Химический состав и свойства металлов, из которых мы производим клещи и молотки
Мы работаем практически с любыми ковкими материалами, по желанию Заказчика. Есть предпочтительные для нас материалы, с которыми накоплен большой опыт и которые отлично себя зарекомендовали в производстве. Это сталь СТ-3, Медь М1 и латунь Л63. С ними мы работаем чаще других. Клещи кузнечные и клещи для термистов мы изготавливаем из стали Ст-3, молотки для деликатной формовки и для работы во взрывоопасной среде — из меди или латуни с содержанием меди до 70%.
Химический состав и свойства меди марки М1:
Fe | до 0,005 | |
Ni | до 0,002 | |
S | до 0,004 | |
Cu | 99,9 | |
As | до 0,002 | |
Pb | до 0,005 | |
Zn | до 0,004 | |
Ag | до 0,003 | |
O | до 0,05 | |
Sb | до 0,002 | |
Bi | до 0,001 | |
Sn | до 0,002 |
Твердость материала: HB 10 -1 = 45 МПа | |
Линейная усадка, %: 2.![]() |
|
Температура литья, °C: 1150 — 1250 | |
Температура плавления, °C: 1083 | |
Коэффициент трения со смазкой: 0.011 | |
Коэффициент трения без смазки: 0.43 |
Механические свойства сплава М1 при Т=20oС | |||||||
Прокат | Размер | Напр. | σв(МПа) | sT (МПа) | δ5 (%) | ψ % | KCU (кДж / м2) |
сплав мягкий | 200-250 | 90-150 | |||||
сплав твердый | 400-490 | 300-450 | 6 |
Физические свойства сплава М1 | ||||||
T (Град) | E 10— 5 (МПа) | a 10 6 (1/Град) | l (Вт/(м·град)) | r (кг/м3) | C (Дж/(кг·град)) | R 10 9 (Ом·м) |
20 | 1.![]() |
387 | 8940 | 390 | 17.8 | |
100 | 1.32 | 16.7 |
Химический состав и свойства латуни марки Л63:
Класс: Латунь, обрабатываемая давлением | |
Использование в промышленности: для деформации в холодном состоянии глубокой вытяжкой, волочением, прокаткой, чеканкой, изгибом; для изготовления изделий криогенной техники; пригоден для пайки и сварки; хорошо полируется |
Fe | до 0,2 | Л63″> |
P | до 0,001 | |
Cu | 62 — 65 | |
Pb | до 0,07 | |
Zn | 34,5 — 38 | |
Sb | до 0,005 | |
Bi | до 0,002 |
Твердость материала: HB 10 -1 = 150 — 160 МПа | |
Температура плавления, °C: 906 | |
Коэффициент трения со смазкой: 0.![]() |
|
Коэффициент трения без смазки: 0.39 |
Механические свойства сплава Л63 при Т=20oС | |||||||
Прокат | Размер | Напр. | σв(МПа) | sT (МПа) | δ5 (%) | ψ % | KCU (кДж / м2) |
сплав твердый | 680-750 | 2-4 | |||||
сплав мягкий | 380-450 | 40-50 |
Физические свойства сплава Л63 | ||||||
T (Град) | E 10— 5 (МПа) | a 10 6 (1/Град) | l (Вт/(м·град)) | r (кг/м3) | C (Дж/(кг·град)) | R 10 9 (Ом·м) |
20 | 1.![]() |
8440 | 74 | |||
100 | 20.5 |
Химический состав и свойства стали марки 40Х:
Марка: 40Х (заменители 45Х, 38ХА, 40ХН, 40ХС, 40ХФ, 40ХР)
Класс: Сталь конструкционная легированная
Использование в промышленности: оси, валы, вал-шестерни, плунжеры, штоки, коленчатые и кулачковые валы, кольца, шпиндели, оправки, рейки, губчатые венцы, болты, полуоси, втулки и другие улучшаемые детали повышенной прочности.
