МЕТАЛЛЫ И ИХ СВОЙСТВА
Чтобы работа шла успешно, нужно знать свойства материала, его технологические и декоративные качества. В настоящее время используют металлы в чистом виде и сплавы. Металлы и их сплавы делятся на черные и цветные.
Для наших целей понадобится обыкновенная углеродистая сталь. Сталь (сплав железа с углеродом и другими элементами) упруга и обладает способностью закаливаться. Нагретый до красного каления и опущенный в воду кусок стали приобретает различные степени твердости и упругости. При нагревании и медленном охлаждении сталь теряет свои свойства, или, как говорят, отпускается. Сталь куется, хорошо режется. Закаленную сталь вообще нельзя обрабатывать инструментами, ее надо сначала отпустить. Чем меньше в стали углерода, тем она мягче. Мягкость стали повышается при отжиге, который состоит в том, что сталь нагревают докрасна и затем медленно охлаждают. Сталь выпускают в виде сортового материала. Для гравирования и других подобных работ используют стали У8 и У10.
Цветные металлы выпускают в виде чушек, полос, лент, трубок, прутков, проволоки, листового материала.
Медь — довольно мягкий, очень ковкий металл оранжево-красного цвета. Обрабатывается медь легко, но при этом нужно иметь в виду ее большую вязкость. Медь очень хорошо паяется оловом и твердым припоем, обладает большой электро- и теплопроводностью. Листовая медь является основным материалом для чеканных, граверных работ и декоративных работ из проволоки.
Бронза представляет собой сплав меди с оловом; от содержания последнего цвет металла меняется и приобретает то розовый, то красный, то желтый и серый оттенок. Если бронзу покрыть патиной (налетом, состоящим из оксидов меди), то она становится зеленоватой или дымчатой. Бронза пригодна для литейных и инкрустационных работ.
Латунь — сплав цинка и меди. Цвет латуни зависит от содержания в сплаве цинка. Латунь более тверда, нежели красная медь, ковкость латуни значительно хуже. По сравнению с медью она хрупка и обладает некоторой упругостью. Латунь легко поддается различной обработке, ее можно применять в наборе инкрустационных вставок — тонких жилок и украшений различных конфигураций, как листовой материал в чеканных работах.
Цинк — металл синевато-белого цвета, плавится при температуре 419°С, куется плохо, легко паяется и обрабатывается инструментами, а также гравируется, и при соответствующей обработке ему можно придать различный вид. Очень хорош для литья как в чистом виде, так и в сплавах с другими металлами.
Олово — мягкий металл серебристо-белого цвета, плавится при 232 °С. Входит в состав различных бронз. Его легко узнать по характерному хрусту при изломе. Олово идет для лужения посуды, для пайки как в чистом виде, так и в сплавах со свинцом, продукты коррозии безвредны. Олово и его сплавы являются подходящим металлом для инкрустации.
Алюминий — серебристо-белого цвета металл, плавится при температуре около 658 °С. Чистый алюминий легок и легко обрабатывается. Литой алюминий довольно хрупок, а прокатный, отожженный — пластичен.
Свинец — мягкий, очень пластичный металл синевато-серого цвета, плавится при 327 °С, хорошо противостоит окислению. Оксиды свинца ядовиты. Пригоден для литейных работ.
Серебро — в декоративных целях используют в виде сплавов с медью, так как чистое серебро слишком мягкое и неудобно при обработке. Серебряные вставки можно применять в инкрустационных работах, обрабатывая вставки способами гравирования, чеканки и черни.
Рассмотрим некоторые свойства металлов, влияющие на качество исполнения художественных изделий.
Ковкие пластичные металлы требуют силы резания, но необходимо учитывать их вязкость. Кусок меди или» свинца надо рубить зубилом до конца, в то время как кусок латуни, цинка или стали можно надрубить и затем сломать. Более твердая латунь при обточке дает гладкую поверхность, медь или алюминий как бы тянутся за резцом.
Хрупкость — способность твердых тел разрушаться при механических воздействиях без заметной пластической деформации, свойство, противоположное пластичности. Сильно закаленная сталь, многие сорта чугуна и бронз от удара разлетаются на куски. Хрупкость металла не всегда является признаком его твердости, например цинковая отливка хрупка, но не тверда. Закаленный нож и хрупок и тверд.
Упругость — свойство металла восстанавливать свою форму и объем после прекращения действия внешних сил или других причин (например, нагревания), вызвавших деформацию. В наибольшей степени этим свойством обладают специальные сорта стали.
Способность металла плавиться при нагревании — это один из самых дешевых способов получения изделий из металла. Части огромных машин и мелкая скульптура из металла по существу изготовляются одинаковым способом.
Когда необходимо закалить деталь, сохранив вязкость металла, используют токи высокой частоты; деталь закаляется на глубину в несколько миллиметров. Вся остальная масса металла внутри изделия остается без изменения. И, наконец, детали из металла можно обрабатывать без нагревания (гравирование и резьба по металлу).
