2. Технология изготовления корпусных деталей
Заготовки корпусных деталей чаще всего отливают из чугуна и алюминиевых сплавов, реже из стали или других литейных сплавов.
Широко применяется литье в песчано-глинистые формы, кокиль, оболочковые формы, под давлением. Реже – литье по выплавляемым моделям.
В качестве исходных заготовок используют поковки. Находит применение и сварка стальных заготовок.
2.1. Технические требования к корпусным деталям
При изготовлении корпусных деталей необходимо обеспечить:
1. Правильность формы
2. Малую шероховатость (мкм)
3. Точность взаимного расположения основных баз деталей.
Так, для привалочных плоскостей допуск прямолинейности равен 0,05…0,2 мм, шероховатость
2. Малую шероховатость
4. Правильность расположения отверстий друг относительно друга (параллельность и перпендикулярность осей, межосевые расстояния и т.д.). Например, допуски параллельности осей отверстий и перпендикулярности торцовых поверхностей к осям отверстий обычно составляют от 0,02 до 0,05 мм соответственно на 100 мм длины или радиуса.
Требования к точности межосевых расстояний устанавливаются по стандартам и условиям обеспечения нормальной работы зубчатых передач (обычно 7-8 степени точности).
Точность формы, размеров и малая шероховатость отверстий необходимы для повышения износостойкости уплотнений и долговечности подшипников качения, для уменьшения потерь на трение, утечек жидкости и газа.
2.2. Предварительная обработка корпусов
Перед отправкой отливок и поковок в механический цех удаляют облой, литники и прибыли. Для этого используют обрезные прессы, фрезерные, шлифовальные, ленточно-отрезные и другие станки, сварочные аппараты, пневматические молотки, зубила и другие средства производства. Кроме того, производят очистку, термическую обработку, предварительную покраску, грунтовку и контроль заготовки.
При очистке удаляют остатки пригоревшей формовочной смеси и мелкие неровности для того, чтобы улучшить внешний вид детали, повысить стойкость наносимой краски, увеличить стойкость режущего инструмента при последующей обработке.
Очистка производится стальными щетками, иглофрезами, травлением серной кислотой с последующей промывкой, обдувкой дробью, водой с крупнозернистым керамзитом и содой.
Термическую обработку (низкотемпературный отжиг отливок из серого чугуна) выполняют для снятия остаточных напряжений и улучшения обрабатываемости отливок.
2.3. Базирование заготовок корпусов
При выборе черновых баз необходимо:
1. Обеспечить равномерность припусков на обработку отверстий
2. Избежать касания внутренних поверхностей корпуса и деталей большого диаметра (зубчатых колес, маховиков, муфт).
Для этого часто на первых операциях заготовки базируют по основному отверстию или двум возможно более удаленным отверстиям, т.к. внутренняя полость корпуса и получаемые в отливке отверстия базируются с помощью общего стержня или связанных друг с другом стержней. Установка осуществляется:
1. В приспособлениях с конусами (рис. 2.1.).
С помощью кулачковых или плунжерных оправок, которые закрепляются в отверстиях заготовки вместе с нею, выступающими шейками устанавливаются на призмы и другие опорные приспособления.
