Термитная сварка с давлением
пер.Каштановый 8/14 51100 пгт.Магдалиновка
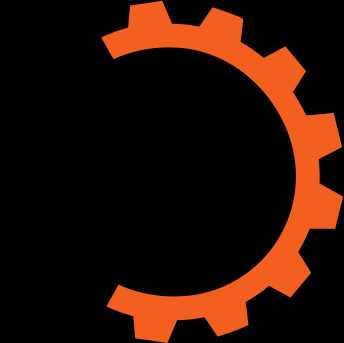
Nikolaenko Dmitrij
Термитная сварка с давлением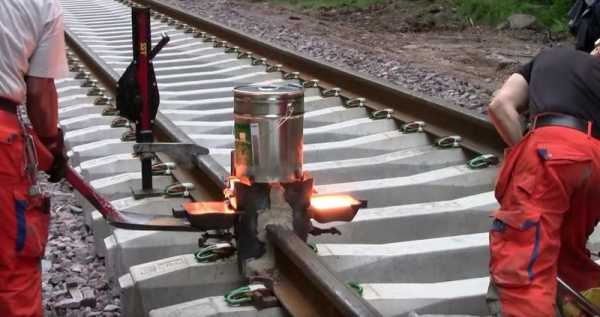
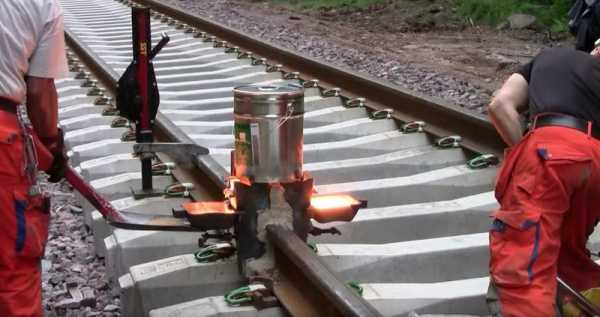
Процесс сварки является уникальным способом соединять металлы на межатомном уровне, позволяющий деталям сращиваться друг с другом. Существуют разные способы это делать и один из них – термитная сварка с давлением. Суть термитной сварки заключается в нагреве свариваемого металла термитом, который состоит из порошкообразной смеси магния или алюминия, а также железной окалины. Пропорционально берут 37% алюминия и 37% оксида железа, при необходимости и больше. Эти металлы в момент возгорания создают большое теплообразование, а железная окалина служит в качестве источника кислорода. Смесь нагретого термита заливают в свариваемый зазор, выдерживают определенное время, в течение которого происходит рекристаллизация металлов.
Технология термитной сварки
Технология термитной сварки протекает следующим образом:
- свариваемая поверхность тщательно зачищается и подготавливается для точной стыковки;
- заформовывают огнеупорным материалом, который закрепляют струбцинами. Форма должна быть сухой, без влаги;
- нагревателем разогревают место стыковки металлов до 900 градусов Цельсия;
- после предварительного нагрева подсоединяется тигли, внутри которого находится термит;
- термит зажигается запальной смесью;
- нагретый термит до 3500 градусов заливается в подготовленную форму, полностью заполняя зазор между деталями обеспечивая надежное соединение;
- через несколько минут форма разбивается и сварочный наплыв зачищается.
Такая технология термитной сварки позволяет достичь лучшего результата соединения металлов. Термиты могут обогащать ферросилицием и ферромарганцем, это улучшает его химический состав, повышает механические свойства, происходит раскисление. Чтобы увеличить выход термитной смеси, обычно добавляют мелкое железо примерно 10-15% от веса смеси термита. Технология термитной сварки алюминиевым термитом выполняют тремя способами:
- Плавлением;
- Давлением;
- Комбинированным.
Есть много общего между этими способами. Комбинированный применяют при сваривании рельсов.
Сварка магниевым термитом протекает при плавлении оксида магния(28000С). Его применяют для сварки стальных телефонных и телеграфных проводов воздушных линий связи.
Обучение термитной сварке
Обучение термитной сварке включает в себя понимание методики соединения металлов и суть технологического процесса. Самостоятельное обучение многие получают в основном для того, чтобы научиться правильно выполнять сварку провода, а для этого необходимо:
- подготовить устройство для сварки ПТСП, термошашки, термопатроны ПАС – от 70 до 300 марки, термитные спички, асбест;
- специальные сварочные клещи готовят под нужный размер провода, который будут сваривать;
- концы этого провода заводят в трубки термитного патрона до упора вкладыша;
- трубка термитного патрона запечатывается четырьмя витками асбеста, чтобы не вытекал расплавленный металл;
- провода зажимаются и закрепляются;
- все готово, термитной спичкой зажигается термопатрон, который потом закрывается кожухом;
- через 1 или 2мин. клещи сжимаются и провода сближаются;
- когда провод остыл, удаляется шлак и освобождение из термопатрона;
- проверяется качество сварки на пережог и перегиб.
Обучение термитной сварке требует практической работы, что придает уверенности при использовании этого вида сварки.
229
Опубликовано/отредактировано: 2019-02-20
metallsmaster.ru
Термитная сварка
Виды сварки — Термитная сварка
Термитная сварка — процесс сварки металлических деталей жидким металлом заданного химического состава, получаемого в результате термитной (алюминотермической) реакции. Сущность термитной реакции заключается в том, что алюминий способен восстанавливать окислы металлов со значительным выделением тепла, в результате чего происходит изменение потенциального состояния энергии и рекристаллизация компонентов, участвующих в процессе:
Значительное количество тепла, выделяемого при термитной реакции, длительное время сохраняет металл в жидком перегретом состоянии и дает возможность использовать его для технологических целей.
В отличие от обычного процесса горения термитная реакция может происходить в замкнутых системах или даже в вакууме, так как реакция происходит за счет кислорода, содержащегося в окислах металлов.
Термитный процесс с железо-алюминиевым составом протекает в соответствии со следующей зависимостью:
Основным высококалорийным горючим, применяющимся в термитных Смесях, является алюминий. После кислорода и кремния алюминий является самым распространенным элементом земной коры и составляет около 8% массы Земли (железо 4,7%).
