Сталь-Максимум: Марка 14Х17Н2
Этот материал представляет собой коррозионно-стойкую жаропрочную сталь. Относится он к классу мартенсито-ферритных. Также в технической литературе вы можете встретить наименования 1Х17Н2 или ЭИ268. Это не аналоги, а другие обозначения данной марки.
Коррозионная стойкость — способность материалов сопротивляться коррозии, определяющаяся скоростью коррозии в данных условиях. Для оценки скорости коррозии используются как качественные, так и количественные характеристики. Изменение внешнего вида поверхности металла, изменение его микроструктуры являются примерами качественной оценки скорости коррозии.
см. Википедию
Из стали 14Х17Н2 производят:
- фасонный и сортовой прокат,
- рабочие лопатки, диски, валы и втулки,
- фланцы, фитинги и крепежи,
- калиброванные и шлифованные прутки,
- запчасти компрессорных машин, предназначенных для работы на нитрозном газе,
- серебрянки,
- тонкостенные и толстостенные листы,
- полосы, поковки и кованные заготовки,
- детали, которые работают с агрессивными средами и при пониженных температурах.
Все эти элементы используются в различных областях промышленности.
Точный химический состав стали 14Х17Н2
Эксплуатационные и технические характеристики изделий из данного материала, а также его химический состав прописаны в нормативе ГОСТ 5632-72. Сплав включает в себя 9 элементов.
Основные из них:
Второстепенные:
- Кремний
- Марганец
- Медь
- Титан
- Углерод
- Фосфор
- Сера
Точное процентное соотношение веществ вы можете посмотреть в таблице и на диаграмме ниже.
Cr |
Ni |
Si |
Mn |
Cu |
Ti |
С |
Р |
S |
от 16 до 18 |
1,5 – 2,5 |
менее 0,8 |
меньше 0,8 |
|
до 0,2 |
0,11 – 0,17 |
до 0,03 |
меньше 0,025 |
Свойства стали 14Х17Н2
Данный сплав обладает отличными техническими характеристиками. Он очень надежный и долговечный. Изделия из этого материала широко используются в различных направлениях современной промышленности.
Удельный вес данного металла составляет 7750 кг/м3. Его термическая обработка осуществляется следующим образом:
- закалка при температуре до 1020oC,
- обработка в масле,
- отпуск при показаниях термометра около +700oC,
- охлаждение на воздухе.
Критические температурные отметки:
- Ac1 = 720
- Ac3(Acm) = 830
- Ar1 = 700
Обрабатываемость резанием возможна в закаленном и отпущенном состоянии. Материал относится к трудносвариваемым, поэтому осуществлять сварку необходимо с предварительным нагревом и дальнейшей термообработкой. При этом стоит учитывать, что сплав склонен к отпускной хрупкости.
Технические характеристики наиболее распространенных изделий из стали 14Х17Н2
Стальные прутки
Во время первого этапа обработки их закаливают маслом при температуре от +975° до +1040°С. Затем отпускают на воздухе при показаниях термометра от +275° до +350°С. При втором шаге изделия закаливаю маслом с температурой 1000°-1030°С, затем вновь следует отпуск на воздухе, но уже при 620°-660°С.
Такие прутки имеют сечение до 60 мм. Их условный предел текучести варьируется от 635 МПа до 835 МПа. Максимальный предел прочности при растяжении составляет 1080 МПа. Показатели относительного удлинения после разрыва варьируются в пределах от 10% до 16%, сужения – от 30% до 55%.
Горячекатаные и холоднокатаные стальные листы
Их закаливают в воде или на воздухе при температуре 960°-1050°С. Отпуск поперечных образцов происходит на воздухе при 275°-350°С.
Условный предел текучести данных листов составляет 882 МПа. Сопротивление на разрыв достигает 1078 МПа. Относительное удлинение после разрыва около 10%, сужение при этом не происходит.
Стальные поковки
Изготовление этих деталей осуществляет двумя методами.
Первый:
Изделие закаливается маслом при температуре 980° — 1020°С и отпускается на воздухе при 680° — 700°С. Его сечение при этом может доходить до 1000 мм. Предел текучести составляет 637 МПа. Временное сопротивление разрыву – 784 МПа. Относительное удлинение после разрыва достигает двенадцати процентов, а сужается деталь до 30%.
Второй:
Поковку закаливают маслом при 1000° — 1030°С. Затем ее ждет двойной отпуск в печи или на воздухе при температуре от 665° до 675°С. Сечение таких деталей доходит до 100 мм. Предел текучести условно достигает 540 МПа. Сопротивление на разрыв – 690 МПа. Удлинение после разрыва может доходить до 15%, а сужение до 40%.
Отечественные и зарубежные аналоги стали 14Х17Н2
Россия |
20Х17Н2 |
Германия |
X22CrNi17, X20CrNi72 |
Франция |
Z15CN16-02 |
Англия |
431S29 |
США |
431 |
Япония |
SUS431 |
Интересует прокат из стали этой марки или остались вопросы?
Звоните нам: |
Пишите на почту: |
stalmaximum.ru
Доска объявлений | Сталь 14Х17Н2 — характеристика, химический состав, свойства, твердостьСталь 14Х17Н2Общие сведения
Химический состав
Механические свойстваМеханические свойства
Механические свойства при повышенных температурах
Механические свойства в зависимости от температуры отпуска
Технологические свойства
Температура критических точек
Ударная вязкостьУдарная вязкость, KCU, Дж/см2
Предел выносливости
Коррозионные свойства
Жаростойкость
Физические свойства
[ Назад ] |
s-metall.com.ua
Нержавеющая сталь 14Х17Н2 — расшифровка марки стали, ГОСТ, характеристика материала
Марка стали — 14Х17Н2
Стандарт — ГОСТ 5632
Заменитель — 20х17Н2
Сталь 14Х17Н2 содержит углерода в среднем 0,14%, Х17 — указывает содержание хрома в стали примерно 17%, Н2 — указывает содержание никеля в стали около 2%. Сталь легированная, коррозионно-стойкая, жаропрочная.
Нержавеющая сталь 14Х17Н2 применяется для изготовления деталей, работающих в агрессивных средах и при пониженных температурах в химической, авиационной и других отраслях промышленности. Наибольшей коррозионно-стойкостью обладает после закалки с высоким отпуском.
