типы, принцип работы, технические характеристики станков СК, СКД, ПШГН, СКДР
Чтобы понять принцип действия плунжерного насоса станка-качалки, нужно разобраться в роли и назначении отдельного станка в структуре всей трубопроводной сети добывающего комплекса. Качалка для нефти – это приводной механизм насоса, которая своим возвратно-поступательным движением, напоминающим качели, приводит в действие плунжерную пару насосного устройства. Оптимальная цикличность действия механизма качалки позволяет нефтяному ресурсу на глубине залегания концентрироваться у фильтра скважины, что способствует эффективности процесса добычи. Вся конструкция станка предусматривает минимизацию износа его отдельных элементов, установка рассчитана на безупречное действие в течение длительного срока эксплуатации.
При изучении устройства станка-качалки необходимо начать с установочной базы. База – это то, из чего состоит основа аппарата. Монтаж станка производится на заранее подготовленную бетонную основу, фундамент.

После того, как все организационные работы по установке платформы завершены, на неё навешивается массивный балансир, который уравновешивает специальную головку с канатным подвесом. Энергетическим приводом станка является мощный электродвигатель, который через редуктор станка-качалки передаёт усилие на балансир. Двигатель размещается иногда снизу под платформой, но такой вариант используется крайне редко, так как он связан с недостаточной безопасностью эксплуатации оборудования.
Через кривошип с шатуном электродвигатель воздействует на балансир, благодаря чему вращение вала двигателя преобразуется в цикличное поступательное движение элементов глубинного насоса.
Пункт управления станком-качалкой изготавливается в коробчатом виде, он содержит всё необходимое электротехническое оборудование комплекса. В станции, в непосредственной близости от управляющего реле, расположен и механический тормоз ручного типа.
Конструктивные особенности
Станки-качалки предназначены для передачи поступательного движения глубинному штанговому насосу, расположенному на дне скважины. Для уменьшения затрат на энергию оборудование должно обладать уникальной кинематической схемой. Дополнительным условием является применение современных комплектующих и компонентов.
Для анализа функциональности и особенности работы необходимо ознакомиться с конструкцией, которой обладает станок-качалка. Он состоит из силовой установки, вращательное движение от которой поступает на ведущий вал редуктора. На нем расположен кривошип с системой противовесов. Для связи кривошипа с балансиром предусмотрены шатуны и траверсы. В свою очередь, балансир установлен на опорной стойке. Для уменьшения затраты энергии на торцевой части балансира расположена откидная головка.
Правильно установленный станок имеет следующие эксплуатационные качества:
- высокий показатель КПД. Обусловлен системой противовесов, которые позволят оптимизировать затраты энергии;
- надежность.
Станок качалка способен работать продолжительное время. Главное — обеспечивать должный уровень смазки подвижных механизмов;
- сложность установки. Для нормальной эксплуатации станки-качалки необходимо устанавливать на обустроенные опорные платформы. Чаще всего их изготавливают методом заливки бетонной смесью.
Наряду с этой конструкцией в нефтедобывающей отрасли применяется безбалансировочное оборудование. Эти модели отличаются относительно небольшими размерами и массой, но при этом обладают более низким показателем КПД. Чаще всего устанавливаются в труднодоступных районах или местах, где обустройство полноценного фундамента затруднено.
В качестве привода чаще всего используются электродвигатели, скорость вращения вала которых не превышает 1500 об/мин. Изменение этого параметра выполняется с помощью коробки передач или ее клиноременного аналога.
Виды станков
Семейство нефтяных качалок представлено на отечественном рынке оборудования большим количеством модификаций. У всех видов станков практически один и тот же принцип работы, но есть и существенные отличия. Наиболее популярны среди нефтяников станки с балансирами, которые относятся к классическому типу добывающего оборудования. В этих станках предусмотрен механизм задней фиксации шатуна и редуктор расположен на одной раме с электродвигателем и балансиром.
Альтернативой классическим станкам являются такие типы станков-качалок, как гидравлические штанговые насосы, закрепляемые на фланце арматуры скважины в самом верху. Штанговые насосы имеют то преимущество перед станками классического типа, что они не требуют при своей установки сооружения мощного фундамента. Особенно важно это свойство штанговых насосов для случаев разработки месторождений в вечной мерзлоте, где заливка любого качественного фундамента сопряжена с большими трудностями. Свайная же установка классических станков не оправдана по экономическим соображениям.
