Технология разработки пасек харвестером.
Технологический процесс харвестера состоит из нескольких операций: наведение режущей головки на дерево и его зажим, спиливание, сталкивание — перенос (подтаскивание) дерева в зону обработки, очистка ствола, раскряжевка, пакетирование, а также переезды с одной технологической стоянки к другой для последующего повала деревьев и их обработки.
На труднодоступных для машин участках и при крупных деревьях, не подлежащих обработке харвестером, используют бензиномоторные пилы для выполнения всех технологических операций. Получаемые при этом крупные сортименты остаются на месте, а средние и мелкие собираются в небольшие кучи.
Технологические схемы:
1. Технология, не предусматривающая разрубку прямолинейных коридоров (пасечных волоков) (рис. 20). Данная технологическая схема наиболее целесообразна при полноте древостоев 0,7…0,9 и наличии на пасеках куртин жизнеспособного подроста. Харвестер, перемещаясь по пасеке, выполняет полностью все технологические операции: валку, обрезку сучьев, раскряжевку и пакетирование. При этом харвестер обрабатывает только те деревья, которые мешают проезду машины, вследствие чего волок и не прямолинеен. По мере продвижения харвестера вглубь пасеки оператор на основании визуальной оценки полупасек равномерно выбирает деревья по всей ширине пасеки, в том числе сухостой и валежник. Ширина пасеки при этом составляет два эффективных вылета манипулятора.
Рис. 20. Схема разработки лесосеки без прямолинейных коридоров:
1 — импровизированный волок; 2 — сортименты
2. Технологическая схема с прямолинейными коридорами (рис. 21). Рассматриваемая технологическая схема, предусматривающая разрубку прямолинейных волоков (коридоров) через расстояния, равные удвоенному эффективному вылету манипулятора, наиболее целесообразна при разработке лесосек с полнотой древостоев 0,8…1,0 при хорошей несущей способности грунтов и в зимний период, а также при отсутствии
Рис. 21 Схема разработки лесосеки с прямолинейными коридорами
Рис. 22. Схема разработки лесосеки с заездом харвестера полупасеки
разреженных участков и куртин жизнеспособного подроста. Харвестер выполняет полностью цикл работ: валка, обрезка сучьев, раскряжевка и пакетирование. При такой схеме имеется возможность разрабатывать пасеки одинаковой площади и обеспечивать при этом равномерную работу системы машин харвестер-форвардер.
При использовании технологических схем (см. рис. 20 и 21) в случае необходимости ширина пасеки может быть значительно увеличена, а валку деревьев в полосе, недоступной для манипулятора харвестера, производят бензопилами. Поваленные перпендикулярно волоку деревья харвестеры разделывают на сортименты при втором проходе по волоку. Харвестер захватывает дерево за вершину или середину и полностью обрабатывает его, одновременно окучивая сортименты и укладывая их на волок. Ширина пасеки может быть увеличина на удвоенную высоту самого низкого из вырубаемых деревьев.
3. Технологическая схема с заездом харвестера на полупасеки
(рис.22).
Она наиболее целесообразна при полноте древостоя 0,7…0,9, наличии свободного пространства и нелесоэксплуатационных участков на полупасеках, разрозненных куртин жизнеспособного подроста и хорошей несущей способности грунтов. Заезд на полупасеки позволяет увеличить ширину пасеки до 30 м, что создает более благоприятные условия для сохранения лесной среды и уменьшения площади лесосеки, занятой технологическими коридорами. Однако при этом наблюдается снижение производительности харвестера в связи с затратами времени на заезды на пасечные волоки и выезды с них.
4. Технологическая схема с вспомогательным (импровизированным)
волоком (рис. 23).
Применение данной схемы позволяет уменьшить отрицательное воздействие на почву, подрост и оставшуюся часть древостоя со стороны форвардера, так как трелевка сортиментов осуществляется только по основным волокам. Причем ширина разрабатываемой пасеки может достигать 3,5 В- эффективных вылетов манипулятора харвестера. Вначале разрубаются основные волоки и прилегающие полуленты и укладываются выпиливаемые сортименты вдоль волоков. Затем харвестер переходит на дополнительный волок, выполняя на нем работу по полному циклу. Однако при движении харвестера и выборе деревьев для валки оператор харвестера стремится максимально сохранить подрост и оставшуюся часть древостоя, а также укладывать сортименты в пакеты на максимальном удалении от машин. Тем самым создаются условия форвардеру, перемещающемуся по основному волоку, для трелевки пачек сортиментов, сформированных с дополнительного волока.
Подобная схема обеспечивает значительное увеличение ширины пасеки в зависимости от минимальной высоты вырубаемых деревьев и может составлять 4…6 В — эффективных вылетов манипулятора. Одновременно уменьшается отрицательное воздействие форвардера на лесную среду, так как он перемещается только по основным волокам. Харвестер, перемещаясь в первый заход по пасечным волокам, выполняет весь цикл работ: валка, очистка стволов от сучьев, разделка и пакетирование. Часть пасеки, недоступная для манипулятора с пасечных волоков, разрабатывается с импровизированного волока. Харвестер в этом случае работает как валочная машина, обеспечивая сталкивание спиленных деревьев вершиной в сторону ближайшего пасечного волока. После чего харвестер вторично проходит по пасечным волокам, обрабатывая лежащие деревья в режиме процессора: захват за вершину, очистка ствола от сучьев, раскряжевка и пакетирование. Подобная схема позволяет разрабатывать лесосеки со слабыми почвами, уменьшая до минимума число проходов машин по вспомогательным волокам и значительно укрепляя основные волоки сучьями поваленных деревьев. Однако производительность харвестера в этом случае будет несколько ниже по сравнению с предыдущей схемой.
При определенных условиях может применяться вариант с двумя импровизированными волоками, что обеспечивает увеличение ширины пасеки до 6…9 В — эффективных вылетов манипулятора (рис. 25). Однако необходимость формирования пакетов с одной стороны вспомогательного волока вызывает снижение производительности харвестера.
Рис.23. Схема разработки лесосеки с импровизированным волоком: 1 — импровизированный волок; 2 — сортименты
![]() |
Рис. 24. Схема разработки лесосеки с импровизированным волоком при работе харвестера в трех режимах: 1 — импровизированный волок; 2 — поваленные деревья
Рис. 25. Схема разработки лесосеки с двумя импровизированными волоками: 1 – импровизированный волок; 2 — сортименты
infopedia.su
49 Харвестеры и процессоры. Устройство рабочих органов, приёмы работы на этих машинах.
Харвестеры
Мировой опыт показывает, что заготовка сортиментов может производиться на базе современных систем машин по различным технологическим схемам. Особенностью технологических и технических решений в области сортиментной заготовки лесоматериалов за последние десятилетия стало совмещение переместительных операций с непосредственно обрабатывающими на основе упрощения производственной схемы и устранения многочисленных перегрузочных операций, что позволило в конечном итоге повысить эффективность производства лесопродукции в целом. В настоящее время на лесозаготовках в качестве основного машинного комплекса для заготовки сортиментов в условиях лесосеки широко применяются валочно-сучкорезно-раскряжевочные машины (харвестеры). Применение эффективных харвестеров при соблюдении лесоводственных требований к рубкам главного и промежуточного пользования обеспечивает экономическую и экологическую целесообразность ведения несплошных рубок различного назначения при заготовке сортиментов с одновременным упрощением технологического процесса лесозаготовок и снижением трудозатрат на подготовительные работы.
Согласно приведенной выше классификации машинных комплексов харвестеры относятся к группе самоходных машин. В зависимости от конструкции технологического оборудования харвестеры подразделяют на одномодульные и двухмодульные.
Конструктивной особенностью одномодульных харвестеров является комбинированный валочно-сучкорезно-раскряжевочный модуль, установленный на манипуляторе с вылетом до 10,5 м и оснащенный электронной системой контроля длины выпиливаемых сортиментов. Одномодульная компоновка харвестерного агрегата позволяет расширить возможности манипуляций со срезанным деревом, формируя пачки сортиментов, способствуя сохранению подроста, снижая вероятность повреждений коры растущих в зоне работы машины деревьев, исключить перехваты обрабатываемого дерева, а значит, повысить производительность.
Двухмодульные харвестеры оснащаются валочным агрегатом, установленным на манипуляторе и сучкорезно-расряжевочным устройством (процессорным агрегатом), смонтированным на раме самоходного шасси. Валочный агрегат выполняет спиливание и валку дерева с его последующим переносом в захватный и протаскивающий модули процессорного агрегата. Полученные сортименты укладываются в пачки у волока. Причем возможность поворота процессорного агрегата в горизонтальной плоскости позволяет формировать несколько пачек в пределах угла поворота (до 270°), осуществляя предварительную сортировку лесоматериалов. Примером двухмодульных харвестеров являются выпускавшиеся в 80-х годах машины «Оса-706» и «Вольво БМ Валмет-902» (рис.3).
Рис.3. Двухмодульный харвестер «Валмет-902»
В зависимости от типа режущего устройства харве герного агрегата выделяются следующие группы машишс механизмом безопилочного резания с консольной пилой.
В качестве механизмов безопилочного резания харвестерные агрегаты оснащаются, как правило, гидроножницами которые приводятся в действие с помощью силовых гидроцилиндров и осуществляют перерезание стволовой древесины при валке-раскряжевке деревьев. С учетом необходимости больших энергозатрат в процессе торцевого перерезания волокон древесины область применения харвестерных агрегатов подобного типа ограничивается различными видами рубок в тонкомерных лесонасаждениях (максимальным диаметром не более 0,25 м). Наиболее широкую известность получили одномодульные харвестеры «Макери-ЗЗТ», созданные для прореживания леса. Харвестерный агрегат смонтирован на раме мини-трактора посредством подъемных рычагов и снабжен накопительным устройством. Мощные гидравлические ножницы способны перерезать ствол толщиной до 25 см. Очистка от сучьев производится за счет протаскивания ствола вальцами через сучкорезные ножи. Машина оснащена энергоустановкой мощностью 25,7 кВт, приводящей в действие гидростатическую трансмиссию и все технологическое оборудование.
