какие бывают способы и технологии для стали
Термообработка — основополагающий химический процесс, проводимый при работе со сплавами. В черной и цветной металлургии методика берется за основу и имеет огромное количество различных вариаций. От правильного проведения операции зависят химические, технические и механические свойства металла. Все виды термообработки стали подразделяются на определённые группы, что позволяет подбирать рациональные вариации.
Основные виды термической обработки
На промышленных предприятиях все процессы автоматизированы и человек принимает в них лишь косвенное участие. Все технологии практически идентичные, но имеют отличия по условиям температуры и другим факторам. В первую очередь сплав нагревается до определённой температуры, далее его выдерживают в этих температурных режимах. На последнем этапе происходит моментальное охлаждение. Таким образом, термообработанная сталь будет иметь уникальные технические характеристики. Основные типы технологий:
- Термическое воздействие включает в себя закалку, старение, отпуск, криогенный нагрев.
- Термомеханические методики. Сопровождаются не только нагревом, но и механическими воздействиями.
- Термохимические технологии. После воздействия температурой происходит обработка различными типами жидкостей или газов, что может упрочнять сплав.
Любой способ подразумевает под собой получение требуемых условий, поэтому в случае возникновения сложностей вторичная обработка будет неприемлемой. Каждая технология по-своему уникальна, но при этом основывается на нагревании металлов.
Поэтому требуется более основательно разобраться с различиями и другими факторами. Это позволит получить более конкретную информацию обо всех интересующих аспектах.
Отжиг металлов в печи
Стандартная методика, при которой заготовки отправляют в печь и нагревают. В дальнейшем остывание происходит не в отдельных камерах, а в той же печи. Таким образом, начинается естественный процесс остывания за счет температуры окружающей среды. Если рассматривать виды термообработки металлов, то представленная технология — одна из самых простых. Технология позволяет получить следующие свойства:
- Уменьшается твердость, в дальнейшем легко перерабатывать сплавы.
- Повышается зернистость структуры.
- Исчезают неоднородные сегменты.
- Исчезает внутреннее напряжение.
В настоящее время представленная технология реализуется в нескольких разнообразных вариациях. Как указывает технологический справочник, для различных нужд создаются оптимальные условия. На промышленных предприятиях данные работы должны проводиться в специальных печах. Сегодня отжиг стальных заготовок применяется для получения высококачественной стали. Такие методики очень важны для промышленности и развития индустрии в этом сегменте.
Технология закалки
Один из самых распространённых методов термической обработки — это закалка. Технология представляет собой термические манипуляции с металлами и нагрев их до критических температур. Результатом технологии становится повышение пластичности и прочности сплавов. Отличием закалки от отжига является довольно быстрое охлаждение. Для этих целей применяются ванны с водой, что в значительной степени ускоряет процессы. С технической точки зрения это уникальная методика. Существует несколько основных разновидностей закалки:
- Технология, где используют только один тип жидкости для охлаждения.
- Прерывистая методика. Сначала металл нагревают до критического показателя и опускают в воду. После остывания до температуры 300 градусов оставляют на воздухе или в масле.
- Ступенчатая. В этом случае применяется методика охлаждения в воде, потом в специальных солях и на последнем этапе оставляют остывать на воздухе. Таким образом, на каждом этапе металл приобретает более уникальные технические характеристики.
- Изотермическая — практически идентична ступенчатой закалке.
- Частичная закалка. Охлаждение происходит только по краям металла, в середине он остается горячим. Такая методика применяется при изготовлении отбойных инструментов, так как сплав получается вязким в середине и прочным по краям.
Технология закалки очень часто используется в кузницах как основной метод термообработки. Его эффективность подтверждается многими годами использования и указывает на невероятные преимущества. В настоящее время на каждом этапе технологического процесса нужно контролировать показатели. Это позволит получить металл с требуемыми характеристиками.
Отпуск и старение сплавов
Если нет информации о том, какая обработка стальных изделий характеризуется улучшением технических показателей, то можно выбрать любую методику. Все связано с тем, что каждая технология имеет определённые преимущества и достоинства. Отпуск — это методика, используемая на последнем этапе обработки металлов, таким образом, за счет нее придаются различные физические свойства конечного формата. Для этого металлическую деталь нагревают до температуры, которая должна быть ниже критической, и проводят охлаждения. В настоящее время известно несколько основных типов отпуска:
- высокий;
- средний;
- низкий.
Процесс старения применяется для обработки чугуна и различных типов цветных металлов. Технология очень распространена, так как позволяет увеличивать пределы текучести и прочности металлов. Проводят старение после отжига при нормальной температуре, это позволяет добиться требуемого эффекта без каких-либо сторонних технологий.
Особенность любого типа термической обработки заключается в профессионализме исполнителей. У каждого специалиста, работающего с металлом, есть свои секреты, которые он применяет на практике. Удается получать металл с уникальными техническими характеристиками. В заводских условиях нужно придерживаться технического регламента, поэтому металл всегда одинакового формата, это иногда является большой проблемой. Технические стандарты остаются постоянными.
Криогенное воздействие
В настоящее время техника и технология постоянно развиваются, появляются новые варианты воздействий на сплавы. Сегодня можно использовать не только высокие температуры, но и низкие. То есть холод также улучшает качество материалов. Существуют специальные криогенные камеры, в которых и проводятся технологические процедуры. Температура, при которой находятся детали и заготовки, равна -196 градусов Цельсия. Преимущество технологии заключается в том, что не требуется повторная обработка.
Конечно же, технология не всегда бывает подходящей и имеет множество различных нюансов. Рекомендуется пользоваться технологическими регламентами, что позволит в значительной степени повысить качество продукта. Также при такой обработке в значительной степени снижаются затраты. Достаточно использовать холодильник, при высоких температурах нужны сторонние ресурсы на разогрев печи и так далее.
Термомеханическое воздействие
Из всех перечисленных технологий представленная методика в промышленных масштабах используется уже давно. Суть заключается в предварительном нагревании металла до пластичного состояния и в дальнейшем механическом воздействии. Термомеханическая обработка может быть нескольких видов:
- Низкотемпературная обработка. Ее отличие заключается в том, что металл нагревается до аустенитного состояния. Технология включает в себя пластическую деформацию, закалку и отпуск. Все делается в соответствии с техническим регламентом.
- Высокотемпературная обработка. Металл нагревается до мартенситного состояния, проводится пластическая деформация.
- Предварительная обработка.
Выбрать нужный метод позволяют практика и те цели, которые вы преследуете. С технологической точки зрения каждый метод любого типа термической обработки подходит только для определённых металлов и сплавов. Именно этим фактором обусловлено разнообразие. То есть ни в коем случае нельзя подвергать сталь воздействию определенного типа, если оно не подходит. Это приведет к ухудшению качества материалов.
Химическая обработка
Химические реакции с металлами в совокупности с термическими воздействием приводят к повышению износостойкости, устойчивости к воздействию кислот и щелочей. В настоящее время существуют специализированные промышленные условия для проведения большого количества процессов. Важно различать методики и использовать их в нужный момент. Типы термохимических реакций:
- Цианирование — металл подвергают одновременному воздействию углерода и азота. Основа методики заключается в насыщении сплава данными элементами.
- Азотирование — технология, позволяющая повысить коррозионную устойчивость металлов до максимальных показателей, также повышается прочность. Для этого сплавы погружают в азотную среду.
- Диффузионная металлизация — очень сложная технология, но схожая с предыдущими. Благодаря ее проведению металл становится более прочным, износостойким и не подвергается воздействию агрессивных средств. Для этого поверхность сплавов обрабатывают бромом, хромом, алюминием.
- Цементация — методика, повышающая прочность металла. Для этого используют углерод, который в газовом состоянии непрерывно подается на металл в печи.
В каждом отдельном случае важно соблюдать все правила технологического сопровождения. Сплав при неправильном воздействии может потерять свои технические характеристики и будет отправлен на дополнительную переплавку. В таких ситуациях используются контрольно-измерительные приборы, исключающие нарушение технологии.