Другой особенностью гидравлических насосов является возможность плавно, бесступенчато регулировать длину обсадной колонны. Благодаря этому появляется возможность точного подбора эксплуатационного режима скважины.
Основные характеристики качалок
Чтобы выбрать более подходящие станки для разработки месторождения нефти, нужно сделать анализ широкого спектра эксплуатационных и технических характеристик всех видов этого оборудования.
При оценке важнейших характеристик станка-качалки обязательно учитывают:
- рабочую штоковую нагрузку;
- максимальный ход плунжера;
- габариты редуктора;
- величину крутящего момента выходного вала;
- частоту качаний.
Определяющим параметром станка является мощность его электродвигателя. На установках классического типа для работы насосных станций достаточна мощность электродвигателя в 25 кВт. Но следует ещё учитывать тип используемых ремней для передачи вращения от двигателя на редуктор, диаметры шкивов ремённой передачи и конструкцию механизма торможения.
Даже если все эксплуатационные параметры рассматриваемого станка устраивают покупателя, ему следует ещё учесть и габариты оборудования. Ведь размеры иногда играют определяющую роль – это те случаи, когда приходится транспортировать станки на большие расстояния в условиях различных климатических и региональных зон страны. Габаритные размеры в большой степени решают вопрос, можно ли произвести установку данного оборудования в конкретной ситуации, в конкретных условиях разрабатываемого месторождения нефти.
Обычно масса станка не превышает 10 т, а его габариты по длине и ширине составляют 7Х2,5 м.
Интересные статьи:
Какой выбрать ручной листогибочный станок для металла?
Какой купить станок для резки арматуры?
Какую купить углевыжигательную печь?
Отдельные модели станков
Специалисту, занимающемуся заказами оборудования для нефтедобычи, необходимо хорошо ознакомиться с отдельными его моделями и их главными характеристиками. Несмотря на то, что каждый такой аппарат рассчитан на долгие годы работы, уже существующие промыслы время от времени производят модернизацию оборудования, закупая более современные его виды. Рассмотрим некоторые модели станков-качалок, сравнивая их характеристики и особенности.
Качалки СК
Распространённая в нефтедобывающей отрасли станок- качалка СК представляет собой скважинный насос с отдельным приводом. Насос при работе опускается в обсадную трубу скважины, и с ним соединён специальный шток привода. Шток составляется из колонны отдельных штанг, обеспечивая тем самым требуемую длину.
Как и в других классических вариантах добывающего насосного оборудования, вращение электродвигателя станка преобразуется с помощью кривошипа в поступательное движение штанговой колонны. Два исполнения станков-качалок СК изготавливаются со своим отдельным количеством типоразмеров. Аппараты СК имеют семь типоразмеров, а СКД – шесть.
Главные отличия станков-качалок СКД от СК заключаются в следующем:
- несимметричность кинематической преобразовательной схемы и более высокое преобразующее кинематическое соотношение;
- уменьшенные габаритные размеры;
- расположение редуктора прямо на станочной раме.
В установках СК используются трёхфазные электрические двигатели асинхронного типа с влагостойким исполнением в искробезопасном корпусе. В зависимости от модификации станка в нём могут применяться двигатели мощностью от 4 до 40 кВт.
Механизм тормоза станка включает в себя две колодки, правую и левую, он предназначен для фиксирования станка в нужном положении в момент его остановки.
Качалки СКДР
Более усовершенствованная модель семейства СК – станок-качалка СКДР. Аппарат развивает тяговое усилие в 60 кН при длине штока от 1,2 до 3 м. Редуктор, используемый в аппарате, имеет типоразмер Ц2НШ-450-28 или Ц3НШ-450-28.
Станки СКДР используются для откачки нефти из скважины со штоковой нагрузкой до 80 000 Н. Они разработаны с учётом последних достижений отечественного и зарубежного машиностроения. Главные элементы кинематики станков изготовлены с учётом всех требований ГОСТов на нефтедобывающее оборудование.
Частота качаний установки СКДР регулируется в диапазоне от 1,7 до 11,8 в мин и зависит от передаточного числа установленного редуктора на раме станка. Мощность двигателя качалки может составлять от 5,5 до 22 кВт в зависимости от передаточного числа редуктора.
