Способ химического полирования алюминия
Изобретение касается способа химического полирования алюминия обработкой полировальным составом, промывкой и обработкой в азотной кислоте. Образцы предварительно подвергают травлению в 50%-ной серной кислоте, промывают водой, осветляют 30%-ной азотной кислотой и после промывания водой полируют в течение 1 — 2 мин при температуре 80 — 90oC в растворе следующего состава, мас. %: экстракционная фосфорная кислота 28 — 28,50, ортофосфорная кислота 28,5 — 30,0, азотная кислота 3 — 7, серная кислота 11 — 16 медь (в пересчете на Cu2+) 0,07 — 0,14, вода — остальное. Медь в состав электролита вводят в виде сульфата или нитрата. После полирования образцы промывают горячей водой и обрабатывают 20 — 30%-ным раствором азотной кислоты для удаления пассивной пленки и следов выделенной металлической меди. В случае необходимости отполированные изделия подвергаются анодированию.
Изобретение касается способа химического полирования алюминия, позволяющее получить высококачественную зеркальную отделку отполированной поверхности и может быть использовано при производстве рефлекторов, деталей для декоративной отделки автомобилей, медицинского оборудования, всевозможных изделий легкой промышленности и т.д.
Азотная кислота — 3 — 7
Серная кислота — 11 — 16
Медь (в пересчете на Cu2+) — 0,07 — 0,14
Вода — Остальное
Медь в состав электролита вводят в виде сульфата или нитрата. После полирования образцы промывают горячей водой и обрабатывают 20 — 30%-ным раствором азотной кислоты для удаления пассивной пленки и следов выделившейся металлической меди. В случае необходимости отполированные изделия подвергаются анодированию. Пример 1. Образцы алюминия чистотой 99,5% подвергали травлению в 50%-ной серной кислоте, промывали водой, затем осветляли в 30%-ной азотной кислоте и после промывки водой полировали в электролите следующего состава, мас.%:
Экстракционная фосфорная кислота — 28
Ортофосфорная кислота — 28
Серная кислота — 11
Азотная кислота — 3
Медь (Cu2+) — 0,07
Вода — Остальное
при температуре 80oC в течение 1 минуты. После полирования образцы промывали горячей водой и обрабатывали 20 — 30%-ным раствором азотной кислоты. Коэффициент зеркального отражения отполированной поверхности 69. Коэффициент суммарного отражения — 96. Пример 2. Образцы алюминия чистоты 99,5% предварительно подвергали травлению в 50%-ной серной кислоте. Затем после промывания водой, осветляли в 30%-ной азотной кислоте и после дальнейшей промывки водой полировали в электролите следующего состава, мас.%:
Экстракционная кислота — 28,5
Ортофосфорная фосфорная кислота — 30
Серная кислота — 16
Азотная кислота — 7
Медь (Cu2+) — 0,14
Вода — Остальное
в течение 2 мин при температуре 90oC с последующей промывкой горячей водой и обработкой в 20 — 30%-ным растворе азотной кислоты. Коэффициент зеркального отражения — 66. Коэффициент суммарного отражения — 92. Пример 3. Образцы алюминия чистоты 99,5% после предварительного травления в 50%-ной серной кислоте промывали водой, осветляли в 30%-ном растворе серной кислоты и дальнейшей промывки водой полировали в ванне следующего состава, мас.%:
Ортофосфорная кислота — 29,25
Серная кислота — 13,5
Азотная кислота — 5
Медь (Cu2+) — 0,105
Вода — Остальное
в течение 1,5 мин при температуре 85oC с последующей промывкой горячей водой и обработкой 20 — 30%-ным раствором азотной кислоты. Коэффициент зеркального отражения обработанной поверхности — 68. Коэффициент суммарного отражения — 91. Пример 4 (по прототипу). Образцы алюминия чистоты 99,5% полировали в ванне следующего состава, мас.%:
Ортофосфорная кислота (уд.в. 1,7) — 77,5
Серная кислота (уд.в. 1,84) — 15,5
Азотная кислота (уд.в. 1,52) — 6,0
Борная кислота (крист.) — 0,5
Медь азотнокислая (крист.) — 0,5
при температуре 105oC в течение 1,5 мин с дальнейшей промывкой в горячей воде и обработкой в 38%-ном растворе азотной кислоты для удаления пассивной пленки и мельчайших красноватых выделений металлической меди. Коэффициент зеркального отражения отполированной поверхности — 59,8. Коэффициент суммарного отражения — 81,1. Из примеров вытекает, что способ химического полирования алюминия по изобретению по сравнению со способом по прототипу имеет значительные преимущества: увеличение коэффициентов зеркального и суммарного отражения отполированной поверхности алюминия с чистотой 99,5%. Литература
1. В. Тегарт Электролитическое и химическое полирование металлов М.: Иностранная литература, 1957, с. 150-152. 2. Л.В. Щиголев Электролитическое и химическое полирование металлов. М.: Академия наук СССР, 1959, с. 95-97.
Формула изобретения
Серная кислота 11 16
Азотная кислота 3 7
Медь (в пересчете на Cu2+) 0,07 0,14
Вода Остальноед
www.findpatent.ru
Алюминий и его сплавы полирование
Растворы 1, 2 используются для обезжиривания черных металлов, 2 — меди и ее сплавов, 3 — цинка и его сплавов, 4 — алюминия, сплавов цинка, свинца и кадмия. Раствор 5 предложен для обезжиривания черных и цветных металлов с использованием переменного тока. В более концентрированных растворах обезжиривают грубо обработанные, сильно загрязненные изделия. Менее концентрированные растворы рекомендуются для обезжиривания изделий, имеющих полированную поверхность. [c.26]При полировании алюминия в кислотном растворе происходит бурное выделение газов и паров кислот. Уменьшение выделения КОг указывает на снижение концентрации НКОз и необходимость добавления азотной кислоты в ванну. Увеличение содержания в ванне воды или понижение температуры раствора приводят к травлению металла и уменьшению его блеска. Добавка мочевины в кислые растворы несколько уменьшает травление металла. По мере накопления в ванне солей алюминия эффективность полирования снижается. Хорошие результаты достигаются при содержании в растворе до 30—40 г/л алюминия. Качество полирования ухудшается также при наличии примесей в металле. Лучше всего полируется чистый металл. Возможно полирование сплавов алюминия с магнием и марганцем. Алюминиевые сплавы, содержащие медь или цинк, полируются значительно хуже, а на сплавах с высоким содержанием кремния не удается достигнуть блеска.
Электрополирование алюминия. Электролитическое полирование изделий из алюминия и его сплавов получило большое распространение, особенно для изделий, подлежащих оксидированию. Поверхность изделия, отполированная электрохимическим способом, после оксидирования приобретает равномерную, слегка блестящую плотную пленку. [c.34]
В отличие от полирования других металлов и сплавов полирование алюминия в фосфорной кислоте происходит при температуре свыше 80° при этом реакция сопровождается бурным выделением газа. [c.62]
Растворы на основе фосфорной и азотной кислот пригодны для обработки технически чистого алюминия и деформированных сплавов, содержащих магний [29] и марганец (N4). Продолжительность обработки в растворах составляет от 15 сек. до 15 мин. Чистый алюминий после Полирования имеет отражательную способность 87% отражательная способность сплавов несколько ниже. [c.63]
Растворы № 1, 2, 3 используются для обезжиривания черных металлов, № 4, 5 — для меди и ее сплавов, № 6, 7—для алюминия и его сплавов. Полированные изделия рекомендуется обезжиривать в растворах №3,4,6. [c.13]
Чаще всего формы из алюминиевых сплавов применя для изготовления точных полых изделий, волноводов, ела ных бесшовных труб, в которых требуется высокая чист внутренней поверхности. В таких случаях форму готовят алюминия путем обточки или отливки с последующим ш фованием и полированием. Затем наращивают на нее мета и по окончании наращивания растворяют форму в подог той щелочи или соляной кислоте. [c.18]
Полирование химическое деталей из алюминия и его сплавов [c.267]
Полусферическую форму имеют так называемые полированные питтинги. Их внутренняя поверхность блестяща, что свидетельствует об изотропном, не зависящем от структуры, растворении, близком по механизму к электрополировке. Такие питтинги наблюдались на железе, нержавеющих сталях, алюминии, тантале, сплавах на основе никеля, титана, кобальта.