Принцип получения трудновосстанавливаемых металлов из их окислов впервые был выдвинут крупнейшим русским ученым-химиком, основоположником современной физической химии Н Н. Бекетовым. В 1865 г. в своей докторской диссертации «Исследования над явлениями вытеснения одних элементов другими» Бекетов превратил этот принцип в научную теорию, заложив основу алюминотермии. Он установил, что алюминий обладает очень большой активностью, соединяясь с кислородом, и что при определенных условиях алюминий легко восстанавливает из окислов другие металлы, стоящие правее его в таблице напряжений химических элементов.
Сварочный термит состоит из порошкообразного металлического алюминия и окислов железа в виде окалины (технологического отхода горячей обработки стали), а также различных присадок, вводимых в шихту для легирования получаемой стали.
Какие условия необходимы для начала термитной реакции?
1 Термитная шихта должна быть рассчитана так, чтобы в ходе реакции выделилось необходимое количество тепла для расплавления и перегрева конечных продуктов термитной реакции
2. Компоненты термитной шихты: алюминиевый порошок и окислы железа должны быть мелких фракций и тщательно перемешаны.
3. Для начала термитной реакции в любой точке термитной шихты необходимо создать температурный толчок не ниже 1350o. после чего термитная реакция быстро распространится на всю шихту.
В результате термитной реакции, которая в течение 15—30 сек. протекает очень активно, образуются металл (около 50% от первоначального веса термитной шихты) и шлак.
В процессе термитной реакции часть тепла расходуется на нагревание стенок тигля, лучеиспускание и т. д. Однако, несмотря на это, количество выделяющегося тепла достаточно для того, чтобы расплавить шихту и перегреть продукты реакции — жидкий металл и шлак до 2600—2700o. Это обусловливает возможность получения чистого металла, так как благодаря значительной разнице в удельных весах жидкий шлак всплывает на поверхность, а металл опускается на дно тигля.
Качество термитного металла определяется физико-химическими свойствами компонентов шихты.
Для получения металла (стали) нужного химического состава в шихту вводят в измельченном состоянии легирующие материалы: ферромарганец, ферромолибден, ферротитан, феррованадий, углерод и т. д.
Измельченная легирующая присадка закладывается в тигель вместе с термитными компонентами.
Участие легирующих элементов в термитной реакции очень многообразно: они легируют термитную сталь, раскисляют и рафинируют ее. Кроме того, они частично теряются — испаряются и переходят в шлак.
Ценные ферросплавы (ферротитан, феррованадий и др.) повышают прочность термитной стали, так как в ходе реакции, находясь в жидком состоянии, они образуют карбидную фазу титана и ванадия. Наличие в стали перечисленных карбидов увеличивает ее мелкозернистость, повышает твердость и т. п.
Длительность термитной реакции oт момента зажигания термита до ее окончания и полного отделения металла от шлака находится в прямой зависимости от количества сжигаемого термита и колеблется от 15 до 40-50 сек.
При одновременном сжигании больших количеств термита реакция протекает с относительно небольшими потерями тепла.
Термитные смеси в зависимости от их назначения можно условно разделить на следующие группы;
1) элементарная термитная смесь — железная окалина плюс алюминиевый порошок в стехиометрическом соотношении;
2) термит для сварки рельсовых стыков. В шихту вводится стальной наполнитель — мелкие кусочки малоуглеродистой проволоки или стальная малоуглеродистая стружка, ферромарганец и порошкообразный графит,
3) термит для сварки легированных сталей. В качестве присадки используются ферротитан, феррованадий и др.;
4) термит для сварки чугуна. В присадку вводится значительное количество кремния. Марганец исключается. Высокое содержание кремния в термитном металле способствует выделению графита в сварочной и переходной зонах и обеспечивает получение достаточно прочных сварных соединений;
6) специальные термиты — пиротехнические, для наварки пода в металлургических печах, уменьшения усадочных раковин в слитках, вторичного дробления минералов и руд, изготовления термитных брикетов и т. п.
История развития производства термита и термитной сварки рельсов
В Москве термитную сварку впервые применили в 1915 г.. когда было сварено 126 стыков. В 1918 г. сварили еще 151 стык. С 1923 г. в трамвайных путях столицы начинают регулярно варить стыки термитом. До 1925 г. стыки сваривали импортным термитом. В 1925 г. на Московском термитно-стрелочном заводе инженером М. Л. Карасевым было налажено промышленное производство термита.
М. А. Карасев внес крупный вклад в развитие алюминотермии, организовав на базе отечественной технологии выпуск термитных смесей для народного хозяйства. Он предложил рациональные способы производства алюминиевого порошка и термита. Ему были выданы авторские свидетельства на «аппарат для получения эерноволокнистого алюминия», «шаровой мельницы для производства алюминиевого порошка», «механической нагрева-тельной печи для обжига железной обсечки и окалины при изготовлении термита» и т. п.
В последующие годы в путях московского трамвая было сварено термитом свыше 100 000 стыков.
Сварка производилась двумя способами: комбинированным и врасклинку. Ввиду того, что стыки, свариваемые последним способом, часто выходили из строя, к 1931 г. этот способ перестали применять Вместо него начали внедрять способ сварки промежуточным литьем. Одновременно начали применять способ сварки «дуплекс» (способ промежуточною литья с последующим прессованием). Однако этот способ не получил широкого распространения из-за сложности технологического процесса.
Качество сварки термитных стыков за первые 10 лет ежегодно улучшалось, и количество лопнувших (в течение года) стыков в среднем не превышало 0,8%.
Применение отечественного термита для сварки рельсовых стыков показало его превосходство перед импортировавшимся термитом. В стыках рельсов, сваренных отечественным термитом, значительно меньше процент брака. Это подтверждают результаты эксплуатации первой очереди Московского метрополитена. Так, например, каждый рельсовый стык на участке Сокольники—Парк культуры в 1938 г, выдержал 13,4 млн. ударов с грузонапряженностью 53 млн. т-км.
В 1936 г. вышло из строя 0,17% от количества эксплуатируемых в путях стыков, в 1937 и 1938 г. — по 0,5%.
Из приведенного количества выбывших из строя стыков 75% разрушились из-за наличия болтовых отверстий в зоне сварки.
В эти же годы термит стали внедрять в другие отрасли народного хозяйства. В частности, была разработана и успешно осуществлена термитная сварка стыков легированных труб первого прямоточного котла высокого давления; начали применять также термитную сварку для ремонта крупногабаритных стальных деталей: валов, колонн и т. п.
