Продление срока службы деревянных шпал
Перед укладкой деревянные шпалы, переводные и мостовые брусья должны быть укреплены от растрескивания одним из следующих способов:
- деревянными винтами по ТУ 32ЦП 229-79 «Винт деревянный для укрепления концов деревянных шпал и брусьев;
- металлическими болтами диаметром 12-13 мм.
Деревянные винты или металлические болты устанавливаются на расстоянии 120-150 мм от торца на высоте 50-60 мм от нижней пласти.
Допускается укрепление шпал, переводных и мостовых брусьев:
- обвязкой проволокой диаметром 5-7 мм на расстоянии 120-150 мм от торцов;
- установкой П-образных скоб длиной 120 мм из стальной полосы 20 х 2 мм в количестве восьми штук на расстоянии 120 и 180 мм от торца с верхней и нижней пласти, с заглублением скоб в тело шпалы или бруса на 50 мм;
- другими установленными МПС России способами. Кроме того, переводные брусья могут укрепляться в средней части одним из перечисленных в выше способов в местах, указанных в табл.
Таблица 5.1. Места установки укрепителей на переводных брусьях
Длина брусьев. см | Расстояние от шнурового конца бруса до места установки укрепителей, см | Длина брусьев, см | Расстояние от шнурового конца бруса до места установки укрепителей, см | ||
1-й укрепитель | 2-й укрепитель | 1-й укрепитель | 2-й укрепитель | ||
325 | 155 | — | 450 | 135 | 300 |
350 | 165 | — | 475 | 135 | 330 |
375 | 175 | — | 500 | 135 | 360 |
400 | 100 | 270 | 525 | 135 | 375 |
425 | 110 | 290 | 550 | 135 | 400 |
При сборке рельсошпальной решетки на производственной базе или одиночной укладке деревянных шпал, переводных и мостовых брусьев в путь необходимо оберегать их от механического повреждения. С этой целью должны применяться машины, механизмы и приспособления, исключающие повреждение пропитанного слоя. Деревянные шпалы, переводные и мостовые брусья должны подбираться примерно равными по толщине.
Забивать костыли и устанавливать шурупы без предварительной насверловки отверстий запрещается. Диаметр отверстия зависит от породы древесины и составляет:
- для костылей в мягкой породе 12,7-13,0 мм, в твердой породе — 14 мм; для шурупов — 16 мм (для упрощения установки, верхнюю часть на глубину 20 мм рассверливают диаметром 20-21 мм). Отверстия высверливаются на глубину 130 мм — под костыли и 155 мм — под шурупы.
- Не допускается устанавливать изогнутые костыли. Наклонная забивка костылей с последующим их отгибанием при окончательной забивке запрещается.
Для защиты деревянных шпал от механического износа древесины под подкладками должны укладываться прокладки согласно утвержденным МПС России чертежам и техническим условиям.
Прокладки на деревянную шпалу устанавливают при сплошной и одиночной замене шпал новыми.
При укладке прокладок на старогодные деревянные шпалы с износом древесины под подкладкой до 5 мм должно производиться удаление изношенной древесины в зоне подкладки с целью выравнивания поверхности шпалы в месте постановки подкладок.
В кривых малого радиуса (менее 600 м) для защиты деревянных шпал от механического износа должны применять специальные несимметричные металлические подкладки.
Для защиты переводных брусьев от механического износа и продления срока их службы должны укладываться прокладки согласно утвержденным МПС России чертежам.
После пришивки рельсов к деревянным шпалам и переводным брусьям в пути выполняется их подбивка. Через два-пять дней, в зависимости от грузонапряженности, уложенные шпалы и переводные брусья подбиваются вновь.
Для исправления пути на пучинах карточки следует укладывать между подкладкой и прокладкой.
В состав работ включаются:
- удаление изношенной древесины с зачисткой заусенцев и антисептирование зачищенных мест;
- постановка во время перешивок пути пластинок-закрепителей при костыльном скреплении и втулок — при шурупном;
- антисептирование отверстий от прикрепителей и трещин на верхней пласти;
- установка П-образных скоб в количестве не менее шести штук на расстоянии 40 мм от нижней пласти на торце.
