Станок холодной штамповки: устройство и принцип действия
При работе с металлом используется разнообразное оборудование. Изготавливать изделия сложной формы можно с помощью станков для холодной штамповки. Методом выдавливания на металлический лист наносят узор, делают отверстия, штампуют изделия сложной формы. Существует два вида штамповки и несколько видов оборудования для проведения этого технологического процесса.
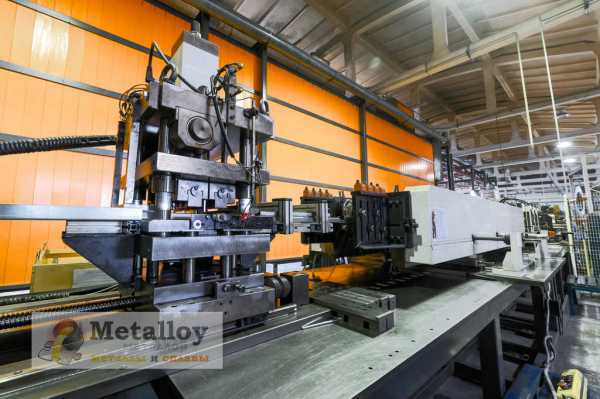
Станок холодной штамповки
Принципы листовой штамповки
Холодная штамповка детали — технологический процесс, при котором на лист металла оказывается сильное давление. Механическое воздействие передаётся на обрабатываемый материал с помощью специальных машин. Помимо холодной существует горячая обработка.
У листовой обработки металла есть сильные и слабые стороны. Преимущества:
- увеличение эффективности производства;
- минимальная дополнительная обработка материалов после выдавливания;
- возможность создания прочных изделий сложной формы;
- актуальность применения технологического процесса при серийном производстве деталей;
- минимальное количество отходов при обработке металлических листов.
Недостатки:
- возникают сложности при проектировании хода работ;
- пресс-формы требуют дополнительных вложений;
- настройка промышленного оборудования требует наличия определённых навыков.
При серийном производстве деталей минусы скрашиваются высокой эффективностью технологического процесса.
Виды обработки и оборудования
Прежде чем говорить о штамповочном оборудовании следует разобраться с видами обработки:
- Холодная — ряд действий, в ходе которых изготавливают детали для вентиляции, корпусов машин, самолётов. Преимущества этого метода — экономия материала, увеличение эффективности производства.
- Горячая — технологический процесс, с помощью которого штампуют металлические листы толщиной до 4 мм. Изначально материал разогревается до определённой температуры, затем используется специальное оборудование для его обработки. Для разогревания используются печи разного типа.
Холодная штамповка металла не требует дополнительных навыков. Горячий метод проводится с учётом определённых особенностей. При остывании материал может изменять форму.
При обработке используются такие станки:
- электромагнитные;
- гидравлические;
- кривошипно-шатунные;
- радиально-ковочные.
Используя специальное оборудование, нужно учитывать ряд особенностей, зависящих от конструкции и возможностей станка.
Принцип работы и устройство оборудования
Штамповка металла проводится с помощью пресса. Существует несколько видов инструмента. Пресс приводится в действие с помощью пара, жидкости или газа.
Кривошипно-шатунный
Это станок, в котором вращающееся движение двигателя становится обратно-поступательным. Нагрузка передаётся штампу, который воздействует на рабочую поверхность материала. Во время работы создаётся давление до 8 тысяч тонн. С их помощью проводят:
- прошивку;
- выдавливание;
- формирование заусенцев.
Кривошипные прессы для листовой штамповки увеличивают эффективность производства, позволяют сэкономить материал.
При работе с материалами большой толщины используют гидравлическое оборудование. Оно оказывает меньше усилий на рабочую поверхность, но достигает большего эффекта. Механические прессы воздействуют на заготовки ударами, что эффективнее при работе с тонколистовым металлом.
Гидравлический
Обработка металлических листов гидравлическими прессами можно назвать продавливанием. Состоит из двух цилиндров, заполненных водой, соединительной трубы, поршней. После запуска механизмов увеличивается давление. Гидравлические прессы используются для штамповки металла большой толщины.
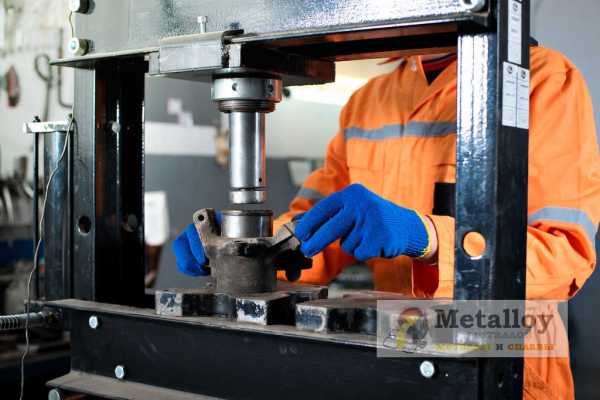
Гидравлический пресс
Радиально-ковочный
Аппарат, который обрабатывает материал теплом. Заготовку отправляют в специальный модуль, который разогревает её по методу индукции. Когда материал будет разогрет до определённой температуры, он перемещается по конвейеру до зоны обработки. Выдавливание производится с помощью бойков. Заготовка крутится, а рабочие части обрабатывают её по всей поверхности. Радиально-ковочный пресс для штамповки листового металла приводится в действия с помощью электромотора.
Электромагнитный
Штамповочный пресс для металла на основе электромагнитов считается новейшей технологией обработки металлических листов. Представляет собой мощный электромагнит, который начинает толкать штамп под воздействием электромагнитного поля. В исходное положение рабочая часть возвращается при разжимании пружин, отключении электромагнита от сети. Это экономичное и долговечное оборудование.
Этапы изготовления штампов
Чтобы выполнить штамповку деталей, нужно уметь проектировать штампы. Если расчёты проведены неправильно, достичь хорошего результата невозможно. Этапы изготовления штампов:
- Чертёж будущего изделия.
- Разбор рабочего процесса, этапов взаимодействия элементов оборудования.
- Подгон окончательных размеров штампа.
Если расчёты проведены верно, нужно изготовить штамп и приступить к обработке металлических листов. Штамповка на кривошипных прессах требует точного расчёта размера заготовки, её толщины и прочности. При работе с толстыми заготовками нужно материал предварительно разогреть. Так уменьшаются показатели твердости, прочности, металл становится податливым к механическим нагрузкам.
