Вентили для баллонов
Вентиль кислородный ВК-94 (Сжатый воздух, азот и другие не агрессивные газы)
Параметры | ВК-94-01 | ||
исп.07 | |||
Ду, мм, не менее | 4,0 | ||
Рабочее давление, МПа (кгс/см2) | 20 (200) | ||
Размеры, мм | 60х62х120 | ||
Масса, кг | 0,55 | ||
Присоединительные размеры | |||
на входе — наружная резьба | W27,8 | W19,2 | |
на выходе — наружная резьба | G3/4 -В |
Вентиль мембранный ВБМ-1 (для инертных газов: гелия, азота, аргона и других не агрессивных газов)
Параметры | |||
Ду, мм, не менее | 4,0 | ||
Рабочее давление, МПа (кгс/см2) | 20 (200) | ||
Размеры, мм | Ø62х130 (без фильтра) | ||
Масса, кг | 0.65 | ||
Присоединительные размеры | |||
на входе — наружная резьба | W27,8 | W19,2 | |
на выходе — наружная резьба | G3/4 -В |
Вентиль мембранный КВБ-53 (кислород, гелий, углекислый газ, сжатый воздух, азот)
Параметры | КВБ-53 | |
Ду, мм | 4 | |
Рабочее давление, МПа (кгс/см2) | 20 (200) | |
Размеры, мм | 63х63х110 | |
Масса, кг | 0,56 | |
Присоединительные размеры | ||
на входе — наружная резьба | W27,8 | |
на выходе — наружная резьба | G3/4-В |
Вентиль водородный ВВ-88
Параметры | ВВ-88 | ||
исп.03 | |||
Ду, мм, не менее | 4,0 | ||
Рабочее давление, МПа (кгс/см2) | 20 (200) | ||
Размеры, мм | 66х62х120 | ||
Масса, кг | 0,60 | ||
Присоединительные размеры | |||
на входе — наружная резьба | W27,8 | W19,2 | |
на выходе — наружная резьба | СП 21,8-14 ниток на 1″ левая |
Вентиль аммиачный (Клапан угловой цапковый для хлорных баллонов)
Параметры | 15лс93бк | |
Ду, мм, не менее | 5 | |
Давление номинальное, МПа (кгс/см2) | 1,6 (16) | |
Масса, кг | 0,52 | |
Присоединительные размеры | ||
на входе — наружная резьба | W27,8 | |
на выходе — наружная резьба | G1/2 |
Вентиль ацетиленовый ВАБ-97
Параметры | ВАБ-97 | |
Ду, мм, не менее | 3,5 | |
Рабочее давление, МПа (кгс/см2) | 3,5 | |
Размеры, мм | 123х41х39 | |
Масса, кг | 0,6 | |
Присоединительная резьба | W27,8 |
Вентиль ацетиленовый ВБА-1
Параметры | ВБА-1 | ||
исп.03 | |||
Ду, мм, не менее | 4 | ||
Рабочее давление, МПа (кгс/см2) | 3,5 (35) | ||
Размеры, мм | 110х45х45 | ||
Масса, кг | 0,65 | ||
Присоединительные размеры | |||
на входе — наружная резьба | W30,3 | W19,2 | |
на выходе — расточка под штуцер с хомутом | Ø10хØ20х5,5 |
Вентиль баллонный Cavagna group (Италия)
Материал | Латунь | |
Рабочее давление, МПа (кгс/см2) | 19,6 (200) | |
Присоединительные размеры | ||
на входе — наружная резьба | W27,8 | |
на выходе — наружная резьба | G3/4-В | |
Материал | Латунь | |
Рабочее давление, МПа (кгс/см2) | 19.6 (200) | |
Присоединительные размеры | ||
на входе — наружная резьба | W19,2 | |
на выходе — наружная резьба | 21,8 |
prom-kapital.ru
Аммиачный вентиль — Большая Энциклопедия Нефти и Газа, статья, страница 1
Аммиачный вентиль
Cтраница 1
Аммиачный вентиль служит для регулирования давления и расхода газообразного аммиака, выходящего из баллона. [1]
Регулирующие аммиачные вентили ( рис. 108, в) состоят из чугунного корпуса с перегородкой, имеющей отверстие под седло клапана. Наличие прорезей на хвосте клапана позволяет постепенно увеличивать проходное сечение в клапане. Это обеспечивает плавное и точное регулирование подачи жидкого аммиака в испарительную систему. На трубопроводах малых диаметров б, 10 и 15 мм специальные регулирующие вентили не ставятся, вместо них используются запорные угловые вентили соответствующего диаметра с малым шагом резьбы. [2]
Терморегулирующие аммиачные вентили монтируют в вертикальном положении на временной опоре вблизи от ввода жидкости в испаритель. [3]
Каждый аммиачный вентиль, рассольную или водяную задвижку полностью разбирают, их детали очищают от грязи, покрывают противокоррозийной смазкой и проверяют на плотность закрытия клапанов и дисков. Несоответствующие стандарту прокладки и сальниковую набивку заменяют. [4]
Сальники аммиачных вентилей уплотняют хлопчатобумажной или асбестовой прографи-ченной набивкой. [5]
Сальники аммиачных вентилей имеют мягкую набивку и уплотняются нажимной гайкой. Во фреоновых запорных вентилях ( рис. 107) применяют в основном мембранное и сильфонное уплотнение шпинделя. [6]
В сальниковом аммиачном вентиле ( рис. II-19) уплотнение золотника представляет собой фторопластовое кольцо 2, которое запрессовано или завальцовано в золотник. Уплотнение крышки выполнено также в виде фторопластового кольца 9, что позволяет при поднятом до отказа шпинделе разгрузить сальниковые уплотнения от давления рабочей среды. [8]
В сальниковом аммиачном вентиле ( рис. II-19) уплотнение золотника представляет собой фторопластовое кольцо 2, которое запрессовано или завальцовано в золотник. Уплотнение крышки выполнено также в виде фторопластового кольца 9, что позволяет при поднятом до отказа шпинделе разгрузить сальниковые уплотнения от давления рабочей среды. [10]
Таким образом, аммиачный вентиль марки 15к21бт означает: вентиль ( 15) из ковкого чугуна, конструкция с ручным приводом по фигуре ( 21), с уплотнением из баббита. [11]
Набивка сальника у аммиачного вентиля — просаленный, пропитанный графитом хлопчатобумажный шнур, у фреонового — асбест с графитом и свинцом. Для предотвращения утечки фреона крышка вентиля закрыта колпаком на резьбе. При открывании вентиля колпак отвинчивается и используется в качестве маховика. [12]
При наличии поверхностных дефектов баббитового пояса клапана аммиачных вентилей производят его протачивание, а при значительных дефектах — перезаливку клапана баббитом с последующим протачиванием пояса. [13]
Коэффициенты местных сопротивлений, так же как для аммиачных вентилей, соответствуют литературным данным испытаний вентилей подобных конструкций, либо определены примерным расчетом. [15]
Страницы: 1 2 3
www.ngpedia.ru
Вентиль на газовый (кислородный) баллон: устройство, замена
Вентиль на газовый баллон является совершенно особым представителем запорно-регулирующей арматуры. Ведь данный узел должен обеспечивать не только точное дозирование потока газа, но и абсолютную герметичность, как корпуса, так и узла крепления арматуры и баллона.