Применение термитной сварки в трамвайных хозяйствах
Сварка стыков рельсов радикально решает проблему борьбы с блуждающими токами, которые наносят значительный ущерб подземным металлическим коммуникациям.
Бесстыковой путь дает возможность уменьшить экономические затраты по текущему содержанию пути, позволяет увеличить скорость движения рельсового транспорта, уменьшает шум и удлиняет срок службы подвижного состава.
Рассматривая применяющиеся в настоящее время различные способы сварки стыков рельсов — электроконтактный, электрошлаковый, газопрессовый, ванный, электродуговой с приваркой накладок и подкладок и термитный, — нельзя не отдать предпочтение последнему, у которого такие преимущества:
1) удобство, маневренность применяющейся оснастки;
2) возможность применения без электроэнергии;
3) высокая производительность;
4) достаточная прочностная характеристика.
Термитная сварка позволила к 1953 г. в Москве и Ленинграде иметь в трамвайных путях бесстыковые соединения.
В трамвайных хозяйствах многих городов отдается предпочтение термитной сварке стыков рельсов. За последние 25—30 лет термитная сварка претерпела небольшие качественные изменения.
Из всех способов термитной сварки — кузнечного, промежуточного литья, комбинированного, «дуплекс» — получил широкое распространение способ промежуточного литья.
С 1950 г. применяется модернизированный способ промежуточного литья — «единый» способ, который хотя и не дает провара по всему сечению рельсов, но благодаря простоте всего технологического процесса позволил расширить внедрение термитной сварки в трамвайных путях.
В связи с массовым применением термитной сварки на транс порте появилась потребность как в качественном улучшении сварного стыка — получение плотного стыка с хорошим проваром и постоянством химического состава термитной стали, так и в изменении количественных характеристик — повышение производительности, уменьшение расхода материалов и т. д.
Условия, необходимые для проведения термитной реакции
Чтобы осуществить термохимическую реакцию между восстановителем и окислителем, необходимо наличие определенных условий, как то: химической чистоты компонентов термитной шихты, соответствующего измельчения их, определенного соотношения составляющих термита в шихте, доведения термитной смеси до температуры начала реакции.
В составе железо-алюминиевого термита восстановителем является алюминий в порошкообразном состоянии, а окислителем — порошок железной окалины. Химическая чистота восстановителя и окислителя необходима для обеспечения определенной активности и теплотворной способности термита, а также для качества сварки.
Окислитель — железная окалина — должен содержать минимальное количество кремния, серы и фосфора.
Кислородный баланс окалины 24,5—26% О2, что недостаточно для получения активной высококалорийной термитной реакции. Чтобы увеличить содержание кислорода в окалине, ее подвергают специальной обработке при высокой температуре в окислительной среде.
Большое влияние на ход реакции оказывает измельчение составляющих термитной шихты. Более крупные компоненты используются в реакциях с большими порциями шихты. Для небольших порций термита применяют более измельченные порошки.
Отклонение от указанных пределов в ту или иную сторону нарушает нормальные соотношения восстановителя и окислителя в термите, что приводит к снижению его калорийности, повышает в термитном металле содержание Al или насыщает металл кислородом, что отрицательно влияет на качество термитной сварки.
Чтобы осуществлялась реакция между алюминием и железной окалиной, термитная шихта должна быть нагрета до температуры воспламенения, которая для железо-алюминиевого термита при правильно выбранном соотношении составляющих достигает 1340-1360o. Это — критическая точка начала активной реакции, хотя медленно протекающие термохимические процессы уже начинаются при нормальной температуре после смешения компонентов термитной шихты.
Медленно протекающие термохимические процессы безопасны, но они снижают теплотворную способность термита, вследствие эгого длительное хранение его нежелательно.
Применение термита
Термит широко применяется в различных отраслях народного хозяйства. Он используется Для сварки крупногабаритных стальных и чугунных конструкций и арматуры железобетонных узлов. Термитом можно сваривать трубы и провода контактной сети, а также провода высоковольтных линий электропередачи.
Термитный металл обладает хорошими литейными свойствами и может употребляться для прицезионного литья.
В технической литературе освещено применение термитной сварки при:
а) производстве крупногабаритных деталей, состоящих из нескольких элементов: коленчатых валов, рулевых рам судов, приварке лопастей к гребным валам судов и пр.;
б) восстановлении цилиндров прессов, поршневых штоков, колонн кузнечных прессов, роторных валов, валков, а также ведущих реверсивных шестерен прокатных станов, всевозможных станин—клетей прокатных станов, станин прессов и главных станин ковочно-высадочных машин и пр.;
в) ремонте чугунного технологического оборудования сталелитейных цехов: изложниц, шлаковых ковшей, поддонов и т. д.
Термитную сварку крупногабаритных деталей лучше всего производить в литейном цехе, где имеется необходимое технологическое оборудование, а также грузоподъемные механизмы.
Термитная сварка крупных чугунных деталей дает большой экономический эффект, особенно для восстановления технологического оборудования металлургического производства: различных ковшей, изложениц, поддонов, а также всевозможных станин.
Приступая к термитной сварке чугунных деталей, нужно учитывать повышенную чувствительность чугуна к температурным изменениям. При нагревании чугуна выше критической точки и охлаждении со скоростью, превышающей 149o в мин., он становится хрупким.
Одним из важнейших условий успешного проведения термитной сварки чугунных деталей является предварительный подогрев. При сварке чугунных деталей, помимо местного подогрева в зоне сварки до 900o, необходимо произвести и общий подогрев всей детали до 450—500o.
Весьма эффективно применение термита для сварки стыков стержней большого диаметра непосредственно в блоках гидросооружений, где нельзя использовать стыковую сварку. При этом повышается экономия металла, используемого на накладки или технологические изгибы сопрягаемых элементов, а также увеличивается производительность сварки по сравнению с электродуговым или ванным способом. Кроме того, облив улучшает работу арматуры в бетонных сооружениях, так как, выступая за габариты стержня, он повышает сцепляемость арматуры с бетоном.
Термитная сварка стыков арматурных стержней, как правило производится без предварительного подогрева, но с несколько большим расходом термита на стык.
При термитной сварке стыков арматурных стержней применяют универсальные огнеупоры, являющиеся одновременно и тиглем и формой.
