ΠΠΎΠ»ΠΎΡΠ΅Π½ΠΈΠ΅ ΠΏΡΠΎΠ²ΠΎΠ»ΠΎΠΊΠΈ β ΠΎΡΠΎΠ±Π΅Π½Π½ΠΎΡΡΠΈ ΡΠ΅Ρ Π½ΠΎΠ»ΠΎΠ³ΠΈΠΈ ΠΈ ΠΎΠ±ΠΎΡΡΠ΄ΠΎΠ²Π°Π½ΠΈΠ΅
ΠΠΎΠ»ΠΎΡΠ΅Π½ΠΈΠ΅, ΠΏΠΎΡΡΠ΅Π΄ΡΡΠ²ΠΎΠΌ ΠΊΠΎΡΠΎΡΠΎΠ³ΠΎ ΠΏΡΠΎΠΈΠ·Π²ΠΎΠ΄ΡΡ ΠΏΡΠΎΠ²ΠΎΠ»ΠΎΡΠ½ΡΡ ΠΏΡΠΎΠ΄ΡΠΊΡΠΈΡ, ΡΠ²Π»ΡΠ΅ΡΡΡ Π½Π΅ΡΠ»ΠΎΠΆΠ½ΠΎΠΉ ΡΠ΅Ρ Π½ΠΎΠ»ΠΎΠ³ΠΈΡΠ΅ΡΠΊΠΎΠΉ ΠΎΠΏΠ΅ΡΠ°ΡΠΈΠ΅ΠΉ. ΠΠ΅ΠΆΠ΄Ρ ΡΠ΅ΠΌ, ΡΡΠΎΠ±Ρ Π² ΠΈΡΠΎΠ³Π΅ Π²ΡΠΏΠΎΠ»Π½Π΅Π½ΠΈΡ ΡΠ°ΠΊΠΎΠΉ ΠΏΡΠΎΡΠ΅Π΄ΡΡΡ ΠΏΠΎΠ»ΡΡΠΈΡΡ ΠΊΠ°ΡΠ΅ΡΡΠ²Π΅Π½Π½ΠΎΠ΅ ΠΈΠ·Π΄Π΅Π»ΠΈΠ΅, ΠΎΡΡΡΠ΅ΡΡΠ²Π»ΡΡΡ Π΅Π΅ Π½Π΅ΠΎΠ±Ρ ΠΎΠ΄ΠΈΠΌΠΎ Π² ΠΏΡΠ°Π²ΠΈΠ»ΡΠ½ΠΎΠΉ ΠΏΠΎΡΠ»Π΅Π΄ΠΎΠ²Π°ΡΠ΅Π»ΡΠ½ΠΎΡΡΠΈ ΠΈ ΠΈΡΠΏΠΎΠ»ΡΠ·ΠΎΠ²Π°ΡΡ Π΄Π»Ρ ΡΡΠΎΠ³ΠΎ ΡΠΎΠΎΡΠ²Π΅ΡΡΡΠ²ΡΡΡΠ΅Π΅ ΠΎΠ±ΠΎΡΡΠ΄ΠΎΠ²Π°Π½ΠΈΠ΅.
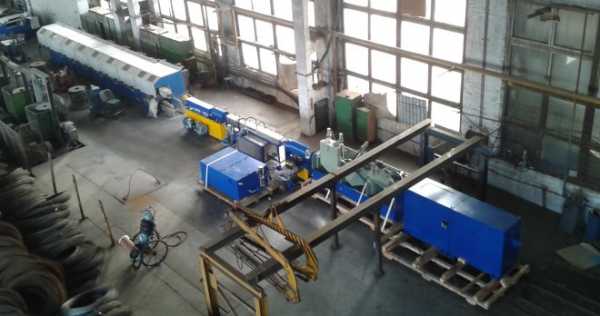
ΠΠΈΠ½ΠΈΡ ΠΏΡΠΎΠΈΠ·Π²ΠΎΠ΄ΡΡΠ²Π° ΠΏΡΠΎΠ²ΠΎΠ»ΠΎΠΊΠΈ ΠΏΠΎ ΠΌΠ΅ΡΠΎΠ΄Ρ Π²ΠΎΠ»ΠΎΡΠ΅Π½ΠΈΡ
ΠΡΠ½ΠΎΠ²Π½ΡΠ΅ ΡΡΠ°ΠΏΡ
Π‘ΡΡΡ ΡΠ΅Ρ Π½ΠΎΠ»ΠΎΠ³ΠΈΠΈ, ΠΏΠΎ ΠΊΠΎΡΠΎΡΠΎΠΉ Π²ΡΠΏΠΎΠ»Π½ΡΡΡ Π²ΠΎΠ»ΠΎΡΠ΅Π½ΠΈΠ΅ ΠΏΡΠΎΠ²ΠΎΠ»ΠΎΠΊΠΈ, Π·Π°ΠΊΠ»ΡΡΠ°Π΅ΡΡΡ Π² ΡΠΎΠΌ, ΡΡΠΎ ΠΌΠ΅ΡΠ°Π»Π»ΠΈΡΠ΅ΡΠΊΡΡ Π·Π°Π³ΠΎΡΠΎΠ²ΠΊΡ ΠΈΠ· ΡΡΠ°Π»ΠΈ, ΠΌΠ΅Π΄ΠΈ ΠΈΠ»ΠΈ Π°Π»ΡΠΌΠΈΠ½ΠΈΡ ΠΏΡΠΎΡΡΠ³ΠΈΠ²Π°ΡΡ ΡΠ΅ΡΠ΅Π· ΡΡΠΆΠ°ΡΡΠ΅Π΅ΡΡ ΠΎΡΠ²Π΅ΡΡΡΠΈΠ΅ β ΡΠΈΠ»ΡΠ΅ΡΡ. Π‘Π°ΠΌ ΠΈΠ½ΡΡΡΡΠΌΠ΅Π½Ρ, Π² ΠΊΠΎΡΠΎΡΠΎΠΌ ΡΠ°ΠΊΠΎΠ΅ ΠΎΡΠ²Π΅ΡΡΡΠΈΠ΅ Π²ΡΠΏΠΎΠ»Π½Π΅Π½ΠΎ, Π½Π°Π·ΡΠ²Π°Π΅ΡΡΡ Π²ΠΎΠ»ΠΎΠΊΠΎΠΉ, Π΅Π³ΠΎ ΡΡΡΠ°Π½Π°Π²Π»ΠΈΠ²Π°ΡΡ Π½Π° ΡΠΏΠ΅ΡΠΈΠ°Π»ΡΠ½ΠΎΠ΅ ΠΎΠ±ΠΎΡΡΠ΄ΠΎΠ²Π°Π½ΠΈΠ΅ Π΄Π»Ρ Π²ΠΎΠ»ΠΎΡΠ΅Π½ΠΈΡ ΠΏΡΠΎΠ²ΠΎΠ»ΠΎΠΊΠΈ. ΠΠ° ΡΠΎ, ΠΊΠ°ΠΊΠΈΠΌΠΈ Π΄ΠΈΠ°ΠΌΠ΅ΡΡΠΎΠΌ, ΡΠ΅ΡΠ΅Π½ΠΈΠ΅ΠΌ ΠΈ ΡΠΎΡΠΌΠΎΠΉ Π±ΡΠ΄Π΅Ρ ΠΎΠ±Π»Π°Π΄Π°ΡΡ Π³ΠΎΡΠΎΠ²ΠΎΠ΅ ΠΈΠ·Π΄Π΅Π»ΠΈΠ΅, ΠΎΠΊΠ°Π·ΡΠ²Π°ΡΡ Π²Π»ΠΈΡΠ½ΠΈΠ΅ ΠΏΠ°ΡΠ°ΠΌΠ΅ΡΡΡ ΡΠΈΠ»ΡΠ΅ΡΡ.
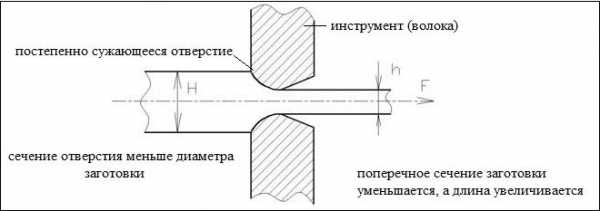
ΠΡΠΈΠ½ΡΠΈΠΏ Π²ΠΎΠ»ΠΎΡΠ΅Π½ΠΈΡ ΠΌΠ΅ΡΠ°Π»Π»Π°
ΠΡΠΏΠΎΠ»Π½Π΅Π½ΠΈΠ΅ Π²ΠΎΠ»ΠΎΡΠ΅Π½ΠΈΡ, Π΅ΡΠ»ΠΈ ΡΡΠ°Π²Π½ΠΈΠ²Π°ΡΡ ΡΠ°ΠΊΡΡ ΡΠ΅Ρ Π½ΠΎΠ»ΠΎΠ³ΠΈΡΠ΅ΡΠΊΡΡ ΠΎΠΏΠ΅ΡΠ°ΡΠΈΡ Ρ ΠΏΡΠΎΠΊΠ°ΡΠΊΠΎΠΉ, ΠΏΠΎΠ·Π²ΠΎΠ»ΡΠ΅Ρ ΠΏΠΎΠ»ΡΡΠ°ΡΡ ΠΈΠ·Π΄Π΅Π»ΠΈΡ, ΠΎΡΠ»ΠΈΡΠ°ΡΡΠΈΠ΅ΡΡ Π±ΠΎΠ»Π΅Π΅ Π²ΡΡΠΎΠΊΠΎΠΉ ΡΠΈΡΡΠΎΡΠΎΠΉ ΠΏΠΎΠ²Π΅ΡΡ Π½ΠΎΡΡΠΈ ΠΈ ΠΈΡΠΊΠ»ΡΡΠΈΡΠ΅Π»ΡΠ½ΠΎΠΉ ΡΠΎΡΠ½ΠΎΡΡΡΡ Π³Π΅ΠΎΠΌΠ΅ΡΡΠΈΡΠ΅ΡΠΊΠΈΡ ΠΏΠ°ΡΠ°ΠΌΠ΅ΡΡΠΎΠ². Π’Π°ΠΊΠΈΠΌΠΈ ΠΈΠ·Π΄Π΅Π»ΠΈΡΠΌΠΈ ΠΌΠΎΠ³ΡΡ Π±ΡΡΡ Π½Π΅ ΡΠΎΠ»ΡΠΊΠΎ ΡΠ°Π·Π»ΠΈΡΠ½ΡΠ΅ ΡΠΈΠΏΡ ΠΏΡΠΎΠ²ΠΎΠ»ΠΎΠΊΠΈ (ΡΠ»Π΅ΠΊΡΡΠΎΡΠ΅Ρ Π½ΠΈΡΠ΅ΡΠΊΠ°Ρ, ΠΈΡΠΏΠΎΠ»ΡΠ·ΡΠ΅ΠΌΠ°Ρ Π΄Π»Ρ ΡΠ²Π°ΡΠΊΠΈ, Π²ΡΠ·ΠΎΡΠ½Π°Ρ ΠΈ Π΄Ρ.), Π½ΠΎ ΡΠ°ΠΊΠΆΠ΅ ΡΠ°ΡΠΎΠ½Π½ΡΠ΅ ΠΏΡΠΎΡΠΈΠ»ΠΈ, ΡΡΡΠ±Ρ ΠΈ ΠΏΡΡΡΠΊΠΈ ΡΠ°Π·Π½ΠΎΠ³ΠΎ Π΄ΠΈΠ°ΠΌΠ΅ΡΡΠ°. ΠΠΎΠ»ΡΡΠ΅Π½Π½ΡΠ΅ ΠΏΠΎ ΡΠ°ΠΊΠΎΠΉ ΡΠ΅Ρ Π½ΠΎΠ»ΠΎΠ³ΠΈΠΈ ΠΈΠ·Π΄Π΅Π»ΠΈΡ ΠΎΡΠ»ΠΈΡΠ°ΡΡΡΡ ΠΈ Π»ΡΡΡΠΈΠΌΠΈ ΠΌΠ΅Ρ Π°Π½ΠΈΡΠ΅ΡΠΊΠΈΠΌΠΈ Ρ Π°ΡΠ°ΠΊΡΠ΅ΡΠΈΡΡΠΈΠΊΠ°ΠΌΠΈ, ΡΠ°ΠΊ ΠΊΠ°ΠΊ Π² ΠΏΡΠΎΡΠ΅ΡΡΠ΅ Π²ΠΎΠ»ΠΎΡΠ΅Π½ΠΈΡ ΠΌΠ΅ΡΠ°Π»Π»Π° Ρ Π΅Π³ΠΎ ΠΏΠΎΠ²Π΅ΡΡ Π½ΠΎΡΡΠ½ΠΎΠ³ΠΎ ΡΠ»ΠΎΡ ΡΠ½ΠΈΠΌΠ°Π΅ΡΡΡ Π½Π°ΠΊΠ»Π΅ΠΏ. Π§ΡΠΎ ΠΊΠ°ΡΠ°Π΅ΡΡΡ ΠΈΠΌΠ΅Π½Π½ΠΎ ΠΏΡΠΎΠΈΠ·Π²ΠΎΠ΄ΡΡΠ²Π° ΠΏΡΠΎΠ²ΠΎΠ»ΠΎΠΊΠΈ, ΡΠΎ ΠΌΠ΅ΡΠΎΠ΄ΠΎΠΌ Π²ΠΎΠ»ΠΎΡΠ΅Π½ΠΈΡ ΠΌΠΎΠΆΠ½ΠΎ ΠΏΠΎΠ»ΡΡΠΈΡΡ ΠΈΠ·Π΄Π΅Π»ΠΈΡ, Π΄ΠΈΠ°ΠΌΠ΅ΡΡ ΠΊΠΎΡΠΎΡΡΡ Π½Π°Ρ ΠΎΠ΄ΠΈΡΡΡ Π² ΠΈΠ½ΡΠ΅ΡΠ²Π°Π»Π΅ ΠΎΡ 1β2 ΠΌΠΈΠΊΡΠΎΠ½ Π΄ΠΎ 10 ΠΈ Π΄Π°ΠΆΠ΅ Π±ΠΎΠ»Π΅Π΅ ΠΌΠΈΠ»Π»ΠΈΠΌΠ΅ΡΡΠΎΠ².
Π’Π΅Ρ Π½ΠΎΠ»ΠΎΠ³ΠΈΡ Π²ΠΎΠ»ΠΎΡΠ΅Π½ΠΈΡ ΡΠ΅Π³ΠΎΠ΄Π½Ρ ΡΠΆΠ΅ Ρ ΠΎΡΠΎΡΠΎ ΠΎΡΡΠ°Π±ΠΎΡΠ°Π½Π°, Π΄Π»Ρ Π΅Π΅ ΡΠ΅Π°Π»ΠΈΠ·Π°ΡΠΈΠΈ ΠΈΡΠΏΠΎΠ»ΡΠ·ΡΡΡΡΡ ΡΠΎΠ²ΡΠ΅ΠΌΠ΅Π½Π½ΡΠ΅ ΠΌΠΎΠ΄Π΅Π»ΠΈ Π²ΠΎΠ»ΠΎΡΠΈΠ»ΡΠ½ΡΡ ΡΡΠ°Π½ΠΊΠΎΠ², ΡΠ°Π±ΠΎΡΠ°ΡΡΠΈΡ Π±Π΅Π· ΡΠ±ΠΎΠ΅Π² ΠΈ ΠΏΠΎΠ·Π²ΠΎΠ»ΡΡΡΠΈΡ Π²ΡΠΏΠΎΠ»Π½ΡΡΡ ΡΠ΅Ρ Π½ΠΎΠ»ΠΎΠ³ΠΈΡΠ΅ΡΠΊΠΈΠΉ ΠΏΡΠΎΡΠ΅ΡΡ Π½Π° ΡΠΊΠΎΡΠΎΡΡΠΈ, Π΄ΠΎΡ ΠΎΠ΄ΡΡΠ΅ΠΉ Π΄ΠΎ 60 ΠΌΠ΅ΡΡΠΎΠ² Π³ΠΎΡΠΎΠ²ΠΎΠ³ΠΎ ΠΈΠ·Π΄Π΅Π»ΠΈΡ Π² ΡΠ΅ΠΊΡΠ½Π΄Ρ. ΠΡΠΏΠΎΠ»ΡΠ·ΠΎΠ²Π°Π½ΠΈΠ΅ ΡΠ°ΠΊΠΎΠ³ΠΎ ΠΎΠ±ΠΎΡΡΠ΄ΠΎΠ²Π°Π½ΠΈΡ Π΄Π»Ρ Π²ΠΎΠ»ΠΎΡΠ΅Π½ΠΈΡ, ΠΊΡΠΎΠΌΠ΅ ΡΠΎΠ³ΠΎ, ΠΏΠΎΠ·Π²ΠΎΠ»ΡΠ΅Ρ ΠΎΠ±Π΅ΡΠΏΠ΅ΡΠΈΡΡ Π·Π½Π°ΡΠΈΡΠ΅Π»ΡΠ½ΡΡ Π²Π΅Π»ΠΈΡΠΈΠ½Ρ ΠΎΠ±ΠΆΠ°ΡΠΈΡ Π·Π°Π³ΠΎΡΠΎΠ²ΠΊΠΈ.
Π’Π΅Ρ Π½ΠΎΠ»ΠΎΠ³ΠΈΡΠ΅ΡΠΊΠ°Ρ ΡΡ Π΅ΠΌΠ° Π²ΠΎΠ»ΠΎΡΠ΅Π½ΠΈΡ ΠΏΡΠΎΠ²ΠΎΠ»ΠΎΠΊΠΈ ΠΈΠ· Π½Π΅ΡΠΆΠ°Π²Π΅ΡΡΠ΅ΠΉ ΡΡΠ°Π»ΠΈ
ΠΠ·Π³ΠΎΡΠΎΠ²Π»Π΅Π½ΠΈΠ΅ ΠΏΡΠΎΠ²ΠΎΠ»ΠΎΠΊΠΈ ΠΏΠΎ ΡΠ΅Ρ Π½ΠΎΠ»ΠΎΠ³ΠΈΠΈ Π²ΠΎΠ»ΠΎΡΠ΅Π½ΠΈΡ Π²ΠΊΠ»ΡΡΠ°Π΅Ρ Π² ΡΠ΅Π±Ρ Π½Π΅ΡΠΊΠΎΠ»ΡΠΊΠΎ ΡΡΠ°ΠΏΠΎΠ².
- ΠΡΡ ΠΎΠ΄Π½Π°Ρ Π·Π°Π³ΠΎΡΠΎΠ²ΠΊΠ° ΠΏΠΎΠ΄Π²Π΅ΡΠ³Π°Π΅ΡΡΡ ΠΏΡΠΎΡΠ΅Π΄ΡΡΠ΅ ΡΡΠ°Π²Π»Π΅Π½ΠΈΡ, Π΄Π»Ρ ΡΠ΅Π³ΠΎ ΠΈΡΠΏΠΎΠ»ΡΠ·ΡΠ΅ΡΡΡ ΡΠ΅ΡΠ½ΠΎΠΊΠΈΡΠ»ΡΠΉ ΡΠ°ΡΡΠ²ΠΎΡ, Π½Π°Π³ΡΠ΅ΡΡΠΉ Π΄ΠΎ 50 Π³ΡΠ°Π΄ΡΡΠΎΠ². Π‘ ΠΏΠΎΠ²Π΅ΡΡ Π½ΠΎΡΡΠΈ ΠΌΠ΅ΡΠ°Π»Π»Π°, ΠΏΡΠΎΡΠ΅Π΄ΡΠ΅Π³ΠΎ ΡΠ°ΠΊΡΡ ΠΏΡΠΎΡΠ΅Π΄ΡΡΡ, Π»Π΅Π³ΠΊΠΎ ΡΠ½ΠΈΠΌΠ°Π΅ΡΡΡ ΠΎΠΊΠ°Π»ΠΈΠ½Π°, Π·Π° ΡΡΠ΅Ρ ΡΠ΅Π³ΠΎ ΡΠ²Π΅Π»ΠΈΡΠΈΠ²Π°Π΅ΡΡΡ ΡΡΠΎΠΊ ΡΠ»ΡΠΆΠ±Ρ ΠΌΠ°ΡΡΠΈΡ Π²ΠΎΠ»ΠΎΡΠΈΠ»ΡΠ½ΡΡ ΡΡΠ°Π½ΠΊΠΎΠ².
- Π§ΡΠΎΠ±Ρ ΡΠ²Π΅Π»ΠΈΡΠΈΡΡ ΠΏΠ»Π°ΡΡΠΈΡΠ½ΠΎΡΡΡ ΠΎΠ±ΡΠ°Π±Π°ΡΡΠ²Π°Π΅ΠΌΠΎΠΉ Π·Π°Π³ΠΎΡΠΎΠ²ΠΊΠΈ, Π° Π΅Π΅ Π²Π½ΡΡΡΠ΅Π½Π½ΡΡ ΡΡΡΡΠΊΡΡΡΡ Π΄ΠΎΠ²Π΅ΡΡΠΈ Π΄ΠΎ ΠΌΠ΅Π»ΠΊΠΎΠ·Π΅ΡΠ½ΠΈΡΡΠΎΠ³ΠΎ ΡΠΎΡΡΠΎΡΠ½ΠΈΡ, Π²ΡΠΏΠΎΠ»Π½ΡΡΡ ΠΏΡΠ΅Π΄Π²Π°ΡΠΈΡΠ΅Π»ΡΠ½ΡΠΉ ΠΎΡΠΆΠΈΠ³ ΠΌΠ΅ΡΠ°Π»Π»Π°.
- ΠΡΡΠ°ΡΠΊΠΈ ΡΡΠ°Π²ΠΈΠ»ΡΠ½ΠΎΠ³ΠΎ ΡΠ°ΡΡΠ²ΠΎΡΠ°, ΠΊΠΎΡΠΎΡΡΠΉ ΡΠ²Π»ΡΠ΅ΡΡΡ Π΄ΠΎΡΡΠ°ΡΠΎΡΠ½ΠΎ Π°Π³ΡΠ΅ΡΡΠΈΠ²Π½ΡΠΌ, Π½Π΅ΠΉΡΡΠ°Π»ΠΈΠ·ΡΡΡ, ΠΏΠΎΡΠ»Π΅ ΡΠ΅Π³ΠΎ Π·Π°Π³ΠΎΡΠΎΠ²ΠΊΡ ΠΏΠΎΠ΄Π²Π΅ΡΠ³Π°ΡΡ ΠΏΡΠΎΠΌΡΠ²ΠΊΠ΅.
- Π§ΡΠΎΠ±Ρ ΠΊΠΎΠ½Π΅Ρ Π·Π°Π³ΠΎΡΠΎΠ²ΠΊΠΈ ΠΌΠΎΠΆΠ½ΠΎ Π±ΡΠ»ΠΎ ΠΏΡΠΎΠΏΡΡΡΠΈΡΡ Π² ΡΠΈΠ»ΡΠ΅ΡΡ, Π΅Π³ΠΎ Π·Π°ΠΎΡΡΡΡΡΡ, Π΄Π»Ρ ΡΠ΅Π³ΠΎ ΠΌΠΎΠΆΠ΅Ρ Π±ΡΡΡ ΠΈΡΠΏΠΎΠ»ΡΠ·ΠΎΠ²Π°Π½ ΠΌΠΎΠ»ΠΎΡ ΠΈΠ»ΠΈ ΠΊΠΎΠ²ΠΎΡΠ½ΡΠ΅ Π²Π°Π»ΠΊΠΈ.
- ΠΠΎΡΠ»Π΅ Π·Π°Π²Π΅ΡΡΠ΅Π½ΠΈΡ Π²ΡΠ΅Ρ ΠΏΠΎΠ΄Π³ΠΎΡΠΎΠ²ΠΈΡΠ΅Π»ΡΠ½ΡΡ ΠΎΠΏΠ΅ΡΠ°ΡΠΈΠΉ Π·Π°Π³ΠΎΡΠΎΠ²ΠΊΠ° ΠΏΡΠΎΠΏΡΡΠΊΠ°Π΅ΡΡΡ ΡΠ΅ΡΠ΅Π· ΡΠΈΠ»ΡΠ΅ΡΡ Π΄Π»Ρ Π²ΠΎΠ»ΠΎΡΠ΅Π½ΠΈΡ ΠΏΡΠΎΠ²ΠΎΠ»ΠΎΠΊΠΈ, Π³Π΄Π΅ ΠΈ ΡΠΎΡΠΌΠΈΡΡΡΡΡΡ ΠΏΡΠΎΡΠΈΠ»Ρ ΠΈ ΡΠ°Π·ΠΌΠ΅ΡΡ Π³ΠΎΡΠΎΠ²ΠΎΠ³ΠΎ ΠΈΠ·Π΄Π΅Π»ΠΈΡ.
- ΠΡΠΎΠΈΠ·Π²ΠΎΠ΄ΡΡΠ²ΠΎ ΠΏΡΠΎΠ²ΠΎΠ»ΠΎΠΊΠΈ Π·Π°Π²Π΅ΡΡΠ°Π΅ΡΡΡ Π²ΡΠΏΠΎΠ»Π½Π΅Π½ΠΈΠ΅ΠΌ ΠΎΡΠΆΠΈΠ³Π°. ΠΠΎΡΠ»Π΅ Π²ΠΎΠ»ΠΎΡΠ΅Π½ΠΈΠΈΡ ΠΈΠ·Π΄Π΅Π»ΠΈΠ΅ ΡΠ°ΠΊΠΆΠ΅ ΠΏΠΎΠ΄Π²Π΅ΡΠ³Π°ΡΡ ΡΡΠ΄Ρ Π΄ΠΎΠΏΠΎΠ»Π½ΠΈΡΠ΅Π»ΡΠ½ΡΡ ΡΠ΅Ρ Π½ΠΎΠ»ΠΎΠ³ΠΈΡΠ΅ΡΠΊΠΈΡ ΠΎΠΏΠ΅ΡΠ°ΡΠΈΠΉ β ΡΠ΅Π·ΠΊΠ΅ Π½Π° ΠΎΡΡΠ΅Π·ΠΊΠΈ ΡΡΠ΅Π±ΡΠ΅ΠΌΠΎΠΉ Π΄Π»ΠΈΠ½Ρ, ΡΠ½ΡΡΠΈΡ ΠΊΠΎΠ½ΡΠΎΠ², ΠΏΡΠ°Π²ΠΊΠ΅ ΠΈ Π΄Ρ.
ΠΡΠΎΠ±Π΅Π½Π½ΠΎΡΡΠΈ ΠΏΡΠΎΡΠ΅Π΄ΡΡΡ
ΠΡΠ±ΠΎΠΉ Π²ΠΎΠ»ΠΎΡΠΈΠ»ΡΡΠΈΠΊ ΠΏΡΠΎΠ²ΠΎΠ»ΠΎΠΊΠΈ Π·Π½Π°Π΅Ρ ΡΠ°ΠΊΠΎΠΉ Π½Π΅Π΄ΠΎΡΡΠ°ΡΠΎΠΊ Π²ΠΎΠ»ΠΎΡΠ΅Π½ΠΈΡ, ΠΊΠ°ΠΊ Π½Π΅Π΄ΠΎΡΡΠ°ΡΠΎΡΠ½ΠΎ Π²ΡΡΠΎΠΊΠ°Ρ ΡΡΠ΅ΠΏΠ΅Π½Ρ Π΄Π΅ΡΠΎΡΠΌΠΈΡΠΎΠ²Π°Π½ΠΈΡ Π³ΠΎΡΠΎΠ²ΠΎΠ³ΠΎ ΠΈΠ·Π΄Π΅Π»ΠΈΡ. ΠΠ±ΡΡΡΠ½ΡΠ΅ΡΡΡ ΡΡΠΎ ΡΠ΅ΠΌ, ΡΡΠΎ ΠΎΠ½ΠΎ, Π²ΡΡ ΠΎΠ΄Ρ ΠΈΠ· Π·ΠΎΠ½Ρ ΠΎΠ±ΡΠ°Π±ΠΎΡΠΊΠΈ Π²ΠΎΠ»ΠΎΡΠΈΠ»ΡΠ½ΠΎΠ³ΠΎ ΡΡΠ°Π½ΠΊΠ°, Π΄Π΅ΡΠΎΡΠΌΠΈΡΡΠ΅ΡΡΡ ΡΠΎΠ»ΡΠΊΠΎ Π΄ΠΎ ΡΡΠ΅ΠΏΠ΅Π½ΠΈ, ΠΎΠ³ΡΠ°Π½ΠΈΡΠ΅Π½Π½ΠΎΠΉ ΠΏΡΠΎΡΠ½ΠΎΡΡΡΡ ΠΊΠΎΠ½ΡΠ° Π·Π°Π³ΠΎΡΠΎΠ²ΠΊΠΈ, ΠΊ ΠΊΠΎΡΠΎΡΠΎΠΌΡ ΠΈ ΠΏΡΠΈΠΊΠ»Π°Π΄ΡΠ²Π°Π΅ΡΡΡ ΡΠΎΠΎΡΠ²Π΅ΡΡΡΠ²ΡΡΡΠ΅Π΅ ΡΡΠΈΠ»ΠΈΠ΅ Π² ΠΏΡΠΎΡΠ΅ΡΡΠ΅ ΠΎΠ±ΡΠ°Π±ΠΎΡΠΊΠΈ.
Π ΠΊΠ°ΡΠ΅ΡΡΠ²Π΅ ΠΈΡΡ ΠΎΠ΄Π½ΠΎΠ³ΠΎ ΠΌΠ°ΡΠ΅ΡΠΈΠ°Π»Π°, ΠΊΠΎΡΠΎΡΡΠΉ ΠΏΠΎΠ΄Π²Π΅ΡΠ³Π°ΡΡ ΠΎΠ±ΡΠ°Π±ΠΎΡΠΊΠ΅ Π½Π° Π²ΠΎΠ»ΠΎΡΠΈΠ»ΡΠ½ΡΡ ΡΡΠ°Π½ΠΊΠ°Ρ , ΡΠ»ΡΠΆΠ°Ρ ΠΌΠ΅ΡΠ°Π»Π»ΠΈΡΠ΅ΡΠΊΠΈΠ΅ Π·Π°Π³ΠΎΡΠΎΠ²ΠΊΠΈ, ΠΏΠΎΠ»ΡΡΠ΅Π½Π½ΡΠ΅ ΠΌΠ΅ΡΠΎΠ΄ΠΎΠΌ Π½Π΅ΠΏΡΠ΅ΡΡΠ²Π½ΠΎΠ³ΠΎ Π»ΠΈΡΡΡ, ΠΏΡΠ΅ΡΡΠΎΠ²Π°Π½ΠΈΠ΅ΠΌ ΠΈ ΠΊΠ°ΡΠ°Π½ΠΈΠ΅ΠΌ ΠΈΠ· ΡΠ³Π»Π΅ΡΠΎΠ΄ΠΈΡΡΡΡ ΠΈ Π»Π΅Π³ΠΈΡΠΎΠ²Π°Π½Π½ΡΡ ΡΡΠ°Π»Π΅ΠΉ, Π° ΡΠ°ΠΊΠΆΠ΅ ΡΠ²Π΅ΡΠ½ΡΡ ΡΠΏΠ»Π°Π²ΠΎΠ². ΠΠ°ΠΈΠ±ΠΎΠ»ΡΡΡΡ ΡΠ»ΠΎΠΆΠ½ΠΎΡΡΡ ΠΏΡΠΎΡΠ΅ΡΡ Π²ΠΎΠ»ΠΎΡΠ΅Π½ΠΈΡ ΠΏΡΠ΅Π΄ΡΡΠ°Π²Π»ΡΠ΅Ρ Π² ΡΠΎΠΌ ΡΠ»ΡΡΠ°Π΅, Π΅ΡΠ»ΠΈ ΠΎΠ±ΡΠ°Π±ΠΎΡΠΊΠ΅ ΠΏΠΎΠ΄Π²Π΅ΡΠ³Π°Π΅ΡΡΡ ΡΡΠ°Π»ΡΠ½ΠΎΠΉ ΡΠΏΠ»Π°Π². Π ΡΠ°ΠΊΠΈΡ ΡΠ»ΡΡΠ°ΡΡ Π΄Π»Ρ ΠΊΠ°ΡΠ΅ΡΡΠ²Π΅Π½Π½ΠΎΠ³ΠΎ Π²ΠΎΠ»ΠΎΡΠ΅Π½ΠΈΡ Π½Π΅ΠΎΠ±Ρ ΠΎΠ΄ΠΈΠΌΠΎ Π΄ΠΎΠ²Π΅ΡΡΠΈ ΠΌΠΈΠΊΡΠΎΡΡΡΡΠΊΡΡΡΡ ΠΌΠ΅ΡΠ°Π»Π»Π° Π΄ΠΎ ΡΡΠ΅Π±ΡΠ΅ΠΌΠΎΠ³ΠΎ ΡΠΎΡΡΠΎΡΠ½ΠΈΡ. Π§ΡΠΎΠ±Ρ ΠΏΠΎΠ»ΡΡΠΈΡΡ ΠΎΠΏΡΠΈΠΌΠ°Π»ΡΠ½ΡΡ Π²Π½ΡΡΡΠ΅Π½Π½ΡΡ ΡΡΡΡΠΊΡΡΡΡ ΡΡΠ°Π»ΠΈ, ΡΠ°Π½ΡΡΠ΅ ΠΈΡΠΏΠΎΠ»ΡΠ·ΠΎΠ²Π°Π»ΠΈ ΡΠ°ΠΊΡΡ ΡΠ΅Ρ Π½ΠΎΠ»ΠΎΠ³ΠΈΡΠ΅ΡΠΊΡΡ ΠΎΠΏΠ΅ΡΠ°ΡΠΈΡ, ΠΊΠ°ΠΊ ΠΏΠ°ΡΠ΅Π½ΡΠΈΡΠΎΠ²Π°Π½ΠΈΠ΅. ΠΠ°ΠΊΠ»ΡΡΠ°Π»ΡΡ ΡΡΠΎΡ ΡΠΏΠΎΡΠΎΠ± ΠΎΠ±ΡΠ°Π±ΠΎΡΠΊΠΈ Π² ΡΠΎΠΌ, ΡΡΠΎ ΡΡΠ°Π»Ρ ΡΠ½Π°ΡΠ°Π»Π° Π½Π°Π³ΡΠ΅Π²Π°Π»ΠΈ Π΄ΠΎ ΡΠ΅ΠΌΠΏΠ΅ΡΠ°ΡΡΡΡ Π°ΡΡΡΠ΅Π½ΠΈΠ·Π°ΡΠΈΠΈ, Π° Π·Π°ΡΠ΅ΠΌ Π²ΡΠ΄Π΅ΡΠΆΠΈΠ²Π°Π»ΠΈ Π² ΡΠ²ΠΈΠ½ΡΠΎΠ²ΠΎΠΌ ΠΈΠ»ΠΈ ΡΠΎΠ»ΡΠ½ΠΎΠΌ ΡΠ°ΡΠΏΠ»Π°Π²Π΅, Π½Π°Π³ΡΠ΅ΡΠΎΠΌ Π΄ΠΎ ΡΠ΅ΠΌΠΏΠ΅ΡΠ°ΡΡΡΡ ΠΎΠΊΠΎΠ»ΠΎ 500Β°.
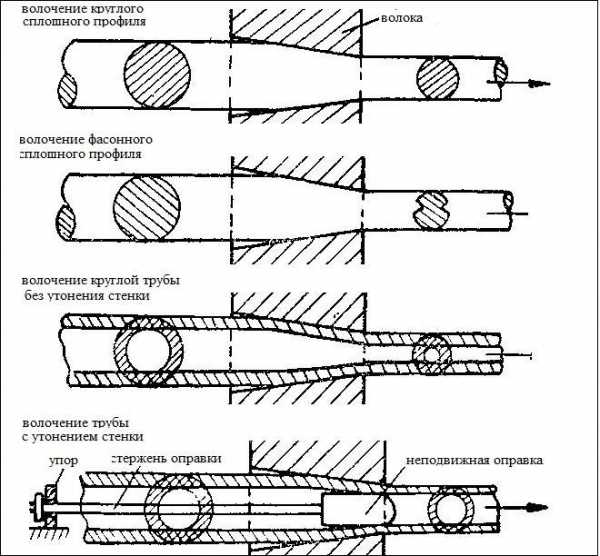
ΠΠ΅ΡΠΎΠ΄Ρ Π²ΠΎΠ»ΠΎΡΠ΅Π½ΠΈΡ
Π‘ΠΎΠ²ΡΠ΅ΠΌΠ΅Π½Π½ΡΠΉ ΡΡΠΎΠ²Π΅Π½Ρ ΡΠ°Π·Π²ΠΈΡΠΈΡ ΠΌΠ΅ΡΠ°Π»Π»ΡΡΠ³ΠΈΡΠ΅ΡΠΊΠΎΠΉ ΠΏΡΠΎΠΌΡΡΠ»Π΅Π½Π½ΠΎΡΡΠΈ, ΠΈΡΠΏΠΎΠ»ΡΠ·ΡΠ΅ΠΌΡΠ΅ Π² Π½Π΅ΠΉ ΡΠ΅Ρ Π½ΠΎΠ»ΠΎΠ³ΠΈΠΈ ΠΈ ΠΎΠ±ΠΎΡΡΠ΄ΠΎΠ²Π°Π½ΠΈΠ΅ Π΄Π»Ρ ΠΏΠΎΠ»ΡΡΠ΅Π½ΠΈΡ ΠΌΠ΅ΡΠ°Π»Π»ΠΎΠ² ΠΈ ΡΠΏΠ»Π°Π²ΠΎΠ² ΠΏΠΎΠ·Π²ΠΎΠ»ΡΡΡ Π½Π΅ Π³ΠΎΡΠΎΠ²ΠΈΡΡ ΠΌΠ΅ΡΠ°Π»Π» ΠΊ Π²ΠΎΠ»ΠΎΡΠ΅Π½ΠΈΡ ΡΠ°ΠΊΠΈΠΌ ΡΠ»ΠΎΠΆΠ½ΡΠΌ ΠΈ ΡΡΡΠ΄ΠΎΠ΅ΠΌΠΊΠΈΠΌ ΡΠΏΠΎΡΠΎΠ±ΠΎΠΌ. Π‘ΡΠ°Π»ΡΠ½Π°Ρ Π·Π°Π³ΠΎΡΠΎΠ²ΠΊΠ°, Π²ΡΡ ΠΎΠ΄ΡΡΠ°Ρ Ρ ΠΏΡΠΎΠΊΠ°ΡΠ½ΠΎΠ³ΠΎ ΡΡΠ°Π½Π° ΡΠΎΠ²ΡΠ΅ΠΌΠ΅Π½Π½ΠΎΠ³ΠΎ ΠΌΠ΅ΡΠ°Π»Π»ΡΡΠ³ΠΈΡΠ΅ΡΠΊΠΎΠ³ΠΎ ΠΏΡΠ΅Π΄ΠΏΡΠΈΡΡΠΈΡ, ΡΠΆΠ΅ ΠΎΠ±Π»Π°Π΄Π°Π΅Ρ Π²Π½ΡΡΡΠ΅Π½Π½Π΅ΠΉ ΡΡΡΡΠΊΡΡΡΠΎΠΉ, ΠΎΠΏΡΠΈΠΌΠ°Π»ΡΠ½ΠΎ ΠΏΠΎΠ΄Ρ ΠΎΠ΄ΡΡΠ΅ΠΉ Π΄Π»Ρ Π²ΠΎΠ»ΠΎΡΠ΅Π½ΠΈΡ.
Π‘Π°ΠΌΠ° ΡΠ΅Ρ Π½ΠΎΠ»ΠΎΠ³ΠΈΡ Π²ΠΎΠ»ΠΎΡΠ΅Π½ΠΈΡ ΠΈ Π²ΠΎΠ»ΠΎΡΠΈΠ»ΡΠ½ΠΎΠ΅ ΠΎΠ±ΠΎΡΡΠ΄ΠΎΠ²Π°Π½ΠΈΠ΅ ΡΠ°ΠΊΠΆΠ΅ ΡΠΎΠ²Π΅ΡΡΠ΅Π½ΡΡΠ²ΠΎΠ²Π°Π»ΠΈΡΡ Π½Π° ΠΏΡΠΎΡΡΠΆΠ΅Π½ΠΈΠΈ ΠΌΠ½ΠΎΠ³ΠΈΡ Π»Π΅Ρ. Π ΡΠ΅Π·ΡΠ»ΡΡΠ°ΡΠ΅ Π²ΠΎΠ»ΠΎΡΠΈΠ»ΡΡΠΈΠΊ ΠΏΡΠΎΠ²ΠΎΠ»ΠΎΠΊΠΈ ΡΠ΅Π³ΠΎΠ΄Π½Ρ ΠΈΠΌΠ΅Π΅Ρ Π²ΠΎΠ·ΠΌΠΎΠΆΠ½ΠΎΡΡΡ ΠΏΡΠΈΠΌΠ΅Π½ΡΡΡ ΡΠΎΠ²ΡΠ΅ΠΌΠ΅Π½Π½ΡΠ΅ Π²ΠΎΠ»ΠΎΡΠΈΠ»ΡΠ½ΡΠ΅ ΡΡΡΡΠΎΠΉΡΡΠ²Π°, ΠΏΠΎΠ·Π²ΠΎΠ»ΡΡΡΠΈΠ΅ Ρ ΠΌΠΈΠ½ΠΈΠΌΠ°Π»ΡΠ½ΡΠΌΠΈ ΡΡΡΠ΄ΠΎΠ·Π°ΡΡΠ°ΡΠ°ΠΌΠΈ Π³Π°ΡΠ°Π½ΡΠΈΡΠΎΠ²Π°Π½Π½ΠΎ ΠΏΠΎΠ»ΡΡΠ°ΡΡ ΠΈΠ·Π΄Π΅Π»ΠΈΡ Π²ΡΡΠΎΠΊΠΎΠ³ΠΎ ΠΊΠ°ΡΠ΅ΡΡΠ²Π°. ΠΠ°ΡΠ΅ΡΡΠ²ΠΎ ΠΈ ΡΠΎΡΠ½ΠΎΡΡΡ ΠΎΠ±ΡΠ°Π±ΠΎΡΠΊΠΈ, Π²ΡΠΏΠΎΠ»Π½ΡΠ΅ΠΌΠΎΠΉ Π½Π° ΡΠ°ΠΊΠΈΡ Π²ΠΎΠ»ΠΎΡΠΈΠ»ΡΠ½ΡΡ ΡΠΏΠ΅ΡΠΈΠ°Π»ΠΈΠ·ΠΈΡΠΎΠ²Π°Π½Π½ΡΡ ΡΡΠ°Π½ΠΊΠ°Ρ , ΠΎΠ±Π΅ΡΠΏΠ΅ΡΠΈΠ²Π°Π΅ΡΡΡ Π½Π΅ ΡΠΎΠ»ΡΠΊΠΎ ΠΈΡ ΠΎΡΠ½Π°ΡΠ΅Π½ΠΈΠ΅ΠΌ ΡΠΎΠ²ΡΠ΅ΠΌΠ΅Π½Π½ΡΠΌ ΡΠ°Π±ΠΎΡΠΈΠΌ ΠΈΠ½ΡΡΡΡΠΌΠ΅Π½ΡΠΎΠΌ, Π½ΠΎ ΠΈ ΠΈΡΠΏΠΎΠ»ΡΠ·ΠΎΠ²Π°Π½ΠΈΠ΅ΠΌ ΠΏΡΠΈ ΠΈΡ ΡΠ°Π±ΠΎΡΠ΅ ΠΊΠΎΠΌΠ±ΠΈΠ½ΠΈΡΠΎΠ²Π°Π½Π½ΠΎΠΉ ΡΠΈΡΡΠ΅ΠΌΡ ΠΎΡ Π»Π°ΠΆΠ΄Π΅Π½ΠΈΡ, Π΄Π»Ρ ΠΊΠΎΡΠΎΡΠΎΠ³ΠΎ ΠΏΡΠΈΠΌΠ΅Π½ΡΡΡΡΡ Π²ΠΎΠ·Π΄ΡΡ ΠΈ Π²ΠΎΠ΄Π°. ΠΡΡ ΠΎΠ΄Ρ Ρ ΡΠ°ΠΊΠΎΠ³ΠΎ ΡΡΠ°Π½ΠΊΠ° Π΄Π»Ρ Π²ΠΎΠ»ΠΎΡΠ΅Π½ΠΈΡ, Π³ΠΎΡΠΎΠ²ΠΎΠ΅ ΠΈΠ·Π΄Π΅Π»ΠΈΠ΅ ΠΎΠ±Π»Π°Π΄Π°Π΅Ρ Π½Π΅ ΡΠΎΠ»ΡΠΊΠΎ ΡΡΠ΅Π±ΡΠ΅ΠΌΡΠΌ ΠΊΠ°ΡΠ΅ΡΡΠ²ΠΎΠΌ ΠΈ ΡΠΎΡΠ½ΠΎΡΡΡΡ Π³Π΅ΠΎΠΌΠ΅ΡΡΠΈΡΠ΅ΡΠΊΠΈΡ ΠΏΠ°ΡΠ°ΠΌΠ΅ΡΡΠΎΠ², Π½ΠΎ ΠΈ ΠΎΠΏΡΠΈΠΌΠ°Π»ΡΠ½ΠΎΠΉ ΠΌΠΈΠΊΡΠΎΡΡΡΡΠΊΡΡΡΠΎΠΉ.
ΠΠ° ΠΊΠ°ΠΊΠΎΠΌ ΠΎΠ±ΠΎΡΡΠ΄ΠΎΠ²Π°Π½ΠΈΠΈ Π²ΡΠΏΠΎΠ»Π½ΡΠ΅ΡΡΡ Π²ΠΎΠ»ΠΎΡΠ΅Π½ΠΈΠ΅ ΠΌΠ΅ΡΠ°Π»Π»ΠΎΠ²
ΠΠ±ΠΎΡΡΠ΄ΠΎΠ²Π°Π½ΠΈΠ΅, ΠΊΠΎΡΠΎΡΠΎΠ΅ Π²ΠΎΠ»ΠΎΡΠΈΠ»ΡΡΠΈΠΊ ΠΏΡΠΎΠ²ΠΎΠ»ΠΎΠΊΠΈ ΠΈΡΠΏΠΎΠ»ΡΠ·ΡΠ΅Ρ Π² ΡΠ²ΠΎΠ΅ΠΉ ΠΏΡΠΎΡΠ΅ΡΡΠΈΠΎΠ½Π°Π»ΡΠ½ΠΎΠΉ Π΄Π΅ΡΡΠ΅Π»ΡΠ½ΠΎΡΡΠΈ, Π½Π°Π·ΡΠ²Π°Π΅ΡΡΡ ΡΡΠ°Π½ΠΎΠΌ. ΠΠ±ΡΠ·Π°ΡΠ΅Π»ΡΠ½ΡΠΌ ΡΠ»Π΅ΠΌΠ΅Π½ΡΠΎΠΌ ΠΎΡΠ½Π°ΡΠ΅Π½ΠΈΡ Π²ΠΎΠ»ΠΎΡΠΈΠ»ΡΠ½ΠΎΠΉ ΡΠΏΠ΅ΡΠΈΠ°Π»ΠΈΠ·ΠΈΡΠΎΠ²Π°Π½Π½ΠΎΠΉ ΠΌΠ°ΡΠΈΠ½Ρ ΡΠ²Π»ΡΠ΅ΡΡΡ Β«Π³Π»Π°Π·ΠΎΠΊΒ» β Π²ΠΎΠ»ΠΎΠΊΠ°. ΠΠΈΠ°ΠΌΠ΅ΡΡ Π²ΠΎΠ»ΠΎΠΊΠΈ, ΡΠ°Π·ΡΠΌΠ΅Π΅ΡΡΡ, Π²ΡΠ΅Π³Π΄Π° Π΄ΠΎΠ»ΠΆΠ΅Π½ Π±ΡΡΡ ΠΌΠ΅Π½ΡΡΠ΅, ΡΠ΅ΠΌ ΡΠ°Π·ΠΌΠ΅ΡΡ ΠΏΠΎΠΏΠ΅ΡΠ΅ΡΠ½ΠΎΠ³ΠΎ ΡΠ΅ΡΠ΅Π½ΠΈΡ ΠΏΡΠΎΡΡΠ³ΠΈΠ²Π°Π΅ΠΌΠΎΠΉ ΡΠ΅ΡΠ΅Π· Π½Π΅Π΅ Π·Π°Π³ΠΎΡΠΎΠ²ΠΊΠΈ.
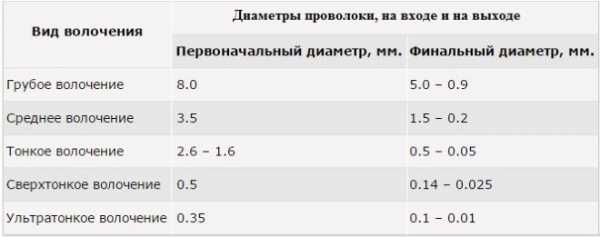
Π‘ΠΎΠΎΡΠ½ΠΎΡΠ΅Π½ΠΈΡ ΠΏΠ΅ΡΠ²ΠΎΠ½Π°ΡΠ°Π»ΡΠ½ΠΎΠ³ΠΎ ΠΈ ΡΠΈΠ½Π°Π»ΡΠ½ΠΎΠ³ΠΎ Π΄ΠΈΠ°ΠΌΠ΅ΡΡΠΎΠ² ΠΏΡΠΎΠ²ΠΎΠ»ΠΎΠΊΠΈ ΠΏΡΠΈ ΡΠ°Π·Π»ΠΈΡΠ½ΡΡ ΡΠΈΠΏΠ°Ρ Π²ΠΎΠ»ΠΎΡΠ΅Π½ΠΈΡ
ΠΠ° ΡΠ΅Π³ΠΎΠ΄Π½ΡΡΠ½ΠΈΠΉ Π΄Π΅Π½Ρ ΠΏΡΠΎΠΈΠ·Π²ΠΎΠ΄ΡΡΠ²Π΅Π½Π½ΡΠ΅ ΠΏΡΠ΅Π΄ΠΏΡΠΈΡΡΠΈΡ ΠΏΡΠΈΠΌΠ΅Π½ΡΡΡ Π²ΠΎΠ»ΠΎΡΠΈΠ»ΡΠ½ΡΠ΅ ΡΠΏΠ΅ΡΠΈΠ°Π»ΠΈΠ·ΠΈΡΠΎΠ²Π°Π½Π½ΡΠ΅ ΡΡΠ°Π½ΠΊΠΈ Π΄Π²ΡΡ ΠΎΡΠ½ΠΎΠ²Π½ΡΡ ΡΠΈΠΏΠΎΠ², ΠΊΠΎΡΠΎΡΡΠ΅ ΠΎΡΠ»ΠΈΡΠ°ΡΡΡΡ Π΄ΡΡΠ³ ΠΎΡ Π΄ΡΡΠ³Π° ΠΊΠΎΠ½ΡΡΡΡΠΊΡΠΈΠ΅ΠΉ ΡΡΠ½ΡΡΠ΅Π³ΠΎ ΠΌΠ΅Ρ Π°Π½ΠΈΠ·ΠΌΠ°. Π’Π°ΠΊ, ΡΠ°Π·Π»ΠΈΡΠ°ΡΡ:
- ΡΡΠ°Π½ΠΊΠΈ, Π² ΠΊΠΎΡΠΎΡΡΡ Π³ΠΎΡΠΎΠ²ΠΎΠ΅ ΠΈΠ·Π΄Π΅Π»ΠΈΠ΅ Π½Π°ΠΌΠ°ΡΡΠ²Π°Π΅ΡΡΡ Π½Π° Π±Π°ΡΠ°Π±Π°Π½, ΡΠ΅ΠΌ ΠΈ ΠΎΠ±Π΅ΡΠΏΠ΅ΡΠΈΠ²Π°Π΅ΡΡΡ ΡΡΠ½ΡΡΠ΅Π΅ ΡΡΠΈΠ»ΠΈΠ΅;
ΠΎΠ±ΠΎΡΡΠ΄ΠΎΠ²Π°Π½ΠΈΠ΅ Ρ ΠΏΡΡΠΌΠΎΠ»ΠΈΠ½Π΅ΠΉΠ½ΡΠΌ Π΄Π²ΠΈΠΆΠ΅Π½ΠΈΠ΅ΠΌ Π³ΠΎΡΠΎΠ²ΠΎΠΉ ΠΏΡΠΎΠ²ΠΎΠ»ΠΎΠΊΠΈ.
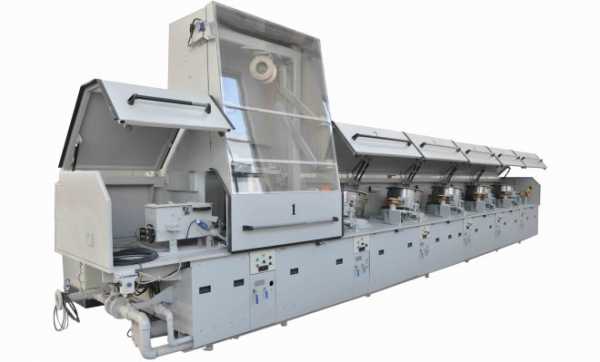
ΠΡΡΠΌΠΎΡΠΎΡΠ½ΡΠΉ Π²ΠΎΠ»ΠΎΡΠΈΠ»ΡΠ½ΡΠΉ ΡΡΠ°Π½ Ρ ΠΏΡΠΎΠ³ΡΠ°ΠΌΠΌΠ½ΡΠΌ ΡΠΏΡΠ°Π²Π»Π΅Π½ΠΈΠ΅ΠΌ
ΠΠ° ΡΡΡΡΠΎΠΉΡΡΠ²Π°Ρ Π²ΡΠΎΡΠΎΠ³ΠΎ ΡΠΈΠΏΠ°, Π² ΡΠ°ΡΡΠ½ΠΎΡΡΠΈ, Π²ΡΠΏΠΎΠ»Π½ΡΡΡ Π²ΠΎΠ»ΠΎΡΠ΅Π½ΠΈΠ΅ ΡΡΡΠ± ΠΈ Π΄ΡΡΠ³ΠΈΡ ΠΈΠ·Π΄Π΅Π»ΠΈΠΉ, ΠΊΠΎΡΠΎΡΡΠ΅ Π½Π΅ ΡΡΠ΅Π±ΡΡΡ Π½Π°ΠΌΠΎΡΠΊΠΈ Π½Π° Π±ΡΡ ΡΡ. ΠΠΌΠ΅Π½Π½ΠΎ ΠΏΡΠΎΠ²ΠΎΠ»ΠΎΠΊΡ, Π° ΡΠ°ΠΊΠΆΠ΅ ΡΡΡΠ±Π½ΡΠ΅ ΠΈΠ·Π΄Π΅Π»ΠΈΡ Π½Π΅Π±ΠΎΠ»ΡΡΠΎΠ³ΠΎ Π΄ΠΈΠ°ΠΌΠ΅ΡΡΠ° ΠΏΡΠΎΠΈΠ·Π²ΠΎΠ΄ΡΡ ΠΏΡΠ΅ΠΈΠΌΡΡΠ΅ΡΡΠ²Π΅Π½Π½ΠΎ Π½Π° ΡΡΠ°Π½ΠΊΠ°Ρ , ΠΎΡΠ½Π°ΡΠ΅Π½Π½ΡΡ Π±Π°ΡΠ°Π±Π°Π½Π½ΡΠΌ ΠΌΠ΅Ρ Π°Π½ΠΈΠ·ΠΌΠΎΠΌ. Π’Π°ΠΊΠΈΠ΅ ΡΡΠ°Π½ΠΊΠΈ Π² Π·Π°Π²ΠΈΡΠΈΠΌΠΎΡΡΠΈ ΠΎΡ ΠΊΠΎΠ½ΡΡΡΡΠΊΡΠΈΠ²Π½ΠΎΠ³ΠΎ ΠΈΡΠΏΠΎΠ»Π½Π΅Π½ΠΈΡ ΠΌΠΎΠ³ΡΡ Π±ΡΡΡ:
- ΠΎΠ΄Π½ΠΎΠΊΡΠ°ΡΠ½ΡΠΌΠΈ;
- ΠΌΠ½ΠΎΠ³ΠΎΠΊΡΠ°ΡΠ½ΡΠΌΠΈ, ΡΠ°Π±ΠΎΡΠ°ΡΡΠΈΠΌΠΈ ΡΠΎ ΡΠΊΠΎΠ»ΡΠΆΠ΅Π½ΠΈΠ΅ΠΌ ΠΈΠ»ΠΈ Π±Π΅Π· Π½Π΅Π³ΠΎ, Π° ΡΠ°ΠΊΠΆΠ΅ ΡΠ΅, Π² ΠΊΠΎΡΠΎΡΡΡ ΠΈΡΠΏΠΎΠ»ΡΠ·ΡΠ΅ΡΡΡ ΠΏΡΠΈΠ½ΡΠΈΠΏ ΠΏΡΠΎΡΠΈΠ²ΠΎΠ½Π°ΡΡΠΆΠ΅Π½ΠΈΡ Π·Π°Π³ΠΎΡΠΎΠ²ΠΎΠΊ.
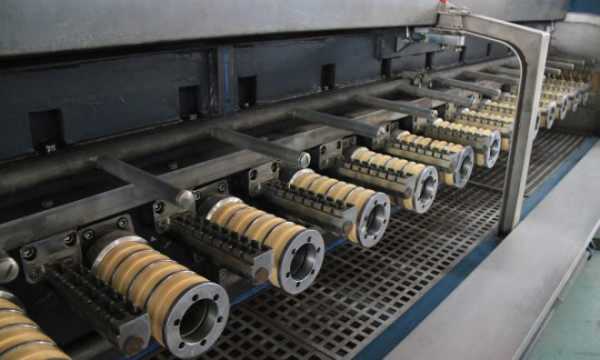
ΠΠ½ΠΎΠ³ΠΎΠ½ΠΈΡΠΎΡΠ½ΡΠΉ Π²ΠΎΠ»ΠΎΡΠΈΠ»ΡΠ½ΡΠΉ ΡΡΠ°Π½ ΠΎΠ±Π»Π°Π΄Π°Π΅Ρ Π±ΠΎΠ»ΡΡΠ΅ΠΉ ΠΏΡΠΎΠΈΠ·Π²ΠΎΠ΄ΠΈΡΠ΅Π»ΡΠ½ΠΎΡΡΡΡ ΠΈ Π²ΡΠ³ΠΎΠ΄Π΅Π½ Π½Π° ΠΊΡΡΠΏΠ½ΡΡ ΠΏΡΠ΅Π΄ΠΏΡΠΈΡΡΠΈΡΡ
ΠΠ°ΠΈΠ±ΠΎΠ»Π΅Π΅ ΠΏΡΠΎΡΡΠΎΠΉ ΠΊΠΎΠ½ΡΡΡΡΠΊΡΠΈΠ΅ΠΉ ΠΎΡΠ»ΠΈΡΠ°Π΅ΡΡΡ ΠΎΠ΄Π½ΠΎΠΊΡΠ°ΡΠ½ΡΠΉ ΡΡΠ°Π½ΠΎΠΊ Π΄Π»Ρ Π²ΠΎΠ»ΠΎΡΠ΅Π½ΠΈΡ. ΠΠ°Π½ΠΈΠΏΡΠ»ΠΈΡΡΡ ΡΠ°ΠΊΠΈΠΌ ΠΎΠ±ΠΎΡΡΠ΄ΠΎΠ²Π°Π½ΠΈΠ΅ΠΌ, Π²ΠΎΠ»ΠΎΡΠΈΠ»ΡΡΠΈΠΊ ΠΏΡΠΎΠ²ΠΎΠ»ΠΎΠΊΠΈ Π²ΡΠΏΠΎΠ»Π½ΡΠ΅Ρ Π΅Π΅ ΠΏΡΠΎΡΡΠ³ΠΈΠ²Π°Π½ΠΈΠ΅ Π·Π° ΠΎΠ΄ΠΈΠ½ ΠΏΡΠΎΡ ΠΎΠ΄. ΠΠ° Π²ΠΎΠ»ΠΎΡΠΈΠ»ΡΠ½ΠΎΠΌ ΡΡΡΡΠΎΠΉΡΡΠ²Π΅ ΠΌΠ½ΠΎΠ³ΠΎΠΊΡΠ°ΡΠ½ΠΎΠ³ΠΎ ΡΠΈΠΏΠ°, ΠΊΠΎΡΠΎΡΠΎΠ΅ ΡΠ°Π±ΠΎΡΠ°Π΅Ρ ΠΏΠΎ Π½Π΅ΠΏΡΠ΅ΡΡΠ²Π½ΠΎΠΉ ΡΡ Π΅ΠΌΠ΅, ΡΠΎΡΠΌΠΈΡΠΎΠ²Π°Π½ΠΈΠ΅ Π³ΠΎΡΠΎΠ²ΠΎΠ³ΠΎ ΠΈΠ·Π΄Π΅Π»ΠΈΡ ΠΎΡΡΡΠ΅ΡΡΠ²Π»ΡΠ΅ΡΡΡ Π·Π° 2β3 ΠΏΡΠΎΡ ΠΎΠ΄Π°. ΠΡΡΠΏΠ½ΡΠ΅ ΠΏΡΠ΅Π΄ΠΏΡΠΈΡΡΠΈΡ, ΠΏΡΠΎΠΈΠ·Π²ΠΎΠ΄ΡΡΠΈΠ΅ ΠΏΡΠΎΠ²ΠΎΠ»ΠΎΠΊΡ Π² ΠΏΡΠΎΠΌΡΡΠ»Π΅Π½Π½ΡΡ ΠΌΠ°ΡΡΡΠ°Π±Π°Ρ , ΠΌΠΎΠ³ΡΡ Π±ΡΡΡ ΠΎΡΠ½Π°ΡΠ΅Π½Ρ Π½Π΅ ΠΎΠ΄Π½ΠΈΠΌ Π΄Π΅ΡΡΡΠΊΠΎΠΌ Π²ΠΎΠ»ΠΎΡΠΈΠ»ΡΠ½ΡΡ ΡΡΠ°Π½ΠΊΠΎΠ² ΡΠ°Π·Π½ΠΎΠΉ ΠΌΠΎΡΠ½ΠΎΡΡΠΈ, Π½Π° ΠΊΠΎΡΠΎΡΡΡ ΠΈΠ·Π³ΠΎΡΠ°Π²Π»ΠΈΠ²Π°Π΅ΡΡΡ ΠΏΡΠΎΠ΄ΡΠΊΡΠΈΡ ΡΠ°Π·Π»ΠΈΡΠ½ΠΎΠ³ΠΎ Π½Π°Π·Π½Π°ΡΠ΅Π½ΠΈΡ.
ΠΡΠ½ΠΎΠ²Π½ΡΠΌ ΡΠ°Π±ΠΎΡΠΈΠΌ ΠΎΡΠ³Π°Π½ΠΎΠΌ Π»ΡΠ±ΠΎΠΉ Π²ΠΎΠ»ΠΎΡΠΈΠ»ΡΠ½ΠΎΠΉ ΠΌΠ°ΡΠΈΠ½Ρ, ΠΊΠ°ΠΊ ΡΠΆΠ΅ Π³ΠΎΠ²ΠΎΡΠΈΠ»ΠΎΡΡ Π²ΡΡΠ΅, ΡΠ²Π»ΡΠ΅ΡΡΡ ΡΠΈΠ»ΡΠ΅ΡΠ°, Π΄Π»Ρ ΠΈΠ·Π³ΠΎΡΠΎΠ²Π»Π΅Π½ΠΈΡ ΠΊΠΎΡΠΎΡΠΎΠΉ ΠΈΡΠΏΠΎΠ»ΡΠ·ΡΡΡ ΡΠ²Π΅ΡΠ΄ΡΠ΅ ΠΌΠ΅ΡΠ°Π»Π»ΠΎΠΊΠ΅ΡΠ°ΠΌΠΈΡΠ΅ΡΠΊΠΈΠ΅ ΡΠΏΠ»Π°Π²Ρ β ΠΊΠ°ΡΠ±ΠΈΠ΄Ρ Π±ΠΎΡΠ°, ΠΌΠΎΠ»ΠΈΠ±Π΄Π΅Π½Π°, ΡΠΈΡΠ°Π½Π°, ΡΠ΅ΡΠΌΠΎΠΊΠΎΡΡΠ½Π΄ ΠΈ Π΄Ρ. ΠΡΠ»ΠΈΡΠΈΡΠ΅Π»ΡΠ½ΡΠΌΠΈ Ρ Π°ΡΠ°ΠΊΡΠ΅ΡΠΈΡΡΠΈΠΊΠ°ΠΌΠΈ ΡΠ°ΠΊΠΈΡ ΠΌΠ°ΡΠ΅ΡΠΈΠ°Π»ΠΎΠ² ΡΠ²Π»ΡΡΡΡΡ ΠΏΠΎΠ²ΡΡΠ΅Π½Π½Π°Ρ ΡΠ²Π΅ΡΠ΄ΠΎΡΡΡ, ΠΈΡΠΊΠ»ΡΡΠΈΡΠ΅Π»ΡΠ½Π°Ρ ΡΡΡΠΎΠΉΡΠΈΠ²ΠΎΡΡΡ ΠΊ ΠΈΡΡΠΈΡΠ°Π½ΠΈΡ, Π° ΡΠ°ΠΊΠΆΠ΅ Π½Π΅Π²ΡΡΠΎΠΊΠ°Ρ Π²ΡΠ·ΠΊΠΎΡΡΡ. Π ΠΎΡΠ΄Π΅Π»ΡΠ½ΡΡ ΡΠ»ΡΡΠ°ΡΡ , ΠΊΠΎΠ³Π΄Π° Π½Π΅ΠΎΠ±Ρ ΠΎΠ΄ΠΈΠΌΠΎ ΠΈΠ·Π³ΠΎΡΠΎΠ²ΠΈΡΡ ΠΎΡΠ΅Π½Ρ ΡΠΎΠ½ΠΊΡΡ ΠΏΡΠΎΠ²ΠΎΠ»ΠΎΠΊΡ ΠΈΠ· ΡΡΠ°Π»ΠΈ, ΡΠΈΠ»ΡΠ΅ΡΠ° ΠΌΠΎΠΆΠ΅Ρ Π±ΡΡΡ ΠΈΠ·Π³ΠΎΡΠΎΠ²Π»Π΅Π½Π° ΠΈΠ· ΡΠ΅Ρ Π½ΠΈΡΠ΅ΡΠΊΠΈΡ Π°Π»ΠΌΠ°Π·ΠΎΠ².
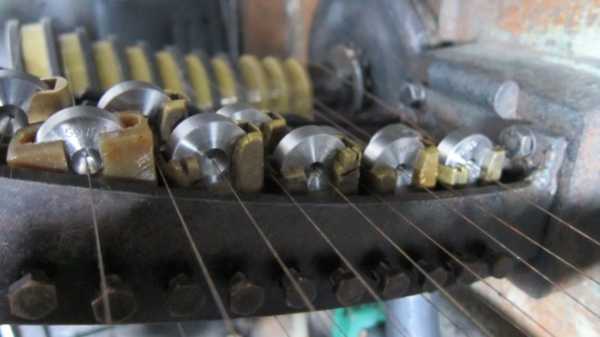
Π€ΠΈΠ»ΡΠ΅ΡΡ Π²ΠΎΠ»ΠΎΡΠΈΠ»ΡΠ½ΠΎΠΉ ΠΌΠ°ΡΠΈΠ½Ρ
Π€ΠΈΠ»ΡΠ΅ΡΠ° ΡΡΡΠ°Π½Π°Π²Π»ΠΈΠ²Π°Π΅ΡΡΡ Π² ΠΏΡΠΎΡΠ½ΡΡ ΠΈ Π²ΡΠ·ΠΊΡΡ ΡΡΠ°Π»ΡΠ½ΡΡ ΠΎΠ±ΠΎΠΉΠΌΡ. ΠΡΠΎ ΡΠ°ΠΊ Π½Π°Π·ΡΠ²Π°Π΅ΠΌΠ°Ρ Π²ΠΎΠ»ΠΎΡΠΈΠ»ΡΠ½Π°Ρ Π΄ΠΎΡΠΊΠ°. ΠΠ° ΡΡΠ΅Ρ ΡΠ²ΠΎΠ΅ΠΉ ΠΏΠ»Π°ΡΡΠΈΡΠ½ΠΎΡΡΠΈ ΡΠ°ΠΊΠ°Ρ ΠΎΠ±ΠΎΠΉΠΌΠ° Π½Π΅ ΠΎΠΊΠ°Π·ΡΠ²Π°Π΅Ρ Π·Π½Π°ΡΠΈΡΠ΅Π»ΡΠ½ΠΎΠ³ΠΎ Π΄Π°Π²Π»Π΅Π½ΠΈΡ Π½Π° ΡΠΈΠ»ΡΠ΅ΡΡ ΠΈ ΠΎΠ΄Π½ΠΎΠ²ΡΠ΅ΠΌΠ΅Π½Π½ΠΎ ΡΠ½ΠΈΠΆΠ°Π΅Ρ ΡΠ°ΡΡΡΠ³ΠΈΠ²Π°ΡΡΠΈΠ΅ Π½Π°ΠΏΡΡΠΆΠ΅Π½ΠΈΡ, ΠΊΠΎΡΠΎΡΡΠ΅ Π² Π½Π΅ΠΉ Π²ΠΎΠ·Π½ΠΈΠΊΠ°ΡΡ.
