Волочильный станок для проволоки
Волочение проволоки: технология и оборудование — волочильные станы и станки
Волочение, посредством которого производят проволочную продукцию, является несложной технологической операцией. Между тем, чтобы в итоге выполнения такой процедуры получить качественное изделие, осуществлять ее необходимо в правильной последовательности и использовать для этого соответствующее оборудование.
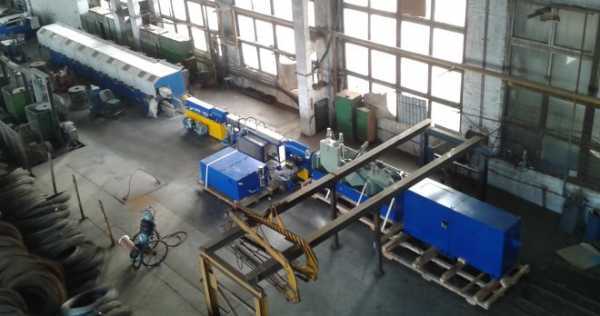
Линия производства проволоки по методу волочения
Основные этапы
Суть технологии, по которой выполняют волочение проволоки, заключается в том, что металлическую заготовку из стали, меди или алюминия протягивают через сужающееся отверстие – фильеру. Сам инструмент, в котором такое отверстие выполнено, называется волокой, его устанавливают на специальное оборудование для волочения проволоки. На то, какими диаметром, сечением и формой будет обладать готовое изделие, оказывают влияние параметры фильеры.
Принцип волочения металла
Выполнение волочения, если сравнивать такую технологическую операцию с прокаткой, позволяет получать изделия, отличающиеся более высокой чистотой поверхности и исключительной точностью геометрических параметров. Такими изделиями могут быть не только различные типы проволоки (электротехническая, используемая для сварки, вязочная и др.), но также фасонные профили, трубы и прутки разного диаметра. Полученные по такой технологии изделия отличаются и лучшими механическими характеристиками, так как в процессе волочения металла с его поверхностного слоя снимается наклеп. Что касается именно производства проволоки, то методом волочения можно получить изделия, диаметр которых находится в интервале от 1–2 микрон до 10 и даже более миллиметров.
Технология волочения сегодня уже хорошо отработана, для ее реализации используются современные модели волочильных станков, работающих без сбоев и позволяющих выполнять технологический процесс на скорости, доходящей до 60 метров готового изделия в секунду. Использование такого оборудования для волочения, кроме того, позволяет обеспечить значительную величину обжатия заготовки.
Технологическая схема волочения проволоки из нержавеющей стали
Изготовление проволоки по технологии волочения включает в себя несколько этапов.
- Исходная заготовка подвергается процедуре травления, для чего используется сернокислый раствор, нагретый до 50 градусов. С поверхности металла, прошедшего такую процедуру, легко снимается окалина, за счет чего увеличивается срок службы матриц волочильных станков.
- Чтобы увеличить пластичность обрабатываемой заготовки, а ее внутреннюю структуру довести до мелкозернистого состояния, выполняют предварительный отжиг металла.
- Остатки травильного раствора, который является достаточно агрессивным, нейтрализуют, после чего заготовку подвергают промывке.
- Чтобы конец заготовки можно было пропустить в фильеру, его заостряют, для чего может быть использован молот или ковочные валки.
- После завершения всех подготовительных операций заготовка пропускается через фильеры для волочения проволоки, где и формируются профиль и размеры готового изделия.
- Производство проволоки завершается выполнением отжига. После волочениия изделие также подвергают ряду дополнительных технологических операций – резке на отрезки требуемой длины, снятию концов, правке и др.
Особенности процедуры
Любой волочильщик проволоки знает такой недостаток волочения, как недостаточно высокая степень деформирования готового изделия. Объясняется это тем, что оно, выходя из зоны обработки волочильного станка, деформируется только до степени, ограниченной прочностью конца заготовки, к которому и прикладывается соответствующее усилие в процессе обработки.
В качестве исходного материала, который подвергают обработке на волочильных станках, служат металлические заготовки, полученные методом непрерывного литья, прессованием и катанием из углеродистых и легированных сталей, а также цветных сплавов. Наибольшую сложность процесс волочения представляет в том случае, если обработке подвергается стальной сплав. В таких случаях для качественного волочения необходимо довести микроструктуру металла до требуемого состояния. Чтобы получить оптимальную внутреннюю структуру стали, раньше использовали такую технологическую операцию, как патентирование. Заключался этот способ обработки в том, что сталь сначала нагревали до температуры аустенизации, а затем выдерживали в свинцовом или соляном расплаве, нагретом до температуры около 500°.
