Радиальный и тангенциальный шпон
Радиальным называется распил, при котором плоскость разреза проходит через сердцевину ствола.
Древесина такого шпона довольно однородна по цвету и текстуре, межкольцевые размеры минимальны. Шпон радиального распила устойчив к внешним воздействиям, практически не подвергается деформации и обладает высокой износостойкостью. Шпон радиального распила имеет коэффициент усушки = 0,19%, а коэффициент разбухания = 0,2%. Эти показатели у шпона радиального распила вдвое лучше, чем у шпона тангенциального распила.
Поскольку выход досок радиального распила составляет 10 — 15% от общего объема, стоимость их довольно высока. Ламель радиального распила должна иметь угол наклона годовых колец к пласти 90 — 60 градусов, угол наклона для полурадиального распила должен составлять не менее 45 градусов.
Тангенциальным называется распил, при котором плоскость разреза проходит на расстоянии от сердцевины, по касательной к годичному слою ствола.
Такой шпон имеют ярко выраженную текстуру и насыщенный волнообразный рисунок годовых колец. Шпон тангенциального распила имеет более высокие коэффициенты усушки и разбухания, но более доступен по цене.
От вида распила зависит текстура шпона или готового изделия.
Текстура — это естественный рисунок, образованный волокнами и слоями древесины и обусловленный особенностями ее структуры.
Зависит от расположения древесных волокон, различимости годовых слоев, цветовой гаммы древесины, количества и размеров сердцевинных лучей.
Пороки древесины — это природные недостатки отдельных участков древесины, снижающие ее качество и ограничивающие ее использование.
Дефектами называют пороки древесины механического происхождения, возникающие в ней в процессе заготовки, транспортирования, сортировки, штабелевки и механической обработки.
Один из пороков древесины — наклон волокон — раньше называли косослоем. Как уже ясно из названия, данный дефект заключается в отклонении волокон от продольной оси ствола. Наклон волокон может быть как тангенциальным, так и радиальным.
Тяговая древесина характеризуется изменением строения в растянутой зоне стволов и сучьев, проявляющимся в резком увеличении ширины годичных слоев. Под действием света такие участки древесины окрашиваются в коричневый цвет. Как правило, тяговая древесина характерна для лиственных пород деревьев.
Свилеватость — извилистое или беспорядочное расположение волокон древесины. Встречается у всех древесных пород, чаще у лиственных.
Завиток — местное искривление годичных слоев около сучков или проростей. Бывает односторонний и сквозной, снижает прочность древесины.
Те же «побочные эффекты» дают и глазки — следы неразвившихся в побег спящих почек. Их диаметр не превышает 5мм. Глазка бывают разбросанные и групповые, светлые и темные.
Кармашек — плотность внутри или между годичными слоями, заполненная смолой или камедями.
Сердцевина — узкая центральная часть ствола, состоящая из рыхлой ткани бурого или более светлого, чем у окружающей древесины, цвета. На торцах сортимента наблюдаются пятна около 5мм различной формы, на радиальной поверхности — в виде узкой полосы. Смещенная сердцевина — эксцентричное расположение сердцевины, сопровождающееся свилеватостью. Двойная сердцевина — наличие в сортименте 2 и более сердцевин с самостоятельными системами годичных слоев, окруженных с периферии одной общей системой.
Сухобокость — участок поверхности ствола, омертвевший в процессе роста дерева как результат повреждения.
Прорость — зарастающая или заросшая рана.
Рак — углубление или вздутие на поверхности растущего дерева в результате деятельности грибов или бактерий.
Ложное ядро — темная, неравномерно окрашенная зона, граница которой не совпадает с годичными слоями, отделенная от заболони темной каймой.
Пятнистость древесины — окраска заболони лиственных пород в виде пятен и полос, близкая по цвету к окраске ядра.
Внутренняя заболонь — смежные годичные слои, расположенные в зоне ядра, окраска и свойства их близки к окраске и свойствам заболони.
Водослоем называют участки ядра или спелой древесины с повышенным содержанием воды.
Твердость древесины в первую очередь зависит от породы древесины, а также в большой степени от условий роста дерева, влажности и пр. В пределах одного вида разброс значений может быть весьма значительным. Обычно указываются средние относительные показатели твердости по Бринелю в процентах по отношению к дубу, относительная твердость дуба принимается за 100%.
Прочностью называется способность древесины сопротивляться разрушению под действием механических нагрузок. Она зависит от направления действующей нагрузки, породы дерева, плотности, влажности, наличия пороков и характеризуется пределом прочности — напряжением, при котором разрушается образец.
Различают основные виды действия сил: растяжение, сжатие, изгиб, скалывание.
Виды распилов древесины
Главная — Статьи — Виды распилов древесины
Уже много веков человечество использует древесину в качестве строительного материала и, несмотря на постоянное появление новых, самих современных материалов, популярность натуральной древесины совершенно не уменьшается.
Как же правильно выбрать пиломатериалы из огромного ассортимента? Чем обусловлены различия в цене и качестве?
Качество готовых материалов из древесины зависит от многих параметров – породы древесины и качества исходного лесоматериала, профессионализма станочников, соблюдения технологии сушки пиломатериалов и производства готовых изделий. Еще одним фактором, который оказывает существенное влияние на качество и внешний вид пиломатериалов, а также их механические свойства, является способ распила древесины, который определяет текстуру доски.
Существуют несколько видов распила древесины — тангенциальный, радиальный, рустикальный и поперечный, из которых наибольшее распространение получили первые два.
При поперечном распиле древесина разрезается поперек волокон. Способ применяется при производстве художественного паркета. Рустикальным распилом называется любой распил, выполненный под острым углом к направлению волокон. Способ используется в производстве пиломатериала для рустикального полового покрытия – самого неоднородного и оригинального по рисунку и оттенку.
При тангенциальном распиле плоскость разреза проходит по касательной к годичным слоям дерева на некотором расстоянии от сердцевины. Так как волокна древесины, как правило, не имеют единого направления, они создают на поверхности доски естественные узоры в форме причудливых «арок», «завитушек», «колец». Текстура полученной доски тангенциального распила неоднородная, возможно наличие древесных пор. На некоторых из сухих досок после чистового строгания на поверхности могут образовываться расслоения.
Для радиального распила древесины плоскость распила располагается перпендикулярно годовым кольцам. При этом способе текстура доски получается довольно однородной с минимальным расстоянием между годовыми слоями. Это не только создает красивый рисунок, но и способствует повышению прочности пиломатериала.
Доски радиального распила отличаются хорошей устойчивостью к внешним воздействиям, имеют большую сопротивляемость деформации и износоустойчивость, чем доски тангенциального распила.
Коэффициенты усушки и разбухания пиломатериалов радиального распила равны соответственно 0,18% и 0,2%, что почти в два раза лучше, чем у пиломатериалов тангенциального распила. Причина этого явления заключается в том, что у досок радиального распила усушка и разбухание происходит по толщине материала, в отличие от досок тангенциального распила, у которых изменение размеров происходит по ширине доски.
Средний коэффициент полезного выхода досок радиального распила составляет всего 10-15%. Этим объясняется их высокая себестоимость. К радиального распилу можно отнести ламели, у которых угол между годовыми кольцами и пластью составляет 60-90°. Если указанный угол находится в диапазоне 45-60°, такие доски относятся к полурадиальному распилу. Наилучшими эксплуатационными качествами обладает пиломатериал, у которого угол между годичными слоями и плоскостью распила составляет 80-90 градусов. С учетом досок полурадиального распила коэффициент полезного выхода может достигать 30%.
Обычно, при радиальной распиловке бревно изначально распиливают на четверти, а затем с каждой четверти отпиливают доски поочередно с двух пластей. Для распиловки бревна радиальным способом могут использоваться, например, продольно-распиловочные станки UP-700. Важное значение имеет микропроцессорная система управления и оптимизации UP-700, которая используется технологами для определения процента выхода доски радиального распила исходя из критериев оптимизации максимального выхода готовой продукции, а также условий радиальности и полурадиальности распила.
Сравнивая радиальный и тангенциальный виды распилов, можно сделать несколько выводов:
- Радиальные пиломатериалы обладают лучшими свойствами усушки и разбухания.
- Доски радиального распила имеют лучшие механические характеристики и стабильность геометрических размеров.
- Древесина досок радиального распила обладает равномерным оттенком и однородной текстурой, что придает особую декоративную ценность готовым изделиям из дерева.
- Благодаря своим характеристикам, радиальные доски находят более широкое применение, хотя и обладают более высокой ценой.
Примеры распилов древесины
Крайние — тангенциальный распил, 2 центральных — радиальный |
Радиальный распил |
Радиальный распил (лиственница) | Тангенциальный распил |
- Ремонт пола из досок
- Особенности палубной доски
- Разновидности распила древесины, сорта и изъяны
Древесина, используемая в производстве гитар.
Древесина, используемая в производстве гитар.
|
Читайте также:
|
Вопрос:
— Чем отличается «Stratocaster» от «Les Paul»?
Ответ:
— «Strat» горит лучше, а «Les Paul» — дольше.
Для производства электрогитар используются различные породы дерева. Существует одно принципиальное требование – древесина должна быть хорошо высушена. Сырое дерево не звучит, т.к. влага, оставшаяся в дереве является своеобразным демпфером, кроме того при высыхании дерево может повести и оно может треснуть. Особенно это принципиально для древесины, из которой делается гриф. В промышленном производстве дерево для гитар сушится в специальных помещениях многие годы. Срок сушки дерева в принципе не ограничен – чем дольше, тем лучше. В домашних условиях дерево сушится вдали от прямых солнечных лучей в сухом месте. В квартирах жилого дома, например, под кроватью. Даже термин такой есть – подкроватная сушка. Для того, чтобы дерево сохло равномерно торцы бревен или досок заливают компаундом. В домашних условиях в качестве такого компаунда можно применять парафин, из которого изготовлены бытовые свечи. На мой взгляд для того, что бы древесину можно было использовать для постройки гитары, ее достаточно выдержать на чердаке минимум 3 года, а в квартире от 5 лет. По этому запасайтесь деревом заранее! Быструю сушку дерева в вакуумных печах применять не рекомендую, т.к. при такой сушке нарушается структура дерева, что практически полностью убивает звук. При изготовлении гитары используются доски только продольных (ни в коем случае не поперечных!) распилов. На рисунке ниже показаны три основных типа продольной распиловки ствола дерева (бревна), которые применяются в деревообрабатывающей промышленности.
Тангентальный распил — плоскость разреза проходит по касательной к годичным слоям и на спиле виден «арочный» рисунок годовых колец.
Радиальный распил — плоскость разреза проходит перпендикулярно годичным кольцам древесины. Рисунок в виде полос.
Смешанный тип распила — имеет радиальный, тангентальный рисунок и переходные структуры.
Для изготовления гитар применяют доски в основном тангентального и радиального распилов, однако на худой конец можно использовать и доски смешанного распила.
Сразу оговорюсь, что дерево в магазинах стройматериалов приобретать не следует по нескольким причинам. Первая – такое дерево сушится в сушильных печах, которые разрушают структуру. Второе – зачастую доски имеют склейки для получения необходимой длины. И т.п. Необходимое дерево можно найти либо на деревообрабатывающих предприятиях (не прошедшее сушку в печах), либо в организациях, занимающихся распиловкой леса, либо в торговых фирмах, специализирующихся на поставках дерева для изготовления музыкальных инструментов, либо, наконец, у гитарных мастеров. В России существует крупная компания по поставке лесоматериалов любых пород дерева – «Buhmans» (www.bohmans.com), услугами которой пользуется много гитаростроителей-любителей. Кроме того деку и гриф любой степени готовности можно заказать у Александра Шамрая (www.shamray.ru). На изготовление гитар идут доски получаемые при распиловке ствола дерева до первых ветвей.
Дерево для корпуса (деки):
1. Ольха (Alder) – стандартный материал для дек. Большинство дек гитар от дешевых до дорогих делается из ольхи. Это объясняется хорошими акустическими характеристиками дерева, его не большим весом, легкостью в обработке и достаточной прочностью.
2. Липа (Basswood – басовое дерево) – один из самых распространенных материалов для дек, особенно бас-гитар. Звук такой деки получается сбалансированный, с хорошей низкочастотной составляющей. Характеризуется также как и ольха достаточной прочностью, средней твердостью и весом.
3. Тополь (Poplar) – по своим свойствам похож на ольху, но более мягкий.
4. Клен (Maple) – хороший материал для дек, но тяжелый. Имеет широкий акустический диапазон, много высоких частот. Материал твердый, и прочный. Клен имеет много разновидностей, таких как клен явор, огненный клен, волнистый клен, «птичий глаз», которые почти все используются в гитаростроении. В основном применяется в качестве топов дек.
5. Ясень (Ash) – прочный и тяжелый материал. По акустическим характеристикам похож на клен.
Существуют еще экзотические для России породы дерева, которые часто используются в гитаростроении типа красного дерева (Mahogany), но на них я не буду останавливаться. Такие породы как береза, бук, осина, ель, сосна, а также другие хвойные и лиственные породы в производстве электрогитар не используются. Очень редко можно встретить дуб и то только как часть деки.
Дерево для грифа.
Лучшим и классическим материалом для грифа является клен, из-за его прекрасных акустических качеств, прочности, прекрасной фактуре и твердости. Кроме клена в качестве дерева для грифа часто используют красное дерево. На других материалах, я останавливаться не буду.
Накладки обычно делают из палисандра (Rosewood) и его разновидностей и клена. Палисандр дерево для России экзотическое, найти его можно только в некоторых специализированных магазинах и фирмах, поставляющих дерево для гитар. На некоторых дорогих гитарах накладки делаются из еще более экзотической породы – черного дерева (Ebony).
Самое подходящее дерево для изготовления гитар, которое можно найти на просторах нашей великой Родины, произрастает на Северном Кавказе. Это липа, кавказский клен явор и ясень. Тополь и ольха — в средней полосе России.
