Предел текучести как показатель надежности конструкции
Предел текучести как показатель надежности конструкции. Выбираем марку стали для складского стеллажа
Гношова Ольга Юрьевна, генеральный директор компании «Юнирек»
Первое, на что стоит обратить внимание при выборе стеллажного оборудования — это марка стали, из которой оно будет изготовлено.
Друзья! Мы находимся в испытательной лаборатории Уральского научно-исследовательского института черных металлов ( ОАО «Уральский институт металлов»).
Мы покажем вам, чем отличаются марки стали с точки зрения грузонесущей способности, способности сопротивляться стационарной и динамической нагрузке и за что, в конечном счете, платит покупатель стеллажей.
Марки стали отличаются по химическому составу и физическим свойствам. Нас интересует как деформируется сталь после воздействия на нее нагрузки.
Деформации разделяют на обратимые (упругие)
Приведем классический пример из жизни склада: погрузчик ударяет стойку стеллажа. Если стойка принимает свое изначальное положение, то это «деформация упругая», а если стойка не возвращается в свое проектное положение, принимает «форму погрузчика», то это называется «пластическая деформация».
Каждый сплав имеет предел или критический момент, после которого упругая деформация переходит в пластическую. Именно этот показатель – «предел текучести» стали, нас с вами интересует.
Чем выше показатель предела текучести стали, тем дольше сталь способна находиться в напряженном состоянии и противостоять стационарным и динамическим нагрузкам.
Самыми популярными в России марками стали для производства стеллажей являются марки Ст08пс, Ст3пс, Ст3сп, Ст3кп, Ст350, S355МС
.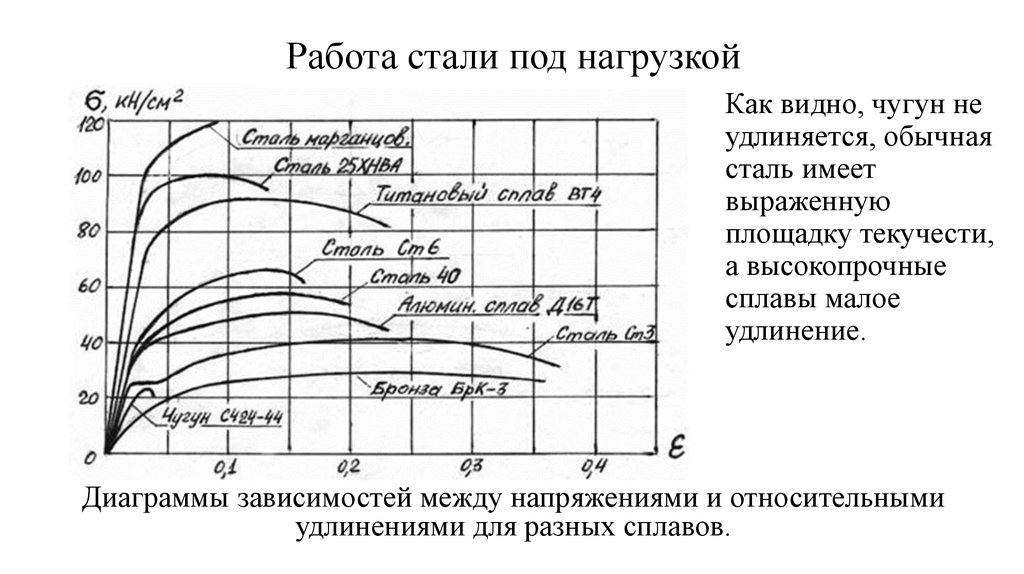
По нашей просьбе, на заводе были изготовлены 4 образца стеллажных стоек. По два образца из стали марок S355MC и Ст3, толщиной 1,5 и 2,0 миллиметра.
Для наглядности их окрасили в разные цвета – сталь Ст3 в оранжевый, а сталь S355MC в синий цвет.
Перед испытаниями в Лаборатории определили химический состав (марку стали) образцов при помощи фотоэлектрического спектрального анализа.
Ниже приведена таблица с ориентировочными показателями различных сталей, используемых при производстве стеллажных комплектующих в России (данные показатели могут отличаться в зависимости от партий проката и при разных условиях).
В Европе при производстве стеллажей используется только сталь с высоким пределом текучести, марки S52 (и других).
σ0,2 — предел текучести условный, МПа
sв — временное сопротивление разрыву (предел прочности при растяжении), МПа
sT — предел пропорциональности (предел текучести для остаточной деформации), МПа
d5 — относительное удлинение после разрыва, %
HB — твердость по Бринеллю
KCU — ударная вязкость, Дж/см2
Итак, мы подвергли стационарной нагрузке (давлением пресса) две пары стоек.
