Как сделать компактный многофункциональный станок
Перевел SaorY для mozgochiny.ru
Всем мозгоремесленникам доброго времени суток! Для тех из вас, у кого нет больших мастерских или малогабаритных стеллажей под инструмент, пригодится самоделка этой статьи, в которой компактно умещены все полезные инструменты, и которую легко можно перемещать на другие рабочие площадки.
При создании этой мозгоподелки я старался сделать ее как можно компактной, чтобы ей можно было удобно пользоваться даже в небольшом пространстве, а перемещать даже при отсутствии у вас автомобиля. Для этого у нее имеются транспортировочные колеса, и передвигать
Этот компактная станок-самоделка включает в себя: циркулярный стол, фрезерный стол и лобзик. А еще в ней имеется большой шкаф в котором вы можете хранить другой свой инструмент.
Полезная ссылочка
Чтобы показать поделку в действии я сделаю пару ящиков из дешевых сосновых досок.
На видео показано как я нарезаю доски для ящиков на циркулярном столе с помощью салазок, для получения требуемых размеров пользуюсь дополнительной планкой с зажимом.
Потом я делаю канавку для основания.
Нужный угол можно получить используя угловой упор с направляющей.
Сняв накладку можно выставить угол наклона диска, в данном случае 45 градусов.
Далее я делаю ручку выдвижного ящика, и для этого использую фрезером, которым навожу округлую фаску. Здесь также имеется направляющая для углового упора, а еще будет полезен выносной подшипник для фрезерования кривых линий. Сам фрезер можно наклонять под углом 45°.
Ящик готов, и он занимает предназначенное ему место.
Соединение паз-шип можно на этом мозгостоле сделать двумя путями. Во-первых, с помощью лобзика, дополнительной планки и углового упора. А во-вторых, на циркулярном столе, используя специальный кондуктор.
С диском самого большого размера, который можно установить на самоделку (235мм), можно получить максимальный рез 70мм. На направляющей имеются небольшие регулировочные болты для уменьшения наклона, а при необходимости даже для блокировки.
Для соединения деталей я выбрал второй способ, для этого одни части следует помещать с одной стороны кондуктора, а другие — со второй.
И вот что получилось, переходим к фрезеру, на этот раз уже используем прижимное устройство, чтобы сделать паз основания. Для этого необходимо поднять циркулярную пилу и выставить фрезер под углом 45°.
Шаг 1: Нарезка деталей
Начинается создание многофункционального стола-самоделки с нарезки всех деталей и их нумерации.
Далее для получения прорези ручки высверливаются 4 угловых отверстия и «допиливаются» лобзиком. Затем высверливаются отверстия тех же размеров, что и диаметр и толщина шайбы системы открывания. Отверстия зенкуются.
После этого подготавливается место для установки кнопок включения питания и аварийного отключения. Затем с помощью дюбелей и 50мм-х саморезов собирается корпус мозгостола. По желанию, детали корпуса обрабатываются лаком, так поделка будет лучше выглядеть и дольше прослужит.
Подготовив корпус, собираются 3 верхние части. Для этого нарезаются детали откидных рамок и в них высверливаются необходимые отверстия. Отверстие под трубку сверлится такого диаметра, чтобы эта трубка свободно в нем вращалась, так как она является осью вращения откидных крышек.
Затем выбирается полость под циркулярную пилу. Я это сделал с помощью своего 3D-фрезера, за неимением подобного это можно сделать обычным фрезером с помощью соответствующих кондукторов и направляющих.
С лицевой стороны крышки циркулярного стола выбирается полость под быстросъемную панель, сняв которую можно будет менять угол наклона диска. Саму панель можно использовать для настройки глубины фрезерования полости.
Установив циркулярную пилу в предназначенную полость размечаются отверстия под ее крепление. Хорошо подходит для этого 3D-фрезер, потому что на сверлильном станке данные отверстия нельзя будет просверлить из-за его ограниченной рабочей поверхности.
Шаг 2: Начало сборки
На данной стадии начинается постепенная сборка портативного многофункционального станка для мастерской самодельщика.
Размечается и выбирается с помощью циркулярного стола паз под направляющую. Две дополнительных фанерки дадут необходимую глубину для прочного крепления планки направляющей. Далее на крышку крепится планка с нанесенной на него самоклеящейся рулеткой.
После этого высверливается отверстие для фрезера. Затем отрезаются трубки для осей вращения и на корпус монтируются рамки откидных крышек. В соответствии с чертежами изготавливаются и устанавливаются фиксирующие подпорки.
К рамке прикладывается крышка фрезера, выравнивается и крепится саморезами посредством отверстий в канале направляющей.
Затем подготавливается крышка лобзика, в ней выбирается паз под этот самый лобзик. Если для крышки используется материал не со скользящей поверхностью, такой как у меламина, то поверхность этой крышки следует обработать лаком, чередуя со шлифовкой.
Сделав это, вырезаются и собираются детали механизма вертикального подъемника фрезера, с помощью которого будет регулироваться глубина фрезерования.
Далее склеиваются вместе две фанерки, чтобы сделать из них держатель самого фрезера. В них высверливается отверстие того же диаметра, или подходящего, что и при создании крышки фрезера. Этот держатель мозгофрезера можно сделать на ЧПУ-станке или даже заказать онлайн.
Готовый держатель фрезера крепится к вертикальному подъемнику, и теперь его можно попробовать в действии.
Для разметки радиуса пазов наклона временно крепятся к вертикальному подъемнику обычные петли, а для изготовления ручек-вертушков используются обрезки фанеры.
