Диаметр электрода от толщины металла (листа или детали), сила тока сварки от диаметра электрода. Режимы — выбор режима ручной дуговой сварки. Траектории движения электрода. Схема, скорость сварки, влияние наклона электрода, силы сварочного тока…
| Адрес этой страницы (вложенность) в справочнике dpva.ru: главная страница / / Техническая информация / / Технологии и чертежи / / Сварка металлов / / Диаметр электрода от толщины металла (листа или детали), сила тока сварки от диаметра электрода. Режимы — выбор режима ручной дуговой сварки. Траектории движения электрода. Схема, скорость сварки, влияние наклона электрода, силы сварочного тока…
|
dpva.ru
Разновидности наливных полов в зависимости от толщины слоя
Наливные полимерные полы существенно различаются по стоимости. Зависит это во многом от толщины пола и его назначения. Самые тонкие покрытия для обеспыливания могут быть толщиной до миллиметра, а полы для промышленных помещений будут раз в 10 толще.
Виды покрытий:
- Обеспыливающие покрытия толщиной в десятые доли миллиметра обычно используются для пропитки бетонных оснований в качестве временной меры или при подготовке к заливке основного полимерного пола. Большая часть вещества проникает в верхний слой основания, а на поверхности создается лишь тончайший слой. Чтобы добиться повышенной текучести состава, в эпоксидную смолу добавляются особые пластифицирующие добавки, которые делают ее более жидкой и позволяют добиться максимального растекания.
- Полиуретановая покраска пола. При такой обработке толщина слоя будет уже около 1 мм. Держится такое покрытие дольше, примерно 4 года.
- Самовыранивающиеся полы толщиной до 3-х мм применяются в помещениях с малыми и средними нагрузками. На производстве прочности такого пола будет недостаточно, а вот для квартиры покрытие толщиной 2-3 мм подойдет, как нельзя лучше.
- Покрытия толще 3-х мм применяются в цехах и других помещениях с высокой нагрузкой на пол. Толщина такого полимерного пола обычно составляет до 5-ти мм, поскольку более толстый слой уже не даст увеличения прочности, зато приведет к повышенному расходу смолы, а, следовательно, удорожанию.
- Наполненные полы отличаются тем, что в состав смеси добавляется какой-либо наполнитель. Используя вместе со смолой, например, песок, можно удешевить монтаж за счет уменьшения количества более дорогой смолы. Количество ингредиентов в смеси можно варьировать, добиваясь той или иной структуры покрытия.
Смотрите также:
иликоновая резина — это незаменимый материал для множества сфер жизни. Формы из силикона используются в косметологии и кулинарной области, в создании любого рода украшений, декора и косметических средств и т.д. Мы расскажем об основных свойствах силиконовой резины, а также приведём способы самостоятельного создания форм из этого материала…Читать далееСтеклоткань — тканый или нетканый материал, изготовленный из стекловолокна, которое, в свою очередь, производится из специальных сортов стекла.
Читать далееСтеклопластики — полимерные композиционные материалы, армированные стеклянными волокнами, которые формируют из расплавленного неорганического стекла.
