Температура газа в доменной печи » Строительный портал
Наивысшие температуры в доменной печи имеют место в горне, где происходит горение. Распределение температуры, выраженное в градусах, в различных точках сечения горна доменной печи не было известно в течение весьма длительного времени. М.А. Павлов рассказывает, что в прежнее время для суждения о тепловом состоянии горна доменщики вдвигали через глаз фурмы длинный железный лом диаметрам около 30—40 мм — до противоположной стены. Лом выдерживался в горне то или иное время, в зависимости от состояния горна, после чего вынимался. По накалу лома судили о степени прогрева горна и о распределении температур по радиусу горна, которое не было и не могло быть равномерным: вблизи фурмы; на некотором расстоянии от глаза ее, где находился фокус горения, лом бывал нагрет до ослепительно белого каления и даже оплавлялся, далее нагрев лома заметно понижался по мере приближения к середине горна.
При ненормальной работе доменной печи, например, при скоплении большого количества мусора в горне, лом оставался темным, не успев прогреться при сравнительно кратковременной выдержке. Наконец, при расстроенном ходе печи бывало, что лом вообще не мог пройти через середину горна, что свидетельствовало о присутствии нерасплавленных масс в этом месте.
Ввиду больших экспериментальных трудностей измерение температур в горне долгое время не производилось. Лишь благодаря работам советских исследователей, создавших специальные измерительные приборы, этот пробел был заполнен. Вместо единичных наблюдений, проведенных зарубежными исследователями, что не давало никакой гарантии их достоверности, советские исследователи произвели сотни измерений, вследствие чего полученные ими данные являются вполне достоверными, лишенными всякого элемента случайности.
Исследования начались с 1934 г. и продолжались в течение нескольких лет подряд. Измерения температур производились посредством графито-вольфрамовых и платино-платинорадиевых термопар, которые вводились в горн при помощи специальной охлаждаемой водой трубки.
На рис. 80 показано изменение температур по радиусу горна доменной печи с полезным объемом 1180 м3 (исследования 1935, 1936 и 1937 гг. ). Каждая кривая построена по данным, представляющим собой среднее из многих наблюдений. Из рисунка видно, что температура в фокусе горения, расположенном на расстоянии около 600 мм от глаза фурмы, составляет примерно 1900° С. Затем по направлению к оси горна температура в зависимости от сорта выплавлявшегося чугуна (литейного или передельного) и условий работы колебалась в пределах 1400—1250° С.
На рис. 81 приведена кривая изменения температуры газа по радиусу горна доменной печи с полезным объемом 1300 м3. Эта кривая отражает ту же самую закономерность в распределении температур, которая была получена для печи объемом 1180 м3.
Измерение температур в распаре и шахте представляет меньшие экспериментальные трудности, хотя и не является простым и легким делом. Поэтому долгое время мы не располагали достаточно достоверными данными о температурах, господствующих в распаре и шахте доменных печей.
Многочисленные данные об измерении температур как по высоте шахты, так и по радиусу ее, полученные советскими исследователями, позволили заполнить этот пробел. В табл. 42 приведены результаты замера температур, по данным некоторых работ советских исследователей. Таблица показывает, что, так же как и в горне, температуры по радиусу распара, по радиусу шахты на различных горизонтах не остаются постоянными. Наибольшая температура наблюдается непосредственно у стенки печи; по направлению к оси печи температура падает. Минимум температуры достигается в зависимости от хода печи либо на некотором расстоянии от стенки печи (после чего температура снова поднимается, достигая второго максимума у оси), либо непосредственно у оси печи. При выплавке литейного и передельного чугуна температура в распаре колеблется в пределах от 1350—1300° С для максимума и до 900—950° С для минимума.
На среднем и верхнем горизонтах шахты распределение температур по радиусу принципиально такое же, как и по распару, но численные значения температуры иные. Для среднего горизонта шахты максимум температуры колеблется, как правило, в пределах 1000—900° С, поднимаясь в виде исключения до 1235° С; минимум температур колеблется в пределах 525—700° С. В верхнем горизонте максимум температур колеблется в пределах от 460 до 690° С, минимум — 125—300° С.
Температура газов, покидающих доменную печь, или, как говорят, температура колошника может колебаться в зависимости от многих факторов. Например, увеличение удельного расхода кокса будет способствовать повышению температуры колошника по той причине, что в этом случае количество газов на единицу чугуна возрастает, в то время как величина рудной сыпи остается без изменений, вследствие чего газы будут уносить с собой больше тепла и температура колошника увеличится. Наоборот, уменьшение удельного расхода кокса будет способствовать снижению температуры колошника.