Методы волочения
Современный уровень развития металлургической промышленности, используемые в ней технологии и оборудование для получения металлов и сплавов позволяют не готовить металл к волочению таким сложным и трудоемким способом. Стальная заготовка, выходящая с прокатного стана современного металлургического предприятия, уже обладает внутренней структурой, оптимально подходящей для волочения.
Сама технология волочения и волочильное оборудование также совершенствовались на протяжении многих лет. В результате волочильщик проволоки сегодня имеет возможность применять современные волочильные устройства, позволяющие с минимальными трудозатратами гарантированно получать изделия высокого качества. Качество и точность обработки, выполняемой на таких волочильных специализированных станках, обеспечивается не только их оснащением современным рабочим инструментом, но и использованием при их работе комбинированной системы охлаждения, для которого применяются воздух и вода. Выходя с такого станка для волочения, готовое изделие обладает не только требуемым качеством и точностью геометрических параметров, но и оптимальной микроструктурой.
На каком оборудовании выполняется волочение металлов
Оборудование, которое волочильщик проволоки использует в своей профессиональной деятельности, называется станом. Обязательным элементом оснащения волочильной специализированной машины является «глазок» – волока. Диаметр волоки, разумеется, всегда должен быть меньше, чем размеры поперечного сечения протягиваемой через нее заготовки.
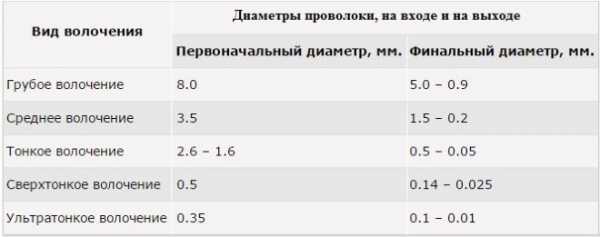
Соотношения первоначального и финального диаметров проволоки при различных типах волочения
На сегодняшний день производственные предприятия применяют волочильные специализированные станки двух основных типов, которые отличаются друг от друга конструкцией тянущего механизма. Так, различают:
- станки, в которых готовое изделие наматывается на барабан, чем и обеспечивается тянущее усилие;
- оборудование с прямолинейным движением готовой проволоки.
i-perf.ru
Линия волочения проволоки | Волочильное оборудование
Применение
Линия волочения проволоки используется для вытягивания медной катанки диаметром 8 мм с целью получения проволоки диаметром 1.2~4.0 мм (или алюминиевой катанки диаметром 9.5 мм для получения проволоки диаметром 1.7~4.8 мм), а также её дальнейшего отжига и сматывания в бухты.
Контактная форма
Компоненты оборудования
Отдатчик, волочильный стан, установка для отжига (только для медной проволоки), натяжной механизм, автоматическая приёмно-намоточная машина с двумя катушками (или стандартная моталка по запросу клиента), острильный станок и съемник, электрическая система управления.
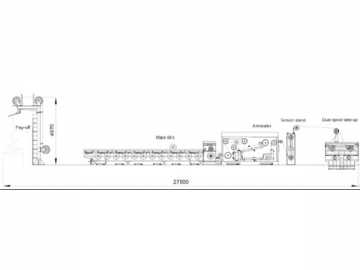
Основные характеристики
1. Волочильная машина имеет цельнолитую станину и характеризуется выверенной конструкцией, низким уровнем шума при работе, высокой производительностью и экономической эффективностью.
2. Тяговые шайбы диаметром 450 мм расположены в один ряд под небольшим наклоном, что позволяет избежать избыточного трения и пережима медной проволоки. Они обладают высокой твердостью и прочностью. Промежуточные и тяговые шайбы приводятся в движение отдельными двигателями. Благодаря оптимизированной электротехнической шине скорость их вращения можно регулировать в синхронном режиме. Волоки можно легко заменить.
4. Для предотвращения протечек охлаждающего масла в коробку передач используются различные способы уплотнения.
5. Тяговые шайбы, промежуточные шайбы и направляющее колесо подвергаются различным видам обработки для повышения их твердости, прочности и износостойкости.
