Способы и виды термической обработки стали
Термическая обработка стали проводится с целью придания материала определенного набора свойств путем изменения его внутренней структуры на молекулярном уровне. Метод подразумевает нагрев или охлаждение металла до определенного температурного уровня с его последующим возвращением к нормальному состоянию. Иногда применяется многофазная термообработка, которая позволяет производить наиболее закаленные марки сталей.
Процедура протекает в специальных печах или холодильных установках, которые дают возможность четко контролировать температуру на каждом этапе технологического процесса. Это очень важное условия успешной закалки, так как несоблюдение технологии может наоборот придать металлу негативные свойства. Режимы термообработки стали зависят от структурного состава материала. Все они были установлены опытным путем в результате многократных испытаний, поэтому современные способы закалки при соблюдении всех условий позволяют получать материалы высокого качества с большим запасом прочности.
Выделяют следующие виды термообработки сталей: закалка, отпуск, отжиг, нормализация, воздействие холодом и химико-термическая обработка.
Закалка стали
Закалка подразумевает прогрев металла до установленной температуры и поддержание достигнутого уровня в течение определенного периода времени. Временной интервал определяется скоростью превращения внутренней структуры сплава устойчивое вещество. После этого сталь быстро охлаждают в воде или масле, так как постепенное остывание может привести к нарушению достигнутой структуры кристаллической решетки.
Закалка придает материалу твердости, но снижает его ударную вязкость, что делает сталь более хрупкой. Такой обработке подвергают детали, которые предназначены для эксплуатации под воздействием статической нагрузки без влияния динамических колебаний. Отпуску подвергаются некоторые детали после закалки.
После нагрева металл вытаскивают из печи и дают остыть естественным путем без применения охладителей. Такая процедура несколько снижает твердость, но при этом повышает ударную вязкость и ковкость. Так что после закалки с последующим отпуском сталь будет тверже и пластичнее, чем необработанный сплав. Отжиг проводится по схеме нагрева металла с последующим медленным остыванием прямо в печи без использования специальных средств. Это убирает неоднородность распределения элементов в сплаве и позволяет создать устойчивое соединение железа с углеродом на межмолекулярном уровне.
Отжиг
После отжига значительно уменьшается твердость стали, но возрастает ее пластичность и ковкость. Такой обработке подвергается материал, предназначенный для последующей штамповки или раскатки. Нормализация технологически повторяет процесс отжига, только после нагрева сплав остывает не непосредственно в печи, а на открытом воздухе. Это позволяет добиться хороших показателей ковкости и пластичности без существенного снижения твердости.
Воздействие холодом
Воздействие холодом необходимо для завершения превращения аустенита в мартенсит. Он придает металлу дополнительную упругость и препятствует образованию рваных трещин при воздействии избыточного давления на деталь. Такой материал хорошо подходит для эксплуатации под влиянием высоких динамических нагрузок. Необходимой твердости ему обычно добавляют с помощью соответствующих присадок.
Химико-термическая обработка
Химико-термическая обработка подразумевает насыщение верхних слоев стали каким-либо элементом под воздействием высокой температуры. Различают несколько видов данной процедуры. Цементация означает пропуск через сталь углерода при температуре 950 градусов по Цельсию. Это придает поверхности дополнительной твердости, не затрагивая при этом внутренние слои материала.
Азотирование позволяет насытить верхний слой стали азотом для повышения его коррозийной стойкости, прочности и предела устойчивости. Проводится процедура путем нагревания сплава до 700 градусов в аммиачной среде. Хромирование позволит придать поверхности материала повышенную устойчивость к пресной и соленой воде и некоторым видам кислотных и оксидных сред. Это позволяет подготовить сталь к эксплуатации в неблагоприятных условиях. Цианирование совмещает в себе одновременное насыщение верхних слоев стали углеродом и азотом. Это позволяет одним махом увеличить твердость материала и защитить его от воздействия коррозии.
Термообработка разных видов стали
Термообработка легированной стали должна производиться с медленным прогревом до необходимой температуры, а затем с медленным остыванием заготовки. В результате добавления легирующих присадок стали данной марки имеют низкую теплопроводность, поэтому резкое изменение температуры может привести к короблению или образованию трещин. Также очень важно, чтобы нагревание происходило равномерно по всей площади детали.
Термообработка нержавеющей стали тоже содержит свои нюансы.После отжига ее необходимо оставить в печи до полного остывания, а затем провести процедуру отпуска, чтобы получить материал оптимального качества. Резкое изменение температур также нежелательно, так как может негативно отразиться на эксплуатационных свойствах.
Термообработка аустенитных сталей проводится в печах при равномерном нагреве заготовки до температуры 1000-1150 градусов по Цельсию. После этого следует быстрое охлаждение в жидкости, что позволяет получить материал с устойчивой ферритной внутренней структурой. Эти стали применяются для изготовления конструкционных материалов, поэтому должны получить повышенную прочность при закалке.
Термообработка быстрорежущей стали является трудоемким процессом. Она относится к классу высоколегированных сплавов, поэтому не переносит резких перепадов температур. Закалка данного материала производится на высокоточном оборудовании, позволяющем четко регулировать каждую фазу технологического процесса. Эта марка используется для производства инструментов для резки, которые даже при нагреве до 600 градусов не теряют своей первоначальной твердости.
Термообработка углеродистой стали сводится к получению устойчивой связи между атомами железа и углерода в кристаллической решетке. Метод зависит от необходимости получения конкретного вещества по завершению процесса.
принцип и назначение отжига стали
Чтобы придать металлам необходимые характеристики, прибегают к термической обработке. Завод металлоконструкций ЧЗМК выполняет закалку и отжиг стали и цветных сплавов.
Назначение термической обработки
Поскольку металлические конструкции и изделия подвергают разнообразным нагрузкам и испытаниям, они должны быть прочными, износостойкими, сопротивляться коррозии и другим разрушительным факторам.
В процессе происходят важнейшие изменения в структуре металла. В зависимости от выбранного вида термообработки, будет отличаться и результат. В металлообрабатывающей промышленности с помощью таких технологий создают сплавы с уникальными характеристиками. Если назначение термической обработки – повысить податливость, пластичность, после нее металл будет легче резать, придавать ему желаемую форму.
Но некоторые операции увеличивают такие характеристики, как твердость, циклическая прочность. Кроме того, при помощи термообработки удается устранить дефекты, которые вызваны ошибками или просчетами на предыдущих производственных этапах.
Преимущества термообработки металлов
При грамотно выбранном режиме и продолжительности процедур удается добиться заданных характеристик. Термическую обработку ценят за следующие достоинства:
- увеличивается стойкость металла к износу;
- за счет улучшения технических показателей возрастает срок службы металлоконструкций и изделий;
- уменьшается количество деталей, непригодных к использованию;
- благодаря повышению прочности, долговечности и износостойкости сокращаются финансовые издержки.
Чтобы стали обрели желаемые свойства, необходимо специальное оборудование. Это высокотехнологичные печи, в которых за счет высоких температур добиваются сильного нагрева, вызывающего изменения в структуре металла. Однако для качественной термообработки важна регулировка мощности, других настроек. Поскольку каждому металлу требуется свой температурный режим. Также его подбирают под цели термической обработки – в зависимости от того, какие именно свойства нужно придать стали или цветному сплаву.
Принцип термической обработки
Хотя процессы отличаются температурным режимом, длительностью и другими тонкостями, в целом процедура протекает по одному и тому же принципу. Термическую обработку стали выполняют в следующей последовательности:
- Нагрев.
- Выдержка.
- Охлаждение.
Для первого этапа крайне важно точно подобрать температуру и выполнить нагрев до указанного предела. Температурный режим предопределяется тем, предстоит ли работать со сталью или с другими сплавами, какие именно свойства следует придать металлу.
Также имеет значение продолжительность выдержки. Сплавы претерпевают желаемые изменения в структуре, только когда температура держится в конкретном диапазоне в течение определенного времени.
Скорость охлаждения – не менее значимая константа. В некоторых случаях в работе со сталью при термообработке ее оставляют в печи, где она очень долго остывает вместе с оборудованием. Но иногда требуется более быстрое понижение температуры металла, чтобы в структуре не произошли нежелательные изменения. И тогда после термической обработки заготовку выставляют остывать на воздухе.
Виды термообработки стали
Имея общий алгоритм действий, предприятия выполняют термическую обработку разными способами. Располагая всего тремя инструментами – нагрев, выдержка и охлаждение, удается решать широчайший круг задач. Если одни виды термической обработки стали предназначены для увеличения ее прочности, то другие повышают пластичность и текучесть. Поэтому важен профессионализм, четкое понимание процессов, протекающих в структуре.
Отжиг
К одним из самых востребованных видов термообработки относят отжиг, который выполняют для понижения твердости и снятия внутреннего напряжения. Зачастую он необходим после горячей обработки стали давлением. Например, такой термической обработке подвергают заготовки после ковки, прокатки и штамповки. Иногда к отжигу прибегают вслед за сваркой. Он же используется, если на предыдущем этапе работы со сталью допущены ошибки и возникли дефекты.
Суть такой термической обработки заключается в нагреве выше критической точки, последующей выдержке и охлаждении. Благодаря этому структура обретает равновесность, впоследствии со сталью проще работать способом резания.
Закалка
Эту термическую обработку выполняют, чтобы увеличить твердость сплава. Если говорить о процессах, которые происходят со сталью, то в ее структуре вместо перлита образовывается мартенсит, проходя через стадию аустенита.
Воздействуя при помощи высоких температур на металл, сначала добиваются аустенитного превращения. Чтобы избежать промежуточную структуру, заготовку помещают в масло. Там происходит быстрое охлаждение стали до мартенситных превращений. Однако далее снижение температур должно замедлиться. Иначе распад аустенита будет неполным и не удастся при помощи термообработки придать стали желаемую твердость.
Отпуск
Такую термическую обработку осуществляют для повышения пластичности одновременно со снижением хрупкости. При этом удается сохранить высокую прочность стали. Отпуск делят на три вида, в зависимости от уровня нагрева металла. Он бывает:
- низкотемпературным;
- среднетемпературным;
- высокотемпературным.
В первом случае термическую обработку выполняют, доведя сплав до 250 градусов. Преимущественно данный способ применим для закаленной стали. Также низкотемпературному отпуску подвергают инструменты из углеродистых и низколегированных металлов.
Второй вид предполагает термическую обработку стали с нагревом до 350-500 градусов. Он обеспечивает повышение упругости и выносливости. Улучшается еще одно ценное свойство – релаксационная стойкость.
Среднетемпературный отпуск протекает с охлаждением в два этапа – сначала в воде, а затем на воздухе. Благодаря этому стали придают сжимающие остаточные напряжения, что улучшает выносливость.
Высокотемпературный отпуск – это нагрев до 500-680 градусов. Благодаря данной термической обработке удается совместить высокую прочность с пластичностью и вязкостью. Подобные свойства особенно ценятся при производстве деталей, на которые будут выпадать повышенные ударные нагрузки. Например, это валы и зубчатые колеса.
Эти виды термообработки приводят к распаду мартенсита. Также в процессе происходит полигонизация и рекристаллизация.
Химико-термическая обработка
Суть подобных мероприятий заключается в нагреве и выдержке в химически активных средах. Посредством такой термообработки удается поменять химический состав, а не только структуру и свойства стали.
Процедура показана по отношению к заготовкам, в которых должна сохраняться твердость поверхности и вязкость сердцевины. Также удается повысить коррозионную стойкость и сопротивление усталости.
Химико-термическую обработку осуществляют, применяя жидкие, твердые и газообразные среды. В зависимости от того, какими веществами насыщается металл, выделяют следующие виды процедур:
- цементация;
- азотирование;
-
цианирование и пр.
Если термообработку совмещают с нанесением углерода, как в первом случае, сталям придают высокую прочность и сопротивление истиранию. Процесс происходит с погружением в порошкообразную смесь, в соляные ванны или в печи с цементирующими газами.
Суть азотирования заключается в насыщении стали азотом. Термообработку выполняют в печи, меняя длительность процесса, в зависимости от нужной глубины проникновения химического вещества.
Цианирование предполагает насыщение углеродом и азотом одновременно. Благодаря этому сталям придают высокую твердость, стойкость к истиранию и к коррозии. Такую термическую обработку выполняют, используя цианистые соли, азотирующие газы, порошки и пасты.
Термомеханическая обработка
Данная методика сравнительно новая. Она позволяет сохранить пластичность, выполнить пластическую деформацию и упрочнить структуру.
Металл доводят до аустетинтного состояния. При быстром охлаждении начинается формирование мартенсита. В это же время выполняют наклеп аустенита – посредством прокатки, штамповки либо ковки. За счет этого и происходит улучшение физико-механических свойств стали.
В зависимости от того, какая используется температура, термомеханическая обработка бывает:
- высокотемпературной;
- низкотемпературной.
В первом случае превышают высшую критическую точку, приступают к пластической деформации и завершают закалкой. Во втором – сначала происходит нагрев, затем охлаждение до температуры, когда сохраняется аустенит, но еще не начинается рекристаллизация. На этой стадии осуществляют пластическую деформацию.
Криогенная обработка
Чтобы поменять свойства металлов, используют не только высокие, но и низкие температуры. Как и при термообработке, удается снять остаточные напряжения и повысить износостойкость деталей. Увеличивается твердость заготовок, их прочность. В процессе остаточный аустенит трансформируется в мартенсит. Данные мероприятия выполняют в криогенном процессоре.
Применяемое оборудование
В термических цехах встречаются разнообразные установки. Поскольку и назначение термической обработки бывает различным, возникает потребность в нескольких видах печей:
- шахтные;
- камерные;
- вакуумные;
- с выдвижным подом.
Первые называют универсальными. В них возможно выполнять термообработку разными способами. В шахтных печах размещаются заготовки любого размера. Сюда отправляют детали для нагрева перед закалкой, для отжига и отпуска, для цементации. Более того, в них работают не только со сталями, но и с цветными металлами.
В камерных печах обрабатывают преимущественно заготовки среднего и мелкого размера. Их устанавливают на различных предприятиях и в качестве самостоятельных единиц, и в составе автоматизированного комплекса.
В вакуумных печах, помимо термической обработки, можно выполнять пайку, спекание материалов. Оборудование ценят за то, что оно в точности придерживается заданных технологических параметров. Температура не откланяется от нужного предела больше чем на 5 градусов. Такие печи используются для термической обработки конструкционной стали. В них проходят разнообразные процедуры титановые сплавы, тугоплавкие металлы.
Печи с выдвижным поддоном особенно удобны, когда необходимо обработать очень крупную деталь либо узел. Для загрузки и выгрузки стали обычно используют специальные краны и кран-балки. Однако оборудование этого типа имеет существенные недостатки. Во-первых, оно громоздкое, поэтому не на каждом предприятии найдется пространство для его установки. Во-вторых, из-за специфики конструкции высоки теплопотери.
В основном печи с выдвижным поддоном применимы для отжига сварных конструкций. В них доводят заготовки крупных габаритов до аустенитного состояния. Еще один способ применения – подготовка для ковки.
Особенности термообработки цветных сплавов
Цветные металлы требуют особого подхода к обработке, в отличие от работы со сталями. Индивидуальный подход обусловлен особенностями строения кристаллической решетки. Режим и характер воздействия подбирают также с учетом теплопроводности, химической активности. Но многие процессы с цветными металлами протекают в тех же печах, где обрабатывают стали.
Завод металлоконструкций ЧЗМК подвергает термической обработке различные стали, цветные металлы. Для этого предприятие оснащено разнообразным современным оборудованием. Высокая квалификация и профессионализм специалистов служат залогом превосходного результата.
Вид термической обработки стали, металла, а также сплава
Обработка металла термическим способом — это изменение внутреннего строения (структуры) металла под воздействием изменения температурных условий и получение вследствие этого необходимых механических и физических свойств металла.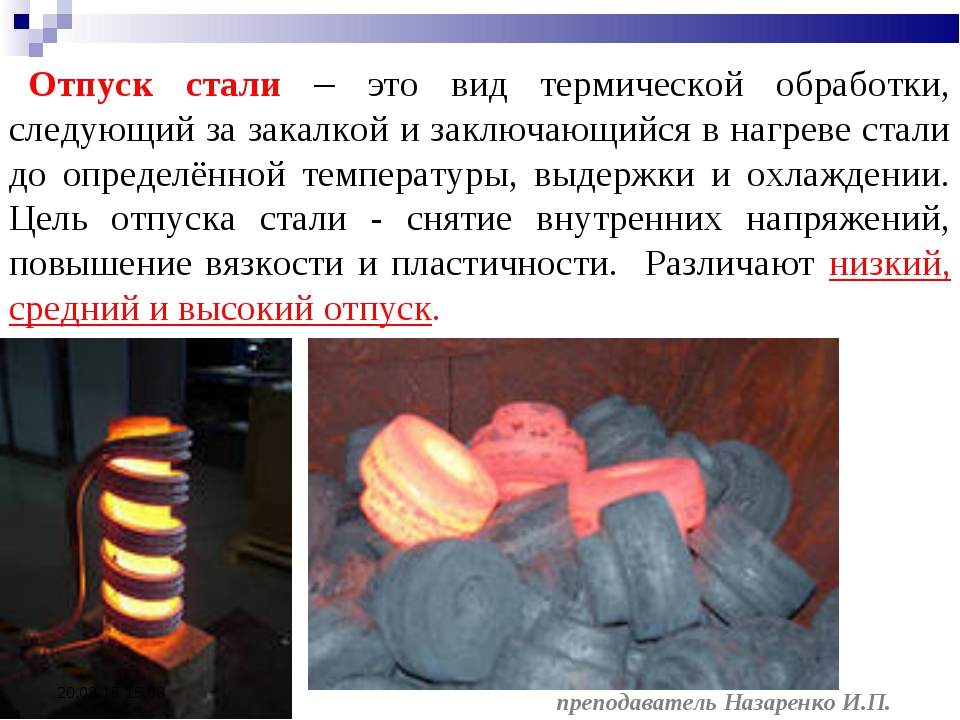
Поэтому термическая обработка металла сводится к трём последовательным операциям и видам:
- нагрев металла с определённой скоростью до заданной температуры;
- выдержка металла в течение некоторого времени при этой температуре;
- охлаждение с заданной по процессу скоростью.
