ПРИНЦИП ДЕЙСТВИЯ, КОНСТРУКТИВНЫЕ СХЕМЫ И ТЕХНИЧЕСКИЕ ХАРАКТЕРИСТИКИ БАРАБАННЫХ МЕЛЬНИЦ
В мельницах с разгрузочной решеткой в качестве измельчающих тел применяют шары или рудную галю, измельченный продукт проходит через отверстия решетки, а затем поднимается лифтерами к центру разгрузочной цапфы мельницы. Разность уровней пульпы h2, между загрузочным и разгрузочным концами барабана (см. рис. 8.1.1, а) значительна. Поэтому скорость движения материала вдоль мельницы сравнительно высокая, что предполагает получение продукта более грубого измельчения, чем в мельницах с центральной загрузкой.
В шаровых мельницах с центральной разгрузкой разность уровней h3 пульпы в загрузочном и разгрузочном концах (см. рис. 8.1.1, б) небольшая, материал перемещается вдоль мельницы сравнительно медленно и получается более тонкий продукт измельчения.
Как шаровые, так и бесшаровые барабанные мельницы имеют ограниченные возможности в части повышения энергонапряженности и удельной производительности.
Шаровая мельница с разгрузочной решеткой (рис. 8.1.3) состоит из барабана 1 с торцовыми крышками 2 и 16, загрузочной 4 и разгрузочной 14 цапф, опирающихся на подшипники 3 и 15. Барабан вращается от электродвигателя посредством малой шестерни 18, насаженной на приводной вал 19, и зубчатого венца 11, закрепленного на барабане. В мельницах больших размеров тихоходный электродвигатель присоединяется к приводному валу с помощью эластичной муфты, а в мельницах малых размеров электродвигатель подключается к этому валу через редуктор.
Исходный материал загружается в мельницу питателем 5 через его центральное отверстие 6, а пески классификатора — улитковым черпаком с козырьком 7. Барабан и торцовые крышки для предотвращения от износа футеруются броневыми плитами 8, которые закрепляются болтами 9, а внутренняя поверхность пустотелых цапф — съемными воронками.
У разгрузочного конца мельницы установлена решетка 10. Пространство между этой решеткой и торцовой крышкой 16 разделено радиальными перегородками — лифтерами 12 — на секторные камеры, открытые в цапфу 14. Наличие решетки и секторных камер позволяет осуществлять принудительную разгрузку измельченного продукта из мельницы и поддерживать в ней низкий уровень пульпы.
При вращении мельницы лифтеры 12 поднимают пульпу до уровня разгрузочной цапфы 14, через которую она удаляется из мельницы. В мельницу загружают стальные или чугунные шары разной крупности (40… 150 мм) примерно на половину ее объема. Во время вращения барабана шары, перекатываясь, скользя и падая, измельчают зерна полезного ископаемого.
Для разгрузки изношенных шаров, введения футеровки внутрь мельницы и ее осмотра служат люки 17. Горловина 13 разгрузочной цапфы имеет несколько больший диаметр, благодаря чему происходит движение пульпы в сторону разгрузки. Номинальные размеры мельницы определяются внутренним диаметром D0 и его длиной L0 без учета толщины футеровки. Сокращенно мельницы с разгрузочной решеткой обозначаются МШР-D0хL0.
Технические характеристики шаровых мельниц с решеткой приведены в табл. 8.1.1.
Барабан мельницы изготовляют сварным или клепаным из листовой стали, а торцовые крышки отливают из чугуна и стали. Они соединяются между собой болтами. Сменные броневые плиты выполняют из износостойких материалов. Толщина новой футеровки h принимается в зависимости от D0.
От профиля и толщины футеровочных плит барабана зависят характер движения измельчающих тел (высота подъема и коэффициент скольжения по футеровке), рабочий объем барабана мельницы, износ футеровки, производительность мельницы, удельный расход электроэнергии и измельчающих тел.
Основными элементами резиновой футеровки (рис. 8.1.4) являются лифтеры /, плиты 2 и секторы решетки 3. На загрузочную крышку барабана мельницы радиально укладывают плиты толщиной 60 мм, которые зажимают лифтерами с размерами в сечении 100×100 мм. На барабане располагают плиты толщиной 55 мм и лифтеры размером 140×125 мм. Резиновые секторы решетки толщиной 54 мм с отверстиями зажимают лифтерами, размер которых 100×110 мм.
На один комплект футеровочных плит и секторов решетки полагается иметь два комплекта лифтеров. Поскольку резиновая футеровка тоньше стальной, рабочий объем мельницы увеличивается примерно на 5…6 %.
Кроме того, срок службы резиновых и стальных футеровок либо одинаковый, либо первые служат на 15…20% дольше вторых. Удельный расход шаров в мельнице с резиновой футеровкой меньше, чем в мельнице со стальной футеровкой, а производительность мельниц с резиновой футеровкой не ниже
(а часто и выше), чем мельниц со стальной футеровкой. К преимуществам резиновых футеровок относятся меньшая трудоемкость монтажа, большая герметичность, низкий уровень шума [4].
Конструкцию футеровок торцовых крышек и разгрузочных решеток подбирают с таким расчетом, чтобы срок их службы был равен или кратен сроку службы футеровки барабана. Это достигается путем подбора их толщины с учетом фактического износа. Футеровка цапф гладкая или спиральная. Направление спирали загрузочной цапфы должно способствовать продвижению исходного материала в мельницу, а в разгрузочной цапфе — возврату шаров и крупного материала.
Обычно футеровка изнашивается неравномерно. Скорость износа футеровочных плит из высокомарганцовистой стали марки 110Г13Л составляет несколько долей миллиметра в сутки. Промышленные испытания футеровок показали, что футеровки волнового профиля из чугуна марок ИЧХ12Г5 и ВУ-4 служат в 2-3 раза дольше, чем из стали марки 110Г13Л.
Питатель. Для загрузки мельницы исходным материалом, поднятым на уровень ее оси, применяют барабанный питатель (рис. 8.1.5, б), состоящий из цилиндрической камеры 1, переходящей в конус, крышки 2 и диафрагмы 3 с секторным отверстием. Питатель крепится болтами к загрузочной цапфе мельницы. Материал проходит через отверстие диафрагмы и попадает на спираль футеровки загрузочной цапфы. Барабанные питатели применяют в мельницах, работающих в открытом цикле, когда пульпу, выходящую из мельницы, не требуется классифицировать по гранулометрическому составу и возвращать в мельницу на доизмельчение.
Для одновременной загрузки в мельницу исходного материала и песков классификатора, работающего в замкнутом цикле с этой мельницей, используют комбинированные питатели. Они кроме центрального отверстия имеют дополнительный один или два хобота, с помощью которых недоизмельченный материал, вышедший из мельницы и отделенный в классификаторе от кондиционного продукта, захватывается из сборника перед мельницей и повторно направляется внутрь мельницы для доизмельчения.
Комбинированный питатель (рис. 8.1.5, б) представляет собой комбинацию барабанного и улиткового питателей. К цилиндрическому барабану 1 прикреплен черпак 2, на конце которого монтируется сменный козырек 3. Питатель крепится болтами к загрузочной цапфе мельницы. Исходный материал загружается через отверстие крышки 4, а пески захватываются черпаками из загрузочной коробки, расположенной ниже уровня оси мельницы, и попадают внутрь барабана 1 питателя [3].
Питатели стержневых мельниц сухого помола представляют собой наклонный желоб, нижний конец которого вводится в цапфу загрузочной части, а верхний расширенный конец имеет горизонтально расположенный фланец, с помощью которого соединяется с питающим конвейером. В нижней части желоба предусмотрено уплотнение, предотвращающее просыпание мелочи и пыли из загрузочной части наружу. Желоб устанавливается перед мельницей на фундаментную плиту переднего подшипника (рис. 8.1.6).
Барабан. Барабан шаровых мельниц состоит из корпуса 1, двух ремонтных люков с крышками 2, резиновых прокладок 3 и футеровок 4 с крепежными деталями 5 (рис. 8.1.7). Корпус барабана представляет собой обечайку, сваренную из стального листа. К ее концам приварены кованые фланцы, которые служат для соединения барабана с загрузочной и разгрузочной частями мельницы.
Для шаровых мельниц обечайку выпол-няеют из листов одинаковой толщины по всей длине обечайки. У стержневых мельниц крайние листы обечайки для уменьшения напряжений от рабочих нагрузок утолщены. Для обеспечения плотного прилегания литых футеровок, снижения шума и устранения гидроабразивного износа между корпусом барабана и футеровками укладывают прокладки из резины.
Основные требования к корпусу барабана — отсутствие овальности в сечениях, прямолинейность образующей барабана, перпендикулярность к продольной оси торцовых фланцев, прочность всех швов. Корпуса барабанов обычно отжигают для снятия внутренних напряжений. Сопряжение торцовой крышки с корпусом барабана является одним из самых ответственных узлов мельницы. При неправильной сборке этих узлов соединительные болты ослабевают и обрываются. Надежного соединения крышки с корпусом достигают путем чистой обработки сопрягаемых поверхностей соединяемых деталей и полного совпадения болтовых отверстий.
Почти 20…25 % болтов должны быть призонными (поставлены с натягом без зазора), остальные следует устанавливать с зазорами < 0,5… 1 мм. Соединительные болты необходимо затягивать равномерно, чего практически достичь невозможно, поэтому часть болтов работает с напряжением, а часть — недогружены. При расчете учитывают только 50 % установленных болтов, которые размещаются с минимальным шагом. Люковые отверстия располагают диаметрально противоположно для равновесия. Крышки люка открываются отжимными винтами.
Футеровки крепятся к корпусу барабана болтами с головками овальной формы. Узлы крепления футеровок барабана уплотняют с помощью резиновых уплотнительных колец и шайб. На стержневых мельницах, работающих в тяжелых режимах эксплуатации, отверстия под футеровочные болты усилены приварными бонками и уплотнение болтового крепления их осуществляют с помощью резинового кольца и грундбуксы.
Разгрузочная часть. Разгрузочная часть стержневых мельниц состоит из торцовой крышки 1, торцовых футеровок 2, разгрузочной воронки 3, горловины воронки 4, бутары 5 и крепежных деталей для крепления зубчатого венца, футеровок, корпуса барабана, горловины воронки и бутары (рис. 8.1.8). Торцовая крышка и разгрузочная воронка сварные, на внутреннюю цилиндрическую поверхность воронки наплавлен износостойкий материал.
Торцовые футеровки загрузочной и разгрузочной частей унифицированы. Горловина воронки чугунная.
Бутара предназначена для вывода из технологического процесса случайно попавших в мельницу недробимых предметов, а также обломков стержней и расколовшихся шаров. Бутара устанавливается на разгрузочной части стержневых и шаровых мельниц с центральной разгрузкой. Она представляет собой перфорированный цилиндр из стального листа или из резиновых элементов. Пульпа через отверстия бутары сливается в приемный желоб, а недробимые предметы с помощью винтовых ребер внутри бутары выводятся из потока.
Стержневые мельницы с низким уровнем слива имеют на внутреннем конце разгрузочной воронки диафрагму в виде кольца, отлитого на ребрах по внутреннему диаметру. Разгрузочная воронка выполняется литой из чугуна, внутренняя поверхность ее конусная, расширяющаяся в сторону разгрузки материала. На входе воронки предусмотрены винтовые ребра, которые предназначены для отбрасывания внутрь мельницы шаров или кусков неизмельченной породы.
В шаровых мельницах с разгрузкой через решетку рабочая полость барабана отделена от разгрузочной камеры системой сменных решеток 1 и крепежных клиньев 2 из высокомарганцовистой стали (рис. 8.1.9). Внутренняя поверхность разгрузочной крышки 3 разделена радиальными ребрами 4 на восемь секторов.
В каждом секторе установлены коробчатые чугунные футеровки (элеваторы) 5 и 6, защищающие ребра крышки и стенку корпуса от износа и служащие черпаками для выливания пульпы из зарешеченного пространства в разгрузочную воронку.