Классификацию запорной арматуры для баллонов выстраивают на основе содержимого емкостей высокого давления.
И на основе этого принципа вентили делятся на:
- Арматуру для баллонов со сжиженным газом
- Арматуру для кислородных баллонов
- Арматуру для пропан-бутановых баллонов
Впрочем, особых конструкционных отличий между вентилями нет. Однако маркировка у данных устройств абсолютно разная. Так, вентиль кислородного баллона маркируется синим цветом, пропановый вентиль – красным, ацетиленовый – белым, водородный – зеленым и так далее, в соответствии с ГОСТами.
↑Устройство вентиля газового баллона
Типовой вентиль на газовый баллон состоит из следующих узлов:
- Корпуса вентиля – стальной детали, напоминающей по своей форме тройник. Причем на нижней части корпуса нарезана коническая резьба – под приемное отверстие баллона. В верхней части нарезана резьба цилиндрическая – под накидную гайку, удерживающую шток клапана. На боковом отводе корпуса нарезана цилиндрическая резьба – под заглушку вентиля.
- Запорного элемента – сборного узла, состоящего из: пропускного клапана – детали, регулирующей движения потока сквозь корпус; штока – управляющего элемента, передающего крутящий момент с маховика на клапан.
- Органов управления – маховика, соединенного со штоком клапана с помощью подпружиненной гайки.
Кроме того, вентили для баллонов высокого давления оборудованы уплотняющими прокладками, размещенными между корпусом и накидной гайкой, между гайкой и маховиком, между клапаном и корпусом.
Подобная конструкция гарантирует высокую надежность регулирующего узла. Причем вся конструкция рассчитана на то, что запорный элемент будет вмонтирован в емкость, функционирующую в условиях постоянного давления.
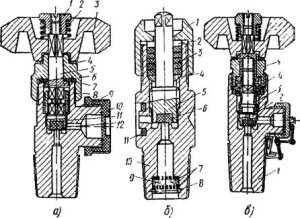
Вентили: а — кислородный, б — ацетиленовый, в — пропан бутановый
Например, вентиль для пропанового баллона работает под давлением в 15 атмосфер. Но и это значение далеко не предельно. Так вентиль баллона с кислородом может выдержать давление в 190-195 атмосфер.
Схема эксплуатации вентиля очень проста: с бокового штуцера корпуса свинчивается заглушка и туда же навинчивается редуктор потребляющей сети; далее, плавным движением, откручивается маховик запорного элемента, который сдвигает клапан и содержимое баллона поступает к потребителю. Для перекрытия потока газа из баллона эту последовательность действий повторяют в обратном порядке.
Как видите, баллонный вентиль не относится к чрезмерно сложным узлам (несмотря на достаточно высокую надежность устройства), а схему эксплуатации этого узла освоит даже ребенок. Некоторые затруднения способна вызвать только процедура замены самого вентиля. Поэтому на этом вопросе мы остановимся более подробно.
↑Монтаж и замена вентиля на газовом баллоне
Приступая к монтажу запорного узла для баллона со сжиженным газом необходимо помнить о том, что данный элемент будет функционировать в условиях высокого давления. Поэтому все работы по монтажу или замене такого узла следует проводить в строгом соответствии с инструкциями.
Технически поменять вентиль на газовом баллоне достаточно легко – устаревший узел просто вывинчивается из входного отверстия в емкости, как обычный штуцер, а новый запорный элемент ввинчивается на его место. Однако при этом нужно соблюдать особые меры предосторожности.
Ведь, повторимся, этот узел находится под давлением (например, на вентиль ацетиленового баллона давят целых 30 атмосфер), следовательно, сам процесс демонтажа и монтажа следует организовывать по такой схеме:
В самом начале запорный узел вентиля следует перевести в положение «открыто». То есть, выкрутить до упора в крайнее верхнее положение. В итоге остатки содержимого баллона уйдут либо в атмосферу, либо в какую-либо емкость.
- После освобождения баллона от опасного содержимого можно приступать к демонтажу корпуса вентиля из резьбового отверстия в верхней части баллона. Для этих целей можно использовать либо специальный инструмент, либо обычный разводной ключ. При этом необходимо понимать, что вентиль был вкручен очень плотно и, возможно, с использованием жидкого уплотнителя, поэтому, перед демонтажем корпус запорного элемента нужно нагреть строительным феном.
- Удалив старый вентиль из баллона нужно подготовить к монтажу новый запорный узел. То есть, нужно просто нанести на конический штуцер в нижней части корпуса гелеобразный или полимерный уплотнитель. В качестве последнего, чаще всего, используется обычная ФУП лента.
- После подготовки вентиль вкручивается в отверстие на корпусе баллона, вначале, руками, а затем и ключом. Причем в качестве ключа, лучше всего, задействовать особый инструмент — динамометрический ключ, который позволяет регулировать усилие при затягивании. Ведь для стальных корпусов нужно создать момент в 480 Нм, а для латунных – 250 Нм.
Завершив монтаж вентиля, следует нанести сведения о дате операции на паспорт баллона – специальную табличку, вмонтированную в корпус емкости.
↑Техника безопасности и методика контроля качества монтажа
По завершению процесса монтажа вентиля необходимо проконтролировать качество выполненных работ.
Для этого нужно сделать следующее:
- К боковому штуцеру корпуса подключают шланг от нагнетателя (компрессора).
- Вентиль переводят в положение «открыто» и закачивают в баллон порцию сжатого воздуха. После этого вентиль баллона переводят в положение «закрыто».
- Далее, к боковому штуцеру корпуса подключают манометрический вентиль с ввинченным измерительным прибором (манометром).
После этого вентиль баллона переводят в положение открыто и такую же операцию проделывают и с манометрическим вентилем. В итоге, на манометре отображается давление в системе и по его колебаниям, наблюдаемым в течение определенного промежутка времени, определяют степень герметичности узла баллон-вентиль.
Разумеется, герметично монтированный вентиль должен удерживать давление на одном уровне в течение достаточно длительного времени.
