенная острота лезвий булатных клинков? Почему методами современной металлургии невозможно выплавлять сталь, подобную древнему булату?
Эти вопросы давно волновали не только металлургов. Автор надеется, что читатель в какой-то мере найдет на них ответы в следующих главах книги.
Харалужные мечи
Холодное оружие до конца XIV века было основным вооружением русского войска. О высоком качестве булатных клинков на Руси знали с незапамятных времен.

Отечественные археологи установили, что в V—VIII веках древние русские кузне¬цы умели делать железные ножи со стальными лезвиями. В IX —X веках в России достигла высокого уровня техника производства сварочного булата. В трактате багдадс¬кого философа Аль-Кинди «О различных видах мечей и железе хороших клинков и о местностях, по которым они называются», написанном в первой половине IX века, ука¬зывается на то, что франкские и слиманские мечи изготовляются из дамасской стали. Современник Аль-Кинди арабский ученый Ибн-Руста называет народ, владевший слиманс-кими мечами, «русами»; Аль-Бируни сооб¬щает: «Русы выделывали свои мечи из ша-буркана (твердой стали -авт.
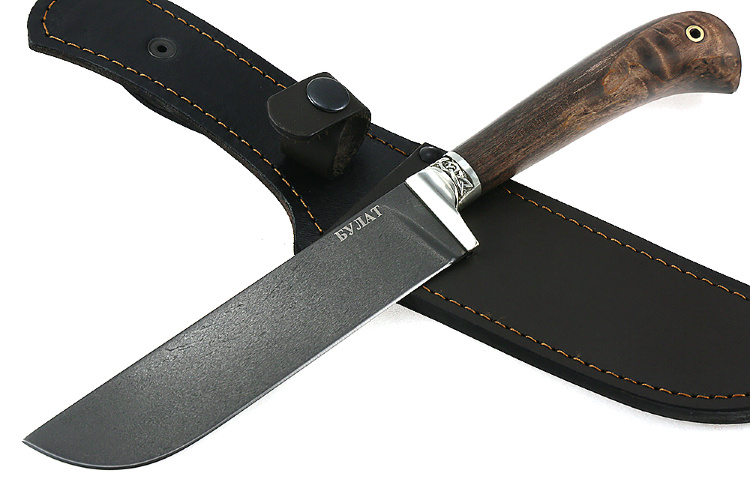
Современный исследователь истории производства холодного оружия в России Б. А. Колчин указывает, что все известные нам древнерусские мечи (их найдено более 75) имеют конструкцию клинка, подобную описанной Аль-Бируни [15]. На основании обнаруженных структурных схем металла древнерусских мечей была реконструирована технология их изготовления.
Основа клинка делалась из железа или сваривалась из трех полос стали и железа. Когда ее сваривали только из стали, то брали малоуглеродистый металл. Довольно широко применялась и узорчатая сварка. В этом случае основа клинка изготавливалась из средней железной и двух крайних стальных специально сваренных полос. Последние состояли из нескольких прутьев (слоев) с разным содержанием углерода, много раз перекрученных и раскованных в полосу.

В работах исследователей В.В.Арентда [16] и С.А. Зыбина [17] есть сведения о мечах из дамасской стали, найденных на территории древнерусских селений Боре, Новоселках, Михайловском и других. Меч, найденный в Михайловском, хранится в Государственном историческом музее в Москве. Полоса дамасской стали наварена на нем поверх дола и состоит из трех прутиков — слоев. Средний из них имеет крупный узор, напоминающий узор литого булата.
Не удивительно, что русские мечи с «ред¬костными» узорами пользовались большим спросом на внешних рынках: в Византии, Средней Азии и других странах.
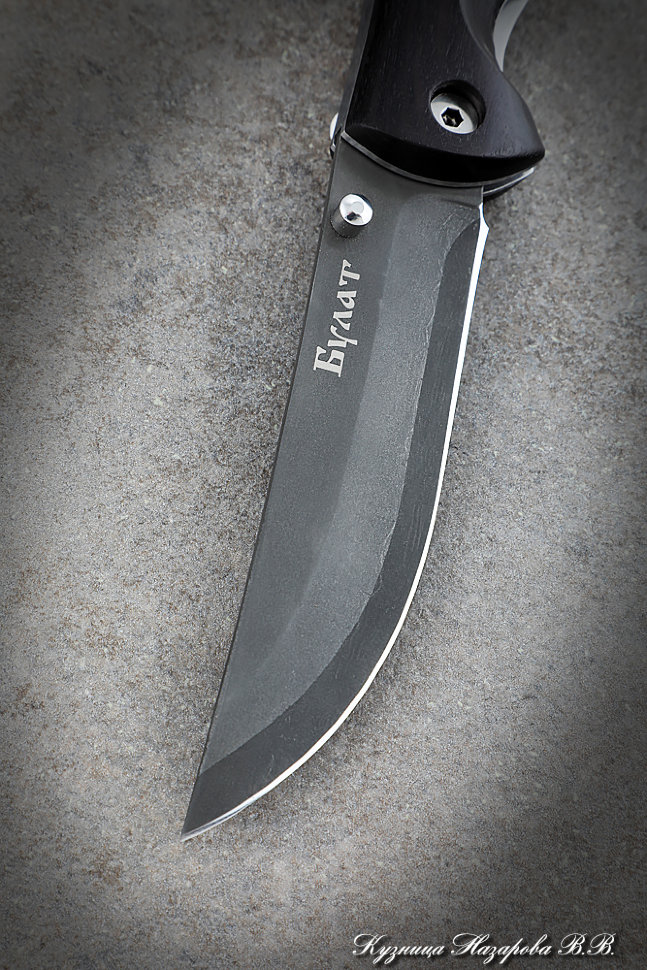
Русское оружие славилось не только качеством стали, но и ее термообработкой. За¬каленную сталь на Руси называли «трьпен-ный оцел» («стойкая сталь»). Наваренные «оцелом» топоры находили в курганах, относящихся к XI веку. «Каленные» стрелы и сабли часто упоминаются в былинах. Известна древняя поговорка: «Пещь искушает оцел во калении». Рогатина тверского князя Бориса Александровича имела рожну из закаленного булата.
В России умели делать дамаск (сварочный булат) вплоть до конца XIX века.

Рижский историк-металловед А. К. Ан-тейн сравнительно недавно приготовил очень эффективный реактив для расчистки проржавевших лезвий древних мечей. На лезвиях древних мечей, обработанных «бальзамом Антенна», выявляют очень тонкие надписи, которые обычно располагались в верхней трети клинка. Они, как правило, инкрустированы в горячем состоянии обычной или перекрученной железной либо стальной проволокой. Так, например, в Киевском историческом музее хранится меч с красивой рукояткой с рисунком в виде перевитых друг с другом чудовищ.
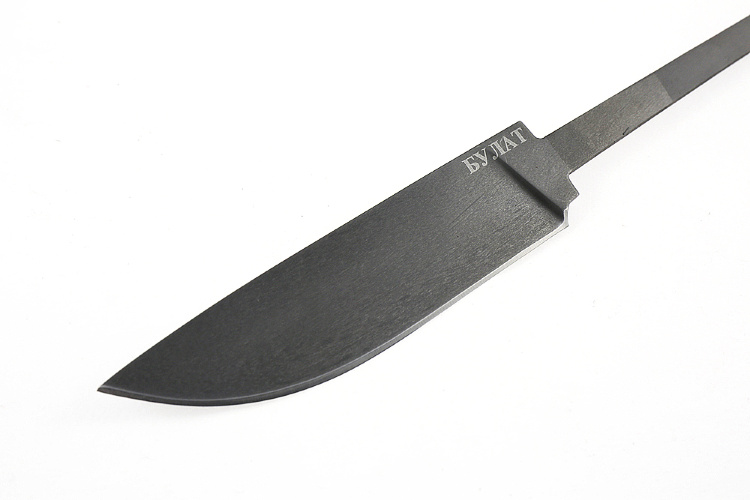
Булат и дамасск: как выбрать настоящий нож
Беседа с Александром Бычковым, мастером-кузнецом, приоткрывает нам тайну создания клинков самого высокого качества.
Фото автора
С Александром мы знакомы давно. Меня всегда поражали его изделия. Не знаю почему, но его клинки я «чувствую», например, когда нахожусь на выставках. Быть может, это происходит потому, что мастер заложил в них какую-то тайну?
БУЛАТ
— Итак, начну нашу беседу с традиционного вопроса: что же такое дамаск и булат?
— Разговоров об этих чудо-металлах ходит много. Мне приходилось слышать о них от людей, которые меньше всего вникают в смысл и суть дамаска и булата, но при этом желают слыть крупнейшими специалистами в данной области.
Чтобы понять суть вопроса, вернемся к истокам зарождения булата, ибо как указывают исторические хроники, сначала был булат, который представляет собой сплав железа с углеродом. Зародилось производство отливаемого металла в Индии.
|
Пакет будущего клинка состоит из слоев разной структуры. ФОТО RIKROSE/FLICKR.COM (CC BY-NC-ND 2.0) |
Установлено, что тот металл с заданными качествами плавился в небольших глиняных чашах с невысокими краями — в тиглях. В тигель закладывали железную руду либо уже готовые слитки железа. Туда же добавляли шихту, в которую входил уголь (преимущественно древесный).
В процессе плавки железо насыщалось углеродом из угля и кислородом из воздуха. Нельзя было допускать перенасыщения металла кислородом. В результате получался слиток в форме полусферы. Его называли «вутц». Впоследствии слиток рубили пополам и в таком виде уже продавали.
|
После сваривания ковкой металл приобретает форму монолита. ФОТО RIKROSE/FLICKR.COM (CC BY-NC-ND 2.0) |
— А как люди могли определить, что им продают булат, а не дешевую подделку?
— В любом случае на поверхности слитка должна проступать кристаллическая структура. Особенно хорошо эта структура была видна как раз на срезе.
— Что делали со слитком потом?
— Далее нужно было правильно отковать этот слиток, для того чтобы впоследствии делать из этого булата клинки. На этой стадии есть свои небольшие тонкости.
Дело в том, что для получения качественного булатного клинка при ковке необходимо сделать булат чище. Для этого необходимо «выгнать» (или выдавить) все содержащиеся в металле газы, которые могут оказать пагубное влияние на качество булата, если останутся в нем.
Это своего рода грязь, порочащая чистоту металла. Чем монолитнее структура булата, тем качественнее будут из него клинки. Но не всем кузнецам это удается.
|
История дамаска и булата насчитывает не одну тысячу лет. |
— Значит ли, что в этом случае качество булата резко снижается?
— Да, это так.
— Я знаю, что процесс ковки настолько ответственен, насколько и интересен. Это настоящее творчество. Рождению клинка зачастую пытаются приписать различные магические действия.
Но, на мой взгляд, у всякого мастера с большой буквы складывается свой стиль общения с металлом. Наверное, кто-то скажет, что железо есть железо.
Но я больше чем уверен, что во все выдающиеся творения, каковыми в нашем случае являются высококачественные клинки, мастер вкладывает частичку своей души. А этого не заменит никакая автоматика производства, существующая на данном этапе развития цивилизации. Как в общих чертах необходимо работать с булатом дальше?
|
Дамаск получают методом ковки из пластин металла. |
— Булат требует к себе большого внимания. При ковке нельзя недогреть металл, так как он может лопнуть, и перегреть его, так как пропадет рисунок, а если перегрев будет еще больше, то металл также может лопнуть.
— Как следить за температурой булата?
— Это возможно определить только по его цвету и дается с наработкой определенного опыта.
У мастеров высокого класса есть свои секреты общения с металлом, но не все любят их озвучивать. Однако в случае с Александром меня поразило, что он готов обо всем подробно рассказать.
И когда я спросил, не боится ли он делиться секретами с конкурентами, смысл его ответа был приблизительно таков: «Если уж дано, так дано. Нет — так нигде не приобретешь!» А дано в данном случае должно быть чувство металла. Но вернемся в нашу кузнецу.
— Какие еще важные детали, возникающие в процессе обработки булата, ты бы отметил?
— Одна из особенностей булата — это способность набирать температуру при ковке. Поэтому приходится останавливать процесс, для того чтобы остудить заготовку. Вместе с тем булат должен быть хорошо прокован, а во время ковки на наковальне часть заготовки все же успевает остыть. И поэтому приходится опять подогревать ее до нужной температуры.
Очень важно держать этот температурный баланс. Самый качественный булат можно получить только при использовании качественного древесного угля. В древесном угле практически отсутствует сера, которая дает металлу хрупкость.
— Итак, у нас есть болванка качественной булатной стали. Что мы делаем с ней дальше?
— Болванка проковывается определенным способом. Получается квадратная заготовка. Во время проковки заготовки из нее «выгоняются» газы и заковываются те полости (или раковины), которые получились в местах выхода газов.
Важно, чтобы вся структура заготовки была наиболее близка к монолиту. Именно этот квадрат и является той «колыбелью», из которой путем ковки вытягивают будущие клинки. Квадрат расковывается в полосу в зависимости от размера клинка (по толщине и длине).
На протяжении всего процесса ковки металл необходимо как можно больше перекладывать, подобно тому как кулинар месит тесто. Но тут, как и в каждом деле, нельзя переусердствовать.