Рис. 2.1. – Схема базирования корпуса по коническим оправкам
Рис. 2.2. – Схема базирования корпуса по разжимной оправке
studfiles.net
ТЕХНОЛОГИЯ ИЗГОТОВЛЕНИЯ КОРПУСОВ
Изготовление корпуса, пожалуй самое ответственное в создании любой радиолюбительской конструкции. Да и многим трудно придумать, как сделать корпус для того или иного самодельного устройства. Поэтому предлагаю рассмотреть такую стандартную универсальную конструкцию, что подойдёт для самого широкого спектра приборов — усилителей, блоков питания, зарядных устройств и т.д.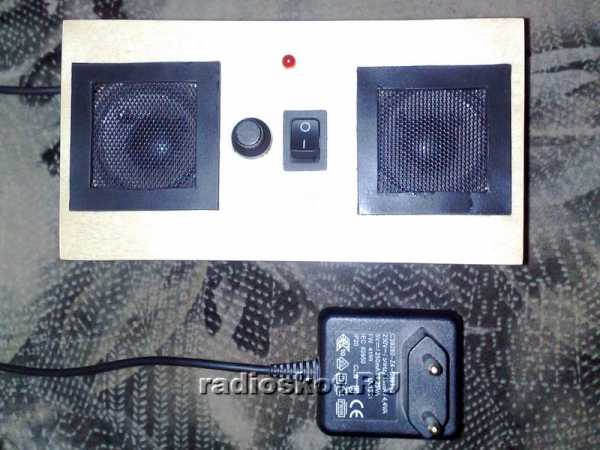
Все размеры чертежа исходят из размеров деталей, в данном случае от габаритов динамиков и размера печатной платы, так как использовал в качестве источника питания обычное зарядное устройство, а не аккумулятор, то размеры корпуса получились значительно меньше. И запомните — корпус можно сделать из чего угодно, например, из пластмассы, дерева, металла. Даже из стекла, главное, чтобы было все очень аккуратно и последовательно. В изготовлении корпуса торопиться нельзя, так например, у меня на воплощение идеи ушло три дня. Спешка может только испортить ценный материал.
Итак, приступим к изготовлению нашего корпуса для «ультразвукового отпугивателя комаров» — эта статья была опубликована на нашем сайте раньше. Для начала необходимо выбрать материал. Недолго думая, решил взять фанеру толщиной 4 мм, так как её не так сложно найти, и легко можно обрабатывать, ну и в конце концов у меня есть пятилетний опыт работы с деревом. Теперь определяемся с расположением всех отверстий на корпусе — под переменный резистор, выключатель , вход питания и форму дырок под динамики.
Разберемся по порядку: переменный резистор взял самый распространённый, но только подобрал к нему пластиковую поворотную ручку и прикпенил его гайкой, подложив шайбу. Выключатель взял из сгоревшего компьютерного блока питания, на нем есть по бокам усики, поэтому его ни чем не крепил.
Вход под провод питания просверлил диаметром 3,5 мм. И наконец дырки под динамики решил сделать квадратными (конечно можно и круглые), чтобы можно было вырезать из резины квадратные прокладки, для скрытия неровностей и перехода от фанеры к сетки от динамиков. И ещё, чуть не забыл об отверстии для светодиода диаметром 4 мм и двух вентиляционных отверстиях по бокам корпуса, на которые тоже приклеены. Резинки — они продаются в строительном магазине, как прокладки для водопроводных труб, их диаметр подбирайте сами. Задняя крышка корпуса выполнена тоже из фанеры, а сверху наклеена резина толщиной 3 мм. Крышка прикручена шестью саморезами — лист фанеры у меня был немного изогнут, но конечно можно и четырьмя.
После изготовления всех деталей, склеил их пва клеем. Затем окончательно зашкурил и покрыл лаком с баллончика для автомобильных дисков. Вот смотрите чертеж этого художества:
Форум по корпусам
Обсудить статью ТЕХНОЛОГИЯ ИЗГОТОВЛЕНИЯ КОРПУСОВ
radioskot.ru
Технология производства пластмассовых корпусов
Технология производства прессованных пластмассовых корпусов
Пластмассовые корпусы обычно применяют для приборов, где преобладающим фактором является стоимость и не требуется высокая герметичность.
На следующем рисунке показан пластмассовый плоский корпус с двухрядным расположением выводов.
Для успешного изготовления формовочной смеси необходимо выбрать соответствующий материал для прессования, который удовлетворял бы требованиям надежности прибора, и надлежащим образом управлять самим процессом прессования. Кроме того, большое значение имеет полная автоматизация процесса сборки (в частности, монтажа кристалла), выполнения проволочных соединений и операции прессования.