Похожие статьи:
poznayka.org
Материалы
Инструментальные и конструкционные материалы Механические свойства металлов Большинство деталей машин, обрабатываемых на металлорежущих станках, изготавливается из металлов и их сплавов. Наибольшее распространение имеют чугуны и стали, в меньшей степени — цветные металлы. Для режущих инструментов широко применяются твердые сплавы и абразивные материалы. Твердость закаленных сталей определяют, вдавливая алмазный конус при нагрузке 1470 Н, по черной шкале и обозначают HRCэ. Испытание твердости шариком с нагрузкой 980 Н на приборе Роквелла предусмотрено для мягких незакаленных металлов. В этом случае отсчет показаний ведут по красной шкале, а твердость обозначают HRB. Прочность — способность металла сопротивляться разрушению под действием внешних сил. Для определения прочности образец металла установленной формы и размера испытывают на наибольшее разрушающее напряжение при растяжении, которое называют пределом прочности (временное сопротивление) и обозначают Σв (сигма). Пластичность — способность металла, не разрушаясь, изменять форму под нагрузкой и сохранять ее после прекращения действия нагрузки. При испытании на растяжение пластичность характеризуется относительным удлинением Δ (дельта), которое соответствует отношению приращения длины образца после разрыва к его первоначальной длине в процентах. Черные металлы Железоуглеродистые сплавы с примесями марганца, кремния, серы, фосфора и некоторых других элементов принято называть черными металлами. В зависимости от содержания углерода они делятся на две группы: чугуны и стали. Чугун — сплав железа с углеродом, содержащий свыше 2,3% углерода (практически от 2,5 до 4,5%). Углерод в нем может находится в химически связанном состоянии в виде карбида железа (цементита) и в свободном состоянии — в виде графита. В соответствии с этим чугуны делятся на белые — передельные и серые — литейные. В сером чугуне большая часть углерода находится в свободном состоянии в виде мелких пластинок графита. Последние, разделяя структуру чугуна и действуя как надрезы, значительно уменьшают его прочность и увеличивают его хрупкость. Такие чугуны имеют в изломе серый цвет, обладают хорошими литейными свойствами, почти не дают усадку в отливках и сравнительно легко обрабатываются резанием. Однако, имея в своем составе твердые зерна цементита, серые чугуны значительно ускоряют изнашивание инструмента, что не позволяет обрабатывать их с высокими скоростями резания. Марки серого чугуна обозначаются буквами СЧ и числами, соответствующими его пределу прочности при растяжении в кгс/мм2. В промышленности также применяются отливки из высокопрочных и ковких чугунов. Высокопрочный чугун получают прибавлением к расплавленному чугуну присадок магния и ферросилиция, благодаря чему выделяющийся углерод приобретает шаровидную форму. Такой чугун обладает повышенной прочностью и пластичностью. Его применяют для деталей, работающих при значительных механических нагрузках. В ковком чугуне графит имеет хлопьевидную форму. Этот чугун получают длительным отжигом отливок из белого чугуна. Такие чугуны обладают повышенной прочностью и пластичностью и по своим свойствам занимают промежуточное положение между серым чугуном и сталью. Высокопрочные и ковкие чугуны маркируются буквами и цифрами: ВЧ — высокопрочный чугун, КЧ — ковкий чугун; первые две цифры — предел прочности при растяжении в кгс/мм Сера и фосфор — вредные примеси. Сера придает хрупкость чугуну, делает его густотекучим и пузырчатым. Фосфор увеличивает хрупкость чугуна, но делает его жидкотекучим. Сталь — это сплав железа с углеродом, содержащий до 1,8% углерода. Стали относятся к пластичным металлам, которым деформированием можно придать необходимую форму. По химическому составу они делятся на углеродистые и легированные; по назначению — на конструкционные, инструментальные, особого назначения (нержавеющие, жаропрочные и др.). Углеродистые конструкционные стали подразделяются на обыкновенного качества, качественные и автоматные. Стали обыкновенного качества обозначаются буквами Ст и цифрами о 0 до 7. Качественные имеют меньше посторонних примесей. Они маркируются цифрами 08, 10, 15, 20 и так далее до 60, указывающие содержание углерода в сотых долях процента. Выпускаются две группы таких сталей: I — с нормальным и II — с повышенным содержанием марганца. Последние в конце маркировки имеют букву Г — марганец. Качественные стали группы II обладают повышенной прочностью и упругостью. Легированные конструкционные стали, кроме обычного состава, содержат хром, ванадий, вольфрам, никель, алюминий и др. Эти элементы придают стали определенные свойства: прочность, твердость, прокаливаемость, износостойкость и т.д. Марки легированных сталей обозначают буквами и цифрами. Первые две цифры указывает среднее содержание углерода в сотых долях процента; затем следуют цифры, обозначающие легирующий элемент; цифры после букв — примерное содержание легирующего элемента в процентах. Если содержание элемента близко к 1%, цифра после буквы не ставится. В маркировке приняты следующие буквенные обозначения элементов: Г — марганец, С — кремний, Х — хром, Н — никель, М — молибден, В — вольфрам, Ф — ванадий, К — кобальт, Ю — алюминий, Т — титан, Д — медь. Буква А в конце марки означает, что сталь высококачественная. Инструментальные стали делятся на углеродистые, легированные и быстрорежущие. Углеродистые инструментальные стали содержат углерода от 0,65 до 1,35%, обладают высокой прочностью, твердостью в закаленном состоянии 63-65 HRCэ и теплостойкостью до 200-250 градусов С. Они делятся на качественные и высококачественные. Последние содержат меньше серы, фосфора и остаточных примесей. Марки этих сталей обозначают буквой У — углеродистая, а цифры после нее указывают среднее содержание углерода в десятых долях процента. У высококачественных сталей в конце маркировки указывается буква А. Углерод существенно влияет на свойства стали. С повышением его содержания твердость, износостойкость и хрупкость стали увеличиваются, но вместе с тем ухудшается его обработка резанием. Легированную инструментальную сталь получают введением в высокоуглеродистую сталь хрома, вольфрама, ванадия и других элементов, которые повышают ее режущие свойства. Благодаря легирующим элементам эта сталь приобретает повышенную вязкость и износостойкость в закаленном состоянии, меньшую склонность к деформациям и трещинам при закалке, более высокую теплостойкость (до 300-350 градусов С) и твердость в состоянии поставки. Легированные инструментальные стали маркируются аналогично конструкционным с той лишь разницей., что первая цифра в начале марки означает содержание углерода в десятых долях процента. Быстрорежущие стали представляют собой легированные инструментальные стали с высоким содержанием вольфрама (до 18%). После термообработки (закалки и многократного отпуска) они приобретают высокую красностойкость до 600 градусов С, твердость 63-66 HRCэ и износостойкость. Быстрорежущие стали маркируются буквами и цифрами. Первая буква Р означает, что сталь быстрорежущая. Цифры после нее указывают среднее содержание вольфрама в процентах. Остальные буквы и цифры означают то же, что и в марках легированных сталей. Быстрорежущие стали, легированные ванадием и кобальтом, имеют повышенные режущие свойства. Они предусмотрены для труднообрабатываемых сталей и сплавов высокой прочности и вязкости. Структура быстрорежущей стали (рисунок слева) — мелкие, твердые, однородно распределенные карбиды и мартенсит, легированный для теплостойкости вольфрамом и (или) молибденом Примерное назначение и свойства быстрорежущих сталей
Цветные металлы Из цветных металлов наибольшее промышленное применение получили медь, алюминий и сплавы на их основе. Твердые сплавы Твердые сплавы выпускаются в виде пластинок различных форм и размеров, получаемых методом порошковой металлургии (прессованием и спеканием). Основой для них служат порошки твердых зерен карбидов тугоплавких металлов (вольфрама, титана, тантала), сцементированных кобальтом. Основные марки вольфрамосодержащих твердых сплавов и области их применения
Минералокерамические материалы В целях экономии дорогостоящих и редких материалов, входящих в состав твердых сплавов, создан минералокерамический материал — микролит марки ЦМ332 на основе корунда (оксида алюминия — Al2O3) в виде пластинок белого цвета. Микролит превосходит твердые сплавы по твердости и красностойкости (1300 градусов С), уступая им значительно по вязкости. Поэтому его применяют в основном для получистового и чистового точения при жесткой технологической системе и безударной нагрузке. Основные характеристики и области применения безвольфрамовых твердых сплавов
Основные характеристики и области применения пластин из минералокерамики
Основные характеристики и области применения сверхтвердых синтетических материалов
|
metall-stroi78.ru
Виды и свойства металлов
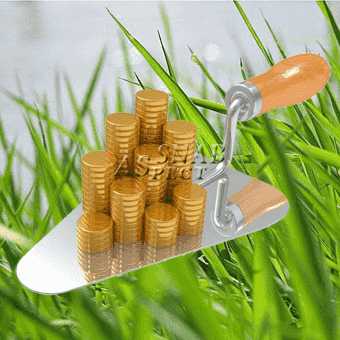
Виды и свойства металлов
Металлы начали обрабатываться человеком сравнительно недавно по историческим меркам
Для того чтобы овладеть навыками мастерства работы с данным видом материала, ему пришлось приобрести необходимые знания по строению и свойствам обрабатываемой поверхности.