Шаг 3: Завершение сборки
Эту стадию сборки самоделки я начну с тех деталей, о которых позабыл ранее. Они придадут стабильности системе подъема.
Для начала нарезаются детали основания, я сделал это на своем циркулярном столе, затем они собираются в рамку, которая крепится к дну корпуса многофункционального мозгостола. Высота этой рамки должна быть такой же, что и высота имеющихся колесиков.
На створки одной из откидных крышек крепится щеколда, а створки другой — замок. Это может быть полезно при транспортировке поделки и выступать в качестве превентивной меры от кражи вашего инструмента.
Далее подготавливается 4-х разъемный электроудлинитель, в два разъема которого будут включаться лобзик и фрезер, а в два оставшихся — дополнительный электроинструмент. Розетка для циркулярной пилы подключается через кнопку включения питания и кнопку аварийного отключения. Провод удлинителя наматывается на специальные сделанные для этого ручки.
Быстросъемные панели сделаны из опалового метакрилата. Они помещаются на свои места, а прорезь в панели циркулярной пилы аккуратно делается самой пилой. В качестве направляющего подшипника я использовал аксессуар из комплекта старого фрезера. Это приспособление будет полезно при фрезеровании изогнутых линий.
После этого уровнем проверяется плоскость всей верхней части поделки, если они откидные крышки не лежат в плоскости центральной части, то это легко исправляется регулировкой наклона фиксирующих подпорок.
Далее проводится проверка перпендикулярности рабочих частей инструментов и плоскости стола. Для проверки фрезера в нем закрепляется трубка, по которой и смотрится перпендикулярность оси фрезера и плоскости стола, а еще проверяется параллельность канала направляющей и циркулярного диска. Ну и наконец, проверяется перпендикулярность полотна лобзика.
После этого крышки стола складываются, чтобы проверить не мешают ли мозгоинструменты друг другу.
Шаг 4: Полезные приспособления
Данный шаг повествует об изготовлении некоторых полезных аксессуарах для стола-самоделки.
Первым делом нарезаются детали салазок, далее выбирается паз под ползунок направляющей. После этого две фанерные детали скрепляются вместе саморезами, при этом положения саморезов следует выбрать так, чтобы они не мешали последующей доработке этой детали. Затем в специально подготовленный паз на нее наклеивается измерительная лента, и этот аксессуар для мозгостола покрывается лаком, чередуя со шлифованием, тем самым создавая на этом приспособлении необходимую гладкую поверхность.
Салазки собираются, помещаются на многофункциональную самоделку и от них отрезается лишнее и прорезается срединный пропил, а затем еще наклеивается измерительная лента.
От саней откручивается ползунок направляющей и делается паз для кондуктора «шип-паз». Такого же как у другого моего циркулярного стола.
Ползунок канала настраивается таким образом, чтобы исчез крен между болтами. Сам ползунок можно при необходимости застопорить просто закрутив бота по максимуму.
Далее нарезаются детали для стойки, она собирается, и лакируется-шлифуется. После сборки стойки изготавливается фиксирующая система для нее. Дюбели, вклеенные в эту фиксирующую систему, используются как направляющие оси. В окончании сборки стойки изготавливается ручка фиксирующей системы, а затем вся стойка проверяется в действии.
Дополнительно на стойку устанавливается пылесборник для фрезера, а в боковую сторону мозгостойки у пылесборника вкручиваются резьбовые втулки для прижимной панели.
Сделав это проверяется параллельность стойки и циркулярного диска, затем в паз боковой стенки вклеивается измерительная лента.
Закончив с этим, нарезаются детали кондуктора «шип-паз», которые затем склеиваются и зачищаются.
Шаг 5: Еще несколько полезных приспособлений
Это последнее видео данного мозгоруководства, и в его первой части показано как сделать угловой упор (для его создания можно наклеить распечатанный шаблон или воспользоваться линейкой). Заготовку упора можно уже нарезать на самом многофункциональном станке.
Резьба в ползунке направляющей дюймовая, если же необходима метрическая, то придется воспользоваться метчиком.
Обязательно стоит временно прикрутить заготовку упора к направляющей, чтобы убедиться, что радиус поворота сделан верно.
Затем нарезаются детали шипового кондуктора, при этом необходимо для уменьшения трения слегка увеличить толщину крепления кондуктора.
Чтобы изготовить прижимную панель на фанерную заготовку наклеивается шаблон, пазы настройки этой панели выбираются с помощью фрезера мозгостанка. В нужных местах крышки с фрезером монтируются резьбовые втулки.
Далее изготавливается направляющая пилки лобзика, фиксирующая система этой направляющей такая же, как и у стойки.
Сначала собирается система регулировки подшипников, чтобы избежать износа фанеры используется металлическая пластина. Одно из отверстий делается большим, чтобы посредством этого производить настройку подшипников.
Тоже самое проделывается с фанеркой.
После этого механизируется система регулировки высоты, и теперь конструкция может перемещаться в трех осях, тем самым получается необходимое положение.
Наконец, готовую направляющую для пилки можно проверить в действии, при этом важно удерживать распиливаемую дощечку двумя руками, чтобы она достаточно прочно прилегала к плоскости стола.
О компактной многофункциональной самоделке всё, удачи в творчестве!
(A-z Source)
ПОДЕЛИТЕСЬ С ДРУЗЬЯМИ!
