40Х :: Металлические материалы: классификация и свойства
Сталь 40Х ГОСТ 4543-71
Группа стали – хромистая
Массовая доля элементов, % | ||||||||
Углерод | Кремний | Марганец | Хром | Никель | Молибден | Алюминий | Титан | Ванадий |
0,36-0,44 | 0,17-0,37 | 0,50-0,80 | 0,80-1,10 | — | — | — | — |
Ac1 | Ac3(Acm) | Ac3(Arcm) | Ar1 | Mн |
743 | 815 | 730 | 693 | 325 |
Число твердости, НВ, не более | |
Отожженный или высокоотпущенный прокат | 217 |
Нагартованный прокат | 269 |
Термообработка | Передел текучести σт, Н/мм2 (кгс/мм2) не менее | Временное сопротивление σв, Н/мм2 (кгс/мм2) | Относительное удлинение δ5,% | Относительное сужение ψ, % | Ударная вязкость KCU, Дж/см2 (кгс·м/см2) | Размер сечения заготовок для термической обработки (диаметр круга или сторона квадрата), мм | |||||
Закалка | Отпуск | ||||||||||
Температура, оС | Среда охлаждения | Температура, оС | Среда охлаждения | ||||||||
1-й закалки или нормализации | 2-й закалки | ||||||||||
не менее | |||||||||||
860 | — | Масло | 500 | Вода или масло | 785(80) | 980(100) | 10 | 45 | 59(6) | 25 |
Температура отпуска, ºС | Предел текучести ,σ0,2 МПа | Временное сопротивление σв, МПа | Относительное удлинение δ5 | Относительное сужение ψ | KCU, Дж/см2 | НВ |
% | ||||||
200 300 400 500 600 | 1560 1390 1180 910 720 | 1760 1610 1320 1150 860 | 8 8 9 11 14 | 35 35 40 49 60 | 29 20 49 69 147 | 552 498 417 326 265 |
Температура испытания, ºС | Предел текучести ,σ0,2 МПа | Временное сопротивление σв, МПа | Относительное удлинение δ5 | Относительное сужение ψ | KCU, Дж/см2 |
% | |||||
Закалка 830 ºС, масло. Отпуск 550 ºС | |||||
200 300 500 | 700 680 610 430 | 880 870 690 490 | 15 17 18 21 | 42 58 68 80 | 118 — 98 78 |
Образец диаметром 10 мм и длиной 50 мм, кованый и отожженый. Скорость деформирования 5 мм/мин. Скорость деформации 0,002 1/с | |||||
700 800 900 1000 1100 1200 | 140 54 41 24 11 11 | 175 98 69 43 26 24 | 33 59 65 68 68 70 | 78 98 100 100 100 100 | — — — — — |
Сечение, мм | Предел текучести, σ0,2 | Временное сопротивление σв, | Относительное удлинение δ5 | Относительное сужение ψ | KCU, Дж/см2 | HB |
МПа | % | |||||
не менее | ||||||
Закалка 840-860 ºС, вода, масло. Отпуск 580-650 ºС, вода, воздух | ||||||
101-200 201-300301-500 | 490 440 345 | 655 635 590 | 15 14 14 | 45 40 38 | 59 54 49 | 212-248 197-235 174-217 |
Предел выносливости | Состояние стали | ||
σ-1, МПа | n | ||
363 470 509 333 372 | — — — 240 — | 106 106 — 5·105 — | σв=690 МПа. σв=940 МПа. σ0,2=870 МПа, σв=960 МПа σв=690 МПа Закалка 860 ºС, мало, отпуск 580 ºС |
Температура, ºС | Термообработка | |||
20 | -25 | -40 | -70 | |
Ударная вязкость KCU, Дж/см2 | ||||
160 91 | 148 82 | 107 — | 85 54 | Закалка 850 ºС, масло. Отпуск 650 ºС Закалка 850 ºС, масло. Отпуск 580 ºС |
Расстояние от торца, мм | Примечание | ||||||||||
1,5 | 4,5 | 6 | 7,5 | 10,5 | 13,5 | 16,5 | 19,5 | 24 | 30 | Закалка 850 ºС | |
Прокаливаемость | |||||||||||
50,5-60,5 | 48-59 | 45-57,5 | 39,5-57 | 35-53,5 | 31,5-50,5 | 28,5-46 | 27-42,5 | 24,5-39,5 | 22-37,5 | Твердость для полос прокаливаемости, HRCЭ | |
Термообработка | Количество мартенсита, % | Критическая твердость HRCЭ | Критический диаметр, мм | |
в воде | в масле | |||
Закалка | 50 90 | 43-46 49-53 | 38-76 23-58 | 16-48 6-35 |
Заменитель – стали: 45Х, 38ХА, 40ХН, 40ХС, 40ХФ, 40ХР.