Для электрохимического полирования алюминия и его сплавов используются в основном растворы на основе ортофосфорной кислоты и щелочные фосфатные растворы (табл. 9.8). В кислотных растворах процесс идет при относительно [c.334]
Однако можно подобрать такой состав электролита, что при определенном режиме работы ванны анодный окислительный процесс будет приводить к образованию гладкой, блестящей поверхности металла. Это процесс электрохимического полирования (глянцевание). Таким путем получают зеркальные поверхности у алюминия, меди, хрома, никеля, серебра, стали и ряда других металлов и сплавов. [c.367]
Из применяющихся в машиностроении способов анодной обработки алюминиевых сплавов наиболее полно исследованы электрохимическое полирование и анодирование [178]. Закономерности электрохимической размерной обработки алюминия и его сплавов изучены недостаточно это относится и к технологий процесса, и к механизму анодного растворения при высоких плотностях тока. Наиболее широко представлены данные по обрабатываемости алюминиевых сплавов методом ЭХО в хлоридных и нитратных электролитах [28, 29, 45, 61 ]. Качество обработанной поверхности после ЭХО в хлоридных электролитах, как пра [c.57]
Для химического полирования поверхностей детали из меди, алюминия и их сплавов погружают в смесь ортофосфорной, серной и азотной кислот при 60—100 °С на 1—5 мин. Этот способ прост, но не обеспечивает получения зеркально-блестящей поверхности. [c.139]
Алюминий, цинк и их сплавы после шлифования или полирования 30 5 30 5 4 1 70—80 5—10 [c.14]
Широко применяют в промышленности метод анодирования (особенно алюминия и его сплавов). В основе этого метода также лежит принцип образования плотного окисного слоя при анодной поляризации металла. Анодные окисные слои могут быть окрашены, чем достигается хороший декоративный вид изделий. Электрохимическое полирование также основано на способности металла пассивироваться. [c.67]
Составы щелочных растворов для обработки деталей представлены в табл. 40. Раствор № 1 применяется для деталей из углеродистых сталей и медных сплавов, загрязненных маслами и смазками раствор № 2—для обезжиривания деталей из алюминия и его сплавов, а также для полированных деталей из меди и ее сплавов раствор № 3 — для струйного обезжиривания заготовок печатных плат раствор № 4 — для удаления полировочных паст с деталей из любых металлов, кроме алюминия раствор № 5 — для удаления смазочно-охлаждающих жидкостей для деталей из любых металлов. [c.72]
Химическое полирование цветных металлов гораздо эффективнее, чем черных, и может применяться для обработки деталей из меди, алюминия и прочих металлов. Так, для деталей из меди и ее сплавов можно применять растворы, сведенные для удобства в табл. 106. [c.190]
Качество химического полирования зависит не только от состава ванны, но и от выбора сплава. Алюминиевые сплавы, содержащие цинк и медь, плохо полируются и анодируются. Особенно плохо полируются сплавы алюминия с высоким содержанием кремния. Наилучшие результаты получаются для алюминия высокой чистоты (99,99%). [c.25]
На Московском фурнитурном заводе внедрен в производство способ химического полирования и анодирования насыпью мелких изделий из алюминия и его сплавов (сплав АМГ). [c.26]
Детали из алюминия и его сплавов, литье У5 У10 Тонкое шлифование Отделка Полирование 6—8 5—4 Паста П-7 Подготовка поверхности перед декоративным анодированием [c.104]
Детали из алюминия и его сплавов, штампованные ую Тонкое шлифование Полирование 6—8 Паста П-7 То же [c.104]
ТАБЛИЦА 9. РЕЖИМ РАБОТЫ И СОСТАВ ВЯЗКИХ ЭЛЕКТРОЛИТОВ для ХИМИЧЕСКОГО ПОЛИРОВАНИЯ АЛЮМИНИЯ И ЕГО СПЛАВОВ [c.220]
Температура растворов 1 — 65—75 °С, 2— 100—П0°С, 3 — 95—110 °С, продолжительность полирования 1—5 мин. В растворе 1 обрабатывают технический алюминий и сплавы типа АМг, АМц, в растворе 2 — чистый алюминий, сплавы типа АМгО, 5, в растворе 3 — алюминий и сплавы АК6, АК8, АМгб, АД31. Режим полирования следует уточнять опытным путем, с учетом конфигурации деталей, состояния поверхности и состава сплава, из которого они изготовлены. В растворе 1 достигается относительно хорошее сглаживание шероховатостей поверхности, но декоративный вид несколько хуже, чем после обработки в растворах 2 и 3. [c.79]
Электролиты № 1 и 2 применяются для обезжиривания черных металлов № 2 — для меди и ее сплавов № 3 — для цинка и его сплавов № 4 — для алюминия, сплавов цинка, свинца и кадмия № 5 предлагается для обезжиривания металлов с использованием переменного тока. В более концентрированных растворах обезжиривают сильно загрязненные детали, нижний предел концентрации рекомендуется для обезжиривания полированных деталей. С. А. Вишенков [20] предлагает для электрохимического обезжиривания нержавеющих сталей 1X13 и 1Х18Н9Т (перед нанесением никель-фосфорного покрытия химическим способом) слегк, опескоструенные детали обрабатывать на аноде в 10—] 5-ном растворе едкого натра при анодной плотности тока 5—10 Щдм температуре раствора 60—70°, в течение 5—10 мин. до получения равномерного красно-коричневого налета по всей поверхности детали. После анодной обработки де- [c.17]
Однако можно подобрать такой состав электролита, что при определенном режиме работы ванны анодный окислительный процесс будет приводить к образованию гладкой, блестяш,ей поверхности металла. Это — процесс электрохимического полирования [злек-трополировка). При этом можно добиться удаления даже очень мелких шероховатостей размером менее 0,01 мк (глянцевание). Таким путем получают зеркальные поверхности у алюминия, меди, хрома, никеля, серебра, стали и ряда других металлов и сплавов. [c.342]
В хромоксидном электролите анодируют детали сложной конфигурации с клепаными и сварными соединениями, литейных сплавов с высоким содержанием кремния Оксидные плевки, полученные из этих электролитов, имеют низкую пористость, бесцветные, стекловидные, практически не изменяют размеров деталей, сохраняют блеск полированного алюминия Их тоувдииа от 2 до 5 мкм. [c.230]
Электролиты 2 и 3 используют для анодного оксидирования алюминии и его сплавов АМ1, АМц, АЛ2, АЛ9 В электролите 2 анодируют детали, имеющие малые юпуски с полированной поверхностью В электролите 3 — неполированные детати с большими допусками. Электролит ие пригоден для анодирования сплавов алюминия с содержанием медн >0,5 %. [c.231]
Растворы № 1, 3, 6 используются для обезжиривания черных металлов № 2, 4, 5, 7, 8 — для меди и ее сплавов №2, ), 10—для алюминия и его сплавов. Раствор № 5 сравнительно более универсален, в нем обезжириваются детали из черных и цветных металлов. Для очист] и полированных деталей рекомендуется использовать растворы № 6, 8, 10 остатки полировальных паст иа стальных деталях лучше отмываются в растворе № 6. Растворы Аг 3, 4, 5 применяют для обработки сильно загрязненных деталей раствор Л 4 — для обезжиривания деталей из медн. ее сплавов, а также детален с серебряными покрытиями, изгоюв-лепными с применением пайки припоями типа ПОС. [c.67]
Растворы № I, 3, 6 используются для обезжиривания черных металлов № 2, 4, 5, 7, 8 — для меди и ее сплавов №2,9, 10—для алюминия и его сплавов. Раствор № 5 сравнительно более универсален, в нем обезжириваются детали из черных н цветных металлов. Для очистки полированных детален рекомендуется использовать растворы Л 6, 8, 10 остати полировальных паст на стальных деталях лучше отмываются в растворе № 6. Растворы Лз 3, 4, 5 применяют для обработки сильно загрязненных деталей раствор [c.67]
К механическим способам относятся щлифование, полирование, струйная обработка (песко-, гидро- и дробеструйная). Мягкие металлы — алюминий и его сплавы, латуни Подвергают гидропеокоструйной обработке, более твердые стальные поверхности — песко- или дробеструйной. [c.192]
Эта реакция неизбежно сопровождает процессы углевосстановительного получения сплавов с высоким содержанием алюминия АЬОС существует в гексагональной форме с параметрами решетки а=0,3119 и с=0,4994 нм, в полированном шлифе имеет белую или светло-голубую окраску с микротвердостью 15690—16670 МПа. [c.228]
Механическое полирование представляет собой процесс, принципиально мало отличающийся от шлифования и, по существу, является дальнейшим сглаживанием неровностей на поверхности металла более тонким абразивным материалом.. Полирование производят на сукне, фетре или бархате до полного удаления рисок, остающихся от шлифования. Во время полирования на полировальный материал непрерывно или периодически наносят суспензию воды с тонкоразмельченными абразивными веществами (окись алюминия, окись железа, окись хрома, окись магния и др.). При полировании мягких металлов (алюминий, магний, олово и их сплавы) на тонкую шлифовальную бумагу наносят слой парафина или раствор парафина в керосине. Механический способ полирования достаточно прост, поэтому широко распространен, однако имеет свои недостатки [46] трудность и длительность, значительный расход полировочного сукна, появление на шлифовальной поверхности (так же как и при шлифовании) деформированного наклепанного слоя, искажающего истинную структуру металла. Последнее нежелательно при микроэлектрохимических исследованиях, при испытании металлов на устойчивость к коррозионному растрескиванию и коррозионноусталостную прочность, при которых увеличение внутренних напряжений в поверхностных слоях металла может отразиться на результатах испытаний. Для удаления внутренних напряжений, связанных с шлифованием и механическим полированием, применяют термообработку, например отпуск при определенной температуре [49], ° С [c.53]
С целью повышения локальности микроспектрального анализа было разработано достаточное число специальных методов и приборов. С шнуровым разрядом от выпрямленной высоковольтной искры (разд. 2.8.5 в [20а]) и при использовании игольчатых электродов из серебра, алюминия или меди можно получать кратеры обыскривания диаметром 0,1—0,2 мм и глубиной 0,01 — 0,02 мм. Этим способом можно непосредственно анализировать большие включения в полированных образцах, а также изучать однородность сплавов [2—5]. Если полированный образец медленно перемещать (со скоростью в несколько миллиметров в секунду) по отношению к неподвижному противоэлектроду и одновременно непрерывно передвигать кассету спектрографа, то можно получать спектры по методике движущаяся проба — движущаяся фотопластинка и, таким образом, следить за изменением концентрации компонентов вдоль трека искры [6—8]. На основании диаграмм, построенных по результатам фотометрирования, и оценки концентрации элементов для отдельных участков спектра движущаяся проба — движущаяся фотопластинка (рис. 3.18) можно сделать выводы о локальных обогащениях и составе включений, наблюдаемых на полированной пробе и находящихся вдоль трека искры. Однако из-за малого объема паров образца в мик- [c.112]