Цветные сплавы
Каждый отдельный цветной металл или сплав отличается от других физическими и химическими свойствами, что не скажешь о черных металлах. Поэтому рекомендуется для каждого отдельного случая подбирать свои методики, чтобы не потерять качество. Рекристализационный отжиг проводится для меди, что в значительной степени повышает качество, и происходит термоупрочнение. Различают такие особенности:
- Латунь ни в коем случае нельзя сильно нагревать, предел — 250−300 градусов Цельсия. При неправильной обработке либо высоких температурах происходит растрескивание структуры.
- Бронзу нужно гомогенизировать и в последующем нагревать до 600 градусов Цельсия.
- Магний можно обрабатывать различными методами: старение, отжиг и так далее.
- Титановые сплавы можно закаливать, отжигать, подвергать старению, цементации.
В настоящее время существуют специальные справочники и технические пособия, позволяющие подбирать соответствующие методики для повышения технических свойств металлов. Специалисты, работающие на промышленных предприятиях, действуют по заранее заложенным планам и техническим документам. Таким образом, каждая методика по-своему уникальна и делает металлы и сплавы более качественными и подходящими для технических и промышленных нужд.
Промышленные компании применяют практически все существующие методы, что дает возможность получить сплавы различного формата. Очень важно придерживаться регламентов и стандартов ГОСТ. Каждая рассмотренная термическая обработка имеет свои стандарты и технические нормативы. Любое отклонение приведет к получению некачественного материала, и, следовательно, будет брак.
obrabotkametalla.info
Термическая обработка сплавов. Виды термообработки
Термообработка сплавов является неотъемлемой частью производственного процесса чёрной и цветной металлургии. В результате такой процедуры металлы способны изменить свои характеристики до необходимых значений. В данной статье мы рассмотрим основные виды термообработки, применяемые в современной промышленности.
Сущность термической обработки
В процессе производства полуфабрикаты, металлические детали подвергаются термической обработке для придания им нужных свойств (прочности, устойчивость к коррозии и износу и т. д.). Термическая обработка сплавов – это совокупность искусственно созданных процессов, в ходе которых в сплавах под действием высоких температур происходят структурные и физико-механические изменения, но сохраняется химический состав вещества.
Назначение термообработки
Металлические изделия, которые используются ежедневно в любых отраслях народного хозяйства, должны отвечать высоким требованиям устойчивости к износу. Металл, как сырьё, нуждается в усилении нужных эксплуатационных свойств, которых можно добиться воздействием на него высокими температурами. Термическая обработка сплавов высокими температурами изменяет изначальную структуру вещества, перераспределяет составляющие его компоненты, преобразует размер и форму кристаллов. Всё это приводит к минимизации внутреннего напряжения металла и таким образом повышает его физико-механические свойства.
Виды термической обработки
Термообработка металлических сплавов сводится к трём незатейливым процессам: нагреву сырья (полуфабриката) до нужной температуры, выдерживанию его в заданных условиях необходимое время и быстрому охлаждению. В современном производстве используется несколько видов термообработки, отличающихся между собой некоторыми технологическими особенностями, но алгоритм процесса в общем везде остаётся одинаковым.
По способу совершения термическая обработка бывает следующих видов:
- Термическая (закалка, отпуск, отжиг, старение, криогенная обработка).
- Термо-механическая включает обработку высокими температурами в сочетании с механическим воздействием на сплав.
- Химико-термическая подразумевает термическую обработку металла с последующим обогащением поверхности изделия химическими элементами (углеродом, азотом, хромом и др.).
Отжиг
Отжиг – производственный процесс, при котором металлы и сплавы подвергаются нагреванию до заданного значения температуры, а затем вместе с печью, в которой происходила процедура, очень медленно естественным путём остывают. В результате отжига удаётся устранить неоднородности химического состава вещества, снять внутренне напряжение, добиться зернистой структуры и улучшить её как таковую, а также снизить твёрдость сплава для облегчения его дальнейшей переработки. Различают два вида отжига: отжиг первого и второго рода.
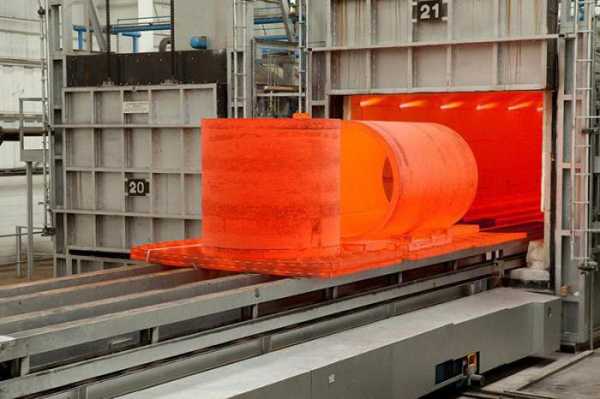
Отжиг первого рода подразумевает термическую обработку, в результате которой изменения фазового состояния сплава незначительны или отсутствуют вовсе. У него также есть свои разновидности: гомогенизированный – температура отжига составляет 1100-1200 , в таких условиях сплавы выдерживают в течение 8-15 часов, рекристаллизационный (при t 100-200 ) отжиг применяется для клёпаной стали, то есть деформированной уже будучи холодной.
Отжиг второго рода приводит к значимым фазовым изменениям сплава. Он также имеет несколько разновидностей:
- Полный отжиг – нагрев сплава на 30-50 выше критической температурной отметки, характерной для данного вещества и охлаждения с указанной скоростью (200 /час – углеродистые стали, 100 /час и 50 /час – низколегированные и высоколегированные стали соответственно).
- Неполный – нагрев до критической точки и медленное охлаждение.
- Диффузионный – температура отжига 1100-1200.
- Изотермический – нагрев происходит так же, как при полном отжиге, однако после этого проводят быстрое охлаждение до температуры несколько ниже критической и оставляют остывать на воздухе.
- Нормализованный – полный отжиг с последующим остыванием металла на воздухе, а не в печи.
Закалка
Закалка – это манипуляция со сплавом, целью которой является достижение мартенситного превращения металл, обеспечивающее понижение пластичности изделия и повышение его прочности. Закалка, равно как и отжиг, предполагает нагрев металла в печи выше критической температуры до температуры закалки, отличие состоит в большей скорости охлаждения, которое происходит в ванне с жидкостью. В зависимости от металла и даже его формы применяют разные виды закалки:
- Закалка в одной среде, то есть в одной ванне с жидкостью (вода – для крупных деталей, масло – для мелких деталей).
- Прерывистая закалка – охлаждение проходит два последовательных этапа: сперва в жидкости (более резком охладителе) до температуры приблизительно 300 , затем на воздухе либо в другой ванне с маслом.
- Ступенчатая – по достижению изделием температуры закалки, его охлаждают какое-то время в расплавленных солях с последующим охлаждением на воздухе.
- Изотермическая – по технологии очень похожа на ступенчатую закалку, отличается только временем выдержки изделия при температуре мартенситного превращения.
- Закалка с самоотпуском отличается от других видов тем, что нагретый метал охлаждают не полностью, оставив в середине детали тёплый участок. В результате такой манипуляции изделие приобретает свойства повышенной прочности на поверхности и высокой вязкости в середине. Такое сочетание крайне необходимо для ударных инструментов (молотки, зубила и др.)

Отпуск
Отпуск – это завершающий этап термической обработки сплавов, определяющий конечную структуру металла. Основная цель отпуска является снижение хрупкости металлического изделия. Принцип заключается в нагреве детали до температуры ниже критической и охлаждении. Поскольку режимы термической обработки и скорость охлаждения металлических изделий различного назначения могут отличаться, то выделяют три вида отпуска:
- Высокий — температура нагрева от 350-600 до значения ниже критической. Данная процедура чаще всего используется для металлических конструкций.
- Средний – термообработка при t 350-500, распространена для пружинных изделий и рессор.
- Низкий — температура нагрева изделия не выше 250 позволяет достичь высокой прочности и износостойкости деталей.
