Токарный станок с ЧПУ: технические характеристики, описание, плюсы
ТокарныйТокарный станок с ЧПУ, технические характеристики которого использует электроника, может работать с высокой точностью. Применяю в мелкосерийном производстве.
В настоящей статье рассмотрим токарный станок с ЧПУ, технические характеристики которого задействованы специальными программами числового управления, а также целой системой приводов, двигателей. Рассматривая описание таких станков, нужно отметить, что они оборудованы специальными револьверными головками, которые обеспечивают автоматическую замену инструментов.
Токарные станки обычно применяют для обрабатывания всевозможных вращательных поверхностей сферического, цилиндрического или конического вида, нарезания внутренней резьбы. Такой агрегат может работать с достаточно высокой точностью. Применяются подобные устройства чаще при мелкосерийном производстве.
Функциональное оснащение токарных приспособлений дает возможность практично применять их в виде не дорогостоящих многозадачных систем, которые способны взять на себя выполнение различных производственных заданий при небольшой их себестоимости за минимально короткие сроки.
Об оснащении и некоторых особенностях
Основные узлы станка и жесткие закаленные направляющие, для гарантии выполнения точных работ, требуют к себе применения специальной импульсной смазки. Охлаждение их смазочно-охлаждающими жидкостями (СОЖ), подведенными непосредственно к каждому инструменту, дает доступность обработки детали, используя высокие режимы резки, что существенно увеличивает сроки их изнашиваемости.
К тому же для улучшения работы оператора:
- пиноль задней бабки управляется гидрофицированным прибором;
- производится автоматическое транспортирование стружки;
- патрон можно разжимать или зажимать механизированным способом;
- станок оснащен специальной борштангой для расточки глубоких отверстий и одной револьверной головкой.
Подобное оснащение оборудования под программным управлениеми и техническими характеристиками такого вида, существенно расширяет область их технологических возможностей, повышается класс точности.
О технических свойствах устройств типа РТ305М
Токарный станок РТ305М с ЧПУ, технические характеристики коего дают возможность выполнять ротационную вытяжку изделий цилиндрического, а также сферического или конического типа, может производить все необходимые действия токарно-производственного режима.
Технические свойства этого устройства, его жесткость дают возможность использования его в качестве твердосплавного или быстрорежущего инструмента для обрабатывания цветных или черных металлов. Основными техническими характеристиками таких установок являются:
- максимальный допуск диаметра детали, установленной над станиной, может быть до 500мм;
- детали, для обработки могут быть диаметром до 350мм;
- отверстия шпинделя допускаются диаметром до 110мм;
- максимальная толщина стального листа имеет предел прочности не более 120кг/мм2;
- максимальный вес деталей, устанавливаемых на оборудовании, может достигать до 3000кг;
- станина имеет ширину 560мм;
- мощность двигателя в киловаттах – 22.
При всех этих характеристиках, такая установка имеет цельную, литую из чугуна, станину, а жесткость ей придают ребра и коробчатые формы конструкции. Также к техническим характеристикам токарного станка относят наличие двух закаленных призматического вида направляющих, которые способны многократно уменьшать диапазон движения и направления каретки станка, что способствует повышению качества обрабатывания деталей.
О назначении
Такие специализированные токарно-давильные устройства программного управления обычно предназначаются для выполнения операций связанных токарной обработкой изделий. Станки с ЧПУ на основе устройств РТ305М, устанавливают для раскатывания деталей, у которых впоследствии завальцовывают и подрезают торцы.
О преимуществах устройств с ЧПУ
Главным преимуществом специального токарно-давильного станка с ЧПУ РТ305М, является высокий показатель степени автоматизации производства, так как вмешательство оператора устройства в его технологический процесс сведено минимально. Главной задачей обслуживающего персонала при числовом управлении установкой, является токарная обработка изделий, практически выполняя только лишь подготовительные и заключительные производственные операции, например:
- установка и закрепление детали;
- снятие уже обработанного изделия;
- техническая наладка инструментов.
Важно. Оператор наладчик, при подобном программном управлении, способен проводить техническое обслуживание одновременно нескольких таких токарных устройств с ЧПУ.
К преимуществам использования токарных приспособлений с числовым управлением также относят:
- производственная гибкость, при которой для обрабатывания разных изделий достаточно только заменить или скорректировать управляющую программу;
- бесконечное число повторяющих циклов при достаточно высоком уровне параметра обработки деталей;
- возможность такой обработки изделий, которая порой недоступна на обычных простых токарных устройствах;
- долгий срок эксплуатации токарных станков с ЧПУ, технические характеристики, которых на порядок выше, по сравнению с обычными станками, особенно при использовании автоматической подачи СОЖ (смазочно-охлаждающих жидкостей) в области резки.
О функциональности токарных устройств
На таких токарных станках ЧПУ благодаря наличию специальных программ, можно выполнять токарные операции в патронах, к примеру:
- расточку;
- обточку;
- нарезку резцами внутренней резьбы;
- обработку таких изделий как крышки, втулки.
Для этого в станке используют специальные центровые инструменты. Применяя закаленные шлифовальные направляющие скольжения можно делать обработку деталей, имеющих большую толщину снимания припуска. При этом все направляющие плоскости шлифуются, имеют специальное антифрикционное покрытие, позволяющее достигать наиболее точного расположения необходимых узлов, перемещений.
vseochpu.ru
Станок 16К20Ф3: технические характеристики и описание
Токарно-винторезное оборудование 16К20Ф3, технические характеристики которого рассмотрим ниже, создано на базе агрегата 16К20, используется преимущественно в мелкосерийном производстве. Оба станка имеют унифицированную конструктивную часть и общий принцип работы. Установка позволяет обрабатывать внешние и внутренние поверхности заготовок, длиной до 1000 миллиметров. Числовое программное обеспечение дает дополнительные возможности и облегчает обслуживание агрегата.
Из чего состоит?
Технические характеристики 16К20Ф3 обусловлены конструкцией и кинематической схемой станка. Агрегат выполнен в традиционной компоновке, которая соответствует универсальным стандартам, а также допускает производство широкого спектра операций.
Комплектующие элементы оборудования:
- Остов (станина).
- Рама.
- Каретка суппорта.
- Резцедержатель поворотного типа.
- Задняя и шпиндельная бабка.
- Автоматическая передающая коробка.
- Направляющие элементы.
- Электромагнитные муфты.
- Поперечные и продольные приводы.
- Гидравлический усилитель.
Принцип работы
Станок 16К20Ф3, технические характеристики которого позволяют выбрать до 9 скоростей вращения вала, работает следующим образом:
- Металлическая деталь крепится в шпинделе, приводимым в действие посредством клиноременной передачи от электрического мотора.
- Скорость обработки корректируется при помощи автоматической коробки и узла шпинделя.
- Коробка-автомат оснащена шестью электромагнитными муфтами, комбинированное включение которых позволяет выбрать требуемую скорость.
- Для увеличения или уменьшения оборотистости используются зубчатые колеса шпиндельной бабки. Они управляются вручную, регулируют до 12 позиций.
- Каретка установки приспособлена к продольному перемещению с применением электромагнитного привода.
- Поперечная сдвижка суппорта и резцедержателя производится через привод, зубчатое колесо и ходовой винт.
- Поворотный резцедержатель может монтироваться в шести положениях со сменой углов обработки и горизонтальной оси вращения плоскости. Кроме того, в этих манипуляциях участвует крепление поперечного суппорта.
- На резцедержателе позиционируется инструментальная головка, рассчитанная на использование не более шести резцов, обрабатывающих заготовку согласно заданной программе.
Гидравлический привод
Этот узел токарного станка 16К20Ф3, технические характеристики это подтверждают, обеспечивает все основные процессы, связанные с функционированием рабочих элементов. Гидропривод состоит из следующих частей:
- Пары гидроусилителей.
- Регулирующего насоса.
- Привода.
- Резервуара с маслом.
- Контрольной аппаратуры.
Маркировка
Токарный агрегат 16К20Ф3, технические характеристики которого рассмотрим далее, имеет маркировку. Ее расшифровка выглядит следующим образом:
- Индекс «1» – токарный.
- 6 – винторезный.
- К – производство.
- 20 – показатель высоты по центрам в сантиметрах.
- Ф3 – оборудование ЧПУ.
Оборудование этой категории имеет стандартную мощность в пределах 10-11 кВт, класс точности соответствует ГОСТУ 8-82-П.