Читать далее
polymax10.ru
Выбор номера наконечника сварочной горелки в зависимости от толщины свариваемого металла
Номер наконечника
1
2
3
4
5
6
7
Примерная толщина свариваемого
металла (стали), мм
до 1,5
1-3
2,5-4 4-7
7-11
10-18
17-30
Таблица А2
Выбор угла наклона сварочной горелки к оси сварного шва в зависимости от толщины свариваемого металла
Угол наклона горелки к шву | 20° | 30° | 40° | 50° | 60° | 70° |
Примерная толщина свариваемого металла (стали), мм | 1-3 | 5-7 | 7-10 | 10-12 | 12-16 |
Таблица А3
Выбор диаметра присадочной проволоки в зависимости
от толщины свариваемого металла
Толщина металла (стали), мм
1-2
2-3
3-5
5-10
10-15
15
и более
Диаметр проволоки (стальной), мм
без проволоки 2
2-4
3-4
4-6
6-8
Диаметр проволоки (медной), мм
1,5
2-3
3-4
5
6
8
Таблица А4
Выбор номера наружного и внутреннего мундштуков
универсального резака и давления кислорода в зависимости
от толщины разрезаемого металла
Толщина разрезае-мого металла, мм
5
25
50
100
200
300
№ наружного
мундштука
1
1
1
2
2
2
№ внутреннего
мундштука
1
2
3
4
5
6
Давление кислорода, МПа
0,2
0,4
0,6
0,8
1,2
1,4
Расстояние головки резака от поверхности металла, мм
2
2,5
3
4
5
6,5
ПРИЛОЖЕНИЕ Б
Пропан-бутано-кислородная сварка
Этот вид сварки применяют для неответственных деталей. Давление рабочих газов при входе в горелку поддерживается в пределах: пропан-бутановой смеси 0,02 — 0,05 МПа, кислорода — 0,02 — 0,04 МПа, при этом поддерживается соотношение рабочих газов -3,5 : 4. При этом виде сварки недопустимо применение в качестве присадочной проволоки Св-08 и Св-08А, рекомендуемых для ацетилено-кислородной резки. Чаще всего используются проволоки марок Св-12ГС, Св-08Г2С, Св-08ГС, хорошо раскисляющие сварочную ванну.
Присадочную проволоку держат под углом 35 — 40° к оси шва, а пламя — под углом 45 -60°. Расстояние от ядра пламени до поверхности сварочной ванны должно поддерживаться в пределах 3-6 мм, а до плавящегося конца присадочной проволоки -2-4 мм. Основные режимы пропан-бутано-кислородной сварки приведены в таблице Б1.
Таблица Б1
studfiles.net
Подбор длины обычного болта в зависимости от толщины стягиваемого пакета
Главная » Вес крепежа » Расчет длины обычного болта по толщине пакетаДанный калькулятор предназначен для расчета длины обычных болтов по ГОСТ 7798-70, ГОСТ Р ИСО 4014-2013.
Для вычисления требуемой длины болта нужны следующие данные: толщина пакета, количество и высота гаек, количество и толщина шайб, шаг резьбы.
Формула подбора длины болта:
Длина болта = толщина пакета (толщина соединяемых деталей, пластин) + высота гаек + толщина шайб + выступающий конец
Минимальная длина болта М16 — 140 мм. Количество витков резьбы выступающих из гайки — 2.2 Максимальная длина болта М16 — 160 мм. Количество витков резьбы выступающих из гайки — 4.5 Длина резьбы болта М16*140 — 54.0 мм. Шаг резьбы — 3.5 мм. Высота гайки по ГОСТ — 19.8 мм. Толщина шайбы — 3.0 мм. |
1. Введите необходимую толщину соединяемых пластин, деталей (толщину пакета)
2. Выберите необходимое количество гаек и шайб
2. Щелкните мышью на любом свободном месте страницы
3. И вот Вы видите длину болта, который Вам необходим!Всё очень просто — с новым калькулятором подбора крепежа в зависимости от толщины соединяемых деталей у Вас нет необходимости копаться в ГОСТах и таблицах!
Теперь подсчет длины болта занимает секунды!Расчет длины болта по толщине пакета. Расчет длины болта онлайн. Толщина пакета болта. Вычисление длины болта.
bashmetiz.ru
Условия применения марок чугуна в зависимости от толщины стенки отливки
Чугун | Толщина стенки отливки, мм, для условий применения | ||||
I | II | III | IV | V | |
СЧ 15 | <2 | 2-6 | 6-10 | 10-20 | >20 |
СЧ 20 | <4 | 4-9 | 9-15 | 15-30 | >30 |
СЧ 25 | <6 | 6-12 | 12-25 | 25-50 | >50 |
СЧ 30 | <10 | 10-15 | 15-40 | >40 | — |
СЧ 35 | <15 | 15-40 | 40-80 | >80 | — |
СЧ 40 | <20 | 20-40 | 40-120 | >120 | — |
Условия применения марок чугуна: I – применение невозможно; II – требуются специальные меры для предупреждения или ликвидации отбела (например, модифицирование чугуна или термическая обработка отливок) и повышенные затраты на механическую обработку отливок; Ш – для отливок высокой износостойкости и прочности при повышенной твердости; IV – для отливок средней твердости и хорошей обрабатываемости резанием; V – только для специальных целей (с использованием модифицирования и легирования).