Виды металлов
Любой металл как и кирпич имеет отношение к одной из двух больших групп: черные и цветные. К черным металлам относится чугун и сталь. Когда содержание углерода в структуре достаточно низкое, образец имеет право называться сталью. При повышении содержания элемента в структуре происходит изменение свойств стали и постепенное превращение в чугун. Но, кроме углерода, в железной руде могут присутствовать и включения иных металлов. Для обработки чугуна и стали может применяться технологическая резка, в том числе и лазерная резка металла. Для производства особых сталей в значительных масштабах могут добавляться медь, цинк, олово. Они способствуют изменению свойств металла и защите его от коррозии.
Строение металлов
В строении кристаллической решетки металлов между атомами, как между кирпичами, существует уникальный вид связи, названной металлической. В их внешнем слое присутствует довольно малое количество электронов, поэтому им проще отдавать частицы, чем их принимать. При данном виде связи одиночные электроны склонны образовывать пары. Связь будет оставаться в исходной форме вне зависимости от агрегатного состояния элемента. Решетки металлов обладают повышенной прочностью. В узлах решетки закрепляются положительные ионы. Так как все частицы, образующие решетку, имеют заряд такого же знака, то такая решетка практически неразрушима. Ионы упаковываются в такую своеобразную тару весьма плотно, практически под завязку. От валентности металла и от того, в каком ряду в таблице он расположен, форма решетки может изменяться.
Свойства металлов
Свойства металлов могут быть самого разного типа. Все они зависят от особенностей атомного и ионного строения. Каждый металл обладает твердостью. Она препятствует проникновению в его структуру более плотного металла. Это свойство можно проследить на примере гибки листового металла. При изменяющихся внешних условиях это свойство может разниться. Если воздействовать на металлический образец достаточно высокой температурой, то он станет более пластичным, нежели твердым. Также важным свойством металла является его упругость. Упругость можно измерить после того, как указанное на образец воздействие приведено в состояние равновесия. Чем металл мягче, тем он пластичнее. Также металлам присуща пластичность, хрупкость, ковкость, сопротивление на изгиб. Все эти свойства позволяют производить с образцом самые различные манипуляции. Металлы можно скручивать, штамповать, волочить и прокатывать.
Технологические свойства металлов
Технологические свойства металла — сродни свойствам камня или свойствам кирпича это его способность подвергаться определенного вида обработке. Под такой обработкой может подразумеваться сваривание листов, порошковая покраска, прокаливаемость. Свойства литья зависят от формы заливки и жидкотекучести образца. При такой обработке существует понятие литейной усадки — разницы между объемом металла в жидком и твердом состояниях. Возможное состояние металла измеряется методом графического и иного вида анализа. Понятие ковкости включает в себя способность образца воспринимать определенную деформацию. При этом признаков разрушения материала не наблюдается. Ковкость присуща как металлам, находящимся в раскаленном состоянии, так и охлажденным металлам. Стали с небольшим содержанием углерода поддаются деформированию много легче, чем образцы жаропрочные и особо стойкие.
Связанные элементы: Блок ЛСР 10.7 NF RAUF / Блок ЛСР 12.35 NF RAUF. / Блок ЛСР 14.3 NF RAUF
as-snab.ru
Элементы периодической системы и их свойства
Металлы. Свойства металлов
Содержание.
- Строение атомов металлов. Положение металлов в периодической системе. Группы металлов
- Физические свойства металлов
- Химические свойства металлов
- Коррозия металлов
- Понятие о сплавах
- Способы получения металлов
- Список использованной литературы
I. Строение атомов металлов. Положение металлов в периодической системе. Группы металлов.
В настоящее время известно 105 химических элементов, большинство из них — металлы. Последние весьма распространены в природе и встречаются в виде различных соединений в недрах земли, водах рек, озер, морей, океанов, составе тел животных, растений и даже в атмосфере.
По своим свойствам металлы резко отличаются от неметаллов. Впервые это различие металлов и неметаллов определил М. В. Ломоносов. «Металлы, — писал он, — тела твердые, ковкие блестящие».
Причисляя тот или иной элемент к разряду металлов, мы имеем в виду наличие у него определенного комплекса свойств:
- Плотная кристаллическая структура.
- Характерный металлический блеск.
- Высокая теплопроводность и электрическая проводимость.
- Уменьшение электрической проводимости с ростом температуры.
- Низкие значения потенциала ионизации, т. е. способность легко отдавать электроны.
- Ковкость и тягучесть.
- Способность к образованию сплавов.
Все металлы и сплавы, применяемые в настоящее время в технике, можно разделить на две основные группы. К первой из них относят черные металлы — железо и все его сплавы, в которых оно составляет основную часть. Этими сплавами являются чугуны и стали. В технике часто используют так называемые легированные стали. К ним относятся стали, содержащие хром, никель, вольфрам, молибден, ванадий, кобальт, титан и другие металлы. Иногда в легированные стали входят 5−6 различных металлов. Методом легирования получают различные ценные стали, обладающие в одних случаях повышенной прочностью, в других — высокой сопротивляемостью к истиранию, в третьих — коррозионной устойчивостью, т. е. способностью не разрушаться под действием внешней среды.
Ко второй группе относят цветные металлы и их сплавы. Они получили такое название потому, что имеют различную окраску. Например, медь светло-красная, никель, олово, серебро — белые, свинец — голубовато-белый, золото -желтое. Из сплавов в практике нашли большое применение: бронза — сплав меди с оловом и другими металлами, латунь — сплав меди с цинком, баббит — сплав олова с сурьмой и медью и др.
Это деление на черные и цветные металлы условно.
Наряду с черными и цветными металлами выделяют еще группу благородных металлов: серебро, золото, платину, рутений и некоторые другие. Они названы так потому, что практически не окисляются на воздухе даже при повышенной температуре и не разрушаются при действии на них растворов кислот и щелочей.
- Физические свойства металлов.
С внешней стороны металлы, как известно, характеризуются прежде всего особым «металлическим» блеском, который обусловливается их способностью сильно отражать лучи света. Однако этот блеск наблюдается обыкновенно только в том случае, когда металл образует сплошную компактную массу. Правда, магний и алюминий сохраняют свой блеск, даже будучи превращенными в порошок, но большинство металлов в мелкораздробленном виде имеет черный или темно-серый цвет. Затем типичные металлы обладают высокой тепло- и электропроводностью, причем по способности проводить тепло и ток располагаются в одном и том же порядке: лучшие проводники — серебро и медь, худшие — свинец и ртуть. С повышением температуры электропроводность падает, при понижении температуры, наоборот, увеличивается.
