Quenching and aging aluminum
Solution heat treatment of aluminium profiles on the extrusion press
Cooling rate aluminum profiles – quenching – immediately after exiting the press should be fast enough, to delay the magnesium and silicon in solid solution. This achieves the maximum mechanical property profile of the material due to their isolation in the subsequent hardening of aging.
The required rate of cooling of the solid solution alloying elements – magnesium and silicon in aluminum – to ensure the hardening effect depends on the cross-sectional dimensions of the aluminum profile and the methods of its cooling:
- calm air,
- fans,
- water mist,
- water cooling or spreyernym
- in water stream.
Figure and table shows the minimum allowable cooling rate profiles for various aluminum alloys of the 6xxx series. For aluminum alloy profiles 6060 usually sufficient cooling in calm air or fans, whereas the profiles of alloy 6061 spreyernoe necessary cooling water or cooling water flow.
Aging aluminum alloys
Aging 6xxx series alloys produced to improve the mechanical properties of aluminum profiles. The degree of this increase depends on the properties of the alloy and aging conditions. These conditions differ for:
- natural aging, that occurs “by itself” at room temperature, and
- artificial aging, is conducted at elevated temperatures, near 160-200 oC.
Strength alloys 6xxx series is directly related to their ability to resist the movement of dislocations during deformation. Upon the application of stress to the material formed in it and move dislocation. With increasing number of stress and dislocation density, moving in the material, increases until, till, finally, the material is not destroyed.
The movement of dislocations is inhibited due to the presence of particles Mg2Si and thus the strength of aged aluminum alloy increases. The dimensions and density of these particles are controlled aging parameters.
If the particles grow too large (β ‘-Mg2Si и b-Mg2Si), they become too small due to the limited content of Mg and Si in the aluminum. In this case, the dislocation easily circumvent these particles and the strength of the material is reduced.
This shows a schematic graph of a typical artificial aging in the figure below.
Fig. thermal treatment of the alloy alyuminevogo 6060Peak strength properties is achieved when a large number of fine particles β”-Mg2Si. For alloys 6xxx typical parameters are the temperature artificial aging 170 ° C when exposed 8 hours or 185 ° C when exposed 6 hours.
T states aluminum alloys
Different parameters correspond to embodiments of aging various designations of the state of aluminum alloys:
- T1 — cooled after pressing to room temperature and naturally aged;
- T4 — after pressing, hardened from separate heating and naturally aged;
- T5 — cooled after pressing to room temperature and artificially aged to the maximum strength properties;
- T6 – hardened after pressing with a separate heating and artificially aged to peak strength properties.
To designate other aging treatments, are specifically designed to obtain mechanical properties, which differ from the maximum strength properties. for instance, state T52 and T591 are applied to aluminum profiles, which are subject to bending, T7 and the state — for profiles, which are applied at elevated temperatures.
Stretching and maturing this mass profiles
The usual practice of manufacturing aluminum extrusions involves stretching them from 0,5 % to 3 % and then aging with a delay of one day of artificial aging for profiles made of low-alloy 6xxx alloys (no more 0,9 % Mg2Si), for example, Aluminum alloys AD31, 6060 and 6063. This contributes to the achievement of optimum mechanical properties after aging profiles.
However, this delay for higher strength aluminum alloys (content Mg2Si more 0,9 %), for example, 6061, It may lead to reduced mechanical properties of the material of aluminum profiles. These alloys contain copper in an amount of not less 0,1 %, which counteracts the influence of delay artificial aging on the final mechanical properties of thermally toughened aluminum profiles.
Закалка алюминиевых сплавов
Растворимость большинства компонентов в алюминии при понижении температуры уменьшается (рис.1), что позволяет упрочнять сплавы путем закалки и старения.
Алюминиевые сплавы не претерпевают полиморфных превращений, и их упрочняющая термическая обработка (закалка и старение) обусловлена уменьшением растворимости легирующих элементов в матричном твердом растворе при понижении температуры от эвтектической или перитектической до комнатной.