На железнодорожном транспорте широко применяется термитная приварка электросоедимениний к рельсам. Для этого используется специальный термит, состоящий из окислов меди, сплава меди с алюминием и ферромарганца. Сжигается этот термит в тигель-форме из жаропрочного графита, способного выдерживать несколько сот плавок.
На действующих газопроводах для предохранения их от разрушения почвенной коррозией осуществляется электродренажная защита — привариваются стальные стержни, которые подключаются к источникам постоянного тока. Стальные стержни приваривают только термитом. Использование других видов сварки — электрической или газовой — недопустимо, так как в ходе сварки может произойти прожог труб, по которым подается горючий газ под давлением. Термит для приварки стержней дренажной защиты состоит из железо-алюминиевой шихты с введением в нее дополнительно магния и ферромарганца.
Для сварки стальных проводов широко применяют спрессованный в цилиндрические шашки термит, который состоит из 25% металлического магния и 75% железной окалины.
Магниевый термит применяется потому, что при сгорании он нe образует жидких шлаков.
Термитно-магниевые шашки можно использовать и при пайке. В паяльник закладывают шашку и поджигают ее обычным способом. Через несколько минут после окончания процесса горения Паяльник прогревается до нужной температуры и становится пригодным для пайки.
При строительстве электрических установок высокого напряжения часто приходится сваривать стыки многопроволочных проводов. Перед сваркой производят механическую подготовку и обезжиривание стыков, закладывают подготовленные концы проводов в цилиндрический термитный патрон и закрепляют их в сварочных клещах.
Стык проводов при поджигании термитного патрона и в процессе сварки должен быть в горизонтальном положении.
При сварке стале-алюминиевых и алюминиевых проводов со сваренного стыка необходимо удалять металлический кокиль—оболочку термитного патрона.
Термитная сварка стыков узкоколейных рельсов без предварительного подогрева может применяться в горной и лесной промышленности. Для этого используют такие же сухие формы, как и при термитной сварке арматурных стержней.
Количество термита для сварки стыка без предварительного подогрева удваивается. Это компенсируется высокой производительностью (7—10 мин.) на один стык и компактностью применяемой оснастки.
Трещины в головке, участки пробуксовки и другие дефекты рельсов устраняют термитной наплавкой.
Термитным способом можно получить термитную перегретую жидкую сталь любого состава, которая имеет высокую жидкотекучесть и хорошие литейные свойства. Это дает возможность получить из термитной стали всевозможные отливки сложной конфигурации.
Высокая жидкотекучесть термитной стали позволяет отливать из нее небольшие сложные детали, которые обычным способом из стали отлить нельзя.
Высокие литейные качества термитной антикоррозийной стали позволяют с успехом отлипать из нее любые скульптурные композиции.
Читать: «Автогенная обработка». Термитная сварка. История развития, Краткие рекомендации по технике безопасности при термитной сварке рельсовых стыков, Кузнечный способ термитной сварки
Источник: Малкин Б.В. Термитная сварка
www.autowelding.ru
что это такое, особенности и виды, видео
При работе с металлическими конструкциями всегда приходится использовать сварку. Но чтобы шов получился гладким и прочным важно выбрать наиболее подходящий способ сваривания. Особым спросом среди многих профессионалом пользуется термитная сварка.
Она получила высокую ценность благодаря высокой скорости и надежности. Также она обладает максимальной простотой и легкостью проведения, во время сварочного процесса не нужно применять электроды и огромные сварочные аппараты.

В чем состоит суть термитной сварки
Многие часто спрашивают, что такое термитная сварка и зачем она используется? Чтобы это понять, стоит рассмотреть ее основную суть. Во время сварочного процесса применяются специальные порошковые составы, которые во время сгорания образуют большое количество тепловой энергии. Часто данные металлические смеси называют термитами.
Термическая сварка — это процедура, во время которой происходит разогревание свариваемого элемента до состояния полужидкой субстанции, но в то же время оно сплавляется в целостный состав при помощи специального порошка. Обычно применяется порошок, который состоит из железа и алюминия.
При смешивании данных элементов на основе алюмотермической реакции на области сварки образуется катализатор с высоким качеством. Основная суть этого процесса состоит в том, что во время него из соответствующего оксида химическим методом происходит полное восстановление металла.
Обратите внимание! Сварка изделий производится за счет оказания воздействия расплавленного металла из термита и сильного жара на кромки, которые начинают активно плавятся на свариваемом участке. Именно термит в данном случае выступает в качестве присадочного материала.
При термическом сварочном процессе проявляется мощный поток тепла с показателем температуры от 2400-27000С, оно выполняет функции горелки при проведении газосварки или электрода при электродуговой сварке. Главная особенность данной технологии состоит в том, что порошкообразный термит способен воспламеняться самостоятельно.
Это связано с наличием кислорода в составе порошка, который выделяется во время химической реакции из оксида железа. Именно это способы позволяет проводить термическое сваривание в среде, которая заполнена негорючими газами, к примеру, углекислым, и даже в вакууме.
Сферы применения
При помощи термита из алюминиевой пудры выполняется наплавка на запасные части или детали. Также данная технология применяется при сваривании рельсов и чугуна, разных сплавов из хрупких металлов. Именно этот вид сваривания позволяет провести быстрый ремонт железнодорожных путей с минимальными затратами.
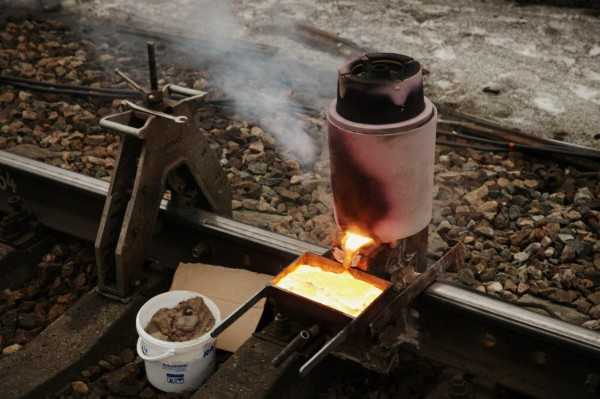
Термит для сварки из производных магния применяется в случаях, когда необходимо сваривать электрические коммуникации, телефонные провода и многое другое. Термитное сваривание часто используется в условиях производства. Этот способ подходит для изготовления крупных деталей — лопасти в речных и морских судах, коленчатые валы автомобилей и другие.
