Медь Исл выплавка — Справочник химика 21
Самые древние следы выплавки меди датируются археологами 7-6-м тыс. до н.э. Еще раньше человек познакомился с самородными металлами золотом, серебром, медью, а затем и с метеоритным железом. Овладение искусством выплавки меди из окисленных медных руд с применением древесного угля и придания ей нужной формы литьем в 5-4-м тыс. до н. э. привело к быстрому росту ее производства и расширению сфер использования. Центром металлургии меди в то время был древний Египет. Этот период развития цивилизации археологи называют медным веком. К середине 2-го тыс. до н. э. относится освоение на Ближнем Востоке и в Центральной Европе получения меди из гораздо более распространенных в природе сульфидных руд с применением предварительного обжига руды на воздухе и рафинирования меди путем повторного плавления с различными флюсами. [c.32]В процессе выплавки меди из руды СигЗ образуется 802. Если предположить, что ежегодно получают
В ряде технологических процессов в металлургической промышленности промежуточным или готовым продуктом являются сульфиды металлов. Сульфидирование металлов и их окислов широко применяют в пирометаллургических процессах, протекающих в цветной и черной металлургии в печах при высоких температурах. Сульфидирование является основны.м процессом при выплавке меди, никеля II кобальта из их окислов. Весьма целесообразно применение ВОС при производстве сульфидов бария, стронция, натрия и др. [c.104]
Пирометаллургические методы выплавки меди нецелесообразно применять для переработки бедных руд, не поддающихся обогащению. К этой категории относятся окисленные руды как бедные, так и более богатые, а также отвалы бедных сульфидных руд и хвостов от обогащения. Для этого сырья применяются методы выщелачивания меди из руды и ее извлечение из растворов посредством осаждения железом или электролиза с нерастворимыми анодами.
[c.219]После получения металла из руды может оказаться необходимой его дальнейшая очистка. Например, губчатая медь, получаемая выплавкой из медных руд, имеет чистоту приблизительно 99%. Она содержит небольшие примеси мышьяка, сурьмы, сере- [c.358]
Выплавку меди из руд, содержащих оксиды, осуществляют путем прокаливания их с углем [c.417]
Первыми используемыми металлами были, вероятно, золото и серебро, поскольку их можно было найти в природ в свободном состоянии. Применяли их в основном в декоративных изделия . Медь начали использовать около 8000 лет до нашей эры для изготовления орудий труда, оружия, кухонной утвари и украшений. Около 3800 лет до нашей эры была изобретена бронза — сплав меди и олова. В результате человечество перешло из каменного в бронзовый век. Затем был найден способ выплавки железа, и начался железный век. По мере того как люди накапливали свой химический опыт, расширялся и круг полезных материалов, которые человек научился получать путем переработки самых разнообразных руд.
Древесный уголь получают сухой перегонкой дерева (нагревание дерева без доступа воздуха). Он употребляется в металлургии для выплавки высокосортного чугуна и рафинирования меди, для очистки спирта от посторонних примесей, для изготовления активированного угля, применяемого в противогазах, для производства черного пороха, в медицине, в быту и т. д. [c.464]
Г. Выплавка меди из руды и металлолома (обрезки и стружки) [c.47]
Важным источником получения диоксида серы служат отходящие газы заводов цветной металлургии. Значение этого источника видно хотя бы из того, что при выплавке 1 т меди образуется 7,5 т SO2, из которого можно получить более 10 т серной кислоты. [c.465]
Кокс используется в различных процессах и в зависимости от них кокс может быть разделен на доменный кокс — для выплавки чугуна в доменных печах литейный кокс — для плавки чугуна и других металлов в вагранках кокс для электротермических производств — для получения фосфора, карбида кальция, ферросплавов кокс для шахтных печей — применяется для обжига руд цветных металлов (медь, олово, цинк, никель, кобальт) и для обжига известняка кокс — для подготовки рудного сырья (агломераты и окатыши) кокс для бытовых целей.
[c.9]Выплавка меди из оксидных руд несравненно проще, чем из сернистых, так как сводится к легко протекающему восстановлению углем. Именно таким путем и добывали, по-видимому, медь в древности. Выработка ее в Египте достигала значительных размеров уже за 3000 лет до н. э. [c.418]
Металлы можно извлекать из их руд непосредственно электролитическим или химическим восстановлением. Электролитическое восстановление, которое уже обсуждалось в разд. 19.6, используется в промышленных масштабах для получения наиболее активных металлов натрия, магния и алюминия. Менее активные металлы — медь, железо и цинк-получают в промышленных масштабах с помощью химического восстановления, причем большую часть менее активных металлов получают методом высокотемпературного восстановления в расплавленном состоянии. Поэтому такие процессы называются выплавкой.
Получение. Выплавка меди и ее сульфидных руд — сложный процесс. При обжиге сернистые концентраты частично окисляются до оксидов меди, которые затем восстанавливаются избытком суль- [c.412]
Так, аргон используют в качестве защитной атмосферы (предохранение от окисления) при выплавке таких металлов, как уран, торий, германий, цирконий и гафний, а также при получении чистого кремния. На практике широко распространен способ электросварки (а также наплавки и резки) металлов в защитной атмосфере инертного газа —обычно аргона (аргонно-дуговая сварка титановых, алюминиевых, магниевых и др. сплавов, меди, вольфрама, нержавеющих сталей и т. д.). Чистые гелий и аргон—непревзойденные защитные газы при работе с химически малоустойчивыми веществами, легко поддающимися окислению.
[c.544]В металлургии фосфорные руды применяются в смеси с железной рудой для выплавки в доменной печи феррофосфора и при переработке в доменной печи малофосфористых железных руд, не пригодных для получения нормального томасовского или литейного фосфористого чугуна. Апатито-нефелиновые руды используются также в литейном деле (для получения металла с повышенным содержанием фосфора), при получении фосфористой меди, в качестве раскислителя при производстве фосфористой бронзы и др. [c.19]
Реальные химические и металлургические реакции совершаются с участием растворов. Расплавленные чугун, сталь, медь, другие цветные металлы представляют собой жидкие растворы различных элементов, преимущественно неметаллов (углерод, кислород, сера и др.) в основном металле. Расплавленные шлаки доменных и сталеплавильных печей являются растворами оксидов. Промежуточный продукт при выплавке меди (штейн) есть раствор сульфидов меди и железа. Подавляющее большинство промышленных сплавов содержит в своем составе твердые растворы. Сталь — твердый раствор углерода в железе. Предшественница железа в истории техники — бронза есть раствор олова и меди. Водные растворы солей, кислот и оснований широко используются в гидрометаллургии при извлечении цветных металлов из руд. Значение водных растворов выходит за рамки техники вследствие их исключительной роли во всех биологических процессах.
Выплавка меди, из ее сернистых руд распадается на несколько стадий. Прежде всего руду обжигают на воздухе для удаления главной массы содержащейся в ней серы. Обожженную руду с добавкой флюсов затеи переплавляют. При этом пустая порода и часть железа переходят в шлак, а СигЗ, Ре8 и небольшие количества других примесей сплавляют в штейн (который собирается на дне печи). Последний переводят в специальные конверторы, где медь освобождается от серы и железа путем продувания сквозь расплавленную массу воздуха.
