Характеристика жаропрочного металла; что собой представляет жаростойкая сталь
Окалино- или жаростойкость – это способность металлов или сплавов длительное время противостоять газовой коррозии в условиях повышенных температур. Жаропрочность же представляет собой способность металлов не разрушаться и не поддаваться пластической деформации при высокотемпературном режиме работы. Сталь жаропрочная представлена на рынке большим разнообразием марок, равно как и жаропрочные сплавы. Большинство специалистов признают ее лучшим материалом для изготовления деталей конструкций и оборудования, эксплуатируемых в агрессивных средах и в иных сложных условиях.
Жаропрочный металл и жаростойкость
Ненагруженные конструкции, эксплуатируемые при температуре порядка 550°С в окислительной газовой атмосфере, изготавливаются обычно из жаростойкой стали. К данным изделиям часто относятся детали нагревательных печей. Сплавы на базе железа при температуре больше 550°С склонны активно окисляться, из-за чего на их поверхности образуется оксид железа. Соединение с элементарной кристаллической решеткой и нехватка атомов кислорода приводит к появлению окалины хрупкого типа.
Для улучшения жаростойкости стали в химический состав вводятся:
- хром;
- кремний;
- алюминий.
Данные элементы, соединяясь с кислородом, способствуют формированию в металле надежных, плотных кристаллических структур, благодаря чему и улучшается способность металла спокойно переносить повышенную температуру.
Тип и количество легирующих элементов, вводимых в состав сплава на базе железа, зависит от температуры, в которой эксплуатируется изделие из него. Лучшая жаростойкость у сталей, легирование которых выполнялось на основе хрома. Наиболее известные марки этих сильхромов:
- 15Х25Т;
- 08Х17Т;
- 36Х18Н25С2;
- Х15Х6СЮ.
С повышением количества хрома в составе жаростойкость увеличивается. С хромом могут создаваться марки металлов, изделия из которых не утратят первоначальных характеристик и при долгом воздействии температуры больше 1000°С.
Особенности жаропрочных материалов
Жаропрочные сплав и стали успешно эксплуатируются при постоянном воздействии больших температур, причем склонность к ползучести не проявляется. Суть данного процесса, которому подвержены стали обыкновенных марок и прочие металлы, в том, что материал, испытывающий воздействие постоянной температуры и нагрузку, медленно деформируется, или ползет.
Ползучесть, которой стараются избежать при создании жаропрочных сталей и металлов другого типа, бывает:
- длительной;
- кратковременной.
Для определения параметров кратковременной ползучести материалы подвергаются испытаниям: помещаются в печь, нагретую до нужной температуры, а к ним на определенное время прикладывается растягивающая нагрузка. За короткое время проверить материал на склонность к длительной ползучести и выяснить, каков ее предел, не удастся. С этой целью испытуемое изделие в печи подвергается длительной нагрузке.
Важность предела ползучести в том, что он характеризует наибольшее напряжение, ведущее к разрушению разогретого образца после воздействия определенное время.
Марки жаростойких и жаропрочных сталей
По внутренней структуре категории следующие:
- мартенситные;
- аустенитные;
- мартенситно-ферритные;
- перлитные.
Жаростойкие стали могут представлять еще два типа:
- ферритные;
- мартенситные, или аустенитно-ферритные.
Среди сталей с мартенситной структурой наиболее известны:
- Х5 (из нее делают трубы, которые будут эксплуатироваться при температуре не больше 650°С).
- Х5М, Х5ВФ, 1 Х8ВФ, Х6СМ, 1 Х12Н2ВМФ (служат для изготовления изделий, которые эксплуатируются при 500-600°С определенное время (1000-10000 ч.).
- 3Х13Н7С2 и 4Х9С2 (изделия из них успешно эксплуатируются при 850-950°С, поэтому из них делают клапаны моторов транспортных средств).
- 1Х8ВФ (изделия из этой стали успешно эксплуатируются при температурах не больше 500°С 10000 ч. и дольше; в частности, из материала делают конструктивные элементы паровых турбин).
Основа мартенситной структуры – это перлит, меняющий состояние, если в составе материала увеличивается содержание хрома. Перлитные марки жаростойких и жаропрочных сталей, которые относятся к хромокремнистым и хромомолибденовым:
- Х6С;
- Х7СМ;
- Х6СМ;
- Х9С2;
- Х10С2М;
- Х 13Н7С2.
Для получения из этих сталей материала со структурой сорбита, отличающегося высокой твердостью (не меньше 25 по HRC), сначала их закаливают при 950-1100°C, а потом подвергают отпуску.
Стальные сплавы с ферритной структурой, из категории жаростойких, содержат 25-33% хрома, определяющего их характеристики. Для придания этим сталям мелкозернистой структуры изделия из них отжигают. В данную категорию сталей входят:
- 1 Х12СЮ;
- Х17;
- Х18СЮ;
- 0Х17Т;
- Х25Т;
- Х 28.
При нагревании их до 850°C и больше зерно внутренней структуры укрупняется, из-за чего повышается хрупкость.
Из жаропрочной нержавейки изготавливаются:
- тонколистовой прокат;
- бесшовные трубы;
- агрегаты химической и пищевой промышленности.
Стали, в основе которых феррит и мартенсит, активно используются в производстве изделий различного назначения в машиностроении. Изделия из таких жаропрочных сплавов даже довольно длительное время успешно эксплуатируются при температуре до 600°C .
Самые распространенные марки данных жаропрочных сталей:
- Х6СЮ;
- 1Х13;
- 1 Х11МФ;
- 1Х12ВНМФ;
- 1 Х12В2МФ;
- 2 Х12ВМБФР.
Хрома в химическом составе этих сплавов – 10-14%. Легирующие добавки, улучшающие состав, здесь – ванадий, вольфрам и молибден.
Аустенитно-ферритные и аустенитные стальные сплавы
Самые значимые особенности аустенитных сталей в том, что внутренняя их структура формируется благодаря никелю в их составе, а жаростойкость связана с хромом.
В сплавах данной категории, отличающихся малым содержанием углерода, иногда присутствуют легирующие элементы титан и ниобий. Стали, основу внутренней структуры которых составляет аустенит, входят в категорию нержавеющих и при длительном воздействии больших температур (до 1000°C) хорошо противостоят формированию окалины.
Наиболее распространенные сегодня стали с аустенитной структурой – это дисперсионно-твердеющие сплавы. С целью улучшения качественных характеристик добавляются карбидные или интерметаллические упрочнители.
Наиболее популярные марки, основа внутренней структуры которых – аустенит:
- Дисперсионно-твердеющие Х12Н20Т3Р, 4Х12Н8Г8МФБ, 4Х14Н14В2М, 0Х14Н28В3Т3ЮР.
- Гомогенные 1Х14Н16Б, 1Х14Н18В2Б, Х18Н12Т, Х18Н10Т, Х23Н18, Х25Н16Г7АР, Х25Н20С2.