Температура ковки, ºС:
начала 1250,
конца 800.
Заготовки сечением до 350 мм охлаждаются на воздухе.
Свариваемость – трудно свариваемая; способы сварки: РДС, ЭШС. Необходимы подогрев и последующая термообработка. КТС – необходима последующая термообработка.
Обрабатываемость резанием – в горячекатаном состоянии при HB 163-168, σв=610 МПа, КV т.в. спл =0,95, КV б. ст =0,95.
Флокеночувствительность – чувствительна.
Склонность к отпускной хрупкости – склонна.
Назначение: оси, валы, вал-шестерни, плунжеры, штоки, коленчатые и кулачковые валы, кольца, шпиндели, оправки, рейки, зубчатые венцы, болты, полуоси, втулки и другие улучшаемые детали повышенной прочности.
Полосы прокаливаемостиПо требованию потребителя, указанному в заказе, пачки, концы или торцы горячекатаных и кованых прутков, а по согласованию изготовителя с потребителем и калиброванных прутков из стали всех марок в зависимости от группы должны маркироваться краской в соответствии с таблицей
Группа стали | Цвет маркировки |
Хромистая | Зеленый + желтый |
Сортамент:
горячекатаная квадратная – ГОСТ 2591-88,
горячекатаная квадратная – ГОСТ 2590-88,
горячекатаная шестигранная – ГОСТ 2879-88,
горячекатаная полосовая – ГОСТ 103-76,
кованая круглая и квадратная – ГОСТ 1133-71,
калиброванная круглая – ГОСТ 7417-75,
калиброванная квадратная – ГОСТ 8559-75,
калиброванная шестигранная – ГОСТ 8560-78,
серебрянка – ГОСТ 14955-77
markmet.ru
Сталь марки 40х13 — характеристики, применение, свойства и термообработка
Сталь 40Х13 всегда в наличии на складе. Весь прокат металла производится по ГОСТ, есть сертификаты. Продажа Ст 40х13 оптом и в розницу по оптимальной цене, доставка по России.
(351) 735-59-79
Химический состав
Сталь 40Х13 входит в группу типа Х13 вместе со сталями 08Х13, 12Х13, 20Х13 и 30Х13. Занимает свой интервал по содержанию углерода — от 0,36 до 0,45 %, количества остальных легирующих элементов и примесей — такие же, как и у других сталей типа Х13 (таблица 1).
Сталь | Массовая доля элементов в ст.40х13, % | |||||
Углерод | Кремний | Марганец | Хром | Сера | Фосфор | |
40Х13 | 0,36-0,45 | <0,8 | <0,8 | 12,0-14,0 | <0,025 | <0,030 |
Структурный класс стали 40Х13 по ГОСТ 5632-72 мартенситный.
Термообработка превращения и микроструктура стали 40х13
- При нагреве сталь 40Х13 имеет полиморфное альфа-гамма превращение в интервале температур от 820°С (Ас1) до 880°С (Ас3).
- При нагреве несколько выше температуры точки Ас3 структура стали состоит из аустенита и карбидов хрома типа Cr23C6. Полное растворение карбидов происходит при 950-1000°С.
- Имеет наилучшую коррозионную стойкость после закалки с температуры, которая обеспечивает полное растворение карбидов.
- Имеет достаточно высокую прокаливаемость: закалка деталей может производиться при охлаждении в масле или на воздухе.