Если распределение материалов ухудшится, то неравномерность в распределении газового потока усилится; это проявляется обычно в том, что в отдельных каналах, проложенных газом в столбе шихтовых материалов, проходит очень много газов, эти газы отдают шихте лишь незначительную часть заключающегося в них тепла и выходят из столба шихты с высокой температурой, что и вызывает повышение температуры колошника.
Существенное понижение уровня засыпи против обычного, уменьшая высоту столба шихты и тем самым сокращая время контакта газов с шихтой, ведет к повышению температуры колошника.
Температура колошника может в значительной степени меняться в зависимости от качества загружаемой шихты. Так, загрузка в шихту горячего агломерата будет способствовать повышению температуры колошника; наоборот, применение сырых бурых железняков с высоким содержанием гигроскопической влаги будет способствовать понижению этой температуры.
Увеличение веса руды по отношению к весу кокса будет способствовать понижению температуры колошника.
Что касается абсолютного значения температуры колошника, то в зависимости от условий работы она может колебаться при выплавке передельных и литейных чугунов от 80—100°С до 300—350° С.
При выплавке доменных ферросплавов — ферросилиция и ферромарганца — температура колошника вследствие высокого расхода кокса бывает значительно выше и может достигать 450—600° С, если для ее снижения не применяется искусственных мер (например, усиленная поливка шихты водой перед загрузкой в печь).
Средние температуры колошника представлены в табл. 43 (по данным 1949—1950 гг.).
В действительных условиях температура колошника никогда не остается постоянной. Загрузка свежей порции материалов вызывает быстрое понижение температуры; по мере подогрева только что опущенной порции шихты температура колошника растет, колебания температуры колошника между двумя завалками колошника могут составлять 150—225° С.
Особенности теплопередачи в доменных печах » Все о металлургии
09.06.2015
Приведенные приемы анализа тепловой стороны доменного процесса основывались на тепловом балансе, рассчитанном по начальному и конечному состоянию системы, т. е. с учетом общего количества выделяющегося тепла, но без учета того, при каких условиях и при каких температурах происходит передача тепла от газов к материалам. Рассмотренный тепловой баланс, независимо от предложенных способов его расчета, базируется на «первом начале», т. е. на обеспечении соблюдения только баланса тепла в доменном процессе в целом. Согласно этому балансу, равные количества тепла, например, на испарение воды и на диссоциацию влаги, учитываются равным числом калорий и одинаково отражаются на расходе кокса. Между тем, фактическое влияние этих факторов на расход кокса неодинаково.
Соблюдение «второго начала», согласно которому тепло может переходить только от тела с более высокой температурой к телу с более низкой, обычным балансом не контролируется.

Эти рассуждения свидетельствуют о недостаточности обычного теплового баланса как средства анализа процесса. Можно обратить внимание и на то, что при составлении обычного баланса формально можно было бы в расчет принять любую высокую температуру дутья или любую низкую температуру колошника, в то время как фактически нельзя подавать в печь дутье с температурой, выше оптимальной в данных условиях, и нельзя никакими мерами снизить температуру колошника ниже определенного уровня.
Примером обусловленности температуры колошниковых газов существом процесса и невозможности ее снижения ниже некоторого уровня является то, что при увеличении высоты печи и, следовательно, пути газов почти вдвое не было достигнуто существенного понижения температуры колошниковых газов, несмотря ка то, что контакт шихты и газов при этом значительно удлинился. В подтверждение сказанного можно указать на следующий пример, приведенный М.А. Павловым: если сравнить две печи, из которых одна имела высоту 14,33 м и объем 170 м3, а вторая соответственно 24,38 м и 440 м3, то температура колошника у первой оказалась 390°, а у второй — 336°, т.