ΠΠ° ΡΠΎΠ²ΡΠ΅ΠΌΠ΅Π½Π½ΡΡ ΠΏΡΠ΅Π΄ΠΏΡΠΈΡΡΠΈΡΡ Π²ΠΎΠ»ΠΎΡΠ΅Π½ΠΈΠ΅ ΠΌΠ΅ΡΠ°Π»Π»ΠΎΠ² ΡΠ°ΡΡΠΎ ΠΏΡΠΎΠ²ΠΎΠ΄ΡΡ Ρ ΠΈΡΠΏΠΎΠ»ΡΠ·ΠΎΠ²Π°Π½ΠΈΠ΅ΠΌ ΡΠ±ΠΎΡΠ½ΡΡ Π²ΠΎΠ»ΠΎΠΊ, ΠΊΠΎΡΠΎΡΡΠ΅ ΠΏΠΎΠ·Π²ΠΎΠ»ΡΡΡ ΡΡΡΠ΅ΠΊΡΠΈΠ²Π½ΠΎ Π²ΡΠΏΠΎΠ»Π½ΡΡΡ ΡΠ°ΠΊΠΎΠΉ ΠΏΡΠΎΡΠ΅ΡΡ Π΄Π°ΠΆΠ΅ Π² ΡΡΠ»ΠΎΠ²ΠΈΡΡ ΠΏΠΎΠ²ΡΡΠ΅Π½Π½ΠΎΠ³ΠΎ Π³ΠΈΠ΄ΡΠΎΠ΄ΠΈΠ½Π°ΠΌΠΈΡΠ΅ΡΠΊΠΎΠ³ΠΎ ΡΡΠ΅Π½ΠΈΡ. ΠΡΠΎΠΌΠ΅ ΡΠΎΠ³ΠΎ, ΠΏΡΠΈΠΌΠ΅Π½Π΅Π½ΠΈΠ΅ ΡΠ°ΠΊΠΎΠ³ΠΎ ΠΈΠ½ΡΡΡΡΠΌΠ΅Π½ΡΠ° ΡΠ½ΠΈΠΆΠ°Π΅Ρ ΡΠ°ΡΡ ΠΎΠ΄ ΡΠ»Π΅ΠΊΡΡΠΎΡΠ½Π΅ΡΠ³ΠΈΠΈ ΠΈ ΡΠ²Π΅Π»ΠΈΡΠΈΠ²Π°Π΅Ρ ΠΏΡΠΎΠΈΠ·Π²ΠΎΠ΄ΠΈΡΠ΅Π»ΡΠ½ΠΎΡΡΡ ΡΠ°Π±ΠΎΡΡ ΠΎΠ±ΠΎΡΡΠ΄ΠΎΠ²Π°Π½ΠΈΡ Π½Π° 20β30%.
ΠΠΎΠ΄Π³ΠΎΡΠΎΠ²ΠΊΠ° ΠΌΠ΅ΡΠ°Π»Π»ΠΈΡΠ΅ΡΠΊΠΈΡ Π·Π°Π³ΠΎΡΠΎΠ²ΠΎΠΊ
ΠΠΎΠ»ΠΎΡΠΈΠ»ΡΡΠΈΠΊ ΠΏΡΠΎΠ²ΠΎΠ»ΠΎΠΊΠΈ, ΠΈΡΠΏΠΎΠ»ΡΠ·ΡΡ ΡΠΏΠ΅ΡΠΈΠ°Π»ΠΈΠ·ΠΈΡΠΎΠ²Π°Π½Π½ΠΎΠ΅ ΠΎΠ±ΠΎΡΡΠ΄ΠΎΠ²Π°Π½ΠΈΠ΅, ΡΠΎΠ»ΡΠΊΠΎ Π² ΡΠΎΠΌ ΡΠ»ΡΡΠ°Π΅ ΡΠΌΠΎΠΆΠ΅Ρ Π΄ΠΎΠ±ΠΈΡΡΡΡ ΠΊΠ°ΡΠ΅ΡΡΠ²Π΅Π½Π½ΠΎΠ³ΠΎ ΠΊΠΎΠ½Π΅ΡΠ½ΠΎΠ³ΠΎ ΡΠ΅Π·ΡΠ»ΡΡΠ°ΡΠ°, Π΅ΡΠ»ΠΈ ΠΏΠΎΠ²Π΅ΡΡ Π½ΠΎΡΡΡ Π·Π°Π³ΠΎΡΠΎΠ²ΠΊΠΈ Π±ΡΠ΄Π΅Ρ ΡΠΎΠΎΡΠ²Π΅ΡΡΡΠ²ΡΡΡΠΈΠΌ ΠΎΠ±ΡΠ°Π·ΠΎΠΌ ΠΏΠΎΠ΄Π³ΠΎΡΠΎΠ²Π»Π΅Π½Π°. Π’Π°ΠΊΠ°Ρ ΠΏΠΎΠ΄Π³ΠΎΡΠΎΠ²ΠΊΠ° Π·Π°ΠΊΠ»ΡΡΠ°Π΅ΡΡΡ Π² ΡΠ΄Π°Π»Π΅Π½ΠΈΠΈ ΠΎΠΊΠ°Π»ΠΈΠ½Ρ, Π΄Π»Ρ ΡΠ΅Π³ΠΎ ΠΌΠΎΠ³ΡΡ Π±ΡΡΡ ΠΈΡΠΏΠΎΠ»ΡΠ·ΠΎΠ²Π°Π½Ρ ΡΠ»Π΅Π΄ΡΡΡΠΈΠ΅ ΠΌΠ΅ΡΠΎΠ΄Ρ:
- ΠΌΠ΅Ρ Π°Π½ΠΈΡΠ΅ΡΠΊΠΈΠΉ;
- Ρ ΠΈΠΌΠΈΡΠ΅ΡΠΊΠΈΠΉ;
- ΡΠ»Π΅ΠΊΡΡΠΎΡ ΠΈΠΌΠΈΡΠ΅ΡΠΊΠΈΠΉ.
ΠΠΎΠ»Π΅Π΅ ΠΏΡΠΎΡΡΡΠΌ ΠΈ ΡΠΊΠΎΠ½ΠΎΠΌΠΈΡΠ΅ΡΠΊΠΈ Π²ΡΠ³ΠΎΠ΄Π½ΡΠΌ ΡΠ²Π»ΡΠ΅ΡΡΡ ΠΌΠ΅Ρ Π°Π½ΠΈΡΠ΅ΡΠΊΠΈΠΉ ΡΠΏΠΎΡΠΎΠ± ΠΎΡΠΈΡΡΠΊΠΈ ΠΎΡ ΠΎΠΊΠ°Π»ΠΈΠ½Ρ, ΠΊΠΎΡΠΎΡΡΠΉ ΠΈΡΠΏΠΎΠ»ΡΠ·ΡΡΡ Π΄Π»Ρ Π·Π°Π³ΠΎΡΠΎΠ²ΠΎΠΊ ΠΈΠ· ΡΠ³Π»Π΅ΡΠΎΠ΄ΠΈΡΡΡΡ ΡΡΠ°Π»Π΅ΠΉ. ΠΡΠΈ Π²ΡΠΏΠΎΠ»Π½Π΅Π½ΠΈΠΈ ΡΠ°ΠΊΠΎΠΉ ΠΎΡΠΈΡΡΠΊΠΈ Π·Π°Π³ΠΎΡΠΎΠ²ΠΊΡ ΠΏΡΠΎΡΡΠΎ Π³Π½ΡΡ Π² ΡΠ°Π·Π½ΡΠ΅ ΡΡΠΎΡΠΎΠ½Ρ, Π° Π·Π°ΡΠ΅ΠΌ ΠΎΠ±ΡΠ°Π±Π°ΡΡΠ²Π°ΡΡ Π΅Π΅ ΠΏΠΎΠ²Π΅ΡΡ Π½ΠΎΡΡΡ ΠΏΡΠΈ ΠΏΠΎΠΌΠΎΡΠΈ ΠΌΠ΅ΡΠ°Π»Π»ΠΈΡΠ΅ΡΠΊΠΈΡ ΡΠ΅ΡΠΎΠΊ.
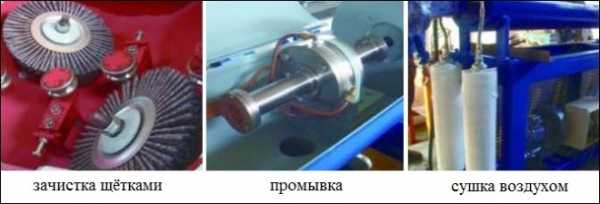
Π’Π΅Ρ Π½ΠΎΠ»ΠΎΠ³ΠΈΡ ΡΠ°Π±ΠΎΡΡ ΠΎΠΊΠ°Π»ΠΈΠ½ΠΎΡΠ½ΠΈΠΌΠ°ΡΠ΅Π»Ρ
ΠΠΎΠ»Π΅Π΅ ΡΠ»ΠΎΠΆΠ½ΠΎΠΉ ΠΈ Π·Π°ΡΡΠ°ΡΠ½ΠΎΠΉ ΡΠ²Π»ΡΠ΅ΡΡΡ Ρ ΠΈΠΌΠΈΡΠ΅ΡΠΊΠ°Ρ ΠΎΡΠΈΡΡΠΊΠ° ΠΎΡ ΠΎΠΊΠ°Π»ΠΈΠ½Ρ, Π΄Π»Ρ Π²ΡΠΏΠΎΠ»Π½Π΅Π½ΠΈΡ ΠΊΠΎΡΠΎΡΠΎΠΉ ΠΈΡΠΏΠΎΠ»ΡΠ·ΡΡΡ ΡΠ°ΡΡΠ²ΠΎΡΡ ΡΠΎΠ»ΡΠ½ΠΎΠΉ ΠΈΠ»ΠΈ ΡΠ΅ΡΠ½ΠΎΠΉ ΠΊΠΈΡΠ»ΠΎΡΡ. Π‘ΠΏΠ΅ΡΠΈΠ°Π»ΠΈΡΡ, Π²ΡΠΏΠΎΠ»Π½ΡΡΡΠΈΠΉ ΡΠ°ΠΊΡΡ ΡΠ»ΠΎΠΆΠ½ΡΡ ΠΈ Π΄ΠΎΡΡΠ°ΡΠΎΡΠ½ΠΎ ΠΎΠΏΠ°ΡΠ½ΡΡ ΠΎΠΏΠ΅ΡΠ°ΡΠΈΡ, Π΄ΠΎΠ»ΠΆΠ΅Π½ Π±ΡΡΡ Ρ ΠΎΡΠΎΡΠΎ ΠΏΠΎΠ΄Π³ΠΎΡΠΎΠ²Π»Π΅Π½ ΠΈ ΡΡΡΠΎΠ³ΠΎ ΡΠΎΠ±Π»ΡΠ΄Π°ΡΡ Π²ΡΠ΅ ΠΏΡΠ°Π²ΠΈΠ»Π° Π±Π΅Π·ΠΎΠΏΠ°ΡΠ½ΠΎΡΡΠΈ ΡΠ°Π±ΠΎΡΡ Ρ Π°Π³ΡΠ΅ΡΡΠΈΠ²Π½ΡΠΌΠΈ ΡΠ°ΡΡΠ²ΠΎΡΠ°ΠΌΠΈ. ΠΠ΅Π· Ρ ΠΈΠΌΠΈΡΠ΅ΡΠΊΠΎΠ³ΠΎ ΡΠΏΠΎΡΠΎΠ±Π° ΠΎΡΠΈΡΡΠΊΠΈ Π½Π΅ ΠΎΠ±ΠΎΠΉΡΠΈΡΡ, Π΅ΡΠ»ΠΈ ΠΏΡΠΎΠ²ΠΎΠ»ΠΎΠΊΡ Π½Π΅ΠΎΠ±Ρ ΠΎΠ΄ΠΈΠΌΠΎ ΡΠ΄Π΅Π»Π°ΡΡ ΠΈΠ· Π·Π°Π³ΠΎΡΠΎΠ²ΠΎΠΊ, Π²ΡΠΏΠΎΠ»Π½Π΅Π½Π½ΡΡ ΠΈΠ· Π½Π΅ΡΠΆΠ°Π²Π΅ΡΡΠΈΡ ΠΈ Π΄ΡΡΠ³ΠΈΡ ΡΠΈΠΏΠΎΠ² Π²ΡΡΠΎΠΊΠΎΠ»Π΅Π³ΠΈΡΠΎΠ²Π°Π½Π½ΡΡ ΡΡΠ°Π»Π΅ΠΉ. Π‘Π»Π΅Π΄ΡΠ΅Ρ ΠΈΠΌΠ΅ΡΡ Π² Π²ΠΈΠ΄Ρ, ΡΡΠΎ ΡΡΠ°Π·Ρ ΠΏΠΎΡΠ»Π΅ Π²ΡΠΏΠΎΠ»Π½Π΅Π½ΠΈΡ Ρ ΠΈΠΌΠΈΡΠ΅ΡΠΊΠΎΠΉ ΠΎΡΠΈΡΡΠΊΠΈ ΠΏΠΎΠ²Π΅ΡΡ Π½ΠΎΡΡΡ Π·Π°Π³ΠΎΡΠΎΠ²ΠΊΠΈ ΡΠ»Π΅Π΄ΡΠ΅Ρ ΡΡΠ°ΡΠ΅Π»ΡΠ½ΠΎ ΠΏΡΠΎΠΌΡΡΡ Π³ΠΎΡΡΡΠ΅ΠΉ, Π° Π·Π°ΡΠ΅ΠΌ Ρ ΠΎΠ»ΠΎΠ΄Π½ΠΎΠΉ Π²ΠΎΠ΄ΠΎΠΉ.
ΠΠ»Π΅ΠΊΡΡΠΎΡ ΠΈΠΌΠΈΡΠ΅ΡΠΊΠΈΠΉ ΡΠΏΠΎΡΠΎΠ± ΠΎΡΠΈΡΡΠΊΠΈ ΠΎΡ ΠΎΠΊΠ°Π»ΠΈΠ½Ρ ΠΎΡΠ½ΠΎΠ²Π°Π½ Π½Π° ΠΌΠ΅ΡΠΎΠ΄Π΅ ΡΡΠ°Π²Π»Π΅Π½ΠΈΡ Π² ΡΠ»Π΅ΠΊΡΡΠΎΠ»ΠΈΡΠΈΡΠ΅ΡΠΊΠΎΠΌ ΡΠ°ΡΡΠ²ΠΎΡΠ΅. Π Π·Π°Π²ΠΈΡΠΈΠΌΠΎΡΡΠΈ ΠΎΡ ΠΎΡΠΎΠ±Π΅Π½Π½ΠΎΡΡΠ΅ΠΉ Π²ΡΠΏΠΎΠ»Π½Π΅Π½ΠΈΡ ΡΠ°ΠΊΠΎΠΉ ΠΌΠ΅ΡΠΎΠ΄ ΠΌΠΎΠΆΠ΅Ρ Π±ΡΡΡ Π°Π½ΠΎΠ΄Π½ΡΠΌ ΠΈ ΠΊΠ°ΡΠΎΠ΄Π½ΡΠΌ.
ΠΠΎΠ»ΠΎΡΠ΅Π½ΠΈΠ΅ ΠΌΠ΅Π΄Π½ΠΎΠΉ ΠΏΡΠΎΠ²ΠΎΠ»ΠΎΠΊΠΈ
Π§ΡΠΎΠ±Ρ Π±ΠΎΠ»Π΅Π΅ ΠΏΠΎΠ΄ΡΠΎΠ±Π½ΠΎ ΠΏΠΎΠ·Π½Π°ΠΊΠΎΠΌΠΈΡΡΡΡ Ρ ΡΠ΅Ρ Π½ΠΎΠ»ΠΎΠ³ΠΈΠ΅ΠΉ Π²ΠΎΠ»ΠΎΡΠ΅Π½ΠΈΡ, ΠΌΠΎΠΆΠ½ΠΎ ΡΠ°ΡΡΠΌΠΎΡΡΠ΅ΡΡ Π΅Π΅ Π½Π° ΠΏΡΠΈΠΌΠ΅ΡΠ΅ ΡΠΎΠ³ΠΎ, ΠΊΠ°ΠΊ Π΄Π΅Π»Π°ΡΡ ΠΌΠ΅Π΄Π½ΡΡ ΠΏΡΠΎΠ²ΠΎΠ»ΠΎΠΊΡ. ΠΠ°Π³ΠΎΡΠΎΠ²ΠΊΠΈ Π΄Π»Ρ Π²ΡΠΏΠΎΠ»Π½Π΅Π½ΠΈΡ ΡΠ°ΠΊΠΎΠΉ ΠΎΠΏΠ΅ΡΠ°ΡΠΈΠΈ ΠΏΠΎΠ»ΡΡΠ°ΡΡ ΠΌΠ΅ΡΠΎΠ΄ΠΎΠΌ Π»ΠΈΡΡΡ, ΠΏΠΎΡΠ»Π΅ ΡΠ΅Π³ΠΎ ΠΈΡ ΡΠΏΠ»Π°Π²Π»ΡΡΡ ΠΌΠ΅ΠΆΠ΄Ρ ΡΠΎΠ±ΠΎΠΉ ΠΈ ΠΏΡΠΎΠΊΠ°ΡΡΠ²Π°ΡΡ. Π§ΡΠΎΠ±Ρ Π²ΠΎΠ»ΠΎΡΠ΅Π½ΠΈΠ΅ ΠΌΠ΅Π΄Π½ΠΎΠΉ ΠΏΡΠΎΠ²ΠΎΠ»ΠΎΠΊΠΈ Π±ΡΠ»ΠΎ Π²ΡΠΏΠΎΠ»Π½Π΅Π½ΠΎ ΠΌΠ°ΠΊΡΠΈΠΌΠ°Π»ΡΠ½ΠΎ ΠΊΠ°ΡΠ΅ΡΡΠ²Π΅Π½Π½ΠΎ, Ρ ΠΏΠΎΠ²Π΅ΡΡ Π½ΠΎΡΡΠΈ Π·Π°Π³ΠΎΡΠΎΠ²ΠΊΠΈ Π½Π΅ΠΎΠ±Ρ ΠΎΠ΄ΠΈΠΌΠΎ ΡΠ΄Π°Π»ΠΈΡΡ ΠΎΠΊΡΠΈΠ΄Π½ΡΡ ΠΏΠ»Π΅Π½ΠΊΡ, Π΄Π»Ρ ΡΠ΅Π³ΠΎ Π΅Π΅ ΠΎΠ±ΡΠ°Π±Π°ΡΡΠ²Π°ΡΡ ΡΠ°ΡΡΠ²ΠΎΡΠΎΠΌ ΠΊΠΈΡΠ»ΠΎΡΡ.
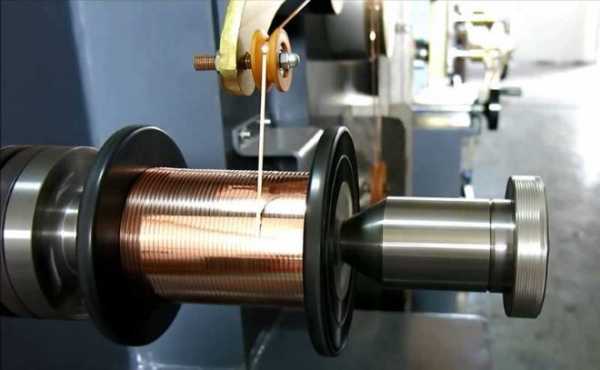
ΠΠ°ΠΌΠΎΡΠΊΠ° Π³ΠΎΡΠΎΠ²ΠΎΠΉ ΠΏΡΠΎΠ²ΠΎΠ»ΠΎΠΊΠΈ Π½Π° Π±Π°ΡΠ°Π±Π°Π½
Π‘Π°ΠΌ ΠΏΡΠΎΡΠ΅ΡΡ Π²ΠΎΠ»ΠΎΡΠ΅Π½ΠΈΡ ΠΌΠ°Π»ΠΎ ΡΠ΅ΠΌ ΠΎΡΠ»ΠΈΡΠ°Π΅ΡΡΡ ΠΎΡ ΠΏΡΠΎΠΈΠ·Π²ΠΎΠ΄ΡΡΠ²Π° ΡΠ²Π°ΡΠΎΡΠ½ΠΎΠΉ ΠΏΡΠΎΠ²ΠΎΠ»ΠΎΠΊΠΈ (ΠΈΠ»ΠΈ Π»ΡΠ±ΠΎΠΉ Π΄ΡΡΠ³ΠΎΠΉ). ΠΡΠΎΠ²ΠΎΠ»ΠΎΡΠ½ΡΠΉ ΡΡΠ°Π½ Π² ΡΠ°ΠΊΠΎΠΌ ΡΠ»ΡΡΠ°Π΅ ΡΡΠ½Π΅Ρ Π·Π°Π³ΠΎΡΠΎΠ²ΠΊΡ, ΠΏΡΠΎΠΏΡΡΠΊΠ°Ρ Π΅Π΅ ΡΠ΅ΡΠ΅Π· ΡΠΈΠ»ΡΠ΅ΡΠ½ΡΠ΅ ΠΎΡΠ²Π΅ΡΡΡΠΈΡ ΠΎΠΏΡΠ΅Π΄Π΅Π»Π΅Π½Π½ΠΎΠ³ΠΎ Π΄ΠΈΠ°ΠΌΠ΅ΡΡΠ°. ΠΠ»Ρ ΠΈΠ·Π³ΠΎΡΠΎΠ²Π»Π΅Π½ΠΈΡ ΠΌΠ΅Π΄Π½ΠΎΠΉ ΠΏΡΠΎΠ²ΠΎΠ»ΠΎΠΊΠΈ ΠΎΡΠ΅Π½Ρ Π½Π΅Π±ΠΎΠ»ΡΡΠΎΠ³ΠΎ Π΄ΠΈΠ°ΠΌΠ΅ΡΡΠ° (Π΄ΠΎ 10 ΠΌΠΊΠΌ) Π΅Π΅ ΡΠΎΡΠΌΠΈΡΠΎΠ²Π°Π½ΠΈΠ΅ ΠΌΠΎΠΆΠ΅Ρ ΠΎΡΡΡΠ΅ΡΡΠ²Π»ΡΡΡΡΡ Π² ΡΠΏΠ΅ΡΠΈΠ°Π»ΡΠ½ΠΎΠΌ ΡΠΌΠ°Π·ΠΎΡΠ½ΠΎΠΌ ΡΠΎΡΡΠ°Π²Π΅ (ΠΏΠΎΠ³ΡΡΠΆΠ½ΠΎΠΉ ΠΌΠ΅ΡΠΎΠ΄). Π ΠΊΠ°ΡΠ΅ΡΡΠ²Π΅ ΡΠ°ΠΊΠΈΡ ΡΠΎΡΡΠ°Π²ΠΎΠ², Π² ΡΠ°ΡΡΠ½ΠΎΡΡΠΈ, ΠΌΠΎΠ³ΡΡ ΠΈΡΠΏΠΎΠ»ΡΠ·ΠΎΠ²Π°ΡΡΡΡ:
- ΠΊΠΎΠΌΠΏΠ»Π΅ΠΊΡΠ½ΡΠ΅ ΡΠ°ΡΡΠ²ΠΎΡΡ;
- ΡΠΏΠ΅ΡΠΈΠ°Π»ΡΠ½ΡΠ΅ ΡΠΌΡΠ»ΡΡΠΈΠΈ;
- ΠΊΠΎΠΌΠΏΠ»Π΅ΠΊΡΠ½ΡΠ΅ Π²Π΅ΡΠ΅ΡΡΠ²Π°.
ΠΡΠΏΠΎΠ»ΡΠ·ΠΎΠ²Π°Π½ΠΈΠ΅ ΡΠ°ΠΊΠΈΡ ΡΠΎΡΡΠ°Π²ΠΎΠ², ΡΠ΅ΡΠ΅Π· ΠΊΠΎΡΠΎΡΡΠ΅ ΠΏΡΠΎΠ²ΠΎΠ»ΠΎΠΊΠ° ΠΏΡΠΎΡ ΠΎΠ΄ΠΈΡ Π² ΠΏΡΠΎΡΠ΅ΡΡΠ΅ ΡΠ²ΠΎΠ΅Π³ΠΎ ΡΠΎΡΠΌΠΈΡΠΎΠ²Π°Π½ΠΈΡ, ΠΏΠΎΠ·Π²ΠΎΠ»ΡΠ΅Ρ ΠΏΠΎΠ»ΡΡΠ°ΡΡ ΠΈΠ·Π΄Π΅Π»ΠΈΡ, Π½Π°ΡΡΠΆΠ½Π°Ρ ΠΏΠΎΠ²Π΅ΡΡ Π½ΠΎΡΡΡ ΠΊΠΎΡΠΎΡΡΡ ΠΎΡΠ»ΠΈΡΠ°Π΅ΡΡΡ ΠΌΠ°ΠΊΡΠΈΠΌΠ°Π»ΡΠ½ΠΎΠΉ ΡΠΈΡΡΠΎΡΠΎΠΉ.
ΠΡΠ΅Π½ΠΊΠ° ΡΡΠ°ΡΡΠΈ:
ΠΠ°Π³ΡΡΠ·ΠΊΠ°…ΠΠΎΠ΄Π΅Π»ΠΈΡΡΡΡ Ρ Π΄ΡΡΠ·ΡΡΠΌΠΈ:
met-all.org
ΠΠΎΠ»ΠΎΡΠΈΠ»ΡΠ½ΡΠ΅ ΡΡΠ°Π½Ρ Π΄Π»Ρ ΠΏΡΠΎΠ²ΠΎΠ»ΠΎΠΊΠΈ β iMachine
ΠΡΡΠΌΠΎΡΠΎΡΠ½ΡΠΉ Π²ΠΎΠ»ΠΎΡΠΈΠ»ΡΠ½ΡΠΉ ΡΡΠ°Π½ Ρ ΠΏΡΠΎΠ³ΡΠ°ΠΌΠΌΠ½ΡΠΌ ΡΠΏΡΠ°Π²Π»Π΅Π½ΠΈΠ΅ΠΌ
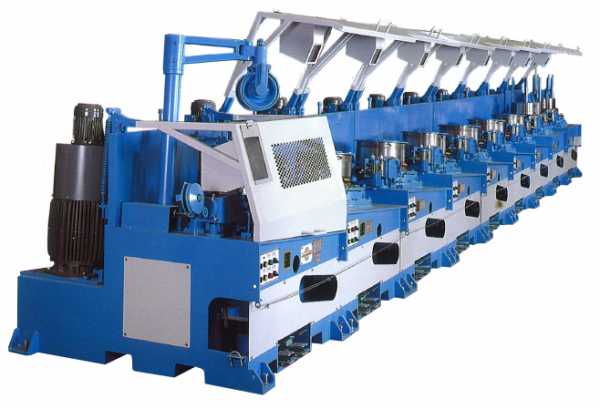
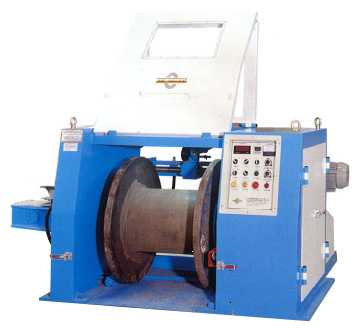
ΠΡΠΈΠΌΠ΅Π½ΠΈΠΌ Π΄Π»Ρ ΠΏΡΠΎΠ²ΠΎΠ»ΠΎΠΊΠΈ ΠΈΠ· Π²ΡΡΠΎΠΊΠΎ/Π½ΠΈΠ·ΠΊΠΎ ΡΠ³Π»Π΅ΡΠΎΠ΄ΠΈΡΡΠΎΠΉ ΡΡΠ°Π»ΠΈ, Π½Π΅ΡΠΆΠ°Π²Π΅ΡΡΠ΅ΠΉ ΡΡΠ°Π»ΠΈ, ΡΠ²Π΅ΡΠ½ΡΡ ΠΌΠ΅ΡΠ°Π»Π»ΠΎΠ². Π₯Π°ΡΠ°ΠΊΡΠ΅ΡΠ½ΡΠ΅ ΠΎΡΠΎΠ±Π΅Π½Π½ΠΎΡΡΠΈ ΠΎΠ±ΠΎΡΡΠ΄ΠΎΠ²Π°Π½ΠΈΡ Π²ΠΊΠ»ΡΡΠ°ΡΡ Π² ΡΠ΅Π±Ρ: Π·Π΅ΡΠΊΠ°Π»ΡΠ½ΠΎ ΠΎΡΠΏΠ°Π»ΠΈΡΠΎΠ²Π°Π½Π½ΡΡ ΠΏΠΎΠ²Π΅ΡΡ Π½ΠΎΡΡΡ Π²ΠΎΠ»ΠΎΡΠΈΠ»ΡΠ½ΡΡ Π±Π°ΡΠ°Π±Π°Π½ΠΎΠ², ΠΏΠΎΠ²Π΅ΡΡ Π½ΠΎΡΡΠ½ΡΠΉ ΡΠ»ΠΎΠΉ ΠΊΠΎΡΠΎΡΡΡ ΠΏΠΎΠΊΡΡΡ ΠΊΠ°ΡΠ±ΠΈΠ΄-Π²ΠΎΠ»ΡΡΡΠ°ΠΌΠ½ΡΠΌ Π½Π°ΠΏΡΠ»Π΅Π½ΠΈΠ΅ΠΌ, Π±Π°ΡΠ°Π±Π°Π½Ρ ΠΏΡΠΎΡΠ»ΠΈ Π±Π°Π»Π°Π½ΡΠΈΡΠΎΠ²ΠΊΡ, ΡΡΠΎΠ±Ρ ΠΏΠ΅ΡΠ΄ΠΎΡΠ²ΡΠ°ΡΠΈΡΡ Π±ΠΈΠ΅Π½ΠΈΠ΅. ΠΡΠ΅ Π±Π»ΠΎΠΊΠΈ ΠΈΠΌΠ΅ΡΡ ΡΠΈΡΡΠ΅ΠΌΡ Π²Π½ΡΡΡΠ΅Π½Π½Π΅Π³ΠΎ Π²ΠΎΠ΄ΡΠ½ΠΎΠ³ΠΎ ΠΎΡ Π»Π°ΠΆΠ΄Π΅Π½ΠΈΡ ΠΈ Π²Π½Π΅ΡΠ½Π΅Π³ΠΎ ΠΎΡ Π»Π°ΠΆΠ΄Π΅Π½ΠΈΡ ΠΏΠΎΡΡΠ΅Π΄ΡΡΠ²ΠΎΠΌ ΠΏΡΠΎΠ΄ΡΠ²Π° Π²ΠΎΠ·Π΄ΡΡ ΠΎΠΌ. ΠΠ»Ρ Π±ΡΡΡΡΠΎΠΉ ΡΠΌΠ΅Π½Ρ Π²ΠΎΠ»ΠΎΠΊ Π½Π° ΠΎΠ±ΠΎΡΡΠ΄ΠΎΠ²Π°Π½ΠΈΠΈ ΠΏΡΠΈΠΌΠ΅Π½ΡΡΡΡΡ Π²ΠΎΠ»ΠΎΠΊΠΎΠ΄Π΅ΡΠΆΠ°ΡΠ΅Π»ΠΈ ΡΡΡΠΌΠ½ΠΎΠ³ΠΎ ΡΠΈΠΏΠ° Ρ ΡΠΈΡΡΠ΅ΠΌΠΎΠΉ Π²Π½ΡΡΡΠ΅Π½Π½Π΅Π³ΠΎ Π²ΠΎΠ΄ΡΠ½ΠΎΠ³ΠΎ ΠΎΡ Π»Π°ΠΆΠ΄Π΅Π½ΠΈΡ; ΠΏΡΠΈΡΠΏΠΎΡΠΎΠ±Π»Π΅Π½ΠΈΡ ΠΎΡΠ²Π΅ΡΠ°ΡΡΠΈΠ΅ Π·Π° Π±Π΅Π·ΠΎΠΏΠ°ΡΠ½ΠΎΡΡΡ ΡΠΊΡΠΏΠ»ΡΠ°ΡΠ°ΡΠΈΠΈ ΠΎΠ±ΠΎΡΡΠ΄ΠΎΠ²Π°Π½ΠΈΡ Π²ΠΊΠ»ΡΡΠ°ΡΡ Π² ΡΠ΅Π±Ρ: Π·Π°ΡΠΈΡΠ½ΡΠΉ ΡΠΊΡΠ°Π½, Π³ΠΈΠ΄ΡΠ°Π²Π»ΠΈΡΠ΅ΡΠΊΠΈΠΉ ΡΠΎΡΠΌΠΎΠ· ΠΈ ΡΠΈΡΡΠ΅ΠΌΡ ΡΠΊΡΡΡΠ΅Π½Π½ΠΎΠΉ ΠΎΡΡΠ°Π½ΠΎΠ²ΠΊΠΈ. ΠΡΠΈΠ²ΠΎΠ΄Π½ΡΠ΅ ΡΠ΅ΡΡΠ΅ΡΠ½ΠΈ ΡΠ΅Π΄ΡΠΊΡΠΎΡΠ° ΠΏΠΎΠ΄Π²Π΅ΡΠ³Π»ΠΈΡΡ ΡΠΏΠ΅ΡΠΈΠ°Π»ΡΠ½ΠΎΠΉ ΡΠ»ΠΈΡΠΎΠ²ΠΊΠ΅, Π΄Π°Π±Ρ ΠΏΡΠΎΠ΄Π»ΠΈΡΡ ΡΡΠΎΠΊ ΡΠΊΡΠΏΠ»ΡΠ°ΡΠ°ΡΠΈΠΈ ΠΈ ΡΠ½ΠΈΠ·ΠΈΡΡ ΡΡΠΎΠ²Π΅Π½Ρ ΡΡΠΌΠ°.
Π‘ΡΠ°Π½ΠΎΠΊ | ΠΠΈΠ°ΠΌΠ΅ΡΡ Π±Π°ΡΠ°Π±Π°Π½Π° (ΠΌΠΌ) | ΠΠΈΠ°ΠΌΠ΅ΡΡ ΠΏΡΠΎΠ²ΠΎΠ»ΠΎΠΊΠΈ Π½Π° Π²Ρ ΠΎΠ΄Π΅ (ΠΌΠΌ) | ΠΠΈΠ°ΠΌΠ΅ΡΡ ΠΏΡΠΎΠ²ΠΎΠ»ΠΎΠΊΠΈ Π½Π° Π²ΡΡ ΠΎΠ΄Π΅ (ΠΌΠΌ) | ΠΠΎΡΠ½ΠΎΡΡΡ Π΄Π²ΠΈΠ³Π°ΡΠ΅Π»Ρ | ||
Π‘ΡΠ΅Π΄Π½ΡΡ | Π’Π²ΡΡΠ΄Π°Ρ | Π‘ΡΠ΅Π΄Π½ΡΡ | Π’Π²ΡΡΠ΄Π°Ρ | |||
YTTD-400H | 400 | 4.0-3.0 | 3.0-2.0 | 1.0-0.8 | 1.0-0.7 | 15kw-23kw |
YTTD-600H | 600 | 8,0-5,5 | 6,5-5,5 | 2.2-1.5 | 2.2-1.8 | 30kw-56kw |
YTTD-750H | 750 | 12-10 | 10-8,0 | 4.0-3.3 | 3.5-2.8 | 75kw-94kw |
ΠΠΎΠ»ΠΎΡΠΈΠ»ΡΠ½ΡΠΉ ΡΡΠ°Π½ Π½Π΅ΠΏΡΠ΅ΡΡΠ²Π½ΠΎΠ³ΠΎ ΡΠΈΠΏΠ° Ρ Π½Π°ΠΌΠ°ΡΡΠ²Π°ΡΡΠΈΠΌ ΠΌΠ΅Ρ Π°Π½ΠΈΠ·ΠΌΠΎΠΌ
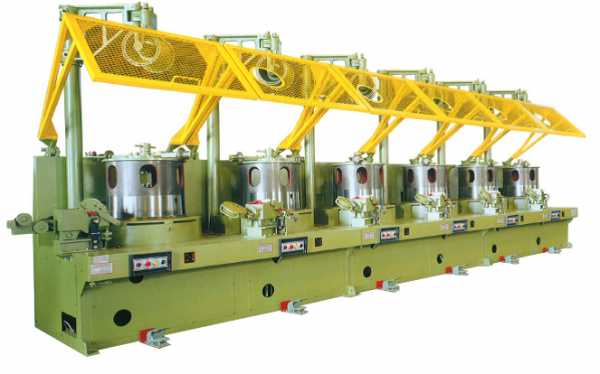
Β
ΠΠΎΠ»ΠΎΡΠΈΠ»ΡΠ½ΡΠΉ ΡΡΠ°Π½ Π½Π΅ΠΏΡΠ΅ΡΡΠ²Π½ΠΎΠ³ΠΎ ΡΠΈΠΏΠ° β ΡΡΠΎ ΠΌΠ½ΠΎΠ³ΠΎΠ±Π»ΠΎΡΠ½ΡΠΉ, ΠΌΠ½ΠΎΠ³ΠΎΠ²ΠΎΠ»ΠΎΠΊΠΎΠ²ΡΠΉ ΡΡΠ°Π½ Ρ ΡΡΠ½ΠΊΡΠΈΡΠΌΠΈ Π²ΠΎΠ»ΠΎΡΠ΅Π½ΠΈΡ ΠΈ ΡΠΌΠ°ΡΡΠ²Π°Π½ΠΈΡ Π² Π±ΡΠ½ΡΡ. ΠΠΎΠ»ΠΎΡΠΈΠ»ΡΠ½ΡΠ΅ Π±Π°ΡΠ°Π±Π°Π½Ρ ΠΏΠΎΠΊΡΡΡΡ Π°Π½ΡΠΈΡΡΠΈΠΊΡΠΈΠΎΠ½Π½ΡΠΌ ΡΠΎΡΡΠ°Π²ΠΎΠΌ, Π΄Π»Ρ ΠΏΡΠ΅Π΄ΠΎΡΠ²ΡΠ°ΡΠ΅Π½ΠΈΡ ΡΡΠ΅Π·ΠΌΠ΅ΡΠ½ΠΎΠ³ΠΎ ΡΡΠ΅Π½ΠΈΡ. ΠΠΎΠ»ΠΎΡΠΈΠ»ΡΠ½ΡΠΉ Π±Π°ΡΠ°Π±Π°Π½ ΠΈΠ·Π³ΠΎΡΠΎΠ²Π»Π΅Π½ Ρ ΠΏΠΎΠΌΠΎΡΡΡ ΡΠΎΡΠ΅ΡΠ½ΠΎΠΉ ΡΠ²Π°ΡΠΊΠΈ, Π° Π΅Π³ΠΎ Π²Π½ΡΡΡΠ΅Π½Π½ΡΡ ΡΡΠΎΡΠΎΠ½Π° ΠΎΡ Π»Π°ΠΆΠ΄Π°Π΅ΡΡΡ Ρ ΠΏΠΎΠΌΠΎΡΡΡ ΠΏΡΠΈΠ½ΡΠ΄ΠΈΡΠ΅Π»ΡΠ½ΠΎΠ³ΠΎ Π²ΠΎΠ΄ΡΠ½ΠΎΠ³ΠΎ ΠΎΡ Π»Π°ΠΆΠ΄Π΅Π½ΠΈΡ. ΠΠΎΠ»ΠΎΠΊΠΎΠ΄Π΅ΡΠΆΠ°ΡΠ΅Π»Ρ ΠΎΡΠ½Π°ΡΡΠ½ Π²ΠΎΠ»ΠΎΠΊΠΎΠΉ ΠΏΠΎΠ΄ Π΄Π°Π²Π»Π΅Π½ΠΈΠ΅ΠΌ Π΄Π»Ρ Π»ΡΡΡΠ΅ΠΉ ΡΠΌΠ°Π·ΠΊΠΈ ΠΈ ΡΡΡΡΠΎΠΉΡΡΠ²ΠΎΠΌ Π²ΠΎΠ΄ΡΠ½ΠΎΠ³ΠΎ ΠΎΡ Π»Π°ΠΆΠ΄Π΅Π½ΠΈΡ. Π¨Π΅ΡΡΠ΅ΡΠ½ΠΈ ΡΠ΅Π΄ΡΠΊΡΠΎΡΠ½ΠΎΠΉ ΠΊΠΎΡΠΎΠ±ΠΊΠΈ ΡΠ΄Π΅Π»Π°Π½Ρ ΠΈΠ· Π²ΡΡΠΎΠΊΠΎΠΏΡΠΎΡΠ½ΠΎΠ³ΠΎ ΡΠΏΠ»Π°Π²Π° ΠΈ ΠΏΡΠΎΡΠ»ΠΈ ΡΠ΅ΡΠΌΠΈΡΠ΅ΡΠΊΡΡ ΠΎΠ±ΡΠ°Π±ΠΎΡΠΊΡ Ρ ΠΏΠΎΡΠ»Π΅Π΄ΡΡΡΠ΅ΠΉ ΡΠ»ΠΈΡΠΎΠ²ΠΊΠΎΠΉ, ΡΡΠΎ ΠΎΠ±Π΅ΡΠΏΠ΅ΡΠΈΠ²Π°Π΅Ρ ΠΈΡ Π±Π΅ΡΡΡΠΌΠ½ΡΡ ΠΈ ΡΡΡΠ΅ΠΊΡΠΈΠ²Π½ΡΡ ΡΠΊΡΠΏΠ»ΡΠ°ΡΠ°ΡΠΈΡ Π½Π° Π±ΠΎΠ»ΡΡΠΈΡ ΡΠΊΠΎΡΠΎΡΡΡΡ . Π‘ΠΊΠΎΡΠΎΡΡΡ Π²ΡΠ°ΡΠ΅Π½ΠΈΡ Π±Π°ΡΠ°Π±Π°Π½Π° ΠΊΠΎΠ½ΡΡΠΎΠ»ΠΈΡΡΠ΅ΡΡΡ Ρ ΠΏΠΎΠΌΠΎΡΡΡ ΠΈΠ½Π²Π΅ΡΡΠΎΡΠ°, ΡΠ°ΠΊΠΈΠΌ ΠΎΠ±ΡΠ°Π·ΠΎΠΌ Π²ΠΎΠ»ΠΎΡΠΈΠ»ΡΠ½ΡΠΉ ΡΡΠ°Π½ ΠΏΡΠΈΠ³ΠΎΠ΄Π΅Π½ Π΄Π»Ρ Π²ΠΎΠ»ΠΎΡΠ΅Π½ΠΈΡ ΠΏΡΠΎΠ²ΠΎΠ»ΠΎΠΊΠΈ ΠΈΠ· ΡΡΠ°Π»ΠΈ, Π½Π΅ΡΠΆΠ°Π²Π΅ΡΡΠ΅ΠΉ ΡΡΠ°Π»ΠΈ, Π° ΡΠ°ΠΊΠΆΠ΅ ΠΈΠ· Π°Π»ΡΠΌΠΈΠ½ΠΈΡ ΠΈ ΠΌΠ΅Π΄ΠΈ.
Π‘ΠΏΠ΅ΡΠΈΡΠΈΠΊΠ°ΡΠΈΡ Π΄Π»Ρ ΡΡΠ°Π½Π΄Π°ΡΡΠ½ΡΡ ΠΌΠΎΠ΄Π΅Π»Π΅ΠΉ
ΠΠΎΠ΄Π΅Π»Ρ | YTD-600SG5/*(N)+ABCD-600G or+ABCD-600B | YTD-600SG5/*(N)+ABCD-600G or+ABCD-600B | ||
ΠΠ°ΡΠ΅ΡΠΈΠ°Π» | ΠΠΈΠ·ΠΊΠΎ, ΡΡΠ΅Π΄Π½Π΅ ΡΠ³Π»Π΅ΡΠΎΠ΄ΠΈΡΡΠ°Ρ ΡΡΠ°Π»Ρ | |||
ΠΠΈΠ°ΠΌΠ΅ΡΡ Π±Π°ΡΠ°Π±Π°Π½Π° | 600 ΠΌΠΌ | 600 ΠΌΠΌ | ||
ΠΠΈΠ°ΠΌΠ΅ΡΡ ΠΏΡΠΎΠ²ΠΎΠ»ΠΎΠΊΠΈ ΠΏΡΠΈ Π²Ρ ΠΎΠ΄Π΅ | Π‘ΡΠ΅Π΄Π½ΡΡ 8,0-6,5 | Π’Π²ΡΡΠ΄Π°Ρ 6,5-5,5 | Π‘ΡΠ΅Π΄Π½ΡΡ 6,5-5,5 | Π’Π²ΡΡΠ΄Π°Ρ 6,5-5,5 |
ΠΠΈΠ°ΠΌΠ΅ΡΡ ΠΏΡΠΎΠ²ΠΎΠ»ΠΎΠΊΠΈ Π½Π° Π²ΡΡ ΠΎΠ΄Π΅ | 2,4-2,0 ΠΌΠΌ | 2,3-1,8 ΠΌΠΌ | 1,8-1,5 ΠΌΠΌ | 2,3-1,8ΠΌΠΌ |
Π‘ΠΊΠΎΡΠΎΡΡΡ Π²ΠΎΠ»ΠΎΡΠ΅Π½ΠΈΡ | 530-700 | 530-700 | 535-800 | 450-600 |
ΠΠΎΡΡΠ΅Π±Π»ΡΠ΅ΠΌΠ°Ρ ΠΌΠΎΡΠ½ΠΎΡΡΡ Π½Π° Π±Π»ΠΎΠΊ | 50ΠΠ‘ | 50ΠΠ‘ | 40ΠΠ‘ | 40ΠΠ‘ |
Π‘ΠΏΠ΅ΡΠΈΡΠΈΠΊΠ°ΡΠΈΡ Π΄Π»Ρ ΡΡΠ°Π½Π΄Π°ΡΡΠ½ΡΡ ΠΌΠΎΠ΄Π΅Π»Π΅ΠΉ
ΠΠΎΠ΄Π΅Π»Ρ | YTD-600SG3/*(N)+ASD-600B | YTD-600SG3/*(N)+ASD-600B | |
ΠΠ°ΡΠ΅ΡΠΈΠ°Π» | ΠΠΈΠ·ΠΊΠΎΡΠ³Π»Π΅ΡΠΎΠ΄ΠΈΡΡΠ°Ρ ΡΡΠ°Π»Ρ | ΠΠ΅ΡΠΆΠ°Π²Π΅ΡΡΠ°Ρ ΡΡΠ°Π»Ρ | |
ΠΠΈΠ°ΠΌΠ΅ΡΡ Π±Π°ΡΠ°Π±Π°Π½Π° | 600 ΠΌΠΌ | 600 ΠΌΠΌ | |
ΠΠΈΠ°ΠΌΠ΅ΡΡ ΠΏΡΠΎΠ²ΠΎΠ»ΠΎΠΊΠΈ ΠΏΡΠΈ Π²Ρ ΠΎΠ΄Π΅ | Π‘ΡΠ΅Π΄Π½ΡΡ 6,5-5,5 | Π’Π²ΡΡΠ΄Π°Ρ 6,5-5,5 | 6,5-5,5 ΠΌΠΌ |
ΠΠΈΠ°ΠΌΠ΅ΡΡ ΠΏΡΠΎΠ²ΠΎΠ»ΠΎΠΊΠΈ Π½Π° Π²ΡΡ ΠΎΠ΄Π΅ | 2,0-1,65 ΠΌΠΌ | 2,0-1,65 ΠΌΠΌ | 2,3-2,0 ΠΌΠΌ |
Π‘ΠΊΠΎΡΠΎΡΡΡ Π²ΠΎΠ»ΠΎΡΠ΅Π½ΠΈΡ | 400-600 | 535-800 | 200-300 |
ΠΠΎΡΠ½ΠΎΡΡΡ Π΄Π²ΠΈΠ³Π°ΡΠ΅Π»Ρ Π½Π° Π±Π»ΠΎΠΊ | 30ΠΠ‘ | 40ΠΠ‘ | 25-30ΠΠ‘ |
Π‘ΠΏΠ΅ΡΠΈΡΠΈΠΊΠ°ΡΠΈΡ Π΄Π»Ρ ΡΡΠ°Π½Π΄Π°ΡΡΠ½ΡΡ ΠΌΠΎΠ΄Π΅Π»Π΅ΠΉ
ΠΠΎΠ΄Π΅Π»Ρ | YTD-400SG2/*(N)+ABΠ‘Π-400B | YTD-400SG2/*(N)+ASD-400B | |
ΠΠ°ΡΠ΅ΡΠΈΠ°Π» | ΠΠΈΠ·ΠΊΠΎΡΠ³Π»Π΅ΡΠΎΠ΄ΠΈΡΡΠ°Ρ ΡΡΠ°Π»Ρ | ΠΠ΅ΡΠΆΠ°Π²Π΅ΡΡΠ°Ρ ΡΡΠ°Π»Ρ | |
ΠΠΈΠ°ΠΌΠ΅ΡΡ Π±Π°ΡΠ°Π±Π°Π½Π° | 400 ΠΌΠΌ | 400 ΠΌΠΌ | |
ΠΠΈΠ°ΠΌΠ΅ΡΡ ΠΏΡΠΎΠ²ΠΎΠ»ΠΎΠΊΠΈ ΠΏΡΠΈ Π²Ρ ΠΎΠ΄Π΅ | Π‘ΡΠ΅Π΄Π½ΡΡ 3,5-3,2 | Π’Π²ΡΡΠ΄Π°Ρ 3,0-2,7 | 2,7-2,0 ΠΌΠΌ |
ΠΠΈΠ°ΠΌΠ΅ΡΡ ΠΏΡΠΎΠ²ΠΎΠ»ΠΎΠΊΠΈ Π½Π° Π²ΡΡ ΠΎΠ΄Π΅ | 1,1-1,0 ΠΌΠΌ | 0,9-0,8 ΠΌΠΌ | 1,0-0,7 ΠΌΠΌ |
Π‘ΠΊΠΎΡΠΎΡΡΡ Π²ΠΎΠ»ΠΎΡΠ΅Π½ΠΈΡ | 600-800 | 600-800 | ΠΠ°ΠΊΡ. 600 |
ΠΠΎΡΠ½ΠΎΡΡΡ Π΄Π²ΠΈΠ³Π°ΡΠ΅Π»Ρ Π½Π° Π±Π»ΠΎΠΊ | 25-30ΠΠ‘ | 25-30ΠΠ‘ | 20-25ΠΠ‘ |
VERTICAL TYPE WIRE DRAWING MACHINE β ΠΠΎΠ»ΠΎΡΠΈΠ»ΡΠ½ΡΠΉ ΡΡΠ°Π½ Π²Π΅ΡΡΠΈΠΊΠ°Π»ΡΠ½ΠΎΠ³ΠΎ ΡΠΈΠΏΠ°
ΠΠ‘ΠΠΠΠΠΠΠ‘Π’Π ΠΠΠΠ Π£ΠΠΠΠΠΠΠ―
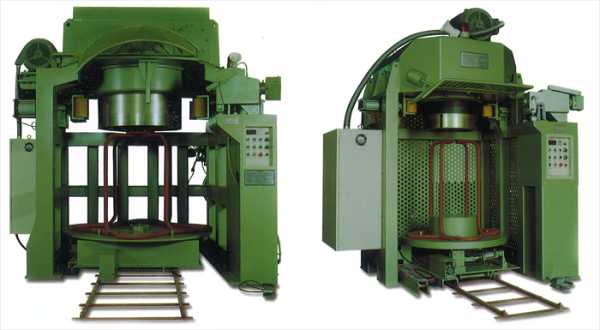
ΠΠΎΠ»ΠΎΡΠΈΠ»ΡΠ½ΡΠΉ ΡΡΠ°Π½ ΠΌΠΎΠ΄Π΅Π»ΠΈ GVY ΡΠΏΡΠΎΠ΅ΠΊΡΠΈΡΠΎΠ²Π°Π½ Π΄Π»Ρ Π²ΡΠΎΡΠΈΡΠ½ΠΎΠΉ ΠΎΠ±ΡΠ°Π±ΠΎΡΠΊΠΈ ΠΌΠ΅ΡΠ°Π»Π»ΠΈΡΠ΅ΡΠΊΠΎΠΉ ΠΏΡΠΎΠ²ΠΎΠ»ΠΎΠΊΠΈ. ΠΠ°Π½Π½ΡΠΉ ΡΡΠ°Π½ ΠΈΠΌΠ΅Π΅Ρ ΡΡΠ½ΠΊΡΠΈΠΈ ΠΊΠ°ΠΊ Π²ΠΎΠ»ΠΎΡΠ΅Π½ΠΈΡ, ΡΠ°ΠΊ ΠΈ Π½Π°ΠΌΠΎΡΠΊΠΈ. ΠΏΡΠΎΠ²ΠΎΠ»ΠΎΠΊΠ° ΠΏΠΎΠ΄Π²Π΅ΡΠ³Π°Π΅ΡΡΡ Π²ΠΎΠ»ΠΎΡΠ΅Π½ΠΈΡ ΠΈ ΡΠΌΠ°ΡΡΠ²Π°Π΅ΡΡΡ Π½Π° ΡΠ΅Π»Π΅ΠΆΠΊΡ. ΠΠΎΠ»ΠΎΡΠΈΠ»ΡΠ½ΡΠΉ ΡΡΠ°Π½ GVY ΠΏΡΠΎΡΡ Π² ΡΠΊΡΠΏΠ»ΡΠ°ΡΠ°ΡΠΈΠΈ, ΡΠΊΠΎΠ½ΠΎΠΌΠΈΡΠ΅Π½ Π² ΠΎΡΠ½ΠΎΡΠ΅Π½ΠΈΠΈ ΡΡΡΠ΄ΠΎΠ·Π°ΡΡΠ°Ρ ΠΈ Π²ΡΠ΅ΠΌΠ΅Π½ΠΈ, ΡΡΡΠ΅ΠΊΡΠΈΠ²Π΅Π½. ΠΠΎΠ΄Π΅Π»Ρ GVY ΠΏΠΎΠΊΡΡΠ²Π°Π΅Ρ ΡΠΈΡΠΎΠΊΠΈΠΉ ΡΠΏΠ΅ΠΊΡΡ ΠΏΡΠΎΠ²ΠΎΠ»ΠΎΠΊΠΈ Π΄Π»Ρ ΠΏΡΠΎΠΈΠ·Π²ΠΎΠ΄ΡΡΠ²Π° ΠΊΡΠ΅ΠΏΠ΅ΠΆΠ°, ΠΌΠ΅Π΄Π½ΠΎΠΉ ΠΏΡΠΎΠ²ΠΎΠ»ΠΎΠΊΠΈ, Π° ΡΠ°ΠΊΠΆΠ΅ ΡΠ°Π·Π»ΠΈΡΠ½ΡΡ Π²ΠΈΠ΄ΠΎΠ² ΡΡΠ°Π»ΡΠ½ΠΎΠΉ ΠΏΡΠΎΠ²ΠΎΠ»ΠΎΠΊΠΈ. ΠΠΎΠΌΠΈΠΌΠΎ Π²ΠΎΠ»ΠΎΡΠ΅Π½ΠΈΡ ΠΈ Π½Π°ΠΌΠΎΡΠΎΡΠ½ΠΎΠΉ ΡΡΠ½ΠΊΡΠΈΠΈ GVY ΡΠ°ΠΊΠΆΠ΅ ΠΏΡΠΈΠΌΠ΅Π½ΠΈΠΌ Π΄Π»Ρ ΠΏΠΎΠ²Π΅ΡΡ Π½ΠΎΡΡΠ½ΠΎΠΉ ΠΎΠ±ΡΠ°Π±ΠΎΡΠΊΠΈ ΠΏΡΠΎΠ²ΠΎΠ»ΠΎΠΊΠΈ.
Π‘ΠΠΠ¦ΠΠ€ΠΠΠΠ¦ΠΠ―
ΠΠΎΠ΄Π΅Π»Ρ | GVY-600T | GVY-750T | GVY-800T | GVY-1000T | GVY-1300T |
ΠΠ°ΡΠ΅ΡΠΈΠ°Π» | ΠΠ΅Π΄Π½Π°Ρ, ΡΠ²ΡΡΠ΄Π°Ρ ΠΈ ΠΌΡΠ³ΠΊΠ°Ρ ΡΡΠ°Π»ΡΠ½Π°Ρ ΠΏΡΠΎΠ²ΠΎΠ»ΠΎΠΊΠ°, ΠΏΡΠΎΠ²ΠΎΠ»ΠΎΠΊΠ° ΠΈΠ· Π½Π΅ΡΠΆΠ°Π²Π΅ΡΡΠ΅ΠΉ ΡΡΠ°Π»ΠΈ ΠΈ Π΄ΡΡΠ³ΠΈΠ΅ | ||||
ΠΠΈΠ°ΠΌΠ΅ΡΡ Π±Π°ΡΠ°Π±Π°Π½Π° | 600ΠΌΠΌ | 750ΠΌΠΌ | 800ΠΌΠΌ | 1000ΠΌΠΌ | 1300ΠΌΠΌ |
ΠΠΈΠ°ΠΌΠ΅ΡΡ ΠΏΡΠΎΠ²ΠΎΠ»ΠΎΠΊΠΈ Π½Π° Π²Ρ ΠΎΠ΄Π΅ | 4-8 ΠΌΠΌ | 8-13 ΠΌΠΌ | 8-14 ΠΌΠΌ | 12-25 ΠΌΠΌ | 20-34 ΠΌΠΌ |
Π‘ΠΊΠΎΡΠΎΡΡΡ | 80-120 ΠΌ/ΠΌΠΈΠ½ | 60-90 ΠΌ/ΠΌΠΈΠ½ | 50-80 ΠΌ/ΠΌΠΈΠ½ | 35-65 ΠΌ/ΠΌΠΈΠ½ | 22-33 ΠΌ/ΠΌΠΈΠ½ |
ΠΠΎΡΠ½ΠΎΡΡΡ Π΄Π²ΠΈΠ³Π°ΡΠ΅Π»Ρ | 25-30 ΠΠ‘ | 50 ΠΠ‘ | 50 ΠΠ‘ | 50-75 ΠΠ‘ | 100 ΠΠ‘ |
taiwan-fasteners.com
ΠΠΎΠ»ΠΎΡΠ΅Π½ΠΈΠ΅ ΠΏΡΠΎΠ²ΠΎΠ»ΠΎΠΊΠΈ: ΡΠ΅Ρ Π½ΠΎΠ»ΠΎΠ³ΠΈΡ, Π²ΠΈΠ΄Ρ ΠΈ ΠΎΠΏΠΈΡΠ°Π½ΠΈΠ΅
ΠΠΎΠ»ΠΎΡΠ΅Π½ΠΈΠ΅ ΠΏΡΠΎΠ²ΠΎΠ»ΠΎΠΊΠΈ — ΡΡΠΎ ΠΎΠ΄Π½Π° ΠΈΠ· ΡΠ°Π·Π½ΠΎΠ²ΠΈΠ΄Π½ΠΎΡΡΠ΅ΠΉ ΡΠΎΡΠΌΡ ΠΎΠ±ΡΠ°Π±ΠΎΡΠΊΠΈ ΠΌΠ΅ΡΠ°Π»Π»ΠΈΡΠ΅ΡΠΊΠΈΡ ΠΈΠ·Π΄Π΅Π»ΠΈΠΉ. ΠΡΠ»ΠΈΡΠΈΡΠ΅Π»ΡΠ½Π°Ρ ΡΠ΅ΡΡΠ° ΠΎΠΏΠ΅ΡΠ°ΡΠΈΠΈ Π·Π°ΠΊΠ»ΡΡΠ°Π΅ΡΡΡ Π² ΡΠΎΠΌ, ΡΡΠΎ ΠΎΠ½Π° ΠΏΡΠΎΠ²ΠΎΠ΄ΠΈΡΡΡ ΠΏΠΎΠ΄ Π²ΡΡΠΎΠΊΠΈΠΌ Π΄Π°Π²Π»Π΅Π½ΠΈΠ΅ΠΌ. ΠΠ½ΠΎ Π²ΠΎΠ·Π΄Π΅ΠΉΡΡΠ²ΡΠ΅Ρ Π½Π° Π·Π°Π³ΠΎΡΠΎΠ²ΠΊΡ, ΠΊΠΎΡΠΎΡΠ°Ρ ΠΈΠΌΠ΅Π΅Ρ ΠΊΡΡΠ³Π»ΠΎΠ΅ ΠΈΠ»ΠΈ ΡΠ°ΡΠΎΠ½Π½ΠΎΠ΅ ΡΠ΅ΡΠ΅Π½ΠΈΠ΅. Π’Π°ΠΊΠ°Ρ Π·Π°Π³ΠΎΡΠΎΠ²ΠΊΠ° ΠΏΡΠΎΡΠ°ΡΠΊΠΈΠ²Π°Π΅ΡΡΡ ΠΏΠΎΠ΄ Π΄Π°Π²Π»Π΅Π½ΠΈΠ΅ΠΌ ΡΠΊΠ²ΠΎΠ·Ρ ΠΎΡΠ²Π΅ΡΡΡΠΈΡ, ΠΊΠΎΡΠΎΡΡΠ΅ ΠΈΠ·Π½Π°ΡΠ°Π»ΡΠ½ΠΎ ΠΌΠ΅Π½ΡΡΠ΅, ΡΠ΅ΠΌ Π΄ΠΈΠ°ΠΌΠ΅ΡΡ, ΠΏΡΠΎΡΡΠ³ΠΈΠ²Π°Π΅ΠΌΠΎΠ³ΠΎ ΠΈΠ·Π΄Π΅Π»ΠΈΡ. Π’Π°ΠΊΠΈΠΌ ΠΎΠ±ΡΠ°Π·ΠΎΠΌ ΠΈ ΠΏΠΎΠ»ΡΡΠ°ΡΡ ΠΏΡΠΎΠ²ΠΎΠ»ΠΎΠΊΡ.
ΠΠΈΠ΄Ρ ΠΎΠΏΠ΅ΡΠ°ΡΠΈΠΈ
ΠΠ° ΡΠ΅Π³ΠΎΠ΄Π½Ρ ΠΈΡΠΏΠΎΠ»ΡΠ·ΡΠ΅ΡΡΡ Π±ΠΎΠ»ΡΡΠΎΠ΅ ΠΊΠΎΠ»ΠΈΡΠ΅ΡΡΠ²ΠΎ ΠΌΠ΅ΡΠΎΠ΄ΠΎΠ² Π²ΠΎΠ»ΠΎΡΠ΅Π½ΠΈΡ ΠΏΡΠΎΠ²ΠΎΠ»ΠΎΠΊΠΈ. ΠΡΠ»ΠΈ Π³ΠΎΠ²ΠΎΡΠΈΡΡ ΠΎ ΡΠΈΠΏΠ°Ρ ΠΎΠΏΠ΅ΡΠ°ΡΠΈΠΈ, ΡΠΎ ΠΎΠ½Π° ΠΌΠΎΠΆΠ΅Ρ Π±ΡΡΡ Π΄Π²ΡΡ Π²ΠΈΠ΄ΠΎΠ². ΠΠ΅ΡΠ²ΡΠΉ Π²ΠΈΠ΄ Π½Π°Π·ΡΠ²Π°Π΅ΡΡΡ ΡΡΡ ΠΈΠΌ. Π Π΄Π°Π½Π½ΠΎΠΌ ΡΠ»ΡΡΠ°Π΅ ΠΏΡΠΎΡΠ΅ΡΡ ΠΏΡΠΎΡΡΠ³ΠΈΠ²Π°Π½ΠΈΡ ΠΎΡΡΡΠ΅ΡΡΠ²Π»ΡΠ΅ΡΡΡ ΡΠ΅ΡΠ΅Π· Π΅ΠΌΠΊΠΎΡΡΡ, Π²Π½ΡΡΡΠΈ ΠΊΠΎΡΠΎΡΠΎΠΉ ΠΌΡΠ»ΡΠ½ΡΠΉ ΠΏΠΎΡΠΎΡΠΎΠΊ.
ΠΠΎΠΊΡΡΠΉ ΡΠΈΠΏ ΠΎΠΏΠ΅ΡΠ°ΡΠΈΠΈ Π²ΡΠΏΠΎΠ»Π½ΡΠ΅ΡΡΡ ΠΏΡΠΈ ΠΏΠΎΠΌΠΎΡΠΈ ΠΌΡΠ»ΡΠ½ΠΎΠΉ ΡΠΌΡΠ»ΡΡΠΈΠΈ. ΠΠ°Π½Π½Π°Ρ ΠΎΠΏΠ΅ΡΠ°ΡΠΈΡ ΠΈΠΌΠ΅Π΅Ρ ΡΠΈΡΡΠΎΡΡ ΠΎΠ±ΡΠ°Π±ΠΎΡΠΊΠΈ, ΠΊΠΎΡΠΎΡΠ°Ρ ΡΠ°ΠΊΠΆΠ΅ ΠΌΠΎΠΆΠ΅Ρ Π±ΡΡΡ Π²ΡΠΏΠΎΠ»Π½Π΅Π½Π° Π² Π΄Π²ΡΡ ΠΊΠ°ΡΠ΅Π³ΠΎΡΠΈΡΡ . ΠΠ΅ΡΠ²Π°Ρ — ΡΡΠΎ ΡΠ΅ΡΠ½ΠΎΠ²Π°Ρ, ΠΈΠ»ΠΈ ΠΆΠ΅ ΠΏΠΎΠ΄Π³ΠΎΡΠΎΠ²ΠΈΡΠ΅Π»ΡΠ½Π°Ρ. ΠΡΠΎΡΠΎΠΉ ΡΠΈΠΏ — ΡΠΈΡΡΠΎΠ²Π°Ρ ΠΎΠ±ΡΠ°Π±ΠΎΡΠΊΠ°. ΠΡΠΎ ΡΠΈΠ½Π°Π»ΡΠ½Π°Ρ ΡΡΠ°Π΄ΠΈΡ, ΠΊΠΎΡΠΎΡΠ°Ρ Π½Π΅ΠΎΠ±Ρ ΠΎΠ΄ΠΈΠΌΠ°, ΡΡΠΎΠ±Ρ ΡΠΎΠ·Π΄Π°ΡΡ Π½ΡΠΆΠ½ΡΡ ΡΠΎΡΠΌΡ ΠΈ ΡΠ°Π·ΠΌΠ΅Ρ ΠΏΡΠΎΠ²ΠΎΠ»ΠΎΠΊΠΈ.
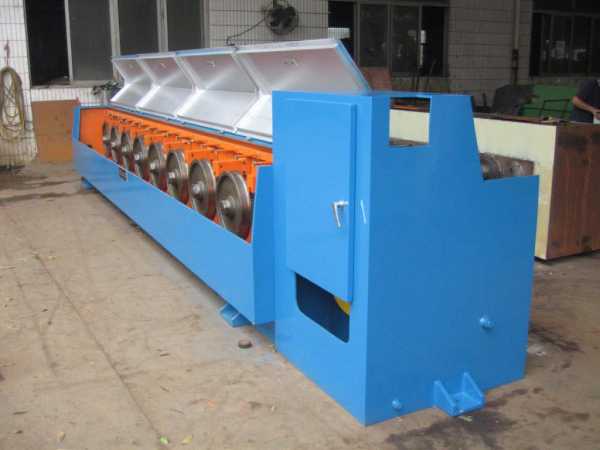
ΠΠΎΠ»ΠΎΡΠ΅Π½ΠΈΠ΅ ΡΠ°ΠΊΠΆΠ΅ ΠΈΠΌΠ΅Π΅Ρ ΡΠ°ΠΊΠΎΠΉ ΡΡΠ°ΠΏ, ΠΊΠ°ΠΊ ΠΊΡΠ°ΡΠ½ΠΎΡΡΡ. ΠΠΎΠ·ΠΌΠΎΠΆΠ΅Π½ ΠΎΠ΄Π½ΠΎΠΊΡΠ°ΡΠ½ΡΠΉ ΠΏΠ΅ΡΠ΅Ρ ΠΎΠ΄ ΠΈΠ»ΠΈ ΠΆΠ΅ ΠΌΠ½ΠΎΠ³ΠΎΠΊΡΠ°ΡΠ½ΡΠΉ. ΠΠΎ Π²ΡΠΎΡΠΎΠΌ ΡΠ»ΡΡΠ°Π΅ ΠΏΡΠ΅Π΄ΠΏΠΎΠ»Π°Π³Π°Π΅ΡΡΡ, ΡΡΠΎ ΠΎΠ΄Π½Π° ΠΈ ΡΠ° ΠΆΠ΅ Π·Π°Π³ΠΎΡΠΎΠ²ΠΊΠ° Π½Π΅ΡΠΊΠΎΠ»ΡΠΊΠΎ ΡΠ°Π· ΠΏΡΠΎΠΉΠ΄Π΅Ρ ΡΠ΅ΡΠ΅Π· ΡΡΠ°Π½ΠΎΠΊ. ΠΡΠΎΠΌΠ΅ ΡΠΎΠ³ΠΎ, ΡΠ°Π±ΠΎΡΠ° ΠΌΠΎΠΆΠ΅Ρ Π²ΡΠΏΠΎΠ»Π½ΡΡΡΡΡ ΠΏΠ°ΡΠ°Π»Π»Π΅Π»ΡΠ½ΠΎ. Π’ΠΎ Π΅ΡΡΡ Π·Π°Π³ΠΎΡΠΎΠ²ΠΊΠ° ΠΌΠΎΠΆΠ΅Ρ Π±ΡΡΡ ΠΎΠ΄Π½ΠΎΠ½ΠΈΡΠΎΡΠ½ΠΎΠΉ, Π° ΠΌΠΎΠΆΠ΅Ρ Π±ΡΡΡ ΠΌΠ½ΠΎΠ³ΠΎΠ½ΠΈΡΠΎΡΠ½ΠΎΠΉ.
ΠΡΠ»ΠΈΡΠ°ΡΡΡΡ ΠΌΠΎΠ³ΡΡ ΡΠ°ΠΊΠΆΠ΅ ΠΈ Π²ΠΎΠ»ΠΎΠΊΠΈ ΡΠ²ΠΎΠ΅ΠΉ ΠΏΠΎΠ΄Π²ΠΈΠΆΠ½ΠΎΡΡΡΡ. ΠΠ½ΠΈ ΠΌΠΎΠ³ΡΡ Π±ΡΡΡ Π»ΠΈΠ±ΠΎ Π²ΡΠ°ΡΠ°ΡΡΠ΅Π³ΠΎΡΡ ΡΠΈΠΏΠ°, Π»ΠΈΠ±ΠΎ Π½Π΅ΠΏΠΎΠ΄Π²ΠΈΠΆΠ½ΠΎΠ³ΠΎ. ΠΠΎΡΠ»Π΅Π΄Π½ΠΈΠΉ ΡΠ»Π΅ΠΌΠ΅Π½Ρ, ΠΊΠΎΡΠΎΡΡΠΉ ΠΎΠΊΠ°Π·ΡΠ²Π°Π΅Ρ Π²Π»ΠΈΡΠ½ΠΈΠ΅ Π½Π° Ρ ΠΎΠ΄ ΠΎΠΏΠ΅ΡΠ°ΡΠΈΠΈ, — ΡΡΠΎ Π½Π°Π³ΡΠ΅Π² Π·Π°Π³ΠΎΡΠΎΠ²ΠΊΠΈ. ΠΡΡΠ΅ΡΡΠ²Π΅Π½Π½ΠΎ, ΡΡΠΎ ΠΎΠ½Π° ΠΌΠΎΠΆΠ΅Ρ Π±ΡΡΡ Ρ ΠΎΠ»ΠΎΠ΄Π½ΠΎΠΉ ΠΈΠ»ΠΈ ΠΆΠ΅ Π³ΠΎΡΡΡΠ΅ΠΉ.