[c.418]Несмотря на высокую стоимость выплавки металла в вакуумных печах, их использование расширяется, так как они окупаются высоким качеством получаемого металла и малым угаром дорогостоящих легирующих присадок. Детали, изготовленные из стали, выплавленной в вакуумных печах, имеют в 2—2,5 раза больший срок службы, а медь — меньшее удельное электрическое сопротивление. [c.149]
Выплавка черновой меди из окисленных медных руд. ……. [c.473]
Возникновение М. относится к глубокой древности, выплавка меди производилась уже в 7-б-м тыс. до н.э. (юго-зап. часть Малой Азии). Вначале человек познакомился с самородными металлами-золотом, серебром, медью и метеоритным железом, а затем научился производить металлы. Первые металлич. изделия изготовлялись в холодном состоянии. После открытия горячей обработки (ковки) металлич. изделия получают более широкое распространение. Первоначально выплавку Си производили из окисленных медных руд (литье, 5-4-е тыс. до н.э.), переработка сульфидных руд, их окисление и рафинирование Си относятся ко 2-му тыс. до н. э. (Ближний Восток и Центр. Европа). Во 2-м тыс. до н.э. медь стала вытесняться ее сплавом — бронзой (бронзовый век). В сер. 2-го тыс. до н.э. осваивается получение Ре из руд (сыродутный процесс). В дальнейшем успехи в произ-ве Ре (овладение процессами его науглероживания и закалки) привели к появлению литого металла и стали. Эти усовершенствования обеспечили главенствующее положение черным металлам среди материалов уже в 1-м тыс. до н.э. (железный век). На протяжении почти трех тысячелетий М. железа не претерпевала принципиальных изменений. В 18 в. в Европе открыт способ произ-ва литой стали (тигельная плавка), а в 19 в.-еще три новых процесса (бессемеровский, мартеновский и тома-совский).
Выплавка меди из ее сульфидных руд или концентратов представляет собою сложный процесс. Обычно он слагаетсн на следующих операций обжиг. [c.570]
Селен и теллур встречаются в таких редких минералах, как СпзЗе, РЬ5е, А 25е, Си2Те, РЬТе, А 2Те и Аи Те, а также в виде примесей в сульфидных рудах меди, железа, никеля и свинца. С промышленной точки зрения важными источниками добычи этих элементов являются медные руды. В процессе их обжига при выплавке металлической меди большая часть селена и теллура остается в меди. При электролитической очистке меди, описанной в разд. 19.6, такие примеси, как селен и теллур, наряду с драгоценными металлами золотом и серебром скапливаются в так называемом анодном иле. При обработке анодного ила концентрированной серной кислотой приблизительно при 400°С происходит окисление селена в диоксид селена, который сублимируется из реакционной смеси [c.307]
Выплавка металлов-процесс получения металлов из руд и шихт, основанный на полном их расплавлении и разделении расплава. Таким образом получают сталь, чугун, никель, кобальт, свинец, черновые медь и кадмий, олово, сурьму и др. (см. Металлургия).
Перспективными в гидрометаллургии меди могут оказаться и другие методы, основанные на обработке сульфидов расплавленной серой, электролизе расплавов или органических растворов солей меди, модернизации традиционных методов выплавки меди. [c.68]
Как увеличение объема переработки медного лома металлургической промышленностью повлияет на доступность этого металла в будущем Ограничена ли чем-нибудь выплавка меди из отходое Почему [c.148]
Большую часть висмута получают переработкой отходов произ-водства свинца и меди (из анодных шламов, образующихся при рафинировании этих металлов, нылей и возгонов, выделяющихся при их выплавке). [c.425]
В процессе восстановительной плавки сопутствующие глинозему окислы восстанавливаются при температурах более низких, чем глинозем (кроме окиси кальция и магния), что и послужило основой для создания этого процесса. Однако восстановление окислов идет не до конца (5—7% окислов остается в электрокорунде). Наличие окислов в больших количествах плохо влияет на рост кристаллов корунда. При оксисульфидной плавке вредные примеси при помощи сульфидирующих агентов (например, РеЗг) предварительно переводят в сульфиды. Сульфидирование металлов и их окислов широко применяют в цветной и черной металлургии. Оно является основным процессом при выплавке меди, никеля и кобальта из их окислов, а также при производстве полупроводников и др. Конец реакции сульфидирования определяют по содержа- [c.33]
В результате в печи образуются два жидких слоя — сверху более легкий шлак, а внизу — расплав, состоящий из FeS и U2S (штейн). Шлак сливают, а жидкий штейн переливают в конвертор, в- который добавляют флюс и вдувают воздух. Конвертор для выплавки меди аналогичен используемому для получения стали, только воздух в него подается сбоку (при подаче воздуха снизу медь сильно охлаждается и затвердевает). В конверторе образуется расплавленная медь, сульфид железа превращается в оксид, который переходит в шлак [c.582]
Литье меди и ее сплавов. При выплавке медных и особенно медно-цинковых сплавов вместо печей, отапливаемых нефтяным топливом, применяют электрические печи. Чистое газовое топливо используют весьма редко. Основные причины, ограничивающие применение газового топлива, — возможность потенциальных потерь металла в виде окиси цинка при выплавке в отапливаемых открытым пламенем печах и опасение загрязнения чистых металлов сульфидами или какими-либо окислами, особенно ряда сплавов, нуждающихся в тщательном рафинировании. Однако имеются примеры успешного использования газового топлива. В ФРГ применяют небольшие закрытого типа тигли, обогреваемые снаружи СНГ. Газовые печи оригинальной конструкции имеются в США. Печь, разработанная фирмой Асарко (рис. 66), загружается сверху медными катодами. Воздух и газ вдуваются внутрь печи по ее окружности вблизи донной части через горелки предварительного смешения. При этом для обеспечения необходимо качества металла следует выдерживать соотношение газ— воздух. Например, избыток воздуха не должен превышать 0,5%, содержание серы в СНГ — 0,001%. В атмосфере печи содержание водорода должно быть не более 1 %. Соблюдение этих условий гарантирует достижение требуемого качества переплавляемой меди. [c.314]
Выплавка меди из ее сульфидных руд или концентратов представляет собой сложный процесс. Обычно он слагается из следующих операций обжиг, плавка, конвертирование, огневое и электролитическое рафинирование. В ходе обжига большая часть сульфидов примесных элементов преврап(ается в оксиды. Так, главная примесь большинства медных руд пирит FeSj превращается в РегОз- Газы, отходящие при обжиге, содержат SO2 и используются для получения серной кислоты. [c.534]