Зависит от того как надо изменить свойства определённого стального изделия и применяют различные виды термической обработки, которые отличаются максимальной температурой нагрева, временем выдержки и скоростью охлаждения. В машиностроении термическая обработка нашла самое широкое применение.
Термическая обработка металла, сплава, стали
Все свойства любого сплава зависят от его структуры. Основной способ, который позволяет изменять эту структуру и является термическая обработка. Её основы разработал Чернов Д.К., а в дальнейшем его работы поддержали Бочвара А.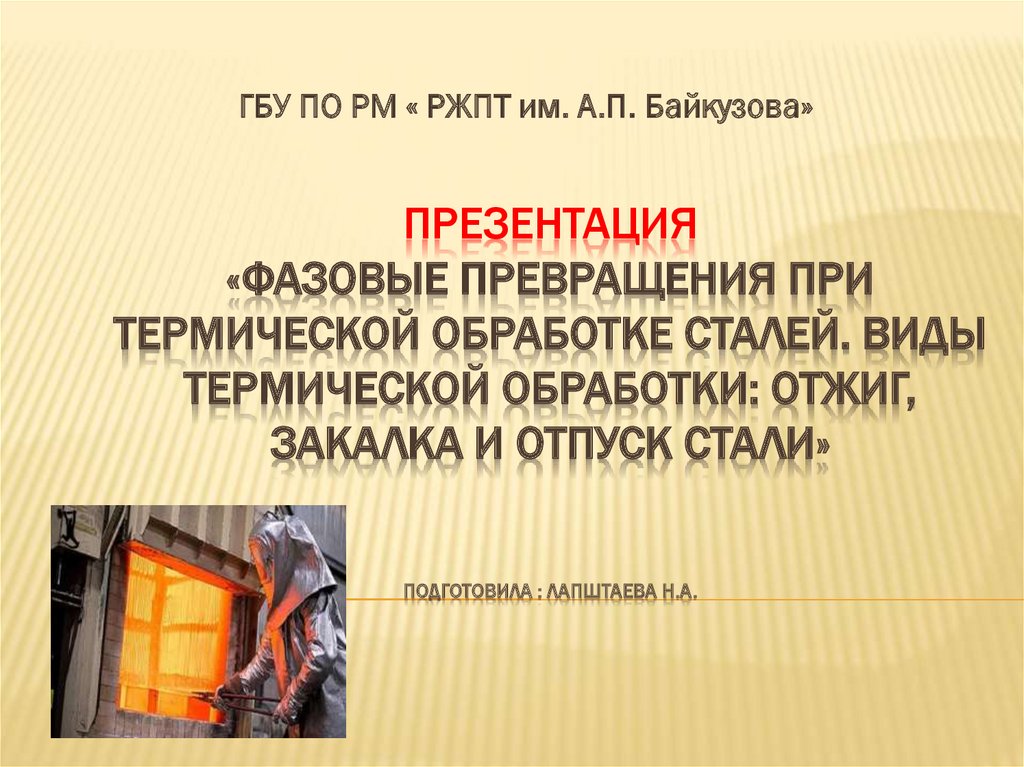
Термическая обработка металла и сплава — это последовательность операций таких как: нагрев, выдержка и охлаждение, которые выполняются в определённой последовательности и при определённом режиме, чтобы изменить внутреннее строение сплава и получения нужных свойств, при этом химический состав металла не изменяется.
В чём заключается термическая обработка металла и сплава?
- В отжиге
- Закалке
- Отпуске
- Нормализации
Отжиг. Это нагрев металла до высокой температуры, а потом происходит медленное охлаждение. Отжиг бывает разного вида — все зависит от температурного режима нагрева и скорости охлаждения.
Закалка. Термообработка стали, сплавов, металла, которая основана на перекристаллизации стали при нагреве выше критической температуры. После выдержки стали при такой температуре следует очень быстрое охлаждение. Такая сталь бывает неравновесной структуры и поэтому после закалки следует — отпуск.
Отпуск. Проводится после закалки, чтобы уменьшить или снять остаточное напряжение в стали и сплавах, повысить вязкость, уменьшить твёрдость и хрупкость металла.
Нормализация. Она похожа на отжиг, различие только в том, что нормализация металла происходит на воздухе, а отжиг — в печи.
Нагрев заготовки
Эта операция очень ответственная. От её правильного проведения зависит, во-первых — качество изделия, а во-вторых — производительность труда. Необходимо знать, что при нагреве металл меняет структуру, свойства и все характеристики поверхностного слоя. Так как при взаимодействии стали или сплава с воздухом происходит окисление железа и на поверхности образуется окалина. Толщина окалины зависит от того — какой химический состав металла, какая была температура и время его нагрева.Сталь начинает интенсивно окисляться при нагреве больше 900 градусов, потом окисляемость увеличивается в два раза — при нагреве 1000 градусов С, а при температуре 1200 градусов С — в 5 раз.
Какое бывает окисление у разных сталей?
Хромоникелевая сталь — её называют жаростойкой потому, что она практически не поддаётся окислению.
Легированная сталь — у неё образуется плотный, но тонкий слой окалины, который защищает от дальнейшего окисления и не даёт растрескиваться при ковке.
Углеродистая сталь — она теряет около 2–4 мм углерода с поверхности при нагреве. Это для металла очень плохо, так как он теряет прочность, твёрдость и сталь ухудшается в закаливании. А особенно очень пагубным является обезуглероживание для ковки небольших деталей с последующей закалкой. Чтобы не было трещин на высоколегированной и высокоуглеродистой стали, их надо нагревать медленно.
Обязательно нужно обращаться к диаграмме «железо-углерод», где определена температура для начала и конца ковки. Делать это надо для того, чтобы металл при нагреве не приобретал крупнозернистую структуру и не снижалась его пластичность.
Но перегрев заготовки можно исправить методом термообработки, но для этого нужно дополнительная энергия и время. Если металл нагреть до ещё большей температуры, то это приведёт к пережогу, что дойдёт до того, что в металле нарушится связь между зёрнами и он полностью разрушится при ковке.
Пережог
Это самый неисправимый брак. При нагреве металла или сплава обязательно нужно следить за температурой, временем и конца нагрева. Окалина растёт, если увеличено время нагрева, а при быстром или интенсивном нагреве могут появиться трещины.Пережог сплава происходит вследствие диффузии кислорода на границах зёрен, где сразу образуются окислы, которые разъединяют зёрна при высокой температуре сплава и при этом сразу резко падает прочность. А пластичность в это время приходит к нулю. Этот брак сразу отправляется на переплавку.
Какой бывает термообработка металла и сплавов
Термическая обработка подразделяется на:
- термическую;
- термомеханическую;
- химикотермическую
В термическую обработку входят основные виды — отжиг 1-го рода, отжиг 2-го рода, закалка и отпуск. Нормализация применяется не ко всем видам стали, все зависит от её степени легированности.
У всех видов термической обработки разная температура нагрева, продолжительность выдержки при этой температуре и скорость охлаждения после окончания выдержки.
1-ый род отжига — это диффузионный отжиг, отжиг для снятия напряжений.
2-ой род отжига подразделяется на неполный, полный, изотермический отжиг, сфероидезацию, нормализацию.
Закалка применяется для того, чтобы изделия были твёрдые, прочные и износостойкие.
Химикотермическая обработка
Это такая термообработка стали, которая совокупляется с насыщением поверхности изделия — углеродом, азотом, алюминием, кремнием, хромом и др., которые образуют с железом твёрдые растворы замещения. Они более длительные и энергоёмкие, чем сталь насыщенная железом и углеродом, образующая с железом твёрдые растворы внедрения.Химико — термическая обработка при создании на поверхности изделий благоприятных остаточных напряжений сжатия увеличивает долговечность и надёжность изделия. Также она повышает коррозионную стойкость, твёрдость.
Такая обработка предназначена для изменения в определённом слое состава стали. К таким методам относятся:
- цементация — при таком методе верхний слой стали обогащается углеродом. При этом получаются изделия с комбинированными свойствами — мягкая сердцевина и твёрдый поверхностный слой;
- азотирование — это обогащение поверхностного слоя азотом, чтобы была повышена коррозионная стойкость и усталостная прочность изделия;
- борирование — это насыщение поверхностных слоёв стали бором, при таком методе у изделия повышается износостойкость, особенно при трении и сухом скольжении. Кроме того при борировании исключается схватываемость или сваривание деталей в холодном состоянии. Детали после борирования делаются очень стойкими к кислоте и щелочи;
- алитирование — это насыщение стали алюминием. Делается это для того, чтобы придать стали стойкость к агрессивным газам — серному ангидриду, сероводороду;
- хромирование — насыщение хромом поверхностного слоя стали. Хромирование малоуглеродистых сталей почти совсем не влияет на их прочностные характеристики. Хромирование стали с более высоким содержанием хрома называется твёрдым хромированием, так как на поверхности деталей образуется карбид хрома, который имеет:
- высокую твёрдость
- окалиностойкость
- коррозионную стойкость
- повышенную износостойкость
Криогенная обработка
Это упрочняющая термическая обработка металла и сплавов при криогенных, очень низких температурах — ниже -153 градусов С. Ранее такая термическая обработка называлась «обработка холодом» или «термическая обработка металла при температуре ниже нуля». Но эти названия не совсем отображали всю суть криогенной обработки.Её суть заключается в следующем: обрабатываемые детали помещают в криогенный процессор, где происходит их медленное охлаждение, а потом выдерживают детали при температуре -196 градусов С определённое время. Затем они постепенно возвращаются опять к комнатной температуре. Когда идёт этот процесс, то в металле происходят структурные изменения. За счёт этого повышается износостойкость, циклическая прочность, коррозионная и эрозионная стойкости.
Основные свойства, полученные при обработке, как холодное охлаждение, сохраняются на весь срок службы обрабатываемой детали и поэтому не требует повторной обработки.
Конечно, криогенная технология не заменит методы термического упрочнения, а при обработке холодом придаст материалу новые свойства.
Инструменты обработанные сверхнизкими температурами позволяют предприятиям сократить расходы потому, что:
- увеличивается износостойкость инструмента, деталей и механизмов;
- снижается количество брака;
- сокращаются затраты на ремонт и замену технологического оснащения и инструмента.
Именно советские учёные позволили полноценно оценить эффект влияния обработки холодом на металл и сплав и положили начало для использования этого метода.
В данное время метод криогенной обработки изделий широко применяется во всех отраслях промышленности.
Машиностроение и металлообработка:
- увеличивает ресурс оборудования и инструмента до 300%;
- увеличивает износостойкость материала;
- увеличивает циклическую прочность;
- увеличивает коррозионную и эрозионную стойкость;
- снимает остаточное напряжение.
Спецтехника и транспорт:
- увеличивает ресурс тормозных дисков на 250%;
- повышает эффективность работы тормозной системы;
- увеличивает циклическую прочность пружин подвески и других упругих элементов на 125%;
- увеличивает ресурс и мощность двигателя;
- снижает расходы на эксплуатацию транспортных средств.
Оборонная промышленность:
- увеличивает живучесть стволов до 200%;
- уменьшает влияние нагрева стволов на результаты стрельбы;
- увеличивает ресурс узлов и механизмов.
Добывающая и обрабатывающая промышленность:
- увеличивает стойкость породоразрушающего инструмента до 200%;
- уменьшает абразивный износ узлов и механизмов;
- увеличивает коррозионную и эрозийную стойкость оборудования;
- увеличивает ресурс промышленного и горнодобывающего оборудования.
Аудиотехника и музыкальные инструменты:
- уменьшает искажение сигнала в проводниках;
- улучшает музыкальную деятельность, ясность и прозрачность звучания;
- расширяет диапазон звучания музыкальных инструментов.
Криогенная обработка применяется практически во всех отраслях, где необходимо повысить ресурс, увеличить прочность и износостойкость, а также поднять производительность.
Для чего нужна термическая обработка?
Надёжность и долговечность металлических конструкций, оборудования, трубопроводов зависит от качества изготовления узлов, деталей, элементов из которых они состоят. Во время эксплуатации они подвергаются статистическим, динамическим и циклическим нагрузкам и влиянию агрессивных сред. Им приходится работать при низких и высоких температурах и находится в условиях быстрого износа.И поэтому эксплуатация любых металлоизделий напрямую зависит от износостойкости, прочности, термо- и коррозионной стойкости элементов из которых они состоят.
Для того чтобы повысить все эти характеристики необходимо правильно подобрать материал для деталей, усовершенствовать их конструкцию, устранить неточности сборки, улучшить методы горячей и холодной обработки.
Таким высоким требованиям редко отвечают материалы в состоянии поставки. Основная часть доставляемых конструкционных элементов нуждается в стабилизации эксплуатационных свойств, чтобы они не изменялись с течением времени. И чтобы повысить механические и физико-химические свойства металлических материалов, применяют термическую обработку. Это последовательность операций нагрева, выдержки и охлаждения металлов и сплавов.
Её проводят для изменения структуры и свойств металлов и сплавов в направлении, которое было задано. Термообработка применяется для изменения структуры фазового состава и перераспределения компонентов, размера и формы кристаллических зёрен, видов дефектов, их количества и распределения. И это все позволяет достаточно легко получить требуемое свойство материала.
Обязательно надо помнить, что свойства металла и сплавов зависит не только от не только от структуры, но и от химического состава, который образуется во время металлургического и литейного процесса.
Задачей термической обработки является ликвидация внутреннего напряжения в металле и сплаве, улучшение механических и эксплуатационных свойств и другое.
Термической обработке подвергается сталь, чугун, сплав на основе цветных металлов.
Нужно знать, что материалам с одним химическим составом при проведении различных режимов термообработки можно получить несколько совершенно разных структур, которые будут обладать абсолютно разными свойствами. При улучшении механических свойств с помощью термической обработки можно использовать сплавы более простого состава. Допускаемые напряжения, уменьшение массы деталей и механизмов, повышение их надёжности и долговечности также можно достичь с помощью термической обработки.
При малых затратах на термообработку результат её может оказывать огромное влияние на трудоёмкость и стоимость работ на смежных участках производства. Многие производители не проводят термическую обработку изделий, тем самым сокращают весь технологический процесс при изготовлении изделий. Иногда это оправдано, а иногда — нет.
Всегда нужно не только тщательно продумывать весь процесс объёмной и местной термообработки, но и строго соблюдать их режимы, чтобы добиться оптимальных структур и высокого уровня физико-механических и эксплуатационных свойств в изделиях для обеспечения их надёжной и длительной работы.
Оцените статью: Поделитесь с друзьями!Термическая обработка металла
Термическая обработка металлов — это процесс температурного воздействия на сплав, с целью изменения его структуры и (или) свойств. Термообработка применяется для изменения структуры и свойств как железоуглеродистых сплавов, так и цветных сплавов.
Основные виды термической обработки металлов
Термическая обработка металла представляет собой не только упрочнение. Во многих случаях применяется разупрочняющая термическая обработка или термообработка на определенную структуру. Для смягчения стали перед холодной пластической деформацией (ХПД) в большинстве случаев делается отжиг с полной перекристаллизацией сплава. Для улучшения обрабатываемости резанием металла применяется нормализация, отжиг на зернистый перлит или улучшение. Отжиг на зернистый перлит применяется и для получения требуемого комплекса механических свойств перед высадкой или холодной штамповкой. Перед волочением проволоки из некоторых марок сталей делается патентирование на трооститную структуру.
Термическая обработка металлов подразделяется на следующие виды:
1. Объёмная термообработка металла — применяется для получения определенной структуры или свойств по всему сечению детали или заготовки.
Основные виды объёмной термической обработки сталей и сплавов:
а) Закалка стали (сплава)
б) Отжиг и нормализация стали (сплава)
в) Отпуск стали или старение сплава
2. Локальная термическая обработка — применяется для получения структуры или свойств в определённом объеме детали или заготовки, при этом термическому воздействию подвергается только определенный объем металла (закалка токами высокой частоты, лазерная закалка, закалка с электроконтактным нагревом)
3. Химико-термическая обработка — применяется для получения структуры или свойств в определённом объеме детали или заготовки, при этом термическому воздействию подвергается весь объем металла (цементация, нитроцементация, азотирование)
Для достижения требований, которые предъявляются к металлу используется множество разновидностей этих видов термообработки. Так например, один только отжиг насчитывает более 10 разновидностей.
Термическая обработка, как способ получения заданного комплекса механических свойств, подразумевает под собой не только высокотемпературное воздействие на металл. Есть определенные группы сталей, для обработки которых применяется так называемая обработка холодом. Это стали, у которых точка конца мартенситного превращения лежит ниже комнатных температур. Соответственно у этих сталей будет идти превращение А-М и при низких температурах. К таким сталям относятся: инструментальные стали, обработка холодом которых позволяет получить максимальную твердость и износостойкость; мерительный инструмент, для которого важна размерная стабильность; изделия из стали, которые работают в условиях низких температур.