Закалка алюминиевых сплавов — заключается в нагреве их до температуры, при которой избыточные интерметаллидные фазы, полностью или большей частью растворяются в алюминии, выдержке при этой температуре и быстром охлаждении до комнатной температуры для получения пересыщенного твердого раствора. Сущность закалки без полиморфных превращений заключается в насыщении твердого раствора легирующими элементами и точечными дефектами до концентраций, соответствующих выбранной температуре нагрева, а также в фиксации полученного состояния сплава в результате резкого охлаждения.
Свойства закаленных алюминиевых деформируемых сплавов и кинетика последующего старения во многом определяются степенью пересыщения твердого раствора легирующими элементами, зеренной структурой, которая окончательно может формироваться в процессе нагрева под закалку, а также плотностью и типом дефектов кристаллического строения закалочного роисхождения. С увеличением степени пересыщения твердого раствора легирующими элементами повышается прочность закаленных сплавов, что можно объяснить непосредственным взаимодействием дислокаций с растворенными атомами, а также с некоторым изменением дислокационной структуры в сплаве. Кроме того, повышение концентрации твердого раствора приводит к уменьшению критического зародыша новой фазы и к увеличению числа промежуточных превращений в процессе старения.
Например, температура закалки сплавов системы Аl—Сu (рис.1) определится линией abc, проходящей выше линии предельной растворимости для сплавов, содержащих <5,6% Сu, и ниже эвтектической линии (548°С) для сплавов, содержащих большее количество меди. При нагреве под закалку сплавов, содержащих до 5,6% Сu, избыточная фаза СuАl2 полностью растворится и при последующем быстром охлаждении фиксируется только пересыщенный α-твердый раствор, содержащий столько меди, сколько ее находится в сплаве. При содержании более 5,6% Сu в структуре сплавов после закалки будет пересыщенный α-твердый раствор состава, отвечающего точке b, и нерастворенные при нагреве кристаллы соединения СuАl2.
При нагреве под закалку в алюминиевых деформируемых сплавах могут протекать рекристаллизационные процессы, приводящие, как правило, к некоторой потере прочности в результате уменьшения плотности дефектов кристаллической решетки и роста зерна.
Однако сохранение нерекристаллизованной структуры после закалки не всегда обеспечивает более высокую прочность в термо-упрочненном состоянии. В процессе нагрева под закалку в алюминиевых сплавах не только растворяются избыточные фазы, но и происходит распад пересыщенного переходными элементами (Mn, Zr, Сr) твердого раствора. Степень распада, размер, плотность и характер распределения дисперсоидов, в какой-то мере обусловленные режимом закалки, оказывают заметное влияние на протекающие при нагреве под закалку рекристаллизационные процессы, на устойчивость твердого раствора, на распределение продуктов распада и дислокаций
Типы термической обработки алюминия
2 ноября 2018 г.
Термическая обработка алюминия — это процесс, посредством которого повышаются прочность и твердость определенного подмножества алюминиевых сплавов, а именно деформируемых и литейных сплавов, способных к дисперсионному твердению. К дисперсионно-твердеющим алюминиевым сплавам относятся серии 2XXX, 6XXX, 7XXX и 8XXX. Кроме того, отжиг может потребоваться для деталей, подвергшихся деформационному упрочнению в процессе формования.
Типичными видами термической обработки алюминия являются отжиг, гомогенизация, термообработка на твердый раствор, естественное старение и искусственное старение (также известное как дисперсионное твердение). В зависимости от того, какой именно процесс используется, температура печи может варьироваться от 240 до 1000°F. Важно иметь в виду, что термическая обработка алюминия сильно отличается от обработки стали.
Отжиг
Алюминиевые сплавы подвергаются деформационному упрочнению, также известному как деформационное упрочнение. Деформационное упрочнение происходит, когда алюминиевый сплав подвергается пластической деформации. Пластическая деформация заставляет зернистые структуры алюминия скользить друг относительно друга вдоль областей, называемых плоскостями скольжения. По мере того, как происходит все большая и большая пластическая деформация, остается все меньше и меньше плоскостей скольжения, которые легко деформировать. В результате для достижения дальнейшей деформации требуется большее усилие. Когда деталь достигает этого состояния, говорят, что она закалена. Для продолжения пластической деформации материала деформационное упрочнение необходимо снять с детали.