Разгрузочная воронка 7 со стороны решеток имеет восемь внутренних секторов, которые при сборке сопрягаются с секторами крышки. Пульпа из элеваторов при повороте барабана попадает в сектор воронки и далее сливается на внутреннюю поверхность воронки, которая выполнена с расширенным концом по ходу разгрузки. Затем пульпа поступает в разгрузочную горловину 8 и выливается наружу.
Зазоры между элеваторами и ребрами крышки заполнены заливкой из быстротвер-деющего глиноземистого цемента. Решетки, клинья, элеваторы и другие элементы разгрузочной части крепятся к разгрузочной крышке с помощью болтов и гаек. Узлы крепления имеют резиновые уплотнения. На мельницах с диаметром барабана 3600 мм разгрузка материала выполняется с помощью литых элеваторов, установленных на торцовую конусную поверхность крышки. Со стороны барабана стоят решетки, которые помещены на открытую сторону элеваторов и закреплены болтами на торцовой крышке.
В центральной части каналы лифтеров сопрягаются с открытым концом разгрузочной воронки. Для снижения уровня шума на горловину разгрузочной части мельницы устанавливают специальные шумопоглощающие экраны, представляющие собой сварные кожухи, изнутри облицованные резиновой обкладкой. В стержневых мельницах сухого помола с периферической разгрузкой готовый продукт удаляется через отверстия, выполненные на цилиндрической части разгрузочной крышки (рис. 8.1.10).
Главные подшипники. Сила тяжести вращающейся части мельницы вместе с мелющими телами и размалываемым материалом, центробежная сила мелющих тел и материала, ударная нагрузка от падающих мелющих тел воспринимаются двумя главными подшипниковыми опорами скольжения. Подшипниковые опоры всех мельниц аналогичны по конструкции и отличаются только размерами (рис. 8.1.11).
Каждый подшипник состоит из фундаментной плиты 1, корпуса подшипника 2, вкладыша с баббитовой заливкой 3, крышки подшипника 4, смотрового фонаря 5, смотрового люка 6, уплотнений 7. Фундаментную плиту после выверки и регулировки закрепляют на фундаменте с помощью анкерных болтов. Корпус подшипника монтируют на фундаментной плите. Для перемещения и фиксирования корпуса на фундаментной плите при установке мельницы и регулировке зубчатого зацепления привода используют четыре регулировочных винта. Вращающаяся часть мельницы цапфами торцовых крышек опирается на баббитовую цилиндрическую поверхность вкладыша, который своей выпуклой сферической поверхностью лежит на вогнутой сферической поверхности корпуса подшипника, что обеспечивает его самоустановку по шейке цапфы и крышки.
Поскольку равнодействующая всех сил, действующих на корпус барабана, направлена постоянно вниз и мало отклоняется от вертикали, угол обхвата баббитовой заливки подшипников всех мельниц принят равным 120… 130°. Для компенсации температурных изменений длины мельницы и возможных отклонений от номинальных размеров при изготовлении ее составных частей один из подшипников является фиксированным, а другой плавающим. При этом ширина вкладышей обоих подшипников одинакова, а компенсирующим элементом служит одна из шеек цапф торцовых крышек, длина которой больше ширины вкладыша.
Шаровая мельница с центральной разгрузкой (рис. 8.1.12) конструктивно идентична мельнице МШР. Она состоит из цилиндрического барабана 1 с торцовыми крышками 2 и 14, имеющими пустотелые цапфы 3 и 13, посредством которых барабан опирается на подшипники 6 и 11. Внутренняя поверхность барабана и крышек покрыта футеровочными плитами 8 и 10. Вращение барабана проводится от электродвигателя посредством ведущей шестерни 16, насаженной на вал 17, и венцовой шестерни 9, закрепленной на барабане. На загрузочной пустотелой цапфе смонтирован комбинированный питатель 5. Полые цапфы снабжены сменными загрузочной 4 и разгрузочной 12 воронками; 7 и 15 — технологические отверстия.
Мельницы с центральной разгрузкой обозначают МШЦ. Мельница МШЦ характеризуется высоким уровнем пульпы в барабане, что предопределяет меньшую скорость движения в продольном направлении и более тонкое измельчение материала. Шаровые мельницы с разгрузкой через решетку более производительны (на 10…15%) и выдают измельченный продукт с меньшим содержанием шламов, чем мельницы с центральной разгрузкой, но более сложны по конструкции.
Мельницы МШР обычно устанавливают в первой стадии измельчения, а МШЦ, обеспечивающие более тонкое измельчение, — во второй и третьей стадиях. Технические характеристики мельниц МШР приведены в табл. 8.1.1, а мельниц МШЦ в табл. 8.1.2.
Стержневая мельница по конструкции аналогична шаровой мельнице с центральной разгрузкой (рис. 8.1.13). Она состоит из горизонтального цилиндрического барабана 1, загрузочного устройства в виде комбинированного питателя 2 и приводного механизма 5. С целью увеличения скорости прохождения материала через стержневую мельницу загрузочную 3 и разгрузочную 6 цапфы делают увеличенных диаметров по сравнению с цапфами шаровой мельницы такого же диаметра. В стержневых мельницах устанавливают футеровки 4 волнистого или ступенчатого профиля.
Стержневые мельницы обозначают МСЦ [4-7]. Их используют как аппараты для мелкого дробления перед шаровыми мельницами, а также для подготовки мелковкрапленных руд перед гравитационными и магнитными способами обогащения (для измельчения до 0,5…3 мм). Технические характеристики стержневых мельниц приведены в табл. 8.1.3.
enciklopediya-tehniki.ru
Техническая характеристика шаровых мельниц[1]
Таблица №2[1]
Показатель | Диаметр * длину барабана, м | ||
0,9*1,8 | 1,5*1,76 | 1,5*3,0 | |
Производительность, т/ч | 5,4* | 6* | 18* |
Частота вращения барабана, об/мин | 39 | 28 | 25 |
Мощность главного двигателя, кВт | 22 | 55 | 100 |
Масса (без электродвигателя и мелющих тел), т | 5 | 13 | 21 |
Масса мелющих тел | 2,3 | 4,8 | 10,5 |
* — при тонкости помола, соответствующей 10% остатка на сите № 0,08
1.3.Конструкция мельниц.[1,2]
Рассмотрим конструкцию шаровой мельницы на примере однокамерной мельницы с разгрузочной диафрагмой (рис. 4).
Однокамерная мельница с диафрагмой представляет собой цилиндрический барабан 6, к которому прикреплены торцовые днища 4. Днища отливают совместно с полыми цапфами, которыми барабан опирается на подшипники, имеющие самоустанавливающиеся вкладыши 2. Барабан и днища со стороны загрузки футерованы стальными бронеплитами, которые к днищу крепятся болтами, а в барабане располагаются параллельными, примыкающими друг к другу кольцами. В каждом кольце рядовые бронеплиты 13 замыкаются клиновой плитой 14, прикрепляемой к барабану двумя болтами. Шары общей массой 3000 кг загружают через люк, который закрывают крышкой 5.
Для облегчения загрузки и разгрузки материала полые цапфы снабжены конусными втулками 3 и 11, расширяющимися в направлении движения материала. При мокром помоле материал в барабан подают улитковым питателем 1, который при каждом обороте барабана зачерпывает порцию материала из бассейна и направляет ее в конусную втулку 3. Производительность мельницы регулируют изменением уровня материала в питающем бассейне. По мере продвижения вдоль барабана материал измельчается и выходит через втулку 11 разгрузочной цапфы.
Рис. 4. Однокамерная мельница[2]
Для ускорения разгрузки мельница снабжена диафрагмой 8, которая имеет радиальные перегородки (лифтеры) 9 и конические 1 отверстия, а для предохранения от повреждения шарами прикрыта колосниковыми плитами 12 и сплошными бронеплитами. Забивая отверстия диафрагмы деревянными пробками, можно регулировать уровень пульпы в мельнице. Для удаления излишка пульпы при случайной перегрузке мельницы служит труба 10. При грубом помоле диафрагма увеличивает производительность мельницы на 15… 30°/о, при тонком поломе ее эффективность снижается. В этом случае обычно применяют мельницы со свободной разгрузкой через полую цапфу. Барабан мельницы вращается от электродвигателя через клиноременную передачу и зубчатую пару с венцовой шестерней 7. Частота вращения барабана в минуту 28. Мощность электродвигателя 55 кВт. Производительность при мокром помоле и измельчении материала от 60 до 0,85 мм равна 6 т/ч, до 0,21 мм —3 т/ч, до 0,07 мм — 1,5 т/ч.
При помоле мягких материалов применяют короткие цилиндрические мельницы с разгрузкой через полую цапфу, у которых вместо шаров мелющими телами являются стальные цилиндрические стержни, примерно равные длине барабана мельницы. Эффективность измельчения мягких материалов в стержневых мельницах объясняется интенсивным истирающим действием стержней при их перекатывании и вращении[1].
Особенности устройства основных деталей шаровых мельниц[2]
Барабаны шаровых мельниц сваривают из стальных листов толщиной от 10 до 60 мм. Толщину листа принимают обычно 0,01 от диаметра барабана для коротких мельниц и 0,02 для трубных. Днища крепят болтами к кольцам (фланцам), приваренным к барабану. Для загрузки мелющих тел, смены футеровки, установки перегородок каждая камера снабжается люком, который перекрывается крышкой, имеющей защитную 6ронеплиту. Барабан мельницы футеруют чугунными или стальными бронеплитами, которые бывают плоскими, ступенчатыми, волнистыми и с выступами (каблуками), облегчающими подъем крупных шаров. Наи6олее стойкими на истирание являются плиты из марганцовистой стали с содержанием марганца 12…14%. На скорость износа плит влияет и их форма. Некоторые из бронеплит и способы их крепления представлены на рис. 5.
Рисунок 5. Виды бронеплит и виды их крепления[2].
Материал измельчают мелющими телами — шарами и короткими цилиндриками (цильпебсом). Шары штампуют, куют или отливают из углеродистой, марганцовистой или хромистой стали. Диаметр шаров 30…100 мм, цилиндриков — 16…25 мм, длина цилиндриков соответствует 1,5 диаметра. Применяют также барабанные мельницы без мелющих тел, в которых происходит самодробление. Особенностью таких мельниц является большой диаметр барабана (5200 мм) при сравнительно малой его длине (1560 мм), футеровка днищ в виде треугольных в сечении концентрических колец, обеспечивающих при вращении барабана отбрасывание кусков в среднюю его часть для лучшего дробления кусков материала размером 12…15 мм и таких мельницах добавляют небольшое количество стальных шаров.
Разгрузку измельченного материала производят воздушным потоком.
Частота вращения барабана. При вращении барабана шаровой мельницы загруженные в него мелющие тела и материал под действием центробежных сил инерции прижимаются к футеровке, поднимаются на некоторую высоту и при падении приобретают кинетическую энергию, используемую для измельчения. В зависимости от угловой скорости или частоты вращения барабана возникает три случая движения шаров:
1. При сравнительно малой угловой скорости вращения 6арабана, на (рис. 6, а) вся масса шаров вместе с измельчаемым материалом смещается в сторону вращения барабана и, когда свободная поверхность загрузки получит наклон, превышающий угол естественного откоса шаров, они скатываются, измельчая материал легкими ударами и истиранием. Такое движение мелющих тел не обеспечивает интенсивного измельчения.
2. При увеличении угловой скорости барабана возрастает действие центробежных сил инерции, шары поднимаются выше горизонтальной плоскости, проходящей через геометрическую ось барабана и, отрываясь от его внутренней поверхности, продолжают двигаться как тело, брошенное под углом к горизонту, Т. е. по параболе (рис. 6, б). Такое движение обеспечивает наиболее интенсивное измельчение материала в основном ударом падающих шаров.
Рисунок 6. Движение шаров в барабане.[2]
3. При дальнейшем увеличении угловой скорости барабана наступает момент, когда центробежные силы инерции, действующие на шары, превзойдут силу тяжести сначала в наиболее удаленном от оси вращения слое, а затем и во внутренних слоях, и шары, прижатые к внутренней поверхности барабана, будут вращаться вместе с ним, не производя никакой работы (рис. 6 в).
studfiles.net
Шаровые мельницы открытого цикла помола — Глава 4
4.1. Достоинства и недостатки шаровых мельниц
Шаровая мельница является традиционным, на протяжении уже более ста лет, оборудованием для достижения требуемой тонкости помола при многотоннажном производстве. В эксплуатации в России на отдельных заводах ещё находятся мельницы производительностью 25 т/час при максимально достигнутой в мире производительности 320 т/час.