Π‘ΡΡΡ Π²ΠΎΠ»ΠΎΡΠ΅Π½ΠΈΡ
Π Π½Π°ΡΡΠΎΡΡΠ΅Π΅ Π²ΡΠ΅ΠΌΡ Π²ΠΎΠ·ΠΌΠΎΠΆΠ½ΠΎ Π²ΠΎΠ»ΠΎΡΠ΅Π½ΠΈΠ΅ Π°Π»ΡΠΌΠΈΠ½ΠΈΠ΅Π²ΠΎΠΉ ΠΏΡΠΎΠ²ΠΎΠ»ΠΎΠΊΠΈ, ΠΌΠ΅Π΄Π½ΠΎΠΉ ΠΈΠ»ΠΈ ΠΆΠ΅ ΡΡΠ°Π»ΡΠ½ΠΎΠΉ. ΠΠ±ΠΎΡΡΠ΄ΠΎΠ²Π°Π½ΠΈΠ΅, Π² ΠΊΠΎΡΠΎΡΠΎΠΌ ΠΈΠΌΠ΅Π΅ΡΡΡ ΠΎΡΠ²Π΅ΡΡΡΠΈΠ΅ Π½ΡΠΆΠ½ΠΎΠ³ΠΎ Π΄ΠΈΠ°ΠΌΠ΅ΡΡΠ°, Π½Π°Π·ΡΠ²Π°Π΅ΡΡΡ Π²ΠΎΠ»ΠΎΠΊΠΎΠΌ, ΠΎΡΡΡΠ΄Π° ΠΈ Π½Π°Π·Π²Π°Π½ΠΈΠ΅ ΠΏΡΠΎΡΠ΅Π΄ΡΡΡ. Π‘Π°ΠΌΠΎ ΠΆΠ΅ ΠΎΡΠ²Π΅ΡΡΡΠΈΠ΅ Π½Π°Π·ΡΠ²Π°Π΅ΡΡΡ ΡΠΈΠ»ΡΠ΅ΡΠΎΠΉ. ΠΡ Π΅Π³ΠΎ ΡΠΎΡΠΌΡ ΠΈ Π±ΡΠ΄Π΅Ρ Π·Π°Π²ΠΈΡΠ΅ΡΡ ΠΊΠΎΠ½Π΅ΡΠ½ΡΠΉ ΡΠ΅Π·ΡΠ»ΡΡΠ°Ρ Π²ΡΠ΅ΠΉ ΠΏΡΠΎΡΠ΅Π΄ΡΡΡ.
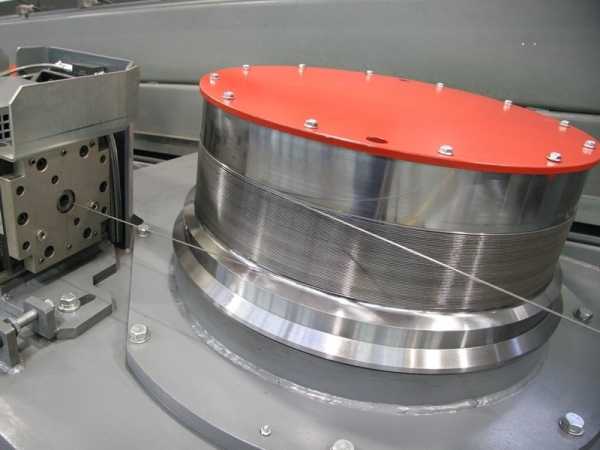
ΠΡΠΎΠΌΠ΅ ΡΠΎΠ³ΠΎ, Π΅ΡΠ»ΠΈ ΡΡΠ°Π²Π½ΠΈΠ²Π°ΡΡ ΠΏΡΠΎΡΠ΅Π΄ΡΡΡ Π²ΠΎΠ»ΠΎΡΠ΅Π½ΠΈΡ ΠΏΡΠΎΠ²ΠΎΠ»ΠΎΠΊΠΈ ΠΈ ΠΏΡΠΎΠΊΠ°Ρ, ΡΠΎ ΠΏΠ΅ΡΠ²ΡΠΉ ΡΠΏΠΎΡΠΎΠ± Π³ΠΎΡΠ°Π·Π΄ΠΎ Π±ΠΎΠ»Π΅Π΅ ΡΡΡΠ΅ΠΊΡΠΈΠ²Π΅Π½, ΡΠ°ΠΊ ΠΊΠ°ΠΊ ΠΎΠ½ ΠΎΠ±Π΅ΡΠΏΠ΅ΡΠΈΡ Π±ΠΎΠ»ΡΡΡΡ ΡΠΈΡΡΠΎΡΡ, Π° ΡΠ°ΠΊΠΆΠ΅ ΡΠΎΡΠ½ΠΎΡΡΡ ΠΏΠΎΠ²Π΅ΡΡ Π½ΠΎΡΡΠΈ ΠΏΡΠΎΠ²ΠΎΠ»ΠΎΠΊΠΈ. Π ΡΠΎΠΌΡ ΠΆΠ΅ ΠΏΡΠΎΡΠ΅Π΄ΡΡΠ° ΡΡΠ° Ρ Π°ΡΠ°ΠΊΡΠ΅ΡΠΈΠ·ΡΠ΅ΡΡΡ Π΅ΡΠ΅ ΠΈ ΡΠ΅ΠΌ, ΡΡΠΎ Π² ΠΏΡΠΎΡΠ΅ΡΡΠ΅ Π΅Π΅ ΠΏΡΠΎΠ²Π΅Π΄Π΅Π½ΠΈΡ ΡΠ»ΡΡΡΠ°ΡΡΡΡ ΠΌΠ΅Ρ Π°Π½ΠΈΡΠ΅ΡΠΊΠΈΠ΅ ΠΏΠΎΠΊΠ°Π·Π°ΡΠ΅Π»ΠΈ, ΡΡΠΎ ΠΎΠ±ΡΡΠ»ΠΎΠ²Π»Π΅Π½ΠΎ ΡΠ½ΡΡΠΈΠ΅ΠΌ Π½Π°ΠΊΠ»Π΅ΠΏΠ°. Π Π½Π°ΡΡΠΎΡΡΠ΅Π΅ Π²ΡΠ΅ΠΌΡ Π΅ΡΡΡ Π²ΠΎΠ·ΠΌΠΎΠΆΠ½ΠΎΡΡΡ ΠΈΠ·Π³ΠΎΡΠ°Π²Π»ΠΈΠ²Π°ΡΡ ΠΏΡΠΎΠ²ΠΎΠ»ΠΎΠΊΡ Ρ Π΄ΠΈΠ°ΠΌΠ΅ΡΡΠΎΠΌ ΠΎΡ 1-2 ΠΌΠΈΠΊΡΠΎΠ½ Π΄ΠΎ 10, Π° Π² ΠΎΡΠ΄Π΅Π»ΡΠ½ΡΡ ΡΠ»ΡΡΠ°ΡΡ ΠΈ Π±ΠΎΠ»Π΅Π΅, ΠΌΠΈΠ»Π»ΠΈΠΌΠ΅ΡΡΠΎΠ².
Π’Π΅Ρ Π½ΠΎΠ»ΠΎΠ³ΠΈΡ ΠΈ ΡΡΠ°ΠΏΡ Π²ΠΎΠ»ΠΎΡΠ΅Π½ΠΈΡ
Π‘ΡΠΎΠΈΡ ΠΎΡΠΌΠ΅ΡΠΈΡΡ, ΡΡΠΎ Ρ Π½ΡΠ½Π΅ΡΠ½ΠΈΠΌ ΡΠ°Π·Π²ΠΈΡΠΈΠ΅ΠΌ ΡΠ΅Ρ Π½ΠΎΠ»ΠΎΠ³ΠΈΠΉ Π²ΠΎΠ»ΠΎΡΠ΅Π½ΠΈΠ΅ ΠΏΡΠΎΠ²ΠΎΠ»ΠΎΠΊΠΈ Π½Π° ΡΠΎΠ²ΡΠ΅ΠΌΠ΅Π½Π½ΠΎΠΌ ΠΎΠ±ΠΎΡΡΠ΄ΠΎΠ²Π°Π½ΠΈΠΈ Π³Π°ΡΠ°Π½ΡΠΈΡΡΠ΅Ρ Π΄ΠΎΡΡΠ°ΡΠΎΡΠ½ΠΎ Π²ΡΡΠΎΠΊΡΡ ΠΏΡΠΎΠΈΠ·Π²ΠΎΠ΄ΠΈΡΠ΅Π»ΡΠ½ΠΎΡΡΡ. Π ΡΡΠΎ ΠΎΡΠ΅Π½Ρ Π²Π°ΠΆΠ½ΡΠΉ ΠΌΠΎΠΌΠ΅Π½Ρ. ΠΠ±ΠΎΡΡΠ΄ΠΎΠ²Π°Π½ΠΈΠ΅ Π΄Π»Ρ Π²ΠΎΠ»ΠΎΡΠ΅Π½ΠΈΡ ΠΏΡΠΎΠ²ΠΎΠ»ΠΎΠΊΠΈ Π²ΠΏΠΎΠ»Π½Π΅ ΠΌΠΎΠΆΠ΅Ρ ΡΡΠ½ΠΊΡΠΈΠΎΠ½ΠΈΡΠΎΠ²Π°ΡΡ Π½Π° Π΄ΠΎΡΡΠ°ΡΠΎΡΠ½ΠΎ Π±ΠΎΠ»ΡΡΠΎΠΉ ΡΠΊΠΎΡΠΎΡΡΠΈ, ΠΏΡΠΈ ΡΡΠΎΠΌ Π±Π΅Π· ΠΊΠ°ΠΊΠΈΡ -Π»ΠΈΠ±ΠΎ Π½Π°ΡΡΡΠ΅Π½ΠΈΠΉ. Π‘ΠΊΠΎΡΠΎΡΡΡ, ΠΊΠΎΡΠΎΡΡΡ ΠΌΠΎΠ³ΡΡ ΡΠ°Π·Π²ΠΈΠ²Π°ΡΡ Π°Π³ΡΠ΅Π³Π°ΡΡ, Π΄ΠΎΡΡΠΈΠ³Π°Π΅Ρ 60 ΠΌ/Ρ.
ΠΡΠΎΡΠ΅ΡΡ ΠΏΡΠΎΡ ΠΎΠ΄ΠΈΡ Π² Π½Π΅ΡΠΊΠΎΠ»ΡΠΊΠΎ ΠΎΡΠ½ΠΎΠ²Π½ΡΡ ΡΡΠ°ΠΏΠΎΠ²:
- ΠΠ΅ΡΠ²Π°Ρ ΡΡΠ°Π΄ΠΈΡ — ΡΡΠΎ ΡΡΠ°Π²Π»Π΅Π½ΠΈΠ΅ ΠΈΡΡ ΠΎΠ΄Π½ΠΈΠΊΠΎΠ². ΠΠ»Ρ ΡΡΠΎΠ³ΠΎ ΠΎΠ±ΡΡΠ½ΠΎ ΠΏΡΠΈΠΌΠ΅Π½ΡΠ΅ΡΡΡ ΡΠ΅ΡΠ½ΠΎΠΊΠΈΡΠ»ΡΠΉ ΡΠ°ΡΡΠ²ΠΎΡ, ΠΊΠΎΡΠΎΡΡΠΉ ΠΏΡΠ΅Π΄Π²Π°ΡΠΈΡΠ΅Π»ΡΠ½ΠΎ Π½Π°Π³ΡΠ΅Π²Π°Π΅ΡΡΡ Π΄ΠΎ ΡΠ΅ΠΌΠΏΠ΅ΡΠ°ΡΡΡΡ Π² 50 Π³ΡΠ°Π΄ΡΡΠΎΠ² ΠΏΠΎ Π¦Π΅Π»ΡΡΠΈΡ. ΠΠΏΠ΅ΡΠ°ΡΠΈΡ Π½Π΅ΠΎΠ±Ρ ΠΎΠ΄ΠΈΠΌΠ° Π΄Π»Ρ ΡΠΎΠ³ΠΎ, ΡΡΠΎΠ±Ρ ΡΠ²Π΅Π»ΠΈΡΠΈΡΡ ΡΡΠΎΠΊ ΡΠΊΡΠΏΠ»ΡΠ°ΡΠ°ΡΠΈΠΈ ΠΏΡΡΠ΅ΠΌ ΡΠ΄Π°Π»Π΅Π½ΠΈΡ ΠΎΠΊΠ°Π»ΠΈΠ½.
- Π‘Π»Π΅Π΄ΡΡΡΠ°Ρ ΠΏΡΠΎΡΠ΅Π΄ΡΡΠ° — ΡΡΠΎ ΠΎΡΠΆΠΈΠ³. ΠΠ½Π° Π½Π΅ΠΎΠ±Ρ ΠΎΠ΄ΠΈΠΌΠ° Π΄Π»Ρ ΡΠΎΠ³ΠΎ, ΡΡΠΎΠ±Ρ ΡΠ²Π΅Π»ΠΈΡΠΈΡΡ ΡΠ°ΠΊΡΡ Ρ Π°ΡΠ°ΠΊΡΠ΅ΡΠΈΡΡΠΈΠΊΡ, ΠΊΠ°ΠΊ ΠΏΠ»Π°ΡΡΠΈΡΠ½ΠΎΡΡΡ, Π° ΡΠ°ΠΊΠΆΠ΅ ΡΡΠΎΡΠΌΠΈΡΠΎΠ²Π°ΡΡ ΠΌΠ΅Π»ΠΊΠΎΠ·Π΅ΡΠ½ΠΈΡΡΠΎΡΡΡ.
- Π’ΡΠ΅ΡΠΈΠΉ ΡΡΠ°ΠΏ — ΡΡΠΎ ΡΠ΄Π°Π»Π΅Π½ΠΈΠ΅ ΠΎΡΡΠ°ΡΠΊΠΎΠ² ΡΠ΅ΡΠ½ΠΎΠΊΠΈΡΠ»ΠΎΠ³ΠΎ ΡΠ°ΡΡΠ²ΠΎΡΠ°. ΠΠ»Ρ ΡΡΠΎΠ³ΠΎ ΠΏΡΠΎΠ²ΠΎΠ΄ΠΈΡΡΡ ΠΏΡΠΎΠΌΡΠ²ΠΊΠ° ΠΈ Π½Π΅ΠΉΡΡΠ°Π»ΠΈΠ·Π°ΡΠΈΡ Π²Π΅ΡΠ΅ΡΡΠ²Π°.
- ΠΡΠΈ ΠΏΠΎΠΌΠΎΡΠΈ ΠΌΠΎΠ»ΠΎΡΠ° ΠΊΠΎΠ½ΡΡ Π·Π°Π³ΠΎΡΠΎΠ²ΠΊΠΈ Π·Π°ΠΎΡΡΡΡΡΡΡΡ.
- ΠΠ° Π΄Π°Π½Π½ΠΎΠΌ ΡΡΠ°ΠΏΠ΅ ΠΏΡΠΎΠΈΡΡ ΠΎΠ΄ΠΈΡ Π½Π΅ΠΏΠΎΡΡΠ΅Π΄ΡΡΠ²Π΅Π½Π½ΠΎΠ΅ Π²ΠΎΠ»ΠΎΡΠ΅Π½ΠΈΠ΅ ΡΡΠ°Π»ΡΠ½ΠΎΠΉ ΠΏΡΠΎΠ²ΠΎΠ»ΠΎΠΊΠΈ ΠΈΠ»ΠΈ Π»ΡΠ±ΠΎΠΉ Π΄ΡΡΠ³ΠΎΠΉ.
- ΠΠΎΡΠ»Π΅Π΄Π½ΠΈΠΉ ΡΡΠ°ΠΏ — ΡΡΠΎ ΡΠ½ΠΎΠ²Π° ΠΎΡΠΆΠΈΠ³ ΡΠΆΠ΅ Π³ΠΎΡΠΎΠ²ΠΎΠ³ΠΎ ΠΈΠ·Π΄Π΅Π»ΠΈΡ.
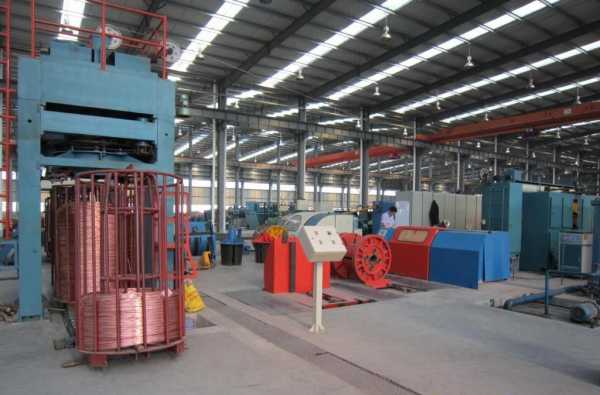
ΠΡΠΎΠ±Π΅Π½Π½ΠΎΡΡΡ ΠΎΠΏΠ΅ΡΠ°ΡΠΈΠΈ
ΠΡΡΠ΅ΡΡΠ²Π΅Π½Π½ΠΎ, Π»ΡΠ±Π°Ρ ΠΎΠΏΠ΅ΡΠ°ΡΠΈΡ ΠΈΠΌΠ΅Π΅Ρ ΡΠ²ΠΎΠΈ Π½Π΅Π΄ΠΎΡΡΠ°ΡΠΊΠΈ. ΠΠ°ΠΊ ΡΡΠΈΡΠ°ΡΡ ΡΠΏΠ΅ΡΠΈΠ°Π»ΠΈΡΡΡ, Π²ΠΎΠ»ΠΎΡΠ΅Π½ΠΈΠ΅ ΠΈΠΌΠ΅Π΅Ρ Π»ΠΈΡΡ ΠΎΠ΄ΠΈΠ½, Π½ΠΎ Π΄ΠΎΡΡΠ°ΡΠΎΡΠ½ΠΎ ΡΠ΅ΡΡΠ΅Π·Π½ΡΠΉ ΠΌΠΈΠ½ΡΡ. ΠΠ°ΠΊΠ»ΡΡΠ°Π΅ΡΡΡ ΠΎΠ½ Π² ΡΠΎΠΌ, ΡΡΠΎ ΠΏΡΠΎΠ²ΠΎΠ»ΠΎΠΊΠ° ΠΏΠΎΠ΄Π²Π΅ΡΠ³Π°Π΅ΡΡΡ Π½Π΅Π·Π½Π°ΡΠΈΡΠ΅Π»ΡΠ½ΠΎΠΉ Π΄Π΅ΡΠΎΡΠΌΠ°ΡΠΈΠΈ Π²ΠΎ Π²ΡΠ΅ΠΌΡ ΠΏΡΠΎΠ²Π΅Π΄Π΅Π½ΠΈΡ ΠΎΠΏΠ΅ΡΠ°ΡΠΈΠΈ. Π§Π°ΡΠ΅ Π²ΡΠ΅Π³ΠΎ ΠΈΡΡ ΠΎΠ΄Π½ΡΠΌ ΡΡΡΡΠ΅ΠΌ Π΄Π»Ρ Π²ΠΎΠ»ΠΎΡΠ΅Π½ΠΈΡ ΠΏΡΠΎΠ²ΠΎΠ»ΠΎΠΊΠΈ ΡΡΠ°Π½ΠΎΠ²ΠΈΡΡΡ Π½Π΅ΠΏΡΠ΅ΡΡΠ²Π½ΠΎ ΠΎΡΠ»ΠΈΡΠ°Ρ, ΡΠΏΡΠ΅ΡΠΎΠ²Π°Π½Π½Π°Ρ, ΡΠΊΠ°ΡΠ°Π½Π½Π°Ρ Π·Π°Π³ΠΎΡΠΎΠ²ΠΊΠ°, ΠΈΠ·Π³ΠΎΡΠΎΠ²Π»Π΅Π½Π½Π°Ρ ΠΈΠ· ΡΠ²Π΅ΡΠ½ΡΡ ΠΌΠ΅ΡΠ°Π»Π»ΠΎΠ², ΡΠ΅ΡΠ½ΡΡ ΠΌΠ΅ΡΠ°Π»Π»ΠΎΠ² ΠΈΠ»ΠΈ ΡΠ³Π»Π΅ΡΠΎΠ΄ΠΈΡΡΡΡ , Π»Π΅Π³ΠΈΡΠΎΠ²Π°Π½Π½ΡΡ ΡΡΠ°Π»Π΅ΠΉ. ΠΡΡΠ³ΠΈΠΌΠΈ ΡΠ»ΠΎΠ²Π°ΠΌΠΈ, ΡΡΠΎΠ±Ρ Π΄ΠΎΡΡΠΈΡΡ Π²ΡΡΠΎΠΊΠΎΠ³ΠΎ ΠΊΠ°ΡΠ΅ΡΡΠ²Π° ΠΏΡΠΎΠ²ΠΎΠ»ΠΎΠΊΠΈ, Π½Π΅ΠΎΠ±Ρ ΠΎΠ΄ΠΈΠΌΠΎ ΠΈΡΠΏΠΎΠ»ΡΠ·ΠΎΠ²Π°ΡΡ Π΄ΠΎΠ²ΠΎΠ»ΡΠ½ΠΎ Π²ΡΡΠΎΠΊΠΎΠΊΠ°ΡΠ΅ΡΡΠ²Π΅Π½Π½ΠΎΠ΅ ΠΈΠ·Π½Π°ΡΠ°Π»ΡΠ½ΠΎΠ΅ ΡΡΡΡΠ΅.
Π Π°Π½Π΅Π΅ Π΄Π»Ρ ΠΏΡΠΎΠΈΠ·Π²ΠΎΠ΄ΡΡΠ²Π° ΠΏΡΠΎΠ²ΠΎΠ»ΠΎΠΊΠΈ Π²ΠΎΠ»ΠΎΡΠ΅Π½ΠΈΠ΅ΠΌ ΠΏΡΠΈΠΌΠ΅Π½ΡΠ»ΠΈΡΡ ΡΡΠ°Π»ΡΠ½ΡΠ΅ Π·Π°Π³ΠΎΡΠΎΠ²ΠΊΠΈ, ΠΊΠΎΡΠΎΡΡΠ΅ ΠΏΠΎΡΠ»Π΅ ΠΏΡΠΎΡ ΠΎΠΆΠ΄Π΅Π½ΠΈΡ ΠΏΡΠΎΡΠ΅Π΄ΡΡΡ ΠΎΠ±ΡΠ°Π±Π°ΡΡΠ²Π°Π»ΠΈΡΡ ΡΠ°ΠΊΠΈΠΌ ΡΠΏΠΎΡΠΎΠ±ΠΎΠΌ, ΠΊΠ°ΠΊ ΠΏΠ°ΡΠ΅Π½ΡΠΈΡΠΎΠ²Π°Π½ΠΈΠ΅. ΠΡΠΎ ΠΏΡΠΎΡΠ΅ΡΡ Π½Π°Π³ΡΠ΅Π²Π°, ΠΏΡΠΈ ΠΎΠΏΡΠ΅Π΄Π΅Π»Π΅Π½Π½ΠΎΠΉ ΡΠ΅ΠΌΠΏΠ΅ΡΠ°ΡΡΡΠ΅ ΠΊΠΎΡΠΎΡΠΎΠ³ΠΎ ΠΏΡΠΎΠΈΡΡ ΠΎΠ΄ΠΈΠ» ΡΠ°ΠΊΠΎΠΉ ΠΏΡΠΎΡΠ΅ΡΡ, ΠΊΠ°ΠΊ Π°ΡΡΡΠ΅Π½ΠΈΠ·Π°ΡΠΈΡ ΠΈ ΡΠΊΡΠΏΠΎΠ·ΠΈΡΠΈΡ Π² ΡΠΎΠ»ΡΠ½ΡΡ ΠΈΠ»ΠΈ ΠΆΠ΅ ΡΠ²ΠΈΠ½ΡΠΎΠ²ΡΡ ΡΠ°ΡΠΏΠ»Π°Π²Π°Ρ . ΠΡΠ΄Π΅ΡΠΆΠΊΠ° ΡΠ°ΠΊΠΎΠ³ΠΎ ΠΏΡΠΎΠ΄ΡΠΊΡΠ° ΠΎΡΡΡΠ΅ΡΡΠ²Π»ΡΠ»Π°ΡΡ ΠΏΡΠΈΠΌΠ΅ΡΠ½ΠΎ ΠΏΡΠΈ 500 Π³ΡΠ°Π΄ΡΡΠ°Ρ ΠΏΠΎ Π¦Π΅Π»ΡΡΠΈΡ.
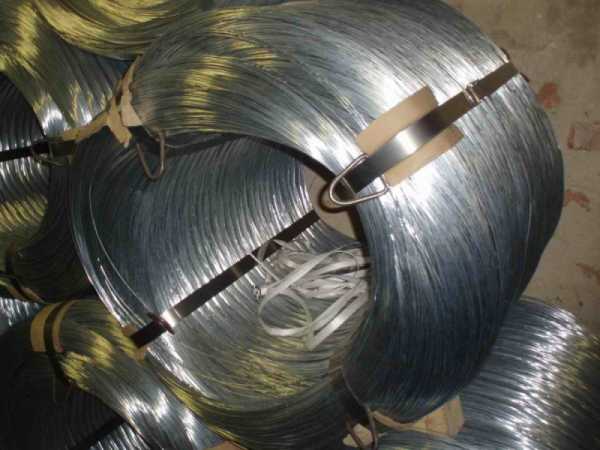
ΠΠ±ΠΎΡΡΠ΄ΠΎΠ²Π°Π½ΠΈΠ΅ Π΄Π»Ρ ΡΠ°Π±ΠΎΡΡ
ΠΠ»Ρ Π²ΠΎΠ»ΠΎΡΠ΅Π½ΠΈΡ ΠΌΠ΅Π΄Π½ΠΎΠΉ ΠΏΡΠΎΠ²ΠΎΠ»ΠΎΠΊΠΈ, Π° ΡΠ°ΠΊΠΆΠ΅ ΡΡΠ°Π»ΡΠ½ΠΎΠΉ, ΠΈΡΠΏΠΎΠ»ΡΠ·ΡΠ΅ΡΡΡ Π°Π³ΡΠ΅Π³Π°Ρ, ΠΊΠΎΡΠΎΡΡΠΉ ΠΏΠΎΠ»ΡΡΠΈΠ» Π½Π°Π·Π²Π°Π½ΠΈΠ΅ «ΡΡΠ°Π½». ΠΡΠ½ΠΎΠ²Π½ΠΎΠΉ ΡΠ°Π±ΠΎΡΠΈΠΉ ΡΠ»Π΅ΠΌΠ΅Π½Ρ ΡΡΠΎΠ³ΠΎ Π°Π³ΡΠ΅Π³Π°ΡΠ° — ΡΡΠΎ «Π³Π»Π°Π·ΠΎΠΊ», ΠΈΠ»ΠΈ ΠΆΠ΅ Π²ΠΎΠ»ΠΎΠΊ. ΠΡΡΠ΅ΡΡΠ²Π΅Π½Π½ΠΎ, ΡΡΠΎ ΡΠ΅ΡΠ΅Π½ΠΈΠ΅ ΠΏΠΎΠ΄Π±ΠΈΡΠ°Π΅ΡΡΡ ΡΠ°ΠΊΠΈΠΌ ΠΎΠ±ΡΠ°Π·ΠΎΠΌ, ΡΡΠΎΠ±Ρ ΠΎΠ½ΠΎ Π±ΡΠ»ΠΎ Π²ΡΠ΅Π³Π΄Π° ΠΌΠ΅Π½ΡΡΠ΅, ΡΠ΅ΠΌ ΠΏΠΎΠΏΠ΅ΡΠ΅ΡΠ½ΠΎΠ΅ ΡΠ΅ΡΠ΅Π½ΠΈΠ΅ Π·Π°Π³ΠΎΡΠΎΠ²ΠΊΠΈ.
ΠΠΈΠ΄Ρ ΡΠΎΠ²ΡΠ΅ΠΌΠ΅Π½Π½ΡΡ Π°Π³ΡΠ΅Π³Π°ΡΠΎΠ²
Π Π½Π°ΡΡΠΎΡΡΠ΅Π΅ Π²ΡΠ΅ΠΌΡ Π½Π° Π·Π°Π²ΠΎΠ΄Π°Ρ ΠΏΠΎ ΠΎΠ±ΡΠ°Π±ΠΎΡΠΊΠ΅ ΠΌΠ΅ΡΠ°Π»Π»Π° ΠΈΡΠΏΠΎΠ»ΡΠ·ΡΠ΅ΡΡΡ Π΄Π²Π° ΡΠΈΠΏΠ° ΠΎΠ±ΠΎΡΡΠ΄ΠΎΠ²Π°Π½ΠΈΡ. ΠΡΠ»ΠΈΡΠ°ΡΡΡΡ ΠΎΠ½ΠΈ Π΄ΡΡΠ³ ΠΎΡ Π΄ΡΡΠ³Π° ΡΠΈΠΏΠΎΠΌ ΡΡΠ½ΡΡΠ΅Π³ΠΎ ΠΌΠ΅Ρ Π°Π½ΠΈΠ·ΠΌΠ°.
- Π ΠΏΠ΅ΡΠ²ΠΎΠΌ ΡΠ»ΡΡΠ°Π΅ ΡΠ΅Ρ Π½ΠΎΠ»ΠΎΠ³ΠΈΡ Π²ΠΎΠ»ΠΎΡΠ΅Π½ΠΈΡ ΠΏΡΠΎΠ²ΠΎΠ»ΠΎΠΊΠΈ Π·Π°ΠΊΠ»ΡΡΠ°Π΅ΡΡΡ Π² ΡΠΎΠΌ, ΡΡΠΎ ΠΈΠ·Π΄Π΅Π»ΠΈΠ΅ Π½Π°ΠΌΠ°ΡΡΠ²Π°Π΅ΡΡΡ Π½Π° Π±Π°ΡΠ°Π±Π°Π½, ΡΠ΅ΠΌ ΡΠ°ΠΌΡΠΌ ΡΠΎΠ·Π΄Π°Π²Π°Ρ ΡΡΠ³ΠΎΠ²ΠΎΠ΅ ΡΡΠΈΠ»ΠΈΠ΅.
- ΠΡΠΎΡΠΎΠΉ ΡΠ»ΡΡΠ°ΠΉ — ΡΡΠΎ ΠΏΡΠΈΠΌΠ΅Π½Π΅Π½ΠΈΠ΅ ΡΡΡΡΠΎΠΉΡΡΠ²Π°, ΠΊΠΎΡΠΎΡΠΎΠ΅ ΡΡΠ½Π΅Ρ Π·Π°Π³ΠΎΡΠΎΠ²ΠΊΡ ΠΏΠΎ ΠΏΡΡΠΌΠΎΠΉ Π»ΠΈΠ½ΠΈΠΈ.
ΠΡΠ»ΠΈ Π³ΠΎΠ²ΠΎΡΠΈΡΡ ΠΎ ΠΏΡΠΈΠΌΠ΅Π½Π΅Π½ΠΈΠΈ, ΡΠΎ Π²ΡΠΎΡΠΎΠΉ ΡΠΈΠΏ Π°Π³ΡΠ΅Π³Π°ΡΠΎΠ² ΡΠ°ΡΠ΅ Π²ΡΠ΅Π³ΠΎ ΠΈΡΠΏΠΎΠ»ΡΠ·ΡΠ΅ΡΡΡ Π² ΡΠΎΠΌ ΡΠ»ΡΡΠ°Π΅, Π΅ΡΠ»ΠΈ Π½Π΅ΠΎΠ±Ρ ΠΎΠ΄ΠΈΠΌΠΎ ΠΏΡΠΎΡΡΠ½ΡΡΡ ΡΡΡΠ±Π½ΡΡ Π·Π°Π³ΠΎΡΠΎΠ²ΠΊΡ, ΠΊΠΎΡΠΎΡΠ°Ρ Π½Π΅ ΡΡΠ΅Π±ΡΠ΅Ρ ΠΏΠΎΡΠ»Π΅Π΄ΡΡΡΠ΅Π³ΠΎ ΡΠ²ΠΎΡΠ°ΡΠΈΠ²Π°Π½ΠΈΡ Π² Π±ΡΡ ΡΡ.
ΠΡΠ½ΠΎΠ²Π½Π°Ρ ΠΌΠ°ΡΡΠ° ΠΏΡΠΎΠ²ΠΎΠ»ΠΎΠΊΠΈ ΠΈ ΡΡΡΠ± ΠΌΠ°Π»ΠΎΠ³ΠΎ ΡΠ΅ΡΠ΅Π½ΠΈΡ ΠΏΡΠΎΠΈΠ·Π²ΠΎΠ΄ΠΈΡΡΡ ΠΈΠΌΠ΅Π½Π½ΠΎ Π½Π° Π±Π°ΡΠ°Π±Π°Π½Π½ΡΡ ΡΡΡΡΠΎΠΉΡΡΠ²Π°Ρ . ΠΡΠΈ ΠΌΠ΅Ρ Π°Π½ΠΈΠ·ΠΌΡ ΠΌΠΎΠ³ΡΡ Π±ΡΡΡ Π»ΠΈΠ±ΠΎ ΠΎΠ΄Π½ΠΎΠΊΡΠ°ΡΠ½ΡΠΌΠΈ, Π»ΠΈΠ±ΠΎ ΠΌΠ½ΠΎΠ³ΠΎΠΊΡΠ°ΡΠ½ΡΠΌΠΈ. ΠΡΡΠ΅ΡΡΠ²Π΅Π½Π½ΠΎ, ΡΡΠΎ Π½Π°ΠΈΠ±ΠΎΠ»Π΅Π΅ ΠΏΡΠΎΡΡΠ°Ρ ΠΊΠΎΠ½ΡΡΡΡΠΊΡΠΈΡ ΠΈΠΌΠ΅Π½Π½ΠΎ Ρ ΠΎΠ΄Π½ΠΎΠΊΡΠ°ΡΠ½ΠΎΠ³ΠΎ ΠΎΠ±ΠΎΡΡΠ΄ΠΎΠ²Π°Π½ΠΈΡ. Π’Π΅Ρ Π½ΠΎΠ»ΠΎΠ³ΠΈΡΠ΅ΡΠΊΠΈΠΉ ΠΏΡΠΎΡΠ΅ΡΡ ΠΏΡΠΎΠΈΠ·Π²ΠΎΠ΄ΡΡΠ²Π° Π² ΡΠ°ΠΊΠΎΠΌ ΡΠ»ΡΡΠ°Π΅ ΠΏΡΠ΅Π΄ΠΏΠΎΠ»Π°Π³Π°Π΅Ρ ΠΏΡΠΎΡΡΠ³ΠΈΠ²Π°Π½ΠΈΠ΅ ΠΏΡΠΎΠ²ΠΎΠ»ΠΎΠΊΠΈ Π² ΠΎΠ΄ΠΈΠ½ ΠΏΡΠΎΡ ΠΎΠ΄. ΠΡΠ»ΠΈ ΠΈΡΠΏΠΎΠ»ΡΠ·ΡΠ΅ΡΡΡ ΠΌΠ½ΠΎΠ³ΠΎΠΊΡΠ°ΡΠ½ΡΠΉ ΡΡΠ°Π½ΠΎΠΊ, ΡΠΎ ΠΏΡΠΎΡΠ΅Π΄ΡΡΠ° ΠΌΠΎΠΆΠ΅Ρ ΠΏΠΎΠ²ΡΠΎΡΡΡΡΡΡ Π΄Π²Π° ΠΈΠ»ΠΈ ΡΡΠΈ ΡΠ°Π·Π° ΠΏΠΎΠ΄ΡΡΠ΄.
Π£ΡΡΡΠΎΠΉΡΡΠ²ΠΎ ΡΠ°Π±ΠΎΡΠΈΡ ΡΡΠ°Π½ΠΊΠΎΠ²
ΠΡΠ½ΠΎΠ²Π½ΡΠΌ ΡΠ°Π±ΠΎΡΠΈΠΌ ΡΠ»Π΅ΠΌΠ΅Π½ΡΠΎΠΌ ΡΠ²Π»ΡΠ΅ΡΡΡ ΠΏΡΠΈΡΠΏΠΎΡΠΎΠ±Π»Π΅Π½ΠΈΠ΅, ΠΊΠΎΡΠΎΡΠΎΠ΅ ΠΏΡΠΈΡΡΡΡΡΠ²ΡΠ΅Ρ Π² Π»ΡΠ±ΠΎΠΌ Π°ΠΏΠΏΠ°ΡΠ°ΡΠ΅ Π΄Π»Ρ Π²ΠΎΠ»ΠΎΡΠ΅Π½ΠΈΡ ΠΏΡΠΎΠ²ΠΎΠ»ΠΎΠΊΠΈ — ΡΠΈΠ»ΡΠ΅Ρ. ΠΡΠΎΡ ΠΌΠ΅Ρ Π°Π½ΠΈΠ·ΠΌ Π²ΡΠ΅Π³Π΄Π° ΡΠΎΠ·Π΄Π°Π΅ΡΡΡ ΠΈΠ· ΠΎΡΠ΅Π½Ρ ΠΏΡΠΎΡΠ½ΠΎΠ³ΠΎ ΠΌΠ΅ΡΠ°Π»Π»ΠΎΠΊΠ΅ΡΠ°ΠΌΠΈΡΠ΅ΡΠΊΠΎΠ³ΠΎ ΡΠΏΠ»Π°Π²Π°. ΠΡΠ»ΠΈΡΠΈΡΠ΅Π»ΡΠ½Π°Ρ ΡΠ΅ΡΡΠ° Π΄Π°Π½Π½ΠΎΠ³ΠΎ ΠΌΠ΅ΡΠ°Π»Π»Π° Π·Π°ΠΊΠ»ΡΡΠ°Π΅ΡΡΡ Π² ΡΠΎΠΌ, ΡΡΠΎ ΠΎΠ½ ΠΎΡΠ΅Π½Ρ ΠΏΡΠΎΡΠ½ΡΠΉ, ΠΎΠ±Π»Π°Π΄Π°Π΅Ρ ΠΏΠΎΠ²ΡΡΠ΅Π½Π½ΠΎΠΉ ΡΠ²Π΅ΡΠ΄ΠΎΡΡΡΡ, Π½ΠΈΠ·ΠΊΠΎΠΉ Π²ΡΠ·ΠΊΠΎΡΡΡΡ, Π° ΡΠ°ΠΊΠΆΠ΅ Π²ΡΡΠΎΠΊΠΎΠΉ ΡΡΡΠΎΠΉΡΠΈΠ²ΠΎΡΡΡΡ ΠΊ ΠΈΡΡΠΈΡΠ°Π½ΠΈΡ. Π ΡΠ΅Π΄ΠΊΠΈΡ ΡΠ»ΡΡΠ°ΡΡ Π΄Π»Ρ ΠΏΡΠΎΠΈΠ·Π²ΠΎΠ΄ΡΡΠ²Π° ΡΠΈΠ»ΡΠ΅ΡΠ° ΠΈΡΠΏΠΎΠ»ΡΠ·ΡΠ΅ΡΡΡ ΡΠ΅Ρ Π½ΠΈΡΠ΅ΡΠΊΠΈΠΉ Π°Π»ΠΌΠ°Π·. ΠΡΠΎ Π΄Π°Π΅Ρ ΡΡΡΠ΅ΡΡΠ²Π΅Π½Π½ΠΎΠ΅ ΠΏΡΠ΅ΠΈΠΌΡΡΠ΅ΡΡΠ²ΠΎ ΠΏΡΠΈ ΠΎΠ±ΡΠ°Π±ΠΎΡΠΊΠ΅ Π±ΠΎΠ»Π΅Π΅ ΡΠ»ΠΎΠΆΠ½ΡΡ ΠΌΠ΅ΡΠ°Π»Π»ΠΎΠ².
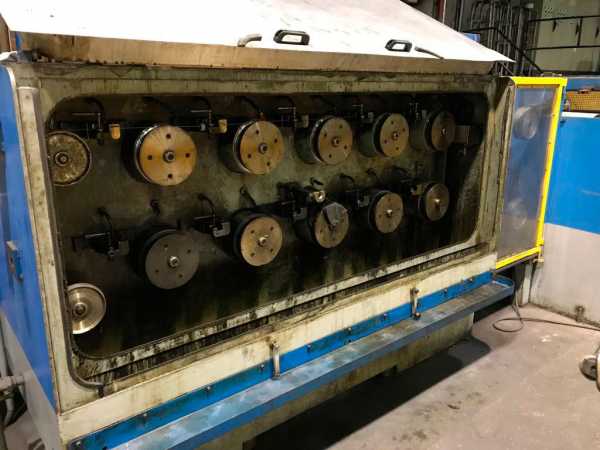
Π Π°Π·ΠΌΠ΅ΡΠ°ΡΡΡΡ ΡΡΠΈ Π΄Π΅ΡΠ°Π»ΠΈ Π² Π΄ΠΎΡΡΠ°ΡΠΎΡΠ½ΠΎ ΠΏΡΠΎΡΠ½ΡΡ ΠΈ Π²ΡΠ·ΠΊΠΈΡ ΡΡΠ°Π»ΡΠ½ΡΡ ΠΎΠ±ΠΎΠΉΠΌΠ°Ρ . Π‘Π°ΠΌΠ° ΠΏΠΎ ΡΠ΅Π±Π΅ ΠΎΠ±ΠΎΠΉΠΌΠ° Π½Π΅ ΡΠΏΠΎΡΠΎΠ±Π½Π° ΠΎΠΊΠ°Π·Π°ΡΡ ΡΠΈΠ»ΡΠ½ΠΎΠ΅ Π²Π»ΠΈΡΠ½ΠΈΠ΅ Π½Π° ΡΠΈΠ»ΡΠ΅ΡΡ, Π½ΠΎ ΠΏΡΠΈ ΡΡΠΎΠΌ Π΅Π΅ Π½Π°Π»ΠΈΡΠΈΠ΅ ΡΡΡΠ΅ΡΡΠ²Π΅Π½Π½ΠΎ ΡΠ½ΠΈΠΆΠ°Π΅Ρ ΡΠ°ΡΡΡΠ³ΠΈΠ²Π°ΡΡΠ΅Π΅ Π½Π°ΠΏΡΡΠΆΠ΅Π½ΠΈΠ΅, ΠΊΠΎΡΠΎΡΠΎΠ΅ Π½Π΅ΠΈΠ·Π±Π΅ΠΆΠ½ΠΎ Π²ΠΎΠ·Π½ΠΈΠΊΠ°Π΅Ρ Π²ΠΎ Π²ΡΠ΅ΠΌΡ ΡΠ°Π±ΠΎΡΡ. ΠΠ° ΡΠΎΠ²ΡΠ΅ΠΌΠ΅Π½Π½ΡΡ ΠΏΡΠ΅Π΄ΠΏΡΠΈΡΡΠΈΡΡ Π΄ΠΎΠ²ΠΎΠ»ΡΠ½ΠΎ ΡΠ°ΡΡΠΎ ΠΈΡΠΏΠΎΠ»ΡΠ·ΡΠ΅ΡΡΡ ΡΠ±ΠΎΡΠ½ΡΠΉ Π²ΠΎΠ»ΠΎΠΊ, ΠΊΠΎΡΠΎΡΡΠΉ ΠΎΡΠ»ΠΈΡΠ°Π΅ΡΡΡ ΡΠ΅ΠΌ, ΡΡΠΎ ΠΏΠΎΡΡΠ΅Π±Π»ΡΠ΅Ρ ΠΌΠ΅Π½ΡΡΠ΅ ΡΠ½Π΅ΡΠ³ΠΈΠΈ, Π° Π΅Π³ΠΎ ΠΊΠΎΡΡΡΠΈΡΠΈΠ΅Π½Ρ ΠΏΠΎΠ»Π΅Π·Π½ΠΎΠ³ΠΎ Π΄Π΅ΠΉΡΡΠ²ΠΈΡ (ΠΠΠ) Π²ΡΡΠ΅ ΠΏΡΠΈΠΌΠ΅ΡΠ½ΠΎ Π½Π° 30 %.
ΠΠΎΠ΄Π³ΠΎΡΠΎΠ²ΠΊΠ° ΠΌΠ΅ΡΠ°Π»Π»Π° ΠΊ ΡΠ°Π±ΠΎΡΠ΅
ΠΡΡΠ΅ΡΡΠ²Π΅Π½Π½ΠΎ, ΡΡΠΎ ΠΏΡΠΎΠ²ΠΎΠ΄ΠΈΡΡ ΡΠ°ΠΊΡΡ ΠΏΡΠΎΡΠ΅Π΄ΡΡΡ Π±Π΅Π· ΠΏΡΠ΅Π΄Π²Π°ΡΠΈΡΠ΅Π»ΡΠ½ΠΎΠΉ ΠΏΠΎΠ΄Π³ΠΎΡΠΎΠ²ΠΊΠΈ ΠΌΠ΅ΡΠ°Π»Π»Π° Π½Π΅Π»ΡΠ·Ρ. ΠΡΠΎΠΌΠ΅ ΡΠΎΠ³ΠΎ, Π±Π΅Π· ΡΡΠΎΠΉ ΠΏΡΠΎΡΠ΅Π΄ΡΡΡ Π½Π΅ ΠΏΠΎΠ»ΡΡΠΈΡΡΡ Π΄ΠΎΠ±ΠΈΡΡΡΡ ΠΊΠ°ΡΠ΅ΡΡΠ²Π΅Π½Π½ΠΎΠ³ΠΎ ΠΈΠ·Π΄Π΅Π»ΠΈΡ. Π‘ΡΡΡ ΠΏΠΎΠ΄Π³ΠΎΡΠΎΠ²ΠΈΡΠ΅Π»ΡΠ½ΡΡ ΡΠ°Π±ΠΎΡ Π·Π°ΠΊΠ»ΡΡΠ°Π΅ΡΡΡ Π² ΡΠΎΠΌ, ΡΡΠΎ Π½Π΅ΠΎΠ±Ρ ΠΎΠ΄ΠΈΠΌΠΎ ΡΠ΄Π°Π»ΠΈΡΡ ΠΎΠΊΠ°Π»ΠΈΠ½Ρ Ρ Π·Π°Π³ΠΎΡΠΎΠ²ΠΊΠΈ. ΠΡΠ΅ΠΆΠ΄Π΅ ΡΠ΅ΠΌ Π½Π°ΡΠ°ΡΡ ΠΏΡΠΎΡΠ΅ΡΡ Π²ΠΎΠ»ΠΎΡΠ΅Π½ΠΈΡ ΠΏΡΠΎΠ²ΠΎΠ»ΠΎΠΊΠΈ, ΠΏΡΠΎΠ²ΠΎΠ΄ΡΡ ΠΎΠ΄Π½Ρ ΠΈΠ· ΡΡΠ΅Ρ ΠΏΡΠΎΡΠ΅Π΄ΡΡ:
- ΠΌΠ΅Ρ Π°Π½ΠΈΡΠ΅ΡΠΊΠ°Ρ ΠΎΠ±ΡΠ°Π±ΠΎΡΠΊΠ°;
- Ρ ΠΈΠΌΠΈΡΠ΅ΡΠΊΠ°Ρ ΠΎΠ±ΡΠ°Π±ΠΎΡΠΊΠ°;
- ΡΠ»Π΅ΠΊΡΡΠΎΡ ΠΈΠΌΠΈΡΠ΅ΡΠΊΠ°Ρ ΠΎΠ±ΡΠ°Π±ΠΎΡΠΊΠ°.
ΠΠ΅Ρ Π°Π½ΠΈΡΠ΅ΡΠΊΠ°Ρ ΠΎΡΠΈΡΡΠΊΠ° Π·Π°Π³ΠΎΡΠΎΠ²ΠΊΠΈ ΡΠ²Π»ΡΠ΅ΡΡΡ ΡΠ°ΠΌΡΠΌ ΠΏΡΠΎΡΡΡΠΌ ΠΈ ΡΠ°ΠΌΡΠΌ Π΄Π΅ΡΠ΅Π²ΡΠΌ ΠΌΠ΅ΡΠΎΠ΄ΠΎΠΌ ΠΎΡΠΈΡΡΠΊΠΈ. Π§Π°ΡΠ΅ Π²ΡΠ΅Π³ΠΎ ΠΏΡΠΈΠΌΠ΅Π½ΡΠ΅ΡΡΡ ΠΎΠ½Π° Π² ΡΠΎΠΌ ΡΠ»ΡΡΠ°Π΅, Π΅ΡΠ»ΠΈ ΠΈΠ·Π΄Π΅Π»ΠΈΠ΅ ΠΈΠ·Π³ΠΎΡΠΎΠ²Π»Π΅Π½ΠΎ ΠΈΠ· ΡΠ³Π»Π΅ΡΠΎΠ΄ΠΈΡΡΠΎΠΉ ΡΡΠ°Π»ΠΈ. ΠΠΎ Π²ΡΠ΅ΠΌΡ ΠΏΡΠΎΡΠ΅Π΄ΡΡΡ ΠΎΠ±ΡΠ°Π±ΠΎΡΠΊΠΈ ΠΊΠ°ΡΠ°Π½ΠΊΠ° ΠΈΠ·Π³ΠΈΠ±Π°Π΅ΡΡΡ Π² ΡΠ°Π·Π½ΡΠ΅ ΡΡΠΎΡΠΎΠ½Ρ. Π ΡΡΠΎ Π²ΡΠ΅ΠΌΡ Π΅Π΅ ΠΏΠΎΠ²Π΅ΡΡ Π½ΠΎΡΡΡ ΠΎΠ±ΡΠ°Π±Π°ΡΡΠ²Π°Π΅ΡΡΡ ΠΌΠ΅Ρ Π°Π½ΠΈΡΠ΅ΡΠΊΠΈΠΌΠΈ ΡΠ΅ΡΠΊΠ°ΠΌΠΈ.
Π₯ΠΈΠΌΠΈΡΠ΅ΡΠΊΠ°Ρ ΠΈ ΡΠ»Π΅ΠΊΡΡΠΎΡ ΠΈΠΌΠΈΡΠ΅ΡΠΊΠ°Ρ ΠΎΠ±ΡΠ°Π±ΠΎΡΠΊΠ°
Π§ΡΠΎ ΠΊΠ°ΡΠ°Π΅ΡΡΡ Ρ ΠΈΠΌΠΈΡΠ΅ΡΠΊΠΎΠ³ΠΎ ΡΠΏΠΎΡΠΎΠ±Π° ΠΎΡΠΈΡΡΠΊΠΈ ΠΎΡ ΠΎΠΊΠ°Π»ΠΈΠ½Ρ, ΡΠΎ ΠΎΠ½ ΡΠ²Π»ΡΠ΅ΡΡΡ Π±ΠΎΠ»Π΅Π΅ ΡΠ»ΠΎΠΆΠ½ΡΠΌ, Π° ΡΠ°ΠΊΠΆΠ΅ ΡΡΡΠ΄ΠΎΠ΅ΠΌΠΊΠΈΠΌ. ΠΠ»Ρ ΡΡΠΎΠ³ΠΎ ΡΠ°ΡΠ΅ Π²ΡΠ΅Π³ΠΎ ΠΈΡΠΏΠΎΠ»ΡΠ·ΡΡΡ Π»ΠΈΠ±ΠΎ ΡΠΎΠ»ΡΠ½ΡΡ, Π»ΠΈΠ±ΠΎ ΡΠ΅ΡΠ½ΡΡ ΠΊΠΈΡΠ»ΠΎΡΡ. ΠΡΠΎΠΌΠ΅ ΡΠΎΠ³ΠΎ, ΡΡΠΎΠ±Ρ Π²ΡΠΏΠΎΠ»Π½ΡΡΡ ΡΠ°ΠΊΡΡ ΠΎΠΏΠ΅ΡΠ°ΡΠΈΡ, Π²ΠΎΠ»ΠΎΡΠΈΠ»ΡΡΠΈΠΊ Π΄ΠΎΠ»ΠΆΠ΅Π½ ΠΎΠ±Π»Π°Π΄Π°ΡΡ Π½Π΅ΠΎΠ±Ρ ΠΎΠ΄ΠΈΠΌΠΎΠΉ ΠΊΠ²Π°Π»ΠΈΡΠΈΠΊΠ°ΡΠΈΠ΅ΠΉ, ΡΡΠΎΠ±Ρ ΡΠ°Π±ΠΎΡΠ°ΡΡ Ρ Ρ ΠΈΠΌΠΈΡΠ΅ΡΠΊΠΈΠΌΠΈ Π²Π΅ΡΠ΅ΡΡΠ²Π°ΠΌΠΈ.
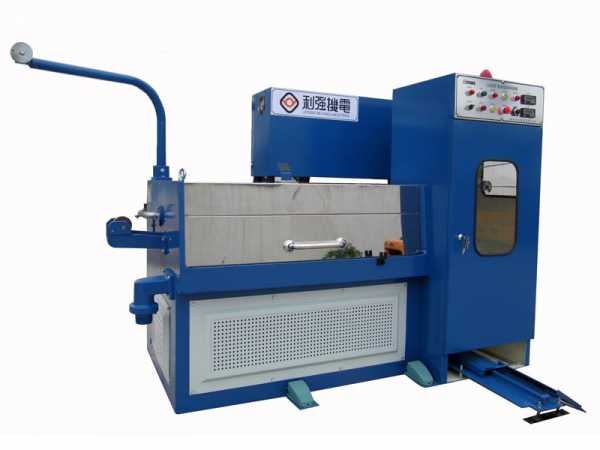
ΠΠ΄Π½Π°ΠΊΠΎ Π·Π΄Π΅ΡΡ Π²Π°ΠΆΠ½ΠΎ ΠΎΡΠΌΠ΅ΡΠΈΡΡ, ΡΡΠΎ Π΄Π°Π½Π½ΡΠΉ ΠΌΠ΅ΡΠΎΠ΄ ΡΠ²Π»ΡΠ΅ΡΡΡ Π½Π΅Π·Π°ΠΌΠ΅Π½ΠΈΠΌΡΠΌ, Π΅ΡΠ»ΠΈ Π½Π΅ΠΎΠ±Ρ ΠΎΠ΄ΠΈΠΌΠΎ ΠΏΠΎΠ΄Π³ΠΎΡΠΎΠ²ΠΈΡΡ ΠΊ Π²ΠΎΠ»ΠΎΡΠ΅Π½ΠΈΡ Π²ΡΡΠΎΠΊΠΎΠ»Π΅Π³ΠΈΡΠΎΠ²Π°Π½Π½ΡΡ ΠΈΠ»ΠΈ ΠΆΠ΅ Π½Π΅ΡΠΆΠ°Π²Π΅ΡΡΡΡ ΡΡΠ°Π»Ρ. ΠΡΠΎΠΌΠ΅ ΡΠΎΠ³ΠΎ, ΠΏΠΎΡΠ»Π΅ ΡΠΎΠ³ΠΎ, ΠΊΠ°ΠΊ Ρ ΠΈΠΌΠΈΡΠ΅ΡΠΊΠ°Ρ ΠΎΡΠΈΡΡΠΊΠ° Π±ΡΠ΄Π΅Ρ Π·Π°Π²Π΅ΡΡΠ΅Π½Π°, ΠΏΠΎΠ²Π΅ΡΡ Π½ΠΎΡΡΡ ΠΌΠ΅ΡΠ°Π»Π»Π° Π½Π΅ΠΎΠ±Ρ ΠΎΠ΄ΠΈΠΌΠΎ ΠΏΡΠΎΠΌΡΡΡ Π²ΠΎΠ΄ΠΎΠΉ.
ΠΠΎΡΠ»Π΅Π΄Π½ΠΈΠΉ ΠΌΠ΅ΡΠΎΠ΄, ΡΠ»Π΅ΠΊΡΡΠΎΡ ΠΈΠΌΠΈΡΠ΅ΡΠΊΠΈΠΉ, Π·Π°ΠΊΠ»ΡΡΠ°Π΅ΡΡΡ Π² ΡΠΎΠΌ, ΡΡΠΎ ΠΏΡΠΎΠ²ΠΎΠ΄ΡΡ ΡΡΠ°Π²Π»Π΅Π½ΠΈΠ΅ ΠΌΠ΅ΡΠ°Π»Π»Π° Π² ΡΠ»Π΅ΠΊΡΡΠΎΠ»ΠΈΡΠΈΡΠ΅ΡΠΊΠΎΠΌ ΡΠ°ΡΡΠ²ΠΎΡΠ΅. ΠΡΠ° ΠΆΠΈΠ΄ΠΊΠΎΡΡΡ ΠΌΠΎΠΆΠ΅Ρ Π±ΡΡΡ Π»ΠΈΠ±ΠΎ Π°Π½ΠΎΠ΄Π½ΠΎΠΉ, Π»ΠΈΠ±ΠΎ ΠΊΠ°ΡΠΎΠ΄Π½ΠΎΠΉ, ΠΈΡΡ ΠΎΠ΄Ρ ΠΈΠ· ΡΠΎΠ³ΠΎ, ΠΊΠ°ΠΊΠΈΠ΅ ΡΡΠΎΡΡ ΡΡΠ»ΠΎΠ²ΠΈΡ, Π° ΡΠ°ΠΊΠΆΠ΅ Π±Π΅ΡΡ Π²ΠΎ Π²Π½ΠΈΠΌΠ°Π½ΠΈΠ΅ ΠΎΡΠΎΠ±Π΅Π½Π½ΠΎΡΡΠΈ ΠΌΠ°ΡΠ΅ΡΠΈΠ°Π»Π°.
ΠΠΎΠ»ΠΎΡΠ΅Π½ΠΈΠ΅ ΠΌΠ΅Π΄Π½ΡΡ Π·Π°Π³ΠΎΡΠΎΠ²ΠΎΠΊ
ΠΠΎ Π²ΡΠ΅ΠΌΡ Π²ΠΎΠ»ΠΎΡΠ΅Π½ΠΈΡ ΠΌΠ΅Π΄Π½ΠΎΠΉ ΠΏΡΠΎΠ²ΠΎΠ»ΠΎΠΊΠΈ ΠΈΠ· ΠΌΠ΅Π΄Π½ΡΡ Π·Π°Π³ΠΎΡΠΎΠ²ΠΎΠΊ Π²ΡΠ΅Π³Π΄Π° ΠΈΡΠΏΠΎΠ»ΡΠ·ΡΡΡΡΡ Π»ΠΈΡΡΠ΅ Π·Π°Π³ΠΎΡΠΎΠ²ΠΊΠΈ, Π½Π° ΡΡΠΎΠΌ ΠΈ ΠΎΡΠ½ΠΎΠ²ΡΠ²Π°Π΅ΡΡΡ Π²Π΅ΡΡ ΠΌΠ΅ΡΠΎΠ΄. ΠΠ»Ρ Π½Π°ΡΠ°Π»Π° Π½Π΅ΠΎΠ±Ρ ΠΎΠ΄ΠΈΠΌΠΎ ΡΠΏΠ»Π°Π²ΠΈΡΡ ΠΌΠ΅ΠΆΠ΄Ρ ΡΠΎΠ±ΠΎΠΉ Π²ΡΠ΅ Π·Π°Π³ΠΎΡΠΎΠ²ΠΊΠΈ. Π‘ΡΠ°Π·Ρ ΠΏΠΎΡΠ»Π΅ ΡΡΠΎΠ³ΠΎ, ΠΏΠΎΠΊΠ° ΠΎΠ½ΠΈ Π΅ΡΠ΅ Π½Π°Ρ ΠΎΠ΄ΡΡΡΡ Π² Π³ΠΎΡΡΡΠ΅ΠΌ ΡΠΎΡΡΠΎΡΠ½ΠΈΠΈ, ΠΈΡ ΠΏΡΠΎΠΊΠ°ΡΡΠ²Π°ΡΡ. ΠΠ΄Π½Π°ΠΊΠΎ ΠΏΡΠΎΠ²Π΅Π΄Π΅Π½ΠΈΠ΅ Π΄Π°Π½Π½ΠΎΠ³ΠΎ ΠΏΡΠΎΡΠ΅ΡΡΠ° Π²Π»Π΅ΡΠ΅Ρ Π·Π° ΡΠΎΠ±ΠΎΠΉ ΠΏΠΎΡΠ²Π»Π΅Π½ΠΈΠ΅ ΠΏΠ»Π΅Π½ΠΊΠΈ ΠΈΠ· ΠΎΠΊΡΠΈΠ΄ΠΎΠ² Π½Π° ΠΏΠΎΠ²Π΅ΡΡ Π½ΠΎΡΡΠΈ ΠΈΠ·Π΄Π΅Π»ΠΈΡ. Π§ΡΠΎΠ±Ρ ΠΈΠ·Π±Π°Π²ΠΈΡΡΡΡ ΠΎΡ ΡΡΠΎΠΉ ΠΏΡΠΎΠ±Π»Π΅ΠΌΡ, Π½Π΅ΠΎΠ±Ρ ΠΎΠ΄ΠΈΠΌΠΎ ΠΏΡΠΎΠ²Π΅ΡΡΠΈ ΠΎΠ±ΡΠ°Π±ΠΎΡΠΊΡ Ρ ΠΈΠΌΠΈΡΠ΅ΡΠΊΠΈΠΌΠΈ ΡΠΎΡΡΠ°Π²Π°ΠΌΠΈ. ΠΠΎΡΠ»Π΅ ΡΡΠΎΠ³ΠΎ ΠΌΠΎΠΆΠ½ΠΎ ΠΏΠ΅ΡΠ΅ΠΉΡΠΈ Π½Π΅ΠΏΠΎΡΡΠ΅Π΄ΡΡΠ²Π΅Π½Π½ΠΎ ΠΊ ΠΏΡΠΎΡΠ΅Π΄ΡΡΠ΅ Π²ΠΎΠ»ΠΎΡΠ΅Π½ΠΈΡ.
ΠΠΎΠ»ΡΡΠ΅Π½ΠΈΠ΅ ΠΌΠ΅Π΄Π½ΠΎΠΉ ΠΏΡΠΎΠ²ΠΎΠ»ΠΎΠΊΠΈ ΠΌΠΎΠΆΠ΅Ρ ΡΠ°ΠΊΠΆΠ΅ ΠΎΡΡΡΠ΅ΡΡΠ²Π»ΡΡΡΡΡ ΠΏΠΎ ΠΏΡΠΈΠ½ΡΠΈΠΏΡ ΠΏΠΎΠ³ΡΡΠΆΠ½ΠΎΠ³ΠΎ ΡΠΎΡΠΌΠΎΠ²Π°Π½ΠΈΡ. ΠΡΠ»ΠΈ ΠΏΡΠΈΠΌΠ΅Π½ΡΡΡ Π΄Π°Π½Π½ΡΠΉ ΠΌΠ΅ΡΠΎΠ΄, ΡΠΎ ΠΏΠΎΠ²Π΅ΡΡ Π½ΠΎΡΡΡ ΠΊΠ°ΡΠ°Π½ΠΊΠΈ Π±ΡΠ΄Π΅Ρ ΠΎΡΡΠ°Π²Π°ΡΡΡΡ ΡΠΈΡΡΠΎΠΉ ΠΈ ΡΠ΄Π°ΡΡΡΡ ΠΈΠ·Π±Π΅ΠΆΠ°ΡΡ ΠΏΡΠΎΡΠ΅Π΄ΡΡΡ ΠΎΡΠΈΡΡΠΊΠΈ. ΠΠΌΠ΅Π½Π½ΠΎ ΡΠ°ΠΊΠΎΠΉ ΡΠΏΠΎΡΠΎΠ± ΠΈΡΠΏΠΎΠ»ΡΠ·ΡΠ΅ΡΡΡ Π΄Π»Ρ ΡΠΎΠ³ΠΎ, ΡΡΠΎΠ±Ρ ΠΈΠ·Π³ΠΎΡΠ°Π²Π»ΠΈΠ²Π°ΡΡ Π½Π°ΠΈΠ±ΠΎΠ»Π΅Π΅ ΡΠΎΠ½ΠΊΠΈΠ΅ ΠΏΡΠΎΠ²ΠΎΠ»ΠΎΠΊΠΈ (Π΄ΠΈΠ°ΠΌΠ΅ΡΡΠΎΠΌ Π΄ΠΎ 10 ΠΌΠΈΠΊΡΠΎΠ½). ΠΠ΄Π½Π°ΠΊΠΎ ΠΏΡΠΈ ΠΈΡΠΏΠΎΠ»ΡΠ·ΠΎΠ²Π°Π½ΠΈΠΈ ΡΠ°ΠΊΠΎΠ³ΠΎ ΠΌΠ΅ΡΠΎΠ΄Π° ΠΎΡΠ΅Π½Ρ Π²Π°ΠΆΠ½ΠΎ ΠΏΠΎΠ΄ΠΎΠ±ΡΠ°ΡΡ ΡΠΎΡΡΠ°Π², ΠΊΠΎΡΠΎΡΡΠΉ Π±ΡΠ΄Π΅Ρ ΠΎΠ±Π»Π°Π΄Π°ΡΡ ΠΏΠΎΠ΄Ρ ΠΎΠ΄ΡΡΠΈΠΌΠΈ ΡΠ²ΠΎΠΉΡΡΠ²Π°ΠΌΠΈ.
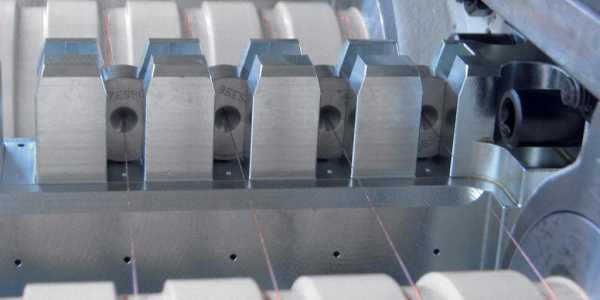
Π‘ΡΠ΅Π΄ΠΈ ΡΠ°ΠΊΠΈΡ ΡΠΎΡΡΠ°Π²ΠΎΠ² Π²ΡΠ΄Π΅Π»ΡΡΡΡΡ:
- ΠΊΠΎΠΌΠΏΠ»Π΅ΠΊΡΠ½ΡΠ΅ ΡΠ°ΡΡΠ²ΠΎΡΡ, Π² ΡΠΎΠ»ΠΈ ΠΊΠΎΡΠΎΡΡΡ ΠΌΠΎΠ³ΡΡ Π²ΡΡΡΡΠΏΠ°ΡΡ ΡΠ΅Π»ΠΎΡΠ½ΡΠ΅ ΡΠΎΡΡΠ°Π²Ρ, ΡΠΎΠ»ΠΈ ΠΆΠΈΡΠ½ΡΡ ΡΡΠ»ΡΡΠΈΡΠΎΠ²Π°Π½Π½ΡΡ ΠΌΠ°ΡΠ΅Π» ΠΈ Π΅ΡΠ΅ Π½Π΅ΡΠΊΠΎΠ»ΡΠΊΠΎ Π²Π΅ΡΠ΅ΡΡΠ²;
- Π²ΠΎΠ·ΠΌΠΎΠΆΠ½ΠΎ ΠΈΡΠΏΠΎΠ»ΡΠ·ΠΎΠ²Π°Π½ΠΈΠ΅ ΡΠ°Π·Π½ΠΎΠ³ΠΎ ΡΠΎΠ΄Π° ΡΠΌΡΠ»ΡΡΠΈΠΉ, ΡΠ°ΠΊΠΈΡ ΠΊΠ°ΠΊ Π°Π½ΠΈΠΎΠ½Π½ΡΠ΅, Π°Π½ΡΠΈΠΏΠ΅Π½Π½ΡΠ΅, ΡΠΈΠ½ΡΠ΅ΡΠΈΡΠ΅ΡΠΊΠΈΠ΅ ΡΡΠΈΡΡ ΠΈ Π΄ΡΡΠ³ΠΈΠ΅;
- ΠΎΡΠ΄Π΅Π»ΡΠ½ΠΎ ΡΠ°ΡΡΠΌΠ°ΡΡΠΈΠ²Π°ΡΡΡΡ ΡΠΈΠ½ΡΠ΅ΡΠΈΡΠ΅ΡΠΊΠΈΠ΅ Π²Π΅ΡΠ΅ΡΡΠ²Π°, ΡΠ°ΠΊΠΈΠ΅ ΠΊΠ°ΠΊ ΡΠΎΠ»ΠΈ ΠΎΡΠ³Π°Π½ΠΈΡΠ΅ΡΠΊΠΎΠ³ΠΎ ΠΈ Π½Π΅ΠΎΡΠ³Π°Π½ΠΈΡΠ΅ΡΠΊΠΎΠ³ΠΎ ΡΠΈΠΏΠ°, Π° ΡΠ°ΠΊΠΆΠ΅ ΡΠ°ΡΡΠ²ΠΎΡΡ ΠΏΠΎΠ»ΠΈΠΌΠ΅ΡΠΎΠ².
ΠΠ°ΡΠΈΠ°Π½ΡΡ ΠΎΠ±ΡΠ°Π±ΠΎΡΠΊΠΈ
Π Π½Π°ΡΡΠΎΡΡΠ΅Π΅ Π²ΡΠ΅ΠΌΡ ΡΡΡΠ΅ΡΡΠ²ΡΠ΅Ρ Π±ΠΎΠ»ΡΡΠΎΠ΅ ΠΊΠΎΠ»ΠΈΡΠ΅ΡΡΠ²ΠΎ ΡΠ°Π·Π½ΠΎΠΎΠ±ΡΠ°Π·Π½ΡΡ Π²Π°ΡΠΈΠ°Π½ΡΠΎΠ² Π΄Π»Ρ ΠΎΠ±ΡΠ°Π±ΠΎΡΠΊΠΈ Π·Π°Π³ΠΎΡΠΎΠ²ΠΊΠΈ.
- ΠΡΡ ΡΠΎΠ²ΡΠΉ ΡΠΈΠΏ ΠΎΠ±ΡΠ°Π±ΠΎΡΠΊΠΈ. ΠΡΠΎ Π²Π°ΡΠΈΠ°Π½Ρ ΡΠ°Π±ΠΎΡΡ Ρ ΡΡΡΠ±Π°ΠΌΠΈ ΠΈΠ· Π·Π°Π³ΠΎΡΠΎΠ²ΠΎΠΊ, ΠΊΠΎΡΠΎΡΡΠ΅ ΡΠΎΠ±ΡΠ°Π½Ρ Π² Π±ΡΡ ΡΡ. Π’Π°ΠΊΠΆΠ΅ ΡΡΠ΄Π° Π²Ρ ΠΎΠ΄ΡΡ ΡΠ΅ ΡΡΡΠ±Ρ, ΠΊΠΎΡΠΎΡΡΠ΅ ΠΏΡΠΎΡΠ»ΠΈ ΠΏΡΠΎΡΠ΅ΡΡ Π²ΠΎΠ»ΠΎΡΠ΅Π½ΠΈΡ, ΠΏΠΎΡΠ»Π΅ ΠΊΠΎΡΠΎΡΠΎΠ³ΠΎ ΠΎΠ½ΠΈ Π±ΡΠ»ΠΈ ΡΠΎΠ±ΡΠ°Π½Ρ Π² Π±ΡΡ ΡΡ.