Целью отжига является существенное восстановление структуры кристаллического зерна, восстановление плоскостей скольжения и обеспечение возможности продолжения формообразования детали без приложения чрезмерных усилий. Для отжига нагартованного алюминиевого сплава металл необходимо нагреть до температуры от 570°F до 770°F в течение установленного времени, от тридцати минут до полных трех часов. Время и температура зависят от двух вещей: размера отжигаемой детали и состава ее сплава.
Отжиг также снимает внутренние напряжения, которые могут возникнуть в детали во время таких процессов, как холодная ковка или литье, стабилизирует размеры детали и устраняет проблемы, возникающие в результате внутренних деформаций (например, деформации). Кроме того, отжиг можно успешно проводить на алюминиевых сплавах, которые считаются нетермообрабатываемыми сплавами. Он обычно используется на кованых, экструдированных или литых алюминиевых деталях.
Гомогенизация
Гомогенизация используется для более равномерного перераспределения осаждающих элементов в алюминиевой детали. Обычно это необходимо при работе с литыми деталями из алюминиевого сплава. Когда деталь начинает остывать, наружный край, непосредственно контактирующий с формой, охлаждается первым. Это приводит к образованию корки из алюминиевых зерен или кристаллов. По мере того как деталь продолжает остывать внутрь, в результате получается довольно чистый алюминий вблизи поверхности и в некоторых областях вблизи центра. Легирующие элементы выпадают в осадок, в результате чего зерна алюминия фиксируются на месте. Литая деталь в конечном итоге имеет некоторые области, которые становятся мягкими, а другие — прочными. Эта сегрегация между областями может быть уменьшена, а полученная часть может быть сделана более пригодной для формования путем прохождения процесса гомогенизации.
Алюминиевая деталь гомогенизируется путем повышения ее температуры почти до точки плавления, которая обычно составляет от 900°F до 1000°F. После того, как вся деталь достигла этой температуры гомогенизации, ей дают медленно охладиться. В результате получается литая деталь с однородной внутренней структурой.
Термическая обработка на твердый раствор
Хотя скорость охлаждения не является фактором при отжиге, она является фактором в другом аналогичном процессе термообработки алюминия, называемом термообработкой на твердый раствор. В процессе термической обработки на твердый раствор элементы, ответственные за старение (что со временем затрудняет работу с металлической деталью), растворяются. Эти растворенные элементы затем становятся сфероидами, и в результате получается гомогенизированная структура. Однако деталь должна быть закалена или быстро охлаждена, чтобы сохранить то окончательное распределение растворенных элементов в сплаве, которое было достигнуто в результате термической обработки. После этого с деталью будет намного легче работать. Однако со временем эти захваченные элементы снова выпадут в осадок и вызовут старение.
Точная температура для термообработки на твердый раствор зависит от состава сплава алюминия, но обычно она находится в диапазоне от 825°F до 980°F, но используемая температура должна быть в пределах ±10°F от заданной температуры . Если эта температура не будет достигнута, термообработка раствора не будет успешной. Если температура будет слишком низкой, прочность будет потеряна; если температура слишком высока, деталь может обесцветиться, критические элементы могут расплавиться или внутри детали может возникнуть повышенная деформация.
Как только деталь достигает узкого интервала заданной температуры, ее необходимо пропитать. Это время замачивания может составлять от 10 минут для тонкой детали до 12 часов для более крупной и толстой детали. Однако у специалистов по термообработке есть общее практическое правило: один час на каждый дюйм поперечного сечения по толщине.
Далее следует этап закалки. Цель закалки здесь состоит в том, чтобы «заморозить» захваченные элементы на месте или достаточно быстро охладить алюминиевую деталь, чтобы у легирующих элементов не было возможности выпасть в осадок при охлаждении детали. Вода является наиболее часто используемой закалкой и, как правило, наиболее эффективной закалкой для алюминиевых сплавов.