Развитие мирового лесного машиностроения показало преимущество тех фирм, которые пошли по пути создания и совершенствования специализированных лесных машин, учитывающих условия эксплуатации и экологические ограничения. Этим критериям в полной мере соответствуют одномодульные харвестеры с консольным пильным аппаратом, позволяющим качественно обрабатывать деревья в широком диапазоне толщин. В настоящее время основными фирмами, производящими такие лесозаготовительные комплексы для сортиментной технологии, являются скандинавские концерны «Раума» («Тимберджек»), «Партек Форест» («Валмет») и их филиалы в Северной и Южной Америке, Австралии и Юго-Восточной Азии. Эти фирмы являются также основными поставщиками многооперационных машин для сортиментной заготовки леса лесопромышленным предприятиям России.
Основные технические характеристики харвестеров «Валмет»:
Модель 901 911 921
Назначение Рубки ухода Сплошные рубки Сплошные рубки
Масса, кг:
4-колесный… 12500 13700
6-колесный… 13500 14500
Дорожный
просвет, мм……. 640
Крутящий момент, Нм:
885
при 1200 об/мин…. —
при 1300 об/мин…,’ 430
при 1400 об/мин…. Тяговое усилие, кН…. 108
В качестве технологического оборудования конструкция харвестеров включает в себя валочно-сучкорезно-раскряжевочный агрегат, установленный шарнирно на манипуляторе. Основными механизмами этого агрегата являются пильный блок, выполненный в виде консольной цепной пилы, 5 сучкорезных ножей, охватывающих обрабатываемую поверхность ствола, протаскивающие вальцы, Еотатор, обеспечивающий вращение агрегата относительно манипулятора. Харвестерный агрегат снабжен гидроприводом и электронной системой контроля и управления.
Рис.7. Харвестерный агрегат:
1 — шарнирная управляемая подвеска; 2 — подающие вальцы с приводными гидродвигателями; 3 — пять подвижных сучкорезных ножей; 4 — механизм пиления; 5 — система измерений и контроля на базе мини-ЭВМ МО 22А; 6-механизм поворота (ротатор)
Механизм поворота харвестерного агрегата позволяет расширить возможность захвата деревьев, особенно при выборочных рубках, а в сочетании с гидроцилиндром наклона агрегата облегчает работу с наклонными деревьями, а также работу на ветровальных и буреломных делянках. I
Подающие вальцы установлены на управляемых с помощью гидроцилиндров шарнирных рычагах. Для привода вальцов используются аксиально-поршневые гидромоторы, которые обеспечивают скорость подачи до 4 м/с с усилием 18 кН. Вальцы выполняют обрезиненными. Управление прижимом имеет два режима: нормальное и дополнительное сжатие. Для повышения силы сцепления вальцов с поверхностью ствола применяют съемные цепи.
Поваленное дерево очищается от сучьев пятью подвижными ножами. Четыре боковых ножа управляются гидроцилиндром. Причем торсионная подвеска передних ножей позволяет регулировать их прижим к обрабатываемой поверхности. При работе ножи копируют поверхность ствола и через установленные на них датчики формируют сигнал для измерения диаметра сортиментов.
Механизм пиления в харвестерном агрегате выполняет две операции: валку и раскряжевку. Он выполнен в виде консольной цепной пилы с приводом от гидромотора и системой надвигания, обеспечивающей максимальную скорость надвигания в зависимости от сил сопротивления, действующих в пропиле. Пильный аппарат состоит из стальной каплеобразной шины длиной 560 мм и универсальной цепи «Сандвик» с шагом 10,3 мм. Для уменьшения сопротивления движению пилы в пропиле некоторые харвестерные агрегаты (мод.965) оснащаются системой «Экосмазчик». Ее назначение состоит в подаче в пропил специальной смазки, которая впоследствии подвергается биологическому разложению с получением безвредных для природной среды веществ.
Измерение длины сортиментов в харвестерном агрегате производится с помощью перекатывающегося вдоль ствола зубчатого измерительного колеса. Датчик импульсов, кинематически связанный с ним, посылает сигналы на блок мини-ЭВМ, которая выдает результат измерения на дисплей и при необходимости на принтер. С помощью бортового компьютера можно также производить раскряжевку по заданной программе.
Процессоры
Самоходные сучкорезно-раскряжевочные машинные комплексы, или иначе самоходные «процессоры», в зависимости от конструкции технологического оборудования подразделяются на одномодульные, двухмодульные и трехмодульные.
Технологическое оборудование процессоров имеет различную компоновку исполнительных механизмов:
В оддномодудьных процессорах оно включает манипулятор с комбинированным сучкорезно-раскряжевочным модулем;
В двухмодульных процессорах комбинированный сучкорезно-раскряжевочный модуль установлен на раме шасси, там же смонтирован и загрузочный модуль в виде манипулятора с грейферным захватом;
В трехмодульных процессорах оно состоит из сдвоенного сучкорезного модуля, разнесенного по краям качающейся балки, протаскивающего модуля в виде подвижной каретки с зажимными рычагами и раскряжевочного модуля, состоящего из консольного пильного аппарата с системой отмера длин.
Отдельную группу составляют так называемые прицепные процессоры или процессорные приставки, которые, как правило, не имеют специального шасси, а выполняются в виде прицепа, оснащенного сучкорезно-раскряжевочным устройством, агрегаты которого приводятся в действие от вала отбора мощности общепромышленного трактора.
Процессоры, выполняя операции технологического процесса заготовки сортиментов, работают как непосредственно на делянке, перемещаясь по технологическому коридору, так и на площадке верхнего лесного склада. При выполнении несплошных рубок целесообразно применение самоходных одно- или двухмодульных и прицепных процессоров обеспечивающих обработку деревьев непосредственно в технологическом коридоре. Наличие манипулятора или лебедки позволяет этим машинам окучить предварительно поваленные деревья вблизи технологического коридора. Применение трехмодулъных процессоров в технологическом коридоре ограничено их низкой маневренностью и неэффективно при несплошных рубках. Возможности этих машин существенно возрастают при работе на площадках верхних лесных складов, где в штабелях складируются заготовленные деревья.
Для заготовки сортиментов на лесосеке при несплошных рубках (рубках ухода, выборочных, постепенных) Карельским научно-исследовательским институтом лесной промышленности (КарНИИЛП) разработан одномодульный процессор ЛО-123 на базе энергетической установки в виде трактора МТЗ-80 и шестиколесного шасси (рис.10.).
Машина
предназначена для обрезки сучьев с
предварительно поваленных деревьев,
раскряжевки хлыстов с частичной
сортировкой сортиментов по длинам
непосредственно в технологическом
коридоре (волоке) при несплошных и
сплошных рубках в насаждениях с объемом
хлыста до 0,30м3.
Рис. 10. Одномодульный процессор ЛО-123:
1 — трактор МТЗ-80; 2 — шасси; 3 — калорифер; 4 — ограждение стекол; 5 — манипулятор; 6 — подвеска; 7 — процессорный агрегат; 8 — тележка ДЗ-122; 9 — пневмогидроаккумулятор; 10 — трансмиссия; 11 — аккумуляторные батареи; 12 — гидросистема; 13 — гидроцилиндр; 14 — защитный поддон; 15 — насосная станция;16 — подножка; 17. — кронштейн; 18 — защита двигателя
Конструкция процессора включает в себя:
— энергетическую установку в виде трактора МТЗ-80;
— активный прицеп на базе задней балансирной тележки авто-грейдера ДЗ-143 с приводом от вала отбора мощности и карданных передач;
— манипулятор ЛВ-184 с сучкорезно-раскряжевочным агрегатом. Технологическое обррудование процессора ЛО-123 представляет
собой гидроманипулятор, оснащенный сучкорезно-раскряжевочным агрегатом, который состоит из рамы с захватами, выдвижной балки с сучкорезными ножами и фиксатором ствола, консольной цепной пилы для раскряжевки хлыста и устройства поворота агрегата в горизонтальной плоскости — ротатора.
Машина работает следующим образом. Манипулятором процессорный агрегат наводится на поваленное дерево, после чего срабатывают захваты, перемещая ствол в пространство между сучкорезными ножами.
Обрезка сучьев производится путем перемещения сучкорезных ножей вдоль неподвижного ствола с помощью гидроцилиндра выдвижной балки. При обратном ходе выдвижной балки с ножами происходит подача очищенной от сучьев части ствола в зону раскряжевки. После очистки от сучьев требуемой длины ствола производится отпиливание сортимента и укладка его у волока с возможной сортировкой в разные пакеты. Система отмера длин работает на основе электронного логического устройства, обрабатывающего сигналы, поступающие от датчиков на балке сучкорезных ножей и на фиксаторе ствола при его перемещении в зону раскряжевки. Обработка поступающей информации и выработка управляющих сигналов выполняется блоком управления в соответствии с программой, заданной оператором нажатием кнопок на пульте управления. Программа может содержать от 1 до 10 длин сортиментов с градацией через 1м.