6. Коробка передач использует шестерни из стали 20CrMnTi, прошедшие прецизионную обработку, науглероживание и закалку.
7. Основной тяговый двигатель, двигатель промежуточных тяговых шайб и двигатель приёмно-намоточной машины оснащены цифровыми регуляторами скорости от Siemens.
Основные технические параметры
Высокоскоростная линия для волочения медной проволокиМодель | LHT450/9 | LHT450/11 | LHT450/13 |
Диаметр медной катанки на входе (мм) | Ø 8 | Ø8 | Ø 8 |
Диаметр медной проволоки на выходе (мм) | Ø 2.0~4.0 | Ø 1.5~4.0 | Ø 1.2~4.0 |
Макс. количество волок | 9 | 11 | 13 |
Диаметр тяговой шайбы (мм) | 450 | ||
Макс. скорость волочения (мм/с) | 20 | 22 | 25 |
Мощность основного двигателя (кВт) | 280 | 280 | 280 |
Мощность установки для отжига | 60V×5000A(6000A) | ||
Обработка тяговых шайб | |||
Размер приёмной катушки (мм) | PND500/630 | ||
Способ охлаждения | Погружение в масло и распыление масла |
Контактная форма
Высокоскоростная линия для волочения проволоки из алюминия/алюминиевых сплавовМодель | LHD450/9 | LHD450/11 | LHD450/13 |
Диаметр медной катанки на входе (мм) | Ø 9/12 | Ø9/12 | Ø9/12 |
Диаметр медной проволоки на выходе (мм) | Ø 2.8~4.8 | Ø 2.2~4.8 | Ø 1.7~4.8 |
Макс. количество волок | 9 | 11 | 13 |
Диаметр тяговой шайбы (мм) | 450 | ||
Макс. скорость волочения (мм/с) | 20 | 22 | 25 |
Мощность основного двигателя (кВт) | 220 | 220 | 250 |
Обработка тяговых шайб | Вольфрамовое покрытие | ||
Размер приёмной катушки (мм) | PND500/630 | ||
Способ охлаждения | Погружение в масло и распыление масла |
Контактная форма
Среднескоростная линия для волочения медной проволокиМодель | LHT400/13 | LHT400/11 | LHT400/9 | LHT400/8 |
Диаметр медной катанки на входе (мм) | Ф8 | |||
Диаметр медной проволоки на выходе (мм) | Ф1.2~Ф3.2 | Ф1.6~Ф3.2 | Ф2.3~Ф3.2 | Ф2.6~Ф3.2 |
Макс. количество волок. | 13 | 11 | 9 | 8 |
Макс. скорость волочения (мм/с) | 20 | 18 | 12 | 12 |
Станина | Цельнолитая, чугунная | |||
Трансмиссия | Зубчатая передача с прецизионно обработанными шестернями | |||
Диаметр тяговой шайбы(мм) | Ф400 | |||
Обработка тяговых шайб | Вольфрамовое покрытие | |||
Мощность основного двигателя (кВт) | 160 | 132 | 132 | 132 |
Способ охлаждения | Погружение в масло | |||
Опциональное оборудование | Установка непрерывного отжига 350T | |||
Приёмно-намоточная машина с двумя катушками | ||||
Моталка | ||||
Приёмно-намоточная машина с одной катушкой QD630 | ||||
Опциональные функции | Система быстрой замены волок | |||
Установка непрерывного отжига 350T | ||||
Модель | 350T | |||
Конструкция | Горизонтальная | |||
Диаметр тяговой шайбы(мм) | Ф350 | |||
Диаметр проволоки (мм) | Ф1.2~Ф3.2 | |||
Защитный газ | Пар или азот | |||
Напряжение | 0~60B | |||
Ток | 0~4500A |
Контактная форма
Среднескоростная линия для волочения алюминиевой проволокиМодель | LHD400/13 | LHD400/11 | LHD400/9 |
Диаметр медной катанки на входе (мм) | Ф9.5 | ||
Диаметр медной проволоки на выходе (мм) | Ф1.8~Ф4.2 | Ф2.3~Ф4.2 | Ф3.0~Ф4.2 |
Макс. количество волок | 13 | 11 | 9 |
Макс. скорость волочения (мм/с) | 20 | 18 | 15 |
Станина | Цельнолитая, чугунная | ||
Трансмиссия | Зубчатая передача с прецизионно обработанными шестернями | ||
Диаметр тяговой шайбы (мм) | Ф400 | ||
Обработка тяговых шайб | Вольфрамовое покрытие | ||
Мощность основного двигателя(кВт) | 132 | 110 | |
Способ смазки | Погружение в масло | ||
Приёмно-намоточная машина | С двумя катушками | ||
С одной катушкой | |||
Опциональные функции | Система быстрой замены волок |
Контактная форма
Вас может также заинтересовать: Линия непрерывного вертикального литья бескислородной медной катанки, машина непрерывного литья заготовок из меди, линия непрерывного литья и прокатки, гидравлическая волочильная линия
www.etwinternational.ru
Волочение проволоки: технология, виды и описание
Волочение проволоки — это одна из разновидностей формы обработки металлических изделий. Отличительная черта операции заключается в том, что она проводится под высоким давлением. Оно воздействует на заготовку, которая имеет круглое или фасонное сечение. Такая заготовка протаскивается под давлением сквозь отверстия, которые изначально меньше, чем диаметр, протягиваемого изделия. Таким образом и получают проволоку.
