Π‘ΠΌΠΎΠ»Π° ΠΠ-20 | HYORTS
ΠΡΠΎΠΌΡΡΠ»Π΅Π½Π½Π°Ρ Ρ ΠΈΠΌΠΈΡ ΠΈ Ρ ΠΈΠΌΠΈΡΠ΅ΡΠΊΠΎΠ΅ ΡΡΡΡΠ΅
ΠΡΠΎΠ΄ΡΠΊΡΠΈΡ
Β | Β | Β |
ΠΠ½Π΅ΡΠ½ΠΈΠΉ Π²ΠΈΠ΄: | ΠΡΠΎΠ·ΡΠ°ΡΠ½Π°Ρ Π²ΡΠ·ΠΊΠ°Ρ ΠΆΠΈΠ΄ΠΊΠΎΡΡΡ ΠΆΠ΅Π»ΡΠΎΠ²Π°ΡΠΎΠ³ΠΎ ΡΠ²Π΅ΡΠ° Π±Π΅Π· Π²ΠΈΠ΄ΠΈΠΌΡΡ ΠΌΠ΅Ρ Π°Π½ΠΈΡΠ΅ΡΠΊΠΈΡ Π²ΠΊΠ»ΡΡΠ΅Π½ΠΈΠΉ | |
ΠΠΠ‘Π’ | 10587-84 | |
ΠΡΠΈΠΌΠ΅Π½Π΅Π½ΠΈΠ΅ | ||
ΠΠ»Ρ ΠΈΠ·Π³ΠΎΡΠΎΠ²Π»Π΅Π½ΠΈΡ ΠΈ ΡΠ΅ΠΌΠΎΠ½ΡΠ° Π΄Π΅ΡΠ°Π»Π΅ΠΉ ΠΊΠΎΡΠΏΡΡΠΎΠ² Π»ΠΎΠ΄ΠΎΠΊ, ΡΡ
Ρ, ΡΠ°ΠΌΠΎΠ»Π΅ΡΠΎΠ², Π°Π²ΡΠΎΠΌΠΎΠ±ΠΈΠ»Π΅ΠΉ ΠΈ Ρ. Π΄. ΠΡΠΈΠΌΠ΅Π½ΡΠ΅ΡΡΡ Ρ ΠΎΡΠ²Π΅ΡΠ΄ΠΈΡΠ΅Π»Π΅ΠΌ ΠΠΠΠ (ΠΏΠΎΠ»ΠΈΡΡΠΈΠ»Π΅Π½ΠΏΠΎΠ»ΠΈΠ°ΠΌΠΈΠ½) ΠΈΠ»ΠΈ Π΄ΡΡΠ³ΠΈΠΌΠΈ ΠΎΡΠ²Π΅ΡΠ΄ΠΈΡΠ΅Π»ΡΠΌΠΈ Π΄Π»Ρ ΡΠΏΠΎΠΊΡΠΈΠ΄Π½ΡΡ ΡΠΌΠΎΠ». Π‘ΠΎΠ΅Π΄ΠΈΠ½Π΅Π½ΠΈΠ΅ ΡΠΌΠΎΠ»Ρ Ρ ΠΎΡΠ²Π΅ΡΠ΄ΠΈΡΠ΅Π»Π΅ΠΌ Π΄ΠΎΠ»ΠΆΠ½ΠΎ ΠΏΡΠΎΠΈΠ·Π²ΠΎΠ΄ΠΈΡΡΡΡ ΠΏΡΠΈ ΡΠ΅ΠΌΠΏΠ΅ΡΠ°ΡΡΡΠ΅ Π½Π΅ Π½ΠΈΠΆΠ΅ 20Β°Π‘. ΠΡΠ΅ΠΌΡ ΠΆΠ΅Π»Π°ΡΠΈΠ½ΠΈΠ·Π°ΡΠΈΠΈ ΠΏΡΠΈΠΌΠ΅ΡΠ½ΠΎ 1,5 ΡΠ°ΡΠ°, Π° Π²ΡΠ΅ΠΌΡ ΠΏΠΎΠ»Π½ΠΎΠ³ΠΎ ΠΎΡΠ²Π΅ΡΠΆΠ΄Π΅Π½ΠΈΡ 24 ΡΠ°ΡΠ°. | ||
ΠΡΠ½ΠΎΠ²Π½ΡΠ΅ Ρ Π°ΡΠ°ΠΊΡΠ΅ΡΠΈΡΡΠΈΠΊΠΈ | ||
1. ΠΠ»ΠΎΡΠ½ΠΎΡΡΡ ΠΏΡΠΈ 20 Β°Π‘ β 1,16-1,25 ΠΊΠ³/ΠΊΡΠ±. ΠΌ. | ||
Π£ΡΠ»ΠΎΠ²ΠΈΡ Ρ ΡΠ°Π½Π΅Π½ΠΈΡ: | Π£ΡΠ»ΠΎΠ²ΠΈΡ Ρ ΡΠ°Π½Π΅Π½ΠΈΡ β ΠΏΠ»ΠΎΡΠ½ΠΎ Π·Π°ΠΊΡΡΡΠ°Ρ ΡΠ°ΡΠ°, ΡΠ΅ΠΌΠΏΠ΅ΡΠ°ΡΡΡΠ° ΠΎΠΊΡΡΠΆΠ°ΡΡΠ΅ΠΉ ΡΡΠ΅Π΄Ρ Π΄ΠΎ 40 Β°Π‘. |
hyorts.ru
ΠΡΠΎΠ±Π΅Π½Π½ΠΎΡΡΠΈ ΡΠ°Π±ΠΎΡΡ Ρ ΡΠΏΠΎΠΊΡΠΈΠ΄ΠΊΠΎΠΉ
ΠΡΠΎΠ±Π΅Π½Π½ΠΎΡΡΠΈ ΡΠ°Π±ΠΎΡΡ Ρ ΡΠΏΠΎΠΊΡΠΈΠ΄ΠΊΠΎΠΉ
ΠΡΠΎΠ±Π΅Π½Π½ΠΎΡΡΠΈ ΡΠ°Π±ΠΎΡΡ Ρ ΡΠΏΠΎΠΊΡΠΈΠ΄ΠΊΠΎΠΉ
ΠΠΏΠΎΠΊΡΠΈΠ΄Π½ΡΠ΅ ΡΠΌΠΎΠ»Ρ β ΡΡΠΎ ΠΏΠΎΠΆΠ°Π»ΡΠΉ ΡΠ°ΠΌΡΠΉ Π΄ΠΎΡΡΡΠΏΠ½ΡΠΉ ΠΌΠ°ΡΠ΅ΡΠΈΠ°Π» Π΄Π»Ρ ΡΠΎΡΠ½ΠΎΠ³ΠΎ Ρ ΠΎΠ»ΠΎΠ΄Π½ΠΎΠ³ΠΎ Π»ΠΈΡΡΡ ΠΏΠ»Π°ΡΡΠΌΠ°ΡΡΠΎΠ²ΡΡ Π΄Π΅ΡΠ°Π»Π΅ΠΉ Π² Π΄ΠΎΠΌΠ°ΡΠ½ΠΈΡ ΡΡΠ»ΠΎΠ²ΠΈΡΡ ΠΈ Π² Π½Π°ΠΈΠ±ΠΎΠ»ΡΡΠ΅ΠΉ ΡΡΠ΅ΠΏΠ΅Π½ΠΈ ΠΏΠΎΠ΄Ρ ΠΎΠ΄ΠΈΡ Π΄Π»Ρ ΠΈΠ·Π³ΠΎΡΠΎΠ²Π»Π΅Π½ΠΈΡ ΡΠΏΠΈΠ½Π½ΠΈΠ½Π³ΠΎΠ²ΡΡ ΠΏΡΠΈΠΌΠ°Π½ΠΎΠΊ ΡΠ»ΠΎΠΆΠ½ΠΎΠΉ ΡΠΎΡΠΌΡ.
ΠΡΠΈ ΡΠ°Π±ΠΎΡΠ΅ Ρ ΡΠΏΠΎΠΊΡΠΈΠ΄ΠΊΠΎΠΉ (ΡΠ°ΠΊ Π½Π°ΡΠΎΠ΄ ΠΎΠΊΡΠ΅ΡΡΠΈΠ» ΡΡΠΎΡ ΠΊΠ»Π°ΡΡ Π²Π΅ΡΠ΅ΡΡΠ²) Π½Π°Π΄ΠΎ Π·Π½Π°ΡΡ ΠΈΡ ΠΎΡΠ½ΠΎΠ²Π½ΡΠ΅ ΡΠ²ΠΎΠΉΡΡΠ²Π° ΠΈ ΠΏΠΎΠ²Π΅Π΄Π΅Π½ΠΈΠ΅ ΠΏΡΠΈ ΡΠ°Π·Π»ΠΈΡΠ½ΡΡ ΡΠΈΠ·ΠΈΡΠ΅ΡΠΊΠΈΡ ΡΡΠ»ΠΎΠ²ΠΈΡΡ .
ΠΠΏΠΎΠΊΡΠΈΠ΄ΠΊΠ° ΠΏΡΠ΅Π΄ΡΡΠ°Π²Π»ΡΠ΅Ρ ΠΈΠ· ΡΠ΅Π±Ρ Π²ΡΠ·ΠΊΡΡ ΡΠΌΠΎΠ»Ρ, ΠΊΠΎΡΠΎΡΠ°Ρ ΠΏΠΎΡΠ»Π΅ ΡΠΌΠ΅ΡΠΈΠ²Π°Π½ΠΈΡ Ρ ΠΎΡΠ²Π΅ΡΠ΄ΠΈΡΠ΅Π»Π΅ΠΌ ΠΏΠΎΠ»ΠΈΠΌΠ΅ΡΠΈΠ·ΡΠ΅ΡΡΡ ΠΈ ΠΏΠ΅ΡΠ΅Ρ ΠΎΠ΄ΠΈΡ Π² ΡΠ²Π΅ΡΠ΄ΡΡ ΡΠ°Π·Ρ. ΠΠΎ ΠΏΠΎΠ»ΠΈΠΌΠ΅ΡΠΈΠ·Π°ΡΠΈΠΈ Π² ΡΠΌΠΎΠ»Ρ ΠΌΠΎΠΆΠ½ΠΎ Π²Π²ΠΎΠ΄ΠΈΡΡ Π²ΡΠ΅Π²ΠΎΠ·ΠΌΠΎΠΆΠ½ΡΠ΅ ΡΠ²Π΅ΡΠ΄ΡΠ΅ Π½Π°ΠΏΠΎΠ»Π½ΠΈΡΠ΅Π»ΠΈ, ΠΊΠΎΡΠΎΡΡΠ΅ Π±ΡΠ΄ΡΡ ΠΌΠ΅Π½ΡΡΡ Π² ΠΆΠ΅Π»Π°Π΅ΠΌΡΡ ΡΡΠΎΡΠΎΠ½Ρ ΡΠ²ΠΎΠΉΡΡΠ²Π° ΠΏΠΎΠ»ΡΡΠ΅Π½Π½ΠΎΠΉ ΠΏΠ»Π°ΡΡΠΌΠ°ΡΡΡ.
ΠΠ°ΠΈΠ±ΠΎΠ»Π΅Π΅ Π΄ΠΎΡΡΡΠΏΠ½ΠΎΠΉ ΠΈ ΡΠΈΡΠΎΠΊΠΎΠΈΠ·Π²Π΅ΡΡΠ½ΠΎΠΉ ΡΠΏΠΎΠΊΡΠΈΠ΄ΠΊΠΎΠΉ ΡΠ²Π»ΡΡΡΡΡ ΡΠΏΠΎΠΊΡΠΈΠ΄Π½ΡΠ΅ ΠΊΠ»Π΅ΠΈ ΠΠΠ ΠΈ ΠΠΠ€. Π‘Π»Π΅Π΄ΡΠ΅Ρ ΠΎΡΠΌΠ΅ΡΠΈΡΡ, ΡΡΠΎ ΡΡΠΎ Π½Π°Π·Π²Π°Π½ΠΈΠ΅ ΡΠ²Π»ΡΠ΅ΡΡΡ ΡΠΊΠΎΡΠ΅Π΅ Π²ΡΠ΅Π³ΠΎ ΡΠΎΡΠ³ΠΎΠ²ΠΎΠΉ ΠΌΠ°ΡΠΊΠΎΠΉ, Π° Π½Π΅ Π½Π°Π·Π²Π°Π½ΠΈΠ΅ΠΌ Π²Π΅ΡΠ΅ΡΡΠ²Π°, ΠΏΠΎΡΡΠΎΠΌΡ Π½Π° ΠΎΡΠ΅ΡΠ΅ΡΡΠ²Π΅Π½Π½ΡΡ Π·Π°Π²ΠΎΠ΄Π°Ρ ΠΏΡΠΈ ΡΠ°ΡΡΠ°ΡΠΎΠ²ΠΊΠ΅ ΡΡΠΈΡ ΠΊΠ»Π΅Π΅Π² Π² ΡΠ°ΡΡ ΠΌΠΎΠ³ΡΡ Π»ΠΈΡΡ ΡΡΠΎ ΡΠ³ΠΎΠ΄Π½ΠΎ ΠΈΠ· ΡΠΏΠΎΠΊΡΠΈΠ΄Π½ΡΡ ΡΠΌΠΎΠ» ΡΠ°Π·Π»ΠΈΡΠ½ΡΡ ΠΌΠ°ΡΠΎΠΊ. ΠΠ΅ ΡΡΠΎΠΈΡ ΡΠΎΠ³Π΄Π° ΡΠ΄ΠΈΠ²Π»ΡΡΡΡΡ, ΡΡΠΎ ΡΠΏΠ°ΠΊΠΎΠ²ΠΊΠΈ ΡΡΠΎΠ³ΠΎ ΠΏΡΠΎΠ΄ΡΠΊΡΠ°, ΠΏΡΠΈΠΎΠ±ΡΠ΅ΡΠ΅Π½Π½ΡΠ΅ Π² ΡΠ°Π·Π½ΠΎΠ΅ Π²ΡΠ΅ΠΌΡ ΠΈΠ»ΠΈ Π² ΡΠ°Π·Π»ΠΈΡΠ½ΡΡ ΠΌΠ΅ΡΡΠ°Ρ Π±ΡΠ΄ΡΡ ΠΎΡΠ»ΠΈΡΠ°ΡΡΡΡ ΠΏΠΎ ΡΠ²ΠΎΠΈΠΌ ΡΠ²ΠΎΠΉΡΡΠ²Π°ΠΌ. ΠΡΠ»ΠΈ Π½Π°Π΄ΠΎ Π²ΡΠΏΠΎΠ»Π½ΠΈΡΡ ΠΊΠ°ΠΊΡΡ-Π»ΠΈΠ±ΠΎ ΡΠ°Π±ΠΎΡΡ, Π½Π° ΠΊΠΎΡΠΎΡΡΡ ΠΏΠΎΡΡΠ΅Π±ΡΠ΅ΡΡΡ Π±ΠΎΠ»Π΅Π΅ ΠΎΠ΄Π½ΠΎΠΉ ΡΠΏΠ°ΠΊΠΎΠ²ΠΊΠΈ β ΡΠΎΠ³Π΄Π° Π»ΡΡΡΠ΅ ΠΏΡΠΈΠΎΠ±ΡΠ΅ΡΡΠΈ ΠΈΡ ΡΡΠ°Π·Ρ ΠΈΠ· ΠΎΠ΄Π½ΠΎΠΉ ΠΏΠ°ΡΡΠΈΠΈ, Π° Π½Π΅ Π·Π°Π½ΠΈΠΌΠ°ΡΡΡΡ ΠΏΠΎΡΠΎΠΌ Π½Π΅ Π½ΡΠΆΠ½ΡΠΌΠΈ ΡΠΊΡΠΏΠ΅ΡΠΈΠΌΠ΅Π½ΡΠ°ΠΌΠΈ. ΠΠ»Π΅ΠΉ ΠΠΠ ΠΏΡΠΈ ΡΠ°ΡΡΠ°ΡΠΎΠ²ΠΊΠ΅ ΠΏΠΎ 280 Π³ ΡΡΠΎΠΈΡ ΠΎΠΊΠΎΠ»ΠΎ 1,5$ ΠΈ ΠΏΡΠΎΠ΄Π°Π΅ΡΡΡ Π² Ρ ΠΎΠ·ΡΠΉΡΡΠ²Π΅Π½Π½ΡΡ ΠΌΠ°Π³Π°Π·ΠΈΠ½Π°Ρ . Π£ΠΏΠ°ΠΊΠΎΠ²ΠΊΠ° ΡΠΎΠ΄Π΅ΡΠΆΠΈΡ Π΄Π²Π° ΠΊΠΎΠΌΠΏΠΎΠ½Π΅Π½ΡΠ° ΡΠΏΠΎΠΊΡΠΈΠ΄Π½ΡΡ ΠΌΠΎΠ΄ΠΈΡΠΈΡΠΈΡΠΎΠ²Π°Π½Π½ΡΡ ΡΠΌΠΎΠ»Ρ ΠΈ ΠΎΡΠ²Π΅ΡΠ΄ΠΈΡΠ΅Π»Ρ, ΠΊΠΎΡΠΎΡΡΠ΅ ΠΏΠ΅ΡΠ΅Π΄ ΡΠΏΠΎΡΡΠ΅Π±Π»Π΅Π½ΠΈΠ΅ΠΌ ΡΠΌΠ΅ΡΠΈΠ²Π°ΡΡΡΡ Π² ΡΠΎΠΎΡΠ½ΠΎΡΠ΅Π½ΠΈΠΈ ΠΎΡ 8:1 Π΄ΠΎ 10:1. ΠΡΠΎΡΠ΅ΡΡ ΠΏΠΎΠ»ΠΈΠΌΠ΅ΡΠΈΠ·Π°ΡΠΈΠΈ ΠΏΡΠΎΠΈΡΡ ΠΎΠ΄ΠΈΡ ΠΏΡΠΈ ΠΊΠΎΠΌΠ½Π°ΡΠ½ΠΎΠΉ ΡΠ΅ΠΌΠΏΠ΅ΡΠ°ΡΡΡΠ΅ Π² ΡΠ΅ΡΠ΅Π½ΠΈΠΈ Π½Π΅ΡΠΊΠΎΠ»ΡΠΊΠΈΡ ΡΠ°ΡΠΎΠ², Π° ΠΏΠΎΠ»Π½Π°Ρ ΠΏΠΎΠ»ΠΈΠΌΠ΅ΡΠΈΠ·Π°ΡΠΈΡ Π·Π°ΠΊΠ°Π½ΡΠΈΠ²Π°Π΅ΡΡΡ ΡΠΏΡΡΡΡ 12 ΡΠ°ΡΠΎΠ². Π§Π΅ΠΌ Π±ΠΎΠ»ΡΡΠ΅ ΡΠΎΠ΄Π΅ΡΠΆΠ°Π½ΠΈΠ΅ ΠΎΡΠ²Π΅ΡΠ΄ΠΈΡΠ΅Π»Ρ Π² ΡΠΊΠ°Π·Π°Π½Π½ΠΎΠΌ Π²ΡΡΠ΅ ΡΠΎΠΎΡΠ½ΠΎΡΠ΅Π½ΠΈΠΈ, ΡΠ΅ΠΌ Π±ΡΡΡΡΠ΅Π΅ ΠΈΠ΄Π΅Ρ ΠΏΡΠΎΡΠ΅ΡΡ ΠΏΠΎΠ»ΠΈΠΌΠ΅ΡΠΈΠ·Π°ΡΠΈΠΈ ΠΈ ΡΡΡ ΡΠ»Π΅Π΄ΡΠ΅Ρ ΠΏΠ΅ΡΠ²ΠΎΠ΅ ΠΏΡΠ°Π²ΠΈΠ»ΠΎ β ΡΠΎΡΠ½ΠΎ ΠΎΡΠΌΠ΅ΡΡΡΡ ΠΈΡΡ ΠΎΠ΄Π½ΡΠ΅ ΠΊΠΎΠΌΠΏΠΎΠ½Π΅Π½ΡΡ ΠΏΡΠΈ ΠΈΠ·Π³ΠΎΡΠΎΠ²Π»Π΅Π½ΠΈΠΈ ΡΠ°Π±ΠΎΡΠ΅ΠΉ ΡΠΌΠ΅ΡΠΈ, Π° Π² ΠΎΡΠ½ΠΎΡΠ΅Π½ΠΈΠΈ ΠΎΡΠ²Π΅ΡΠ΄ΠΈΡΠ΅Π»Ρ β Π»ΡΡΡΠ΅ Π΅Π³ΠΎ Π½Π΅ΠΌΠ½ΠΎΠ³ΠΎ «ΠΏΠ΅ΡΠ΅Π»ΠΎΠΆΠΈΡΡ», ΡΠ΅ΠΌ «Π½Π΅Π΄ΠΎΠ»ΠΎΠΆΠΈΡΡ».
ΠΡΠΎΡΠΎΠΉ ΠΈΠ· ΠΎΡΠ΅ΡΠ΅ΡΡΠ²Π΅Π½Π½ΡΡ ΡΠΏΠΎΠΊΡΠΈΠ΄Π½ΡΡ ΡΠΌΠΎΠ», ΠΏΡΠΈΠ³ΠΎΠ΄Π½ΠΎΠΉ Π΄Π»Ρ Π΄ΠΎΠΌΠ°ΡΠ½Π΅Π³ΠΎ ΡΠ²ΠΎΡΡΠ΅ΡΡΠ²Π°, ΡΠ²Π»ΡΠ΅ΡΡΡ ΡΠΏΠΎΠΊΡΠΈΠ΄Π½Π°Ρ ΡΠΌΠΎΠ»Π° ΠΠ-20. Π‘Π²ΠΎΠΉΡΡΠ²Π° Π΅Π΅ Π±ΠΎΠ»Π΅Π΅ ΠΏΡΠ΅Π΄ΡΠΊΠ°Π·ΡΠ΅ΠΌΡ, ΡΠ΅ΠΌ ΡΠ²ΠΎΠΉΡΡΠ²Π° ΠΠΠ, Π΄Π° ΠΈ ΠΊΠΎΠ½Π΅ΡΠ½Π°Ρ ΡΡΠΎΠΈΠΌΠΎΡΡΡ ΠΏΡΠΎΠ΄ΡΠΊΡΠ° ΠΏΠΎΠ»ΡΡΠ°Π΅ΡΡΡ ΠΏΠΎΡΡΠΈ Π² Π΄Π²Π° ΡΠ°Π·Π° Π½ΠΈΠΆΠ΅, Π½ΠΎ ΠΊ ΡΠΎΠΆΠ°Π»Π΅Π½ΠΈΡ ΠΏΡΠΈΠΎΠ±ΡΠ΅ΡΡΠΈ Π΅Π΅ Π² ΠΌΠ°Π»ΠΎΠΉ ΡΠ°ΡΡΠ°ΡΠΎΠ²ΠΊΠ΅ ΠΏΡΠ°ΠΊΡΠΈΡΠ΅ΡΠΊΠΈ Π½Π΅Π²ΠΎΠ·ΠΌΠΎΠΆΠ½ΠΎ. ΠΠΈΠ½ΠΈΠΌΠ°Π»ΡΠ½ΡΡ ΡΠ°ΡΡΠ°ΡΠΎΠ²ΠΊΡ, ΠΊΠΎΡΠΎΡΡΡ ΠΌΠ½Π΅ ΡΠ΄Π°Π»ΠΎΡΡ ΠΎΠ±Π½Π°ΡΡΠΆΠΈΡΡ ΡΡΠΎ ΡΠΌΠΎΠ»Π° ΠΠ-20 β 6 ΠΊΠ³. ΠΈ ΠΎΡΠ²Π΅ΡΠ΄ΠΈΡΠ΅Π»Ρ β 1 ΠΊΠ³. (ΡΠΌΠΎΠ»Π° ΠΈ ΠΎΡΠ²Π΅ΡΠ΄ΠΈΡΠ΅Π»Ρ ΠΏΡΠΎΠ΄Π°ΡΡΡΡ ΠΎΡΠ΄Π΅Π»ΡΠ½ΠΎ Π΄ΡΡΠ³ ΠΎΡ Π΄ΡΡΠ³Π°).
ΠΠΏΠΎΠΊΡΠΈΠ΄ΠΊΠ° ΠΏΠ»ΠΎΡ ΠΎ ΠΏΡΠΈΡΡΠ°Π΅Ρ ΠΊ ΡΠ°ΠΊΠΈΠΌ Π²Π΅ΡΠ΅ΡΡΠ²Π°ΠΌ, ΠΊΠ°ΠΊ ΠΏΠΎΠ»ΠΈΡΡΠΈΠ»Π΅Π½ (ΠΏΡΠ°ΠΊΡΠΈΡΠ΅ΡΠΊΠΈ Π½Π΅ ΠΏΡΠΈΡΡΠ°Π΅Ρ), ΠΏΠΎΠ»ΠΈΡΡΠΈΡΠΎΠ», ΠΎΡΠ³ΡΡΠ΅ΠΊΠ»ΠΎβ¦ ΠΡΠ»ΠΈ Π½Π° ΡΡΠΈ ΠΌΠ°ΡΠ΅ΡΠΈΠ°Π»Ρ Π½Π°Π½Π΅ΡΡΠΈ Π·Π°ΡΠΈΡΠ½ΡΠΉ ΡΠ»ΠΎΠΉ (Π½Π°ΠΏΡΠΈΠΌΠ΅Ρ ΠΈΠ· ΠΌΠ°ΡΡΠΈΠΊΠΈ Π΄Π»Ρ ΠΏΠ°ΡΠΊΠ΅ΡΠ°), ΡΠΎ ΠΏΠΎΡΠ»Π΅ ΠΏΠΎΠ»ΠΈΠΌΠ΅ΡΠΈΠ·Π°ΡΠΈΠΈ ΡΠΏΠΎΠΊΡΠΈΠ΄ΠΊΠ° Π»Π΅Π³ΠΊΠΎ ΠΎΡ Π½ΠΈΡ ΠΎΡΠ΄Π΅Π»ΡΠ΅ΡΡΡ. ΠΠ°ΡΠΈΡΠ° ΠΌΠ°ΡΡΠΈΠΊΠΎΠΉ ΠΌΠ΅ΡΠ°Π»Π»ΠΈΡΠ΅ΡΠΊΠΈΡ ΠΏΠΎΠ²Π΅ΡΡ Π½ΠΎΡΡΠ΅ΠΉ, ΠΏΠΎΠ²Π΅ΡΡ Π½ΠΎΡΡΠ΅ΠΉ ΠΈΠ· Π΄ΡΡΠ³ΠΈΡ ΠΏΠ»Π°ΡΡΠΌΠ°ΡΡ ΠΈ ΠΏΠΎΠ²Π΅ΡΡ Π½ΠΎΡΡΠ΅ΠΉ ΠΈΠ· ΡΠΏΠΎΠΊΡΠΈΠ΄ΠΊΠΈ ΠΏΠΎΠ·Π²ΠΎΠ»ΡΠ΅Ρ ΡΠ°ΠΊΠΆΠ΅ Π»Π΅Π³ΠΊΠΎ ΠΎΡΠ΄Π΅Π»ΠΈΡΡ ΠΎΡΠ»ΠΈΠ²ΠΊΡ ΠΈΠ· ΡΠΏΠΎΠΊΡΠΈΠ΄ΠΊΠΈ ΠΏΠΎΡΠ»Π΅ Π΅Π΅ ΠΏΠΎΠ»ΠΈΠΌΠ΅ΡΠΈΠ·Π°ΡΠΈΠΈ.
ΠΡΠΎΡΠ΅ΡΡ ΠΏΠΎΠ»ΠΈΠΌΠ΅ΡΠΈΠ·Π°ΡΠΈΠΈ ΡΠΏΠΎΠΊΡΠΈΠ΄ΠΊΠΈ ΡΠ²ΡΠ·Π°Π½ Ρ Ρ ΠΈΠΌΠΈΡΠ΅ΡΠΊΠΎΠΉ ΡΠ΅Π°ΠΊΡΠΈΠ΅ΠΉ ΠΌΠ΅ΠΆΠ΄Ρ Π΅Π΅ ΠΊΠΎΠΌΠΏΠΎΠ½Π΅Π½ΡΠ°ΠΌΠΈ, Π² Ρ ΠΎΠ΄Π΅ ΠΊΠΎΡΠΎΡΠΎΠΉ Π½Π°Π±Π»ΡΠ΄Π°Π΅ΡΡΡ Π²ΡΠ΄Π΅Π»Π΅Π½ΠΈΠ΅ ΡΠ΅ΠΏΠ»Π°. Π‘ Π΄ΡΡΠ³ΠΎΠΉ ΡΡΠΎΡΠΎΠ½Ρ ΡΠ°ΠΌΠ° Ρ ΠΈΠΌΠΈΡΠ΅ΡΠΊΠ°Ρ ΡΠ΅Π°ΠΊΡΠΈΡ ΠΈΠ΄Π΅Ρ Π±ΠΎΠ»Π΅Π΅ ΠΈΠ½ΡΠ΅Π½ΡΠΈΠ²Π½ΠΎ ΠΏΡΠΈ Π±ΠΎΠ»Π΅Π΅ Π²ΡΡΠΎΠΊΠΈΡ ΡΠ΅ΠΌΠΏΠ΅ΡΠ°ΡΡΡΠ°Ρ . ΠΠΎ ΡΡΠΎΠΉ ΠΏΡΠΈΡΠΈΠ½Π΅ (Π΅ΡΠ»ΠΈ Π½Π΅Ρ Π΄ΠΎΡΡΠ°ΡΠΎΡΠ½ΠΎΠ³ΠΎ ΠΎΡΠ²ΠΎΠ΄Π° ΡΠ΅ΠΏΠ»Π° ΠΎΡ ΠΏΠΎΠ»ΠΈΠΌΠ΅ΡΠΈΠ·ΡΡΡΠ΅ΠΉΡΡ ΠΌΠ°ΡΡΡ) ΠΏΡΠΎΠΈΡΡ ΠΎΠ΄ΠΈΡ Π΅Π΅ ΡΠ°Π·ΠΎΠ³ΡΠ΅Π², Π° Π² ΡΠ»ΡΡΠ°Π΅ ΠΊΠ»Π΅Ρ ΠΠΠ ΠΈΠ½ΠΎΠ³Π΄Π° ΡΠ΅ΠΌΠΏΠ΅ΡΠ°ΡΡΡΠ° ΠΌΠΎΠΆΠ΅Ρ ΠΏΠΎΠ΄Π½ΡΡΡΡΡ Π΄ΠΎ 50 β 60 Π³ΡΠ°Π΄ΡΡΠΎΠ². ΠΡΠΎ ΡΠ»Π΅Π΄ΡΠ΅Ρ ΡΡΠΈΡΡΠ²Π°ΡΡ ΠΏΡΠΈ Π²ΡΠ±ΠΎΡΠ΅ ΠΌΠ°ΡΠ΅ΡΠΈΠ°Π»Π° Π΄Π»Ρ ΠΈΠ·Π³ΠΎΡΠΎΠ²Π»Π΅Π½ΠΈΡ ΡΠΎΡΠΌΡβ¦ (ΠΏΡΠΈ ΡΠ°ΠΊΠΈΡ ΡΠ΅ΠΌΠΏΠ΅ΡΠ°ΡΡΡΠ°Ρ ΡΠΎΡΠΌΠ° ΠΈΠ· ΠΏΠ»Π°ΡΡΠΈΠ»ΠΈΠ½Π° ΠΏΠΎΠΏΠ»ΡΠ²Π΅Ρ, Π° ΠΎΡΠ»ΠΈΠ²ΠΊΠ° Π±ΡΠ΄Π΅Ρ Π±Π΅Π·Π½Π°Π΄Π΅ΠΆΠ½ΠΎ ΠΈΡΠΏΠΎΡΡΠ΅Π½Π°).
Π Π΅Π°ΠΊΡΠΈΡ ΠΏΠΎΠ»ΠΈΠΌΠ΅ΡΠΈΠ·Π°ΡΠΈΠΈ ΠΈΠ΄Π΅Ρ Π½Π°ΠΈΠ±ΠΎΠ»Π΅Π΅ ΠΈΠ½ΡΠ΅Π½ΡΠΈΠ²Π½ΠΎ Π² ΠΏΡΠΈΠ³ΡΠ°Π½ΠΈΡΠ½ΠΎΠΌ ΡΠ»ΠΎΠ΅. ΠΡΠΈ ΠΈΡΠΏΠΎΠ»ΡΠ·ΠΎΠ²Π°Π½ΠΈΠΈ ΡΠΏΠΎΠΊΡΠΈΠ΄ΠΊΠΈ Ρ ΡΠ²Π΅ΡΠ΄ΡΠΌ Π½Π°ΠΏΠΎΠ»Π½ΠΈΡΠ΅Π»Π΅ΠΌ (ΡΠ΅ΠΌΠ΅Π½Ρ, Π³ΠΈΠΏΡ ΠΈ Ρ.Π΄.) ΠΏΠΎΠ²Π΅ΡΡ Π½ΠΎΡΡΡ ΡΡΠΎΠ³ΠΎ ΠΏΡΠΈΠ³ΡΠ°Π½ΠΈΡΠ½ΠΎΠ³ΠΎ ΡΠ»ΠΎΡ ΡΠ΅Π·ΠΊΠΎ Π²ΠΎΠ·ΡΠ°ΡΡΠ°Π΅Ρ ΠΈ ΠΏΡΠΎΡΠ΅ΡΡ ΠΏΠΎΠ»ΠΈΠΌΠ΅ΡΠΈΠ·Π°ΡΠΈΠΈ ΠΈΠ΄Π΅Ρ Π±ΡΡΡΡΠ΅Π΅, ΡΠ΅ΠΌ Π±Π΅Π· Π½Π°ΠΏΠΎΠ»Π½ΠΈΡΠ΅Π»Ρ. ΠΡΠΎΠΌΠ΅ ΡΠΎΠ³ΠΎ ΠΎΡΠ²ΠΎΠ΄ ΡΠ΅ΠΏΠ»Π° Ρ ΡΡΠΎΠ³ΠΎ ΠΏΡΠΈΠ³ΡΠ°Π½ΠΈΡΠ½ΠΎΠ³ΠΎ ΡΠ»ΠΎΡ ΠΎΠ³ΡΠ°Π½ΠΈΡΠ΅Π½ ΠΈ Π½Π°Π±Π»ΡΠ΄Π°Π΅ΡΡΡ ΡΠ°ΠΌΠΎΡΠ°Π·ΠΎΠ³ΡΠ΅Π² ΡΠΌΠ΅ΡΠΈ, ΡΡΠΎ ΡΠ°ΠΊΠΆΠ΅ Π½Π΅ΠΎΠ±Ρ ΠΎΠ΄ΠΈΠΌΠΎ ΡΡΠΈΡΡΠ²Π°ΡΡ.
ΠΡΠΈ ΠΏΠΎΠ²ΡΡΠ΅Π½ΠΈΠΈ ΡΠ΅ΠΌΠΏΠ΅ΡΠ°ΡΡΡΡ ΡΠΌΠΎΠ»Π° ΠΏΠΎΠ²ΡΡΠ°Π΅Ρ ΡΠ²ΠΎΡ ΡΠ΅ΠΊΡΡΠ΅ΡΡΡ ΠΈ ΡΠ½ΠΈΠΆΠ°Π΅Ρ Π²ΡΠ·ΠΊΠΎΡΡΡ, ΠΏΠΎΡΡΠΎΠΌΡ Π΄Π»Ρ Π·Π°Π»ΠΈΠ²ΠΊΠΈ ΠΌΠ΅Π»ΠΊΠΈΡ Π΄Π΅ΡΠ°Π»Π΅ΠΉ ΡΠ°ΡΡΠ²ΠΎΡ Π½Π΅ΠΎΠ±Ρ ΠΎΠ΄ΠΈΠΌΠΎ ΠΏΠ΅ΡΠ²ΠΎΠ½Π°ΡΠ°Π»ΡΠ½ΠΎ Π½Π°Π³ΡΠ΅Ρ Π΄ΠΎ 25 β 30 Π³ΡΠ°Π΄ΡΡΠΎΠ². ΠΠ°Π»Π΅Π΅ Π² Π½Π΅Π³ΠΎ Π΄ΠΎΠ±Π°Π²Π»ΡΠ΅ΠΌ Π½Π°ΠΏΠΎΠ»Π½ΠΈΡΠ΅Π»Ρ ΠΈ ΡΠΎΠ»ΡΠΊΠΎ ΠΏΠΎΡΠ»Π΅ ΡΡΠΎΠ³ΠΎ ΠΎΡΠ²Π΅ΡΠ΄ΠΈΡΠ΅Π»Ρ. Π’Π°ΠΊΠ°Ρ ΠΏΠΎΡΠ»Π΅Π΄ΠΎΠ²Π°ΡΠ΅Π»ΡΠ½ΠΎΡΡΡ ΠΏΡΠΈΠ³ΠΎΡΠΎΠ²Π»Π΅Π½ΠΈΡ ΠΈΡΡ ΠΎΠ΄Π½ΠΎΠΉ ΠΌΠ°ΡΡΡ Π² Π½Π°ΠΈΠ±ΠΎΠ»ΡΡΠ΅ΠΉ ΡΡΠ΅ΠΏΠ΅Π½ΠΈ Π±ΡΠ΄Π΅Ρ Π³Π°ΡΠ°Π½ΡΠΈΡΠΎΠ²Π°ΡΡ ΠΎΠ΄Π½ΠΎΡΠΎΠ΄Π½ΠΎΡΡΡ ΠΊΠΎΠ½Π΅ΡΠ½ΠΎΠΉ ΠΏΠ»Π°ΡΡΠΌΠ°ΡΡΡ. ΠΡΠΈ ΠΏΠΎΠ½ΠΈΠΆΠ΅Π½ΠΈΠΈ ΡΠ΅ΠΌΠΏΠ΅ΡΠ°ΡΡΡΡ ΠΈ Π²ΠΎ Π²Π»Π°ΠΆΠ½ΠΎΠΉ Π°ΡΠΌΠΎΡΡΠ΅ΡΠ΅ ΠΏΡΠΎΡΠ΅ΡΡ ΠΏΠΎΠ»ΠΈΠΌΠ΅ΡΠΈΠ·Π°ΡΠΈΠΈ ΡΠΌΠΎΠ»Ρ Π·Π°ΠΌΠ΅Π΄Π»ΡΠ΅ΡΡΡ, Π° ΠΏΡΠΈ Π²ΡΡΠΎΠΊΠΎΠΉ Π²Π»Π°ΠΆΠ½ΠΎΡΡΠΈ ΠΏΠΎΠ»ΠΈΠΌΠ΅ΡΠΈΠ·Π°ΡΠΈΡ Π²ΠΎΠΎΠ±ΡΠ΅ ΠΌΠΎΠΆΠ΅Ρ Π½Π΅ ΠΏΡΠΎΠΈΠ·ΠΎΠΉΡΠΈ Π΄ΠΎ ΠΊΠΎΠ½ΡΠ°.
ΠΠΎ ΡΠ΅Ρ ΠΏΠΎΡ, ΠΏΠΎΠΊΠ° ΡΠΏΠΎΠΊΡΠΈΠ΄ΠΊΠ° Π½Π΅ ΠΏΠΎΠ»ΠΈΠΌΠ΅ΡΠΈΠ·ΠΎΠ²Π°Π»Π°ΡΡ, ΠΎΠ½Π° Π²Π΅Π΄Π΅Ρ ΡΠ΅Π±Ρ ΠΊΠ°ΠΊ Π²ΡΠ·ΠΊΠ°Ρ ΠΆΠΈΠ΄ΠΊΠΎΡΡΡ ΡΠΎ Π²ΡΠ΅ΠΌΠΈ Π²ΡΡΠ΅ΠΊΠ°ΡΡΠΈΠΌΠΈ ΠΎΡΡΡΠ΄Π° ΠΏΠΎΡΠ»Π΅Π΄ΡΡΠ²ΠΈΡΠΌΠΈ. ΠΠ²Π΅Π΄Π΅Π½ΡΠΉ Π² ΡΠΏΠΎΠΊΡΠΈΠ΄ΠΊΡ Π½Π°ΠΏΠΎΠ»Π½ΠΈΡΠ΅Π»Ρ Π² Π·Π°Π²ΠΈΡΠΈΠΌΠΎΡΡΠΈ ΠΎΡ Π΅Π³ΠΎ ΡΠ΄Π΅Π»ΡΠ½ΠΎΠ³ΠΎ Π²Π΅ΡΠ° Π»ΠΈΠ±ΠΎ ΠΎΠΏΡΡΠΊΠ°Π΅ΡΡΡ Π²Π½ΠΈΠ· (ΡΠ΅ΠΌΠ΅Π½Ρ Π½Π°ΠΏΡΠΈΠΌΠ΅Ρ) Π»ΠΈΠ±ΠΎ Π²ΡΠΏΠ»ΡΠ²Π°Π΅Ρ (Π΄Π΅ΡΠ΅Π²ΡΠ½Π½Π°Ρ ΠΊΡΠΎΡΠΊΠ°, ΠΎΡΠ΄Π΅Π»ΡΠ½ΡΠ΅ ΠΏΡΠ·ΡΡΡΠΊΠΈ Π²ΠΎΠ·Π΄ΡΡ Π°). ΠΡΠΎ Π½Π΅ΠΎΠ±Ρ ΠΎΠ΄ΠΈΠΌΠΎ ΡΡΠΈΡΡΠ²Π°ΡΡ Π΄Π»Ρ ΠΏΡΠ°Π²ΠΈΠ»ΡΠ½ΠΎΠΉ ΠΎΡΠΈΠ΅Π½ΡΠ°ΡΠΈΠΈ Π»ΠΈΡΡΠ΅Π²ΠΎΠΉ ΡΠΎΡΠΌΡ Π² ΡΠ΅ΡΠ΅Π½ΠΈΠΈ ΠΏΡΠΎΡΠ΅ΡΡΠ° ΠΏΠΎΠ»ΠΈΠΌΠ΅ΡΠΈΠ·Π°ΡΠΈΠΈ, ΡΡΠΎΠ±Ρ Π½Π° ΠΎΡΠ²Π΅ΡΡΡΠ²Π΅Π½Π½ΡΡ ΠΏΠΎΠ²Π΅ΡΡ Π½ΠΎΡΡΡΡ Π½Π΅ ΠΎΠ±ΡΠ°Π·ΠΎΠ²Π°Π»ΠΈΡΡ Π½Π΅ΠΆΠ΅Π»Π°ΡΠ΅Π»ΡΠ½ΡΠ΅ ΡΠ°ΠΊΠΎΠ²ΠΈΠ½Ρ ΠΎΡ Π²ΠΎΠ·Π΄ΡΡΠ½ΡΡ ΠΏΡΠ·ΡΡΠ΅ΠΉ ΠΈ Ρ.ΠΏ.
ΠΡΠ½ΠΎΠ²Π½Π°Ρ Π±Π΅Π΄Π° ΠΎΡΠ΅ΡΠ΅ΡΡΠ²Π΅Π½Π½ΠΎΠΉ ΡΠΏΠΎΠΊΡΠΈΠ΄ΠΊΠΈ β ΡΡΠΎ ΡΡΡΠ΄Π½ΠΎΡΡΡ ΠΈΠ·Π±Π°Π²Π»Π΅Π½ΠΈΡ ΠΎΡ Π²ΠΎΠ·Π΄ΡΡΠ½ΡΡ ΠΏΡΠ·ΡΡΡΠΊΠΎΠ², ΠΊΠΎΡΠΎΡΡΠ΅ ΠΎΠ±ΡΠ°Π·ΡΡΡΡΡ Π² ΠΏΡΠΎΡΠ΅ΡΡΠ΅ ΠΏΡΠΈΠ³ΠΎΡΠΎΠ²Π»Π΅Π½ΠΈΡ ΠΈ ΠΏΠ΅ΡΠ΅ΠΌΠ΅ΡΠΈΠ²Π°Π½ΠΈΡ ΠΈΡΡ ΠΎΠ΄Π½ΠΎΠΉ ΠΌΠ°ΡΡΡ. Π Π΅ΡΠ΅ΠΏΡ ΡΡΡ ΠΎΠ΄ΠΈΠ½ β Π΄Π°Π²Π°ΡΡ ΠΎΡΡΡΠΎΡΡΡΡΡ ΡΠΌΠ΅ΡΠΈ, ΡΡΠΎΠ±Ρ ΠΏΡΠ·ΡΡΠΈ Π²ΡΠΏΠ»ΡΠ»ΠΈ, ΠΏΠΎΠ²ΡΡΠΈΡΡ ΡΠ΅ΠΊΡΡΠ΅ΡΡΡ ΡΠΌΠΎΠ»Ρ ΠΏΠΎΠ²ΡΡΠ΅Π½ΠΈΠ΅ΠΌ Π΅Π΅ ΡΠ΅ΠΌΠΏΠ΅ΡΠ°ΡΡΡΡ ΠΈ ΡΠΈΠ·ΠΈΡΠ΅ΡΠΊΠΎΠ΅ ΡΠ΄Π°Π»Π΅Π½ΠΈΠ΅ ΠΏΡΠ·ΡΡΠ΅ΠΉ, ΠΏΡΠΈΠ»ΠΈΠΏΡΠΈΡ ΠΊ ΠΏΠΎΠ²Π΅ΡΡ Π½ΠΎΡΡΡΠΌ ΡΠΎΡΠΌΡ ΠΏΡΠΈ ΠΏΠΎΠΌΠΎΡΠΈ ΠΎΡΡΡΠΎΠ³ΠΎ ΠΏΡΠ΅Π΄ΠΌΠ΅ΡΠ° (Π½Π°ΠΏΡΠΈΠΌΠ΅Ρ Π·ΡΠ±ΠΎΡΠΈΡΡΠΊΠΈ). ΠΠΎΠΌΠΎΠ³Π°Π΅Ρ ΡΠ°ΠΊ-ΠΆΠ΅ Π·Π°Π»ΠΈΠ²ΠΊΠ° ΡΠ°ΡΡΠ²ΠΎΡΠ° Π² ΡΠΎΡΠΌΡ Π½Π΅ Π½Π°ΠΏΡΡΠΌΡΡ, Π° ΡΠ΅ΡΠ΅Π· ΠΏΡΠΎΠΌΠ΅ΠΆΡΡΠΎΡΠ½ΡΠΉ ΠΏΡΠ΅Π΄ΠΌΠ΅Ρ ΡΠΎΠ½ΠΊΠΎΠΉ ΡΡΡΡΠΉΠΊΠΎΠΉ (ΡΠΎΠ³Π΄Π° Π±ΠΎΠ»ΡΡΠΈΠ½ΡΡΠ²ΠΎ ΠΌΠΈΠΊΡΠΎΠΏΡΠ·ΡΡΠ΅ΠΉ ΠΈΡΡΠ΅Π·Π½Π΅Ρ Π½Π° ΠΏΡΠΎΠΌΠ΅ΠΆΡΡΠΎΡΠ½ΡΡ ΠΏΠΎΠ²Π΅ΡΡ Π½ΠΎΡΡΡΡ Π² ΠΏΡΠΎΡΠ΅ΡΡΠ΅ Π·Π°Π»ΠΈΠ²ΠΊΠΈ).
