Устройство и принцип работы мартеновской печи
На рис. 131 представлена схема мартеновской печи, отапливаемой высококалорийным топливом. Печь состоит из рабочего пространства, головок, топливосжигающих устройств (горелок или форсунок), шлаковиков, регенераторов, боровов с перекидными устройствами, котлов-утилизаторов, системы газоочистки и дымовой трубы. Регулирование давления в печи, а в случае необходимости и перекрывание дымового тракта осуществляется при помощи шиберов. Печь оборудована контрольно-измерительными приборами, системами управления и охлаждения, устройствами для подъема заслонок рабочих окон и другими механизмами.
Рабочее пространство ограничено подиной, продольными и поперечными откосами, передней и задней стенками неводом (рис. 132). Нижняя часть рабочего пространства до уровня порога рабочих окон называется ванной. Произведение длины ванны L на ее ширину В на уровне порога рабочих окон называется площадью пода S, которая составляет для 100-т и 900-т мартеновских печей соответственно 48 и 160 м2.
Дымовые газы, выходящие из рабочего пространства, содержат большое количество пыли (до 35— 40 г/м3). Во избежание засорения насадок регенератора газы предварительно проходят шлаковик, где оседают крупные частицы пыли. Камеры регенераторов заполнены огнеупорной насадкой (рис. 133).
Отдельные элементы печи (рамы рабочих окон, заслонки и т. д.) охлаждаются либо проточной водой, либо паро-водяной эмульсией при паро-испарительной системе охлаждения. Паро-испарительное охлаждение носит замкнутый характер: химически чистая вода поступает самотеком из бака-сепаратора к охлаждаемому элементу, а паро-водяная эмульсия поднимается по трубе вновь в бак-сепаратор (рис. 134). Стойкость элементов печи при такой системе охлаждения возрастает, уменьшается расход воды.
Мартеновская печь работает следующим образом. Топливо, подаваемое на схеме рис. 131 через правую горелку (форсунку), сгорает в потоке нагретого в правом регенераторе воздуха, который нагнетается вентилятором. Подводящая (на рис. 131 правая) головка обеспечивает организацию факела в рабочем пространстве печи. Отходящие газы с температурой 1550—1650° С направляются в отводящую (на рис. 131 левую) головку, через вертикальный канал и шлаковик попадают в левый регенератор и, проходя через его насадку, нагревают ее. После регенератора при 500—700° С дымовые газы направляются в котел-утилизатор, а затем через систему газоочистки в дымовую трубу.
На одну сторону печь работает в течение 5—20 мин. Затем по мере охлаждения — насадки регенератора на подводящей стороне и нагрева их на отводящей происходит перекидка клапанов. Шибер после левого регенератора опускается, а шибер после правого регенератора поднимается. Таким образом, воздух от вентилятора поступает уже в левый регенератор, а правый регенератор соединяется с трубой. Подача топлива переключается с правой на левую головку, и первая головка становится подводящей, а вторая — отводящей.
metallurgy.zp.ua
Устройство мартеновской печи и принцип ее работы — реферат
Устройство мартеновской печи и принцип ее работы
Для получения высоких температур в печи воздух и газы подают нагретыми до 1100—1300°. Для нагрева воздуха и газа используют отходящие из мартеновской печи горячие газы. Для более интенсивного нагрева печи в современной практике используют обогащенное кислородом дутье.
На рис. 20 показана принципиальная схема устройства мартеновской печи. Плавильное пространство печи А подвергается действию высоких температур и химическому взаимодействию расплавленного металла 1 и жидкого шлака 2. Плавильное пространство ограничивается сверху сводом 3, снизу — подом 4, задней 5 и передней 6 стенками. В передней стенке имеются загрузочные окна 7, количество которых зависит от размеров печи. Заднюю стенку 5 устанавливают с наклоном для лучшего прилипания к ней порошкообразных огнеупорных материалов при текущем ремонте. В этой стенке сделано выпускное отверстие — летка 8, которое во время плавки закрыто огнеупорными материалами 9. Перед выпуском готовой стали огнеупорный материал 9, тощий отверстие, разрушается, и отверстие 8 пробивают стальным
Рис. 1. Схема устройства мартеновской печи:
1 — расплавленный металл; 2 — расплавленный шлак; 3 — свод; 4 — под; 5 — задняя стенка- 6 — передняя стенка; 7 — загрузочные окна. 8 — выпускная летка для металла и шлака; 9 — огнеупорный материал; 10 — воздушный регенератор: 11 — газовый регенератор; 12 — рабочий уровень площадки; 13 и 13 — каналы для подвода воздуха и отвода продуктов горения; 14 и 14′ — каналы для подвода газа и отвода продуктов горения, 15 — перекидные клапаны; 16 — головка; 17 — дымовой канал; 18 — тележка для шлака; 19 — волоохлаждаемыс кислородные фурмы
Под печи конструктивно выполнен с уклоном к выпускному отверстию, чтобы весь металл и шлак могли полностью вытекать из печи. Рабочее плавильное пространство расположено на высоте 4,5 -8 м от уровня пола с таким расчетом, чтобы под выпускной желоб можно было подводить разливочный ковш.
В настоящее время на отечественных заводах повышается удельный вес крупных мартеновских печей, повышается емкость действующих печей, разработаны типовые мартеновские печи ёмкостью 600—700 т и 800—900 т. Работа мартеновских печей переведена на автоматическое управление с применением в отдельных случаях счетно-решающих машин.
Регенераторы 10—11 (рис. 20) расположены под печью или под рабочей площадкой. Как показано на рис. 21, они занимают первый этаж и углублены значительно ниже уровня пола. Регенераторы устанавливают с двух сторон печи попарно. При этом одна пара нагревается, вторая пара отдает тепло.
Регенераторы 10 (рис. 20) нагревают воздух, а регенераторы 11 нагревают газ. Если печь работает на жидком топливе или высококалорийном природном или коксовом газе, то регенераторы нагревают только воздух.
Для предохранения отдельных частей металлической арматуры печей последние охлаждаются водой. Мартеновская печь работает по следующему принципу. Через правую пару регенераторов (рис. 20) по каналам подают газ и воздух, которые, проходя регенераторы 10 и 11, постепенно нагреваются до 1100° и выше. Нагретые газ и воздух смешиваются в. головке печи и сгорают. Образующиеся продукты сгорания направляются на поверхность металлической ванны и удаляются из рабочего пространства через каналы 13°, 14° в левую пару регенераторов. Температура отходящих газов в верхней части регенераторов 1600°; по мереих опускания температура их понижается: из газового регенератора они удаляются с температурой 600° и через дымовые каналы отводятся в трубу.
Спустя некоторое время, движение газов в печи переключают в противоположном направлении так, чтобы левая пара регенераторов нагревала воздух и газ, а правая нагревалась.
Направление отходящих газов и подачу холодного воздуха и газа регулируют с помощью специальных клапанных перекидных устройств 15 (рис. 20). Регулирование теплового режима мартеновской печи осуществляется автоматически. Для этой цели в местах заданных температур устанавливают приборы для измерения температуры связанные с автоматическими устройствами. В настоящее время более 90% стали выплавляется на автоматизированных мартеновских печах. Мартеновские печи имеют устройства для подачи кислорода для форсирования горения топлива или для окисления примесей в жидкой ванне.
Кислород для окисления примесей подается через сводовые водоохлаждаемые фурмы 19 (рис. 1). При подаче кислорода в жидкую ванну его используют для введения порошкообразных флюсов непосредственно в жидкий металл. В отдельных случаях для этой цели используют воздух. Ввод порошкообразных материалов в жидкий металлускоряет процессы шлакования вредных примесей.
Поперечный разрез мартеновского цеха показан на рис. 2. Металл из печи через отверстие 5 выпускают по желобу в разливочные ковши 4. Загрузка печей производится специальным» крановыми или напольными завалочными машинами 10. Материалы подаются в печь металлическими ящиками-мульдами 7. Доставляются материалы с шихтового двора на рабочую площадку вагонетками 8. Готовая сталь краном разливается из ковшей в изложницы 2. Изложницы устанавливаются на тележках или в специально оборудованных канавах.
