Спецсплавы и стали в ассортименте
ГлавнаяМагазин Спецстали и сплавы
Вам нужен металл? Купить сталь и прочие сплавы предлагает наша компания. У нас купить сталь модно по привлекательной цене. Мы предлагаем купить сталь, которая имеет наивысший уровень качества. Но для начала давайте разберемся, что же они собой представляют.
Что такое металл, и какие существуют сплавы железа? Что вообще такое металлический сплав?
Металлом называют кристаллическое вещество, которое имеет определённые свойства, позволившие сгруппировать разнообразные химические элементы под общим названием. Итак, что же это за свойства? Металлам присуща высокая тепло- и электропроводность, особый металлический блеск. Кроме этого, металлы за исключением ртути (тоже относится к этой категории) обладают повышенной прочностью к механическим воздействиям и пластичностью. Они, особенно под воздействием повышенных температур, легко поддаются ковке — деформируются при воздействии на них механическим путем. Металлы самая крупная группа элементов в периодической таблице Менделеева. Их 75 % от общего количества.
Металлическими сплавами называется однородная смесь веществ (металлов), которая образуется в процессе затвердевания после доведения их до расплавленного состояния. В сплав входит минимум два элемента, максимальное их количество может быть бесчисленным.
Металлические сплавы могут состоять из металлов и могут иметь в своем составе примеси прочих элементов — неметаллов. Для примера, к металлическим сплавам относится латунь, бронза. К неметаллическим — чугун, сталь, так как они содержат примесь углерода, который не относится к этой группе химических элементов.
Возможность смешивания разных металлов, позволяет получать в конечном итоге
сплавы, имеющие разные свойства и характеристики, получать материал, который востребован в том или ином виде хозяйственной деятельности.Сплавы металлов или твердые растворы с химической точки зрения образуются двумя способами:
- замещения
- внедрения
В первом случае, атомы одного металла замещают часть атомов кристаллической решетки другого металла. Для примера это сплавы железа и никеля, меди и никеля и прочие. При смешанном способе из молекулы попросту перемешиваются.
Где используются сплавы металлов?
Находят они себе применение повсеместно. В доме любого человека, куда ни глянь, обязательно найдешь какой ни, будь сплав. Современная техника зачастую состоит из сплавов, потому что они обладают повышенной конструктивной прочностью, устойчивы к воздействию пониженных и повышенных температур, к окислению, и обладают прочими полезными человеку химико-физическими свойствами.
Некоторые сплавы металлов постепенно вытесняют другие. Например, все чаще вместо стали в некоторых конструкциях и механизмах стали использовать сплав алюминия.
Научно-технический прогресс вносит в нашу жизнь все большее количество сплавов. Их разнообразие непрерывно растет, насыщая рынок высокотехнологичными товарами, которые обладают все большим количеством полезных для человека свойств. Появление новых сплавов, открыло для людей все больше перспектив для развития, но все также востребованной остается сталь, сплав которой неизменно пользуется повышенным спросом и широко используется в промышленном производстве. Сталь – сплав железа и углерода. Несмотря на то, что в нем содержится неметаллический элемент углерод, он очень прочен на разрыв и к механическим повреждениям. Благодаря чему
спецсталь – сплав железа и углерода, так востребован в разных отраслях экономики особенно в промышленности.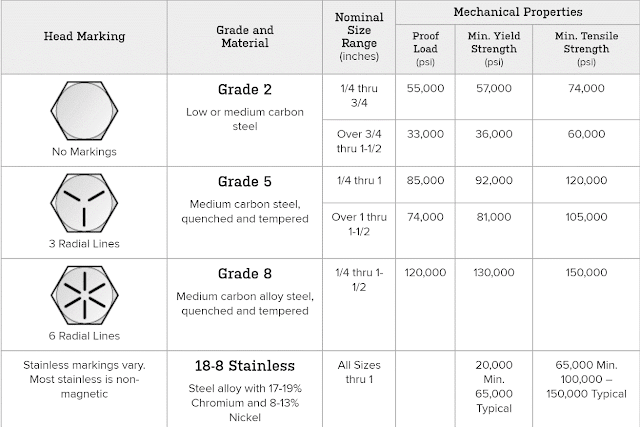
Что предлагает наша компания?
Вы ищете, где купить стали и сплавы? Вы пришли по адресу. У нас есть стали и сплавы в широком ассортименте.
Мы предлагаем купить сплав разных металлов высокого уровня качества. В ассортименте имеются как традиционные соединения разнообразных элементов, так и сплавы редких металлов, а также спецсталь. У нас имеется спецсталь самого высокого уровня качества. Купить спецсталь можно как мелкими партиями, так и крупными.
Мы реализует
Мир сталей и сплавов . Занимательно о железе
Сталь — сплав железа с другими элементами: углеродом, кремнием, марганцем, серой, фосфором. Это известно нам сейчас. Однако люди научились получать и использовать сталь гораздо раньше, чем узнали ее состав. Египтянам, например, еще до нашей эры известно было, что некоторые сорта железа при погружении в нагретом состоянии в воду “принимают закалку”, другие не принимают. Свойство стали “принимать закалку” и служило потом долгие века единственным признаком для разграничения железа и стали.
Французский ученый Реомюр в 1722 году высказал мысль, что железо и сталь отличаются друг от друга по химическому составу только присутствием какой-то примеси, названной им летучей солью, которая и определяет различие их свойств. Лишь в 1814 году немецкий исследователь Карстен указал, что такой примесью является углерод. Наконец-то была доказана единая материальная природа всех железоуглеродистых сплавов — чугуна, стали и железа. Только во второй половине XIX века выработалось в основном верное представление о железе и его сплавах.
Появление в XIX веке новых областей применения металла — машиностроения, железнодорожного строительства — потребовало более точных представлений о качестве металла. Для этого определяли химический состав железных руд, шлаков и различных железоуглеродистых сплавов. Постепенно выявилось более точное влияние на углеродистое железо примесей — кремния, марганца, серы, фосфора.
П.П. Аносов впервые занялся систематическим изучением влияния различных элементов на сталь. Он исследовал добавки золота, платины, марганца, хрома, алюминия, титана и других элементов и первым доказал, что физико-химические и механические свойства стали могут быть значительно изменены и улучшены добавками некоторых легирующих элементов. Ученый заложил основы металлургии легированных сталей. Замечательное свойство железа — давать сплавы с различными элементами и при этом проявлять новые качества — широко используется в современной технике. Известно более 8 тысяч сплавов, обработка которых дает десятки тысяч марок сталей различного назначения. Созданы самые удивительные марки стали: “деревянная”, свинцовистая, алмазная и мягкая, графитизированная, платинистая и серебряная.
В старину пытались получать стали с добавками благородных металлов. Так, в 1825 году в России были описаны опыты на Гороблагодатских казенных заводах по сплавлению стали с платиной. Шесть фунтов стали расплавили в тигле с восемью золотниками очищенной платины. Жидкую массу вылили в чугунную форму и быстро охладили в холодной воде. “По разломе стального бруска сталь оказалась весьма однородной сыпи и столь мелкой, что простыми глазами невозможно было усмотреть ее сложения. Будучи выточена и закалена без отпуска, она резала стекло, как алмаз, рубила чугун и железо, не притуплялся”.
Позже нашли более дешевые и широко распространенные легирующие элементы, дающие лучшие результаты. Например, в сплаве платинит нет платины (содержится 48% никеля, 0,15% углерода, остальное железо). Сплав имеет такой же коэффициент теплового расширения, как и у стекла, поэтому применяется для замены платиновых вводов в электролампах. Сплав ковар (29% никеля, 18% кобальта) имеет коэффициент линейного расширения такой же, как у молибденового стекла, и предназначается для спайки с этими стеклами, давая прочное и совершенно газонепроницаемое соединение.
В 1927 году в Берлине на выставке показывали небольшую кастрюльку с двумя ручками из разных металлов. В ней кипела вода и одна из ручек, сделанная из железа, была горячая, другая теплая. Ручка была сделана из так называемой деревянной стали, в состав которой входили 35% никеля, 1% хрома и 64% железа. Называлась она так потому, что по теплопроводности была подобна дереву. Она относится к прецизионным сплавам, свойства которых достигаются только при совершенно точном составе. Малейшее отступление от рецепта вызывает потерю этих свойств.
Автором одного из таких сплавов был швейцарский физик и метролог, ставший затем директором Международного бюро мер и весов, профессор Гийом. В 1898 году он определил зависимость физических свойств стали от содержания в ней никеля. Оказалось, что сталь, содержащая более 25% никеля, при нагревании теряет магнитные свойства; сталь, содержащая 36% никеля, отличается самым малым коэффициентом линейного расширения (в 10 раз меньше, чем у платины).
Замечательные свойства инвара позволили применять его в измерительной технике и приборостроении, в частности в вакуумной технике для спайки с различными сортами стекла. Из инвара изготовляют также вставки для разрезных алюминиевых поршней, чтобы уменьшить их тепловое расширение и устранить заедание в цилиндре во время работы двигателя.
Алмазной сталью названа легированная инструментальная сталь, содержащая 1,25–1,45% углерода, 0,4–0,7% хрома и 4–5% вольфрама. Такая сталь имеет очень высокую твердость, близкую к твердости алмаза. Ее применяют для снятия тонкой стружки с твердых материалов (отбеленного чугуна, стекла).
Стали с новыми свойствами создаются чаще при комплексном использовании нескольких элементов. Использование редкоземельных элементов в сталях специалисты считают самым выдающимся успехом в сталеварении за последние полвека.
Для создания новых марок сталей используют, например, азот. Газы в металле — всегда нежелательная примесь, снижающая качество металла. А вот в Институте электросварки им. Е.О. Патона АН УССР в плазменную печь, где расплавляется металл, специально нагнетается азот. После охлаждения получается сталь, о которой давно мечтали машиностроители: жаропрочная, устойчивая к воздействию кислот и щелочей. Азот превращается в полезный элемент: за счет образования нитридов ванадия, титана, молибдена идет измельчение зерна. Применение азота позволило сократить добавки никеля и совсем не использовать ферросплавы.
Японским специалистам удалось получить в твердом виде аморфный металл, т. е. без кристаллической структуры. Для этого смешивают железо или никель (90%) с фосфором и углеродом, кремнием, алюминием и бором. Смесь нагревают до 1200°С. Затем сплав очень быстро охлаждают, подвергая вращению со скоростью 5 тысяч оборотов в минуту. Такая сталь во много раз тверже известных сталей и обладает высокой химической стойкостью. Новую марку стали можно применять на атомных электростанциях, в приборах для исследования моря, в химической аппаратуре.
Специалисты Института прецизионных сплавов ЦНИИчермета занимаются разработкой способов превращения металла в “металлическое стекло”. Принцип получения металла со “стеклообразной” структурой таков: заставить расплавленный металл затвердеть с такой скоростью, чтобы не успела сформироваться кристаллическая решетка. Для этого струя расплавленного металла через профильную форсунку “выстреливается” на холодную движущуюся поверхность.
Затвердевший металл расплющивается и сматывается серебристой лентой на катушку.
Структура “металлического стекла” предопределяет уникальное свойство этого материала, названного аморфным прецизионным сплавом. В обычной стали уязвимым местом являются границы между зернами. Именно здесь появляются тонкие трещины, развивается коррозия. Поскольку у нового материала нет кристаллической решетки, он в десятки раз прочнее традиционной стали, обладает повышенной устойчивостью к коррозии, легко поддается намагничиванию. Металлическое стекло незаменимо для изготовления приборов, работающих в агрессивных средах, при низких температурах или высоких механических нагрузках.
В создании сплавов и марок сталей участвуют прежде всего электрометаллурги. Они ведут плавку в электропечах наиболее совершенным процессом из ныне существующих для массового получения литой стали. Электропечь емкостью 100–200 тонн обслуживают сталевар и один — два подручных. Возможность создать более высокие температуры в электропечи (2500–3000°С) позволяет получать стали и специальные сплавы с высоким содержанием тугоплавких легирующих элементов.
Большой интерес представляет сплав никеля с титаном — нитинол. При проведении опытов с этим металлом было замечено, что он обладает способностью “запоминать”. Нагревая нитинол, придавали ему определенную форму, затем охлаждали и сплющивали. Потом снова нагревали. И сплав принимал свою первоначальную форму, с высокой точностью повторяя все изгибы и закругления, полученные при первом нагреве.