Разбавитель акриловый универсальный — https://www.dcpt.ruНазначение и виды термической обработки — Режущий инструмент
Назначение и виды термической обработки
Термическая обработка формирует физико-механические свойства инструмента: теплостойкость, прочность, твердость, износостойкость. Для изготовления инструмента используют такие виды термической обработки, как отжиг, закалка, отпуск, химико-термическая обработка. При неправильно выбранных или при нарушении заданных режимов термической обработки инструмент может оказаться вообще неработоспособным. Поэтому высокая культура термической обработки, особенно закалки и отпуска, предопределяет высокое качество инструмента.
Отжиг.
Отжиг осуществляют для снятия внутренних напряжений и понижения твердости после горячей обработки давлением (прокатка, ковка, штамповка) и сварки заготовок. Перед повторной закалкой инструментов, если первичная выполнена неправильно, инструменты также отжигают. Для этого заготовку или инструмент нагревают до температуры 830—850 °С, выдерживают при этой температуре 3—4 часа, а затем охлаждают с различными скоростями. Приблизительный режим отжига быстрорежущей стали представлен диаграммой рис. 3.18. Более предпочтительный — изотермический отжиг по диаграмме рис. 3.19.
Повышение температуры отжига и увеличение выдержки при этой температуре способствуют более полному растворению карбидов в аустените. После закалки и отпуска получается более легированный мартенсит, что повышает красностойкость инструмента. Однако увеличивается опасность окисления и обезуглероживания поверхностных слоев заготовки или инструмента. Поэтому обычно стремятся сокращать время нагрева стали при высоких температурах. Для повышения пластичности быстрорежущей стали перед холодной обработкой давлением (волочение, редуцирование, ротационное обжатие, прокат тонких листов, рубка, штамповка) рекомендуют термическую обработку, занимающую промежуточное место между отжигом и неполной закалкой. Сталь нагревают до 720—780 °С, выдерживают при этой температуре один час, после чего охлаждают в масле или на воздухе. Закалка.
Цель закалки — увеличить твердость инструмента, превратив исходную перлитную структуру быстрорежущей стали в мартенсит. Для этого необходимо исходный перлит превратить в аустенит, нагревая сталь до температуры аустенитных превращений. Затем сталь быстро охлаждают в масле до температуры мартенситных превращений, чтобы аустенит не превратился в промежуточные структуры. После этого охлаждение должно быть медленным, чтобы обеспечить более полный распад аустенита.
Нагрев. Быстрорежущая сталь обладает пониженной теплопроводностью. Поэтому нагрев до закалочной температуры 1200—1300 °С необходимо осуществлять медленно, для того чтобы избежать появления закалочных трещин — следствия высоких внутренних растягивающих напряжений в сердцевине инструмента от разности объемов горячих поверхностных слоев инструмента и относительно холодной сердцевины. Инструмент сначала медленно подпревают до температуры 780—840 °С, а затем быстро нагревают до окончательной температуры. Быстрый нагрев уменьшает рост зерна стали и обезуглероживание поверхностных слоев инструмента. Крупногабаритные и фасонные инструменты подогревают дважды, сначала до 400—500 °С, а затем до 780—840 °С.
Температура окончательного нагрева, продолжительность подогрева и окончательного нагрева зависят от целого ряда факторов:
а) требуемых физико-механических свойств инструмента;
б) химсостава стали;
в) теплоемкости и теплопроводности стали,
г) продолжительности фазовых превращений и процессов растворения карбидов в аустените;
д) физических свойств нагревающей среды;
е) конфигурации и размера нагреваемого инструмента.
Поэтому режим термической обработки назначают и экспериментально проверяют не только для конкретного инструмента из стали данной марки, но и для каждого номера плавки стали этой же марки, и даже для каждого проката стали той же плавки. Установленный таким образом режим нагрева строго контролируется и поддерживается. Например, отклонение температуры нагрева допускается в пределах ± 10°С. Время выдержки при окончательном нагреве быстрорежущей стали в хлорбариевых ваннах 6—7 с на каждый миллиметр сечения инструмента, а в печах с газовой средой 10—12 с. Температура окончательного нагрева, в зависимости от марки стали, колеблется в пределах 1200—1300 °С. Уточненные значения температуры и времени выдержки при нагреве под закалку можно найти в специальной литературе, например, [14; 170]. Инженеру-механику важно знать, что повышение температуры окончательного нагрева и увеличение времени выдержки при этой температуре способствует более полному растворению карбидов. В результате после закалки и отпуска получаем более легированный мартенсит, что повышает твердость и теплостойкость инструмента. Однако при этом увеличивается опасность окисления и обезуглероживания поверхности инструмента, структура металла становится крупнозернистой, появляется ледобу- ритная сетка, что понижает прочность инструмента. Кроме того, уменьшение содержания свободных карбидов в стали вследствие их более полного растворения понижает износостойкость инструмента. Поэтому повышенные температуры нагрева и увеличенные выдержки можно рекомендовать лишь для простых инструментов, работающих с высокими скоростями, например, для резцов общего назначения. Дня сложнорежущих и мелкопрофильных инструментов, протяжек, зуборезных, резьбонарезных и других подобных инструментов такой нагрев неприемлем.
Охлаждение. Выбор метода охлаждения и охлаждающих сред зависит от состава стали, сложности инструмента и требуемых свойств.
Охлаждение до температуры мартенситного превращения следует вести быстро, чтобы аустенит не превратился в промежуточные структуры. Для каждой марки стали существует своя постоянная скорость охлаждения, а стало быть, и своя охлаждающая среда.
Охлаждение в интервале температур мартенситного превращения (300—200 °С) следует вести более медленно, так как при быстрых структурных превращениях объем металла изменяется быстро, что может явиться причиной появления трещин. Поэтому для разных марок сталей и форм инструмента чаще всего применяется комбинированное охлаждение: сначала в одной среде, а затем в другой.
Охлаждающими средами могут быть: вода, масло, расплавы и растворы солей, щелочей, воздух.
Инструменты из углеродистой стали сложной конфигурации сначала охлаждают в воде до температуры 300—250 °С, а затем в масле. Простые инструменты охлаждают только в воде.
Быстрорежущие инструменты простой формы охлаждают в масле, а небольшого поперечника (3—5 мм) даже на спокойном воздухе или под вентилятором.
Инструменты сложной формы, фасонные, подвергают ступенчатой закалке, т.е. комбинированному охлаждению, с целью снижения деформаций и возможности появления трещин. Сначала инструмент охлаждают в расплавленной калиевой селитре (хуже — в натриевой, разъедает инструмент) до температуры 500—450 °С с выдержкой при этой температуре 2—5 мин, в зависимости от сечения инструмента. Это область температур наибольшей устойчивости аустенита. Затем инструмент охлаждают на воздухе.
Для инструментов особо сложной формы, а также крупных размеров и большой длины рекомендуется изотермическая закачка, значительно уменьшающая внутренние напряжения и деформацию. При этом инструмент сначала охлаждают в соли с температурой 250—300 °С, выдерживают 40—60 мин., а затем на воздухе. Если температура соли 200—250 °С, то выдержка при этой темперагуре 30—40 мин, дальнейшее охлаждение на воздухе. Охлаждающая среда — смесь едких щелочей NaOH и КОН в различной пропорции в зависимости от требуемой температуры. Можно использовать смесь селитр KN03 (56 %) и NaN03 (44 %).
Светлая закалка. Нагрев инструмента обычный, в соляных ваннах, а охлаждение в растворе щелочей: 80 % КОН + 20 % NaOH + + 6 частей воды на 100 частей щелочей. Чтобы поверхность инструмента не была пятнистой, перед нагревом его обезжиривают в горячем растворе следующего состава: на 1 л воды 250 г NaOH и 15 г Na3PG4. Затем инструмент высушивают при температуре 400—500 °С и только после этого переносят в ванну для нагрева под закалку, так как попадание влаги в соляную ванну может вызвать взрыв и выплескивание солей. После охлаждения инструмент промывают в горячей воде для удаления солей и высушивают или сразу же отпускают. Такая промывка с просушкой предохраняет инструмент от коррозии.
Отпуск.
Нормальный отпуск. После закалки быстрорежущей стали в ее структуре остается около 20 % аустенита. В результате — пониженная твердость инструмента. Кроме того, во время работы инструмента под воздействием температуры резания аустенит как бы самопроизвольно распадается, превращаясь в мартенсит. Казалось бы, это неплохо. Но беда в том, что при таких структурных превращениях изменяется объем стали, причем только в отдельных частях инструмента. Возникают внутренние напряжения, которые, складываясь с напряжениями от действия сил резания, могут привести к поломке инструмента. Таким образом, прочность инструмента понижена. Понижена также и износостойкость, так как аустенит мягкий и быстро размазывается по детали. Поэтому оставшийся после закалки аустенит необходимо перевести в мартенсит. Этой цели служит отпуск. Закаленные инструменты загружают в печь, нагревают до 525—575 °С, выдерживают 1,0—1,5 часа и выгружают для остывания на воздухе. Так повторяют два-три раза, т.е. делают двух-, трехкратный отпуск. В это время происходит превращение остаточного аустенита в мартенсит и выделение мелкодисперсных, устойчивых против коагуляции карбидов, что вызывает дисперсионное твердение, называемое вторичной твердостью. В результате остается 2—3 % аустенита, повышается твердость инструмента на 2—3 единицы HRC3. Во время последнего отпуска окончательно снимаются внутренние напряжения, что является второй задачей отпуска. Первая задача — перевод остаточного аустенита в мартенсит.
Обработка холодом. Сразу после закалки инструмент можно обработать холодом в жидком азоте (-197 °С) или в твердой углекислоте, растворенной в бензине (-80… -100 °С). После такой обработки в стали практически не остается аустенита и можно обойтись только одним отпуском для снятия внутренних напряжений. Кроме того, обработка в жидком азоте даже готового инструмента повышает его стойкость тем значительнее, чем больше нарушен режим термообработки инструмента.
Высокий отпуск. Задние поверхности многих инструментов после закалки и отпуска не шлифуют, как, например, у стандартных фасонных фрез, резьбонарезных гребенчатых фрез, резьбонарезных плашек. Не шлифуют фасонные поверхности инструментов, если в инструментальном цехе конкретного завода по той или иной причине сделать это невозможно. Тем не менее шероховатость таких поверхностей должна быть минимальной, и ее надо обеспечить лезвийной обработкой. Для этой цели делают неполную закалку инструмента с последующим высоким отпуском, нагрев до 920—950 °С, охлаждение на воздухе или в масле и высокий отпуск при температуре 700—720 °С. После отпуска сталь имеет твердость 260—270 НВ, несколько труднее обрабатывается, но обеспечивает меньшую шероховатость обработанной поверхности.
Такой закалке с высоким отпуском подвергают также протяжки перед чистовой лезвийной обработкой, хотя после последующей нормальной закалки и отпуска их шлифуют.
Высокий отпуск делают лапкам конусов инструментов и ушкам ножовочных полотен для понижения их твердости.
Низкий отпуск. Его проводят при температурах 200—250 °С для ответственных режущих инструментов, например, внутренних протяжек, чтобы исключить их поводку во время эксплуатации под действием остаточных внутренних напряжений. Такому отпуску подвергают уже готовые инструменты или инструменты перед чистовым шлифованием.
Смотрите также
Термическая обработка металлов. Особенности каждого вида обработки
Многие металлические изделия практически всегда подлежат термообработке, задача которой — управление последующими механическими параметрами и структурой изделия. Целями операций термообработки является изменение твёрдости, микро- и макроструктуры деталей.
Классификация
Согласно требованиям чертежа или по условиям последующих формоизменяющих (либо сборочных операций), термообработка металлических деталей классифицируется по следующим признакам:
- По величине итоговой твёрдости изделия – упрочняющая или разупрочняющая.
- По наличию изменений в структуре – поверхностная или глубинная.
- По источнику внешнего воздействия – пламенная или высокоэнергетическая.
- По месту процесса в общей – последовательности технологических операций – предварительная, промежуточная, конечная (финишная).
- По уровню температурных воздействий – обработка при повышенных или пониженных температурах.
Наиболее распространённые виды термической обработки металлов различают по параметрам необходимой температуры и времени обработки. Главным образом, термообработке подвергают изделия из стали, а также из некоторых металлов и сплавов – например, дюралюминия, титана.
Отжиг, его задачи и технология проведения
Цель отжига – обеспечить выравнивание механических свойств, структуры, а также добиться ликвидации внутренних напряжений, которые практически всегда появляются в результате формоизменяющих операций (преимущественно ковки или холодной объёмной штамповки). Отожжённые детали характеризуются повышенной технологической обрабатываемостью, но уменьшенной твёрдостью.
Отжиг может быть:
- Рекристаллизационным, вследствие которого понижается предел прочности. Такой отжиг может быть низко-, средне- и высокотемпературным;
- Диффузионным, после чего структура стали становится более равномерной;
- Сфероидизирующим, который обеспечивает улучшенную обрабатываемость.
В общем случае, технология проведения отжига состоит из переходов нагрева заготовки в пламенной печи до требуемой температуры, выдержки её при этой температуре некоторое время и последующее медленное охлаждение: вначале в печи, а далее — на спокойном воздухе.
Нормализация и её необходимость
Под нормализацией понимают повышение температуры детали до значений, на 30…600С превышающих температуру структурных превращений, после чего заготовка/изделие находится под воздействием этих температур, а далее медленно охлаждается.
Нормализации подвергают преимущественно конструкционные стали, поскольку после неё обрабатываемость металла увеличивается, а внутренние напряжения исчезают. С увеличением процентного содержания углерода в стали, требуемые температуры для проведения увеличиваются. Как и отжиг, ее ведут преимущественно в пламенных печах.
Нормализация часто является промежуточной стадией процессов термообработки, поскольку достигаемая при этом твёрдость не обеспечивает должной стойкости детали при её работе в составе какого-либо узла или конструкции.
Закалка: разновидности, технология
Суть закалки – быстрый нагрев до температур начала формирования неравновесных структур – мартенсита, аустенита и высокотемпературных карбидов. Для определённых групп сталей (сложнолегированных) при закалке происходят процессы дисперсионного твердения, в результате которых повышение твёрдости достигается не вследствие повышенного карбидообразования, а как результат осаждения интерметаллидных составляющих, главным образом, титана, кобальта, молибдена. Твёрдость таких сталей возрастает особенно интенсивно.
При необходимых температурах структурных превращений металл выдерживают определённое время, после чего интенсивно охлаждают, фиксируя неравновесные структуры в конечном изделии. Закалку проводят полностью погружая изделие в воду или (для особо ответственных деталей сложной конфигурации) в масло.
Закалка – одна из наиболее ответственных операций термообработки. Выбор способа определяется многими факторами: химическим составом сплава, заданным уровнем твёрдости, предельными значениями остаточных внутренних напряжений, конфигурацией детали и т.д.
Закалка может быть по объёму и по поверхностному слою детали. В первом случае, процесс ведут в пламенных печах с контролируемой атмосферой. Для поверхностной закалки используют высокочастотные электрические установки, которые обеспечивают требуемый комплекс физико-механических свойств лишь в относительно небольшом по толщине слое.
Основными дефектами закалки являются перегрев и пережог готового изделия. В результате перегрева формируется грубодисперсная структура с неравномерной твёрдостью и сниженной пластичностью. Этот дефект можно исправить повторным проведением данной операции. При значительном превышении верхнего предела закалочной температуры в микроструктуре металла происходят необратимые изменения: его кристаллическая структура разрушается, а в межзёренных промежутках появляются жидкие фазы легкоплавких примесей – серы и фосфора. Это – пережог, необратимый дефект термической обработки, потому как пережжённые детали разрушаются при малейших механических нагрузках на них.
Отпуск и улучшение
Часто наличие внутренних напряжений в закалённой детали приводят к её короблению и потере пластических свойств, что особенно недопустимо для инструментальных и легированных конструкционных сталей. Поэтому практически во всех случаях после закалки термообрабатываемые изделия подвергают отпуску.
Отпуск заключается в нагреве изделия до температур, которые несколько меньше температур начала структурных превращений, последующей выдержке и дальнейшему медленному охлаждению. Отпуск подразделяют на одно- и многократный. После него хрупкость металлов уменьшается, а показатели пластичности и вязкости возрастают.
Разновидностью отпуска считается улучшение. Оно проводится с целью эксплуатационных свойств изделий, которые в дальнейшем будут подвергаться значительным знакопеременным нагрузкам. Поэтому температура выдержки при улучшении несколько выше, чем при отпуске.
Криогенная обработка
Желаемого изменения структуры и физико-механических характеристик металлов можно достичь не только при их нагреве, но и при глубоком охлаждении. Многие конструкционные стали обрабатывают холодом при температурах -60…-1200С.
Криогенной обработкой решаются следующие задачи:
- Повышается стойкость изделий к износу;
- Размеры деталей становятся стабильными;
- Улучшается качество последующей поверхностной доводки и полирования;
- Увеличивается твёрдость.
Особенно эффективна обработка холодом для легированных сталей, которые содержат значительный процент сравнительно мягкого остаточного аустенита. В процессе глубокого охлаждения аустенит превращается в значительно более твёрдую структурную составляющую – мартенсит.
Кроме объёмных процессов термической обработки широкое распространение получили также процессы, при которых повышается твёрдость лишь тонкого поверхностного слоя изделия. Такая термообработка выполняется электрофизическими методами (воздействием на поверхность металла теплом искрового или дугового разрядов) или электрохимическими методами – термообработкой в расплавах или в атмосфере различных веществ.
