Технология листовой штамповки: горячая, холодная, резиной, взрывом, жидкостью
Листовая штамповка — метод изготовления плоских и объемных тонкостенных изделий из листового материала, ленты или полосы с помощью штампов на прессах или без применения прессов. Листовая штамповка подразделяется на горячую и холодную.
Горячая штамповка. Применяется главным образом в производстве котельных днищ, полушариев, буев и других корпусных деталей для судостроения. Изготовляются они из стального листа толщиной 3 … 4 мм. Операции горячей листовой штамповки аналогичны операциям холодной штамповки. Однако при составлении технологического процесса всегда учитывается нагрев. Составляя чертеж заготовки, надо учитывать утяжку металла при вырубке, пробивке и гибке, а также и степень коробления при остывании детали, так как ее размеры при этом несколько сокращаются. Это обстоятельство заставляет увеличивать допуски на размеры в сравнении с холодной штамповкой. Нагревают заготовки в пламенных и электрических печах, а также в электронагревательных устройствах.
Холодная штамповка. Это наиболее прогрессивный метод обработки давлением, так как он позволяет получить детали, не требующие в большинстве случаев дальнейшей обработки резанием. Холодной листовой штамповкой изготовляют как крупные, так и мелкие детали (рамы и кузова автомобилей, шасси самолетов, элементы обшивки судов, детали часовых механизмов и др.).
Листовая штамповка дает большую экономию в использовании металла, обеспечивая в то же время высокую производительность. Но наибольший эффект она дает при массовом и крупносерийном производстве.
При холодной листовой штамповке применяются углеродистая и легированная стали, алюминий и его сплавы, медь и ее сплавы, а также неметаллические материалы: картон, эбонит, кожа, резина, фибра, пластмасса, поставляемые в виде листов, лент и полос.
Технология листовой штамповки. Основным технологическим оборудованием для изготовления изделий методом листовой штамповки являются вибрационные ножницы (рис. 77), кривошипные (см. рис. 87 и рис. 88) и гидравлические прессы. Операции листовой штамповки могут быть разделены на два основных вида: разделительные и формоизменяющие. К основным разделительным операциям относятся: резка, вырубка и пробивка.
Рис. 77
Рис. 87
Рис. 88
Резкой называют операцию, где происходит последовательное отделение части заготовки по прямой или кривой линии. Применяется резка для получения как готовых деталей, так и раскроя листа на полосы нужной ширины. При раскрое листа необходимо, чтобы выход деталей из листа был максимальным, а отходы были минимальными. Рациональность раскроя определяется на основании подсчета коэффициента использования материала. Под коэффициентом понимается отношение площади вырубленных деталей к площади листа. Операция резки производится с помощью вибрационных, дисковых, гильотинных и других ножниц.
Вибрационные ножницы (рис. 77) представляют собой станок с короткими ножами. Верхний нож 5 получает колебательные движения от электродвигателя 1 через эксцентриковый механизм. Листовой металл устанавливают на столе 7 и подвигают между верхним 5 и нижним 6 ножами до упора 3, который может передвигаться и закрепляться в скобе станины, 2,4 — головку, 8 — стойка станины.
Вырубка — операция по получению заготовки замкнутого контура (рис. 78). На рис. 79 приведены чертеж (I) и схема (II) типовой детали, изготовляемой из полосы вырубкой.
Рис. 78
Рис. 79
Пробивка — получение отверстий в детали нужной формы (рис. 80).
Рис. 80
К основным формоизменяющим операциям* относят гибку, вытяжку, отбортовку, обжим и формовку.
Гибка — операция, при которой плоской заготовке придают изогнутую форму (рис. 81: 1 — пуасон; 2 — нейтральный слой; 3 — матрица): R и г — внешний и внутренние радиусы гибки, S — толщина материала. Она может быть V -образная, U-образная и др. (рис. 82).
Рис. 81
Рис. 82
На рис. 83 представлен чертеж детали, отверстия в которой получены пробивкой. После этого деталь изогнута на штампе.
Рис. 83
Вытяжка — операция, превращающая плоскую заготовку в полую пространственную деталь или полуфабрикат 2 (рис. 84). Вытяжкой изготовляют не только цилиндрические детали, но и сложные по форме коробчатые, конические и полусферические. При вытяжке плоская заготовка 5 втягивается пуансоном 1 в отверстие матрицы 3. Для предотвращения в заготовке при сжимающем напряжении образования складок применяют прижимы 4.
Рис. 84
Вытяжка может быть без утонения и с утонением. В первом случае она происходит без заметного изменения, во втором изменяется не только форма заготовки, но и толщина ее стенок. В случае, когда нужно получить глубокую вытяжку, ее ведут в несколько проходов. На рис. 85 показан чертеж типовой детали и из металлического листа 1, изготовленной штамповкой с вытяжкой.
Рис. 85
Отбортовка — операция образования бортов по наружному контуру листовой заготовки или вокруг заранее пробитых отверстий (рис. 86). Она применяется главным образом для образования горловин у плоских деталей 2, необходимых как для нарезания резьбы, так и сварки или сборки. Обычно она выполняется последовательно (I, II, III) за один или несколько проходов в штампах, состоящих из пуансона 1 и матрицы 3. Операцию отбортовки очень часто выполняют на концах труб при подсоединении к ним фланцев, с помощью которых трубы будут в дальнейшем соединяться.
Рис. 86
Обжим — операция сужения (уменьшения) концевой части полых или объемных деталей. Осуществляется она путем обжатия материала штампом снаружи в конической матрице. При этом конфигурация обжимаемой части целиком зависит от формы штампа.
Формовка — операция, связанная с местным изменением формы с сохранением конфигурации наружного контура детали. Примером формовки может служить изготовление ребер жесткости на машиностроительных деталях, а также увеличение размеров по диаметру средней части полой детали.
Технологический процесс обработки различных материалов давлением, как упоминалось выше, производят на прессах. Прессы бывают гидравлические и механические (кривошипные, винтовые, реечные и т. д.). По назначению прессы подразделяют на ковочные, штамповочные, листоштамповочные, чеканочные, обрезные, трубопрофильные, гибочные, правильные, брикетировочные (для изготовления брикетов из кусковатых или порошкообразных материалов), кузнечно-штамповочные автоматы, термо- пластавтоматы и др.
Кривошипные горячештамповочные прессы ГОСТ 6809-87Е (рис. 87) изготавливаются в России давлением от 61,78 до 617,8 кН (mc — единица силы и веса). Они состоят из станины 1, ползуна 2, шатуна 3, кривошипного вала 4, стажных колонн 5, зубчатого колеса 6 и фрикционной муфты 7. Применение прессов для горячей объемной штамповки очень эффективно в сравнении с другим технологическим оборудованием. Они обеспечивают более высокую точность поковок при значительной экономии металла. Наличие в них индукционного электрического нагрева способствует улучшению условий труда в цехе: уменьшаются шум и сотрясение здания, устраняется задымленность производственных помещений. Управление прессом осуществляется органами регулирования и с помощью сжатого воздуха из цеховой магистрали.