Двумя основными типами приборов в пластмассовых корпусах являются прибор с корпусом, прессуемым из пластмассы после сборки, смонтированный в плоском корпусе с двухрядным расположением вертикальных выводов, и прибор с предварительно спрессованным из пластмассы корпусом, например, кристаллодержатель. Для герметизации приборов с прессованием корпуса после сборки используют термореактивные (с поперечными связями) кремнийорганические соединения и эпоксидные смолы; при этом запрессовка комплекса выводная рамка-кристалл производится после присоединения кристалла к выводной рамке. Процесс прессовки пластмассой после сборки не является достаточно технологичным. Для того чтобы избежать контакта кристалла и его проводников или соединения на ленточном носителе с вязкой формовочной смесью, была разработана технология изготовления предварительно спрессованного из пластмассы корпуса. Согласно этой технологии, предварительно прессуют корпус, а затем выполняют монтаж кристалла и межкомпонентные соединения. Для прессования могут использоваться термореактивные материалы, упомянутые выше, или термопластичные полимеры, такие как полифениленсульфид. Предварительно спрессованный корпус является пластмассовым эквивалентом керамического корпуса из тугоплавкой керамики с углублением для кристалла и получит в будущем широкое применение в технологии СБИС.
Для герметизации ИС обычно используют эпоксидные смолы и кремнийорганические соединения. Специальную эпоксидную смолу «Эпокси-А» получают конденсацией эпихлоргидрина с бис-фенолом А.
Эпоксидные новолачные клеи в настоящее время являются более предпочтительными из-за их термостойкости, связанной с тем, что каждая повторяющаяся группа содержит эпоксидный радикал. Эти смолы, называемые «Эпокси-В», получают путем реакции эпихлоргидрина с новолачной фенольной смолой и основой. В процессе синтеза смолы в качестве побочного продукта образуется хлорид натрия. Ионы натрия и хлора оказывают вредное воздействие на надежность прибора, и поэтому, эти побочные продукты должны быть тщательно отделены от смол перед составлением искомой формовочной смеси.
studfiles.net
Изготовление корпусов. Краткий обзор технологий.
22.03.2015 Корпус должен отвечать различным требованиям, которые, зачастую конфликтуют между собой. Так, к корпусу для РЭА предъявляют следующие требования: удобство, функциональность, надёжность, современный и функциональный дизайн, и при всё при этом, конечно же, низкая цена.На сегодняшний день у разработчика прибора имеется широкий выбор возможностей для решения проблемы выбора корпуса для своего изделия. Попытаемся структурировать эти возможности.
По материалу изготовления корпуса делятся на пластмассовые и металлические. Металлические корпуса, в зависимости от того, в каких условиях внешней среды будет работать корпус, могут изготавливаться из углеродистой («чёрной») стали, алюминия, меди и нержавеющей стали.
Выбор материала корпуса зависит чаще всего от предназначения прибора. Приборы бытового назначения чаще всего изготавливаются из полимерных материалов. Этому способствует лёгкость полимерных материалов, их долголетие и возможность придать им практически любую форму, а значит, реализовать любой, даже самый капризный запрос конечного потребителя в области дизайна.
В настоящее время выбор технологий для производства пластмассовых корпусов не велик. Для разработки и производства опытных образцов чаще всего используют полимерное пластмассовое прототипирование, для производства крупных серий используют технологию пресс-форм и пластмассового литья под давлением.
Когда же дело касается приборов промышленного или военного назначения, чаще всего выбор принадлежит металлу из-за его вполне очевидных свойств. Надёжность и дешевизна металлических корпусов до сих пор остаётся решающим фактором выбора их в качестве оболочки для промышленного электронного прибора.
В области изготовления металлических корпусов для РЭА выбор технологий несколько шире, чем при производстве корпусов из пластмассы. До сих пор остаётся востребованным одна из старейших технологий – технология холодной листовой штамповки, при которой для производства партии корпусов создаётся металлический штамп, с помощью которого происходит штамповка элементов корпуса. Стоит заметить, что данный способ актуален на сегодняшний день только для производства крупных партий корпусных металлических изделий. Для изготовления корпусов средних, малых и сверхмалых серий данный способ производства нерентабелен в силу высокой стоимости разработки и изготовления матрицы штампа.