C | 0,36 — 0,44 | |
Si | 0,17 — 0,37 | |
Mn |
0,5 — 0,8 | |
Ni | до 0,3 | |
S | до 0,035 | |
P | до 0,035 | |
Cr | 0,8 — 1,1 | |
Cu | до 0,3 | |
Fe | ~97 |
Удельный вес: 7820 кг/м3
Твердость материала: HB 10 -1 = 217 МПа
Температура критических точек: Ac1 = 743 , Ac3(Acm) = 815 , Ar3(Arcm) = 730 , Ar1 = 693
Флокеночувствительность: чувствительна
Свариваемость: трудносвариваема.
Обрабатываемость резанием: в горячекатаном состоянии при HB 163-168 и σв=610 МПа, К υ тв. спл=1,2 и Кυ б.ст=0,95
Температура ковки, °С: начала 1250, конца 800. Сечения до 350 мм охлаждаются на воздухе.
Склонность к отпускной хрупкости: склонна
Механические свойства стали 40Х | |||||||||
ГОСТ | Состояние поставки, режим термообработки | Сечение, мм | КП | σ0,2 (МПа) |
δ5 (%) | ψ % | KCU (кДж / м2) | НВ, не более | |
4543-71 | Пруток.![]() |
25 | 780 | 980 | 10 | 45 | 59 | ||
8479-70 | Поковки: нормализация |
500-800 300-500 |
245 275 |
245 275 |
470 530 |
15 15 |
30 32 |
34 29 |
143-179 156-197 |
закалка, отпуск | 500-800 | 275 | 275 | 530 | 13 | 30 | 29 | 156-197 | |
нормализация | до 100 100-300 |
315 | 315 | 570 | 17 14 |
38 35 |
39 34 |
167-207 | |
закалка, отпуск | 300-500 500-800 |
315 | 315 | 570 | 12 11 |
30 30 |
29 29 |
167-207 | |
нормализация | до 100 100-300 300-500 |
345 | 345 345 |
590 | 18 17 14 |
45 40 38 |
59 54 49 |
174-217 | |
закалка, отпуск | до 100 100-300 300-500 |
395 | 395 | 615 | 17 15 13 |
45 40 35 |
59 54 49 |
187-229 |
Механические свойства стали 40Х в зависимости от сечения |
||||||
Сечение, мм | σ0,2 (МПа) | σв(МПа) | δ4 (%) | ψ % | KCU (кДж / м2) | HB |
Закалка 840-860 °С, вода, масло.![]() |
||||||
101-200 | 490 | 655 | 15 | 45 | 59 | 212-248 |
201-300 | 440 | 635 | 14 | 40 | 54 | 197-235 |
301-500 | 345 | 590 | 14 | 38 | 49 | 174-217 |
Механические свойства стали 40Х в зависимости от температуры отпуска | ||||||
Температура отпуска, °С | σ0,2 (МПа) | σв(МПа) | δ5 (%) | ψ % | KCU (кДж / м2) | HB |
200 | 1560 | 1760 | 8 | 35 | 29 | 552 |
300 | 1390 | 1610 | 8 | 35 | 20 | 498 |
400 | 1180 | 1320 | 9 | 40 | 49 | 417 |
500 | 910 | 1150 | 11 | 49 | 69 | 326 |
600 | 720 | 860 | 14 | 60 | 147 | 265 |
Механические свойства стали 40Х при повышенных температурах | |||||
Температура испытаний, °С | σ0,2 (МПа) | σв(МПа) | δ5 (%) | ψ % | KCU (кДж / м2) |
Закалка 830 °С, масло.![]() |
|||||
200 300 400 500 |
700 680 610 430 |
880 870 690 490 |
15 17 18 21 |
42 58 68 80 |
118 98 |
Образец диаметром 10 мм, длиной 50 мм кованый и отоженный. Скорость деформирования 5 мм/мин, скорость деформации 0,002 1/с | |||||
700 800 900 1000 1100 1200 |
140 54 41 24 11 11 |
175 98 69 43 26 24 |
33 59 65 68 68 70 |
78 98 100 100 100 100 |