Штамповка металлических листов считается популярным технологическим процессом. С его помощью изготавливают детали, использующиеся в автомобилестроении, самолётостроении, судостроении, строительстве. Учитывая особенности используемого оборудования, правильно изготавливая штампы, можно увеличить эффективность производства, сделать его экономичнее.
metalloy.ru
Кузнечно-прессовое оборудование: классификация
Машины для выполнения ковочно-штамповочных операций (так вернее, ибо какое-либо оборудование обычно создаётся под разработанную технологию, а не наоборот) – распространённый вид устройств для металлообработки.
Например, на машино- и приборостроительных предприятиях или заводах по производству металлоконструкций на каждые 5 металлорежущих станков обязательно приходится одна единица оборудования для обработки давлением. Причём не только металлов: например, те же ПЭТ-бутылки производятся на термопластавтоматах, которые тоже представляют специализированное штамповочное оборудование.
Виды кузнечно-прессового оборудования
Всё многообразие конструкций и схем кузнечно-штамповочного оборудования (КШО) классифицируют по следующим показателям:
По температуре обрабатываемой заготовки
Машины для ковки, горячей штамповки, холодной листовой штамповки, холодной объёмной штамповки.
По виду операций, которые выполняются на машине
Различают заготовительное, основное КШО, а также КШО для заключительных стадий обработки давлением.
По способу подачи и удаления изделий из зоны обработки
Неавтоматизированное оборудование, штамповочные комплексы, машины-автоматы, автоматизированные штамповочные линии.
По типу энергоносителя
В качестве которого может использоваться электроэнергия, сжатый воздух, пар, жидкость высокого давления, а также несколько указанных источников одновременно.
По характеру обработки металла
Выделяют машины статического и динамического действия. Сюда же принято относить и установки для высокоэнергетической штамповки.
По основному технологическому параметру
Которым может быть номинальное усилие (для механических прессов), предельное усилие (для гидравлических и пневматических прессов), крутящий момент (для машин ротационного действия), энергия удара (для молотов).
Все остальные классификационные признаки – последовательность размещения основных узлов
Способ управления и т.д. — носят вспомогательный характер
Следует отметить: в вопросах названия определённых типов КШО элемент терминологической путаницы вносят различия в обозначениях технологических процессов, которые исторически приняты в отечественной и иностранной профильной литературе.
Так, машины для холодной объёмной штамповки часто именуют оборудованием для холодной ковки металла. Происходит это из-за буквального перевода английского термина cold forging (холодная ковка), который некритично воспринимается производителями КШО, в частности, из Китая, Тайваня и т.д.
Аналогично случилось и с термином forging (в иностранной литературе понятие hot forging практически не употребляется: всё, что не делает cold forging, автоматически зачисляется в горячештамповочное оборудование). Таким образом, следует точно различать принципиальные различия в областях применения КШО у нас в стране, и за рубежом, и использовать их в дальнейшем:
Оборудование для ковки
Ковка, как операция горячей обработки штучных заготовок давлением, отличается от горячей штамповки тем, что в последнем случае для формоизменения металла обязательно нужна технологическая оснастка – штамп. Чисто ковочное КШО предназначается для заготовительных операций – чаще осадки, расплющивания, открытой прошивки – а потому не содержит повышенных требований к точности полуфабриката (который в дальнейшем ещё будет обрабатываться различными способами, в том числе, и штамповкой). Поэтому оно должно обеспечивать лишь необходимую мощность формоизменения.
Для горячей ковки металла
Применяются два различных вида КШО: ковочные молоты (см. рис. 1) и гидравлические прессы (см. рис.3). Крупные ковочные молоты могут использовать в качестве энергоносителя пар и сжатый воздух, мелкие – только сжатый воздух (см. рис.2). Гораздо реже используются газовые и гидравлические молоты. Молоты имеют преимущественно вертикальную компоновку.
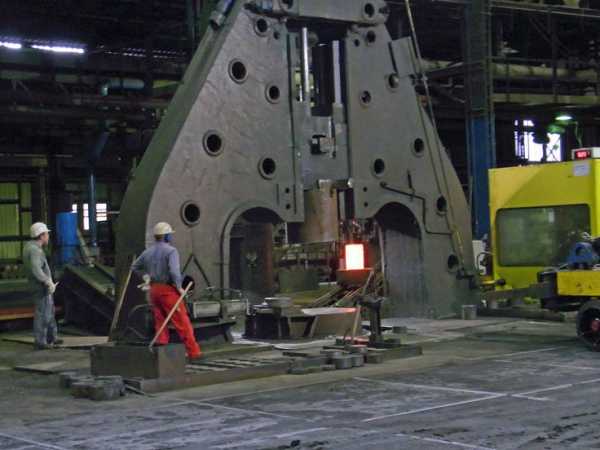
Рисунок 1 – ковочный паровоздушный молот
Поскольку при ковке создаются большие динамические нагрузки, то фундамент ковочного молота с подштамповой плитой обычно отделяется от остальных его узлов, что хорошо заметно на рис.1.
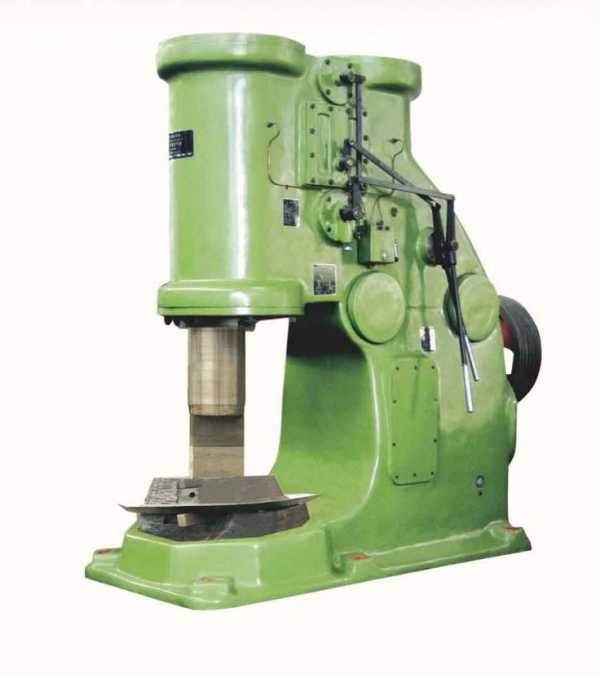
Рисунок 2 – Пневматический ковочный молот.