- Образец из стали Ст3 показал, что пределом его текучести является нагрузка в 94,14 кН, что соответствует 9600 кгс.
- Образец из стали S355МС показал, что пределом его текучести является нагрузка в 109,8 кН, что соответствует 11200 кгс.
Таким образом, образец из стали S355МС оказался на 16,7% устойчивее к стационарной нагрузке, чем образец из стали Ст3.
Видео показывает, что после наступления критического момента, даже после снижения нагрузки от пресса, образец продолжает деформироваться.
Данное поведение металла стоек следует принимать во внимание в процессе эксплуатации стеллажного оборудования.
Необходимо помнить, что деформированная стойка выносит меньшую нагрузку, чем «целая», и поэтому ее нельзя подвергать прежней нагрузке.
Вторая пара из стали толщиной 2,0 мм
- Образец из стали Ст3 показал, что пределом его текучести является нагрузка в 127,5кН, что соответствует 13000 кгс.
- Образец из стали S355МС показал, что пределом его текучести является нагрузка в 164,75 кН, что соответствует 16800 кгс.
Таким образом, образец из стали S355МС оказался на 29,5% устойчивее к стационарной нагрузке, чем образец из стали Ст3.
Кстати, европейский концерн «Mecalux» не использует для производства паллетных стеллажей сталь толщиной менее 1,8мм.
Для определения устойчивости стали разных марок к динамическим нагрузкам, были произведены испытания образцов по показателю «Предел прочности на растяжение»
.
Предел прочности на растяжение есть пороговая величина постоянного (для статического предела прочности) или, соответственно, переменного (для динамического предела прочности) механического напряжения, превышая который механическое напряжение в результате (за конечный достаточно короткий промежуток времени) разорвет тело из конкретного материала.
Нами были подготовлены два образца в виде металлических пластин из стали Ст3 и S355МС, которые поочередно подвергли растяжению- Образец из стали Ст3 показал, что пределом его прочности является нагрузка в 8,24кН, что соответствует 840 кгс.
- Образец из стали S355МС показал, что пределом его прочности является нагрузка в 10,2 кН, что соответствует 1040 кгс.
Таким образом, образец из стали S355МС оказался на 23,85% прочнее на растяжение, чем образец из стали Ст3.
Сегодняшними испытания мы хотели наглядно показать, что образцы из разных марок стали ведут себя по-разному после воздействия нагрузки. ![]()
Вы увидели, что образцы из S355MC стали держат гораздо большие стационарные и динамические нагрузки, чем образцы из стали Ст3.
Поэтому, при выборе стеллажного оборудования марка стали имеет значение!
Надеемся, что приведенная информация покажется Вам интересной и полезной.
ООО «Юнирек» проектирует и поставляет стеллажное оборудование уже более 8-ми лет, безаварийная служба поставленного оборудования обеспечена политикой компании – мы не идем на компромиссы в вопросах качества и безопасности.
определение, измерение характеристик стали, проверка сплава
Современное производство нуждается в большом количестве прочных стальных изделий. При строительстве мостов, домов, сложных конструкций используют различные стали. Одним из главнейших вопросов является расчет прочности металла и значения величины напряжения стальной арматуры. Чтобы конструкции служили долго и были безопасны необходимо точно знать предел текучести стального материала, который подвергается основной нагрузке.
- Основное определение
- Состав стальных сплавов
- Добавки углерода и прочность
- Марганец и кремний
- Сера и фосфор
- Азот и кислород
- Поведение легирующих добавок
- Проверка сплава
- Проведение испытаний
- Невыраженная точка текучести
- Характеристика пластичности
- Показатель хрупкости
- Прочность материала
Основное определение
В процессе использования на любое сооружение приходятся разные нагрузки в виде сжатий, растяжений или ударов. Они могут действовать как обособленно, так и совместно.
Современные конструкторы стремятся уменьшить массу стальных деталей для экономии материала, но при этом не допустить критичного снижения несущей способности всей конструкции. Происходит это засчет уменьшения сечения стальных арматур.
В зависимости от назначения объектов, могут меняться некоторые требования к стали, но имеется перечень стандартных и важных показателей. Их величины рассчитывают на этапе проектирования деталей и узлов будущего сооружения. Заготовка должна обладать высокой прочностью при соответствующей пластичности.
В первую очередь при расчетах прочности изделия из стали обращают внимание на предел текучести. Это значение характеризующее поведение деталей при воздействиях на них.