Виды термитной сварки
Сварка, во время которой применяется специальный порошковый термит из алюминия и железа, может производиться при помощи тигельного и муфельного способа. Первый способ также имеет другое известное название — алюминотермитная сварка. Она часто используется при установке заземляющих контуров, металлических конструкций.
Стоит отметить! Перед проведением сварки делается термит из оксида железа и алюминиевого порошка в пропорциях 70:23. Во время его сгорания стыки деталей соединяются расплавленным железом, который восстанавливается из окалины.
Алюмотермитная сварка часто применяется при проведении ремонта поврежденных поверхностей методом наплавки. Главное преимущество данной технологии состоит в возможности сваривании чугунных элементов без образования стыков. Но ее невозможно применять для наложения швов на алюминиевые изделия, в этих случаях стоит использовать муфельный сварочный процесс.

При проведении термитной сварки своими руками оказывается высокая температура, которая вызывает сильное расплавление алюминия, в результате этого он начинает испаряться. Муфельная технология проводится с использованием термита на основе магния, при повышенных температурах он не растекается, а впитывается в поверхность и образует ровный шов.
Оборудование
При проведении термитной сварки сварщик должен применять следующие элементы и оборудование:
- тигель из керамики или тугоплавкого металла. Он должен иметь устройство для безопасного слива расплава;
- для создания отливок потребуется применение форм и матриц. Они могут быть одноразовыми или для многократного применения;
- устройства для закрепления и сжатия деталей;
- термитный карандаш. Этот элемент применяется в домашних условиях для сваривания и резки металлов;
- комплект инструментов, которые должен иметь в составе такие элементы, как кислородный резак, газовая горелка, ножовка по металлу, полосковый термометр;
- для зачистки поверхностей стоит применять абразивный круг или металлическую щетку.
Проведение термического сварочного процесс стоит соблюдать важные особенности и правила. Несмотря на то, что он простой и не требует использования дорогого оборудования, все равно не нужно забывать про разновидности сварки и некоторые нюансы, от которых зависит прочность и внешний вид шва.
Интересное видео
osvarka.com
Термитная сварка рельсов. Видео на железной дороге
Многим известен такой вид сварки, как электродуговая и газовая. Они широко применяются как на производстве, так и в строительстве. Но термитная сварка мало кому известна. Поэтому речь пойдет о ней. Благодаря использованию термитной сварки, получаются, ничем не хуже по качеству соединения, как при электро или газосварке, притом не требуется источник электропитания или газовые баллоны.
Сферы применения
Термитную сварку на сегодняшний день используют для сваривания чугуна, электрических и телефонных коммуникаций, труб, частей двигателя и так далее. Особо часто термит используют для сваривания железнодорожных рельсов. Соединения получаются достаточно надёжные. Место ремонта может быть на любом участке дороги, даже в несколько сот километров от населенного пункта.
Термитная сварка
Появление термитной сварки было обусловлено необходимостью стыкового соединения металлов без использования громоздкого оборудования и наличия электросети. Поэтому в 1859 г. Бекетов Н. Н. обнаружил способ, в основе которого лежит алюминотермия ― процесс получения металла восстановлением их окислов алюминия. Он определил, что смесь порошка алюминия и оксида железа, горя при 3000° C, превращаются в сталь и шлак.
В 1898 г. исследователь из Германии Гольдшмидт, впервые применил термитную сварку на практике, соединив два железных бруска. Сделал он это, образовав форму вокруг места стыка и засыпав его термитным порошком. Сгорев, термитный порошок превратился в расплавленное железо, соединив таким образом два металлических бруска. При этом шлак всплывал на поверхность и мог свободно отделиться.
С того времени состав термита практически не изменился. Чаще всего термит имеет в своём составе опилки алюминия ― 23%, и окись железа― 77%. Фракция порошка составляет ― 0,5 мм. В момент поджига порошка, возникает химическая реакция, благодаря которой выделяется много тепла. Плавясь, окись железа переходит в чистое железо, а расплавленный алюминий окисляется.
Термитная сварка рельсов
Процесс сваривания рельсов термитом заключается в следующем:
- обрезка рельс с двух сторон, чтобы промежуток между ними был 23 ― 25 мм. Притом они должны быть выставлены горизонтально и вертикально;
- в зазор между рельсами вставляется пластина из углеродистой стали, для образования зазора;
- стык рельсов зажимается прессом;
- на место соединения монтируется огнеупорная форма, а стыки формы с рельсами, засыпаются песком, или замазываются специальной пастой;
- поверх форм прикрепляется тигель (конус в виде лейки из огнеупорного материала) в котором первоначально сжигается термит. Расплавленный жидкий металл полученный в тигле, в последствии выливают в форму на стыке рельс;
- термит в тигле поджигается термитным карандашом, после чего происходит горение основной смеси 20 ― 30 секунд;
- снизу в воронке тигля установлена заглушка, которая расправляется и освобождает проход жидкому металлу в форму. Сталь и шлак заполняя форму, образуют соединительный шов, притом шлак частично вытесняется наружу в специальные чаши, прикрепленные сбоку тигля;
- горячая сталь заливаемая в форму, проплавляет торцы рельс. После, убирается тигель, и форма сжимается прессом;
- форму снимают, и пока металл ещё горячий, удаляют его избыток;
- получившийся шов, тщательно шлифуют до образования однородной плоскости с рельсой.
Термитные карандаши
В продаже можно найти термитные карандаши. Это кусок проволоки состоящей из углеродистой стали, диаметром до 5 мм. На неё наносят термитную смесь перемешанную с клеем. С одной стороны карандаша имеется место для запала. Что-то вроде бертолетового шнура, но нанесенного в виде дорожки на сам карандаш. Карандаш вставляют в держатель ― как для электросварки, ― и поджигают верхнюю часть. Когда огонь доходит до основного состава на другом конце карандаша, происходит запал термита. Сварку необходимо производить с защитным щитком и рукавицами. Этот же карандаш применяется для поджига основной смеси в тигле. Его поджигают и бросают в тигель с термитной смесью.
Кроме карандашей, существуют ещё термитные шашки и патроны. По принципу работы они схожи с термитным карандашом.
Достоинства термитной сварки
- крепкое и надежное сварочное соединение с высокой стойкостью к разрушению;
- технология сварки отличается простотой и доступностью, что предполагает ее использование как в промышленности, так и в быту;
- самый оптимальный вариант сварки при аварийных ситуациях.