Предел выносливости стали 40Х | |||
σ-1, МПА |
J-1, МПА |
n | Состояние стали |
363 470 509 333 372 |
240 |
106 106 5*106 |
σв=690 МПа σв=690 МПа σ0,2=690 МПа, σв=690 МПа σв=690 МПа Закалка 860 °С, масло, отпуск 550 °С |
Ударная вязкость стали 40Х KCU, (Дж/см2) | ||||
Т= +20 °С | Т= -25 °С | Т= -40 °С | Т= -70 °С | Термообработка |
160 91 |
148 82 |
107 | 85 54 |
Закалка 850 °С, масло, отпуск 650 °С Закалка 850 °С, масло, отпуск 580 °С |
Прокаливаемость стали 40Х (ГОСТ 4543-71) | ||||||||||
Расстояние от торца, мм | Примечание | |||||||||
1,5 | 4,5 | 6 | 7,5 | 10,5 | 13,5 | 16,5 | 19,5 | 24 | 30 | Закалка 860 °С |
20,5-60,5 | 48-59 | 45-57,5 | 39,5-57 | 35-53,5 | 31,5-50,5 | 28,5-46 | 27-42,5 | 24,5-39,5 | 22-37,5 | Твердость для полос прокаливаемости, HRC |
Химический состав и свойства стали марки СТ-3:
Ст3 представляет собой конструкционную углеродистую сталь обыкновенного качества, востребованную при изготовлении несущих и ненесущих конструкций, эксплуатируемых при плюсовых температурах. Это самый распространенный конструкционный материал среди сталей данного класса, производится конвертерным или мартеновским способом.
Сталь изготавливается по ГОСТу 380-2005, согласно которому расшифровка обозначения материала выглядит следующим образом:
- Ст – первые буквы;
- цифра – отображает условный номер марки, зависящий от состава;
- буква «Г» – присутствует при наличии марганца 0,8% и более;
- «пс», «сп», «кп» – обозначают степень раскисления стали.
Дополнительно к буквенно-цифровой, на прокат наносится несмываемая цветовая маркировка – красная.
По степени раскисления (удаления кислорода, ухудшающего механические характеристики сплава) выделяют:
- Ст3сп – спокойная, раскисленная марганцем, алюминием, кремнием, это наиболее дорогой и качественный вид продукции;
- сталь марки Ст3пс – полуспокойная, для ее раскисления используют алюминий, титан, ферросилиций+алюминий, ферросилиций+титан, это наиболее распространенная разновидность, занимающая промежуточное положение по стоимости и уровню механических характеристик между кипящими и спокойными сплавами;
- Ст3кп – без раскисления или раскисленная только ферромарганцем, это самый низкокачественный вид марки Ст3.
Химический состав Ст3 в зависимости от степени раскисления
Марка |
Углерод, % |
Марганец, % |
Кремний, % |
Ст3кп |
0,14-0,22 |
0,30-0,60 |
до 0,05 включительно |
Ст3пс |
0,14-0,22 |
0,4-0,65 |
0,05-0,15 |
Ст3сп |
0,14-0,22 |
0,4-0,65 |
0,15-0,3 |
Плотность при +20°C – 7850 кг/м3, твердость – HB 10-1=131 МПа.
Ст3 всех видов раскисления не имеет ограничений по свариваемости. Основные способы сварки – ручная электродуговая, полу- и автоматическая электродуговая, контактно-точечная.
