виды, свойства и области применения
Сегодня алюминий используется практически во всех отраслях промышленности, начиная с производства пищевой посуды и заканчивая созданием фюзеляжей космических кораблей. Для тех или иных производственных процессов подходят только определенные марки алюминия, которые обладают определенными физико-химическими свойствами.
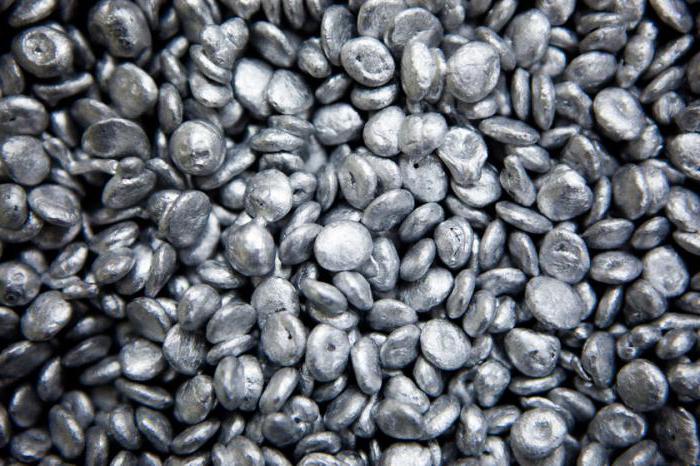
Виды алюминия
Все марки металла описаны и внесены в единую систему признанных национальных и международных стандартов: Европейских EN, Американских ASTM и международных ISO. В нашей стране марки алюминия определены ГОСТом 11069 и 4784. Во всех документах алюминий и его сплавы рассматриваются отдельно. При этом сам металл подразделяется именно на марки, а сплавы не имеют конкретно определенных знаков.
В соответствии с национальными и международными стандартами, следует выделить два вида микроструктуры нелегированного алюминия:
- высокой чистоты с процентным содержанием более 99,95%;
- технической чистоты, содержащей около 1% примесей и добавок.
В качестве примесей чаще всего рассматривают соединения железа и кремния. В международном стандарте ISO для алюминия и его сплавов выделена отдельная серия.
Марки алюминия
Технический вид материала делится на определенные марки, которые закреплены за соответствующими стандартами, например АД0 по ГОСТ 4784-97. При этом в классификацию входит и металл высокой частоты, чтобы не создавать путаницу. Данная спецификация содержит следующие марки:
- Первичный (А5, А95, А7Е).
- Технический (АД1, АД000, АДС).
- Деформируемый (АМг2, Д1).
- Литейный (ВАЛ10М, АК12пч).
- Для раскисления стали (АВ86, АВ97Ф).
Кроме того, выделяют и категории лигатуры – соединения алюминия, которые используются для создания сплавов из золота, серебра, платины и других драгоценных металлов.
Первичный алюминий
Первичный алюминий (марка А5) – типичный пример данной группы. Его получают путем обогащения глинозема. В природе металл в чистом виде не встречается ввиду его высокой химической активности. Соединяясь с другими элементами, он образует бокситы, нефелины и алуниты. Впоследствии из этих руд получают глинозем, а из него с помощью сложных химико-физических процессов — чистый алюминий.
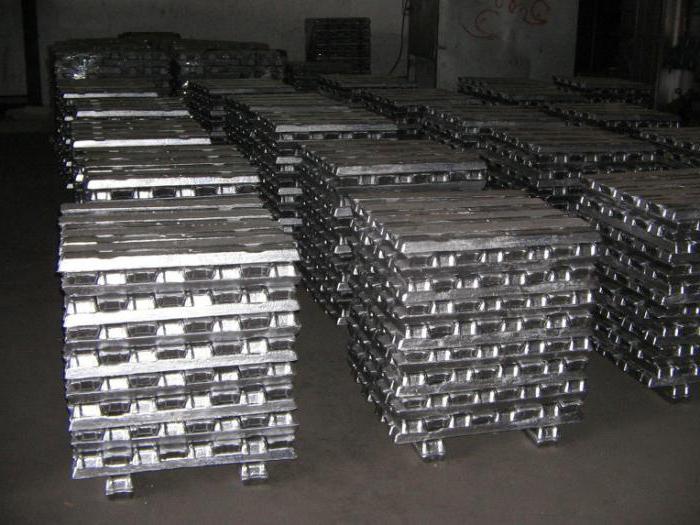
ГОСТ 11069 устанавливает требования к маркам первичного алюминия, которые следует отметить путем нанесения вертикальных и горизонтальных полос несмываемой краской различных цветов. Данный материал нашел широкое применение в передовых отраслях промышленности, главным образом там, где от сырья требуются высокие технические характеристики.
Технический алюминий
Техническим алюминием называют материал с процентным содержанием инородных примесей менее 1%. Очень часто его также называют нелегированным. Технические марки алюминия по ГОСТу 4784-97 характеризуются очень низкой прочностью, но высокой антикоррозионной стойкостью. Благодаря отсутствию в составе легирующих частиц на поверхности металла быстро образуется защитная оксидная пленка, которая отличается устойчивостью.
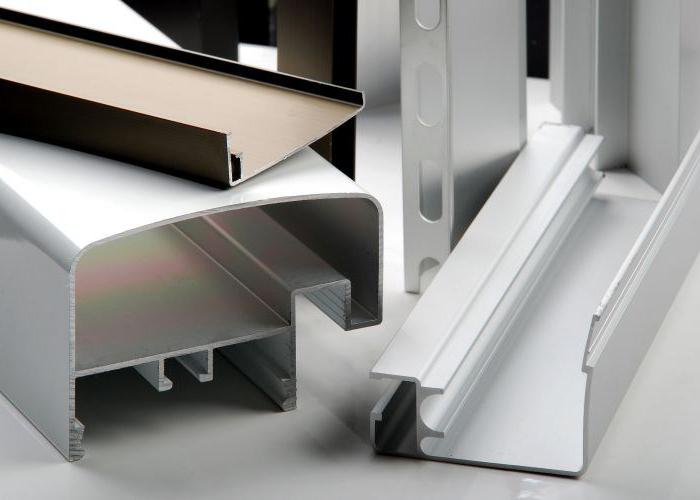
Деформируемый алюминий
К деформируемому алюминию относят материал, который подвергают горячей и холодной обработке давлением: прокатке, прессованию, волочению и другим видам. В результате пластических деформаций из него получают полуфабрикаты различного продольного сечения: алюминиевый пруток, лист, ленту, плиту, профили и другие.
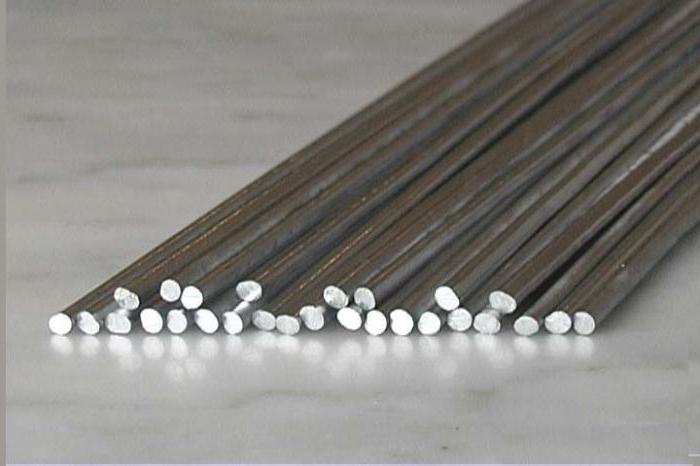
Область применения деформируемого алюминия, как и та, где применяется алюминиевый пруток, достаточно обширна. Он используется как в областях, требующих высоких технических характеристик от материалов — в корабле- и самолетостроении, так и на строительных площадках в качестве сплава для сварки.
Литейный алюминий
Литейные марки алюминия используются для производства фасонных изделий. Их главной особенностью является сочетание высокой удельной прочности и низкой плотности, что позволяет отливать изделия сложных форм без образования трещин.
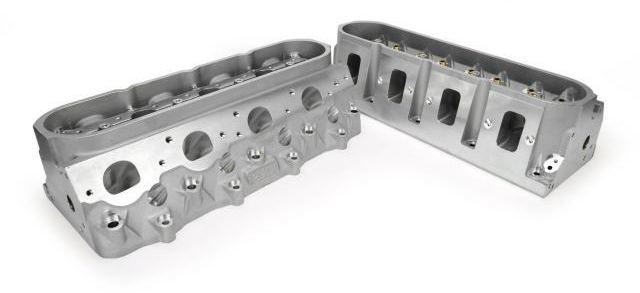
- Высокогерметичные материалы (АЛ2, АЛ9, АЛ4М).
- Материалы с высокой прочностью и жароустойчивостью (АЛ 19, АЛ5, АЛ33).
- Вещества с высокой антикоррозионной устойчивостью.
Очень часто эксплуатационные характеристики изделий из литейного алюминия повышают различными видами термической обработки.
Алюминий для раскисления
На качество изготавливаемых изделий оказывает влияние и то, какие имеет алюминий физические свойства. И применение низкосортных сортов материала не ограничивается созданием полуфабрикатов. Очень часто он используется для раскисления стали – удаления из расплавленного железа кислорода, который растворен в нем и повышает тем самым механические свойства металла. Для проведения данного процесса чаще всего применяются марки АВ86 и АВ97Ф.
Алюминий и его сплавы
Алюминий (Al) — это легкий цветной металл (его плотность составляет 2,71 г/см3) с невысокой температурой плавления (660 °С). По распространенности в земной коре Аl занимает первое место — 8,8 % (для сравнения Fe — 4,65 %, Mg — 2,4 %, Ti — 6,3·10-3 %, Ni — 8·10-3 %, Сu — 4,7·10-3 %). Его предел прочности при растяжении σв = 80…100 МПа; твердость — 25 НВ. Алюминий отличается пластичностью, легко поддается обработке давлением. После холодной прокатки алюминия его предел прочности (σв) увеличивается до 180…250 МПа, а твердость — до 45…60 НВ. Впервые алюминий в свободном виде получил в 1825 г. датский ученый Х.К. Эрстед. Однако высокая химическая активность алюминия и, следовательно, высокая стойкость образуемых химических соединений долго не позволяли наладить его производство. Кроме того, производство алюминия требует больших энергетических затрат. Наличие мощных электростанций и создание надежных технологий получения этого металла из руды, выдвинули алюминий и его сплавы на одно из ведущих мест среди цветных металлов по значимости и объему применения в современном машиностроении.
В полупроводниковой и ядерной технике и химической промышленности используется алюминий высокой чистоты (марок А995, А99, А97, А95), содержащий от 0,005 до 0,05 % примесей. Алюминий промышленной чистоты (марок А85, А8, А7, А6, А5, А0, А, АЕ), содержащий от 0,15 до 1 % примесей, используется в электротехнической промышленности, а также для производства сплавов. Чистый алюминий в машиностроении используется незначительно (в основном, применяются сплавы алюминия).
Для получения сплавов используется алюминий, выпускаемый в виде чушек.
Сплавы на основе алюминия классифицируются по степени упрочнения после термической обработки, по эксплуатационным свойствам, по технологии изготовления деталей. По последнему признаку различают алюминиевые сплавы литейные и деформируемые. Основными примесями в алюминии и его сплавах являются Fe и Si. Железо, образуя интерметаллиды, снижает пластичность алюминия и его сплавов. В отношении термической обработки сплавы алюминия бывают не упрочняемые и упрочняемые термической обработкой.
Алюминиевые сплавы образуют твердые растворы, эвтектики, интерметаллидные фазы. Для них применяют закалку и старение, а также отжиг. При закалке температура нагрева сплава находится в интервале 485…525 °С. При этом для каждого сплава используется более узкий интервал в пределах этих температур, поскольку повышение температуры выше закалочной ведет к пережогу (оплавлению по границам зерен). Выдержка при нагреве должна быть минимальной, обеспечивающей полное растворение избыточных фаз в твердом растворе. После охлаждения детали подвергают старению. Старение производится при комнатной температуре (естественное старение) и продолжается несколько суток или при температуре 150…200 °С — 10…24 часа (искусственное старение). Закалка и старение увеличивают твердость и σв обрабатываемых сплавов. Для некоторых сплавов при оптимальных условиях старения эти показатели могут увеличиться в два раза.