Молоты
Для свободной ковки отечественного производства маркируются буквой М/МА и четырьмя цифрами, две первых определяют тип энергоносителя (13,15 – паровоздушный молот, 41 – пневматический молот). Две последних цифры обозначают основной параметр оборудования – массу падающих частей в тоннах. Например, марка молота МА 4134 соответствует пневматическому молоту с массой падающих частей (мпч) 250 кг, а М1345 – паровоздушному молоту с мпч 3150 кг.
Гидравлические прессы
Применяются для горячей ковки заготовок, которые отличаются особо большими габаритными размерами. Например, поковку вала океанского судна куют с несколькими нагревами металла в течение суток и даже более. В молоте такая заготовка не сможет разместиться, поэтому деформацию производит ползун ковочного пресса. Такое оборудование отличается весьма большими габаритными размерами, поскольку только в таком случае можно обеспечить необходимое давление на металл.
Для механизации
Транспортных операций – подачи, кантовки заготовки в процессе ковки и т.д. – применяются специальные манипуляторы, которые могут быть безрельсового (для сравнительно небольших поковок) и рельсового типа.
Маркировка ковочных
Гидропрессов отечественного производства выполняется буквой П, после которой указываются конструктивное исполнение пресса (первые две цифры) и его номинальное усилие в тоннах (вторые две цифры). Например, марка ПБ1341 соответствует ковочному гидропрессу усилием 12500 кН.
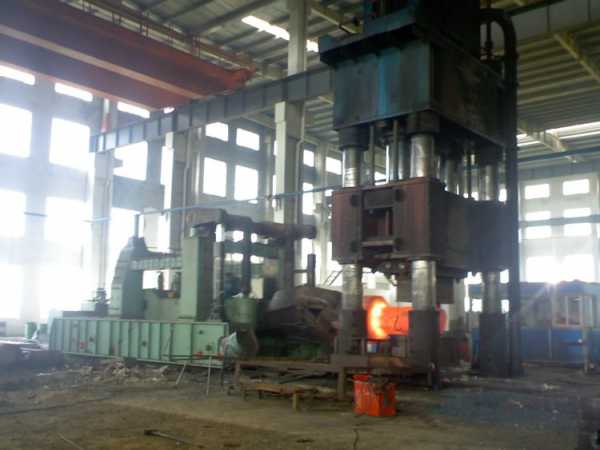
Рисунок 3 – Ковочный гидравлический пресс с манипулятором.
Оборудование для горячей объёмной штамповки
Точность горячей штамповки должна быть по определению выше, чем ковки: во многих случаях непосредственно после деформирования деталь не нуждается в последующей доработке.
Поэтому класс горячештамповочного оборудования дополняется, кроме штамповочных молотов, ещё кузнечными бульдозерами, кривошипными горячештамповочными прессами (КГШП) и горячештамповочными автоматами. В эксплуатации продолжает оставаться некоторое количество горизонтально-ковочных машин (ГКМ).
Паровоздушные
Штамповочные молоты конструктивно отличаются от ковочных меньшими значениями энергии удара и более жёсткой конструкцией, которая связывает между собой шабот, подштамповую плиту и стойки молота (в которых перемещается баба) в единую топологическую систему.
Поскольку усилия, возникающие при штамповке, всегда больше ковочных (сказывается более сложная конфигурация штампованной поковки), то сжатый воздух как энергоноситель в данной ситуации неэффективен.
Даже при использовании мощных паровоздушных штамповочных молотов (ППШМ) по заготовке приходится наносить несколько ударов, пока она не приобретёт форму, установленную штампом. Горячая штамповка выполняется обычно с одного нагрева, поэтому скорость деформирования имеет очень большое значение. Поэтому все ППШМ — молоты двойного действия, в которых баба дополнительно разгоняется основным энергоносителем.
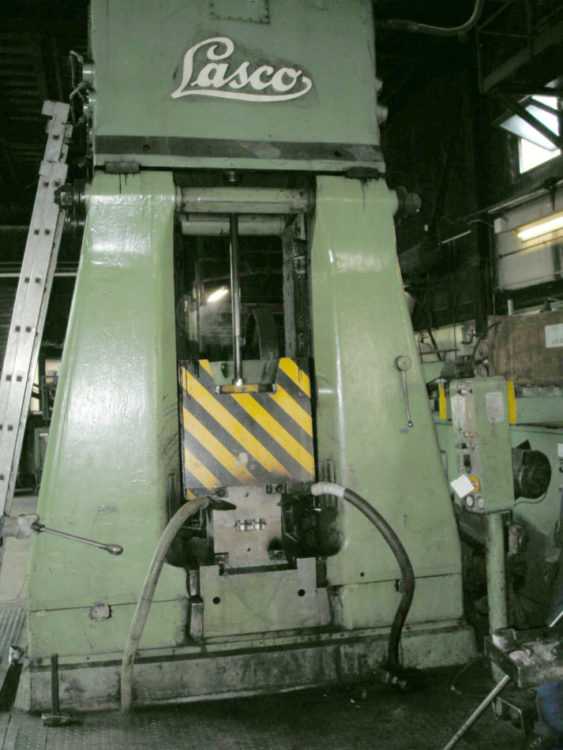
Рисунок 4 – Паровоздушный штамповочный молот.
ППШМ
Простые с конструктивной точки зрения машины, но надлежащую точность горячей объёмной штамповки они не всегда обеспечивают. Причины:
- Вибрация элементов оборудования и штампа;
- Остывание поковки при многократных ударах бабы молота;
- Износ рабочих элементов гравюры штампа.
Кроме того, автоматизировать штамповку на молоте в большинстве случаев невозможно. Поэтому для точной штамповки процесс проектируют на КГШП, а снижение энергии деформирования (КГШП формоизменяют металл с гораздо более низкими скоростями) компенсируют увеличением позиций штамповки.
Виду этого штампы на КГШП – составные (а не цельные, как на молотах), и представляют собой совокупность отдельных вставок, которые располагаются в последовательности, соответствующей стадиям деформирования заготовки. Это облегчает переналадку штампа, оптимизирует время вспомогательных операций и снижает вибрации при работе оборудования.
Фото общего вида современного КГШП представлено на рис. 5.