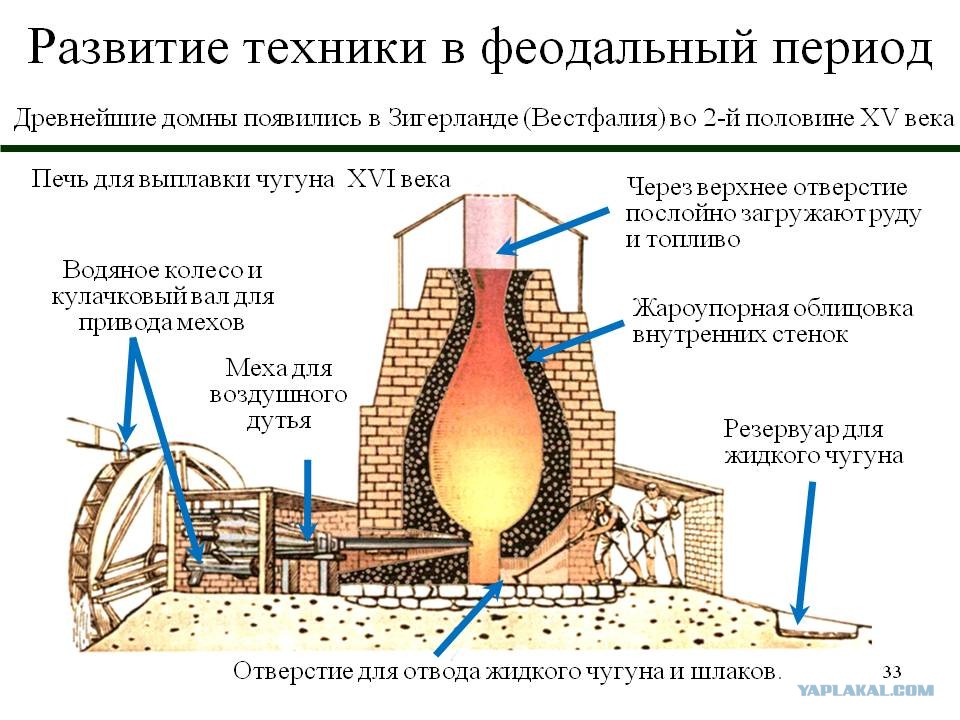
Можно отметить также, что невысокие печи небольшого объема, работающие на влажной лимонитовой рудеминетт, имеют часто температуру колошника 60—70°, а печи Магнитогорского завода объемом 1386 м3, работающие на офлюсованном агломерате, при незначительном количестве летучих в шихте имеют температуру колошника 350—400°, причем использование углерода в последних неизмеримо выше, чем у первых.
Таким образом, температура отходящих газов не зависит от высоты и размеров печи, а определяется главным образом потреблением тепла в верхних горизонтах печи. Она зависит также и от количества тепла, выделенного в результате экзотермических реакций верхней части печи. Доказательством этого является весьма высокая температура колошниковых газов при выплавке ферромарганца из руды, содержащей пиролюзит (MnO2), в связи с выделением большого количества тепла при восстановлении от MnO2 до Mn2O3.

He приходится говорить о том, что «низкотемпературное» тепло, теряемое в колошник с газами, нагретыми до 400—300°, не может быть использовано в печи, так как в других местах печи температура еще выше. Для снабжения нижних горизонтов нужным теплом необходимо, как известно, подвести это тепло в соответствующие участки печи, причем теплоноситель должен иметь соответственно более высокую температуру; тепло должно быть «высокотемпературным» и доставляться путем увеличения количества сжигаемого углерода либо повышением нагрева дутья.
При увеличении количества руды, приходящейся на прежнее количество кокса, возможно снижение температуры отходящих газов; но в нижних частях печи, где избытка тепла нет, неизбежен тепловой «перегруз» — похолодание печи.
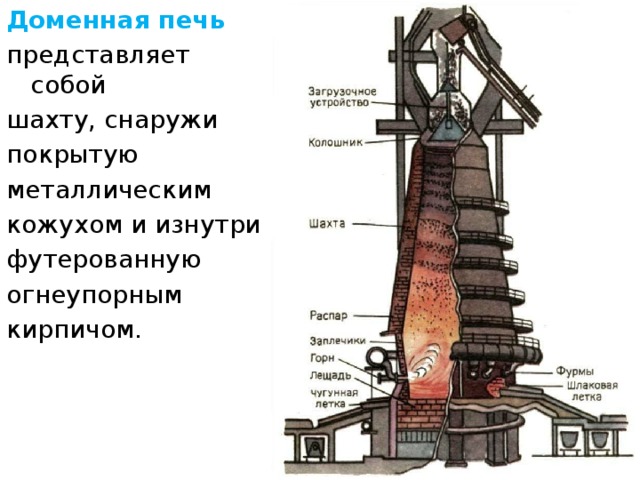
Таким образом, возрастание количества неиспользованного тепла, уносимого газами в колошник, может быть следствием либо экзотермических реакций в верхних частях печи, либо следствием малого потребления тепла в шахте на удаление летучих (h3O, CO2) и испарение влаги, либо результатом возросшей потребности «высокотемпературного» тепла в нижних частях печи, вызывающей больший расход углерода. С этим связано образование большего количества газов, которые, переходя в шахту, не могут найти потребителя содержащегося в них тепла. Поэтому часто производственники, желая предохранить железные конструкции колошника от действия высоких температур, намеренно увлажняют руду, искусственно охлаждая этим газы. При этом, кстати, уменьшается скорость газов на колошнике и снижается вынос руды в виде пыли.
Все приведенные факты и основанные на них рассуждения заставляют предположить, что условия теплопередачи в нижних и верхних частях печи различны: внизу «высокотемпературное» тепло утилизируется полностью, причем приход тепла от горения топлива в горячем дутье без избытка покрывает потребность в нем нижней части печи; вверху же печи «низкотемпературного» тепла, принесенного сюда газами, пришедшими снизу, оказывается часто больше, чем необходимо для процесса, поэтому колошниковые газы выходят из печи с повышенной температурой.

