Станки для производства шпона — особенности, виды, применение и назначение
Дорогостоящие сорта лесоматериалов являются прекрасным сырьем для создания предметов мебели, однако не все люди могут себе позволить такую дорогую продукцию. С целью экономии ценных пород древесины и снижения стоимости конечного продукта и был придуман шпон. Этот материал сегодня крайне популярен для облицовки мебели. Шпон на 100% повторяет узор, текстуру и оттенок натуральной древесины.
Для создания шпона на производствах пользуются специальными станками. Шпон бывает:
- лущеный
- строганый
- пиленый.
Соответственно и станок для производства шпона бывает трех типов.
Лущильный станок для производства шпона
Для реализации лущения шпона сырье необходимо предварительно обработать паром для того, чтобы увеличить пластичность. После этого кряжи подаются на окорочный станок, где с заготовки удаляется кора, а вместе с ней грязь и песок, которые часто становятся причиной быстрого затупления лущильных ножей. При помощи пилы кряжи раскраивают на чураки определенной длины. Чурак нужно предварительно оцилиндровать, после чего можно приступать к лущению. Лента шпона, которая выходит из лущильного станка, кладется на конвейер, подающий ее к ножницам. Ножницы режут шпон на листы необходимого формата. По конвейеру шпон укладывается в пачку, которая выносится из-под ножниц и при помощи электрического погрузчика доставляется в сушилку. Сушат продукцию в роликовой сушилке, далее на конвейере его сортируют и складывают по сортам в пачки. Дефектные листы можно склеить. Если на листах имеются сучки, их отправляют на шпонопочиночный станок, где удаляют изъяны и декорируют их вставками из шпона.
Такой станок для шпона позволяет получить листовой материал толщиной от 1,5 до 5 мм из разнообразных сортов лесоматериалов. На большинстве станков имеется система, которая позволяет в автоматическом режиме устанавливать бревно для последующей обработки.
Чтобы повысить производительность и удобство работы оператора станки оборудуют гидравлическими подъемниками-центроискателями, которые сами определяют подходящую ось вращения заготовки и совмещают ее с осью вращения центровочных валов.
Лущение пропаренной древесины используется для сосновых, ольховых, березовых лесоматериалов. Из лущеного шпона изготавливают фанеру.
Станок для строгания шпона
Прежде всего, кряжи подвергают поперечному раскрою. Во время этой процедуры кряжи распиливают на отрезки необходимой длины. Все отрезки распиливают вдоль, вследствие чего образуется двухкантный брус. Иногда его распиливают пополам. После этого ванчесы подвергают тепловой обработке в пропарочной камере или автоклаве.
Далее ванчесы нужно острогать на шпонострогальном станке. Строганный шпон сушат в роликовых сушилках, торцуют и пакуют в пачки. В каждом наборе составляется конкретный рисунок. Оттенок и узор древесины должны совпадать в каждом наборе. Именно по этой причине листы шпона, которые получаются из каждого ванчеса во время строгания, складывают, сушат и пакуют в пачки точно в том порядке, в каком они выходили из строгального станка. Когда строгаются одновременно три ванчеса, шпон из каждого из них складывают в три разные пачки. Укомплектованную, высушенную, запакованную и перетянутую шпагатом пачку шпона называют кнолем.
Станок для изготовления шпона позволяет создать из дорогостоящих сортов лесоматериалов, которые отличаются необычной текстурой, тонкие листы. Такой материал отлично подходит для фанерования. Методы создания шпона:
- радиальный
- тангенциальный
- радиально-тангенциальный
- тангенциально-торцовый.
Наиболее привлекательным сырьем для создания шпона является дубовая древесина. Такой шпон используют для облицовки рустикальных предметов мебели элитного сегмента.
Кроме дубового шпона в специализированных магазинах можно встретить кленовый, буковый, липовый материал, а также из красного дерева.
Станок для сшивки шпона
Шпон режут на специализированных аппаратах. Он отличается довольно тонкой и хрупкой структурой. Для того, чтобы отделать поверхность шпоном, его необходимо соединить между собой для получения полотна, скатываемого в рулоны. Шпон соединяют двумя способами:
- склейка
- сшивка.
Эти методы одинаково популярны на мебельных производствах. Сшивку шпона осуществляют на станке или ручным способом. Для небольших мастерских разработаны ручные устройства для склейки или сшивки шпона. При помощи особого устройства клеевую или термонить разогревают, и в виде зигзага наносят на основную сторону.
Сегодня станки для сшивки шпона представляют собой небольшие аппараты, функционирующие в автономном режиме. Управление такой машиной осуществляет один специалист. Вся работа на них производится четко, качественно и достаточно быстро.
Ручная сшивка встречается все реже, главным образом, в антикварных, реставрационных и авторских мастерских.
wood-prom.ru
Оборудование для производства фанеры: линия и технология изготовления
Производство фанеры является очень сложным, но прибыльным бизнесом. Для открытия предприятия по производству фанеры необходимо, прежде всего, приобрести оборудование, которое используется для этого процесса. Стоит помнить, что качественное оборудование способно значительно упростить процесс производства фанеры.
