Виды закалки металла
По способу охлаждения различают следующие виды закалки.
Закалка в одной среде
Такая закалка проще по выполнению, но не для любой стали и не для любых изделий ее можно применять.
Быстрое охлаждение в большом интервале температур изделий переменного сечения способствует возникновению температурной неравномерности и больших внутренних напряжений, называемых термическими.
Помимо термических напряжений, при превращении аустенита в мартенсит создаются дополнительно так называемые структурные напряжения, связанные с тем, что превращение аустенита в мартенсит происходит с увеличением объема.
Если деталь сложной формы или переменного сечения, то увеличение объема проходит неравномерно и вызывает возникновение внутренних напряжений.
Наличие больших напряжений может вызвать коробление изделия, поводку, а иногда и растрескивание, если величина внутренних напряжений превзойдет предел прочности.
Чем больше углерода, тем больше объемные изменения и структурные напряжения, тем больше опасность возникновения трещин.
Сталь с содержанием углерода более 0,8% закаливают в одной среде, если изделия простой формы (шарики, ролики и т.д.). В противном случае предпочитают закалку либо в двух средах, либо по способу ступенчатой закалки.
Закалка в двух средах
Этот способ нашел широкое применение для закалки инструмента из высокоуглеродистой стали.
Состоит он в следующем:
деталь вначале замачивают в воде и охлаждают до температур 500—550°,
затем быстро переносят в масло, где оставляют до полного охлаждения.
Ступенчатая закалка
При этом способе деталь быстро охлаждается погружением в соляную ванну с температурой 300—250°. Выдержка при этой температуре в течение 1,5—2 мин. должна обеспечить выравнивание температур по всему сечению изделия, устраняя тем самым термические внутренние напряжения. Последующее охлаждение производят на воздухе.
В качестве охлаждающей среды используют расплавленные соли, селитры, легкоплавкие металлы.
Ступенчатая закалка уменьшает внутренние напряжения, коробление и возможность растрескивания деталей.
Недостатки ступенчатой закалки
Недостаток этого вида закалки в том, что охлаждение в горячих средах не может обеспечить большую скорость охлаждения в интервале 400—600°.
В связи с этим ступенчатую закалку для углеродистой стали можно применять для изделий небольшого сечения (диаметр до 10 мм, например, сверла).
Для легированных сталей, имеющих небольшие значения критической скорости закалки, ступенчатая закалка применима к изделиям большего сечения.
Закалка с подстуживанием
При таком способе деталь вынимают из печи и перед погружением в охлаждающую жидкость некоторое время выдерживают на воздухе. Время выдержки на воздухе должно быть таким, чтобы не произошел
распад на структуру перлита или сорбита. Это время определяется практикой закалки.
Подстуживание уменьшает внутренние напряжения и коробление и применяется для тонких и длинных деталей.
Поверхностная закалка стали
От некоторых деталей в эксплуатации требуется высокая поверхностная твердость при сохранении достаточно вязкой сердцевины, например зуб шестерни, шейка коленчатого вала и др.
В этом случае сталь сознательно закаливают на небольшую глубину. Существует несколько методов поверхностной закалки стали.
Поверхностная закалка при нагреве ацетилено-кислородным пламенем
Нагрев изделия производится ацетилено-кислородным пламенем. Пламенная горелка (рис. 67), движущаяся вдоль изделия с определенной скоростью, нагревает его поверхность.
Вслед за горелкой с той же скоростью движется трубка, подающая воду, с помощью которой производится охлаждение изделия.
Глубина прогрева и температура нагрева регулируются скоростью перемещения горелки и расстоянием горелки от изделия.
Поверхностная закалка токами высокой частоты
Нагрев изделий токами высокой частоты вызывает разогрев поверхностного слоя изделия.
Это объясняется тем, что токи высокой частоты распространяются с неравномерной плотностью по сечению. Чем больше частота тока, тем на меньшую глубину изделия токи проникают.
Благодаря этому возникает большая плотность тока у поверхности изделия, вызывающая весьма быстрый разогрев поверхностных слоев металла.
Этот метод имеет ряд преимуществ: высокую производительность, достаточную легкость регулирования глубины закаленного слоя, получение большей твердости, чем при обычных методах закалки, отсутствие окалины и коробления.
Применяемый для этой цели электрический ток получают от специальных генераторов, дающих переменный ток с частотой до 10 млн. гц (т.е. перемен направления тока в секунду). Ток городской сети имеет частоту 50 гц.
