характеристики и расшифовка, применение и свойства стали
- Стали
- Стандарты
Всего сталей
Страна | Стандарт | Описание | ||||||||||
---|---|---|---|---|---|---|---|---|---|---|---|---|
Россия | ГОСТ 4543-2016 | ![]() | ||||||||||
Россия | ГОСТ 10702-2016 | Прокат из качественной конструкционной углеродистой и легированной стали для холодного выдавливания и высадки. Технические условия | ||||||||||
Россия | ГОСТ Р 53932-2010 | Заготовка трубная. Общие технические условия |
Механические свойства стали 30ХМА
Свойства по стандарту ГОСТ 4543-2016
Тип образца | Образец | Предел текучести, σ0,2, МПа | Временное сопротивление разрыву, σв, МПа | Относительное удлинение при разрыве, δ5, % | Относительное сужение, ψ, % | Ударная вязкость KCU при 20°С, Дж/см2 |
Продольный | Термически обработанный | > 735 | > 930 | > 12 | > 50 | > 88 |
Свойства по стандарту ГОСТ Р 53932-2010
Обработка | Диаметр или толщина, мм | Предел текучести, σ0,2, МПа | Временное сопротивление разрыву, σв, МПа | Относительное удлинение при разрыве, δ5, % | Относительное сужение, ψ, % | Ударная вязкость KCU при 20°С, Дж/см2 | Твердость, НВ | Диаметр отпечатка, мм |
Без обработки | - | > 735 | > 930 | > 12 | > 50 | > 88 | - | - |
Отожженный или высокоотпущенный | > 5 | - | - | - | - | - | < 229 | > 4 |
Нагартованный | > 5 | - | - | - | - | - | < 269 | > 3,7 |
×
Отмена Удалить
×
Выбрать тариф
×
Подтверждение удаления
Отмена Удалить
×
Выбор региона будет сброшен
Отмена
×
×
Оставить заявку
×
Название | |||
Отмена
×
К сожалению, данная функция доступна только на платном тарифе
Выбрать тариф
30ХМА — Юнисталь Урал
Марка: | 30ХМА |
---|---|
Классификация: | Сталь жаропрочная релаксационностойкая |
Применение: | поковки общего назначения, валы, роторы и диски паровых турбин, фланцы, крепежные детали с рабочей температурой до 450 град.![]() |
C | Si | Mn | Ni | S | P | Cr | Mo | Cu |
---|---|---|---|---|---|---|---|---|
0,26 — 0,33 | 0,17 — 0,37 | 0,4 — 0,7 | до 0,3 | до 0,025 | до 0,025 | 0,8 — 1,1 | 0,15 — 0,25 |
Ac1 = 757, | Ac3(Acm) = 807 |
Сортамент | Размер, мм | Напр.![]() |
SВ, МПа | SТ, МПа | d5, % | y, % | KCU, кДж/м2 | Термообр. |
---|---|---|---|---|---|---|---|---|
Пруток | Ж 15 | 930 | 735 | 12 | 50 | 880 | Закалка 880 0С, масло Отпуск 540 0С, вода |
Твердость материала 30ХМА после отжига | HB 10 -1 = 229 МПа |
Т, град | Е 10-5, МПа | a 106, 1/град | l, Вт/(м·град) | r, кг/м3 | С, Дж/(кг·град) | R 109, Ом·м |
---|---|---|---|---|---|---|
20 | 2,08 | 7820 | 230 | |||
100 | 2,07 | 11,6 | 46 | 7800 | 462 | |
200 | 2,04 | 12,5 | 44 | 7770 | ||
300 | 1,97 | 13,2 | 42 | 7740 | ||
400 | 1,88 | 13,8 | 42 | 7700 | ||
500 | 1,76 | 14,3 | 39 | 7660 | ||
600 | 1,6 | 37 | ||||
700 | 36 | |||||
800 | 32 |
Свариваемость: | ограниченно свариваемая |
Флокеночувствительность: | чувствительна |
Склонность к отпускной хрупкости: | не склонна |
Механические свойства: | ||
---|---|---|
SВ | Предел кратковременной прочности, МПа | |
SТ | Предел пропорциональности (предел текучести для остаточной деформации), МПа | |
d5 | Относительное удлинение при разрыве, %) | |
y | Относительное сужение, % | |
KCU | Ударная вязкость, кДж/м2 | |
HB | Твердость по Бринеллю, МПа | |
Физические свойства: | ||
T | Температура, при которой получены данные свойства, Град | |
E | Модуль упругости первого рода, МПа | |