Дата добавления: 2015-10-30; просмотров: 109 | Нарушение авторских прав
| | следующая страница ==> | |
Регулировка высоты датчиков | | | К разделу о склеивании деки и грифа |
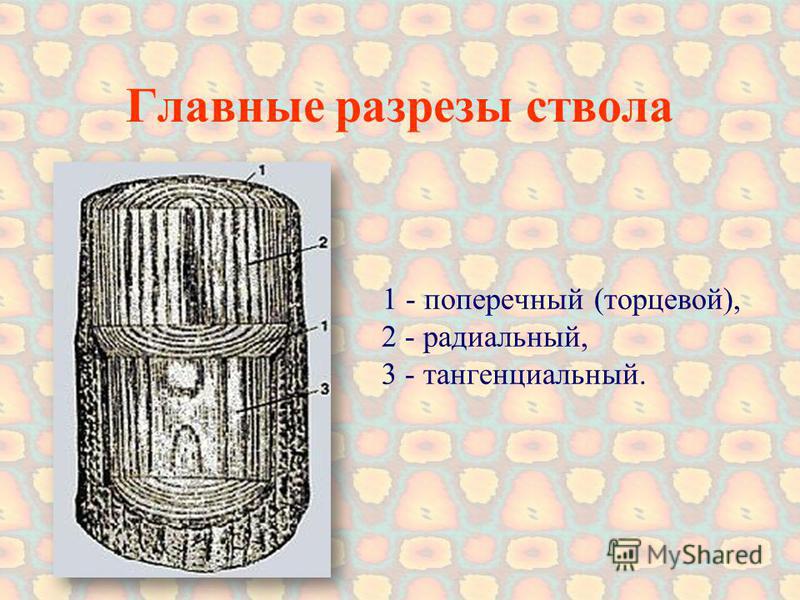
лущеный, пиленый, строганый тангенциальный и радиальный, производство файн-лайн
Желание потребителей иметь мебель, внутренние и межкомнатные конструкции из натурального дерева не всегда выполнимо из-за высокой стоимости природного материала. Особенно сожалеть об этом не имеет смысла, потому что изделия, сделанные из цельного дерева, имеют большой вес, к тому же по истечении времени могут рассыхаться, деформироваться. В связи с этим часто для отделки применяют шпон.
Изделия из натурального шпона очень похожи внешне на массив дерева, при этом продукция стоит значительно дешевле и эксплуатируется без проблем.
Что называют шпоном
Шпон – слово немецкого происхождения, обозначающее щепу. По-видимому, во времена заимствования термина они были синонимами. Сейчас под щепой подразумевают измельченную рублением древесину. Существует несколько типов щепы, лучшие из которых называются технологическими. После дополнительной химической обработки некоторые их них используют в производстве плит из древесных волокон и стружки.
Все современные виды шпона получают более тонкими механическими приемами обработки древесины, для которых применяют специальное технологическое оборудование. В результате образуются пластины маленькой толщины и относительно большой (для измельченного сырья) поверхностной площади. Они совсем не похожи на щепу.
Достоинства шпонированной продукции заключаются в следующем:
- покрытие имеет красивый узор, который дополнительно усиливается при обработке;
- шпоном экзотических пород можно задекорировать основу, сделанную из недорогой древесины;
- при небольших повреждениях вид поверхности легко корректируется мелким ремонтом;
- шпон позволяет отреставрировать старые конструкции и изделия без больших финансовых затрат;
- тонкий слой покрытия позволяет проводить работу самостоятельно с помощью обычных инструментов.
При работе с цельным натуральным деревом приходится прилагать большие физические усилия, применять деревообрабатывающие станки и специальные инструменты, а работать со шпоном гораздо проще.
Способы разделки древесины
Пластины шпона можно снимать с древесных полуфабрикатов несколькими способами. Их выбор определяется породой сырья, его состоянием, направлением будущего использования продукта, оснащенностью предприятия-изготовителя.
Главные типы механических действий следующие:
- строгание;
- лущение;
- пиление.
Каждая процедура требует специального оборудования, использования древесины необходимого качества, степени ее подготовки. Готовый шпон отличается эстетическими особенностями, соответственно, возможностью использования и ценой.
Строганый материал
Строганием получают шпон дуба, красного дерева, ясеня, бука и двух основных хвойных пород: сосны и лиственницы. Изделия имеют красивую текстуру, используются преимущественно в качестве облицовочного материала. Для производственного процесса берут распиленные брусья или так называемые ванчесы, наросты, которые после обработки паром разделывают на особых строгальных станках.
Обратите внимание! Строгание может проводиться по отличающимся направлениям, в результате на пластинках получается разный рисунок.
После радиального состругивания шпона, выполняемого строго по торцу, на нем образуется рисунок из параллельных колец, расположенных равномерно по всей поверхности. Радиальный шпон, сделанный таким способом, обозначается буквой Р.
Вследствие наполовину радиального состругивания рисунок колец занимает приблизительно ¾ площади образовавшейся пласты. Шпон, полученный в результате такого механического действия, обозначается буквосочетанием ПР.
В результате тангенциальной обработки кольца имеют вид искривленных полосок. Пластинки, полученные строганием по тангенсу (по касательной к годовому кольцу), обозначают буквой Т. Иногда встречается название «тангентальный». Его нельзя назвать неправильным, так как мастера часто применяют такой термин.
После тангенциально-торцевого строгания рисунок образуется закольцованными овальными кривыми линиями, на которых видны штриховые сердцевинные лучи. Вид такого шпона, образующийся в результате технологии строгания по оси между торцом и тангенциальной плоскостью, обозначают буквосочетанием ТТ.
Сорта и толщина строганого шпона
Согласно показателями качества древесины и тщательности обработки, строганая продукция подразделяется на два сорта. Виды натурального шпона из 1-й группы имеют минимальные изъяны в виде пятнистости, внутренней заболони, темной прорости, трещин, царапин или вовсе их не содержит. Виды шпона из 2-й сортовой группы контролируются гораздо лояльнее, потому что стандартом допускается наличие в изделиях изъянов.
Значения толщины пластин из древесины варьируются в интервале от 0,5 до 1 мм. Шпон, полученный тангенциальной, полностью или наполовину радиальной разделкой, имеет длину, достигающую 900 мм, ширину, достигающую 120 мм. Продукция с обозначением ТТ обычно имеет меньшие размеры. Показатель допустимой шершавости поверхности различается. Для дуба, красного дерева, ясеня, сосны, лиственницы он равен 200 мкм, остальной древесины – 100 мкм.
Весь шпон, произведенный строганием, высушивают до достижения массовой доли влаги, равной 8 %, затем упаковывают.
Лущеный шпон
Похожий на ленту шпон называют лущеным . Его снимают с поверхности древесины на специальном станке. Длинные ленты высушивают, разрезают на куски с заданными размерами и применяют как полуфабрикат для производства фанеры, многослойных панелей, клееных элементов строительных конструкций, облицовок, пищевых упаковок.
Внешние покрытия, которые образует лущеный шпон, выглядят немного хуже, чем сделанные из строганых кусочков. Преимущество этого вида заключается в большей площади поверхности пластинок. Ценные породы древесины обрабатывать лущением не всегда целесообразно, а полуфабрикат из повсеместного сырья, например тополя, после фанеровки превращается в востребованный товар.
Длина каждой единицы продукции варьируется в интервале от 800 до 3750 мм. Ширина изменяется от 150 до 3750 мм, шаг в линейке варьируется от 50 мм до 100 мм. Требования к показателям толщины зависят от породы древесины. Для тонких пластин из лиственного сырья максимум составляет 4 мм, для более толстых 6,5 мм.
Шпон подразделяют на 5 сортов: элитный и остальные, включающие от 1-го до 4-го сорта. Рядом с цифровым обозначением сортности изделий из хвойной древесины присутствует буква Х.
Читайте также: Ламинированная фанера: виды, размер, вес, фото, производители, описание
Влажность готового шпона не должна превышать 6 %, показатель шероховатости для лиственной продукции не может превышать 200 мкм, хвойной – 320 мкм.
Пиленый шпон
Распиливать древесину на пласты человек научился давным-давно. Сделать тонкие листы с помощью пилы, даже самой современной формы, сложно, к тому же процесс сопровождается получением большого количества отходов. Ламели, сделанные распиливанием, имеют толщину от 1 до 12 мм.
Обратите внимание! Пиленый вид шпона применяют для инкрустирования дорогой мебели и декоративных элементов интерьера.
Особенность пиленого шпона в том, что его можно подобрать по рисунку основной части древесины изделия. Результат получится очень красивый, впечатляющий, но за это придется заплатить немалые деньги. Листовой шпон, спиленный из древесины кедра, ели, пихты, часто применяют для формирования согнутых элементов оформления мебели или лестниц. Изделия используются в отдельности или в сочетании с МДФ-материалом.
В некоторых источниках можно увидеть информацию о применении пиленых видов шпона для отделки музыкальных инструментов. Содержание государственного стандарта свидетельствует о том, что для этих целей берут лущеные или строганые шпоновые пластины. Так, для черновой облицовки пианино применяют виды, полученные лущением лиственных пород, для чистовой облицовки – строганые куски шпона ясеня, груши, грецкого или американского ореха, клена, вяза, дуба и даже красного дерева (для самых дорогих инструментов).
Рустикальный распил: дает весьма неоднородную по фактуре поверхность
Этот тип распила считают наиболее простым, ведь его можно производить под любым углом относительно ствола. Полученная доска выделяется неоднородным рисунком и расцветкой, так как в ней могут попадаться сучки (с Ø до 5 мм), заболонь (поверхностные слои древесины, окрашенные светлее глубинных).
Паркетная доска, созданная методом рустикального распила, считается самой бюджетной. В Европе именно этот тип древесных полов пользуется большим спросом за натуральность и естественность облика. Сучки, мелкие трещинки и разнородность расцветки прекрасно вписываются в так называемые деревенские стили (кантри, шале и пр.).
Но следует учитывать, что паркет рустикального распила слабее по прочности и мягче, чем иные типы досок, поэтому его относят к 3-му сорту. Из-за смешивания заболони и глубинных слоев древесины материал способен «играть», деформироваться, если в доме будут перепады влаги и температур. А так как разные древесные слои дают неодинаковое качество плотности плашек, то ходить по такому полу на каблуках-шпильках нежелательно, иначе могут остаться вмятины.
Современные технологии производства
Помимо традиционных способов, многие предприятия внедрили и успешно применяют новые подходы к изготовлению шпоновых изделий.
Популярностью пользуется пестрый, разнохарактерный мультишпон, на поверхности которого могут иметься светлые или темные коричневые оттенки, серые тона с отличающейся фактурой. Существуют дизайнерские работы, создающие строго определенный или хаотичный рисунок, непохожий на натуральную расцветку, но с текстурой дерева. Продукция востребована в кругу ценителей нестандартных решений в оформлении интерьеров.
Особенности файн-лайн
Изделия со своеобразным названием, понятным любому человеку, изучавшему английский в школе, действительно, имеют прекрасные линии на поверхности. Материал делают из древесных отходов, вследствие чего его стоимость более доступна, чем у первоклассного натурального шпона. Такой вид шпона называют также реконструированным. Продукция вида файн-лайн представлена в ассортименте, имеет большую цветовую гамму, легко претерпевает дальнейшую обработку.
Технологический цикл производства реконструированного шпона включает в себя следующие этапы:
- снятие пластин на лущильных станках;
- высушивание и сортировка;
- пропитывание красителем в емкостях;
- обработка клеящими средствами;
- прессование;
- форматирование строганием.
Таким образом, продукция является лущеной и при этом строганой. Влажность материала должна укладываться в диапазон от 8 до 12 %. Наибольшим спросом пользуются виды реконструированных пластин файн-лайн толщиной 0,35…5 мм, плотностью от 450 до 600 кг/м3. Конечный продукт имеет до 94 % натуральной древесины, приблизительно 6 % склеивающего вещества, не более 2 % красящих пигментов.
Файн-лайн-покрытия могут имитировать текстуру любых древесных пород, создавать текстильные рисунки, например сатиновый узор поверхности. Шпон вида файн-лайн обладает большой пластичностью и термостойкостью, не реагирует на влажное окружение воздуха, легко покрывается лаком.
Минусы и плюсы
По внешнему виду двери со шпоном очень сложно отличить от аналогов, изготовленных из древесины, поскольку они покрываются натуральным срезом дерева.
Такие двери имеют много преимуществ:
- Изделие по составу на 99% является натуральным, поскольку оно включает массив древесины и срез ценной породы дерева снаружи.
- Двери со шпоном изготавливаются из экологически чистых материалов, поэтому часто применяются не только для спален или гостиных, но также для детских комнат.
- Привлекательный внешний вид изделия достигается благодаря применению натурального дерева, которое характеризуется оригинальным и неповторимым принтом и текстурой.
Деревянные двери со шпоном позволяют создать хороший микроклимат в помещении. Они отлично пропускают воздух через микропоры. Лёгкость шпонированных моделей позволяет осуществлять их установку даже на очень тонкие стены. Если двери установлены правильно, то они в редких случаях могут провиснуть. Хорошее сочетание качества и цены изделия. Если сравнивать стоимость шпонированной и деревянной модели, то вариант со шпоном стоит значительно дешевле
Если модель с натуральным шпоном является тоже дорогой, тогда можно обратить внимание на варианты с экошпоном или другим искусственным покрытием. Модели со шпоном очень часто передают фактуру ценного дерева. Красиво смотрится шпон вишни, сосны, венге, красного дерева или ясеня
К дорогостоящим породам деревьев принадлежат такие, как чёрный орех, мадрона.
- Шпонированные модели можно отремонтировать, если в процессе транспортировки или эксплуатации повредилось полотно. Необходимо применить специальный состав для окрашивания шпона или произвести полировку повреждённого места.
- Изделие со шпоном характеризуется отменными шумоизоляционными свойствами, а также способностью великолепно удерживать тепло, если говорить о вариантах, изготовленных из цельного массива сосны.
- Современные производители предлагают широкий модельный ряд шпонированных дверей, среди которых можно подобрать не только материал, но также цветовое исполнение и необходимые размеры. Двери представлены в естественных тонах. Чтобы придать шпону глубины цвета, часто осуществляется его окрашивание.
Двери со шпоном имеют и некоторые недостатки, с которыми стоит ознакомиться перед выбором дверей:
- Натуральные материалы всегда стоят дорого, поэтому шпонированные модели являются дорогостоящими.
На цену дверей также влияет известность производителя.
- Натуральный шпон практически не отличается от искусственного, что позволяет мошенникам выдавать некачественный шпон за натуральный.
- Для обеспечения длительной эксплуатации изделия необходимо осуществлять бережный уход. Для очистки дверей стоит использовать специальные средства, разработанные на основе воска.
Для изготовления ламинированной двери используется специальная ламинатная плёнка. Она идеально передаёт фактуру массива. Конечно, такие изделия отличаются доступной стоимостью, повышенной износостойкостью и надежной защитой от попадания влаги.
Качество | лестницы из массива дерева
Фрагменты межэтажных лестниц, изготовленные фирмой «Мир бука», имеют исключительно высокое качество. Они делаются из экологически чистых бука и дуба, произрастающих на Кавказе. Бук и дуб — ценные твердые породы древесины, идеальные для внутренней отделки респектабельного жилища и для деревянной межэтажной лестницы. Мебель из бука и дуба обладает высокими прочностными характеристиками.
Качество продукции — наша повседневная забота:
— заготовка лучшего сырья, правильный раскрой древесины, антисептирование, мягкая камерная сушка пиломатериалов;
— производство, оснащенное современным оборудованием и высококачественным инструментом;
— подбор заготовок в изделии по цвету, фактуре и виду распила;
— склейка древесины на специализированном оборудовании с использованием лучших импортных клеев;
— тщательная сортировка и приемка продукции;
— строгий контроль за соблюдением технологических процессов на всех этапах производства;
— добротная упаковка продукции.