- ΠΠΎΠΊΡΡΠΉ ΡΠΈΠΏ ΠΎΠ±ΡΠ°Π±ΠΎΡΠΊΠΈ ΠΏΡΠ΅Π΄ΠΏΠΎΠ»Π°Π³Π°Π΅Ρ, ΡΡΠΎ Π²ΠΎΠ»ΠΎΠΊ Π²ΠΎ Π²ΡΠ΅ΠΌΡ ΡΠ°Π±ΠΎΡΡ Π±ΡΠ΄Π΅Ρ ΠΏΠΎΠ³ΡΡΠΆΠ΅Π½ Π² ΠΆΠΈΠ΄ΠΊΡΡ ΡΠΌΠ°Π·ΠΊΡ.
- ΠΠ°ΠΈΠ±ΠΎΠ»Π΅Π΅ ΡΠ°ΡΡΠΎ ΠΈΡΠΏΠΎΠ»ΡΠ·ΡΠ΅ΠΌΡΠΉ ΠΏΡΠΈΠΌΠ΅Π½Π΅Π½ΠΈΠ΅ Π²ΠΎΠ»ΠΎΠΊΠ° Π½Π° Π·Π°ΠΊΡΠ΅ΠΏΠ»Π΅Π½Π½ΡΡ ΠΎΠΏΡΠ°Π²ΠΊΠ°Ρ .
- ΠΡΡΡ ΡΠΏΠΎΡΠΎΠ± ΠΎΠ±ΡΠ°Π±ΠΎΡΠΊΠΈ, Π² ΠΊΠΎΡΠΎΡΠΎΠΌ Π΄ΠΎΠΏΡΡΠΊΠ°Π΅ΡΡΡ ΠΈΡΠΏΠΎΠ»ΡΠ·ΠΎΠ²Π°Π½ΠΈΠ΅ ΡΡΡΠ±, Π½Π΅ ΠΈΠΌΠ΅ΡΡΠΈΡ ΠΊΡΡΠ³Π»ΠΎΠΉ (ΡΠ°ΡΠΎΠ½Π½ΠΎΠΉ) ΡΠΎΡΠΌΡ.
- ΠΠ»Π΅ΠΊΡΡΠΎΠΏΠ»Π°ΡΡΠΈΡΠ΅ΡΠΊΠΈΠΉ ΠΌΠ΅ΡΠΎΠ΄ ΠΈΡΠΏΠΎΠ»ΡΠ·ΡΠ΅ΡΡΡ Π² ΡΠΎΠΌ ΡΠ»ΡΡΠ°Π΅, Π΅ΡΠ»ΠΈ Π΅ΡΡΡ Π½Π΅ΠΎΠ±Ρ ΠΎΠ΄ΠΈΠΌΠΎΡΡΡ ΡΠ°Π±ΠΎΡΡ Ρ ΠΏΡΠΎΡΡΠ³ΠΈΠ²Π°Π½ΠΈΠ΅ΠΌ ΠΌΠ΅ΡΠ°Π»Π»Π°, ΠΊΠΎΡΠΎΡΡΠΉ Π΄ΠΎΡΡΠ°ΡΠΎΡΠ½ΠΎ ΡΡΡΠ΄Π½ΠΎ ΠΏΠΎΠ΄Π΄Π°Π΅ΡΡΡ Π΄Π΅ΡΠΎΡΠΌΠ°ΡΠΈΠΈ.
- ΠΡΠ΅ ΠΎΠ΄ΠΈΠ½ ΠΈΠ· ΠΌΠ΅ΡΠΎΠ΄ΠΎΠ² ΠΎΠ±ΡΠ°Π±ΠΎΡΠΊΠΈ — ΡΡΠ΅ΡΠΆΠ½Π΅Π²ΠΎΠΉ. Π Π·Π°Π³ΠΎΡΠΎΠ²ΠΊΡ Π²Π²ΠΎΠ΄ΠΈΡΡΡ ΡΡΠ΅ΡΠΆΠ΅Π½Ρ Π΄Π»Ρ ΡΠΎΠ³ΠΎ, ΡΡΠΎΠ±Ρ ΠΏΡΠΎΡΡΠ³ΠΈΠ²Π°ΡΡ Π΅Π³ΠΎ Π²ΠΌΠ΅ΡΡΠ΅ Ρ ΡΡΡΠ±ΠΎΠΉ. ΠΠΎΡΠ»Π΅ ΠΏΡΠΎΡ ΠΎΠΆΠ΄Π΅Π½ΠΈΡ Π²ΠΎΠ»ΠΎΠΊΠ° Π²ΡΡΠ°Π²Π»Π΅Π½Π½ΡΠΉ ΡΡΠ΅ΡΠΆΠ΅Π½Ρ Π½Π΅ΠΎΠ±Ρ ΠΎΠ΄ΠΈΠΌΠΎ Π΄ΠΎΡΡΠ°ΡΡ ΠΎΠ±ΡΠ°ΡΠ½ΠΎ.
Π Π°Π·Π½ΠΎΡΡΡ Π΄ΠΈΠ°ΠΌΠ΅ΡΡΠΎΠ²
ΠΡΠΎΡΠ΅ΡΡ Π²ΠΎΠ»ΠΎΡΠ΅Π½ΠΈΡ Π΄Π΅Π»ΠΈΡΡΡ Π΅ΡΠ΅ Π½Π° Π½Π΅ΡΠΊΠΎΠ»ΡΠΊΠΎ Π²ΠΈΠ΄ΠΎΠ², Π² Π·Π°Π²ΠΈΡΠΈΠΌΠΎΡΡΠΈ ΠΎΡ ΡΠΎΠ³ΠΎ, ΠΊΠ°ΠΊΠΎΠ² Π±ΡΠ» Π½Π°ΡΠ°Π»ΡΠ½ΡΠΉ Π΄ΠΈΠ°ΠΌΠ΅ΡΡ Π·Π°Π³ΠΎΡΠΎΠ²ΠΊΠΈ ΠΈ ΠΊΠ°ΠΊΠΎΠΉ ΠΎΠ½ ΠΏΠΎΠ»ΡΡΠΈΠ»ΡΡ Π² ΠΈΡΠΎΠ³Π΅. ΠΡΡΠ±ΡΠΌ Π²ΠΎΠ»ΠΎΡΠ΅Π½ΠΈΠ΅ΠΌ Π½Π°Π·ΡΠ²Π°Π΅ΡΡΡ ΠΏΡΠΎΡΠ΅Π΄ΡΡΠ°, ΠΏΡΠΈ ΠΊΠΎΡΠΎΡΠΎΠΉ Π½Π°ΡΠ°Π»ΡΠ½ΡΠΉ Π΄ΠΈΠ°ΠΌΠ΅ΡΡ Π±ΡΠ» 8 ΠΌΠΌ, Π° ΠΏΠΎΡΠ»Π΅ ΠΏΡΠΎΡ ΠΎΠΆΠ΄Π΅Π½ΠΈΡ Π²ΠΎΠ»ΠΎΠΊΠ° ΡΡΠ°Π» ΠΎΡ 5 Π΄ΠΎ 0,9 ΠΌΠΌ. Π‘ΡΠ΅Π΄Π½ΠΈΠΌ Π²ΠΎΠ»ΠΎΡΠ΅Π½ΠΈΠ΅ΠΌ ΡΡΠΈΡΠ°Π΅ΡΡΡ ΠΎΠΏΠ΅ΡΠ°ΡΠΈΡ, ΠΏΡΠΈ ΠΊΠΎΡΠΎΡΠΎΠΉ Π·Π°Π³ΠΎΡΠΎΠ²ΠΊΠ° ΠΈΠΌΠ΅Π»Π° Π΄ΠΈΠ°ΠΌΠ΅ΡΡ 3,5 ΠΌΠΌ, Π° Π² ΡΠ΅Π·ΡΠ»ΡΡΠ°ΡΠ΅ ΠΎΠ½ ΡΠΌΠ΅Π½ΡΡΠΈΠ»ΡΡ Π΄ΠΎ 1,5-0,2 ΠΌΠΌ. Π ΡΠΎΠ½ΠΊΠΎΠΌ Π²ΠΎΠ»ΠΎΡΠ΅Π½ΠΈΠΈ ΠΈΡΠΏΠΎΠ»ΡΠ·ΡΡΡΡΡ Π·Π°Π³ΠΎΡΠΎΠ²ΠΊΠΈ ΠΎΡ 2,6 Π΄ΠΎ 1,6 ΠΌΠΌ. Π ΡΠ΅Π·ΡΠ»ΡΡΠ°ΡΠ΅ ΠΏΠΎΠ»ΡΡΠ°Π΅ΡΡΡ ΠΏΡΠΎΠ΄ΡΠΊΡΠΈΡ Ρ ΡΠ΅ΡΠ΅Π½ΠΈΠ΅ΠΌ ΠΎΡ 0,5 Π΄ΠΎ 0,05 ΠΌΠΌ.
fb.ru
ΠΠΎΠ»ΠΎΡΠ΅Π½ΠΈΠ΅ ΠΏΡΠΎΠ²ΠΎΠ»ΠΎΠΊΠΈ — ΠΎΡΠΎΠ±Π΅Π½Π½ΠΎΡΡΠΈ ΡΠ΅Ρ Π½ΠΎΠ»ΠΎΠ³ΠΈΠΈ ΠΈ ΠΎΠ±ΠΎΡΡΠ΄ΠΎΠ²Π°Π½ΠΈΠ΅
ΠΠ΄Π½ΠΈΠΌ ΠΈΠ· ΡΠΏΠΎΡΠΎΠ±ΠΎΠ² ΠΊΠ°ΡΠ΅ΡΡΠ²Π΅Π½Π½ΠΎΠΉ ΠΎΠ±ΡΠ°Π±ΠΎΡΠΊΠΈ ΠΌΠ΅ΡΠ°Π»Π»ΠΈΡΠ΅ΡΠΊΠΈΡ Π·Π°Π³ΠΎΡΠΎΠ²ΠΎΠΊ ΡΠ²Π»ΡΠ΅ΡΡΡ Π²ΠΎΠ»ΠΎΡΠ΅Π½ΠΈΠ΅ ΠΏΡΠΎΠ²ΠΎΠ»ΠΎΠΊΠΈ. ΠΡΠΎ ΠΎΡΠΎΠ±Π°Ρ ΡΠ΅Ρ Π½ΠΎΠ»ΠΎΠ³ΠΈΡ Π½Π° ΡΡΠ°Π½ΠΊΠ°Ρ , ΠΏΡΠΈ ΠΊΠΎΡΠΎΡΠΎΠΉ ΡΠ²Π΅ΡΠ½ΡΠ΅ ΠΌΠ΅ΡΠ°Π»Π»Ρ ΠΏΡΠΎΡΡΠ³ΠΈΠ²Π°ΡΡ ΡΠΊΠ²ΠΎΠ·Ρ ΠΊΡΡΠ³Π»ΠΎΠ΅ ΠΈΠ»ΠΈ ΡΠ°ΡΠΎΠ½Π½ΠΎΠ΅ ΠΎΡΠ²Π΅ΡΡΡΠΈΠ΅ (ΡΠΈΠ»ΡΠ΅ΡΡ) ΡΠΏΠ΅ΡΠΈΠ°Π»ΡΠ½ΠΎΠ³ΠΎ ΠΈΠ½ΡΡΡΡΠΌΠ΅Π½ΡΠ° β Π²ΠΎΠ»ΠΎΠΊΠΈ. Π Π΅Π·ΡΠ»ΡΡΠ°ΡΠΎΠΌ ΠΏΡΠΎΡΠ΅ΡΡΠ° ΡΠ²Π»ΡΠ΅ΡΡΡ ΡΠΌΠ΅Π½ΡΡΠ΅Π½ΠΈΠ΅ Π·Π°Π³ΠΎΡΠΎΠ²ΠΊΠΈ ΠΈ ΡΠ²Π΅Π»ΠΈΡΠ΅Π½ΠΈΠ΅ Π΅Π΅ Π΄Π»ΠΈΠ½Ρ. ΠΡΠΎ Π°ΠΊΡΡΠ°Π»ΡΠ½ΠΎ Π΄Π»Ρ ΠΏΡΠΎΠΈΠ·Π²ΠΎΠ΄ΡΡΠ²Π° ΠΏΡΠΎΠ²ΠΎΠ»ΠΎΠΊΠΈ ΡΠ°Π·Π½ΠΎΠ³ΠΎ ΠΏΡΠΎΡΠΈΠ»Ρ ΠΈ Π΄ΡΡΠ³ΠΎΠΉ ΠΏΡΠΎΠ²ΠΎΠ»ΠΎΡΠ½ΠΎΠΉ ΠΏΡΠΎΠ΄ΡΠΊΡΠΈΠΈ, ΠΏΡΠΈΠΌΠ΅Π½ΡΠ΅ΠΌΠΎΠΉ Π²ΠΎ Π²ΡΠ΅Ρ ΠΎΠ±Π»Π°ΡΡΡΡ ΡΠ΅Π»ΠΎΠ²Π΅ΡΠ΅ΡΠΊΠΎΠΉ Π΄Π΅ΡΡΠ΅Π»ΡΠ½ΠΎΡΡΠΈ.
ΠΡΠΎΠ±Π΅Π½Π½ΠΎΡΡΠΈ ΠΏΡΠΎΡΠ΅Π΄ΡΡΡ
ΠΡΠΎΡΠ΅ΡΡ Π²ΠΎΠ»ΠΎΡΠ΅Π½ΠΈΡ Π½Π΅ΡΠ»ΠΎΠΆΠ½ΡΠΉ. Π ΠΊΠ°ΡΠ΅ΡΡΠ²Π΅ ΠΈΡΡ ΠΎΠ΄Π½ΠΎΠ³ΠΎ ΡΡΡΡΡ ΠΈΡΠΏΠΎΠ»ΡΠ·ΡΡΡ ΠΊΠ°ΡΠ°Π½ΡΡ, Π»ΠΈΡΡΡ ΠΈΠ»ΠΈ ΠΏΡΠ΅ΡΡΠΎΠ²Π°Π½Π½ΡΡ Π·Π°Π³ΠΎΡΠΎΠ²ΠΊΠΈ. Π Π°Π±ΠΎΡΡ Π²ΡΠΏΠΎΠ»Π½ΡΡΡ Π½Π° ΡΠΏΠ΅ΡΠΈΠ°Π»ΡΠ½ΠΎΠΌ ΠΎΠ±ΠΎΡΡΠ΄ΠΎΠ²Π°Π½ΠΈΠΈ β Π²ΠΎΠ»ΠΎΡΠΈΠ»ΡΠ½ΡΡ ΡΡΠ°Π½ΠΊΠ°Ρ . Π€ΠΎΡΠΌΠ°, Π΄ΠΈΠ°ΠΌΠ΅ΡΡ ΠΈ ΡΠ΅ΡΠ΅Π½ΠΈΠ΅ Π³ΠΎΡΠΎΠ²ΠΎΠ³ΠΎ Π΄Π»ΠΈΠ½Π½ΠΎΠΌΠ΅ΡΠ½ΠΎΠ³ΠΎ ΠΈΠ·Π΄Π΅Π»ΠΈΡ Π·Π°Π²ΠΈΡΡΡ ΠΎΡ ΠΏΠ°ΡΠ°ΠΌΠ΅ΡΡΠΎΠ² ΡΠΈΠ»ΡΠ΅ΡΡ. ΠΠΎ ΡΡΠ°Π²Π½Π΅Π½ΠΈΡ Ρ ΠΏΡΠΎΠΊΠ°ΡΠΊΠΎΠΉ ΠΌΠ΅ΡΠ°Π»Π»Π°, ΡΠ΅Ρ Π½ΠΎΠ»ΠΎΠ³ΠΈΡΠ΅ΡΠΊΠ°Ρ ΠΎΠΏΠ΅ΡΠ°ΡΠΈΡ ΠΈΠΌΠ΅Π΅Ρ ΠΌΠ½ΠΎΠ³ΠΎ ΠΏΡΠ΅ΠΈΠΌΡΡΠ΅ΡΡΠ²:
- ΠΡΡΠΎΠΊΠ°Ρ ΠΏΡΠΎΠΈΠ·Π²ΠΎΠ΄ΠΈΡΠ΅Π»ΡΠ½ΠΎΡΡΡ Π·Π° ΡΡΠ΅Ρ Π°Π²ΡΠΎΠΌΠ°ΡΠΈΠ·Π°ΡΠΈΠΈ ΠΏΡΠΎΡΠ΅ΡΡΠΎΠ² ΡΡΠ°Π½ΠΊΠΎΠ².
- ΠΠΎΠ»ΠΎΡΠ΅Π½ΠΈΠ΅ ΠΏΡΠΎΠ²ΠΎΠ»ΠΎΠΊΠΈ Π½Π°ΠΏΡΠ°Π²Π»Π΅Π½ΠΎ Π½Π° ΠΏΠΎΠ»ΡΡΠ΅Π½ΠΈΠ΅ Π³Π΅ΠΎΠΌΠ΅ΡΡΠΈΡΠ΅ΡΠΊΠΈ ΠΏΡΠ°Π²ΠΈΠ»ΡΠ½ΠΎΠΉ ΠΏΡΠΎΠ΄ΡΠΊΡΠΈΠΈ, Ρ ΡΠΎΠ²Π½ΠΎΠΉ ΠΈ ΡΠΈΡΡΠΎΠΉ ΠΏΠΎΠ²Π΅ΡΡ Π½ΠΎΡΡΡΡ. ΠΡΠΎ ΠΏΠΎΠ·Π²ΠΎΠ»ΡΠ΅Ρ ΡΠ½ΠΈΠ·ΠΈΡΡ ΠΎΠ±ΡΠ΅ΠΌ ΠΏΠΎΡΠ»Π΅Π΄ΡΡΡΠ΅ΠΉ ΠΎΠ±ΡΠ°Π±ΠΎΡΠΊΠΈ.
- ΠΠ·Π΄Π΅Π»ΠΈΡ ΠΎΠ±Π»Π°Π΄Π°ΡΡ ΡΠ»ΡΡΡΠ΅Π½Π½ΡΠΌΠΈ ΠΌΠ΅Ρ Π°Π½ΠΈΡΠ΅ΡΠΊΠΈΠΌΠΈ Ρ Π°ΡΠ°ΠΊΡΠ΅ΡΠΈΡΡΠΈΠΊΠ°ΠΌΠΈ.
- ΠΠΎΠ·ΠΌΠΎΠΆΠ½ΠΎΡΡΡ ΠΏΡΠΎΠΈΠ·Π²ΠΎΠ΄ΠΈΡΡ ΡΠ°Π·Π½ΡΠ΅ Π²ΠΈΠ΄Ρ ΠΌΠ΅ΡΠ°Π»Π»ΠΈΡΠ΅ΡΠΊΠΎΠ³ΠΎ ΡΠ½ΡΡΠ°, Π² ΡΠΎΠΌ ΡΠΈΡΠ»Π΅ ΠΏΠΎΡΠΎΡΠΊΠΎΠ²ΠΎΠΉ ΠΏΡΠΎΠ²ΠΎΠ»ΠΎΠΊΠΈ, Π° ΡΠ°ΠΊΠΆΠ΅ ΠΊΠ°Π»ΠΈΠ±ΡΠΎΠ²Π°Π½Π½ΡΠ΅ ΠΏΡΡΡΠΊΠΈ, ΡΠΎΠ½ΠΊΠΎΡΡΠ΅Π½Π½ΡΠ΅ ΡΡΡΠ±Ρ Π΄ΠΈΠ°ΠΌΠ΅ΡΡΠΎΠΌ Π΄ΠΎ 5 ΠΌΠΌ.
- ΠΠΈΠ°ΠΌΠ΅ΡΡ ΠΈΠ·Π΄Π΅Π»ΠΈΠΉ Π²Π°ΡΡΠΈΡΡΠ΅ΡΡΡ ΠΎΡ 1 Π΄ΠΎ 10 ΠΌΠΈΠΊΡΠΎΠ½.
- ΠΠΈΠ·ΠΊΠΈΠ΅ Π·Π°ΡΡΠ°ΡΡ Π½Π° Π²ΠΎΠ»ΠΎΡΠΈΠ»ΡΠ½ΡΠ΅ ΡΡΠ°Π½ΠΊΠΈ.
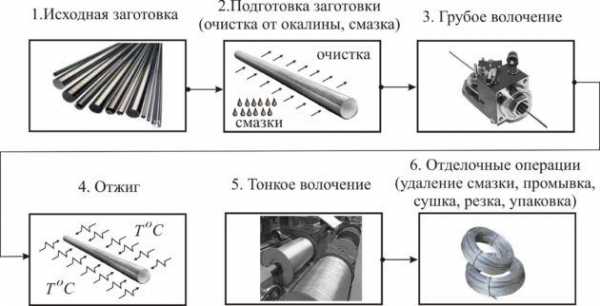
Π‘Ρ Π΅ΠΌΠ° ΠΏΡΠΎΡΠ΅ΡΡΠ° Π²ΠΎΠ»ΠΎΡΠ΅Π½ΠΈΡ
ΠΡΠ°ΠΏΡ Π²ΠΎΠ»ΠΎΡΠ΅Π½ΠΈΡ
Π’Π΅Ρ Π½ΠΎΠ»ΠΎΠ³ΠΈΡ ΠΏΡΠΎΠΈΠ·Π²ΠΎΠ΄ΡΡΠ²Π° ΠΏΡΠΎΠ²ΠΎΠ»ΠΎΠΊΠΈ ΡΠ°Π·Π΄Π΅Π»Π΅Π½Π° Π½Π° ΠΏΡΡΡ ΡΡΠ°ΠΏΠΎΠ².
ΠΡΠ°ΠΏ β1
ΠΡΠΎΡΠ΅Π΄ΡΡΠ° ΡΡΠ°Π²Π»Π΅Π½ΠΈΡ Ρ ΡΠ΅Π»ΡΡ ΡΠ΄Π°Π»Π΅Π½ΠΈΡ ΠΏΠΎΠ²Π΅ΡΡ Π½ΠΎΡΡΠ½ΠΎΠ³ΠΎ ΡΠ»ΠΎΡ ΠΌΠ°ΡΠ΅ΡΠΈΠ°Π»Π° β ΠΎΠΊΠ°Π»ΠΈΠ½Ρ, ΠΊΠΎΡΠΎΡΠ°Ρ ΠΌΠ΅ΡΠ°Π΅Ρ Π²ΠΎΠ»ΠΎΡΠ΅Π½ΠΈΡ:
Π’ΡΠ°Π²Π»Π΅Π½ΠΈΠ΅ ΠΌΠ΅ΡΠ°Π»Π»Π° Π² Π½Π΅ΠΏΡΠ΅ΡΡΠ²Π½ΠΎΠΌ ΡΡΠ°Π²ΠΈΠ»ΡΠ½ΠΎΠΌ Π°Π³ΡΠ΅Π³Π°ΡΠ΅
- ΠΠΎΠ΄Π³ΠΎΡΠΎΠ²ΠΊΠ° ΠΏΠΎΠ²Π΅ΡΡ Π½ΠΎΡΡΠΈ: ΠΎΠ±Π΅Π·ΠΆΠΈΡΠΈΠ²Π°Π½ΠΈΠ΅, ΡΠ»ΠΈΡΠΎΠ²Π°Π½ΠΈΠ΅, ΠΏΠΎΠ»ΠΈΡΠΎΠ²ΠΊΠ°, Π²ΡΡΠ΅Π·Π°Π½ΠΈΠ΅ Π±ΡΠ°ΠΊΠΎΠ²Π°Π½Π½ΡΡ ΡΡΠ°ΡΡΠΊΠΎΠ².
- Π ΠΎΠΊΠ°Π»ΠΈΠ½Π΅ ΠΏΡΠΈΡΡΡΡΡΠ²ΡΡΡ ΡΠ»ΠΎΠΆΠ½ΡΠ΅ ΡΠΎΠ΅Π΄ΠΈΠ½Π΅Π½ΠΈΡ Π΄ΡΡΠ³ΠΈΡ ΡΠ»Π΅ΠΌΠ΅Π½ΡΠΎΠ², ΠΏΠΎΡΡΠΎΠΌΡ ΠΈΡΡ ΠΎΠ΄Π½ΠΎΠ΅ ΡΡΡΡΠ΅ ΠΏΠΎΠ΄Π²Π΅ΡΠ³Π°ΡΡ Ρ ΠΈΠΌΠΈΡΠ΅ΡΠΊΠΎΠΉ ΠΈΠ»ΠΈ ΠΌΠ΅Ρ Π°Π½ΠΈΡΠ΅ΡΠΊΠΎΠΉ ΠΎΠ±ΡΠ°Π±ΠΎΡΠΊΠ΅.
- ΠΡΠ±ΠΎΡ ΠΌΠ΅ΡΠΎΠ΄Π° ΡΡΠ°Π²Π»Π΅Π½ΠΈΡ Π·Π°Π²ΠΈΡΠΈΡ ΠΎΡ ΠΏΡΠΈΡΠΎΠ΄Ρ ΠΌΠ΅ΡΠ°Π»Π»Π°. Π£Π΄Π°Π»Π΅Π½ΠΈΠ΅ ΠΎΠΊΠ°Π»ΠΈΠ½Ρ ΠΏΡΠΎΠΈΠ·Π²ΠΎΠ΄ΡΡ ΡΠΎΡΡΠΎΡΠ½ΠΎΠΉ, ΡΠΎΠ»ΡΠ½ΠΎΠΉ, Π°Π·ΠΎΡΠ½ΠΎΠΉ, ΠΏΠ»Π°Π²ΠΈΠΊΠΎΠ²ΠΎΠΉ ΠΈΠ»ΠΈ ΡΠ΅ΡΠ½ΠΎΠΉ ΠΊΠΈΡΠ»ΠΎΡΠΎΠΉ, Π½Π°Π³ΡΠ΅ΡΠΎΠΉ Π΄ΠΎ 50 0C.
- ΠΠ±ΡΠ°Π±Π°ΡΡΠ²Π°Π΅ΠΌΡΡ ΠΏΠΎΠ²Π΅ΡΡ Π½ΠΎΡΡΡ ΠΎΡΠΈΡΠ°ΡΡ ΠΎΡ ΠΏΡΠΎΠ΄ΡΠΊΡΠΎΠ² ΡΡΠ°Π²Π»Π΅Π½ΠΈΡ. ΠΡΠΎ ΠΏΡΠΎΠΌΡΠ²ΠΊΠ° Π·Π°Π³ΠΎΡΠΎΠ²ΠΎΠΊ Ρ ΠΏΠΎΠΌΠΎΡΡΡ ΡΠΏΠ΅ΡΠΈΠ°Π»ΡΠ½ΠΎΠ³ΠΎ ΡΠ°ΡΡΠ²ΠΎΡΠΈΡΠ΅Π»Ρ ΠΈΠ»ΠΈ Π²ΠΎΠ΄Ρ.
- ΠΠΎΡΠ»Π΅ ΠΏΡΠΎΡΠ΅Π΄ΡΡΡ ΠΌΠ΅ΡΠ°Π»Π» Π΄ΠΎΠ»ΠΆΠ΅Π½ ΠΏΡΠΈΠΎΠ±ΡΠ΅ΡΡΠΈ ΠΌΠ°ΡΠΎΠ²ΡΠΉ ΠΎΡΡΠ΅Π½ΠΎΠΊ.
- Π‘ΡΡΠΊΠ° ΠΏΡΠΎΠ²ΠΎΠ»ΠΎΠΊΠΈ Π² ΡΠ΅ΡΠ΅Π½ΠΈΠ΅ ΡΠ°ΡΠ° ΠΏΡΠΈ ΡΠ΅ΠΌΠΏΠ΅ΡΠ°ΡΡΡΠ΅ 75β100 0C. ΠΠ»Ρ ΡΡΠΎΠ³ΠΎ ΠΈΡΠΏΠΎΠ»ΡΠ·ΡΡΡ ΡΠΏΠ΅ΡΠΈΠ°Π»ΡΠ½ΡΠ΅ ΡΡΠ°Π½ΠΊΠΈ Ρ ΡΡΡΠΈΠ»ΡΠ½ΡΠΌΠΈ ΠΊΠ°ΠΌΠ΅ΡΠ°ΠΌΠΈ.
ΠΡΠ°ΠΏ β2
Π ΡΠ΅ΡΠΌΠΈΡΠ΅ΡΠΊΠΎΠΉ ΠΎΡΠ½ΠΎΡΡΡ ΠΏΡΠΎΡΠ΅ΡΡΡ
Π’Π΅ΡΠΌΠΈΡΠ΅ΡΠΊΠ°Ρ ΠΎΠ±ΡΠ°Π±ΠΎΡΠΊΠ° ΠΏΡΠΎΠ²ΠΎΠ΄ΠΈΡΡΡ Π΄Π»Ρ ΡΠΎΠ³ΠΎ, ΡΡΠΎΠ±Ρ Π·Π°Π³ΠΎΡΠΎΠ²ΠΊΡ ΡΠ΄Π΅Π»Π°ΡΡ ΠΏΠΎΠ»ΡΠΌΡΠ³ΠΊΠΎΠΉ, Ρ ΠΌΠ΅Π»ΠΊΠΎΠ·Π΅ΡΠ½ΠΈΡΡΠΎΠΉ ΡΡΡΡΠΊΡΡΡΠΎΠΉ, ΡΠ²ΠΎΠ±ΠΎΠ΄Π½ΠΎΠΉ ΠΎΡ Π²Π½ΡΡΡΠ΅Π½Π½ΠΈΡ Π½Π°ΠΏΡΡΠΆΠ΅Π½ΠΈΠΉ. ΠΠ΅ΡΠ°Π»Π» Π½Π°Π³ΡΠ΅Π²Π°ΡΡ Π΄ΠΎ ΠΎΠΏΡΠ΅Π΄Π΅Π»Π΅Π½Π½ΠΎΠΉ ΡΠ΅ΠΌΠΏΠ΅ΡΠ°ΡΡΡΡ, Π½Π΅ΠΊΠΎΡΠΎΡΠΎΠ΅ Π²ΡΠ΅ΠΌΡ Π²ΡΠ΄Π΅ΡΠΆΠΈΠ²Π°ΡΡ Π² ΡΠ°ΠΊΠΈΡ ΡΡΠ»ΠΎΠ²ΠΈΡΡ , ΠΎΡ Π»Π°ΠΆΠ΄Π°ΡΡ.
ΠΡΠΆΠΈΠ³ ΠΈΠ·ΠΌΠ΅Π½ΡΠ΅Ρ ΡΠ²ΠΎΠΉΡΡΠ²Π° ΠΌΠ°ΡΠ΅ΡΠΈΠ°Π»Π° ΠΈ ΠΎΠ±Π»Π΅Π³ΡΠ°Π΅Ρ ΠΏΡΠΎΡΠ΅ΡΡ Π²ΠΎΠ»ΠΎΡΠ΅Π½ΠΈΡ ΠΏΡΠΎΠ²ΠΎΠ»ΠΎΠΊΠΈ. Π‘ΠΊΠΎΡΠΎΡΡΡ Π½Π°Π³ΡΠ΅Π²Π° Π·Π°Π²ΠΈΡΠΈΡ ΠΎΡ ΡΠ΅ΠΏΠ»ΠΎΠΏΡΠΎΠ²ΠΎΠ΄Π½ΠΎΡΡΠΈ ΠΌΠ΅ΡΠ°Π»Π»Π°. ΠΡΡΡΡΠΎΡΠ° ΠΎΡ Π»Π°ΠΆΠ΄Π΅Π½ΠΈΡ ΠΎΠΏΡΠ΅Π΄Π΅Π»ΡΠ΅ΡΡΡ ΡΠ²Π΅ΡΠ΄ΠΎΡΡΡΡ, ΠΊΠΎΡΠΎΡΡΡ Π½ΡΠΆΠ½ΠΎ Π΄ΠΎΡΡΠΈΡΡ ΠΏΠΎΡΠ»Π΅ ΠΎΡΠΆΠΈΠ³Π°. Π‘ΡΠ°Π»ΡΠ½ΡΠ΅ ΠΏΡΠΎΠ²ΠΎΠ»ΠΎΠΊΠΈ ΠΎΡ Π»Π°ΠΆΠ΄Π°ΡΡΡΡ ΠΌΠ΅Π΄Π»Π΅Π½Π½Π΅Π΅, ΡΠ΅ΠΌ ΡΠ³Π»Π΅ΡΠΎΠ΄ΠΈΡΡΡΠ΅ ΡΠΎΠ΅Π΄ΠΈΠ½Π΅Π½ΠΈΡ.
ΠΡΠ°ΠΏ β3
ΠΡΠΈ ΠΏΠΎΠΌΠΎΡΠΈ ΡΠΏΠ΅ΡΠΈΠ°Π»ΡΠ½ΠΎΠ³ΠΎ ΠΌΠΎΠ»ΠΎΡΠ° ΠΈΠ»ΠΈ ΠΊΠΎΠ²ΠΎΡΠ½ΡΡ Π²Π°Π»ΠΎΠΊ ΠΊΠΎΠ½ΡΡ Π·Π°Π³ΠΎΡΠΎΠ²ΠΊΠΈ ΡΠΏΠ»ΡΡΠΈΠ²Π°ΡΡ ΠΈ Π²ΡΡΠ°Π²Π½ΠΈΠ²Π°ΡΡ. ΠΡΠΎΡΠ΅Π΄ΡΡΠ° ΠΏΠΎΠ·Π²ΠΎΠ»ΡΠ΅Ρ Π·Π°ΠΊΡΠ΅ΠΏΠ»ΡΡΡ ΠΌΠ΅ΡΠ°Π»Π» Π½Π° Π±Π°ΡΠ°Π±Π°Π½Π΅ ΡΡΠ°Π½ΠΊΠ° ΠΈ ΠΏΡΠΎΠΏΡΡΠΊΠ°ΡΡ ΡΠΊΠ²ΠΎΠ·Ρ ΡΠΈΠ»ΡΠ΅ΡΡ.
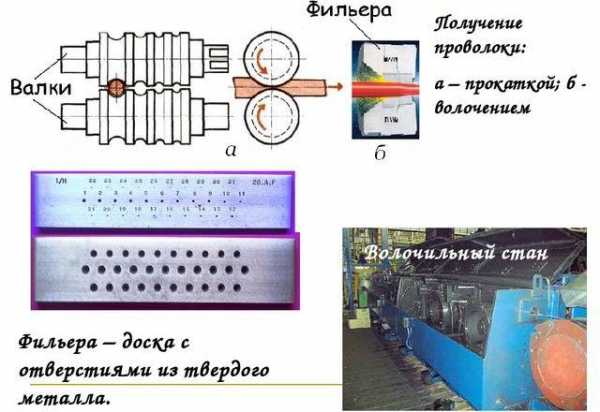
Π€ΠΈΠ»ΡΠ΅ΡΠ° Π΄Π»Ρ Π²ΠΎΠ»ΠΎΡΠ΅Π½ΠΈΡ ΠΏΡΠΎΠ²ΠΎΠ»ΠΎΠΊΠΈ
ΠΡΠ°ΠΏ β4
ΠΠΎΠ»ΠΎΡΠ΅Π½ΠΈΠ΅ ΠΏΡΠΎΠ²ΠΎΠ»ΠΎΠΊΠΈ: ΠΏΡΠΎΡΡΠ°Π²Π»Π΅Π½Π½ΠΎΠ΅ ΠΎΠ±ΡΠ°Π±ΠΎΡΠ°Π½Π½ΠΎΠ΅ ΡΡΡΡΠ΅ ΠΏΡΠΎΡΡΠ³ΠΈΠ²Π°ΡΡ Π½Π° ΡΡΠ°Π½ΠΊΠ΅ Ρ ΠΌΠ°ΠΊΡΠΈΠΌΠ°Π»ΡΠ½ΠΎΠΉ ΡΠΊΠΎΡΠΎΡΡΡΡ ΡΠ΅ΡΠ΅Π· ΠΏΠ»Π°Π²Π½ΠΎ ΡΡΠΆΠ°ΡΡΠΈΠΉΡΡ ΠΊΠ°Π½Π°Π». ΠΠΎ ΡΠΈΡΠ»Ρ ΠΎΠ΄Π½ΠΎΠ²ΡΠ΅ΠΌΠ΅Π½Π½ΠΎ ΠΏΡΠΎΡΡΠ³ΠΈΠ²Π°Π΅ΠΌΡΡ ΠΏΡΡΡΠΎΠ² ΠΏΡΠΎΡΠ΅ΡΡ Π±ΡΠ²Π°Π΅Ρ:
- ΠΠ΄Π½ΠΎΠ½ΠΈΡΠΎΡΠ½ΡΠΉ.
- ΠΠ½ΠΎΠ³ΠΎΠ½ΠΈΡΠΎΡΠ½ΡΠΉ.
ΠΠΎ ΡΠΈΠΏΡ ΠΊΠΎΠ½Π΅ΡΠ½ΠΎΠ³ΠΎ ΠΏΡΠΎΠ΄ΡΠΊΡΠ°:
- ΠΠ»ΠΈΠ½Π½ΠΎΠΌΠ΅ΡΠ½ΡΠ΅ ΠΈΠ·Π΄Π΅Π»ΠΈΡ Π² Π²ΠΈΠ΄Π΅ ΠΌΠΎΡΠΊΠΎΠ² ΠΈΠ»ΠΈ ΠΊΠ°ΡΡΡΠ΅ΠΊ.
- ΠΠ°Π»ΠΈΠ±ΡΠΎΠ²Π°Π½Π½ΡΠ΅ ΠΏΡΡΡΠΊΠΈ.
ΠΠΎ ΠΊΠΎΠ»ΠΈΡΠ΅ΡΡΠ²Ρ ΠΏΠ΅ΡΠ΅Ρ ΠΎΠ΄ΠΎΠ² Π²ΠΎΠ»ΠΎΡΠ΅Π½ΠΈΠ΅ ΠΏΡΠΎΠ²ΠΎΠ»ΠΎΠΊΠΈ ΠΈΠΌΠ΅Π΅Ρ Π΄Π²Π΅ ΡΠ°Π·Π½ΠΎΠ²ΠΈΠ΄Π½ΠΎΡΡΠΈ:
- ΠΠ΄Π½ΠΎΠΊΡΠ°ΡΠ½ΠΎΠ΅ β ΠΏΡΠΈ ΠΊΠΎΡΠΎΡΠΎΠΌ ΠΏΡΠΎΡΡΠ³ΠΈΠ²Π°Π½ΠΈΠ΅ ΠΎΡΡΡΠ΅ΡΡΠ²Π»ΡΠ΅ΡΡΡ ΡΠ΅ΡΠ΅Π· ΠΎΠ΄Π½Ρ Π²ΠΎΠ»ΠΎΠΊΡ. ΠΡΠΎΡΠ΅ΡΡ ΠΏΠΎΠ΄Ρ ΠΎΠ΄ΠΈΡ Π΄Π»Ρ ΡΠΎΠ»ΡΡΠΎΠΉ, ΠΏΠ»ΠΎΡ ΠΎ Π΄Π΅ΡΠΎΡΠΌΠΈΡΡΠ΅ΠΌΠΎΠΉ ΠΏΡΠΎΠ²ΠΎΠ»ΠΎΠΊΠΈ.
- ΠΠ½ΠΎΠ³ΠΎΠΊΡΠ°ΡΠ½ΠΎΠ΅, ΠΊΠΎΠ³Π΄Π° ΠΌΠ°ΡΠ΅ΡΠΈΠ°Π» ΠΏΠΎΠ΄Π²Π΅ΡΠ³Π°Π΅ΡΡΡ ΡΠΆΠ°ΡΠΈΡ ΠΏΠΎΡΠ»Π΅Π΄ΠΎΠ²Π°ΡΠ΅Π»ΡΠ½ΠΎ Π½Π° Π½Π΅ΡΠΊΠΎΠ»ΡΠΊΠΈΡ Π²ΠΎΠ»ΠΎΠΊΠ°Ρ .
Π‘ΡΠ°Π½ΠΎΠΊ Π΄Π»Ρ Π²ΠΎΠ»ΠΎΡΠ΅Π½ΠΈΡ ΡΠΎΡΠΌΠΈΡΡΠ΅Ρ ΠΏΡΠΎΡΠΈΠ»Ρ ΠΈ ΡΠ°Π·ΠΌΠ΅ΡΡ Π³ΠΎΡΠΎΠ²ΠΎΠΉ ΠΏΡΠΎΠ΄ΡΠΊΡΠΈΠΈ.
ΠΡΠ°ΠΏ β5
ΠΠ°Π²Π΅ΡΡΠ°ΡΡΠΈΠΉ ΡΡΠ°ΠΏ ΠΏΡΠ΅Π΄ΠΏΠΎΠ»Π°Π³Π°Π΅Ρ Π²ΡΠΏΠΎΠ»Π½Π΅Π½ΠΈΠ΅ ΠΎΡΠΆΠΈΠ³Π°. ΠΡΠΎ Π΄Π΅Π»Π°Π΅ΡΡΡ Ρ ΡΠ΅Π»ΡΡ ΡΡΡΡΠ°Π½ΠΈΡΡ Π²ΡΠ΅Π΄Π½ΠΎΠ΅ Π½Π°ΠΏΡΡΠΆΠ΅Π½ΠΈΠ΅ ΠΏΠΎΡΠ»Π΅ Π²ΠΎΠ»ΠΎΡΠ΅Π½ΠΈΡ. ΠΠ·Π΄Π΅Π»ΠΈΠ΅ ΡΡΠ°Π½ΠΎΠ²ΠΈΡΡΡ ΠΌΡΠ³ΠΊΠΈΠΌ, ΡΡΡΠΎΠΉΡΠΈΠ²ΡΠΌ ΠΊ ΡΠ°Π·ΡΡΠ²Π°ΠΌ, ΠΏΠΎΠ΄Π°ΡΠ»ΠΈΠ²ΡΠΌ ΠΊ Π·Π°Π³ΠΈΠ±Π°ΠΌ, ΡΠ΄Π»ΠΈΠ½Π΅Π½ΠΈΡ ΠΈ ΡΠΊΡΡΡΠΈΠ²Π°Π½ΠΈΡ. ΠΠΎΡΠ»Π΅ ΡΠ΅ΡΠΌΠΈΡΠ΅ΡΠΊΠΎΠΉ ΠΎΠ±ΡΠ°Π±ΠΎΡΠΊΠΈ ΠΏΡΠΎΠ²ΠΎΠ΄ΡΡ Π΄ΠΎΠΏΠΎΠ»Π½ΠΈΡΠ΅Π»ΡΠ½ΡΠ΅ ΠΎΡΠ΄Π΅Π»ΠΎΡΠ½ΡΠ΅ ΠΎΠΏΠ΅ΡΠ°ΡΠΈΠΈ, ΡΡΠ΅Π΄ΠΈ ΠΊΠΎΡΠΎΡΡΡ :
- Π¦ΠΈΠ½ΠΊΠΎΠ²Π°Π½ΠΈΠ΅ ΠΏΡΠΎΠ²ΠΎΠ»ΠΎΠΊΠΈ.
- ΠΠΎΠ½ΡΠ΅ΡΠ²Π°ΡΠΈΠΎΠ½Π½Π°Ρ ΡΠΌΠ°Π·ΠΊΠ°.
- Π Π°Π·ΡΠ΅Π·Π°Π½ΠΈΠ΅ Π½Π° ΡΠ°ΡΡΠΈ.
- ΠΠ°ΡΠΊΠΈΡΠΎΠ²ΠΊΠ°.
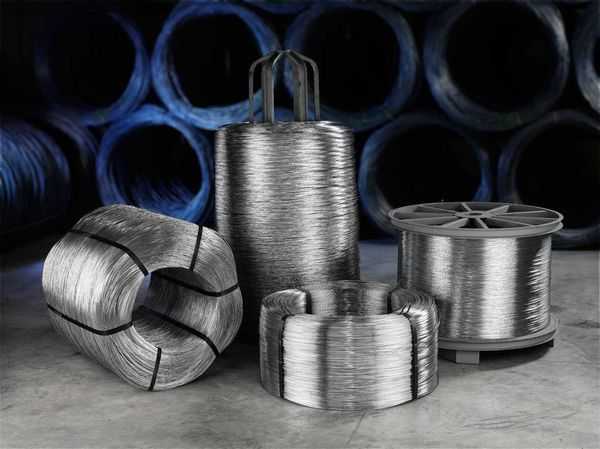
ΠΠΈΠ΄ Π³ΠΎΡΠΎΠ²ΠΎΠΉ ΠΏΡΠΎΠ²ΠΎΠ»ΠΎΠΊΠΈ ΠΏΠΎΡΠ»Π΅ Π²ΡΠ΅Ρ ΠΏΡΠΎΡΠ΅ΡΡΠΎΠ² ΠΎΠ±ΡΠ°Π±ΠΎΡΠΊΠΈ
ΠΠ±ΠΎΡΡΠ΄ΠΎΠ²Π°Π½ΠΈΠ΅ Π΄Π»Ρ Π²ΡΠΏΠΎΠ»Π½Π΅Π½ΠΈΡ Π²ΠΎΠ»ΠΎΡΠ΅Π½ΠΈΡ ΠΏΡΠΎΠ²ΠΎΠ»ΠΎΠΊΠΈ
ΠΠΎΠ»ΠΎΡΠ΅Π½ΠΈΠ΅ ΠΏΡΠΎΠ²ΠΎΠ»ΠΎΠΊΠΈ ΠΏΡΠΎΠΈΡΡ ΠΎΠ΄ΠΈΡ Π½Π° ΡΡΠ°Π½ΠΊΠ΅, ΠΎΠ±ΠΎΡΡΠ΄ΠΎΠ²Π°Π½Π½ΠΎΠΌ ΡΠΏΠ΅ΡΠΈΠ°Π»ΡΠ½ΡΠΌ ΠΈΠ½ΡΡΡΡΠΌΠ΅Π½ΡΠΎΠΌ β Π²ΠΎΠ»ΠΎΠΊΠΎΠΌ Ρ ΠΎΡΠ²Π΅ΡΡΡΠΈΠ΅ΠΌ, ΠΊΠΎΡΠΎΡΠΎΠ΅ Π½Π°Π·ΡΠ²Π°Π΅ΡΡΡ Β«Π³Π»Π°Π·ΠΊΠΎΠΌΒ». ΠΡΠ²Π΅ΡΡΡΠΈΠ΅ ΠΈΠΌΠ΅Π΅Ρ ΠΏΠΎΡΡΠ΅ΠΏΠ΅Π½Π½ΠΎ ΡΠΌΠ΅Π½ΡΡΠ°ΡΡΠ΅Π΅ΡΡ ΡΠ΅ΡΠ΅Π½ΠΈΠ΅, ΡΠ΅ΡΠ΅Π· ΠΊΠΎΡΠΎΡΠΎΠ΅ ΠΏΡΠΎΡΡΠ³ΠΈΠ²Π°ΡΡ Π·Π°Π³ΠΎΡΠΎΠ²ΠΊΡ.
ΠΠΎΠ½ΡΡΡΡΠΊΡΠΈΡ ΠΎΠ±ΠΎΡΡΠ΄ΠΎΠ²Π°Π½ΠΈΡ Π·Π°Π²ΠΈΡΠΈΡ ΠΎΡ ΠΎΡΠΎΠ±Π΅Π½Π½ΠΎΡΡΠ΅ΠΉ ΡΡΠ½ΡΡΠ΅Π³ΠΎ ΠΌΠ΅Ρ Π°Π½ΠΈΠ·ΠΌΠ°:
- Π‘ΡΠ°Π½ΠΎΠΊ Π΄Π»Ρ Π²ΠΎΠ»ΠΎΡΠ΅Π½ΠΈΡ, Π² ΠΊΠΎΡΠΎΡΠΎΠΌ ΠΌΠ΅ΡΠ°Π»Π» Π½Π°ΠΌΠ°ΡΡΠ²Π°ΡΡ Π½Π° Π±Π°ΡΠ°Π±Π°Π½ ΠΈ ΡΠ½ΠΈΠΌΠ°ΡΡ Π² Π²ΠΈΠ΄Π΅ ΠΌΠΎΡΠΊΠ° ΠΈΠ»ΠΈ ΠΊΠ°ΡΡΡΠΊΠΈ. ΠΠ°ΡΠ°Π±Π°Π½Π½ΡΠ΅ ΠΌΠ°ΡΠΈΠ½Ρ Π±ΡΠ²Π°ΡΡ ΠΎΠ΄Π½ΠΎΠΊΡΠ°ΡΠ½ΡΠΌΠΈ ΠΈ ΠΌΠ½ΠΎΠ³ΠΎΠΊΡΠ°ΡΠ½ΡΠΌΠΈ.
- ΠΠ³ΡΠ΅Π³Π°Ρ, ΠΎΠ±Π΅ΡΠΏΠ΅ΡΠΈΠ²Π°ΡΡΠΈΠΉ ΠΏΡΡΠΌΠΎΠ»ΠΈΠ½Π΅ΠΉΠ½ΠΎΠ΅ Π΄Π²ΠΈΠΆΠ΅Π½ΠΈΠ΅ Π·Π°Π³ΠΎΡΠΎΠ²ΠΊΠΈ. Π£ΡΡΡΠΎΠΉΡΡΠ²Π° ΡΡΠΎΠΉ Π³ΡΡΠΏΠΏΡ ΡΠ°Π·Π΄Π΅Π»ΡΡΡΡΡ Π½Π° ΡΠ΅ΠΏΠ½ΡΠ΅, ΡΠ΅Π΅ΡΠ½ΡΠ΅ ΠΈ Π²ΠΈΠ½ΡΠΎΠ²ΡΠ΅.
ΠΡΠ½ΠΎΠ²Π½ΠΎΠΉ ΡΠ°Π±ΠΎΡΠΈΠΉ ΠΈΠ½ΡΡΡΡΠΌΠ΅Π½Ρ ΡΡΠ°Π½ΠΊΠ° Π΄Π»Ρ ΠΏΡΠΎΠΈΠ·Π²ΠΎΠ΄ΡΡΠ²Π° ΠΏΡΠΎΠ²ΠΎΠ»ΠΎΠΊΠΈ β Π²ΠΎΠ»ΠΎΠΊΠ°. ΠΠ½ ΡΠΎΡΡΠΎΠΈΡ ΠΈΠ· Π΄Π²ΡΡ ΡΠ»Π΅ΠΌΠ΅Π½ΡΠΎΠ²: Π½Π΅ΠΏΠΎΡΡΠ΅Π΄ΡΡΠ²Π΅Π½Π½ΠΎ Π²ΠΎΠ»ΠΎΠΊΠΈ ΠΈ ΠΎΠ±ΠΎΠΉΠΌΡ. Π’Π°ΠΊΠ°Ρ ΠΊΠΎΠ½ΡΡΡΡΠΊΡΠΈΡ ΠΎΠ±ΡΡΠ»ΠΎΠ²Π»Π΅Π½Π° ΡΡΠ»ΠΎΠ²ΠΈΡΠΌΠΈ ΡΠΊΡΠΏΠ»ΡΠ°ΡΠ°ΡΠΈΠΈ ΠΈ ΠΌΠ°ΡΠ΅ΡΠΈΠ°Π»ΠΎΠΌ, ΠΈΠ· ΠΊΠΎΡΠΎΡΠΎΠ³ΠΎ ΡΠ΄Π΅Π»Π°Π½Π° ΡΠΈΠ»ΡΠ΅ΡΠ°. ΠΠ΅ ΠΈΠ·Π³ΠΎΡΠ°Π²Π»ΠΈΠ²Π°ΡΡ ΠΈΠ· ΠΊΠ°ΡΠ΅ΡΡΠ²Π΅Π½Π½ΡΡ ΡΠ²Π΅ΡΠ΄ΡΡ ΡΠΏΠ»Π°Π²ΠΎΠ², ΠΊΠΎΡΠΎΡΡΠ΅ ΡΡΡΠΎΠΉΡΠΈΠ²Ρ ΠΊ ΠΈΡΡΠΈΡΠ°Π½ΠΈΡ, ΡΠ°ΡΠΊΠΎΠ»Ρ ΠΈ ΠΌΠ΅Ρ Π°Π½ΠΈΡΠ΅ΡΠΊΠΎΠΌΡ Π²ΠΎΠ·Π΄Π΅ΠΉΡΡΠ²ΠΈΡ. ΠΠ½ΡΡΡΡΠΌΠ΅Π½Ρ ΡΡΠ°Π½ΠΊΠ° ΡΡΠ»ΠΎΠ²Π½ΠΎ ΡΠ°Π·Π΄Π΅Π»Π΅Π½ Π½Π° ΡΠ΅ΡΡΡΠ΅ ΡΠ°Π±ΠΎΡΠΈΠ΅ Π·ΠΎΠ½Ρ:
- Π²Ρ ΠΎΠ΄Π½Π°Ρ;
- ΡΠΌΠ°Π·ΠΎΡΠ½Π°Ρ;
- Π΄Π΅ΡΠΎΡΠΌΠΈΡΡΡΡΠ°Ρ;
- ΠΊΠ°Π»ΠΈΠ±ΡΡΡΡΠ°Ρ.
ΠΠΎΠ»ΠΎΠΊΠΈ Π΄Π»Ρ Π²ΠΎΠ»ΠΎΡΠ΅Π½ΠΈΡ ΠΏΡΠΎΠ²ΠΎΠ»ΠΎΠΊΠΈ
ΠΠΎΠ»ΠΎΠΊΠΈ Π±ΡΠ²Π°ΡΡ ΠΌΠΎΠ½ΠΎΠ»ΠΈΡΠ½ΡΠΌΠΈ ΠΈ ΡΠΎΡΡΠ°Π²Π½ΡΠΌΠΈ ΠΈΠ· Π½Π΅ΡΠΊΠΎΠ»ΡΠΊΠΈΡ ΡΠΎΠΏΡΡΠΆΠ΅Π½Π½ΡΡ ΡΠ°ΡΡΠ΅ΠΉ. Π‘Π±ΠΎΡΠ½Π°Ρ ΠΊΠΎΠ½ΡΡΡΡΠΊΡΠΈΡ ΡΠΊΠΎΠ½ΠΎΠΌΠΈΡΠ½Π΅Π΅ ΠΌΠΎΠ½ΠΎΠ»ΠΈΡΠ½ΠΎΠ³ΠΎ ΠΌΠ΅Ρ Π°Π½ΠΈΠ·ΠΌΠ° ΠΏΠΎ ΡΠ°ΡΡ ΠΎΠ΄Ρ ΡΠ»Π΅ΠΊΡΡΠΎΡΠ½Π΅ΡΠ³ΠΈΠΈ.
ΠΠΎ Π²ΡΠ΅ΠΌΡ Π²ΠΎΠ»ΠΎΡΠ΅Π½ΠΈΡ ΠΏΡΠΎΠ²ΠΎΠ»ΠΎΠΊΡ ΡΠΊΠ»Π°Π΄ΡΠ²Π°ΡΡ Π² ΡΡΠ°Π»ΡΠ½ΡΡ ΠΎΠ±ΠΎΠΉΠΌΡ, ΠΊΠΎΡΠΎΡΠ°Ρ ΡΠ»ΡΠΆΠΈΡ ΠΈΠ·Π΄Π΅Π»ΠΈΡ Π·Π°ΡΠΈΡΠΎΠΉ ΠΎΡ ΠΈΠ·Π»ΠΈΡΠ½Π΅Π³ΠΎ ΡΠΆΠΈΠΌΠ°Π½ΠΈΡ.
ΠΠ° ΠΌΠ½ΠΎΠ³ΠΈΡ Π±ΠΎΠ»ΡΡΠΈΡ ΠΏΡΠ΅Π΄ΠΏΡΠΈΡΡΠΈΡΡ ΠΊΠ°Π»ΠΈΠ±ΡΠΎΠ²ΠΎΡΠ½ΡΠ΅ ΡΠ΅Ρ Π° ΠΎΡΠ½Π°ΡΠ΅Π½Ρ ΡΠ°Π·Π½ΠΎΠΏΠ»Π°Π½ΠΎΠ²ΡΠΌΠΈ ΡΡΠ°Π½ΠΊΠ°ΠΌΠΈ ΠΏΠΎΠ΄ Π²ΡΠ΅Π²ΠΎΠ·ΠΌΠΎΠΆΠ½ΡΠ΅ Π²ΠΈΠ΄Ρ ΠΏΡΠΎΠ΄ΡΠΊΡΠΈΠΈ.
Π£Π΄Π°Π»Π΅Π½ΠΈΠ΅ ΠΎΠΊΠ°Π»ΠΈΠ½Ρ
ΠΠΎΠ»ΠΎΡΠ΅Π½ΠΈΠ΅ ΠΏΡΠΎΠ²ΠΎΠ»ΠΎΠΊΠΈ Π±ΡΠ΄Π΅Ρ ΡΡΠΏΠ΅ΡΠ½ΡΠΌ ΠΏΡΠΈ ΡΡΠ»ΠΎΠ²ΠΈΠΈ ΠΊΠ°ΡΠ΅ΡΡΠ²Π΅Π½Π½ΠΎΠΉ ΠΎΠ±ΡΠ°Π±ΠΎΡΠΊΠΈ ΠΏΠΎΠ²Π΅ΡΡ Π½ΠΎΡΡΠΈ Π·Π°Π³ΠΎΡΠΎΠ²ΠΊΠΈ. Π£Π΄Π°Π»ΠΈΡΡ ΠΎΠΊΠ°Π»ΠΈΠ½Ρ Ρ ΠΏΠΎΠ²Π΅ΡΡ Π½ΠΎΡΡΠΈ ΠΌΠΎΠΆΠ½ΠΎ ΡΡΠ΅ΠΌΡ ΡΠΏΠΎΡΠΎΠ±Π°ΠΌΠΈ.
ΠΠ»Π΅ΠΊΡΡΠΎΡ ΠΈΠΌΠΈΡΠ΅ΡΠΊΠΈΠΉ
ΠΠ»ΠΈ ΡΠ»Π΅ΠΊΡΡΠΎΠ»ΠΈΡΠΈΡΠ΅ΡΠΊΠΈΠΉ ΠΌΠ΅ΡΠΎΠ΄ ΠΏΠΎΠ·Π²ΠΎΠ»ΡΠ΅Ρ ΡΠ²Π΅Π»ΠΈΡΠΈΡΡ ΡΠΊΠΎΡΠΎΡΡΡ ΡΠ½ΡΡΠΈΡ ΡΠΆΠ°Π²ΡΠΈΠ½Ρ ΠΈ ΠΎΠΊΠ°Π»ΠΈΠ½Ρ Ρ ΠΏΠΎΠ²Π΅ΡΡ Π½ΠΎΡΡΠΈ ΠΌΠ΅ΡΠ°Π»Π»Π° ΠΏΠΎΠ΄ Π²ΠΎΠ·Π΄Π΅ΠΉΡΡΠ²ΠΈΠ΅ΠΌ ΡΠ»Π΅ΠΊΡΡΠΈΡΠ΅ΡΠΊΠΎΠ³ΠΎ ΡΠΎΠΊΠ° ΠΈ ΡΠ°ΡΡΠ²ΠΎΡΠ° ΠΊΠΈΡΠ»ΠΎΡΡ. ΠΡΠΎΡΠ΅ΡΡΡ ΡΠ»Π΅ΠΊΡΡΠΎΡ ΠΈΠΌΠΈΡΠ΅ΡΠΊΠΎΠΉ ΠΎΠ±ΡΠ°Π±ΠΎΡΠΊΠΈ Π²ΠΊΠ»ΡΡΠ°ΡΡ Π² ΡΠ΅Π±Ρ Π΄Π²Π° Π²Π°ΡΠΈΠ°Π½ΡΠ°.
ΠΡΠΈΡΡΠΊΠ° Π΄Π΅ΡΠ°Π»Π΅ΠΉ ΠΎΡ ΡΠΆΠ°Π²ΡΠΈΠ½Ρ ΡΠ»Π΅ΠΊΡΡΠΎΡ ΠΈΠΌΠΈΡΠ΅ΡΠΊΠΈΠΌ ΡΠΏΠΎΡΠΎΠ±ΠΎΠΌ
ΠΠ½ΠΎΠ΄Π½ΡΠΉ β ΠΎΡΠ½ΠΎΠ²Π°Π½ Π½Π° ΡΠ°ΡΡΠ²ΠΎΡΠ΅Π½ΠΈΠΈ ΠΌΠ΅ΡΠ°Π»Π»Π° Π² ΠΊΠΎΠ½ΡΠ°ΠΊΡΠ΅ Ρ ΠΏΠΎΠ»ΠΎΠΆΠΈΡΠ΅Π»ΡΠ½ΡΠΌ ΠΏΠ»ΡΡΠΎΠΌ ΠΈΡΡΠΎΡΠ½ΠΈΠΊΠ° ΡΠΎΠΊΠ°. ΠΡΠ΄Π΅Π»ΡΡΡΠΈΠΉΡΡ ΠΊΠΈΡΠ»ΠΎΡΠΎΠ΄ ΡΠΏΠΎΡΠΎΠ±ΡΡΠ²ΡΠ΅Ρ ΠΌΠ΅Ρ Π°Π½ΠΈΡΠ΅ΡΠΊΠΎΠΌΡ ΠΎΡΡΡΠ²Π°Π½ΠΈΡ ΠΎΠΊΡΠΈΠ΄ΠΎΠ². ΠΡΠΈΠΌΠ΅Π½ΡΠ΅ΡΡΡ Π΄Π»Ρ Π»Π΅Π³ΠΈΡΠΎΠ²Π°Π½Π½ΠΎΠΉ ΠΈ ΡΠ³Π»Π΅ΡΠΎΠ΄ΠΈΡΡΠΎΠΉ ΡΡΠ°Π»ΠΈ Ρ ΡΠ΅Π»ΡΡ ΡΠ΄Π°Π»Π΅Π½ΠΈΡ ΡΠΎΠ½ΠΊΠΈΡ ΠΏΠ»Π΅Π½ΠΎΠΊ.
ΠΠ°ΡΠΎΠ΄Π½ΡΠΉ β ΠΎΠΊΡΠΈΠ΄Ρ ΠΆΠ΅Π»Π΅Π·Π° Π²ΠΎΡΡΡΠ°Π½Π°Π²Π»ΠΈΠ²Π°ΡΡΡΡ ΠΏΠΎΠ΄ Π²ΠΎΠ·Π΄Π΅ΠΉΡΡΠ²ΠΈΠ΅ΠΌ Π°ΡΠΎΠΌΠΎΠ² Π°ΠΊΡΠΈΠ²Π½ΠΎ ΠΎΠ±ΡΠ°Π·ΡΡΡΠ΅Π³ΠΎΡΡ Π²ΠΎΠ΄ΠΎΡΠΎΠ΄Π°. ΠΡΠΎ ΠΎΠΏΠ°ΡΠ½ΡΠΉ ΡΠΏΠΎΡΠΎΠ± ΠΏΠΎ ΡΡΠ°Π²Π½Π΅Π½ΠΈΡ Ρ ΠΏΡΠ΅Π΄ΡΠ΄ΡΡΠΈΠΌ, ΡΠ°ΠΊ ΠΊΠ°ΠΊ ΠΎΡΡΡΠ² ΠΎΠΊΠ°Π»ΠΈΠ½Ρ ΠΏΠ»ΠΎΡ ΠΎ ΠΊΠΎΠ½ΡΡΠΎΠ»ΠΈΡΡΠ΅ΡΡΡ, ΠΈ ΠΈΠ·Π΄Π΅Π»ΠΈΠ΅ ΠΎΠ±ΡΠ΅ΡΠ°Π΅Ρ ΡΡΠ°Π²ΠΈΠ»ΡΠ½ΡΡ Ρ ΡΡΠΏΠΊΠΎΡΡΡ.
Π₯ΠΈΠΌΠΈΡΠ΅ΡΠΊΠΈΠΉ ΡΠΏΠΎΡΠΎΠ±
ΠΠ΅Π·Π°ΠΌΠ΅Π½ΠΈΠΌ, ΠΊΠΎΠ³Π΄Π° Π² ΠΊΠ°ΡΠ΅ΡΡΠ²Π΅ ΡΡΡΡΡ ΠΈΡΠΏΠΎΠ»ΡΠ·ΡΠ΅ΡΡΡ ΠΊΠΈΡΠ»ΠΎΡΡΠΎΠΉΠΊΠ°Ρ ΡΡΠ°Π»Ρ. ΠΡΡΠ°ΡΠΊΠΈ ΡΠ»ΡΡΠΎΠ² ΠΈ ΠΎΠΊΠΈΡΠ»ΠΎΠ² ΡΠ΄Π°Π»ΡΡΡ Ρ ΠΏΠΎΠΌΠΎΡΡΡ ΡΠ°ΡΡΠ²ΠΎΡΠ° Ρ Π»ΠΎΡΠΈΡΡΡΡ ΡΠΎΠ»Π΅ΠΉ, ΡΠ΅Π»ΠΎΡΠΈ ΠΈΠ»ΠΈ ΠΊΠΈΡΠ»ΠΎΡΡ. ΠΡΠ±ΠΎΠ΅ Ρ ΠΈΠΌΠΈΡΠ΅ΡΠΊΠΎΠ΅ Π²Π΅ΡΠ΅ΡΡΠ²ΠΎ ΡΡΠ΅Π±ΡΠ΅Ρ ΡΠΏΠ΅ΡΠΈΠ°Π»ΡΠ½ΡΡ Π·Π½Π°Π½ΠΈΠΉ ΠΈ ΠΎΡΡΠΎΡΠΎΠΆΠ½ΠΎΠ³ΠΎ ΠΎΠ±ΡΠ°ΡΠ΅Π½ΠΈΡ.
Π’ΡΠ°Π΄ΠΈΡΠΈΠΎΠ½Π½ΠΎΠ΅ ΠΊΠΈΡΠ»ΠΎΡΠ½ΠΎΠ΅ ΡΡΠ°Π²Π»Π΅Π½ΠΈΠ΅ ΠΏΡΠ΅Π΄ΠΏΠΎΠ»Π°Π³Π°Π΅Ρ ΠΏΠΎΡΠ»Π΅Π΄ΠΎΠ²Π°ΡΠ΅Π»ΡΠ½ΡΡ ΠΎΠ±ΡΠ°Π±ΠΎΡΠΊΡ ΠΌΠ΅ΡΠ°Π»Π»Π° Π² Π΄Π²ΡΡ Π²Π°Π½Π½Π°Ρ β ΡΠ΅ΡΠ½ΠΎΠΊΠΈΡΠ»ΠΎΡΠ½ΠΎΠΉ ΠΈ Π°Π·ΠΎΡΠ½ΠΎΠΊΠΈΡΠ»ΠΎΡΠ½ΠΎΠΉ ΠΏΡΠΈ ΠΎΠΏΡΠ΅Π΄Π΅Π»Π΅Π½Π½ΠΎΠΉ ΡΠ΅ΠΌΠΏΠ΅ΡΠ°ΡΡΡΠ΅.
ΠΡΡΡ ΠΌΠ½ΠΎΠ³ΠΎ Π²Π°ΡΠΈΠ°Π½ΡΠΎΠ² ΡΡΠΎΠ³ΠΎ ΡΠΏΠΎΡΠΎΠ±Π°. ΠΡΠ±ΠΎΡ ΡΠ°ΡΡΠ²ΠΎΡΠ° ΠΈ ΡΡΠ»ΠΎΠ²ΠΈΡ ΠΎΠ±ΡΠ°Π±ΠΎΡΠΊΠΈ Π·Π°Π²ΠΈΡΡΡ ΠΎΡ ΡΠΎΡΡΠ°Π²Π° ΠΈ ΡΡΡΡΠΊΡΡΡΡ ΠΎΠΊΠΈΡΠ½ΠΎΠΉ ΠΏΠ»Π΅Π½ΠΊΠΈ.
ΠΠ΅Ρ Π°Π½ΠΈΡΠ΅ΡΠΊΠΈΠΉ
ΠΠΎΠ΄ΡΠ°Π·ΡΠΌΠ΅Π²Π°Π΅Ρ ΡΠ»ΠΈΡΠΎΠ²ΠΊΡ, Π³Π°Π»ΡΠΎΠ²ΠΊΡ, ΠΏΠΎΠ»ΠΈΡΠΎΠ²ΠΊΡ ΠΈ ΠΊΡΠ°ΡΠ΅Π²Π°Π½ΠΈΠ΅. Π ΠΎΡΠ½ΠΎΠ²Π΅ ΠΌΠ΅ΡΠΎΠ΄Π° Π»Π΅ΠΆΠ°Ρ ΡΠ°ΠΊΠΈΠ΅ ΠΏΡΠΎΡΠ΅ΡΡΡ:
- Π΄Π΅ΡΠΎΡΠΌΠ°ΡΠΈΡ ΠΈΠ·Π³ΠΈΠ±ΠΎΠΌ;
- ΡΠΊΡΡΡΠΈΠ²Π°Π½ΠΈΠ΅, ΡΠ°ΡΡΡΠΆΠ΅Π½ΠΈΠ΅;
- ΠΏΡΡΠΌΠΎΠ΅ Π²ΠΎΠ·Π΄Π΅ΠΉΡΡΠ²ΠΈΠ΅ Π½Π° ΠΏΠΎΠ²Π΅ΡΡ Π½ΠΎΡΡΡ ΠΈΠ·Π΄Π΅Π»ΠΈΡ ΡΠΏΠ΅ΡΠΈΠ°Π»ΡΠ½ΡΡ ΡΠ΅Π°Π³Π΅Π½ΡΠΎΠ² ΠΈΠ»ΠΈ Π°Π±ΡΠ°Π·ΠΈΠ²Π½ΡΡ ΠΌΠ°ΡΠ΅ΡΠΈΠ°Π»ΠΎΠ²;
- ΠΈΡΠΏΠΎΠ»ΡΠ·ΠΎΠ²Π°Π½ΠΈΠ΅ ΠΈΠ½ΡΡΡΡΠΌΠ΅Π½ΡΠΎΠ²: ΡΠ΅ΡΠΊΠΈ, ΠΈΠ³Π»ΠΎΡΠ΅Π·Ρ, ΠΌΠΈΠΊΡΠΎΡΠ΅Π·ΡΠΎΠ²ΡΠ΅ ΠΏΡΠΈΠ±ΠΎΡΡ.