Стальные сплавы на основе смеси аустенита и феррита отличает очень высокая жаропрочность, которая по показателям превышает аналогичный параметр даже у высокохромистых материалов. Характеристики жаропрочности достигаются и за счет высокой стабильности внутренней структуры сталей этой категории. Изделия из них успешно эксплуатируются даже при температурах до 1150°С.
Жаропрочные стали с аустенитно-мартенситной структурой характеризуются повышенной хрупкостью, поэтому не могут использоваться в производстве изделий, которые эксплуатируются под высокой нагрузкой.
Из жаропрочных сталей этой категории делаются изделия такого назначения:
- Жаропрочные трубы, конвейеры для печей, емкости для цементации (Х20Н14С2 и 0Х20Н14С2).
- Пирометрические трубки (Х23Н13).
Тугоплавкие материалы
Стальные сплавы на базе тугоплавких металлов используются для производства изделий, которые эксплуатируются при 1000–2000°C .
Тугоплавкие металлы, которые входят в химический состав таких сталей, характеризуются температурами плавления:
Благодаря тому, что тугоплавкие стали этой категории имеют высокую температуру перехода в хрупкое состояние, при серьезном нагреве происходит их деформация. Для повышения жаропрочности таких сталей в их состав вводят специальные добавки, а для повышения жаростойкости легируют титаном, молибденом, танталом и др.
Самые распространенные соотношения химических элементов в тугоплавких сплавах:
- основа – вольфрам и 30% рений;
- 60% ванадий и 40% ниобий;
- основа – 48% железо, 15% ниобий, 5% молибден, 1% цирконий;
- 10% вольфрама и тантала.
Сплавы на основе никеля и никель с железом
Сплавы на базе никеля (55% Ni) или выполненные на основе смеси его с железом (65%) — жаропрочные с высокими качествами жаростойкости. Базовый легирующий элемент для любых сталей этой категории – хром, которого содержится 14-23%.
Высокая стойкость и прочность сохраняется при повышенных температурах. Этими качествами обладают стальные сплавы на основе никеля.
Наиболее популярные:
- ХН60В;
- ХН67ВМТЮ;
- ХН70МВТЮБ;
- ХН70;
- ХН77ТЮ;
- ХН78Т;
- ХН78МТЮ;
- ХН78Т.
Некоторые марки – это жаропрочные стаи, остальные – жаростойкие. При нагревании на поверхности изделий из данных сплавов появляется оксидная пленка на базе алюминия и хрома. В твердых растворах структуры этих металлов формируются соединения никеля и алюминия или никеля и титана, что обеспечивает устойчивость материалов к высоким температурам. Более подробные характеристики приводятся в специальных справочниках.
Из сталей никелевой группы изготавливают:
- Элементы газовых конструкций и коммуникаций (ХН5ВМТЮ).
- Конструктивные элементы турбинных устройств (ХН5ВТР).
- Конструктивные элементы компрессоров – лопатки, диски (ХН35ВТЮ).
- Роторы для оснащения турбин (ХН35ВТ и ХН35ВМТ).
Итак, жаропрочные марки способны долгое время функционировать в условиях высоких температур без деформаций и противостоят газовой коррозии. Посредством сплавов разных элементов добиваются оптимальных свойств материалов в зависимости от условий эксплуатации.
tokar.guru
жаропрочные стали, жаростойкость, температура плавления
Развитие новых промышленных технологий, ракетной техники, сложного турбинного оборудования в середине пятидесятых годов прошлого века, повлекло за собой модернизацию металлургической отрасли в целом. В отдельное направление выделились работы по созданию жаропрочных сплавов. С течением времени они нашли применение в атомном машиностроении, энергетике, химической промышленности и заняли место в цепочке высокотехнологических производств.
Жаропрочные и жаростойкие материалы
Жаропрочные и жаростойкие сплавы — это большая группа легированных материалов с присадками молибдена, титана, хрома и ряда других элементов. Все эти сплавы изготавливаются на железной, никелевой и кобальтовой основах. Их главной особенностью является сохранение повышенной прочности при высоких температурах.
Основные типы
Наиболее распространены сплавы на основе железа. Это хромистые, хромоникелевые, а также хромомарганцевые стали с молибденовыми, титановыми и вольфрамовыми присадками. Также производят сплавы с такими легирующими элементами, как алюминий, ниобий, ванадий, бор, но в меньших количествах.
В большинстве случаев процент добавления присадок в сталь достигает от 15 до 50%
Вторая, весьма востребованная группа — сплавы на никелевой основе. В качестве присадки используется хром. Жаропрочность также повышают добавки титана, церия, кальция, бора и сходных по составу элементов. В отдельных технологических комплексах востребованы сплавы на основе никеля с молибденом.
К третьей группе относятся термостойкие сплавы на кобальтовой основе. Легирующими элементами для них служат углерод, вольфрам, ниобий, молибден.
В металлургии существует целый ряд материалов, который используется при легировании сталей:
- хром,
- никель,
- молибден,
- ванадий,
- ниобий,
- титан,
- марганец,
- Вольфрам.
- кремний,
- тантал,
- алюминий,
- медь,
- бор,
- кобальт,
- цирконий.
Широко используются редкоземельные элементы.
Химический состав
Определение химического состава жаростойких материалов — сложный процесс. Необходимо учитывать не только основные легирующие элементы, но и то, что попадает в продукцию как примеси или остаётся в результате химических реакций, протекающих во время плавки.
Специально добавленные легирующие элементы вводятся для получения необходимых технологических, физических и механических свойств. А примеси и образовавшиеся при плавке химические элементы могут ухудшать свойства высоколегированного металла.
Для хромоникелевых сплавов и огнеупорных материалов на основе кобальта опасно присутствие серы более 0,005%, следов олова, свинца, сурьмы и других легкоплавких металлов.
Структура и свойства
Жаропрочность определяется не только химическим составом металлов, но и формой, в которой примеси находятся в сплаве. Например, сера в виде сульфидов никеля снижает температуру плавления. А та же сера, соединённая с цирконием, церием, магнием образует тугоплавкие структуры. Большое влияние на жаропрочность оказывает чистота никеля или хрома. Однако следует учитывать, что свойства сплавов варьируются в зависимости от применяемой технологии.
Главное свойство, по которому определяют жаростойкость материала — ползучесть. Это явление постоянной деформации под непрерывным напряжением. Сопротивляемость материала разрушению под действием температуры
Классификация сплавов
Первый параметр классификации сплавов — это жаропрочность, то есть способность материала выдерживать механические деформации при высоких температурах, без деформации.
Во-вторых, это жаростойкость (окалиностойкость). Способность материала противостоять газовой коррозии при высоких температурах. При описании процессов до шестисот градусов Цельсия используется термин «теплоустойчивость».
Одной из основных характеристик является предел ползучести. Это напряжение, при котором деформация материала за определённый период достигает заданной величины. Время деформации является сроком службы детали или конструкции.