Любая формовка, которую необходимо выполнить для детали, подвергнутой термообработке на твердый раствор, должна выполняться вскоре после завершения закалки. В противном случае начнется естественное старение и деталь станет сложнее в работе. Это противоположно тому, что происходит с термообработанными сталями, которые после закалки становятся чрезвычайно хрупкими и твердыми.
Естественное старение
После термообработки алюминия растворенные элементы со временем начнут выпадать в осадок. Это приводит к тому, что зерна фиксируются на месте, что, в свою очередь, увеличивает естественную прочность алюминия и называется старением.
Процесс естественного старения или возрастного упрочнения происходит при комнатной температуре в течение периода времени от четырех до пяти дней, при этом 90% упрочнения происходит в течение первого дня. Из-за этого эффекта алюминиевые детали часто необходимо формовать довольно быстро после прохождения процесса термообработки на твердый раствор.
Искусственное старение, также известное как дисперсионное твердение
Чтобы некоторые алюминиевые сплавы могли достичь максимальной твердости, из них необходимо полностью выделить растворенные элементы. Не все алюминиевые сплавы могут достичь достаточной твердости в процессе естественного старения при комнатной температуре. Некоторые из них могут затвердевать только до определенной точки, но это можно решить с помощью дисперсионного твердения, которое иногда называют искусственным старением.
При дисперсионном твердении алюминий нагревают до определенной температуры сплава от 240°F до 460°F, в пределах ±5°F от заданной температуры. Затем он замачивается на период от шести до двадцати четырех часов с последующим охлаждением до комнатной температуры. Результат включает значительное увеличение предела текучести алюминия, несколько меньшее увеличение предела прочности при растяжении и снижение пластичности.
Проблемы с закалкой алюминиевых сплавов
Как обсуждалось ранее, цель закалки состоит в том, чтобы сохранить растворенные элементы в той форме, которая достигается в конце фактического процесса нагрева. Если закалка требуется как часть термической обработки алюминия, то очень важно закаливать деталь, как только она выходит из печи для термической обработки. Задержка более 15 секунд может быть очень вредной. Разумно располагать закалочный бак как можно ближе к печи для термообработки.
Вода при температуре окружающей среды обычно используется для закалки алюминиевых сплавов, но для более сложных форм с переменным поперечным сечением могут быть рассмотрены другие закалки или методы. Другие варианты закалки алюминия включают:
- Кипящая вода
- Солевые растворы
- Нагнетание струи воздуха
- Неподвижный воздух
- Полимеры
- Гликоли
- Быстро закалочные масла
Имейте в виду, что один из недостатков быстрой закалка — это деформация детали (например, коробление или скручивание) и развитие остаточных напряжений, что делает закалку горячей водой еще одним распространенным выбором.
Печи для термообработки алюминия
Почти все упомянутые выше способы термообработки алюминия требуют очень точного контроля температуры для достижения желаемого эффекта. Это включает в себя использование высококачественных печей и сушильных шкафов, которые могут обеспечить равномерное распределение температуры, чрезвычайно точные контрольно-измерительные приборы и квалифицированных специалистов, знающих, как правильно использовать оборудование.
Должны быть не только достигнуты правильные температуры, но циклы температура-время для процесса термообработки должны быть однородными и непрерывными. Кроме того, печь должна быть сконструирована таким образом, чтобы обрабатываемая деталь достигала равномерной температуры на всем протяжении.
ASM2705E
При изготовлении алюминиевых деталей для аэрокосмической и автомобильной промышленности используется глобальная спецификация пирометрии ASM2750E (Спецификации аэрокосмических материалов). Эта спецификация была выпущена SAE International и использовалась Nadcap при сертификации и аудите оборудования для термообработки, используемого в авиационном и автомобильном производстве. Он включает такие факторы, как размещение и тип термопар, используемых для определения температуры печи, калибровки и точности системы тестирования. Идеальным решением для достижения соответствия требованиям ASM2705E является добавление пакета пирометрии для поддержки необходимого аудита и тестирования.