Двухмодульные процессоры не имеют пока отечественных аналогов. К этой группе машин относятся процессор на базе колесного трактора «Локомо 930» для сплошных и несплошных рубок и процессор «Брюнет мини» для рубок ухода. Эти машины представляют продукцию концерна «Раума». К машинам этой группы относится и канадский процессор «Инчворм», который широко применяется на сплошных рубках в лесах Северной Америки. Конструкция технологического оборудования двухмодульных процесЬоров включает в себя манипулятор с грейферным захватом и смонтированный на раме самоходного шасси сучкорезно-раскряжевочный агрегат, который может занимать транспортное и рабочее положения. Процессор «Брюнет мини» состоит из двухсекционного шарнирно сочлененного восьмиколесного шасси с гидростатико-механической трансмиссией, полноповоротного манипулятора «Кранаб»
и поворотного сучкорезно-раскряжевочного устройства, ориентируемого в горизонтальной и вертикальной плоскостях с помощью двух гидроцилиндров. Рабочее положение процессорного агрегата перпендикулярно направлению движения машины. Правая по ходу движения машины сторона процессорного агрегата содержит сучкорезный модуль, а левая -раскряжевочный модуль. Между ними раоположень! два обрезиненных протаскивающих вальца, имеющих гидравлический механизм прижима. В первоначальный момент грейферный захват манипулятора переносит комлевую часть ствола предварительно сваленного дерева в пространство между протаскивающими вальцами и разведенными ножами сучкорезного-раскряжевочного модуля. Далее ножи охватывают ствол, после чего вальцы протаскивают его на требуемую по программе раскроя длину в зону раскряжевки, в которой с помощью консольной цепной пилы происходит отпиливание сортимента. Раскладка сортиментов по группам в зависимости от длин ведется манипулятором.
Трехмодульные сучкорезно-раскряжевочные машины предназначены в основном для работы на верхних лесных складах, но могут применяться и в технологическом процессе сплошнолесосечных работ в системе с валочно-пакетирующей машиной, формирующей пакеты деревьев с одной стороны перпендикулярно волоку. При этом процессор перемещается по волоку и ведет очистку от сучьев и раскряжевку непосредственно на волоке. Из-за необходимости применения большого количества машин (ВПМ, процессор, форвардер), перемещающихся по одному технологическому коридору, возрастает количество проходов тяжелых машин по лесным почвам с их разрушением, а также слишком большими становятся удельные энергозатраты. Поэтому более рациональным следует считать применение трехмодульных процессоров на верхнем лесном складе.
В настоящее время серийно выпускаются Трехмодульные процессоры ЛО-120 и ЛО-126 (рис.11.). Причем процессор ЛО-126 после модернизации на Кудымкарском механическом заводе получил марку процессор лесной ПЛ-1. Конструктивно машины выполнены по единой кинематической схеме. Процессоры ЛО-120, ЛО-126 (ПЛ-1) созданы на базе сучкорезных машин ЛП-3 ОБ Сыктывкарского механического завода и ЛП-ЗЗА завода «Екатеринбургские лесные машины». На сучкорезных машинах установлено дополнительное технологическое оборудование: устройство для отмерз длин, пильный механизм от валочно-трелевочной машины ЛП-49. Устройство для отмера длин позволяет выпиливать несколько сортиментов длиной от 4 до 6 м с соответствующей переналадкой. Одновременно без переналадки можно выпиливать сортименты только двух длин. Модернизированная машина ПЛ-1, оснащенная измерительным барабаном и электронной системой, может без переналадок выпиливать неограниченное число сортиментов по длине.
studfiles.net
Tekhnologia_lesozagotovki / Лекции ПДФ / РК2 / Лекция 7
Лекция №4 ТЕХНОЛОГИИ РАЗРАБОТКИ ЛЕСОСЕК СИСТЕМАМИ
ВАЛОЧНО-СУЧКОРЕЗНО-РАСКРЯЖЕВОЧНАЯМАШИНА И ФОРВАРДЕР
1. Основные принципы и технология работы Технология разработки лесосек системаши машин валочно-сучкорезно-
раскряжевочная машина + трелевочный трактор манипуляторного типа предназначена для проведения сортиментной лесозаготовки. Она не требует дополнительных механизмов для обработки деревьев в процессе получения сортиментов.
Валочно-сучкорезно раскряжевочные машины(ВСРМ) или харвестеры – это лесосечные машины, получающие в процессе лесозаготовки круглые лесоматериалы (сортименты).
Основными частями ВСРМ являются:
1)шасси на гусеничной или колесной базе
2)поворотная платформа, объединяющая кабину оператора и манипуляторное оборудование
3)манипулятор с валочно-сучкорезно-раскряжевочнойголовкой
4)кабина оператора
Харвестеры производят на лесосеке следующие операции:
1)валка деревьев
2)обрезка сучьев
3)раскряжевка хлыстов
Форвардер – это специализированный трелевочный трактор манипуляторного типа для сбора сортиментов.
Он состоит из следующих основных частей:
1)колесное шасси
2)поворотная платформа, объединяющая кабину оператора и манипуляторное оборудование
3)манипулятор
4)кабина оператора
5)емкость для сбора сортиментов
Работа систем машин харвестер+ форвардер происходит согласно технологических схем указанных на рис. 4.1, 4.2, 4.3.
Подготовительные работы при разработке лесосеки комплексом машин харвестер + форвардер состоят в разметке границ пасек и делянок, обозначении оси направления движения харвестера, устройстве погрузочных площадок, полосы безопасности и мастерского участка, прокладке магистральных волоков и лесовозных усов. Все подготовительные работы производятся перед началом основных работ.
Прокладка пасечных волоков и уборка опасных деревьев на делянке выполняется в процессе проведения основных операций
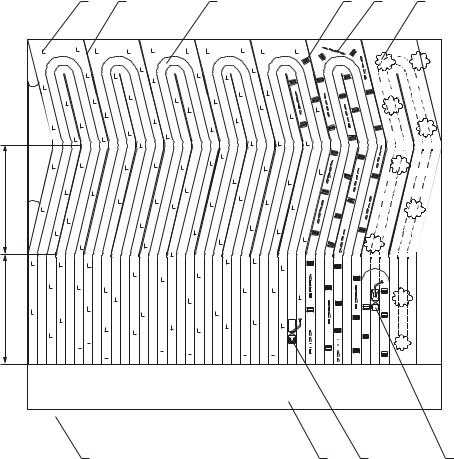
При проведении сплошных и сплошных чересполосных рубок перед началом освоения лесосеки, в процессе подготовительных работ, делянка разбивается на параллельные пасеки шириной 18 м, выделяются деревья диаметром более 50 см, а также намечается затесками на деревьях ось направления движения харвестера. Для исключения ветровальных «сквозняков» эта ось должна через каждые 100 м иметь поворот в сторону, под углом не менее 30°.
100 м
|
|
|
|
|
|
|
|
|
|
|
|
|
|
|
|
|
|
|
|
|
|
|
|
|
|
|
|
|
|
|
|
|
|
|
|
|
|
|
|
|
|
|
|
|
|
|
|
|
|
|
|
|
|
|
|
|
|
|
|
|
|
|
|
|
|
|
|
|
|
|
|
|
|
|
|
|
|
|
|
|
|
|
|
|
|
|
|
|
|
|
|
|
|
|
|
|
|
|
|
|
|
|
|
|
|
|
|
|
|
7 |
|
|
|
|
|
|
|
|
|
|
|
| 8 | 9 | 10 |
Рисунок 4.1 – Технологическая схема разработки лесосек комплексом харвестер + форвардер при сплошных рубках
1 – вырубка; 2 – граница пасек; 3 – след харвестера; 4 – пачка сортиментов; 5 – хлыст, разделанный вальщиком; 6 – растущий лес; 7 – лесовозный ус; 8 – штабель сортиментов; 9 – форвардер; 10 – харвестер.
Валка деревьев диаметром до 50 см (кроме тонкомера), обрезка сучьев и раскряжевка хлыстов на сортименты осуществляются харвестером по всей ширине пасеки при его движении вдоль визира к дальней границе делянки. Им же укладываются сортименты в пачки справа и слева от колеи машины с подсортировкой лесоматериалов по породам и качеству, или без неё. Пасека разрабатывается путем последовательного перехода харвестера с одной технологической стоянки на другую, при его движении от лесовозного уса. Дойдя до конца пасеки, машина переезжает на смежную пасеку и продолжает работу, двигаясь в обратном направлении, к лесовозному усу.
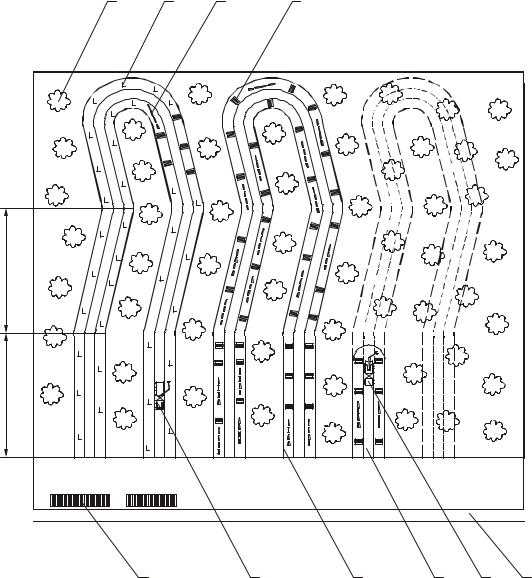
Валку деревьев диаметром более 50 см производит вальщик, оснащенный | ||||||
бензиномоторной пилой, гидроклином, рулеткой и крючьями для откатки |
| |||||
сортиментов. Он осуществляет валку деревьев, обрезку сучьев, разметку хлыстов и | ||||||
их раскряжевку на сортименты, а также откатку сортиментов в сторону с целью | ||||||
освобождения пути движения форвардеру. Один вальщик, как правило, обеспечивает | ||||||
работу двух комплексов машин. |
|
|
|
|
| |
1 | 2 | 3 | 4 |
|
|
|
100 м |
|
|
|
|
|
|
100 м |
|
|
|
|
|
|
| 5 | 6 | 7 | 8 | 9 | 10 |
Рисунок 4.2 – Технологическая схема разработки лесосек комплексом |
| |||||
харвестер + форвардер при сплошных чересполосных рубках |
1 – растущий лес; 2 – вырубка; 3 – хлыст, разделанный вальщиком; 4 – пачки сортиментов; 5 – штабеля сортиментов; 6 – форвардер; 7 – граница ленты, разрабатываемой харвестером; 8 – след харвестера; 9 – харвестер; 10 – лесовозный ус.