ΠΡΠΈ ΡΠ°Π±ΠΎΡΠ΅ Ρ ΡΠΏΠΎΠΊΡΠΈΠ΄ΠΊΠΎΠΉ Π½Π΅ΠΎΠ±Ρ ΠΎΠ΄ΠΈΠΌΠΎ ΠΈΡΠΏΠΎΠ»ΡΠ·ΠΎΠ²Π°ΡΡ ΠΎΠ΄Π½ΠΎΡΠ°Π·ΠΎΠ²ΡΡ (Π»ΡΡΡΠ΅ ΠΏΠ»Π°ΡΡΠΈΠΊΠΎΠ²ΡΡ) ΠΏΠΎΡΡΠ΄Ρ Π΄Π»Ρ ΠΏΡΠΈΠ³ΠΎΡΠΎΠ²Π»Π΅Π½ΠΈΡ ΠΊΠ°ΠΆΠ΄ΠΎΠΉ Π½ΠΎΠ²ΠΎΠΉ ΠΏΠ°ΡΡΠΈΠΈ ΡΠΌΠ΅ΡΠΈ. ΠΠ»Ρ ΡΡΠΎΠ³ΠΎ ΠΈΡΠΏΠΎΠ»ΡΠ·ΡΠ΅ΡΡΡ Π²ΡΠ΅Π²ΠΎΠ·ΠΌΠΎΠΆΠ½Π°Ρ ΡΠ°ΡΠ° ΠΈΠ· ΠΏΠΎΠ΄ ΡΠ°Π·Π»ΠΈΡΠ½ΡΡ ΠΏΠΈΡΠ΅Π²ΡΡ ΠΏΡΠΎΠ΄ΡΠΊΡΠΎΠ² β Π°Π»ΡΠΌΠΈΠ½ΠΈΠ΅Π²ΡΠ΅ Π±Π°Π½ΠΊΠΈ ΠΈΠ· ΠΏΠΎΠ΄ ΠΏΠΈΠ²Π° ΠΈ ΡΠΎΠΊΠΎΠ², ΠΏΠ»Π°ΡΡΠΈΠΊΠΎΠ²ΡΠ΅ ΠΊΠΎΡΠΎΠ±ΠΊΠΈ ΠΈΠ· ΠΏΠΎΠ΄ Π²ΡΠ΅Π²ΠΎΠ·ΠΌΠΎΠΆΠ½ΡΡ ΠΌΠΎΠ»ΠΎΡΠ½ΡΡ ΠΏΡΠΎΠ΄ΡΠΊΡΠΎΠ², ΠΏΠ»Π°ΡΡΠΈΠΊΠΎΠ²ΡΠ΅ ΠΏΠ΅Π½Π°Π»Ρ ΠΈΠ· ΠΏΠΎΠ΄ ΡΠΎΡΠΎΠΏΠ»Π΅Π½ΠΊΠΈ ΠΈ Ρ.ΠΏ. ΠΠ»Π°Π²Π½ΠΎΠ΅, ΡΡΠΎΠ±Ρ Π±ΡΠ»ΠΎ Π½Π΅ ΠΆΠ°Π»ΠΊΠΎ Π²ΡΠ±ΡΠ°ΡΡΠ²Π°ΡΡ ΠΏΠΎΡΠ»Π΅ ΠΈΡΠΏΠΎΠ»ΡΠ·ΠΎΠ²Π°Π½ΠΈΡ ΡΠΌΠ΅ΡΠΈ. Π―, Π½Π°ΠΏΡΠΈΠΌΠ΅Ρ, ΡΠ°Π·Π²ΠΎΠΆΡ ΡΠΏΠΎΠΊΡΠΈΠ΄ΠΊΡ Π² Π±Π°Π½ΠΊΠ°Ρ ΠΈΠ· ΠΏΠΎΠ΄ ΠΉΠΎΠ³ΡΡΡΠΎΠ² β Π΄Π΅ΡΠ΅Π²ΠΎ ΠΈ ΡΠ΅ΡΠ΄ΠΈΡΠΎ!
ΠΡΡ ΠΎΠ΄Π½ΡΠ΅ ΠΊΠΎΠΌΠΏΠΎΠ½Π΅Π½ΡΡ ΡΠΏΠΎΠΊΡΠΈΠ΄ΠΊΠΈ ΡΡΠ΅Π±ΡΡΡ ΡΡΠ°ΡΠ΅Π»ΡΠ½ΠΎΠΉ Π΄ΠΎΠ·ΠΈΡΠΎΠ²ΠΊΠΈ, Π΄Π»Ρ ΠΎΡΡΡΠ΅ΡΡΠ²Π»Π΅Π½ΠΈΡ ΠΊΠΎΡΠΎΡΠΎΠΉ ΡΠ΄ΠΎΠ±Π½ΠΎ ΠΈΡΠΏΠΎΠ»ΡΠ·ΠΎΠ²Π°ΡΡ ΠΎΠ΄Π½ΠΎΡΠ°Π·ΠΎΠ²ΡΠ΅ ΠΏΠ»Π°ΡΡΠΈΠΊΠΎΠ²ΡΠ΅ ΡΠΏΡΠΈΡΡ (Π²ΡΠΏΡΡΠΊΠ°ΡΡΡΡ ΠΎΠ±ΡΠ΅ΠΌΠΎΠΌ 2, 5 ΠΈ 10 ΡΠΌ3). Π‘ΠΌΠΎΠ»Π° Π·Π°Π»ΠΈΠ²Π°Π΅ΡΡΡ Π² ΡΠΏΡΠΈΡ ΡΠ²Π΅ΡΡ Ρ.
ΠΡΠ²Π΅ΡΠ΄ΠΈΡΠ΅Π»Ρ ΠΌΠΎΠΆΠ½ΠΎ Π½Π°Π±ΡΠ°ΡΡ Π² ΡΠΏΡΠΈΡ ΠΎΠ±ΡΠΊΠ½ΠΎΠ²Π΅Π½Π½ΡΠΌ ΠΎΠ±ΡΠ°Π·ΠΎΠΌ.
ΠΠ»Ρ Π½Π°Π½Π΅ΡΠ΅Π½ΠΈΡ Π½Π° ΡΠΎΡΠΌΡ Π·Π°ΡΠΈΡΠ½ΠΎΠ³ΠΎ ΡΠ»ΠΎΡ, ΠΎΡΠΎΠ±Π΅Π½Π½ΠΎ Π² ΡΡΡΠ΄Π½ΠΎΠ΄ΠΎΡΡΡΠΏΠ½ΡΡ ΠΌΠ΅ΡΡΠ°Ρ ΡΠ΄ΠΎΠ±Π½ΠΎ ΠΏΠΎΠ»ΡΠ·ΠΎΠ²Π°ΡΡΡΡ Π²Π°ΡΠ½ΡΠΌΠΈ ΠΏΠ°Π»ΠΎΡΠΊΠ°ΠΌΠΈ. ΠΡΠΈ ΠΈΡ ΠΏΠΎΠΌΠΎΡΠΈ ΡΠ°ΠΊΠΆΠ΅ ΡΠ΄Π°Π»ΡΡΡ ΠΈΠ·Π»ΠΈΡΠΊΠΈ ΠΌΠ°ΡΡΠΈΠΊΠΈ.
ΠΠ»Ρ ΡΠ΄Π°Π»Π΅Π½ΠΈΡ Π²ΠΎΠ·Π΄ΡΡΠ½ΡΡ ΠΏΡΠ·ΡΡΠ΅ΠΉ Π²ΡΠ΅ ΡΠ³Π»ΡΠ±Π»Π΅Π½ΠΈΡ Π² ΡΠΎΡΠΌΠ΅ ΠΏΠΎΡΠ»Π΅ Π·Π°Π»ΠΈΠ²ΠΊΠΈ «ΠΏΡΠΎΡ ΠΎΠ΄ΡΡΡΡ» ΠΎΡΡΡΠΎΠΉ Π΄Π΅ΡΠ΅Π²ΡΠ½Π½ΠΎΠΉ Π·ΡΠ±ΠΎΡΠΈΡΡΠΊΠΎΠΉ. ΠΠ΅ΡΠ΅Π²ΠΎ Π½Π΅ ΠΏΡΠΈΠ½ΠΎΡΠΈΡ Π²ΡΠ΅Π΄Π° ΡΠΎΡΠΌΠ΅ ΠΈ Π·Π°ΡΠΈΡΠ½ΠΎΠΌΡ ΡΠ»ΠΎΡ, Π½ΠΎ ΠΏΠΎΠΌΠΎΠ³Π°Π΅Ρ Π²ΠΎΠ·Π΄ΡΡΠ½ΡΠΌ ΠΏΡΠ·ΡΡΡΠΌ ΠΎΡΠΎΡΠ²Π°ΡΡΡΡ ΠΎΡ ΠΏΠΎΠ²Π΅ΡΡ Π½ΠΎΡΡΠΈ ΡΠΎΡΠΌΡ ΠΈ Π²ΡΠΏΠ»ΡΡΡβ¦
Π’Π΅ΠΏΠ΅ΡΡ Π½Π΅ΡΠΊΠΎΠ»ΡΠΊΠΎ ΡΠ»ΠΎΠ² ΠΎ Π½Π°ΠΏΠΎΠ»Π½ΠΈΡΠ΅Π»ΡΡ .
Π ΠΊΠ°ΡΠ΅ΡΡΠ²Π΅ Π½Π°ΠΏΠΎΠ»Π½ΠΈΡΠ΅Π»Π΅ΠΉ ΡΠ°ΡΠ΅ Π²ΡΠ΅Π³ΠΎ ΠΈΡΠΏΠΎΠ»ΡΠ·ΡΡΡ ΡΠ΅ΠΌΠ΅Π½Ρ, Π°Π»Π΅Π±Π°ΡΡ (ΡΡΡΠΎΠΈΡΠ΅Π»ΡΠ½ΡΠΉ Π³ΠΈΠΏΡ), ΠΌΠ΅Π» (Π·ΡΠ±Π½ΠΎΠΉ ΠΏΠΎΡΠΎΡΠΎΠΊ), Π΄ΡΠ΅Π²Π΅ΡΠ½ΡΡ ΠΊΡΠΎΡΡ. ΠΡΠΎΡΠ΅Π½ΡΠ½ΠΎΠ΅ ΡΠΎΠ΄Π΅ΡΠΆΠ°Π½ΠΈΠ΅ Π½Π°ΠΏΠΎΠ»Π½ΠΈΡΠ΅Π»Ρ Π² ΡΠΌΠ΅ΡΠΈ (ΠΏΠΎ ΠΎΠ±ΡΠ΅ΠΌΡ) ΠΌΠΎΠΆΠ΅Ρ Π΄ΠΎΡ ΠΎΠ΄ΠΈΡΡ Π΄ΠΎ 50% (ΠΏΠΎΠΊΠ° ΡΠΌΠ΅ΡΡ Π½Π΅ ΠΏΠΎΡΠ΅ΡΡΠ΅Ρ ΡΠ²ΠΎΡ ΡΠ΅ΠΊΡΡΠ΅ΡΡΡ). Π― ΡΠ΅ΠΊΠΎΠΌΠ΅Π½Π΄ΡΡ Π΄ΠΎΠ±Π°Π²Π»ΡΡΡ Π½Π°ΠΏΠΎΠ»Π½ΠΈΡΠ΅Π»Ρ ΠΎΠΊΠΎΠ»ΠΎ 30-40%. ΠΡΠΈ ΡΠ°ΠΊΠΎΠΌ ΡΠΎΠΎΡΠ½ΠΎΡΠ΅Π½ΠΈΠΈ ΡΠ΄Π°Π΅ΡΡΡ ΠΏΠΎΠ»ΡΡΠΈΡΡ ΠΊΠΎΠ½Π΅ΡΠ½ΡΠΉ ΠΏΠ»Π°ΡΡΠΈΠΊ Ρ ΡΡΠ΅Π±ΡΠ΅ΠΌΡΠΌΠΈ ΡΠ²ΠΎΠΉΡΡΠ²Π°ΠΌΠΈ, ΡΠ½ΠΈΠΆΠ°Π΅ΡΡΡ ΡΠ°ΡΡ ΠΎΠ΄ ΡΠΏΠΎΠΊΡΠΈΠ΄ΠΊΠΈ, ΠΈ, Π² ΡΠΎΠΆΠ΅ Π²ΡΠ΅ΠΌΡ, ΡΠΎΡ ΡΠ°Π½ΡΠ΅ΡΡΡ Π΅Π΅ Π΄ΠΎΡΡΠ°ΡΠΎΡΠ½Π°Ρ ΠΏΠΎΠ΄Π²ΠΈΠΆΠ½ΠΎΡΡΡ Π² ΠΏΡΠΎΡΠ΅ΡΡΠ΅ Π»ΠΈΡΡΡ.
Π¦Π΅ΠΌΠ΅Π½Ρ, ΠΊΠ°ΠΊ Π½Π°ΠΏΠΎΠ»Π½ΠΈΡΠ΅Π»Ρ Ρ ΠΎΡΠΎΡΠΎ ΠΏΡΠΈΠΌΠ΅Π½ΡΡΡ ΠΏΡΠΈ ΠΈΠ·Π³ΠΎΡΠΎΠ²Π»Π΅Π½ΠΈΠΈ Π²ΡΠ΅Π²ΠΎΠ·ΠΌΠΎΠΆΠ½ΡΡ ΡΠΎΡΠΌ Π΄Π»Ρ Π»ΠΈΡΡΡ. ΠΠΎΠ½Π΅ΡΠ½ΡΠΉ ΠΏΠ»Π°ΡΡΠΈΠΊ ΠΏΠΎΠ»ΡΡΠ°Π΅ΡΡΡ ΠΏΡΠΎΡΠ½ΡΠΌ (Π²ΠΈΠ΄ΠΈΠΌΠΎ ΡΠΊΠ°Π·ΡΠ²Π°Π΅ΡΡΡ ΠΈ Π½Π΅ΠΊΠΎΡΠΎΡΠΎΠ΅ «ΡΡ Π²Π°ΡΡΠ²Π°Π½ΠΈΠ΅» ΡΠ΅ΠΌΠ΅Π½ΡΠ°). Π‘Π»Π΅Π΄ΡΠ΅Ρ ΡΠΎΠ»ΡΠΊΠΎ ΡΡΠ΅ΡΡΡ, ΡΡΠΎ ΠΈΠΌΠ΅ΡΡΠΈΠΉΡΡ Π² ΠΏΡΠΎΠ΄Π°ΠΆΠ΅ ΡΠ΅ΠΌΠ΅Π½Ρ ΠΏΠ΅ΡΠ΅Π΄ ΠΏΡΠΈΠ³ΠΎΡΠΎΠ²Π»Π΅Π½ΠΈΠ΅ΠΌ ΡΠΌΠ΅ΡΠΈ Π½Π΅ΠΎΠ±Ρ ΠΎΠ΄ΠΈΠΌΠΎ ΠΏΡΠΎΡΠ΅ΡΡΡ ΡΠ΅ΡΠ΅Π· ΠΌΠ°ΡΠ»Ρ, Ρ.ΠΊ. Π² Π½Π΅ΠΌ ΠΌΠ½ΠΎΠ³ΠΎ ΠΊΠΎΠΌΠΊΠΎΠ² Π±ΠΎΠ»ΡΡΠΎΠ³ΠΎ ΡΠ°Π·ΠΌΠ΅ΡΠ°.
ΠΠ»Π΅Π±Π°ΡΡΡ. ΠΠ΅ΠΌΠ½ΠΎΠ³ΠΎ Ρ ΡΠΆΠ΅, ΡΠ΅ΠΌ ΡΠ΅ΠΌΠ΅Π½Ρ, Ρ ΡΠΎΡΠΊΠΈ Π·ΡΠ΅Π½ΠΈΡ Π½Π°ΠΏΠΎΠ»Π½ΠΈΡΠ΅Π»Ρ, Π½ΠΎ Π²ΠΏΠΎΠ»Π½Π΅ ΠΏΠΎΠ΄Ρ ΠΎΠ΄ΠΈΡ Π΄Π»Ρ ΡΠΊΠΎΠ½ΠΎΠΌΠΈΠΈ ΡΠΏΠΎΠΊΡΠΈΠ΄ΠΊΠΈ.
ΠΠ΅Π» (Π·ΡΠ±Π½ΠΎΠΉ ΠΏΠΎΡΠΎΡΠΎΠΊ). ΠΠΏΠΎΠ»Π½Π΅ ΠΏΡΠΈΠ΅ΠΌΠ»Π΅ΠΌ Ρ ΡΠΎΡΠΊΠΈ Π·ΡΠ΅Π½ΠΈΡ ΡΠ²ΠΎΠΉΡΡΠ², ΠΊΠ°ΠΊ Π½Π°ΠΏΠΎΠ»Π½ΠΈΡΠ΅Π»Ρ, Π½ΠΎ ΠΎΠ±Π»Π°Π΄Π°Π΅Ρ ΠΎΠ΄Π½ΠΎΠΉ ΠΏΠ°ΡΡΠΈΠ²ΠΎΠΉ ΠΎΡΠΎΠ±Π΅Π½Π½ΠΎΡΡΡΡ β ΠΎΡΠ΅Π½Ρ Π³ΠΈΠ³ΡΠΎΡΠΊΠΎΠΏΠΈΡΠ΅Π½, Π° ΡΠΏΠΎΠΊΡΠΈΠ΄ΠΊΠ° Π½Π΅ Π»ΡΠ±ΠΈΡ Π²ΠΎΠ΄Ρ. ΠΠΎΡΡΠΎΠΌΡ ΠΎΡ ΠΏΡΠΈΠΌΠ΅Π½Π΅Π½ΠΈΡ ΠΌΠ΅Π»Π° Π»ΡΡΡΠ΅ Π²ΠΎΠ·Π΄Π΅ΡΠΆΠ°ΡΡΡΡ ΠΈΠ»ΠΈ Π² ΠΊΡΠ°ΠΉΠ½Π΅ΠΌ ΡΠ»ΡΡΠ°Π΅ ΠΏΠ΅ΡΠ΅Π΄ Π·Π°ΡΡΠΏΠΊΠΎΠΉ Π΅Π³ΠΎ Π² ΡΠΌΠ΅ΡΡ Ρ ΠΎΡΠΎΡΠ΅Π½ΡΠΊΠΎ ΠΏΡΠΎΡΡΡΠΈΡΡ Π΄Π»Ρ ΡΠ΄Π°Π»Π΅Π½ΠΈΡ Π²Π»Π°Π³ΠΈ.
ΠΡΠ΅Π²Π΅ΡΠ½Π°Ρ ΠΊΡΠΎΡΠΊΠ°. ΠΠ±Π»Π°Π΄Π°Π΅Ρ Π½ΠΈΠ·ΠΊΠΈΠΌ ΡΠ΄Π΅Π»ΡΠ½ΡΠΌ Π²Π΅ΡΠΎΠΌ ΠΈ Π½Π΅Π·Π°ΠΌΠ΅Π½ΠΈΠΌΠ° ΠΏΡΠΈ ΠΈΠ·Π³ΠΎΡΠΎΠ²Π»Π΅Π½ΠΈΠΈ ΠΏΠ»Π°ΡΡΠΈΠΊΠ° Ρ ΡΠ΄Π΅Π»ΡΠ½ΡΠΌ Π²Π΅ΡΠΎΠΌ Π½ΠΈΠΆΠ΅, ΡΠ΅ΠΌ Ρ ΠΈΡΡ ΠΎΠ΄Π½ΠΎΠΉ ΡΠΏΠΎΠΊΡΠΈΠ΄ΠΊΠΈ. ΠΡΠΈΠΌΠ΅Π½ΡΠ΅ΡΡΡ Π΄Π»Ρ ΠΈΠ·Π³ΠΎΡΠΎΠ²Π»Π΅Π½ΠΈΡ ΡΠΌΠ΅ΡΠΈ ΠΏΠΎΠ΄ Π²ΡΠ΅Π²ΠΎΠ·ΠΌΠΎΠΆΠ½ΡΠ΅ Π²ΠΎΠ±Π»Π΅ΡΡ ΠΈ Ρ.ΠΏ. Π§Π΅ΠΌ ΠΌΠ΅Π»ΡΡΠ΅ ΠΊΡΠΎΡΠΊΠ° β ΡΠ΅ΠΌ Π»ΡΡΡΠ΅ Π±ΡΠ΄Π΅Ρ ΠΊΠΎΠ½Π΅ΡΠ½ΡΠΉ ΠΏΠ»Π°ΡΡΠΈΠΊ. Π ΠΏΡΠΎΡΠ΅ΡΡΠ΅ ΡΠΌΠ΅ΡΠΈΠ²Π°Π½ΠΈΡ Ρ ΡΠΏΠΎΠΊΡΠΈΠ΄ΠΊΠΎΠΉ Π΄ΡΠ΅Π²Π΅ΡΠ½Π°Ρ ΠΊΡΠΎΡΠΊΠ° ΠΏΡΠΎΠΏΠΈΡΡΠ²Π°Π΅ΡΡΡ ΡΠΌΠΎΠ»ΠΎΠΉ ΠΈ ΠΎΠ±ΡΠ°Π·ΡΡΡΡΡ ΠΌΠ΅Π»ΠΊΠΈΠ΅ Π»ΠΎΠΊΠ°Π»ΡΠ½ΡΠ΅ ΡΠ°ΡΡΠΈΡΡ Ρ ΡΠ²Π΅ΡΠ΄ΠΎΠΉ ΠΏΠΎΠ²Π΅ΡΡ Π½ΠΎΡΡΡΡ, ΠΊΠΎΡΠΎΡΡΠ΅ Π½Π΅ Π²ΠΏΠΈΡΡΠ²Π°ΡΡ Π²Π»Π°Π³Ρ. ΠΠΎΠ»ΡΡΠΈΡΡ ΠΏΡΠΈΠ΅ΠΌΠ»Π΅ΠΌΡΡ Π΄ΡΠ΅Π²Π΅ΡΠ½ΡΡ ΠΊΡΠΎΡΠΊΡ ΠΌΠΎΠΆΠ½ΠΎ Π»ΠΈΠ±ΠΎ Π·Π°ΠΆΠ°Π² Π΄Π΅ΡΠ΅Π²ΡΠ½Π½ΡΡ Π±ΠΎΠ»Π²Π°Π½ΠΊΡ Π² ΡΠΎΠΊΠ°ΡΠ½ΠΎΠΌ ΡΡΠ°Π½ΠΊΠ΅ ΠΏΠΎ Π΄Π΅ΡΠ΅Π²Ρ ΠΈ ΠΎΠΏΠΈΠ»ΠΈΠ²Π°Ρ Π΅Π΅ ΠΏΠΎΠ²Π΅ΡΡ Π½ΠΎΡΡΡ ΠΎΡΠ΅Π½Ρ Π³ΡΡΠ±ΠΎΠΉ Π½Π°ΠΆΠ΄Π°ΡΠ½ΠΎΠΉ Π±ΡΠΌΠ°Π³ΠΎΠΉ, Π»ΠΈΠ±ΠΎ ΠΈΡΠΏΠΎΠ»ΡΠ·ΡΡ ΠΊΡΡΠ³-Π½Π°ΡΠ°Π΄ΠΊΡ Π΄Π»Ρ ΡΠ»Π΅ΠΊΡΡΠΎΠ΄ΡΠ΅Π»ΠΈ Ρ Π³ΡΡΠ±ΠΎΠΉ ΡΠΊΡΡΠΊΠΎΠΉ, ΠΎΠΏΠΈΠ»ΠΈΠ²Π°Ρ Π΅Ρ Π΄Π΅ΡΠ΅Π²ΡΠ½Π½ΡΡ Π±ΠΎΠ»Π²Π°Π½ΠΊΡβ¦ Π² Π»ΡΠ±ΠΎΠΌ ΡΠ»ΡΡΠ°Π΅ Π΄Π΅ΡΠ΅Π²ΡΠ½Π½Π°Ρ Π±ΠΎΠ»Π²Π°Π½ΠΊΠ° Π΄ΠΎ Π΅Π΅ «ΠΏΠ΅ΡΠ΅Π²ΠΎΠ΄Π° Π² ΠΎΠΏΠΈΠ»ΠΊΠΈ» Π΄ΠΎΠ»ΠΆΠ½Π° Π±ΡΡΡ ΠΏΡΠΎΡΡΡΠ΅Π½Π°. ΠΠ»Ρ ΠΈΠ·Π³ΠΎΡΠΎΠ²Π»Π΅Π½ΠΈΡ ΠΏΠ»Π°ΡΡΠΈΠΊΠ° ΠΏΠΎΠ΄ Π²ΠΎΠ±Π»Π΅ΡΡ Π²ΠΏΠΎΠ»Π½Π΅ ΠΏΡΠΈΠ³ΠΎΠ΄Π½Ρ Π»Π΅Π³ΠΊΠΈΠ΅ ΠΏΠΎΡΠΎΠ΄Ρ Π΄ΡΠ΅Π²Π΅ΡΠΈΠ½Ρ: Π»ΠΈΠΏΠ°, ΡΠΎΠΏΠΎΠ»Ρ, ΡΠΎΡΠ½Π°, ΠΏΡΠΎΠ±ΠΊΠ° ΠΈ Ρ.Π΄. ΠΎΠ΄Π½Π°ΠΊΠΎ ΡΠ»Π΅Π΄ΡΠ΅Ρ ΡΡΠ°Π·Ρ ΠΎΡΠΌΠ΅ΡΠΈΡΡ, ΡΡΠΎ ΡΡΡΠ΅ΡΡΠ²Π΅Π½Π½ΠΎ ΡΠ½ΠΈΠ·ΠΈΡΡ ΡΠ΄Π΅Π»ΡΠ½ΡΠΉ Π²Π΅Ρ ΠΏΠ»Π°ΡΡΠΈΠΊΠ°, ΠΊΠ°ΠΊ ΠΏΡΠ°Π²ΠΈΠ»ΠΎ Π½Π΅ ΡΠ΄Π°Π΅ΡΡΡ, ΠΏΠΎΡΡΠΎΠΌΡ ΠΏΡΠΈ ΠΈΠ·Π³ΠΎΡΠΎΠ²Π»Π΅Π½ΠΈΠΈ ΠΏΠ»Π°Π²Π°ΡΡΠΈΡ ΠΌΠΎΠ΄Π΅Π»Π΅ΠΉ ΠΏΡΠΈΠΌΠ°Π½ΠΎΠΊ ΠΏΡΠΈΡ ΠΎΠ΄ΠΈΡΡΡ Π² ΠΏΡΠΎΡΠ΅ΡΡΠ΅ ΠΈΡ ΠΈΠ·Π³ΠΎΡΠΎΠ²Π»Π΅Π½ΠΈΡ ΠΏΠΎΠΌΠ΅ΡΠ°ΡΡ Π²Π½ΡΡΡΡ Π΄ΠΎΠ²ΠΎΠ»ΡΠ½ΠΎ Π±ΠΎΠ»ΡΡΠΈΠ΅ Π²ΡΡΠ°Π²ΠΊΠΈ ΠΈΠ· ΡΠ΅Π»ΠΎΠ³ΠΎ ΠΊΡΡΠΊΠ° Π΄ΡΠ΅Π²Π΅ΡΠΈΠ½Ρ ΠΈΠ»ΠΈ Π΄ΡΡΠ³ΠΎΠ³ΠΎ ΠΌΠ°ΡΠ΅ΡΠΈΠ°Π»Π° Ρ Π½ΠΈΠ·ΠΊΠΈΠΌ ΡΠ΄Π΅Π»ΡΠ½ΡΠΌ Π²Π΅ΡΠΎΠΌ.
ΠΠ΅ΡΠ΅ΡΠΈΡΠ»Π΅Π½Π½ΡΠ΅ Π²ΡΡΠ΅ ΡΠ²Π΅ΡΠ΄ΡΠ΅ Π½Π°ΠΏΠΎΠ»Π½ΠΈΡΠ΅Π»ΠΈ ΠΏΠΎΠ·Π²ΠΎΠ»ΡΡΡ ΠΏΠΎΠ»ΡΡΠΈΡΡ Π΄ΠΎΠ²ΠΎΠ»ΡΠ½ΠΎ ΠΊΠ°ΡΠ΅ΡΡΠ²Π΅Π½Π½ΡΠΉ ΡΠ²Π΅ΡΠ΄ΡΠΉ ΠΏΠ»Π°ΡΡΠΈΠΊ, Π½ΠΎ ΡΠ»Π΅Π΄ΡΠ΅Ρ ΡΡΠΈΡΡΠ²Π°ΡΡ, ΡΡΠΎ ΠΈΠ½ΠΎΠ³Π΄Π° ΠΎΠ½ Π±ΡΠ΄Π΅Ρ ΠΈ Ρ ΡΡΠΏΠΊΠΈΠΌβ¦ (Π²ΡΠΏΠΎΠΌΠ½ΠΈΠΌ, ΡΡΠΎ Ρ ΠΎΡΠΎΡΠ°Ρ ΡΡΠ°Π»Ρ Ρ Π²ΡΡΠΎΠΊΠΎΠΉ ΡΠ²Π΅ΡΠ΄ΠΎΡΡΡΡ Π»Π΅Π³ΠΊΠΎ Π»ΠΎΠΌΠ°Π΅ΡΡΡβ¦, β Π°Π½Π°Π»ΠΎΠ³ΠΈΡΠ½ΡΡ ΠΊΠ°ΡΡΠΈΠ½Ρ ΠΌΡ ΠΈΠΌΠ΅Π΅ΠΌ ΠΈ Ρ ΡΠ°ΠΌΠΎΠ΄Π΅Π»ΡΠ½ΡΠΌ ΠΏΠ»Π°ΡΡΠΈΠΊΠΎΠΌ). ΠΠ»Ρ ΡΠ½ΠΈΠΆΠ΅Π½ΠΈΡ Ρ ΡΡΠΏΠΊΠΎΡΡΠΈ ΠΈ ΠΏΠΎΠ²ΡΡΠ΅Π½ΠΈΡ ΠΏΠ»Π°ΡΡΠΈΡΠ½ΠΎΡΡΠΈ Π² ΡΠΌΠ΅ΡΡ ΠΌΠΎΠΆΠ½ΠΎ Π²Π²ΠΎΠ΄ΠΈΡΡ ΠΆΠΈΠ΄ΠΊΠΈΠ΅ ΠΏΠ»Π°ΡΡΠΈΡΠΈΠΊΠ°ΡΠΎΡΡ, Π½Π°ΠΈΠ±ΠΎΠ»Π΅Π΅ Π΄ΠΎΡΡΡΠΏΠ½ΡΠΌ ΠΈΠ· ΠΊΠΎΡΠΎΡΡΡ ΡΠ²Π»ΡΠ΅ΡΡΡ ΠΊΠ°ΡΡΠΎΡΠΎΠ²ΠΎΠ΅ ΠΌΠ°ΡΠ»ΠΎ.
ΠΡΠΎΡΠ΅Π½ΡΠ½ΠΎΠ΅ ΡΠΎΠ΄Π΅ΡΠΆΠ°Π½ΠΈΠ΅ ΠΏΠ»Π°ΡΡΠΈΡΠΈΠΊΠ°ΡΠΎΡΠ° ΠΎΠΏΡΠ΅Π΄Π΅Π»ΡΠ΅ΡΡΡ ΡΠΊΡΠΏΠ΅ΡΠΈΠΌΠ΅Π½ΡΠ°Π»ΡΠ½ΠΎ Π² ΠΊΠ°ΠΆΠ΄ΠΎΠΌ ΠΊΠΎΠ½ΠΊΡΠ΅ΡΠ½ΠΎΠΌ ΡΠ»ΡΡΠ°Π΅ Π΄Π»Ρ ΡΠΎΠΎΡΠ½ΠΎΡΠ΅Π½ΠΈΡ ΡΠΌΠΎΠ»Π°-ΠΎΡΠ²Π΅ΡΠ΄ΠΈΡΠ΅Π»Ρ-Π½Π°ΠΏΠΎΠ»Π½ΠΈΡΠ΅Π»Ρβ¦ (ΠΊΠ°ΠΊ ΠΏΡΠ°Π²ΠΈΠ»ΠΎ ΡΡΠΎ ΠΎΠ΄Π½Π°-Π΄Π²Π΅ ΠΊΠ°ΠΏΠ»ΠΈ ΠΌΠ°ΡΠ»Π°).
ΠΠ΅ΠΌΠ½ΠΎΠΆΠΊΠΎ ΠΏΠΎ ΡΠ΅ΠΌΠΏΠ΅ΡΠ°ΡΡΡΠ½ΡΠΌ ΡΠ΅ΠΆΠΈΠΌΠ°ΠΌ ΠΏΠΎΠ»ΠΈΠΌΠ΅ΡΠΈΠ·Π°ΡΠΈΠΈ ΡΠΏΠΎΠΊΡΠΈΠ΄Π½ΠΎΠΉ ΡΠΌΠ΅ΡΠΈ.
ΠΡΠΈ ΠΈΠ·Π³ΠΎΡΠΎΠ²Π»Π΅Π½ΠΈΠΈ ΠΎΡΠ²Π΅ΡΡΡΠ²Π΅Π½Π½ΡΡ ΠΈΠ·Π΄Π΅Π»ΠΈΠΉ, ΠΊΠΎΡΠΎΡΡΠ΅ Π΄ΠΎΠ»ΠΆΠ½Ρ Π±ΡΠ΄ΡΡ Π²ΡΠ΄Π΅ΡΠΆΠΈΠ²Π°ΡΡ Π·Π½Π°ΡΠΈΡΠ΅Π»ΡΠ½ΡΠ΅ Π½Π°Π³ΡΡΠ·ΠΊΠΈ Π»ΡΡΡΠ΅ Π²ΡΠ΅Π³ΠΎ Π΅ΡΠ»ΠΈ ΠΏΡΠΎΡΠ΅ΡΡ ΠΏΠΎΠ»ΠΈΠΌΠ΅ΡΠΈΠ·Π°ΡΠΈΠΈ ΡΠΏΠΎΠΊΡΠΈΠ΄ΠΊΠΈ Π±ΡΠ΄Π΅Ρ ΠΏΡΠΎΡ ΠΎΠ΄ΠΈΡΡ ΠΏΡΠΈ ΠΊΠΎΠΌΠ½Π°ΡΠ½ΠΎΠΉ ΡΠ΅ΠΌΠΏΠ΅ΡΠ°ΡΡΡΠ΅, Ρ.Π΅. ΡΠ΅ΠΌΠΏΠ΅ΡΠ°ΡΡΡΠ΅, ΠΏΡΠΈ ΠΊΠΎΡΠΎΡΠΎΠΉ Π² Π΄Π°Π»ΡΠ½Π΅ΠΉΡΠ΅ΠΌ ΠΈ Π±ΡΠ΄Π΅Ρ ΡΠΊΡΠΏΠ»ΡΠ°ΡΠΈΡΠΎΠ²Π°ΡΡΡΡ Π΄Π°Π½Π½ΠΎΠ΅ ΠΈΠ·Π΄Π΅Π»ΠΈΠ΅. ΠΡΠΎ ΡΠΏΠΎΡΠΎΠ±ΡΡΠ²ΡΠ΅Ρ ΠΏΠΎΠ»ΡΡΠ΅Π½ΠΈΡ ΠΈΠ·Π΄Π΅Π»ΠΈΡ Ρ ΠΌΠΈΠ½ΠΈΠΌΠ°Π»ΡΠ½ΡΠΌΠΈ Π²Π½ΡΡΡΠ΅Π½Π½ΠΈΠΌΠΈ Π½Π°ΠΏΡΡΠΆΠ΅Π½ΠΈΡΠΌΠΈ. ΠΠ΅ Π·Π°Π±ΡΠ²Π°ΠΉΡΠ΅, ΡΡΠΎ ΡΠΏΠΎΠΊΡΠΈΠ΄ΠΊΠ° ΠΎΠ±Π»Π°Π΄Π°Π΅Ρ Π΄ΠΎΡΡΠ°ΡΠΎΡΠ½ΠΎ Π±ΠΎΠ»ΡΡΠΈΠΌ ΠΊΠΎΡΡΡ. Π»ΠΈΠ½Π΅ΠΉΠ½ΠΎΠ³ΠΎ ΡΠ°ΡΡΠΈΡΠ΅Π½ΠΈΡ ΠΈ ΡΠ°Π·Π½ΠΈΡΠ° Π² 20 Π³ΡΠ°Π΄ΡΡΠΎΠ² ΠΌΠ΅ΠΆΠ΄Ρ ΡΡΠ°Π΄ΠΈΠ΅ΠΉ ΠΏΠΎΠ»ΠΈΠΌΠ΅ΡΠΈΠ·Π°ΡΠΈΠΈ ΠΈ ΡΠ°Π±ΠΎΡΠΈΠΌΠΈ ΡΡΠ»ΠΎΠ²ΠΈΡΠΌΠΈ ΠΌΠΎΠΆΠ΅Ρ ΡΡΡΠ΅ΡΡΠ²Π΅Π½Π½ΠΎ ΠΏΠΎΠ²Π»ΠΈΡΡΡ Π½Π° ΠΊΠΎΠ½Π΅ΡΠ½ΡΠ΅ ΡΠ΅Π·ΡΠ»ΡΡΠ°ΡΡ. ΠΠΎ Π²ΡΠ΅ΠΌΠ΅Π½ΠΈ ΡΡΠΎ ΠΎΠΊΠΎΠ»ΠΎ 12 ΡΠ°ΡΠΎΠ².
Π‘ΠΎΠΊΡΠ°ΡΠΈΡΡ Π²ΡΠ΅ΠΌΡ ΠΏΠΎΠ»ΠΈΠΌΠ΅ΡΠΈΠ·Π°ΡΠΈΠΈ Π±Π΅Π· ΡΠΎΠ·Π΄Π°Π½ΠΈΡ ΠΈΠ·Π»ΠΈΡΠ½ΠΈΡ Π½Π°ΠΏΡΡΠΆΠ΅Π½ΠΈΠΉ ΠΌΠΎΠΆΠ½ΠΎ ΠΏΠΎΠ²ΡΡΠΈΠ² ΡΠ΅ΠΌΠΏΠ΅ΡΠ°ΡΡΡΡ ΡΠΌΠΎΠ»Ρ ΡΠΏΡΡΡΡ 4 ΡΠ°ΡΠ° ΠΏΠΎΡΠ»Π΅ Π΅Π΅ ΠΏΡΠΈΠ³ΠΎΡΠΎΠ²Π»Π΅Π½ΠΈΡ Π΄ΠΎ 40-50 Π³ΡΠ°Π΄ΡΡΠΎΠ² ΠΈ Π²ΡΠ΄Π΅ΡΠΆΠ°Π² Π΅Π΅ ΠΏΡΠΈ ΡΡΠΎΠΉ ΡΠ΅ΠΌΠΏΠ΅ΡΠ°ΡΡΡΠ΅ Π² ΡΠ΅ΡΠ΅Π½ΠΈΠΈ ΡΠ°ΡΠ°.
ΠΠ»Ρ Π»ΠΈΡΡΡ ΠΌΠ΅Π½Π΅Π΅ ΠΎΡΠ²Π΅ΡΡΡΠ²Π΅Π½Π½ΡΡ ΠΈΠ·Π΄Π΅Π»ΠΈΠΉ ΠΌΠΎΠΆΠ½ΠΎ Ρ ΡΠ°ΠΌΠΎΠ³ΠΎ Π½Π°ΡΠ°Π»Π° ΠΏΠΎΠΌΠ΅ΡΡΠΈΡΡ ΡΠΎΡΠΌΡ Ρ Π·Π°Π»ΠΈΠ²ΠΊΠΎΠΉ Π² Π΄ΡΡ ΠΎΠ²ΠΊΡ ΠΈ Π²ΡΡΡΠ°Π²ΠΈΡΡ ΡΠ΅ΠΌΠΏΠ΅ΡΠ°ΡΡΡΡ 60 β 70 Π³ΡΠ°Π΄ΡΡΠΎΠ². ΠΡΠ΄Π΅ΡΠΆΠ°Π² ΠΏΡΠΈ ΡΠ°ΠΊΠΎΠΉ ΡΠ΅ΠΌΠΏΠ΅ΡΠ°ΡΡΡΠ΅ 1 ΡΠ°Ρ Π΅ΡΠ΅ ΡΠ΅ΡΠ΅Π· ΠΏΠ°ΡΡ ΡΠ°ΡΠΎΠ² ΠΏΠΎΠ»ΡΡΠ°Π΅ΠΌ Π³ΠΎΡΠΎΠ²ΠΎΠ΅ ΠΈΠ·Π΄Π΅Π»ΠΈΠ΅. Π‘Π»Π΅Π΄ΡΠ΅Ρ ΠΎΡΠΌΠ΅ΡΠΈΡΡ, ΡΡΠΎ ΠΏΡΠΈ ΡΠ°ΠΊΠΎΠΌ ΡΠ΅ΠΆΠΈΠΌΠ΅ ΠΏΠΎΠ»ΠΈΠΌΠ΅ΡΠΈΠ·Π°ΡΠΈΠΈ ΡΠΌΠΎΠ»Π° Π² ΡΠ°ΠΌΠΎΠΌ Π½Π°ΡΠ°Π»Π΅ ΠΏΡΠΎΡΠ΅ΡΡΠ° ΡΡΠ°Π½ΠΎΠ²ΠΈΡΡΡ ΠΎΡΠ΅Π½Ρ ΡΠ΅ΠΊΡΡΠ΅ΠΉ ΠΈ Π²ΡΠ΅ ΠΎΡΡΠ°Π²ΡΠΈΠ΅ΡΡ Π² Π΅Π΅ ΠΎΠ±ΡΠ΅ΠΌΠ΅ Π²ΠΎΠ·Π΄ΡΡΠ½ΡΠ΅ ΠΏΡΠ·ΡΡΠΈ ΠΎΠ±ΡΠ΅Π΄ΠΈΠ½ΡΡΡΡΡ Π² ΠΎΠ΄ΠΈΠ½ ΠΈ ΠΏΠΎΠ΄Π½ΠΈΠΌΠ°ΡΡΡΡ ΠΊ Π²Π΅ΡΡ Ρ ΡΠΎΡΠΌΡ, ΡΡΠΎ ΠΌΠΎΠΆΠ΅Ρ ΠΏΡΠΈΠ²Π΅ΡΡΠΈ ΠΊ ΠΎΠ±ΡΠ°Π·ΠΎΠ²Π°Π½ΠΈΡ ΡΠ°ΠΊΠΎΠ²ΠΈΠ½Ρ Π² ΠΎΡΠ»ΠΈΠ²ΠΊΠ΅, ΠΏΡΠΈ ΠΈΡΠΏΠΎΠ»ΡΠ·ΠΎΠ²Π°Π½ΠΈΠΈ ΡΠΎΡΠΌΡ Π·Π°ΠΌΠΊΠ½ΡΡΠΎΠ³ΠΎ ΠΎΠ±ΡΠ΅ΠΌΠ°.
ΠΠΎΡ Π²ΡΠΎΠ΄Π΅ ΠΈ Π²ΡΠ΅ ΠΎΡΠ½ΠΎΠ²Π½ΡΠ΅ «ΡΠΎΠ½ΠΊΠΎΡΡΠΈ» ΡΠ°Π±ΠΎΡΡ Ρ ΠΎΡΠ΅ΡΠ΅ΡΡΠ²Π΅Π½Π½ΠΎΠΉ ΡΠΏΠΎΠΊΡΠΈΠ΄ΠΊΠΎΠΉ, ΠΊΠΎΡΠΎΡΡΠ΅ ΠΏΠΎΠ»ΡΡΠ΅Π½Ρ Π½Π° ΠΏΡΠ°ΠΊΡΠΈΠΊΠ΅ ΠΈ ΠΊΠΎΡΠΎΡΡΠ΅ ΠΏΠΎΠΌΠΎΠ³ΡΡ Π²Π°ΠΌ ΠΈΠ·Π±Π΅ΠΆΠ°ΡΡ ΡΠ°Π·ΠΎΡΠ°ΡΠΎΠ²Π°Π½ΠΈΡ ΠΏΡΠΈ ΠΈΠ·Π³ΠΎΡΠΎΠ²Π»Π΅Π½ΠΈΠΈ ΠΏΡΠΈΠΌΠ°Π½ΠΎΠΊ Π² Π΄ΠΎΠΌΠ°ΡΠ½ΠΈΡ ΡΡΠ»ΠΎΠ²ΠΈΡΡ .
Π. ΠΠ»Π°ΡΠ΅Π½ΠΊΠΎ
Π³. ΠΠΎΡΠΊΠ²Π°, 22.03.2001
ΠΠ½ΠΈΠΌΠ°Π½ΠΈΠ΅!
Π ΠΊΠ°ΡΠ΅ΡΡΠ²Π΅ ΠΈΡΡ ΠΎΠ΄Π½ΠΎΠ³ΠΎ ΠΌΠ°ΡΠ΅ΡΠΈΠ°Π»Π° ΠΈΡΠΏΠΎΠ»ΡΠ·ΠΎΠ²Π°Π½Π° ΡΡΠ°ΡΡΡ Ρ ΡΠ°ΠΉΡΠ° «ΠΠΎΡΠΎΠ΄Π°ΡΠ°Ρ ΡΡΡΠ°Π½ΠΈΡΠ°«
ο»Ώ
yug-fishing.ru
Π Π°Π±ΠΎΡΠ° Ρ ΡΠΏΠΎΠΊΡΠΈΠ΄Π½ΡΠΌΠΈ ΡΠΌΠΎΠ»Π°ΠΌΠΈ, ΡΠΎΠ²Π΅ΡΡ ΠΈ ΡΠ΅ΠΊΠΎΠΌΠ΅Π½Π΄Π°ΡΠΈΠΈ
Β Β Β Β Β Β Β Β Β Β Β Β Β Β Β Β Β Β Β Β Β Β Β Β Π Π°Π±ΠΎΡΠ° Ρ ΡΠΏΠΎΠΊΡΠΈΠ΄Π½ΡΠΌΠΈ ΡΠΌΠΎΠ»Π°ΠΌΠΈ
Β
Β Β Β ΠΡΠΈΠ²Π΅Π΄Π΅Π½Π½ΡΠΉ ΠΌΠ°ΡΠ΅ΡΠΈΠ°Π» Π½Π΅ ΡΠ²Π»ΡΠ΅ΡΡΡ ΠΎΡΠΈΡΠΈΠ°Π»ΡΠ½ΠΎΠΉ ΠΈΠ½ΡΡΡΡΠΊΡΠΈΠ΅ΠΉ ΠΏΠΎ ΠΈΡΠΏΠΎΠ»ΡΠ·ΠΎΠ²Π°Π½ΠΈΡ ΠΈ Π½ΠΎΡΠΈΡ Π»ΠΈΡΡ ΡΠ΅ΠΊΠΎΠΌΠ΅Π½Π΄Π°ΡΠ΅Π»ΡΠ½ΡΠΉ Ρ Π°ΡΠ°ΠΊΡΠ΅Ρ.