Из нержавеющей стали 14Х17Н2 изготовляют детали и узлы основного оборудования АЭС, рабочие лопатки, диски, валы, втулки, фланцы, крепеж, детали компрессорных машин и другие детали, работающие при температуре до 800°С.
Массовая доля основных химических элементов, % | |||||
---|---|---|---|---|---|
C — углерода | Si — кремния | Mn — марганца | Cr — хрома | Ni — никеля | |
0,11-0,17 | Не более 0,80 | Не более 0,80 | 16,00-18,00 | 1,50-2,50 |
Температура критических точек, °С | |||
---|---|---|---|
Ac1 | Ac3 | Ar1 | Ar3 |
720 | 830 | 700 | — |
Технологические свойства | |
---|---|
Ковка | Температура ковки, °С: начала 1250, конца 900. Сечения до 350 мм охлаждаются на воздухе. |
Свариваемость | Трудносвариваемая. Способы сварки: ручная дуговая сварка, аргонодуговая сварка, контактная сварка. Сварные соединения в зоне термического влияния обладают пониженной коррозионной стойкостью, поэтому после сварки необходим отпуск при 680-700°С в течении 30-60 мин. |
Обрабатываемость резанием | В закаленном и опущенном состоянии при HB 330: Kv твердый сплав = 0,6 Kv быстрорежущая сталь = 0,3 |
Склонность к отпускной хрупкости | Склонна |
Физические свойства | Температура испытаний, °С | |||||||||
---|---|---|---|---|---|---|---|---|---|---|
20 | 100 | 200 | 300 | 400 | 500 | 600 | 700 | 800 | 900 | |
Модуль нормальной упругости E, ГПа | 193 | — | — | 164 | — | 148 | 133 | — | — | — |
Модуль упругости при сдвиге кручением G, ГПа | — | — | — | — | — | — | — | — | — | — |
Плотность ρn, кг/м3 | 7750 | — | — | — | — | — | — | — | — | — |
Коэффициент теплопроводности λ Вт/(м*К) | 21 | 22 | 23 | 24 | 24 | 25 | 26 | 27 | 28 | 30 |
Удельное электросопротивление ρ, нОм*м | 720 | 780 | 840 | 890 | 990 | 1040 | 1110 | 1130 | 1160 | 1170 |
20-100 | 20-200 | 20-300 | 20-400 | 20-500 | 20-600 | 20-700 | 20-800 | 20-900 | 20-1000 | |
Коэффициент линейного расширения α*106, K-1 | 9,8 | 10,6 | 11,8 | 11,0 | 11,1 | 11,3 | 11,0 | 10,7 | 11,4 | 11,5 |
Удельная теплоемкость c, Дж/(кг*К) | 462 | — | — | — | — | — | — | — | — | — |
tekhnar.ru
Сталь 14Х17Н2: характеристики, ГОСТ, аналоги, применение
Сталь – смесь железа и углерода, которую активно использует как в строительстве, так и в машиностроительной отрасли. Данный материал получил популярность благодаря увеличенной износостойкости, прочности и низкой цене, но свойства каждой заготовки будут значительно отличаться друг от друга, и тут всё зависит от химического состава (по этому параметру определяют качество и назначение металлопроката). И для создания высокосортной детали или прочной конструкции нужно уделять внимание именно дополнительным компонентам.
Большинство металлических деталей используются в неблагоприятных условиях: повышенные температуры, сильное механическое действие, высокая влажность и прочее. И если большинство сплавов легко переносят первые факторы, то жидкость считается главным врагом любого железа. Однако современная металлургическая отрасль нашла выход из этой ситуации, и создала модель Ст 14Х17Н2, относящаяся к коррозионно-стойкому типу. Ещё она является жаростойкой, и её можно использовать практически при любых обстоятельствах.
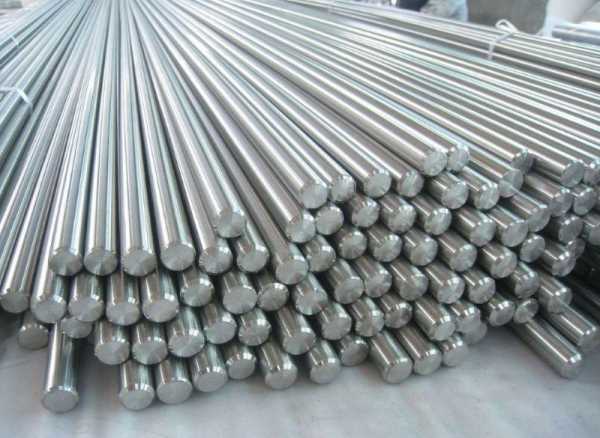
Сталь 14Х17Н2 — характеристики
Характеристики материала
Применение металлопроката можно встретить в следующих случаях:
- Создание рабочих и направляющих лопаток для турбин. На такие предметы ложится серьёзная ответственность, и от их сорта будет завесить стабильная работа всего агрегата. Лопасти подвергаются быстрым оборотам, а внешние факторы в виде газа или горячего пара создают дополнительную нагрузку. Ещё, в спокойном состоянии, на поверхности может скапливаться конденсат, который начнёт разрушать обычный металл.
- Изготовление крепежей. Сюда входят болты, гайки, штифты, шпильки и другие. Эти компоненты также играют ключевую роль, и от их прочности будет зависеть надёжность и безопасность всей конструкций.
- Производство втулок. Эти составляющие встречаются в подвеске автомобилей, поэтому они должны выдержать не только силовое давление, но и отлично отталкивать воду после дождя, переносить повышенную температуру в летнее время и низкую в зимнее, служить без деформации. Также втулки разрешено устанавливать и в другие механизированные приборы.
- Выпуск валов. Подобные запчасти передают крутящий момент от одного звена механизма к другому. Тут тоже имеются негативные факторы в виде силы трения, давления, температуры и другого.