Сбор и транспортировку сортиментов с пасеки к месту складирования осуществляет форвардер. Для набора пачки форвардер задним ходом по следу харвестера заходит в глубь пасеки на расстояние, обеспечивающее полную загрузку
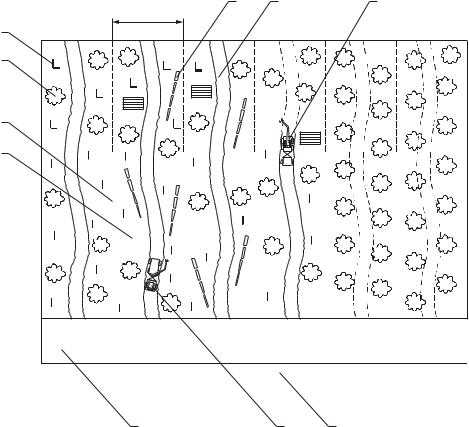
платформы. Затем форвардер останавливается и приступает к формированию пачки сортиментов в приемном устройстве (платформе) трактора. Собрав гидроманипулятором все лесоматериалы, лежащие по обе стороны машины, форвардер движется в сторону лесовозного уса к следующей технологической стоянке. Заполнив платформу сортиментами, форвардер транспортирует их к месту складирования у лесовозного уса. Обычно приемное устройство загружается лесоматериалами одного типоразмера, что упрощает их сортировку и штабелевку при выгрузке с платформы. Штабеля сортиментов формируются вдоль лесовозного уса, высотой не более 2…3 м. При этом сортименты в штабеля укладываются перпендикулярно оси лесовозного уса верхними отрезами в сторону дороги, с удалением от обочины на расстояние 1,5… 2 м.
18 м
4
5
6
7
|
|
|
|
|
|
|
|
|
|
|
|
|
|
|
|
|
|
|
|
|
|
|
|
|
|
|
|
|
|
|
|
|
|
|
|
|
|
|
|
|
|
|
|
|
|
|
|
|
|
|
|
|
|
|
|
|
|
|
|
|
|
|
|
|
|
|
|
|
|
|
|
|
|
|
|
|
|
|
|
|
|
|
|
|
|
|
|
|
|
|
|
|
|
|
|
|
|
|
|
|
|
|
|
|
|
|
|
|
|
|
|
|
|
|
|
|
|
|
|
|
|
|
|
|
|
|
|
|
|
|
|
|
|
|
|
|
|
|
|
|
|
|
|
|
|
|
|
|
|
|
|
|
|
|
|
|
|
|
|
|
|
|
|
|
|
|
|
|
|
|
|
|
|
|
|
|
|
|
|
|
|
|
|
|
|
|
|
|
|
|
|
|
|
|
|
|
|
|
|
|
|
|
|
|
|
|
|
|
|
|
|
|
|
|
|
|
|
|
|
|
|
|
|
|
|
|
|
|
|
|
|
|
|
|
|
|
|
|
|
|
|
|
|
|
|
|
|
|
|
|
|
|
|
|
|
|
|
|
|
|
|
|
|
|
|
|
|
|
|
|
|
|
|
|
|
|
|
|
|
|
|
|
|
|
|
|
|
|
|
|
|
|
|
|
|
|
|
|
|
|
|
|
|
|
|
|
|
|
|
|
|
|
|
|
|
|
|
|
|
|
|
|
|
|
|
|
|
|
|
|
|
|
|
|
|
|
|
|
|
|
|
|
|
|
|
|
|
|
|
|
|
|
|
|
|
|
|
|
|
|
|
|
|
|
|
|
|
|
|
|
|
|
|
|
|
|
|
|
|
|
|
|
|
|
|
|
|
|
|
|
|
|
|
|
|
|
|
|
|
|
|
|
|
|
|
|
|
|
|
|
|
|
|
|
|
|
|
|
|
|
|
|
|
|
|
|
|
|
|
|
|
|
|
|
|
|
|
|
|
|
|
|
|
|
|
|
|
|
|
|
|
|
|
|
|
|
|
|
|
|
|
|
|
|
|
|
|
|
|
|
|
|
|
|
|
|
|
|
|
|
|
|
|
|
|
|
|
|
|
|
|
|
|
|
|
|
|
|
|
|
|
|
|
|
|
|
|
|
|
|
|
|
|
|
|
|
|
|
|
|
|
|
|
|
|
|
|
|
|
|
|
|
|
|
|
|
|
|
|
|
|
|
|
|
|
|
|
|
|
|
|
|
|
|
|
|
|
|
|
|
|
|
|
|
|
|
|
|
|
|
|
|
|
|
|
|
|
|
|
|
|
|
|
|
|
|
|
|
|
|
|
|
|
|
|
|
|
|
|
|
|
|
|
|
|
|
|
|
|
|
|
|
|
|
|
|
|
|
|
|
|
|
|
|
|
|
|
|
|
|
|
|
|
|
|
|
|
|
|
|
|
|
|
|
|
|
|
|
|
|
|
|
|
|
|
|
|
|
|
|
|
|
|
|
|
|
|
|
|
|
|
|
|
|
|
|
|
|
|
|
|
|
|
|
|
|
|
|
|
|
|
|
|
|
|
|
|
|
|
|
|
|
|
|
|
|
|
|
|
|
|
|
|
|
|
|
|
|
|
|
|
|
|
|
|
|
|
|
|
|
|
|
|
|
|
|
|
|
|
|
|
|
|
|
|
|
|
|
|
|
|
|
|
|
|
|
|
|
|
|
|
|
|
|
|
|
|
|
|
|
|
|
|
|
|
|
|
|
|
|
|
|
|
|
|
|
|
|
|
|
|
|
|
|
|
|
|
|
|
|
|
|
|
|
|
|
|
|
|
|
|
|
|
|
|
|
|
|
|
|
|
|
|
|
|
|
|
|
|
|
|
|
|
|
|
|
|
|
|
|
|
|
|
|
|
|
|
|
|
|
|
|
|
|
|
|
|
|
|
|
|
|
|
|
|
|
|
|
|
|
|
|
|
|
|
|
|
|
|
|
|
|
|
|
|
|
|
|
|
|
|
|
|
|
|
|
|
|
|
|
|
|
|
|
|
|
|
|
|
|
|
|
|
|
|
|
|
|
|
|
|
|
|
|
|
|
|
|
|
|
|
|
|
|
|
|
|
|
|
|
|
|
|
|
|
|
|
|
|
|
|
|
|
|
|
|
|
|
|
|
|
|
|
|
|
|
|
|
|
|
|
|
|
|
|
|
|
|
|
|
|
|
|
|
|
|
|
|
|
|
|
|
|
|
|
|
|
|
|
|
|
|
|
|
|
|
|
|
|
|
|
|
|
|
|
|
|
|
|
|
|
|
|
|
|
|
|
|
|
|
|
|
|
|
|
|
|
|
|
|
|
|
|
|
|
|
|
|
|
|
|
|
|
|
|
|
|
|
|
|
|
|
|
|
|
|
|
|
|
|
|
|
|
|
|
|
|
|
|
|
|
|
|
|
|
|
|
|
|
|
|
|
|
|
|
|
|
|
|
|
|
|
|
|
|
|
|
|
|
|
|
|
|
|
|
|
|
|
|
|
|
|
|
|
|
|
|
|
|
|
|
|
|
|
|
|
|
|
|
|
|
|
|
|
|
|
|
|
|
|
|
|
|
|
|
|
|
|
|
|
|
|
|
|
|
|
|
|
|
|
|
|
|
| 8 |
|
|
|
|
|
|
| 9 |
|
|
|
| 10 |
|
|
|
Рисунок 4.3 – Технологическая схема разработки лесосек комплексом харвестер + форвардер при выборочных рубках
1 – хлыст, разделанный вальщиком; 2 – технологический коридор; 3 – харвестер; 4 – вырубка; 5 – растущий лес; 6 – граница пасеки; 7 – сортименты; 8 – штабель
сортиментов; 9 – форвардер; 10 – лесовозный ус.
При проведении постепенных чересполосных рубок технология разработки лесосеки остается прежней. Отличие состоит в том, что между двумя смежными пасеками оставляют стену леса шириной 18…20 м для обеспечения семенного самосева.
Контрольные вопросы:
1.Что такое харвестеры? Объясните из каких частей они состоят и какова последовательность их работы.
2.Как происходит заготовка древесины системой харвестер + форвардер по технологии сплошных рубок?
3.Как осуществляется заготовка древесины системой харвестер + форвардер по технологиям несплошных рубок?
4.Какова роль вальщика в обеспечении эффективной работы комплекса харвестер + форвардер?
