Робот-манипулятор в современной промышленности
В условиях современной промышленности уделяется особое внимание минимизации риска получения производственных травм, и в этом плане немаловажную роль играет робот-манипулятор. Он способен заменить человека при выполнении многих операций. Не так давно для этих целей применялись разнообразные бронекостюмы и скафандры, но их использование также подразумевало непосредственное участие работника, выполняющего те или иные промышленные операции. Развитие кибернетической науки позволяет снижать важность непосредственного участия человека в решении тех или иных задач. В определённых отраслях промышленности применение получают различные роботы, оснащенные манипуляторами для выполнения самых различных функций.
Устройство и конструкция
Важнейшей конструктивной особенностью робота-манипулятора является возможность выполнения работ в условиях, недоступных для человека в принципе. Кроме того, промышленные роботы и манипуляторы позволяют существенно повысить общий уровень качества и сложности производимой продукции, а также снизить себестоимость её изготовления. Более того, благодаря использованию подобных машин существенно возрастает производительность труда на предприятии.
Немаловажную роль играет и тот факт, что в случае использования человеческого труда очень высок риск ошибки. В частности, даже лучшие сотрудники с огромным опытом физически не способны выполнить нарезку материала, обеспечив абсолютно точные размеры каждой из частей. В свою очередь, с точки зрения функциональности оснащённого манипулятором робота подобная процедура может считаться примитивнейшей.
Роботизированный манипулятор промышленного назначения — это технический агрегат высокой сложности, включающий в себя целый ряд компонентов, для соединения которых между собой используются сервомоторы. Простейшее устройство, применяемое в современной промышленности, состоит из двух-трёх подобных звеньев. Роботизированная рука, являющаяся манипулятором подобного агрегата, позволяет выполнять целый ряд простейших операций, включая захват объекта и его перемещение в указанную точку. Первые модели подобных механизмов не предусматривали наличия датчиков и были рассчитаны на выполнение одной-единственной заданной команды. Для обеспечения выполнения этой функции механизм должен был располагаться точно перед целевым объектом, с которым и осуществлялось взаимодействие.
Следующие поколения агрегатов отличались наличием простейших датчиков. С развитием науки телематики происходило превращение роботов-манипуляторов в сложнейшие устройства, способные адекватно анализировать окружающую обстановку и принимать соответствующие решения. Серьёзные преобразования претерпевала и рука, получавшая увеличенное количество степеней свободы и включавшая в себя уже не
два-три, а целый набор звеньев.
Современные роботы оснащаются компьютерами, способными функционировать по более совершенной программе, в которой закладываются не строгие и явные, а лишь общие указания и моменты.
Программное обеспечение установки осуществляет анализ данных, получаемых датчиками, и вырабатывает оптимальное для конкретной ситуации поведение. Система управления робота-манипулятора рассчитывает исходные и требуемые координаты каждого из звеньев руки, передавая соответствующие команды на сервоприводы. Фактически в случае современного манипулятора практически невозможно предугадать поведение заранее: даже в случае осуществления одних и тех же операций все выполняемые действия в каждом конкретном случае отличаются.
Вернуться к оглавлениюКлассификация и применение
В современной промышленности применяются различные роботы-манипуляторы. Одним из преимуществ таких устройств перед человеком является тот факт, что промышленный робот не предъявляет таких же требований к рабочему месту, то есть не нуждается в обеспечении надлежащей циркуляции воздуха, ярком освещении и многих других условиях. Конечно, промышленные роботы требуют соблюдения определённых условий эксплуатации, обеспечивающих максимальный ресурс и производительность оборудования, но эти требования минимальны в сравнении с потребностями живого работника.
С точки зрения способа управления современные промышленные роботы-манипуляторы могут быть автоматическими (выполняющими свои задачи в соответствии с заданной оператором программой) и управляемыми дистанционно (производящие необходимые манипуляции по команде с удалённого пульта управления). Промышленные агрегаты могут отличаться с точки зрения конструкции, предусматривающей наличие одной или нескольких рук. Чаще всего роботы оснащаются одним вычислительным блоком, а также набором модулей, формируемым на основании требований и особенностей деятельности заказчика.
Эти модули определяют целый ряд характеристик агрегата.
- Предельный вес перемещаемых объектов.
- Точность позиционирования устройства.
- Степень свободы, присущая манипуляторной установке.
Благодаря вычислительному блоку обеспечивается внесение самых различных изменений в программу робота-манипулятора. В частности, оператор может своими руками оптимизировать точность перемещения захвата, скорость выполнения работ и многие другие параметры. Решение практически любой задачи подразумевает разработку и внедрение собственной уникальной программы, включающей в себя комплект алгоритмов предполагаемых операций и манипуляций, в соответствии с которыми робот и выполняет свои обязанности.
С точки зрения подвижности роботы-манипуляторы могут быть свободно перемещающимися на гусеницах (колёсах) либо ограниченными, предназначенными для выполнения работ на конкретном участке. Рабочие показатели ограниченных моделей чаще всего находятся в зависимости от конкретных условий работы, поэтому такие роботы обычно предусматривают дистанционное управление.
Вернуться к оглавлениюМанипулятор робота
Манипулятором принято называть специальное устройство, посредством которого выполняется перемещение самых различных объектов и предметов в пространстве. В состав оборудования входит определённое количество звеньев двух типов, работающих за счёт пневматического или гидравлического привода. Одна категория звеньев манипулятора отвечает за поступательные движения, вторая — за перемещения под углом. Узлы, работающие за счёт гидравлики, характеризуются более высокой мощностью.
Рука-манипулятор, сконструированная по примеру человеческой рабочей конечности, предусматривает наличие высокотехнологичного захватного механизма, осуществляющую работу с деталями и объектами. Рассмотрим подробнее этот и другие параметры.
Аспекты | Характеристики |
Захват предметов. | Непосредственно схватывание предметов в большинстве подобных устройств производится механическими пальцами. В работы с плоскими поверхностями эти пальцы оснащаются специальными присосками, а если необходимо работать сразу со многими аналогичными заготовками, для захвата используется крупная конструкция особой формы. |
Крепление руки. | Крепление механической руки-манипулятора может быть как статическим, так и подвижным, предусматривающим полную или ограниченную свободу действий. |
Насадки. | В некоторых моделях роботов-манипуляторов вместо руки может устанавливаться другое оборудование, такое как сварочный аппарат, пульверизатор, отвертка и т. д. |
Использование промышленных роботов-манипуляторов позволяет существенно повысить эффективность, производительность и безопасность производства, поэтому тысячи подобных агрегатов уже применяются на многих предприятиях самых различных отраслей.
kranigruz.ru
Промышленные роботы
Промышленные роботы представляют из себя полностью механизированное и автоматическое устройство, состоящее из манипулятора и системы управления С помощью этой системы производится перепрограммирование. Кроме того можно менять траекторию, задавать другие необходимые параметры.
