Добыча и производство алюминия в России
В современной промышленности наибольшую популярность завоевала алюминиевая руда. Алюминий представляет собой самый распространенный метал из всех, существующих на сегодняшний день, металлов на земле. Кроме того, ему принадлежит третье место в рейтинге по численности залежей в недрах Земли. Также, алюминий является и самым легким металлом. Алюминиевой рудой называется горная порода, служащая материалом, из которого и происходит получение металла. Алюминий обладает определенными химическими и физическими свойствами, которые позволяют адаптировать его применение к совершенно различным областям человеческой деятельности. Таким образом, алюминий нашел свое широкое применение в таких отраслях, как машиностроение, автомобилестроение, строительство, при производстве различной тары и упаковки, электротехники, иных потребительских товаров. Практически каждый бытовой прибор, ежедневно используемый человеком, в том или ином количестве содержит в себе алюминий.
Добыча алюминия
Минералов, в составе которых было в свое время обнаружено наличие данного металла, существует огромное количество. Ученые пришли к выводу, что данный металл можно добывать из более, чем 250 минералов. Однако, абсолютно из всех руд добывать металл не выгодно, поэтому среди всего существующего разнообразия есть наиболее ценные алюминиевые руды, из которых и осуществляется получение металла. Таковыми являются: бокситы, нефелины, а также алуниты. Из всех алюминиевых руд максимальное содержание алюминия отмечено в бокситах. Именно в них находится порядка 50% оксидов алюминия. Как правило, залежи бокситов располагаются непосредственно на земной поверхности в достаточных количествах.
Бокситы представляют собой непрозрачную горную породу, имеющую красный или серый цвет. Самые прочные бокситные образцы по минералогической шкале оцениваются в 6 баллов. Они бывают разной плотности от 2900 до 3500 кг/м3, которая напрямую зависит от химического состава.
Бокситные руды отличаются своим сложным химическим составом, в который входят гидроксиды алюминия, оксиды железа и кремния, а также от 40% до 60% глинозема, являющегося главным сырьем для получения алюминия. Стоит сказать, что экваториальный и тропический земные пояса являются основной местностью, которая славится залежами бокситной руды.
Для зарождения бокситов необходимо участие нескольких компонентов, среди которых одноводный гидрат глинозема, бемит, диаспор, а также различные минералов гидроокиси железа наряду с оксидом железа. Выветривание кислых, щелочных, а в некоторых случаях и основных пород, а также медленное оседание глинозема на дне водоемов и приводит к формированию бокситной руды.
Из двух тонн глинозема алюминия получается вдвое меньше – 1 тонна. А для двух тонн глинозема необходимо добыть порядка 4,5 тонн боксита. Алюминий допустимо получать и из нефелинов и алунитов.
Первые, в зависимости от своего сорта, могут содержать в своем составе от 22% до 25% глинозема. В то время, как алуниты, немногим уступают бокситам, и на 40% состоят из оксида алюминия.
Алюминиевые руды России
Российская Федерация расположилась на 7-ой строке рейтинга среди всех стран мира по количеству добываемых алюминиевых руд. Стоит отметить, что данное сырье на территории российского государства добывается в колоссальном количестве. Однако, страна испытывает существенный дефицит этого металла, и не в состоянии предоставить его в объеме, необходимом для абсолютного обеспечения промышленности. В этом кроется приоритетная причина, из-за которой России приходится приобретать алюминиевые руды у других государств, а также осваивать месторождения с низким качеством минеральных руд.
В государстве существует порядка 50 месторождений, наибольшее число которых располагается в европейской части государства. Однако, Радынкское – наиболее старое месторождение алюминиевых руд в России. Местом его расположения является Ленинградская область. Оно состоит из бокситов, являющиеся с далеких времен главным и незаменимым материалом из которого и производят в последствии алюминий.
Наименование | Содержание % | Процент от общих запасов | Степень промышленного освоения | |
---|---|---|---|---|
AL2O3 | SiO2 | |||
«Красная шапочка» г. Североуральск | 53.7 | 3.7 | 3.1 | В разработке |
Кальинское г. Североуральск | 56.0 | 2.6 | 3.6 | В разработке |
Черемузовское, Свердлоская обл | 54.2 | 4.0 | 11.0 | В разработке |
Ново — Кальинское, г. Североуральск | 55.0 | 3.1 | 7.0 | В разработке |
Иксинское, ст. Наволок | 53.5 | 17.4 | 11.4 | В разработке |
Вежаю-Ворыквинское,. Республика Коми | 49.2 | 0.1 | 11.3 | В стадии подготовки |
Висловское г. Белгород | 49.1 | 7.9 | 12.1 | В резерве |
Производство алюминия в России
В начале ХХ столетия в России произошло зарождение алюминиевой промышленности. Именно в 1932 году в Волхове появилось первый производственный комбинат по выпуску алюминия. И уже 14 мая того же года на предприятии удалось впервые получить партию металла. Ежегодно на территории государства осваивались все новые месторождения алюминиевых руд и запускались в работу новые мощности, которые существенно были расширены в период Второй мировой войны. Послевоенное время для страны было отмечено открытием новых предприятий, основной деятельностью которых было производство фабрикатов, основным материалом для чего служили алюминиевые сплавы. Тогда же был произведен запуск в работу Пикалевского глиноземного предприятия.
Россия славится своим разнообразием заводов, благодаря работе которых страна производит алюминий. Из них наиболее масштабным не только в рамках российского государства, но и во всем мире, считается ОК «Русал». Ему удалось произвести в 2015 году порядка 3,603 млн тонн алюминия, а в 2012 году предприятие достигло показателя в 4,173 млн тонн металла.
mining-prom.ru
пошаговая инструкция. Технология плавки алюминия в домашних условиях :: BusinessMan.ru
Алюминий – один из самых распространенных металлов на земле. Он присутствует даже в человеческом организме, так что уж говорить об окружающей действительности. В каждом доме или личном автомобиле есть алюминиевые функциональные элементы, детали или узлы, которые, увы, достаточно часто ломаются. Это мебельная и оконная фурнитура, направляющие для дверей и ставен, защелки замков и другие нужные мелочи.
Их можно заменить покупными новыми изделиями, отремонтировать или изготовить самостоятельно. В последних двух случаях и может понадобиться плавка алюминия в домашних условиях.
Характеристики алюминия
Все характеристики металла для домашних самоделок знать необязательно. Но есть несколько моментов, которые могут стать значительными или даже опасными в работе.
Алюминий хорошо поддается литью, плавится при относительно невысокой температуре в 660 °С. Для справки: чугун начинает плавиться при температуре 1100°С, а сталь – 1300 °С.
Поэтому плавка алюминия в домашних условиях на газовой плите трудно осуществима, так как домашние газовые приборы такую температуру обеспечить не могут. Правда, отечественные «кулибины» могут все, но об этом позже.
Снизить температуру плавления алюминия можно, растерев его в порошок или используя в качестве сырья готовый порошковый продукт. Но здесь важным становится еще одно свойство алюминия. Он достаточно активный металл, который при соединении с кислородом воздуха может воспламениться или просто окислиться. А температура плавления оксида алюминия — больше 2000 °С. При плавлении оксид все равно образуется, но в небольших количествах, именно он формирует окалину.
Та же активность может сыграть плохую шутку, если в расплавленный металл попадет вода. При этом происходит взрыв. Поэтому если в процессе плавки нужно сырье добавлять, то нужно следить, чтобы оно было сухим.
Сырье для плавки
Если предстоит плавка алюминия в домашних условиях, из-за сложности работы с порошковым металлом его в качестве сырья не используют.
Можно приобрести алюминиевую чушку или использовать обычную алюминиевую же проволоку, которую нарезать ножницами на небольшие кусочки и для уменьшения площади контакта с воздухом плотно спрессовать пассатижами.