Для каждого материала установлена максимальная величина пластической деформации. К примеру, у лопаток паровых турбин эти деформации должны быть не больше 1% за 10 лет. Лопатки газовых турбин — не больше 1−2% за 500 часов. Трубы паровых котлов, работающих под давлением не должны деформироваться больше чем на 1% за 100 000 часов работы.
По способу получения материала жаропрочные марки классифицируют следующим образом.
- Хромистые стали мартенситного класса: Х5, Х5М, Х5ВФ, 1Х8ВФ, 4Х8С2,1Х12Н2ВМФ.
- Хромистые стали мартенситно-ферритного класса: Х6СЮ, 1Х11МФ, 1Х12ВНМФ, 15Х12ВМФ, 18Х11МФБ, 1Х12В2МФ.
- Хромистые стали ферритного класса:1х12СЮ, 0Х13, Х14, Х17, Х18СЮ, Х25Е, Х28.
- Стали аустенито-мартенситного и аустенито-ферритного класса: 2Х13Н4Г9, Х15Н9Ю, Х17Н7Ю, 2Х17Н2, 0Х20Н14С2, Х20Н14С2.
- Стали аустенитного класса: 0Х18Н10, 0Х18Н11, 1Х18Н9, 0Х18Н12Т, 1Х18Н12Т.
Маркировка сталей разнится по ГОСТам и техническим условиям. В вышеприведённом списке применяется классификация ГОСТ 5632–61 , в которой легко проследить наличие легирующего элемента по буквам. Х — хром, В — ванадий, М — молибден. Например, шифр 09Г2С означает, что в сплаве присутствует 0,09% углерода, 2% марганца и кремний, которого меньше 1%. Цифра впереди показывает содержание углерода (без цифры — до одного процента). Цифра после буквы показывает содержание определённого легирующего элемента в процентах. При содержании какого-либо элемента менее одного процента цифры не ставятся.
Ещё одним нормативным документом служит ГОСТ 5632–61 , с применением специальных обозначений. Для того чтобы быстро соотносить разные ГОСТы и Технические Условия можно воспользоваться соответствующим справочником или сортаментом отдельных выпусков.
По ГОСТ 5632–61 сплавы классифицируются следющим образом:
- Стали аустенитного класса с высоким содержание хрома: ЭИ813 (1Х25Н25ТР), ЭИ835, ЭИ417.
- Стали с карбидным уплотнением: ЭИ69, ЭИ481, ЭИ590, ЭИ388, ЭИ572.
- Стали сложнолегированные повышенной жаропрочности аустенитного класса: ЭИ694Р, ЭИ695, ЭП17, ЭИ726, ЭИ680, ЭП184.
- Стали с интерметаллидным упрочнением аустенитного класса: ЭИ696, ЭП33, ЭИ786, ЭИ 612, ЭИ787, ЭП192, ЭП105, ЭП284.
За рубежом применяется своя классификация материалов. Например, AISI 309, AISI 310S.
Технология и применение
По структуре и способу получения специальные стали подразделяются на следующие: аустенитные, мартенситные, перлитные, мартенсито-ферритные. Мартенситные и аустенитные стали применяются, если температура достигает 450−700о С и по объёму плавки занимают первое место.
С повышением температуры до 700−1000о С используются никелевые сплавы, при ещё более высоких температурах необходимо включать в технологический процесс кобальтовые сплавы, графит, тугоплавкие металлы и термическую керамику.
Аустенитные — самые жаропрочные стали, которые используются, если температура среды достигает 600о С. Основа легирования — хром и никель. Присадки Ti, Nb, Cr, Mo, W, Al.
Стали мартенситного класса предназначены для производства изделий, работающих при температуре в диапазоне 450−600о С. Повышенная жаропрочность у мартенситных сталей достигается уменьшением (до 0.10−0.15%) содержания углерода и легированием хромом 10−12%, молибденом, ниобием, вольфрамом, либо средним (0,4%) содержанием углерода и легированием кремнием (до 2−3%) и хромом (в пределах 5−10%).
Применение специальных сталей и сплавов узконаправленное и наиболее эффективно в сложных областях производства. К примеру, жаропрочные стали марки 30Х12Н7С2 и 30Х13Н7С2С нашли широкое применение в современном двигателестроении. Марки 15ХМ и 12Х12ВНМФ — в производстве котлов и сосудов под давлением. Марка стали ХН70ВМТЮ идёт на производство лопаток газовых турбин, а 08Х17Т используется при изготовлении топочных элементов печей. К жаропрочным также относится нержавеющая сталь.
Марки нержавеющей стали
Прежде всего это ЭИ417 или 20Х23Н18 по ГОСТ 5632–61 . Аналог западноевропейских и американских производителей — известная AISI 310. Аустенитная сталь, изделия из которой востребованы для работы в среде с температурой, достигающей 1000 °C.
20Х25Н20С2, она же ЭИ283 — аустенитный сплав, устойчивый к температурам в 1200о С и выше.
Низкоуглеродистые сплавы с содержанием хрома от 4 до 20% используется для производства листовой нержавеющей стали. Жаропрочная нержавейка по сортаменту выпускается холоднокатаной и горячекатаной, толстолистовой и тонколистовой.
Достоинства и недостатки
Свойства жаропрочных сталей делают незаменимым этот материал в таких сферах, как ракетостроение и космическая отрасль, сложное двигателестроение, авиапромышленность, производство ключевых элементов газовых турбин и многих других. Их доля в прокате высокотехнологичной стали достигает 50%. Некоторые сплавы способны работать при температуре свыше 7000° С.
Этот сложный в производстве материал, изготовление которого невозможно без специального оборудования и квалифицированного персонала, имеет высокую себестоимость. Использование подобных сталей не может быть универсальным, поэтому для его эффективного применения необходимо наличие развитой научно-технической базы.
Оцените статью: Поделитесь с друзьями!chebo.pro
Жаропрочность металлов
Жаростойкие и жаропрочные материалы
1. Жаропрочность
Жаропрочные стали и сплавы предназначены для изготовления деталей котлов, газовых турбин, реактивных двигателей, ракет, атомных устройств и др., работающих при высоких температурах.
Повышение температуры сильно понижает механические свойства. При этом следует иметь в виду, что если при высокой температуре нагрузить металл постоянно действующим напряжением, даже ниже предела текучести при этой температуре, и оставить его под нагрузкой длительное время, то металл в течение всего времени действия температуры и нагрузки будет формироваться с определенной скоростью. Это явление получило название ползучести или крипа. Развитие ползучести может привести к разрушению металла.
Сопротивление металла ползучести и разрушению в области высоких температур при длительном действии нагрузки называют жаропрочностью. Жаропрочность характеризуется условным приделом ползучести и пределом длительной прочности.
Явление ползучести наблюдается тогда, когда рабочая температура выше температура рекристаллизации, действующее напряжение выше предела упругости.