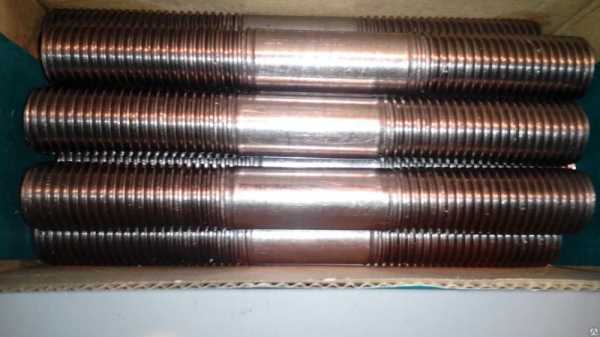
Шпилька М16 14Х17Н2
Такие предметы допускается использовать в различных сферах, и, от части, их можно отнести к универсальному типу. Даже долю медицинских приборов и инструментов делают из этого проката. Что касается свойств, то у 14Х17Н2 характеристики выглядят следующим образом:
- нержавеющая поверхность;
- способность работать при Т = до +400 °C;
- устойчивость к статическим и динамическим влияниям;
- малый уровень деформации.
Трудно найти сплав, который смог бы соответствовать аналогичным параметрам. Поэтому он и цениться на всех производственных предприятиях.
Химический состав
Сталь относится к коррозионностойкому жаропрочному веществу, и к мартенсита-ферритному классу. В соединении имеется 10 химических элементов:
- Углерод (С) – 0,11-0,17%. Придаёт веществу плотность.
- Кремний (Si) и марганец (Mn) – не более 0,8%. Первый необходим для закаливаемости, второй – для удаления лишнего кислорода.
- Никель (Ni) – 1,5-2,5%. Защищает плоскость от ржавчины.
- Фосфор (P) – 0,03%. Снижает хрупкость предмета.
- Сера (S) – 0,025%. Необходима для будущей обработки плоскости.
- Хром (Cr) – 16-18%. Добавляется во все нержавеющие стали, и даёт сопротивляемость коррозии.
- Титан (Ti) – не более 0,2%. Уменьшает массу объекта и увеличивает устойчивость к повреждениям.
- Медь (Cu) – до 0,3%. Придаёт металлу пластичность, и защищает его от надломов.
- Железо (Fe) – 78%. Основная составляющая, являющаяся неотъемлемой частью любой стали.
Несмотря на высокие показатели, хранить сталь 14Х17Н2 можно только в удалённом от воды месте. Особенно, если период складирования будет достигать нескольких лет. В этом случае продукт сохранит свою первоначальную гладкость, и не утратит эксплуатационные опции.
Маркировка и расшифровка
Каждое изделие подобного рода должно иметь соответствующий знак, указывающий на характеристики и качество. Товар без маркировки запрещено продавать, поскольку от потребителя будет скрыта достоверная информация. Следует отметить, что сталь 14Х17Н2 относится к ГОСТ 5632 72. Этот государственный стандарт относится к нержавеющим, окалиностойким и жаропрочным металлопрокатом, которые способны работать в нагруженном состоянии и в экстремальных условиях. Также в требовании к 14Х17Н2 ГОСТ прописано точное соотношение всех элементов, входящих в структуру слитка.
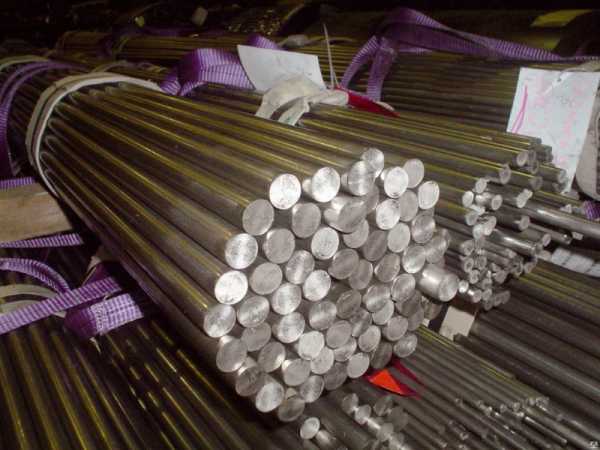
Пруток 26 мм 14Х17Н2
Символы, входящие в название, носят информационный характер: начальная цифра (14) указывает на среднее соотношение (в сотых долях процента) углерода. Символ «Х» обозначает наличие хрома, а значение 17 говорит о количестве этого вещества (в целых процентах). А знак «Н» говорит о присутствии никеля и его количестве. Из названия данной марки можно сказать, что сталь содержит примерно 0,14% (С), 17% (Cr) и 2% (Ni). Идентичным образом можно расшифровать любую аббревиатуру.
Скачать ГОСТ 5632-72
Аналоги стали 14Х17Н2
В качестве альтернативного варианта рекомендуется обратить внимание на зарубежные варианты. Например, на аналог AISI 431 американского производства. Состав этого сплава отличается лишь наличием 0,8% марганца (Mn). Что касается опций, то они выглядят следующим образом: При 5-ти часовом погружении в дистиллированную жидкость с Т = 300 °С начинает образовываться коррозия размером в 0,08 мм. Такой же эффект появляется по истечении одного года хранения в ненадлежащих условиях. Если плоскость подвергнуть воздействию Т = 100 °С, то его модуль упругости будет составлять 1,97 МПа, плотность составит 7750кг/м3, а коэффициент расширения – 9,81 °С.
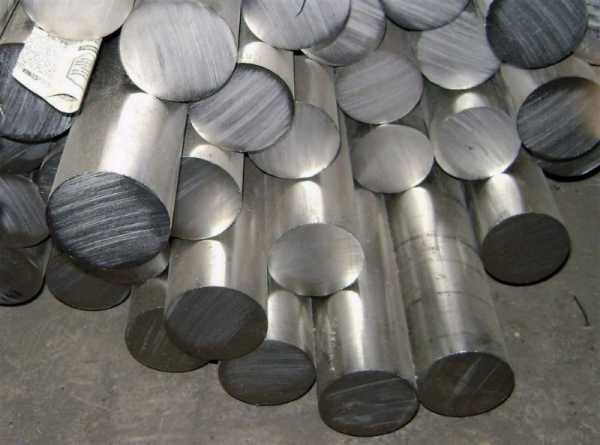
AISI 431
Но такой заменитель имеет ряд недостатков:
- ограниченная свариваемость;
- повышение хрупкости при отпуске;
- перед сварными работами изделие важно разогреть до 300 °С;
- после сварки объект нужно подвергнуть тепловому воздействию.
Однако эта модель полностью заслуживает интереса покупателей.