Рассмотрим подробнее условия теплопередачи в верхней и нижней областях доменной печи, предположив вначале, что в шихте не содержится влаги. Оценим раздельно теплопередачу в областях с температурой ниже 900°, где не происходит разложения карбонатов и прямого восстановления, и в областях с температурой выше 900°, где, кроме разложения карбонатов и прямого восстановления Fe, Si, Mn, P и других элементов и перевода серы в шлак, происходит еще плавление чугуна, шлака, их перегрев и диссоциация водяного пара.

В нижней же части печи, кроме обычного теплообмена, есть еще теплопередача, при которой газы, как и вверху, охлаждаясь, понижают температуру, а встречные твердые и жидкие вещества, воспринимая тепло, температуры не повышают. Именно такое явление имеет место при разложении карбонатов, плавлении, прямом восстановлении. На эту существенную разницу потребления тепла в верхней и нижней частях печи впервые в 1910 г. указал А.С. Саркисьянц, а позже — Дипшлаг, Н.А. Костылев, В. Матезиус, Б.И. Китаев и др.
P — вес сухих материалов;
р — количество газов;
T0 и T — температуры материалов в начале верхней зоны, т. е. при загрузке на колошнике, и в конце верхней зоны;
t0 и t — температуры газов при входе и выходе из верхней зоны;
С и с — теплоемкости материалов и газов.

Так как количество тепла, отданного газами, охладившимися от t0 до t, равно теплу, воспринятому материалами, нагретыми от T0 до T, то баланс тепла выразится так:
Произведения рс = Wg и PC = Ws принято называть водяными эквивалентами. Нетрудно видеть, что рс > РС Так, например, при расходе сырых материалов P = 3,2 кг на 1 кг чугуна, теплоемкости их C = 0,22 ккал/кг °С, величина PC=Ws = 3,2*0,22 = 0,7. При выходе газа на 1 кг чугуна р = 3,5 м3 и его теплоемкости с = 0,33 ккал/м3 °C получим
рс = Wg = 3,5 * 0,33 = 1,15.
Отношение pc/PC = 1,15/0,7 = 1,65. При всех возможных изменениях значений Р, р, С и с отношение это всегда превышает единицу, откуда следует, что T-T0/t0-t > 1, т. е. материалы нагреваются в большей степени, чем охлаждаются газы.
Действительно, материалы в верхней зоне нагреваются от 0 до 900°, а газы на соответствующем участке охлаждаются примерно на 550°. Если в той зоне, где материалы нагрелись до 900°, температура газов составляет 950—1000°, то температура газа при выходе из печи будет 400—450°. Именно такой и бывает температура колошника при отсутствии влаги в шихте. В действительности температура колошника несколько ниже вследствие расхода тепла на удаление влаги и на некоторые эндотермические процессы (разложение некоторой части карбонатов до 900°), протекающие в шахте.
Температура колошника t, таким образом, тем ниже, чем выше отношение водяных эквивалентов шихты и газа Ws/Wg = PC/pc или выше P/p, т. е. чем больше отношение количества шихтовых материалов к количеству газов или чем ниже расход кокса. Температура колошника зависит также от t0 и Т, но эти величины, как видно из предыдущего, изменяются мало.
Формула показывает, что с повышением нагрева дутья, вызывающим снижение расхода кокса, или с обогащением дутья кислородом снижается температура колошника: в обоих случаях снижается количество газов на единицу чугуна, т. е. увеличивается Р/р.
Рассмотрим баланс тепла в нижней зоне. Здесь тепло газов лишь частично используется для дальнейшего нагрева материалов и продуктов плавки; значительная же часть этого тепла используется на «скрытые» расходы. Обозначим сумму этих расходов через Q. Тогда получим, подобно предыдущему,
Уравнения (VI, 35), (VI, 36), (VI, 38), (VI, 39) условно отражают действительное течение процесса: ведь количества введенных и вышедших продуктов изменяются от начала к концу каждой зоны, так как в зонах происходят восстановительные и иные процессы, изменяющие значения P и P’. То же следует сказать и о количествах газа и теплоемкостях, в каждом расчете принимаемых приблизительно постоянными. Эти неточности не изменяют, однако, качественной стороны выводов.
Из уравнения (VI, 39) нетрудно заключить, что в нижней зоне, в противоположность верхней, отношение T’-T0’/t0′-t’ меньше единицы. В самом деле, если p’c’/P’C’ и в этом случае больше единицы, но меньше двух, то член Q/P’C'(t0′-t’) всегда равен или больше единицы, почему вся левая часть, а с ней и правая меньше единицы.