Запоминающие сплавы — теперь не сенсация, с ними работают, изучают их новые свойства. Исследования показали, что временные нагрузки, вызывающие в металле те или иные напряжения, после снятия их оставляют в металле какие-то “следы”, и металл постепенно суммирует их. Оказалось, что наиболее легко металлы воспринимают и прочно “запоминают” нагрузки, “перенесенные” ими при очень высокой температуре.
Попутно исследуются возможные сферы инженерного применения этого необычного свойства. Представьте конструкцию, которая способна собирать самое себя. Антенну для космической станции размером в десятки метров можно упаковать, к примеру, в небольшой контейнер и доставить на орбиту. Достаточно затем прогреть багаж электрическим током или солнечными лучами, и начинается самосборка. С помощью охлаждения антенну можно снова упаковать.
В наш век повсеместной механизации и автоматизации основным материалом для механизмов остается сталь. А движущиеся металлические части — это неизбежный шум, вибрации. Для борьбы с первопричиной шума ищут новые материалы. Стальной сплав, обладающий свойством гасить колебания и превращать их в тепловую энергию, а также в значительной степени свободный от резонанса, получен на заводе японского концерна “Ниппон Кокан”. В состав сплава входит 12% хрома, причем сплав подвергается специальной термообработке. Перспективы у “тихой” стали большие. Это производство станков, локомотивов, различных крышек и клапанов, головок цилиндров, некоторых приборов. Детали из нее создают меньше шума и обладают большим сопротивлением усталости.
Оригинальную марку “мягкой” стали создали челябинские специалисты. Добавки свинца и селена делают металл “мягким”, легко обрабатываемым. По другим качествам он не уступает обычной стали, зато производительность труда станочников при обработке деталей повышается, служба инструмента увеличивается.
Прозрачную нержавеющую сталь выпускают на металлургическом заводе “Меллори” (США). Пропуская свет, она совершенно не пропускает воду. Однако листы, изготовленные из этой стали, скорее напоминают сито, чем стекло: на просвет можно увидеть множество крохотных отверстий (десять тысяч на один сантиметр поверхности), полученных электрохимическим способом.
На заводе сталь новой марки получают непрерывной прокаткой. Сталь хорошо сваривается, паяется, легко обрабатывается на станках. Помимо прозрачности, она обладает еще способностью исключительно хорошо поглощать шумы. Столь неожиданное свойство, по мнению специалистов, позволит использовать ее для изготовления кожухов турбореактивных двигателей. Однако наиболее перспективное применение дырчатой стали — полости для сыпучих материалов. Продувая сквозь поры воздух, можно заставить муку, цемент, угольную пыль течь, подобно жидкости. Разгрузка железнодорожных вагонов с днищем из такой стали, приспособленных для перевозки порошкообразных материалов, значительно упростится. Новинку можно использовать в строительстве и для декоративной отделки.
Современной технике нужны металлы и сплавы с самыми необычными свойствами. Нужны стали для работы при давлении в сотни и тысячи атмосфер (в производстве аммиака давление на 100 МПа) и при глубоком вакууме, когда давление близко к нулю (в электронных приборах давление до 0,000133 Па). Хладостойкие стали должны сохранять прочность при температурах, близких к абсолютному нулю (-273°С). Для атомных реакторов требуется металл с наибольшей магнитопроводностью, для двигателей реактивных самолетов и ракет — сталь, способная сохранять прочность при весьма высоких температурах и больших нагрузках. Теперь такие стали и сплавы есть!
состав, свойства, маркировка и применение
Нержавеющая сталь представляет собой сплав, состоящий из железа и добавок углерода. Эти элементы считаются основными. Помимо них в сплаве присутствуют лигирующие вещества, которые придают ему дополнительные свойства. В качестве основной добавки используется хром. Он должен присутствовать в коррозийном сплаве в количестве не меньшим 10,5 процентов. Никель также является основополагающим элементом, который регулирует технические характеристики.
Таблица марок аустенитных сталей по ГОСТу и AISI, их основные области применения
Марка по ГОСТу 5632 | Марка по AISI | Области применения |
12Х18Н10Т | 321 | Технологические линии химической индустрии и предприятий нефтепереработки |
08Х18Н10 | 304 | Технологические трубопроводные системы в химической и пищевой индустрии, ограниченный ассортимент посуды, не включающий изделия для горячей обработки пищи |
08Х17Н13М2 | 316 | Технологическое оборудование химической индустрии, использование в качестве «пищевого» материала |
12Х15Г9НД | 201 | Емкости и трубопроводы, контактирующие с органическими кислотами и умеренно агрессивными средами |
Методы классификации нержавеющей стали
В зависимости от количества разнообразных добавок проводится классификация сталей по структуре. Выделяются следующие виды:
Ферритная. Малоуглеродистая сталь с содержанием данного элемента до 0,15 процентов. Хрома в таком составе должно быть до 30 процентов. Сплав обладает высокой пластичностью и прочностью. Относится к классу ферромагнитных. Хорошо переносит холодную деформацию. В основном обрабатывается отжигом, который снимает наклеп. Данный процесс придает стали стойкость к коррозии.
Мартенситная. Содержание углерода у этой марки составляет до 0,5 процента, хрома до 17 процентов. Структура сплава получается вследствие закалки и последующего отпуска. Она обладает свойством устойчивости к коррозии, стойкостью, повышенной твердостью, упругостью. Используется для изготовления деталей, которые предназначены для работы в агрессивных средах.
Аустенитная. Это целый класс сталей, для которых характерна повышенная стойкость к коррозии и пластичность в различных состояниях. Хорошо подвергается обработке и сварке. Данный класс делится на два подкласса, к которым относятся стабилизированные и нестабилизированные стали. В стабилизированные марки добавляется титан и ниобий, которые укрепляют кристаллическую решетку и защищают ее от коррозии.
Таблица марок нержавеющих сталей ферритного класса по ГОСТу и AISI, основные сферы использования
Марка по ГОСТу 5632 | Марка по AISI | Области применения |
08Х13 | 409 | Столовые приборы |
12Х13 | 410 | Емкости для жидких алкогольсодержащих продуктов |
12Х17 | 430 | Емкости для высокотемпературной обработки пищевой продукции |
Наиболее популярные марки и сферы их применения нержавеющей стали
Все марки нержавеющей стали можно разделить на несколько типов: 200-я, 300-я, 400-я. К каждому из этих классов относится несколько разновидностей. К 200-й относится марка AISI 201. Она практически не отличается от классов выше, но немного уступает им по своим антикоррозийным свойствам. Однако, имеет весьма существенное отличие в цене. К 300-й серии относятся такие марки:
AISI 304. Хорошо сваривается. Нашла широкое применение в пищевой промышленности.
AISI 316. От предыдущей марки отличается тем, что в ее состав входит молибден (2%), это делает сталь более устойчивой к коррозии. Способна сохранять свои свойства под воздействием высоких температур и кислотных сред. Используется в судостроительной, химической и нефтегазовой промышленности.
AISI 316T. В данной стали присутствует титан, который дает возможность использовать изделия при высоких температурах и под воздействием хлорид-ионов. Применяется в химической, газовой и пищевой промышленности.
AISI 321. Содержит большое количество титана. По этой причине способна переносить высокие температуры до 800 градусов. Хорошо подвергается сваркой. Из нее изготавливаются бесшовные трубы.
400-я серия отличается тем, что в ней практически отсутствуют посторонние элементы. Все они заменяется содержанием большого количества хрома. Углерод в данной стали присутствует в минимальных количествах. Сплав очень пластичен и хорошо сваривается. Сталь данного класса представлена маркой AISI 430.
Правила маркировки нержавеющей стали
При маркировке создается обозначение, которое содержит цифры и буквы. Первое двузначное число указывает на наличие углерода и его количество. После этого значения идут буквы, которые показывают наличие лигирующих добавок. После указания этих элементов в виде цифры указывается их количество с округлением до целого числа. В случае, когда это число составляет 1-1,5 процента цифра будет отсутствовать.
Как расшифровать маркировку
Каждая буква, которая содержится в маркировке стали имеет свое определенное значение:
- Х – содержание хрома;
- Н – содержание никеля;
- Т – содержание титана;
- В – содержание вольфрама;
- Г – содержание марганца;
- Д – содержание меди;
- М – присутствие молибдена.
В каких сферах применимы свойства нержавеющей стали
Нержавеющая сталь обладает высокими антикоррозийными свойствами, которые позволяют ее применять при изготовлении различного рода деталей, которые предназначены для эксплуатации в неблагоприятных условиях. Она используется практически во всех сферах производства: в химической, пищевой, авиационной промышленности, электроэнергетике, транспортном машиностроении. Некоторые марки способны сохранять свои свойства даже под воздействием высоких температур, которые доходят до 800 градусов.
Конструкционные стали и сплавы RMS
Конструкционные стали и сплавы
Конструкционными называются стали, предназначенные для изготовления деталей машин (машиностроительные стали), конструкций и сооружений (строительные стали).
Углеродистые конструкционные стали
Углеродистые конструкционные стали подразделяются на стали обыкновенного качества и качественные.
Стали обыкновенного качества изготавливают следующих марок Ст0, Ст1, Ст2,…, Ст6 (с увеличением номера возрастает содержание углерода). Ст4 — углерода 0.18-0.27%, марганца 0.4-0.7%.
Стали обыкновенного качества, особенно кипящие, наиболее дешевые. Стали отливают в крупные слитки, вследствие чего в них развита ликвация и они содержат сравнительно большое количество неметаллических включений.
С повышением условного номера марки стали возрастает предел прочности (sв) и текучести (s0.2) и снижается пластичность (d,y). Ст3сп имеет sв=380¸490МПа, s0.2=210¸250МПа, d=25¸22%.
Из сталей обыкновенного качества изготовляют горячекатаный рядовой прокат: балки, швеллеры, уголки, прутки, а также листы, трубы и поковки. Стали в состоянии поставки широко применяют в строительстве для сварных, клепанных и болтовых конструкций.
С повышением содержания в стали углерода свариваемость ухудшается. Поэтому стали Ст5 и Ст6 с более высоким содержанием углерода применяют для элементов строительных конструкций, не подвергаемых сварке.
Качественные углеродистые стали выплавляют с соблюдением более строгих условий в отношении состава шихты и ведения плавки и разливки. Содержание S<=0.04%, P<=0.035¸0.04%, а также меньшее содержание неметаллических включений.
Качественные углеродистые стали маркируют цифрами 08, 10, 15,…, 85, которые указывают среднее содержание углерода в сотых долях процента.
Низкоуглеродистые стали (С<0.25%) 05кп, 08, 07кп, 10, 10кп обладают высокой прочностью и высокой пластичностью. sв=330¸340МПа, s0.2=230¸280МПа, d=33¸31%.
Стали без термической обработки используют для малонагруженных деталей, ответственных сварных конструкций, а также для деталей машин, упрочняемых цементацией.
Среднеуглеродистые стали (0.3-0.5% С) 30, 35,…, 55 применяют после нормализации, улучшения и поверхностной закалки для самых разнообразных деталей во всех отраслях промышленности. Эти стали по сравнению с низкоуглеродистыми имеют более высокую прочность при более низкой пластичности (sв=500¸600МПа, s0.2=300¸360МПа,d =21¸16%). В связи с этим их следует применять для изготовления небольших деталей или более крупных, но не требующих сквозной прокаливаемости.
Стали с высоким содержанием углерода (0.6-0.85% С) 60, 65,…, 85 обладают высокой прочностью, износостойкостью и упругими свойствами. Из этих сталей изготавливают пружины и рессоры, шпиндели, замковые шайбы, прокатные валки и т.д.
Легированные конструкционные стали
Легированные стали широко применяют в тракторном и сельскохозяйственном машиностроении, в автомобильной промышленности, тяжелом и транспортном машиностроении в меньшей степени в станкостроении, инструментальной и других видах промышленности. Это стали применяют для тяжело нагруженных металлоконструкций.
Стали, в которых суммарное количество содержание легирующих элементов не превышает 2.5%, относятся к низколегированным, содержащие 2.5-10% — к легированным, и более 10% к высоколегированным (содержание железа более 45%).
Наиболее широкое применение в строительстве получили низколегированные стали, а в машиностроении — легированные стали.
Легированные конструкционные стали маркируют цифрами и буквами. Двухзначные цифры, приводимые в начале марки, указывают среднее содержание углерода в сотых долях процента, буквы справа от цифры обозначают легирующий элемент. Пример, сталь 12Х2Н4А содержит 0.12% С, 2% Cr, 4% Ni и относится к высококачественным, на что указывает в конце марки буква ²А².