Что могут делать такие машины? Во-первых, различные технологичные операции, например, сварочные работы, сборку или покраску чего-либо. Во-вторых, разнообразные вспомогательные технологичные операции – выгрузка или загрузка оборудования и других рабочих элементов. Чтобы повысить экономическую выгоду многие фирмы используют промышленных роботов вместе с другими автоматизированными устройствами.
К их появлению привело возникновение механических манипуляторов, а позже и системного программирования. Самый первый робот появился в 50-х годах в Америке. Нашел широкое применение и довольно быстро набирал обороты популярности. Робот состоит из 2-х частей: механизм и управление этим механизмом. В эту систему поступают сигналы от сенсора. Механизм же состоит из манипуляционной системы перемещения. В манипуляционную систему входит устройство для захвата.
Устройство промышленных роботов
Манипулятор состоит из устройства, которое обеспечивает поступательное движение, и механизма, необходимого для вращения. Их сочетание дает подвижность. В звеньях чаще всего устанавливаются приводы пневматические, гидравлические или электрические. Захватное устройство также входит в манипулятор и представляет собой подобие человеческих рук с механическими пальцами.
Если необходимо совершить захват плоского предмета, то здесь используется присоска пневматическая. А если это множество деталей – используется специализированная конструкция. Кроме того, вместо устройства для захвата робот может быть оснащен любыми другими рабочими инструментами, например, отверткой, пульверизатором или сварочными клещами.
Передвигается промышленный робот по напольной колее вдоль монорельсов – это в случае, если он находится внутри помещения. А если необходимо его движениев на неровной или наклонной поверхности, то применяются своеобразные шагающие конструкции на пневматических присосках.
Принцип работы и управление промышленными роботами
Управление ими может быть следующих типов:
1. При помощи программы. Такой способ является самым простым. У промышленных роботов нет сенсорной части, его действия полностью фиксированы и постоянно повторяются.
2. Адаптивное. В данном случае присутствует сенсорное устройство, а передаваемые сигналы проходят анализ , и уже потом совершается какое-либо действие.
3. Метод своеобразного искусственного интеллекта.
4. Действует за счет управления человеком на расстоянии.
Роботы действуют по принципу подчиненного управления. Применяются вышеописанные машины в промышленности. Они могут выполнять главные и второстепенные действия. Но самыми распространенными действиями у роботов являются разгрузка или загрузка, укладка или сортировка деталей, их транспортировка, перемещение предметов от одного места к другому, точечная сварка и сварка швов, сборка деталей механических или электрических, а также электронных, покраска.
Огромный положительный момент промышленных роботов в том, что они полностью исключают действие человеческого фактора, кроме того характерна высокая точность действий, рациональное использование помещения.
О цене таких машин говорить трудно. Она варьирует от функциональности робота и от производителя.
promplace.ru
УСТРОЙСТВО ПРОМЫШЛЕННЫХ РОБОТОВ
Оборудование заводов по переработке пластмасс
Производим и продаем электроприводы ЭТУ, ЭПУ для двигателей постоянного тока, тел./email +38 050 4571330 / [email protected]Привод ЭПУ 25А с дросселем — 5500грн
Конструкция манипуляторов. Манипулятор — механическая рука робота — представляет собой многозвенный разомкнутый механизм с вращательными или поступательными сочленениями, заканчивающийся рабочим органом в виде схвата или какого-либо специального технологического инструмента. Универсальность манипулятора определяется числом степеней подвижности руки. Для работы с неориентированными объектами необходимо иметь не менее шести степеней подвижности: три степени— для перемещения схвата в заданную точку пространства и еще три — для ориентации схвата в пространстве. Увеличение числа степеней подвижности диктуется стремлением повысить маневренность манипулятора, но одновременно приводит к существенному усложнению его конструкции, поэтому большинство промышленных роботов имеет от 4 до 7 степеней подвижности.
На рис. 12.1 показан манипулятор отечественного промышленного робота ТУР-10, предназначенного для обслуживания станков с ЧПУ, литьевых машин, прессов, штампов, а также для окраски, сварки и других технологических операций.
Каждый манипулятор имеет свою рабочую зону (зону обслуживания). Эта зона представляет собой объемную фигуру в виде совокупности точек пространства, до которых может дотянуться схват во всех крайних положениях. Конфигурация рабочей зоны определяется числом степеней подвижности, типом кинематических пар, их взаимной ориентацией и относительными размерами звеньев руки. Типам рабочих зон соответствуют различные системы координат, в которых осуществляется движение схвата манипулятора: прямоугольная, цилиндрическая и сферическая.
Движение руки по каждой координате осуществляется с помощью трех основных механизмов: привода, передаточного механизма и исполнительного устройства. Последним может быть схват, кисть, рука и манипулятор в целом. В качестве приводов используются гидродвигатели, пневмодвигатели, электродвигатели и комбинированные приводы.
Конструкции передаточных механизмов отличаются большим разнообразием и содержат цилиндрические или конические зубчатые, червячные, цепные, троссовые, рычажные, шари-
Рис. 12.1. Конструктивная, схема манипулятора промышленного робота ТУР-10:
І — неподвижное основание; 2 — подвижные звенья руки; 3 — схват.
Ковинтовые, винтовые, планетарные /
И другие передачи.
В основе классификации манипуляторов лежит конструктивно — компоновочный признак, а именно — способ размещения приводных устройств и принцип передачи движения от них соответствующим звеньям руки. В соответствии с этой классификацией все известные конструкции манипуляторов можно разделить на четыре группы, различающиеся расположением приводов: 1) приводы расположены непосредственно на местах связи звеньев руки так, что корпус привода связан с одним звеном, а ведущий элемент — с другим; 2) приводы всех звеньев расположены на неподвижном основании манипулятора, а связь каждого привода со своим звеном осуществляется через передаточные механизмы; 3) один привод используется для перемещения нескольких звеньев руки; 4) используются комбинации трех основных способов размещения приводов.
Преимущество манипуляторов первой группы заключается в простоте кинематических связей между звеньями, а недостатки связаны с трудностью создания компактной и гибкой конструкции и с ухудшением динамических характеристик манипулятора по сравнению с приводами других конструкций. Манипуляторы второй группы имеют более сложные передаточные механизмы и более длинные кинематические цепи, но обладают лучшими динамическими характеристиками. Достоинством манипуляторов третьей группы является сокращение числа приводов. Однако поскольку управление звеньями руки осуществляется здесь последовательно с помощью распределительных механизмов, снижается быстродействие манипулятора. Из комбинированных конструктивных схем манипуляторов (четвертая группа) чаще всего используется комбинация способов расположения приводных устройств, характерных для первой и второй группы с преимущественным применением принципов, принятых для первой группы.