Жаропрочность в первую очередь зависит от температуры плавления металла. Чем выше температура плавления металла, тем выше его температура рекристаллизации. Между названными температурами существует следующая зависимость:
Тр = αТпл К,
где α = 0,3…0,4 для технически чистых металлов, α = 0,6 …0,8 для сплавов.
Под условным приделом ползучести понимают напряжение, которое за установленное время испытания при данной температуре вызывает заданное удлинение образца или заданную скорость деформации (ползучести).
Ползучесть представляет собой медленное нарастание пластической деформации под действием напряжений, меньших предела текучести. Типичная зависимость деформации от времени нагружения представлена на рис. 1.

Рис. 1. Кривая ползучести: I – неустановившаяся стадия; II – установившаяся стадия; III – стадия разрушения
Кривая ползучести состоит из трех участков. Стадия I так называемой неустановившейся ползучести отличается постепенным затуханием скорости деформации до определенного постоянного значения. Стадия II – установившейся ползучести – характеризуются постоянной скоростью деформации. На стадии III– стадии разрушения – скорость деформации нарастает до момента разрушения. Как правило, она непродолжительна и для деталей недопустима.
Предел ползучести обозначают через σ и числовыми индексами. Так, σ7000,2/100 означает предел ползучести при допуске на деформацию 0,2% за 100 ч. испытания при 700О С. В случае определения предела ползучести его обозначают буквой σ с двумя числовыми индексами. Нижний индекс означает заданную скорость ползучести (%/ч), верхний индекс – температуру испытания, О С; так, σ60010-5 – предел ползучести при скорости ползучести 1* 10-5% /ч при 600 О С.
Предел длительной прочности, т.е. наибольшее напряжение, вызывающее разрушение металла за определенное время при постоянной температуре, обозначают σ с двумя числовыми индексами. Так σ7001000 означает придел длительной прочности за 1000 ч. при 700О С.
Повышения жаропрочности достигают легированием твердого раствора, приводящим к увеличению энергии связи между атомами, в результате чего процессы диффузии и самодиффузии задерживаются, а температура рекристаллизации возрастает, созданием у сплава специальной структуры, состоящей из вкрапленных в основной твердый раствор и по границам зерен дисперсных карбидных и особенно интерметаллидных фаз. Такая структура получается в результате закалки с высоких температур и последующего старения. Наличие равномерно распределенных дисперсных избыточных фаз затрудняет пластическую деформацию при высоких температурах. Чем крупнее зерно, тем выше жаропрочность.
Жаропрочные сплавы для работы при высоких температурах (до 700 – 950 О С) создаются на основе железа, никеля и кобальта, а для работы при еще более высоких температурах (до 1200–1500О С) – на основе хрома, молибдена и других тугоплавких металлов.
Рабочие температуры жаропрочных сталей составляют 500 – 750О С. При температурах до 600 О С чаще используют стали на основе α-твердого раствора, а при более высоких температурах – на основе γ-твердого раствора с гранецентрированной кубической решеткой.
2. Стали перлитного класса (ГОСТ 20072–79)
Для изготовления малонагруженных деталей и узлов энергетических установок, работающих при температурах не выше 500 – 580 О С, используют низкоуглеродистые стали перлитного класса, содержащие не менее 1% хрома, молибдена и ванадия. Эти элементы, повышая температуру рекристаллизации феррита и затрудняя диффузионные процесс, повышают жаропрочность стали.
Для изготовления деталей котельных установок, работающих при 510 О С и давлении 1000–1100 МПа, применяют сталь 15ХМ или более жаропрочную 12Х1МФ. Сталь 12Х1МФ удовлетворительно обрабатывается давлением и сваривается. После нормализации 960 – 980 О С и отпуска при 740 О С предел ползучести этой стали σ56010-4 = 85 МПа; предел длительной прочности σ560104 = 140 МПа.
3. Стали мартенситно-ферритного класса
Детали и узлы газовых турбин и паросиловых установок изготавливают из мартенситных сложнолегированных сталей 18Х12ВМБФР и 15Х12ВНМФ, в состав которых входят Mo, W, V, Nb, B. Эти элементы повышают температуру рекристаллизации. Они образуют карбиды типа М23 С6 , М7 С3 , М2 С, МС и соединение Fe2 Mo, в результате повышается жаропрочность стали.
Рабочие температуры этих сталей могут достигать 600 – 620 О С.
Для получения оптимальной жаропрочности высокохромистые стали закаливают на мартенсит. Структура сталей после отпуска – сорбит и троостит. Для стали 18Х12ВМБФР при 550 О С σ105 = 250÷300, а для стали 15Х12ВНМФ – 200 МПа.
4. Стали аустенитного класса (ГОСТ 5632–72)
Для получения структуры аустенита эти стали должны содержать большое количества хрома, никеля и марганца. Для достижения высокой жаропрочности их дополнительно легируют Mo, W, V, Nb и B. Эти стали идут для изготовления деталей, работающих при 500–750О С. Жаропрочность аустенитных сталей выше, чем перлитных и мартенситно-ферритных. Сталей.
Аустенитные стали пластичны и хорошо свариваются, однако обработка их резанием затруднена.
Аустенитные стали по способу упрочнения делят на три группы:
1. твердые растворы, содержащие сравнительно мало легирующих элементов;
2. твердые растворы с карбидным упрочнением. В этом случае упрочняющими фазами могут быть как первичные (TiC, VC, ZrC, NbC и др.), так и вторичные карбиды (М23 С6 , М7 С3 , М6 С), выделяющиеся из твердого раствора;
3. твердые растворы с интерметаллидным упрочнением. Упрочняющей фазой в этих сталях является γ-фаза типа Ni3 Ti, Ni3 Al, Ni3 Nb и др.
Стали с интеметаллидным упрочнением более жаропрочны, чем стали с карбидным упрочнением.
Аустенитные жаропрочные стали со структурой твердых растворов (например, 09Х14Н16Б и 09Х14Н18В2БР) предназначены для работы при 600–700О С, их применяют после закалки с 1100–1160О С в воде или на воздухе.
Для достижения высокой жаропрочности аустенитные стали с карбидным и интерметаллидным упрочнением подвергают закалке с 1050–1200О С в воде, масле или на воздухе для растворения карбидных и интерметаллидных фаз в твердом растворе – аустените – и получения после охлаждения однородного высоколегированного твердого раствора и старению при 600–850О С для выделения дисперсных фаз из твердого раствора, упрочняющих сталь.
Высокая жаропрочность сталей с карбидным упрочнением достигается введением в хромоникелевый или хромоникельмарганцовистый аустенит 0,3 – 0,5% С и карбидообразующих элементов Mo, W, V, Nb и др. К этим сталям относятся, например, стали 45Х14Н14В2М и 40Х12Н8Г8МФБ, а также сталь 40Х15Н7Г7Ф2МС, в которой никель частично заменен марганцем. Длительная прочность σ600100 этой стали составляет 400 МПа.