a | Коэффициент температурного (линейного) расширения (диапазон 20o — T ), 1/Град | |
l | Коэффициент теплопроводности (теплоемкость материала), Вт/(м·град) | |
r | Плотность материала, кг/м3 | |
C | Удельная теплоемкость материала (диапазон 20o — T ), Дж/(кг·град) | |
R | Удельное электросопротивление, Ом·м |
Без ограничений: | сварка производится без подогрева и без последующей термообработки |
Ограниченно свариваемая: | сварка возможна при подогреве до 100-120 град.![]() |
Трудносвариваемая: | для получения качественных сварных соединений требуются дополнительные операции: подогрев до 200-300 град. при сварке, термообработка после сварки — отжиг |
Сталь 30ХМА принадлежит к среднеуглеродистым низколегированным сталям. Эта сталь характеризуется резко выраженной неравномерностью распределения серы и фосфора по толщине проката. Введение в сталь 30ХМА небольшого количества меди (0,3%) повышает стойкость стали против коррозии (атмосферной и в морской воде). Для изготовления сварных конструкций 30ХМА используют в горячекатаном состоянии. Легирующие элементы, вводимые в сталь 30ХМА, образуя с железом, углеродом и другими элементами твердые растворы и химические соединения, изменяют ее свойства. Это повышает, механические свойства стали и, в частности, снижает порог хладноломкости. В результате появляется возможность снизить массу конструкций.
Сталь 30ХМА используется для производства машиностроительных деталей: ведущие валы, оси, ответственные болты, детали паровых турбин. Также из этой стали делают крепежную арматуру (болты, гайки, шпильки и др.), работающую при температуре до 500 0С. Немаловажную роль эта сталь играет в химической и нефтехимической промышленности: из нее делают трубы для установок нефтехимических производств.
У нас вы можете купить круг 30ХМА — прокат круглого сечения. Размер и цена указаны в каталоге.
Также есть другие легированные стали: 15Х5М, 5ХМ, 12Х1МФ.
Купить сталь или узнать цены вы можете, связавшись с нашими менеджерами:
- 8 (343) 382-14-33
- 8 (343) 382-11-41
- 8 (343) 286-97-68
- [email protected]
Los Angeles Abrasion – Pavement Interactive
Обзор
Испытание на истирание в Лос-Анджелесе (L. A.) (рис. 1) является распространенным методом испытаний, используемым для определения совокупной прочности и характеристик истирания. Характеристики абразивного износа заполнителя важны, потому что заполнитель, входящий в состав HMA, должен сопротивляться раздавливанию, деградации и распаду, чтобы производить HMA высокого качества.
Стандартное испытание на истирание в Лос-Анджелесе подвергает образец крупного заполнителя (оставленный на сите № 12 (1,70 мм)) истиранию, удару и измельчению во вращающемся стальном барабане, содержащем определенное количество стальных сфер.
После обработки во вращающемся барабане вес заполнителя, оставшегося на сите № 12 (1,70 мм), вычитается из исходного веса, чтобы получить процент от общего веса заполнителя, который раздробился и прошел через сито. Сито № 12 (1,70 мм). Таким образом, значение потерь на истирание L.A., равное 40, указывает на то, что 40% исходного образца прошло через сито № 12 (1,70 мм).
Стандартное испытание на истирание в Лос-Анджелесе:
- AASHTO T 96 или ASTM C 131: Устойчивость к разложению крупнозернистого заполнителя малого размера при истирании и ударе в машине Лос-Анджелеса .