Диффузионный (гомогенизирующий) отжиг сплава производится перед его обработкой давлением для устранения в слитках дендритной ликвации, которая приводит к неоднородности структуры, и измельчению зерна. Такой отжиг производится при температуре 450…520 °С с последующим охлаждением сплава вместе с печью или на воздухе.
Рекристаллизационный отжиг производят при нагреве сплава до температуры 350…500 °С (в зависимости от состава сплава).
Для разупрочнения закаленных сплавов производят их отжиг при температуре 350…460 °С с выдержкой при этой температуре 1,5…2 часа. При этом происходит полный распад пересыщенных твердых растворов и коагуляция упрочняющих фаз.
Сплавы для изготовления фасонных отливок (кроме свойств, определяемых условиями эксплуатации) должны обладать хорошими литейными свойствами.
Алюминиевые литейные сплавы (ГОСТ 1583—93) маркируются буквами и цифрами. Буква «А» в марке сплава означает, что сплав алюминиевый литейный, а остальные буквы обозначают элементы, входящие в его состав:
- К — кремний;
- М — медь;
- Н — никель;
- Ц — цинк;
- Су — сурьма;
- Мг — магний;
- Кд — кадмий;
- Мц — марганец.
Цифры после букв обозначают среднюю массовую долю соответствующего элемента (в %). Буквы в конце марки сплава обозначают следующее:
- «ч» — чистый;
- «пч» — повышенной чистоты;
- «оч» — особой чистоты;
- «л» — литейные сплавы;
- «с» — селективный.
Рафинированные сплавы в чушках обозначают буквой «р», которую ставят после обозначения марки сплава.
В составе литейных сплавов (при литье в песчаные формы) допускается содержание 0,5…1 % Fe, а при литье в кокиль — 0,8…1,4 % Fe. Кремний не оказывает вредного влияния на литейные сплавы и используется в качестве основного или вспомогательного легирующего элемента.
Для производства основной массы изготавливаемых деталей применяются пять групп литейных алюминиевых сплавов. Это Al–Si (силумины), Al–Cu–Si (алькусины), Al–Cu, Al–Mg и сложнолегированные сплавы.
Выделено семь элементов, которые могут служить основными легирующими элементами в алюминиевых сплавах,— серебро (Ag), германий (Ge), литий (Li), цинк (Zn), магний (Mg), медь (Сu), кремний (Si). Все они образуют с алюминием системы эвтектического типа, но из-за высокой стоимости Ag, Ge и Li сплавы, легированные этими элементами, применяются очень ограниченно. Цинк применяется для растворного упрочнения литейных сплавов, но он не образует интерметаллидов и не обеспечивает значительного упрочнения. В этой связи основными легирующими элементами в алюминиевых сплавах являются Mg, Сu и Si. Образование интерметаллидов в сплавах Al–Cu, Al–Mg и Al–Mg–Si, а также отличная жидкотекучесть и малая усадка (линейная усадка для большинства сплавов составляет 0,9…1,3 %) Al–Si сплавов, переменная растворимость элементов в твердом состоянии в сплавах Al–Cu и Al–Mg позволяют получать качественные отливки и использовать различные методы упрочнения сплавов, включая дисперсное твердение путем закалки и старения. Вспомогательные легирующие элементы (Mn, Cr, V, Ti, Zr, Mo, Ni и др.) дополнительно упрочняют отливки по растворному типу, улучшают пластичность сплавов и повышают их жаропрочность, а другие вспомогательные легирующие элементы (Na, К, Be, Ca, Cd и др.) используются в виде небольших добавок (до 0,2 %) для улучшения технологических свойств в качестве модификаторов.
Основными особенностями алюминиевых сплавов, которые необходимо учитывать при плавке, являются склонность этих сплавов к газопоглощению (особенно водорода) и легкая окисляемость. В последующем водород, выделяясь при кристаллизации и охлаждении, способствует образованию газовой пористости в отливках, а включения А12O3 существенно снижают механические свойства сплава. Для защиты от этих нежелательных явлений производят плавку алюминиевых сплавов под слоем флюса, перед заливкой проводят дегазацию расплава, его рафинирование хлором и азотом, а для получения мелкозернистой структуры и улучшения механических свойств сплава применяют модифицирование фтористыми и хлористыми соединениями.
Твердость литейных алюминиевых сплавов (в зависимости от их состава и методов термической обработки) составляет от 500 до 1000 НВ, а σв — от 130 до 360 МПа.
Максимальная рабочая температура применяемых в промышленности алюминиевых сплавов составляет 300…350 °С.
Для изготовления отливок в промышленности используют пять групп алюминиевых сплавов (ГОСТ 1583–93):
- Сплавы на основе системы «алюминий—кремний» (силумины): марки АК12; АК13; АК9; АК9с; АК9ч; АК9пч; АК8л; АК7; АК7ч; АК7пч; АК10Су;
- Сплавы на основе системы «алюминий—медь—кремний» (алькусины) : марки АК5М; АК5Мч; АК5М2; АК5М7; АК6М2; АК8М; АК5М4; АК8М3; АК8М3ч; АК9М2; АК12М2; АК12ММгН; АК12М2МгН; АК21М2,5Н2,5;
- Сплавы на основе системы «алюминий—медь»: марки АМ5; АМ4,5Кд;
- Сплавы на основе системы «алюминий—магний»: марки АМг4К1,5М; АМг5К; АМг3Мц; АМг6л; АМг6лч; АМг10; АМг10ч; АМг11; АМг7;
- Сплавы алюминия с прочими компонентами (сложнолегированные): марки АК7Ц9; АК9Ц6; АЦ4Мг.
Сплавы системы алюминий–кремний (силумины) получили наибольшее распространение. Они обладают лучшими из всех алюминиевых сплавов литейными свойствами и широко применяются для отливок деталей, отличающихся сложностью очертаний или несущих большие нагрузки. Силумины обладают удовлетворительной коррозионной стойкостью. Изготавливаемые из них детали защищают анодированием и лакокрасочными покрытиями. Силумины широко используют в промышленности (авиационной, машиностроительной, судостроительной и электротехнической).
Добавление меди к сплавам Al—Si повышает их твердость и предел прочности при растяжении, а также значительно улучшает обрабатываемость резанием. Тройные сплавы Al—Cu—Si (алькусины) применяются при изготовлении особо ответственных деталей (например, головок цилиндров двигателей, поршней, деталей, работающих при повышенной температуре, и др.). Эти сплавы используют в промышленности для изготовления деталей необходимой прочности, сохраняющих постоянство размеров в процессе эксплуатации и имеющих высокую чистоту обработанной поверхности.
Сплавы системы Al–Cu имеют пониженные литейные свойства, малую коррозионную стойкость и недостаточную пластичность, но хорошо обрабатываются резанием. Эти сплавы применяют для отливки небольших ответственных деталей машин и приборов, несущих высокую нагрузку (статическую и ударную).
Сплавы системы Al–Mg обладают малой плотностью, высокой коррозионной стойкостью и прочностью. Их применяют для изготовления сильно нагруженных деталей. Однако эти сплавы плохо работают при повышенных температурах. Из этих сплавов изготавливают арматуру и корпуса машин, устанавливаемых на морских судах.
Сложнолегированные сплавы алюминия применяют для изготовления отливок, работающих при повышенных температурах и давлениях, с повышенной стабильностью размеров, а также для изготовления сварных конструкций и деталей, хорошо обрабатывающихся резанием.
Области применения некоторых марок литейных алюминиевых сплавов представлены в таблице 1.
Таблица 1. Области применения литейных алюминиевых сплавов
Группа | Марка сплава | Области применения |
I | АК12 | Герметичные детали небольших размеров. Детали, испытывающие ударные нагрузки, тонкостенные детали сложной конфигурации. Детали, применяемые в автомобиле- и тракторостроении (картеры, блоки цилиндров, поршни двигателей внутреннего сгорания). Изделия пищевого назначения (теплообменники, мясорубки) |
АК9 АК7 | Отливки сложных по конфигурации, статически нагруженных деталей (корпуса водяных насосов, компрессоров, картеры и блоки цилиндров двигателей внутреннего сгорания, системы водяного охлаждения, турбинные колеса турбохолодильников, вентиляторов, арматура и посуда) | |
АК7пч | Сложные по конфигурации детали агрегатов и приборов, испытывающие средние нагрузки и работающие при температуре до 200 °С | |
АК8л | Отливки крупных корпусных деталей, сложных по конфигурации и работающих под большим внутренним давлением газа или жидкости | |
II | АК8М | Нагруженные детали (блоки цилиндров, головки блоков и другие детали автомобильных двигателей) |
АК8М3ч | Силовые и герметичные детали с рабочими температурами до 250 °С, изготовляемые литьем под давлением и другими методами точного литья | |
АК5М | Головки цилиндров двигателей воздушного охлаждения, детали агрегатов и приборов, работающих при температуре не выше 250 °С | |
III | АМ5 | Крупногабаритные отливки ответственных деталей, работающих в условиях повышенных статических и ударных нагрузок, при низких и повышенных (до 300 °С) температурах |
IV | АМг10, АМг10ч | Используются вместо дефицитных бронз, латуней, коррозионно-стойких сталей Силовые детали, работающие при температурах от –60 до +60 °С.. Детали, работающие в различных климатических условиях, включая воздействие морской воды и тумана |
Для повышения механических свойств отливок из алюминиевых сплавов их часто подвергают термической обработке, после которой в некоторых случаях прочность отливок увеличивается почти в два раза.
К группе деформируемых относятся сплавы на основе алюминия (табл. 2), перерабатываемые в изделия методами деформирования (прессованием, волочением, ковкой, штамповкой, прокаткой). Среди этих сплавов различают сплавы, упрочняемые и не упрочняемые термической обработкой.
Таблица 2. Состав деформируемых алюминиевых сплавов
Марка сплава | Содержание элементов в сплаве (остальное Al), % | |||
Cu | Mg | Mn | прочие | |
АМц* | – | – | – | – |
АМг2* | – | 1,8…2,6 | 0,2…0,6 | – |
АМг6* | – | 5,8…6,8 | 0,5…0,8 | 0,02…0,1 Ti |
Д1** | 3,8…4,8 | 0,4…0,8 | 0,4…0,8 | 0,002…0,005 Be |
Д16** | 3,8…4,9 | 1,2…1,8 | 0,3…0,9 | – |
Д18** | 2,2…3,0 | 0,2…0,5 | – | – |
В95*** | 1,4…2,0 | 1,8…2,8 | 0,2…0,6 | 0,01…0,25Cr 5…7 Zn |
АК6*** | 1,8…2,6 | 0,4…0,8 | 0,4…0,8 | 0,7…1,2 Si |
АК8*** | 3,9…4,8 | 0,4…0,8 | 0,4…1,0 | 0,6…1,2 Si |
* Механические свойства после отжига. ** Механические свойства после закалки и естественного старения. *** Механические свойства после закалки и искусственного старения |
В группе деформируемых сплавов алюминия, упрочняемых термической обработкой, различают сплавы нормальной прочности, высокопрочные сплавы, жаропрочные сплавы и сплавы для ковки и штамповки.
Типичным представителем сплавов нормальной прочности являются дуралюмины, относящиеся к системе А1–Сu–Mg, которые маркируются буквой «Д». Марганец повышает коррозионную стойкость, температуру рекристаллизации и улучшает механические свойства дуралюминов (табл. 3).