Примеры применения серых чугунов для типовых деталей машин и оборудования приведены в табл.4.
Таблица 4
Применение серых чугунов для типовых деталей машин и оборудования
Область применения | Виды деталей или отливок | Марки чугуна | Особенности химического состава, % | Твердость НВ |
1 | 2 | 3 | 4 | 5 |
Автотракторостроение | Блоки цилиндров карбюраторных и дизельных двигателей | СЧ 20 СЧ 25 | до 0,6Cr, до 0,5Ni, до 0,6Cu, до 0,08Ti | 183-217 |
Головки цилиндров дизельных двигателей | СЧ 20, СЧ 25 | до 0,3Cr, до 0,5Cu, до 0,25Ti | до 235 |
Продолжение таблицы 4
1 | 2 | 3 | 4 | 5 |
Автотракторостроение | Блоки цилиндров тяжелонагруженных автомобильных и судовых двигателей | СЧ 25- СЧ 35 | 0,2-0,5Cr, до 0,85Ni, 0,35-0,85Mo | 207-248 |
Головки тяжелонагруженных двигателей | СЧ 25 | 3,5-3,7C, 02-0,4Cr, 0,5-0,7Mo | 180-229 | |
Гильзы цилиндров карбюраторных и дизельных двигателей | СЧ 20, СЧ 25 | 0,15-0,45Cr, 0,15-0,30Ni | 200-250*) | |
Гильзы цилиндров автомобильных и тракторных двигателей | СЧ 20, СЧ 25 | до 0,9P, до 0,8Cu, дo 0,6Мo | 180-240 | |
Распределительные валы дизельных и карбюраторных двигателей | СЧ 25, СЧ 30 | до 1,5Cr, до 1,3Ni, до 0,8Mo, до 0,1B | 217-321**) | |
Тормозные барабаны и диски средней нагруженности | СЧ 20, СЧ 25 | до 0,6Сг, до 0,9Ni,. до 0,6Cu, до 0,8Mo, | до 255 | |
Маховики | СЧ 25- СЧ 35 | до 0,6Cr, до 0,5Ni, до 0,6Cu, до 0,08Ti | 210-300 | |
Крышки коренных подшипников | СЧ 25 | — | ≥200 | |
Выпускные коллекторы | СЧ 15, СЧ 20 | до 0,5Mo, до 0,4Cu, до 0,05Ti | 163-255 | |
Станкостроение | Легкие отливки (толщина стенки а до 10 мм, масса М до 100кг) | СЧ 25, СЧ 30 | _ | ≥180 |
Средние отливки (а =10-20 мм, М=100-4000 кг) | .СЧ 25, СЧ 30 | _ | ≥180 | |
Тяжелые отливки (а =20-30 мм, М= 4000- 10000 кг) | СЧ 25- СЧ 35 | _ | ≥170 | |
Особо тяжелые отливки (а>30 мм, М=10000-30000 кг) | СЧ 25- СЧ 35 | _ | ≥170 |
Окончание таблицы 4
1 | 2 | 3 | 4 | 5 |
Станкостроение | Уникальные отливки (М>30000 кг) | СЧ 25- СЧ 35 | легирование Сг, Ni, Cu, Sn, Mo | ≥170 |
Тяжелое машино-строение | Крупные отливки | СЧ 15- СЧ 25 | 2,8-3,2C, 0,2-0,5Cr | _ |
Электротехническая промышленность. | Станины электродвигателей | СЧ 15 | до 0,3P, до 0,15Cr | _ |
Сантехни-ческая промыш-ленность. | Отопительные ради-аторы, секции котлов, гарнитура, ванны, трубы, раковины | СЧ 10 | 3,5-3,7C, 0,3-0,6P | _ |
Примечания: *) твердость на рабочей поверхности не менее HRC 42, **) на кулачках не менее HRC 45.