Очень важным свойством металлов является их сравнительно легкая механическая деформируемость. Металлы пластичны, они хорошо куются, вытягиваются в проволоку, прокатываются в листы и т. п.
Характерные физические свойства металлов находятся в связи с особенностями их внутренней структуры. Согласно современным воззрениям, кристаллы металлов состоят из положительно заряженных ионов и свободных электронов, отщепившихся от соответствующих атомов. Весь кристалл можно себе представить в виде пространственной решетки, узлы которой заняты ионами, а в промежутках между ионами находятся легкоподвижные электроны. Эти электроны постоянно переходят от одних атомов к другим и вращаются вокруг ядра то одного, то другого атома. Так как электроны не связаны с определенными ионами, то уже под влиянием небольшой разности потенциалов они начинают перемещаться в определенном направлении, т. е. возникает электрический ток.
Наличием свободных электронов обусловливается и высокая теплопроводность металлов. Находясь в непрерывном движении, электроны постоянно сталкиваются с ионами и обмениваются с ними энергией. Поэтому колебания ионов, усилившиеся в данной части металла вследствие нагревания, сейчас же передаются соседним ионам, от них — следующим и т. д., и тепловое состояние металла быстро выравнивается; вся масса металла принимает одинаковую температуру.
По плотности металлы условно подразделяются на две большие группы: легкие металлы, плотность которых не больше 5 г/см3, и тяжелые металлы — все остальные. Плотность, а также температуры плавления некоторых металлов приведены в таблице № 1.
Таблица № 1
Плотность и температура плавления некоторых металлов.
Название | Атомный вес | Плотность, г/см3 | Температура плавления, C |
Легкие металлы. | |||
Литий | 6,939 | 0,534 | 179 |
Калий | 39,102 | 0,86 | 63,6 |
Натрий | 22,9898 | 0,97 | 97,8 |
Кальций | 40,08 | 1,55 | 850 |
Магний | 24,305 | 1,74 | 651 |
Цезий | 132,905 | 1,90 | 28,5 |
Алюминий | 26,9815 | 2,702 | 660,1 |
Барий | 137,34 | 3,5 | 710 |
Тяжелые металлы | |||
Цинк | 65,37 | 7,14 | 419 |
Хром | 51,996 | 7,16 | 1875 |
Марганец | 54,9380 | 7,44 | 1244 |
Олово | 118,69 | 7,28 | 231,9 |
Железо | 55,847 | 7,86 | 1539 |
Кадмий | 112,40 | 8,65 | 321 |
Никель | 58,71 | 8,90 | 1453 |
Медь | 63,546 | 8,92 | 1083 |
Висмут | 208,980 | 9,80 | 271,3 |
Серебро | 107,868 | 10,5 | 960,8 |
Свинец | 207,19 | 11,344 | 327,3 |
Ртуть | 200,59 | 13,546 | -38,87 |
Вольфрам | 183,85 | 19,3 | 3380 |
Золото | 196,967 | 19,3 | 1063 |
Платина | 195,09 | 21,45 | 1769 |
Осмий | 190,2 | 22,5 | 2700 |
Частицы металлов, находящихся в твердом и жидком состоянии, связаны особым типом химической связи — так называемой металлической связью. Она определяется одновременным наличием обычных ковалентных связей между нейтральными атомами и кулоновским притяжением между ионами и свободными электронами. Таким образом, металлическая связь является свойством не отдельных частиц, а их агрегатов.
- Химические свойства металлов.
Основным химическим свойством металлов является способность их атомов легко отдавать свои валентные электроны и переходить в положительно заряженные ионы. Типичные металлы никогда не присоединяют электронов; их ионы всегда заряжены положительно.
Легко отдавая при химических реакциях свои валентные электроны, типичные металлы являются энергичными восстановителями.
Способность к отдаче электронов проявляется у отдельных металлов далеко не в одинаковой степени. Чем легче металл отдает свои электроны, тем он активнее, тем энергичнее вступает во взаимодействие с другими веществами.
Опустим кусочек цинка в раствор какой-нибудь свинцовой соли. Цинк начинает растворяться, а из раствора выделяется свинец. Реакция выражается уравнением:
Zn + Pb (NO3)2 = Pb + Zn (NO3)2
Из уравнения следует, что эта реакция является типичной реакцией окисления-восстановления. Сущность ее сводится к тому, что атомы цинка отдают свои валентные электроны ионам двухвалентного свинца, тем самым превращаясь в ионы цинка, а ионы свинца восстанавливаются и выделяются в виде металлического свинца. Если поступить наоборот, то есть погрузить кусочек свинца в раствор цинковой соли, то никакой реакции не произойдет. Это показывает, что цинк более активен, чем свинец, что его атомы легче отдают, а ионы труднее присоединяют электроны, чем атомы и ионы свинца.
Вытеснение одних металлов из их соединений другими металлами впервые было подробно изучено русским ученым Бекетовым, расположившим металлы по их убывающей химической активности в так называемый «вытеснительный ряд». В настоящее время вытеснительный ряд Бекетова носит название ряда напряжений.
Страницы: 1 2 3 4
www.55referatov.ru
Строение металлов и их свойства
Все металлы имеют кристаллическую структуру. В расплавленном состоянии атомы металлов находятся в беспорядочном движении, а при переходе в твердое состояние они ориентируются определенным образом в пространстве, образуя кристаллическую решетку. Строение решетки и расположение в ней атомов зависит от вида металла. Наиболее распространенными типами кристаллической решетки являются кубическая – у железа и гексагональная – у алюминия.
Рассмотренные виды кристаллических решеток характерны для идеальных кристаллов. Для реальных металлов и сплавов характерно наличие различных дефектов. Дефекты бывают точечные, линейные, и поверхностные. К самым простым точечным дефектам относятся вакансии и межузельные атомы.
Вакансией называется пустой узел кристаллической решетки. Межузельным атомом называется атом, перемещенный из узла в позицию между атомами. Вакансии и межузельные атомы имеются в кристаллах при любой температуре выше абсолютного нуля из-за тепловых колебаний атомов.
К линейным дефектам относятся дислокации. Дислокации образуются за счет нарушения правильного чередования атомных плоскостей при кристаллизация, а также в результате большого числа вакансий.
Поверхностные дефекты образуются в более крупных структурах металла, например, на границе зерен, т.е. групп кристаллов, которые могут быть сориентированы в пространстве различным образом.
Все физико-механические свойства металлов и их особенности являются следствием кристаллической решетки. Высокая прочность металлов объясняется наличием сил, удерживающих атомы в определенных местах кристаллической решетки. В основе упругих деформаций лежит обратимое смещение атомов кристаллической решетки от положения равновесия. В основе пластического деформирования металлов лежит перемещение дислокаций практически при любых температурах и нагрузках.