Слишком долгая проковка ведет к измельчению кристаллической структуры металла. При этом рисунок практически исчезает. Теряется качество булата. Заготовка на конкретное изделие отрубается от квадрата после вытяжки.
|
Клинок из дамаска состоит из сотен тончайших слоев, сваренных методом ковки. ФОТО ДМИТРИЯ ВСТОВСКОГО |
— Я слышал, что многие из наших современных мастеров заканчивают работу с металлом именно на этой стадии. Так ли это?
— К сожалению, так. После того как заготовка вырублена, придать форму будущему изделию пытаются с помощью наждака. При этом стачиваются самые ценные слои металла, несущие наибольшую твердость. Такие «мастера» концентрируются только на том, чтобы придать клинку как можно более привлекательный внешний вид.
Сделать это в принципе просто. Но при этом на карту ставятся утилитарные качества изделия. А точнее сказать, они сводятся на очень низкий уровень.
Мне известны случаи, когда «мастера» сваривают металлические пакеты или даже просто прутки «в ребро», затем путем ковки придают им вид выкованного изделия.
При таком способе внутренняя структура металла не может быть и рядом поставлена с настоящим булатом или дамаском. Я всегда довожу заготовку до конца ковкой и таким образом позволяю металлу сохранить свою монолитную структуру, а это приводит к высокому качеству клинка.
— Но, как известно, мало выковать клинок, необходимо его еще правильно закалить и отпустить. Как это делаешь ты?
— Закалка и отпуск — это составляющие единого процесса. Они служат для повышения режущих свойств клинка. Это сугубо индивидуальный процесс.
Например, изделия, выкованные из одного слитка булата, закаливаются и отпускаются в одинаковом режиме. Для другого слитка этот режим может быть иным.
— Как затачиваются клинки из булата?
— Все зависит от вида изделия и его практического назначения. Способы заточки различны. Есть комбинированная заточка. Это когда в одном месте (обычно ближе к рукоятке) клинок делается более толстым (а отсюда и заточка будет больше похожа на клин), а далее лезвие затачивается, как бритва. Так можно затачивать охотничьи ножи.
Той частью клинка, что находится у рукоятки, обычно выполняется более грубая работа: резка шкуры животного, строгание и резка деревянных поверхностей, сучков, в то время как более тонко заточенная центральная и носовая части клинка помогут выполнить работы по снятию шкуры и разделке мяса животного, а также другие более деликатные работы.
|
Булат изготавливается методом литья, после чего заготовка распиливается пополам, чтобы оценить качество полученного металла. |
ДАМАССКАЯ СТАЛЬ
— Александр, давай теперь вернемся к дамасской стали. Об изделиях из нее ходит много легенд, но еще больше небылиц по причине малой осведомленности. Так что же это такое?
— В отличие от булата, который выплавляется, дамасская сталь сварная. Она может быть сварена из различных сортов стали или стали и железа.
Предположительно в своем историческом начале кричное железо, получаемое из руды путем плавления, имело пористую структуру. Причиной этого было наличие большого количества примесей. Это железо проковывалось. Часть железа оставалась мягкой, часть науглероживалась.
В процессе дальнейшей ковки смешивали твердое и мягкое железо. Твердое служило основой, к которой с двух сторон проковывалось более мягкое.
Таким образом, получался пакет, где более мягкие слои стачивались быстрее, чем середина с более твердым слоем. При таком раскладе получалось, что клинок затачивался самопроизвольно. Ярким примером такого ножа служит древний скифский нож «Акинак».
Основой дамасской стали является пакет из разных марок стали или стали и железа. При кузнечной сварке металлов важно избежать перегрева, при котором выходит углерод.
По сравнению с булатной сталью дамаск был более простым в изготовлении. Я делаю фактически три пакета: один для середины и два на боковые слои «щечки».
На некоторых изделиях я пробовал расковывать пакеты до 50 000 слоев в общей сложности. Но увлекаться большим количеством слоев не стоит, так как при столь длительной обработке металла из него выходит углерод. Во внешних слоях моих изделий в основном 400–450 слоев, во внутренних — более 1000.
От того, как пройдет этот процесс, и зависит качество будущего клинка. Чем плотнее и монолитнее мастеру удастся связать все слои пакета, тем выше будет качество.
|
Александр закончил Суздальское художественно-реставрационное училище. |
— А что ты можешь сказать о легенде, по которой мечи из дамасской стали в древние времена носили под широким поясом восточной одежды?
— Легенд было во все времена больше, чем в этом была необходимость. Безусловно, такие мечи были. Но их было не так много, как привыкли утверждать некоторые. Само сочетание эластичности металла и его твердости малосопоставимо, на первый взгляд.
Но некоторым мастерам древности удавалось добиваться этого. Вряд ли таких изделий могло быть много. Доподлинно известно о четырех мечах подобного рода, находящихся в Иране.
Само собой разумеется, что такие изделия имеют статус народного достояния. К ним было такое же отношение, как к знаменитым мечам самураев в Японии.
— Александр, давай попробуем сравнить производство клинков из булата и дамаска. Каковы характерные особенности этого процесса для каждого из них?
— В целом булат более пластичен за счет кристаллической структурной решетки. При этом он может иметь гораздо более высокую твердость. Если взять 60 единиц твердости по Rockwell (для стали это очень высокое число), то она характерна лишь для инструментальных сталей, которыми обрабатывают металл.
Все основные виды охотничьих ножей имеют твердость от 54 до 58 единиц по той же шкале. Но те же 60 единиц для дамасской стали — норма.
Для булата нормой являются 64 единицы. Это твердость надфиля. Но при такой твердости булатный клинок может гнуться в дугу.
Высокая плотность, коррозионная стойкость и высокие режущие свойства — характерные особенностиклинков из булата. И это благодаря тому, что булат изначально должен быть более монолитным и не рыхлым.
|
Цена на клинки из дамаска довольно высока.ФОТО VADIMDEM/DEPOSITPHOTOS.COM |
— Александр, проанализируй, пожалуйста, те изделия, которые мы видим на витринах охотничьих магазинов. Прежде всего я имею в виду клинки из дамасской стали, а точнее сказать, то, что пытаются выдать за дамасскую сталь.
— Честно говоря, не очень хотелось бы это обсуждать по многим причинам. Но вкратце могу сказать следующее. Те изделия, которые можно порой увидеть на прилавках магазинов, даже с натяжкой нельзя назвать тем, за что их выдают продавцы.
Я уже говорил, что в последнее время появилось много умельцев, которые могут вам выдать около 100 (!) изделий из «дамасской» стали в месяц. Как вы думаете, какими будут эти клинки? В основной массе на прилавках магазинов мы видим изделия с количеством слоев от 100 до 300 максимум.
Настоящий дамасский клинок даже не начинается с такого количества слоев. Цена таких изделий говорит сама за себя. Кто из нас видел, например, «Мерседес» по цене «Запорожца»? Уверен, никто и никогда.
— Что бы ты посоветовал тем, кто хочет приобрести нож из настоящего булата или дамаска?
— Если человек всерьез интересуется такого рода ножами, он должен получить определенные знания о предмете своего интереса. Это можно узнать из книг или же у специалистов в этом вопросе. Мне порой достаточно нескольких минут, чтобы объяснить человеку разницу между клинком из настоящей булатной стали и подделкой.
Если человек ориентируется в предмете разговора, он сразу все поймет, а впоследствии даже с гордостью расскажет об этом другим. И это, я считаю, очень хорошо.
P.S. От имени читателей выражаю огромную благодарность Александру Бычкову — мастеру с большой буквы, продолжателю русских традиций кузнечного дела за то, что он ввел нас в таинственный мир работы с металлом, и желаю ему богатырского здоровья и дальнейших творческих успехов.
Беседовал Дмитрий Встовский 4 мая 2017 в 09:43
Как он получил свое название и как это сделано
Дамасская сталь — это знаменитый тип стали, который можно распознать по водянистому или волнистому светлому и темному рисунку металла. Дамасская сталь не только была красивой, но и ценилась за то, что она сохраняла острый край, но при этом была твердой и гибкой. Оружие, сделанное из дамасской стали, значительно превосходило оружие, сделанное из железа! Хотя современные высокоуглеродистые стали, изготовленные с использованием бессемеровского процесса XIX века, превосходят по качеству дамасскую сталь, она остается выдающимся материалом, особенно для своего времени.Существует два типа дамасской стали: литая дамасская сталь и дамасская сталь, полученная методом узорчатой сварки.
Откуда дано название дамасской стали
Непонятно, почему именно дамасская сталь называется дамасской сталью. Три популярных вероятных источника:
- Относится к стали, произведенной в Дамаске.
- Это сталь, купленная или проданная в Дамаске.
- Относится к сходству стального узора с дамасской тканью.
Хотя сталь могла быть сделана в Дамаске в какой-то момент, а узор действительно несколько напоминает дамасскую, это, безусловно, правда, что дамасская сталь стала популярным предметом торговли для города.
Литая дамасская сталь
Никто не повторил оригинальный метод изготовления дамасской стали, потому что она была отлита из вутца, типа стали, первоначально производимой в Индии более двух тысяч лет назад. Индия начала производить вуц задолго до Рождества Христова, но оружие и другие предметы, сделанные из вуца, стали по-настоящему популярными в 3-м и 4-м веках в качестве торговых предметов, продаваемых в городе Дамаск, на территории современной Сирии. В 1700-х годах методы изготовления вуца были утеряны, поэтому исходный материал для дамасской стали был утерян.Несмотря на то, что большое количество исследований и обратного инжиниринга пытались воспроизвести литой дамасской стали, никто не смог успешно отлить подобный материал.
Литая сталь Wootz была изготовлена путем плавления железа и стали вместе с древесным углем в восстановительной атмосфере (с минимальным содержанием кислорода или без него). В этих условиях металл поглощал углерод из древесного угля. Медленное охлаждение сплава привело к образованию кристаллического материала, содержащего карбид. Дамасская сталь изготавливалась путем ковки из мастеров мечей и других предметов.Чтобы производить сталь с характерным волнистым рисунком, требовалось немало навыков, чтобы поддерживать постоянную температуру.
Дамасская сталь, сваренная по шаблону
Если вы покупаете современную дамасскую сталь, вы можете получить металл, который был просто протравлен (поверхность обработана), чтобы получить светлый / темный узор. На самом деле это не дамасская сталь, так как узор стирается.
Ножи и другие современные предметы, изготовленные из дамасской стали, сваренной по образцу, имеют водянистый узор на всем протяжении металла и обладают многими из тех же характеристик, что и оригинальный дамасский металл.Сталь, полученная сваркой по шаблону, изготавливается путем наслаивания железа и стали и ковки металлов вместе путем их обработки молотком при высокой температуре для образования сварного соединения. Флюс герметизирует соединение, чтобы не допустить проникновения кислорода. Многослойная кузнечная сварка дает эффект водянистости, характерный для этого типа дамасской стали, хотя возможны и другие формы.
Список литературы
Фигиль, Лео С. (1991). Дамасская сталь . Atlantis Arts Press. С. 10–11. ISBN 978-0-9628711-0-8.
Джон Д. Верховен (2002). Материаловедение . Исследования стали 73 нет. 8.
К. С. Смит, История металлографии, Издательство Юниверсити, Чикаго (1960).
Годдард, Уэйн (2000). Чудо изготовления ножей . Краузе. С. 107–120. ISBN 978-0-87341-798-3.
Дамасская сталь — Руководство для начинающих
Читатели нашего Руководства по ножевой стали часто спрашивают меня о Дамасская сталь .Эта привлекательная, но загадочная сталь захватила воображение многих, поэтому я постараюсь объяснить, что это такое и как ее производят.
Слово «Дамаск» восходит к средневековым западным культурам и относится к более раннему стилю мастерства, впервые появившемуся в Индии около 300 г. до н. Э. В то время это мастерство было плодотворным и, вероятно, было названо в честь региона, который прославил его.
Примерно в то же время арабская культура представила сталь Wootz в сирийском городе Дамаск, где этот материал привел к процветанию оружейной промышленности.Дамаск импортировал сталь Wootz из Персии и Шри-Ланки для производства и использования гибридных стальных лезвий, известных своей прочностью. По-видимому, люди, стоящие за этим технологическим развитием, понимали, как сочетание различных металлов может создать оружие большей прочности по сравнению с оружием, сделанным из чистой стали.
>> Рекомендуемые ножи из дамасской стали на BladeHQ <<
Следовательно, дамасская сталь не является чистой. На самом деле, в этой уникальности его очарование и его загадка. Материал характеризуется множеством полос и пятен, сваренных вместе узорным способом для создания декоративных лезвий любой формы и / или длины, не способных разбиться. Идентификация композитов в оригинальной дамасской стали до сих пор остается неизвестной, так как не существует записей, описывающих их. Тем не менее, современное производство стали в Дамаске следует практике комбинирования чистых металлов в зависимости от личных предпочтений и потребностей. Хотя слесарии могут выбирать и смешивать материалов для формования стальных заготовок, железо пользуется популярностью из-за его твердости и стойкости с повышенным содержанием карбидов.
Исторически сложилось так, что дамасская сталь приобрела несколько загадочную репутацию, поскольку первые упоминания о ней исчезли примерно в 1700 году нашей эры, что указывает на упадок узорчатых мечей, производство которых прекратится примерно через пятьдесят лет. Однако древние традиции и значение дамасской стали никогда не забывались, отсюда и бурно развивающаяся промышленность, существующая сегодня.