5.В чем состоят преимущества и недостатки заготовки древесины системой харвестер + форвардер?
studfiles.net
Технология разработки лесосеки с заездом харвестера на полупасеки.
Количество просмотров публикации Технология разработки лесосеки с заездом харвестера на полупасеки. — 1144
Обе пасеки разрабатываются одновременно с волоком. Направление валки должна быть как перпендикулярно волку так и вдоль волока вершиной на себя. На участках с групповым размещением подроста деревья спиливают и валят перпендикулярно волоку, но с учетом расположения групп подроста и молодняка хозяйственно ценных пород.
Рис. 4.3 Схема работа харвестера с заездом на полупасеки
1 – растущие деревья;2 – волок; 3- харвестер; 4 – пакет сортиментов; 5 – порубочные остатки; 6 – заезд на пасеку.
Технология разработки лесосеки со вспомогательным технологическим коридором и применением на валке и раскряжевке хпрвестера, а на подвозке сортиментов – форвардера. Форвардер работает лишь на волоках, удаленных друг от друга на расстояние 30 м. При работе харвестера во вспомогательном коридоре, как и на волоке, выполняется весь цикл вспомогательных опреций: валка, обрезка сучьев, раскряжевка и пакетирование, однако пакеты сортиментов при этом укладываются на максимальном удалении от машины. Этим обеспечивается доступность пакетов, сформированных харвестером при работе во вспомогательном коридоре, манипулятору форвардера, перемещающегося по волоку.
Рис.4.4 Схема разработки пасеки со вспомогательным коридором.
1 – путь движения харвестера; 2 – границы волока; 3 – границы ленты; 4 – пакеты сортиментов, сформированные при разрубке волока; 5 – пакеты сортиментов, сформированные при разрубке вспомогательной ленты.
Технология разработки лесосеки при работе харвестера в трех режимах и форвардера на подвозке сортиментов. (рис 4.6) В корне этой технологии лежит возможность использования харвестера по неполному циклу. Сначала разрубаются смежные пасечные волока, отстоящие друг от друга на расстоянии до 40 м, и прилегающие ленты, досягаемые для манипулятора харвестера. Работа при этом ведется по полному циклу. Далее харвестер переходит для работ на оставленную между волоками ленту леса. Перемещаясь по центру этой полосы таким образом, что бы нанести минимальный ущерб насаждению, харвестер валит деревья, назначенные в рубку, под прямым углом к волоку вершиной в направлении ближайшего волока. Обрезка сучьев и раскряжевка поваленных деревьев осуществляется во время следующего прохода харвестера по разрубленным волокам. Обрезка сучьев производится способом ʼʼза вершинуʼʼ, а раскряжевка хлыста͵ после перехвата его харвестерным агрегатом – ʼʼза комельʼʼ.
Рис 4.6 Схема разработки пасеки харвестером в трех режимах.
1 – растущие деревья; 2 – волок; 3 – харветер; 4 – поваленные деревья; 5 – пакет сортиментов; 6 – пеньки; 7 – движение харвестера при работе в режиме ʼʼвалкаʼʼ; 8 – порубочные остатки; 9 – форвардер.
В данных условиях целесообразно применять как технологию с валкой бензомоторными пилами, которая используется в парке на данный момент, так и на базе харвестеров.
Выбор технологии с использованием харвестера во I группе леса обусловлено следующими причинами:
· хорошей несущей способностью грунтов;
· экономическими показателями;
· экологической безопасностью.
Для разработки лесосек бензомоторной пилой выбираем метод узких пасек с подкладочным деревом (рис 4.1). Ширина пасек при этой технологии не превышает 20 м. Разработку ведут с подкладочным деревом, что облегчает обрезку сучьев, перемещение стволов в пределах пасеки. При разработке пасек таким способом посреди волока образуется вал сучьев, который значительно улучшает проходимость форвардера и предотвращает деформацию волока. После трелевки сортиментов на пасеке не требуется дополнительной очистки, поскольку все сучья сконцентрированы на волоке и уплотнены проходами форвардера.
Для разработки лесосек с помощью харвестера принимаем технологию со вспомогательным коридором и подвозкой сортиментов форвардером (рис 4.4). Данный вариант позволяет существенно уменьшить длину пасечных волоков на лесосеке. Технология рекомендуется для реализации постепенных и выборочных рубок средней и высокой интенсивности. .
В защитных лесах целесообразно проводить выборочные рубки. Выборочная рубка – многоприемная рубка, при которой вырубают в первую очередь фаутные, спелые, перестойные деревья, включая деревья главных пород с пониженным ростом, а также деревья, мешающие росту подросту или деревьям главных пород. Выборочная рубка не имеет законченного процесса, обеспечивает непрерывность возобновления и выращивания леса, позволяет сохранить защитные и средообразующие функции леса. По интенсивности рубки древостоев делятся: на слабые 10–15% их запаса, умеренные — 15–25% и сильные — 25–35%. При слабой интенсивности повторяемость рубки составляет 10–15 лет, при высокой – 20–30 лет. Принимем выборочные рубки с интенсивностью 20% и сроком повторяемости 15 лет.
referatwork.ru
ЛАБОРАТОРНАя работа Тема- Валочносучкорезнорасряжевочные машины харвестеры Цель занятия- детальное из
Работа добавлена на сайт samzan.ru: 2016-03-13Тема: Валочно-сучкорезно-расряжевочные машины (харвестеры)
Цель занятия: детальное изучение конструкций навесного технологического оборудования харвестерови правил их эксплуатации
Структура отчета:
1. Назначение, область применения харвестеров;
2. Устройство и принцип работы навесного технологического оборудования харвестеров;
3. Правила эксплуатации и техника безопасности при работе на валочно-сучкорезно-расряжевочных
Конструкции харвестеров
Конструкции современных харвестеров рассмотрим с учетом их классификации (раздел 1) на примерах харвестеров «Valmet-911» и «Timberjack-1270С».
Харвестер «Valmet-911» является одномодульной машиной. Может использоваться при проведении различных видов рубок. Конструкция харвестера включает в себя следующие основные узлы (рис. 6):
дизельный силовой агрегат, приводящий в действие все системы харвестера;
шарнирно-сочлененную раму на базе трехосного колесного шасси;
качающуюся кабину оператора, установленную на поворотной платформе;
комбинированный шарнирно-рычажно-телескопический манипулятор;
харвестерную валочно-сучкорезно-раскряжевочную головку.
Рис. 6. Устройство харвестера: 1 рама; 2 двигатель; 3 манипулятор; 4, 5 передний и задний мосты; 6 харвестерная головка; 7 тандемы
Силовой агрегат харвестера представляет собой 6-цилиндровый дизель с непосредственным впрыском и турбонаддувом. К особенностям двигателя харвестера можно отнести устойчивую работу при изменении оборотов коленчатого вала от 780 до 2400 об/мин, достаточную мощность 130 кВт, а также наличие турбокомпрессора, который состоит из газовой турбины и соосного компрессора. Турбина, раскручиваемая выхлопными газами, приводит в действие компрессор, подающий сжатый воздух под давлением в цилиндры (давление наддува). Увеличение количества воздуха в цилиндрах дает возможность увеличить количество впрыскиваемого топлива, которое интенсивно сгорает. В результате получается большая мощность при меньшем расходе топлива и более чистых выхлопных газах.
Рама харвестера состоит из двух частей: передней и задней, которые соединены вместе центральным шарниром. Гидроцилиндры управления поворотом машины установлены между передней и задней рамами и обеспечивают изменение угла между ними. На раме имеется механизм наклона кабины и манипулятора, который установлен между поворотной платформой и рамой. Гидроцилиндры наклона кабины позволяют не только изменять ее ориентацию при работе на склонах, но и уменьшают боковые колебания машины при движении по неровной дороге. Поворот кабины с манипулятором в горизонтальной плоскости во время работы осуществляется с помощью мотор-редуктора и зубчатой передачи. Максимальный угол поворота 315°.
Харвестер «Valmet-911» оснащается валочно-сучкорезно-раскряжевочной головкой модели 960, которая позволяет успешно применять харвестер как на выборочных, так и на сплошных рубках. Им можно обрабатывать как уже поваленные, так и стоящие деревья. Головка шарнирно подвешивается к манипулятору. Конструкция харвестерной головки показана на рис.9. Для привода всех механизмов харвестерная головка имеет электрическую и гидравлическую системы.
Механизм поворота харвестерной головки позволяет расширить возможность захвата дерева, особенно при выборочных рубках, а в сочетании с гидроцилиндром наклона головки облегчает работу с наклонными деревьями, а также работу на ветровальных и буреломных участках лесосеки.
Подающие вальцы установлены на управляемых с помощью гидроцилиндров шарнирных рычагах. Для привода вальцов используются аксиально-поршневые гидромоторы, которые обеспечивают скорость подачи до 4 м/с с усилием 18 кН. Вальцы имеют специальное резиновое покрытие. Управление прижимом имеет два режима: нормальное и дополнительное сжатие. Для повышения силы сцепления вальцов с поверхностью ствола применяют съемные цепи.
Поваленное дерево очищается от сучьев пятью подвижными ножами. Четыре боковых ножа управляются гидроцилиндром. Причем торсионная подвеска передних ножей позволяет регулировать их прижим к обрабатываемой поверхности. При работе ножи копируют поверхность ствола и через установленные на них датчики формируют сигнал для измерения диаметра сортиментов.