Предел текучести материала — это величина критического напряжения, при которой материал продолжает самостоятельную деформацию без увеличения нагрузки. Эта характеристика измеряется в Паскалях и позволяет рассчитывать максимально возможное напряжение для пластичной стали.
После прохождения этого предела в материале происходят невосстановимые процессы искажения кристаллической решетки. При последующем увеличении силы воздействия на заготовку и преодолении площадки текучести, деформация увеличивается.
Предел текучести иногда путают с пределом упругости. Это похожие понятия, но предел упругости — это величина максимального сопротивления металла и она чуть ниже предела текучести.
Величина текучести примерно на пять процентов превышает предел упругости.
Состав стальных сплавов
Свойства металла зависят от сформированной кристаллической решетки, которая, в свою очередь, определяется содержанием углерода. Зависимость типов решетки от количества углерода хорошо прослеживается на структурной диаграмме. Если, например, в решетке стали насчитывается до 0.06% углерода, то это классический феррит, который имеет зернистую структуру. Такой материал непрочный, но текучий и имеет большой предел ударной вязкости.
По структуре стали делятся на:
- ферритную;
- перлитно-ферритовую;
- цементитно-ферритную;
- цементитно-перлитовую;
- перлитную.
Добавки углерода и прочность
Закон аддитивности подтверждается процентными изменениями цементита и феррита в стали. Если количество углеродной добавки составляет около 1,2%, то предел текучести стального материала увеличивается и повышается твердость, прочность и температуростойкость. При последующем увеличении содержания углерода технические параметры ухудшаются. Сталь плохо сваривается и неохотно поддается штамповке. Самым лучшим образом при сварке ведут себя сплавы с небольшим содержанием углерода.
Марганец и кремний
В виде добавки, чтобы увеличить степень раскисления, дополнительно добавляют марганец. Кроме того, этот элемент уменьшает вредное воздействие серы. Содержание марганца обычно не более 0.8% и он не влияет на технологические свойства сплава. Присутствует как твердый компонент.
Кремний тоже особо не влияет на характеристики металла. Он необходим для увеличения качества сварки деталей. Содержание этого элемента не превышает 0.38% и он добавляется во время процесса раскисления.
Сера и фосфор
Сера содержится в виде хрупких сульфитов. Повышенное количество этого элемента влияет на механические показатели сплава. Чем больше серы, тем хуже пластичность, текучесть и вязкость сплава. Если превышен предел в 0.06%, то изделие сильнее подвержено коррозии и становится способным к сильному истиранию.
Наличие фосфора увеличивает показатель текучести, но при этом уменьшается пластичность и вязкость. В общем, завышенное содержание фосфора значительно ухудшает качество металла. Особенно вредно сказывается на характеристиках совместное высокое содержание фосфора и углерода. Допустимыми пределами содержания фосфора считаются значения от 0.025 до 0.044%.
Азот и кислород
Это неметаллические примеси, которые понижают механические свойства сплава. Если содержание кислорода больше чем 0.03%, то металл быстрее стареет, падают значения пластичности и вязкости. Азотные добавки увеличивают прочность, но в этом случае предел текучести уменьшается. Увеличенное содержание азота делает сталь ломкой и способствует быстрому старению металлической конструкции.
Поведение легирующих добавок
Для улучшения всех физических показателей стали, в сплав добавляют специальные легирующие элементы. Такими добавками могут быть вольфрам, молибден, никель, хром, титан и ванадий. Совместное добавление в необходимых пропорциях, дает самые приемлемые результаты.
Легирование значительно повышает показатель текучести, ударной вязкости и препятствует деформации и растрескиванию.
Проверка сплава
Перед запуском в производство для изучения свойств металлического сплава, проводят испытания. На образцы металла воздействуют различными нагрузками до полной потери всех свойств.
Нагрузки бывают:
- Статистическая нагрузка.
- Проверка на выносливость и усталость стали.
- Растягивание элемента.
- Тестирование на изгиб и кручение.
- Совместная выносливость на изгиб и растяжение.
Для этих целей применяют специальные станки и создают условия, максимально приближенные к режиму эксплуатации будущей конструкции.
Проведение испытаний
Для проведения испытаний на цилиндрический образец сечением в двадцать миллиметров и расчетной длиной в десять миллиметров применяют нагрузку на растяжение. Сам образец имеет длину более десяти миллиметров, чтобы была возможность надежно его захватить, а на нем отмечена длина в десять миллиметров и именно она называется расчетной. Силу растяжения увеличивают и замеряют растущее удлинение образца. Для наглядности данные наносят на график. Он носит название диаграммы условного растяжения.