Продукцию нашей фирмы можно узнать по чернильным штампам на тыльных поверхностях изделий и ярлыку с логотипом и названием фирмы. Чернильные штампы несут информацию о бригаде, изготовившей изделие, о дате изготовления и сортности, и о бригаде, осуществившей приемку и упаковку. Такая маркировка позволяет обеспечить персональную ответственности за качество производимого изделия.
Фирма «Мир бука» несет ответственность за качество своей продукции. Гарантийные обязательства действуют в течение шести месяцев со дня продажи изделия.
Немногие фирмы отваживаются изготовливать и поставлять свою продукцию из 100%-ного массива твердого дерева без декоративного и защитного лакового покрытия. Дело в том, что с помощью лака и современных средств декоративной отделки легко скрыть любые незначительные естественные дефекты древесины, которые расцениваются покупателем как недопустимые. Это требование к отсутствию незначительных дефектов на лицевых поверхностях серьезно затрудняет изготовление высококачественных изделий. Кроме этого, отсутствие покрытия делает изделия уязвимыми к разного рода внешним воздействиям (пыль, грязь). Несмотря на эти трудности, специалисты нашей фирмы обеспечивают необходимое качество лицевых поверхностей и без отделочного покрытия. Таким образом, мы даем возможность нашим клиентам пользоваться для отделки своих лестниц любыми отделочными материалами.
Контроль качества продукции регламентируется внутренними документами фирмы — «техническими условиями». Техусловия созданы на основе стандартов РФ и мирового опыта производства изделий из древесины твердых пород. ТУ оговаривают признаки, определяющие классность изделий и условия их хранения, а также формулируют требования к используемому сырью и определяют параметры сухого пиломатериала.
Качество изделий определяется состоянием лицевых поверхностей. Наша фирма производит и поставляет продукцию высшего сорта «Экстра» и 1-го сорта «классов «А» и «Б». Изделия изготавливаются из древесины, подобранной по цветовой гамме и виду распила (радиальный, тангентальный). Из древесины, имеющей однородную цветовую окраску, делаются изделия высшего сорта «Экстра». Из древесины, имеющей биохимические пятна или ложное ядро, делаются изделия и 1-го сорта классов «А» и «Б». Каких-либо других отличий изделия высшего и первого сортов не имеют. Биохимические пятна или ложное ядро не изменяют прочностных характеристик древесины. Цены на изделия класса «Б» значительно ниже, чем на изделия высшего сорта. Изделия высшего сорта рекомендуются для отделки бесцветным лаком или, если это 1 сорт «класса А», с очень легкой тонировкой. Для изделий 1-го сорта «класса Б» рекомендуется отделка с глубокой тонировкой.
Коллектив инженеров нашей фирмы постоянно совершенствует технологические процессы, используемые в нашем производстве, обновляет инструментарий и станочный парк с целью поддержания качества выпускаемой продукции на высоком уровне.
Стандарт предприятия.
Фрагменты межэтажных деревянных лестниц из бука.
Общие технические условия.
Настоящий стандарт распространяется на фрагменты (изделия) деревянных межэтажных лестниц из бука, изготавливаемых фирмой «Мир бука». Наименование и виды стандартных фрагментов лестниц приведены в прайс-листе фирмы «Мир бука».
1. Размеры.
1.1. Размеры стандартных фрагментов лестниц должны соответствовать указанным в прайс-листе фирмы «Мир бука».
1.2. Размеры заказных изделий должны быть указаны в технической документации на изделие.
2. Технические требования.
2.1. Фрагменты лестниц должны соответствовать требованиям настоящего стандарта, технической документации и образцу-эталону, утвержденному в установленном порядке.
2.2. Характеристики.
2.2.1. Предельные допустимые отклонения от линейных размеров изделий приведены в п.п. 4.4.1.1; 4.4.2.1; 4.4.3.1.
2.2.2. Предельные отклонения угловых размеров — не более ± 1 град.
2.2.3. Предельное отклонение неперпендикулярности сторон — не более ± 1,0 мм на 300 мм длины.
2.2.4. Покоробленность щитовых деталей длинной и (или) шириной 300 мм и менее не нормируется.
2.2.5. Допустимая покоробленность щитовых фрагментов лестниц приведена в п.п.: 4.4.1.2; 4.4.2.2; 4.4.3.2.
2.2.6. Влажность деталей из массивной древесины должна быть (8 ± 2) %. Сушка древесины выполняется
в соответствии с требованиями «Руководящих материалов по технологии камерной сушки древесины» (Архангельск, ЦНИИМОД 1985). Сушка материалов должна выполняться по нормальным или мягким режимам.
2.2.7. В процессе хранения изделия могут принимать равновесную влажность от 4% до 13 %. Перед монтажом рекомендуем выдерживать изделие в условиях эксплуатационной влажности до тех пор, пока равновесная влажность изделия не станет равной эксплуатационной.
2.2.8. Прочность клеевого соединения должна быть не ниже предела прочности на скалывание древесины данной породы. Прочность клеевого соединения определяется по ГОСТ 15613 — 70; ГОСТ 14348 — 69 и ГОСТ 14349 — 63; водостойкость по ГОСТ 17005 — 82 (не хуже, чем Д3 по стандарту ДИН ЕН 204).
2.2.9. Варианты склеивания заказных изделий оговариваются в технической документации заказа. Варианты склеивания стандартных изделий производятся согласно утвержденным образцам.
2.2.10. Склеивание древесины по толщине и ширине при ширине изделия до 590 мм должно производиться на гладкую фугу по ГОСТ 9330 — 76, а по длине — на зубчатые шипы по ГОСТ 19414 — 79 или конструктив Хофмана. Соединения по длине с шипом до 10 мм допускаются во всех деталях без ограничения. Соединения по длине с шипом длинной свыше 10 мм не допускаются.
2.2.11. Число соединений по длине должно быть не более двух на 1 м погонной длины при длине склеиваемых заготовок не менее 400 мм.
2.2.12. Длина заготовок, из которых склеиваются поручень, подперильник, опорные столбы, — не менее 800 мм.
2.2.13. При изготовлении заказных ступеней и площадок длинной до 1200 мм допускается сращивание заготовок в длину и по кромке «вразбежку». При этом заготовка, из которой изготавливается передняя кромка ступени, не должна иметь стыков по длине.
2.2.14. Не допускается, чтобы на лицевую поверхность попадал технологический узел сращивания (минишип, микрошип, шпонка, шкант, «ласточкин хвост», конструктив Хофмана).
2.2.15. Шлифовку лицевых поверхностей производить вдоль волокон древесины.
2.2.16. Шлифовка лицевых поверхностей должна производиться в два приема. Первый раз поверхность обрабатывать наждачной бумагой зернистостью 16 мкм. Вторую, чистовую обработку, производить наждачной бумагой зернистостью 8 мкм.
2.2.17. Торцевые кромки, если они являются лицевыми поверхностями, шлифовать.
2.2.18. Нормы ограничения пороков древесины на поверхностях фрагментов лестниц приведены в п.п. 4.4.1.7.; 4.4.2.8.; 4.4.3.6. Виды пороков древесины, допустимых на лицевых поверхностях изделий приведены ниже.
3. Древесина бук.
3.1. Бук — одна из наиболее ценных твердолиственных пород дерева. Бук используется для изготовления высококачественной мебели, столярных изделий, паркета.
3.2. Натуральный цвет древесины имеет очень широкую гамму оттенков. Диапазон оттенков простирается от нежного, почти белого, серо-розового до глубокого коричнего-серого. Глубина оттенка зависит от возраста дерева, условий произрастания, и заболонной грибной окраски, технологии сушки. Изменение цвета бука возможно наблюдать даже на небольшой заготовке. Это затрудняет подборку заготовок для каждого изделия. Для удобства подборки и однозначной идентификации вся цветовая гамма бука разделена нами на 4 группы оттенков.
оттенки
3.3. Внешний вид поверхности бука зависит от вида распила древесины.
Примеры разных видов распилов: тангентальный, радиальный
Внешний вид
3.3.1. Тангенциальный распил — лицевая плоскость поверхности доски близка или совпадает с плоскостью, касательной к поверхности годовых колец дерева.
3.3.2. Радиальный распил — лицевая плоскость поверхности доски близка или совпадает с плоскостью радиуса годовых колец дерева.
3.3.3. Рустикальный распил — лицевая плоскость поверхности доски расположена под углом, близким к 45 град. по отношению к радиальной или тангентальной плоскости.
3.4. Наиболее однородной, по виду распила, будет поверхность доски, взятой из ствола дерева большого диаметра. Выдержать однородность вида распила в реальных изделиях практически невозможно. Более того, вид распила даже в пределах одной заготовки практически всегда будет неоднородным. Подборка заготовок по виду распила может классифицироваться как условная.
3.5. При изменении влажности окружающей среды, древесина изменяет свои линейные размеры. Причем изменение линейных размеров сильно зависит от направления (тангентальное, радиальное, продольное). Поэтому невозможно сделать изделие из цельного массивного куска дерева. При усушке большой заготовки обязательно появятся трещины и разрывы, делающие изделие полностью непригодным к эксплуатации. Единственным способом сделать изделие заданных размеров из 100% массива натуральной древесины — это склейка между собой подобранных по виду распила и цветовой гамме ламелей (заготовок). Причем, изделие будет вести себя тем стабильнее, при изменении внешних условий, чем мельче ламели, из которых оно склеено. Влажность и вид распила всех заготовок в изделии должна быть строго равной, иначе, спустя некоторое время после изготовления, между соседними ламелями возможно появление «ступенек». Это результат выравнивания влажности древесины каждой из ламелей. Так как идеальный подбор ламелей невозможен, эффект «ступенек» будет наблюдаться всегда.
Фирма «Мир бука» в своих изделиях стремится свести этот эффект к минимуму. Для полного же избежания эффекта «ступенек» мы рекомендуем производить окончательную отделку (шлифовку и лакировку) лестницы после её монтажа и длительной выдержки при эксплуатационной (комнатной) температуре и влажности.
Образцы поверхностей из ламелей, подобранных по цвету и виду распила (на примере тетивы)
тетива
3.6. Натуральная древесина всегда имеет пороки строения и грибные поражения. Их присутствие на обработанных поверхностях изделий также естественна, как сама природа. Лучшая пластмассовая имитация древесины «оживляется» изображением пороков. Пороки строения древесины и грибные поражения, встречающиеся на поверхностях наших изделий, не являются вульгарными. Они не нарушают внешнего вида и механической прочности изделий. Деловая древесина, из которой изготавливаются наши изделия, отбирается из первосортного пиловочника.
3.7. Виды дефектов, встречающиеся на поверхности изделий из бука.
3.7.1 Виды пороков строения древесины бука: глазок, свилеватая древесина, живой сучок, прорость, наклон волокон, ложное ядро.
бук
3.7.2. Виды поверхностных и заболонных грибных поражений: грибные окраски.
бук
3.7.3. Виды трещин: трещины боковые, трещины пластевые.
бук
3.7.4. Причиной неустраняемой покоробленности может быть использование неравномерно напряженной древесины в процессе изготовления изделий. Допустимые пределы неустраняемой покоробленности указаны п.4 настоящего документа.
4. Сортность.
Фирма «Мир бука» производит и поставляет продукцию в соответствии с настоящими техническими требованиями к изделиям соответствующих сортов. Технические требования к качеству изделий фирмы «Мир бука» значительно выше, чем требования ГОСТа Российской Федерации. В зависимости от назначения изделий мы рекомендуем выбор — изделия двух сортов (Высший сорт «Экстра», 1 сорт «А класс», 1 сорт «Б класс»). Изделия 1-го сорта подразделяются на 2 вида — » класс А» и «класс Б». Изделия высшегого и 1-го сорта изготавливаются по одинаковой технологии на одинаковом оборудования с использованием одинакового высококачественного клея.
4.1. Поверхности изделий: «лицевые» и «внутренние».
4.1.1. «Лицевые» поверхности изделий — это те, которые составляют внешний вид смонтированной межэтажной лестницы. «Лицевые» поверхности изделий шлифуются. Для изделий высшего сорта «Экстра», 1-го сорта «А класса» на лицевых поверхностях подбирается вид распила ламелей, а для высшего сорта «Экстра»еще и подбирается и цветовой оттенок ламелей.
4.1.2. «Внутренние» поверхности изделий — это те поверхности, которые не составляют внешний вид смонтированной межэтажной лестницы. «Внутренние» поверхности не шлифуются и не подбираются по виду распила и цветовому оттенку.
4.2. Предназначение изделий разных сортов.
4.2.1. Изделия высшего сорта «Экстра» имеют тщательно подобранную по виду распила и по цветовому оттенку лицевую поверхность с незначительными пороками строения древесины. Изделия высшего сорта «Экстра» предназначаются для строительства высококачественных межэтажных лестниц, имеющих лицевую поверхность натуральных светлых оттенков. Такие изделия рекомендуем отделывать бесцветным лаком. Изделия высшего сорта «Экстра» наиболее дорогие.
4.2.2. Изделия 1-го сорта «А класса» также, как и высшего сорта «Экстра», имеют на лицевой поверхности незначительные пороки строения древесины, а подборка ламелей сделана только по виду распила. Подборка ламелей по цветовому оттенку в изделиях 1-го сорта «А класса» не делается. Изделия 1-го сорта «А класса» предназначаются для строительства высококачественных межэтажных лестниц с глубокой тонировкой лицевых поверхностей. Изделия 1-го сорта «А класса» значительно дешевле изделий высшего сорта «Экстра».
4.2.3. Изделия 1-го сорта «Б класса» могут иметь более заметные пороки строения древесины на лицевой поверхности Подборка ламелей по виду распила и цветовому оттенку в изделиях 1-го сорта «Б класса» не производится. Изделия 1-го сорта «Б класса» предназначены для строительства высококачественных межэтажных лестниц, отделанных укрывистыми красками или лаком с очень глубокой тонировкой лицевых поверхностей. Изделия 1-го сорта «Б класса» имеют цену, соизмеримую с изделиями из мягких пород дерева.
4.3. Сортность изделий определяется:
4.3.1. по количеству и видам пороков строения древесины на лицевых поверхностях;
4.3.2. по качеству шлифовки лицевых поверхностей изделий;
4.3.3. по тщательности подборки древесины на лицевой поверхности по виду распила;
4.3.4. по тщательности подборки древесины на лицевой поверхности по цветовому оттенку;
4.3.5. по точности геометрических размеров изделий;
4.3.6. по количеству и видам производственных дефектов на лицевых поверхностях изделий.
4.4. Перечень дефектов и пороков древесины, допустимых на лицевых поверхностях изделий. Неупомянутые дефекты и пороки недопустимы.
4.4.1. Дефекты и пороки древесины, допустимые в изделиях высшего сорта «Экстра».