↑Методика упрощенного контроля
Такая методика практикуется в полевых условиях или при отсутствии «под руками» измерительных приборов.
Для ее реализации нужно выполнить следующее:
- В баллон закачивают сжатый воздух и перекрывают вентиль.
- Поверх вентиля наносят помазком для бритья взбитую мыльную пену.
- Герметичность узла баллон-вентиль контролируют по отсутствию «пузырей» в мыльной «шапке» на вентиле.
Несмотря на простоту, этот метод считается достаточно действенным и используется большинством специалистов по напорным трубопроводам.
vsetrybu.ru
Вентиль запорный аммиачный — Справочник химика 21
Рис. 13. Амлгаачная схема фризера ОФА 1 — запорный жидкостный вентиль, 2 — фильтр, 3 — ПРВ, 4 — аккумулятор, 5 — рубашка, в — маслоотделитель, г — отбойник, 8 — фильтр, 9 — бародросселирующий вентиль, 10 — запорный газовый вентиль, 11 — запорный аммиачный кран, 12 — аммиачный мановакуумметр, 13 — маслоспускной вентиль, 14 — предохранительный клапан | ![]() |
К запорной арматуре относятся, главным образом, запорные проходные и угловые вентили (рис. 108), а также задвижки (рис. 109) и обратные клапаны. Каждый запорный вентиль состоит из следующих основных частей корпуса, клапана, шпинделя, сальника и маховика. Конструкция запорных вентилей зависит от диаметра условного прохода. Запорные вентили малого диаметра (6, 10 и 15 мм) имеют стальной кованый корпус, а клапаном служит конец шпинделя, обработанный на конус. Запорные аммиачные [c.168]
Рис. 15. Фризер ОФИ i — приемная коробна, 2 — насос 1 ступени, з — воздушный клапан, 4 — насос И ступени, 6 — цилиндровый блок, б — выпускной патрубок, 7 — трехходовой кран, 8 — клапан противодавления, 9 — насадка для заполнения гильз, 10 — насадка для заполнения металлических лотков, 11 — жидкостный аммиачный патрубок, 12 — запорный аммиачный вентиль перед редукционным вентилем, 23 — трехходовой запорный аммиачный кран, 14 — пусковая панель, 15 — маховичок регулятора скорости | ![]() |
Контроль за процессами в автоклавах проводится по температуре и давлению. Для регулирования режима автоклавы оборудуются запорными вентилями, предохранительными клапанами, манометрами, термометрами и т. п. Манометр, установленный на автоклаве, должен быть обязательно дублирован. При несовпадении показаний обоих манометров аппарат не может быть допущен к эксплуатации до проверки и замены неисправного прибора. Для наблюдения за давлением в процессах аминирования применяют специальные аммиачные манометры, которые имеют устройство, предохраняющее от коррозии медные части прибора. Простое и надежное устройство, предохраняющее манометр от воздействия вредных газов, показано на рис. 57. Наличие масла в сосуде предохраняет манометрическую трубу от попадания в нее коррозионноактивных веществ. [c.172]
Наиболее распространенными работами при ремонте запорной арматуры являются смена набивки сальников, притирка клапанов и гнезд в аммиачных вентилях, шабрение и шлифование уплотнительных колец и клинкеров в рассольных и водяных задвижках, замена дефектного шпинделя. [c.592]
ЩИТ регулирующей станции, 2 — соленоидный вентиль, 3 —аммиачный фильтр, 4 — терморегулирующий вентиль, 5 — запорные вентили обводного мостика, 6 — ручной регулирующий вентиль, 7 — манометры, 8 — вентиль для заполнения системы аммиаком [c.302]
Вентили аммиачные и фреоновые. Принцип действия и назначение аналогичны вентилям запорным, регулирующим и дросселирующим. Гнезда и плоскости прилегания клапанов этих вентилей выполняются из баббита. На штоках имеется конус, залитый баббитом, служащий для закрытия сальников при полностью открытом клапане. Фланцы выполняются с выступом и впадиной. Большая часть типов аммиачных и фреоновых вентилей оборудована герметичными колпаками, закрывающими крышку вентиля. [c.92]
Запорные аммиачные вентили 0 19-4-250 мм имеют литой чугунный корпус, чугунный клапан с направляющими ребрами, свободно надетый на шпиндель. В вентилях диаметром до 125 мм резьба шпинделя выполнена внутри нижней части крышки (рис. 119, в), а вентили диаметром 150- 250 мм имеют для шпинделя траверсу на колонках. [c.195]
Аммиачная система. Согласно схеме, проверяют открытие всех запорных и регулирующих вентилей на аммиачной системе. [c.111]
Регулирующие и запорные аммиачные вентили снабжены обратным торцовым уплотнением, это позволяет заменить сальниковую набивку без выключения машины при полностью открытом вентиле. [c.47]
Регулирующие и запорные аммиачные и фреоновые вентили снабжаются также обратным торцевым уплотнением (стальное кольцо и баббитовая канавка), позволяющим производить смену сальниковой набивки при полностью открытом вентиле, без остановки машин. [c.111]
Переполнение жидким аммиаком сосудов или аппаратов. В новом издании правил техники безопасности на аммиачных холодильных установках [101] предписана установка предохранительных клапанов на аппаратах установок производительностью 10 тыс. ккал/час. Ранее этого пункта не было, поэтому на одной из установок, где всю жидкость собрали в испаритель и закрыли запорный вентиль, произошел взрыв. Предохранительные клапаны должны ежегодно проверяться и пломбироваться механиком холодильной установки. Перед клапаном, установленным на аппарате, в целях удобства ремонта и проверки разрешается поместить запорный вентиль, опломбированный в открытом положении. При обратном заполнении баллонов следует подавать не более 0,57 кг аммиака на 1 л емкости баллона. [c.206]
Запорные вентили состоят из корпуса, клапана, шпинделя, сальника и маховичка. Движение жидкости или паров при проходе вентилей должно быть по направлению подъема клапана. Конструкция вентилей зависит от диаметра условного прохода. Для аммиачных машин при спуске масла, воздуха и заполнения системы аммиаком применяют угловые вентили диаметром 6—10 мм, клапаны которых, обработанные на конус, притерты к гнезду в корпусе. Запорные вентили с условным проходом от 32 до 200 мм (табл. 137) выполняют из специального чугунного или стального литья. Конструкции некоторых аммиачных запорных вентилей приведены на фиг. 182. [c.275]
Аммиачные системы испытывают с помощью двухступенчатого воздушного компрессора типа ВК-25. Перед началом испытаний открывают все вентили системы, за исключением запорных вентилей компрессоров. Давление в системе поднимают постепенно. При достижении 0,4 и 0.6 испытательного давления приступают к осмотру системы для выявления больших утечек, явившихся следствием некачественной сварки стыков трубы и сборки болтовых соединений, неустановленных прокладок и других причин. [c.407]