Особенности термообработки
Эта процедура необходима для улучшения пробы материала. В результате таких работ происходят процессы, которые способны изменить свойства заготовки. При этом обрабатывать можно как обычные болванки, так и готовые части. Термообработка стали 14Х17Н2 всегда проходит по одному сценарию:
- закалка в печи 980-1020 °С;
- отпуск в масле до 680-700 °С;
- охлаждение на открытом воздухе.
Этот процесс придаёт сплавам твёрдость, и прибавляет коэффициент износостойкости, а это очень важный показатель, поскольку материал может быть использован для создания сложных технических устройств или массивных конструкций. Суть такого способа заключается в постепенном нагревании с дальнейшим резким охлаждением, и так делается несколько подходов.
Следует отметить, что при закаливании есть шанс возникновения дефектов: перегрев, пережог, окисление, трещины и прочее. Чтобы избежать таких неприятностей нужно строго следовать всем правилам термической обработки.
Если вы нашли ошибку, пожалуйста, выделите фрагмент текста и нажмите Ctrl+Enter.
stankiexpert.ru
Круг 14Х17Н2, шестигранник ст.14Х17Н2, сталь 14Х17Н2 (ЭИ268, 1Х17Н2), нержавеющий квадрат 14Х17Н2, полоса ЭИ-268
сделать заявку
Сталь 14Х17Н2 (ЭИ268, 1Х17Н2) коррозионностойкая жаропрочная мартенсито-ферритного класса
Заменители: Сталь 20Х17Н2
Сталь 14Х17Н2 применяется: для изготовления рабочих лопаток, дисков, валов, втулок, фланцев, крепежных и других деталей; деталей компрессорных машин, работающих на нитрозном газе; деталей, работающих в агрессивных средах и при пониженных температурах в химической и других отраслях промышленности; фасонных отливок и отливок по выплавляемым моделям для авиастроения I группы — нагруженных деталей с определенными требованиями по плотности и механическим свойствам: высоконагруженных кронштейнов, герметичных корпусов приборов, рам гироскопов, стабилизаторов и т.д. и II группы — ненагруженных и малонагруженных деталей: колец, фланцев, соединительных деталей, негерметичных корпусов приборов и т.д. Рекомендуемая максимальная температура эксплуатации в течение длительного времени +400 °C. Температура начала интенсивного окалинообразования в воздушной среде +800 °C. Наибольшей коррозионной стойкостью сталь обладает после закалки с высоким отпуском.
Технические характеристики
Химический состав в % |
НТД | C | S | P | Mn | Cr | W | V | Ti | Si | Ni | N | Mo | Cu | Al |
ОСТ 1 90090-79 | 0,05-0,10 | ≤0,025 | ≤0,025 | 0,30-0,80 | 15,0-18,0 | ≤0,20 | ≤0,050 | ≤0,050 | 0,80-1,50 | 2,80-3,80 | ≤0,050 | ≤0,20 | ≤0,30 | ≤0,10 |
ТУ 14-1-2186-77, ГОСТ 5632-72 | 0,11-0,17 | ≤0,025 | ≤0,030 | ≤0,80 | 16,00-18,00 | ≤0,20 | ≤0,20 | ≤0,20 | ≤0,80 | 1,50-2,50 | — | ≤0,30 | ≤0,30 | — |
По ОСТ 1 90090-79 химический состав приведен дл стали 14Х17Н2Л (ЭИ268Л). В стали допускается содержание азота до 0,070 %.
По ТУ 14-1-2186-77 для стали, выплавленной электрошлаковым переплавом содержание S ≤ 0,015 %.
Механические свойства |
Механические свойства при 20°С |
Состояние поставки | Сечение
(мм) | t испыт.
(°C) | t отпуска
(°C) | sТ | s0,2 (МПа) | sB (МПа) | d5 (%) | d4 | d | d10 | y
(%) | KCU
(кДж/м2) | HB | HRC | HRB | HV | HSh |
---|---|---|---|---|---|---|---|---|---|---|---|---|---|---|---|---|
Градация показателей свойств готовых термообработанных деталей по ОСТ 1 90005-91 | ||||||||||||||||
830-1030 | 229-321 | 21,0-30,0 | ||||||||||||||
930-1130 | 255-363 | 27,0-32,0 | ||||||||||||||
Заготовки (поковки и штамповки) по ОСТ 95-10-72. Закалка в масло с 950-1040 °С + Отпуск, охлаждение в масле или на воздухе (образцы) | ||||||||||||||||
≤100 | 600-650 | 229-285 | 20-29 | |||||||||||||
≤100 | 275-350 | 35-43 | ||||||||||||||
КТ0 | ≤60 | 275-350 | ≥1079 | ≥10 | ≥392 | 321-415 | ||||||||||
КТ55 | ≤100 | 600-680 | ≥540 | ≥686 | ≥15 | ≥40 | ≥588 | 207-285 | ||||||||
Заготовки деталей трубопроводной арматуры по СТ ЦКБА 016-2005. Закалка в масло с 975-1040 °C + Отпуск, охлаждение на воздухе | ||||||||||||||||
≤60 | 275-370 | ≥834 | ≥1080 | ≥10 | ≥25 | ≥490 | 331-388 | 37,0-42,5 | ||||||||