На рисунке 4.1. представлены две компоновки современных шаровых мельниц. Они обе имеют опоры на башмаки подшипников скольжения гидродинамического типа. Одна из них имеет боковой редукторный привод, а вторая центральный.
Рисунок 4.1. – Компоновка современных шаровых мельниц, где:
1 – загрузка мельницы, 2 – разгрузка мельницы, 3 – опоры башмаков подшипников скольжения, 4 – главный редуктор, 5 – двигатель мельницы, 6 – вспомогательный привод
Достоинствами шаровых мельниц кроме большой единичной мощности, достижения тонкости помола, соответствующей удельной поверхности 5000 см2/г, простоты конструкции, высокой надежности, является также хорошо разработанное научное обоснование, в которое внесла вклад и советская цементная наука. При этом был рассмотрен механизм измельчения с образованием первой и последующих трещин в измельчаемом материале с использованием аппарата дислокаций, а также обнаружено наличие на новой поверхности ненасыщенных валентных связей при разрыве сплошных кристаллов [57, 58]. Исследовалась кинетика измельчения клинкера [59, 60], представляющего собой сложную ионно–ковалентную, смешанную со стеклообразной фазой, частично пористую структуру. Разрабатывались математические модели структуры потока материала в мельницах [61, 62, 63], вопросы интенсификации их работы [64] и управления зерновым составом цемента [65]. Изучался также и зарубежный опыт [66].
К недостаткам шаровых мельниц относится их значительные металлоемкость и износ мелющих тел, а также сильный шум. Большая часть энергии при работе шаровой мельницы теряется бесполезно, коэффициент полезного действия низок – по разным оценкам от 2 до 20% [6]. Но даже значительный удельный расход электроэнергии на помол цемента окупается полезным эффектом при использовании мельницы. Это не исключает поиска решений по экономии электроэнергии при помоле, чем и занимаются цементники всего мира.
Ещё одним недостатком шаровых мельниц открытого цикла является переизмельчение порошка. Оно связано с необходимостью совместного разрушения отличающихся по размалываемости компонентов [67], таких как клинкер, гипс, гранулированный шлак и других добавок. Невозможна ситуация, при которой частица, достигшая требуемого размера, была бы выведена из мельницы, а размалывающие силы использовались бы только для частиц завышенного размера. Наоборот эта частица должна ждать, когда трудно размалываемая достигнет требуемого размера, а сама к этому времени переизмельчается. То есть ради необходимого по тонине измельчения трудно размалываемых составляющих цемента производится переизмельчение его легче размалываемых частей. Для открытых циклов помола всё, что выходит из мельницы, должно уже быть цементом. При переизмельчении частицы, задержавшиеся в мельнице, получают окатанную форму, и гидравлическая активность их снижается. Так для одинаковой прочности при компенсации этого недостатка, удельная поверхность цемента, произведенного в мельнице открытого цикла, должна быть на 300 см2/г больше чем для замкнутого.
4.2. Усовершенствование помола в шаровых мельницах
Тенденции развития технологии помола в шаровых мельницах просматриваются в сравнении нового и старого оборудования, длительно находящегося в эксплуатации.
При строительстве новых цементных заводов наращивалась единичная производительность шаровых мельниц. Крупные системы вводились в Юго–Восточной Азии. Развитие коснулось отказа от открытого цикла помола. Мельницы были оснащены сепараторами, которые в своем развитии прошли несколько поколений.
За длительное время жизни шаровой мельницы из-за износа не один раз сменяются комплекты мелющих тел. Остается неизменным вращающийся барабан, который служит базой для последующих модернизаций. Старые мельницы переоснащались, а новые оснащались современными бронеплитами с оптимизированной геометрией, износостойкими мелющими шарами смешанного ассортимента, заменившими цильпебс [68], и регулируемыми диафрагмами. Цапфовые опоры уже более двадцати лет не используются, в новых мельницах они заменены опорами на башмаки подшипников скольжения гидродинамического типа. Используются также боковые редукторные приводы.
В середине прошлого века с началом использования интенсификаторов помола был совершен рывок в повышении производительности шаровых мельниц. Внедрением впрыска воды в зону мелкого измельчения мельницы был решен вопрос со стабилизацией температуры цемента, не достигающей температуры его ложного схватывания, и дополнительно повышена производительность.
Мельницы оснащались компьтерными системами управления, лазерными гранулометрами, работающими в потоке цемента. Быстродействие этих систем позволило разработать и внедрить экспертные системы управления мельницами, исключившими участие в этом оператора.
Использование устройств ЭКОФОР [69, 70, 71, 72] для дополнительного повышения производительности работающих мельниц с одновременным снижением удельного расхода электроэнергии позволяет надеяться на очередной шаг в усовершенствовании помола.
Технология помола цемента в России отстала от зарубежной, высокие результаты достигались за счет квалификации цементников. В связи с дешевизной электроэнергии в СССР было принято ошибочное решение о повсеместном использовании открытого цикла помола цемента и только в 80-х годах были построены несколько заводов сухого способа производства, где использовались замкнутые системы помола на базе отечественного оборудования. Рост единичной производительности мельниц, выпускаемых заводом «Волгоцеммаш» и достигший 100 т/час, был остановлен переориентацией на иностранных производителей.
В настоящее время заканчивается переоснащение мельниц весовыми дозаторами вместо объемных. Многие заводы произвели модернизацию отдельных мельниц с установкой сепараторов. Новые заводы строятся с участием зарубежных фирм с использованием современных замкнутых систем помола и автоматизации [73]. Но большинство цементных мельниц в России продолжают использоваться в открытом цикле помола и поэтому необходимо улучшать показатели их работы. Остается ориентация на использование во второй камере старых мельниц цильпебса и пневмокамерных насосов в системе их разгрузки. На многих заводах имеются трудности со сжатым воздухом, и это ограничивает возможности по повышению производительности мельниц.
На ОАО «Осколцемент» была предпринята попытка внедрения на базе шаровой мельницы открытого цикла оригинальной непрерывно–дискретной системы помола [74] с внутренним рециклом и устройством регулирования выгрузки материала на выходе мельницы. Эта новация расширяла возможности открытых систем помола. Был получен обнадеживающий научный результат, но из–за низкой надежности дискретной системы выгрузки внедрение было остановлено.
4.3. Электризация в шаровой мельнице
Измельчение по ходу шаровой мельницы идет с нарастающим сопротивлением материала. Сначала трещины проходят через крупные поры, поскольку пористость клинкера составляет 17–26%. Потом количество пор уменьшается, и молоть становится тяжелее. Далее до удельной поверхности 1500 – 1700 см2/г измельчение идет по границам раздела фаз, а после 2500 см2/г сопротивление помолу начинает резко расти, происходит разрушение уже отдельных кристаллов [59].
Этот процесс был рассмотрен с позиций физики диэлектриков [75], поскольку клинкер, гипс, шлак и другие добавки являются диэлектриками. В общем сопротивлении измельчению была выделена электростатическая составляющая, поскольку клинкер относится к кристаллическим классам, которые электризуются – приобретают электрический заряд под действием механических сил.
Появление свободных электрических зарядов в материале при этом соответствует принципу термодинамического подвижного равновесия Ле Шателье. Этот принцип предусматривает возникновение в системе, находившейся в состоянии равновесия и оказавшейся под каким-либо воздействием, процессов, ослабляющих это воздействие. Так, при измельчении имеет место процесс электризации материала, который ослабляет силовое механическое воздействие.
То есть вследствие механических воздействий, таких как удар, сдавливание и истирание измельчаемого материала, в нем появляется свободные электрические носители. Действие этих носителей электрического заряда следует рассматривать как реакцию материала на энергетическое, в данном случае механическое, воздействие. Поступающие на измельчение материалы стремятся сохранить состояние термодинамического равновесия. Они сопротивляются измельчению, но с помощью механического воздействия это сопротивление подавляется. Применением активной электронейтрализации удалось ослабить действие свободных электрических носителей при помоле. Электростатическая реакция измельчаемого материала, его противодействие, были снижены и в результате этого получены необходимые технологические преимущества.
Рисунок 4.2. – Последствие удара по материалу
Несмотря на то, что мельница заземлена, часть освобожденных электрических носителей остается на материале, поскольку заземление может принять и релаксировать только ограниченное количество электричества. Удары производят трещины в измельчаемом материале, на стенках этих трещин появляется электрический заряд [76]. Часть гранул материала, как это показано на рисунке 4.2., раскалывается по трещинам на более мелкие куски, а некоторые трещины смыкаются после удара под действием противоположных по знаку зарядов. При этом наиболее сложная ситуация создается в последней камере мельницы, где помол происходит на уровне кристаллов. Перед выходом материала из мельницы в результате электростатического взаимодействия размолотых сверхтонких частиц происходит их агрегация. Такие дисперсные системы частично утрачивают текучесть. Недостаточная текучесть цемента снижает производительность пневмокамерных насосов и тем самым ограничивает потенциальные возможности мельниц, а также увеличивает время выгрузки цемента. Агрегация, возникающая при помоле, является обратимой, способной при определенных условиях к разобщению частиц. Если не используются интенсификаторы помола или производится цемент без добавки шлака, то на мелющих рабочих поверхностях и перегородках вследствие адгезии, сила которой имеет электростатическую составляющую, образуется твердая, демпфирующая удары, не способствующая помолу оболочка. Налипание усиливается при выпуске цементов высоких марок, а также при повышенной температуре клинкера.
Таким образом свободные электрические носители, возникающие в процессе помола, снижают его эффективность, а их возникновение является проявлением электростатической составляющей сопротивления обрабатываемого материала механическому воздействию [77].
4.4. Активная электронейтрализация в шаровой мельнице
Устройство ЭКОФОР нейтрализует свободные электрические носители в ходе помола. Оно действует в мельнице совместно с естественно происходящей нейтрализацией заряда в результате коронного разряда и действия заземления. Таким образом оно дополнительно снижает электростатические проявления в ходе помола и устраняет их негативные последствия. При этом активно используется металлическая поверхность мелющих тел. Устройство преобразует процессы, протекающие на границе измельчаемого материала и приповерхностного слоя мелющих тел, обеспечивая воздействие на обе взаимодействующие фазы.
Подключение устройств к цапфе выходного подшипника мельницы показано на рисунке 4.3. При подключении место контакта для обеспечения его надежности должно быть очищено от масла и цементной пыли. Подключение должно быть выполнено медным проводом сечением не менее, чем 1,5 мм², защищенным от механических воздействий. Прокладка провода должна исключать воздействие на него силовых и высокочастотных электрических полей.
Рисунок 4.3. – Место подключение устройства ЭКОФОР к шаровой мельнице
Измельчаемый материал связан с устройством по распределенной электрической цепи через мелющие тела, броневые плиты, корпус и вал мельницы, корпус подшипника и вход устройства.
Динамика улучшения зависит от наличия оболочки на поверхности мелющих тел до подключения устройства. Если она имеется, то после подключения устройства мельница должна поработать с устройством 8…12 часов без изменения подачи. Это дает возможность разрядить «дебри–слой» дислокаций на поверхности мелющих тел. С нормализацией структуры их приповерхностных слоев они начнут очищаться от налипшей оболочки и образовывать вероятностную металлическую токопроводящую связь между измельчаемым материалом и входом устройства ЭКОФОР. При этом остаток на контрольном сите в первые часы может увеличиться, что связано с очисткой от твердой оболочки выходной диафрагмы и части мелющих тел, находящихся рядом с ней. Через несколько часов рост остатка на контрольном сите прекращается. Полная очистка мелющих тел происходит не ранее трех – пяти дней работы, а иногда в связи с крайне тяжелыми условиями помола достижимой является лишь “рябая” их поверхность, однако, достаточная для отвода заряда.