Таблица 3. Механические свойства деформируемых алюминиевых сплавов
Марка сплава | Механические свойства сплава | Вид полуфабриката | ||||
σв | σ0,2 | σ–1 | δ, % | НВ, МПа | ||
МПа | ||||||
АМц* | 130 | 50 | 55 | 20 | 300 | Листы |
АМг2* | 190 | 100 | 125 | 23 | 450 | Листы |
АМг6* | 340 | 170 | – | 20 | 700 | Листы |
Д1** | 400 | 240 | 105 | 20 | 950 | Листы, прессованные прутки. |
480 | 320 | 125 | 14 | – | ||
Д16** | 440 | 330 | 115 | 18 | 1050 | Листы, плиты, прессованные прутки |
530 | 400 | 140 | 11 | – | ||
Д18** | 300 | 170 | 95 | 24 | 700 | Проволока |
В95*** | 540 | 470 | 150 | 10 | 1500 | Листы, плиты, прессованные прутки |
600 | 560 | 150 | 8 | 1500 | ||
АК6*** | 400 | 299 | 125 | 12 | 1000 | Поковки |
АК8*** | 480 | 380 | 130 | 9 | 1350 | Поковки |
* Механические свойства после отжига. ** Механические свойства после закалки и естественного старения. *** Механические свойства после закалки и искусственного старения |
Для упрочнения сплавов применяют закалку с последующим охлаждением в холодной воде. Закаленные дуралюмины подвергают старению, способствующему увеличению их коррозионной стойкости. В процессе естественного (несколько суток) или искусственного старения (10…24 ч) повышается прочность сплава вследствие распада пересыщенного твердого раствора.
Дуралюмины широко применяются в авиации. Так, из сплава Д1 изготовляют лопасти винтов, из Д10 — несущие элементы фюзеляжей самолетов, а сплав Д1В является одним из основных заклепочных материалов. Из дуралюминов обработкой давлением производят полуфабрикаты (прутки, полосы, листы и т. д.)
К высокопрочным сплавам алюминия относят сплавы (В95, В96), системы Al–Zn–Mg–Сu. В качестве легирующих добавок используют марганец и хром, которые увеличивают коррозионную стойкость и эффект старения сплава. Для достижения требуемых прочностных свойств (σв = 600…700 МПа) сплавы закаливают при температуре 460…480 °С с последующим искусственным старением при температуре 120…140 °С. Высокопрочные сплавы превосходят дуралюмины но прочностным показателям, но менее пластичны и более чувствительны к концентраторам напряжений, а также воздействию коррозионных сред под напряжением. Для повышения коррозионной стойкости изделий их плакируют сплавом Al+1% Zn. Высокопрочные сплавы применяют в авиастроении для изготовления наружных конструкций с температурой длительной эксплуатации до 120 °С.
Для изделий, эксплуатируемых при температурах до 300 °С, используют жаропрочные сплавы АК-4, АК-4-1. Они имеют сложный химический состав, легированы железом, никелем, медью и другими элементами, образующими упрочняющие фазы СuAl2, CuMgAl2, Al12Mg2Cu и др. Жаропрочность сплавам придает легирование медью, марганцем и титаном, замедляющими диффузионные процессы. Детали из жаропрочных сплавов используют после закалки и искусственного старения.
Сплавы для ковки и штамповки обладают высокой пластичностью и удовлетворительно перерабатываются литьем. При горячем деформировании в этих сплавах не образуются трещины. Типичными представителями таких материалов являются сплавы системы А1—Cu—Mg с добавками кремния (АК 0, АК 8). Ковку и штамповку этих сплавов производят при температуре 450…475 °С. Затем применяют закалку и старение. Из этих сплавов изготавливают поковки и прокат.
К неупрочняемым термической обработкой деформируемым сплавам относят сплавы систем А1–Мn, А1–Mg. Они отличаются высокой пластичностью, коррозионной стойкостью, хорошо свариваются. Сплавы этой группы используют в отожженном, нагартованном и полунагартованном видах.
Для устранения дендритной ликвации деформируемых сплавов проводят гемогенизирующий отжиг слитков при температуре 450…520 °С в течение 4…40 ч с последующим охлаждением на воздухе или в печи. Деформированные заготовки подвергают рекристаллизационному отжигу при температуре 350…500 °С в течение 0,5…2 ч. Эта операция способствует снятию наклепа и получению мелкозернистой структуры металла. Из неупрочняемых сплавов изготовляют емкости для жидкостей, трубы, корабельные конструкции, детали вагонов.
Просмотров: 639
Литейные алюминиевые сплавы: свойства, применение, обработка
В последнее время достаточно большое распространение получили алюминиевые сплавы. Это связано с тем, что они обладают исключительными эксплуатационными качествами. Существует просто огромное количество различных видов алюминия, классификация зависит от химического состава и многих других показателей. Довольно большое распространение получили литейные алюминиевые сплавы. Они могут применяться для изготовления самых различных деталей, в большинстве случаев, корпусов. Рассмотрим особенности литейных алюминиевых сплавов подробнее.


Общая характеристика и свойства
Существует довольно большое количество разновидностей литейных алюминиевых сплавов, каждый из которых обладает своими особенностями. Алюминиевый литейный сплав характеризуется следующими эксплуатационными качествами:
- Высокие литейные качества. Подобный металл довольно часто применяется для литья по форме. Высокие литейные качества позволяют создавать детали сложной формы.
- Плотность. Химический состав алюминиевых литейных сплавов определяет то, что их плотность относительно невелика. За счет этого вес получаемой конструкции относительно небольшой.
- Коррозионная стойкость также высокая. Она может снижаться за счет добавления различных легирующих элементов.
- Рассматривая свойства сплавов следует отметить и повышенную прочность, а также твердость. Эти качества достигаются путем добавления самых различных веществ.
- Высокая степень обрабатываемости. Путем литья достаточно часто получают заготовки, которые в дальнейшем доводят до готового состояния путем механической обработки на фрезерном или другом оборудовании.
Подобные материалы обладают хорошими литейными свойствами, что позволяет получать детали со сложными поверхностями. Сплавы с высоким содержанием магния или других легирующих элементов могут подвергаться дополнительной термообработке.
В большинстве случаев к данному материалу предъявляют следующие требования:
- Хорошие литейные свойства. Именно они считаются наиболее важными при рассмотрении алюминиевых сплавов данной группы. Чем менее выражены литейные качества, тем хуже раствор заполняет созданную форму. Литейные свойства могут определяться самыми различными методами.
- Небольшая усадка. Процесс усадки практически неизбежен при литье по форме. Однако некоторые составы более склонны к образованию раковин и других дефектов при литье, другие меньше. Чем меньше усадка, тем более качественным получается изделие.
- Высокая жидкотекучесть. Если созданная форма для литья имеет большое количество сложных поверхностей, то для их заполнения состав должен обладать повышенным показателем жидкотекучести.
- Малая склонность к образованию горячих трещин. При выполнении литейных операций возникает вероятность появления трещин, которые снижают прочность структуры и эксплуатационные качества материала.
- Низкая склонность к пористости. Пористая структура обладает менее привлекательными эксплуатационными качествами, так как она имеет меньшею прочность, впитывает влагу и может быть подвержена воздействию коррозии.
- Оптимальные механические и химические свойства. Современные методы легирования позволяют сделать легкий материал более прочным. Для этого проводится добавление самых различных компонентов. Оптимальные механические свойства представлены сочетанием легкости и прочности, а также другими качествами.
- Мелкозернистая однородная структура. При рассмотрении особенностей структуры получаемых изделий следует отметить, что однородная лучше воспринимает оказываемые нагрузки и вероятность появления дефектов существенно снижается. Неоднородную структуру можно охарактеризовать тем, что изделие может иметь разный показатель твердости поверхности, на одной части может появляться коррозия, другая может оказаться быть более устойчивой к подобному воздействию.
Исключить вероятность образования многих дефектов можно путем соблюдения технологии отливки и обработки полученного сплава. Кроме этого, используемый состав также в той или иной степени определяет вероятность образования дефектов.


Литейные алюминиевые сплавы в чушках
Наиболее важным качеством можно назвать жидкотекучесть. Она определяет способность заполнения литейной формы. Кроме этого уделяют внимание тому, какова склонность состава к образованию газовых и усадочных пустот. Измеряется показатель жидкотекучести тем, какая емкость и за какое время может заполниться. Стоит учитывать, что повышенное содержание оксидов становится причиной снижения показателя жидкотекучести.
Процесс литья также определяет высокую вероятность образования усадочных раковин. При охлаждении расплав уменьшается в объеме. Выделяют два основных типа образующейся раковины:
- крупную;
- макроусадочную.
Для определения степени усадки используются различные методы.
При литье также часто встречается деформация, которая становится причиной образования трещин. Она связана с процессом, который определяется сжимающим напряжением между уже затвердевшим и кашеобразным составом.
Различают несколько разновидностей алюминиевых литейных сплавов, о которых далее поговорим подробнее.
Виды литейных алюминиевых сплавов
Все литейные сплавы алюминия можно условно разделить на несколько основных групп:
- Высокопрочные и жаропрочные сплавы. Наиболее распространенным материалом из этой группы можно назвать алюминиевый сплав АЛ19. Его легируют путем добавления титана, за счет чего придаются более высокие механические свойства. Добавление легирующих элементов может проводится при низких или комнатных температурах. Жаропрочность определяет то, что механические свойства и линейные размеры остаются неизменными даже при нагреве состава до температуры 350 градусов Цельсия. Сплавы этой группы хорошо свариваются, а также обладают высокой обрабатываемостью. Стоит учитывать, что за счет легирования коррозионная стойкость относительно невысокая. Существенно повысить прочность можно путем закалки или старения. Подобные марки литейных алюминиевых сплавов широко используются при литье крупногабаритных отливок по песчаной форме.
- Конструкционные герметичные алюминиевый сплав обладают более высокими литейными свойствами. Распространенные марки: АЛ4 и АЛ9. Также следует отметить достаточно высокую коррозионную стойкость. Стоит учитывать тот момент, что термическая обработка в этом случае не проводится. При закалке или старении эксплуатационные качества не улучшаются. Хороший комплекс технологических свойств определяет популярность алюминиевого сплава.
- Коррозионностойкие металлы. К данной группе относится маркировка АЛ27 и АЛ8. Следует учитывать, что подобный тип металла обладает высокой стойкостью к воздействию повышенной влажности. Высокая коррозионная стойкость во многих агрессивных средствах существенно расширяет область применения металла. Кроме этого, структура определяет хорошую свариваемость и обрабатываемость резанием. Однако отметим, что металл обладает низкой жаропрочностью – структура не может выдержать воздействие температуры выше 80 градусов Цельсия. За счет легирования снижаются и литейные свойства. Исключением можно назвать сплав АЛ24, основные свойства которого сохраняются при температуре до 150 градусов Цельсия.
Последняя группа сплавов получила достаточно широкое распространение при изготовлении корпусов и деталей, на которые оказывается воздействие морской воды. Из-за высокой концентрации соли на поверхности довольно часто образуется коррозия.
К литейным сплавам принято относить составы, в которых есть от 10 до 13% кремния. Довольно часто в состав добавляются магний, медь и другие присадки, способные существенно повысить прочность. Также в состав добавляют титан и цирконий. В свою очередь, марганец может существенно повысить антикоррозионные свойства.
Несмотря на то, что в большинстве случаев железо и никель считаются вредными примесями, в данном случае они добавляются для существенного повышения жаропрочности.
Рассматривая маркировку отметим, что для этого применяется обозначение от АЛ2 до АЛ20. Эти материалы сегодня еще называют силуминами. Их химический состав, от которого зависят механические качества, может существенно отличаться. Именно поэтому следует подробно рассматривать состав каждой марки.
Применение
Алюминиевый литейный сплав сегодня применяется при производстве фасонных отливок. Отметим, что разделают как чистый алюминий, так и полученный после вторичной переработки. В химической и пищевой промышленности может использоваться чистый алюминий. Этот материал применим и в электротехнике. Важным моментом является то, что на алюминий приходится более 20% литейных сплавов.


Детали из литейных алюминиевых сплавов
Рассматривая особенности производства отметим, что первичный металл производится в чушках на специализированных алюминиевых заводах. Есть и вторичная цветная металлургия, которая предусматривает применение вторичного лома или отходов. За счет применения менее дорого сырья существенно снижается стоимость материалов.
В России только 50% заводов проводит использование лома в качестве основы. В более развитых странах мира, к примеру, США, Японии, Германии сегодня при производстве алюминиевых сплавов вторичное сырье применяется не менее чем в 90%. За счет этого существенно снижается стоимость различных изделий, а также повышается экологическая чистота.
Применение литейного алюминия весьма обширно:
- Изготовление корпусных деталей. Именно при производстве корпусных деталей чаще всего применяют литейные алюминиевые сплавы. Это связано с тем, что подобным образом существенно снижается их стоимость. Для получения сложных изделий из стандартной заготовки применяют современное фрезерное оборудование, которое стоит дорого и требует соответствующей оснастки.