Рис. 87
На рис. 88 показан пресс для холодной штамповки ГОСТ 9408-89Е, состоящий из стойки 1, электродвигателя 2, цилиндра уравновешивания ползуна 3, зубчатого колеса 4, направляющих 5, ползуна 6 и стола пресса 7. На подобных прессах изготавливают как мелкие, так и крупные листовые детали, например, кузова автомобилей. Возможное давление пресса — 30,89 кН.
Рис. 88
Гидравлические прессы обладают наилучшей характеристикой для глубокой вытяжки и других операций листовой штамповки, так как осуществляют деформирование металла с постоянной скоростью. Подобные прессы широко применяют в авиационной и ракетостроительной промышленности.
На рис. 89 и 90 показаны крупные сборочные единицы самолетов, детали которых изготовлены прессованием. Так, каркас пола пассажирской кабины самолета (рис. 89) включает: обшивку 1, шпангоут 2, стрингеры 3, поперечные балки 4 и продолжные балки 5. А гондола турбо-винтового двигателя самолета (рис. 90) состоит из обтекателя втулки винта — 1, воздухозаборника 2, крышки переднего капота 3, крышки заднего капота 4, люка 5, силовой фермы в, кожуха 7, стекателя 8, хвостовой части гондолы 9, силового шпангоута 10, рамы маслорадиатора 11, силового шпангоута 12 и боковой балки 13.
Рис. 89
Рис. 90
Штамповка резиной. С ее помощью осуществляются разделительные и формоизменяющие операции. При этом пуансоном или матрицей является резина. Штамповку резиной чаще всего применяют для изделий из тонколистового металла толщиной до 2 мм (алюминия, медных сплавов, малоуглеродистой стали).
Штамповка жидкостью. В этом случае металл деформируется под давлением жидкости, принимая форму матрицы. Данный способ применяют для вытяжки полых деталей разной формы.
Штамповка взрывом. Для пластического формоизменения заготовки применяют и взрывчатые вещества (взрывчатые газовые смеси из метана, пропана, гиксогена и др.), создающие высокое давление, под действием которого заготовка принимает форму штампа.
Штамповку взрывом применяют для изготовления крупных деталей и деталей сложной формы, когда изготовление их другими способами невозможно (например, сплавы труднодеформируемые) или неэкономично. Такая
штамповка не требует сложного и дорогостоящего оборудования.
Электрогидравлическая штамповка. Этот метод характерен тем, что энергоносителем является высоковольтный электрический заряд в жидкости. Разряд вызывает появление ударной волны, которая и деформирует заготовку, придавая ей необходимую форму.
Этот вид штамповки дает возможность выполнять все операции холодной листовой штамповки с большой точностью и с сравнительно малыми затратами.
Магнитно-импульсная формовка. Формирование изделий этим методом происходит при создании импульсного магнитного поля вокруг заготовки и взаимодействия этого поля с импульсными токами, протекающими в заготовке. В результате такого взаимодействия в заготовке возбуждаются вихревые токи, что приводит к образованию вокруг нее также электромагнитного поля. Это создает предпосылки для динамического воздействия на заготовку и ее деформирование.
Этим методом осуществляют обжатие трубных заготовок, рельефную формовку, вырубку и др.
Существуют и другие прогрессивные методы листовой штамповки, но мы их рассматривать не будем.
* Формоизменяющими операциями называют такие, при помощи которых из плоской заготовки получают детали пространственной формы
cherch.ru
Горячая объемная штамповка и сущность процесса
Метод горячей объемной штамповки использует одно из основных физических свойств металлов — пластичность. Это свойство металлического поликристалла изменять свои размеры при приложении к нему усилия.
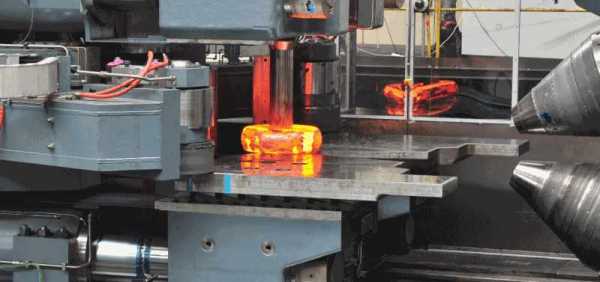
Горячая объемная штамповка
Пластичность растет с повышением температуры, поэтому для изготовления сложных объемных деталей заготовки нагревают.
Таким способом изготавливают детали самой разнообразной формы — от деталей часов до колесных дисков автомобиля.
Процесс горячей объемной штамповки
Метод заключается в том, что при приложении высокого давления металл горячей болванки подвергается серии последовательных деформаций, и, не нарушая своей целостности, затекает в свободное пространство специально подготовленных штампов, повторяя их пространственную форму и приходя к заданным размерам. Выступы и впадины в соответствующих локальных областях штампа ограничивают и направляют движение металла, приближая с каждым проходом конфигурацию и габариты болванки к параметрам конечного изделия. При последнем рабочем проходе они формируют замкнутый единый ручей (полость), совпадающий с конфигурацией готового изделия.
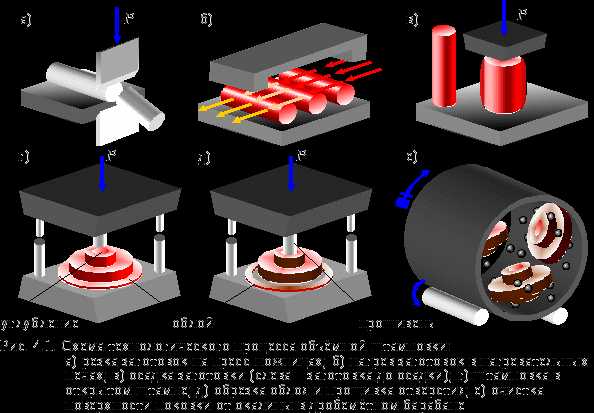
Технологический процесс горячей объемной штамповки
Термин горячая объемная штамповка металла указывает на то, что габариты и геометрия заготовки меняются не в одном, а в двух или трех измерениях.
Горячая штамповка в качестве болванок использует круглый или прямоугольный прокат, а также горячекатаный лист. Горячая объемная штамповка проводится и прямо из прутка, если конфигурация детали не очень сложная и достаточно одного-двух проходов. Впоследствии отдельные детали отрубают от прутка.
По своей форме конечные поковки подразделяют на два основных класса:
- Дисковые: фланцы, крышки, ступицы, прочие круглые (прямоугольные) поковки с длиной, малой относительно диаметра. Здесь выбирают базовую технологическую схему осадки в торец исходной болванки.
- Удлиненные: рычаги, валы, шатуны и похожие на них по конфигурации детали. Болванка располагается на штампе плашмя, и в ходе нескольких черновых и штамповочных операций ей придают окончательную форму. До завершающего прохода исполняют формовку в ручьях и на вальцах.