Станки с ЧПУ 16К20Ф3: технические характеристики
Параметры рассматриваемого оборудования:
- Габариты – 3,7/2,2/1,65 м.
- Масса – 400 кг.
- Количество скоростей –22.
- Диаметр отверстия – 53 мм.
- Центр пиноли – Морзе 5.
- Рабочий диапазон – от 12,5 до 2000 оборотов в минуту, в зависимости от выбранной скорости.
- Размер шага – 0,01-40 мм.
- Высота резца – 25 мм.
- Продольные/поперечные ходы – 5000/7500 мм/мин.
Описание
Станок токарный 16К20ФЗ, технические характеристики которого указаны выше, оборудован чугунной станиной, подвергающейся шлифовке, что обеспечивает длительный период эксплуатации. В качестве основного привода используется электрический двигатель мощностью 11 кВт. Он гарантирует крутящий момент в пределах до 800 Нм. Это позволяет корректировать обработку заготовки с максимальной точностью до необходимых размеров.
Шпиндель агрегата имеет отверстие диаметром 55 мм с возможностью фиксации штыревых деталей различного диаметра. Специальные револьверные головки используются для проведения особых операций, значительно расширяя возможности токарного оборудования. Этот узел более всего подвержен изнашиванию, поскольку происходит деформация планетарного редуктора в виде выкрашивания зубцов или разрушения эксцентрика. Избежать таких последствий поможет регулярный контроль состояния механизмов и своевременные профилактические работы. Смазка деталей осуществляется при включении оборудования направлено на различные элементы. Программное управление в автоматическом режиме определяет цикл подачи смазочной смеси на узлы оборудования. Имеется возможность запуска этой операции вручную. При этом запрограммированный цикл не нарушается.
Универсальность
Технические характеристики токарно-винторезного станка 16К20Ф3 позволяют использовать его для проведения следующих операций:
- Сверления отверстий различного диаметра.
- Обработки заготовок с торцевых частей.
- Зенкерования.
- Резьбовой нарезки.
- Расточки и отделки поверхностей конического и фасонного типа.
В качестве защиты винторезных пар выступают специальные ограничители, которые позволяют предотвратить преждевременную поломку механизмов. Модернизация рассматриваемых агрегатов заключается в оснащении комплектами ЧПУ отечественного и зарубежного производства с заменяемыми системами электрооснащения. Переоборудование дает возможность усилить мощность в 2-3 раза, в зависимости от состояния агрегатов. Все эти решения повышают производительность оборудования, сокращают режим трансформации заготовок. Модернизацию желательно производить одновременно с капитальным ремонтом.
Что дает усовершенствование?
Токарно-винторезный станок 16К20Ф3, технические характеристики которого можно улучшить путем модернизации тремя способами:
- Путем полной модернизации.
- Улучшение комплектующих и рабочих приспособлений.
- Реорганизация тягового оборудования.
Модернизация дает возможность увеличить число диапазонов обработки деталей, а также точность проведения манипуляций.
Для максимального повышения рабочего ресурса оборудования используют систему адаптивного управления. Она позволяет выключать агрегат при критических нагрузках, а также способствует следующим показателям:
- Снижению срока отделки деталей.
- Увеличению периода службы комплектующих элементов.
- Понижению случаев выхода из строя оснастки.
- Повышению общей работоспособности оборудования.
Технические характеристики токарного станка 16К20Ф3 с ЧПУ позволяют менять нагрузку на шпиндель. При этом имеется возможность корректировки подачи используемого инструмента, с учетом типа материала обрабатываемой заготовки. Это способствует увеличению срока службы всех деталей агрегата.
ЧПУ
При использовании числового программного обеспечения операции по обработке заготовок выполняются при помощи заранее установленных программ. Они дают возможность откорректировать информацию, поданную с операторского пульта, а также использовать кассеты внешней памяти. Итоговые данные выводятся на специальный дисплей, после анализа которых, можно принять решение по настройке последующего процесса.
Автоматизация процесса сопровождается 6-ю, 8-ю или 12-ю позициями, позволяющими менять диаметр обработки или ось поворота по горизонтали. Рабочая головка оборудована диском, на который можно монтировать три осевых и шесть радиальных элементов. Кроме того, она может эксплуатироваться с 8-12 блоками под различный инструмент.
Повысить эффективность станка 16К20Ф3, технические характеристики и описание которого приведены выше, можно дополнительно модернизировать посредством смены кинематической схемы либо установки современной энергосберегающей конструкции. Значительно расширяет функционал рассматриваемого агрегата комплекс ЧПУ. Благодаря нему улучшается точность и скорость обработки деталей, а также режим отделки. Станки с ЧПУ имеют диапазон продольных и поперечных перемещений – 0,005 и 0,01 миллиметров, соответственно.
fb.ru
Плоскошлифовальный станок: технические характеристики
Плоскошлифовальными называются особые станки, используемые для очистки поверхности изделий от ненужных слоев. Чаще всего этот вид оборудования используется для обработки деревянных заготовок. Однако плоскошлифовальный станок по металлу — это также довольно-таки распространенный вид агрегатов. Используются они для обработки деталей из стали, алюминия, меди и т. д.
Немного истории
Изобретен плоскошлифовальный станок был в 1874 году в Америке. Первоначально в качестве рабочего инструмента в нем использовались круги, вырезанные из цельных кусков разного рода абразивных пород. Поскольку менять их приходилось часто, особого распространения такие агрегаты в то время не получили. Однако уже в 1893 году, после изобретения искусственных абразивов, плоскошлифовальные станки стали очень востребованными и популярными.
Для чего используются
Применяется оборудование этого типа для:
обдирки заготовок;
резки и отрезки;
точной обработки поверхностей деталей;
очистки зубьев колес;
чистовой обработки резьбы и т. д.
Основной особенностью этих станков является то, что они предназначены именно для чистовой отделки деталей с плоской поверхностью. Для доводки формы заготовки их не используют.
Принцип действия
Работа оборудования этого типа построена на очень простом принципе. Обточка заготовки производится посредство вращающегося с большой скоростью абразивного круга. В движение последний приводится при помощи электродвигателя. При этом обработка может производиться как поверхностью круга, так и его торцом. Сегодня в продаже существуют в том числе и станки этого типа с двумя кругами, отличающиеся очень большой производительностью.
Функционирует в большинстве случаев плоскошлифовальный станок следующим образом:
Электродвигатель вращает шестеренчатый насос, нагнетающий масло в каналы гидравлической системы.
Последнее, попав в коробку переключения, подходит к пусковому крану.
При включении крана масло перетекает в цилиндр подачи детали и сдвигает поршень, а заодно и скрепленный с ним стол.
В конце своего хода стол поворачивает кран переключателя, отвечающий за направление масла в то или иную сторону золотника цилиндра подачи.
Направление тока масла при этом меняется на обратное и стол начинает передвигаться вслед за ним.
Особенности конструкции
Шлифовальные станки этого типа обычно отличаются повышенной прочностью, поскольку обрабатываемые на них детали в большинстве случаев имеют значительный вес. Наибольшая допустимая масса заготовки составляет 600 кг, а высота — 280 мм.
Колонна станка этого типа крепится на тумбе, отлитой в одно целое со станиной. В средней своей части она имеет углубление, по обеим сторонам от которого расположены направляющие. По последним движется каретка. На ней закреплены горизонтальные направляющие, предназначенные под шпиндельную бабку.
Заготовка в таких станках крепится либо непосредственно на столе, либо с использованием специальных магнитных зажимов. Иногда для фиксации детали применяются и механические приспособления.
Стол плоскошлифовальный станок может иметь круглый или прямоугольный. В зависимости от этого выбирается способ подачи детали: продольная или круговая. Иногда оборудование этого типа используется для обработки деталей очень большой площади. В этом случае применяется поперечная методика подачи. Поверхность стола плоскошлифовального станка оснащается специальным фторопластовым покрытием. Это обеспечивает плавность его движения и износоустойчивость.
Шпиндель плоскошлифовального станка может располагаться по-разному. По этому признаку оборудование подразделяют на вертикальное и горизонтальное. Каждая из этих групп имеет как свои достоинства, так и недостатки.
Как и любые другие, плоскошлифовальные станки обозначаются условными заводскими номерами. Определить по такой надписи функционал оборудования невозможно. Для этого нужно изучить паспорт плоскошлифовального станка.