- Получение различных заготовок в сфере кораблестроения и авиастроения. На протяжение нескольких столетий алюминий используется для изготовления деталей, которые применяются при сборе самолетов и различных летательных аппаратов.
- Изготовление деталей сложной формы и различных размеров. Детали, представленные телами вращения и плоскими поверхностями сложны в изготовлении при применении оборудования по механической обработке.
- Получение элементов, которые применяются для осуществления подачи электричества. При добавлении легирующих элементов получаются сплавы, обладающие хорошими токопроводящими способностями.
Очень большое количество деталей в моторостроении получается также путем литья. Данный метод изготовления позволяет получить детали с высокоточными размерами и качественной поверхностью.
В заключение отметим, что сегодня данный тип металла получил широкое применение в самых различных областях промышленности. Это также можно связать с тем, что стоимость производства подобного металла относительно невысока. Сочетание высоких эксплуатационных качеств с низкой стоимостью и определяют широкое распространение металла в самых различных отраслях промышленности.
Все об алюминиевых профилях
Как изготавливают алюминиевые профили
Алюминиевый профиль – это почти всегда прессованный алюминиевый профиль. Значительно реже применяются другие виды алюминиевых профилей, например, гнутые или катаные.
Рисунок 1.1 – Метод прямого прессования [1]
Рисунок 1.2 – Типичный пресс для прямого прессования алюминиевых сплавов [4]
Рисунок 1.3 – Типичный комплект прессового инструмента для прямого прессования [1]
Рисунок 1.4 – Метод обратного прессования [1]
с применением матрицы типа “портхол” [1]
Рисунок 1.6- Метод прессования труб с применением матрицы и оправки [1]
Рисунок 1.7 – Доля готовой продукции и технологических отходов
из экструзионного алюминиевого слитка (столба) [4]
Выход готовой продукции из алюминиевого слитка-столба:
- 75 % – готовые профили;
- 4,5 % – лом при изготовлении алюминиевой продукции из алюминиевых профилей;
- 4,5 % – заготовки для разогрева матриц; опрессовка матриц, дефекты прессования;
- 11 % – отходы смятых концов профилей после растяжной машины;
- 4 % – пресс-остатки; 1 % – отходы горячей резки столба на заготовки
Рисунок 1.8 – Технологические отходы экструзии алюминия,
которые сразу идут на переплавку и литье новых экструзионных слитков [4]
Элементы и детали конструкций, машин и изделий
Каждый алюминиевый профиль имеет свое назначение, свои свойства и характеристики. Если это просто декоративный элемент, главное назначение которого – быть красивым, радовать глаз, то основная его характеристика – хорошее качество поверхности, однородный цвет его декоративного покрытия, порошкового или анодного.
Если для алюминиевого профиля задано, например – матовое бесцветное анодное покрытие, то оно должно быть действительно матовым. Эта самая «матовость» должна быть совершенно однородной при взгляде с заданного расстояния и под заданным углом, без видимых полос и других визуальных неоднородностей поверхности. Чтобы обеспечить все это, необходимо применить алюминиевый сплав с особым химическим составом, особую технологию его изготовления и особую технологию обработки его поверхности.
Алюминиевые профили, как элементы несущих строительных или других конструкций, требуют особого внимания к их механическим характеристикам:
- пределу прочности,
- пределу пластичности,
- относительному сужению,
- вязким свойствам.
В этом случае важен выбор правильного сплава, его состояния (степени нагартовки или термической обработки), а также необходимой точности размеров при его изготовлении.
В других видов профилей надо принять во внимание такие свойства, как коррозионная стойкость в той среде, в которой будет работать профиль, иногда – электропроводность или теплостойкость.
Рисунок 1.9 – Пространственный каркас автомобиля Ауди А8 из алюминиевых сплавов [1]
Рисунок 1.10 – Проектирование алюминиевых профилей
с повышенной жесткостью [1]
Заготовки для волочения, холодного прессования и ковки
Кроме того, прессованные алюминиевые профили применяют в качестве исходных заготовок для таких технологий обработки алюминия как волочение, холодное прессование и ковка.
Рисунок 1.11 – Назначение алюминиевых профилей,
в том числе для волочения, холодного прессования и ковки [1]
Рисунок 1.12 – Волочение трубы из прессованной алюминиевой полой заготовки [3]
Сплавы для алюминиевых профилей
Прессованные алюминиевые профили могут изготавливаться из большого количества сплавов в различных состояниях с тем, чтобы удовлетворить требованиям различных сфер их применения – от бытовых изделий до космических ракетоносителей.
В принципе, из любого деформируемого алюминиевого сплава (и даже литейного) так или иначе можно отпрессовать алюминиевый профиль. Однако, течение металла через отверстия и полости матрицы при высоких температурах прессования требует особых характеристик течения, чтобы металл:
- наполнял все отверстия на выходе из матрицы с одинаково высокой скоростью,
- обеспечивал нужную микроструктуру,
- достигал заданных прочностных и других свойств,
- формировал оптимальное качество поверхности.
Поэтому разрабатывают специальные алюминиевые сплавы специально для прессования (экструзии). Химический состав этих сплавов оптимизируют таким образом, чтобы они максимально подходили для условий процесса прессования и обеспечивали нужное качество прессованной продукции.
В мировой практике алюминиевые профили из сплавов серии 6ххх дают более 75 % объема всех профилей.
Рисунок 1.13 – Содержание магния и кремния
в алюминиевых сплавах 6060 и 6063,
а также других некоторых сплавах серии 6ххх [1]
Самые популярные алюминиевые сплавы для профилей – это сплавы:
- 6060/6063 (АД31) и
- 6061(АД33).
Набирают популярности “более конструкционные” сплавы
Марки алюминия серии 1ххх, например, 1100, применяют для деталей и изделий, к которым не предъявляются требования по прочности. Они лучше всего прессуются – имеют самую высокую прессуемость.
Из сплавов серии 3ххх, например, сплава 3103 прессуют трубы для жидкостных трубопроводов.
Другие сплавы, которые чаще других применяют для изготовления профилей – это “дюрали”:
- 2017(Д1),
- 2014(АК8),
- 2024(Д16),
а также
- 5083(АМг4,5),
- 6101,
- 7005(1915) и
- 7075.
которые производят в виде прессованных изделий [1]
Рисунок 1.15 – Механические свойства некоторых алюминиевых сплавов,
которые производят в виде прессованных изделий [1]
Прессуемость сплавов: способность к прессованию
Рисунок 2.1 – Относительная прессуемость алюминиевых сплавов [1]
Рисунок 2.2 – Прессуемость различных алюминиевых сплавов [1]
Минимальная толщина стенки профиля
Влияние сложности поперечного сечения профиля из сплава 6063 на нормальную минимальную толщину стенки/
Рисунок 2.3 – Рекомендации по минимальной толщине стенки
профилей различной сложности из сплава 6063 [1]
Рисунок 2.4 – Минимальная толщина стенки алюминиевых профилей
(сплошных, труб, полых)
для экструзионных прессов усилием 10-80 МН [2]
Диаметр описанной окружности профиля
Обобщенным размером алюминиевого профиля является диаметр окружности, описывающий его поперечное сечение (рисунки 3.1 и 3.2). Этот параметр называют «диаметр описанной окружности».
Рисунок 3.1 – Диаметр описанной окружности профиля
Диаметр описанной окружности (ДОО) действительно связан со сложностью прессования алюминиевого профиля. При прессовании металл стремится течь через различные участки матрицы с различной скоростью: чем дальше от оси заготовки, тем медленнее. Поэтому, чем больше ДОО, тем сложнее контролировать размеры алюминиевого профиля.
При прессовании больших и тонких профилей, особенно, если эти тонкие стенки профилей находятся на периферии матрицы, необходимо предпринимать специальные меры, чтобы течение металла было равномерным по всему сечению профиля. Поэтому с увеличением ДОО все стандарты на алюминиевые профили снижают требования по предельным отклонениям геометрических размеров.
Рисунок 3.2 – Круглая заготовка
Рисунок 3.3 – Прямоугольная заготовка для прямоугольного контейнера[1]
Рисунок 3.4 – Полые прессованные алюминиевые профили,
которые производят с применением прямоугольного контейнера [1]
Виды алюминиевых профилей
Действующие стандарты на алюминиевые профили – например, российские ГОСТ 22233-2018 и ГОСТ 8617-91, европейские ЕN 755-9 и EN 12020-2 – подразделяют весь сортамент алюминиевых профилей на различные виды:
- профили полые и
- профили сплошные, а также
- С- и П-образные или профили «с открытым концом».
Полый профиль
По определению этих стандартов полые алюминиевые профили – это те, которые имеют в поперечном сечении хотя бы одну замкнутую полость.
Рисунок 4.1 – Полый профиль
Сплошной профиль
Сплошные алюминиевые профили не имеют замкнутых полостей.
Рисунок 4.2 – Сплошной профиль [1]
Сплошные матрицы имеют одно или более отверстий и предназначены для изготовления прессованных профилей без полостей. Отверстие в сплошной матрице в точности повторяет поперечное сечение прессуемого алюминиевого изделия.
Рисунок 5.1 – Матрица для прессования сплошных профилей методом прямого прессования [1]
Рисунок 5.2 – Течение металла при прямом прессовании [1]
Профиль с открытым концом
«Открытый конец» может быть как у полого, так и у сплошного профиля. Для этих трех видов профилей задаются различные требования по предельным отклонениям геометрических размеров.
Рисунок 6 – Контролируемые размеры алюминиевых профилей по ГОСТ 22233-2018 [5]
(EN 12020-2 [6]: h2 – расстояние между открытыми концами)
Полузамкнутые и полуоткрытые профили
Полые алюминиевые профили включают, в том числе, и профили с так называемыми полузамкнутыми (полуоткрытыми) полостями. Часто профили такого вида называют полузамкнутыми (полуоткрытыми). Они имеют частично замкнутую полость, например, круг или прямоугольник, с входом в нее с одной стороны (рисунок 6).
Рисунок 7 – Полузамкнутый (полуоткрытый) профиль [1]
Не каждая частично замкнутая полость превращает профиль из сплошного полузамкнутый: ее площадь А должна быть существенно больше квадрата ширины ее входа b (А > b), в зависимости от ширины входа – в 2,0-4,5 раза (см. рисунок 6).
“Полые” матрицы
Полые и полузамкнутые алюминиевые профили объединяются в один вид, потому что они изготавливают на так называемых «полых» матрицах (рисунки 7 и 8). Полые матрицы бывают трех видов:
- мостиковые (bridge),
- портхол (porthole) и
- крестообразные (spider).
Профили, изготавливаемые на таких матрицах, имеют один или несколько продольных сварочных швов из-за течения металла вокруг мостиков, которые поддерживают оправку. Оправка задает внутренний контур профиля. После прохождения этих мостиков, металл перед выходом из матрицы снова сваривается в сварочной камере. Сварка происходить за счет большого давления и высокой температуры. Сплошные профили прессуют на сплошных матрицах – стальных дисках с одним или больше отверстиями с таким же поперечным сечением, что и прессуемый профиль.
Рисунок 7 – Комбинированная матрица для прессования полузамкнутых (полуоткрытых) профилей
Рисунок 8- Комбинированная матрица для прессования полых профилей
Категории сложности алюминиевых профилей
Каждый вид профилей – сплошных, полузамкнутых и полых – различаются на типы по сложности их поперечного сечения. Эту сложность оценивают по коэффициенту формы алюминиевого профиля.
Коэффициент формы
Коэффициент формы алюминиевого профиля вычисляется как площадь всех поверхностей, образующихся при прессовании единицы массы металла. Очевидно, что этот коэффициент прямо пропорционален длине периметра поперечного сечения. Коэффициент формы влияет на производительность прессования профиля, а также на стоимость производства и технического обслуживания матриц. Поэтому он нередко применяется производителями-прессовщиками в качестве основы для установки цены профиля и дает разработчикам профилей определенный инструмент для сравнения альтернативных вариантов разрабатываемых алюминиевых профилей.
Рисунок 9.1 – Коэффициенты формы различных типов профилей [1]
Классификация сложности алюминиевых профилей
Классификация типов прессованных алюминиевых профилей по степени сложности их изготовления представлена в таблице ниже. Типы сложности от A до N расположены в порядке повышения сложности. Каждый тип иллюстрируется несколькими примерами.