В том, что второй член левой части уравнения (VI, 39) больше единицы, нетрудно убедиться при любом подсчете, если подставить в это выражение конкретные величины.
Следовательно, в нижней части печи вследствие значительного увеличения теплопотребления шихты («скрытые» расходы тепла) температура твердых и жидких веществ изменяется всегда меньше, чем температура газов.
Сопоставляя закономерности изменения температур верхней и нижней зон печи и предполагая, что газы охлаждаются равномерно, получим схематическую картину, изображенную на рис. 190.
Прямая наклонная линия относится к газам, а ломаная — к материалам и жидким продуктам плавки. Разность температур, как это следует из выражений (VI, 36), (VI, 39) и рис. 190, будучи максимальной в низу печи, уменьшается к середине; здесь (при 900—1000°) перепад температур достигает минимального значения, а затем вновь возрастает. Заметная разность температур вверху соответствует тому, что газы уходят из печи при сравнительно высокой температуре.
В важнейших точках диаграммы буквами обозначены температуры, соответствующие входящим в формулы (VI, 36) и (VI, 39), причем очевидно, T = T0′ и t0 = t’, так как газ, оставляющий нижнюю зону, переходит в верхнюю с той же температурой, а материалы из верхней — в нижнюю с той же температурой. Из рис. 190 видно, что в верхней зоне изменение температур материалов больше, чем газов (VI, 36), а в нижней — наоборот (VI, 39).
Б.И. Китаев рядом расчетов и экспериментальных исследований показал, что область T, Т0′ и t0, t’ не фиксируется на одном горизонте, а распространяется на некоторую высоту печи. Сказанное иллюстрируется рис. 191, согласно которому печь по высоте делится не на две (как на рис. 190), а на три зоны, причем средняя зона, где разность температур газа и материалов незначительна, названа «холостой» высотой, а верхняя и нижняя области, соответствующие верхней и нижней зонам рис. 190, названы первой и второй ступенями теплообмена. Нетрудно видеть, что закономерности теплообмена, вытекающие из предыдущих рассуждений и отраженные на рис. 190, имеют место и на рис. 191: уменьшение разности температур между газами и продуктами плавки по мере движения газов снизу вверх во второй ступени (нижняя зона) и возрастание разности в первой ступени (верхняя зона). Искривление линий на рис. 191 объясняется учетом некоторых деталей, опущенных при схематическом построении рис. 190. В частности, на рис. 191 учтено, что в первой ступени, кроме простого теплообмена, имеет место и некоторый «скрытый» расход тепла — на испарение влаги, разложение гидратов и легкоразложимых карбонатов (FeCO3, MgCO3), — чему соответствует сравнительно более резкое падение температуры близ колошника.
Соображения Б.И. Китаева критиковались А.П. Любаном и другими, причем указывалось на то, что температуры измерялись термопарами, опущенными в печь через шомпольные отверстия, т. е. на периферии; поэтому незначительные изменения температур в «холостой» части печи характерны не для всего объема печи, соответствующего холостой высоте, а только некоторой небольшой периферийной части объема, содержащей мало руды и много шлака.
Б. И. Китаев, считая, что холостой является значительная часть объема доменной печи по высоте, поставил вопрос об уменьшении высоты печей.
Такой вывод вызвал серьезные возражения, основанные на том, что если даже и есть холостая высота, то она является результатом не конструкции (чрезмерной общей высоты) печи, а существа доменного процесса. Что это действительно так, доказывается измерением температур в модели доменной печи (1/20 нормальной высоты), полезной высотой 1225 мм. И.Ф. Коваль показал, что даже на такой маленькой печи при протекании в ней обычного процесса тоже имеется холостая высота, составляющая около 30% всей высоты. Следовательно, при уменьшении высоты печи холостой участок останется.
Ослабленный теплообмен на определенной высоте печи объясняется существенным изменением характера теплопередачи при 800—950°, которая не может осуществиться мгновенно или в небольшом участке пространства ввиду малой разности температур нагревающихся и охлаждающихся тел. Это изменение условий теплообмена как раз характеризуется незначительной разницей температур газа и материалов. Следует учесть, что восстановительные процессы при температурах 800—950° (область холостой высоты) идут с выделением тепла, а разложение карбонатов в той же области — с поглощением. Это способствует некоторой стабилизации температуры на известной высоте.
Резкое изменение температур в верхней и нижней зонах печи и слабое их изменение в средних подтверждается не только исследованиями, упомянутыми выше, но и более ранними измерениями температур газов по высоте печен США, проведенными Кинни (рис. 192).