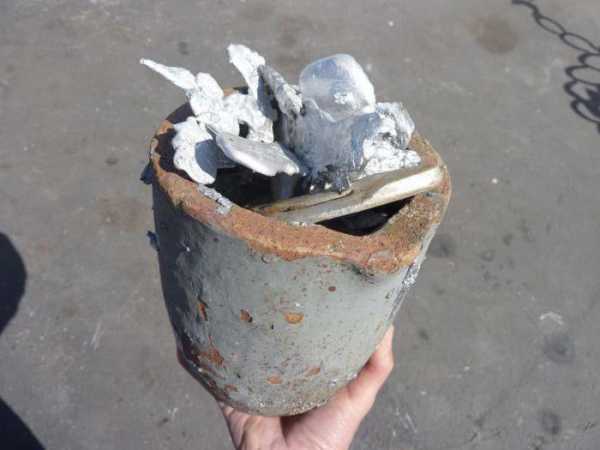
Вторичное сырье может быть окрашено или испачкано, это не страшно, лишние составляющие отойдут в виде шлаков. Только нужно помнить, что вдыхать пары сгоревшей краски нельзя.
Чтобы из вторичного сырья получилась качественная плавка алюминия в домашних условиях, флюсы, задача которых состоит в том, чтобы связывать и выводить на поверхность расплавленного металла все примеси и загрязнения, лучше приобрести готовые. Но можно сделать самостоятельно из технических солей.
Покровный флюс готовится из 10 % криолита и по 45 % хлорида натрия и хлорида калия.
В рафинирующий флюс для получения алюминия без пористости добавляют еще 25 % от общей массы фтористого натрия.
Средства индивидуальной защиты при плавке
Плавка алюминия в домашних условиях – процесс небезопасный. Поэтому нужно пользоваться средствами индивидуальной защиты (СИЗ). Даже если такая плавка нужна один раз на минимальном оборудовании, то по меньшей мере нужно защитить руки, например специальными перчатками сварщика, отлично предохраняющими от ожогов, ведь температура жидкого алюминия — больше 600 °С.
Глаза тоже желательно защищать, особенно если плавка происходит достаточно часто, очками или маской. И совсем в идеале работать нужно в специальном костюме металлурга с повышенной стойкостью к огню и высоким температурам.
Если нужен очень чистый алюминий с использованием рафинирующего флюса, то работать следует в химическом респираторе.
Литейная форма
Если требуется только отлить чистый алюминий для припоя, то литейная форма не нужна. Достаточно использовать стальной лист, на котором расплавленный металл остынет. Но если нужно отлить хотя бы простенькую деталь, то понадобится литейная форма.
Литейную форму можно сделать из скульптурного гипса, именно гипса, а не алебастра. Жидкий гипс заливается в смазанную маслом форму, ему дают немного застыть, периодически встряхивая, чтобы вышли пузырьки воздуха, вставляют в него модель и накрывают второй емкостью с гипсом. В удобном месте нужно в гипс вставить цилиндрический предмет, чтобы в итоге в форме появилось отверстие, так называемый канал, в который будет заливаться расплавленный алюминий. Когда гипс окончательно застынет, две части формы разъединяются, вынимается модель, и форма с готовым слепком соединяется опять.
Изготовить литейную форму можно и из смеси 75 % формовочного песка, 20 % глины и 5 % каменноугольного песка, которая засыпается в специальный ящик из досок и трамбуется. В утрамбованную землю отжимается модель, получившийся отпечаток присыпается тальком и графитом (угольной пылью), чтобы остывшую алюминиевую деталь можно было легко отделить от формы.
Тигель для плавки
Плавка алюминия в домашних условиях требует наличия специальной емкости с носиком из тугоплавкого материала. Это так называемый тигель. Тигли могут быть фарфоровые, кварцевые, стальные, чугунные, изготовленные из корунда или графита. В домашних условиях можно использовать покупной тигель или изготовить его, например, из отрезка стальной трубы достаточно большого диаметра. Правда, для этого нужна болгарка, сварочный аппарат и навыки владения этими инструментами.
Размеры тигля зависят от необходимого количества алюминия, который нужно расплавить. Этот ковш должен равномерно прогреваться, а его тепло — передаваться к сырью.
Печи для плавки
Технология плавки алюминия в домашних условиях достаточно проста. В специальном ковше нагревается лом алюминия до температуры, превышающей температуру плавления этого металла, расплав некоторое время выдерживается в разогретом состоянии, с его поверхности снимается шлак, затем чистый металл разливается в форму для остывания. Время плавки зависит от конструкции печи, то есть той температуры, которую она способна обеспечить.
Если используется паяльная лампа или газовая горелка, то они нагревают алюминий сверху. Правда, печь при этом все равно складывается из кирпичей колодцем без связующего раствора, внутри которого будут прогорать угли для нагревания емкости снизу и поддержания ее в нагретом состоянии.
Примерно так же выглядит конструкция печи, если тигель прогревается снизу с помощью обычных дров и фена для сушки волос. Только в этом случае дрова укладываются в кирпичном колодце не на дно, а на решетку, расположенную на первом ряду кирпичей, а в этом ряду оставляется отверстие для металлической трубы, надетой на горловину фена и закрепленной на ней изолентой. Тиглем в этом случае служит консервная банка, естественно, не алюминиевая, в которой на небольшом расстоянии от верха проделываются диаметрально противоположные сквозные отверстия. В эти отверстия продевается стальной прут, за который банка должна подвешиваться в печи. Фен нужен для нагнетания горячего воздуха в пространство между кирпичами и тиглем. Иногда вместо кирпичей используют металлическую бочку.
Если плавка должна происходить достаточно часто, то можно своими руками изготовить муфельную печь с вертикальной загрузкой тигля или купить готовую.
Плавка с помощью паяльной лампы
Плавка алюминия в домашних условиях паяльной лампой должна происходить не в помещении. Кроме сырья, паяльной лампы, тиглей и кирпичей, нужно подготовить дрова, пассатижи и стальной прут.
Итак, из кирпичей изготовлен небольшой колодец так, чтобы сверху можно было установить ковш с алюминием и стальной небольшой лист. В колодце разжигается костер, который должен немного прогореть, чтобы образовались угли. Дальше и происходит, собственно, плавка алюминия в домашних условиях. Пошаговая инструкция процесса:
— На кирпичи устанавливается емкость с сырьем. Ее нужно греть примерно 15 минут.
— После этого на полную мощность включается горелка паяльной лампы и алюминий прогревается сверху.
— В течение нескольких секунд начинается процесс, но для того чтобы прогрев был равномерным, металл в емкости нужно аккуратно перемешивать стальным прутом, придерживая ее пассатижами (не забыв при этом надеть рукавицы). Можно обойтись и без прута, периодически встряхивая ковш с помощью тех же плоскогубцев, но очень осторожно.
— Когда жидкость становится однородной, нужно пассатижами взять емкость и вылить содержимое на прокаленный стальной лист таким образом, чтобы вся образовавшаяся окалина осталась в ковше, а на лист для застывания попал только чистый металл.
Так обычно из вторичного сырья получают чистый алюминий, если с его помощью нужно запаять алюминиевые детали.
Плавка на дровах или газе
Плавка алюминия в домашних условиях на дровах происходит в легких разборных печах. Минусом такого способа является неконтролируемость процесса. Увеличить или уменьшить температуру нагрева невозможно. Вмешаться в процесс возможно, только сняв емкость с алюминием с огня.
Плавка алюминия в домашних условиях на газу — это единственно возможный вариант для квартиры. Греть емкость нужно долго, периодически сливая расплавленный металл. В таком случае отливка выполняется слоями. Для работы понадобятся две металлические емкости таких диаметров, чтобы одна надевалась на другую. Меньшая служит тиглем. Она с ломом, например нарезанной алюминиевой проволокой, ставится на конфорку, с которой нужно снять рассекатель пламени, бытовой газовой плиты. Над большей емкостью придется предварительно поработать. В ее днище выполняются около десятка небольших отверстий. В два или три из них вкручиваются болты, которые исполняют роль рукояток, за которые пассатижами раскаленную емкость можно поднять.
Эта емкость кверху дном надевается на тигель. Такая конструкция и позволяет прогревать алюминий. Периодически верхнюю емкость нужно снимать и металлическим прутом или ножом перемешивать лом. Перед тем как слить расплавленный металл, с его поверхности нужно снять шлак.
Плавка алюминия в муфельной печи
Муфельная печь – это уже достаточно серьезное оборудование для получения качественного расплавленного металла. Поэтому при плавке используют флюс для очистки алюминия от примесей. И это уже почти производственный процесс, а не плавка алюминия в домашних условиях. Пошаговая инструкция включает еще и несколько пунктов по подготовке сырья:
- Сначала в тигле расплавляется флюс, которого нужно взять в количестве от 2 до 5 % от веса алюминия, а затем в него добавляется лом.