Рисунок 9.2 – Типы сложности алюминиевых профилей
Сложность прессования возрастает в следующем порядке типов профилей:
- Прутки – простые или профильные.
- Стандартные алюминиевые профили и простые сплошные профили,
- Полузамкнутые профили,
- Профили со сложными язычками матриц,
- Трубы,
- Простые полые профили,
- Сложные полые профили.
- Широкие полые профили.
Оптимизация алюминиевых профилей
Рисунок 10 – Оптимизация поперечного сечения алюминиевых профилей [2]
Цена алюминиевых профилей
Цена алюминиевых профилей обычно напрямую связана с его категорией сложности. Однако, вместе с тем, сложные многофункциональные алюминиевые профили открывают более эффективные технические возможности, и их более высокая цена часто бывает вполне оправданной.
Источники:
- TALAT 1302
- TALAT 2202
- Drawing Types – University of Liverpool
- Презентация компании SAPA
- ГОСТ 22233-2018
- EN 12020-2
Литейные алюминиевые сплавы
Если оказалось, что проектируемая деталь должна быть литой и алюминиевой, правильный выбор сплава может оказаться проблемой, как для конструктора, так и для литейщика.
Литая алюминиевая деталь?
Обычно считается, что применение алюминиевого литья для нагруженных деталей оправдано только тогда, когда сложная форма литой детали дает существенное преимущество в массе по сравнению с простой по форме, например, кованой, деталью.
Обычно литейщики-производственники работают только несколькими литейными сплавами, что оправдано более экономичным использованием литейного оборудования, сокращением запасов сырья и снижением риска смешивания различных сплавов. С точки зрения качества литья более разумно работать со сплавом, который является технологичным, чем с тем, который может быть на бумаге и показывает несколько лучшие свойства, но более труден технологически.
С точки зрения литейщиков эти сплавы являются частным случаем литейных сплавов и поэтому могут называться немного по-другому – алюминиевые литейные сплавы.
Методы литья алюминия
Наиболее важными методами литья изделий из алюминиевых сплавов являются:
Литье под давлением, при котором расплавленный металл под действием давления «вдавливается» в стальную пресс-форму, обычно применяется при массовом производстве. Детали, отлитые под давлением, почти не требуют последующей механической обработки.
При литье в кокиль расплавленный металл разливается в, как правило, разъемные и обычно стальные формы многократного использования.
Технология литья в песчаные формы – это более медленный процесс, но обычно самый экономичный для малых партий, сложных конфигураций и больших отливок.
ГОСТ 1583-93: литейные алюминиевые сплавы
Отечественную классификацию литейных алюминиевых сплавов в настоящее время определяет ГОСТ 1583-93. Он включает системы с различными комбинациями алюминия с легирующими элементами Si, Cu, Mg, Mn и Zn:
- двойные сплавы Al–Si, Al–Cu, Al–Zn и Al–Mg;
- тройные сплавы Al–Si–Mg и Al–Si–Cu;
- четверные сплавы Al–Si–Mg–Cu.
Каждый сплав в этом стандарте имеет двойное обозначение: первое – для чушек и второе (в скобках) – для отливок, например, АК12(АЛ2). Это связано с тем, что в свое время, в конце 1980-х, ГОСТ 1583-89 объединил и заменил в один три стандарта:
- ГОСТ 1583-73 на литейные алюминиевые сплавы в чушках,
- ГОСТ 2685-75 на литейные алюминиевые сплавы в отливках и
- ГОСТ 1521-76 на силумин в чушках.
От ГОСТ 2685-75 и остались буквенно-цифровые обозначения типа АЛ2, АЛ4 или АЛ11. ГОСТ 1583-93 разрешает для отливок применять эти обозначения сплавов без дублирования обозначениями для чушек. Интересно, что ссылки на ГОСТ 2685-75, отмененный более 20 лет назад, все еще встречается, например, на сайтах некоторых литейных предприятий.
Силумины нормальные
Из литейных алюминиевых сплавов наиболее часто применяют силумины – сплавы с большим содержанием кремния. Сплавы алюминия только с медью, магнием и цинком применяют значительно реже. Дело в основном в том, что для получения плотной структуры отливки необходим сплав с узким интервалом кристаллизации, а для этого лучше подходят сплавы эвтектической концентрации или близкой к ней. В этом смысле система Al–Si имеет решающее преимущество над другими системами – ее эвтектика имеет сравнительно низкое содержание кремния 11,7 %, тогда как в системе Al–Cu эвтектика имеет 33 % меди, а в системе Al–Mg – 34,5 %.
Двойные сплавы Al–Si имеют самые лучшие литейные свойства. К ним относится обычный (нормальный) силумин с содержанием кремния от 10 до 13 % (сплав АЛ2), который применяют для отливок сложной формы при отсутствии требований высоких механических свойств.
Силумины специальные
При более высоких требованиях к прочностным свойствам применяют специальные силумины – доэвтектические силумины с содержанием кремния от 4 до 10 % и добавками меди, магния и марганца в различных комбинациях и количествах. Сплавы АЛ4 и АЛ9 – силумины с пониженным содержанием кремния и с небольшим добавками магния и марганца (АЛ4) и магния (АЛ9), что улучшает их механические свойства. Низкокремнистые силумины, легируют медью, а также небольшими количествами магния – сплав АЛ5, магния и марганца (и титана) – сплав АК5М2. Они обладают худшими литейными свойствами, чем нормальный силумин, но превосходят его по механическим свойствам. Эти силумины после термической обработки имеют прочность от 200 до 250 МПа и относительное удлинение от 1 до 6 % – прочность близкая к прочности деформируемых сплавов, но при относительно низкой пластичности. Это связано с более грубой структурой, не раздробленной пластической деформацией. Сплав АЛ11 относится к цинковистым силуминам – добавка цинка таких больших количествах (10-14 %) улучшает его литейные свойства, что дает возможность отливать из него особо сложные детали.
Термическая обработка литейных алюминиевых сплавов
Термическая обработка литейных алюминиевых сплавов, по сравнению с деформированными, имеет свои особенности. Это связано в первую очередь с различиями в химическом составе, а также более грубой и крупнозернистой структурой литых сплавов. Литые сплавы почти не подвержены естественному старению, поэтому максимальная прочность обычно достигается за счет искусственного старения в течение 10-20 часов при 150-180 °С. Упрочнение происходит за счет выделения из пресыщенного твердого раствора интерметаллических соединений CuAl2,Mg2Si, Al3Mg2 и т.д. Нередко уже одна закалка повышает прочность и пластичность за счет растворения интерметаллических соединений, которые в литом состоянии скапливаются на границах зерен. Старение еще больше повышает прочность, но чаще всего в ущерб пластичности.
Выбор литейных алюминиевых сплавов
К факторам, которые принимают во внимание при выборе литейного сплава для конкретного конструкторского решения, относятся следующие.
Примеси в алюминиевых сплавах
Каждый литейный алюминиевый сплав по ГОСТ 1583-93 и для чушек, и для отливок имеет в целом одинаковый состав основных легирующих элементов. Требования же по содержанию примесей могут значительно отличаться для чушек и отливок, с одной стороны, и для применяемых способов литья – с другой. При этом ограничения по каждой из таких примесей как марганец, медь, цинк, никель, свинец, олово и кремний, как правило, одинаковы для чушек и отливок. Однако ограничения по их сумме, а также отдельно по содержанию железа различаются как для чушек и отливок, так и для способов литья: в песчаные формы, в кокиль, под давлением. Для чушек требования по примесям выше, чем для отливок. Для литья под давлением допускается максимальное содержание железа и суммы примесей, для литья в песчаные формы – минимальное.
Вторичные алюминиевые сплавы
Количество примесей, особенно железа, является одним из важных качеств литейного сплава. С понижением количества примесей в сплаве повышается его коррозионная стойкость и пластичность. Однако надо принимать во внимание и то, что более чистый сплав и стоить будет дороже. Вторичные литейные сплавы обычно изготавливают из лома по тому же ГОСТ 1583-93 и они могут иметь более низкий по сравнению с первичными сплавами уровень пластичности и коррозионной стойкости именно из-за большего количеств примесей. Однако существует множество изделий, для которых эти механические свойства и коррозионная стойкость вполне приемлемы, и поэтому вторичные сплавы широко применяются. Как видно из требований ГОСТ 1583-93 более «грязный» сплав может потребовать более сложного способа литья.
Прочностные свойства алюминиевых сплавов
В зависимости от требований к механическим свойствам будущей отливки сплав выбирают из следующих условных «прочностных» категорий:
«Прочные и пластичные». В эту группу входят наиболее важные упрочняемые старением сплавы, например, Al–Cu. С помощью различных видов термической обработки их свойства «регулируют» или на высокую прочность или на высокое относительное удлинение.
«Твердые». Литейные сплавы этой группы имеют определенную прочность при растяжении и твердость без особых требований к относительному удлинению. Прежде всего, это сплавы Al–Si–Cu.
«Пластичные». Сплавы с повышенной пластичностью – это, в основном, нормальные и низкокремнистые силумины.
Литейные свойства алюминиевых сплавов
Литейные свойства сплава, такие как жидкотекучесть и особенности затвердевания, ставят литейщику определенные ограничения. Не каждую отливку можно отлить из любого сплава. Выбор оптимального сплава для конкретной детали обычно требует взаимодействия конструктора и литейщика.
Жидкотекучесть металлического расплава определяют с помощью технологической пробы, например, длины заполнения расплавом специальной спирали. Казалось бы при низкой жидкотекучести надо просто увеличить температуру разливки. Однако в этом случае обычно сталкиваются с другими проблемами, такими как окисление расплава, насыщение его водородом или повышенный износ литейной формы. Эвтектические силумины имеют самую высокую жидкотекучесть, низкокремнистые силумины – среднюю, а сплавы Al–Cu и Al–Mg – самую низкую.
Склонность к горячему растрескиванию является почти противоположностью жидкотекучести. Под горячим растрескиванием понимают отделение друг от друга уже кристаллизовавшихся фаз, например, при усадке. Эти трещины или разрывы могут залечиваться при подаче в форму оставшегося металла. У эвтектических алюминиевых литейных сплавов почти нет проблем с образованием трещин, тогда как для алюминиевых литейных сплавов Al–Cu и Al–Mg эта проблема весьма актуальна.
Источники:
- Гуляев А.П. Металловедение, 1986.
- Aluminum and Aluminum Alloys, ASM International, 1993.
Сплав алюминия и меди: состав, характеристики, сферы применения
Сплавы алюминия и меди востребованы в различных производственных сферах, так как обладают относительно небольшим весом, высокой прочностью, пластическими свойствами, однородной плотностью. Хорошо поддаются литью, ковке и другим видам обработки. Отличаются относительно простой технологией получения.

История открытия
История сплавов алюминия с медью начинается с опытов Х. Эрстеда в 1825 году, когда он хотел получить чистый Al методом электролиза. В действительности он получил некий состав, в который входили и другие элементы, участвующие в эксперименте.
Дальнейшие опыты по открытию чистого алюминия провёл Ф. Велер в 1827 году, когда получил 30 грамм порошка Al, а в 1845 году — расплавленные шарики. Однако метод получения был слишком трудоёмким и требовал усовершенствования.
В 1856 году А. Девиль разработал со своей исследовательской группой промышленный метод получения алюминия и открыл первое его массовое производство. В 1886 году П. Эру и Ч. Холл открыли электролитический способ, который оказался дешевле и эффективнее химического.
С 1888 по 1895 в Нейгаузене (Швейцария) открываются предприятия по массовому производству Al.
В 1906 году А. Вильм на собственном предприятии начинает разрабатывать высокопрочные алюминиево-медные сплавы. Путем опытов он получил образец, который обладал свойством самоупрочнения. Его производство было продолжено в 1911 году в Германии.
Массовые исследования сплавов пришлись на период с 1920 по 1940 год в СССР, Германии, США. Стали явно разделяться два направления экспериментов — изучение чистых и легированных составов.