Механические характеристики проката толщиной до 20 мм
Марка | Предел прочности при растяжении, Ϭв, МПа | Предел текучести, Ϭт, МПа | Относительное удлинение, δ5, % |
Ст3кп | 360-460 | 235 | 27 |
Ст3пс | 370-480 | 245 | 26 |
Ст3сп | 380-490 | 245 | 26 |
Ст3Гпс | 370-490 | 245 | 26 |
Ст3Гсп | 390-570 | 245 | 24 |
Области применения стали СТ-3:
Сталь используется в производстве:
- фасонного и листового проката толщиной до 10 мм, применяемого для создания несущих участков сварных конструкций, эксплуатируемых при воздействии знакопеременных усилий; толщиной 11-25 мм с гарантируемой свариваемостью, предназначенного для производства несущих элементов конструкций;
- гладкопрофильной арматуры, применяемой при создании ж/б элементов;
- фасонных профилей для с/х машиностроения;
- просечно-вытяжных листов;
- заготовок деталей трубопроводной арматуры;
- соединительных элементов трубопроводов с ограничением рабочих температур от -20°C до +200°C;
- электросварных труб;
- двухслойных коррозионностойких листов в роли основного слоя.
Краткие обозначения: | ||||
σв | — временное сопротивление разрыву (предел прочности при растяжении), МПа | ε | — относительная осадка при появлении первой трещины, % | |
σ0,05 | — предел упругости, МПа | Jк | — предел прочности при кручении, максимальное касательное напряжение, МПа | |
σ0,2 | — предел текучести условный, МПа | σизг | — предел прочности при изгибе, МПа | |
δ5,δ4,δ10 | — относительное удлинение после разрыва, % | σ-1 | — предел выносливости при испытании на изгиб с симметричным циклом нагружения, МПа | |
σсж0,05 и σсж | — предел текучести при сжатии, МПа | J-1 | — предел выносливости при испытание на кручение с симметричным циклом нагружения, МПа | |
ν | — относительный сдвиг, % | n | — количество циклов нагружения | |
sв | — предел кратковременной прочности, МПа | R и ρ | — удельное электросопротивление, Ом·м | |
ψ | — относительное сужение, % | E | — модуль упругости нормальный, ГПа | |
KCU и KCV | — ударная вязкость, определенная на образце с концентраторами соответственно вида U и V, Дж/см2 | T | — температура, при которой получены свойства, Град | |
sT | — предел пропорциональности (предел текучести для остаточной деформации), МПа | l и λ | — коэффициент теплопроводности (теплоемкость материала), Вт/(м·°С) | |
HB | — твердость по Бринеллю | C | — удельная теплоемкость материала (диапазон 20o — T ), [Дж/(кг·град)] | |
HV | — твердость по Виккерсу | pn и r | — плотность кг/м3 | |
HRCэ | — твердость по Роквеллу, шкала С | а | — коэффициент температурного (линейного) расширения (диапазон 20o — T ), 1/°С | |
HRB | — твердость по Роквеллу, шкала В | σtТ | — предел длительной прочности, МПа | |
HSD | — твердость по Шору | G | — модуль упругости при сдвиге кручением, ГПа |
40Х КРЕПЕЖ МАТЕРИАЛ СТ.
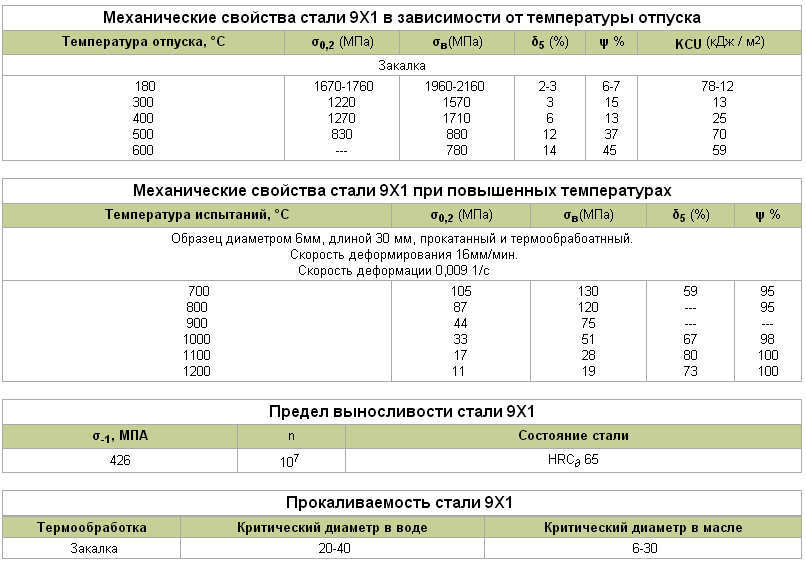
Характеристика материала ст. 40Х.