Недостатки
- высокое поглощение влаги;
- смесь из-за способности воспламенятся, считается пожароопасной, что требует бережного отношения и хранения;
- попадание влаги на термитную шашку приводит к образованию взрыва;
- неспособность контролировать процесс горения термита.
Оборудование для термитной сварки рельс
- вольфрамовый или керамический тигель с плавящейся заглушкой, и приспособленный для слива жидкого металла в форму;
- отливочные формы для придания расплавленному металлу формы рельсов;
- пресс для сжатия форм после заливки металла;
- дополнительное оборудование: подставка для тигля, термометр, горелка;
- дополнительные материалы и инструменты: болгарка, шлифовальные круги, кувалда, зубило, металлическая щётка, термостойкая одежда, рукавицы, защитные очки для глаз и другое.
Все это обеспечит качественную работу и защитит персонал от разрушительного воздействия тепла и грязи получаемых при сгорании термосмеси.
Условия для сварки рельс термитом
Чтобы соединение при процессе сварки получилось качественным и крепким, необходимо соблюдать следующие условия:
- количество порошка термита необходимо просчитать столько, сколько нужно для заполнения металлом формы вокруг рельса;
- важно, чтобы смесь шихты была тщательно измельчена и перемешана;
- температура горения зажигательного элемента (шашка, карандаш), как катализатора поджига основной смеси, должна быть не менее 1400° C.
Несмотря на свои незначительные недостатки, термитная сварка может с успехом конкурировать по безопасности и качеству с такими сварками, как электродуговая и газовая. Например, газовая взрывоопасна, а электрическая не исключает поражение электротоком. Да и многое в этих видах сварок напрямую зависит от квалификации самого сварщика. В термитной же, большую роль играет качество смеси и сохранение технологии, а остальное получится само ― собой.
proinstrumentinfo.ru
Термитная сварка
Процесс соединения металлических заготовок с помощью жидкого металла с определенными химическими свойствами получил название термитной сварки. В качестве источника теплоты при этом используется перегретый металлический расплав, который образуется вследствие реакции горения термитов. Объем тепла, выделяющийся в процессе такой термитной (чаще всего алюминотермической) реакции, способствует сохранению жидкого состояния металла в подогретом виде на протяжении долгого времени, что необходимо в данной технологии.
Что такое сварочный термит?
Сварочные термиты представляют собой порошковые смеси из металлов и их оксидов. Обычно они включают алюминий, магний и другие порошковые металлы с железными окислами в виде окалины, получаемой как технический отход в процессе горячей обработки сталей. Окислы железа служат источниками кислорода, а металлические порошки – источников теплоты. Также в составе термита присутствуют разнообразные присадки, которые вводятся в шихту с целью получения легированных сталей. Эти легирующие элементы способствуют улучшению механических характеристик свариваемого изделия. Чаще всего для термитной сварки сварщики пользуются смесью, состоящей на 20% из алюминиевого порошка и на 80% из железной окалины. Помимо этого допускается введение в термит наполнителя из металла, например, железной обсечки, способствующей увеличению выхода жидкого расплава в ходе реакции.
Основным элементом, используемым в термитных смесях в качестве горючего, служит алюминий. Этот металл, обладая повышенной химической активностью, в соединении с кислородом и при соблюдении определенных условий способен легко восстанавливать различные металлы из их окислов. А его большое распространение в земной породе (алюминий занимает третье место по распространенности после кислорода и кремния) позволяет широко использовать восстановительные свойства данного металла в алюминотермии.
Технологии термитной сварки
Принцип действия сварки термитным способом с железо-алюминиевой смесью основан на способности алюминия восстанавливать металлы из окислов. При этом выделяется значительное количество теплоты, что ведет к изменению энергетического потенциала и способствует рекристаллизации элементов, принимающих участие в процессе. Отличием термитной реакции от традиционного горения служит то, что она возможна в любых системах замкнутого типа вплоть до вакуумных.
Это объясняется тем, что сварка термитным карандашом осуществляется посредством кислорода, который присутствует в металлических окислах. Характерной особенностью термитного процесса сварки служит сгорание термитной смеси за несколько секунд с выделением полного объема теплоты. Причем количество тепла, которое выделяется от сгорания горючих материалов, превышает необходимое для окисного разложения, этим и объясняется получаемый в ходе термитной реакции тепловой эффект.
Сварку данным способом разделяют на термитно-муфельную и термитно-тигельную. При последней характерно использование сухих порошкообразных термитных смесей. При соединении стержней из стали и полос применяют железо-алюминиевый термит, процентное соотношение железной окалины с алюминием в котором зависит от чистоты металлического порошка и сортности окалины. Чтобы выход выделяемого в ходе сгорания термита железа был больше, а температура реакции ниже, в термитную смесь нередко добавляются отходы из стали, например, от производства гвоздей.
При термитно-тигельной сварке полосок стали и стержней эффективно использование специального вкладыша, выполненного из стали в форме окружности. Он применяется для закрывания отверстия тигеля. Для проведения термитной сварки ЭХЗ вскрывать индивидуальную упаковку термокоарандаша необходимо непосредственно перед его использованием с выводом шнура замедленного горения из тигель-формы наружу. Стабильность процесса горения термитной смести во многом зависит от размерности входящих в нее элементов. Наиболее интенсивен он при использовании гранул величиной до 1,5 мм. Отличительной особенностью термитно-тигельного процесса сварки является оплавление концов свариваемых стержней с соединением их посредством металла, выделяемого от сгорания термита.
Используемые при термитно-муфельной сварке алюминиевых проводов термитные шашки должны иметь проходящее насквозь продольное отверстие. Причем необходимо, чтобы его диаметр соответствовал размеру соединяемых проводов. Такие термитные шашки изготавливают путем прессования из смесей, состоящих на 75% из железной окалины и на 25% из специального пиротехнического магния. Для связывания данных компонентов применяется нитролак. Его добавляют в объеме 14% к общей массе смеси в сухом состоянии. Отличие термитно-муфельной сварки от термитно-тигельной заключается в отсутствии жидких продуктов реакции от сгорания термита. Образующаяся при этом пористая субстанция из окисленного магния, впитывая железный расплав, не позволяет растекаться шлаковой жидкости.