About SaorY
mozgochiny.ru
Удивительная мастерская старого канадца — Виталий Чихарин
Давно хотел перевести эту страницу, наконец решился. Ниже (под «катом») фоторепортаж из хоббийной мастерской одного уже очень пожилого канадца, любителя поработать руками. Ему 74 года и на площади 170 квадратных метров он собрал «коллекцию» станков и ручного инструмента, которой позавидуют многие производства. Репортаж выполнен Матиасом Ванделом, тоже замечательным мастером, его канал в Ютьбе весьма популярен. Перевод с английского мой.Удивительная мастерская Жака Жодуа
Я недавно встретил Жака Жодуа, человека, известного среди местных специалистов по деревообработке своей огромной мастерской со множеством инструментов. Он предложил мне показать свою мастерскую и позволил сделать её фотографии. Его мастерская полностью занимает подвал большого бунгало площадью 170 кв. м. Сложно запечатлеть эту мастерскую в нескольких фотографиях, так что я сделал их много и включил в этот отчет.
Мне 74 года, я стал заниматься деревообработкой в 14 лет, так что могу сказать что опыт в этой области у меня 60 лет. Хотя я выполнял некоторые заказы чтобы иметь возможность купить инструмент, для меня деревообработка была и остается хобби. Я делал мебель для трех моих детей и для семи внуков и внучек. Многие думают, что владеть таким количеством инструмента и не зарабатывать с его помощью деньги — это безумие.
Я столяр-самоучка1. Когда я начинал в 1950-м, было только три журнала (Popular Science, Popular Mechanics и Mechanics Illustrated), в которых только небольшой раздел был посвящен деревообработке. В наше время этому занятию посвящены десятки узкоспециализированных журналов. Конечно, статьи в них повторяются и оценка инструментов иногда не слишком честная (давайте не будем обижать рекламодателей). Я начал писать для Canadian Woodworking и Home Improvement и обнаружил, что объяснять разные технические приемы — это очень интересно и непросто.
В 1950-м, в возрасте четырнадцати лет, я принял участие в соревновании, которое проводил Mechanics Illustrated с первым изготовленным мной предметом мебели (кофейным столиком для моей матери). Я выиграл второй приз, так что вероятно конкуренция не была слишком большой. Пятьдесят лет после этого я не принимал участия в конкурсах вплоть до марта 2002-го когда я поучаствовал в конкурсе на лучшую североамериканскую мастерскую, проводимом Wood Magazine совместно с DeWalt. Я выиграл приз — три тысячи долларов от DeWalt.
Журнал Wood Magazine, март 2002-го. |
Все фотографии мастерской в этой статье увеличивается по клику на них.
![]() | Верстак на переднем плане поднимается и опускается ножничными столами китайского производства. Это означает, что они дешевы, но зато и клапаны не держат давление дольше десяти минут. Решение — фиксировать их на необходимой высоте. Верстак может быть опущен до двадцати восьми сантиметров или полнят до девяноста, это очень удобно для работы с высокими элементами мебели или для работы вместе с внуками. Верстак на заднем плане размером 137 на 335 сантиметров изготовлен из мебельного щита из красного дуба толщиной 9 сантиметров. Вокруг верстаков расположены восемь электрических розеток и десять коннекторов для пылеудаления, соединенных со специальным пылесосом для этих верстаков. |
![]() | В этой мастерской я работаю двадцать пять лет. Первые несколько лет у меня был только один верстак у левой стены (без холодильника и ящиков для фрез). Я думал что хорошим решением будет оставить центральную часть свободной для сборочных работ. Проблема оказалась в том, что я не мог работать со всех сторон верстака, а такая возможность — значительное преимущество при склеивании больших деталей. Когда я получил ящики для фрез, я решил пожертвовать этим открытым пространством ради гигантских двойных верстаков. Хотя сейчас из-за уменьшения места для сборки появляются некоторые трудности, возможность работать со всех сторон верстаков перевешивает. |
![]() | Это вид со стороны входа в мастерскую. Долбежный станок General Int. установлен на основании с колесами, это позволяет отодвинуть его с прохода или освободить место при работе с длинными заготовками. У верстака такая же столешница из твердого дуба как и повсеместно в мастерской, на переднем плане на нем установлен стационарный ламельный фрезер. Он очень часто используется так как позволяет точно и быстро соединить маленькие детали. Для больших кусков фанеры я использую ручной ламельный фрезер. |
![]() | Эти ящики использовались для хранения тяжелых автомобильных головок в Home Depot. Покупатели нередко ломали их когда выдвигали. Когда Home Depot перешел на новую систему (с крючками), я купил 336 ящиков за 5 долларов. |
Эти самодельные «вагонные колеса» удобны для хранения небольшого количества маленьких саморезов. Я собрал маленькие баночки от детского питания когда мои дети были малышами. Они дешёвые и практичные. |
![]() | Передняя струбцина ламельного фрезера может быть использована вертикально или горизонтально. Стол можно наклонять. Единственным плохим моментом фрезера является то, что мотор подается вперед напольной педалью. Лезвие должно выйти на определенное расстояние чтобы сделать паз достаточной глубины, педалью не всегда возможно это сделать. Чтобы исправить этот недостаток, потребовалось сделать рычаг с эксцентриком в задней части чтобы добиться нужной траектории (на фотографии рычага нет, он был добавлен уже после того, как фотография сделана). |