4.4.1.1. Предельные допустимые отклонения от линейных размеров не более ±1 мм. Для изделий, линейные размеры которых превышают 1м, допустимые отклонения составляют не более ±0,1% данного размера.
4.4.1.2. Допускается незначительная покоробленность изделий, не устраняемая в процессе монтажа: продольная — на длине 1 м — менее ±1 мм; поперечная — на длине 0,3 м — менее ±1 мм.
4.4.1.3. Допускается незначительное несоответствие вида распила между соседними ламелями на лицевой поверхности изделия. Максимальный угол между лицевой поверхностью и идеальной радиальной (тангентальной, рустикальной) поверхностью не более ±20 град.
4.4.1.4. Несоответствие цветовых оттенков между соседними ламелями на лицевой поверхности допускается в пределах одной группы оттенков (см. п. 3.2.). Максимальное несоответствие цветовых оттенков ламелей на лицевой поверхности одного изделия может составлять 2 группы оттенков. Все сказанное в этом пункте относится к шлифованной нелакированной поверхности. После отделки изделия бесцветным лаком цветовой оттенок ламелей может изменится.
4.4.1.5. В случае, если изделие имеет более одной лицевой поверхности, подборка ламелей по виду распила и цветовому оттенку может быть сделана только на одной из лицевых поверхностей (на какой именно — оговаривается при оформлении заказа).
4.4.1.6. В случае, когда изготавливается комплект заказных изделий (несколько изделий) для одной лестницы, допускается делать подборку лицевых поверхностей, лежащих в перпендикулярных плоскостях с разными цветовыми оттенками и с разными видами распила, если не оговорено обратное.
4.4.1.7. Допускается наличие не более одного порока древесины на каждой из лицевых поверхностей изделия. Образцы допустимых пороков изображены на рис.3 — рис.7. Суммарная площадь, занимаемая каждым из пороков, не должна превышать 0,02% площади каждой из лицевых поверхностей изделия.
4.4.1.8. На внутренних поверхностях изделий допускаются отремонтированные столярными методами все виды пороков древесины, трещины и производственные дефекты. Эти отремонтированные пороки и дефекты не должны уменьшать механическую прочность изделия в целом.
4.4.1.9. Допускается отсутствие шлифовки на внутренних поверхностях изделий.
4.4.1.10 Допускаются зашпатлеванные боковые трещины на внутренних торцевых поверхностях, не влияющие на механическую прочность изделий и конструкцию лестницы в целом.
4.4.1.11. Допускается на внутренних поверхностях изделия использовать акриловую шпатлевку цвета «бук» для заделки небольших производственных дефектов, сучков, трещин.
4.4.2. Дефекты и пороки древесины, допустимые в изделиях 1-го сорта «А класса».
4.4.2.1. Предельные допустимые отклонения от линейных размеров не более ±1 мм. Для изделий, линейные размеры которых превышают 1м, допустимые отклонения составляют не более ±0,1% данного размера.
4.4.2.2. Допускается незначительная покоробленность изделий, не устраняемая в процессе монтажа:
продольная — на длине 1 м — менее ±1 мм;
поперечная — на длине 0,3 м — менее ±1 мм.
4.4.2.3. Допускается незначительное несоответствие вида распила между соседними ламелями на лицевой поверхности изделия. Максимальный угол между лицевой поверхностью и идеальной радиальной (тангентальной, рустикальной) поверхностью — не более ±30 град.
4.4.2.4. В случае, если изделие имеет более одной лицевой поверхности, подборка ламелей по виду распила может быть сделана только на одной из лицевых поверхностей (на какой именно — оговаривается при оформлении заказа).
4.4.2.5. В случае, когда изготавливается комплект заказных изделий (несколько изделий) для одной лестницы, допускается делать подборку лицевых поверхностей лежащих в перпендикулярных плоскостях с разными видами распила, если не оговорено обратное.
4.4.2.6. Допускается несоответствие цветовых оттенков на лицевой поверхности между соседними ламелями.
4.4.2.7. Допускается на лицевой поверхности ложное ядро, поверхностные и заболонные грибные окраски. Ложное ядро и грибные окраски не изменяют твердость и структуру древесины. Такие пороки древесины хорошо скрываются в процессе отделки глубокой тонировкой лицевых поверхностей.
4.4.2.8. Допускается наличие не более одного порока древесины на каждой из лицевых поверхностей изделия. Образцы допустимых пороков изображены на рис.3…рис.9. Суммарная площадь, занимаемая каждым из пороков, не должна превышать 0,05% площади каждой из лицевых поверхностей изделия.
4.4.2.9. На внутренних поверхностях изделий допускаются отремонтированные столярными методами все виды пороков древесины, трещины и производственные дефекты. Эти отремонтированные пороки и дефекты не должны уменьшать механическую прочность изделия в целом.
4.4.2.10. Допускается отсутствие шлифовки на внутренних поверхностях изделий.
4.4.2.11. Допускаются зашпаклеванные боковые трещины на внутренних торцевых поверхностях, не влияющие на механическую прочность изделий и конструкцию лестницы в целом.
4.4.2.12. Допускается на внутренних поверхностях изделия использовать акриловую шпатлевку цвета «бук» для заделки небольших производственных дефектов, сучков, трещин.
4.4.3. Дефекты и пороки древесины, допустимые на изделиях 1-го сорта «Б класса».
4.4.3.1. Предельные допустимые отклонения от линейных размеров не более ±2 мм. Для изделий, линейные размеры которых превышают 1м, допустимые отклонения составляют не более ±0,02% данного размера.
4.4.3.2. Допускается незначительная покоробленность изделий, не устраняемая в процессе монтажа: продольная — на длине 1 м менее ±1,5 мм; поперечная — на длине 0,3 м менее ±1,5 мм.
4.4.3.3. Допускается несоответствие вида распила межу соседними ламелями на лицевой поверхности изделия.
4.4.3.4. Допускается несоответствие цветовых оттенков на лицевой поверхности между соседними ламелями.
4.4.3.5. Допускается на лицевой поверхности ложное ядро, поверхностные и заболонные грибные окраски. Ложное ядро и грибные окраски не изменяют твердость и структуру древесины. Такие пороки древесины хорошо скрываются в процессе отделки глубокой тонировкой лицевых поверхностей.
4.4.3.6. Допускается наличие более одного порока древесины на всех лицевых поверхностях одного изделия. Образцы допустимых пороков изображены на рис.3…рис.9. Суммарная площадь, занимаемая каждым из пороков, не должна превышать 0,2% площади каждой из лицевых поверхностей изделия.
4.4.3.7. На внутренних поверхностях изделий допускаются отремонтированные столярными методами все виды пороков древесины, трещины и производственные дефекты. Эти отремонтированные пороки и дефекты не должны уменьшать механическую прочность изделия в целом.
4.4.3.8. Допускается отсутствие шлифовки на внутренних поверхностях изделий.
4.4.3.9. Допускаются зашпатлеванные боковые трещины на внутренних торцевых поверхностях, не влияющие на механическую прочность изделий и конструкцию лестницы в целом.
4.4.3.10. Допускается на лицевых и внутренних поверхностях изделия использовать акриловую шпатлевку цвета «бук» для заделки небольших производственных дефектов, сучков, трещин.
5. Маркировка.
5.1. Изделия, производимые фирмой «Мир бука», маркируются тремя чернильными штампами: бригада-изготовитель, дата изготовления, сорт изделия. Чернильные штампы ставятся на внутренней поверхности изделия.
5.2. Изделия, производимые фирмой «Мир бука», маркируются двумя бумажными ярлыками: ярлык с логотипом фирмы-изготовителя и ярлык с отметкой о виде распила и цветовом оттенке лицевой поверхности изделия.
5.2.1. На изделиях высшего сорта «Экстра» наклеивается ярлык с указанием вида распила и цветового оттенка.
5.2.2. На изделиях 1-го сорта «А класса» наклеивается ярлык только с указанием вида распила.
5.2.3. На изделиях 1-го сорта «Б класса» ярлыки с указанием вида распила и цветового оттенка не наклеиваются.
6. Упаковка.
6.1. Изделия упаковываются прозрачной полиэтиленовой пленкой толщиной 100 мкм. Края полиэтиленовой пленки проклеиваются прозрачной клеящей лентой.
6.2. На внутреннюю поверхность изделия наклеивается ярлык с логотипом фирмы «Мир бука». Для защиты изделий от подделки внешний вид фирменного ярлыка может изменяться.
6.3. На поверхность полиэтиленовой пленки наклеивается ярлык с указанием вида распила и цветового оттенка.
6.4. На поверхности упаковки могут быть сделаны служебные пометки.
7. Хранение.
7.1. Хранение изделий должно производится в сухом, отапливаемом, вентилируемом помещении при температуре +5 — +30 °С при относительной влажности воздуха 30-60%.
7.2. В период хранения не допускается попадание на изделия тепловой и солнечной энергии.
7.3. Хранение производить в упаковке производителя.
7.4. Срок хранения при соблюдении условий, изложенных в п.п. 7.1…7.3, — не более 10 месяцев.
Виды пиломатериалов в зависимости от обработки
Уникальные свойства древесины – прочность, длительный срок эксплуатации, экологичность, приятный эстетичный вид, сделали ее востребованным стройматериалом, сырьем для производства мебели, декоративного покрытия, народного творчества. Люди, работающие с деревянными заготовками после их распила, призваны хорошо ориентироваться в видах пиломатериалов, знать их технические характеристики.
Содержание
- Разновидность сырья и его подготовка к распилу
- Классификация обработанных пиломатериалов
- Влияние размера детали на его классификацию
- Дополнительная классификация материалов по предназначению
- Породы деревьев для пиломатериалов
- Особенности хвойных материалов
- Лиственный ряд материалов
Разновидность сырья и его подготовка к распилу
Классифицируя древесину по степени подготовки, учитывают показатель влажности материала. Абсолютная влажность определяется соотношением масс – влаги и сухой древесины на единицу объема.
Различают несколько видов пиломатериалов
Внешний пиломатериал с показателем воздушно-сухой или естественной влажности более 18–20%, полученный после длительного пребывания на воздухе. Используется в строительстве и для сооружения деревянных конструкций.
Универсальный пиломатериал, имеющий влажность до 15%, он идет для обустройства плинтусов, наличников, бруса.
Специальный бокс для сушки пиломатериалов
Материал камерной сушки – в специальном боксе при высокой температуре. Влажность – в пределах 8–10%. Абсолютно сухая древесина обрабатывается защитным составом для предохранения от впитывания влаги из атмосферы.
Недостаточно просушенная или не надлежаще хранящаяся древесина подвержена деформации, гниению или разрушению. Чтобы этого не случилось, пиломатериал нуждается в дополнительной обработке в паровых камерах.
Вся древесина подразделяется на несколько видов:
- обрезной материал, когда заготовка обрабатывается со всех сторон;
- необрезные куски – обработка лишь с одной стороны.
По методу обработки:
- нефрезерованный пиломатериал;
- фрезерованный или же строганный.
Различают способы распила по отношению к годичным кольцам древесины:
- Радиальный распил ориентирован к центру колец. Заготовки – с различными размерами, шириной, ограниченной поперечным сечением бревна.
- Тангентальный – направлен распил к этим кольцам по касательной и способствует получению длинных досок с одинаковыми размерами и формой сечения.
Варианты распиловки древесины
Каждый вид раскроя пиломатериалов служит для создания различных форм изделий. Именно многообразие размеров и форм позволяет применять обработанную древесину во всех сферах человеческой деятельности.
Классификация обработанных пиломатериалов
Различают несколько видов пиломатериалов, зависящих от степени обработки.
Пластина – половина бревна, полученная при распиле дерева по центру. Ее применяют для изготовления шпал, бруса, массивной доски.
Брус – распространенный результат деревообработки. Применяют при обустройстве обшивки и в виде самостоятельной конструкции в постройках. Брус имеет толщину, не превышающую 100 мм, а ширину – меньшую, чем удвоенная толщина.
В зависимости от количества обработанных сторон, бывает двух-, трех- и четырехкантный брус. Существуют его разновидности:
- простой брус;
- профилированный брус;
- оцилиндрованный брус.
Два варианта профилированного бруса
Влияние размера детали на его классификацию
Виды пиломатериалов
Брусок – тот же брус, но с меньшими размерами, стандартный размер сечения 40×40 или 50×50 мм. Используется в мебельной промышленности и для производства столярных изделий.
Рейка – вид бруска, более плоская и узкая, встречается разных размеров. Часто подобное изделие распиливается непосредственно на месте строительства, его ширина и высота подгоняются под необходимые габариты.
Доска – обрезная продукция, у которой ширина колеблется от 85 до 140 мм, а толщина – в пределах от 27 до 45 мм. Изделия нужны в капитальном строительстве, для отделки помещений, при производстве мебели.
Подразделяется доска на 5 сортов:
- Отборный – применим в судостроении, обрешетке автомобильных бортов и создании интерьеров элитного класса.
- Пиломатериалы первого и второго сорта пригодны в производстве мебельных фасадов.
- Применение третьесортной доски – строительные объекты.
- Для досок четвертого сорта – производство ящиков. С их помощью упаковывают для отправки крупные механизмы.
Востребованные разновидности доски:
Структура паркетной доски
- Паркетная – ее нижний слой делают из грубо обработанной древесины, а для верха берут породы из числа элитных.
- Террасная – прочная и легкая, ее производят из лучшей древесины.
- Подоконная – хорошо просушенная, с особой пропиткой.
- Инженерная – с верхом из древесины и нижним слоем из фанеры.
Дополнительная классификация материалов по предназначению
Вагонка – пиломатериал, используемый для внутренней и наружной обшивки. В технической документации ее называют обшивочной доской. Уличная обшивка выполняется исключительно твердыми пиломатериалами.
Шпалы производят из древесины ценных пород, с отличным состоянием дерева, так как они подвержены неблагоприятному влиянию внешней среды и большим нагрузкам со стороны тяжелого железнодорожного состава.
Подбирают пиломатериал, способный надежно удерживать рельсы и гасить вибрацию поездов. Для изготовления железнодорожных шпал часто используют сосну, а иногда их делают из ели, пихты, красного клена и сибирского кедра. Чтобы предотвратить гниение и быстрое разрушение, их пропитывают особым веществом.
Погонажные деревянные изделия
Мелкий погонаж – к этим изделиям относятся уголки, плинтусы, наличники, штапики – различных габаритов, чтобы удовлетворить потребность в подборе оптимальных вариантов.
Горбыль – отход распиловки бревна на доски, боковая его часть. Его применяют для сооружения временных построек, в качестве обрешетки под крышу. Некоторые дизайнеры советуют заказчикам делать декоративную отделку при помощи этого пиломатериала. Низкая стоимость такой древесины, сделала горбыль востребованным.