Строительные низколегированные стали
Низко легированными называют стали, содержащие не более 0.22% С и сравнительно небольшое количество недефицитных легирующих элементов: до 1.8% Mn, до 1,2% Si, до 0,8% Cr и другие.
К этим сталям относятся стали 09Г2, 09ГС, 17ГС, 10Г2С1, 14Г2, 15ХСНД, 10ХНДП и многие другие. Стали в виде листов, сортового фасонного проката применяют в строительстве и машиностроении для сварных конструкций, в основном без дополнительной термической обработки. Низколегированные низкоуглеродистые стали хорошо свариваются.
Для изготовления труб большого диаметра применяют сталь 17ГС (s0.2=360МПа, sв=520МПа).
Арматурные стали
Для армирования железобетонных конструкций применяют углеродистую или низкоуглеродистую сталь в виде гладких или периодического профиля стержней.
Сталь Ст5сп2 — sв=50МПа, s0.2=300МПа, d=19%.
Стали для холодной штамповки
Для обеспечения высокой штампуемости отношение sв/s0.2 стали должно быть 0.5-0.65 при y не менее 40%. Штампуемость стали тем хуже, чем больше в ней углерода. Кремний, повышая предел текучести, снижает штампуемость, особенно способность стали к вытяжке. Поэтому для холодной штамповки более широко используют холоднокатаные кипящие стали 08кп, 08Фкп (0.02-0.04% V) и 08Ю (0.02-0.07% Al).
Конструкционные (машиностроительные) цементируемые (нитроцементуемые) легированные стали
Для изготовления деталей, упрочняемых цементацией, применяют низкоуглеродистые (0.15-0.25% С) стали. Содержание легирующих элементов в сталях не должно быть слишком высоким, но должно обеспечить требуемую прокаливаемость поверхностного слоя и сердцевины.
Хромистые стали 15Х, 20Х предназначены для изготовления небольших изделий простой формы, цементируемых на глубину 1.0-1.5мм. Хромистые стали по сравнению с углеродистыми обладают более высокими прочностными свойствами при некоторой меньшей пластичности в сердцевине и лучшей прочности в цементируемом слое. , чувствительна к перегреву, прокаливаемость невелика.
Сталь 20Х — sв=800МПа, s0.2=650МПа, d=11%, y=40%.
Хромованадиевые стали. Легирование хромистой стали ванадием (0.1-0.2%) улучшает механические свойства (сталь 20ХФ). Кроме того, хромованадиевые стали менее склонны к перегреву. Используют только для изготовления сравнительно небольших деталей.
Хромоникелевые стали применяются для крупных деталей ответственного значения, испытывающих при эксплуатации значительные динамические нагрузки. Повышенная прочность, пластичность и вязкость сердцевины и цементированного слоя. Стали малочувствительны к перегреву при длительной цементации и не склонны к перенасыщению поверхностных слоев углеродом
Сталь 12Х2Н4А — sв=1150МПа, s0.2=950МПа, d=10%, y=50%.
Хромомарганцевые стали применяют во многих случаях вместо дорогих хромоникелевых. Однако они менее устойчивы к перегреву и имеют меньшую вязкость по сравнению с хромоникелевыми.
В автомобильной и тракторной промышленности, в станкостроении применяют стали 18ХГТ и 25ХГТ.
Сталь 25ХГМ — sв=1200МПв, s0.2=1100МПа, d=10%, y=45%.
Хромомарганцевоникелевые стали. Повышение прокаливаемости и прочности хромомарганцевых сталей достигается дополнительным легированием их никелем.
На ВАЗе широко применяют стали 20ХГНМ, 19ХГН и 14ХГН.
После цементации эти стали имеют высокие механические свойства.
Сталь 15ХГН2ТА — sв=950МПа, s0.2=750МПа, d=11%, y=55%.
Стали, легированные бором. Бор увеличивает прокаливаемость стали, делает сталь чувствительной к перегреву.
В промышленности для деталей, работающих в условиях износа при трении, применяют сталь 20ХГР, а также сталь 20ХГНР.
Сталь 20ХГНР — sв=1300МПа, s0.2=1200МПа, d=10%, y=09%.
Конструкционные (машиностроительные) улучшаемые легированные стали
Стали имеют высокий предел текучести, малую чувствительность к концентраторам напряжений, в изделиях, работающих при многократном приложении нагрузок, высокий предел выносливости и достаточный запас вязкости. Кроме того, улучшаемые стали обладают хорошей прокаливаемостью и малой чувствительностью к отпускной хрупкости.
При полной прокаливаемости сталь имеет лучшие механические свойства, особенно сопротивление хрупкому разрушению — низкий порог хладноломкости, высокое значение работы развития трещины КСТ и вязкость разрушения К1с.
Хромистые стали 30Х, 38Х, 40Х и 50Х применяют для средненагруженных деталей небольших размеров. С увеличением содержания углерода возрастает прочность, но снижаются пластичность и вязкость. Прокаливаемость хромистых сталей невелика.
Сталь 30Х — sв=900МПа, s0.2=700МПа, d=12%, y=45%.
Хромомарганцевые стали. Совместное легирование хромом (0.9-1.2%) и марганцем (0.9-1.2%) позволяет получить стали с достаточно высокой прочностью и прокаливаемостью (40ХГ). Однако хромомарганцевые стали имеют пониженную вязкость, повышенный порог хладноломкости (от 20 до −60°С), склонность к отпускной хрупкости и росту зерна аустенита при нагреве.
Сталь 40ХГТР — sв=1000МПа, s0.2=800МПа, d=11%, y=45%.
Хромокремнемарганцевые стали. Высоким комплексом свойств обладают хромокремнемарганцевые стали (хромансил). Стали 20ХГС, 25ХГС и 30ХГС обладают высокой прочностью и хорошей свариваемостью. Стали хромансил применяют также в виде листов и труб для ответственных сварных конструкций (самолетостроение). Стали хромансил склонны к обратимой отпускной хрупкости и обезуглероживанию при нагреве.
Сталь 30ХГС — sв=1100МПа, s0.2=850МПа, d=10%, y=45%.
Хромоникелевые стали обладают высокой прокаливаемостью, хорошей прочностью и вязкостью. Они применяются для изготовления крупных изделий сложной конфигурации, работающих при динамических и вибрационных нагрузках.
Сталь 40ХН — sв=1000МПа, s0.2=800МПа, d=11%, y=45%.
Хромоникелемолибденовые стали. Хромоникелевые стали обладают склонностью к обратимой отпускной хрупкостью, для устранения которой многие детали небольших размеров из этих сталей охлаждают после высокого отпуска в масле, а более крупные детали в воде для устранения этого дефекта стали дополнительно легируют молибденом (40ХН2МА) или вольфрамом.
Сталь 40ХН2МА — sв=1100МПа, s0.2=950МПа, d=12%, y=50%.
Хромоникелемолибденованадиевые стали обладают высокой прочностью, пластичностью и вязкостью и низким порогом хладноломкости. Этому способствует высокое содержание никеля. Недостатками сталей являются трудность их обработки резанием и большая склонность к образованию флокенов. Стали применяют для изготовления наиболее ответственных деталей турбин и компрессорных машин.
Сталь 38ХН3МФА — sв=1200МПа, s0.2=1100МПа, d=12%, y=50%.
Стали с повышенной обрабатываемостью резанием
Наиболее часто применяют автоматные стали А12, А20, А40, имеющие повышенное содержание серы (0.08-0.3%), фосфора (<=0.05%) и марганца (0.7-1.0%). Сталь 40Г содержит 1.2-1.55% Mn.
Фосфор, повышая твердость, прочность и охрапчивая сталь, способствует образованию ломкой стружки и получению высокого качества поверхности.
Стали обладают большой анизотропией механических свойств, склонны к хрупкому разрушению, имеют пониженный предел выносливости. Поэтому сернистые автоматные стали применяют лишь для изготовления неответственных изделий — преимущественно нормалей или метизов.
Мартенсито-стареющие высоко прочные стали
Широкое применение в технике получила высокопрочная мартенсито-стареющая сталь Н18К9М5Т (<=0.03% С, ~18% Ni, ~9% Co, ~5% Mo, ~0.6 Ti).
Кроме стали Н18К9М5Т нашли применение менее легированные мартенсито-стареющие стали: Н12К8М3Г2, Н10Х11М2Т (sв=1400¸1500МПа), Н12К8М4Г2, Н9Х12Д2ТБ (sв=1600¸1800МПа), KCU=0.35¸0.6 МДж/м2, s0.2=1800¸2000МПа. Мартенсито-стареющие стали имеют высокий предел упругости s0.002=1500МПа.
Мартенсито-стареющие стали применяют в авиационной промышленности, в ракетной технике, в судостроении, в приборостроении для упругих элементов, в криогенной технике и т.д. Эти стали дорогостоящие.
Высокопрочные стали с высокой пластичностью
(ТРИП- или ПНП-стали)
Метастабильные высокопрочные аустенитные стали называют ТРИП-сталями или ПНП-сталями. Эти стали содержат 8-14% Cr, 8-32% Ni, 0. 5-2.5% Mn, 2-6% Mo, до 2% Si (30Х9Н8М4Г2С2 и 25Н25М4Г1).
Механические свойства ПНП-сталей: sв=1500¸1700МПа, s0.2=1400¸1550МПа, d=50¸60%. Характерным для это группы сталей является высокое значение вязкости разрушения и предела выносливости.
Широкому применению ПНП-сталей препятствует их высокая легированность, необходимость использования мощного оборудования для деформации при сравнительно низких температурах, трудность сварки. Эти стали используют для изготовления высоконагруженных деталей, проволоки, тросов, крепежных деталей и др.
Рессорно-пружинные стали общего назначения
Рессорно-пружинные стали предназначены для изготовления пружин, упругих элементов и рессор различного назначения. Они должны обладать высоким сопротивлением малым пластическим деформациям, пределом выносливости и релаксационной стойкостью при достаточной пластичности и вязкости.
Для пружин малого сечения применяют углеродистые стали 65, 70,75, 85. Сталь 85 — s0.2=1100МПа, sв=1150МПа, d=8%, y=30%.
Более часто для изготовления пружин и рессор используют легированные стали.
Стали 60С2ХФА и 65С2ВА, имеющие высокую прокаливаемость, хорошую прочность и релаксационную стойкость применяют для изготовления крупных высоконагруженных пружин и рессор. Сталь 65С2ВА — s0.2=1700МПа, sв=1900МПа, d=5%, y=20%. Когда упругие элементы работают в условиях сильных динамических нагрузок, применяют сталь с никелем 60С2Н2А.
Для изготовления автомобильных рессор широко применяют сталь 50ХГА, которая по техническим свойствам превосходит кремнистые стали. Для клапанных пружин рекомендуется сталь 50ХФА, не склонная к перегреву и обезуглероживанию.
Шарикоподшипниковые стали.
Для изготовления тел качения и подшипниковых колец небольших сечений обычно используют высокоуглеродистую хромистую сталь ШХ15 (0.95-1.0% С и 1.3-1.65% Cr), а больших сечений — хромомарганцевую сталь ШХ15СГ (0.95-1.05% С, 0.9-1.2% Cr, 0.4-0.65% Si и 1.3-1.65% Mn), прокаливающуюся на большую глубину. Стали обладают высокой твердостью, износостойкостью и сопротивлением контактной усталости. К сталям предъявляются высокие требования по содержанию неметаллических включений, так как они вызывают преждевременное усталостное разрушение. Недопустима также карбидная неоднородность.
Для изготовления деталей подшипников качения, работающих при высоких динамических нагрузках, применяют цементуемые стали 20Х2Н4А и 18ХГТ. После газовой цементации, высокого отпуска, закалки и отпуска детали подшипника из стали 20Х2Н4А имеют на поверхности 58-62 HRC и в сердцевине 35-45 HRC.
Износостойкие стали
Для деталей, работающих на износ в условиях абразивного трения и высоких давлений и ударов, применяют высокомарганцевую литую аустенитную сталь 110Г13Л, содержащую 0.9-1.3% С и 11,5-14.5% Mn. Она обладает следующими механическими свойствами: s0.2=250¸350МПа, sв=800¸1000МПа, d=35¸45%, y=40¸50%.
Сталь 110Г13Л обладает высокой износостойкостью только при ударных нагрузках. При небольших ударных нагрузках в сочетании с абразивным изнашиванием либо при чистом абразивном изнашивании мартенситное превращение не протекает и износостойкость стали 110Г13Л невысокая.