Оборудование для изготовления фанеры
Для производства фанеры чаще всего используются лущильный, калибровочный и раскроечный станки. С помощью лущильного станка осуществляется получение тонкой поперечной стружки. На этих станках обрабатываются короткие бревна, которые по-другому называются чураки. На суппорте станка устанавливается нож, который при вращении бревна срезает с него слой древесины. Этот слой древесины имеет слой толстой и беспрерывной ленты, которую называют шпоном.
Для улучшения качества шпона и увеличения его прочности во время лущения шпона производится обжим древесины. Для этого используется прижимная линейка.
Калибровочный станок используется для пропуска бревен с сечениями. Благодаря этому станку обеспечивается удаление участков бревен, которые выступают за просветы в нем. Закомелистая часть наиболее толстых бревен обтачивается благодаря наличию калибрующих ножей. Благодаря возможности регулировать положение ножей на роторе можно обрабатывать на этом станке бревна различного сечения. Раскроечные станки предназначаются для раскройки фанеры. Они характеризуются большими габаритами, что позволяет разрезать фанеру на листы разнообразных разрезов.
Для того, чтобы просканировать недостатки отобранного материала используются специальные станки. Ими являются измерители количества влаги, а также конвейеры.
Иногда на производстве фанеры используются линии, благодаря которым осуществляется сортировка шпона.
Технология производства фанеры
Производство фанеры состоит из нескольких этапов. К основным из них относится:
- Подбор материала;
- Снятие коры;
- Снятие слоя шпона на лущильном станке;
- Просушка шпона.
К подбору материала для фанеры необходимо подходить очень тщательно. Зачастую для производства фанеры используют шпон из березы, ольхи, бука, сосны и т.д. Для создания удобств в работе материал проваривается в специальном бассейне. Этот процесс значительно повышает качество сырья.
После этого с древесины снимается кора, а также проверяется материал на наличие металлических элементов. Далее материал поступает на специальное оборудование, которое предназначается для производства фанеры.
На лущильном станке снимаются первый слой шпона, после чего его разделяют на отдельные листы. Качество шпона зависит от вида древесины. При наличии в шпоне большого количества влаги его отправляют на просушку. Далее производится склеивание листов шпона.
Вы можете прямой сейчас узнать какое оборудование для производства сетки рабицы нужно и открыть прибыльный бизнес в этом направлении.
Производство профнастила — замечательный бизнес. Всё об этом Вы можете узнать тут.
Для склеивания шпона используются специальные материалы. Клеящие составы изготавливаются в механизированных смесителях, после чего они подаются желобки нескольких клеевых вальцов. Прокатывается клеящий состав с обеих сторон пиломатериала. Далее промазанные клеем листы шпона склеиваются с помощью пневматических, гидравлических или винтовых прессах.
При склеивании фанеры в комнатной температуре их необходимо продержать в помещении около 6 часов. Наиболее эффективным является прессование фанеры при повышенной температуре. В таких условиях на склеивание шпона уходит всего несколько минут.
В том случае, если производится гнутая фанера, используется специальные инструментальные плиты, которые характеризуются наличием нескольких пресс-форм. Далее фанера поступает на раскроечный станок, где осуществляется ее резка на листы различных размеров. Технология изготовления фанеры напрямую зависит от вида производимого строительного материала.
Линия по производству фанеры
Выпуск фанеры требует наличия специальных линий. Это специализированное оборудование, которое значительно упрощает процесс производства. Работа линии заключается в следующем. Древесина в виде бревна или чурака очищается от разнообразных загрязнений, а также с нее снимается кора. Для этого в течение нескольких часов применяется влаготермическая обработка.
После того, как древесина прошла процесс размягчения, ее закрепляют в специальном станке, который вращается вокруг своей оси. К чураку подводится лущильный нож и с его помощью снимается с него тонкий слой древесины. Благодаря этой процедуре вырабатывается стружка. Эта стружка и становится основой будущей фанеры.
Шпон раскраивается на листы. Эти листы проходят процесс сортировки согласно их качеству. При этом учитывается наличие трещин, сучков и разнообразных незначительных дефектов. Далее листы проходят процесс сушки, после чего их собирают в пакеты. Улаживаются листы в пакеты по принципу перпендикулярности.
Базовый лист фанеры должен быть расположен симметрично. После того, как пакет сформирован, его смазывают специальным клеящим составом. Благодаря клею из отдельных листов шпона образуется единый и цельный лист фанеры. После этого фанера проходит процесс высыхания и охлаждения. На этом процесс производства на линии заканчивается.
Во время производства шлифованной фанеры используются специальные шлифовальные станки, на которых она проходит соответствующую обработку.