Печи L&L, используемые для термообработки алюминия
Когда дело доходит до термообработки алюминиевых деталей, L&L Special Furnace Co. , Inc. предлагает несколько различных решений. Печи, хорошо приспособленные для работы с алюминием, включают:
- Серия DRQ печей высокоравномерного отжига DRQ2436 с полуавтоматическими закалочными ваннами, охладителями закалочной среды и централизованной станцией промывки обработка печей 1100°F (593°C) / 400°F (260°C)
- Серия VB настольных рециркуляционных закалочных печей 1300°F (700°C)
- Серия DV/DR для тяжелых условий эксплуатации на полу газовые или электрические рециркуляционные печи закалки 1300°F (700°C)
- GS1714A из серии GS небольших печей , которые обычно имеются на складе для немедленной отгрузки
Каждая из этих печей может быть оснащена нашим авиационным пирометром Пакет для поддержки соответствия стандарту ASM2705E, а также другие опции, позволяющие убедиться, что вы можете получить печь, которая действительно соответствует вашим потребностям в термообработке алюминия.
Модель DRQ246 проходит заводские испытания, проверяя ручное управление нагрузкой и время от нагревания раствора до закалки.
Термическая обработка алюминия – Позвольте L&L помочь
Термическая обработка алюминия может быть сложным процессом с очень небольшим количеством ошибок или задержек. Вот почему мы разработали наши печи с учетом ASM2705E. Наши печи оснащены высокоточными контроллерами, а внутренняя часть всех наших печей разработана для обеспечения равномерного распределения температуры. Мы даже предлагаем современные закалочные ванны для обеспечения точности на этом последнем, но решающем этапе термообработки на твердый раствор.
Идеальным решением для клиентов, выполняющих термообработку алюминия, является одна из печей, предназначенных для использования с алюминием вместе с пирометрическим комплектом для поддержки калибровки, испытаний и необходимой документации. L&L Special Furnace предлагает и то, и другое. Свяжитесь с нами сегодня, чтобы узнать, как мы можем вам помочь.
Термическая обработка алюминия: дисперсионное твердение | L&L печь
23 июля 2020 г.
Дисперсионное твердение, также иногда называемое искусственным старением, представляет собой процесс термообработки , используемый для доведения некоторых алюминиевых сплавов до максимальной твердости, когда одного естественного старения недостаточно. Это выполняется после завершения термической обработки раствора, и процесс позволяет полностью осаждаться растворенным элементам от предыдущей термической обработки.
Процесс дисперсионного тверденияАтмосфера
Дисперсионное твердение осуществляется либо в вакууме, либо в атмосфере инертного газа при рабочих температурах в диапазоне от 300 до 1400°F (от 149 до 760°C). Вакуум или атмосфера инертного газа предотвращает дальнейшее взаимодействие химических реакций, происходящих внутри алюминия, с внешними элементами, что может вызвать негативные побочные эффекты.
Термическая обработка
Процесс дисперсионного твердения начинается после термообработки на твердый раствор и завершения первого цикла закалки. Затем алюминиевый сплав снова нагревают до определенной температуры от 240 до 460°F +/- 5°F (от 116 до 238°C +/- 3°C). Точная температура, до которой нагревается алюминий, зависит от конкретных легирующих элементов в нем.
Этот нагрев заставляет атомы, из которых состоит сплав, формировать упорядоченные массивы. Определенные массивы атомов могут привести к увеличению физических преимуществ, таких как повышенная прочность или твердость. Наиболее известным примером этого является то, как атомы углерода могут располагаться в определенном порядке из-за температуры и давления, образуя алмаз — чрезвычайно твердый материал. Дисперсионное твердение алюминиевых сплавов следует тому же принципу.
Наконец, растворенные в сплаве элементы осаждаются из детали. Это устраняет любые нежелательные свойства, которые могли появиться на стадии термообработки на раствор в процессе.