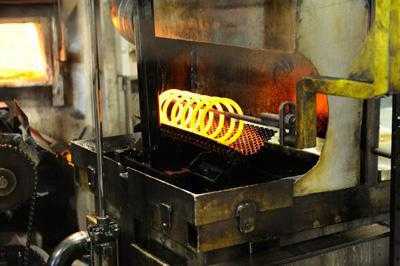
Старение
Старение – это термическая обработка сплавов, обуславливающая процессы распада пересыщенного металла после закалки. Результатом старения является увеличение пределов твёрдости, текучести и прочности готового изделия. Старению подвергаются не только чугун, но и цветные металлы, в том числе и легко деформируемые алюминиевые сплавы. Если металлическое изделие, подвергнутое закалке выдержать при нормальной температуре, в нём происходят процессы, приводящие к самопроизвольному увеличению прочности и уменьшению пластичности. Это называется естественное старение металла. Если эту же манипуляцию проделать в условиях повышенной температуры, она будет называться искусственным старением.
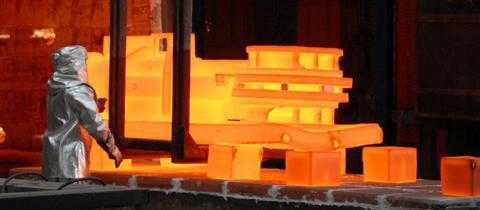
Криогенная обработка
Изменения структуры сплавов, а значит, и их свойств можно добиться не только высокими, но и крайне низкими температурами. Термическая обработка сплавов при t ниже нуля получила название криогенной. Данная технология широко используется в самых разных отраслях народного хозяйства в качестве дополнения к термообработкам с высокими температурами, поскольку позволяет существенно снизить расходы на процессы термического упрочнение изделий.
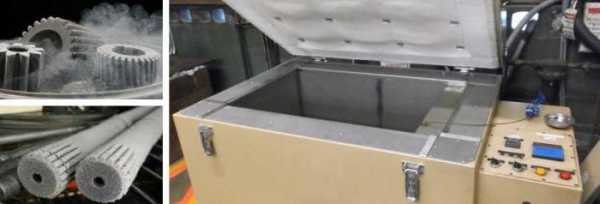
Криогенная обработка сплавов проводится при t -196 в специальном криогенном процессоре. Данная технология позволяет существенно увеличить срок службы обработанной детали и антикоррозионные свойства, а также исключить необходимость повторных обработок.
Термомеханическая обработка
Новый метод обработки сплавов сочетает в себе обработку металлов при высоких температурах с механической деформацией изделий, находящихся в пластичном состоянии. Термомеханическая обработка (ТМО) по способу совершения может быть трёх видов:
- Низкотемпературная ТМО состоит из двух этапов: пластической деформации с последующим закалкой и отпуском детали. Главное отличие от других видов ТМО – температура нагрева до аустенитного состояния сплава.
- Высокотемпературная ТМО подразумевает нагрев сплава до мартенситного состояния в сочетании с пластической деформацией.
- Предварительная – деформация производится при t 20 с последующей закалкой и отпуском металла.
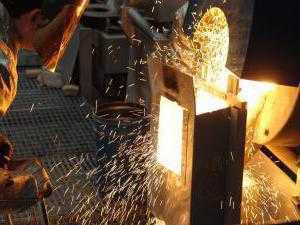
Химико-термическая обработка
Изменить структуру и свойства сплавов возможно и с помощью химико-термической обработки, которая сочетает в себе термическое и химическое воздействие на металлы. Конечной целью данной процедуры помимо придания повышенной прочности, твёрдости, износостойкости изделия является и придание детали кислотоустойчивости и огнестойкости. К данной группе относятся следующие виды термообработки:
- Цементация проводится для придания поверхности изделия дополнительной прочности. Суть процедуры заключается в насыщении металла углеродом. Цементация может быть выполнена двумя способами: твёрдая и газовая цементация. В первом случае обрабатываемый материал вместе с углём и его активатором помещают в печь и нагревают до определённой температуры с последующей выдержкой его в данной среде и охлаждением. В случае с газовой цементацией изделие нагревается в печи до 900 под непрерывной струёй углеродосодержащего газа.
- Азотирование – это химико-термическая обработка металлических изделий путём насыщения их поверхности в азотных средах. Результатом данной процедуры становится повышение предела прочности детали и увеличение его коррозионной устойчивости.
- Цианирование – насыщение металла одновременно и азотом и углеродом. Среда может быть жидкой (расплавленные углерод- и азотсодержащие соли) и газообразной.
- Диффузионная металлизация представляет собой современный метод придания металлическим изделиям жаростойкости, кислотоустойчивости и износостойкости. Поверхность таких сплавов насыщают различными металлами (алюминий, хром) и металлоидами (кремний, бор).
Особенности термической обработки чугуна
Литейные сплавы чугуна повергаются термической обработке по несколько иной технологии, чем сплавы цветных металлов. Чугун (серый, высокопрочный, легированный) проходит следующие виды термообработки: отжиг (при t 500-650 ), нормализация, закалка (непрерывная, изотермическая, поверхностная), отпуск, азотирование (серые чугуны), алитирование (перлитные чугуны), хромирование. Все эти процедуры в результате значительно улучшают свойства конечных изделий чугуна: увеличивают эксплуатационный срок, исключают вероятность возникновения трещин при использовании изделия, повышают прочность и жаростойкость чугуна.
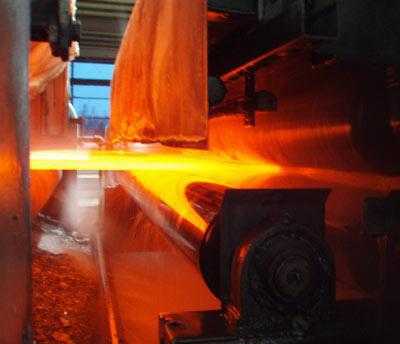
Термообработка цветных сплавов
Цветные металлы и сплавы обладают отличными друг от друга свойствами, поэтому обрабатываются разными методами. Так, медные сплавы для выравнивания химического состава подвергаются рекристаллизационному отжигу. Для латуни предусмотрена технология низкотемпературного отжига (200-300 ), поскольку этот сплав склонен при влажной среде к самопроизвольному растрескиванию. Бронза подвергается гомогенизации и отжигу при t до 550 . Магний отжигают, закаляют и подвергают искусственному старению (естественное старение для закалённого магния не происходит). Алюминий, равно как и магний, подвергается трём методам термообработки: отжигу, закалке и старению, после которых деформируемые алюминиевые сплавы значительно повышают свою прочность. Обработка титановых сплавов включает: рекристаллизационный отжиг, закалку, старение, азотирование и цементацию.
Резюме
Термическая обработка металлов и сплавов является основным технологическим процессом, как в чёрной, так и в цветной металлургии. Современные технологии располагают множеством методов термообработки, позволяющих добиться нужных свойств каждого вида обрабатываемых сплавов. Для каждого металла свойственна своя критическая температура, а это значит, что термообработка должна производиться с учётом структурных и физико-химических особенностей вещества. В конечном итоге это позволит не только достичь нужных результатов, но и в значительной степени рационализировать производственные процессы.
fb.ru
МЕТАЛЛОВ ТЕРМИЧЕСКАЯ ОБРАБОТКА — это… Что такое МЕТАЛЛОВ ТЕРМИЧЕСКАЯ ОБРАБОТКА?
- МЕТАЛЛОВ ТЕРМИЧЕСКАЯ ОБРАБОТКА
определенный временной цикл нагрева и охлаждения, которому подвергают металлы для изменения их физических свойств. Термообработка в обычном смысле этого термина проводится при температурах, не достигающих точки плавления. Процессы плавления и литья, оказывающие существенное влияние на свойства металла, в это понятие не включаются. Изменения физических свойств, вызываемые термической обработкой, обусловлены изменениями внутренней структуры и химических соотношений, происходящими в твердом материале. Циклы термической обработки представляют собой различные комбинации нагрева, выдерживания при определенной температуре и быстрого или медленного охлаждения, соответствующие тем структурным и химическим изменениям, которые требуется вызвать.