При небольшой нагрузке образец удлиняется пропорционально. Когда сила растяжения достаточно увеличится, то будет достигнут предел пропорциональности. После прохождения этого предела начинается непропорциональное удлинение материала при равномерном изменении силы растяжения. Затем достигается предел, после прохождения которого образец не может возвратиться к первоначальной длине. При прохождении этого значения, изменение испытываемой детали происходит без увеличения силы растяжения. Например, для стального прута Ст. 3 эта величина равна 2450 кг на один квадратный сантиметр.
Невыраженная точка текучести
Если при постоянной силе воздействия, материал способен длительное время самостоятельно деформироваться, то его называют идеально пластическим.
При испытаниях часто бывает, что площадка текучести нечетка определена, тогда вводят определение условного предела текучести. Это означает, что сила, действующая на металл, вызвала деформацию или остаточное изменение около 0.2%. Значение остаточного изменения зависит от пластичности металла.
Чем металл пластичнее, тем выше значение остаточной деформации. Типичными сплавами, в которых нечетко выражена такая деформация, являются медь, латунь, алюминий, стали с малым содержанием углерода. Образцы этих сплавов называют уплотняющимися.
Когда металл начинает «течь» то, как демонстрируют опыты и исследования, в нём происходят сильные изменения в кристаллической решетке. На её поверхности появляются линии сдвига и слои кристаллов значительно сдвигаются.
После того как металл самопроизвольно растянулся, он переходит в следующее состояние и опять приобретает способность сопротивления. Затем сплав достигает своего предела прочности и на детали четко проявляется наиболее слабый участок, на котором происходит резкое сужение образца.
Площадь поперечного сечения становится меньше и в этом месте происходит разрыв и разрушение. Величина силы растяжения в этот момент падает вместе со значением напряжения и деталь рвётся.
Высокопрочные сплавы выдерживают нагрузку до 17500 килограмм на сантиметр квадратный. Предел прочности стали СТ.3 находится в пределах 4−5 тыс. килограммов на сантиметр квадратный.
Характеристика пластичности
Пластичность материала является важным параметром, который должен учитываться при проектировании конструкций. Пластичность определяется двумя показателями:
- остаточным удлинением;
- сужением при разрыве.
Остаточное удлинение вычисляют путем замера общей длины детали после того, как она разорвалась. Она состоит из суммы длин каждой половины образца. Затем в процентах определяют отношение к первоначальной условной длине. Чем прочнее металлический сплав, тем меньше значение относительного удлинения.
Остаточное сужение — это отношение в процентах самого узкого места разрыва к изначальной площади сечения исследуемого прута.
Показатель хрупкости
Самым хрупким металлическим сплавом считается инструментальная сталь и чугун. Хрупкость — это свойство обратное пластичности, и оно несколько условно, поскольку сильно зависит от внешних условий.
Такими условиями могут являться:
- Температура окружающей среды. Чем ниже температура, тем хрупче становится изделие.
- Скорость изменения прилагаемого усилия.
- Влажность окружающей среды и другие параметры.
При изменении внешних условий, один и тот же материал ведет себя по-разному. Если чугунную болванку зажать со всех сторон, то она не разбивается даже при значительных нагрузках. А, например, когда на стальном пруте есть проточки, то деталь становиться очень хрупкой.
Поэтому на практике применяют не понятие предела хрупкости, а определяют состояние образца как хрупкое или довольно пластичное.
Прочность материала
Это механическое свойство заготовки и характеризуется способностью выдерживать нагрузки полностью не разрушаясь. Для испытываемого образца создают условия наиболее отражающие будущие условия эксплуатации и применяют разнообразные воздействия, постепенно увеличивая нагрузки. Повышение сил воздействия вызывают в образце пластические деформации. У пластичных материалов деформация происходит на одном, ярко выраженном участке, который называется шейка. Хрупкие материалы могут разрушаться на нескольких участках одновременно.
Сталь проходит испытание для точного выяснения различных свойств, чтобы получить ответ о возможности её использования в тех или иных условиях при строительстве и создании сложных конструкций.
Значения текучести различных марок сталей занесены в специальные Стандарты и Технические Условия. Предусмотрено четыре основных класса. Значение текучести изделий первого класса может доходить до 500 кг/см кв., второй класс отвечает требованиям к нагрузке до 3 тыс. кг/см кв., третий — до 4 тыс. кг/см кв. и четвертый класс выдерживает до 6 тыс. кг/см кв.
Прочность на растяжение и предел текучести стали
← Вернуться в Центр знаний
Posted on Среда, 25 ноября 2020 г.
Прочность на растяжение и предел текучести стали
В чем разница между пределом текучести и пределом текучести?