Β
Β Β Β ΠΠ°Π½Π½ΡΠΉ ΠΌΠ°ΡΠ΅ΡΠΈΠ°Π» ΡΠΎΠ΄Π΅ΡΠΆΠΈΡ ΠΈΠ½ΡΠΎΡΠΌΠ°ΡΠΈΡ ΠΎ ΡΠ°Π±ΠΎΡΠ΅ Ρ ΡΠΏΠΎΠΊΡΠΈΠ΄Π½ΡΠΌΠΈ ΡΠΌΠΎΠ»Π°ΠΌΠΈ Π² Π½Π°ΠΈΠ±ΠΎΠ»Π΅Π΅ ΡΠΈΠΏΠΈΡΠ½ΠΎΠΉ ΠΎΠ±Π»Π°ΡΡΠΈ ΠΈΡ ΠΏΡΠΈΠΌΠ΅Π½Π΅Π½ΠΈΡ β ΠΈΠ·Π³ΠΎΡΠΎΠ²Π»Π΅Π½ΠΈΠ΅ ΡΠΏΠΎΠΊΡΠΈΠ΄Π½ΠΎΠ³ΠΎ ΠΊΠ»Π΅Ρ, Π² ΠΊΠ°ΡΠ΅ΡΡΠ²Π΅ ΠΏΡΠΎΠΏΠΈΡΠΎΡΠ½ΠΎΠ³ΠΎ ΠΌΠ°ΡΠ΅ΡΠΈΠ°Π»Π° Π²ΠΌΠ΅ΡΡΠ΅ ΡΠΎ ΡΡΠ΅ΠΊΠ»ΠΎΡΠΊΠ°Π½ΡΡ Π΄Π»Ρ ΠΈΠ·Π³ΠΎΡΠΎΠ²Π»Π΅Π½ΠΈΡ ΠΈ ΡΠ΅ΠΌΠΎΠ½ΡΠ° ΡΠ°Π·Π»ΠΈΡΠ½ΡΡ ΠΊΠΎΡΠΏΡΡΠΎΠ² (Π»ΠΎΠ΄ΠΊΠΈ, ΡΠ»Π΅ΠΌΠ΅Π½ΡΡ ΠΊΡΠ·ΠΎΠ²Π° Π°Π²ΡΠΎΠΌΠΎΠ±ΠΈΠ»Ρ ΠΈ Π΄Ρ.) ΠΈΠ»ΠΈ Π²ΡΠΏΠΎΠ»Π½Π΅Π½ΠΈΡ Π³ΠΈΠ΄ΡΠΎΠΈΠ·ΠΎΠ»ΡΡΠΈΠΈ ΠΏΠΎΠΌΠ΅ΡΠ΅Π½ΠΈΠΉ (ΠΏΠΎΠ» ΠΈ ΡΡΠ΅Π½Ρ ΠΏΠΎΠ΄Π²Π°Π»ΡΠ½ΡΡ ΠΏΠΎΠΌΠ΅ΡΠ΅Π½ΠΈΠΉ, Π±Π°ΡΡΠ΅ΠΉΠ½Ρ) ΠΈ Ρ.ΠΏ.
Β 1). ΠΠ°ΡΡΠΎΡΡΠ΅Π»ΡΠ½ΠΎ ΡΠ΅ΠΊΠΎΠΌΠ΅Π½Π΄ΡΠ΅ΠΌ Π²ΡΠ±ΡΠ°ΡΡ ΠΎΠΏΡΠΈΠΌΠ°Π»ΡΠ½ΠΎΠ΅ Π΄Π»Ρ ΠΠ°ΡΠΈΡ ΡΠ΅Π»Π΅ΠΉ ΡΠΎΠΎΡΠ½ΠΎΡΠ΅Π½ΠΈΠ΅ ΡΠΌΠΎΠ»Ρ, ΠΎΡΠ²Π΅ΡΠ΄ΠΈΡΠ΅Π»Ρ ΠΈ ΠΏΠ»Π°ΡΡΠΈΡΠΈΠΊΠ°ΡΠΎΡΠ° ΠΏΡΡΠ΅ΠΌ ΠΈΠ·Π³ΠΎΡΠΎΠ²Π»Π΅Π½ΠΈΡ Π½Π΅Π±ΠΎΠ»ΡΡΠΈΡ ΠΏΡΠΎΠ±Π½ΡΡ ΠΎΠ±ΡΠ°Π·ΡΠΎΠ². Π Π΅Π°ΠΊΡΠΈΡ ΡΠΌΠΎΠ»Ρ Ρ ΠΎΡΠ²Π΅ΡΠ΄ΠΈΡΠ΅Π»Π΅ΠΌ Π½Π΅ΠΎΠ±ΡΠ°ΡΠΈΠΌΠ°, Π² ΡΠ»ΡΡΠ°Π΅ ΠΎΡΠΈΠ±ΠΊΠΈ — ΡΠΌΠΎΠ»Π° Π±ΡΠ΄Π΅Ρ ΠΈΡΠΏΠΎΡΡΠ΅Π½Π°.
Β 2). ΠΡΠ΅ΠΌΡ ΠΏΠΎΠ»ΠΈΠΌΠ΅ΡΠΈΠ·Π°ΡΠΈΠΈ (ΠΆΠ΅Π»Π°ΡΠΈΠ½ΠΈΠ·Π°ΡΠΈΠΈ, Π³Π΅Π»Π΅ΠΎΠ±ΡΠ°Π·ΠΎΠ²Π°Π½ΠΈΡ) — Π²ΡΠ΅ΠΌΡ, Π½Π΅ΠΎΠ±Ρ ΠΎΠ΄ΠΈΠΌΠΎΠ΅ Π΄Π»Ρ Π΄Π°Π½Π½ΠΎΠΉ ΠΌΠ°ΡΡΡ ΡΠΏΠΎΠΊΡΠΈΠ΄Π½ΠΎΠΉ ΡΠΌΠΎΠ»Ρ Π΄Π»Ρ Π΅Π΅ ΠΎΠ±ΡΠ°ΡΠ΅Π½ΠΈΠ΅ Π² ΡΠ²Π΅ΡΠ΄ΠΎΠ΅ ΡΠΎΡΡΠΎΡΠ½ΠΈΠ΅ ΠΈ ΡΠΎΠΎΡΠ²Π΅ΡΡΡΠ²ΡΠ΅Ρ ΡΠ»Π΅Π΄ΡΡΡΠ΅ΠΌΡ ΠΏΡΠ°Π²ΠΈΠ»Ρ: Π²ΡΠ΅ΠΌΡ ΠΏΠΎΠ»ΠΈΠΌΠ΅ΡΠΈΠ·Π°ΡΠΈΠΈ Π·Π°Π²ΠΈΡΠΈΡ ΠΎΡ ΡΠ΅ΠΌΠΏΠ΅ΡΠ°ΡΡΡΡ ΡΠΌΠ΅ΡΠΈ ΠΈ ΠΎΡΠ½ΠΎΡΠ΅Π½ΠΈΡ ΠΏΠ»ΠΎΡΠ°Π΄ΠΈ ΠΊ ΠΌΠ°ΡΡΠ΅ ΡΠΌΠΎΠ»Ρ. Π ΠΏΡΠΈΠΌΠ΅ΡΡ , Π΅ΡΠ»ΠΈ 100 Π³ ΡΠΌΠ΅ΡΠΈ ΡΠΏΠΎΠΊΡΠΈΠ΄Π½ΠΎΠΉ ΡΠΌΠΎΠ»Ρ Ρ ΠΎΡΠ²Π΅ΡΠ΄ΠΈΡΠ΅Π»Π΅ΠΌ Β ΠΠΠΠ ΠΎΠ±ΡΠ°ΡΠ°ΡΡΡΡ Π² ΡΠ²Π΅ΡΠ΄ΠΎΠ΅ ΡΠΎΡΡΠΎΡΠ½ΠΈΠ΅ Π·Π° 30-50 ΠΌΠΈΠ½ΡΡ ΠΏΡΠΈ ΠΈΡΡ ΠΎΠ΄Π½ΠΎΠΉ ΡΠ΅ΠΌΠΏΠ΅ΡΠ°ΡΡΡΠ΅ Π² 22-24Β°Π‘, ΡΠΎ ΠΏΡΠΈ ΠΈΡΡ ΠΎΠ΄Π½ΠΎΠΉ ΡΠ΅ΠΌΠΏΠ΅ΡΠ°ΡΡΡΠ΅ Π² 15Β°Π‘ Π½Π° ΡΡΠΎ ΠΏΠΎΡΡΠ΅Π±ΡΠ΅ΡΡΡ Π±ΠΎΠ»Π΅Π΅ ΡΠ°ΡΠ° Π²ΡΠ΅ΠΌΠ΅Π½ΠΈ. Π Π΅ΡΠ»ΠΈ ΠΏΡΠΈ ΡΠ΅Ρ ΠΆΠ΅ 22-24Β°Π‘ ΡΡΠΈ 100 Π³ ΡΠΌΠ΅ΡΠΈ ΡΠΏΠΎΠΊΡΠΈΠ΄Π½ΠΎΠΉ ΡΠΌΠΎΠ»Ρ Ρ ΠΎΡΠ²Π΅ΡΠ΄ΠΈΡΠ΅Π»Π΅ΠΌ ΡΠ°Π·ΠΌΠ°Π·Π°ΡΡ ΠΏΠΎ ΠΏΠ»ΠΎΡΠ°Π΄ΠΈ Π² 1 ΠΌΠ, ΠΏΠΎΠ»ΠΈΠΌΠ΅ΡΠΈΠ·Π°ΡΠΈΡ Π·Π°ΠΉΠΌΠ΅Ρ ΡΠ²ΡΡΠ΅ 2 ΡΠ°ΡΠΎΠ².
ΠΠΎΡΡΠΎΠΌΡ Π·Π°ΠΌΠ΅ΡΠΈΠ²Π°ΠΉΡΠ΅ ΡΡΠΎΠ»ΡΠΊΠΎ ΡΠΌΠΎΠ»Ρ, ΡΠΊΠΎΠ»ΡΠΊΠΎ Π²Ρ ΠΌΠΎΠΆΠ΅ΡΠ΅ Π΅Π΅ Π²ΡΡΠ°Π±ΠΎΡΠ°ΡΡ Π΄ΠΎ ΠΌΠΎΠΌΠ΅Π½ΡΠ° ΡΡ Π²Π°ΡΡΠ²Π°Π½ΠΈΡ (ΠΆΠ΅Π»Π°ΡΠΈΠ½ΠΈΠ·Π°ΡΠΈΠΈ).
ΠΡΠ»ΠΈ ΠΡ Π²ΡΠ΅ ΠΆΠ΅ Π½Π°Π΄ΡΠΌΠ°Π»ΠΈ ΠΏΠΎΡΠ°Π±ΠΎΡΠ°ΡΡ Ρ Π±ΠΎΠ»ΡΡΠΈΠΌ ΠΊΠΎΠ»ΠΈΡΠ΅ΡΡΠ²ΠΎΠΌ β ΡΠ΅ΠΊΠΎΠΌΠ΅Π½Π΄ΡΠ΅ΠΌ, ΡΡΠ°Π·Ρ ΠΆΠ΅ ΠΏΠΎΡΠ»Π΅ ΡΠΌΠ΅ΡΠΈΠ²Π°Π½ΠΈΡ ΡΠΌΠΎΠ»Ρ ΠΈ ΠΎΡΠ²Π΅ΡΠ΄ΠΈΡΠ΅Π»Ρ ΡΠ°Π·Π»ΠΈΡΡ Π΅Π΅ Π½Π° Π±ΠΎΠ»Π΅Π΅-ΠΌΠ΅Π½Π΅Π΅ ΠΌΠ΅Π»ΠΊΠΈΠ΅ ΠΏΠΎΡΡΠΈΠΈ — ΠΈΠ½Π°ΡΠ΅ ΠΌΠΎΠΆΠ½ΠΎ ΠΏΡΠΎΡΡΠΎ Π½Π΅ ΡΡΠΏΠ΅ΡΡ Ρ Π½Π΅ΠΉ ΠΏΠΎΡΠ°Π±ΠΎΡΠ°ΡΡ, ΡΠΌΠΎΠ»Π° Π±ΡΡΡΡΠΎ Π²ΡΡΠ°Π½Π΅Ρ, Π° ΡΠΎ ΠΈ Π²ΡΠΊΠΈΠΏΠΈΡ.
Β 3). Π‘ΠΊΠΎΡΠΎΡΡΡ ΠΏΠΎΠ»ΠΈΠΌΠ΅ΡΠΈΠ·Π°ΡΠΈΠΈ ΡΠΌΠ΅ΡΠΈ ΡΠΏΠΎΠΊΡΠΈΠ΄Π½ΠΎΠΉ ΡΠΌΠΎΠ»Ρ Ρ ΠΎΡΠ²Π΅ΡΠ΄ΠΈΡΠ΅Π»Π΅ΠΌ Ρ ΠΎΡΡ ΠΈ Π·Π°Π²ΠΈΡΠΈ ΠΎΡ ΠΏΠ΅ΡΠ²ΠΎΠ½Π°ΡΠ°Π»ΡΠ½ΠΎΠΉ ΡΠ΅ΠΌΠΏΠ΅ΡΠ°ΡΡΡΡ — ΡΠ°ΠΌ ΠΌΠ΅Ρ Π°Π½ΠΈΠ·ΠΌ ΠΏΠΎΠ»ΠΈΠΌΠ΅ΡΠΈΠ·Π°ΡΠΈΠΈ ΠΎΡ Π½Π΅Π΅ Π½Π΅ Π·Π°Π²ΠΈΡΠΈΡ. Π Π΅Π°ΠΊΡΠΈΡ ΡΠΏΠΎΠΊΡΠΈΠ΄Π½ΠΎΠΉ ΡΠΌΠΎΠ»Ρ Ρ ΠΎΡΠ²Π΅ΡΠ΄ΠΈΡΠ΅Π»Π΅ΠΌ Π½Π΅ΠΎΠ±ΡΠ°ΡΠΈΠΌΠ°.Β
Β Β Π Π΅Π°ΠΊΡΠΈΡ ΡΠΌΠ΅ΡΠΈ Π² ΠΆΠΈΠ΄ΠΊΠΎΠΌ ΡΠΎΡΡΠΎΡΠ½ΠΈΠΈ ΠΏΡΠΎΡΠ΅ΠΊΠ°Π΅Ρ Π±ΡΡΡΡΠ΅Π΅. ΠΠΎ Ρ ΠΎΠ΄Ρ ΠΏΠΎΠ»ΠΈΠΌΠ΅ΡΠΈΠ·Π°ΡΠΈΠΈ ΡΠΌΠΎΠ»Π° ΠΌΠ΅Π½ΡΠ΅Ρ ΡΠ²ΠΎΠ΅ ΡΠΎΡΡΠΎΡΠ½ΠΈΠ΅ Ρ ΠΆΠΈΠ΄ΠΊΠΎΠ³ΠΎ Π½Π° Π»ΠΈΠΏΠΊΠΎΠ΅, Π²ΡΠ·ΠΊΠΎ-Π³Π΅Π»Π΅ΠΎΠ±ΡΠ°Π·Π½ΠΎΠ΅. ΠΠΎ ΠΌΠ΅ΡΠ΅ Π½Π°ΡΠ°ΡΡΠ°Π½ΠΈΡ ΡΠ²Π΅ΡΠ΄ΠΎΡΡΠΈ, ΡΠΊΠΎΡΠΎΡΡΡ ΡΠ΅Π°ΠΊΡΠΈΠΈ Π·Π°ΠΌΠ΅Π΄Π»ΡΠ΅ΡΡΡ, ΠΏΠΎΡΡΠ΅ΠΏΠ΅Π½Π½ΠΎ ΡΠ΅ΡΡΠ΅ΡΡΡ Π»ΠΈΠΏΡΡΠ΅ΡΡΡ. Π‘ΠΎ Π²ΡΠ΅ΠΌΠ΅Π½Π΅ΠΌ Π»ΠΈΠΏΡΡΠ΅ΡΡΡ ΠΈΠ·ΡΠ΅Π·Π½Π΅Ρ, Π½ΠΎ ΡΠΌΠΎΠ»Π° ΠΏΡΠΎΠ΄ΠΎΠ»ΠΆΠΈΡ Π½Π°Π±ΠΈΡΠ°ΡΡ ΡΠ²ΠΎΡ ΡΠ²Π΅ΡΠ΄ΠΎΡΡΡ ΠΈ ΠΏΡΠΎΡΠ½ΠΎΡΡΡ. Π‘ΡΠΈΡΠ°Π΅ΡΡΡ, ΡΡΠΎ ΠΎΠΊΠΎΠ½ΡΠ°ΡΠ΅Π»ΡΠ½ΠΎΠ΅ ΠΎΡΠ²Π΅ΡΠΆΠ΄Π΅Π½ΠΈΠ΅ Π΄ΠΎΡΡΠΈΠ³Π°Π΅ΡΡΡ ΡΠΏΡΡΡΡ 24 ΡΠ°ΡΠ° ΠΏΡΠΈ ΡΠ΅ΠΌΠΏΠ΅ΡΠ°ΡΡΡΠ΅ 22-24Β°Π‘.
ΠΠ΄Π½Π°ΠΊΠΎ ΡΡΠ΅ΠΏΠ΅Π½Ρ ΠΎΡΠ²Π΅ΡΠΆΠ΄Π΅Π½ΠΈΡ ΠΈ ΠΏΠΎΡΠ»Π΅ 24 ΡΠ°ΡΠΎΠ² Π½Π΅ ΠΏΡΠ΅Π²ΡΡΠΈΡ 65 — 70% ΠΎΠΊΠΎΠ½ΡΠ°ΡΠ΅Π»ΡΠ½ΠΎΠΉ ΠΏΡΠΎΡΠ½ΠΎΡΡΠΈ. ΠΡΠΎ ΡΡΠ²Π΅ΡΠΆΠ΄Π΅Π½ΠΈΠ΅ ΠΎΡΠΎΠ±Π΅Π½Π½ΠΎ Π°ΠΊΡΡΠ°Π»ΡΠ½ΠΎ Β Π΅ΡΠ»ΠΈ ΠΈΡΠΏΠΎΠ»ΡΠ·ΡΡΡΡΡ Β ΡΠ΅Π°ΠΊΡΠΈΠ²Π½ΡΠ΅ ΠΎΡΠ²Π΅ΡΠ΄ΠΈΡΠ΅Π»ΠΈ, Π½Π°ΠΏΡΠΈΠΌΠ΅Ρ ΡΠ°ΠΊΠΈΠ΅ ΠΊΠ°ΠΊ ΠΠΠΠ, Π° Π΄Π»Ρ ΠΎΡΠ²Π΅ΡΠ΄ΠΈΡΠ΅Π»Π΅ΠΉ Π½ΠΎΠ²ΠΎΠ³ΠΎ ΠΏΠΎΠΊΠΎΠ»Π΅Π½ΠΈΡ, Π½Π°ΠΏΡΠΈΠΌΠ΅Ρ ANCAMINE-1618; 2519 ΡΡΠΎ ΠΌΠ΅Π½Π΅Π΅ Π°ΠΊΡΡΠ°Π»ΡΠ½ΠΎ.
Β Β ΠΠ»Ρ ΠΏΠΎΠ²ΡΡΠ΅Π½ΠΈΡ ΠΏΡΠΎΡΠ½ΠΎΡΡΠΈ (Ρ ΠΈΡΠΏΠΎΠ»ΡΠ·ΠΎΠ²Π°Π½ΠΈΠ΅ΠΌ ΡΠΎΠΉ ΠΆΠ΅ ΠΠΠΠ) ΡΠ΅ΠΊΠΎΠΌΠ΅Π½Π΄ΡΠ΅ΡΡΡ ΠΏΡΠΎΠ²ΠΎΠ΄ΠΈΡΡ ΡΠ΅ΡΠΌΠΎΠΎΠ±ΡΠ°Π±ΠΎΡΠΊΡ ΠΏΡΠΈ 60-100Β°Π‘ Π² ΡΠ΅ΡΠ΅Π½ΠΈΠΈ 2-12ΡΠ°ΡΠΎΠ².
Β Β ΠΡΠ»ΠΈ ΡΠ΅ΡΠΌΠΎΠΎΠ±ΡΠ°Π±ΠΎΡΠΊΠ° Π½Π΅ ΠΏΡΠΎΠ²ΠΎΠ΄ΠΈΠ»Π°ΡΡ, ΠΎΡΠ²Π΅ΡΠΆΠ΄Π΅Π½ΠΈΠ΅ ΡΠΏΠΎΠΊΡΠΈΠ΄Π½ΠΎΠΉ ΡΠΌΠΎΠ»Ρ Π±ΡΠ΄Π΅Ρ ΠΏΡΠΎΠ΄ΠΎΠ»ΠΆΠ°ΡΡΡΡ Π² ΡΠ΅ΡΠ΅Π½ΠΈΠ΅ ΠΏΠΎΡΠ»Π΅Π΄ΡΡΡΠΈΡ Π½Π΅ΡΠΊΠΎΠ»ΡΠΊΠΈΡ Π½Π΅Π΄Π΅Π»Ρ, Π΄ΠΎΡΡΠΈΠ³Π½ΡΠ² Π² ΠΊΠΎΠ½ΡΠ΅ ΠΊΠΎΠ½ΡΠΎΠ² ΡΠΎΡΠΊΠΈ, ΠΊΠΎΠ³Π΄Π° Π΄Π°Π»ΡΠ½Π΅ΠΉΡΠ΅Π΅ ΠΎΡΠ²Π΅ΡΠΆΠ΄Π΅Π½ΠΈΠ΅ ΡΠΆΠ΅ Π±ΡΠ΄Π΅Ρ Π½Π΅Π²ΠΎΠ·ΠΌΠΎΠΆΠ½ΠΎ.
Β 4). ΠΠ΅Π·Π°ΡΠΈΡΠ΅Π½Π½Π°Ρ ΡΠΏΠΎΠΊΡΠΈΠ΄Π½Π°Ρ ΡΠΌΠΎΠ»Π° ΠΏΠ»ΠΎΡ ΠΎ ΠΏΠ΅ΡΠ΅Π½ΠΎΡΠΈΡ ΡΠΎΠ»Π½Π΅ΡΠ½ΡΠΉ ΡΠ²Π΅Ρ (Π£Π€ ΠΈΠ·Π»ΡΡΠ΅Π½ΠΈΡ). ΠΡΠΈΠΌΠ΅ΡΠ½ΠΎ ΡΠ΅ΡΠ΅Π· ΠΏΠΎΠ»Π³ΠΎΠ΄Π° (Π²ΡΠ΅ΠΌΡ Π΄ΠΎΠ²ΠΎΠ»ΡΠ½ΠΎ ΡΡΠ»ΠΎΠ²Π½ΠΎ ΠΈ Π·Π°Π²ΠΈΡΠΈΡ ΠΎΡ ΠΌΠ½ΠΎΠ³ΠΈΡ ΡΠ°ΠΊΡΠΎΡΠΎΠ²),Π½Π°ΡΠΈΠ½Π°Π΅ΡΡΡ Π΅Π΅ ΠΏΠΎΠΌΡΡΠ½Π΅Π½ΠΈΠ΅, ΡΠ°Π·ΡΡΡΠ΅Π½ΠΈΠ΅ Ρ ΡΠ°ΡΡΠΈΡΠ½ΠΎΠΉ ΠΏΠΎΡΠ΅ΡΠ΅ΠΉ Π΅Π΅ ΡΠΈΠ·ΠΈΡΠ΅ΡΠΊΠΈΡ ΡΠ²ΠΎΠΉΡΡΠ². ΠΠΎΡΡΠΎΠΌΡ Π³ΠΎΡΠΎΠ²ΠΎΠ΅ ΠΈΠ·Π΄Π΅Π»ΠΈΠ΅ Π½Π΅ΠΎΠ±Ρ ΠΎΠ΄ΠΈΠΌΠΎ Π·Π°ΡΠΈΡΠ°ΡΡ ΠΏΡΠΈ ΠΏΠΎΠΌΠΎΡΠΈ ΠΊΡΠ°ΡΠΎΠΊ, Π»Π°ΠΊΠΎΠ² ΠΈ Ρ.Π΄. ΡΠΎΠ΄Π΅ΡΠΆΠ°ΡΠΈΡ Π£Π€ Π·Π°ΡΠΈΡΡ.
Β Π Π½Π°ΡΡΠΎΡΡΠ΅Π΅ Π²ΡΠ΅ΠΌΡ Ρ ΠΏΠΎΡΠ²Π»Π΅Π½ΠΈΠ΅ΠΌ Π½ΠΎΠ²ΠΎΠΉ Π³Π΅Π½Π΅ΡΠ°ΡΠΈΠΈ ΠΎΡΠ²Π΅ΡΠ΄ΠΈΡΠ΅Π»Π΅ΠΉ ΠΏΡΠΎΠ±Π»Π΅ΠΌΠ° ΡΠ»ΡΡΡΠ°ΡΠΈΠΎΠ»Π΅-ΡΠΎΠ²ΠΎΠΉ Π·Π°ΡΠΈΡΡ ΡΠ΅ΡΠ΅Π½Π° Π±Π΅Π· ΠΏΡΠΈΠΌΠ΅Π½Π΅Π½ΠΈΡ Π΄ΠΎΠΏΠΎΠ»Π½ΠΈΡΠ΅Π»ΡΠ½ΡΡ ΠΌΠ΅Ρ. Π ΡΠ°ΡΠ½ΠΎΡΡΠΈ ΠΊ Π½ΠΈΠΌ ΠΎΡΠ½ΠΎΡΡΡΡΡ
ΠΎΡΠ²Π΅ΡΠ΄ΠΈΡΠ΅Π»ΠΈ ΡΠ°ΠΊΠΈΠ΅ ΠΊΠ°ΠΊ ANCAMINE-1618; 2519. ΠΠΎ ΡΡΠΈ ΠΎΡΠ²Π΅ΡΠ΄ΠΈΡΠ΅Π»ΠΈ Π±ΠΎΠ»Π΅Π΅ Π΄ΠΎΡΠΎΠ³ΠΈΠ΅ ΠΈ ΡΡΠ΅- Π±ΡΡΡΡΡ Π² Π±ΠΎΠ»ΡΡΠ΅ΠΌ ΠΊΠΎΠ»ΠΈΡΠ΅ΡΡΠ²Π΅: Π² ΠΏΡΠΎΠΏΠΎΡΡΠΈΠΈ 50-60% ΠΊ ΠΌΠ°ΡΡΠ΅ ΡΠΌΠΎΠ»Ρ, (Ρ.Π΅. 500-600Π³ ΠΎΡΠ²Π΅ΡΠ΄ΠΈΡΠ΅Π»Ρ Π½Π° 1ΠΊΠ³ ΡΠΏΠΎΠΊΡΠΈΠ΄Π½ΠΎΠΉ ΡΠΌΠΎΠ»Ρ). Π‘ ΡΠ°ΠΊΠΈΠΌΠΈ ΠΎΡΠ²Π΅ΡΠ΄ΠΈΡΠ΅Π»ΡΠΌΠΈ ΠΏΡΠΈΡΡΠ½ΠΎ ΡΠ°Π±ΠΎΡΠ°ΡΡ β ΠΎΠ½ΠΈ Π»Π΅Π³ΠΊΠΎ ΠΏΠ΅ΡΠ΅ΠΌΠ΅ΡΠΈΠ²Π°ΡΡΡΡ ΡΠΎ ΡΠΌΠΎΠ»ΠΎΠΉ, ΠΏΡΠ°ΠΊΡΠΈΡΠ΅ΡΠΊΠΈ Π½Π΅ ΠΈΠΌΠ΅ΡΡ Π·Π°ΠΏΠ°Ρ Π°, ΠΏΡΠ°ΠΊΡΠΈΡΠ΅ΡΠΊΠΈ Π±Π΅ΡΡΠ²Π΅ΡΠ½ΡΠ΅, ΡΡΠΎ Π½Π° Β«ΡΡΠ°Β» ΠΈΡΠΏΠΎΠ»ΡΠ·ΡΠ΅ΡΡΡ Π² ΠΈΠ·Π³ΠΎΡΠΎΠ²Π»Π΅Π½ΠΈΠΈ ΡΠ°Π·Π»ΠΈΡΠ½ΠΎΠΉ Π±ΠΈΠΆΡΡΠ΅ΡΠΈΠΈ, ΡΡΠ²Π΅Π½ΠΈΡΠΎΠ² β¦, Ρ.Π΅.
ΡΠ°ΠΌ, Π³Π΄Π΅ Π½Π΅ΠΎΠ±Ρ ΠΎΠ΄ΠΈΠΌΠ° Β ΠΏΡΠΎΠ·ΡΠ°ΡΠ½ΠΎΡΡΡ ΠΈΠ·Π΄Π΅Π»ΠΈΡ.Β
Β 5). ΠΠΏΠΎΠΊΡΠΈΠ΄Π½ΡΠ΅ ΡΠΌΠΎΠ»Ρ ΠΌΠΎΠ³ΡΡ Π² ΠΏΡΠΎΡΠ΅ΡΡΠ΅ ΠΎΡΠ²Π΅ΡΠΆΠ΄Π΅Π½ΠΈΡ ΠΎΠ±ΡΠ°Π·ΠΎΠ²ΡΠ²Π°ΡΡ Π½Π° ΡΠ²ΠΎΠ΅ΠΉ ΠΏΠΎΠ²Π΅ΡΡ Π½ΠΎΡΡΠΈ ΡΠΎΠ½ΠΊΡΡ, Π»ΠΈΠΏΠΊΡΡ ΠΏΠ»Π΅Π½ΠΊΡ. ΠΠ½Π° ΡΠΎΡΠΌΠΈΡΡΠ΅ΡΡΡ Π² ΠΏΡΠΈΡΡΡΡΡΠ²ΠΈΠΈ ΡΠ³Π»Π΅ΠΊΠΈΡΠ»ΠΎΠ³ΠΎ Π³Π°Π·Π° ΠΈ ΠΏΠ°ΡΠΎΠ² Π²ΠΎΠ΄Ρ, ΠΎΡΠΎΠ±Π΅Π½Π½ΠΎ Π² Ρ ΠΎΠ»ΠΎΠ΄Π½ΡΡ, ΡΡΡΡΡ ΠΏΠΎΠ³ΠΎΠ΄Ρ. ΠΡΠ° ΠΏΠ»Π΅Π½ΠΊΠ° Π²ΠΎΠ΄ΠΎΡΠ°ΡΡΠ²ΠΎΡΠΈΠΌΠ° ΠΈ Π΄ΠΎΠ»ΠΆΠ½Π° Π±ΡΡΡ ΡΠ΄Π°Π»Π΅Π½Π° ΠΌΠ΅Ρ Π°Π½ΠΈΡΠ΅ΡΠΊΠΈ ΠΏΠ΅ΡΠ΅Π΄ ΡΠ»ΠΈΡΠΎΠ²ΠΊΠΎΠΉ ΠΈΠ»ΠΈ ΠΏΠΎΠΊΡΠ°ΡΠΊΠΎΠΉ.
Β Β ΠΡΠΈ Π½Π΅ΠΎΠ±Ρ ΠΎΠ΄ΠΈΠΌΠΎΡΡΠΈ ΡΠ°Π·ΠΎΠ³ΡΠ΅Π²Π° ΡΠΌΠΎΠ»Ρ, ΠΊΠΎΠΌΠΏΠΎΠ½Π΅Π½ΡΠΎΠ² ΠΈΠ»ΠΈ ΡΠΌΠ΅ΡΠΈ, Π½Π°ΠΏΡΠΈΠΌΠ΅Ρ Π΄Π»Ρ ΠΎΠ±Π»Π΅Π³ΡΠ΅Π½ΠΈΡ ΠΏΠ΅ΡΠ΅ΠΌΠ΅ΡΠΈΠ²Π°Π½ΠΈΡ, ΡΠΌΠ΅Π½ΡΡΠ΅Π½ΠΈΡ Π²Π΅ΡΠΎΡΡΠ½ΠΎΡΡΠΈ ΠΎΠ±ΡΠ°Π·Π°Π·ΠΎΠ²Π°Π½ΠΈΡ ΠΏΡΠ·ΡΡΡΠΊΠΎΠ² Π²ΠΎΠ·Π΄ΡΡ Π°,ΡΠ»ΡΡΡΠ΅Π½ΠΈΡ ΠΈΡ Π²ΡΡ ΠΎΠ΄Π° Π½Π° ΠΏΠΎΠ²Π΅ΡΡ Π½ΠΎΡΡΡ ΡΠΌΠ΅ΡΠΈ, ΠΏΡΠΈΠΌΠ΅Π½ΡΡΡ ΡΠ°ΠΊ Π½Π°Π·ΡΠ²Π°Π΅ΠΌΡΡ Β«Π²ΠΎΠ΄ΡΠ½ΡΡ Π±Π°Π½ΡΒ»,ΠΏΡΠΈ ΡΡΠΎΠΌ Π΅ΡΡΡ ΡΠΈΡΠΊ ΠΏΠΎΠΏΠ°Π΄Π°Π½ΠΈΡ Π²ΠΎΠ΄Ρ Π² ΡΠΌΠ΅ΡΡ, ΡΡΠΎ Π½Π΅ Π΄ΠΎΠΏΡΡΡΠΈΠΌΠΎ.Β Β Β Β Β
Β ΠΡΠ΅ ΠΎΠ΄Π½ΠΎΠΉ ΠΏΡΠΈΡΠΈΠ½ΠΎΠΉ ΠΎΠ±ΡΠ°Π·ΠΎΠ²Π°Π½ΠΈΡ Π»ΠΈΠΏΠΊΠΎΠΉ, ΠΌΡΡΠ½ΠΎΠΉ ΠΏΠ»Π΅Π½ΠΊΠΈ Π½Π° ΠΏΠΎΠ²Π΅ΡΡ Π½ΠΎΡΡΠΈ β Π½Π΅ ΡΠΎΠ±Π»ΡΠ΄Π΅Π½ΠΈΠ΅
ΡΡΠ΅Π±ΡΠ΅ΠΌΠΎΠ³ΠΎ ΡΠΎΠΎΡΠ½ΠΎΡΠ΅Π½ΠΈΡ ΡΠΌΠΎΠ»Ρ ΠΈ ΠΎΡΠ²Π΅ΡΠ΄ΠΈΡΠ΅Π»Ρ.
Β ΠΡΠ΅ Π·Π½Π°ΡΡ, ΡΡΠΎ ΠΏΡΠΈ ΡΠ°Π±ΠΎΡΠ΅ Ρ ΡΠΏΠΎΠΊΡΠΈΠ΄Π½ΠΎΠΉ ΡΠΌΠΎΠ»ΠΎΠΉ ΠΌΠ°ΡΠΊΠΈ ΠΠ-20, ΠΎΡΠ²Π΅ΡΠ΄ΠΈΡΠ΅Π»Ρ ΠΌΠΎΠΆΠ½ΠΎ Π΄ΠΎΠ±Π°Π²Π»ΡΡΡ ΡΠΊΠ°ΠΆΠ΅ΠΌ ΡΠ°ΠΊ, Β«Π½Π° Π³Π»Π°Π·ΠΎΠΊΒ» — 1 ΠΊ 10. ΠΡΠ° ΡΠΌΠΎΠ»Π° Π΄ΠΎΠΏΡΡΠΊΠ°Π΅Ρ ΠΎΠΏΡΠ΅Π΄Π΅Π»Π΅Π½Π½ΡΠ΅ ΠΎΡΠΊΠ»ΠΎΠ½Π΅Π½ΠΈΡ Π² ΡΡ ΠΈΠ»ΠΈΒ ΠΈΠ½ΡΡ ΡΡΠΎΡΠΎΠ½Ρ. ΠΠ½Π° Π²ΡΠ΅ ΡΠ°Π²Π½ΠΎ ΡΡΠ°Π±ΠΎΡΠ°Π΅Ρ.
Β ΠΡΡΠ³ΠΎΠ΅ Π΄Π΅Π»ΠΎ ΡΠ°Π±ΠΎΡΠ°Ρ Ρ ΡΠΏΠΎΠΊΡΠΈΠ΄Π½ΡΠΌΠΈ ΡΠΌΠΎΠ»Π°ΠΌΠΈ ΠΈΠΌΠΏΠΎΡΡΠ½ΠΎΠ³ΠΎ ΠΏΡΠΎΠΈΠ·Π²ΠΎΠ΄ΡΡΠ²Π°. ΠΠ΄Π΅ΡΡ Π½Π΅ΠΎΠ±- Ρ ΠΎΠ΄ΠΈΠΌΠΎ ΡΠΎΡΠ½ΠΎ ΡΠΎΠ±Π»ΡΠ΄Π°ΡΡ ΠΏΡΠΎΠΏΠΎΡΡΠΈΠΈ Π² ΡΠΎΠΎΡΠ½ΠΎΡΠ΅Π½ΠΈΠΈ ΡΠΌΠΎΠ»Π°-ΠΎΡΠ²Π΅ΡΠ΄ΠΈΡΠ΅Π»Ρ. Π’ΡΡ Π½Π΅ ΠΎΠ±ΠΎΠΉΡΠΈΡΡ Π±Π΅Π· ΡΠ»Π΅ΠΊΡΡΠΎΠ½Π½ΡΡ Π²Π΅ΡΠΎΠ². ΠΠ±ΡΡΠ½ΠΎ ΡΡΠΎ 13% ΠΎΡΠ²Π΅ΡΠ΄ΠΈΡΠ΅Π»Ρ ΠΊ Π²Π΅ΡΡ ΡΠΌΠΎΠ»Ρ.
Β ΠΡΠΈ Π·Π°ΠΌΠ΅ΡΠ½ΠΎΠΌ ΠΎΡΠΊΠ»ΠΎΠ½Π΅Π½ΠΈΠΈ Π² ΠΏΡΠΎΠΏΠΎΡΡΠΈΠΈ, Π² ΠΈΡΠΎΠ³Π΅ ΡΡΡΠ°Π΄Π°Π΅Ρ ΡΠ°ΠΌΠ° ΠΏΡΠΎΡΠ½ΠΎΡΡΡ Π³ΠΎΡΠΎΠ²ΠΎΠ³ΠΎ ΠΈΠ·Π΄Π΅Π»ΠΈΡ, Π° Π² ΡΠ»ΡΡΠ°Π΅ ΠΈΠ·Π±ΡΡΠΊΠ° ΠΎΡΠ²Π΅ΡΠ΄ΠΈΡΠ΅Π»Ρ, ΡΠΌΠΎΠ»Π° ΡΡΠ°Π½ΠΎΠ²ΠΈΡΡΡ ΠΊΠΎΡΡΠΎΠ·ΠΈΠΎΠ½Π½ΠΎ-Π°ΠΊΡΠΈΠ²Π½ΠΎΠΉ.
Β 6). ΠΠ»Ρ ΡΠΎΠ³ΠΎ, ΡΡΠΎΠ±Ρ Π³ΠΎΡΠΎΠ²ΠΎΠ΅ ΠΈΠ·Π΄Π΅Π»ΠΈΠ΅ Π±ΡΠ»ΠΎ ΠΏΠ»Π°ΡΡΠΈΡΠ½ΠΎ, Π½Π΅ Π»ΠΎΠΌΠ°Π»ΠΎΡΡ, Π½Π΅ ΡΡΠ΅ΡΠΊΠ°Π»ΠΎΡΡ Ρ ΡΠ΅ΡΠ΅Π½ΠΈΠ΅ΠΌ Π²ΡΠ΅ΠΌΠ΅Π½ΠΈ Π² ΡΠΏΠΎΠΊΡΠΈΠ΄Π½ΡΡ ΡΠΌΠΎΠ»Ρ Π½ΡΠΆΠ½ΠΎ Π΄ΠΎΠ±Π°Π²Π»ΡΡΡ ΠΏΠ»Π°ΡΡΠΈΡΠΈΠΊΠ°ΡΠΎΡ. ΠΠ»Π°ΡΡΠΈΡΠΈΠΊΠ°ΡΠΎΡ ΠΎΠ±ΡΠ·Π°ΡΠ΅Π»ΡΠ½ΠΎ Π½Π΅ΠΎΠ±Ρ ΠΎΠ΄ΠΈΠΌΠΎ ΠΈΡΠΏΠΎΠ»ΡΠ·ΠΎΠ²Π°ΡΡ ΠΏΡΠΈ ΠΈΠ·Π³ΠΎΡΠΎΠ²Π»Π΅Π½ΠΈΠΈ Π΄ΠΎΡΡΠ°ΡΠΎΡΠ½ΠΎ Π±ΠΎΠ»ΡΡΠΈΡ ΠΈΠ·Π΄Π΅Π»ΠΈΠΉ, ΠΏΠΎΡΠΊΠΎΠ»ΡΠΊΡ Π²ΠΎΠ·ΠΌΠΎΠΆΠ½ΠΎ ΠΏΠΎΡΠ²Π»Π΅Π½ΠΈΠ΅ ΡΡΠ΅ΡΠΈΠ½ Π΅ΡΠ΅ Π½Π° ΡΡΠ°Π΄ΠΈΠΈ Π·Π°ΡΠ²Π΅ΡΠ΄Π΅Π²Π°Π½ΠΈΡ.
Β 7). ΠΡΠΈΠΌΠ΅Π½Π΅Π½ΠΈΠ΅ ΡΠ½ΠΈΠ²Π΅ΡΡΠ°Π»ΡΠ½ΠΎΠ³ΠΎ ΠΏΠ»Π°ΡΡΠΈΡΠΈΠΊΠ°ΡΠΎΡΠ° ΠΠΠΠ£Π’ΠΠΠ€Π’ΠΠΠΠ’ (ΠΠΠ€):
Β ΠΠ±Π»Π°ΡΡΡ ΠΏΡΠΈΠΌΠ΅Π½Π΅Π½ΠΈΡ ΠΠΠ€ Π²Π΅ΡΡΠΌΠ° ΡΠΈΡΠΎΠΊ, ΠΎΠ΄Π½ΠΎ ΠΈΠ· Π½ΠΈΡ — ΠΏΠ»Π°ΡΡΠΈΡΠΈΠΊΠ°ΡΠΈΡ ΡΠΏΠΎΠΊΡΠΈΠ΄Π½ΡΡ ΡΠΌΠΎΠ». ΠΠΠ€ Π΄ΠΎΡΡΠ°ΡΠΎΡΠ½ΠΎ ΠΏΠ»ΠΎΡ ΠΎ ΡΠ΅Π°Π³ΠΈΡΡΠ΅Ρ (ΠΏΠ΅ΡΠ΅ΠΌΠ΅ΡΠΈΠ²Π°Π΅ΡΡΡ) Ρ ΡΠΏΠΎΠΊΡΠΈΠ΄Π½ΠΎΠΉ ΡΠΌΠΎΠ»ΠΎΠΉ, ΡΡΠΎ Π΄Π°Π΅Ρ Π½Π΅Π±ΠΎΠ»ΡΡΠΎΠΉ ΠΏΠ»Π°ΡΡΠΈΡΠ΅ΡΠΊΠΈΠΉ ΡΡΡΠ΅ΠΊΡ, Π½ΠΎ Π΅Π³ΠΎ ΠΎΠ±ΡΡΠ½ΠΎ Π±ΡΠ²Π°Π΅Ρ Π΄ΠΎΡΡΠ°ΡΠΎΡΠ½ΠΎ Π΄Π»Ρ ΠΏΡΠ΅Π΄ΠΎΡΠ²ΡΠ°ΡΠ΅Π½ΠΈΡ ΡΠ°ΡΡΡΠ΅ΡΠΊΠΈΠ²Π°Π½ΠΈΡ Π³ΠΎΡΠΎΠ²ΠΎΠ³ΠΎ ΠΈΠ·Π΄Π΅Π»ΠΈΡ ΠΏΡΠΈ Π·Π°ΡΠ²Π΅ΡΠ΄ΡΠ²Π°Π½ΠΈΠΈ ΠΈ Π½Π° ΠΌΠΎΡΠΎΠ·Π΅. ΠΠ»Ρ ΡΠ²Π΅Π»ΠΈΡΠ΅Π½ΠΈΡ Π΄Π°Π½ΠΎΠ³ΠΎ ΡΡΡΠ΅ΠΊΡΠ°, ΡΠΏΠΎΠΊΡΠΈΠ΄Π½ΡΡ ΡΠΌΠΎΠ»Ρ Ρ ΠΏΠ»Π°ΡΡΠΈΡΠΈΠΊΠ°ΡΠΎΡΠΎΠΌ (ΠΠΠ€) Π½Π΅ΠΎΠ±Ρ ΠΎΠ΄ΠΈΠΌΠΎ «Π²Π°ΡΠΈΡΡ». ΠΠ»Ρ ΡΡΠΎΠ³ΠΎ ΡΠ΄ΠΎΠ±Π½ΠΎ ΠΈΡΠΏΠΎΠ»ΡΠ·ΠΎΠ²Π°ΡΡ «Π²ΠΎΠ΄ΡΠ½ΡΡ Π±Π°Π½Ρ» — ΠΎΠΏΡΡΡΠΈΡΡ Π΅ΠΌΠΊΠΎΡΡΡ ΡΠΎ ΡΠΌΠΎΠ»ΠΎΠΉ Π² Π²ΠΎΠ΄Ρ ΠΈ ΠΏΠΎΡΡΠΎΡΠ½Π½ΠΎ ΠΏΠ΅ΡΠ΅ΠΌΠ΅ΡΠΈΠ²Π°Ρ Π΄ΠΎΠ²Π΅ΡΡΠΈ Π΄ΠΎ 50-60Β°Π‘.