- Принцип Павлова
- Обогащение дутья кислородом в доменном процессе
- Значение горячего дутья в доменном процессе
- Показатели тепловой работы доменной печи
- Способы составления теплового баланса доменной плавки
- Материальный баланс доменной плавки
- Определение количества и диаметра фурм
- Окисление составных частей чугуна и их повторное восстановление в горне
- Возгонка окислов и металлов в горне доменной печи
- Температуры в окислительной зоне и в фокусе горения
Химия сталеплавильного производства.

| ||||||||||
|
|
|
| ||||||||||
|
Процесс доменной печи — tec-science
В доменной печи железная руда вступает в реакцию с углеродом, содержащимся в коксе, с образованием серого или белого чугуна.
- 1 Combustion process
- 2 Boudouard reaction
- 3 Preheating
- 4 Indirect reduction zone
- 5 Direct reduction zone
- 6 Carburizing zone
- 7 Melting zone
- 8 Tapping zone
Combustion process
The железо в перерабатываемых рудах должно быть растворено химическими процессами. Для этого требуется элемент, который связывает кислород сильнее, чем железо. Это именно то, что углерод может сделать как восстановитель . Углерод подается в доменную печь в виде кокса (пиролизного угля) с коксового завода.
При достаточно высоких температурах углерод может непосредственно участвовать в восстановлении железа ( прямое восстановление ). При более низких температурах восстановление происходит косвенно с помощью образующегося при сгорании оксида углерода ( косвенное восстановление ). В обоих случаях оксид железа восстанавливается до железа.
Рисунок: Зоны в доменной печи Использование углерода в качестве восстанавливающего агента обусловлено не только его высокой доступностью, но и тем преимуществом газообразного вещества, что окись углерода имеет то преимущество, что она может хорошо проникать в пористые руды и реагировать с оксидами железа. По этой причине железные руды также перерабатываются как можно более пористыми в виде агломерата и окатышей.
Углерод не только обеспечивает необходимое тепло для плавления железной руды, но и служит особым восстановителем для восстановления оксидов железа до железа!
Отдельные химические процессы в доменной печи более подробно описаны в следующих разделах.
Для получения необходимого тепла и восстановительного газа угарного газа (\(CO\)), кокс сжигается в нижней части доменной печи с подачей горячего дутья. Углерод (\(C\)), содержащийся в коксе, сначала реагирует с кислородом воздуха в горячем дутье (\(O_2\)) в соответствии со следующим химическим уравнением с двуокисью углерода (\(CO_2\)):
\begin{выравнивание}
\label{колендиоксид}
& C + O_2 \rightarrow CO_2 ~~~ \text{(экзотермический)} \\[5px]
\end{align}
Это горение очень сильно экзотермическое, т.е. обычно в процессе горения. Это приводит к повышению температуры до 2000 °С. Углекислый газ (\(CO_2\)) реагирует с углеродом, содержащимся в коксе (\(C\)) из-за очень высоких температур, и образует монооксид углерода (\(CO\)) в качестве восстановителя:
\begin{align}
\label{kohlenmonoxid}
& CO_2 + C \rightleftharpoons 2~CO ~~~ \text{(эндотерма)} \\[5px]
\end{align}
Образование окиси углерода эндотермическое, т.е. с энергией поглощения, так что температура газа падает примерно до 1700°С. Однако следует избегать чрезмерного падения температуры, поскольку реакция двуокиси углерода с окисью углерода происходит только при достаточно высоких температурах.
Слишком низкая температура снова будет означать обратную реакцию (обозначенную двойной стрелкой в химическом уравнении) монооксида углерода в диоксид углерода. Но именно эта окись углерода необходима для восстановления окислов железа и должна производиться в достаточном количестве.
Реакция Будуара
Реакция диоксида углерода и углерода с образованием монооксида углерода и ее обратная реакция зависят от температуры и описываются так называемой реакцией Будуара .
Ситуацию можно проиллюстрировать на примере испарения воды в закрытом помещении, наполненном воздухом. В зависимости от температуры воздух может поглощать определенное количество воды. Если воздух полностью насыщен водой, он не может больше поглощать воду, и остаток жидкой воды остается в помещении. Со временем установится баланс между водой, которая все еще находится в жидком состоянии, и водой, содержащейся в воздухе.
В то время как жидкая вода может кратковременно испаряться в локальной точке из-за статистических флуктуаций («реакция»), вода снова локально конденсируется из перенасыщенного воздуха в другой точке («обратная реакция»). Однако в глобальном масштабе наступит равновесие между этими фазами или между реакцией и ее обратной реакцией жидкости и воды, связанной с воздухом. Говорят также о динамическом равновесии .