Поиск оптимальных компоновочных решений в конструкциях манипуляторов позволяет наблюдать две принципиально различные тенденции: создание универсальных, но дорогих и сложных конструкций с большим числом степеней подвижности и разработку простых, недорогих, узкоспециализированных манипуляторов.
В последние годы успешно развивается третий путь, основанный на применении системы модулей — функционально и
конструктивно независимых элементов, каждый из которых может использоваться как индивидуально, так и в различных комбинациях с другими модулями. Соединение модулей между собой происходит с помощью унифицированных стыковочных поверхностей и не требует никаких дополнительных проектных или монтажных работ, кроме операции сочленения. Состав системы конструктивных модулей определяется технологическими требованиями к геометрическим, точностным и динамическим характеристикам перемещения объектов производства.
Для увеличения рабочей зоны манипулятора и автоматизации транспортных операций некоторые модели манипуляторов оснащают средствами передвижения, среди которых чаще всего применяются колесные устройства, имеющие электрические или гидравлические приводы. При управлении приводами используются датчики, которые либо непрерывно измеряют путь перемещения манипулятора относительно неподвижной базы, либо подключаются (как кинематически, так и электрически) только в районе обслуживаемого оборудования. В целях повышения точности позиционирования манипуляторов и упрощения системы управления ими траекторию их движения обычно ограничивают подвесными или расположенными на полу рельсовыми путями.
Захватные устройства манипуляторов. Роботы применяются на самых разнообразных операциях и работают с деталями, различными по прочности, массе, габаритам, шероховатости поверхности. Поэтому для манипуляторов разработано большое количество всевозможных захватных устройств — схватов, которые можно подразделить на: механические с жесткими или пружинящими губками; с вакуумными присосками; электромагнитные; приспособления в виде кронштейнов для крепления технологического инструмента. В некоторых конструкциях манипуляторов схваты могут автоматически заменяться в соответствии с записанной программой.
Наиболее часто применяются механические схваты с регулируемым усилием или моментом, состоящие из механизма зажима и сменных губок. У значительной части роботов, особенно простых, движение захватного устройства осуществляется в одной плоскости по декартовым или полярным координатам. На 12.2 показан схват шарнирной конструкции с губками для удержания изделий цилиндрической формы. На штоке 2 пневмоцилиндра 1 смонтированы шарниры 3, несущие зажимные губки 4. Губки схватов могут быть универсальными или изготовленными из быстротвердеющих материалов типа силиконовых резин методом формообразования по профилю захватываемого изделия. Для взятия хрупких предметов применяются губки в виде надувных подушек или схваты с несколькими резиновыми пальцами в виде полых разностенных трубок, несимметрично деформирующихся при подаче в них воздуха и мягко охватывающих переносимый предмет с разных сторон.
Рис. 12.2. Схват для изделий ци — ? 4
Линдрической формы. Пояснения. в тексте.
Вакуумные схваты с Г’ присосками из резины или ]_Г другого эластичного поли — мера используются преиму — щественно при работе с изделиями в виде листов или относительно легких объемных фигур с плавными обводами. Эти схваты очень просты по конструкции, имеют небольшую массу и достаточно универсальны.’ Для перемещения крупногабаритных изделий и заготовок применяют схваты с несколькими присосками, расположение и ориентация которых в пространстве зависит от конфигурации изделия.
Область применения электромагнитных схватов несколько шире, чем вакуумных. Они могут работать с более мелкими и более тяжелыми изделиями разной формы. Однако возможность взаимодействия только с изделиями из магнитных материалов сужает диапазон их использования. Недостатком таких схватов является остаточный магнетизм и захват посторонних частиц, способных повредить поверхность обрабатываемого изделия.
На схватах промышленных роботов, если это необходимо по условиям технологического процесса, устанавливают чувствительные элементы, дающие информацию об объекте и внешней среде, в которой функционирует робот. Схваты оснащают тактильными (измеряющими усилие сжатия), фотоэлектрическими, ультразвуковыми и другими датчиками, которые помогают ориентировать схват относительно детали, компенсируя неточности положения схвата, обусловленные неизбежными ошибками системы жесткого программирования манипулятора, а также уменьшают вероятность повреждения детали.
Приводы манипуляторов. Движения рабочих органов манипуляторов осуществляются с помощью гидравлических, электрических и пневматических приводов, а также комбинированных — электрогидравлических, пневмогидравлических и др. Около 30% манипуляторов имеют гидравлические приводы. Небольшая масса гидроагрегатов, приходящаяся на единицу их мощности, жесткие статические и высокие динамические характеристики, сравнительно небольшие потери при передаче энергии в значительной мере способствуют их широкому применению. В качестве силовых двигателей здесь используются гидромоторы, осуществляющие непрерывное вращение выходного вала; мо — ментные и поршневые гидроцилиндры, преобразующие энергию потока жидкости в поступательное перемещение выходного штока. Регулирование скорости движения гидродвигателей обеспечивается с помощью дросселей, управляемых в ручном или ав
томатическом режимах. Недостатки гидродвигателей связаны с зависимостью скорости их работы от температуры окружающей среды, которая влияет на вязкость жидкости и динамические характеристики привода.
Манипуляторы с электродвигателями дискретного или непрерывного действия используются реже. Они имеют широкий диапазон грузоподъемности. Внешние условия слабо влияют на их работу. К преимуществам электропривода относятся легкость монтажа и наладки, отсутствие трубопроводов и низкий уровень шума при работе. Ограниченность применения электроприводов в роботостроении обусловлена тем, что использование существующих высокоскоростных двигателей вращательного типа требует сложных передаточных механизмов, введения устройств фиксации положения звеньев типа фрикционных тормозов и применения самотормозящих передач, которые существенно снижают к. п.д. привода.
Пневматические приводы в виде поршневых цилиндров и поворотных пневмодвигателей широко используются в конструкциях наиболее простых манипуляторов небольшой грузоподъемности, имеющих обычно от двух до четырех степеней подвижности. Привод одной степени подвижности состоит из исполнительного двигателя, распределительного устройства, дросселей-регуляторов скорости и редуктора. Пневматический привод во многом сходен с гидравлическим, но не имеет обратного трубопровода. Он значительно дешевле, надежнее, проще в изготовлении и эксплуатации. Основной недостаток пневмопривода — трудность управления им в следящем режиме из-за высокой сжимаемости воздуха.
Из комбинированных приводов наиболее часто применяются электрогидравлические и пневмогидравлические.
Развитие рынка вакуумного оборудования идет полным ходом. Ассортимент продукции регулярно пополняется новыми системами, а характеристики уже производимых компрессоров, воздуходувок, осушителей и прочих агрегатов постоянно улучшаются. Движущей силой эволюции вакуумной техники …
Промышленные роботы первого поколения еще не обладают способностью контролировать свои действия, используя при этом зрительные, звуковые и другие достаточно сложные в техническом отношении средства анализа состояния окружающей среды. Их информационная …
Действия промышленного робота первого поколения при выполнении им любой технологической операции определяются жесткой программой, реализуемой с помощью системы управления роботом. При этом все движения манипулятора могут быть согласованы во времени …
msd.com.ua
Роботы-манипуляторы. Манипуляторы — Робототехника- Портал искусственного интеллекта
Роботы-манипуляторы.