Основные свойства металлов:
Наличие плоскостей скольжения.
Плоскость скольжения обычно возникает в кристалле в месте наибольшей концентрации атомов.
Наклеп.
Наклеп – это упрочнение металла в процессе его пластической деформации.
Сущность наклепа состоит в том, что при перемещении одних частей кристаллов относительно других по плоскостям скольжения, искажается их форма, они поворачиваются, часть кристаллов может претерпеть излом, что приводит к образованию структуры типа мозаичной. Это приводит к увеличению сопротивления металла деформациям, а следовательно, к повышению его прочности.
Полиморфность.
Свойство металла иметь несколько модификаций. Многие металлы, например железо, могут переходить из одной модификации в другую, т.е. могут иметь различные типы кристаллической решетки.
Применение металлов в строительстве
По применению, стали подразделяются на конструкционные и инструментальные. Конструкционные стали используются для изготовления различных строительных конструкций и деталей машин, а инструментальные – для изготовления инструмента (применяются высокоуглеродистые стали).
Строительные стали, являются малоуглеродистыми. Среднеуглеродистые стали, в основном применяют в машиностроении.
Строительные и машиностроительные стали относят к группе конструкционных сталей.
По механическим характеристикам конструкционные стали делят на семь марок: СтО, Ст1, Ст2, СТЗ, Ст4, Ст5, Ст6. Основными строительными сталями являются СтЗ и Ст5, из которых изготавливают несущие металлические конструкции и арматуру для железобетона. Из сталей Ст4 и Ст5 изготавливают также болты, шурупы и т.д.
Углеродистые стали обыкновенного качества в зависимости от гарантируемых свойств объединяют в группы А, Б и В. В маркировке эту букву добавляют спереди, а в конце маркировки — способ раскисления: спокойный — сп, полуспокойный — пс, кипящий — кп, например: АСтЗпс, ВСт4пс. По группе А стали поставляют с гарантированными механическими свойствами, по группе Б — химическому составу, по группе В — по механическим свойствам и химическому составу.
По требованиям ударной вязкости в зависимости от температурных условий эксплуатации и назначения конструкций углеродистые стали разделяют на 6 категорий (номер категории указывают в конце маркировки после обозначения способа раскисления), например, ВСтЗкп2.
Легированные конструкционные, в том числе и строительные стали маркируют следующим образом. Первые две цифры показывают содержание углерода в сотых долях процента. Затем следуют условные обозначения легирующих элементов. Цифра, стоящая за условным обозначением, показывает приблизительное содержание элемента в процентах. Например, сталь 18Гсп в среднем содержит 0,18% углерода и приблизительно 1% марганца. Буквы «сп» обозначают, что сталь спокойная (по способу раскисления). Сталь 20ХГ2С в среднем содержит 0,2% углерода, приблизительно 1% хрома, приблизительно 2% марганца и приблизительно 1% кремния. Если количество легирующих добавок менее 0,3%, то обозначение легирующего элемента не проставляется. Буква А в конце марки означает, что сталь высококачественная. В строительстве применяют низколегированные стали (по экономическим соображениям): 18Г, 09Г2; 10Г2С1;20ХГ2С и др.
Большое влияние на механические характеристики сталей оказывает содержание углерода. С повышением содержания углерода твердость стали увеличивается, а пластичность уменьшается. Упругость сталей изменяется мало. Модуль упругости изменяется в пределах 2*105 — 2,06-105 Мпа. Предел прочности увеличивается до содержания углерода 0,8-1,0%, а затем снижается.
В строительстве сталь применяют в виде прокатных изделий, имеющих различную форму поперечного сечения – профиль. Используют сталь в строительстве для изготовления несущих конструкций: колонн, балок, ферм. Из низколегированных сталей изготавливают различные виды арматуры периодического профиля (для железобетона). Также сталь используется для изготовления оконных и дверных переплетов.
Основным способом получения стальных изделий являются горячая прокатка. Этим способом получают различные профили, листы, стержни, трубы. Изделия в этом случае называют горячекатанными.
Важной особенностью сталей является способность улучшать свои физико-механические свойства и, в частности, прочность в результате термической и механической обработки.
К термическим видам обработки, применяемым для строительной стали, относят закалку и отпуск. Закалка стали заключается в нагреве ее до высоких температур с последующим охлаждением в воде, масле, расплавленном свинце. Структура и свойства закаленных сталей зависят от скорости охлаждения. Стали, прошедшие закалку, имеют повышенную прочность и твердость, однако при этом имеют склонность к хрупкому разрушению.
Отпуск стали производят с целью уменьшения внутренних напряжений, возникающих при закалке, а также для снижения хрупкости и твердости закаленной стали. Стали при этом нагревают до температуры не выше 600°С и после изотермической выдержки постепенно охлаждают.
Проволоку изготовляют путем вытяжки (волочения). Некоторые виды арматуры периодического профиля изготовляют путем холодного сплющивания. И в том и в другом случае сталь упрочняется за счет наклепа. Арматуру при этом называют холоднотянутой.
Арматуру классифицируют по четырем признакам:
в зависимости от технологии изготовления различают стержневую и проволочную арматуру. Под стержневой в данной классификации подразумевают арматуру любого диаметра в пределах d=6…40 мм;
в зависимости от способа последующего упрочнения горячекатаная арматура может быть термически упрочненной, т.е. подвергнутой термической обработке, или упрочненной в холодном состоянии — вытяжкой, волочением
по форме поверхности арматура бывает периодического профиля и гладкой. Выступы в виде ребер на поверхности стержневой арматуры периодического профиля, рифы или вмятины на поверхности проволочной арматуры значительно улучшают сцепление с бетоном;
по способу применения при армировании железобетонных элементов различают напрягаемую арматуру, т.е. подвергаемую предварительному натяжению, и ненапрягаемую.
Стержневая горячекатаная арматура в зависимости от ее основных механических характеристик подразделяется на шесть классов с условным обозначением: А-I, А-II, А-III, А-IV, А-V, А-VI. Термическому упрочнению подвергают стержневую арматуру четырех классов; упрочнение в ее обозначении отмечается дополнительным индексом «т»: Ат-III, Ат-IV, Ат-V, Ат-VI. Дополнительной буквой С указывается на возможность стыкования сваркой, буквой К — на повышенную коррозионную стойкость. Подвергнутая вытяжке в холодном состоянии стержневая арматура класса А-III, отмечается дополнительным индексом В.
Каждому классу арматуры соответствуют определенные марки арматурной стали с одинаковыми механическими характеристиками, но различным химическим составом. В обозначении марки стали отражается содержание углерода и легирующих добавок.
Стержневая арматура всех классов имеет периодический профиль за исключением круглой (гладкой) арматуры класса А-I.