При использовании интенсификаторов помола или выпуске цемента с добавкой шлака мелющие тела, как правило, не имеют оболочки даже у разгрузочной части. В этом случае уже в течение первого часа после включения устройства происходит разрушение агрегатов и залповый вынос составляющих их мелких частиц из мельницы. Это можно заметить по импульсному в течение нескольких минут увеличению нагрузки электродвигателя элеватора или временному уменьшению времени заполнения емкостей пневмокамерных насосов.
Размалываемость материала постепенно улучшается, поскольку большее количество трещин с нейтрализованной поверхностью открывается после ударов. Пропускная способность мельницы увеличивается, она продолжает освобождаться от материала. Наблюдается временное, пока мельница очень сильно не опустела, улучшение качества помола, которым необходимо воспользоваться для повышения производительности мельницы.
Скорость прохождения материала через мельницу, текучесть цемента и шум мельницы постепено увеличиваются. Если своевременно не отреагировать на улучшение качества помола, то значительная часть материала может покинуть мельницу, а качество помола ухудшится.
Рисунок 4.4. – Пример зависимости качества помола от заполнения пространства между мелющими телами
Для мельницы характерна оптимальная зависимость качества помола, например, удельной поверхности от содержания в ней материала, представленная на рисунке 4.4. Жирно выделена та часть этой характеристики, в пределах которой обычно работает оператор. За 100% принимается степень заполнения, при которой материал при остановке мельницы находится на уровне мелющих тел. Скорость измельчения материала в соответствии с уравнением кинетики измельчения [60] прямо пропорциональна количеству материала, находящегося в мельнице. То есть чем его меньше, тем меньше и вероятность попадания частиц под удар при прохождении через мельницу. Этим определяется левая падающая ветвь зависимости, представленной на рисунке 4.4. Наличие же правой её падающей части обусловлено тем, что увеличение содержания материала в мельнице приводит к смягчению ударов мелющих тел, нарушению их траектории, а, следовательно, к снижению качества помола.
Оптимальный по качеству помола уровень измельчаемого материала в мельнице при включении устройства постепенно сдвигается в сторону его увеличения. Устройство предоставляет возможность увеличить содержание материала внутри на 10 – 30 %, без всякой опасности переполнить («заработать») мельницу. Это нужно также для лучшего истирания материала в последней камере мельницы. Необходимо за счет увеличенного питания перевести работу мельницы из точки «а» в точку «b». Если этого не сделать, то мельница останется работать на левой, необычной для оператора ветви новой, переместившейся оптимальной зависимости. Например, если оператор, привыкший снижать питание при ухудшении качества помола, будет в новых условиях поступать аналогично, то он усугубит ситуацию. Работа мельницы на уровне прежней производительности будет сопровождаться большим шумом, а новые возможности по повышению питания не будут использованы. Производительность же необходимо ступенчато увеличить суммарно на 12 – 25 %, причем в большей степени при выпуске высоких марок цемента.
Питание мельницы после получения данных об улучшенном показателе качества помола следует увеличивать из расчета, что каждые 100 см2/г удельной поверхности, превышающие норматив, требуют 4% дополнительного питания. Таким образом, увеличенное питание будет гарантировать нахождение новой рабочей точки на правой ветви переместившейся оптимальной характеристики. В дальнейшем увеличение питания может идти по 1 – 2 т/час после получения очередного превышающего норматив показателя качества помола. Не следует перегружать мельницу, а если это случилось, то необходимо резко уменьшить подачу материала на 5 – 15 минут, так как по пропускной способности мельница нечувствительна для небольшого снижения питания после её переполнения.
Разрежение на выходе мельницы, если температура цемента это позволяет, должно быть снижено на 20 – 40% для удержания в ней ставшего более текучим материала. Это помогает и в том случае, если материал «убегает» из первой камеры во вторую, то есть для баланса загрузки камер. Звук первой камеры должен при этом стать глуше, чем раньше, а второй более четким и звонким.
Износ мелющих тел снижается под воздействием устройств ЭКОФОР в результате преобразования приповерхностной структуры мелющих тел. При этом количество дефектов этой поверхности уменьшается и происходит её упрочнение. По данным завода на Кипре Vassiliko Cement Works Ltd, использовавших пять устройств ЭКОФОР в течение двенадцати лет, износ мелющих тел марки Hardalloy бельгийской фирмы Magotteaux на трех помольных системах уменьшился в результате действия устройств ЭКОФОР с 25–40 г/т цемента до 9–13 г/т, то есть почти в три раза.
4.5. Особенности работы шаровой мельницы при электронейтрализации
Медленная, продолжительностью несколько часов, реакция мельницы на включение устройства связана с необходимостью постепенной аннигиляции дислокаций «дебри – слоя» поверхности мелющих тел. Их рабочая поверхность становится более гладкой, приобретает большую твердость. Не следует сравнивать эту реакцию с реакцией на подачу интенсификаторов помола, которые показывают первый результат уже через час. Интенсификаторы действуют в объёме измельчаемого материала, а электронейтрализация проводится по распределенной металлической цепи через поверхность мелющих тел, которая претерпевает значительные изменения с течением времени.
Действие интенсификаторов помола заканчивается также в основном через один час после прекращения их подачи. Устройство ЭКОФОР обладает длительным последействием – до трёх недель для систем помола открытого цикла.
После отключения устройства, например, при перестановке его для демонстрации на следующую систему помола, мельница продолжает длительное время работать с улучшенными, медленно возвращающимися к прежнему уровню показателями, пока не износится упрочненная, ставшая малодефектной, поверхность мелющих тел.
Мельница под воздействием устройства должна содержать внутри на 10–30% большее количество материала. Это достигается увеличением питания мельницы и, если это возможно по условиям охлаждения, снижением уровня аспирации – разрежения на её выходе. Мощность, потребляемая электродвигателем мельницы, при этом несколько уменьшается.
Обновляется оптимальная зависимость качества помола от степени заполнения мельницы материалом. Появляется ошибочная возможность работы с прежней производительностью в неоптимальном режиме. Повышается текучесть измельченного, нейтрализованного цемента.
Так, время разгрузки камер пневмокамерного насоса на китайском заводе «Дианнан», где в январе 1997 года проводилось испытание устройств ЭКОФОР и особое внимание уделялось текучести цемента, уменьшилось на 27%.
Возможности по повышению производительности мельниц открытого цикла и снижению удельного расхода электроэнергии на производство тонны цемента при использовании устройства представлены в таблице 4.1.
Таблица 4.1. – Эффективность устройства для шаровой мельницы
Тип цикла помола | Интенси-фикаторы помола | Питание мельницы, т/час | Увеличение питания, % | Снижение удельного расхода энергии, % | Количество устройств, шт. |
Открытый | Нет | 25 – 100 | 12 – 25 | 11 – 20 | 1 |
Открытый | Есть | 25 – 100 | 8 – 12 | 8 – 11 | 1 |
Увеличение выпуска продукции для мельниц производительностью менее 20 т/час иногда достигало 40 – 60%. Режим работы мельницы с устройством всегда носит более стабильный характер. Если не требуется увеличение объемов выпуска цемента, то появляется возможность сократить рабочее время мельницы, а, следовательно, и затраты электроэнергии.
4.6. Условия испытания мельницы, требующие согласования
Для того, чтобы получить достоверный результат и исключить технологические помехи и психологические сложности, следует перед испытанием согласовать условия его проведения.
– Испытания должны проводиться на помольной системе, если её вспомогательное оборудование имеет резерв повышения производительности. Например, если пневмокамерные насосы или элеватор работают на пределе своей производительности, то они не смогут принять от мельницы дополнительное количество материала;
– Для сравнимости результатов необходимо использовать клинкер с относительно стабильными характеристиками, такими же, как и до подключения устройства;
– Не допускается изменять калибровку весоизмерительных устройств в течение испытания для обеспечения сравнимости результатов;
– Перед подключением устройства необходимо усреднить и зафиксировать с ответственным за испытание заводским специалистом усредненные значения питания мельницы и качества помола за период 8 – 12 часов её стабильной работы;
– Измерение питания и качества помола нужно делать каждый час;
– Составляющие питания мельницы (клинкер, гипс, другие добавки) необходимо изменять в постоянной пропорции;
– Операторы всех рабочих смен должны быть осведомлены о проходящем испытании и должны быть ознакомлены с инструкцией по работе с устройством;
– После включения устройства требуется его адаптация к оборудованию в течение 2 – 12 часов;
– После улучшения качества помола и/или опустошения мельницы питание должно быть увеличено ступенчато. Для мельниц производительностью 45 – 60 т/час сначала на 3 т/час затем по 1 т/час. Для мельниц 100 т/час сначала на 7 т/час затем по 2 – 1 т/час;
– Решение об изменении питания принимается каждый час в зависимости от текущего значения качества помола. Процесс изменения питания может продолжаться в течение 12 – 24 часов работы;
– При разбалансировке работы камер мельницы или её повышенном шуме необходимо снизить разрежение на её выходе на 20 – 40%, но не допускать перегрев цемента;
– Необходимо достичь уровня питания, близкого к максимальному, при нормативном качестве помола и стабилизировать режим в течение не менее 8 – 12 часов;
– Определение прироста производительности мельницы производится по усредненным значениям питания стабильных режимов после и до включения устройства при выпуске одной и той же марки цемента;
– После выключения устройства мельница продолжает работать с повышенной производительностью в течение длительного времени пока не износится упрочненная под действием устройства поверхность мелющих тел.
4.7. Динамика интенсификации помола при включении устройства
Первое испытание устройства ЭКОФОР по помолу цемента было проведено в 1995 году на опытном заводе Гипроцемент на мельнице производительностью 10 т/час при производстве жаростойкого цемента. Устройство было подключено к редуктору бокового привода мельницы. Остаток на сите 80 мкм после включения устройства, как это показано на рисунке 4.5 уменьшился со временем с 11 до 7%. Такое повышение качества помола свидетельствовало о возможности увеличения производительности мельницы и о целесообразности проведения испытаний в заводских условиях.
Рисунок 4.5. – Результаты испытания устройства ЭКОФОР на опытной мельнице Гипроцемент
На рисунке 4.6. представлены результаты испытания устройства в цехе силикатного кирпича [78] АО «Стройматериалы», г. Белгород.
Рисунок 4.6. – Результаты испытания в АО «Стройматериалы»
Устройство подключалось к выходному подшипнику мельницы. Результаты оценивались по времени освобождения бункера извести и по качеству помола. Бункер извести без устройства освобождался за 130 минут, а с устройством за 105 минут. Повышение производительности мельницы составило 19,2%., а качество помола осталось в допуске.
В 1996 году началось внедрение устройств ЭКОФОР за рубежом [79, 80]. Сначала они были внедрены на четырех заводах Египта: Tourah Portland Cement, Helwan Portland Cement, Ameriyah Cement, Alexandria Portland Cement и на Кипре на Vassiliko Cemеnt Works. За прошедшие годы проведены испытания в 42 странах мира. Идет активное внедрение устройств на цементных заводах Турции [81], где министерство энергетики требует снизить электропотребление цементных заводов на 10%.
На Tourah Cement – рисунок 4.7. после включения устройства удельная поверхность цемента увеличилась на 300 см2/г, после чего питание мельницы было в два приема увеличено с 75 до 85 т/час, то есть на 13%.
Рисунок 4.7. – Результаты испытания в Tourah Cement Company, Египет
На Ameriyah Cement в Египте до и после испытания из мельницы вынимали мелющие шары, представленные на рисунке 4.8. Шары оказались полностью очищенными от имевшейся на них до испытания твердой оболочки. Питание мельницы было увеличено с 87.0 до 100.5 т/час, на 15%.
Рисунок 4.8. – Мелющие шары до и после ЭКОФОР
Рисунок 4.9. – Результаты испытания на заводе «Китай», КНР
На рисунке 4.9. представлены результаты испытания устройства в Китае на одноименном цементном заводе «Китай», на трехкамерной мельнице производительностью 18 т/час с наружным водяным охлаждением. Её питание регулировали изменением оборотов привода транспортера дозатора. После включения устройства мельница значительно, на 400 см2/г увеличила удельную поверхность. После этого её питание было в три приема увеличено на 26%. Получено снижение удельного расхода электроэнергии на 9,0 кВт час/т цемента.