Второй способ изготовления металлических корпусов – производство путём обработки листового металла. Но прежде чем более подробно остановиться на нём, требуется обосновать выбор именно этого метода.
После того, как разработчик конечного электронного продукта сделал свой выбор в пользу металлического корпуса, он должен определиться, нужен ли ему корпус, разработанный индивидуально под его электронное изделие, или можно обойтись теми готовыми решениями, которые уже есть на рынке, немного доработав их под себя. Зависеть этот выбор будет, во-первых , от того, какой величины планируется тираж. Если серия будет большой, то тогда есть резон разработать и изготовить корпус именно под свой прибор на крупном предприятии штамповочного метода производства. Если же партия намечается средняя или мелкая, и будущее электронного продукта не ясно, то тогда выбор, скорее всего, будет за готовыми корпусами, которые можно при необходимости немного доработать и получить нужную для себя конфигурацию.
Однако в последнее время всё более популярным становится третий путь производства корпусов для РЭА. Благодаря появлению и всё более глубокому внедрению в производственный процесс промышленных роботизированных систем ЧПУ, изготовление небольших серий корпусов на заказ становится всё более совершенным технологически и всё более доступным по цене. Речь в данном случае может идти даже о количестве от 20-30 штук. Совершенство этих высокоточных промышленных систем позволяет осваивать весь цикл производства корпусных изделий, имея всего лишь два-три разнопрофильных станка с ЧПУ, например, с лазерной резкой и гибкой листового металла. Их относительно небольшие размеры позволяет резко сократить арендуемую под них производственную площадь, а их производительность и высокая точность обработки листовых материалов также резко уменьшает количество отходов производства. Благодаря практически полной автоматизации, количество обслуживающих их рабочих рук также сокращается до минимума. Все эти факторы вкупе и дают эффект резкого снижения себестоимости производства корпусов для приборов РЭА в условиях средних, малых и сверхмалых партий.
Эта тенденция на резкое уменьшение себестоимости небольшим партий корпусных изделий позволяет средним и малым разработчикам активнее выходить на рынок электротехнической и электронной продукции, подчас составляя конкуренцию крупным производителям, и входя в те ниши рынка, в которых гибкость и активность в освоении новых разработок наиболее важны.
К тому же, использование промышленных систем ЧПУ оказывается целесообразным не только при выпуске мелких и средних партий корпусной продукции, но также и при крупных партиях. Всё зависит от величины станочного парка конкретного производителя и его рабочего ресурса.
Таким образом, можно с уверенностью сказать, что наиболее перспективным на сегодняшний день методом для производства корпусов РЭА является метод обработки листового металла на станках ЧПУ. Причём, стоить отметить, что этот вывод подтверждает и западный опыт. Там также давно уже наметилась тенденция, когда функции подрядчика в производстве металлических корпусов переходит к мелким и средним металлообрабатывающим центрам.
metallistyar.ru
Технологический процесс изготовления корпуса
Министерство образования и науки Российской Федерации
Тольяттинский государственный университет
Механико-технологическое отделение
Кафедра «Технология машиностроения»
Дипломный проект
на тему:
Технологический процесс изготовления корпуса
Дипломант Орловский С.Ю.
Тольятти « » 2007г.
УДК 621.9..6
Технологический процесс изготовления корпуса.
Кафедра: Технология машиностроения.
ТГУ: Тольятти, 2007г., — с., 10 л. формата А1.
Целью дипломного проекта является разработка технологического процесса изготовления корпуса в условиях серийного производства.
На основе научных исследований рассмотрены вопросы нового метода обработки – высокоскоростной обработки алюминия. Разработан новый полный технологический процесс изготовления корпуса.
Эффективность внедрения нового технологического процесса изготовления подтверждена экономическим расчетом, а так же обеспечена экологичность проекта.