Рис.2. Поперечный разрез главного здания типового
цеха с мартеновскими печами:
1-механизм для открывания стопора; 2-изложницы; 3-ковшпри заливке металла в форму; 4-ковш при выходе металла из печи; 5-выпускное отверстие-летка; 6-мартеновские печь; 7-мульда; 8-вагонетка; 9-регенераторы; 10-заволочная машина
myunivercity.ru
Схема устройства мартеновской печи и принцип ее работы
Выплавка стали производится в мартеновских или электроплавильных печах, а также в кислых или основных конверторах. Наибольшее количество выплавляемой стали получают в настоящее время в мартеновских печах.
Для выплавки стали в рабочем пространстве мартеновской печи необходимо поддерживать температуру до 1700°. В качестве топлива для мартеновских печей применяют генераторный или коксовальный газ, смесь одного из них с доменным газом, природный и попутный нефтяной газы, а также жидкое топливо в виде мазута или смолы. Кроме этого, используется смесь газообразного и жидкого топлива. Требуемую высокую температуру в печи можно получить только при условии сжигания любого из этих видов топлива в среде нагретого воздуха, причем генераторный и коксовый газы, а также смесь их с доменным газом должны быть также предварительно нагреты. Нагрев воздуха и газообразного топлива производится путем пропуска их через предварительно нагретые отходящими продуктами горения с температурой 1600—1650° насадки из огнеупорного кирпича, выложенные в регенераторах.
На рис. 1 приведена схема движения газа, воздуха и продуктов горения мартеновской печи, работающей с подогревом газа и воздуха. Газ из газопровода через открытый газовый клапан / поступает по газовому каналу-борову 2 в газовый регенератор 3, где нагревается до температуры 1100—1300°, проходя через раскаленную насадку. Из регенератора нагретый газ через газовый шлаковик 4, вертикальный газовый канал 5 и головку печи 6 поступает в рабочее пространство 7.
Левый газовый шибер 8 и правый газовый клапан 10 при этом закрыты, а правый газовый шибер 9 — открыт.
Параллельно с газом воздух из атмосферы засасывается при помощи вентилятора при закрытом левом воздушном шибере 16 н открытом правом воздушном шибере 17 и направляется через воздушный клапан 11 по воздушному каналу-борову 12 в воздушный регенератор 13, в котором, проходя через насадку нагревается, до температуры 1100—1300°. Из регенератора нагретый воздух через воздушный шлаковик 14, воздушный вертикальный канал 15 и головку печи 6 поступает также в рабочее пространство 7. Нагретые газ и воздух при выходе из головки смешиваются, газ воспламеняется и образует факел, заполняющий почти все рабочее пространство печи.
Продукты горения через противоположную головку печи направляются двумя раздельными трактами — воздушным и газовым через вертикальные каналы, шлаковики и регенераторы. Отдав свое тепло кирпичу насадок и нагрев их до 1200—1300°, они, охлажденные до 800—900°, проходят по боровам через от¬крытые Шиберы 9 и 17 и далее через шибер 20 и котел-утилизатор или непосредственно через шибер 19 и поступают в дымовую трубу 18. После нагрева насадок до необходимой температуры происходит автоматическое переключение клапанов и шиберов, в результате чего газ и воздух направляют в рабочее пространство через правую сторону печи, а продукты горения уходят через левую сторону. Правая и левая стороны печи совершенно одинаковы по своей конструкции. В результате периодического изменения направления движения газа, воздуха и продуктов го-рения в мартеновскую печь постоянно поступают нагретые до нужной температуры газ и воздух, что и обеспечивает при сжигании газа требуемую температуру в рабочем пространстве печи.
metallurgy.zp.ua
Устройство мартеновской печи — Энциклопедия по машиностроению XXL
Фиг. 14. Схема устройства мартеновской печи / — воздушный канал 2 — газовый канал 3 — воздушный регенератор 4 — газовый регенератор 5 — вертикальные каналы б — головка 7 — рабочее пространство 8 — головка 9 — вертикальные каналы J0 — газовый регенератор и — воздушный регенератор 12 — газовый канал 3 — воздушный канал 14 — боров 15 — дымовая труба 16 — газовый клапан 17 — воздушный клапан 18 — шлаковики. | ![]() |
Рис. 70, Схема перекидных устройств мартеновской печи | ![]() |
Схема устройства мартеновской печи, работающей на газе, приведена на фиг. 20 [9]. [c.398]
Устройство мартеновской печи [c.38]
Каково устройство мартеновских печей, работающих на газе [c.74]
Рис. 27. Схема устройства мартеновской печи. | ![]() |
Устройство мартеновской печи. В мартеновских печах сжигают мазут или предварительно подогретые газы с использованием горячего дутья. Температура факела пламени равна примерно 1800— 1900° С.
Схема устройства мартеновской печи представлена а рис. 18. Основной частью печи является рабочее пространство А, ограниченное сверху сводом 1, снизу подом [c.50]
Устройство мартеновской печи. Мартеновская печь называется пламенной регенеративной, так как принцип ее работы основан на регенерации тепла, обеспечивающей высокую температуру печи, необходимую для ведения плавки. Схема устройства мартеновской печи с распределительными клапанами представлена на фиг. 39. [c.82]
II. Устройство мартеновской печи и принцип ее работы [c.48]
Рис. 20. Схема устройства мартеновской печи | ![]() |
Фиг. 14. Схема устройства мартеновской печи и движения в ней газа, воздуха и продуктов сгорания. | ![]() |
При технологических аппаратах периодического действия устанавливают одно утилизирующее устройство, использующее вторичные энергоресурсы за несколькими технологическими агрегатами. Примером такого решения является установка котла-утилизатора за несколькими мартеновскими печами. [c.38]
В черной металлургии при традиционной схеме производства металла чугун — сталь — прокат (с учетом производств, обслуживающих металлургические заводы) к агрегатам-источникам ВЭР могут быть отнесены доменные печи, кауперы, агломерационные машины, ферросплавные печи, мартеновские печи, кислородные конвертеры, нагревательные устройства (методи- [c.39]
В топку из форсунки (а при механическом распыливании из форсунки и воздушного регистра или другого устройства) поступают распыленное жидкое топливо и воздух. Только в исключительно редких случаях (например, в мартеновской печи) воздух нагрет настолько, что обеспечивает испарение и воспламенение топлива без дополнительного нагрева. Обычно же для воспламенения необходимо испарить некоторую часть топлива и подогреть смесь паров топлива с воздухом до такой температуры, при которой за счет реакции горения выделялось бы больше тепла, чем требуется для испарения оставшегося топлива и покрытия потерь на охлаждение факела. Тогда температура смеси будет уже возрастать без подвода тепла извне, произойдет воспламенение, и дальнейшее горение будет определяться в значительной мере тем, как аэродинамические условия обеспечат необходимую доставку окислителя к топливу, и какова скорость испарения отдельных капель. [c.220]
Однако мазут пока еще не применяется для камер сгорания газовых или парогазовых турбин. Газообразное же топливо даже при высоком качестве его смешения с воздухом дает пламена с невысокой излучательной способностью. Именно поэтому для повышения излучательной способности газовых пламен (например, в мартеновских печах, а этот вид теплообмена в плавильных печах вообще является основным) производят подсвечивание газовых факелов путем ввода 20—25% мазута. В рассматриваемых же нами топочных устройствах (камеры сгорания газовых или парогазовых турбин) или в парогенераторах энергетического значения основными видами топлива пока являются газ или продукты газификации топлив, а для транспортных газотурбинных установок — керосин или дизельное топливо, т. е. те виды топлива, которые при хорошем смесеобразовании образуют только слабо светящиеся пламена. [c.30]
Все это в конечном счете приводит к понижению температуры, которая практически никогда не достигает своего теоретического уровня. Вследствие этого топочные устройства имеют некоторый максимум температуры, который может достигать 1800—2000° К в высокофорсированных камерах горения и мартеновских печах. В котельных же топках с нормальными форсировками и в нагревательных печах с интенсивным теплоотводом этот максимум не превышает 1700—1800° К. [c.222]
Впервые материалы по методам приготовления, некоторым свойствам и результатам использования угле-мазутных систем в топочных устройствах и мартеновских печах были обобщены в 1942 г. В. Ф. Кустовым [208]. [c.264]
Процесс плавки в мартеновских печах их устройство и работа исходные материалы ход процесса сравнение качества стали, полученной в конвертерах и мартеновских печах. [c.613]