В Казахстане на Бухтарминской цементной компании цемент ПЦ500 Д0 производился с использованием триэтаноламина. После включения устройства ЭКОФОР мельница опустошилась, удельная поверхность цемента выросла на 600 см2/г. Производительность была увеличена, как это показано на рисунке 4.10., с 18,9 до 22.9 т/час, то есть на 21%. Снижение удельного расхода электроэнергии составило 8 кВт час/т цемента.
Рисунок 4.10. – Результаты испытания на Бухтарминской цементной компании, Казахстан
На рисунке 4.11 представлена диаграмма роста производительности мельницы ОАО «Сухоложцемент» после включения устройства ЭКОФОР при производстве цемента ПЦТ I-50. Питание мельницы увеличено с 35,6 до 39 т/час, на 9,5%. Снижение удельного расхода энергии 5 кВт час/т цемента.
Рисунок 4.11. – Результаты испытания на ОАО «Сухоложцемент»
Рисунок 4.12. – Результаты испытания на ЗАО «Пикалевский цемент»
На рисунке 4.12 представлены результаты испытания устройства на мельнице ЗАО «Пикалевский цемент» при производстве цемента ПЦ400-Д20.
После включения устройства питание мельницы увеличено с 57 до 62 т/час, на 9,0%. Снижение удельного расхода энергии составило 3 кВт час/т.
На рисунке 4.13 представлены результаты испытания устройства на мельнице ОАО «Жигулевские стройматериалы» при производстве цемента ПЦ500-Д0. После включения устройства питание мельницы увеличено с 35 до 46 т/час, то есть на 31,0%. Снижение удельного расхода энергии составило 10 кВт час/т цемента.
Рисунок 4.13. – Результаты испытания на ОАО «Жигулевские стройматериалы»
4.8. Результаты испытаний шаровых мельниц открытого цикла
В приложении 1 приведены данные по испытаниям, проведенным на системах помола открытого цикла с применением устройства ЭКОФОР, с 1995 по 2010 год. Это 57 мельниц, из них 23 в России, 20 в странах СНГ и 14 в дальнем зарубежье. Они представляют третью часть всех проведенных испытаний, остальные прошли на мельницах замкнутого цикла помола.
Диапазон полученного повышения производительности мельниц составлял от 3 до 30%, также как это отмечается [5] для жидких интенсификаторов помола.
Снижение удельного расхода электроэнергии на помол тонны цемента находится при этом в диапазоне от 3 до 11 кВт час/ т, в среднем 7 кВт час/т. Если принять среднюю производительность цементной мельницы в России 45 т/час, то одно устройство ЭКОФОР на такой средне–статистической мельнице может сберечь 300 кВт час за каждый час её работы.
Отличия в эффективности устройств зависят от технического состояния оборудования и в основном от размалываемости клинкера. Она определяется его пористостью, химическим и минералогическим составом, микроструктурой клинкера и кристаллографией клинкерных материалов [82].
Не удалось повысить производительность мельницы на цемзаводе «Октябрь» ОАО «Новоросцемент». При производстве сульфатостойкого цемента ССПЦ400 Д20 с добавкой 10% опоки она работала на уровне 58 т/час, больше чем аналогичная мельница без использования опоки. Измерения цифровым мультиметром электрического потенциала опоки по отношению к земле показали, что эта добавка имеет отрицательный потенциал на уровне – 500 … 800 мВ. То есть она играет роль природного интенсификатора помола, за счет аниона кислотного остатка кремнезема нейтрализуя положительный заряд материала и повышая производительность мельницы. Такими свойствами обладает также пуццолан, и некоторые другие добавки. На фоне пуццолана и опоки ЭКОФОР и интенсификаторы помола не могут дать эффекта.
ecofor.com
Ударная шаровая мельница «ТРИБОКИНЕТИКА» или новая техника механического диспергирования
Эффективность — результативность процесса или операции,
по отношению результата к затратам,
обеспечившим его получение
1. Тонкий помол сегодня и завтра
В настоящее время существуют различные способы получения высокодисперсных порошков твердых тел. При этом механический способ является наиболее простым и широко распространенным. Для диспергирования минерального сырья находят применение машины, отличающиеся способом воздействия на материал. В одном случае это может быть раздавливание, в другом – удар, истирание или их комбинация [1].
Сегодня основными агрегатами тонкого помола являются шаровые и аналогичные им мельницы. Их рабочие элементы — это броневые плиты барабана и загруженные в него мелющие тела — шары, стержни, диски, а в мельницах самоизмельчения — крупные куски материала. Вращение барабана вызывает подъем мелющих тел, которые, достигнув определенной высоты, падают и скатываются вниз (Рис.1).
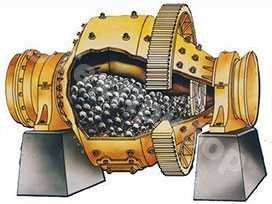
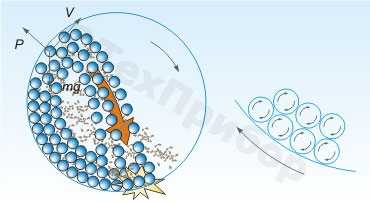
Разрушение материала в шаровых мельницах происходит как в результате медленного раздавливания — истирания при скатывании шаров, так и быстрого сжатия от ударов при их падении.
Несмотря на абсолютное лидерство среди агрегатов тонкого помола, используемых в многотоннажном производстве порошкообразных материалов, шаровым мельницам присущи и серьезные недостатки. Только от 2 до 20% всей потребляемой энергии расходуется непосредственно на измельчение [2], остальная ее часть идет на преодоление сил трения, образование тепла, звуковых колебаний, вибрации и т.д. В результате проведенных исследований было установлено, что только каждый тысячный удар шара производит работу непосредственно по измельчению [3]. И если грубый помол с получением частиц, размерами в сотые доли миллиметра, не вызывает серьезных затруднений, при более тонком помоле коэффициент полезного действия шаровой мельницы снижается настолько, что ее дальнейшее использование становится экономически не целесообразно. Ограниченность самого способа измельчения, как и реализующего его оборудования прекрасно отражают слова советского учёного, доктора технических наук Александра Васильевича Волженского: «…большое уменьшение затрат энергии могут дать лишь те способы, при которых материалы измельчались бы под влиянием прямых разрывающих воздействий на них, а не в результате первоначальных сжимающих сил» [4].
2. Удар и сжатие
Все твердые материалы характеризуются присущим им сопротивлением измельчению. Разрушение твердого тела происходит в том случае, если подведенной энергии достаточно для преодоления сил внутреннего сцепления. Обычно при механическом диспергировании обрабатываемый материал подвергается действию сжимающих сил с двух сторон (статическое раздавливание — истирание) или с одной стороны (свободный удар). Первый способ измельчения реализуется, например, в щековых, конусных и валковых дробилках, шаровых и вибрационных мельницах, второй способ характерен для дезинтеграторов, мельниц струйных и ударно-отражательных дробилок. Но в любом случае кинетической энергии действующих мелющих тел должно быть достаточно для создания таких напряжений, которые по достижению предельных значений приведут к разрыву целого куска с образованием более мелких фрагментов. При этом расход энергии, необходимой для создания критических напряжений, может существенно различаться, в зависимости как от физико-механических свойств самого измельчаемого материала, так и способа приложения разрушающих сил.
Минеральное сырье, обычно используемое в производстве порошков твердых тел, характеризуется прочностью на сжатие, в 6-12 раз превосходящей прочность на растяжение, поэтому для его диспергирования целесообразно использовать быстрый удар, а не медленное сжатие. Одни и те же результаты измельчения могут быть достигнуты с разными показателями экономичности процесса, и существующий опыт использования самого распространенного инструмента тонкого помола подтверждает такую возможность.
Хотя шаровые мельницы лишь условно можно назвать агрегатом ударного действия, теория и практика их применения позволяет установить четкую зависимость между преобладающим способом разрушения и эффективностью тонкого помола.
Как говорилось выше, способ разрушения материала в шаровых мельницах комбинированный, то есть присутствует и раздавливание — истирание от качения шаров и удары от их падения. От того, какой способ будет преобладающим, зависит количество энергии расходуемой на образование единицы новой поверхности. Несмотря на простоту устройства и принципа действия шаровой мельницы, результаты ее технико-экономического использования зависят от множества факторов. Ключевыми из них являются: крупность питания, размер и распределение мелющих тел, объем загрузки, скорость вращения барабана. Последний в большей степени и определяет эффективность работы мельницы, так как ударная составляющая помола — это, прежде всего, масса и скорость шаров.
Механизм «бросания» мелющих тел в шаровой мельнице достаточно хорошо изучен, и большинство вышеперечисленных факторов работают на интенсификацию именно ударного воздействия. Вращение корпуса мельницы увлекает шары, которые, поднявшись на некоторую высоту, отрываются от стенки и падают вниз. При этом шары падают не отвесно, а по параболе. После отрыва от стенки шар продолжает двигаться как тело, брошенное под углом к горизонту со скоростью равной скорости вращения барабана. Акт измельчения происходит в том случае, если кинетической энергии брошенного шара достаточно для преодоления внутренних связей в частицах материала. Чем больше энергия шара, тем выше и его размольная мощность.
Так как масса шара постоянная, увеличение его кинетической энергии возможно, только за счет повышения скорости вращения барабана. Однако, сам принцип работы шаровой мельницы исключает такую возможность, как только действующие центробежные силы начинают сильнее прижимать мелющие тела к стенкам барабана, падение шаров, а значит и помол, прекращаются. Поэтому главной задачей расчета параметров шаровой мельницы является определение критической скорости вращения барабана. Если она выбрана верно, достигается большая высота подъема и скорость «бросания» шаров, если нет — процесс измельчения резко замедляется, а энергорасход мельницы возрастает. Но центробежная составляющая ставит предел максимально допустимой скорости вращения барабана, а значит, эффективность тонкого помола с использованием шаровых мельниц не может быть существенно увеличена, что в свою очередь вызывает необходимость в изыскании таких способов диспергирования, где ударная составляющая была бы реализована в максимально полном объеме.
3. Разнообразие вариантов и отсутствие альтернативы
В настоящее время разработана большая номенклатура аппаратов измельчения свободным ударом. Однако в крупнотоннажном производстве нашли применение только ударно-отражательные дробилки, серьезно потеснив, а в некоторых областях и практически полностью заменив, «тихоходные» агрегаты дробления. Ударные мельницы же, несмотря на безупречность теоретических посылов для их создания, не могут похвастаться подобными успехами, сферой их применения является относительно грубый помол мягких материалов до размеров частиц в 100 мкм, с невысокой производительностью и относительно большими затратами энергии. Редкие исключения, когда рассматриваемые машины все же используются для помола мягких, малоабразивных материалов только лишний раз указывают на серьезные проблемы технической реализации принципов ударного диспергирования.
Даже спустя десятилетия научных исследований, экспериментов, масштабных испытаний, модернизаций и улучшений современные мельницы свободного удара, используемые в производстве высокодисперсных порошков (Sуд ? 3000 см2/г), не имеют существенных преимуществ перед шаровыми мельницами ни по одному из ключевых показателей. Напротив, попытки промышленного использования наиболее ярких представителей быстроходных машин ударного диспергирования: струйных и вихревых мельниц, дезинтеграторов и дисмембраторов выявили целый ряд их серьезнейших недостатков.
В частности, расход энергии центробежной мельницы при помоле цементного клинкера до удельной поверхности 2500 см2/г превышает 200 кВт на тонну, что почти в десять раз больше, чем затрачивают многокамерные шаровые мельницы, используемые в производстве цемента [5]. Не приходится удивляться и весьма низкой технической надежности вихревых, центробежных, а также подобных им быстроходных мельниц, учитывая высокую скорость движения помольных элементов, находящихся в постоянном контакте с материалами различной степени абразивности.