Нагрев изделия осуществляется индуктором, по которому проходят токи высокой частоты и большой силы.
Индуктор наводит (индуктирует) токи в изделии, помещенном внутри него (рис. 68).
Индуктор изготовляют из полых медных трубок, внутри которых циркулирует охлаждающая вода, поэтому он сам не разогревается за тот короткий промежуток времени, за который деталь успевает нагреться до необходимой температуры.
Форма индуктора должна точно повторить форму изделия, только тогда изделие закалится да одну и ту же глубину по всему сечению. Затруднения бывают при сложной форме детали, что ограничивает применение этого метода.
Охлаждение нагретой детали осуществляется чаще всего либо дополнительным дождевым устройством, либо водой, циркулирующей внутри индуктора.
В связи с тем что новый тип детали требует изготовления нового индуктора, этот метод целесообразно применять при наличии однотипных деталей в массовом или крупносерийном производстве.
§
Закалка металла — виды, способы и методы
Содержание
- 1 Скорость разогрева
- 2 Среды охлаждения
- 3 Типы закаливания
- 4 Дефекты, которые возникают при закаливании
Закалка металла представляет собой термообработку, при которой заготовки из стали разогревают до температуры, превышающую критическую, выдерживают при нем определенное время, резко остужают в воде либо масле.
Главное предназначение закалки стали – получить твердый, прочный, износостойкий металл. Качество закалки зависит от температуры и быстроты разогрева/охлаждения, времени выдержки.
Температуру разогрева под закаливание для большей части металлов устанавливают по расположению критических точек. Закалку металлов типа нержавейки осуществляют при более высоком температурном уровне, чем закаливание обычной стали. К примеру, нержавейка 4Х13 закаливается при 1100 градусах. Сталь Р18 закаляется при 1250 градусах. Это необходимо, чтобы обеспечить полное растворение лишних карбидных элементов.
Содержание
- Скорость разогрева
- Среды охлаждения
- Типы закаливания
- Дефекты, которые возникают при закаливании
Скорость разогрева
Быстрота разогрева зависима от формы заготовок, их прокаливаемости, вида нагревающих печей и среды нагревания. К примеру, шаровая деталь разогревается в 3 раза, а цилиндровая – в 2 раза медленнее, чем пластина. Чем выше скорость разогрева, тем производительнее нагревающая печь.
Если заготовки расположены рядом друг с другом плотным образом, то на их нагрев придется потратить много времени. Для определения времени разогрева изделий специалисты обыкновенно используют технологические карты. В них включен список всех процедур обрабатывания заготовок, указана вся нужная информация (температурный уровень, продолжительность прогрева, метод охлаждения, используемые устройства).
Среднее время разогрева заготовок таково (указано время для нагрева одного миллиметра):
- электропечь (800 градусов) – 50 секунд;
- пламенная печь (1300 градусов) – 18 секунд;
- соляная ванна (1300 градусов) – 9 секунд.
Среды охлаждения
Для того чтобы охлаждать изделия из стали, обычно используют разные среды закаливания: воду, соляные растворы, плавленую соль, минеральные масла и так далее. Среды закалки значительно различаются по физическим характеристикам.
Самой лучшей средой для закаливания металла является та, в которой охлаждение проходит быстро при 500-650 градусах и медленно – при 200-300 градусах. Универсальной среды в данный момент не существует.
Типы закаливания
Разные виды закалки отличаются по методу охлаждения. Чем более сложная форма у заготовки, тем ответственнее нужно отнестись к подбору охлаждающей среды. Изделия должны становиться твердыми, не иметь трещинок.
Полная закалка делится на такие разновидности:
1. В одном охладителе. Самый легкий и популярный метод. Заготовку, разогретую до температуры закаливания, опускают в охлаждающую среду. Она располагается там, пока полностью не остынет. Данный метод применяют при закаливании простых изделий, которые изготовлены из углеродистой/легированной стали. Заготовки из углеродистой стали остужаются в воде (кроме изделий радиусом менее 2 миллиметров), из легированной – в масляной жидкости. Этот метод можно использовать при осуществлении механизированной закалки металлов.
2. В 2 средах (прерывистая). Метод, при котором изделие остужают в воде, а потом опускают в другую охлаждающую среду для закалки (масляная жидкость). Способ используется при обработке инструмента, произведенного из металла с большим содержанием углерода.