Шлифовка деталей торцом
Существует несколько видов подобной обработки деталей:
Многопроходная. В этом случае заготовка устанавливается на рабочую поверхность и движется со скоростью порядка 45 м/с. При этом деталь передвигается под кругом по нескольку раз, а последний постепенно подается на глубину до тех пор, пока не будет снят слой металла или дерева необходимой толщины.
Однопроходная. Эта методика используется на станках с круглым столом. В данном случае инструмент подается на всю глубину вертикально за один проход.
Двухсторонняя. На таком оборудовании одновременно обрабатываются сразу оба торца заготовки.
Шлифовка периферией
Этот способ используют для обработки деталей, изготовленных из не слишком жестких материалов. Периферийное шлифование бывает:
Глубинным. В данном случае за каждый цикл обработки снимается очень большой слой материала.
С врезной подачей. Эта методика применяется для обработки тех заготовок, у которых высота больше чем ширина.
С прерывистой подачей. Эта технология позволяет производить максимально качественную шлифовку даже очень больших заготовок.
Круги плоскошлифовальных станков
Изготавливаться эти инструменты могут в виде шайбы или цилиндра. Состоят они из зерен разного рода абразивных материалов высокой жесткости, скрепленных между собой керамической, вулканитовой или бакелитовой связкой. Шлифовальные круги могут иметь разные размеры и профиль. Подбираются они в зависимости от марки станка и типа обрабатываемых на нем деталей.
Дополнительное оборудование
Очень часто к плоскошлифовальному станку подключается такое оборудование, как охладительный агрегат. Он необходим для того чтобы снижать температуру рабочих органов станка в процессе обработки деталей. Это позволяет значительно продлить срок их службы.
Также в станках этого типа может использоваться такое дополнительное оборудование, как подающий и принимающий рольганг, инверторы скорости, разного рода агрегаты для очистки охлаждающей жидкости и т. д.
Технические характеристики
Станки этого типа могут различаться по мощности, производительности и функционалу. Схемы плоскошлифовальных станков представлены на этой странице. Технические характеристики у этого вида оборудования могут быть разными. Далее посмотрим, какие параметры могут иметь такие станки на примере очень популярной модели 3Г71. Этот агрегат предназначен только для периферийного шлифования заготовок. В его конструкцию входят станина, колонка с бабкой, рабочий стол и гидравлическая система.
Из представленной ниже таблицы можно узнать, какие имеет этот станок плоскошлифовальный технические характеристики.
Параметр | Значение |
Минимальный размер обрабатываемой детали высота/ширина/длина | 320/200/630 мм |
Максимальная масса заготовки | 100 кг |
Максимальное расстояние от оси шпинделя до стола | 80 мм |
Размеры стола | 630х200 мм |
Перемещение стола продольное/поперечное | 70-710/235 мм |
Диапазон скоростей продольного перемещения | 5-20 м/мин |
Скорость автоматической поперечной подачи | 0.7 м/мин |
Размеры шлифовального круга | 250х25х75 мм |
Частота вращения круга | 3740 об/мин |
Габариты станка | 1870х1550х1980 мм |
Масса станка | 1900 кг |
Несмотря на то что разработан плоскошлифовальный станок 3Г71 были еще в СССР, он до сих пор используется на производствах и считается вполне производительным и надежным. На его основе сконструированы более совершенные и дорогие станки 3Г71М.
fb.ru
Токарный станок 1а616 – технические характеристики, паспорт
Токарный станок 1А616 имеет давнюю историю: выпускать его начали еще в середине 50-х годов прошлого века. Выпуском данного станка, который многие специалисты узнают даже по фото, занимался Средневолжский станкостроительный завод. Эту модель и сегодня можно встретить на многих производственных предприятиях
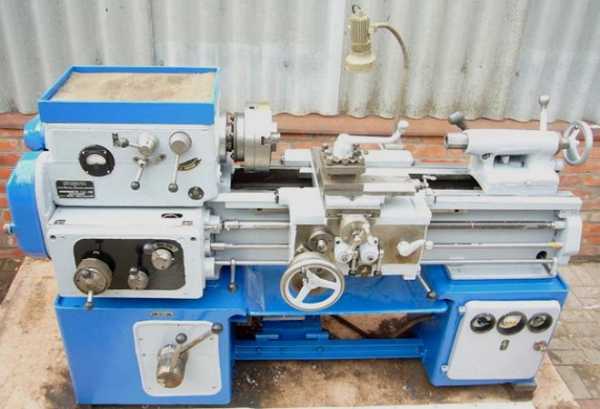
Токарно-винторезный станок 1А616
Характеристики станка
Токарно-винторезный станок 1А616, конструкцию которого разработали более 60-ти лет назад, преимущественно используется для обработки заготовок, отличающихся небольшими габаритными размерами. Среди технических характеристик станка можно выделить следующие:
- максимальная длина выполняемого обтачивания — 660 мм;
- максимальная длина обрабатываемой заготовки — 710 мм;
- максимальный диаметр заготовки, располагаемой над суппортом — 180 мм, размещенной над станиной — 320 мм;
- масса оборудования — 1500 кг;
- диаметр сквозного отверстия, выполненного в шпинделе — 35 мм;
- резьбовой конец шпинделя выполнен в соответствии с ГОСТ 12593-72 и относится к типу 6К;
- прямое, а также обратное вращение шпинделя может осуществляться в интервале 9–1800 об/мин, регулировка данного параметра может выполняться по 21 ступеням;
- габаритные размеры оборудования — 2135х1225х1220 мм.
Более подробно все технические характеристики токарного станка 1А616 представлены ниже в формате таблиц:
- Общие характеристики и основные размеры
- Характеристики суппорта
- Характеристики резцовых салазок, шпинделя, задней бабки
- Характеристики электродвигателя, ремней, подшипников шпинделя, муфт
В поперечном направлении суппорт токарного станка перемещается по винту вручную, предельная величина такого перемещения составляет 195 мм. Продольное перемещение суппорта обеспечивается винтом или валиком, его максимальное значение может составлять 670 мм. Характеристики рабочих подач 1А616 при этом одинаковы и могут выбираться в пределах от 0,065 до 0,91 об/мин.
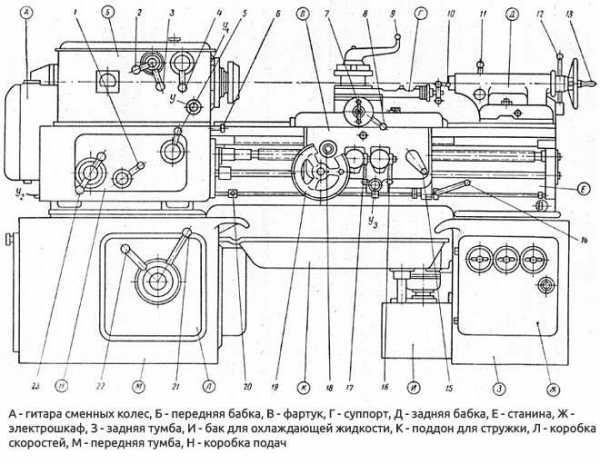
Основные узлы станка 1А616
Даже без использования сменных зубчатых колес на токарно-винторезном станке данной модели допустимо нарезать высокоточную резьбу со следующими характеристиками:
- питчевую — с шагом 2–128 питч;
- модульную, шаг которой находится в пределах 0,25–5,5 мм;
- дюймовую — с шагом 1–56 ниток на дюйм;
- метрическую — с шагом 0,5–24 мм.
Обрабатываемые детали можно фиксировать в обычном патроне токарного станка или использовать для этого пневматические и гидравлические зажимные устройства.
Конструкция и принцип работы
В конструкции 1А616 можно выделить следующие основные узлы:
- тумбы — передняя и задняя;
- задняя бабка;
- передняя бабка, где находится несколько механизмов: реверсивное устройство, звено, отвечающее за повышение шага, переборный механизм;
- блок, состоящий из сменных колес;
- шкаф, в котором размещена электрическая система;
- фартук, в котором находится механизм подач;
- несущая станина;
- коробка подач;
- система, отвечающая за охлаждение режущего инструмента;
- коробка переключения скоростей;
- поддон, где собирается стружка и отработанная охлаждающая жидкость.