При соединении алюминиевых проводов термитная сварка в термитно-тигельном варианте неприемлема, а использование термитно-муфельной сварки с прямым контактированием муфельной шашки и алюминиевого провода нежелательно в силу ряда причин. Вступающий в реакции при сгорании термитного муфеля алюминий способствует выгоранию поверхностного металла соединяемых жил. Кроме того, попадающие в сварочную ванну продукты реакции способны ухудшить качество соединения, а оплавление проводов при выходе из термитного муфеля уменьшает их сечение, что может привести к перегоранию отдельных жил в многопроволочных проводниках. Для сварки таких проводов существуют термитные патроны, отличающиеся от шашек наличием металлического кокиля.
Чаще всего соединяют термитной сваркой рельсы, провода, линии электропередачи и связи, а также стыки арматуры. Эффективен данный способ для сваривания отломившихся элементов изделий из стали, таких как зубья в больших шестеренках. Благодаря своим преимуществам термитный сварочный процесс активно используется в ремонтных работах чугунных и стальных конструкций.
promplace.ru
Термитная сварка : описание процесса
(описание процесса)
Темы: Технология сварки.
Термитная сварка подразумевает, что источником теплоты служит перегретый расплавленный металл, образовавшийся в результате горения термитов — порошкообразных смесей металлов с оксидами других металлов.
Для сварки чаще всего применяют алюминиевые термиты, содержащие 20–25% алюминиевого порошка и 75–80% железной окалины. Кроме того, в термиты можно вводить легирующие элементы для улучшения механических свойств и металлический наполнитель — железную обсечку для увеличения выхода жидких продуктов реакции.
Воспламенение термитной смеси происходит при температуре более 1300 °С. Для этого применяют термитные спички или электрозапальные устройства. Начавшееся горение протекает бурно, быстро распространяется на весь объем смеси, и термит полностью сгорает за 20–30 с. Термит сжигают в огнеупорном тигле. Размер тигля зависит от величины сжигаемой порции термита. После сжигания термита в тигле находится жидкая сталь и шлак в сильно перегретом состоянии: на 1 кг термитной смеси образуется 550 г расплавленной стали и 450 г шлака, состоящего из оксида алюминия.
Термитной сваркой сваривают в основном рельсы, стыки арматуры, провода, линии связи и электропередачи. Ее можно использовать для ремонта крупных стальных и чугунных деталей, а также для приливки отломанных частей стальных деталей, например зубьев крупных шестерен.
Другие страницы по теме
Термитная сварка
:
Чтобы удержать жидкий металл в месте сварки, применяют сварочные разъемные формы. Наиболее распространена сварка способом промежуточного литья с предварительным подогревом стыка или без подогрева. В первом случае стык собирают с зазором 12–14 мм, устанавливают и закрепляют форму. Закрепленную форму промазывают огнеупорной глиной. Затем через отверстие в наружной половине формы вставляют горелку, и концы стыкуемых деталей нагревают до 850–900 °С. Термитный металл, расплавленный в тигле, после выдержки в течение 4–6 с выпускают в форму.
Для термитной сварки способом промежуточного литья без предварительного подогрева стыка тигель и форма составляют одно целое. Тигельное пространство отделено от заливаемого заформованного пространства запорной пластиной, толщина которой выбрана так, чтобы она расплавилась после окончания термитной реакции. Перегретый металл заливают в форму, оплавляют концы стыкуемых деталей, и образуется сварное соединение. Первая порция металла, которая стекает в дополнительное пространство, образуя прибыль, подогревает концы стыкуемых деталей. Расход термита для сварки без подогрева почти в 2 раза больше, чем для сварки с подогревом, однако производительность сварки значительно выше, так как предварительный подогрев занимает 15–20 мин.
Поперечное сечение тигля для термитной сварки и принципиальная схема арматурных стержней показаны на рисунке.
Наличие влаги в форме, на соединяемых кромках, недопустимо, так как при заливке расплавленного металла образовавшийся пар может привести к выбросу жидкого металла. Согласно правилам техники безопасности персонал должен иметь защитную одежду, лицо закрывать прозрачным щитком.
![]() |
Рисунок. Термитная сварка арматуры: 1 — тигель; 2 — термитная смесь; 3 — огнеупорная глина; 4 — свариваемое изделие; 5 — асбестовое уплотнение |
- < Режимы сварки
- Лазерная технология >
weldzone.info
Термитная сварка крупногабаритных деталей | Сварка и сварщик
При эксплуатации в металлургической промышленности прокатного, кузнечнопрессового и другого оборудования, испытывающего большие динамические нагрузки и выдерживающего высокие температуры, происходят разрушение крупных деталей и выход из строя станин прокатных станов, прессов и ковочно-высадочных машин. Термитная сварка позволяет восстанавливать разрушенные детали. При этом необходимо обеспечить минимальную деформацию восстанавливаемого узла. Если, например, прямоугольная замкнутая рама разрушена с одного конца, то необходимо производить предварительный подогрев не только места сварки, но и противоположной стороны, чтобы компенсировать температурные деформации при сварке.
Нагрев противоположной стороны необходимо продолжить и после сварки до тех пор, пока сваренная часть несколько охладиться, а температура противоположных сторон рамы выровняется.
В технической литературе освещено применение термитной сварки при:
а) производстве крупногабаритных деталей, состоящих из нескольких элементов: коленчатых валов, рулевых рам судов, приварке лопастей к гребным валам судов и пр.;
б) восстановлении цилиндров прессов, поршневых штоков, колонн кузнечных прессов, роторных валов, валков, а также ведущих реверсивных шестерен прокатных станов, всевозможных станин-клетей прокатных станов, станин прессов и главных станин ковочно-высадочных машин и пр.;
в) ремонте чугунного технологического оборудования сталелитейных цехов: изложниц, шлаковых ковшей, поддонов и т. д.
Термитную сварку крупногабаритных деталей лучше всего производить в литейном цехе, где имеется необходимое технологическое оборудование, а также грузоподъемные механизмы.
Летом в сухую погоду термитную сварку можно производить и под открытым небом — на монтажной площадке, удаленной от огнеопасных объектов.
Перед сваркой крупногабаритной детали следует сделать химический анализ на содержание в металле основных примесей. На основании полученных данных определяют, какими элементами нужно легировать термитную сталь, и производят расчет количества легирующих элементов и стального наполнителя для введения в термитную шихту. Необходимо также рассчитать количество термитной шихты для сварки данной детали. Для этого подсчитывают объемы всей сварочной зоны, литниковой и выпорной систем, а также прибыльной части.