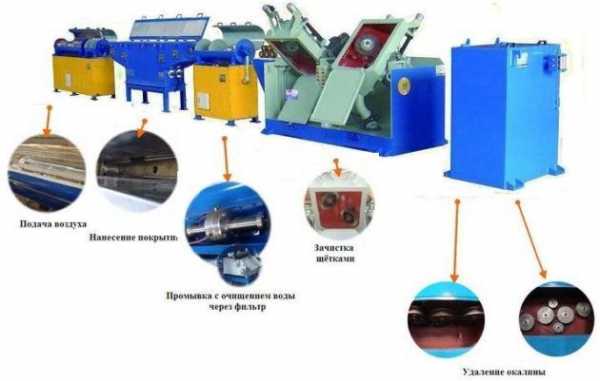
ΠΠ±ΠΎΡΡΠ΄ΠΎΠ²Π°Π½ΠΈΠ΅ Π΄Π»Ρ ΠΌΠ΅Ρ Π°Π½ΠΈΡΠ΅ΡΠΊΠΎΠ³ΠΎ ΡΠ΄Π°Π»Π΅Π½ΠΈΡ ΠΎΠΊΠ°Π»ΠΈΠ½Ρ Π½Π° ΠΏΡΠΎΠ²ΠΎΠ»ΠΎΠΊΠ΅
ΠΠΎΠΌΠ±ΠΈΠ½ΠΈΡΠΎΠ²Π°Π½Π½ΡΠΉ
Π‘ΠΏΠΎΡΠΎΠ± ΠΎΡΠ½ΠΎΠ²Π°Π½ Π½Π° ΠΏΡΠΈΠΌΠ΅Π½Π΅Π½ΠΈΠΈ Ρ ΠΈΠΌΠΈΡΠ΅ΡΠΊΠΎΠ³ΠΎ ΠΈ ΡΠ»Π΅ΠΊΡΡΠΎΡ ΠΈΠΌΠΈΡΠ΅ΡΠΊΠΎΠ³ΠΎ ΠΌΠ΅ΡΠΎΠ΄ΠΎΠ².
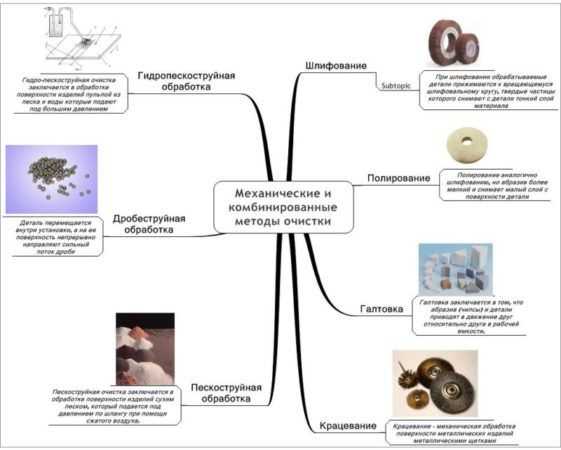
ΠΠ΅Ρ Π°Π½ΠΈΡΠ΅ΡΠΊΠΈΠ΅ ΠΈ ΠΊΠΎΠΌΠ±ΠΈΠ½ΠΈΡΠΎΠ²Π°Π½Π½ΡΠ΅ ΠΌΠ΅ΡΠΎΠ΄Ρ ΠΎΡΠΈΡΡΠΊΠΈ
ΠΡΠΎΠ±Π΅Π½Π½ΠΎΡΡΠΈ ΠΏΡΠΈ Π²ΠΎΠ»ΠΎΡΠ΅Π½ΠΈΠΈ ΠΌΠ΅Π΄Π½ΠΎΠΉ ΠΏΡΠΎΠ²ΠΎΠ»ΠΎΠΊΠΈ
ΠΠ·Π΄Π΅Π»ΠΈΡ, ΠΏΠΎΠ»ΡΡΠ΅Π½Π½ΡΠ΅ ΠΏΡΡΠ΅ΠΌ Π²ΠΎΠ»ΠΎΡΠ΅Π½ΠΈΡ Π½Π° ΡΡΠ°Π½ΠΊΠ°Ρ , Π½Π°Ρ ΠΎΠ΄ΡΡ ΡΠΈΡΠΎΠΊΠΎΠ΅ ΠΏΡΠΈΠΌΠ΅Π½Π΅Π½ΠΈΠ΅ Π² ΡΠ»Π΅ΠΊΡΡΠΎΠ½Π½ΠΎΠΉ ΠΈ ΡΠ»Π΅ΠΊΡΡΠΈΡΠ΅ΡΠΊΠΎΠΉ ΠΎΠ±Π»Π°ΡΡΡΡ . ΠΠ°ΠΊ ΠΏΡΠ°Π²ΠΈΠ»ΠΎ, ΠΈΡΠΏΠΎΠ»ΡΠ·ΡΡΡ ΠΏΡΠΎΠ²ΠΎΠ»ΠΎΠΊΡ ΡΠΎΠ»ΡΠΈΠ½ΠΎΠΉ ΠΎΡ 20 ΠΌΠΌ Π΄ΠΎ 10 ΠΌΠΊΠΌ.
ΠΠ·Π³ΠΎΡΠ°Π²Π»ΠΈΠ²Π°ΡΡ ΠΏΡΠΎΠ²ΠΎΠ»ΠΎΠΊΡ ΠΈΠ· ΠΌΠ΅Π΄ΠΈ ΡΠ»Π΅Π΄ΡΠ΅Ρ Π½Π° ΠΎΡΠ½ΠΎΠ²Π΅ Π»ΠΈΡΡΡ Π·Π°Π³ΠΎΡΠΎΠ²ΠΎΠΊ ΡΠΎΠΎΡΠ²Π΅ΡΡΡΠ²ΡΡΡΠ΅Π³ΠΎ ΠΏΡΠΎΡΠΈΠ»Ρ. ΠΡ ΠΏΠΎΠ΄Π²Π΅ΡΠ³Π°ΡΡ ΠΏΠ»Π°Π²Π»Π΅Π½ΠΈΡ, Π·Π°ΡΠ΅ΠΌ Π² Π³ΠΎΡΡΡΠ΅ΠΌ Π²ΠΈΠ΄Π΅ ΠΏΡΠΎΠΊΠ°ΡΡΠ²Π°ΡΡ. ΠΠΎΡΠΊΠΎΠ»ΡΠΊΡ ΠΏΡΠΎΡΠ΅Π΄ΡΡΠ° ΡΠΏΠΎΡΠΎΠ±ΡΡΠ²ΡΠ΅Ρ ΠΏΠΎΡΠ²Π»Π΅Π½ΠΈΡ ΡΠΎΠ½ΠΊΠΎΠΉ ΠΎΠΊΡΠΈΠ΄Π½ΠΎΠΉ ΠΏΠ»Π΅Π½ΠΊΠΈ, ΠΏΠ΅ΡΠ΅Π΄ Π²ΠΎΠ»ΠΎΡΠ΅Π½ΠΈΠ΅ΠΌ ΠΏΡΠΎΠ²ΠΎΠ»ΠΎΠΊΡ ΠΎΠ±ΡΠ°Π±Π°ΡΡΠ²Π°ΡΡ Π²ΠΎΠ΄Π½ΡΠΌ ΡΠ°ΡΡΠ²ΠΎΡΠΎΠΌ ΡΠ΅ΡΠ½ΠΎΠΉ ΠΊΠΈΡΠ»ΠΎΡΡ ΠΏΡΠΈ ΡΠ΅ΠΌΠΏΠ΅ΡΠ°ΡΡΡΠ΅ 45β50 0C.
ΠΡΠ½ΠΎΠ²Π½ΠΎΠΉ ΡΠ΅Ρ Π½ΠΎΠ»ΠΎΠ³ΠΈΡΠ΅ΡΠΊΠΈΠΉ ΠΏΡΠΎΡΠ΅ΡΡ ΡΠ°ΠΊΠΎΠΉ ΠΆΠ΅, ΠΊΠ°ΠΊ ΠΈ Π² ΠΏΡΠΎΠΈΠ·Π²ΠΎΠ΄ΡΡΠ²Π΅ ΠΏΡΠΎΠ΄ΡΠΊΡΠΈΠΈ ΠΈΠ· Π΄ΡΡΠ³ΠΈΡ ΠΌΠ΅ΡΠ°Π»Π»ΠΎΠ²:
- ΠΠ΅Π΄Π½ΡΡ Π·Π°Π³ΠΎΡΠΎΠ²ΠΊΡ ΠΎΡ Π»Π°ΠΆΠ΄Π°ΡΡ Π²ΠΎΠ·Π΄ΡΡ ΠΎΠΌ, Π²ΠΎΠ΄ΠΎΠΉ ΠΈΠ»ΠΈ ΡΠΏΠ΅ΡΠΈΠ°Π»ΡΠ½ΡΠΌ ΡΠ°ΡΡΠ²ΠΎΡΠΎΠΌ.
- ΠΠΎΠ²Π΅ΡΡ Π½ΠΎΡΡΡ ΡΠΌΠ°Π·ΡΠ²Π°ΡΡ ΠΌΡΠ»ΡΠ½ΠΎ-ΠΌΠ°ΡΠ»ΡΠ½ΠΎΠΉ ΡΠΌΡΠ»ΡΡΠΈΠ΅ΠΉ.
- ΠΠΎΠ»ΠΎΡΠ΅Π½ΠΈΠ΅ ΠΏΡΠΎΠ²ΠΎΠ»ΠΎΠΊΠΈ ΠΏΡΠΎΠ²ΠΎΠ΄ΡΡ Π½Π° 22-Ρ ΠΈ 18-ΠΊΡΠ°ΡΠ½ΡΡ ΡΡΠ°Π½ΠΊΠ°Ρ Ρ ΠΏΡΠΈΠΌΠ΅Π½Π΅Π½ΠΈΠ΅ΠΌ ΠΏΡΠΎΡΠ½ΠΎΠΉ Π°Π»ΠΌΠ°Π·Π½ΠΎΠΉ Π²ΠΎΠ»ΠΎΠΊΠΈ.
- Π ΠΏΡΠΎΡΠ΅ΡΡΠ΅ Π²ΡΡΡΠ³ΠΈΠ²Π°Π½ΠΈΡ Π·Π°Π³ΠΎΡΠΎΠ²ΠΊΠΈ ΠΈΡΠΏΠΎΠ»ΡΠ·ΡΡΡ Π²ΠΎΠ»ΠΎΠΊΠΈ, ΠΎΡΠ²Π΅ΡΡΡΠΈΡ ΠΊΠΎΡΠΎΡΡΡ ΡΠ΅ΡΠΊΠΎ ΡΠΎΠΎΡΠ²Π΅ΡΡΡΠ²ΡΡΡ Π΄ΠΈΠ°ΠΌΠ΅ΡΡΡ ΠΈΠ·Π΄Π΅Π»ΠΈΠΉ.
- Π Π°Π±ΠΎΡΠΈΠΉ ΠΈΠ½ΡΡΡΡΠΌΠ΅Π½Ρ ΠΌΠΎΠΆΠ΅Ρ ΠΈΠΌΠ΅ΡΡ ΠΎΠ΄Π½Ρ ΠΈΠ»ΠΈ Π½Π΅ΡΠΊΠΎΠ»ΡΠΊΠΎ ΠΌΠ°ΡΡΠΈΡ.
- ΠΠ·Π΄Π΅Π»ΠΈΡ Π΄ΠΈΠ°ΠΌΠ΅ΡΡΠΎΠΌ Π΄ΠΎ 0,05 ΠΌΠΌ ΠΎΡΡΠ°Π²Π»ΡΡΡ Π±Π΅Π· ΠΏΡΠΎΠΌΠ΅ΠΆΡΡΠΎΡΠ½ΠΎΠ³ΠΎ ΠΎΡΠΆΠΈΠ³Π°. Π Π½ΠΈΠΌ ΠΏΡΠΈΠΌΠ΅Π½ΡΠ΅ΡΡΡ ΡΠ΅Ρ Π½ΠΎΠ»ΠΎΠ³ΠΈΡ ΠΏΠΎΠ³ΡΡΠΆΠ½ΠΎΠ³ΠΎ ΡΠΎΡΠΌΠΎΠ²Π°Π½ΠΈΡ.
- ΠΠ»Ρ ΠΌΠ°ΠΊΡΠΈΠΌΠ°Π»ΡΠ½ΠΎ ΡΠΎΠ½ΠΊΠΎΠ³ΠΎ ΠΌΠ°ΡΠ΅ΡΠΈΠ°Π»Π° Π²Π°ΠΆΠ½ΠΎ ΠΏΡΠ°Π²ΠΈΠ»ΡΠ½ΠΎ ΠΏΠΎΠ΄ΠΎΠ±ΡΠ°ΡΡ ΡΠΌΠ°Π·ΠΎΡΠ½ΡΠΉ ΡΠΎΡΡΠ°Π². ΠΡΠΎ ΠΌΠΎΠ³ΡΡ Π±ΡΡΡ ΠΊΠΎΠΌΠΏΠ»Π΅ΠΊΡΠ½ΡΠ΅ Ρ ΠΈΠΌΠΈΡΠ΅ΡΠΊΠΈΠ΅ ΡΠ°ΡΡΠ²ΠΎΡΡ, ΡΠΌΡΠ»ΡΡΠΈΠΈ ΠΈΠ»ΠΈ ΡΠΈΠ½ΡΠ΅ΡΠΈΡΠ΅ΡΠΊΠΈΠ΅ Π²Π΅ΡΠ΅ΡΡΠ²Π°.
- ΠΡΠΈ Π½Π΅ΠΎΠ±Ρ ΠΎΠ΄ΠΈΠΌΠΎΡΡΠΈ ΠΌΠ΅Π΄Ρ ΠΏΠΎΠ΄Π²Π΅ΡΠ³Π°ΡΡ ΡΠ΅ΡΠΌΠΈΡΠ΅ΡΠΊΠΎΠΉ ΠΎΠ±ΡΠ°Π±ΠΎΡΠΊΠ΅ Π±Π΅Π·ΠΎΠΊΠΈΡΠ»ΠΈΡΠ΅Π»ΡΠ½ΠΎΠ³ΠΎ ΡΠΈΠΏΠ° Π² ΡΠΏΠ΅ΡΠΈΠ°Π»ΡΠ½ΡΡ ΡΠ»Π΅ΠΊΡΡΠΎΠΏΠ΅ΡΠ°Ρ , Π»ΠΈΡΠ΅Π½Π½ΡΡ Π΄ΠΎΡΡΡΠΏΠ° Π²ΠΎΠ·Π΄ΡΡ Π°.
- ΠΡΠΎΠΌΠ΅ ΡΡΠ°Π½Π΄Π°ΡΡΠ½ΠΎΠ³ΠΎ ΠΎΠ±ΠΎΡΡΠ΄ΠΎΠ²Π°Π½ΠΈΡ, Π΄Π»Ρ ΠΌΠ΅Π΄Π½ΡΡ Π·Π°Π³ΠΎΡΠΎΠ²ΠΎΠΊ ΠΌΠΎΠ³ΡΡ ΠΈΡΠΏΠΎΠ»ΡΠ·ΠΎΠ²Π°ΡΡΡΡ ΡΡΠ°Π½ΠΊΠΈ Ρ ΡΠΎΠ»ΠΈΠΊΠ°ΠΌΠΈ Π²ΠΌΠ΅ΡΡΠΎ ΠΎΡΠ²Π΅ΡΡΡΠΈΠΉ Π΄Π»Ρ ΠΏΡΠΎΡ ΠΎΠΆΠ΄Π΅Π½ΠΈΡ ΠΊΠ°ΡΠ°Π½ΠΊΠΈ.
- ΠΠ»Π°Π³ΠΎΠ΄Π°ΡΡ ΡΠ°ΠΊΠΎΠΉ ΡΠ΅Ρ Π½ΠΎΠ»ΠΎΠ³ΠΈΠΈ, Π³ΠΎΡΠΎΠ²ΡΠ΅ ΠΈΠ·Π΄Π΅Π»ΠΈΡ ΠΈΠΌΠ΅ΡΡ Π³Π»Π°Π΄ΠΊΡΡ Π±Π»Π΅ΡΡΡΡΡΡ ΠΏΠΎΠ²Π΅ΡΡ Π½ΠΎΡΡΡ ΠΈ ΡΠΎΠΎΡΠ²Π΅ΡΡΡΠ²ΡΡΡΠΈΠΉ Π΄ΠΈΠ°ΠΌΠ΅ΡΡ.
ΠΠ½ΠΎΠ³ΠΈΠ΅ ΠΏΡΠΎΠΌΡΡΠ»Π΅Π½Π½ΡΠ΅ ΠΏΡΠ΅Π΄ΠΏΡΠΈΡΡΠΈΡ ΡΠΊΡΠΏΠ»ΡΠ°ΡΠΈΡΡΡΡ ΡΡΠ°Π½ΠΊΠΈ Ρ ΡΠΎΠ²ΠΌΠ΅ΡΠ΅Π½ΠΈΠ΅ΠΌ ΠΎΠΏΠ΅ΡΠ°ΡΠΈΠΉ Π²ΠΎΠ»ΠΎΡΠ΅Π½ΠΈΡ ΠΈ ΠΎΡΠΆΠΈΠ³Π°. ΠΠ°Π½Π½ΡΠΉ ΠΌΠ΅ΡΠΎΠ΄ ΠΏΠΎΠ·Π²ΠΎΠ»ΡΠ΅Ρ Π½Π΅ ΡΠΎΠ»ΡΠΊΠΎ ΠΈΠ·Π³ΠΎΡΠ°Π²Π»ΠΈΠ²Π°ΡΡ ΠΏΡΠΎΠ²ΠΎΠ»ΠΎΠΊΡ ΠΈΠ· ΠΌΠ΅Π΄ΠΈ, Π½ΠΎ ΠΈ ΠΏΡΠΎΠΈΠ·Π²ΠΎΠ΄ΠΈΡΡ ΠΌΠ΅Π΄Π½ΡΠ΅ ΡΡΡΠ±Ρ.
ΠΠΈΠ΄Π΅ΠΎ ΠΏΠΎ ΡΠ΅ΠΌΠ΅:Β ΠΠΎΠ»ΠΎΡΠ΅Π½ΠΈΠ΅ ΠΏΡΠΎΠ²ΠΎΠ»ΠΎΠΊΠΈ β ΠΊΠ°ΠΊ ΡΡΠΎ ΠΏΡΠΎΠΈΡΡ ΠΎΠ΄ΠΈΡ
promzn.ru
1.4 ΠΡΠΎΠ΄ΡΠΊΡΠΈΡ, ΠΏΠΎΠ»ΡΡΠ°Π΅ΠΌΠ°Ρ Π²ΠΎΠ»ΠΎΡΠ΅Π½ΠΈΠ΅ΠΌ
ΠΠ²Π΅Π΄Π΅Π½ΠΈΠ΅
ΠΡΠΎΠΈΠ·Π²ΠΎΠ΄ΡΡΠ²ΠΎ ΠΌΠ΅ΡΠΈΠ·ΠΎΠ² ΡΠ²Π»ΡΠ΅ΡΡΡ ΡΠ°ΠΌΠΎΡΡΠΎΡΡΠ΅Π»ΡΠ½ΠΎΠΉ ΠΎΠ±Π»Π°ΡΡΡΡ ΠΌΠ΅ΡΠ°Π»Π»ΠΎΠΎΠ±ΡΠ°Π±ΠΎΡΠΊΠΈ. ΠΠ΅ΡΠΈΠ·Π°ΠΌΠΈ ΡΡΠ»ΠΎΠ²Π½ΠΎ ΠΏΡΠΈΠ½ΡΡΠΎ Π½Π°Π·ΡΠ²Π°ΡΡ Π³ΡΡΠΏΠΏΡ ΡΠΈΡΠΎΠΊΠΎ ΠΏΡΠΈΠΌΠ΅Π½ΡΠ΅ΠΌΡΡ Π² Π½Π°ΡΠΎΠ΄Π½ΠΎΠΌ Ρ ΠΎΠ·ΡΠΉΡΡΠ²Π΅ ΠΌΠ΅ΡΠ°Π»Π»ΠΈΡΠ΅ΡΠΊΠΈΡ ΠΈΠ·Π΄Π΅Π»ΠΈΠΉ ΠΏΡΠΎΠΌΡΡΠ»Π΅Π½Π½ΠΎΠ³ΠΎ Π½Π°Π·Π½Π°ΡΠ΅Π½ΠΈΡ, Π΄Π»Ρ ΠΈΠ·Π³ΠΎΡΠΎΠ²Π»Π΅Π½ΠΈΡ ΠΊΠΎΡΠΎΡΡΡ ΠΈΡΠΏΠΎΠ»ΡΠ·ΡΡΡ ΠΊΠ°ΡΠ°Π½ΠΊΡ, ΠΌΠ΅Π»ΠΊΠΎΡΠΎΡΡΠ½ΡΠΉ ΠΏΡΠΎΠΊΠ°Ρ, ΠΊΠ°Π»ΠΈΠ±ΡΠΎΠ²Π°Π½Π½ΡΠΉ ΠΌΠ΅ΡΠ°Π»Π», ΠΏΡΠΎΠ²ΠΎΠ»ΠΎΠΊΡ ΠΈ ΠΊΠ°ΡΠ°Π½ΡΠ΅ ΠΏΠΎΠ»ΠΎΡΡ. Π ΡΡΠΎΠΉ Π³ΡΡΠΏΠΏΠ΅ ΠΈΠ·Π΄Π΅Π»ΠΈΠΉ, ΠΎΡΠ½ΠΎΡΡΡΠ΅ΠΉΡΡ ΠΊ ΠΏΡΠΎΠ΄ΡΠΊΡΠΈΠΈ ΡΠ΅ΡΠ²Π΅ΡΡΠΎΠ³ΠΎ ΠΏΠ΅ΡΠ΅Π΄Π΅Π»Π° ΡΠ΅ΡΠ½ΠΎΠΉ ΠΌΠ΅ΡΠ°Π»Π»ΡΡΠ³ΠΈΠΈ (ΡΡΠΈΡΠ°Ρ ΠΏΠ΅ΡΠ²ΡΠΌ — ΠΏΡΠΎΠΈΠ·Π²ΠΎΠ΄ΡΡΠ²ΠΎ ΡΡΠ³ΡΠ½Π°, Π²ΡΠΎΡΡΠΌ β ΡΡΠ°Π»ΠΈ, ΡΡΠ΅ΡΡΠΈΠΌ β ΠΏΡΠΎΠΊΠ°ΡΠ°), ΠΎΡΠ½ΠΎΡΡΡΡΡ: ΠΏΡΠΎΠ²ΠΎΠ»ΠΎΠΊΠ°, ΠΊΠ°Π½Π°ΡΠ½ΡΠ΅ ΠΈΠ·Π΄Π΅Π»ΠΈΡ, ΠΌΠ΅ΡΠ°Π»Π»ΠΎΠΊΠΎΡΠ΄, Π²ΠΈΡΠ°Ρ Π°ΡΠΌΠ°ΡΡΡΠ°, ΠΌΠ΅ΡΠ°Π»Π»ΠΈΡΠ΅ΡΠΊΠΈΠ΅ ΡΠ΅ΡΠΊΠΈ, ΠΊΡΠ΅ΠΏΠ΅ΠΆΠ½ΡΠ΅ ΠΈΠ·Π΄Π΅Π»ΠΈΡ ΠΈ Π΄Ρ.
ΠΠ±ΡΠ°Π±ΠΎΡΠΊΠ° ΠΌΠ΅ΡΠ°Π»Π»Π° Π²ΠΎΠ»ΠΎΡΠ΅Π½ΠΈΠ΅ΠΌ, Ρ.Π΅. ΠΏΡΠΎΡΡΠ³ΠΈΠ²Π°Π½ΠΈΠ΅ Π·Π°Π³ΠΎΡΠΎΠ²ΠΊΠΈ ΡΠ΅ΡΠ΅Π· ΠΎΡΠ²Π΅ΡΡΡΠΈΠ΅, Π²ΡΡ ΠΎΠ΄Π½ΡΠ΅ ΡΠ°Π·ΠΌΠ΅ΡΡ ΠΊΠΎΡΠΎΡΠΎΠ³ΠΎ ΠΌΠ΅Π½ΡΡΠ΅, ΡΠ΅ΠΌ ΠΈΡΡ ΠΎΠ΄Π½ΠΎΠ΅ ΡΠ΅ΡΠ΅Π½ΠΈΠ΅ Π·Π°Π³ΠΎΡΠΎΠ²ΠΊΠΈ, Π½Π°Ρ ΠΎΠ΄ΠΈΡ ΡΠ°ΠΌΠΎΠ΅ ΡΠΈΡΠΎΠΊΠΎΠ΅ ΠΏΡΠΈΠΌΠ΅Π½Π΅Π½ΠΈΠ΅ Π² ΡΠ°Π·Π»ΠΈΡΠ½ΡΡ ΠΎΡΡΠ°ΡΠ»ΡΡ ΠΏΡΠΎΠΌΡΡΠ»Π΅Π½Π½ΠΎΡΡΠΈ. ΠΠ·Π΄Π΅Π»ΠΈΡ, ΠΏΠΎΠ»ΡΡΠ°Π΅ΠΌΡΠ΅ Π²ΠΎΠ»ΠΎΡΠ΅Π½ΠΈΠ΅ΠΌ, ΠΎΠ±Π»Π°Π΄Π°ΡΡ Π²ΡΡΠΎΠΊΠΈΠΌ ΠΊΠ°ΡΠ΅ΡΡΠ²ΠΎΠΌ ΠΏΠΎΠ²Π΅ΡΡ Π½ΠΎΡΡΠΈ ΠΈ Π²ΡΡΠΎΠΊΠΎΠΉ ΡΠΎΡΠ½ΠΎΡΡΡΡ ΡΠ°Π·ΠΌΠ΅ΡΠΎΠ² ΠΏΠΎΠΏΠ΅ΡΠ΅ΡΠ½ΠΎΠ³ΠΎ ΡΠ΅ΡΠ΅Π½ΠΈΡ.
ΠΠΎΠ»ΠΎΡΠ΅Π½ΠΈΠ΅ Π²ΡΠ³ΠΎΠ΄Π½ΠΎ ΠΎΡΠ»ΠΈΡΠ°Π΅ΡΡΡ ΠΎΡ ΠΌΠ΅Ρ Π°Π½ΠΈΡΠ΅ΡΠΊΠΎΠΉ ΠΎΠ±ΡΠ°Π±ΠΎΡΠΊΠΈ ΠΌΠ΅ΡΠ°Π»Π»Π° ΡΠ΅Π·Π°Π½ΠΈΠ΅ΠΌ (ΡΡΡΠΎΠ³Π°Π½ΠΈΠ΅ΠΌ), ΡΡΠ΅Π·Π΅ΡΠΎΠ²Π°Π½ΠΈΠ΅ΠΌ, ΠΎΠ±ΡΠΎΡΠΊΠΎΠΉ ΠΈ ΠΏΡ., ΡΠ°ΠΊ ΠΊΠ°ΠΊ ΠΏΡΠΈ ΡΡΠΎΠΌ ΠΎΡΡΡΡΡΡΠ²ΡΡΡ ΠΎΡΡ ΠΎΠ΄Ρ ΠΌΠ΅ΡΠ°Π»Π»Π° Π² Π²ΠΈΠ΄Π΅ ΡΡΡΡΠΆΠΊΠΈ, Π° ΡΠ°ΠΌ ΠΏΡΠΎΡΠ΅ΡΡ Π·Π°ΠΌΠ΅ΡΠ½ΠΎ ΠΏΡΠΎΠΈΠ·Π²ΠΎΠ΄ΠΈΡΠ΅Π»ΡΠ½Π΅Π΅ ΠΈ ΠΌΠ΅Π½Π΅Π΅ ΡΡΡΠ΄ΠΎΠ΅ΠΌΠΎΠΊ.
ΠΠΎΠ»ΠΎΡΠ΅Π½ΠΈΠ΅ ΠΏΡΠ΅Π΄ΡΡΠ°Π²Π»ΡΠ΅Ρ ΡΠΎΠ±ΠΎΠΉ ΠΎΠ΄ΠΈΠ½ ΠΈΠ· Π΄ΡΠ΅Π²Π½Π΅ΠΉΡΠΈΡ ΡΠΏΠΎΡΠΎΠ±ΠΎΠ² ΠΎΠ±ΡΠ°Π±ΠΎΡΠΊΠΈ ΠΌΠ΅ΡΠ°Π»Π»Π° Π΄Π°Π²Π»Π΅Π½ΠΈΠ΅ΠΌ. ΠΠΏΠ΅ΡΠ²ΡΠ΅ Π²ΠΎΠ»ΠΎΡΠ΅Π½ΠΈΠ΅ Π½Π°ΡΠ°Π»ΠΈ ΠΏΡΠΈΠΌΠ΅Π½ΡΡΡ 3-3,5 ΡΡΡ. Π»Π΅Ρ Π΄ΠΎ Π½Π°ΡΠ΅ΠΉ ΡΡΡ. Π Π½Π°ΡΠ°Π»Π΅ XYIII Π²Π΅ΠΊΠ° Π½Π° Π·Π°Π²ΠΎΠ΄Π°Ρ Π£ΡΠ°Π»Π° ΡΠ°Π±ΠΎΡΠ°Π»ΠΎ 16 Π²ΠΎΠ»ΠΎΡΠΈΠ»ΡΠ½ΡΡ ΡΡΠ°Π½ΠΎΠ² ΠΎΡ Π²ΠΎΠ΄ΡΠ½ΠΎΠ³ΠΎ ΠΏΡΠΈΠ²ΠΎΠ΄Π°, Π²ΡΠΏΡΡΠΊΠ°Π²ΡΠΈΡ ΠΎΠΊΠΎΠ»ΠΎ 45 ΡΠΎΠ½Π½ ΠΆΠ΅Π»Π΅Π·Π½ΠΎΠΉ ΠΏΡΠΎΠ²ΠΎΠ»ΠΎΠΊΠΈ Π² Π³ΠΎΠ΄. Π 1838 Π³ΠΎΠ΄Ρ Π²ΠΏΠ΅ΡΠ²ΡΠ΅ Π±ΡΠ»ΠΎ ΠΏΡΠΈΠΌΠ΅Π½Π΅Π½ΠΎ ΠΌΠ½ΠΎΠ³ΠΎΠΊΡΠ°ΡΠ½ΠΎΠ΅ Π²ΠΎΠ»ΠΎΡΠ΅Π½ΠΈΠ΅ Π½Π° Π±ΠΎΠ»ΡΡΠΈΡ ΡΠΊΠΎΡΠΎΡΡΡΡ 30-60 ΠΌ/ΠΌΠΈΠ½. Π 1922 Π³ΠΎΠ΄Ρ Π½Π° ΠΠ΅Π»ΠΎΡΠ΅ΡΠΊΠΎΠΌ ΡΡΠ°Π»Π΅ΠΏΡΠΎΠ²ΠΎΠ»ΠΎΡΠ½ΠΎ-ΠΊΠ°Π½Π°ΡΠ½ΠΎΠΌ Π·Π°Π²ΠΎΠ΄Π΅ Π±ΡΠ» Π²Π½Π΅Π΄ΡΠ΅Π½ ΡΠΏΠ΅ΡΠΈΠ°Π»ΡΠ½ΡΠΉ Π²ΠΈΠ΄ ΡΠ΅ΡΠΌΠΈΡΠ΅ΡΠΊΠΎΠΉ ΠΎΠ±ΡΠ°Π±ΠΎΡΠΊΠΈ ΠΊΠ°ΡΠ°Π½ΠΊΠΈ — ΠΏΠ°ΡΠ΅Π½ΡΠΈΡΠΎΠ²Π°Π½ΠΈΠ΅, Ρ ΠΏΠΎΠΌΠΎΡΡΡ ΠΊΠΎΡΠΎΡΠΎΠ³ΠΎ Π±ΡΠ»Π° ΠΏΠΎΠ»ΡΡΠ΅Π½Π° ΠΏΡΠΎΡΠ½Π°Ρ ΡΡΠ°Π»ΡΠ½Π°Ρ ΠΏΡΠΎΠ²ΠΎΠ»ΠΎΠΊΠ°. ΠΠ΅ΡΠ΅Ρ ΠΎΠ΄ ΠΎΡ Π²ΠΎΠ»ΠΎΡΠ΅Π½ΠΈΡ Π½Π° ΠΎΠ΄Π½ΠΎΠΊΡΠ°ΡΠ½ΡΡ ΠΌΠ°ΡΠΈΠ½Π°Ρ ΠΊ Π²ΠΎΠ»ΠΎΡΠ΅Π½ΠΈΡ Π½Π° ΠΌΠ½ΠΎΠ³ΠΎΠΊΡΠ°ΡΠ½ΡΡ ΡΡΠ°Π½Π°Ρ ΠΏΠΎΠ·Π²ΠΎΠ»ΠΈΠ» Π·Π½Π°ΡΠΈΡΠ΅Π»ΡΠ½ΠΎ ΠΏΠΎΠ΄Π½ΡΡΡ ΠΏΡΠΎΠΈΠ·Π²ΠΎΠ΄ΠΈΡΠ΅Π»ΡΠ½ΠΎΡΡΡ. Π‘ΠΊΠΎΡΠΎΡΡΡ Π²ΠΎΠ»ΠΎΡΠ΅Π½ΠΈΡ Π²ΠΎΠ·ΡΠΎΡΠ»Π° Π±ΠΎΠ»Π΅Π΅ ΡΠ΅ΠΌ Π² 15 ΡΠ°Π·.
Π‘ΡΠ°Π»Π΅ΠΏΡΠΎΠ²ΠΎΠ»ΠΎΡΠ½ΠΎΠ΅ ΠΏΡΠΎΠΈΠ·Π²ΠΎΠ΄ΡΡΠ²ΠΎ ΡΠ΅Ρ Π½ΠΈΡΠ΅ΡΠΊΠΈ ΠΏΠΎΡΡΠΎΡΠ½Π½ΠΎ ΡΠΎΠ²Π΅ΡΡΠ΅Π½ΡΡΠ²ΡΠ΅ΡΡΡ. ΠΠ·ΠΌΠ΅Π½Π΅Π½Π° ΡΡΡΡΠΊΡΡΡΠ° ΠΏΡΠΎΠΈΠ·Π²ΠΎΠ΄ΡΡΠ²Π°: ΡΠ²Π΅Π»ΠΈΡΠ΅Π½Π° Π΄ΠΎΠ»Ρ Π²ΡΠΏΡΡΠΊΠ° ΠΏΡΠΎΠ²ΠΎΠ»ΠΎΠΊΠΈ ΠΎΡΠ²Π΅ΡΡΡΠ²Π΅Π½Π½ΠΎΠ³ΠΎ Π½Π°Π·Π½Π°ΡΠ΅Π½ΠΈΡ, Π±ΠΎΠ»Π΅Π΅ ΡΠΎΠ½ΠΊΠΎΠΉ ΠΈ ΠΏΡΠΎΡΠ½ΠΎΠΉ. ΠΡΠ²ΠΎΠ΅Π½Ρ Π²ΡΡΠΎΠΊΠΈΠ΅ ΡΠΊΠΎΡΠΎΡΡΠΈ Π²ΠΎΠ»ΠΎΡΠ΅Π½ΠΈΡ.
ΠΡΠΎΠ²ΠΎΠ»ΠΎΠΊΡ ΠΎΡΠ½ΠΎΠ²Π½ΠΎΠ³ΠΎ ΡΠΎΡΡΠ°ΠΌΠ΅Π½ΡΠ° ΠΏΡΠΎΠΈΠ·Π²ΠΎΠ΄ΡΡ ΠΏΠΎ ΡΠΎΠ²ΡΠ΅ΠΌΠ΅Π½Π½ΡΠΌ, Π΄ΠΎΡΡΠ°ΡΠΎΡΠ½ΠΎ ΡΡΡΠ΅ΠΊΡΠΈΠ²Π½ΡΠΌ ΡΠ΅Ρ Π½ΠΎΠ»ΠΎΠ³ΠΈΡΠ΅ΡΠΊΠΈΠΌ ΡΡ Π΅ΠΌΠ°ΠΌ Π½Π° Π²ΡΡΠΎΠΊΠΎΠΏΡΠΎΠΈΠ·Π²ΠΎΠ΄ΠΈΡΠ΅Π»ΡΠ½ΠΎΠΌ ΠΎΠ±ΠΎΡΡΠ΄ΠΎΠ²Π°Π½ΠΈΠΈ. Π‘ΡΠ°Π»Π΅ΠΏΡΠΎΠ²ΠΎΠ»ΠΎΡΠ½ΠΎΠ΅ ΠΏΡΠΎΠΈΠ·Π²ΠΎΠ΄ΡΡΠ²ΠΎ ΠΎΡΠ½Π°ΡΠ΅Π½ΠΎ ΠΏΠΎΡΠΎΡΠ½ΡΠΌΠΈ Π°Π³ΡΠ΅Π³Π°ΡΠ°ΠΌΠΈ, Π½Π° ΠΊΠΎΡΠΎΡΡΡ ΡΠΎΠ²ΠΌΠ΅ΡΠ΅Π½Ρ ΠΎΠΏΠ΅ΡΠ°ΡΠΈΠΈ ΡΠ΅ΡΠΌΠΈΡΠ΅ΡΠΊΠΎΠΉ ΠΎΠ±ΡΠ°Π±ΠΎΡΠΊΠΈ ΠΈ ΠΏΠΎΠ΄Π³ΠΎΡΠΎΠ²ΠΊΠΈ ΠΏΠΎΠ²Π΅ΡΡ Π½ΠΎΡΡΠΈ, Π²ΠΊΠ»ΡΡΠ°Ρ Π½Π°Π½Π΅ΡΠ΅Π½ΠΈΠ΅ ΠΌΠ΅ΡΠ°Π»Π»ΠΈΡΠ΅ΡΠΊΠΈΡ ΠΏΠΎΠΊΡΡΡΠΈΠΉ.
ΠΠ΅ΡΠΈΠ·Π½Π°Ρ ΠΏΡΠΎΠΌΡΡΠ»Π΅Π½Π½ΠΎΡΡΡ ΠΎΠ±Π΅ΡΠΏΠ΅ΡΠΈΠ²Π°Π΅Ρ ΠΏΠ΅ΡΠ΅ΡΠ°Π±ΠΎΡΠΊΡ 90-95% ΠΏΡΠΎΠΈΠ·Π²ΠΎΠ΄ΠΈΠΌΠΎΠΉ ΠΊΠ°ΡΠ°Π½ΠΊΠΈ Π² ΠΏΡΠΎΠ²ΠΎΠ»ΠΎΠΊΡ. ΠΠ°ΡΡΠ΄Ρ Ρ ΠΏΠΎΠ²ΡΡΠ΅Π½ΠΈΠ΅ΠΌ ΠΏΡΠΎΡΠ½ΠΎΡΡΠΈ ΠΏΡΠΎΠ²ΠΎΠ»ΠΎΠΊΠΈ ΠΈ ΡΠ½ΠΈΠΆΠ΅Π½ΠΈΠ΅ΠΌ Π²Π΅Π»ΠΈΡΠΈΠ½Ρ Π΅Π΅ ΠΏΠ»ΡΡΠΎΠ²ΡΡ Π΄ΠΎΠΏΡΡΠΊΠΎΠ² Π½Π° Π΄ΠΈΠ°ΠΌΠ΅ΡΡ Π·Π½Π°ΡΠΈΡΠ΅Π»ΡΠ½ΠΎ ΡΠΊΠΎΠ½ΠΎΠΌΠΈΡΡΡ ΠΌΠ΅ΡΠ°Π»Π». ΠΡΠΎΠΌΡ ΠΆΠ΅ ΡΠΏΠΎΡΠΎΠ±ΡΡΠ²ΡΠ΅Ρ ΡΠ²Π΅Π»ΠΈΡΠ΅Π½ΠΈΠ΅ Π΄ΠΎΠ»ΠΈ Π²ΡΠΏΡΡΠΊΠ° ΠΏΡΠΎΠ²ΠΎΠ»ΠΎΠΊΠΈ Ρ Π·Π°ΡΠΈΡΠ½ΡΠΌΠΈ ΠΏΠΎΠΊΡΡΡΠΈΡΠΌΠΈ ΠΈ Ρ ΡΠ°ΡΠΎΠ½Π½ΡΠΌ ΠΏΠΎΠΏΠ΅ΡΠ΅ΡΠ½ΡΠΌ ΡΠ΅ΡΠ΅Π½ΠΈΠ΅ΠΌ Π²ΠΌΠ΅ΡΡΠΎ ΠΊΡΡΠ³Π»ΠΎΠΉ, ΡΡΠΎ ΠΏΠΎΠ·Π²ΠΎΠ»ΡΠ΅Ρ ΡΠ½ΠΈΠ·ΠΈΡΡ ΠΌΠ°ΡΡΡ ΡΠ°ΠΌΠΎΠ³ΠΎ ΠΈΠ·Π΄Π΅Π»ΠΈΡ ΠΈ Π²ΡΠ΅ΠΉ ΠΏΠΎΡΡΠ΅Π±Π»ΡΠ΅ΠΌΠΎΠΉ ΠΏΡΠΎΠ²ΠΎΠ»ΠΎΠΊΠΈ.
ΠΠΠ Β«Π§Π‘ΠΠΒ» ΡΠ²Π»ΡΠ΅ΡΡΡ ΠΊΡΡΠΏΠ½ΡΠΌ ΠΏΡΠ΅Π΄ΠΏΡΠΈΡΡΠΈΠ΅ΠΌ ΠΌΠ΅ΡΠΈΠ·Π½ΠΎΠΉ ΠΏΡΠΎΠΌΡΡΠ»Π΅Π½Π½ΠΎΡΡΠΈ, Π² Π½ΠΎΠΌΠ΅Π½ΠΊΠ»Π°ΡΡΡΠ΅ ΠΈΠ·Π΄Π΅Π»ΠΈΠΉ ΠΊΠΎΡΠΎΡΠΎΠ³ΠΎ ΠΏΡΠ΅Π΄ΡΡΠ°Π²Π»Π΅Π½Π° ΡΠΈΡΠΎΠΊΠ°Ρ Π³Π°ΠΌΠΌΠ° ΠΌΠ΅ΡΠΈΠ·ΠΎΠ². Π Π½Π°ΡΡΠΎΡΡΠ΅Π΅ Π²ΡΠ΅ΠΌΡ Π΄ΠΎΠ»Ρ Β«Π§Π‘ΠΠΒ» Π² ΠΎΡΠ³ΡΡΠ·ΠΊΠ΅ ΡΠΎΠ²Π°ΡΠ½ΠΎΠΉ ΠΏΡΠΎΠ΄ΡΠΊΡΠΈΠΈ ΡΡΠ΅Π΄ΠΈ ΠΏΡΠ΅Π΄ΠΏΡΠΈΡΡΠΈΠΉ Π°ΡΡΠΎΡΠΈΠ°ΡΠΈΠΈ Β«ΠΡΠΎΠΌΠΌΠ΅ΡΠΈΠ·Β» ΡΠΎΡΡΠ°Π²Π»ΡΠ΅Ρ 38%.
30 Π΄Π΅ΠΊΠ°Π±ΡΡ 1967 Π³ΠΎΠ΄Π° Π±ΡΠ» ΠΈΠ·Π΄Π°Π½ ΠΏΡΠΈΠΊΠ°Π· ΠΠΈΠ½ΠΈΡΡΠ΅ΡΡΡΠ²Π° ΡΠ΅ΡΠ½ΠΎΠΉ ΠΌΠ΅ΡΠ°Π»Π»ΡΡΠ³ΠΈΠΈ Π‘Π‘Π‘Π ΠΎ ΡΠΎΠ·Π΄Π°Π½ΠΈΠΈ Π§Π΅ΡΠ΅ΠΏΠΎΠ²Π΅ΡΠΊΠΎΠ³ΠΎ ΡΡΠ°Π»Π΅ΠΏΡΠΎΠΊΠ°ΡΠ½ΠΎΠ³ΠΎ Π·Π°Π²ΠΎΠ΄Π° Π½Π° Π±Π°Π·Π΅ Π²ΡΠ²Π΅Π΄Π΅Π½Π½ΠΎΠ³ΠΎ ΠΈΠ· ΡΠΎΡΡΠ°Π²Π° ΠΌΠ΅ΡΠ°Π»Π»ΡΡΠ³ΠΈΡΠ΅ΡΠΊΠΎΠ³ΠΎ Π·Π°Π²ΠΎΠ΄Π° ΠΌΠ΅ΡΠΈΠ·Π½ΠΎΠ³ΠΎ ΠΏΡΠΎΠΈΠ·Π²ΠΎΠ΄ΡΡΠ²Π°.
Π Π½Π°ΡΡΠΎΡΡΠ΅Π΅ Π²ΡΠ΅ΠΌΡ ΠΠΠ Β«Π§Π‘ΠΠΒ» ΡΠ°Π·Π΄Π΅Π»Π΅Π½ΠΎ Π½Π° ΡΡΠΈ Π±ΠΎΠ»ΡΡΠΈΡ ΠΏΡΠΎΠΈΠ·Π²ΠΎΠ΄ΡΡΠ²Π°:
ΠΌΠ΅ΡΠΈΠ·Π½ΠΎΠ΅ ΠΏΡΠΎΠΈΠ·Π²ΠΎΠ΄ΡΡΠ²ΠΎ Π² ΡΠΎΡΡΠ°Π²Π΅ ΡΡΠ°Π»Π΅ΠΏΡΠΎΠ²ΠΎΠ»ΠΎΡΠ½ΠΎΠ³ΠΎ ΡΠ΅Ρ Π° β 1 ΠΌΠΎΡΠ½ΠΎΡΡΡΡ 450 ΡΡΡ. ΡΠΎΠ½Π½ ΠΏΡΠΎΠ²ΠΎΠ»ΠΎΠΊΠΈ Π² Π³ΠΎΠ΄; Π³Π²ΠΎΠ·Π΄ΠΈΠ»ΡΠ½ΠΎΠ³ΠΎ ΡΠ΅Ρ Π° ΠΌΠΎΡΠ½ΠΎΡΡΡΡ 70 ΡΡΡ. ΡΠΎΠ½Π½ Π³Π²ΠΎΠ·Π΄Π΅ΠΉ Π² Π³ΠΎΠ΄; ΡΠ΅Ρ Π° ΠΌΠ΅ΡΠ°Π»Π»ΠΈΡΠ΅ΡΠΊΠΈΡ ΡΠ΅ΡΠΎΠΊ ΠΌΠΎΡΠ½ΠΎΡΡΡΡ 30 ΡΡΡ. ΡΠΎΠ½Π½ ΡΠ΅ΡΠΊΠΈ ΠΈ ΡΠ΅ΡΡΠ°ΡΡΡ ΠΊΠΎΠ½ΡΡΡΡΠΊΡΠΈΠΉ Π² Π³ΠΎΠ΄; ΡΠ»Π΅ΠΊΡΡΠΎΠ΄Π½ΠΎΠ³ΠΎ ΡΠ΅Ρ Π° ΠΌΠΎΡΠ½ΠΎΡΡΡΡ 66 ΡΡΡ. ΡΠΎΠ½Π½ ΡΠ»Π΅ΠΊΡΡΠΎΠ΄ΠΎΠ² ΠΈ ΠΏΠΎΡΠΎΡΠΊΠΎΠ²ΠΎΠΉ ΠΏΡΠΎΠ²ΠΎΠ»ΠΎΠΊΠΈ Π² Π³ΠΎΠ΄;
ΠΊΠ°Π»ΠΈΠ±ΡΠΎΠ²ΠΎΡΠ½ΠΎΠ΅ ΠΏΡΠΎΠΈΠ·Π²ΠΎΠ΄ΡΡΠ²ΠΎ Π² ΡΠΎΡΡΠ°Π²Π΅ ΠΊΠ°Π»ΠΈΠ±ΡΠΎΠ²ΠΎΡΠ½ΠΎΠ³ΠΎ ΡΠ΅Ρ Π° ΠΌΠΎΡΠ½ΠΎΡΡΡΡ 500 ΡΡΡ. ΡΠΎΠ½Π½ ΠΊΠ°Π»ΠΈΠ±ΡΠΎΠ²Π°Π½Π½ΠΎΠ³ΠΎ ΠΌΠ΅ΡΠ°Π»Π»Π° Π² Π³ΠΎΠ΄; ΠΊΡΠ΅ΠΏΠ΅ΠΆΠ½ΠΎΠ³ΠΎ ΡΠ΅Ρ Π° ΠΌΠΎΡΠ½ΠΎΡΡΡΡ 15 ΡΡΡ. ΡΠΎΠ½Π½ ΠΊΡΠ΅ΠΏΠ΅ΠΆΠ° Π² Π³ΠΎΠ΄; ΡΠ΅Ρ Π° ΡΡΠ°Π»ΡΠ½ΡΡ ΡΠ°ΡΠΎΠ½Π½ΡΡ ΠΏΡΠΎΡΠΈΠ»Π΅ΠΉ ΠΌΠΎΡΠ½ΠΎΡΡΡΡ 20 ΡΡΡ. ΡΠΎΠ½Π½ ΡΠ°ΡΠΎΠ½Π½ΡΡ ΠΏΡΠΎΡΠΈΠ»Π΅ΠΉ Π² Π³ΠΎΠ΄;
ΡΡΠ°Π»Π΅ΠΏΡΠΎΠ²ΠΎΠ»ΠΎΡΠ½ΠΎ-ΠΊΠ°Π½Π°ΡΠ½ΠΎΠ΅ ΠΏΡΠΎΠΈΠ·Π²ΠΎΠ΄ΡΡΠ²ΠΎ Π² ΡΠΎΡΡΠ°Π²Π΅ ΡΡΠ°Π»Π΅ΠΏΡΠΎΠ²ΠΎΠ»ΠΎΡΠ½ΠΎΠ³ΠΎ ΡΠ΅Ρ Π° β 2 ΠΌΠΎΡΠ½ΠΎΡΡΡΡ 120 ΡΡΡ. ΡΠΎΠ½Π½ ΠΏΡΠΎΠ²ΠΎΠ»ΠΎΠΊΠΈ Π² Π³ΠΎΠ΄ ΠΈ ΠΊΠ°Π½Π°ΡΠ½ΠΎΠ³ΠΎ ΡΠ΅Ρ Π° ΠΌΠΎΡΠ½ΠΎΡΡΡΡ 75 ΡΡΡ. ΡΠΎΠ½Π½ ΡΡΠ°Π»ΡΠ½ΡΡ ΠΈ Π°ΡΠΌΠ°ΡΡΡΠ½ΡΡ ΠΊΠ°Π½Π°ΡΠΎΠ² Π² Π³ΠΎΠ΄.
Π ΡΡΡΡΠΊΡΡΡΡ Π·Π°Π²ΠΎΠ΄Π° Π²ΠΊΠ»ΡΡΠ΅Π½ ΡΡΠ΄ ΡΠ»ΡΠΆΠ± ΠΈ Π²ΡΠΏΠΎΠΌΠΎΠ³Π°ΡΠ΅Π»ΡΠ½ΡΡ ΡΠ΅Ρ ΠΎΠ²: ΡΠ½Π΅ΡΠ³ΠΎΡΠ΅Ρ , ΠΈΠ½ΡΡΡΡΠΌΠ΅Π½ΡΠ°Π»ΡΠ½ΡΠΉ, ΡΠ΅ΠΌΠΎΠ½ΡΠ½ΠΎ-ΠΌΠ΅Ρ Π°Π½ΠΈΡΠ΅ΡΠΊΠΈΠΉ, ΡΠ°ΡΠ½ΡΠΉ, ΡΡΡΠΎΠΈΡΠ΅Π»ΡΠ½ΡΠΉ, ΡΡΠ°Π½ΡΠΏΠΎΡΡΠ½ΠΎ-Π³ΡΡΠ·ΠΎΠ²ΠΎΠΉ, ΠΈ Π΄Ρ. ΠΠ±Π΅ΡΠΏΠ΅ΡΠ΅Π½ΠΈΠ΅ ΠΏΡΠΎΠΈΠ·Π²ΠΎΠ΄ΡΡΠ²Π° ΡΡΡΡΠ΅ΠΌ ΠΈ ΠΌΠ°ΡΠ΅ΡΠΈΠ°Π»Π°ΠΌΠΈ ΠΎΡΡΡΠ΅ΡΡΠ²Π»ΡΠ΅Ρ Π΄ΠΈΡΠ΅ΠΊΡΠΈΡ ΠΏΠΎ ΠΎΠ±Π΅ΡΠΏΠ΅ΡΠ΅Π½ΠΈΡ ΠΌΠ°ΡΠ΅ΡΠΈΠ°Π»ΡΠ½ΠΎ-ΡΠ΅Ρ Π½ΠΈΡΠ΅ΡΠΊΠΈΠΌΠΈ ΡΠ΅ΡΡΡΡΠ°ΠΌΠΈ, Π΄ΠΈΡΠ΅ΠΊΡΠΈΡ ΠΏΠΎ ΠΌΠ°ΡΠΊΠ΅ΡΠΈΠ½Π³Ρ ΠΈ ΡΠ±ΡΡΡ ΠΎΡΡΡΠ΅ΡΡΠ²Π»ΡΠ΅Ρ ΡΠ°Π±ΠΎΡΡ Ρ ΠΊΠ»ΠΈΠ΅Π½ΡΠ°ΠΌΠΈ, ΠΏΠ»Π°Π½ΠΈΡΠΎΠ²Π°Π½ΠΈΠ΅ ΠΏΡΠΎΠ΄Π°ΠΆ ΠΈ ΠΈΠ·ΡΡΠ΅Π½ΠΈΠ΅ ΡΡΠ½ΠΊΠ° ΡΠ±ΡΡΠ°.
ΠΡΠΏΠΎΠ»ΡΠ·ΠΎΠ²Π°Π½Π° ΠΈΠ½ΡΠΎΡΠΌΠ°ΡΠΈΡ ΠΈΠ· βΠΠΎΡΠΎΠ±ΠΈΡ Π²ΠΎΠ»ΠΎΡΠΈΠ»ΡΡΠΈΠΊΠ°β.
1. ΠΠ»Π°ΡΡΠΈΡΠΈΠΊΠ°ΡΠΈΡ Π²ΠΎΠ»ΠΎΡΠΈΠ»ΡΠ½ΡΡ ΡΡΠ°Π½ΠΎΠ²
ΠΠΎΠ»ΠΎΡΠΈΠ»ΡΠ½ΡΠΉ ΡΡΠ°Π½ — ΡΡΠΎ ΠΌΠ°ΡΠΈΠ½Π°, ΡΠ»ΡΠΆΠ°ΡΠ°Ρ Π΄Π»Ρ ΠΎΠ±ΡΠ°Π±ΠΎΡΠΊΠΈ ΠΌΠ΅ΡΠ°Π»ΒΠ»Π° Π²ΠΎΠ»ΠΎΡΠ΅Π½ΠΈΠ΅ΠΌ, .Ρ.Π΅.ΠΏΡΠΎΡΡΠ³ΠΈΠ²Π°Π½ΠΈΠ΅ΠΌ ΠΌΠ΅ΡΠ°Π»Π»ΠΈΡΠ΅ΡΠΊΠΈΡ Π·Π°Π³ΠΎΡΠΎΠ²ΠΎΠΊ Π² Ρ ΠΎΠ»ΠΎΠ΄ΒΠ½ΠΎΠΌ ΡΠΎΡΡΠΎΡΠ½ΠΈΠΈ ΡΠ΅ΡΠ΅Π· Π²ΠΎΠ»ΠΎΡΠΈΠ»ΡΠ½ΡΠΉ ΠΈΠ½ΡΡΡΡΠΌΠ΅Π½Ρ Π΄Π»Ρ ΠΏΠΎΠ»ΡΡΠ΅Π½ΠΈΡ ΠΌΠ΅Π½ΡΡΠΈΡ ΡΠ°Π·ΠΌΠ΅ΡΠΎΠ² ΠΏΠΎΠΏΠ΅ΡΠ΅ΡΠ½ΠΎΠ³ΠΎ ΡΠ΅ΡΠ΅Π½ΠΈΡ Π³ΠΎΡΠΎΠ²ΠΎΠ³ΠΎ ΠΈΠ·Π΄Π΅Π»ΠΈΡ — ΠΏΡΠΎΠ²ΠΎΠ»ΠΎΠΊΠΈ. ΠΠΎΠ»ΠΎΒΡΠ΅Π½ΠΈΠ΅ΠΌ ΠΎΠ±ΡΠ°Π±Π°ΡΡΠ²Π°Π΅ΡΡΡ ΠΏΡΠΎΠ²ΠΎΠ»ΠΎΠΊΠ° ΠΊΡΡΠ³Π»ΡΡ ΠΈ ΡΠ°ΡΠΎΠ½Π½ΡΡ ΡΠ΅ΡΠ΅Π½ΠΈΠΉ ΠΈ ΠΎΠ±Π΅ΡΒΠΏΠ΅ΡΠΈΠ²Π°Π΅ΡΡΡ Π²ΡΡΠΎΠΊΠ°Ρ ΡΠΎΡΠ½ΠΎΡΡΡ ΠΏΡΠΎΡΠΈΠ»Ρ ΠΈ ΡΠΈΡΡΠ°Ρ Π³Π»Π°Π΄ΠΊΠ°Ρ ΠΏΠΎΠ²Π΅ΡΡ Π½ΠΎΡΡΡ. ΠΡΠΈ Ρ ΠΎΠ»ΠΎΠ΄Π½ΠΎΠΌ Π²ΠΎΠ»ΠΎΡΠ΅Π½ΠΈΠΈ Π·Π½Π°ΡΠΈΡΠ΅Π»ΡΠ½ΠΎ ΠΏΠΎΠ²ΡΡΠ°Π΅ΡΡΡ ΠΏΡΠ΅Π΄Π΅Π» ΡΠ΅ΠΊΡΡΠ΅ΡΡΠΈ ΠΈ ΠΏΡΠΎΡΠ½ΠΎΡΡΠΈ, Π° ΡΠ°ΠΊΠΆΠ΅ ΡΠ²Π΅ΡΠ΄ΠΎΡΡΡ ΠΏΡΠΎΡΡΠ³ΠΈΠ²Π°Π΅ΠΌΠΎΠ³ΠΎ ΠΌΠ΅ΡΠ°Π»Π»Π°.
Π Π·Π°Π²ΠΈΡΠΈΠΌΠΎΡΡΠΈ ΠΎΡ ΠΊΠΎΠ½ΡΡΡΡΠΊΡΠΈΠ²Π½ΡΡ ΠΎΡΠΎΠ±Π΅Π½Π½ΠΎΡΡΠ΅ΠΉ ΠΈ Π½Π°Π·Π½Π°ΡΠ΅Π½ΠΈΡ Π²ΠΎΠ»ΠΎΡΠΈΠ»ΡΠ½ΡΠ΅ ΡΡΠ°Π½Ρ Π΄Π΅Π»ΡΡΡΡ Π½Π° Π΄Π²Π΅ Π³ΡΡΠΏΠΏΡ: ΡΡΠ°Π½Ρ Ρ ΠΊΡΡΠ³ΠΎΠ²ΡΠΌ Π΄Π²ΠΈΠΆΠ΅ΒΠ½ΠΈΠ΅ΠΌ ΠΏΡΠΎΠ²ΠΎΠ»ΠΎΠΊΠΈ ΠΏΡΠΈ Π½Π°ΠΌΠΎΡΠΊΠ΅ Π½Π° Π±Π°ΡΠ°Π±Π°Π½ ΠΈ Ρ ΠΏΡΡΠΌΠΎΠ»ΠΈΠ½Π΅ΠΉΠ½ΡΠΌ Π΄Π²ΠΈΠΆΠ΅Π½ΠΈΠ΅ΠΌ Π³ΠΎΡΠΎΠ²ΠΎΠ³ΠΎ ΠΈΠ·Π΄Π΅Π»ΠΈΡ ΠΏΡΠΈ ΠΏΠΎΠΌΠΎΡΠΈ ΡΡΠ½ΡΡΠΈΡ ΡΠ΅Π»Π΅ΠΆΠ΅ΠΊ. ΠΠΎ ΠΏΡΠΈΠ½ΡΠΈΠΏΡ ΡΠ°Π±ΠΎΡΡ Π²ΠΎΠ»ΠΎΡΠΈΠ»ΡΠ½ΡΠ΅ ΡΡΠ°Π½Ρ ΠΊΠ»Π°ΡΡΠΈΡΠΈΡΠΈΡΡΡΡΡΡ Π½Π° Π²ΠΎΠ»ΠΎΡΠΈΠ»ΡΠ½ΡΠ΅ ΡΡΠ°Π½Ρ Π±Π΅Π· ΡΠΊΠΎΠ»ΡΠΆΠ΅Π½ΠΈΡ ΠΏΡΠΎΠ²ΠΎΠ»ΠΎΠΊΠΈ Π½Π° ΡΡΠ³ΠΎΠ²ΡΡ Π±Π°ΡΠ°Π±Π°Π½Π°Ρ ΠΈ ΡΡΠ°Π½Ρ ΡΠΎ ΡΠΊΠΎΠ»ΡΠΆΠ΅Π½ΠΈΠ΅ΠΌ ΠΏΡΠΎΠ²ΠΎΠ»ΠΎΠΊΠΈ Π½Π° Π±Π°ΡΠ°Π±Π°Π½Π°Ρ , ΠΊΡΠΎΠΌΠ΅ ΠΏΠΎΡΠ»Π΅Π΄Π½Π΅Π³ΠΎ, ΡΠΈΡΡΠΎΠ²ΠΎΠ³ΠΎ.
ΠΠ΅ΡΠ²ΡΠ΅, Π² ΡΠ²ΠΎΡ ΠΎΡΠ΅ΡΠ΅Π΄Ρ, ΠΏΠΎΠ΄ΡΠ°Π·Π΄Π΅Π»ΡΡΡΡΡ Π½Π° ΡΡΠ°Π½Ρ Ρ Π½Π°ΠΊΠΎΠΏΠ»Π΅ΒΠ½ΠΈΠ΅ΠΌ ΠΏΡΠΎΠ²ΠΎΠ»ΠΎΠΊΠΈ Π½Π° ΠΏΡΠΎΠΌΠ΅ΠΆΡΡΠΎΡΠ½ΡΡ Π±Π°ΡΠ°Π±Π°Π½Π°Ρ ΠΈ Π½Π° ΡΡΠ°Π½Ρ Ρ Π°Π²ΡΠΎΠΌΠ°ΡΠΈΒΡΠ΅ΡΠΊΠΈΠΌ ΡΠ΅Π³ΡΠ»ΠΈΡΠΎΠ²Π°Π½ΠΈΠ΅ΠΌ ΡΠ°ΡΡΠΎΡΡ Π²ΡΠ°ΡΠ΅Π½ΠΈΡ ΠΏΡΠΎΠΌΠ΅ΠΆΡΡΠΎΡΠ½ΡΡ Π±Π°ΡΠ°Π±Π°Π½ΠΎΠ² Π½Π° ΠΏΡΡΠΌΠΎΡΠΎΡΠ½ΡΡ ΡΡΠ°Π½Π°Ρ .
ΠΠΎ ΠΊΡΠ°ΡΠ½ΠΎΡΡΠΈ Π²ΠΎΠ»ΠΎΡΠ΅Π½ΠΈΡ Π²ΠΎΠ»ΠΎΡΠΈΠ»ΡΠ½ΡΠ΅ ΡΡΠ°Π½Ρ ΠΏΠΎΠ΄ΡΠ°Π·Π΄Π΅Π»ΡΡΡΡΡ Π½Π°
ΠΎΠ΄Π½ΠΎΠΊΡΠ°ΡΠ½ΡΠ΅ ΠΈ ΠΌΠ½ΠΎΠ³ΠΎΠΊΡΠ°ΡΠ½ΡΠ΅. ΠΠΎ ΠΊΠΈΠ½Π΅ΠΌΠ°ΡΠΈΡΠ΅ΡΠΊΠΎΠΌΡ ΠΏΡΠΈΠ½ΡΠΈΠΏΡ — ΡΡΠ°Π½Ρ Ρ ΠΈΠ½Π΄ΠΈΠ²ΠΈΠ΄ΡΠ°Π»ΡΠ½ΡΠΌ ΠΏΡΠΈΠ²ΠΎΠ΄ΠΎΠΌ ΠΊΠ°ΠΆΠ΄ΠΎΠ³ΠΎ Π±Π°ΡΠ°Π±Π°Π½Π° ΠΈ ΡΡΠ°Π½Ρ Ρ Π³ΡΡΠΏΠΏΠΎΠ²ΡΠΌ ΠΏΡΠΈΒΠ²ΠΎΠ΄ΠΎΠΌ Π²ΡΠ΅Ρ Π±Π°ΡΠ°Π±Π°Π½ΠΎΠ². Π Π·Π°Π²ΠΈΡΠΈΠΌΠΎΡΡΠΈ ΠΎΡ Π΄ΠΈΠ°ΠΌΠ΅ΡΡΠ° ΠΏΡΠΎΡΡΠ³ΠΈΠ²Π°Π΅ΠΌΠΎΠΉ ΠΏΡΠΎΠ²ΠΎΠ»ΠΎΠΊΠΈ ΡΡΠ°Π½Ρ ΠΏΠΎΠ΄ΡΠ°Π·Π΄Π΅Π»ΡΡΡΡΡ: Π΄Π»Ρ ΠΎΡΠΎΠ±ΠΎ ΡΠΎΠ»ΡΡΠΎΠ³ΠΎ Π²ΠΎΠ»ΠΎΡΠ΅Π½ΠΈΡ (ΠΏΡΠΈ Π΄ΠΈΠ°ΠΌΠ΅ΡΡΠ΅ ΠΏΡΠΎΠ²ΠΎΠ»ΠΎΠΊΠΈ Π±ΠΎΠ»Π΅Π΅ 6.0 ΠΌΠΌ), Π³ΡΡΠ±ΠΎΠ³ΠΎ Π²ΠΎΠ»ΠΎΡΠ΅Π½ΠΈΡ (3.0-6.0 ΠΌΠΌ), ΡΡΠ΅Π΄Π½Π΅Π³ΠΎ Π²ΠΎΠ»ΠΎΡΠ΅Π½ΠΈΡ (1.8-3.0 ΠΌΠΌ), ΡΠΎΠ½ΠΊΠΎΠ³ΠΎ Π²ΠΎΠ»ΠΎΡΠ΅Π½ΠΈΡ (0.8-1.8 ΠΌΠΌ), ΡΠΎΠ½ΡΠ°ΠΉΡΠ΅Π³ΠΎ Π²ΠΎΠ»ΠΎΡΠ΅Π½ΠΈΡ (0.5-0.8 ΠΌΠΌ), Π½Π°ΠΈΡΠΎΠ½ΡΠ°ΠΉΡΠ΅Π³ΠΎ Π²ΠΎΠ»ΠΎΡΠ΅Π½ΠΈΡ (0.1-0.5 ΠΌΠΌ) ΠΈ Π²ΠΎΠ»ΠΎΡΠ΅Π½ΠΈΡ ΠΏΡΠΎΠ²ΠΎΠ»ΠΎΠΊΠΈ Π΄ΠΈΠ°ΠΌΠ΅ΡΡΠΎΠΌ ΠΌΠ΅Π½Π΅Π΅ 0.1 ΠΌΠΌ.
ΠΠΎ ΡΠ΅ΡΠΌΠΈΡΠ΅ΡΠΊΠΈΠΌ ΡΡΠ»ΠΎΠ²ΠΈΡΠΌ Π΄Π΅ΡΠΎΡΠΌΠ°ΡΠΈΠΈ Π²ΠΎΠ»ΠΎΡΠ΅Π½ΠΈΠ΅ ΠΏΡΠΎΠ²ΠΎΠ»ΠΎΠΊΠΈ ΠΏΠΎΠ΄ΒΡΠ°Π·Π΄Π΅Π»ΡΠ΅ΡΡΡ Π½Π°:
Π³ΠΎΡΡΡΠ΅Π΅ Π²ΠΎΠ»ΠΎΡΠ΅Π½ΠΈΠ΅ — Π²ΠΎΠ»ΠΎΡΠ΅Π½ΠΈΠ΅ Π² ΡΡΠ»ΠΎΠ²ΠΈΡΡ Π·Π°ΡΠ΅ΠΊΡΠΈΡΡΠ°Π»Π»ΠΈΠ·Π°ΡΠΈΠΎΠ½Π½ΡΡ ΡΠ΅ΠΌΠΏΠ΅ΡΠ°ΡΡΡ (Π΄ΠΎ 900Β°Π‘), ΠΏΡΠΈΠΌΠ΅Π½ΡΠ΅ΠΌΠΎΠ΅ Π΄Π»Ρ ΡΠ°ΠΊΠΈΡ ΠΌΠ΅ΡΠ°Π»Π»ΠΎΠ², ΠΊΠ°ΠΊ Π²ΠΎΠ»ΡΡΡΠ°ΠΌ, ΠΌΠΎΠ»ΠΈΠ±Π΄Π΅Π½, ΡΠΏΠ»Π°Π²Ρ ΡΠΈΡΠ°Π½Π° ΠΈ Π°Π»ΡΠΌΠΈΠ½ΠΈΡ, ΡΠ°ΠΊ ΠΊΠ°ΠΊ ΠΎΠ½ΠΈ ΠΎΠ±Π»Π°Π΄Π°ΡΡ ΠΏΡΠΈ ΠΎΠ±ΡΡΠ½ΡΡ ΡΠ΅ΠΌΠΏΠ΅ΡΠ°ΡΡΡΠ°Ρ Π½Π΅Π΄ΠΎΡΡΠ°ΡΠΎΡΠ½ΠΎΠΉ ΠΏΠ»Π°ΡΡΠΈΡΠ½ΠΎΡΡΡΡ ΠΈ ΠΏΡΠΎΡΠ²Π»ΡΡΡ Ρ ΡΡΠΏΠΊΠΎΡΡΡ; ΡΠ΅ΠΏΠ»ΠΎΠ΅ Π²ΠΎΠ»ΠΎΡΠ΅Π½ΠΈΠ΅ — Π²ΠΎΠ»ΠΎΡΠ΅Π½ΠΈΠ΅ Π² ΡΡΠ»ΠΎΠ²ΠΈΡΡ Π΄ΠΎ ΠΈΠ»ΠΈ ΠΎΠΊΠΎΠ»ΠΎ ΡΠ΅ΠΊΡΠΈΡΡΠ°Π»Π»ΠΈΠ·Π°ΡΠΈΠΎΠ½Π½ΠΎΠ³ΠΎ ΠΏΠΎΡΡΠ΄ΠΊΠ° (Π΄ΠΎ 500Β°Π‘,) ΠΈΡΠΏΠΎΠ»ΡΠ·ΡΠ΅ΡΠ΅Π΅ΡΡ Π΄Π»Ρ Π²ΠΎΒΠ»ΠΎΡΠ΅Π½ΠΈΡ ΠΏΡΠΎΠ²ΠΎΠ»ΠΎΠΊΠΈ ΠΈΠ· Π±ΡΡΡΡΠΎΡΠ΅ΠΆΡΡΠΈΡ ΠΌΠ°ΡΠΎΠΊ ΡΡΠ°Π»Π΅ΠΉ ΡΠΈΠΏΠ° Π -9, Π -18; Π½ΠΈΠ·ΠΊΠΎΡΠ΅ΠΌΠΏΠ΅ΡΠ°ΡΡΡΠ½ΠΎΠ΅ Π²ΠΎΠ»ΠΎΡΠ΅Π½ΠΈΠ΅ — Π²ΠΎΠ»ΠΎΡΠ΅Π½ΠΈΠ΅ Π² ΠΈΠ½ΡΠ΅ΡΠ²Π°Π»Π΅ ΡΠ΅ΠΌΒΠΏΠ΅ΡΠ°ΡΡΡ ΠΎΡ 60Β°Π‘ Π΄ΠΎ 180Β°Π‘, ΠΏΡΠΈΠΌΠ΅Π½ΡΡΡΠ΅Π΅ΡΡ ΠΏΡΠΈ ΠΏΡΠΎΠΈΠ·Π²ΠΎΠ΄ΡΡΠ²Π΅ ΠΏΡΠΎΠ²ΠΎΠ»ΠΎΠΊΠΈ ΠΈΠ· Π²ΡΡΠΎΠΊΠΎΠ»Π΅Π³ΠΈΡΠΎΠ²Π°Π½Π½ΡΡ ΡΡΠ°Π»Π΅ΠΉ Ρ Π°ΡΡΡΠ΅Π½ΠΈΡΠ½ΠΎΠΉ ΠΈ Π°ΡΡΡΠ΅Π½ΠΈΡΠ½ΠΎ-ΡΠ΅ΡΡΠΈΡΠ½ΠΎΠΉ ΡΡΡΡΠΊΡΡΡΠΎΠΉ.