- Насколько флюс активен, можно определить по поверхности расплава – она должна быть зеркальной. Если это не так, в расплав добавляется еще немного флюса, затем нужно будет добавить его перед окончанием плавки, чтобы шлак было легче удалять с поверхности металла стальной ложкой.
- Плавку нужно вести примерно при 700-750 °С. Это температура красного свечения.
- В процессе плавки может потребоваться добавлять сырье в тигель, так как расплавленный металл сильно уменьшается в объеме.
- Рафинирующий флюс добавляют при необходимости в конце плавки в количестве 0,25 % от веса расплавленного металла. Выдерживание такой пропорции в домашних условиях – задача непростая. После добавления флюса расплав нужно перемешать ложкой, дать постоять около 5 минут, затем снять шлак.
- Когда в результате нагрева алюминий превратился в однородную блестящую каплю, тигель нужно еще некоторое время подержать в печи, чтобы металл стал более текучим.
- Затем алюминий из тигля через носик (в этот момент становится понятно, зачем нужен именно такой ковш) заливается тонкой непрерывной струйкой в форму.
- После полного остывания форма аккуратно разделяется на половинки, из нее извлекается готовая деталь, которую еще нужно окончательно обработать: просверлить отверстия, если нужно, зачистить и наждачной бумагой отшлифовать поверхность. Вот и все. Процесс завершен.
Так что не стоит заранее пугаться, если предстоит в домашних условиях расплавить алюминиевый лом, чтобы получить чистый металл или изготовить деталь взамен поломавшейся. Серьезные профессиональные навыки для организации такого литейного производства совсем не нужны. Желание и умелые руки обычного мастера-любителя способны творить чудеса.
businessman.ru
Алюминиевая руда. От добычи до получения металла. Страны-лидеры по добыче алюминия
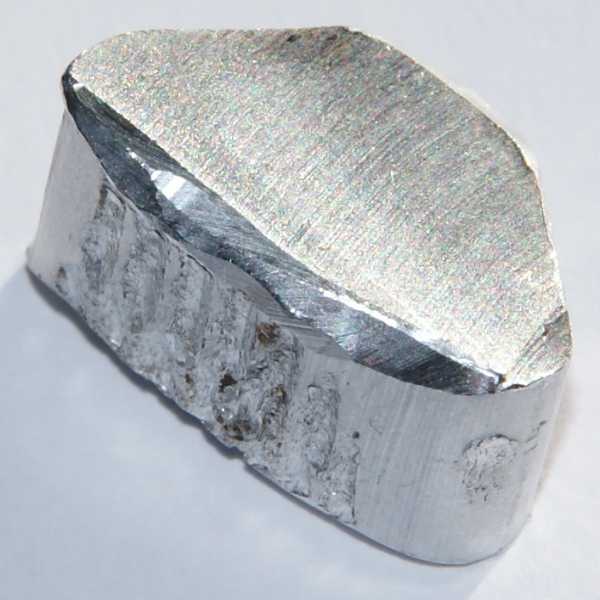
Содержание статьи:
В сравнении с традиционными металлами (сталью, медью, бронзой), алюминий молодой металл. Современный способ его получения был разработан только в 1886 году, а до этого он был очень редким. Промышленные масштабы «крылатого» металла начались лишь в 20 веке. Сегодня, это один из востребованных материалов в различных отраслях от электроники до космической и авиационной промышленности.
Впервые алюминиевая руда в виде серебристого металла была получена в 1825 году в объеме всего лишь нескольких миллиграмм, и до появления массового производства этот металл был дороже золота. Например, одна из королевских корон Швеции имела в своем составе алюминий, а Д. И. Менделеев в 1889 году получил от британцев дорогой подарок – весы из золота и алюминия.
Какое сырье необходимо для получения алюминиевой руды? Как производят один из самых необходимых в современности материалов?
Бокситовая руда – основа мирового производства алюминия
Непосредственно сам серебристый металл получают из глинозема. Это сырье представляет собой оксид алюминия (Аl2О3), получаемый с руд:
- Бокситов;
- Алунитов;
- Нефелиновых сиенитов.
Самый распространенный источник получения исходного материала это бокситы, их и считают основной алюминиевой рудой.
Несмотря на уже более чем 130 летнюю историю открытия, понять происхождение алюминиевой руды до сих пор не удалось. Возможно, что попросту в каждом регионе сырье образовалось под воздействием определенных условий. И это создает затруднения, чтобы вывести одну универсальную теорию об образовании бокситов. Основных гипотез происхождения алюминиевого сырья три:
- Они образовались вследствие растворения некоторых типов известняков, как остаточный продукт.
- Боксит получился в результате выветривания древних пород с дальнейшим их переносом и отложением.
- Руда является результатом химических процессов разложения железных, алюминиевых и титановых солей, и выпала как осадок.
Однако, алунитовые и нефелиновые руды образовывались в отличных условиях от бокситов. Первые формировались в условиях активной гидротермальной и вулканической деятельности. Вторые — при высоких температурах магмы.
Как результат, алуниты, в основном, имеют рассыпчатую пористую структуру. В их составе имеется до 40% различных оксидных соединений алюминия. Но, кроме собственно самой алюмниеносной руды в залежах, как правило, имеются добавки, что влияет на рентабельность их добычи. Считается выгодным разрабатывать месторождение при 50-ти процентном соотношении алунитов к добавкам.
Нефелины обычно представлены кристаллическими образцами, которые кроме алюминиевого оксида содержат добавки в виде различных примесей. Зависимо от состава, такой тип руды классифицируют по типам. Самые богатые имеют в своем составе до 90% нефелинов, второсортные 40-50%, если минералы беднее этих показателей, то не считается нужным вести их разработку.
Имея представления, о происхождении полезных ископаемых, геологическая разведка может довольно точно определить места нахождения залежей алюминиевых руд. Также условия формирования, влияющие на состав и структуру минералов, определяют способы добычи. Если месторождение считается рентабельным, налаживают его разработку.
Свойства алюминиевой руды
Боксит представляет собой сложное соединение оксидов алюминия, железа и кремния (в виде различных кварцев), титана, а также с небольшой примесью натрия, циркония, хрома, фосфора и прочих.
Медная руда: свойства, применение, добыча
Самым важным свойством в производстве алюминия является «вскрываемость» бокситов. То есть насколько просто будет отделить от него ненужные кремниевые добавки, чтобы получить исходное сырье для выплавки металла.
Основа получения алюминия – глинозем. Чтобы он образовался, руду перемалывают в мелкий порошок, и прогревают паром, отделяя большую часть кремния. И уже эта масса будет сырьем для выплавки.
Чтобы получить 1 тонну алюминия, потребуется около 4-5 тонн бокситов, с которых после обработки образуется около 2 тонн глинозема, а уже потом можно получить металл.
Технология разработки алюминиевых залежей. Способы добычи алюминиевой руды
При незначительной глубине залегания алюминиеносных пород их добыча ведется открытым способом. Но, сам процесс срезания пластов руды будет зависеть от ее вида, и структуры.
- Кристаллические минералы (чаще бокситы, или нефелины), снимают фрезерным способом. Для этого используются карьерные комбайны. Зависимо от модели такая машина может вести срез пласта толщиной до 600 мм. Толща породы разрабатывается постепенно, образуя после прохода одного слоя полки.
Это делается для безопасного положения кабины оператора и ходовых механизмов, которые в случае непредвиденного обвала будут находиться на безопасном расстоянии.
- Рыхлые алюминиевоносные породы исключают использование фрезерной разработки. Так как их вязкость забивает режущую часть машины. Чаще всего такие типы пород могут срезать при помощи карьерных экскаваторов, которые тут же грузят руду на самосвалы, для дальнейшей транспортировки.
Транспортирование сырья — это отдельная часть всего процесса. Обычно обогатительные комбинаты по возможности стараются возводить неподалеку от разработок. Это позволяет использовать ленточные транспортеры для подачи руды на обогащение. Но, чаще изъятое сырье перевозят самосвалами.
Следующий этап, обогащение и подготовка породы для получения глинозема.
- Руду при помощи ленточного транспортера перемещают в цех подготовки сырья, где может использоваться насколько дробильных аппаратов, измельчающих минералы поочередно до фракции приблизительно в 110 мм.
- Второй участок подготовительного цеха осуществляет подачу подготовленной руды, и дополнительных добавок на дальнейшую переработку.