Аннотация
Введение
1. Состояние вопроса
1.1 Анализ служебного назначения детали
1.2 Анализ технологичности конструкции детали
1.3 Определение типа производства и обоснование формы его организаии
1.4 Анализ базового варианта технологического процесса
2. Выбор и проектирование заготовки
2.1 Выбор вида и методов получения заготовки
2.2 Технико-экономическое сравнение методов получения заготовки
3. Разработка схем базирования
4. Технологический маршрут и план обработки
5. Размерный анализ технологического процесса
6. Разработка технологических операций
6.1 Выбор оборудования
6.2 Выбор последовательности переходов
6.3 Выбор режущего инструмента и технологической оснастки
6.4 Расчет режимов резания
6.5 Расчет норм времени
7. Расчет и проектирование станочного приспособления. Расчет режущего инструмента
7.1 Расчет и проектирование станочного приспособления
7.2 Расчет режущего инструмента
8. Расчет и проектирование контрольного приспособления
9. Научные исследования по совершенствованию процесса обработки аллюминиевых сплавов
10. Патентные исследования
11. Проектирование производственного участка
12. Безопасность и экологичность объекта
13. Экономческая эффективность проекта
Заключение
Литература
Цель дипломного проектирования по технологии машиностроения — научится правильно применять теоретические знания, полученные в процессе учебы, использовать свой практический опыт работы на машиностроительных предприятиях для решения профессиональных технологических и конструкторских задач.
Целью данного проекта является снижение трудоемкости изготовления корпуса угловой передачи промышленного робота, путем разработки прогрессивного технологического процесса, базирующегося на современных достижениях в области станкостроения и инструментального производства.
К мероприятиям по разработке новых прогрессивных технологических процессов относится и автоматизация, на ее основе проектируется высокопроизводительное технологическое оборудование, осуществляющее рабочие и вспомогательные процессы без непосредственного участия человека.
Для достижения цели решаются следующие задачи:
1.Расширение, углубление, систематизация и закрепление теоретических знаний, и применение их для проектирования прогрессивных технологических процессов изготовления деталей, включая проектирование средств технологического оснащения.
2.Развитие и закрепление навыков ведения самостоятельной творческой инженерной работы.
3.Овладение методикой теоретико-экспериментальных исследований технологических процессов механосборочного производства.
В дипломном проекте должна отображаться экономия затрат труда, материала, энергии. Решение этих вопросов возможно на основе наиболее полного использования возможностей прогрессивного технологического оборудования и оснастки, создания гибких технологий.
1.1 Анализ служебного назначения детали
Деталь – корпус (рис 1.) и предназначена (деталь) для базирования в нём основных узлов и агрегатов для воспроизводства угловой передачи. Деталь по сути дела воспринимает на себе все колебания узлов и механизмов находящихся в ней. Она работает в условиях циклических знакопеременных нагрузках. Исполнительные поверхности, корпуса работают в условиях постоянного трения.
Материал детали — алюминиевый сплав АЛ9-1 ГОСТ 2685-75. Химический состав и механические свойства представлены в табл. 1.1 и 1.2. соответственно.
Таблица 1.1.
Химический состав сплава АЛ9-1 ГОСТ 2685-75,%
Таблица 1.2.
Механические свойства сплава АЛ9-1 ГОСТ 2685-75
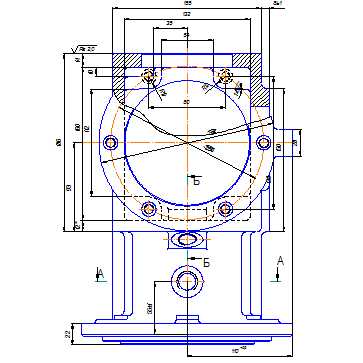
Рис 1. Деталь — корпус
В таблице1.3 представлена классификация поверхностей детали. Номера поверхностей указаны на технологическом чертеже представленном на рис. 2.
Таблица 1.3
1.2 Анализ технологичности конструкции детали
Рабочий чертеж корпуса угловой передачи содержит необходимую графическую информацию для полного представления о его конструкции. Указаны размеры с их отклонениями, проставлены необходимая шероховатость и допуски формы и расположения поверхностей.