Как область практич. деятельности X. уходит корнями в глубокую древность. Так, задолго до нашей эры в разл. регионах Древнего мира (Египет, Китай, Индия) возникли ремесла, основанные на использовании хим. процессов выплавка металлов (железо, медь) из руд, изготовление сплавов (бронза) получение кожи из шкур животных с помощью дубильных в-в крашение тканей прир. красителями произ-во стекла и керамики. Отсюда берут начало примитивные хим. знания. Никаких науч. представлений о составе в-ва и его превращениях в Древнем мире не существовало. Отсутствовало само понятие хим. элемента его заменяло неопределенное натурфилософское учение о стихиях, или элементах (огне, воде, воздухе, земле), получившее т1аиб. законченный вид у Аристотеля. Эти отвлеченные представления не были связаны с практикой. [c.651]
История химии. Как основанная на опыте практика, X. возникла вместе с зачатками человеческого общества (использование огня, приготовление пищи, дубление шкур) и в форме ремесел рано достигла изощренности (получение красок и эмалей, ядов и лекарств). Вначале человек использовал хим. изменения биол. объектов (брожение, гниение), а с полным освоением огня и горения — хим. процессы спекания и сплавления (гончарное и стекольное произ-ва), выплавку металлов. Состав древнеегипетского стекла (4 тыс. лет до н. э.) существенно не отличается от состава совр. б)ггылочного стекла. В Египте уже за 3 тыс. лет до н.э. выплавляли в больших кол-вах медь, используя уголь в качестве восстановителя (самородная медь применялась с незапамятных времен). Согласно клинописным источникам, развитое произ-во железа, меди, серебра и свинца существовало в Месопотамии также за 3 тыс. лет до н. э. Освоение хим. процессов произ-ва меди и бронзы, а затем и железа являлось ступенями эволюции [c.257]
Туман фосфорной кислоты Ваграночная пыль Колошниковая (доменная) пыль Пыль известковых печей Пыль, содержащая окислы цинка, из печей, выплавляющих латунь Щелочной аэрозоль из известковых печей Аэрозоль сульфата меди Дурногихнущие вещества мыльных фабрик Пыль мартеновских печей, работающих на дутье, обогащенном кислородом Пыль мартеновских пе- ей, работающих на воздушном дутье Пыль из томасовского конвертера Пыль, образующаяся при выплавке 45уо ферросилиция в закрытых электроне 1зх Пыль, образующаяся в печах производства целлюлозы Производство черного щелока обработка предварительно увлажненные газов обработка сухих газов [c.145]
Локальные загрязнения биосферы. Зафязнение окружающей среды происходит весьма неравномерно. Основные очаги анфопогенного воздействия на природу расположены в регионах с развитой промыщ-ленностью, максимальной конценфацией населения и интенсивным сельскохозяйственным производством. Такие зафязнения, обычно наблюдающиеся вокруг какого-либо промышленного предприятия, крупного рудника, населенного пункта, называются локальными. Их химизм определяется, с одной стороны, отраслевой принадлежностью источника зафязнения, с другой — рельефом, климатическими особенностями и другими природными условиями места зафязнения. Так, почва вокруг рудников полиметаллических руд и комбинатов по выплавке цветных металлов всегда содержит повышенное количество тяжелых металлов — меди, цинка, свинца, кадмия. Такое же локальное зафязнение почвы свинцом наблюдается вдоль автострад с напряженным движением. [c.48]
Восстановительная способность углерода широко используется в пирометаллургии. Для этого служит кокс — высокопористая прочная форма углерода, получаемая обжигом каменного угля. Кокс применяют для выплавки чугуна, при восстановительном обжиге большинства цветных металов меди, никеля, свинца, цинка, олова, сурьмы, мышьяка и др. Восстановление коксом обычно протекает через стадию образования монооксида углерода по схеме [c.147]
Кадмий открыт в 1817 г. немецким ученым Ф. Штромейером в карбонате цинка и назван им по греческому названию руды цннка кадменя или кадмиа , которую древние греки добавляли к меди при выплавке латуни. [c.104]
chem21.info
Технология производства и добычи меди. Минеральные базы.
Добыча меди тесно связана с технологией извлечения металла из руды и производится экономически выгодными способами с учетом специфики месторождения.
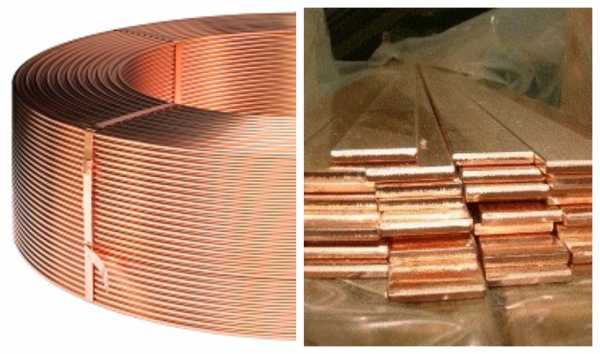
Технология производства медных изделий.
Минеральная база для извлечения металла
Сырьем для добычи медной руды являются естественные образования минералов, в которых металлический компонент содержится в количестве, необходимом для экономически выгодной промышленной разработки.
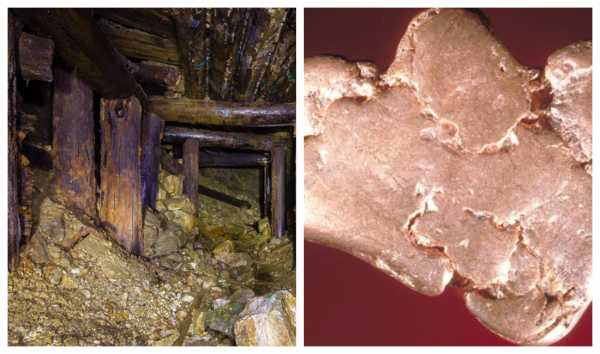
Сырье для добычи медной руды.
Рудные месторождения представлены силикатными, карбонатными, сульфатными соединениями, оксидами, образовавшимися в зоне окисления.
Среди разведанных минералов для промышленной разработки можно выделить:
- халькопирит;
- халькозин;
- борнит;
- куприт;
- самородная медь;
- брошантит;
- азурит;
- кубанит;
- малахит;
- хризотил.
В руде концентрация металла составляет 0,3–5%, а в минералах показатель концентрации составляет 22–100% (самородный металл). Месторождения меди находятся в генетической взаимосвязи с другими ценными компонентами, которые добываются как дополнительные химические элементы к основному процессу.
Среди попутных компонентов встречаются:
- платаноиды;
- серебро;
- золото;
- теллур;
- галлий;
- молибден;
- висмут;
- никель;
- титан;
- цинк.
Руда для извлечения меди содержит мышьяк, сурьму, реже ртуть. В зависимости от вида попутных химических элементов различают типы месторождений, среди которых главное значение имеют:
- медно-никелевый;
- медно-колчеданный;
- медистых песчаников и сланцев;
- медно-порфировый.
Скарновые месторождения металла и кварцево-сульфидные образования имеют подчиненное значение. В перспективе в качестве сырья для промышленного производства металла рассматриваются железомарганцевые конкреции, находящиеся в донных отложениях Мирового океана.
Способы добычи
Как добывают медь на рудных месторождениях? Низкая концентрация металла в породе предусматривает обработку большого количества материала. Для получения единицы массы металла требуется переработать 200 единиц руды.
Медь, добыча которой в основном производится открытым способом, находится на глубине до 1000 м. Глубина открытых разработок достигает 150–300 м, а в отдельных случаях до 600 м. Подземным способом разрабатываются залежи, находящиеся на глубине до 1000 м.
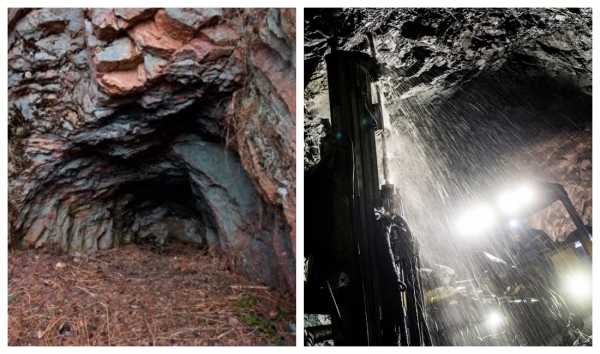
Переработка руды в поисках меди.