≤60 | 560-600 | ≥735 | ≥931 | ≥10 | ≥30 | ≥490 | 277-331 | 30,0-37,0 | ||||||||
≤60 | 680-700 | ≥568 | ≥784 | ≥14 | ≥50 | ≥588 | 229-285 | 22,5-31,0 | ||||||||
60-100 | 680-700 | ≥540 | ≥687 | ≥12 | ≥43 | ≥490 | 229-285 | 22,5-31,0 | ||||||||
>100-300 | 680-700 | ≥540 | ≥687 | ≥12 | ≥40 | ≥392 | 229-285 | 22,5-31,0 | ||||||||
Заготовки деталей трубопроводной арматуры по СТ ЦКБА 016-2005. Отжиг при 680-700 °C (выдержка 20 ч), охлаждение на воздухе с печью | ||||||||||||||||
≤60 | ≥490 | ≥735 | ≥14 | ≥50 | ≥588 | 240-260 | 25,0-28,0 | |||||||||
Листовой горячекатаный (1,5-3,9 мм) и холоднокатаный (0,7-3,9 мм) прокат по ГОСТ 5582-75. Закалка в масло с 950-975 °C + Отпуск при 275-350 °C, охлаждение на воздухе | ||||||||||||||||
Образец | ≥1080-1370 | ≥10 | ||||||||||||||
Литье по выплавляемым моделям и в керамические формы. Закалка в масле или растворе жидкого стекла с 1040-1060 °C + Отпуск при 540-560 °C (3 часа), охлаждение на воздухе | ||||||||||||||||
≥736 | ≥932 | ≥8 | ≥20 | ≥245 | 229-321 | |||||||||||
Литье по выплавляемым моделям и в керамические формы. Закалка в масле или растворе жидкого стекла с 1040-1060 °C + Отпуск при 670-690 °C (3 часа), охлаждение на воздухе | ||||||||||||||||
≥638 | ≥834 | ≥8 | ≥20 | ≥245 | 229-321 | |||||||||||
Поковки для деталей стойких к МКК. Закалка в масло или на воздухе с 970-1020 °C + Отпуск при 620-670 °C, охлаждение на воздухе | ||||||||||||||||
≤60 | ≥540 | ≥687 | ≥12 | ≥60 | ≥590 | 228-277 | ||||||||||
100-300 | ≥540 | ≥687 | ≥12 | ≥40 | ≥393 | 228-277 | ||||||||||
60-100 | ≥540 | ≥687 | ≥12 | ≥50 | ≥492 | 228-277 | ||||||||||
Поковки. Закалка в масло или на воздухе с 970-1000 °C + Отпуск при 600-650 °C, охлаждение на воздухе | ||||||||||||||||
≤60 | ≥638 | ≥736 | ≥12 | ≥45 | ≥600 | 241-321 | ||||||||||
100-300 | ≥638 | ≥736 | ≥10 | ≥35 | 241-321 | |||||||||||
60-100 | ≥638 | ≥736 | ≥11 | ≥40 | ≥500 | 241-321 | ||||||||||
Поковки. Закалка в масло или на воздухе с 970-1000 °C + Отпуск при 300-350 °C, охлаждение на воздухе | ||||||||||||||||
≤300 | 321-388 | |||||||||||||||
Поковки. Закалка в масло с 980-1020 °C + Отпуск при 680-700 °C, охлаждение на воздухе | ||||||||||||||||
60-100 | ≥637 | ≥784 | ≥12 | ≥30 | ≥490 | |||||||||||
Сортовой прокат горячекатаный и кованый по ГОСТ 5949-75. Закалка в масло с 1000-1030 °C + Отпуск при 620-660 °C, охлаждение на воздухе | ||||||||||||||||
Образец | ≥635 | ≥835 | ≥16 | ≥55 | ≥784 | |||||||||||
Сортовой прокат горячекатаный и кованый по ГОСТ 5949-75. Закалка в масло с 975-1040 °C + Отпуск при 275-350 °C, охлаждение на воздухе | ||||||||||||||||
Образец | ≥835 | ≥1080 | ≥10 | ≥30 | ≥490 | |||||||||||
Сортовой прокат горячекатаный и кованый по СТП 26.260.484-2004. Закалка в масло с 975-1040 °C + Отпуск, охлаждение на воздухе | ||||||||||||||||
Образец | 275-350 | ≥850 | ≥1100 | ≥10 | ≥30 | ≥490 | ||||||||||
Образец | 680-700 | ≥600 | ≥750 | ≥18 | ≥45 | ≥686 | ||||||||||
Штамповки по ОСТ 1 90176-75. Закалка в масло с 1010-1030 °C + Отпуск при 670-690 °C, охлаждение на воздухе | ||||||||||||||||
Образец | ≥638 | ≥834 | ≥16 | ≥55 | ≥784 | 255-302 | ||||||||||
Штамповки по ОСТ 1 90176-75. Закалка в масло с 975-1040 °C + Отпуск при 275-350 °C, охлаждение на воздухе | ||||||||||||||||
Образец | ≥834 | ≥1079 | ≥10 | ≥30 | ≥490 | 321-388 |
Механические свойства в зависимости от температуры отпуска |
Состояние поставки | Сечение
(мм) | t испыт.
(°C) | t отпуска
(°C) | sТ | s0,2 (МПа) | sB (МПа) | d5 (%) | d4 | d | d10 | y
(%) | KCU
(кДж/м2) | HB | HRC | HRB | HV | HSh |
---|---|---|---|---|---|---|---|---|---|---|---|---|---|---|---|---|
Пруток. Отжиг при 760-780 °С (выдержка 2 ч), охлаждение с печью + Закалка в масло с 950-975 °С (выдержка 1 ч) | ||||||||||||||||
300 | 930-950 | 1260-1280 | ≥16 | 59-61 | 400-444 | |||||||||||
400 | 980-1050 | 1290-1330 | 16-17 | 60-62 | 388-444 | |||||||||||
500 | 970-1000 | 1110-1200 | 14-15 | ≥60 | 363-388 |
Механические свойства при повышенных температурах |
Состояние поставки | Сечение
(мм) | t испыт.