Жировая и маршалитовая пасты применяются для окончательного шлифования крокусная — для полирования меди и ее сплавов, серебра известковая—для полирования никеля, латуни, алюминия, серебра и других металлов хромовая — для полирования хрома, нержавеющей стали и других металлов и покрытий алюминиевая и хромокрокусная — для полирования медных и никелевых покрытий. [c.69]
Из указанных электролит № 1 рекомендуется для полирования углеродистых и низколегированных сталей электролит №2 —для коррозионно-стойких марок стали (может быть пригоден также для алюминия и его сплавов) электролит №3—для сталей типа 12Х18Н9Т. В качестве катодов может быть использован рольный свинец марки ССУ1 с содержанием 4—6% сурьмы, которая придает ему более высокую твердость. Пригодна для этой цели и сталь марки 08Х18Н10Т. [c.195]
Электрополирование алюминия. Алюминий и его сплавы можно электрополировать в щелочных, фосфатных и борфтористоводородных электролитах, однако наибольшее применение для этой цели нашли сернофосфорнохромовокислые электролиты. При полировании в этих электролитах поверхность приобретает блеск высокой степени и увеличивается ее стойкость против коррозии. Эти электролиты не сложны по составу и легко корректируются. [c.153]
Изделия из алюминия и его сплавов обрабатывают в смеси ортофосфорной кислоты (500—1100 г/л), хромового ангидрида (30—80 г/л), серной кислоты (250— 500 г/л плотность раствора 1,63—1,72 г/см ). Медь и ее сплавы полируют в растворе ортофосфорной кислоты (850—900 г/л) с добавлением хромового ангидрида (100—150 г/л плотность раствора 1,60—1,61 г/см ). В качестве материалов для катодов используются сталь марки 12Х18Н9Т, алюминий и свинец. Эффект сглаживания поверхности при электрохимическом полировании обусловлен тем, что скорость травления металла на микровыступах больше по сравнению с микроуглублениями вследствие различных условий пассивирования поверхности в растворах. В микроуглублениях образуется пассивная, более толстая и устойчивая пленка, которая растворяется медленнее, чем на микровыступах. [c.162]
Весьма подробно освещены составы растворов, протекающие реакции и оптимальные режимы при химическом и электрохимическом полировании алюминия и его сплавов, железа и стали, меди и медных сплавов. Растворы классифицируются по их вязкости, ско рости съема металла и степени сглаживания поверхности. Помимо составов растворов и их режимов, для химического и элбктрохимическото полирования приведены различные теории, предложенные для объяснения механизма протекающих процессов. [c.6]
Из перечисленных в табл. 1 составов электролитов в Германии наибольшее распространение получил состав Алюполь IV. Он применяется главным образом для глянцевания алюминия чистотой не менее 99,9%- На этих сортах достигается эффект глянцевания, часто превышающий эффект, получаемый при использовании состава Алюполь II. Для глянцевания сплавов с содержанием кремния свыше 2% она менее подходит. При приготовлении этой ванны необходимо требуемое количество борной кислоты растворить при комнатной температуре в отмеренном количестве концентрированной серной кислоты и только после этого добавить к фосфорной кислоте серную кислоту с содержащейся в ней борной кислотой. Часть рекомендуемой карб-оксиметилцеллюлозы (СМС) следует добавлять только в недавно приготовленные ванны, чтобы смягчить сильную вначале реакцию полирования. [c.222]
chem21.info
Полировка алюминия. Виды полировки.
Алюминий относится к цветным металлам, и представляет мягкий, устойчивый к коррозии металл, широкоиспользующийся не только в строительной сфере, но и в других областях.
Наряду с положительными свойствами алюминия, у него есть и недостатки, один из которых потеря декоративными изделиями товарного вида в связи с окислением.
Выходом из данной ситуации является полировка алюминия.
Можно выделить три вида данной процедуры:
— химическая полировка;
— электрополировка;
— декоративное травление.
Давайте рассмотрим каждый из этих способов в отдельности.
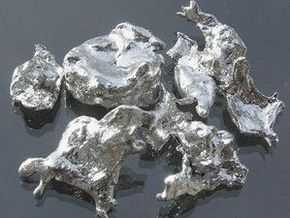
Химическая полировка
Данный способ полировки является быстрым и достаточно экономичным. Данный способ, как правило, используют для полировки мелких деталей из алюминия.
Процесс химической полировки представляет собой процесс воздействия на алюминий специальных химических веществ.
Выглядит это так, в специальную полировочную ванну (из кислотоустойчивой стали) где находится специальный раствор кислот (серная, азотная, ортофосфорная) и некоторые добавки, опускают алюминиевую деталь. При этом температура раствора составляет от 90 до 120 градусов. Опускание делателей производится на 5-6 секунд, в течении полуминуты.
Следующим этапом является промывка детали в специальном сборнике-улавливателе.
Для повышения качества полировки обработанную деталь помещают в специальный вращающейся барабан, где они дополнительно подвергаются обработке раствором с большей степенью предварительного использования.
После этого на изделии остаётся плёнка контактной меди, для снятия которой алюминиевое изделие промывается под проточной водой (вода должна быть низкой температуры) и обрабатывают 30% азотной кислотой.
Кроме этого для химического полирования изделий из алюминия используют различные растворы щелочей (каустическая сода, нитрат натрия, натриевая селитра, тринатрийфосфат), при этом их температура должна быть более высокой, нежели у растворов кислот и составляет 120-140 градусов.
Естественно при использовании химического способа полировки, как и в других способах, наблюдаются потери алюминия. В данном случае они составляют 7-8 мкм. от слоя.
Электрополировка
Кроме химической полировки достаточно распространена электрополировка.
Электрополировка представляет собой полировку алюминия высокого качества с помощью электричества, с использованием ортофосфорной и серной кислоты, температура кислоты гораздо ниже, нежели при химической полировке (60-90%). Процесс занимает 3-5 минут, при этом используется электрический ток в 10-50 А/дм².
Кроме кислоты и тока в процессе полировки используют свинцовые катоды, дюралевые подвески и электролитные ванны с обработкой фторопластом, а так же свинцовой и полиэтиленовой обработкой.
Наряду с этим зачастую используют щелочные электролиты, которые дешевле и проще, но процесс выглядит немного иначе.
Декоративное травление
Декоративное травление представляет собой анодное травление в фосфорно-хромовом электролите и по своей сути является электрической полировкой.
При этом на алюминии образуется кристаллический рисунок, который напоминает изморозь.
Процесс декоративного травления выглядит следующим образом, детали, завешенные на анодную штангу обрабатывают под напряжением 25-30 В постепенно поднимая до 35-40 В.
В начальной стадии плотность тока будет составлять — 8-12 А/дм², а температура – 70-80°C. Как правило, появление рисунка на алюминиевой поверхности начинает появляться через 15-20 минут.
После того, как напряжение в самопроизвольном порядке начинает подниматься, это означает, что процесс декоративного травления закончен. Теперь изделие необходимо промыть, просушить произвести анодное оксидирование (или лакировку), после чего произвести покраску (органической краской).
Кроме промышленной полировки алюминиевых изделий существуют и способы полировки в ручном режиме, на дому:
Читайте так же:
Винт установочный.
Наплавка, применение, виды наплавки
Газы и пыли пирометаллургических процессов, виды металлургических пылей и газов
www.junona-2.ru
Химическое полирование позволяет быстро и качественно обработать поверхности металлических деталей. Большое преимущество такой технологии заключается в том, что с помощью ее (и только ее!) удается отполировать в домашних условиях детали со сложным профилем. Составы растворов для химического полирования Для углеродистых сталей (содержание компонентов указывается в каждом конкретном случае в тех или иных единицах (г/л, процентах, частях)
Для нержавеющей стали
Последний состав применим для полирования чугуна и любых сталей. Для меди
Внимание! В растворы хлористый натрий вводят в последнюю очередь, причем раствор должен быть предварительно охлажден!
Для латуни
Для бронзы
Для никеля и его сплавов (мельхиора и нейзильбера)
Для алюминия и его сплавов
Автор: Л.А. Ерлыкин Читайте еще: |
www.sdelaysam.info
Промышленные методы электрохимического и химического полирования металлов
Электрохимический и химический методы полирования в настоящее время наиболее широко применяют для обработки поверхности изделий, изготовленных из алюминия и его сплавов. Это объясняется широким применением алюминия в электротехнической, машиностроительной и приборостроительной промышленности. В ряде случаев полированный электрохимическим или химическим способом алюминий подвергается последующему анодированию и окрашиванию, в результате чего поверхность изделий приобретает красивый (декоративный) вид. Электрополированный алюминий высокой чистоты имеет высокий коэффициент отражения света в весьма большом диапазоне как в красном, так и в ультрафиолетовом спектре.
Для электролитического полирования алюминия различают три основных процесса: Бриталь-процесс, разработанный в Англии, Альзак- и Баттель-процессы, разработанные в США. Во всех этих процессах съем металла весьма незначителен и правильнее называть их процессами глянцевания. Процессы электрополирования сопровождаются образованием на поверхности тонкой окисной пленки, которой, однако, недостаточно для защиты от коррозии основного металла, а также для сохранения оптических показателей электрополированной поверхности. Поэтому изделия подвергают дополнительному кратковременному анодированию, в результате чего коэффициент отражения света несколько снижается, но остается практически постоянным; кроме того, искусственно полученная окисная пленка является хорошим адсорбентом органических красителей и электрополированные изделия можно окрашивать в красивые тона (рис. 9).