Общая масса агрегата СКДР составляет 13 100 кг, а его габариты равны 7200х6350х 3100 мм.
Качалки ПШГН
Приводная часть глубинного нефтяного насоса шагового типа или станок-качалка ПШГН через систему штанг передаёт движение головки на насосный плунжер, расположенный глубоко в обсадной трубе скважины. Головка балансира аппарата соединяется со штоком насоса с помощью тросовой подвески.
По производительности качалка ПШГН может регулироваться путём увеличения или уменьшения числа качаний в минуту, амплитуды этих качаний и размеров насосного плунжера. Чтобы произвести регулировку длины хода штока, необходимо выполнить перестановку пальцев кривошипно-шатунного механизма в другие отверстия.
Как и все предыдущие нефтяные качалки, разновидность ПШГН не является отдельным их видом, а представляет собой разновидность главного механизма установки для добычи нефти.
Шкивы электродвигателя
Шкивы электродвигателя выполняют быстросменными за счёт конусной расточки тела и применения конусной втулки, закрепляемой гайкой. При помощи сменных шкивов регулируется число ходов точки подвеса штанг.
Поворотные салазки предназначены для крепления электродвигателя, обеспечивают быструю смену и натяжение клиновидных ремней. Выполнены в виде рамы, которая шарнирно укреплена на заднем конце рамы станка-качалки в трёх точках, а на большегрузных СК (длина хода свыше 3,5, и) — в четырёх и прикреплённых к ней поперечно болтами двух салазок, на которые устанавливается электро- двигатель. Поворотные салазки поворачиваются вращением ходового винта.
Обслуживание нефтяных качалок
Специальный персонал нефтедобывающего предприятия выполняет обслуживание станка-качалки. Для удобства его работы конструкторами предусмотрены различные вспомогательные устройства и механизмы. При обслуживании балансира с траверсой и кривошипа на установке устроена специальная площадка, снабжённая системами привода. Операторы, располагаясь на этой площадке, производят управление балансировкой и уравновешиванием станка, проверяют крепление всех узлов кривошипно-шатунного механизма.
Вся кинематика системы привода нефтедобывающей качалки сконструирована для того, чтобы головка станка и кривошип совершала движение в оптимальном ритме и этот режим можно бы было легко перенастраивать.
Функции операторов станков и обслуживающего персонала необходимо разделять. Технический персонал занимается обслуживанием нефтяных насосов во время их интенсивной эксплуатации, в их обязанности входит слежение за рабочими показателями всех механизмов станции и техническое обслуживание насосного оборудования. В случае необходимости они производят и ремонт станков-качалок. Особенно важно в их работе создавать благоприятные режимы функционирования узлов и механизмов станка в моменты возникновения в нём максимальных, пиковых нагрузок.
В функции же операторов установок входят обязанности по регулированию самого процесса выкачки нефтяных ресурсов из глубины месторождения, по установке оптимальных режимов работы станка на каждом периоде освоения запасов углеводородов.
Обработка дерева и металла
Цель обкатки: выявить возможные дефекты сборки и дать приработаться сопрягаемым поверхностям трения.
К обкатке приступают, убедившись, что все сборочные единицы и механизмы закреплены и обеспечена их доброкачественная смазка и что все ограждающие устройства находятся на своих местах. Перед пуском станка проверяют нормальную работу механизмов, проворачивая соответствующие сборочные единицы вручную и переключая рукоятки скоростей и подач. Одновременно следят, как поступает масло к трущимся поверхностям.
Обкатку сначала ведут на холостом ходу и на самых малых скоростях, затем последовательно включают все рабочие скорости вплоть до наибольшей. На этой максимальной скорости станок должен работать не менее ч без перевыва. Точно так же, как механизмы вращения, проверяют работу механизмов привода подач.
В процессе обкатки определяют температуру нагрева подшипников, которая в станках должна быть не выше 50—60 °С, выявляют стук и шум. Все механизмы должны работать плавно, без толчков и вибраций; их пуск и реверсирование должны осуществляться легко и не сопровождаться рывками или ударами.
Все органы управления должны быть сблокированы (связаны между собой) таким образом, чтобы при включениях исполнительных органов перемещения и подачи происходили строго согласованно во времени и полностью исключалась возможность самопроизвольного движения даже на самые малые расстояния каких-либо деталей механизмов, частей агрегата. Упоры, кулачки и другие детали автоматически действующих устройств должны обеспечивать надежное выключение подач, а механизмы зажатых деталей и инструментов — многократное и безотказное их закрепление и раскрепление. Необходимо, чтобы системы смазки и охлаждения подавали к соответствующим местам достаточное количество масла и охлаждающей жидкости.