(°C) | t отпуска
(°C) | sТ | s0,2 (МПа) | sB (МПа) | d5 (%) | d4 | d | d10 | y
(%) | KCU
(кДж/м2) | HB | HRC | HRB | HV | HSh |
---|---|---|---|---|---|---|---|---|---|---|---|---|---|---|---|---|
Деформированное состояние. Скорость деформирования 2,5 мм/мин | ||||||||||||||||
700 | ≥215 | ≥58 | ≥90 | |||||||||||||
800 | ≥145 | ≥70 | ≥92 | |||||||||||||
900 | ≥98 | ≥75 | ≥88 | |||||||||||||
1000 | ≥59 | ≥80 | ≥90 | |||||||||||||
1100 | ≥29 | ≥80 | ≥90 | |||||||||||||
1200 | ≥20 | ≥80 | ≥88 | |||||||||||||
1250 | 20 | 68 | 80 | |||||||||||||
Поковки дисков диаметром 700 мм и высотой 30-80 мм. Отжиг с двумя переохлаждениями 200-230 °С и 140-180 °С. Закалка в масло с 960-980 °С + Отпуск при 640-670 °С (образцы тангенциальные). При 20 °С НВ=285 | ||||||||||||||||
20 | 680-690 | 870-890 | ≥16 | 52-55 | ||||||||||||
200 | 630-650 | 780 | 12-15 | 47-53 | ||||||||||||
300 | 610-630 | 730-760 | 11-13 | 50-53 | ||||||||||||
400 | 600-630 | 730-750 | 11-12 | ≥45 | ||||||||||||
500 | 500-540 | 560-610 | ≥15 | 54-56 | ||||||||||||
600 | 280-310 | 330-340 | 28-30 | 83-84 | ||||||||||||
Пруток. Отжиг при 760-780 °С (выдержка 2 ч), охлаждение с печью + Закалка в масло с 950-975 °С (выдержка 1 ч) + Отпуск при 600 °С (выдержка 3-6 ч). При 20 °С НВ=269-302 | ||||||||||||||||
20 | 680-710 | 860-880 | 19-22 | 60-63 | ||||||||||||
300 | 620-640 | ≥720 | ≥16 | 65-67 | ||||||||||||
400 | 580-590 | 670-680 | 14-15 | 63-64 | ||||||||||||
500 | 510 | 550-570 | 17-18 | 68-70 | ||||||||||||
550 | ≥430 | ≥460 | ≥20 | ≥81 |
Механические свойства при испытании на длительную прочность |
Предел ползучести, МПа | Скорость позучести, %/ч | Температура испытания, °C | Предел длительной прочности, МПа | Длительность испытания, ч | Температура отпуска, °C |
---|---|---|---|---|---|
274 | 2/100 | 450 | 608-686 | 1000 | 400 |
588-666 | 2000 | ||||
617 | 200 | 450 |
Дополнительная информация |
Нагрев отливок до температур свыше 900 °С должен производиться либо с эмалевым покрытием, либо в защитной среде (гелий, аргон, с точкой росы 52°С согласно ГОСТ 10157). Для тонколистового горячекатаного (1,5-3,9 мм) и холоднокатаного (0,7-3,9 мм) проката по ГОСТ 5582-75 рекомендуется режим термообработки: Отжиг или отпуск при 650-700 °C, при этом уровень механических свойств готового проката устанавливается по согласованию производителя и потребителя. По ГОСТ 7350-77 для листового горячекатаного (4,0-25,0 мм) и холоднокатаного (4,0-5,0 мм) проката рекомендуется режим термообработки: отжиг или отпуск при 650-700 °C, при этом уровень механических свойств готового проката устанавливается по согласованию производителя и потребителя. По ОСТ 1 90176-75 вариант термической обработки штамповок оговаривается в заказе. При отсутствии указания в заказе заводу-поставщику предоставляется право выбирать режим термической обработки по своему усмотрению. |
Технологические свойства |
Обрабатываемость резаньем | В закаленном и отпущенном состоянии при НВ 330 Kn тв.спл.=0,4 Kn б.ст.=0,3. Для улучшения обрабатываемости и получения твердости НВ ≤ 229 заготовки подвергают отжигу при 620-670 °C в течение 4-8 ч с охлаждением на воздухе. |
Особенности термической обработки | Сталь мартенсито-ферритного класса применяют в закаленном и отпущенном состоянии. Для достижения максимальной прочности изделия из стали 14Х17Н2 подвергают закалке с 975 — 1040 °С, выдержка при толщине изделия до 10 мм — 15 мин, свыше 10 мм — 15 мин + 1 мин на 1 мм максимальной толщины, охлаждение — в масле. Отпуск — при 275 — 350 °С в течение 2 ч + 1 мин на 1 мм максимальной толщины, охлаждение — на воздухе. Нагрев деталей (заготовок) в интервале температур от 500 °С до 800 °С должен производиться со скоростью не более 200 °С в час. В интервале температур 750 — 800 °С необходимо дать выдержку до полного прогрева садки. Дальнейший нагрев до температуры закалки производится по мощности печи. Для деталей толщиной (диаметром) до 120 мм скорость нагрева не лимитируется и выдержка при температуре от 750 °С до 800 °С не производится. Для обеспечения среднего уровня прочности после закалки, изделия подвергают отпуску при 560-650 °С в течение 1 ч + 1 мин на 1 мм максимальной толщины материала, охлаждение на воздухе. Термическая обработка по этому режиму вызывает в изделии склонность к межкристаллитной коррозии. Для достижения высокой коррозионной стойкости изделия из стали 14Х17Н2 после закалки подвергают отпуску при 680-700 °С в течение 30 мин + 1 мин на 1 мм максимальной толщины материала. Температуру нагрева под закалку для изделий, изготовленных из листовой стали 14Х17Н2, можно понижать до 950-975 °С. Сварные изделия из стали 14Х17Н2 обладают пониженной коррозионной стойкостью в зоне термического влияния. Поэтому их необходимо подвергать отпуску при 680-720 °С. Время выдержки -30 мин + 1 мин на 1 мм максимальной толщины изделия. Для уменьшения остаточной магнитной индукции в деталях магнитопровода электромагнитов детали (заготовки) должны подвергаться длительному отжигу. Детали, входящие в узлы трения и уплотнения затвора трубопроводной арматуры, могут подвергаться поверхностной закалке с нагревом токами высокой частоты (ТВЧ) с целью повышения твердости при одновременном сохранении высоких механических свойств в сердцевине детали. Поверхностная закалка с нагревом ТВЧ применяется для деталей толщиной (диаметром) не менее 15 мм и производится только после предварительной улучшающей термической обработки на твердость до 22-31 HRC. Подкалка деталей ТВЧ допускается только при отсутствии требования стойкости стали к межкристаллитной коррозии. Длительный отжиг заготовок применяется для уменьшения остаточной магнитной индукции в деталях магнитопровода электромагнитов и обеспечивает магнитные характеристики для стали марки 14Х17Н2 наименьшая коэрцитивная сила Нс равна 0,1 ка/м при остаточной индукции Вч 0,5 Тл, индукция насыщения Bs равна 1,5 Тл при максимальной коэрцитивной силе Нm 20 ка/м. Сварные узлы и изделия из стали 14Х17Н2 для повышения коррозионной стойкости подвергают отжигу по режиму: нагрев до 680-700 °С, выдержка — 2-3 ч, охлаждение на воздухе при отсутствии требований стойкости к МКК; нагрев до 680-700 °С, выдержка — 3-5 ч, охлаждение на воздухе при требовании стойкости к МКК. |