Зернистая структура металлов. Всякий металл обычно состоит из множества соприкасающихся друг с другом кристаллов (называемых зернами), как правило, имеющих микроскопические размеры, но иногда и видимых простым глазом. Внутри каждого зерна атомы расположены так, что образуют правильную трехмерную геометрическую решетку. Тип решетки, называемый кристаллической структурой, является характеристикой материала и может быть определен методами рентгеноструктурного анализа. Правильное расположение атомов сохраняется в пределах всего зерна, если не считать небольших нарушений, таких, как отдельные узлы решетки, случайно оказавшиеся вакантными. Все зерна имеют одинаковую кристаллическую структуру, но, как правило, по-разному ориентированы в пространстве. Поэтому на границе двух зерен атомы всегда менее упорядочены, чем внутри них. Этим объясняется, в частности, то, что границы зерен легче поддаются травлению химическими реагентами. На полированной плоской поверхности металла, обработанной подходящим травителем, обычно выявляется четкая картина границ зерен. Физические свойства материала определяются свойствами отдельных зерен, их воздействием друг на друга и свойствами границ зерен. Свойства металлического материала существенным образом зависят от размеров, формы и ориентации зерен, и цель термической обработки состоит в том, чтобы управлять этими факторами.
Атомные процессы при термической обработке. При повышении температуры твердого кристаллического материала его атомам становится все легче переходить из одного узла кристаллической решетки в другой. Именно на этой диффузии атомов и основана термическая обработка. Наиболее эффективный механизм движения атомов в кристаллической решетке можно представить себе как движение вакантных узлов решетки, которые всегда имеются в любом кристалле. При повышенных температурах благодаря увеличению скорости диффузии ускоряется процесс перехода неравновесной структуры вещества в равновесную. Температура, при которой заметно повышается скорость диффузии, неодинакова для разных металлов. Она обычно выше для металлов с высокой температурой плавления. В вольфраме с его температурой плавления, равной 3387° C, рекристаллизация не происходит даже при красном калении, тогда как термическую обработку алюминиевых сплавов, плавящихся при низких температурах, в некоторых случаях оказывается возможным проводить при комнатной температуре.
Во многих случаях термической обработкой
предусматривается очень быстрое охлаждение, называемое закалкой, цель которого — сохранить структуру, образовавшуюся при повышенной температуре. Хотя, строго говоря, такую структуру нельзя считать термодинамически устойчивой при комнатной температуре, практически она вполне устойчива благодаря низкой скорости диффузии. Очень многие полезные сплавы обладают подобной «метастабильной» структурой. Изменения, вызываемые термической обработкой, могут быть двух основных видов. Во-первых, и в чистых металлах, и в сплавах возможны изменения, затрагивающие только физическую структуру. Это могут быть изменения напряженного состояния материала, изменения размеров, формы, кристаллической структуры и ориентации его кристаллических зерен. Во-вторых, изменяться может и химическая структура металла. Это может выражаться в сглаживании неоднородностей состава и образовании выделений другой фазы, во взаимодействии с окружающей атмосферой, созданной для очистки металла или придания ему заданных поверхностных свойств. Изменения того и другого вида могут происходить одновременно.
См. МЕТАЛЛОВЕДЕНИЕ ФИЗИЧЕСКОЕ.
Снятие напряжений. Деформация в холодном состоянии повышает твердость и хрупкость большинства металлов. Иногда такое «деформационное упрочнение» желательно. Цветным металлам и их сплавам обычно придают ту или иную степень твердости холодной прокаткой. Малоуглеродистые стали тоже часто упрочняют холодным деформированием. Высокоуглеродистые стали, доведенные холодной прокаткой или холодным волочением до повышенной прочности, необходимой, например, для изготовления пружин, обычно подвергают отжигу для снятия напряжений — нагревают до сравнительно низкой температуры, при которой материал остается почти столь же твердым, как и раньше, но в нем исчезают неоднородности распределения внутренних напряжений. Благодаря этому ослабевает тенденция к растрескиванию, особенно в коррозионных средах. Такое снятие напряжений происходит, как правило, за счет локального пластического течения в материале, не приводящего к изменениям общей структуры.
Рекристаллизация. При разных методах обработки металлов давлением нередко требуется сильно изменять форму заготовки. Если формообразование должно проводиться в холодном состоянии (что часто диктуется практическими соображениями), то приходится разбивать процесс на ряд ступеней, в промежутках между ними проводя рекристаллизацию. После первой ступени деформации, когда материал упрочнен настолько, что дальнейшее деформирование может привести к разрушению, заготовку нагревают до температуры, превышающей температуру отжига для снятия напряжений, и выдерживают для рекристаллизации. Благодаря быстрой диффузии при такой температуре за счет атомной перестройки возникает совершенно новая структура. Внутри зеренной структуры деформированного материала начинают расти новые зерна, которые с течением времени полностью ее заменяют. Сначала образуются мелкие новые зерна в местах наибольшего нарушения старой структуры, а именно на старых границах зерен. При дальнейшем отжиге атомы деформированной структуры перестраиваются так, что тоже становятся частью новых зерен, которые растут и в конце концов поглощают всю старую структуру. Заготовка сохраняет прежнюю форму, но она теперь — из мягкого, ненапряженного материала, который может быть подвергнут новому циклу деформирования. Такой процесс можно повторять несколько раз, если этого требует заданная степень деформирования. Холодная обработка — это деформирование при температуре, слишком низкой для рекристаллизации. Для большинства металлов данному определению соответствует комнатная температура. Если деформирование производится при достаточно высокой температуре, так что рекристаллизация успевает следовать за деформированием материала, то такая обработка называется горячей. Пока температура остается достаточно высокой, его можно сколь угодно сильно деформировать. Горячее состояние металла определяется, в первую очередь, тем, насколько его температура близка к точке плавления. Высокая ковкость свинца означает, что он легко рекристаллизуется, т.е. его «горячую» обработку можно проводить при комнатной температуре.
Контроль текстуры. Физические свойства зерна, вообще говоря, неодинаковы в разных направлениях, так как каждое зерно — это монокристалл с собственной кристаллической структурой. Свойства металлического образца представляют собой результат усреднения по всем зернам. В случае беспорядочной ориентации зерен общие физические свойства одинаковы во всех направлениях. Если же некоторые кристаллические плоскости или атомные ряды большинства зерен параллельны, то свойства образца становятся «анизотропными», т.е. зависящими от направления. В этом случае у чашечки, полученной глубоким выдавливанием из круглой пластинки, будут «язычки», или «фестоны», на верхней кромке, объясняющиеся тем, что в одних направлениях материал деформируется легче, чем в других. При механическом формообразовании анизотропия физических свойств, как правило, нежелательна. Но в листах магнитных материалов для трансформаторов и других устройств очень желательно, чтобы направление легкого намагничения, которое в монокристаллах определяется кристаллической структурой, во всех зернах совпадало с заданным направлением магнитного потока. Таким образом, «предпочтительная ориентация» (текстура) может быть желательна или нежелательна в зависимости от назначения материала. Вообще говоря, при рекристаллизации материала его предпочтительная ориентация меняется. Характер этой ориентации зависит от состава и чистоты материала, от вида и степени холодной деформации, а также от длительности и температуры отжига.
Контроль размера зерен. Физические свойства металлического образца в значительной мере определяются средним размером зерен. Наилучшим механическим свойствам почти всегда соответствует мелкозернистая структура. Уменьшение размера зерна часто является одной из целей термической обработки (а также плавления и литья). При повышении температуры ускоряется диффузия, а потому средний размер зерна увеличивается. Границы зерен смещаются так, что более крупные зерна растут за счет мелких, которые, в конце концов, исчезают. Поэтому завершающие процессы горячей обработки обычно проводят при возможно более низкой температуре, чтобы были минимальны размеры зерен. Часто специально предусматривают низкотемпературную горячую обработку, в основном для уменьшения размеров зерен, хотя того же результата можно достичь холодной обработкой с последующей рекристаллизацией.