Для изготовления лопастей гидротурбин и гидронасосов, судовых гребных винтов и других деталей, работающих в условиях изнашивания при кавитационной эрозии, применяют стали с нестабильным аустенитом 30Х10Г10, 0Х14АГ12 и 0Х14Г12М, испытывающим при эксплуатации частичное мартенситное превращение.
Коррозийно-стойкие и жаростойкие стали и сплавы
Жаростойкие стали и сплавы. Повышение окалиностойкости достигается введением в сталь главным образом хрома, а также алюминия или кремния, т. е. Элементов, находящихся в твердом растворе и образующих в процессе нагрева защитные пленки оксидов (Cr, Fe)2O3, (Al, Fe)2O3.
Для изготовления различного рода высокотемпературных установок , деталей печей и газовых турбин применяют жаростойкие ферритные (12Х17, 15Х25Т и др.) и аустенитные (20Х23Н13, 12Х25Н16Г7АР, 36Х18Н25С2 и др.) стали, обладающие жаропрочностью.
Сталь 12Х17 — sв=520МПа, s0.2=350МПа, d=30%, y=75%.
Коррозионно-стойкие стали устойчивы к электрохимической коррозии.
Стали 12Х13 и 20Х13 применяют для изготовления деталей с повышенной пластичностью, подвергающихся ударным нагрузкам (клапанов гидравлических прессов, предметов домашнего обихода), а также изделий, испытывающих действие слабо агрессивных сред (атмосферных осадков, водных растворов солей органических кислот).
Стали 30Х13 и 40Х13 используют для карбюраторных игл, пружин, хирургических инструментов и т. д.
Стали 15Х25Т и 15Х28 используют чаще без термической обработки для изготовления сварных деталей, работающих в более агрессивных средах и не подвергающихся действию ударных нагрузок, при температуре эксплуатации не ниже −20°С.
Сталь 12Х18Н10Т получила наибольшее распространение для работы в окислительных средах (азотная кислота).
Сталь 12Х13 — sв=750МПа, s0.2=500МПа, d=20%, y=65%.
Коррозионно-стойкие сплавы на железоникелевой и никелевой основе. Сплав 04ХН40МДТЮ предназначен для работы при больших нагрузках в растворах серной кислоты.
Для изготовления аппаратуры, работающей в солянокислых средах, растворах серной и фосфорной кислоты, применяют никелевый сплав Н70МФ. Сплавы на основе Ni-Mo имеют высокое сопротивление коррозии в растворах азотной кислоты.
Для изготовления сварной аппаратуры, работающей в солянокислых средах, применяют сплав Н70МФ.
Наибольшее распространение получил сплав ХН65МВ для работы при повышенных температурах во влажном хлоре, солянокислых средах, хлоридах, смесях кислот и других агрессивных средах.
Сталь Н70МФ — sв=950МПа, s0.2=480МПа, d=50%.
Двухслойные стали нашли применение для деталей аппаратуры (корпусов аппаратов, днищ, фланцев, патрубков и др.), работающих в коррозионной среде. Эти стали состоят из основного слоя — низколегированной (09Г2, 16ГС, 12ХМ, 10ХГСНД) или углеродистой (Ст3) стали и коррозийно-стойкого плакирующего слоя толщиной 1-6мм из коррозийно-стойких сталей (08Х18Н10Т, 10Х17Н13М2Т, 08Х13) или никелевых сплавов (ХН16МВ, Н70МФ).
Сталь ХН65МВ — sв=1000МПа, s0.2=600МПа, d=50%.
Криогенные стали
Криогенные стали обладают достаточной прочностью при нормальной температуре в сочетании с высоким сопротивлением хрупкому разрушению при низких температурах. К этим сталям нередко предъявляют требования высокой коррозийной стойкости. В качестве криогенных сталей применяют низкоуглеродистые никелевые стали и стали аустенитного класса, несклонные к хладноломкости. Для сварных конструкций, работающих при температуре до −196°С, используют стали с 6-7% Ni (ОН6А) и 8.5-9.5% Ni (ОН9А), обладающие низким порогом хладноломкости.
Из этих сталей изготовляют цилиндрические или сферические резервуары для хранения и транспортировки сжиженных газов при температуре не ниже −196°С.
Сталь 10Х14Г14Н4Т — sв=620МПа, s0.2=280МПа, d=45%, y=60%.
Жаропрочные стали и сплавы
Жаропрочными называют стали и сплавы, способные работать под напряжением при высоких температурах в течение определенного времени и обладающие при этом достаточной жаростойкостью.
Жаропрочные стали и сплавы применяют для изготовления многих деталей котлов, газовых турбин, реактивных двигателей, ракет и т. д., работающих при высоких температурах.
Жаропрочные стали благодаря невысокой стоимости широко применяются в высокотемпературной технике, их рабочая температура 500-750°С.
Механические свойства сталей перлитного класса (12К, 15К, 18К, 22К, 12Х1МФ): sв=360¸490МПа, s0.2=220¸280МПа, d=24¸19%. Чем больше в стали углерода, тем выше прочность и ниже пластичность.
Стали мартенситного и мартенсито-ферритного классов (15Х11МФ, 40Х9С2, 40Х10С2М) применяют для деталей и узлов газовых турбин и паросиловых установок.
Стали аустенитного класса (10Х18Н12Т, 08Х15Н24В4ТР, 09Х14Н18В2БР) предназначены для изготовления пароперегревателей и турбоприводов силовых установок высокого давления.
Жаропрочные сплавы на никелевой основе находят широкое применение в различных областях техники (авиационные двигатели, стационарные газовые турбины, химическое аппаратостроение и т. д.).
Часто используют сплав ХН70ВТЮ, обладающий хорошей жаропрочностью и достаточной пластичностью при 700-800°С.
Никелевые сплавы для повышения их жаростойкости подвергают алитированию.
От кельтов до современности. Как производится сталь
После угля, цемента, нефти и древесины сталь является самым используемым материалом в мире. Из нее делают детали для автомобилей, самолетов и поездов, ее применяют в производстве бытовой техники, посуды, труб и много где еще. Причина такой востребованности проста. Дело в том, что сталь — материал ковкий и крайне прочный, он легко принимает форму, а при наличии правильного количества примесей практически не поддается коррозии.
О том, как она производится, читайте в этом материале.
Немного истории
Первые изделия из стали были созданы еще до нашей эры. Тогда для производства использовались так называемые сыродутные печи. Механизм их работы был прост: древесный уголь и куски железа слоями закладывали в выкопанную яму. В процессе горения между ними продували холодный воздух, что приводило к соединению кислорода с углеродом, находящимся в руде. В результате образовывался кусок «запеченного» железа с примесями шлаков, который после нагревали и выковывали.
Именно этой технологией несколько сотен лет пользовались люди в разных странах, чаще всего, для создания оружия. Так, например, около 200 лет до нашей эры кельты модернизировали этот способ: они резали кованое железо на тонкие полоски, складывали их в контейнер с обожженными костями, а затем нагревали его 10–12 часов на сильном огне. Позже получившиеся куски сваривали между собой и ковали ножи. Именно такой «кельтский» способ производства в 1050 г. нашей эры скопировали викинги и немцы, которые так делали стальные клинки. Стальное оружие изготавливали в Европе, Японии и других странах.
Проблема заключалась лишь в том, что наши предки не могли разогреть железо до температуры плавления — 1540 градусов по Цельсию. Поэтому им и приходилось спекать куски, что было очень трудоемко. Однако в XVIII веке все изменилось, когда английский металлург Бенджамин Гентсман открыл производство литейной стали. Для этого он переплавлял куски чугуна и сварного железа с примесью флюса, то есть вещества, которое помогало отделять металл от пустой породы. В континентальную Европу этот метод просочился только в начале XIX века благодаря предпринимателю Фридриху Круппу, основавшему первый литейный завод в Германии.
С тех пор сталь получила широкое распространение и применялась, прежде всего, в военной промышленности.
Производственный процесс
Сталь — это сплав железа с углеродом, в котором содержится не менее 45% железа и от 0,02 до 2,14% углерода. Именно от последнего элемента зависят основные свойства стали.
Чтобы производить сталь, нужно для начала добыть руду и каменный уголь, а затем обработать их специальным способом. Железную руду необходимо обогатить. Для этого ее дробят, а затем магнитом отделяют кусочки, в которых присутствует металл. С углем тоже не все так просто, поскольку в природном виде он содержит большое количество примесей, поэтому его также перемалывают, а затем просушивают в специальной «духовке», получая кокс.
Когда обогащенная железная руда и кокс подготовлены, их смешивают с известью и отправляют в печь, где при высокой температуре выплавляется чугун. А уже из чугуна производится сталь.
Чугун обогащен углеродом, который придает сплаву хрупкость. Также в нем все еще много ненужных примесей. Поэтому главные задачи при производстве качественной стали — вывести из состава как можно больше ненужных веществ, а также уменьшить концентрацию углерода до необходимых значений (от 0,02 до 2,14%).
Три основных стадии производства стали
• Расплавление
На данном этапе в ванну, расположенную в печи, закладывается шихта — в нашем случае, смесь чугуна с примесями других элементов. Смесь нагревается и расплавляется, а железо окисляется (то есть, забирает кислород), при этом оно окисляет примеси металлов, а именно фосфор, кремний и марганец. Главная задача первой стадии технологического процесса — удаление фосфора.
Итак, ванна нагревается. Под действием температуры часть примесей отделяются и поднимаются на поверхность, превращаясь в шлак. В это время оксид фосфора с оксидом железа создает неустойчивое соединение, которое реагирует с поднявшимся в шлак оксидом кальция. В результате еще одной химической реакции ненужный фосфор остается на поверхности, откуда его можно легко удалить.
• Кипение
Температуру в печи повышают, а внутрь нагнетают чистый кислород. Из-за этого углерод, находящийся в смеси, начинает окисляться — то есть взаимодействовать с кислородом. Соединившись с ним, он превращается в газообразный оксид углерода и с пузырьками покидает смесь. Это создает эффект кипения ванны.
В результате такого взаимодействия количество углерода снижается. А мы с вами помним: чем меньше углерода — тем крепче сплав. Так чугун начинает превращаться в сталь.
Еще один побочный, но полезный эффект процесса заключается в том, что к всплывающим пузырькам «прилипают» неметаллические примеси, что приводит к улучшению качества расплавленного металла. При этом вредная для стали сера также удаляется на этом этапе: когда температура повышается, она в составе сульфида железа реагирует с кальцием и отправляется в шлак. При этом металл остается в смеси.
• Раскисление
Итак, количество углерода снизили. Однако в результате химических реакций в смеси теперь достаточно много кислорода, который негативно влияет на свойства стали. Очевидно, что его необходимо удалить. Этот процесс и называется раскислением.
Способов существует несколько, но самых распространенных два. Смысл в том, что в ванну добавляют металлы, которые реагируют с кислородом гораздо активнее, чем железо. В одном случае их примешивают к непосредственно к сплаву, в другом — к шлаку. В результате химической реакции чистое железо отделяется от кислорода и остается в смеси, в то время как кислород с добавленными металлами собирается на поверхности.
В результате концентрация железа увеличивается, кислорода — уменьшается. Так получается сталь. Добавим, что отделившийся шлак не выбрасывают, а пускают в производство. Например, из него делают черепицу и кирпич, добавляют в цемент и так далее.
Разновидности и применение
Сталь можно классифицировать несколькими способами. Прежде всего, она делится по химическому составу с учетом наличия или отсутствия примесей:
• Углеродистые стали не содержат примесей. В зависимости от количества углерода в составе, бывают низкоуглеродистые (до 0,25%), среднеуглеродистые (0,3–0,55%) и высокоуглеродистые (0,6–2,14% С). Напоминаем, чем больше углерода в составе, тем более прочной, но менее пластичной она становится.
• Легированные содержат различные примеси, в зависимости от их количества делятся на низколегированные — до 4% легирующих элементов, среднелегированные — до 11% и высоколегированные — свыше 11% примесей.
По назначению стали делятся на множество категорий, расскажем об основных.
• Конструкционные. Используются для изготовления деталей, механизмов и конструкций в строительстве и машиностроении. Бывают легированными и углеродистыми, в зависимости от необходимых свойств сплава.
Что делают: проволоку, гвозди, крепежные детали, пружины, железнодорожные и трамвайные вагоны, детали автомобилей.