Важно знать предел текучести и предел прочности при растяжении, поскольку каждый из них влияет на производство и использование стали (и многих других материалов, но мы сосредоточимся на стали). Итак, в чем разница между пределом текучести и пределом прочности? Самая большая разница в том, что предел прочности при растяжении катастрофичен, а предел текучести — это всего лишь остаточная деформация. Ниже мы более подробно остановимся на обоих из них, а также поговорим о том, что такое удлинение по отношению к прочности на растяжение.
Что такое предел прочности при растяжении?
Растяжимый по определению означает способность растягиваться или растягиваться. Прочность на растяжение – это сопротивление стали разрушению при растяжении. Он используется для указания точки, когда сталь переходит от упругой (временной) к пластической (постоянной) деформации. Обычно она измеряется в единицах силы на площадь поперечного сечения. Как только кусок стали вытягивается за пределы точки растягивающего напряжения, он распадается на части.
Прочность стали на растяжение покажет нам, какое напряжение растяжения сталь может выдержать, пока оно не приведет к разрушению двумя способами: вязкому или хрупкому разрушению.
Вязкое разрушение — рассматривайте это как предварительную стадию разрушения, когда оно выталкивается за пределы предела текучести до остаточной деформации.
Хрупкое разрушение – это заключительный этап, на котором проводится измерение предела прочности при растяжении.
По сути, предел прочности при растяжении измеряется максимальным напряжением, которое сталь может выдержать при растяжении или растяжении до разрыва.
Что такое предел текучести?
Предел текучести — это максимальное напряжение, которое можно приложить до того, как оно начнет постоянно менять форму. Это приближение к пределу упругости стали. Если к металлу добавляется напряжение, но оно не достигает предела текучести, он вернется к своей первоначальной форме после того, как напряжение будет снято. Когда напряжения превышают предел текучести, сталь не сможет прийти в норму. Предел текучести представляет собой верхний предел нагрузки, которую можно безопасно приложить к металлу, что делает его очень важным числом, которое необходимо знать при проектировании компонентов.
Удлинение
Удлинение — это процент растяжения от исходной длины стали до точки разрыва, показывающий, насколько пластична сталь. Пластичность — это способность стали растягиваться, не становясь при этом более хрупкой или слабой. Чем пластичнее он, тем более пластичен продукт. Удлинение — это хороший показатель, на который следует обратить внимание, чтобы определить, правильный ли продукт вы выбираете для своего проекта. Стальной круглый пруток, испытанный
Хотя прочность на растяжение важна, вы не должны принимать решение, основываясь исключительно на ней. Вы также хотите принять во внимание предел текучести, разницу между пределом текучести и пределом текучести и процентное удлинение.
Если вам понравился этот пост, ознакомьтесь с нашим постом «Твердость и прокаливаемость», чтобы узнать о различиях между ними в сталелитейной промышленности!
Значения модуля Юнга, предела прочности при растяжении и предела текучести для некоторых материалов
Модуль растяжения — или модуль Юнга альт. Модуль упругости — это мера жесткости упругого материала. Он используется для описания упругих свойств таких объектов, как провода, стержни или колонны, когда они растягиваются или сжимаются.
Модуль упругости при растяжении определяется как
«отношение напряжения (силы на единицу площади) вдоль оси к деформации (отношение деформации к начальной длине) вдоль этой оси»
Его можно использовать для прогнозирования удлинения или сжатие объекта до тех пор, пока напряжение меньше, чем предел текучести материала. Подробнее об определениях ниже таблицы.