Рис. 9. Харвестерная головка: 1 шарнирная управляемая подвеска; 2 протаскивающие вальцы с приводными гидродвигателями; 3 пять подвижных сучкорезных ножей; 4 пильный аппарат; 5 система измерений и контроля на базе мини-ЭВМ MD 22A; 6 механизм поворота (ротатор)
Пильный аппарат в харвестерной головке выполняет две операции: валку и раскряжевку. Он выполнен в виде консольной цепной пилы с приводом от гидромотора и системой надвигания, обеспечивающей максимальную скорость надвигания в зависимости от сил сопротивления, действующих при пилении. Пильный аппарат состоит из стальной каплеобразной шины длиной 560 мм и универсальной цепи «Сандвик» с шагом 10,3 мм. Для уменьшения сопротивления движению пилы в пропиле некоторые харвестерные агрегаты оснащаются системой «Экосмазчик». Ее назначение состоит в подаче в пропил специальной смазки, которая впоследствии подвергается биологическому разложению с получением безвредных для природной среды веществ.
Измерение длины сортиментов в харвестерном агрегате производится с помощью перекатывающегося вдоль ствола зубчатого измерительного колеса. Датчик импульсов, кинематически связанный с ним, посылает сигналы на блок ЭВМ, которая выдает результат измерения на дисплей и при необходимости на принтер. С помощью бортового компьютера можно также производить раскряжевку по заданной программе.
Харвестер «Timberjack-1270С» представляет последнее поколение машин такого класса. Он имеет колесную формулу 6К6 и оснащен системой сбалансированных тандемных тележек, что позволяет достичь большого тягового усилия. Трансмиссия гидростатическая с двухдиапазонной раздаточной коробкой. Передний и задний ведущие мосты имеют блокировку дифференциала, приводимую в действие электрогидравлической системой. Передний мост с балансирными тандемными тележками, задний одинарный. Харвестер оснащен дизельным двигателем «Cummins 6CT8.3» мощностью 165 кВт, который обеспечивает увеличенный крутящий момент и большую мощность при низких оборотах.
Управление поворотом шарнирно-сочлененных полурам осуществляется двумя гидроцилиндрами. Рабочий и вспомогательный тормоза многодисковые в масляной ванне, приводимые в действие гидравликой. Стояночный и аварийный тормоза приводятся в действие пружинами.
Харвестер имеет комбинированный шарнирно-рычажно-телескопический манипулятор параллельного действия с максимальным вылетом 10 м и грузовым моментом 178 кН×м. Харвестерная головка оснащена шестью сучкорезными ножами. Из них две пары подвижные, а одна стационарная. При этом один стационарный нож имеет верхнее расположение, а второй нижнее. Подвижные ножи приводятся в движение посредством одного гидроцилиндра. Протаскивающий механизм представляет собой 4 вальца, поверхность которых резиновая, а при необходимости оснащается специальными цепями. Привод вальцов осуществляется аксиально-поршневыми гидродвигателями с повышенным крутящим моментом.
Кабина оператора имеет системы обогрева и кондиционирования воздуха, эргономичное сиденье и остеклена тонированными стеклами из ударопрочного материала (лексан).
Харвестер «Timberjack-1270С» оснащен системами управления двигателем, балансирными тележками, раскряжевкой ствола дерева и передачи информации потребителям лесоматериалов. Кроме того харвестер имеет систему нанесения цветной маркировки на торцы лесоматериалов и обработки пней химическими жидкостями.
Конструкции и технические характеристики наиболее распространенных в настоящее время харвестеров и харвестерных головок приведены в приложении.
Системы управления харвестерами
Системы управления современными харвестерами представляют собой сложные технические комплексы, реализующие одновременно несколько функций: управление базовой машиной, исполнительными органами технологического оборудования, принятие решений.
Операции перемещения машины, валки, очистки стволов от сучьев и раскряжевки требуют соблюдения ряда требований: технологии, ГОСТов, экономики, экологии, эргономики, охраны труда.
Важной составляющей систем управления харвестером является оператор. В его функции входит не только управление харвестером, но и принятие решений по оптимальной работе машины и раскряжевке хлыстов, что обеспечивает максимальную прибыль.
Система управления харвестером включает следующие подсистемы:
управление базовой машиной;
управление манипулятором;
управление харвестерным процессором;
управление системой отмера длин;
управление в комплексе: харвестер (оценка лесосечного фонда отводимого в рубку и заготовка лесоматериалов), транспорт лесоматериалов и их переработка.
Системы управления манипуляторами
Системы управления манипуляторами современных харвестеров базируются на идентичных принципах, практически независимо от фирмы изготовителя, типа и основных параметров манипулятора. В харвестерах в основном используются манипуляторы двух кинематических схем: шарнирно-рычажные и комбинированные (с телескопической вставкой). Принципиальная схема управления гидравликой манипулятора комбинированного типа представлена на рис. 10.
Сервоуправление гидравликой манипулятора выполняется с помощью системы сервоуправления «ЕНС-35», в которую входит регулировочный блок «IPS» для индивидуальной регулировки каждой рабочей операции манипулятора. Рычаги управления манипулятором расположены у сиденья. Предусмотренными в рычагах управления потенциометрами регулируется сила тока, идущего через регулировочный блок «IPS» на клапаны управления. Для обеспечения надежной работы системы «ЕНС» ее регулировочные вставки должны быть проверены уполномоченным специалистом через каждые 1000 моточасов или как минимум один раз в год. Кроме вышеуказанного, регулировка системы «ЕНС» необходима также в том случае, если манипулятор работает неудовлетворительно или гидросистема вырабатывает слишком много тепла.
Перспективные системы управления харвестерами
Информационная система харвестеров позволяет устанавливать связь между оператором харвестера и лесопильным предприятием либо потребителем. Лесопильное предприятие имеет возможность следить за процессом заготовки древесины и постоянно располагать информацией об ее объеме, количестве деревьев, длине сортиментов. Вновь разрабатываемые в Скандинавских странах системы, использующие спутниковую связь и выход в Интернет (рис. 13), на основе геоинформационных технологий позволяют: выполнять оценочный прогноз на будущую рубку; планировать лесозаготовительные работы в зависимости от спроса, корректировать и оптимизировать их проведение в рамках системы «лес харвестер потребитель», включая маршрутизацию перевозок сортиментов; обмениваться встречной информацией между операторами харвестеров, форвардеров и водителями сортиментовозов; также основываясь на данные, полученные ЭВМ харвестера во время рубки, моделировать возобновление нового поколения леса.
С харвестером, как источником многих данных о производимой продукции и с лучшими сведениями о растущем лесе, в базисе составляются банки данных о древесине, которые позволяют осуществлять полный количественный контроль над складируемой древесиной. Этот контроль охватывает всю цепь от леса к промышленности и обратно к заказчику. С помощью новой системы управления можно получать отчет о поставках древесины, выбирать вид рубки, средства, продолжительность (от 2 до 10 лет). Кроме того, можно производить детальную годовую и месячную планировку мероприятий по рубке древостоев.
Рис. 13. Информационная система харвестера: 1 спутник; 2 харвестер; 3 сервер; 4 лесопильный завод; 5 форвардер
Рис. 14. Система дистанционного управления заготовки древесины харвестером
В Шведской фирме EU-PRQJEKTES PROMOTE разработана программа «SkogForsk» для персонального компьютера по поставкам отходов из леса, подбору подходящего вида рубки, а также прогнозу месячной поставки древесины. Данная система представлена на рис. 14.
Система «ProLog» определяет объемы образующихся на лесопильном заводе сортиментов и другой готовой продукции, а также все заказы на пиломатериалы в районе. Заказы пересчитываются в круглые лесоматериалы. С помощью «ProLog» лесопильный завод узнает, кроме того, какие лесосеки выбраны для рубки. На основании всей информации дается заказ на круглые лесоматериалы, определяются длина и диаметр сортиментов, их количество. В лесу подбираются насаждения, которые лучше всего подходят для рубки. Для харвестера устанавливается очередность вырубки насаждений. Затем прогноз ожидаемых качественных и количественных характеристик сортиментов предстоящего периода поставок передается на лесопильный завод. Достоверный прогноз размера поставки на следующий месяц как минимум в два раза увеличивает горизонт планирования работы лесопильного завода и значительно облегчает управление заказами покупателей.
С полными сведениями о составе и положении древесины, а также с бортовыми компьютерами в лесовозных транспортных средствах, которые имеют GPS-доступ (интернет-доступ), появляется возможность оптимизации транспортных перевозок. Это означает уменьшение холостых пробегов и более лучшее использование автопарка.
Ориентированная на нужды потребителей и движимая изменениями рыночных тенденций, торговля круглыми лесоматериалами предъявляет повышенные требования к точности измерительного оборудования и передаче компьютеризированных данных при работе харвестеров.
Чтобы достичь желаемой производительности и рентабельности, оператор харвестера должен принимать быстрые решения по качеству и оптимальному использованию каждого заготавливаемого дерева. В используемых в настоящее время харвестерах применяются системы измерения и управления, которые осуществляют автоматическую оценку ствола, во время того, как происходит очистка ствола от сучьев и выбирают оптимальные места для распила, тем самым позволяя оператору сконцентрироваться на контроле за качеством древесины. С помощью таких систем быстро и эффективно может задаваться множество требуемых параметров процесса заготовки древесины. Возможен также большой набор автоматических функций: автоматизация управления подачи пильной шины; регулирование прижима сучкорезных ножей и протяжных вальцов либо гусениц; поднятие харвестерного процессора после завершения раскряжевки. Системы обладают функциями диагностики, которые позволяют оператору определить неисправности не покидая кабины.
Наряду с этим оператору предоставляется ряд возможностей доступ к электронной почте, глобальной навигационной системе GPS, интегрированному программному обеспечению, комплексной системе управления харвестером. Информация по всем перечисленным аспектам представляется на одном дисплее.