Обапол (четвертина) – недоработанный вариант доски, у нее плоской является лишь одна сторона, ширина на всей протяженности – неодинаковая, поэтому продольный срез имеет неправильную форму.
Широкий ассортимент древесины и обилие пиломатериалов, отличающихся по сортаменту – реальная возможность подобрать с выгодой все детали интерьера.
Породы деревьев для пиломатериалов
Известны виды пиломатериалов из различных пород деревьев, они могут относиться к двум массивам древесины:
- хвойным;
- лиственным.
Виды пород древесины
Практически все лиственные пиломатериалы, обладающие эстетичным внешним видом и эксплуатационными свойствами, подходят для отделки помещений.
И хвойные, и лиственные породы древесины разной ценовой группы относятся к экологичным материалам. Они сейчас популярны для внутренних отделочных и наружных работ при строительстве частных домов.
Но необходимо правильно подбирать древесину и учитывать эксплуатационные качества различных видов пиломатериалов.
Особенности хвойных материалов
Лиственница – устойчива к воздействию воды, не повреждается насекомыми и грибками, загнивание происходит редко.
Сосна – менее прочна, склонна к возгоранию больше чем другие виды древесины, благодаря выступающим на ее поверхности смолам.
Текстура хвойной древесины
Кедр – близок по качественным характеристикам к сосне и обладает выраженной и насыщенной текстурой древесины, стойкий к загниванию и способен дезинфицировать воздух в помещения, где есть изделия из него. Пиломатериал применяется редко из-за высокой цены.
Тис – древесина красно-бурого цвета с прожилками, отличается прочностью и твердостью, имеет много сучков. Не подвержен материал червоточине, нечувствителен к атмосферным осадкам. Тисовые бруски хороши для резьбы, а шпон – для мозаичных работ.
Пихта – легкая и не слишком упругая древесина, удобна в деревообработке. Из нее производят кровельные материалы, вагонку для обшивки зданий. Отсутствие характерного запаха живицы, позволяет использовать материал для изготовления пищевой тары (бочек и ящиков).
Лиственный ряд материалов
Акация – твердая древесина желтого цвета с ярко выраженными годичными кольцами. Не трескается и не коробится, обладает упругостью, высоким сопротивлением трению, прекрасно поддается полировке. Из нее делают детали деревообрабатывающих инструментов и столярных верстаков, а шпон хорош для мозаичных работ.
Дуб – востребованная древесина в строительстве домов и сооружений. У него красивая текстура, высокая прочность, устойчивость к гниению, он способен гнуться и долговечен. Дубовые заготовки идут на производство мебели и паркета, декоративно-прикладное творчество.
Текстура лиственной древесины
Ясень – с близкими к дубу механическими свойствами. Высокая способность к сгибанию и прочность – достоинства древесины. Но она легко повреждается червоточиной, и нуждается в антисептической обработке. Применяют пиломатериал из ясеня для изготовления мебели и гимнастических стенок.
Осина – из лиственных пиломатериалов она легко поддается обработке, применяется для изготовления спичек, в разных работах. Наиболее часто ее древесину расходуют на сооружение бани или сауны, из нее производят фанеру или ДСП.
Ольха – мягкая древесина не поддается загниванию, идет на изготовление мебели, строительство домов, кладовых и срубов колодцев, материал не пахнет и не впитывает сторонних ароматов.
Береза – прочная древесина с красивой текстурой, легкая в обработке, но неустойчива к гниению. Ее используют для изготовления фанеры, ДСП и лущеного шпона, применяемых для производства мебели.
Граб или белый бук принадлежит к породе деревьев с прочной и твердой древесиной. После сушки этот показатель возрастает, превышая качества дуба. Трудно обрабатывается режущими инструментами, но хорошо отделывается.
Клен – с твердой светло-желтой древесиной поддается обработке и полировке, не коробится, легко режется. Востребована древесина для декоративно-прикладного творчества, особенно удачными получаются резные изделия из нее.
Видео: Виды пиломатериалов
Понимание тангенциальной силы резания при фрезеровании
Изображение предоставлено Sandvik Coromat
[Примечание редактора. который написал автору, ищущему формулу для определения крутящего момента, необходимого режущему инструменту при фрезеровании титанового сплава Ti6Al4V.]
Тангенциальная сила резания, если конечные пользователи знают, как ее определить, и скорость резания, которая выбирается как один из нескольких параметров обработки, позволяющих рассчитать требуемую мощность обработки для операции. Когда требуемое значение мощности обработки примерно равно номинальной мощности фрезерного станка, производительность фрезерования приближается к своему максимуму.
Крутящий момент (T s ), который приложен к шпинделю и, следовательно, к фрезе, создается тангенциальной силой резания (F t ) и может быть рассчитан по формуле:
T s = F t × R (1)
Где R — радиус фрезы. (Формулы далее обозначены номером в скобках.)
Концепция расчета тангенциальной силы резания при фрезеровании основана на авторском аналитическом исследовании принципов металлообработки и экспериментальном исследовании фрез с положительно-отрицательной и двойно-положительной геометрией.
Эта концепция основана на отношениях между следующими параметрами:
- Предел прочности при растяжении (σ) металлических рабочих материалов в зависимости от их твердости,
- Площадь поперечного сечения необработанной стружки (А),
- Количество зубьев в зацеплении с заготовкой (Z c ),
- Коэффициент сцепления материала заготовки (E f ) и
- Коэффициент износа режущего инструмента (T f ).
Следующая формула тангенциальной силы резания была разработана в соответствии с этими соотношениями:
F t = σ × A × Z c × E f × T f (2)
Поскольку конечный пользователь заинтересован в фрезеровании конкретного титанового сплава, ниже представлена информация о Ti6Al4V. , альфа-бета титановый сплав. Он используется для изготовления дисков и лопаток авиационных газовых турбин, элементов конструкции планера и других изделий, требующих высокой прочности при температурах до 600° F (315° C).
Предел прочности на растяжение Ti6Al4V в отожженном состоянии составляет 137 000 фунтов на кв. дюйм (945 МПа в метрической системе), имеющий твердость 36 HRC.
Форма поперечного сечения несрезанной стружки зависит от геометрии режущей пластины и угла в плане фрезы. Квадратные, шестигранные или восьмиугольные пластины имеют прямые режущие кромки и производят стружку с прямоугольным поперечным сечением, когда фреза имеет угол в плане 0°, или с поперечным сечением в виде параллелограмма, когда фреза имеет угол в плане больше 0°.
Для расчета площади поперечного сечения необработанной стружки рекомендуется следующая формула:
A = a p × f (3)
Где a p – осевой DOC, а f – подача на зуб или нагрузка на стружку.
Количество зубьев в зацеплении с заготовкой (Z c ) зависит от количества зубьев в фрезе (Z) и угла зацепления (α). Формула для расчета Z c :
Z c = Z × α ÷ 360° (4)
Угол зацепления зависит от радиального WOC (W). Если радиальный WOC равен диаметру фрезы (D), угол зацепления имеет максимальное значение 180°, а количество зацепляемых зубьев составляет половину количества зубьев в фрезе:
Z c = Z × 180° ÷ 360º = 0,5 Z (5)
Если угол зацепления меньше 180°, он рассчитывается по формулам, содержащим тригонометрические функции. Подробное описание этих формул и подтверждающие иллюстрации были опубликованы в июльском номере CTE за 2010 г. (см. «Новая мельница» Е. Исакова, стр. 44).
Коэффициенты зацепления
Коэффициент зацепления материала заготовки (E f ) представляет собой безразмерный коэффициент, включенный в формулу (2) для соотнесения тангенциальной силы резания с отношением радиального ВЗК к диаметру фрезы (W ÷ Д).
Фрезерование более эффективно, когда образуется достаточно толстая и однородная стружка. Отношение W/D влияет на однородность толщины стружки. Когда радиальный WOC равен диаметру фрезы (W ÷ D = 1), образующаяся стружка начинается с нулевой толщины в точке входа. Затем он увеличивается до максимальной толщины по центральной линии фрезы и утончается до нуля в точке выхода. Этот тип реза образует неравномерную стружку, создает максимальное трение на режущей кромке и, как следствие, увеличивает сопротивление стружки резанию. Эффективное фрезерование достигается, когда радиальный WOC составляет около двух третей диаметра фрезы. Такой рез дает однородную и достаточно толстую стружку, создает меньшее трение на режущей кромке и снижает сопротивление резанию.
Коэффициент износа режущего инструмента
Коэффициент износа режущего инструмента (T f ) представляет собой безразмерный коэффициент, включенный в формулу (2) для корреляции тангенциальной силы резания с увеличением износа режущих пластин при фрезеровании. При применении новых или только что индексированных режущих пластин в течение короткого времени (от 20 до 25 процентов стойкости инструмента) коэффициент износа режущего инструмента (T f ) составляет 1,0; при фрезеровании до тех пор, пока пластины не должны быть индексированы или заменены (100 процентов стойкости инструмента), в зависимости от типа операции рекомендуются следующие коэффициенты износа режущего инструмента (Справочник по машиностроению, 29). издание, с. 1086).
Табл. Ответы специалистов по металлообработке с описанием операций фрезерования по оптимальным диапазонам осевого DOC и подачи на зуб.
- Легкая и средняя торцевая обработка: от 1,10 до 1,25
- Торцевое фрезерование сверхтяжелых режимов: от 1,30 до 1,60
К сожалению, в рассмотренных автором публикациях отсутствуют данные, которые могли бы идентифицировать каждую фрезерную операцию. Поэтому автор подготовил анкету с запросом данных обработки, которые лучше всего описывали бы операции фрезерования по оптимальным диапазонам осевого DOC и подачи на зуб. Анкета была разослана более чем 100 промышленным специалистам, обладающим практическими знаниями и опытом в области фрезерования, и более 80 процентов ответили. Статистическая обработка их ответов дала данные, показанные в таблице выше.
Мощность обработки
Рассчитав тангенциальное резание (F t ), требуемую мощность обработки на шпинделе (P s ) и главном приводе (P m ) можно рассчитать по следующим формулам.
Стандартные единицы измерения США:
Мощность на шпинделе: P s = F t × V c ÷ 33 000 (л.с.) (6)
Мощность на главном приводе14 P 0 9 0 90 с ÷ E (л.с.) (7)
Где F t выражено в фунтах, V c – скорость резания в фут/мин, 33 000 – коэффициент, переводящий футы-фунты. в минуту в лошадиных силах, а E — коэффициент эффективности основного привода, выраженный в процентах.
Метрические единицы измерения:
Мощность на шпинделе: P с = F t × В c ÷ 60 000 (кВт) (8)
Мощность на главном приводе: P
0 40 м ÷ E (кВт) (9)
Где F t в ньютонах, В c – скорость резания, выраженная в м/мин, 60 000 – коэффициент, пересчитывающий ньютон × м/мин. в киловаттах, а E — коэффициент полезного действия главного привода, выраженный в процентах.
Расчеты
Результаты расчета значений тангенциальной силы резания, крутящего момента и мощности обработки при фрезеровании Ti6Al4V основаны на выбранной геометрии торцевой фрезы и параметрах обработки, предоставленных конечным пользователем.
Торцевая фреза
Элемент по каталогу: SOF 8/16-D2.0
Диаметр: 2,0 «(50,8 мм)
Угол свинца: 44 °
Количество индексируемых вставки: шесть
Каталог INSERT. : 0,100 дюйма (2,54 мм)
Радиальный WOC: 2,0 дюйма (50,8 мм)
Подача на зуб: 0,006 дюйма (0,15 мм)
Скорость резания: 180 футов в минуту (55 м/мин)
Коэффициент эффективности станка: 90 процентов, или 0,9
Автор произвел расчеты с помощью своего Advanced Milling Calculators (один для единиц США, другой для метрических единиц).