Струйные мельницы характеризуются также большим расходом энергии, который дополняется и относительно быстрым износом деталей, контактирующих с измельчаемым материалом, высокой сложностью самого агрегата, а также его периферии. Так как размольная мощность струйных мельниц не велика, получение высокодисперсных порошков возможно только в замкнутой схеме помола при интенсивной циркуляции материала. В некоторых случаях эта циркуляция в десятки раз превосходит производительность самой мельницы. Дополнительные сложности применения струйных мельниц создает необходимость очистки больших объемов отходящего воздуха и неизбежный унос наиболее высокодисперсной фракции материала с отработанным носителем.
Из перечисленных агрегатов дезинтегратор является примером, пожалуй, наиболее успешной реализации ударного измельчения твердых материалов. Существует обширный опыт промышленного использования дезинтеграторных мельниц-активаторов в производстве оригинального строительного материала – силикальцита, получаемого путем совместного помола извести и кварцевого песка [6]. Однако применение быстроходных дезинтеграторов ограничено относительно грубым помолом. Получение порошков с удельной поверхностью до 2000 см2/г включительно можно считать естественным пределом для данного вида оборудования. Предпринимаемые попытки увеличения размольной мощности дезинтеграторов за счет большей частоты вращения помольных органов вызывают ускоренный износ последних, уменьшая и без того небольшие сроки безремонтной эксплуатации (Рис.2).
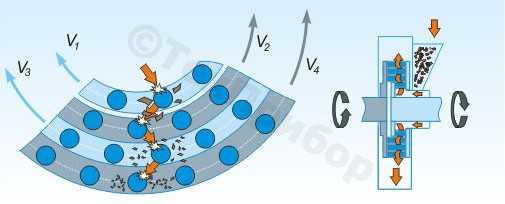
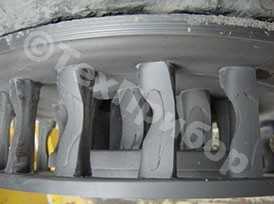
Для того, чтобы понять, почему применение измельчителей ударного действия сегодня ограничено только грубым помолом мягких материалов, необходимо пересмотреть способы реализации ударного разрушения твердого тела с позиции основных законов Ньютоновской механики: инерции, действия и противодействия. Именно здесь и скрывается ответ на вопрос: почему ударные дробилки успешно используются во всем мире, а мельницы свободного удара, так и не реализовав и малой части своих потенциальных возможностей, нашли очень ограниченное применение.
4. Скорость, масса, размер
В мельницах ударного действия разрушение частиц материала происходит вследствие ударных нагрузок. Эти нагрузки могут возникнуть в самых разнообразных условиях и обстоятельствах. Например, при падении мелющих тел, при столкновении летящей частицы с неподвижной преградой или, напротив, столкновения мелющих тел с неподвижной или движущейся частицей, так же возможны и взаимные соударения частиц в полете. Но в любом случае кусок материала или само мелющее тело должно обладать таким количеством кинетической энергии, которой хватило бы для преодоления внутренних связей между частицами.
При ударном измельчении разрушающий эффект зависит от массы тела и его скорости. Кинетическая энергия тела в момент удара определяется по известной формуле: E=mV2/2, где m — масса тела, а V — его скорость. Чем больше вес куска материала и выше его скорость, тем эффективней работа ударного диспергирования. Если уменьшить массу тела, для достижения тех же результатов измельчения нужно увеличить его скорость и наоборот, но в любом случае недостаток одного должен компенсироваться избытком другого — это основа способа измельчения ударом.
Несмотря на все разнообразие конструкций измельчительных машин ударного действия, механика разрушения твердого тела различается лишь некоторыми нюансами, что хорошо прослеживается на примере центробежной мельницы и ударно-отражательной дробилки. В последней материал, подлежащий измельчению, подается на быстро вращающийся ротор-ускоритель, частицы приобретают скорость, равную скорости ротора, и выбрасываются в пространство помольной камеры, их разрушение происходит при ударе об отражательные плиты и столкновении друг с другом в полете (Рис.3).
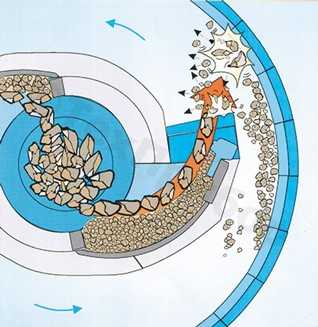
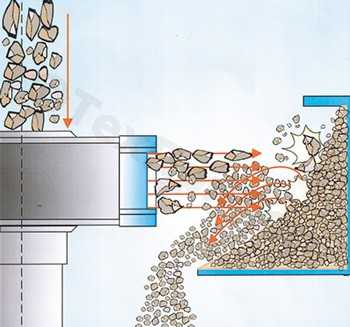
В ударно-отражательных дробилках материал после столкновения с преградой практически сразу выводится из агрегата, а в центробежных мельницах часть материала отправляется на дополнительное измельчение. Частицы, ударившись о препятствие, отскакивают от него, возвращаются к ротору-ускорителю, снова отбрасываются им. Таким образом, цикл может повторяться до тех пор, пока частицы не достигнут требуемых размеров и не будут выведены из мельницы.
Ударно-отражательные дробилки, выпуск которых налажен такими известными производителями измельчительного оборудования как: «BHS sonthofen», «Barmak Associates», «Sandvic», «Krupp», позволяют получать продукт высокого качества с меньшими затратами. Однако по мере изменения массы частиц, характер их взаимодействия с рабочими органами измельчительной машины кардинально меняется.
Одной из особенностей измельчения свободным ударом является тот факт, что разрушение материала происходит по наиболее слабым связям, дефектам структуры в местах соединения кристаллов, зерен, слоев и т.д. В производстве фракционированного щебня или искусственного песка это несомненное преимущество, так как продукт ударного дробления представлен зернами изометрической формы без внутренних дефектов с небольшим содержанием переизмельченного продукта. В тоже время для получения большей тонины помола, упрочнение частиц которое происходит вместе с уменьшением их размеров, создает дополнительные трудности.
В определенный момент, когда структурная прочность каждой отдельной частицы достигает своего максимума, а ее масса ничтожно мала, свободный удар практически полностью замещается истиранием. Ротор центробежной мельницы перестает выполнять функцию ускорителя и работает скорее как завихритель материаловоздушных потоков (Рис. 4). Увлекаемые к стенкам помольной камеры крупные частицы вытесняют более мелкие, которые, перемещаясь от периферии к центру, измельчаются исключительно за счет взаимного истирания в турбулентных потоках.
Если судить по расходу энергии на образование единицы новой поверхности твердых материалов — это один из самых неэффективных способов измельчения.
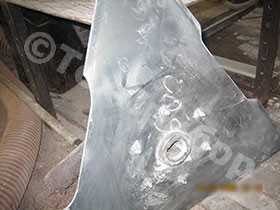
5. Рациональное ускорение, способ
Совершенно очевидно, что для поддержания высокого уровня эффективности ударного диспергирования кинетическая энергия мелющих тел, кусков, зерен, частиц и т.д. не должна уменьшаться. Данное условие ставит под сомнение саму возможность промышленного использования эффекта самоистирания твердых материалов (? 3 по шкале Мооса) в производстве высокодисперсных порошков (Sуд ?3000 см2/г), так как расход энергии в этом случае в десятки раз превышает общепринятые нормы. Естественно, это вовсе не означает, что ударное измельчение ограничено диспергированием только мягких, непрочных, малоабразивных веществ, напротив, приведенные факты только указывают на необходимость создания других типов мельниц, способных реализовать все преимущества разрушающего удара.
Интенсификация механического диспергирования возможна только за счет увеличения работы мелющих тел, масса которых серьезно не меняется в течение всего процесса. Данное условие отчасти реализуется в вибрационных, планетарных и центробежно-эллиптических шаровых мельницах, используемых в настоящее время для тонкого помола минерального сырья. Принцип действия этих машин основан на интенсивном побуждении мелющих тел, когда взамен сил гравитации, вызывающей падение шаров, используется инерция, центробежные силы и т.д.
Вращение вала вибратора, а за ним и самого корпуса мельницы заставляет мелющие тела совершать движения в соответствии с величиной эксцентриситета или радиуса водила. Передача энергии мелющей загрузки осуществляется через корпус мельницы. Под действием инерции, центробежных сил, знакопеременных нагрузок шары внутри корпуса движутся по сложной траектории, прижимаются к стенкам барабана, ударяются друг об друга, а также о частицы измельчаемого материала, разбивая, раздавливая и перетирая их (Рис.5).
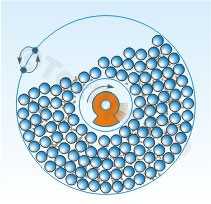
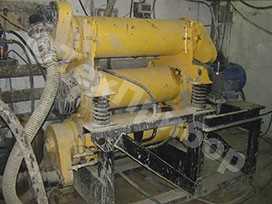
Минусом данного способа являются техническая сложность его реализации. Целый ряд конструктивных и технологических недостатков вибрационных и аналогичных им мельниц препятствует созданию машин, в которых высокая эффективность помола сочеталась бы с технической надежностью оборудования. Трудности уравновешивания массивных движущихся частей, разрушающее воздействие вибрации и большие ударные нагрузки, сложная кинематика привода барабана — все эти факторы самым негативным образом сказываются на надежности и безотказности агрегатов. В настоящее время вибрационные и подобные им мельницы в основном используются в качестве лабораторного и полупромышленного оборудования, позволяющего осуществлять тонкий и особо тонкий помол минерального сырья с производительностью до 500 кг/ч. В крупнотоннажном производстве данные мельницы широкого применения не нашли.
Однако в данном случае проблему масштабируемости процесса следует отнести не к реализуемому способу измельчения, а скорее к его аппаратному обеспечению. Уже тот факт, что более интенсивное побуждение шаров позволило выйти на новый уровень механического диспергирования указывает на перспективность данного направления. Основной вопрос заключается только в выборе наиболее рационального способа сообщить мелющим телам достаточно высокую скорость.
Но увеличить работу мелющей загрузки возможно и не приводя в движение весь корпус мельницы, а, например, разогнав только относительно легкий ротор-ускоритель, который и будет разбрасывать или «выстреливать» шары вместе с измельчаемым материалом. Ведь сообщить большую кинетическую энергию мелющим телам возможно как минимум двумя способами: или напрямую, разогнав в ускорителе шары вместе с измельчаемым материалом, или опосредовано, через корпус мельницы. При этом первый способ является более эффективным, так как энергия передается непосредственно действующему телу и объекту разрушения, исключая передаточные звенья, а значит и дополнительные затраты.
6. Kinetik?s — приводящий в движение
Если в центр ротора-ускорителя вместе с материалом подать также и мелющие тела, преобладающим способом измельчения будет не раздавливание-истирание, а именно удар (Рис.6). Такую мельницу можно назвать ударно-шаровой, так как именно шар является действующим мелющим телом. Данный способ успешно реализован в высокоэффективной мельнице «ТРИБОКИНЕТИКА», разработанной машиностроительным предприятием «ТЕХПРИБОР» г. Щекино. Новая мельница, как и реализуемый ею способ измельчения, открывает совершенно новые возможности диспергирования твердых тел, позволяя серьезно пересмотреть существующую практику получения порошкообразных материалов.
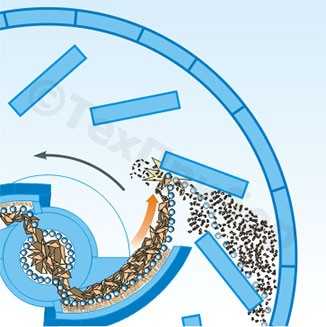
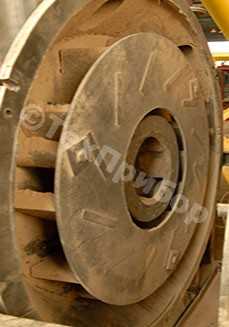
Удачно сочетая преимущества «классических» шаровых и быстроходных центробежных мельниц, «ТРИБОКИНЕТИКА» демонстрирует наибольшую в классе степень измельчения, техническую надежность, возможность проведения полного спектра механохимических реакций и превращений. Ее основным отличием от рассмотренного выше оборудования является высокая эффективность на всех стадиях измельчения, от мелкого дробления до сверхтонкого помола.