Использование манипуляторов стало обыденным явлением еще в 20-м веке. На сегодняшний день ни одно крупное промышленное про- изводство не обходится без них. Кроме того, манипуляторы устанавли- вают и на мобильных роботах, чтобы расширить возможности управле- ния в труднодоступных для человека местах. При однообразных и мо- нотонных действиях робот также может заменить человека, например раскладывать пирожные по коробочкам. Итак, определим манипулятор как управляемое устройство, пред- назначенное для выполнения сложных действий, аналогичных движе- ниям руки человека. В том числе, это механизм для управления поло- жением предметов.
Стрела манипулятора
Для освоения управления манипулятором следует вернуться к контролю положения двигателя с помощью П-регулятора, которое описано
в главе «Алгоритмы управления». Только конструкция будет несколько отличаться от описанной (рис. 8.148-8.149).
Рис. 8.148. Крепление мотора к корпусу NXT горизонтально на уровне по- верхности. Штифт-полуось вствляется в вал мотора снизу.
Рис. 8.149. Первое колено манипулятора.
Стрела манипулятора расположена горизонтально. Алгоритм управления состоит из двух параллельных задач. В первой работает
П-регулятор, который удерживает мотор в положении alpha. Во второй положение alpha изменяется со временем (рис. 8.150).
Рис. 8.150. Управление горизонтальным положением стрелы манипулятора.
Учитывая, что нулевое положение определяется на старте, задайте отрицательный угол во второй параллельной задаче и осуществите по-
следовательный переход через нуль. Если все получается, следует приступить к установке второго мотора с захватом.
Манипулятор с захватом
Рис. 8.151. Установка захвата на второй мотор.
Рис. 8.152. Мотор с захватом закрепляется на диске первого мотора.
Рис. 8.152. Мотор с захватом закрепляется на диске первого мотора.
Программирование робота с двумя степенями свободы (рис. 8.151-8.152) осуществляется аналогично. Новая переменная beta будет
определять положение второго мотора. Расширьте вторую задачу, подобрав подходящие значения для открывания и закрывания захвата
(рис. 8.153). Не забывайте, что стартовое положение определяет все.
Рис. 8.153. Заготовка для управления двумя моторами на основе П-регуля- торов. Необходимо продолжить цикл в параллельной задаче.
Точное позиционирование. Дискретный регулятор.
Библиографическое описание: Мусаев Г. М. Моделирование системы позиционирования отражателя концентратора солнечной энергии [Текст] / Г. М. Мусаев // Молодой ученый. — 2013. — №3. — С. 81-83.
Целью создания системы точного углового позиционирования является разработка и изготовление аппаратных и программных средств, необходимых для обеспечения управления с помощью ЭВМ системой позиционирования различных объектов. В качестве исполнительного устройства используются двигатели постоянного тока с редукторами и датчиками углового перемещения различных типов.
Для решения научно-практических задач требуется обеспечить угловое позиционирование объектов с высокой точностью [1].
К основным параметрам системы можно отнести:
Системы управления динамическими объектами с цифровыми регуляторами представляют собой достаточно сложный для описания класс. Непрерывная часть системы (объект управления) задается дифференциальными уравнениями, тогда как микропроцессоры, реализующие алгоритмы управляющих устройств, представлены разностными уравнениями. Смешанное описание в виде дифференциальных и разностных уравнений, дополненных соотношениями для преобразователей аналог-код и код-аналог, создает значительные трудности при решении типовых задач анализа и синтеза. Поэтому в практике управления получили распространение модели, которые описывают поведение систем лишь в дискретные (тактовые) моменты времени. При этом удается ограничиться лишь разностными уравнениями, что радикально упрощает описание рассматриваемых систем и решение соответствующих задач синтеза регуляторов.
Альтернативный подход, напротив, предлагает ограничиться исходным описанием системы дифференциальными уравнениями и синтезировать непрерывные регуляторы, которые уже после синтеза реализуются на микропроцессорах. Оба этих подхода широко используются в практике управления, хотя каждый их них имеет свои методические погрешности.
Альтернативный подход к синтезу дискретных регуляторов предлагает решать задачи управления, оставаясь в рамках непрерывных систем. При этом синтезируется непрерывный регулятор, который затем реализуется цифровыми методами. Физически ясно, что поведение дискретной системы будет приближаться к поведению непрерывной с уменьшением периода квантования. Чтобы оценить изменения, вносимые в динамику непрерывных систем применением микропроцессоров, рассмотрим сначала частотные характеристики экстраполятора нулевого порядка
(1)
Заменяя экспоненту тригонометрическими функциями, после простых преобразований найдем
(2)
Из последнего соотношения видно, что коэффициент передачи экстраполятора равен периоду квантования. Экстраполятор создает чистое запаздывание, величина которого равна половине периода квантования. При проектировании частота квантования выбирается существенно большей диапазона рабочих частот системы.
Преобразователи вносят в систему дополнительное запаздывание, равное половине периода квантования. Поэтому синтез регуляторов при их последующей реализации на микропроцессоре следует выполнять для модифицированного объекта, отличающегося от исходного наличием звена чистого запаздывания
(3)
В качестве системы управления динамическим объектом с цифровыми регуляторами рассмотрим устройство управления двигателем постоянного тока. Двигатели постоянного тока применяют в приводах, требующих плавного регулирования частот вращения в широком диапазоне.
Основным звеном устройства управления двигателем постоянного тока, выполняющим роль преобразователя и источника управляющих сигналов, может быть микроконтроллер (МК).
Свойства двигателей постоянного тока, определяются пусковыми, рабочими, механическими и регулировочными характеристиками.
Индексами «в» и «я» отмечены параметры и переменные цепей возбуждения и якоря; L — индуктивность, R — активное сопротивление, U — напряжение, i — ток; М — электромагнитный момент двигателя, е — ЭДС якоря.
От двигателя, применяемого в следящих системах, требуется преобразование электрического сигнала (управляющего напряжения) в пропорциональную величине сигнала скорость вращения якоря. Как правило, используются двигатели постоянного тока с независимым возбуждением. Принципиальная схема двигателя приведена на рис.1.
Рис. 1. Принципиальная схема двигателя постоянного тока.
Управление двигателем возможно путем изменения напряжений или по цепи якоря UЯ, или по цепи обмотки управления UB..