При получении отливок из серого чугуна для предупреждения отбела или плохой обрабатываемости резанием в тонких сечениях чугун в жидком состоянии перед разливкой модифицируют специальными добавками. Модифицирование обеспечивает также получение в структуре чугуна тонкостенных отливок преимущественно пластинчатого равномерно распределенного графита, что приводит к выравниванию структуры и свойств чугуна в различных сечениях отливок и повышает общую прочность чугуна.
Чаще всего в качестве универсальных кодификаторов применяют ферросилиций марки ФС 75, содержащий около 75% Si, около 1,5% Al и до 0,8% Са, а также ферросилиций в смеси с графитом, силикокальцием и лигатурами РЗМ (редкоземельных металлов). Количество вводимого модификатора составляет обычно от 0,2 до 0,6% от массы жидкого чугуна в зависимости от марки чугуна (чем выше марка чугуна, тем больше добавка модификатора).
При производстве отливок из серого чугуна с пластинчатым графитом иногда используют термическую обработку отливок. Ее применяют для снятия внутренних напряжений, обеспечения минимальных деформаций при эксплуатации, для улучшения обрабатываемости резанием, повышения механических свойств и износостойкости.
Закалку с отпуском проводят для получения мартенситной структуры и обеспечения высокой твердости и износостойкости чугуна. Нагрев под закалку проводят обычно до температур на 50-700 выше критической точки aci. Во избежание деформации деталей применяют после закалки стабилизирующий отпуск при 180-200°С.
Улучшение (закалку с высокотемпературным отпуском) применяют для получения структуры зернистого сорбита и обеспечения достаточно высоких значений прочности и твердости.
Нормализация проводится для отливок с исходной ферритной иди ферритно-перлитной структурой с целью получения перлитной структуры и повышения механических свойств и износостойкости чугуна. Нагрев проводят так же, как и при закалке, с выдержкой около 1 часа на 25 мм толщины стенки отливки. Сложные отливки рекомендуется охлаждать на воздухе до 500°С, а далее в печи со скоростью 40 градусов в час для снятия напряжений.
Высокотемпературный (880-950°С, выдержка до 5 часов) отжиг применяют для снижения твердости отбеленного чугуна.
Отжиг для снятая напряжений проводят чаще всего при температурах 500-600°С в зависимости от марки чугуна. Длительность выдержки составляет обычно 1,0-1,5 часа для отливок с толщиной стенки до 20 мм и увеличивается на 1,0-1,5 часа на каждые последующие 25 мм толщины сечения. Скорость охлаждения после отжига не должна превышать 10-30 градусов в час для отливок сложной конфигурации и 150 градусов в час для простых отливок.
Иногда проводят низкотемпературный (700-750°С) отжиг отливок для улучшения обрабатываемости резанием. Такой отжиг обеспечивает распад эвтектоидного цементита и получение мягкой ферритно-графитной структуры с твердостью НВ 130-180.
Важной характеристикой чугуна является показатель качества ПК, представляющий собой отношение значений предела прочности и твердости НВ чугуна (ПК = / HB), причем чаще всего выражают в МПа, а твердость НВ в обычных единицах твердости, условно принимаемых безразмерными.
Показатель качества, прежде всего, зависит от структуры чугуна. Поэтому его опенку удобно проводить по структурным зонам, характерным для структурных структурно-прочностных диаграмм (см. рис.1 и 2).
На
рис.3 представлена область значений ПК
для чугунов различного химического
состава (т.е. с разными значениями
углеродного эквивалента СЭ).
Зависимость 1 (для нелегированных
чугунов) получена на основе данных рис.1
для стандартных проб диаметром 30 мм
(или при толщине стенки отливки 15 мм в
случае применения формовки “по-сырому”).
Видно, что в области химических составов,
соответствующих перлитным чугунам, с
понижением углеродного эквивалента
от 4,3 до 3,3 показатель качества существенно
возрастает (до ПК ≈ 1,5), но при дальнейшем
снижения углеродного эквивалента (до
областейIIи I) начинает
резко уменьшаться, что связано с
появлением отбела в структуре чугуна.