- В стали 40Х13 перед перлитным превращением аустенита из него выделяются карбиды Cr23C6. После обеднения аустенита по углероду происходит перлитное превращение аустенита.
- Интервал мартенситного превращения в стали 40Х13 составляет 270-80 °С. При закалке с температур 980-1000 °С происходит практически полное превращение аустенита в мартенсит.
- Промежуточное (бейнитное) превращение в стали 40Х13 отсутствует.
- Отпуск закаленной стали 40Х13 приводит к распаду мартенсита на феррито-карбидную смесь. С повышением температуры отпуска твердость снижается. При отпуске в интервале 480-520 °С происходит существенное снижение пластичности и ударной вязкости из-за развития процессов отпускной хрупкости.
- В зависимости от заданной твердости применяют или после низкотемпературного отпуска при 200-400 °С, или после высокого отпуска при 600-650 °С. Для промежуточных температур отпуска характерно снижение коррозионной стойкости.
Твердость 40Х13 после закалки и отпуска , | HB 10 -1 = 460 — 550 МПа |
Твердость 40Х13 после отжига, Пруток ГОСТ 5949-75 | HB 10 -1 = 143 — 229 МПа |
Механические свойства
- По ГОСТ 5582-75 сталь 40Х13 после смягчающей термической обработки в виде отжига или отпуска при 740-800 °С должна иметь предел прочности при растяжении не менее 560 МПа и относительное удлинение не менее 15 %.
- По ГОСТ 5949-75 твердость горячекатаной, кованой, калиброванной и шлифованной стали 40Х13 в отожженном или отпущенном состояниях должна составлять 229-143 НВ.
Механические свойства 40Х13 при Т=20oС
Сортамент | Размер | Напр. | sв | sT | d5 | y | KCU | Термообр. |
— | мм | — | МПа | МПа | % | % | кДж / м2 | — |
Лист, ГОСТ 5582-75 | 550 | 15 | Отжиг 740 — 800oC, | |||||
Пруток, заданой прочности , ГОСТ 18907-73 | 590-810 | 10 | ||||||
Проволока, ГОСТ 18143-72 | 640-880 | 10-14 |
Механические свойства стали 40Х13 при повышенных температурах
Влияние повышения температуры на механические свойства стали 40Х13 после закалки с 1050 °С и отпуска при 600 °С показано в таблице 2.
Температура испытания | Предел прочности при растяжении | Предел текучести 0,2МПа | Относительное удлиннение |
20°С | 1140 | 910 | 13 |
200°С | 960 | 830 | 11 |
300°С | 920 | 730 | 10 |
400°С | 795 | 685 | 12 |
500°С | 530 | 475 | 20 |
600°С | 310 | 260 | 21 |
Коррозионная стойкость стали 40Х13
Сталь 40Х13 обладает после закалки и низкого отпуска хорошей коррозионной стойкостью в атмосферных условиях (кроме морской атмосферы), слабых растворах азотной кислоты при умеренных температурах, речной и водопроводной воде, обеспечивающей полное растворение карбидов. Повышение температуры отпуска сопровождается снижением их стойкости к общей коррозии. Причиной снижения коррозионной стойкости является обеднение твердого раствора по хрому вследствие выделения карбидов хрома. Снижение коррозионной стойкости наблюдается при отпуске до 600°С, затем происходит некоторое ее увеличение. Однако коррозионная стойкость не достигает уровня, который имеют обе стали в закаленном или низкоотнущенном состоянии.
Коррозионная стойкость существенно зависит от качества поверхности изделий. Рекомендуется применять шлифованную и полированную поверхность.
Таким образом, сталь 40Х13 целесообразно применять либо после температурного отпуска при 200-400 °С (с целью получения высоких твердости и коррозионной стойкости), либо после высокого отпуска при 600-650 °С с целью получения конструкционного материала.
Специальные свойства
При работе в водороде предельные допустимые параметры атмосферы составляют 600 °С и 80 МПа.
Плотность — 7,68 г/см3.