История вопроса
Заполнители подвергаются значительному износу в течение всего срока службы. Как правило, они должны быть достаточно твердыми и прочными, чтобы противостоять раздавливанию, деградации и разрушению в результате любых сопутствующих действий, включая производство (Рисунок 2), складирование (Рисунок 3), производство (Рисунок 4), размещение (Рисунок 5) и уплотнение (Рисунок 6). ) (Робертс и др., 1996 [1] ). Кроме того, они должны быть в состоянии адекватно передавать нагрузки от поверхности дорожного покрытия к нижележащим слоям и, в конечном счете, к земляному полотну. Эти свойства особенно важны для HMA с открытой или щелевой градацией, которые не получают выгоды от амортизирующего эффекта мелкого заполнителя и где крупные частицы подвергаются высоким контактным напряжениям (Wu et al. , 1998 [2] ). Заполнители, недостаточно устойчивые к истиранию и полировке, могут привести к преждевременному разрушению конструкции и/или потере сопротивления скольжению. Кроме того, плохая стойкость к истиранию может привести к чрезмерному запылению во время производства HMA, что может привести к проблемам с окружающей средой, а также к проблемам с контролем смеси.
Рисунок 2: Агрегатное производство. | Рисунок 3: Совокупные запасы. |
Рисунок 5: Размещение HMA. | Рисунок 6: Уплотнение HMA. |
Из-за вышеперечисленных проблем важно провести испытание для прогнозирования совокупной ударной вязкости и сопротивления истиранию. Испытание на истирание в Лос-Анджелесе является преобладающим испытанием в США; его используют 47 государств (Wu et al. , 1998 [2] ).
Концепция испытания
Испытание на истирание методом L.A. измеряет разрушение образца крупного заполнителя, помещенного во вращающийся барабан со стальными сферами (рис. 7). По мере вращения барабана заполнитель разрушается за счет истирания и ударов о другие частицы заполнителя и стальные шарики (так называемый «заряд»). После завершения испытания расчетная масса заполнителя, который распался на более мелкие частицы, выражается в процентах от общей массы заполнителя. Таким образом, более низкие значения потерь на истирание в L.A. указывают на то, что заполнитель является более прочным и устойчивым к истиранию.
Рисунок 7: Стальные сферы.Адекватность испытаний
Испытание на истирание в Лос-Анджелесе является эмпирическим испытанием; это не имеет прямого отношения к производительности агрегатов в полевых условиях. Полевые наблюдения, как правило, не показывают хорошей взаимосвязи между значениями истирания в Лос-Анджелесе и полевыми показателями. Ву и др. (1998 [2] ) обнаружили, что потери на истирание в Лос-Анджелесе не могут предсказать эксплуатационные характеристики. В частности, тест может быть неудовлетворительным для некоторых типов заполнителей. Некоторые заполнители, такие как шлак и некоторые известняки, как правило, имеют высокие потери на истирание LA, но адекватно работают в полевых условиях. Потери на истирание LA, по-видимому, хорошо коррелируют с образованием пыли во время обработки и производством HMA, поскольку заполнители с более высокими значениями потерь на истирание LA обычно производят больше пыли.
Wu et al. (1998 [2] ) обнаружил, что прибор Micro-Deval является единственным широко используемым тестом, который имеет адекватные возможности прогнозирования в отношении ударной вязкости и сопротивления истиранию. В Micro-Deval также используется вращающийся барабан (рис. 8) со стальными сферами, но барабан намного меньше, чем сферы (рис. 9). В результате тест Micro-Deval имеет тенденцию к полировке (сглаживанию) частиц заполнителя (рис. 10), в то время как тест на истирание в Лос-Анджелесе имеет тенденцию к их разрушению. На видео 1 показан ход испытания Micro-Deval.
Рисунок 8: Барабан, используемый в аппарате Micro-Deval. | Рисунок 9: Стальные сферы, использованные в тесте Micro-Deval. | Рисунок 10: Частицы заполнителя до и после теста Micro-Deval. |
Видео 1: Тест Micro-Deval.