Состав стали
Науки, лежащие в основе дамасской стали и производства стали, весьма сложны, но они подтверждают изобретательность и сложность, с которой методы и процессы Дамаска стали известны и уважаемы.Металлургия и химия служат основой для состава и множества областей применения, необходимых для производства и использования стали.
Интересно, что дамасская сталь считалась чем-то вроде «суперпластика» не из-за некоторой идеи, что это не настоящий металл — хотя она никогда не была чистым в этом смысле, — а из-за долговечности, приписываемой предыдущему образцу. Несмотря на то, что различные типы современной стали заменили лезвия из дамасской стали по своим характеристикам, химическая структура, присущая первоначальным производственным процессам, в которых использовались последние, делала лезвия того времени исключительно жесткими и мощными.
С 1973 года современные лезвия из дамасской стали изготавливаются из различных сортов стали, свариваемых вместе в заготовок . Эти заготовки также обычно содержат полосы железа для обеспечения необходимой прочности на молекулярном уровне. В результате они растягиваются и накладываются друг на друга в соответствии с потребностями, обозначенными конкретным применением лезвия и предпочтениями владельца лезвия. Это означает, что лезвия из дамасской стали производятся не на конвейере, а по индивидуальному заказу.
Процедура проста: стальные слитки образуют заготовки, которые складываются как «бутерброды» внутри других типов металлов. Полученный продукт может состоять из сотен слоев и обязательно будет иметь твердую плотность и разнообразный дизайн. Этот проверенный процесс каждый раз обеспечивает целостность и уникальность дамасской стали.
Тем не менее, основной состав дамасской стали состоит из двух дихотомических структурных типов: пластичности и хрупкости. Первый допускает сжатие материала для поглощения увеличения энергии, которая в противном случае минимизировала бы или исключила нарушение целостности лезвия. Последнее вводит в заблуждение, поскольку хрупкость обычно связана со слабостью. Однако в данном случае это слово относится к степени гибкости, необходимой для предотвращения разрушения или поломки, а также для облегчения остроты кромок.
Это структурное явление гарантирует, что дамасское лезвие легко режется и остается прочным. Выпуклая шлифовка обеспечивает остроту тонкости кромки, так что нарезанный материал отходит в стороны во время хода и, таким образом, сводит к минимуму «прилипание», которое часто происходит с лезвиями с более гладкими кромками.Таким образом, структурная хрупкость требует выпуклой шлифовки.
На более глубоком уровне углеродные нанотрубки образуются в стали, что обеспечивает пластичность и постоянную прочность в процессе ковки. Высокая концентрация углерода обеспечивает решающее качество целостности стали, что гарантирует высокую производительность. Это объясняет, почему углерод имеет решающее значение при разработке лезвий из дамасской стали.
В процессе ковки небольшие стальные слитки постепенно принимают желаемую форму лезвия. Это приводит к объединению карбидов железа в полосы, образующие уникальные узоры. Эти узоры напоминают зерна стали Wootz из древней Индии и отражают старую эстетику и стиль производства. Сегодня мастера по металлу могут воспроизвести многое в том же порядке, в котором, как известно, существовала дамасская сталь много веков назад.
Нагрев и отделка
Ниже приведены списки общих процессов нагрева и отделки для подготовки дамасской стали. Опять же, особенности меняются в зависимости от потребностей и желаний, а также от типа металлов, соединяемых вместе.Основные процессы всегда остаются неизменными.
Термообработка дамасской стали включает заданную температуру от 1500F до 2000F, в зависимости от полосы, и смесь цементита и аустернита.
- Соответственно заданная температура печи.
- Установить металлический блок в печь. Нагрейте весь цикл до начальной температуры.
- После нагрева выдержите сталь в течение десяти минут, чтобы она остыла.
- Закаленная сталь в масле.
Перенести в жидкий азот на один час.
- Закалка стали в течение одного часа при температуре 350 ° F. Это нужно сделать дважды.
Следующие шаги иллюстрируют последующую финишную обработку.
- Нанесите на лезвие абразивную обработку.
- Протравить без предварительной полировки в 50/50 разбавленном растворе хлорида железа и дистиллированной воды. Оставьте лезвие в растворе минимум на десять минут.
- Снимите лезвие и промойте его в проточной воде.
- Повторяйте цикл с пятиминутными интервалами до достижения желаемого результата.
- Погрузите лезвие в тринатрийфосфат для нейтрализации отделки.
Как сделать лезвие из дамасской стали
На предыдущих этапах описывается, как нагревать и чистить дамасскую сталь, а ниже показан весь процесс. Следовательно, знание первых двух необходимо заранее, чтобы изготовитель металла мог выполнить то, что указано ниже. Этот порядок указывает как на особенности, так и на то, как все работает вместе.
Изготовление лезвий из дамасской стали — это несложный процесс, но он требует постоянного ухода и кропотливости.Тем не менее, этот процесс требует много времени. Это необходимо как для обеспечения желаемого внешнего вида, так и для создания эффективного, хорошо сбалансированного лезвия.
- Соберите ингредиенты в тигель. Эти ингредиенты включают стекло и листья, которые, как известно, предотвращают окисление.
- Нагрейте тигель, чтобы ингредиенты расплавились.
- Когда тигель достигнет точки охлаждения, осторожно извлеките металлические слитки и нагрейте их до температуры, необходимой для ковки.
- Молоток по металлу, пока он горячий.Этот этап включает в себя описанное выше «прослоение». После того, как металл остынет, повторно нагрейте металл, чтобы снова выковать его. При необходимости повторите этот цикл, чтобы заострить края и придать форму лезвию.
- Когда окончательная форма будет достигнута, обрежьте лезвие и выковайте окончательные детали вручную.
- Удалите излишки науглероженного металла с поверхности лезвия.
- Вставьте канавки и просверлите отверстия в поверхности лезвия по мере необходимости или по желанию.
- Разогреть. Снова сожмите лезвие. Отполируйте, чтобы лезвие приобрело почти окончательную форму.
- Протравите поверхность лезвия кислотой для улучшения рисунка.
- По окончании тщательно удалите кислоту с поверхности лезвия.
Вот отличное видео, демонстрирующее процесс:
Ножи из дамасской стали
Ножи из дамасской стали бывают разных типов для любого числа целей, от кемпинга и выживания до рубки леса и охоты. Композитные материалы, соединенные вместе для изготовления дамасского ножа, обязательно зависят от типа ножа и условий, в которых он предполагается и / или предназначен для использования.Некоторые распространенные типы перечислены ниже:
- Ножи для разделки
- Охотничьи ножи
- Зубчатые ножи
- Шлепки
- Такелажные ножи
- Тактильные складные ножи
- Тактильные фиксированные лезвия
Прекрасная вещь о любом типе Дамасский нож таков, что по своей конструкции он выдерживает любые приложенные к нему силы. Дамасский нож не только прочен, но и долговечен.
Ниже приведены несколько прекрасных примеров дамасских клинков, с которыми я столкнулся.Большинство ведущих мировых брендов, таких как Spyderco, Benchmade, Kershaw и другие, недавно выпустили ограниченные серии в Дамаске.
Почему мы любим ножи из дамасской стали
Любители ножей любят ножи из дамасской стали по многим причинам. Это замечательно, потому что такое разнообразие отражает присущую Дамаску универсальность, которой нет у других клинков. История дамасской стали также привлекает внимание, поскольку она содержит тайну, которая создает ощущение интриги и значительно усиливает древние традиции.
Наиболее распространенные черты ножей из дамасской стали, которые энтузиасты считают идеальными, — это эстетика и высокая производительность. Ножи из дамасской стали украшены стильными узорами, которые металлисты выгравируют на лезвии в процессе ковки. Нет двух одинаковых дамасских ножей. На самом деле каждый нож уникален и ценен как выразительное произведение искусства.
>> Рекомендуемые ножи из дамасской стали на BladeHQ <<
Что касается высоких характеристик, то богатые углеродом металлы, кованные вместе, дают ощущение силы за счет заготовки и обвязки, что чуждо многим современным конструкциям лезвий.Это распространяется на молекулярный состав лезвия, а также на точность и осторожность, которые типичны при производстве, что делает такую мощность синонимом дизайна Дамаска.
Стоит ли владеть и использовать ножи из дамасской стали? Опять же, ответ субъективен. Владельцы клинков, вероятно, согласятся, что ножи из дамасской стали лучше подходят в определенных контекстах по сравнению с другими. Два широко приветствуемых сценария, как описано выше, — это любовь к уникальности стиля и художественных узоров, а также использование оружия, как это видно на охоте и военных подвигах, хотя многие повара также владеют дамасскими ножами.Эти ножи совершенно особенные и ценятся. Действительно, сегодня они пользуются уникальным авторитетом среди коллекционеров ножей.
По прошествии 2000 лет стиль и традиции Дамаска все еще укрепляются, и, в свете их загадочности и особого качества, они, несомненно, просуществуют еще долгое время.
Ключевая роль примесей в лезвиях из древней дамасской стали
Ключевая роль примесей в лезвиях из древней дамасской сталиАрхеотехнология
Дж.Д. Верховен, А.Х. Пендрей, У. Даукш
Искусство изготовления знаменитых лезвий из дамасской стали 16-18 веков, найденных во многих музеях, было давно утеряно. Однако недавно исследования установили убедительные доказательства, подтверждающие теорию о том, что отчетливый рисунок поверхности на этих лезвиях является результатом явления образования карбидных полос, вызванного микросегрегацией небольших количеств карбидообразующих элементов, присутствующих в слитках Wootz, из которых были выкованы лезвия. .Кроме того, вполне вероятно, что лезвия Wootz Damascus с дамасскими узорами могли быть произведены только из слитков Wootz, доставленных из тех регионов Индии, где имеются соответствующие месторождения руды, содержащие примеси .
Примечание автора: Все составы даны в массовых процентах, если не указано иное. В разделе оружия и доспехов большинства крупных музеев представлены образцы оружия из дамасской стали. Эти стали бывают двух разных типов, сваренные по шаблону Damascus и wootz Damascus, обе из которых, по-видимому, впервые были произведены примерно до 500 г. 1,2 Эти стали имеют привлекательный узор на поверхности, состоящий из закрученных узоров светотравленных участков на почти черном фоне. Стали с модельной сваркой получали путем ковочной сварки чередующихся листов высокоуглеродистых и низкоуглеродистых сталей. Затем этот композит сгибали и сваривали вместе, и цикл складывания / штамповки повторяли до тех пор, пока не было получено большое количество слоев.
Эта статья посвящена второму типу дамасской стали, иногда называемому восточным дамасцем.Наиболее распространенными примерами этих сталей являются мечи и кинжалы, хотя известны также примеры бронежилетов. Название Дамаск, по-видимому, произошло от этих сталей. Сама сталь производилась не в Дамаске, а в Индии и стала известна в английской литературе в начале 19 века 3 как сталь wootz, как ее здесь называют. Подробные изображения многих таких дамасских мечей представлены в книге Фигиэля, 4 , а металлургия этих клинков обсуждается в книге Смита. 5
К сожалению, технология изготовления лезвий из дамасской стали
потерянное искусство. Дата выпуска последних клинков из высококачественного дамаска.
закономерности нет, но, вероятно, около 1750 г .; маловероятно, что лезвия
отображение низкокачественных дамасковых узоров было произведено позже, чем ранние
19 век. Споры продолжаются в металлургическом сообществе в прошлом.
200 лет тому, как были сделаны эти лезвия и почему появился рисунок на поверхности. 6-8 Исследования, проводившиеся на протяжении многих лет, заявили об открытии методов воспроизведения
Wootz Damascus Steel Blades, 9-12 но все эти
методы страдают той же проблемой — современные кузнецы не могут
использовать методы воспроизведения лопастей. Успешное воспроизведение wootz
Лезвия из дамасской стали требуют производства лезвий, соответствующих химическому составу,
обладают характерным дамасским поверхностным рисунком и обладают такими же внутренними
микроструктура, которая вызывает узор на поверхности.