Технологические параметры
Сталь 40Х13 имеет хорошую технологичность при горячей пластической деформации. Температурный интервал горячей пластической деформации составляет от 1100 до 850 °С. Сталь 40Х13 склонна к образованию при больших скоростях нагрева и охлаждения. Поэтому нагрев под прокатку и ковку проводят медленно до 830 °С. После горячей деформации применяют медленное охлаждение.
Холодная пластическая деформация стали 40Х13 ограничена. В качестве смягчающей термической обработки после горячей или холоной пластической деформации применяют отжиг при 750-800 °С с последующим охлаждением с печью до 500 °С и далее на воздухе. Окончательной термической обработкой является закалка с 950-1000 °С с охлаждением в масле или на воздухе на заданную твердость и коррозионную стойкость.
Применение
- как коррозионностойкий материал с высокой твердостью для:
— режущего, измерительного и хирургического инструментов;
— пружин, подшипников и других изделий, работающих на износ в слабоагрессивных средах;
— бытовых приборах и предметах домашнего обихода.; - как жаропрочный и жаростойкий материал при работе до 400-450 °С для крепежных изделий, валов, упругих элементов, испытывающих воздействие слабоагрессивных сред, например, при переработке нефти.
ГОСТы на прокат стали 40х13
- ГОСТ 19903-2015
- ГОСТ 1133-71 «Кованая круглая и квадратная. Сортамент»;
- ГОСТ 18143-72 «Проволока из высоколегированной коррозионно-стойкой и жаростойкой стали. Технические условия.»;
- ГОСТ 18907-73 «Прутки нагартованные, термически обработанные шлифованные из высоколегированной и коррозионно-стойкой стали. Технические условия.»;
- ГОСТ 5582-75 «Прокат тонколистовой коррозионно-стойкий, жаростойкий и жаропрочный. Технические условия»;
- ГОСТ 5632-72 «Высоколегированные и сплавы коррозионностойкие, жаростойкие и жаропрочные. Марки»;
- ГОСТ 5949-75 «Сортовая и калиброванная коррозионностойкая, жаростойкая и жаропрочная.
- ГОСТ 4405-75 «Полосы горячекатаные и кованые из инструментальной стали. Сортамент.»;
- ГОСТ 14955-77 «Качественная круглая со специальной отделкой поверхности. Технические условия.»;
- ГОСТ 2590-2006 «Прокат сортовой стальной горячекатаный круглый. Сортамент.»;
- ГОСТ 2591-2006 «Прокат сортовой стальной горячекатаный квадратный. Сортамент.»;
- ГОСТ 7417-75 «Калиброванная круглая. Сортамент.»;
- ГОСТ 4405-75 «Полосы горячекатаные и кованые из инструментальной стали. Сортамент.»;
- ГОСТ 8559-75 «Калиброванная квадратная. Сортамент.»;
- ГОСТ 8560-78 «Прокат калиброванный шестигранный. Сортамент.»;
- ГОСТ 1133-71 «Кованая круглая и квадратная. Сортамент.»;
- ГОСТ 5632-72 «Стали высоколегированные и сплавы коррозионностойкие, жаростойкие и жаропрочные. Марки.»;
- ГОСТ 103-2006 «Прокат сортовой стальной горячекатаный полосовой. Сортамент.»;
- ГОСТ 5949-75 «Сортовая и калиброванная коррозионно-стойкая, жаростойкая и жаропрочная. Технические условия.»;
- ГОСТ 2879-2006 «Прокат сортовой стальной горячекатаный шестигранный. Сортамент.»;
- ТУ 14-11-245-88 «Профили стальные фасонные высокой точности. Технические условия.»;
- ОСТ 3-1686-90 «Заготовки из конструкционной стали для машиностроения. Общие технические условия.»;
www.promgroupchel.ru
Доска объявлений | Сталь 40Х — характеристика, химический состав, свойства, твердостьСталь 40ХОбщие сведения
Химический состав
Механические свойстваМеханические свойства
Механические свойства при повышенных температурах
Механические свойства в зависимости от температуры отпуска
Механические свойства в зависимости от сечения
Технологические свойства
Температура критических точек
Ударная вязкостьУдарная вязкость, KCU, Дж/см2
Предел выносливости
ПрокаливаемостьЗакалка 850 С. Твердость для полос прокаливаемости HRCэ.