Рис. 9. Влияние анодирования электрополированного алюминия на коэффициент отражения света:
1 — зеркальное отражение; 2 — диффузное отражение
Бриталь-процесс предусматривает электрополировку алюминия высокой чистоты в растворе, содержащем 15—30% (по массе) безводного Na2CO3 и 5—10% Na3PO4. Процесс протекает при температуре 80—90° С и плотности тока 5—6 А/дм2.
В Альзак-процессе основным компонентом является борофтористоводородная кислота (2,5%-ная HBF4).
Напряжение поддерживается в пределах 10—25 В, плотность тока 2—6 А/дм2, температура около 30° С, продолжительность процесса 5—10 мин. Для охлаждения электролита в процессе полирования через медный змеевик, который может быть одновременно использован в качестве катода, пропускают холодную воду.
Баттель-процесс применим для электролитического полирования технического алюминия и деформированных сплавов на его основе, типа дюралюминия, АМГ, АМЦ и др. Постоянным компонентом электролитов служит ортофосфорная кислота; помимо нее, присутствуют серная, хромовая или азотная кислоты в различных соотношениях. В отличие от щелочных электролитов рекомендуется перемешивание путем движения анодных штанг. В табл. 9 приведены типичные составы электролитов, режимы.
Хромовая кислота пассивирует поверхность полируемых изделий и предупреждает их разъедание в момент выключения тока. Серная кислота повышает электропроводность раствора и предупреждает образование питтинга.
Для электролитического полирования алюминия применяют электролиты, содержащие фосфорную кислоту и другие компоненты, а также смесь хлорной кислоты с уксусным ангидридом.
В литературе приводятся также электролиты для химического полирования алюминия и его сплавов. Американская алюминиевая компания (AlCoA) предложила раствор состава, % (объемн):
H3РO4 (плотность 1,7) . . 73—83
HNO3 (плотность 1,52) . . 2—5
H2O……… 14-23
При температуре 90° С время выдержки в пределах 1—5 мин. В настоящее время лучшими растворами для химического полирования алюминия считаются алюполь IV и алюполь V. Ниже приводятся составы этих растворов, % (по массе):
К раствору алюполь V в качестве смачивающего вещества добавляют 0,05% (по массе) карбоксилметил-целлюлозы. Процесс протекания при температуре 100° С в течение 1—4 мин. Съем металла составляет 3,75 мкм/мин.
В ФРГ большое применение получил способ «Эрфт-верк».
Ниже приводится состав раствора, % (по массе) и его режим:
HNO3….. 13—14 Температура, °С . 55—75
NH4HF2 …. 16 Выдержка, с . . 15—20
Pb(NO3)2 ….0,02 Съем металла, мкм 2,5—5
В этом растворе хорошо полируется алюминий высокой чистоты и сплавы типа АМГ (коэффициент отражения ~90%). Полирующий эффект резко снижается после обработки 167 дм2 поверхности в 3,8 л электролита; после добавления 4 г HF на каждые 10 дм2 обработанной поверхности восстанавливаются прежние показатели.
Второе место после алюминия и его сплавов в области электрополировки занимают стали, в особенности высоколегированные. Коррозионная стойкость электрополированной стали в результате дополнительной пассивации повышается. Изделия из стали типа нержавеющей, да еще сложной формы, механически трудно полируются.
Одним из главных компонентов электролита для полирования стальных изделий является ортофосфорная кислота, которая в сочетании с серной кислотой часто дает надлежащий эффект. Стали некоторых марок можно электролитически полировать в одной серной кислоте, но для этого плотность тока необходимо повысить до 250 А/дм2, что связано с большими затруднениями эксплуатационного характера, да и результаты получаются невоспроизводимыми. То же можно сказать относительно применения одной фосфорной кислоты. При смешивании одна кислота оказывает благоприятное влияние на другую, что сокращает продолжительность полировки, понижает необходимую плотность тока и расширяет номенклатуру марок сталей, поддающихся эффективной полировке. Кстати, можно отметить, что в смеси фосфорной и серной кислот эффективно полируются не только стали, но и ряд металлов и сплавов, трудно полируемых механически. Концентрация серной кислоты в зависимости от состава стали (или другого сплава) может колебаться от 15 до 60% (по массе), концентрация фосфорной кислоты — соответственно от 70 до 30% (по массе), содержание воды около 10%. Иногда вводят ангидрид хромовой кислоты, который благоприятно сказывается на течении процесса.
Повышенное содержание фосфорной кислоты позволяет понизить плотность тока и напряжение, повышение содержания серной кислоты позволяет расширить допустимые пределы изменения плотности и тока. Наиболее широкий рабочий интервал соответствует смеси, состоящей из 16—40% H2SO4 и 44—67% H3РO4. При содержании в электролите 63—67% (по массе) фосфорной кислоты минимальная плотность тока для стали 18—8 равна 7—12,5 А/дм2. Рекомендуется поддерживать плотность тока в пределах 10—50 А/дм2 и температуру 45— 65° С. С изменением основных легирующих компонентов должен быть изменен и режим.
Существенным недостатком электролитов, приготовленных на основе фосфорной и серной кислот, является их ограниченный срок службы. Электролиты выходят из строя по мере накопления в них продуктов анодного растворения, связывающих кислоты в соли, в то время как на катодах в сильно кислой среде разряжаются ионы гидроксония. Сульфаты железа и никеля не растворяются в таких количествах, которые могут отрицательно сказываться на результатах электролитической полировки, но растворимость их повышается в присутствии хромовой кислоты, наличие которой в электролите не зависит от того, вводился хромовый ангидрид или не вводился, так как при электрополировке нержавеющей стали хром растворяется в виде шестивалентных ионов.
Шестивалентные ионы хрома восстанавливаются на катодах до трехвалентных, а на анодах (полируемых изделиях) вновь окисляются до шестивалентных. Вредное влияние оказывает трехвалентный хром, который при содержании в электролите в количестве 2% нарушает нормальное течение процесса. Рассчитать точно поверхность, которую можно обработать до выхода электролита из строя, нельзя, так как состояние исходной поверхности не всегда одинаково.
Хорошие результаты дает электролит примерного состава: 70% H3РО4. 12% H2SO4, 9% CrO3 и 9% H2O; температура 70—90° С, плотность тока 15—20 А/дм2 и выше. Этот электролит можно применять для широкой номенклатуры сталей как легированных, так и углеродистых.
Электролиты, содержащие в качестве компонента глицерин, можно успешно применять для электролитической полировки нержавеющей стали и других сплавов. Глицерин оказывает положительное влияние в смеси с фосфорной кислотой, с серной или смесью обеих кислот, а также с фтористоводородной кислотой. Лучшие результаты получаются при электролитической полировке нержавеющей стали 18—8 в смеси фосфорной кислоты с глицерином. Преимущества таких электролитов сводятся к следующему: 1) можно получить поверхность с высоким коэффициентом отражения света при сравнительно низкой плотности тока; 2) полированная поверхность получается при небольшом съеме металла; 3) точечное разъедание наблюдается редко. При хорошо подготовленной предварительно механическим путем поверхности в результате последующей электрополировки можно получить поверхность с хорошим зеркальным отражением.
На рис. 10 показано влияние на отражение света нержавеющей стали концентрации 85%-ной H3РO4 (плотности 1,71) в 96%-ном глицерине (плотности 1,25) при анодной плотности тока 7,8 А/дм2, температуре 100° С и продолжительности обработки 15 мин. Лучшие показания (93% зеркального отражения) получаются при концентрации фосфорной кислоты 35—45% (объемн.)
Рис. 10. Влияние концентрации 85%-ной H3РO4, (плотность 1,71) в 96%-ном глицерине (плотность 1,25) при анодной плотности тока 7,8 А/дм2, температуре 100° С на коэффициент зеркального отражения света нержавеющей стали
В Японии применяют в промышленности электролиты, в которых главным компонентом является фосфорная кислота, а процесс протекает при комнатной температуре и переменном токе. Так, для полирования изделий из углеродистой стали применяют следующий состав электролита и режим процесса:
при
H3РO4 (плотность 1,7), мл….. 1000
Желатина, г………. 10
H2C2O4, г……….. 40
H6C4O6 г………… 15
Температура, °С……… 20
Плотность переменного тока, А/дм2 . 8
Для полирования пружинной стали состав электролита и режим процесса следующие:
H3РO4 (плотность 1,7), мл . . . . . 1000
Желатина, г……….. 1
Температура, °С . . . …… 20
Плотность переменного тока, А/дм2 . . 10—20
Напряжение, В………. 15
При электролитическом полировании быстрорежущей стали встречаются затруднения, поскольку она содержит такие элементы, как вольфрам, который растворяется в щелочах, и кобальт, растворяющийся в кислотах. Для этой цели используют постоянный ток высокой плотности. Главным компонентом таких электролитов является азотная кислота. Помимо нее, вводят фтористоводородную, щавелевую, хромовую, серную кислоты, а также соли железа, никеля, кобальта. Ниже приводится состав (мл) одного из таких электролитов и режим:
HNO3 …. 1000
HF….. 100—360
H2C2O4 . . . 20—40
H2O….. 600
Плотность тока, А/дм2. . . 140—160
Напряжение, В 6
Температура, °С……….20—50
Время, с . . . 10—30
Коррозионная стойкость аустенитных хромоникелевых и хромистых сталей повышается в результате электрополировки. Электронографически установлено, что в результате селективного растворения на поверхности хромоникелевой стали образуется пленка NiO·Cr2O3, а на поверхности хромистой стали FeO·Cr2O3. Эти пленки и повышают сопротивление коррозии полируемых изделий.
Турбинные лопатки изготовляют из жаропрочной хромомарганцовистой стали. Электролитическая полировка повышает их механические и химические свойства. Процесс осуществляется при следующем режиме и составе электролита.