Β Π‘Π½Π°ΡΠ°Π»Π° Π² ΡΠΌΠΎΠ»Ρ Π΄ΠΎΠ±Π°Π²Π»ΡΡΡ ΠΏΠ»Π°ΡΡΠΈΡΠΈΠΊΠ°ΡΠΎΡ. ΠΠΏΠΎΠΊΡΠΈΠ΄Π½ΡΡ ΡΠΌΠΎΠ»Ρ Π²ΠΌΠ΅ΡΡΠ΅ Ρ ΠΠΠ€ Π½Π΅ΠΎΠ±Ρ ΠΎΠ΄ΠΈΠΌΠΎ ΠΌΠ΅Π΄Π»Π΅Π½Π½ΠΎ Π½Π°Π³ΡΠ΅Π²Π°Ρ Π΄ΠΎ ΡΠ΅ΠΌΠΏΠ΅ΡΠ°ΡΡΡΡ 50-60Β°Π‘ ΠΏΠΎΡΡΠΎΡΠ½Π½ΠΎ ΠΏΠ΅ΡΠ΅ΠΌΠ΅ΡΠΈΠ²Π°ΡΡ Π² ΡΠ΅ΡΠ΅Π½ΠΈΠ΅ 2-3 ΡΠ°ΡΠΎΠ². ΠΡΠΎ Π½Π΅ΠΎΠ±Ρ ΠΎΠ΄ΠΈΠΌΠΎ Π΄Π»Ρ ΡΡΠΏΠ΅ΡΠ½ΠΎΠ³ΠΎ ΠΏΡΠΎΡΠ΅ΠΊΠ°Π½ΠΈΡ Ρ ΠΈΠΌΠΈΡΠ΅ΡΠΊΠΎΠΉ ΡΠ΅Π°ΠΊΡΠΈΠΈ ΠΌΠ΅ΠΆΠ΄Ρ ΡΠΌΠΎΠ»ΠΎΠΉ ΠΈ ΠΠΠ€, Π² ΠΏΡΠΎΡΠΈΠ²Π½ΠΎΠΌ ΡΠ»ΡΡΠ°Π΅ ΠΏΠΎΠ»ΡΡΠΈΡΡΡ ΡΠΌΠ΅ΡΡ, ΠΊΠΎΡΠΎΡΠ°Ρ Π½Π΅ Π±ΡΠ΄Π΅Ρ ΠΎΠ±Π»Π°Π΄Π°ΡΡ Π½Π΅ΠΎΠ±Ρ ΠΎΠ΄ΠΈΠΌΡΠΌΠΈ ΡΠ²ΠΎΠΉΡΡΠ²Π°ΠΌΠΈ.
Β ΠΠ½ΠΈΠΌΠ°Π½ΠΈΠ΅!
Β β’ Π½Π΅ΠΎΠ±Ρ ΠΎΠ΄ΠΈΠΌΠΎ ΠΈΠ·Π±Π΅Π³Π°ΡΡ ΠΏΠΎΠΏΠ°Π΄Π°Π½ΠΈΡ Π²ΠΎΠ΄Ρ Π² ΡΠΌΠΎΠ»Ρ:
Β β’ Π½Π΅ΠΎΠ±Ρ ΠΎΠ΄ΠΈΠΌΠΎ ΠΈΠ·Π±Π΅Π³Π°ΡΡ Π½Π°Π³ΡΠ΅Π²Π° ΡΠΌΠΎΠ»Ρ Π²ΡΡΠ΅ 60Β°Π‘ , Ρ.ΠΊ. Π²ΠΎΠ·ΠΌΠΎΠΆΠ½ΠΎ Β«Π·Π°ΠΊΠΈΠΏΠ°Π½ΠΈΠ΅Β» ΡΠΌΠΎΠ»Ρ (ΡΠΌΠΎΠ»Π° ΡΡΠ°Π½Π΅Ρ ΠΌΠ°ΡΠΎΠ²ΠΎ-Π±Π΅Π»ΠΎΠΉ ΠΈ ΠΏΠΎΠΊΡΠΎΠ΅ΡΡΡ ΠΏΠ΅Π½ΠΎΠΉ) β ΡΠ°ΠΊΠ°Ρ ΡΠΌΠΎΠ»Π° Π½Π΅ΠΏΡΠΈΠ³ΠΎΠ΄Π½Π° ΠΊ ΠΈΡΠΏΠΎΠ»ΡΠ·ΠΎΠ²Π°Π½ΠΈΡ.
Β ΠΠΎΡΠΊΠΎΠ»ΡΠΊΡ Π²ΡΠΏΠΎΠ»Π½ΠΈΡΡ Π²ΡΡΠ΅ΠΎΠΏΠΈΡΠ°Π½Π½ΡΡ ΠΏΡΠΎΡΠ΅Π΄ΡΡΡ Π·Π°ΡΡΡΠ΄Π½ΠΈΡΠ΅Π»ΡΠ½ΠΎ, Π»ΡΡΡΠ΅, Π² ΡΠΎΠΌ ΡΠΈΡΠ»Π΅ Π΄Π»Ρ ΠΏΡΠΈΠ΄Π°Π½ΠΈΡ Π±ΠΎΠ»Π΅Π΅ ΠΌΠΎΡΠ½ΠΎΠ³ΠΎ ΠΏΠ»Π°ΡΡΠΈΡΠ΅ΡΠΊΠΎΠ³ΠΎ ΡΡΡΠ΅ΠΊΡΠ°, ΠΈΡΠΏΠΎΠ»ΡΠ·ΠΎΠ²Π°ΡΡ ΠΏΠ»Π°ΡΡΠΈΡΠΈΠΊΠ°ΡΠΎΡ ΠΠΠΠ ΠΠΠ‘ΠΠ Β ΠΠΠ-1.
Β 8). ΠΠΠΠ ΠΠΠ‘ΠΠ Β ΠΠΠ-1 ΡΠ°ΠΌΠ° ΠΏΠΎ ΡΠ΅Π±Π΅ ΡΠΏΠΎΠΊΡΠΈΠ΄Π½Π°Ρ ΡΠΌΠΎΠ»Π°, ΡΠ°ΠΊΠΆΠ΅ ΡΠ²Π»ΡΠ΅ΡΡΡ ΠΏΠ»Π°ΡΡΠΈΡΠΈΠΊΠ°ΡΠΎΡΠΎΠΌ ΠΈ Π°ΠΊΡΠΈΠ²Π½ΡΠΌ ΡΠ°Π·Π±Π°Π²ΠΈΡΠ΅Π»Π΅ΠΌ. ΠΠΠ-1 ΠΏΡΠ΅ΠΊΡΠ°ΡΠ½ΠΎ ΡΠΌΠ΅ΡΠΈΠ²Π°Π΅ΡΡΡ Ρ ΡΠΏΠΎΠΊΡΠΈΠ΄Π½ΠΎΠΉ ΡΠΌΠΎΠ»ΠΎΠΉ, ΡΡΠΎ Π΄Π°Π΅Ρ ΠΌΠΎΡΠ½ΡΠΉ ΠΏΠ»Π°ΡΡΠΈΡΠ΅ΡΠΊΠΈΠΉ ΡΡΡΠ΅ΠΊΡ. ΠΡΠΎΠΏΠΎΡΡΠΈΡ 5-7% ΠΠΠ-1 ΠΊ ΠΌΠ°ΡΡΠ΅ ΡΠΌΠΎΠ»Ρ. ΠΠΏΠΎΠΊΡΠΈΠ΄Π½Π°Ρ ΡΠΌΠΎΠ»Π° Π²ΠΌΠ΅ΡΡΠ΅ Ρ ΠΠΠΠ ΠΠΠ‘ΠΠ Β ΠΠΠ-1 ΠΌΠΎΠΆΠ΅Ρ Ρ ΡΠ°Π½ΠΈΡΡΡΡ ΡΠΊΠΎΠ»Ρ ΡΠ³ΠΎΠ΄Π½ΠΎ Π΄ΠΎΠ»Π³ΠΎ, ΡΠ°ΠΊΡΡ ΡΠΌΠΎΠ»Ρ Π½Π°Π·ΡΠ²Π°ΡΡ
ΠΌΠΎΠ΄ΠΈΡΠΈΡΠΈΡΠΎΠ²Π°Π½Π½ΠΎΠΉ ΡΠΏΠΎΠΊΡΠΈΠ΄Π½ΠΎΠΉ ΡΠΌΠΎΠ»ΠΎΠΉ, Ρ.Π΅. Ρ ΠΈΠ·ΠΌΠ΅Π½Π΅Π½Π½ΡΠΌΠΈ ΡΠ²ΠΎΠΉΡΡΠ²Π°ΠΌΠΈ.
Β 9). ΠΠΎΡΠ»Π΅ ΡΠΌΠ΅ΡΠ΅Π½ΠΈΡ ΡΠΌΠΎΠ»Ρ Ρ ΠΏΠ»Π°ΡΡΠΈΡΠΈΠΊΠ°ΡΠΎΡΠΎΠΌ Π² Π½Π΅Π΅ Π΄ΠΎΠ±Π°Π²Π»ΡΡΡ ΠΎΡΠ²Π΅ΡΠ΄ΠΈΡΠ΅Π»Ρ. Π‘ΠΌΠΎΠ»Ρ Π½Π΅ΠΎΠ±Ρ ΠΎΠ΄ΠΈΠΌΠΎ ΠΎΡ Π»Π°Π΄ΠΈΡΡ Π΄ΠΎ 22-24Β°Π‘ (ΠΏΡΠΈ ΠΏΡΠΈΠΌΠ΅Π½Π΅Π½ΠΈΠΈ ΠΠΠ€), ΡΡΠΎΠ±Ρ ΡΠΌΠ΅Π½ΡΡΠΈΡΡ ΡΠΈΡΠΊ Β«Π·Π°ΠΊΠΈΠΏΠ°Π½ΠΈΡΒ» ΡΠΌΠΎΠ»Ρ. Π‘ΡΠ°Π½Π΄Π°ΡΡΠ½ΠΎΠ΅ ΡΠΎΠΎΡΠ½ΠΎΡΠ΅Π½ΠΈΠ΅ (Π΄Π»Ρ ΠΠ-20) ΡΠΌΠΎΠ»Π° — ΠΎΡΠ²Π΅ΡΠ΄ΠΈΡΠ΅Π»Ρ β 1:10. Π Π½Π΅ΠΊΠΎΡΠΎΡΡΡ ΡΠΏΠ΅ΡΠΈΡΠΈΡΠ΅ΡΠΊΠΈΡ ΡΠ΅Ρ Π½ΠΎΠ»ΠΎΠ³ΠΈΡΠ΅ΡΠΊΠΈΡ ΠΏΡΠΎΡΠ΅ΡΡΠ°Ρ ΠΎΠ½ΠΎ ΠΌΠΎΠΆΠ΅Ρ ΡΠΈΠ»ΡΠ½ΠΎ ΠΎΡΠ»ΠΈΡΠ°ΡΡΡΡ ΠΎΡ ΠΎΠ±ΡΠ΅ΠΏΡΠΈΠ½ΡΡΠΎΠ³ΠΎ β Π±ΡΡΡ ΠΎΡ 1:5 Π΄ΠΎ 1:20, Π½ΠΎ Π² ΠΏΠΎΠ΄Π°Π²Π»ΡΡΡΠ΅ΠΌ Π±ΠΎΠ»ΡΡΠΈΠ½ΡΡΠ²Π΅ ΡΠ»ΡΡΠ°Π΅Π² ΠΈΡΠΏΠΎΠ»ΡΠ·ΡΠ΅ΡΡΡ ΡΠΎΠΎΡΠ½ΠΎΡΠ΅Π½ΠΈΠ΅, Π±Π»ΠΈΠ·ΠΊΠΎΠ΅ ΠΊ ΡΡΠ°Π½Π΄Π°ΡΡΠ½ΠΎΠΌΡ. ΠΠ»Ρ ΡΠΌΠΎΠ» ΠΈΠΌΠΏΠΎΡΡΠ½ΠΎΠ³ΠΎ ΠΏΡΠΎΠΈΠ·Π²ΠΎΠ΄ΡΡΠ²Π° ΡΠ°ΠΊΠΎΠ΅ ΡΠΎΠΎΡ- Π½ΠΎΡΠ΅Π½ΠΈΠ΅ 13% ΠΎΡΠ²Π΅ΡΠ΄ΠΈΡΠ΅Π»Ρ ΠΊ ΠΌΠ°ΡΡΠ΅ ΡΠΌΠΎΠ»Ρ.
Β 10). ΠΡΠ²Π΅ΡΠ΄ΠΈΡΠ΅Π»Ρ Π½Π΅ΠΎΠ±Ρ ΠΎΠ΄ΠΈΠΌΠΎ Π»ΠΈΡΡ Π² ΡΠΏΠΎΠΊΡΠΈΠ΄Π½ΡΡ ΡΠΌΠΎΠ»Ρ ΠΎΡΠ΅Π½Ρ ΠΌΠ΅Π΄Π»Π΅Π½Π½ΠΎ, ΡΡΠ°ΡΠ΅Π»ΡΠ½ΠΎ ΠΈ ΠΏΠΎΡΡΠΎΡΠ½Π½ΠΎ ΠΏΠ΅ΡΠ΅ΠΌΠ΅ΡΠΈΠ²Π°Ρ, ΡΠ°ΠΊ ΡΡΠΎ Π±Ρ Π² ΠΈΡΠΎΠ³Π΅ ΠΎΡΠ²Π΅ΡΠ΄ΠΈΡΠ΅Π»Ρ ΡΠ°Π²Π½ΠΎΠΌΠ΅ΡΠ½ΠΎ ΠΏΡΠΈΡΡΡΡΡΠ²ΠΎΠ²Π°Π» Π²ΠΎ Π²ΡΠ΅ΠΌ ΠΎΠ±ΡΠ΅ΠΌΠ΅ ΡΠΌΠΎΠ»Ρ (ΡΡΠΎ ΠΊΠ°ΡΠ°Π΅ΡΡΡ ΠΈ ΠΏΠ»Π°ΡΡΠΈΡΠΈΠΊΠ°ΡΠΎΡΠΎΠ²).
Β Β Π‘ΠΈΠ»ΡΠ½Π°Ρ ΠΏΠ΅ΡΠ΅Π΄ΠΎΠ·ΠΈΡΠΎΠ²ΠΊΠ° ΠΎΡΠ²Π΅ΡΠ΄ΠΈΡΠ΅Π»Ρ Π΄Π°ΠΆΠ΅ Π²ΡΠ΅ΠΌΠ΅Π½Π½ΠΎ Π² ΡΠ°ΡΡΠΈ Π΅ΠΌΠΊΠΎΡΡΠΈ, ΠΌΠΎΠΆΠ΅Ρ ΠΏΡΠΈΠ²Π΅ΡΡΠΈ ΠΊ Β«Π·Π°ΠΊΠΈΠΏΠ°Π½ΠΈΡΒ» ΡΠΌΠΎΠ»Ρ (ΡΠΌΠΎΠ»Π° ΡΡΠ°Π½Π΅Ρ ΠΌΠ°ΡΠΎΠ²ΠΎ-Π±Π΅Π»ΠΎΠΉ ΠΈ ΠΏΠΎΠΊΡΠΎΠ΅ΡΡΡ ΠΏΠ΅Π½ΠΎΠΉ), Π² ΡΡΠΎΠΌ ΡΠ»ΡΡΠ°Π΅ Π²ΡΡ ΡΠΌΠΎΠ»Π° Π±ΡΠ΄Π΅Ρ ΠΈΡΠΏΠΎΡΡΠ΅Π½Π°. ΠΠ΅ΠΎΠ±Ρ ΠΎΠ΄ΠΈΠΌΠΎ ΠΈΠΌΠ΅ΡΡ Π² Π²ΠΈΠ΄Ρ, ΡΡΠΎ ΠΏΡΠΎΡΠ΅ΡΡ ΡΠΌΠ΅ΡΠΈΠ²Π°Π½ΠΈΡ ΡΠΌΠΎΠ»Ρ Ρ ΠΎΡΠ²Π΅ΡΠ΄ΠΈΡΠ΅Π»Π΅ΠΌ ΡΠΊΠ·ΠΎΡΠ΅ΡΠΌΠΈΡΠ΅ΡΠΊΠΈΠΉ (Π²ΡΠ΄Π΅Π»ΡΠ΅ΡΡΡ ΡΠ΅ΠΏΠ»ΠΎ), ΡΠΌΠΎΠ»Π° Π±ΡΠ΄Π΅Ρ Π½Π°Π³ΡΠ΅Π²Π°ΡΡΡΡ. ΠΠ½ΠΎΠ³Π΄Π° Π² ΠΏΡΠΎΡΠ΅ΡΡΠ΅ Π΄ΠΎΠ±Π°Π²Π»Π΅Π½ΠΈΡ ΠΎΡΠ²Π΅ΡΠ΄ΠΈΡΠ΅Π»Ρ ΠΈΠ»ΠΈ ΡΡΠ°Π·Ρ ΠΏΠΎ ΠΎΠΊΠΎΠ½ΡΠ°Π½ΠΈΠΈ ΡΠΌΠ΅ΡΠΈΠ²Π°Π½ΠΈΡ Π²ΠΎΠ·Π½ΠΈΠΊΠ°Π΅Ρ Π»Π°Π²ΠΈΠ½ΠΎΠΎΠ±ΡΠ°Π·Π½ΡΠΉ ΠΏΡΠΎΡΠ΅ΡΡ β ΡΠΌΠΎΠ»Π° ΠΎΡΠ΅Π½Ρ Π±ΡΡΡΡΠΎ ΡΠΈΠ»ΡΠ½ΠΎ Π½Π°Π³ΡΠ΅Π²Π°Π΅ΡΡΡ ΠΈ ΠΏΡΠ°ΠΊΡΠΈΡΠ΅ΡΠΊΠΈ ΠΌΠΎΠΌΠ΅Π½ΡΠ°Π»ΡΠ½ΠΎ Β«Π²ΡΡΠ°Π΅ΡΒ» (Π·Π°ΡΠ²Π΅ΡΠ΄Π΅Π²Π°Π΅Ρ). ΠΡΠΎ ΡΠ²ΡΠ·Π°Π½ΠΎ Ρ ΠΏΠ΅ΡΠ΅Π΄ΠΎΠ·ΠΈΡΠΎΠ²ΠΊΠΎΠΉ ΠΎΡΠ²Π΅ΡΠ΄ΠΈΡΠ΅Π»Ρ ΠΈΠ»ΠΈ Ρ Π²ΡΡΠΎΠΊΠΎΠΉ ΠΈΡΡ ΠΎΠ΄Π½ΠΎΠΉ ΡΠ΅ΠΌΠΏΠ΅ΡΠ°ΡΡΡΠΎΠΉ ΡΠΌΠΎΠ»Ρ.
Β 11). ΠΠΈΠ·Π½Π΅ΡΠΏΠΎΡΠΎΠ±Π½ΠΎΡΡΡ ΡΠΌΠ΅ΡΠΈ ΡΠΌΠΎΠ»Ρ Ρ ΠΎΡΠ²Π΅ΡΠ΄ΠΈΡΠ΅Π»Π΅ΠΌ ΠΎΠ±ΡΡΠ½ΠΎ ΠΎΡ 30 ΠΌΠΈΠ½. Π΄ΠΎ 1 Ρ. (Π·Π°Π²ΠΈΡΠΈΡ ΠΎΡ ΡΠ΅ΠΌΠΏΠ΅ΡΠ°ΡΡΡΡ ΡΠΌΠΎΠ»Ρ, ΡΠΈΠΏΠ° ΠΎΡΠ²Π΅ΡΠ΄ΠΈΡΠ΅Π»Ρ ΠΈ Π΅Π³ΠΎ ΠΊΠΎΠ»ΠΈΡΠ΅ΡΡΠ²Π°).
Β 12). ΠΠ»Ρ ΠΎΡΠ²Π΅ΡΠΆΠ΄Π΅Π½ΠΈΡ ΡΠΏΠΎΠΊΡΠΈΠ΄Π½ΠΎΠΉ ΡΠΌΠΎΠ»Ρ Π² Ρ ΠΎΠ»ΠΎΠ΄Π½ΠΎΠ΅ Π²ΡΠ΅ΠΌΡ Π³ΠΎΠ΄Π° ΡΠ΅ΠΊΠΎΠΌΠ΅Π½Π΄ΡΠ΅ΡΡΡ Π΄ΠΎΠ±Π°Π²Π»ΡΡΡ Π² ΠΌΠ°ΡΡΡ 1 -2 % ΡΡΠΊΠΎΡΠΈΡΠ΅Π»Ρ.
Β ΠΡΡΡ ΡΠΏΠΎΠΊΡΠΈΠ΄Π½ΡΠ΅ ΡΠΌΠΎΠ»Ρ ΠΏΡΠ΅Π΄Π½Π°Π·Π½Π°ΡΠ΅Π½Π½ΡΠ΅ Π΄Π»Ρ ΡΠ°Π±ΠΎΡΡ Π² Ρ ΠΎΠ»ΠΎΠ΄Π½ΠΎΠ΅ Π²ΡΠ΅ΠΌΡ Π³ΠΎΠ΄Π°. ΠΠ°ΠΏΡΠΈΠΌΠ΅Ρ ΡΠΌΠΎΠ»Π°Β DER-353, ΠΊΠΎΡΠΎΡΠ°Ρ ΠΈ ΠΏΡΠΈ ΠΌΠΈΠ½ΡΡΠΎΠ²ΠΎΠΉ ΡΠ΅ΠΌΠΏΠ΅ΡΠ°ΡΡΡΠ΅ ΠΎΡΡΠ°Π΅ΡΡΡ ΠΆΠΈΠ΄ΠΊΠΎΠΉ.
Β Β 13). ΠΠ»Ρ ΠΊΠ°ΠΆΠ΄ΠΎΠ³ΠΎ ΠΊΠΎΠ½ΠΊΡΠ΅ΡΠ½ΠΎΠ³ΠΎ Π²ΠΈΠ΄Π° ΡΠ°Π±ΠΎΡ, Π½Π΅ΠΎΠ±Ρ ΠΎΠ΄ΠΈΠΌΠΎ Π²ΡΡΠ°Π±ΠΎΡΠ°ΡΡ ΡΠ²ΠΎΡ ΡΠΎΠ±ΡΡΠ²Π΅Π½Π½ΡΡ, Π½Π°ΠΈΠ±ΠΎΠ»Π΅Π΅ ΠΏΠΎΠ΄Ρ ΠΎΠ΄ΡΡΡΡ ΡΠ΅Ρ Π½ΠΎΠ»ΠΎΠ³ΠΈΡ, ΠΊΠΎΡΠΎΡΠ°Ρ Π±ΡΠ΄Π΅Ρ Π²ΠΊΠ»ΡΡΠ°ΡΡ Π² ΡΠ΅Π±Ρ ΠΏΡΠ΅Π΄ΠΏΠΎΡΡΠΈΡΠ΅Π»ΡΠ½ΡΠ΅ ΠΌΠ°ΡΠΊΠΈ ΡΠΏΠΎΠΊΡΠΈΠ΄Π½ΠΎΠΉ ΡΠΌΠΎΠ»Ρ ΠΈ ΠΊΠΎΠΌΠΏΠΎΠ½Π΅Π½ΡΠΎΠ², ΠΈΡ ΡΠΎΡΠ½ΡΠ΅ ΠΏΡΠΎΠΏΠΎΡΡΠΈΠΈ ΠΈ ΠΎΡΠΎΠ±Π΅Π½Π½ΠΎΡΡΠΈ ΡΠ΅Ρ Π½ΠΎΠ»ΠΎΠ³ΠΈΡΠ΅ΡΠΊΠΎΠ³ΠΎ ΠΏΡΠΎΡΠ΅ΡΡΠ°.
Β Π’Π°ΠΊ, ΠΏΡΠΈΠ²Π΅Π΄Π΅ΠΌ Π½Π΅ΠΊΠΎΡΠΎΡΡΠ΅ ΠΏΡΠΈΠΌΠ΅ΡΡ:
— ΠΏΡΠΈ ΡΠ°Π±ΠΎΡΠ΅ Ρ ΡΠΏΠΎΠΊΡΠΈΠ΄Π½ΠΎΠΉ ΡΠΌΠΎΠ»ΠΎΠΉ ΠΠ-20 Π² ΡΠ΅ΠΌΠΏΠ΅ΡΠ°ΡΡΡΠ½ΠΎΠΌ ΡΠ΅ΠΆΠΈΠΌΠ΅ ΠΎΡ +18-30Β°Π‘ Ρ ΠΈΡΠΏΠΎΠ»Ρ- Π·ΠΎΠ²Π°Π½ΠΈΠ΅ΠΌ ΠΠΠΠ, ΠΎΡΠ²Π΅ΡΠ΄ΠΈΡΠ΅Π»Ρ Π½Π΅ΠΎΠ±Ρ ΠΎΠ΄ΠΈΠΌΠΎ ΠΎΡ 9-10% ΠΎΡ ΠΌΠ°ΡΡΡ ΡΠΌΠΎΠ»Ρ;
— ΠΏΡΠΈ ΡΠ°Π±ΠΎΡΠ΅ Ρ ΠΠ-20, ΠΏΡΠΈ Π±ΠΎΠ»Π΅Π΅ Π½ΠΈΠ·ΠΊΠΈΡ ΡΠ΅ΠΌΠΏΠ΅ΡΠ°ΡΡΡΠ°Ρ ΠΎΡ +2 Π΄ΠΎ +18Β°Π‘ ΠΈΡΠΏΠΎΠ»ΡΠ·ΡΡΡ ΠΎΡΠ²Π΅Ρ-
Π΄ΠΈΡΠ΅Π»Ρ Π£Π-583Π, Π² ΠΏΡΠ΅Π΄Π΅Π»Π°Ρ 18-22%;
— ΠΈΡΠΏΠΎΠ»ΡΠ·ΡΡ ΠΊΠΎΠΌΠΏΠ°ΡΠ½Π΄Ρ Π-115;Π-153;Π-153Π ΠΎΡ +18 Π΄ΠΎ +30Β°Π‘Β Ρ ΠΎΡΠ²Π΅ΡΠ΄ΠΈΡΠ΅Π»Π΅ΠΌ ΠΠΠΠ —
Π΅Π³ΠΎ Π½Π΅ΠΎΠ±Ρ ΠΎΠ΄ΠΈΠΌΠΎ 7-8%;
— ΠΏΡΠΈΠΌΠ΅Π½ΡΡ ΡΠ΅ ΠΆΠ΅ ΠΊΠΎΠΌΠΏΠ°ΡΠ½Π΄Ρ Π-115;Π-153;Π-153Π ΠΏΡΠΈ ΡΠ΅ΠΌΠΏΠ΅ΡΠ°ΡΡΡΠ΅ +2 Π΄ΠΎ +18Β°Π‘Β Ρ ΠΎΡΠ²Π΅Ρ-
Π΄ΠΈΡΠ΅Π»Π΅ Π£Π-583Π ΠΏΠΎΡΠ»Π΅Π΄Π½Π΅Π³ΠΎ Π½ΡΠΆΠ½ΠΎ 15-16%;
ΠΡΠΈΠΌΠ΅ΡΠ°Π½ΠΈΠ΅: ΡΠ΅ΠΌ Π½ΠΈΠΆΠ΅ ΡΠ΅ΠΌΠΏΠ΅ΡΠ°ΡΡΡΠ° ΠΏΡΠΈ ΠΊΠΎΡΠΎΡΠΎΠΉ Π²Ρ ΡΠ°Π±ΠΎΡΠ°Π΅ΡΠ΅ Ρ ΡΠΏΠΎΠΊΡΠΈΠ΄Π½ΡΠΌΠΈ ΡΠΌΠΎΠ»Π°ΠΌΠΈ,
ΡΠ΅ΠΌ Π±ΠΎΠ»ΡΡΠ΅ Π½Π΅ΠΎΠ±Ρ ΠΎΠ΄ΠΈΠΌΠΎ Π΄ΠΎΠ±Π°Π²Π»ΡΡΡ ΠΎΡΠ²Π΅ΡΠ΄ΠΈΡΠ΅Π»Ρ.
— Π³ΠΎΡΠΎΠ²ΠΎΠ΅ ΠΈΠ·Π΄Π΅Π»ΠΈΠ΅, ΠΊΠΎΡΠΎΡΠΎΠ΅ Π±ΡΠ΄Π΅Ρ ΡΠΊΡΠΏΠ»ΡΠ°ΡΠΈΡΠΎΠ²Π°ΡΡΡΡ ΠΏΡΠΈ ΡΠ΅ΠΌΠΏΠ΅ΡΠ°ΡΡΡΠ΅ +90;+100Β°Π‘, ΠΈΡΠΏΠΎΠ»ΡΠ·ΡΡ ΠΠ-20 Ρ ΠΠΠΠ (ΠΎΠ±ΡΡΠ½ΠΎ ΠΎΡΠ²Π΅ΡΠ΄ΠΈΡΠ΅Π»Ρ 10%), ΠΈΠ·Π΄Π΅Π»ΠΈΠ΅ Π±ΡΠ΄Π΅Ρ ΡΠ°Π·ΠΌΡΠ³ΡΠ°ΡΡΡΡ,ΡΡΠ°Π½ΠΎΠ²ΡΡΡ Π½Π΅ΡΠΊΠΎΠ»ΡΠΊΠΎ ΡΠ»Π°ΡΡΠΈΡΠ½ΡΠΌ, Π½ΠΎ ΠΏΡΠΈ ΡΡΠΎΠΌ ΠΏΠΎΠ»Π½ΠΎΡΡΡΡ ΡΠΎΡ ΡΠ°Π½ΠΈΡ ΡΠ²ΠΎΠΈ ΡΠ²ΠΎΠΉΡΡΠ²Π°;
— ΠΏΡΠΈ ΡΠ΅Ρ ΠΆΠ΅ +100Β°Π‘ ΠΈΠ·Π΄Π΅Π»ΠΈΠ΅ ΠΎΡΡΠ°Π½Π΅ΡΡΡ ΠΆΠ΅ΡΠΊΠΈΠΌ (ΡΠ°Π·ΠΌΡΠ³ΡΠ°ΡΡΡΡ Π½Π΅ Π±ΡΠ΄Π΅Ρ) Ρ ΠΈΡΠΏΠΎΠ»ΡΠ·ΠΎΠ²Π°Π½ΠΈΠ΅ΠΌ ΠΎΡΠ²Π΅ΡΠ΄ΠΈΡΠ΅Π»Ρ Π£Π-583;Π£Π-583Π Ρ ΠΏΡΠΎΠΏΠΎΡΡΠΈΠ΅ΠΉ 16% ΠΎΡ Π²Π΅ΡΠ° ΡΠΌΠΎΠ»Ρ;
— Π£Π-583;Π£Π-583Π — 20% ΠΊ ΠΠ-20, ΠΏΡΠΈ 100Β°Π‘ β ΠΏΠΎΠ²Π΅ΡΡ Π½ΠΎΡΡΡ ΠΆΠ΅ΡΠΊΠ°Ρ;
— ΠΊΠΎΠΌΠΏΠ°ΡΠ½Π΄Ρ Π-115; Π-153; Π-153Π Ρ ΠΈΡΠΏΠΎΠ»ΡΠ·ΠΎΠ²Π°Π½ΠΈΠ΅ΠΌ Π£Π-583; Π£Π-583Π (16%), ΠΏΠΎΠ²Π΅ΡΡ Π½ΠΎΡΡΡ ΠΆΠ΅ΡΠΊΠ°Ρ;
— ΡΠΏΠΎΠΊΡΠΈΠ΄Π½ΡΠ΅ ΡΠΌΠΎΠ»Ρ ΠΈΠΌΠΏΠΎΡΡΠ½ΠΎΠ³ΠΎ ΠΏΡΠΎΠΈΠ·Π²ΠΎΠ΄ΡΡΠ²Π°, Π·Π°ΠΌΠ΅ΡΠΈΠ²Π°ΡΡ Ρ ΠΠΠΠ (13%), ΠΏΡΠΈ ΠΎΠΏΡΠΈΠΌΠ°Π»ΡΠ½ΠΎΠΉ ΠΊΠΎΠΌΠ½Π°ΡΠ½ΠΎΠΉ ΡΠ΅ΠΌΠΏΠ΅ΡΠ°ΡΡΡΠ΅ 22-24Β°Π‘;
— ΡΠΏΠΎΠΊΡΠΈΠ΄Π½ΡΠ΅ ΡΠΌΠΎΠ»Ρ ΠΈΠΌΠΏΠΎΡΡΠ½ΠΎΠ³ΠΎ ΠΏΡΠΎΠΈΠ·Π²ΠΎΠ΄ΡΡΠ²Π°, ΠΏΡΠΈΠΌΠ΅Π½ΡΡ ΠΎΡΠ²Π΅ΡΠ΄ΠΈΡΠ΅Π»ΠΈ Π£Π-583; Π£Π-583Π — Β (22-25%), ΠΏΡΠΈ ΡΠ΅Ρ ΠΆΠ΅ 22-24Β°Π‘;
Β Β ΠΡΠΈΠΌΠ΅ΡΠ°Π½ΠΈΠ΅: Β ΠΈΠ·Π΄Π΅Π»ΠΈΡ, ΠΊΠΎΡΠΎΡΡΠ΅ Π±ΡΠ΄ΡΡ ΡΠΊΡΠΏΠ»ΡΠ°ΡΠΈΡΠΎΠ²Π°ΡΡΡΡ ΠΏΡΠΈ ΡΠ΅ΠΌΠΏΠ΅ΡΠ°ΡΡΡΠ°Ρ +90; +100Β°Π‘,
ΠΈΠ·Π³ΠΎΡΠΎΠ²Π»Π΅Π½Π½ΡΠ΅ Ρ ΠΈΡΠΏΠΎΠ»ΡΠ·ΠΎΠ²Π°Π½ΠΈΠ΅ΠΌ ΡΠΏΠΎΠΊΡΠΈΠ΄Π½ΡΡ ΡΠΌΠΎΠ» ΠΈΠΌΠΏΠΎΡΡΠ½ΠΎΠ³ΠΎ ΠΏΡΠΎΠΈΠ·Π²ΠΎΠ΄ΡΡΠ²Π° Π±ΡΠ΄ΡΡ Π²Π΅ΡΡΠΈ ΡΠ΅Π±Ρ ΠΏΡΠΈΠ±Π»ΠΈΠ·ΠΈΡΠ΅Π»ΡΠ½ΠΎ ΡΠ°ΠΊ ΠΆΠ΅, ΠΊΠ°ΠΊ ΠΈ Ρ ΠΠ-20.Β Β
Β 14). ΠΡΠ»ΠΈ ΡΠΏΠΎΠΊΡΠΈΠ΄Π½Π°Ρ ΡΠΌΠΎΠ»Π° Π΄ΠΎΠ»Π³ΠΎ Ρ ΡΠ°Π½ΠΈΠ»Π°ΡΡ, ΠΏΠ΅ΡΠ΅Π΄ Π½Π°ΡΠ°Π»ΠΎΠΌ ΡΠ°Π±ΠΎΡ ΡΠ±Π΅Π΄ΠΈΡΠ΅ΡΡ, ΡΡΠΎ ΡΠΌΠΎΠ»Π° Π½Π΅ ΠΊΡΠΈΡΡΠ°Π»ΠΈΠ·ΠΈΡΠΎΠ²Π°Π»Π°ΡΡ, ΡΡΠΎ ΠΎΠ½Π° ΠΏΠΎΡΠΎΠ·ΡΠ°ΡΠ½Π°Ρ, Π½Π΅ ΠΌΡΡΠ½Π°Ρ, Π² ΠΏΡΠΎΡΠΈΠ²Π½ΠΎΠΌ ΡΠ»ΡΡΠ°Π΅ ΠΏΠΎΠΏΡΡΠ°ΠΉΡΠ΅ΡΡ Π½Π°Π³ΡΠ΅Π²Π°Π½ΠΈΠ΅ΠΌ Π΄ΠΎ 40-50Β°Π‘ Ρ ΠΈΠ½ΡΠ΅Π½ΡΠΈΠ²Π½ΡΠΌ ΠΏΠ΅ΡΠ΅ΠΌΠ΅ΡΠΈΠ²Π°Π½ΠΈΠ΅ΠΌ Π²Π΅ΡΠ½ΡΡΡ Π΅Π΅ Π² ΠΏΡΠΎΠ·ΡΠ°ΡΠ½ΠΎΠ΅ ΡΠΎΡΡΠΎΡΠ½ΠΈΠ΅.
Β 15). ΠΡΠ»ΠΈ ΠΈΠ·Π³ΠΎΡΠ°Π²Π»ΠΈΠ²Π°Π΅ΡΡΡ ΠΈΠ·Π΄Π΅Π»ΠΈΠ΅ Ρ Π΄ΠΎΡΡΠ°ΡΠΎΡΠ½ΠΎ ΡΠΎΠ»ΡΡΡΠΌ ΡΠ»ΠΎΠ΅ΠΌ Ρ ΡΠΏΠΎΠΊΡΠΈΠ΄Π½ΠΎΠΉ ΡΠΌΠΎΠ»Ρ, ΡΠΎ ΠΌΠ°ΡΠ΅ΡΠΈΠ°Π» Π½Π°ΠΊΠ»Π°Π΄ΡΠ²Π°Π΅ΡΡΡ ΡΠ»ΠΎΡΠΌΠΈ, Π΄ΠΎΠΆΠΈΠ΄Π°ΡΡΡ ΠΏΠ΅ΡΠ²ΠΈΡΠ½ΠΎΠΉ ΠΏΠΎΠ»ΠΈΠΌΠ΅ΡΠΈΠ·Π°ΡΠΈΠΈ ΠΏΡΠ΅Π΄ΡΠ΄ΡΡΠ΅Π³ΠΎ ΡΠ»ΠΎΡ ΠΏΠ΅ΡΠ΅Π΄ Π½Π°Π½Π΅ΡΠ΅Π½ΠΈΠ΅ΠΌ ΡΠ»Π΅Π΄ΡΡΡΠ΅Π³ΠΎ.
Β 16). ΠΡΠ»ΠΈΠ²Π°Ρ ΡΠΏΠΎΠΊΡΠΈΠ΄Π½ΡΡ ΡΠΌΠΎΠ»Ρ Π² ΡΠΎΡΠΌΡ, Π΄Π»Ρ ΠΎΠ±Π»Π΅Π³ΡΠ΅Π½ΠΈΡ Π²ΠΎΠ·ΠΌΠΎΠΆΠ½ΠΎΡΡΠΈ ΠΎΡΠ΄Π΅Π»Π΅Π½ΠΈΡ Π³ΠΎΡΠΎΠ²ΠΎΠ³ΠΎ ΠΈΠ·Π΄Π΅Π»ΠΈΡ ΠΎΡ ΡΠΎΡΠΌΡ, ΡΠΎΡΠΌΠ° ΡΠ»Π°Π·ΡΠ²Π°Π΅ΡΡΡ ΠΆΠΈΡΠΎΠΌ, Π½Π°ΠΏΡΠΈΠΌΠ΅Ρ — ΡΠ΅Ρ Π½ΠΈΡΠ΅ΡΠΊΠΈΠΌ Π²Π°Π·Π΅Π»ΠΈΠ½ΠΎΠΌ.
Β Β ΠΠΏΠΎΠΊΡΠΈΠ΄ΠΊΠ° ΠΎΡΠ΅Π½Ρ ΠΏΠ»ΠΎΡ ΠΎ ΠΏΡΠΈΡΡΠ°Π΅Ρ ΠΊ ΡΠ°ΠΊΠΈΠΌ Π²Π΅ΡΠ΅ΡΡΠ²Π°ΠΌ, ΠΊΠ°ΠΊ ΠΏΠΎΠ»ΠΈΡΡΠΈΠ»Π΅Π½, ΠΏΠΎΠ»ΠΈΡΡΠΈΡΠΎΠ», ΠΎΡΠ³ΡΡΠ΅ΠΊΠ»ΠΎ, ΡΡΠΎΡΠΎΠΏΠ»Π°ΡΡ ΠΈ Ρ.Π΄., Π° Π΅ΡΠ»ΠΈ Π½Π° ΡΡΠΈ ΠΌΠ°ΡΠ΅ΡΠΈΠ°Π»Ρ Π΅ΡΠ΅ ΠΈ Π½Π°Π½Π΅ΡΡΠΈ Π·Π°ΡΠΈΡΠ½ΡΠΉ ΡΠ»ΠΎΠΉ (Π½Π°ΠΏΡΠΈΠΌΠ΅Ρ ΠΈΠ· ΠΌΠ°ΡΡΠΈΠΊΠΈ Π΄Π»Ρ ΠΏΠ°ΡΠΊΠ΅ΡΠ° ΠΈΠ»ΠΈ ΡΠΎΡ ΠΆΠ΅ ΡΠ΅Ρ Π½ΠΈΡΠ΅ΡΠΊΠΈΠΉ Π²Π°Π·Π΅Π»ΠΈΠ½), ΡΠΎ ΠΏΠΎΡΠ»Π΅ ΠΏΠΎΠ»ΠΈΠΌΠ΅ΡΠΈΠ·Π°ΡΠΈΠΈ ΡΠΏΠΎΠΊΡΠΈΠ΄ΠΊΠ° Π»Π΅Π³ΠΊΠΎ ΠΎΡ Π½ΠΈΡ ΠΎΡΠ΄Π΅Π»ΡΠ΅ΡΡΡ. ΠΡΠ»ΠΈΡΠΎΠ΅ ΠΈΠ·Π΄Π΅Π»ΠΈΠ΅ Π² Π΄Π°Π»ΡΠ½Π΅ΠΉΡΠ΅ΠΌ ΠΌΠΎΠΆΠ½ΠΎ ΠΏΠΎΠ΄Π²Π΅ΡΠ³Π°ΡΡ ΠΌΠ΅Ρ Π°Π½ΠΈΡΠ΅ΡΠΊΠΎΠΉ ΠΎΠ±ΡΠ°Π±ΠΎΡΠΊΠ΅.
Β 17). ΠΠ΅ΡΠ΅ΡΡΠ΅Ρ Β«ΠΏΠΎΠΊΠ°Π·Π°ΡΠ΅Π»Ρ ΡΠΏΠΎΠΊΡΠΈΠ΄Π½Π½ΠΎΠ³ΠΎ ΡΠΊΠ²ΠΈΠ²Π°Π»Π΅Π½ΡΠ½ΠΎΠ³ΠΎ Π²Π΅ΡΠ°Β» (Π³/ΡΠΊΠ²), ΠΊΠΎΡΠΎΡΡΠΉ ΡΠΊΠ°Π·ΡΠ²Π°Π΅ΡΡΡ Π² ΡΠ΅Ρ Π½ΠΈΡΠ΅ΡΠΊΠΈΡ Ρ Π°ΡΠ°ΠΊΡΠ΅ΡΠΈΡΡΠΈΠΊΠ°Ρ ΡΠΏΠΎΠΊΡΠΈΠ΄Π½ΡΡ ΡΠΌΠΎΠ» ΠΈΠΌΠΏΠΎΡΡΠ½ΠΎΠ³ΠΎ ΠΏΡΠΎΠΈΠ·Π²ΠΎΠ΄ΡΡΠ²Π°, Π² ΠΏΡΠΈΠ²ΡΡΠ½ΡΠΉ Π΄Π»Ρ Π½Π°Ρ ΠΏΠΎΠΊΠ°Π·Π°ΡΠ΅Π»Ρ β Β«ΠΌΠ°ΡΡΠΎΠ²ΡΡ Π΄ΠΎΠ»Ρ ΡΠΏΠΎΠΊΡΠΈΠ΄Π½ΡΡ Π³ΡΡΠΏΠΏΒ» Π² %,
Β y = 43 / x * 100 , Π³Π΄Π΅
Β y β ΠΌΠ°ΡΡΠΎΠ²Π°Ρ Π΄ΠΎΠ»Ρ ΡΠΏΠΎΠΊΡΠΈΠ΄Π½ΡΡ Π³ΡΡΠΏΠΏ, Π² %
Β x β ΡΠΏΠΎΠΊΡΠΈΠ΄Π½ΡΠΉ Π²Π΅Ρ, Π³/ΡΠΊΠ²,
Β ΠΠ°ΠΏΡΠΈΠΌΠ΅Ρ, Π΅ΡΠ»ΠΈ Π² ΠΏΠ°ΡΠΏΠΎΡΡΠ΅ ΡΠΏΠΎΠΊΡΠΈΠ΄Π½ΠΎΠΉ ΡΠΌΠΎΠ»Ρ ΠΈΠΌΠΏΠΎΡΡΠ½ΠΎΠ³ΠΎ ΠΏΡΠΎΠΈΠ·Π²ΠΎΠ΄ΡΡΠ²Π° Β«ΡΠΏΠΎΠΊΡΠΈΠ΄Π½ΡΠΉ ΡΠΊΠ²ΠΈΠ²Π°Π»Π΅Π½ΡΠ½ΡΠΉ Π²Π΅ΡΒ» Π½Π°Ρ ΠΎΠ΄ΠΈΡΡΡ Π² ΠΏΡΠ΅Π΄Π΅Π»Π°Ρ 186-192, ΡΠΎ Π² ΠΏΠ΅ΡΠ΅ΡΡΠ΅ΡΠ΅, ΡΠΎΠ³Π»Π°ΡΠ½ΠΎ ΡΠΎΡΠΌΡΠ»Ρ, Β«ΠΌΠ°ΡΡΠΎΠ²Π°Ρ Π΄ΠΎΠ»Ρ ΡΠΏΠΎΠΊΡΠΈΠ΄Π½ΡΡ Π³ΡΡΠΏΠΏΒ» ΡΠΎΡΡΠ°Π²ΠΈΡ 22,39-23,11 %.