- Следующий этап подготовки, это спекание породы в печах.
Также на этом этапе, возможна обработка сырья выщелачиванием крепкими щелочами. Результатом становится жидкий алюминатный раствор (гидрометаллургическая обработка).
- Алюминатный раствор проходит стадию декомпозиции. На данном этапе получают алюминатную пульпу, которую в свою очередь отправляют на сепарацию, и выпаривание жидкой составляющей.
- После чего данную массу очищают от ненужных щелочей, и направляют на прокалку в печах. В результате такой цепочки образуется сухой глинозем необходимый для получения алюминия путем гидролизной обработки.
Сложный технологический процесс требует большого количества топлива, и известняка, а также электроэнергии. Это является основным фактором расположения алюминиевых комбинатов – возле хорошей транспортной развязки, и нахождения рядом залежей необходимых ресурсов.
Все о железной руде
Однако существует и шахтный способ извлечения, когда порода из пластов вырубается по принципу добычи каменного угля. После чего руду отправляют на подобные производства по обогащению, и извлечению алюминия.
Одна из самых глубоких «алюминиевых» штолен находится на Урале в России, ее глубина достигает 1550 метров!
Страны лидеры по добыче алюминиевых руд
Основные месторождения алюминия сосредоточены в регионах с тропическим климатом, а большая часть 73% залежей приходятся на всего 5 стран: Гвинею, Бразилию, Ямайку, Австралию и Индию. Из них самые богатые запасы имеет Гвинея более 5 млрд. тонн (28%от мировой доли).
Если разделить запасы и объемы по добыче, то можно получить следующую картину:
1-е место – Африка (Гвинея).
2-е место – Америка.
3-е место – Азия.
4-е место – Австралия.
5-е – Европа.
Пятерка лидеров стран по добыче алюминиевой руды представлена в таблице
Страна | Объемы добычи млн. тонн |
Китай | 86,5 |
Австралия | 81,7 |
Бразилия | 30,7 |
Гвинея | 19,7 |
Индия | 14,9
|
Также к основным добытчикам алюминиевых руд относятся: Ямайка (9,7 млн. т.), Россия (6,6), Казахстан (4,2), Гайана (1,6).
Разработка месторождений алюминиевых руд в России
В нашей стране есть несколько богатых залежей алюминиевых руд, сосредоточенных на Урале, и в Ленинградской области. Но, основным способом добычи бокситов у нас, является более трудоемкий закрытый шахтный метод, которым извлекают около 80% от общей массы руд в России.
Иностранные инвестиции в промышленности России
Лидеры по разработке месторождений – акционерное общество «Севуралбокситруда», АО Бакситогорский глинозем, Южно-Уральские бокситовые рудники. Однако их запасы исчерпываются. Вследствие чего России приходится импортировать около 3 млн. тонн глинозема в год.
Месторождение | Запасы |
Красная Шапочка (Урал) | На 19 лет добычи |
Горностайское и Горностайско-Краснооктябрьское | На 18 лет добычи
|
Блиново-Каменское | 10 лет |
Кургазское | 10 лет |
Радынский карьер | 7 лет |
В общей сложности на территории страны разведано 44 месторождения различных алюминиевых руд (бокситов, нефелинов), которых по оценкам, должно хватить на 240 лет, при такой интенсивности добычи как сегодня.
Импорт глинозема обусловлен низким качеством руды в залежах, например, на месторождении Красная Шапочка добывают боксит с 50% глиноземным составом, тогда как в Италии извлекают породу с 64% оксида алюминия, а в Китае 61%.
Применение алюминиевой руды
В основном до 60% рудного сырья используется для получения алюминия. Однако богатый состав позволяет извлекать из него, и другие химические элементы: титан, хром, ванадий и прочие цветные металлы, необходимые в первую очередь в качестве легирующих добавок для улучшения качеств стали.
Как вспоминалось выше технологическая цепочка получения алюминия обязательно проходит через стадию образования глинозема, который также используют в качестве флюсов в черной металлургии.
Как распределяются расходы на поддержку промышленности?
Богатый состав элементов в алюминиевой руде используется и для производства минеральной краски. Также способом плавки производится глиноземный цемент – быстро застывающая прочная масса.
Еще один материал, получаемый из бокситов – электрокорунд. Его получают путем плавления руды в электропечах. Это очень твердое вещество, уступающее только алмазу, что делает его востребованным в качестве абразива.
Также в процессе получения чистого металла образуются отходы – красный шлам. Из него извлекают элемент – скандий, который применяется в производстве алюминиево-скандиевых сплавов, востребованных в автомобильной промышленности, ракетостроении, выпуске электроприводов, и спортивного оборудования.
Альтернатива алюминиевым рудам
Развитие современного производства требует все больших объемов алюминия. Однако не всегда рентабельно разрабатывать месторождения, или импортировать глинозем из-за границы. Поэтому все чаще используется выплавка металла с использованием вторичного сырья.
Импортозамещение — фактор экономической безопасности страны
Например, такие страны как США, Япония, Германия, Франция, Великобритания в основном производят вторичный алюминий, по объемам составляющий до 80% от общемировой выплавки.
Вторичный металл обходится намного дешевле, в сравнении с первичным, для получения которого тратится 20000 кВт энергии/1 тонну.
На сегодня алюминий, получаемый с различных руд, один из востребованных материалов позволяющих получать прочные и легкие изделия, не поддающиеся коррозии. Альтернатив металлу пока не найдено, и в ближайшие десятилетия объемы добычи руды, и выплавки будут только расти.
promdevelop.ru
Выплавка — алюминий — Большая Энциклопедия Нефти и Газа, статья, страница 1
Выплавка — алюминий
Cтраница 1
Выплавка алюминия весьма энергоемка: каждая тонна металла требует затраты около 16 тыс. кет-ч электроэнергии. Первичная его очистка осуществляется продувкой хлора. Продажный металл содержит обычно 99 7 % алюминия. Наряду с другими примесями ( главным образом Si и Ре) в нем имеются и следы галлия. [1]
Выплавка алюминия весьма энергоемка: каждая тонна металла требует затраты около 16 тыс. квт-ч электроэнергии. Первичная его очистка осуществляется продувкой хлора. Продажный металл содержит обычно 99 7 % алюминия. Наряду с другими примесями ( главным образом Si и Fe) в нем имеются и следы галлия. [3]
Выплавка алюминия производится в большинстве случаев не на месте добычи, а в районах, располагающих большими ресурсами гидроэлектрической энергии. [4]
Для выплавки алюминия в электропечах используют криолит. Криолит получают обработкой плавиковой кислотой смеси, содержащей гидроксид алюминия и гидроксид натрия. [5]
Основы выплавки алюминия электролизом сохранились неизменными до настоящего времени, только увеличился объем электролизеров, а издержки производства резко сократились. [6]
На выплавку алюминия массой 2 кг расходуется оксид алюминия массой 4 кг. [7]
Электролизер для выплавки алюминия представляет собой железный кожух, выложенный изнутри огнеупорным кирпичом. Его дно ( под), собранное из блоков спрессованного угля, служит катодом. Аноды ( один или несколько) располагаются сверху: это — алюминиевые каркасы, заполненные угольными брикетами. На современных заводах электролизеры устанавливают сериями; каждая серия состоит из 150 и большего числа электролизеров. [8]
Электролизер для выплавки алюминия представляет собой железный кожух, выложенный изнутри огнеупорным кирпичом. Его дно ( под), собранное из блоков спрессованного угля, служит катодом. Аноды ( один или несколько) располагаются сверху: это — алюминиевые каркасы, заполненные угольными брикетами. На современных заводах электролизеры устанавливают сериями; каждая — серия состоит из 150 и большего числа электролизеров. [9]
Электролизер для выплавки алюминия представляет собой железный кожух, выложенный изнутри огнеупорным кирпичом. Его дно ( под), собранное из блоков спрессованного угля, служит катодом. Аноды ( один или несколько) располагаются сверху: это — алюминиевые каркасы, заполненные угольными брикетами. На современных заводах электролизеры устанавливают сериями; каждая серия состоит из 150 и большего числа электролизеров. [10]
Электролизер для выплавки алюминия представляет собой железный кожух, выложенный изнутри огнеупорным кирпичом. Его дно ( под), собранное из блоков спрессованного угля, служит катодом. Аноды ( один или несколько) располагаются сверху: это — алюминиевые каркасы, заполненные угольными брикетами. На современных заводах электролизеры устанавливают сериями; каждая серия состоит из 150 и большего числа электролизеров. [11]
Электролизер для выплавки алюминия представляет собой железный кожух, выложенный изнутри огнеупорным кирпичом. Его дно ( под), собранное из блоков спрессованного угля, служит катодом. [12]
Трудности осуществления так называемой термохимической выплавки алюминия различны. [14]
Удельный расход электроэнергии при выплавке алюминия на сернистой анодной массе был практически на уровне обычных норм, принятых для малосернистой анодной массы. Работа на опытных ваннах с сернистыми анодами проходила спокойно и даже с меньшими технологическими отклонениями, чем на ваннах с обычными анодами из пекового кокса. Расход фторалюми-ния и криолита примерно одинаков для электролизеров, работающих на сернистой и на обычной анодной массе. [15]
Страницы: 1 2 3 4
www.ngpedia.ru
Алюминиевая промышленность — Википедия
Материал из Википедии — свободной энциклопедии
Алюминиевая промышленность — отрасль цветной металлургии, объединяющая предприятия по выработке металлического алюминия[1]. По масштабам производства и потребления алюминий занимает первое место среди подотраслей цветной металлургии, а среди отраслей металлургии по объёму уступает лишь производству стали[2]. Важнейшими потребителями продукции алюминиевой промышленности являются: авиационная, электротехническая, автомобильная и ряд других отраслей машиностроительной и металлообрабатывающей промышленности, а также строительство, железнодорожный транспорт, химическая, пищевая промышленность.