Минус подобного метода состоит в том, что непросто определить продолжительность нахождения изделия в воде. Если передержать деталь в воде, она покоробится, на ней появятся трещинки. Специалист, использующий подобные способы закалки, должен быть опытным и высококвалифицированным.
3. Струйчатая. Заготовки, для которых достигнута температура закалки, остужаются водной струей. Подобный используется при обработке внутренних участков, штампов высадки, матриц, иного штамповочного инструмента, у которого рабочая часть должна располагать мартенситной структурой.
Если использовать такие способы закалки, паровая рубашка не формируется. Детали прокаливаются глубже, чем при обыкновенном закаливании в воде. Быстрота остывания зависит от температурного уровня, водного напора, радиуса и числа отверстий в брызгале, угла, который образует струя с заготовкой.
4. С самоотпуском. Метод заключается в том, что изделия держат в охладителе не до полного остывания. В некоторый момент охлаждение останавливают, чтобы обеспечить сохранение в середине заготовки тепла, нужного для самоотпуска. Данный момент определяется опытным путем. Качество термообработки прямо зависимо от квалификации рабочего.
Закалка и отпуск контролируются по цветам побежалости, которые возникают на светлой части заготовки. Возникновение цветов побежалости при 200-300 градусах обусловлено появлением на изделии оксидной пленки небольшой толщины.
Такие способы закалки используют для обработки ударного инструментария (зубила, бородки, керны). У данных приспособлений твердость должна снижаться равномерным и постепенным образом.
5. Ступенчатая. Разогретые заготовки остужают в медленно охлаждающейся среде (плавленая соль, горячая масляная жидкость). За время небольшой выдержки происходит выравнивание температурного уровня. После этого выполняется финальное охлаждение.
Ступенчатая полная закалка позволяет уменьшить напряжения внутри детали. Ее часто используют в промышленности, в особенности при производстве инструмента. Она дает возможность осуществлять правку и рихтовку раскаленных изделий.
6. Изотермическая. Такая полная закалка заключается в том, что изделие нагревается до нужного температурного уровня и охлаждается в изотермической среде до 230-340 градусов. Выдержки заготовок в среде закаливания должно быть достаточно, чтобы аустенит полностью превратился в троостит. После превращения закаленное изделие остужается на воздухе.
Такой вид закаливания применяют тогда, когда цель закалки – сделать изделие максимально прочным, пластичным и вязким.
Дефекты, которые возникают при закаливании
Когда осуществляется закалка и отпуск изделия, внутри его возникают напряжения. Образуются трещинки, деталь деформируется, коробится, обезуглероживается, окисляется, появляются мягкие пятна.
- Трещинки. Этот брак нельзя исправить, он образуется при термообработке. В больших изделиях, к примеру, в матрицах и штампах для ковки, трещинки могут возникать даже при закаливании в масляной жидкости. Ввиду этого подобные изделия нужно остужать до ста пятидесяти градусов с резким отпуском.
Трещинки возникают при ошибках разогрева, а также тогда, когда скорость охлаждения при закалке слишком высокая. Обычно они появляются в уголках заготовок, выглядят дугообразно либо извилисто. - Деформирование, коробление. Возникают из-за того, что преобразования структуры, объема проходят неравномерно, внутри детали появляются напряжения при остывании. Ввиду этого при опускании изделия в среду закалки нужно принимать во внимание его форму, величину. К примеру, заготовки, которые имеют толстые/тонкие элементы, опускают в среду закаливания сначала той частью, которая толще.
В крупносерийном производстве для каждого изделия производятся особые приспособления. Цена их разработки окупается. Такие изделия, как колеса с зубцами, диски, плиты проходят закаливание в прессовочных/штамповочных устройствах. Это позволяет избежать коробления.
- Обезуглероживание. Этот процесс, по определению, заключается в том, что из металла уходит большая часть углерода. Деталь может обезуглеродиться при нагревании в электропечах, жидкостях (соляных ваннах). Это значительный дефект, сильно снижающий прочность изделия. Обнаружить его сложно. Обычно для этого применяется микрошлиф.
- Мягкие пятна. Представляют собой области заготовки, имеющие сниженную твердость. Дефект может быть обусловлен наличием окалины, грязи, обезуглероживанием, паровой рубашкой. От него избавляются струйчатым закаливанием в соленой воде.