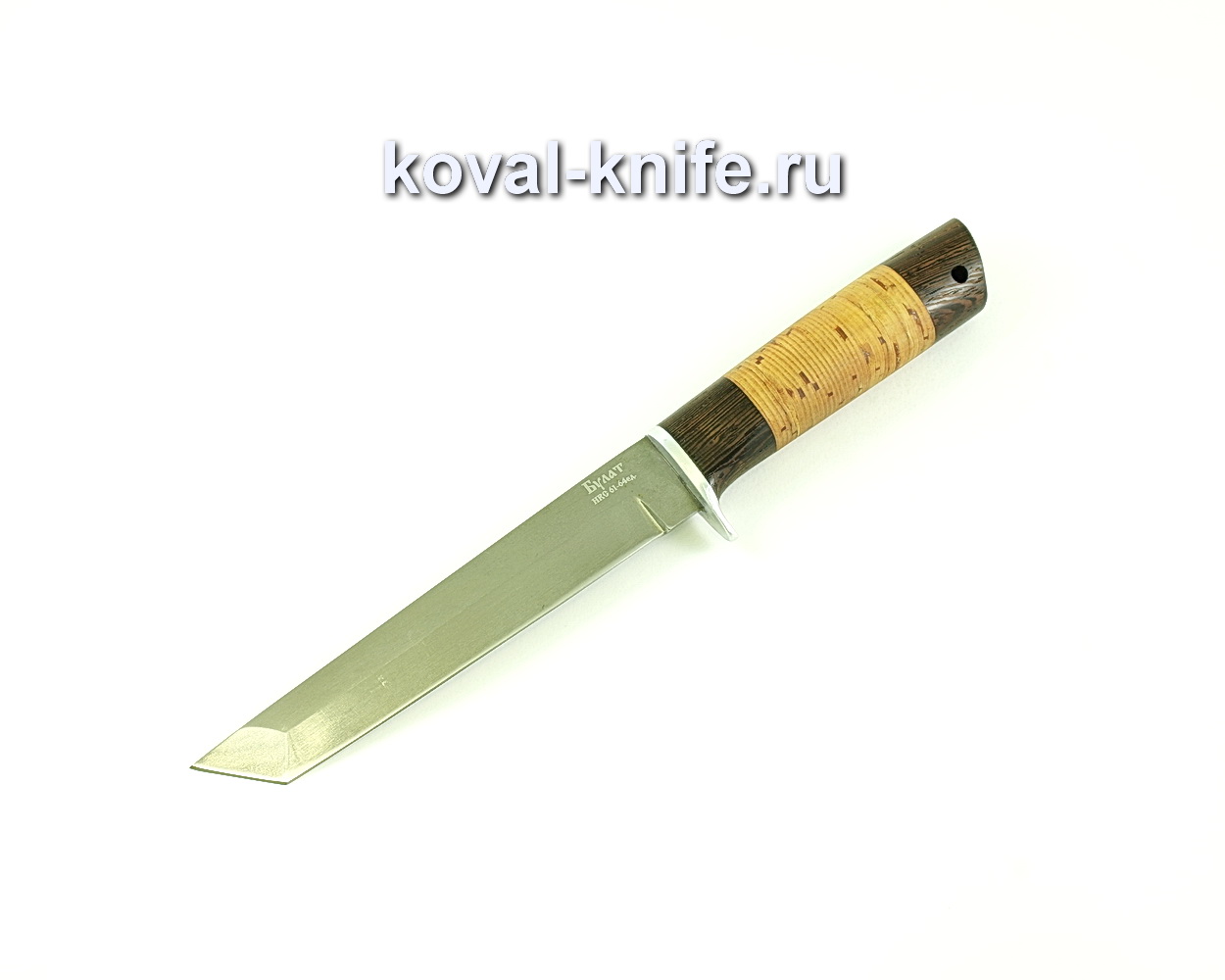
б |
Рис. 1. (a) Реконструированный клинок из дамасского дамаска, на котором виден дамасский узор поверхности, содержащий комбинированный узор лестницы Мухаммеда и узор розы. (b) Продольный разрез той же лопасти, показывающий полосы частиц цементита, ответственные за рисунок поверхности. |

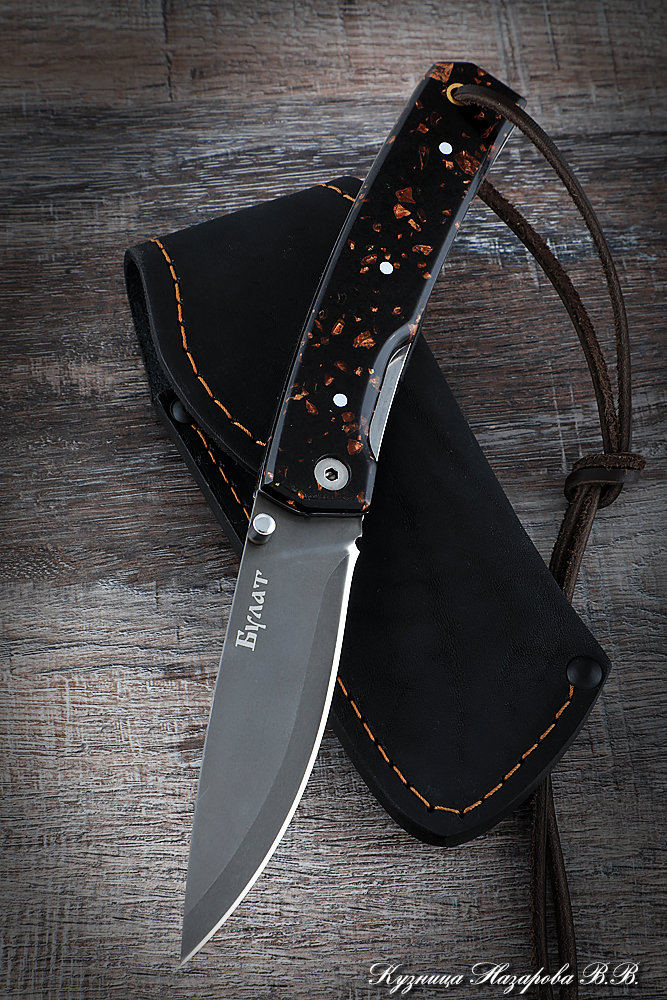
Подробное графическое описание процесса производства этого лезвия было недавно опубликовано. 14 Кроме того, методика была полностью описана в литературе, 15-17 , и было показано, что лезвия, обладающие высококачественными дамасскими узорами, могут быть повторно изготовлены с использованием этой техники.Этот метод, по сути, является простым воспроизведением общего метода, описанного более ранними исследователями. Небольшой стальной слиток правильного состава (Fe + 1,5C) получают в закрытом тигле, а затем выковывают его в форму лезвия. Однако теперь уточняются некоторые ключевые факторы. К ним относятся запись времени / температуры подготовки слитка, температура операций ковки, а также тип и уровень примесных элементов в стали Fe + 1. 5C. Представляется, что наиболее важным фактором является тип примесных элементов в стальном слитке.Недавняя работа 17-18 показала, что полосы из сгруппированных частиц Fe 3 C могут быть образованы в лезвиях путем добавления очень небольших количеств (0,03% или меньше) одного или нескольких карбидообразующих элементов, таких как V , Mo, Cr, Mn и Nb. Элементы ванадий и молибден, по-видимому, являются наиболее эффективными элементами, вызывающими образование полос. Очевидный вопрос, поднятый этими результатами, заключается в том, присутствуют ли эти элементы в небольших количествах в дамасских клинках 16-18 веков?
Рисунок 2. Макрофотографии клинков меча Жшокке. |
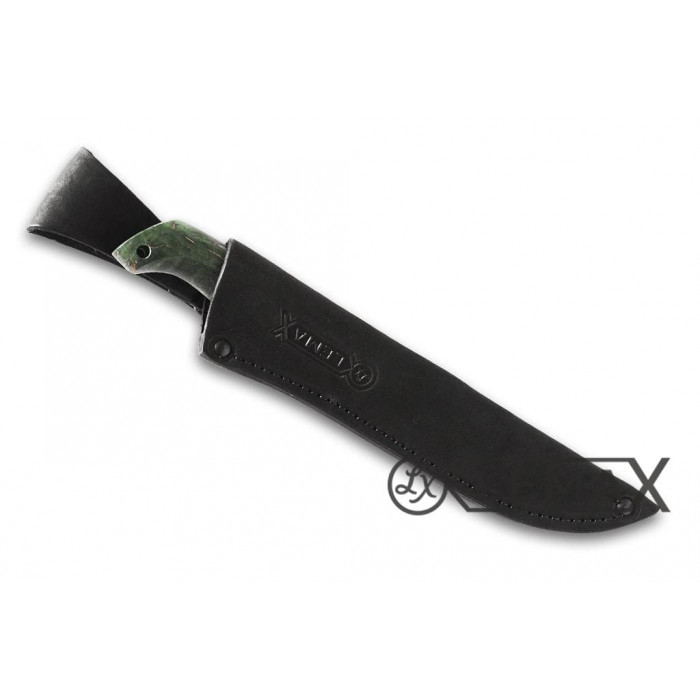
В данной статье представлены результаты исследования этих четырех образцов.Кроме того, были приобретены и включены в комплект четыре дополнительных лезвия из дамасского войлока, которым, как считается, несколько сотен лет. Следовательно, всем изученным здесь клинкам более двух столетий, и они предположительно были изготовлены из вутцовой стали. Эти лезвия называются настоящими лезвиями из дамасского войса, чтобы отличать их от реконструированных лезвий из дамасского войса, изготовленных по методике, разработанной авторами.
С одного конца каждого образца вырезали кусочки тонкой алмазной пилой.Отрезок длиной 2 см отрезали для исследований химического анализа, а образец длиной 8 мм использовали для анализа микроструктуры. Химические анализы были выполнены с использованием эмиссионной спектроскопии на калиброванной машине Nucor Steel Corporation. В таблице I представлены результаты химического анализа вместе со значениями, указанными Zschokke. Согласие между анализом, проведенным Zschokke в 1924 г., и настоящими данными достаточно хорошее.
Таблица I. Сравнение текущих химических анализов с анализами Зшокке 13 * | ||||||||
---|---|---|---|---|---|---|---|---|
Меч 7 | Меч 8 | Меч 9 | Меч 10 | |||||
Материал | Текущий | Zschokke | Текущий | Zschokke | Текущий | Zschokke | Текущий | Zschokke |
С | 1.71 | 1,87 | 0,65 | 0.![]() | 1,41 | 1,34 | 1,79 | 1,73 |
Mn | 150 | 50 | 1,600 | 1,590 | <100 | 190 | 300 | 280 |
п. | 1,010 | 1,270 | 1 975 | 2,520 | 980 | 1,080 | 1,330 | 1,720 |
S | 95 | 130 | 215 | 320 | 60 | 80 | 160 | 200 |
Si | 350 | 490 | 1,150 | 1,190 | 500 | 620 | 500 | 620 |
* Анализы даны в частях на миллион по весу, за исключением C, который выражается в% по весу.![]() |
Меч 8 является доэвтектоидом и, следовательно, не может быть настоящей дамасской сталью Wootz, потому что такие стали не будут образовывать частицы Fe 3 C при охлаждении. Металлографическое исследование подтвердило это ожидание и показало, что рисунок поверхности, видимый на этой шпаге (рис. 2), обусловлен полосами феррита в перлитной матрице. Следовательно, этот меч не будет считаться подлинным дамасским мечом в нижеследующем обсуждении.
Микрофотографии поверхности и поперечных сечений остальных трех мечей показаны на рисунке 3.Микрофотографии поверхностей, по сути, представляют собой конические сечения полос, видимых на микрофотографиях сечений, и, как и ожидалось, ширина полос увеличена на видах поверхности.
Таблица II представляет собой сводку микроструктурных наблюдений сталей. Все три дамасских меча показывают расстояние между полосами в диапазоне 40-50 мм. Меч 7 содержит графитовые стрингеры, не показанные на микрофотографиях.
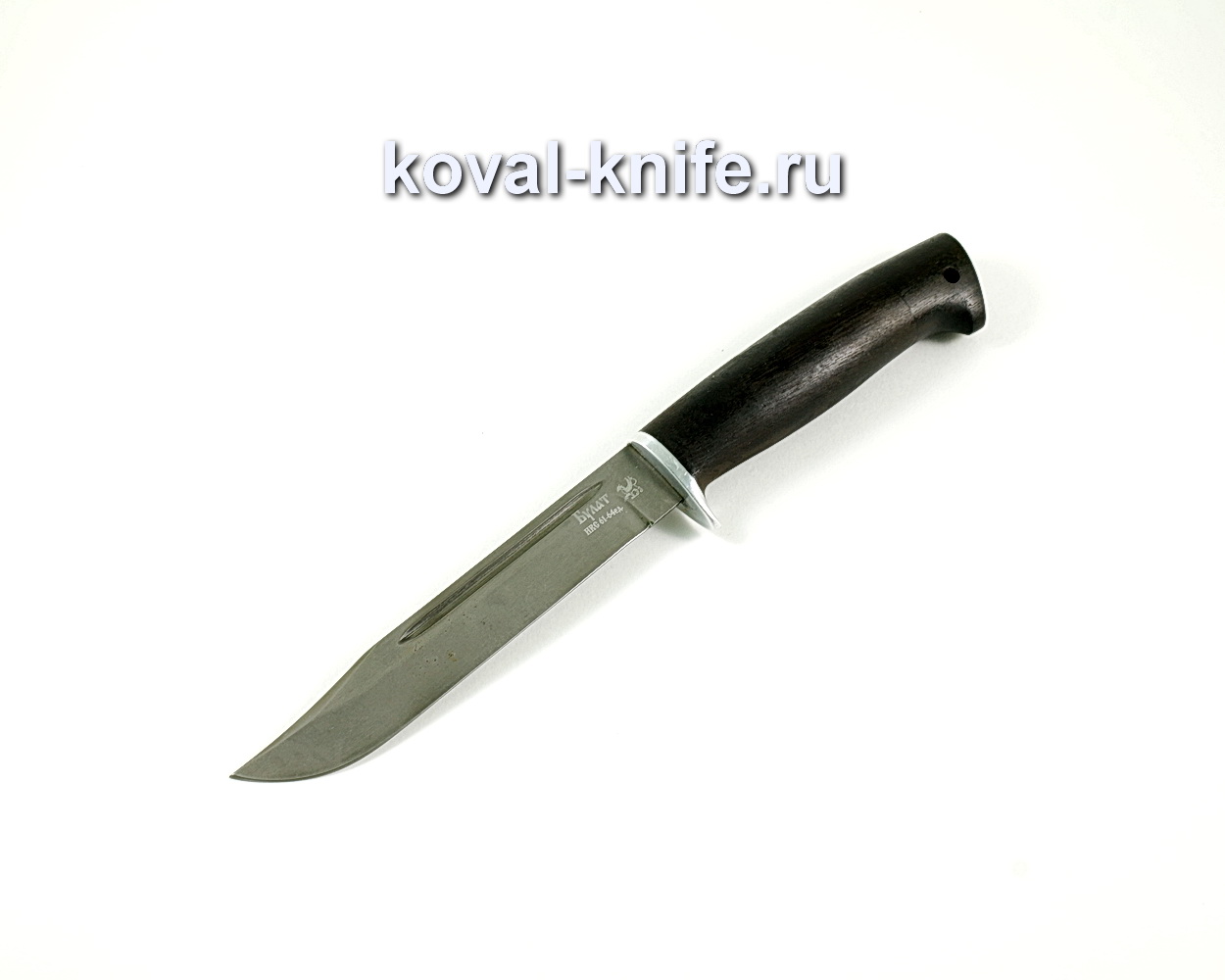
Данные твердости по шкале С по Роквеллу были взяты вдоль средней линии поперечных сечений всех четырех мечей, чтобы их более полно охарактеризовать. Был обнаружен большой разброс твердости, который представлен в Таблице II. Твердость коррелировала с микроструктурой матрицы. В матричной структуре лопаток произошел переход от перлита на тонком острие к разведенному эвтектоидному ферриту + цементит на толстом конце (толщина = 3-4 мм). Эти структуры согласуются с недавними кинетическими исследованиями эвтектоидной реакции в заэвтектоидных сталях. 19-20 Исследования показывают, что в двухфазных сталях (аустенит + Fe 3 C) преобразование разведенного эвтектоида (DET) преобладает при низких скоростях охлаждения, а перлитная реакция — при более высоких скоростях охлаждения; DET предпочтительнее, поскольку плотность частиц Fe 3 C в трансформирующемся аустените увеличивается. Следовательно, микроструктуры матрицы указывают на то, что лезвия охлаждались воздухом с преобладанием перлита около режущей кромки с более быстрым охлаждением. Преобладание матричной структуры DET в мечах 7 и 10, вероятно, является результатом большего количества межзонного Fe 3 C, присутствующего в этих мечах.