Тангенциальная сила резания, формула (2)
Формула содержит пять элементов со следующими значениями:
1. Предел прочности при растяжении, σ = 137 000 psi (945 МПа)
2. Площадь поперечного сечения несрезанной стружки , A = 0,1 × 0,006 = 0,0006 дюйма 2 (0,381 мм 2 )
3. Количество зубьев в зацеплении с заготовкой, Z c = 6 × 180° ÷ 360° = 3 (полное зацепление)
4. Коэффициент зацепления, E f = 1,7 (для заготовки из титанового сплава при полном зацеплении)
5. Коэффициент износа режущего инструмента, T f = 1,1 (соответствует «легкому фрезерованию», см. таблицу)
Тангенциальная сила резания (обычные единицы измерения США):
F т = 137 000 × 0,0006 × 3 × 1,7 = 419,2 фунта. (новые или только что индексированные вставки)
F t = 137 000 × 0,0006 × 3 × 1,7 × 1,1 = 461,1 фунта. (индексация вкладышей обязательна)
Тангенциальная сила резания (метрические единицы измерения):
F t = 945 × 0,381 × 3 × 1,7 = 1836,2 Н (новые или только что индексированные пластины)
F t 3,7 × 0 = 9381 × 945 × 1,1 = 2019,8 Н (требуется индексация пластин)
Крутящий момент на шпинделе (фрезе), формула (1)
Единицы США:
T с = F t × 2 R = 419. дюймов-фунтов = 34,9 футо-фунта. (новые или только что индексированные пластины)
T s = F t × R = 461,1 × 1 = 461,1 дюйм-фунт. = 38,4 футо-фунта. (Требуется индексация вставки)
Метрические единицы:
T S = F T × R = 1 836,2 × 0,0254 = 46,6 нм (новый или только вставка индексации)
T S = F T)
T S = F T)
T S = F )
T S = F ). × R = 2019,8 × 0,0254 = 51,3 Нм (требуется индексация пластин)
Требуемая мощность обработки на шпинделе:
Единицы США, формула (6)
P с = 419,9 × 3320 0л.с. (новые или только что индексированные пластины)
P s = 461,1 × 180 ÷ 33 000 = 2,52 л.с. (требуется индексация пластин)
Требуемая мощность на главном приводе:
Единицы США, формула (7) 900
P м = 2,29 ÷ 0,9 = 2,54 л.с. (новые или только что индексированные пластины)
P м = 2,52 ÷ 0,9 = 2,80 л.с. (требуется индексация пластин)
мощность шпинделя: Метрические единицы, формула (8)
P s = 1 836,2 × 55 ÷ 60 000 = 1,68 кВт (новые или только что индексированные вставки)
P s = 2 019,8 × 55 ÷ 60 000 = 1,890 кВт при 2090 мощности (требуется индексация пластин0) главный привод:
Метрические единицы, формула (9)
P м = 1,68 ÷ 0,9 = 1,87 кВт (новые или только что индексированные вставки)
P м = 1,85 ÷ 0,9 кВт (индексация вставок = 2,06 кВт) требуется)
Формулы для расчета силы резания при фрезеровании описаны в различных технических документах и книгах. Некоторые формулы чрезвычайно сложны и состоят из двух матриц и восьми тригонометрических уравнений. Другой пример, формула силы резания, представляет собой дифференциальное уравнение второго порядка:
Где (M) — матрица масс режущей системы, (C) — матрица демпфирования режущей системы, а (K) — матрица жесткости режущей системы. Две точки над X означают, что это вторая производная от X; одна точка над X — первая производная X. X — комплексная функция, содержащая шесть переменных: X = (x 1 x 2 y 1 y 2 z 1 z 2 ) Т . К сожалению, определения x, y, z и T не были предоставлены. Такие сложные формулы бесполезны в практических инженерных расчетах, потому что их могут выполнить только математики, хорошо разбирающиеся в вычислениях. Поэтому рекомендуются простые инженерные формулы, подобные представленным в этой статье. Они обеспечивают, по крайней мере, 85-процентную точность. При фрезеровании Ti6Al4V понимание тангенциальной силы резания и возможность расчета требуемой мощности обработки являются первыми шагами к максимальному повышению производительности. Все текстовые материалы и изображения на этих страницах защищены авторским правом © W. Одно из основных правил инженерного проектирования заключается в том, что оно «выполняется с помощью чисел», а не с помощью расплывчатых утверждений о свойствах проектируемой системы. Бессмысленно говорить, что мы хотим, чтобы наши системы крепления были «действительно жесткими и прочными», не уточняя, что это означает. Подумайте, как бы вы отреагировали, если бы покупатель пришел в ваш магазин, чтобы узнать цены, и сказал, что он хочет, чтобы размеры детали были «очень точными», а поверхность — «супергладкой». Вы, наверное, подумали, что клиент был наивен! Когда вы покупаете системы крепления, очень важно знать, какой уровень производительности вам нужен, чтобы не стать таким же клиентом. В этом духе мы научимся оценивать величину сил резания во время операции механической обработки. Используя эту информацию, мы можем указать, какая производительность нам требуется от компонентов, выбранных для нашей системы крепления. К системам крепления заготовки предъявляются два наиболее важных требования: Первое требование просто означает, что, как бы заготовка ни удерживалась в приспособлении, она не будет ослаблена или вытянута из приспособления силами резания. Второе требование признает, что должны соблюдаться допуски и чистота поверхности, а это означает, что система крепления не может чрезмерно прогибаться или вибрировать. Конечно, если мы пытаемся разумно спроектировать или выбрать систему крепления, нам необходимо знать, насколько велики эти силы резания, чтобы мы могли оценить реакцию системы крепления. При фрезеровании кромка вращающегося инструмента проходит сквозь неподвижную заготовку, образуя стружку. Большинство фрез имеют несколько режущих кромок, и по мере вращения инструмента каждая кромка входит в зацепление с заготовкой, удаляет стружку и выходит из заготовки. На рисунке ниже показан вид сверху на операцию прорезания пазов с использованием фрезы с двумя канавками. Фреза вращается по часовой стрелке и подается в заготовку вправо. Область в форме полумесяца, ограниченная пунктирной линией, является чипом, который будет удален этим ребром. Следующее ребро удалит область аналогичной формы. Толщина стружки при ее удалении равна нулю, когда кромка впервые входит в заготовку, увеличивается до максимального значения после поворота фрезы на 90 градусов, а затем снова падает до нуля, когда она выходит после поворота на 180 градусов. В любой момент во время вращения существует составляющая силы резания, известная как тангенциальная сила резания, F t , действующая на кромку фрезы, касательную к корпусу фрезы. Величина тангенциальной силы пропорциональна осевой глубине резания b , мгновенной толщине стружки t и зависит от типа разрезаемого материала. Максимальное значение толщины стружки, f , равно подачи на зуб , или загрузка чипа , выбранная программатором. Существуют также составляющие силы резания, направленные от кромки к центру инструмента и вдоль его оси. Однако на практике эти радиальные и осевые составляющие силы резания обычно составляют небольшую часть тангенциальной силы; поэтому мы сосредоточимся только на тангенциальной силе резания, назвав ее сила резания . Как видно из этого рисунка, сила резания не является постоянной ни по величине, ни по направлению. Это характерно почти для всех фрезерных операций и отличается от токарных операций, когда единственная режущая кромка постоянно контактирует с заготовкой при ее вращении, а результирующая сила резания номинально постоянна. Еще одна вещь, которую следует учитывать, это то, что если инструмент имеет более двух режущих кромок, каждая из которых вносит свою собственную силу резания, а система крепления должна быть спроектирована таким образом, чтобы противодействовать их общей сумме. Расчет силы резания может показаться безнадежно сложным. Поскольку они постоянно изменяются во время резки, удерживаемые заготовки могут существенно различаться по размеру, форме и материалу, и для каждой обрабатываемой детали может использоваться множество разных фрез. К счастью, в инженерном проектировании мы обычно не пытаемся анализировать каждую ситуацию нагрузки, с которой может столкнуться конструкция при эксплуатации. Вместо этого мы хотим создать нашу конструкцию так, чтобы она была способна выдерживать самые высокие ожидаемые нагрузки. Например, проектировщик моста не утруждает себя расчетом напряжения каждого сварного шва моста для случая, когда маленький ребенок переезжает один велосипедный переход. Механическая обработка представляет собой субтрактивный процесс, в котором каждая заготовка начинается с начального объема и заканчивается меньшим конечным объемом. Вообще говоря, чем больше объем удаляемого материала, тем больше времени требуется для его удаления. Одним из ключей к минимизации времени цикла является максимизация скорости съема материала или MRR; а высокие MRR обычно означают более высокие силы резания и требуют более высокой мощности шпинделя. При большинстве резов не потребляется полная мощность шпинделя, хотя рекомендуется максимально увеличить MRR, учитывая ограничения на поломку и износ инструмента, а также чистоту поверхности. Тем не менее, имеет смысл посмотреть, насколько высоки силы резания, когда шпиндель работает на полную мощность, а MRR максимален, и использовать эти значения при анализе компонентов системы крепления. Для большинства операций обработки легко рассчитать максимальное значение общей силы резания, которое может быть достигнуто при номинальной мощности двигателя шпинделя. В приведенной ниже простой формуле используются только три входа: мощность шпинделя, P , в лошадиных силах, скорость вращения шпинделя, n, в об/мин и радиус инструмента, rtool, в дюймах; и дает силу резания F t в фунтах. Эта взаимосвязь сохраняется, несмотря на разрезаемый материал, тип используемой фрезы, траекторию движения инструмента или выбранные подачи и скорости. Например, предположим, что ваш фрезерный центр имеет шпиндель мощностью 30 л.с., и вы выполняете резку инструментом диаметром 1 дюйм со скоростью вращения шпинделя 2500 об/мин. Тангенциальная сила резания будет F t,max =1512 фунтов , когда шпиндель работает на максимальной мощности, и несколько меньше, чем при любой операции, которая не потребляет полную мощность шпинделя. Вышеприведенная формула показывает, что для заданной мощности и скорости шпинделя по мере увеличения диаметра инструмента максимальная сила резания, которую может создать шпиндель, уменьшается, поэтому фреза диаметром 2 дюйма может создавать силы резания, вдвое меньшие, чем для фрезы. 1-дюймовый резак или 506 фунтов. Увеличение скорости шпинделя также может снизить максимальную силу резания, особенно для инструментов меньшего диаметра. Однако в какой-то момент, когда мы пытаемся максимизировать MRR для инструментов меньшего диаметра, силы резания могут стать настолько большими, что инструмент либо сломается, либо преждевременно изнашивается. В данном случае ограничение MRR не вызвано недостаточной мощностью шпинделя; и сила резания, как правило, будет ниже, чем для случая максимальной мощности. Электродвигатели с регулируемой скоростью, такие как шпиндели станков, обычно не способны развивать свою полную номинальную мощность на всех скоростях. Точно так же они обычно не могут развивать свой полный номинальный крутящий момент на всех скоростях. Не все OEM-производители станков предоставляют информацию о крутящем моменте шпинделя своим клиентам, и в этом случае нам нужно будет полагаться на максимальную мощность для оценки максимальной силы резания, которая может воздействовать на деталь и, следовательно, на систему крепления. . Если вы знаете максимальный номинальный крутящий момент двигателя шпинделя, T max , максимальное усилие резания легко рассчитать по приведенной ниже формуле, где T max в дюйм-фунтах, и r инструмент в дюймах. Если максимальная сила резания, рассчитанная по номинальному крутящему моменту шпинделя, выше, чем по максимальной номинальной мощности, то мы будем использовать это значение. На практике эти две оценки обычно схожи, и поскольку мы будем использовать щедрые коэффициенты запаса, любой из них подходит для наших целей. На этой диаграмме также видно, что одна режущая кромка не может зацепить заготовку более чем на 180 градусов при вращении инструмента при долблении. Большинство фрезерных операций используют меньше, чем долбление, поэтому угол зацепления зуба в работе еще меньше. Если радиальная глубина резания мала, зуб может войти в зацепление только на небольшую часть оборота инструмента. Например, рассмотрим чистовую операцию с использованием концевой фрезы диаметром один дюйм с четырьмя зубьями, как показано на рисунке ниже. Если при чистовом проходе удаляется 0,010 дюйма материала, режущая кромка входит в заготовку в позиции A и выходит из нее в позиции B . Сила резания здесь на самом деле представляет собой серию коротких импульсов, возникающих на частоте прохождения зуба, и любой, кто работал на фрезерном станке, теперь поймет, что отчетливый звук процесса на самом деле вызван различной силой, когда каждый зуб входит в зацепление и покидает заготовку. Это часть всех операций фрезерования и может привести к чрезмерным вибрациям, если система крепления заготовки не спроектирована должным образом. В крайних случаях, если система крепления слишком гибкая, вибрации могут превратиться в полномасштабную вибрацию, что приведет к ухудшению качества поверхности и даже повреждению. Динамическая вибрационная реакция системы крепления заготовки на периодические изменения силы резания в идеале никогда не должна быть ограничивающим фактором того, насколько агрессивной может быть операция обработки в стремлении максимизировать MRR для сокращения времени цикла. В этом посте мы узнали, как использовать максимальную номинальную мощность шпинделя станка для оценки максимальной силы резания, которую станок может создать и, следовательно, воздействовать на заготовку и ее систему крепления. Мы также увидели, что сила резания не постоянна при фрезеровании, а изменяется в зависимости от частоты прохождения зуба, потенциально вызывая вибрации, которые могут привести к ухудшению качества поверхности. Будет справедливо поделиться… Укажите свой источник
МДА
АПА
Чикаго Опубликовано 15 мая 2019 г. автором wecreate Растачивание — это внутренняя токарная операция, используемая для увеличения отверстий. Одноточечные режущие инструменты — расточные оправки — являются наиболее часто используемыми инструментами. Когда борштанга режет, сила резания может быть приложена далеко от того места, где инструмент поддерживается. Жесткость принимает две формы. Динамическая жесткость противостоит вибрации. Статическая жесткость сопротивляется прогибу. В этой статье основное внимание уделяется статической жесткости. Простое понимание основного уравнения, управляющего отклонением расточной оправки, может показать, какие шаги будут наиболее эффективными для повышения жесткости процесса расточки. Сила резания, действующая на расточной оправку, может быть определена тремя компонентами: тангенциальной силой, силой подачи и радиальной силой. (См. рис. 1 ниже.) Ft – тангенциальная сила
Fr – радиальная сила
Ff – осевая сила
Do – внешний диаметр борштанги
Di – внутренний диаметр расточной оправки для СОЖ При растачивании тангенциальная сила резания является наибольшей. Сила подачи является второй по величине. Он действует параллельно центральной линии и не отклоняет борштангу. Как правило, сила силы подачи составляет от 50 до 60 процентов силы касательной. Радиальная сила перпендикулярна обеим этим силам и отталкивает стержень от стенки отверстия. Эта сила составляет от 25 до 30 процентов тангенциальной силы. Таким образом, расточная оправка испытывает отклонения как в тангенциальном, так и в радиальном направлениях. Отклонение расточной оправки Отклонение расточной оправки аналогично отклонению консольной балки. Это балка с неподвижной опорой на одном конце и свободной частью, или консолью, на другом. (См. рис. 2 ниже.) Из-за сходства формула, описывающая прогиб консольной балки, также будет описывать расточный стержень: (Формула 1) Y = (F x L 3 ) / (3E x I) Где. Ft – тангенциальная сила
Fr – радиальная сила
Ff – осевая сила
Do – внешний диаметр борштанги
Di – внутренний диаметр расточной оправки для СОЖ В большинстве случаев расточные оправки представляют собой круглые оправки со сплошным или трубчатым поперечным сечением. Последний член в приведенном выше списке, момент инерции (I), рассчитывается по формуле 2 для сплошного сечения или по формуле 3 для трубчатого сечения. Расточная оправка с подачей СОЖ через инструмент будет иметь трубчатое поперечное сечение. (Формула 2) Y = (F x L 3 ) / (3E x I) (Формула 3) Y = (F x L 3 x I) / (3E x L 3 x I) / (3E x I) Где. Расчет тангенциальной силы (Ft) в формуле 1 включает коэффициент для единиц. Тангенциальная сила в фунтах может быть рассчитана как: (Формула 4) Y = (F x L 3 ) / (3E x I) Тангенциальная сила в ньютонах может быть рассчитана как: (Формула 5) Y = (F x L 3 ) / (3E x I) Где. . . Радиальная сила резания (Fr) может быть найдена как: (формула 6) Y = (F x L 3 ) / (3E x I) Формула 1 предлагает все следующие рекомендации по улучшению статической жесткости расточной оправки: Причина: в формуле свес вычисляется в кубе. Даже небольшой дополнительный выступ может значительно увеличить прогиб. Причина: Прогиб стержня уменьшается пропорционально моменту инерции поперечного сечения стержня. А формулы 2 и 3 показывают, что момент инерции увеличивается с увеличением диаметра. Причина: Эта характеристика не фигурирует ни в одном из уравнений. Распространенной ошибкой является предположение, что расточная оправка с более высокой твердостью или сделанная из более качественной стали будет меньше прогибаться. Фактически, свойство материала, определяющее прогиб, — это модуль упругости. Твердость не фигурирует. Гивенс Расчет сил резания: Момент инерции рассчитывается по формуле 3: Прогиб расточной оправки рассчитывается по формуле 1: Стадник Т. Алюминиевый сплав ◽ Сила резания ◽ Силы резания ◽ Тангенциальный компонент ◽ Промышленные роботы ◽ Процесс измельчения ◽ Стабильность процесса ◽ Ленточное шлифование ◽ Отношение ◽ Режимы резки Абстрактный. Мельница Паломар
Palomar Mill Wayne’s Word Index Noteworthy Plants Trivia Lemnaceae Biology 101 Botany Поиск Анатомия дерева Стебли и корни Лиственные породы Окаменелое дерево Араукариас
at Palomar College Фото 1. Распил соснового бревна в Паломарском колледже. Большинство досок на этом изображении распилены на тангенциальные секции. Разрез по центру так, чтобы кольца располагались под прямым углом к поверхности доски, называется радиальным разрезом или радиальным разрезом. В радиальном разрезе годовые кольца параллельны. Центральные доски в этом бревне близки к радиальным сечениям, потому что кольца расположены почти под прямым углом к лицевой стороне досок. В досках, распиленных на четыре части, бревно распиливается на четыре части, а затем из каждой четверти вырезаются доски так, чтобы кольца располагались почти под прямым углом к лицевой стороне доски (см. Следующее изображение). Все пиломатериалы распиливаются радиально, но не все пиломатериалы радиально распиливаются. Радиальные пропилы можно делать прямо по центру бревна, не разделяя бревно на четверти.