Определенные стандарты регламентируют целесообразность углубления разработок с целью извлечения рудного сырья. Это связано с технологией добычи, дополнительными затратами и снижением производительности оборудования, увеличивающими себестоимость сырья.
Поэтому в металлургической отрасли широко используется открытый способ, отличающийся незначительными потерями при разработке. Хотя и здесь есть свои минусы, связанные со складированием пустой породы.
Например, в 2013 году в США на медном карьере Kennecott Utah Copper Bingham Canyon Mine произошел оползень. Глубина карьера Бингем Каньон около 1 км, а диаметр около 4 км. Добыча руды здесь производилась в течение 150 лет.
Доставка сырья к месту переработки осуществлялась автомашинами грузоподъемностью 231 т. Горняки были предупреждены об опасном явлении и были готовы к развитию событий. Стена карьера двигалась со скоростью несколько дюймов в сутки, а предпринятые попытки укрепления не дали желаемого результата.
Условия добычи сырья предполагают использование технологии последовательной разработки с использованием:
- самоходного оборудования;
- ведения работ во время добычи сырья;
- закладки специальными материалами выработанного пространства с целью безопасности дальнейшей разработки.
Каждый технологический процесс предусматривает снижение потерь при разработке месторождений, улучшение показателей по выпуску руды.
При выемке руды слоями обеспечивается полное использование запасов. В условиях глубоких карьеров применяют циклично-поточную технологию, учитывающую особенности залегания руды.
Технология извлечения металла
Для отделения породы, не содержащей ценный компонент, используют метод флотации. Только незначительное количество сырья, содержащего медь в повышенной концентрации, подвергается непосредственной плавке. Выплавка металла предполагает сложный процесс, включающий такие операции:
- обжиг;
- плавка;
- конвертирование;
- рафинирование огневое и электролитическое.

Плавка сырья.
В процессе обжига сырья содержащиеся в нем сульфиды и примеси превращаются в оксиды (пирит превращается в оксид железа). Газы, выделяющиеся при обжиге, содержат оксид серы и используются для производства кислоты.
Оксиды металлов, образованные в результате влияния температурного градиента на породу, при обжиге отделяются в виде шлака. Жидкий продукт, полученный при переплавке, подвергается конвертированию.
Из черновой меди извлекают ценные компоненты и удаляют вредные примеси путем огневого рафинирования и другие металлы путем насыщения жидкой смеси кислородом с последующим разливом в формы. Отливки используются в качестве анода для электролитического способа очистки меди.
Сырье, в котором находятся медь и никель, подвергается обогащению по схеме выборочной флотации с целью получения концентрата металлов. Железомедные руды подвергаются магнитной сепарации.
Руды медистых песчаников и сланцев, жильных пород и самородного металла перерабатываются с целью извлечения медного концентрата. Обогащение производится гравитационным способом.
Метод флотации применяется для смешанных и окисленных руд, но чаще используется химический способ и бактериальное выщелачивание.
Высокое содержание меди характерно для концентратов, извлеченных из халькозина и борнита, а низкое — для халькопирита.
Обогащение руды с незначительным содержанием меди могут проводить гидрометаллургическим способом, состоящим в выщелачивании меди серной кислотой. Из полученного в результате процесса раствора выделяют медь и сопутствующие металлы, в том числе драгоценные.
Похожие статьи
ometallah.com
Плавка меди
Медь и медные сплавы можно приготовить во всех печах, обеспечивающих получение температур 1000—1300°С. Однако предпочтительнее использовать агрегаты, в которых перегрев до этих температур осуществляется в более короткое время. В этом отношении применяемые в современной практике печи для плавки меди и медных сплавов можно расположить в следующей последовательности: электрические индукционные (высокочастотные, низкочастотные и на промышленной частоте) печи, электродуговые с косвенной дугой (ДМ), тигельные и отражательные (пламенные) печи, отапливаемые мазутом или газом. Выбор печи обусловлен типом сплава, потребностью в металле, требованиями, предъявляемыми к отливкам, территориальными условиями производства, экономическими соображениями и др. В меднолитейных цехах поэтому можно встретить и допотопные горны, отапливаемые коксом, и современные электрические печи. Наилучшее качество металла получается при плавке в индукционных печах, но при правильном ведении плавки хороших результатов можно добиться, используя любой из перечисленных печной агрегат.
Плавка меди, бронз и латуней в различных печах в основном похожа, но имеются специфические особенности в зависимости от конструкции печей, времени плавки, возможности применения флюсов, разнообразия шихты и др. Общим является требование, чтобы время плавки металла было минимальным, металл был чистым от окислов, газов и вредных примесей, безвозвратные потери металла были небольшими; технология была проста и надежна, а затраты на материалы и обслуживание были минимальными.
Чистая медь применяется в технике в основном в виде проката (проволока, листы, прутки и др.). Фасонные литые изделия из меди трудно получить из-за низких литейных свойств ее. Слитки под прокатку получают отливкой в водоохлаждаемые изложницы или непрерывным методом.
Плавку меди, если необходимо сразу большое количество металла, производят в пламенных отражательных печах емкостью до 50 т и выше. При небольшом производстве медь можно плавить в электрических, а также в тигельных печах. Особо чистую бескислородную медь плавят в вакуумных индукционных печах или в печах с контролируемой атмосферой, исключающей контакт с кислородом.
Плавка меди заключается либо в простом расплавлении и перегреве ее до нужных температур с последующим раскислением, либо одновременно в процессе плавки производят рафинирование (очистку) ее от примесей, если применяемая шихта содержит значительное количество примесей (5—10%).
Рафинировочная плавка проводится в отражательных пламенных печах, где можно легко изменять атмосферу. Процесс окислительно-рафинировочной плавки состоит последовательно из окисления примесей, удаления образовавшихся окислов примесей и восстановления растворенной закиси меди.
Окисление происходит с начала плавки и в течение всего периода расплавления шихты, для этого в печи поддерживают сильно окислительную атмосферу. Окисляются цинк, железо и Другие примеси. Естественно, одновременно окисляется также и медь. Для более полного удаления вредных примесей ванну расплавленной меди продувают сжатым воздухом или кислородом. Окисление примесей происходит в последовательности, соответствующей упругости диссоциации их окислов, как в результате прямой реакции между кислородом и примесью, так и благодаря взаимодействию закиси меди Cu2O с примесями, обладающими большим, чем у меди, химическим сродством к кислороду:
Cu2O + Me = MeО + 2Cu.
По закону действующих масс наибольшая часть примесей окисляется через посредство Cu2O, кроме того, Cu2O хорошо растворяется в меди и обеспечивает удобные условия окисления примесей по всему объему металла. Последовательность окисления примесей, присутствующих в меди, следующая: цинк, железо, сера, олово, свинец, мышьяк, сурьма и т. д. Если имеются примеси алюминия, магния, кремния, то они окисляются в первую очередь, как обладающие более высоким сродством к кислороду.
Образующиеся окислы, имеющие основной характер, всплывают и ошлаковываются кремнеземом шлака:
ZnO + SiO2 → (ZnO • SiO2),
FeO + SiO2 → (FeO • SiO2)
и т. д.
Вместе с примесями в шлак переходит также и Cu2O в количествах, определяемых химическим равновесием между металлом и шлаком:
[Cu2O] + (SiO2) → (Cu2O • SiO2).