Безотказной должна быть и работа электрооборудования. В рубильниках, переключателях, реостатах и всех других аналогичных устройствах и аппаратах не допускаются даже малейшие неисправности. Недостаточно быстрое включение или выключение электроаппаратуры, чрезмерный нагрев пускового реостата, гудение реле и другие подобные неполадки при обкатке станка или машины свидетельствуют о дефектах сборки или ремонта вообще. Их устраняют соответствующими регулировками, а если нужно, полностью разбирают те или иные механизмы.
Под нагрузкой отремонтированный и собранный станок испытывают путем обработки деталей-образцов на различных скоростях в соответствии с техническими данными паспорта станка. Испытание ведут с нагружением станка до величины номинальной мощности привода, снимая стружку все большего сечения. Допускается кратковременная перегрузка станка, однако не более чем на 25% его номинальной мощности.
Все механизмы станка при его испытании под нагрузкой должны работать исправно, допустимо лишь незначительное повышение шума в зубчатых передачах. Устройства, предохраняющие станок от перегрузок, должны действовать надежно; легко и плавно должна включаться пластинчатая фрикционная муфта. При наибольшей перегрузке станка (на 25%) муфта не должна самовключаться или буксовать.
На точность и шероховатость обработки станок проверяют после его испытания под нагрузкой. Перед новым испытанием нужно прогреть шпиндель, подшипники, гидросистему и другие основные элементы станка обкаткой его на холостом ходу.
Испытание на получение требуемой шероховатости обработанной поверхности производится точением образца при определенных режимах резания. На обработанных поверхностях не должно быть следов дробления.
Для испытания на точность обработки станок необходимо установить на фундаменте или стенде и тщательно выверить при помощи клиньев, башмаков или другими средствами. Его надо привести в то же положение, при котором он был выверен на стадии сборки после окончания ремонта. Приемка отремонтированного станка из капитального ремонта производится по нормам точности, установленным ГОСТ 18097—72 для приемки новых токарных станков.
Проверка станка на жесткость производится (по ГОСТ 7035—75) g целью определения качества сборки передней бабки, суппорта и задней бабки. Жесткость станка уменьшается из-за неровностей на соприкасающихся поверхностях, а также из-за деформации подшипников, клиньев, планок, болтов и других промежуточных деталей вследствие их плохой пригонки.
Показатель жесткости — степень деформации испытываемых сборочных единиц относительно станины под действием внешней силы определенной величины. Проверяют жесткость динамометром и индикатором, применяя при необходимости оправки и упоры. Воздействуя через динамометр на шпиндель или суппорт с определенной силой, выявляют отклонение вследствие деформации по индикатору, установленному с противоположной стороны шпинделя или суппорта.
Испытанием на мощность (производится после испытаний станка на холостом ходу, в работе и на жесткость) определяют коэффициент полезного действия станка при наибольшей допустимой для него нагрузке. Во время испытания обрабатывают болванку или производственную деталь, предварительно выбрав сечение стружки и Другие режимы резания по паспортным данным станка Продолжительность пробной обработки с использованием полной мощности станка не более 30 мин. Допускается перегрузка электродвигателя на 10—15% против его номинальной мощности.
Геометрическую точность станка проверяют в соответствии о ГОСТ 18097—72 после испытания станка на холостом ходу и в работе.
17)Конструирование и принцип действие станка качалки.
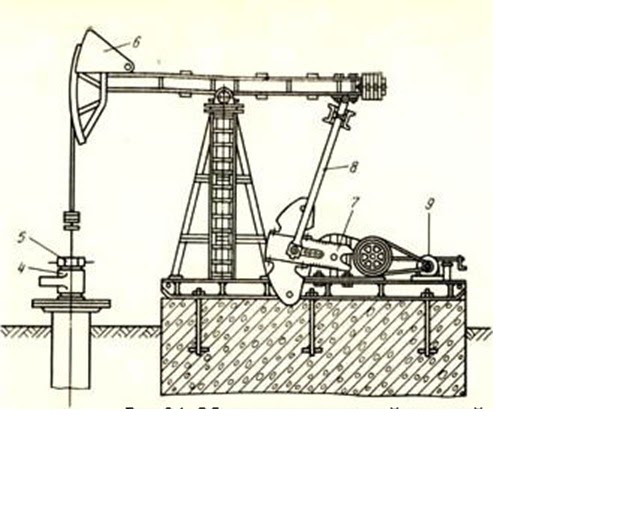
Станок качалка (СК), (СКН), (СКД).