В случае изготовления ламинированной фанеры используется специальная пленка, которая наклеивается сверху на фанеру.
Благодаря этой пленке фанера имеет отличные технические характеристики, а также повышенный уровень износоустойчивости. Ламинирование фанеры может быть выполнено как с одной, так и с двух сторон. Водостойкую фанеру во время производства обрабатывают специальными смолами.
Популярные модели оборудования
Лущильный станок СЛ-720
На производствах фанеры используются разнообразные станки. От качества оборудования зависит скорость процесса изготовления фанеры, а также его качество. Именно поэтому к подбору оборудования необходимо подходить очень ответственно. Существует множество фирм, которые занимаются производством оборудования для изготовления фанеры. Наиболее популярными среди станков для производства фанеры считаются:
- Лущильный станок для производства шпона СЛ-720 (1600). С помощью этого станка древесина обрабатывается без дополнительных усилий. Определение оптимального положения оси обеспечивается благодаря наличию специального приспособления. Наличие дебаркера обеспечивает высокое качество начальной обработки чурака. С помощью хорошей фрезы заготовке придается правильная форма. Наличие гибкого гофрированного шланга позволяет беззаботно удалять отходы во время работы.
Хотите открыть свое дело по производству плитки, но не знаете с чего начать? Сперва узнайте, как осуществляется изготовление керамической плитки.
Всё об изготовлении бетона здесь.
Как наладить производство брусчатки? Информация на странице http://buisiness-oborudovanie.com/dlya-dorozhnyx-pokrytij-kamnya/oborudovanie-dlya-proizvodstva-bruschatki/.
- Станок для производства лущенного шпона CЛ-800 (1600) характеризуется наличием специального устройства, с помощью которого устанавливается бревно для его обработки. С помощью этого станка можно обрабатывать заготовки, диаметр которых составляет от 110 до 740 миллиметров. Этот станок способен производить четыре метра шпона в час.
Делительный станок СД-800
Станок делительный для рубки шпона СД-800 (1600). С помощью этого агрегата осуществляется деление ленты шпона на отдельные дощечки или листы необходимой ширины. Задается ширина листа с помощью специального электронного устройства. Использовать этот агрегат необходимо на одной линии со станком по производству шпона. Ширина обрабатываемого шпона может составлять до 1600 миллиметров.
- Калибровочный станок по дереву производится на основе станков эстакадного типа. Наличие высокооборотного привода позволяет управлять скоростью работы станка. Удобства при работе на станке придаются благодаря возможности автоматического управления столом. Благодаря этому агрегату осуществляется калибровка поверхности плиты.
Раскроечный станок по дереву FDB Maschinen FR 6020 предназначается для обработки фанеры. Это изделие характеризуется компактностью, высоким уровнем сборки и наличием специальных устройств, благодаря которым значительно упрощается процесс обработки дерева.
Все станки производятся из материалов высокого качества, что обеспечивает им прочность, надежность и длительный срок эксплуатации. После производства все станки проходят ряд испытаний, что обеспечивает им высокий уровень износоустойчивости, а также значительно упрощает процесс производства фанеры.
Видео про изготовление фанеры
buisiness-oborudovanie.com
Обзор технологий изготовления шпона
Особое место в деревообработке занимает производство шпона. Существует несколько способов его изготовления, каждый из которых обладает как своими преимуществами, так и недостатками.
Шпоном (от немецкого слова Span – стружка) принято называть тонкие листы древесины определенной толщины, используемые в деревообрабатывающей промышленности как для производства фанеры, древесно-слоистых пластиков, так и для облицовывания изделий из древесины и древесных материалов для улучшения их механических свойств и внешнего вида. По способу производства шпон различают лущеный и строганый.
Заготовкой для получения лущеного шпона является чурак – бревно определенной длины, которому перед лущением придают форму цилиндра. Процесс получения шпона способом лущения происходит на лущильных станках. Режущий нож подается на вращающуюся цилиндрическую заготовку по всей ее длине, распуская древесину на тонкую стружку, словно разматывая рулон бумаги.
Шпон с оригинальной текстурой получается в случае, когда заготовка обрабатывается аналогично карандашу в точилке. Чтобы такой шпон не завивался в спираль, вдоль всего чурака по его образующей пропиливается радиальный паз, проходящий до оси его вращения. Этот шпон применяется для облицовывания деталей в виде розетки, например крышки круглого стола. Оборудование для получения такого декоративного шпона серийно не выпускается.
Строганый шпон получают способом строгания на шпонострогальных станках. Его получают из заготовок – ванчесов, чаще всего способом поперечного строгания. В настоящее время наиболее распространены два способа строгания шпона. В первом случае нож при строгании двигается параллельно плоской поверхности ванчеса, срезая тонкую плоскую пластину древесины. Во втором случае нож, надвигаясь на эксцентрично вращающийся ванчес параллельно оси его вращения, срезает тонкую стружку по дугообразной траектории.