Перед наполнением системы аммиаком ее предварительно освобождают от воздуха с помощью аммиачного компрессора. Для этого открывают все вентили в системе, кроме тех, которые имеют сообщение с атмосферой. Запорный вентиль на нагнетательной стороне компрессора закрывают, а фланец отсоединяют от фланца компрессора для выброса отсасываемого воздуха из системы. [c.421]
Сальники аммиачных вентилей имеют мягкую набивку и уплотняются нажимной гайкой. Во фреоновых запорных вентилях (рис. 107) применяют в основном мембранное и сильфонное уплотнение шпинделя. [c.209]
Запорные вентили при ремонте полностью разбирают, конусы клапанов при необходимости шлифуют или просто притирают по месту к седлу. Сальники аммиачных вентилей заполняют хлопчатобумажной набивкой, пропитанной маслом и мелким порошком графита. На фреоновых вентилях сальники набивают уплотнительными кольцами, вырубленными из листовой маслобензостойкой резины. Плотность прилегания вентиля в сборе проверяется в двух крайних положениях шпинделя давлением воздуха 16 10 Па. Вентиль должен плотно перекрываться без применения рычагов и особых усилий. [c.291]
Ремонт арматуры заключается в очистке вентилей и задвижек от загрязнений, проточке, притирке и замене уплотняющих поверхностей клапанов, золотников и седел, смене сальниковых уплотнений, восстановлении или замене поврежденных и изношенных шпинделей и их гаек. Основной и самой существенной работой при ремонте арматуры является восстановление седел, а также ремонт уплотняющих поясков у клапанов вентилей и у золотников задвижек. Изношенные уплотняющие пряски у клапанов запорных аммиачных вентилей восстанавливают путем перезаливки их баббитом с последующей проточкой на станке или опиловкой их пилой по плите на краску. Незначительно изношенные уплотняющие детали задвижек ремонтируют путем притирки поясков золотника к пояскам опорных колец седла. Притирка производится вручную или с помощью приспособления (рис. 248). При износе шпинделей (повреждение резьбы и изгиб) их исправляют или заменяют. Существенное значение имеет правильная набивка и затяжка сальника. Кольца для набивки сальников у аммиачных вентилей изготовляют из просаленного хлопчатобумажного шнура квадратного сечения размерами 6, 10, 12 и 16 мм. Для сальников рассольных и водяных задвижек применяют просаленные хлопчатобумажный шнур или пеньковую набивку. Чтобы набивочные сальниковые кольца имели плотные стыки, отмеренный кусок набивки отрезают острым ножом под углом 45°. Набивочные кольца вставляют на место таким образом, чтобы стыки колец были расположены в разбежку . После ремонта проверяют герметичность арматуры. Запорные вентили проверяют рабочим давлением холодильного агента, а задвижки — рабочим давлением рассола или воды. Если арматура для ремонта снималась со своего места, то ее герметичность проверяют на специальном стенде [c.301]
Все запорные вентили на аммиачных газовых нагнетательных трубопроводах должны быть запломбированы в открытом положении, за исключением основных запорных вентилей компрессоров. [c.65]
Повышение давления нагнетания. В аммиачных компрессорах предусмотрена установка предохранительного клапана, который при разности давлений нагнетания и всасывания 16 кг]см соединяет их между собой. Однако срабатывание клапана весьма нежелательно. Поэтому для защиты от опасного повышения давления нагнетания используют реле высокого давления, присоединяемое. между цилиндром и запорным вентилем. [c.206]
А — компрессора Б — маслоотделитель, В — конденсатор. Г — ресивер, Д — отделитель жидкости, Е — аммиачные батареи, Ж — дренажный ресивер, 3 — маслосборник, И — регулирующий вентиль, —10 — запорные вентили [c.295]
Трубопроводную арматуру устанавливают на горизонтальных и вертикальных участках трубопроводов в любом положении, за исключением положения маховиком вниз. Запорно-регулирующую арматуру устанавливают по ходу движения транспортируемой среды под клапан, за исключением соленоидных вентилей и аммиачного запорного вентиля диаметром 200 мм типа 5С29бт, которые устанавливают по ходу движения среды на клапан. [c.356]
Для трубопроводов малых диаметро1В устанавливаются вместо регулирующих вентилей проходные или угловые запорные вентили. Они применяются в качестве запорной арматуры на паровых и жидкостных линиях. Для удобства обслуживания холодильной машины конструкция запорных аммиачных вентилей зависит от диаметра условного прохода. Аммиачные угловые вентили 0 6 10 15 мм (рис. 119, б) имеют стальной кованый корпус прямоугольной формы с нарезными штуцерами. Клапаном служит нижняя часть шпинделя, обработанная на конус и притертая к седлу. [c.195]
I — запорный аммиачный вентиль, 2 — регулирукиций вентиль, 3 — отделитель жидкоста, — поплавковый регулирующий вентиль, 5 — дистанциовнЯВ указатель уровня аммиака, 6 — мановакуумметр, 7 — вентиль аммиачный проходной,.8 — газовый коллектор, 9 — вентиль аммиачный угловой, 10 — жидкостный коллектор, // — газовый шланг, /2 — жидкостный шланг, 13 — жидкостный вентиль для присоединения гибкого шланга, 4 —газовый вентиль для присоединения гибкого шланга, 15 — автомобиль-холодильник под зарядкой [c.424]
Защита от недопустимого повышения давления нагнетания. Для этой цели служат предохранительные клапаны, устанавливаемые на нагнетательной стороне компрессора, между цилиндром и запорным вентилем. В аммиачных компрессорах эти клапаны должны открываться при разности давлений между лагнетательной и всасывающей стороной 16 атм, а во фреоновых установках (фреон-12) не более 10 атм, и перепускать холодильный агент во всасывающий трубопровод. В малых фреоновых компрессорах предохранительные клапаны не устанавливают. [c.83]
На нагнетательной линии аммиачного компрессора между цилиндром и запорным вентилем необходимо установить пружинный предохранительный клапан, перепускающий аммиак во всасывающий трубопровод в случае чрезмерного повышения давления. Пружинный предохранительный клапан должен открываться прн разности давления паров аммиака 16 kTJ m (начало откры-вания) и при давлении 18,4 кГ1см (полное открывание). На перепускной линии не должно быть никаких запорных приспособлений. [c.329]
I — цистерны, 2 — вентиль на цистерне с сифонной трубйой для жидкого аммиака 3 — вентиль на цистерне для газообразного аммиака 4 — специальные аммиачные гибкие резиновые шланги для присоединения вентилей цистерны к трубопроводам 5 — запорные вентили на трубопроводах 6 — манометры на трубопроводах. [c.347]
