Закалка | Материаловедение
Закалка заключается в нагреве стали до температуры на 30…50°С выше критических точек. Затем следует выдержка при этой температуре для прогрева изделия но всему сечению и быстрое охлаждение. Закалка возможна, если при изменении температуры в сплаве происходят фазовые изменения, и при понижении температуры происходит уменьшение растворимости одного компонента в другом. Целью закалки является получение пересыщенного твердого раствора. При этом сплав переходит в неравновесное состояние: при нагреве выше критических точек происходят фазовые превращения, а при быстром охлаждении обратные процессы не успевают произойти полностью. В частности, при охлаждении аустенита со скоростью выше некоторой критической получается пересыщенный твердый раствор углерода в α-железе — мартенсит, обладающий высокой твердостью, хрупкостью и низкой пластичностью. Углеродистую сталь подвергают закалке для повышения ее прочности и твердости.
Критической скоростью охлаждения (VK) называют минимальную скорость охлаждения, при которой избыточный углерод не успевает выделиться из аустенита, и весь аустенит превращается в мартенсит (рисунок 22). При малой скорости охлаждения Vi аустенит распадается на крупнодисперсную смесь феррита и цементита (перлит), а при больших скоростях V2 распадается на более мелкодисперсные смеси (сорбит, троостит). Если охлаждать сталь со скоростью, не пересекающей кривую начала распада аустенита (линия А), т.е. со скоростью V3, то образуется мартенсит.
Превращение аустенита в мартенсит начинается при определенной температуре, называемой температурой начала мартенситного превращении МН. Для того чтобы мартенситное превращение протекало, необходимо непрерывное охлаждение аустенита ниже точки МН. При достижении определенной температуры дальнейшее превращение аустенита в мартенсит прекращается.
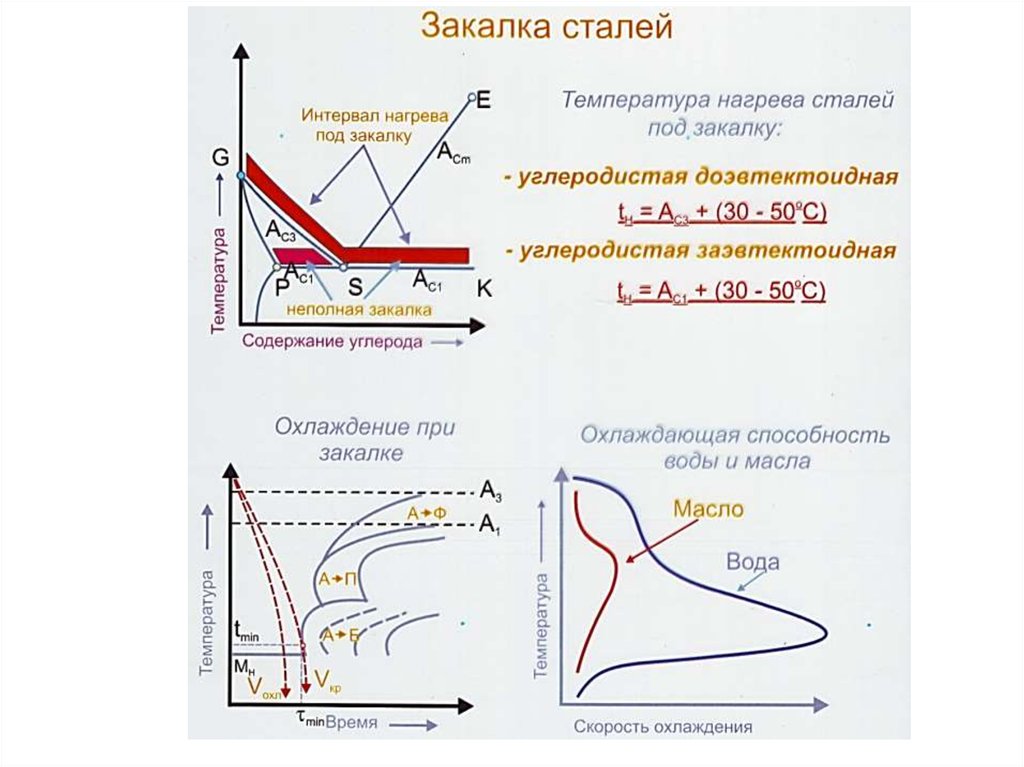
В зависимости от температуры нагрева стали различают полную закалку и неполную. Полная закалка состоит в нагреве стали выше критической точки Аc3 на 30…50°С, а неполная — выше критической точки Ac1

Заэвтектоидные стали подвергают неполной закалке, после которой получается мартенсито-цементитная смесь, имеющая высокую твердость (цементит имеет твердость даже выше, чем у мартенсита).