Закалка
После нагрева детали наступает время второго цикла закалки. На этот раз деталь замачивается от 6 до 24 часов. Обычно алюминий закаливают в воде, но иногда вместо этого используют легкий рассол. Различные закалочные среды будут иметь разную скорость закалки и по-разному воздействуют на детали. Важно знать, какую среду использовать для детали, которую вы закаливаете, и желаемые свойства.
После завершения замачивания деталь оставляют остывать на воздухе при комнатной температуре. Продолжительность времени, в течение которого деталь остается остывать, зависит от детали. Все алюминиевые сплавы требуют закалки в воде (или слабом соляном растворе), но некоторые сплавы также твердеют по мере старения на воздухе. Такие детали, как заклепки, являются одним из примеров тех, которые выигрывают от старения на воздухе.
Дисперсионное твердение позволяет получить более твердый и прочный металл. Алюминий является довольно мягким металлом, поэтому этот процесс может значительно увеличить его предел текучести, увеличить предел прочности на растяжение и повысить его износостойкость. Предел текучести относится к тому, какое напряжение деталь может выдержать без необратимой деформации. Прочность на растяжение относится к тому, какое усилие на растяжение и растяжение деталь может выдержать без разрушения. А износостойкость — это просто то, насколько хорошо деталь выдерживает поверхностные царапины и точечную коррозию. Все эти три полезных свойства продлевают срок службы детали, подвергнутой дисперсионному твердению.
Дополнительным преимуществом является снижение пластичности детали. Это почти сочетание увеличения текучести и прочности на растяжение. Это означает, что деталь сможет выдержать большее растягивающее напряжение, прежде чем деформируется, что немного отличается от разрушения из-за растягивающего напряжения. И разрушение, и деформация часто не идеальны, поэтому хорошо иметь высокую прочность на растяжение и низкую пластичность.
Последним преимуществом дисперсионного твердения алюминия является то, что оно не приводит к деформации детали. Деформация является довольно распространенной проблемой, с которой приходится сталкиваться как при термической обработке, так и при закалке. Однако дисперсионное твердение предполагает гораздо меньший риск этого.
Применение дисперсионно-твердеющих алюминиевых деталей Алюминий, подвергнутый дисперсионному твердению, обычно используется в тех случаях, когда требуется легкий вес и прочность. Когда дело доходит до деталей двигателей, деталей самолетов и других аэрокосмических приложений, легкие детали являются необходимостью, но нельзя ставить под угрозу прочность.
Алюминий является одним из наиболее предпочтительных металлов для использования в автомобильной и аэрокосмической промышленности, поскольку его малый вес обеспечивает более эффективное передвижение. Более тяжелые автомобили требуют больше энергии для движения, поэтому снижение веса везде, где это возможно, экономит время и деньги в долгосрочной перспективе. Тем не менее, использование самых легких материалов не является хорошей идеей, если эти материалы не в состоянии выдержать рабочие нагрузки. Стандартный алюминий просто недостаточно прочен для многих из этих применений, поэтому необходима дисперсионная закалка. Он сохраняет полезные свойства алюминия, такие как малый вес, при этом добавляя столь необходимую прочность для обеспечения безопасности транспортных средств.
Заключение Дисперсионное твердение — это один из процессов термической обработки, с помощью которого алюминиевые сплавы можно упрочнить различными способами. И этот процесс, также известный как искусственное старение, на самом деле выполняется после предыдущего цикла термообработки на раствор и закалки. Цель использования дисперсионного твердения состоит в том, чтобы удалить любые отрицательные свойства, добавленные к материалу в результате термообработки на твердый раствор, а также повысить как предел текучести, так и предел прочности на растяжение. После закалки алюминиевый сплав часто используется как в автомобильной, так и в аэрокосмической промышленности, где ценятся прочные и легкие материалы.
Если ваша компания производит детали для автомобильной и аэрокосмической промышленности, возможность искусственного старения алюминиевых сплавов просто необходима. Вы можете зайти так далеко только с естественно состаренным алюминием, поэтому вам нужна специально разработанная печь от L&L. Мы производим широкий спектр промышленных печей, в том числе специально предназначенных для дисперсионного твердения.