- Недостаточная твердость. Обычно дефект проявляется при обработке инструмента, может быть обусловлен медленным охлаждением в закаливающей среде, малой температурой. Для его исправления изделие отпускают при температуре шестьсот градусов, после чего нормально закаливают.
- Перегревание. Структура перегретой детали крупнозерниста, изломана. Из-за этого механические характеристики металла невысоки. Для того чтобы измельчить зерна и подготовить заготовку к новому закаливанию, металл отжигают.
- Недогрев. При данном дефекте структура металла заключает в себе мартенситные и ферритные зерна. Они располагают малой твердостью. Дефект устраняется отжигом металла с повторным закаливанием.
Что такое закаливаемость? Это свойство металла, характеризующее его способность к закалке. Для каждого вида металла нужно подбирать оптимальный закалочный метод. При его выборе необходимо принимать во внимание также тип изделия. Ни в коем случае нельзя допускать превышения критической скорости закалки. Это может привести к возникновению разнообразных дефектов, которые придется устранять. Также нужно охлаждать деталь достаточное количество времени.
Если вы интересуетесь покупкой металлического сейфа, то в компании ООО «НПО Промет» вы сможете найти сейфы, металлическую и производственную мебель, автоматические системы хранения и электронные замки любого класса взломостойкости. Чтобы ознакомиться со всем ассортиментом достаточно перейти на сайт. Гармоничное сочетание многолетнего опыта и инновационных технологий позволяют создавать надежную и безопасную продукцию.
Типы процессов закалки металлов
Обновлено 26 ноября 2018 г.
Автор: Rachelle Dragani
Металл известен тем, что является прочным веществом, способным выдержать большой износ, но, возможно, он изначально не был таким. Многие типы металлов прошли процесс закалки, чтобы сделать их более подходящими для работы, которую они должны выполнять. Существуют различные типы закалки, которые посредством сложных процессов нагрева и охлаждения помогают сделать металлы прочными, долговечными и удобными в работе.
TL;DR (слишком длинное; не читал)
Каждый процесс закалки металла включает три основных этапа: нагрев, замачивание и охлаждение металла. Некоторые распространенные типы упрочнения включают деформационное упрочнение, упрочнение на твердый раствор, дисперсионное упрочнение, а также закалку и отпуск.
Разогреть
В то время как инженеры и рабочие-металлисты придумали несколько различных типов закалки в зависимости от типа металла и результатов, которые они хотят получить, каждый тип включает в себя три основных этапа: нагрев металла, его замачивание. а затем его охлаждение.
На первом этапе термообработки рабочие по металлу нагревают материал, часто при очень высоких температурах. Иногда они делают это, чтобы изменить физический или химический состав металла, часто для того, чтобы с ним было легче манипулировать и работать с ним. Например, когда некоторые металлы подвергаются воздействию температур выше 1000 градусов по Фаренгейту, их внутренняя структура изменяется. Это может быть временным, чтобы рабочие по металлу могли изменить его форму, а затем вернуть его в исходное состояние. В других металлах изменение является постоянным. Иногда эта внутренняя структура становится прочнее и жестче, что делает ее лучшим материалом для использования в чем-то, что требует прочности, например, при строительстве небоскреба. В других случаях термическая обработка используется для повышения пластичности металла. Металлы с высоким уровнем пластичности способны выдерживать силы, тянущие их с любого конца. Это важное качество для таких металлов, как медь, которую нужно вытягивать в тонкие полоски медной проволоки, или золото, которое часто вытягивают в тонкие нити для изготовления украшений.
Замачивание и охлаждение
Второй частью процесса является замачивание металла. Хотя слово «замачивание» может натолкнуть вас на мысль о том, как вы отмачиваете собаку в ванне после пробежки по грязному заднему двору, замачивание в процессе закалки металла немного отличается. Металл не замачивают в ванне с жидким веществом. Вместо этого замачивание в данном случае относится к обеспечению того, чтобы после того, как металл достиг желаемой температуры в процессе нагрева, он «пропитывался» этим теплом. Сроки различны для всех типов закалки, но в целом рабочий по металлу должен убедиться, что все куски металла достигают нужной температуры в течение определенного периода времени.