H2SO4, мл … 300
H3РO4, мл . . . 700
CrO3, г/л …. 50—100
Температура, °С . 100
Плотность постоянного тока, А/дм2 10—50
Время, мин . . . 2—6
Химическое полирование стальных изделий не применяется столь широко, как электрохимическое, однако для изделий малых размеров и сложной формы этот метод имеет определенные преимущества.
Для изделий из низкоуглеродистой стали предложен электролит следующего состава, г/л:
H2O2 (30%-ная) . . 13
H2C2O4·2H2O … 25
H2SO4 … 0,1
Температура процесса 20° С, продолжительность 30—60 мин.
За 1 ч снимается слой металла около 10 мкм. Эффект выравнивания поверхности тем больше, чем грубее исходная поверхность.
В Японии для химического полирования углеродистых сталей применяют электролит состава (объемных частей):
H3РO4 ….400
H2SO4 ….200—600
HNO3 …. 100—200
HCl …. 25
Продолжительность процесса зависит от температуры следующим образом:
Температура, °С . 80 100 120
Продолжительность процесса, с . 60 30 10
С повышением температуры улучшается блеск и повышается интенсивность выделения окислов азота. Чем выше содержание углерода в стали, тем меньше воды должно быть в полируемом растворе и выше температура.
Химическое полирование мелких деталей в оптической и часовой промышленности успешно осуществляется в обезвоженной H3РO4. Для этого ее длительно нагревают при температуре 250° С так, что она частично переходит в пирофосфорную кислоту. Реакция длится около 1,5 ч, конец ее узнается по прекращению выделения водорода. После охлаждения добавляют около 10% H2SO4. Точное соотношение кислот выбирают в зависимости от содержания углерода в полируемых деталях — чем оно больше, тем меньше должно быть содержание серной кислоты. Процесс протекает при 200° С и длится от нескольких секунд до нескольких минут. Выгруженные детали тщательно промывают в слабощелочном растворе. Оптимальный полирующий эффект наблюдается при содержании в стали 0,6% С, т. е. при чисто перлитной структуре. В дегидратированной смеси фосфорной и серной кислот можно химически полировать также хромистую сталь (13% Cr) и хромоникелевую сталь (18% Cr, 8% №).
Хотя основные закономерности электролитического полирования металлов были установлены на основе анодного поведения меди в растворах ортофосфорной кислоты и первые промышленные установки были рассчитаны на обработку изделий из меди и ее сплавов, в настоящее время этот процесс находит ограниченное применение. В значительной степени это объясняется тем, что для неответственных целей изделия из меди и медных сплавов быстро подвергают травящей полировке (химической) в смеси серной и азотной кислот в присутствии небольших количеств соляной кислоты. В ответственных случаях медные изделия анодно полируют в концентрированной фосфорной кислоте.
Начиная с пятидесятых годов, промышленное применение получил запатентованный в США способ химического полирования меди и латуни в растворе состава, % (объемн.):
H3РO4 (плотность 1,75) … 65
СH3СООН (ледяная) …. 20
HNO3 (плотность 1,42) … 15
Главный недостаток этого электролита, в котором процесс протекает при температуре 60—70° С, заключается в большом съеме металла (25—40 мкм), а также в выделении вредных газов и в ограниченном сроке службы — явлении, характерном для всех электролитов, содержащих уксусную кислоту и работающих при повышенных температурах.
Хорошие результаты получаются при химическом полировании медных или латунных изделий в растворе состава, мл:
H3РO4 (плотность 1,7) . . 550
СНзСООН (ледяная) … 250
HNO3 (плотность 1,4) . . . 200
Тиомочевина, г…..0,2
при комнатной температуре в течение 2—6 мин.
Рекомендуется покачивание обрабатываемых изделий.
Электролитическое полирование никеля успешно осуществляется в растворах серной кислоты (плотность 1,6) при температуре 35° С, плотность тока 40 А/дм2 и продолжительности 3—5 с. Применительно к никелированным изделиям процесс не получил промышленного применения из-за возможности оголения основного металла в углублениях, где толщина покрытия меньше средней и из-за выявления различного рода дефектов, которые при механической полировке «замазываются».
Серебряные и серебренные изделия можно электрополировать в цианистом электролите для серебрения при анодной плотности тока 2—3 А/дм2. Рекомендуется прерывать ток (через 3—4 с), чтобы дать возможность раствориться образующейся пленке AgCN и вновь образоваться. При электрополировке серебренных изделий удобнее поступать следующим образом. После окончания процесса серебрения изделия в той же ванне включают в качестве анодов, а штангу с серебряными анодами соединяют с отрицательным полюсом. Ток прерывают через 3—4 с; анодная плотность тока должна быть в 4— 5 раз больше, чем в процессе серебрения. Общая продолжительность такой обработки составляет 1—3 мин.
Золото можно электрополировать в растворе состава, г/: 67,5—KCN; 15—KNaC4H4O6·4H2O; 18,5—H3РO4; 0,9 NH4OH, температура до 60° С; напряжение на ванне 5—10 В, катоды — медные. Необходимо сильное перемешивание электролита.
Другой электролит для электрополировки золота имеет состав, г/л: 10СH3СООН; 3H2SO4; 25C6H5NH2S, температура процесса 25—45° С, плотность тока 1,5—3,5 А/дм2.
www.stroitelstvo-new.ru
Электрохимическое полирование — Химическая обработка
Электрохимическое полирование
Категория:
Химическая обработка
Электрохимическое полирование
Электрохимическое полирование представляет собой процесс, обратный гальваническому осаждению металлов: обрабатываемую деталь помещают в качестве анода в ванну с электролитом и при заданном режиме (плотности тока, температуре и времени погружения) осуществляют съем металла. Процесс анодного растворения используют в операциях очистки поверхности металла, удаления заусенцев и грата, заострения, полирования.
Наибольший интерес представляет электрохимическое полирование. Такое полирование наиболее широко распространено в промышленности, но оно весьма трудоемко, плохо поддается механизации и автоматизации. Этим процессом определяются такие важнейшие критерии качества поверхностного слоя, как макро- и микрогеометрия, наклеп, микроструктура, остаточные напряжения. В прямой зависимости от этих критериев находятся эксплуатационные свойства деталей машин и механизмов — усталостная прочность, отражательная, теплоизлучающая и теплопоглощающая способность, обтекаемость жидкостями и газами, коррозийная стойкость.
Полирование определяет также эстетику изделия.
Сущность процесса
Электрохимическое полирование основано на анодном растворении обрабатываемой поверхности при режимах, которые обеспечивают интенсивное растворение микровыступов шероховатой поверхности и замедленное растворение во впадинах. В результате неравномерной скорости растворения шероховатая поверхность сглаживается, и появляется заметный блеск.
Только в случае преимущественного растворения микровыступов на поверхности металла происходит полирование (сглаживание).
Преимущественное растворение микровыступов может происходить тогда, когда у поверхности металла в результате электролиза образуется пленка низкой электропроводности, состоящая из продуктов анодного растворения.
Рис. 1. Схема образования вязкой пленки:
а — впадины; б — вязкая пленка; в — выступы; г — силовые линии тока.
В этом случае толщина пленки, а следовательно, и электрическое сопротивление ее в микровпадинах будут больше, чем на выступах, что и приведет к более интенсивному растворению выступов.
Растворимость анодных продуктов в электролите, скорость диффузии их в электролит, состав и физико-химические свойства анодной пленки имеют существенное значение для процесса полирования. Поэтому этот процесс у различных материалов происходит неодинаково. У многих металлов и сплавов (медь, никель, алюминий, нержавеющие хромистые и хромоникелевые стали) сглаживание сопровождается появлением блеска на обработанной поверхности. У некоторых сплавов (стали карбидного класса, бронзы, латуни) наблюдается блеск без заметного сглаживания шероховатостей. Ряд металлов и сплавов (олово, свинец, серый чугун, высококремнистые стали) вовсе не полируется. Вместо сглаживания образуется’ сильно травленая поверхность с толстыми темными пленками.
Существует несколько гипотез, по-разному объясняющих процесс электрохимического полирования, причем следует отметить, что ни одна из них не объясняет полностью все данные опыта. Наиболее вероятной и логически объясняющей сущность процесса является гипотеза вязкой пленки. Согласно этой гипотезе, электрохимическое полирование может происходить лишь при образовании на поверхности анода в процессе анодного растворения вязкой пленки.
Вязкая пленка состоит из продуктов анодного растворения, обладающих высоким электрическим сопротивлением. Покрывая тонким слоем шероховатую поверхность полируемого металла, эта пленка приобретает неодинаковую толщину на различных участках поверхности. На выступах толщина пленки и соответственно ей критическое сопротивление меньше, чем во впадинах.
Вследствие различного сопротивления пленки и способности электрического тока концентрироваться на остриях плотность тока на выступах будет больше, чем во впадинах. Поэтому скорость растворения вершин выступов будет больше скорости растворения дна впадин. В результате неравномерного распределения плотности тока и вследствие этого различной скорости растворения возникает сглаживание шероховатой поверхности.
Достоинства и недостатки электрохимического полирования
Электрохимическое полирование металлов имеет свои достоинства и недостатки. Главное достоинство метода — высокая производительность. Время полирования практически составляет не более 10 мин., причем габариты детали и форма ее не влияют на производительность. Возможна одновременная обработка такого количества деталей, какое помещается в ванне. Производительность процесса не зависит от твердости и вязкости обрабатываемого материала. Электрохимическое полирование позволяет обрабатывать детали не только простых очертаний, но и сложного профиля, а также внутренние полости, трудно доступные или вовсе не доступные при механическом полировании.