Рассмотрим вначале уравнения статики. Ток в цепи якоря /Я, магнитный поток возбуждения ФВ, вращающий момент Мвр, скорость вращения вала двигателя ω и противоэлектродвижущая сила еп,наводимая в обмотке якоря, связаны следующими соотношениями:
(4)
где
N — число проводников якоря, Р — число пар полюсов, а — число пар параллельных ветвей, Rя — активное сопротивление цепи якоря. Исключая из уравнения еп и iя получим
(5)
Из формулы (4), которая определяет механическую характеристику двигателя, видно, что при постоянном потоке возбуждения Фв, создаваемом неизменяемым напряжением возбуждения Uв,вращающий момент линейно зависит от управляющего сигнала по цепи якоря Uя. Это позволяет плавно изменять скорость двигателя в широком диапазоне. В связи с этим обстоятельством в рассматриваемой следящей системе управление двигателем осуществляется именно по цепи якоря. Составим уравнение динамики для двигателя постоянного тока, управляемого по цепи якоря.
Уравнение движения якоря двигателя имеет вид
(6)
Здесь J — момент инерции всех вращающихся масс, приведенных к валу двигателя, с —коэффициент вязкого трения, Мс — момент сопротивления.
Из (5) и (6) получим
или
(7)
где Тм — постоянная времени двигателя, Км — коэффициент передачи двигателя по управлению, Кс— коэффициент передачи двигателя по возмущению:
;
;
(8)
Соответственно передаточные функции двигателя по управлению и возмущению (моменту сопротивления) относительно угловой скорости имеют вид
;
(9)
Уравнение (7) можно записать относительно угла поворота. Учитывая, что получаем следующее уравнение:
(10)
Двигателю, описываемому уравнением (11), соответствуют две передаточные функции — по управлению и по возмущению относительно угла поворота:
(11)
(12)
intellect.ml
Роботы манипуляторы. Структура промышленного робота.
Принципиальная схема промышленного робота включает в себя механическую систему и систему программного управления, а так же связующие информационные цепи между ними. Система программного управления (СПУ) предназначена для сохранения в запоминающем устройстве управляющей программы – набора инструкций, объявленных на некотором формальном языке программирования, точное, последовательное выполнение которых позволяет добиваться поставленной цели.
Основное требование, предъявляемое к управляющей программе – полное и точное описание всех инструкций, которые необходимо соблюдать. В общем случае, для нормального функционирования промышленного робота, блок управления должен получить помимо полного описания инструкций (включая время их выполнения, начала и окончания) еще и информацию о положении всех степеней подвижности, полученную на основании расчетов (автооператоры) или по показателям контролирующих датчиков (адаптивные механизмы). Совокупность всей информации и носит название управляющей программы.
Она записывается на материальный носитель, который называют программоносителем, постоянным запоминающим устройством (ПЗУ), или просто «жестким диском», блоком памяти. Впрочем, в ПЗУ может быть реализован любой удобный принцип записи информации, от магнитной или перфорированной ленты до современных оптических и лазерных дисков. По физическому принципу различают механические (копиры, упоры), быстросъемные («винчестеры», диски, flash накопители и т.д.) носители, коммутаторы (барабаны). Соответственно изменяется и способ считывания записанной информации (различают контактный, бесконтактный и магнитный).
Современные системы позволяют записывать управляющую информация прямо с пульта управления, путем программирования, или выбора последовательности уже готовых программных блоков (с пульта управления). Помимо указанных задач, СПУ выполняет функции обратной связи, усиления сигнала, сравнения. Обратная связь – это восприятие, передача и усиление аналоговых или цифровых сигналов от контрольно-измерительных датчиков в блок управления (включая преобразование аналоговых сигналов в цифровые). Сравнение – это сопоставление заложенных в программу данных с информацией, поступающей от датчиков, выявление расхождений (ошибок) и их устранение. Усиление сигнала обычно необходимо при передаче информации от задающего блока исполнительному и рабочему органу.
Управляющая программа может составляться методами самообучения (применяется крайне редко, только в адаптивных механизмах), обучения (самый распространенный вариант, при котором оператор последовательно выполняет набор операций, а машина их запоминает) и путем предварительного расчета. Составленная программа записывается в постоянное запоминающее устройство или на съемный носитель. В процессе работы инструкции по выполнению текущей операции передаются в оперативное запоминающее устройство (ОЗУ). Для ОЗУ и ПЗУ справедливо понятие объема памяти, которое для станков с числовым программным управлением (ЧПУ) измеряется в байтах, а для станков с цикловым программным управлением (ЦПУ) – количеством операций (циклов).
С понятием СПУ неразрывно связано понятие информационной системы (ИС), которая включает в себя систему устройств обратной связи (УОС), набор датчиков обратной связи (ДОС) и устройство сравнения сигналов (УС). Всю поступающую информацию можно разделить на две категории: о внешней и внутренней среде. Причем одним и те же датчики могут получать и отправлять информацию сразу из обеих систем. На основе полученной информации принимаются решения об изменении положения степеней подвижности, остановке или возобновлении производства. К внешней ИС относят сведения касательно объекта труда (заготовка, деталь, материал) и рабочего органа (инструментов), а так же систем и параметров работы степеней подвижности. Информация считывается датчиками контактного и бесконтактного типа.
Контактные датчики используются для обеспечения возможности работы промышленного робота (установление момента контакта с заготовкой, ее положения, веса, давления на рабочем инструменте), а так же для соблюдения техники безопасности. Бесконтактные, или дистантные (дистанционные) датчики выполняют те же функции, однако, с некоторыми ограничениями. Например, их невозможно использовать для захвата и обработки хрупких заготовок, т.к. высоки риски их повреждения. Невозможно бесконтактным путем снять многие показатели, например, тепло- и электропроводность, шероховатость поверхности и т.п. Во внутренней системе собирается информация о положении, скорости движения или вращения степеней подвижности, анализируются поломки и остановки оборудования, прогнозируется неизрасходованный срок службы.
Во внутренней системе применяются датчики разных конструкций, функционирующих на разных физических принципах (в зависимости от типа приводов: гидравлический, пневматический, электродинамический). Здесь активно эксплуатируются всевозможные выключатели и переключатели, реле, срабатывающие в момент, когда значение контролируемого параметра выходит за установленные рамки. Значимость разных датчиков, и контролируемой ими информации разница от производственного цикла к циклу. Всего в работе промышленного робота выделяют три фазы: захват, транспортировка, обработка. Под обработкой понимается изменение ориентации объекта, его крепление к другому объекту, механическая обработка (сверление, штамповка, окраска и т.д.). Например, при транспортировке требуется информация только от датчиков движения, а при захвате – еще и от датчиков давления.