ΠΡΠΎΠΌΠ΅ ΡΡΠΎΠ³ΠΎ, ΠΏΡΠΎΡΠ΅ΡΡ Π²ΠΎΠ»ΠΎΡΠ΅Π½ΠΈΡ ΠΌΠΎΠΆΠ΅Ρ ΠΏΡΠΎΠ²ΠΎΠ΄ΠΈΡΡΡΡ Ρ ΠΏΡΠΎΡΠΈΠ²ΠΎΠ½Π°-ΡΡΠΆΠ΅Π½ΠΈΠ΅ΠΌ, ΠΊΠ°ΠΊ ΡΡΠΎ ΠΏΡΠΎΠΈΡΡ ΠΎΠ΄ΠΈΡ Π½Π° ΠΏΡΡΠΌΠΎΡΠΎΡΠ½ΡΡ Π²ΠΎΠ»ΠΎΡΠΈΠ»ΡΠ½ΡΡ ΡΡΠ°Π½Π°Ρ -ΠΏΠ΅ΡΠ΅Π΄ ΡΠΎΠΎΡΠ²Π΅ΡΡΡΠ²ΡΡΡΠ΅ΠΉ Π²ΠΎΠ»ΠΎΠΊΠΎΠ½ ΠΏΡΠΎΡΡΠ³ΠΈΠ²Π°Π΅ΠΌΠΎΠΉ ΠΏΡΠΎΠ²ΠΎΠ»ΠΎΠΊΠ΅ ΡΠΎΠ·Π΄Π°Π΅ΡΡΡ ΠΏΡΠ΅Π΄Π²Π°ΡΠΈΡΠ΅Π»ΡΠ½ΠΎΠ΅ Π½Π°ΡΡΠΆΠ΅Π½ΠΈΠ΅ ΠΎΡ ΠΏΡΠ΅Π΄ΡΠ΄ΡΡΠ΅Π³ΠΎ Π±Π°ΡΠ°Π±Π°Π½Π°.
ΠΠΈΠ±ΡΠ°ΡΠΈΠΎΠ½Π½ΠΎΠ΅ Π²ΠΎΠ»ΠΎΡΠ΅Π½ΠΈΠ΅ — Π²ΠΎΠ»ΠΎΡΠ΅Π½ΠΈΠ΅ Ρ Π½Π°Π»ΠΎΠΆΠ΅Π½ΠΈΠ΅ΠΌ Π²ΠΈΠ±ΡΠ°ΡΠΈΠΉ Π½Π° ΠΏΡΠΎΠ²ΠΎΠ»ΠΎΠΊΡ ΠΈΠ»ΠΈ Π²ΠΎΠ»ΠΎΠΊΡ Ρ ΡΠ°ΡΡΠΎΡΠΎΠΉ ΠΎΡ 200 Π΄ΠΎ 1000 ΠΡ, ΡΡΠΎ ΠΏΡΠΈΠ²ΠΎΒΠ΄ΠΈΡ ΠΊ ΡΠΌΠ΅Π½ΡΡΠ΅Π½ΠΈΡ ΡΠΈΠ»Ρ Π²ΠΎΠ»ΠΎΡΠ΅Π½ΠΈΡ Π½Π° 35-45%.
ΠΠΎΠ»ΠΎΡΠ΅Π½ΠΈΠ΅ ΡΠ΅ΡΠ΅Π² Π²ΡΠ°ΡΠ°ΡΡΡΡΡΡ Π²ΠΎΠ»ΠΎΠΊΡ ΡΠ°ΠΊΠΆΠ΅ ΡΠΌΠ΅Π½ΡΡΠ°Π΅Ρ ΡΠΈΠ»Ρ Π²ΠΎΠ»ΠΎΡΠ΅Π½ΠΈΡ, Π½ΠΎ Π΄Π»Ρ Π²ΡΠ°ΡΠ΅Π½ΠΈΡ Π²ΠΎΠ»ΠΎΠΊΠΈ Π½Π΅ΠΎΠ±Ρ ΠΎΠ΄ΠΈΠΌ ΡΠΏΠ΅ΡΠΈΠ°Π»ΡΠ½ΡΠΉ ΠΏΡΠΈΠ²ΠΎΠ΄.
ΠΠΎΠ»ΠΎΡΠ΅Π½ΠΈΠ΅ ΠΏΡΠΎΠ²ΠΎΠ»ΠΎΠΊΠΈ ΡΠ΅ΡΠ΅Π· Π½Π΅ΠΏΡΠΈΠ²ΠΎΠ΄Π½ΡΠ΅ ΡΠΎΠ»ΠΈΠΊΠΎΠ²ΡΠ΅ Π²ΠΎΠ»ΠΎΠΊΠΈ, ΠΏΡΠΈΒΠΌΠ΅Π½ΡΡΡΠΈΠ΅ΡΡ Π΄Π»Ρ Π²ΡΡΠΎΠΊΠΎΠΏΡΠΎΡΠ½ΡΡ ΡΡΠ°Π»Π΅ΠΉ, Π°Π½Π°Π»ΠΎΠ³ΠΈΡΠ½ΠΎ ΠΎΠ±ΡΠ°Π±ΠΎΡΠΊΠ΅ Π΄Π°Π²Π»Π΅ΒΠ½ΠΈΠ΅ΠΌ ΠΌΠ΅ΡΠΎΠ΄ΠΎΠΌ ΠΏΡΠΎΠΊΠ°ΡΠΊΠΈ Ρ Π½Π΅ΠΏΡΠΈΠ²ΠΎΠ΄Π½ΡΠΌΠΈ Π²Π°Π»ΠΊΠ°ΠΌΠΈ.
ΠΠΎΡΠ²Π»Π΅Π½ΠΈΠ΅ Π² 1927-28 Π³Π³. ΡΠ²Π΅ΡΠ΄ΠΎΡΠΏΠ»Π°Π²Π½ΠΎΠ³ΠΎ Π²ΠΎΠ»ΠΎΡΠΈΠ»ΡΠ½ΠΎΠ³ΠΎ ΠΈΠ½ΡΡΡΡΒΠΌΠ΅Π½ΡΠ° ΠΏΡΠΎΠΈΠ·Π²Π΅Π»ΠΎ ΡΠ²ΠΎΠ΅Π³ΠΎ ΡΠΎΠ΄Π° ΡΠ΅Π²ΠΎΠ»ΡΡΠΈΡ Π² Π²ΠΎΠ»ΠΎΡΠΈΠ»ΡΠ½ΠΎΠΌ ΠΏΡΠΎΠΈΠ·Π²ΠΎΠ΄ΡΡΠ²Π΅.
1.1 ΠΠΎΠ»ΠΎΡΠΈΠ»ΡΠ½ΡΠ΅ ΡΡΠ°Π½Ρ Π΄Π»Ρ ΠΎΠ΄Π½ΠΎΠΊΡΠ°ΡΠ½ΠΎΠ³ΠΎ Π²ΠΎΠ»ΠΎΡΠ΅Π½ΠΈΡ ΠΏΡΠΎΠ²ΠΎΠ»ΠΎΠΊΠΈ
ΠΠ΄Π½ΠΎΠΊΡΠ°ΡΠ½ΡΠ΅ Π²ΠΎΠ»ΠΎΡΠΈΠ»ΡΠ½ΡΠ΅ ΡΡΠ°Π½Ρ ΠΏΡΠ΅Π΄Π½Π°Π·Π½Π°ΡΠ΅Π½Ρ Π΄Π»Ρ Π²ΠΎΠ»ΠΎΡΠ΅Π½ΠΈΡ ΠΏΡΠΎΠ²ΠΎΠ»ΠΎΠΊΠΈ ΠΈΠ· Π·Π°Π³ΠΎΡΠΎΠ²ΠΎΠΊ ΡΠΎΠ»ΡΡΡΡ ΡΠ°Π·ΠΌΠ΅ΡΠΎΠ² — ΠΎΡ 8.0 Π΄ΠΎ 20.0 ΠΌΠΌ. ΠΠΈΠ°ΠΌΠ΅ΡΡ ΡΡΠ½ΡΡΠΈΡ Π±Π°ΡΠ°Π±Π°Π½ΠΎΠ² ΡΠΎΡΡΠ°Π²Π»ΡΠ΅Ρ 550-750 ΠΌΠΌ.
Π‘Ρ Π΅ΠΌΠ° ΡΠ°Π±ΠΎΡΡ ΠΎΠ΄Π½ΠΎΠΊΡΠ°ΡΠ½ΠΎΠ³ΠΎ Π²ΠΎΠ»ΠΎΡΠΈΠ»ΡΠ½ΠΎΠ³ΠΎ ΡΡΠ°Π½Π° ΠΏΠΎΠΊΠ°Π·Π°Π½Π° Π½Π° ΡΠΈΡ.1.1. ΠΡΠΎΡΡΠ³ΠΈΠ²Π°Π΅ΠΌΠ°Ρ Π·Π°Π³ΠΎΡΠΎΠ²ΠΊΠ° 2 ΡΠΌΠ°ΡΡΠ²Π°Π΅ΡΡΡ Ρ ΡΠ°Π·ΠΌΠΎΡΠΎΡΠ½ΠΎΠ³ΠΎ ΡΡΡΡΠΎΠΉΡΡΠ²Π° 1. ΠΠΎΡΠ»Π΅ ΠΏΡΠΎΡ ΠΎΠΆΠ΄Π΅Π½ΠΈΡ ΡΠ΅ΡΠ΅Π· Π²ΠΎΠ»ΠΎΡΠΈΠ»ΡΠ½ΡΠΉ ΠΈΠ½ΡΡΡΡΠΌΠ΅Π½Ρ (Π²ΠΎΒΠ»ΠΎΠΊΡ) 3, ΠΏΡΠΎΡΡΠ½ΡΡΠ°Ρ Π½Π° Π½Π΅ΠΎΠ±Ρ ΠΎΠ΄ΠΈΠΌΡΠΉ ΡΠ°Π·ΠΌΠ΅Ρ (Π΄ΠΈΠ°ΠΌΠ΅ΡΡ) ΠΏΡΠΎΠ²ΠΎΠ»ΠΎΠΊΠ° 4 Π½Π°ΠΌΠ°ΡΡΠ²Π°Π΅ΡΡΡ Π½Π° ΡΡΠ½ΡΡΠΈΠΉ Π±Π°ΡΠ°Π±Π°Π½ Π±, ΠΊΠΎΡΠΎΡΡΠΉ ΠΏΡΠΈΠ²ΠΎΠ΄ΠΈΡΡΡ Π²ΠΎ Π²ΡΠ°ΡΠ΅Π½ΠΈΠ΅ ΠΎΡ ΡΠ»Π΅ΠΊΡΡΠΎΠ΄Π²ΠΈΠ³Π°ΡΠ΅Π»Ρ 7 ΡΠ΅ΡΠ΅Π· ΡΠ΅Π΄ΡΠΊΡΠΎΡ ΠΈΠ»ΠΈ ΠΊΠΎΡΠΎΠ±ΠΊΡ ΡΠΊΠΎΡΠΎΡΡΠ΅ΠΉ 6.
ΠΠΎΠ»ΠΎΡΠΈΠ»ΡΠ½ΡΠΉ ΡΡΠ°Π½ (ΡΠΈΡ.1.2) ΠΏΡΠ΅Π΄ΡΡΠ°Π²Π»ΡΠ΅Ρ ΡΠΎΠ±ΠΎΠΉ ΡΠ°ΠΌΠΎΡΡΠΎΡΡΠ΅Π»ΡΒΠ½ΡΠΉ Π±Π»ΠΎΠΊ, ΡΠΎΡΡΠΎΡΡΠΈΠΉ ΠΈΠ· Π»ΠΈΡΠΎΠ³ΠΎ ΠΊΠΎΡΠΏΡΡΠ° 11, Π½Π° ΠΊΠΎΡΠΎΡΠΎΠΌ ΡΠΌΠΎΠ½ΡΠΈΡΠΎΠ²Π°Π½ ΡΡΠ³ΠΎΠ²ΡΠΉ Π²ΠΎΠ»ΠΎΡΠΈΠ»ΡΠ½ΡΠΉ Π±Π°ΡΠ°Π±Π°Π½ 5.ΠΠ°ΡΠ°Π±Π°Π½ ΠΏΠΎΠ»ΡΡΠ°Π΅Ρ Π²ΡΠ°ΡΠ΅Π½ΠΈΠ΅ ΠΎΡ ΡΠ»Π΅ΠΊΡΒΡΠΎΠΏΡΠΈΠ²ΠΎΠ΄Π°, ΡΠΎΡΡΠΎΡΡΠ΅Π³ΠΎ ΠΈΠ· ΡΠ»Π΅ΠΊΡΡΠΎΠ΄Π²ΠΈΠ³Π°ΡΠ΅Π»Ρ 3, ΠΊΠ»ΠΈΠ½ΠΎΡΠ΅ΠΌΠ΅Π½Π½ΠΎΠΉ ΠΏΠ΅ΡΠ΅Π΄Π°ΒΡΠΈ, ΡΠ΅ΡΡΡΠ΅Ρ ΡΠΊΠΎΡΠΎΡΡΠ½ΠΎΠΉ ΠΊΠΎΡΠΎΠ±ΠΊΠΈ ΠΏΠ΅ΡΠ΅Π΄Π°Ρ 4, ΠΊΠΎΠ½ΠΈΡΠ΅ΡΠΊΠΎΠΉ ΠΈ ΡΠΈΠ»ΠΈΠ½Π΄ΡΠΈΡΠ΅ΡΒΠΊΠΎΠΉ ΠΏΠ°Ρ Π·ΡΠ±ΡΠ°ΡΡΡ ΠΊΠΎΠ»Π΅Ρ.
ΠΡΠ½Ρ Π·Π°Π³ΠΎΡΠΎΠ²ΠΊΠΈ, ΠΏΠΎΠ΄Π»Π΅ΠΆΠ°ΡΠ΅ΠΉ Π²ΠΎΠ»ΠΎΡΠ΅Π½ΠΈΡ, Π½Π°Π΄Π΅Π²Π°Π΅ΡΡΡ Π½Π° ΠΊΠΎΠ½ΡΠΎΠ»Ρ 1 ΠΈΠ»ΠΈ ΡΠΈΠ³ΡΡΠΊΡ 2. ΠΠΎΠ½Π΅Ρ ΠΏΡΠΎΠ²ΠΎΠ»ΠΎΠΊΠΈ ΠΏΠΎΡΠ»Π΅ Π·Π°ΠΎΡΡΡΠ΅Π½ΠΈΡ Π½Π° ΠΎΡΡΡΠΈΠ»ΡΠ½ΠΎΠΌ ΡΡΠ°Π½ΠΊΠ΅ ΠΏΡΠΎΠΏΡΡΠΊΠ°ΡΡ ΡΠ΅ΡΠ΅Π· ΠΎΡΠ²Π΅ΡΡΡΠΈΠ΅ Π²ΠΎΠ»ΠΎΠΊΠΈ 9, ΠΏΠΎΡΠ»Π΅ ΡΠ΅Π³ΠΎ Π·Π°Ρ Π²Π°ΡΡΠ²Π°ΒΡΡ Π²ΡΡΡΠΆΠ½ΡΠΌΠΈ ΠΊΠ»Π΅ΡΠ°ΠΌΠΈ. ΠΠ»Π΅ΡΠΈ ΠΏΡΠΈ ΠΏΠΎΠΌΠΎΡΠΈ ΠΏΠ»Π°ΡΡΠΈΠ½ΡΠ°ΡΠΎΠΉ ΡΠ΅ΠΏΠΈ Ρ ΠΊΡΡΠΊΠΎΠΌ Π½Π° Π΄ΡΡΠ³ΠΎΠΌ ΠΊΠΎΠ½ΡΠ΅ ΡΠΎΠ΅Π΄ΠΈΠ½ΡΡΡΡΡ Ρ Π±Π°ΡΠ°Π±Π°Π½ΠΎΠΌ 5.ΠΠ° Π·Π°ΠΏΡΠ°Π²ΠΎΡΠ½ΠΎΠΉ (ΠΌΠ΅Π΄Π»Π΅Π½ΒΠ½ΠΎΠΉ) ΡΠΊΠΎΡΠΎΡΡΠΈ Π½Π° Π±Π°ΡΠ°Π±Π°Π½ Π½Π°ΠΌΠ°ΡΡΠ²Π°Π΅ΡΡΡ Π½Π΅ΡΠΊΠΎΠ»ΡΠΊΠΎ Π²ΠΈΡΠΊΠΎΠ² ΠΏΡΠΎΠ²ΠΎΠ»ΠΎΒΠΊΠΈ, ΠΏΠΎΡΠ»Π΅ ΡΠ΅Π³ΠΎ ΠΊΠ»Π΅ΡΠΈ ΡΠ½ΠΈΠΌΠ°ΡΡΡΡ, Π° ΡΠ²ΠΎΠ±ΠΎΠ΄Π½ΡΠΉ ΠΊΠΎΠ½Π΅Ρ ΠΏΡΠΎΠ²ΠΎΠ»ΠΎΠΊΠΈ Π·Π°ΠΊΒΡΠ΅ΠΏΠ»ΡΠ΅ΡΡΡ Π·Π° ΡΠΏΠΈΡΡ 6 Π±Π°ΡΠ°Π±Π°Π½Π°. ΠΠΎΡΠ»Π΅ ΡΡΠΎΠ³ΠΎ ΡΡΠ°Π½ Π²ΠΊΠ»ΡΡΠ°Π΅ΡΡΡ Π½Π° ΡΠ°ΒΠ±ΠΎΡΡΡ ΡΠΊΠΎΡΠΎΡΡΡ.
ΠΠΎΡΠ»Π΅ Π½Π°ΠΊΠΎΠΏΠ»Π΅Π½ΠΈΡ Π½Π° Π±Π°ΡΠ°Π±Π°Π½Π΅ ΠΎΠΏΡΠ΅Π΄Π΅Π»Π΅Π½Π½ΠΎΠ³ΠΎ ΠΊΠΎΠ»ΠΈΡΠ΅ΡΡΠ²Π° Π²ΠΈΡΠΊΠΎΠ² ΠΏΡΠΎΠ²ΠΎΠ»ΠΎΠΊΠΈ, ΡΡΠ°Π½ ΠΎΡΡΠ°Π½Π°Π²Π»ΠΈΠ²Π°Π΅ΡΡΡ, ΠΏΠΎΠ»ΡΡΠ΅Π½Π½ΡΠΉ ΠΌΠΎΡΠΎΠΊ ΠΏΡΠΎΠ²ΠΎΠ»ΠΎΠΊΠΈ (ΠΈΠ»ΠΈ ΠΏΠ΅ΡΠ΅Π΄Π΅Π»ΡΠ½ΠΎΠΉ Π·Π°Π³ΠΎΡΠΎΠ²ΠΊΠΈ) ΡΠ½ΠΈΠΌΠ°Π΅ΡΡΡ ΠΈ ΡΠΊΠ»Π°Π΄ΡΠ²Π°Π΅ΡΡΡ Π½Π° ΡΠ²ΡΠ·ΠΎΡΠ½ΡΡ ΡΠΈΒΠ³ΡΡΠΊΡ 8.
ΠΡΠ΅ ΠΎΠΏΠ΅ΡΠ°ΡΠΈΠΈ ΠΏΠΎ ΡΠΊΠ»Π°Π΄ΠΊΠ΅ Π±ΡΠ½ΡΠ° Π·Π°Π³ΠΎΡΠΎΠ²ΠΊΠΈ Π½Π° ΡΠ°Π·ΠΌΠΎΡΠΎΡΠ½ΠΎΠ΅ ΡΡΡΒΡΠΎΠΉΡΡΠ²ΠΎ ΠΈ ΡΡΠ΅ΠΌ ΠΌΠΎΡΠΊΠ° ΠΏΡΠΎΠ²ΠΎΠ»ΠΎΠΊΠΈ ΠΌΠ΅Ρ Π°Π½ΠΈΠ·ΠΈΡΠΎΠ²Π°Π½Ρ.
ΠΠΎΠ»ΠΎΡΠΈΠ»ΡΠ½ΡΠΉ Π±Π°ΡΠ°Π±Π°Π½ ΠΎΠ±ΡΠ»ΡΠΆΠΈΠ²Π°Π΅ΡΡΡ ΠΏΠΎΠ΄ΡΠ΅ΠΌΠ½ΠΈΠΊΠ°ΠΌΠΈ, Π° ΡΠΊΠ»Π°Π΄ΠΊΠ° Π±ΡΠ½ΡΠ° ΠΎΡΡΡΠ΅ΡΡΠ²Π»ΡΠ΅ΡΡΡ ΡΠ΅Π»ΡΡΠ΅ΡΠΎΠΌ 7. ΠΠ°ΡΡΠ° Π±ΡΠ½ΡΠΎΠ² Ρ ΠΏΡΠΎΠ²ΠΎΠ»ΠΎΡΠ½ΡΡ ΠΏΡΠΎ ΠΊΠ°ΡΠ½ΡΡ ΡΡΠ°Π½ΠΎΠ² ΡΠΎΡΡΠ°Π²Π»ΡΠ΅Ρ 1.0-1.5 Ρ, Π΄Π»Ρ ΠΈΡ ΡΠΊΡΡΠΏΠ½Π΅Π½ΠΈΡ ΠΏΡΠΈΠΌΠ΅Π½ΡΠ΅ΡΡΡ ΡΡΡΠΊΠΎΠ²Π°Ρ ΡΠ²Π°ΡΠΊΠ° Ρ ΠΏΠΎΠΌΠΎΡΡΡ ΡΠΏΠ΅ΡΠΈΠ°Π»ΡΠ½ΡΡ ΡΠ²Π°ΡΠΎΡΠ½ΡΡ Π°ΠΏΠΏΠ°ΡΠ°ΡΠΎΠ² 10, ΠΊΠΎΒΡΠΎΡΡΠΌΠΈ ΠΎΠ±ΠΎΡΡΠ΄ΠΎΠ²Π°Π½ ΠΊΠ°ΠΆΠ΄ΡΠΉ ΡΡΠ°Π½.
ΠΠ°ΠΌΠΎΡΠΊΠ° ΠΏΡΠΎΠ²ΠΎΠ»ΠΎΠΊΠΈ ΠΌΠΎΠΆΠ΅Ρ ΠΏΡΠΎΠΈΠ·Π²ΠΎΠ΄ΠΈΡΡΡΡ Π½Π΅ ΡΠΎΠ»ΡΠΊΠΎ Π² Π±ΡΠ½ΡΡ, Π½ΠΎ ΠΈ Π½Π° ΠΊΠ°ΡΡΡΠΊΠΈ Π²ΠΌΠ΅ΡΡΠΈΠΌΠΎΡΡΡΡ Π΄ΠΎ 2.0 Ρ ΠΏΡΠΈ ΠΏΠΎΠΌΠΎΡΠΈ ΡΠΏΠ΅ΡΠΈΠ°Π»ΡΠ½ΡΡ Π½Π°ΠΌΠΎΒΡΠΎΡΠ½ΡΡ ΡΡΡΡΠΎΠΉΡΡΠ², ΠΊΠΎΡΠΎΡΡΠ΅ ΠΌΠΎΠ³ΡΡ Π±ΡΡΡ ΡΡΡΠ°Π½ΠΎΠ²Π»Π΅Π½Ρ Π² ΠΎΠ΄Π½ΠΎΠΉ Π»ΠΈΠ½ΠΈΠΈ Ρ Π²ΠΎΠ»ΠΎΡΠΈΠ»ΡΠ½ΡΠΌΠΈ ΡΡΠ°Π½Π°ΠΌΠΈ. ΠΡΠΎ ΠΏΠΎΠ·Π²ΠΎΠ»ΡΠ΅Ρ ΠΏΠΎΠ²ΡΡΠΈΡΡ ΠΏΡΠΎΠΈΠ·Π²ΠΎΠ΄ΠΈΡΠ΅Π»ΡΠ½ΠΎΡΡΡ Π²ΠΎΠ»ΠΎΡΠΈΠ»ΡΠ½ΠΎΠ³ΠΎ ΡΡΠ°Π½Π° Π·Π° ΡΡΠ΅Ρ ΡΠ½ΠΈΠΆΠ΅Π½ΠΈΡ Π²ΡΠ΅ΠΌΠ΅Π½ΠΈ Π½Π° ΡΡΡΠ½ΡΠ΅ ΠΎΠΏΠ΅ΡΠ°ΡΠΈΠΈ (ΡΡΠ΅ΠΌ ΠΌΠΎΡΠΊΠ° ΠΏΡΠΎΠ²ΠΎΠ»ΠΎΠΊΠΈ Ρ Π±Π°ΡΠ°Π±Π°Π½Π° ΠΈ Π΄Ρ.) ΠΈ ΡΠ²Π΅Π»ΠΈΡΠ΅Π½ΠΈΡ ΠΌΠ°ΡΠΈΠ½Π½ΠΎΠ³ΠΎ Π²ΡΠ΅ΠΌΠ΅Π½ΠΈ. ΠΡΠΈ ΡΡΠΎΠΌ ΡΠ»ΡΡΡΠ°Π΅ΡΡΡ ΠΊΠ°ΡΠ΅ΡΡΠ²ΠΎ Π³ΠΎΡΠΎΠ²ΠΎΠΉ ΠΏΡΠΎΠ΄ΡΠΊΡΠΈΠΈ, ΡΠΌΠ΅Π½ΡΡΠ°ΒΡΡΡΡ ΠΎΡΡ ΠΎΠ΄Ρ, ΠΈΡΠΊΠ»ΡΡΠ°Π΅ΡΡΡ ΠΏΠ΅ΡΠ΅ΠΏΡΡΡΠ²Π°Π½ΠΈΠ΅ ΠΏΡΠΎΠ²ΠΎΠ»ΠΎΠΊΠΈ ΠΈ Ρ.Π΄.
ΠΡΠΈΠ²ΠΎΠ΄ Π² ΡΡΠ°Π½Π°Ρ ΠΎΠ΄Π½ΠΎΠΊΡΠ°ΡΠ½ΠΎΠ³ΠΎ Π²ΠΎΠ»ΠΎΡΠ΅Π½ΠΈΡ ΠΌΠΎΠΆΠ΅Ρ ΠΎΡΡΡΠ΅ΡΡΠ²Π»ΡΡΡΡΡ ΠΎΡ ΡΠ»Π΅ΠΊΡΡΠΎΠ΄Π²ΠΈΠ³Π°ΡΠ΅Π»Π΅ΠΉ ΠΊΠ°ΠΊ ΠΏΠ΅ΡΠ΅ΠΌΠ΅Π½Π½ΠΎΠ³ΠΎ, ΡΠ°ΠΊ ΠΈ ΠΏΠΎΡΡΠΎΡΠ½Π½ΠΎΠ³ΠΎ ΡΠΎΠΊΠ°.
ΠΡΠΈΠ²ΠΎΠ΄ Π΄ΠΎΠ»ΠΆΠ΅Π½ ΠΎΠ±Π΅ΡΠΏΠ΅ΡΠΈΠ²Π°ΡΡ:
Π·Π°ΠΏΡΡΠΊ ΡΡΠ°Π½Π° ΠΏΡΠΈ Π·Π°ΠΏΡΠ°Π²ΠΊΠ΅ Π½Π° ΠΌΠ΅Π΄Π»Π΅Π½Π½ΠΎΠΉ, ΠΏΠΎΠ»Π·ΡΡΠ΅ΠΉ ΡΠΊΠΎΡΠΎΡΡΠΈ ΠΈ ΠΏΠ»Π°Π²Π½ΡΠΉ ΡΠ°Π·Π³ΠΎΠ½, ΠΈΡΠΊΠ»ΡΡΠ°ΡΡΠΈΠΉ ΠΎΠ±ΡΡΠ² ΠΏΡΠΎΠ²ΠΎΠ»ΠΎΠΊΠΈ;
Π±ΡΡΡΡΡΠΉ ΡΠ°Π·Π³ΠΎΠ½ Π΄Π»Ρ ΠΎΠ±Π΅ΡΠΏΠ΅ΡΠ΅Π½ΠΈΡ ΠΌΠ°ΠΊΡΠΈΠΌΠ°Π»ΡΠ½ΠΎΠΉ ΠΏΡΠΎΠΈΠ·Π²ΠΎΠ΄ΠΈΡΠ΅Π»ΡΒ Π½ΠΎΡΡΠΈ;
ΡΠΈΡΠΎΠΊΠΈΠΉ Π΄ΠΈΠ°ΠΏΠ°Π·ΠΎΠ½ ΡΠ΅Π³ΡΠ»ΠΈΡΠΎΠ²Π°Π½ΠΈΡ ΡΠΊΠΎΡΠΎΡΡΠΈ Π²ΠΎΠ»ΠΎΡΠ΅Π½ΠΈΡ Π² Π·Π°Π²ΠΈΒ ΡΠΈΠΌΠΎΡΡΠΈ ΠΎΡ Π²Π΅Π»ΠΈΡΠΈΠ½Ρ ΠΏΠΎΠΏΠ΅ΡΠ΅ΡΠ½ΠΎΠ³ΠΎ ΡΠ΅ΡΠ΅Π½ΠΈΡ ΠΈ ΠΌΠ°ΡΠΊΠΈ ΠΏΡΠΎΡΡΒ Π³ΠΈΠ²Π°Π΅ΠΌΠΎΠ³ΠΎ ΠΌΠ°ΡΠ΅ΡΠΈΠ°Π»Π°;
Π±ΡΡΡΡΡΡ ΠΎΡΡΠ°Π½ΠΎΠ²ΠΊΡ ΡΡΠ°Π½Π° Π² Π°Π²Π°ΡΠΈΠΉΠ½ΡΡ ΡΠ»ΡΡΠ°ΡΡ .
ΠΠ΅ΡΠΌΠΎΡΡΡ Π½Π° ΡΠΎ, ΡΡΠΎ ΡΠΎΠ²ΡΠ΅ΠΌΠ΅Π½Π½ΡΠ΅ ΠΎΠ΄Π½ΠΎΠΊΡΠ°ΡΠ½ΡΠ΅ ΡΡΠ°Π½Ρ ΠΏΡΠΎΠ΅ΠΊΡΠΈΡΡΒΡΡ Π΄Π»Ρ ΡΠ°Π±ΠΎΡΡ Ρ ΠΏΠΎΠ²ΡΡΠ΅Π½Π½ΡΠΌΠΈ ΡΠΊΠΎΡΠΎΡΡΡΠΌΠΈ Π²ΠΎΠ»ΠΎΡΠ΅Π½ΠΈΡ, ΠΎΠ½ΠΈ ΠΈΠΌΠ΅ΡΡ ΡΠ»Π΅ΒΠ΄ΡΡΡΠΈΠ΅ Π½Π΅Π΄ΠΎΡΡΠ°ΡΠΊΠΈ:
Π·Π° ΠΎΠ΄Π½Ρ, Π° ΠΈΠ½ΠΎΠ³Π΄Π° Π·Π° Π΄Π²Π΅ ΠΏΡΠΎΡΡΠΆΠΊΠΈ (ΠΏΡΠΈ ΡΡΡΠΏΠ΅Π½ΡΠ°ΡΠΎΠΌ, ΡΠ΄Π²ΠΎΠ΅Π½Β Π½ΠΎΠΌ Π±Π°ΡΠ°Π±Π°Π½Π΅) Π½Π΅Π»ΡΠ·Ρ ΠΏΠΎΠ»ΡΡΠ°ΡΡ Π²ΡΡΠΎΠΊΠΈΠ΅ ΠΎΠ±ΠΆΠ°ΡΠΈΡ;
ΠΎΠ³ΡΠ°Π½ΠΈΡΠ΅Π½Π½Π°Ρ ΡΠΊΠΎΡΠΎΡΡΡ Π²ΠΎΠ»ΠΎΡΠ΅Π½ΠΈΡ Π²ΡΠ΅ΡΠ΅Π»ΠΎ ΠΎΠΏΡΠ΅Π΄Π΅Π»ΡΠ΅ΡΡΡ Π΄ΠΎΠΏΡΡΡΠΈΠΌΠΎΠΉ ΡΠΊΠΎΡΠΎΡΡΡΡ ΡΡ ΠΎΠ΄Π° Π·Π°Π³ΠΎΡΠΎΠ²ΠΊΠΈ Ρ ΡΠΈΠ³ΡΡΠΊΠΈ;
— Π²Π²ΠΈΠ΄Ρ ΡΠΎΠ³ΠΎ, ΡΡΠΎ Π΄ΠΈΠ°ΠΌΠ΅ΡΡ Π·Π°Π³ΠΎΡΠΎΠ²ΠΊΠΈ Π΄ΠΎΠ²ΠΎΠ»ΡΠ½ΠΎ Π²Π΅Π»ΠΈΠΊ, Π° ΠΌΠ°ΡΠΈΠ½Β Π½ΠΎΠ΅ Π²ΡΠ΅ΠΌΡ Π½Π° ΠΎΠ΄ΠΈΠ½ Π±ΡΠ½Ρ Π·Π°Π³ΠΎΡΠΎΠ²ΠΊΠΈ ΠΌΠ°Π»ΠΎ, ΡΡΠ°Π½ ΡΠ°ΡΡΠΎ ΠΏΡΠΈΡ ΠΎΠ΄ΠΈΡΡΡ ΠΎΡΒ ΡΠ°Π½Π°Π²Π»ΠΈΠ²Π°ΡΡ Π΄Π»Ρ Π·Π°ΠΌΠ΅Π½Ρ Π±ΡΠ½ΡΠ°, Π° ΡΠ°ΠΊΠΆΠ΅ ΡΡΠ΅ΠΌΠ° ΠΌΠΎΡΠΊΠ° ΠΏΡΠΎΠ²ΠΎΠ»ΠΎΠΊΠΈ, Π΅ΡΠ»ΠΈ ΠΏΠΎΡΠ»Π΅Π΄Π½ΡΡ Π½Π°ΠΊΠ°ΠΏΠ»ΠΈΠ²Π°Π΅ΡΡΡ Π½Π° Π±Π°ΡΠ°Π±Π°Π½Π΅.
ΠΠ΄Π½ΠΎΠΊΡΠ°ΡΠ½ΡΠ΅ Π²ΠΎΠ»ΠΎΡΠΈΠ»ΡΠ½ΡΠ΅ ΡΡΠ°Π½Ρ Π½Π°Ρ ΠΎΠ΄ΡΡ ΡΠΈΡΠΎΠΊΠΎΠ΅ ΠΏΡΠΈΠΌΠ΅Π½Π΅Π½ΠΈΠ΅ Π΄Π»Ρ ΠΏΡΠΎΠΈΠ·Π²ΠΎΠ΄ΡΡΠ²Π° ΠΏΡΠΎΠ²ΠΎΠ»ΠΎΠΊΠΈ ΡΠ°ΡΠΎΠ½Π½ΡΡ ΠΏΡΠΎΡΠΈΠ»Π΅ΠΉ (ΡΠ΅ΡΠ΅Π½ΠΈΠΉ), ΠΏΡΠΈ Π²ΠΎΠ»ΠΎΡΠ΅Π½ΠΈΠΈ ΡΡΡΠ΄Π½ΠΎΠ΄Π΅ΡΠΎΡΠΌΠΈΡΡΠ΅ΠΌΡΡ ΠΌΠ°ΡΠΎΠΊ ΡΡΠ°Π»Π΅ΠΉ, ΠΏΡΠΈ ΠΊΠ°Π»ΠΈΠ±ΡΠΎΠ²ΠΊΠ΅ ΡΠΎΠ»ΡΡΠΎΠΉ ΠΏΡΠΎΠ²ΠΎΠ»ΠΎΒΠΊΠΈ, Π° ΡΠ°ΠΊΠΆΠ΅ ΠΏΡΠΈ ΡΠ΅ΠΏΠ»ΠΎΠΌ Π²ΠΎΠ»ΠΎΡΠ΅Π½ΠΈΠΈ Ρ ΠΏΡΠ΅Π΄Π²Π°ΡΠΈΡΠ΅Π»ΡΠ½ΡΠΌ ΠΏΠΎΠ΄ΠΎΠ³ΡΠ΅Π²ΠΎΠΌ ΠΌΠ΅ΒΡΠ°Π»Π»Π° (Π·Π°Π³ΠΎΡΠΎΠ²ΠΊΠΈ).
Π ΡΠ°Π±Π».2.1 ΠΏΡΠΈΠ²Π΅Π΄Π΅Π½Π° ΡΠ΅Ρ Π½ΠΈΡΠ΅ΡΠΊΠ°Ρ Ρ Π°ΡΠ°ΠΊΡΠ΅ΡΠΈΡΡΠΈΠΊΠ° Π½Π°ΠΈΠ±ΠΎΠ»Π΅Π΅ ΡΠ°ΡΠΏΡΠΎΡΡΡΠ°Π½Π΅Π½Π½ΡΡ ΡΠΈΠΏΠΎΠ² Π²ΠΎΠ»ΠΎΡΠΈΠ»ΡΠ½ΡΡ ΡΡΠ°Π½ΠΎΠ² ΠΊΠ°ΠΊ Π΄Π»Ρ ΠΎΠ΄Π½ΠΎΠΊΡΠ°ΡΠ½ΠΎΠ³ΠΎ, ΡΠ°ΠΊ ΠΈ Π΄Π»Ρ ΠΌΠ½ΠΎΠ³ΠΎΠΊΡΠ°ΡΠ½ΠΎΠ³ΠΎ Π²ΠΎΠ»ΠΎΡΠ΅Π½ΠΈΡ ΠΊΠΎΠ½ΡΡΡΡΠΊΡΠΈΠΈ ΠΠΠΠΠΠΠ’ΠΠΠ¨Π°.
ΠΠΈΠ½Π΅ΠΌΠ°ΡΠΈΡΠ΅ΡΠΊΠΈΠ΅ ΡΡ Π΅ΠΌΡ ΠΏΡΠΈΠ²ΠΎΠ΄ΠΎΠ² ΡΡΠ°Π½ΠΎΠ² ΠΠ‘Π 1/650, ΠΠ‘Π 1/550 ΠΈ ΠΠ‘Π 1/750 ΠΏΡΠΈΠ²Π΅Π΄Π΅Π½Ρ Π½Π° ΡΠΈΡ. 1.3-1.5.
Π ΠΈΡ.1.1. Π‘Ρ Π΅ΠΌΠ° ΡΠ°Π±ΠΎΡΡ ΠΎΠ΄Π½ΠΎΠΊΡΠ°ΡΠ½ΠΎΠ³ΠΎ Π²ΠΎΠ»ΠΎΡΠΈΠ»ΡΠ½ΠΎΠ³ΠΎ ΡΡΠ°Π½Π°:
1 — ΡΠ°Π·ΠΌΠΎΡΠΎΡΠ½ΠΎΠ΅ ΡΡΡΡΠΎΠΉΡΡΠ²ΠΎ; 2 — ΠΏΡΠΎΠ²ΠΎΠ»ΠΎΠΊΠ° — Π·Π°Π³ΠΎΡΠΎΠ²ΠΊΠ°; 3 — Π²ΠΎΠ»ΠΎΡΠΈΠ»ΡΠ½ΡΠΉ ΠΈΠ½ΡΡΡΡΠΌΠ΅Π½Ρ; 4 — ΠΏΡΠΎΡΡΠ½ΡΡΠ°Ρ ΠΏΡΠΎΠ²ΠΎΠ»ΠΎΠΊΠ°; 5 — ΡΡΠ½ΡΡΠΈΠΉ Π±Π°ΡΠ°Π±Π°Π½; 6 — ΡΠ΅Π΄ΡΠΊΡΠΎΡ; 7 — ΡΠ»Π΅ΠΊΡΡΠΎΠ΄Π²ΠΈΠ³Π°ΡΠ΅Π»Ρ
Π ΠΈΡ.1.2. ΠΠ±ΡΠΈΠΉ Π²ΠΈΠ΄ Π²ΠΎΠ»ΠΎΡΠΈΠ»ΡΠ½ΠΎΠ³ΠΎ ΡΡΠ°Π½Π° ΠΠ‘Π 1/650:
1-ΠΊΠΎΠ½ΡΠΎΠ»Ρ Π΄Π»Ρ Π·Π°Π³ΠΎΡΠΎΠ²ΠΊΠΈ Π² ΠΌΠΎΡΠΊΠ°Ρ ; 2-Π²ΡΠ°ΡΠ°ΡΡΠΈΠ΅ΡΡ ΡΠΈΠ³ΡΡΠΊΠΈ Π΄Π»Ρ ΠΌΠΎΡΠΊΠΎΠ²;3-ΡΠ»Π΅ΠΊΡΡΠΎΠ΄Π²ΠΈΠ³Π°ΡΠ΅Π»Ρ ΠΏΡΠΈΠ²ΠΎΠ΄Π°; 4-ΠΊΠΎΡΠΎΠ±ΠΊΠ° ΠΏΠ΅ΡΠ΅Π΄Π°Ρ; 5-Π²ΠΎΠ»ΠΎΡΠΈΠ»ΡΠ½ΡΠΉ,ΡΡΠ½ΡΡΠΈΠΉ Π±Π°ΡΠ°Π±Π°Π½;6-ΡΠΏΠΈΡΡ Π΄Π»Ρ Π½Π°ΠΊΠΎΠΏΠ»Π΅Π½ΠΈΡ ΠΏΡΠΎΠ²ΠΎΠ»ΠΎΠΊΠΈ; 7-ΠΊΠΎΠ»ΠΎΠ½Π½Π° ΡΡΠ΅ΠΌΠ½ΠΈΠΊΠ°: 8-ΡΠΈΠ³ΡΡΠΊΠ° Π΄Π»Ρ ΡΠ²ΡΠ·ΠΊΠΈ ΠΌΠΎΡΠΊΠ°; 9-ΡΠΈΠ»ΡΠ΅ΡΠΎΠ΄Π΅ΡΠΆΠ°ΡΠ΅Π»Ρ; 10-ΡΠ²Π°ΡΠΎΡΠ½ΡΠΉ Π°ΠΏΠΏΠ°ΡΠ°Ρ; 11-ΠΊΠΎΡΠΏΡΡ Π±Π»ΠΎΠΊΠ° ΡΡΠ°Π½Π°; 12-ΡΠ»Π΅ΠΊΡΡΠΎΡΠΊΠ°Ρ; 13-Π½Π°ΠΆΠ΄Π°ΠΊ
. 1.2 ΠΠΎΠ»ΠΎΡΠΈΠ»ΡΠ½ΡΠ΅ ΡΡΠ°Π½Ρ Π΄Π»Ρ ΠΌΠ½ΠΎΠ³ΠΎΠΊΡΠ°ΡΠ½ΠΎΠ³ΠΎ Π²ΠΎΠ»ΠΎΡΠ΅Π½ΠΈΡ
ΠΏΡΠΎΠ²ΠΎΠ»ΠΎΠΊΠΈ
ΠΠ° ΠΌΠ½ΠΎΠ³ΠΎΠΊΡΠ°ΡΠ½ΡΡ Π²ΠΎΠ»ΠΎΡΠΈΠ»ΡΠ½ΡΡ ΡΡΠ°Π½Π°Ρ ΠΏΡΠΎΠ²ΠΎΠ»ΠΎΠΊΠ° — Π·Π°Π³ΠΎΡΠΎΠ²ΠΊΠ° ΠΏΡΠΎΒΡ ΠΎΠ΄ΠΈΡ ΠΏΠΎΡΠ»Π΅Π΄ΠΎΠ²Π°ΡΠ΅Π»ΡΠ½ΠΎ ΡΠ΅ΡΠ΅Π· Π½Π΅ΡΠΊΠΎΠ»ΡΠΊΠΎ Π²ΠΎΠ»ΠΎΠΊ, ΠΈΠ·ΠΌΠ΅Π½ΡΡ ΠΏΠΎΡΠ»Π΅ ΠΊΠ°ΠΆΠ΄ΠΎΠΉ
ΠΠΎΠ»ΠΎΡΠΈΠ»ΡΠ½ΡΠΉ ΡΡΠ°Π½ ΡΠΈΠΏΠ° UDZSA 5000/6
Π¨Π΅ΡΡΠΈΠΊΡΠ°ΡΠ½ΡΠΉ Π²ΠΎΠ»ΠΎΡΠΈΠ»ΡΠ½ΡΠΉ ΡΡΠ°Π½ Π±Π»ΠΎΡΠ½ΠΎΠ³ΠΎ ΡΠΈΠΏΠ° ΠΌΠΎΠ΄Π΅Π»ΠΈ UDZSA 5000/6 Ρ ΠΌΠ°ΠΊΡΠΈΠΌΠ°Π»ΡΠ½ΡΠΌ ΡΡΠΈΠ»ΠΈΠ΅ΠΌ Π²ΠΎΠ»ΠΎΡΠ΅Π½ΠΈΡ Π½Π° ΠΏΠ΅ΡΠ²ΠΎΠΌ ΡΠ΅ΡΠ½ΠΎΠ²ΠΎΠΌ Π±Π»ΠΎΠΊΠ΅ ΡΠ°Π²Π½ΡΠΌ 50 ΠΊΠ (5000 ΠΊΠ³), ΠΏΡΠ΅Π΄Π½Π°Π·Π½Π°ΡΠ΅Π½ Π΄Π»Ρ Π²ΠΎΠ»ΠΎΡΠ΅Π½ΠΈΡ ΡΡΠ°Π»ΡΠ½ΠΎΠΉ ΡΠ³Π»Π΅ΒΡΠΎΠ΄ΠΈΡΡΠΎΠΉ ΠΏΡΠΎΠ²ΠΎΠ»ΠΎΠΊΠΈ ΠΏΡΠΈ Π΄ΠΈΠ°ΠΌΠ΅ΡΡΠ΅ Π·Π°Π³ΠΎΡΠΎΠ²ΠΊΠΈ Π΄ΠΎ 12 ΠΌΠΌ. ΠΡΠΈ Π²ΠΎΠ»ΠΎΡΠ΅Π½ΠΈΠΈ ΠΌΠ΅Π΄Π½ΠΎΠΉ ΠΈΠ»ΠΈ Π°Π»ΡΠΌΠΈΠ½ΠΈΠ΅Π²ΠΎΠΉ ΠΏΡΠΎΠ²ΠΎΠ»ΠΎΠΊΠΈ Π΄ΠΈΠ°ΠΌΠ΅ΡΡ Π·Π°Π³ΠΎΡΠΎΠ²ΠΊΠΈ ΠΌΠΎΠΆΠ΅Ρ Π±ΡΡΡ Π±ΠΎΠ»ΡΡΠ΅. ΠΠ±ΡΠΈΠΉ Π²ΠΈΠ΄ Π²ΠΎΠ»ΠΎΡΠΈΠ»ΡΠ½ΠΎΠ³ΠΎ ΡΡΠ°Π½Π° UDZSA 5000/6 ΠΏΡΠΈΠ²Π΅Π΄Π΅Π½ Π½Π° ΡΠΈΡ.3.1.
ΠΡΠ΅ Π±Π»ΠΎΠΊΠΈ Π΄Π°Π½Π½ΠΎΠ³ΠΎ ΡΡΠ°Π½Π° ΠΈΠΌΠ΅ΡΡ ΠΎΠ΄ΠΈΠ½Π°ΠΊΠΎΠ²ΡΡ ΠΊΠΎΠ½ΡΡΡΡΠΊΡΠΈΡ. ΠΡΠ»ΠΈΒΡΠΈΡΠ΅Π»ΡΠ½ΡΡ ΠΎΡΠΎΠ±Π΅Π½Π½ΠΎΡΡΡ ΠΈΠΌΠ΅Π΅Ρ ΡΠΈΡΡΠΎΠ²ΠΎΠΉ Π±Π°ΡΠ°Π±Π°Π½, ΡΠ½Π°Π±ΠΆΠ΅Π½Π½ΡΠΉ ΡΠΏΠ΅ΡΠΈΒΠ°Π»ΡΠ½ΡΠΌΠΈ ΡΠΏΠΈΡΠ°ΠΌΠΈ Π΄Π»Ρ ΡΠ±ΠΎΡΠ° Π²ΠΈΡΠΊΠΎΠ² Π³ΠΎΡΠΎΠ²ΠΎΠΉ ΠΏΡΠΎΠ²ΠΎΠ»ΠΎΠΊΠΈ Π² ΠΌΠΎΡΠΎΠΊ. ΠΡΠ»ΠΈ Π²ΠΎΠ»ΠΎΡΠΈΠ»ΡΠ½ΡΠΉ ΡΡΠ°Π½ ΡΠ½Π°Π±ΠΆΠ΅Π½ Π½Π°ΠΌΠΎΡΠΎΡΠ½ΡΠΌ Π°ΠΏΠΏΠ°ΡΠ°ΡΠΎΠΌ, ΡΠΎ Π³ΠΎΡΠΎΠ²Π°Ρ ΠΏΡΠΎΠ²ΠΎΒΠ»ΠΎΠΊΠ° Π½Π°ΠΌΠ°ΡΡΠ²Π°Π΅ΡΡΡ Π½Π° ΠΊΠ°ΡΡΡΠΊΠΈ Π²ΠΌΠ΅ΡΡΠΈΠΌΠΎΡΡΡΡ Π΄ΠΎ 1000 ΠΊΠ³.
ΠΠ°ΠΆΠ΄ΡΠΉ Π±Π»ΠΎΠΊ ΡΡΡΠ°Π½Π°Π²Π»ΠΈΠ²Π°Π΅ΡΡΡ Π½Π° ΡΠΎΠ±ΡΡΠ²Π΅Π½Π½ΠΎΠΌ ΠΆΠ΅Π»Π΅Π·ΠΎΠ±Π΅ΡΠΎΠ½Π½ΠΎΠΌ ΡΡΠ½Π΄Π°ΠΌΠ΅Π½ΡΠ΅, ΠΏΡΠΎΡΠ½ΠΎ ΠΏΡΠΈΠΊΡΠ΅ΠΏΠ»ΡΠ΅ΡΡΡ ΠΊ Π½Π΅ΠΌΡ Π°Π½ΠΊΠ΅ΡΠ½ΡΠΌΠΈ Π±ΠΎΠ»ΡΠ°ΠΌΠΈ. Π Π±Π»ΠΎΒΠΊΠ°ΠΌ ΠΏΠΎΠ΄Π²ΠΎΠ΄ΡΡΡΡ Π½Π΅ΠΎΠ±Ρ ΠΎΠ΄ΠΈΠΌΡΠ΅ ΠΊΠΎΠΌΠΌΡΠ½ΠΈΠΊΠ°ΡΠΈΠΈ: ΡΡΡΠ±ΠΎΠΏΡΠΎΠ²ΠΎΠ΄Ρ Π΄Π»Ρ Π²ΠΎΠ΄ΡΠ½ΠΎΒΠ³ΠΎ ΠΎΡ Π»Π°ΠΆΠ΄Π΅Π½ΠΈΡ Π±Π°ΡΠ°Π±Π°Π½ΠΎΠ² ΠΈ Π²ΠΎΠ»ΠΎΠΊΠΎΠ΄Π΅ΡΠΆΠ°ΡΠ΅Π»Π΅ΠΉ, ΡΠ»Π΅ΠΊΡΡΠΎΠΏΠΈΡΠ°Π½ΠΈΠ΅ , ΡΠΈΡΒΡΠ΅ΠΌΡ ΡΠΏΡΠ°Π²Π»Π΅Π½ΠΈΡ ΠΈ Ρ.Π΄.
Π Π·Π°Π²ΠΈΡΠΈΠΌΠΎΡΡΠΈ ΠΎΡ ΡΠ΅Ρ Π½ΠΎΠ»ΠΎΠ³ΠΈΡΠ΅ΡΠΊΠΈΡ ΠΎΡΠΎΠ±Π΅Π½Π½ΠΎΡΡΠ΅ΠΉ ΠΈΠ·Π³ΠΎΡΠΎΠ²Π»Π΅Π½ΠΈΡ ΠΏΡΠΎΠ²ΠΎΠ»ΠΎΠΊΠΈ ΠΈ ΠΏΠΎΠ»ΡΡΠ΅Π½ΠΈΡ Π½Π΅ΠΎΠ±Ρ ΠΎΠ΄ΠΈΠΌΡΡ ΠΌΠ΅Ρ Π°Π½ΠΈΡΠ΅ΡΠΊΠΈΡ ΡΠ²ΠΎΠΉΡΡΠ² Π½Π° Π³ΠΎΡΠΎΠ²ΠΎΠΌ ΡΠ°Π·ΠΌΠ΅ΡΠ΅ Π²ΠΎΠ»ΠΎΡΠΈΠ»ΡΠ½ΡΠ΅ ΡΡΠ°Π½Ρ ΠΌΠΎΠ³ΡΡ ΠΊΠΎΠΌΠΏΠ»Π΅ΠΊΡΠΎΠ²Π°ΡΡΡΡ Π² ΠΎΠ΄Π½ΠΎΠΉ Π»ΠΈΠ½ΠΈΠΈ Ρ ΡΠ°Π·Π»ΠΈΡΠ½ΡΠΌ ΡΠΈΡΠ»ΠΎΠΌ Π±Π»ΠΎΠΊΠΎΠ² (ΠΎΡ ΠΎΠ΄Π½ΠΎΠ³ΠΎ Π΄ΠΎ ΡΠ΅ΡΡΠΈ).ΠΡΠ½ΠΎΠ²Π½ΡΠ΅ ΡΠ΅Ρ Π½ΠΈΡΠ΅ΡΠΊΠΈΠ΅ Ρ Π°ΡΠ°ΠΊΡΠ΅ΡΠΈΡΡΠΈΠΊΠΈ Π²ΠΎΠ»ΠΎΡΠΈΠ»ΡΠ½ΡΡ ΡΡΠ°Π½ΠΎΠ² UDZSA 5000/1-6, 2500/1-6, 1250/1-10 ΠΈ 630/1-10 ΠΏΡΠΈΠ²Π΅Π΄Π΅Π½Ρ Π² ΡΠ°Π±Π».3.2.
ΠΠ»ΠΎΠΊΠΈ Π²ΠΎΠ»ΠΎΡΠΈΠ»ΡΠ½ΠΎΠ³ΠΎ ΡΡΠ°Π½Π° UDZSA 5000/6 ΠΈΠΌΠ΅ΡΡ Π² ΡΠ²ΠΎΠ΅ΠΌ ΡΠΎΡΡΠ°Π²Π΅ ΠΏΡΠΈΠ²ΠΎΠ΄ ΠΎΡ ΡΠ»Π΅ΠΊΡΡΠΎΠ΄Π²ΠΈΠ³Π°ΡΠ΅Π»Ρ ΠΏΠ΅ΡΠ΅ΠΌΠ΅Π½Π½ΠΎΠ³ΠΎ ΡΠΎΠΊΠ°, ΠΊΠ»ΠΈΠ½ΠΎΡΠ΅ΠΌΠ΅Π½Π½ΡΡ ΠΏΠ΅ΡΠ΅ΒΠ΄Π°ΡΡ, ΡΠ΅ΡΡΡΠ΅Ρ ΡΡΡΠΏΠ΅Π½ΡΠ°ΡΡΡ ΠΊΠΎΡΠΎΠ±ΠΊΡ ΠΏΠ΅ΡΠ΅Π΄Π°Ρ, Π΄Π²Π΅ ΡΠΈΠ»ΠΈΠ½Π΄ΡΠΈΡΠ΅ΡΠΊΠΈΠ΅ ΠΈ ΠΎΠ΄Π½Ρ ΠΊΠΎΠ½ΠΈΡΠ΅ΡΠΊΡΡ Π·ΡΠ±ΡΠ°ΡΡΡ ΠΏΠ΅ΡΠ΅Π΄Π°ΡΡ, ΠΏΡΠΈΠ²Π΅Π΄Π΅Π½Π½ΡΠ΅ Π½Π° ΡΠΈΡ.3.2. ΠΡΠ΅ ΠΌΠ΅Ρ Π°Π½ΠΈΠ·ΠΌΡ ΡΡΡΠ°Π½ΠΎΠ²Π»Π΅Π½Ρ Π² Π»ΠΈΡΠΎΠΌ ΡΡΠ°Π»ΡΠ½ΠΎΠΌ ΠΊΠΎΡΠΏΡΡΠ΅, ΠΎΠ±Π΅ΡΠΏΠ΅ΡΠΈΒΠ²Π°ΡΡΠ΅ΠΌ Π΄ΠΎΡΡΠ°ΡΠΎΡΠ½ΡΡ ΠΏΡΠΎΡΠ½ΠΎΡΡΡ ΠΈ ΠΆΠ΅ΡΡΠΊΠΎΡΡΡ. ΠΠ°Π»Ρ Π·ΡΠ±ΡΠ°ΡΡΡ ΠΊΠΎΠ»Π΅Ρ ΠΈΠΌΠ΅ΡΡ ΠΎΠΏΠΎΡΡ Π½Π° ΠΏΠΎΠ΄ΡΠΈΠΏΠ½ΠΈΠΊΠ°Ρ ΠΊΠ°ΡΠ΅Π½ΠΈΡ. Π‘ΠΌΠ°Π·ΠΊΠ° Π·ΡΠ±ΡΠ°ΡΡΡ ΠΊΠΎΠ»Π΅Ρ ΠΈ ΠΏΠΎΠ΄ΡΠΈΠΏΠ½ΠΈΠΊΠΎΠ²ΡΡ ΡΠ·Π»ΠΎΠ² — ΠΊΠ°ΡΡΠ΅ΡΠ½Π°Ρ, ΠΎΠΊΡΠ½Π°Π½ΠΈΠ΅ΠΌ ΠΈ ΡΠ°Π·Π±ΡΡΠ·Π³ΠΈΠ²Π°Π½ΠΈΠ΅ΠΌ. ΠΡΠ±ΡΡ ΠΊΠΎΠ»Π΅Ρ Π΄Π»Ρ ΡΠ²Π΅Π»ΠΈΡΠ΅Π½ΠΈΡ ΡΡΠΎΠΉΠΊΠΎΡΡΠΈ ΠΏΠΎΠ΄Π²Π΅ΡΠ³Π°ΡΡΡΡ Π·Π°ΠΊΠ°Π»ΠΊΠ΅ ΠΈ ΡΠ»ΠΈΒΡΠΎΠ²Π°Π½ΠΈΡ Π»ΠΈΠ±ΠΎ ΠΏΡΠΈΡΠΈΡΠΊΠ΅. Π£ΠΏΡΠΎΡΠ½Π΅Π½ΠΈΡ Π·Π°ΠΊΠ°Π»ΠΊΠΎΠΉ ΠΏΠΎΠ΄Π²Π΅ΡΠ³Π°ΡΡΡΡ ΠΈ ΡΠΎΠ»ΠΈΒΠΊΠΈ Π΄ΠΈΡΡΠ΅ΡΠ΅Π½ΡΠΈΠ°Π»Π°, ΡΠ°Π±ΠΎΡΠ°ΡΡΠΈΠ΅ Π² ΡΡΠ»ΠΎΠ²ΠΈΡΡ ΡΡΠΆΠ΅Π»ΠΎΠ³ΠΎ Π½Π°Π³ΡΡΠΆΠ΅Π½ΠΈΡ.
ΠΠ°ΠΆΠ΄ΡΠΉ Π²ΠΎΠ»ΠΎΡΠΈΠ»ΡΠ½ΡΠΉ ΡΡΠ°Π½ ΠΎΡΠ½Π°ΡΠ°Π΅ΡΡΡ Π·Π°ΠΏΡΠ°Π²ΠΎΡΠ½ΠΎΠΉ ΡΠ°Π½Π³ΠΎΠΉ Π΄Π»Ρ ΠΏΡΠΎΡΡΠ³ΠΈΠ²Π°Π½ΠΈΡ ΠΊΠΎΠ½ΡΠ° ΠΏΡΠΎΠ²ΠΎΠ»ΠΎΠΊΠΈ ΡΠ΅ΡΠ΅Π· Π²ΠΎΠ»ΠΎΡΠΈΠ»ΡΠ½ΡΠΉ ΠΈΠ½ΡΡΡΡΠΌΠ΅Π½Ρ ΠΈ Π½Π°ΠΌΠ°ΒΡΡΠ²Π°Π½ΠΈΡ Π½Π° Π±Π°ΡΠ°Π±Π°Π½ Π½Π΅ΡΠΊΠΎΠ»ΡΠΊΠΈΡ Π²ΠΈΡΠΊΠΎΠ² ΠΏΡΠΎΠ²ΠΎΠ»ΠΎΠΊΠΈ Π΄Π»Ρ Π΄Π°Π»ΡΠ½Π΅ΠΉΡΠ΅Π³ΠΎ Π²ΠΎΠ»ΠΎΡΠ΅Π½ΠΈΡ. ΠΡΡΠ³ΠΎΠΉ ΠΊΠΎΠ½Π΅Ρ ΡΠ°Π½Π³ΠΈ ΠΈΠΌΠ΅Π΅Ρ ΠΊΡΡΡΠΎΠΊ, ΠΊΠΎΡΠΎΡΡΠΉ Π·Π°ΡΠ΅ΠΏΠ»ΡΠ΅ΡΡΡ Π·Π° ΡΠΏΠ΅ΡΠΈΠ°Π»ΡΠ½ΡΠ΅ ΠΎΡΠ²Π΅ΡΡΡΠΈΡ Π² Π±Π°ΡΠ°Π±Π°Π½Π΅. ΠΠΎΡΠ»Π΅ Π½Π°ΠΌΠ°ΡΡΠ²Π°Π½ΠΈΡ Π½Π΅ΡΠΊΠΎΠ»ΡΠΊΠΈΡ Π²ΠΈΡΠΊΠΎΠ² ΠΏΡΠΎΠ²ΠΎΠ»ΠΎΠΊΠΈ (ΠΎΠΊΠΎΠ»ΠΎ 10) ΡΠ°Π½Π³Π° ΡΠ½ΠΈΠΌΠ°Π΅ΡΡΡ ΠΈ ΡΡΠ°Π½ Π²ΠΊΠ»ΡΡΠ°Π΅ΡΡΡ Ρ Π·Π°ΠΏΡΠ°Π²ΠΎΡΠ½ΠΎΠΉ ΡΠΊΠΎΡΠΎΡΡΠΈ Π½Π° Π½ΠΎΡΠΌΠ°Π»ΡΠ½ΡΡ ΡΠ°Π±ΠΎΡΡΡ. ΠΠΎ Π²ΡΠ΅ΠΌΡ Π·Π°ΠΏΡΠ°Π²ΠΊΠΈ Π½ΡΠΆΠ½ΠΎ Π±ΡΡΡ ΠΎΡΠ΅Π½Ρ Π²Π½ΠΈΠΌΠ°ΡΠ΅Π»ΡΠ½ΡΠΌ ΠΈ ΠΏΡΠ΅Π΄ΠΎΡ ΡΠ°Π½ΡΡΡ ΡΡΠΊΠΈ ΠΎΡ Π²ΠΎΠ·ΠΌΠΎΠΆΠ½ΠΎΠ³ΠΎ Π·Π°ΡΡΠ³ΠΈΠ²Π°Π½ΠΈΡ ΠΈΡ Π²ΠΈΡΠΊΠ°ΠΌΠΈ Π½Π°ΠΌΠ°ΡΡΠ²Π°Π΅ΠΌΠΎΠΉ ΠΏΡΠΎΠ²ΠΎΠ»ΠΎΠΊΠΈ.
ΠΠ±ΡΠΈΠΉ Π²ΠΈΠ΄ ΠΏΡΠΎΠΌΠ΅ΠΆΡΡΠΎΡΠ½ΠΎΠ³ΠΎ Π±Π°ΡΠ°Π±Π°Π½Π° Π²ΠΎΠ»ΠΎΡΠΈΠ»ΡΠ½ΠΎΠ³ΠΎ ΡΡΠ°Π½Π° UDZSA 5000/ΠΏ ΠΏΠΎΠΊΠ°Π·Π°Π½ Π½Π° ΡΠΈΡ.3.2.
ΠΠ°Π³ΠΎΡΠΎΠ²ΠΊΠ° ΠΈΠ»ΠΈ ΠΏΡΠΎΠ²ΠΎΠ»ΠΎΠΊΠ° ΠΏΡΠΎΠΌΠ΅ΠΆΡΡΠΎΡΠ½ΠΎΠ³ΠΎ ΡΠ°Π·ΠΌΠ΅ΡΠ°, ΠΏΡΠΎΡ ΠΎΠ΄Ρ ΡΠ΅ΡΠ΅Π· Π²ΠΎΠ»ΠΎΡΠΈΠ»ΡΠ½ΡΠΉ ΠΈΠ½ΡΡΡΡΠΌΠ΅Π½Ρ, ΡΡΡΠ°Π½ΠΎΠ²Π»Π΅Π½Π½ΡΠΉ Π² Π²ΠΎΠ»ΠΎΠΊΠΎΠ΄Π΅ΡΠΆΠ°ΡΠ΅Π»Π΅ 10, Π½Π°ΠΌΠ°ΒΡΡΠ²Π°Π΅ΡΡΡ Π½Π° ΡΡΠ³ΠΎΠ²ΡΠΉ Π±Π°ΡΠ°Π±Π°Π½ ΠΈ ΠΏΠΎΡΠ»Π΅ Π½Π°ΠΊΠΎΠΏΠ»Π΅Π½ΠΈΡ Π½Π΅ΠΊΠΎΡΠΎΡΠΎΠ³ΠΎ ΠΎΠ±ΡΠ΅ΠΌΠ° ΠΏΡΠΎΠΏΡΡΠΊΠ°Π΅ΡΡΡ ΡΠ΅ΡΠ΅Π· ΡΠΎΠ»ΠΈΠΊ 13 ΡΠΎΡΠΌΠΎΠ·Π½ΠΎΠ³ΠΎ Π΄ΠΈΡΡΠ΅ΡΠ΅Π½ΡΠΈΠ°Π»Π° ΠΈ Π΄Π°Π»Π΅Π΅ ΡΠ΅ΒΡΠ΅Π· Π½Π°ΠΏΡΠ°Π²Π»ΡΡΡΠΈΠΉ Π±Π»ΠΎΠΊ 14, ΡΡΡΠ°Π½ΠΎΠ²Π»Π΅Π½Π½ΡΠΉ Π½Π° Π²Π΅ΡΡΠΈΠΊΠ°Π»ΡΠ½ΠΎΠΉ ΡΡΠΎΠΉΠΊΠ΅, ΠΊ Π²ΠΎΠ»ΠΎΠΊΠΎΠ΄Π΅ΡΠΆΠ°ΡΠ΅Π»Ρ ΡΠ»Π΅Π΄ΡΡΡΠ΅Π³ΠΎ Π±Π»ΠΎΠΊΠ° Π²ΠΎΠ»ΠΎΡΠΈΠ»ΡΠ½ΠΎΠ³ΠΎ ΡΡΠ°Π½Π°.
ΠΠΊΠ»ΡΡΠ΅Π½ΠΈΠ΅ Π±Π»ΠΎΠΊΠ° Π²ΠΎΠ»ΠΎΡΠΈΠ»ΡΠ½ΠΎΠ³ΠΎ ΡΡΠ°Π½Π° ΠΏΡΠΎΠΈΠ·Π²ΠΎΠ΄ΠΈΡΡΡ ΠΊΠ½ΠΎΠΏΠΊΠΎΠΉ 9.. «ΠΡΡΠΊ», Π° ΠΎΡΡΠ°Π½ΠΎΠ²ΠΊΠ° ΠΊΠ½ΠΎΠΏΠΊΠΎΠΉ 8 «Π‘ΡΠΎΠΏ». Π£ΠΏΡΠ°Π²Π»Π΅Π½ΠΈΠ΅ ΡΠΈΡΡΠ΅ΠΌΠΎΠΉ ΠΎΡ Π»Π°ΠΆΒΠ΄Π΅Π½ΠΈΡ Π²ΠΎΠ»ΠΎΡΠΈΠ»ΡΠ½ΠΎΠ³ΠΎ ΠΈΠ½ΡΡΡΡΠΌΠ΅Π½ΡΠ° ΠΎΡΡΡΠ΅ΡΡΠ²Π»ΡΠ΅ΡΡΡ ΠΏΠ΅ΡΠ΅ΠΏΡΡΠΊΠ½ΡΠΌ ΠΊΠ»Π°ΠΏΠ°ΒΠ½ΠΎΠΌ 7, Π° ΠΎΡ Π»Π°ΠΆΠ΄Π΅Π½ΠΈΠ΅ Π±Π°ΡΠ°Π±Π°Π½Π° — ΠΊΠ»Π°ΠΏΠ°Π½ΠΎΠΌ 6.
ΠΠΎ Π²ΡΠ΅ΠΌΡ Π·Π°ΠΏΡΠ°Π²ΠΊΠΈ ΠΏΡΠΎΠ²ΠΎΠ»ΠΎΠΊΠΈ Π½Π° Π±Π°ΡΠ°Π±Π°Π½Π΅ ΠΈ Π½Π°ΡΡΠΎΠΉΠΊΠ΅ ΡΡΠ°Π½Π° Π½ΠΎΠΆΠ½ΠΎΠΉ Π²ΡΠΊΠ»ΡΡΠ°ΡΠ΅Π»Ρ «ΠΏΠΎΠ»Π·ΡΡΠ΅ΠΉ» ΠΌΠ΅Π΄Π»Π΅Π½Π½ΠΎΠΉ ΡΠΊΠΎΡΠΎΡΡΠΈ ΠΏΡΠΈΠ²ΠΎΠ΄Π° Π±Π»ΠΎΠΊΠ° -ΠΊΠΎΠ½Π΅ΡΠ½ΡΠΉ Π²ΡΠΊΠ»ΡΡΠ°ΡΠ΅Π»Ρ 1. Π§Π°ΡΡΠΎΡΠ° Π²ΡΠ°ΡΠ΅Π½ΠΈΡ Π±Π°ΡΠ°Π±Π°Π½Π° ΠΊΠΎΠ½ΡΡΠΎΠ»ΠΈΡΡΠ΅ΡΡΡ ΡΠ°Ρ ΠΎΠ³Π΅Π½Π΅ΡΠ°ΡΠΎΡΠΎΠΌ 2.