Физические свойства
[ Назад ] |
s-metall.com.ua
Марка стали |
Вид поставки Сортовой прокат – ГОСТ 4543–71. Поковки – ГОСТ 8479–70. Трубы – ГОСТ 8733–74. |
||||||||||||||||||||||||||||||||||||||||
40Х |
|||||||||||||||||||||||||||||||||||||||||
Массовая доля элементов, % по ГОСТ 4543–71 |
Температура критических точек, ºС |
||||||||||||||||||||||||||||||||||||||||
C |
Si |
Mn |
S |
P |
Cr |
Ni |
Cu |
N |
Ас1 |
Ас3 |
Аr1 |
Аr3 |
|||||||||||||||||||||||||||||
0,36– 0,44 |
0,17–0,37 |
0,50–0,80 |
≤ 0,035 |
≤ 0,035 |
0,80– 1,10 |
≤ 0,30 |
≤ 0,30 |
≤ 0,008 |
743 |
815 |
693 |
730 |
|||||||||||||||||||||||||||||
Механические свойства при комнатной температуре |
|||||||||||||||||||||||||||||||||||||||||
НД |
Режим термообработки |
Сечение, мм |
σ0,2, Н/мм2 |
σВ, Н/мм2 |
δ, % |
Ψ, % |
KCU, Дж/см2 |
HRC |
НВ |
||||||||||||||||||||||||||||||||
Операция |
t, ºС |
Охлаждающая среда |
не менее |
||||||||||||||||||||||||||||||||||||||
ГОСТ 4543–71 |
Отжиг |
820–840 |
С печью |
Свыше 5 до 250 |
Не определяются |
|
≤ 217 |
||||||||||||||||||||||||||||||||||
Закалка Отпуск |
845–875 450–550 |
Вода Вода или масло |
До 80 Свыше 80 до 150 Свыше 150 до 250 |
785 785
785 |
980 980
980 |
10 8
7 |
45
40
35 |
59 54
51 |
–
|
– |
|||||||||||||||||||||||||||||||
ГОСТ 8479–70 |
Закалка
Отпуск |
840–860
550–650 |
Вода или масло
Вода, масло, воздух или печь |
До 100
100–300
300–500
500–800 |
490
490
395
315 |
655
655
615
570 |
16
13
13
11 |
45
40
35
30 |
59
54
49
29 |
|
212–248 218–248 187–229 167–207 |
||||||||||||||||||||||||||||||
Нормализация
Отпуск
|
850–870
560–650 |
Воздух
Воздух
|
До 100
100–300
300–500
500–800 |
345
315
275
245 |
590
570
530
470 |
18
14
15
15 |
45
35
32
30 |
59
34
29
34 |
|
174–217 167–207 156–197 143–179 |
|||||||||||||||||||||||||||||||
ГОСТ 8733–74 |
В термически обработанном состоянии |
|
|
ø 5–250
s 5–24 |
– |
618 |
14 |
– |
– |
|
≤ 217 |
||||||||||||||||||||||||||||||
Назначение. Оси, валы-шестерни, плунжеры, штоки, коленчатые и кулачковые валы, кольца, шпиндели, оправки, рейки, кулачки, зубчатые венцы, болты, полуоси, пиноли, втулки и другие детали повышенной прочности. Валы, диски и роторы паровых турбин, трубы.