Арматурную проволоку диаметром 3…8 мм подразделяют на два класса: Вр-I — обыкновенная арматурная проволока (холоднотянутая, низкоуглеродистая), предназначенная главным образом для изготовления сварных сеток; В-II, Вр-II—высокопрочная арматурная проволока (многократно волоченная, углеродистая), применяемая в качестве напрягаемой арматуры предварительно напряженных элементов. Периодический профиль обозначается дополнительным индексом «р»: Вр-I, Вр-II.
Применение в строительстве алюминиевых сплавов:
Чистый алюминий применяют для устройства кровли здания.
Из лент алюминия, переплетенных друг с другом, делают бесчердачные покрытия большого пролета. Остается лишь положить теплую кровлю.
Из прокатных профилей изготавливают оконные и дверные переплеты.
Из проката изготовляют фермы и арки для перекрытия больших пролетов. Выигрыш малый вес.
Сборно-разборочные сооружения различного типа.
Несущие конструкции верхних этажей зданий в сейсмических районах, а также в зданиях с агрессивными средами.
Листы из алюминиевых сплавов применяют для облицовки внутренних и наружных стен.
studfiles.net
Строение и свойства металлов
Характерными свойствами металлов являются наличие металлического блеска и пластичности, высокая электро- и теплопроводность. Характерные свойства металлов обусловлены их строением.
Атомы металлов не однородны. Атом состоит из положительно заряженного тяжелого ядра, и окружающих ядро отрицательно заряженных электронов. Число электронов равно порядковому номеру элемента в таблице Д.И. Менделеева. В ядре атома находятся положительно заряженные элементарные частицы, называемые протонами. Количество протонов равно количеству окружающих ядро электронов. Кроме протонов, в ядре находятся тяжелые электрически нейтральные частицы – нейтроны. Масса электрона в 1840 раз меньше массы протона или нейтрона. Таким образом, вся масса атома сосредоточена в его ядре.
Электроны быстро вращаются вокруг ядра. Внешние, так называемые валентные, электроны у всех металлов относительно слабо связаны с ядром. Слабой связью внешних валентных электронов с ядром и объясняются характерные металлические свойства.
Замечание
Между понятием «металл» как химический элемент и как вещество есть некоторая разница. Химия делит все элементы на металлы и неметаллы по их поведению в химических реакциях. Теория металлического состояния рассматривает крупные скопления атомов металлов, в котором они обладают характерными металлическими свойствами: пластичностью, высокой тепло- и электропроводностью, металлическим блеском. Эти свойства характерны для больших групп атомов. У отдельных атомов таких свойств нет.
Атомы в металле находятся в ионизированном состоянии. Атомы металлов, отдавая часть внешних валентных электронов, превращаются в положительно заряженные ионы. Свободные электроны непрерывно перемещаются между ними, образуя подвижный электронный газ.
При комнатной температуре все металлы, кроме ртути, представляют собой твердые тела, имеющие кристаллическое строение. Для кристаллов характерно строго определенное расположение в пространстве ионов, образующих кристаллическую решетку.
Металлы имеют кристаллические решетки различных типов. Каждая кристаллическая решетка может быть охарактеризована элементарной кристаллической ячейкой.
Элементарная кристаллическая ячейка – наименьший комплекс атомов, повторяя который многократно, можно построить весь кристалл.
У металлов чаще всего встречаются три типа элементарных кристаллических ячеек:
В кубической объемноцентрированной (ОЦК) решетке восемь ионов располагаются по вершинам и один в центре куба, на пересечении диагоналей. Объемноцентрированную кубическую решетку имеют кристаллы железа при комнатной температуре, хрома, вольфрама, молибдена, ванадия и др. Эта решетка характеризуется всего одним параметром решетки – расстоянием между центрами двух ионов, расположенных по одному ребру, обозначенным на рисунке а.
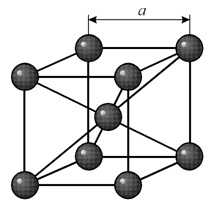
Многие металлы, используемые в технике, имеют гранецентрированную кубическую решетку. В элементарной решетке гранецентрированного куба ионы расположены по вершинам куба и в центре каждой грани (на пересечении ее диагоналей). Центр куба остается свободным. Такую кристаллическую решетку имеют кристаллы меди, никеля, алюминия, свинца, серебра и др. гранецентрированная решетка также характеризуется одним параметром – длиной ребра куба а.
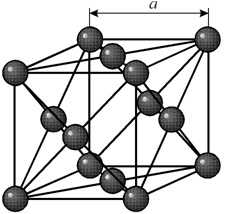
Элементарная ячейка гексагональной плотноупакованной решетки представляет собой шестигранную призму. По основаниям призмы расположены правильные шестиугольники по вершинам которых и в их центрах находятся ионы. Посередине между основаниями вклинивается правильный треугольник с ионами по вершинам.
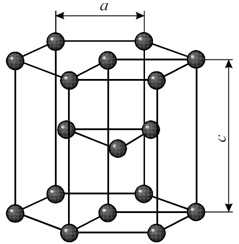
Гексагональная решетка характеризуется двумя параметрами: а и с. Наибольшая плотность упаковки достигается при соотношении параметров с/а = 1.633. Гранецентрированная решетка с таким соотношением параметров называется гранецентрированной плотноупакованной. Такую решетку имеют титан, цирконий, кобальт, цинк, магний и др.
Строение металлических сплавов
Под металлическим сплавом понимают вещество, получаемое сплавлением двух или более элементов, обладающее характерными металлическими свойствами.
Металлические сплавы получают сплавлением элементов – металлов или металлов с неметаллами при преимущественном содержании металлов. Строение сплавов сложнее, чем чистых металлов.
При кристаллизации жидкого сплава могут получаться твердые металлические сплавы с различным строением.
Механическая смесь двух чистых металлов А и В получается в том случае, когда в процессе кристаллизации сплава из жидкого состояния разнородные атомы не входят в общую кристаллическую решетку. В механической смеси каждый металл образует самостоятельные кристаллы. Кристаллы каждого их металлов, находящиеся в этом сплаве, обладают теми же строением и свойствами, которыми они обладают в куске чистого металла.
Твердый раствор – сплав, у которого атомы растворимого элемента размещены в кристаллической решетке растворителя. На микрошлифе твердого раствора кристаллы после травления выглядят одинаково. В кристаллах твердого раствора существует только один тип кристаллической решетки. Растворителем является тот элемент, кристаллическую решетку которого имеет твердый раствор. Растворимый элемент может либо замещать элемент-растворитель в узлах кристаллической решетки, либо располагаться в междоузлиях. По типу расположения атомов растворимого элемента в кристаллической решетке твердые растворы делят на две группы: замещения и внедрения.
Твердые растворы внедрения образуют металлы с неметаллами. Атомы неметаллов меньше атомов металлов. Поэтому атомы неметаллов могут располагаться в междоузлиях кристаллической решетки металлов. Внедрившийся атом вызывает искажение решетки металла-растворителя. Все твердые растворы внедрения – растворы с ограниченной растворимостью.