Казалось бы всегда можно отключить КУ мартеновских печей, которые устанавливают на обводных газоходах. Однако применяемые для очистки отходящих газов мартеновских печей от уноса системы газоочистки (например, электрофильтры) не могут эффективно работать при высоких температурах газов. Нужное охлаждение газов достигается в КУ. Если КУ отключены, надо предусмотреть специальные охлаждающие газ устройства (впрыск воды и т. п.). Отходящие газы печей прокатного производства, как правило, более чистые, поэтому здесь можно отключать КУ, если система газоходов позволяет обеспечить приемлемую температуру отходящих газов. Однако ликвидация сброса пара УУ в атмосферу путем отключения тех или иных УУ не является решением, которое можно рекомендовать к применению. Для выбора оптимального решения вопроса нужно проведение соответствующих исследований и мероприятий. [c.123]
Перекидные клапаны. Система перекидки клапанов (рис. 70) предназначена для изменения направления потоков газа и воздуха с одной стороны печи в другую. Для этого в боровах, газопроводах устанавливают перекидные и регулирующие устройства газовые клапаны, воздушные клапаны, дымовые клапаны и воздушные задвижки, переключение которых осуществляется специальными устройствами при помощи блоков. Операция перекидки клапанов в современных мартеновских печах автоматизирована. [c.151]
Устройство и работа мартеновской печи. Мартеновская печь (рис. 2.3) — пламенная отражательная регенеративная печь, Она имеет рабочее плавильное пространство, ограниченное снизу подиной [c.36]
Емкость мартеновских печей достигает 900 т. Около 60% всей стали выплавляется в мартеновских печах. Устройство и принцип работы показаны на рнс. 3. [c.28]
Мартеновские печи существующих конструкций благодаря устройству наклонных стенок имеют своды с очень большими пролетами кроме того, вдоль стен между уровнем ванны и сводом расстояние уменьшено, что способствует быстрому износу этих участков свода. Опыт работы мартеновской печи новой конструкции с обратным наклоном подвесных стен (внутрь печи), что значительно уменьшает пролет и вес свода, показал возможность повышения стойкости динасового свода примерно на 70% [17]. [c.411]
Автоматизация энерго снабжающих установок увеличивает надежность работы, повышает их к. п. д., производительность труда и качество выпускаемой продукции, способствует в некоторых случаях снижению капитальных затрат, улучшает условия работы обслуживающего персонала и сокращает его количество. Так, например, применение автоматических устройств для доменных и мартеновских печей увеличивает выпуск металла на 7—10% и экономит 4—6% топлива. Тем не менее до настоящего времени [c.298]
До настоящего времени на испарительное охлаждение переведен уже ряд сталеплавильных (мартеновских) печей. Выход пара от испарительного охлаждения мартеновских печей составляет 0,22 /и на 1 т чугуна (в пересчете на чугун) при давлении 1,6— А ата. Капиталовложения при устройстве системы испарительного охлаждения на мартеновской печи для вновь строящихся цехов в два раза меньше, чем при водяном охлаждении. [c.254]
Мартеновская печь (рис. 14) по устройству и принципу работы является пламенной регенеративной печью. В ее плавильном про- [c.46]Мартеновские печи, работающие на мазуте с С = 35ч-45 МДж/кг (8500-г-Ю 500 ккал/кг), снабжены с каждой стороны только одним регенератором — для нагрева воздуха. В последнее время в качестве топлива в мартеновских печах начали широко применять природный газ с д = 35 МДж/м (8500 ккал/м ). Его добавляют к коксо-домен-ной газовой смеси или сжигают с добавкой мазута (для подсвечивания факела пламени). Форсунки и другие устройства для подачи [c.47]
Фиг. 20. Схема устройства мартеновской печи / — воздушный канал 7 — газовый канал 3 — воздушный регенератор —газовый регенератор 5 — вертикальные каналы 5 —головка 7— ра( .очев пространство 5 — головка 9 — вертикальные каналы — газовый регенератор — воздушный регенератор /2 — газовый канал воздушный канал / —боров /дымовая труба / — газовый кла1.а 1 воздушный клапвн — шлаковики. | ![]() |
С — яетали дизелей и газотурбинных установок, интенсивно греющиеся узлы котлотурбинной техники, детали цементационных и отжигательных производственных печей, трубы-рекуператоры, электронагревательные элементы печей сопротивления, детали атомных реакторов, проволочные сопротивления различных назначений, конструкции химико-металлургической промышленности, детали насосов для транспортировки расплавленных металлов, разнообразные емкости для обжига химических продуктов, передняя арматура и засыпные устройства мартеновских печей, заготовки металлов и сплавов в процессах их термообработки и другие. [c.279]
Устройство И работа мартеновской печи. Мартеновская печь (рис. 2.3) — пламенная отражательная регенеративная печь. Она имеет рабочее плавильное пространство, ограниченное снизу подиио /2, сверху сводо . //, а с боков передней 5 и задней J0 стенками Подина имеет форму ванны с откосами по направлению к стенкам печи. Футеровка печи может быть основной и кислой. Если в npoiie e плавки стали в шлаке преобладают основные окислы, проиесс называют основным мартеновским процессом, а если кислые — кислым. Основную мартеновскую печь футеруют магнезитовым кирпичом, на который набивают магнезитовый порошок. Кислую мартеновскую печь футеруют динасовым кирпичом, а подину [c.32]
Ротационные машины Рольганги Нажимные устройства валков прокатных станов Многие металлорежущие станки с вращательным движением зонтального наведения артиллерийских орудий .Деррик-краны Пневматические молоты Различные ножницы Ткацкие станки Зарядные устройства в артиллерии Качающиеся мартеновские печи Плоскопечатные машины приводы шины Бумажные роллы Фрикционные молоты Шлифовальные станки Дорновые станки [c.30]
В качестве дополнительного внешнего теплоиспользующего устройства КУ обычно не оказывает влияния на характер основного технологического процесса. Однако в ряде случаев КУ способствует улучшению условий работы технологического агрегата. Так, например, расположение КУ за мартеновской печью дает возможность на охлажденных уходяпдах газах установить дымосос, что благоприятно сказывается на работе печи (улучшает тягу). [c.34]
Тетообменные аппараты — устройства, в которых теплота передается от одного теплоносителя к другому. По принципу действия теплообменные аппараты (теплообменники) разделяются на рекуперативные, регенеративные и смесительные. В рекуперативных теплообменниках (подогревателях, испарителях, конденсаторах и др.) теплота от горячей среды к холодной передается через разделяющую их стенку. В регенеративных теплообменниках (воздухоподогревателях доменных и мартеновских печей, котельных установок, газотурбинных установок, утилизаторах теплоты вентиляционных выбросов и др.) одна и та же поверхность некоторого тела (насадки) омывается то горячим, то холодным теплоносителем. В первый период насадка нагревается греющей средой, а во второй — охлаждается, отдавая ранее аккумулированную теплоту нагреваемой среде. Смесительные теплообменники предназначены для осуществления тепло-и массообменных процессов при непосредственном контакте теплоносителей. К ним относятся полые, насадочные и барботажные скрубберы скрубберы Вентури, пенные аппараты, широко применяемые для охлаждения газов и в системах газоочистки [69] оросительные камеры систем кондиционирования воздуха (см. [6]) выпарные аппараты с погружными горелками (см. п. 4.2.9) струйные во-до-водяные (элеваторы, см. п. [68]) и пароводяные подогреватели типа фисоник или транссоник , применяемые в системах теплоснабжения, отопления, вентиляции и горячего водоснабжения [82]. [c.167]
Снижение тепловых потерь промышленных печей и сушил, а также улучшение санитарно-гигиенических условий обслуживающего персонала наряду с применением тепловой изоляции достигается устройством отражающих экранов. Промышленные печи и сушила в эксплуатационных условиях являются источниками теплового излучения и конпех тив-ного нагрева воздуха, вызывающими значительное повышение температуры в производственных помещениях. Особенно интенсивное тепловое излучение происходит при ведении технологического процесса и при загрузке и выгрузке печей и сушил. В зависимости от температуры источника излучения и расстояния от него степень облучения обслуживающего персонала, по данным А. Ф. Бабалова, онределяется (в кал1см мин). у молотов 3—5, у нагревательных нечей 4—5, у мартеновских печей 8-12. [c.313]
В регенеративных колодцах тепло отходящих продуктов горения используется для подогрева в регенерат ях газа и воздуха перед их сжиганГ колодце. Устройство и работа регс торов нагревательных колодцев и много общего с устройством и работ регенераторов мартеновских печей. [c.235]
mash-xxl.info
Устройство мартеновской печи
Дом Устройство мартеновской печипросмотров — 80
Мартеновский процесс выплавки стали
Тема 8. Технология производства стали
Начало существования мартеновского процесса относится к 1864 году, его автор Пьер Мартен.