По технологическим схемам активно применяются две наиболее употребительных:
- штамповка в закрытых штампах
- штамповка в открытых штампах
Горячая объемная штамповка в закрытых штампах осуществляется в штампе с небольшим зазором между его половинами. Подразумевается, что объемы заготовки и готового изделия совпадают. Эту оснастку снабжают двумя поверхностями разъединения, находящимися под некоторым углом. Схема используется в производстве сравнительно несложных по своей форме деталей и позволяет добиться наибольшей однородности внутреннего строения детали и меньшей шероховатости.
При применении схемы горячей объемной штамповки в открытых штампах нет точного соответствия объемов между заготовкой и конечным изделием, происходит активное перераспределение массы металла между частями поковки. Часть металла выдавливается за пределы штампа в специальную канавку и называется облоем. Схема позволяет штамповать детали практически любой конфигурации, поскольку позволяет проводить большое количество черновых и завершающих проходов с промежуточным кантованием болванки.
Преимущества и недостатки процесса
Горячая объемная штамповка обладает такими достоинствами, как:
- Изготовление поковок весьма сложной формы.
- Снижение потерь материалов.
- Снижение удельной трудоемкости.
- Нет необходимости в высокой квалификации штамповщика.
- Точность соблюдения габаритов и конфигурации.
К минусам метода горячей объемной штамповки относят
- Сложность операций
- Значительная энергоемкость
- Существенная стоимость и трудоемкость проектирования и изготовления оснастки. Штамп приходится делать из высококачественных материалов, и применим он только к данному изделию.
- Необходимость использовать большее усилие, чем при ковке
- Лимит веса готового изделия до 3-4 тонн.
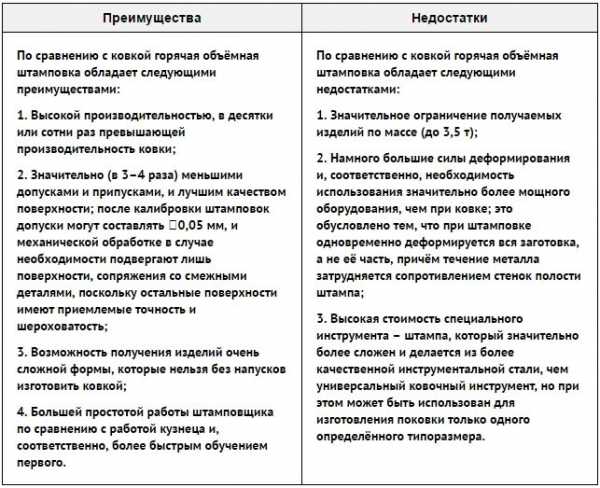
Преимущества и недостатки
В целом горячую объемную штамповку имеет смысл применять при выпуске средних и больших серий, а также, если сложность формы и толщина детали не допускают применение обойтись холодной формовкой.
Технологический процесс горячей объемной штамповки охватывает множество подготовительных и рабочих операций, от поступления материала и до получения конечного изделия.
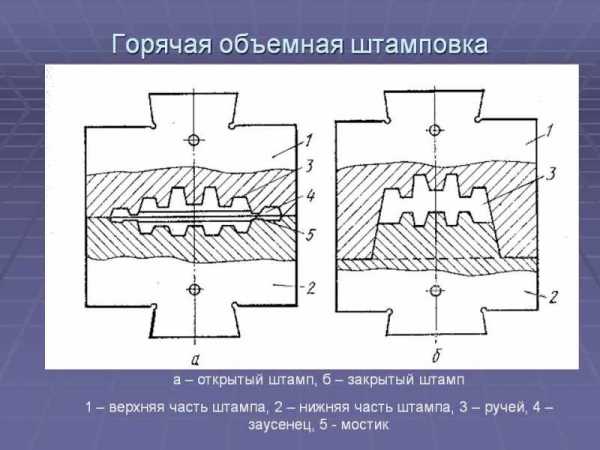
Схема горячей объемной штамповки
Проработка технологии включает такие этапы, как:
- Определяется схема горячей объемной штамповки — в открытых штампах или закрытая, выпускается конструкторская документация.
- Определяют переходы процесса, с учетом допусков выставляют размеры болванки.
- Исходя из потребного усилия горячей объемной штамповки выбирают оборудование (пресс, молот, и т. д.).
- Проектируются штампы.
- Задается метод нагревания и температурно — временной режим для каждой операции.
- Определяются отделочно-завершающие операции.
- Определяются технико-экономические характеристики проектируемого техпроцесса.
Горячая объемная штамповка требует от технологов, конструкторов и цехового персонала глубоких знаний по материаловедению и обширного практического опыта работы с данным процессом.
Сам процесс горячей объемной штамповки разделяется на следующие этапы:
- Нарезка проката на болванки,
- Доведение заготовок до рабочей температуры
- Штамповочные операции
- Удаление облоя
- Коррекция формы (при необходимости)
- Термообработка
- Удаление окалины
- Калибровка,
- Прием службой технического контроля.
Смазка для процесса горячей объемной штамповки
До подачи на штамп болванки требуется полностью и равномерно прогреть. На современных предприятиях этим процессом управляет автоматика, обеспечивая заданных график повышения температуры, равномерное прогревание всех заготовок по всему их объему и исключение образования оксидных пленок и зон пониженного содержания углерода. В качестве нагревателей применяют:
- электроконтактные установки. Нагрев осуществляется путем включения болванки в электрическую цепь и прохождению по ней сильного тока.
- индукционные системы. Нагрев производится вихревыми токами, возбуждаемыми в приповерхностном слое заготовки;
- газовые печи. Повышение температуры проходит в изолированной от атмосферы камере, заполненной инертным газом, исключающим образование окалины.
Удаление облоя и пробивка пленок применяется в случае открытой схемы горячей объемной штамповки. При этом используют специальные обрезные и пробивные штампы и кривошипные прессы.
Иногда в ходе выемки изделий из штампа, обрубки облоя или термообработки происходит искривление осей изделия либо нарушение поперечных сечений. Тогда применяют операцию коррекции формы, или правку. Заготовки больших размеров либо изготовленные из высококачественных сталей подвергаются правке, будучи горячими. Операция проводится в чистовом ручье после удаления облоя. Иногда операцию правки совмещают с обрезкой. Изделия небольшого размера корректируют винтовыми прессами по окончании термообработки и остывания.
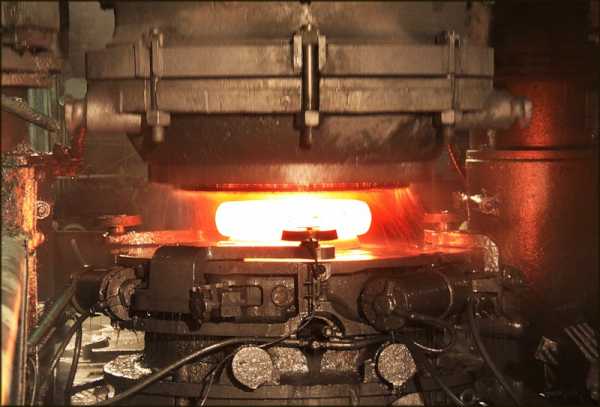
Термообработка в горячей объемной штамповке
Термообработку проводят с целью доведения физических свойств изделий до заданных параметров и для облегчения финальной обработки. Операция позволяет также снять остаточные напряжения, уменьшить зернистость, повысить вязкость и пластичность.