Таблица II. Данные о микроструктуре и твердости мечей Wootz Zschokke | ||
---|---|---|
Меч | Микроструктура | Диапазон твердости |
7 | Диффузные полосы вытянутых частиц Fe 3 C в матрице.![]() Значительные графитовые стрингеры. Расстояние между полосами = 42 мкм. Матрица: перлит, выступающий на 7 мм от режущей кромки; остаток = DET | R c = 32, Перлитная матрица R c = 8, матрица DET * |
9 | Очень четкие полосы частиц Fe 3 C в матрице. Расстояние между полосами = 50 мкм. Матрица: перлит, за исключением тонкой области DET около толстого конца | R c = 23, Перлитная матрица R c = 9, матрица DET * |
10 | Отчетливые полосы частиц Fe 3 C в матрице. Расстояние между полосами = 46 мкм. Перлит, выступающий на 3 мм от режущей кромки; остаток = DET | R c = 37, Перлитная матрица R c = 5, матрица DET * |
* Матрица с разделенной эвтектоидной трансформацией, дающая частицы Fe 3 C в феррите.![]() |
Из-за уникальной исторической ценности этих лезвий было проведено довольно тщательное исследование, чтобы охарактеризовать морфологию карбидных частиц, составляющих полосы, образующие дамасские узоры. Грани на образцах длиной 2 см, использованных для анализа эмиссионного спектрографа, были закреплены, отполированы и протравлены в пикрале. Эти лицевые поверхности вместе с поперечными и продольными сечениями мечей, подготовленными с помощью аналогичной металлографии, затем были исследованы с помощью цифровой камеры высокого разрешения.Программное обеспечение для анализа изображений использовалось для определения средней площади, максимального диаметра и минимального диаметра частиц Fe 3 C (Таблица III). Для каждого зарегистрированного измерения были исследованы три региона. Среднее значение из 20 самых больших несвязанных частиц в поле образца из 500-600 частиц было определено в каждой области, и в таблице представлено среднее значение трех средних измерений.

В мечах 7 и 10 частицы имеют преимущественно пластинчатую форму с тонким направлением, выровненным в плоскости ковки лезвий меча. Следовательно, площадь частиц на лицевой стороне меча обычно больше, чем на секциях. Стандартное отклонение данных постоянно находится в диапазоне 20-25%, так что различия в площадях на трех поверхностях проблематичны, тогда как различия в минимальном и максимальном диаметрах значительны. Для лезвий 7 и 10 максимальное / минимальное соотношение размеров частиц в среднем составляет около трех на поперечном и продольном сечениях и около двух на лицевых сторонах меча.Соотношения немного меньше для лопатки 9, что отражает более шаровидную форму частиц и наблюдение, что у продолговатых частиц нет хорошо выровненной широкой поверхности в плоскости ковки, как у лопаток 7 и 10.
Таблица III. Резюме измерений размера частиц Fe 3 C * | ||||
---|---|---|---|---|
Раздел | ||||
Меч | Размер | Лицо | продольный | Поперечный |
7 | Диаметр (макс.![]() Площадь | 13 / 7,4 88 | 16 / 4,6 69 | 10 / 3,230 |
9 | Диаметр (макс. / Мин.) Площадь | 11 / 5,7 59 | 12 / 5,6 65 | 11 / 3,9 41 |
10 (малый) | Диаметр (макс. / Мин.) Площадь | 13 / 6,6 76 | 16/4.8 62 | 15,4.9 63 |
10 (большой) | Диаметр (макс. / Мин.) Площадь | 54/27 1,300 | 44/14 590 | 46/15 640 |
Kard Blade | Диаметр (макс.![]() Площадь | 8,0 / 4,0 30 | ||
* Диаметр измеряется в мм; площадь в мм 2 . |
Крупные частицы в лезвии 10 представляют значительно большую площадь на поверхности лезвия, и можно ожидать, что они улучшат дамасский узор. Это усиление не было обнаружено на образце, повторно отполированном для этого исследования. Однако трудно вызвать потемнение матрицы на лезвиях 7 и 10 из-за большого количества феррита, производимого DET-структурой матрицы в этих лезвиях. При травлении по пикралю поверхности лезвия показывают очень слабый узор из-за этой проблемы, в отличие от блестящего рисунка на лезвии 9 с его перлитной матрицей.При протравливании трением с хлоридом железа матрица травится темнее, но все же не так темнее, как лезвие 9, как показано на рисунке 2. Возможно, что Зшокке, который отполировал лезвия для своего исследования 1924 года, использовал превосходную технику травления, которая была способный вытравить DET-матрицу лезвия 10 темнее и, таким образом, произвести более отчетливые полосы, что привело к заключению, что его дамасский узор лучше, чем у лезвия 9.

Таблица IV. Химический анализ семи лезвий Wootz Damascus * | |||||||
---|---|---|---|---|---|---|---|
Элемент | 7 | 9 | 10 | Старый B | Фигиль | Voigt | Кард |
С | 1,71 | 1.![]() | 1,79 | 1,51 | 1,64 | 1,00 | 1,49 |
Mn | 150 | <100 | 300 | 100 | 200 | 500 | 100 |
п. | 1,010 | 980 | 1,330 | 950 | 1,620 | 260 | 1,440 |
S | 95 | 60 | 160 | 53 | 85 | 115 | 90 |
Si | 350 | 500 | 500 | 470 | 460 | 975 | 500 |
Ni | 600 | 400 | 700 | <100 | 180 | <100 | 200 |
Cr | <100 | <100 | <100 | <100 | <100 | <100 | <100 |
Пн | <100 | <100 | <100 | <100 | <100 | <100 | <100 |
Cu | 1,750 | 900 | 1830 | 330 | 780 | 300 | 900 |
Al | <10 | <10 | 10 | 12 | 8 | 25 | 30 |
В | 145 | 50 | 270 | 40 | 40 | <10 | 60 |
Nb | <100 | <100 | <100 | <100 | <100 | <100 | <100 |
Pb | <10 | <10 | <10 | <10 | 10 | 10 | 40 |
Sn | <10 | 10 | <10 | <10 | <10 | 15 | <10 |
Ti | 9 | 11 | 6 | 13 | 16 | 7 | 19 |
Zr | <10 | <10 | <10 | <10 | <10 | <10 | <10 |
B | <1 | <1 | <1 | <1 | 2 | <1 | <1 |
Ca | 19 | 17 | 15 | 11 | 2 | 13 | <1 |
* Все анализы даны в массовых частях на миллион, за исключением C, который выражен в массовых процентах.![]() |
Клинок карда, упомянутый в таблицах III и IV, представляет собой нож в стиле персидского карда, недавно полученный от Л. Фигиэля. У него есть рукоять из моржовой кости (известная как шамони) и резьба на поверхности лезвия, которая примыкает к рукоятке, как показано на рис. 4. Он был приобретен в Индии Фигилом и считается подлинным дамасским клинком, произведенным в 18-ый век. Этот клинок был изучен для расширения базы данных и демонстрации возможности получения данных химического анализа с использованием эмиссионного спектрометрического анализа без постоянной потери дамасского рисунка.Электрическая дуга, используемая в этом анализе, создает обесцвеченный диск в форме кратера диаметром около 1 см на поверхности, на которой испаряются поверхностные атомы, а узор разрушается. Для успешного выполнения дуги лезвия необходимо очистить обе стороны лезвия, окружающие область кратера, наждачной бумагой для достижения надлежащего электрического контакта. На рис. 4а показана поверхность лезвия карда после легкой полировки наждачной бумагой и искры в эмиссионном спектрометре.

б |
Рис. 4. (a) Поверхность лезвия карты, показывающая царапины наждачной бумагой и следы ожога, нанесенные анализом эмиссионного спектрографа. (b) Область возле ожога после повторной отделки. |
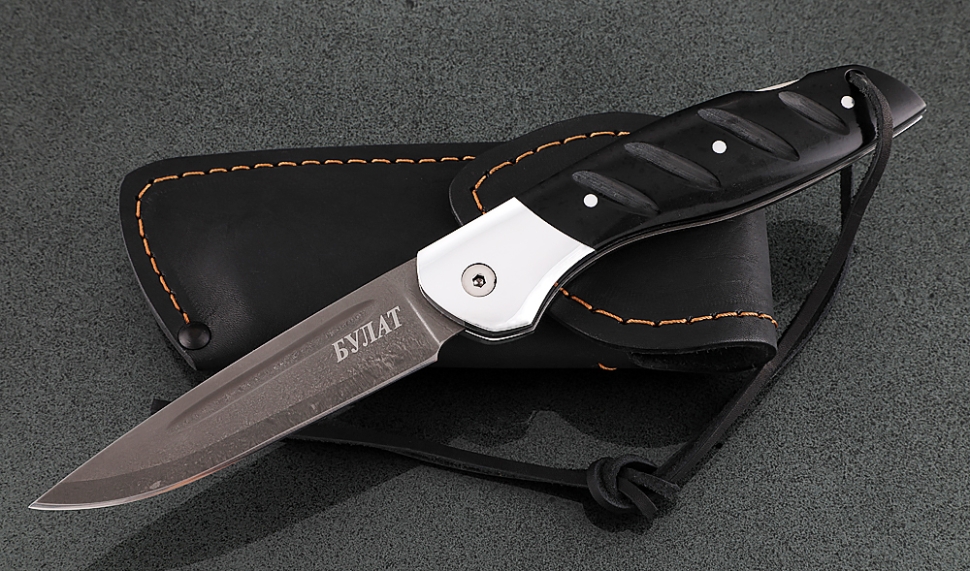

Рис. 5. (a) Продольный разрез после надреза, прорезанного поперек лезвия- (b) Деформация карбидных лент в результате ковки. (c) Схема поверхности лопатки, показывающая расстояние между полосами после потока ковки. |
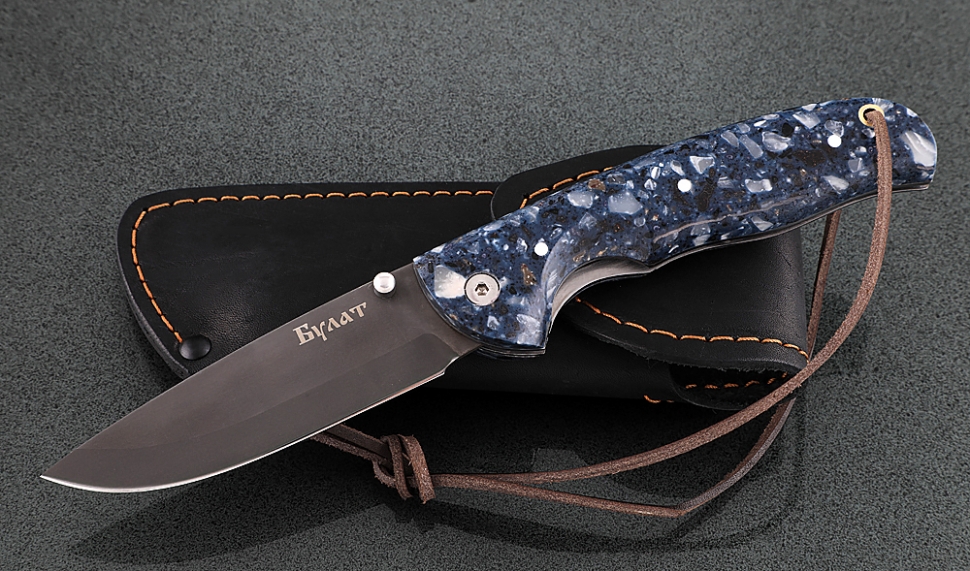
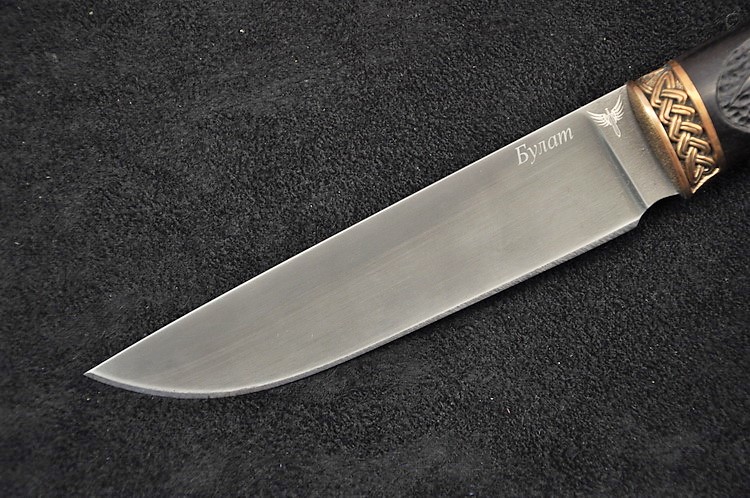
Эксперименты проводились на реконструированных лопастях из дамасского уотца, на которых рисунок лестницы и розетки был изготовлен как методом нарезания канавок, так и методом ковки. Узоры на лезвии на Рисунке 1 были сделаны с помощью техники вырезания канавок, и недавно были опубликованы подробные фотографии этого процесса (Рисунок 6a). 14 Эти узоры можно сравнить с аналогичными узорами «лестница / розетка», изготовленными методом штамповки (рис. 6b). Круговой узор на рисунке 6b (называемый розовым узором на древних лезвиях) был получен с помощью полого цилиндрического штампа, в то время как узор на рисунке 6а был получен путем удаления металла твердым сверлом специальной формы. В случае штампованных моделей гребни, образовавшиеся в результате осадки штампа, были удалены с помощью ленточно-шлифовального станка перед дополнительной ковкой.