Химические соединения металлы образуют как с металлами так и с неметаллами. Химическое соединение характеризуется определенной температурой плавления, скачкообразным изменением свойств при изменении состава. Химические соединения металлов с неметаллами образуются при строго определенных соотношениях входящих в них элементов, соответствующих нормальным валентностям. Химические соединения обладают повышенной твердостью и пониженной пластичностью. Кристаллическая решетка химического соединения имеет сложное строение.
Диаграмма состояния
Диаграмма состояния представляет собой графическое изображение состояния сплава. Если изменится состав сплава, его температура, давление, то состояние сплава изменится, и это находит отражение в диаграмме состояния.
Диаграмма состояния показывает устойчивые состояния, которые при данных условиях обладают минимальным уровнем свободной энергии. Поэтому диаграмма состояния может также называться диаграммой равновесия, поскольку показывает, какие при данных условиях существуют равновесные фазы. Следовательно, и изменения в состоянии, которые отображены на диаграмме, относятся к равновесным условиям, т.е. при отсутствии перенагрева или переохлаждения. Так как превращения в отсутствии перенагрева или переохлаждения в действительности не могут совершаться, поэтому диаграмма состояния представляет собой теоретический случай.
Общие закономерности сосуществования устойчивых фаз, отвечающих теоретическим условиям равновесия, описываются правилом фаз или законом Гиббса.
Закон Гиббса дает количественную зависимость между степенью свободы системы и количеством фаз и компонентов.
Фазой называется однородная часть системы, отделенная от других частей системы (фаз) поверхностью раздела, при переходе через которую химический состав или структура вещества изменяется скачком.
Однородная жидкость – однофазная система.
Смесь двух видов кристаллов – двухфазная система.
Компонентами называются вещества, образующие систему.
Чистый металл – однокомпонентная система.
Сплав двух металлов – двухкомпонентная система.
Среди диаграмм состояния металлических сплавов самое большое значение имеет диаграмма состояния системы железо-углерод. Это объясняется наиболее широким применением в технике железоуглеродистых сплавов.
Диаграмма железо-углерод относится к диаграммам состояния для сплавов с ограниченной растворимостью. Диаграмма железо-углерод, как ясно из названия, должна распространяться от железа до углерода. Железо образует с углеродом ряд химических соединений, но надежно установлено лишь одно Fe3C – карбид железа или цементит. Каждое устойчивое химическое соединение можно рассматривать как компонент, а диаграмму изучать по частям.
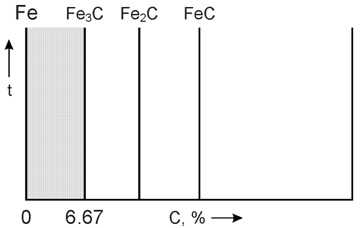
Следовательно, рассматривая диаграмму железо-углерод на участке от железа до цементита, мы можем компонентами системы считать железо и цементит.
Рассмотрим свойства отдельных компонентов.
Железо. Температура плавления 1539 °С. Железо аллотропическое вещество. Атомы элемента могут образовывать, если исходить только из геометрических соображений, любую кристаллическую решетку. Однако устойчивым, а, следовательно, реально существующим типом является решетка, обладающая наиболее низким запасом свободной энергии.
В ряде случаев (и для железа в том числе) при изменении температуры или давления может оказаться, что для одного и того же металла более устойчивой будет другая решетка, чем та, которая была при другой температуре или давлении.
Так для железа характерны две кристаллические решетки:
• объемноцентрированный куб;
• гранецентрированный куб.
Существование одного металла в нескольких кристаллических формах носит название полиморфизма или аллотропии. Различные кристаллические формы одного и того же вещества называются полиморфными или аллотропическими модификациями. Аллотропические формы обозначаются греческими буквами α, β, γ и т.д., которые в виде индексов добавляются к символу, обозначающему элемент. Аллотропическая форма, существующая при самой низкой температуре, обозначается через α, следующая через β и т.д. Превращение одной аллотропической формы в другую при нагреве чистого металла сопровождается поглощением тепла и происходит при постоянной температуре. На термической кривой превращение отмечается горизонтальным участком. При охлаждении происходит выделение тепла теоретически при той же температуре, что и при нагреве, но практически при более низкой вследствие переохлаждения.
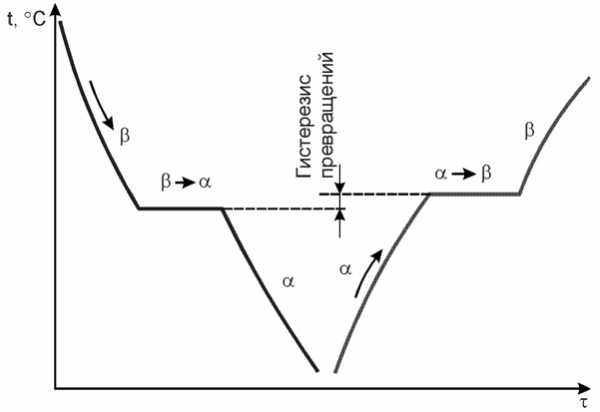
Явление полиморфизма основано на едином законе об устойчивости состояния с наименьшим запасом энергии.
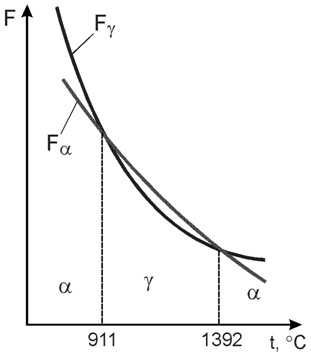
Запас свободной энергии зависит от температуры. Поэтому в одном интервале температур более устойчивой является модификация α, а в другом модификация γ.
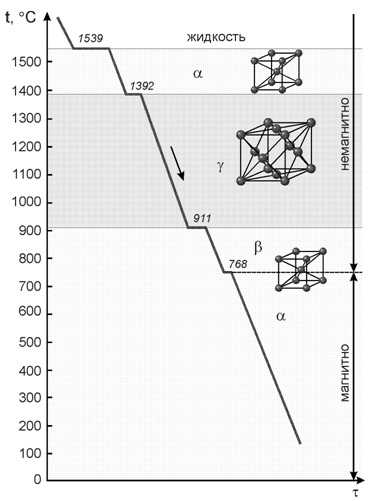
Железо имеет две температуры полиморфного превращения: 911 и 1392 °С.
Особо следует рассмотреть образование растворов углерода в железе. Растворимость С в Fe существенно зависит от того, в какой кристаллической форме существует железо.
Диаметр атома углерода (в свободном состоянии) равен 1.54 A. В объемноцентрированной решетке имеется 12 свободных мест в середине ребер. Диаметр такого свободного места 0.62 A. Такой объем явно недостаточен для помещения в нем атома углерода.