Реакция эта нежелательна: она увеличивает потери меди. Поэтому шлак подбирают таким образом, чтобы в его состав входили окислы, у которых основность выше, чем у закиси меди, и они вытесняли бы Cu2O из шлака в металл по реакции
(Cu2O • SiO2) + (Me`O) → (Me`O • SiO2) + [Cu2O].
Такими окислами могут быть CaO, MnO, FeO и др. На практике для этой цели находит применение основной мартеновский шлак состава: 24—40% СаО, 10—15% FeO, 10—15% Аl2О3, 8—12% MnО и 25—30% SiO2. Шлак наводят на поверхность меди при плавке в количестве 1,5—2% от массы шихты. Для разжижения шлака в него дополнительно добавляют плавиковый шпат CaF2, криолит Na3AlF6, кальцинированную соду Na2CO3 и др.
Ошлакование примесей ускоряют перемешиванием металла со шлаком. Перемешивание металла облегчает также удаление из меди свинца, так как он вследствие большей плотности оседает на дне. Сера удаляется в окислительный период в виде газообразного продукта SO2 по реакции:
Cu2S + 2Cu2O ↔ 6Cu + SO2.
Во время удаления серы наблюдается «кипение» металла.
Полноту окисления расплава определяют путем взятия проб на излом. Плотный, неноздреватый грубокристаллический излом коричневого цвета свидетельствует об окончании окислительного периода плавки. С поверхности жидкого металла снимают шлак и приступают к восстановлению закиси меди, которой содержится в растворе после снятия шлака до 10%. Такая медь в твердом состоянии хрупкая и без раскисления непригодна для отливки слитков. Атмосферу печи делают восстановительной, т. е.
горение факела происходит с избытком топлива и недостатком воздуха (коптящее пламя). Восстановление меди из закиси усиливается операцией, которую принято называть «дразнением» металла. Дразнение производится погружением в расплав сырых осиновых или березовых бревен. При сгорании дерева выделяются водяные пары и продукты перегонки древесины (водород и углеводороды), вследствие чего металл бурно кипит, хорошо перемешивается и более активно взаимодействует с восстановительной атмосферой печи.
Поверхность ванны на этот период покрывают древесным углем для усиления восстановительной атмосферы. Закись меди, растворенная в металле, соприкасаясь с такой атмосферой, восстанавливается: Cu2O + CO = 2Cu + CO2.
Поскольку медь в этот момент содержит большое количество кислорода, погружение сырых бревен относительно неопасно в отношении возможности насыщения металла водородом, так как его растворимость в меди при значительном количестве кислорода очень мала.
Проба на излом хорошо раскисленной меди имеет плотный, мелкозернистый излом светло-розового цвета. Металл считается готовым к разливке, когда содержание закиси меди доводится примерно до 0,4%, дальнейшее уменьшение содержания Cu2O не считается желательным, так как с этого момента возрастает опасность насыщения меди водородом, который при последующей кристаллизации разлитой меди способен взаимодействовать с кислородом с образованием пузырьков паров воды, снижающих плотность и свойства меди.
Плавка меди из чистой шихты состоит из расплавления, перегрева, раскисления и разливки. Для этой цели в заготовительных цехах применяют электрические индукционные печи. Плавку ведут обычно под защитным покровом прокаленного древесного угля, который предохраняет металл от окисления. После расплавления шихты в ванну вводят раскислитель — фосфористую медь в количестве 0,1—0,3% от массы шихты. Затем расплав тщательно перемешивают, контролируют по излому, выдерживают в течение 3—5 мин, а затем по достижении температуры 1150—1200°С разливают.
Для удаления кислорода применяется также литий, который является хорошим раскислителем меди. Иногда применяют комплексный раскислитель из лития и фосфора (когда надо получить особо чистый металл), а также магний.
Однако почти все раскислители, оставаясь в меди, снижают ее важнейшее свойство — электропроводность, поэтому стремятся, чтобы их количество в меди было минимальным, а наиболее качественную бескислородную медь плавят в печах со специальной защитной атмосферой в виде генераторного газа или же в вакууме, при котором не требуется раскисления.
Бескислородная медь содержит не менее 99,97% Cu — она пластичнее меди обычного состава, более коррозионноустойчива и имеет высокую электропроводность.
Несмотря на плохие литейные свойства меди, в частности низкую жидкотекучесть, из нее можно получить довольно сложные пустотелые отливки литьем в песчаные или металлические формы. Медь в этом случае должна быть очень хорошо раскислена и очищена от водорода (продувкой азотом). Для улучшения ее литейных свойств вводят до 1,0% Sn + Zn + Pb. Чем при меньших количествах этих элементов возможно получение фасонной отливки, тем выше ее свойства (электропроводность и теплопроводность). Из такой меди отливают фурмы доменных печей, задвижки, кольца и другие детали.
www.teh-lib.ru
Выплавка меди по Агриколе « Попаданцев.нет
Как я уже описывал, в медный век медь была гадкого качества.
В Древнем Египте великолепно волочили проволоку из золота или даже серебра — но с медью это не получалось.
Однако, уже в Римской Империи выплавка металлов поднялась на новую высоту, но была ли там медная проволока — я не нашел сведений. Если посмотреть на весь список медных артефактов Римской Империи, то они разделены историками на три группы «литье», «ковка» и «неизвестно» (примерно 20% артефактов). При этом именно медных вещей фактически не осталось — либо бронза, либо латунь (вполне понятно почему, это описано в статье про медь).
Ситуация усугубляется тем, что письменных источников о технологиях меди Римская Империя не оставила. Первым таким трактатом стали 12 томов Георгия Агриколы «О горном деле и металлургии», 1556 года.
Давайте посмотрим, какую именно медную технологию предложил нам Георгий Агрикола…
Разбираться в творении Агриколы непросто.
С одной стороны — он оставил исчерпывающее описание печей и инструментов для работы, а с другой стороны — у него описание не делится на выплавку разных металлов, у него идет исключительно «выплавка руд». При этом его описание — итерационное. То есть берется руда и выплавляется. А уже судя по богатству руды и ее составу вносятся изменение в технологию плавки.
То есть, если сравнивать с современными технологиями, это два типа наводки ракеты — по датчикам GPS и управление по самонаведению или радиолокации.
В первом случае — мы знаем точные координаты цели и отправляем туда ракету. Ракета знает где она находится по этому же GPS и рассчитывает оптимальный маршрут к цели. Это современные методы выплавки, когда мы знаем что именно и в каких концентрациях укладывается в печь, имеем точную температуру в градусах и знаем теплотворную способность кокса. Мы можем все рассчитать заранее и получить именно то, что требуется.
Второй случай — управление по радиолокации. Ракета выпущена в сторону локатора РЛС. Ракета не знает где она находится и не знает где находится цель. Но в каждый момент времени она получает поправки и доворачивает пока не попадет куда требуется. Это методы плавки по Агриколе. Мы не знаем, что засыпаем в печь и мы не знаем что получиться из литника, вплоть до того, что металл вообще не пойдет. Но методом итераций мы доводим технологию до стабильного результата, и весь смысл Агриколы — он описывает что нужно рулить.
Конечно, такая аналогия верна только в самом-самом первом приближении. В реальности две стратегии смешиваются и истина где-то посередине. Поэтому перекопаем Агриколу и найдем место где более-менее описан рецепт. Ситуация усугубляется тем, что по прочтению Агриколы возникает впечатление — у него главной целью была выплавка золота, ну или серебра на худой конец. А медная руда содержит серебро в большинстве случаев (пусть даже в следовых количествах) и поэтому большая часть рецепта — выплавка серебра из медной руды.