А. Тангенциальные разрезы выполняются перпендикулярно лучам и касательные к годичным кольцам (красные кружки) и торцу бревна. Этот рубанок еще называют горбыльным или плоскопиленным (плоскопиленным) пиломатериалом. Годовые кольца имеют неправильную волнистую форму (см. Фото 2 и Фото 3 ниже). Это плоскость, в которой на лесопилке распиливается большая часть фанеры и пиломатериалов.
Фото 2. Тангенциальная плоскость фанеры пихты Дугласа ( Pseudotsuga menziesii ), показывающая привлекательный волнистый рисунок годичных колец. Также см. дубовый блок на фото 5 ниже. Фото 3. Кабинет из мореного ясеня, показывающий тангенциальную плоскость дерева. Это самый распространенный разрез на дверцах шкафов и мебели. Б. Радиальные разрезы делают по лучам или радиусу бревна, под прямым углом к годичным кольцам. [Обратите внимание, что радиальные распилы в основном расположены под прямым углом к красным годовым кольцам.] Эта плоскость также называется пиломатериалом, распиленным на четверть (четвертью), потому что бревна фактически распиливаются на четверти. Кольца выглядят как близко расположенные параллельные полосы (см. фото 4 ниже). Поскольку из бревна можно вырезать относительно немного больших, идеальных, распиленных на четверть досок, они стоят дороже. Поскольку густые темные летние полосы (годовые кольца) расположены близко друг к другу, эта плоскость также более износостойкая.
Фото 4. Радиальная плоскость сосны пондероза ( Pinus ponderosa ), показывающая близко расположенные параллельные годовые кольца. Это также называется четвертьпиленной (квадрораспиленной) доской. Он более устойчив к износу, потому что плотные (темные) летние полосы расположены очень близко друг к другу.
Фото 5. Дубовое бревно, распиленное в колледже Паломар. Большинство досок на этом изображении распилены на тангенциальные секции. Разрез по центру так, чтобы кольца располагались под прямым углом к поверхности доски, называется радиальным разрезом или радиальным разрезом. В радиальном разрезе годовые кольца параллельны. Центральные доски в этом бревне близки к радиальным сечениям, потому что кольца расположены почти под прямым углом к лицевой стороне досок. В досках, распиленных на четыре части, бревно распиливают на четыре части, а затем из каждой четверти нарезают доски так, чтобы кольца располагались почти под прямым углом к лицевой стороне доски. Все пиломатериалы распиливаются радиально, но не все пиломатериалы радиально распиливаются. Радиальные пропилы можно делать прямо по центру бревна, не разделяя бревно на четверти.
Фото 6. Дубовый брусок, показывающий тангенциальную плоскость (T) и радиальную плоскость (R). Параллельные линии на радиальной стороне — годовые кольца. Пятна клеток под прямым углом к годичным кольцам представляют собой лучи (лентовидные скопления клеток, проходящие радиально через ткань ксилемы). Вернуться на главную страницу WAYNE’S WORD
Вернуться на страницу ЗАМЕЧАТЕЛЬНЫЕ РАСТЕНИЯ
Перейти на страницу биологии GEE WHIZ TRIVIA
Перейти на страницу
ОНЛАЙН-страница РЯСКИХ P. Армстронг
Практическая мудрость
Силы резания при фрезеровании
Поэтому сила резания достигает своего максимального значения, когда кромка находится под углом 90 градусов, а толщина стружки максимальна.
Если в резке используется частичное радиальное зацепление (меньше, чем полный паз), ситуация снова меняется в отношении того, когда кромки находятся внутри или вне заготовки. Если радиальное зацепление меньше половины диаметра фрезы, максимальная толщина стружки никогда не достигает значения «подача на зуб», ф .
Оценка максимальной силы резания
Вместо этого они основывают свой анализ на своей оценке самых больших нагрузок, которые могут когда-либо встречаться, например, близко расположенная военная колонна танков, пересекающих мост. Проделаем то же самое для систем крепления.
Система крепления должна быть достаточно прочной, чтобы силы такой величины не ослабляли деталь, а возникающие в результате прогибы или вибрации не вызывали проблем с допусками или чистотой поверхности.
Тем не менее, мы должны спроектировать нашу систему крепления так, чтобы она могла выдерживать силы резания, вызванные корпусом максимальной мощности.
Мощность шпинделя в зависимости от крутящего момента шпинделя
Как насчет вибрации?
Небольшая тригонометрия показывает нам, что зуб взаимодействует с заготовкой только на 11,5 градусов вращения. Следующий зуб не входит в зацепление с заготовкой еще на 78,5 градусов, что означает отсутствие контакта с заготовкой примерно в 88% случаев. В это время сила резания равна нулю.
Резюме
Основы растачивания — Компания промышленного снабжения Эри
Расстояние без опоры между местом резания и местом зажима расточной оправки называется ее вылетом. С большим вылетом расточная оправка может обрабатывать более глубокие отверстия. Но больший вылет также увеличивает риск чрезмерного прогиба и вибрации. Для эффективного сверления глубоких отверстий расточная оправка должна иметь высокую жесткость.
Силы резания, действующие на расточной оправку
Надписи:
Он действует перпендикулярно передней поверхности режущей пластины и толкает борштангу «вниз», то есть ниже центральной линии.
. .
Y = тангенциальное или радиальное отклонение, в дюймах (дюймах) или миллиметрах (мм)
F = тангенциальное усилие (Ft) или радиальное усилие (Fr), в фунтах (фунтах) или ньютонах (Н)
L = длина без опоры стержень или выступ, в дюймах или мм
E = модуль упругости при растяжении, в фунтах на квадратный дюйм или Н/мм2
I = момент инерции поперечного сечения стержня, в дюймах или мм4 Заголовки:
. .
Do = внешний диаметр стержня, в дюймах или мм
Di = внутренний диаметр стержня для охлаждающей жидкости, в дюймах или мм
396,000 = коэффициент пересчета, фунт·дюйм/л.с.мин
1,000 = коэффициент пересчета, Н·см/кВт·сек
d = глубина резания, в дюймах или мм
f = подача, в дюймах на оборот ( ipr) или миллиметры на оборот (мм/об)
Kp = постоянная мощности материала заготовки в л.с./дюйм3/мин или кВт/см3/сек Рекомендации
Материал Давление Сталь от 28 до 30 миллионов фунтов на кв. дюйм Тяжелые металлы от 45 до 52 миллионов фунтов на кв. дюйм Цементированные карбиды
(содержание кобальта от 10 до 15 процентов) 80 миллионов фунтов на квадратный дюйм Цементированные карбиды
(содержание кобальта от 3 до 8 процентов) 90 миллионов фунтов на квадратный дюйм Пример расчета
Do = 1,00 дюйма (25,4 мм)
Di = 0,156 дюйма (3,96 мм)
L = 5,00 дюйма (127 мм)
E = 30 x 106 фунтов на кв. дюйм (207000 Н/мм2)
Хвостовик из легированной стали 4340
Легированная сталь AISI 4140, твердость 250 HB
Kp = 0,84 л.с./дюйм3/мин (2,29 кВт/см3/сек) (из Machinery’s Handbook, 26-е издание, Industrial Press Inc. )
d = 0,080 дюйма (2,03 мм)
f = 0,008 дюйм/об (0,203 мм/об)
По формуле 4, Ft = 396000 x 0,08 x 0,008 x 0,84 = 212,9 фунта
Используя формулу 6, Fr = 0,3 x 212,9 = 63,9 фунта
I = x (1,04 – 0,1564)/64 = 0,049 дюйма4.
Yt = 212,9 x 53/(3 x 30 x 106 x 0,049) = 0,0060 в
Yr = 63,9 x 53/(3 x 30 x 106 x 0,049) = 0,0018 дюйма Влияние технологических режимов на тангенциальную составляющую силы резания при ленточно-вращательном шлифовании заготовок из алюминиевых сплавов Д 16
В настоящее время при изготовлении узлов и механизмов кораблей, самолетов и других технологических машин, промышленных роботов применяют длинномерные изделия из алюминиевого сплава Д 16 (Стандарт ГОСТ-Р), для обработки которых используется комплекс ленточно-вращательных Разработано измельчение. Результаты процесса шлифования с вращающейся лентой зависят от сил резания, возникающих в процессе обработки. По силам резания диагностируют устойчивость процесса, рассчитывают значения показателей шероховатости поверхности, температур и режимов резания по уравнению баланса перемещений. Статья посвящена получению математической модели, устанавливающей связь между тангенциальной составляющей силы резания и режимами резания при ленточно-вращательном шлифовании алюминиевого сплава Д 16.
Экспериментальное исследование характеристики и модели усилий при фрезеровании алюминиевого сплава
Цзэн Хуэй Ань ◽
Сю Ли Фу ◽
Я Нан Пан ◽
Ай Джун Тан
Алюминиевый сплав ◽
Сила резания ◽
Силы резания ◽
Высокоскоростной ◽
Резка металла ◽
Концевое фрезерование ◽
Факторы влияния ◽
Скорость резки ◽
Глубина резания ◽
Фрезерные силы
Силы резания являются одним из важных физических явлений в процессе резания металлов. Это напрямую влияет на качество обрабатываемой поверхности, срок службы инструмента и стабильность резания. Были проведены ортогональные эксперименты по силе резания и влияющим факторам со сменными и цельными концевыми фрезами, и была создана прогнозирующая модель силы фрезерования во время высокоскоростного концевого фрезерования алюминиевого сплава 7050-T7451. В статье в основном исследуется влияние скорости резания, глубины резания и подачи на силу резания. Экспериментальные результаты одного фактора показали, что силы резания увеличиваются раньше и падают позже с увеличением скорости резания, а скорость резания на изгиб для 7050-T7451 составляет 1100 м/мин. По мере увеличения осевой глубины резания, радиальной глубины резания и скорости подачи сила резания возрастает в разной степени. Сила резания особенно чувствительна к осевой глубине резания и немного к радиальной глубине резания.
Модель силы резания алюминиевого сплава 2014 при точении с анализом ANOVA
Юн Цзе Ма ◽
Йи Ду Чжан ◽
Сяо Ци Чжао
Алюминиевый сплав ◽
Сила резания ◽
Поверхность отклика ◽
Силы резания ◽
Параметры резки ◽
Квадратичная модель ◽
Поверхностная модель ◽
Силовая модель ◽
Параметры обработки ◽
Модель силы резания
В настоящем исследовании в качестве материала заготовки был выбран алюминиевый сплав 2014, силы резания измерялись в условиях токарной обработки. Для организации тестовых исследований учитывались параметры резания, глубина резания, подача, скорость резания. Математическая модель поворотной силы была решена с помощью методологии поверхности отклика (RSM). Подгонка модели поверхности отклика для данных изучалась с помощью дисперсионного анализа (ANOVA). Квадратичная модель RSM, связанная с методом оптимизации отклика и совокупной желательностью, использовалась для нахождения оптимальных значений параметров обработки по отношению к значениям силы резания. Коэффициенты силы поворота в модели были откалиброваны по результатам испытаний, и предложенные модели сил резания адекватно отображают в пределах рассматриваемых параметров резания. Экспериментальные результаты показали, что наибольшая сила резания среди трех сил резания была основной силой резания. Основной фактор, влияющий на силы резания, был получен с помощью моделей сил резания и корреляционного анализа. Сила резания оказывает существенное влияние на качество детали. На основе модели силы резания можно представить несколько тематических исследований для изучения прецизионной обработки тонкостенных деталей из алюминиевого сплава 2014.
О нестабильности инструмента во время обработки
К. Сахай ◽
Р. Н. Дубей
Сила резания ◽
Деформация сдвига ◽
Статический анализ ◽
Силы резания ◽
Толщина стружки ◽
Толщина неразрезанной стружки ◽
Фрикционное взаимодействие ◽
Система обработки ◽
Отношение
Абстрактный В настоящей статье описывается роль инструмента в вибрациях обрабатывающей системы. Сила резания считается постоянной. Учитывается сдвиговая деформация инструмента. Квазистатический анализ ситуации дает максимально допустимую толщину несрезанной стружки, которая показывает, как фрикционное взаимодействие на торце инструмента и соотношение составляющих сил резания меняют эту величину. Отношение также выражает влияние размеров инструмента и рабочего материала на вибрацию инструмента.
Проверка и оптимизация параметров резания для токарной обработки Ti-6Al-4V с использованием моделирования DEFORM 3D и метода Тагучи
Джафет Ойрере Обико ◽
Фредрик Мадарака Мвема ◽
Майкл Олуватосин Бодунрин
Сила резания ◽
Скорость подачи ◽
Силы резания ◽
Сигнал-шум ◽
Скорость резки ◽
Параметры резки ◽
Температура интерфейса ◽
Глубина резания ◽
Оптимизация параметров резки ◽
Отношение
В этом исследовании мы показываем, что оптимизация сил резания как реакции на механическую обработку обеспечивает наиболее благоприятные условия для токарной обработки сплава Ti-6Al-4V. Используя комбинацию вычислительных методов, включающих моделирование DEFORM, план эксперимента Тагути (DOE) и дисперсионный анализ (ANOVA), стало возможным минимизировать типичные характеристики обработки, такие как сила резания, мощность резания и температура поверхности раздела стружки и инструмента. Параметры токарной обработки, которые варьировались в этом исследовании, включают скорость резания, глубину резания и скорость подачи. Оптимальные комбинации параметров токарной обработки, которые минимизируют реакцию обработки, были установлены с использованием критерия «чем меньше, тем лучше» и выбора самого высокого значения отношения сигнал/шум. Подтверждающее моделирование показало, что при скорости резания 120 м/мин, глубине резания 0,25 мм и скорости подачи 0,1 мм/об можно получить наименьшее усилие резания 88,21 Н и температуру поверхности раздела стружка-инструмент 387,24 °C. Регрессионный анализ показал, что самый высокий коэффициент корреляции 0,97 был получен между силами резания и параметрами токарной обработки.
Взаимосвязь между силами резания и параметрами токарной обработки была линейной, поскольку регрессионной модели первого порядка было достаточно.