Марка : | 40Х | ||
Заменитель: | 45Х, 38ХА, 40ХН, 40ХС, 40ХФ, 40ХР | ||
Классификация: | Сталь конструкционная легированная | ||
| |||
Применение: | оси, валы, вал-шестерни, плунжеры, штоки, коленчатые и кулачковые валы, кольца, шпиндели, оправки, рейки, губчатые венцы, болты, полуоси, втулки и другие улучшаемые детали повышенной прочности.![]() |
Химический состав в % материала 40Х
C | Si | Mn | Ni | S | P | Cr | Cu |
0.36 — 0.44 | 0.17 — 0.37 | 0.5 — 0.8 | до 0.3 | до 0.035 | до 0.035 | 0.![]() | до 0.3 |
Температура критических точек материала 40Х.
Ac1 = 743, Ac3(Acm) = 782, Ar3(Arcm) = 730, Ar1 = 693 |
Механические свойства при Т=20°C материала 40Х.
Сортамент | Размер | Напр. | sв | sT | d5 | y | KCU | Термообр.![]() |
— | мм | — | МПа | МПа | % | % | кДж / м2 | — |
Диск | Танг. | 570 | 320 | 17 | 35 | 400 | ||
Пруток | Ж 28 — 55 | Прод.![]() | 940 | 800 | 13 | 55 | 850 | |
Пруток | Ж 25 | 980 | 785 | 10 | 45 | 590 | Закалка 860°C, масло, Отпуск 500°C, вода, |
Твердость материала 40Х после отжига, | HB 10 -1 = 217 МПа |
Физические свойства материала 40Х.
T | E 10- 5 | a 10 6 | l | r | C | R 10 9 |
Град | МПа | 1/Град | Вт/(м·град) | кг/м3 | Дж/(кг·град) | Ом·м |
20 | 2.![]() | 7820 | 210 | |||
100 | 2.11 | 11.9 | 46 | 7800 | 466 | 285 |
200 | 2.06 | 12.5 | 42.7 | 7770 | 508 | 346 |
300 | 2.![]() | 13.2 | 42.3 | 7740 | 529 | 425 |
400 | 1.85 | 13.8 | 38.5 | 7700 | 563 | 528 |
500 | 1.76 | 14.1 | 35.![]() | 7670 | 592 | 642 |
600 | 1.64 | 14.4 | 31.9 | 7630 | 622 | 780 |
700 | 1.43 | 14.6 | 28.8 | 7590 | 634 | 936 |
800 | 1.![]() | 26 | 7610 | 664 | 1100 | |
900 | 26.7 | 7560 | 1140 | |||
1000 | 28 | 7510 | 1170 | |||
1100 | 28.![]() | 7470 | 120 | |||
1200 | 7430 | 1230 | ||||
T | E 10- 5 | a 10 6 | l | r | C | R 10 9 |
Технологические свойства материала 40Х.