К сталям с интерметаллидным упрочнением относится большая группа сложнолегированных сталей, содержащих, кроме хрома и никеля, титан, алюминий, вольфрам, молибден и бром. Содержание углерода в этих сталях должно быть небольшое, так как он связывает молибден и вольфрам в карбиды, что понижает жаропрочность аустенита. Бор упрочняет границы зерен аустенита в результате образования боридов.
К этой группе относится сталь 10Х11Н2Т3Р, применяемая в виде листов для изготовления сварных деталей, работающих при температурах 550 – 750 О С, а также сталь 10Х11Н23Т3МР. Длительная прочность σ600100 и σ700100 этих сталей составляет 550 – 600 и 300 – 400 МПа соответственно.
сталь сплав жаропрочный деталь
5. Жаропрочные стали на никелевой основе (ГОСТ 56321–32)
Жаропрочные сплавы на основе никеля называют нимониками. Эти сплавы предназначены для изготовления деталей с длительным сроком службы при 650–850О С.
Для получения высокой окалиностойкости никель легируют хромом (20%), а для повышения жаропрочности – титаном (1,0–2,8%) и алюминием (0,55–5,5%). В этом случае при старении закаленного сплава в основном γ-твердом растворе образуется интерметаллидная γ-фаза [типа Ni3 (Ti, Al)], а также карбиды TiC и нитриды TiN, увеличивающие прочность при высоких температурах. Дальнейший рост жаропрочности достигается легированием сплавов 2,0–11% Мо и 2,0–11% W, повышающими температуру рекристаллизации и затрудняющими процесс диффузии в твердом растворе, определяющий коагуляцию избыточных фаз и рекристаллизацию. Добавление к сложнолегированным сплавам 4–16% Со еще больше увеличивает жаропрочность и технологическую пластичность сплавов. Для упрочнения границ зерен γ-твердого раствора сплав легируют бором и цирконием. Они устраняют вредное влияние примесей, связывая их в тугоплавкие соединения. Примеси серы, сурьмы, свинца и олова понижают жаропрочность сплавов и затрудняют их обработку давлением.
mirznanii.com
жаропрочные стали, жаростойкость, температура плавления
Развитие новых промышленных технологий, ракетной техники, сложного турбинного оборудования в середине пятидесятых годов прошлого века, повлекло за собой модернизацию металлургической отрасли в целом. В отдельное направление выделились работы по созданию жаропрочных сплавов. С течением времени они нашли применение в атомном машиностроении, энергетике, химической промышленности и заняли место в цепочке высокотехнологических производств.
Жаропрочные и жаростойкие материалы
Жаропрочные и жаростойкие сплавы — это большая группа легированных материалов с присадками молибдена, титана, хрома и ряда других элементов. Все эти сплавы изготавливаются на железной, никелевой и кобальтовой основах. Их главной особенностью является сохранение повышенной прочности при высоких температурах.
Основные типы
Наиболее распространены сплавы на основе железа. Это хромистые, хромоникелевые, а также хромомарганцевые стали с молибденовыми, титановыми и вольфрамовыми присадками. Также производят сплавы с такими легирующими элементами, как алюминий, ниобий, ванадий, бор, но в меньших количествах.
В большинстве случаев процент добавления присадок в сталь достигает от 15 до 50%
Вторая, весьма востребованная группа — сплавы на никелевой основе. В качестве присадки используется хром. Жаропрочность также повышают добавки титана, церия, кальция, бора и сходных по составу элементов. В отдельных технологических комплексах востребованы сплавы на основе никеля с молибденом.
К третьей группе относятся термостойкие сплавы на кобальтовой основе. Легирующими элементами для них служат углерод, вольфрам, ниобий, молибден.
В металлургии существует целый ряд материалов, который используется при легировании сталей:
- хром,
- никель,
- молибден,
- ванадий,
- ниобий,
- титан,
- марганец,
- Вольфрам.
- кремний,
- тантал,
- алюминий,
- медь,
- бор,
- кобальт,
- цирконий.
Широко используются редкоземельные элементы.
Химический состав
Определение химического состава жаростойких материалов — сложный процесс. Необходимо учитывать не только основные легирующие элементы, но и то, что попадает в продукцию как примеси или остаётся в результате химических реакций, протекающих во время плавки.
Специально добавленные легирующие элементы вводятся для получения необходимых технологических, физических и механических свойств. А примеси и образовавшиеся при плавке химические элементы могут ухудшать свойства высоколегированного металла.
Для хромоникелевых сплавов и огнеупорных материалов на основе кобальта опасно присутствие серы более 0,005%, следов олова, свинца, сурьмы и других легкоплавких металлов.
Структура и свойства
Жаропрочность определяется не только химическим составом металлов, но и формой, в которой примеси находятся в сплаве. Например, сера в виде сульфидов никеля снижает температуру плавления. А та же сера, соединённая с цирконием, церием, магнием образует тугоплавкие структуры. Большое влияние на жаропрочность оказывает чистота никеля или хрома. Однако следует учитывать, что свойства сплавов варьируются в зависимости от применяемой технологии.
Главное свойство, по которому определяют жаростойкость материала — ползучесть. Это явление постоянной деформации под непрерывным напряжением. Сопротивляемость материала разрушению под действием температуры
Классификация сплавов
Первый параметр классификации сплавов — это жаропрочность, то есть способность материала выдерживать механические деформации при высоких температурах, без деформации.
Во-вторых, это жаростойкость (окалиностойкость). Способность материала противостоять газовой коррозии при высоких температурах. При описании процессов до шестисот градусов Цельсия используется термин «теплоустойчивость».
Одной из основных характеристик является предел ползучести. Это напряжение, при котором деформация материала за определённый период достигает заданной величины. Время деформации является сроком службы детали или конструкции.
Для каждого материала установлена максимальная величина пластической деформации. К примеру, у лопаток паровых турбин эти деформации должны быть не больше 1% за 10 лет. Лопатки газовых турбин — не больше 1−2% за 500 часов. Трубы паровых котлов, работающих под давлением не должны деформироваться больше чем на 1% за 100 000 часов работы.
По способу получения материала жаропрочные марки классифицируют следующим образом.
- Хромистые стали мартенситного класса: Х5, Х5М, Х5ВФ, 1Х8ВФ, 4Х8С2,1Х12Н2ВМФ.
- Хромистые стали мартенситно-ферритного класса: Х6СЮ, 1Х11МФ, 1Х12ВНМФ, 15Х12ВМФ, 18Х11МФБ, 1Х12В2МФ.
- Хромистые стали ферритного класса:1х12СЮ, 0Х13, Х14, Х17, Х18СЮ, Х25Е, Х28.
- Стали аустенито-мартенситного и аустенито-ферритного класса: 2Х13Н4Г9, Х15Н9Ю, Х17Н7Ю, 2Х17Н2, 0Х20Н14С2, Х20Н14С2.