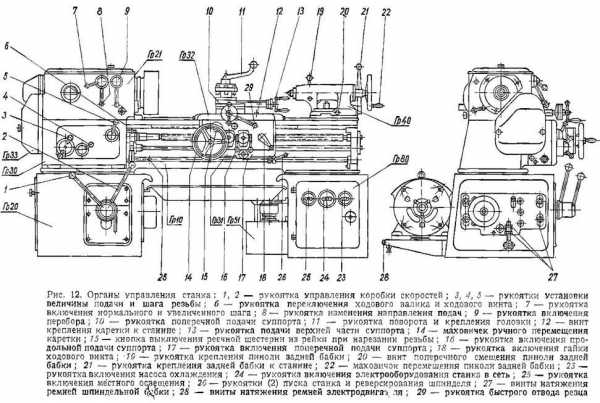
Органы управления станка 1А616 (нажмите, чтобы увеличить)
Принцип работы данной модели токарного станка можно представить в виде следующей схемы.
- Заготовку, которую необходимо обработать, фиксируют в патроне станка или между его центрами.
- Резцы закрепляются в резцедержателе, размещенном на суппорте агрегата. Одновременно в таком резцедержателе можно закрепить до 4 резцов.
- Если в заготовке необходимо выполнить сверление, расточку отверстий или нарезание внутренней резьбы, то соответствующий инструмент закрепляют в пиноли задней бабки.
- Обработка на 1А616, как и на токарно-винторезных станках других моделей, обеспечивается за счет комбинирования двух движений: поступательного перемещения режущего инструмента и вращения детали. Благодаря сочетанию таких движений на станке можно выполнять обработку деталей цилиндрической, конической и фасонной конфигурации, винтовых поверхностей, торцов заготовки.
Передача вращения на шпиндель устройства и, соответственно, на обрабатываемую заготовку осуществляется при помощи ременного шкива, установленного между его опорами. Можно менять приводной клиновой ремень, если в этом возникла необходимость, не снимая шпиндель, что обеспечивает специальное устройство его задней опоры. В конструкции токарного станка этой модели реализован принцип раздельной передачи движения на его суппорт, который может перемещаться за счет ходового винта или ходового валика. В обмотку двигателя оборудования подключен статор постоянного тока, что позволяет обеспечить эффективное торможение привода агрегата.
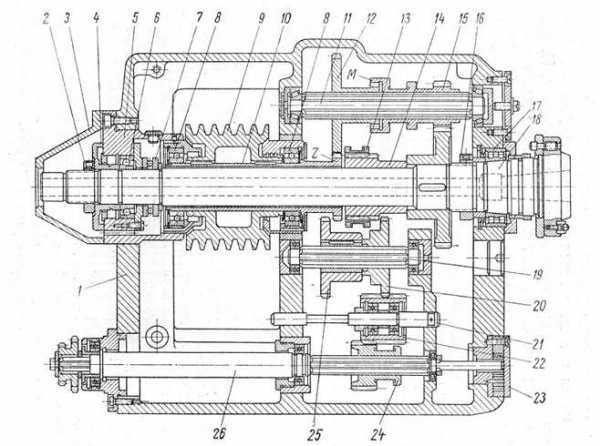
Передняя бабка 1А616
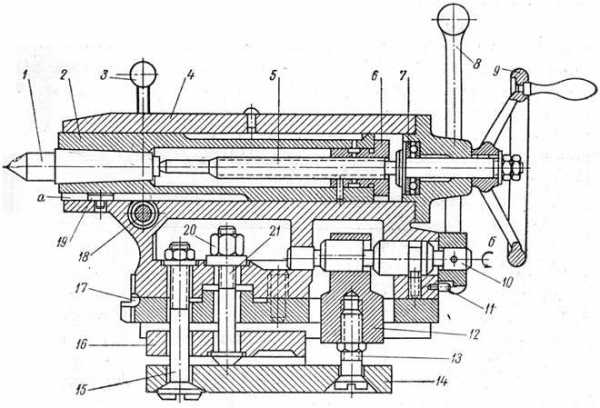
Задняя бабка 1А616
Электрическая система станка
Электросхема токарного станка данной модели включает в себя следующие элементы:
- три предохранителя плавкого типа;
- выключатель, устанавливаемый на вводе;
- лампу для освещения рабочей зоны;
- реле напряжения;
- выключатель для лампы освещения;
- контакторы, управляющие остановкой двигателя, включением его рабочего и обратного хода;
- выключатель, обеспечивающий поступление напряжения на насос, подающий охлаждающую жидкость;
- реле, отвечающее за контроль скорости вращения двигателя;
- реле, отвечающее за управление контактором остановки двигателя;
- понижающий трансформатор;
- переключатель управления станком;
- указатель уровня нагрузки;
- выпрямитель селенового типа.
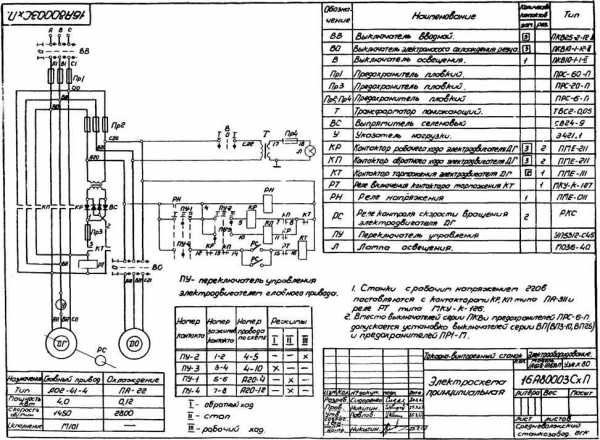
Электрическая принципиальная схема станка 1А616 (нажмите, чтобы увеличить)
На станке установлено два электродвигателя, каждый из которых решает свою задачу:
- трехфазный электродвигатель ПА22 мощностью 0,12 кВт, со скоростью вращения 2800 об/мин, работающий от напряжения 220/380 В, — приводит в действие насос, подающий охлаждающую жидкость в зону резания;
- трехфазный электродвигатель А02-41-4 мощностью 4 кВт, со скоростью вращения 1430 об/мин, работающий от напряжения 220/380 В, — используется в качестве главного привода станка.
Для оснащения промышленных предприятий используются токарные станки, работающие от напряжения 380 В, а для эксплуатации в домашней мастерской оптимальными являются модели, работающие от электрической сети с напряжением 220 В. Кроме того, по специальному заказу могут выпускаться модификации токарного станка, работающего от электрической сети с напряжением 500 В.
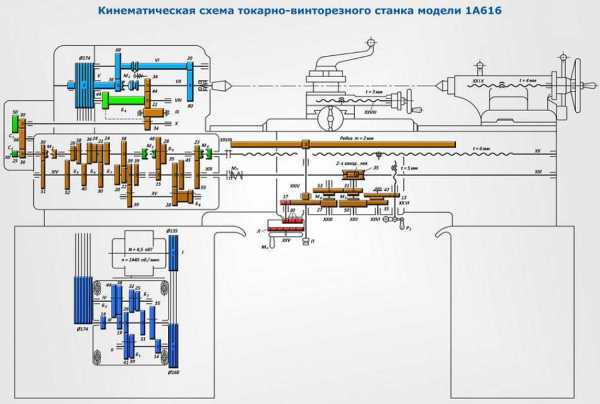
Кинематическая схема станка 1А616 (нажмите, чтобы увеличить)
Питание на лампу освещения, которая работает от напряжения 36В, поступает от понижающего трансформатора, присутствующего в электросхеме станка. Особенностью данного токарного станка является то, что в его конструкции нет двигателя, отвечающего за быстрый ход его суппорта. Быстрая и одновременно плавная остановка двигателя, при которой он не нагревается, обеспечивается за счет использования постоянного тока.
Обеспечение движения подачи и резания
Движение подачи, которое совершает суппорт токарного станка, сообщается ему от шпиндельного узла. Фактически коробка подач станка данной модели может обеспечить 48 скоростей, но по причине того, что некоторые из этих скоростей совпадают, в паспорте устройства их указано всего 22. Для того чтобы сообщить суппорту продольное перемещение, необходимо задействовать зубчатую муфту, а за поперечную подачу данного узла отвечает ходовой винт агрегата.