Наладку работы холодильной установки проводят с целью достижения параметров, характеризующих нормальную ее работу. Подачу жидкого аммиака в испаритель регулируют, вращая регулировочный шпиндель терморегулирующего венТйля (ТРВА). При вращении шпинделя против часовой стрелки перегрев уменьшается, при повороте по часовой стрелке — увеличивается. Регулирование ведут ак, чтобы перегрев в испарителе был в пределах 1,5—2° С, а перегрев на всасывании компрессора составлял 5—8 С. Подачу жидкого фреона в испаритель регулируют обычно через соленоидный вентиль (СВМ), работой которого управляет двухпозиционная система питания (Приборы ПТРД-2 и ТСП-24). Прибор ПТРД-2 регулируют, вращая ручку настройки на величину перепада температур, ручкой резистора и тумблером. Регулирование ведут так, чтобы перегрев был в аналогичных для аммиачной системы пределах. При пробной работе конденсатора следят за тем, чтобы подача охлаждающей воды была достаточной, наблюдают за давлением в конденсаторе и состоянием предохранительных устройств, герметичностью соединений и сальников запорной арматуры. При работе оросительного конденсатора контролируют равномерное распределение воды по секциям и в случае необходимости регулируют водораспределительные устройства. Скорость движения воды в кожухотрубных и элементных конденсаторах Должна быть не менее 1 м/с, В период пробной работы испарителя периодически контролируют концентрацию рассола и поддерживают ее такой, чтобы температура замерзания рассола была ниже температуры кипения хладагента на 8° С для испарителей закрытого типа и на 5° С для испарителей открытого типа. Для проверки герметичности испарителя проводят анализ рассола на присутствие в нем аммиака. Для нормальной работы ресиверов поддерживают определенный уровень жидкого хладагента в ресивере, который проверяют по смотровому стеклу. [c.451]
В схемах аммиачных установок можно отключать компрессоры от одной группы камер и подключать их к другой по мере необходимости (в случае изменения у них тепловых нагрузок). Для этого на всасывающих трубопроводах установки предусматривают епеди-альные мосты трубных переключений с запорными вентилями. При верхней разводке трубопроводов компрессоров мосты трубных переключений у всасывающих трубопров одов чаще всего монтируют на одной из стен компрессорного помещения, где, кроме того, размещают всасывающие трубопроводы и трубные перемычки с запорными вентилями в местах и положениях, легко доступных и удобных для обслуживания. Чтобы надежно защитить компрессор от поступления жидкости в цилиндры в аммиачных системах с автоматическими приборами подачи жидкого аммиака или системах с увеличенными теплопритоками и удаленными на большие расстояния приборами охлаждения всасывающие трубопроводы снабжают отделителя и жидкого аммиака, которые размещают перед компрессорами. При монтаже системы оснащают защитными приспособлениями, которые улавливают жидкий аммиак. У компрессоров их устанавливают в случае выброса жидкости из батареи во всасывающий трубопровод при неисправности приборов, регулирующих подачу жидкости в батареи, или при вскипании аммиака в батареях при повышенных, даже кратковременных, теплопритоках к батареям. Эти отделители снабжают приборами сигнализации и защиты, останавливающими компрессоры при повышении уровня жидкости в отделителе выше допустимого. Монтаж обвязочных трубопроводов сложен, так как их выполняют с ответвлениями для присоединения к нескольким компрессорам. [c.142]
Запорную арматуру на холодильных трубопроводах можно монтировать на горизонтальных и вертикальных участках трубопроводов в любом положении, за исключением положения маховиком вниз. При монтаже арматуры следует учитывать движение среды в трубопроводе. Запорную и регулирующую арматуру аммиачных и фреоновых вентилей устанавливают по ходу движения среды под клапан, за исключением аммиачного запорного вентиля диаметром 200 мм типа 15С29бт, который устанавливается по движению среды на клапан. [c.281]
При пусконаладочных работах проверяют установленные на аппаратах предохранительные клапаны по их условному проходу. Предохранительные клапаны должны быть установлены на нагнетательной стороне компрессора, между цилиндром и запорным вентилем, а также на кожухотрубных испарителях и конденсаторах, элементных конденсаторах, ресиверах и промсосудах. Устанавливать вместо предохранительных клапанов заглушки или запорные вентили запрещается. Перед конденсатором должен быть установлен аммиачный обратный клапан. Заполнение установок аммиаком выполняют прошедшие специальное обучение лица. При заполнении аммиаком из баллонов, авто- или железнодорожной аммиачной цистерны должны быть наготове аммиачные противогазы марки К и резиновые перчатки. Применяемые при сливе аммиака в холодильную систему резиновые шланги должны иметь несколько внутренних прокладок и выдерживать давление 20 кгс1см . Нагревать баллоны для ускорения заполнения системы категорически воспрещается. [c.329]
Рис, 1Х.6. Аммиачный кожухо-трубиый ко нденсатор / — кожух 2 — трубные решетки . — водяные трубы 4 —крышки 5 — маслоотстойник в — запорный вентиль 7 — спускной клапан 8 — предохранительный клапан [c.216]
Аммиачные и фреоновые вентили, работающие при температуре до —40 °С, изготовляют из углеродистой стали, а в случае воздействия более низких температур — из сталей марок 20ХНЗА и Х18Н9Т. Мелкая резьба на шпинделе и особая форма золотника (удлиненный конус с малым углом у вершины или цилиндр с треугольными продольными вырезамк) в регулирующих вентилях позволяют плавно регулировать поступление аммиака (фреона) в испаритель. Сальники аммиачных вентилей набиваются асбесто-графито-свинцовой массой, сальники фреоновых запорных вентилей — специальным фторопластовым материалом (ФУМ). Особенностью конструкции фреоновых вентилей особой герметичности является наличие над сальниковой грундбуксой ввертного колпачка, предотвращающего утечку фреона. [c.118]
Регулирующие аммиачные вентили (рис. 108, в) состоят из чугунного корпуса с перегородкой, имеющей отверстие под седло клапана. Клапан вентиля 4 имеет удлинение в виде цилиндрического хвоста, нр котором профрезерованы три наклонных прореза «треугольного сечения. Клапан свободно сидит на шпинделе 3, ввернутом на резьбе в крышку вентиля 2. Наличие прорезей на хвосте клапана позволяет постепенно увеличивать проходное сечение в клапане. Это обеспечивает плавное и точное регулирование подачи жидкого аммиака в испарительную систему. Подъем клапана обеспечивается поворотом маховичка 7, надетого на шпиндель 3. Шпиндель уплотняется сальником 6 и нажимной втулкой 5. На трубопроводах малых диаметров 6, 10 и 15 мм специальные регулирующие вентили не ставятся, вместо них используются запорные угловые вентили соответствующего диаметра с малым шагом резьбы. [c.171]
chem21.info
Вентили для газовых баллонов
Предлагаем ознакомиться с перечнем поставляемых вентилей:
Вентиль ВК-94
Вентили кислородные баллонные ВК-94 являются запорными приспособлениями баллонов при наполнении, хранении и расходовании из них кислорода, азота, воздуха и др. неагрессивных газов.