основные виды, плюсы и минусы
Термообработка металла является важной частью производственного процесса в цветной и чёрной металлургии. После этой процедуры материалы приобретают необходимые характеристики. Термообработку использовали довольно давно, но она была несовершенна. Современные методы позволяют достичь лучших результатов с меньшими затратами, и снизить стоимость.
Особенности термической обработки
Для придания нужных свойств металлической детали она подвергается термической обработке. Во время этого процесса происходит структурное изменение материала.
Металлические изделия, используемые в хозяйстве, должны быть устойчивыми к внешнему воздействию. Чтобы этого достичь, металл необходимо усилить при помощи воздействия высокой температуры. Такая обработка меняет форму кристаллической решётки, минимизирует внутреннее напряжение и улучшает его свойства.
Виды термической обработки стали
Термообработка стали сводится к трём этапам: нагреву, выдержке и быстрому охлаждению. Существует несколько видов этого процесса, но основные этапы у них остаются одинаковыми.
Выделяют такие виды термической обработки:
- Техническая (отпуск, закалка, криогенная обработка, старение).
- Термомеханическая, при которой используют не только высокую температуру, но и физическое воздействие на металл.
- Химико-термическая включает в себя термическую обработку металла с последующим воздействием на поверхность азотом, хромом или углеродом.
Отжиг
Это производственный процесс нагрева металла до заданной температуры, а затем медленного охлаждения, которое происходит естественным путём. В результате этой процедуры устраняется неоднородность металла, снижается внутреннее напряжение, и уменьшается твёрдость сплава, что значительно облегчает его переработку. Существует два вида отжига: первого и второго рода.
При отжиге первого рода фазовое состояние сплава изменяется незначительно. У него есть разновидности:
- Гомогенизированный — температура составляет 1100−1200 °C, металл выдерживается от 7−14 часов в таких условиях.
- Рекристаллизационный — температура отжига 100−200 °C, эта процедура используется для клёпаной стали.
При отжиге второго рода происходит фазовое изменения металла. Процесс имеет несколько видов:
- Полный отжиг — металл нагревается на 25−40 °C выше критического значения для этого материала и охлаждается со специальной скоростью.
- Неполный — сплав нагревается до критической точки и долго остывает.
- Диффузионный — отжиг производится при температуре 1100−1200 °C.
- Изотермический — нагрев металла происходит как при полном отжиге, но охлаждение ниже критической температуры, остывание на открытом воздухе.
- Нормализованный — производится полный отжиг металла с остыванием на воздухе.
Закалка
Это процесс манипуляции металлом для достижения мартенситного превращения, чем обеспечивается повышенная прочность и уменьшенная пластичность изделия. При закалке сплав нагревают до критического значения, как и при отжиге, но процесс охлаждения производится значительно быстрее, и для этого используют ванную с жидкостью. Существует несколько видов закалки:
- Закалка в одной жидкости, для мелких деталей используют масло, а для крупных — воду.
- Прерывистая закалка — понижение температуры происходит в два этапа: резкое охлаждение до температуры в 300 °C, с помощью воды, а затем изделие помещают в масло или на открытый воздух.
- Ступенчатая — при достижении металла необходимой температуры, его охлаждают в расплавленных солях, а затем на открытом воздухе.
- Изотермическая — сходный со ступенчатой, отличается во времени выдержки.
- Закалка с самоотпуском, сплав охлаждается не полностью, оставляется тёплый участок в середине. В результате металл получает повышенную прочность и высокую вязкость. Такое сочетание отлично подходит для ударных инструментов.
Неправильно сделанная закалка может привести к появлению таких дефектов:
- обезуглероживание;
- трещины;
- коробление или поводки.
Главная причина поводок и трещин — неравномерное изменение размера детали при охлаждении или нагреве. Они также могут возникнуть при резком повышении прочности в отдельных местах. Лучший способ избежать этих проблем — медленное охлаждение металла до значения мартенситного превращения.
Поводка и коробление возникает при неравномерном охлаждении искривлённых деталей. Эти дефекты довольно невелики и могут быть исправлены шлифованием. Предварительный отжиг деталей и их постепенный и равномерный нагрев помогут избежать коробления.
Обезуглероживание металла происходит в результате выгорания углерода при длительном нагреве. Интенсивность процесса зависит от температуры нагрева, чем она выше, тем быстрее процесс. Для исправления деталь нагревают в нейтральной среде (муфельной печи).
Окалины на поверхности металла приводят к угару и деформации изделия. Это снижает скорость нагрева и делает механическую обработку более трудной. Окалины удаляются химическим или механическим способом. Для того чтобы избежать их появления, нужно использовать специальную пасту (100 г жидкого стекла, 25 г графита, 75 г огнеупорной глины, 14 г буры, 100 г воды, 30 г карборунда). Состав наносится на изделия и оставляется до полного высыхания, а затем нагревается как обычно.
Отпуск
Он смягчает воздействие закалки, снимает напряжение, уменьшает хрупкость, повышает вязкость. Отпуск производится с помощью нагрева детали, закалённой до критической температуры. В зависимости от значения температуры можно получить состояния тростита, мартенсита, сорбита. Они отличаются от похожих состояний в закалке по свойствам и структуре, которая более точечная. Это увеличивает пластичность и прочность сплава. Металл с точечной структурой имеет более высокую ударную вязкость.
В зависимости от температуры различают такие виды отпуска: низкий, средний, высокий.
Для точного определения температуры используют таблицу цветов. Плёнка окислов железа придаёт металлу разные цвета. Она появляется, если изделие очистить от окалин и нагреть до 210 °C, при повышении температуры толщина плёнки увеличивается.
При низком отпуске (температура до 300 °C) в составе сплава остаётся мартенсит, который изменяет структуру материала. Кроме того, выделяется карбид железа. Это увеличивает вязкость стали и уменьшает её твёрдость. При низком отпуске металл охлаждают в соляных и масляных ваннах.
Высокий отпуск значительно улучшает механические свойства стали, увеличивает вязкость, пластичность, прочность. Её широко используют для изготовления рессор, шатунов двигателей, кузнечных штампов, осей автомобилей. Для мелкозернистой легированной стали отпуск проводят сразу после нормализации.
Чтобы увеличить обрабатываемость металла, его нормализацию производят при высокой температуре (970 °C), что повышает его твёрдость. Для уменьшения этого параметра делают высокий отпуск.
Криогенная обработка
Изменения структуры металла можно добиться не только высокой температурой, но и низкой. Обработка сплава при температуре ниже 0 °C широко применяется в разных отраслях производства. Процесс происходит при температуре 195 °C.
Плюсы криогенной обработки:
- Снижает количество аустенита, что придаёт устойчивость размерам деталей.
- Не требует последующего отпуска, что сокращает производственный цикл.
- После такой обработки детали лучше поддаются шлифовке и полировке.
Химико-термическая обработка
Химико-термическая обработка включает в себя не только воздействие с помощью высокой температуры, но и химическое. Результатом этой процедуры является повышенная прочность и износостойкость металла, а также придание огнестойкости и кислотоустойчивости.
Различают такие виды обработки:
- Цементация.
- Азотирование.
- Нитроцементация.
- Борирование.
Цементация стали — представляет собой процесс дополнительной обработки металла углеродом перед закалкой и отпуском. После проведения процедуры повышается выносливость изделия при кручении и изгибе.
Перед началом цементации производится тщательное очищение поверхности, после чего её покрывают специальными составами. Процедуру производят после полного высыхания поверхности.
Различают несколько видов цементации: жидкая, твёрдая, газовая. При первом виде используют специальную печь-ванную, в которую засыпают 75% соды, 10% карбида кремния, 15% хлористого натрия. После чего изделие погружают в ёмкость. Процесс протекает в течение 2 часов при температуре 850 °C.
Твёрдую цементацию удобно выполнять в домашней мастерской. Для неё используют специальную пасту на основе кальцинированной соды, сажи, щавелево-кислого натрия и воды. Полученный состав наносят на поверхность и ждут высыхания. После этого изделие помещают в печь на 2 часа при температуре в 900 °C.
При газовой цементации используют смеси газов, содержащие метан. Процедура происходит в специальной камере при температуре в 900 °C.
Азотирование стали — процесс насыщения поверхности металла азотом при помощи нагрева до 650 °C в аммиачной атмосфере. После обработки сплав увеличивает свою твёрдость, а также приобретает сопротивление к коррозии. Азотирование, в отличие от цементации, позволяет сохранить высокую прочность при больших температурах. А также изделия не коробятся при охлаждении. Азотирование металла широко применяется в промышленности для придания изделию износостойкости, увеличения твёрдости и защиты от коррозии.
Нитроцементация стали заключается в обработке поверхности углеродом и азотом при высокой температуре с дальнейшей закалкой и отпуском. Процедура может осуществляться при температуре 850 °C в газовой среде. Нитроцементацию используют для инструментальных сталей.
При борировании стали на поверхность металла наносят слой бора. Процедура происходит при температуре 910 °C. Такая обработка используется для повышения стойкости штампового и бурового инструментов.
Термомеханическая обработка
При использовании этого метода применяют высокую температуру и пластическую деформацию. Различают такие виды термомеханической обработки:
- Высокотемпературная.
- Низкотемпературная.
- Предварительная.
При высокотемпературной обработке деформация металла происходит после разогрева. Сплав подогревают выше температуры рекристаллизации. После чего производится закалка с отпуском.
Высокотемпературная обработка металла:
- Повышает вязкость.
- Устраняет отпускную хрупкость.
Такой обработке подвергают конструкционные, инструментальные, углеродистые, пружинные, легированные стали.
При низкотемпературной обработке заготовку после охлаждения выдерживают при температуре ниже значения рекристаллизации и выше мартенситного превращения. На этом этапе делают пластическую деформацию. Такая обработка не даёт устойчивости металлу при отпуске, а для её осуществления необходимо мощное оборудование.
Для осуществления термомеханической обработки необходимо применять специальные приспособления для давления, нагрева и охлаждения заготовки.
Термообработка цветных сплавов
Цветные металлы отличаются по своим свойствам друг от друга, поэтому для них применяют свои виды термообработки. Для выравнивания химического состава меди её подвергают рекристаллизационному отжигу. Латунь обрабатывают при низкой температуре (200 °C). Бронзу подвергают отжигу при температуре 550 °C. Магний закаляют, отжигают и подвергают старению, алюминий подвергают похожей обработке.
В чёрной и цветной металлургии широко применяются разные виды термической обработки металлов. Их используют для получения нужных свойств у сплавов, а также экономии средств. Для каждой процедуры и металла подбираются свои значения температуры.
4 типа термической обработки стали
В нашем последнем сообщении в блоге мы рассмотрели три этапа термообработки, которые включают нагрев металла до заданной температуры (этап нагрева), поддержание его при этой температуре в течение определенного периода времени. время (стадия выдержки) и охлаждение до комнатной температуры с помощью метода, который зависит от типа металла и желаемых свойств (стадия охлаждения). В этом посте мы рассмотрим четыре основных типа термической обработки стали, которой сегодня подвергается: отжиг, нормализация, закалка и отпуск.
Позвольте нам удовлетворить ваши потребности в термообработке
Kloeckner работает с рядом партнеров по термообработке стали, чтобы предоставить нашим клиентам качественные детали, соответствующие их спецификациям. Мы предлагаем термически обработанные изделия под ключ из нашего общенационального склада листового, пруткового и листового проката.
Сталь для термической обработки: отжиг
Целью отжига является обратное закалке. Вы отжигаете металлы, чтобы снять напряжение, смягчить металл, повысить пластичность и улучшить структуру их зерен.
Без соответствующей стадии предварительного нагрева сварка может привести к получению металла с неравномерной температурой, даже с расплавленными участками рядом с участками, имеющими комнатную температуру. В таких условиях сварка может сделать металл более слабым: по мере охлаждения сварного шва, наряду с твердыми и хрупкими пятнами, возникают внутренние напряжения. Отжиг — это один из способов решения таких распространенных проблем и снятия внутренних напряжений.
Отжиг стали
Для отжига сталей и других черных металлов для получения наивысшего уровня пластичности необходимо медленно нагреть металл до соответствующей температуры, замочить его, а затем дать ему медленно остыть, либо закопав его в какой-нибудь изоляционного материала или просто выключив печь и давая печи и детали медленно остыть вместе.
Время, в течение которого металл впитается, зависит как от его типа, так и от его массы. Если это низкоуглеродистая сталь, для нее потребуется максимально возможная температура отжига, а по мере увеличения содержания углерода температура отжига будет снижаться. Для получения дополнительной информации об отжиге вы можете просмотреть наше руководство по отжигу для более подробного объяснения.
Сталь термической обработки: нормализация
Целью нормализации является устранение любых внутренних напряжений в результате термической обработки, механической обработки, ковки, формовки, сварки или литья.Разрушение металла может быть результатом неконтролируемого напряжения, поэтому нормализация стали перед закалкой может помочь обеспечить успех проектов.
В чем разница между отжигом и нормализацией?
Нормализация применяется только к черным металлам, таким как сталь. Но есть еще одно ключевое отличие процесса термообработки: при нормализации, когда металл нагревается до более высокой температуры, он охлаждается воздухом после извлечения из печи.
Нормализованная сталь прочнее отожженной стали.Обладая высокой прочностью и высокой пластичностью, она прочнее, чем отожженная сталь. Если металлическая деталь должна выдерживать удар или иметь максимальную ударную вязкость, чтобы противостоять внешним воздействиям, обычно рекомендуется нормализовать ее, а не отжигать.
Поскольку нормализованные металлы охлаждаются воздухом, масса металла является ключевым фактором, определяющим скорость охлаждения и полученный уровень твердости детали. Во время нормализации более тонкие кусочки будут быстрее остывать на воздухе и станут тверже, чем более толстые.Но при отжиге и его печном охлаждении твердость как толстых, так и тонких деталей будет сопоставимой.
Термическая обработка стали: закалка
Целью закалки является не только упрочнение стали, но и ее усиление. К сожалению, в закалке есть не только плюсы. Хотя закалка действительно увеличивает прочность, она также снижает пластичность, делая металл более хрупким. После закалки металл может потребоваться отпустить, чтобы удалить часть хрупкости.
Для упрочнения большинства сталей вы должны использовать первые две стадии термообработки (медленное нагревание с последующей выдержкой в течение определенного времени до однородной температуры), третий этап отличается.Когда вы закаливаете металлы, вы быстро охлаждаете их, погружая в воду, масло или рассол. Большинству сталей для закалки требуется быстрое охлаждение, называемое закалкой, но есть некоторые, которые можно успешно охлаждать на воздухе.
По мере добавления сплавов к стали скорость охлаждения, необходимая для ее упрочнения, снижается. В этом есть положительный момент: более низкая скорость охлаждения снижает риск растрескивания или деформации. Твердость углеродистой стали зависит от содержания в ней углерода: до 0,80% углерода способность к упрочнению увеличивается вместе с содержанием углерода.При превышении 0,80% вы можете повысить износостойкость за счет образования твердого цементита, но не можете повысить твердость.
Когда вы добавляете в сталь сплавы для повышения ее твердости, вы также увеличиваете способность углерода к упрочнению и упрочнению. Это означает, что содержание углерода, необходимое для получения наивысшего уровня твердости, ниже в легированных сталях по сравнению с обычными углеродистыми сталями. В результате легированные стали обычно обладают лучшими характеристиками, чем простые углеродистые стали. .
При закалке углеродистой стали ее необходимо охладить до температуры ниже 1000 ° F менее чем за одну секунду.Но как только вы добавляете в сталь сплавы и увеличиваете эффективность углерода, вы увеличиваете этот временной предел более чем на одну секунду. Это позволяет вам выбрать более медленную закалочную среду, чтобы получить заданную твердость.
Обычно углеродистые стали закаливают в рассоле или воде, тогда как легированные стали закаливают в масле. К сожалению, закалка — это процесс, при котором возникает высокое внутреннее напряжение, и для разгрузки стали одним из вариантов является ее отпуск. Непосредственно перед тем, как деталь остынет, вы вынимаете ее из закалочной ванны при температуре 200 ° F и даете остыть на воздухе.Диапазон температур от комнатной до 200 ° F называется «диапазоном растрескивания», и вы не хотите, чтобы сталь в закалочной среде проходила через него. Читайте дальше, чтобы узнать больше о темперировании.
Сталь для термической обработки: закалка
После закалки металла, будь то корпус или пламя, и создания внутренних напряжений после быстрого охлаждения, присущего процессу, сталь часто оказывается тверже, чем необходимо, и слишком хрупкой. Ответ может заключаться в отпуске стали для уменьшения хрупкости и снятия или снятия внутренних напряжений.
Во время отпуска вы:
- Нагреваете сталь до заданной температуры ниже ее температуры закалки
- Удерживаете сталь при этой температуре в течение определенного периода
- Охлаждаете сталь, обычно на неподвижном воздухе
Если это звучит знакомо, ты прав! Закалка состоит из тех же трех этапов, что и термообработка. Основное отличие — это температура отпуска и ее влияние на твердость, прочность и, конечно же, пластичность.
При отпуске стальной детали снижается твердость, вызванная закалкой, и развиваются определенные физические свойства.Отпуск всегда следует за закалкой, и, хотя он снижает хрупкость, он также смягчает сталь. К сожалению, смягчение стали при отпуске неизбежно. Но степень потери твердости можно регулировать в зависимости от температуры во время отпуска.
В то время как другие процессы термообработки, такие как отжиг, нормализация и закалка, всегда включают температуры выше верхней критической точки металла, отпуск всегда проводится при температурах ниже ее.