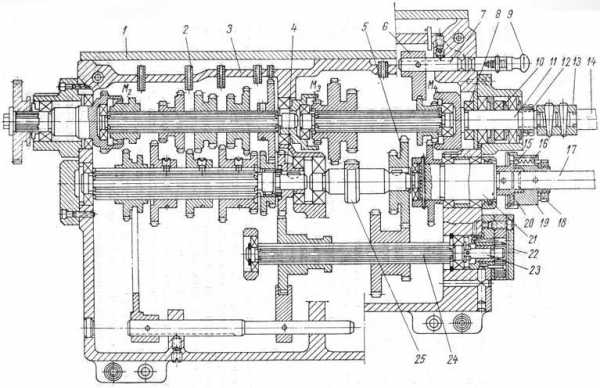
Коробка подач 1А616 (нажмите, чтобы увеличить)
В том случае, если на обрабатываемой детали необходимо нарезать резьбу, шаг которой не превышает 6 мм, суппорт связывается со шпинделем станка напрямую. Если необходимо нарезать резьбу с большим шагом, то для связи суппорта и шпинделя включается перебор, и используется промежуточное звено увеличения шага.
Главным движением в данном токарном станке, как и в устройствах других моделей, является движение резания, которое совершают шпиндель и закрепленная в нем заготовка из металла. От этого движения, как уже говорилось выше, приводится в действие и суппорт станка, который может перемещаться в продольном и поперечном направлениях. Основными элементами привода, отвечающего за движение резания, выступают:
- две клиноременные передачи;
- 12-ступенчатая коробка скоростей.
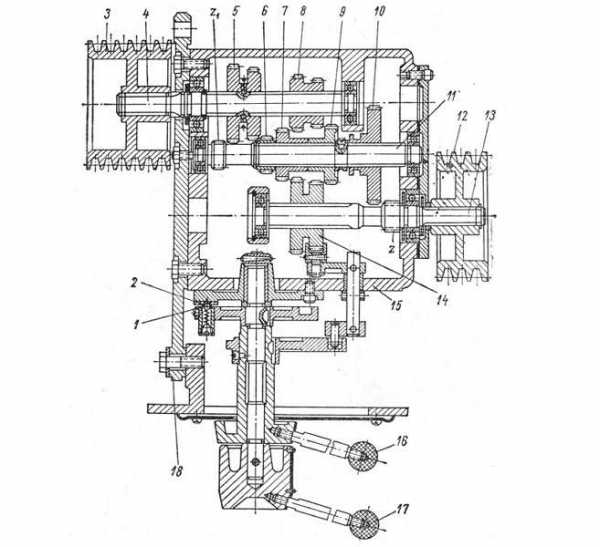
Коробка скоростей 1А616
Коробка скоростей токарного станка состоит из трех валов, установленных в узлы с подшипниками, трех подвижных блоков, каждый из которых состоит из двух шестерен, одиночной подвижной шестерни. За счет введения в зацепление шестерен с разными параметрами шпинделю станка сообщаются различные скорости вращения. Вращение от коробки скоростей передается полому валу, а далее, через ряд зубчатых передач — шпинделю станка. В том случае, если шпинделю необходимо придать большие скорости вращения, он напрямую соединяется с полым валом, для чего задействуется специальная кулачковая муфта.
Для управления токарным станком, которое, по отзывам даже начинающих специалистов, не представляет большой сложности, необходимо совершать и ряд ручных операций. К ним относятся:
- поворот резцедержателя и его установка в требуемое положение;
- передвижение задней бабки, в которой размещается пиноль станка;
- установка суппорта в требуемое положение.
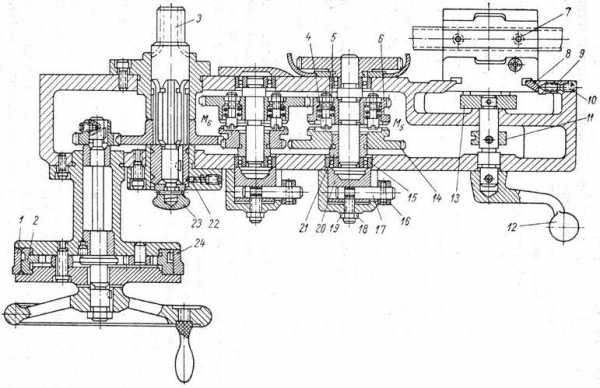
Фартук 1А616 (нажмите, чтобы увеличить)
Паспорт 1А616 и руководство по электрооборудованию
Скачать бесплатно паспорт токарно-винторезного станка 1А616 в pdf-формате можно здесь: Паспорт 1А616
Скачать руководство по уходу и обслуживанию электрооборудования 1А616 можно здесь: Электрооборудование 1А616
Технические возможности станка данной модели позволяют использовать его как при производстве изделий крупными сериями, так и при изготовлении единичных деталей. Оснащаться такой токарно-винторезный станок может инструментом, изготовленным из быстрорежущих сталей, а также резцами с твердосплавными пластинами. На станке, оснащенном подобным инструментом, можно не только выполнять различные операции по токарной обработке, но и нарезать резьбу: метрическую, питчевую, дюймовую.
Оценка статьи:
Загрузка…Поделиться с друзьями:
met-all.org
описание, технические характеристики. Фрезы по металлу для фрезерного станка
Фрезерный станок 676 представляет собой универсальное оборудование, используемое для фрезерной обработки различных деталей. Агрегат может работать со шпоночными, концевыми, дисковыми и другими типами фрез. Конфигурация станка дает возможность фрезеровать заготовки по горизонтали и вертикали, что существенно расширяет возможности агрегата.
Описание
Многофункциональный фрезерный станок 676 может комплектоваться поворотно-вертикальным шпинделем или его горизонтальным аналогом. Первый вариант позволяет обрабатывать детали при помощи торцовых и шпоночных фрез, а во втором случае используются фасонные фрезы, а также дисковые и цилиндрические аналоги.
Главным отличием рассматриваемого оборудования от аналогичных станков является наличие второй головки шпинделя, которая регулируется в перпендикулярных плоскостях. Рассматриваемый агрегат может задействовать в работе одновременно оба шпинделя. Кроме фрезерования, оборудование рассчитано на проведение сверления, зенкерования и растачивания.
В промышленной сфере универсальный фрезерный станок 676 используется для выполнения ряда операций, а именно:
- Проведения обработки внутренних и наружных поверхностей, в том числе и вращательных тел, способом обточки.
- Нарезания уступов и пазов.
- Обточки шлицев на валах.
- Формирования конфигурации зубчатых колес.
Особенности
Фрезерный станок 676 причисляется к категории высокоточных фрезеров (класса Н). Максимальная точность обработки достигается, если во время работы рядом с агрегатом отсутствуют источники вибрации, температура окружающего воздуха находится в пределах 20 °C, влажность – около 65%.
Рассматриваемое оборудование используется в единичном и мелкосерийном производстве, преимущественно на машиностроительных предприятиях и инструментальных комбинатах. На популярность фрезерного станка 676 влияет ряд преимуществ по сравнению с конкурентами:
- Остов оборудования выполнен из чугуна, имеет большую массу, обеспечивающую надежную устойчивость без возникновения вибраций, что гарантирует высокоточную обработку.
- Универсальность оборудования позволяет работать с малоразмерными заготовками и деталями длиной до 0,8 м при ширине – 0,25 м.
- Агрегат может комплектоваться долбежным наконечником, с возможностью выполнения соответствующих операций.
- Относительно небольшие габариты станка дают возможность его размещения даже в обычном гараже.
- Многоуровневый спектр вращения шпиндельных головок способствует оптимальному подбору режимов отделки металлов, в зависимости от их твердости.
Ниже представлены технические параметры рассматриваемого оборудования:
- Размер горизонтального/вертикального рабочего стола – 250*800/250*630 мм.
- Предельная масса устанавливаемой для обработки заготовки – 100 кг.
- Осевое расстояние от шпинделя до стола – 80-450 мм.
- Вынос шпинделя – 125-375 мм.
- Ход шпиндельной бабки по осям X/Y (максимальный) – 300/380 мм.
- Оборотистость шпинделя (горизонталь/вертикаль) – 1630/2040 оборотов в минуту.
- Число скоростей – 16 штук.
- Габаритные размеры – 1200/1240/1005 мм.
- Масса – 1000 кг.
- Мощность электропривода – 3 кВт.
Кроме того, универсальный фрезерный станок 676 оснащается вспомогательной системой подачи СОЖ с мотором, от которого активируется электронасос производительностью 23 литра в минуту.