Гомогенизация. Процессы, о которых говорилось выше, протекают и в чистых металлах, и в сплавах. Но существует ряд других процессов, которые возможны лишь в металлических материалах, содержащих два или большее число компонентов. Так, например, в отливке сплава почти наверняка будут неоднородности химического состава, что определяется неравномерным процессом затвердевания. В затвердевающем сплаве состав твердой фазы, образующейся в каждый данный момент, не таков, как в жидкой, находящейся с ней в равновесии. Следовательно, состав твердого вещества, возникшего в начальный момент затвердевания, будет иным, нежели в конце затвердевания, а это и ведет к пространственной неоднородности состава в микроскопическом масштабе. Такая неоднородность устраняется простым нагреванием, особенно в сочетании с механическим деформированием.
Очистка. Хотя чистота металла определяется в первую очередь условиями плавления и литья, очистка металла часто достигается термической обработкой в твердом состоянии. Примеси, содержащиеся в металле, реагируют на его поверхности с атмосферой, в которой он нагревается; так, атмосфера водорода или другого восстановителя может превратить значительную часть оксидов в чистый металл. Глубина такой очистки зависит от способности примесей диффундировать из объема на поверхность, а поэтому определяется длительностью и температурой термической обработки.
Выделение вторичных фаз. В основе большинства режимов термической обработки сплавов лежит один важный эффект. Он связан с тем, что растворимость в твердом состоянии компонентов сплава зависит от температуры. В отличие от чистого металла, в котором все атомы одинаковы, в двухкомпонентном, например твердом, растворе имеются атомы двух разных сортов, случайно распределенные по узлам кристаллической решетки. Если увеличивать количество атомов второго сорта, то можно достичь состояния, когда они не смогут просто замещать атомы первого сорта. Если количество второго компонента превышает этот предел растворимости в твердом состоянии, в равновесной структуре сплава появляются включения второй фазы, отличающиеся по составу и структуре от исходных зерен и обычно разбросанные между ними в виде отдельных частиц. Такие частицы второй фазы могут оказывать сильное влияние на физические свойства материала, что зависит от их размера, формы и распределения. Эти факторы можно изменять термической обработкой. Растворимость в твердом состоянии обычно увеличивается с повышением температуры, как показано на рис. 1. Здесь видно, что при равновесных условиях материал, который по своему составу и температуре лежит слева от кривой, существует в виде одной фазы — твердого раствора. Справа же от кривой состав и температура соответствуют структуре, содержащей вторую фазу, каким-то образом диспергированную в первой. Если состав сплава определяется абсциссой X0, то его равновесная структура может быть либо однофазной, либо двухфазной в зависимости от температуры. График, по осям которого откладываются состав и температура, показывающий фазы в равновесных условиях, называется фазовой диаграммой или диаграммой состояний. Следует иметь в виду, что такая диаграмма (график рис. 1 лишь часть ее) иллюстрирует структуры, которые могут существовать лишь в равновесных условиях, а при низких температурах для достижения равновесия требуется много времени. Если сплав состава X0 поддерживать при температуре T1, то в конце концов он станет однофазным твердым раствором. Вторая фаза, присутствовавшая в нем первоначально, исчезнет вследствие диффузии ее атомов, которые станут частью твердого раствора. Такая обработка называется термической обработкой на твердый раствор. Если после этого медленно охлаждать материал, то при температуре T0 начнут возникать частицы второй фазы, которые будут расти при дальнейшем понижении температуры. Это приведет к тому, что образуется небольшое количество довольно крупных частиц, наличие которых будет сказываться, например, на механических свойствах. Однако процесс выделения второй фазы можно проводить иначе. Если твердый раствор, соответствующий температуре T1, достаточно быстро охладить до комнатной температуры, то сохранится однофазный твердый раствор. Хотя его равновесная структура должна быть двухфазной, скорость диффузии при комнатной температуре столь мала, что структуру твердого раствора можно считать практически стабильной. Если же теперь материал нагреть до температуры, не выходящей за пределы двухфазной области, но обеспечивающей быструю диффузию, то можно вызвать выделение второй фазы в высокодисперсной форме. Такую обработку часто называют старением раствора. Выбирая нужную длительность и температуру старения, можно контролировать размеры зерна, что позволяет добиться дисперсности частиц, существенно повышающей прочность материала.
Рис. 1. ФАЗОВАЯ ДИАГРАММА двухкомпонентного сплава показывает, что растворимость в твердом состоянии увеличивается с повышением температуры. Сплав, температура и состав которого соответствуют точкам, лежащим слева от кривой, — однофазный, т.е. представляет собой твердый раствор.
Таким способом можно упрочнять многие практически полезные сплавы, например, серебряный припой «стерлинг», содержащий несколько процентов меди. Важным примером могут служить алюминиевые сплавы, содержащие несколько процентов меди и составляющие основу дюралюмина. Упрочняющим старением таких сплавов достигается очень высокое отношение предела прочности к весу. Особенно интересно то, что их упрочняющее старение в какой-то мере может происходить за счет диффузии при комнатной температуре. После термической обработки на твердый раствор и закалки до комнатной температуры прочность таких сплавов постепенно увеличивается в 2 раза на протяжении нескольких дней вследствие выделения второй фазы, происходящего при комнатной температуре. Чтобы сохранить состояние твердого раствора, материал приходится хранить при пониженной температуре. Например, дюралюминовая заклепка, выдерживаемая в сухом льду после термической обработки на твердый раствор, остается мягкой до установки на место, а затем за несколько дней сама по себе упрочняется при комнатной температуре. Другой интересный пример — сплавы «алнико» (на железной основе, содержащие алюминий, никель и кобальт) для постоянных магнитов. Чтобы такой сплав приобрел магнитные свойства, оптимальные для постоянных магнитов, его после термической обработки на твердый раствор подвергают закалке и старению при условиях, обеспечивающих определенные размеры, форму и распределение частиц вторичных фаз. Для повышения эффективности старение проводят в магнитном поле.
Кинетика и закалка. Фазовую диаграмму, представленную на рис. 1 и показывающую фазовую структуру, которой будет обладать сплав, когда достигнет равновесного состояния, следует дополнить данными о скорости его приближения к такому состоянию. На графике рис. 2 по вертикальной оси тоже откладывается температура, но по горизонтальной — не состав, а время. Кривая этого графика, имеющая С-образную форму, описывает поведение сплава, состав которого соответствует точке X0, T0 на рис. 1. Если образец состава X0 выдержать при температуре выше T0 до завершения обработки на твердый раствор, а затем закалить до более низкой температуры, скажем T2, то после некоторого периода «ожидания» начнут возникать частицы выделившейся второй фазы и их количество будет расти, пока не будет достигнут равновесный уровень, отвечающий этой температуре. Кривая рис. 2 показывает время, необходимое при разных температурах для того, чтобы началось такое фазовое превращение в сплаве, первоначально подвергнутом термической обработке на твердый раствор. Аналогичную С-образную форму имеют кривые, показывающие время, необходимое для полного превращения или для достижения некоторого промежуточного состояния. Форма кривой указывает на то, что скорость превращения нарастает до максимума при некоторой температуре Tm, лежащей значительно ниже T0, а затем снова уменьшается. Это объясняется совместным действием двух противоположных эффектов. При температурах выше T0 стабильной фазой является твердый раствор, и он будет существовать как угодно долго. Если же его охладить до температуры, несколько меньшей T0, то, как явствует из фазовой диаграммы (рис. 1), должно образоваться некоторое количество второй фазы. Но С-образная кривая свидетельствует, что для этого потребуется очень много времени. Дело в том, что в данном случае мала степень охлаждения, т.е. разность температуры T0 и фактической температуры, а именно эта разность является движущей силой процесса перехода к термодинамическому равновесию. Чем больше охлаждение, тем больше движущая сила и тем быстрее движется система к равновесию, на что указывает крутой загиб книзу в левой части С-образной кривой. Однако чем больше понижается температура, тем меньше становится скорость диффузии. Ниже температуры Tm движущая сила продолжает увеличиваться, но подвижность атомов настолько уменьшается, что время, необходимое для превращения, снова начинает увеличиваться и в конце концов становится практически бесконечно большим.