Свариваемость | Трудносвариваемая. Способ сварки РДС, АрДС. Сварные соединения в зоне термического влияния обладают пониженной стойкостью к МКК и общей коррозии, поэтому после сварки необходим отпуск при 680-700 °С в течение 30-60 мин. |
Склонность к отпускной хрупкости | Склонна. |
Температура ковки | Начала — 1250 °C, конца — 900 °C. Сечения до 350 мм охлаждаются на воздухе. |
Температура критических точек |
Критическая точка | Температура °C |
---|---|
AC1 | 720 |
AC3 | 830 |
AR3 | |
AR1 | 700 |
MN |
Ударная вязкость |
Состояние поставки температура | +20 | -20 | -40 | -60 |
---|---|---|---|---|
Лист толщиной 10 мм в состоянии поставки. Образцы поперечные. | ≥560 | ≥510 | ≥490 | ≥470 |
Лист толщиной 10 мм в состоянии поставки. Образцы продольные. | ≥710 | ≥530 | ≥530 | ≥520 |
Состояние поставки, режим термообработки | HRCэ поверхности | HRCэ сердцевины | HRB | HB | HV | HSD |
---|---|---|---|---|---|---|
ГОСТ 18907-73. Пруток ≥ 5,0 мм, после отжига | ≤302 | |||||
ГОСТ 5949-75. Прокат г/к и кованый. Отжиг или отпуск | ≤285 |
Предел выносливости |
Термообработка, состояние стали | s-1 (МПа) | t-1 (МПа) | n | sB (МПа) | s0,2 (МПа) |
---|---|---|---|---|---|
451 | 1Е+7 |
Коррозионные свойства |
Среда | Температура испытания °C | Скорость коррозии, мм/год | Длительность испытания, ч | Глубина мм/год |
---|---|---|---|---|
Вода дистиллированная | 300 | 50 | 0,08 | |
Пар—воздух | 100 | 100 | 0,005 |
Жаростойкость |
|
Физические свойства |
Температура испытания, °С | 0 | 20 | 100 | 200 | 300 | 400 | 500 | 600 | 700 | 800 | 900 | 1000 | 1200 |
---|---|---|---|---|---|---|---|---|---|---|---|---|---|
Модуль нормальной упругости (Е, ГПа) | 193 | 197 | 164 | 148 | 133 | ||||||||
Модуль упругости при сдвиге кручением (G, ГПа) | |||||||||||||
Плотность (r, кг/м3) | 7750 | 7750 | |||||||||||
Коэффициент теплопроводности (l, Вт/(м · °С)) | 21 | 20,9 | 22 | 23 | 24 | 24 | 25 | 26 | 27 | 28 | 30 | ||
Уд. электросопротивление (R, НОм · м) | 720 | 720 | 780 | 840 | 890 | 990 | 1040 | 1110 | 1130 | 1160 | 1170 | 1180 | |
Коэффициент линейного расширения (a, 10-6 1/°С) | 9,8 | 10,6 | 11,8 | 11 | 11,1 | 11,3 | 11 | 10,7 | 11,4 | 11,4 | 11,5 | ||
Удельная теплоемкость (С, Дж/(кг · °С)) | 462 |
Обозначения |
Механические свойства:
|
mmetallurg.ru
Коррозионно-стойкая жаропрочная сталь 14Х17Н2
Справочник металлопроката
Ни для кого не секрет, что качество, долговечность и надежность эксплуатации металлоконструкций, применяющихся в производстве и строительстве, напрямую зависят от качественности используемых при их изготовлении материалов. Необходимость применения конкретного типа сырья определяется, исходя из будущего предназначения изделия и среды, в которой будет работать та или иная металлоконструкция. Так, для создания металлопродукции, предназначенной для работы в условиях низких температур и агрессивных сред, традиционно применяется коррозийно-стойкая и жароустойчивая сталь 14х17н2.
Преимущества 14х17н2
От других видов стали вышеназванный сплав отличает:
- отличная устойчивость к повышенным температурам (свыше +500 °C), причём при +400 °C эта сталь работает в обычном режиме;
- видимая эффективность работы при колебаниях температуры и её значительном понижении;
- повышенная стойкость к разного рода механическим воздействиям и повреждениям;
- хорошая устойчивость к коррозионному воздействию и пагубному влиянию со стороны агрессивных сред (кислот, влажности и даже щелочей).
Химический состав и свойства стали 14х17н2
Химсостав данного материала включает в себя: хром (на него приходится 16 — 18 процентов), никель (1,6 — 2,5% сплава), марганец и кремний (по 0,8% тот и другой), медь (примерно 0,3проц.), титан (не более 0,2 %), а также малые количества углерода, фосфора и серы.
Сталь 14Х17Н2 принадлежит к категории трудносвариваемых материалов, потому для получения по-настоящему качественных соединений требуется проведение целого ряда допопераций. Необходимой является процедура нагревания деталей до 200 – 300 град., а также дальнейшая термообработка – т.н. отжиг детали. Кроме того, используется дуговая ручная сварка и аргонодуговая сварка. Ввиду того, что места сварки склонны к возникновению коррозии и имеют низкую стойкость к МКК, требуется дополнительный отпуск детали (в течение получаса — часа) при t 680 — 700град.
Максимальная температура, выдерживаемая данной сталью – 400 град. по Цельсию (если воздействие будет длительным). Если же на 14х17н2 воздействовать вдвое большей температурой, 800 град., формируется интенсивная окалина. Наивысшей коррозионной стойкостью материал обладает после процедуры закалки с максимально высоким отпуском.
В качестве заменителя жаропрочной стали марки 14х17н2 применяется сплав марки 20х17н2.
Применение 14х17н2
Хромоникелевую нержавейку 14х17н2 отличает широчайшая область применения. Традиционно она используется для производства валов, дисков, рабочих лопаток, втулок, крепежных деталей и деталей компрессоров, эксплуатирующихся на нитрозном газе, а кроме того, запчастей для машин, работающих в тяжёлых эксплуатационных условиях (при пониженных температурах и в сложных средах).
Благодаря хорошим технологическим и физическим качествам данной стали, она применяется в самых разных отраслях промышленности. Например, сталь данной марки незаменима в авиационной промышленности — её используют при производстве фасонных отливок. Довольно часто 14х17н2 применяется и в химической промышленности.