- Стали аустенитного класса: 0Х18Н10, 0Х18Н11, 1Х18Н9, 0Х18Н12Т, 1Х18Н12Т.
Маркировка сталей разнится по ГОСТам и техническим условиям. В вышеприведённом списке применяется классификация ГОСТ 5632–61 , в которой легко проследить наличие легирующего элемента по буквам. Х — хром, В — ванадий, М — молибден. Например, шифр 09Г2С означает, что в сплаве присутствует 0,09% углерода, 2% марганца и кремний, которого меньше 1%. Цифра впереди показывает содержание углерода (без цифры — до одного процента). Цифра после буквы показывает содержание определённого легирующего элемента в процентах. При содержании какого-либо элемента менее одного процента цифры не ставятся.
Ещё одним нормативным документом служит ГОСТ 5632–61 , с применением специальных обозначений. Для того чтобы быстро соотносить разные ГОСТы и Технические Условия можно воспользоваться соответствующим справочником или сортаментом отдельных выпусков.
По ГОСТ 5632–61 сплавы классифицируются следющим образом:
Стали аустенитного класса с высоким содержание хрома: ЭИ813 (1Х25Н25ТР), ЭИ835, ЭИ417.
- Стали с карбидным уплотнением: ЭИ69, ЭИ481, ЭИ590, ЭИ388, ЭИ572.
- Стали сложнолегированные повышенной жаропрочности аустенитного класса: ЭИ694Р, ЭИ695, ЭП17, ЭИ726, ЭИ680, ЭП184.
- Стали с интерметаллидным упрочнением аустенитного класса: ЭИ696, ЭП33, ЭИ786, ЭИ 612, ЭИ787, ЭП192, ЭП105, ЭП284.
За рубежом применяется своя классификация материалов. Например, AISI 309, AISI 310S.
Технология и применение
По структуре и способу получения специальные стали подразделяются на следующие: аустенитные, мартенситные, перлитные, мартенсито-ферритные. Мартенситные и аустенитные стали применяются, если температура достигает 450−700о С и по объёму плавки занимают первое место.
С повышением температуры до 700−1000о С используются никелевые сплавы, при ещё более высоких температурах необходимо включать в технологический процесс кобальтовые сплавы, графит, тугоплавкие металлы и термическую керамику.
Аустенитные — самые жаропрочные стали, которые используются, если температура среды достигает 600о С. Основа легирования — хром и никель. Присадки Ti, Nb, Cr, Mo, W, Al.
Стали мартенситного класса предназначены для производства изделий, работающих при температуре в диапазоне 450−600о С. Повышенная жаропрочность у мартенситных сталей достигается уменьшением (до 0.10−0.15%) содержания углерода и легированием хромом 10−12%, молибденом, ниобием, вольфрамом, либо средним (0,4%) содержанием углерода и легированием кремнием (до 2−3%) и хромом (в пределах 5−10%).
Применение специальных сталей и сплавов узконаправленное и наиболее эффективно в сложных областях производства. К примеру, жаропрочные стали марки 30Х12Н7С2 и 30Х13Н7С2С нашли широкое применение в современном двигателестроении. Марки 15ХМ и 12Х12ВНМФ — в производстве котлов и сосудов под давлением. Марка стали ХН70ВМТЮ идёт на производство лопаток газовых турбин, а 08Х17Т используется при изготовлении топочных элементов печей. К жаропрочным также относится нержавеющая сталь.
Марки нержавеющей стали
Прежде всего это ЭИ417 или 20Х23Н18 по ГОСТ 5632–61 . Аналог западноевропейских и американских производителей — известная AISI 310. Аустенитная сталь, изделия из которой востребованы для работы в среде с температурой, достигающей 1000 °C.
20Х25Н20С2, она же ЭИ283 — аустенитный сплав, устойчивый к температурам в 1200о С и выше.
Низкоуглеродистые сплавы с содержанием хрома от 4 до 20% используется для производства листовой нержавеющей стали. Жаропрочная нержавейка по сортаменту выпускается холоднокатаной и горячекатаной, толстолистовой и тонколистовой.
Достоинства и недостатки
Свойства жаропрочных сталей делают незаменимым этот материал в таких сферах, как ракетостроение и космическая отрасль, сложное двигателестроение, авиапромышленность, производство ключевых элементов газовых турбин и многих других. Их доля в прокате высокотехнологичной стали достигает 50%. Некоторые сплавы способны работать при температуре свыше 7000° С.
Этот сложный в производстве материал, изготовление которого невозможно без специального оборудования и квалифицированного персонала, имеет высокую себестоимость. Использование подобных сталей не может быть универсальным, поэтому для его эффективного применения необходимо наличие развитой научно-технической базы.
obrabotkametalla.info
Жаропрочность металлов — часть 2
Наиболее широко используют никелевый сплав ХН77ТЮР. После закалки с 1080–1120О С он имеет структуру, состоящую из пересыщенного γ-раствора с г.ц.к. решеткой, и поэтому небольшую прочность и высокую пластичность, допускающую глубокую штамповку, гибку и полирование. Сплав удовлетворительно сваривается. После закалки и старения при 700О С сплав получает высокую жаропрочность.
Широко применяют сплав ХН70ВМТЮ, обладающий хорошей жаропрочностью и достаточной пластичностью при 700 – 800 О С.
Предел длительной прочности сплава σ800100 = 200÷250 МПа.
6. Тугоплавкие металлы и сплавы на их основе
Тугоплавкими называют металлы, температура плавления которых выше, чем у железа.
Наибольшее значение в технике имеют тугоплавкие металлы Nb, Mo, Cr, Ta и W с температурой плавления соответственно 2468, 2625, 1275, 2996 и 3410 О С.
Интерес к тугоплавким металлам и сплавам на их основе возрос в связи со строительством ракет, космических кораблей, атомных реакторов и развитием энергетических установок, отдельные детали и узлы которых работают при температурах до 1500–2000 О С.
Молибден, вольфрам и хром обладают высокой жаропрочностью, однако они склонны к хрупкому разрушению из-за высокой температуры порога хладноломкости, которую особенно сильно повышают примеси внедрения С, N, Н и О. после деформации ниже температуры рекристаллизации (1100–1300О С) порог хладноломкости молибдена и вольфрама понижается. Ниобий и тантал в отличие от вольфрама и молибдена – металлы с хорошей пластичностью и сворачиваемостью.
Молибден и вольфрам в Чистов виде используют в радио- и электронной промышленности (нити накаливания, листовые аноды, сетки, пружины катодов, нагреватели и т.д.) вследствие малого поперечного сечения захвата нейтронов и отсутствия взаимодействия с расплавленными щелочными металлами ниобий применяют для изготовления теплообменников атомных реакторов.