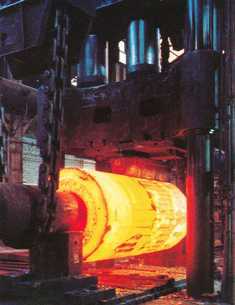
Объемная штамповка
Чтобы упростить операции контроля, обеспечить прецизионное позиционирование болванки и снизить износ инструмента на стадии механической обработки, проводят очистку изделий от окалины. Для этого применяются дробеструйные комплексы. В изолированной камере поковки воздухом под большим напором разгоняют стальную дробь и направляют ее на движущиеся, на транспортере изделия. Многочисленные соударения сбивают пленки и хлопья окислов в поверхности, придавая ей матовый внешний вид и одновременно уплотняя приповерхностный слой. Для мелких изделий применяют другую установку — галтовочный барабан. В нем большое количество деталей пересыпается вместе с добавляемыми к ним металлическими шариками или звездочками. Благодаря многочисленным соударениям деталей с них сбивается окалина.
Иногда в последовательность добавляют еще один переход — калибровку. Она проводится с целью избежать финишной обработки, оставляя только шлифовку. Посредством плоскостной калибровки достигают точности габаритов по вертикали. Объемная калибровка служит для доведения габаритов в нескольких направлениях, позволяя также и снизить шероховатость. Для калибровки используют специальные штампы с особо точными ручьями, повторяющими конфигурацию поковки.
Штамповочные ручьи и их виды
Для простых конфигураций изделий горячая объемная штамповка выполняется за один проход.
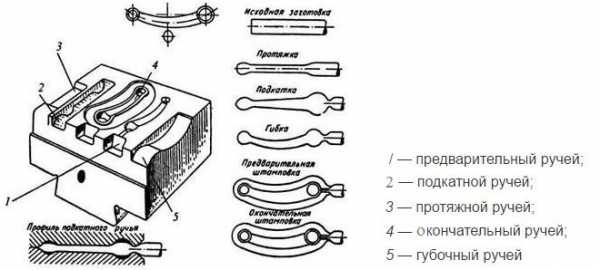
Штамповочные ручьи и их виды
Если же предстоит отштамповать замысловатое изделие с перепадами толщин и высот, выступы и изгибы — изготовление проводят за несколько проходов, в каждом из которых формовка делается отдельной впадиной на штампе — ручьем. Их подразделяются на два вида:
Заготовительные
Используются для фасонирования приведения материала болванки к пространственной конфигурации, позволяющей провести операции горячей объемной штамповки с минимальными потерями материала.
Заготовительные ручьи
Виды заготовительных ручьев:
- Протяжной — растягивает определенные части болванки, сужая их сечение. Применяется серия несильных ударов с переворотом болванки
- Податной — утолщает сечение болванки, «перегоняя» на это место материал с соседних участков. Применяется также серия несильных ударов с переворотом болванки
- Пережимной — плющит болванку в месте применения, вызывая увеличение местной ширины. Используется 1-3 сильных удара,
- Гибочный – используется для деталей с выгнутой осью
- Осадочный — применяется для изделий, близких к круглой форме. Уменьшает высоту болванки, добиваясь нужной высоты и радиуса
Штамповочные
Используются в завершающей формовке, бывают черновыми и чистовыми.
Черновой используется для изделий сложной конфигурации и в целях снижения износа чистового. Предназначен для приближения габаритов и конфигурации болванки к окончательному изделию. Он глубже и уже, чем чистовой ручей, обладает большими радиусами и уклонами. Эти меры применяются для свободного размещения болванки в чистовом ручье.
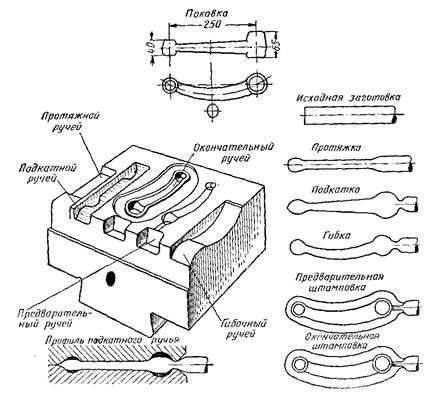
Штамповочные ручьи
Чистовой ручей используется для формовки конечной продукции, изготавливается с припуском на усадку при охлаждении. Устанавливается в середине штампа, поскольку давление и возникающие напряжения при чистовой штамповке максимальны. Для отвода выдавливаемого металла вокруг ручья расположена облойная канавка.
Схемы штамповки
Конкретная конфигурация горячей объемной штамповки выбирается опытным технологом, принимающим во внимание следующие параметры:
- Размеры детали.
- Материал.
- Форма.
- Доступное оборудование.
- Лимиты трудоемкости и материальных затрат.
На текущий момент применяется две основные схемы горячей объемной штамповки:
- с открытым штампом;
- с закрытым штампом.
Штамповка в закрытом штампе проводится с небольшим зазором между его половинами. Подразумевается, что объемы болванки и конечной детали точно совпадают. Иногда делают две линии примыкания, находящиеся под углом друг к другу. Схема используется для формовки сравнительно несложных по конфигурации поковок и позволяет добиться наибольшей однородности внутреннего строения детали и меньшей шероховатости.
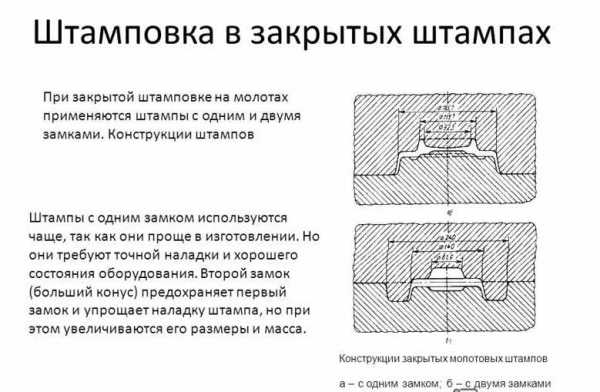
Схема штамповки в закрытых штампах
При применении схемы горячей объемной штамповки в открытых штампах нет соответствия объемов болванки и конечного изделия, происходит активное перераспределение массы металла между ее частями. Некоторая часть металла выдавливается за пределы штампа в приспособленную для этого канавку и называется облоем. Схема позволяет штамповать детали практически любой конфигурации, поскольку позволяет проводить большое количество черновых и завершающих проходов с промежуточными поворотами болванки.