Большая размольная мощность ударно-шаровой мельницы обеспечивает и целый ряд дополнительных преимуществ в создании участков дробления-помола за счет сокращения единиц оборудования, задействованного в процессе. Если крупность питания вибрационных мельниц обычно не превышает 3-5 мм, «ТРИБОКИНЕТИКА» загружается кусками материала размерами до 70 мм включительно. Так как их масса достаточно высока, покидая ротор-ускоритель со скоростью порядка 40-60 м/с, крупные куски разрушаются при ударе об отражательные плиты статора мельницы. С уменьшением размеров частиц их дальнейшее измельчение происходит в результате ударов шаров, кинетическая энергия которых составляет от 6 до 40Дж (в зависимости от массы шара и скорости ротора), что вполне достаточно для разрушения самых прочных материалов, используемых в производстве порошков. Таким образом, на всех стадиях помола ударная составляющая не замещается истиранием, а значит и не теряет своей эффективности, изменяются только виды удара.
Так, при грубом помоле преобладающим является свободный удар, когда материал разрушается по слабым спаям и дефектам. По мере уменьшения размеров частиц их дальнейшее разрушение происходит в местах сосредоточения наибольших нагрузок, то есть в результате стесненного удара. С учетом наибольшей крупности питания степень измельчения в ударно-шаровой мельнице «ТРИБОКИНЕТИКА» достигает 1000 и выше, что превосходит возможности практически всех существующих в настоящее время агрегатов тонкого помола. И эти впечатляющие результаты достигаются при относительно невысоких скоростях вращения ротора-ускорителя (от 1000 до 3000 об/мин), что положительно сказывается на ресурсе изнашивающихся частей, приводной части и общей надежности оборудования.
Но «ТРИБОКИНЕТИКА» — это не только большая размольная мощность, но и прежде всего высокая экономичность измельчения. Ведь создание предельной концентрации энергии в ограниченном объеме помольной камеры не является самоцелью, эффективность тонкого помола определяется тем, на что расходуется большая часть подведенной энергии. При истирающем помоле – это, прежде всего, нагрев, вибрация, создание паразитных воздушных и циркуляционных потоков, непродуктивное нагружение тонких фракций продукта помола и т.д. «ТРИБОКИНЕТИКА» практически полностью лишена перечисленных недостатков, даже воздушные потоки, образованные вращающимся ротором-ускорителем, используются максимально продуктивно.
Хорошо известно, что эффективность механического диспергирования, оцениваемая по оптимальному гранулометрическому составу порошка и минимальному удельному расходу электроэнергии, тем выше, чем быстрее и полнее выделяются из материала наиболее тонкие фракции, тормозящие процесс измельчения. В существующих мельницах процессы помола и классификации, как правило, разделены. То есть мельница состоит из отдельного измельчителя и устройства, где происходит разделение продукта помола на товарную фракцию и крупку, отправляемую на домол. В новой ударно-шаровой мельнице «ТРИБОКИНЕТИКА» процессы измельчения и разделения совмещены в одном устройстве — мельнице-классификаторе. Воздушные потоки захватывают частицы нужных размеров и выводят их из помольной камеры, улучшая тем самым условия работы мельницы. Таким образом, большая часть подведенной энергии расходуется именно на разрушение относительно крупных частиц, а не на повторное нагружение мелких.
Встроенный классификатор также позволяет изменять границу разделения, переключать систему на возврат крупки в замкнутых схемах измельчения или выдачу до трех фракций продукта помола в открытых схемах.
7. Итоги и перспективы
Измельчение является основой большинства современных технологий и широко используется в самых различных областях материального производства. Знаковые достижения человеческой цивилизации от хлебной муки до извести неразрывно связаны с процессами дробления и помола.
В век информационных технологий механическое диспергирование не только не утратило своего значения, но приобрело статус базового передела, результаты которого в конечном итоге и определяют основные свойства коммерческого продукта. Проблема рационализации процесса измельчения, как и создания новых типов мельниц, никогда еще не стояла так остро как в настоящее время. Сегодня реальная потребность в высокодисперсных порошках значительно превышает возможности «классических» мельниц тонкого помола, как в части себестоимости, так и качества продукта. При этом некоторые типы измельчительного оборудования практически полностью исчерпали резервы для серьезной модернизации.
Рост потребления порошкообразных материалов, в том числе субмикронной размерности, предъявляет все более жесткие требования не только к гранулометрическим характеристикам порошков, но также к форме отдельных частиц, структуре пограничных слоев, реакционной способности новообразованной поверхности, себестоимости помола и т.д. В этой связи показатели эффективности измельчения приобретают совершенно новое значение. И если при относительно грубом помоле расход или точнее перерасход энергии не превышает общепринятых норм, а ее доля в себестоимости конечного продукта незначительна, то производство высокодисперсных порошков, которое всегда связанно с более высокими энергетическими затратами, попросту не может позволить себе использование недостаточно эффективных способов диспергирования. В противном случае самые прогрессивные технологии становятся пленниками устаревших взглядов, традиций и технических решений «…времен Очаковских и покоренья Крыма…».
А.Б. Липилин, главный инженер МП «ТЕХПРИБОР»;
М.В. Векслер, инженер, ведущий специалист;
Н.В. Коренюгина, главный технолог.
Конструкторские решения, использованные при создании ударно-шаровой мельницы «ТРИБОКИНЕТИКА», защищены патентами РФ.
Список литературы:
- П. М. Сиденко Измельчение в химической промышленности. Москва, 1977, 365 С.
- В. И. Акунов О выборе оптимальных типов измельчителей. //Строительные материалы. 1962. №11, С. 21-22.
- А. Рулли, Х. Тедер Форма и характер поверхности зерен кварцевого песка в зависимости от способа помола и их влияние на фракционный способ при воздушной сепарации. В сб.тр. НИПИ силикатобетона.1971.Таллин, №6, С.103-118.
- А.В. Волженский Минеральные вяжущие вещества.Стройиздат, 1986. С. 216-217.
- П. М. Сиденко Измельчение в химической промышленности. Москва, 1977, 158 С.
- И. А. Хинт Основы производства силикальцитных изделий. Госстройиздат, 1962.
www.tpribor.ru
Барабанно-шаровые мельницы
Барабанно-шаровые мельницы применяются для измельчения и тонкого помола твердых каменистых пород, строительных обломков, керамики, угля и других материалов. Их используют на горнорудных комбинатах, на производстве для изготовления строительных материалов (гипс, цемент, сухие сыпучие смеси), на производстве фаянса и керамики, на производстве асфальта, для приготовления сухих примесей, которые добавляют в смесь асфальта, для улучшения качеств верхнего слоя, в лабораториях и т.д.
Шаровые мельницы могут быть барабанными (диаметр барабана не намного меньше длины барабана) и трубными (длина барабана намного превышает диаметр барабана). Трубные шаровые мельницы обычно имеют две камеры.
Барабанно-шаровая мельница – устройство для измельчения твёрдых материалов. Применяется в основном в горнорудной промышленности, для создания порошка для использования в красках, пиротехнических средствах, и в керамике. Барабанные мельницы используются для измельчения материала до частиц размером менее десятых долей миллиметра.
Принцип работы барабанно-шаровой мельницы
Помол твердых тел осуществляется с помощью твердых мелющих тел сферической формы, которые загружают в барабан вместе с материалом, требующим измельчения. Барабан крутится, что приводит мелющие тела в движение. Высокая скорость вращения барабана шаровой мельницы ведет к тому, что мелющие шары внутри него падают с высоты и разбивают, тем самым измельчая материал, это так называемый водопадный способ помола. Низкая скорость приводит к тому, что между мелющими шарами возникает трение, за счет которого происходит измельчение материала, такой способ называют каскадным.
Для повышения качества измельчения, мелющие шары могут быть разных размеров. Мелющие элементы большого размера дробят основную массу, а мелющие элементы малого размера позволяют добиться более тонкой степени помола материала, превращая его в пыль. Главная особенность шаровых мельниц заключается в том, что твердость мелющих элементов должна быть выше, чем твердость перемалываемых материалов. Мелющие шары могут быть сделаны из чугуна, стали, керамики.
В барабанных мельницах материал измельчается внутри полого вращающегося барабана. При вращении мелющие тела и измельчаемый материал сначала движутся по круговой траектории вместе с барабаном, а затем падают по параболе. Часть перемалываемого материала, расположенная ближе к оси вращения, скатывается вниз по подстилающим слоям. Материал измельчается в результате истирания при относительном перемещении мелющих тел и частиц материала, а также вследствие удара.
Конструкционные особенности барабанно-шаровой мельницы
Барабанно-шаровая мельница представляет собой сварную конструкцию из толстолистовой стали в форме цилиндрического барабана в виде трубы. Торцы трубы заварены листами круглой формы, в которых имеются отверстия для загрузки и разгрузки барабана. Внутренняя поверхность барабана футерирована твердыми плитами или накладками, чтобы снизить механические повреждения и повысить срок службы конструкции. Чаще всего мелющие элементы, которые загружают в барабан выполняют из того же материала, что футеровка. При помощи электродвигателя барабан вращается. Существуют шаровые мельницы беспрерывного и периодического действия. В случае беспрерывной работы загрузка и выгрузка материалов осуществляется беспрерывно, а при периодическом действии, загрузку и выгрузку материалов проводят, когда работа шаровой мельницы остановлена.
Количество мелющих элементов, которое загружают в барабан, получают расчетным путем. Чем больше мелющих элементов, тем выше качество помола. Но если мелющих шаров будет слишком много, то это приведет к перерасходу энергии и снижению эффективности работы агрегата, возможным поломкам. В процессе разгрузки барабана, чтобы мелющие шары не выпали, используют специальный стакан, в котором сделаны отверстия меньшего диаметра, чем мелющие шары. Нередко барабанно-шаровые мельницы снабжают ситом, чтобы разделить перемолотую массу на фракции, в этом случае крупные элементы отправляют снова в барабан для вторичного помола.
Мельницы шаровые работают в различных технологических схемах (в открытом или закрытом цикле) и позволяет получать однородный по тонкости продукт измельчения с помощью мелющих тел (шаров и цильпебсов). Производительность мельницы зависит от свойств измельчаемых материалов (прочность, размолоспособность), крупности материалов на входе (до 50 мм), влажности материалов (до 0,5 %), тонкости помола, равномерности питания, заполнения мелющими телами и материалом.
Типы барабанно-шаровых мельниц
Шаровые мельницы отличаются по размеру барабана (барабанные, трубные), форме (конические, цилиндрические), количеству камер (однокамерные и двухкамерные), способу работы (беспрерывная и периодическая), виду материала из которого выполнена футеровка и мелющие элементы, типу двигателя (периферийный, центральный). Барабанно-шаровые мельницы делятся на промышленные и лабораторные. Промышленные барабанно-шаровые мельницы представляют собой крупногабаритные агрегаты, их используют на производстве. Лабораторные барабанно-шаровые мельницы меньше по размеру, они бывают настольные и напольные, их применяют для работы в лаборатории или для тестирования и моделирования помола разных типов материалов. Барабанно-шаровые мельницы могут применяться для сухого измельчения материалов и для мокрого, либо комбинированные варианты, сочетающие оба способа. Лабораторные шаровые мельницы для мокрого помола могут использовать агрессивные растворяющие жидкости для повышения эффективности работы.
Достоинства и недостатки барабанно-шаровых мельниц
К числу достоинств барабанно-шаровых мельниц можно отнести высокую степень тонкости помола и возможность ее регулировать, возможность сушки материала в процессе работы мельницы, простоту конструкции и эксплуатации, надежность, универсальность. Барабанно-шаровые мельницы позволяют осуществлять помол пород различной твердости, для этого достаточно правильно подобрать мелющие тела (относительно твердости перемалываемого материала и размер шаров). Основной недостаток барабанно-шаровых мельниц – это энергоемкость, процесс помола требует значительного расхода электроэнергии, а также большой вес оборудования и размеры, сильный шум во время работы. Несмотря на все недостатки, барабанно-шаровые мельницы эффективно применяются в различных отраслях промышленности.
www.bmpa.ru
Шаровые мельницы
Строительные машины и оборудование, справочник
Шаровые мельницыКатегория:
Дорожные машины 2
Шаровые мельницы
Шаровые мельницы применяют для очень мелкого дробления (тонкого помола) каменных материалов в минеральный порошок, который используется в качестве заполнителя при приготовлении верхнего слоя асфальтобетона. Измельчение материала в этих мельницах производится с помощью шаров или стержней.