![]() | На этой стойке хранятся все небольшие дрели и специализированные ручные инструменты. Секция из 110-мм труб из ABS хорошо подходит для их хранения. Крюк на задней стенке защищает сетевые кабели от спутывания. А рядом настоящее вагонное колесо. В банках большего размера можно хранить большие вещи, но надо позаботиться о балансировке содержимого, иначе колесо будет крутится какое-то время. |
![]() | Этот старый фрезер Craftsman тех времен когда инструменты делались из металла, а не из пластика. Фрезеры эволюционировали за последние пятьдесят лет. У того, что у меня в руках, очень опасная незащищенная кнопка запуска. |
![]() | В первые тридцать лет у меня был только фрезер Rockwell мощностью 1100 Ватт (сделанный из металла), который я в итоге установил во фрезерный стол с копировальным штифтом2. А затем произошел взрыв новых конструкций, который сделал фрезеры намного эффективнее и интереснее для всех технологий и соединений. Пока я работал для Home Depot, а потом для Porter Cable, у меня было много возможностей чтобы покупать фрезеры по цене, которой невозможно сопротивляться. Самые серьезные столяры владеют тремя или четырьмя фрезерами. У меня немного больше. Есть шутка, что я просто не люблю менять фрезы. Точила и ленточные шлифовальные станки установлены на вращающиеся и вытаскиваемые столы для лучшего доступа. |
![]() | Так выглядит четверть моей мастерской. Она загромождена, но так как большинство среднеразмерных станков установлены на платформах с колесиками, пространство все еще используется довольно эффективно. Мастерская находится в подвале, так что за аренду платить не надо, вода и электричество легко доступны, но нет солнца, летом влажно, а потолки только 2,34 м высотой. В конце концов я отделаю потолок чтобы в мастерской было поярче, но я колеблюсь, так как использую стропила как место для хранения. Мастерская имеет прямоугольную форму со сторонами 8 на 21 метр. Такая длина означает, что надо много ходить. Если бы я должен был строить здание именно под мастерскую, я бы приблизил её к квадрату. |
![]() | Большой фрезерный станок3 Rockwell слева был куплен в 1970-м за 1500 долларов. Учитывая инфляцию, фрезерный станок такого качества и размера сегодня должен был бы стоить 5000 долларов. На самом деле, такой можно сейчас купить менее, чем за 1500 долларов. Суть в том, что инструменты и оборудование сейчас дешевле, чем когда-либо благодаря улучшению методов производства и конкуренции, но до некоторой степени упало их качество. Справа фрезерный станок Delta меньшего размера, который я приобрел за бесценок у кого-то, у кого он был отнят за долги. Он очень полезен для быстрых настроек4. |
![]() | Пятидесятисантиметровая ленточная пила Delta, которая показана на этом фото, это рабочая лошадка в мастерской. Я пользуюсь ею каждый день и безоговорочно предпочитаю распускать на ней, а не на круглопильном станке. Я считаю что это безопаснее, легче и у меня больше места и легче доступ благодаря двум наборам рольгангов, которые регулируются по высоте и имеют подставку на колесах для использования с другими станками. У этой ленточной пилы есть своя система пылеотсоса. Хотя этой пиле сорок пять лет, она до сих пор работает как новая. Я добавил лучший упор и сейчас заменяю направляющие на подшипниковую систему Carter. |
![]() | Главный сверлильный станок. Его особенность — педаль, которой можно погружать сверло когда обе руки заняты деталью. Ход сверла 15 сантиметров и нет люфтов. Рычага для поднимания или опускания стола нет, так что я сделал противовес с системой блоков чтобы уравновешивать вес стола. У этого сверлильного станка также есть две скорости работы и установленный как дополнительный аксессуар лазерный указатель точки сверления. Есть два вакуумных шланга (с двух сторон). Единственное, что плохо в этом сорокалетнем сверлильном станке, это стол. Производители в последнее время сильно улучшили столы. Я изготовил два дополнительных стола с Т-образными пазами и специальными прижимами. Я также использую пару магнитных крепежей MAG для быстрого крепления тисков к столу. |
![]() | Слева фрезерный стол с копировальным штифтом на подставке и маленький рольганг. Красный и оранжевый ящики удобны для быстрого доступа к сверлам, приспособлениям, кондукторам и т.п. Кресло нужно чтобы смотреть по ночам телевизор. |
На этой фотографии на главном плане двойной барабанный шлифовальный станок (барабаны 8 и 15 см). Он производит много пыли, поэтому большие сборники подсоединены к мощному пылеотсосу. Справа тридцатисантиметровый5 токарный станок Delta с двумя копирами. Станки американского производства дорогие и очень качественные. Китайский дёшев, но почти бесполезен. Мне потребовалось произвести дорогостоящие изменения просто чтобы заставить его работать. Слева (едва виден) вертикальный ленточный шлифовальный станок6 (15 на 513 см). Это один из наиболее часто использующихся инструментов. |
![]() | Монтажный стол Kreg очень эффективен при изготовлении основ для шкафов. Я пользуюсь кондукторами Kreg в течение последних двадцати лет и всегда находил их продукты очень искусными и качественными. В правой части фото на потолке система воздухообмена, так как барабанный шлифовальный станок и токарный станок производят много пыли несмотря на то, что они подсоединены к эффективным системам пылеотсоса |
![]() | Синий станок в самой правой части фотографии заменяет ручной кондуктор для косых карманов. Он предназначен для промышленного использования. Другой синий станок на заднем плане — малярный компрессор HLVP и на переднем плане шестнадцатидюймовый шаблон Porter Cable для фрезерования ласточкиных хвостов. |
Но погодите… Эти фотографии сделаны после прогулки только вдоль одной стены мастерской.