Мартеновский процесс осуществляется на поду пламенной отражательной печи, оснащенной регенеративными насадками. В печь загружают шихту (чугун, лом и другие компоненты), которая под воздействием факела сжигаемого топлива нагревается и постепенно плавится.
После расплавления в ванну вводят различные добавки с тем, чтобы получить металл крайне важного состава и температуры и затем готовый металл выпускают в разливочный ковш.
Благодаря возможности иметь в шихте мартеновской плавки дешевый лом, себестоимость мартеновской стали была ниже, чем в конвертерных процессах и даже в электросталеплавильных печах. Такое положение сохранялось до середины XX столетия, когда появился кислородно-конвертерный процесс и стали применять кислород для интенсификации электроплавки стали, а широкое применение методов внепечной (ковшевой) металлургии обеспечило высокое качество металла, выплавляемого и в конвертерных и электросталеплавильных цехах.
В СССР мартеновский процесс был доминирующим, в связи с этим в России сохранился указанный способ выплавки стали, хотя доля его постоянно сокращается.
Схема мартеновской печи представлена на рис. 8.1‑1 в положении подачи топлива и воздуха с правой стороны и отводов продуктов сгорания через левую головку и регенератор.
Проходя через предварительно нагретую насадку правого регенератора, воздух нагревается до 1100…1200оС и через головку вводится в рабочее пространство и одновременно через эту же головку в печь подается топливо (газ, мазут). В результате сгорания топлива образуется факел с температурой 1900…2000оС, интенсивно отдающий (преимущественно излучением) тепло ванне и внутренней поверхности ограждения рабочего пространства.
Высоконагретые продукты сгорания уходят через левую головку в насадку левого регенератора, отдавая ей свое тепло, а затем через систему дымовых каналов и трубу выбрасываются в атмосферу. Через определенный промежуток времени осуществляется автоматическое реверсирование пламени, чтобы поддержать максимальный КПД регенерации тепла и избежать перегрева насадок регенераторов. По конструкции мартеновские печи бывают стационарные и качающиеся, наибольшее распространение получили стационарные печи. По составу футеровки пода их разделяют на основные и кислые.
Рабочее пространство мартеновской печи ограждено сводом, подом и стенками. Окна для загрузки шихты и заливки чугуна расположены в передней стенке. Материал для футеровки выбирают в зависимости от типа процесса и используют либо динас или магнезитохромит.
Торцы рабочего пространства ограничены головками, предназначенными для формирования жесткого, настильного факела, обеспечивающего наибольшую полноту сгорания топлива. При работе на высококаларийном топливе, нужнобность в подогреве его отпадает, конструкция головок (одноканальная) упрощается, и печь оснащается только одним регенератором с каждой стороны для подогрева воздуха. При такой схеме работы регенераторов – один охлаждается, а другой – нагревается до перекидки факела.
Важным элементом мартеновской печи является подина, на которой осуществляют нагрев, расплавление и рафинирование металла. Выбор футеровки печи определяется характеристикой шлаков. Учитывая зависимость оттипа шлака подину выполняют или из базовых или из кислых футеровочных материалов. Устройство подов мартеновской печи представлено на рис. 8.1‑2.
Своды мартеновских печей можно изготавливать как из кислых, так и из базовых огнеупоров. В практике чаще всего используют магнезитохромитовый кирпич, который обладает высокой термостойкостью и выдерживает до 1000 плавок. Конструкция свода распорно − подвесная.
Мартеновская печь – агрегат реверсивного действия, в котором направление движения газов в системе печи периодически меняется. Для этого в дымоходах и воздухопроводах устанавливают систему шиберов, клапанов, задвижек, объединенных общим названием «перекидные клапаны». Операция «перекидки клапанов» осуществляется в автоматическом режиме.
У каждой мартеновской печи есть своя дымовая труба. Высоту трубы рассчитывают таким образом, чтобы создаваемая ее тяга (разрежение) была достаточной для преодоления сопротивления движения дымовых газов на всем пути. Высота трубы достигает 100 м.
Многие элементы печей охлаждают с помощью воды. Современные большегрузные печи потребляют более 400 м3 воды в один час. С охлаждающей водой теряется от 15 до 25 % общего количества тепла, вводимого в печь. Для уменьшения расхода воды на охлаждение используют испарительное охлаждение, в котором химочищенную воду нагревают до 100 оС и более. Τᴀᴋᴎᴍ ᴏϬᴩᴀᴈᴏᴍ, сокращается расход воды на охлаждение печи и попутно можно получать до 10 т пара в час для технологических и энергетических целей.
Топливом для мартеновских печей служит высококалорийный природный газ, при сжигании образующий малосветящийся факел. Для обеспечения светящегося факела одновременно с газом подают мазут (до 30 %) от тепловой нагрузки. Применение мазута обеспечивает также настильность (жесткость) факела, обладающего высокой излучательной способностью при температуре 1800–1900 оС.
Отходящие газы могут захватывать из рабочего пространства капли шлака и пыли, для улавливания которых печь оснащается с каждой стороны шлаковиками. Крупные частицы пыли осаждаются в шлаковике, а более мелкая пыль уносится в регенератор. Насадки регенераторов забиваются пылью и их периодически продувают сжатым воздухом или промывают водой под давлением. К концу кампании насадки регенераторов оказываются сильно занесенными пылью и зашлакованными. Для повышения срока службы регенераторов верхние ряды насадок выкладывают из более термостойкого магнезитохромитового или форстеритового кирпича, а нижние ряды выполняют из шамотного огнеупора.
Отходящие газы, проходя через насадку регенератора отдают ей свое тепло (температура газов на входе в насадку составляет 1500–1600 оС) и из поднасадочного пространства уходят с температурой ~ 800 оС, направляются к котлу-утилизатору, где дополнительно охлаждаются, проходят через газоочистку и далее уходят к дымовой трубе.
oplib.ru
Производство стали в мартеновских печах. устройство и работа мартеновской печи / дальский 2002, с. 36; 77 – с. 46 /
1.8. Производство стали в мартеновских печах.
Устройство и работа мартеновской печи /Дальский 2002, с. 36; 77 – с. 46/. Мартеновская печь (рис. 1.8) — это пламенная отражательная регенеративная печь. Она имеет рабочее плавильное пространство, ограниченное снизу подиной 12, сверху сводом 7, а с боков передней 5 и задней 10 стенками.
Рис. 1.8. Схема мартеновской печи
Подина имеет форму ванны с откосами по направлению к стенкам печи. Футеровка печи может быть основной и кислой. Если в процессе плавки стали в шлаке преобладают кислотные окислы, процесс называется кислым мартеновским процессом, а если преобладают основные окислы — основным. При высоких температурах шлаки могут взаимодействовать с футеровкой печи, разрушая ее. Для уменьшения этого взаимодействия необходимо, чтобы при кислом процессе футеровка печи была кислой, а при основном — основной. Футеровку кислой мартеновской печи изготовляют из динасового кирпича, а верхний рабочий слой подины набивают из кварцевого песка. Футеровку основной мартеновской печи выполняют из магнезитового кирпича, на который набивают магнезитовый порошок. Свод мартеновской печи не соприкасается со шлаком, поэтому его делают из динасового или магнезитохромитового кирпича независимо от типа процесса, осуществляемого в печи. В передней стенке печи находятся загрузочные окна 4 для подачи шихтовых материалов (металлической шихты, флюса) в печь. В задней стенке печи расположено сталевыпускное отверстие 9 для выпуска готовой стали.