История
Рост производства алюминия в XX веке Принцип работы электролизной ванны по выплавке алюминияВ 1854 году французским учёным Анри Этьеном Сент-Клер Девилем (Sainte-Claire Deville), был открыт способ промышленного производства алюминия, основанный на вытеснении алюминия металлическим натрием из двойного хлорида натрия и алюминия NaCl·AlCl3. За 36 лет его применения, с 1855 по 1890 гг., способом Сент-Клер Девиля было получено 200 т металлического алюминия[3].
В 1856 году на заводе братьев Тисье в Руане Девилль организовал первое промышленное предприятие по выпуску алюминия. При этом стоимость 1 кг алюминия сначала равнялась 300 франкам. Через несколько лет удалось снизить продажную цену до 200 франков за 1 кг, но все равно она оставалась исключительно высокой. Алюминий в это время употребляли почти как драгоценный металл для производства различных изделий. Изделия из этого металла даже пользовались популярностью благодаря своему белому цвету и приятному блеску. По мере совершенствования химических методов выделения алюминия цена на него с годами падала. Например, завод в Олбери (Англия) в середине 1880-х годов выпускал до 250 кг алюминия в день и продавал его по цене 30 шиллингов за кг, иными словами, цена его за 30 лет снизилась в 25 раз. Уже в середине XIX века некоторые химики указывали на то, что алюминий можно получать путём электролиза. В 1854 году Бунзен получил алюминий путём электролиза расплава хлористого алюминия. Для производства алюминия путём электролиза уже более 100 лет используется технология Эру-Холла[4]. Этот способ производства алюминия придумали независимо друг от друга француз Эру и американец Холл. Благодаря широкому распространению этого метода во всём мире, стало возможным производить алюминий в широких масштабах и цены на него упали в десятки раз.
Рост производства был особенно быстрым во время и после Второй мировой войны. Производство первичного алюминия (без учёта производства Советского Союза) составляло только 620 тыс. т в 1939 году. В 1943 году оно возросло до 1,9 млн т. В 1956 году во всем мире производилось 3,4 млн т первичного алюминия, в 1965 году мировое производство алюминия составило 5,4 млн т, в 1980 — 16,1 млн т, а в 1990 — 18 млн т. Производство алюминия в мире в 2007 году составило 37,41 млн тонн (по данным Международного института алюминия (International Aluminium Institute, IAI)[5] и продолжает развиваться очень большими темпами. Применяются Технология Содерберга и другие технологии.
Видео по теме
Структура алюминиевой промышленности
Алюминиевая промышленность охватывает следующие основные производства,
Основным природным сырьём для получения глинозёма с целью последующего получения из него алюминия, являются бокситы. Для производства одной тонны металлического алюминия требуется примерно 1930 кг глинозёма, 50 кг фтористых солей, 550 кг угольных электродов (анодной массы или обожжённых анодов) и до 18 000 квт-ч электроэнергии. Алюминиевая промышленность — одна из наиболее энергоёмких отраслей промышленности, поэтому важнейшим условием её развития является наличие мощных источников дешёвой электроэнергии.
Развитие и размещение алюминиевой промышленности в мире
Сырьевая база
Основные мировые месторождения, на которых добывают бокситыБоксит является основным минеральным сырьём для алюминиевой промышленности. Его запасы в мире распределены очень неравномерно и ограничены. В мире существует семь бокситоносных районов:
По данным Геологической службы США мировые ресурсы бокситов оцениваются в 55 — 75 млрд. т, которые распределяются между отдельными регионами следующим образом: Африка — 32%, Океания — 23%, Южная Америка и страны Карибского бассейна — 21%, Азия — 18%, прочие регионы — 6%. В целом мировые запасы природных ресурсов бокситов достаточны для удовлетворения мировых потребностей в алюминии в течение продолжительного времени [6].
Понимая важность сырьевой базы, крупнейшие производители алюминия в мире поделили основные месторождения бокситов высокого качества, с содержанием глинозёма не менее 50%. Другим компаниям остается либо приобретать глинозём на открытом рынке и быть всецело зависимыми от рыночного колебания цен, либо объединять усилия с владельцами месторождений[2].
Основные производители алюминия в мире
Производство первичного алюминия по континентам земного шара Крупнейшие производители алюминия в миреСписок стран, крупнейших производителей алюминия
По данным Геологической службы США[7] крупнейшими производителями алюминия в мире явились следующие страны:
Список компаний — крупнейших производителей алюминия
Десятка крупнейших компаний-производителей алюминия выглядит следующим образом[8]:
Самым крупным предприятием по производству алюминия является Братский алюминиевый завод, который первым в мире стал производить более 1 миллиона тонн алюминия в год. Завод производит 30% российского алюминия и 4% мирового. Завод потребляет 75% электроэнергии, вырабатываемой Братской ГЭС[9].