Оборудование, используемое для горячей объемной штамповки
Оборудование для горячей объемной штамповки включает в себя:
- Молоты
- Кривошипные прессы
- Горизонтально-ковочные машины
Технология применения каждого класса установок связана с их конструкцией. Молоты допускают такие схемы, как открытая штамповка и штамповка в закрытых штампах
Горячая объемная штамповка на молотах
Технология использует явление преобразования кинетической энергии падающего массивного молота в энергию ударной деформации заготовки. Молоты поднимаются в исходное состояние сжатым воздухом или паром и имеют массу от 0.5 до 25 тонн.
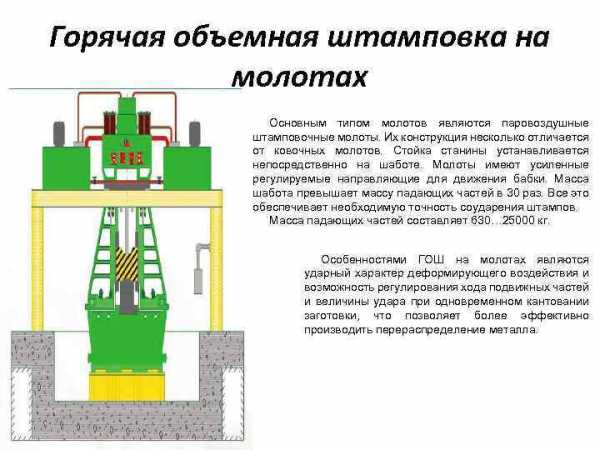
Горячая объемная штамповка на молотах
Изменяя высоту подъема молота, можно регулировать силу удара. Ход молота также регулируется, это дает возможность для поворота заготовки во время очередного подъема молота и более точной штамповки. Доступны все подготовительные операции, включая протяжку и подкат.
Точность изготовления деталей на молотах оставляет желать лучшего, что объясняется неминуемым сдвигом частей штампа друг относительно друга в момент удара. Допуски при использовании молотов приходится давать большими, а для обеспечения возможности выемки изделий из пресса делаются большие штамповочные уклоны.
Горячая объемная штамповка на прессах
Горячая штамповка металла проводится и на кривошипных прессах. Главная характеристика оборудования — это развиваемое им усилие, варьирующееся от 6 до 110 МН.
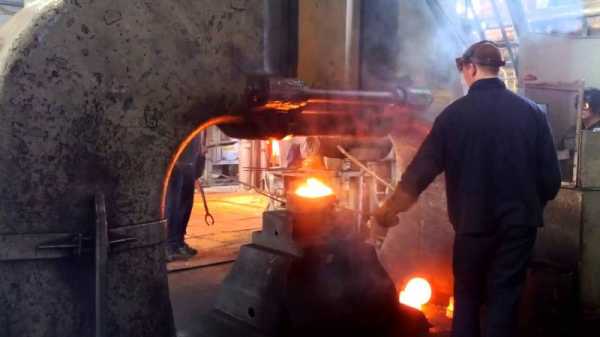
Горячая объемная штамповка на прессах
Конструкция кривошипного горячештамповочного пресса имеет жесткий привод и не дает возможности регулировать ход пресса и его усилие. Эти факторы исключают из перечня допустимых операций протяжку и подкат, поскольку для них нужно постепенно увеличиваемое давление.
Отсутствие ударов, постоянный ход штампа и использование направляющих исключает сдвиг, что позволяет добиться точности обработки, принципиально недостижимой на молотах.
Соответственно допустимо задание существенно меньших допусков, штамповочных радиусов и уклонов, что снижает потери материалов и повышает производительность оборудования.
Кроме того, статическая деформация глубже проникает в болванку, чем динамическая, и это делает доступными для обработки материалы с низкой пластичностью.
Отрицательными особенностями кривошипных горячештамповочных прессов являются:
- окалина запрессовывается в поверхность, для борьбы с этим применяют нагрев в инертной атмосфере или глубокую зачистку болванки;
- ввиду продолжительного соприкосновения с пуансоном болванка остывает, снижается ее пластичность и заполняемость.
Штамповка на горизонтально-ковочных машинах
При горячей объемной штамповке этим методом, установка также приводится в действие кривошипным механизмом, главное деформирующее усилие прикладывается по горизонтали. В дополнение к этому применяется еще один ползун, размещенный под прямым углом. Матрица соответственно также составлена из двух частей, одна из которых является подвижной.
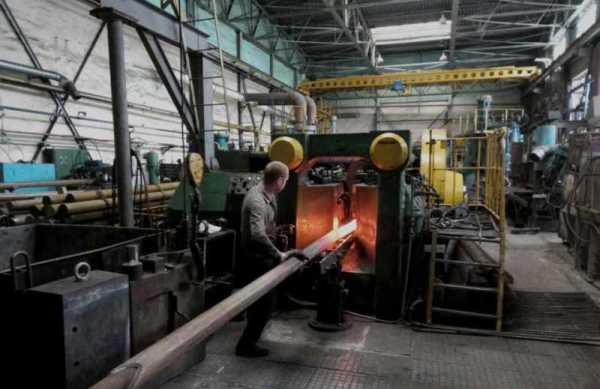
Штамповка на горизонтально-ковочных машинах
Доступны такие переходы, как высадка, прошивка и пробивка. Для штамповки стержней, колец, труб с утолщениями и отверстиями в качестве заготовок применяют круглый или квадратный пруток.
Эти специализированные устройства позволяют добиваться существенного повышения эффективности. В качестве минусов можно отметить узкую применимость и дороговизну.
Если вы нашли ошибку, пожалуйста, выделите фрагмент текста и нажмите Ctrl+Enter.
stankiexpert.ru
Холодная штамповка металла
Холодная штамповка металлаОбщая информация (#Холоднаяштамповка_иннов_описание)
Холодная штамповка — это процесс пластической деформации металла, в результате чего он приобретает заданные размеры и формы без термического влияния.
Описание назначения (#Холоднаяштамповка_иннов_назначение)
Холодная штамповка предназначена для получения изделий достаточно сложных форм (изогнутых сразу в нескольких направлениях) экономически эффективным методом — наиболее быстро с наименьшим колическом отходов, затраченной энергии и постобработки.
Используемые материалы (#Холоднаяштамповка_иннов_материалы)
Материал для холодной листовой штамповки — тонкий пластичный листовой металл: сталь, алюминий, нержавейка, медь и т.д.
При холодной объемной штамповке выдавливанием мелких деталей типа болтов используется нелистовой металл вроде прутка и другого проката.
Описание технологического процесса (#Холоднаяштамповка_иннов_процессы)
Материал помещается в пресс, после чего с помощью сильного давления металлу придается необходимая форма. Пресс может одновременно деформировать и вырезать изделие из материала. При создании сильной кривизны, штамповка может производиться в несколько этапов с промежуточным обжигом для сняния внутреннего напряжения и восстановления пластичности металла.
Серийность (#Холоднаяштамповка_иннов_серийность)
Холодная штамповка характеризуется высокой серийностью, производительностью и скоростью.
Возможно изготовление от нескольких десятков до сотен изделий в минуту на одном прессе.