Текстура строганого шпона, образованная в первую очередь расположением волокон древесины, более красива и разнообразна, чем у лущеного. Строганый шпон уже с ХХ в. широко применяется для облицовывания деталей мебели из малоценных пород древесины. Пик его потребления пришелся на 1960–1970-е гг. в связи с широким использованием ДСП для производства мебели при облицовывании ее лицевых фасадов. Однако с появлением двухсторонних ламинированных плит строганый шпон из древесины ценных пород стал использоваться для чистового облицовывания лицевых элементов мебели высокого качества, отделки интерьеров внутренних помещений коттеджей и офисов.
Облицовывание – это приклеивание покрытия из листов на основу с целью улучшения ее свойств или изменения внешнего вида. Облицовка, служащая окончательным (наружным) покрытием, называется чистовой. Подбором смежных листов шпона создают определенный естественный текстурный зеркально-симметричный рисунок древесины облицовки, что позволяет декоративно оформлять детали и узлы, входящие в изделие.
Облицовывание детали должно быть симметричным, т.е. одновременно оклеиваются две противоположные плоскости, поскольку вследствие односторонней усадки клеевого шва возможно коробление детали вогнутостью в сторону облицовки. Для облицовывания внутренней поверхности детали используют строганый шпон той же толщины менее ценных пород древесины, а зачастую и лущеный березовый шпон.
Строганый шпон должен изготавливаться, транспортироваться и храниться в соответствии с требованиями ГОСТ 2977-82 «Шпон строганый. Технические условия». Для его производства чаще всего используется древесина лиственных пород (дуб, бук, ясень, красное дерево, вяз, ильм и др.), хотя не забыты и хвойные (тис, лиственница, сосна).
По текстуре строганый шпон подразделяется на следующие виды: радиальный (Р), полурадиальный (ПР), тангентальный (Т), тангентально-торцовый (ТТ). У строганого шпона радиального вида годовые слои имеют вид параллельных прямых линий по всей поверхности листа, а сердцевинные лучи древесины хорошо различимы в виде полос и расположены не менее чем на 75% площади листа. Для текстуры строганого шпона полурадиального вида характерны годовые слои в виде прямых параллельных линий, занимающие не менее 75% площади листа, и сердцевинные лучи в виде наклонных полос, расположенных не менее чем на 50% листа. У шпона тангентального вида годовые слои образуют в стволе дерева конусы нарастания, имеющие вид углов или кривых линий, а сердцевинные лучи – вид продольных или наклонных штрихов или линий. Тангентально-торцовый шпон получают из наплывов дерева, текстуру которого определяют годовые слои в виде замкнутых кривых линий и сердцевинные лучи в виде кривых линий и штрихов.
Согласно ГОСТу длина листов строганого шпона должна составлять от 550 мм и выше с градацией 100 мм (для текстуры ТТ – от 300 мм), предельные отклонения ±10 мм; ширина от 80 мм и выше с градацией 10 мм (для текстуры ТТ – от 100 мм), предельные отклонения +5 и -4 мм; тол щина 0,4; 0,6; 0,8 и 1 мм, предельные отклонения ±0,05 мм. В соответствии с этими размерами производитель обрезает пачки шпона со всех четырех сторон. По качеству исходного сырья (наличию и величинам пороков древесины) и дефектам обработки (царапинам, рискам, волнистости) шпон подразделяется на 1-й и 2-й сорта. При этом ограничивается шероховатость его поверхностей: для дуба, ясеня, ильма, лиственницы, сосны максимальная высота неровностей должна быть не более 200 мкм, для остальных пород – не более 100 мкм. Влажность листов шпона должна соответствовать 8% (±2%).
Листы шпона укладываются в пачки (кноли) в порядке выхода их при строгании ванчеса. Пачки формируются раздельно по породам, видам и сортам. Количество листов в пачке должно быть четным и составлять не менее 10 листов. Каждую пачку маркируют, указывая породу, размеры, вид текстуры, сорт, количество шпона в листах и квадратных метрах.
Особенности производства
Изготовление строганого шпона включает в себя ряд процессов: подготовку древесного сырья к строганию; строгание шпона; сушку; прирезку пачек листов; контроль качества и упаковку.
Подготовка сырья начинается с раскроя неокоренных лесоматериалов. Длинномерные бревна на складе распиливаются на мерные отрезки (кряжи), наибольшая длина которых должна соответствовать технической характеристике шпонострогального станка. Операция раскряжевки (поперечной распиловки) бревен может выполняться на оборудовании, оснащенном либо круглыми, либо цепными пилами. Чтобы получить заготовки (ванчесы) для строгания шпона, кряжи проходят операцию продольного раскроя (распиловки): сначала получают двухкантный брус, который затем по высоте раскраивается на два одинаковых трехкантных бруса – ванчеса. Эти операции могут выполняться на круглопильных, ленточнопильных станках, а также на горизонтальных пилорамах.