Третий и последний этап процесса закалки — охлаждение. После того, как металл был нагрет и пропитан этим теплом, его необходимо охладить. Иногда после этого процесса металлы возвращаются к своей первоначальной химической или физической структуре. В других случаях рабочие по металлу следят за тем, чтобы металлы изменялись навсегда.
Типы закалки металла
Существует несколько различных типов процессов закалки металла, в зависимости от типа металла, с которого начинают работать рабочие, и материала, в который они хотят его превратить.
Одним из наиболее распространенных является мартенситное превращение, также известное как закалка и отпуск. Это сложный процесс закалки стали, и рабочие по металлу должны тщательно выполнять каждый шаг. Во-первых, они должны нагреть сталь до экстремальной температуры. Затем кристаллическая структура внутри стали изменяется, позволяя растворить больше углерода. В этот момент металл должен быть закален или охлажден достаточно быстро, чтобы у углерода не было времени на образование других нежелательных материалов в металле. Быстрое охлаждение заставляет его оставаться в закаленном состоянии, что делает его более прочным материалом, лучше приспособленным к износу. Различные состояния, которые он проходит во время процесса, называются аустенитным и мартенситным, а ресурс по аустенитному и мартенситному отпуску может дать вам больше информации об этом процессе.
Другие типы процессов закалки включают поверхностную закалку, отжиг и дисперсионную закалку. Каждый работает по-разному, чтобы сделать металлы более прочными, пластичными, жесткими или ковкими, чтобы помочь инженерам использовать их различными способами. В окружающем вас мире есть все виды металлов, и, скорее всего, слесарь использовал процесс закалки, чтобы привести их в то состояние, в котором они находятся сегодня.
Упрочнение поверхности стали (цементация) — процесс и методы
Закаленная стальИзображение предоставлено Shutterstock/PHOTOCREO Михал Беднарек
Поверхностное упрочнение (цементация)
Во многих областях применения требуется высокая твердость или прочность, в первую очередь на поверхности, а сложные эксплуатационные нагрузки часто требуют не только твердой, износостойкой поверхности, но также прочности и ударной вязкости сердцевины, чтобы противостоять ударным нагрузкам.
Для достижения этих различных свойств используются два основных процесса: 1) Химический состав поверхности изменяется до или после закалки и отпуска; используемые процессы включают науглероживание, азотирование, цианирование и карбонитрирование; и 2) в процессе нагрева и закалки упрочняется только поверхностный слой; наиболее распространенными процессами, используемыми для поверхностной закалки, являются закалка пламенем и индукционная закалка.
Науглероживание: углерод рассеивается на поверхности детали на контролируемую глубину путем нагрева детали в углеродсодержащей среде. Результирующая глубина науглероживания, обычно называемая глубиной слоя, зависит от углеродного потенциала используемой среды, а также от времени и температуры обработки науглероживанием. Наиболее подходящими для науглероживания для повышения ударной вязкости стали стали с достаточно низким содержанием углерода, обычно ниже 0,3%. Температуры науглероживания колеблются от 1550 до 1750°F (от 843 до 9°С).
Наиболее часто используются три вида науглероживания: —
- Жидкая цементация включает нагрев стали в расплавленном цианиде бария или цианиде натрия. Корпус поглощает некоторое количество азота в дополнение к углероду, что повышает твердость поверхности.
- Газовая науглероживание включает нагрев стали в газе с контролируемым содержанием углерода. При использовании уровень углерода в корпусе можно точно контролировать.
- Науглероживание упаковки , которое включает запечатывание стали и твердого углеродсодержащего материала в газонепроницаемом контейнере с последующим нагревом этой комбинации.
При использовании любого из этих методов деталь может быть либо закалена после цикла науглероживания без повторного нагрева, либо подвергнута воздушному охлаждению с последующим повторным нагревом до температуры аустенизации перед закалкой. Глубина гильзы может варьироваться в зависимости от условий нагрузки при эксплуатации. Однако рабочие характеристики часто требуют, чтобы только отдельные области детали должны были быть закалены. Покрытие областей, не подлежащих покрытию, медным покрытием или слоем коммерческой пасты позволяет углероду проникать только в открытые области. Другой метод включает науглероживание всей детали, затем удаление корпуса в выбранных областях путем механической обработки перед закалкой.