При повторном нагреве закаленной стали вы начинаете отпуск при 212 ° F и продолжаете до тех пор, пока не достигнете критической точки.Чтобы выбрать желаемую твердость и прочность, вы можете установить температуру отпуска. Минимальная продолжительность отпуска должна составлять один час, если толщина детали меньше одного дюйма; если его толщина превышает один дюйм, вы можете добавить еще час на каждый дополнительный дюйм толщины.
Скорость охлаждения после отпуска не влияет на большинство сталей. После извлечения стальной детали из закалочной печи ее обычно охлаждают на неподвижном воздухе, как и в процессе нормализации. Но, как и во всех других процессах термообработки, есть некоторые отличия, которые выходят за рамки этого сообщения в блоге.
Если вас интересует отпуск, просто знайте, что отпуск снимает внутренние напряжения, возникающие при закалке, снижает хрупкость и твердость и может фактически повысить предел прочности закаленной стали при отпуске до температуры 450 ° F; при температуре выше 450 ° F прочность на разрыв снижается.
Kloeckner работает с рядом партнеров по термообработке стали, чтобы предоставить нашим клиентам качественные детали, соответствующие их спецификациям. Мы предлагаем термически обработанные изделия под ключ из нашего общенационального склада листового, пруткового и листового проката.Пожалуйста, свяжитесь с Kloeckner Louisville или позвоните по телефону (678) 259-8800 для получения информации о термообработке.
Позвольте нам удовлетворить ваши потребности в термообработке
Kloeckner работает с рядом партнеров по термообработке стали, чтобы предоставить нашим клиентам качественные детали, соответствующие их спецификациям. Мы предлагаем термически обработанные изделия под ключ из нашего общенационального склада листового, пруткового и листового проката.
Виды термической обработки | Металлургия для чайников
Термическая обработка стали
Термическая обработка — это контролируемый нагрев и охлаждение металлов для изменения их физических и механических свойств без изменения формы продукта.Термическая обработка иногда выполняется случайно из-за производственных процессов, которые нагревают или охлаждают металл, например, при сварке или формовке.
Обработка термической обработки
Термическая обработка — это группа промышленных и металлообрабатывающих процессов, используемых для изменения физических, а иногда и химических свойств материала. Чаще всего применяется в металлургии. Термическая обработка также используется при производстве многих других материалов, таких как стекло. Термическая обработка включает использование нагрева или охлаждения, обычно до экстремальных температур, для достижения желаемого результата, такого как отверждение или размягчение материала.
Методы термообработки включают отжиг, цементирование, дисперсионное упрочнение, отпуск и закалку. Примечательно, что хотя термин термическая обработка применяется только к процессам, в которых нагрев и охлаждение выполняются с конкретной целью преднамеренного изменения свойств, нагрев и охлаждение часто происходят случайно во время других производственных процессов, таких как горячая штамповка или сварка.
Термическая обработка часто связана с увеличением прочности материала, но ее также можно использовать для изменения определенных целей технологичности, таких как улучшение механической обработки, улучшение формуемости, восстановление пластичности после операции холодной обработки.Таким образом, это очень эффективный производственный процесс, который может не только помочь другим производственным процессам, но также может улучшить характеристики продукта за счет увеличения прочности или других желаемых характеристик.
Сегодня используются четыре основных типа термической обработки. Это отжиг, нормализация, закалка и отпуск. В следующих параграфах описаны методы, используемые в каждом процессе, и их отношение к металлургу.
ЗАКАЛКА
Закалка сталей проводится для повышения прочностных и износостойких свойств.При достаточном содержании углерода сталь можно сразу закалить. Закалка для большинства сталей заключается в нагреве стали до заданной температуры с последующим ее быстрым охлаждением путем погружения в масло, воду или рассол. Большинству сталей для закалки требуется быстрое охлаждение (закалка), но некоторые из них можно охлаждать воздухом с теми же результатами. Закалка увеличивает твердость и прочность стали, но делает ее менее пластичной. Чтобы удалить часть хрупкости, после закалки сталь следует отпустить.
Многие цветные металлы можно упрочнить и повысить их прочность за счет контролируемого нагрева и быстрого охлаждения. Чистое железо, кованое железо и чрезвычайно низкоуглеродистые стали обладают очень низкими упрочняющими свойствами, и их трудно закалить при термической обработке. Чугун имеет ограниченные возможности к закалке. При быстром охлаждении чугуна образуется белое железо, твердое и хрупкое. В простой углеродистой стали максимальная твердость, получаемая при термообработке, почти полностью зависит от содержания углерода в стали.
По мере увеличения содержания углерода упрочняющая способность стали увеличивается; однако эта способность к упрочнению с увеличением содержания углерода сохраняется только до определенного момента. Когда вы увеличиваете содержание углерода выше 0,80 процента, твердость не увеличивается, но увеличивается износостойкость. Когда вы легируете сталь для повышения ее твердости, сплавы делают углерод более эффективным в увеличении твердости и прочности. Из-за этого содержание углерода, необходимое для получения максимальной твердости, ниже, чем для простых углеродистых сталей.Обычно легированные стали превосходят углеродистые стали.
Углеродистые стали обычно закаливают в рассоле или воде, а легированные стали обычно закаливают в масле. При закалке углеродистой стали помните, что вы должны охладить сталь до температуры ниже 1000 ° F менее чем за 1 секунду. Закалка вызывает чрезвычайно высокие внутренние напряжения в стали, и для их снятия вы можете отпустить сталь непосредственно перед тем, как она станет холодной.
Закалка корпуса
Цементная закалка — это термохимический диффузионный процесс, при котором легирующий элемент, чаще всего углерод или азот, диффундирует в поверхность монолитного металла.Полученный твердый раствор внедрения тверже основного материала, что улучшает износостойкость без ущерба для прочности. Лазерная обработка поверхности — это обработка поверхности с высокой универсальностью, селективностью и новыми свойствами. Поскольку скорость охлаждения при лазерной обработке очень высока, этим методом можно получить даже метастабильное металлическое стекло.
Цементная закалка идеально подходит для деталей, которым требуется износостойкая поверхность и которые должны быть достаточно прочными изнутри, чтобы выдерживать большие нагрузки.Лучше всего для цементной закалки подходят стали низкоуглеродистые и низколегированные. При цементировании высокоуглеродистой стали твердость проникает в сердцевину и вызывает хрупкость. В случае закалки вы изменяете поверхность металла химически, вводя высокое содержание карбида или нитрида. Ядро остается химически незатронутым. При термообработке поверхность с высоким содержанием углерода реагирует на упрочнение, и сердцевина становится более жесткой.
Науглероживание
Науглероживание — это процесс цементации, при котором углерод добавляется к поверхности низкоуглеродистой стали.В результате получается науглероженная сталь с высокоуглеродистой поверхностью и низкоуглеродистой внутренней частью. Когда науглероженная сталь подвергается термообработке, корпус становится более твердым, а сердечник остается мягким и прочным.
Для науглероживания стали используются два метода. Один из методов заключается в нагреве стали в печи, содержащей атмосферу оксида углерода. В другом методе сталь помещается в контейнер, заполненный древесным углем или другим богатым углеродом материалом, а затем нагревается в печи. Чтобы остудить детали, вы можете оставить емкость в печи для охлаждения или вынуть ее и дать остыть на воздухе.В обоих случаях при медленном охлаждении детали отжигаются. Глубина проникновения углерода зависит от продолжительности периода замачивания. В современных методах науглероживание почти исключительно осуществляется в газовой атмосфере.
Цианирование
Этот процесс представляет собой быстрый и эффективный способ поверхностного упрочнения. Предварительно нагретую сталь погружают в нагретую цианистую ванну и дают ей впитаться. После удаления его охлаждают, а затем промывают для удаления остатков цианида. Этот процесс дает тонкую твердую оболочку, которая тверже, чем оболочка, полученная путем науглероживания, и может быть завершена за 20-30 минут или несколько часов.Главный недостаток в том, что цианидные соли — смертельный яд.
Азотирование
Этот метод цементации дает самую твердую поверхность из всех процессов упрочнения. Он отличается от других методов тем, что перед азотированием отдельные детали прошли термообработку и отпуск. Затем детали нагревают в печи, имеющей атмосферу газообразного аммиака. Закалка не требуется, поэтому можно не беспокоиться о короблении или других типах искажений. Этот процесс используется для упрочнения деталей, таких как шестерни, гильзы цилиндров, распределительные валы и другие детали двигателя, которые должны быть износостойкими и работать в зонах с высокой температурой.
Закалка пламенем
Закалка пламенем — это еще одна процедура, применяемая для упрочнения поверхности металлических деталей. Когда вы используете кислородно-ацетиленовое пламя, тонкий слой на поверхности детали быстро нагревается до критической температуры, а затем сразу же гасится комбинацией струи воды и холодного основного металла. В результате этого процесса получается тонкая, упрочненная поверхность, и в то же время внутренние детали сохраняют свои первоначальные свойства. Независимо от того, является ли процесс ручным или механическим, необходимо внимательно следить, поскольку горелки быстро нагревают металл, а температура обычно определяется визуально.
ЗАКАЛКА
Термин «отпуск» используется для описания нагрева после предварительной закалки, холодной обработки (холодное выравнивание) или сварки до температуры от комнатной до температуры ниже точки превращения Ac1 и выдержки при этой температуре с последующим охлаждением в зависимости от цели (DIN 17022 часть 1 -5). Микроструктура, которая была быстро преобразована в результате быстрого охлаждения, не находится в стабильном состоянии равновесия, что означает, что при повторном нагреве ударная вязкость увеличивается, и в то же время твердость может снижаться.Степень снижения твердости определяется температурой и периодом времени отпуска.
После закалки сталь часто оказывается тверже, чем необходимо, и слишком хрупкой для большинства практических применений. Кроме того, при быстром охлаждении от температуры затвердевания возникают серьезные внутренние напряжения. Для снятия внутренних напряжений и уменьшения хрупкости после закалки сталь следует отпускать. Закалка заключается в нагреве стали до определенной температуры (ниже температуры ее закалки), выдержке при этой температуре в течение необходимого периода времени, а затем в охлаждении, как правило, с подачей воздуха.Результирующие прочность, твердость и пластичность зависят от температуры, до которой сталь нагревается в процессе отпуска.
Для снятия внутренних напряжений и снижения хрупкости после закалки сталь следует отпускать. Закалка заключается в нагреве стали до определенной температуры (ниже температуры ее закалки), выдержке при этой температуре в течение необходимого периода времени, а затем в охлаждении, как правило, с подачей воздуха. Результирующие прочность, твердость и пластичность зависят от температуры, до которой сталь нагревается в процессе отпуска.
Закалка всегда следует за закалкой, но никогда не предшествует ей. Помимо снижения хрупкости, отпуск смягчает сталь. Это неизбежно, и степень потери твердости зависит от температуры, до которой нагревается сталь в процессе отпуска. Это верно для всех сталей, кроме быстрорежущей. Отпуск увеличивает твердость быстрорежущей стали.
В большинстве случаев требуется отпуск закаленных деталей. Отпуск состоит из нагрева стали ниже нижней критической температуры (часто от 400 до 1105 ° F или от 205 до 595 ° C, в зависимости от желаемых результатов) для придания некоторой прочности.Закалка также может производиться на нормализованных сталях. Отпуск всегда проводится при температурах ниже критической точки стали. Когда закаленная сталь повторно нагревается, отпуск начинается при 212 ° F и продолжается по мере увеличения температуры до низкокритической точки. Выбирая определенную температуру отпуска, вы можете заранее определить конечную твердость и прочность.
Минимальное температурное время отпуска должно составлять 1 час. Обычно скорость охлаждения от температуры отпуска не влияет на сталь.После извлечения из закалочной печи стальные детали обычно охлаждаются на неподвижном воздухе; однако есть несколько типов стали, которые необходимо закалить при температуре отпуска, чтобы предотвратить хрупкость. Эти голубые хрупкие стали могут стать хрупкими, если их нагреть в определенных температурных диапазонах и дать им медленно остыть. Некоторые хромоникелевые стали подвержены этой отпускной хрупкости.
Свежешлифованная или отполированная сталь при нагревании образует оксидные слои. Это приводит к появлению цветов на поверхности стали.С повышением температуры слой оксида железа увеличивается в толщине, меняя цвет. Эти цвета, называемые цветами закалки, веками использовались для измерения температуры металла. По цветам отпуска можно судить об окончательных свойствах закаленной стали. Очень твердая инструментальная сталь часто закаляется в диапазоне от светлой до темно-соломенной, тогда как пружинная сталь часто закаляется до синего цвета.
Однако окончательная твердость закаленной стали будет варьироваться в зависимости от состава стали.После нормализации сталь может быть подвергнута закалке при условии ее твердости. Отожженная сталь не поддается отпуску. Отпуск снимает закалочные напряжения и снижает твердость и хрупкость. Фактически, предел прочности закаленной стали может увеличиваться по мере отпуска стали до температуры около 450 ° F. Закалка увеличивает мягкость, пластичность, пластичность и ударопрочность. Твердость быстрорежущей стали повышается при отпуске, если она подвергается отпуску при высокой температуре (около 1550 ° F).Помните, что вся сталь должна быть удалена из закалочной ванны и отпущена до того, как она полностью остынет. Неправильный отпуск приводит к быстрому выходу из строя закаленной детали.
ОТЖИГ
Технологический отжиг используется для обработки упрочненных деталей из низкоуглеродистой стали (<0,25% углерода). Это позволяет деталям быть достаточно мягкими для дальнейшей холодной обработки без разрушения. Технологический отжиг осуществляется путем повышения температуры до уровня чуть ниже области феррит-аустенит, линия A1 на диаграмме.Эта температура составляет примерно 727 ºC (1341 ºF), поэтому достаточно нагреть ее до примерно 700 ºC (1292 ºF). Это выдерживается достаточно долго, чтобы позволить перекристаллизацию ферритной фазы, а затем охлаждают на неподвижном воздухе. Поскольку материал остается в одной и той же фазе на протяжении всего процесса, единственное изменение, которое происходит, - это размер, форма и распределение зернистой структуры. Этот процесс дешевле, чем полный отжиг или нормализация, поскольку материал не нагревается до очень высокой температуры и не охлаждается в печи.
В общем, отжиг противоположен закалке. Вы отжигаете металлы, чтобы снять внутренние напряжения, смягчить их, сделать их более пластичными и улучшить структуру их зерен. Отжиг состоит из нагревания металла до определенной температуры, выдерживания его при этой температуре в течение заданного времени, а затем охлаждения металла до комнатной температуры. Метод охлаждения зависит от металла и желаемых свойств. Некоторые металлы охлаждают в печи, а другие охлаждают, закапывая их в золе, извести или других изоляционных материалах.
Мягкий отжиг
Мягкий отжиг выполняется при температуре чуть ниже Ac1 *, иногда также выше Ac1 или путем колебания около Ac1 с последующим медленным охлаждением для достижения мягкого состояния (DIN 17022 часть 1-5). Благодаря этой термообработке цементитный слой перлита трансформируется в сферическую форму, известную как гранулированный цементит. Этот тип микроструктуры обеспечивает наилучшую обрабатываемость сталей с содержанием углерода более прибл. 0,5%. Гранулированный цементит обеспечивает наилучшую обрабатываемость для любого типа холодной обработки. E.грамм. для холодной высадки, волочения или холодной экструзии.
Полный отжиг
Полный отжиг — это процесс медленного повышения температуры примерно на 50 ºC (90 ºF) выше линии аустенитной температуры A3 или линии ACM в случае доэвтектоидных сталей (стали с содержанием углерода <0,77%) и 50 ºC (90 ºF) в Область аустенит-цементит в случае заэвтектоидных сталей (стали с содержанием углерода> 0,77%). Его выдерживают при этой температуре в течение достаточного времени, чтобы весь материал превратился в аустенит или аустенит-цементит, в зависимости от обстоятельств.Затем его медленно охлаждают со скоростью примерно 20 ºC / час (36 ºF / час) в печи до примерно 50 ºC (90 ºF) в диапазоне феррит-цементит. Теперь его можно охлаждать на воздухе комнатной температуры с естественной конвекцией.
Отжиг для снятия напряжения
Отжиг для снятия напряжений используется для снижения остаточных напряжений в крупных отливках, сварных деталях и деталях холодной штамповки. Такие детали имеют тенденцию испытывать напряжения из-за термоциклирования или наклепа. Детали нагревают до температуры 600–650 ºC (1112–1202 ºF), выдерживают в течение длительного времени (около 1 часа или более), а затем медленно охлаждают на неподвижном воздухе.
Сфероидизация
Сфероидизация — это процесс отжига, используемый для высокоуглеродистых сталей (углерод> 0,6%), которые впоследствии будут подвергнуты механической обработке или холодной штамповке. Это делается одним из следующих способов:
1. Нагрейте деталь до температуры чуть ниже линии феррит-аустенит, линия A1 или ниже линии аустенит-цементит, существенно ниже линии 727 ºC (1340 ºF). Удерживайте температуру в течение длительного времени, после чего следует довольно медленное охлаждение. Или
2.Несколько раз переключитесь между температурами немного выше и немного ниже 727 ºC (1340 ºF), например, между 700 и 750 ºC (1292–1382 ºF), и медленно охладите. Или
3. Для инструментальной и легированной стали нагреть до 750-800 ºC (1382-1472 ºF) и выдержать несколько часов с последующим медленным охлаждением.
Все эти методы приводят к получению структуры, в которой весь цементит находится в форме небольших глобул (сфероидов), рассеянных по ферритной матрице. Эта структура позволяет улучшить обработку при непрерывных операциях резания, таких как токарные и винтовые станки.Сфероидизация также повышает устойчивость к истиранию.