![]() | Лучше показан вертикальный ленточный шлифовальный станок. Он много используется на сложной древесине (например, на клёне с волнистым волокном). |
![]() | Тридцатисантиметровый5 токарный станок с регулируемой скоростью вращения. Справа видна часть 400-амперного распределительного шкафа. |
![]() | Круглопильный станок находится в загроможденном месте. Это затрудняет работу с длинными или широкими заготовками, так что я пользуюсь форматно-раскроечной пилой, которую вы потом увидите. Выше (на потолке) податчик для круглопильного станка. Он очень тяжелый, поэтому опускается электрическим тельфером. Из-за этого я использую его только если надо много пилить в сжатые сроки. |
![]() | Я слишком много раз бился о рукоятку, блокирующую направляющую, так что заменил эту рукоятку на съемную. Рольганг за пилой наклонен чтобы помочь движению отрезанных кусков древесины. |
![]() | Пара роликовых подставок с изменяемой высотой, которые используются с круглопильным станком. Они ножничного типа и могут подниматься до двух сантиметров, этого достаточно для компенсации разницы в высоте между двумя столами. Они прикручены к фанере, так что могут использоваться и в других местах. |
![]() |
Сейчас мы достигли дальней стороны мастерской Жака. Но это была прогулка только по одному из проходов. Во втором проходе есть ещё оборудование.
![]() | На переднем плане стальная вертикальная ленточная пила с наклоняемым пильным узлом, которую я интенсивно использую при изготовлении кондукторов. |
![]() | Это 36-сантиметровая радиально-консольная пила Delta, которую я купил в 1970-м, когда радиально-консольные пилы были последним писком моды7. Сейчас я использую её главным образом для отрезания больших кусков древесины или продольной распиловки широких досок, так как там стоит очень мощный 2200-ваттный двигатель. |
![]() | Это старая 36-сантиметровая радиально-консольная пила DeWALT, которую я переделал в радиально-консольный фрезер, выбросив двигатель и вставив 2200-ваттный фрезерный мотор Porter Cable. |
![]() | Радиально-консольный фрезер оснащен большим рольгангом, который лучше виден на этой фотографии. На переднем плане слева вы можете видеть ленточный/дисковый шлифовальный станок фирмы General. Это промышленная чугунная модель канадского производства. Ей вероятно 40 лет, но она всё ещё как новая. Инструмент такого качества не изнашивается. |
![]() | На этой фотографии 2,4-метровый калибровочно-шлифовальный станок который я использую для шлифования дверей или столешниц. Кольцевой ремень имеет размеры 1,8 метра на 510 сантиметров. Так как от этого станка много пыли, он подсоединен к расположенному рядом самому мощному моему пылеотсосу с циклонной системой очистки. |
33-сантиметровый рейсмус DeWALT смонтирован на старом фрезерном столе Craftsman чтобы можно было пропускать под ним длинные заготовки, обрабатываемые на двадцатисантиметровом фуганке. Его также можно наклонить (см. петли) когда мне требуется обработать на фуганке края больших досок. Большинство завершающих стадий работ я делаю на этом маленьком рейсмусе, на нём гораздо проще получить хороший результат, чем на пятидесятисантиметровом рейсмусе Delta, показанном на следующей фотографии. |
![]() | На этой фотографии часть пятидесятисантиметрового рейсмуса Delta. Как вы видите, он почти сразу подключен к большому стружкоотсосу с циклонной системой очистки, так как этот станок даёт большую и тяжелую стружку. Я использую его главным образом для грубой обработки чтобы увидеть волокно или дефекты. |
![]() | Стол для выгрузки отрезанных на круглопильном станке заготовок. Рольганги слегка наклонены чтобы заготовки быстрее убирались из рабочей зоны. Также рольганги можно поднять чтобы опирать на них широкие заготовки при работе на фуганке. |
![]() | Здесь лучше виден пятидесятисантиметровый рейсмус Delta. С обеих сторон от него рольганги, которые можно поднять или опустить при помощи автомобильных ножничных домкратов чтобы они соответствовали высоте рабочей поверхности. |
![]() | В этом проходе пол из плитки чтобы легче было двигать станки, установленные на подставках с колесиками. В другом проходе пол покрыт толстым вспененным материалом, чтобы меньше нагружать ноги и спину. Там нет необходимости перекатывать станки. |
![]() |
![]() | Тридцатисантиметровая торцовочная пила Hitachi без протяга и такая же пила Hitachi с протягом. Обе они активно используются. Я почти не делаю торцевание на радиально-консольной пиле или на круглопильном станке. |
![]() | Это маленький, но очень эффективный и отлично сделанный сверлильный станок Ryobi. Сверлильный узел и столик поворачиваются относительно центральной опоры. Рычагом поднимается и опускается именно сверлильный узел, а не столик. Скорость меняется без перекидывания приводного ремня. На заднем плане (справа) моя сорокосантиметровая новая ленточная пила Laguna HD для продольного распила, которая используется в основном как для изготовления толстого шпона, так и для роспуска кругляка. |
![]() | Обратная сторона пилы Laguna и деревянные струбцины, которые я сделал из списанных школьных скамеек. |
На заднем плане (за сверлильным станком) самодельный пресс для шпонирования, который используется с электрическим тельфером, висящим на потолке. Тельфер поднимает верхний стол. Это облегчает установку шпона убирая необходимость снимать проставки8 или верхний стол. |
Это форматно-раскроечная пила. Она очень хороша для раскроя листов фанеры, но не так хороша для распиловки, так как вес верхней части зажимает диск пилы. Я пытаюсь решить эту проблему, а также заменить недостаточно мощный мотор. |