• Нержавеющие. Легированная сталь, которая устойчива к коррозии в атмосфере и агрессивных средах. Ее получают путем добавления в сплав азота, алюминия, серы, кремния, хрома, никеля, меди, титана и других элементов.
Что делают: кухонную технику (плиты, холодильники, микроволновки), сантехнику, посуду, части мебели и окон, ограждения и водостоки, ключевые узлы в автомобилях (двигатели, коробки передач), трубы в химической промышленности, элементы фильтров и так далее.
• Инструментальные. Сталь с содержанием углерода от 0,7% и выше. Отличается твердостью и плотностью и, как не трудно догадаться, из нее изготавливают инструменты.
Что делают: колуны, молотки, кусачки, плоскогубцы, пилы, стамески, напильники, бритвенные лезвия и ножи, хирургические инструменты, отвертки, заклепки и многое другое.
• Жаропрочные. Легированная сталь, которая отличается способностью работать под напряжением в условиях повышенных температур без заметной остаточной деформации и разрушения.
Что делают: детали конструкций двигателей внутреннего сгорания, клапаны авиационных поршневых моторов, элементы газовых турбин, части реактивных двигателей и так далее.
• Криогенные. Легированные стали, которые могут выдерживать температуру ниже точки кипения кислорода, то есть ниже -183 градусов по Цельсию. Для получения этих свойств в сплав добавляются никель, хром и марганец.
Что делают: детали арматуры, части авиакосмической техники, детали сверхпроводящих магнитов и установок термоядерного синтеза.
Сталь сегодня. Крупнейшие российские производители
В 2021 г. мировое производство стали достигло рекордного значения — 1950,5 млн тонн. Лидером, несмотря на снижение выпуска, остается Китай. На втором месте находится Индия, на третьем — Япония. Четвертую строчку в рейтинге занимает США. Россия в этом списке располагается на пятой позиции.
Крупнейшие российские производители стали — НЛМК, ММК, Северсталь и Евраз.
НЛМК
Это международная сталелитейная компания с активами в России, США и странах Европы. Основное предприятие — Новолипецкий металлургический комбинат, построенный в 1930-ых гг. В группу входят площадки, на которых происходит полный производственный цикл — от добычи сырья до выпуска готовой продукции.
Металлопродукция НЛМК применяется в стратегических отраслях экономики: от машиностроения и строительства до производства труб большого диаметра и энергетического оборудования.
На 2021 г. компания — крупнейший производитель стали в России.
ММК
Магнитогорский металлургический комбинат — одно из крупнейших предприятий отрасли в СНГ. Его строительство началось в 1929 г. ММК входит в число крупнейших мировых производителей стали, имеет сталеплавильное производство в Турции.
ММК производит различную металлопродукцию, которая используется в автопроме, судо- и мостостроении, в производстве бытовой техники, трубной промышленности, а также в производстве товаров народного потребления.
В 2021 г. выручка ММК выросла на 86,6% относительно предыдущего года. Компания поставляет продукцию в регионы РФ и страны ближнего зарубежья.
Северсталь
Череповецкий металлургический комбинат должны были построить в 1940-х гг. , однако этого не произошло из-за начала Великой отечественной войны. Поэтому свою историю компания отчитывает с 1955 г., когда было запущено производство. Комбинат является одним из ведущих производителей стали в России на листовом прокате. Также занимается производством труб, добычей и обогащением железной руды
По итогам 2021 г. компания представила сильные результаты. Ее выручка увеличилась, несмотря на снижение цены на стальную продукцию.
Евраз
В феврале 1992 г. была основана компания Евразметалл, которая занималась продажей металлопродукции. В 1995 г. ее в состав вошел Нижнетагильский металлургический комбинат (НТМК), в 2002 г. — Западно-Сибирский металлургический комбинат (ЗСМК).
Evraz Group имеет активы в России, Канаде, США, Италии, Казахстане и Чехии. Штаб-квартира находится в Лондоне.
НТМК занимается доменным, коксохимическим, прокатным, сталеплавильным и кислородным производствами. Комбинат выпускает чугун, шлак, сталь для железнодорожного транспорта, в том числе, профили для вагоностроения, рельсы и колеса. Также из стали на предприятии делают трубы большого диаметра для магистральных газопроводов. НТМК производит более 1200 марок стали.
В ЗСМК занимаются доменным, сталепрокатным, коксохимическим и другими видами производств. Выпускаются проволока, стальные трубы, рельсы, товары народного потребления, металлургическая продукция для строительной отрасли.
Интересные факты
• Сталь — один из самых перерабатываемых металлов в мире, потому что его легко переплавить. По статистике, более 60% сплава перерабатывается. Это значит, что больше половины всей стали используется повторно.
• Нержавеющую сталь изобрели случайно. Английский металлург Гарри Брирли пытался создать сплав, который бы защитил жерла пушек от эрозии, то есть от износа, связанного с высокими температурами. Однако в процессе исследования выяснилось, что если сталь содержит от 12 до 20% хрома, то она сопротивляется кислотной коррозии.
• Существует мыло из нержавеющей стали. Если подержать его в руках какое-то время, оно удалит любой, даже самый неприятный запах.
• Высота Эйфелевой башни в зависимости от времени года может меняться на 15 сантиметров. Это связано с тем, что стальные элементы конструкции имеют свойство сжиматься при охлаждении и расширяться при нагреве.
• Для постройки некоторых спутников, измеряющих радиацию в космосе, в 1950-ых гг. американцы подняли со дна стальные части затонувшего в 1919 г. корабля «Кронпринц Вильгельм».
Читайте также: Есть даже на Марсе, но трудно добыть на Земле. Как производят алюминий
БКС Мир инвестиций
Углеродистая сталь — РИНКОМ
Углеродистые стали – это обширная категория сплавов. Их ключевое отличие – отсутствие легирующих элементов и повышенное содержание углерода. Материал востребован при изготовлении сортового проката и металлорежущего инструмента.
В материале:
- Химический состав
- Преимущества и недостатки
- Классификация углеродистых сталей
- Дополнительная классификация
- Расшифровка маркировки
- Пример расшифровки
- Изготавливаемая продукция
- Сверла из углеродистой стали
- Ручной инструмент
- Заточка инструмента из углеродистой стали
- Стандарты, регламентирующие качество проката из углеродистой стали
- Аналоги
- Термическая обработка углеродистых сталей
- Отжиг
- Нормализация
- Закалка
- Отпуск
Химический состав
Химический состав зависит от марки углеродистой стали. При этом все сплавы данной группы содержат стандартное количество определенных элементов:
- углерод – до 2,14%;
- кремний – до 1%;
- марганец – до 1%;
- сера – до 0,05%;
- фосфор – до 0,06%.
Показатели серы и фосфора превышают аналогичные параметры у легированных сталей. Это негативно сказывается на прочности продукции из углеродистых сплавов.
Рис. 1 Изменение структуры углеродистой стали с ростом процентного содержания углерода
Преимущества и недостатки
Углеродистые стали имеют немало преимуществ и недостатков. К преимуществам материалов относятся:
- высокие показатели ударной вязкости;
- длительное сохранение заточки;
- повышенные прочностные характеристики;
- приемлемая стоимость ввиду отсутствия легирующих элементов.
Недостатки углеродистых сплавов:
- уязвимость к коррозионному поражению;
- повышенное содержание вредных примесей в сравнении с легированными сталями;
- необходимость многоуровневой термической обработки для придания сплаву требуемых свойств.
Металлические конструкции из углеродистой стали подвергаются окрашиванию. Это исключает их окисление под действием внешних факторов.
Рис. 2 Коррозионное поражение необработанного участка опор из углеродистой стали
Классификация углеродистых сталей
ГОСТ 308-2005 предусматривает изготовление двух типов сплавов: инструментальные углеродистые стали и конструкционные углеродистые стали. Первые используются при производстве металло- и деревообрабатывающего инструмента, вторые – сортового проката для металлоконструкций.
Конструкционные стали бывают качественными и обычными, инструментальные – качественными и высококачественными.
Конструкционные стали обычного качества делятся на три группы:
- А – материал, поставляемый по механическим свойствам;
- Б – материал, поставляемый по химсоставу;
- В – материал, поставляемый по химсоставу и механическим свойствам.
Качественные стали конструкционного типа также делятся на 3 группы:
- специальные;
- с содержанием марганца до 0,7%;
- с содержанием марганца свыше 0,7%.
Внутригруппового деления для инструментальных сплавов не предусмотрено.
Рис. 3 Классификация углеродистых сталей
Дополнительная классификация
Углеродистые сплавы могут различаться по ряду дополнительных параметров.
- По способу получения: выплавка в мартеновских печах, электропечах или кислородно-конвертерным способом.
- По взаимодействию с химически активными средами: спокойные, полуспокойные и кипящие.
- По содержанию углерода:
- низкоуглеродистые – до 0,29%;
- среднеуглеродистые – от 0,3 до 0,6%;
- высокоуглеродистые – более 0,6%.
Сплавы, в которых содержание углерода превышает 2,4%, относятся к чугунам.
Расшифровка маркировки
Маркировка углеродистых сталей зависит от класса и состава, содержит следующие параметры.
- Ст – принадлежность сплава к сталям обычного качества.
- Цифры от 1 до 6 – условный номер, соответствующий содержанию углерода.
- Б – гарантия механического состава сплава.
- В – гарантия химического состава сплава.
- ПС или КП – степень взаимодействия стали с химически активными средами, ПС – полуспокойная, КП – кипящая.
- Г – повышенное содержание марганца.
- У – принадлежность сплава к качественным сталям.
Если в маркировке отсутствуют обозначения ПС или КП, то сталь относится к спокойным. Сплавы повышенного качества и инструментальные стали обозначаются буквой А.
Таблица №1 Химический состав сталей обычного качества в соответствии с условными номерами от 1 до 6
Пример расшифровки
Сталь БСт5пс имеет следующую расшифровку маркировки: углеродистый полуспокойный сплав обычного качества с гарантированным механическим составом и содержанием углерода 0,28-0,37% в соответствии с условным номером.
Также при обозначении стали могут использоваться особые цвета, информирующие о ее марке.
Таблица №2 Цвет обозначения стали в соответствии с маркой
Изготавливаемая продукция
Из углеродистой стали производятся сверла, коронки и прочий металлорежущий инструмент. Продукция широко используется на производстве и в быту.
Сверла из углеродистой стали
Выпуск сверл из углеродистой стали осуществляется по техническим условиям. Изделия отличаются доступной ценой, эффективно справляются с деревом, пластиком и металлом.
Рис. 4 Спиральные сверла из углеродистой стали
Сверла из углеродистой стали входят в состав многих наборов.
Рис. 5 Набор, включающий сверла из углеродистой стали
Ручной инструмент
Высокая твердость углеродистой стали делает ее отличной основой для ручного инструмента: топоры, стамески, зубила и т. д.
Рис. 6 Стамеска из углеродистой стали
Заточка инструмента из углеродистой стали
Заточка режущего инструмента из углеродистой стали производится посредством абразивных кругов. Мастер постепенно снижает зернистость круга, что обеспечивает формирование качественной рабочей части.
Для обслуживания ручного инструмента (топоры, стамески) может использоваться универсальный круг или брусок. Главное – обеспечить равномерный контакт лезвия с абразивным материалом.
Рис. 7 Заточка стамески
Стандарты, регламентирующие качество проката из углеродистой стали
Прокат из углеродистой стали выпускается согласно следующим стандартам:
- ГОСТ 14637-89 – толстолистовой прокат;
- ГОСТ 16532-97 – тонколистовой прокат;
- ГОСТ 535-2005 – фасонный прокат;
- ГОСТ 2590-2006 – круг.
Из углеродистой стали также производятся швеллеры, уголки и балки. Для каждого типа изделий предусмотрен собственный стандарт. В отдельных случаях используются технические условия.
Рис. 8 Рифленый листовой прокат из углеродистой стали
Аналоги
Углеродистая сталь имеет множество аналогов в странах СНГ и дальнего зарубежья.
Таблица №3 Аналоги отечественных углеродистых сталей
Термическая обработка углеродистых сталей
Термическая обработка углеродистых сплавов осуществляется путем отжига, нормализации, закалки и отпуска.
Отжиг
Отжиг углеродистой стали производится с целью снятия внутренних напряжений и выравнивания структуры. Нагрев происходит в электрических печах, его температура зависит от процентного содержания углерода. Материал охлаждается в воздушной среде.