Свариваемость: | трудносвариваемая. |
Флокеночувствительность: | чувствительна. |
Склонность к отпускной хрупкости: | склонна. |
Обозначения:
Механические свойства : | |
sв | — Предел кратковременной прочности , [МПа] |
sT | — Предел пропорциональности (предел текучести для остаточной деформации), [МПа] |
d5 | — Относительное удлинение при разрыве , [ % ] |
y | — Относительное сужение , [ % ] |
KCU | — Ударная вязкость , [ кДж / м2] |
HB | — Твердость по Бринеллю , [МПа] |
Физические свойства: | |
T | — Температура, при которой получены данные свойства , [Град] |
E | — Модуль упругости первого рода , [МПа] |
a | — Коэффициент температурного (линейного) расширения (диапазон 20o — T ) , [1/Град] |
l | — Коэффициент теплопроводности (теплоемкость материала) , [Вт/(м·град)] |
r | — Плотность материала , [кг/м3] |
C | — Удельная теплоемкость материала (диапазон 20o — T ), [Дж/(кг·град)] |
R | — Удельное электросопротивление, [Ом·м] |
Свариваемость: | |
без ограничений | — сварка производится без подогрева и без последующей термообработки |
ограниченно свариваемая | — сварка возможна при подогреве до 100-120°C и последующей термообработке |
трудносвариваемая | — для получения качественных сварных соединений требуются дополнительные операции: подогрев до 200-300 град.![]() |
- О компании
- Производство
- Контакты
- Клиентам
- Услуги
- Продукция
- Справочник
- Документация
- Трубопроводы
- Статьи
- Объявления
- Карта сайта
- Пользовательское соглашение
- Cookies
- © «МФЗ», 2003-2023
Данные о морфологии и химическом состоянии покрытий на основе TiN, полученных методом конденсации с ионной бомбардировкой на различных подложках
- Список журналов
- Краткое описание данных
- т.
27; 2019 дек.
- PMC6864333
Краткий обзор данных. 2019 декабрь; 27: 104737.
Published online 2019 Nov 4. doi: 10.1016/j.dib.2019.104737
, a, ∗ , a , a , b , b , b и c
Информация об авторе Примечания к статье Информация об авторских правах и лицензиях Отказ от ответственности
В данной статье представлено влияние подложки на морфологию и химический состав покрытий из нитрида титана, сформированных методом конденсации с ионной бомбардировкой. Различные стали, спеченный твердый сплав (карбид вольфрама – 92%, кобальт – 8%) и сплав на основе титана. В работе представлены данные РФЭС, полученные на различных глубинах от поверхности. Также в статье приведены данные по износостойкости покрытий дорожных фрез.
Ключевые слова: Конденсация с ионной бомбардировкой, CIB, Нитрид титана, Покрытие, Рентгенофотоэлектронная спектроскопия, РФЭС, СЭМ
Таблица технических характеристик0049
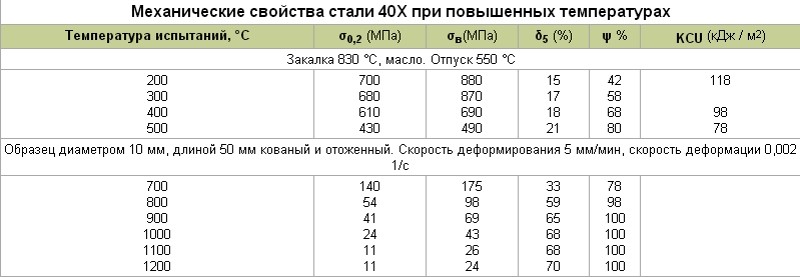
Значение данных
|
Открыть в отдельном окне
В наборе данных данной статьи представлена информация о влиянии подложки на морфологию и химическое состояние покрытий TiN на сталях, спеченных твердых сплавах (WC – 92%, Co – 8%) и сплав на основе титана (). Также в датасете представлена информация об элементном составе и химическом состоянии, а также данные об износостойкости покрытий дорожных фрез.
Таблица 1
Покрытие на различных основаниях.