СКН – станок качалка нормального ряда.
Наиболее распространённый вид насосов
на буровых, СК предназначен для
механического привода плунжера глубинного
насоса. В России эксплуатируется СК
около 15-17 видов (СКН;СКД) это российское
производство, и “Вулкан” – Румыния.
Состав: рама установлена на фундамент,
редуктор, электродвигатель, балансир
установлен на пирамиде, соединён с
редуктором через кривошипы и шатуны
через траверсу. На другом конце балансира
головка, на которую подвешивают колонну
штанг через канатную подвеску. Имеется
площадка на которую установлена станция
управления. На кривошипах редуктора
установлены по два контргруза, которые
можно перемещать по кривошипу для
выравнивания веса, но в зависимости от
количества и веса штанг. На кривошипах
имеются отверстия, при помощи которых
можно изменить длину хода плунжера,
устанавливая шатуны на определённом
месте. Имеется возможность изменять
число качаний. Изменяя диаметр шкивов,
изменяется число качаний.
18)Понятие газового фактора.
Газовый фактор – это количество газа в одном кубическом метре растворенного в одной тонне нефти в пластовых условиях. Количество растворенного газа зависит от насыщенного давления, это давление газа при котором газ находится в растворённом состоянии. Газ добываемый с нефтью называют попутным газом. Составляющая газа является метан. Чем выше газовый фактор, тем больше газа- вода- проявления открытых фонтанов.
19)Назначение устройства и принцип работы электроконтактного манометра.
Электроконтактный манометр предназначен для поддержания заданного давления в трубопроводе или аппарате. Вмонтированы два контакта на минимальное и максимальное давление. В момент максимального давления двигатель отключается, при достижении минимального давления включается.
20)Первая помощь при поражении током.
Алгоритм действий:
1)Обезопасить себя;
2)Вывести пострадавшего из опасной зоны;
3)Оценить состояние, вызвать тех.
При поражении током могут быть ожоги и остановка сердца.
Клиническая смерть – это если не оказать помощь, через 5-7 минут переходит в биологическую, поэтому необходимо проведения реанимации. Участвуют 3, 2 или 1 спасатель.
Порядок действий: Пострадавшего
уложить на твёрдой поверхности, защитить
от простуды, освободить от стесняющей
одежды, положить валик под шейный
позвонок на уровне лопаток, очистить
полость рта, выдвинуть нижнюю челюсть,
приложить к голове холод. Первый спасатель
становится слева от пострадавшего и
находит точку на груди над сердцем, и
наносит удар по этой точке с высоты
20-30 сантиметров. От этого удара сердце
может сразу запуститься. Второй спасатель
становится справа от пострадавшего и
производит искусное дыхание. На каждый
вдох первый спасатель осуществляет 5
надавливаний на глубину 4 сантиметра,
это называется непрямой массаж сердца.
Продолжительность надавливаний 0,5
секунды третий спасатель приподнимает
ноги. Если третьего спасателя нет то
под ноги подставляем табурет.
Принцип работы и правила эксплуатации перфоратора
Перфораторы — это инструменты, используемые для непосредственной добычи камня. Он бурит взрывные скважины в скальных образованиях, чтобы разместить взрывчатые вещества, чтобы взорвать скалы, чтобы завершить добычу камня или другой каменной кладки.
Кроме того, перфоратор можно использовать в качестве отбойного молотка для разрушения твердых слоев, таких как бетон. Перфораторы можно разделить на четыре категории в зависимости от их источников питания: пневматические перфораторы, перфораторы внутреннего сгорания, электрические перфораторы и гидравлические перфораторы.
Основная классификация:
Перфораторы можно разделить на четыре категории в зависимости от их источников питания: пневматические перфораторы, перфораторы внутреннего сгорания, электрические перфораторы и гидравлические перфораторы.