Таблица №4 Температура отжига углеродистой стали
Нормализация
Нормализация предполагает температурную обработку с целью изменения размерности зерна. Уровень нагрева определяется согласно общему графику термической обработки.
Рис. 9 Общий график термической обработки
Закалка
Закалка углеродистой стали осуществляется путем нагрева и резкого охлаждения заготовок. По завершении операции материал увеличивает твердость, но снижает пластичность.
Рис. 10 Закалка металла в печи
Отпуск
Отпуск углеродистой стали производится с целью увеличения пластичности. Выделяют три типа процедур:
- низкий отпуск при температуре 150 – 260 градусов;
- умеренный отпуск при температуре 300 – 400 градусов;
- высокий отпуск при температуре 500 – 650 градусов.
Металл остывает в воде, масле или воздушной среде.
Часто задаваемые вопросы
Чем углеродистые стали отличаются от легированных?
Углеродистые сплавы не содержат легирующих присадок. Их основными компонентами являются железо и углерод. Легированные стали могут включать никель, хром и прочие элементы, повышающие их эксплуатационные свойства.
Чем отличается качественная углеродистая сталь от стали обыкновенного качества?
Качественная углеродистая сталь содержит меньшее количество серы, фосфора и прочих вредных примесей. Она обладает более высокой пластичностью и ударной вязкостью.
Чем отличается низкоуглеродистая сталь от высокоуглеродистой?
Материалы различаются процентным содержанием углерода. В первом случае показатель составляет не более 0,29%, во втором – превышает 0,6%.
Что такое легированная сталь | Легированная сталь VS Углеродистая сталь
跳过内容 ЧТО ТАКОЕ ЛЕГИРОВАННАЯ СТАЛЬ — Легированная сталь VS Углеродистая сталь Прежде чем мы рассмотрим все, что касается легированной стали, давайте поразимся нескольким фактам о стали, о которых, я уверен, вы никогда раньше не слышали.
- Сталь примерно в тысячу раз прочнее самой чистой формы железа и может быть переработана без потери прочности.
- Сталелитейная промышленность открывает дома для более чем 2 миллионов человек по всему миру по мере увеличения уровня занятости.
- 25% среднего компьютера состоит из стали.
- При нагревании сталь и железо расширяются. Это свойство стали увеличивает высоту Эйфелевой башни летом на шесть дюймов.
- Ежегодно из стали производится 200 миллиардов банок.
- Ежегодно в Северной Америке перерабатывается более восьмидесяти миллионов тонн стали.
- Крыши из стали служат более пятидесяти лет, в то время как традиционные крыши служат только семнадцать лет.
Довольно интересно, правда? В этой статье мы обсудим легированную сталь и ее связь с нержавеющей и углеродистой сталью.
Что такое легированная сталь?
О нержавеющей стали наверняка слышали все. Это лучший материал для посуды, такой как кастрюли и сковородки. Но знаете ли вы, из чего состоит нержавеющая сталь? Это смесь железа, хрома, кремния, углерода и марганца (все они добавляются в разных количествах). Любая смесь металлов называется сплавом. Другой пример сплава, который мы сегодня обсудим, — это легированная сталь. Это тип стали, смешанный с различными уровнями одного или нескольких из следующих элементов: марганец, кремний, никель, титан, медь, хром и алюминий. Разница между нержавеющей сталью и легированной сталью заключается в том, что легированная сталь состоит из таких элементов, как никель и медь.
- Марганец упрочняет сталь при более высоких температурах, поскольку устраняет образование ненужных соединений, таких как сульфид железа.
- Никель и медь повышают прочность и твердость стали, а также сохраняют устойчивость к коррозии и окислению.
- Медь добавляется в очень небольших количествах, но она также повышает прочность и коррозионную стойкость стали. Алюминий
- ограничивает образование и рост любых примесей, таких как аустенитные зерна.
- Хром является ключевым легирующим элементом, обладающим значительной устойчивостью к коррозии и износу. Это также помогает стали упрочняться, так как положительно реагирует на термическую обработку.
Рассмотрим некоторые свойства легированной стали: Теплопроводность (способность материала проводить тепло) легированной стали составляет около 26-48,6 Вт/м·К, что считается низким. Поскольку большинство легированных сталей содержат титан и никель, которые обладают низкой теплопроводностью. Прочность на растяжение легированных сталей составляет от 758 до 1882 МПа, что выше, чем у нержавеющей стали. Сталь смешивается с другими элементами для улучшения их механических свойств, закалки стали, что делает легированную сталь более прочной и устойчивой к коррозии.
Существует два типа легированной стали: высоколегированная и низколегированная сталь. Это зависит от процентного содержания легирующих элементов; высоколегированная сталь имеет более высокий процент. Низколегированная сталь обычно содержит 1-5% легирующих элементов, что делает ее более подходящей для применений, требующих механических свойств. Наиболее распространенным примером высоколегированной стали является нержавеющая сталь. Уровень хрома варьируется, что приводит к различным типам нержавеющей стали. Хрома не менее 12%, а в некоторых сталях оно может увеличиваться до 27%; в зависимости от их использования. Забавный факт, знаете ли вы, что нержавеющая сталь может удалять запахи с поверхности кожи! Низколегированная сталь имеет повышенную твердость и сопротивление износу и разрыву, но не обладает такой же прочностью на растяжение, как высоколегированная сталь. Высоколегированная сталь также может противостоять износу даже при высоких температурах.
Каково использование легированной стали?
Легированная сталь является одной из часто используемых сталей. Существует широкий спектр применений легированной стали, включая:
- Трубы, используемые в энергетических приложениях, таких как бурение нефтяных и газовых скважин.
Они способны выдерживать нагрузку и давление, которые будут воздействовать на эти части машины.
Подшипники - изготовлены из легированной стали, поскольку это придает им прочность, чтобы противостоять растрескиванию или контактной усталости при качении.
- Архитектура использует легированную сталь, чтобы избежать коррозии, в строительстве используется высоколегированная сталь.
- Железные дороги, безопасные сейфы и броня — другие распространенные области применения легированной стали. Марганец и никель, содержащиеся в легированной стали, в основном ответственны за это применение.
- Предметы домашнего обихода, такие как посуда, столовые приборы, столешницы и т. д., изготовлены из нержавеющей стали, так как им легко придать форму при высоких температурах.
- Artwork использует стальные сплавы в качестве материала для изобразительного искусства. Художники используют его в качестве основы для холста, чтобы придать художественному произведению блеск.
Легированная сталь используется почти во всех отраслях промышленности. В дополнение к перечисленным выше применениям, сталь может использоваться в транспорте, жилищном строительстве, энергетике и машиностроении.
Легированная сталь VS Углеродистая сталь
«Упорство в характере человека, как углерод в стали», Наполеон Хилл.
Другим типом стали, о котором пойдет речь в этой статье, является углеродистая сталь. Основным элементом в этом типе стали является не железо, а углерод. Чем выше количество углерода, тем легче вы можете закалить металл при его нагревании. Существует также низко-, средне- и высокоуглеродистая сталь. В малоуглеродистой стали содержание углерода не превышает 0,25 % в смеси с 0,4 % марганца. Это самая дешевая углеродистая сталь, но ее можно использовать во многих областях, поскольку она легко поддается формованию. Среднеуглеродистая сталь состоит максимум из 0,54% углерода и 1,65% марганца. Более высокое содержание углерода делает этот тип стали прочнее, а также придает ему устойчивость к износу. Это, однако, снижает их способность легко формироваться. В то время как в высокоуглеродистой стали содержание углерода может достигать 0,9%.
Этот тип углеродистой стали является самым прочным и трудно поддающимся формованию, поэтому он используется только тогда, когда это действительно необходимо. Некоторые из его применений — пружины, провода и ножи. Если вы любитель химии, вы должны знать, что различные формы углерода очень прочны. Алмазы, самый прочный материал на земле, на самом деле состоят из углерода. Таким образом, это может объяснить, почему, когда углерод смешивается с железом, его достаточно самого по себе без каких-либо дополнительных элементов для его укрепления.
Теперь, когда мы создали хорошую основу для того, что такое углеродистая сталь, давайте углубимся в различия между углеродистой сталью и легированной сталью. Их состав сильно отличается друг от друга. Углеродистая сталь изготавливается из максимум 2,1% углерода (очень высокоуглеродистая сталь) и железа. Любой другой элемент, обнаруженный в этом типе стали, рассматривается как примесь.
Однако легированная сталь не была бы легированной без добавления дополнительных элементов для улучшения ее свойств. Именно это делает легированную сталь более устойчивой к коррозии, имеет более высокую прочность на растяжение и твердость. Чем выше содержание легирующих элементов, тем чаще используется легированная сталь. С другой стороны, чем выше содержание углерода, тем тверже и менее пригодной для использования становится сталь. Тем не менее, углеродистая сталь занимает первое место в ценовой категории. Углеродистая сталь относительно дешевле, особенно из-за более низкого содержания углерода. Легированная сталь может стать очень дорогой из-за добавленных легирующих элементов и их количества.
Сколько это стоит?
Прежде чем совершить покупку, давайте рассмотрим плюсы и минусы легированных сталей. Легированные стали имеют высокое отношение прочности к весу. Они также имеют низкую плотность, уменьшая их вес, чтобы они могли противостоять стрессу и давлению. С помощью тепла им можно придать любую требуемую форму, что расширяет возможности их применения. С другой стороны, по сравнению с нержавеющей сталью, легированная сталь в целом имеет более низкую прочность (особенно при более высоких температурах), а также более высокую вероятность коррозии.
При выборе легированной стали необходимо учитывать несколько моментов: форму легированной стали, толщину, ширину и длину стальных труб. А также марку трубы, которая представляет собой процентное содержание легирующих элементов. Двумя основными странами, поставляющими легированную сталь, являются Индия и Китай. США занимают третье место. По данным глобальных торговых онлайн-сайтов (таких как Alibaba.com и made-in-china), цена на легированную сталь начинается с 450 долларов и может достигать 2800 долларов за тонну. Одна тонна — минимальный вес для заказа.
В заключение, куда бы вы ни посмотрели, вы найдете сталь в любой форме. Он был интегрирован почти во все аспекты жизни. В зависимости от элементов, с которыми смешивается железо, образуются разные типы стали. Каждый тип стали, будь то легированная, углеродистая или нержавеющая сталь, имеет свой собственный набор свойств, которые делают их более подходящими для конкретных применений. Но общими свойствами всех них являются их прочность, твердость и способность принимать желаемую форму. Использование стали широко варьируется от посуды до промышленности, строительства и сельского хозяйства.
Songshun Steel2020-10-10T03:54:47-04:00 Ссылка для загрузки страницыЧто такое нержавеющая сталь и как она производится?
Как изготавливается нержавеющая сталь Точный процесс для марки нержавеющей стали будет отличаться на более поздних этапах. То, как марка стали формируется, обрабатывается и обрабатывается, играет важную роль в определении того, как она выглядит и работает.
Прежде чем вы сможете создать готовое стальное изделие, вы должны сначала создать расплавленный сплав.
Из-за этого большинство марок стали имеют общие начальные этапы.
Этап 1: ПлавлениеПроизводство нержавеющей стали начинается с плавки металлолома и добавок в электродуговой печи (ЭДП). Используя мощные электроды, электродуговая печь нагревает металлы в течение многих часов, создавая расплавленную жидкую смесь.
Поскольку нержавеющая сталь на 100 % подлежит вторичной переработке, многие заказы на нержавеющую сталь содержат до 60 % переработанной стали. Это помогает не только контролировать расходы, но и уменьшить воздействие на окружающую среду.
Точная температура зависит от марки созданной стали.
Этап 2: Удаление углерода Углерод помогает повысить твердость и прочность железа. Однако слишком много углерода может создать проблемы, такие как осаждение карбида во время сварки.
Перед разливкой расплавленной нержавеющей стали необходимо выполнить калибровку и снизить содержание углерода до надлежащего уровня.
Существует два способа контроля содержания углерода в литейном производстве.
Первый – аргонно-кислородное обезуглероживание (AOD). Впрыск газовой смеси аргона в расплавленную сталь снижает содержание углерода с минимальной потерей других важных элементов.
Другим используемым методом является вакуумно-кислородное обезуглероживание (VOD). В этом методе расплавленная сталь переносится в другую камеру, где в сталь впрыскивается кислород при одновременном нагревании. Затем с помощью вакуума удаляются газы из камеры, что еще больше снижает содержание углерода.