Сравнение схем лестниц, полученных путем шлифовки и ковки, показывает почти идентичные характеристики (рис. 6).Фигиль указывает на то, что узор полос на нескольких примерах, представленных в его книге, сильно различается. 4 Таким образом, это исследование позволяет сделать вывод о том, что древние кузнецы создавали лестничные узоры, делая параллельные канавки на поверхности почти готовых лезвий путем ковки или резки / шлифования.
б |
Рисунок 6. Рисунок лестницы и розетки, образованный (a), канавкой, прорезанной в поверхности почти законченного лезвия, и (b) канавкой, выкованной на поверхности почти законченного лезвия. |
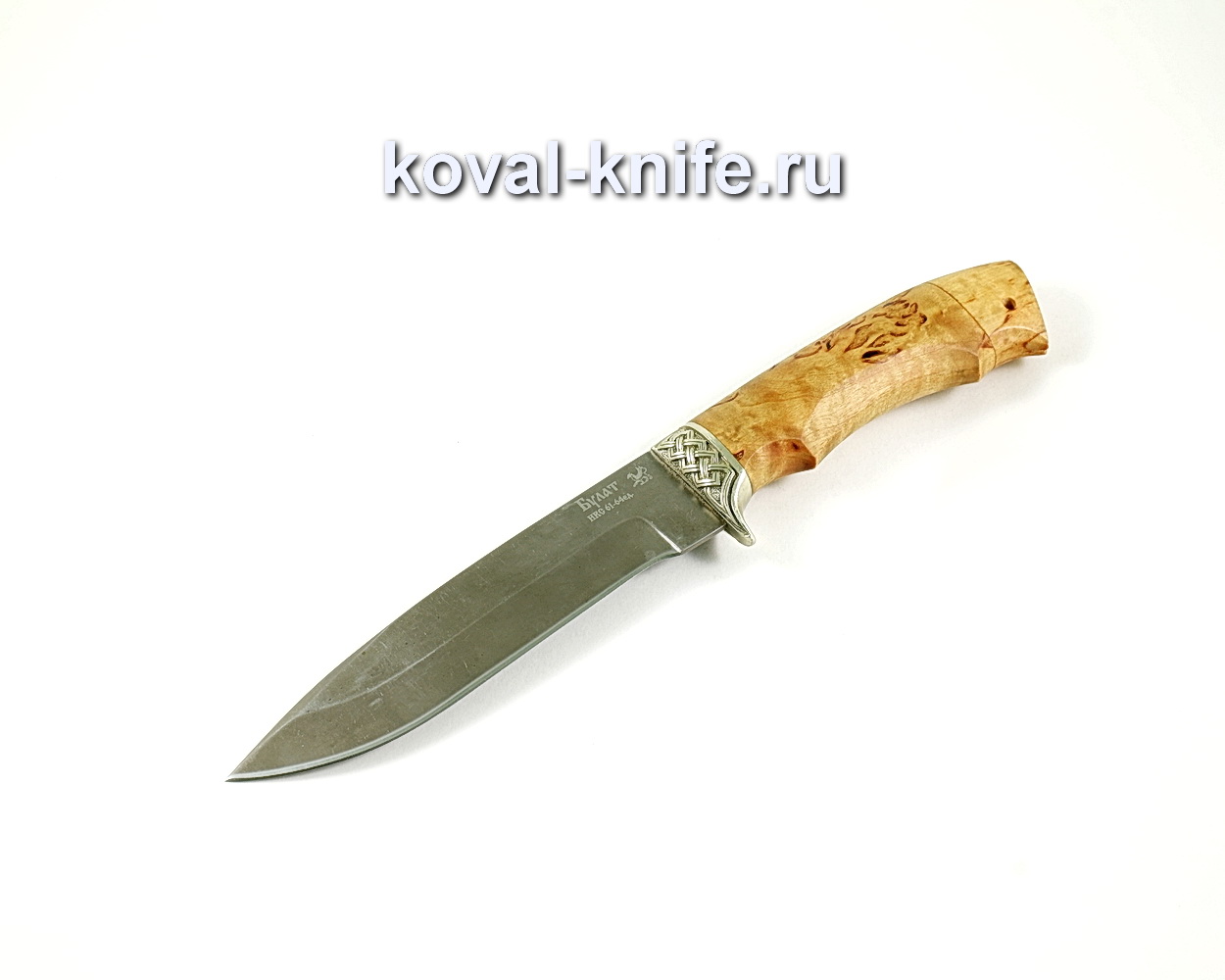
Хорошо известно 25-28 , что образование полос феррит / перлит в доэвтектоидных сталях является результатом микросегрегации элемента X в сплавах Fe-C-X, где X обычно представляет собой марганец, фосфор или добавку сплава. Для примера X = P установлено, что микросегрегация фосфора в междендритные области (IR) вызывает зарождение феррита преимущественно в IR.Если скорость охлаждения достаточно низкая, феррит растет как блочные аллотриоморфы на границах зерен и выталкивает углерод перед фронтом роста до тех пор, пока перлит не образуется между соседними IR. По-видимому, деформация прокаткой или ковкой весьма эффективна для выравнивания IR затвердевших слитков в плоские массивы, поскольку феррит выглядит как плоские полосы, параллельные плоскости деформации, разделенные полосами перлита. Ферритно-перлитные полосы меча 8, вероятно, образовались из-за этого типа полос, вызванного, скорее всего, микросегрегацией фосфора.
Был получен убедительный объем доказательств 16-18 , которые подтверждают теорию о том, что слоистые структуры в обычных заэвтектоидных дамасских сталях образуются по механизму, аналогичному механизму, вызывающему образование полос из феррита / перлита в доэвтектоидных сталях с одним важным отличием в феррите. / перлитная окантовка, полосы образуются за один термический цикл. Например, полосы феррита / перлита могут быть разрушены путем полной аустенизации при низких температурах (чуть выше температуры A 3 ) с последующим быстрым охлаждением и затем преобразованы за один нагрев до аустенита с последующим достаточно медленным охлаждением. 26 (Низкотемпературная аустенизация необходима, чтобы избежать гомогенизации микросегрегированного элемента X.) Карбидные ленты из дамасской стали Wootz разрушаются полной аустенизацией при низких температурах (чуть выше температуры A см ) с последующим охлаждением любой скоростью, медленной или быстрой. Однако, если сталь затем многократно подвергать циклической обработке до максимальных температур примерно 50-100 ° C ниже A см , полосы карбида начнут развиваться после нескольких циклов и станут прозрачными после 6-8 циклов.
Механизм образования карбидов, селективно сгруппированных вдоль ИК-диапазона во время циклического нагрева процесса ковки, не решен. Однако кажется вероятным, что он включает в себя процесс избирательного укрупнения, в результате чего частицы цементита, лежащие на ИК, медленно становятся больше своих соседей, лежащих на участках дендритов, и вытесняют их. Была представлена модель такого избирательного процесса огрубления. 17 Во время стадии нагрева каждого термического цикла более мелкие частицы цементита будут растворяться, и только более крупные частицы останутся при температуре ковки, которая находится чуть ниже температуры A см .Модель требует, чтобы сегрегированные примесные атомы, лежащие в ИК-диапазоне, избирательно снижали подвижность границ раздела цементит / аустенит в этих областях. В этом случае более крупные частицы будут появляться в ИК-диапазоне при температуре ковки. Они, вероятно, сохраняют свое доминирование при охлаждении, потому что нельзя было ожидать, что мелкие частицы, которые растворились, будут повторно образовывать ядро при охлаждении в присутствии соседних частиц цементита.
Эти находящиеся поблизости частицы будут обеспечивать места для роста цементита до адекватного локального переохлаждения, достаточного для зарождения новых частиц.
Основываясь на этом опыте, кажется вероятным, что доля индийской тигельной стали, которая была успешно выкована в поврежденные лезвия, была, вероятно, довольно небольшой; Большинство сохранившихся клинков из дамасского войлока, вероятно, имеют некачественный рисунок поверхности. Крэддок 29 пришел к такому же выводу на основе анализа литературы по сталям с дамасским узором. Результаты для четырех лезвий Moser, изученных Zschokke, подтверждают тот же вывод. Предположительно, эти клинки представляли собой высококачественные дамасцированные клинки с востока, и все же из четырех только меч 9 имеет высококачественные ленты Fe 3 C, характерные для лучших клинков из дамасского войса музейного качества.
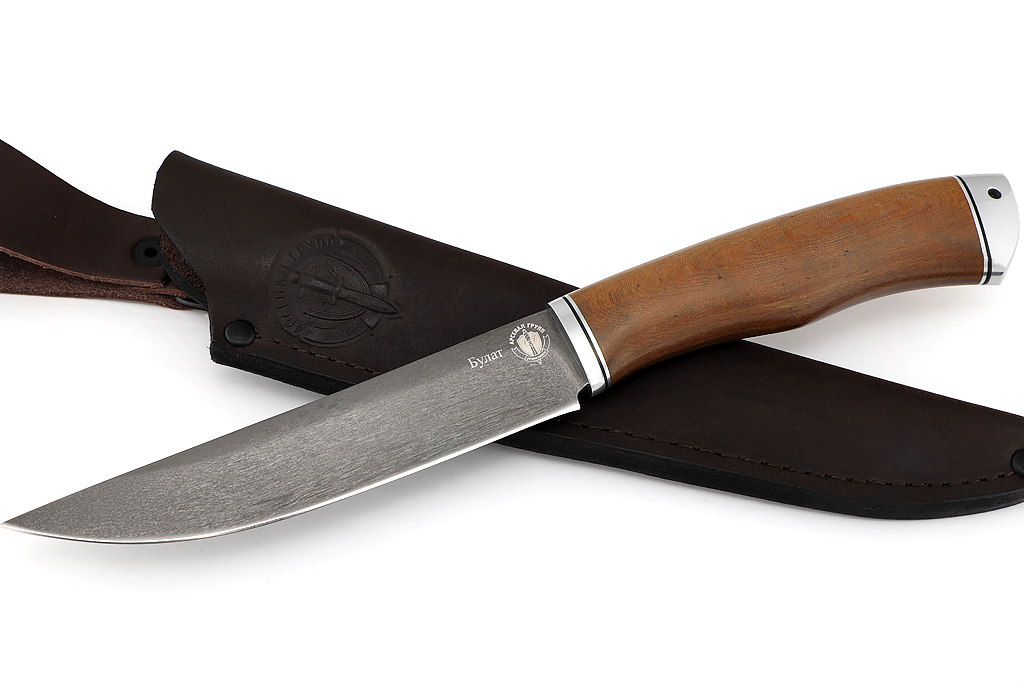
Одна из самых больших загадок дамасской стали заключалась в том, почему было утрачено искусство изготовления этих лезвий. Уровни ванадия составляют основу теории. Основываясь на наших исследованиях, ясно, что для создания дамасского узора дамасского клинка музейного качества кузнецу необходимо выполнить как минимум три требования. Во-первых, слиток Wootz должен был быть получен из рудного месторождения, которое обеспечивало значительные уровни определенных микроэлементов, в частности Cr, Mo, Nb, Mn или V.Эта идея согласуется с теорией некоторых авторов 30 , которые полагают, что лезвия с хорошими узорами были произведены только из слитков, сделанных в южной Индии, по-видимому, около Хайдарабада. Во-вторых, данные Таблицы IV подтверждают предыдущие знания о том, что лезвия из дамасского войлока с хорошими рисунками характеризуются высоким уровнем фосфора. Это означает, что слитки этих лезвий будут сильно короткими, что объясняет, почему кузнецы 19-го века Брэнта 9 в Париже не могли ковать слитки Wootz.Следовательно, как было показано ранее, успешная ковка 15 потребует разработки методов термообработки, обезуглероживающих поверхность, чтобы получить пластичный поверхностный обод, достаточный для удержания горячих коротких внутренних областей. В-третьих, кузнец, который разработал технику термообработки, которая позволила выковать слитки горячего короткого замыкания, возможно, еще не научился создавать поверхностные узоры, потому что они не появляются до тех пор, пока поверхность с декарбовой областью не стачивается с лезвий; этот процесс измельчения — непростое дело.