НОРМАЛИЗАЦИЯ
Нормализация — это метод, используемый для обеспечения однородности размера зерна и состава во всем сплаве. Этот термин часто используется для черных сплавов, которые были нагреты выше верхней критической температуры, а затем охлаждались на открытом воздухе. При нормализации сталь нагревается до температуры (примерно от 20 ° C до 50 ° C) выше верхней точки превращения Ac3 для заэвтектоидных сталей выше Ac1, а затем охлаждается в статическом воздухе.Он используется для получения ровной мелкозернистой микроструктуры.
Нормализация — это процесс повышения температуры выше 60 º C (108 ºF) выше линии A3 или линии ACM полностью в пределах аустенитного диапазона. Его выдерживают при этой температуре, чтобы полностью преобразовать структуру в аустенит, а затем удаляют из печи и охлаждают до комнатной температуры в условиях естественной конвекции. Это приводит к зернистой структуре мелкодисперсного перлита с избытком феррита или цементита. Полученный материал получается мягким; степень мягкости зависит от реальных условий охлаждения.Этот процесс значительно дешевле полного отжига, поскольку не требует дополнительных затрат на контролируемое охлаждение печи.
Для доэвтектоидных сталей микроструктура состоит из перлита и феррита, а для заэвтектоидных сталей — из перлита и цементита. Чем выше скорости нагрева и охлаждения, тем мельче становятся зерна в микроструктуре, при условии, что превращение во время охлаждения происходит на стадии перлита.
Нормализация позволяет устранить неравномерную и крупнозернистую микроструктуру, образовавшуюся во время горячей штамповки.Кроме того, для сталей с содержанием углерода менее 0,5%, которые легко трансформируются, корректировка перлитно-ферритной микроструктуры с в значительной степени равномерным распределением приводит к хорошим механическим свойствам. Нормализация — это вид термической обработки, применимый только к черным металлам. Он отличается от отжига тем, что металл нагревается до более высокой температуры, а затем удаляется из печи для охлаждения на воздухе.
Нормализованные стали тверже и прочнее отожженных сталей. В нормализованном состоянии сталь намного прочнее, чем в любом другом структурном состоянии.Детали, подверженные ударам, и те, которые требуют максимальной прочности с устойчивостью к внешним нагрузкам, обычно нормализуются. При нормализации масса металла влияет на скорость охлаждения и получаемую структуру. Тонкие кусочки остывают быстрее и после нормализации тверже, чем толстые. При отжиге (охлаждение в печи) твердость обоих примерно одинакова.
Возможно вам понравится
Случайные столбы
- Явление хрупкого разрушения
Существуют ситуации, в которых сопротивление разрушению определяется не прочностью, а несущей способностью t… - Процессы формовки металла
Деформации металла возникают из-за приложения внешних сил к заготовке, которые уравновешены … - Что такое золото?
Золото сопротивляется воздействию отдельных кислот, но оно может быть растворено царской водкой (нитро-соляной кислотой), так называемой … - Медное покрытие
Гальваника — это процесс использования электрического тока для нанесения электрического покрытия проводящий объект с тонким слоем… - Фазовая диаграмма железа и углерода — Fe-Fe3C и диаграмма TTT
Кривые преобразования время-температура соответствуют началу и окончанию преобразований, которые простираются до …
5 Типы термической обработки и Их назначение в прецизионной обработке
Есть много способов изменить поведение металлов и их реакцию на прецизионную обработку. Один из таких методов — термическая обработка. Термическая обработка может быть применена к детали до того, как сделать материал более поддающимся механической обработке, или компоненты могут быть подвергнуты механической обработке перед стадиями окончательной закалки и нагрева.Термическая обработка может влиять на ряд различных аспектов металла, включая прочность, твердость, ударную вязкость, обрабатываемость, формуемость, пластичность и эластичность. Это также может повлиять на физические и механические свойства металла, чтобы изменить использование металла или изменить будущую работу с ним. Здесь мы более подробно рассмотрим различные типы термообработки и их влияние на детали во время прецизионной обработки.
ЗАКАЛКА
При термообработке для упрочнения металла металл нагревается до температуры, при которой элементы в металле превращаются в раствор.До этого дефекты в структуре кристаллической решетки металла являются основным источником «отдачи» или пластичности. Термическая обработка устраняет эти недостатки, превращая металл в надежный раствор с мелкими частицами для упрочнения металла. После того, как металл полностью нагревается до нужной температуры для образования твердого раствора, его быстро охлаждают, чтобы уловить частицы в растворе.
При дисперсионном твердении частицы примесей добавляются к металлическому сплаву для дальнейшего повышения прочности.
УПЛОТНЕНИЕ КОРПУСА
В процессе цементации внешний слой металла упрочняется, а внутренний металл остается мягким. Для металлов с низким содержанием углерода, таких как железо и сталь, в поверхность необходимо ввести дополнительный углерод. Упрочнение — это процесс, который часто используется в качестве заключительного этапа после того, как деталь уже была обработана. Высокая температура используется в сочетании с другими элементами и химикатами для создания твердого внешнего слоя. Поскольку закалка может сделать металлы более хрупкими, упрочнение может быть полезно в тех случаях, когда требуется гибкий металл с прочным износостойким слоем.
ОТЖИГ
Отжиг — это метод термообработки, при котором металл, такой как алюминий, медь, сталь, серебро или латунь, нагревают до определенной температуры, выдерживают при этой температуре в течение некоторого времени, чтобы произошло превращение, а затем охлаждают на воздухе. Этот процесс увеличивает пластичность металла и снижает твердость, чтобы металл стал более пригодным для обработки. Медь, серебро и латунь можно охлаждать быстро или медленно, тогда как черные металлы, такие как сталь, всегда нужно охлаждать постепенно, чтобы произошел отжиг.Отжиг может использоваться перед обработкой металла для повышения его стабильности, что снижает вероятность растрескивания или разрушения более твердых материалов.
НОРМАЛИЗАЦИЯ
Нормализация — это процесс отжига стали, при котором она нагревается на 150-200 ° F выше, чем при отжиге, и выдерживается при критической температуре, достаточной для того, чтобы произошло превращение. Обработанная таким образом сталь должна охлаждаться на воздухе. Термическая обработка при нормализации приводит к более мелким аустенитным зернам, тогда как воздушное охлаждение дает более мелкие ферритные зерна.Этот процесс улучшает обрабатываемость, пластичность и прочность стали. Стандартизация также полезна для удаления столбчатых зерен и дендритной сегрегации, которые могут возникнуть во время литья детали.
ТЕМПЕРИЗАЦИЯ
Закалка — это метод термической обработки, используемый для повышения упругости сплавов на основе железа, таких как сталь. Металлы на основе железа очень твердые, но часто слишком хрупкие, чтобы их можно было использовать в большинстве случаев. Отпуск может использоваться для изменения твердости, пластичности и прочности металла, что обычно облегчает его обработку.Металл будет нагреваться до температуры ниже критической точки, поскольку более низкие температуры уменьшают хрупкость при сохранении твердости. Для повышения пластичности при меньшей твердости и прочности требуются более высокие температуры.
Другой вариант — приобрести закаленный материал или упрочнить материал перед обработкой. Хотя это затрудняет обработку, это устраняет риск изменения размеров деталей, в отличие от процесса термообработки после обработки. Это также может устранить необходимость в шлифовальном цехе для получения жесткой отделки или допусков.
INVERSE SOLUTIONS, INC. ЯВЛЯЕТСЯ ОДНИМ ИЗ МАШИНОСТРОИТЕЛЬНЫХ МАГАЗИНОВ, КОТОРЫЕ МОГУТ ПРИОБРЕСТИ УЖЕ ЗАКАЛЕННЫЙ МАТЕРИАЛ.Термическая обработка может быть важной частью процесса прецизионной обработки для преобразования металлов и обеспечения того, чтобы ваши детали и детали работали так, как вам нужно. Поговорите с одним из наших квалифицированных инженеров по точному производству о ваших требованиях и о том, как найти правильный метод термообработки для вашего проекта точного машиностроения.
Обзор методов термообработки и их преимуществ
Термическая обработка — это процесс нагрева и охлаждения металлов с использованием определенных заранее определенных методов для получения желаемых свойств .Как черные, так и цветные металлы перед использованием проходят термическую обработку.
Со временем было разработано множество различных методов. Даже сегодня металлурги постоянно работают над улучшением результатов и рентабельности этих процессов.
Для этого они разрабатывают новые графики , или цикла, для производства различных марок. Каждый график относится к разной скорости нагрева, выдержки и охлаждения металла.
При тщательном соблюдении этих методов можно производить металлы различных стандартов с удивительно специфическими физическими и химическими свойствами.
Преимущества
Есть разные причины для проведения термообработки. Некоторые процедуры делают металл мягким, а другие повышают твердость. Они также могут повлиять на электрическую и теплопроводность этих материалов.
Некоторые методы термообработки снимают напряжения, возникшие в более ранних процессах холодной обработки. Другие придают металлам желаемые химические свойства. Выбор идеального метода зависит от типа металла и требуемых свойств.
В некоторых случаях металлическая деталь может пройти несколько процедур термообработки.Например, некоторые суперсплавы, используемые в авиастроении, могут пройти до шести различных этапов термообработки, чтобы оптимизировать их для применения.
Этапы процесса термообработки
Проще говоря, термическая обработка — это процесс нагрева металла, выдержки его при этой температуре и последующего охлаждения. В процессе обработки металлическая деталь претерпевает изменения в своих механических свойствах. Это связано с тем, что высокая температура изменяет микроструктуру металла.И микроструктура играет важную роль в механических свойствах материала.
Конечный результат зависит от множества различных факторов. К ним относятся время нагрева, время выдержки металлической детали при определенной температуре, скорость охлаждения, окружающие условия и т. Д. Параметры зависят от метода термообработки, типа металла и размера детали.
В ходе этого процесса свойства металла изменятся. Среди этих свойств — электрическое сопротивление, магнетизм, твердость, вязкость, пластичность, хрупкость и коррозионная стойкость.
Отопление
Детали реактивного двигателя, идущие в печьКак мы уже говорили, микроструктура сплавов будет изменяться в процессе термообработки. Нагрев осуществляется в соответствии с заданным термическим профилем.
Сплав может находиться в одном из трех различных состояний при нагревании. Это может быть механическая смесь, твердый раствор или их комбинация.
Механическая смесь аналогична бетонной смеси, в которой цемент связывает песок и гравий.Песок и гравий все еще видны как отдельные частицы. В случае металлических сплавов механическая смесь удерживается основным металлом.
С другой стороны, в твердом растворе все компоненты смешиваются гомогенно. Это означает, что их невозможно идентифицировать индивидуально даже под микроскопом.
Каждый штат приносит с собой разные качества. По фазовой диаграмме возможно изменение состояния путем нагрева. Однако охлаждение определяет конечный результат.Сплав может оказаться в одном из трех состояний, в зависимости только от метода.
Холдинг
Во время выдержки или выдержки металл поддерживается при достигнутой температуре. Продолжительность зависит от требований.
Например, поверхностная закалка требует только структурных изменений поверхности металла для увеличения твердости поверхности. В то же время для других методов требуются единые свойства. В этом случае период владения больше.
Время замачивания также зависит от типа материала и размера детали. Для более крупных деталей требуется больше времени, если целью является единообразие свойств. Просто требуется больше времени, чтобы сердцевина большой детали достигла необходимой температуры.
Охлаждение
После завершения стадии пропитывания металл необходимо охладить в установленном порядке. На этом этапе тоже происходят структурные изменения. Твердый раствор при охлаждении может оставаться таким же, полностью или частично превращаться в механическую смесь, в зависимости от различных факторов.
Различные среды, такие как рассол, вода, масло или принудительный воздух, регулируют скорость охлаждения. Вышеупомянутая последовательность охлаждающих сред находится в порядке убывания эффективной скорости охлаждения. Рассол быстрее всего поглощает тепло, а воздух — медленнее всего.
Также можно использовать печи в процессе охлаждения. Контролируемая среда обеспечивает высокую точность, когда необходимо медленное охлаждение.
Фазовые диаграммы
Каждый металлический сплав имеет свою фазовую диаграмму. Как уже было сказано ранее, термическая обработка проводится по этим схемам.Они показывают структурные изменения, происходящие при разных температурах и различном химическом составе.
Давайте возьмем фазовую диаграмму железо-углерод в качестве примера, так как это наиболее известная и широко используемая в университетах диаграмма.
Фазовая диаграмма железо-углерод является важным инструментом при изучении поведения различных углеродистых сталей при термообработке. По оси абсцисс показано содержание углерода в сплаве, а по оси ординат — температура.
Обратите внимание, что 2,14% углерода — это предел, при котором сталь превращается в чугун,
На диаграмме показаны различные области, где металл находится в различных микросостояниях, таких как аустенит, цементит, перлит. Эти области обозначены границами A1, A2, A3 и Acm. На этих границах раздела фазовые изменения происходят, когда через них проходит значение температуры или содержания углерода.
A1: Верхний предел фазы цементита / феррита.
A2: Предел, при котором железо теряет свой магнетизм.Температура, при которой металл теряет свой магнетизм, также называется температурой Кюри.
A3: граница раздела фаз аустенит + феррит от γ (гамма) аустенитной фазы.
Acm: граница раздела, которая отделяет γ-аустенит от поля аустенит + цементит.
Фазовая диаграмма — важный инструмент для определения того, будет ли термическая обработка полезной или нет. Каждая структура придает конечному продукту определенные качества, и выбор термообработки зависит от этого.
Общие методы термообработки
Есть несколько методов термообработки на выбор. Каждый из них обладает определенными качествами.
К наиболее распространенным методам термообработки относятся:
- Отжиг
- Нормализация
- Закалка
- Старение
- Снятие напряжения
- Закалка
- Науглероживание
Отжиг
При отжиге металл нагревается выше верхней критической температуры, а затем медленно охлаждается.
Отжиг проводится для размягчения металла. Это делает металл более пригодным для холодной обработки и формовки. Он также улучшает обрабатываемость, пластичность и вязкость металла.
Отжиг также полезен для снятия напряжений в детали, вызванных предшествующими процессами холодной обработки. Имеющиеся пластические деформации устраняются во время рекристаллизации, когда температура металла пересекает верхнюю критическую температуру.
Металлы могут подвергаться множеству методов отжига, таких как рекристаллизационный отжиг, полный отжиг, частичный отжиг и окончательный отжиг.
Нормализация
Нормализация — это процесс термообработки, используемый для снятия внутренних напряжений, вызванных такими процессами, как сварка, литье или закалка.
В этом процессе металл нагревается до температуры, которая на 40 ° C выше его верхней критической температуры.
Эта температура выше, чем температура, используемая для закалки или отжига. После выдержки при этой температуре в течение определенного периода времени его охлаждают на воздухе. Нормализация создает однородный размер зерна и состав по всей детали.
Нормализованная сталь тверже и прочнее отожженной стали. Фактически, в нормализованном виде сталь прочнее, чем в любом другом состоянии. Вот почему детали, которые требуют ударной вязкости или должны выдерживать большие внешние нагрузки, почти всегда будут нормализованы.
Закалка
Закалка, наиболее распространенный из всех процессов термообработки, используется для увеличения твердости металла. В некоторых случаях затвердеть может только поверхность.
Заготовку закаляют, нагревая ее до заданной температуры, а затем быстро охлаждая, погружая в охлаждающую среду.Можно использовать масло, рассол или воду. Полученная деталь будет иметь повышенную твердость и прочность, но одновременно возрастет и хрупкость.
Цементная закалка — это процесс упрочнения, при котором упрочняется только внешний слой заготовки. Используемый процесс такой же, но поскольку тонкий внешний слой подвергается обработке, полученная рабочая деталь имеет твердый внешний слой, но более мягкую сердцевину.
Это обычное дело для валов. Твердый внешний слой защищает его от износа материала.В противном случае при установке подшипника на вал он может повредить поверхность и сместить некоторые частицы, которые ускорят процесс износа. Закаленная поверхность обеспечивает защиту от этого, а сердечник по-прежнему обладает необходимыми свойствами, чтобы выдерживать усталостные напряжения.
Индукционная закалка
Другие типы процессов закалки включают индукционную закалку, дифференциальную закалку и закалку пламенем. Однако закалка пламенем может привести к образованию зоны термического влияния, которая возникает после охлаждения детали.
Старение
График старения алюминия 6061Старение или дисперсионное твердение — это метод термообработки, который в основном используется для повышения предела текучести ковких металлов. В ходе процесса образуются равномерно диспергированные частицы в структуре зерна металла, что приводит к изменению свойств.
Осадочное твердение обычно происходит после еще одного процесса термообработки, при котором достигаются более высокие температуры. Однако старение только повышает температуру до среднего уровня и снова быстро снижает ее.
Некоторые материалы могут стареть естественным образом (при комнатной температуре), в то время как другие стареют только искусственно, то есть при повышенных температурах. Для естественно стареющих материалов может быть удобно хранить их при более низких температурах.
Снятие стресса
Снятие напряжения особенно часто используется для деталей котлов, баллонов с воздухом, аккумуляторов и т. Д. Этот метод нагревает металл до температуры чуть ниже его нижней критической границы. Процесс охлаждения медленный и, следовательно, равномерный.
Это делается для снятия напряжений, которые возникли в деталях из-за более ранних процессов, таких как формовка, механическая обработка, прокатка или правка.
Закалка
Закалка — это процесс уменьшения избыточной твердости и, следовательно, хрупкости, возникающей в процессе закалки. Также снимаются внутренние напряжения. Прохождение этого процесса может сделать металл пригодным для многих применений, в которых требуются такие свойства.