Пластинки-закрепители следует изготавливать из твердых пород древесины — березы, бука или дуба и пропитывать их смесью каменноугольного масла (50 %) с битумом 3 (50 %). Допускается пропитка их фтористым натрием.
Допускается изготовление пластинок-закрепителей из здоровой древесины старогодных шпал.
Ширина пластинок-закрепителей должна быть 14-15 мм, высота 110 мм, толщина должна превышать величину сдвижки при перешивке колеи на 1-2 мм, но быть не более б мм.
Пластинки-закрепители устанавливаются в костыльное отверстие со стороны противоположной выполняемой сдвижки рельса или подкладки.
При разработке костыльных отверстий, когда деревянная шпала не может быть отремонтирована без изъятия из пути, допускается на путях 3-4-го классов (на путях 3-го класса при скоростях движения поездов до 60 км/ч) производить поперечную сдвижку не более трех шпал подряд на величину 8-10 см в кривых — наружу колеи, в прямых — в сторону полевой нитки, кроме стыковых и предстыковых шпал. При забивке костылей и установке шурупов в новые места старые отверстия необходимо заделывать антисептированными пробками, обеспечивающими полное заполнение разработанных отверстий.
На путях 1-го и 2-го класса такие деревянные шпалы подлежат изъятию из пути.
Деревянные шпалы, переводные и мостовые брусья, имеющие дефекты, указанные в гр. 5 и 6 подлежат изъятию из пути. К первоочередной замене должны назначаться деревянные шпалы, переводные и мостовые брусья, не обеспечивающие стабильность рельсовой колеи.
Негодные деревянные шпалы, переводные и мостовые брусья от двух и более, лежащие подряд, считаются «кустом». При наличии в пути «кустов» из трех и более негодных деревянных шпал, переводных и мостовых брусьев подряд до их ликвидации путь эксплуатируется со скоростями, приведенными в приложении 2 к настоящей Инструкции.
Замена негодных деревянных шпал при текущем содержании должна производиться в объемах, исключающих образование «кустов» до проведения очередного осмотра пути. Минимальная (расчетная) потребность замены негодных деревянных шпал при текущем содержании пути приведена в табл. 5.2.
Таблица 5.2. Минимальная потребность замены негодных деревянных шпал
Количество негодных шпал на 1 км пути | Минимальная укладка шпал для замены негодных | Количество негодных шпал на 1 км пути | Минимальная укладка шпал для замены негодных | Количество негодных шпал на 1 км пути | Минимальная укладка шпал для замены негодных |
100 | 3 | 300 | 25 | 500 | 77 |
110 | 3 | 310 | 27 | 510 | 81 |
120 | 4 | 320 | 29 | 520 | 85 |
130 | 5 | 330 | 530 | 89 | |
140 | 5 | 340 | 33 | 540 | 96 |
150 | 6 | 350 | 35 | 550 | 97 |
160 | 7 | 360 | 37 | 560 | 101 |
170 | 8 | 370 | 39 | 570 | 105 |
180 | 9 | 380 | 41 | 580 | 110 |
190 | 10 | 390 | 44 | 590 | 114 |
200 | 11 | 400 | 47 | 600 | 119 |
210 | 11 | 410 | 49 | 610 | 124 |
220 | 13 | 420 | 52 | 620 | 129 |
230 | 15 | 430 | 55 | 630 | 134 |
240 | 16 | 440 | 58 | 640 | 140 |
250 | 17 | 450 | 61 | 650 | 146 |
260 | 19 | 460 | 64 | 152 | |
270 | 20 | 470 | 67 | 670 | 157 |
280 | 20 | 480 | 70 | 680 | 163 |
290 | 24 | 490 | 74 | 690 | 170 |
700 | 176 |
Для исключения повышенного силового воздействия на вновь укладываемые отдельные деревянные шпалы, переводные и мостовые брусья при разрядке «кустов» их следует размещать так, чтобы число остающихся подряд негодных не превышало двух, а между ними лежало не менее двух вновь уложенных. Вновь укладываемые при разрядке кустов деревянные шпалы должны зашиваться на полное число костылей.