Β 18). ΠΠ΅ΡΠ΅ΡΡΠ΅Ρ ΠΏΠΎΠΊΠ°Π·Π°ΡΠ΅Π»Ρ Β«ΡΠΎΠ΄Π΅ΡΠΆΠ°Π½ΠΈΠ΅ ΡΠΏΠΎΠΊΡΠΈΠ΄Π½ΡΡ Π³ΡΡΠΏΠΏΒ» (ΠΌΠΌΠΎΠ»Ρ/ΠΊΠ³), Π² ΠΏΠΎΠΊΠ°Π·Π°ΡΠ΅Π»Ρ Β«ΠΌΠ°ΡΡΠΎΠ²Π°Ρ Π΄ΠΎΠ»Ρ ΡΠΏΠΎΠΊΡΠΈΠ΄Π½ΡΡ Π³ΡΡΠΏΠΏΒ» Π² %,
Β y = x * 43 / 10000, Π³Π΄Π΅
Β y β ΠΌΠ°ΡΡΠΎΠ²Π°Ρ Π΄ΠΎΠ»Ρ ΡΠΏΠΎΠΊΡΠΈΠ΄Π½ΡΡ Π³ΡΡΠΏΠΏ, Π² %
Β x β ΡΠΎΠ΄Π΅ΡΠΆΠ°Π½ΠΈΠ΅ ΡΠΏΠΎΠΊΡΠΈΠ΄Π½ΡΡ Π³ΡΡΠΏΠΏ, ΠΌΠΌΠΎΠ»Ρ/ΠΊΠ³,
Β ΠΠ°ΠΏΡΠΈΠΌΠ΅Ρ, Π΅ΡΠ»ΠΈ Π² ΠΏΠ°ΡΠΏΠΎΡΡΠ΅ ΡΠΏΠΎΠΊΡΠΈΠ΄Π½ΠΎΠΉ ΡΠΌΠΎΠ»Ρ ΠΈΠΌΠΏΠΎΡΡΠ½ΠΎΠ³ΠΎ ΠΏΡΠΎΠΈΠ·Π²ΠΎΠ΄ΡΡΠ²Π° Β«ΡΠΎΠ΄Π΅ΡΠΆΠ°Π½ΠΈΠ΅ ΡΠΏΠΎΠΊΡΠΈΠ΄Π½ΡΡ Π³ΡΡΠΏΠΏΒ» Π½Π°Ρ ΠΎΠ΄ΠΈΡΡΡ Π² ΠΏΡΠ΅Π΄Π΅Π»Π°Ρ 2000 β 3320 ΠΌΠΌΠΎΠ»Ρ/ΠΊΠ³, ΡΠΎ Π² ΠΏΠ΅ΡΠ΅ΡΡΠ΅ΡΠ΅, ΡΠΎΠ³Π»Π°ΡΠ½ΠΎ ΡΠΎΡΠΌΡΠ»Ρ Β«ΠΌΠ°ΡΡΠΎΠ²Π°Ρ Π΄ΠΎΠ»Ρ ΡΠΏΠΎΠΊΡΠΈΠ΄Π½ΡΡ Π³ΡΡΠΏΠΏΒ» ΡΠΎΡΡΠ°Π²ΠΈΡ 8.6 β 14.2 %
Β 19). ΠΠ΅ΡΠ΅ΡΡΠ΅Ρ ΠΏΠΎΠΊΠ°Π·Π°ΡΠ΅Π»Ρ Β«ΡΠΎΠ΄Π΅ΡΠΆΠ°Π½ΠΈΠ΅ Π³ΠΈΠ΄ΡΠΎΠ»ΠΈΠ·ΠΎΠ²Π°Π½Π½ΠΎΠ³ΠΎ Ρ Π»ΠΎΡΠ° ΠΈΠΎΠ½ΠΎΠ² Β» Π² ppm, ΡΠΊΠ°Π·Π°Π½Π½ΡΠΉ Π² Ρ Π°ΡΠ°ΠΊΡΠ΅ΡΠΈΡΡΠΈΠΊΠ°Ρ ΡΠΏΠΎΠΊΡΠΈΠ΄Π½ΡΡ ΡΠΌΠΎΠ» ΠΈΠΌΠΏΠΎΡΡΠ½ΠΎΠ³ΠΎ ΠΏΡΠΎΠΈΠ·Π²ΠΎΠ΄ΡΡΠ²Π° Π² ΠΏΡΠΈΠ²ΡΡΠ½ΡΠΉ Π΄Π»Ρ Π½Π°Ρ ΠΏΠΎΠΊΠ°Π·Π°ΡΠ΅Π»Ρ Β«ΠΌΠ°ΡΡΠΎΠ²Π°Ρ Π΄ΠΎΠ»Ρ ΠΎΠΌΡΠ»ΡΠ΅ΠΌΠΎΠ³ΠΎ Ρ Π»ΠΎΡΠ°Β» Π² %,
Β y = x / 10000, Π³Π΄Π΅
Β y β ΠΌΠ°ΡΡΠΎΠ²Π°Ρ Π΄ΠΎΠ»Ρ ΠΎΠΌΡΠ»ΡΠ΅ΠΌΠΎΠ³ΠΎ Ρ Π»ΠΎΡΠ° Π² %;
Β x β ΡΠΎΠ΄Π΅ΡΠΆΠ°Π½ΠΈΠ΅ Π³ΠΈΠ΄ΡΠΎΠ»ΠΈΠ·ΠΎΠ²Π°Π½Π½ΠΎΠ³ΠΎ Ρ Π»ΠΎΡΠ° ΠΈΠΎΠ½ΠΎΠ² Π² ppm,
Β ΠΠ°ΠΏΡΠΈΠΌΠ΅Ρ, Π΅ΡΠ»ΠΈ Π² ΠΏΠ°ΡΠΏΠΎΡΡΠ΅ ΡΠΏΠΎΠΊΡΠΈΠ΄Π½ΠΎΠΉ ΡΠΌΠΎΠ»Ρ ΠΈΠΌΠΏΠΎΡΡΠ½ΠΎΠ³ΠΎ ΠΏΡΠΎΠΈΠ·Π²ΠΎΠ΄ΡΡΠ²Π° Β«ΡΠΎΠ΄Π΅ΡΠΆΠ°Π½ΠΈΠ΅ Π³ΠΈΠ΄ΡΠΎΠ»ΠΈΠ·ΠΎΠ²Π°Π½Π½ΠΎΠ³ΠΎ Ρ Π»ΠΎΡΠ° ΠΈΠΎΠ½ΠΎΠ²Β» ΡΠ°Π²Π½ΠΎ 500 ppm, ΡΠΎ Β«ΠΌΠ°ΡΡΠΎΠ²Π°Ρ Π΄ΠΎΠ»Ρ ΠΎΠΌΡΠ»ΡΠ΅ΠΌΠΎΠ³ΠΎ Ρ Π»ΠΎΡΠ°Β» Π±ΡΠ΄Π΅Ρ Π½Π΅ Π±ΠΎΠ»Π΅Π΅ 0,05%.
Β 20). Π‘ΠΎΠΎΡΠ½ΠΎΡΠ΅Π½ΠΈΠ΅ ΠΊΠΎΠ»ΠΈΡΠ΅ΡΡΠ²Π° ΠΎΡΠ²Π΅ΡΠ΄ΠΈΡΠ΅Π»Ρ ΠΊ ΡΠΌΠΎΠ»Π΅.
Β ΠΡΠΏΠΎΠ»ΡΠ·ΡΠΉΡΠ΅ ΡΠ°ΠΊ Π½Π°Π·ΡΠ²Π°Π΅ΠΌΡΠΉ ΡΡΠ΅Ρ ΠΈΠΎΠΌΠ΅ΡΡΠΈΡΠ΅ΡΠΊΠΈΠΉ ΠΊΠΎΡΡΡΠΈΡΠΈΠ΅Π½Ρ (ΠΡ) (Π.Π―.ΠΠΎΡΠΈΠ½ΡΠΊΠΈΠΉ). ΠΡΠΈ ΡΠΌΠ½ΠΎΠΆΠ΅Π½ΠΈΠΈ ΡΠΏΠΎΠΊΡΠΈΠ΄Π½ΠΎΠ³ΠΎ ΡΠΈΡΠ»Π° Π½Π° ΠΊΠΎΡΡΡΠΈΡΠΈΠ΅Π½Ρ (ΠΡ) ΠΏΠΎΠ»ΡΡΠ°Π΅ΠΌ ΠΊΠΎΠ»ΠΈΡΠ΅ΡΡΠ²ΠΎ ΠΎΡΠ²Π΅ΡΠ΄ΠΈΡΠ΅Π»Ρ Π² Π³ΡΠ°ΠΌΠΌΠ°Ρ , Π½Π΅ΠΎΠ±Ρ ΠΎΠ΄ΠΈΠΌΠΎΠ΅ Π΄Π»Ρ ΠΎΡΠ²Π΅ΡΠΆΠ΄Π΅Π½ΠΈΡ 100 Π³ ΡΠΏΠΎΠΊΡΠΈΠ΄Π½ΠΎΠΉ ΡΠΌΠΎΠ»Ρ. ΠΡΠΈΠ²ΠΎΠ΄ΠΈΠΌ ΡΠΈΠΏΠΎΠ²ΡΠ΅ Π²Π΅Π»ΠΈΡΠΈΠ½Ρ ΠΡ Π΄Π»Ρ Π½Π΅ΠΊΠΎΡΠΎΡΡΡ ΡΠΈΡΠΎΠΊΠΎ ΡΠ°ΡΠΏΠΎΡΡΡΠ°Π½Π΅Π½Π½ΡΡ ΠΌΠ°ΡΠΎΠΊ ΠΎΡΠ²Π΅ΡΠ΄ΠΈΡΠ΅Π»Π΅ΠΉ Ρ ΠΎΠ»ΠΎΠ΄Π½ΠΎΠ³ΠΎ ΠΎΡΠ²Π΅ΡΠΆΠ΄Π΅Π½ΠΈΡ: ΠΠΠΠ — 0,65…0,72 Π² Π·Π°Π²ΠΈΡΠΈΠΌΠΎΡΡΠΈ ΠΎΡ ΡΠΎΡΡΠ°Π²Π° ΠΠΠΠ ΠΈ ΡΡΠ»ΠΎΠ²ΠΈΠΉ ΠΎΡΠ²Π΅ΡΠΆΠ΄Π΅Π½ΠΈΡ; ΠΠ-300 — 3,0; ΠΠ€-2 — 0,85; Π£Π-583Π — 0,9; Π£Π-0633Π — 1,0; ΠΠ’Π-2 — 2,77.
Β Π£ΡΠΈΡΡΠ²Π°Ρ Π·Π½Π°ΡΠΈΡΠ΅Π»ΡΠ½ΡΠ΅ ΠΎΡΠΊΠ»ΠΎΠ½Π΅Π½ΠΈΡ ΠΏΠ°ΡΠ°ΠΌΠ΅ΡΡΠΎΠ² ΠΎΡΠ²Π΅ΡΠ΄ΠΈΡΠ΅Π»Π΅ΠΉ ΠΎΡ ΡΡΠ΅Π΄Π½ΠΈΡ Π·Π½Π°ΡΠ΅Π½ΠΈΠΉ, Π²ΠΎ Π²ΡΠ΅Ρ ΡΠ»ΡΡΠ°ΡΡ ΡΠ΅ΠΊΠΎΠΌΠ΅Π½Π΄ΡΠ΅ΡΡΡ ΠΏΡΠΎΠ²Π΅Π΄Π΅Π½ΠΈΠ΅ ΡΠ΅Ρ Π½ΠΎΠ»ΠΎΠ³ΠΈΡΠ΅ΡΠΊΠΈΡ ΠΏΡΠΎΠ± ΠΈ ΠΏΡΠΎΠ²Π΅ΡΠΊΠ° Π²ΡΠ΅ΠΌΠ΅Π½ΠΈ ΠΆΠ΅Π»Π°ΡΠΈΠ½ΠΈΠ·Π°ΡΠΈΠΈ ΡΠΌΠ΅ΡΠΈ Π² ΡΡΠ°Π½Π΄Π°ΡΡΠ½ΡΡ ΡΡΠ»ΠΎΠ²ΠΈΡΡ . Π ΠΎΡΠΎΠ±Π΅Π½Π½ΠΎΡΡΠΈ Π΄Π»Ρ ΠΠΠΠ ΡΠ΅ΠΊΠΎΠΌΠ΅Π½Π΄ΡΠ΅ΡΡΡ ΠΏΡΠΎΠ²Π΅ΡΠΊΠ° Π°ΠΌΠΈΠ½Π½ΠΎΠ³ΠΎ ΡΠΈΡΠ»Π° ΠΎΡΠ²Π΅ΡΠ΄ΠΈΡΠ΅Π»Ρ.
21). ΠΡΠΈ Π½Π΅ΠΎΠ±Ρ ΠΎΠ΄ΠΈΠΌΠΎΡΡΠΈ Π² ΡΠΏΠΎΠΊΡΠΈΠ΄Π½ΡΡ ΡΠΌΠΎΠ»Ρ Π΄ΠΎΠ±Π°Π²Π»ΡΡΡ ΡΠ°Π·Π»ΠΈΡΠ½ΡΠ΅ Π½Π°ΠΏΠΎΠ»Π½ΠΈΡΠ΅Π»ΠΈ. ΠΡΠΎ ΠΌΠΎΠΆΠ΅Ρ Π±ΡΡΡ ΠΏΡΠ°ΠΊΡΠΈΡΠ΅ΡΠΊΠΈ Β ΡΡΠΎ ΡΠ³ΠΎΠ΄Π½ΠΎ, Π½ΠΎ ΡΠΎΠ»ΡΠΊΠΎ ΡΡΡ ΠΈΠ΅ Π½Π°ΠΏΠΎΠ»Π½ΠΈΡΠ΅Π»ΠΈ β Π°Π»ΡΠΌΠΈΠ½ΠΈΠ΅Π²ΡΡ ΠΏΡΠ΄ΡΡ,ΠΌΡΠΊΡ,Β ΠΌΠ΅ΡΠ°Π»Π»ΠΈΡΠ΅ΡΠΊΠΈΠ΅ ΠΈ Π΄Π΅ΡΠ΅Π²ΡΠ½Π½ΡΠ΅ ΠΎΠΏΠΈΠ»ΠΊΠΈ, ΡΠ΅ΠΌΠ΅Π½Ρ, Π΄ΠΎ Π²ΡΠ΅Π²ΠΎΠ·ΠΌΠΎΠΆΠ½ΡΡ ΡΡΡ ΠΈΡ ΠΏΠΈΠ³ΠΌΠ΅Π½ΡΠΎΠ², ΠΈ Ρ.Π΄.
Β ΠΠ°ΠΏΠΎΠ»Π½ΠΈΡΠ΅Π»Ρ Π»ΡΡΡΠ΅ Π²Π²ΠΎΠ΄ΠΈΡΡ ΠΏΠΎΡΠ»Π΅ ΡΠΌΠ΅ΡΠΈΠ²Π°Π½ΠΈΡ ΡΠΌΠΎΠ»Ρ Ρ ΠΎΡΠ²Π΅ΡΠ΄ΠΈΡΠ΅Π»Π΅ΠΌ — ΡΠ½ΠΈΠΆΠ°Π΅ΡΡΡ ΡΠΈΡΠΊ Π½Π°ΡΡΡΠ΅Π½ΠΈΡ ΠΏΡΠΎΠΏΠΎΡΡΠΈΠΈ.
22).Β ΠΠ»Ρ ΡΠΌΠ΅Π½ΡΡΠ΅Π½ΠΈΡ Π²ΡΠ·ΠΊΠΎΡΡΠΈ ΡΠΏΠΎΠΊΡΠΈΠ΄Π½ΠΎΠΉ ΡΠΌΠΎΠ»Ρ, Π΅Π΅ ΡΠ°Π·Π±Π°Π²Π»ΡΡΡ ΡΠ°Π·Π»ΠΈΡΠ½ΠΎΠ³ΠΎ ΡΠΎΠ΄Π° ΡΠ°ΡΡΠ²ΠΎΡΠΈΡΠ΅Π»ΡΠΌΠΈ, Π½Π°ΠΏΡΠΈΠΌΠ΅Ρ: Π°ΡΠ΅ΡΠΎΠ½ΠΎΠΌ, ΡΠΏΠΈΡΡΠΎΠΌ, ΡΠ°ΡΡΠ²ΠΎΡΠΈΡΠ΅Π»ΡΠΌΠΈ 646, 650 ΠΈ Ρ.Π΄. ΠΡΠΈ ΡΡΠΎΠΌ
ΡΠ΅ΠΊΠΎΠΌΠ΅Π½Π΄ΡΠ΅ΡΡΡ ΠΈΡ Π²Π²ΠΎΠ΄ΠΈΡΡ Π½Π΅ΠΏΠΎΡΡΠ΅Π΄ΡΡΠ²Π΅Π½Π½ΠΎ ΠΏΠ΅ΡΠ΅Π΄ ΡΠ°ΠΌΠΈΠΌ ΠΈΡΠΏΠΎΠ»ΡΠ·ΠΎΠ²Π°Π½ΠΈΠ΅ΠΌ ΠΈ Π½Π΅ Π±ΠΎΠ»Π΅Π΅ 10% ΠΎΡ ΠΌΠ°ΡΡΡ ΡΠΌΠ΅ΡΠΈ. Π Π°Π·Π±Π°Π²Π»Π΅Π½Π½Π°Ρ ΡΠΏΠΎΠΊΡΠΈΠ΄ΠΊΠ° ΠΏΡΠΈ ΡΡΠΎΠΌ ΠΈΠΌΠ΅Π΅Ρ Π½Π΅Π±ΠΎΠ»ΡΡΡΡ ΡΡΠ°Π΄ΠΊΡ ΠΈ ΡΠ΅ΡΡΠ΅Ρ Π² ΠΈΡΠΎΠ³Π΅ Π²
ΠΏΡΠΎΡΠ½ΠΎΡΡΠΈ, Π° ΠΏΠΎΠ²Π΅ΡΡ Π½ΠΎΡΡΡ ΠΌΠΎΠΆΠ΅Ρ Π±ΡΡΡ ΠΏΠΎΡΠΈΡΡΠΎΠΉ. ΠΡΠΈ ΡΠΎΠ±Π»ΡΠ΄Π΅Π½ΠΈΠΈ ΡΡΠΎΠ³ΠΎ ΠΏΡΠ°Π²ΠΈΠ»Π° (Π½Π΅ Π±ΠΎΠ»Π΅Π΅ 10%), Π΄ΠΎ ΡΠΎΠ³ΠΎ, ΠΊΠ°ΠΊ ΡΠΏΠΎΠΊΡΠΈΠ΄ΠΊΠ° Π²ΡΡΠ°Π½Π΅Ρ, Π²Π΅ΡΡ ΡΠ°ΡΡΠ²ΠΎΡΠΈΡΠ΅Π»Ρ ΠΊ ΡΡΠΎΠΌΡ ΠΌΠΎΠΌΠ΅Π½ΡΡ ΠΈΡΠΏΠ°ΡΠΈΡΡΡ ΠΈ Π² ΠΈΡΠΎΠ³Π΅
Π½Π΅ ΠΏΠΎΡΡΡΠ°Π΄Π°ΡΡ Π΅Π΅ ΡΠ²ΠΎΠΉΡΡΠ²Π°. Β Β
Π ΡΠ°Π±Π»ΠΈΡΠ΅ ΠΏΡΠΈΠ²Π΅Π΄Π΅Π½Ρ ΡΠ΅ΠΊΠΎΠΌΠ΅Π½Π΄ΡΠ΅ΠΌΡΠ΅ ΡΠΎΠΎΡΠ½ΠΎΡΠ΅Π½ΠΈΡ ΠΎΡΠ²Π΅ΡΠ΄ΠΈΡΠ΅Π»Π΅ΠΉ ΠΊ ΡΠΏΠΎΠΊΡΠΈΠ΄Π½ΡΠΌ ΡΠΌΠΎΠ»Π°ΠΌ Π² % ΠΏΡΠΈ ΡΠ΅ΠΌΠΏΠ΅ΡΠ°ΡΡΡΠ΅ 22-24Β°Π‘
Β |
ΠΠΠΠ |
ΠΠΠ’Π |
Π’ΠΠ’Π |
Π£Π-583Π |
Π£Π-0633Π |
Ancamine |
DER-331Β |
13 |
11-14 |
13 |
20-22 |
19-25 |
50-55 |
DER-353Β |
13 |
11-14Β |
13 |
20-22 |
19-25 |
50-55 |
Epikote 828Β |
13 |
11-14Β |
13 |
20-22 |
19-25 |
50-55 |
Epoxy 520 |
13 |
11-14Β |
13 |
20-22 |
19-25 |
50-55 |
Epoxy 525Β |
13 |
11-14Β |
13 |
20-22 |
19-25 |
50-55 |
XZ-92466 |
13 |
11-14Β |
13 |
20-22 |
19-25 |
50-55 |
Π-115Β |
8 |
9-10 |
10 |
16 |
16 |
40-45 |
Π-153 |
8 |
9-10 |
10 |
16 |
16 |
40-45 |
ΠΠ-20 |
10 |
10 |
10 |
20 |
20 |
50 |
ΠΠ-16 |
10 |
10 |
10 |
20 |
20 |
50 |
ΠΠΏΠΈΠ΄ΠΈΠ°Π½-6 |
12 |
11-14Β |
13 |
20-22 |
19-25 |
50-55 |
Π£ΠΠΠ§ΠΒ ΠΒ Π ΠΠΠΠ’Π
dafna.com.ua
Vimas
0 .
Π‘ΠΠΠΠ ΠΠΠΠΠ‘ΠΠΠΠ-ΠΠΠΠΠΠΠΠ― ΠΠ-20/ΠΠ-16
ΠΠΠ‘Π’ 10587-84
Π‘ΠΌΠΎΠ»Π° ΡΠΏΠΎΠΊΡΠΈΠ΄Π½ΠΎ-Π΄ΠΈΠ°Π½ΠΎΠ²Π°Ρ ΠΌΠ°ΡΠΊΠΈ ΠΠ-20/16 ΠΈΡΠΏΠΎΠ»ΡΠ·ΡΠ΅ΡΡΡ Π² ΡΠ°Π΄ΠΈΠΎ-ΡΠ»Π΅ΠΊΡΡΠΎΠ½Π½ΠΎΠΉ, ΡΠ»Π΅ΠΊΡΡΠΎΡΠ΅Ρ Π½ΠΈΡΠ΅ΡΠΊΠΎΠΉ ΠΏΡΠΎΠΌΡΡΠ»Π΅Π½Π½ΠΎΡΡΠΈ, Π°Π²ΠΈΠ°-, ΡΡΠ΄ΠΎ-, ΠΌΠ°ΡΠΈΠ½ΠΎΡΡΡΠΎΠ΅Π½ΠΈΠΈ, Π² ΡΡΡΠΎΠΈΡΠ΅Π»ΡΡΡΠ²Π΅ Π² ΠΊΠ°ΡΠ΅ΡΡΠ²Π΅ ΠΊΠΎΠΌΠΏΠΎΠ½Π΅Π½ΡΠ° Π·Π°Π»ΠΈΠ²ΠΎΡΠ½ΡΡ ΠΈ ΠΏΡΠΎΠΏΠΈΡΠΎΡΠ½ΡΡ ΠΊΠΎΠΌΠΏΠ°ΡΠ½Π΄ΠΎΠ², ΠΊΠ»Π΅Π΅Π², Π³Π΅ΡΠΌΠ΅ΡΠΈΠΊΠΎΠ², ΡΠ²ΡΠ·ΡΡΡΠΈΡ Π΄Π»Ρ Π°ΡΠΌΠΈΡΠΎΠ²Π°Π½Π½ΡΡ ΠΏΠ»Π°ΡΡΠΈΠΊΠΎΠ².
Π€ΠΈΠ·ΠΈΠΊΠΎ-Ρ ΠΈΠΌΠΈΡΠ΅ΡΠΊΠΈΠ΅ Ρ Π°ΡΠ°ΠΊΡΠ΅ΡΠΈΡΡΠΈΠΊΠΈ.Β
Π₯Π°ΡΠ°ΠΊΡΠ΅ΡΠΈΡΡΠΈΠΊΠΈ | ΠΠ-20 | ΠΠ-16 |
ΠΠ½Π΅ΡΠ½ΠΈΠΉ Π²ΠΈΠ΄ | ΠΡΡΠΎΠΊΠΎΠ²ΡΠ·ΠΊΠ°Ρ, ΠΏΡΠΎΠ·ΡΠ°ΡΠ½Π°Ρ Π±Π΅Π· Π²ΠΈΠ΄ΠΈΠΌΡΡ ΠΌΠ΅Ρ Π°Π½ΠΈΡΠ΅ΡΠΊΠΈΡ Π²ΠΊΠ»ΡΡΠ΅Π½ΠΈΠΉ ΠΈ ΡΠ»Π΅Π΄ΠΎΠ² Π²ΠΎΠ΄Ρ | |
Π¦Π²Π΅Ρ ΠΏΠΎ ΠΆΠ΅Π»Π΅Π·ΠΎΠΊΠΎΠ±Π°Π»ΡΡΠΎΠ²ΠΎΠΉ ΡΠΊΠ°Π»Π΅, Π½Π΅ Π±ΠΎΠ»Π΅Π΅ | 4 | 12 |
ΠΠ°ΡΡΠΎΠ²Π°Ρ Π΄ΠΎΠ»Ρ ΡΠΏΠΎΠΊΡΠΈΠ΄Π½ΡΡ Π³ΡΡΠΏΠΏ, % | 19,9 Γ· 22,0 | 19,9 Γ· 22,0 |
ΠΠ°ΡΡΠΎΠ²Π°Ρ Π΄ΠΎΠ»Ρ ΠΈΠΎΠ½Π° Ρ Π»ΠΎΡΠ°, %, Π½Π΅ Π±ΠΎΠ»Π΅Π΅ | 0,003 | 0,006 |
ΠΠ°ΡΡΠΎΠ²Π°Ρ Π΄ΠΎΠ»Ρ ΠΎΠΌΡΠ»ΡΠ΅ΠΌΠΎΠ³ΠΎ Ρ Π»ΠΎΡΠ°, %, Π½Π΅ Π±ΠΎΠ»Π΅Π΅ | 0,5 | 0,9 |
ΠΠ°ΡΡΠΎΠ²Π°Ρ Π΄ΠΎΠ»Ρ Π³ΠΈΠ΄ΡΠΎΠΊΡΠΈΠ»ΡΠ½ΡΡ Π³ΡΡΠΏΠΏ, %, Π½Π΅ Π±ΠΎΠ»Π΅Π΅ | 1,7 | — |
ΠΠ°ΡΡΠΎΠ²Π°Ρ Π΄ΠΎΠ»Ρ Π»Π΅ΡΡΡΠΈΡ Π²Π΅ΡΠ΅ΡΡΠ², %, Π½Π΅ Π±ΠΎΠ»Π΅Π΅ | 0,5 | 0,9 |
ΠΠΈΠ½Π°ΠΌΠΈΡΠ΅ΡΠΊΠ°Ρ Π²ΡΠ·ΠΊΠΎΡΡΡ, ΠΠ°’Π‘, ΠΏΡΠΈ 25Β°Π‘ | 12 Γ·18 | 12 Γ· 25 |
ΠΡΠ΅ΠΌΡ ΠΆΠ΅Π»Π°ΡΠΈΠ½ΠΈΠ·Π°ΡΠΈΠΈ Ρ ΠΎΡΠ²Π΅ΡΠ΄ΠΈΡΠ΅Π»Π΅ΠΌ, ΡΠ°Ρ, Π½Π΅ ΠΌΠ΅Π½Π΅Π΅ | 5,0 | 4,0 |
Β ΠΠ΅ΡΡ ΠΏΡΠ΅Π΄ΠΎΡΡΠΎΡΠΎΠΆΠ½ΠΎΡΡΠΈ.
- Π Π°Π±ΠΎΡΠ°ΡΡΠΈΠ΅ Ρ ΡΠΏΠΎΠΊΡΠΈΠ΄Π½ΡΠΌΠΈ ΡΠΌΠΎΠ»Π°ΠΌΠΈ Π΄ΠΎΠ»ΠΆΠ½Ρ Π±ΡΡΡ ΠΎΠ±Π΅ΡΠΏΠ΅ΡΠ΅Π½Ρ ΡΠΏΠ΅ΡΠΎΠ΄Π΅ΠΆΠ΄ΠΎΠΉ ΠΈ ΠΈΠ½Π΄ΠΈΠ²ΠΈΠ΄ΡΠ°Π»ΡΠ½ΡΠΌΠΈ ΡΡΠ΅Π΄ΡΡΠ²Π°ΠΌΠΈ Π·Π°ΡΠΈΡΡ (ΡΠ΅Π·ΠΈΠ½ΠΎΠ²ΡΠ΅ ΠΏΠ΅ΡΡΠ°ΡΠΊΠΈ, Π·Π°ΡΠΈΡΠ½ΡΠ΅ ΠΎΡΠΊΠΈ).
- ΠΡΠ΅ ΠΎΠΏΠ΅ΡΠ°ΡΠΈΠΈ ΠΏΡΠΈ ΡΠ°Π±ΠΎΡΠ΅ Ρ ΡΠΏΠΎΠΊΡΠΈΠ΄Π½ΡΠΌΠΈ ΡΠΌΠΎΠ»Π°ΠΌΠΈ Π΄ΠΎΠ»ΠΆΠ½Ρ ΠΏΡΠΎΠ²ΠΎΠ΄ΠΈΡΡΡΡ Π² ΠΏΠΎΠΌΠ΅ΡΠ΅Π½ΠΈΡΡ , ΠΎΠ±ΠΎΡΡΠ΄ΠΎΠ²Π°Π½Π½ΡΡ ΠΏΡΠΈΡΠΎΡΠ½ΠΎ-Π²ΡΡΡΠΆΠ½ΠΎΠΉ Π²Π΅Π½ΡΠΈΠ»ΡΡΠΈΠ΅ΠΉ.
Π£ΠΏΠ°ΠΊΠΎΠ²ΠΊΠ°.
Π‘ΠΌΠΎΠ»Π° ΡΠΏΠΎΠΊΡΠΈΠ΄Π½ΠΎ-Π΄ΠΈΠ°Π½ΠΎΠ²Π°Ρ ΡΠΏΠ°ΠΊΠΎΠ²Π°Π½Π° Π² ΠΌΠ΅ΡΠ°Π»Π»ΠΈΡΠ΅ΡΠΊΠΈΠ΅ Π±Π°ΡΠ°Π±Π°Π½Ρ. ΠΠ°ΡΡΠ° Π½Π΅ΡΡΠΎ Π΅Π΄ΠΈΠ½ΠΈΡΡ ΠΏΡΠΎΠ΄ΡΠΊΡΠΈΠΈ 50-60ΠΊΠ³.
Π₯ΡΠ°Π½Π΅Π½ΠΈΠ΅.
- ΠΠΏΠΎΠΊΡΠΈΠ΄Π½ΠΎ-Π΄ΠΈΠ°Π½ΠΎΠ²ΡΡ ΡΠΌΠΎΠ»Ρ Ρ ΡΠ°Π½ΡΡ Π² ΠΏΠ»ΠΎΡΠ½ΠΎ Π·Π°ΠΊΡΡΡΠΎΠΉ ΡΠ°ΡΠ΅ Π² Π·Π°ΠΊΡΡΡΡΡ ΡΠΊΠ»Π°Π΄ΡΠΊΠΈΡ ΠΏΠΎΠΌΠ΅ΡΠ΅Π½ΠΈΡΡ ΠΏΡΠΈ ΡΠ΅ΠΌΠΏΠ΅ΡΠ°ΡΡΡΠ΅ Π½Π΅ Π²ΡΡΠ΅ 40Β°Π‘.
- ΠΠ°ΡΠ°Π½ΡΠΈΠΉΠ½ΡΠΉ ΡΡΠΎΠΊ Ρ ΡΠ°Π½Π΅Π½ΠΈΡ 1,5 Π³ΠΎΠ΄Π° Ρ Π΄Π°ΡΡ ΠΈΠ·Π³ΠΎΡΠΎΠ²Π»Π΅Π½ΠΈΡ.
Π’ΠΠ₯ΠΠΠΠΠΠΠ― ΠΠ ΠΠΠΠΠΠΠΠ―:
- ΠΠ΅ΡΠ΅Π΄ ΠΈΡΠΏΠΎΠ»ΡΠ·ΠΎΠ²Π°Π½ΠΈΠ΅ΠΌ ΡΠΌΠΎΠ»Ρ Π½Π΅ΠΎΠ±Ρ ΠΎΠ΄ΠΈΠΌΠΎ ΠΏΠΎΠ΄Π³ΠΎΡΠΎΠ²ΠΈΡΡ ΠΏΠΎΠ²Π΅ΡΡ Π½ΠΎΡΡΡ ΠΈΠ»ΠΈ ΠΌΠ°ΡΡΠΈΡΡ ΠΈ Π½Π°Π½Π΅ΡΡΠΈ ΡΠ°Π·Π΄Π΅Π»ΠΈΡΠ΅Π»ΡΠ½ΡΠΉ ΡΠΎΡΡΠ°Π².
- ΠΠΎΡΠ»Π΅ ΡΠΌΠ΅ΡΠΈΠ²Π°Π½ΠΈΡ ΡΠΌΠΎΠ»Ρ Ρ ΠΎΡΠ²Π΅ΡΠ΄ΠΈΡΠ΅Π»Π΅ΠΌ Π½Π°ΡΠΈΠ½Π°Π΅ΡΡΡ Π½Π΅ΠΎΠ±ΡΠ°ΡΠΈΠΌΡΠΉ ΠΏΡΠΎΡΠ΅ΡΡ ΠΎΡΠ²Π΅ΡΠΆΠ΄Π΅Π½ΠΈΡ
- ΠΠΎΠΌΠΏΠ΅ΠΊΡΠ°ΡΠΈΡ:
- ΠΠ° 100 ΠΌΠ°ΡΡΠΎΠ²ΡΡ
ΡΠ°ΡΡΠ΅ΠΉ ΡΠΌΠΎΠ»Ρ 6-10 ΠΌΠ°ΡΡΠΎΠ²ΡΡ
ΡΠ°ΡΡΠ΅ΠΉ ΠΎΡΠ²Π΅ΡΠ΄ΠΈΡΠ΅Π»Ρ (ΠΠΠΠ, Π-4, Π’ΠΠ’Π).
- ΠΠ΅ΡΠ΅ΠΌΠ΅ΡΠΈΠ²Π°Π½ΠΈΠ΅ ΡΠΌΠΎΠ»Ρ Ρ ΠΊΠΎΠΌΠΏΠΎΠ½Π΅Π½ΡΠ°ΠΌΠΈ ΡΠ»Π΅Π΄ΡΠ΅Ρ ΠΏΡΠΎΠ²ΠΎΠ΄ΠΈΡΡ ΡΠ°ΠΊ, ΡΡΠΎΠ±Ρ ΠΈΠ·Π±Π΅ΠΆΠ°ΡΡ ΠΏΠΎΠΏΠ°Π΄Π°Π½ΠΈΡ Π² ΠΌΠ°ΡΡΡ ΠΏΡΠ·ΡΡΡΠΊΠΎΠ² Π²ΠΎΠ·Π΄ΡΡ
Π°.
- ΠΠΏΡΠΈΠΌΠ°Π»ΡΠ½Π°Ρ ΡΠ΅ΠΌΠΏΠ΅ΡΠ°ΡΡΡΠ° ΠΈΡΠΏΠΎΠ»ΡΠ·ΠΎΠ²Π°Π½ΠΈΡ ΡΠΌΠΎΠ»Ρ +20Π‘.
- Π‘ΡΠ΅Π΄Π½ΡΡ ΠΆΠΈΠ·Π½Π΅ΡΠΏΠΎΡΠΎΠ±Π½ΠΎΡΡΡ ΡΠΌΠΎΠ»Ρ ΡΠΎΡΡΠ°Π²Π»ΡΠ΅Ρ 30-90 ΠΌΠΈΠ½ΡΡ Π² Π·Π°Π²ΠΈΡΠΈΠΌΠΎΡΡΠΈ ΠΎΡ ΠΊΠΎΠ»ΠΈΡΠ΅ΡΡΠ²Π° ΠΎΡΠ²Π΅ΡΠ΄ΠΈΡΠ΅Π»Ρ (6-10% ΠΏΠΎ ΠΌΠ°ΡΡΠ΅).
- ΠΡΠΈ Π±ΠΎΠ»Π΅Π΅ ΡΡΠΊΠΎΡΠ΅Π½Π½ΠΎΠΌ ΠΎΡΠ²Π΅ΡΠΆΠ΄Π΅Π½ΠΈΠΈ Π²ΠΎΠ·ΠΌΠΎΠΆΠ΅Π½ ΡΠΈΠ»ΡΠ½ΡΠΉ ΡΠ°Π·ΠΎΠ³ΡΠ΅Π² ΠΈ Π²ΠΏΠΎΡΠ»Π΅Π΄ΡΡΠ²ΠΈΠΈ Π±ΠΎΠ»ΡΡΠ°Ρ ΡΡΠ°Π΄ΠΊΠ°.
- ΠΠΎΠ»Π½ΠΎΠ΅ ΠΎΡΠ²Π΅ΡΠΆΠ΄Π΅Π½ΠΈΠ΅ ΡΠΌΠΎΠ»Ρ ΠΏΡΠΎΠΈΡΡ
ΠΎΠ΄ΠΈΡ Π² ΡΡΠ΅Π΄Π½Π΅ΠΌ Π·Π° 2-5 Π΄Π½Π΅ΠΉ. Π ΡΠ΅ΡΠ΅Π½ΠΈΠ΅ ΠΏΠ΅ΡΠΈΠΎΠ΄Π° ΠΎΡΠ²Π΅ΡΠΆΠ΄Π΅Π½ΠΈΡ ΠΈΠ·Π΄Π΅Π»ΠΈΠ΅ ΡΠΎΡ
ΡΠ°Π½ΡΠ΅Ρ Π½Π΅ΠΊΠΎΡΠΎΡΡΡ ΡΡΠ΅ΠΏΠ΅Π½Ρ Π³ΠΈΠ±ΠΊΠΎΡΡΠΈ.
- ΠΠΏΡΠ΅Π΄Π΅Π»ΠΈΡΡ ΠΏΠΎΠ»Π½ΠΎΠ΅ ΠΎΡΠ²Π΅ΡΠ΄Π΅Π²Π°Π½ΠΈΠ΅ ΡΠΌΠΎΠ»Ρ ΠΌΠΎΠΆΠ½ΠΎ ΠΏΡΠΈ ΠΏΠΎΠΌΠΎΡΠΈ Π°ΡΠ΅ΡΠΎΠ½Π°. ΠΠ΅ΠΎΠ±Ρ
ΠΎΠ΄ΠΈΠΌΠΎ Π²ΡΠ»ΠΈΡΡ Π½Π΅Π±ΠΎΠ»ΡΡΠΎΠ΅ ΠΊΠΎΠ»ΠΈΡΠ΅ΡΡΠ²ΠΎ Π°ΡΠ΅ΡΠΎΠ½Π° Π½Π° ΠΎΡΠ²Π΅ΡΠ΄Π΅Π²ΡΡΡ ΠΏΠΎΠ²Π΅ΡΡ
Π½ΠΎΡΡΡ ΡΠΌΠΎΠ»Ρ ΠΈ ΡΠ°ΡΡΠ΅ΡΠ΅ΡΡ Π΅Π³ΠΎ ΡΡΡΠΏΠΊΠΎΠΉ Π΄ΠΎ ΠΏΠΎΠ»Π½ΠΎΠ³ΠΎ Π²ΡΡΡΡ
Π°Π½ΠΈΡ. Π ΡΠ»ΡΡΠ°Π΅, Π΅ΡΠ»ΠΈ ΠΏΠΎΡΠ»Π΅ Π²ΡΡΡΡ
Π°Π½ΠΈΡ Π°ΡΠ΅ΡΠΎΠ½Π° ΠΏΠΎΠ²Π΅ΡΡ
Π½ΠΎΡΡΡ ΡΡΠ°Π»Π° Π»ΠΈΠΏΠΊΠΎΠΉ β ΠΎΡΠ²Π΅ΡΠΆΠ΄Π΅Π½ΠΈΠ΅ ΡΠΌΠΎΠ»Ρ Π΅ΡΠ΅ Π½Π΅ Π·Π°Π²Π΅ΡΡΠΈΠ»ΠΎΡΡ.
Π‘ΡΠΎΠΈΠΌΠΎΡΡΡ ΡΠΎΠ²Π°ΡΠ° ΠΌΠΎΠΆΠ½ΠΎ ΡΡΠΎΡΠ½ΠΈΡΡΒ Π² ΠΈΠ½Ρ-ΠΌΠ°Π³Π°Π·ΠΈΠ½Π΅Β Β http://krovli100.ru
www.vimas.ru
ΠΡΠΎΠ±Π΅Π½Π½ΠΎΡΡΠΈ, Ρ Π°ΡΠ°ΠΊΡΠ΅ΡΠΈΡΡΠΈΠΊΠΈ ΠΈ ΠΏΡΠ°Π²ΠΈΠ»Π° ΠΏΡΠΈΠΌΠ΅Π½Π΅Π½ΠΈΡ ΡΠΏΠΎΠΊΡΠΈΠ΄Π½ΠΎΠΉ ΡΠΌΠΎΠ»Ρ ΠΌΠ°ΡΠΊΠΈ ΡΠ΄-20 β ΠΠ·ΡΡΠΊΠ°Π½Π½ΡΠΉ ΡΠ΅ΠΌΠΎΠ½Ρ
Π‘ΠΌΠΎΠ»Ρ Π½Π° ΡΠΏΠΎΠΊΡΠΈΠ΄Π½ΠΎΠΉ ΠΎΡΠ½ΠΎΠ²Π΅ β ΠΌΠ½ΠΎΠ³ΠΎΡΠ΅Π»Π΅Π²ΠΎΠΉ ΠΎΠ»ΠΈΠ³ΠΎΠΌΠ΅ΡΠ½ΡΠΉ ΠΌΠ°ΡΠ΅ΡΠΈΠ°Π», ΠΏΡΠΈΠΌΠ΅Π½ΡΡΡΠΈΠΉΡΡ Π΄Π»Ρ ΠΈΠ·Π³ΠΎΡΠΎΠ²Π»Π΅Π½ΠΈΡ ΠΊΠΎΠΌΠΏΠ°ΡΠ½Π΄ΠΎΠ², ΠΊΠΎΠΌΠΏΠΎΠ·ΠΈΡΠΎΠ², Π° Π΅ΡΠ΅ Π΄Π»Ρ Π·Π°Π»ΠΈΠ²ΠΊΠΈ ΠΏΠΎΠ²Π΅ΡΡ Π½ΠΎΡΡΠ΅ΠΉ ΡΠ°Π·Π»ΠΈΡΠ½ΠΎΠ³ΠΎ Ρ Π°ΡΠ°ΠΊΡΠ΅ΡΠ° ΠΈ ΠΈΠ·Π³ΠΎΡΠΎΠ²Π»Π΅Π½ΠΈΡ ΠΊΠ»Π΅Ρ, Π³Π΅ΡΠΌΠ΅ΡΠΈΠΊΠ°. ΠΠ»Π°Π³ΠΎΠ΄Π°ΡΡ ΡΠ½ΠΈΠΊΠ°Π»ΡΠ½ΠΎΠΌΡ ΠΊΠΎΠΌΠ±ΠΈΠ½ΠΈΡΠΎΠ²Π°Π½ΠΈΡ Ρ ΠΎΡΠΎΡΠΈΡ ΡΠ²ΠΎΠΉΡΡΠ² ΡΠΏΠΎΠΊΡΠΈΠ΄ΠΊΠ° ΠΏΡΠΈΠ³ΠΎΠ΄ΠΈΡΡΡ ΠΈ Π² ΠΏΡΠΎΠΌΡΡΠ»Π΅Π½Π½ΠΎΡΡΠΈ, ΠΈ Π² Π±ΡΡΠΎΠ²ΡΡ ΡΠ΅Π»ΡΡ . ΠΠ· Π±ΠΎΠ»ΡΡΠΎΠ³ΠΎ ΡΠ°Π·Π½ΠΎΠΎΠ±ΡΠ°Π·ΠΈΡ ΠΏΡΠΎΠ΄ΡΠΊΡΠΎΠ² Π²ΡΠ΄Π΅Π»ΡΠ΅ΡΡΡ ΡΠΏΠΎΠΊΡΠΈΠ΄ΠΊΠ° ΠΠ-20 β Π½Π΅Π΄ΠΎΡΠΎΠ³ΠΎΠ΅ ΡΡΠ΅Π΄ΡΡΠ²ΠΎ ΠΎΡΠ»ΠΈΡΠ½ΠΎΠ³ΠΎ ΠΊΠ°ΡΠ΅ΡΡΠ²Π°.
Π‘Π²ΠΎΠΉΡΡΠ²Π° ΡΠΌΠΎΠ»Ρ ΠΠ-20 ΠΈ ΠΈΡΠΏΠΎΠ»ΡΠ·ΠΎΠ²Π°Π½ΠΈΠ΅
ΠΠΏΠΎΠΊΡΠΈΠ΄Π½ΠΎ-Π΄ΠΈΠ°Π½ΠΎΠ²Π°Ρ ΡΠΌΠΎΠ»Π° ΠΠ-20 β ΡΠ²Π΅ΡΠΎΠΏΡΠΎΠ·ΡΠ°ΡΠ½Π°Ρ Π²ΡΠ·ΠΊΠ°Ρ ΠΆΠΈΠ΄ΠΊΠΎΡΡΡ ΠΆΡΠ»ΡΠΎΠ³ΠΎ, ΠΊΠΎΡΠΈΡΠ½Π΅Π²Π°ΡΠΎΠ³ΠΎ ΡΠ²Π΅ΡΠ° Π±Π΅Π· ΠΌΠ΅Ρ ΠΏΡΠΈΠΌΠ΅ΡΠ΅ΠΉ, Π²ΠΊΠ»ΡΡΠ΅Π½ΠΈΠΉ. ΠΠ½Π° ΡΠΎΠ±ΠΎΠΉ ΠΏΡΠ΅Π΄ΡΡΠ°Π²Π»ΡΠ΅Ρ ΠΏΠ»Π°Π²ΠΊΠΈΠΉ ΡΠ΅Π°ΠΊΡΠΈΠΎΠ½Π½ΠΎΡΠΏΠΎΡΠΎΠ±Π½ΡΠΉ ΠΏΡΠΎΠ΄ΡΠΊΡ Π½Π° ΠΎΡΠ½ΠΎΠ²Π΅ Π΄ΠΈΡΠ΅Π½ΠΈΠ»ΠΎΠ»ΠΏΡΠΎΠΏΠ°Π½Π° ΠΈ ΡΠΏΠΈΡ Π»ΠΎΡΠ³ΠΈΠ΄ΡΠΈΠ½Π°. ΠΠ·Π³ΠΎΡΠΎΠ²ΠΈΡΠ΅Π»Ρ ΡΠΌΠΎΠ»Ρ ΡΡΠΎΠΉ ΠΌΠ°ΡΠΊΠΈ β Π€ΠΠ ΠΠ°Π²ΠΎΠ΄ ΠΈΠΌ. Π‘Π²Π΅ΡΠ΄Π»ΠΎΠ²Π°, ΡΠ°ΠΊΠΆΠ΅ Π΅Π΅ Π²ΡΠΏΡΡΠΊΠ°Π΅Ρ ΡΡΠ΄ Π΄ΡΡΠ³ΠΈΡ ΠΊΠΎΠΌΠΏΠ°Π½ΠΈΠΉ. Π‘ΡΠ΅Π΄Π½ΡΡ ΠΌΠ½ΠΎΠ³ΠΎΡΠΈΡΠ»Π΅Π½Π½Π°Ρ Π΄ΠΎΠ»Ρ ΡΠΏΠΎΠΊΡΠΈΠ΄Π½ΡΡ Π³ΡΡΠΏΠΏ Π² ΡΠΌΠΎΠ»Π΅ ΡΠ°Π²Π½Π° 20%, ΠΎΡΡΡΠ΄Π° ΠΈ ΠΎΠ±ΠΎΠ·Π½Π°ΡΠ΅Π½ΠΈΠ΅ ΠΌΠ°ΡΠ΅ΡΠΈΠ°Π»Π°.