![]() | Это калибровочно-шлифовальный станок General Int 33 на 99 сантиметров. Очень полезен для подгонки шпона к определенной толщине. Подача несколько медленная, но в целом станок хорошо изготовлен. Рольганги с каждой стороны (тоже производства General) могут растягиваться до 152 см чтобы поддерживать длинные заготовки. |
![]() | Справа доска для лекций. Длинная зеленая ручка — это 111-сантиметровая гильотина для резки шпона (не видна). За экраном большой компрессор, снабжающий всю мастерскую сжатым воздухом. Стол — это горизонтальная форматно-раскроечная пила. Пильный узел (не показан) двигается по направляющей и я использую его для раскроя листов фанеры. |
![]() | Здесь показан четвертый угол. За стеной из перфорированной плиты находятся полки со шпоном. Фрезерный стол производства Jessem. Справа три осциллирующих дисковых и барабанных шлифовальных станка Delta. Инструменты слева лучше видны на следующей фотографии. |
![]() | Слева тридцатисантиметровый отрезной станок Milwaukee. В центре осциллирующий шлифователь General Int. Справа самодельный плоскошлифователь. |
![]() | Стальные стеллажи для хранения древесины за всеми перфорированными плитами. |
![]() | Слева зажимная система для изготовления мебельных щитов Lee Valley Tools. |
В правом нижнем углу старый вертикальный фуганок Delta. Да, это фуганок. Он сделан в 1960-х. Предполагалось что такая конструкция будет безопаснее для обучающихся. Ножи представляют собой небольшие лезвия, насаженные на вертикальный диск. Станок не очень хороший. |
Учитывая размер своей коллекции, Жак вынужден был сказать следующее:
«Мой брат говорит, что однажды двое покрытые белыми перьями придут и заберут меня. Кто-то сказал: „Будь они мужчинами, они бы посмотрели на мастерскую и забыли бы зачем пришли, я бы остался“. Некоторые друзья обвиняют меня в коллекционировании инструментов. В этом есть доля истины, но учитывая, что я провожу от тридцати до сорока часов в неделю используя этот инструмент для чистого и неприкрытого удовольствия, это больше чем мертвая коллекция предметов. Кроме того, коммерческая деятельность тяжела и вы теряете своё хобби. Мне нужно хобби больше, чем деньги».
Я сделал короткий видеорепортаж о прогулке по мастерской Жака чтобы дать вам лучшее понятие как всё соединено.
Большое спасибо Жаку, что он показал мне свою поразительную мастерскую, позволил мне её сфотографировать и прокомментировал все фотографии.
Здесь ссылка http://forum.woodtools.ru/index.php?topic=30197.0на обсуждение мастерской Жака на форуме woodtools.
1В оригинале woodworker, это может означать мастера, выполняющего и плотницкие, и столярные работы. Хотя в плотницкие работы включают кроме деревянного домостроения и изготовление простой мебели и т.п., всё же мне кажется, что Жак скорее столяр в нашем понимании.
2pin router table. В этом видео показано, как работает это остроумное приспособление для копирования с шаблоном на фрезерном столе.
3shaper. По сути, специализированный фрезерный станок для обработки кромок. См.
4 It is very useful for quick set ups. Я не понял до конца эту фразу. Вероятно, имеются в виду какие-то черновые работы или подгонка?
5 vertical edge sander
6 Как я понимаю, расстояние от центра вращения до станины.
7 А сейчас их почти не найти в продаже, их заменили торцовочно-усовочные с протягом.
8 Cauls. Не знаю как этот термин точно звучит на русском. Используются для зажима, в т.ч. при шпонировании, чтобы распределить нагрузку от струбцин на большую площадь. См.
chva.livejournal.com
Чертежи ЧПУ станка из фанеры
Сегодня представляю вашему вниманию разработку ЧПУ станка из фанеры.
Этот самодельный ЧПУ станок легко сделать своими руками. Чертежи ЧПУ станка можно скачать по ссылке в конце статьи.
Как и самодельный ЧПУ станок Графа, данный станок является фрезером с ЧПУ управлением.
Это все детали для сборки самодельного ЧПУ станка своими руками. Пилить с помощью лобзика их придется долго. Лучше заказать нарезку через объявление в газете или у знакомого, кто уже имеет ЧПУ станок.
А это набор фурнитуры, которая используется при сборке ЧПУ станка. Многовато конечно, но, всяко выйдет дешевле, чем покупать готовый ЧПУ станок где то на стороне.
Этот ЧПУ станок рассчитан на обработку дерева с небольшой подачей, пластика, может нарезать фанеру или быть гравером по мягкому металлу. Грызть сталь или цветмет он не сможет в силу конструктивных особенностей — слишком хлипкая конструкция. Однако, в домашних условиях для модельных дел — это оптимальный выбор. Всегда можно частично разобрать и упаковать станок, что бы домашние не ругались по поводу того, что он занимает место.
Основой самодельного ЧПУ станка является рабочий стол. Чем он прочнее, тем прочнее будет и станок, а значит и выше точность изготавливаемых деталей.
В данном случае стол ЧПУ станка изготавливается из фанеры, форма — решетчатая, это повышает прочностные характеристики и уменьшает искажения стола при работе станка.
Крепление всех деталей производится за счет фурнитуры.
При желании к фурнитуре можно добавить и клей — например ПВА столяр, тогда ЧПУ станок станет крепче, но потеряет разборность.
Направляющие изготовлены из алюминиевого уголка.
Фиксатором служит распорный болт. Для уменьшения искажений используются фанерные вставки во длине направляющей.
Каретки так же собирается из фанеры. По направляющим катятся подшипники, для их фиксации используются те же болты и шайбы.
В качестве фрезера используется обычный дремель. Можно вместо него и любой китайский гравер с мощностью в 120 или больше Ватт поставить.
Вот так он выглядит во время работы.
Я не буду останавливаться подробно на всех этапах сборки ЧПУ станка своими руками. Смотрите сборочные чертежи, там все достаточно ясно.