Так система «Тимберматик 300» полностью компьютеризирована и использует оперативную систему Windows 2000, простой графический интерфейс и два уровня меню. При использовании системы «Тимберматик 300» не нужны отдельный ноутбук и отдельный дисплей для комплексной системы управления харвестером. Оператор может использовать любые программные обеспечения и системы, такие как e-mail, карты, программы глобальной навигационной системы GPS, доступные пользователю PC. Для управления системой «Тимберматик 300» могут использоваться клавиатура, мышь, панель управления либо джойстик. Это упрощает ряд операций, особенно процесс ввода письменной информации.
Ведущие фирмы, выпускающие харвестеры, работают над созданием мультимедийной системы «помощь» (help), которая помимо прочего объединит в себе инструкции, гидравлические и электрические схемы, фотографии и другой визуальный материал для оказания помощи оператору при любых обстоятельствах.
Принципы работы харвестеров
Харвестер во время работы перемещается задним ходом. С любой стоянки он валит и обрабатывает деревья, растущие в рабочей зоне гидроманипулятора. Перед захватом очередного дерева технологическое оборудование поворачивают в вертикальное положение (рис. 22, а) и направляют на дерево, которое захватывают по возможности ниже с противоположной стороны от направления валки (рис. 20, б) и спиливают.
Рукоятью гидроманипулятора осуществляется толчок и дерево падает на растущий лес, что гасит скорость падения и предотвращает резкие динамические усилия на грейфер и гидроманипулятор. Далее дерево обрабатывают аналогично как процессором в горизонтальном положении с очисткой ствола от сучьев и раскряжевкой на сортименты (рис. 20, в, г, д). При глубоком снеге дерево захватывают на высоте 0,5…1 м и включением протаскивающего механизма грейфер опускают по стволу (рис. 20, е).
Рис. 20. Технология работы харвестера: а поворот грейфера в вертикальное положение; б захват и спиливание дерева; в подтаскивание дерева в зону обработки; г процесс обработки; д перенос сучьев на волок для его укрепления; е опускание грейфера по дереву
samzan.ru
Харвестер John Deere 1270D – устройство и технические характеристики
Харвестер John Deere 1270D – это специальная техника, предназначенная для работ по заготовке леса и окончательного прореживания.
Модель John Deere 1270D стала эталоном качества и образцом для подражания. На сегодняшний день техника 1270D считается самой мощной, а в ее производительности сомневаться не приходиться вовсе.
С новым харвестером 1270E заготовка леса больше никогда не будет такой, как раньше. Мощный 9-литровый дизельный двигатель и гидравлическая система с двумя насосами обеспечивают превосходную производительность этой машины.
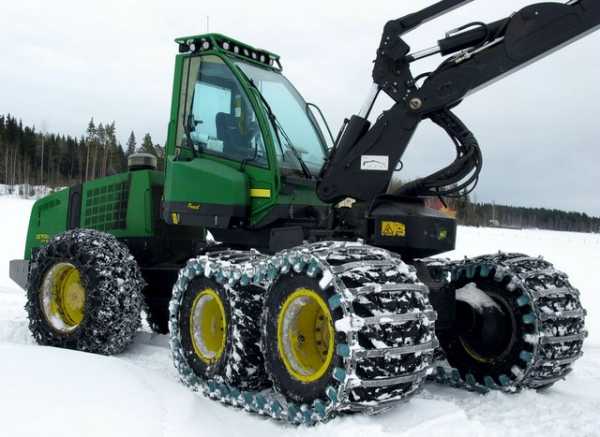
Харвестер оснащен интеллектуальной системой измерения и контроля TimberMatic H-12, позволяющей использовать клавиши быстрого доступа к основным функциям машины, а также настраивать параметры работы навесного оборудования.
Удобство работы оператора, эргономичные органы управления, прекрасная обзорность – в этой машине все сделано для повышения производительности. Попробуйте и убедитесь сами.
Одной из характеристик харвестера 1270D является самое современное автоматизированное оснащение кабины. Все процессы работы совершаются при помощи компьютера., в результате чего многократно повышается эффективность работы машины. Кроме полного комфорта для оператора (кондиционер, система защиты от шума и др.) харвестер 1270D имеет максимальную проходимость, мощный двигатель, благодаря которому легко справляется с самыми тяжелыми работами.
Устройство харвестера John Deere 1270D
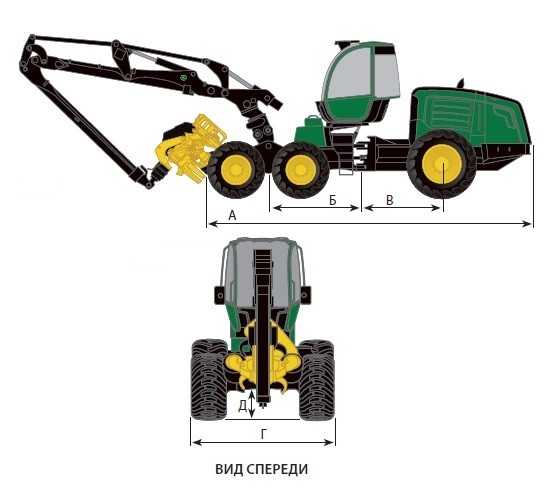
Масса харвестеров John Deere 1270 — 18,4 тонн. В харвестере установлен мощный 6-цилиндровый двигатель 228 л.с., объемом 9 литров. Усовершенствованный манипулятор СН7 имеет максимальный вылет стрелы 8,6 / 10, 11,7 м. Угол поворота стрелы — 220⁰. Гидравлическая система имеет управление по нагрузке. Трансмиссия оснащена блокировкой дифференциала на заднем и переднем мостах.
Вариантов кабины предлагается два: фиксированная и поворотная с возможностью выравнивания. Кабина отличается низким уровнем шума и вибрации, а также оснащена кондиционером и прочими, делающими работу оператора более комфортной, опциями.
Кабина оператора
Просторная, светлая, комфортабельная с эргономическим сиденьем, оснащена простыми в использовании мини-джойстиками управления. Оборудована эффективным отоплением и кондиционированием воздуха. Обеспечивает хорошую обзорность рабочего участка и хорошие условия работы оператора. Кабина испытана на безопасность в соответствии с промышленными стандартами ISO (ROPS, FOPS, OPS, BC).
Уровень шума в кабине соответствует международному стандарту. Кабина снабжена радиомагнитолой, имеет тонированные стекла из ударопрочного материала и гнездо для подключения сотового телефона. В качестве дополнительного оборудования на харвестере «Джон Дир 1270D» устанавливается автоматическая система выравнивания и поворота кабины, повышающая уровень эргономики и снижающая вероятность повреждения кабины деревьями, которые остаются при проведении выборочных рубок.
Двигатель
Джон Дир JD 6081 HTJ D3 с турбонадувом, дизельный, шестицилиндровый, рабочий объем цилиндров 8,1 л, максимальная мощность 160 кВт при частоте вращения коленчатого вала 2000 мин –1, крутящий момент 1100 Нм при частоте вращения коленчатого вала 1400 мин –1, емкость топливного бака 480 л.
Крутящий момент двигателя дает возможность одновременно включать моторы протяжки харвестерной головки и использовать функции гидроманипулятора, что позволяет повысить производительность харвестера. В эксплуатационных условиях двигатель можно использовать на более низких частотах вращения его коленчатого вала, что приводит к снижению расхода топлива, увеличению срока службы кривошипно-шатунного механизма и снижению уровня шума.
Трансмиссия
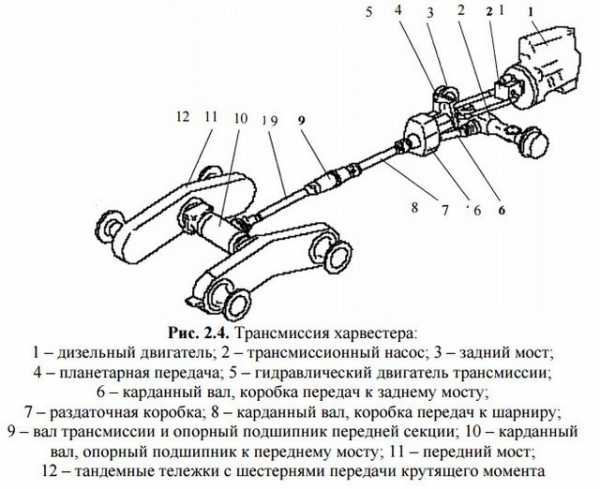
Гидростатическо-механическая с двухдиапазонной раздаточной коробкой передач. Скорость движения V = 0…24 км/ч, максимальное тяговое усилие Рк = 160 кН. Трансмиссия включает в себя гидравлический насос и двигатель, двухступенчатую раздаточную коробку (высшая и низшая передачи), карданные валы. Гидростатический элемент трансмиссии включает в себя гидравлический насос и гидравлический двигатель, которые соединены между собой всасывающим и нагнетательным контуром.
Гидравлический насос и двигатель поршневого типа – с регулируемыми рабочими объемами. Рабочий объем гидравлического насоса находится в пределах 0…100 см3, двигателя – 140…160 см3. При пуске гидравлический двигатель всегда имеет максимальный рабочий объем. Раздаточная коробка распределяет крутящий момент от гидравлического двигателя между передним и задним мостами. Она представляет собой механическую зубчатую передачу и обеспечивает диапазоны высшей и низшей передач, а также позволяет отключить привод на передний мост.