Примечания
Ссылки
См. также
wiki2.red
Алюминий выплавка — Справочник химика 21
В 1854 г. французский ученый Сент-Клер Девиль предложил электрохимический способ получения алюминия, восстанавливая натрием двойной хлорид алюминия-натрия. По способу Сент-Клер Девиля с 1855 по 1890 г. было получено всего 200 тонн алюминия, а за оставшиеся до конца XIX в. 10 лет выплавка алюми- [c.330]Главным потребителем кокса является алюминиевая промышленность, где кокс служит восстановителем (анодная масса) при выплавке алюминия из алюминиевых руд. Кроме того, кокс используют в качестве сырья при изготовлении графитированных электродов для сталеплавильных печей, для получения карбидов (кальция, кремния) и сероуглерода. [c.29]
Электролизер для выплавки алюминия представляет собой железный кожух, выложенный изнутри огнеупорным кирпичом. Его ДЕЮ (под), собранное из блоков спрессованного угля, служит катодом. Аноды (один или несколько) располагаются сверху это— алюминиевые каркасы, заполненные угольными брикетами. На современных заводах электролизеры устанавливают сериями каждая серия состоит из 150 и большего числа электролизеров. [c.634]
Нефтяной кокс — ценный углеродистый материал, используемый для изготовления электродной продукции, применяемой в первую очередь для выплавки алюминия и высококачественных сталей. Графитированный (прокаленный при температуре 2300—3000° С) кокс весьма термически стоек, имеет высокую теплопроводность, устойчив против коррозии. Он используется как конструкционный материал для изготовления химической аппаратуры и оборудования, в том числе для футеровки атомных реакторов. При переработке высокосернистого и высокозольного сырья кокс получается низкого качества и используется как топливо. [c.145]
Газовая печная среда, образующаяся при горении природного газа в рабочей камере печи, имеет высокое парциальное давление водяных паров. Химический ее состав, температура и давление зависят от режима сжигания. При неконтролируемой среде возможно протекание ряда сопутствующих физических и химических процессов, которые отрицательно влияют на качество получаемых продуктов. Например, ири выплавке алюминия и его сплавов происходит насыщение расплава газами, которое ведет к образованию газовых раковин, резко выраженной пористости, появлению неметаллических включений, являющихся концентраторами напряжения, снижающими прочность и предел усталости, к снижению пластических свойств металла, к образованию дефектов типа окисных плен, име ющих большую твердость и нулевую пластичность, к появлению пузырей при окончательной термообработке готовых изделий, что ухудшает механические свойства при закалке и старении сплавов. [c.76]
При выплавке алюминия к анодам, изготовляемым из различных коксов, подводится при помощи металлических штырей электрический ток напряжением 4—5 в и силой 15 000— 20 000 а. Температура вверху самообжигающегося анода около 150°С и внизу, на границе с расплавленным электролитом, около 950 °С. На границе штырь — анод возникает ток, направление которого может совпадать с направлением основного тока или быть противоположным ему. Опубликованных данных [c.213]
Анодная масса и обожженные аноды — это основные материалы, используемые в процессе электрохимического получения алюминия. Расход энергии на выплавку [c.13]
Постановка и контроль выполнения этой задачи на таком высоком уровне объяснялись актуальностью создания отечественной сырьевой базы по прокаленному коксу для обеспечения быстро растущих потребностей цветной и черной металлургии. Для производства 1 т алюминия расходуется до 0,5 т прокаленного нефтяного кокса, для выплавки 1 т электростали — до 6 кг электродов на основе высококачественных коксов игольчатой структуры. Специальные сорта нефтяных коксов изотропной структуры используются в атомной энергетике и в специзделиях в оборонной и космической технике. [c.22]
Фториды поражают растения уже при концентрации 5 частей на миллиард (7— 9 сут. экспозиции). Они содержатся в значительных количествах в отходящих газах заводов по производству минеральных удобрений, выплавке алюминия и других, где фтористые соединения входят в состав сырья или флюсов. ПДК для фтористых газов равна 3 млн . [c.22]
Мешок фильтра регулярно очищают путем изменения направления движения потока осевшая на фильтре пыль поступает снова в кипящий слой. В слой непрерывно подается глинозем, по качеству соответствующий глинозему, используемому в электропечах для выплавки алюминия пройдя через псевдоожиженный слой, он выгружается (время пребывания в слое составляет от 2 до 14 ч) и используется для выплавки алюминия. Соотношение оксида алюминия и очищаемого воздуха колеблется в пределах 30—150 1, потеря напора составляет 0,75—1,5 кПа, Эффективность абсорбции газа превышает 99%, тогда как эффективность удаления твердых частиц превышает 90% (таблица X -2). [c.544]
Печи для выплавки алюминия Закрытая со входом с одной сто- 0,75—1 [c.577]
Выплавка стекла. Стекло может быть прозрачным или полупрозрачным, бесцветным или окрашенным. Оно является продуктом высокотемпературного переплава смеси кремния (кварц или песок), соды и известняка. Для получения специфических или необычных оптических и других физических свойств в качестве присадки к расплаву или заменителя части соды и известняка в шихте применяют другие материалы (алюминий, поташ, борнокислый натрий, силикат свинца или карбонат бария). Цветные расплавы образуются в результате добавок окислов железа или хрома (желтые или зеленые цвета), сульфида кадмия (оранжевые), окислов кобальта (голубые), марганца (пурпурные) и никеля (фиолетовые). Температуры, до которых должны быть нагреты эти ингредиенты, превышают 1500 °С. Стекло не имеет определенной точки плавления и размягчается до жидкого состояния при температуре 1350—1600 °С. Энергопотребление даже в хорошо сконструированных печах составляет около 4187 кДж/кг производимого стекла. Необходимая температура пламени (1800— 1950 °С) достигается за счет сжигания газа в смеси с воздухом, подогреваемым до 1000 °С в регенеративном теплообменнике, который сооружается из огнеупорного кирпича и нагревается отходящими продуктами сгорания. Газ вдувается в поток горячего воздуха через боковые стенки верхней головки регенератора, которая является основной камерой сгорания, а продукты сгорания, отдав тепло стекломассе, покидают печь и уходят в расположенный напротив регенератор. Когда температура подогрева воздуха, подаваемого на горение, снизится значительно, потоки воздуха и продуктов сгорания реверсируются и газ начнет подаваться в поток воздуха, подогреваемого в расположенном напротив регенераторе. [c.276]
Твердые и высокопрочные УНС после обжига или после обжига, графитации и соответствующей обработки (механическая обработка, нанесение защитного покрытия и др.) используют в электротермических производствах в качестве электродной продукции (электродов). Электродную продукцию применяют для подвода тока в рабочую зону электролизеров и электропечей, предназначенных для выплавки алюминия, магния, высококачественных сталей и других металлов, а также ферросплавов и карбидов. В зависимости от эксплуатационных характеристик и условий применения различают два вида электродов. [c.99]
Кокс широко применяют в различных областях народного хозяйства. Наибольшее количество кокса потребляет цветная металлургия, в частности при производстве алюминия (для приготовления анодной массы и обожженных анодов алюминиевых электролизеров, графитированных электродов и углеграфитовых конструкционных изделий). Так, для выплавки 1 т алюминия требуется до 500 кг нефтяного электродного кокса. Используют кокс и в качестве реагента в химической промышленности — для приготовления сероуглерода, сульфида натрия, карбидов (кальция, кремния, бора), ферросплавов и т. п., а также как строительный, футеровочный материал и как топливо. [c.393]
Производства, основанные на базе коксующихся углей,—химическая промышленность и электротермические производства (выплавка алюминия, различных сортов сталей, карбидов, получение хлора, магния, сероуглерода, производство углеграфитовых материалов, всевозможных восстановителей н сульфидирующих агентов и др.) — должны искать новые источники сырья. [c.8]
Очевидно, импортируемый кокс в этих странах прежде всего применяется для получения электродной продукции-—анодной массы, предназначенной для выплавки алюминия и графитированных электродов. [c.12]
Обычно прокалку кокса в промышленных условиях завершают прн 1200—1300 С. Поскольку для обессеривания нефтяного кокса необходимы температура и продолжительность процесса более высокие, чем при обычной прокалке, то все физико-химические изменения, которые происходят с коксом, более глубокие. Таким образом, при термическом обессеривании кокса исключается необходимость в его повторной прокалке. Термический метод обессеривания кокса -проверен в промышленных условиях на электрокальцинаторе. Впервые для обессеривания кокса был применен способ нагрева пропусканием тока через прокаливаемый продукт. Испытания обессеренного этим способом кокса при выплавке алюминия на [c.150]
Этим объясняется и то, что извлечение металлов из руд требует затраты большого количества энергии (тепловой — в доменном процессе, электрической — при производстве алюминия). Коррозия, по существу, является естественным процессом, обратным искусственному металлургическому. В результате коррозии высвобождается и рассеивается использованная при выплавке металлов из руды и связанная в металле энергия. [c.10]
Потребность в нефтяном коксе, как более дешевом и высококачественном материале, чем кокс, получаемый на основе угля (так называемый пековый), весьма значительна и непрерывно возрастает. Основной потребитель нефтяного кокса — алюминиевая промышленность кокс служит восстановителем (анодная масса) при выплавке алюминия из алюминиевых руд. Удельный расход кокса на производство алюминия весьма значителен и составляет 550-600 кг на 1 т алюминия. Из других областей применения нефтяного кокса следует назвать использование его в качестве сырья для изготовления графитированных электродов для сталеплавильных печей, для получения карбидов (кальция, кремния) и сероуглерода. Специальные сорта нефтяного кокса применяют как конструкционный материал для изготовления химической аппаратуры, работающей в условиях агрессивных сред. [c.43]
Металлы можно извлекать из их руд непосредственно электролитическим или химическим восстановлением. Электролитическое восстановление, которое уже обсуждалось в разд. 19.6, используется в промышленных масштабах для получения наиболее активных металлов натрия, магния и алюминия. Менее активные металлы — медь, железо и цинк-получают в промышленных масштабах с помощью химического восстановления, причем большую часть менее активных металлов получают методом высокотемпературного восстановления в расплавленном состоянии. Поэтому такие процессы называются выплавкой. [c.356]