А вот так выглядит этот самодельный ЧПУ станок в сборе рядом с компьютером. Накладка на монитор вырезана и отфрезерована (надписи) именно на этом стане.
Скачать чертежи самодельного ЧПУ станка из фанеры можно тут.
В архиве версия 1.2 и 2.0.
Самодельный ЧПУ станок
homecnc.ru
Сверлильный станок своими руками 1500 фото, чертежи, инструкции
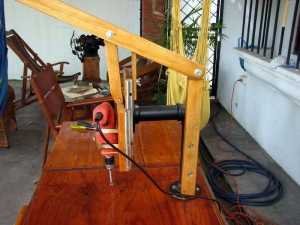
Первую дрель придумали еще в эпоху неолита, уже тогда без этого инструмента было никуда – дерево просверлить, в камне отверстие сделать, да даже огонь развести. С тех пор ничего не изменилось, дрель все так же популярна, только ее немного усовершенствовали. Сегодня большинство работ по сверлению, в зависимости от сложности, выполняют или на специальных станках или ручным инструментом.
Понятно, что заводские станки, предназначенные для выполнения серийных операций в домашней мастерской ни к чему, но с другой стороны, иногда необходима особая точность сверления. Вот тогда мастера и задумываются, как сделать сверлильный станок своими руками и желательно, из подручных материалов. Просто найти нужные детали в магазине вряд ли получится, поэтому для изготовления необходима особая фантазия.
Здесь представлены десятки самодельных сверлильных станков – лучшие идеи, которые удалось найти в интернете. А также узнаете, как сделать стол для сверлильного станка, тиски, органайзер для хранения сверл, тумбочку под самодельный станок и даже устройство для охлаждения сверла.
Как сделать сверлильный станок своими руками
Каждый мастер, кто работает с деревом, знает, что невозможно вручную сделать сотни отверстий совершенно прямо и с одинаковой глубиной. Этот подробный мастер класс с пошаговыми фотографиями покажет, как сделать сверлильный станок своими руками, который поможет сэкономить много времени и усилий при сверлении точных отверстий по дереву, пластику, металлу или в любом другом материале, с чем вы работаете. Инструмент очень полезен для сверления прямых отверстий с минимальным усилием, в сочетании с высокой
скоростью может быть хорошим подспорьем, чтобы вырезать границы на ту же высоту, как показано на картинке. Также благодаря регулируемой высоте инструмента можно вырезать участки определенного размера в древесине, например, заготовки квадратной формы.
По желанию, можно внести некоторые усовершенствования, например, добавить пружину в верхней части основания, чтобы получить автоматический подъем дрели. Здесь показаны только фото, если интересует подробное описание процесса, необходимые материалы и инструменты, под галереей находится ссылка на сайт первоисточника.
Источник фото www.instructables.com/id/Drill-press-for-20-21/
Безпроводной сверлильный станок из дерева
Интересная идея самодельного сверлильного станка, изготовленного только из дерева. Установка полностью портативная, так как автор использовал беспроводную дрель на аккумуляторах. Конструкция включает в себя деревянную коробку, которую удобно использовать для сверления прямолинейных отверстий в заготовках большого размера. Предоставлять конкретный чертеж автор посчитал нецелесообразным, так как станок изготовлен под определенную дрель, которая была у автора, так что, возможно, придется внести некоторые изменения в размеры, которые будут соответствовать вашей дрели.
Источник фото www.instructables.com/id/The-Cordless-Drill-Press/
Мини сверлильный станок своими руками
Точный, прочный и недорогой самодельный мини сверлильный станок, который без труда можно сделать с помощью простых инструментов. Все дрели разные, поэтому вам для начала надо нарисовать детали будущей конструкции. Автор использовал МДФ толщиной 1,8 см, рекомендую вам тоже использовать этот материал. Чтобы прикрепить дрель, надо просверлить 4 отверстия в МДФ для крепления хомутов. Сложить левую и правую сторону и выровнять заднюю часть (смотрите на фото). Как только это сделано, просверлить еще 4 отверстия для винтов, и склейте все части, дальше надо установить мини дрель и прикрутить нижнюю часть. Для рычага подойдет обычная деревянная палка, как ручка ложки. А чтобы подтянуть мини дрели, можно использовать резиновые жгуты из старой воздушной камеры. В перспективе автор планирует добавить светодиодные лампочки и сделать маленькие тиски для крепления печатной платы при сверлении.
Источник фото www.instructables.com/id/Easy-Mini-Drill-Press
Самодельный сверлильный станок
Дрель, инструмент многофункциональный, но на весу, без хорошего упора, долбится высокой точности, мягко говоря, довольно затруднительно. Хороший выход из ситуации, самодельный сверлильный станок, в общем, любая стойка, чтобы закрепить инструмент. Обычно мастера используют те детали и подручный материал, которые имеются в любом частном гараже. Как видите, представленный здесь вариант особой сложностью не отличается, автор использовал трубу, уголки и два фланца. Стойка для дрели просто крепиться к столу болтами. Алюминиевые дорожки взяты из картинной рамы, для распорок использовались палочки от эскимо. Дрель закреплена обычными хомутами.
В общем, на фото все хорошо показано, пожалуй, ни у кого не возникнет трудностей с изготовлением такой конструкции.
Источник фото www.instructables.com/id/Drill-press
Похожий вариант, только крепится на деревянной основе. Саморезами прикрепляем мебельную направляющую. В доске делаем отверстия по диаметру дрели, крепим уголок и металлическую пластину. Всю конструкцию прикручиваем к направляющей. Затем крепим стальную пластину на платформе, делаем ручку и прикрепляем саморезами. Хомутами зажимаем дрель, фиксируем пружину. Возможно, немного путано, но по фотографиям разберетесь, ничего сложного.