Кузнецы, которые производили высококачественные лезвия, скорее всего, держали бы процесс изготовления этих лезвий в строжайшем секрете, который передавался бы только своим ученикам. Кузнецы смогут научить учеников второму и третьему перечисленным пунктам, но первый пункт — это то, чего они не знали бы. Нет никакой разницы во внешнем виде между слитком с присутствующими надлежащими второстепенными элементами и слитком без них. Предположим, что в течение нескольких поколений все слитки из Индии происходили из рудного тела с надлежащим количеством присутствующих второстепенных элементов, и производились лезвия с хорошими узорами.Затем, по прошествии нескольких столетий, источник руды мог быть исчерпан или стал недоступен для кузнецов; следовательно, техника больше не работала. Со временем кузнецы, которые знали об этой технике, вымерли, не передав ее своим ученикам (поскольку она больше не работала), поэтому, даже если позже был найден аналогичный источник, знаний для его использования уже не было. Возможная обоснованность этой теории могла бы быть исследована, если бы были доступны данные об уровне карбидообразующих элементов в различных рудных месторождениях Индии, используемых для производства вутц-стали.
2. Б. Бронсон, «Создание и продажа Wootz», Archeomaterials, 1 (1986), стр. 13-51.
3. У. Ростокер и Б. Бронсон, «Доиндустриальное железо, его технология и этнология», Монография по археоматериалам № 1 (Филадельфия, Пенсильвания: Археоматериалы, 1990), с. 127.
4. Л.С. Figiel, On Damascus Steel (Atlantas, FL: Atlantas Arts Press, 1991).
5. C.S. Smith, История металлографии , главы 3 и 4 (Кембридж, Массачусетс: MIT Press, 1988).
6. C.S. Smith, «Damascus Steel», Science, 216 (1983), стр. 242-244.
7. Дж. Уодсворт, О.Д. Шерби, «Damascus Steel-Making», Science, 216 (1983), стр. 328–330.
8. Дж. Д. Верховен и Д. Т. Петерсон, «Что такое дамасская сталь?» Мат. Char., 29 (1992), стр. 355-341.
9. М. Бреант, «Описание процесса изготовления булатной стали», Annals of Philosophy, 8 (1824), стр.267-271.
10. П. Аносов, О. Булатах, Горный журнал (2) (1841), стр. 157-318.
11. N.T. Белаев, «Убер Дамаст», Металлургия, 8 (1911), стр. 449-456; «Damast, seine Struktur und Eigenschaften», Metallurgie, 8 (1911), стр. 699-704; «Damascene Steel», J. Iron and Steel Inst., 97 (1918), стр. 417-439.
12. Дж. Уодсворт, О.Д. Шерби, «Возвращение к булатско-дамасской стали», Прогр. Мат. Sci., 25 (1980), стр. 35-68.
13. Б. Зшокке, «Du Damasse et des Lames de Damas», Rev. Met., 21 (1924), стр. 635-669.
14. Дж. Д. Верховен и А. Х. Пендрей, «Тайна дамасского меча», Muse, 2 (2) (апрель 1998 г.), стр. 35-43.
15. J.D. Verhoeven и A.H. Pendray, «Эксперименты по воспроизведению узора лезвий из дамасской стали», Mat. Char., 29 (1992), стр. 195-212.
16. J.D. Verhoeven, A.H. Pendray, P.M. Берге, «Исследования лезвий из дамасской стали: Часть II, Разрушение и реформирование узора», Матем.Char., 30 (1993), стр. 187-200.
17. J.D. Verhoeven, A.H. Pendray, E.D. Гибсон, «Wootz Damascus Steel Blades», Мат. Char., 37 (1996), стр. 9-22.
18. J.D. Verhoeven и др., «Микросегрегация и образование полос в сверхэвтектоидной стали: дамасская сталь», ISS Trans., 25 (в печати).
19. E.M. Taleff et al., «Перлит в сверхвысокоуглеродистых сталях: термическая обработка и механические свойства», Met. Мат. Пер. A, 27A (1996), стр. 111-118.
20. Дж.Д. Верховен, Э. Гибсон, «Разведенное эвтектоидное преобразование (DET) в стали», Met. Мат. Пер. A, 29A (1998), стр. 1181-1189.
21. Д. Т. Петерсон, Х. Х. Бейкер, Дж. Д. Верховен, «Дамасская сталь, характеристика одного меча из дамасской стали», Матем. Char., 24 (1990), стр. 355-374.
22. Massalski, «Preparation de l’acier Damasse en Perse», Ann. Du Journal des Mines de Russie (1841), стр. 297-308.
23. H.T.P. J. duc de Luynes, Memoire sur la Fabrication de l’acier Foundu et Damassee (Париж: 1844 г.).
24. К. Пансери, «Дамасская сталь в легендах и реальности», Gladius, IV (1965), стр. 5-66.
25. Р.А. Grange, «Эффект микроструктурных полос в стали», Met. Мат. Пер. А, 2 (1971), стр. 417-426.
26. L.E. Samuals, Оптическая микроскопия углеродистой стали (Metals Park, OH: ASM, 1980), стр. 154-161.
27. S.W. Томпсон и П.Р. Хауэлл, «Факторы, влияющие на полосчатость феррита / перлита и происхождение крупных перлитных конкреций в доэвтектоидной пластинчатой стали», Матем.Sci. Tech., 8 (1992), стр. 777-784.
28. Р. Гросстерлинден и др., «Формирование перлитных полосчатых структур в ферритно-перлитных сталях», Steel Research, 63 (1992), стр. 331-336.
29. P.T. Крэддок, «Чугун, оцинкованный чугун, тигельная сталь: жидкое железо в древнем мире», Prehistory of Mining and Extractive Metallurgy, ed. P.T. Крэддок и Дж. Лэнг (Лондон: Британский музей, в печати).
30. Х. Марион, «Сварка образцов и натягивание лезвий мечей-Часть 2», J.Междунар. Inst. по сохранению хист. and Art Works, 5 (1960), стр. 52-60.
ОБ АВТОРАХ
J.D. Verhoeven в настоящее время является профессором материаловедения Департамент науки и техники в Айове Государственный университет. А.Х. Пендрей в настоящее время является президентом Гильдии мастеров ножей. МЫ. Даукш ушел с поста вице-президента и генерального директора Nucor. Стальная корпорация.
За дополнительной информацией обращайтесь к J.Д. Верховен, Университет штата Айова, факультет материаловедения и инженерии, 104 Wilhelm Hall, Ames, Iowa 50011; (515) 294-9471; факс (515) 294-4291; [email protected].
Авторские права принадлежат Обществу минералов, металлов и материалов, 1998 г.
Направляйте вопросы об этой или любой другой странице JOM по адресу [email protected].
Дамасская сталь — Материаловедение
Дж.Хорнинг
Крупный план лезвия из дамасской стали:
Около 500 г. н.э. кузнецы Ближнего Востока начали производить ножи и мечи с силой и режущими способностями, не имеющими аналогов ни у одной другой цивилизации того времени. Превосходство этого оружия исходило от стали, из которой его изготавливали. Сталь была тверже и могла удерживать лезвие дольше, чем другие стали. Утверждается, что одно из этих лезвий могло разрезать падающий шелковый шарф.Европейцы, увидевшие этот подвиг, были поражены: их оружие не способно ни на что подобное. Лезвия этого оружия также имели характерный волнистый рисунок. Поскольку изначально предполагалось, что сталь будет изготавливаться в Дамаске, сталь получила название «дамасская».
Многие люди в Европе видели эти стали и пытались воссоздать эффект путем обработки. Однако они не смогли раскрыть секрет, да и не смогли его раскрыть. Несмотря на то, что дамасская сталь пользовалась спросом, в 19 веке ее производство прекратили.Эту сталь производили в течение 11 веков, и буквально за одно поколение средства ее производства были полностью утеряны. Причина его исчезновения оставалась загадкой всего несколько лет назад.
Как выясняется, техника не пропала, она просто перестала работать. «Секрет» изготовления такого высококачественного оружия заключался не в технике кузнецов, а скорее в составе материала, который они использовали. Стальные слитки мастера получали из Индии.В XIX веке горнодобывающий регион, откуда добывали эти слитки, изменился. Эти новые слитки имели немного другие примеси, чем предыдущие слитки. Из-за нового состава новые слитки нельзя было выковывать в дамасскую сталь. Поскольку кузнецы не понимали природу материала, который они использовали, при изменении этого материала дамасская сталь была утеряна.
В 1998 году J.D. Verhoeven заново открыл композицию, которая позволила создать эту сталь. Его статью по этой теме можно найти на сайте JOM.Теперь снова можно покупать изделия из настоящей дамасской стали (а не из сваренной по образцу).
Что такое дамасская сталь? | Ф. Sharp
Легендарная дамасская сталь, неуловимый процесс ковки которой охраняли немногие избранные, пережила современное возрождение. На протяжении веков эта уникальная техника ковки считалась утерянной в истории, поскольку исчезли все известные традиции создания этой великолепно обработанной изысканной стали.К счастью, как для профессиональных металлургов, так и для любителей, современные технологии и металлургическая наука продвинулись достаточно далеко, чтобы ученые открыли современные способы воссоздания упругой и изысканно сложной дамасской стали.
Новое изобретение дамасской стали
Дамасская сталь, названная в честь нынешней столицы Сирии, изначально была недокументированной техникой ковки, которую использовали производители мечей на Ближнем и Среднем Востоке. Хотя некоторые свидетельства позволяют предположить, что дамасская сталь датируется 300 годом до н.C., первые упоминания о знаменитой стали относятся к периоду между 300 и 500 годами нашей эры.
Западная Европа впервые ощутила настоящий вкус дамасской стали во время крестовых походов 11 века, когда крестоносцы стали свидетелями явной остроты знаменитого клинка в действии в руках арабских воинов. Свирепость этих арабских воинов с их уникальными клинками породила легенды, распространившиеся по Ближнему Востоку и Европе.
Традиционную дамасскую сталь можно отличить по разнообразным завиткам на плоскости лезвия.Считается, что эти уникальные узоры изначально были получены из блоков индийской и шри-ланкийской вутц-стали. Эти стальные слитки содержали различные «примеси», такие как вольфрам и ванадий, которые в сочетании с традиционным индийским процессом плавки, а также с многочисленными раундами наслоения, используемыми для изготовления каждого лезвия, создали великолепные лезвия из дамасской стали.
Арабы веками успешно импортировали слитки Wootz. Однако по мере изменения границ, разорения войн и исчерпания резервов мир начал терять связь с мастерами этой бесподобной стали.К сожалению, к середине 18 века клинки исчезли, как и методы их создания.
Современное изобретение
К счастью, человечество просто стойкое и ностальгирующее. Металлурги, историки и коллекционеры со всего мира в сочетании с радикальным развитием технологий смогли реконструировать общий процесс ковки дамасской стали и, конечно же, по ходу дела добавили свои особые штрихи.
Статья в New York Times от 29 сентября 1981 года раскрыла, что два ученых из Стэнфордского университета, исследующие металлы со сверхпластичными характеристиками, случайно обнаружили секрет создания дамасской стали.Их исследования показали, что сталь, используемая для создания древних клинков, требовала высокого содержания углерода и относительно низкой температуры для процессов ковки и ковки, а затем требовалось быстрое нагревание с последующим быстрым охлаждением.
Помимо тех, кто любит кровавую историю, процесс «закалки» или охлаждения лезвий из древней дамасской стали — это пища для небылиц. Легенда гласит, что именно в процессе закалки лезвия приобрели свою магическую силу.Считалось, что фальсификаторы вонзили раскаленные лезвия в рабов, чтобы передать свою силу в лезвие, или что лезвия были «закалены» кровью дракона.
Хотя идея закаливания стали кровью для придания прочности может показаться нереальной, некоторые современные Ученые считают, что азот в крови на самом деле укрепил сплав.
В настоящее время известно, что дамасская сталь не является чистым металлом, поскольку она основана на различных примесях и высоком содержании углерода, что обеспечивает красоту, прочность и долговечность, которые открывают путь возрождению современной дамасской стали.Пластичность нагретого металла и долговечность охлаждаемого продукта позволяют использовать эту сталь в самых разных инструментах, от шестеренок и автозапчастей до стильных высококачественных кухонных ножей.
Гайки и болты из дамасской стали
Создание современной дамасской стали по-прежнему является видом искусства. От выбора подходящей стали с подходящими сплавами и содержанием углерода до различных температур для ковки, формовки и закалки стали — процесс является обширным и точным.