Рисунок 22 — Диаграмма превращения аустенита при непрерывном охлаждении. А — линия начала перлитного превращения; Б — линия конца перлитного превращения; МН-линия начала мартенситного превращения;МК — линия конца мартенситного превращения
Прокаливаемость — способность стали получать закаленный слой на ту или иную глубину. Прокаливаемость повышается легированием стали марганцем, хромом, молибденом, бором, а также при увеличении размера зерна. За глубину закаленного слоя условно принимают расстояние от поверхности до полумартеснситной зоны (50% мартенсита+50% троостита), которую легко определить по микроструктуре и по твердости.
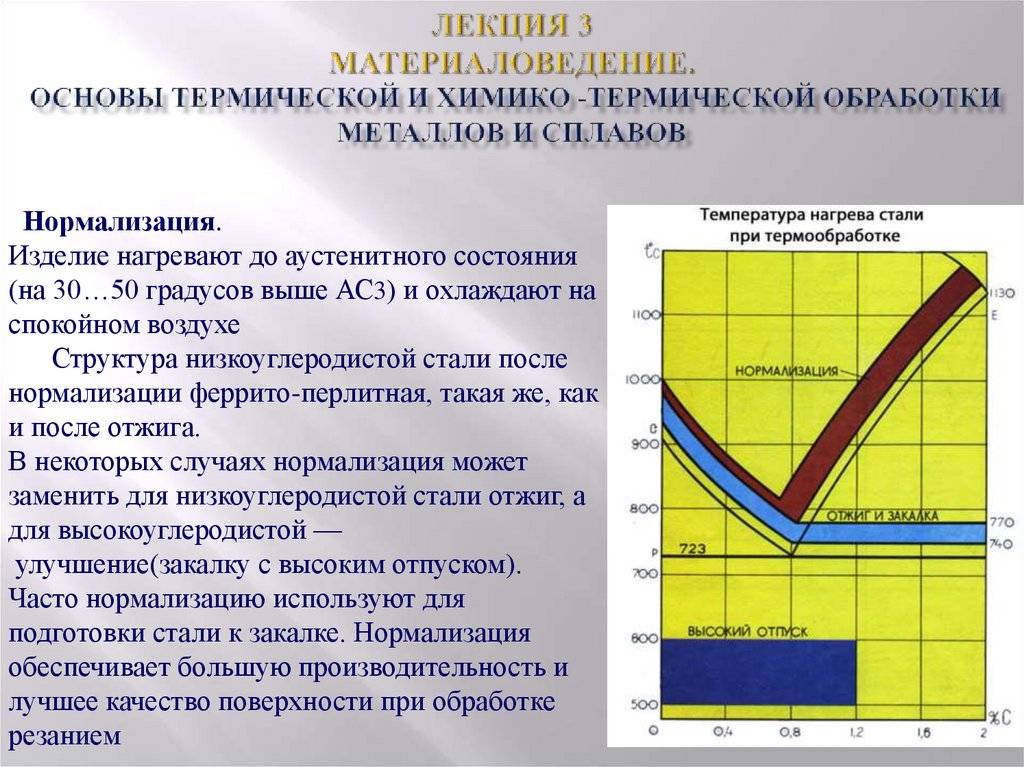
Охлаждающими средами при закалке могут быть воздух, вода, растворы солей или минеральное масло. После закажи углеродистая сталь имеет высокую прочность, твердость, износостойкость, низкую пластичность и приобретает внутренние напряжения. Чтобы уменьшить хрупкость и внутренние напряжения, вызванные закалкой, и получить требуемые механические свойства, сталь после закалки всегда подвергают отпуску.