На станционных и подъездных путях с маневрово-вывозным характером движения (5-й класс) допускается чередование деревянных шпал с железобетонными по схеме, установленной службой пути железной дороги, а на путях 4-го класса — с разрешения МПС России.
Переход от деревянных шпал к железобетонным осуществляется комбинированным звеном, собранным из деревянных и железобетонных шпал. Место перехода от одного вида шпал к другому должно располагаться на расстоянии не менее 6,0 м от стыка рельсов.
ОАО ‘БШПЗ’ — Рекомендации по эксплуатации и продлению срока службы деревянных шпал и брусьев.
- Правила транспортирования, погрузки, выгрузки и хранения деревянных шпал, переводных и мостовых брусьев.
Отгрузка пропитанных деревянных шпал, переводных и мостовых брусьев производится в соответствии с требованиями ГОСТ 78, ГОСТ 8816 и ГОСТ 28450.
Транспортирование пропитанных деревянных шпал, переводных и мостовых брусьев производится в полувагонах с соблюдением технических условий погрузки и крепления грузов, а также автотранспортом с учетом обеспечения механизированной их выгрузки.
Выгрузка деревянных шпал, переводных и мостовых брусьев должна производиться кранами и специальными механизмами.
При погрузке, транспортировании и выгрузке деревянных шпал, переводных и мостовых брусьев должны обеспечиваться меры, предупреждающие повреждение пропитанного слоя древесины.
Хранение деревянных шпал, переводных и мостовых брусьев должно осуществляться в штабелях. Площадка под штабеля и территория вокруг них на расстоянии не менее 3 м должна быть очищена от легковоспламеняющихся материалов, растительного покрова и мусора и, кроме того, должна быть оборудована системой водоотводов, обеспечивающих отвод поверхностных вод с территории складирования. Штабеля должны быть выложены на подштабельное основание из пропитанной древесины или на негодные железобетонные шпалы. Расстояние между соседними подштабельными основаниями должно быть не менее 1,5 м.
Ленточные штабеля деревянных шпал, переводных и мостовых брусьев должны укладываться параллельно железнодорожному пути на расстоянии не менее 30м от строений и не ближе 6 м, а на звеносборочных базах не ближе 3 м от ближайшего рельса. Они не должны находиться так же под проводами электропередачи, связи и автоблокировки. Запрещается складировать штабеля деревянных шпал на расстоянии менее 6 м от кабельных трасс устройств СЦБ, связи, ДИСК ЖТСМ.
На производственных базах расстояние от штабелей деревянных шпал, переводных и мостовых брусьев до ближайшего рельса определяется возможностями выгрузочных кранов.
Штабеля деревянных шпал укладываются в клетку плотно по 100 штук. Верхнему ряду придается наклон для стока вод.
Штабеля располагают вплотную друг к другу с разрывом не менее 1 м через каждые четыре штабеля.
Переводные и мостовые брусья должны быть уложены в штабелях (комплектами или по размерам). При укладке переводных брусьев комплектами необходимо брусья большей длины размещать в нижних рядах штабеля.
Затенение штабелей шпал и брусьев от воздействия солнечных лучей обеспечит предохранение их от растрескивания в процессе хранения.
- Предохранение шпал и брусьев перед укладкой в путь.
Не допускается повреждение пропитанного слоя древесины шпалы и брусьев при выгрузке и в процессе производства работ.
Перед укладкой шпал и брусьев в путь в них должны быть
обязательно просверлены перпендикулярно к верхней постели отверстия
для постановки костылей и шурупов. Забивать костыли и устанавливать шурупы в шпалы и брусья без предварительной сверловки отверстий в древесине запрещается.