Требования по обеспечению производства (#Холоднаяштамповка_иннов_обеспечение)
Используемое оборудование (#Холоднаяштамповка_иннов_оборудование)
Оборудование для холодной штамповки — механический пресс, гидравлический пресс.
Требования к заготовке (#Холоднаяштамповка_иннов_заготовка)
Основное требование — высокая пластичность, что определяет выбор подходящих металлов и тонкость листа. Холодная штамповка возможна только с тонким листовым металлом или маленькими нелистовыми заготовками, например для выдавливания болтов из прутка.
Требования к температуре (#Холоднаяштамповка_иннов_температура)
При холодной штамповке нагревание не требуется. Однако, если нужно получить существенное изменение формы (например, из листа металла сделать высокую вазу или чайник), то штамповка может производиться в несколько этапов с промежуточным отжигом для снятия внутреннего напряжения и восстановления пластичности металла.
Требования к давлению (#Холоднаяштамповка_иннов_давление)
Пресс оказывает сильное механическое давление на материал, что определяет большой размер и вес оборудования.
Ограничения по форме и конструкции (#Холоднаяштамповка_иннов_ограничения)
Возможно использование только тонкого листового металла или маленьких нелистовых заготовок. Чем толще и массивнее материал, тем «горячее» требуется его штамповка, чтобы он был достаточно пластичным. Также существуют ограничения на размер отверстий и радиусы скруглений, т.к. изготовление малых отверстий приводят к быстому износу оборудования из-за высокого давления, а высокая кривизна требует штамповки в несколько этапов и промежуточного обжига.
Постобработка (#Холоднаяштамповка_иннов_обработка)
Среди горячей, теплой и холодной штамповки, у последней самая низкая потребность в постобработке.
Характеристики готовых деталей (#Холоднаяштамповка_иннов_характеристики)
Механические свойства (#Холоднаяштамповка_иннов_механика)
Среди горячей, теплой и холодной штамповки, у последней самая высокая точность изготовления и наилучшее качество поверхности. При штамповке металл упрочняется сам по себе вдобавок к получению криволинейной формы, что делает итоговое изделие прочным, но при этом «пустотелым» и следовательно легким.
Оптические свойства (#Холоднаяштамповка_иннов_оптика)
Оптические свойства определяются свойствами металла.
Тепло/электро проводность (#Холоднаяштамповка_иннов_проводимость)
Тепло/электопроводность высока, т.к. используется тонкий металл.
Тактильные (#Холоднаяштамповка_иннов_тактильность)
Тактильные свойства изделия определяются свойствами материала. На ощупь изделия ощущаются как металл.
Внешние признаки применяемой технологии (#Холоднаяштамповка_иннов_признаки)
Преимущества технологии: наименьший расход материала, наименьшие энергозатраты, высокая точность и качество поверхности. Также преимуществом является возможность использовать дешевые материалы (стали и цветные металлы) с более низкими прочностными свойствами. Эти материалы упрочняются в ходе штамповки, что позволяет получить изделия с требуемыми характеристиками.
Видео материалы по теме:
https://youtu.be/0hGYYZIUcwc
https://youtu.be/0Aq2bpLbYsA
https://youtu.be/bYW-Mkb6yPY
1. Каковы основные требования к заготовке при холодной штамповке?
2. Каковы основные эстетические и технологические ограничения технологии?
3. Каковы основные преимущества технологии перед горячей штамповкой и литьем?
alterozoom.com
Прессы для холодной штамповки — Энциклопедия по машиностроению XXL
Оборудованием для горячей штамповки служат молоты, в которых работа формоизменения производится за счет энергии удара падающих частей, а также механические или гидравлические прессы, по конструкции аналогичные прессам для холодной штамповки. [c.92]Кривошипные штамповочные прессы по принципу действия аналогичны прессам для холодной штамповки (см. 5), но отличаются более жесткой конструкцией и более быстроходны, так как поковки не должны успеть охладиться к моменту [c.95]
Штампы для обрезки заусенцев и прошивки отверстий. Удаление заусенцев, получающихся при штамповке, а также образование отверстий путем прошивки перемычек в углублениях поковки производится на специальных обрезных прессах, напоминающих прессы для холодной штамповки. [c.106]
По технологическому признаку прессы для холодной штамповки подразделяют на универсальные и специальные. На универсальных прессах выполняют операции гибки, резки, вырубки, пробивки, обрезки, прошивки, просечки и неглубокой вытяжки. [c.26]
ГИДРАВЛИЧЕСКИЕ ПРЕССЫ ДЛЯ ХОЛОДНОЙ ШТАМПОВКИ, ИХ ЭКСПЛУАТАЦИЯ И РЕМОНТ [c.149]
Многие гидравлические прессы для холодной штамповки имеют насосный (индивидуальный) привод, в котором в качестве рабочей жидкости используют масло. [c.238]
ПРЕССЫ ДЛЯ ХОЛОДНОЙ ШТАМПОВКИ [c.73]
Раздел четвертый ПРЕССЫ ДЛЯ ХОЛОДНОЙ ШТАМПОВКИ [c.493]
Подобно прессу конструируется и многоточечная машина, независимо от конфигурации изделия она представляет собой станок, назначение которого в сварке то же, что и пресса в холодной штамповке. Для данного узла проектируется сварочный штамп. Последний, как и штамп в прессе для холодной штамповки, имеет верхнюю и нижнюю плиты, закрепляемые на станке болтами. Нижняя плита перемещается относительно верхней плиты на колонках. На верхней плите расположены сварочные пистолеты в соответствии с формой данной детали. [c.192]
Основным оборудованием заводов П. м. являются прессы для холодной штамповки и автоматы. Ниже приводятся цифры оборудования механич. и прессового цехов америк. з-да и з-да СССР, а равно показатели необходимого оборудования на выпуск 10 ООО шт. П. м. при работе в три смены (табл. 4). [c.245]
Специализированные прессы для холодной штамповки выдавливанием. Основное преимущество холодной штамповки выдавливанием — возможность изготовления точных поковок, шероховатость поверхности которых в ряде случаев удовлетворяет предъявляемым к деталям требованиям или предусматривает незна- [c.203]
Привод прессов для холодной штамповки выдавливанием может быть насосным без аккумулятора и насосно-аккумуляторным. Наиболее экономичным для прессов с номинальным усилием до 50 МН является привод без аккумулятора с регулируемой производительностью. В качестве рабочей жидкости применяют минеральное масло. [c.204]
При выборе оборудования для холодной штамповки необходимо учитывать вид операции, материал, размеры и сложность конфигурации заготовки. Основной вопрос, решаемый при выборе оборудования,— определение усилия пресса. Для холодной объемной штамповки требуемое усилие определяют по таким же зависимостям, как для горячей штамповки с учетом особенностей холодной штамповки [6, 29]. Усилия здесь получаются больше, так как пластичность металлов в холодном состоянии гораздо ниже, чем в горячем. [c.151]
Асинхронные короткозамкнутые электродвигатели широко используются в машинных агрегатах металлургических машин (волочильные станы для волочения при постоянной скорости, острильные машины, ножницы [64], [116]), прессов-автоматов для холодной штамповки [83], угледобывающих машин [51], машин текстильной и легкой промышленности [10]. [c.5]