Читайте также Отпуск
ОБРАТИТЕ ВНИМАНИЕ! На нашем сайте Вы можете заказать любые задания по всем разделам материаловедения. Решение предоставляется в печатном виде с детальными комментариями |
Закалка (термообработка) стали в Набережных Челнах
Закалка — термическая обработка, заключается в нагревании стали до температуры выше критической (Ас3 — для доэвтектоидной и Ас1 — для заэвтектоидной сталей) или температуры растворения избыточных фаз, выдержке и последующем охлаждении со скоростью, превышающей критическую.
Какие металлы подлежат калению
Закалка металла — это термическая обработка, которой чаще всего подвергаются углеродистые и легированные стали с целью повышения их твердости и улучшения прочностных характеристик. Несколько реже встречается термообработка цветных металлов, в частности отпуск, отжиг и закалка меди, латуни и бронзы, а также сплавов алюминия и титана. Необходимо отметить, что закаливание этих соединений в отличие от углеродистых сталей не всегда приводит к их упрочнению, некоторые сплавы меди после этого, наоборот, становятся более пластичными и мягкими. Гораздо чаще изделия из цветных металлов подвергаются отпуску для снятия напряжения после отливки, штамповки, прокатки или волочения.
Свойства стали после закалки
Углеродистая сталь в процессе нагрева проходит через ряд фазовых изменений своей структуры, при которых меняется ее состав, а также форма и элементов кристаллической решетки.

Заказать звонок
Нужна закалка стали в Набережных Челнах? Закажите звонок и мы обсудим с Вами все нюансы предстоящей работы!
Мы перезвоним Вам в рабочее время.
Имя
Телефон
Нажимая кнопку, Вы даете согласие на обработку персональных данных в соответствии с условиями,указанными по ссылке
Классификация каления стали
Виды закалки сталей классифицируют по типу источника нагрева и способу охлаждения металла. Основным оборудованием для нагрева деталей перед закаливанием по-прежнему являются муфельные печи, в которых можно равномерно разогревать металлические изделия любых размеров. Высокую скорость нагрева при поточной обработке изделий обеспечивает закалка с применением токов высокой частоты (индукционная закалка сталей) (см. фото ниже). Для закаливания верхних слоев стальных изделий применяют довольно недорогую и эффективную газопламенную закалку, главный недостаток которой — невозможность точно задать глубину прогрева. Этих недостатков лишена лазерная закалка, но ее возможности ограничены небольшой мощностью источника излучения. Способы охлаждения закаливаемой детали обычно классифицируют по виду охлаждающей среды, а также совокупностям и циклам рабочих операций. Некоторые из них включают процедуры отпуска, а для других, таких как разные виды изотермической закалки, он не нужен.
Закаливание в одной среде
При таком способе закалки нагретое до заданной температуры изделие из стали помещают в жидкость, где она остается до полного остывания. В качестве закалочной среды для углеродистых сталей используют воду, а для легированных — минеральное масло. Недостаток этого метода заключается в том, что после такого закаливания в металле сохраняются значительные напряжения, поэтому в ряде случаев может потребоваться дополнительная термообработка (отпуск).
Ступенчатая закалка
Ступенчатое закаливание проходит в два этапа. На первом изделие помещается в среду с температурой, превышающей на несколько десятков градусов точку начала возникновения мартенсита. После того, как температура выравнивается по всему объему металла, деталь медленно охлаждается, в результате чего в нем равномерно формируется мартенситная структура.