Состав и структура
Фазовая диаграмма состояния алюминиевых сплавов Al-Cu имеет следующие особенности:
- Максимальная растворимость меди в алюминии в твёрдой фазе составляет 5,65%, которая снижается с понижением температуры. Это делает возможным проведение закалки и старения. Фаза CuAl2 играет роль упрочняющей по методу растворов, придаёт механическую и термическую прочность.
- Эвтектическая точка находится на 33% концентрации меди, состоит из хрупкой, но прочной фазы CuAl2, которая делает материал непригодным для практического применения. Большое количество меди существенно повышает плотность образцов. Для литья используются сплавы с концентрацией от 1 до 1,5% (для получения упрочнения) и от 6 до 8% (чтобы исключить количество хрупкой фазы CuAl2).
- Хорошая растворимость Cu в Al и низкая температура плавления эвтектики +5480С становятся причиной появления широкого интервала кристаллизации.
Низкая жидкотекучесть, образование пор, трещин, ликвация — характерные признаки необходимости поиска компромисса между литейными и прочностными свойствами.
Основным легирующим элементом является медь, которая приводит к созданию неравновесной эвтектической фазы. Поэтому при термообработке закалкой проводят ступенчатый нагрев расплава до +5300С с последующей выдержкой до получения стабильной фазы.
Значительное количество электронов проводимости в сплавах Cu-Al существенно снижают удельное электросопротивление до уровня менее 0,02 мкОм*м. Наличие примесей железа или легирующих элементов на данную величину практически не влияют.

Характеристики и свойства сплава
Применение алюминия в чистом виде не выгодно по причине его малой прочности. Даже в изготовлении электронных компонентов он практически не применяется.
Свойства алюминия при добавлении меди существенно улучшаются: сохраняется пластичность, повышается прочность. В однофазных сплавах отсутствует текучая жидкая фаза, которая способна заполнять пустоты, образуемых в процессе усадки, снимать внутренние напряжения. Трудные составы имеют сложный процесс твердения и необходимо применять особые меры в процессе литья.
Существуют такие виды сплавов:
- деформируемые, получаемые путём термической закалки и последующего старения — используются в средне нагружаемых конструкциях, выпускаются в виде проволоки, прутка, листов, профилей и труб;
- литейные — используются для отливки сложных конструкций, обладают высокой прочностью, плохо поддаются пайке.
Чтобы улучшить литейные свойства смеси, в состав добавляют немного кремния, который увеличивает текучесть, снижает вероятность растрескивания. Негативным фактором является понижение уровня пластичности.
Механические свойства сплавов с содержанием меди от 9 до 11%:
- высокая прочность от 500 МПа;
- износостойкость;
- самоупрочнение;
- жаростойкость.
Для улучшения характеристик используются легирующие элементы:
- марганец и титан формируют интерметаллиды, которые находятся по границам дендритных ячеек Cu-Al образуют твёрдый каркас, применяются для повышения жаропрочности образцов;
- кремний повышает механические свойства, на снижает литейные, может применяться без термической обработки.
Изготовление
Медные сплавы с алюминием производят методом расплавления в электрических печах. Особенностью является возможность многократных циклов плавки и твердения, при которых не теряются основные свойства.
Сначала расплавляют алюминий, затем в него добавляют медь, а после получения однородного состава и легирующие элементы (железо, марганец, магний). Следующим этапом является закалка, которая позволяет избавиться от метастабильных фаз и добиться однородной плотности. Время выдержки выбирается на основе используемых легирующих компонентов и процентного содержания меди.
Где применяют сплав
Применение конструкций из алюминиево-медных сплавов:
- пищевая промышленность;
- автомобиле-, корабле- и самолётостроение;
- отделочные декоративные материалы;
- для защиты металлических изделий от коррозии;
- в электротехнике — радиоэлементы, высоковольтные линии передач, кабеля;
- в качестве отражателей света в лампах;
- для изготовления дорожных знаков, указателей, таблиц.

Достоинства и недостатки
Основные преимущества:
- высокая прочность, пластичность;
- хорошая обрабатываемость —резание, штамповка, ковка, вытяжка, литьё;
- сохранение механических свойств до температуры +1750С;
- сверхпроводимость, позволяющая использовать образцы в научных исследованиях или применять в инновационных разработках;
- высокая коррозионная стойкость;
- возможность эксплуатации в деталях конструкций с повышенной взрывоопасностью;
- химическая нейтральность;
- простота сварки.
Основным недостатком является низкая коррозионная стойкость.
После закалки некоторое время сплав имеет отличную пластичность и ему можно придавать необходимую форму. Чтобы избежать чрезмерного образования дислокаций, требуется прогрев до +3500С с последующим остыванием в воздушной среде.
Деформируемые алюминиевые сплавы: ГОСТ, химический состав
Кроме него отношение к химическому составу деформируемых сплавов имеют еще два стандарта:
- ГОСТ 1131-76 на сплавы алюминиевые деформируемые в чушках
- ГОСТ 11069-2001 на алюминий первичный в чушках.
Чушки из первичного алюминия и деформируемых сплавов переплавляют и получают слитки, пригодные для обработки горячей или холодной деформацией.
Марки алюминия и алюминиевых сплавов
Будем для удобства в наименовании алюминиевых сплавов опускать слово «марка», например, «алюминиевый сплав АД33», а не «алюминиевый сплав марки АД33». На мой взгляд, при наименовании сплавов слово «марка» представляется совершенно излишним – совершенно достаточно слова “сплав”.
Чтобы различать различные варианты чистого алюминия применяют термин “марка алюминия”, например, марка алюминия АД00. В этом случае это полезно, потому что марки алюминия не являются по определению алюминиевыми сплавами.
В стандартах стран СНГ применяет три вида обозначений марок алюминия и алюминиевых сплавов: традиционные бессистемные буквенно-цифровые и системные цифровые, а также международные цифровые и химические для имеющихся международных аналогов. Например, для сплава Д1 это: Д1, 1110, AlCu4MgSi и 2017.
Обозначения алюминиевых сплавов
Чисто цифровые обозначения были введены в конце шестидесятых прошлого века и были задуманы как часть общей системы обозначений всех сплавов всех металлов. Первая цифра 1 была закреплена за алюминиевыми сплавами. Вторая цифра должна обозначать систему легирования. Тогда первые две цифры, судя по ГОСТ 4784, обозначают алюминиевые сплавы различных систем легирования, например:
- 10хх – алюминий технический;
- 11хх – сплавы алюминиевые системы Al-Cu-Mg;
- 12хх – сплавы алюминевые системы Al-Cu-Mn;
- 13хх – сплавы алюминевые системы Al-Mg-Si;
- 14хх – сплавы алюминевые системы Al-Mn;
- 15хх – сплавы алюминевые системы Al-Mg;
- 19хх – сплавы системы Al-Zn-Mg.
Последние две цифры определяют порядковый номер сплава внутри конкретной системы, причем, как будто бы, нечетные числа должны обозначать деформируемые сплавы, а четные – литейные. Однако в ГОСТ 1583-93 на литейные алюминиевые сплавы никаких следов таких цифровых обозначений не видно.
По-существу, эта цифровая система обозначений так полностью и не прижилась и мало употребляется. Большинство сплавов обозначают «старыми», бессистемными буквенно-цифровыми обозначениями, а стандарты, например ГОСТ 4784, дублируют оба варианта. Правда, некоторые сплавы имеют только одно, цифровое обозначение, например, сплав 1105, который применяется для изготовления лент и у которого нет ни «старого» обозначения, ни “официального” международного аналога.
Деформируемые сплавы: ГОСТ 4784-97
ГОСТ 4784-97 распространяется на алюминий и деформируемые алюминиевые сплавы, предназначенные для изготовления полуфабрикатов (лент в рулонах, листов, плит, полос, прутков, профилей, шин, труб, проволоки, поковок и штамповок) методом горячей или холодной деформации, а также слябов и слитков для дальнейшей деформационной переработки.
Железо и кремний являются неизбежными постоянными примесями в алюминии и алюминиевых сплавах. Они образуют с алюминием тройные химические соединения, которые, особенно, если они находятся на границах зерен, снижают пластичность алюминия. Поэтому стандарт требует, чтобы в марках алюминия, а также сплаве АМцС, содержание железа было больше чем кремния.
ГОСТ 4784 относит к деформируемым сплавам легированный алюминий с суммарным содержанием легирующих элементов и примесей более 1,0 %. Таблица ниже представляет собой обзор сплавов ГОСТ 4784. Для большей ясности опущены специфические сварочные сплавы и варианты сплавов для проволоки для холодной высадки.
Мягкие сплавы
Марки алюминия (серия 1ххх)
Содержание примесей (или легирующих элементов) не более 1,00 %.
Алюминиевые сплавы Al-Mn (серия 3ххх)
Термически неупрочняемые сплавы.
(Заметим, что мы применяем слово “неупрочняемые” со слитным написанием частицы “не”. Это слово в данном случае – прилагательное, а не причастие. Прилагательные пишутся с частицей “не” слитно, а вот причастия – раздельно. Это мы помним со школьной скамьи. 🙂 )
Интересно, что эта система формально имеет соединение Al6Mg с переменной растворимостью и ее сплавы должны бы быть термически упрочняемыми. Однако, оказывается, в присутствии неизбежной примеси – железа – вместо растворимой фазы образуется нерастворимое в алюминии соединение Al6(Mn, Fe). Марганец, в отличие от других легирующих элементов, не ухудшает, а улучшает коррозионную стойкость сплава. Поэтому эти сплавы превосходят технический алюминий и по прочности, и коррозионной стойкости.
Сплавов этой системы в стандарте не так уж много:
- ММ,
- АМц,
- АМцС
- Д12.
Все они применяются, в основном, в виде листов и лент в различных нагартованных состояниях.
Обозначения сплавов этой системы пример полной бессистемности (извините за каламбур!) обозначений сплавов в наших стандартах. Похоже на тест для оценки IQ: “Д1, Д16, Д18, Д19 – дюралюмины. Является ли сплав Д12 также дюралюмином?” Правильный ответ – нет.
Умеренно прочные алюминиевые сплавы
Алюминиевые сплавы Al-Mg(серия 5ххх)
Термически не упрочняемые.
Магний в количестве до 6 % дает упрочнение твердого раствора сплава и высокую эффективность деформационного упрочнения. Поэтому сплавы серии 5ххх имеют довольно высокие прочностные свойства. Эти сплавы широко имеют хорошую коррозионную стойкость, особенно сопротивление коррозии в морской воде и морской атмосфере, и поэтому широко применяются в судостроении, в основном в виде листов. Из этих сплавов изготавливают штампованные детали корпуса и шасси автомобилей благодаря хорошей комбинации их прочности и формуемости.
Алюминиевые сплавы Al-Mg-Si (серия 6ххх)
Эти сплавы иногда (только у нас) называют «авиалями».
Упрочняющей фазой является соединение Mg2Si.
Алюминиевый сплав АД31 – полный аналог «американского» сплава 6063 и, частично, «европейского» сплава 6060. Соотношение среднего содержания кремния и магния в нем близко к стехиометрическому соотношению 1:1,73 для соединения Mg2Si.
- АД31 (6060/6063) – самый популярный промышленный алюминиевый сплав. Широко применяется для изготовления алюминиевых профилей для строительных ограждающих конструкций (окон, дверей, фасадов) и других, как правило, не несущих конструкций.
- Алюминиевый сплав АД33 – аналог сплава 6061. Большее содержание магния и кремния, чем у АД31 (кремний в избытке), а также добавки меди. Более прочный, чем АД31. Применяется в несущих строительных конструкциях.
- Алюминиевый сплав АД35 – аналог сплава 6082. По сравнению со сплавом АД33 магния почти столько же, как и у сплава АД33, а кремния раза в полтора больше и дополнительно до 1 % марганца. Поэтому сплав АД35 еще более прочный, чем АД33. Применяется в несущих строительных конструкциях.
Твердые алюминиевые сплавы
Серия 2ххх – Алюминиевые сплавы Al-Cu-Mg и Al-Cu-Mn
Термически упрочняемые сплавы.
Так называемые дуралюмины или дюралюмины. В зависимости от содержания меди и магния, а также соотношения их концентраций, в них могут образовываться различные упрочняющие фазы: двойные или тройные соединения алюминия с медью, магнием и марганцем.