Размеры плавильного пространства зависят от емкости печи. В нашей стране работают мартеновские печи емкостью 20…900 т жидкой стали. Важной характеристикой рабочего пространства является площадь пода печи, которую условно подсчитывают на уровне порогов загрузочных окон. Например, для печи емкостью 900 т площадь пода составляет 115 м2. С обоих торцов плавильного пространства расположены головки печи 2. Головки печи служат для смешивания топлива с воздухом и подачи этой смеси в плавильное пространство. В качестве топлива в мартеновских печах используют природный газ или мазут.Для подогрева воздуха при работе на газообразном топливе печь имеет два регенератора 1. Регенератор представляет собой камеру, в которой размещена насадка — огнеупорный кирпич, выложенный в клетку. Температура отходящих из печи газов 1500…1000 °С. Попадая в регенераторы, они нагревают насадку до 1250…1280 °С, а охлажденные до 500…600 °С газы уходят из печи через дымовую трубу. Затем через один из регенераторов, например правый, в печь подают воздух, который, проходя через насадку, нагревается до 1100…1200 °С. Нагретый воздух поступает в головку печи, где смешивается с топливом; на выходе из головки образуется факел 7, направленный на шихту 6. Отходящие газы проходят через противоположную головку (правую), очистные устройства (шлаковики) для отделения мелких частиц шлака и пыли, уносимых из печи потоком газов, и направляются во второй (левый) регенератор, нагревая его насадку. Охлажденные газы покидают печь через дымовую трубу 8 высотой до 120 м. После охлаждения насадки правого регенератора до определенной температуры происходит автоматическое переключение клапанов, и поток газов в печи изменяет направление: через нагретый левый регенератор и головку в печь поступает воздух, а правый нагревается теплотой отходящих газов.
Температура факела пламени достигает 1750…1800 °С. Факел нагревает рабочее пространство печи и шихту. Факел имеет окислительный характер, что создает условия для окисления примесей шихты на протяжении всей плавки.
Разновидности мартеновского процесса. При плавке в мартеновских печах составляющими металлической шихты могут быть стальной скрап, жидкий и твердый чугуны. В зависимости от состава металлической шихты, используемой при плавке, различают следующие разновидности мартеновского процесса:
скрап-процесс, при котором основной частью шихты является
стальной скрап; применяют на металлургических заводах, где нет доменных
печей, но расположенных в крупных промышленных центрах, где много
металлолома; кроме скрапа в состав шихты входит 25…46 % чушкового пере
дельного чугуна;скрап-рудный процесс, при котором основная часть
шихты состоит из жидкого чугуна (55…75 %), а твердая составляющая ших
ты — скрап и железная руда; этот процесс чаще применяют на металлурги
ческих заводах, имеющих доменные печи.
Наибольшее количество стали получают в мартеновских печах с основной футеровкой, так как в этом случае возможно переделывать в сталь различные шихтовые материалы, в том числе и с повышенным содержанием фосфора и серы. При этом используют обычно скрап-рудный процесс, как наиболее экономичный.
Кислым мартеновским процессом выплавляют качественные стали. Стали, выплавляемые в кислых мартеновских печах, содержат значительно меньшее количество растворенных газов (водорода и кислорода), неметаллических включений, чем сталь, выплавленная в основной печи. Поскольку в печах с кислой футеровкой нельзя навести основный шлак, способствующий удалению фосфора и серы, то при плавке в кислой печи применяют металлическую шихту с низким содержанием этих составляющих. Благодаря этому кислая сталь имеет более высокие показатели механических свойств, особенно ударной вязкости и пластичности, и ее используют для ответственных деталей: коленчатых валов крупных двигателей, роторов мощных турбин, шарикоподшипников, стволов орудий и т. д.
Плавка стали скрап-рудным процессом в основной мартеновской печи происходит следующим образом. После осмотра и ремонта пода печи с помощью завалочной машины загружают железную руду и известняк и после их прогрева подают скрап. По окончании прогрева скрапа в печь заливают жидкий чугун, который, проходя через слой скрапа, взаимодействует с железной рудой. В период плавления за счет окислов железа руды и скрапа интенсивно окисляются примеси чугуна:
2Fe2O3+3Si=3SiO2+4Fe;
2Fe2O3+3Mn=3MnO+2Fe;
5Fe2O3+6P=3Р2O5+10Fe;
Fe2O3+3C=3CO+2Fe
Окислы SiO2, MnO, Р2O5, а также CaO без извести образуют шлак с высоким содержанием MnO и FeO, а выделяющаяся окись углерода (СО) вспенивает шлак, который выпускают из печи в шлаковые чаши. Образование и спуск шлака продолжаются почти до полного расплавления шихты. В этот период плавления полностью окисляется кремний и почти полностью марганец и большая часть углерода, а также интенсивно удаляется фосфор.
Завалка шихты, заливка чугуна и плавление протекают медленно при большом расходе топлива. Для ускорения плавления и окисления примесей после окончания заливки чугуна ванну продувают кислородом, подаваемым в печь через водоохлаждаемые фурмы, которые опускаются в отверстия в своде печи. При этом выделяется значительное количество теплоты, металл интенсивно перемешивается, что позволяет в 2…3 раза сократить период плавления, уменьшить расход топлива и железной руды.
По окончании расплавления шихты наступает период кипения ванны. Для этого после расплавления шихты в печь подают некоторое количество железной руды или продувают ванну кислородом, подаваемым по трубам 3 (см. рис. 1. 8). Углерод, содержащийся в металле, начинает интенсивно окисляться, образуется окись углерода. В это время отключают подачу топлива и воздуха в печь, давление газов в плавильном пространстве печи падает и выделяющаяся окись углерода вспенивает шлак. Шлак начинает вытекать из печи через порог завалочного окна в шлаковые чаши. Эта операция называется скачиванием шлака. Вместе со шлаком удаляется значительное количество фосфора и серы. После этого вновь включают подачу топлива и воздуха, давление газов в печи возрастает, шлак перестает вспениваться, и его скачивание прекращается.
Для более полного удаления из металла фосфора и серы в печи наводят новый шлак путем подачи на зеркало металла извести с добавлением боксита или плавикового шпата для уменьшения вязкости шлака.
Окислительная атмосфера в печи способствует образованию на поверхности шлак — газ окиси железа (Fе203). Окись железа диффундирует через шлак и на поверхности шлак-металл реагирует с жидким железом, восстанавливаясь до FеО, который также отдает свой кислород металлу. Поступивший в металл кислород взаимодействует с углеродом металла с образованием окиси углерода, которая выделяется в виде пузырьков, вызывая кипение ванны. Поэтому для кипения ванны шихта должна содержать избыток углерода (на 0,5…0,6 %) сверхзаданного в выплавляемой стали. Эта реакция является главной в мартеновской плавке, так как в процессе кипения ванны металл обезуглероживается, выравнивается его температура по объему ванны, частично удаляются из него газы и неметаллические включения, увеличивается поверхность соприкосновения металла со шлаком и облегчается удаление фосфора и серы из металла.
Начиная с расплавления шихты, до выпуска металла из печи, регулярно отбирают пробы металла и шлака для анализа химического состава. Процесс кипения считают окончившимся, если содержание углерода в металле по результатам анализов соответствует заданному, а содержание серы и фосфора минимально.
После этого приступают к раскислению металла. Металл раскисляют в два этапа: в период кипения, путем прекращения подачи руды в печь, вследствие чего раскисление происходит за счет углерода металла и подачи в ванну раскислителей — ферромарганца, ферросилиция, алюминия и окончательно раскисляют алюминием и ферросилицием в ковше при выпуске стали из печи. После отбора контрольных проб плавку выпускают из печи через сталевыпускное отверстие в задней стенке. По желобу сталь сливается в сталеразливочный ковш.
При выплавке легированных сталей легкоокисляющиеся легирующие элементы вводят в ванну после раскисления перед выпуском металла из печи.
Основные технико-экономические показатели. Эти показатели производства стали в мартеновских печах следующие: производительность в сутки (т/м2-сутки), и расход топлива на тонну выплавленной стали (кг/т). Средний съем стали с 1 м2 площади пода в сутки составляет ~ 10 т/м2 в сутки, а расход условного топлива от 120 кг/т для обычной плавки до 80 кг/т для плавки с применением кислорода.
Технико-экономические показатели работы мартеновских печей можно повысить путем применения печей повышенной емкости, улучшения их конструкции, интенсификации технологического процесса плавки. Увеличение емкости печей способствует более полному использованию их тепловой мощности. В нашей стране эксплуатируют экономически оптимальные мартеновские печи с ванной емкостью до 500-600 т.
Все более широкое применение находят двухванные мартеновские печи, позволяющие полнее использовать теплоту отходящих газов (рис. 1.9).