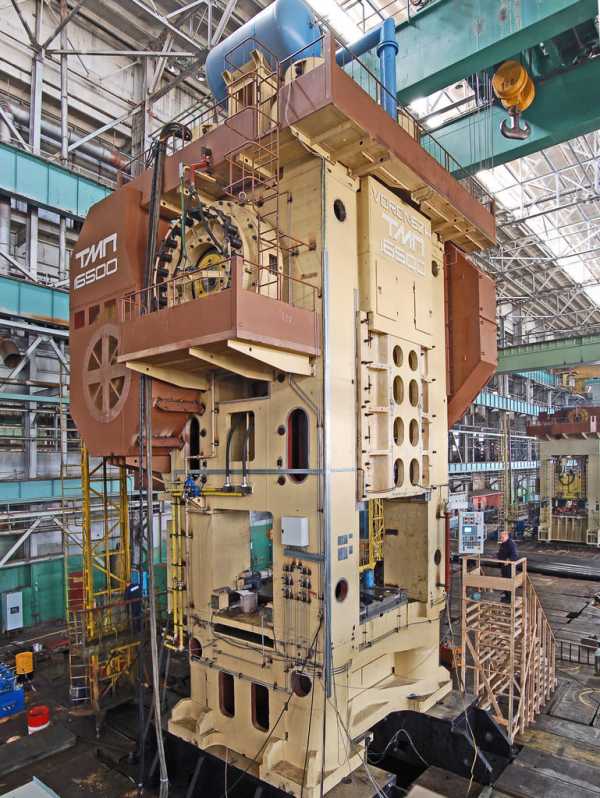
Рисунок 5 – КГШП номинальным усилием 165 МН.
Маркировка
Такого оборудования отечественного производства также представляет собой комбинированное буквенно-цифровое обозначение: первой идёт буква К, последующие две первых цифры (80 или 85) указывают на конструктивные особенность машины, а две последних – на её номинальное усилие. Например, КГШП модели КБ8544 обладает номинальным усилием 25 МН.
В условиях массового производства
Мелких и средних поковок типа толкателей клапанов, железнодорожных костылей, крупных метизов экономически целесообразно применять горячештамповочные автоматы (ГША).
В отличие от ГКМ
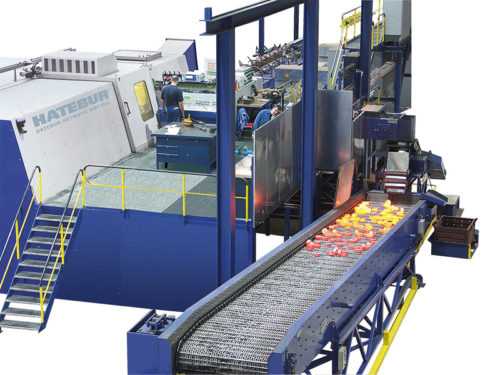
Рисунок 6 – Общий вид горячештамповочного комплекса на базе ГША модели АМР-70.
Свою нишу в производстве поковок методом горячей объёмной штамповки достойно заполняют винтовые прессы с дугостаторным приводом (см. рис. 7).
Эти машины сочетают в себе принципы статического и динамического деформирования, поскольку работают со скоростями ниже, чем молоты, но выше, чем КГШП. Штамповка происходит перемещающимся внгих винтом, который получает движение от гайки, раскручиваемой специализированным дугостаторным двигателем с бегущим электромагнитным полем.
Винтовые прессы
Применяются для производства поковок из алюминиевых сплавов, мелких и средних стальных поковок, изделий, которые имеют тонкие рёбра и перемычки. Из-за простоты управления, возможности автоматизации и низкой стоимости винтовые машины нашли широкое применение и в холодной штамповке.
Маркировка машин включает в себя букву Ф (первоначально источником привода винта являлись не электромагнитные силы, а силы трения от диска, фрикционно сцеплявшегося с элементами приводного вала) с последующими четырьмя цифрами (17 — тип привода: дугостаторный и – далее – две цифры, указывающие на номинальное усилие).
Например, обозначение АКФ 1730 указывает на автоматизированный комплекс на базе винтового пресса с дугостаторным приводом номинальным усилием 1 МН.
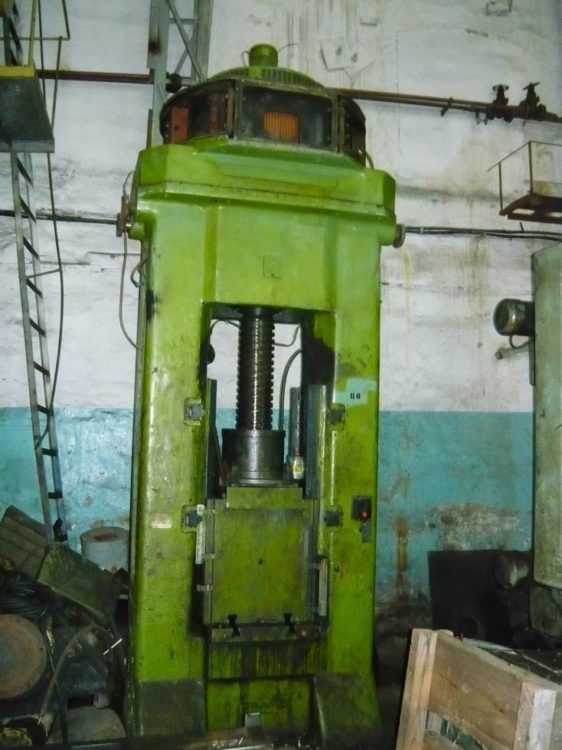
Рисунок 7 – Винтовой пресс с дугостаторным приводом усилием 1600 кН.
Кузнечные бульдозеры
(или горизонтально-гибочные машины, см. рис. 8) применяются для горячей гибки заготовок из толстой полосы.
Это — оборудование, которое отличается простотой конструкции и высокими эксплуатационными показателями. Используются кузнечные бульдозеры преимущественно в средне- и мелкосерийном производстве, поскольку не отличаются высокой производительностью.
Их маркировка
Включает в себя букву И (этот индекс присваивается всем видам КШО, которые выполняют гибку заготовок) и 4 цифры; две последние традиционно указывают на номинальное усилие оборудования. Например, И1230 – горизонтально-гибочная машина усилием 1000 кН.
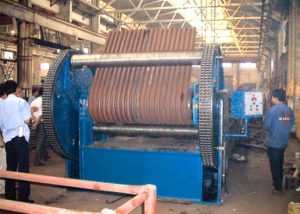
Рисунок 8 – Горизонтально-гибочная машина.
Оборудование для холодной штамповки
Холодноштамповочное КШО различают по выполняемым операциям, среди которых:
- Разделительные/заготовительные.
- Штамповка листового материала.
- Штамповка из полосы или ленты.
- Формообразующие операции с листовым металлом (вытяжка, гибка).
- Холодная объёмная штамповка – выдавливание, высадка.
- Комбинированная штамповка из листа – листообрабатывающие центры.