Электролизер для выплавки алюминия представляет собой железный кожух, выложенный изнутри огнеупорным кирпичом. Его дно (под), собранное из блоков спрессованного угля, служит катодом. Аноды (один или несколько) [c.677]
Ниже (см. табл. на с. 123) приведены данные о составе шамотного кирпича, которым была выложена электропечь для выплавки алюминия, до работы и после долгих лет работы. [c.122]
Железо — четвертый по распространенности элемент на Земле (4,7 о после кислорода, кремния и алюминия) и наиболее распространенный из тяжелых металлов. Железо известно с глубокой древности ( железный век — период в развитии человечества, наступивший в начале 1-го тысячелетия гю н. э. и связанный с началом выплавки железа и изготовлением железных орудий труда и оружия). [c.191]
В течение семилетки в восточных р-пах получат быстрое развитие такие отрасли П., как топливно-энергетическая, химическая, произ-во алюминия, выплавка стали, машиностроение. Темпы роста П. вост. р-]юв будут примерно в 2 раза превышать средние темпы роста П. ССС Р. Добыча угля в вост. р-пах (без Урала) возрастет за 7 лет на 40—45%, а в р-нах Сибири и Казахстана, где сосредоточены наиболее эффективные угольные месторождения, прирост добычи угля будет равен примерно (>0% общего прироста добычи угля в стране. В резулг.тате уд. вес вост. р-)(ов страны возрастет в 1965 в добыче угля примерно до 50%, в произ-ве стали до 48%, электроэнергии до 46%, меди рафинированной до 88%, алюминия до 71%. На дешевых углях в вост. р-нах в течение семилетия будут созданы мощные тепловые электростанции. Будет также развернуто строительство крупных На этой базе будет создан крупный комплекс энергоемких ироиз-в, в частности произ-во алюминия. На востоке создается 3-я металлургич. база страны в составе 2 новых сибирских предприятий — Тайшетского и Зап.-Сибирского (Кузбасс), Карагандинского металлургич. комби1гата, завода ферросплавов и других предприятий. Крупные центры лесной и лесохнмич. Г[. возникнут в р-нах Етшсейска, Красноярска, Братска. Пром. комплекс вост. р-нов дополняется вая нейшими отраслями — нефтепереработкой и нефтехимич. И. В Сибири строится несколько крупных нефтеперерабатывающих заводов. В Зап. Якутии создается крупная алмазная 11. Выпуск отечественных алмазов вырастет за годы семилетки в 15—16 раз. В Каз. ССР будут расширены действующие [c.365]Поэтому процесс выплавки стали обычно заканчивается ее раскислением — уменьшением количества растворенного в жидкой стали кислорода. Существуют различные способы раскисления стали. Чаще всего применяется добавкг к стали небольших количеств элементов, активно соединяющиеся с кислородом. Обычно в качестве раскислптелей применяют марганец, кремний, алюминий, титан. Образующиеся оксиды этих элементов переходят в шлак. [c.682]
При выплавке алюминия на базе сернистого нефтяного кокса для штырей предпочтительнее применять сталь ЭЯ1Т. Она стойка против сероводородной коррозии, а т. э. д. с. на контакте с этой сталью — наименьшая и имеет положительный знак. [c.216]
Потребность стран мира в коксе для производства анодов, которые используют для выплавки алюминия, в период 1985-2000 гг. будет составлять 41-43% общего производства. Значительное количество нефтяного кокса будет расходоваться на изготовление электродной продукции. В СССР для этих целей в настоящее время применяют кокс, получаемый на кубовых установках из специально подобранного и подготовленного сырья. Стабильная работа крупногабаритных электродов при повышенных токовых нагрузках обеспечивается благодаря высокой их электрической проводимости и низкому коэффициенту термического расщирения. Для получения электродной продукции с подобными свойствами требуется кокс определенной структуры — так называемый игольчатый кокс (Иеед.1е соке). Игольчатый кокс получают из высокоароматизированных малосернистых дистиллятных остатков. Его производят в США, СССР, Англии, Японии и других странах. [c.8]
Нефтяной малозольный кокс используют в качестве анодной массы и обожженных анодов при производстве алюминия и в качестве электродов при выплавке специальных марок сталей и различных цветных металлов. Для указанных целей кокс получают преимущественно на установках замедленного коксования. У нас в стране кокс до термической обработки (прокаливания) назгша- [c.12]
Основными производствами, составляющими технологическую цепочку Руда- Глинозем Алюминий, является производства глинозема и алюминия. Территориально они обычно разделены. Вследствие высокой энергоемкости процесса электролитического восстановления алюминия алюминиевые заводы располагаются в районах с дешёвой электроэнергией ГЭС. Производства глинозема, наоборот, базируются в местах добычи алюминиевых руд с тем, чтобы сократить расходы на перевозку сырья. Примером производства с полным циклом (от руды до рафинированного металлического алюминия) являются Волховский и Каменец-Уральский заводы. На других предприятиях этой отрасли осуществляется только часть технологической цепочки производство глинозема (Ачинск, Вокситогорск) или выплавка алюминия (Кандалакша, Волгоград, Новокузнецк, Братск, Красноярск). [c.19]
Хлор и хлориды. Абсорбция газообразного хлористого водорода водой, в которой он очень хорошо растворяется, является обычной стадией производства соляной кислоты. Хлориды присутствуют в отходящих газах выплавки алюминия из лома, где соль (Na l) входит в состав флюса. Абсорбция элементарного хлора является одной из основных стадий очистки этого газа перед его дальнейшим использованием. [c.140]
Некоторые вещества обладают клейкими свойствами (пылевидные выбросы дуговых печей, пыль оксида цинка и газообразные отходы процесса выплавки алюминия), в результате для удаления ворса может потребоваться опаление поверхности ткани. В целях лучшего удаления пылевых отложений применялась также обработка ткани кремнийорганическими смолами, этот процесс особенно эффективен в условиях присутствия влаги [71а]. [c.351]
Нефтяной кокс применяется для изготовления анодов к печам для выплавки алюминия и графитированных электродов для сталеплавильных лечей. В связи с бурным развитием электрометаллургии потребность в нефтяном коксе ежегодно возрастает. [c.149]
Конечное содержание серы в прокаленном коксе из гудрона арланской нефти такое же, как в коксе из крекинг-остатка ромашкинской нефти, т. е. менее 1%. Остальные показатели в основном одинаковы, за исключением содержания ванадия (для арланского кокса в 1,5 раза выше), железа и других металлов. Повышенное содержание ванадия в обессеренном коксе объясняется высоким его содержанием в арланской нефти. Из-за этого такой кокс нельзя применять в алюминиевой промышленности. При выплавке алюминия ванадий, как и другие металлы, из кокса по- [c.155]
Основными вндами продукции, выпускаемыми электродными предприятиями являются графитированные и угольные электроды, применяемые для выплавки стали, чугуна и кремния катодные и анодные блоки, товарные массы, необходимые для вьшлавки алюминия и производства ферросплавов конструкционные углеродные материалы и изделия из них, широко применяемые во всех отраслях промышленности, атомной энергетике, сельском хозяйстве, в том числе, машиностроении, самолетостроении, ракетостроении и др. [c.41]
Самыми распространенными породами, содержащими алюминий, являются каолины и глины. В настоящее время, однако, эти руды применяются только для получения силикоалюминия электротермическим методом. Для выплавки сплавов алюминия с кремнием используют силлиманитовые руды, запасы которых в СССР очень велики. [c.479]
ФЛЮОРИТ (плавиковый шпат) — минерал aFj, хрупок, окрашен в различные цвета желтый, голубой, фиолетовый, фиолетово-черный. Иногда содержит примеси редкоземельных элементов, урана и др. Чистые кристаллы Ф.— очень прозрачные в ультрафиолетовом и инфракрасном свете, ярко люминесцируют в катодных лучах и под действием ультрафиолетового излучения, светятся при нагревании (термолюминесценция). Ф. применяют в металлургии для образования легкоплавких шлаков, при выплавке алюминия, для получения фтора, искусственного криолита, фторидных соединений, в керамике — эмали и глазури. Прозрачные, бесцветные кристаллы Ф. применяют для изготовления линз и т. п. [c.263]
Многие лантаноиды и их соединения применяются в различных областях науки и техники. Они используются в виде мишметалла (сплава лантаноидов с преобладающим содержанием церия и лантана) в металлургии при выплавке стали, чугуна и сплавов цветных металлов. Добавление малых количеств мишметалла повышает качество нержавеющих, быстрорежущих, жаропрочных сталей и чугуна. При введении 0,35% мишметалла в нихром срок его службы при 1000°С возрастает в 10 раз. Заметно увеличивается прочность при высоких температурах сплавов алюминия и магния при добавлении лантаноидов. Основным потребителем лантаноидов является стекольная промышленность. Цериевое стекло устойчиво по отношению к радиоактивному излучению (не тускнеет) и применяется в атомной технике. Оксиды лантаноидов входят в состав оптических стекол. Некоторые оксиды придают стеклу различную окраску. Лантаноиды и их оксиды используются как катализаторы при химических синтезах, а также в качестве материалов в радио- и электротехнике. [c.323]
Применение. Из алюминия делают теплообменники, радиаторы, химическую аппаратуру, электрические провода, рефлекторы, тонкую (до 0,01 мм) фольгу для электроконденсаторов и упаковки пищевых продуктов и фармацевтических препаратов. В больших количествах алюминий расходуется на изготовление сплавав, широко применяемых в машиностроении, авиационной и космической технике. Сплавы на основе алюминия бывают двух типов ковкие (пластичные) и литьевые (хрупкие). К первым относится дюралюмин (дюраль), содержащий 4% Си и по 0,5% Лg, Ре и 81. Ко вторым—силумин, в который входит до 14% 81 и 0,1% N3. Прочность дюралюмина после закалки и вылеживания возрастает в 6 раз. Из сплавов алюминия с магнием — магналия — делают корпуса легких судов и во все возрастающих количествах консервные банки, фольгу для сыров и для тушения мяса, крышки для бутылок с молочнокислыми продуктами, банки для пива. Применяют алюминий и для выплавки других металлов методом алюмотермии. [c.306]
chem21.info
Методы и способы плавления алюминия на производстве и в домашних условиях
Алюминий и его сплавы используются почти во всех сферах промышленности, а также в процессе изготовления предметов домашнего обихода. В условиях комнатной температуры на алюминии образуется тонкая пленка окиси (А12O3), прочно защищающая его от последующего окисления. Время окисления алюминия с ростом температуры резко увеличивается. Именно по этой причине в процессе плавки алюминия и его сплавов в плавильных печах поверхность расплавляемого материала и зеркало ванны очень быстро покрывается пленкой окиси.