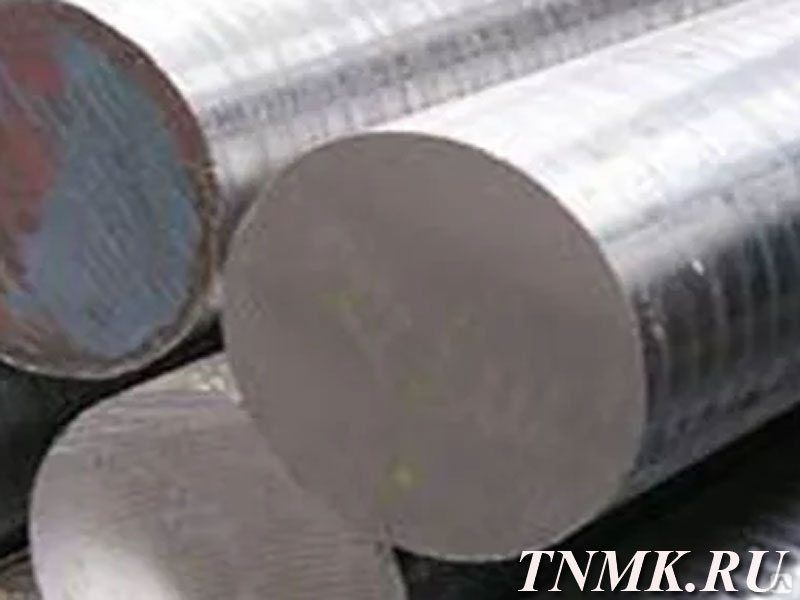
Стандартный тест Micro-Deval:
- AASHTO TP 58: Устойчивость крупнозернистого заполнителя к разложению под действием истирания в аппарате Micro-Deval
Описание теста
Следующее описание является кратким описанием теста на истирание в Лос-Анджелесе. Это не полная процедура, и ее не следует использовать для выполнения теста. Полную процедуру испытаний можно найти в:
- AASHTO T 96 или ASTM C 131: Устойчивость к разложению мелкого крупнозернистого заполнителя при истирании и ударе в машине Los Angeles
Резюме
Образец заполнителя, оставшийся на сите № 12 (1,70 мм), помещают во вращающийся стальной барабан, содержащий определенное количество стальных сфер или «загрузок». При вращении барабана полка внутри барабана собирает заполнитель и стальные шарики. Полка переносит их до тех пор, пока они не упадут на противоположную сторону барабана, подвергая заполнитель ударам и дроблению. Затем заполнитель подвергается истиранию и измельчению при вращении барабана до тех пор, пока полка не подхватит содержимое, и процесс повторяется. Барабан вращается на заданное число оборотов. После этого заполнитель снимают с барабана и просеивают на сите № 12 (1,70 мм). Заполнитель, оставшийся на сите, взвешивают, и разницу между этим весом и первоначальным весом выражают в процентах и сообщают как значение потерь при истирании L.A. На рис. 11 показано основное оборудование, использовавшееся при испытании на истирание в Лос-Анджелесе.
Приблизительное время тестирования
3 дня с момента взятия пробы до окончательного определения веса. Ниже приводится разбивка времени тестирования:
Уменьшение выборки до размера тестирования | 5 – 10 минут |
Промывка образца | 5 – 10 минут |
Сушка до постоянной массы | 8-12 часов (ночь) |
Время во вращающемся барабане | 15 минут |
Просеивание и повторная промывка | 30 минут |
Сушка до постоянной массы | 8-12 часов (ночь) |
Окончательное взвешивание | 5 – 10 минут |
Основная процедура
- Получите совокупный образец для тестирования и уменьшите его до необходимого размера (рис.
12).
Рисунок 12: Разделение образца заполнителя для испытания на истирание в Лос-Анджелесе.
- Промойте образец и высушите в печи до постоянной массы при 230ºF (110ºC).
- После сушки материал просеивают на отдельные фракции и рекомбинируют до одной из четырех указанных градаций, которые наиболее точно отражают градацию заполнителя в том виде, в каком он был получен. Запишите общую массу образца. Общая масса образца должна быть около 5000 г.
- Поместите образец и указанное количество стальных сфер в барабан и проверните его на 500 оборотов со скоростью от 30 до 33 об/мин (Видео 2). Требуемая плата зависит от используемой градации.
- Получите совокупный образец для тестирования и уменьшите его до необходимого размера (рис.