В качестве заготовительного оборудования используются кривошипные или дисковые ножницы. Первые могут резать как сортовой, так и профильный прокат, в то время, как дисковые ножницы предназначены для роспуска только тонколистового металла в виде рулонов или широкой ленты.
Сортовые ножницы
Для резки прутка чаще встречаются в цехах горячей или холодной объёмной штамповки. Они представляют собой однокривошипные механические прессы с устройствами для подачи прутка и его удерживания во время разрезания.
Листовые ножницы
Машины горизонтального исполнения, которые оснащаются двумя шатунами, поскольку зона реза должна быть несколько больше ширины листа. Листовые ножницы могут иметь гидравлический привод, что используется в моделях, работающих с металлом толщиной более 16 мм.
Комплексы
На базе кривошипных ножниц оснащаются приводными рольгангами, поворотными столами и другими механизмами, снижающими трудоёмкость резки.
Маркировка ножниц отечественного производства начинается в буквы Н. Характерно, что последними двумя цифрами маркировки листовых ножниц обозначают не усилие, а толщину разрезаемого металла (одновременно указывается и предел прочности в МПа, для которого было рассчитано это усилие).
Например, модель Н1830 – кривошипные сортовые ножницы усилием 1000 кН, а НК3414 – листовые ножницы для резки листа толщиной до 2,5 мм. Внешний вид оборудования представлен на рис. 9, 10, 11.
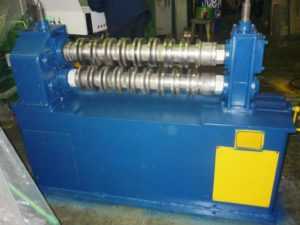
Рисунок 9 – Многодисковые ножницы.
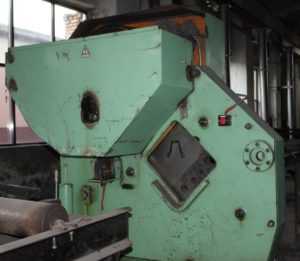
Рисунок 10 – Сортовые ножницы.
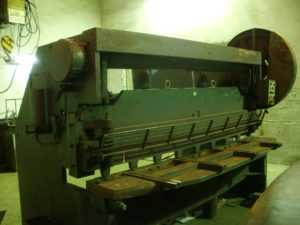
Рисунок 12 – Листовые ножницы с наклонным ножом
Листовую холодную штамповку ведут на механических или гидравлических прессах вертикального исполнения
Механические прессы различаются по следующим характеристикам
Количеству кривошипов
Один, два или четыре.
По форме станины
Открытая или закрытая.
По количеству стоек
Одна или две.
По наличию или отсутствию узлов
Автоматизации штамповки.
По количеству ползунов
Простого или двойного действия.
Для операций листовой штамповки, не требующих большого хода ползуна (пробивка, вырубка, гибка, неглубокая вытяжка) используются однокривошипные открытые прессы вертикального типа. Для глубокой вытяжки применяют прессы двойного действия.
Габаритные заготовки, деформирование которых не сопровождается большими технологическими усилиями, производят на двухкривошипных открытых прессах, а при значительных усилиях деформации применяют закрытые кривошипные прессы.
Гидравлические прессы в холодной штамповке используются реже, поскольку не отличаются высокой производительностью.
Общей тенденцией для холодноштамповочного КШО считается удобство управления оборудованием, для чего прессы часто оснащают автоматическими подачами, сбрасывателями, питателями.
Кривошипные механические прессы
Отечественного производства маркируются буквой К, а гидравлические – буквой Г. Принцип формирования остальных символов в маркировке не отличается от рассмотренного выше.
Отдельную категорию холодноштамповочного КШО составляют
Листообрабатывающие центры
Они особенно эффективны в условиях мелкосерийного производства, когда из одного и того же листа можно штамповать (в основном, вырубкой и пробивкой) одновременно несколько различных по конфигурации деталей. Такое оборудование имеет роторное исполнение.
Типовые представители КШО для холодной листовой штамповки представлены на рис. 13, 14, 15.
КШО
Для холодной объёмной штамповки разделяют на две группы
Прессы для холодного выдавливания, а автоматы для холодной высадки.
Первую группу составляют
Вертикальные (реже – горизонтальные) прессы с механическим или гидравлическим приводом. Поскольку при холодном выдавливании требуется развивать большие технологические усилия, обеспечивая оборудованию одновременно и значительную жёсткость, то вместо традиционной кривошипной схемы в данном случае применяется схема кВ кривошипно-коленчатым механизмом.
Она даёт возможность при сравнительной компактности конструкции обеспечивать необходимые нагрузки деформирования заготовки. Такие машины маркируются обозначением К00 или К83/82 (последние две цифры, которые здесь не указаны, определяют номинальное усилие пресса).
Поскольку холодная высадка – технология, адаптированная под массовый выпуск продукции типа болтов, гаек, винтов и прочего крепежа, то реализуется она исключительно на автоматизированном оборудовании. Выпускаются отдельно автоматы для изготовления стержневых деталей, и для холодной высадки коротких изделий.
Для накатывания резьбы на полуфабрикатах
Выпускаются резьбонакатные станки. Они могут быть трёх исполнений:
Плашечного
Где резьба получается работой двух плашек – подвижной и неподвижной:
Роликового
Пригодного для накатки резьбы на изделиях без головки;
Планетарного
При котором накатка выполняется инструментом типа «ролик-сегмент».
Многие холодновысадочные автоматы снабжаются резьбонакатными головками, и могут производить полностью готовые метизы. Примеры современного оборудования , предназначенного для операций холодной объёмной штамповки показаны на рис. 16 и 17.
Примеры работы различных видов КШО можно посмотреть на многих видео YouTube.
Например, на видеоролике представлена работа паровоздушного молота с мпч 8000 кг.
Здесь:можно наглядно увидеть работу кривошипного пресса для холодной контурной гибки по задаваемой программе.
В ролике разъясняется устройство многопозиционного холодновысадочного автомата для изготовления болтов.
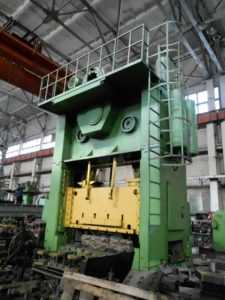
Рисунок 13 – Двухкривошипный пресс простого действия со станиной закрытого типа.
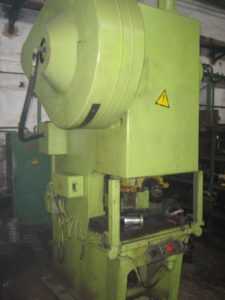
Рисунок 14 – Однокривошипный открытый пресс с С-образной станиной.