В то же время можно отметить и ряд недостатков:
— на чертеже не указаны отклонения на некоторые свободные поверхности корпуса;
— шероховатость проставлена по старому госту;
— симметричность стенок паза проставлена относительно двух баз;
— отсутствуют технические требования;
— невидимые поверхности показаны штриховыми линиями;
На технологическом чертеже корпуса угловой передачи сделаны необходимые доработки.
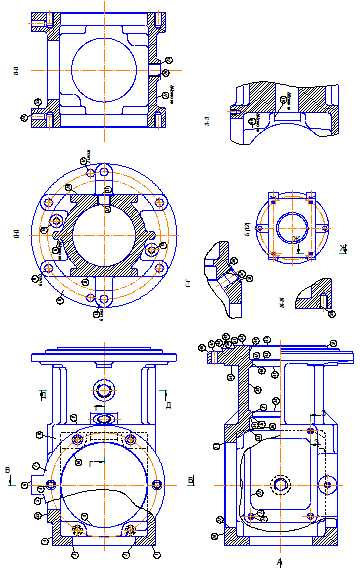
Рис 2. Эскиз с нумерацией поверхностей
В отношении других поверхностей деталь технологична и позволяет применить высокопроизводительные методы обработки.
Общую технологичность детали можно определить с помощью коэффициентов:
-коэффициент точности
; (1.1) ; (1.2)где, ТCP — среднее значение точности;
Ti — квалитет i -ой поверхности;
n — число поверхностей с текущим квалитетом;
ТCP = 13;
Кточ = 0,92;
— коэффициент шероховатости
; (1.3.) ; (1.4.)где, ШСР – средняя шероховатость, Ra ;
Шi — текущая шероховатость поверхности;
ni — число поверхностей с данной шероховатостью;
ШСР = 6,8;
Кш = 0,85.
В учебных целях тип производства определяем по таблице 4.1 [1]. При массе детали до 8 кг. и годовой программе выпуска 500 – 5000 дет/год (N = 1200 дет/год) тип производства – среднесерийное.
Для серийного производства рекомендуется групповая форма организации производства, когда запуск деталей осуществляется партиями.
шт в месяц (1.5)где а – периодичность запуска деталей, при запуске раз в месяц а = 12.
С учетом типа производства предполагается применение оснастки с механизированным силовым приводом и режущего инструмента со сменными многогранными пластинами.
Материал корпуса выключателя – алюминиевый сплав АЛ9-1, по этому заготовку можно получить только методами литья. Наиболее предпочтительными являются литье в оболочковые формы и литье в землю.
В базовом технологическом процессе обработка ведется на универсальном оборудовании, что увеличивает число операций. Применяется унифицированный инструмент и оснастка.
Базовый маршрут обработки детали включает в себя следующие операции:
000 Заготовительная.
005 Токарная.
010 Фрезерная.
015 Фрезерная.
020 Фрезерная.
025 Токарная.
030 Фрезерная.
035 Токарная.
040 Фрезерная.
045 Токарная.
050 Контрольная.
055 Протяжная.
060 Слесарная.
065 Моечная.
070 Контрольная.
075 Окрасочная.
Для максимальной концентрации операций на одном оборудовании предлагается использовать обрабатывающий центр МАНО МС50. Также предлагается применение оснастки с механизированным силовым приводом и прогрессивного режущего инструмента.
На выбор метода получения заготовки оказывает влияние: материал детали, ее назначение и технические требования на изготовление; объем и серийность выпуска; форма поверхностей и размеры детали.
mirznanii.com
Технология производства керамических корпусов
Технология производства керамических корпусов
Керамические корпусы обычно применяют для герметизации современных приборов, где требуется максимальная надежность.