Жаропрочность чистых металлов сравнительно невелика. Более высокой жаропрочностью обладают сплавы на основе тугоплавких металлов. Повышение жаропрочности достигается в результате образования легированного твердого раствора или твердого раствора, который добавочно упрочняется мелкодисперсными выделениями типа карбидов ZrC, (Ti, Zr) C и др., оксидов (ZrO2 ) и т.д. Все тугоплавкие металлы обладают низкой жаропрочностью. Поэтому при температурах 600 – 800 О С их нужно защищать от окисления.
Для молибдена и вольфрама лучшими считаются термодиффузионные силицидные покрытия (MoSi2 , WSi2 ).
Поверхностные покрытия чаще применяют для деталей, работающих малый срок службы, или одноразового действия.
Под жаростойкостью (окалиностойкостью) понимают способность металла сопротивляться окислению при высоких температурах. Для повышения окалиностойкости стали легируют элементами, которые существенно изменяют состав и строение окалины. Железо при температурах выше 570 О С образует три окисла: FeO (вюстит), Fe3 O4 (магнетит), Fe2 O3 (гематит), которые слабо защищают поверхность металла от воздействия кислорода. При введении в железо хрома, алюминия или кремния, обладающих большим сродством к кислороду, на поверхности образуются плотные окислы Cr2 O3 , Al2 O3 , SiO2 , затрудняющие процесс дальнейшего окисления.
Чем выше содержание хрома, алюминия или кремния в стали, тем выше окалиностойкость стали и тем выше может быть рабочая температура. Количество хрома, необходимое для обеспечения окалиностойкости при разных температурах, можно определить по рис. 2. следует подчеркнуть, что окалиностойкость не зависит от структуры стали, а зависит только от химического состава.
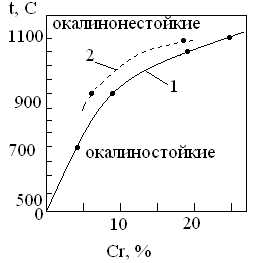
Рис. 2. Влияние хрома на окалиностойкость: 1 – ферритные стали; 2 – аустенитные стали
Сравнительная оценка жаростойкости чистых металлов по скорости окисления на воздухе в интервале допустимых рабочих температур приведена в табл. 1.
Таблица 1. Жаростойкость чистых металлов
Очень плохая жаростойкость магния при температурах выше 450 О С связана с образованием рыхлого оксида MgO, у которого коэффициент объема φ = 0,79. В интервале 500 – 600 О С скорость окисления магния лежит в пределах 10-1 – 101 г / (м2 * ч).
Металлы Nb, Ta, Mo, W имеют плотные оксиды, но их защитные свойства ухудшаются при нагреве выше 550 О С. Это объясняется тем, что у них φ > 2,5, поэтому возникают большие напряжения, вызывающие растрескивание оксидов. Кроме того, оксид молибдена при нагреве испаряется. Оксиды титана и циркония, образующиеся при нагреве, теряют кислород вследствие его большой растворимости в металле и не защищают от дальнейшего окисления. Это явление называют деградацией оксида. При высоких температурах и длительных выдержках оксид становится даже рыхлым. Для тугоплавких металлов скорости окисления на воздухе в интервале 700 – 800 О С лежат в пределах 101 –103 г / (м2 * ч).
Металлы Cu, Fe, Ni, Co (см. табл. 1) в интервале 500–600О С окисляются на воздухе со скоростью от 10-3 до 103 г / (м2 *ч), а в интервале 700–800О С – от 101 до 1 г / (м2 *ч). относительно высокие скорости окисления у этих металлов связывают с большой дефектностью образующихся при нагреве оксидов.
В процессе окисления железа и стали на поверхности растут несколько оксидов, у которых химический состав, кристаллическая структура и защитные свойства различны.
Температурная зависимость скорости окисления железа на воздухе отражает изменения состава и структуры образующихся на поверхности оксидов (рис. 3.). До 560О С окисление идет медленнее, так как на поверхности образуются оксиды Fe3 O4 и Fe2 O3 с хорошими защитными свойствами. При дальнейшем нагреве единственным защитным оксидом становится FeO с худшими защитными свойствами, чем у Fe3 O4 и Fe2 O3 . именно по этой причине предельно допустимая рабочая температура нагрева на воздухе для чистого железа составляет 560 О С. Благодаря легированию эту температуру удается повысить до 1000–1200 О С.
Рис. 3. Влияние температуры на скорость окисления Δm железа на воздухе
Металлы Al, Zn, Sn, Hb, Cr, Mn, Be (см. таб. 1.) обладают хорошей жаростойкостью. Скорость окисления хрома на воздухе в интервале 400 – 600 О С менее 10-6 г / (м2 * ч), а в интервале 700–800О С составляет 10-4 – 10-3 г/(м2 *ч).
Жаростойкость промышленных медных сплавов – латуней и бронз – выше жаростойкости чистой меди. Легирующие элементы в медных сплавах (см. табл. 1.) имеют большее химическое сродство к кислороду, чем медь, и при достаточном их количестве образуют при нагреве собственные оксиды, обладающие лучшими защитными свойствами, чем Cu2 O. Сплавы меди с бериллием, алюминием, марганцем отличаются высокой жаростойкостью; несколько уступают им сплавы меди с цинком, оловом и кремнием.
Титановые и циркониевые сплавы поглощают кислород, поэтому защитные оксиды на поверхности не образуются и жаростойкость титана при легировании не улучшается. Повысить жаростойкость удается лишь применением жаростойких покрытий.
Жаростойкость железа и сталей повышают легированием хромом, алюминием и кремнием. Наибольшее распространение при объемном и поверхностном легировании железа и сталей получил хром, содержание которого доходит до 30%. С увеличением количества хрома в стали, а также ростом температуры и выдержки содержание хрома в оксиде возрастает. Легированные оксиды железа заменяются оксидами хрома, что ведет к повышению жаростойкости.
Жаростойкими являются высоколегированные хромистые стали ферритного и мартенситного класса, хромоникелевые и хромомарганцевые стали аустенитного класса. Чем больше хрома содержит сталь, тем выше максимальная температура ее применения и больше срок эксплуатации изделий. Жаростойкость определяется главным образов химическим составом стали (т.е. содержанием хрома) и сравнительно мало зависит от ее структуры.
Дополнительное легирование жаростойких сталей кремнием (до 2–3%) и алюминием (до 1–2% в сталях и до 4–5% в сплавах с высоким электрическим сопротивлением) повышает температуру эксплуатации.
Низкоуглеродистая сталь при большом содержании хрома приобретает однофазную ферритную структуру. В процессе длительной работы при высоких температурах кристаллы феррита растут, что сопровождается понижением ударной вязкости. Для предотвращения охрупчивания сталь дополнительно легируют карбидообразующими элементами (например, Ti). Карбиды затрудняют рост зерна феррита. Химический состав и свойства некоторых жаростойких сталей приведены в табл. 2.