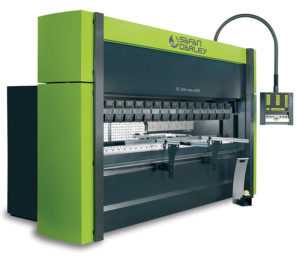
Рисунок 15 – Современный листообрабатывающий центр.
stanki-info.ru
Автоматические штамповочные комплексы | World Machinery
Оборудование для изготовления деталей методом штамповки листового металла, заранее подготовленного на линии продольной резки.
Принцип работы
Единожды заправив штрипс, получаем показатели машинной выработки. Автоматическая линия подачи рулонного металла повышает скорость выпуска деталей в 3,5 раза и снижает затраты на металл до 30% по сравнению с ручной подачей заготовки из листа.
Роботизированная подача
Благодаря комплексному оборудованию, детали проходят каждый этап обработки с помощью автоматизированной подачи, без необходимости вручную перекладывать изделие. Сортировка деталей происходит автоматически, операциями управляет контроллер. Человеческий фактор сведен к минимуму — производительность труда увеличена!
Подача детали
Изготовление детали на многопозиционном штампе с греферной подачей
Работа правильно-подающего устройства
На видео представлена подача металла из рулона на пресс.
Готовые изделия
- Элементы кузовов автомобилей
- Детали корпусов морских и речных судов
- Элементы крыльев и фюзеляжей самолетов
- Элементы электродвигателей
- Металлическая посуда
- Корпуса осветительных приборов
- Узлы и детали станков
- Лотки, подвесы, крабы, зацепы, зажимы, закладные
Конфигурация получаемых деталей разнообразна: плоские, с отогнутыми под углами краями, с выдавленной пуклевкой, перфорацией, чеканкой. В зависимости от вида штампуемой продукции, которую определяет заказчик в техническом задании, состав комплекса подбирается индивидуально.
Преимущества
- Низкая стоимость оборудования
- Скорость выпуска деталей выше
- Снижает затраты на металл до 30%
- Обработка металла в шахматном порядке
- Обработка метала с высокой текучестью
- Большой диапазон ширины и длины подачи металла
- Высокая жесткость корпуса
- Высокий крутящий момент
- Низкий уровень шума
- Централизованное управление
- Добавление рабочих устройств
- Автоматическая система смазки
- Высокая износоустойчивость
- Высокая точность операций
- Низкая ударная нагрузка
- Регулируемая высота плиты
- Безопасность управления
Оборудование
Основным инструментом в линии является пресс для комплексной штамповки деталей. Конструкция и электронная система пресса позволяет добавлять дополнительные рабочие устройства. Пресс подбирается индивидуально под техническое задание заказчика специалистами компании. Как пример представлен кривошипный штамповочный пресс с С-образной станиной. Гидравлическое оборудование также вписывается в линию штамповочного комплекса.
В автоматическую линию входят: подающее и разматывающее устройство для
w-m.group
§ 3. Оборудование для объемной штамповки
Горячая объемная штамповка осуществляется на штамповочных молотах, прессах, горизонтально-ковочных машинах и специальных машинах узкого назначения.
Штамповочные молоты используются для штамповки поковок различной формы в основном в многоручьевых открытых штампах. Основным типом таких молотов являются паровоздушные штамповочные молоты с массой падающих частей 0,63 – 16 т, реже применяются фрикционные молоты с массой падающих частей 0,5 – 15 т.
Паровоздушные штамповочные молоты различают простого и двойного действия. Эти молоты отличаются от ковочных молотов конструкцией станины и шабота, но они обеспечивают большую точность перемещения частей штампов. Для точного совпадения положения верхней половины штампа, прикрепленной к бабе, относительно нижней, укрепляемой на штамподержателе левую и правую стойки станины молота монтируют на шаботе и устанавливают на доном фундаменте. Кроме того, штамповочные молоты имеют более совершенные направляющие, прикрепляемые к стойкам, для обеспечения строго определенного направления движения бабы на всей длине рабочего хода. Для нормальной работы штамповочного молота необходимо, чтобы масса шабота была в 20 – 30 раз больше массы падающих частей.
Применяют также бесшаботные паровоздушные штамповочные молоты. У этих молотов вместо тяжелых шаботов имеются две бабы (верхняя и нижняя), которые при работе движутся навстречу друг другу по направляющим общей станины. На нижней бабе устанавливают нижнюю половину штампа с заготовкой, верхняя половина штампа крепится к верхней бабе. Штамповка происходит при соударении обеих баб. Привод у бесшаботных молотов паровой или воздушный. Число ударов — 6 – 20 в мин.
Применяются также молоты гидравлические и фрикционные с доской.
Штамповка на молотах осуществляется как правило, за 3 – 5 ударов. В конце последнего удара обе части штампа стыкуются по плоскости разъема. Средняя масса поковок при массе падающих частей 1000 кг составляет 0,5 – 5 кг, при 10 000 кг – 40 – 100 кг.
Штамповочные прессы применяют винтовые фрикционные, гидравлические и кривошипные.
Винтовые фрикционные прессы применяют для штамповки в открытых и закрытых штампах небольших поковок (до 20 кг) и используются в мелкосерийном производстве.
Гидравлические прессы для штамповки аналогичны ковочным гидравлическим прессам, но имеют более жесткую конструкцию и выталкиватели для удаления поковок из штампа. На этих прессах штампуют главным образом крупные поковки (массой 100 – 350 кг) в открытых и закрытых штампах с одной или несколькими плоскостями разъема.
Кривошипные ковочноштамповочные прессы относятся к числу наиболее прогрессивных ковочных машин. Внедрение кривошипных прессов обеспечивает повышение производительности штамповки в 1, 5 – 2 раза по сравнению со штамповкой на молотах, экономию металла – проката, применяемого в виде заготовок на 10 – 30%, а штамповка в закрытых штампах сокращает производственный цикл (т. е. уменьшает число операций). Изготовление поковок на этих прессах с наименьшими припусками на механическую обработку позволяет на 15 – 30% сэкономить время на их последующую обработку в механических цехах.
Рабочий орган пресса – ползун, несущий верхнюю часть инструмента (штампа), приводится в возвратно-поступательное движение при помощи кривошипно-шатунного механизма.
В отличие от молотов кривошипные прессы имеют жесткий график движения ползуна. Полный ход (путь) ползуна равен удвоенному радиусу кривошипа. Каждому углу поворота кривошипного вала соответствует определенное положение ползуна и определенная его скорость, которая в крайних точках (вверху и внизу) равна 0.