СПУ управляет механической системой (МС), под которой часто и обозначают манипулятор. Манипулятор – это открытая чаще всего пространственная сложная (иногда простая) кинематическая цепь, последнее звено которой имеет всего одну кинематическую пару. Состоит из исполнительного механизма, захвата, передаточных устройств, приводов, основания (базы, несущей конструкции). Под кинематической парой понимается соединение двух звеньев. В промышленных роботах наибольшее распространение получили кинематические пары V класса (возвратно-поступательное, взаимосвязанное вращательное движения, вращение вокруг поперечной оси).
Исполнительный механизм – это набор звеньев, оказывающих воздействие на обрабатываемый объект (в случае манипулятора – перемещение). Захватывающий механизм – устройство для захвата и удержания объекта, выполняется, как правило, сменным, а сам манипулятор оснащается набором типовых захватов, отличающихся размером, весом. Оснащается системой датчиков контактного типа. Все механизмы в зависимости от их функционального назначения группируются в четыре блока: основание (подвижное или неподвижное), корпус, механическая рука, рабочий орган (захват).
Важнейшей характеристикой механической системы является число степеней свободы. Как правило, в промышленных роботах применяются кинематические пары, каждая с одной степенью свободы, их совокупность определяет общее количество степеней подвижности (рассчитывается по формуле Сосиева–Малышева). Обычно механизм имеет до 10-12 степеней свободы (против 28 у руки человека, которая считается прообразом всех подобных устройств). Все движения промышленного робота принято разделять на локальные (ориентирующие, перемещения инструмента соизмеримые с его размером), региональные (транспортирующие, соизмеримые с размерами, площадью рабочего места) и глобальные (координатные, превышающие размеры всего промешенного робота и его рабочей зоны). Совокупность всех возможных региональных движений называется основными движениями, они формируют систему координат перемещения промышленного робота.
Так же МС характеризуется степенью подвижности каждой функциональной группы, манёвренностью (способностью руки манипулятора обходить препятствия с полностью неподвижным в пространстве захватом), коэффициентом сервиса (возможностью подведения захвата к объекту с разных сторон). Коэффициент сервиса оценивается телесным углом, или углом, который может образовывать ось захвата в заданной точке пространства для беспрепятственного доступа к заготовке. При 100% коэффициенте сервиса захват может быть подведен с любого направления, под любым углом.
Если рассматривать не только заданную точку пространства, но весь объем рабочей зоне, то следует говорить о полном коэффициенте сервиса, который дает общее представление о кинематических свойствах механической системе, ее подвижности. При проектировании промышленного робота именно этот показатель становится ключевым и перед конструкторами ставится задача его максимизации.
xn—-8sbb4apdidbgjdltho3kl6e.xn--p1ai
11 Манипуляторы и промышленные роботы
11.1 Виды манипуляторов и промышленных роботов
Манипулятором называется техническое устройство, предназначенное для воспроизведения рабочих функций руки человека (латинское «manipulus» -пригоршня).
Механизм манипулятора образован из пространственной незамкнутой кинематической цепи (рисунок 11.1). Звенья этой цепи имеют названия
0 – корпус
1 – плечо
2 – предплечье
3 – кисть (захват)
4 – палец. Кинематические пары: А – плечевой сустав Р3 В – локтевой сустав Р1 С – кистевой сустав Р3.
Рисунок 11.1
Звено – 4 (палец) при структурном анализе объединяется со звеном 3. Поэтому цепь состоит из стойки и трех подвижных звеньев и имеет степень подвижности W = 7, так как число степеней свободы незамкнутой кинематической цепи равно сумме подвижностей кинематических пар или
W = 6n – 5Р1 – 4Р2 – 3Р3 – 2Р4 – Р5 = 6. 3 – 5. 1 – 3. 2 = 7.
Вдальнейшем появились манипуляторы с большим числом звеньев и кинематических пар, и внешнее сходство с рукой человека стало утрачиваться, но во всех вариантах сохранилось назначение манипулятора – воспроизводить движения подобные движениям рук человека (степень подвижности руки человека, без учета движения пальцев, W = 12). Число степеней подвижности манипуляторов обычно не превышает 7.
Взависимости от вида системы управления различают манипуляторы с ручным управлением и манипуляторы с автоматическим управлением.
Вманипуляторах с ручным управлением оператор, ориентируя рукоятку задающего устройства, создает нулевую ориентацию звеньев исполнительного механизма. Недостаток – отсутствие обратной связи по усилию, т.е. оператор не ощущает действие нагрузки.
В манипуляторах с автоматическим управление звенья исполнительного механизма получают движение от сервоприводов (т.е. вспомогательных приводов, которые приводят в движение отдельные звенья по заданной программе). Программа может многократно использоваться для управления манипулятором.
Манипуляторы с автоматическим управлением называются промышленными роботами. Они используются не только для работы во вредных условиях, но и для механизации однообразных и утомительных работ на быстродействующих конвейерах. Отличаются от других машинавтоматов возможностью быстрой переналадки на выполнение другой программы.
Промышленные роботы по степени совершенства принято делить на роботов 1-го,2-гои3-гопоколений.
Роботы 1-гопоколения имеют «жесткую»программу и требуют точного позиционирования деталей, с которыми работают. Большинство применяемых в настоящее время в промышленности роботов относятся к 1- му поколению. Робот1-гопоколения состоит из манипулятора и программных блоков. Первоначальная программа действий записывается в память робота. Это называется этапом обучения. Различают три метода обучения:
а) с помощью настройки механических устройств типа кулачков, конечных переключателей — «обучение по точкам»;
б) с помощью пульта управления, аналогично как у станков с ЧПУ – «обучение с пульта»;
в) непосредственно рукой оператора – «обучение показом».
Роботы 2-гопоколения представляют собой устройства, приспособленные к изменяющейся внешней обстановке и не требующие точного позиционирования деталей. Их по этому называют адаптивными. Элементами адаптации являются различные датчики фотометрические, магнитные, измерители температуры, цвета, химического состава и т.п.
Роботы 3-гопоколения способны выбирать способ движения в зависимости от окружающей обстановки. Их называют «интегральными» или «интеллектуальными». Человек выступает не как оператор, а как диспетчер (выдает задание, принимает доклады об исполнении).
Термин «поколение» надо понимать лишь как степень развития технических возможностей.
11.2 Структура и геометрия манипуляторов
Движения, совершаемые человеком и воспроизводимые роботом, можно разделить на три класса: глобальные, региональные, локальные.
Глобальные движения – это перемещения на расстояния, превышающие размеры робота, например перемещение робота по монорельсу для обслуживания группы станков.
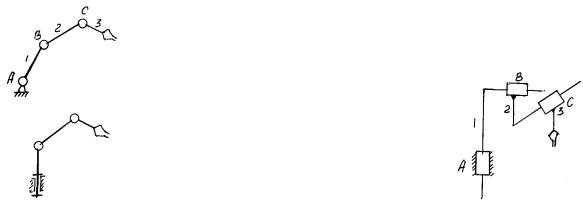
Движения, совершаемые рукой робота в пределах его рабочей зоны, называются региональными, или переносными, так как они обеспечивают перенос объекта в требуемую точку.