Вентиль ВВ-55
Вентили мембранные ВВ-55 предназначены для установки на водородные баллоны малого и среднего объема с рабочим давлением до 19,6 МПа в качестве запорно-пускового приспособления.
Вентиль КВБ-53 (КВБ-53М, КВБ-53С)
Вентили мембранные КВБ-53, КВБ-53М и КВБ-53С являются запорно-пусковыми механизмами для баллонов малого и среднего объема наполняемых кислородом, гелием, и др. газовыми смесями.
Вентиль КВ-1П (КВ-1М)
Вентили мембранные КВ-1П и КВ-1М являются запорно-пусковыми механизмами для баллонов, малого объема наполняемых кислородом, гелием, и др. газами. Рассчитаны на рабочее давление до P ≤ 19,6 МПа (200 кгс/см²).
Вентиль КВ-1МС
Вентиль мембранный нержавеющий КВ-1МС предназначен для установки на малолитражные баллоны в качестве запорно-пускового приспособления. Применяется для работы с агрессивными и коррозионными газами.
Вентиль ВВ-400
Вентиль ВВ-400 является запорным устройством баллона при заполнении, хранении и отборе газа. Предназначены для установки на стальные баллоны для воздуха, азота, кислорода на рабочее давление до Pр=40 МПа.
Вентиль точной регулировки ВТР
Вентили ВТР предназначены для точной регулировки расхода для сред с давлением до 14,7 МПа. Применяются на газовом баллоне взамен редуктора, в частности, для подачи поверочной газовой смеси на прибор.
Вентиль ВВБ-54
Мембранный вентиль ВВБ-54 является запорно-пусковым приспособлением для водорода. Предназначен для установки на баллонах средней емкости с максимальным рабочим давлением до 14,7 МПа.
Вентиль ВБ-15Л
Вентиль предназначен для установки на баллоны малого и среднего объёма для неагрессивных газов в качестве запорного устройства. Рассчитан на рабочее давление до P ≤ 15 МПа (150 кгс/см²).
Вентиль ВБМ-1
Вентили ВБМ-1 предназначены для установки на стальные баллоны малого или среднего объема для азота, аргона, гелия и других инертных и неагрессивных газов на рабочее давление до Pр=20 МПа.
Вентиль ВБ-2
Вентили ВБ-2 предназначены для установки на стальные баллоны для сжиженных углеводородных газов, вместимостью 5, 12, 27, 50 литров на рабочее давление до 1,6 МПа..
Вентиль ВБВ-40
Вентиль водородный ВБВ-40 является запорным устройством баллона при заполнении, хранении и отборе газа. Вентили предназначены для установки на баллоны для водорода на рабочее давление до Pр=40 МПа.
Вентиль ВАБ-97
Вентиль ацетиленовый ВАБ-97. Предназначен для установки на ацетиленовых баллонах средней и малой вместимости с рабочим давлением 3,5 МПа. Является запорным устройством при хранении и расходовании ацетилена.
Смотрите также:
В случае заинтересованности, Вы можете связаться с нами по следующим контактам:
- Тел.: +7 (8443) 56-88-35, 56-88-34
- Факс: +7 (8443) 56-88-42
- E-Mail: [email protected]
vpk-vlz.ru
Аммиачный запорный вентиль — Большая Энциклопедия Нефти и Газа, статья, страница 1
Аммиачный запорный вентиль
Cтраница 1
Аммиачные запорные вентили под фланцевое соединение марки 15с12бт ( рис. 18 s; табл. 42) имеют кованый стальной корпус, в который ввернуты шпильки для присоединения фланцев трубопроводов. Крышка, накидная гайка и маховик отлиты из ковкого чугуна, остальные детали выполнены из стали. [1]
Трубопроводную арматуру устанавливают на горизонтальных и вертикальных участках трубопроводов в любом положении, за исключением положения маховиком вниз. Запорно-регулирующую арматуру устанавливают по ходу движения транспортируемой среды под клапан, за исключением соленоидных вентилей и аммиачного запорного вентиля диаметром 200 мм типа 15С29бт, которые устанавливают по ходу движения среды на клапан. [2]
Вентили с ручным управлением монтируют на вертикальных и на горизонтальных участках трубопроводов в любом пространственном положении, кроме положения маховиком вниз. Запорные и регулирующие аммиачные и фреоновые вентили, как и вентили для воды, должны быть расположены по ходу движения среды под клапан в соответствии со стрелкой на корпусе арматуры. Исключение составляют аммиачные запорные вентили диаметром 200 мм, которые следует устанавливать по ходу среды на клапан. [3]
При монтаже арматуры следует учитывать движение среды в трубопроводе. Запорную и регулирующую арматуру аммиачных и фреоновых вентилей устанавливают по ходу движения среды под клапан, за исключением аммиачного запорного вентиля диаметром 200 мм типа 15С29бт, который устанавливается по движению среды на клапан. [4]
Запорная арматура служит для отключения отдельных машин и аппаратов от системы. На аммиачных трубопроводах устанавливают стальные фланцевые вентили и задвижки. Они делаются проходными или угловыми. Каждый аммиачный запорный вентиль ( рис. 64) состоит из корпуса, клапана, шпинделя, сальника и маховика. Шпиндели холодильной арматуры имеют приспособления, предохраняющие их от полного вывертывания. Давление рабочей среды подается под клапан вентиля. Вентили малых диаметров делаются цапковыми ( рис. 64, в) ввертными с резьбой на цапках. [6]
Запорные вентили состоят из корпуса, клапана, шпинделя, сальника и маховичка. Движение жидкости или паров при проходе вентилей должно быть по направлению подъема клапана. Конструкция вентилей зависит от диаметра условного прохода. Для аммиачных машин при спуске масла, воздуха и заполнения системы аммиаком применяют угловые вентили диаметром 6 — 10 мм, клапаны которых, обработанные на конус, притерты к гнезду в корпусе. Запорные вентили с условным проходом от 32 до200 мм ( табл. 137) выполняют из специального чугунного или стального литья. Конструкции некоторых аммиачных запорных вентилей приведены на фиг. [7]
Запорные вентили состоят из корпуса, клапана, шпинделя, сальника и маховичка. Движение жидкости или паров при проходе вентилей должно быть по направлению подъема клапана. Конструкция вентилей зависит от диаметра условного прохода. Для аммиачных машин при спуске масла, воздуха и заполнения системы аммиаком применяют угловые вентили диаметром 6 — 10 мм, клапаны которых, обработанные на конус, притерты к гнезду в корпусе. Запорные вентили с условным проходом от 32 до 200 мм ( табл. 137) выполняют из специального чугунного или стального литья. Конструкции некоторых аммиачных запорных вентилей приведены на фиг. [8]
Страницы: 1