1. Перфоратор внутреннего сгорания
В перфораторе внутреннего сгорания нет необходимости заменять внутренние части головки машины, просто перемещайте рукоятку, как требуется для работы. Он имеет преимущества удобной работы, большей экономии времени, экономии труда, высокой скорости резки и высокой эффективности. В скале бурятся отверстия, которые могут быть вертикально вниз, горизонтально вверх под углом менее 45° и вертикально вниз до самой глубокой скважины до шести метров. Будь то высокие горы или равнины, работает ли она в жарком районе 40° или в холодном районе минус 40°, эта машина обладает широким диапазоном приспособляемости.
Перфоратор внутреннего сгорания выполняет функции добычи полезных ископаемых, бурения, строительства зданий, цементного покрытия, асфальта и других функций растрескивания, дробления, трамбовки, лопаты и других функций. Он широко используется в горнодобывающей промышленности, строительстве, тушении пожаров, геологоразведке, строительстве дорог, разработке карьеров, строительстве, оборонной технике и т. д. через кривошипный механизм, чтобы разбить камень. Механизм выброса порошка используется для выброса каменной крошки, а тип внутреннего сгорания использует принцип двигателя внутреннего сгорания для привода поршня, который ударяет по стальному припою и разбивает камень взрывной силой бензина. Применяется на строительных площадках без электроснабжения и без источника газа. Гидравлический тип основан на гидравлическом давлении для воздействия на сталь инертным газом и ударным телом для удара по породе. Когда ударный механизм этих перфораторов находится в обратном ходе, вращающийся механизм заставляет сталь поворачиваться на угол, так что долото меняет положение и продолжает долбить породу. Благодаря взрывной силе дизельного топлива поршень воздействует на стальной припой, так что он непрерывно ударяется и вращается, а механизм выброса камней используется для выброса каменной крошки, чтобы можно было выдолбить взрывную скважину.
В-третьих, пневматический тип использует сжатый воздух для перемещения поршня вперед в цилиндре, так что сталь просверливается и раскачивается, что является наиболее распространенным. Конструкция буровой установки состоит из трех частей: главного двигателя, насосной станции и консоли. Большой рабочий диапазон, высокая надежность и простота в эксплуатации;
Буровая установка с погружным пневмоударником: с вращением и ударом. Вращательное движение обеспечивает вращение буровой установки вне скважины и передается на погружной пневмоударник через бурильную трубу, тем самым приводя погружной пневмоударник во вращение. Ударное движение обеспечивается сжатым воздухом или водой под высоким давлением из буровой установки снаружи скважины, а давление передается на погружной пневмоударник через полую бурильную трубу. Перфоратор со скрытым отверстием преобразует энергию, содержащуюся в напорной среде, в энергию удара возвратно-поступательного движения, воздействующего на буровое долото, при этом сверло глубокое и глубокое. Скорость бурения, как правило, выше, чем у роторных буровых установок, но ниже, чем у установок с перфоратором. Преимущество заключается в том, что можно делать более глубокие отверстия, а скорость остается постоянной, поскольку сила удара не уменьшается с увеличением глубины отверстия. Шлам выносится воздухом или водой из петли между бурильной трубой и стенкой скважины.
Перфоратор: с вращением и ударом. И вращение, и удар обеспечиваются сверлом вне отверстия. Удар всегда действует на верхнюю часть бурильной трубы. По мере увеличения глубины сверления бурильная труба удлиняется и мощность удара передается на забой скважины. Таким образом, глубина бурения, как правило, не превышает 20 метров, но и до 30 метров, но редко, это также очень медленно. Буровой шлам также осуществляется сжатым воздухом или водой.
Роторная буровая установка: только вращение, бурение только вращением при определенных условиях движения. Буровое долото на рисунке представляет собой шарошечную буровую установку, которая обычно бурит относительно большую скважину в горной породе. Существует также вращающаяся дрель, представляющая собой алмазный резак, или инструмент из других относительно твердых материалов, используемый для резки камней в пласте. Обычно скорость бурения такой буровой машины относительно низкая, но преимущество в том, что она может быть глубокой, и можно пройти любые геологические условия, а прямолинейность бурения не пострадает.