Например, F.N. Sharp использует комбинацию стали VG10 и VG2, чтобы показать узор с перьями из дамасской стали. VG10 содержит примерно 1% углерода и молибдена, 15% хрома, 1,5% кобальта и менее 1% ванадия, марганца и фосфора, в то время как VG2 состоит из примерно 1% углерода, 15% хрома и менее 1% меди, молибдена. и никель. Добавление марганца в VG10 дает сталь более темного цвета, а включение никеля в VG2 дает яркий серебряный оттенок.
Разные элементы из стали также имеют разное назначение.Например, добавление углерода улучшает твердость лезвия, удержание кромки, прочность на разрыв и сопротивление износу и истиранию, в то время как добавление марганца улучшает зернистую структуру, прокаливаемость, прочность и износостойкость. Добавление хрома, который является одним из наиболее важных элементов нержавеющей стали (для нержавеющей стали требуется не менее 13% хрома), улучшает жгут, прочность на разрыв и устойчивость к износу и коррозии.
При создании Дамаска две стали укладываются в чередующиеся слои для создания заготовок, которые затем скручиваются, складываются, нагреваются и забиваются молотком.После того, как заготовки были многократно согнуты и забиты молотком и горячий металл приобрел надлежащий оттенок темно-красного (светло-красный указывает на высокую температуру, которая приведет к растрескиванию металла), сталь затем закаливают для упрочнения конструкции. Наконец, мастер заканчивает процесс формовки, ударяя молотком, удлиняя и сплющивая металл, пока не будет обнаружен уникальный узор Дамаска.
Типы стали, из которых делают дамасские ножи
Сталь, необходимая для изготовления дамасских клинков, различается в зависимости от назначения клинка.Основными требованиями являются высокоуглеродистая сталь, нержавеющая сталь или их комбинация. Лезвия из высокоуглеродистой стали известны своими острыми кромками, а лезвия из нержавеющей стали известны своей непроницаемостью к окислению. Некоторые обычно используемые марки стали включают VG1, VG2, VG10, AUS8 и AUS10.
AUS8, японская сталь, производимая Aichi Foundry, представляет собой нержавеющую сталь, которая считается сталью среднего уровня по сравнению с высококачественной сталью VG10 или AUS10. Эта сталь имеет высокое содержание углерода, что позволяет использовать ее в качестве жесткого ножа, но, как известно, требует частой заточки.Эта проблема с удержанием кромки отличает ножи, изготовленные из этой стали, от ножей более высокого качества, изготовленных из стали VG10 или AUS10. Это позволяет сделать ножи из этой стали более доступными и простыми в массовом производстве.
AUS10 — это японская сталь, также производимая Aichi Foundry. Это нержавеющая сталь с твердостью от 58 до 60 по шкале Роквелла. Хотя его кромка остается лучше, чем у AUS8, для этой стали это все еще проблема. AUS10 похож на VG10 и обычно используется для создания высококачественных и кухонных ножей.
СтальVG1 — это японская сталь, созданная Takefu Special Steel Company, которая в основном является нержавеющей сталью, но имеет более высокое содержание углерода, чем большинство других сталей VG. Эта сталь была предшественницей VG10. В VG1, известном своей остротой и отличными кромками, отсутствуют добавки кобальта и ванадия, а это означает, что лезвия, изготовленные из этой стали, склонны к сколам и коррозии.
СтальVG2, также созданная компанией Takefu Special Steel Company, представляет собой твердую нержавеющую сталь с 62 по шкале Роквелла.Содержание углерода ниже, чем у VG1 и VG10, но его сочетание с другими металлами, такими как хром, никель и медь, делает его чрезвычайно устойчивым к коррозии.
VG10 — это знаменитая японская нержавеющая сталь, также созданная Takefu Special Steel Company, которая в сочетании с определенным рядом других металлов, включая кобальт, углерод, хром и ванадий, дает сталь, которая не только не подвержена окислению, но и отличается жесткий, результат от 60 до 62 по шкале Роквелла. VG10 также известен своей пугающе острой кромкой, что делает его одной из самых почитаемых сталей на рынке кухонных ножей.
F.N. Sharp с гордостью использует сталь VG2 и VG10 для создания наших исключительно острых и потрясающе красивых кухонных ножей из дамасской стали.
Насколько прочна дамасская сталь и подходит ли она для кухонных ножей?
Прочность любого изделия из дамасской стали напрямую зависит от того, какая сталь использовалась для изготовления лезвия. Качественная дамасская сталь обеспечит не только красивое изделие с уникальным и замысловатым дизайном, но и прочное лезвие с долговечной острой кромкой.
Carbon — настоящий герой в создании прочного и прочного ножа. Количество углерода, используемого в вышеописанных стальных сплавах, хотя и более мягкое для работы, затвердевает сильнее, чем обычная нержавеющая сталь, но при этом обеспечивает некоторую гибкость стали во избежание поломки.
Кухонные ножи Damascus нашли применение на домашних кухнях по всему миру. Красивые узоры делают их произведением искусства для кухни, а их исключительная резкость и удержание краев позволяют быстро справиться с повседневным приготовлением еды.
В зависимости от стали, использованной для ее создания, дамасская сталь обеспечивает идеальное соотношение углерода и микроэлементов нержавеющей стали, чтобы предложить идеальный баланс пластичности, коррозионной стойкости и остроты, что является ключом к требованию любого шеф-повара к универсальности использования ножа.
Уход и очистка дамасской стали
Лучший способ обеспечить долговечность дамасской стали — это следовать инструкциям производителя по уходу и очистке лезвия.Важно быстро мыть и сушить лезвие после каждого использования, чтобы удалить любой органический материал, который может разрушить сталь.
Если вы выберете лезвия из углеродистой дамасской стали, не менее важно полностью высушить излишки воды перед хранением лезвий, поскольку углеродные лезвия склонны к ржавчине и коррозии. Вам также необходимо регулярно затачивать их, чтобы сохранить острие. Чтобы усилить и сохранить красоту замысловатых узоров, еженедельно полируйте лезвие неабразивной полировальной тканью.Если лезвие предназначено для декоративных целей, а не для утилитарных, регулярная смазка лезвия маслом сохранит яркий блеск, который усилит дамасский узор.
Если вы не хотите заниматься дополнительным обслуживанием, лучше всего выбрать ножи из дамасской стали, изготовленные из нержавеющей стали. Нержавеющая сталь Damascus намного проще в обслуживании, и в зависимости от типа используемой стали она может быть непроницаемой для ржавчины и коррозии. Например, мы здесь, в F.N. Компания Sharp выбрала комбинацию нержавеющей стали VG10 и VG2, чтобы создать исключительно острые и простые в обслуживании ножи из дамасской стали для людей с большими жизнями — ведь ни у кого (занятые домашние повара) нет времени каждый день полировать и точить свои ножи.
Дополнительные советы о том, как держать кухонные ножи (и пальцы) в идеальном состоянии, можно найти в книге F.N. Руководство по безопасности кухонных ножей и выбору лучшей разделочной доски.
Король (или королева) кухни
Благодаря исследованиям и экспериментам энтузиастов клинков и ученых из Стэнфорда, дамасская сталь превратилась из потрясающе устрашающих клинков мавританской легенды в универсальный материал с бесконечным применением.
Из-за прочности и долговечности лезвий, выкованных с использованием техник дамасской стали, все большее число профессиональных поваров выбирают кухонные ножи из дамасской стали в качестве основных лезвий. Отчасти очарование этих кухонных ножей заключается в их необычайно острой кромке; однако новичку может быть сложно их правильно затачивать. Если вы позволите специалисту заточить ваши ножи из дамасской стали, они прослужат вам долгие годы.
Почувствуйте красоту кухонных ножей из дамасской стали вместе с F.Н. Шарп! Наши кухонные ножи премиум-класса доступны в наборах из 3 и 6 ножей, и каждый поставляется с бесплатным блоком для ножей, поэтому вам не придется беспокоиться о поиске лучшего варианта хранения ножей. Изготовленный из красивой древесины акации, F.N. Блок Sharp Knife Block оснащен внешними магнитами и внутренними гибкими стержнями для дополнительного хранения.
Нужны ножи для стейка? Они у нас тоже есть! И если вы просто ищете один нож, чтобы все сделать, нет лучшего соперника, чем F.N. Острый поварской нож.В любом случае, если вы ищете лучшие ножи из дамасской стали для своей кухни, тогда вам не стоит искать дальше, чем F.N. Острый!
Прочна ли дамасская сталь? · Вегас Фордж
Ножи, огнестрельное оружие и другие металлические изделия из дамасской стали становятся все более популярными среди мастеров и заново открывают для себя искусство. По мере того, как на рынке появляется все больше ножей из дамасской стали, покупатели и кузнецы, плохо знакомые с этим материалом, хотят знать: прочна ли дамасская сталь?
Не весь Дамаск создан равным
Дамаск состоит из нескольких металлов, которые сплавлены вместе, образуя единое целое.Контраст между типами стали создает эти отличительные узоры, особенно когда они протравлены и смазаны маслом.
Как и практически любой другой металлический продукт на рынке, прочность дамасской стали напрямую зависит от ее качества. Great Damascus изготовлен из высококачественных материалов, а процесс ковки тщательно продуман, чтобы гарантировать отсутствие пустот, трещин или риска расслоения во время работы с металлом.
Распространено заблуждение, что при работе с Дамаском риск расслоения — разделения слоев — просто то, с чем вам нужно иметь дело.
На самом деле это не так.
Дамаск хорошего качества не расслаивается. Конечно, любой кузнец может получить плохую партию, но любая марка дамасской стали, которая имеет повторяющиеся расслоения, вероятно, имеет слабые места в металле. Трещины, пустоты и расслоения — верный признак того, что вы работаете с Дамаском низкого качества, а прочность вашей стали, вероятно, невысока.
Спросите у окружающих, прежде чем выбрать марку Дамаска для использования в своих проектах, и если вы услышите несколько историй о расслоениях или пустотах в материале, вероятно, будет разумным выбрать марку получше.
Между тем, работаете ли вы со стальными заготовками из дамасской стали или покупаете готовое изделие из дамасской стали для использования…
Beware Cheap Damascus
Мусор — это мусор.
Если вы решите купить дешевый дамасский нож или бюджетные заготовки, скорее всего, вы получите что-то красивое, но не особенно практичное.
На рынке много дешевых подделок «Дамаск». Они немного дороже, чем обычные, бюджетные лезвия, но по цене намного ниже, чем лезвия из высококачественной дамасской стали из надежных источников.
В случае изделий из металла вы обычно получаете то, за что платите.
Создание надежного и прочного Дамаска требует времени и тщательного внимания к деталям. Как и в любом кустарном ремесле, такая добросовестность стоит дорого.
Если вы собираетесь приобрести качественный дамасский нож, вы можете разумно рассчитывать, что заплатите как минимум 200 долларов. Остерегайтесь «дешевых» лезвий в диапазоне от 50 до 100 долларов.
Относитесь к своему Дамаску правильно
Еще одна вещь, которая влияет на прочность вашего готового изделия из дамасской стали, — это то, как вы его термически обрабатываете.
Углерод и нержавеющая сталь Damascus подвергаются аустенизации и закалке при различных температурах, а некоторые виды Damascus также могут подвергаться крио-закалке. Если вы работаете с заготовками или заготовками из дамасской стали, обязательно подвергайте их термообработке в соответствии с типом металла.
Правильный отжиг, термообработка и отпуск куска дамасской стали — важная часть процесса, которая сильно влияет на качество конечного продукта.
Офорт Дамаск помогает выделить контрастные цвета в узоре.На плохо протравленных предметах часто бывают пятна.
Если у вас есть кусок дамасской стали, не забудьте о нем должным образом ухаживать. Держите металл смазанным и избегайте длительного хранения дамасских лезвий в кожаных ножнах, потому что кожа может удерживать влагу на металле, вызывая ржавчину. Чтобы узнать больше о полировке, заточке и чистке Дамаска, см. Это краткое руководство по уходу за Дамаском.
Так прочна ли хорошая дамасская сталь?
Высококачественная дамасская сталь — это , а не — самый прочный металл, который вы можете получить.Однако для большинства проектов и применений он достаточно прочен и долговечен.
Существуют некоторые современные металлические сплавы, которые невероятно прочны, и если вы работаете над проектом, который должен выдерживать самые суровые условия, которые только можно представить, вам, вероятно, следует использовать один из них.
Однако для чего-то вроде охотничьего ножа, головки клюшки для гольфа или даже компонента огнестрельного оружия хороший нержавеющий дамаск подойдет.
Damascus имеет дополнительное преимущество для таких вещей, как кухонные ножи, так как сочетание металлов создает микрозубцы на краю, которые делают ваше лезвие очень острым.Дамаск также имеет тенденцию оставаться острее дольше, что является несомненным преимуществом при нарезке ломтиками и кубиками.
Помните также, что есть разные виды Дамаска.
Карбон Дамаск мягче в работе, но после затвердевания он тверже нержавеющей стали. С нержавеющим дамаском обращаются немного по-другому, поэтому, если вы собираетесь с ним работать, убедитесь, что вы правильно обрабатываете его.
Идея о том, что дамасская сталь слишком мягкая, хрупкая или ненадежная для практического применения, связана с преобладанием дешевых, плохо изготовленных металлов.Если вы используете материалы хорошего качества из авторитетной кузницы, Дамаск достаточно прочен.