Изотермическая закалка
При изотермическом закаливании изделие также выдерживается в закалочной ванне при температуре, превышающей точку мартенсита, но несколько дольше. В результате этого аустенит трансформируется в бейнит — одну из разновидностей троостита. Такая сталь сочетает в себе повышенную прочность с пластичностью и вязкостью. Кроме того, после изотермической закалки в изделии снижаются остаточные напряжения.
Закалка с самоотпуском
Этот вид термообработки используется для закаливания ударного инструмента, который должен обладать твердым поверхностным слоем и вязкой серединой. Его особенность заключается в том, что изделие извлекается из закалочной емкости при неполном охлаждении. В этом случае его внутренняя часть еще содержит достаточное количество тепла, чтобы прогреть весь объем металла до температуры отпуска. Так как повторный нагрев изделия осуществляется без внешнего воздействия за счет внутренней тепловой энергии, такой вид термической обработки называют закалкой с самоотпуском.
Светлая закалка
Светлая закалка применяется для стальных изделий, поверхности которых при термообработке не должны подвергаться окислению. При такой термообработке сталь нагревается в вакуумных печах (см. фото ниже) или в инертных газовых средах (азот, аргон и пр.), а охлаждается в неокисляющих жидкостях или расплавах. Этим способом закаливают изделия, которые не должны подвергаться дальнейшей шлифовке, а также детали, критичные к содержанию углерода в поверхностном слое.
Оборудование для термообработки сталей
Основное оборудование, на котором проводится термическая обработка изделий из сталей и цветных металлов, состоит из двух основных групп: установок для нагрева заготовок и закалочных ванн. Нагревательные устройства включают в себя следующие виды оборудования:
- муфельные термопечи;
- устройства индукционного нагрева;
- установки для нагрева в расплавах;
- газоплазменные установки;
- аппараты лазерной закалки.
Первые три вида могут выполнять прогрев всего объема изделия до требуемой температуры, а последние — только поверхностного слоя металла. Кроме того, выпускаются и широко используются печи для закалки металлов, в которых нагрев осуществляется в вакууме или в среде инертного газа. Закалочные ванны представлены стальными емкостями-охладителями для различных жидкостей, а также специальными тиглями из графита и печами для расплавов солей или металлов. В качестве закалочных жидкостей чаще всего используют минеральное масло, воду и водополимерные смеси. Для расплавов металлов обычно применяют свинец или олово, а для расплавов солей — соединения натрия, калия и бария. Закалочные ванны для жидких сред имеют системы нагрева и охлаждения рабочей жидкости до требуемой температуры, а также мешалки для равномерного распределения жидкости и разрушения паровой рубашки.
Видео оборудования
Температура для закалки
Нормативная температура нагрева стали при ее закалке напрямую зависит от массовой доли углерода и легирующих добавок. В целом наблюдается следующая зависимость: чем меньше содержание углерода, тем выше температура закалки. При недогреве изделия не успевает сформироваться требуемая структура, а при значительном перегреве происходит обезуглероживание, окисление поверхностного слоя, изменение формы и размера структурных элементов, а также рост внутреннего напряжения. В таблице ниже приведены температуры закалки, отжига и отпуска некоторых марок углеродистых и легированных сталей. Марка стали Температура, С закалки отжига отпуска
Марка стали | Температура, С | ||
---|---|---|---|
закалки | отжига | отпуска | |
15Г | 800 | 780 | 200 |
65Г | 815 | 790 | 400 |
15Х, 20Х | 800 | 870 | 400 |
30Х, 35Х | 850 | 880 | 450 |
40Х, 45Х | 840 | 860 | 400 |
50Х | 830 | 830 | 400 |
50Г2 | 805 | 830 | 200 |
40ХГ | 870 | 880 | 550 |
ОХ13 | 1050 | 860 | 750 |
3Х13 | 1050 | 880 | 450 |
35ХГС | 870 | 860 | 500 |
30ХГСА | 900 | 860 | 210 |
У7, У7А | 800 | 780 | 170 |
Р9, Р12 | 1250 | 860 | 580 |
Р9Ф5, Р9К5 | 1250 | 860 | 590 |
Р18Ф2 | 1300 | 900 | 590 |
ШХ15 | 845 | 780 | 400 |
9ХС | 860 | 730 | 170 |
Р18К5Ф2 | 1280 | 860 | 580 |
1Х14Н18Б2БРГ | 1150 | 860 | 750 |
4Х14Н1482М | 1200 | 860 | 750 |
Определение температуры нагрева в промышленном производстве осуществляется посредством контактных и бесконтактных пирометров. В последние десятилетия широкое распространение получили инфракрасные приборы, позволяющие дистанционно замерять температуру в любой точки поверхности нагретой детали. Кроме того, приблизительную температуру разогрева стали можно определить по цветовым таблицам.