Рис. 1.9. Схема двухванной мартеновской печи /Кнорозов, с. 50/
В этих печах имеются две ванны: в то время как в одной из них протекают процессы, требующие большой затраты теплоты (завалка, прогрев, плавление), в другой происходит продувка ванны кислородом; при этом возникающий избыток теплоты с отходящими газами используется в первой ванне. К моменту выпуска металла из одной ванны печи, в другой начинают продувку, а выделяющиеся газы направляют в первую ванну, в которой после выпуска начинают завалку шихты. Окись углерода, выделяющаяся при продувке ванны, догорает над шихтой другой ванны, благодаря чему шихта быстро нагревается и плавится. В таких печах топлива расходуется в 2…3 раза меньше, чем в обычных мартеновских печах, резко сокращается расход огнеупоров, повышается производительность печи.
Процесс плавки интенсифицируют широким применением кислорода, что повышает температуру в печи, ускоряет процесс окисления примесей, уменьшает продолжительность плавки и повышает производительность печи (на 20…25 %), снижает расход топлива. Широко применяют кислородный процесс, используя природный малосернистый высококалорийный газ, что снижает содержание серы в стали. Существенно повысить производительность мартеновских печей можно, применяя качественно подготовленные шихтовые материалы с минимальным содержанием вредных примесей, а также автоматизируя контроль и управление ходом мартеновской плавки. Более полное использование мартеновских печей достигается высокой организацией труда при проведении плавки.
1.9. Производство стали в электропечах /Дальский 77, с. 54/
Электроплавильные печи. Эти печи имеют преимущества по сравнению с другими плавильными агрегатами. В электропечах можно получить высокую температуру, создавать окислительную, восстановительную, нейтральную атмосферу или вакуум. В этих печах можно выплавлять сталь и сплавы любого состава, более полно раскислить металл с образованием минимального количества неметаллических включений—продуктов раскисления. Поэтому электропечи используют для выплавки конструкционных сталей ответственного назначения, высоколегированных, инструментальных, коррозионно-стойких (нержавеющих) и других специальных сталей и сплавов.
Для плавки смтали используются дуговыми и индукционные электропечи.
Дуговая электросталеплавильная печь. В этих печах в качестве источника теплоты используют электрическую дугу, возникающую между электродами и металлической шихтой. Дуговая электросталеплавильная печь (рис. 1. 10) питается трехфазным переменным током и имеет три цилиндрических электрода 9, изготовленных из графитированной массы.
Электрический ток от трансформатора гибкими кабелями 7 и медными шинами подводится к электрододержателям 8, а через них к электродам 9. Между электродами и металлической шихтой 4 возникает электрическая дуга, электроэнергия превращается в теплоту, которая передается металлу и шлаку излучением. Рабочее напряжение 180…600 В, сила тока 1…10 кА. Во время работы печи длина дуги регулируется автоматически путем вертикального перемещения электродов. Печь имеет стальной сварной кожух 3. Кожух печи изнутри футерован теплоизоляционным и огнеупорным кирпичом 7, который может быть основным (магнезитовый, магнезитохромитовый) или кислым (динасовый). Подина 12 печи набивается огнеупорной массой. Плавильное пространство ограничено стенками 5, подиной 12 и сводом 6, изготовляемым также из огнеупорного кирпича и имеющим отверстия для прохода электродов. В стенках печи имеются рабочее окно 10 для управления ходом плавки и летка для выпуска готовой стали по желобу 2 в ковш.
Рис. 1.10. Схема дуговой электрической плавильной печи
Печь загружают при снятом своде. Механизмом 11 печь может наклоняться в сторону загрузочного окна и летки. Емкость дуговых электропечей 0,5—400 т. В металлургических цехах обычно используют дуговые электропечи с основной футеровкой, а в литейных цехах — с кислой.
Основная дуговая печь. Применяют два вида технологии плавки в дуговой основной печи: на шихте из легированных отходов (методом переплава) и на углеродистой шихте (с окислением примесей).
Плавку на шихте из легированных отходов с низким содержанием фосфора проводят без окисления примесей. Шихта для такой плавки, кроме пониженного содержания фосфора, должна иметь меньшее, чем в выплавляемой стали, количество марганца и кремния. По сути это переплав. Однако в процессе плавки за счет кислорода некоторые примеси (алюминия, титана, кремния, марганца, хрома) окисляются. Кроме того, шихта может содержать окислы. Поэтому после расплавления шихты металл раскисляют, удаляют серу, наводят основный шлак, при необходимости науглероживают и доводят металл до заданного химического состава. Раскисляют ферросилицием, алюминием, молотым коксом. При этом окислы легирующих элементов восстанавливаются и переходят из шлака в металл. Таким способом плавки получают легированные стали из отходов машиностроительных заводов.
Плавку на углеродистой шихте чаще применяют для производства конструкционных углеродистых сталей. Эту плавку проводят за два периода: окислительный и восстановительный. После заправки печи, удаления остатков металла и шлака предыдущей плавки, исправления поврежденных мест футеровки в печь загружают шихту: стальной лом (до 90 %), чушковый передельный чугун (до 10 %), электродный бой или кокс для науглероживания металла и 2…3 % извести. По окончании завалки шихты электроды опускают вниз и включают ток; шихта под электродами плавится, металл накапливается на подине печи. Во время плавления шихты начинается окислительный период плавки: за счет кислорода воздуха, окислов шихты и окалины окисляется кремний, марганец, углерод, железо. Вместе с окисью кальция, содержащейся в извести, окислы этих элементов образуют основный железистый шлак, способствующий удалению фосфора из металла.
После нагрева металла и шлака до 1500…1540 °С в печь загружают руду и известь. Содержащийся в руде кислород интенсивно окисляет углерод и вызывает кипение ванны жидкого металла за счет выделяющихся пузырьков окиси углерода. Шлак вспенивается, уровень его повышается; для выпуска шлака печь наклоняют в сторону рабочего окна и он стекает в шлаковую чашу. Кипение металла ускоряет нагрев ванны, удаление из металла газов, неметаллических включений, способствует удалению фосфора. Шлак удаляют, руду и известь добавляют 2…3 раза. В результате содержание фосфора в металле снижается до 0,01 % и одновременно за счет образования окиси углерода при кипении уменьшается и содержание углерода. Когда содержание углерода становится меньше заданного на 0,1 %, кипение прекращают и полностью удаляют из печи шлак. Этим заканчивается окислительный период плавки.
Восстановительный период плавки включает раскисление металла, удаление серы и доведение химического состава до заданного. После удаления окислительного шлака в печь подают ферромарганец в количестве, обеспечивающем заданное содержание марганца в стали, а также производят науглероживание, если выплавляют высокоуглеродистые стали (до 1,5 % С). Затем в печь загружают флюс, состоящий из извести, плавикового шпата и шамотного боя. После расплавления флюсов и образования шлака в печь вводят раскислительную смесь, состоящую из извести, плавикового шпата, молотого кокса и ферросилиция. Молотый кокс и ферросилиций вводят в порошкообразном виде. Они очень медленно проникают через слой шлака. В шлаке восстанавливается закись железа:
FeO+C=Fe+CO;
2FeO+Si=Fe+SiO2
При этом содержание закиси железа в шлаке снижается и она из металла согласно закону распределения начинает переходить в шлак. Этот процесс называют диффузионным раскислением стали. Раскислительную смесь вводят в печь несколько раз. По мере раскисления и понижения содержания FеО цвет шлака изменяется и он становится почти белым. Раскисление под белым шлаком длится 30…60 мин.
Во время восстановительного периода сера удаляется из металла, что объясняется высоким (до 55…60 %) содержанием СаО в белом шлаке и низким (менее 0,5 %) содержанием FеО. Это способствует интенсивному удалению серы из металла:
FeS+CaO=CaS+FeO.
По ходу восстановительного периода берут пробы для определения химического состава металла. При необходимости в печь вводят ферросплавы для достижения заданного химического состава металла. Когда достигнуты заданные состав металла и температура, выполняют конечное раскисление стали алюминием и силикокальцием. После этого следует выпуск металла из печи в ковш.
При выплавке легированных сталей в дуговых печах в сталь вводят легирующие элементы в виде ферросплавов. Порядок ввода определяется сродством легирующих элементов к кислороду. Никель, молибден обладают меньшим сродством к кислороду, чем железо, и их вводят в период плавления или в окислительный период. Хром легко окисляется и его вводят в восстановительный период; кремний, ванадий, титан — перед выпуском металла из печи в ковш, так как они легко окисляются.