Отличия между моделями 676П и СФ-676
Модификация 676П от СФ-676 отличается незначительно:
- Имеет расстояние по оси от стола к шпинделю на 10 мм меньше.
- Перемещение бабки шпинделя по вертикали составляет 250 мм.
- Показатель мощности основного электропривода – 2,2 кВт.
- Масса – 910 кг.
- Габариты – 1260/1210/1780 мм.
Широкоуниверсальный фрезерный станок 676П относится к устаревшим модификациям, и сейчас не выпускается. Приобрести его можно только на вторичном рынке.
Устройство
Станина станка 676 изготовлена из чугуна, служит несущим основанием с закрепленными на нем основными конструктивными элементами. На левой стороне станины установлен блок скоростей и короб подачи. На верхней поверхности остова перемещается бабка с установленным горизонтальным шпинделем. На этом элементе, при необходимости, устанавливается вертикальное шпинделное устройство.
Суппорт смонтирован на вертикальных направляющих, стол – на горизонтальных элементах. Станок оборудован основным горизонтальным столом и дополнительным вертикальным аналогом. На основном верстаке фиксируются заготовки размером до 800 мм по длине и 250 мм по ширине.
Электропривод агрегата находится в нижней части остова, размещен на опоре в виде плиты, внутри которой предусмотрена емкость для охлаждающей жидкости. Все электрическая начинка станка расположена под крышкой станины в верхней части. Такая конструкция не затрудняет доступ к узлам для ремонта или обслуживания.
Главными функциональными деталями фрезерного станка является суппорт и шпиндельная головка. Предназначение суппорта – удержание и перемещение рабочего стола в поперечно-продольной плоскости. В действие элемент приводится при помощи ходового вала, передающего крутящий момент от силового агрегата к подающей коробке.
Шпиндельная бабка агрегирует с коробкой подач через барабанные шестеренки, сам шпиндель смонтирован на радиальных и шариковых подшипниках. Точность его перемещения обеспечивает индикаторный держатель.
Техническое обслуживание
Широкоуниверсальный станок СФ-676 требует регулярного техобслуживания. Необходимо:
- Проводить через 10 часов работы смазку специальным машинным маслом направляющих и ходовых винтов.
- Покрывать машинной смазкой линейные подшипники каждые 40 часов.
- Через 400 отработанных часов осматривать и регулировать ремни в подающей коробке, а также подтягивать винтовые узлы.
Перед первым рабочим пуском станка необходимо проверить надежность фиксации предохранительных кожухов, очистить рабочий стол от жидкостей и смазочных материалов, включить агрегат и проверить его работу на холостых оборотах.
Проверка работоспособности
Этот процесс начинают с прогонки оборудования на минимальной скорости, постепенно увеличивая ее до максимального показателя. На основной рабочей передачи вращения станок должен проработать не менее двух часов, при этом шпиндельные опоры не могут подвергаться нагреву свыше 50 градусов.
После проверки агрегата на холостых оборотах, он подвергается нагрузке. Фрезер должен проработать на предельном режущем усилии в режиме кратковременной 25-процентной перегрузке. При нормальной работе в таком режиме не наблюдается появление вибраций и сохраняется высокая точность обработки.
Фрезы по металлу для фрезерного станка
Многообразие конфигураций фрез позволяет выполнить выборку материала на самых труднодоступных участках, благодаря чему деталь принимает требуемые размеры и очертания.
Фрезы классифицируются по расположению резцов, типу конструкции, направлению, форме зубьев, способу крепления и материалу режущего инструмента.
Модификации:
- Дисковые фрезы используются для обрезки заготовок, выборке пазов, металла, снятия фасок. Режущая часть таких элементов может размещаться с одной или с двух сторон.
- Торцовые фрезы работают с плоскими заготовками ступенчатого типа. Рабочей частью инструмента является торец, ось его вращения перпендикулярна поверхности заготовки.
- Цилиндрическая фреза по металлу для фрезерного станка может быть с винтовыми или прямыми зубцами. Первый вариант позволяет обрабатывать плавно заготовку, а вторая конфигурация – отделывать узкие плоскости, поэтому такой инструмент относится к универсальной категории.
- Угловые варианты. Такие фрезы используются для обработки наклонных поверхностей, имеют коническую конфигурацию. Различают одно и двухугловые модификации, отличающиеся размещением режущей кромки.
- Концевые фрезы предназначаются для создания пазов, контурных выемок, уступов и обработки взаимно перпендикулярных частей.
Также существуют фасонные, червячные и кольцевые фрезы. Они служат для обработки фасонных поверхностей и заготовок неординарных конфигураций и еще больше расширяют возможности станка 676.
fb.ru
Определение технических характеристик станка
Стр 1 из 3Следующая ⇒
Содержание
1. Определение технических характеристик станка
2. Разработка кинематики станка, описание компоновки
3. Проектирование и описание кинематической схемы станка
4. Динамические, прочностные и др. расчеты узлов проектируемых узлов и деталей станка
5. Описание конструкции и системы смазки спроектированных узлов
6. Описание систем управления станком
Заключение
Список литературы
Введение
Современные металлорежущие станки — это высокоразвитые машины, включающие механические, электрические, электронные, гидравлические, пневматические и другие методы осуществления движением и управления циклом.
По конструкции и назначению трудно найти более разнообразные машины, чем металлорежущие станки. На них обрабатывают всевозможные детали – от мельчайших элементов часов и приборов до деталей, размеры которых достигают многих метров (турбины), прокатных станов. На станках обрабатывают и простые цилиндрические, и поверхности, описываемые сложными математическими уравнениями или заданные графически. При этом достигаются высокая точность обработки, измеряемая нередко долями микрометра. На станках обрабатывают детали из сталей и чугунов, из цветных, специальных жаропрочных, мягких твердых и других материалов. Современное станкостроение развивается быстрыми темпами. В решениях правительства по развитию станкостроения особое внимание обращено на опережающее развитие выпуска станков с числовым программным управлением, развитием производства тяжелых и уникальных станков.
Сверлильные станки предназначены для сверления глухих и сквозных отверстий, рассверливания, зенкерования, развертывания, растачивания и нарезания резьбы. Сверлильные станки подразделяются на вертикально-сверлильные настольные и наклонные, радиально-сверлильные, для глубокого сверления, центровальные и многошпиндельные.
Определение технических характеристик станка
Общий вид наиболее распространенного универсального одношпиндельного вертикально-сверлильного станка показан на рис. 1. Станок предназначен для работы в основных производственных цехах, а также в условиях единичного и мелкосерийного производства, в ремонтно-механических и инструментальных цехах.
Рис.1 — Вертикально-сверлильный станок.
На фундаментной плите 1 смонтирована колонна 3 коробчатой формы. В ее верхней части размещена шпиндельная головка 6, несущая электродвиатель 5 и шпиндель 7 с инструментом 8. На вертикальных направляющих колонны установлена шпиндельная бабка 4, внутри которой размещён механизм подачи, осуществляющий вертикальное перемещение шпинделя. Поднимать и опускать шпиндель можно механически и вручную, с помощью штурвала 2. Для установки и закрепления приспособления с обрабатываемыми заготовками имеется стол 9. Его устанавливают на различной высоте, в зависимости от размеров обрабатываемых деталей.
Синтез методов и кинематики формообразования поверхностей резанием
Кп+Сл Кп+Cл
ФV(В1) ФV(В1)
ФS(П2) ФS(П2)
Уст(П3) Уст(П3)
Кп+Кс
ФV(В1)
ФS(П2)
Уст(П3)
Основные технические характеристики вертикально-сверлильных станков, близких по типоразмеру:
Параметры | 2А150 | 2Г175 | 2Н175М |
Наибольший условный диаметр сверления в стали | |||
Рабочая поверхность стола | 500х560 | 560х630 | 710х1250 |
Наибольшее расстояние от торца шпинделя до рабочей поверхности стола | |||
Вылет шпинделя | 200-760 | ||
Наибольший ход шпинделя | - | - | |
Наибольшее вертикальное перемещение | |||
сверлильной (револьверной) головки | |||
стола | - | - | |
Конус Морзе отверстия шпинделя | 1,2 или 3 | ||
Число скоростей шпинделя | |||
Частота вращения шпинделя об/мин | 22-1000 | 18-800 | 22-1000 |
Число подач шпинделя (револьверной головки) | |||
Подача шпинделя (револьверной головки), мм/об | 0,05-2,25 | 0,018-4,5 | 0,05-2,24 |
Мощность электродвигателя в кВт | 7,0 | ||
Габаритные размеры: | |||
длина | |||
ширина | |||
высота | |||
Масса, кг. |
В качестве станка-прототипа выбираю вертикально-сверлильный станок 2А150 исходя из анализа его кинематики и технических характеристик.