Технология каления металла
Технология закалки сталей требует соблюдения ряда требований к процессам нагрева и охлаждения закаливаемых деталей. В первую очередь это относится к скорости разогрева и охлаждения металла. Экономические показатели термического процесса требуют максимально быстрого повышения температуры до номинальной, т. к. при этом расходуется меньше энергии. Однако скоростной нагрев приводит к большому перепаду температур между поверхностным слоем и сердцевиной изделия, что может привести к его деформации и возникновению трещин. Поэтому прогрев на всю глубину детали до полного ее разогрева должен проходить плавно, а его время определяется технологом-термистом с помощью эмпирических формул и табличных значений. От скорости и температурных параметров охлаждения стали, разогретой выше критической точки, напрямую зависит процесс формирования структуры и состава закаленного металла. К примеру, при быстром охлаждении в воде с комнатной температурой можно получить углеродистую сталь с мартенситной структурой, а при охлаждении в масле или горячей воде получается троостит. Каждой марке стали соответствуют свои характеристики и температурные режимы закалки, которые, помимо прочего, зависят от размера и формы детали. Поэтому на производстве термическая обработка деталей проводится в соответствии с маршрутной технологией и операционными картами, разрабатываемыми для каждого изделия.
Фото оборудования
Контакты
Адрес: 423825, Республика Татарстан, г. Набережные Челны, ул. Профильная, 106
Тел: +7 (8552) 77-83-68
Email: mail@proftermo.com
Металлообработка — Закалка | Linde
Каждая техника отличается своими требованиями и степенью закалки стали. Прежде чем выбирать процесс закалки стали, рассмотрите предполагаемое применение вашего компонента.
Закалка и отпуск
Закалка и отпуск, также известный как мартенситное превращение, представляет собой процесс закалки, в ходе которого стальной компонент нагревается, а затем быстро охлаждается и нагревается до тех пор, пока его молекулярная структура не изменится в достаточной степени.
Нагрев стали выше температуры сольвуса, когда молекулярная структура стали начинает превращаться в аустенитную. Металл с аустенитной структурой зерна очень мягкий, поэтому его нужно закаливать.
Закалка – это процесс погружения или «закалки» горячего металла в охлаждающую среду. Газ, нефть, вода и рассол являются распространенными примерами закалочной среды. Выбор среды во многом будет зависеть от желаемых результатов. Например, газовая закалка стали в таком газе, как аргон или гелий, обеспечивает высокую степень контроля над процессом охлаждения и устраняет осадок, который часто остается при закалке в воде или масле.
При закалке аустенитной стали ее зернистая структура превращается в более твердую структуру. Полученная структура может быть мартенситной, ферритной, цементитной или перлитной в зависимости от того, насколько быстро остывает металл. На этом этапе сталь твердая, но очень хрупкая.
Для повышения пластичности и устранения внутренних напряжений закалите сталь или повторно нагрейте ее до более низкой температуры. Как правило, вместо повторной закалки детали можно дать постепенно остыть до температуры закалки стали.
Закаленная и отпущенная сталь имеет множество потенциальных применений, в том числе:
- Детали тяжелого оборудования
- Износостойкие накладки для грузовиков
- Строительные опоры
- Резервуары для хранения
- Режущие кромки
Отжиг
Отжиг – это процесс термообработки , который снижает твердость, в результате чего компонент становится более пластичным и легче поддается формованию. Обычно это делается между другими процессами металлообработки, чтобы уменьшить внутреннее напряжение и улучшить микроструктуру стали.