Поэтому для серого нелегированного
чугуна следует выбирать оптимальные
составы в интервале значений СЭ=3,3-3,7%,
причем следует учитывать, что эта
рекомендация относится лишь к отливкам
стандартного сечения. В случае отливок
с другой толщиной стенки необходимо
строить зависимости, подобные кривой
1 на рис.3, для соответствующего сечения.
Из рис.3 и данных табл.2 следует, что в отливках стандартного сечения можно использовать лишь чугуны до марки СЧ 30. Применение для таких отливок чугунов более высоких марок невозможно из-за частичного или полного отбела в их структуре. Нелегированный чугун марки СЧ 35 можно использовать в основном в отливках большего сечения.
При выборе состава чугуна необходимо исходить из условия наибольшей простоты технологического процесса. Так, например, термическую обработку отливок следует назначать только в случаях предъявления к ним особых требований или при необходимости исправления структуры и повышения свойств в уже изготовленных отливках.
Более широко используется метод модифицирования, позволяющий получать высокие марки чугуна (СЧ 25, СЧ 30) без использования легирующих элементов в составе или при ограниченном их использовании. Чугуны наиболее высоких марок (СЧ 35 и СЧ 40) получают обычно с помощью легирования (см. табл.2) и модифицирования, реже с применением термической обработки. В этом случае можно обеспечить и получение высоких значений показателя качества чугуна. Примером могут служить легированные чугуны, разработанные в БГИТА. Зависимости показателя качества таких чугунов от углеродного эквивалента приведены на рис.3 в литом состоянии (кривая 2) и после термической обработки (кривая 2’), а различие в прочностных свойствах по сравнению с нелегированным чугуном – на рис.4.
Высокопрочные чугуны с шаровидным графитом (ВЧШГ)
Существенное повышение механических свойств чугуна достигается при переходе от пластинчатой формы графита к шаровидной или вермикулярной (промежуточной). Для чугуна с шаровидным графитом (ЧШГ) характерны не только высокая прочность (отсюда и название – высокопрочный чугун), но и значительные пластичность и вязкость, в связи с чем во многих зарубежных стандартах его называют пластичным чугуном.
ВЧШГ имеют широкий диапазон механических и эксплуатационных свойств. Ферритные чугуны характеризуются наивысшей среди чугунов пластичностью и вязкостью, обеспечивают литым деталям высокие хладо- и ударостойкость, хорошую свариваемость и обрабатываемость резанием. Перлитные ЧШГ хорошо сопротивляются статическим и циклическим нагрузкам, обладают высокими износо- и задиростойкостъю. В бейнитных ЧШГ сочетаются максимально высокая прочность с достаточной пластичностью, что обеспечивает высокие значения износостойкости, усталостной прочности и контактной выносливости литых изделий.
Все марки ЧШГ имеют высокий модуль упругости и значительно большую, чем у стали, демпфирующую способность. Предел текучести у бейнитных чугунов в 2,5-3 раза выше, чем у обычных конструкционных сталей.
По способности выдерживать высокие механические нагрузки при наименьших деформациях и массе деталей ЧШГ значительно превосходит сталь, ковкий и серый чугун. Масса литых деталей из ЧШГ может быть на 5-10% ниже по сравнению с литой сталью и ковким чугуном и на 10-20% меньше по сравнению со стальными поковками и штамповками.
ВЧШГ успешно заменяет углеродистую сталь и другие виды чугунов в деталях, работающих в условиях тепловых ударов, термоусталости (при температурах цикла до 600°С), низких температур (до -100°С), умеренно агрессивных сред, высоких давлений, знакопеременных динамических нагрузок.
ВЧШГ обладают хорошими литейными свойствами, что позволяет изготавливать из них высококачественные отливки с толщиной стенок от 2,5 до 1000 мм и массой от нескольких десятков граммов (например, поршневые кольца) до 200 т (станины, цилиндры, контейнеры и др.).
Высокая герметичность в сочетания с ударо- и коррозионностойкостью позволяют эффективно использовать ВЧШГ в виде наиболее экономичного материала для напорных труб и фитингов. Почти половина мирового производства ЧШГ используется на эти цели.
Свойства ВЧШГ регламентированы ГОСТ 7293-85, в котором предусмотрены 8 марок чугуна (табл.5).