Основное отличие электрохимически полированной поверхности от механически полированной — отсутствие на ней каких-либо следов деформации и структурных изменений. Это — естественное следствие сущности электрохимического процесса, который осуществляется не только без приложения каких бы то ни было механических усилий к обрабатываемой поверхности, но и вовсе без физического прикосновения к ней.
Больше того, электрохимическое полирование удаляет механически деформированный поверхностный слой металла и восстанавливает его истинное строение. В результате анодного растворения поверхность оказывается свободной от механических и термических изменений. Улучшается микрогеометрия; блеск поверхности оказывается больший, чем у механически полированной.
Электрохимическое полирование выявляет дефекты в металле (неметаллические включения, трещины, волосовины, неоднородность структуры).
Поверхности, электрохимически полированные, пассивируются и благодаря этому в 4—6 раз лучше сопротивляются коррозии; они обладают повышенными оптическими свойствами.
Процесс не требует применения полировальных станков, фетровых кругов, абразивных порошков, паст. Возможны автоматизация обработки и одновременное обслуживание нескольких ванн. Значительно облегчаются и оздоровляются условия труда.
Перечисленные достоинства характеризуют несомненное превосходство электрохимического метода над механическим. Однако на нынешней ступени развития этому методу присущи и серьезные недостатки, которые ограничивают применение электрохимического полирования.
Один из основных недостатков — незначительная эффективность сглаживания. Электрохимическим полированием можно улучшить чистоту поверхности на 1—2 класса, причем оно эффективно, если исходная шероховатость не грубее 4—5-го классов. Поэтому при необходимости достигнуть 12—13-го классов приходится механически подготовлять поверхности до 10—11-го классов. Грубо обработанная поверхность (после точения, фрезерования, шлифования), подвергнутая электрохимическому полированию, почти сохраняет макрорельеф поверхности. Сглаживаются полностью лишь отдельные микровыступы и наблюдается закругление гребешков.
Попытки многих исследователей повысить эффективность сглаживания и, по существу, решить задачу электрохимического шлифования практически не привели к положительным результатам. Повышение эффективности сглаживания требует прежде всего применения высоких плотностей тока (более 100 а/см2), что, в свою очередь, приводит к растворению больших толщин металла (0,5—1 мм).
Необходимое время полирования обычно определяется опытным путем и находится, как правило, в пределах 8—10 мин. при полировании сталей. Увеличение производительности полирования сверх 10 мин. не только не ведет к улучшению качества поверхности, но часто, наоборот, ухудшает ее.
Сглаживание следов механической обработки происходит постепенно: после первых 3—4 мин. электрохимического полирования наблюдается уничтожение мелких рисок и появление гладких полированных площадок; после 10 мин. на поверхности остается рельеф грубых рисок, которые в дальнейшем полностью не исчезают, а лишь закругляются, образуя волнистую поверхность. Мы проводили исследования сглаживания при изменении времени полирования от 2 до 20 мин.
Увеличение времени полирования приводит к еще большему растворению металла. Кроме того, оно может вызвать в сплавах вытравливание отдельных структурных составляющих.
Данные этой таблицы показывают, что при возрастании времени полирования шероховатость поверхности улучшается. Однако, начиная с 10 мин. выдержки, улучшение это незначительно, и через 15 и 20 мин. сглаживание наших образцов (сталь У10 закаленная) происходило примерно с одинаковой эффективностью. К этому следует добавить, что значительная эффективность сглаживания сопровождается большим съемом металла. В процессе полирования за 10 мин. растворяется слой металла толщиной 60—100 мк.
Это резко искажает форму и размеры деталей, подвергаемых полированию, и превосходит припуски, оставляемые обычно на полирование.
Кроме того, интенсивное растворение металла приводит к накоплению в электролите большого количества железа (Ре20з). При накоплении Fe203 в количестве 6% к весу электролита полирование становится невозможным.
Так, например, ванна емкостью 10 л при полировании деталей с поверхностью 0,5 дм2 способна практически работать 4—6 суток. Затем железо должно быть удалено из раствора или электролит следует заменить вновь приготовленным.
Однако еще задолго до полного насыщения электролита железом состав электролита в процессе эксплуатации изменяется. Контроль его производят ежедневно, определяя удельный вес, и соответственно корректируют. Убыль воды в результате испарения восполняют довольно частым добавлением горячей воды.
Помимо контроля удельного веса электролита необходимо периодически осуществлять анализ на содержание Сг03, Cr203, h3S04, Н3РО4 и Fe203 и корректировать состав электролита.
При накоплении в электролите 1,5% Сг20з производят под действием тока окисление трехвалентного хрома в шестивалентный, а после окисления электролит прогревают в течение часа при 90—110 °С.
Анализ и корректировка кислот и удаление железа из электролита являются еще более затруднительными операциями. Таким образом, сложность корректировки состава электролита и, в конечном счете, короткий срок службы электролита являются еще одним весьма существенным недостатком электрохимического полирования. Расчеты показывают, что в результате непродолжительного действия электролита и, следовательно, большого удельного расхода кислот электрохимическое полирование в ряде случаев оказывается экономически нерентабельным.
Рис. 2. Зависимость съема металла от времени полирования (углеродистые стали).
Оборудование для электрохимического полирования
Оборудование, предназначенное для осуществления процесса электрохимического полирования, весьма сходно по конструкции с оборудованием, имеющимся в цехах металлопокрытий для операции хромирования.
Основным оборудованием являются ванны, источники постоянного тока низкого напряжения и приборы для измерения и регулирования электрического режима.
Ванны.
Ванны должны быть снабжены электронагревателями, помещенными в защитных, химически стойких, оболочках внутри самой ванны, и водяной рубашкой. Применение двойного нагрева необходимо потому, что при приготовлении и проработке электролита приходится нагревать его до 110—120°С, а в процессе полирования необходимо поддерживать температуру 70—80 °С. Применение водяной рубашки исключает возможность перегрева электролита. Кроме того, она используется для охлаждения проточной водой электролита, который часто перегревается в процессе полирования.
Внутренняя поверхность ванны должна быть облицована химически и температуростойким материалом. В качестве таких материалов для наиболее агрессивного сернофосфорнохромового электролита следует применять свинец, фторопласт-4 либо покрытия из суспензии фторопласта ЗМ или химически стойкой силикатной эмали марки ЛК-1.
В лабораторных условиях могут быть использованы жаростойкое стекло, фарфор, керамика.
Источником питания ванн обычно служат выпрямители селеновые марки ВСГ-ЗМ, купрокеный ВКГ-100 либо германиевый ВАГЗ-9/12-600. При необходимости возможна совместная работа нескольких выпрямителей.
Регулирование тока осуществляется по-разному, в зависимости от режима работы ванны и источника питания. В последнее время в промышленности применяется плавное бесступенчатое регулирование тока изменением напряжения в первичной обмотке трансформатора. Трансформатор смонтирован совместно с селеновым или германиевым выпрямителем. Подробное описание оборудования и схем для регулирования электрического режима можно найти в специальной литературе.
Составы электролитов, их приготовление и корректирование
Для электрохимического полирования предложены сотни различных по составу электролитов.
Это свидетельствует прежде всего о том, что до сих пор не найден состав электролита, который бы удовлетворял следующим основным требованиям:
1) высокой сглаживающей способностью;
2) длительной работоспособностью;
3) способностью полирования многих металлов и сплавов;
4) безопасностью в эксплуатации.
В результате испытаний разных электролитов установлено, что наиболее универсальным в современной технике является электролит, основой которого служит фосфорная кислота с добавлением серной кислоты и хромового ангидрида (фосфорносернохромовый электролит). Всестороннее изучение указанного электролита показало, что в нем практически возможно полировать большое количество марок сталей — от углеродистых до высоколегированных, включая нержавеющие и инструментальные стали. В этом электролите также возможно полировать медь, алюминий и некоторые марки сплавов на их основе.
Рис. 3. Ванна для электрохимического полирования:
1 — корпус наружной ванны; 2 — корпус внутренней ванны; 3 — нагреватель.
Приготовление и корректирование электролита
Порядок приготовления электролита следующий: смешивают фосфорную кислоту уд. веса 1,54 и серную кислоту уд. веса 1,82.
В отдельном сосуде растворяют в воде хромовый ангидрид. После отстаивания сливают его в ванну полирования. Затем вливают в ванну расчетное количество ортофосфорной кислоты уд. веса 1,54, а затем серной уд. веса 1,82. Полученную смесь прогревают при 140° С в течение примерно 1,5—2 час. до достижения уд. веса 1,73—1,74 (для полирования углеродистых сталей) и при 110—120 °С — до удельного веса 1,64 (для полирования нержавеющих сталей).
Опыт эксплуатации фосфорносернохромового электролита показывает, что работоспособность его во многом зависит от того, насколько поддерживается в процессе полирования соотношение соединений шестивалентного и трехвалентного хрома.
Если прикатодное пространство не изолировано от общего объема ванны, то в процессе полирования на катоде происходит восстановление хромовой кислоты, причем продукты восстановления повышают вязкость электролита, доводя его до непригодного состояния. Поэтому рекомендуется прикатодную зону изолировать пористой диафрагмой.
Диафрагма представляет собой узкий керамический пористый сосуд (прямоугольный или цилиндрический), в который помещается катод. Материалом для изготовления диафрагм служит смесь красной и шамотной глины (30% шамотной глины) и песка. В зависимости от габаритов катодов и ванны диафрагма формуется с возможно более тонкими стенками и обжигается при 1000— 1100 °С.
При пользовании диафрагмой срок службы электролита возрастает в 5—6 раз. Анодное окисление трехвалентного хрома при накоплении его свыше 2% ведут при анодной плотности тока 10—15 а/дм2, напряжении 10—12 в и температуре электролита 60 °С. Соотношение анода к катоду 1 : 10. Материалом анодов и катодов служит свинец. После окисления электролит рекомендуют прогреть в течение часа при 90—110 °С.