Нагрейте стальной компонент выше температуры сольвуса, а затем дайте ему пропитаться в течение заданного периода времени перед охлаждением. Это позволяет атомам в зерне смещаться и создавать конфигурацию с более низкой энергией. Поддержание контролируемой среды имеет решающее значение для управления примесями в процессе отжига — азот, например, эффективно предотвращает окисление поверхности и обеспечивает более яркую поверхность металла.
Для черных металлов, таких как сталь, лучше дать им медленно остыть при комнатной температуре. Металл рекристаллизуется и затвердевает по мере охлаждения, способствуя росту новых зерен и устраняя деформации.
Дисперсионное твердение
Дисперсионное твердение экспоненциально увеличивает предел текучести и долговечность компонента, что делает ковкие материалы, такие как стальные сплавы, способными выдерживать более высокие нагрузки при использовании.
Цементация
Цементная закалка или науглероживание — это процесс закалки стали, при котором создается твердый, износостойкий поверхностный слой с прочной сердцевиной.
Чтобы науглерожить сталь, вы нагреваете ее до температуры выше температуры сольвуса, а затем позволяете ей пропитаться. Эта температура может изменяться в зависимости от конкретного используемого сплава. Поместите деталь в газовую атмосферу, содержащую углерод, введенный в печь, и дайте детали пропитаться.
При этой температуре изменяется зернистая структура стали, что позволяет ей поглощать углерод из атмосферы. По окончании периода замачивания вы можете либо дать детали остыть, либо сразу же закалить ее в масле.
Тщательно контролируемая, воспроизводимая атмосфера на основе ацетилена имеет решающее значение для успешного цементирования. Случайное воздействие кислорода может привести к окислению поверхности, что препятствует закалке стали до необходимого уровня. Вакуумная цементация, также известная как цементация при низком давлении (LPC), представляет собой метод, в котором используется вакуумная печь для нагрева и пропитки металла, что устраняет риск воздействия кислорода.
Типичными областями применения цементируемой стали являются автомобильные детали, такие как шестерни и поршни. Процесс закалки защищает эти компоненты от чрезмерного износа, продлевая срок их службы.
Техника состоит из трех этапов:
- Обработка на твердый раствор: нагревают сталь выше температуры сольвуса и выдерживают до образования однородного твердого раствора без осадков.
- Закалка: после выдержки стали в течение необходимого времени извлеките ее из источника тепла и немедленно закалите до образования осадков — закалка в таких газах, как аргон, азот или гелий, позволяет лучше контролировать процесс охлаждения и снижает внутреннее напряжение. или искажение.
- Старение: Наконец, повторно нагрейте компонент ниже температуры сольвуса, чтобы образовался тонкий слой осадка. Этот процесс создает прочную внутреннюю решетку, в результате чего металл становится более прочным.
Следующие отрасли промышленности обычно используют дисперсионно-твердеющую сталь в своей работе:
- Авиакосмическая промышленность
- Химическая
- Еда и напитки
- Нефть и газ
Закалка пламенем
Закалка пламенем повышает пластичность стального компонента при одновременном упрочнении его поверхности. Обычно вы обрабатываете металл пламенем перед началом других производственных процессов. Быстро нагрейте металл за счет прямого контакта с контролируемым высокотемпературным пламенем газовой горелки. Ацетилен — оптимальное топливо для закалки пламенем — в смеси с кислородом он может нагреваться до 3160 градусов по Цельсию. Пропан также эффективен для этой цели. После нагревания и замачивания немедленно гасите компонент. Этот шаг позволяет ему быстро охлаждаться и образовывать твердую, износостойкую и коррозионно-стойкую поверхность.