Рис. 2. С-ОБРАЗНАЯ КРИВАЯ описывает поведение сплава, состав которого соответствует точке X0, T0 на рис. 1, после закалки. Кривая определяет время, необходимое при разных температурах для того, чтобы началось послезакалочное выделение второй фазы. При температурах выше T0 стабильной фазой является твердый раствор.
Цель закалки металла после термической обработки на твердый раствор в том, чтобы очень быстро, не дав времени на превращение, охладить его ниже точки Tm до температуры T3, при которой скорость превращения ничтожно мала. Максимально возможная скорость закалки металлического образца (или изделия) определяется скоростью отвода тепла с его поверхности, а также его размерами и коэффициентом теплопроводности. Первый фактор ограничивается кипением закалочной среды (по большей части воды или соляного раствора) и, попросту говоря, всегда одинаков. Поэтому предельные размеры детали, которая может быть закалена без фазового превращения, зависят от теплопроводности ее материала, так как именно теплопроводностью определяется скорость охлаждения в объеме детали, даже если считать бесконечно большой скорость отвода тепла с ее поверхности.
См. также
МЕТАЛЛОВЕДЕНИЕ ФИЗИЧЕСКОЕ;
МЕТАЛЛОВ ОБРАБОТКА ДАВЛЕНИЕМ.
ЛИТЕРАТУРА
Металловедение и термическая обработка стали. М., 1961-1962 Кристиан Дж. Теория превращений в металлах и сплавах. М., 1978 Павлов П.А. Механические состояния и прочность материалов. Л., 1980
Энциклопедия Кольера. — Открытое общество. 2000.
- МЕТАЛЛОВЕДЕНИЕ ФИЗИЧЕСКОЕ
- ПОЛИГРАФИЯ
Смотреть что такое «МЕТАЛЛОВ ТЕРМИЧЕСКАЯ ОБРАБОТКА» в других словарях:
Термическая обработка — металлов, процесс обработки изделий из металлов и сплавов путём теплового воздействия с целью изменения их структуры и свойств в заданном направлении. Это воздействие может сочетаться также с химическим, деформационным, магнитным и др.… … Большая советская энциклопедия
ТЕРМИЧЕСКАЯ ОБРАБОТКА — металлов процесс тепловой обработки металлов и сплавов с целью изменения их структуры, а следовательно, и св в, заключающийся в нагреве до определ. темп ры. выдержке при этой темп ре и последующем охлаждении с заданной скоростью. Т. о. одно из… … Большой энциклопедический политехнический словарь
ТЕРМИЧЕСКАЯ ОБРАБОТКА (металлов) — технолог. процесс, заключающийся в нагревании и охлаждении металл. изделий, полуфабрикатов или сплавов с целью изменения их структуры и свойств (хим., физических или механ.) для повышения качества готовых изделий. В зависимости от сложности… … Технический железнодорожный словарь
ТЕРМИЧЕСКАЯ ОБРАБОТКА — ТЕРМИЧЕСКАЯ ОБРАБОТКА, тепловая обработка в основном металлов и сплавов для изменения их структуры и свойств. Основные виды: закалка (быстрое охлаждение с повышением температуры для увеличения прочности), отжиг (нагрев до высокой температуры,… … Современная энциклопедия
ТЕРМИЧЕСКАЯ ОБРАБОТКА — изменение механических свойств металлов путем соответственного температурного режима, иногда в соединении с действием химических реагентов. К термической обработке относится закалка, отжиг, цементация, отпуск, нитрирование и т. д. Самойлов К. И.… … Морской словарь
ТЕРМИЧЕСКАЯ ОБРАБОТКА — совокупность технологических операций, связанных с нагреванием, охлаждением и направленных на изменение свойств материалов в результате изменения их внутреннего или поверхностного строения. Особенно широкое промышленное распространение получила Т … Большая политехническая энциклопедия
термическая обработка — совокупность операций теплового воздействия на материалы (главным образом металлы и сплавы) с целью изменения структуры и свойств в нужном направлении. Основные виды термической обработки: закалка, отпуск, отжиг, нормализация, старение… … Энциклопедический словарь
Термическая обработка металлов — Металл в термопечи Термическая обработка металлов и сплавов процесс тепловой обработки металлических изделий, целью которого является изменение структуры и свойств в заданном направлении … Википедия
термическая обработка — [heat (thermal treatment (processing)] совокупность операций теплового воздействия на материал с целью изменения его структуры и свойств в нужном направлении (Смотри Термообработка). Смотри также: Обработка электроэрозионная обработка … Энциклопедический словарь по металлургии
термическая обработка металлов — процесс обработки изделий из металлов и сплавов путём теплового воздействия для целенаправленного изменения их структуры и свойств. Термическая обработка металлов подразделяется на собственно термическую, заключающуюся только в тепловом… … Энциклопедия техники
dic.academic.ru
Термическая обработка — Мегаэнциклопедия Кирилла и Мефодия — статья
Терми́ческая обрабо́тка, технологический способ воздействия на структурное и фазовое состояние материала с помощью различных режимов нагрева и охлаждения, в процессе которых достигается приближение к равновесному состоянию или та или иная степень отклонения от него. Понятие режимов нагрева и охлаждения включает скорость этих процессов, температуру, среду, продолжительность изотермических выдержек. Режимы термической обработки подбирают с учетом фазовых и структурных превращений в материале с целью получения необходимого комплекса свойств.
Термическая обработка может быть предварительной или окончательной.
Предварительную термообработку применяют для подготовки структуры и свойств материала к последующим технологическим операциям (для обработки давлением, улучшения обрабатываемости резанием). При окончательной термообработке формируются свойства готового изделия.
Термическую обработку применяют на стадии производства различных материалов и изделий, а также для снятия напряжения в них. Основные виды термообработки: отжиг (1-го и 2-го рода) и закалка без полиморфного превращения и с полиморфным превращением. Термическая обработка является основным способом воздействия на свойства металлов и сплавов. Специальные процессы термообработки, такие как возврат, рекристаллизация, полигонизация, старение, отпуск, нормализация, патентирование разработаны и подробно изучены по отношению к металлам и сплавам.Если сплав однофазен и не испытывает в твердом состоянии никаких фазовых превращений, то возможные отклонения от равновесия в таких сплавах могут быть связаны с химической неоднородностью твердого раствора или с наличием структурных дефектов, созданных пластической деформацией. Приближение к равновесию в таких случаях реализуется чаще всего за счет диффузионных процессов и достигается с помощью операций отжига I рода, под которым понимают относительно продолжительный высокотемпературный нагрев с последующим, как правило, медленным охлаждением.
Наличие фазовых превращений в сплаве значительно расширяет возможности термической обработки. Отжиг II рода — отжиг металлов и сплавов, испытывающих фазовые превращения в твердом состоянии при нагреве и охлаждении — проводится для сплавов, в которых имеются полиморфные или эвтектоидные превращения, а также переменная растворимость компонентов в твердом состоянии. Отжиг II рода проводят с целью получения более равновесной структуры и подготовки ее к дальнейшей обработке. В результате отжига измельчается зерно, повышаются пластичность и вязкость, снижаются прочность и твердость, улучшается обрабатываемость резанием.Чтобы зафиксировать высокотемпературное фазовое или метастабильное фазовое состояние, промежуточное между высоко- и низкотемпературным, применяют быстрое охлаждение от высоких температур. Такая операция называется закалкой. Закалка проводится для сплавов, испытывающих фазовые превращения в твердом состоянии при нагреве и охлаждении, с целью повышение твердости и прочности путем образования неравновесных структур (сорбит, троостит, мартенсит).Низкотемпературный нагрев после закалки (старение или отпуск) приближает систему к равновесному состоянию. Благодаря малой диффузионной подвижности атомов при низких температурах процесс легко остановить на промежуточных стадиях, отличающихся разной степенью приближения к равновесию, а следовательно, и свойствами. Отпуск проводится с целью снятия внутренних напряжений, снижения твердости и увеличения пластичности и вязкости закаленных сталей.