Перед сваркой обрезают газом поверхности, которые будут свариваться, а затем зачищают их. После этого фиксируют взаимное положение частей, подлежащих сварке. Свариваемые элементы прихватываются электросваркой по зазору при помощи технологических перемычек. После прихватки одна из свариваемых частей должна быть раскреплена для свободного перемещения от температурного воздействия.
Термитная сварка деталей из серого чугуна
Термитная сварка крупных чугунных деталей дает большой экономический эффект, особенно для восстановления технологического оборудования металлургического производства: различных ковшей, изложении, поддонов, а также всевозможных станин.
Приступая к термитной сварке чугунных деталей, нужно учитывать повышенную чувствительность чугуна к температурным изменениям. При нагревании чугуна выше критической точки и охлаждении со скоростью, превышающей 149^ в мин., он становится хрупким.
В процессе сварки в зоне, прилегающей к термитному металлу, чугун разогревается выше критической точки. Чтобы ликвидировать отрицательное влияние температуры на эту зону, необходимо уменьшать скорость ее охлаждения за счет предварительного нагрева смежных участков.
Одним из важнейших условий успешного проведения термитной сварки чугунных деталей является предварительный подогрев. При сварке чугунных деталей, помимо местного подогрева в зоне сварки до 900 , необходимо произвести и общий подогрев всей детали до 450-500°.
Сваривая жесткие конструкции типа чугунных замкнутых рам, нужно предотвращать появление в них напряжений, которые могут привести к разрушению детали. Для этого с успехом применяют общий компенсационный подогрев.
Усадка термитного металла почти в два раза превышает усадку чугуна; при слишком большом отношении длины свариваемого сечения к толщине могут образоваться поперечные трещины — поэтому термитную сварку чугунных деталей целесообразно применять лишь тогда, когда ширина деталей превосходит ее толщину не более чем в восемь раз.
Если в относительно тонкой детали имеются длинные трещины, ее целесообразно разделить по оси трещины на две части и произвести сварку всего сечения. Узкие трещины нужно расширить и несколько удлинить. Это необходимо для качественного провара.
При сварке удлиненных стыков их по возможности следует располагать в вертикальном положении, чтобы создать наиболее благоприятные условия для удаления в прибыльную часть песка и шлака. Если сварку производят в горизонтальном положении, шов нужно «промыть» термитным металлом, чтобы освободить его от вредных включений.
Приварка стыковых соединений к рельсам
На железнодорожном транспорте широко применяется термитная приварка электросоединений к рельсам. Для этого используется специальный термит, состоящий из окислов меди, сплава меди с алюминием и ферромарганца. Сжигается этот термит в тигельформе из жаропрочного графита, способного выдержать несколько сот плавок.
При сгорании термитной шихты получается марганцовистая бронза, которая приваривает стыковой соединитель к рельсу. Таким же термитом, но с применением специальной сварочной оснастки производится приварка заземляющих устройств к мечтам линий высоковольтных электропередач и контактной сети.
Термитная наплавка рельсов
Трещины в головке, участки пробуксовки и другие дефекты рельсов устраняют термитной наплавкой, которая состоит из следующих операций:
- поврежденное место рельса вырезается газом до здорового металла;
- устанавливается форма;
- производится предварительный подогрев горелкой наплавляемого участка до 900-950°. При этом желательно применять горелку с прямолинейным соплом, рабочая ширина которого равна ширине головки рельса;
- заливка термитной сталью. Чтобы получился качественный провар, термитную сталь из тигля льют непосредственно на ремонтируемый участок рельса. Между запорным устройством тигля и наплавляемой поверхностью рельса необходимо выдерживать расстояние не более 150 мм, чтобы уменьшить разбрызгивание заливаемой стали;
- после этого удаляют формы, обрубают шлак, обрезают газом излишки наплавленного металла и шлифуют рабочие поверхности.
Для повышения износоустойчивости наплавляемой термитной стали в термитную шихту вводят несколько повышенное количество легирующих элементов-ферромарганца и углерода.
Термитная сварка стыков узкоколейных рельсов
Термитная сварка стыков узкоколейных рельсов без предварительного подогрева может применяться в горной и лесной промышленности. Для этого используют такие же сухие формы, как и при термитной сварке арматурных стержней.
Количество термита для сварки стыка без предварительного подогрева удваивается. Это компенсируется высокой производительностью (7-10 мин.) на один стык и компактностью применяемой оснастки.
Приварка элементов заземления к металлоконструкциям
На действующих газопроводах для предохранения их от разрушения почвенной коррозией осуществляется электродренажная защита — привариваются стальные стержни, которые подключаются к источникам постоянного тока. Стальные стержни приваривают только термитом. Использование других видов сварки — электрической или газовой — недопустимо, так как в ходе сварки может произойти прожог труб, по которым подается горючий газ под давлением. Термит для приварки стержней дренажной защиты состоит из железоалюминиевой шихты с введением в нее дополнительно магния и ферромарганца.
Для сварки стальных проводов широко применяют спрессованный в цилиндрические шашки термит, который состоит из 25% металлического магния и 75% железной окалины.
Магниевый термит применяется потому, что при сгорании он не образует жидких шлаков.
Термитно-муфельная шашка, сгорая в течение нескольких секунд, выделяет большое количество тепла, причем размеры шашки после окончания термитной реакции остаются неизменными. Это и позволяет с большим успехом использовать магниевый термит в качестве концентрированного источника местного подогрева стыков проводов, которые после необходимой выдержки осаживаются специальными клещами.
Термитная сварка многопроволочных проводов
При строительстве электрических установок высокого напряжения часто приходится сваривать стыки многопроволочных проводов. Перед сваркой производят механическую подготовку и обезжиривание стыков, закладывают подготовленные концы проводов в цилиндрический термитный патрон и закрепляют их в сварочных клещах.
Стык проводов при поджигании термитного патрона и в процессе сварки должен быть в горизонтальном положении.
После осадки проводов клещами процесс сварки заканчивается. Остывший шлак необходимо сбить.
При сварке сталеалюминевых и алюминиевых проводов со сваренного стыка необходимо удалять металлический кокиль — оболочку термитного патрона.
weldering.com