Мельницы бывают однокамерные и двухкамерные, в зависимости т мелющих тел — шароЕые и стержневые, с сухим или мокрым помолом. Кроме того, шаровые мельницы бывают непрерывного действия, когда загрузка дробимого материала и выгрузка дробленого происходит непрерывно; периодического действия, в которых загрузка-выгрузка производится при овта-новке барабана через специальные люки; периодической загрузкой и непрерывной выгрузкой дробимого материала, когда часть цилиндрической поверхности барабана закрыта проволочной сеткой.
Рис. 5.18. Схема шаровой мелькицы
По форме барабана шаровые мельницы бывают цилиндрические, цилиндрические длинные (трубные) и конические. По способу выхода измельченного материала мельницы могут быть со свободным выходом через полую центральную цапфу, с выходом через поперечное сито и G выходом через наружное цилиндрическое сито.
Основными узлами и деталями шаровой мельницы являются (рис, 5.18) барабан, загрузочное устройство, подшипники и приводное устройство. Барабан — полый, сварной, изготовляется из толстолистовой стали. К цилиндрической части барабана на болтах крепятся торцовые днища. Внутри барабан выложен футеровкой из стальных плит для предохранения от износа. На цилиндрической части барабана имеется люк, который служит для осмотра мельницы, ее ремонта и для заполнения дробильной камеры шарами.
Торцовые днища для предохранения их от износа и непосредственных ударов мелющих шаров также выложены футеровкой. В центре днищ имеются круглые отверстия, переходящие в полые цапфы, которыми барабан опирается на два массивных коренных подшипника. Через одну цапфу производится загрузка мельницы дробимым материалом, а через другую удаляется измельченный , материал. Загрузочное устройство обеспечивает равномерную подачу материала, подлежащего дроблению. Питатель крепится болтами к загрузочной цапфе. При вращении барабана вращается и улитка питателя, черпая загрузочным носком материал, находящийся в ящике. При движении улитки материал скользит по спирали, поступая через полую цапфу в барабан.
Коренные подшипники представляют собой массивные корпуса G большой площадью прилегания к фундаменту, так как каждый из них несет половину веса барабана. Нижние вкладыши подшипника, залитные баббитом, опираются на корпус подшипника сферической формы. Такая форма дает возможность еамоцентровки подшипника, а также сглаживает дефекты монтажа, компенсирует неравномерную усадку фундамента и прогиб барабана и обеспечивает равномерное распределение нагрузки на корпус подшипника. Привод шаровой мельницы производится от электродвигателя с помощью клиноременной передачи. Вращение от двигателя передается промежуточному валу, на котором установлена цилиндрическая шестерня, приводящая во вращение зубчатый венец, прикрепленный болтами к барабану.
Мелющие шары изготовляют из отбеленного чугуна или марганцовистой стали, диаметр их от 40 до 135 мм. Эффективность дробления зависит от размеров и массы шаров. Для обеспечения тонкого помола вместе е крупными шарами загружают и более мелкие, которые дополнительно дробят мелкий материал до нужной тонкости. Мелких шаров (по весу) должно быть больше, чем крупных.
Реклама:
Читать далее: Установки дробильно-сортировочные
Категория: — Дорожные машины 2
Главная → Справочник → Статьи → Форум
stroy-technics.ru
Барабанные шаровые и стержневые мельницы
Завод нестандартного оборудования «Машинопромышленное объединение» проектирует и изготавливает оборудование для предприятий горной, химической и нефтегазовой промышленности. в том числе и производит оборудование для замены футеровки барабанных мельниц (перефутеровочные машины различных видов). Барабанная шаровая (стержневая) мельница в общем случае — это специальное оборудование предназначенное для эффективного измельчения твёрдых материалов.
Определение «барабанная» здесь означает, что основной конструктивный элемент мельницы — ее корпус исполнен в виде цилиндрического барабана, приводимого во вращение в процессе измельчения материала.
Определение «шаровая» или «стержневая» в свою очередь означает, что измельчение материала в рассматриваемой мельнице происходит при помощи специальных мелющих тел в виде шаров или стержней.
В зависимости от своих масштабов барабанные шаровые мельницы могут быть промышленными и лабораторными. Нас интересуют конечно же первые, о них и будем говорить. Так же по особенностям технологического процесса барабанные шаровые мельницы могут быть сухими и мокрыми (измельчение в присутствии воды), иметь периодическую или непрерывную загрузку. Важной особенностью барабанной шаровой (стержневой) мельницы является способ разгрузки.
Маркировка барабанных шаровых (стержневых) мельниц.
Таким образом барабанные мельницы в зависимости от применяемых мелющих тел и способа разгрузки изготавливаются следующих типов:
- Тип МСЦ ― мельницы стержневые с центральной разгрузкой;
- Тип МСП ― мельницы стержневые с периферической разгрузкой;
- Тип МШР ― мельницы шаровые с разгрузкой через решетку;
- Тип МШЦ― мельницы шаровые с центральной разгрузкой.
Так же возможны модификации (вариации исполнения) мельниц, учитывающие требования заказчика, такие как мельница с низким уровнем слива (маркируется «Н») и мельница с удлиненным валом (маркируется «В»).
У барабанных мельниц с центральной разгрузкой удаление результатов измельчения происходит свободным сливом через пустотелую разгрузочную цапфу. У барабанных мельниц с разгрузкой через решетку предусмотрено специальное устройство для подъема барабана, обеспечивающее разгрузку, поэтому их так же называют мельницами с принудительной разгрузкой.
Полная структура условного обозначения мельниц может иметь следующий вид:
МСЦ (МСП, МШР, МШЦ) ― ДхL ―X ―X, где
- М — означает мельница
- С ― стержневая, Ш — шаровая (характеризует применяемые в мельнице мелющие тела ― стержни или шары)
- Ц ― с центральной разгрузкой, Р― с разгрузкой через решетку, П ― с периферической разгрузкой (характеризует способ разгрузки продукта из мельницы)
- Д ― Внутренний диаметр барабана (без футеровок), мм
- L ― Длина барабана, мм
- Н ―с низким уровнем слива, В ― с удлиненным валом (исполнение мельницы)
Дополнительно указывается климатическое исполнение и категория размещения
Пример записи при заказах и в документации условных обозначений мельниц:
- Мельница шаровая с разгрузкой через решетку, диаметр барабана 2100 мм и длина 3000 мм, исполнения УХЛ, категории размещения 4 с указанием технических условий:
- Мельница МШР-2100хЗ000 ― УХЛ4 ТУ
- Мельница стержневая с центральной разгрузкой, диаметром барабана 3200 мм, длиной 4500 мм, с удлиненным валом, в исполнении О, для категории размещения 4, с указанием технических условий:
- Мельница МСЦ — 3200х4500 ―В ―04 ТУ
Конструктивные особенности барабанных шаровых (стержневых) мельниц.
Основной принцип измельчения материала в барабанных мельницах — перемешивание и соприкосновение с мелющими телами (шарами, стержнями) внутри полого вращающегося барабана. При вращении мелющие тела (шары, стержни) и измельчаемый материал, так же называемый «загрузкой» сначала получают импульс к движению по круговой траектории вместе с барабаном, а затем, отделившись от стенок барабана падают по параболе. Материал измельчается в результате истирания при взаимном перемещении мелющих тел и частиц материала, а также в результате удара.
Основная деталь конструкции мельниц этого вида — вращающийся барабан, частично заполненный шариками рассчитываемого диаметра из стали, чугуна и разных сплавов.
В конструкции барабанных мельниц предусматривается обязательно:
- загрузочное устройство (питатель), исключающее выплескивание пульпы;
- специальные разгрузочные устройства способные разделять на выходе пульпу, мелющие тела и остатки не размолотого материала;
- установку футеровочных деталей и решеток из износостойких материалов без пересверловки отверстий на барабане;
- взаимозаменяемость основных сборочных единиц и деталей привода, подшипников, барабана в сборе с торцевыми крышками, сменных деталей для мельниц одного типоразмера.
В конструкции барабанных мельниц рекомендуется предусматривать:
- возможность их встраивания в автоматические линии, действующие на предприятии;
- исключение циркуляции пульпы в местах соединения частей и других креплениях;
- футеровки в корпусе барабана;
- возможность применения устройств механизации для проведения ремонтных работ;
- возможность выгрузки мелющих тел и подачу всех футеровочных деталей и элементов решетки через люки;
- возможность замены решетки без снятия разгрузочной крышки (для мельниц типа МШР диаметром 3,6 м и более).
Варианты исполнения приводов барабанных мельниц:
- один привод со стороны загрузочной или разгрузочной части;
- один привод на разгрузочной цапфе или барабане;
- два привода с загрузочной или разгрузочной стороны.
Барабанные шаровые (стержневые) мельницы с периодической загрузкой и разгрузкой наиболее просты по конструкции, но так же и менее производительны и их сложнее встроить в непрерывный технологический процесс.
Для обеспечения автоматизации процессов измельчения предпочтительнее барабанные шаровые (стержневые) мельницы с непрерывной загрузкой. В конструкции барабанов таких мельниц предусмотрены встроенные полые цапфы, через входную непрерывно загружается исходный материал, а через выходную удаляется измельченный материал. Это может происходить самотеком или принудительно, при помощи устройств всасывания установленных в приемных трубопроводах.
Механизмы приводящие в движение барабан шаровой (стержневой) мельницы могут быть боковыми или центральными. Боковой привод вращения барабана осуществляется от электродвигателя через редуктор или непосредственно на зубчатую шестерню передающую вращение на венец, закрепленный на барабане. Центральный или осевой привод вращения барабана производится от электродвигателя, через редуктор на цапфу установленную по оси барабана.
Особенности использования мелющих тел барабанных шаровых (стержневых) мельниц.
При измельчении материала в барабанных мельницах, использующих стальные мелющие тела расходы на износ шаров, стержней и футеровки поверхности барабана одна из главных статей затрат. В связи с этим производились множество исследований по выбору оптимальной формы мелющих тел и в конечном итоге шары оказались лучшим вариантом как по эффективности измельчения, так и по износу. Так же неплохо показали себя и стержни — короткие цилиндрические куски металла.
Изнашивание мелющих тел (шаров, стержней) сложный процесс, зависящий от свойств используемого металла, их размеров, абразивных свойств измельчаемого материала и его размеров, а так же скорости вращения барабана мельницы. В случае мокрого измельчения к абразивному износу добавляются процессы коррозии.
Чтобы компенсировать износ мелющих тел, в процессе работы барабанной мельницы, необходимо обеспечить их подачу внутрь барабана. Износ мелющего тела сопровождается изменением его размеров и таким образом в процессе измельчения в мельнице одновременно находятся шары или стержни различных размеров, что отражается на результатах работы. Так что расчеты оптимального количества подаваемых мелющих тел для обеспечения эффективной работы мельницы это целая наука, в которой есть свои теории и гипотезы.
Барабанные шаровые (стержневые) мельницы мокрого измельчения с непрерывной загрузкой нашли широкое применяется на предприятиях горнорудной промышленности. Процесс измельчения на подобных агрегатах отличается большой энергоёмкостью и стоимостью, но дает необходимый результат. Производительность барабанных шаровых (стержневых) мельниц зависит в первую очередь от свойств измельчаемых материалов, крупности кусков на входе и заданной тонкости измельчения, а так же равномерности подачи исходного сырья и заполнения мелющими телами.
Об особенностях перефутеровки поверхностей барабанов шаровых (стержневых) мельниц будем писать в дальнейшем. А на страницах нашего сайта можно ознакомится с описанием:
ПЕРЕФУТЕРОВОЧНАЯ МАШИНА ДЛЯ МЕЛЬНИЦ
МАШИНА ДЛЯ ЗАМЕНЫ ФУТЕРОВКИ МЕЛЬНИЦЫ ММС
Приглашаем к сотрудничеству
www.mpoltd.ru