Процесс формирования многослойной заготовки из тугоплавкой керамики начинается с подготовки керамической пасты и протекает в следующей последовательности:
Отливка
Формирование заготовки корпуса
Трафаретная печать
Образование многослойной структуры
Перфорирование
Спекание
На первом этапе готовят жидкую пасту из керамического порошка и жидкой компоненты (растворитель и смола-пластификатор). Затем из этой пасты отливают тонкие листы, пропуская над ней сглаживающее лезвие. После сушки листы разрезают в соответствии с необходимыми размерами. Далее механическим путем пробивают в них сквозные отверстия (отверстия в диэлектрических слоях, через которые осуществляются межкомпонентные соединения) и углубление для кристалла, наносят на поверхность проводящие дорожки (обычно пасту на основе порошка вольфрама) и заполняют сквозные отверстия металлом. Некоторые пластины спрессовывают друг с другом с помощью зажимного приспособления с точным совмещением. Готовая структура подвергается отжигу при температуре 1600 °С для образования монолитного спеченного материала.
После отжига пластина готова для заключительных операций по присоединению выводов и металлизации. Для подготовки к пайке выводов на вольфрам наносят никель. Выводы изготавливают из сплава Fe—Ni—Co, называемого коваром, пайку выводов осуществляют эвтектическим сплавом серебро-медь. Все внешние металлические поверхности подвергаются гальванической или электролитической обработке (обычно наносят золото на никель) для повышения качества соединения и защиты от окружающей среды. Многослойные керамические корпусы могут иметь размеры до 100×100 мм с допуском ±0.5% и содержать до 30 слоев.
Технология производства керамических корпусов очень эффективна для конструирования сложных корпусов с большим числом сигнальных, заземляющих, питающих, соединительных и герметизирующих слоев. Однако ей присущи три недостатка: трудность получения необходимых допусков размера корпуса из-за большой усадки во время обработки; высокая диэлектрическая проницаемость керамики (= 9,5) и недостаточная теплопроводностьAl2O3. Проблема допусков затрудняет использование краевой области пластины, высокая диэлектрическая проницаемость оказывает вредное воздействие на емкостную нагрузку сигнальной линии. ЗаменаAl2O3наBeOдолжна значительно улучшить тепловые характеристики и уменьшить диэлектрическую проницаемость корпусов. Корпусы изBeOнайдут широкое применение в будущем благодаря потенциальной возможности улучшения рабочих характеристик керамических корпусов.
studfiles.net
ЗАО СТАМП: Технология производства корпусов.
Конструкция.
Каждый элемент корпусов разработан и смоделирован в специализированном трехмерном ПО. В терминалах предусмотрены места для установки Пинпада и функциональных клавиатур (дублирующие функции тачскрина), кардридера (для считывания информации с пластиковых карт), штрихридера (для считывания штрихкодов), диспенсера карт, которые по умолчанию комплектуются заглушками. Все терминалы соответствуют требованиям стандартов ISO. Компания СТАМП располагает всеми необходимыми мощностями, что позволило нам наладить производство корпусов и предоставлять Вам только качественные услуги. Кроме того, стоимость наших аппаратов и услуг остается такой же доступной для каждого клиента. Условия сотрудничества и оплаты Вы можете уточнить у менеджеров нашей компании и заказать изготовление необходимого аппарата или комплектующие.
Каждая деталь корпуса изготовлена на высокотехнологичном и точном оборудовании:
- Лазерная резка заготовок.
Помимо высокой точности и качества реза лазерная резка позволяет при моделировании проектировать детали произвольной конфигурации, в том числе с любыми радиусами, что улучшает эстетические и эргономические свойства продукции. - Современное гибочное оборудование
обеспечивает высокое качество гибки и точную повторяемость последовательных гибов, изготовление сложных пространственных деталей, благодаря чему производство корпусов проходит на высоком уровне. Гнутый профиль имеет ряд преимуществ по сравнению со сварным: отсутствуют дефекты, присущие сварочному шву (горячие и холодные трещины, непровары, поры и др.), отсутствует термическое влияние и, отсутствуют дополнительные операции по обработке швов. Таким образом широкое использование гибки улучшает внешний вид изделия в целом, повышает качество. - Конденсаторная сварка
Каждая модель терминалов ЗАО «СТАМП» прошла ускоренные ресурсные испытания в собственной сети, что гарантирует стабильную надёжную работу всего оборудования.