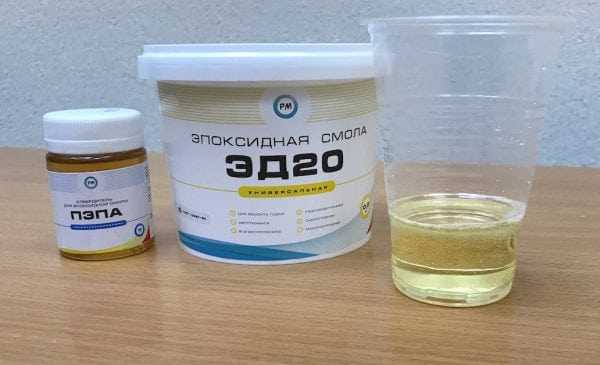
ΠΠ-20 ΡΠΎΡΠ΅ΡΠ°Π΅ΡΡΡ Ρ ΡΠ°Π·Π»ΠΈΡΠ½ΡΠΌΠΈ ΠΎΡΠ²Π΅ΡΠ΄ΠΈΡΠ΅Π»ΡΠΌΠΈ, Π² Π±ΠΎΠ»ΡΡΠΈΠ½ΡΡΠ²Π΅ ΡΠ»ΡΡΠ°Π΅Π² ΡΡΠ΅Π±ΡΠ΅ΡΡΡ Π΄ΠΎΠ±Π°Π²Π»Π΅Π½ΠΈΠ΅ Π²ΠΎΠ΄Π½ΡΡ ΠΈΠ½Π³ΠΈΠ±ΠΈΡΠΎΡΠΎΠ² (ΠΠ»Ρ ΡΠ½ΠΈΠΆΠ΅Π½ΠΈΡ ΠΆΠ΅ΡΡΠΊΠΎΡΡΠΈ Π³ΠΎΡΠΎΠ²ΠΎΠ³ΠΎ ΠΈΠ·Π΄Π΅Π»ΠΈΡ). ΠΡΠ²Π΅ΡΠΆΠ΄Π΅Π½ΠΈΠ΅ Π²ΠΎΠ·ΠΌΠΎΠΆΠ½ΠΎ Ρ ΠΎΠ»ΠΎΠ΄Π½ΡΠΌ ΠΈ Π³ΠΎΡΡΡΠΈΠΌ ΡΠΏΠΎΡΠΎΠ±ΠΎΠΌ (ΠΏΡΠΈ ΠΊΠΎΠΌΠ½Π°ΡΠ½ΠΎΠΉ ΠΈΠ»ΠΈ ΠΎΡΠ΅Π½Ρ Π²ΡΡΠΎΠΊΠΎΠΉ ΡΠ΅ΠΌΠΏΠ΅ΡΠ°ΡΡΡΠ΅), Π΄Π»Ρ Π΄Π°Π½Π½ΠΎΠ³ΠΎ ΠΏΡΠΎΡΠ΅ΡΡΠ° Π½Π΅ ΠΏΠΎΡΡΠ΅Π±ΡΠ΅ΡΡΡ ΠΏΡΠ΅ΡΡΠΎΠ²ΠΎΠ΅ ΠΈ ΡΠ΅ΡΠΌΠΈΡΠ΅ΡΠΊΠΎΠ΅ ΠΎΠ±ΠΎΡΡΠ΄ΠΎΠ²Π°Π½ΠΈΠ΅. Π‘Π²ΠΎΠΉΡΡΠ²Π° ΠΠ-20 ΡΠ°ΠΊΠΈΠ΅:
- Π±ΠΎΠ»ΡΡΠ°Ρ ΠΏΠ»ΠΎΡΠ½ΠΎΡΡΡ, Π±Π΅ΡΠΏΠΎΡΠΈΡΡΠΎΡΡΡ Π³ΠΎΡΠΎΠ²ΠΎΠ³ΠΎ ΠΏΡΠΎΠ΄ΡΠΊΡΠ°;
- Π·Π°ΠΌΠ΅ΡΠ°ΡΠ΅Π»ΡΠ½Π°Ρ ΡΠ²Π΅ΡΠ΄ΠΎΡΡΡ, ΡΡΡΠΎΠΉΡΠΈΠ²ΠΎΡΡΡ ΠΊ ΡΠ΄Π°ΡΠ°ΠΌ ΡΠ°ΡΠ°ΠΏΠΈΠ½Π°ΠΌ ΠΈ ΡΠ°ΠΊ Π΄Π°Π»Π΅Π΅, Π°Π³ΡΠ΅ΡΡΠΈΠ²Π½ΠΎΠΉ ΠΎΠ±ΡΡΠ°Π½ΠΎΠ²ΠΊΠ΅, Π²ΠΎΠ·Π΄Π΅ΠΉΡΡΠ²ΠΈΡ Π²Π»Π°Π³ΠΈ;
- ΡΠ΅ΡΠΌΠΈΡΠ΅ΡΠΊΡΡ ΡΡΡΠΎΠΉΡΠΈΠ²ΠΎΡΡΡ;
- Π΄ΠΈΡΠ»Π΅ΠΊΡΡΠΈΡΠ΅ΡΠΊΠΈΠ΅ ΠΈ ΠΏΡΠΎΡΠΈΠ²ΠΎΠΊΠΎΡΡΠΎΠ·ΠΈΠΎΠ½Π½ΡΠ΅ ΡΠΏΠΎΡΠΎΠ±Π½ΠΎΡΡΠΈ;
- Ρ ΠΎΡΠΎΡΠ°Ρ Π°Π΄Π³Π΅Π·ΠΈΡ Ρ ΠΏΠ»Π°ΡΡΠΈΠΊΠΎΠΌ, ΠΌΠ΅ΡΠ°Π»Π»ΠΎΠΌ, ΡΡΠ΅ΠΊΠ»ΠΎΠΌ, ΠΊΠ΅ΡΠ°ΠΌΠΈΠΊΠΎΠΉ, Π΄Π΅ΡΠ΅Π²ΠΎΠΌ, ΠΊΠ΅Π²Π»Π°ΡΠΎΠΌ, ΡΠ³Π»Π΅Π²ΠΎΠ»ΠΎΠΊΠ½ΠΎΠΌ ΠΈ ΠΏΡΠΎΡΠΈΠΌΠΈ ΠΌΠ°ΡΠ΅ΡΠΈΠ°Π»Π°ΠΌΠΈ;
- ΠΏΡΠΎΡΡΠΎΡΠ° Π² ΡΠ°Π±ΠΎΡΠ΅;
- Π½Π΅Π±ΠΎΠ»ΡΡΠ°Ρ ΡΡΠ°Π΄ΠΊΠ°, Π½Π΅Π²ΡΡΠΎΠΊΠΈΠΉ ΡΠ΄Π΅Π»ΡΠ½ΡΠΉ Π²Π΅Ρ.
ΠΠΏΠΎΠΊΡΠΈΠ΄ΠΊΠ° ΠΈΠΌΠ΅Π΅Ρ Π±ΠΎΠ»ΡΡΠΎΠ΅ ΠΈΡΠΏΠΎΠ»ΡΠ·ΠΎΠ²Π°Π½ΠΈΠ΅ Π² ΡΠ°Π·Π½ΡΡ ΠΎΠ±Π»Π°ΡΡΡΡ Π½Π°ΡΠΎΠ΄Π½ΠΎΠ³ΠΎ Ρ ΠΎΠ·ΡΠΉΡΡΠ²Π°. ΠΠ΅ ΠΈΡΠΏΠΎΠ»ΡΠ·ΡΡΡ Π΄Π»Ρ ΡΠ°Π±ΠΎΡ ΠΏΠΎ ΡΠ΅ΠΌΠΎΠ½ΡΡ ΡΠ΅Ρ Π½ΠΈΠΊΠΈ Π½Π° ΡΠ»Π΅ΠΊΡΡΠΈΡΠ΅ΡΠΊΠΎΠΌ Ρ ΠΎΠ΄Ρ, ΠΊΠΎΠΌΠΏΡΡΡΠ΅ΡΠΎΠ², ΡΠ°Π΄ΠΈΠΎΡΠ»Π΅ΠΊΡΡΠΎΠ½ΠΈΠΊΠΈ, Π΄Π΅ΡΠ°Π»Π΅ΠΉ ΠΈ ΠΊΠΎΡΠΏΡΡΠΎΠ² ΡΡ Ρ, Π»ΠΎΠ΄ΠΎΠΊ, ΠΊΠ°ΡΠ΅ΡΠΎΠ², Π΄Π»Ρ ΠΌΠ΅Π±Π΅Π»ΡΠ½ΡΠ΅ ΠΏΡΠΎΠΈΠ·Π²ΠΎΠ΄ΡΡΠ²Π° β ΡΡΠΎΠ»ΠΎΠ², ΡΡΡΠ»ΡΠ΅Π².
Π‘Β ΠΏΠΎΠΌΠΎΡΡΡ ΠΠ-20 Π΄Π΅Π»Π°ΡΡ ΠΏΡΠ΅ΠΊΡΠ°ΡΠ½ΡΠ΅ ΡΡΠΎΠ»Π΅ΡΠ½ΠΈΡΡ, Π³Π°Π»Π°Π½ΡΠ΅ΡΠ΅Ρ, ΠΈΠ·Π΄Π΅Π»ΠΈΡ Π² Π²Π°Π½Π½ΡΡ ΠΊΠΎΠΌΠ½Π°ΡΡ. ΠΠ°ΡΠ΅ΡΠΈΠ°Π» ΠΏΡΠ΅ΠΊΡΠ°ΡΠ½ΠΎ ΠΏΠΎΠ΄ΠΎΠΉΠ΄Π΅Ρ Π΄Π»Ρ ΡΡΡΠΎΠΈΡΠ΅Π»ΡΡΡΠ²Π°, Π°Π²ΡΠΎΠΌΠΎΠ±ΠΈΠ»Π΅ΡΡΡΠΎΠ΅Π½ΠΈΡ, Π°Π²ΠΈΠ° ΠΏΡΠΎΠΌΡΡΠ»Π΅Π½Π½ΠΎΡΡΠΈ, ΠΏΡΠΈΠ±ΠΎΡΠΎΡΡΡΠΎΠ΅Π½ΠΈΡ. ΠΠ³ΠΎ ΠΏΡΠΈΠΌΠ΅Π½Π΅Π½ΠΈΠ΅ Π΄Π»Ρ ΠΏΠΎΠΊΡΡΡΠΈΡ ΠΏΠΎΠ²Π΅ΡΡ Π½ΠΎΡΡΠΈ ΡΡΠ΅Π½, ΡΠΎΠ·Π΄Π°Π½ΠΈΡ 3D-ΠΏΠΎΠ»ΠΎΠ² ΠΏΠΎΠΌΠΎΠ³Π°Π΅Ρ Π² ΡΠ°ΠΌΡΡ ΠΎΡΠ²Π°ΠΆΠ½ΡΡ ΡΠ΅ΡΠ΅Π½ΠΈΡΡ ΠΎΡ Π΄ΠΈΠ·Π°ΠΉΠ½Π΅ΡΠΎΠ².
ΠΠ-20 Π²Ρ ΠΎΠ΄ΠΈΡ Π² ΡΠΎΡΡΠ°Π² ΡΠ°ΠΌΡΡ ΡΠ°Π·Π½ΡΡ Π»Π°ΠΊΠΎΠΊΡΠ°ΡΠΎΡΠ½ΡΡ ΠΌΠ°ΡΠ΅ΡΠΈΠ°Π»ΠΎΠ² β Π³ΡΡΠ½ΡΠΎΠ²ΠΎΡΠ½ΡΡ ΡΠΌΠ΅ΡΠ΅ΠΉ, ΠΏΡΠΎΠΏΠΈΡΠΎΡΠ½ΡΡ Π»Π°ΠΊΠΎΠ², ΡΠΌΠ°Π»Π΅ΠΉ, Π·Π°Π»ΠΈΠ²ΠΎΡΠ½ΡΡ ΡΠΌΠ΅ΡΠ΅ΠΉ. ΠΠ° ΠΎΡΠ½ΠΎΠ²Π΅ ΡΠΏΠΎΠΊΡΠΈΠ΄ΠΊΠΈ Π΄Π΅Π»Π°ΡΡ Π°ΡΠΌΠΈΡΠΎΠ²Π°Π½Π½ΡΠΉ Π°ΠΊΡΠΈΠ», ΡΡΠ΅ΠΊΠ»ΠΎΠΊΠΎΠΌΠΏΠΎΠ·ΠΈΡ, ΡΡΠ΅ΠΊΠ»ΠΎΠ²ΠΎΠ»ΠΎΠΊΠ½ΠΎ.
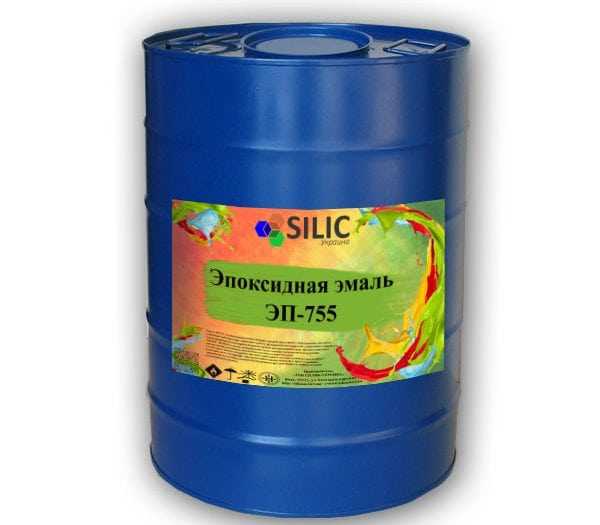
Π’Π΅Ρ ΠΏΠ°ΡΠ°ΠΌΠ΅ΡΡΡ
ΠΡΠ΅ΠΌΡ ΠΆΠ΅Π»Π°ΡΠΈΠ½ΠΈΠ·Π°ΡΠΈΠΈ ΡΠΏΠΎΠΊΡΠΈΠ΄ΠΊΠΈ ΡΠΎΡΡΠ°Π²Π»ΡΠ΅Ρ 8 ΡΠ°ΡΠΎΠ², Π° ΠΏΠ΅ΡΠΈΠΎΠ΄ ΠΏΠΎΠ»Π½ΠΎΠ³ΠΎ ΠΎΡΠ²Π΅ΡΠΆΠ΄Π΅Π½ΠΈΡ ΡΠ°Π²ΡΠ½ 24 ΡΠ°ΡΠ°ΠΌ. Π ΠΎΠΏΠΈΡΠ°Π½ΠΈΠΈ Π²ΡΡΡΠ΅Π³ΠΎ ΡΠΎΡΡΠ° ΠΌΠ°ΡΠ΅ΡΠΈΠ°Π»Π° ΡΠΊΠ°Π·Π°Π½Ρ ΡΠ»Π΅Π΄ΡΡΡΠΈΠ΅ Ρ Π°ΡΠ°ΠΊΡΠ΅ΡΠΈΡΡΠΈΠΊΠΈ Π² ΡΠ΅Ρ Π½ΠΈΡΠ΅ΡΠΊΠΎΠΌ ΠΏΠ»Π°Π½Π΅:
- ΠΏΠ»ΠΎΡΠ½ΠΎΡΡΡ ΠΏΡΠΈ Ρ ΠΎΠ»ΠΎΠ΄Π½ΠΎΠΌ ΠΎΡΠ²Π΅ΡΠΆΠ΄Π΅Π½ΠΈΠΈ β 1110β1230 ΠΊΠ³ ΠΌ3, ΠΏΡΠΈ Π³ΠΎΡΡΡΠ΅ΠΌ ΠΎΡΠ²Π΅ΡΠΆΠ΄Π΅Π½ΠΈΠΈ β 1200β1270;
- ΠΌΠ½ΠΎΠ³ΠΎΡΠΈΡΠ»Π΅Π½Π½Π°Ρ Π΄ΠΎΠ»Ρ ΠΈΠΎΠ½ΠΎΠ² Cl β 0,001%, ΠΎΠΌΡΠ»ΡΠ΅ΠΌΠΎΠ³ΠΎ Ρ Π»ΠΎΡΠ° β 0,3%;
- ΠΌΠ½ΠΎΠ³ΠΎΡΠΈΡΠ»Π΅Π½Π½Π°Ρ Π΄ΠΎΠ»Ρ Π³ΠΈΠ΄ΡΠΎΠΊΡΠΈΠ»ΡΠ½ΡΡ Π³ΡΡΠΏΠΏ β 1,7%, Π»Π΅ΡΡΡΠΈΡ Π²Π΅ΡΠ΅ΡΡΠ² β 0,2%;
- Π²ΡΠ·ΠΊΠΎΡΡΡ Π΄ΠΈΠ½Π°ΠΌΠΈΡΠ΅ΡΠΊΠ°Ρ β 13β20 ΠΠ/ΡΠ΅ΠΊΡΠ½Π΄Ρ;
- ΡΠ΅ΠΆΠΈΠΌ ΡΠ΅ΠΌΠΏΠ΅ΡΠ°ΡΡΡ Π΄Π»Ρ ΡΠ°Π·ΠΌΡΠ³ΡΠ΅Π½ΠΈΡ β Π΄ΠΎ ΡΠ΅ΡΡΠΈΠ΄Π΅ΡΡΡΠΈ Π³ΡΠ°Π΄ΡΡΠΎΠ².
ΠΠ½Π°Π»ΠΎΠ³ΠΈ ΠΌΠ°ΡΠ΅ΡΠΈΠ°Π»Π°
ΠΠΎ Π²Ρ ΠΎΠ΄ΡΡΠΈΠΌ Π² ΡΠΎΡΡΠ°Π² ΠΊΠΎΠΌΠΏΠΎΠ½Π΅Π½ΡΠ°ΠΌ, ΠΎΡΠΎΠ±Π΅Π½Π½ΠΎΡΡΡΠΌ ΠΈ ΠΈΡΠΏΠΎΠ»ΡΠ·ΠΎΠ²Π°Π½ΠΈΡ Π΅ΡΡΡ ΡΡΠ΄ ΠΏΠΎΠ΄ΠΎΠ±Π½ΡΡ ΡΠΌΠΎΠ» Π½Π° ΡΠΏΠΎΠΊΡΠΈΠ΄Π½ΠΎΠΉ ΠΎΡΠ½ΠΎΠ²Π΅ ΠΈΠ· Π³ΡΡΠΏΠΏ ΠΠ, Π’ΠΠ, ΠΠΠ. ΠΡΠ»ΠΈ Π±ΡΠ΄Π΅Ρ Π½Π΅ΠΎΠ±Ρ ΠΎΠ΄ΠΈΠΌΠΎΡΡΡ ΠΈΠΌΠΈ ΠΌΠΎΠΆΠ½ΠΎ ΡΠΌΠ΅Π½ΠΈΡΡ ΠΠ-20. ΠΠΈΠΆΠ΅ ΠΏΠΎΠΊΠ°Π·Π°Π½Ρ ΠΎΡΠ΅Π½Ρ Π·Π½Π°ΠΌΠ΅Π½ΠΈΡΡΠ΅ ΡΠΌΠΎΠ»Ρ.
ΠΠ-8
ΠΠΏΠΎΠΊΡΠΈΠ΄ΠΊΠ° ΠΠ-8 Π²ΡΠΏΠΎΠ»Π½ΡΠ΅ΡΡΡ ΡΠΎΠ³Π»Π°ΡΠ½ΠΎ ΠΠΠ‘Π’ 10587-84. ΠΠ½Π° ΡΠΎΠ±ΠΎΠΉ ΠΏΡΠ΅Π΄ΡΡΠ°Π²Π»ΡΠ΅Ρ ΡΠ°ΡΡΠ²ΠΎΡΠΈΠΌΡΠΉ ΠΏΠ»Π°Π²ΠΊΠΈΠΉ ΠΎΠ»ΠΈΠ³ΠΎΠΌΠ΅ΡΠ½ΡΠΉ ΠΏΡΠΎΠ΄ΡΠΊΡ ΠΈΠ· ΡΠ΅Ρ ΠΆΠ΅ Π²Π΅ΡΠ΅ΡΡΠ², ΡΡΠΎ ΠΈ ΠΠ-20 (Π΄ΠΈΡΠ΅Π½ΠΈΠ»ΠΎΠ»ΠΏΡΠΎΠΏΠ°Π½ ΠΈ ΡΠΏΠΈΡ Π»ΠΎΡΠ³ΠΈΠ΄ΡΠΈΠ½). Π‘ΠΌΠΎΠ»Π° ΠΏΠΎΠ²ΡΠ΅ΠΌΠ΅ΡΡΠ½ΠΎ ΠΈΡΠΏΠΎΠ»ΡΠ·ΡΠ΅ΡΡΡ Π² Π°Π²ΠΈΠ°ΡΠΈΠΎΠ½Π½ΠΎΠΉ, ΡΡΠ΄ΠΎΡΡΡΠΎΠΈΡΠ΅Π»ΡΠ½ΠΎΠΉ, ΠΌΠ°ΡΠΈΠ½ΠΎΡΡΡΠΎΠΈΡΠ΅Π»ΡΠ½ΠΎΠΉ ΠΏΡΠΎΠΌΡΡΠ»Π΅Π½Π½ΠΎΡΡΠΈ, Π² ΠΏΡΠΎΡΠ΅ΡΡΠ΅ ΠΈΠ·Π³ΠΎΡΠΎΠ²Π»Π΅Π½ΠΈΡ Π»Π°ΠΊΠΎΠΊΡΠ°ΡΠΎΡΠ½ΡΡ ΠΌΠ°ΡΠ΅ΡΠΈΠ°Π»ΠΎΠ², Π½Π° ΡΡΡΠΎΠΉΠΊΠ΅, Π² ΡΠ΅ΠΌΠΎΠ½ΡΠ΅ ΡΠ΅Ρ Π½ΠΈΠΊΠΈ, ΡΠ»Π΅ΠΊΡΡΠΎΠ½ΠΈΠΊΠΈ. ΠΠΏΠΎΠΊΡΠΈΠ΄ΠΊΠ° ΡΠ»ΡΠΆΠΈΡ ΠΈ ΠΊΠ°ΠΊ ΡΠ²ΡΠ·ΡΡΡΠΈΠΉ ΡΠ»Π΅ΠΌΠ΅Π½Ρ Π΄Π»Ρ Π°ΡΠΌΠΈΡΠΎΠ²Π°Π½Π½ΡΠΉ Π°ΠΊΡΠΈΠ».
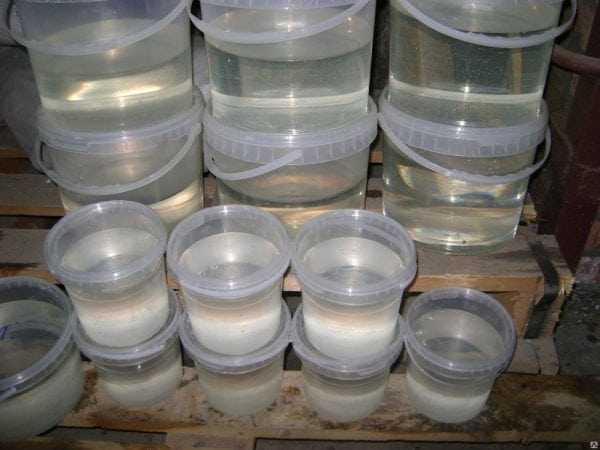
ΠΠΎ ΡΠΈΠ·ΠΈΠΊΠΎ-Ρ ΠΈΠΌΠΈΡΠ΅ΡΠΊΠΈΠΌ ΠΏΠΎΠΊΠ°Π·Π°ΡΠ΅Π»ΡΠΌ ΠΠ-8 ΡΠ°ΠΊΠΆΠ΅ ΠΌΠ°Π»ΠΎ ΡΠ°Π·Π½ΠΈΡΡΡ ΠΎΡ ΠΠ-20. Π‘ΠΎΠ΄Π΅ΡΠΆΠ°Π½ΠΈΠ΅ ΠΈΠΎΠ½ΠΎΠ² Cl ΠΈ ΠΎΠΌΡΠ»ΡΠ΅ΠΌΠΎΠ³ΠΎ Ρ Π»ΠΎΡΠ° ΠΏΠΎΠ΄ΠΎΠ±Π½ΠΎΠ΅, Π·Π°ΡΠΎ Π³ΠΈΠ΄ΡΠΎΠΊΡΠΈΠ»ΡΠ½ΡΠ΅ Π³ΡΡΠΏΠΏΡ Π² ΠΌΠ°ΡΡΠ΅ Π½Π΅ ΠΎΠ±Π½Π°ΡΡΠΆΠΈΠ²Π°ΡΡΡΡ. ΠΡΠ·ΠΊΠΎΡΡΡ ΠΈ ΡΠ΅ΠΌΠΏΠ΅ΡΠ°ΡΡΡΠ° ΡΠ°Π·ΠΌΡΠ³ΡΠ΅Π½ΠΈΡ Π°Π½Π°Π»ΠΎΠ³ΠΈΡΠ½ΡΠ΅. ΠΠ°ΠΆΠ½ΠΎΠ΅ ΠΎΡΠ»ΠΈΡΠΈΠ΅ β Π² ΠΌΠ°ΡΡΠΎΠ²ΠΎΠΉ Π΄ΠΎΠ»Π΅ ΡΠΏΠΎΠΊΡΠΈΠ΄Π½ΡΡ Π³ΡΡΠΏΠΏ (8%) ΠΈ Π²ΡΠ΅ΠΌΠ΅Π½ΠΈ ΠΆΠ΅Π»Π°ΡΠΈΠ½ΠΈΠ·Π°ΡΠΈΠΈ (3 ΡΠ°ΡΠ°).
ΠΠ-16
ΠΠΏΠΎΠΊΡΠΈΠ΄ΠΊΠ° ΠΠ-16 ΠΈΠΌΠ΅Π΅Ρ ΡΠ΅ ΠΆΠ΅ ΠΏΡΠΈΠΌΠ΅Π½Π΅Π½ΠΈΠ΅ ΠΈ ΡΠ²ΠΎΠΉΡΡΠ²Π°, Π½ΠΎ Π²ΠΊΠ»ΡΡΠ°Π΅Ρ ΠΈΠ½ΠΎΠ΅ ΠΊΠΎΠ»ΠΈΡΠ΅ΡΡΠ²ΠΎ ΡΠΏΠΎΠΊΡΠΈΠ΄Π½ΡΡ Π³ΡΡΠΏΠΏ β ΠΎΠΊΠΎΠ»ΠΎ 16%. ΠΡΠ·ΠΊΠΎΡΡΡ ΠΏΡΠΎΠ΄ΡΠΊΡΠ° ΠΌΠ΅Π½ΡΡΠ΅, ΡΠ΅ΠΌ Ρ ΠΠ-20, ΡΡΠ°Π»ΠΎ Π±ΡΡΡ, ΠΆΠ΅Π»Π°ΡΠΈΠ½ΠΈΠ·Π°ΡΠΈΡ ΠΏΡΠΎΠΈΡΡ ΠΎΠ΄ΠΈΡ Π±ΡΡΡΡΠ΅Π΅ (ΠΎΡΠΈΠ΅Π½ΡΠΈΡΠΎΠ²ΠΎΡΠ½ΠΎ 4 ΡΠ°ΡΠ°). Π‘ΡΠ΅Π΄ΡΡΠ²ΠΎ ΡΠ°Π·Π»ΠΈΡΠ°Π΅ΡΡΡ Π²ΡΡΠΎΠΊΠΈΠΌΠΈ ΠΏΠΎΠΊΠ°Π·Π°ΡΠ΅Π»ΡΠΌΠΈ ΠΏΡΠΎΡΠ½ΠΎΡΡΠΈ ΠΊΠ»Π΅Π΅Π²ΠΎΠ³ΠΎ ΡΠ²Π°, ΠΎΠ΄Π½Π°ΠΊΠΎ Π² Π½Π΅ΠΌ ΠΎΡΠ΅Π½Ρ Π²ΡΡΠΎΠΊΠΎΠ΅ ΠΊΠΎΠ»-Π²ΠΎ Ρ Π»ΠΎΡΠ°.
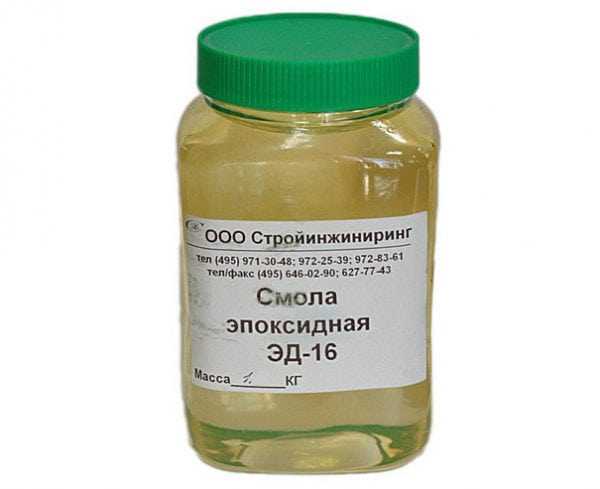
ΠΠ-22
ΠΡΠ΅ ΠΎΠ΄Π½Π° ΡΠΏΠΎΠΊΡΠΈΠ΄ΠΊΠ° Π½Π° ΠΎΡΠ½ΠΎΠ²Π΅ ΡΠΏΠΈΡ Π»ΠΎΡΠ³ΠΈΠ΄ΡΠΈΠ½Π° ΠΈ Π΄ΠΈΡΠ΅Π½ΠΈΠ»ΠΎΠ»ΠΏΡΠΎΠΏΠ°Π½Π°, Π΄ΠΎΠ»Ρ ΡΠΏΠΎΠΊΡΠΈΠ΄Π½ΡΡ Π³ΡΡΠΏΠΏ β 22%. Π‘ΠΌΠΎΠ»Π° ΠΠ-22 ΡΡΠ΅Π΄ΠΈ ΡΠ²ΠΎΠΉΡΡΠ² ΠΈΠΌΠ΅Π΅Ρ ΠΎΡΠ΅Π½Ρ Π²ΡΡΠΎΠΊΠΎΠ΅ Π²ΡΠ΅ΠΌΡ ΠΆΠ΅Π»Π°ΡΠΈΠ½ΠΈΠ·Π°ΡΠΈΠΈ β 18 ΡΠ°ΡΠΎΠ², ΠΏΡΠΈ ΡΡΠΎΠΌ Π΄ΠΈΠ½Π°ΠΌΠΈΡΠ΅ΡΠΊΠ°Ρ Π²ΡΠ·ΠΊΠΎΡΡΡ ΡΠΎΡΡΠ°Π²Π»ΡΠ΅Ρ 8β12 ΠΠ/ΡΠ΅ΠΊΡΠ½Π΄Ρ.
Π-40
ΠΡΠΎΠΈΠ·Π²ΠΎΠ΄ΡΡΠ²Π΅Π½Π½Π°Ρ ΡΠ΅Ρ Π½ΠΎΠ»ΠΎΠ³ΠΈΡ ΡΠΏΠΎΠΊΡΠΈΠ΄ΠΊΠΈ Π-40 Π½Π΅ΠΌΠ½ΠΎΠ³ΠΎ Π²ΡΠ΄Π΅Π»ΡΠ΅ΡΡΡ ΠΎΡ ΡΠΎΠ·Π΄Π°Π½ΠΈΡ ΠΌΠ°ΡΠ΅ΡΠΈΠ°Π»ΠΎΠ² ΠΌΠ°ΡΠΊΠΈ ΠΠ. ΠΡΠΎΠ΄ΡΠΊΡ ΠΏΠΎΠ»ΡΡΠ°ΡΡ ΠΏΡΡΠ΅ΠΌ ΠΊΠΎΠ½Π΄Π΅Π½ΡΠ°ΡΠΈΠΈ ΡΠΏΠΈΡ Π»ΠΎΡΠ³ΠΈΠ΄ΡΠΈΠ½Π° ΠΈ Π΄ΠΈΡΠ΅Π½ΠΈΠ»ΠΎΠ»ΠΏΡΠΎΠΏΠ°Π½Π° Π² ΡΠ΅Π»ΠΎΡΠ½ΠΎΠΉ ΠΎΠ±ΡΡΠ°Π½ΠΎΠ²ΠΊΠ΅ Ρ Π΄ΠΎΠ±Π°Π²ΠΊΠΎΠΉ ΡΠ°ΡΡΠ²ΠΎΡΠΈΡΠ΅Π»Ρ ΡΠΎΠ»ΡΠΎΠ»Π°. Π‘ΡΠ΅Π΄ΡΡΠ²ΠΎ ΠΌΠΎΠΆΠ½ΠΎ ΠΏΠ΅ΡΠ΅Π²ΠΎΠ΄ΠΈΡΡ Π² Π½Π΅ΠΏΠ»Π°Π²ΠΊΠΎΠ΅ ΡΠΎΡΡΠΎΡΠ½ΠΈΠ΅ ΠΏΡΡΠ΅ΠΌ ΠΈΡΠΏΠΎΠ»ΡΠ·ΠΎΠ²Π°Π½ΠΈΡ ΠΎΡΠ²Π΅ΡΠ΄ΠΈΡΠ΅Π»Π΅ΠΉ β ΠΏΠΎΠ»ΠΈΠΊΠ°ΡΠ±ΠΎΠ½ΠΎΠ²ΡΡ ΠΊΠΈΡΠ»ΠΎΡ, ΠΈΡ Π°Π½Π³ΠΈΠ΄ΡΠΈΠ΄ΠΎΠ², ΠΏΠΎΠ»ΠΈΠ°ΠΌΠΈΠ½ΠΎΠ².
ΠΠ±Π»Π°ΡΡΡ ΠΈΡΠΏΠΎΠ»ΡΠ·ΠΎΠ²Π°Π½ΠΈΡ ΠΌΠ°ΡΠ΅ΡΠΈΠ°Π»Π° β ΠΏΡΠΈΠ³ΠΎΡΠΎΠ²Π»Π΅Π½ΠΈΠ΅ ΡΠΌΠ°Π»Π΅ΠΉ, ΠΎΠ±Π»Π°Π΄Π°ΡΡΠΈΡ Π²ΡΡΠΎΠΊΠΈΠΌΠΈ ΡΠ²ΠΎΠΉΡΡΠ²Π°ΠΌΠΈ Π·Π°ΡΠΈΡΡ, Π° Π΅ΡΠ΅ ΡΠΎΠ·Π΄Π°Π½ΠΈΠ΅ Π»Π°ΠΊΠΎΠ² ΠΈ ΡΠΏΠ°ΠΊΠ»Π΅Π²ΠΎΠΊ. ΠΠΎΠ»Π΅Π΅ ΡΠΎΠ³ΠΎ, Π-40 Π²ΡΡΡΡΠΏΠ°Π΅Ρ ΠΊΠ°ΠΊ ΠΏΠΎΠ»ΡΡΠ°Π±ΡΠΈΠΊΠ°Ρ Π΄Π»Ρ ΠΏΡΠΎΠΈΠ·Π²ΠΎΠ΄ΡΡΠ²Π° ΠΈΠ½ΡΡ ΡΠΌΠΎΠ» Π½Π° ΡΠΏΠΎΠΊΡΠΈΠ΄Π½ΠΎΠΉ ΠΎΡΠ½ΠΎΠ²Π΅, ΠΊΠ»Π΅Π΅Π² ΠΈ ΠΊΠΎΠΌΠΏΠ°ΡΠ½Π΄ΠΎΠ² Π΄Π»Ρ Π·Π°Π»ΠΈΠ²ΠΊΠΈ. Π‘ΠΌΠΎΠ»Π° Π²Π»Π°Π΄Π΅Π΅Ρ Π±ΠΎΠ»ΡΡΠ΅ΠΉ ΠΏΠ»Π°ΡΡΠΈΡΠ½ΠΎΡΡΡΡ, Π²ΠΎΠ΄ΠΎΡΡΠΎΠΉΠΊΠΎΡΡΡΡ, Π² ΠΏΠΎΠ»ΠΈΠΌΠ΅ΡΠΈΠ·ΠΎΠ²Π°Π½Π½ΠΎΠΌ Π²ΠΈΠ΄Π΅ Π½Π΅ ΡΠ΅Π°Π³ΠΈΡΡΠ΅Ρ Π½Π° Π²ΠΎΠ·Π΄Π΅ΠΉΡΡΠ²ΠΈΠ΅ ΡΠ΄Π΅ΡΠΆΠ°Π½Π½ΠΎ Π°Π³ΡΠ΅ΡΡΠΈΠ²Π½ΡΡ ΠΊΠΈΡΠ»ΠΎΡ, ΡΠ΅Π»ΠΎΡΠ΅ΠΉ.
ΠΠ½ΡΡΡΡΠΊΡΠΈΡ ΠΏΠΎ ΠΏΡΠΈΠΌΠ΅Π½Π΅Π½ΠΈΡ ΠΠ-20
Π Π΅Π·ΡΠ»ΡΡΠ°Ρ ΡΠΌΠ΅ΡΠΈΠ²Π°Π½ΠΈΡ ΡΠΌΠΎΠ»Ρ ΠΈ ΠΎΡΠ²Π΅ΡΠ΄ΠΈΡΠ΅Π»Ρ Π±ΡΠ΄Π΅Ρ ΡΠΈΠ»ΡΠ½ΠΎ Π·Π°Π²ΠΈΡΠ΅ΡΡ ΠΎΡ ΠΈΡ ΠΏΡΠΎΠΏΠΎΡΡΠΈΠΈ, ΡΡΠ»ΠΎΠ²ΠΈΠΉ Π²Π½Π΅ΡΠ½Π΅ΠΉ ΡΡΠ΅Π΄Ρ, ΠΊΠ°ΡΠ΅ΡΡΠ²Π° ΠΏΠΎΠ΄Π³ΠΎΡΠΎΠ²ΠΊΠΈ ΡΠ°ΡΡ ΠΈ ΡΡΠ΄Π° ΠΈΠ½Π΄ΠΈΠ²ΠΈΠ΄ΡΠ°Π»ΡΠ½ΡΡ ΡΠ°ΠΊΡΠΎΡΠΎΠ². ΠΠ½ΡΡΡΡΠΊΡΠΈΡ ΠΏΠΎ ΠΈΡΠΏΠΎΠ»ΡΠ·ΠΎΠ²Π°Π½ΠΈΡ Π½Π΅ Π²ΡΠ΅Π³Π΄Π° ΠΏΠΎΡΠ°Π³ΠΎΠ²Π°Ρ, Π² Π½Π΅ΠΉ Π² Π±ΠΎΠ»ΡΡΠΈΠ½ΡΡΠ²Π΅ ΡΠ»ΡΡΠ°Π΅Π² ΡΠΊΠ°Π·ΡΠ²Π°ΡΡΡΡ Π»ΠΈΡΡ ΡΠΎΡΠ½ΡΠ΅ ΡΠΎΠΎΡΠ½ΠΎΡΠ΅Π½ΠΈΡ ΡΠ»Π΅ΠΌΠ΅Π½ΡΠΎΠ² ΠΈ Π³Π»Π°Π²Π½ΡΠ΅ ΡΡΠ΅Π±ΠΎΠ²Π°Π½ΠΈΡ ΠΊ ΠΏΡΠΎΡΠ΅ΡΡΡ ΠΏΠΎΠ»ΠΈΠΌΠ΅ΡΠΈΠ·Π°ΡΠΈΠΈ. Π Π΅ΠΊΠΎΠΌΠ΅Π½Π΄ΡΠ΅ΡΡΡ Π²Π½Π°ΡΠ°Π»Π΅ ΠΏΡΠΈΠΎΠ±ΡΠ΅ΡΡΠΈ ΡΠΊΠ°Π·Π°Π½Π½ΡΠΉ ΠΈΠ·Π³ΠΎΡΠΎΠ²ΠΈΡΠ΅Π»Π΅ΠΌ ΠΆΠΈΠ΄ΠΊΠΈΠΉ ΠΎΡΠ²Π΅ΡΠ΄ΠΈΡΠ΅Π»Ρ (Π΅ΡΠ»ΠΈ ΠΎΠ½ Π½Π΅ ΠΊΠΎΠΌΠΏΠ»Π΅ΠΊΡΡΠ΅ΡΡΡ) ΠΈ ΠΏΠ΅ΡΠ΅ΠΌΠ΅ΡΠ°ΡΡ Π΅Π³ΠΎ ΡΠΎ ΡΠΌΠΎΠ»ΠΎΠΉ Π² ΡΠ°ΠΌΡΡ ΠΎΡΠ΅Π½Ρ ΠΌΠ°Π»Π΅Π½ΡΠΊΠΈΡ Π΄ΠΎΠ·ΠΈΡΠΎΠ²ΠΊΠ°Ρ . ΠΡΠΎ Π΄Π°ΡΡ Π²ΠΎΠ·ΠΌΠΎΠΆΠ½ΠΎΡΡΡ ΡΠ²ΠΈΠ΄Π΅ΡΡ ΡΠ΅Π·ΡΠ»ΡΡΠ°Ρ ΠΈ ΡΠ΄Π΅Π»Π°ΡΡ Π²ΡΠ²ΠΎΠ΄Ρ ΠΎ ΠΏΡΠ°Π²ΠΈΠ»ΡΠ½ΠΎΡΡΠΈ ΠΏΡΠΎΠΏΠΎΡΡΠΈΠΉ.
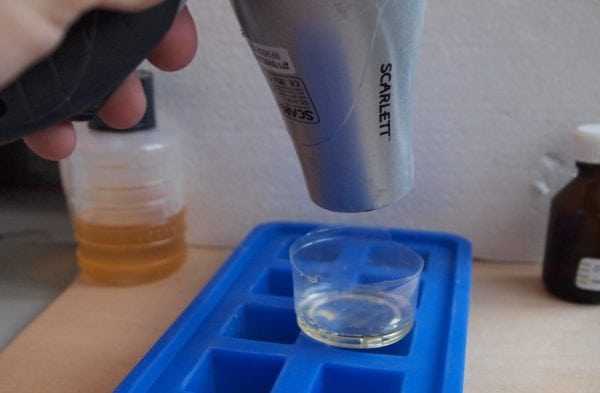
ΠΠ΅ΡΠ΅ΠΌΠ΅ΡΠΈΠ²Π°Π½ΠΈΠ΅ ΡΠΌΠΎΠ»Ρ Π² ΠΌΠ°Π»ΡΡ ΠΎΠ±ΡΠ΅ΠΌΠ°Ρ ΡΠ»ΠΎΠΆΠ½ΠΎΡΡΠ΅ΠΉ Π½Π΅ ΠΏΡΠ΅Π΄ΡΡΠ°Π²Π»ΡΠ΅Ρ. ΠΠ»Ρ Π΄Π°Π½Π½ΠΎΠΉ ΡΠ΅Π»ΠΈ ΠΏΡΠ΅ΠΊΡΠ°ΡΠ½ΠΎ ΠΏΠΎΠ΄Ρ ΠΎΠ΄ΠΈΡ ΠΌΠ΅ΡΠΎΠ΄ΠΈΠΊΠ° Ρ ΠΎΠ»ΠΎΠ΄Π½ΠΎΠ³ΠΎ ΠΎΡΠ²Π΅ΡΠΆΠ΄Π΅Π½ΠΈΡ, ΠΊΠΎΠ³Π΄Π° Π²ΡΠ΅ ΡΠ°Π±ΠΎΡΡ ΠΏΡΠΎΠ²ΠΎΠ΄ΡΡΡΡ ΠΏΡΠΈ ΠΊΠΎΠΌΠ½Π°ΡΠ½ΡΡ ΡΠ΅ΠΌΠΏΠ΅ΡΠ°ΡΡΡΠ°Ρ . ΠΠ΅ΡΠ΅Π΄ ΡΠΌΠ΅ΡΠΈΠ²Π°Π½ΠΈΠ΅ΠΌ ΡΠΏΠΎΠΊΡΠΈΠ΄ΠΊΠΈ Π² Π·Π½Π°ΡΠΈΡΠ΅Π»ΡΠ½ΠΎΠΌ ΠΎΠ±ΡΠ΅ΠΌΠ΅ ΠΏΡΠΈΠ΄Π΅ΡΡΡ ΠΏΡΠΈΠ³ΠΎΡΠΎΠ²ΠΈΡΡ ΠΏΠΎΡΡΠ΄Ρ Π΄Π»Ρ Π½Π°Π³ΡΠ΅Π²Π° ΡΠΌΠΎΠ»Ρ, ΡΠ°ΠΊ ΠΊΠ°ΠΊ ΠΏΡΠΈΠΌΠ΅Π½ΡΠ΅ΡΡΡ ΠΌΠ΅ΡΠΎΠ΄ Π³ΠΎΡΡΡΠ΅Π³ΠΎ ΠΎΡΠ²Π΅ΡΠΆΠ΄Π΅Π½ΠΈΡ. ΠΠΏΠΎΠΊΡΠΈΠ΄ΠΊΡ Π³ΡΠ΅ΡΡ Π½Π° Π²ΠΎΠ΄ΡΠ½ΠΎΠΉ Π±Π°Π½Π΅ Π΄ΠΎ ΡΠ΅ΠΌΠΏΠ΅ΡΠ°ΡΡΡΡ 50β55 Π³ΡΠ°Π΄ΡΡΠΎΠ², ΠΏΠΎΡΠ»Π΅ ΡΡΠΎΠ³ΠΎ Π΄Π΅Π»Π°ΡΡ ΠΏΠΎΡΠ»Π΅Π΄ΡΡΡΠΈΠ΅ ΡΠ°Π±ΠΎΡΡ Π² Π±ΡΡΡΡΠΎΠΌ ΡΠ΅ΠΆΠΈΠΌΠ΅.
ΠΠ»Π°Π²Π½ΠΎΠ΅ ΠΏΡΠ΅Π΄ΡΡΠΌΠΎΡΡΠ΅ΡΡ, ΡΡΠΎ ΠΏΠΎΡΠ»Π΅ Π΄ΠΎΠ±Π°Π²ΠΊΠΈ ΠΎΡΠ²Π΅ΡΠ΄ΠΈΡΠ΅Π»Ρ ΡΠ΅Π°ΠΊΡΠΈΡ ΠΏΠΎΠ»ΠΈΠΌΠ΅ΡΠΈΠ·Π°ΡΠΈΠΈ ΡΡΠΈΡΠ°Π΅ΡΡΡ Π½Π΅ΠΎΠ±ΡΠ°ΡΠΈΠΌΠΎΠΉ, ΠΎΡΡΠ°Π½ΠΎΠ²ΠΈΡΡ Π΅Π΅ Π½Π΅ ΠΏΡΠ΅Π΄ΡΡΠ°Π²Π»ΡΠ΅ΡΡΡ Π²ΠΎΠ·ΠΌΠΎΠΆΠ½ΡΠΌ, Π΅ΡΡΡ ΡΠ°Π½Ρ Π»ΠΈΡΡ Π½Π΅ΠΌΠ½ΠΎΠ³ΠΎ Π·Π°ΠΌΠ΅Π΄Π»ΠΈΡΡ ΡΠ½ΠΈΠΆΠ΅Π½ΠΈΠ΅ΠΌ ΡΠ΅ΠΌΠΏΠ΅ΡΠ°ΡΡΡΡ Π²ΠΎΠ·Π΄ΡΡ Π°. ΠΠ»ΠΎΡ ΠΎ ΡΠ΄Π΅Π»Π°Π½Π½ΡΠ΅ Π΄Π΅ΠΉΡΡΠ²ΠΈΡ ΠΏΡΠΈΠ²Π΅Π΄ΡΡ ΠΊ ΠΏΠΎΡΡΠ΅ ΠΏΠΎΡΡΠΈΠΈ ΡΠΏΠΎΠΊΡΠΈΠ΄ΠΊΠΈ, Π±Π»Π°Π³ΠΎΠ΄Π°ΡΡ ΡΡΠΎΠΌΡ Π²ΡΠ΅ ΡΠ°ΡΡΠ΅ΡΡ Π΄ΠΎΠ»ΠΆΠ½Ρ Π±ΡΡΡ ΡΠ΄Π΅Π»Π°Π½Ρ Π·Π°Π±Π»Π°Π³ΠΎΠ²ΡΠ΅ΠΌΠ΅Π½Π½ΠΎ.