Sample name | Substrate (Russian classification) | Analog (Germany classification) | |||||||||||||||||||||||||||||||||||||||||||||||||||||||||||||||||||||||||||||||||||||||||||||||||||||||||||||||
---|---|---|---|---|---|---|---|---|---|---|---|---|---|---|---|---|---|---|---|---|---|---|---|---|---|---|---|---|---|---|---|---|---|---|---|---|---|---|---|---|---|---|---|---|---|---|---|---|---|---|---|---|---|---|---|---|---|---|---|---|---|---|---|---|---|---|---|---|---|---|---|---|---|---|---|---|---|---|---|---|---|---|---|---|---|---|---|---|---|---|---|---|---|---|---|---|---|---|---|---|---|---|---|---|---|---|---|---|---|---|---|---|---|
S1 | Steel (110G13L) | GX120Mn12, GX120Mn13 | |||||||||||||||||||||||||||||||||||||||||||||||||||||||||||||||||||||||||||||||||||||||||||||||||||||||||||||||
S2 | Sintered hard alloy (VK8) | HG30,HG40 | |||||||||||||||||||||||||||||||||||||||||||||||||||||||||||||||||||||||||||||||||||||||||||||||||||||||||||||||
S3 | Сталь (40X) | 41Cr4 | |||||||||||||||||||||||||||||||||||||||||||||||||||||||||||||||||||||||||||||||||||||||||||||||||||||||||||||||
S4 | Стопный твердый сплав (VK8) с TIC Coating | HG30, HG40 | |||||||||||||||||||||||||||||||||||||||||||||||||||||||||||||||||||||||||||||||||||||||||||||||||||||||||||||||
S5 | на основе титана (VT-5) | 3,7114, 3,7115 | 9999
S1 | |||||||
---|---|---|---|---|---|---|---|
Spectrum | Concentration, at.![]() | ||||||
[C] | [N] + [O] | [Al] | [Ti] | [ Mn] | [Fe] | ||
1 | 12.19 | 39.54 | 0.68 | 39.56 | 1.54 | 6.49 | |
2 | 15.83 | 38.22 | 0.73 | 36.6 | 1.63 | 6.99 | |
3 | 12.![]() | 42.02 | 0.71 | 37.67 | 1.38 | 5.99 | |
4 | 13.1 | 42.2 | 0.55 | 37.02 | 1.43 | 5.7 | |
S2 | |||||||
Spectrum | [C] | [N] + [O] | [Al] | [Ti] | [Fe] | [Co] | [W] |
1 | 16.![]() | 44.49 | 1.52 | 31.51 | 0.05 | 0.48 | 5.09 |
2 | 15.54 | 48.92 | 0.76 | 28.18 | 0.07 | 1.53 | 5.00 |
3 | 19.50 | 46.80 | 0.62 | 25.27 | 0.05 | 2.65 | 5.11 |
4 | 18.![]() | 46.70 | 0.56 | 23.63 | 0.13 | 7.27 | 2.73 |
S3 | |||||||
Spectrum | [C] | [N] + [O] | [Si] | [Ti] | [Cr] | [Fe] | |
1 | 5.75 | 23.32 | 1.65 | 15.94 | 1.![]() | 51.36 | |
2 | 5.40 | 25.17 | 0.58 | 19.03 | 3.50 | 46.31 | |
3 | 8.08 | 22.66 | 0.39 | 23.07 | 3.56 | 42.24 |
Открыть в отдельном окне
показывает СЭМ изображения поверхности образцов S4 и S5 до и после формирования покрытия. Как видно, покрытия повторяют рельеф поверхности подложек. Это свидетельствует о высокой адгезии покрытий к подложкам. В показаны данные EDX для образцов S4 и S5.
Открыть в отдельном окне
РЭМ-изображения образцов: (а) S4 без покрытия, (b) S4 с покрытием; (в) S5 без покрытия, (d) S5 с покрытием.