Штампы для холодной штамповки Пресс-формы………. [c.39]
Для холодной штамповки крупногабаритных изделий используют гидравлические прессы. [c.343]
Назначение. Метчики ручные, напильники, шаберы слесарные штампы для холодной штамповки обрезные и вырубные небольших размеров и без резких переходов по сечению, холодно-высадочные пуансоны и штемпели мелких размеров калибры простой формы и пониженных классов точности, пресс-формы для пластмасс в приборостроении. [c.245]
Конструкция современных однопозиционных прессов для холодного выдавливания в наибольшей степени отвечает требованиям получения высокого качества штампованных заготовок, улучшения условий работы штампа и устойчивости технологического процесса штамповки в целом. У прессов минимальные размеры стола, скорость движения ползуна соответствуют заданной скорости деформирования (обычно 60—160 мм/с) по-вышенные продольная и поперечная жесткость отсутствуют угловые деформации незначительны отклонения от плоскостности стола и ползуна (до [c.17]
Многопозиционные штампы устанавливают на специализированные прессы для холодного выдавливания (обычно механические, реже — гидравлические). Исходные заготовки получают в штампе для точной отрезки. В некоторых случаях при крупносерийном и массовом производстве отрезка заготовок, их калибровка и предварительное фасонирование проводятся на однопозиционном прессе-автомате (при диаметре заготовки до 22—25 мм). После этого заготовку подвергают РТО, очистке от окалины и загрязнений, покрытию носителем смазочного материала и смазыванию. В зависимости от сложности формы готовой детали и деформируемости заготовки проводится штамповка на одной или двух машинах. В некоторых [c.18]
Прессы для холодной листовой штамповки выпускаются усилием от 10 до 80 ООО—100 ООО кН расстояние между колоннами в продольном направлении доходит до 8 м. [c.310]
Для холодной штамповки применяют прессы кривошипные с ры чажной передачей фрикционные гидравлические. [c.395]
Машины-орудия для холодной штамповки — кривошипные, фрикционные, эксцентриковые и гидравлические прессы. При массовом производстве изделий штамповка производится за несколько операций, выполняемых на специальных прессах-автоматах. На рис. 145, а показано устройство фрикционного пресса. Он состоит из станины /, на опорах которой помещен [c.283]
Износостойкое хромирование применяется нри покрытии штампов для холодной штамповки металла матриц, пуансонов и пресс-форм, предназначенных для прессования пластмасс, резины, форм для литья металла под давлением. [c.565]
Слесарное, где осуществляется слесарная обработка, сборка и испытание оснастки. В зависимости от характера продукции инструментального цеха это отделение может иметь следующие участки штампов для горячей и для холодной штамповки, пресс-форм и форм для литья, приспособлений, режущего и измерительного инструмента. [c.4]
Оборудованием для холодной штамповки служат прессы различных типов и в сравнительно редких случаях молоты. [c.29]
Штампы для работы под прессами более сложны по конструкции, чем молотовые, и несколько напоминают штампы для холодной штамповки. Они имеют верхнюю и нижнюю плиты (их иногда называют башмаками и державками), направляющие колонки со втулками, обоймы для крепления в них вставок с формующими полостями и выталкиватели. [c.105]
Изготовление штампов для механических прессов. Как было указано выше, каждый штамп состоит из вставок с формующими полостями и вспомогательных деталей, служащих для соединения штампа с прессом и удаления поковки. Технология изготовления вставок, в общем, не отличается от технологии изготовления небольших молотовых штампов, т. е. заготовки проходят механическую обработку, закалку и отпуск, после чего следует слесарная доводка и полировка рабочих поверхностей. Что касается блоков и вспомогательных деталей, то технология их обработки и сборки сходна с соответствующими этапами технологического процесса изготовления штампов для холодной штамповки. Контроль собранного штампа производится так же путем заливки его свинцом или селитрой. [c.114]
Описаны устройства механических листоштамповочных, гидравлических прессов, штампов для холодной штамповки, а также монтаж, наладка и эксплуатация прессов различных конструкций. Даны сведения о механизации и автоматизации процессов холодной штамповки, особенностях ремонтных работ. В четвертое издание (3-е в 1977 г. Холодноштамповочное оборудование и его наладка ) включен материал по штамповке эластичной средой. [c.2]
ХВС Ножницы для холодной резки металла резьбопакат-ные плашки, пуансоны и обмсимные матрицы для холодной штамповки, пресс-формы для литья под давлением деревообделочные инструменты [c.327]
Привод ог насосов ротационного типа — радиально-плунжерных, аксиально-плунжерных, а также лопастных и щестерённых — получил щирокое применение, особенно к прессам для холодной листовой штамповки. Рабочей жидкостью для этих насосов является минеральное масло с давлением в радиально- и аксиальноплунжерных насосах преимущественно до 200 ат. Насосы монтируются или непосредственно на самом прессе или (для мелких прессов) рядом с прессом. [c.452]
Группы станков режущего инстру- мента мери- тельного инстру- мента вспомо- гатель- ного инстру- мента приспо- соблений восста- новления инстру- мента штампов для холодной штамповки штампов для горячей штамповки металли- ческих моделей пресс- форм кокилей [c.20]
Последнее условие связано с тем, что в номенклатуре шаровых пальцев больше половины деталей имеют массу 1—3 кг. В то же время программа их изготовления недостаточна для обеспечения полной загрузки дорогостои-щих многопозиционных автоматов. Таким образом, применив однопозиционные прессы для холодной объемной штамповки и оснастив их соответствующими средствами автоматизации, можно получить достаточный технико-экономический эффект. [c.363]
В зависимости от формы, размеров и материала собираемых деталей штампосборочные операции производят на кривошипных или гидравлических прессах в штампах для холодной штамповки и для холодной сварки. Кроме того, штампосборочные операции можно осуществлять штамповкой взрывом, штамповкой электрическим разрядом в жидкости и штамповкой магнитными полями высокой напряженности. Сборку деталей производят с использованием формоизменяющих операций холодной штамповки, показанных на рис. 2. Ниже рассмотрены отдельные примеры сборки деталей в сборочные единицы. [c.277]
Линия штамповки обоймы привода состоит из пресса для холодной высадки 9 и пресса для выдавливания 10. Оба пресса оборудованы автохматическими устройствами для загрузки заготовок. Шестерни приводов штампуются на одном прессе 11, оборудованном поворотным столом и двумя автоматическими подачами. На прессе прямым выдавливанием одновременно изготовляют две детали. [c.315]
mash-xxl.info
Пресс штамповочный и его различные аналоги + видео
Холодная ковка по силам каждому, достаточно взять в руки молоток и нанести по листовому металлу несколько ударов, чтобы придать ему некоторую деформацию, по такому же принципу работает и пресс штамповочный.