Локальные движения – это перемещения, соответствующие движениям кисти руки. Основное назначение – ориентирование объекта манипулирования, поэтому их также называют ориентирующими.
Пространственный манипулятор в общем случае должен иметь шесть степеней подвижности, три для отработки региональных (переносны) движений и три – для локальных (ориентирующих).
Для промышленных роботов обычно оказывается достаточным для выполнения рабочих операций 4 –5степеней (3 переносных и 1 – 2 ориентирующих). Простейшие, не перепрограммируемые роботы называемые автооператорами, могут иметь 1–2степени подвижности.
Кинематическая цепь региональных движений обычно содержит три звена и три кинематические пары V класса (вращательных и поступательных) и носит название руки. Возможны следующие расположения кинематических пар (рисунок 11.2) ВВВ,ВВП,ВПВ,ПВВ,ППВ,ПВП,
ВПП,ППП. Оси соседних кинематических пар могут | иметь самое |
различное относительное расположение, поэтому схемы | манипуляторов |
весьма разнообразна. |
|
| … … … … … … |
ВВВ | ППП |
Рисунок 11.2
Одной из простейших схем является схема ППП с прямоугольной системой координат, форма ее рабочей зоны – параллелепипед. Такая схема наиболее удобна для выполнения прямолинейных движений. Применяется в станках с ЧПУ.
В настоящее время наибольшее распространение получили манипуляторы ВПП с цилиндрической системой координат (рисунок 11.3).
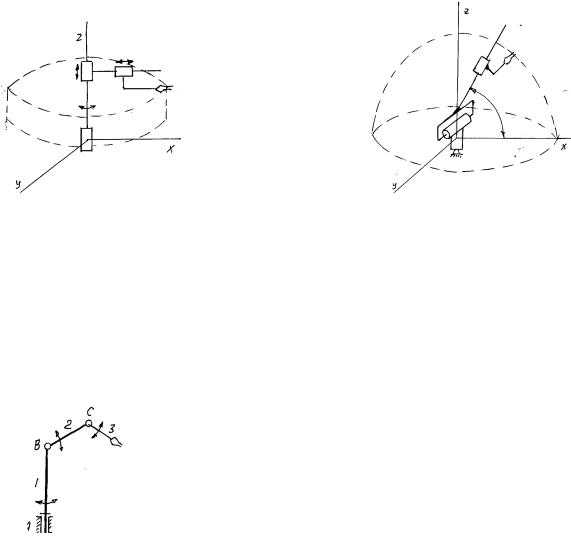
Рабочее пространство имеет форму цилиндра или его части. Рука может осуществлять движения по горизонтали и вертикали, и поворот вокруг оси колонны. Такую схему имеют обычно транспортные роботы.
Рисунок 11.3 | Рисунок 11.4 |
Манипулятор исполнения ВВП имеет сферическую систему координат, его рабочее пространство – сферический сегмент (рисунок 11.4). Такие манипуляторы сложнее чем с цилиндрической, однако, компактнее, обслуживают большой объем. Имеют повышенную жесткость, что позволяет использовать при повышенных нагрузках, например при точечной сварке.
Манипулятор исполнения ВВВ имеет сложную сферическую систему координат (рисунок 11.5).
Он называется ангулярным, шарнирным или антропоморфным. Имеет значительно меньшие габариты, чем у ППП при большей зоне обслуживания. Может применяться в стесненной зоне обслуживания.
Рисунок 11.5
Каждая их рассмотренных схем обладает определенными достоинствами и недостатками, поэтому выбор схемы является компромиссным решением и ведется с учетом предъявляемых к данному роботу разнообразных требований. Нет такой схемы робота, которая была бы оптимальной во всех случаях – для каждой задачи нужно искать наилучшую компановку.
Кинематическая цепь, реализующая локальные движения зазывается кистью робота. Назначение – выполнять ориентирующие движения.
Для удержания объекта манипулирования кисть снабжается захватным
устройством. |
|
|
|
Назначение переносных и ориентирующих движений — | поместить | ||
захватное устройство в любую точку рабочей зоны. |
| ||
Рабочей зоной (зоной обслуживания) называется часть рабочего объема | |||
манипулятора, | в которой можно | выполнять данную | операцию, |
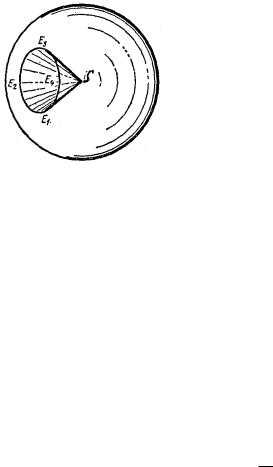
характеризуемую | расположением захвата по | отношению | к | объекту | ||||||
манипулирования. |
|
|
|
|
|
|
|
|
| |
Для каждой | точки | рабочего объема манипулятора можно определить | ||||||||
некоторый телесный угол ψ, внутри которого захват можно | подвести к этой | |||||||||
точке. Этот угол называется углом сервиса (рисунок 11.6). |
|
|
|
| ||||||
|
|
|
| Телесный | угол | это | часть | |||
|
|
|
| пространства, |
| ограничения | ||||
|
|
|
| прямыми, проведенными из одной | ||||||
|
|
|
| точки (S) ко всем точкам какой | ||||||
|
|
|
| либо | замкнутой | кривой. | Мерой | |||
|
|
|
| телесного | угла является площадь, | |||||
|
|
|
| вырезаемая телесным | углом | на | ||||
|
|
|
| сфере | единичного | радиуса | с | |||
|
|
|
| центром в вершине. Максимальное | ||||||
Рисунок 11.6 | значение телесного угла равно 4π. | |||||||||
|
|
|
|
|
|
| ||||
Отношение | ψ | = θ | называется коэффициентом сервиса в данной точке. | |||||||
4π |
Значение этого коэффициента может меняться от 0 для точек на границе рабочего объема до1 для точек зоны полного сервиса (схват совершает полное сферическое движение вокруг данной точки).
Качество манипулятора в отношении возможностей выполнения различных операций оценивается средней величиной коэффициента сервиса θср в рабочем объемеV, который называется полным коэффициентом сервиса манипулятора.
θ ср V1 ò θdV .
(V)
Под маневренностью манипулятора понимается его число степеней свободы при неподвижном захвате. Одну степень маневренности имеет манипулятор со сферическими парами (m = 1), у которого при неподвижном захвате его звенья могут вращаться вокруг оси проходящей через центры сферических пар, т.е. как бы «ометают» некоторый объем.
В манипуляторах с одноподвижными кинематическими парами маневренности равна нулю m = 0, т.е. каждому положению захвата соответствует единственное расположение всех звеньев.