Разработка кинематики станка, описание компоновки
Выбор и описание компоновки станка
Компоновка станка в значительной степени влияет на технико-экономические показатели. От компоновки зависит: жёсткость конструкции; тепловой баланс и температурная деформация; универсальность станка и его переналаживаемость; металлоёмкость; трудоёмкость изготовления, сборки; ремонтопригодность.
Рассмотрим три варианта компоновки вертикально-сверлильного станка и выберем один:
Структурная формула данной компоновки: 0ZCv
Недостаток: ограниченные габариты обрабатываемой детали, трудность в сборки, при износе стола, куда устанавливается деталь, нету возможности замены его, при малых габаритах обрабатываемой детали уменьшается жесткость шпинделя, т.к. увеличивается величина вылета.
Структурная формула данной компоновки: Z0ZCv
Рисунок 2 — Структурная схема вертикально-сверлильного станка.
Основным формообразующими движениями при сверлильных операциях являются: главное – вращательное движение В1 и движение подачи П2 шпинделя станка. Кинематические цепи, осуществляющие эти движения, имеют самостоятельные органы настройки iv и is, посредством которых устанавливается необходимая скорость вращения инструмента и его подача.
Вращение шпинделя осуществляется по цепи: от электродвигателя М по коробки скоростей iv, которая обеспечивает 12 частот вращения, передаётся на шпиндель 2. (М- iv-2)
Подача осуществляется по цепи: от электродвигателя М через коробку скоростей iv, через коробку подач is, которая обеспечивает 9 подач, вращение сообщается реечному колесу К, которое передаёт вращение на пиноль шпинделя с рейкой t. (М- iv-1- is-К-t)
Рисунок 5 — Кинематическая схема привода.
Заключение
Вертикально-сверлильные станки классифицируются по основным размерам: наибольшему диаметру обрабатываемого отверстия D.
По точности различают станки нормальной точности – Н, повышенной точности – П, высокой точности – В, особо высокой точности – А, особо точные – С.
Станком-прототипом данного спроектированного станка является вертикально-сверлильный станок модели 2А150.
На спроектированном станке могут выполняться следующие операции:
• сверление глухих, сквозных и ступенчатых отверстий;
• зенкерование отверстий;
• развёртывание отверстий;
• нарезание внутренней резьбы метчиком;
СПИСОК ИСПОЛЬЗОВАННОЙ ЛИТЕРАТУРЫ
1. Металлорежущие станки / Под. ред. Тепинкиевича. М:. Машиностроение, 1973.-472 с.
2. Металлорежущие станки/ Под. ред. Пуша. М. Машиностроение, 1985.-256 с.
3. Станки с числовым программным управлением / Под. ред. Лещенко. М:. Машиностроение, 1988
4. Общемашиностроительные нормативы режимов резания для технического нормирования работ на металлорежущих станках. В 2-х частях –М.: Машиностроение,1974 ч.1 — 406 с., ч.2 – 200 с.
5. Свирщевский Ю.Н., Макейчик Н.П. Расчет и конструирование коробок скоростей и подач. – Минск: Вышэйшая шк.,1976 – 590 с.
6. Анурьев В.И. Справочник конструктора-машиностроителя М:. Машиностроение, т.11980 – 728 с., т.2 1981 – 559 с., т.3 1982 – 557 с.
7. Ничипорчик. Детали машин в примерах и задачах М:. Машиностроение, 1981.
8. Кузьмин. Расчеты деталей машин. М:. Машиностроение, 1985
Содержание
1. Определение технических характеристик станка
2. Разработка кинематики станка, описание компоновки
3. Проектирование и описание кинематической схемы станка
4. Динамические, прочностные и др. расчеты узлов проектируемых узлов и деталей станка
5. Описание конструкции и системы смазки спроектированных узлов
6. Описание систем управления станком
Заключение
Список литературы
Введение
Современные металлорежущие станки — это высокоразвитые машины, включающие механические, электрические, электронные, гидравлические, пневматические и другие методы осуществления движением и управления циклом.
По конструкции и назначению трудно найти более разнообразные машины, чем металлорежущие станки. На них обрабатывают всевозможные детали – от мельчайших элементов часов и приборов до деталей, размеры которых достигают многих метров (турбины), прокатных станов. На станках обрабатывают и простые цилиндрические, и поверхности, описываемые сложными математическими уравнениями или заданные графически. При этом достигаются высокая точность обработки, измеряемая нередко долями микрометра. На станках обрабатывают детали из сталей и чугунов, из цветных, специальных жаропрочных, мягких твердых и других материалов. Современное станкостроение развивается быстрыми темпами. В решениях правительства по развитию станкостроения особое внимание обращено на опережающее развитие выпуска станков с числовым программным управлением, развитием производства тяжелых и уникальных станков.
Сверлильные станки предназначены для сверления глухих и сквозных отверстий, рассверливания, зенкерования, развертывания, растачивания и нарезания резьбы. Сверлильные станки подразделяются на вертикально-сверлильные настольные и наклонные, радиально-сверлильные, для глубокого сверления, центровальные и многошпиндельные.
Определение технических характеристик станка
Общий вид наиболее распространенного универсального одношпиндельного вертикально-сверлильного станка показан на рис. 1. Станок предназначен для работы в основных производственных цехах, а также в условиях единичного и мелкосерийного производства, в ремонтно-механических и инструментальных цехах.
Рис.1 — Вертикально-сверлильный станок.
На фундаментной плите 1 смонтирована колонна 3 коробчатой формы. В ее верхней части размещена шпиндельная головка 6, несущая электродвиатель 5 и шпиндель 7 с инструментом 8. На вертикальных направляющих колонны установлена шпиндельная бабка 4, внутри которой размещён механизм подачи, осуществляющий вертикальное перемещение шпинделя. Поднимать и опускать шпиндель можно механически и вручную, с помощью штурвала 2. Для установки и закрепления приспособления с обрабатываемыми заготовками имеется стол 9. Его устанавливают на различной высоте, в зависимости от размеров обрабатываемых деталей.
Синтез методов и кинематики формообразования поверхностей резанием
Кп+Сл Кп+Cл
ФV(В1) ФV(В1)
ФS(П2) ФS(П2)
Уст(П3) Уст(П3)
Кп+Кс
ФV(В1)
ФS(П2)
Уст(П3)
Основные технические характеристики вертикально-сверлильных станков, близких по типоразмеру:
Параметры | 2А150 | 2Г175 | 2Н175М |
Наибольший условный диаметр сверления в стали | |||
Рабочая поверхность стола | 500х560 | 560х630 | 710х1250 |
Наибольшее расстояние от торца шпинделя до рабочей поверхности стола | |||
Вылет шпинделя | 200-760 | ||
Наибольший ход шпинделя | - | - | |
Наибольшее вертикальное перемещение | |||
сверлильной (револьверной) головки | |||
стола | - | - | |
Конус Морзе отверстия шпинделя | 1,2 или 3 | ||
Число скоростей шпинделя | |||
Частота вращения шпинделя об/мин | 22-1000 | 18-800 | 22-1000 |
Число подач шпинделя (револьверной головки) | |||
Подача шпинделя (револьверной головки), мм/об | 0,05-2,25 | 0,018-4,5 | 0,05-2,24 |
Мощность электродвигателя в кВт | 7,0 | ||
Габаритные размеры: | |||
длина | |||
ширина | |||
высота | |||
Масса, кг. |
В качестве станка-прототипа выбираю вертикально-сверлильный станок 2А150 исходя из анализа его кинематики и технических характеристик.
Рекомендуемые страницы:
lektsia.com
Станки трубонарезные: модели, характеристики. Промышленное оборудование
Станки трубонарезные относятся к классу токарного оборудования. Они предназначены для обработки труб и соединений. При необходимости, агрегат может использоваться для нарезания разных типов резьбы. Сфера применения устройства распространяется в промышленном и частном масштабе. На отечественном рынке представлена широкая линейка подобных приспособлений. Рассмотрим некоторые виды станков, их особенности и возможности.