www.ngpedia.ru
Баллоны для аммиака — Справочник химика 21
Полярность связи N — Н обусловливает между молекулами ИдЫ водородную связь. Поэтому температуры плавления (—77,75 С) и кипения (—33,42°С) аммиака довольно высоки, он характеризуется значительной энтальпией испарения и легко сжижается. На этом основано его применение в холодильных маитинах. Жидкий аммиак хранят в стальных баллонах. [c.347]Сериая кислота эфир углекислый газ (из баллона) аммиак (из баллона) [c.89]
Примечания I. Рабочее давление для баллонов типов А,- Б В, Г, Н соответственно равно 15,0 12,5 3,0 0.6 и 3,0 МПа. 2. Наполнение баллонов аммиаком 0.57, хлором —1,25 кг/л. [c.698]
Наполнение и опорожнение баллонов должны производиться в соответствии с инструкцией (приложение 9). При этом наполнение баллонов аммиаком не должно превышать 0,5 кг на 1 л емкости баллона. Проверка наполнения баллонов должна выполняться взвешиванием. [c.56]
Сварные соединения труб с трубной решеткой подвергаются пневмоиспытаниям (подача в межтрубное пространство сжатого воздуха от заводской сети под избыточным давлением 6—7 кгс/см ), испытаниям аммиаком (подача в межтрубное пространство аммиака из баллона под избыточным давлением 42 кгс/см ). На одной трубной решетке пневмоиспытаниями было обнаружено около 2% труб, имеющих дефекты (в том числе дефекты самой трубы). После каждого этапа испытания трубного пучка дефекты исправляют ручной аргонодуговой сваркой горелкой АР-9. Приварка алюминиевых труб к алюминиевым трубным решеткам производится ручной аргонодуговой сваркой неплавящимся электродом с присадочной проволокой. Перед сваркой вокруг каждого отверстия выполняется кольцевая канавка. Сварку производят с обязательным предварительным подогревом трубной решетки для сплава АМцС температура подогрева 200—250°С, для сплава АМ — 100° С. [c.177]Заполнение и хранение баллонов с хладагентом возможно только в том случае, если не и гек срок их освидетельствования и баллоны находятся в исправном состоянии исправен запорный вентиль, не поврежден корпус и башмак, имеются клеймо, надлежащая окраска и надписи. Баллоны, находящиеся в эксплуатации, проходят периодическое освидетельствование через 5 лет. Освидетельствование производится на заводах, где осуществляется их заправка, или на специально организованных испытательных пунктах. После освидетельствования на баллоне ввгбивают-ся цифры, указывающие дату проведенного -и последующего освидетельствования. Например, клеймо 9-75-80 означает, что баллон был испытан в сентябре 1975 г. и подлежит следующему освидетельствованию в 1980 г. Нормы заполнения 1 л емкости баллонов аммиаком 0,5 кг, фреоном-12 1,1 кг, фрео-ном-22 0,9 кг. [c.91]
На 100 м швов расходуется один баллон аммиака, 1 л спирта и 0,1 кг фенолфталеина. [c.234]
Наполнение баллонов аммиаком допускается только при непросроченных сроках их технического освидетельствования. [c.56]
Наполнение баллонов аммиаком должно производиться только машинистом под наблюдением начальника компрессорного цеха. [c.142]
Подобные аварии происходили при наливе хлорных железнодорожных цистерн и других сосудов, и все они были вызваны смешением несовместимых продуктов. Такого рода аварии являются следствием неудовлетворительной подготовки цистерн под налив сжиженными газами и нарушений действующих правил и инструкций. При проведении сливо-наливных операций следует строго руководствоваться инструкциями по безопасной эксплуатации цистерн, контейнеров (бочек) и баллонов для жидкого хлора, аммиака и сжиженных углеводородных газов и др. Смешение несовместимых продуктов, приводящее к взрывам и пожарам, чаще наблюдается на транспортных емкостях, так как при транспортировке используется большое число емкостей. Чтобы исключить подобные аварии, запрещено применять цистерны, предназначенные для перевозки сжиженных углеводородов, под налив перекисью водорода и другими окислителями или несовместимыми продуктами. [c.190]
Запорный вентиль на выходе из ресивера закрывают, а регулирующий вентиль оставляют открытым. При открытии зарядного вентиля и вентиля на баллоне аммиак через регулирующий вентиль поступает в испаритель и отсасывается компрессором. При полном опорожнении баллона нижняя его часть (около вентиля) покрывается инеем. Для отсоединения баллона закрывают вентиль на баллоне и зарядный вентиль. Ставят на место заглушку и колпак и взвешивают баллон, записывая массу тары и количество заряженного аммиака. На крупных холодильниках иногда систему заряжают аммиаком прямо из железнодорожных цистерн согласно инструкции [8, приложение 10]. При заполнении системы аммиаком необходимо иметь противогаз и резиновые перчатки, запрещается подогревать баллоны, нельзя ремонтировать неисправные баллоны с аммиаком с надписью Полный . Такой баллон возвращают на завод. [c.269]
Заполнение баллонов аммиаком из холодильной установки не должно превышать 0,5 кг/л. Проверяют заполнение взвешиванием. Баллоны должны быть с непросроченным сроком клеймения. [c.347]
Нормы наполнения баллонов и цистерн регламентируются. Максимальное количество аммиака на 1 л емкости баллона или цистерны не должно превышать 0,57 кг, а минимальная емкость баллона или цистерны для 1 кг аммиака равна 1,76 л. При заполнении баллона аммиаком нз холодильной установки норма наполнения установлена равной 0,5 кг/л. [c.317]
Заполнение баллонов аммиаком из системы холодильной установки показано на рис. Х1У.37. [c.586]
При разборе этих аварий выяснилось, что предприятие не имело разрешения органов Госгортехнадзора на проведение освидетельствования и наполнение баллонов и не имело квалифицированных кадров для проведения этих работ. На предприятии не выполнялись соответствующие требования по оформлению документации по заполнению баллонов. В результате этих нарушений неоднократно допускалось заполнение баллонов аммиаком сверх допустимой нормы. Взвешивание баллонов, находящихся на складе, показало, что они были переполнены. [c.151]
Работу провели с маслом МС-20. Состав и свойства этого масла описаны Баллонный аммиак был очищен перегонкой и содержал не более 2- 10- масла на литр жидкости. [c.79]