Однако это динамическое равновесие может смещаться в пользу или за счет жидкой воды, в зависимости от температуры. При высоких температурах воздух может поглощать больше воды, поэтому больше воды испаряется, а остаточное содержание жидкости уменьшается. Таким образом, равновесие смещается в сторону процесса испарения. Однако при понижении температуры часть воды, связанной в воздухе, конденсируется, и содержание жидкости в почве повышается. Затем равновесие смещается в сторону процесса конденсации (этот эффект также очень хорошо виден на охлажденных банках для напитков, где вода, содержащаяся в воздухе, конденсируется и образуются водяные жемчужины).
Таким же образом, существует температурно-зависимое равновесие между реакцией углекислого газа в монооксид углерода и соответствующей обратной реакцией монооксида углерода в диоксид углерода. На рисунке выше показано соотношение между монооксидом углерода и диоксидом углерода в соответствующих равновесных состояниях при разных температурах. Становится очевидным, что при температурах выше 1000 °С углекислый газ распадается почти исключительно на монооксид углерода.
При высоких температурах углерод реагирует преимущественно с диоксидом углерода с образованием монооксида углерода (как важного восстановителя). При низких температурах монооксид углерода в основном разлагается на диоксид углерода и углерод!
Предварительный нагрев
При сжигании кокса образуются горячие газы, состоящие в основном из монооксида углерода, диоксида углерода, азота и (газообразной) воды. Эти горячие газы поднимаются вверх в доменной печи и охлаждаются. От максимальной 2000 °C на уровне сопел горячего дутья (фурмы) температура снижается примерно до 200 °C вплоть до горловины. При этой температуре наполненную шихту сначала сушат и предварительно нагревают. Поэтому эта зона доменной печи называется 9-й.0395 зона предварительного нагрева .
В зоне подогрева происходит предварительный подогрев и сушка шихты!
Зона непрямого восстановления
Дальнейшее понижение содержания железной руды в доменной печи приводит к температурной зоне от 400 °C до 800 °C. В этом районе происходит так называемое косвенное восстановление железных руд до железа монооксидом углерода.
Угарный газ (\(CO\)) окисляется до двуокиси углерода (\(CO_2\)) за счет поглощения кислорода, содержащегося в оксиде железа (\(O\)). Непрямое восстановление можно разделить на несколько промежуточных реакций, в результате которых содержание железа в рудах постоянно увеличивается, и в конечном итоге получается чистое железо.
Сначала слабожелезистый гематит (\(Fe_2O_3\)) восстанавливается монооксидом углерода (\(CO\)) до более железистого магнетита (\(Fe_3O_4\)). Затем магнетит восстанавливается до так называемого вюстита (\(FeO\)) перед тем, как окончательно восстановиться до железа (\(Fe\)):
\begin{align}
\label{indirekt}
3~ Fe_2O_3 &~+~ CO &&\rightarrow~ 2~Fe_3O_4 &&+ ~CO_2 ~~~~~~ \text{(гематит} \rightarrow \text{магнетит)} \\[5px]
Fe_3O_4 &~+~ CO && \rightarrow~ 3~FeO &&+ ~CO_2 ~~~~~~ \text{(магнетит} \rightarrow \text{вюстит)} \\[5px]
FeO &~+~ CO &&\rightarrow~ Fe &&+ ~CO_2 ~~~~~~ \text{(wüstite} \rightarrow \text{железо)} \\[5px]
\end{align}
последняя химическая реакция вюстита с железом экзотермическая и дает тепло. Однако выделяющегося тепла достаточно для подачи тепла для первых двух эндотермических реакций. Таким образом, общий баланс остается экзотермическим. Тем не менее, температура в этой зоне непрямого восстановления от 400 °C до максимум 800 °C слишком низка для расплавления восстановленного железа! Таким образом, консистенция железа остается твердой.
Нерасплавленные железные руды все еще содержат невосстановленные оксиды железа. Неблагоприятное накопление руды в точках контакта также может затруднить поток газа и, таким образом, оставить невосстановленную железную руду. Однако самое позднее, когда процесс плавки происходит в более глубоких и горячих зонах доменной печи, железные руды могут быть почти полностью восстановлены.
В зоне непрямого восстановления оксид железа, содержащийся в железной руде, восстанавливается окисью углерода, при этом железная руда не расплавляется!
Зона прямого восстановления
Если железная руда, которая еще не была восстановлена, перемещается дальше в доменной печи, то углерод также может непосредственно восстанавливать оксиды железа, содержащиеся в руде, благодаря высоким температурам. Углерод (\(C\)) окисляется до монооксида углерода (\(CO\)) за счет поглощения кислорода (\(O\)). Из-за прямого восстановления оксидов железа углеродом говорят также о прямом восстановлении .