Кривошипные прессы для горячей штамповки обладают высокой жесткостью конструкции, которая необходима для снижения упругих деформаций и получения наиболее точных размеров поковок. Пресс имеет выталкиватели в столе и ползуне для автоматического удаления поковок из штампа.
К недостаткам таких прессов относится:
необходимость точного определения массы заготовок;
требования отсутствия окалины на заготовках;
стоимость в 3 – 4 раза больше , чем молотов.
Горизонтально-ковочные машины применяются для горячей высадки различных деталей (типа стержня с утолщением, со сквозным отверстием, с глухой полостью, а также сложной конфигурации) из пруткового материала или из труб в многоручьевых штампах. Конструкция штампов позволяет осуществлять также пробивку отверстий, обрезку по контуру, отрезку от прутка. ГКМ различают с разъемом матриц в вертикальной и горизонтальной плоскостях. Две плоскости разъема состоят из 3 частей: неподвижной и подвижной матриц и пуансона.
Двойная плоскость разъема штампов дает возможность штамповать большинство поковок без штамповочных уклонов и облоя. Заготовку (пруток) устанавливают в неподвижную матрицу до упора. Главный ползун с пуансоном приводится в движение от кривошипно-шатунного механизма. Прежде чем пуансон соприкоснется с торцем заготовки, подвижная матрица прижимает ее к неподвижной матрице, а упор отводится в сторону. Ползун с неподвижной матрицей перемещается от бокового ползуна , который в свою очередь, приводится в движение от кулачков, закрепленных на главном валу.
Исходным материалом для штамповки на ГКМ служит круглый, реже квадратный или прямоугольный прокат повышенной точности, диаметром до 270 мм и массой до 100 кг.
ГКМ изготавливают с усилием 100 – 3150 т и числом ходов 95 – 21 в минуту. Производительность высокая – 400 – 900 поковок в час.
studfiles.net
Производство штампов для станков-молотов
Штампы широко используются в разных отраслях машиностроения на всех массовых и серийных производствах, для изготовления различного рода деталей, поковок и заготовок. Это инструменты, с помощью которых можно получить одинаковые изделия и детали, поковки и заготовки, методом пластической деформации. Они пластически деформируют заготовку, сообщая ей форму рабочей части штампа. Устанавливаются штампы на оборудование, предназначенное для штамповки (прессы, молоты), оно и приводит его в действие.
Производство штампов может происходить либо внутри самого предприятия – в инструментальных цехах, либо их можно заказать по индивидуальным чертежам на предприятиях, имеющих для этого квалифицированный персонал и высокопроизводительное оборудование. Второй вариант экономически выгоден мелким производителям.
С развитием и совершенствованием технологий, количество новых изделий соответственно увеличивается, а их многообразие форм требует новых деталей. Для их производства соответственно требуются новые штампы и этот процесс постоянен. Так, как штампы используются в разных отраслях производства, то их конструкция сильно отличается в зависимости от предназначения. Штампы условно можно подразделить по технологии их использования и по оборудованию для их установки. По технологии: штампы для горячей штамповки и штампы для холодной штамповки. По оборудованию: для прессов, молотовые и для горизонтально ковочных машин — ГКМ.
Разнообразие штампов
Конструкция и производство штампов сильно отличается между собой в зависимости от их предназначения. Так штампы, предназначенные для станков-молотов, имеют, в отличие от устанавливаемых на другое оборудование, небольшое количество деталей. Это обусловлено тем, что формовка протекает в ручьях – участках поверхности половинок штампа, которые повторяет форму конечного изделия. Как уже замечено, штамп состоит из двух половин, сходящиеся с довольно высокой точностью по поверхности раздела штампа. Поверхности раздела штампа иногда могут иметь несколько ручьев: окончательный и высадочный, протяжной и подкатной, отрубной и гибочный.
Как минимум половина, из огромного количества разнообразнейших прессов, в качестве рабочего инструмента нуждаются в штампах. Особенно это заметно в листовой штамповке, где они довольно широко используются. Именно там они имеют наиболее характерное устройство в виде двух плит, направляющих и рабочих деталей (пуансона, матрицы и т.д.). Хотя иногда применяются и довольно необычные варианты штампов.
Технология штамповки металла
Штамповка, как правило, технологически подразделяется на холодную и горячую и обе они подразумевают применение определенного давления, а также специальных форм, которые локализуют течение металла, что позволяет получить максимально точные образцы изделий. Методом штамповки получают разнообразные детали – фланцы, шестерни, корпуса, крышки, платы и прочее, имеющую плоскую или изогнутую конструкцию.
![]() | ![]() | |
формоизменяющие — гибочные штампы | подкладной штамп |
Любая штамповка металла, подразумевает использование различного оборудования – это гидравлические прессы и горячештамповочные прессы, горизонтально-ковочные агрегаты и кузнечно-штамповочные машины, молоты и пресс – молоты и так далее.
В ассортименте компании ООО «Станметалломаркет» имеется высокотехнологичное оборудование, используемое для штамповки металла. Оно выпущено лучшими европейскими производителями, дающие гарантии на высокое качество своей продукции. Штамповочное оборудование обладает высокими эксплуатационными характеристиками, и оно отличается надежностью при длительном сроке эксплуатации. Основными достоинствами поставляемого оборудования предназначенного для штамповки являются: лёгкость использования, удобство эксплуатации, экономичность.
![]() | ![]() | |
холодная штамповка | горячая штамповка |
Некоторые особенности и отличия холодной и горячей штамповки
Современную штамповку металла обычно подразделяют на два разных способа, имеющих принципиальное отличие, – холодную и горячую. Холодная штамповка или холодная деформация считается одним из наиболее экономически обоснованных способов производства большой номенклатуры деталей. Применение холодной штамповки экономически выгодный процесс обработки металла, так, как зачастую не требует дальнейшей механической доводки деталей, и они отличаются высокой взаимозаменяемостью, а также хорошей прочностью и жесткостью.
В холодной штамповке используются штампы: разделительные и формоизменяющие - гибочные. Разделительные штампы осуществляют отрезку или вырезку, пробивку или просечку, и т.д. Для гибки, завивки, обтяжки, вытяжки, формовки и т.д. применяют формоизменяющие или как ещё их называют гибочные штампы. Холодная штамповка по исходному материалу разделяется на листовую и объёмную.
В листовой используется лист, полоса, лента и иногда проволока. Можно к этому добавить и следующее, что в листовой штамповке допускается использование разных материалов, включая и неметаллические. В объёмной штамповке используется толстая полоса, профильный прокат, пруток.