Виды операции
На сегодня используется большое количество методов волочения проволоки. Если говорить о типах операции, то она может быть двух видов. Первый вид называется сухим. В данном случае процесс протягивания осуществляется через емкость, внутри которой мыльный порошок.
Мокрый тип операции выполняется при помощи мыльной эмульсии. Данная операция имеет чистоту обработки, которая также может быть выполнена в двух категориях. Первая — это черновая, или же подготовительная. Второй тип — чистовая обработка. Это финальная стадия, которая необходима, чтобы создать нужную форму и размер проволоки.
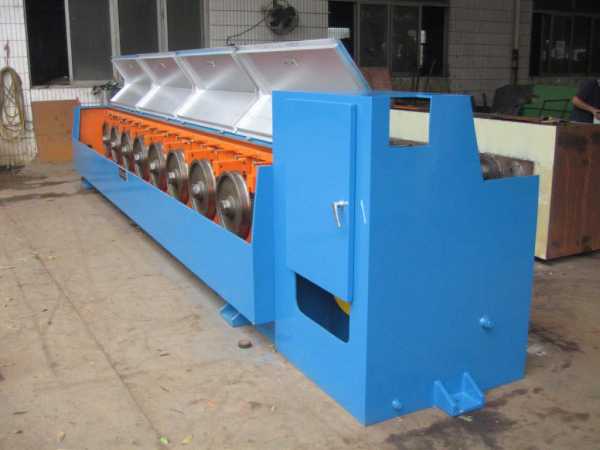
Волочение также имеет такой этап, как кратность. Возможен однократный переход или же многократный. Во втором случае предполагается, что одна и та же заготовка несколько раз пройдет через станок. Кроме того, работа может выполняться параллельно. То есть заготовка может быть однониточной, а может быть многониточной.
Отличаться могут также и волоки своей подвижностью. Они могут быть либо вращающегося типа, либо неподвижного. Последний элемент, который оказывает влияние на ход операции, — это нагрев заготовки. Естественно, что она может быть холодной или же горячей.
Суть волочения
В настоящее время возможно волочение алюминиевой проволоки, медной или же стальной. Оборудование, в котором имеется отверстие нужного диаметра, называется волоком, отсюда и название процедуры. Само же отверстие называется фильерой. От его формы и будет зависеть конечный результат всей процедуры.
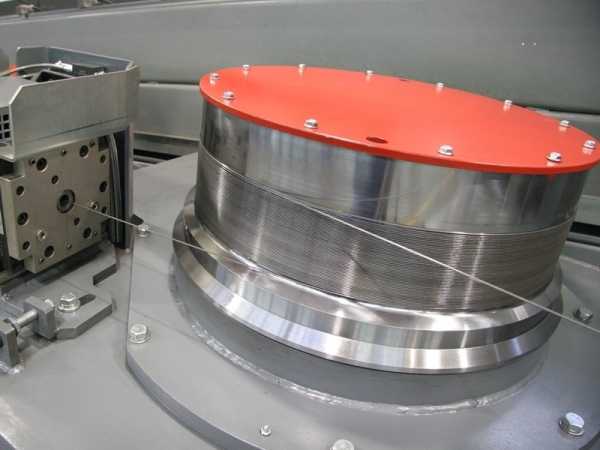
Кроме того, если сравнивать процедуру волочения проволоки и прокат, то первый способ гораздо более эффективен, так как он обеспечит большую чистоту, а также точность поверхности проволоки. К тому же процедура эта характеризуется еще и тем, что в процессе ее проведения улучшаются механические показатели, что обусловлено снятием наклепа. В настоящее время есть возможность изготавливать проволоку с диаметром от 1-2 микрон до 10, а в отдельных случаях и более, миллиметров.