1 Кривошипный и гидравлический пресс штамповочный
Работа кузнеца или, как звучало это слово в некоторых диалектах славян, коваля всегда была одной из самых почетных. Опытные мастера, используя несколько разных молотов, способны были выполнить из металла практически любую вещь. Со временем штучная ручная работа стала недостаточной для обеспечения всех желающих металлическими изделиями, которые начали выпускаться в промышленных масштабах с помощью специальных станков.
Среди прочих весьма востребованным агрегатом стал аналог молота – пресс штамповочный, необходимый для холодной обработки металла. Используется он для придания необходимой формы металлической заготовке путем деформации некоторых участков, выбивания заданного рельефа или вырубания фрагментов. Различают кривошипный и гидравлический штамповочный пресс, разница между назначениями которых заключается только в том, что первый используется для простейших холодных обработок металла.
Рекомендуем ознакомиться
Кривошипный механизм работает по принципу преобразования вращательного движения привода через кривошипно-шатунную передачу в возвратно-поступательное действие, совершаемое ползуном, который и воздействует на заготовку. Гидравлический прессовальный агрегат оснащен двумя резервуарами с водой, которые являются рабочими камерами с поршнями, создающими в жидкости избыточное давление. Вода поступает в цилиндр, где движется поршень, связанный с ударным ползуном.
2 Горячая обработка металла – радиально-ковочная машина
Ни одно производство металлических деталей не может обойтись без заготовок, которые обрабатываются на станках в огромных количествах. В частности, для токарных операций требуется много валов с различными диаметрами, главным образом от 6 до 15 сантиметров. Только при таких условиях оправдано приобретение такого агрегата, как радиально-ковочная машина, которая отличается крайне высокой стоимостью. На этом станке можно производить до 300 тысяч заготовок в год, которых должно быть достаточно даже при самых крупных промышленных масштабах. Ввиду высокой сложности настройки оборудования, крайне желательно, чтобы выпуск валов был обусловлен необходимостью больших партий заготовок определенного диаметра.
Процесс радиальной ковки осуществляется следующим образом. Заготовка подается в нагревательный блок, работающий по индукционному принципу, где металлу придается нужная температура. По достижении необходимой степени пластичности заготовка направляется через рольганг (конвейер) в захватное устройство, которое направляет ее непосредственно в зону горячей штамповки или ковки. Здесь заготовку перехватывает следующий захватный механизм для дальнейшей обработки бойками. В процессе ковки металлическая болванка постоянно вращается захватом, для того чтобы поверхность подвергалась воздействию равномерно.
Станок для радиальной ковки работает от электродвигателя, который клиноременной передачей сообщает крутящий момент четырем валам с эксцентриковыми буксами. Каждый вал установлен вертикально и, в свою очередь, передает движение шатуну с бойком, между которыми закреплен ползун. За синхронное сближение бойков с последующим движением заготовки отвечают копирные барабаны – основа автоматики механизма. Вращение захвата с зажатой в нём заготовкой обеспечивается через червячные передачи от электродвигателя, а торможение в момент ковки выполняется с помощью пружинной муфты.
Параллельно земле располагается заготовка и в таком агрегате, как горизонтально-ковочная машина. На данном оборудовании отковываются торцевые утолщения на стержнях различного диаметра, для фиксации которых используются разъемные матрицы с горизонтально-ориентированными каналами. Одна половина зажима является неподвижной, в нее укладывается заготовка, после чего активируется механизм, посредством коленчатого вала связанная с ним ползуном вторая часть матрицы придвигается, плотно охватывая стержень. Одновременно коленчатый вал воздействует на шатун, от которого начинается работа ударных пуансонов, расположенных напротив каналов матрицы. Затем все движущиеся части агрегата возвращаются в исходное положение, а матрица размыкается.
3 В помощь кузнецу – молот ковочный пневматический
Сегодня редко где можно наблюдать работу кузнеца, но представить себе, как она выполняется – довольно просто. На наковальню укладывается придерживаемый клещами кусок металла, по которому наносятся удары тяжелым молотом. Работа сложная, сил нужно прикладывать немало. Именно поэтому в помощь кузнецам был создан молот ковочный пневматический. Это сравнительно небольшой агрегат, доступный по стоимости многим предприятиям, а также достаточно легко транспортируемый. Механизм имеет встроенный компрессор, с помощью которого в рабочем цилиндре сжимается и разряжается воздух за счет возвратно-поступательного движения поршня, сообщающегося от электродвигателя.
В отключенном состоянии компрессорный поршень пневматического молота находится в крайнем верхнем положении, а рабочий поршень – в крайнем нижнем. Когда агрегат включается, поршни приходят в движение навстречу друг другу, из-за чего воздух сжимается, и его напряжение передается на кривошип, соединенный с бойком. На каждый оборот кривошипного механизма приходится один удар рабочей части молота. Таким образом, чем чаще работает поршень компрессора, тем быстрее работает боёк станка. Масса удара может достигать одной тонны.
Похожим образом работает штамповочный паровоздушный молот, однако основным источником энергии движения поршня в нём является пар, подающийся от специального котла под собственным давлением, либо горячий воздух, нагнетаемый с помощью компрессорной установки. Сила ударов паровоздушного молота может превышать 8 тонн, в зависимости от модели, а скорость движения бойка способна достигать 50 метров в секунду. Механизмы делятся на два типа: автоматического и ручного действия. В первом случае удары по заготовке наносятся непрерывно, а во втором – когда боек достигает крайнего верхнего положения, то остается в нем до пускового сигнала с пульта или педали.
Бывают разные виды механических молотов: для ковки и штамповки, только штамповочного назначения, для обработки листового металла, а также выколоточные, для получения деталей по шаблону.
4 Вальцы и ротационно-ковочная машина – обработка вращением
Поковка деталей бывает не только штучной, но и конвейерной. Для последней удобнее всего использовать специальные вальцы ковочные, осуществляющие обжимное штампование фасонных заготовок. Принцип работы данного оборудования очень прост – на вращающихся в противоположных направлениях валах равноудаленные сектора снабжены штамповочными накладками.
В тот момент, когда секторные штампы расходятся, между вальцами вставляется заготовка, которая обжимается до нужного состояния вновь сошедшимися по мере вращения ковочными накладками. Некоторые модели ротационного механизма снабжаются ползуном, который выполняет функции гильотины и отсекает готовую деталь. Процесс обработки заготовок в таком механизме, как ротационно-ковочная машина, также основан на движении вращения.
В центре, между расположенными в кольцевой обойме роликами, с большой скоростью крутится шпиндель, внутри которого крестообразно размещены четыре бойка. Центробежная сила откидывает бойки, и они прижимаются к обойме, но когда их тыльные части надвигаются на ролики, снова сдвигаются к центру, нанося удары по заготовке. Встречаются и другие варианты действия механизма, в частности, когда вокруг неподвижного шпинделя вращается обойма с роликами, а бойки выталкиваются из центра пружинами. Возможно и противоположно направленное движение шпинделя и обоймы.
tutmet.ru