Продольному раскрою бревен на деревообрабатывающих предприятиях уделяют особое внимание, поскольку от способа раскроя кряжа зависит полезное использование древесины, выход наиболее ценных видов шпона, его качество и трудоемкость производства.
Перед строганием заготовки подвергаются гидротермической обработке – воздействию высокой температуры и пара. Это позволяет изменить физико-механические свойства древесины, создать благоприятные условия для ее резания, уменьшить вероятность образования трещин в шпоне и вырывов на его поверхностях. Гидротермическую обработку осуществляют в специальных устройствах: автоклавах, парильных ямах и камерах. После гидротерми ческой обработки выполняется окорка ванчесов, поскольку после пропарки кора легче отделяется от древесины. Окорка чаще всего производится вручную. Окоренный ванчес закрепляется в шпонострогальном станке, где и происходит строгание шпона.
Срезанные листы укладывают в кноли и транспортиру ют к сушильной камере. Шпон по одному листу в строгой последовательности, как выходил из станка при срезании с заготовки, поступает в сушилку, где достигает влажности 6–10%. Высушенные листы шпона в той же последовательности укладываются в пачки.
Следующей операцией является прирезка пачек шпона по длине, а затем и по ширине. Прирезка происходит обычно на гильотинных ножницах со всех четырех сторон пачки. В дальнейшем выполняют формирование пакета из нескольких пачек шпона, обвязывают его лентой и маркируют перед отправкой на склад готовой продукции.
Последнее время достаточно широко применяется разновидность строганого шпона «файн-лайн». Это материал, изготовленный из натурального шпона малоценных пород чаще всего лиственной древесины, листы которого предварительно склеены между собой по особой технологии в массивные блоки, внешне напоминающие многослойный брус LVL. Особенностью технологии «файн-лайн» является возможность передать специфичную оригинальную текстуру древесины ценных пород. Этот материал широко используется для облицовывания на вакуумных прессах элементов межкомнатных дверей, наличников, элементов мебели и интерьера жилья.
Для изготовления «файн-лайн» используется лущеный шпон, который получается на лущильных станках. Непрерывная лента рубится на полосы заданной ширины и поступает в сушильную камеру. После процесса сушки шпон сортируется по цвету. Далее он поступает в специальные емкости с красящим раствором, где выдерживается заданное время. После дополнительной сушки листы шпона склеиваются между собой по толщине в блок с про дольным направлением волокон древесины, который затем подвергается прессованию под высоким давлением. Шпон «файн-лайн» производится традиционным способом на шпонострогальных станках, когда вместо ванчеса используется клееный блок, раскраиваемый в нужном направлении волокон на полосы заданных размеров, имитируя требуемую текстуру – радиальную, тангентальную и т.д.
Шпон «файн-лайн» является фактически натуральным продуктом, поскольку практически полностью (до 94%) состоит из натуральной древесины с небольшими включениями красителя и клеевой композиции (не более 8% в зависимости от исходной породы шпона). А технологии покраски и строгания позволяют с большим приближением создавать рисунок шпона, аналогичный текстуре ценных пород древесины. Так, например, Московский завод деревоизделий, ранее созданный при ЗИЛе, успешно выпускает широкую номенклатуру дверей и сопутствующей продукции (коробок, наличников, доборов и т.д.), облицованной шпоном «файн-лайн».
Особенности процесса строгания
Шпон, получаемый на шпонострогальном станке, представляет собой стружку-продукт, получаемую при поперечном резании древесины. Резец (нож), внедряясь в древесину, деформирует подрезанную лезвием стружку своей передней гранью. В начале резания стружка контактирует с передней поверхностью ножа, а затем отделяется от него, закручиваясь вследствие неодинаковой деформации своих наружного и внутреннего слоев, что вызывает сжатие и изгиб в поперечном сечении стружки в зоне резания. Так как растягивающие напряжения от изгиба по величине обычно больше, чем сжимающие, у лезвия на стружку (примерно на половину-треть ее толщины) будут действовать преобладающие растягивающие напряжения. Из-за слабой сопротивляемости древесины растяжению вдоль волокон по мере внедрения резца, растягивающие напряжения первыми достигают предела прочности древесины, что ведет к образованию трещин по нижней поверхности стружки. Трещины образуются с определенным шагом и не выходят на поверхность стружки, поскольку там превалируют сжимающие усилия. В результате образуется стружка лентообразной формы с трещинами на внутренней стороне, что отрицательно сказывается на механической прочности и внешнем виде шпона и облицованных им изделий.
Для предотвращения образования трещин при производстве шпона используют минимальные углы резания с применением резцов с углом заострения порядка 16°, что позволяет снизить растягивающие напряжения. Обязательной технологической операцией, предшествующей процессу строгания древесины, является гидротермическая обработка заготовок. Повышение влажности и температуры древесины повышает ее способности деформироваться под воздействием одного и того же напряжения. При этом при одной и той же деформации стружки (отгибании ее передней гранью ножа на некоторый угол) создаст по толщине стружки растягивающие напряжения при резании пропаренной древесины меньшие, чем при резании сухой древесины с температурой окружающей среды. Следовательно, предварительная гидротермическая обработка древесины позволяет существенно предотвратить возможность образования трещин по нижней поверхности шпона.