На современный рынок стройматериалов данная марка стали поступает как фасонный и сортовой прокат, серебрянка, шлифованный и калиброванный пруток, толстого и тонкого листа, в виде поковки, полос и кованой заготовки. Заказать любые разновидности металлопродукции из этого сырья в Челябинской области вы можете в компании «ЧНСК». Вы оцените по достоинству широчайший ассортимент предлагаемых изделий, возможность поставок любого объёма, а также более чем доступные цены.
Круг 14х17н2
Круг 14х17н2 представляет собой прокат с круглым сечением, изготовляемый из коррозионно-стойкой стали, принадлежащей к мартенситно — ферритному классу. Данный прокат выпускается в различных длинах — от 3-рёх до 6-сти метров и классифицируется в зависимости от точности прокатки как обычной (В), повышенной (Б), либо высокой точности (А). Как и исходный материал, на протяжении длительного времени способен выдерживать эксплуатацию при температуре +400 °C.
Круг 14х17н2 серебрянка отличает хорошая устойчивость к механическим повреждениям и воздействию агрессивных сред, кроме того, без проблем может эксплуатироваться в условиях низких температур, что сделало данный вид проката чрезвычайно востребованным в различных сферах промышленности – в судостроении, машиностроении, а также строительной, нефтехимической и бытовой сфере.
Круг сталь 14х17н2 — посмотреть в каталоге
Шестигранник сталь 14х17н2- посмотреть в каталоге
А также можно заказать по телефонам: (351) 725-34-00, (351) 725-42-40, (351)735-96-89.
chnsk.ru
Cталь 14Х17Н2 — ГП Стальмаш
Справочная информация
Характеристика материала сталь 14Х17Н2.
Марка : | 14Х17Н2 | |
Заменитель: | 20Х17Н2 | |
Классификация : | Сталь коррозионно-стойкая жаропрочная | |
| ||
Применение: | рабочие лопатки, диски, валы, втулки, фланцы, крепежные и другие детали, детали компрессорных машин, работающие на нитрозном газе, детали, работающие в агрессивных средах и при пониженных температурах; сталь мартенсито — ферритного класса | |
|
Химический состав в % материала 14Х17Н2
C | Si | Mn | Ni | S | P | Cr | Ti | Cu |
0.11 — 0.17 | до 0.8 | до 0.8 | 1.5 — 2.5 | до 0.025 | до 0.03 | 16 — 18 | до 0.2 | до 0.3 |
Температура критических точек материала 14Х17Н2.
Ac1 = 720 , Ac3(Acm) = 830 , Ar1 = 700 |
Механические свойства при Т=20oС материала 14Х17Н2 .
Сортамент | Размер | Напр. | sв | sT | d5 | y | KCU | Термообр. |
— | мм | — | МПа | МПа | % | % | кДж / м2 | — |
Поковки | до 1000 | 784 | 637 | 12 | 30 | 490 | Закалка 980 — 1020oC, масло, Отпуск 680 — 700oC, воздух, | |
Сорт | 60 | 1080 | 835 | 10 | 30 | 490 | Закалка 975 — 1040oC, масло, Отпуск 275 — 350oC, воздух, | |
Сорт | 60 | 835 | 635 | 16 | 55 | 750 | Закалка 1000 — 1030oC, масло, Отпуск 620 — 660oC, воздух, |
Твердость материала 14Х17Н2 после закалки и отпуска , | HB 10 -1 = 228 — 293 МПа |
Твердость материала 14Х17Н2 после отжига , | HB 10 -1 = 285 МПа |
Физические свойства материала 14Х17Н2 .
T | E 10— 5 | a 10 6 | l | r | C | R 10 9 |
Град | МПа | 1/Град | Вт/(м·град) | кг/м3 | Дж/(кг·град) | Ом·м |
20 | 1.97 | 20.9 | 7750 | 720 | ||
100 | 9.8 | 21.7 | 780 | |||
200 | 10.6 | 22.6 | 840 | |||
300 | 1.67 | 10.8 | 23.4 | 890 | ||
400 | 11 | 24.3 | 990 | |||
500 | 1.51 | 11.1 | 25.1 | 1040 | ||
600 | 1.36 | 11.8 | 25.9 | 1110 | ||
700 | 11 | 26.8 | 1130 | |||
800 | 10.7 | 28 | 1160 | |||
900 | 11.4 | 29.7 | 1170 | |||
1000 | 11.5 | 1180 | ||||
T | E 10— 5 | a 10 6 | l | r | C | R 10 9 |
Технологические свойства материала 14Х17Н2 .
Свариваемость: | трудносвариваемая. |
Склонность к отпускной хрупкости: | склонна. |
Зарубежные аналоги материала 14Х17Н2
Внимание! Указаны как точные, так и ближайшие аналоги.США | Германия | Япония | Франция | Англия |
— | DIN,WNr | JIS | AFNOR | BS |
Обозначения:
Механические свойства : | |
sв | — Предел кратковременной прочности , [МПа] |
sT | — Предел пропорциональности (предел текучести для остаточной деформации), [МПа] |
d5 | — Относительное удлинение при разрыве , [ % ] |
y | — Относительное сужение , [ % ] |
KCU | — Ударная вязкость , [ кДж / м2] |
HB | — Твердость по Бринеллю , [МПа] |
Физические свойства : | |
T | — Температура, при которой получены данные свойства , [Град] |
E | — Модуль упругости первого рода , [МПа] |
a | — Коэффициент температурного (линейного) расширения (диапазон 20o — T ) , [1/Град] |
l | — Коэффициент теплопроводности (теплоемкость материала) , [Вт/(м·град)] |
r | — Плотность материала , [кг/м3] |
C | — Удельная теплоемкость материала (диапазон 20o — T ), [Дж/(кг·град)] |
R | — Удельное электросопротивление, [Ом·м] |
Свариваемость : | |
без ограничений | — сварка производится без подогрева и без последующей термообработки |
ограниченно свариваемая | — сварка возможна при подогреве до 100-120 град. и последующей термообработке |
трудносвариваемая | — для получения качественных сварных соединений требуются дополнительные операции: подогрев до 200-300 град. при сварке, термообработка после сварки — отжиг |
yaruse.ru