Печи для плавки алюминия
Зачастую в производстве вторичного алюминия используют отражательные (подовые) печи. Такой тип печей для плавки алюминия отличается большим количеством модификаций. Однако все они приспособлены под стандартную отражательную печь, под специальные условия работы и особую шихту.
Не меньшей популярность пользуются и тигельные печи, в особенностях, на малых производствах.
Производства вторичного алюминия часто используют в качестве плавильных печей роторные печи, в особенности для того, чтобы переплавить лом с высокой удельной поверхностью, к примеру, алюминиевую стружку, а также очень грязный алюминиевый лом.
Всех производителей вторичного алюминия делят на две категории:
- компании, создающие литейные сплавы для изготовителей алюминиевых отливок
- компании, создающие алюминий для раскисления стали.
Обе категории компаний используют в качестве сырья «старый» лом и производственные отходы литейных заводов. На таких заводах помимо введения легирующих составляющих для доводки определенного сплава используют оснащение для очистки алюминиевого расплава и ликвидации нежелательных химических элементов и прочих примесей. Роторными плавильными печами пользуются именно эти переработчики алюминиевого лома.
Плавление алюминия на литейных предприятиях, которые занимаются производством алюминиевых отливок из вторичного литейного алюминия, осуществляется главным образом в тигельных печах – газовых и электрических, индукционных и сопротивления, и для плавки, и для выдержки алюминия, а также для разливки алюминиевого расплава в подготовленные формы.
Температура плавления окиси алюминия составляет примерно 2050° С, что почти в три раза выше, чем градус плавления алюминия металлического.
На сегодняшний день наиболее популярной является плавка алюминия в пламенных отражательных печах, которые работают на углеродистом топливе, и в электрических печах. В ходе плавки алюминия в отражательных пламенных печах и в камерных электропечах сопротивления прогрев обособленных кусков садки стартует в области самых высоких температур, т. е. в верхней части. В тоже время поверхность садки с большой скоростью окисляется и поглощает много газов.
Внутри канальной индукционной электропечи расплавление кусков алюминия осуществляется в области наивысших температур под слоем жидкого металла, поверхность которого накрыта пленкой окиси алюминия. Области наивысших температур в канальных электропечах расположена в узком канале и в прилегающих к нему частях шихты.
Металл на поверхности шахты имеет самую низкую температуру, вследствие чего получившиеся отливки из канальных электропечей, имеют в своем составе более низкое количество окислов, чем отливки из печей других видов. Таким же преимуществом отличаются тигельные индукционные электропечи, в которых по технологическим требованиям в тигле по окончанию каждой плавки остается некоторое количество жидкого металла, примерно 20—35% от емкости тигля печи.
Важное свойство жидкого алюминия и его сплавов заключается в его способности поглощать газы, в особенности водород. В пламенных печах много водорода собирается в топочных газах. Помимо этого, в плавильные печи всех видов его можно внести сырой шихтой.
Жидкий алюминий является хорошим растворителем для многих металлов, к примеру, железа. При этом образуются хрупкие соединения FeAl2 и Fe2Al7, которые снижают качество отливок.
Плавление алюминия в домашних условиях
Очень печально, если в доме выходят из строя маленькие, но важные функциональные составляющие, к примеру, направляющие рольставен или раздвижных дверей (могут лопнуть), фурнитура и прочее. Чаще всего такие элементы создают из алюминия. Искать им замену проблематично, а иногда ликвидировать поломку в функционале двери или окна нужно немедленно, хотя бы временно. Если вы имеете опыт паяния, но большую часть поломок алюминиевой фурнитуры или профиля можно устранить самостоятельно.
Основная проблема – это получение рабочего материала, то есть расплавленного алюминия, при помощи которого будет осуществляться пайка сломанных деталей.
Многие не знают, какая температура плавления алюминия. Она составляет около 660 градусов. Стандартная газовая плита не способна разогреть металл до такой температуры. Что же делать?
Для начала необходимо приобрести алюминиевую чушку, но можно и использовать обрезки старого профиля. Чтобы расплавить алюминий понадобится портативная газовая горелка или паяльная лампа. Разные модели этих устройств способны дать температуру в пределах 1000 – 1300 градусов.
Подготовленный материал нужно положить в тугоплавкую емкость, к примеру, из нержавеющей стали. Кроме этого, нужна прокаленная стальная пластина или еще одна емкость, в которую мы будем выливать расплавленный металл.
Последовательность работы:
- создание небольшого «колодца». Сверху нужно будет поставить емкость для плавки
- розжиг костра в «колодце». Это необходимо для поддержания тары в нагретом состоянии, после использования горелки. Также костер поможет прогреть алюминий снизу
- после образования жарких углей можно установить емкость с алюминием. Время плавления алюминия таким образом составляет примерно 15 – 20 минут. Тут же вы можете оставить прогреваться и вторую емкость или пластину
- далее нужно включить газовую горелку на максимум и греть алюминий сверху
- плавка металла начинается почти мгновенно, но цель еще не получена. Главная задача – получение однородного прогрева. Чтобы этого добиться нужно периодически встряхивать емкость
- в процессе плавки образуется оксид алюминия, формирующий окалину
- после этого расплавленный металл нужно вылить на прокаленную стальную поверхность, аккуратно, чтобы не высыпалась окалина. Теперь расплавленный алюминий готов к дальнейшей работе.
Степень чистоты, % | 99,25 | 99,40 | 99,75 | 99.97 | 99,996 | 99.9998 |
Плотность при 20°С, г/см3 | 2,727 | 2,706 | 2,703 | 2,6996 | 2,6989 | 2,69808 |
Степень чистоты, % | 99,25 | 99.40 | 99.75 |
Плотность, г/см3 | 2,311 | 2,291 | 2,289 |
Степень чистоты, % | 99,2 | 99,5 | 99,6 | 99,97 | 99,996 |
Температура плавления, °С | 657 | 658 | 659,7 | 659,8 | 660,24 |
mining-prom.ru