Оба метода обеспечивают точный контроль содержания углерода, чтобы обеспечить правильную смесь и точные характеристики конечного продукта из нержавеющей стали.
Этап 3: Настройка После восстановления углерода происходит окончательная балансировка и гомогенизация температуры и химии. Это гарантирует, что металл соответствует требованиям, предъявляемым к его предполагаемой марке, и что состав стали одинаков во всей партии.
Образцы тестируются и анализируются. Затем вносятся коррективы до тех пор, пока смесь не будет соответствовать требуемому стандарту.
Этап 4: Формовка или литьеПосле создания расплавленной стали литейный цех должен теперь создать примитивную форму, используемую для охлаждения и обработки стали. Точная форма и размеры будут зависеть от конечного продукта.
Общие формы включают:
- Блюмы
- Заготовки
- Плиты
- Стержни
- Трубы
Затем формы маркируются идентификатором для отслеживания различных процессов партии.
Отсюда шаги будут различаться в зависимости от предполагаемого сорта и конечного продукта или функции. Плиты становятся пластинами, полосами и листами. Блюмы и заготовки становятся стержнями и проволокой.
В зависимости от заказанной марки или формата сталь может пройти некоторые из этих этапов несколько раз, чтобы получить желаемый внешний вид или характеристики.
Следующие шаги являются наиболее распространенными.
Горячая прокаткаЭтот этап, выполняемый при температурах выше температуры рекристаллизации стали, помогает установить приблизительные физические размеры стали. Точный контроль температуры на протяжении всего процесса позволяет сохранять сталь достаточно мягкой для работы без изменения структуры.
В процессе используются повторные проходы для медленной регулировки размеров стали. В большинстве случаев для достижения желаемой толщины требуется прокатка на нескольких станах с течением времени.
Холодная прокаткаЧасто используется, когда требуется точность, холодная прокатка происходит ниже температуры рекристаллизации стали. Несколько поддерживаемых роликов используются для придания формы стали. Этот процесс создает более привлекательную однородную отделку.
Однако он также может деформировать структуру стали и часто требует термической обработки для рекристаллизации стали до ее первоначальной микроструктуры.
После прокатки большинство сталей подвергается отжигу. Это включает в себя контролируемые циклы нагрева и охлаждения. Эти циклы помогают размягчить сталь и снять внутреннее напряжение.
Точные значения температуры и времени зависят от марки стали, при этом скорость нагрева и охлаждения влияет на конечный продукт.
Удаление окалины или травлениеПоскольку сталь проходит различные этапы обработки, на ее поверхности часто накапливается окалина.
Это скопление не просто непривлекательно. Это также может повлиять на устойчивость к пятнам, долговечность и свариваемость стали. Удаление этой накипи необходимо для создания оксидного барьера, который придает нержавеющей стали ее характерную коррозионную стойкость и устойчивость к пятнам.
При удалении накипи или травлении эта накипь удаляется либо с помощью кислотных ванн (известных как кислотное травление), либо путем контролируемого нагрева и охлаждения в бескислородной среде.
В зависимости от конечного продукта металл может возвращаться в прокат или экструзию для дальнейшей обработки. Затем следуют повторяющиеся фазы отжига до достижения желаемых свойств.
РезкаПосле того, как сталь обработана и готова, партия разрезается в соответствии с требованиями заказа.
Наиболее распространенными методами являются механические методы, такие как резка гильотинными ножами, дисковыми ножами, высокоскоростными лезвиями или пробивка штампами.
Однако для сложных форм можно также использовать газовую или плазменную резку.
Оптимальный вариант будет зависеть как от требуемой марки стали, так и от желаемой формы поставляемого изделия.
Отделка Нержавеющая сталь доступна в различных вариантах отделки от матовой до зеркальной. Отделка является одним из последних этапов производственного процесса. Общие методы включают травление кислотой или песком, пескоструйную очистку, ленточное шлифование, полировку ленты и полировку ленты.
На этом этапе сталь собирается в своей окончательной форме и готовится к отправке покупателю. Рулоны и рулоны являются обычными способами хранения и транспортировки больших количеств нержавеющей стали для использования в других производственных процессах. Однако окончательная форма будет зависеть от требуемого типа стали и других факторов, характерных для заказа.
Заключительные мыслиПонимание правильных марок и типов нержавеющей стали для конкретных применений и сред является важной частью обеспечения долгосрочных результатов и оптимизации затрат. Если вы ищете что-то прочное и устойчивое к коррозии для морской среды или что-то потрясающее и легкое в уходе для использования в ресторане, у вас есть сплав из нержавеющей стали, который удовлетворит ваши потребности.
Если вам интересно, как нержавеющая сталь может подойти для вашего следующего проекта, проконсультируйтесь с Unified Alloys. Являясь ведущим поставщиком нержавеющей стали в Канаде уже более 40 лет, мы обладаем знаниями и ресурсами, чтобы помочь вам найти идеальный продукт для ваших требований.
Углеродистая сталь и стальные сплавы: часть первая
УГЛЕРОДИСТАЯ СТАЛЬ
Углеродистая сталь – это сталь, свойства которой в основном состоят из углерода, а ее структура зависит от содержания углерода. Самой твердой углеродной структурой в мире является алмаз, который на 100% состоит из углерода. Углерод присутствует во всех сталях и является основным упрочняющим элементом, который определяет уровень твердости или прочности, достигаемый закалкой. Он повышает прочность на растяжение, твердость и сопротивление износу и истиранию по мере увеличения содержания углерода в стали. Однако это также может снизить пластичность, ударную вязкость и обрабатываемость.
Холоднотянутая углеродистая сталь обычно нумеруется префиксом «10» в системе нумерации AISI, за которым следуют два числа, представляющие номинальный процент углерода в продукте (до 1,00%). Например, 1018 содержит 0,18% углерода, а 1045 — 0,45%.
Углерод придает материалу твердость, повышая его износоустойчивость. При содержании углерода более 0,30 % продукт может подвергаться прямой закалке («сквозной закалке»). Углеродистая сталь ниже этого уровня обычно требует науглероживания при термической обработке. Во время науглероживания вводятся молекулы углерода, так что на поверхности образуется затвердевшая «кожа», создающая «корпус». Именно здесь встречается понятие упрочнения корпуса.
Максимальное содержание углерода в стали составляет менее 1,00 %, поскольку более высокое содержание делает материал хрупким. Чем выше содержание углерода, тем труднее обрабатывать углеродистую сталь.
Точно так же, как соль снижает температуру фазового перехода воды, углерод снижает температуру фазового перехода железа.
ЛЕГИРОВАННЫЕ СТАЛИ
Легированные стали являются производными углеродистых сталей, в которые добавляются или удаляются элементы для придания определенных свойств. Обычно эти свойства включают обрабатываемость, износостойкость и прочность. Смесь на основе железа считается легированной сталью, если в ней присутствует марганец более 0,165 %, кремний более 0,5 %, медь более 0,6 % или другие минимальные количества легирующих элементов, таких как хром, никель, молибден или вольфрам.
Железные сплавы являются наиболее распространенными железными сплавами. Сталь представляет собой твердый раствор железа и углерода. Углерод растворяется в железе – железо является растворителем, а углерод – растворенным веществом.
Сталь, как и вода, может изменять свою фазу. В воде фазы бывают твердые, жидкие и газообразные. В углеродистой стали фазами являются жидкая, аустенитная и ферритная. Если в воду добавить соль, температура перехода между фазами сместится. Вот почему соль является распространенным соединением таяния льда. Соль понизит температуру перехода из твердого состояния в жидкое, но повысит температуру перехода из жидкого в газообразное. При добавлении углерода к железу температуры меняются точно так же. Чем больше углерода добавлено (до точки), тем ниже температура, при которой произойдет фазовый переход. Углерод также создает новые фазы, которые не существуют в железе сами по себе. Перлит представляет собой смесь цементита (Fe 3 C) плюс феррит. Максимальное количество углерода, которое может быть растворено в аустените, составляет 0,80%. Это называется «эвтектика». Другие сплавы могут быть описаны как эвтектические сплавы. Эти сплавы имеют максимальное количество легирующих элементов, которые могут быть растворены в исходном материале. Важно отметить, что термическая история изделия также играет роль в его фазовом развитии.
Для большинства низколегированных и углеродистых сталей: чем больше углерода добавляется (выше 0,20%), тем больше перлита получается, вплоть до 0,80%. Выше 0,80% вы получаете карбиды. Если сталь содержит менее 0,20% углерода, все, что вы можете получить, это феррит. Если в стали 0,40% углерода, вы получите перлит и феррит. Если сталь имеет 0,90% углерода, вы получаете перлит и карбиды. См. иллюстрацию ниже.
Чтобы узнать химический состав стали, зная ее марку, запомните следующие правила: простые углеродистые стали относятся к классам 10xx. 10 — простой углерод, а следующие две цифры — содержание углерода. Все 10 сортов также содержат марганец, фосфор и кремний. Последние две цифры ВСЕХ марок обозначают содержание углерода. Если марка 12L14 или 10B21, L означает, что она содержит свинец для обрабатываемости, а B означает, что она содержит бор для повышения прокаливаемости. Если вы знаете химический состав сплава, вы будете знать его твердость, прочность и будет ли вообще работать термическая обработка.
Обычные углеродистые стали и стальные сплавы
Одним из наиболее распространенных сплавов является 1144, углеродистая сталь, в которой легирующие элементы улучшают механическую обработку. StressProof™, продукт LaSalle Steel, является примером сплава 1144 с хорошей обрабатываемостью и прокаливаемостью, который обладает высокой прочностью и может подвергаться сквозной закалке.
Стали, легированные хромом, такие как 4130, 4140 и 4340, названы так из-за высокого содержания хрома (около 1,00%), который является основным легирующим элементом. Стали из сплава хрома начинаются с префикса «40» и заканчиваются двумя цифрами, которые соответствуют номинальному процентному содержанию углерода. Например, 4140 имеет 0,40% углерода и 1,00% хрома.
Стали, легированные никелем, заменяют никель вместо примерно половины стандартного содержания хрома для хромовых сплавов. Например, в то время как 4140 содержит 0,00 % никеля и 1,00 % хрома, 8630 содержит 0,60 % никеля и 0,50 % хрома. Эти сплавы начинаются с префикса «80».
Трудно проводить механические сравнения между сплавами хрома и сплавами никеля, поскольку они похожи, но уникальны для марки. Никелевые сплавы могут быть вытянуты до более точного размера отделки и, следовательно, более распространены в сталях конечного использования, таких как замковый материал.
УЗНАЙТЕ БОЛЬШЕ О ПРОИЗВОДСТВЕ В G.L. HUYETT
Категории: AISI, сплав, углерод, содержание, закалка, прокаливаемость, твердость, обрабатываемость, сталь, прочность, растяжение, сквозной марки или сплавы, а 409 и 430 являются наиболее распространенными. Сплавы хрома и железа с ограниченным содержанием углерода, обычно ниже 0,12% (442, 446 имеют 0,20). Содержание хрома может варьироваться от 10,5 до 30,0%. Эти марки не могут быть упрочнены термической обработкой, но они являются магнитными. Они обладают хорошей коррозионной стойкостью (особенно к коррозионному растрескиванию под воздействием хлоридов), но обычно не выбираются из-за ударной вязкости.