ΠΠΎΠ΄Π³ΠΎΡΠΎΠ²ΠΊΠ° ΡΠΌΠΎΠ»Ρ
ΠΠ»Ρ Ρ ΠΎΠ»ΠΎΠ΄Π½ΠΎΠ³ΠΎ ΠΎΡΠ²Π΅ΡΠΆΠ΄Π΅Π½ΠΈΡ Π½ΠΈΠΊΠ°ΠΊΠΎΠΉ ΠΎΡΠΎΠ±ΠΎΠΉ ΠΏΠΎΠ΄Π³ΠΎΡΠΎΠ²ΠΊΠΈ ΠΌΠ°ΡΠ΅ΡΠΈΠ°Π»Π° Π½Π΅ ΠΏΠΎΡΡΠ΅Π±ΡΠ΅ΡΡΡ. ΠΠ»Ρ Π³ΠΎΡΡΡΠ΅Π³ΠΎ ΡΠΏΠΎΡΠΎΠ±Π° ΠΈ ΡΡΠΊΠΎΡΠ΅Π½ΠΈΡ ΠΏΡΠΎΠΏΠΈΡΠΊΠΈ (Π·Π°Π»ΠΈΠ²ΠΊΠΈ) ΡΠ΅ΠΊΠΎΠΌΠ΅Π½Π΄ΡΠ΅ΡΡΡ ΠΎΠ±ΠΎΠ³ΡΠ΅Π²Π°ΡΡ ΠΎΡΠΌΠ΅ΡΡΠ½Π½ΡΡ ΠΏΠΎΡΡΠΈΡ ΡΡΠ΅Π΄ΡΡΠ²Π°. ΠΠ»Ρ ΡΡΠΎΠ³ΠΎ ΡΡΡΠ°Π½Π°Π²Π»ΠΈΠ²Π°ΡΡ Π²ΠΎΠ΄ΡΠ½ΡΡ Π±Π°Π½Ρ, ΡΠ°ΡΠΏΠΎΠ»Π°Π³Π°ΡΡ Π½Π° Π½Π΅ΠΉ Π΅ΠΌΠΊΠΎΡΡΡ Ρ ΡΠΌΠΎΠ»ΠΎΠΉ Π½Π° ΡΠΏΠΎΠΊΡΠΈΠ΄Π½ΠΎΠΉ ΠΎΡΠ½ΠΎΠ²Π΅. ΠΠ»Π°Π²Π½ΠΎΠ΅ ΡΠΌΠΎΡΡΠ΅ΡΡ, ΡΡΠΎΠ±Ρ Π½ΠΈ ΠΊΠ°ΠΏΠ»ΠΈ Π²ΠΎΠ΄Ρ Π½Π΅ ΠΏΡΠΎΠ±ΡΠ°Π»ΠΎΡΡ Π² ΠΌΠ°ΡΡΡ, ΡΡΠΎ ΠΏΠΎΠ²ΡΠ΅Π΄ΠΈΡ Π΅Π΅. Π’Π°ΠΊΠΆΠ΅ Π½Π΅Π»ΡΠ·Ρ Π½Π°Π³ΡΠ΅Π²Π°ΡΡ ΠΌΠ°ΡΠ΅ΡΠΈΠ°Π», ΡΠ΅Π°ΠΊΡΠΈΡ ΠΏΠΎΠΉΠ΄ΡΡ ΠΎΡΠ΅Π½Ρ Π±ΡΡΡΡΠΎ, Π° Π΄ΠΎΠ²ΠΈΠ΄Π΅Π½ΠΈΠ΅ Π΄ΠΎ ΠΊΠΈΠΏΠ΅Π½ΠΈΡ ΠΏΡΠΈΠ²Π΅Π΄Π΅Ρ ΡΠΌΠΎΠ»Ρ Π² Π½Π΅Π³ΠΎΠ΄Π½ΠΎΡΡΡ. Π₯ΠΎΡΠΎΡΠΈΠΌ Π±ΡΠ΄Π΅Ρ Π½Π°Π³ΡΠ΅Π² Π΄ΠΎ 55 Π³ΡΠ°Π΄ΡΡΠΎΠ² ΠΈΠ»ΠΈ ΠΌΠ΅Π½ΡΡΠ΅. ΠΠΎΠΆΠ½ΠΎ ΠΈ ΡΠΎΠ²ΡΠ΅ΠΌ ΠΎΠΏΡΡΡΠΈΡΡ Π΅ΠΌΠΊΠΎΡΡΡ Ρ ΠΌΠ°ΡΠ΅ΡΠΈΠ°Π»ΠΎΠΌ Π² ΠΏΠΎΡΡΠ΄Ρ Ρ Π³ΠΎΡΡΡΠ΅ΠΉ Π²ΠΎΠ΄ΠΎΠΉ, Π΄Π°ΡΡ ΠΏΠΎΡΡΠΎΡΡΡ Π±Π΅Π· ΠΊΠΈΠΏΡΡΠ΅Π½ΠΈΡ Π²ΠΎΠ΄Ρ. ΠΠ½ΠΎΠ³Π΄Π° ΡΠΌΠ΅ΡΠΈΠ²Π°ΡΡ ΠΌΠ°ΡΡΡ Π΄Π»Ρ ΡΠ°Π²Π½ΠΎΠΌΠ΅ΡΠ½ΠΎΡΡΠΈ Π½Π°Π³ΡΠ΅Π²Π°.
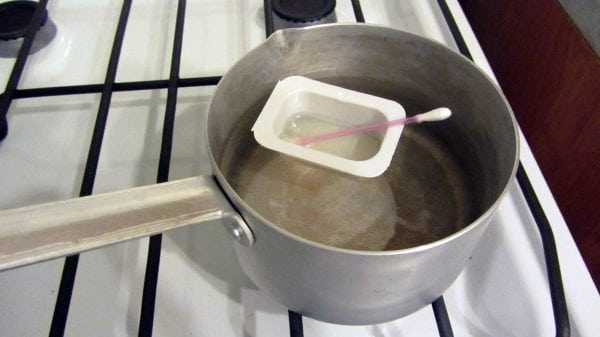
ΠΡΠΈ Ρ ΡΠ°Π½Π΅Π½ΠΈΠΈ ΠΈΠ»ΠΈ ΠΏΡΠ΅Π²ΡΡΠ΅Π½ΠΈΠΈ ΡΡΠΎΠΊΠ° Π³ΠΎΠ΄Π½ΠΎΡΡΠΈ ΡΠΏΠΎΠΊΡΠΈΠ΄ΠΊΠ° ΡΠΏΠΎΡΠΎΠ±Π½Π° ΠΊΡΠΈΡΡΠ°Π»Π»ΠΈΠ·ΠΎΠ²Π°ΡΡΡΡ. ΠΠ΅ΠΎΠ±Ρ ΠΎΠ΄ΠΈΠΌΠΎ ΡΠ±Π΅Π΄ΠΈΡΡΡ, ΡΡΠΎ Π² Π½Π΅ΠΉ Π½Π΅Ρ ΠΊΡΠΈΡΡΠ°Π»Π»ΠΎΠ², ΠΌΡΡΠ½ΠΎΡΡΠ΅ΠΉ, Π² Π΄ΡΡΠ³ΠΎΠΌ ΡΠ»ΡΡΠ°Π΅ Π΅Π΅ ΠΏΠΎΠ΄ΠΎΠ³ΡΠ΅Π²Π°ΡΡ Π΄ΠΎ +40 Π³ΡΠ°Π΄ΡΡΠΎΠ² Ρ ΠΈΠ½ΡΠ΅Π½ΡΠΈΠ²Π½ΡΠΌ ΠΏΠ΅ΡΠ΅ΠΌΠ΅ΡΠΈΠ²Π°Π½ΠΈΠ΅ΠΌ. ΠΡΠΎ ΠΏΠΎΠΌΠΎΠΆΠ΅Ρ Π²Π΅ΡΠ½ΡΡΡ ΠΌΠ°ΡΠ΅ΡΠΈΠ°Π»Ρ ΠΏΡΠΎΠ·ΡΠ°ΡΠ½ΠΎΡΡΡ.
ΠΡΠΈΠΌΠ΅Π½Π΅Π½ΠΈΠ΅ Π²ΠΎΠ΄Π½ΠΎΠ³ΠΎ ΠΈΠ½Π³ΠΈΠ±ΠΈΡΠΎΡΠ°
ΠΠΎΠ±Π°Π²Π»Π΅Π½ΠΈΠ΅ ΡΡΠ΄Π° ΡΠ»Π΅ΠΌΠ΅Π½ΡΠΎΠ² ΠΏΠΎΠΌΠΎΠΆΠ΅Ρ ΠΏΠ»Π°ΡΡΠΈΡΠΈΡΠΈΡΠΎΠ²Π°ΡΡ ΡΠΌΠΎΠ»Ρ Π½Π° ΡΠΏΠΎΠΊΡΠΈΠ΄Π½ΠΎΠΉ ΠΎΡΠ½ΠΎΠ²Π΅. ΠΠ»Ρ ΡΠ΅Π³ΠΎ ΡΡΠΎ Π½Π΅ΠΎΠ±Ρ ΠΎΠ΄ΠΈΠΌΠΎ? ΠΡΠ»ΠΈ ΠΈΠ·Π΄Π΅Π»ΠΈΠ΅ Π² Π΄Π°Π»ΡΠ½Π΅ΠΉΡΠ΅ΠΌ Π΄ΠΎΠ»ΠΆΠ½ΠΎ Π΄Π΅ΡΠΆΠ°ΡΡ Π²ΡΡΠΎΠΊΠΈΠ΅ ΡΠ΄Π°ΡΠ½ΡΠ΅ ΠΈΠ»ΠΈ Π΄ΡΡΠ³ΠΈΠ΅ Π½Π°Π³ΡΡΠ·ΠΊΠΈ ΠΌΠ΅Ρ Π°Π½ΠΈΡΠ΅ΡΠΊΠΎΠ³ΠΎ ΡΠ²ΠΎΠΉΡΡΠ²Π°, ΡΡΠΈΠ»ΠΈΠ΅ Π½Π° ΠΈΠ·Π»ΠΎΠΌ Ρ ΠΏΡΠΈΠΌΠ΅Π½Π΅Π½ΠΈΠ΅ΠΌ ΡΡΡΠ°Π³Π°, Π΅Π³ΠΎ ΡΠΏΡΡΠ³ΠΎΡΡΡ Π½ΡΠΆΠ½ΠΎ ΡΠ²Π΅Π»ΠΈΡΠΈΡΡ. ΠΠΎΠ±Π°Π²Π»Π΅Π½ΠΈΠ΅ ΠΎΡΠΎΠ±ΡΡ Π²ΠΎΠ΄Π½ΡΡ ΠΈΠ½Π³ΠΈΠ±ΠΈΡΠΎΡΠΎΠ² Π΄Π°Π΅Ρ Π²ΠΎΠ·ΠΌΠΎΠΆΠ½ΠΎΡΡΡ Π½Π΅ΠΌΠ½ΠΎΠ³ΠΎ Π³Π°ΡΠΈΡΡ ΠΏΠΎΠ΄ΠΎΠ±Π½ΡΠ΅ Π½Π°Π³ΡΡΠ·ΠΊΠΈ. Π’Π°ΠΊΠΆΠ΅ ΠΈΡ Π²Π²Π΅Π΄Π΅Π½ΠΈΠ΅ ΡΠΎΠ²Π΅ΡΡΠ΅ΡΡΡ Π΄Π»Ρ ΡΡΠΈΠ»Π΅Π½ΠΈΡ Π³ΠΈΠ±ΠΊΠΎΡΡΠΈ ΡΠ²ΠΎΠ², Π΅ΡΠ»ΠΈ ΡΠΏΠΎΠΊΡΠΈΠ΄ΠΊΠ° Π±ΡΠ΄Π΅Ρ ΠΈΡΠΏΠΎΠ»ΡΠ·ΠΎΠ²Π°ΡΡΡΡ Π΄Π»Ρ ΠΏΡΠΈΠΊΠ»Π΅ΠΈΠ²Π°Π½ΠΈΡ ΠΈ Π·Π°Π»ΠΈΠ²ΠΊΠΈ.
ΠΠΎΠ΄Π½ΡΠΉ ΠΈΠ½Π³ΠΈΠ±ΠΈΡΠΎΡ ΠΠΠ€
ΠΠΈΠ±ΡΡΠΈΠ»ΡΡΠ°Π»Π°Ρ, ΠΈΠ»ΠΈ ΠΠΠ€ β Π½Π°ΠΈΠ±ΠΎΠ»Π΅Π΅ ΡΠ°ΡΠΏΡΠΎΡΡΡΠ°Π½Π΅Π½Π½ΡΠΉ Π²ΠΎΠ΄Π½ΡΠΉ ΠΈΠ½Π³ΠΈΠ±ΠΈΡΠΎΡ Π΄Π»Ρ ΡΠΏΠΎΠΊΡΠΈΠ΄ΠΊΠΈ, Π΅Π³ΠΎ Π΄ΠΎΠ±Π°Π²Π»ΡΡΡ Π² Π½Π΅Π±ΠΎΠ»ΡΡΠΎΠΌ ΠΊΠΎΠ»ΠΈΡΠ΅ΡΡΠ²Π΅ β Π΄ΠΎ 2β5% ΠΎΡ Π²ΡΠ΅Π³ΠΎ ΠΎΠ±ΡΠ΅ΠΌΠ°. Π‘ΡΠ΅Π΄ΡΡΠ²ΠΎ ΠΌΠΎΠΆΠ΅Ρ ΠΎΠ±Π΅Π·ΠΎΠΏΠ°ΡΠΈΡΡ ΠΈΠ·Π΄Π΅Π»ΠΈΡ ΠΎΡ ΡΡΠ΅ΡΠΈΠ½Ρ ΠΏΡΠΈ ΠΌΠΎΡΠΎΠ·Π΅, ΡΠ΄Π°ΡΠ΅. Π ΠΎΡΠΎΠ±Π΅Π½Π½ΠΎΡΡΠΈ ΠΏΠΎΠΊΠ°Π·Π°Π½ΠΎ Π²Π²ΠΎΠ΄ΠΈΡΡ ΠΠΠ€ Π²ΠΎ Π²ΡΠ΅ΠΌΡ ΠΈΡΠΏΠΎΠ»ΡΠ·ΠΎΠ²Π°Π½ΠΈΡ ΠΎΡΠ²Π΅ΡΠ΄ΠΈΡΠ΅Π»Π΅ΠΉ ΠΠΠΠ ΠΈ Π’ΠΠ’Π. ΠΡΠ»ΠΈ ΠΆΠ΅ ΠΏΡΠΈΠΌΠ΅Π½ΡΠ΅ΡΡΡ ΠΎΡΠ²Π΅ΡΠ΄ΠΈΡΠ΅Π»Ρ ΠΡΠ°Π» 45Π, Π΄ΠΎΠ±Π°Π²ΠΊΠΈ Π²ΠΎΠ΄Π½ΠΎΠ³ΠΎ ΠΈΠ½Π³ΠΈΠ±ΠΈΡΠΎΡΠ° Π½Π΅ ΠΏΠΎΡΡΠ΅Π±ΡΠ΅ΡΡΡ. ΠΠ΅Π΄ΠΎΡΡΠ°ΡΠΊΠΎΠΌ ΠΠΠ€ ΠΌΠΎΠΆΠ½ΠΎ ΠΈΠΌΠ΅Π½ΠΎΠ²Π°ΡΡ ΡΡΡΠ΄Π½ΠΎΠ΅ ΡΠΎΠ΅Π΄ΠΈΠ½Π΅Π½ΠΈΠ΅ ΡΠΎ ΡΠΌΠΎΠ»ΠΎΠΉ, Π±Π»Π°Π³ΠΎΠ΄Π°ΡΡ ΡΡΠΎΠΌΡ Π½Π΅ΠΎΠ±Ρ ΠΎΠ΄ΠΈΠΌΠΎ ΠΈΡΠΏΠΎΠ»ΡΠ·ΠΎΠ²Π°ΡΡ Π΄Π»ΠΈΡΠ΅Π»ΡΠ½ΠΎΠ΅ ΡΠΌΠ΅ΡΠΈΠ²Π°Π½ΠΈΠ΅ Ρ Π½Π°Π³ΡΠ΅Π²ΠΎΠΌ.
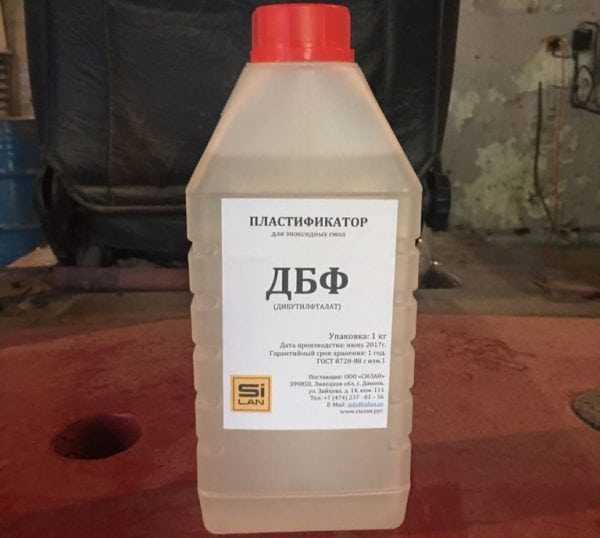
ΠΠΈΠ·ΠΊΠΎΠΌΠΎΠ»Π΅ΠΊΡΠ»ΡΡΠ½ΡΠ΅ ΠΎΡΠ³Π°Π½ΠΈΡΠ΅ΡΠΊΠΈΠ΅ Π²Π΅ΡΠ΅ΡΡΠ²Π° ΠΠΠ 1 ΠΈ Π’ΠΠ 1
ΠΠΈΡΡΠΈΠ»Π΅Π½Π³Π»ΠΈΠΊΠΎΠ»Ρ, ΠΈΠ»ΠΈ ΠΠΠ 1, ΡΠ°ΠΌ ΠΏΠΎ ΡΠ΅Π±Π΅ ΡΡΠΈΡΠ°Π΅ΡΡΡ ΡΠΏΠΎΠΊΡΠΈΠ΄ΠΊΠΎΠΉ, ΠΏΡΠΈ ΡΡΠΎΠΌ Π³ΠΎΠ΄ΠΈΡΡΡ Π΄Π»Ρ ΡΠ°Π·Π±Π°Π²ΠΊΠΈ Π±ΠΎΠ»ΡΡΠΎΠΉ ΠΌΠ°ΡΡΡ Π² ΠΊΠ°ΡΠ΅ΡΡΠ²Π΅ Π²ΠΎΠ΄Π½ΠΎΠ³ΠΎ ΠΈΠ½Π³ΠΈΠ±ΠΈΡΠΎΡΠ°. Π Π°Π±ΠΎΡΠ°Ρ ΠΊΠΎΠ½ΡΠ΅Π½ΡΡΠ°ΡΠΈΡ Π΄Π»Ρ ΠΠ-20 ΡΠΎΡΡΠ°Π²Π»ΡΠ΅Ρ 3β10% β ΡΠ΅ΠΌ Π±ΠΎΠ»ΡΡΠ΅ ΡΡΠ΅Π΄ΡΡΠ²Π° Π΄ΠΎΠ±Π°Π²Π»Π΅Π½ΠΎ, ΠΎΡΠΎΠ±Π΅Π½Π½ΠΎ ΡΠΌΠΎΠ»Π° ΡΡΠ°Π½Π΅Ρ Π½Π°ΠΏΠΎΠΌΠΈΠ½Π°ΡΡ ΡΠ΅Π·ΠΈΠ½Ρ. ΠΠΠ-1 Π»Π΅Π³ΠΊΠΎ ΡΠΎΠ²ΠΌΠ΅ΡΠ°Π΅ΡΡΡ Ρ ΡΠΏΠΎΠΊΡΠΈΠ΄ΠΊΠΎΠΉ, Π΅Π³ΠΎ ΠΎΡΠ΅Π½Ρ ΠΈ ΠΎΡΠ΅Π½Ρ ΠΏΡΠΎΡΡΠΎ ΠΈΡΠΏΠΎΠ»ΡΠ·ΠΎΠ²Π°ΡΡ, Π΅ΡΠ»ΠΈ Π½Π΅Π²Π°ΠΆΠ½Π° Π±Π΅ΡΡΠ²Π΅ΡΠ½ΠΎΡΡΡ. ΠΠ·-Π·Π° ΠΎΡΠ°Π½ΠΆΠ΅Π²ΠΎΠ³ΠΎ ΠΎΡΡΠ΅Π½ΠΊΠ° Π΄Π°Π½Π½ΡΠΉ Π²ΠΎΠ΄Π½ΡΠΉ ΠΈΠ½Π³ΠΈΠ±ΠΈΡΠΎΡ ΠΏΠΎΠ΄Ρ ΠΎΠ΄ΠΈΡ Π½Π΅ Π² Π»ΡΠ±ΠΎΠΌ ΡΠ»ΡΡΠ°Π΅.
Π’ΠΠ 1 ΠΏΠΎ ΡΠ²ΠΎΠΈΠΌ Ρ Π°ΡΠ°ΠΊΡΠ΅ΡΠΈΡΡΠΈΠΊΠ°ΠΌ ΠΈ ΠΈΡΠΏΠΎΠ»ΡΠ·ΠΎΠ²Π°Π½ΠΈΡ ΠΏΠΎΡ ΠΎΠΆ Ρ ΠΠΠ 1, Π½ΠΎ Π½Π΅ΠΌΠ½ΠΎΠ³ΠΎ Π±ΠΎΠ»Π΅Π΅ Π²ΡΠ·ΠΊΠΈΠΉ ΠΏΠΎ ΠΊΠΎΠ½ΡΠΈΡΡΠ΅Π½ΡΠΈΠΈ, ΠΈΠΌΠ΅Π΅Ρ ΠΊΠΎΡΠΈΡΠ½Π΅Π²ΡΠΉ ΠΈΠ»ΠΈ ΠΆΡΠ»ΡΡΠΉ ΡΠ²Π΅Ρ. ΠΠ°ΠΆΠ½ΠΎΠ΅ ΠΎΡΠ»ΠΈΡΠΈΠ΅ Π² ΡΠΎΡΡΠ°Π²Π΅ β Π²Π·Π°ΠΌΠ΅Π½ Π΄ΠΈΡΡΠΈΠ»Π΅Π½Π³Π»ΠΈΠΊΠΎΠ»Ρ Π² Π’ΠΠ 1 Π΅ΡΡΡ ΡΡΠΈΡΡΠΈΠ»Π΅Π½Π³Π»ΠΈΠΊΠΎΠ»Ρ.
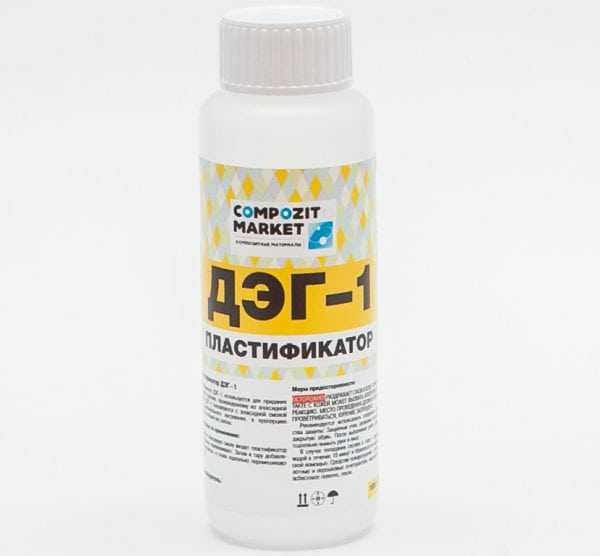
ΠΡΠΈΠΌΠ΅Π½Π΅Π½ΠΈΠ΅ ΠΎΡΠ²Π΅ΡΠ΄ΠΈΡΠ΅Π»Ρ
ΠΡΠ²Π΅ΡΠ΄ΠΈΡΠ΅Π»Ρ β Π½Π°ΡΡΠΎΡΡΠΈΠΉ ΡΠΎΡΡΠ°ΡΡΠ½ΠΈΠΊ Ρ ΠΈΠΌΡΠ΅Π°ΠΊΡΠΈΠΈ ΠΏΠΎΠ»ΠΈΠΌΠ΅ΡΠΈΠ·Π°ΡΠΈΠΈ ΡΠΌΠΎΠ»Ρ Π½Π° ΡΠΏΠΎΠΊΡΠΈΠ΄Π½ΠΎΠΉ ΠΎΡΠ½ΠΎΠ²Π΅. ΠΠ½ Π²Π²ΠΎΠ΄ΠΈΡΡΡ Π² ΠΌΠ°ΡΡΡ ΠΏΠΎΡΠ»Π΅ Π΄ΠΎΠ±Π°Π²ΠΊΠΈ Π²ΠΎΠ΄Π½ΡΡ ΠΈΠ½Π³ΠΈΠ±ΠΈΡΠΎΡΠΎΠ². ΠΠ»Ρ ΡΠΌΠ΅Π½ΡΡΠ΅Π½ΠΈΡ ΡΠΈΡΠΊΠ° Π·Π°ΠΊΠΈΠΏΠ°Π½ΠΈΡ ΡΠΏΠΎΠΊΡΠΈΠ΄ΠΊΠΈ Π΅Π΅ ΡΠ΅ΠΌΠΏΠ΅ΡΠ°ΡΡΡΠ° Π² ΠΌΠΎΠΌΠ΅Π½Ρ ΡΠΌΠ΅ΡΠΈΠ²Π°Π½ΠΈΡ Ρ ΠΎΡΠ²Π΅ΡΠ΄ΠΈΡΠ΅Π»Π΅ΠΌ Π΄ΠΎΠ»ΠΆΠ½Π° ΡΠΎΡΡΠ°Π²Π»ΡΡΡ Π½Π΅ Π±ΠΎΠ»ΡΡΠ΅ 30β40 Π³ΡΠ°Π΄ΡΡΠΎΠ².
Π Π±ΠΎΠ»ΡΡΠΈΠ½ΡΡΠ²Π΅ ΡΠ»ΡΡΠ°Π΅Π² Π²Π²ΠΎΠ΄ΡΡ 1 ΡΠ°ΡΡΡ ΠΎΡΠ²Π΅ΡΠ΄ΠΈΡΠ΅Π»Ρ Π½Π° 10 ΡΠ°ΡΡΠ΅ΠΉ ΡΠΌΠΎΠ»Ρ, Π½ΠΎ ΠΏΡΠΎΠΏΠΎΡΡΠΈΠΈ Π±ΡΠ΄ΡΡ ΠΏΠΎΠ΄ΡΠΈΠ½ΡΡΡΡΡ ΠΎΡ Π½ΡΠΆΠ΄, ΡΠΈΠΏΠ° Π³ΠΎΡΠΎΠ²ΠΎΠ³ΠΎ ΠΈΠ·Π΄Π΅Π»ΠΈΡ. ΠΠΎ ΠΌΠ½ΠΎΠ³ΠΈΡ ΡΠ»ΡΡΠ°ΡΡ Π΄ΠΎΡΡΠ°ΡΠΎΡΠ½ΠΎ ΡΠΎΠΎΡΠ½ΠΎΡΠ΅Π½ΠΈΡ 20:1, Π° ΠΏΠΎΡΠΎΠΉ, Π½Π°ΠΏΡΠΎΡΠΈΠ², ΡΡΠ΅Π±ΡΠ΅ΡΡΡ 5:1. ΠΡΠ²Π΅ΡΠ΄ΠΈΡΠ΅Π»Ρ Π΄ΠΎΠ±Π°Π²Π»ΡΡΡ Π² Π³Π»Π°Π²Π½ΡΡ ΠΌΠ°ΡΡΡ ΠΌΠ΅Π΄Π»Π΅Π½Π½Π΅Π΅, ΠΏΠΎΡΠΎΠΌΡ ΠΊΠ°ΠΊ ΠΏΡΡΠΊ ΡΠ΅ΠΏΠ»ΠΎΠ²ΠΎΠΉ ΡΠ΅Π°ΠΊΡΠΈΠΈ ΠΌΠΎΠΆΠ΅Ρ Π²ΡΠ·Π²Π°ΡΡ ΠΏΠ΅ΡΠ΅Π³ΡΠ΅Π² ΠΈ ΠΏΠΎΡΡΡ ΡΠΌΠΎΠ»Ρ. ΠΡΡΡΡΠΎΠ΅ Π²Π»ΠΈΠ²Π°Π½ΠΈΠ΅ Π² Π±ΠΎΠ»ΡΡΠΈΠ½ΡΡΠ²Π΅ ΡΠ»ΡΡΠ°Π΅Π² Π²ΡΠ·ΡΠ²Π°Π΅Ρ Π»Π°Π²ΠΈΠ½ΠΎΠΎΠ±ΡΠ°Π·Π½ΡΠΉ ΠΏΡΠΎΡΠ΅ΡΡ, ΠΊΠΎΠ³Π΄Π° ΠΌΠ°ΡΡΠ° ΠΏΠ΅ΡΠ΅Π³ΡΠ΅Π²Π°Π΅ΡΡΡ ΠΈ ΠΎΡΠ΅Π½Ρ Π±ΡΡΡΡΠΎ Π·Π°ΡΡΡΠ²Π°Π΅Ρ. Π ΡΠ΅ΠΌ ΠΆΠ΅ ΠΏΠΎΡΠ»Π΅Π΄ΡΡΠ²ΠΈΡΠΌ ΠΏΡΠΈΠ²ΠΎΠ΄ΡΡ ΡΠ»ΠΈΡΠΊΠΎΠΌ Π·Π½Π°ΡΠΈΡΠ΅Π»ΡΠ½ΠΎΠ΅ ΠΊΠΎΠ»ΠΈΡΠ΅ΡΡΠ²ΠΎ ΠΎΡΠ²Π΅ΡΠ΄ΠΈΡΠ΅Π»Ρ, Π±ΠΎΠ»ΡΡΠ°Ρ Π½Π°ΡΠ°Π»ΡΠ½Π°Ρ ΡΠ΅ΠΌΠΏΠ΅ΡΠ°ΡΡΡΠ° ΡΠΏΠΎΠΊΡΠΈΠ΄ΠΊΠΈ.
ΠΠΠΠ, Π’ΠΠ’Π ΠΈ ΠΠΠ’Π
ΠΠΎΠ»ΠΈΡΡΠΈΠ»Π΅Π½ΠΏΠΎΠ»ΠΈΠ°ΠΌΠΈΠ½, ΠΈΠ»ΠΈ ΠΠΠΠ, β Π΄Π΅ΡΠ΅Π²ΡΠΉ ΠΈ Π΄ΠΎΠ²ΠΎΠ»ΡΠ½ΠΎ ΡΠ°ΡΠΏΡΠΎΡΡΡΠ°Π½Π΅Π½Π½ΡΠΉ ΠΎΡΠ²Π΅ΡΠ΄ΠΈΡΠ΅Π»Ρ, ΠΎΠ½ ΡΡΠ½ΠΊΡΠΈΠΎΠ½ΠΈΡΡΠ΅Ρ ΠΏΡΠΈ ΠΊΠΎΠΌΠ½Π°ΡΠ½ΠΎΠΉ ΠΈΠ»ΠΈ Π½ΠΈΠ·ΠΊΠΎΠΉ ΡΠ΅ΠΌΠΏΠ΅ΡΠ°ΡΡΡΠ΅, Π½Π΅ ΠΏΡΠΎΡΠΈΡ Π½Π°Π³ΡΠ΅Π²Π°Π½ΠΈΡ ΠΈΡΡ ΠΎΠ΄Π½ΠΎΠΉ ΠΌΠ°ΡΡΡ. ΠΠΠΠ Π½Π΅ ΡΠΌΠ΅Π½ΡΡΠ°Π΅Ρ ΡΠΎΠ±ΡΡΠ²Π΅Π½Π½ΡΡ ΠΏΠ°ΡΠ°ΠΌΠ΅ΡΡΠΎΠ² Π΄Π°ΠΆΠ΅ ΠΏΡΠΈ ΠΎΡΠ΅Π½Ρ Π±ΠΎΠ»ΡΡΠΎΠΉ Π²Π»Π°ΠΆΠ½ΠΎΡΡΠΈ. ΠΠ½ ΠΈΠΌΠ΅Π΅Ρ ΠΆΡΠ»ΡΡΠΉ, ΠΊΠΎΡΠΈΡΠ½Π΅Π²ΡΠΉ ΡΠ²Π΅Ρ, ΠΏΠΎΡΠΎΠΉ ΡΡΡΡ Π·Π΅Π»Π΅Π½ΠΎΠ²Π°ΡΡΠΉ, Π² Π΅Π³ΠΎ ΠΎΡΠ½ΠΎΠ²Π΅ β ΡΡΠΈΠ»Π΅Π½ΠΎΠ²ΡΠ΅ Π°ΠΌΠΈΠ½Ρ. ΠΠΎΠ΄Ρ ΠΎΠ΄ΡΡΠ΅Π΅ ΠΊΠΎΠ»-Π²ΠΎ Π΄Π»Ρ Π΄ΠΎΠ±Π°Π²ΠΊΠΈ Π² ΡΠΏΠΎΠΊΡΠΈΠ΄ΠΊΡ β 13,7%, Π³Π»Π°Π²Π½ΠΎΠ΅ Π²ΠΎΠΉΡΠΈ Π² Π΄ΠΈΠ°ΠΏΠ°Π·ΠΎΠ½ 10β15%.
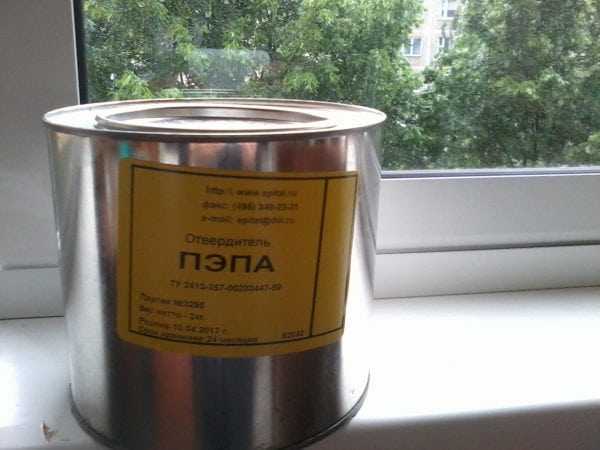
Π’ΡΠΈΡΡΠΈΠ»Π΅Π½ΡΠ΅ΡΡΠ°ΠΌΠΈΠ½ Π’ΠΠ’Π β Π΅ΡΠ΅ 1 Π·Π½Π°ΠΌΠ΅Π½ΠΈΡΡΠΉ ΠΊΠ»Π°ΡΡΠΈΡΠ΅ΡΠΊΠΈΠΉ ΠΎΡΠ²Π΅ΡΠ΄ΠΈΡΠ΅Π»Ρ, ΠΏΠΎΠ·Π²ΠΎΠ»ΡΠ΅Ρ Π³ΠΎΡΠΎΠ²ΠΈΡΡ ΡΠΌΠΎΠ»Ρ ΠΏΡΠΈ ΡΠ΅ΠΌΠΏΠ΅ΡΠ°ΡΡΡΠ΅ +15β¦+25 Π³ΡΠ°Π΄ΡΡΠΎΠ². Π Π½Π΅Π΄ΠΎΡΡΠ°ΡΠΊΠ°ΠΌ ΠΊΠ°ΠΊ ΠΏΡΠ°Π²ΠΈΠ»ΠΎ ΠΎΡΠ½ΠΎΡΡΡ Π΅Π΄ΠΊΠΈΠΉ Π°ΡΠΎΠΌΠ°Ρ, ΡΠ΄ΠΎΠ²ΠΈΡΠΎΡΡΡ Π²Π΅ΡΠ΅ΡΡΠ²Π°. ΠΠ½ΠΎ ΡΡΠ΅Π±ΡΠ΅Ρ ΡΡΡΠΎΠΆΠ°ΠΉΡΠ΅Π³ΠΎ Π²ΡΠΏΠΎΠ»Π½Π΅Π½ΠΈΡ ΠΏΡΠΎΠΏΠΎΡΡΠΈΠΉ (Π΄Π»Ρ ΠΠΠΠ ΡΡΠΎ ΡΠΎΠ²Π΅ΡΡΠ΅Π½Π½ΠΎ Π½Π΅ ΡΠ°ΠΊ Π²Π°ΠΆΠ½ΠΎ).
ΠΡΠ²Π΅ΡΠ΄ΠΈΡΠ΅Π»Ρ ΠΠΠ’Π ΠΎΡΠ½ΠΎΡΠΈΡΡΡ ΠΊ ΡΠΎΠΉ ΠΆΠ΅ Π³ΡΡΠΏΠΏΠ΅ Π²Π΅ΡΠ΅ΡΡΠ² Π΄Π»Ρ Ρ ΠΎΠ»ΠΎΠ΄Π½ΠΎΠΉ ΠΏΠΎΠ»ΠΈΠΌΠ΅ΡΠΈΠ·Π°ΡΠΈΠΈ ΡΠΌΠΎΠ» Π½Π° ΡΠΏΠΎΠΊΡΠΈΠ΄Π½ΠΎΠΉ ΠΎΡΠ½ΠΎΠ²Π΅. Π₯Π°ΡΠ°ΠΊΡΠ΅ΡΠ½ΠΎΠΉ ΡΠ΅ΡΡΠΎΠΉ ΡΡΠΈΡΠ°Π΅ΡΡΡ ΡΡ Π²Π°ΡΡΠ²Π°Π½ΠΈΠ΅ ΠΈΠ· Π²ΠΎΠ·Π΄ΡΡ Π° Π²Π»Π°Π³ΠΈ ΠΈ ΡΠ³Π»Π΅ΡΠΎΠ΄Π°, Π±Π»Π°Π³ΠΎΠ΄Π°ΡΡ ΡΡΠΎΠΌΡ ΡΠΎΡ ΡΠ°Π½ΡΡΡ Π΅Π³ΠΎ Π½ΡΠΆΠ½ΠΎ ΠΏΠ»ΠΎΡΠ½ΠΎ Π·Π°ΠΊΡΡΡΡΠΌ. Π‘ΡΠ΅Π΄ΡΡΠ²ΠΎ ΠΎΡΠ²Π΅ΡΠΆΠ΄Π°Π΅Ρ ΡΠΌΠΎΠ»Ρ Π·Π° 1,5 ΡΠ°ΡΠ°.
ΠΠ’ΠΠ 45Π
ΠΡΠΎΡ ΠΌΠ½ΠΎΠ³ΠΎΡΠ΅Π»Π΅Π²ΠΎΠΉ ΠΎΡΠ²Π΅ΡΠ΄ΠΈΡΠ΅Π»Ρ Π²Π»Π°Π΄Π΅Π΅Ρ Β«Π·Π°Π΄Π°Π½Π½ΠΎΠΉ ΠΏΠ»Π°ΡΡΠΈΡΠ½ΠΎΡΡΡΡΒ», Π±Π»Π°Π³ΠΎΠ΄Π°ΡΡ ΡΡΠΎΠΌΡ Π½Π΅ ΠΏΡΠΎΡΠΈΡ Π²Π²Π΅Π΄Π΅Π½ΠΈΡ Π²ΠΎΠ΄Π½ΡΡ ΠΈΠ½Π³ΠΈΠ±ΠΈΡΠΎΡΠΎΠ². ΠΠ³ΠΎ ΠΊΠΎΠ½ΡΠΈΡΡΠ΅Π½ΡΠΈΡ Π±Π»ΠΈΠ·ΠΊΠ° ΠΊ ΡΠ°ΠΌΠΎΠΉ ΡΠΌΠΎΠ»Π΅ ΠΠ-20, ΡΠΌΠ΅ΡΠΈΠ²Π°Π½ΠΈΠ΅ Π±ΡΠ΄Π΅Ρ Π½Π΅ ΡΡΠΆΠ΅Π»ΡΠΌ. Π’Π΅ΠΌΠΏΠ΅ΡΠ°ΡΡΡΠ½Π°Ρ ΡΠ΅Π°ΠΊΡΠΈΡ ΠΎΡ Π΄ΠΎΠ±Π°Π²ΠΊΠΈ ΠΡΠ°Π» 45Π ΠΌΠ΅Π½Π΅Π΅ ΠΊΠΈΠΏΡΡΠ°Ρ, ΡΡΠΎΠΈΡ Π΅ΡΠ΅ ΡΠΊΠ°Π·Π°ΡΡ, ΡΡΠΎ ΠΎΠ½ Π½Π΅ ΡΠΎΠΊΡΠΈΡΠ½ΡΠΉ, Π½Π΅ Π°Π»Π»Π΅ΡΠ³ΠΈΡΠ΅Π½, Π±Π΅Π· ΠΏΡΠΎΡΠΈΠ²Π½ΠΎΠ³ΠΎ Π·Π°ΠΏΠ°Ρ Π°.
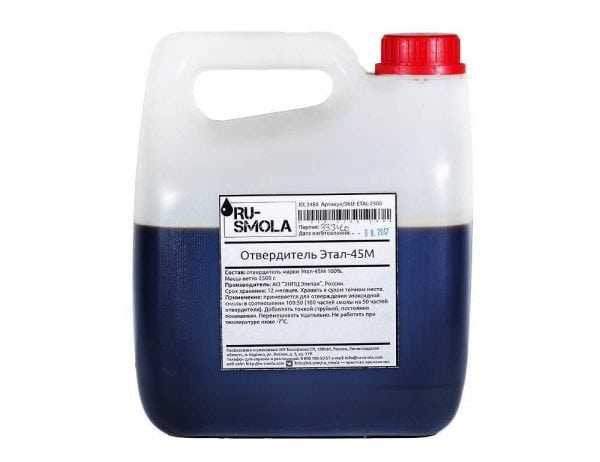
Π‘ΠΏΠΎΡΠΎΠ±Π½ΠΎΡΡΡ ΠΊ ΠΆΠΈΠ·Π½ΠΈ ΡΠΏΠΎΠΊΡΠΈΠ΄ΠΊΠΈ
ΠΡΠ΅ΠΌΠ΅Π½Π΅ΠΌ ΠΆΠΈΠ·Π½ΠΈ Π½Π°Π·ΡΠ²Π°ΡΡ Π²ΡΠ΅ΠΌΠ΅Π½Π½ΠΎΠΉ ΠΏΡΠΎΠΌΠ΅ΠΆΡΡΠΎΠΊ, Π² ΠΊΠΎΡΠΎΡΡΠΉ ΡΠ±Π΅ΡΠ΅Π³Π°Π΅ΡΡΡ ΠΆΠΈΠ΄ΠΊΠΎΠ΅ ΠΈΠ»ΠΈ Π²ΡΠ·ΠΊΠΎΠ΅ ΡΠΎΡΡΠΎΡΠ½ΠΈΠ΅ ΠΌΠ°ΡΡΡ ΠΏΠΎΡΠ»Π΅ Π²Π²Π΅Π΄Π΅Π½ΠΈΡ ΠΎΡΠ²Π΅ΡΠ΄ΠΈΡΠ΅Π»Ρ. Π Π΄Π°Π½Π½ΡΠΉ ΠΏΠ΅ΡΠΈΠΎΠ΄ ΡΠΏΠΎΠΊΡΠΈΠ΄ΠΊΠ° ΠΏΡΠΈΠ³ΠΎΠ΄Π½Π° ΠΊ ΡΠ°Π±ΠΎΡΠ΅. Π£ ΡΠ°Π·Π»ΠΈΡΠ½ΡΡ ΡΠΌΠΎΠ» ΡΠΏΠΎΡΠΎΠ±Π½ΠΎΡΡΡ ΠΊ ΠΆΠΈΠ·Π½ΠΈ ΡΠ°Π·Π»ΠΈΡΠ½Π°Ρ, ΠΊΠ°ΠΊ ΠΈ Ρ ΠΎΡΠ²Π΅ΡΠ΄ΠΈΡΠ΅Π»Π΅ΠΉ. Π Π±ΠΎΠ»ΡΡΠΈΠ½ΡΡΠ²Π΅ ΡΠ»ΡΡΠ°Π΅Π² Π΄Π°Π½Π½ΡΠΉ ΠΏΠΎΠΊΠ°Π·Π°ΡΠ΅Π»Ρ ΡΠΎΡΡΠ°Π²Π»ΡΠ΅Ρ 30β60 ΠΌΠΈΠ½ΡΡ.
ΠΡΠΈ Π΄ΠΎΠ±Π°Π²Π»Π΅Π½ΠΈΠΈ ΠΠΠΠ Π² ΠΠ-20 Π²ΡΠ΅ΠΌΡ ΠΆΠΈΠ·Π½ΠΈ ΡΠ°Π²Π½ΠΎ 30β50 ΠΌΠΈΠ½ΡΡ ΠΈ Π·Π°Π²ΠΈΡΠΈΡ ΠΎΡ ΡΠ΅ΠΌΠΏΠ΅ΡΠ°ΡΡΡΡ, ΠΊΠΎΠ»ΠΈΡΠ΅ΡΡΠ²Π° ΠΎΡΠ²Π΅ΡΠ΄ΠΈΡΠ΅Π»Ρ. ΠΠΎΠ»Π½Π°Ρ ΠΏΠΎΠ»ΠΈΠΌΠ΅ΡΠΈΠ·Π°ΡΠΈΡ ΠΏΡΠΎΠ΄ΠΎΠ»ΠΆΠ°Π΅ΡΡΡ ΠΎΡ 24 ΡΠ°ΡΠΎΠ² Π΄ΠΎ Π½Π΅ΡΠΊΠΎΠ»ΡΠΊΠΈΡ ΡΡΡΠΎΠΊ. ΠΠ»Ρ ΠΡΠ°Π» 45Π ΡΠΏΠΎΡΠΎΠ±Π½ΠΎΡΡΡ ΠΊ ΠΆΠΈΠ·Π½ΠΈ Π² 3 ΡΠ°Π·Π° Π±ΠΎΠ»ΡΡΠ΅, Π° ΠΏΠΎΠ»Π½Π°Ρ ΠΏΠΎΠ»ΠΈΠΌΠ΅ΡΠΈΠ·Π°ΡΠΈΡ Π°Π½Π°Π»ΠΎΠ³ΠΈΡΠ½Π°Ρ, ΡΡΠΎ ΠΊΠΎΠΌΡΠΎΡΡΠ½ΠΎ Π΄Π»Ρ ΠΌΠ°ΡΡΠ΅ΡΠ°.