- Алюминиевый сплав Д1 – «классический», нормальный дюралюминий с упрочняющей фазой CuAl2.
- Сплав Д16 – более прочный, так называемый «супердюралюмин», по сравнению с Д1 содержит повышенное количество магния (в среднем 1,5 %). Поэтому основной упрочняющей фазой у него является уже тройная фаза CuMgAl2, что и дает более высокую прочность.
Буква Д не обязательно означает “дюралюминий, дюраль”, как это может показаться. Существует алюминиево-марганцевый сплав Д12 – мягкий и пластичный.
Прочность дюралюминиев зависит от вида полуфабриката: в прутках больше, в листах – меньше. Предел прочности нормального листового Д1 достигает 410 МПа, а листового Д16 – 440 МПа.
- Алюминиевый сплав Д18 специально предназначен для заклепок, он содержит пониженное количество меди и магния и поэтому имеет существенно более низкую прочность, но и более высокую пластичность, чем, скажем, дюралюминий Д1.
- Алюминиевый сплав В65 предназначен для заклепок, которые работают при температуре не выше 100 °С.
- Алюминиевые сплавы АК (АК4, АК6 и АК8) – близкие «родственники» дюралюминия — предназначены для поковок и штамповок. Буква К как раз и обозначает: Ковочный.
Серия 7ххх – Алюминиевые сплавы Al-Zn-Cu-Mg
Термически упрочняемые сплавы.
Включают самый прочный алюминиевый сплав – сплав В95. Известен еще более прочный алюминиевый сплав – В96, но он не включен в ГОСТ 4784-97.
- Алюминиевый сплав В95 имеет содержание цинка от 5 до 7 %, магния от 1,8 до 2,8 % и меди от 1,4 до 2 % при пределе прочности до 600 МПа. Сплав В96 имеет прочность под 700 МПа при содержании цинка от 8 до 9 % и увеличенном содержании магния и меди.
- Алюминиевые сплавы 1915 и 1925 удобны тем, что являются, так сказать, самозакаливающимися. Их прочность мало зависят от вида закалочной среды (вода, воздух). Поэтому при прессовании из них профилей с толщиной полок до 10 мм их охлаждают на воздухе. Старение проводят как при комнатной, так и при повышенных температурах.
Источники:
ГОСТ 4784-97 Алюминий и сплавы алюминиевые деформируемые
Гуляев А.П. Металловедение. М: Металлургия, 1986.
Все о 6061 Алюминий (свойства, прочность и применение)
Металлический алюминий и его сплавы используются в большинстве, если не во всех, современных промышленных процессах из-за его широкой доступности и огромного количества применений. Сплав — это металл, полученный путем объединения двух или более металлических элементов для достижения улучшенных свойств материала. Процесс легирования включает добавление определенных металлических «легирующих» элементов в основной металл для придания ему отличительных свойств, таких как повышенная прочность, коррозионная стойкость, проводимость, ударная вязкость и т. Д., или желаемое сочетание этих черт. Сплавы с низким процентным содержанием легирующих элементов (около <4%) классифицируются как деформируемые сплавы и являются обрабатываемыми, тогда как сплавы с более высоким процентным содержанием (до 22%) классифицируются как литые и обычно хрупкие. Алюминиевая ассоциация (AA Inc.) является ведущим авторитетом в области алюминиевых сплавов и разработала четырехзначную систему именования, используемую для отличия деформируемых сплавов друг от друга на основе их основных легирующих элементов. В этой статье будет подробно рассмотрен алюминиевый сплав 6061, выделены его физические свойства, а также общие области применения этого очень полезного материала.
Алюминий типа 6061 относится к алюминиевым сплавам 6ххх, в состав которых входят те смеси, в которых в качестве основных легирующих элементов используются магний и кремний. Вторая цифра указывает на степень контроля примесей основного алюминия. Когда эта вторая цифра равна «0», это означает, что основная часть сплава представляет собой технический алюминий, содержащий существующие уровни примесей, и не требуется особой осторожности для ужесточения контроля. Третья и четвертая цифры — это просто обозначения для отдельных сплавов (обратите внимание, что это не относится к алюминиевым сплавам 1xxx).Номинальный состав алюминия типа 6061: 97,9% Al, 0,6% Si, 1,0% Mg, 0,2% Cr и 0,28% Cu. Плотность алюминиевого сплава 6061 составляет 2,7 г / см 3 (0,0975 фунта / дюйм 3 ). Алюминиевый сплав 6061 поддается термической обработке, легко формируется, сваривается и хорошо сопротивляется коррозии.
Механические свойства
Механические свойства алюминиевого сплава 6061 различаются в зависимости от того, как он подвергается термообработке или становится прочнее с помощью процесса отпуска. Чтобы упростить эту статью, значения прочности для этого сплава будут взяты из закаленного алюминиевого сплава 6061 (6061-T6), который является обычным для алюминиевых листов и прутков.Его модуль упругости составляет 68,9 ГПа (10000 фунтов на квадратный дюйм), а его модуль сдвига составляет 26 ГПа (3770 фунтов на квадратный дюйм). Эти значения измеряют жесткость сплава или сопротивление деформации и приведены в таблице 1. Как правило, этот сплав легко соединяется сваркой и легко деформируется в самые желаемые формы, что делает его универсальным материалом для изготовления.
Два важных фактора при рассмотрении механических свойств — это предел текучести и предел прочности. Предел текучести описывает максимальное напряжение, необходимое для упругой деформации детали при заданном нагружении (растяжение, сжатие, скручивание и т. Д.).). Предел прочности, с другой стороны, описывает максимальное напряжение, которое материал может выдержать до разрушения (подвергаясь пластической или остаточной деформации). Для статических приложений предел текучести является более важным конструктивным ограничением в соответствии с отраслевыми стандартами проектирования; тем не менее, максимальная прочность может быть полезна для определенных приложений, в которых она необходима. Алюминиевый сплав 6061 имеет предел текучести при растяжении 276 МПа (40000 фунтов на квадратный дюйм) и предел прочности на разрыв 310 МПа (45000 фунтов на квадратный дюйм).Эти значения приведены в таблице 1.
Прочность на сдвиг — это способность материала противостоять сдвигу противодействующими силами вдоль плоскости, подобно тому, как ножницы разрезают бумагу. Когда два лезвия ножниц закрываются, их противодействующие силы действуют на плоскость поперечного сечения бумаги и заставляют ее разрушаться «при сдвиге». Это значение полезно при скручивании (валы, стержни и т. Д.), Где скручивание может вызвать такое напряжение сдвига в материале. Прочность на сдвиг алюминиевого сплава 6061 составляет 207 МПа (30000 фунтов на квадратный дюйм), и эти значения приведены в таблице 1.
Усталостная прочность — это способность материала противостоять разрушению при циклической нагрузке, когда небольшая нагрузка постоянно передается на материал с течением времени. Это значение полезно для приложений, где деталь подвергается повторяющимся циклам нагрузки, например, оси транспортного средства или поршни. Усталостная прочность алюминиевого сплава 6061 составляет 96,5 МПа (14000 фунтов на квадратный дюйм), что рассчитано с использованием 500000000 циклов непрерывного циклического нагружения ниже предела текучести. Эти значения приведены в таблице 1.
Таблица 1: Обзор механических свойств алюминиевого сплава 6061.
Механические свойства | Метрическая система | Английский |
Предел прочности на разрыв | 310 МПа | 45000 фунтов на кв. Дюйм |
Предел текучести при растяжении | 276 МПа | 40000 фунтов на кв. Дюйм |
Прочность на сдвиг | 207 МПа | 30000 фунтов на кв. Дюйм |
Прочность по усталости | 96.5 МПа | 14000 фунтов на кв. Дюйм |
Модуль упругости | 68,9 ГПа | 10000 тысяч фунтов / кв. Дюйм |
Модуль сдвига | 26 ГПа | 3770 тысяч фунтов / кв. Дюйм |
Коррозионная стойкость
При воздействии воздуха или воды алюминиевый сплав 6061 образует слой оксида, который не позволяет ему вступать в реакцию с элементами, вызывающими коррозию лежащего под ним металла.Степень коррозионной стойкости зависит от атмосферных / водных условий; однако при температуре окружающей среды коррозионное воздействие в воздухе / воде обычно незначительно. Важно отметить, что из-за содержания меди 6061 он немного менее устойчив к коррозии, чем другие типы сплавов (например, алюминиевый сплав 5052, который не содержит меди). При контакте с щелочной почвой могут возникнуть некоторые коррозионные эффекты, такие как точечная коррозия, но это сильно зависит от условий почвы.6061 особенно хорошо сопротивляется коррозии от концентрированной азотной кислоты, а также аммиака и гидроксида аммония. Коррозионные воздействия можно полностью устранить, нанеся на сплав защитный слой, на который сплав 6061 хорошо реагирует.
Применения типа 6061 Алюминий
Алюминий типа 6061 — один из наиболее широко используемых алюминиевых сплавов. Его свариваемость и формуемость делают его пригодным для многих приложений общего назначения. Его высокая прочность и коррозионная стойкость делают сплав 6061 особенно полезным в архитектурных, конструкционных и автомобильных приложениях.Список его применений является исчерпывающим, но некоторые основные области применения алюминиевого сплава 6061 включают:
Резюме
В этой статье представлен краткий обзор свойств, прочности и областей применения алюминия 6061. Для получения информации о других продуктах ознакомьтесь с нашими дополнительными руководствами или посетите платформу Thomas Supplier Discovery Platform, чтобы найти потенциальные источники поставок или просмотреть подробную информацию о конкретных продуктах. У нас также есть направляющие для других типов алюминия, включая алюминий 5052, алюминий 3003 и алюминий 7075.