АБС-пластик | 1,4 — 3,1 | 40 | |||||||||||||||||||||||||||||||
A53 Seamless and Welded Standard Steel Pipe — Grade A | 331 | 207 | |||||||||||||||||||||||||||||||
A53 Seamless and Welded Standard Steel Pipe — Grade B | 414 | 241 | |||||||||||||||||||||||||||||||
A106 Бесшовные трубы из углеродистой стали класса A | 330 | 205 | |||||||||||||||||||||||||||||||
A106 Бесшовные трубы из углеродистой стали класса B | 415 | 240 | |||||||||||||||||||||||||||||||
A106 Seamless Carbon Steel Pipe — Grade C | 485 | 275 | |||||||||||||||||||||||||||||||
A252 Piling Steel Pipe — Grade 1 | 345 | 207 | |||||||||||||||||||||||||||||||
A252 Piling Steel Pipe — Grade 2 | 414 | 241 | |||||||||||||||||||||||||||||||
A252 Сваебойная стальная труба — класс 3 | 455 | 310 | |||||||||||||||||||||||||||||||
A501 Горячеформованная углеродистая сталь класса | A5010070 | 400 | 248 | ||||||||||||||||||||||||||||||
A501 Hot Formed Carbon Steel Structural Tubing — Grade B | 483 | 345 | |||||||||||||||||||||||||||||||
A523 Cable Circuit Steel Piping — Grade A | 331 | 207 | |||||||||||||||||||||||||||||||
A523 Стальной трубопровод кабельной цепи — класс B | 414 | 241 | |||||||||||||||||||||||||||||||
A618 Горячеформованные высокопрочные низколегированные конструкционные трубы — класс Ia и Ib | 483 | 345 | |||||||||||||||||||||||||||||||
A618 Hot-Formed High-Trangle Структурные трубки-Степень II | 414 | 345 | |||||||||||||||||||||||||||||||
345 | |||||||||||||||||||||||||||||||||
90 | 345 | ||||||||||||||||||||||||||||||||
345 | |||||||||||||||||||||||||||||||||
345 | |||||||||||||||||||||||||||||||||
9070.![]() | 448 | 345 | |||||||||||||||||||||||||||||||
API 5L Line Pipe | 310 — 1145 | 175 — 1048 | |||||||||||||||||||||||||||||||
Acetals | 2.8 | 65 | |||||||||||||||||||||||||||||||
Acrylic | 3.2 | 70 | |||||||||||||||||||||||||||||||
Aluminum Bronze | 120 | ||||||||||||||||||||||||||||||||
Aluminum | 69 | 110 | 95 | ||||||||||||||||||||||||||||||
Aluminum Alloys | 70 | ||||||||||||||||||||||||||||||||
Сурьма | 78 | ||||||||||||||||||||||||||||||||
Арамид | 70 — 112 | 0068 | Beryllium (Be) | 287 | |||||||||||||||||||||||||||||
Beryllium Copper | 124 | ||||||||||||||||||||||||||||||||
Bismuth | 32 | ||||||||||||||||||||||||||||||||
Bone, compact | 18 | 170 (сжатие) | |||||||||||||||||||||||||||||||
Кость губчатая | 76 | ||||||||||||||||||||||||||||||||
Бор | 7 3100068 | Brass | 102 — 125 | 250 | |||||||||||||||||||||||||||||
Brass, Naval | 100 | ||||||||||||||||||||||||||||||||
Bronze | 96 — 120 | ||||||||||||||||||||||||||||||||
CAB | 0.![]() | ||||||||||||||||||||||||||||||||
Кадмий | 32 | ||||||||||||||||||||||||||||||||
Пластик, армированный углеродным волокном | 150 | 1000 | |||||||||||||||||||||||||||||||
Cast Iron 4.5% C, ASTM A-48 | 170 | ||||||||||||||||||||||||||||||||
Cellulose, cotton, wood pulp and regenerated | 80 — 240 | ||||||||||||||||||||||||||||||||
Cellulose acetate, Литье | 12 — 58 | ||||||||||||||||||||||||||||||||
Ацетат целлюлозы, лист | 30 — 52 | ||||||||||||||||||||||||||||||||
NITRAT0070 | |||||||||||||||||||||||||||||||||
Chlorinated polyether | 1.1 | 39 | |||||||||||||||||||||||||||||||
Chlorinated PVC (CPVC) | 2.9 | ||||||||||||||||||||||||||||||||
Chromium | 248 | ||||||||||||||||||||||||||||||||
Cobalt | 207 | ||||||||||||||||||||||||||||||||
Бетон | 17 | ||||||||||||||||||||||||||||||||
Бетон, высокопрочный (сжатие) | 30 | 40 (compression) | |||||||||||||||||||||||||||||||
Copper | 117 | 220 | 70 | ||||||||||||||||||||||||||||||
Diamond (C) | 1220 | ||||||||||||||||||||||||||||||||
Douglas fir Wood | 13 | 50 (сжатие) | |||||||||||||||||||||||||||||||
Эпоксидные смолы | 3-2 | 26 — 85 | |||||||||||||||||||||||||||||||
Фибранная доска, средняя плотность | 4 | 9007 | |||||||||||||||||||||||||||||||
Flax fiber | 58 | ||||||||||||||||||||||||||||||||
Glass | 50 — 90 | 50 (compression) | |||||||||||||||||||||||||||||||
Glass reinforced polyester matrix | 17 | ||||||||||||||||||||||||||||||||
Gold | 74 | ||||||||||||||||||||||||||||||||
Гранит | 52 | ||||||||||||||||||||||||||||||||
Графен | 1000 | ||||||||||||||||||||||||||||||||
0069 Grey Cast Iron | 130 | ||||||||||||||||||||||||||||||||