Горячая штамповка чаще всего используется в серийном производстве. У этого способа высокая безотходность и точность получаемых изделий и деталей, а также возможность изготовления довольно сложных форм. Главными способами горячей штамповки являются прессование и объёмная штамповка, а также ковка на молотах в подкладных штампах.
stanmetallomarket.ru
Штамповочные станки по металлу. Пресс штамповочный и другие механизмы для ковки
Один из самых востребованных способов металлообработки, позволяющий получить как плоские, так и объемные детали сложной конфигурации — штамповка металла.
Данная технология позволяет производить изделия весом до 2 тонн, более крупные изделия изготавливаются методом ковки.
Принцип штамповки и технологические процессы при ней
Штамповка изделий и деталей из металла относится к металлообработке давлением, при этом возможности данной технологии достаточно широки. При помощи штамповочного оборудования выполняется резка заготовок по заданным размерам и конфигурации, изменение формы путем пластической деформации и другие преобразования исходного материала.
К основным штамповочным операциям относятся:
- Гибка — процесс позволяющий изменить форму заготовки по заданным радиусам.
- Формовка позволяет изменить форму отдельных участков детали при сохранении основных ее контуров.
- Обжим применяется для сужения частей полых объемных заготовок. Для этого применяется объемные штампы различной конфигурации, которые воздействуют на обрабатываемую деталь снаружи. От формы штампа и матрицы зависит будущая конфигурация изделия.
- При осуществлении вытяжки заготовки из листовой стали формируются в объемные плоские изделия. Данная операция позволяет получать цилиндрические, полусферические или конические детали.
- Отбортовка позволяет получить отогнутый край по контуру заготовки или вокруг пробитых в ней отверстий. Данный метод применяется для изготовления горловин, фланцев и других подобных узлов.
Штамповка изделий из металла предполагает выполнение и различных отрезных (разделительных) операций:
- Резка может выполняться как по прямой линии, так и по кривой различной конфигурации. Предназначена для получения заготовок с определенными параметрами из листа металла.
- Вырубка применяется для отделения заготовки, имеющей замкнутый контур.
- Пробивка используется для получения отверстий различного диаметра.
Виды штамповки
На сегодняшний день существует несколько разновидностей технологии штамповки, они отличаются источником энергии, создающим давление на штамп, температурным режимом и другими характеристиками.
На практике чаще всего используют следующие технологии:
- Холодная штамповка
Холодная штамповка изделий из металла применяется при обработке легированной или углеродистой стали, меди и алюминия, а также их сплавов. Выполнение этих работ не требует предварительного разогрева заготовок. Данная технология позволяет получать изделия с высокой точностью размеров, достигается это благодаря отсутствию термической усадки, которая характерна для других технологий, предполагающих предварительный разогрев заготовок.
При помощи холодной штамповки можно получать детали, имеющие минимальные размеры и массу. Применяемое оборудование и технологические линии позволяют организовать производство, как в серийном, так и в единичном масштабе. Оборудование достаточно просто перенастраивается для изготовления деталей с различными параметрами.
К недостатку технологии стоит отнести тот факт, что с ее помощью можно изготовить только сравнительно небольшие изделия, максимальная масса которых не превышает 1 тонны. Изготовление более крупных деталей требует приложения значительных усилий и является экономически нецелесообразным.
Горячая штамповка листового металла и профиля имеет большую сферу применения. Применяется данная технология для производства деталей из периодического проката, профилей различного сечения (квадрат, круг, прямоугольник). Заготовку после предварительного прогрева в электрических, индукционных или пламенных печах формуют при помощи штампа, имеющего полость, соответствующую форме будущего изделия. Нагрев заготовки позволяет выполнять обработку с приложением меньших усилий, поэтому данная технология позволяет получать изделия весом до 2 тонн.
Учитывая энергоемкость технологии (основная часть тратится именно на разогрев металла), ее применение целесообразно только при серийном производстве деталей различной конфигурации, единичная штамповка металла на заказ таким способом не выгодна.
- Валковая технология штамповки
Валковая технология штамповки применяется для работы с заготовками цилиндрического сечения. В процессе обработки происходит формовка изделия под воздействием перемещающегося пуансона и радиальный изгиб при помощи обкатки специальными валками.
К преимуществам данной технологии относятся низкая стоимость оборудования и оснастки, что делает экономически выгодным производство любых партий изделий. Качество и точность получаемых деталей достаточно высоко, как и чистота обрабатываемых поверхностей.
Применяемое оборудование
На производстве в промышленных масштабах применяется разнообразное оборудование для штамповки металла, обеспечивающее создание необходимого давления на обрабатываемые заготовки:
- Механические молоты.
- Различные по конструкции прессы (чаще всего применяют гидравлические или кривошипные модификации).
- Кузнечно-штамповочные автоматы.
- Горизонтально-ковочные машины.
Высокую производительность и максимально возможное качество продукции обеспечивают производственные линии с автоматизированным управлением. Обычный пресс для штамповки металла, управляемый непосредственно оператором, не способен обеспечить высокую интенсивность производство. Именно поэтому все современное оборудование развивается в направлении автоматизации и компьютеризации.
Станок для штамповки листового металла обычно создается на основе гидравлического пресса, характеристики которого идеально подходят для работы с толстым материалом. К преимуществам этого оборудование стоит отнести его устойчивость к возможным перегрузкам и достаточно простую конструкцию, которая значительно упрощает техническое обслуживание.
Для выполнения холодной штамповки чаще всего применяют кривошипный пресс, при этом его конструкция может содержать от одного до четырех кривошипных ползунов. Оборудование данного типа позволяет производить изделия сложной конфигурации, в том числе и ассиметричные.
Технология штамповки металла позволяет организовать изготовление различной продукции с минимальными потерями материала, благодаря чему при выпуске крупных серийных партий продукции достигается существенная экономия.
Именно низкая себестоимость производства и предопределило развитие данной технологии обработки металла давлением.
При разработке технологического процесса штамповки выполняют технологические расчеты, которые включают определение необходимого усилия вырубки и пробивки, усилие пресса, формы и размеров заготовки, необходимого количества операций и их последовательности.
Усилие вырубки и пробивки, необходимое для штампа, у которого соответствующие режущие грани пуансона и матрицы параллельны между собой, зависит от периметра вырубки р, толщины штампуемого материала s, сопротивления срезуматериала заготовки, формы и состояния рабочих кромокпуансона и матрицы и зазора между ними, скорости деформирования и глубины внедрения пуан
netrs.ru