Амиламины получают взаимодействием продуктов хлорирования пентана с аммиаком в спиртовом растворе. Схема промышленной установки представлена на рис. 49. Раствор аммиака в спирте перекачивается насосом из аммиачного абсорбера 1 в приемник 2. Смесь хлорамилов из бака 3 вместе со спиртовым аммиаком поступает в бак 4, оттуда направляется в автоклавы 5. После добавки свежего аммиака из баллона 6 и перемешивания при 160—165° в течение 2 час. температура в автоклаве настолько повышается, что давление возрастает при.мерно до 30 ат. Реакция завершается приблизительно за 2 часа. Реакционную смесь переводят затем в куб 7, где при небольшом избыточном давлении отгоняется аммиак, который снова абсорбируется в абсорбере 1 спиртом. Этот абсорбер состоит из трех последовательно соединенных колонн, через которые циркулирует спирт, охлаждаемый в выносном [c.227]
Для получения амида натрия нарезанный кусками металлический натрий расплавляют (температура плавления 98°) в стальном аппарате с электронагревом, нагревают до 360° и барботируют через него сухой газообразный аммиак из баллонов. Аммиак предварительно осушают пропусканием через колонку с твердой щелочью. Выделяющийся в результате реакции водород выпускают через выхлопную трубу и зажигают. По интенсивности водородного пламени судят о ходе процесса, который продолжается несколько часов. [c.369]
Переносный баллон вмещает около 22,5 кг жидкого аммиака. Какой объем азота и водорода при взаимодействии даст такую массу аммиака, если принять массу [c.155]
Стальные баллоны для аммиака окрашены в желтый цвет и имеют надпись Аммиак черного цвета. Вентили баллонов должны быть стальными. Медные или бронзовые вентили применять не разрешается, так как при соприкосновении с аммиаком они разрушаются. [c.90]
Резиновые 1Йанги, применяемые для слива аммиака в холодильную систему из баллонов или цистерн, а также при заполнении баллонов аммиаком, должны выдерживать избыточное давление 20 ати. Фреон подается в систему из баллонов через медную трубку-компенсатор. [c.327]
Особенности работы с жидким алшиаком, амидами металлов и ацетиленовыми баллонами. Аммиак выпускается в сжиженном состоянии в баллонах желтого цвета с надписью черными буквами аммиак . Он содержит примесь 5 10 весовых частей воды (азеотропной) и обычно хранится при комнатной температуре под давлением не более 30 атм. При отборе жидкого аммиака баллон устанавливают так, чтобы запирающий вентиль был направлен вниз, и жидкость выпускают через игольчатый вентиль в сосуд Дьюара. Отбор производят на улице в противогазе. [c.202]
Простая установка для получения жидкого аммиака и правила работы с ним оиисаны в книге [55 . Можно также пользоваться баллонным аммиаком, сразу наливая его в реакционную колбу. [c.136]
I — крекер 2 — холодильник 3 — колоакв о активированным углем 4 — гидрозатвор 5—колонка восстановления катализатора и магнетита 6 — конденсатор 7—влагоотделитель В— колоакв с силикагелем 9 — газодувка 10 — баллоны азота И — баллоны аммиака. [c.115]
Дихлорэтан, дшслордвфторметан [76]. Определение хлора в газообразных и легколетучих галогенсодержащих органических веществах основано на поглощении анализируемого вещества активированным углем (ВАУ или РР-3), находящимся в кварцевом аппарате. Газ просасывают через кварцевый аппарат с углем 20—30 сек., жидкость наносят капилляром. После введения вещества в аппарат его взвешивают, после чего нагревают до 750—800° С и пропускают из баллона аммиак 10—15 мин. Образовавшийся хлорид аммония смывают водой и определяют хлорид-ион потенциометрическим титрованием раствором 0,1 N AgNOg с серебряным и каломельным электродами. [c.150]
Из баллонного аммиака. Собирают установку (рис. 63). Баллон с аммиаком 1 устанавливают и закрепляют на подставке 2. Баллон соединяют с пустой промежуточной склянкой 3, к которой присоединены две поглотительные склянки 4 с раствором NaOH для поглощения СО2. Аммиак, очищенный от СО2, поступает в приемник 5, где находится дважды перегнанная дистиллированная вода, не содержащая СО2. Насыщение аммиаком проводят до достижения плотности раствора в приемнике 0,907 г/см что соответствует 25% раствору аммиака. [c.111]
Заполнение баллонов аммиаком из системы холодильной установки показано на рис. 14.36. Заполнение баллонов производится из линейного ресивера через вентиль 5. Норма заполнения не превышает 0,5 кг на 1 л емкости. Для ускорения заполнения баллонов жидкий аммиак в линейном ресивере иногда предварительно переохлаждают до температуры (—5)—(—10)° С. С этой целью ресивер отключают от конденсатора и переохладителя закрытием вентилей 1,2 я 4. Затем понижают давление в ресивере до давления кипения, используя для этого трубопровод с вентилем 3 для отбора паровоздушной смеси. Переохлаждение аммиака уменьшает парообразование при заполнении баллона и убыстряет процесс заполнения. После того как осуществлено переохлаждение к ВозВтотвелителю жидкости, которое наблюда- [c.527]
Запорный вентиль на выходе из ресивера закрывают а регулирующий вентиль оставляют открытым. При откры тии зарядного вентиля и вентиля на баллоне аммиак через регулирующий вентиль поступает в испаритель и отсасывается компрессором. При полном опорожнении баллона нижняя его часть (около вентиля) покрьшается инеем. Для отсоединения баллона закрывают вентиль на баллоне и зарядный вентиль. Ставят на место заглушку и колпак и взвешивают баллон, записывая массу тары и количество заряженного аммиака. [c.402]
Жидкий аммиак перевозят в стальных баллонах, железнодорожных и автомобильных цистернах, а также водным транспортом на специальных судах. Ведутся работы по сооружению аммнакопроводов. [c.84]
Сжиженные углеводородные газы, аммиак и хлор перевозят под давлением в железнодорожных и автомобильных цистернах или в баллонах и наполняют из стационарных хранилищ, расположенных, как правило, на предприятиях, производящих эти сжиженные газы. Заправка транспортных сосудов и слив сжиженных газов представляют собой весьма опасные операции. Многие аварии, происщедщие за последние годы за рубежом и в нашей стране, были связаны именно с этими операциями. Поэтому на заправочных станциях должны строго выполняться специфические требования по технике безопасности. [c.191]
chem21.info