ΠΠ΅ΡΠ΅ΠΊΠ»ΡΡΠ΅Π½ΠΈΠ΅ ΡΡΡΠΏΠ΅Π½Π΅ΠΉ Π·ΡΠ±ΡΠ°ΡΡΡ ΠΏΠ΅ΡΠ΅Π΄Π°Ρ ΠΊΠΎΡΠΎΠ±ΠΊΠΈ ΡΠΊΠΎΡΠΎΡΡΠ΅ΠΉ Π½Π° Π±Π»ΠΎΠΊΠ΅ ΠΎΡΡΡΠ΅ΡΡΠ²Π»ΡΠ΅ΡΡΡ ΡΡΡΠ°Π³Π°ΠΌΠΈ 16 ΠΈ 17, ΠΏΡΠΈΡΠ΅ΠΌ ΠΎΠ΄Π½ΠΎΠ²ΡΠ΅ΠΌΠ΅Π½Π½ΠΎ ΠΎΠ΄Π½Π° ΠΈ ΡΠ°ΠΆΠ΅ ΡΠΊΠΎΡΠΎΡΡΡ (ΠΏΠ΅ΡΠ΅Π΄Π°ΡΠ°) ΡΡΡΠ°Π½Π°Π²Π»ΠΈΠ²Π°Π΅ΡΡΡ Π½Π° Π²ΡΠ΅Ρ Π±Π»ΠΎΠΊΠ°Ρ . Π£Π²Π΅Π»ΠΈΒΡΠ΅Π½ΠΈΠ΅ Π»ΠΈΠ½Π΅ΠΉΠ½ΠΎΠΉ ΡΠΊΠΎΡΠΎΡΡΠΈ Π²ΠΎΠ»ΠΎΡΠ΅Π½ΠΈΡ ΠΈΠ»ΠΈ ΠΎΠΊΡΡΠΆΠ½ΠΎΠΉ ΡΠΊΠΎΡΠΎΡΡΠΈ Π±Π°ΡΠ°Π±Π°Π½ΠΎΠ² ΠΎΡ ΠΏΠ΅ΡΠ²ΠΎΠ³ΠΎ Π΄ΠΎ ΠΏΠΎΡΠ»Π΅Π΄Π½Π΅Π³ΠΎ ΡΠΈΡΡΠΎΠ²ΠΎΠ³ΠΎ ΠΎΡΡΡΠ΅ΡΡΠ²Π»ΡΠ΅ΡΡΡ Π·Π° ΡΡΠ΅Ρ ΡΠ°Π·Π»ΠΈΡΒΠ½ΠΎΠ³ΠΎ ΡΠΈΡΠ»Π° Π·ΡΠ±ΡΠ΅Π² Za ΠΈ Zb Π² ΠΊΠΈΠ½Π΅ΠΌΠ°ΡΠΈΡΠ΅ΡΠΊΠΎΠΉ ΡΡ Π΅ΠΌΠ΅ Π² ΠΊΠ°ΠΆΠ΄ΠΎΠΌ Π±Π»ΠΎΠΊΠ΅.
ΠΠ»ΠΎΠΊΠΈΡΡΡΡΠΈΠΉ ΠΊΠΎΠ½ΡΠ°ΠΊΡ 15 ΠΎΡΠΊΠ»ΡΡΠ°Π΅Ρ Π³Π»Π°Π²Π½ΡΠΉ ΠΏΡΠΈΠ²ΠΎΠ΄Π½ΠΎΠΉ ΡΠ»Π΅ΠΊΡΡΠΎΠ΄ΒΠ²ΠΈΠ³Π°ΡΠ΅Π»Ρ ΠΏΡΠΈ ΠΎΡΠΊΡΡΡΠΎΠΉ Π΄Π²Π΅ΡΡΠ΅ Π·Π°ΡΠΈΡΡ. ΠΡΠ΅ ΠΌΠ΅Ρ Π°Π½ΠΈΠ·ΠΌΡ ΡΠΌΠΎΠ½ΡΠΈΡΠΎΠ²Π°Π½Ρ Π½Π° Π»ΠΈΡΠΎΠΌ ΠΊΠΎΡΠΏΡΡΠ΅ 18.
ΠΠ° ΡΠΈΡ. 3.3 ΠΏΡΠ΅Π΄ΡΡΠ°Π²Π»Π΅Π½Π° ΠΊΠΈΠ½Π΅ΠΌΠ°ΡΠΈΡΠ΅ΡΠΊΠ°Ρ ΡΡ Π΅ΠΌΠ° ΠΎΠ΄Π½ΠΎΠ³ΠΎ Π±Π»ΠΎΠΊΠ° Π²ΠΎΠ»ΠΎΡΠΈΠ»ΡΠ½ΠΎΠ³ΠΎ ΡΡΠ°Π½Π° UDZSA 5000/6, Π° Π² ΡΠ°Π±Π». 3.3 — Π΄Π°Π½Π½ΡΠ΅ ΡΠΈΡΠ΅Π»
Π ΠΈΡ. 3.2. ΠΠ±ΡΠΈΠΉ Π²ΠΈΠ΄ Π±Π»ΠΎΠΊΠ° Π²ΠΎΠ»ΠΎΡΠΈΠ»ΡΠ½ΠΎΠ³ΠΎ ΡΡΠ°Π½Π° UDZSA 5000/ΠΏ: 1 — Π½ΠΎΠΆΠ½Π°Ρ ΠΊΠ½ΠΎΠΏΠΊΠ°»Π‘ΡΠΎΠΏ»; 2 — ΡΠ°Ρ ΠΎΠ³Π΅Π½Π΅ΡΠ°ΡΠΎΡ; 3 — ΡΠ»Π΅ΠΊΡΡΠΎΠ΄Π²ΠΈΠ³Π°ΡΠ΅Π»Ρ; 4 — Π³Π»Π°Π²Π½ΡΠΉ ΠΏΡΠΈΠ²ΠΎΠ΄Π½ΠΎΠΉ ΡΠ»Π΅ΠΊΡΡΠΎΠ΄Π²ΠΈΠ³Π°ΡΠ΅Π»Ρ; 5 — ΠΊΠΎΡΠΎΠ±ΠΊΠ° ΡΠ»Π΅ΠΊΡΡΠΎΠΊΠ»Π΅ΠΌΠΌ; 6 — ΠΏΠ΅ΡΠ΅ΠΏΡΡΠΊΠ½ΠΎΠΉ ΠΊΠ»Π°ΠΏΠ°Π½ Π΄Π»Ρ ΠΎΡ Π»Π°ΠΆΠ΄Π΅Π½ΠΈΡ Π±Π°ΡΠ°Π±Π°Π½Π°; 7 — ΠΏΠ΅ΡΠ΅ΠΏΡΡΠΊΠ½ΠΎΠΉ ΠΊΠ»Π°ΠΏΠ°Π½ Π΄Π»Ρ ΠΎΡ Π»Π°ΠΆΠ΄Π΅Π½ΠΈΡ ΠΈΠ½ΡΡΡΡΠΌΠ΅Π½ΡΠ°; 8 — ΠΊΠ½ΠΎΠΏΠΊΠ° «Π‘ΡΠΎΠΏ»; 9 — ΠΊΠ½ΠΎΠΏΠΊΠ° «ΠΡΡΠΊ»; 10 — Π½Π°ΠΏΡΠ°Π²Π»ΡΡΡΠΈΠΉ ΡΠΎΠ»ΠΈΠΊ ΠΏΠ΅ΡΠ΅Π΄ ΡΠΈΠ»ΡΠ΅ΡΠΎΠ΄Π΅ΡΠΆΠ°ΡΠ΅Π»Π΅ΠΌ; 11 -ΠΊΡΡΡΠΊΠ° Π±Π°ΠΊΠ° Ρ ΠΎΡ Π»Π°ΠΆΠ΄Π°ΡΡΠ΅ΠΉ ΠΆΠΈΠ΄ΠΊΠΎΡΡΡΡ; 12 — ΡΡΠ½ΡΡΠΈΠΉ Π±Π°ΡΠ°Π±Π°Π½; 13 -ΡΠΎΡΠΌΠΎΠ· Π΄ΠΈΡΡΠ΅ΡΠ΅Π½ΡΠΈΠ°Π»Π°; 14 — Π²Π΅ΡΡ Π½ΠΈΠΉ Π½Π°ΠΏΡΠ°Π²Π»ΡΡΡΠΈΠΉ ΡΠΎΠ»ΠΈΠΊ; 15 — Π±Π»ΠΎΒΠΊΠΈΡΡΡΡΠΈΠΉ ΠΊΠΎΠ½ΡΠ°ΠΊΡ ΠΏΡΠΈ ΠΎΡΠΊΡΡΠ²Π°Π½ΠΈΠΈ Π·Π°ΡΠΈΡΠ½ΠΎΠ³ΠΎ ΠΎΠ³ΡΠ°ΠΆΠ΄Π΅Π½ΠΈΡ; 16 — ΡΡΡΠ°Π³ Π΄Π»Ρ Π²ΠΊΠ»ΡΡΠ΅Π½ΠΈΡ 2-ΠΉ ΠΈ 4-ΠΉ ΠΏΠ΅ΡΠ΅Π΄Π°ΡΠΈ; 17 — ΡΡΡΠ°Π³ Π΄Π»Ρ Π²ΠΊΠ»ΡΡΠ΅Π½ΠΈΡ 1-ΠΉ ΠΈ 3-ΠΉ ΠΏΠ΅ΡΠ΅Π΄Π°Ρ; 18 — ΠΊΠΎΡΠΏΡΡ Π±Π»ΠΎΠΊΠ°
1.3 ΠΠΎΠ»ΠΎΡΠΈΠ»ΡΠ½ΡΠ΅ ΡΡΠ°Π½ΡΒ ΡΠ°Π·Π΄Π΅Π»ΡΡΡ Π½Π° Π΄Π²Π° ΡΠΈΠΏΠ°: Π±Π°ΡΠ°Π±Π°Π½Π½ΡΠ΅ ΠΈ ΡΠ΅ΠΏΠ½ΡΠ΅.
Β
Π ΠΈΡ.
1.3.1. ΠΡΠΎΠ΄ΠΎΠ»ΡΠ½ΡΠΉ ΡΠ°Π·ΡΠ΅Π· Π²ΠΎΠ»ΠΎΠΊΠΈ (Π°) ΠΈ ΡΡ
Π΅ΠΌΡ
Π±Π°ΡΠ°Π±Π°Π½Π½ΠΎΠ³ΠΎ (Π±) ΠΈ ΡΠ΅ΠΏΠ½ΠΎΠ³ΠΎ (Π²) Π²ΠΎΠ»ΠΎΡΠΈΠ»ΡΠ½ΡΡ
ΡΡΠ°Π½ΠΎΠ²
ΠΠ°ΡΠ°Π±Π°Π½Π½ΡΠ΅ ΡΡΠ°Π½ΡΒ (ΡΠΈΡ. 1.3.1, Π±) ΡΠ»ΡΠΆΠ°Ρ Π΄Π»Ρ Π²ΠΎΠ»ΠΎΡΠ΅Π½ΠΈΡ ΠΏΡΠΎΠ²ΠΎΠ»ΠΎΠΊΠΈ ΠΈ ΡΡΡΠ± Π½Π΅Π±ΠΎΠ»ΡΡΠΎΠ³ΠΎ Π΄ΠΈΠ°ΠΌΠ΅ΡΡΠ°, Π½Π°ΠΌΠ°ΡΡΠ²Π°Π΅ΠΌΡΡ Π½Π° Π²Π΅ΡΡΡΡΠΊΡ 1. ΠΡΠ΅Π΄Π²Π°ΡΠΈΡΠ΅Π»ΡΠ½ΠΎ Π·Π°ΠΎΡΡΡΠ΅Π½Π½ΡΠΉ ΠΊΠΎΠ½Π΅Ρ ΠΏΡΠΎΠ²ΠΎΠ»ΠΎΠΊΠΈ ΠΏΡΠΎΠΏΡΡΠΊΠ°Π΅ΡΡΡ ΡΠ΅ΡΠ΅Π· ΠΎΡΠ²Π΅ΡΡΡΠΈΠ΅ Π²ΠΎΠ»ΠΎΠΊΠΈ 2 ΠΈ Π·Π°ΠΊΡΠ΅ΠΏΠ»ΡΠ΅ΡΡΡ Π½Π° Π±Π°ΡΠ°Π±Π°Π½Π΅ 3, ΠΊΠΎΡΠΎΡΡΠΉ ΠΏΡΠΈΠ²ΠΎΠ΄ΠΈΡΡΡ Π²ΠΎ Π²ΡΠ°ΡΠ΅Π½ΠΈΠ΅ ΠΎΡ ΡΠ»Π΅ΠΊΡΡΠΎΠ΄Π²ΠΈΠ³Π°ΡΠ΅Π»Ρ ΡΠ΅ΡΠ΅Π· ΡΠ΅Π΄ΡΠΊΡΠΎΡ ΠΈ Π·ΡΠ±ΡΠ°ΡΡΡ ΠΏΠ΅ΡΠ΅Π΄Π°ΡΡ 4. Π‘ΡΡΠ΅ΡΡΠ²ΡΡΡ ΡΠ°ΠΊΠΆΠ΅ ΡΡΠ°Π½Ρ ΠΌΠ½ΠΎΠ³ΠΎΠΊΡΠ°ΡΠ½ΠΎΠ³ΠΎ Π²ΠΎΠ»ΠΎΡΠ΅Π½ΠΈΡ, ΠΈΠΌΠ΅ΡΡΠΈΠ΅ Π΄ΠΎ 20 Π±Π°ΡΠ°Π±Π°Π½ΠΎΠ² Ρ ΡΡΡΠ°Π½ΠΎΠ²Π»Π΅Π½Π½ΡΠΌΠΈ ΠΏΠ΅ΡΠ΅Π΄ ΠΊΠ°ΠΆΠ΄ΡΠΌ ΠΈΠ· Π½ΠΈΡ Π²ΠΎΠ»ΠΎΠΊΠ°ΠΌΠΈ.
Π¦Π΅ΠΏΠ½ΡΠ΅ ΡΡΠ°Π½ΡΒ Ρ ΠΏΡΡΠΌΠΎΠ»ΠΈΠ½Π΅ΠΉΠ½ΡΠΌ Π΄Π²ΠΈΠΆΠ΅Π½ΠΈΠ΅ΠΌ ΡΡΠ½ΡΡΠ΅Π³ΠΎ ΡΡΡΡΠΎΠΉΡΡΠ²Π° (ΡΠΈΡ. 1.3.1, Π²) ΠΏΡΠΈΠΌΠ΅Π½ΡΡΡ Π΄Π»Ρ Π²ΠΎΠ»ΠΎΡΠ΅Π½ΠΈΡ ΠΏΡΡΡΠΊΠΎΠ² ΠΈ ΡΡΡΠ±, ΠΊΠΎΡΠΎΡΡΠ΅ Π½Π΅ ΠΌΠΎΠ³ΡΡ Π½Π°ΠΌΠ°ΡΡΠ²Π°ΡΡΡΡ Π² Π±ΡΠ½ΡΡ. ΠΠ° ΡΡΠΎΠΌ ΡΡΠ°Π½Π΅ ΠΊΠΎΠ½Π΅Ρ ΠΏΡΡΡΠΊΠ° ΠΏΡΠΎΠΏΡΡΠΊΠ°ΡΡ ΡΠ΅ΡΠ΅Π· ΠΎΡΠ²Π΅ΡΡΡΠΈΠ΅ Π²ΠΎΠ»ΠΎΠΊΠΈ 2 ΠΈ Π·Π°Ρ Π²Π°ΡΡΠ²Π°ΡΡ ΠΊΠ»Π΅ΡΠ°ΠΌΠΈ 5, ΠΊΠΎΡΠΎΡΡΠ΅ Π·Π°ΠΊΡΠ΅ΠΏΠ»Π΅Π½Ρ Π½Π° ΠΊΠ°ΡΠ΅ΡΠΊΠ΅ 6. ΠΠ°ΡΠ΅ΡΠΊΠ° ΡΠ΅ΡΠ΅Π· ΡΡΠ³ΠΎΠ²ΡΠΉ ΠΊΡΡΠΊ 7 ΠΏΠ΅ΡΠ΅ΠΌΠ΅ΡΠ°Π΅ΡΡΡ ΠΏΠ»Π°ΡΡΠΈΠ½ΡΠ°ΡΠΎΠΉ ΡΠ΅ΠΏΡΡ 8, ΠΏΡΠΈΠ²ΠΎΠ΄ΠΈΠΌΠΎΠΉ Π² Π΄Π²ΠΈΠΆΠ΅Π½ΠΈΠ΅ ΠΎΡ Π·Π²Π΅Π·Π΄ΠΎΡΠΊΠΈ 9, ΠΊΠΎΡΠΎΡΠ°Ρ Π²ΡΠ°ΡΠ°Π΅ΡΡΡ ΠΎΡ ΡΠ»Π΅ΠΊΡΡΠΎΠ΄Π²ΠΈΠ³Π°ΡΠ΅Π»Ρ 11 ΡΠ΅ΡΠ΅Π· ΡΠ΅Π΄ΡΠΊΡΠΎΡ 10.
ΠΠΎΠ»ΠΎΡΠ΅Π½ΠΈΠ΅, ΠΊΠ°ΠΊ ΠΏΡΠ°Π²ΠΈΠ»ΠΎ, ΠΎΡΡΡΠ΅ΡΡΠ²Π»ΡΡΡ Π² Ρ ΠΎΠ»ΠΎΠ΄Π½ΠΎΠΌ ΡΠΎΡΡΠΎΡΠ½ΠΈΠΈ, Π° ΠΏΠΎΡΠΎΠΌΡ ΠΎΠ½ΠΎ ΡΠΎΠΏΡΠΎΠ²ΠΎΠΆΠ΄Π°Π΅ΡΡΡ ΡΠΏΡΠΎΡΠ½Π΅Π½ΠΈΠ΅ΠΌ (Π½Π°ΠΊΠ»Π΅ΠΏΠΎΠΌ) ΠΌΠ΅ΡΠ°Π»Π»Π°. ΠΡΡ ΠΎΠ΄Π½ΡΠΌΠΈ Π·Π°Π³ΠΎΡΠΎΠ²ΠΊΠ°ΠΌΠΈ ΡΠ»ΡΠΆΠ°Ρ ΠΏΡΠΎΠΊΠ°ΡΠ°Π½Π½ΡΠ΅ ΠΈΠ»ΠΈ ΠΏΡΠ΅ΡΡΠΎΠ²Π°Π½Π½ΡΠ΅ ΠΏΡΡΡΠΊΠΈ ΠΈ ΡΡΡΠ±Ρ ΠΈΠ· ΡΡΠ°Π»ΠΈ, ΡΠ²Π΅ΡΠ½ΡΡ ΠΌΠ΅ΡΠ°Π»Π»ΠΎΠ² ΠΈ ΠΈΡ ΡΠΏΠ»Π°Π²ΠΎΠ². ΠΠ΅Π»ΠΈΡΠΈΠ½Π° Π΄Π΅ΡΠΎΡΠΌΠ°ΡΠΈΠΈ Π·Π° ΠΎΠ΄ΠΈΠ½ ΠΏΡΠΎΡ ΠΎΠ΄ ΠΎΠ³ΡΠ°Π½ΠΈΡΠ΅Π½Π°:Β = 1,25-1,45. ΠΡΠ»ΠΈ Π΄Π»Ρ ΠΏΠΎΠ»ΡΡΠ΅Π½ΠΈΡ Π½Π΅ΠΎΠ±Ρ ΠΎΠ΄ΠΈΠΌΡΡ ΠΏΡΠΎΡΠΈΠ»Π΅ΠΉ ΡΡΠ΅Π±ΡΠ΅ΡΡΡ Π±ΠΎΠ»ΡΡΠ°Ρ Π΄Π΅ΡΠΎΡΠΌΠ°ΡΠΈΡ, ΡΠΎ ΠΏΡΠΈΠΌΠ΅Π½ΡΡΡ Π²ΠΎΠ»ΠΎΡΠ΅Π½ΠΈΠ΅ Π·Π° Π½Π΅ΡΠΊΠΎΠ»ΡΠΊΠΎ ΠΏΠ΅ΡΠ΅Ρ ΠΎΠ΄ΠΎΠ² ΠΏΡΠΎΡΡΠ³ΠΈΠ²Π°Π½ΠΈΠ΅ΠΌ ΡΠ΅ΡΠ΅Π· ΡΡΠ΄ ΠΏΠΎΡΡΠ΅ΠΏΠ΅Π½Π½ΠΎ ΡΠΌΠ΅Π½ΡΡΠ°ΡΡΠΈΡ ΡΡ ΠΏΠΎ Π²Π΅Π»ΠΈΡΠΈΠ½Π΅ ΠΎΡΠ²Π΅ΡΡΡΠΈΠΉ. ΠΠ»Ρ ΡΠ½ΡΡΠΈΡ Π½Π°ΠΊΠ»Π΅ΠΏΠ° ΠΏΠΎΡΠ»Π΅ ΠΊΠ°ΠΆΠ΄ΠΎΠ³ΠΎ ΠΏΠ΅ΡΠ΅Ρ ΠΎΠ΄Π° ΠΌΠ΅ΡΠ°Π»Π» ΠΏΠΎΠ΄Π²Π΅ΡΠ³Π°ΡΡ ΠΏΡΠΎΠΌΠ΅ΠΆΡΡΠΎΡΠ½ΠΎΠΌΡ ΠΎΡΠΆΠΈΠ³Ρ. ΠΠ»Ρ ΡΠΌΠ΅Π½ΡΡΠ΅Π½ΠΈΡ ΡΠΈΠ»Ρ ΡΡΠ΅Π½ΠΈΡ ΠΌΠ΅ΡΠ°Π»Π»Π° ΠΎΠ± ΠΈΠ½ΡΡΡΡΠΌΠ΅Π½Ρ ΠΏΠΎΠ»ΠΈΡΡΡΡ ΠΎΡΠ²Π΅ΡΡΡΠΈΠ΅ Π² Π²ΠΎΠ»ΠΎΠΊΠ΅ ΠΈ ΠΏΡΠΈΠΌΠ΅Π½ΡΡΡ ΡΠ°Π·Π»ΠΈΡΠ½ΡΠ΅ ΡΠΌΠ°Π·ΠΊΠΈ — ΠΌΠΈΠ½Π΅ΡΠ°Π»ΡΠ½ΡΠ΅ ΠΌΠ°ΡΠ»Π°, ΠΎΠ»ΠΈΡΡ, Π³ΡΠ°ΡΠΈΡ, ΡΠ°Π»ΡΠΊ, ΠΌΡΠ»Π°, ΡΠΎΡΡΠ°ΡΠ½ΡΠ΅ ΠΈ ΠΌΠ΅ΡΠ°Π»Π»ΠΈΡΠ΅ΡΠΊΠΈΠ΅ ΠΏΠΎΠΊΡΡΡΠΈΡ ΠΈ Π΄Ρ.
Π‘ΠΎΡΡΠ°ΠΌΠ΅Π½Ρ ΠΈΠ·Π΄Π΅Π»ΠΈΠΉ, ΠΈΠ·Π³ΠΎΡΠΎΠ²Π»Π΅Π½Π½ΡΡ Π²ΠΎΠ»ΠΎΡΠ΅Π½ΠΈΠ΅ΠΌ, ΠΎΡΠ΅Π½Ρ ΡΠ°Π·Π½ΠΎΠΎΠ±ΡΠ°Π·Π΅Π½: ΠΏΡΠΎΠ²ΠΎΠ»ΠΎΠΊΠ° 0,002-10 ΠΌΠΌ ΠΈ ΡΠ°ΡΠΎΠ½Π½ΡΠ΅ ΠΏΡΠΎΡΠΈΠ»ΠΈ (ΡΠΈΡ. 1.3.1, Π±), ΡΡΡΠ±Ρ Π΄ΠΈΠ°ΠΌΠ΅ΡΡΠΎΠΌ ΠΎΡ 0,3 Π΄ΠΎ 500 ΠΌΠΌ Ρ ΡΠΎΠ»ΡΠΈΠ½ΠΎΠΉ ΡΡΠ΅Π½ΠΊΠΈ ΠΎΡ 0,05 Π΄ΠΎ 5-6 ΠΌΠΌ.
Β
Π ΠΈΡ.
3.47. Π‘Ρ
Π΅ΠΌΠ° Π²ΠΎΠ»ΠΎΡΠ΅Π½ΠΈΡ ΡΡΡΠ±Ρ (Π°) ΠΈ ΠΏΡΠΈΠΌΠ΅ΡΡ
ΠΏΡΠΎΡΠΈΠ»Π΅ΠΉ, ΠΏΠΎΠ»ΡΡΠ°Π΅ΠΌΡΡ
Π²ΠΎΠ»ΠΎΡΠ΅Π½ΠΈΠ΅ΠΌ (Π±)
ΠΠΎΠ»ΠΎΡΠ΅Π½ΠΈΠ΅ ΡΡΡΠ± ΠΌΠΎΠΆΠ½ΠΎ Π²ΡΠΏΠΎΠ»Π½ΡΡΡ Π±Π΅Π· ΠΎΠΏΡΠ°Π²ΠΊΠΈ, Π΄Π»Ρ ΡΠΌΠ΅Π½ΡΡΠ΅Π½ΠΈΡ ΡΠΎΠ»ΡΠΊΠΎ Π²Π½Π΅ΡΠ½Π΅Π³ΠΎ Π΄ΠΈΠ°ΠΌΠ΅ΡΡΠ°Β (ΡΠ΅Π΄ΡΡΠΈΡΠΎΠ²Π°Π½ΠΈΠ΅), ΠΈ Ρ ΠΎΠΏΡΠ°Π²ΠΊΠΎΠΉ (Π΄Π»Ρ ΡΠΌΠ΅Π½ΡΡΠ΅Π½ΠΈΡ Π²Π½Π΅ΡΠ½Π΅Π³ΠΎ Π΄ΠΈΠ°ΠΌΠ΅ΡΡΠ° ΠΈ ΡΠΎΠ»ΡΠΈΠ½Ρ ΡΡΠ΅Π½ΠΊΠΈ). ΠΠ° ΡΠΈΡ. 3.47, Π°, ΠΏΠΎΠΊΠ°Π·Π°Π½Π° ΡΡ Π΅ΠΌΠ° Π²ΠΎΠ»ΠΎΡΠ΅Π½ΠΈΡ ΡΡΡΠ±Ρ 1 Π½Π° Π΄Π»ΠΈΠ½Π½ΠΎΠΉ Π·Π°ΠΊΡΠ΅ΠΏΠ»Π΅Π½Π½ΠΎΠΉ ΠΎΠΏΡΠ°Π²ΠΊΠ΅ 3. Π ΡΡΠΎΠΌ ΡΠ»ΡΡΠ°Π΅ ΠΏΡΠΎΡΠΈΠ»Ρ ΠΏΠΎΠ»ΡΡΠ΅Π½Π½ΠΎΠΉ ΡΡΡΠ±Ρ ΠΎΠΏΡΠ΅Π΄Π΅Π»ΡΠ΅ΡΡΡ Π·Π°Π·ΠΎΡΠΎΠΌ ΠΌΠ΅ΠΆΠ΄Ρ Π²ΠΎΠ»ΠΎΠΊΠΎΠΉ 2 ΠΈ ΠΎΠΏΡΠ°Π²ΠΊΠΎΠΉ 3. ΠΠΎΠ»ΠΎΡΠ΅Π½ΠΈΠ΅ ΠΎΠ±Π΅ΡΠΏΠ΅ΡΠΈΠ²Π°Π΅Ρ Π²ΡΡΠΎΠΊΡΡ ΡΠΎΡΠ½ΠΎΡΡΡ ΡΠ°Π·ΠΌΠ΅ΡΠΎΠ² (ΡΡΠ°Π»ΡΠ½Π°Ρ ΠΏΡΠΎΠ²ΠΎΠ»ΠΎΠΊΠ° Π΄ΠΈΠ°ΠΌΠ΅ΡΡΠΎΠΌ 1,0-1,6 ΠΌΠΌ ΠΈΠΌΠ΅Π΅Ρ Π΄ΠΎΠΏΡΡΠΊ 0,02 ΠΌΠΌ), Π²ΡΡΠΎΠΊΠΎΠ΅ ΠΊΠ°ΡΠ΅ΡΡΠ²ΠΎ ΠΏΠΎΠ²Π΅ΡΡ Π½ΠΎΡΡΠΈ, ΠΏΠΎΠ»ΡΡΠ΅Π½ΠΈΠ΅ ΠΎΡΠ΅Π½Ρ ΡΠΎΠ½ΠΊΠΈΡ ΠΏΡΠΎΡΠΈΠ»Π΅ΠΉ. ΠΠ΅ΡΠΎΠ΄ Π΄Π°Π΅Ρ Π²ΠΎΠ·ΠΌΠΎΠΆΠ½ΠΎΡΡΡ ΡΠΈΡΠΎΠΊΠΎ Π²Π°ΡΡΠΈΡΠΎΠ²Π°ΡΡ (Π·Π° ΡΡΠ΅Ρ Π½Π°ΠΊΠ»Π΅ΠΏΠ°, Π° ΡΠ°ΠΊΠΆΠ΅ ΡΠ΅ΡΠΌΠΈΡΠ΅ΡΠΊΠΎΠΉ ΠΎΠ±ΡΠ°Π±ΠΎΡΠΊΠΈ) Π΄ΠΈΠ°ΠΏΠ°Π·ΠΎΠ½ ΠΏΡΠΎΡΠ½ΠΎΡΡΠ½ΡΡ ΠΈ ΠΏΠ»Π°ΡΡΠΈΡΠ΅ΡΠΊΠΈΡ ΡΠ²ΠΎΠΉΡΡΠ² ΠΌΠ΅ΡΠ°Π»Π»Π° Π³ΠΎΡΠΎΠ²ΠΎΠ³ΠΎ ΠΈΠ·Π΄Π΅Π»ΠΈΡ, ΡΠ΅Π·ΠΊΠΎ ΡΠΎΠΊΡΠ°ΡΠ°Π΅Ρ ΠΎΡΡ ΠΎΠ΄Ρ ΠΈ ΡΠ²Π΅Π»ΠΈΡΠΈΠ²Π°Π΅Ρ ΠΏΡΠΎΠΈΠ·Π²ΠΎΠ΄ΠΈΡΠ΅Π»ΡΠ½ΠΎΡΡΡ. ΠΡΠ»ΠΈΡΠΈΡΠ΅Π»ΡΠ½ΠΎΠΉ ΡΠ΅ΡΡΠΎΠΉ ΠΏΡΠΎΡΠ΅ΡΡΠ° Π²ΠΎΠ»ΠΎΡΠ΅Π½ΠΈΡ ΡΠ²Π»ΡΠ΅ΡΡΡ Π΅Π³ΠΎ ΡΠ½ΠΈΠ²Π΅ΡΡΠ°Π»ΡΠ½ΠΎΡΡΡ (ΠΏΡΠΎΡΡΠΎΡΠ° ΠΈ Π±ΡΡΡΡΠΎΡΠ° Π·Π°ΠΌΠ΅Π½Ρ ΠΈΠ½ΡΡΡΡΠΌΠ΅Π½ΡΠ°), ΡΡΠΎ Π΄Π΅Π»Π°Π΅Ρ Π΅Π³ΠΎ ΠΎΡΠ΅Π½Ρ ΡΠ°ΡΠΏΡΠΎΡΡΡΠ°Π½Π΅Π½Π½ΡΠΌ.
2. Π₯Π°ΡΠ°ΠΊΡΠ΅ΡΠΈΡΡΠΈΠΊΠ° Π²ΡΠΏΠΎΠΌΠΎΠ³Π°ΡΠ΅Π»ΡΠ½ΠΎΠ³ΠΎ ΠΎΠ±ΠΎΡΡΠ΄ΠΎΠ²Π°Π½ΠΈΡ Π²ΠΎΠ»ΠΎΡΠΈΠ»ΡΠ½ΡΡ ΡΡΠ°Π½ΠΎΠ².
2.1 Π Π°Π·ΠΌΠΎΡΠΎΡΠ½ΡΠ΅ ΡΡΡΡΠΎΠΉΡΡΠ²Π°
Π Π°Π·ΠΌΠΎΡΠΎΡΠ½ΡΠ΅ ΡΡΡΡΠΎΠΉΡΡΠ²Π° ΠΏΡΠ΅Π΄Π½Π°Π·Π½Π°ΡΠ΅Π½Ρ Π΄Π»Ρ ΡΠ°Π·ΠΌΠ°ΡΡΠ²Π°Π½ΠΈΡ ΠΏΡΠΎΒΠ²ΠΎΠ»ΠΎΠΊΠΈ-Π·Π°Π³ΠΎΡΠΎΠ²ΠΊΠΈ ΠΏΠ΅ΡΠ΅Π΄ Π²ΠΎΠ»ΠΎΡΠΈΠ»ΡΠ½ΡΠΌ ΡΡΠ°Π½ΠΎΠΌ Ρ ΡΠ΅Π»ΡΡ Π΅Π΅ ΠΏΠΎΡΠ»Π΅Π΄ΡΡΒΡΠ΅Π³ΠΎ Π²ΠΎΠ»ΠΎΡΠ΅Π½ΠΈΡ. Π Π·Π°Π²ΠΈΡΠΈΠΌΠΎΡΡΠΈ ΠΎΡ ΡΠΎΠ³ΠΎ, Π² ΠΊΠ°ΠΊΠΎΠΌ Π²ΠΈΠ΄Π΅ ΠΏΠΎΡΡΡΠΏΠ°Π΅Ρ ΠΏΡΠΎΠ²ΠΎΠ»ΠΎΠΊΠ° Π΄Π»Ρ Π΄Π°Π»ΡΠ½Π΅ΠΉΡΠ΅ΠΉ ΠΏΠ΅ΡΠ΅ΡΠ°Π±ΠΎΡΠΊΠΈ: Π² ΠΌΠΎΡΠΊΠ°Ρ (Π±ΡΠ½ΡΠ°Ρ ) ΠΈΠ»ΠΈ Π½Π° ΠΊΠ°ΒΡΡΡΠΊΠ°Ρ Π±ΠΎΠ»ΡΡΠΎΠΉ Π²ΠΌΠ΅ΡΡΠΈΠΌΠΎΡΡΠΈ (Π΄ΠΎ 1000 ΠΊΠ³ ΠΈ Π±ΠΎΠ»Π΅Π΅), ΠΊΠΎΠ½ΡΡΡΡΠΊΡΠΈΠ²Π½ΠΎ ΡΠ°Π·ΠΌΠ°ΡΡΠ²Π°ΡΡΠΈΠ΅ ΡΡΡΡΠΎΠΉΡΡΠ²Π° ΡΠ°Π·Π΄Π΅Π»ΡΡΡΡΡ Π½Π° ΡΡΠΈ ΡΠΈΠΏΠ°:
ΡΠ°Π·ΠΌΠΎΡΠΊΠ° Ρ Π²ΡΠ°ΡΠ°ΡΡΠΈΡ ΡΡ ΡΠΈΠ³ΡΡΠΎΠΊ;
ΡΠ°Π·ΠΌΠΎΡΠΊΠ° ΡΠΎ ΡΡΠ°ΡΠΈΠΎΠ½Π°ΡΠ½ΠΎ ΡΡΡΠ°Π½ΠΎΠ²Π»Π΅Π½Π½ΡΡ ΠΊΡΠΎΠ½ΡΡΠ΅ΠΉΠ½ΠΎΠ², ΠΊΠΎΠ½ΡΠΎΒ Π»Π΅ΠΉ;
ΡΠ°Π·ΠΌΠΎΡΠΊΠ° Ρ ΡΡΡΡΠΎΠΉΡΡΠ²Π° ΠΏΠΈΠ½ΠΎΠ»ΡΠ½ΠΎΠ³ΠΎ ΡΠΈΠΏΠ° Π΄Π»Ρ ΡΡΡΠ°Π½ΠΎΠ²ΠΊΠΈ ΠΊΠ°ΡΡΒ ΡΠ΅ΠΊ.
Π ΡΠ°Π·ΠΌΠΎΡΠΎΡΠ½ΡΠΌ ΡΡΡΡΠΎΠΉΡΡΠ²Π°ΠΌ ΠΏΡΠ΅Π΄ΡΡΠ²Π»ΡΡΡΡΡ ΡΡΠ΅Π±ΠΎΠ²Π°Π½ΠΈΡ:
ΠΎΠ±Π΅ΡΠΏΠ΅ΡΠ΅Π½ΠΈΠ΅ ΡΠ°Π²Π½ΠΎΠΌΠ΅ΡΠ½ΠΎΠ³ΠΎ ΡΡ ΠΎΠ΄Π° ΠΏΡΠΎΠ²ΠΎΠ»ΠΎΠΊΠΈ-Π·Π°Π³ΠΎΡΠΎΠ²ΠΊΠΈ Π±Π΅Π· Π·Π°Β ΠΏΡΡΡΠ²Π°Π½ΠΈΡ ΠΈ ΠΏΠΎΠ΄ ΠΎΠΏΡΠ΅Π΄Π΅Π»Π΅Π½Π½ΡΠΌ ΡΠ³Π»ΠΎΠΌ;
Π²ΠΎΠ·ΠΌΠΎΠΆΠ½ΠΎΡΡΡ ΡΠ΅Π³ΡΠ»ΠΈΡΠΎΠ²Π°Π½ΠΈΡ ΡΠΈΠ»Ρ Π½Π°ΡΡΠΆΠ΅Π½ΠΈΡ Π² Π·Π°Π²ΠΈΡΠΈΠΌΠΎΡΡΠΈ ΠΎΡ Π΄ΠΈΠ°ΠΌΠ΅ΡΡΠ° ΠΏΡΠΎΠ²ΠΎΠ»ΠΎΠΊΠΈ;
Π²ΠΎΠ·ΠΌΠΎΠΆΠ½ΠΎΡΡΡ ΡΠ²Π°ΡΠΈΠ²Π°Π½ΠΈΡ ΠΊΠΎΠ½ΡΠΎΠ² ΠΏΡΠΎΠ²ΠΎΠ»ΠΎΠΊΠΈ Π±Π΅Π· ΠΎΡΡΠ°Π½ΠΎΠ²ΠΊΠΈ Π²ΠΎΒ Π»ΠΎΡΠΈΠ»ΡΠ½ΠΎΠ³ΠΎ ΡΡΠ°Π½Π°;
ΠΎΠ±Π΅ΡΠΏΠ΅ΡΠ΅Π½ΠΈΠ΅ Π±Π΅Π·ΠΎΠΏΠ°ΡΠ½ΠΎΠΉ ΡΠ°Π±ΠΎΡΡ ΠΎΠ±ΡΠ»ΡΠΆΠΈΠ²Π°ΡΡΠ΅Π³ΠΎ ΠΏΠ΅ΡΡΠΎΠ½Π°Π»Π°;
ΠΌΠ΅Ρ Π°Π½ΠΈΠ·Π°ΡΠΈΡ Π·Π°Π³ΡΡΠ·ΠΊΠΈ ΡΠ°Π·ΠΌΠ°ΡΡΠ²Π°ΡΡΠΈΡ ΡΡΡΡΠΎΠΉΡΡΠ²;
Π²ΠΎΠ·ΠΌΠΎΠΆΠ½ΠΎΡΡΡ ΠΈΡΠΏΠΎΠ»ΡΠ·ΠΎΠ²Π°Π½ΠΈΡ Π±ΠΎΠ»ΡΡΠΈΡ ΡΠΊΠΎΡΠΎΡΡΠ΅ΠΉ ΡΡ ΠΎΠ΄Π° ΠΏΡΠΎΠ²ΠΎΠ»ΠΎΒ ΠΊΠΈ Ρ ΡΠ°Π·ΠΌΠ°ΡΡΠ²Π°ΡΡΠΈΡ ΡΡΡΡΠΎΠΉΡΡΠ² Π΄Π»Ρ ΠΎΠ±Π΅ΡΠΏΠ΅ΡΠ΅Π½ΠΈΡ ΡΠΊΠΎΡΠΎΡΡΠ½ΠΎΠ³ΠΎ ΠΈ Π²ΡΡΠΎΠΊΠΎΡΠΊΠΎΡΠΎΡΡΠ½ΠΎΠ³ΠΎ Π²ΠΎΠ»ΠΎΡΠ΅Π½ΠΈΡ ΠΏΡΠΎΠ²ΠΎΠ»ΠΎΠΊΠΈ.
ΠΡΠΈ ΡΠ°Π·ΠΌΠΎΡΠΊΠ΅ ΠΏΡΠΎΠ²ΠΎΠ»ΠΎΠΊΠΈ ΠΈΠ· ΠΌΠΎΡΠΊΠΎΠ², ΡΠ»ΠΎΠΆΠ΅Π½Π½ΡΡ Π½Π° Π²ΡΠ°ΡΠ°ΡΡΡΡΡΡ ΡΠΈΠ³ΡΡΠΊΡ, ΠΏΠΎΠ»ΠΎΠΆΠΈΡΠ΅Π»ΡΠ½ΡΠΌ ΠΏΡΠ΅ΠΈΠΌΡΡΠ΅ΡΡΠ²ΠΎΠΌ ΡΠ²Π»ΡΠ΅ΡΡΡ ΡΠΎ, ΡΡΠΎ ΠΏΡΠΎΠ²ΠΎΠ»ΠΎΠΊΠ°., ΡΠΌΠ°ΡΡΠ²Π°ΡΡΡ Ρ ΡΠΈΠ³ΡΡΠΊΠΈ, Π½Π΅ Π·Π°ΠΊΡΡΡΠΈΠ²Π°Π΅ΡΡΡ Π²ΠΎΠΊΡΡΠ³ ΡΠ²ΠΎΠ΅ΠΉ ΠΎΡΠΈ, ΡΡΠΎ Π²Π°ΠΆΒΠ½ΠΎ ΠΏΡΠΈ Π²ΠΎΠ»ΠΎΡΠ΅Π½ΠΈΠΈ ΠΏΡΠΎΠ²ΠΎΠ»ΠΎΠΊΠΈ ΡΠ°ΡΠΎΠ½Π½ΠΎΠ³ΠΎ ΠΏΡΠΎΡΠΈΠ»Ρ ΠΏΠΎ ΡΠ΅ΡΠ΅Π½ΠΈΡ. ΠΠΎ ΠΏΡΠΈ Π±ΠΎΠ»ΡΡΠΈΡ ΠΌΠ°ΡΡΠ°Ρ ΠΌΠΎΡΠΊΠ° ΠΈ Π±ΠΎΠ»ΡΡΠΎΠΉ ΡΠ°ΡΡΠΎΡΠ΅ Π²ΡΠ°ΡΠ΅Π½ΠΈΡ ΡΠΈΠ³ΡΡΠΊΠΈ ΠΈΠ·-Π·Π° Π½Π΅ΒΡΠΎΡΠ½ΠΎΠΉ Π±Π°Π»Π°Π½ΡΠΈΡΠΎΠ²ΠΊΠΈ ΠΌΠΎΡΠΊΠ° ΠΎΡΠ½ΠΎΡΠΈΡΠ΅Π»ΡΠ½ΠΎ ΠΎΡΠΈ Π²ΡΠ°ΡΠ΅Π½ΠΈΡ Π²ΠΎΠ·Π½ΠΈΠΊΠ°ΡΡ Π±ΠΎΠ»ΡΡΠΈΠ΅ ΡΠ΅Π½ΡΡΠΎΠ±Π΅ΠΆΠ½ΡΠ΅ ΡΠΈΠ»Ρ ΠΈΠ½Π΅ΡΡΠΈΠΈ, ΠΊΠΎΡΠΎΡΡΠ΅ Π²ΡΠ·ΡΠ²Π°ΡΡ Π±ΡΡΡΡΡΠΉ ΠΈΠ·Π½ΠΎΡ ΠΏΠΎΠ΄ΡΠΈΠΏΠ½ΠΈΠΊΠΎΠ²ΡΡ ΠΎΠΏΠΎΡ, Π° ΡΠ»Π΅Π΄ΠΎΠ²Π°ΡΠ΅Π»ΡΠ½ΠΎ, ΠΈ ΡΠ°ΡΡΡΠΉ ΠΈΡ ΡΠ΅ΠΌΠΎΠ½Ρ. ΠΠ° Π²ΡΠ°ΒΡΠ°ΡΡΠΈΡ ΡΡ ΡΡΡΡΠΎΠΉΡΡΠ²Π°Ρ ΠΌΠΎΠΆΠ½ΠΎ ΡΠ°Π·ΠΌΠ°ΡΡΠ²Π°ΡΡ ΠΏΡΠΎΠ²ΠΎΠ»ΠΎΠΊΡ ΡΠΎΠ»ΡΡΡΡ ΠΈ ΡΡΠ΅Π΄ Π½ΠΈΡ ΡΠ°Π·ΠΌΠ΅ΡΠΎΠ². Π‘Π²Π°ΡΠΊΠ° ΠΆΠ΅ ΠΊΠΎΠ½ΡΠΎΠ² ΠΏΡΠΎΠ²ΠΎΠ»ΠΎΠΊΠΈ Π±Π΅Π· ΠΎΡΡΠ°Π½ΠΎΠ²ΠΊΠΈ ΡΠΈΠ³ΡΡΠΊΠΈ, Π° ΡΠ»Π΅Π΄ΠΎΠ²Π°ΡΠ΅Π»ΡΠ½ΠΎ, ΠΈ Π²ΠΎΠ»ΠΎΡΠΈΠ»ΡΠ½ΠΎΠ³ΠΎ ΡΡΠ°Π½Π° Π½Π΅Π²ΠΎΠ·ΠΌΠΎΠΆΠ½Π°, ΠΏΠΎΡΡΠΎΠΌΡ ΡΠ²Π΅Π»ΠΈΒΡΠΈΠ²Π°Π΅ΡΡΡ Π²ΡΠ΅ΠΌΡ, Π·Π°ΡΡΠ°ΡΠΈΠ²Π°Π΅ΠΌΠΎΠ΅ Π½Π° ΡΡΡΠ½ΡΠ΅ ΠΎΠΏΠ΅ΡΠ°ΡΠΈΠΈ.
ΠΡΠΈ ΡΡΡΠ°Π½ΠΎΠ²ΠΊΠ΅ ΠΌΠΎΡΠΊΠΎΠ² ΠΏΡΠΎΠ²ΠΎΠ»ΠΎΠΊΠΈ Π½Π° ΠΊΡΠΎΠ½ΡΡΠ΅ΠΉΠ½Π°Ρ ΠΈΠΌΠ΅Π΅ΡΡΡ Π²ΠΎΠ·ΠΌΠΎΠΆΒΠ½ΠΎΡΡΡ ΡΠ²Π°ΡΠΈΠ²Π°Π½ΠΈΡ ΠΊΠΎΠ½ΡΠΎΠ² ΠΏΡΠΎΠ²ΠΎΠ»ΠΎΠΊΠΈ ΠΏΡΠΈ ΡΠ°Π±ΠΎΡΠ°ΡΡΠ΅ΠΌ ΡΡΠ°Π½Π΅. ΠΠΎ ΠΏΡΠΈ ΡΡΠΎΠΌ ΡΠΏΠΎΡΠΎΠ±Π΅ ΡΠ°Π·ΠΌΠ°ΡΡΠ²Π°Π½ΠΈΡ ΠΏΡΠΎΠ²ΠΎΠ»ΠΎΠΊΠ°, ΡΡ ΠΎΠ΄Ρ Ρ ΠΊΡΠΎΠ½ΡΡΠ΅ΠΉΠ½Π°, ΠΏΠΎΠ»ΡΡΠ°Π΅Ρ ΠΎΡΠ΅Π²ΠΎΠ΅ Π·Π°ΠΊΡΡΡΠΈΠ²Π°Π½ΠΈΠ΅ Π·Π° ΠΊΠ°ΠΆΠ΄ΡΠΉ Π²ΠΈΡΠΎΠΊ Π½Π° ΠΎΠ΄ΠΈΠ½ ΠΏΠΎΠ»Π½ΡΠΉ ΠΎΠ±ΠΎΡΠΎΡ, Ρ.Π΅. Π½Π° 360Β°. ΠΡΠΎΠ²ΠΎΠ»ΠΎΠΊΠ° ΠΏΠΎΠ΄Ρ ΠΎΠ΄ΠΈΡ ΠΊ ΠΏΠ΅ΡΠ²ΠΎΠΌΡ Π²ΠΎΠ»ΠΎΠΊΠΎΠ΄Π΅ΡΠΆΠ°ΡΠ΅Π»Ρ ΡΡΠ°Π½Π° Π²ΠΎΠ»ΒΠ½ΠΈΡΡΠΎΠΉ. Π§ΡΠΎΠ±Ρ ΡΠΌΠ΅Π½ΡΡΠΈΡΡ ΡΡΠ΅ΠΏΠ΅Π½Ρ Π²ΠΎΠ»Π½ΠΈΡΡΠΎΡΡΠΈ, ΠΊΡΠΎΠ½ΡΡΠ΅ΠΉΠ½Ρ ΡΡΡΠ°Π½Π°Π²ΒΠ»ΠΈΠ²Π°ΡΡΡΡ Π½Π° Π·Π½Π°ΡΠΈΡΠ΅Π»ΡΠ½ΠΎ Π±ΠΎΠ»ΡΡΠ΅ΠΌ ΡΠ°ΡΡΡΠΎΡΠ½ΠΈΠΈ, ΡΠ΅ΠΌ Π²ΡΠ°ΡΠ°ΡΡΠΈΠ΅ΡΡ ΡΠΈΒΠ³ΡΡΠΊΠΈ, ΠΎΡ Π²ΠΎΠ»ΠΎΡΠΈΠ»ΡΠ½ΠΎΠ³ΠΎ ΡΡΠ°Π½Π°, ΡΡΠΎ ΡΠ²Π΅Π»ΠΈΡΠΈΠ²Π°Π΅Ρ ΠΏΡΠΎΠΈΠ·Π²ΠΎΠ΄ΡΡΠ²Π΅Π½Π½ΡΠ΅ ΠΏΠ»ΠΎΡΠ°Π΄ΠΈ.
ΠΠ»Ρ ΠΏΡΠ΅Π΄ΠΎΡ ΡΠ°Π½Π΅Π½ΠΈΡ ΡΠ°ΠΌΠΎΠΏΡΠΎΠΈΠ·Π²ΠΎΠ»ΡΠ½ΠΎΠ³ΠΎ ΡΡ ΠΎΠ΄Π° Π²ΠΈΡΠΊΠΎΠ² ΠΈ ΠΈΡ Π·Π°ΠΏΡΒΡΡΠ²Π°Π½ΠΈΡ Π½Π° ΠΊΡΠΎΠ½ΡΡΠ΅ΠΉΠ½Π΅ ΡΡΡΠ°Π½Π°Π²Π»ΠΈΠ²Π°Π΅ΡΡΡ ΡΠΏΠ΅ΡΠΈΠ°Π»ΡΠ½ΡΠΉ ΡΡΡΠ°Π³, Π·Π°Π΄Π΅ΡΒΠΆΠΈΠ²Π°ΡΡΠΈΠΉ Π²ΠΈΡΠΊΠΈ ΡΠΈΠ»ΠΎΠΉ ΡΠΎΠ±ΡΡΠ²Π΅Π½Π½ΠΎΠΉ ΠΌΠ°ΡΡΡ. ΠΠΈΠΆΠ½ΠΈΠΉ ΡΡΡΠ°Π³ ΡΠ°ΠΊΠΆΠ΅ ΠΏΡΠ΅ΒΠΏΡΡΡΡΠ²ΡΠ΅Ρ Π²ΠΈΡΠΊΠ°ΠΌ ΠΏΡΠΎΠΈΠ·Π²ΠΎΠ»ΡΠ½ΠΎΠ³ΠΎ ΡΡ ΠΎΠ΄Π°. ΠΠ°ΠΆΠ΄ΡΠΉ ΡΠ½ΠΈΠΌΠ°Π΅ΠΌΡΠΉ Π²ΠΈΡΠΎΠΊ ΠΏΡΠΈΒΠΏΠΎΠ΄Π½ΠΈΠΌΠ°Π΅Ρ ΡΡΡΠ°Π³ΠΈ ΠΈ ΠΎΠ½ΠΈ, ΡΠ΄Π°ΡΡΡΡΡ ΠΎ ΡΠ²ΠΎΠΈ ΠΎΠΏΠΎΡΡ, ΠΈΠ·Π΄Π°ΡΡ ΡΡΡΠΊ-Ρ Π»ΠΎ ΠΏΠΎΠΊ. ΠΠ΅ΡΠΊΠΎΠ»ΡΠΊΠΎ ΡΠ°ΠΊΠΈΡ ΡΠ°Π±ΠΎΡΠ°ΡΡΠΈΡ ΡΠ°Π·ΠΌΠ°ΡΡΠ²Π°ΡΠ΅Π»Π΅ΠΉ ΡΠΎΠ·Π΄Π°ΡΡ Π² ΡΠ΅Ρ Π΅ Π΄ΠΎΒΠΏΠΎΠ»Π½ΠΈΡΠ΅Π»ΡΠ½ΡΠΉ ΡΡΠΌ Π² Π²ΠΈΠ΄Π΅ ΠΏΠ΅ΡΠΈΠΎΠ΄ΠΈΡΠ΅ΡΠΊΠΈΡ ΡΠ΄Π°ΡΠΎΠ².
Π Π°Π·ΠΌΠ°ΡΡΠ²Π°ΡΠ΅Π»Ρ Π² Π²ΠΈΠ΄Π΅ ΠΏΠΎΠ΄Π²Π΅ΡΠΊΠΈ Π΄Π»Ρ Π΄Π²ΡΡ Π±ΡΠ½ΡΠΎΠ² ΠΎΠ΄Π½ΠΎΠ²ΡΠ΅ΠΌΠ΅Π½Π½ΠΎ ΡΡΠ°Π½ΡΠΏΠΎΡΡΠΈΡΡΠ΅ΡΡΡ ΠΊΡΠ°Π½ΠΎΠΌ ΠΈΠ»ΠΈ ΠΊΡΠ°Π½-Π±Π°Π»ΠΊΠΎΠΉ ΠΈΠ· ΠΎΡΠ΄Π΅Π»Π΅Π½ΠΈΡ Π΄Π»Ρ ΠΏΠΎΠ΄Π³ΠΎΒΡΠΎΠ²ΠΊΠΈ ΠΏΠΎΠ²Π΅ΡΡ Π½ΠΎΡΡΠΈ ΠΏΡΠΎΠ²ΠΎΠ»ΠΎΠΊΠΈ ΠΊ Π²ΠΎΠ»ΠΎΡΠ΅Π½ΠΈΡ Π² Π²ΠΎΠ»ΠΎΡΠΈΠ»ΡΠ½ΠΎΠ΅ ΠΎΡΠ΄Π΅Π»Π΅Π½ΠΈΠ΅. ΠΠ±ΡΠ°Ρ Π³ΡΡΠ·ΠΎΠΏΠΎΠ΄ΡΠ΅ΠΌΠ½ΠΎΡΡΡ ΠΏΠΎΠ΄Π²Π΅ΡΠΊΠΈ Π΄ΠΎ 1.5 Ρ. ΠΠΎΠΊΠ° Ρ ΠΎΠ΄Π½ΠΎΠΉ ΠΏΠΎΠ΄Π²Π΅ΡΠΊΠΈ ΠΈΠ΄Π΅Ρ ΡΠ°Π·ΠΌΠ°ΡΡΠ²Π°Π½ΠΈΠ΅, Π½Π° Π²ΡΠΎΡΠΎΠΉ ΠΏΠΎΠ΄Π³ΠΎΡΠ°Π²Π»ΠΈΠ²Π°Π΅ΡΡΡ ΠΊΠΎΠ½Π΅Ρ Π±ΡΠ½ΡΠ° Π΄Π»Ρ ΡΠ²Π°ΡΠΊΠΈ Ρ Π·Π°Π΄Π½ΠΈΠΌ ΠΊΠΎΠ½ΡΠΎΠΌ ΠΏΠ΅ΡΠ²ΠΎΠ³ΠΎ Π±ΡΠ½ΡΠ°.
Π Π°Π·ΠΌΠΎΡΠΊΠ° ΠΏΡΠΎΠ²ΠΎΠ»ΠΎΠΊΠΈ Ρ ΠΊΠ°ΡΡΡΠΊΠΈ Π² Π½Π°ΡΡΠΎΡΡΠ΅Π΅ Π²ΡΠ΅ΠΌΡ ΠΈΠΌΠ΅Π΅Ρ ΡΠ°ΠΌΠΎΠ΅ Π±ΠΎΠ»ΡΡΠΎΠ΅ ΡΠ°ΡΠΏΡΠΎΡΡΡΠ°Π½Π΅Π½ΠΈΠ΅ ΠΈ, Π³Π΄Π΅ ΡΡΠΎ Π²ΠΎΠ·ΠΌΠΎΠΆΠ½ΠΎ, Π·Π°ΠΌΠ΅Π½ΡΠ΅Ρ ΡΠ°Π·ΠΌΠΎΡΠΊΡ ΠΈΠ· Π±ΡΠ½ΡΠΎΠ². Π’Π°ΠΊ ΠΊΠ°ΠΊ ΠΌΠ°ΡΡΠ° ΠΏΡΠΎΠ²ΠΎΠ»ΠΎΠΊΠΈ Π½Π° ΠΊΠ°ΡΡΡΠΊΠ°Ρ Π±ΠΎΠ»ΡΡΠΎΠΉ Π²ΠΌΠ΅ΡΡΠΈΠΌΠΎΡΡΠΈ Π² Π½Π΅ΡΠΊΠΎΠ»ΡΠΊΠΎ ΡΠ°Π· Π±ΠΎΠ»ΡΡΠ΅ ΠΌΠ°ΡΡΡ ΠΌΠΎΡΠΊΠ°, Π·Π½Π°ΡΠΈΡΠ΅Π»ΡΠ½ΠΎ ΡΠΎΠΊΡΠ°ΡΠ°Π΅ΡΡΡ ΡΡΡΠ½ΠΎΠ΅ Π²ΡΠ΅ΠΌΡ Π½Π° Π·Π°ΠΌΠ΅Π½Ρ Π·Π°Π³ΠΎΡΠΎΠ²ΠΊΠΈ. Π£Π»ΡΡΡΠ°ΡΡΡΡ ΡΡΠ»ΠΎΠ²ΠΈΡ ΡΡΠ°Π½ΡΠΏΠΎΡΡΠΈΡΠΎΠ²ΠΊΠΈ ΠΈ Ρ ΡΠ°Π½Π΅Π½ΠΈΡ ΠΏΡΠΎΠ²ΠΎΠ»ΠΎΠΊΠΈ, ΡΠΌΠ΅Π½ΡΡΠ°Π΅ΡΡΡ Π²ΠΎΠ·ΠΌΠΎΠΆΠ½ΠΎΡΡΡ Π·Π°ΠΏΡΡΡΠ²Π°Π½ΠΈΡ Π²ΠΈΡΠΊΠΎΠ², Π° ΡΠ»Π΅Π΄ΠΎΠ²Π°ΡΠ΅Π»ΡΠ½ΠΎ, ΡΠ½ΠΈΠΆΠ°ΡΡΡΡ ΠΎΡΡ ΠΎΠ΄Ρ ΠΌΠ΅ΡΠ°Π»Π»Π°. ΠΡΠ°ΠΊΡΠΈΡΠ΅ΡΠΊΠΈ Π²ΠΎΠ·ΠΌΠΎΠΆΠ½Π° Π»ΡΠ±Π°Ρ ΡΠΊΠΎΡΠΎΡΡΡ ΡΠΌΠ°ΡΡΠ²Π°Π½ΠΈΡ, Π½Π΅ΠΎΠ±Ρ ΠΎΠ΄ΠΈΠΌΠ°Ρ ΠΏΡΠΈ Π²ΠΎΠ»ΠΎΡΠ΅Π½ΠΈΠΈ, ΡΠ°Π±ΠΎΡΠ° ΡΠ°Π·ΒΠΌΠΎΡΠΎΡΠ½ΠΎΠ³ΠΎ ΡΡΡΡΠΎΠΉΡΡΠ²Π° Π±Π΅ΡΡΡΠΌΠ½Π°Ρ.
Π Π°Π·ΠΌΠΎΡΠΎΡΠ½ΠΎΠ΅ ΡΡΡΡΠΎΠΉΡΡΠ²ΠΎ ΠΈΠΌΠ΅Π΅Ρ Π΄Π²Π΅ ΡΠ°ΠΌΠΎΡΡΠΎΡΡΠ΅Π»ΡΠ½ΡΠ΅ ΡΡΠΎΠΉΠΊΠΈ Ρ Π²ΡΠ°ΡΠ°ΡΡΠΈΠΌΠΈΡΡ ΠΏΠΈΠ½ΠΎΠ»ΡΠΌΠΈ. ΠΠ΄Π½Π° ΠΈΠ· ΠΏΠΈΠ½ΠΎΠ»Π΅ΠΉ Π΄ΠΎΠ»ΠΆΠ½Π° ΠΈΠΌΠ΅ΡΡ ΠΏΠ΅ΡΠ΅ΠΌΠ΅ΡΠ΅Π½ΠΈΠ΅
Π²Π΄ΠΎΠ»Ρ ΡΠ²ΠΎΠ΅ΠΉ ΠΎΡΠΈ Π΄Π»Ρ ΠΎΠ±Π΅ΡΠΏΠ΅ΡΠ΅Π½ΠΈΡ ΡΡΡΠ°Π½ΠΎΠ²ΠΊΠΈ ΠΊΠ°ΡΡΡΠ΅ΠΊ ΡΠ°Π·Π»ΠΈΡΠ½ΡΡ ΠΏΠΎ ΡΠ²ΠΎΠ΅ΠΉ ΡΠΈΡΠΈΠ½Π΅. Π’Π°ΠΊ, Π½Π°ΠΏΡΠΈΠΌΠ΅Ρ, Π½Π° ΠΎΠ΄Π½ΠΎΠΌ ΡΠ°Π·ΠΌΠ°ΡΡΠ²Π°ΡΡΠ΅ΠΌ ΡΡΡΡΠΎΠΉΡΡΠ²Π΅ ΠΌΠΎΠ³ΡΡ ΠΏΡΠΈΠΌΠ΅Π½ΡΡΡΡΡ ΠΊΠ°ΡΡΡΠΊΠΈ ΡΠ°Π·ΠΌΠ΅ΡΠΎΠΌ 630, 800 ΠΈ 1000 ΠΌΠΌ ΠΏΠΎ Π΄ΠΈΠ°ΠΌΠ΅ΡΡΡ Π΄ΠΈΡΠΊΠ°. ΠΠ»Ρ Π±ΠΎΠ»ΡΡΠ΅Π³ΡΡΠ·Π½ΡΡ ΠΊΠ°ΡΡΡΠ΅ΠΊ ΠΏΡΠ΅Π΄ΡΡΠΌΠ°ΡΡΠΈΠ²Π°ΡΡΡΡ Π³ΡΡΠ·ΠΎΠΏΠΎΠ΄ΡΠ΅ΠΌΠ½ΡΠ΅ ΡΡΡΡΠΎΠΉΡΡΠ²Π°, ΠΎΠ±ΡΡΠ½ΠΎ Π³ΠΈΠ΄ΡΠ°Π²Π»ΠΈΡΠ΅ΡΠΊΠΎΠ³ΠΎ ΡΠΈΠΏΠ°. ΠΠ»Ρ ΠΎΠ±Π΅ΡΠΏΠ΅ΡΠ΅Π½ΠΈΡ ΡΠΎΡΠΌΠΎΠΆΠ΅ΒΠ½ΠΈΡ ΠΊΠ°ΡΡΡΠ΅ΠΊ, Π΄Π»Ρ ΡΠΎΠ·Π΄Π°Π½ΠΈΡ Π½Π°ΡΡΠΆΠ΅Π½ΠΈΡ ΡΡ ΠΎΠ΄ΡΡΠ΅ΠΉ ΠΏΡΠΎΠ²ΠΎΠ»ΠΎΠΊΠΈ ΠΈΠΌΠ΅Π΅ΡΡΡ ΡΠΎΡΠΌΠΎΠ·Π½ΠΎΠ΅ ΡΡΡΡΠΎΠΉΡΡΠ²ΠΎ ΠΊΠΎΠ»ΠΎΠ΄ΠΎΡΠ½ΠΎΠ³ΠΎ ΠΈΠ»ΠΈ Π»Π΅Π½ΡΠΎΡΠ½ΠΎΠ³ΠΎ ΡΠΈΠΏΠ°, ΠΏΠΎΠ·Π²ΠΎΠ»ΡΡΡΠ΅Π΅ ΡΠ΅Π³ΡΠ»ΠΈΡΠΎΠ²Π°ΡΡ ΡΠΈΠ»Ρ Π½Π°ΡΡΠΆΠ΅Π½ΠΈΡ ΠΏΡΠΎΠ²ΠΎΠ»ΠΎΠΊΠΈ Π² Π·Π°Π²ΠΈΡΠΈΠΌΠΎΡΡΠΈ ΠΎΡ Π΅Π΅ Π΄ΠΈΠ°ΠΌΠ΅ΡΒΡΠ°.
Π Π½Π΅ΠΊΠΎΡΠΎΡΡΡ ΡΠ»ΡΡΠ°ΡΡ ΡΡΠΈΠΊΡΠΈΠΎΠ½Π½ΡΠ΅ ΡΠΎΡΠΌΠΎΠ·Π½ΡΠ΅ ΡΠΈΡΡΠ΅ΠΌΡ ΡΠ°Π±ΠΎΡΠ°ΡΡ Π½Π΅Π΄ΠΎΡΡΠ°ΡΠΎΡΠ½ΠΎ ΠΏΠ»Π°Π²Π½ΠΎ ΠΈ ΡΡΡΠΎΠΉΡΠΈΠ²ΠΎ. ΠΠΎΡΡΠΎΠΌΡ Π² ΡΡΠΈΡ ΡΠ»ΡΡΠ°ΡΡ Π² ΠΊΠ°ΡΠ΅ΡΡΒΠ²Π΅ ΡΠΎΡΠΌΠΎΠ·Π° ΡΡΡΠ°Π½Π°Π²Π»ΠΈΠ²Π°ΡΡ ΡΠ»Π΅ΠΊΡΡΠΎΠ΄Π²ΠΈΠ³Π°ΡΠ΅Π»Ρ, ΡΠ°Π±ΠΎΡΠ°ΡΡΠΈΠΉ Π² Π³Π΅Π½Π΅ΡΠ°ΒΡΠΎΡΠ½ΠΎΠΌ ΡΠ΅ΠΆΠΈΠΌΠ΅ ΠΈ ΡΠΎΠ·Π΄Π°ΡΡΠΈΠΉ ΠΏΠ»Π°Π²Π½ΠΎΠ΅ ΡΠΎΡΠΌΠΎΠΆΠ΅Π½ΠΈΠ΅. ΠΠ΅Π»ΠΈΡΠΈΠ½ΠΎΠΉ Π½Π°Π³ΡΡΠ·ΠΊΠΈ Π½Π° ΡΠ»Π΅ΠΊΡΡΠΎΠ΄Π²ΠΈΠ³Π°ΡΠ΅Π»Ρ-Π³Π΅Π½Π΅ΡΠ°ΡΠΎΡ ΠΌΠΎΠΆΠ½ΠΎ Π² ΡΠΈΡΠΎΠΊΠΈΡ ΠΏΡΠ΅Π΄Π΅Π»Π°Ρ ΡΠ΅Π³ΡΠ»ΠΈΡΠΎΒΠ²Π°ΡΡ ΡΠΈΠ»Ρ Π½Π°ΡΡΠΆΠ΅Π½ΠΈΡ ΠΏΡΠΎΠ²ΠΎΠ»ΠΎΠΊΠΈ, ΡΠΌΠ°ΡΡΠ²Π°ΡΡΠ΅ΠΉΡΡ Ρ ΠΊΠ°ΡΡΡΠΊΠΈ.
ΠΠ°ΠΆΠ½ΡΠΌ ΡΠ»Π΅ΠΌΠ΅Π½ΡΠΎΠΌ ΡΠ°Π·ΠΌΠ°ΡΡΠ²Π°ΡΡΠΈΡ ΡΡΡΡΠΎΠΉΡΡΠ², ΠΎΡΠΎΠ±Π΅Π½Π½ΠΎ Ρ ΠΌΠΎΡΠΊΠΎΠ², ΡΠ²Π»ΡΠ΅ΡΡΡ Π½Π°Π»ΠΈΡΠΈΠ΅ ΠΊΠΎΠ½Π΅ΡΠ½ΡΡ Π²ΡΠΊΠ»ΡΡΠ°ΡΠ΅Π»Π΅ΠΉ, ΠΏΡΠ΅Π΄Π½Π°Π·Π½Π°ΡΠ΅Π½Π½ΡΡ Π΄Π»Ρ ΠΎΡΠΊΒΠ»ΡΡΠ΅Π½ΠΈΡ Π²ΠΎΠ»ΠΎΡΠΈΠ»ΡΠ½ΠΎΠ³ΠΎ ΡΡΠ°Π½Π° Π² ΡΠ»ΡΡΠ°Π΅ Π·Π°ΠΏΡΡΡΠ²Π°Π½ΠΈΡ Π²ΠΈΡΠΊΠΎΠ² ΠΏΡΠΎΠ²ΠΎΠ»ΠΎΠΊΠΈ ΠΈ Π΅Π΅ Π·Π°ΡΡΠΆΠΊΠΈ, Π° ΡΠ°ΠΊΠΆΠ΅ ΠΏΡΠΈ ΠΎΠΊΠΎΠ½ΡΠ°Π½ΠΈΠΈ ΠΌΠΎΡΠΊΠ° ΠΏΡΠΎΠ²ΠΎΠ»ΠΎΠΊΠΈ. ΠΠ½ΠΈ ΡΡΡΠ°Π½Π°Π²ΒΠ»ΠΈΠ²Π°ΡΡΡΡ ΠΌΠ΅ΠΆΠ΄Ρ ΡΠ°Π·ΠΌΠΎΡΠΎΡΠ½ΡΠΌ ΡΡΡΡΠΎΠΉΡΡΠ²ΠΎΠΌ ΠΈ Π²ΠΎΠ»ΠΎΡΠΈΠ»ΡΠ½ΡΠΌ ΡΡΠ°Π½ΠΎΠΌ.