Итак, цитируем рецепт:
К смеси, состоящей из трех частей обожженной свинцовой или медной руды и одной часто сырой руды, добавляют концентраты, полученные промывкой этой же руды, и шлаки. Все это закладывают в печь с постоянно открытым выпускным отверстием. Из этой шихты получают штейн, охлаждают его водой и обжигают. Четыре части его смешивают с одной частью сырых колчеданов и переплавляют в той же печи. Из этой шихты опять получают штейн.
….
Если в нем содержится больше количество меди, последнюю извлекают непосредственно после отжига и повторной плавки. Если же в штейне содержится немного меди, то он подвергнется обжигу, но плавка его производится с добавлением небольшого количества мягкого шлака. При этом способе расплавленный свинец на переднем горне поглощает серебро. Из колчеданов, плавающих поверх переднего горна, в третий раз делают штейн и, после обжига и плавки, из него извлекают медь.
….
Чистая медная руда независимо от того, имеет ли она цвет меди, окрашена ли малахитом или азуритом, имеет ли цвет свинца, коричневый или черный цвет — плавится в печи, выпускное отверстие которой закрывается лишь на весьма короткий срок или же постоянно открыто … Если руда содержит много серебра, то большая часть его поглощается расправленным свинцом на переднем горне; остаток же вместе с медью продается владельцу завода, где отделяют серебро от меди.
….
В случае, если такая руда содержит некоторые ископаемые вещества, трудно поддающиеся плавке, как то: колчеданы, цинковые (или кобальтовые) руду, или же представляют собой руду, из которой получают железо, то к ней добавляют сырой легкоплавкий колчедан и шлаки и ведут плавку на штейн. Последний обжигается столько раз, сколько требуется, а медь извлекают из него путем повторной плавки. Если же в штейне содержится некоторое количество серебра, для извлечения которого нужен свинец, то последний прежде всего помещают на переднем горне и, будучи расплавлен, он поглощает серебро.
….
Сырая медная руда низшего качества, имеющая пепельный цвет, или пурпурный, или же черноватый или местами синий, плавится по способу, принятому в Тироле в печи с постоянно открытым выпускным отверстием. К сырой медной руде, взятой в количестве, достаточным для наполнения 18 сосудов (по семь римских модулей), добавляют три тачки свинцовых шлаков, одну тачку сланцев, 20 фунтов легкоплавких камней, а также немного концентратов, полученных из медного шлака и настылей. Все это он плавит в течении 12 часов и получает 6 центнеров первичного штейна и 1/2 центнера смеси, скапливающейся на поду переднего горна и представляющий собой наполовину сплав меди с серебром. В каждом центнере штейна содержится 1/2 фунта серебра.
….
Второй плавильщик извлекает серебро из первичного штейна, переплавляя его со свинцом … Смесь плавят в течении 12 часов и получают 13 центнеров третьего штейна и 11 центнеров смеси меди, свинца и серебра.
….
Третий плавильщик берет 11 тачек третьего штейна, добавляет три тачки трудноплавких шлаков с незначительным содержанием серебра вместе со шлаками, полученными при плавке второго штейна, и концентратами, полученными от промывки настылей, обычно образующихся в это время. После плавки этой шихты получают 12 центнеров четвертого штейна, имеющего название «твердого штейна» и 15 центнеров трудноплавких шлаков. Эти штейны первый и второй плавильщик добавляет к первому и второму штейну при их переплавке. Из 11 тачек четвертого, твердого штейна после трехкратного обжига получают так называемый последний штейн, 1 центнер которого содержит только 1/2 унции серебра. Эти шлаки, как я уже сказал, третий плавильщик добавляет при переплавке третьего штейна.
Из последнего штейна после трехкратного обжига и переплавки получают черновую медь, из которой получают чистую медь … Полученные ковриги после семикратного обжига переплавляются, при этом выделяется медь. Ковриги из меди переносят в другую печь, где подвергают плавке в третий раз для того, чтобы в материале, полученном на поду печи содержалось больше серебра, чем в верхней части.
Итак, что можно сказать по этим рецептам?
Во-первых — для выделения серебра к медной руде добавлялся свинец, и часть свинца оставалась в меди. Свинец в малых количествах не влияет на качество оловянной бронзы, но в латуни или в чистой меди он сильно портит качество.
Во-вторых — основные техпроцессы это обжигание-плавка-обжигание-плавка. Обжиг нужен для того, чтобы некоторые вещества выделились в газовую фазу и улетели (например, мышьяк), чтобы некоторые компоненты окислились и перешли в другую форму и чтобы в из карбонатов удалить углекислоту (перевести в углекислый газ). Поэтому так часто обжигают промежуточный штейн и поэтому шлак используют много раз — чтобы он впитывал примеси.
Ну что же, мы в результате имеем медь.
Это не чистая электролитическая медь. И это даже не химически чистая медь. В ней хватает висмута и свинца, чтобы создать проблемы при волочении проволоки. Однако. скорее всего проволоку сделать можно было бы. Не очень тонкую, но возможно.
Хотя есть также подозрения, что такая медь обрабатывалась никак не лучше римской. Историки на эту тему почему-то молчат, видимо именно историей технологий мало кто занимается.
В любом случае попаданцу придется освоить хотя бы химические методы очистки меди, если его цель — не проволока, а провод.
www.popadancev.net
Способы плавления меди в домашних условиях
Медные изделия получили широкое распространение не только в промышленности, но и в быту. Это дает повод домашним мастерам задуматься о том, как самостоятельно изменить качество материала для дальнейшего изготовления металлических предметов. Плавка меди – особая технология, обеспечивающая ее переход из твердого состояния в жидкое под влиянием высоких температур.
Основные характеристики меди
Металл легко поддается обработке. О его уникальных свойствах знали еще наши предки, о чем свидетельствуют исторические сведения и археологические находки. В природе он встречается как в соединениях, так и в самородном варианте. Поверхность меди мягкая, желтовато-бурого оттенка. Контактируя с воздухом, она затягивается оксидной пленкой. Технические характеристики меди следующие:
Физические свойства меди
- Занимает второе место после серебра по электропроводности и теплопроводности.
- Невысокая температура плавления: для чистой меди она составляет 1083 градусов, для медных сплавов – от 930 до 1140 градусов.
- При температуре 2560 градусов материал начинает закипать.
- Медь является диамагнетиком.
- Подбирая лом для вторичной переработки, важно помнить, что электротехническая медь является самой чистой – без примесей.
- Сплавы из бронзы и латуни, из которых сделаны многие раритетные вещи, могут содержать в себе ядовитые вещества, например, мышьяк.
С такими веществами нужна особая осторожность.
Медь является красивым материалом. Изделия из него выглядят роскошно, благородно. Этим свойством продукт привлекает к себе внимание многих домашних умельцев.
Характеристика способов плавления меди
Плавка меди дома и на производстве проходит одинаково. Процесс изменения состояния осуществляется под влиянием повышения температуры. При достаточном количестве тепла металлическая структура предмета разрушается. Добиться такого эффекта можно несколькими способами.