Прочие изделия из алюминия
- Лучшие поставщики и производители алюминия в США
- Различные типы марок алюминия (свойства и применение)
- Все о 7075 Алюминий (свойства, прочность и применение)
- Все о 5052 Алюминий (свойства, прочность и применение)
- All About 2024 Aluminium (Свойства, прочность и применение)
- Все о 6063 Алюминий (свойства, прочность и применение)
- Все о 3003 Алюминий (свойства, прочность и применение)
- 6061 Алюминий vs.7075 Алюминий — Различия в свойствах, прочности и областях применения
- Алюминий 6061 и алюминий 6063 — Различия в свойствах, прочности и областях применения
- Алюминий 6061 и алюминий 5052 — Различия в свойствах, прочности и областях применения
- 6061 Алюминий и алюминий 2024 г. — Различия в свойствах, прочности и областях применения
- Алюминий 3003 и алюминий 6061 — различия в свойствах, прочности и областях применения
Источники:
- https: // материалыданные.nist.gov/bitstream/handle/11115/173/Aluminium%20and%20Aluminium%20Alloys%20Davis.pdf?sequence=3&isAllowed=y
- https://sites.esm.psu.edu
- https://www.nrc.gov/docs/ML0633/ML0633
- .pdf
- https://materialsdata.nist.gov/bitstream/handle/11115/185/Understanding%20Waught%20and%20Cast%20Al%20Alloy%20Designations.pdf?isAllowed=y&sequence=3
Другие товары от Metals & Metal Products
.% PDF-1.6 % 59 0 объект > endobj xref 59 145 0000000016 00000 н. 0000003596 00000 н. 0000003790 00000 н. 0000003854 00000 н. 0000003979 00000 п. 0000004418 00000 н. 0000005467 00000 н. 0000005494 00000 п. 0000005522 00000 н. 0000005634 00000 н. 0000006513 00000 н. 0000007448 00000 н. 0000008284 00000 н. 0000009337 00000 н. 0000010216 00000 п. 0000011071 00000 п. 0000011910 00000 п. 0000012737 00000 п. 0000013584 00000 п. 0000014632 00000 п. 0000015511 00000 п. 0000016351 00000 п. 0000017276 00000 п. 0000018323 00000 п. 0000018489 00000 п. 0000019360 00000 п. 0000069088 00000 н. 0000069157 00000 п. 0000069249 00000 п. 0000069331 00000 п. 0000069418 00000 п. 0000069442 00000 п. 0000069639 00000 п. 0000069727 00000 п. 0000069751 00000 п. 0000069880 00000 п. 0000069968 00000 н. 0000069992 00000 н. 0000070110 00000 п. 0000070198 00000 п. 0000070222 00000 п. 0000070363 00000 п. 0000070452 00000 п. 0000070477 00000 п. 0000070591 00000 п. 0000070677 00000 п. 0000070702 00000 п. 0000070835 00000 п. 0000070922 00000 п. 0000070947 00000 п. 0000071070 00000 п. 0000071159 00000 п. 0000071184 00000 п. 0000071286 00000 п. 0000071373 00000 п. 0000071398 00000 п. 0000071524 00000 п. 0000071611 00000 п. 0000071636 00000 п. 0000071750 00000 п. 0000071837 00000 п. 0000071862 00000 п. 0000071984 00000 п. 0000072072 00000 п. 0000072097 00000 п. 0000072225 00000 п. 0000072313 00000 п. 0000072338 00000 п. 0000072456 00000 п. 0000072545 00000 п. 0000072570 00000 п. 0000072692 00000 п. 0000072780 00000 п. 0000072805 00000 п. 0000072916 00000 п. 0000073003 00000 п. 0000073028 00000 п. 0000073189 00000 п. 0000073245 00000 п. 0000073270 00000 п. 0000073385 00000 п. 0000073480 00000 п. 0000073606 00000 п. 0000073693 00000 п. 0000073718 00000 п. 0000073839 00000 п. 0000073928 00000 п. 0000073953 00000 п. 0000074091 00000 п. 0000074180 00000 п. 0000074205 00000 п. 0000074333 00000 п. 0000074420 00000 п. 0000074445 00000 п. 0000074559 00000 п. 0000074647 00000 п. 0000074672 00000 п. 0000074807 00000 п. 0000074894 00000 п. 0000074919 00000 п. 0000075050 00000 п. 0000075139 00000 п. 0000075164 00000 п. 0000075298 00000 п. 0000075387 00000 п. 0000075412 00000 п. 0000075550 00000 п. 0000075637 00000 п. 0000075662 00000 п. 0000075796 00000 п. 0000075883 00000 п. 0000075908 00000 п. 0000076026 00000 п. 0000076082 00000 п. 0000076107 00000 п. 0000076219 00000 п. 0000076307 00000 п. 0000076332 00000 п. 0000076477 00000 п. 0000076566 00000 п. 0000076591 00000 п. 0000076701 00000 п. 0000076788 00000 п. 0000076813 00000 п. 0000076903 00000 п. 0000076928 00000 п. 0000077041 00000 п. 0000077131 00000 п. 0000077156 00000 п. 0000077289 00000 п. 0000077379 00000 п. 0000077404 00000 п. 0000077569 00000 п. 0000077659 00000 п. 0000077684 00000 п. 0000077810 00000 п. 0000077899 00000 н. 0000077924 00000 п. 0000078067 00000 п. 0000078123 00000 п. 0000078148 00000 п. 0000078204 00000 п. 0000078229 00000 п. 0000078318 00000 п. 0000003196 00000 п. трейлер ] / Назад 802226 >> startxref 0 %% EOF 203 0 объект > поток hb«f`c`e`H
.Типы сплавов и их применение
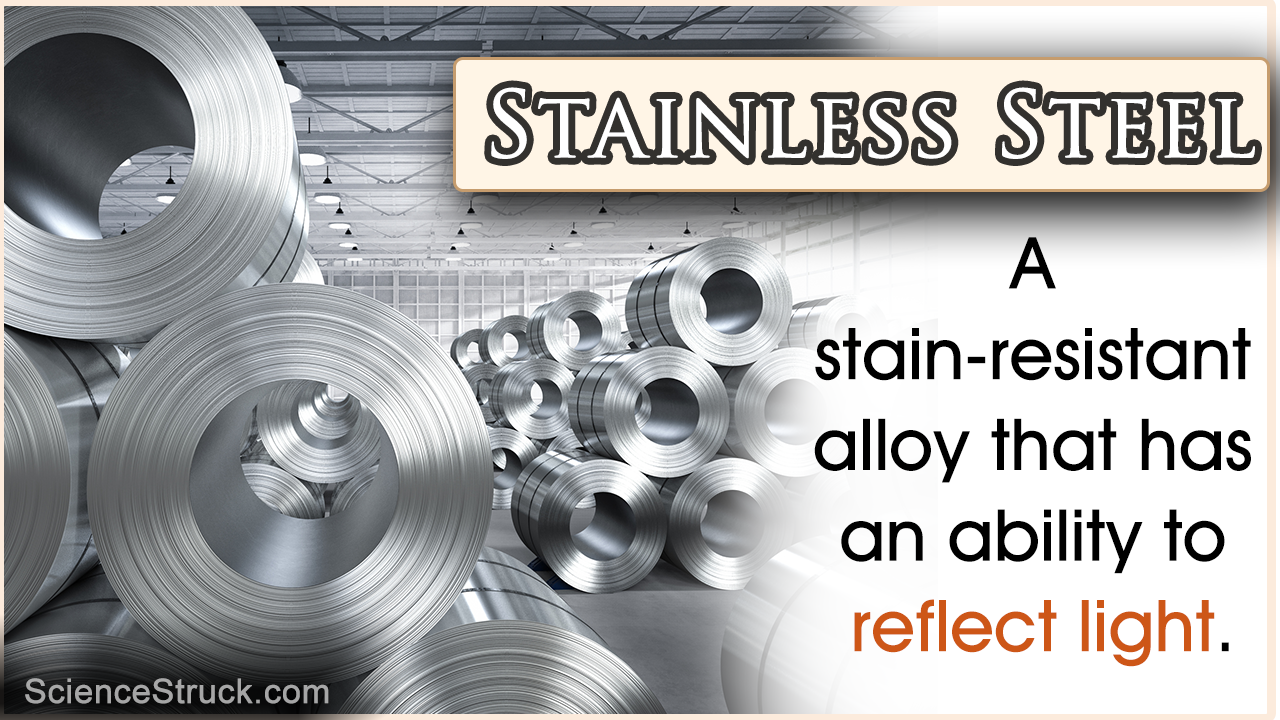
В повседневной жизни мы сталкиваемся с различными типами сплавов. Они все вокруг нас; в посуде, которую мы используем, в декоративных предметах по дому и т. д.
Металлические материалы, содержащие комбинацию более чем одного металла и некоторого другого элемента или металла, называются сплавами.
Хотите написать для нас? Что ж, мы ищем хороших писателей, которые хотят распространять информацию. Свяжитесь с нами, и мы поговорим…
Давайте работать вместе!
Когда два или более металлов или неметаллов соединяются вместе и тщательно смешиваются путем плавления, электролитического осаждения и т. Д., Полученный конечный продукт или сплав становится прочнее и долговечнее для практического использования по сравнению с основным металлом. Различные металлы, которые используются для получения сплавов, — это цинк, медь, олово, алюминий, хром, никель, серебро и т. Д. Более того, различные неметаллические элементы, используемые для изготовления сплавов, — это углерод, бор, сера, цинк и т. Д.В зависимости от состава металла или неметалла в сплаве мы получаем разные типы сплавов.
Существует множество различных типов сплавов, которые получают из комбинации металлов и неметаллов. Могут быть разные типы сплавов металлов, такие как бинарные сплавы, которые создаются путем объединения двух материалов, либо двух металлов, либо одного металла и одного неметалла, или трехкомпонентных сплавов, которые создаются сочетанием трех элементов. Для образования сплава необходимо присутствие по крайней мере одного металла.В этой статье мы рассмотрим только некоторые распространенные типы и способы их использования.
Сплав нержавеющей стали и его применение
Состав
Этим названием нержавеющая сталь обычно называют те металлические сплавы, содержащие 10,5% или более хрома (Cr) и 50% железа (Fe). Присутствующий в нем хром придает нержавеющей стали свойства высокой коррозионной стойкости. Чистое железо нестабильно и подвержено естественной коррозии за счет образования ржавчины. Добавление хрома предотвращает соединение железа с кислородом и водой с образованием ржавчины.Этот очень устойчивый к пятнам сплав выглядит ярким из-за его способности отражать свет. В зависимости от содержания в них хрома, железа и других металлов существуют разные типы нержавеющей стали.
Тип нержавеющей стали | Состав |
Мартенситный | Железо, 12-14% хрома, 0,1-1% углерода, 0,2-1% молибдена |
Ферритный | Железо, 11-18% (17%) хрома, 0.08-0,2% углерода |
Аустенитный | Железо, 17-25% хрома, 10-20% никеля, 0,15-2% углерода |
Дуплекс | Железо, 19-28% хрома, менее 5% молибдена, 1-6% никеля |
Где используется?
Используется для изготовления кухонной утвари, поскольку нержавеющая сталь является одной из самых гигиеничных поверхностей для хранения и приготовления пищи. Они не влияют на вкус пищи и не вступают в реакцию с кислой пищей во время приготовления.Кроме того, поскольку на его поверхности нет пор, он не собирает микробы, грязь или мусор, что упрощает очистку. Помимо кухонной посуды, нержавеющая сталь также используется для изготовления хирургических инструментов, арматурных стержней, опоры для каменной кладки, барабанов стиральных машин, кораблей, танкеров-химовозов и т. Д.
Латунный сплав и его применение
Состав
Латунь, образованная комбинацией цинка и меди, представляет собой сплав красновато-коричневого цвета от светло-желтоватого до темного.Цветовая гамма будет отличаться в зависимости от количества цинка в латуни. Чем выше содержание цинка, тем светлее будет цвет. Опять же, латунь можно разделить на несколько типов в зависимости от ее состава. Вот несколько из них.
Типы латунных сплавов | Состав |
Адмиралтейство Латунь | Медь, 28% цинк, 1% олово |
Красная латунь | Медь, 5% олова, 5% свинца и 5% цинка |
Желтая латунь | Медь, 33% цинка |
Белая латунь | Медь,> 50% цинка |
Алюминий латунь | 76% медь, 22% цинк, 2% алюминий |
Никелевая латунь | 70% медь, 24.5% цинка и 5,5% никеля |
Бессвинцовая латунь | Медь, цинк и менее 0,25% свинца |
Марганцевая латунь | 70% меди, 29% цинка и 1,3% марганца |
Где используется?
Латунь пластична, хорошо проводит тепло, устойчива к коррозии в соленой воде и т.д.Прекрасные акустические свойства латуни делают ее подходящей для духовых музыкальных инструментов. Такие инструменты, как эуфониум, тромбоны, саксофон, тубы, валторны и т. Д., Сделаны из латуни. Кроме того, поскольку латунь не тускнеет, ее также используют для изготовления посуды, столовых приборов и других небольших декоративных предметов. Его теплопроводные свойства делают его полезным при производстве радиаторов и теплообменников, таких как маслоохладители, кондиционеры и сердечники обогревателей.
Хотите написать для нас? Что ж, мы ищем хороших писателей, которые хотят распространять информацию.Свяжитесь с нами, и мы поговорим …
Давайте работать вместе!
Сплав стерлингового серебра и его применение
Состав
Серебро в чистом виде податливо, пластично и чрезвычайно мягко. Эта чрезвычайная мягкость облегчает работу, однако имеет и свои недостатки. Это приводит к тому, что серебро легко царапается и деформируется, что делает его непригодным для изготовления функциональных предметов. Таким образом, чистое серебро (92,5%) сочетается с 7.5% металлической меди, чтобы получить серебро 925 пробы. Металлическая медь дает серебро, необходимую прочность. Помимо меди, в серебро можно добавить даже германий, платину и цинк, чтобы получить чистое серебро.
Где используется?
Серебро 925 пробы используется для изготовления ювелирных изделий из серебра 925 пробы. Еще одно популярное применение стерлингового серебра — это изготовление посуды. Серебряные ножи, ложки, вилки, подносы и чайные сервизы изготавливаются и используются элитой. Поскольку чистое серебро по своей природе является асептическим, а также устойчиво к воздействию антисептиков, термической стерилизации и биологических жидкостей, оно используется в производстве медицинских инструментов.Кроме того, из него также делают музыкальные инструменты, такие как флейта и саксофоны.
Это всего лишь три типа сплавов и их применение. Сплавы действительно полезны, потому что металлы в чистом виде в большинстве случаев очень деликатны для изготовления функциональных предметов. Однако благодаря образованию сплавов мы смогли найти хорошее применение всем этим металлам.