Принцип действия
Станки трубонарезные работают по простой схеме: обрабатываемая деталь пропускается по шпинделю и зажимается парой патронов. Затем труба начинает вращаться, ее второй конец вставляется в люнет, где и происходит необходимая обработка изделия.
Питается агрегат от электрической энергии, может иметь как автоматическое, так и механическое управление. Поскольку диаметр шпинделя имеет значительный разбег по размерам, устройство способно обрабатывать трубы различного диаметра, включая водяные и нефтегазовые трубопроводы.
Некоторые станки данной категории оснащены системой ЧПУ (числовым программным управлением), которая позволяет выполнять большинство токарных манипуляций в автоматическом режиме. В комплектацию приспособления может входить дополнительная система гребенок для нарезания резьбы, а также головки и мобильные подставки. Такой широкий спектр приспособлений позволяет проводить несколько операций с минимальными затратами рабочего ресурса и времени.
Критерии выбора
Выбирая рассматриваемый инструментарий, необходимо учитывать несколько основных факторов:
- Диаметр отверстия шпинделя.
- Наличие револьверной головки или ее аналогов.
- Дистанцию между рабочими центрами.
- Присутствие полуавтоматического режима при нарезании резьбы.
- Показатель прочности и жесткости станины.
Модели с ЧПУ
Эти станки трубонарезные предназначены для нарезки дюймовых, конических, треугольных и прочих видов резьбы. Основные станины защищены методом накала и шлифования. Это, в сочетании с надежностью главных узлов, гарантирует длительный срок эксплуатации без потери параметра точности. Обрубка дефектного края трубы, а также нарезка нужного формата резьбы выполняется в автоматическом режиме.
Ниже приведены характеристики системы ЧПУ марки STC4100 и 1835. Показатели второй модели указаны в скобках:
- Показатель высоты от центра шпинделя до направляющих элементов – 45 (317) см.
- Внешний диаметр используемого патрона – 114-340 (60-180) мм.
- Длина обработки элемента по максимуму – 1 (0,35) м.
- Скорость вращения шпинделя – 310 (306) оборотов в минуту.
- Мощность основного мотора – 18,5 (11) кВт.
- Револьверная головка – вертикального четырехпозиционного типа.
- Типы электрического/гидравлического/пневматического патрона – стандарт.
- Точность обработки – стандарт IT-7/IT-7.
- Масса – 9 (6) тонн.
- Габариты – 3,78/2,08/2,02 (3,07/1,69/1,74) м.
- Задняя бабка в диаметре – 100 миллиметров при возможности перемещения до 250 мм.
СТ-832,8
Эти трубонарезные станки ориентированы на токарную обработку труб и их соединений. Диаметр изделия не должен превышать 210 мм. Конечный продукт преимущественно используется в нефтегазовой сфере. Длина обрабатываемой конструкции по максимуму составляет шесть метров. Устройства оснащены линейкой конусного типа и парой люнетов с пинолями.
Ниже приведены параметры технического плана этой серии:
- Высота по центрам – 41,7 см.
- Диаметры обработки над станиной, суппортом и выемкой – 83/51/100 см.
- Ширина остова – 56 см.
- Диаметр шпинделя – 21 см.
- Максимальное число оборотов – 400 вращений в минуту.
- Число подач при нарезании резьбы – 160.
- Шаги резьб (модульной/дюймовой/диаметральной/миллиметровой) – 37,5/64/240/150 мм.
- Перемещение поперечных/продольных салазок – 51/25 см.
- Задняя бабка оснащена пинолей диаметром 125 миллиметров, ход которой составляет 265 мм.
- Длина/ширина/высота – 4/1,74/1,84 м.
- Питание – насосный, основной мотор и двигатель смазки. Мощность главного привода составляет 18,5 кВт.
Станок трубонарезной 1А983
Устройства этой модификации предназначены для обработки краев труб и идентичных соединений. Ниже представлены характеристики этого приспособления:
- Значения диаметров обрабатываемой заготовки – от 73 до 299 миллиметров.
- Аналогичные показатели над станиной и суппортом – 800/450 мм.
- Максимальное сечение резцов – 32*32 мм.
- Число позиций устройства – 4 значения.
- Длина обрабатываемого изделия по точению с учетом конусной линейки – не более 420 мм.
- Продольное/поперечное перемещение суппорта – 500/800 мм.
- Скорость вращения шпинделя – до 355 оборотов в минуту.
- Количество скоростей – 12.
- Шаги резьбы (метрической/дюймовой) – от 1 до 28 миллиметров.
- Угол поворота конусной линейки – до 10 градусов.
- Мощность электрического мотора – 16 кВт.
- Длина/ширина/высота – 3,6/1,9/1,5 м.
- Максимальный вес – 9,2 т.
Модификация 1Н983
Трубонарезные станки, характеристики которых приведены ниже, используются для обтачивания концов труб и нарезания резьбы в условиях единичного производства. Параметры оборудования:
- Диаметр обрабатываемой конструкции – от 73 до 299 мм.
- Максимальная длина значения – до 800 мм.
- Оборотистость – 355 вращений в минуту при наличии 12 скоростей шпинделя.
- Максимальная масса приспособления составляет 9100 килограмм.
Остальные характеристики оборудования практически идентичны рассмотренному выше станку типа 1А983.
Устройства STC-1535 и STC-1450
Далее указаны параметры трубонарезного станка STC-1535 (в скобках – значения для модели STC-1450):
- Система ЧПУ – Fanuc Oi-TC /Fanuc Oi-TC.
- Высота от центра шпинделя до направляющих элементов – 315 (420) мм.
- Наружный диаметр обрабатываемых заготовок – 156 (140) мм.
- Длина трубы по максимуму – 203 (500) мм.
- Показатель мощности основного мотора – 15 (54) кВт.
- Скорость вращения шпинделя – 660 (906) оборотов в минуту.
- Тип патрона – опрокинутый (стандартный).
- Револьверная головка – вертикальная с четырьмя диапазонами (аналог с 8-ми позициями).
- Стандарт точности обработки изделия – IT7 (IT6).
- Масса устройства – 6 (15) тонн.
- Длина/ширина/высота – 3,24/1,66/1.7 (5,1/2,36/2,1) метра.
REMS Tornado 2010
Эти специальные станки имеют неподвижный остов и вращающийся механизм для заготовки. Прочная конструкция инструмента оптимально подходит для эксплуатации на различных строительных площадках. Компактность и небольшой вес (50 кг) обеспечивают хорошую транспортабельность и упрощают обслуживание приспособления. В комплектацию входит вместительный поддон для стружки, а также регулируемая подставка по высоте.
Производитель предусмотрел две модификации рассматриваемого промышленного оборудования:
- Мобильная вариация оснащена тремя ножками, имеет большую масляную ванну и резервуар для отработанного материала.
- Модель с встроенным поддоном для масла и стружки. Она ориентирована для эксплуатации на верстаке.
Мощный и скоростной привод рассматриваемого агрегата позволяет нарезать резьбу на 2 дюйма за 15 секунд.
Устройство
Станки трубонарезные марки REMS оборудуются несколькими типами двигателей. Среди них:
- Универсальный мотор мощностью 1,7 кВт. Он защищен от перегрузок, обладает скоростью оборотов шпинделя 53 вращения в минуту.
- Силовой агрегат конденсаторного типа. Он оснащен регулятором полярности, имеет мощность 2,1 кВт, пару режимов работы и очень тихий ход. Скорость работы шпинделя составляет от 26 до 52 оборотов в минуту.
- Трехфазный мотор с переключением полярности на 2 кВт. Присутствует педаль для защиты включения автоматического патрона. Кроме того, предусмотрено два режима работы.
Особенностью рассматриваемого станка является наличие двух автоматических патронов с быстрым зажимом. Это позволяет точно и быстро зафиксировать и обработать заготовку без проскальзывания трубы.
Итог
Большинство самоцентрирующихся труборезных станков оборудовано надежными рамами из прочной стали, специальной рукояткой для подачи шпинделя, а также режущим диском, который рассчитан на длительный период эксплуатации. Кроме того, подобные устройства позволяют производить нарезку различной резьбы без особых затрат. При выборе устройства обращайте внимание на его производительность. Также стоит учесть мощность и универсальность агрегата и непосредственно его основное предназначение. Если станок требуется для промышленного использования, лучше обратить внимание на мощные и многофункциональные модели, а для эксплуатации в частном хозяйстве отлично подойдет легкая мобильная модификация.
fb.ru