Муфельная печь
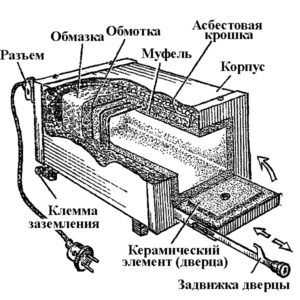
Из чего состоит муфельная печь
Литье с использованием лабораторной муфельной печи, в которой имеется регулировка температуры нагрева. Это довольно простой метод. Сырье предварительно измельчают на части. Чем они меньше, тем быстрее будет плавление.
Подготовленный материал кладут в графитовый тигель и помещают в предварительно разогретую печь. Форма для заливки должна иметь температуру плавления больше, чем у меди. Нагревательное устройство серийного производства оборудовано специальным окном, позволяющим следить за технологическим процессом.
Когда медь достигнет жидкого состояния, тигель железными щипцами извлекают из печи. Проволочным крюком с поверхности расплавленного металла к краям тигля убирают оксидную пленку. После проделанных манипуляций жидкую консистенцию аккуратно заливают в заранее приготовленную емкость.
Газовая горелка
Также осуществляется плавка меди с применением газовой горелки. При отсутствии тигельной печи вполне подойдет ручная портативная газовая горелка. Ее нужно разместить под дном емкости с металлом и следить за тем, чтобы пламя полностью охватывало днище.
Метод позволяет быстро окислять материал, так как предполагает наличие тесного контакта с воздухом. Чтобы не образовывалась толстая оксидная пленка, расплавленную массу присыпают измельченным древесным углем.
Паяльная лампа
Литье меди на основе паяльной лампы происходит так же, как и с газовой горелкой. Способ применим для легкоплавких металлов.
Горн
Растопить медь или её сплавы можно горном. Для этого на хорошо раскаленный древесный уголь помещают тигель с измельченным металлом. Для ускорения процесса используют домашний пылесос, включенный на режиме выдувания.
Труба должна быть небольшого диаметра с железным наконечником, так как пластик расплавится под влиянием высокой температуры. Метод идеально подходит тем людям, кто регулярно занимается литьем металла и в больших объемах.
Микроволновка
Расплавить медь поможет мощная микроволновая печь с измененной конструкцией. Для этого убирают вращающуюся тарелку-поддон. Из огнеупорного кирпича делают муфельную печь, в которую помещают исходный материал. Устройство необходимо для повышения теплосберегающих свойств сырья и защиты элементов техники от перегрева.
Чистую медь трудно плавить, поскольку она в жидком виде обладает плохой текучестью. Специалисты не советуют из такого материала делать мелкие и сложные детали. Для этого подойдут многокомпонентные соединения на основе латуни, олова или цинка, которым высокие температуры не нужны.
Самостоятельная выплавка меди
Для многих людей плавка меди и изготовление из нее всевозможных изделий является увлекательным хобби. Тем, кто мечтает посвятить плавлению металла свободное время, нужно приготовить для работы такие приспособления:
- муфельная печка;
- чистое сырье;
- жаропрочный тигель;
- огнеупорная подставка;
- крюк из стальной проволоки;
- щипцы для извлечения тигля из печки;
- средства индивидуальной защиты: костюм, очки, перчатки.
Действия выполняют согласно инструкции:
- Надевают специальный костюм.
- Исходное сырье измельчают, кладут в тигель.
- Помещают в печь, устанавливают нужный температурный режим. Нельзя допускать, чтобы металл закипал.
- При достижении заданной температуры открывают дверцу, захватывают тигель щипцами, достают из печи, ставят на огнеупорную подставку.
- Стальным крюком к краям емкости сдвигают, образовавшуюся в результате плавления, окисную пленку.
- Жидкую медную массу заливают в специальную емкость, охлаждают.
- В мощных муфельных печах можно подвергать плавлению красную медь и всевозможные сплавы.
Плавление горелкой
Следует помнить, что при плавлении важна азотная среда. Под легкоплавкие медные сплавы, латунь или некоторые марки бронзы можно использовать обычную газовую горелку. Для этого понадобится:
- исходное сырье;
- специальные формы;
- щипцы для извлечения металла с раскаленной рабочей поверхности;
- горелка высокого давления, работающая на газе;
- средства защиты: костюм, очки, перчатки.
Технология плавления сплавов следующая:
- Сырье сильно измельчают. Сделать это можно при помощи напильника, превратив материал в опилки.
- Кладут в специальную форму, сделанную из термостойкого материала.
- Надевают защитный костюм, очки, толстые перчатки.
- Зажигают горелку.
- Нагревательное устройство направляют свободными движениями по корпусу емкости. Для достижения быстрого результата пламя должно касаться поверхности кончиком синего цвета. В этом месте факела – наибольшая температура.
- После того как твердое тело расплавится, тигель захватывают щипцами.
- Жидкую массу выливают в нужную форму.
Если нет газовой горелки, можно использовать обыкновенную паяльную лампу.
Выполняя литье цветных сплавов, каждый мастер должен помнить о технике безопасности:
- В помещении, где ведутся работы, должна быть хорошая вентиляция.
- Во избежание получения ожогов необходимо работать в средствах индивидуальной защиты.
Оптимальная температура воздуха, допустимая влажность воздуха, чистота рабочего места, низкая концентрация вредных веществ атмосферы, хорошая освещенность пространства – факторы, помогающие избежать травматизма.
Видео по теме: Проба плавки меди в домашних условиях
promzn.ru
ВЫПЛАВКА МЕДИ ИЗ СУЛЬФИДНЫХ КОНЦЕНТРАТОВ И РУД
В современной практике не все сульфидные руды меди подвергают флотации. Некоторые из них, более богатые и содержащие мало металлов-спутников, выгодно непосредственно плавить.
Состав минералов при обогащении не изменяется, поэтому между составами руды и концентрата имеются только количественные различия. Следовательно, переработка руд и концентратов имеет одну и ту же физико-химическую основу.
Если сульфидную руду или полученный из нее концентрат расплавить, то расплавленная масса разделится на два жидких слоя: сплав сульфидов и сплав окислов. Расслаивание объясняется различной плотностью и малой взаимной растворимостью расплавленных сульфидов и окислов. Сплав сульфидов называют штейном (от немецкого Stein – камень), а сплав окислов – шлаком. Шлак всплывает над штейном, так как плотность штейнов около 5, а шлаков – около 3.
Еще до плавления при нагревании минералы меди и железа существенно изменяют состав, разлагаясь с образованием простых сульфидов и паров серы:
2FeS2 →2FeS + S2
4CuS → 2Cu2S + S2,
4CuFeS2 → 2Cu2S + 4FeS + S2,
2Cu5FeS4 → 5Cu2S + 2FeS + 1/2S2.
Простые сульфиды железа и меди устойчивы при высоких температурах, поэтому штейн, независимо от минералогического состава сырья, – всегда сплав Cu2S и FeS.
Пустая порода (SiO2, CaO, Аl2О3) переходит при плавке в шлак, который можно легко отделить от штейна и вывести из производства. Следовательно, даже простое расплавление руды или концентрата позволяет сконцентрировать медь в штейне.
Чтобы перевести в шлак и часть железа, надо его сульфид превратить в оксид действием кислорода воздуха:
2FeS + 3О2 → 2FeO + 2SO2.
Но одновременно возможно подобное окисление Cu2S:
2Cu2S + 3О2 → 2Cu2O + SO2.
Однако практически окисляется только сера FeS: оксид меди (I) вновь сульфидируется остаточным сернистым железом:
Cu2O + FeS → Cu2S + FeO.