Термическая обработка используется как способ воздействия на состав точечных дефектов и структурное совершенство в кристаллах полупроводников и твердых растворах на их основе как с целью изучения свойств материала, так и с целью поиска пути управления ими. Понимание механизмов дефектообразования в кристаллах полупроводников при термообработке очень важно, так как кристаллы полупроводников подвергаются термообработкам в процессе изготовления приборов. При этом, как ансамбль собственных точечных дефектов, так и микродефекты могут претерпевать различные превращения, что в дальнейшем может негативно повлиять на характеристики приборов. При термообработке кристаллов может происходить распад пересыщенного твердого раствора как примесей, так и собственных точечных дефектов, если их концентрация превышает растворимость при температуре термообработки. Может происходить развитие ростовых и образование новых микродефектов или их растворение в результате ухода точечных дефектов или примесей, образующих микродефект, на поверхность кристалла. В результате таких процессов происходит не только структурное превращение в матрице кристалла, но существенным образом изменяются его электрофизические свойства: могут измениться концентрация и подвижность носителей заряда, тип проводимости (термоконверсия), оптические и люминесцентные свойства полупроводников.Термическая обработка материалов подразделяется на собственно термическую, заключающуюся только в тепловом воздействии на металл, химико-термическую, сочетающую тепловое и химическое воздействия, и термомеханическую, сочетающую тепловое воздействие и пластическую Разновидности термической обработки — обработка стали холодом, электротермическая обработка.
- Металловедение и термическая обработка стали. М., 1961-1962.
- Кристиан Дж. Теория превращений в металлах и сплавах. М., 1978.
- Павлов П. А. Механические состояния и прочность материалов. Л., 1980.
- Волокушин В. Ф. Металловедение и термическая обработка. — Винница: Кн.-Вега, 2005.
- Колачев Б. А. Металловедение и термическая обработка цветных металлов и сплавов. — М.: МИСИС, 2005.
- Кульбовский И. К. Теория и технология термической и химико-термической обработки. — Брянск: Изд-во БГТУ, 2005.
- Новые методы химико-термической обработки в машиностроении. – М.: МАДИ, 2004.
- Абраимов Н. В. Химико-термическая обработка жаропрочных сталей и сплавов. — М.: Интермет Инжиниринг, 2001.
megabook.ru
Термическая обработка металлов Википедия
Металл в термопечиТермической (или тепловой) обработкой называется совокупность операций нагрева, выдержки и охлаждения твёрдых металлических сплавов с целью получения заданных свойств за счёт изменения внутреннего строения и структуры. Тепловая обработка используется либо в качестве промежуточной операции для улучшения обрабатываемости давлением, резанием, либо как окончательная операция технологического процесса, обеспечивающая заданный уровень свойств изделия.
Общая длительность нагрева металла при тепловой обработке складывается из времени собственного нагрева до заданной температуры и времени выдержки при этой температуре. Время нагрева зависит от типа печи, размеров изделий, их укладки в печи; время выдержки зависит от скорости протекания фазовых превращений.
Нагрев может сопровождаться взаимодействием поверхности металла с газовой средой и приводить к обезуглероживанию поверхностного слоя и образованию окалины. Обезуглероживание приводит к тому, что поверхность изделий становится менее прочной и теряет твёрдость.
При нагреве и охлаждении стали происходят фазовые превращения, которые характеризуются температурными критическими точками. Принято обозначать критические точки стали буквой А. Критические точки А1 лежат на линии PSK (727 °С) диаграммы железо-углерод и соответствуют превращению перлита в аустенит. Критические точки А2 находятся на линии МО (768 °С), характеризующей магнитное превращение феррита. A3 соответствует линиям GS и SE, на которых соответственно завершается превращение феррита и цементита в аустенит при нагреве.
Для обозначения критических точек при нагреве и охлаждении вводят дополнительные индексы: букву «с» в случае нагрева и «r» в случае охлаждения, например Ас1, Ac3, Ar1, Ar3.
Виды термической обработки[ | ]
Среди основных видов термической обработки следует отметить:
- Отжиг
- Отжиг 1 рода (гомогенизация, рекристаллизация, снятие напряжений). Целью является получение равновесной структуры. Такой отжиг не связан с превращениями в твердом состоянии (если они и происходят, то это — побочное явление).
- Отжиг 2 рода связан с превращениями в твердом состоянии. К отжигу 2 рода относятся: полный отжиг, неполный отжиг, нормализация, изотермический отжиг, патентирование, сфероидизирующий отжиг.
- Закалку проводят с повышенной скоростью охлаждения с целью получения неравновесных структур. Критическая скорость охлаждения, необходимая для закалки, зависит от химического состава сплава. Закалка может сопровождаться полиморфным превращением, при этом из исходной высокотемпературной фазы образуется новая неравновесная фаза (например, превращение аустенита в мартенсит при закалке стали). Существует также закалка без полиморфного превращения, в процессе которой фиксируется высокотемпературная метастабильная фаза (например, при закалке бериллиевой бронзы происходит фиксация альфа фазы, пересыщенной бериллием).
- Отпуск необходим для снятия внутренних напряжений, а также для придания материалу требуемого комплекса механических и эксплуатационных свойств. В большинстве случаев материал становится более пластичным при некотором уменьшении прочности.
- Нормализация. Изделие нагревают до аустенитного состояния (на 30…50 градусов выше АС3) и охлаждают на спокойном воздухе
- Дисперсионное твердение (старение). После проведения закалки (без полиморфного превращения) проводится нагрев на более низкую температуру с целью выделения частиц упрочняющей фазы. Иногда проводится ступенчатое старение при нескольких температурах с целью выделения нескольких видов упрочняющих частиц.
- Криогенная обработка — это упрочняющая термическая обработка металлопродукции при криогенных, сверхнизких температурах (ниже минус 153°С).
Ранее для обозначения этого процесса использовалась иная терминология — «обработка холодом», «термическая обработка стали при температурах ниже нуля», но они не совсем точно отражали суть процесса криогенной обработки.
Суть криогенной обработки заключается в следующем: детали и механизмы помещаются в криогенный процессор, где они медленно охлаждаются и после выдерживаются при температуре минус 196˚С в течение определенного времени. Затем обрабатываемые изделия постепенно возвращаются к комнатной температуре. Во время этого процесса в металле происходят структурные изменения. Они существенно повышают износостойкость, циклическую прочность, коррозионную и эрозионную стойкость.
Эта технология позволяет повысить ресурс инструментов, деталей и механизмов до 300 % за счет улучшения механических характеристик материала в результате обработки сверхнизкими температурами.
Наибольшего эффекта удается достичь при обработке таких металлических изделий, как специальный режущий, штамповый, прессовый, прокатный, мелющий инструмент
ru-wiki.ru
Термическая обработка металлов — WiKi
Металл в термопечиТермической (или тепловой) обработкой называется совокупность операций нагрева, выдержки и охлаждения твёрдых металлических сплавов с целью получения заданных свойств за счёт изменения внутреннего строения и структуры. Тепловая обработка используется либо в качестве промежуточной операции для улучшения обрабатываемости давлением, резанием, либо как окончательная операция технологического процесса, обеспечивающая заданный уровень свойств изделия.
Общая длительность нагрева металла при тепловой обработке складывается из времени собственного нагрева до заданной температуры и времени выдержки при этой температуре. Время нагрева зависит от типа печи, размеров изделий, их укладки в печи; время выдержки зависит от скорости протекания фазовых превращений.
Нагрев может сопровождаться взаимодействием поверхности металла с газовой средой и приводить к обезуглероживанию поверхностного слоя и образованию окалины. Обезуглероживание приводит к тому, что поверхность изделий становится менее прочной и теряет твёрдость.
При нагреве и охлаждении стали происходят фазовые превращения, которые характеризуются температурными критическими точками. Принято обозначать критические точки стали буквой А. Критические точки А1 лежат на линии PSK (727 °С) диаграммы железо-углерод и соответствуют превращению перлита в аустенит. Критические точки А2 находятся на линии МО (768 °С), характеризующей магнитное превращение феррита. A3 соответствует линиям GS и SE, на которых соответственно завершается превращение феррита и цементита в аустенит при нагреве.