Технология и этапы волочения
Стоит отметить, что с нынешним развитием технологий волочение проволоки на современном оборудовании гарантирует достаточно высокую производительность. А это очень важный момент. Оборудование для волочения проволоки вполне может функционировать на достаточно большой скорости, при этом без каких-либо нарушений. Скорость, которую могут развивать агрегаты, достигает 60 м/с.
Процесс проходит в несколько основных этапов:
- Первая стадия — это травление исходников. Для этого обычно применяется сернокислый раствор, который предварительно нагревается до температуры в 50 градусов по Цельсию. Операция необходима для того, чтобы увеличить срок эксплуатации путем удаления окалин.
- Следующая процедура — это отжиг. Она необходима для того, чтобы увеличить такую характеристику, как пластичность, а также сформировать мелкозернистость.
- Третий этап — это удаление остатков сернокислого раствора. Для этого проводится промывка и нейтрализация вещества.
- При помощи молота концы заготовки заостряются.
- На данном этапе происходит непосредственное волочение стальной проволоки или любой другой.
- Последний этап — это снова отжиг уже готового изделия.
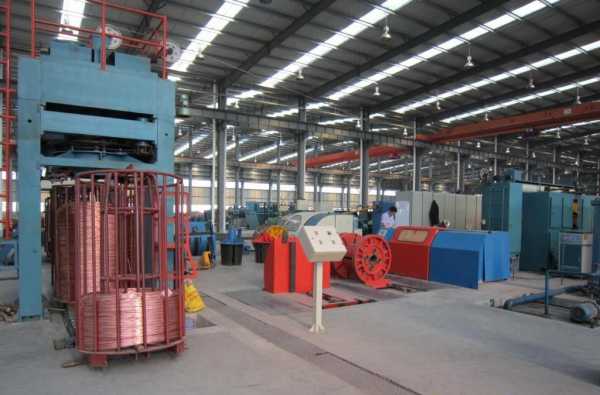
Особенность операции
Естественно, любая операция имеет свои недостатки. Как считают специалисты, волочение имеет лишь один, но достаточно серьезный минус. Заключается он в том, что проволока подвергается незначительной деформации во время проведения операции. Чаще всего исходным сырьем для волочения проволоки становится непрерывно отлитая, спресованная, скатанная заготовка, изготовленная из цветных металлов, черных металлов или углеродистых, легированных сталей. Другими словами, чтобы достичь высокого качества проволоки, необходимо использовать довольно высококачественное изначальное сырье.
Ранее для производства проволоки волочением применялись стальные заготовки, которые после прохождения процедуры обрабатывались таким способом, как патентирование. Это процесс нагрева, при определенной температуре которого происходил такой процесс, как аустенизация и экспозиция в соляных или же свинцовых расплавах. Выдержка такого продукта осуществлялась примерно при 500 градусах по Цельсию.
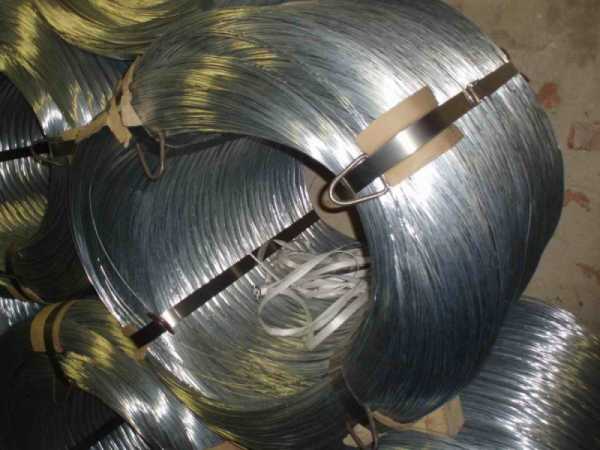
Оборудование для работы
Для волочения медной проволоки, а также стальной, используется агрегат, который получил название «стан». Основной рабочий элемент этого агрегата — это «глазок», или же волок. Естественно, что сечение подбирается таким образом, чтобы оно было всегда меньше, чем поперечное сечение заготовки.