Марка | Описание | Применение |
---|---|---|
304 | General Purpose | Air sensor bags Automotive wiper arms Baggage handling equipment Baking equipment Bar and fountain equipment Beer barrels Bottling machinery Burial caskets Chemical processing equipment Chimney liners Clothes washer /внутренняя часть сушилки Кофеварки Column covers Cookware Counter tops Cryogenic vessels and components Dairy handling equipment Dishwasher drums Elevator interiors Entry Doors Escalators Evaporators Fire doors Fireplace fronts Flatware Food processing equipment Gutters and downspouts Hardware, hinges Хомуты для шлангов Больничные тележки Компоненты HVAC Ювелирные изделия Кухонные шкафы Кухонные вытяжки Meat processing equipment Metal roofing Microwave oven interiors Milking machines Nuclear storage containment Nuclear vessels Oven parts Rapid transit cars Refrigerator panels Retractor springs Roofing tiles Seat belt anchors Signs Sinks Splash shield Spring зажимы Топки для плит Уличная мебель Кузова и шасси автоцистерн Выхлопные системы грузовиков Бензобаки грузовиков Зеркала для грузовиков Грузовые двери и передние углы грузовых прицепов Оконные рамы Оконные жалюзи (солнцезащитные экраны) Винные баки |
305 | Повышение содержания никеля для снижения деформационного упрочнения | Крышки кофейных урн Детали глубокой вытяжки Детали из расширенного металла Формованные детали (требующие сверхнизких характеристик деформационного упрочнения) Операции свободного прядения Чаши для смешивания 4 Отражатели |
309S | Cr и Ni с повышенной для высоких температур | Ящики для отжига, Химическое технологическое оборудование (повышенная температура), Детали конвейеров, Сушилки, Элементы электроплит, Детали печей |
310S | То же, что и 309, только больше | Ящики для отжига, Ленты печей, Химическое технологическое оборудование (повышенная температура), Детали конвейеров Сушилки, Детали печей |
316 | Мо добавлен для повышения коррозионной стойкости | Автобусные/дорожные навесы Оборудование для химической обработки Резервуары для перевозки химикатов Входные двери Оборудование для обработки удобрений Противопожарные двери Оборудование для пищевой промышленности Резервуары для горячей воды Металлическая кровля Оборудование для нефтепереработки Фармацевтическое технологическое оборудование Фотооборудование Компоненты морской воды Оборудование для обработки мыла Уличные резервуары ( городская) мебель Оборудование для бассейнов Билетные автоматы Оборудование для очистки воды Оконные рамы Резервуары для хранения вина |
317 | Добавление большего количества Mo и Cr для повышения коррозионной стойкости | Химическое технологическое оборудование, оборудование для производства чернил, фармацевтическое технологическое оборудование, оборудование для обработки удобрений |
321 | Ti добавлен для предотвращения осаждения карбилов | Выпускной коллектор и фланцы самолетов, химическое оборудование, противопожарные перегородки, резервуары высокого давления |
347 | Cb добавлен для предотвращения осаждения карбилов | Выпускной коллектор и фланцы самолетов, Компенсаторы, Трубы печей и заслонки, Сварные резервуары для хранения органических химикатов |
330 | Увеличенный кремний для обеспечения максимальной термостойкости | Ящики для отжига, камеры сгорания, детали горелок и выхлопных газов |
409 | Нижний Cr В основном используется для выхлопных газов автомобилей | Автомобильные выхлопные системы Рамы автобусов Грузовые контейнеры Ребра для труб обогревателя Перфорированный лист для корпусов глушителей Воздуховод дымоудаления Корпуса трансформаторов и конденсаторов |
410/410S | Общего назначения | Втулки, лотки для башен фракционирования масла, оборудование, столовые приборы, плиты пресса |
420 | Повышенное содержание углерода для улучшения механических свойств | Столовые приборы/ножницы, стоматологическое оборудование, хирургическое оборудование |
430 | Добавлены P и S для улучшения обработки | Архитектурные приложения (интерьер), отделка автомобилей, кухонная утварь, оборудование для пищевой промышленности |
434 | Mo добавлен для повышения коррозионной стойкости в отделке автомобилей | Отделка автомобилей |
Марка | Описание | Применение |
- Хорошая коррозионная стойкость
- Типичная прочность 65–75 тысяч фунтов на квадратный дюйм — растяжение, 35–50 тысяч фунтов на квадратный дюйм — текучесть и относительное удлинение 20–35 %
- Магнитный
- Использование при ограниченной температуре
- Можно полировать
- УНС С40500
- С40910
- С40920
- С40930
- S43000
- С43400
- S43600
- С43035
- С44400
- С44660
- С44735
Содержание углерода, классификация сталей и легированные стали
Как правило, углерод является наиболее важным коммерческим стальным сплавом. Увеличение содержания углерода повышает твердость и прочность, а также улучшает прокаливаемость. Но углерод также увеличивает хрупкость и снижает свариваемость из-за склонности к образованию мартенсита. Это означает, что содержание углерода может быть как благословением, так и проклятием, когда речь идет о коммерческой стали.
И хотя существуют стали с содержанием углерода до 2 процентов, они являются исключением. Большинство сталей содержит менее 0,35% углерода. Чтобы представить это в перспективе, имейте в виду, что это 35/100 от 1 процента.
Теперь любая сталь с содержанием углерода от 0,35 до 1,86% может быть закалена с использованием цикла закалка-закалка-отпуск. Большинство товарных сталей подразделяются на одну из трех групп:
- Нелегированные углеродистые стали
- Низколегированные стали
- Высоколегированные стали
Простые углеродистые стали
Эти стали обычно представляют собой железо с содержанием углерода менее 1%, а также небольшими количествами марганца, фосфора, серы и кремния. Свариваемость и другие характеристики этих сталей в первую очередь зависят от содержания углерода, хотя легирующие и остаточные элементы оказывают незначительное влияние.
Простые углеродистые стали подразделяются на четыре группы:
- Низкая
- Средняя
- Высокая
- Очень высокая
Низкий . Часто называемые мягкими сталями, низкоуглеродистые стали содержат менее 0,30% углерода и являются наиболее часто используемыми марками. Они хорошо обрабатываются и свариваются и более пластичны, чем стали с более высоким содержанием углерода.
Средний . Среднеуглеродистые стали содержат от 0,30 до 0,45% углерода. Повышенное содержание углерода означает повышенную твердость и прочность на растяжение, пониженную пластичность и более сложную обработку.
Высокий . Эти стали с содержанием углерода от 0,45 до 0,75% могут быть сложными для сварки. Предварительный нагрев, последующий нагрев (для контроля скорости охлаждения), а иногда даже нагрев во время сварки становятся необходимыми для получения качественных сварных швов и для контроля механических свойств стали после сварки.
Очень высокий . Высокоуглеродистые стали с содержанием углерода до 1,50% используются для изготовления изделий из твердой стали, таких как металлорежущие инструменты и рессоры грузовых автомобилей. Как и высокоуглеродистые стали, они требуют термической обработки до, во время и после сварки для сохранения своих механических свойств.
Низколегированные стали
Когда эти стали предназначены для сварки, содержание углерода в них обычно ниже 0,25%, а часто ниже 0,15%. Типичные сплавы включают никель, хром, молибден, марганец и кремний, которые повышают прочность при комнатной температуре и повышают ударную вязкость при низких температурах.
Эти сплавы в правильном сочетании могут улучшить коррозионную стойкость и повлиять на реакцию стали на термообработку. Но добавленные сплавы также могут отрицательно влиять на восприимчивость к трещинам, поэтому рекомендуется использовать с ними процессы сварки с низким содержанием водорода. Предварительный нагрев также может оказаться необходимым. Это можно определить, используя формулу углеродного эквивалента, которую мы рассмотрим в следующем выпуске.
Высоколегированные стали
По большей части мы говорим здесь о нержавеющей стали, наиболее важной коммерческой высоколегированной стали. Нержавеющие стали содержат не менее 12 процентов хрома, и многие из них имеют высокое содержание никеля. Три основных типа нержавеющей стали:
- Аустенитная
- Ферритная
- Мартенситная
Мартенситная нержавеющая сталь входит в состав столовых приборов. Они имеют наименьшее количество хрома, обладают высокой прокаливаемостью и требуют как предварительного, так и последующего нагрева при сварке для предотвращения растрескивания в околошовной зоне (ЗТВ).
Ферритные нержавеющие стали содержат от 12 до 27 процентов хрома с небольшим количеством аустенитообразующих сплавов.
Аустенитная 9Нержавеющие стали 0094 обладают отличной свариваемостью, но аустенит нестабилен при комнатной температуре. Следовательно, для стабилизации аустенита необходимо добавлять специальные сплавы. Наиболее важным стабилизатором аустенита является никель, другие включают углерод, марганец и азот.
Особые свойства, включая коррозионную стойкость, стойкость к окислению и прочность при высоких температурах, можно придать аустенитным нержавеющим сталям путем добавления определенных сплавов, таких как хром, никель, молибден, азот, титан и ниобий. И хотя углерод может повысить прочность при высоких температурах, он также может снизить коррозионную стойкость, образуя соединение с хромом. Важно отметить, что аустенитные сплавы нельзя упрочнять термической обработкой. Это означает, что они не затвердевают в зоне термического влияния при сварке.
* Нержавеющие стали всегда имеют высокое содержание хрома, часто значительное количество никеля, а иногда содержат молибден и другие элементы.![]() Рисунок 1 |
Системы классификации стали
Прежде чем мы рассмотрим пару общих систем классификации стали, давайте рассмотрим еще один высокоуглеродистый металл — чугун. Содержание углерода в чугуне составляет 2,1% и более. Существует четыре основных типа чугуна:
- Серый чугун , относительно мягкий. Он легко обрабатывается и сваривается, и вы обнаружите, что он используется для блоков цилиндров двигателей, труб и конструкций станков.
- Белый чугун , твердый, хрупкий и не поддающийся сварке. Он имеет прочность на сжатие более 200 000 фунтов на квадратный дюйм (PSI), а после отжига превращается в ковкий чугун.
- Ковкий чугун , представляющий собой отожженный белый чугун.
Он поддается сварке, механической обработке, пластичен и обладает хорошей прочностью и ударопрочностью.
- Ковкий чугун , который иногда называют чугуном с шаровидным или шаровидным графитом. Он получил такое название, потому что его углерод имеет форму маленьких сфер, а не чешуек. Это делает его пластичным и податливым. Он также поддается сварке.
Теперь давайте взглянем на типичную систему классификации стали (см. Рисунок 1 ). И Общество автомобильных инженеров (SAE), и Американский институт черной металлургии (AISI) используют практически идентичные системы. Оба основаны на четырехзначной системе, где первое число обычно указывает на основной тип стали, а первые два числа вместе указывают серию в группе основного сплава.
Имейте в виду, что в группе основных сплавов может быть несколько серий в зависимости от количества основных легирующих элементов. Последние две-три цифры относятся к примерно допустимому диапазону содержания углерода в пунктах (сотых долях процента).
Эти системы классификации могут быть довольно сложными, и Рисунок 1 является лишь их основным представлением. Не забудьте ознакомиться с последними версиями AISI и SAE.
Это обзор некоторых основ, касающихся соотношения железо-углерод-сталь и его влияния на сварку и металлические сплавы. В следующий раз мы рассмотрим закалку и способы упрочнения металлов. Мы также рассмотрим влияние некоторых ключевых легирующих элементов и влияние сварки на металлургию.
Что такое легированная сталь? (с картинками)
`;
Адам Хилл Сталь
представляет собой металлический сплав, состоящий в основном из железа, а также небольшого количества углерода, в зависимости от марки и качества стали. Легированная сталь — это любой тип стали, в который преднамеренно добавлены один или несколько элементов, помимо углерода, для получения желаемого физического свойства или характеристики. Обычными элементами, которые добавляют для изготовления легированной стали, являются молибден, марганец, никель, кремний, бор, хром и ванадий.
часто подразделяют на две группы: высоколегированные стали и низколегированные стали. Разница между ними определяется несколько произвольно. Тем не менее, большинство согласны с тем, что любая сталь, в состав которой входят другие элементы, помимо железа и углерода, составляет более восьми процентов ее веса, является высоколегированной сталью. Немного более распространены низколегированные стали. Физические свойства этих сталей модифицируются другими элементами, чтобы придать им большую твердость, долговечность, коррозионную стойкость или ударную вязкость по сравнению с углеродистой сталью. Для достижения таких свойств эти сплавы часто требуют термической обработки.
Если уровень углерода в низколегированной стали находится в диапазоне от среднего до высокого, сварка может быть затруднена. Если содержание углерода снизить до диапазона от 0,1% до 0,3%, а некоторые легирующие элементы уменьшить, сталь может достичь большей свариваемости и формуемости при сохранении прочности, которой известна сталь. Такие металлы относятся к высокопрочным низколегированным сталям.
Пожалуй, самой известной легированной сталью является нержавеющая сталь. Это стальной сплав с содержанием хрома не менее 10%. Нержавеющая сталь более устойчива к пятнам, коррозии и ржавчине, чем обычная сталь. Он был обнаружен в 1913 Гарри Брирли из Шеффилда, Англия, но об открытии не было объявлено миру до 1915 года. Нержавеющая сталь обычно используется в столовых приборах, ювелирных изделиях, ремешках для часов, хирургических инструментах, а также в авиационной промышленности. Его знакомый блеск также использовался во многих известных архитектурных проектах, таких как Арка Ворот в Сент-Луисе, штат Миссури, и вершина Крайслер-билдинг в Нью-Йорке.