Для обозначения критических точек при нагреве и охлаждении вводят дополнительные индексы: букву «с» в случае нагрева и «r» в случае охлаждения, например Ас1, Ac3, Ar1, Ar3.
Среди основных видов термической обработки следует отметить:
- Отжиг
- Отжиг 1 рода (гомогенизация, рекристаллизация, снятие напряжений). Целью является получение равновесной структуры. Такой отжиг не связан с превращениями в твердом состоянии (если они и происходят, то это — побочное явление).
- Отжиг 2 рода связан с превращениями в твердом состоянии. К отжигу 2 рода относятся: полный отжиг, неполный отжиг, нормализация, изотермический отжиг, патентирование, сфероидизирующий отжиг.
- Закалку проводят с повышенной скоростью охлаждения с целью получения неравновесных структур. Критическая скорость охлаждения, необходимая для закалки, зависит от химического состава сплава. Закалка может сопровождаться полиморфным превращением, при этом из исходной высокотемпературной фазы образуется новая неравновесная фаза (например, превращение аустенита в мартенсит при закалке стали). Существует также закалка без полиморфного превращения, в процессе которой фиксируется высокотемпературная метастабильная фаза (например, при закалке бериллиевой бронзы происходит фиксация альфа фазы, пересыщенной бериллием).
- Отпуск необходим для снятия внутренних напряжений, а также для придания материалу требуемого комплекса механических и эксплуатационных свойств. В большинстве случаев материал становится более пластичным при некотором уменьшении прочности.
- Нормализация. Изделие нагревают до аустенитного состояния (на 30…50 градусов выше АС3) и охлаждают на спокойном воздухе
- Дисперсионное твердение (старение). После проведения закалки (без полиморфного превращения) проводится нагрев на более низкую температуру с целью выделения частиц упрочняющей фазы. Иногда проводится ступенчатое старение при нескольких температурах с целью выделения нескольких видов упрочняющих частиц.
- Криогенная обработка — это упрочняющая термическая обработка металлопродукции при криогенных, сверхнизких температурах (ниже минус 153°С).
Ранее для обозначения этого процесса использовалась иная терминология — «обработка холодом», «термическая обработка стали при температурах ниже нуля», но они не совсем точно отражали суть процесса криогенной обработки.
Суть криогенной обработки заключается в следующем: детали и механизмы помещаются в криогенный процессор, где они медленно охлаждаются и после выдерживаются при температуре минус 196˚С в течение определенного времени. Затем обрабатываемые изделия постепенно возвращаются к комнатной температуре. Во время этого процесса в металле происходят структурные изменения. Они существенно повышают износостойкость, циклическую прочность, коррозионную и эрозионную стойкость.
Эта технология позволяет повысить ресурс инструментов, деталей и механизмов до 300 % за счет улучшения механических характеристик материала в результате обработки сверхнизкими температурами.
Наибольшего эффекта удается достичь при обработке таких металлических изделий, как специальный режущий, штамповый, прессовый, прокатный, мелющий инструмент, подшипники, ответственные пружины.
Основные свойства металла, приобретенные в ходе глубокого охлаждения, сохраняются в течение всего срока их службы, поэтому повторной обработки не требуется.
Криогенная технология не заменяет существующие методы термического упрочнения, а позволяет придать материалу, обработанному холодом, новые свойства, которые обеспечивают максимальное использование ресурса материала, заданного металлургами.
Использование инструмента, обработанного сверхнизкими температурами, позволяет предприятиям значительно сократить расходы за счет:
- увеличения износостойкости инструмента, деталей и механизмов
- снижения количества брака
- сокращения затрат на ремонт и замену технологического оснащения и инструмента.
Теоретическая разработка и практическое освоение процесса криогенной обработки считается достижением советской науки. Работы таких учёных, как Г. В. Курдюмова, исследования А. П. Гуляева, В. Г. Воробьева и других связаны с обработкой холодом для улучшения качественных характеристик закаленной стали.
Спустя несколько лет после публикации исследований советских учёных появились первые аналогичные работы в иностранной печати, авторы которых ссылались на советские работы как первоисточник. Именно работы советских учёных позволили полно оценить эффективность влияния обработки холодом на свойства стали и положили начало современному развитию и использования этого способа обработки. В 1940—1950-е годы на советских промышленных предприятиях пытались внедрить криогенную обработку инструмента из быстрорежущих сталей в жидком азоте, но это не только не давало ожидаемого результата, но и приводило к снижению прочности инструмента, поскольку появлялись микротрещины из-за резкого и неравномерного охлаждения. От метода, позволяющего преобразовать остаточный аустенит в мартенсит, пришлось отказаться, в основном из-за экономической нецелесообразности — высокой стоимости азота, как основного хладагента.
В США, Японии, Германии, Южной Корее тему криогенной обработки как эффективного способа обработки конструкционных и инструментальных сталей развивали, и десятилетия исследований и опытов привели к результату — в настоящее время технология криогенной обработки успешно применяется во многих отраслях промышленности.
Металлообработка и машиностроение:
- увеличение ресурса инструмента и оборудования до 300 %
- увеличение износостойкости материалов
- увеличение циклической прочности
- увеличение коррозионной и эрозионной стойкости
- снятие остаточных напряжений
Транспорт и спецтехника:
- увеличение ресурса тормозных дисков до 250 %
- повышение эффективности работы тормозной системы
- увеличение циклической прочности пружин подвески и других упругих элементов на 125 %
- увеличение ресурса и мощности двигателя
- снижение расходов на эксплуатацию транспортных средств
Оборонная промышленность:
- увеличение эксплуатации оружия до 200 %
- уменьшение влияния нагрева оружия на результаты стрельбы
- увеличение ресурса узлов и механизмов
Добывающая и обрабатывающая промышленность:
- увеличение стойкости породоразрушающего инструмента до 200 %
- уменьшение абразивного износа машин и механизмов
- увеличение коррозийной и эрозийной стойкости оборудования
- увеличение ресурса промышленного и горнодобывающего оборудования
Аудиотехника и музыкальные инструменты:
- уменьшение искажения сигнала в проводниках
- уменьшение рассеиваемого проводниками тепла на 30-40 %
- улучшение музыкальной детальности, ясности и прозрачности звучания
- расширение диапазона звучания музыкальных инструментов
Применение криогенной обработки актуально практически для любой отрасли, где есть необходимость повышения ресурса, увеличения усталостной прочности и износостойкости, а также требуется рост производительности.
Гомогенизационный отжиг + старение
Например, для суперсплавов на базе никеля (типа «Инконель 718») типичной является следующая термическая обработка:
Гомогенизация структуры и растворение включений (англ. Solution Heat Treatment) при 768—782 °C с ускоренным охлаждением. Затем производится двухступенчатое старение (англ. Precipitation Heat Treatment) — 8 часов при температуре 718 °C, медленное охлаждение в течение 2 часов до 621—649 °C и выдержка в течение 8 часов. Затем следует ускоренное охлаждение.
Закалка + высокий отпуск (улучшение)
Многие стали проходят упрочнение путём закалки — ускоренного охлаждения (на воздухе, в масле или в воде). Быстрое охлаждение приводит, как правило, к образованию неравновесной мартенситной структуры. Сталь непосредственно после закалки отличается высокой твёрдостью, остаточными напряжениями, низкой пластичностью и вязкостью. Так, сталь 40ХНМА (SAE 4340) сразу после закалки имеет твёрдость выше 50 HRC, в таком состоянии материал непригоден для дальнейшего использования из-за высокой склонности к хрупкому разрушению. Последующий отпуск — нагрев до 450 °C — 500 °C и выдержка при этой температуре приводят к уменьшению внутренних напряжений за счёт распада мартенсита закалки, уменьшения степени тетрагональности его кристаллической решётки (переход к отпущенному мартенситу). При этом твёрдость стали несколько уменьшается (до 45 — 48 HRC). Подвергаются улучшению стали с содержанием углерода 0,3 — 0,6 % C.
ru-wiki.org