Виды современных агрегатов
В настоящее время на заводах по обработке металла используется два типа оборудования. Отличаются они друг от друга типом тянущего механизма.
- В первом случае технология волочения проволоки заключается в том, что изделие наматывается на барабан, тем самым создавая тяговое усилие.
- Второй случай — это применение устройства, которое тянет заготовку по прямой линии.
Если говорить о применении, то второй тип агрегатов чаще всего используется в том случае, если необходимо протянуть трубную заготовку, которая не требует последующего сворачивания в бухту.
Основная масса проволоки и труб малого сечения производится именно на барабанных устройствах. Эти механизмы могут быть либо однократными, либо многократными. Естественно, что наиболее простая конструкция именно у однократного оборудования. Технологический процесс производства в таком случае предполагает протягивание проволоки в один проход. Если используется многократный станок, то процедура может повторяться два или три раза подряд.
Устройство рабочих станков
Основным рабочим элементом является приспособление, которое присутствует в любом аппарате для волочения проволоки — фильер. Этот механизм всегда создается из очень прочного металлокерамического сплава. Отличительная черта данного металла заключается в том, что он очень прочный, обладает повышенной твердостью, низкой вязкостью, а также высокой устойчивостью к истиранию. В редких случаях для производства фильера используется технический алмаз. Это дает существенное преимущество при обработке более сложных металлов.
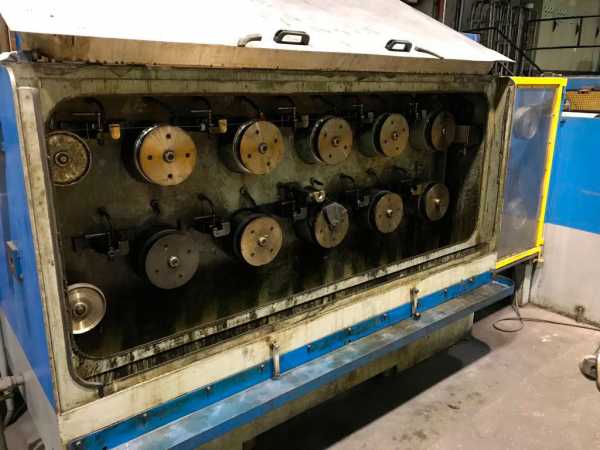
Размещаются эти детали в достаточно прочных и вязких стальных обоймах. Сама по себе обойма не способна оказать сильное влияние на фильеру, но при этом ее наличие существенно снижает растягивающее напряжение, которое неизбежно возникает во время работы. На современных предприятиях довольно часто используется сборный волок, который отличается тем, что потребляет меньше энергии, а его коэффициент полезного действия (КПД) выше примерно на 30 %.
Подготовка металла к работе
Естественно, что проводить такую процедуру без предварительной подготовки металла нельзя. Кроме того, без этой процедуры не получится добиться качественного изделия. Суть подготовительных работ заключается в том, что необходимо удалить окалину с заготовки. Прежде чем начать процесс волочения проволоки, проводят одну из трех процедур:
Механическая очистка заготовки является самым простым и самым дешевым методом очистки. Чаще всего применяется она в том случае, если изделие изготовлено из углеродистой стали. Во время процедуры обработки катанка изгибается в разные стороны. В это время ее поверхность обрабатывается механическими щетками.
Химическая и электрохимическая обработка
Что касается химического способа очистки от окалины, то он является более сложным, а также трудоемким. Для этого чаще всего используют либо соляную, либо серную кислоту. Кроме того, чтобы выполнять такую операцию, волочильщик должен обладать необходимой квалификацией, чтобы работать с химическими веществами.