Таблица 3
Данные EDX для образцов S4 и S5 до и после формирования покрытий.
Sample S4 without coating | |||||||||||||||||||||||||||||||||||||||||||||||||||||||||||||||||||||||||||||||||||||||||||||||||||||||||||||||||
---|---|---|---|---|---|---|---|---|---|---|---|---|---|---|---|---|---|---|---|---|---|---|---|---|---|---|---|---|---|---|---|---|---|---|---|---|---|---|---|---|---|---|---|---|---|---|---|---|---|---|---|---|---|---|---|---|---|---|---|---|---|---|---|---|---|---|---|---|---|---|---|---|---|---|---|---|---|---|---|---|---|---|---|---|---|---|---|---|---|---|---|---|---|---|---|---|---|---|---|---|---|---|---|---|---|---|---|---|---|---|---|---|---|
Spectrum | [C] | [Ti] | |||||||||||||||||||||||||||||||||||||||||||||||||||||||||||||||||||||||||||||||||||||||||||||||||||||||||||||||
1 | 43.61 | 56.39 | |||||||||||||||||||||||||||||||||||||||||||||||||||||||||||||||||||||||||||||||||||||||||||||||||||||||||||||||
S4 | |||||||||||||||||||||||||||||||||||||||||||||||||||||||||||||||||||||||||||||||||||||||||||||||||||||||||||||||||
Spectrum | [C] | [N+O] | [Ti] | ||||||||||||||||||||||||||||||||||||||||||||||||||||||||||||||||||||||||||||||||||||||||||||||||||||||||||||||
1 | 31.![]() | 15.66 | 52.62 | ||||||||||||||||||||||||||||||||||||||||||||||||||||||||||||||||||||||||||||||||||||||||||||||||||||||||||||||
2 | 32.12 | 12.56 | 55.25 | ||||||||||||||||||||||||||||||||||||||||||||||||||||||||||||||||||||||||||||||||||||||||||||||||||||||||||||||
3 | 29.86 | 13.35 | 56.76 | ||||||||||||||||||||||||||||||||||||||||||||||||||||||||||||||||||||||||||||||||||||||||||||||||||||||||||||||
Sample S5 without coating | |||||||||||||||||||||||||||||||||||||||||||||||||||||||||||||||||||||||||||||||||||||||||||||||||||||||||||||||||
Spectrum | [C] | [O] | [Al] | [Ti] | |||||||||||||||||||||||||||||||||||||||||||||||||||||||||||||||||||||||||||||||||||||||||||||||||||||||||||||
1 | 0.![]() | 7.51 | 9.23 | 82.44 | |||||||||||||||||||||||||||||||||||||||||||||||||||||||||||||||||||||||||||||||||||||||||||||||||||||||||||||
S5 | |||||||||||||||||||||||||||||||||||||||||||||||||||||||||||||||||||||||||||||||||||||||||||||||||||||||||||||||||
Spectrum | [C] | [N+O] | [Al] | [Ti] | |||||||||||||||||||||||||||||||||||||||||||||||||||||||||||||||||||||||||||||||||||||||||||||||||||||||||||||
1 | 2.82 | 19.72 | 4.62 | 72.83 | |||||||||||||||||||||||||||||||||||||||||||||||||||||||||||||||||||||||||||||||||||||||||||||||||||||||||||||
2 | 1.71 | 21.48 | 4,42 | 72,39 | |||||||||||||||||||||||||||||||||||||||||||||||||||||||||||||||||||||||||||||||||||||||||||||||||||||||||||||
3 | 18,39 | 18,06 | 1,68 | 61,87 |
| |||||||||||||||||||||||||||||||||||||||||||||||||||||||||||||||||||||||||||||||||||||||||||||||||||||||||||||||||
| |||||||||||||||||||||||||||||||||||||||||||||||||||||||||||||||||||||||||||||||||||||||||||||||||||||||||||||||||
|