|
|||||||||||||||||||||||||||||||||||||||||
Предел выносливости, Н/мм2 |
Термообработка |
Ударная вязкость, KCU, Дж/см2, при t, ºС |
Термообработка |
||||||||||||||||||||||||||||||||||||||
σ-1 |
τ-1 |
+ 20 |
0 |
– 25 |
– 40 |
– 70 |
– 80 |
||||||||||||||||||||||||||||||||||
380 2301
|
–
|
Закалка с 860 ºС в масле, отпуск при 550 ºС |
163 |
– |
151 |
109 |
87 |
– |
Закалка с 860 ºС в масле, отпуск при 550 ºС |
||||||||||||||||||||||||||||||||
1 Образец с надрезом. |
93 |
– |
84 |
– |
55 |
– |
То же, отпуск при 580 ºС |
||||||||||||||||||||||||||||||||||
Технологические характеристики |
|||||||||||||||||||||||||||||||||||||||||
Ковка |
Охлаждение поковок, изготовленных |
||||||||||||||||||||||||||||||||||||||||
Вид полуфабриката |
Температурный интервал ковки, ºС |
из слитков |
из заготовок |
||||||||||||||||||||||||||||||||||||||
Размер сечения, мм |
Условия охлаждения |
Размер сечения, мм |
Условия охлаждения |
||||||||||||||||||||||||||||||||||||||
Слиток |
1250–800 |
|
|
До 350
|
На воздухе |
||||||||||||||||||||||||||||||||||||
Заготовка |
1250–800 |
||||||||||||||||||||||||||||||||||||||||
Свариваемость |
Обрабатываемость резанием |
Флокеночувствительность |
|||||||||||||||||||||||||||||||||||||||
Трудно свариваемая. Способы сварки: РД, РАД и КТ. Необходимы подогрев и последующая термообработка.
|
В горячекатаном состоянии при 163–168 НВ и σВ = 620 Н/мм2 К√ = 1,20 (твердый сплав), К√ = 0,95 (быстрорежущая сталь) |
Чувствительна |
|||||||||||||||||||||||||||||||||||||||
Склонность к отпускной хрупкости |
|||||||||||||||||||||||||||||||||||||||||
Склонна |
stalmaximum.ru
40Х сталь химический состав
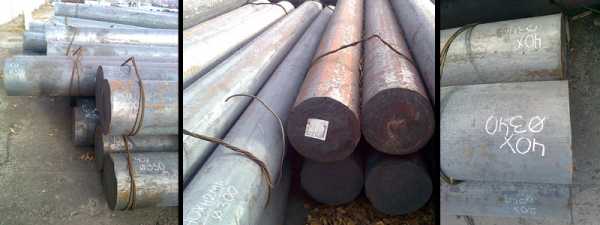
Механические свойства стали 40Х | |||||||||
ГОСТ | Состояние поставки, режим термообработки | Сечение, мм | КП | σ0,2 (МПа) | σв(МПа) | δ5 (%) | ψ % | KCU (кДж / м2) | НВ, не более |
4543-71 | Пруток. Закалка 860 °С, масло.
Отпуск 500 °С, вода или масло | 25 | 780 | 980 | 10 | 45 | 59 | ||
8479-70 | Поковки: нормализация | 500-800 300-500 | 245 275 | 245 275 | 470 530 | 15 15 | 30 32 | 34 29 | 143-179 156-197 |
закалка, отпуск | 500-800 | 275 | 275 | 530 | 13 | 30 | 29 | 156-197 | |
нормализация | до 100 100-300 | 315 | 315 | 570 | 17 14 | 38 35 | 39 34 | 167-207 | |
закалка, отпуск | 300-500 500-800 | 315 | 315 | 570 | 12 11 | 30 30 | 29 29 | 167-207 | |
нормализация | до 100 100-300 300-500 | 345 | 345 345 | 590 | 18 17 14 | 45 40 38 | 59 54 49 | 174-217 | |
закалка, отпуск | до 100 100-300 300-500 | 395 | 395 | 615 | 17 15 13 | 45 40 35 | 59 54 49 | 187-229 |
Механические
свойства стали 40Х в зависимости от сечения | ||||||
Сечение, мм | σ0,2 (МПа) | σв(МПа) | δ4 (%) | ψ % | KCU (кДж / м2) | HB |
Закалка 840-860 °С, вода, масло. Отпуск 580-650 °С, вода, воздух. | ||||||
101-200 | 490 | 655 | 15 | 45 | 59 | 212-248 |
201-300 | 440 | 635 | 14 | 40 | 54 | 197-235 |
301-500 | 345 | 590 | 14 | 38 | 49 | 174-217 |
Механические свойства стали 40Х в зависимости от температуры отпуска | ||||||
Температура отпуска, °С | σ0,2 (МПа) | σв(МПа) | δ5 (%) | ψ % | KCU (кДж / м2) | HB |
200 | 1560 | 1760 | 8 | 35 | 29 | 552 |
300 | 1390 | 1610 | 8 | 35 | 20 | 498 |