Hemp fiber | 35 | ||||||||||||||||||||||||||||||||
Inconel | 214 | ||||||||||||||||||||||||||||||||
Iridium | 517 | ||||||||||||||||||||||||||||||||
Iron | 210 | ||||||||||||||||||||||||||||||||
Свинец | 13,8 | ||||||||||||||||||||||||||||||||
Магний металлический 90 (0069 45 | |||||||||||||||||||||||||||||||||
Manganese | 159 | ||||||||||||||||||||||||||||||||
Marble | 15 | ||||||||||||||||||||||||||||||||
MDF — Medium-density fiberboard | 4 | ||||||||||||||||||||||||||||||||
Mercury | |||||||||||||||||||||||||||||||||
Молибден (Mo) | 329 | ||||||||||||||||||||||||||||||||
Монель-металл | 0 | 0 | 179 | ||||||||||||||||||||||||||||||
Nickel | 170 | ||||||||||||||||||||||||||||||||
Nickel Silver | 128 | ||||||||||||||||||||||||||||||||
Nickel Steel | 200 | ||||||||||||||||||||||||||||||||
Niobium (Columbium) | 103 | ||||||||||||||||||||||||||||||||
Нейлон-6 | 2 — 4 | 45 — 90 | 45 | ||||||||||||||||||||||||||||||
70069 Нейлон-6669 60 — 80 | |||||||||||||||||||||||||||||||||
Oak Wood (along grain) | 11 | ||||||||||||||||||||||||||||||||
Osmium (Os) | 550 | ||||||||||||||||||||||||||||||||
Phenolic cast resins | 33 — 59 | ||||||||||||||||||||||||||||||||
Фенолформальдегидные формовочные соединения | 45 — 52 | ||||||||||||||||||||||||||||||||
Фосфор Бронза | 116 | ||||||||||||||||||||||||||||||||
Pine) | |||||||||||||||||||||||||||||||||
9999999 | |||||||||||||||||||||||||||||||||
Pine)0070 | 9 | 40 | |||||||||||||||||||||||||||||||
Platinum | 147 | ||||||||||||||||||||||||||||||||
Plutonium | 97 | ||||||||||||||||||||||||||||||||
Polyacrylonitrile, fibers | 200 | ||||||||||||||||||||||||||||||||
Polybenzoxazole | 3,5 | ||||||||||||||||||||||||||||||||
Поликарбонаты | 2,6 | 52 — 62 | |||||||||||||||||||||||||||||||
Полиэтилен HDPE (высокой плотности) | 0.![]() | 15 | |||||||||||||||||||||||||||||||
Polyethylene Terephthalate, PET | 2 — 2.7 | 55 | |||||||||||||||||||||||||||||||
Polyamide | 2.5 | 85 | |||||||||||||||||||||||||||||||
Polyisoprene, hard rubber | 39 | ||||||||||||||||||||||||||||||||
Полиметилметакрилат (ПММА) | 2,4–3,4 | ||||||||||||||||||||||||||||||||
Полиимидные ароматические соединения | 3,1 | 68 | 0075|||||||||||||||||||||||||||||||
Polypropylene, PP | 1.5 — 2 | 28 — 36 | |||||||||||||||||||||||||||||||
Polystyrene, PS | 3 — 3.5 | 30 — 100 | |||||||||||||||||||||||||||||||
Polyethylene, LDPE (low density) | 0.11 — 0.45 | ||||||||||||||||||||||||||||||||
Polytetrafluoroethylene (PTFE) | 0.4 | ||||||||||||||||||||||||||||||||
Polyurethane cast liquid | 10 — 20 | ||||||||||||||||||||||||||||||||
Polyurethane elastomer | 29 — 55 | ||||||||||||||||||||||||||||||||
Polyvinylchloride (PVC) | 2.![]() | ||||||||||||||||||||||||||||||||
Potassium | |||||||||||||||||||||||||||||||||
Rhodium | 290 | ||||||||||||||||||||||||||||||||
Резина, малая деформация | 0,01 — 0,1 | ||||||||||||||||||||||||||||||||
Сапфир | 435 | ||||||||||||||||||||||||||||||||
Selenium | 58 | ||||||||||||||||||||||||||||||||
Silicon | 130 — 185 | ||||||||||||||||||||||||||||||||
Silicon Carbide | 450 | 3440 | |||||||||||||||||||||||||||||||
Silver | 72 | ||||||||||||||||||||||||||||||||
Натрий | |||||||||||||||||||||||||||||||||
Сталь, высокопрочный сплав ASTM A-514 | 760 | 690 | |||||||||||||||||||||||||||||||
Steel, stainless AISI 302 | 180 | 860 | 502 | ||||||||||||||||||||||||||||||
Steel, Structural ASTM-A36 | 200 | 400 | 250 | ||||||||||||||||||||||||||||||
Tantalum | 186 | ||||||||||||||||||||||||||||||||
Thorium | 59 | ||||||||||||||||||||||||||||||||
Tin | 47 | ||||||||||||||||||||||||||||||||
Titanium | |||||||||||||||||||||||||||||||||
Titanium Alloy | 105 — 120 | 900 | 730 | ||||||||||||||||||||||||||||||
Tooth enamel | 83 | ||||||||||||||||||||||||||||||||
Tungsten (W) | 400 — 410 | ||||||||||||||||||||||||||||||||
Трайфлендский карбид (WC) | 450 — 650 | ||||||||||||||||||||||||||||||||
Уран | 170 | 170 | 170 | 170 | 170 | 0076 | |||||||||||||||||||||||||||
Vanadium | 131 | ||||||||||||||||||||||||||||||||
Wrought Iron | 190 — 210 | ||||||||||||||||||||||||||||||||
Wood | |||||||||||||||||||||||||||||||||
Zinc | 83 |
- 1 Па (Н/м 2 ) = 1×10 -6 Н/мм 2 = 1,4504×10 -4 фунтов на кв.