Таблица 5
Марки и свойства ВЧШГ (но ГОСТ 7293-85)
Марка чугуна | В | 0,2 | , %, не менее | Твердость НВ | Ударная вязкость КС при +200С, Дж/см 2 |
МПа, не менее | |||||
ВЧ 35 | 343 | 216 | 22 | 140-170 | 80-150 |
ВЧ 40 | 392 | 245 | 15 | 140-202 | 30-80 |
ВЧ 45 | 441 | 304 | 10 | 140-225 | 30-60 |
ВЧ 50 | 491 | 314 | 7 | 153-245 | 30-50 |
ВЧ 60 | 589 | 363 | 3 | 192-277 | 10-30 |
ВЧ 70 | 687 | 412 | 2 | 228-302 | 10-25 |
ВЧ 80 | 785 | 471 | 2 | 248-351 | 10-30 |
ВЧ 100 | 981 | 687 | 2 | 270-360 | 10-20 |
Относительное удлинение, твердость НВ, а также ударную вязкость КС определяют при наличии требований в нормативно-технической документации на отливки, причем значения этих свойств могут отличаться от приведенных в табл.5.
Механические свойства ВЧШГ должны быть обеспечены в литом состоянии или после термической обработки. Механические испытания проводят на образцах, вырезанных из отдельно отлитых или прилитых к отливкам проб.
Механические свойства ЧШГ зависят от толщины стенки отливки, хотя и в меньшей степени, чем у серого чугуна. Прочность и твердость чугуна в пробах обычно выше, чем в реальных отливках. В табл.6 приведено соотношение значений механических свойств (В и НВ) в отливках и в литых трефовидных пробах, причем за единицу приняты свойства в литой пробе.
Влияние скорости охлаждения и толщины стенки отливки связано с тем, что в толстых сечениях повышается количество феррита, увеличивается опасность флотации графита и ухудшения его формы и распределения, усиливается микроликвация элементов.
Таблица 6
studfiles.net
ГОСТ 14802-85
ГОСТ 14802-85
Группа Г34
ЗАКЛЕПКИ (ПОВЫШЕННОЙ ТОЧНОСТИ)
Диаметры отверстий под заклепки, размеры замыкающих
головок и подбор длин заклепок
Rivets (high precision). Hole diameters for rivets,
upset head dimensions and length selection
ОКП 128500
Дата введения 1986-07-01
Постановлением Государственного комитета СССР по стандартам от 27 марта 1985 г. N 905 срок действия установлен с 01.07.86 до 01.07.96*
_______________
* Ограничение срока действия снято по протоколу N 5-94 Межгосударственного Совета по стандартизации, метрологии и сертификации (ИУС N 11/12, 1994 год). — Примечание «КОДЕКС».
ВЗАМЕН ГОСТ 14802-83
ПЕРЕИЗДАНИЕ. Март 1991 г.
1. Настоящий стандарт устанавливает размеры, необходимые для установки заклепок при выполнении соединений ударной и прессовой клепкой.
2. Размеры замыкающих головок и отверстий под заклепки должны соответствовать указанным на чертеже и в таблице.
_____________
* Размеры для справок.
мм
1,0 | 1,4 | 1,6 | 2,0 | 2,6 | 3,0 | 3,5 | ||
Пред. откл. по h22 | 1,1 | 1,5 | 1,7 | 2,1 | 2,7 | 3,1 | 3,6 | |
Номин. | 1,5 | 2,1 | 2,4 | 3,0 | 3,9 | 4,5 | 5,2 | |
Пред. откл. | ±0,10 | ±0,15 | ±0,20 | ±0,25 | ±0,30 | |||
, не менее | 0,4 | 0,6 | 0,7 | 0,8 | 1,1 | 1,2 | 1,4 |
Продолжение
мм
4,0 | 5,0 | 6,0 | 7,0 | 8,0 | 10,0 | ||
Пред. откл. по h22 | 4,1 | 5,1 | 6,1 | 7,1 | 8,1 | 10,1 | |
Номин. | 6,0 | 7,5 | 8,7 | 10,2 | 11,6 | 14,5 | |
Пред. откл. | ±0,40 | ±0,50 | ±0,80 | ±1,00 | |||
, не менее | 1,6 | 2,0 | 2,4 | 2,8 | 3,2 | 4,0 |
3. Длину заклепок в зависимости от толщины пакета следует рассчитывать по формуле
,
где — номинальный диаметр стержня заклепки;
— наибольший допустимый диаметр отверстия;
— расчетная толщина пакета.