температура обычно намного ниже температуры застывания. Чем выше температура, тем мягче становится конечная заготовка. Скорость охлаждения не влияет на структуру металла во время отпуска, и обычно металл охлаждается на неподвижном воздухе.
Науглероживание
Науглероживание корпуса
В этом процессе термообработки металл нагревается в присутствии другого материала, который выделяет углерод при разложении.
Освободившийся углерод абсорбируется поверхностью металла. Содержание углерода на поверхности увеличивается, что делает ее более твердой, чем внутреннее ядро.
Какие металлы подходят для термической обработки?
Хотя черные металлы составляют большинство термообработанных материалов, сплавы меди, магния, алюминия, никеля, латуни и титана также могут подвергаться термообработке.
Около 80% термически обрабатываемых металлов — это стали различных марок. Черные металлы, которые можно подвергать термической обработке, включают чугун, нержавеющую сталь и различные марки инструментальной стали.
Такие процессы, как закалка, отжиг, нормализация, снятие напряжений, поверхностная закалка, азотирование и отпуск, обычно выполняются на черных металлах.
Медь и медные сплавы подвергаются таким методам термической обработки, как отжиг, старение и закалка.
Алюминий подходит для таких методов термообработки, как отжиг, термообработка в растворе, естественное и искусственное старение.Термическая обработка алюминия — это точный процесс. Объем процесса должен быть установлен, и его следует тщательно контролировать на каждом этапе для достижения желаемых характеристик.
Очевидно, не все материалы подходят для термической обработки. Точно так же не обязательно использовать каждый метод для отдельного материала. Поэтому каждый материал нужно изучать отдельно, чтобы добиться желаемого результата. Использование фазовых диаграмм и доступной информации о влиянии вышеупомянутых методов является отправной точкой.
Процессы термообработки: виды, методы, цели [PDF]
Из этой статьи вы узнаете, что такое процесс термообработки ? Его методы , типы и цель , процедура , применение термообработки. Термическая обработка является важной операцией в процессе производства деталей машин и инструментов.
Что такое термическая обработка?Термическая обработка определяется как операция, включающая нагрев и охлаждение металла или сплава в твердом состоянии для получения определенных желаемых свойств без изменения состава.
Процесс термообработки выполняется для изменения размера зерна, модификации структуры материала и снятия напряжений, возникающих в материале после горячей или холодной обработки.
- Термическая обработка проводится для улучшения обрабатываемости.
- Для улучшения магнитных и электрических свойств.
- Для повышения устойчивости к износу, нагреву и коррозии и многому другому.
Термическая обработка заключается в нагревании металла до температуры, близкой к критической или превышающей ее, удерживаемой в течение определенного времени, с последующим охлаждением металла в некоторой среде, которая может быть воздухом, водой, рассолом или расплавом солей.Процесс термообработки включает отжиг, поверхностную закалку, отпуск, нормализацию и закалку, азотирование, цианирование и т. Д.
Типы процессов термообработкиНиже приведены различных типов процессов термообработки:
- Отжиг
- Нормализация
- закалка
- Закалка
- Азотирование
- Цианирование
- Индукционная закалка
- Закалка пламенем
Читайте также:
Типы термообработки 1.ОтжигОтжиг — один из важнейших процессов термообработки. Это одна из наиболее широко используемых операций термической обработки чугуна и стали, которая определяется как процесс размягчения.
Нагрев на 30–50 ° C выше верхней критической температуры и очень медленное охлаждение путем поиска печи. Основная цель отжига — сделать сталь более пластичной и ковкой, а также снять внутренние напряжения. Этот процесс делает сталь мягкой, поэтому ее можно легко обрабатывать.
1.1 Цель отжига- Смягчает сталь и улучшает ее обрабатываемость.
- Для измельчения зерна и удаления газов.
- Устраняет внутренние напряжения, возникшие во время предыдущего процесса.
- Для получения желаемой пластичности, пластичности и вязкости.
- Изменяет электрические и магнитные свойства.
В зависимости от содержания углерода сталь нагревается до температуры примерно на 50–55 ° C выше критического диапазона температур.При такой температуре ее выдерживают в течение определенного времени в зависимости от типа печи и характера работы. Затем стали позволяют постоянно остывать внутри печи.
1.3 Применение отжигаПрименяется для отливок и поковок.
2. НормализацияНормализация: Основная цель нормализации — это устранение внутренних напряжений, возникающих после процесса холодной обработки. При этом сталь нагревается на 30-50 ° C выше ее верхней критической температуры и охлаждается на воздухе.
Улучшает механические и электрические свойства, обрабатываемость и прочность на разрыв. Нормализация — это процесс термической обработки, проводимый для восстановления структуры нормального состояния.
2.1 Цель нормализации- Содействовать единообразию структуры.
- Для измельчения зерна.
- Для достижения желаемых изменений свойств стали.
Сталь нагревают до температуры примерно на 40-50 ° C выше ее верхней критической температуры.При этой температуре его выдерживают непродолжительное время. Затем стали дают остыть на неподвижном воздухе при комнатной температуре, что называется закалкой на воздухе.
2.3 Применение нормализации- Применяется отливок и поковок для улучшения зернистой структуры и снятия напряжений.
- Применяется после холодной обработки, такой как прокатка, штамповка и ковка.
Закалка: Основная цель процесса закалки — сделать сталь твердой и вязкой.В этом процессе сталь нагревается на 30-40 ° C выше верхней критической температуры, а затем продолжается охлаждение до комнатной температуры путем закалки в воде или масле. Это процесс, противоположный отжигу.
3.1 Назначение закалки- Закалкой увеличивает твердость стали.
- Устойчивость к износу
- Позволяет стали резать другие металлы
Сталь нагревается выше критического диапазона температур.Он выдерживается при этой температуре в течение определенного периода времени. Затем сталь быстро охлаждают в среде закалки.
Закалочная среда выбирается в соответствии с желаемой степенью твердости. В качестве закалочных сред используются воздух, вода, газы, масла и расплавленные соли. Тонкое сечение лезвий таких ножей охлаждается на воздухе. Вода — широко используемая среда, но она приводит к образованию пузырьков на поверхности металла.
Следовательно, для предотвращения этого используется рассол. Масло используется, когда есть риск деформации трещин, и подходит для легированных сталей.Расплавленные соли используются для охлаждения тонкого сечения с целью получения без трещин и ударопрочных продуктов.
3.3 Применение закалкиПрименяется для стамески, кувалды, ручного молотка, кернеров, метчиков, штампов, фрез, лезвий ножей и зубчатых колес.
4. ОтпускОтпуск: когда в процессе закалки стальной образец затвердевает, он становится хрупким и имеет высокое остаточное напряжение. Это операция, используемая для изменения свойств стали, закаленной закалкой, с целью повышения ее полезности.
Отпуск или вытяжка приводят к снижению хрупкости и устранению внутренних деформаций, возникающих во время закалки. После закалки сталь необходимо отпустить.
Отпуск подразделяется на три категории в зависимости от полезности используемой стали.
- Низкотемпературный отпуск.
- Среднетемпературный отпуск.
- Высокотемпературный отпуск.
- Для снятия внутренних напряжений, вызванных закалкой.
- Для уменьшения хрупкости.
- Повышение пластичности, прочности и вязкости.
- Для повышения износостойкости.
- Для получения желаемых механических свойств.
Сталь после закалки в процессе закалки повторно нагревается до температуры, немного превышающей температурный диапазон, в котором она будет использоваться, но ниже нижней критической температуры. Температура здесь колеблется от 100 ° C до 700 ° C.
Повторный нагрев осуществляется в ванне из масла, расплавленного свинца или расплавленной соли. Образец выдерживают в ванне некоторое время до достижения равномерной температуры, время зависит от состава и желаемого качества стали. Теперь образец вынимают из ванны и дают медленно остыть на неподвижном воздухе.
4.3 Применение закалкиПрименяется к режущим инструментам, инструментам и зубчатым колесам, закаленным в процессе закалки.
5.АзотированиеАзотирование — это процесс поверхностного упрочнения, при котором газообразный азот используется для получения твердой корки металла. В этом процессе сталь нагревается в присутствии аммиака.
За счет этого осаждается атом азота, что делает материал твердым. Предметы индукционной закалки и закалки пламенем нагреваются кислородно-ацетиленовым пламенем.
5.1 Назначение азотирования- Для упрочнения поверхности стали на определенную глубину.
- Повышение сопротивления износу и усталости.
- Для повышения коррозионной стойкости.
Это делается в электропечи, где поддерживается температура от 450 ° до 510 ° C. Деталь хорошо обработана и обработана и помещена в герметичный контейнер, снабженный выпускными и впускными трубками, по которым циркулирует газообразный аммиак.
Емкость с деталью помещается в печь и пропускается газообразный аммиак, пока печь нагревается.
В процессе нагрева из аммиака выделяется газообразный азот в виде атомарного азота, который вступает в реакцию с поверхностью детали и образует нитрат железа.
Глубина входа зависит от продолжительности времени, проведенного при температуре азотирования. Деталь вынимается и не требует закалки и дальнейшей термообработки.
5.3 Применение азотирования- Применяется для упрочнения поверхности среднеуглеродистых легированных сталей.
Цианирование: В этом процессе сталь нагревается в присутствии среды цианида натрия. Благодаря этому атомы углерода и азота откладываются на поверхности стали и делают ее твердой.
6.1 Назначение цианирования- Этот метод эффективен для повышения предела выносливости деталей среднего и малого размера, таких как шестерни, валы, пальцы и т. Д.
- Для увеличения твердости поверхности.
- Повышение износостойкости.
- Для придания чистой, яркой и приятной поверхности затвердевшей поверхности.
Обрабатываемые детали погружают в ванну с расплавом цианидной соли, поддерживаемую при температуре 950 ° C. Используемые расплавленные соли представляют собой хлорид натрия, карбонат натрия, цианид натрия и кальцинированную соду.
Погруженное изделие оставляют в расплаве цианидной соли при температуре 950 ° C примерно на 15-20 минут. При разложении цианида натрия из окиси углерода выделяется азот и углерод, которые диффундируют в поверхность, что приводит к ее упрочнению.Затем деталь вынимают из ванны и закаливают в воде или масле.
6.3 Применение цианирования- Применяется для небольших изделий, таких как шестерни, втулки, винты, штифты и небольшие ручные инструменты, для которых требуется тонкая и твердая износостойкая поверхность.
Науглероживание: в этом процессе сталь нагревается в присутствии углерода. За счет этого атомы углерода откладываются на поверхности металла и делают ее твердой.
8. Поверхностная закалка или поверхностная закалкаОсновная цель этого процесса — сделать единственную внешнюю поверхность стали твердой, а внутреннюю сердцевину — мягкой. Это процесс науглероживания, т. Е. Насыщения поверхностного слоя стали углеродом, или какой-либо другой процесс, при котором корпус упрочняется, а сердечник остается мягким.
8.1 Назначение упрочнения- Для придания твердости и износостойкости деталям машин.
- Путем поверхностного упрочнения получается прочная сердцевина.
- Для получения более высокого предела выносливости и высоких механических свойств сердечника.
Ниже приведены цели термической обработки.
- Для улучшения механических свойств, таких как прочность на разрыв, твердость, пластичность, ударопрочность и устойчивость к коррозии.
- Улучшить обрабатываемость.
- Для снятия внутренних напряжений металла, возникающих при холодной или горячей обработке.
- Для изменения или уточнения размера зерна.
- Улучшение магнитных и электрических свойств.
- Повышение устойчивости к износу и коррозии.
- Для повышения твердости поверхности.
Загрузите эту статью в формате PDF.
Заключение
Итак, теперь мы надеемся, что мы развеяли все ваши сомнения относительно процесса термообработки. Если у вас все еще есть сомнения по поводу процесса термообработки или методов, типов, применения, вы можете задать вопрос в комментариях.
У нас также есть сообщество на Facebook для вас, ребята. Если вы хотите, вы можете присоединиться к нашему сообществу, вот ссылка на нашу группу в Facebook.
Спасибо, что прочитали. Если вам понравилась наша статья, поделитесь ею с друзьями. Если у вас есть какие-либо вопросы по какой-либо теме, вы можете задать их в разделе комментариев.
Подпишитесь на нашу рассылку, чтобы получать уведомления, когда мы загружаем новые сообщения.
Подробнее о Mechanical Engg на нашем сайте:
- Свойства и типы формовочного песка
- Чугун: типы, свойства и влияние примесей
- Список из 20 различных типов гаек и болтов
Понимание различных типов термообработки
В прошлой статье мы обсудили множество различных типов отжига и уменьшение искажений с помощью отжига для снятия напряжения.В этой статье мы обсудим основные методы закалки стали.
Закалка и отпуск
Самый распространенный метод закалки стали в настоящее время в промышленности заключается в нагреве стальной детали до температуры аустенизации; закалка в подходящем закалочном растворе; и отпуск до желаемой твердости. Это схематично показано на рисунке 1.
Рисунок 1: Схема, представляющая типичную закалку и отпуск до типичной кривой TTT.В этом примере деталь подвергается аустенитизации, а затем закалке в закалочной среде достаточно быстро, чтобы поверхность и центр детали не попадали в «нос» кривой TTT и полностью закаливались.Самая медленная закалка для достижения сквозного твердения соответствует скорости закалки, достаточной для того, чтобы просто пропустить «вершину» кривой TTT. Более низкие скорости закалки, чем минимальные, приведут к образованию продуктов немартенситного превращения феррита, перлита и бейнита. Следует отметить, что кривая ТТТ не влияет на реакцию отпуска.
Это наиболее распространенный тип термообработки сталей, применимый к широкому спектру термообработок всех типов компонентов, включая детали аэрокосмической, автомобильной и сельскохозяйственной техники.В большинстве случаев температура аустенизации примерно на 25-30 градусов Цельсия выше температуры A c3 . После надлежащей выдержки при температуре деталь быстро закаливают в рассоле, воде, полимере или масле. Охлаждающая жидкость обычно составляет менее 80 ° C для масла и при температуре окружающей среды для охлаждающих средств на водной основе (вода, рассол и полимер). Деталь остается в закалочной среде до тех пор, пока она не достигнет температуры, примерно равной температуре закалки. Затем деталь снимается с закалки и немедленно отпускается.Если деталь не закаляется сразу (обычно в течение 90 минут после закалки), деталь может иметь склонность к образованию трещин при закалке. Этот вид термообработки подвержен деформации и остаточным напряжениям. Чтобы свести к минимуму деформацию и остаточные напряжения, закалка выбирается для достижения свойств и минимизации деформации.
Закупка
Закалка — это специализированный процесс, который используется только тогда, когда возникает проблема деформации и высоких остаточных напряжений. В этом процессе детали закаливают от температуры аустенизации до горячего масла или расплавленной соли при приблизительной начальной температуре мартенсита (100-200 градусов C).Деталь выдерживают при температуре масла до тех пор, пока температура поверхности и центра детали не станет почти одинаковой. Как только центр детали достигнет температуры охлаждающей жидкости, деталь удаляют из охлаждающей жидкости и дают ей остыть любым удобным способом (обычно воздушным охлаждением). Это предотвращает образование термических напряжений из-за неравномерного охлаждения между центром и поверхностью (рис. 2).
Рисунок 2: Схематическое изображение темперирования.Если должно произойти полное затвердевание, аустенит должен остыть достаточно быстро, чтобы не допустить, чтобы средняя скорость охлаждения не попала в «нос» диаграммы TTT.Поскольку диаграмма TTT показывает начальную температуру мартенсита, M s , диаграмма TTT полезна для выбора оптимальной температуры закалки и оценки времени, в течение которого деталь должна выдерживаться при температуре, чтобы предотвратить образование бейнита.
Мартемперинг, скорее всего, используется для науглероженных деталей. Карбюризированный корпус детали имеет большее содержание углерода, чем сердечник. Поскольку корпус имеет большее содержание углерода, температура M s в корпусе ниже, чем в активной зоне.Деталь закаливают в масло или расплав соли при температурах чуть выше температуры M s науглероженного корпуса. Это означает, что сердечник часто трансформируется раньше, чем корпус, в результате чего возникают полезные сжимающие остаточные напряжения на поверхности науглероженных деталей.
Легированные стали обычно более поддаются отпуску. По большей части, любая сталь, подвергающаяся закалке в масле, может быть подвергнута закалке в масле. Стали с высоким углеродным эквивалентом (CE), склонные к образованию трещин при закалке, часто подвергаются закалке во избежание растрескивания.В этом случае углеродный эквивалент определяется как [1]:
Другое уравнение для углеродного эквивалента [2]:
В каждом случае было определено, что растрескивание при закалке представляет собой проблему, если углеродный эквивалент (CE)> 0,52 процента. Если углеродный эквивалент стали превышает 0,50 процента, то сталь является хорошим кандидатом для закалки. В таблице 1 показан углеродный эквивалент для некоторых распространенных сталей.
Таблица 1: Обычные сплавы и их начальные температуры мартенсита, а также углеродные эквиваленты.Из обычно термообработанных сплавов в таблице 1 только AISI 8630 и AISI 4130 не склонны к образованию трещин при закалке. AISI 1045 подвергается термообработке путем закалки, закалки и отпуска. Это часто зависит от геометрии детали или склонности к деформации, от того, закаливается ли AISI 1045 с помощью закалки или отпуска. Тонкие секции чаще всего подвергаются закалке из-за низкой закаливаемости AISI 1045.