Технико-экономические показатели. Эти показатели плавки в дуговых печах зависят от емкости печи и технологии плавки. Расход электроэнергии на 1 т стали зависит от емкости печи. С увеличением емкости печи расход электроэнергии на 1 т выплавленной стали уменьшается. Например, для печи емкостью 25 т он составляет 750 кВт -ч, а для печи емкостью 100 т —575 кВт-ч. Расход графитированных электродов составляет 6—9 кг/т выплавленной стали.
Технико-экономические показатели работы дуговых печей и качество металла повышаются за счет интенсификации плавки, увеличения емкости печи, мощности трансформаторов, механизации загрузки шихты, применения электромагнитного перемешивания металла. Значительной эффективности можно достигнуть при выплавке легированных сталей, применяя дуплекс-процесс: выплавка стали в основном кислородном конвертере, а рафинирование и доводка по химическому составу в электропечи. Эффективным является применение кислорода для продувки ванны стали в окислительный период, что интенсифицирует процесс плавки, увеличивает на 15…20 % производительность печи, снижает расход электроэнергии и экономит легирующие добавки.
Электроиндукционные печи. Индукционная тигельная сталеплавильная печь (рис. 1.11) состоит из водоохлаждаемого индуктора 5, внутри которого находится тигель 4 с металлической шихтой.
Через индуктор проходит однофазный переменный ток повышенной частоты (500…1000 кГц). Ток создает переменный магнитный поток, пронизывая куски металла в тигле, наводит в них мощные вихревые токи (Фуко), нагревающие металл 1 до расплавления и необходимых температур перегрева.
Тигель может быть изготовлен из кислых (кварцит) или основных (магнезитовый порошок) огнеупорных материалов. Емкость тигля от 60 до 25 т. Ток к индуктору подводится от генератора высокой частоты -лампового (лабораторные печи) или машинного. Для уменьшения потерь теплоты при плавке можно применить съемный свод 2. Индукционные печи имеют преимущества перед дуговыми: 1) в них отсутствует электрическая дуга, что позволяет выплавлять металлы с низким содержанием углерода, газов и малым угаром элементов, это особенно важно при выплавке высококачественных сталей и сплавов;
Рис. 1.11. Схема индукционной тигельной электрической плавильной печи
2) при плавке в металле возникают электродинамические силы, которые перемешивают металл в печи и способствуют выравниванию химического состава, всплыванию неметаллических включений;
3) индукционные печи имеют небольшие габаритные размеры, что позволяет помещать их в закрытые камеры, в которых можно создавать любую атмосферу, а также вакуум. Однако эти печи имеют малую стойкость футеровки, шлак в них нагревается теплотой металла и температура его недостаточна для интенсивного протекания металлургических процессов между металлом и шлаком.
Обычно в индукционных печах выплавляют сталь и сплавы или из легированных отходов методом переплава, или из чистого шихтового железа и скрапа с добавкой ферросплавов методом сплавления. В большинстве случаев печи имеют кислую футеровку. Основную футеровку используют для выплавки сталей и сплавов с высоким содержанием марганца, никеля, титана и алюминия.
При загрузке тщательно подбирают химический состав шихты в соответствии с заданным, так как плавка протекает быстро, и полного анализа металла по ходу плавки не делают. Поэтому необходимое количество ферросплавов (ферровольфрам, ферромолибден, феррохром, никель) для получения заданного химического состава металла загружают на дно тигля вместе с остальной шихтой. После расплавления шихты на поверхность металла загружают шлаковую смесь. Основное назначение шлака при индукционной плавке — уменьшить тепловые потери металла, защитить его от насыщения газами, уменьшить угар легирующих элементов. При плавке в кислой печи после расплавления и удаления плавильного шлака наводят шлак из боя стекла (SiO2). Металл раскисляют ферросилицием, ферромарганцем и алюминием перед выпуском его из печи.
refdb.ru
Главнейшие конструктивные элементы мартеновских печей
На рис. 2 показана современная основная 500-т мартеновская печь, работающая на смешанном газе.
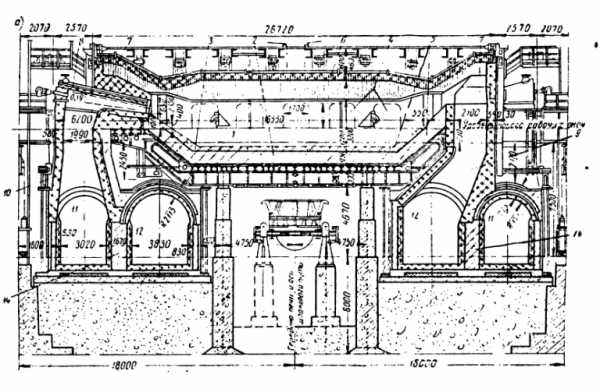
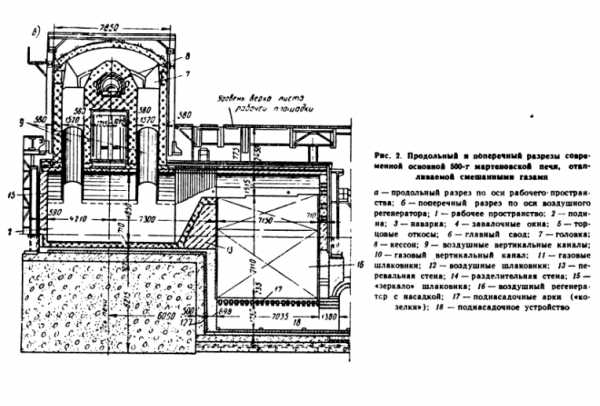
Рабочим пространством называется часть мартеновской печи, в которой ведутся сжигание топлива и плавка стали. Огнеупорная кладка его включает в себя подину, стены и главный свод.
Подина является нижним основанием или дном рабочего пространства. Она выполняется из огнеупорных материалов, имеет разную толщину в зависимости от емкости (веса садки) печи и покрывается сверху наваркой.
Задняя стена рабочего пространства выполняется с наклоном 45—55°. При таком наклоне наносимые на стену заправочные материалы хорошо удерживаются и не сползают с нее. В задней стене устраивают сталевыпускное и шлаковое отверстия и отверстие для заливки чугуна. В связи с тем, что задняя стена имеет большую площадь, через нее теряется много тепла, для предотвращения чего она должна иметь хорошую теплоизоляцию.
Передняя стена у современных мартеновских печей для увеличения ее стойкости делается также наклонной. В передней стене расположены загрузочные окна, которые разделяются между собой простенками или столбиками. Верх загрузочных окон раньше оформлялся арками. В настоящее время в связи с частыми разрушениями арок от ударов завалочных машин и в результате оплавления применяется безарочная конструкция завалочных окон. В этом случае пяты главного свода опираются на охлаждаемые балки. Для увеличения стойкости простенков завалочные окна обрамляются охлаждаемыми металлическими амбразурами или рамами, плотно прилегающими к кладке простенков. Загрузочные окна закрываются охлаждаемыми стальными заслонками, футерованными изнутри огнеупорным кирпичом или жаростойким бетоном; посередине заслонок имеются отверстия для наблюдения за работой печи.
С торцовых сторон ванна рабочего пространства ограничена откосами, выше которых расположены головки.
Главный свод является элементом, перекрывающим рабочее пространство. По своей конструкции своды могут быть распорными (на печах малой емкости), распорно-подвесными и подвесными. Последний тип сводов применяется очень редко. Распорно-подвесной свод является наиболее распространенным видом главного свода мартеновской печи. Этот свод набирается кольцами из прямых и клиновых кирпичей; через систему шты-рей и удлиненных стальных пластин свод подвешен к металло-конструкциям каркаса печи. Подвески фиксируют положение свода при его охлаждении. Для повышения стойкости распорно-подвесного свода его делают ребристым, в этом случае часть колец свода делают из кирпича большого размера (по длине).
В современных мартеновских печах распорные усилия от главного свода воспринимаются охлаждаемыми подпятовыми балками. Свод имеет небольшие наклонные участки (пережимы) при подходе к головкам печи.
Огнеупорная кладка рабочего пространства заключена в современных печах в жесткий стальной каркас, состоящий из системы мощных колонн, балок и облицовочных плит.