Гидросистема
Постоянного давления, чувствительная к нагрузке, рабочее давление – 24…28 МПа. Производительность насоса – 288 л/мин при частоте вращения 1800 мин –1 вала гидронасоса. Гидросистема харвестера включает в себя:
- гидравлический насос двигателя;
- гидрораспределитель HV09 движения манипулятора;
- гидромотор;
- напорные аккумуляторы;
- гидроклапаны;
- тормоза и т. д.
Тормозная система
Гидравлическая. Рабочий и служебный (вспомогательный) тормозы многодисковые в масляной ванне с гидроприводом. Передний мост оснащен рабочими тормозами перед дифференциалом. Во время обработки дерева, чтобы обеспечить одинаковое усилие на все колеса, блокировка дифференциала срабатывает одновременно с тормозами. Рабочие тормоза заднего моста смонтированы на ступицах. Стояночный тормоз смонтирован перед корпусом заднего моста и имеет механическое пружинное включение и гидравлическое отключение.
Рулевое управление
Бесступенчатое с электроприводом, осуществляется с помощью ручного манипулятора типа «джойстик» поворотом шарнирно-сочлененных полурам двумя гидроцилиндрами. Угол поворота полурам ±42º.
Гидроманипулятор
Со стрелой параллельного действия моделей TJ 210H90, 210H97, 210h215 с максимальным вылетом стрелы (с головкой) 9,3; 10 и 11,8 м и подъемным моментом (брутто) 178 кНм. Угол поворота стрелы – 220º, угол наклона стойки гидроманипулятора – 25º вперед и 13º назад/
Электрооборудование
Генератор 288 В/140 А; две аккумуляторные батареи по 140 А и напряжением 24 В. Установлено 14 сдвоенных рабочих фар и четыре одинарных на гидроманипуляторе с освещенностью в рабочей зоне в темное время суток не менее 30 лк.
Харвестерные (процессорные) головки
Широкий выбор харвестерных головок позволяет использовать харвестер Джон Дир 1270D в разнообразных условиях. Мощные головки Н762 и 758 разработаны для применения на рубках главного пользования, а головки Н754, 745 и Н752D – для использования на рубках ухода. Харвестерные головки 758, Н754 и 745 позволяют работать с деревьями, которые имеют искривленные стволы с толстыми сучьями.
Головка оснащена четырьмя подвижными сучкорезными ножами, мощным четырехвальцовым приводом, гидротормозами, цепным пильным механизмом с гидростатическим приводом.
Механизм валки и раскряжевки харвестерной головки
Включает в себя цепную пилу с гидростатическим приводом. Длина пильной шины составляет 750 мм, шаг пильной цепи – 10 мм, скорость пильной цепи – 40 м/с, рекомендуемая производительность гидронасоса харвестера – 250 л/мин при рабочем давлении в системе 24 МПа. Максимальный диаметр среза дерева (за один прием резания) – 56 см.
Механизм протяжки дерева
Включает в себя четыре гидромотора, которые работают совместно и осуществляют привод двух закрепленных на раме и двух подвижных протяжных вальцов. Усилие протяжки – 22,0…27,0 кН. Скорость протяжки дерева – 4,7 м/с, максимальная величина открытия протяжных вальцов – 70 см.
Механизм обрезки сучьев харвестерной головки
Включает в себя четыре подвижных сучкорезных ножа с гидроприводом. Диаметр ствола дерева в зоне обрезки сучьев, охватываемого сучкорезными ножами на 100 %, – 48 см. Сдвоенный потенциометр, расположенный над сучкорезными ножами, измерительное колесо, прижимаемое к стволу дерева, проводят точное измерение его диаметра и длины.
Технические характеристики John Deere 1270D
Двигатель | ||
Марка | John Deere | |
Модель | 6090HTJ | |
Мощность | 160 кВт | |
Мощность | кВт | |
Мощность | 1400 оборотов в минуту | |
Литраж | 9 л | |
Максимальный крутящий момент | 1100 Нм | |
При частоте вращения | 1400 оборотов в минуту | |
Наддув | Turbocharged | |
Колличество цилиндров | 6 | |
Эксплуатационные параметры | ||
Эксплуатационная масса | 17499 кг | |
Объем топливного бака | 480.7 л | |
Емкость жидкости гидросистемы | 290 л | |
Объем системы охлаждения | 28 л | |
Рабочее напряжение | 24 В | |
Генератор тока, в амперах | 140 ампер | |
Максимальная скорость | 24.9 км/ч | |
Шасси | ||
Дорожный просвет | 624 мм | |
Давление на грунт | 69.6 кПа | |
DRIVE SYSTEM | ||
Tire Size — front | 600 x 26.5, 20 PR Forest King F NK | |
Tire Size — rear | 600 x 34, 14 PR TRS NK | |
Стрела | ||
Максимальная дальность | 9296 мм | |
Размеры | ||
Наклон вперед | 11 градусов | |
Наклон в сторону | 15 градусов | |
Высота до верха кабины | 3709 мм | |
Габаритная ширина | 2767 мм | |
Колесная база | 4038 мм |
Видео обзор харвестера John Deere 1270D
tpscom.ru
Харвестерная головка — основная часть харвестера
Харвестерная головка и её дополнительные устройства
Харвестерная головка состоит из металлического каркаса, соединенного с ним механизма наклона (поворот из вертикального в горизонтальное положение), протаскивающих вальцов и направляющих пластин, сучкорезных ножей, пильного блока, автоматики пилы и отдельных датчиков.
Выпускаемые модели харвестерных головок обычно делят на 2-3 класса по размеру и массе: лёгкие (300-600 кг) преимущественно для рубок прореживания (оптимальная толщина ствола 5-40 см), средние (700-1000 кг) общего назначения (оптимальная толщина ствола 5-50 см) и тяжёлые (1000-1200 кг) для рубок главного пользования (оптимальная толщина ствола 10-60 см). На рынке есть модели массой до 3500 кг, способные обрабатывать стволы толщиной более метра.
Принцип действия харвестерной головки довольно прост. При ее раскрытии цилиндры раздвигают сучкорезные ножи и протаскивающие вальцы. Устройство подводят к комлю дерева и закрывают, цилиндры прижимают вальцы и сучкорезные лезвия к стволу. Дерево спиливается обычной цепной пилой и валится с помощью наклонного (валочного) механизма головки. Протаскивающие вальцы (обычно 2-4 штуки) начинают вращаться и двигать (протаскивать) ствол, при этом срезаются ветки, попадающие под сучкорезные ножи. Раскряжевкой и измерением длины протаскиваемого ствола управляет отдельная автоматика.
Рисунок 1. Харвестерная головка включает: 1 — ограждение пилы, 2 — цепную пилу, 3 — гидродвигатель пилы, 4 — нижние сучкорезные ножи, 5 — гидроцилиндр нижних сучкорезных ножей, 6 — протаскивающие вальцы, 7 — гидродвигатели вальцов, 8 — гироцилиндры захватных рычагов вальцов, 9 — верхние сучкорезные ножи, 10 — гидроцилиндр верхних сучкорезных ножей, 11 — согласующую тягу верхних сучкорезных ножей, 12 — верхний нож, 13 — наклонный механизм, 14 — гидроцилиндр наклонного механизма, 15 — ролик хода, 16 — колесо измерителя длины.
Новые валочные головки для заготовки энергетической древесины отличаются от традиционных тем, что ствол срезается с помощью ножа, приводимого в действие силовым гидроцилиндром, и на головке нет протаскивающих вальцов и сучкорезных ножей. Для промежуточного накопления срезанных деревьев валочная головка имеет дополнительные захватные рычаги.
На рынке также есть модели харвестерных головок, которые осуществляют протаскивание ствола при обрезке сучьев по челночному принципу. На верхней части корпуса головки установлена выдвижная стрела с сучкорезными ножами. После валки дерева эта стрела проходит по стволу, срезая сучья. На конце вылета ножи зажимают ствол и подтягивают его к головке примерно на 2 метра. Операция повторяется необходимое количество раз. Раскряжевка ствола выполняется цепной пилой или ножом (маленькие модели). Такая схема протаскивания ствола менее производительна, но более надежна. Кроме того, она меньше повреждает ствол, поэтому лучше подходит для обрезки сучьев у крупных лиственных деревьев.
Харвестерная головка может быть оснащена дополнительными устройствами. Одно из них — устройство для обработки пней в бесснежный период с целью предотвращения распространения дереворазрушающих грибов. Фунгицид наносят при пропиливании через форсунки, расположенные на специальной шине пилы или отдельной форсункой, установленной на кожухе пилы или на кулачке шины. К форсункам препарат подается по шлангу из бачка на каркасе харвестера, разбрызгивание включается автоматически.
Рисунок 2. Принцип действия устройства для обработки пней. Бачок с препаратом можно установить на передней или задней части машины. Из него препарат по шлангу вдоль гидроманипулятора попадает на харвестерную головку.
Харвестерная головка может быть оборудована маркирующим устройством, которое впоследствии облегчает сортировку схожих сортиментов. Нанесение краски происходит через форсунки, установленные на корпусе головки или в пильном блоке. Обычно применяют 2 форсунки и 2 цвета, которые дают 3 комбинации (синий, красный, синий + красный). Краска наносится на верхний торец бревна в тот момент, когда закончен пропил, и оно начинает падать. Краска по тонким шлангам подается на форсунки из 2-х бачков на каркасе харвестера. Сведения о цветовой маркировке определенных сортиментов обычно посылаются оператору вместе с указаниями по раскряжевке. Процесс маркировки контролируется автоматикой харвестера.
Фото 1. Автоматика харвестера управляет цветовой маркировкой так, чтобы правильные комбинации цветов разбрызгивались на торцы соответствующих им сортиментов в нужные моменты.
lesotehnika.com