Π£ΠΏΡΠ°Π²Π»Π΅Π½ΠΈΠ΅ ΠΊΠΎΠ½Π΅ΡΠ½ΡΠΌ Π²ΡΠΊΠ»ΡΡΠ°ΡΠ΅Π»Π΅ΠΌ ΠΎΡΡΡΠ΅ΡΡΠ²Π»ΡΠ΅ΡΡΡ ΠΏΠΎΠ²ΠΎΡΠΎΡΠ½ΡΠΌ ΡΡΡΠ°Π³ΠΎΠΌ-ΡΠΊΠΎΠ±ΠΎΠΉ, ΡΠ΅ΡΠ΅Π· ΠΊΠΎΡΠΎΡΡΡ ΠΏΡΠΎΠΏΡΡΠΊΠ°Π΅ΡΡΡ ΠΏΡΠΎΠ²ΠΎΠ»ΠΎΠΊΠ°. ΠΠ° Π½Π΅ΠΊΠΎΡΠΎΒΡΡΡ Π²ΠΎΠ»ΠΎΡΠΈΠ»ΡΠ½ΡΡ ΡΡΠ°Π½Π°Ρ ΡΡΡΠ°Π½Π°Π²Π»ΠΈΠ²Π°ΡΡΡΡ ΠΏΠ΅ΡΠ»Π΅Π²ΡΠ΅ ΠΊΠΎΠΌΠΏΠ΅Π½ΡΠ°ΡΠΎΡΡ, ΠΊΠΎΒΡΠΎΡΡΠ΅ Π·Π° ΡΡΠ΅Ρ ΡΠ΄Π»ΠΈΠ½Π΅Π½ΠΈΡ ΠΈΠ»ΠΈ ΡΠΊΠΎΡΠΎΡΠ΅Π½ΠΈΡ ΠΏΠ΅ΡΠ»ΠΈ ΠΏΡΠΎΠ²ΠΎΠ»ΠΎΠΊΠΈ ΡΠΎΠ³Π»Π°ΡΡΡΡ ΡΠ°Π±ΠΎΡΡ ΡΠ°Π·ΠΌΠΎΡΠΎΡΠ½ΠΎΠ³ΠΎ ΡΡΡΡΠΎΠΉΡΡΠ²Π° Ρ Π²ΠΎΠ»ΠΎΡΠΈΠ»ΡΠ½ΡΠΌ ΡΡΠ°Π½ΠΎΠΌ, ΡΠ°ΠΊΠΆΠ΅ ΠΏΡΠ΅ΒΠ΄ΠΎΡ ΡΠ°Π½ΡΡ ΠΎΠ±ΡΡΠ²Π½ΠΎΡΡΡ ΠΏΡΠΎΠ²ΠΎΠ»ΠΎΠΊΠΈ.
ΠΠ° ΡΠ°Π±ΠΎΡΠ΅ΠΉ ΠΏΠ»ΠΎΡΠ°Π΄ΠΊΠ΅ ΡΠ°Π·ΠΌΠΎΡΠΎΡΠ½ΡΡ ΡΡΡΡΠΎΠΉΡΡΠ² ΡΡΡΠ°Π½Π°Π²Π»ΠΈΠ²Π°ΡΡΡΡ Π½ΠΎΠΆΠ½ΠΈΡΡ Π΄Π»Ρ ΠΎΠ±ΡΠ΅Π·ΠΊΠΈ ΠΊΠΎΠ½ΡΠΎΠ² ΠΏΠ΅ΡΠ΅Π΄ ΡΠ²Π°ΡΠΊΠΎΠΉ. ΠΡΠΎΠ²ΠΎΠ»ΠΎΠΊΠ° ΡΠΎΠ½ΠΊΠΈΡ ΠΈ ΡΡΠ΅Π΄Π½ΠΈΡ Π΄ΠΈΠ°ΠΌΠ΅ΡΡΠΎΠ² ΠΌΠΎΠΆΠ΅Ρ Π±ΡΡΡ ΠΎΠ±ΡΠ΅Π·Π°Π½Π° ΠΌΠ΅Ρ Π°Π½ΠΈΡΠ΅ΡΠΊΠΈΠΌΠΈ Π½ΠΎΠΆΠ½ΠΈΡΠ°ΠΌΠΈ, ΡΡΡΠ°Π½Π°Π²Π»ΠΈΠ²Π°Π΅ΠΌΡΠΌΠΈ Π½Π° ΠΎΡΡΡΠΈΠ»ΡΠ½ΡΡ Π°ΠΏΠΏΠ°ΡΠ°ΡΠ°Ρ . ΠΠ»Ρ Π±ΠΎΠ»Π΅Π΅ ΡΠΎΠ»ΡΡΠΎΠ³ΠΎ Π΄ΠΈΠ°ΒΠΌΠ΅ΡΡΠ° ΠΎΡ 0.8 ΠΌΠΌ ΠΈ Π±ΠΎΠ»Π΅Π΅ ΡΠΈΡΠΎΠΊΠΎ Π·Π°ΡΠ΅ΠΊΠΎΠΌΠ΅Π½Π΄ΠΎΠ²Π°Π»ΠΈ ΡΠ΅Π±Ρ Π² ΡΠ°Π±ΠΎΡΠ΅ Π½ΠΎΠΆΒΠ½ΠΈΡΡ Ρ Π³ΠΈΠ΄ΡΠΎΠΏΡΠΈΠ²ΠΎΠ΄ΠΎΠΌ Ρ ΡΠΈΠ»ΠΎΠΉ ΡΠ΅Π·Π°Π½ΠΈΡ Π΄ΠΎ 150 ΠΊΠ (15 ΡΡ), ΠΈΠΌΠ΅ΡΡΠΈΠ΅ Π°Π²ΡΠΎΠ½ΠΎΠΌΠ½ΡΡ ΡΡΠ°Π½ΡΠΈΡ ΡΠΎ Π²ΡΠ΅ΠΌ Π½Π΅ΠΎΠ±Ρ ΠΎΠ΄ΠΈΠΌΡΠΌ ΠΎΠ±ΠΎΡΡΠ΄ΠΎΠ²Π°Π½ΠΈΠ΅ΠΌ. Π Π°Π±ΠΎΡΠ΅Π΅ Π΄Π°Π²ΒΠ»Π΅Π½ΠΈΠ΅ Π² Π³ΠΈΠ΄ΡΠΎΡΠΈΡΡΠ΅ΠΌΠ΅ Π΄ΠΎΡΡΠΈΠ³Π°Π΅Ρ 16 ΠΠΠ° (160 ΠΊΠ³Ρ/ΡΠΌ2).
Π Π°Π·ΠΌΠΎΡΠΎΡΠ½ΡΠ΅ ΡΡΡΡΠΎΠΉΡΡΠ²Π° Ρ ΠΊΠ°ΡΡΡΠ΅ΠΊ AVS 630T ΠΈ AVS 800T
Π Π°Π·ΠΌΠΎΡΠΎΡΠ½ΡΠ΅ ΡΡΡΡΠΎΠΉΡΡΠ²Π° ΡΠΊΠ°Π·Π°Π½Π½ΡΡ ΡΠΈΠΏΠΎΠ² ΠΏΡΠ΅Π΄Π½Π°Π·Π½Π°ΡΠ΅Π½Ρ Π΄Π»Ρ ΡΠ°Π·ΠΌΠ°ΡΡΠ²Π°Π½ΠΈΡ ΠΏΡΠΎΠ²ΠΎΠ»ΠΎΠΊΠΈ-Π·Π°Π³ΠΎΡΠΎΠ²ΠΊΠΈ ΠΏΠ΅ΡΠ΅Π΄ Π²ΠΎΠ»ΠΎΡΠΈΠ»ΡΠ½ΡΠΌ ΡΡΠ°Π½ΠΎΠΌ Ρ ΠΊΠ°ΡΡΒΡΠ΅ΠΊ Π΄ΠΈΠ°ΠΌΠ΅ΡΡΠΎΠΌ 315-630 ΠΌΠΌ Π½Π° AVS 630T ΠΈ Π΄ΠΈΠ°ΠΌΠ΅ΡΡΠΎΠΌ 500-800 ΠΌΠΌ Π΄Π»Ρ AVS 800T. ΠΠ°ΠΊΡΠΈΠΌΠ°Π»ΡΠ½ΠΎ Π΄ΠΎΠΏΡΡΡΠΈΠΌΠ°Ρ ΠΌΠ°ΡΡΠ° ΠΏΡΠΎΠ²ΠΎΠ»ΠΎΠΊΠΈ Π΄Π»Ρ ΠΏΠ΅ΡΠ²ΠΎΠ³ΠΎ ΡΡΡΒΡΠΎΠΉΡΡΠ²Π° Π΄ΠΎ 700 ΠΊΠ³, Π° Π΄Π»Ρ Π²ΡΠΎΡΠΎΠ³ΠΎ — Π΄ΠΎ 1200 ΠΊΠ³.
Π ΡΠ²Π°ΡΠ½ΠΎΠΌ ΠΊΠΎΡΠΏΡΡΠ΅1 (ΡΠΈΡ.2.1) ΡΠ°ΡΠΏΠΎΠ»ΠΎΠΆΠ΅Π½Ρ Π΄Π²Π΅ ΡΡΡΠ°ΠΆΠ½ΡΠ΅ ΠΎΠΏΠΎΡΡ 5 ΠΈ 7. ΠΠΏΠΎΡΡ ΠΏΠ΅ΡΠ΅ΠΌΠ΅ΡΠ°ΡΡΡΡ ΠΏΠΎΡΡΡΠΏΠ°ΡΠ΅Π»ΡΠ½ΠΎ ΠΏΠΎ ΠΎΡΠΈ 4 ΠΏΡΠΈ ΠΏΠΎΠΌΠΎΡΠΈ Ρ ΠΎΠ΄ΠΎΠ²ΠΎΠ³ΠΎ Π²ΠΈΠ½ΡΠ° 6 Ρ Π»Π΅Π²ΠΎΠΉ ΠΈ ΠΏΡΠ°Π²ΠΎΠΉ ΡΠ΅Π·ΡΠ±ΠΎΠΉ, Π²ΡΠ°ΡΠ°ΡΡΠ΅Π³ΠΎΡΡ Π²ΡΡΡΠ½ΡΡ ΠΎΡ ΡΡΡΡΠ²Π°Π»Π° 3. ΠΠ°ΠΆΠΈΠΌΠ½ΡΠ΅ ΠΊΠΎΠ½ΡΡΡ 9 ΠΈΠΌΠ΅ΡΡ ΡΠΏΠ΅ΡΠΈΠ°Π»ΡΠ½ΡΡ ΡΠΎΡΠΌΡ, ΡΡΠΈΡΡΠ²Π°ΡΡΡΡ ΡΠ°Π·ΠΌΠ΅ΡΡ ΠΎΡΠ²Π΅ΡΡΡΠΈΠΉ ΠΊΠ°ΡΡΡΠ΅ΠΊ ΡΠ°Π·Π»ΠΈΡΠ½ΡΡ Π΄ΠΈΠ°ΠΌΠ΅ΡΡΠΎΠ². ΠΠ»Ρ ΠΏΠΎΠ΄ΡΠ΅ΠΌΠ° ΠΊΠ°ΡΡΡΠ΅ΠΊ ΡΠΎ ΡΡΠ°Π½ΠΈΠ½Ρ, ΠΏΠΎΡΠ»Π΅ Π·Π°ΠΆΠ°ΡΠΈΡ ΠΈΡ ΠΊΠΎΠ½ΡΡΠ°ΠΌΠΈ, ΡΠ»ΡΠΆΠΈΡ ΡΠΊΡΡΠ΅Π½ΡΡΠΈΠΊΠΎΠ²ΡΠΉ ΠΌΠ΅Ρ Π°Π½ΠΈΠ·ΠΌ 2 Ρ ΠΏΡΠΈΠ²ΠΎΠ΄ΠΎΠΌ ΠΎΡ ΡΡΠΊΠΎΡΡΠΊΠΈ-ΡΡΡΠ°Π³Π° 8. ΠΠΏΡΡΠΊΠ°Ρ ΡΡΡΠ°Π³ Π΄ΠΎ Π³ΠΎΡΠΈΠ·ΠΎΠ½ΡΠ°Π»ΡΠ½ΠΎΠ³ΠΎ ΠΏΠΎΠ»ΠΎΠΆΠ΅Π½ΠΈΡ, ΠΊΠ°ΡΡΡΠΊΠ° ΡΡΡΠ°Π½Π°Π²Π»ΠΈΠ²Π°Π΅ΡΡΡ Π² ΡΠ°Π±ΠΎΡΠ΅Π΅ ΠΏΠΎΠ»ΠΎΠΆΠ΅Π½ΠΈΠ΅. ΠΠ° ΠΎΠ΄Π½ΠΎΠΌ ΠΈΠ· ΠΊΠΎΠ½ΡΡΠΎΠ² ΡΡΡΠ°Π½ΠΎΠ²Π»Π΅Π½ ΡΠΎΡΠΌΠΎΠ·Π½ΠΎΠΉ ΡΠΊΠΈΠ² 10, ΡΠ°Π±ΠΎΡΠ°ΡΡΠΈΠΉ ΠΏΠΎ ΠΏΡΠΈΠ½ΡΠΈΠΏΡ Π»Π΅Π½ΡΠΎΡΠ½ΠΎΠ³ΠΎ ΡΠΎΡΠΌΠΎΠ·Π°, ΠΈ ΡΠ΅Π³ΡΠ»ΠΈΡΠΎΠ²Π°Π½ΠΈΠ΅ Π½Π°ΡΡΠΆΠ΅Π½ΠΈΡ ΡΡ ΠΎΠ΄ΡΡΠ΅ΠΉ Π·Π°Π³ΠΎΡΠΎΠ²ΠΊΠΈ ΠΏΡΠΎΠΈΠ·Π²ΠΎΠ΄ΠΈΡΡΡ Π²ΠΈΠ½ΡΠΎΠΌ Π’-ΠΎΠ±ΡΠ°Π·Π½ΠΎΠΉ ΡΠΎΡΠΌΡ.
Π ΠΈΡ.2.1. Π Π°Π·ΠΌΠΎΡΠΎΡΠ½ΠΎΠ΅ ΡΡΡΡΠΎΠΉΡΡΠ²ΠΎ AVS 630T ΠΈ AVS 800T
ΠΠ°ΠΌΠΎΡΠΎΡΠ½ΡΠ΅ Π°ΠΏΠΏΠ°ΡΠ°ΡΡ Π΄Π»Ρ Π²ΠΎΠ»ΠΎΡΠΈΠ»ΡΠ½ΡΡ ΡΡΠ°Π½ΠΎΠ²
ΠΠ°ΠΌΠΎΡΠΎΡΠ½ΡΠ΅ Π°ΠΏΠΏΠ°ΡΠ°ΡΡ, ΡΡΡΠ°Π½Π°Π²Π»ΠΈΠ²Π°Π΅ΠΌΡΠ΅ Π² ΠΎΠ΄Π½ΠΎΠΉ Π»ΠΈΠ½ΠΈΠΈ Ρ Π²ΠΎΠ»ΠΎΡΠΈΠ»ΡΠ½ΡΠΌΠΈ ΡΡΠ°Π½Π°ΠΌΠΈ, ΠΏΡΠ΅Π΄Π½Π°Π·Π½Π°ΡΠ΅Π½Ρ Π΄Π»Ρ Π½Π°ΠΌΠ°ΡΡΠ²Π°Π½ΠΈΡ ΠΏΡΠΎΠ²ΠΎΠ»ΠΎΠΊΠΈ Π³ΠΎΡΠΎΠ²ΠΎΠ³ΠΎ ΡΠ°Π·ΠΌΠ΅ΡΠ° Π½Π° ΠΊΠ°ΡΡΡΠΊΠΈ Π±ΠΎΠ»ΡΡΠΎΠΉ Π²ΠΌΠ΅ΡΡΠΈΠΌΠΎΡΡΠΈ: 250, 500 ΠΈ 1000 ΠΊΠ³, Π° ΠΈΠ½ΠΎΠ³Π΄Π° ΠΈ Π±ΠΎΠ»Π΅Π΅. ΠΠ»Π°Π³ΠΎΠ΄Π°ΡΡ Π±ΠΎΠ»ΡΡΠΎΠΉ Π²ΠΌΠ΅ΡΡΠΈΠΌΠΎΡΡΠΈ ΠΊΠ°ΡΡΡΠΊΠΈ ΠΏΠΎ ΡΡΠ°Π²Π½Π΅Π½ΠΈΡ Ρ ΠΌΠ°ΡΡΠΎΠΉ ΠΌΠΎΡΠΊΠ° Π½Π° ΡΠΈΡΡΠΎΠ²ΠΎΠΌ Π±Π°ΡΠ°Π±Π°Π½Π΅ Π²ΠΎΠ»ΠΎΡΠΈΠ»ΡΠ½ΠΎΠ³ΠΎ ΡΡΠ°Π½Π°, ΠΎΠ±ΡΡΠ½ΠΎ Π½Π΅ ΠΏΡΠ΅Π²ΡΡΠ°ΡΡΠ΅ΠΉ 70-80 ΠΊΠ³, ΡΠ²Π΅Π»ΠΈΡΠΈΠ²Π°Π΅ΡΡΡ ΠΏΡΠΎΠΈΠ·Π²ΠΎΠ΄ΠΈΡΠ΅Π»ΡΠ½ΠΎΡΡΡ ΡΡΠ°Π½Π° Π·Π° ΡΡΠ΅Ρ ΡΠΎΠΊΡΠ°ΡΠ΅Π½ΠΈΡ ΡΠΈΡΠ»Π° Π΅Π³ΠΎ ΠΎΡΡΠ°Π½ΠΎΠ²ΠΎΠΊ Π΄Π»Ρ ΡΡΠ΅ΠΌΠ° Π³ΠΎΡΠΎΠ²ΠΎΠΉ ΠΏΡΠΎΠ²ΠΎΠ»ΠΎΠΊΠΈ, Ρ.Π΅. ΡΠ²Π΅Π»ΠΈΡΠΈΠ²Π°Π΅ΡΡΡ Π΄ΠΎΠ»Ρ ΠΌΠ°ΡΠΈΠ½Π½ΠΎΠ³ΠΎ Π²ΡΠ΅ΠΌΠ΅Π½ΠΈ ΠΈ ΡΠΎΠΊΡΠ°ΡΠ°Π΅ΡΡΡ Π²ΡΠ΅ΠΌΡ Π½Π° ΡΡΡΠ½ΡΠ΅ ΠΎΠΏΠ΅ΡΠ°ΡΠΈΠΈ.
ΠΠ°ΠΌΠΎΡΠ°Π½Π½Π°Ρ ΠΏΡΠΎΠ²ΠΎΠ»ΠΎΠΊΠ° Π½Π° ΠΊΠ°ΡΡΡΠΊΠ°Ρ Π»Π΅Π³ΠΊΠΎ ΡΠ°Π·ΠΌΠ°ΡΡΠ²Π°Π΅ΡΡΡ Π±Π΅Π· Π·Π°ΠΏΡΡΡΠ²Π°Π½ΠΈΡ ΠΏΡΠΈ ΠΏΠΎΡΠ»Π΅Π΄ΡΡΡΠΈΡ ΡΠ΅Ρ Π½ΠΎΠ»ΠΎΠ³ΠΈΡΠ΅ΡΠΊΠΈΡ ΠΏΡΠΎΡΠ΅ΡΡΠ°Ρ , Π½Π°ΠΏΡΠΈΠΌΠ΅Ρ, ΠΏΡΠΈ ΠΏΠ΅ΡΠ΅ΠΌΠΎΡΠΊΠ΅ ΠΏΡΠΎΠ²ΠΎΠ»ΠΎΠΊΠΈ Π½Π° Π·Π°ΡΡΠ΄Π½ΡΠ΅ ΠΊΠ°ΡΡΡΠΊΠΈ Π² ΠΊΠ°Π½Π°ΡΠ½ΡΡ ΡΠ΅Ρ Π°Ρ . Π ΡΠ΅Π·ΡΠ»ΡΡΠ°ΡΠ΅ ΡΠΌΠ΅Π½ΡΡΠ°Π΅ΡΡΡ ΠΊΠΎΠ»ΠΈΡΠ΅ΡΡΠ²ΠΎ ΠΎΡΡ ΠΎΠ΄ΠΎΠ² ΠΏΡΠΈ ΠΏΠ΅ΡΠ΅ΠΌΠΎΡΠΊΠ΅.
ΠΠ° ΡΡΠ°Π½Π°Ρ Π±Π»ΠΎΡΠ½ΠΎΠ³ΠΎ ΡΠΈΠΏΠ° Π½Π°ΠΌΠΎΡΠΎΡΠ½ΡΠ΅ Π°ΠΏΠΏΠ°ΡΠ°ΡΡ ΡΠ²Π»ΡΡΡΡΡ ΡΠ°ΠΌΠΎΡΡΠΎΡΡΠ΅Π»ΡΠ½ΡΠΌΠΈ Π°Π³ΡΠ΅Π³Π°ΡΠ°ΠΌΠΈ, ΡΠ°Π±ΠΎΡΠ° ΠΊΠΎΡΠΎΡΡΡ Π΄ΠΎΠ»ΠΆΠ½Π° Π±ΡΡΡ ΡΡΡΠΎΠ³ΠΎ ΡΠΎΠ³Π»Π°ΡΠΎΠ²Π°Π½Π½ΠΎΠΉ Ρ ΡΠ°Π±ΠΎΡΠΎΠΉ Π²ΠΎΠ»ΠΎΡΠΈΠ»ΡΠ½ΠΎΠ³ΠΎ ΡΡΠ°Π½Π°, ΡΠΎΡΠ½Π΅Π΅ ΡΠΊΠΎΡΠΎΡΡΡ Π½Π°ΠΌΠΎΡΠΊΠΈ ΠΏΡΠΎΠ²ΠΎΠ»ΠΎΠΊΠΈ Π½Π° ΠΊΠ°ΡΡΡΠΊΡ Π΄ΠΎΠ»ΠΆΠ½Π° Π±ΡΡΡ ΡΠΈΠ½Ρ ΡΠΎΠ½ΠΈΠ·ΠΈΡΠΎΠ²Π°Π½Π° ΡΠΎ ΡΠΊΠΎΡΠΎΡΡΡΡ Π΅Π΅ Π΄Π²ΠΈΠΆΠ΅Π½ΠΈΡ Ρ ΡΠΈΡΡΠΎΠ²ΠΎΠ³ΠΎ Π±Π°ΡΠ°Π±Π°Π½Π°.
ΠΠ°ΠΌΠΎΡΠΎΡΠ½ΡΠ΅ Π°ΠΏΠΏΠ°ΡΠ°ΡΡ, ΠΊΠ°ΠΊ ΡΠ°ΠΌΠΎΡΡΠΎΡΡΠ΅Π»ΡΠ½ΡΠ΅ Π°Π³ΡΠ΅Π³Π°ΡΡ, ΠΈΠΌΠ΅ΡΡ ΠΈΠ½Π΄ΠΈΠ²ΠΈΠ΄ΡΠ°Π»ΡΠ½ΡΠ΅ ΠΏΡΠΈΠ²ΠΎΠ΄Ρ, ΠΊΠΎΡΠΎΡΡΠ΅ Π΄ΠΎΠ»ΠΆΠ½Ρ ΠΎΠ±Π΅ΡΠΏΠ΅ΡΠΈΠ²Π°ΡΡ ΡΠΈΡΠΎΠΊΠΈΠΉ Π΄ΠΈΠ°ΠΏΠ°Π·ΠΎΠ½ ΡΠΊΠΎΡΠΎΡΡΠ΅ΠΉ Π½Π°ΠΌΠΎΡΠΊΠΈ Π² ΡΠΎΠΎΡΠ²Π΅ΡΡΡΠ²ΠΈΠΈ ΡΠΎ ΡΠΊΠΎΡΠΎΡΡΡΠΌΠΈ Π²ΠΎΠ»ΠΎΡΠ΅Π½ΠΈΡ ΠΏΡΠΎΠ²ΠΎΠ»ΠΎΠΊΠΈ Π½Π° Π²ΠΎΠ»ΠΎΡΠΈΠ»ΡΠ½ΠΎΠΌ ΡΡΠ°Π½Π΅. ΠΡΠΈΠ²ΠΎΠ΄ Π½Π°ΠΌΠΎΡΠΎΡΠ½ΠΎΠ³ΠΎ Π°ΠΏΠΏΠ°ΡΠ°ΡΠ° Π΄ΠΎΠ»ΠΆΠ΅Π½ ΠΎΠ±Π΅ΡΠΏΠ΅ΡΠΈΠ²Π°ΡΡ ΠΏΠΎΡΡΠΎΡΠ½Π½ΠΎΠ΅ ΠΈ ΡΠ°Π²Π½ΠΎΠΌΠ΅ΡΠ½ΠΎΠ΅ Π½Π°ΡΡΠΆΠ΅Π½ΠΈΠ΅ ΠΏΡΠΎΠ²ΠΎΠ»ΠΎΠΊΠΈ ΠΏΡΠΈ Π΅Π΅ Π½Π°ΠΌΠΎΡΠΊΠ΅ Π½Π° ΠΊΠ°ΡΡΡΠΊΡ ΠΈ ΠΏΠΎ ΠΌΠ΅ΡΠ΅ ΡΠ²Π΅Π»ΠΈΡΠ΅Π½ΠΈΡ Π΄ΠΈΠ°ΠΌΠ΅ΡΡΠ° Π½Π°ΠΌΠΎΡΠΊΠΈ. ΠΠΎ Π²ΡΠ΅ΠΌΡ ΠΏΡΡΠΊΠ° Π²ΠΎΠ»ΠΎΡΠΈΠ»ΡΠ½ΠΎΠ³ΠΎ ΡΡΠ°Π½Π° Π½Π΅ Π΄ΠΎΠ»ΠΆΠ½ΠΎ Π±ΡΡΡ ΡΠ»Π°Π±ΠΈΠ½Ρ ΠΏΡΠΎΠ²ΠΎΠ»ΠΎΠΊΠΈ, ΠΈΠ½Π°ΡΠ΅ ΠΏΡΠΎΠΈΠ·ΠΎΠΉΠ΄Π΅Ρ ΠΏΡΠΎΡΠΊΠ°Π»ΡΠ·ΡΠ²Π°Π½ΠΈΠ΅ Π²ΠΈΡΠΊΠΎΠ² ΠΏΡΠΎΠ²ΠΎΠ»ΠΎΠΊΠΈ Π½Π° ΡΠΈΡΡΠΎΠ²ΠΎΠΌ Π±Π°ΡΠ°Π±Π°Π½Π΅ Π²ΠΎΠ»ΠΎΡΠΈΠ»ΡΠ½ΠΎΠ³ΠΎ ΡΡΠ°Π½Π° ΠΈ, ΠΊΠ°ΠΊ ΡΠ»Π΅Π΄ΡΡΠ²ΠΈΠ΅, ΠΎΠ±ΡΡΠ² ΠΏΡΠΎΠ²ΠΎΠ»ΠΎΠΊΠΈ. ΠΠ½Π°Π»ΠΎΠ³ΠΈΡΠ½ΠΎ, ΠΏΡΠΈ ΠΎΡΡΠ°Π½ΠΎΠ²Π΅ ΡΡΠ°Π½Π°, ΡΠΎΡΠΌΠΎΠΆΠ΅Π½ΠΈΠΈ Π½Π΅ Π΄ΠΎΠ»ΠΆΠ½ΠΎ Π±ΡΡΡ ΡΡΠ΅Π·ΠΌΠ΅ΡΠ½ΠΎΠ³ΠΎ Π½Π°ΡΡΠΆΠ΅Π½ΠΈΡ ΠΏΡΠΎΠ²ΠΎΠ»ΠΎΠΊΠΈ ΠΌΠ΅ΠΆΠ΄Ρ ΠΊΠ°ΡΡΡΠΊΠΎΠΉ ΠΈ ΡΠΈΡΡΠΎΠ²ΡΠΌ Π±Π°ΡΠ°Π±Π°Π½ΠΎΠΌ.
studfiles.net
ΠΠΎΠ»ΠΎΡΠΈΠ»ΡΠ½ΡΠΉ ΡΡΠ°Π½ — Ρ Π°ΡΠ°ΠΊΡΠ΅ΡΠΈΡΡΠΈΠΊΠΈ ΠΈ ΠΏΡΠΈΠΌΠ΅Π½Π΅Π½ΠΈΠ΅
Π‘Π΅Π³ΠΎΠ΄Π½Ρ ΠΏΡΠΎΠΈΠ·Π²ΠΎΠ΄ΡΡΠ²ΠΎ ΠΌΠ΅ΡΠ°Π»Π»ΠΈΡΠ΅ΡΠΊΠΈΡ ΠΈΠ·Π΄Π΅Π»ΠΈΠΉ ΡΠ²Π»ΡΠ΅ΡΡΡ Π½Π°ΠΈΠ±ΠΎΠ»Π΅Π΅ Π²ΠΎΡΡΡΠ΅Π±ΠΎΠ²Π°Π½Π½ΠΎΠΉ ΠΎΡΡΠ°ΡΠ»ΡΡ ΠΏΡΠΎΠΈΠ·Π²ΠΎΠ΄ΡΡΠ²Π°. Π ΡΡΠΈΠΌ ΡΠΈΠΏΠ°ΠΌ ΠΏΡΠΎΠΈΠ·Π²ΠΎΠ΄ΡΡΠ²Π° ΠΌΠΎΠΆΠ½ΠΎ ΠΎΡΠ½Π΅ΡΡΠΈ ΠΈ ΠΈΠ·Π³ΠΎΡΠΎΠ²Π»Π΅Π½ΠΈΠ΅ ΡΠ°ΠΊΠΈΡ ΠΈΠ·Π΄Π΅Π»ΠΈΠΉ ΠΈΠ· ΠΌΠ΅ΡΠ°Π»Π»Π°, ΠΊΠ°ΠΊ ΠΏΡΠΎΠ²ΠΎΠ»ΠΎΠΊΠ°, ΠΆΠ΅Π»Π΅Π·Π½ΡΠ΅ ΠΏΡΡΡΡ, ΠΏΡΠΎΡΠΈΠ»ΡΠ½ΠΎΠ³ΠΎ ΠΌΠ°ΡΠ΅ΡΠΈΠ°Π»Π° ΠΈ ΡΡΡΠ±Ρ Π½Π΅ ΡΠ»ΠΈΡΠΊΠΎΠΌ Π±ΠΎΠ»ΡΡΠΈΠ΅ ΠΏΠΎ Π΄ΠΈΠ°ΠΌΠ΅ΡΡΡ. Π‘ΡΠΎΠΈΡ ΠΎΡΠΌΠ΅ΡΠΈΡΡ, ΡΡΠΎ Π΄Π»Ρ ΠΈΠ·Π³ΠΎΡΠΎΠ²Π»Π΅Π½ΠΈΡ Π²ΡΠ΅Ρ ΡΡΠΈΡ ΠΌΠ΅ΡΠ°Π»Π»ΠΈΡΠ΅ΡΠΊΠΈΡ ΠΈΠ·Π΄Π΅Π»ΠΈΠΉ ΡΡΠ΅Π±ΡΠ΅ΡΡΡ Π½Π°Π»ΠΈΡΠΈΠ΅ ΡΠΏΠ΅ΡΠΈΠ°Π»ΡΠ½ΠΎΠ³ΠΎ ΠΎΠ±ΠΎΡΡΠ΄ΠΎΠ²Π°Π½ΠΈΡ, ΠΊ Π½Π΅ΠΌΡ Π½Π΅ΠΏΠΎΡΡΠ΅Π΄ΡΡΠ²Π΅Π½Π½ΠΎ ΠΎΡΠ½ΠΎΡΠΈΡΡΡ Π²ΠΎΠ»ΠΎΡΠΈΠ»ΡΠ½ΡΠΉ ΡΡΠ°Π½.
Π£ΡΡΡΠΎΠΉΡΡΠ²ΠΎ Π²ΠΎΠ»ΠΎΡΠΈΠ»ΡΠ½ΠΎΠ³ΠΎ ΡΡΠ°Π½Π°.
ΠΠ°Π½Π½ΠΎΠ΅ ΠΎΠ±ΠΎΡΡΠ΄ΠΎΠ²Π°Π½ΠΈΠ΅ ΠΏΡΠ΅Π΄Π½Π°Π·Π½Π°ΡΠ΅Π½ΠΎ Π΄Π»Ρ ΡΠΎΠ³ΠΎ, ΡΡΠΎΠ±Ρ ΠΏΡΠΎΡΡΠ³ΠΈΠ²Π°ΡΡ ΠΈΠ·Π΄Π΅Π»ΠΈΠ΅ ΡΠ΅ΡΠ΅Π· ΡΠ°ΠΊ Π½Π°Π·ΡΠ²Π°Π΅ΠΌΡΡ Π²ΠΎΠ»ΠΎΠΊΡ, ΠΈΠ½ΡΠΌΠΈ ΡΠ»ΠΎΠ²Π°ΠΌΠΈ ΡΠΏΠ΅ΡΠΈΠ°Π»ΡΠ½ΡΠΉ Π³Π»Π°Π·ΠΎΠΊ, Β ΠΏΡΠΈ ΡΡΠΎΠΌ ΡΠ°Π·ΠΌΠ΅Ρ Π΅Π³ΠΎ ΡΠ΅ΡΠ΅Π½ΠΈΡ ΡΠ²Π»ΡΠ΅ΡΡΡ ΠΌΠ΅Π½ΡΡΠΈΠΌ, Π½Π΅ΠΆΠ΅Π»ΠΈ ΡΠ°Π·ΠΌΠ΅Ρ ΡΠ΅ΡΠ΅Π½ΠΈΡ ΠΈΡΡ
ΠΎΠ΄Π½ΠΎΠ³ΠΎ ΠΌΠ°ΡΠ΅ΡΠΈΠ°Π»Π°. ΠΠΎΠ»ΠΎΡΠΈΠ»ΡΠ½ΡΠ΅ ΡΡΠ°Π½Ρ, Π² Π½Π΅ΠΏΠΎΡΡΠ΅Π΄ΡΡΠ²Π΅Π½Π½ΠΎΠΉ Π·Π°Π²ΠΈΡΠΈΠΌΠΎΡΡΠΈ ΠΎΡ ΠΈΡ
ΠΏΡΠΈΠ½ΡΠΈΠΏΠ° ΡΠ°Π±ΠΎΡΡ ΠΌΠΎΠ³ΡΡ ΠΏΠΎΠ΄ΡΠ°Π·Π΄Π΅Π»ΡΡΡΡΡ Π½Π° ΡΡΠ°Π½Ρ Π΄Π²ΠΈΠΆΠ΅Π½ΠΈΠ΅ ΠΌΠ΅ΡΠ°Π»Π»Π°, Π² ΠΊΠΎΡΠΎΡΡΡ
ΡΠ²Π»ΡΠ΅ΡΡΡ ΠΏΡΡΠΌΠΎΠ»ΠΈΠ½Π΅ΠΉΠ½ΡΠΌ. Π ΡΡΠ°Π½Ρ, Π² ΠΊΠΎΡΠΎΡΡΡ
ΠΎΠ±ΡΠ°Π±Π°ΡΡΠ²Π°Π΅ΠΌΡΠΉ ΠΌΠ΅ΡΠ°Π»Π» Π½Π°ΠΌΠ°ΡΡΠ²Π°Π΅ΡΡΡ Π½Π° Π±Π°ΡΠ°Π±Π°Π½Π½ΠΎΠ΅ ΡΡΡΡΠΎΠΉΡΡΠ²ΠΎ.
ΠΠΎΠ»ΠΎΡΠΈΠ»ΡΠ½ΡΠ΅ ΡΡΠ°Π½Ρ ΠΏΠ΅ΡΠ²ΠΎΠΉ ΠΊΠ°ΡΠ΅Π³ΠΎΡΠΈΠΈ ΠΌΠΎΠ³ΡΡ Π±ΡΡΡ ΡΠ΅Π΅ΡΠ½ΡΠΌΠΈ ΠΈ ΡΠ΅ΠΏΠ½ΡΠΌΠΈ. ΠΡ
ΠΈΡΠΏΠΎΠ»ΡΠ·ΡΡΡ Π΄Π»Ρ Π²ΠΎΠ»ΠΎΡΠ΅Π½ΠΈΡ ΠΈ ΠΊΠ°Π»ΠΈΠ±ΡΠΎΠ²ΠΊΠΈ ΡΠ°ΠΊΠΈΡ
ΠΈΠ·Π΄Π΅Π»ΠΈΠΉ, ΠΊΠ°ΠΊ ΠΏΡΡΡΠΊΠΈ, ΡΡΡΠ±Ρ Π½Π΅Π±ΠΎΠ»ΡΡΠΎΠ³ΠΎ Π΄ΠΈΠ°ΠΌΠ΅ΡΡΠ° ΠΈ Π΄ΡΡΠ³ΠΈΡ
ΠΏΠΎΠ΄ΠΎΠ±Π½ΡΡ
ΠΈΠ·Π΄Π΅Π»ΠΈΠΉ. Π’Π°ΠΊΠΎΠΉ ΠΌΠ°ΡΠ΅ΡΠΈΠ°Π» Π½Π΅ Π½ΡΠΆΠ½ΠΎ ΡΠΌΠ°ΡΡΠ²Π°ΡΡ Π² ΡΠΏΠ΅ΡΠΈΠ°Π»ΡΠ½ΡΠ΅ Π±ΡΡ
ΡΡ.
Β
Β
ΠΡΠΎΡΠΎΠΉ ΡΠΈΠΏ Π²ΠΎΠ»ΠΎΡΠΈΠ»ΡΠ½ΡΡ ΡΡΠ°Π½ΠΎΠ², ΠΌΠ΅ΡΠ°Π»Π» Π² ΠΊΠΎΡΠΎΡΡΡ Π½Π°ΠΌΠ°ΡΡΠ²Π°Π΅ΡΡΡ Π½Π° Π±Π°ΡΠ°Π±Π°Π½Π½ΠΎΠ΅ ΡΡΡΡΠΎΠΉΡΡΠ²ΠΎ, ΠΈΡΠΏΠΎΠ»ΡΠ·ΡΠ΅ΡΡΡ Π½Π°ΠΈΠ±ΠΎΠ»Π΅Π΅ ΡΠ°ΡΡΠΎ Π΄Π»Ρ ΠΈΠ·Π³ΠΎΡΠΎΠ²Π»Π΅Π½ΠΈΡ ΡΠ°ΠΊΠΈΡ ΠΌΠ°ΡΠ΅ΡΠΈΠ°Π»ΠΎΠ², ΠΊΠ°ΠΊ ΠΌΠ΅ΡΠ°Π»Π»ΠΈΡΠ΅ΡΠΊΠ°Ρ ΠΏΡΠΎΠ²ΠΎΠ»ΠΎΠΊΠ°, Π° ΡΠ°ΠΊ ΠΆΠ΅ ΡΠΏΠ΅ΡΠΈΠ°Π»ΡΠ½ΡΠΉ ΠΏΡΠΎΡΠΈΠ»ΡΠ½ΡΠΉ ΠΌΠ°ΡΠ΅ΡΠΈΠ°Π». Π‘ΡΠΎΠΈΡ ΠΎΡΠΌΠ΅ΡΠΈΡΡ, ΡΡΠΎ Π΄Π°Π½Π½ΡΠΉ ΡΠΈΠΏ ΡΡΠ°Π½Π° ΠΌΠΎΠΆΠ½ΠΎ, Π² ΡΠ²ΠΎΡ ΠΎΡΠ΅ΡΠ΅Π΄Ρ, ΠΏΠΎΠ΄ΡΠ°Π·Π΄Π΅Π»ΡΡΡ Π½Π° ΡΡΠ°Π½Ρ ΠΎΠ΄Π½ΠΎΠΊΡΠ°ΡΠ½ΠΎΠ³ΠΎ Π΄Π΅ΠΉΡΡΠ²ΠΈΡ. ΠΠ° ΠΌΠ½ΠΎΠ³ΠΎΠΊΡΠ°ΡΠ½ΡΠ΅ ΡΡΠ°Π½Ρ, ΠΊΠΎΡΠΎΡΡΠ΅ ΡΠ°Π±ΠΎΡΠ°ΡΡ ΡΠΎ ΡΠΊΠΎΠ»ΡΠΆΠ΅Π½ΠΈΠ΅ΠΌ. ΠΠ° ΡΡΠ°Π½Ρ ΠΌΠ½ΠΎΠ³ΠΎΠΊΡΠ°ΡΠ½ΡΠ΅, ΠΊΠΎΡΠΎΡΡΠ΅ ΡΠ°Π±ΠΎΡΠ°ΡΡ Π±Π΅Π· ΡΠΊΠΎΠ»ΡΠΆΠ΅Π½ΠΈΡ, ΠΈ Π½Π°ΠΊΠΎΠ½Π΅Ρ, Π½Π° ΡΡΠ°Π½Ρ ΠΌΠ½ΠΎΠ³ΠΎΠΊΡΠ°ΡΠ½ΠΎΠ³ΠΎ Π΄Π΅ΠΉΡΡΠ²ΠΈΡ, ΠΊΠΎΡΠΎΡΡΠ΅ ΡΠ°Π±ΠΎΡΠ°ΡΡ Ρ ΠΏΡΠΎΡΠΈΠ²ΠΎΠ½Π°ΡΡΠΆΠ΅Π½ΠΈΠ΅ΠΌ.
ΠΠ°Π½Π½ΠΎΠ΅ ΠΎΠ±ΠΎΡΡΠ΄ΠΎΠ²Π°Π½ΠΈΠ΅ Π²ΠΊΠ»ΡΡΠ°Π΅Ρ Π² ΡΠ΅Π±Ρ ΡΡΠΈ ΠΎΡΠ½ΠΎΠ²Π½ΡΡ
ΡΠ°Π±ΠΎΡΠΈΡ
ΡΠ»Π΅ΠΌΠ΅Π½ΡΠ°, ΡΡΠΈΠΌΠΈ ΡΠ°Π±ΠΎΡΠΈΠΌΠΈ ΡΠ°ΡΡΡΠΌΠΈ ΡΠ²Π»ΡΡΡΡΡ ΡΡΡΡΠΎΠΉΡΡΠ²ΠΎ Π΄Π»Ρ ΡΠ°Π·ΠΌΠΎΡΠΊΠΈ ΠΌΠ΅ΡΠ°Π»Π»ΠΈΡΠ΅ΡΠΊΠΎΠ³ΠΎ ΠΌΠ°ΡΠ΅ΡΠΈΠ°Π»Π°, ΡΠ°ΠΌΠ° ΡΠ°ΡΡΡ, ΠΊΠΎΡΠΎΡΠΎΠ΅ ΠΏΡΠΎΠΈΠ·Π²ΠΎΠ΄ΠΈΡ Π²ΠΎΠ»ΠΎΡΠ΅Π½ΠΈΠ΅, ΠΈ ΡΡΡΡΠΎΠΉΡΡΠ²ΠΎ Π΄Π»Ρ Π½Π°ΠΌΠΎΡΠΊΠΈ Π³ΠΎΡΠΎΠ²ΠΎΠ³ΠΎ ΠΈΠ·Π΄Π΅Π»ΠΈΡ.
ΠΡΠΈΠ½ΡΠΈΠΏ ΡΠ°Π±ΠΎΡΡ Π²ΠΎΠ»ΠΎΡΠΈΠ»ΡΠ½ΠΎΠ³ΠΎ ΡΡΠ°Π½Π°.
Β
Β
Β
ΠΡΠΈΠ½ΡΠΈΠΏ ΡΠ°Π±ΠΎΡΡ Π΄Π°Π½Π½ΠΎΠ³ΠΎ ΡΡΡΡΠΎΠΉΡΡΠ²Π° Π²ΡΠ³Π»ΡΠ΄ΠΈΡ ΡΠ»Π΅Π΄ΡΡΡΠΈΠΌ ΠΎΠ±ΡΠ°Π·ΠΎΠΌ. ΠΠ°ΡΠ΅ΡΠΈΠ°Π» ΠΏΠΎΠ΄Π»Π΅ΠΆΠ°ΡΠΈΠΉ Π²ΠΎΠ»ΠΎΡΠ΅Π½ΠΈΡ ΡΠ΅ΡΠ΅Π· ΠΊΠΎΡΠ·ΠΈΠ½Ρ ΠΏΡΠΈΠ΅ΠΌΠΎΡΠ½ΠΎΠ³ΠΎ ΠΎΡΠ΄Π΅Π»Π΅Π½ΠΈΡ Π° ΡΠ°ΠΊΠΆΠ΅ ΡΠ΅ΡΠ΅Π· ΡΠΏΠ΅ΡΠΈΠ°Π»ΡΠ½ΡΠ΅ ΡΠΎΠ»ΠΈΠΊΠΎΠ²ΡΠ΅ ΡΡΡΡΠΎΠΉΡΡΠ²Π°, Π½Π°ΠΏΡΠ°Π²Π»ΡΡΡΠ΅Π³ΠΎ Ρ Π°ΡΠ°ΠΊΡΠ΅ΡΠ° Π²ΡΠ΄Π°Π΅ΡΡΡ Π½Π° ΡΠΎΠ»ΠΈΠΊ, ΠΈ Π΄Π°Π»Π΅Π΅ Π½Π° ΡΠΎΠ»ΠΈΠΊ ΡΡΡΠ°Π½ΠΎΠ²Π»Π΅Π½Π½ΡΠΉ Π² ΠΊΠ°ΡΠ΅ΡΠΊΠ΅ ΠΊΠΎΠΌΠΏΠ΅Π½ΡΠΈΡΡΡΡΠ΅Π³ΠΎ ΡΠΈΠΏΠ°. Π£ΠΆΠ΅ Ρ ΡΡΠΎΠΉ ΠΊΠ°ΡΠ΅ΡΠΊΠΈ ΠΌΠ°ΡΠ΅ΡΠΈΠ°Π» Π²ΡΠ΄Π°Π΅ΡΡΡ ΠΏΡΡΠΌΠΎ Π½Π° ΡΠ°ΠΌΠΎ Π²ΠΎΠ»ΠΎΡΠΈΠ»ΡΠ½ΠΎΠ΅ ΡΡΡΡΠΎΠΉΡΡΠ²ΠΎ.
ΠΡΠΏΠΎΠ»ΡΠ·ΠΎΠ²Π°Π½ΠΈΠ΅ ΡΠ°ΠΊΠΎΠ³ΠΎ ΠΎΡΠ³Π°Π½Π°, ΠΊΠ°ΠΊ ΠΊΠΎΠΌΠΏΠ΅Π½ΡΠΈΡΡΡΡΠ°Ρ ΠΊΠ°ΡΠ΅ΡΠΊΠ° Π²Π°ΠΆΠ½ΠΎ Π΄Π»Ρ ΡΠΎΠ³ΠΎ, ΡΡΠΎΠ±Ρ ΠΏΡΠ΅Π΄ΠΎΡΠ²ΡΠ°ΡΠΈΡΡ ΠΎΠ±ΡΡΠ² ΠΏΡΠΎΠ²ΠΎΠ»ΠΎΠΊΠΈ, Π² ΡΠ»ΡΡΠ°Π΅ ΡΠ΅Π·ΠΊΠΎΠ³ΠΎ ΡΠΎΡΠΌΠΎΠΆΠ΅Π½ΠΈΡ Π²ΠΎΠ»ΠΎΠΊΠΈ ΠΈΠ»ΠΈ ΡΠ΅Π·ΠΊΠΎΠΉ ΠΎΡΡΠ°Π½ΠΎΠ²ΠΊΠΈ ΡΠ°Π±ΠΎΡΡ Π²ΡΠ΅Π³ΠΎ ΡΡΡΡΠΎΠΉΡΡΠ²Π°. Π‘ΡΡΡ ΡΡΠΎΠ³ΠΎ ΡΠ°Π±ΠΎΡΠ΅Π³ΠΎ ΠΌΠ΅Ρ
Π°Π½ΠΈΠ·ΠΌΠ° ΡΡΠ΅Π·Π²ΡΡΠ°ΠΉΠ½ΠΎ ΠΏΡΠΎΡΡΠ°: Π²ΠΎ Π²ΡΠ΅ΠΌΡ Π²Π½Π΅Π·Π°ΠΏΠ½ΠΎΠΉ ΠΎΡΡΠ°Π½ΠΎΠ²ΠΊΠΈ ΠΏΡΠΈ ΠΏΠΎΠ΄Π°ΡΠ΅ Π·Π°Π³ΠΎΡΠΎΠ²ΠΊΠΈ, Π±Π»ΠΎΠΊΠΈ ΠΎΠ±ΠΎΡΡΠ΄ΠΎΠ²Π°Π½ΠΈΡ Π΅ΡΠ΅ ΠΊΠ°ΠΊΠΎΠ΅-ΡΠΎ Π²ΡΠ΅ΠΌΡ ΠΏΡΠΎΠ΄ΠΎΠ»ΠΆΠ°ΡΡ Π²ΡΠ°ΡΠ΅Π½ΠΈΠ΅ ΠΈ ΡΠΎΠΎΡΠ²Π΅ΡΡΡΠ²Π΅Π½Π½ΠΎ ΡΡΠ΅Π±ΡΡΡ Π²ΡΠ΄Π°ΡΠΈ Π΅ΡΠ΅ ΠΊΠ°ΠΊΠΎΠ³ΠΎ-ΡΠΎ ΠΎΠΏΡΠ΅Π΄Π΅Π»Π΅Π½Π½ΠΎΠ³ΠΎ ΠΊΠΎΠ»ΠΈΡΠ΅ΡΡΠ²Π° Π·Π°Π³ΠΎΡΠΎΠ²ΠΎΡΠ½ΠΎΠ³ΠΎ ΠΌΠ°ΡΠ΅ΡΠΈΠ°Π»Π°. Π ΡΡΠΎ Π²ΡΠ΅ΠΌΡ ΠΊΠ°ΡΠ΅ΡΠΊΠ° ΠΊΠΎΠΌΠΏΠ΅Π½ΡΠΈΡΡΡΡΠ΅Π³ΠΎ ΡΠΈΠΏΠ° Π²ΠΎΠ»ΠΎΡΠΈΠ»ΡΠ½ΠΎΠ³ΠΎ ΡΡΠ°Π½Π° ΠΏΡΠΎΠΈΠ·Π²ΠΎΠ΄ΠΈΡ Π΄Π²ΠΈΠΆΠ΅Π½ΠΈΠ΅ ΠΏΠΎ Π½Π°ΠΏΡΠ°Π²Π»Π΅Π½ΠΈΡ Π²Π²Π΅ΡΡ
ΠΈ ΡΠ°ΠΊΠΈΠΌ ΠΎΠ±ΡΠ°Π·ΠΎΠΌ Β ΠΎΡΠ²ΠΎΠ±ΠΎΠΆΠ΄Π°Π΅Ρ Π½Π΅ΠΎΠ±Ρ
ΠΎΠ΄ΠΈΠΌΠΎΠ΅ ΠΊΠΎΠ»ΠΈΡΠ΅ΡΡΠ²ΠΎ ΠΌΠ°ΡΠ΅ΡΠΈΠ°Π»Π°, ΠΊΠΎΡΠΎΡΡΠΉ ΡΠΎΠ±ΡΡΠ²Π΅Π½Π½ΠΎ ΠΏΠΎΡΡΡΠΏΠ°Π΅Ρ Π½Π° Π²ΠΎΠ»ΠΎΡΠΈΠ»ΡΠ½ΠΎΠ΅ ΡΡΡΡΠΎΠΉΡΡΠ²ΠΎ ΠΈ ΡΠ°ΠΊΠΈΠΌ ΠΎΠ±ΡΠ°Π·ΠΎΠΌ ΠΎΠ±ΡΡΠ² Π½Π΅ ΠΈΠΌΠ΅Π΅Ρ ΠΌΠ΅ΡΡΠΎ.
ΠΠ° ΠΏΠΎΡΠ»Π΅Π΄Π½Π΅ΠΉ ΡΡΠ°Π΄ΠΈΠΈ Π²ΠΎΠ»ΠΎΡΠ΅Π½ΠΈΡ ΠΌΠ°ΡΠ΅ΡΠΈΠ°Π» ΠΏΡΠΎΡ
ΠΎΠ΄Ρ ΠΏΠΎΠ΄Π²Π΅ΡΠ³Π½ΡΡΡΠΉ Π²ΠΎΠ»ΠΎΡΠ΅Π½ΠΈΡ ΠΏΠΎΡΡΡΠΏΠ°Π΅Ρ Π½Π° Π½ΠΈΠΆΠ½ΠΈΠΉ Π²ΠΎΠ»ΠΎΡΠΈΠ»ΡΠ½ΡΠΉ Π±Π°ΡΠ°Π±Π°Π½ ΡΠ΄Π²ΠΎΠ΅Π½Π½ΠΎΠ³ΠΎ ΡΠΈΠΏΠ°, ΠΏΠΎΡΠ»Π΅ ΡΠ΅Π³ΠΎ ΠΏΠΎΡΡΠ΅Π΄ΡΡΠ²ΠΎΠΌ ΡΠΎΠ»ΠΈΠΊΠ° ΠΏΠ΅ΡΠ΅ΠΊΠΈΠ΄Π½ΠΎΠ³ΠΎ ΡΠΈΠΏΠ° ΠΎΠ½ Π²ΡΠ΄Π°Π΅ΡΡΡ Π½Π° Π±Π°ΡΠ°Π±Π°Π½ ΡΠ°ΡΠΏΠΎΠ»ΠΎΠΆΠ΅Π½Π½ΡΠΉ Π²Π²Π΅ΡΡ
Ρ, ΠΊΠΎΡΠΎΡΡΠΉ ΡΠ²Π»ΡΠ΅ΡΡΡ Π½Π°ΠΊΠΎΠΏΠΈΡΠ΅Π»ΡΠ½ΡΠΌ. ΠΠΌΠ΅Π½Π½ΠΎ ΠΏΠΎΡΡΠ΅Π΄ΡΡΠ²ΠΎΠΌ ΡΠΎΠ³ΠΎ, ΡΡΠΎ Π²Π΅ΡΡ
Π½ΠΈΠΉ Π±Π°ΡΠ°Π±Π°Π½ Π½Π°ΠΊΠ°ΠΏΠ»ΠΈΠ²Π°Π΅Ρ ΠΏΡΠΎΠ²ΠΎΠ»ΠΎΠΊΡ, Π΅Π΅ ΠΌΠΎΠΆΠ½ΠΎ Π±ΡΠ΄Π΅Ρ ΠΏΠΎΠ΄Π°ΡΡ Π² ΡΠ»ΡΡΠ°Π΅ ΡΠ΅Π·ΠΊΠΎΠ³ΠΎ ΡΠΎΡΠΌΠΎΠΆΠ΅Π½ΠΈΡ ΡΡΡΡΠΎΠΉΡΡΠ²Π°.
ΠΠΎΡΠ»Π΅ ΠΏΡΠΎΡΠ΅Π΄ΡΡΡ Π²ΠΎΠ»ΠΎΡΠ΅Π½ΠΈΡ, ΠΏΡΠΎΠ²ΠΎΠ»ΠΎΠΊΠ° Π²ΡΠ΄Π°Π΅ΡΡΡ Π½Π° ΡΠΏΠ΅ΡΠΈΠ°Π»ΡΠ½ΠΎΠ΅ ΡΠΈΡ
ΡΠΎΠ²Π°Π»ΡΠ½ΠΎΠ΅ ΡΡΡΡΠΎΠΉΡΡΠ²ΠΎ, ΠΊΠΎΡΠΎΡΠΎΠ΅ ΡΠ»ΡΠΆΠΈΡ Π΄Π»Ρ ΡΠΎΠ³ΠΎ, ΡΡΠΎΠ±Ρ ΠΏΡΠΈΠ΄Π°Π²Π°ΡΡ ΠΈΠ·Π΄Π΅Π»ΠΈΡ ΠΈΠ·Π³ΠΈΠ±Ρ ΠΈ Π·Π°Π΄Π°Π½Π½ΡΡ ΡΠΎΡΠΌΡ. Π Π°Π±ΠΎΡΠ° Π²ΠΎΠ»ΠΎΡΠΈΠ»ΡΠ½ΠΎΠ³ΠΎ ΡΡΠ°Π½Π° ΠΏΡΠΎΠΈΡΡ
ΠΎΠ΄ΠΈΡ Π½Π΅ΠΏΠΎΡΡΠ΅Π΄ΡΡΠ²Π΅Π½Π½ΠΎ ΠΎΡ ΡΠ»Π΅ΠΊΡΡΠΈΡΠ΅ΡΠΊΠΎΠ³ΠΎ Π΄Π²ΠΈΠ³Π°ΡΠ΅Π»Ρ.
promplace.ru
ΠΠΎΠ»ΠΎΡΠΈΠ»ΡΠ½ΡΠ΅ ΡΡΠ°Π½Ρ Π΄Π»Ρ ΠΏΡΠΎΠ²ΠΎΠ»ΠΎΠΊΠΈ
ΠΠΠ Β«ΠΠ°Π½ΡΠ°ΡΒ» ΠΏΡΠ΅Π΄Π»Π°Π³Π°Π΅Ρ ΠΎΠ±ΠΎΡΡΠ΄ΠΎΠ²Π°Π½ΠΈΠ΅ Π²ΠΎΠ»ΠΎΡΠ΅Π½ΠΈΡ — Π²ΠΎΠ»ΠΎΡΠΈΠ»ΡΠ½ΡΠ΅ ΡΡΠ°Π½Ρ Π΄Π»Ρ ΠΏΡΠΎΠ²ΠΎΠ»ΠΎΠΊΠΈ.
ΠΠ·Π³ΠΎΡΠΎΠ²Π»Π΅Π½ΠΈΠ΅ ΠΎΠ±ΠΎΡΡΠ΄ΠΎΠ²Π°Π½ΠΈΡ Π²ΠΎΠ»ΠΎΡΠ΅Π½ΠΈΡ ΠΈ ΠΊΠΎΠΌΠΏΠ»Π΅ΠΊΡΠ°ΡΠΈΡΒ ΠΎΡΠ½Π°ΡΡΠΊΠΎΠΉ ΠΏΡΠΎΠΈΠ·Π²ΠΎΠ΄ΠΈΡΡΡ ΠΈΠ½Π΄ΠΈΠ²ΠΈΠ΄ΡΠ°Π»ΡΠ½ΠΎ. ΠΠΎΠ·ΠΌΠΎΠΆΠ½ΠΎ ΠΈΠ·Π³ΠΎΡΠΎΠ²Π»Π΅Π½ΠΈΠ΅ ΠΊΠΎΠΌΠΏΠ»Π΅ΠΊΡΠΎΠ² ΠΎΠ±ΠΎΡΡΠ΄ΠΎΠ²Π°Π½ΠΈΡ Ρ Π½Π΅ΠΎΠ±Ρ ΠΎΠ΄ΠΈΠΌΠΎΠΉ ΠΠ°ΠΌ ΠΏΡΠΎΠΈΠ·Π²ΠΎΠ΄ΠΈΡΠ΅Π»ΡΠ½ΠΎΡΡΡΡ. Π’Π΅Ρ Π½ΠΈΡΠ΅ΡΠΊΠΈΠ΅ Ρ Π°ΡΠ°ΠΊΡΠ΅ΡΠΈΡΡΠΈΠΊΠΈ ΠΏΡΠ΅Π΄ΠΎΡΡΠ°Π²Π»ΡΡΡΡΡ ΠΏΠΎ Π·Π°ΠΏΡΠΎΡΡ.
Π€ΠΎΡΠΎΠ³Π°Π»Π΅ΡΠ΅Ρ ΠΎΠ±ΠΎΡΡΠ΄ΠΎΠ²Π°Π½ΠΈΡ Π΄Π»Ρ Π²ΠΎΠ»ΠΎΡΠ΅Π½ΠΈΡ ΠΏΡΠΎΠ²ΠΎΠ»ΠΎΠΊΠΈ — Π²ΠΎΠ»ΠΎΡΠΈΠ»ΡΠ½ΡΠ΅ ΡΡΠ°Π½Ρ
ΠΠ‘-1-50 (ΠΠΎΠ»ΠΎΡΠΈΠ»ΡΠ½ΡΠΉ ΡΡΠ°Π½)
ΠΠ°ΠΌΠΎΡΠΊΠ° (ΠΠΎΠ»ΠΎΡΠΈΠ»ΡΠ½ΡΠΉ ΡΡΠ°Π½)
ΠΠ‘-2-1000 (ΠΠΎΠ»ΠΎΡΠΈΠ»ΡΠ½ΡΠΉ ΡΡΠ°Π½)
ΠΠ‘-2-1000 (ΠΠΎΠ»ΠΎΡΠΈΠ»ΡΠ½ΡΠΉ ΡΡΠ°Π½)
ΠΠ‘-2-1000 (ΠΠΎΠ»ΠΎΡΠΈΠ»ΡΠ½ΡΠΉ ΡΡΠ°Π½)
ΠΠ‘ (ΠΠΎΠ»ΠΎΡΠΈΠ»ΡΠ½ΡΠΉ ΡΡΠ°Π½)
ΠΠΏΠΈΡΠ°Π½ΠΈΠ΅ Π²ΠΎΠ»ΠΎΡΠΈΠ»ΡΠ½ΡΡ ΡΡΠ°Π½ΠΎΠ² Π΄Π»Ρ Π²ΠΎΠ»ΠΎΡΠ΅Π½ΠΈΡ ΠΏΡΠΎΠ²ΠΎΠ»ΠΎΠΊΠΈ
ΠΡΠ΅Π΄Π½Π°Π·Π½Π°ΡΠ΅Π½ΠΈΠ΅ ΠΎΠ±ΠΎΡΡΠ΄ΠΎΠ²Π°Π½ΠΈΡ: Π΄Π»Ρ ΠΏΡΠΎΠΈΠ·Π²ΠΎΠ΄ΡΡΠ²Π° ΠΌΠ΅Π΄Π½ΠΎΠΉ, Π°Π»ΡΠΌΠΈΠ½ΠΈΠ΅Π²ΠΎΠΉ ΠΈΠ»ΠΈ ΡΡΠ°Π»ΡΠ½ΠΎΠΉ ΠΏΡΠΎΠ²ΠΎΠ»ΠΎΠΊΠΈ ΡΠ°Π·Π»ΠΈΡΠ½ΠΎΠ³ΠΎ Π΄ΠΈΠ°ΠΌΠ΅ΡΡΠ°. ΠΠΎΠ½ΡΡΡΡΠΊΡΠΈΡ ΠΎΠ±ΠΎΡΡΠ΄ΠΎΠ²Π°Π½ΠΈΡ Π΄Π»Ρ Π²ΠΎΠ»ΠΎΡΠ΅Π½ΠΈΡ ΠΏΡΠΎΠ²ΠΎΠ»ΠΎΠΊΠΈ ΡΠΊΠ»Π°Π΄ΡΠ²Π°Π΅ΡΡΡ ΠΈΠ· ΡΡΠ΄Π° ΠΌΠΎΠ΄ΡΠ»Π΅ΠΉ, ΠΊΠΎΡΠΎΡΡΠ΅ ΠΏΡΠΈ Π½Π΅ΠΎΠ±Ρ ΠΎΠ΄ΠΈΠΌΠΎΡΡΠΈ ΡΠΎΡΡΠ°Π²Π»ΡΡΡ ΠΎΠ±ΡΡΡ ΡΠΈΡΡΠ΅ΠΌΡ. ΠΡΠ΄Π΅Π»ΡΠ½ΠΎ ΠΊ Π²ΠΎΠ»ΠΎΡΠΈΠ»ΡΠ½ΡΠΌ ΡΡΠ°Π½Π°ΠΌ ΠΌΠΎΠΆΠ½ΠΎ Π·Π°ΠΊΠ°Π·ΡΠ²Π°ΡΡ ΠΈΠ·ΠΎΠ»ΠΈΡΠΎΠ²ΠΎΡΠ½ΡΠ΅ ΠΌΠ°ΡΠΈΠ½Ρ, Π½Π°ΠΌΠΎΡΠΎΡΠ½ΡΠ΅, ΠΏΠΎΠ΄Π°ΡΡΠΈΠ΅, ΠΏΡΠΈΠ΅ΠΌΠ½ΡΠ΅ ΠΈ Π΄ΡΡΠ³ΠΈΠ΅ ΡΡΡΡΠΎΠΉΡΡΠ²Π°.
Π Π°Π·Π½ΡΠ΅ ΠΌΠΎΠ΄Π΅Π»ΠΈ Π΄Π»Ρ ΠΌΠΎΠΊΡΠΎΠ³ΠΎ Π²ΠΎΠ»ΠΎΡΠ΅Π½ΠΈΡ Π°Π»ΡΠΌΠΈΠ½ΠΈΠ΅Π²ΠΎΠΉ ΠΏΡΠΎΠ²ΠΎΠ»ΠΎΠΊΠΈ Π½Π° ΠΆΠΈΠ΄ΠΊΠΎΠΉ ΡΠ΅Ρ Π½ΠΎΠ»ΠΎΠ³ΠΈΡΠ΅ΡΠΊΠΎΠΉ ΡΠΌΠ°Π·ΠΊΠ΅ ΡΠΎ ΡΠΊΠΎΠ»ΡΠΆΠ΅Π½ΠΈΠ΅ΠΌ ΠΎΡΠ»ΠΈΡΠ°ΡΡΡΡ Π΄ΡΡΠ³ ΠΎΡ Π΄ΡΡΠ³Π° ΠΏΡΠΎΠΈΠ·Π²ΠΎΠ΄ΠΈΡΠ΅Π»ΡΠ½ΠΎΡΡΡΡ ΠΈ Π½Π°Π·Π½Π°ΡΠ΅Π½ΠΈΠ΅ΠΌ. Π‘Π»Π΅Π΄ΡΠ΅Ρ ΠΎΡΠΌΠ΅ΡΠΈΡΡ, ΡΡΠΎ ΡΠ΅Π½Π° Π½Π° ΡΠ°ΠΊΠΈΠ΅ ΠΌΠ°ΡΠΈΠ½Ρ ΠΎΡΠ΅ΡΠ΅ΡΡΠ²Π΅Π½Π½ΠΎΠ³ΠΎ ΠΏΡΠΎΠΈΠ·Π²ΠΎΠ΄ΡΡΠ²Π° Π·Π½Π°ΡΠΈΡΠ΅Π»ΡΠ½ΠΎ Π½ΠΈΠΆΠ΅, ΡΠ΅ΠΌ Π½Π° Π·Π°ΡΡΠ±Π΅ΠΆΠ½ΡΠ΅ Π°Π½Π°Π»ΠΎΠ³ΠΈ.
ΠΡΠΈ Π²ΠΎΠ»ΠΎΡΠ΅Π½ΠΈΠΈ Π²ΡΡΠΎΠΊΠΎΠΊΠ°ΡΠ΅ΡΡΠ²Π΅Π½Π½ΠΎΠΉ ΠΌΠ΅Π΄Π½ΠΎΠΉ ΠΏΡΠΎΠ²ΠΎΠ»ΠΎΠΊΠΈ ΡΡΠ°Π½Ρ, ΡΠ°Π±ΠΎΡΠ°ΡΡΠΈΠ΅ ΠΏΠΎ ΠΊΠΎΠ½Π²Π΅Π½ΡΠΈΠΎΠ½Π°Π»ΡΠ½ΠΎΠΌΡ ΠΏΡΠΈΠ½ΡΠΈΠΏΡ, ΡΡΡΡΠΏΠ°ΡΡ ΡΠ΅ΠΌ, ΠΊΠΎΡΠΎΡΡΠ΅ ΠΎΡΠ½Π°ΡΠ΅Π½Ρ ΡΠ΅Ρ Π½ΠΎΠ»ΠΎΠ³ΠΈΠ΅ΠΉ ΠΊΠΎΠ½ΡΡΠΎΠ»Ρ ΡΠΊΠΎΠ»ΡΠΆΠ΅Π½ΠΈΡ. ΠΡΠΎΡ ΠΌΠ΅ΡΠΎΠ΄ ΠΏΠΎΠ·Π²ΠΎΠ»ΡΠ΅Ρ ΠΈΠ·Π±Π΅ΠΆΠ°ΡΡ ΠΈΠ·Π±ΡΡΠΎΡΠ½ΠΎΠ³ΠΎ ΠΏΡΠΎΡΠΊΠ°Π»ΡΠ·ΡΠ²Π°Π½ΠΈΡ ΠΈ ΠΏΠΎΠ²ΡΠ΅ΠΆΠ΄Π΅Π½ΠΈΡ ΠΏΡΠΎΠ²ΠΎΠ»ΠΎΠΊΠΈ Π² Ρ ΠΎΠ΄Π΅ ΠΏΡΠΎΠΈΠ·Π²ΠΎΠ΄ΡΡΠ²Π°, ΠΎΠ±Π΅ΡΠΏΠ΅ΡΠΈΠ²Π°Π΅Ρ ΠΎΠ΄ΠΈΠ½Π°ΠΊΠΎΠ²ΡΡ ΡΡΡΡΠΊΡΡΡΡ ΠΏΡΠΎΠ΄ΡΠΊΡΠ° ΠΈ Π² ΡΠ΅ΡΠ΄ΡΠ΅Π²ΠΈΠ½Π΅, ΠΈ ΡΠ½Π°ΡΡΠΆΠΈ, Π° ΡΠ°ΠΊΠΆΠ΅ ΡΠ²Π΅Π»ΠΈΡΠΈΠ²Π°Π΅Ρ ΡΡΠΎΠΊ ΠΈΠ·Π½ΠΎΡΠ° Π΄Π΅ΡΠ°Π»Π΅ΠΉ ΠΌΠ°ΡΠΈΠ½Ρ.
ΠΠ»Ρ ΠΏΠΎΠ»ΡΡΠ΅Π½ΠΈΡ Π³Π½ΡΡΠΎΠ³ΠΎ ΠΏΡΠΎΡΠΈΠ»Ρ ΠΈΡΠΏΠΎΠ»ΡΠ·ΡΡΡ ΠΏΡΡΠΌΠΎΡΠΎΡΠ½ΡΠΉ Π²ΠΎΠ»ΠΎΡΠΈΠ»ΡΠ½ΡΠΉ ΡΡΠ°Π½ ΠΈ ΠΏΡΠΎΡΠΈΠ»Π΅Π³ΠΈΠ±ΠΎΡΠ½ΡΠΉ ΡΡΠ°Π½, Π³Π΄Π΅ ΠΌΠ΅ΡΠ°Π»Π» ΠΎΠ±ΡΠ°Π±Π°ΡΡΠ²Π°Π΅ΡΡΡ Π΄Π°Π²Π»Π΅Π½ΠΈΠ΅ΠΌ.
Β
Β
www.kantar-ts.ru