Головками называются конструктивные элементы мартеновской печи, расположенные по торцам рабочего пространства и предназначенные для смешивания топлива с подогретым воздухом, правильного направления факела, а также отвода продуктов горения из рабочего пространства. В головках проис-ходит воспламенение топлива. Головки должны обеспечивать правильное и наиболее рациональное направление факела, при котором максимум тепловой энергии должен передаваться ванне печи. Направление пламени на ограждающие конструкции рабочего пространства должно быть исключено.
Мартеновская печь имеет две головки. В то время как из одной головки в рабочее пространство поступает факел пламени, вторая (противоположная) головка отводит продукты горения.
Для современных мартеновских печей, работающих на по-догретом газе, приняты и наиболее распространены головки, в. которых воздух с боков и сверху полукольцом окружает струю газа, обеспечивая наиболее полное их смешение. Газовый пролет головки представляет из себя водоохлаждаемый стальной кессон, футерованный изнутри и снаружи огнеупорным кирпичом.
Для погашения усилий от теплового расширения, предотвращения трещин и обеспечения устойчивости огнеупорной кладки головок и верхней части вертикальных каналов они заключаются в стальной каркас.
Вертикальные каналы мартеновской печи предназначены для подачи подогретых в регенераторах газа и воздуха в головки печи и отвода продуктов горения из рабочего пространства.
В поперечном сечении они представляют собой каналы прямоугольной формы, выложенные из огнеупорного кирпича, опирающиеся на своды шлаковиков, в которых устроены отверстия, соответствующие по размерам сечению вертикальных каналов.
В ряде печей на уровне рабочей площадки предусмотрены дополнительные опоры для стен вертикальных каналов, выпол-ненные из литых стальных конструкций. Устройство дополни-тельных опор, помимо разгрузки свода шлаковиков, позволяет вести в два яруса кладку каналов при строительстве и ремонте печей, что значительно сокращает срок выполнения работ.
Для увеличения срока службы вертикальных каналов необходимо, чтобы они имели достаточное сечение и достаточную толщину стенок. Проникание газа или воздуха из одного канала в другой не допускается, поэтому кладка разделяющей стены между газовым и воздушными каналами должна быть выполнена особенно тщательно.
Шлаковика ми называются камеры, служащие для сбора частиц пыли и шлака, увлекаемых продуктами горения при выходе их из рабочего пространства. Шлаковики расположены под вертикальными каналами. Для уменьшения скорости движения отходящих газов и создания условий осаждения пыли и частиц шлака поперечное сечение шлаковиков делается больше поперечного сечения вертикальных каналов. Объем шлаковиков должен быть достаточным для скопления уносимой пыли и шлаков в течение всего межремонтного срока работы печи. Если в качестве топлива для мартеновской печи применяется мазут, природный
или попутный газ, то по обеим сторонам печи устраивается по одному воздушному шлаковику, чаще всего с плоским подвесным сводом, в остальных случаях с каждой стороны печи устраивается по два шлаковика — воздушный и газовый — с устройством между ними разделительной стены и перекрытием их арочными сводами.
Камеры шлаковиков имеют прямоугольную форму в плане; выкладываются из огнеупорного крипича и
ограждаются с трех сторон глухими стенами, а с четвертой стороны — перевальной стеной, отделяющей шлаковик от регенератора (снизу — подиной, а сверху — сводом с отверстиями для вертикальных каналов). Стена со стороны разливочного пролета (зеркало) закладывается без перевязки с продольными стенами
и разбирается при каждом холодном ремонте для уборки шлака и ремонта кладки.
Для облегчения труда и сохранения стен камер шлаковиков от механических повреждений при уборке шлака на некоторых заводах в конструкциях шлаковиков применяют дополнительные устройства.
Наиболее простым из них является устройство ложных стенок (рис. 3).
Поперечныйразрез шлаковика
/ — продольные стены шлаковика; 2 —
ложная стенка; 3 —
засыпка песком
В других случаях применяют устройство выкатных подов шлаковиков на шарах или роликах с возведенными на подах стенками. Удаление шлака при таких условиях осуществляется выкаткой пода со скопившимся на нем шлаком с помощью разливочного мостового крана. Применение для облицовки стен шлаковиков хромомагнезитового кирпича значительно упрощает задачу уборки шлака, так как в этом случае шлак, как правило, получается сравнительно рыхлым.
Регенераторами называются конструктивные элементы мартеновской печи, предназначенные для отбора тепла от отходящих продуктов горения с последующей передачей его газу и воздуху, направляемым к месту горения — рабочему пространству.
В зависимости от вида применяемого топлива с каждой стороны печи может быть по одному регенератору — воздушному или по два генератора — воздушному и газовому с соответствующим устройством разделительной стены и сводов.
Регенератор представляет собою камеру, заполненную насадкой, которая и регенерирует тепло отходящих газов.
Камеры регенераторов, так же как и шлаковики, имеют в плане прямоугольную форму и выкладываются из огнеупорного кирпича. Сверху камеры перекрыты сводом, внизу имеют поди-ну, а с боков ограждены стенами и со стороны шлаковика перевальной стеной.
Для получения насадки требуемого объема камеры регенераторов заглубляются ниже уровня пола примерно на 2/3 высоты.
Торцовая стена камеры, представляющая собой большое ремонтное окно, выкладывается без перевязки с продольными стенами и разбирается при холодном ремонте для частичной или полной смены насадок и ремонта других частей регенера-торов. В продольных наружных стенах камер устраиваются не-большие ремонтные окна, предназначенные для ускорения работ по подаче материалов, уборке отходов при сменах насадок и охлаждения насадок перед разборкой.
Перевальная стена, с одной стороны, служит ограждением насадки регенератора, а с другой,— торцовым элементом, организующим выход отходящих газов из шлаковика в верхней его части.
Огнеупорная кладка стен шлаковиков и регенераторов, начиная с отметки низа кладки шлаковиков, заключается в об-щий стальной каркас с кожухом. Каркас воспринимает усилия, возникающие в кладке в результате ее нагревания, чем обеспе-чивает устойчивость кладки, а кожух обеспечивает газонепро-ницаемость наружных стен. Газонепроницаемость сводов шлаковиков и регенераторов повышается за счет нанесения газоуплотнительных обмазок.
Насадки современных мартеновских печей представляют собой систему вертикальных каналов, выложенных из огнеупорного кирпича и размещенных в регенераторах.
Насадки через поднасадочный опорный ряд, набираемый из специального фасонного кирпича, опираются на прочны.е арки, сложенные из крупных фасонных огнеупорных изделий. Арки в свою очередь опираются на продольные стенки каналов, выло-женные на подине камеры регенераторов. Система стенок и поддерживаемых ими арок называется поднасадочным устройством, высота которого должна обеспечивать свободный проход пропускаемых через насадки отходящих продуктов горения с учетом отложения в поднасадочном устройстве части пыли и сажи, выносимых из рабочего пространства печи и не осевших в шлаковике.
Очистка насадки от загрязнений (пыль, сажа и пр.) произ-водится продувкой ее сжатым воздухом или паром.
Насадка должна иметь достаточно большую, омываемую газами поверхность нагрева и малое сопротивление решетки для прохода газов и обладать необходимой теплоемкостью.
Боровами мартеновской печи называются система кана-лов, выполненных в основном из обыкновенного глиняного кирпича и футерованных внутри огнеупорным кирпичом, предназначенных для отвода продуктов горения от регенераторов к дымовой трубе непосредственно или через котел-утилизатор. Часть боровов (от клапанов до регенераторов) выполняют и другие функции — подачу топливного газа и воздуха или (в зависимости от применяемого вида топлива) только воздуха в регенераторы.
Выполнение этих функций, а также регулирование тяги обеспечивается с помощью системы клапанов и шиберов, имеющих общее наименование — перекидные устройства.
Перевод системы клапанов и шиберов из одного положения в другое производится автоматически с помощью электроприво-дов по получении импульсов от соответствующих регулирующих приборов. Перекидные устройства должны обеспечивать герметичность при перекрытии каналов и плавное движение газов без резких поворотов.
Для удобства обслуживания мартеновских печей и создания вокруг них свободной территории борова устраиваются подземными с заглублением верха борова ниже уровня пола.
Условия безопасной эксплуатации печей предъявляют осо-бые требования в части газоплотности боровов. В этих целях борова после их возведения покрывают специальными обмазками, приготовляемыми на месте работ, составы которых указываются проектирующей организацией на рабочих чертежах.
metallurgy.zp.ua