Источник фото usamodelkina.ru/4288-delaem-sverlilnyy-stanok-iz-dreli.html
Простой сверлильный станок своими руками
Простая конструкция самодельного сверлильного станка, можете взять ее за образец. Вам понадобится любой толщины фанера, механизм выдвижного ящика, широкая доска или ПВХ, металлический стержень и необходимой длины винты. Да и клей, обязательно. Фанера нужна для базы, поэтому желательно, чтобы она была гладкой и ровной. Вертикальную заднюю стенку можно сделать как деревянной, так и металлической. Дрель устанавливается на ползуне ящика со спейсером. С электрикой здесь вопрос особый, автор придумал, чтобы дрель включалась при опускании ручки. Этот шаг необязательный и очень не рекомендуется, если вы не знаете, как это делать, а если разбираетесь, то конечно можно попробовать, правда, автор подробной схемы не предоставил, а по фотографиям понять сложно.
Источник фото www.instructables.com/id/Easy-Drill-Press
Самодельный сверлильный станок с подвеской
Если столярное дело для вас хобби, а не бизнес, профессиональный станок не нужен. Но чтобы сделать самодельный сверлильный станок, нужен творческий подход. Но не важно, профессионал вы или любитель, при выполнении сверлильных работ необходима точность. Автор проекта решил преобразовать проводную дрель в сверлильный станок и вот что у него получилось. Основной материал, из которого изготовлена конструкция, можно найти в любом гараже, главная фишка, чем автор очень гордится, четыре мощные резинки. Обычно дрель довольно тяжелая, но с четырьмя резинками она будет колебаться примерно на 20 см выше поверхности стола. В общем, стоит попробовать, если интересуют подробности, ссылка на сайт автора под галереей.
Источник фото www.instructables.com/id/DIY-Drill-Press-with-Rubber-Band-Suspension
Как сделать дешевый сверлильный станок своими руками
Этот простой самодельный станок сделан из деревянных отходов (кусок доски, несколько брусков и лист толстой фанеры для основания) и старой проводной дрели. Еще вам понадобится зажим для шлангов и шурупы. Вначале нарисуйте схему и разметьте детали, Затем соедините все это вместе, как на фотографии, используйте бумагу в качестве прокладок между деревянными деталями. Натрите воском скользящие поверхности. Прикрепите хомуты для шлангов и закрепите дрель на скользящей дощечке, при необходимости используйте клинья. Добавьте ручку для подачи дрели и пружину, чтобы работал механизм возврата. Все это можно сделать за 2 – 3 часа и финансово обойдется практически бесплатно.
Источник фото www.instructables.com/id/Cheap-Drill-Press-DIY/
Самодельный сверлильный станок из труб ПВХ
Трубы ПВХ, это материал, который без труда можно найти. Они подходят не только для водопровода, из них можно сделать много полезных вещей, даже самодельный сверлильный станок. Все материалы можно купить в магазине, главное, правильно подобрать комплектацию. Ниже на фото показаны необходимые материалы и инструменты.
Порядок сборки стойки смотрите на пошаговых фото, никаких сложных операций, рама собирается, как конструктор. Немного усовершенствовать и можно работать использовать, как стойку для фрезера.
Источник фото www.instructables.com/id/PVC-Dremel-drill-press
Как сделать самодельный сверлильный станок
Данный станок можно назвать универсальным, так как по этому проекту вы можете изготовить различные варианты по размерам и производительности. Для этой стойки подойдет любая ручная дрель вне зависимости от мощности. Конечно, представленные выше самодельные модели из дерева сделать легче, но металл, само собой, надежней, хотя без сварочного аппарата не обойтись. Для изготовления понадобится металлическая пластина для основы и уголки для подставок.
Стойка для подъемного механизма сделана из квадратной металлической трубы.
Для изготовления механизма регулировки применяют разные способы, в данном случае сделан тросиковый привод, для чего нужно изготовить скобу для крепления и вращающийся барабан. Для крепления петли тросика в основу приваривается болт. Рукоятку можно сделать любую, из подручных материалов, главное, чтобы удобно было пользоваться. Для фиксирующего устройства использовалась обычная струбцина, закрепленная на металлической пластине. После завершения работы покрасьте все детали, чтобы защитить от ржавчины, а трущиеся поверхности смажьте технической смазкой.
Источник фото mainavi.ru/dom/sverlilnyj-stanok-svoimi-rukami
Автор проекта Алексей Шамборский
Сверлильный станок из дрели
Автор использовал простой подход, зачем изобретать велосипед, если можно использовать готовые алюминиевые профили. Нужно просто отрезать 4 одинаковые части, обработать шлифовальной машинкой, просверлить отверстия и нарезать в них резьбу. Ползунки для подъемного механизма можно использовать от выдвижных ящиков. Стенд выполнен из двух частей, соединенных друг с другом, но можно сделать только из одного. Подсоединяется к базе четырьмя болтами и специальными гайками. Рычаг установлен с помощью длинного болта, ввинчен в гайку. Он сделан из куска трубы диаметром немного меньше, чем диаметр сверлильного станка.
Труба разрезана в продольном направлении и добавлено два тонких листа с отверстиями. С обратной стороны приваривают квадратную трубу и кусочек листа, чтобы закрепить его на стенде. В роли рабочего стола просто кусок дерева, приклеенный силиконовым клеем.
novamett.ru