Π Π°Π·Π»ΠΈΡΠ½ΠΎΠ΅ ΠΊΠ°ΡΠ΅ΡΡΠ²ΠΎ ΠΏΡΠΈΠΊΠ»Π΅ΠΈΠ²Π°Π½ΠΈΡ
ΠΠ°ΡΠ΅ΡΡΠ²ΠΎ ΡΠΏΠΎΠΊΡΠΈΠ΄ΠΊΠΈ ΠΌΠΎΠΆΠ΅Ρ ΠΎΡΠ»ΠΈΡΠ°ΡΡΡΡ Π² Π·Π°Π²ΠΈΡΠΈΠΌΠΎΡΡΠΈ ΠΎΡ ΠΌΠ°ΡΠΊΠΈ ΠΎΡΠ²Π΅ΡΠ΄ΠΈΡΠ΅Π»Ρ, Π²ΠΎΠ΄Π½ΠΎΠ³ΠΎ ΠΈΠ½Π³ΠΈΠ±ΠΈΡΠΎΡΠ°. Π§Π΅ΠΌ Π½Π°ΠΌΠ½ΠΎΠ³ΠΎ Π΄ΠΎΡΠΎΠ³ΠΈΠ΅ ΠΈ ΡΡΡΠ΅ΠΊΡΠ½ΡΠ΅ Π΄ΠΎΠ±Π°Π²ΠΊΠΈ ΠΈΡΠΏΠΎΠ»ΡΠ·ΡΡΡΡΡ, ΡΠ΅ΠΌ Π±ΠΎΠ»ΡΡΠ΅ Π³ΠΎΡΠΎΠ²ΠΎΠ΅ ΠΈΠ·Π΄Π΅Π»ΠΈΠ΅ Π±ΡΠ΄Π΅Ρ ΠΏΠΎΠ΄Ρ ΠΎΠ΄ΠΈΡΡ ΡΡΠ΅Π±ΠΎΠ²Π°Π½ΠΈΡΠΌ. ΠΠ»Π°Π³ΠΎΠ΄Π°ΡΡ ΡΡΠΎΠΌΡ ΡΠΊΠΎΠ½ΠΎΠΌΠΈΡΡ Π½Π΅ Π½ΡΠΆΠ½ΠΎ ΠΈ ΠΏΡΠΈΠΎΠ±ΡΠ΅ΡΠ°ΡΡ Π½Π°ΠΈΠ±ΠΎΠ»Π΅Π΅ Π΄Π΅ΡΠ΅Π²ΡΠ΅ Π½Π°ΠΏΠΎΠ»Π½ΠΈΡΠ΅Π»ΠΈ.
Π£ΠΏΠ°ΠΊΠΎΠ²ΠΊΠ°, Ρ ΡΠ°Π½Π΅Π½ΠΈΠ΅ ΠΈ ΠΏΠ΅ΡΠ΅Π²ΠΎΠ·ΠΊΠ°
Π‘ΠΌΠΎΠ»Ρ Π½Π° ΡΠΏΠΎΠΊΡΠΈΠ΄Π½ΠΎΠΉ ΠΎΡΠ½ΠΎΠ²Π΅ ΡΠΏΠ°ΠΊΠΎΠ²ΡΡΡ Π² ΡΠ°ΡΡ ΠΏΠΎ 50β220 ΠΊΠ³ (Π±Π°ΡΠ°Π±Π°Π½Ρ), Π° Π΅ΡΠ΅ Π² ΠΊΠ°Π½ΠΈΡΡΡΡ, Π΅ΠΌΠΊΠΎΡΡΠΈ ΠΈΠ· ΠΏΠ»Π°ΡΡΠΈΠΊΠ° ΠΎΡ 0,5 ΠΊΠ³ ΠΈ Π±ΠΎΠ»Π΅Π΅. Π’ΡΠ°Π½ΡΠΏΠΎΡΡΠΈΡΡΡΡ ΡΡΠ΅Π΄ΡΡΠ²ΠΎ Π½Π° ΠΊΡΡΡΠΎΠΌ ΡΡΠ°Π½ΡΠΏΠΎΡΡΠ΅. Π Π°Π·ΡΠ΅ΡΠ°Π΅ΡΡΡ Ρ ΡΠ°Π½Π΅Π½ΠΈΠ΅ ΠΌΠ°ΡΠ΅ΡΠΈΠ°Π»Π° ΠΏΡΠΈ ΡΠ΅ΠΌΠΏΠ΅ΡΠ°ΡΡΡΠ΅ +15β¦+40 Π³ΡΠ°Π΄ΡΡΠΎΠ², ΠΏΠ»ΠΎΡΠ½ΠΎ Π·Π°ΠΊΡΡΡΡΠΌ, Π²Π΄Π°Π»Π΅ΠΊΠ΅ ΠΎΡ ΡΠΎΠ»Π½ΡΠ°. ΠΠ΅Π»ΡΠ·Ρ ΡΠΎΡ ΡΠ°Π½ΡΡΡ Π΅Π³ΠΎ ΡΡΠ΄ΠΎΠΌ Ρ ΠΊΠΈΡΠ»ΠΎΡΠ°ΠΌΠΈ ΠΈ ΠΎΠΊΠΈΡΠ»ΠΈΡΠ΅Π»ΡΠΌΠΈ.
ΠΠ΅Π·ΠΎΠΏΠ°ΡΠ½ΠΎΡΡΡ ΠΠ-20
Π Π°Π±ΠΎΡΡ Ρ Π΄Π°Π½Π½ΡΠΌ ΡΡΠ΅Π΄ΡΡΠ²ΠΎΠΌ Π΄ΠΎΠ»ΠΆΠ½Ρ ΠΏΡΠΎΠ²ΠΎΠ΄ΠΈΡΡΡΡ Π² ΠΏΡΠ΅ΠΊΡΠ°ΡΠ½ΠΎ ΠΏΡΠΎΠ²Π΅ΡΡΠΈΠ²Π°Π΅ΠΌΠΎΠΌ ΠΏΠΎΠΌΠ΅ΡΠ΅Π½ΠΈΠΈ ΠΈΠ»ΠΈ Π΅ΡΠ»ΠΈ Π΅ΡΡΡ Π½Π°Π»ΠΈΡΠΈΠ΅ Π²ΡΡΠΎΠΊΠΎΠΊΠ°ΡΠ΅ΡΡΠ²Π΅Π½Π½ΠΎΠΉ Π²Π΅Π½ΡΠΈΠ»ΡΡΠΈΠΈ. ΠΠ»Ρ Π·Π°ΡΠΈΡΡ Π½Π΅ΠΎΠ±Ρ ΠΎΠ΄ΠΈΠΌΠΎ ΠΈΡΠΏΠΎΠ»ΡΠ·ΠΎΠ²Π°ΡΡ ΡΠ΅ΡΠΏΠΈΡΠ°ΡΠΎΡ, ΠΎΡΠΊΠΈ, ΠΏΠ΅ΡΡΠ°ΡΠΊΠΈ, ΠΏΠ»ΠΎΡΠ½ΡΡ ΠΎΠ΄Π΅ΠΆΠ΄Ρ ΠΈΠ»ΠΈ ΡΠ°ΡΡΡΠΊ. ΠΠ-20 Π½Π΅ Π²Π·ΡΡΠ²ΠΎΠΎΠΏΠ°ΡΠ½Π°, ΠΎΠ΄Π½Π°ΠΊΠΎ ΠΏΡΠΈ ΠΏΠΎΠΏΠ°Π΄Π°Π½ΠΈΠΈ Π² ΠΎΠ³ΠΎΠ½Ρ Π³ΠΎΡΠΈΡ.
Π‘ΡΠ΅ΠΏΠ΅Π½Ρ ΠΎΠΏΠ°ΡΠ½ΠΎΡΡΠΈ ΡΠΌΠΎΠ»Ρ ΡΠ²ΠΎΠΉΡΡΠ²Π΅Π½Π½Π° Π΄Π»Ρ Π²Π΅ΡΠ΅ΡΡΠ² 2-Π³ΠΎ ΠΊΠ»Π°ΡΡΠ° Π²Π»ΠΈΡΠ½ΠΈΡ Π½Π° ΡΠ΅Π»ΠΎΠ²Π΅ΡΠ΅ΡΠΊΠΈΠΉ ΠΎΡΠ³Π°Π½ΠΈΠ·ΠΌ. ΠΡΠΈ ΠΏΠΎΠΏΠ°Π΄Π°Π½ΠΈΠΈ Π½Π° ΠΏΠΎΠΊΡΠΎΠ² ΠΊΠΎΠΆΠΈ Π½Π΅ΡΠ΅Π΄ΠΊΠΎ ΠΏΠΎΡΠ²Π»ΡΡΡΡΡ Π°Π»Π»Π΅ΡΠ³ΠΈΠΈ, Π΄Π΅ΡΠΌΠ°ΡΠΈΡΡ. ΠΠΎΡΠ°ΠΆΠ΅Π½Π½ΠΎΠ΅ ΠΌΠ΅ΡΡΠΎ Π½ΡΠΆΠ½ΠΎ ΠΏΠΎΠΌΡΡΡ Ρ ΠΌΡΠ»ΠΎΠΌ, Π²ΡΡΠ΅ΡΠ΅ΡΡ ΡΠΏΠΈΡΡΠΎΠΌ, ΠΏΠΎΡΠ»Π΅ ΠΏΡΠΎΠΌΠ°Π·Π°ΡΡ Π²Π°Π·Π΅Π»ΠΈΠ½ΠΎΠΌ, ΠΊΠ°ΡΡΠΎΡΠΎΠ²ΡΠΌ ΠΌΠ°ΡΠ»ΠΎΠΌ.
ΠΊΠ°ΠΊ ΠΈΡΠΏΠΎΠ»ΡΠ·ΠΎΠ²Π°ΡΡ ΡΠΏΠΎΠΊΡΠΈΠ΄Π½ΡΡ ΠΏΠ°Π»ΠΊΡ Π΄Π»Ρ Π·Π°ΠΏΠΎΠ»Π½Π΅Π½ΠΈΡ ΠΎΡΠ²Π΅ΡΡΡΠΈΠΉ ΠΈ ΡΡΠ΅ΡΠΈΠ½ β Π·Π°ΠΏΠ΅ΡΠ°ΡΠ°ΡΡ Π¦ΠΠ’Π
versace-promo.ru
Π‘ΠΌΠΎΠ»Π° ΠΠ-20 ΠΠΠ‘Π’ 10587-84
Π‘ΠΌΠΎΠ»Π° ΠΠ-20 ΠΏΡΠ΅Π΄ΡΡΠ°Π²Π»ΡΠ΅Ρ ΡΠΎΠ±ΠΎΠΉ ΡΠ°ΡΡΠ²ΠΎΡΠΈΠΌΡΠΉ ΠΈ ΠΏΠ»Π°Π²ΠΊΠΈΠΉ ΡΠ΅Π°ΠΊΡΠΈΠΎΠ½Π½ΠΎ-ΡΠΏΠΎΡΠΎΠ±Π½ΡΠΉ ΠΎΠ»ΠΈΠ³ΠΎΠΌΠ΅ΡΠ½ΡΠΉ ΠΏΡΠΎΠ΄ΡΠΊΡ Π½Π° ΠΎΡΠ½ΠΎΠ²Π΅ ΡΠΏΠΈΡ
Π»ΠΎΡΠ³ΠΈΠ΄ΡΠΈΠ½Π° ΠΈ Π΄ΠΈΡΠ΅Π½ΠΈΠ»ΠΎΠ»ΠΏΡΠΎΠΏΠ°Π½Π°. ΠΠ-20 ΠΈΡΠΏΠΎΠ»ΡΠ·ΡΠ΅ΡΡΡ Π² ΠΏΡΠΎΠΌΡΡΠ»Π΅Π½Π½ΠΎΡΡΠΈ Π² ΡΠΈΡΡΠΎΠΌ Π²ΠΈΠ΄Π΅, ΠΈΠ»ΠΈ Π² ΠΊΠ°ΡΠ΅ΡΡΠ²Π΅ ΠΊΠΎΠΌΠΏΠΎΠ½Π΅Π½ΡΠΎΠ² ΠΊΠΎΠΌΠΏΠΎΠ·ΠΈΡΠΈΠΎΠ½Π½ΡΡ
ΠΌΠ°ΡΠ΅ΡΠΈΠ°Π»ΠΎΠ² — Π·Π°Π»ΠΈΠ²ΠΎΡΠ½ΡΡ
ΠΈ ΠΏΡΠΎΠΏΠΈΡΠΎΡΠ½ΡΡ
ΠΊΠΎΠΌΠΏΠ°ΡΠ½Π΄ΠΎΠ², ΠΊΠ»Π΅Π΅Π², Π³Π΅ΡΠΌΠ΅ΡΠΈΠΊΠΎΠ², ΡΠ²ΡΠ·ΡΡΡΠΈΡ
Π΄Π»Ρ Π°ΡΠΌΠΈΡΠΎΠ²Π°Π½Π½ΡΡ
ΠΏΠ»Π°ΡΡΠΈΠΊΠΎΠ², Π·Π°ΡΠΈΡΠ½ΡΡ
ΠΏΠΎΠΊΡΡΡΠΈΠΉ.
ΠΠ΅ΠΎΡΠ²Π΅ΡΠΆΠ΄Π΅Π½Π½Π°Ρ Π΄ΠΈΠ°Π½ΠΎΠ²Π°Ρ ΡΠΏΠΎΠΊΡΠΈΠ΄Π½Π°Ρ ΡΠΌΠΎΠ»Π° ΠΠ-20 ΠΌΠΎΠΆΠ΅Ρ Π±ΡΡΡ ΠΏΠ΅ΡΠ΅Π²Π΅Π΄Π΅Π½Π° Π² Π½Π΅ΠΏΠ»Π°Π²ΠΊΠΎΠ΅ ΠΈ Π½Π΅ΡΠ°ΡΡΠ²ΠΎΡΠΈΠΌΠΎΠ΅ ΡΠΎΡΡΠΎΡΠ½ΠΈΠ΅ Π΄Π΅ΠΉΡΡΠ²ΠΈΠ΅ΠΌ ΠΎΡΠ²Π΅ΡΠΆΠ΄Π°ΡΡΠΈΡ
Π°Π³Π΅Π½ΡΠΎΠ² (ΠΎΡΠ²Π΅ΡΠ΄ΠΈΡΠ΅Π»Π΅ΠΉ) ΡΠ°Π·Π»ΠΈΡΠ½ΠΎΠ³ΠΎ ΡΠΈΠΏΠ° — Π°Π»ΠΈΡΠ°ΡΠΈΡΠ΅ΡΠΊΠΈΡ
ΠΈ Π°ΡΠΎΠΌΠ°ΡΠΈΡΠ΅ΡΠΊΠΈΡ
Π΄ΠΈ- ΠΈ ΠΏΠΎΠ»ΠΈΠ°ΠΌΠΈΠ½ΠΎΠ², Π½ΠΈΠ·ΠΊΠΎΠΌΠΎΠ»Π΅ΠΊΡΠ»ΡΡΠ½ΡΡ
ΠΏΠΎΠ»ΠΈΠ°ΠΌΠΈΠ΄ΠΎΠ², Π΄ΠΈ- ΠΈ ΠΏΠΎΠ»ΠΈΠΊΠ°ΡΠ±ΠΎΠ½ΠΎΠ²ΡΡ
ΠΊΠΈΡΠ»ΠΎΡ ΠΈ ΠΈΡ
Π°Π½Π³ΠΈΠ΄ΡΠΈΠ΄ΠΎΠ², ΡΠ΅Π½ΠΎΠ»ΡΠΎΡΠΌΠ°Π»ΡΠ΄Π΅Π³ΠΈΠ΄Π½ΡΡ
ΡΠΌΠΎΠ» ΠΈ Π΄Ρ ΡΠΎΠ΅Π΄ΠΈΠ½Π΅Π½ΠΈΠΉ. Π Π·Π°Π²ΠΈΡΠΈΠΌΠΎΡΡΠΈ ΠΎΡ ΠΏΡΠΈΠΌΠ΅Π½ΡΠ΅ΠΌΠΎΠ³ΠΎ ΠΎΡΠ²Π΅ΡΠ΄ΠΈΡΠ΅Π»Ρ ΡΠ²ΠΎΠΉΡΡΠ²Π° ΠΎΡΠ²Π΅ΡΠΆΠ΄Π΅Π½Π½ΠΎΠΉ ΡΠΏΠΎΠΊΡΠΈΠ΄Π½ΠΎΠΉ ΡΠΌΠΎΠ»Ρ ΠΠ-20 ΠΌΠΎΠ³ΡΡ ΠΈΠ·ΠΌΠ΅Π½ΡΡΡΡΡ Π² ΡΠ°ΠΌΡΡ
ΡΠΈΡΠΎΠΊΠΈΡ
ΠΏΡΠ΅Π΄Π΅Π»Π°Ρ
.
ΠΠΏΠΎΠΊΡΠΈΠ΄Π½Π°Ρ ΡΠΌΠΎΠ»Π° ΠΠ-20 Π½Π΅ Π²Π·ΡΡΠ²ΠΎΠΎΠΏΠ°ΡΠ½Π°, Π½ΠΎ Π³ΠΎΡΠΈΡ ΠΏΡΠΈ Π²Π½Π΅ΡΠ΅Π½ΠΈΠΈ Π² ΠΈΡΡΠΎΡΠ½ΠΈΠΊ ΠΎΠ³Π½Ρ. ΠΠ΅ΡΡΡΠΈΠ΅ ΠΊΠΎΠΌΠΏΠΎΠ½Π΅Π½ΡΡ (ΡΠΎΠ»ΡΠΎΠ» ΠΈ ΡΠΏΠΈΡ
Π»ΠΎΡΠ³ΠΈΠ΄ΡΠΈΠ½) ΡΠΎΠ΄Π΅ΡΠΆΠ°ΡΡΡ Π² ΡΠΌΠΎΠ»Π΅ Π² ΠΊΠΎΠ»ΠΈΡΠ΅ΡΡΠ²Π°Ρ
, ΠΎΠΏΡΠ΅Π΄Π΅Π»ΡΠ΅ΠΌΡΡ
ΠΈΡΠΊΠ»ΡΡΠΈΡΠ΅Π»ΡΠ½ΠΎ Π°Π½Π°Π»ΠΈΡΠΈΡΠ΅ΡΠΊΠΈΠΌΠΈ ΠΌΠ΅ΡΠΎΠ΄Π°ΠΌΠΈ, ΠΈ ΠΎΡΠ½ΠΎΡΡΡΡΡ ΠΊ Π²Π΅ΡΠ΅ΡΡΠ²Π°ΠΌ 2-Π³ΠΎ ΠΊΠ»Π°ΡΡΠ° ΠΎΠΏΠ°ΡΠ½ΠΎΡΡΠΈ ΠΏΠΎ ΡΡΠ΅ΠΏΠ΅Π½ΠΈ Π²ΠΎΠ·Π΄Π΅ΠΉΡΡΠ²ΠΈΡ Π½Π° ΠΎΡΠ³Π°Π½ΠΈΠ·ΠΌ ΡΠ΅Π»ΠΎΠ²Π΅ΠΊΠ°.
Π₯Π°ΡΠ°ΠΊΡΠ΅ΡΠΈΡΡΠΈΠΊΠΈ ΡΠΌΠΎΠ»Ρ ΠΠ-20
Β | ΠΡΡΡΠΈΠΉ ΡΠΎΡΡ | ΠΠ΅ΡΠ²ΡΠΉ ΡΠΎΡΡ |
ΠΠ½Π΅ΡΠ½ΠΈΠΉ Π²ΠΈΠ΄ | ΠΡΠ·ΠΊΠ°Ρ, ΠΏΡΠΎΠ·ΡΠ°ΡΠ½Π°Ρ | ΠΡΠ·ΠΊΠ°Ρ, ΠΏΡΠΎΠ·ΡΠ°ΡΠ½Π°Ρ |
Π¦Π²Π΅Ρ ΠΏΠΎ ΠΆΠ΅Π»Π΅Π·ΠΎ-ΠΊΠΎΠ±Π°Π»ΡΡΠΎΠ²ΠΎΠΉ ΡΠΊΠ°Π»Π΅, Π½Π΅ Π±ΠΎΠ»Π΅Π΅ | 3 | 8 |
ΠΠ°ΡΡΠΎΠ²Π°Ρ Π΄ΠΎΠ»Ρ ΡΠΏΠΎΠΊΡΠΈΠ΄Π½ΡΡ Π³ΡΡΠΏΠΏ, % | 20-22,5 | 20,2-22,5 |
ΠΠ°ΡΡΠΎΠ²Π°Ρ Π΄ΠΎΠ»Ρ ΠΈΠΎΠ½Π° Ρ Π»ΠΎΡΠ°, %, Π½Π΅ Π±ΠΎΠ»Π΅Π΅ | 0,001 | 0,005 |
ΠΠ°ΡΡΠΎΠ²Π°Ρ Π΄ΠΎΠ»Ρ ΠΎΠΌΡΠ»ΡΠ΅ΠΌΠΎΠ³ΠΎ Ρ Π»ΠΎΡΠ°, %, Π½Π΅ Π±ΠΎΠ»Π΅Π΅ | 0,3 | 0,8 |
ΠΠ°ΡΡΠΎΠ²Π°Ρ Π΄ΠΎΠ»Ρ Π³ΠΈΠ΄ΡΠΎΠΊΡΠΈΠ»ΡΠ½ΡΡ Π³ΡΡΠΏΠΏ, %, Π½Π΅ Π±ΠΎΠ»Π΅Π΅ | 1,7 | — |
ΠΠ°ΡΡΠΎΠ²Π°Ρ Π΄ΠΎΠ»Ρ Π»Π΅ΡΡΡΠΈΡ Π²Π΅ΡΠ΅ΡΡΠ², %, Π½Π΅ Π±ΠΎΠ»Π΅Π΅ | 0,2 | 0,8 |
ΠΠΈΠ½Π°ΠΌΠΈΡΠ΅ΡΠΊΠ°Ρ Π²ΡΠ·ΠΊΠΎΡΡΡ, ΠΠ°*ΡΠ΅ΠΊ, ΠΏΡΠΈ (25Β±0.1)Β°C ΠΏΡΠΈ (50Β±0.1)Β°C | Β 13-20— | Β 12-25— |
Π’Π΅ΠΌΠΏΠ΅ΡΠ°ΡΡΡΠ° ΡΠ°Π·ΠΌΡΠ³ΡΠ΅Π½ΠΈΡ ΠΏΠΎ ΠΌΠ΅ΡΠΎΠ΄Ρ Β«ΠΊΠΎΠ»ΡΡΠΎ ΠΈ ΡΠ°ΡΒ», Β°C, Π½Π΅ Π²ΡΡΠ΅ | — | — |
ΠΡΠ΅ΠΌΡ ΠΆΠ΅Π»Π°ΡΠΈΠ·Π°ΡΠΈΠΈ, ΡΠ°Ρ., Π½Π΅ ΠΌΠ΅Π½Π΅Π΅ | 8 | 4 |
ΠΠΏΠΎΠΊΡΠΈΠ΄Π½Π°Ρ ΡΠΌΠΎΠ»Π° ΠΠ-20 — Π΄Π²ΡΡ ΠΊΠΎΠΌΠΏΠΎΠ½Π΅Π½ΡΠ½Π°Ρ ΡΠΌΠΎΠ»Π°. ΠΠ»Ρ Π΅Ρ ΠΎΡΠ²Π΅ΡΠΆΠ΄Π΅Π½ΠΈΡ ΡΡΠ΅Π±ΡΡΡΡΡ ΠΎΡΠ²Π΅ΡΠ΄ΠΈΡΠ΅Π»ΠΈ Π΄Π»Ρ ΡΠΏΠΎΠΊΡΠΈΠ΄Π½ΡΡ ΡΠΌΠΎΠ» (ΠΠΠΠ, Π’ΠΠ’Π, ΠΈ Ρ.Π΄.). ΠΡΠΈ ΠΈΡΠΏΠΎΠ»ΡΠ·ΠΎΠ²Π°Π½ΠΈΠΈ ΠΎΡΠ²Π΅ΡΠ΄ΠΈΡΠ΅Π»Ρ ΠΌΠ°ΡΠΊΠΈ ΠΠΠΠ (ΠΏΠΎΠ»ΠΈΡΡΠΈΠ»Π΅Π½ΠΏΠΎΠ»ΠΈΠ°ΠΌΠΈΠ½), Π΅Π³ΠΎ ΡΡΠ΅Π±ΡΠ΅ΡΡΡ ΠΎΡ 5 Π΄ΠΎ 30 %, Π² Π·Π°Π²ΠΈΡΠΈΠΌΠΎΡΡΠΈ ΠΎΡ Π²ΠΈΠ΄Π° ΡΠ°Π±ΠΎΡ. Π‘ΡΠ΅Π΄Π½Π΅Π΅ ΡΠΎΠΎΡΠ½ΠΎΡΠ΅Π½ΠΈΠ΅ 10 -15% ΠΎΡ ΠΌΠ°ΡΡΡ ΡΠΌΠΎΠ»Ρ.
Π‘ΠΎΠ΅Π΄ΠΈΠ½Π΅Π½ΠΈΠ΅ ΡΠΌΠΎΠ»Ρ Ρ ΠΎΡΠ²Π΅ΡΠ΄ΠΈΡΠ΅Π»Π΅ΠΌ Π΄ΠΎΠ»ΠΆΠ½ΠΎ ΠΏΡΠΎΠΈΠ·Π²ΠΎΠ΄ΠΈΡΡΡ ΠΏΡΠΈ ΡΠ΅ΠΌΠΏΠ΅ΡΠ°ΡΡΡΠ΅ Π½Π΅ Π½ΠΈΠΆΠ΅ ΡΠ΅ΠΌ 20 Β°C. ΠΡΠ΅ΠΌΡ ΠΆΠ΅Π»Π°ΡΠΈΠ½ΠΈΠ·Π°ΡΠΈΠΈ ΡΠΎΡΡΠ°Π²Π»ΡΠ΅Ρ, ΠΏΡΠΈΠΌΠ΅ΡΠ½ΠΎ — 1,5 ΡΠ°ΡΠ°, Π° Π²ΡΠ΅ΠΌΡ ΠΏΠΎΠ»Π½ΠΎΠ³ΠΎ ΠΎΡΠ²Π΅ΡΠΆΠ΄Π΅Π½ΠΈΡ — 24 ΡΠ°ΡΠ°.
Π‘ΡΠΎΠΊ Ρ ΡΠ°Π½Π΅Π½ΠΈΡ:
ΠΠ°ΡΠ°Π½ΡΠΈΠΉΠ½ΡΠΉ ΡΡΠΎΠΊ Ρ ΡΠ°Π½Π΅Π½ΠΈΡΒ β 12 ΠΌΠ΅ΡΡΡΠ΅Π²Β Ρ Π΄Π°ΡΡ ΠΏΡΠΎΠΈΠ·Π²ΠΎΠ΄ΡΡΠ²Π°.
Β
ΠΠ’ΠΠΠ Π ΠΠΠΠΠΠΠ¦ΠΠ:
Π’Π΅Π»Π΅ΡΠΎΠ½/ΡΠ°ΠΊΡ: +7 (4852) 28-88-73 -ΠΌΠ½ΠΎΠ³ΠΎΠΊΠ°Π½Π°Π»ΡΠ½ΡΠΉ
ΠΠ»Π΅ΠΊΡΡΠΎΠ½Π½Π°Ρ ΠΏΠΎΡΡΠ°:
npklkp.ru
Π‘ΠΌΠΎΠ»Π° ΠΠ-20
Π‘ΠΠΠΠ ΠΠ-20ΠΠΠ‘Π’ 10587-84
ΠΏΡΠΈΠΌΠ΅Π½Π΅Π½ΠΈΠ΅:
ΠΠΏΠΎΠΊΡΠΈΠ΄Π½ΠΎ-Π΄ΠΈΠ°Π½ΠΎΠ²Π°Ρ ΡΠΌΠΎΠ»Π° ΠΌΠ°ΡΠΊΠΈ ΠΠ-20 ΠΈΡΠΏΠΎΠ»ΡΠ·ΡΠ΅ΡΡΡ Π² ΡΠ»Π΅ΠΊΡΡΠΎΡΠ΅Ρ
Π½ΠΈΡΠ΅ΡΠΊΠΎΠΉ ΠΈ ΡΠ°Π΄ΠΈΠΎΡΠ»Π΅ΠΊΡΡΠΎΠ½Π½ΠΎΠΉ ΠΏΡΠΎΠΌΡΡΠ»Π΅Π½Π½ΠΎΡΡΠΈ, ΠΏΡΠΈΠ±ΠΎΡΠΎ-, Π°Π²ΠΈΠ°-, ΡΡΠ΄ΠΎ- ΠΈ ΠΌΠ°ΡΠΈΠ½ΠΎΡΡΡΠΎΠ΅Π½ΠΈΠΈ ΠΈ Π² ΡΡΡΠΎΠΈΡΠ΅Π»ΡΡΡΠ²Π΅ Π² ΠΊΠ°ΡΠ΅ΡΡΠ²Π΅ ΠΊΠΎΠΌΠΏΠΎΠ½Π΅Π½ΡΠ° Π·Π°Π»ΠΈΠ²ΠΎΡΠ½ΡΡ
ΠΈ ΠΏΡΠΎΠΏΠΈΡΠΎΡΠ½ΡΡ
ΠΊΠΎΠΌΠΏΠ°ΡΠ½Π΄ΠΎΠ², ΠΊΠ»Π΅Π΅Π² Ρ
ΠΎΠ»ΠΎΠ΄Π½ΠΎΠ³ΠΎ ΠΎΡΠ²Π΅ΡΠΆΠ΄Π΅Π½ΠΈΡ, Π³Π΅ΡΠΌΠ΅ΡΠΈΠΊΠΎΠ² ΠΈ ΡΠ²ΡΠ·ΡΡΡΠΈΡ
Π΄Π»Ρ Π°ΡΠΌΠΈΡΠΎΠ²Π°Π½Π½ΡΡ
ΠΏΠ»Π°ΡΡΠΈΠΊΠΎΠ².
ΠΎΡΠΎΠ±Π΅Π½Π½ΠΎΡΡΠΈ:
Π‘ΠΌΠΎΠ»Π° ΠΠ-20 ΡΠ°ΠΊΠΆΠ΅ ΠΏΡΠ΅Π΄Π½Π°Π·Π½Π°ΡΠ΅Π½Π° Π΄Π»Ρ Π΄ΠΎΠ»Π³ΠΎΠ²ΡΠ΅ΠΌΠ΅Π½Π½ΠΎΠΉ Π·Π°ΡΠΈΡΡ ΠΌΠ΅ΡΠ°Π»Π»ΠΈΡΠ΅ΡΠΊΠΈΡ
, ΡΡΠ°Π»ΡΠ½ΡΡ
ΠΈ Π±Π΅ΡΠΎΠ½Π½ΡΡ
ΠΈΠ·Π΄Π΅Π»ΠΈΠΉ, ΡΠ°Π±ΠΎΡΠ°ΡΡΠΈΡ
Π² ΡΠΈΠ»ΡΠ½ΠΎ ΠΊΠΎΡΡΠΎΠ·ΠΈΠΉΠ½ΠΎΠΉ ΡΡΠ΅Π΄Π΅ ΠΈ ΠΏΠΎΠΊΡΡΠΆΠ΅Π½Π½ΡΡ
Π² ΠΆΠΈΠ΄ΠΊΠΎΡΡΡ, Π½Π° ΠΏΡΠΈΠΌΠ΅Ρ Π²Π½ΡΡΡΠ΅Π½Π½ΠΈΡ
ΠΏΠΎΠ²Π΅ΡΡ
Π½ΠΎΡΡΠ΅ΠΉ ΡΠΈΡΡΠ΅ΡΠ½ Π΄Π»Ρ ΡΡΡΠΎΠΉ Π½Π΅ΡΡΠΈ ΠΈ ΠΌΠ°Π·ΡΡΠ°.
ΠΡΡΠΎΠΊΠΎΠ²ΡΠ·ΠΊΠ°Ρ ΠΏΡΠΎΠ·ΡΠ°ΡΠ½Π°Ρ ΠΆΠΈΠ΄ΠΊΠΎΡΡΡ Π±Π΅Π· Π²ΠΈΠ΄ΠΈΠΌΡΡ
ΠΌΠ΅Ρ
Π°Π½ΠΈΡΠ΅ΡΠΊΠΈΡ
Π²ΠΊΠ»ΡΡΠ΅Π½ΠΈΠΉ ΠΈ ΡΠ»Π΅Π΄ΠΎΠ² Π²ΠΎΠ΄Ρ. ΠΠ΅ΠΎΡΠ²Π΅ΡΠΆΠ΄ΡΠ½Π½ΡΠ΅ ΡΠΌΠΎΠ»Ρ ΠΌΠΎΠ³ΡΡ Π±ΡΡΡ ΠΏΠ΅ΡΠ΅Π²Π΅Π΄Π΅Π½Ρ Π² Π½Π΅ΠΏΠ»Π°Π²ΠΊΠΎΠ΅ ΠΈ Π½Π΅ΡΠ°ΡΡΠ²ΠΎΡΠΈΠΌΠΎΠ΅ ΡΠΎΡΡΠΎΡΠ½ΠΈΠ΅ Π΄Π΅ΠΉΡΡΠ²ΠΈΠ΅ΠΌ ΠΎΡΠ²Π΅ΡΠΆΠ΄Π°ΡΡΠΈΡ
Π°Π³Π΅Π½ΡΠΎΠ² ΡΠ°Π·Π»ΠΈΡΠ½ΠΎΠ³ΠΎ ΡΠΈΠΏΠ°. ΠΠΏΠΎΠΊΡΠΈΠ΄Π½ΡΠΉ ΡΠΊΠ²ΠΈΠ²Π°Π»Π΅Π½Ρ 269-239.
Π ΠΎΡΠ²Π΅ΡΠΆΠ΄ΡΠ½Π½ΠΎΠΌ ΡΠΎΡΡΠΎΡΠ½ΠΈΠΈ ΠΠ-20 ΠΎΡΠ»ΠΈΡΠ°ΡΡΡΡ Π²ΡΡΠΎΠΊΠΈΠΌ Π΄ΠΈΡΠ»Π΅ΠΊΡΡΠΈΡΠ΅ΡΠΊΠΈΠΌ ΠΏΠΎΠΊΠ°Π·Π°ΡΠ΅Π»Π΅ΠΌ, Ρ ΠΎΡΠΎΡΠ΅ΠΉ ΠΌΠ΅Ρ Π°Π½ΠΈΡΠ΅ΡΠΊΠΎΠΉ ΠΏΡΠΎΡΠ½ΠΎΡΡΡΡ ΠΈ ΡΡΠΎΠΉΠΊΠΎΡΡΡΡ ΠΊ ΡΠ°Π·Π»ΠΈΡΠ½ΡΠΌ ΡΠ°ΡΡΠ²ΠΎΡΠΈΡΠ΅Π»ΡΠΌ.
ΠΎΡΠ½ΠΎΠ²Π½ΡΠ΅ Ρ
Π°ΡΠ°ΠΊΡΠ΅ΡΠΈΡΡΠΈΠΊΠΈ:
ΠΠ°ΡΠ΅ΡΠΈΠ°Π» Π΄Π²ΡΡ
ΡΠΏΠ°ΠΊΠΎΠ²ΠΎΡΠ½ΡΠΉ, Π½Π° ΠΎΡΠ½ΠΎΠ²Π΅ ΡΠΏΠΈΡ
Π»ΠΎΡΠ³ΠΈΠ΄ΡΠΈΠ½Π° ΠΈ Π΄ΠΈΡΠ΅Π½ΠΈΠ»ΠΎΠ»ΠΏΡΠΎΠΏΠ°Π½Π°.
Π¦Π²Π΅Ρ: ΠΏΡΠΎΠ·ΡΠ°ΡΠ½Π°Ρ ΠΆΠΈΠ΄ΠΊΠΎΡΡΡ.
ΠΠ½Π΅ΡΠ½ΠΈΠΉ Π²ΠΈΠ΄: Π²ΡΠ·ΠΊΠ°Ρ.
Π¦Π²Π΅Ρ ΠΏΠΎ ΠΆΠ΅Π»Π΅Π·ΠΎΠΊΠΎΠ±Π°Π»ΡΡΠΎΠ²ΠΎΠΉ ΡΠΊΠ°Π»Π΅, Π½Π΅ Π±ΠΎΠ»Π΅Π΅ — 4
ΠΠ°ΡΡΠΎΠ²Π°Ρ Π΄ΠΎΠ»Ρ ΡΠΏΠΎΠΊΡΠΈΠ΄Π½ΡΡ
Π³ΡΡΠΏΠΏ, % — 20-22,5
ΠΠ°ΡΡΠΎΠ²Π°Ρ Π΄ΠΎΠ»Ρ ΠΈΠΎΠ½Π° Ρ
Π»ΠΎΡΠ°, %, Π½Π΅ Π±ΠΎΠ»Π΅Π΅ — 0,001-0,005
ΠΠ°ΡΡΠΎΠ²Π°Ρ Π΄ΠΎΠ»Ρ ΠΎΠΌΡΠ»ΡΠ΅ΠΌΠΎΠ³ΠΎ Ρ
Π»ΠΎΡΠ°, %, Π½Π΅ Π±ΠΎΠ»Π΅Π΅ — 0,3-0,8
ΠΠ°ΡΡΠΎΠ²Π°Ρ Π΄ΠΎΠ»Ρ Π³ΠΈΠ΄ΡΠΎΠΊΡΠΈΠ»ΡΠ½ΡΡ
Π³ΡΡΠΏΠΏ, %, Π½Π΅ Π±ΠΎΠ»Π΅Π΅ — 1,7
ΠΠ°ΡΡΠΎΠ²Π°Ρ Π΄ΠΎΠ»Ρ Π»Π΅ΡΡΡΠΈΡ
Π²Π΅ΡΠ΅ΡΡΠ², %, Π½Π΅ Π±ΠΎΠ»Π΅Π΅ — 0,2-0,8
ΠΠΈΠ½Π°ΠΌΠΈΡ. Π²ΡΠ·ΠΊΠΎΡΡΡ
-ΠΏΡΠΈ (25Β±0,1)oΠ‘ ΠΠ°*ΡΒ Β Β Β Β Β Β 13-25
-ΠΏΡΠΈ (50Β±0,1)oΠ‘ ΠΠ°*ΡΒ Β Β Β Β Β 13-25
ΠΡΠ΅ΠΌΡ ΠΆΠ΅Π»Π°ΡΠΈΠ½ΠΈΠ·Π°ΡΠΈΠΈ, Ρ, Π½Π΅ ΠΌΠ΅Π½Π΅Π΅ — 4
ΠΠ°ΡΠ°Π½ΡΠΈΠΉΠ½ΡΠΉ ΡΡΠΎΠΊ Ρ
ΡΠ°Π½Π΅Π½ΠΈΡ Π³ΡΡΠ½ΡΠΎΠ²ΠΎΠΊ — 18 ΠΌΠ΅ΡΡΡΠ΅Π² ΡΠΎ Π΄Π½Ρ ΠΈΠ·Π³ΠΎΡΠΎΠ²Π»Π΅Π½ΠΈΡ.
Π€Π°ΡΠΎΠ²ΠΊΠ°: Π±Π°ΡΠ°Π±Π°Π½Ρ 53 ΠΊΠ³.
ΠΈΠ½ΡΠΎΡΠΌΠ°ΡΠΈΡ ΠΎΠ± ΠΎΠΏΠ°ΡΠ½ΠΎΡΡΠΈ:
Π’Π΅ΠΌΠΏΠ΅ΡΠ°ΡΡΡΠ° ΠΊΠΈΠΏΠ΅Π½ΠΈΡ 0Π‘ — 222-224
ΠΠ΅ΡΡΡΠ΅ΡΡΡ (ΡΠΏΡΡΠ³ΠΎΡΡΡ ΠΏΠ°ΡΠ°) — Π½Π΅ Π»Π΅ΡΡΡΠΈ
ΠΠ»ΠΎΡΠ½ΠΎΡΡΡ (ΠΏΠΎ Π²ΠΎΠ΄Π΅) — 1166ΠΊΠ³/ΠΌ3
Π’Π΅ΠΌΠΏΠ΅ΡΠ°ΡΡΡΠ° Π²ΡΠΏΡΡΠΊΠΈ (Π²ΠΎΡΠΏΠ»Π°ΠΌΠ΅Π½Π΅Π½ΠΈΡ), 0Π‘ — Π²ΡΡΠ΅ 244 ΠΎ.Ρ.
Π’Π΅ΠΌΠΏΠ΅ΡΠ°ΡΡΡΠ° ΡΠ°ΠΌΠΎΠ²ΠΎΡΠΏΠ»Π°ΠΌΠ΅Π½Π΅Π½ΠΈΡ, 0Π‘ — 570
ΠΡΠ΅Π΄Π΅Π»Ρ Π²ΠΎΡΠΏΠ»Π°ΠΌΠ΅Π½Π΅Π½ΠΈΡ, 0Π‘ — Π½ΠΈΠΆΠ½ΠΈΠΉ:122 Π²Π΅ΡΡ
Π½ΠΈΠΉ: 225.
ΠΏΠΎΠ΄Π³ΠΎΡΠΎΠ²ΠΈΡΠ΅Π»ΡΠ½ΡΠ΅ ΡΠ°Π±ΠΎΡΡ:
ΠΠ΅ΡΠ΅Π΄ ΠΏΡΠΈΠΌΠ΅Π½Π΅Π½ΠΈΠ΅ΠΌ ΡΠΌΠ΅ΡΠΈΠ²Π°ΡΡ ΡΠΌΠΎΠ»Ρ Ρ ΠΎΡΠ²Π΅ΡΠ΄ΠΈΡΠ΅Π»Π΅ΠΌ Π² ΠΌΠ°ΡΡΠΎΠ²ΠΎΠΌ ΡΠΎΠΎΡΠ½ΠΎΡΠ΅Π½ΠΈΠΈ: Π½Π° 1 000 Π³Ρ. ΡΠΌΠΎΠ»Ρ 120 Π³Ρ. ΠΎΡΠ²Π΅ΡΠ΄ΠΈΡΠ΅Π»Ρ ΠΠΠΠ. ΠΡΠΈ Π½Π΅ΠΎΠ±Ρ
ΠΎΠ΄ΠΈΠΌΠΎΡΡΠΈ ΡΠ°Π·Π±Π°Π²Π»ΡΡΡ ΡΠ°ΡΡΠ²ΠΎΡΠΈΡΠ΅Π»ΡΠΌΠΈ Π -4, Π -4Π.
ΡΠ΅ΠΌΠΏΠ΅ΡΠ°ΡΡΡΠ° Π½Π°Π½Π΅ΡΠ΅Π½ΠΈΡ:
Π Π΅ΠΊΠΎΠΌΠ΅Π½Π΄ΡΠ΅ΡΡΡ ΡΠ»Π΅Π΄ΡΡΡΠΈΠΉ ΡΠ΅ΠΌΠΏΠ΅ΡΠ°ΡΡΡΠ½ΡΠΉ ΡΠ΅ΠΆΠΈΠΌ: ΠΎΡ + 50Π‘ Π΄ΠΎ + 300Π‘.
Π₯ΡΠ°Π½ΠΈΡΡ ΡΠΌΠΎΠ»Ρ Π² ΠΏΠΎΠΌΠ΅ΡΠ΅Π½ΠΈΠΈ, ΠΈΡΠΊΠ»ΡΡΠΈΠ² ΠΏΠΎΠΏΠ°Π΄Π°Π½ΠΈΠ΅ Π½Π° Π½ΠΈΡ ΠΏΡΡΠΌΡΡ ΡΠΎΠ»Π½Π΅ΡΠ½ΡΡ Π»ΡΡΠ΅ΠΉ ΠΈ Π²Π»Π°Π³ΠΈ ΠΏΡΠΈ ΡΠ΅ΠΌΠΏΠ΅ΡΠ°ΡΡΡΠ΅ Π½Π΅ Π²ΡΡΠ΅ 400Π‘.
ΠΌΠ΅ΡΡ ΠΏΡΠ΅Π΄ΠΎΡΡΠΎΡΠΎΠΆΠ½ΠΎΡΡΠΈ:
Π‘ΠΌΠΎΠ»Ρ Π½Π΅ Π²Π·ΡΡΠ²ΠΎΠΎΠΏΠ°ΡΠ½Ρ, Π½ΠΎ Π³ΠΎΡΡΡ ΠΏΡΠΈ Π²Π½Π΅ΡΠ΅Π½ΠΈΠΈ Π² ΠΈΡΡΠΎΡΠ½ΠΈΠΊ ΠΎΠ³Π½Ρ. ΠΠ΅ΡΡΡΠΈΠ΅ ΠΊΠΎΠΌΠΏΠΎΠ½Π΅Π½ΡΡ ΡΠΏΠΎΠΊΡΠΈΠ΄Π½ΠΎ-Π΄ΠΈΠ°Π½ΠΎΠ²ΡΡ ΡΠΌΠΎΠ» — ΡΠΎΠ»ΡΠΎΠ» ΠΈ ΡΠΏΠΈΡ Π»ΠΎΡΠ³ΠΈΠ΄ΡΠΈΠ½ — ΠΎΡΠ½ΠΎΡΡΡΡΡ ΠΊ Π»Π΅Π³ΠΊΠΎΠ³ΠΎΡΡΡΠΈΠΌ Π²Π΅ΡΠ΅ΡΡΠ²Π°ΠΌ, ΠΏΠΎ ΡΡΠ΅ΠΏΠ΅Π½ΠΈ Π²ΠΎΠ·Π΄Π΅ΠΉΡΡΠ²ΠΈΡ Π½Π° ΠΎΡΠ³Π°Π½ΠΈΠ·ΠΌ — ΠΊ Π²Π΅ΡΠ΅ΡΡΠ²Π°ΠΌ 2-Π³ΠΎ ΠΊΠ»Π°ΡΡΠ° ΠΎΠΏΠ°ΡΠ½ΠΎΡΡΠΈ.
ΠΠ΅ΡΠ΅ΡΡ ΠΎΡ Π΄Π΅ΡΠ΅ΠΉ!
Β
germes-vvp.kz