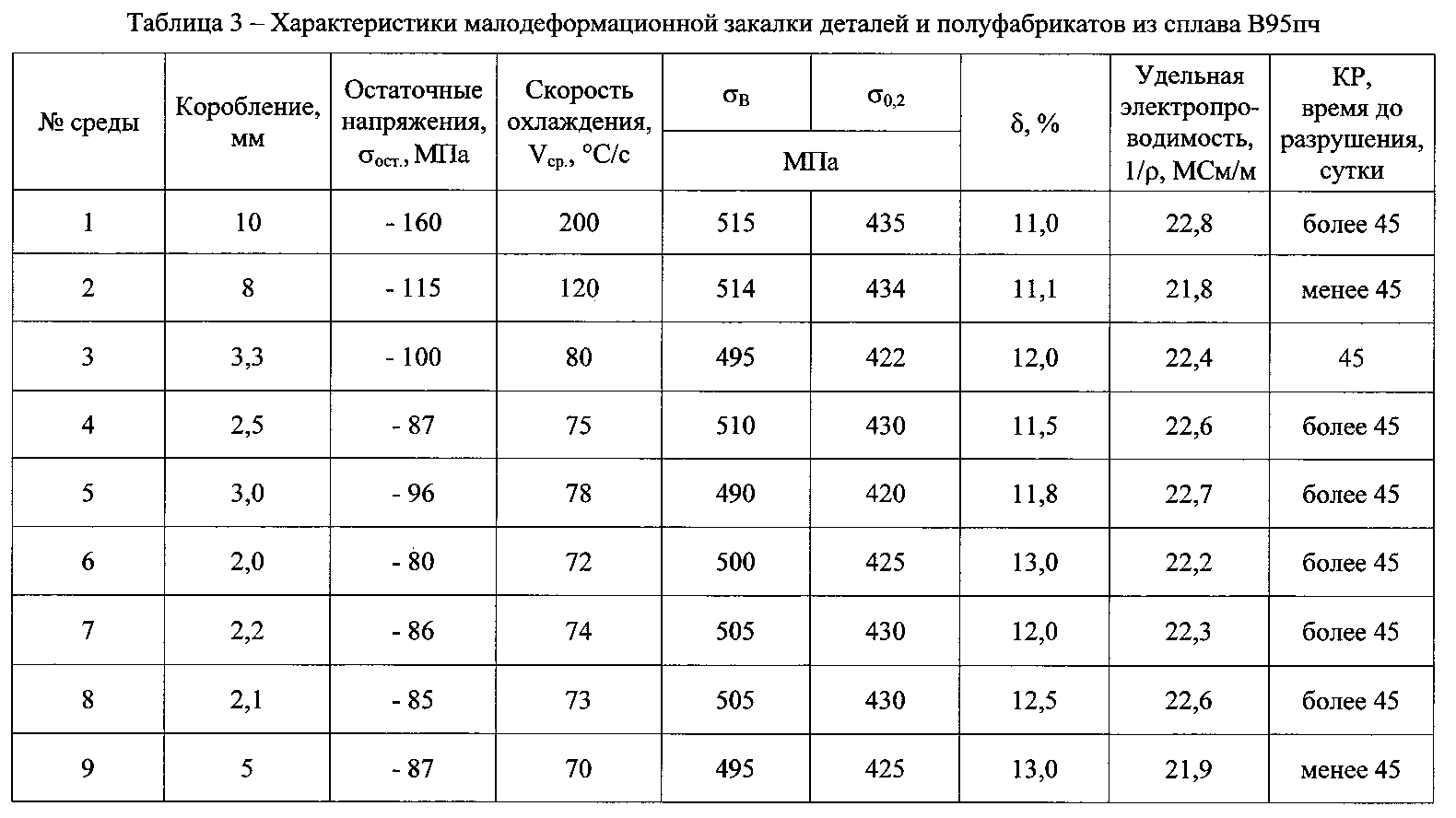