400 | 1180 | 1320 | 9 | 40 | 49 | 417 |
500 | 910 | 1150 | 11 | 49 | 69 | 326 |
600 | 720 | 860 | 14 | 60 | 147 | 265 |
Механические свойства стали 40Х при повышенных температурах | |||||
Температура испытаний, °С | σ0,2 (МПа) | σв(МПа) | δ5 (%) | ψ % | KCU (кДж / м2) |
Закалка 830 °С, масло. Отпуск 550 °С | |||||
200 300 400 500 | 700 680 610 430 | 880 870 690 490 | 15 17 18 21 | 42 58 68 80 | 118 98 78 |
Образец диаметром 10 мм, длиной 50 мм кованый и отоженный. Скорость деформирования 5 мм/мин, скорость деформации 0,002 1/с | |||||
700 800 900 1000 1100 1200 | 140 54 41 24 11 11 | 175 98 69 43 26 24 | 33 59 65 68 68 70 | 78 98 100 100 100 100 |
Предел выносливости стали 40Х | |||
σ-1,
МПА | J-1,
МПА | n | Состояние стали |
363 470 509 333 372 | 240 | 106 106 5*106 | σв=690 МПа σв=690 МПа σ0,2=690 МПа, σв=690 МПа σв=690 МПа Закалка 860 °С, масло, отпуск 550 °С |
Ударная вязкость стали 40Х KCU, (Дж/см2) | ||||
Т= +20 °С | Т= -25 °С | Т= -40 °С | Т= -70 °С | Термообработка |
160 91 | 148 82 | 107 | 85 54 | Закалка 850 °С, масло, отпуск
650 °С Закалка 850 °С, масло, отпуск 580 °С |
Прокаливаемость стали 40Х (ГОСТ 4543-71) | ||||||||||
Расстояние от торца, мм | Примечание | |||||||||
1,5 | 4,5 | 6 | 7,5 | 10,5 | 13,5 | 16,5 | 19,5 | 24 | 30 | Закалка 860 °С |
20,5-60,5 | 48-59 | 45-57,5 | 39,5-57 | 35-53,5 | 31,5-50,5 | 28,5-46 | 27-42,5 | 24,5-39,5 | 22-37,5 | Твердость для полос прокаливаемости, HRC |
Физические свойства стали 40Х | ||||||
T (Град) | E 10— 5 (МПа) | a 10 6 (1/Град) | l (Вт/(м·град)) | r (кг/м3) | C (Дж/(кг·град)) | R 10 9 (Ом·м) |
20 | 2.14 | 7820 | 210 | |||
100 | 2.11 | 11.9 | 46 | 7800 | 466 | 285 |
200 | 2.06 | 12.5 | 42.7 | 7770 | 508 | 346 |
300 | 2.03 | 13.2 | 42.3 | 7740 | 529 | 425 |
400 | 1.85 | 13.8 | 38.5 | 7700 | 563 | 528 |
500 | 1.76 | 14.1 | 35.6 | 7670 | 592 | 642 |
600 | 1.64 | 14.4 | 31.9 | 7630 | 622 | 780 |
700 | 1.43 | 14.6 | 28.8 | 7590 | 634 | 936 |
800 | 1.32 | 26 | 7610 | 664 | 1100 | |
900 | 26.7 | 7560 | 1140 | |||
1000 | 28 | 7510 | 1170 | |||
1100 | 28.8 | 7470 | 120 | |||
1200 | 7430 | 1230 |
Преимущества термообработки изделий из стали 40Х в кипящем слое по сравнению с традиционными способами: был исследован нагрев под закалку высокопрочных болтов из сталей 40Х и 38ХС. Из опытов следует, что при горизонтальном положении болта М24 в кипящем слое частиц корунда диаметром 0,32 мм, отапливаемом природным газом, медленнее всего температура повышается на оси болта в месте стыка его тела и головки. Скорость нагрева в этой точке почти вдвое меньше, чем на поверхности в середине болта, так что во избежание перегрева температура кипящего слоя не должна заметно превышать конечную температуру нагрева. В слое с температурой 900° С болт прогревается до 860° С примерно за 3 мин (термопара зачеканена на оси под головкой), в то время как в применяемых в настоящее время электропечах К-160 нагрев до 860° С длится, по нашим экспериментальным данным, 40 мин. За это время в электропечах образуется значительный слой отслаивающейся окалины, в то время как при нагреве в кипящем слое с двухступенчатым сжиганием поверхность получается чистой. Эксперименты показали, что для аустенизации достаточна выдержка болтов из обеих сталей при температуре слоя 860-870° С в течение 10-15 мин. Поскольку скорость охлаждения этих изделий в кипящем слое оказалась недостаточной, закалку осуществляли в масле. Отпущенные после закалки (410° С, 80 мин) болты отличались высокими показателями прочности при достаточной пластичности:
Сталь 40Х: σв=147-150 кгс/мм2, ан=3,84-3,27 кгс*м/см2, HB 345-360
Сталь 38ХС: σв=165-173,5 кгс/мм2, ан=3,18-4,41 кгс*м/см2, HB 400-430
(ударную вязкость ан определяли на образцах, предел прочности σв на целых болтах).
Параллельно болты М24 из стали 38ХС после выдержки в кипящем слое с температурой 910° С (15 мин) охлаждали в соляной ванне при 360° С (20 мин) с целью получения структуры нижнего бейнита. При достаточно высокой прочности (σв = 163 кгс/мм2) была получена значительно большая ударная вязкость (8,65- 10,6 кгс-м/см2). Наконец, часть болтов из стали 38ХС после такого же нагрева выдерживали в масле в течение 42 с, а затем переносили в кипящий слой температурой 360° С. Такой режим позволил повысить предел прочности до 171,5-173 кгс/мм2, но несколько снизил ударную вязкость (ан = 6,25-6,72 кгс.м/см2). Как показали исследования, нагрев в течение 8-10 мин в слое температурой 910° С обеспечивает превращение исходной ферритокарбидной смеси в аустенит и получение достаточно однородных свойств.
Краткие обозначения: | ||||
σв | — временное сопротивление разрыву (предел прочности при растяжении), МПа | ε | — относительная осадка при появлении первой трещины, % | |
σ0,05 | — предел упругости, МПа | Jк | — предел прочности при кручении, максимальное касательное напряжение, МПа | |
σ0,2 | — предел текучести условный, МПа | σизг | — предел прочности при изгибе, МПа | |
δ5,δ4,δ10 | — относительное удлинение после разрыва, % | σ-1 | — предел выносливости при испытании на изгиб с симметричным циклом нагружения, МПа | |
σсж0,05 и σсж | — предел текучести при сжатии, МПа | J-1 | — предел выносливости при испытание на кручение с симметричным циклом нагружения, МПа | |
ν | — относительный сдвиг, % | n | — количество циклов нагружения | |
sв | — предел кратковременной прочности, МПа | R и ρ | — удельное электросопротивление, Ом·м | |
ψ | — относительное сужение, % | E | — модуль упругости нормальный, ГПа | |
KCU и KCV | — ударная вязкость, определенная на образце с концентраторами соответственно вида U и V, Дж/см2 | T | — температура, при которой получены свойства, Град | |
sT | — предел пропорциональности (предел текучести для остаточной деформации), МПа | l и λ | — коэффициент теплопроводности (теплоемкость материала), Вт/(м·°С) | |
HB | — твердость по Бринеллю | C | — удельная теплоемкость материала (диапазон 20o — T ), [Дж/(кг·град)] | |
HV | — твердость по Виккерсу | pn и r | — плотность кг/м3 | |
HRCэ | — твердость по Роквеллу, шкала С | а | — коэффициент температурного (линейного) расширения (диапазон 20o — T ), 1/°С | |
HRB | — твердость по Роквеллу, шкала В | σtТ | — предел длительной прочности, МПа | |
HSD | — твердость по Шору | G | — модуль упругости при сдвиге кручением, ГПа |
xn--40-1mc.xn--p1ai