Видео 2: Испытание на истирание LA.

- Высыпьте материал и просейте заполнитель через сито крупнее 1,70 мм (№ 12) (рис. 13).
Рисунок 13: Просеивание образца после испытания на истирание в Лос-Анджелесе.
- Просеять более мелкий материал на сите № 12 (1,70 мм).
- Промойте заполнитель крупнее, чем сито № 12 (1,70 мм), и высушите в печи до постоянной массы при 230ºF (110ºC). После охлаждения определяют массу.
Результаты
Измеренные параметры
L.A. Потери на истирание в весовых процентах.
Спецификации
Таблица 1: Исходное свойство L.A. Спецификации истирания
Примечание 1 Для смеси Superpave не существует стандартной спецификации L.A. спецификации обычно устанавливаются государственными или местными органами. Обычно спецификации штатов США ограничивают истирание крупного заполнителя для использования HMA максимальным значением в диапазоне от 25 до 55 процентов, при этом в большинстве штатов используются спецификации на уровне 40 или 45 процентов (рис. 14). Требования к бетону на портландцементе (PCC), как правило, аналогичны, в то время как требования к специализированным смесям, таким как асфальт с каменной матрицей (SMA), как правило, ниже; AASHTO указывает максимальную потерю абразивного износа в Лос-Анджелесе в размере 30 процентов для SMA.
Рис. 14. Спецификации агентства L.A. по абразивному износу. Включает 49 штатов (Мэн использует Micro-Deval), FHWA, FAA и спецификацию округа 2 Калифорнии, всего 52 «агентства». (из Uhlmeyer, 2003)
Типичные значения
Типичные значения истирания для L.A. показаны в таблице 2.
Таблица 2: Типичные значения потерь на истирание для L.A.
На рис. 15 показаны типичные образцы заполнителей до и после истирания в Лос-Анджелесе.
Рисунок 15: Образцы до и после испытания на истирание в Лос-Анджелесе.Расчеты (интерактивное уравнение)
Определите процент потерь в процентах от исходной массы образца.
Где:
M исходный = масса исходного образца (г)
M конечный = масса конечного образца (г)
Запишите это значение как процент потери.
Сноски (↵ возвращается к тексту)
- Roberts, F.L.; Кандхал, PS; Браун, ER; Ли, Д.Ю. и Кеннеди, Т.В. (1996). Асфальтовые материалы для горячей смеси, расчет и конструкция смеси . Образовательный фонд Национальной ассоциации асфальтобетонных покрытий. Lanham, MD.↵
- Wu, Y.; Паркер Ф. и Кандхал К. (1998). . Отчет NCAT 98-4. Национальный центр асфальтовых технологий. Оберн, А.Л. http://www.eng.auburn.edu/center/ncat/reports/rep98-4.pdf. По состоянию на 23 июня 2004 г. ↵
HMA-SCA Зажимной болт для пилы по металлу | МАНИОТИНСТРУМЕНТЫ
- МИСУМИ Главная>
- Инструменты и аксессуары> org/ListItem»> Станки>
- Держатели инструментов>
- Оправки фрезерных станков>
- HMA-SCA Зажимной болт для пилы по металлу
MANYOTOOLS
MANYOTOOLS
[Характеристики]
· Специальные стяжные болты подходят для пил по металлу различной толщины.
· Специальные тонкие болты уменьшают взаимодействие с наконечником, повышая эффективность обработки.
Part Number |
---|
HMA8-SCA12 |
HMA10-SCA13 |
HMA16-SCA25.4 |
HMA16-SCA31.75 |
Part Номер | Скидка за объем | Количество дней до отгрузки | Размер D1 (мм) | Размер M | Размер E (мм) | Размер D2 (мм) | SLOT | Применимый держатель | |||||||
---|---|---|---|---|---|---|---|---|---|---|---|---|---|---|---|
7 Дней | 12 | М 8 | 5 | 16,5 | МСШ-32 | БТ,ХСК,СТ-ХМА 8 | 5247 дней | 13 | M10 | 6 | 21 | MSSH-40 | BT, HSK, ST-HMA10 | ||