Некоторые преимущества процесса закалки пламенем включают:
- Улучшенная износостойкость поверхности
- Уменьшение внутренних искажений
- Сокращение времени обработки
- Больше контроля над локализацией закалки
- Экономичность
Обычно закаленная пламенем сталь используется в компонентах автомобилей и оборудования, таких как шестерни и лезвия. Поскольку он настолько износостойкий, он может выдерживать тяжелые условия, такие как строительство, в течение длительного периода времени.
Закалка металла | Процесс поверхностной закалки
Существует множество процессов для изменения свойств стальных инструментов. К ним относятся отпуск стали, закалка в масле, дисперсионное твердение и многое другое. Когда дело доходит до долговечности, упрочнение металлического корпуса является одним из наиболее эффективных методов.
Что такое поверхностное упрочнение металла?
Цементная закалка металла – часто называемая поверхностной закалкой – представляет собой процесс термической обработки, при котором химические свойства поверхности стали изменяются и упрочняются путем добавления на поверхность деталей тонкого слоя углерода или обогащенного азотом покрытия. Упрочнение поверхности стали помогает продлить срок службы стали, делая ее более устойчивой к истиранию и прямым ударам.
Сталь под закаленным слоем (внутренняя сердцевина) остается минимально измененной в процессе термической обработки. Это внутреннее ядро более пластичное или «более мягкое», чем закаленный поверхностный слой. Цементируемая закалка не только улучшает износостойкость поверхности стали, но также значительно повышает прочность стали, помогая ей достичь максимальной долговечности.
Методы закалки
Прежде чем рассматривать преимущества, давайте рассмотрим различные способы закалки стали.
Науглероживание (вливание углерода)
При науглероживании поверхностная твердость стали увеличивается за счет добавления углерода к компоненту. Деталь, требующая закалки, нагревается и подвергается воздействию углеродной среды. Углерод проникает в поверхность металла и упрочняет его.
Этот процесс должен проводиться в контролируемой среде, чтобы предотвратить присутствие кислорода в процессе, который изменяет результат закалки металла. Частичные вакуумные процессы сокращают затрачиваемое время и обеспечивают несколько экономических преимуществ цементации.
Газовое азотирование (с использованием газа, богатого азотом)
В этом процессе материал нагревается, а затем подвергается воздействию атомарного азота, который может проникать в сталь или железо. Атомарный азот вступает в реакцию с металлом, увеличивая его твердость и сопротивление. Этот процесс обеспечивает высокую степень твердости, но не может использоваться со всеми легированными сталями.
После этого процесса возможны дополнительные производственные затраты в виде процесса шлифовки для удаления тонкого белого слоя, который образуется на поверхности. Однако обычно за азотированием не следуют другие тепловые процессы, что означает меньшую деформацию объекта.
Преимущества цементации
Общие преимущества цементации включают:
- Повышение прочности и долговечности стали
- Повышение износостойкости стали Облегчает сварку стали
Какие типы металлов можно подвергать цементации?
- Нержавеющая сталь
- Чугун
- Низко- и высокоуглеродистая сталь
- Инструментальная сталь
- Низколегированная сталь
Низколегированная и низкоуглеродистая сталь лучше всего реагирует в процессе цементации. Высокоуглеродистые стали можно подвергать поверхностной закалке, но необходимо соблюдать особые меры, чтобы гарантировать, что процесс закалки не повлияет на внутренний сердечник.
Области применения для цементируемой стали
Цементируемая сталь имеет множество применений в промышленности. Например, в автомобильной и железнодорожной промышленности шестерни, подшипники, карданные валы, поршни, двигатели и коробки передач обычно подвергаются цементации. Цементное упрочнение не только защищает сопрягаемые поверхности (зубья) этих компонентов во время контакта, но также обеспечивает защиту от внезапных ударных нагрузок, способствуя увеличению усталостной долговечности.
В аэрокосмической отрасли, где компании должны соблюдать строгие правила аккредитации и сертификации, все, начиная от цилиндров, подшипников, клапанов, лопаток двигателей и шасси, требует закалки. Фактически, SST является единственной коммерчески одобренной компанией в Соединенных Штатах по термообработке некоторых критически важных для полета компонентов.