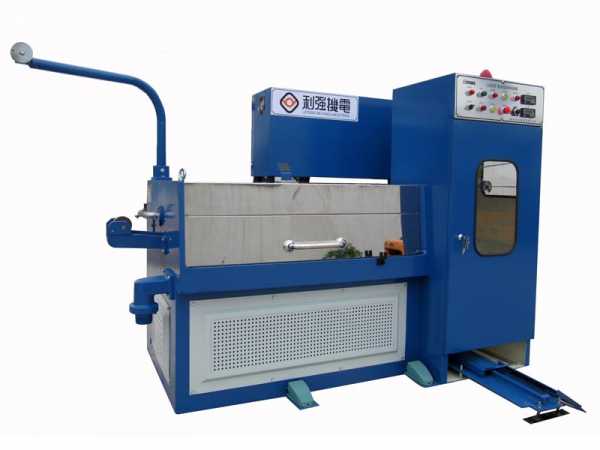
Однако здесь важно отметить, что данный метод является незаменимым, если необходимо подготовить к волочению высоколегированную или же нержавеющую сталь. Кроме того, после того, как химическая очистка будет завершена, поверхность металла необходимо промыть водой.
Последний метод, электрохимический, заключается в том, что проводят травление металла в электролитическом растворе. Эта жидкость может быть либо анодной, либо катодной, исходя из того, какие стоят условия, а также беря во внимание особенности материала.
Волочение медных заготовок
Во время волочения медной проволоки из медных заготовок всегда используются литые заготовки, на этом и основывается весь метод. Для начала необходимо сплавить между собой все заготовки. Сразу после этого, пока они еще находятся в горячем состоянии, их прокатывают. Однако проведение данного процесса влечет за собой появление пленки из оксидов на поверхности изделия. Чтобы избавиться от этой проблемы, необходимо провести обработку химическими составами. После этого можно перейти непосредственно к процедуре волочения.
Получение медной проволоки может также осуществляться по принципу погружного формования. Если применять данный метод, то поверхность катанки будет оставаться чистой и удастся избежать процедуры очистки. Именно такой способ используется для того, чтобы изготавливать наиболее тонкие проволоки (диаметром до 10 микрон). Однако при использовании такого метода очень важно подобрать состав, который будет обладать подходящими свойствами.
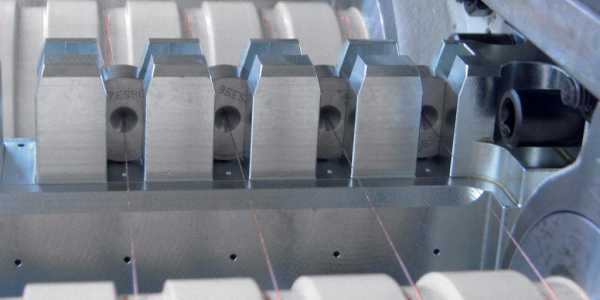
Среди таких составов выделяются:
- комплексные растворы, в роли которых могут выступать щелочные составы, соли жирных сульфированных масел и еще несколько веществ;
- возможно использование разного рода эмульсий, таких как анионные, антипенные, синтетические эфиры и другие;
- отдельно рассматриваются синтетические вещества, такие как соли органического и неорганического типа, а также растворы полимеров.
Варианты обработки
В настоящее время существует большое количество разнообразных вариантов для обработки заготовки.
- Бухтовый тип обработки. Это вариант работы с трубами из заготовок, которые собраны в бухты. Также сюда входят те трубы, которые прошли процесс волочения, после которого они были собраны в бухты.
- Мокрый тип обработки предполагает, что волок во время работы будет погружен в жидкую смазку.
- Наиболее часто используемый применение волока на закрепленных оправках.
- Есть способ обработки, в котором допускается использование труб, не имеющих круглой (фасонной) формы.
- Электропластический метод используется в том случае, если есть необходимость работы с протягиванием металла, который достаточно трудно поддается деформации.
- Еще один из методов обработки — стержневой. В заготовку вводится стержень для того, чтобы протягивать его вместе с трубой. После прохождения волока вставленный стержень необходимо достать обратно.
Разность диаметров
Процесс волочения делится еще на несколько видов, в зависимости от того, каков был начальный диаметр заготовки и какой он получился в итоге. Грубым волочением называется процедура, при которой начальный диаметр был 8 мм, а после прохождения волока стал от 5 до 0,9 мм. Средним волочением считается операция, при которой заготовка имела диаметр 3,5 мм, а в результате он уменьшился до 1,5-0,2 мм. В тонком волочении используются заготовки от 2,6 до 1,6 мм. В результате получается продукция с сечением от 0,5 до 0,05 мм.
fb.ru