Кроме того, для минимизации растягивающих напряжений по толщине шпона к стружке в зоне резания с помощью прижимной линейки прикладывают сжимающую силу, в большой степени компенсирующую растягивающие напряжения за счет трения линейки и стружки. Установка линейки на некотором расстоянии перед лезвием резца позволяет также избавиться от опережающей трещины, что значительно сказывается на снижении шероховатости поверхности шпона и повышении его качества.
Режущим инструментом станка является нож, представляющий собой плоскую пластину, по одной продольной (тыльной) стороне которой выбраны открытые пазы для его крепления болтами на суппорте. Причем пазы выбраны не по нормали к тыльной кромке, а под углом порядка 5–10°, что соответствует углу наклона положения суппорта станка на направляющих. С противоположной стороны пластины сформировано режущее лезвие ножа, образованное снятой с пластины фаской под углом порядка 16° к плоскости ножа, формирующей угол заострения ножа. Задний угол ножа составляет, как правило, 1–2°.
От длины ножа зависит максимальный размер по длине срезаемой пластины шпона. В зависимости от типа станка длина может достигать значения более 5 м. Ширина ножей составляет от 150 до 265 мм. По толщине строгальные ножи подразделяются на тонкие – от 3 до 6 мм, и толстые – 8–22 мм. Наиболее часто для строгания применяются ножи толщиной 15–16 мм. Передняя кромка толстых ножей выполняется двухслойной. Сама пластина изготавливается из недорогой углеродистой стали (например, сталь 15), а на выбранную вдоль пластины четверть наносится режущая часть из легированной стали 9ХС, HSS (или ее аналогов). Толщина режущей части выбирается от четверти до трети толщины ножа, а ширина составляет от трети до половины его ширины. Нож имеет значительную массу, поэтому операции по установке и съему ножа для заточки производятся с помощью специальных приспособлений.
Прижимная линейка шпонострогального станка имеет ту же длину, что и нож. Она изготавливается либо в виде пластины со скошенной кромкой, либо в виде бруса с выступающим ребром. Материалом для линейки служит углеродистая сталь.
Строгание ванчеса может осуществляться за одну или за две установки. В первом случае брус строгается до конца (до оструга). На шпон распускается и сердцевинная его часть (сердцевинная трубка), резко снижающая качество шпона, а часть качественной древесины уходит в отструг. Во втором случае брус строгается приблизительно до половины, затем его разворачивают и укладывают на остроганную поверхность, которая будет выполнять уже роль базы. При этом сердцевинная трубка сводится в отструг, который в любом случае остается в процессе строгания в виде доски толщиной 25–30 мм. Одновременно обеспечивается оптимальное направление строгания против наклона годичных слоев древесины.
Станки для строгания шпона
Шпонострогальными станкам и называют оборудование, в котором рабочим процессом является поперечное (или поперечно-продольное) строгание заготовок из древесины. Для реализации процесса строгания шпона необходимо конструктивно обеспечить сочетание возвратно поступательного движения режущего ножа (или заготовки) и периодического взаимного перемещения заготовки и ножа на толщину срезаемой стружки. Ведущими производителями оборудования для строгания шпона в мире являются фирмы Cremona (Италия), Grenzebach (Германия) и Capital Machine Co., Inc. (США). Во времена СССР основным импортером шпонострогального оборудования по СЭВ являлась Чехословакия, станки которой до сего времени продолжают эксплуатироваться на ряде российских деревообрабатывающих предприятий. По пространственной компоновке основных элементов различают шпонострогальные станки горизонтального, вертикального и ротационного типа.
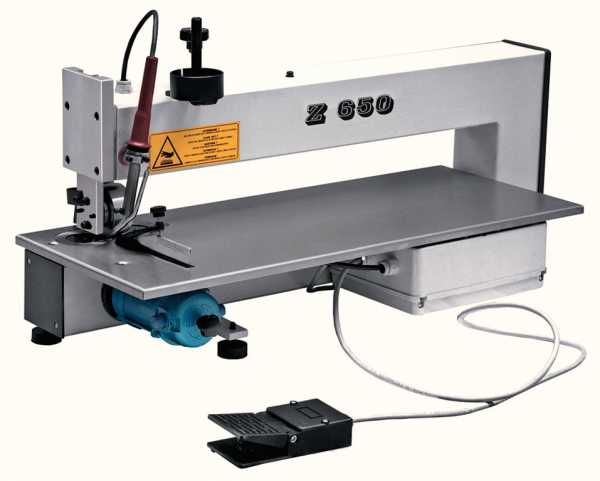
Классические шпонострогальные станки горизонтального типа состоят из ряда агрегатов, смонтированных на массивной станине. Обрабатываемая заготовка закрепляется с помощью механических или гидравлических зажимов на горизонтальном столе, который имеет возможность циклического вертикального перемещения по высоте на заданную толщину шпона. По двум направляющим, расположенным вдоль стола по обеим его сторонам, возвратно-поступательно перемещается режущий суппорт, представляющий собой массивный корпус, в котором установлен нож и прижимная линейка. Суппорт приводится в движение от кривошипно-ползунного механизма. Маховики кривошипы получают вращение от электродвигателя через ряд зубчатых передач и муфту скольжения, что позволяет плавно регулировать скорость резания.