Особенности электрохимического полирования
Исследование работы фосфорносернохромового электролита показывает, что все три кислоты оказывают взаимно благоприятное влияние. Увеличение содержания фосфорной кислоты позволяет понизить плотность тока и напряжение, тогда как увеличение содержания серной кислоты повышает пределы плотности тока. Изменяя концентрацию и соотношение кислот, возможно установить области полирования для заданной марки материала.
Рис. 4. Схема изоляции прикатодной зоны:
1 — электролит в ванне; 2 — диафрагма; 3 — электролит прикатодной зоны; 4 — катод; 5 — анод.
Рис. 5. Полирующая способность фосфорносернохромовых электролитов при полировании:
а — углеродистых и низколегированных сталей; б — нержавеющих хромистых сталей.
Полирование сталей. Фосфорносернохромо-вые электролиты обладают полирующей способностью в широких пределах концентраций: от 60 до 85% фосфорной кислоты и от 15 до 40% —серной кислоты. На рис. 26 приведены диаграммы, иллюстрирующие области полирующей способности электролита углеродистых и нержавеющих групп сталей. Электрохимическое полирование каждой группы сталей имеет свою особенность. При полировании углеродистых сталей, если необходимо максимально сгладить шероховатости и не требуется блеск, следует увеличить содержание воды в электролите до 30—35%, а хромовой кислоты — до 12—15%. В этом случае при плотности тока 15—25 а/дм2 и температуре электролита 70 °С обрабатываемая поверхность приобретает серебристый цвет. Если необходимо сгладить шероховатость с получением блеска, то целесообразнее осуществить процесс в двух растворах: сгладить в электролите с большим содержанием воды и придать блеск в другом электролите с меньшим содержанием воды.
Рис. 6. Профилограммы шероховатости механически обработанных и электрохимически полированных поверхностей нержавеющей стали:
а — фрезерованная и электрохимически полированная после фрезерования; о — шлифованная и электрохимически полированная после шлифования.
Качество поверхности зависит от содержания углерода в стали и ее структуры. Наиболее легко полируются стали со структурой равномерно распределенного феррита и перлита. С увеличением содержания углерода в стали изменяется величина предельного тока, при котором наступает анодная пассивность.
Наименьший ток соответствует низкоуглеродистой стали (0,1%) с почти ферритной структурой; наибольший — среднеуглеродистой стали (0,45%) при соотношении феррита и перлита 1:1. При дальнейшем увеличении содержания углерода, когда структура становится более однородной и преобладает перлитная составляющая, предельный ток вновь снижается.
При полировании хромистых нержавеющих сталей в электролите при плотности тока 20—30 а/дм2 поверхность получается травленой и сглаживания не наблюдается. При плотности тока 40 а/дм2 наблюдается блеск без сглаживания. Наиболее эффективное сглаживание, сопровождаемое блеском, происходит при плотности тока в пределах 50—70 а/дм2. Этой плотности соответствуют профилограммы шероховатости поверхностей различно обработанной нержавеющей стали марки 2X13.
Из профилограмм следует, что поверхность, шлифованную абразивным кругом зернистостью 12 до 7-го класса, возможно отполировать до 9-го класса. Фрезерованную поверхность с шероховатостью 6-го класса возможно отполировать до 9-го класса.
Следует заметить, что в ряде случаев волнистость поверхности не мешает улучшению ее эксплуатационных свойств. Так, например, исходная фрезерованная поверхность после электрохимического полирования, будучи волнистой, обладает повышенной усталостной прочностью, лучшим сопротивлением коррозии и полным отсутствием деформированного слоя.
Температура электролита
Значительное влияние на качество поверхности оказывает температура. При низких температурах (30— 40 °С) полирования не происходит, и поверхность оказывается травленой, матовой. С повышением температуры поверхность становится более блестящей, но травление сохраняется. При температурном интервале 70—80°С получены лучшие результаты.
Для каждого электролита, режима полирования и полируемого сплава существуют пределы температур электролита, отвечающие лучшему качеству поверхности. При чрезмерном снижении температуры электролита против оптимальной повышается вязкость электролита и соответственно вязкость пленки на аноде, а также затрудняется диффузия продуктов анодного растворения. В результате замедляется процесс анодного растворения, полирующее действие электролита ослабляется или полностью прекращается и наблюдается травленая поверхность.
Чрезмерное повышение температуры ускоряет процесс анодного растворения, снижает вязкость электролита и пленки на аноде, облегчает диффузию и уменьшает омическое сопротивление электролита. С повышением температуры усиливается газообразование, на обрабатываемой поверхности появляются полосы и наблюдаются травленые участки.
Несоблюдение главным образом электрического и температурного режимов приводит к появлению различных дефектов при электрохимическом полировании.
Расстояние между электродами и их перемешивание
Расстояние между электродами оказывает заметное влияние на равномерность удаляемого слоя. Так, при расстоянии 20—40 мм происходит значительное растворение (от 0,2 до 0,6 мм). Увеличение расстояния до 150 мм не приводит к существенному улучшению равномерности съема. Увеличение расстояния не позволяет использовать необходимый ток вследствие высокого удельного сопротивления электролита.
Перемешивание электролита ухудшает качество поверхности, покрывая ее темным налетом, причем эффективность сглаживания не возрастает.
Особенности полирования меди
Возможно полирование меди и некоторых ее сплавов (латуней) и в одной ортофосфорной кислоте уд. веса 1,5 (716 г/л Н3Р04). Однако добавление к ортофосфорной кислоте хромового ангидрида позволяет осуществлять процесс полирования в широких пределах плотности тока (20—70 а/дм2) и сократить время полирования до 1—3 мин. Катодами служат свинцовые пластины. Соотношение поверхностей анода и катода 1 : 3.
В процессе полирования меди, как и при полировании сталей, уменьшается содержание воды, кислоты и происходит восстановление Сг03 до Сг20з. Корректирование электролита осуществляется так же, как и при полировании сталей. Вода добавляется до необходимого удельного веса, а кислота — по данным химического анализа. Сгг03 окисляется на аноде в Сг03.
Эффективность сглаживания электролита невелика. Поэтому подготовка механическим шлифованием должна заканчиваться на зернистости 5. Хорошо полируется без всякой предварительной подготовки листовой холоднокатаный материал. В этом случае должна быть проявлена забота о тщательном сохранении поверхности листа от царапин, забоин и других повреждений.
Следует иметь в виду, что раковины, поры и включения хорошо выявляются электрохимическим полированием. Скорость растворения меди при плотности тока 50 а/дм2 составляет 1 мк/мин, причем снижение удельного веса электролита с 1,5 до 1,3 ускоряет процесс растворения.
Особенности полирования алюминия
Характерная особенность полирования алюминия — интенсивное пассивирование полируемой поверхности и вследствие этого снижение плотности тока до очень малых плотностей (1—2 а/дм2) и повышение напряжения до 15—25 в. Эта особенность не должна смущать, хотя она наступает через 2—4 мин. после завешивания детали и несколько ухудшает блеск.
Если полирование осуществляется с целью получения высокой отражательной способности, рекомендуется в этом случае разрушать образующуюся окисную пленку кратковременным переключением тока с анода на катод (реверсированием) либо выключением тока на несколько секунд.
Резкое ухудшение качества полированной поверхности алюминия наступает в результате анодного растворения алюминия. При накоплении в электролите 30 г/л алюминия, по существу, прекращается работа ванны. Контроль и корректирование раствора осуществляют так же, как и в процессе полирования сталей.
Применение электрохимического полирования
Несмотря на существенные недостатки электрохимического полирования и все продолжающиеся исследования в данной области, этот процесс уже сейчас находит эффективное применение в некоторых производствах.
В то же время из-за отсутствия объективных данных и незнания особенностей электрохимического полирования часто возникают значительные затруднения или принимаются ошибочные решения в выборе этого метода.
Применение электрохимического полирования на нынешней стадии развития целесообразно прежде всего там, где затруднено или невозможно механическое полирование (недостаточные для механического полирования поверхности, недопустим нагрев или силовое воздействие, дефекты материала или механической обработки). Так, например, электрохимическому полированию подвергают различные детали арматуры.
Электрохимически полируют детали карбюратора (в частности, клапан подачи горючего из нержавеющей стали или фольги), тончайшую ленту, проволоку и трубы. Особый интерес представляет полирование труб длиной 6—8 м из нержавеющей стали Х18Н9Т. Механическая очистка внутренней поверхности длинных труб вызывает значительные трудности. Химическая очистка труб не решает задачи—она растравливает поверхность и не полностью очищает от окалины. Электрохимическим полированием внутренняя поверхность становится более гладкой, блестящей, повышается коррозийная стойкость, уменьшается трение жидкости и газов о стенки, обеспечивается высокая производительность процесса.
При полировании длинных труб крупного диаметра (больше 100 мм) и других крупных полых деталей внутренняя полость используется в качестве ванны-электро-лизера. Катод в этом случае монтируется в центре трубы. Полирование ведется с протоком электролита через трубу. Трудности полирования больших поверхностей труб заключаются в необходимости применения тока порядка 10 000 а. Столь большой ток вызывает чрезмерный разогрев электролита и выделение большого количества газов. К тому же трудно выполнима подводка большого тока, поэтому трубы крупных диаметров полируют на небольших участках, непрерывно подвигая катод вдоль трубы. Длина катода зависит от диаметра трубы. Например, для трубы диаметром 200 мм длина катода должна быть 170 мм. Электролит циркулирует под давлением до 4 атм, скорость перемещения катода — до 8 м/мин.