Внешний вид.
Если Вы решили воспользоваться услугами компании СТАМП (ремонт аппаратов, производство платежных терминалов, корпусов), то можете быть уверены, что получите действительно качественный автомат.
Эксклюзивный дизайн и качественное исполнение придают изделию оригинальность, узнаваемость, выразительность. Продуманное расположение узлов придётся по душе владельцам – оно обеспечивает лёгкость обслуживания. Реализована возможность установки дополнительного 17-ти дюймового монитора либо лайт-бокса. Все корпуса окрашены порошковой краской. Связавшись с нашими менеджерами, Вы сможете заказать изготовление необходимого аппарата и обсудить с сотрудниками все детали. Таким образом, Вы гарантировано получите аппарат с высокими техническими характеристиками и с эксклюзивным дизайном корпуса. Стоимость услуг Вы также можете уточнить у менеджеров компании СТАМП.
В результате получается долговечное, стойкое, высококачественное и привлекательное на вид покрытие с отличными защитными свойствами. Для окраски уличных моделей терминалов используется специальная уличная краска, особо стойкая к солям, ультрафиолету, химикатам, всепогодным условиям и прочим воздействиям.
Надёжность, взломостойкость.
Преимущественно, корпусные детали терминалов выполнены из высококачественной стали 2-3 мм, благодаря чему увеличивается механическая стойкость к физическим повреждениям. Все корпуса полностью сварные, а ответственные элементы конструкции выполнены с усилением до 6 мм стали, что предотвращает несанкционированный доступ внутрь. Предусмотрена установка усиленных дверей с упором, усиленных замков, дополнительной защитной дверцы. Терминал может комплектоваться надёжным стальным сейфом с «хитрым» замком из 6 мм стали. Дверь снабжена ригельной системой запора 3 стороны (плоскости), и запирается на механический замок сувальдного типа высокой степени секретности с защитой от сверления. В стальной корпус терминала предусмотрен доступ через фронтальную дверь.
Стекла мониторов, а также информационных панелей имеют антивандальное утолщение, что позволяет расширять круг возможных мест установки терминалов. Защитное антивандальное 6 мм (8 мм для уличных терминалов) стекло устойчиво к проявлению «внимания» со стороны вандалов, а также, при попытке взлома, терминал известит хозяина SMS-кой или по ICQ.
Уличные терминалы компании «СТАМП» по защищённости не уступают банковскому оборудованию. Наши терминалы «не боятся» прямого попадания осадков (снег и дождь), обладают металлическими губками для купюроприёмника и термопринтера, с помощью которых полностью обеспечивается герметичность терминала. Данные губки защищают от попадания влаги и конденсата внутрь терминала. Обладают системой климат-контроля, которая регулирует соотношение температуры и уровня влажности внутри терминалов. Все модели уличных терминалов прошли проверку в холодильных камерах при температурах – 20 °C.
Терминалы по желанию Заказчика могут быть оборудованы промышленным компьютером, который более стоек к температурным перепадам, конденсату, и вообще к работе в уличных условиях и предназначен для работы круглый год, день и ночь, каждые сутки без перебоя. Модульная конструкция корпусов облегчает транспортировку и сборку (можно производить непосредственно на месте установки). Конструкция уличного корпуса (для модели TF–Standart ) предусматривает возможность установки небьющихся боковых щитов толщиной 10 мм из монолитного тонированного поликарбоната, которые, в свою очередь, создают клиенту удобство и защищённость в любых погодных условиях, нет бликового эффекта в дневное время. Специальное основание корпуса утяжеляет конструкцию и делает её максимально устойчивой (возможно также крепление к полу анкерными болтами).
Мы регулярно производим модернизацию корпусов наших терминалов с целью повышения взломостойкости, надёжности оборудования, более удобного и экономичного расположения узлов и комплектующих внутри терминалов, улучшения дизайна.
www.stampservice.ru