Таблица 2. Химический состав (ГОСТ 5632–72) и химические свойства жаростойких сталей
Следует отметить, что стали 08Х17Т и 15Х25Т ферритного класса (в структуре преобладает феррит) не жаропрочны, поэтому их используют в изделиях, которые не испытывают больших нагрузок, особенно ударных. Сплавы 20Х23Н18 и 20Х25Н20С2 аустенитного класса не только жаростойки, но жаропрочны. Области применения жаростойких сталей и сплавов указаны в табл. 3.
mirznanii.com
Жаропрочный металл — Большая Энциклопедия Нефти и Газа, статья, страница 1
Жаропрочный металл
Cтраница 1
Жаропрочные металлы представляют интерес для ядерных конструкций, особенно при создании реакторов на быстрых нейтронах, когда от материалов требуется сочетание стойкости к высоким температурам и соответствующих ядерных свойств. Так, ниобий, имея плотность 8 6 г / см3, плавится яри 2415 С и кипит при 3300 С. Он устойчив к действию большинства химических реагентов. Из всех четырех металлов указанной группы ниобий наиболее легко обрабатывается. Подобно танталу, из него можно изготавливать тонкостенные бесшовные трубы и при соответствующих мерах предосторожности сваривать их с образованием ковких швов. [1]
Конструкционные жаропрочные металлы вольфрам и молибден широко применяются в технике современного аппарато — и приборостроения. Исследованию их теплофизических характеристик особенно в области высоких температур посвящено много отечественных и зарубежных работ. [2]
Жаропрочными металлами являются металлы, имеющие температуры плавления до 1600 С. К ним относятся никель, кобальт и железо. [4]
В качестве жаропрочных металлов применяют тугоплавкие. Высокая температура плавления этих металлов объясняется высокими значениями сил межатомной связи. [5]
Поэтому применение жаропрочных металлов и их сплавов является актуальной государственной задачей. Например, температура газов внутри цилиндра в период сгорания топлива в двигателях внутреннего сгорания ( ДВС) достигает 2000 — 2500 С. В табл. 1 приведены примерные значения температуры деталей, ограничивающих внутрицилиндровое пространство ДВС. [7]
Низкая обрабатываемость жаропрочных металлов определяется их физико-химическими свойствами. В этих условиях весьма важно раскрыть причины, влияющие на обрабатываемость этих металлов, и изыскать способы и средства увеличения производитель — — ности их обработки на металлорежущих станках. [8]
Низкая теплопроводность жаропрочных металлов является причиной высокой температуры резания и пониженной скорости резания по сравнению с обычными конструкционными сталями. [9]
При обработке вязких, жаропрочных металлов, наоборот, иногда приходится места обработки подкаливать, для того чтобы увеличить вероятность появления стружки скалывания. [10]
Для нарезания в жаропрочных металлах резьб диаметром от 36 до 60 мм целесообразно применять усовершенствованные резьбонарезные головки конструкции ЦНИИТмаш. [11]
Какое практическое применение имеют жаропрочные металлы и сплавы. [12]
Какое практическое применение имеют жаропрочные металлы и сплавы. [13]
Молибден, вольфрам и другие жаропрочные металлы используют для изготовления высокотемпературных термометров сопротивления, однако они недостаточно стабильны и не нашли широкого применения. [14]
Испытания применяются преимущественно для жаропрочных металлов и сплавов. [15]
Страницы: 1 2 3 4
www.ngpedia.ru
Жаростойкий металл — Большая Энциклопедия Нефти и Газа, статья, страница 1
Жаростойкий металл
Cтраница 1
Жаростойкие металлы мало окисляются в области высоких температур: это нихромы, оксидный слой которых предохраняет их от окисления. [2]
Жаростойкие металлы и сплавы хорошо сопротивляются коррозии в сухих газах при высокой температуре. [3]
Жаростойкие металлы, за исключением тех, которые содержат слишком много углерода, обычно удовлетворительно прокатываются, что позволяет изготовлять из этих сталей сортовой прокат, лист и проволоку. [4]
Титан не является жаростойким металлом. Скорость его окисления при высоких температурах довольно высока. Процессы, протекающие при окислении титана, очень сложны. Известно, что чистый титан в атмосфере воздуха или кислорода начинает окисляться с заметной скоростью при температурах выше 500 С. При высоких температурах ( 700 — 1000 С) окалина на поверхности титана пориста и даже склонна к отслаиванию. При окислении титана в воздухе по мере повышения температуры наблюдается переход от логарифмического к кубическому закону роста пленки, далее параболический, затем линейный и снова параболический закон. [6]
Водород используют при производстве жаростойких металлов и сплавов, что обеспечивает высокое качество получаемого продукта. Прокатка молибдена облегчается в атмосфере чистого водорода, в такой атмосфере происходит светлый отжиг нержавеющей стали. Для предупреждения окислительных процессов термообработку стали проводят в атмосфере водорода. Он необходим для получения металлического вольфрама, молибдена, осмия, тантала, кремния, малоуглеродистых черных металлов, в порошковой металлургии. [7]
Вольфрам является типичным представителем жаростойких металлов, поэтому из примера четко видны преимущества цветовой пирометрии и недостатки радиационной. [8]
Схема была реализована для изучения жаростойких металлов в диапазоне температур от 900 до 3000 С. [9]
Получить изделия требуемой конфигурации из жаростойкого металла наиболее легко путем отливки. Действительно, из множества жаростойких хромоникелевых сплавов, как, например, 25 — 12 и 25 — 20, легко получить отливки, особенно если к ним добавить 1 — 1 5 % Si, который повышает жидко-текучесть металла. [10]
В последнее время наряду с жаростойкими металлами и сплавами широкое применение в промышленности получили металло-керамика, устойчивая при высоких температурах, а также теплостойкие пластические массы. [11]
Автор статьи поставил перед собой задачу показать, какими ресурсами жаростойких металлов располагают металлурги для промышленных печей, особенно для нефтеперерабатывающих заводов. [12]
При химическом воздействии металла и газовой среды образующийся на поверхности жаростойкого металла защитный слой приспособляется по своей структуре к структуре металла. [13]
Эти печи сложны в изготовлении и эксплуатации, требуют большого расхода жаростойкого металла, а при больших размерах не обеспечивают необходимой герметичности. Газовое топливо позволяет использовать в печах радиационные трубы, в которых сжигается газ. Тепло нагреваемым изделиям передается в этом случае главным образом за счет излучения стенок труб, отделяющих пространство горения газа от рабочего пространства печи. Такие печи по качеству нагрева не уступают электрическим, но значительно ( в 2 — 3 раза) экономичнее их. [14]
Описаны [38] корундовые изделия на алюмофосфат-ном связующем, армированные проволокой из жаростойкого металла диаметром 0 3 — 0 5 мм. Изделия обладают высоким разрушающим напряжением при изгибе и рекомендуются для применения при 1400 — 1450 С. [15]
Страницы: 1 2 3 4
www.ngpedia.ru