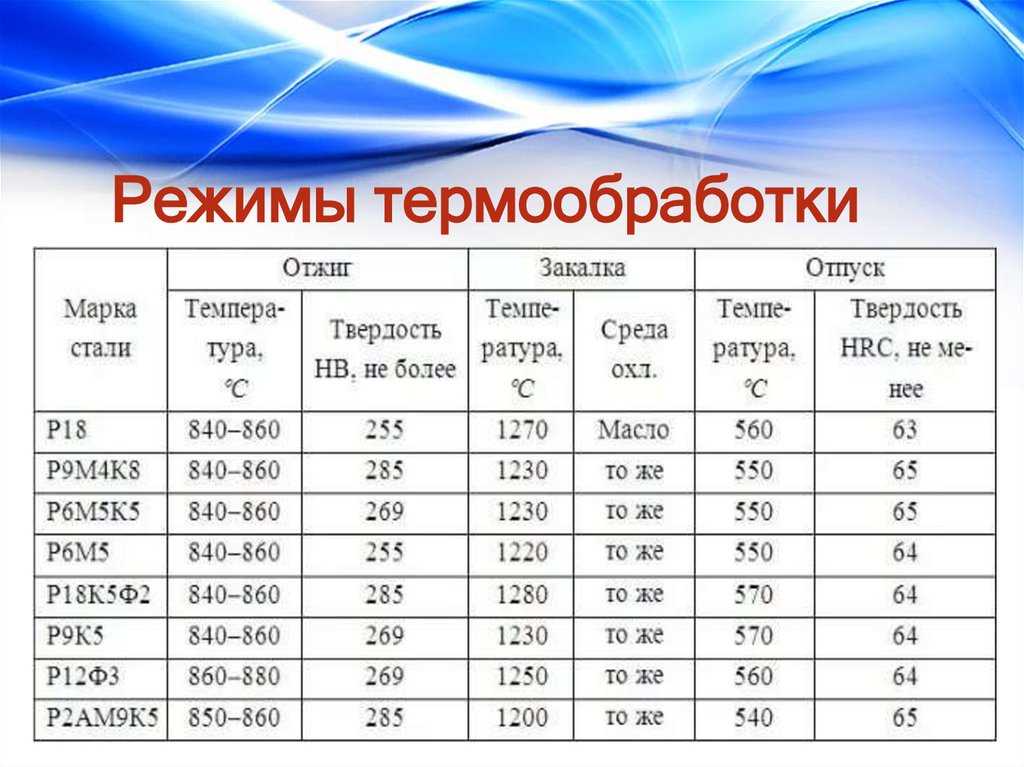
Этот процесс включает нагрев детали в ванне с цианистым натрием до температуры немного выше диапазона превращения с последующей закалкой для получения тонкого корпуса высокой твердости.
Этот процесс аналогичен цианированию, за исключением того, что поглощение углерода и азота осуществляется путем нагревания детали в газовой атмосфере, содержащей углеводороды и аммиак. Для деталей, подлежащих закалке, используются температуры от 1425 до 1625°F (от 774 до 885°C), а более низкие температуры — от 1200 до 1450°F (649°C).до 788°C), может использоваться там, где не требуется жидкая закалка.
Этот процесс включает в себя быстрый нагрев прямым высокотемпературным газовым пламенем, так что поверхностный слой детали нагревается выше диапазона превращения с последующим охлаждением со скоростью, вызывающей желаемое упрочнение. Стали для закалки пламенем обычно содержат 0,30-0,60% углерода, а прокаливаемость соответствует желаемой глубине слоя и используемой закалке. Закалку обычно распыляют на поверхность на небольшом расстоянии позади нагревательного пламени. Требуется немедленная закалка, которую можно провести в обычной печи или в процессе закалки пламенем, в зависимости от размера детали и стоимости.
Этот процесс во многом похож на закалку пламенем, за исключением того, что нагрев вызывается высокочастотным электрическим током, проходящим через катушку или индуктор, окружающий деталь. Глубина нагрева зависит от частоты, скорости теплопроводности с поверхности и продолжительности цикла нагрева. Тушение обычно осуществляется водяной струей, подаваемой в нужное время через форсунки внутри или рядом с блоком индуктора или катушкой. Однако в некоторых случаях детали закаливают в масле, погружая их в ванну с маслом после того, как они достигнут температуры закалки.
Резюме
В этой статье описаны основные методы упрочнения поверхности стали. Узнайте больше о свойствах материалов из Справочника по машинному оборудованию, 30-е издание, которое опубликовано и доступно в Industrial Press на Amazon.