Маневренность зависит не только от числа степеней свободы захвата, но и от расположения сферических пар. Повышение маневренности манипулятора позволяет выполнять движения более высоких классов, которые подразделяются на четыре класса.
studfiles.net
Роботы манипуляторы. Основные понятия.
Робот – специальное техническое устройство, используемое для автоматизации некоторых операций, выполняемых в иных случаях человеком. Наибольшее распространение роботы получили в промышленности, где применяются для автоматизации как основных, так и вспомогательных технологических операций.
Обыкновенно имеют перепрограммируемый блок управления, благодаря чему с помощью одного и того же механизма удается выполнять различные по назначению и составу работы (ряд специалистов выделяет наличие перепрограммируемого устройства управления в качестве отличительной черты робота, позволяющей их однозначно идентифицировать среди прочих средств механизации и автоматизации).
Наиболее совершенные роботы являются адаптационными механизмами, т.е. могут самостоятельно приспосабливаться к изменяющейся окружающей среде. Существует множество типов конструкций роботов, отличающихся по типу и способу управления, перечню исполнительных органов, техническому уровню, количеству доступных к выполнению операций. Совокупность роботов, выполняющих одну и ту же задачу, называется робототехнической системой (РТС). Различают информационные и управляющие, мобильные и манипуляционные системы.
Информационные и управляющие робототехнические системы – это совокупность контрольно-измерительных устройств, усилителей сигнала и блока (блоков) управления, вычислительных центров. Предназначение систем заключается в сборе и обработке информации, ее анализе и формировании на ее основании управляющих сигналов.
Подобные системы нашли широкое распространение во многих отраслях человеческой деятельности, от проведения исследовательских работ (в атмосфере, под водой, в космосе и на других планетах) и спасательных, саперных операций до контроля производственных процессов в промышленности.
Мобильные РТС предназначены для перемещения объектов на небольшие расстояния, как по вертикали, так и по горизонтали. Подобные системы могут перемещать объект по заранее составленному маршруту, или же по принципу адресации цели, когда заранее известна только конечная точка маршрута. Бывают гусеничными, колесными, шагающими, ракетными, винтовыми, водометными, в зависимости от типа движителя. Часто мобильные транспортные устройства оснащаются манипуляторами для захвата объекта, удержания его и перемещения. В промышленности мобильные РТС применяются для внутрицеховой транспортировки деталей, заготовок, сырья и материалов. Нашли применения и на складах.
Манипуляционные механизмы, как видно из названия, предназначены для манипуляций с объектами, имитации движения человеческой руки (с той лишь разницей, что человеческая рука имеет 28 степеней свободы, в то время, как для выполнения подавляющего большинства технологических операций производственного цикла достаточно 10-12 степеней свободы).
Для этого все подобные конструкции оснащаются роботами манипуляторами типа «рука». Под объектом манипуляции может пониматься любой предмет (заготовка, изделие, материал, рабочий инструмент), необходимый в производственном процессе и перемещаемый с помощью манипулятора. Часто манипуляционные устройства называются промышленными роботами.
Любой манипулятор состоит из следующих блоков:
- задающего, предназначенного для формирования управленческих сигналов;
- исполнительного (функционального), реализующего команды от задающего блока;
- связующего, передающего управленческие сигналы от задающего к исполнительному механизму, или в обратном направлении различные контрольные сигналы;
- рабочего (захваты, инструменты), выполняющего технологические операции (обработка, перемещение, удержание и т.д.).
По способу управления все манипуляторы принято разделять на два больших класса: биотические (управляемые человеком, дистанционно или непосредственно, путем перемещения рабочего органа) и автоматические. Признаком биотической РТС является отсутствие блока памяти, который содержал бы набор команд, следствием чего является необходимость в постоянном присутствии оператора.
На стыке этих двух классов формируется класс интерактивных систем, систем со смешанным управлением. В свою очередь, биотические механизмы подразделяются на копирующие, командные и полуавтоматические; а автоматические – на автооператоры и перепрограммируемые системы. Человек, осуществляющий управление биотическим манипулятором, называется оператором.
В копирующем манипуляторе движение рабочего механизма повторяет движение кисти оператора, обычно инструмент управления (рычаг, джойстик) передает в заданном масштабе усилие, возникающее на рабочем органе оператору. Таким образом, задающее устройство имеет кинематическую связь с рабочим органом.
В командной системе кинематическая связь между задающим и рабочим органами не предусмотрена, а управление осуществляется с помощью системы рычагов, кнопок и переключателей (в современных механизмах с помощью сенсорного экрана). Каждая кнопка или рычаг отвечает за управление по одной степени свободы. Такую систему управления называют управлением раздельного типа.
Полуавтоматические РТС управляются с помощью одной единственной или нескольких рукояток, отвечающих сразу за несколько степеней свободы (подвижностей). Рукоятки являются аналоговыми инструментами, поэтому задающее устройство имеет помимо вычислительного центра или микро-ЭВМ еще и преобразователь (оба устройства могут быть совмещены в одном механизме).
На долю блока управления приходится решение задачи по преобразованию сигналов, поступающих с рукоятки в сигналы, отправляемые на рабочий механизм. Наибольшее распространение в промышленности получил и сбалансированные системы шарнирного типа (шарнирные сбалансированные), имеющие систему уравновешивания рабочего органа.
Автоматические РТС не требуют перманентного присутствия человека. Они могут выполнять работу по заранее составленной программе, не подлежащей изменению (автооператоры), или быть перепрограммируемыми (собственно промышленные роботы). Возможность перепрограммирования подразумевает не только смену управляющей программы оператором (человеком), но и возможность самостоятельного ее изменения в виду меняющихся условий окружающей среды (адаптационные механизмы). При этом перепрограммирование должно занимать минимально возможное время.
Оба типа механизмов, и автооператоры и перепрограммируемые промышленные роботы конструктивно состоят из одного или нескольких манипуляторов, выполняются мобильными или стационарными и работают практически без участия человека (за исключением операций по настройке, наладке и техническому обслуживанию). Перепрограммируемые роботы, помимо этого, имеют набор датчиков за контролем одного или нескольких факторов рабочего процесса.
Интерактивные РТС – это биотехнические системы имеющие блок памяти, а потому способные запоминать и повторять некую последовательность действий. Человек принимает участие во всех операциях, чередуясь в этом с роботом (возможно, по принципу автоматического выполнения ряда простейших операций с передачей управленческих функций человеку для контроля над самыми сложными и емкими процессами), или же только в стыковочных операциях, исключительно для переключения робота с выполнения одной работы на другую.
Первый тип управления получил название автоматизированного, второй – супервизорного. Технологически интерактивное управление может быть кнопочным, рычажным и диалоговым (включая подачу команд голосом, редко используется во флективных языках, к которым относится русский, текстом, на любом языке программирования).
xn—-8sbb4apdidbgjdltho3kl6e.xn--p1ai