дюйм
- 1 11201 6 Pa (N/m 2 ) = 0.145×10 3 psi (lb f /in 2 ) = 0.145 ksi
- 1 GPa = 10 9 N/m 2 = 10 6 N/cm 2 = 10 3 N/mm 2 = 0.145×10 6 psi (lb f /in 2 )
- 1 МПа = 10 6 пси = 10 3 ksi
- 1 psi (lb/in 2 ) = 0.001 ksi = 144 psf (lb f /ft 2 ) = 6,894.8 Pa (N/m 2 ) = 6.895 x10 -3 N/мм 2
Блок преобразования натяжения и натяжения печати
Пример — преобразовать между единицами натяжения
10000 PSI . Может быть, преобразовать до
10000 PSI . 10 тысяч фунтов на кв. дюйм , как указано в таблице ниже:
Внимание! — этот онлайн-конвертер давления также можно использовать для преобразования единиц модуля упругости при растяжении.
Деформация —
εДеформация — это «деформация твердого тела из-за напряжения» — изменение размера, деленное на исходное значение размера — и может быть выражена как
ε = / L (1)
, где
ε = штамм (м/м, в/дюйм)
DL = удлинение или сжатие (смещение) объекта (м, в)
L = длина) из
L = длина = длина). Объект (M, IN)
Назначение —
σПресс. Приказ на единицу площади и может быть выражен как
σ = F / A (2)
, где 8 (2)
Стол 9 (2)
Стол 8 (2)
Стол
σ = stress (N/m 2 , lb/in 2 , psi)
F = applied force (N, lb)
A = площадь напряжения объекта (m 2 , in 2 )
- растягивающее напряжение — напряжение, которое стремится растянуть или удлинить материал — действует нормально к напряженной области
- напряжение сжатия, которое имеет тенденцию к сжатию или укорачиванию материала — действует нормально к напряженной зоне
- напряжение сдвига — напряжение, стремящееся к сдвигу материала — действует в плоскости напряженной области под прямым углом к сжимаемому или растягивающему напряжению
- Расчет напряжения в балках Упругость — E
Модуль Юнга можно выразить как
E = напряжение/деформация
= σ
7 / 1209
= (f / a) / (DL / L) (3)
, где
E = Модул молодых эластично , lb/in 2 , psi)
- назван в честь английского врача и физика XVIII века Томаса Янга первоначальная форма после искажения.
Примером упругого объекта является пружина. При растяжении она создает восстанавливающую силу, которая стремится вернуть ее к исходной длине. Эта возвращающая сила в целом пропорциональна растяжению, описываемому законом Гука.
Закон Гука
Чтобы растянуть пружину вдвое больше, требуется примерно вдвое больше силы. Эта линейная зависимость смещения от силы растяжения называется законом Гука и может быть выражена как
F с = -k dL (4)
where
F s = force in the spring (N)
k = spring constant (N/m)
dL = удлинение пружины (м)
Обратите внимание, что закон Гука также может применяться к материалам, подвергающимся трехмерному напряжению (трехосное нагружение).
Предел текучести —
σ yПредел текучести определяется в технике как величина напряжения (предел текучести), которому может подвергаться материал перед переходом от упругой деформации к пластической деформации.
- назван в честь английского врача и физика XVIII века Томаса Янга первоначальная форма после искажения.