Прямое восстановление происходит в температурной зоне между прибл. от 800 °C до прибл. 1600 °С. Прямое восстановление можно снова разделить на промежуточные этапы, на которых содержание железа в рудах увеличивается в каждом случае:
\begin{align}
\label{direct}
3 Fe_2O_3 &~+~ C &&\rightarrow~ 2~Fe_3O_4 &&+ ~CO ~~~~~~ \text{(гематит} \rightarrow \text{магнетит )} \\[5px]
Fe_3O_4 &~+~ C &&\rightarrow~ 3~FeO &&+ ~CO ~~~~~~ \text{(магнетит} \rightarrow \text{вюстит)} \\[5px]
FeO &~+~ C &&\rightarrow~ Fe &&+ ~CO ~~~~~~ \text{(wüstite} \rightarrow \text{железо)} \\[5px]
\end{align}
Все эти реакции эндотермические. Необходимое для этого тепло обеспечивается за счет (экзотермического) сжигания кокса. Соединения кремния, марганца и фосфора (и многие другие соединения), содержащиеся в пустой породе, также восстанавливаются эндотермически. Необходимое для этого тепло также должно быть получено за счет сжигания кокса. Для того чтобы по энергетическим причинам поступление тепла было как можно меньше, в рудах должно содержаться как можно меньше пустой породы. Это делает необходимой переработку руды, описанную выше.
Восстановленные примеси в доменной печи затем реагируют с добавленным в шихту флюсом и связываются в образующемся шлаке.
В зоне прямого восстановления углерод принимает непосредственное участие в восстановлении оксидов железа!
Зона науглероживания
Хотя углерод восстанавливает оксиды железа и производит железо, образующееся железо частично обогащается самим углеродом. Это делается либо газообразным угарным газом, либо, при более высоких температурах, непосредственно углеродом. При этом образуется карбид железа \(Fe_3C\), также известный как цементит .
Обогащение твердого железа углеродом в диапазоне температур от 900 °C до 1200 °C также называется науглероживанием . Соответствующие химические реакции следующие:
\begin{align}
\label{aufkohlen}
3 Fe &~+~ 2 CO &&\rightarrow~ Fe_3C ~+~CO_2 \\[5px]
3 Fe &~+ ~ C &&\rightarrow~ Fe_3C \\[5px]
\end{align}
За счет поглощения углерода температура затвердевания железа снижается с 1536 °C до прибл. 1200 °С (см. фазовая диаграмма железо-углерод ).
В зоне науглероживания восстановленное железо обогащается углеродом и образует промежуточное соединение карбид железа (\(Fe_3C\), цементит)! Науглероживание снижает температуру затвердевания железа!
Зона плавления
Из-за снижения точки затвердевания диффундирующим углеродом в восстановленное железо оно начинает плавиться в более горячих зонах доменной печи. Теперь внутренние слои руды также вступают в контакт с углеродом или газообразным угарным газом и могут быть восстановлены до железа, а затем науглерожены. Постепенно вся железная руда восстанавливается, науглероживается и плавится. Поглощенный углерод остается растворенным в расплавленном железе. По этой причине чугун имеет относительно высокое содержание углерода.
В зоне плавки железо начинает плавиться с образованием высокоуглеродистого чугуна!
Зона выпуска
Расплавленный чугун окончательно собирается в горне доменной печи вместе со шлаком, который также является жидким. Из-за более высокой плотности чугуна его можно отрезать в самой нижней точке доменной печи (называется выпуском ). Он имеет высокое содержание углерода около 4,5%. Дополнительные сопутствующие элементы перечислены ниже, хотя состав может значительно различаться в зависимости от типа чугуна.
- 4,5 % углерода
- 2,5 % кремния
- 1,5 % марганца
- 0,5 % фосфора
- 0,1 % серы
Другие элементы, такие как титан, медь и т.д.
Когда жидкий чугун затвердевает, содержание кремния, в частности, определяет, выделяется ли растворенный углерод в чистом виде в виде графита (\(C\)) в микроструктуре или в виде карбида железа (\(Fe_3C\), цементита).
Графитовое осаждение предпочтительно для высоких концентраций кремния. Образованию графита также способствует относительно низкое содержание марганца и медленное охлаждение. С другой стороны, при относительно низком содержании кремния предпочтительно осаждение цементита при затвердевании чугуна. Этому, в свою очередь, способствуют относительно высокие концентрации марганца и более высокая скорость охлаждения.
Поскольку при высоких температурах и длительном времени отжига образовавшийся цементит разлагается обратно на составляющие его компоненты (железо и углерод), эта форма затвердевания также называется метастабильное затвердевание в термодинамическом смысле. Напротив, графит является термодинамически стабильным соединением, которое сохраняется даже при длительном отжиге. Поэтому этот тип отверждения также называют стабильным отверждением .
Благодаря графиту в стабильной затвердевшей микроструктуре поверхность излома чугуна выглядит матово-серой.