Подбор длин заклепок производить по таблице обязательного приложения.
4. Подбор длин заклепок для соединений, в которых замыкающая головка должна быть потайной, производить по технической документации на заклепочные соединения.
ПРИЛОЖЕНИЕ (обязательное). Таблица для подбора длин заклепок в зависимости от толщины пакета
ПРИЛОЖЕНИЕ
Обязательное
мм
Продолжение
мм
Продолжение
мм
Продолжение
мм
Примечание. Заклепки для толщин пакетов, указанных ниже ломаной линии, не рекомендуется применять при выполнении соединений ударной клепкой.
Текст документа сверен по:
официальное издание
Заклепки повышенной точности.
ГОСТ 14797-85 — ГОСТ 14803-85: Сб. ГОСТов. —
М.: Издательство стандартов, 1991
docs.cntd.ru
Выбор толщины утеплителя в зависимости от стенового материала
Для того чтобы эффективно сланировать и выполнить строительный процесс, нужны точные данные о материалах которые будут использоваться.
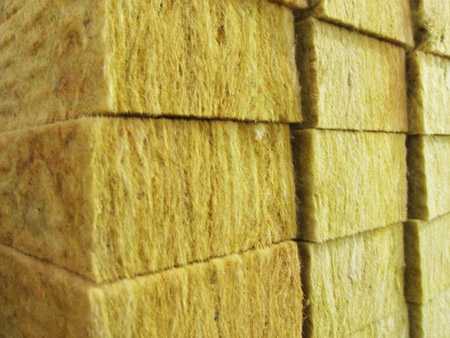
Часто на стенах дома, здания можно сэкономить. В таких случаях используют не толстую каменную стену, а стену, толщины которой бы хватало нести нагрузку от вышележащих конструкций здания. То есть стена выполняет несущую функцию. А с наружной стороны стена отделана утеплителем. Это комбинированная схема (прочность + -защита от холода) самое эффективное решение для стен дома или здания. Этим мы получаем существенный выигрыш в бюджете строительства. Ниже приведены табличные данные о зависимости толщины стены и толщины утеплителя для разных климатических регионов России и стран СНГ. Стоит отметить что количество современных утеплителей очень велико, поэтому всегда можно найти компромиссные варианты.
Зависимость толщины стены от выбранного материала и региона страны
t,°C наиболее холодной пятидневки | Район строительства | Материал стены и ее плотность | |||
Камень, известняк плотность 1800 | Кирпич плотность 1600 | Керамический блок плотность 1200 | Бетон плотность 800 | ||
Толщина стены | |||||
-60 | Верхоянск | 90 | 70 | 45 | |
-40 | Новосибирск | 90 | 70 | 45 | |
-30 | Москва | 80 | 64 | 50 | 35 |
-20 | Ереван, Львов | 60 | 51 | 30 | 20 |
-10 | Тбилиси, Красноводск | 45 | 38 | 25 | 16 |
Зависимость толщины утеплителя от выбранного материала и региона страны при толщине несущей стены из кирпича толщиной 25 сантиметров
t,°C наиболее холодной пятидневки | Район строительства | Материал, плотность утеплителя, кгм3 | |||
Пенопласт плотность 100 | Минеральная вата, плотность 200 | Фибролит, плотность 1200 | Бетон плотность 800 | ||
Толщина стены | |||||
-60 | Верхоянск | 6 | 10 | 20 | 40 |
-40 | Новосибирск | 4 | 6 | 12 | 26 |
-30 | Москва | 3 | 5 | 10 | 22 |
-20 | Ереван, Львов | 2 | 3 | 6 | 13 |
-10 | Тбилиси, Красноводск | 1 | 2 | 4 | 9 |
promplace.ru