Анализ сил резания при прямом и наружном фрезеровании литого алюминиевого сплава EN AC-AlSi10Mg
Юзеф Кучмашевский ◽
Павел Пешко ◽
Магдалена Завада-Михаловская
Алюминиевый сплав ◽
Сила резания ◽
Силы резания ◽
Высокоскоростной ◽
Скорость резки ◽
Глубина резания ◽
Литой алюминиевый сплав ◽
Литой алюминий ◽
Технологические параметры ◽
Высокоскоростная резка
Представлен анализ сил резания при фрезеровании с прямым и наружным резанием литого алюминиевого сплава EN AC-AlSi10Mg. Исследования включали измерение составляющих суммарной силы резания: Ff, Fp и Fc (Fx, Fy, Fz соответственно) и определение их амплитуд при постоянной величине подачи на зуб и принятых переменных технологических параметрах, т. е.: глубине резания ap, ширина фрезерования ae и скорость резания vc. На основании полученных результатов установлено, что с увеличением глубины резания и ширины фрезерования увеличиваются значения выбранных составляющих и их амплитуды как при прямоточном, так и при наружном фрезеровании. При увеличении скорости резания наблюдалось, что составляющие полной силы резания увеличиваются до скорости vc = 450 м/мин, затем их значения начинают уменьшаться. Это связано с переходом от традиционной обработки к диапазону высокоскоростной резки. Важно отметить, что более высокие значения сил резания были отмечены при фрезеровании врезным, а не врезным способом.
Режущие механизмы и их влияние на динамические силы, вибрации и стабильность при микроконцевом фрезеровании
Синью Лю ◽
Мартин Б. Г. Джун ◽
Ричард Э. ДеВор ◽
Шив Г. Капур
Сила резания ◽
Силы резания ◽
Эластичное восстановление ◽
Толщина стружки ◽
Стабильность процесса ◽
Минимальная толщина стружки ◽
Модель вибрации ◽
Динамическая сила резания ◽
Динамические силы ◽
Режущие механизмы
Динамическая модель силы резания и вибрации процесса микроконцевой фрезы, учитывающая динамику микроконцевой фрезы, влияние стабильной наплавленной кромки, влияние минимальной толщины стружки, упругое восстановление и упруго-пластическую природа вспашки/протирания развита. Была проведена экспериментальная проверка, и показано, что модель предсказывает силу резания и вибрацию инструмента в среднем в пределах 12%. Используя разработанную модель, было исследовано влияние минимальной толщины стружки и упругого восстановления на силы резания и вибрации, а также на стабильность процесса микроконцевого фрезерования. Результаты показывают, что большой радиус кромки по отношению к скорости подачи приводит к тому, что стабильность процесса чувствительна к скорости подачи, что приводит к явлению нестабильности низкой скорости подачи. Упругое восстановление значительно увеличивает силы резания от пика до впадины и расширяет диапазон нестабильной скорости подачи.
Повышение эффективности ленточной шлифовки материалов с высокими эксплуатационными характеристиками с помощью роботов
Эккарт Ульманн ◽
Флориан Хайтмюллер
Газовые турбины ◽
Высокая производительность ◽
Масштабные эффекты ◽
Лопасти турбины ◽
Процесс ремонта ◽
Промышленные роботы ◽
С помощью робота ◽
Ленточное шлифование ◽
Экономия от масштаба ◽
Человек
В газовых турбинах и турбореактивных двигателях для изготовления лопаток широко используются материалы с высокими эксплуатационными характеристиками, такие как сплавы на основе никеля. При ремонте доводка сложных лопаток турбин из высокопрочных материалов осуществляется преимущественно вручную. Поэтому процесс ремонта занимает довольно много времени. А стоимость доступных в настоящее время стратегий ремонта, особенно для составных частей, высока из-за индивидуального планирования процесса и большого количества операций, выполняемых вручную. Кроме того, существуют серьезные риски частичного повреждения при ручном ремонте. Все это приводит к тому, что эффект масштаба остается малоиспользуемым для ремонтных задач, хотя количество ремонтируемых деталей значительно увеличивается. В будущем должна быть достигнута постоянная автоматизация цепочки ремонтных процессов за счет разработки адаптивных стратегий чистовой обработки с помощью роботов. Целью данного исследования является использование потенциала автоматизации для задач ремонта путем разработки технологии, которая позволяет промышленным роботам изменять контур лопаток турбины посредством ленточной шлифовки с регулируемым усилием.
Подход к оптимизации с использованием суррогатов для многофункционального концевого фрезерования алюминиевого сплава AA3105
Тамал Гош ◽
Йи Ван ◽
Кристиан Мартинсен ◽
Кешен Ван
Шероховатость поверхности ◽
Алюминиевый сплав ◽
Скорость съема материала ◽
Силы резания ◽
Удаление материала ◽
Концевое фрезерование ◽
Скорость удаления ◽
Параметры резки ◽
Управление данными ◽
Оптимальные параметры резки
Абстрактный
Оптимизация процесса концевого фрезерования является комбинаторной задачей из-за вовлечения большого количества переменных процесса и характеристик производительности. Цифровые модели или математические функции для конкретных процессов необходимы для оценки комбинаций параметров, чтобы улучшить качество обрабатываемых деталей и время обработки. Эту проблему можно охарактеризовать как проблему автономной оптимизации на основе данных. Для таких задач полезны суррогатные или прогностические модели, которые можно использовать для аппроксимации целевых функций для алгоритмов оптимизации. В этой статье представлен управляемый данными суррогатный оптимизатор для моделирования обработки концевой фрезой алюминиевого сплава на настольном фрезерном станке. Для этого скорость съема материала (MRR), шероховатость поверхности (Ra) и силы резания рассматриваются как функции диаметра инструмента, скорости вращения шпинделя, скорости подачи и глубины резания. Основная методология разработана с использованием байесовской регуляризованной нейронной сети (заменитель) и алгоритма поиска усиков жука (оптимизатор) для выполнения оптимизации процесса. Отношения между откликами процесса изучаются с помощью самоорганизующейся карты Кохонена. Предлагаемая методология успешно сравнивается с тремя различными методами оптимизации и показывает, что она превосходит их с улучшением на 40,9.8% для MRR и 10,56% для Ra. Предлагаемый метод оптимизации с помощью суррогатов является быстрым и эффективным при обработке данных автономной обработки.
Наконец, проверка была проведена с использованием экспериментального торцевого фрезерования, выполненного на алюминиевом сплаве, для измерения шероховатости поверхности, скорости съема материала и силы резания с использованием динамометра для определения оптимальных параметров резания на настольном фрезерном центре. При расчетном значении шероховатости поверхности 0,4651 мкм оптимальные параметры резания дали максимальную скорость съема материала 44,027 мм3/с с меньшей амплитудой силы резания на заготовке. Полученные результаты испытаний показывают, что при оптимальном наборе параметров можно добиться более оптимального качества поверхности и съема материала.
Использование акустической эмиссии для обнаружения изменений в контактных механизмах, вызванных износом инструмента в процессе шлифования с абразивной лентой.
Виньяшвара Пандиян ◽
Тегоэ Тьяджовидодо
Износ инструмента ◽
Акустическая эмиссия ◽
Процесс измельчения ◽
Ленточное шлифование ◽
Абразивный пояс
Исследование температуры и сил резания на основе метода расчета Тагучи при высокоскоростном фрезеровании композитов с титановой матрицей инструментом PCD
Ин Фэй Гэ ◽
Хай Сян Хуань ◽
Цзю Хуа Сюй
Сила резания ◽
Скорость подачи ◽
Силы резания ◽
Высокоскоростной ◽
Объемная доля ◽
Температура резки ◽
Скорость резки ◽
Глубина резания ◽
Высокоскоростное фрезерование ◽
Радиальная глубина
Испытания на высокоскоростное фрезерование проводились на об. (5%-8%) композит TiCp/TC4 в диапазоне скоростей 50-250 м/мин с использованием инструментов PCD для исследования температуры резания и сил резания. Результаты показали, что радиальная глубина резания и скорость резания были двумя существенными факторами, влияющими на силы резания, основанными на прогнозе Тагучи. Увеличение радиальной глубины резания и скорости подачи увеличит силу резания, а увеличение скорости резания уменьшит силу резания. Сила резания увеличилась менее чем на 5%, когда объемная доля армирования в композитах увеличилась с 0% до 8%. Радиальная глубина резания была единственным существенным фактором, влияющим на температуру резания. Температура резания увеличивается с увеличением радиальной глубины резания, скорости подачи или скорости резания. Температура резания титановых композитов составляла 40-9°С.на 0 °С выше, чем у матрицы ТС4. Однако температура резания снизилась на 4% при увеличении объемной доли арматуры с 5% до 8%.
Главная | Better MRO
Innovate
Металлообрабатывание
Металлообрабатывание
Личное защитное оборудование
Обработка
Видео: 3 клавиши к успешному производству с Mitch Free, Zyci CNC Machining
Mitch Free, основатель Zyci CNCINC MACHININC, Share Machine, Share Machine, Share Machingc, Share Machingc, Share Machine, Share, Share, Share Machingc, Share Machingc, Share Machingc, Share Machingc, Share Machingc, Share Machingc, Share Maching почему точность деталей, качество и своевременная доставка являются ожиданиями, а не отличительными чертами.
Культура безопасности
5 способов улучшения психического здоровья сотрудников
Обработка
ВИДЕО: Инструменты — почему вы должны включить в свой процесс обработки
. Безопасность
Металлообработка
Как удобные для пользователя инновации Acu-Rite делают работу механических цехов более бесперебойной
IMTS ВОЗВРАЩАЕТСЯ
УЗНАЙТЕ О ПОСЛЕДНИХ ИННОВАЦИОННЫХ ИНСТРУМЕНТАХ И РЕШЕНИЯХ…
Независимо от того, посещаете ли вы IMTS 2022 лично или нет, мы познакомим вас с последними и лучшими инновациями в области металлообработки и механической обработки.
Вот что происходит на стенде MSC # 431854:* Практические демонстрации удостоенных наград MSC Millmax
* Специалисты по металлу. Предупреждение: вы не должны пропустить этих экспертов отрасли!)
Partner Insights
Innovate
Видео: Инновация, рост, возможность: это Showa
Читать Подробнее. Какой лучший вариант для вашей работы?
Производители электроники говорят, что когда-то революционная 3D-печать дополняет обработку на станках с ЧПУ и другие более традиционные производственные процессы, что делает ее еще одним (хотя и очень мощным) инструментом в их наборах инструментов.
Фрезерование
Алюминиевые фрезерные инструменты OSG нового поколения удваивают их конкурентоспособность
Инструментальный производитель премиум-класса OSG решает проблему компромисса между сроком службы инструмента и производительностью, что является трудным препятствием для механических мастерских, с концевыми фрезами A Brand AE-N, которые улучшают оба.
Механическая обработка
Механическое удаление заусенцев: Osborn повышает эффективность благодаря инновациям
Ваши рабочие могут быть заняты удалением заусенцев вручную, но ваш бизнес может быть более прибыльным, если вы перейдете на механический процесс с использованием правильной щетки с правильными параметрами . Объясняют эксперты Osborn.
Робототехника
Это решение Norton Abrasives доказывает ценность автоматизации
Группа по разработке решений для абразивных процессов из Norton | Saint-Gobain Abrasives предоставляет производителям возможность использовать автоматизацию для работы с абразивами.
СОВЕТЫ ПО МЕТАЛЛООБРАБОТКЕ
Технология
Обработка жаропрочных сплавов: советы экспертов для труднообрабатываемых материалов
Узнайте об интеллектуальных подходах к обработке жаропрочных сплавов.
Механическая обработка
5 причин поддерживать чистоту охлаждающей жидкости при механической обработке
От дерматита до сокращения срока службы инструмента чистая охлаждающая жидкость просто лучше и делает станочников более счастливыми, а производственный цех более продуктивным.
Технология
Почему вам нужно перестать покупать дешевые режущие инструменты
Вот почему покупка самых дешевых режущих инструментов иногда может привести к неудаче.
СТРАТЕГИЯ ЦЕПИ ПОСТАВОК
Цепочка поставок
Управление кризисом цепочки поставок: как производителям справиться с дефицитом
Что производители могут сделать, чтобы справиться с кризисом цепочки поставок.
Бережливое производство
Изучение стратегий цепочки поставок: «точно вовремя» или «точно в случае необходимости»
Своевременное управление запасами в целом полезно для бизнеса, но является ли оно лучшей практикой во время глобальных пандемий, стихийных бедствий и торговли войны? Взгляните на варианты.
Цепочка поставок
Лучшее управление цепочкой поставок: возьмите под контроль расходы на ТОиР
Не позволяйте расходам на ТОиР выйти из-под контроля. Обуздайте это, лучше понимая, где найти скрытые расходы и как преодолеть разрыв между закупками и цехом.
Навыки Gap
GAPLE DAP
ВИДЕО: Инструменты — обращение к США по производству навыков
Связь с вакансией
Разрыв на обработке обработки CNC: A Q & A с Tony Schmitz на тренировочном рабочем месте 9.

- DOL здесь, чтобы помочь
- Обязанность защищать
- Защита осведомителей
Производительность обработки
Инновации
Видео: Guhring RF100 Sharp Введение
Содержание поставщиков
Новые RF100 Sharp Milling Rutters от Guhring — это отличные материалы для Sharing Spearing Speaking Shire Shire Speaking Shire Shi.
Обработка
Как концевая фреза Kennametal HARVI I TE повышает производительность и срок службы инструмента
Материалы для партнеров
Узнайте о новейшем пополнении Kennametal в линейке инструментов.
Фрезерование
ВИДЕО: ИНСТРУМЕНТАЛЬНАЯ ИНСТРУМЕНТАЦИЯ — высокоэффективные концевые фрезы SGS серии 77 H-Carb с 7 канавками
Контент для поставщиков
Крис Диксон, инженер по применению в Kyocera SGS Precision Tools, Inc., за обсуждение в режиме реального времени и демонстрацию высокоэффективных концевых фрез серии 77 H-Carb с 7 канавками.
соответствие требованиям
Безопасность на рабочем месте
Объяснение уровня безопасности OSHA DART и способы его расчета
Узнайте о коэффициенте DART, который разработан, чтобы помочь учреждениям измерить свои показатели безопасности.
Безопасность сотрудников
10 основных нарушений техники безопасности по версии OSHA: во что они обходятся в 2021 году включая респираторы, лестницы, строительные леса и блокировку/маркировку. Компании были оштрафованы на миллионы долларов.
Соблюдение нормативных требований
Управление по охране труда и промышленной гигиене США запрашивает дополнительные сведения о производственных травмах с высоким уровнем риска
Управление по охране труда и здоровья США рассматривает вопрос о введении правила, требующего от предприятий с повышенным риском сообщать более подробную информацию о производственных травмах.
Технология
Что такое соответствие требованиям TAA? 5 вещей, которые вы должны знать
Узнайте о соответствии требованиям TAA и о том, как избежать проблем или справиться с ними.