В настоящее время разработано несколько конструкций установок для полирования внутренней и наружной поверхностей труб различных диаметров.
Электрохимическое полирование находит применение и в производстве режущего инструмента. Образующийся при шлифовании инструмента дефектный слой легко снимается электрохимическим полированием. В результате повышаются стойкость инструмента и защита от коррозии. Например, электрохимическое полирование канавок сверл обеспечивает более легкий сход стружки при сверлении и меньший разогрев сверла.
Полирование сверл осуществляется партиями, а не по одному сверлу, как при механическом полировании. Объем ванны емкостью 150 л позволяет загружать одновременно до 30 сверл диаметром 10— 15 мм. Для быстрой загрузки сверл сконструированы приспособления — рамки.
Рис. 7. Полирование сверл:
а — механическое; б — электрохимическое.
Для полирования 1000 сверл диаметром 10 мм в среднем расход электролита составляет 8,7 кг. Соответственно расходуется ортофосфорной кислоты 5,4 кг, серной кислоты — 2,5 кг и хромового ангидрида — 0,8 кг.
Уже указывалось, что электрохимическое полирование удаляет поверхностный слой металла, а многие дефекты материала выступают наружу. Когда преследуют цель декоративной отделки деталей, это свойство является недостатком метода. В случаях необходимости контроля качества поверхности это — несомненное достоинство.
Высокая чувствительность электрохимического полирования к неоднородности состава все больше используется в практике металловедческих лабораторий для контроля качества сталей: выявления микро- и макроструктуры, трещин, флокенов, волосовин, неметаллических включений и других нарушений сплошности металла; определения карбидной неоднородности, склонности сплавов к интеркристаллитной коррозии; обнаружения деформированных участков, явлений термического отпуска тонкого поверхностного слоя. При подготовке шлифов для микроскопического исследования достоинства электрохимического полирования особенно заметны. Поверхность шлифа, полированная электрохимически, освобождается от всех термических и механических изменений (наклепа), неизбежных при механических способах обработки. Она свободна также от каких-либо загрязнений полирующими веществами и пленок, в том числе и окисных, образовавшихся ранее. И хотя полированная поверхность анодно пассивированная, она остается чистой и активной.
Отсутствие на поверхности следов термических воздействий и деформаций и повышенная чистота полированной поверхности позволяют наблюдать истинную, неискаженную структуру исследуемого материала. Электрохимически полированная поверхность особенно удобна для рассмотрения при больших увеличениях. Здесь отчетливо выявляются тончайшие детали структуры, обычно искаженные при механической подготовке (первичное зерно, микроликвация). Электрохимическое полирование в сочетании с химико-механическим методом ускоряет процесс приготовления шлифов.
Реклама:
Читать далее:
Электро-химико-механическая обработка
Статьи по теме:
pereosnastka.ru
способ химического полирования алюминия — патент РФ 2101386
Изобретение относится к области химического полирования металлов, в частности алюминия и его сплавов, и может быть использовано в металлургической и машиностроительной промышленности. Способ полирования алюминия и его сплавов включает обработку поверхности металлов в растворе, содержащем, г/л: полифосфорная кислота (1,95 кг/дм3) 670 — 720, серная кислота (1,8 кг/дм3) 210 — 330, азотная кислота (1,4 кг/дм3) 88 — 220, медь сернокислая пятиводная 3,6 — 7,3, ортофосфорная кислота (1,57 кг/дм3) 660 — 680, при 95 — 110oC в течение 1 — 5 мин в две стадии с промежуточным перерывом между стадиями в течение 0,5 — 1 мин. Использование способа позволяет значительно увеличит чистоту обрабатываемой поверхности и интенсивности сглаживания металла. Изобретение относится к области химического полирования металлов, в частности алюминия и его сплавов, и может быть использовано в металлургической и машиностроительной промышленности. Для полирования алюминия и его сплавов наиболее применимы способы полирования в кислых растворах, содержащих серную, азотную, фосфорную кислоты [1]Полирование металлов в указанных растворах не обеспечивает высокой производительности, в частности, для достижения 10 класса чистоты обрабатываемой поверхности. Наиболее близким по технической сущности к предложенному является способ химического полирования в растворе, содержащем, г/л [2]
Ортофосфорная кислота ( 1,70 кг/дм3 77,5
Серная кислота ( r 1,80 кг/дм3) 15,5
Азотная кислота ( r 1,50 кг/дм3) 6,0
Медь азотнокислая 0,5
Борная кислота 0,5
Карбоксиметилцеллюлоза 0,83
Полирование проводят при 95 110oC в течение 1 5 мин. Недостатком данного способа является низкая чистота обрабатываемой поверхности, особенно при обработке труднополируемых сплавов. Задачей изобретения является создание такого способа химического полирования алюминия и его сплавов, при котором обеспечивается высокая чистота обрабатываемой поверхности и более интенсивное сглаживание поверхности. Поставленная задача достигается путем нанесения на поверхность алюминия и его сплавов полировального состава при следующем содержании компонентов, г/л:
Полифосфорная кислота ( r 1,95 кг/дм3 670 720
Серная кислота ( r 1,8 кг/дм3) 210 330
Азотная кислота ( r 1,40 кг/дм3) 88 220
Медь сернокислая пятиводная CuSO4 5H2O 3,6 7,3
Ортофосфорная кислота ( r 1,57 кг/дм3) 660 680
Способ осуществления при 95 110oC в течение 1 5 мин в две стадии с промежуточным перерывом между стадиями в течение 0,5 1 мин. Изобретение иллюстрируется следующими примерами. Пример 1. Пластинки алюминиевого сплава АК 6 размером 0,09 0,13 м2 обрабатывались полировочным составом при следующем соотношении компонентов, г/л:
Полифосфорная кислота ( r 1,95 кг/дм3) 670
Серная кислота ( r 1,8 кг/дм3) 210
Азотная кислота ( r 1,4 кг/дм3) 88
Медь сернокислая пятиводная CuSO4 5H2O 3,6
Ортофосфорная кислота ( r 1,57 кг/дм3) 660
В течение 1 мин при 95oC, затем находились на воздухе в течение 0,5 мин, затем обрабатывались повторно тем же составом. Чистота обработанной поверхности соответствовала 10 классу. Интенсивность сглаживания металла — 0,093 мин. Пример 2. Пластинки сплавов алюминия АК6 размерами 0,09 0,13 м2 обрабатывали полировочным составом при следующем соотношении компонентов, г/л:
Полифосфорная кислота ( r 1,95 кг/дм3) 720
Серная кислота ( r 1,8 кг/дм3) 330
Азотная кислота ( r 1,4 кг/дм3) 220
Медь сернокислая пятиводная CuSO4 5H2O 7,3
Ортофосфорная кислота ( r 1,57 кг/дм3) 680
В течение 5 мин при 110oC, затем находились на воздухе в течение 1 мин, затем обрабатывались повторно тем же составом. Чистота обработанной поверхности соответствовала 10 классу. Интенсивность сглаживания составила 0,100. Пример 3. Пластинки алюминиевого сплава АК6 размером 0,09 0,13 м2 обрабатывались полировочным составом при следующем соотношении компонентов, г/л:
Полифосфорная кислота ( r 1,95 кг/дм3) 695
Серная кислота ( r 1,8 кг/дм3) 270
Азотная кислота ( r 1,4 кг/дм3) 88
Медь сернокислая пятиводная CuSO4 5H2O 5,45
Ортофосфорная кислота (r=1,57 кг/дм3) 670
В течение 2,5 мин при 100oC, затем находились на воздухе в течение 0,8 мин и повторно обрабатывались тем же составом. Чистота обрабатываемой поверхности соответствовала 10 классу. Интенсивность сглаживания металла — 0,096. Пример 4 (по прототипу). Пластинки сплава алюминия АК 6 0,09 0,13 м2 обрабатывали полировальным составом при следующем соотношении компонентов, г/л:
Ортофосфорная кислота ( r 1,70 кг/дм3) 77,5
Серная кислота ( r 1,80 кг/дм3) 15,5
Азотная кислота ( r 1,50 кг/дм3) 6,0
Медь азотнокислая 0,5
Борная кислота 0,5
Карбоксиметилцеллюлоза 0,83
В течение 3 мин при 100oC. Чистота обрабатываемой поверхности соответствовала 9 классу. Интенсивность сглаживания металла 0,078 мм. Из приведенных примеров видно, что использование предлагаемого способа полирования позволяет значительно увеличить чистоту обрабатываемой поверхности и интенсивность сглаживания металла. Источники информации:
1. Я. Н. Липкин, Т.М. Бершадская Химическое полирование металлов,с.83 (аналог). 2. С.Я. Грилихсс. Электрохимическое и химическое полирование,с. 143 144 (прототип).
ФОРМУЛА ИЗОБРЕТЕНИЯ
Способ химического полирования алюминия и его сплавов, включающий обработку поверхности металла при 95 110oС в течение 1 5 мин в растворе, содержащем ортофосфорную, серную, азотную кислоты и соль меди, отличающийся тем, что обработку проводят в две стадии с промежуточным перерывом 0,5 1 мин в растворе, дополнительно содержащем полифосфорную кислоту, а в качестве соли меди медь сернокислую при следующем соотношении компонентов, г/л:Полифосфорная кислота ( = 1,95 кг/дм3) 670 720
Серная кислота ( = 1,8 кг/дм3) 210 330
Азотная кислота ( = 1,4 кг/дм3) 88 220
Медь сернокислая пятиводная 3,6 7,3
Ортофосфорная кислота ( = 1,57 кг/дм3) 660 680в
www.freepatent.ru