Привод перемещения стола кинематически связан с приводом перемещения суппорта. Это позволяет перемещать стол с помощью храпового механизма и подъемных винтов по высоте на толщину срезаемого шпона во время холостого хода суппорта. Быстрый отвод стола в исходное положение для загрузки новой заготовки осуществляется от отдельного привода, с помощью которого происходит и настройка значений перемещения стола по высоте и, естественно, толщины срезаемого шпона. Существуют станки, в которых передвижения стола обеспечиваются с помощью гидропривода. Поскольку процесс строгания в станках этой группы выполняется способом поперечного резания, который характеризуется значительной шероховатостью получаемой поверхности шпона, для минимизации высоты неровностей на его поверхностях суппорт с ножом и прижимной линейкой разворачивается под углом 5–12° к нормали вектора скорости резания. Разворот суппорта позволяет одновременно снизить и ударные нагрузки при строгании за счет более плавного врезания ножа в древесину.
Срезанный шпон удаляется из ножевого суппорта либо вручную (на станках с невысокой производительностью), либо специальными приемными устройства ми, как на большинстве современных шпонострогальных станков. При большом числе двойных ходов ручная приемка листов шпона становится операцией весьма утомительной и далеко не безопасной. Примером шпонострогального станка горизонтального типа может являться станок марки TN фирмы Cremona, использующийся для строгания толстого шпона толщиной 3–6 мм, который применяется, например, для производства лицевого слоя многослойной паркетной доски.
Шпонострогальные станки вертикального типа, в отличие от горизонтальных, обеспечивают главное движение с помощью подвижного стола с закрепленным на нем ванчесом по вертикальным направляющим, расположенным под небольшим углом в плоскости резания к вертикали. Привод перемещения стола, как и в горизонтальных станках, может быть кривошипно-ползунным от электродвигателя через набор зубчатых передач. Перемещение режуще госуппорта, как правило, обеспечивается от электродвигателя стола через храповой механизм, а его ускоренное передвижение при настройке – от отдельного двигателя через электромагнитную муфту. В более современных станках возвратно-поступательное перемещение стола обеспечивается с помощью гидропривода. Суппорт с ножом и прижимной линейкой установлен на каретке и перемещается благодаря серво приводам по горизонтальным направляющим на величину, равную толщине срезаемого шпона с помощью прецизионных винтовых пар, позволяющих строго выдерживать стабильность подачи. Аналогичные приводы применяются и в современных горизонтальных шпонострогальных станках.
При прочих равных условиях в сравнении с горизонтальными станками, вертикальные станки занимают меньшую производственную площадь, в них проще принимать лист шпона, однако на них сложнее крепить ванчес. Практически все станки этого типа оснащены встроенными в суппорт устройствами для выноса листов шпона из зоны резания и укладчиками в стопу. К примеру, станок марки BHS фирмы Grenzebach при рабочей ширине в 4 и 5,2 м обеспечивает производительность до 105 листов в минуту за счет использования в станке современных гидравлических и линейных приводов.
Станки ротационного типа (этот тип еще называют стейлог) напоминают лущильные станки, в которых заготовка-чурак совершает вращательное движение. В ротационном станке заготовка-ванчес эксцентрично устанавливается на вращающемся вокруг горизонтальной оси столе, а режущий суппорт непрерывно подается на заготовку. Срезание шпона происходит не по плоскости, а по дуге окружности, при этом осуществляется чисто поперечное резание древесины. Текстурный рисунок зависит от способа раскроя кряжей на ванчесы.
В некоторых конструкциях станков стейлог-нож разворачивается под углом до 5–7° к оси вращения ванчеса. В зависимости от вида ванчеса (в виде четверти бревна) и расположения ножа под разными углами к его плоским граням можно получать различные виды текстуры шпона в диапазоне от чисто радиальной до сугубо тангентальной. Например, станок типа стейлог фирмы Capital Machine Co., Inc. может выпускать шпон толщиной от 0,13 до 6,35 мм при длине строгального ножа 5700 мм. Оборудование оснащено компьютеризированной системой выгрузки шпона и контроля его толщины, что позволяет экономить до получаса рабочего времени в смену.