Принцип работы:
Перфоратор работает по принципу ударного дробления. При работе поршень совершает высокочастотные возвратно-поступательные движения и непрерывно ударяет по хвостовику. Под действием ударной силы клиновидная буровая головка дробит горную породу и прорезает ее на определенную глубину, образуя вмятину. После отвода поршня сверло поворачивается на определенный угол, поршень движется вперед, и при повторном ударе по хвостовику молотка образуется новая вмятина. Веерообразная порода между двумя ямками измельчается горизонтальной составляющей, генерируемой долотом. Поршень непрерывно воздействует на хвостовик и непрерывно подает сжатый воздух или воду под давлением из центрального отверстия сверла для выгрузки шлака из отверстия, тем самым формируя круглое отверстие определенной глубины.
Рабочие процедуры:
1. Проверьте целостность и вращение каждого компонента (включая перфоратор, кронштейн или буровую установку) перед бурением, добавьте необходимое смазочное масло, проверьте воздуховод, не заблокирован ли суставы крепкие.
2. Верхняя часть рабочей поверхности называется верхней частью рабочей поверхности, то есть проверьте верхнюю пластину и вторую связку рядом с рабочей поверхностью на наличие живого камня и бирюзы и выполните необходимую обработку.
3. Положение взрывной скважины с плоской рабочей поверхностью необходимо предварительно пробурить во избежание соскальзывания или смещения шпура.
4. Категорически запрещается сушить глаза. Необходимо придерживаться бурения мокрой породы. При работе сначала откройте воду, затем откройте ветер, сначала остановите ветер, затем выключите воду. Начните с низкой скорости при открывании глаз и сверлите на полной скорости после сверления на определенную глубину.
5. Персоналу, выполняющему пайку, не разрешается носить перчатки при сверлении.
6, при использовании газовой ножки для сверления проушины обратите внимание на положение и положение стоя, не следует полагаться на тело для повышения давления, но не может стоять под буровым долотом перед перфоратором, чтобы предотвратить поломку. кусочек.
7. Если при бурении горной породы обнаружен ненормальный звук, если выброс порошковой воды не соответствует норме, прекратите осмотр, выясните причину и устраните ее, прежде чем продолжить бурение.
8. При выходе из перфоратора или замене бурильной штанги перфоратор может работать на низкой скорости, обращая внимание на положение перфоратора перфоратора, избегая автоматического падения бурильной штанги и травмирования людей. , и своевременное закрытие газового тракта.
9. При использовании перфоратора с пневматической опорой для бурения горных пород необходимо плотно прижимать верхнюю часть, чтобы предотвратить ее скольжение и причинение вреда людям.
10. При использовании направленного вверх перфоратора для усадки кронштейна необходимо придерживать буровую штангу, чтобы она не упала автоматически.
Каков принцип работы и характеристики поворотного устройства коромысла большого автоматического трубогибочного станка с ЧПУ?
Бесплатные пресс-формы Нержавеющая сталь Алюминий Медь Полностью автоматический гидравлический трубогиб с ЧПУ Полуавтоматический сервоэлектрический трубогибочный станок с ЧПУ
Трубогибочный станок представляет собой разновидность оборудования для резки, широко используемого при механической обработке, которое может резать стальные листы различной толщины. Производство трубогиба в основном связано с тем, что людям нужно согнуть объект, и это занимает много времени, а эстетика не так хороша, как у машины. Таким образом, продукт трубогиба разработан, чтобы сделать изгиб объекта более красивым. Трубогибочный станок – самый распространенный станок в нашей жизни. Он в основном изгибает объект, что снижает трудозатраты и значительно повышает эффективность работы в традиционном режиме.
Трубогибочный станок состоит из приводного устройства, направляющего колеса, устройства предварительного сжатия, устройства вращения коромысла, зажимного устройства, основания, источника питания промежуточной частоты, гидравлической системы и других компонентов. Поворотное устройство коромысла является основным компонентом трубогибочного оборудования. Его функция заключается в изгибе нагретой трубы по радиусу, соответствующему заданным требованиям, и имеет функции изгиба, поворота и уменьшения диаметра. Поворотное устройство коромысла в основном состоит из большого подвижного стола, привода коромысла, коромысла, среднего подвижного стола, поворотного подшипника, небольшого подвижного стола и других компонентов. Приводное устройство коромысла установлено сбоку от большого стола скольжения, коромысло закреплено на большом столе скольжения через поворотный подшипник, а средний стол скольжения закреплен на коромысле, а положения большого и изменены средние столы салазок, так что центр вращения и патрон отрегулированы.