В гранецентрированной кристаллической решетке в центре имеется пора диаметром 1.02 A. В этой поре атом углерода может поместиться, вызывая естественно некоторое увеличение размера решетки γ-железа.
Таким образом, геометрические соображения подсказывают, что α-железо не растворяет, а γ-железо растворяет углерод. В действительности α-железо растворяет углерод, но в очень небольшом количестве ≈ 0.02%.
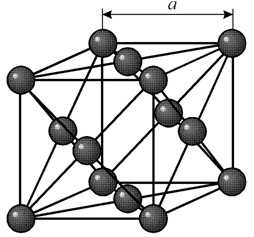
Твердый раствор углерода в α-железе называется ферритом, а в γ-железе аустенитом.
Цементит. Цементит – это химическое соединение углерода с железом (карбид железа Fe3C).
Так как растворимость углерода в α-железе мала, то при нормальных температурах в подавляющем большинстве случаев в структуру стали входят высокоуглеродистые фазы в виде цементита.
Кристаллическая структура цементита очень сложна.
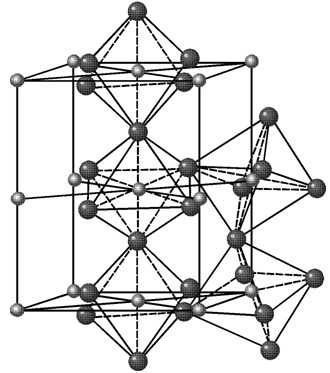
Температура плавления цементита 1600 °С. Аллотропических превращений не испытывает. Цементит имеет высокую прочность ~ 800 НВ и практически нулевую пластичность.
Цементит — соединение неустойчивое и при определенных условиях распадается с образованием свободного углерода в виде графита. Процесс имеет огромное практическое значение.
Историческая справка. Начало изучению диаграммы железо-углерод (а также железоуглеродистых сплавов и процессов термической обработки) было положено работой Чернова Д.К. «Критический обзор статей Лаврова и Калакуцкого о стали и стальных орудиях и собственные исследования Д.К.Чернова по этому же предмету», опубликованной в 1868 году. Этот год можно считать годом возникновения науки металловедения.
В этой работе Чернов впервые указал на существование в стали критических точек, и на зависимость их положения от содержания углерода. Таким образом, Чернов дал первое представление о диаграмме железо-углерод.
Диаграмма железо-цементит имеет двойную концентрационную ось абсцисс. Содержание углерода и содержание цементита.
Линия ABCD является ликвидусом. Это линия – геометрическое место точек начала кристаллизации. Линия AHJECF – солидус. Геометрическое место точек конца кристаллизации.
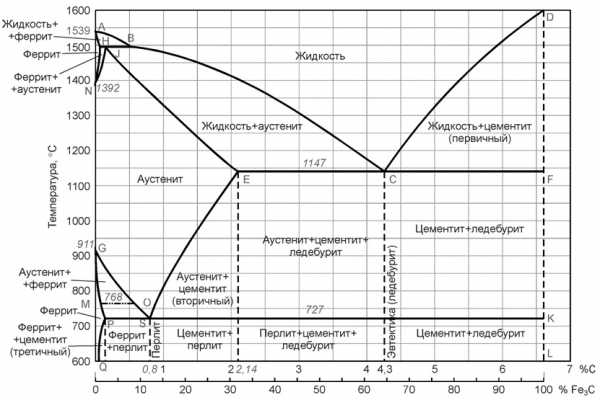
Так как железо с углеродом образует химическое соединение Fe3C, и еще имеет две аллотропические формы α и γ следовательно в системе существуют следующие фазы:
• жидкость (жидкий раствор углерода в железе) располагается выше линии ликвидус и обозначается Ж;
• цементит Fe3C – вертикаль DFKL, обозначается Ц;
• феррит – структурная составляющая, которая представляет собой α-железо, растворяющая в незначительном количестве углерод, область феррита левее линий GPQ и AHN, обозначается Feα;
• аустенит – структура, представляющая собой твердый раствор углерода в γ-железе, область аустенита на диаграмме NJESG, обозначается Feγ.
Три горизонтальные линии на диаграмме HJB, ECF, PSK указывают на протекание трех нонвариантных реакций. Вариантность – это число степеней свободы системы. Если число степеней свободы равно нулю (нонвариантная система), то нельзя изменить внешние и внутренние факторы системы (температуру, давление, концентрацию) без того, чтобы это не вызвало изменение числа фаз.
При 1499 °С (линия HJB) протекает перитектическая реакция:
Ж + Feα → Feγ
Перитектическая реакция представляет собой реакцию, когда жидкость реагирует с ранее выпавшими кристаллами и образует новый вид кристаллов.
В результате перитектической реакции образуется аустенит. Реакция имеет место только у сплавов, содержащих углерода от 0.1 до 0.5%.
При температуре 1147 °С (горизонталь ECF) протекает эвтектическая реакция:
Ж → Feγ + Ц
Эвтектическая реакция – реакция кристаллизации одновременно двух (или более) видов кристаллов из жидкости. Механическая смесь двух (или более) видов кристаллов называется эвтектикой. В результате этой реакции образуется эвтектическая смесь. Эвтектическая смесь аустенита и цементита называется ледебуритом. Эта реакция протекает у всех сплавов, содержащих углерода > 2.14%.
При температуре 727 °С (горизонталь PSK) протекает эвтектоидная реакция:
Feγ → Feα + ЦII
Превращение протекает аналогично кристаллизации эвтектики, но исходным раствором является не жидкость, а твердый раствор.
Такое превращение называется эвтектоидным, а смесь полученных кристаллов эвтектоидом. Эвтектоидная смесь феррита и цементита называется перлитом и имеет вид перламутра. У всех сплавов, содержащих свыше 0.02% углерода, т.е. практически у всех промышленных железоуглеродистых сплавов имеет место перлитное (эвтектоидное) превращение.
Кристаллы выделившиеся из твердого раствора называются вторичными кристаллами и обозначаются символом II (например Цп) в отличие от первичных кристаллов, выделяющихся из жидкости.
У всех сплавов, содержащих менее 2.14% углерода, в результате первичной кристаллизации получается структура аустенита; у всех сплавов содержащих более 2.14% углерода, структура состоит из ледебурита с избыточным аустенитом или цементитом.
Это различие в структуре при высоких температурах и создает существенное отличие в технологических и механических свойствах сплавов.
Наличие эвтектики делает сплав нековким, вместе с тем более низкая температура плавления высокоуглеродистых сплавов облегчает применение их как литейных материалов.
Железоуглеродистые сплавы, содержащие менее 2.14% углерода называются сталями, а более 2.14% — чугунами.
Различают три группы сталей:
• эвтектоидные, содержащие около 0.8% углерода, их структура перлит;
• доэвтектоидные, содержащие II + П (цементит вторичный + перлит).
all4study.ru