Станок оснащен вакуумным столом для крепления ванчеса, благодаря чему снижаются потери древесины на срезки (необрабатываемые остатки ванчеса), а его производительность увеличивается на 7–10%. При этом время загрузки и зажима бруса составляет не более полминуты. Производительность стан ка составляет до 80–90 листов шпона в минуту.
Станок типа стейлог фирмы Grenzebach (Германия) выполнен на линейных гидравлических приводах, что позволяет ему обеспечить еще более высокую производительность – до 120 листов шпона в минуту. В этом оборудовании реализована возможность «косого» расположения ножа под углом к оси вращения.
Японская фирма Marunaka предлагает гамму шпонострогальных станков челночного типа, в которых брус неограниченной длины при резании совершает реверсивное движение. Станок по схеме напоминает большой ручной перевернутый фуганок. У него режущий суппорт представляет собой два горизонтальных стола – передний (подвижный) и задний (неподвижный), установленные на единой станине. Вместо ножевого вала между столами на поворотном основании установлены нож и прижимная линейка. При настройке станка лезвие ножа устанавливается в плоскости заднего стола.
Прижимная линейка и передний стол перемещаются при настройке агрегата на нужную толщину шпона. Нож и линейка разворачиваются на угол 72–85° к вектору скорости подачи, за счет чего выполняется продольно-поперечное резание, позволяющее достичь высокого качества шпона при толщине от 0,2 до 7 мм. При ширине бруса в 250 мм используется нож длиной 1500 мм. Прижим, подача и возврат заготовки осуществляются подающим конвейером с обрезиненной рабочей поверхностью, который после каждого цикла строгания опускается на толщину шпона.
В Японии эти станки широко используются в том числе и для производства верхней дощечки паркетной доски, вытеснив с предприятий ленточнопильное оборудование, на котором ее изготавливали ранее. Данный станок предназначен для строгания бруса с поперечным сечением 250 х 250 мм. Станок может развивать скорость подачи до 68 м/мин. Максимальная ширина строгания на станках этой гаммы достигает 450 мм.
На этом оборудовании можно строгать и более тонкий шпон, однако при этом за счет внутренних напряжений в листе происходит его закручивание в неправильную спираль, что резко усложняет процесс последующей сушки и приводит к растрескиванию листов шпона по торцам.
Существует еще одна группа шпонострогальных станков – наклонные. Это либо горизонтальные станки, у которых направляющие суппорта наклонены к уровню пола на 12–20°, либо вертикальные станки, установленные наклон но, с целью облегчения установки ванчесов на столе. Совершенствование конструкций шпонострогальных станков в настоящее время происходит в основном за счет использования быстродействующих автоматизированных приводов, широкого внедрения компьютерных технологий, манипуляторов, околостаночного оборудования, а также все более износостойких материалов для повышения стойкости режущего инструмента.
www.lesindustry.ru
Оборудование для производства и раскроя лущеного шпона
На сегодняшний день лущение — это наиболее самый распространенный способ получения шпона. Это не удивительно, ведьизделия из шпона так удобны, экологичны и разнообразны — гнутоклееные детали для мебели, ящики и корзины для ягод, овощей и фруктов, различные виды упаковки, спички, палочки для мороженного, медицинские шпатели, LVL брус и фанера, заготовки для шпонирования столярных изделий. Кроме того, производство лущеного шпона весьма малоотходно и высокопроизводительно, что также немаловажно в современных условиях и напрямую связано с размером получаемой прибыли.
Для получения лущеного шпона из фанерного кряжа лиственных и хвойных пород предназначены лущильные станки марки СЛ. Они же позволяют производить одновременно с лущением раскрой шпона на полосы заданной ширины.
Для повышения производительности и удобства работы оператора станки оснащены гидравлическим поъемником-центроискателем, который позволяет автоматически определить оптимальную ось вращения заготовки и совместить ее с осью вращения центровочных валов.
Делительные станки или, как их еще называют, станки для нарезки шпона, предназначены для деления ленты шпона на заготовки различной ширины. Чаще всего их изготавливают по «гильотинному» принципу: движущаяся лента шпона останавливается под ножом, который, опускаясь, «рубит» ее в нужном месте. Гильотины для рубки шпона часто не выдерживают размеров отделяемой заготовки и работают очень медленно, что заставляет устанавливать между лущильным и делительным станками множество разноскоростных энергоемких транспортеров, занимающих немало места.
для производства и раскроя лущеного шпона используют в двух модифуикациях:
- Комплект оборудования для производства лущеного шпона, включающий в себя лущильный станок СЛ-800 и делительный станок СД-800, чаще всего используют как оборудование для производства тарной дощечки. Станки могут работать как в паре, так и в комплекте с оборудованием других производителей.
- Линия для производства лущеного шпона, в которую входятлущильный станок СЛ-1700, конвейер-накопитель К-800 иделительный станок СД-1700 чаще всего используются на начальном этапе производства фанеры, LVL бруса, заготовок для последующего шпонирования столярных изделий.
tehnomarket46.ru