Martempering особенно подходит для науглероженных деталей (особенно подшипников, шестерен и валов), где детали более дорогостоящие в изготовлении и изготавливаются с более близкими размерами [3].Это проиллюстрировано на Рисунке 3, где показано искажение как функция температуры закалки [4].
Рисунок 3: Деформация дорожек подшипников SAE 52100 в зависимости от температуры закалки.Ограничения толщины сечения также должны быть приняты во внимание для пригодности для закалки. При заданной степени закалки существует предел толщины сечения, при котором сталь больше не будет полностью закаливаться или превращаться в мартенсит. Однако в зависимости от области применения может быть допустимо, чтобы центр детали не полностью превратился в мартенсит.Часто допустимо, чтобы твердость сердцевины была меньше твердости поверхности. В этом случае размер для закалки можно увеличить. Влияние полученной смешанной микроструктуры на механические свойства необходимо будет оценивать для каждого применения.
Аустемперинг
Аустемперинг — это изотермический процесс для достижения исключительно бейнитной структуры. Это достигается путем нагрева детали в пределах аустенитного диапазона и последующей закалки детали в ванне с горячим маслом или расплавом соли, поддерживаемой при постоянной температуре 260-400 ° C (выше температуры сплава M s ).Затем детали дают возможность изотермически трансформироваться для достижения бейнитной структуры и охладиться удобным способом, обычно на воздухе. Этот процесс показан на рисунке 4.
Рис. 4: Типичная схема процесса аустеплирования, где конечная микроструктура является бейнитной.Преимущества аустемперинга:
- Повышенная пластичность или ударная вязкость.
- Пониженные искажения.
- Уменьшено общее время цикла.
Для истинного закаливания деталь должна быть охлаждена так, чтобы центр и поверхность детали не совпадали с вершиной кривой TTT.
Выбор стали для закалки в первую очередь основан на кривой TTT сплава. При использовании данной стали для закалки следует учитывать три важных момента:
- Местоположение носика кривой TTT и время, необходимое для обхода носа;
- Время, необходимое для полного превращения в бейнит; и
- Температура начала мартенситного превращения, М с .
Углеродистые стали, как правило, не подходят для закалки, потому что время, необходимое для обхода вершины кривой TTT, очень короткое.Среднеуглеродистые легированные стали, такие как 5140, хорошо подходят для закалки, потому что вершина кривой TTT находится достаточно вправо, так что можно обойти кончик без образования перлита. Полностью бейнитная структура достигается в течение 1-10 минут при температуре 315-400 ° C. Чугун с шаровидным графитом с шаровидным графитом является обычным применением для закалки, поскольку он улучшает износостойкость и обеспечивает микроструктуру ударопрочности.
Максимальная толщина секции важна для определения самой медленной скорости закалки, которая не соответствует вершине кривой TTT.Из-за этого ограничения для достижения полностью бейнитной микроструктуры на участках более 13 мм требуются стали с очень высокой закаливаемостью. Когда допустимо присутствие перлита в микроструктуре, допустимая толщина сечения может быть увеличена. Из-за ограничений по размеру сечения диапазон применений для закалки обычно ограничивается деталями, изготовленными из прутков небольшого диаметра или полос с тонким поперечным сечением.
Осторожный отпуск может быть заменен обычным закаливанием или операциями закалки и отпуска при условии, что сплав имеет достаточную прокаливаемость и тонкое поперечное сечение.Повышенная прочность и пластичность могут привести к уменьшению деформации. В зависимости от области применения технологические затраты могут быть меньше, чем при обычных операциях по закалке и отпуску, поскольку отпуск не требуется после закалки.
Список литературы
- К. Лоренц и К. Дюрен, «Оценка свариваемости труб большого диаметра с помощью углеродного эквивалента», Proc. Int. Конф. Стали для трубопроводов и трубопроводной арматуры, Лондон, 1981.
- Т. Кунитаке и С. Сусигава, «Устойчивость стали к растрескиванию при закалке», Sumitomo Search, стр.16-25 мая 1971 г.
- Д. С. Маккензи, «Металлургические аспекты деформации», на 23-м Международном конгрессе IFHTSE 2016, Саванна, Джорджия, 2016.
- Д. С. Маккензи, «Влияние температуры на деформацию закаленных деталей», в «Технология закалки и деформации», Нагоя, Япония, 2018.
Термическая обработка — обзор
4.4.5 Сплавы Al – Zn – Mg – Cu (серия 7xxx)
Этим сплавам уделяется особое внимание, потому что уже давно установлено, что они особенно хорошо реагируют на старение.Например, Розенхайн и его коллеги из Национальной физической лаборатории в Великобритании в 1917 году получили предел прочности на разрыв 580 МПа для состава Al – 20Zn – 2.5Cu – 0.5Mg – 0.5Mn, когда значение для дюралюминия составляло 420 МПа. Однако этот и другие сплавы, произведенные в течение следующих двух десятилетий, оказались непригодными для использования в конструкции из-за высокой чувствительности к SCC. Из-за критической важности сплавов Al – Zn – Mg – Cu для авиастроения эта проблема является предметом постоянных исследований и разработок и теперь будет рассмотрена более подробно.
Военные потребности конца 1930-х и 1940-х годов в авиационных сплавах с более высоким соотношением прочности и веса в конечном итоге привели к появлению нескольких сплавов Al-Zn-Mg-Cu, из которых 7075, пожалуй, самый известный. Позже этот сплав и аналогичные материалы, такие как DTD 683 в Великобритании, также были приняты для строительства большинства гражданских самолетов. Более прочные сплавы, например, 7178-T6 с пределом прочности на разрыв 600 МПа, были введены для элементов, находящихся под напряжением при сжатии, а другой сплав 7079-T6 был разработан специально для больших поковок, для которых его более низкая чувствительность к закалке была преимуществом.Однако сохраняющиеся проблемы с SCC, особенно с ранним сплавом 7079-T6, который позже был снят с производства, а также недостатки в других свойствах стимулировали потребность в дальнейших улучшениях. Некоторые авиастроители фактически вернулись к использованию более низкопрочных сплавов на основе системы Al – Cu – Mg, даже несмотря на значительное снижение веса.
До этого времени было обычной практикой закалка компонентов в холодной воде после обработки раствором, что могло вызвать высокие уровни остаточного напряжения.Пример показан на рис. 4.27, в котором механическая обработка концевого выступа поковки самолета, закаленной в холодной воде, обнажила лежащие в основе остаточные растягивающие напряжения, которые способствовали возникновению SCC. Интересно отметить, что, хотя трещины в канале ствола были впервые обнаружены, когда поковка находилась в эксплуатации, трещины на сторонах выступов распространялись впоследствии после того, как поковка была удалена и подвергалась воздействию коррозионной атмосферы в отдельных случаях с разницей в несколько лет. Из-за проблемы закалочных напряжений в Великобритании была предпринята попытка использовать сплавы, не содержащие хрома, для поковок и других компонентов, которые не могли снимать напряжения.Такие сплавы могут выдерживать более мягкую закалку, например, в кипящей воде, без ухудшения реакции на старение.
Рисунок 4.27. Напряжение-коррозионные трещины в поковке из сплава Al – Zn – Mg – Cu, закаленного в холодной воде.
Еще одна ранняя практика заключалась в проведении однократной обработки старением при температурах в диапазоне 120–135 ° C, при которых наблюдалась высокая реакция на упрочнение из-за выделения зон GP (раздел 2.2.1). Было известно, что старение этих сплавов при более высокой температуре 160–170 ° C, при которой образуется фаза η ′ (или η), действительно привело к значительному увеличению сопротивления SCC, но свойства при растяжении были значительно снижены (см. Кривую a на рис.4.28). Впоследствии была введена дуплексная обработка старением, обозначенная как состояние T73, при которой более тонкая дисперсия осадка η ‘(или η) могла быть получена за счет зародышеобразования из ранее существовавших зон GP. Как показано на рис. 4.28 (кривая b) свойства 7075-T73 на растяжение примерно на 15% ниже, чем у состояния T6, но теперь сопротивление SCC значительно улучшилось. Например, испытания образцов, нагруженных в коротком поперечном направлении, показали, что сплав 7075, состаренный до состояния T73, не имеет трещин при уровнях напряжения 300 МПа, тогда как в состоянии T6 тот же сплав разрушился при напряжениях всего 50 МПа в в той же среде.Уверенность в характере T73 была продемонстрирована использованием 7075-T73 для критических компонентов самолета, таких как большая штамповка, как показано на рис. 4.29. Другая дуплексная обработка старением, обозначенная T76, была успешно применена к сплавам 7xxx для повышения устойчивости к отслаивающей (послойной) коррозии (рис. 2.37).
Рисунок 4.28. Сравнение пределов текучести (0,2% предела текучести) листа 7075, полученного в результате изотермической (171 ° C) (кривая а) и двухстадийной (121 ° C / 171 ° C) (кривая b) термообработки с осаждением.Повышенный предел текучести сплава 7050 при двухступенчатой обработке показан на кривой c.
Из Hunsicker, HY: Rosenhain Centenary Conf. о вкладе физического металлургии в инженерную практику , Королевское общество, Лондон, 1976.Рисунок 4.29. Штампованная интегральная центральная опора двигателя 7075 – T73 и лонжерон вертикального стабилизатора для самолета McDonnell-Douglas DC-10. В каждом самолете использовалось четыре одинаковых поковки.
Из Hunsicker, HY: Rosenhain Centenary Conf.о вкладе физической металлургии в инженерную практику , Королевское общество, Лондон, 1976.Использование сплавов с состоянием T73 потребовало изменения конструкции некоторых компонентов самолета и снижения веса при замене сплавов, выдержанных до состояния T6. По этой причине большое количество исследований было направлено на разработку сплавов, которые могли бы сочетать высокую стойкость к SCC с максимальным уровнем свойств при растяжении. Некоторый успех был достигнут с добавлением 0.25–0,4% серебра, поскольку этот элемент модифицирует процесс осаждения в сплавах на основе системы Al – Zn – Mg – Cu, обеспечивая высокую чувствительность к упрочнению при старении за одну обработку старением при 160–170 ° C. Один немецкий промышленный высокопрочный сплав, обозначенный AZ74 (7009), который содержал этот элемент, использовался для некоторых поковок в двух европейских самолетах, изготовленных в 1970-х годах. Совсем недавно Alcoa в США разработала сплав 7050 (Al – 6.2Zn – 2.25Mg – 2.3Cu – 0.12Zr), в котором уровень меди, обычно присутствующей в сплавах, таких как 7075, был повышен для увеличения упрочнения. связанный со вторым этапом лечения Т73 (кривая c на рис.4.28). Современные производные 7050 — это еще один высокопрочный сплав 7150, который имел немного большее количество Zn и Mg, и более поздние сплавы 7055, 7449 и 7085, все из которых имеют значительно более высокие уровни цинка (8% по сравнению с 6,2%).
Была разработана другая термообработка, которая позволяет сплавам, таким как 7075, демонстрировать высокий уровень свойств растяжения, ожидаемых от состояния T6, в сочетании с сопротивлением SCC, равным условию T73. Это известно как регресс и повторное старение (RRA), которое включает следующие этапы для 7075:
- 1.
Применяют обработку Т6, т.е. обработку раствором при 465 ° C, закалку в холодной воде, выдержку 24 часа при 120 ° C.
- 2.
Нагрейте в течение короткого времени (например, 5 минут) при температуре в диапазоне 200–280 ° C и закалите в холодной воде.
- 3.
Повторная выдержка 24 часа при 120 ° C.
Изменения свойств при растяжении схематично показаны на рис. 4.30. Общепринято, что обработка RRA приводит к микроструктуре, имеющей матрицу, аналогичную матрице, полученной для состояния T6, в сочетании с зонами границ зерен, характерными для состояния T73, в котором выделения являются более крупными и более разделенными.Сниженная восприимчивость к SCC была приписана этому последнему изменению (раздел 2.5.4). Однако из-за короткого временного интервала, первоначально предложенного для этапа (2), например, 1–5 минут, лечение RRA было трудно применить к толстым сечениям. Совсем недавно были оптимизированы временные и температурные условия для этой стадии процесса (например, 1 час при 200 ° C), и обработке RRA было присвоено коммерческое обозначение T77. Он был нанесен на высоколегированный состав 7055 (Al – 8Zn – 2.05Mg – 2.3Cu – 0.16Zr), который использовался для конструктивных элементов крыльев пассажирского самолета Boeing 777 (раздел 4.6.1).
Рисунок 4.30. Схематическое изображение влияния RRA на предел текучести сплава, такого как 7075.
From Kaneko, RS: Met. Progr ., 41 (4), 1980.Как упоминалось в разделе 4.1.5, термомеханическая обработка предлагает другой метод оптимизации свойств сплавов, упрочненных старением. На рис. 4.31 схематично показан способ сочетания старения с деформацией с целью достижения дислокационного упрочнения, чтобы компенсировать потерю прочности, которая обычно происходит во время изношенной части обработки T73, упомянутой ранее.Деформация достигается теплой обработкой после процедуры старения Т6 и до истощения. Сообщалось, что термомеханическая обработка некоторых сплавов 7ххх таким способом может привести к повышению прочности примерно на 20% без потери ударной вязкости, или наоборот. Однако коммерческое внедрение представляет трудности из-за проблем с контролем температуры и уровня деформации, которую необходимо проводить на материале, который уже находится в состоянии старения.
Рисунок 4.31. Схематическое изображение FTMT-упрочнения сплава 7ххх.
От Патона, штат Северная Каролина, и Соммера, AW: Proc. 3-го Интер. Конф. по прочности металлов и сплавов, , Metals Society, London, 1, 101, 1973.Были внесены другие изменения в состав. Одним из примеров является снижение уровней примесей железа и кремния в сплавах, таких как 7075 (Fe + Si максимум 0,90%), до суммарного максимума 0,22% в сплаве 7475 более высокой чистоты (таблица 4.4). 7475 также имеет пониженное содержание марганца с 0.Максимум от 30% до 0,06%, в то время как содержание других легирующих элементов по существу такое же, как у 7075. Размер и количество интерметаллических соединений, которые способствуют распространению трещин, значительно уменьшены в 7475 и, для аналогичных термообработок T735 и свойств на растяжение, значения трещиностойкости ( K 1c ) могут превышать 50 МПа м 1/2 , тогда как типичное значение для 7075 составляет 30 МПа м 1/2 . Стоимость производства 7475 составляет около 10%, но он широко используется в самолетах.
Другая модификация заключалась в использовании 0,08–0,25% циркония в качестве ингибитора перекристаллизации вместо хрома или марганца или в сочетании с меньшими количествами этих элементов, чтобы снизить чувствительность к закалке, чтобы можно было использовать более низкие скорости закалки без потерь. прочности при последующем старении. Примерами являются сплавы 7050, 7150, 7055, 7085 и британский сплав 7010. Это также особенно важно для сплавов, используемых для толстых листов, поскольку возможно снижение затрат, если большие сборные узлы могут быть заменены механически обработанными монолитными структурами.
В целом, прогресс, достигнутый в борьбе с SCC в материалах серии 7xxx за счет разработки сплавов и изменений в термообработке, можно оценить по результатам для некоторых составов, показанных на рис. 4.32. В отличие от сплавов серии 2ххх (рис. 4.21), улучшения произошли за счет значительных изменений значений плато для скорости роста трещин, а не за счет увеличения уровней пороговой интенсивности напряжений, необходимых для возникновения трещин.
Рисунок 4.32. Скорость распространения трещин при стресс-коррозионных испытаниях на сплавах 7ххх.Условия испытаний описаны на рис. 4.21. Образцы DCB изготовлены из коротких поперечных направлений штамповок и пластин.
из Шпейдел, штат Миссури: Металл. Пер. A , 6A, 631, 1975.Уже упоминалось, что сплавы серии 7xxx имеют тенденцию показывать более высокие значения вязкости разрушения, чем серия 2xxx (например, рис. 4.20). Были достигнуты дальнейшие улучшения, некоторые примеры которых показаны на рис. 4.33. Здесь показана обратная зависимость между вязкостью разрушения и пределом текучести при растяжении для более старых сплавов 7075 – T651 и 7178 – T651.Модификации легирующих добавок, чистоты и термообработки позволили сохранить относительно высокие значения вязкости разрушения в сплавах, таких как 7150 – T651 и 7055 – T7751, несмотря на повышение уровня предела текучести. Как упоминалось ранее, одна из композиционных тенденций заключалась в повышении отношения Zn: Mg, которое увеличилось с 2,25 для раннего сплава 7075 до 2,7 для 7050, 3,9 для 7055 и до 5,0 для последнего сплава 7085. Еще одно изменение касалось увеличить содержание меди со значений около 1.5% в пределах 2,0–2,6%, что, как было установлено, улучшает устойчивость к SCC. Кроме того, допустимые пределы содержания марганца, хрома и примесей железа и кремния были снижены до уровня ниже 0,1% или менее. В 7085 (Fe 0,08%, Si 0,06%) последующее уменьшение интерметаллических соединений в микроструктуре привело к снижению чувствительности к закалке этого сплава, так что очень толстые секции (например, 150 мм) можно подвергать термообработке, сохраняя при этом более высокие характеристики растяжения. чем более ранние авиационные сплавы, такие как 7050.Эта разработка была основным фактором при выборе 7085 для больших экструдированных лонжеронов крыла и штампованных компонентов нервюр для европейского A380 Airbus (раздел 4.6.1).
Рисунок 4.33. Соотношения прочности и вязкости для сплавов серии 7ххх в виде листового проката.
От Hyatt, MV и Axter, SE: Proc. Интер. Конф. о последних достижениях в науке.