Эта реакция считается основной в пирометаллургии меди: она позволяет отделить медь от железа, распределив их между жидкими расплавами – штейном и шлаком.
Чем больше железа переведено из сульфида в оксид, тем меньше остается FeS в штейне, а процентное содержание в нем меди увеличивается. Степень десульфуризации, характеризующую выгорание серы, измеряют отношением количества сгоревшей серы (по массе) к исходному содержанию ее в сырье. Чем выше десульфуризация, тем богаче медью получаемый при плавке штейн.
Часть серы можно окислить перед плавкой посредством обжига (иногда обжиг применяют для сырья с высоким содержанием серы). Если при обжиге или плавке окислить всю серу, связанную с железом, все железо перейдет в шлак. Полученный штейн окажется близким по составу к чистой полусернистой меди 79,9 % Сu. Такой штейн называют белым штейном, а на заводах – также «белым маттом».
Для получения меди расплавленный белый штейн продувают воздухом; полусернистая медь окисляется при этом до оксида (I), который в момент образования реагирует с остатком сульфида:
2Cu2S + 3О2 → 2Cu2O + 2SO2;
Cu2S + 2Cu2O → 6Cu + SO2.
Непосредственно при плавке руды или концентрата белый штейн получать невыгодно, так как с увеличением содержания меди в штейне возрастают механические потери в шлаках из-за неполного отстаивания мелких капель штейна. Лучше сначала получать сравнительно бедный штейн и, значит, бедный отвальный шлак, а остатки железа из штейна удалять в конвертере – аппарате, предназначенном для продувки жидкого штейна воздухом.
В начале продувки протекают реакции окисления сульфида железа. Оксид (II) железа ошлаковывается добавленным в конвертер кварцем.
После получения белого штейна конвертерный шлак сливают и отправляют на повторную переработку: он еще богат медью. Белый штейн продолжают продувать воздухом до получения черновой меди. Черновую медь затем рафинируют – очищают от примесей плавкой в других печах и электролизом.
Смешанные медные руды содержат меньше серы, чем сульфидные, поэтому их можно перерабатывать тем же способом, но при меньшей степени десульфуризации.
Окисленные руды можно плавить в смеси с сульфидными рудами. Следовательно, плавка на штейн пригодна для любого сырья, если серы в нем достаточно для образования штейна.
Общая схема пирометаллургии меди дана на рис. 25. Схема показывает, что медные руды либо обогащают, либо сразу плавят на штейн (штрихпунктирная линия). После обогащения полученный концентрат можно сразу плавить (штриховая линия), а можно сначала обжечь для удаления части серы. Предварительный обжиг позволяет использовать серу для производства серной кислоты и получить более богатый штейн.
Штейн, независимо от варианта его получения, продувают в конвертере. Конвертерный шлак богат медью, поэтому его не отбрасывают, а, как уже указывалось, возвращают в рудную плавку.
Благородные металлы (золото и серебро) при плавке руды или концентрата переходят в штейн, а из него – в черновую медь. При рафинировании черновой меди электролизом благородные металлы, а также часть селена и теллура удается извлечь и затем получить в чистом виде.
www.42buketa.ru
Сырье для получения меди
Для получения меди применяют медные руды, а также отходы меди и ее сплавов. В рудах содержится 1-6% меди.
В рудах медь обычно находится в виде сернистых соединений (медный колчедан или халькопирит CuFeS2, халькозинCu2S, ковелин CuS), оксидов (купритCu2O, теноритCuO) или гидрокарбонатов (малахитCuCO3 Cu(OH2), азурит2CuCO3 Cu(OH)2).
Пустая порода состоит из пирита FeS, кварцаSiO2, карбонатов магния и кальция (MgCO3 и CaCO3), а также из различных силикатов, содержащихAl2O3,CaO, MgOи оксиды железа.
В рудах иногда содержится значительное количество других металлов: цинк, олово, никель, золото, серебро, кремний и другие.
Руда делится на сульфидные, окисленные и смешанные. Сульфидные руды бывают обычно первичного происхождения, а окисленные руды образовались в результате окисления металлов сульфидных руд.
В небольших количествах встречаются так называемые самородные руды, в которых медь находится в свободном виде.
Пирометаллургический способ производства меди.
Известны два способа извлечения меди из руд и концентратов: гидрометаллургический и пирометаллургический.
Первый из них не нашел широкого применения. Его используют при переработке бедных окисленных и самородных руд. Этот способ в отличии от пирометаллургического не позволяет извлечь попутно с медью драгоценные металлы.
Второй способ пригоден для переработки всех руд и особенно эффективен в том случае, когда руды подвергаются обогащению.
Основу этого процесса составляет плавка, при которой расплавленная масса разделяется на два жидких слоя: штейн-сплав сульфидов и шлак-сплав окислов. В плавку поступают либо медная руда, либо обожженные концентраты медных руд. Обжиг концентратов осуществляется с целью снижения содержания серы до оптимальных значений.
Жидкий штейн продувают в конвертерах воздухом для окисления сернистого железа, перевода железа в шлак и выделения черновой меди.
Черновую медь далее подвергают рафинированию – очистке от примесей.
Подготовка руд к плавке.
Большинство медных руд обогащают способом флотации. В результате получают медный концентрат, содержащий 8-35% Cu, 40-50% S, 30-35% Fe и пустую породу, главным образом составляющими которой являются SiO2, Al2O3 и CaO.
Концентраты обычно обжигают в окислительной среде с тем, чтобы удалить около 50% серы и получить обожженный концентрат с содержанием серы, необходимым для получения при плавке достаточно богатого штейна.
Обжиг обеспечивает хорошее смешение всех компонентов шихты и нагрев ее до 550-600 0С и, в конечном итоге, снижение расхода топлива в отражательной печи в два раза. Однако при переплавке обожженной шихты несколько возрастают потери меди в шлаке и унос пыли. Поэтому обычно богатые медные концентраты (25-35% Cu) плавят без обжига, а бедные (8-25% Cu) подвергают обжигу.
Температура обжига концентратов применяют многоподовые печи с механическим перегреванием. Такие печи работают непрерывно.
Выплавка медного штейна
Медный штейн, состоящий в основном из сульфидов меди и железа (Cu2S+FeS=80-90%) и других сульфидов, а также окислов железа, кремния, алюминия и кальция, выплавляют в печах различного типа.
Комплексные руды, содержащие золото, серебро, селен и теллур, целесообразно обогащать так, чтобы в концентрат была переведена не только медь, но и эти металлы. Концентрат переплавляют в штейн в отражательных или электрических печах.
Сернистые, чисто медные руды целесообразно перерабатывать в шахтных печах.
При высоком содержании серы в рудах целесообразно применять так называемый процесс медно-серной плавки в шахтной печи с улавливанием газов и извлечением из них элементарной серы.
В печь загружают медную руду, известняк, кокс и оборотные продукты. Загрузку ведут отдельными порциями сырых материалов и кокса.
В верхних горизонтах шахты создается восстановительная среда, а в нижней части печи – окислительная. Нижние слои шихты плавятся, и она постепенно опускается вниз навстречу потоку горячих газов. Температура у фурм достигается 1500 0С на верху печи она равна примерно 450 0С.
Столь высокая температура отходящих газов необходима для того, чтобы обеспечить возможность из очистки от пыли до начала конденсации паров серы.
В нижней части печи, главным образом у фурм, протекают следующие основные процессы:
а) Сжигание углерода кокса
C + O2 = CO2
studfiles.net