Диаметр просверливаемого отверстия зависит от породы древесины. В шпалах и брусьях из мягких пород — отверстия под костыли просверливают сверлом диаметром 12,7-13,0 мм, а в твердых породах — 14 мм. Отверстия под шурупы высверливают сверлом 16 мм. Чтобы предотвратить растрескивание древесины и упростить установку шурупов рекомендуется верхнюю часть отверстия на глубину 20 мм от верхней постели рассверливать сверлом диаметром 21 мм. Отверстия должны быть высверлены на глубину: для костылей 130 мм: для шурупов 155 мм.
Перед укладкой в путь новые шпалы и брусья для предохранения от растрескивания укрепляют одним из перечисленных способов:
металлическими или деревянными винтами; металлическими болтами — шпильками; проволокой диаметром 3-7 мм или торцевыми металлическими пластинами.
Разрешается укреплять шпалы П-образными скобами не менее 8 шт.: 4 шт. – на верхнюю постель и 4 шт. — на нижнюю.
Расположение укрепителей на переводных брусьях зависит от их длины. Расстояние от нижней постели до оси винта или болта должно быть 50-60 мм. Укрепители по концам брусьев устанавливают на том же расстоянии, что и у шпал — 120-150 мм.
- Предохранение шпал и брусьев при укладке в путь.
При укладке шпал и брусьев в путь необходимо оберегать их от механического повреждения. С этой целью должны применяться машины, механизмы и приспособления, исключающие повреждения пропитанного слоя.
Уложенные в путь новые шпалы или брусья при необходимости устанавливаются на место при помощи скоб и ломов.
При одиночной замене шпалы должны подбираться по толщине примерно соответствующей толщине шпал соседних заменяемой.
Перед пришивкой рельсов к шпалам и брусьям необходимо
проверить правильность ширины колеи по шаблону, а шпалу или брус установить так, чтобы предварительно просверленные костыльные отверстия совпадали с отверстиями в подкладке. Шпалу или брус следует подвесить, подштопать с тем, чтобы подкладки всей своей плоскостью плотно прилегали к подошвам рельсов и верхней постели шпал и брусьев.
Костыли при забивке и шурупы при завинчивании должны
устанавливаться перпендикулярно верхней постели уложенных в путь
шпал или брусьев. Не допускается устанавливать (забивать) изогнутые костыли.
Забивать шурупы в шпалы и брусья запрещается. Шурупы должны завертываться в шпалы и брусья только электрическими или торцовыми ключами.
Запрещается исправлять ширину колеи наклонной забивкой костылей с последующим их отгибанием при окончательной забивке.
После пришивки рельсов к шпале выполняется первая подбивка. Через 2-5 дней, в зависимости от грузовой напряженности участка, уложенные шпалы или брусья подбиваются вновь.
С целью снижения интенсивности износа шпал и брусьев и продления срока их службы необходимо под подкладки укладывать шпальные прокладки, которые должны соответствовать утвержденным чертежам и техническим условиям.
Для защиты переводных брусьев от механического износа и продления срока их службы должны укладываться комплекты прокладок, которые могут быть прибиты или приклеены.
- Предохранение шпал и брусьев при перешивках рельсовой колеи.
При перешивках пути необходимо применять пропитанные пластинки-закрепители установленного размера. Пластинки закрепители устанавливаются в костыльное отверстие со стороны, противоположной выполняемой сдвижке рельса или подкладки.
Ширина пластинки-закрепителя должна быть на 1 мм меньше чем у костыля. При перешивке пути с подачей перешиваемой рельсовой нити до 3 мм толщина пластинки-закрепителя должна быть 4 мм, а при подаче от 4 до 6 мм — 6 мм. Длина пластинки должна соответствовать длине части костыля, находящейся в шпале, и быть не менее 110 мм.
При забивке костылей в новые места старые костыльные отверстия необходимо заделывать пробками.
Для шпал пробки изготавливаются поперечным сечением 18х16 мм. При установке пробки более широкая сторона должна располагаться параллельно продольной оси шпалы. Такая установка пробок обеспечивает более плотное заполнение отверстия вдоль волокон древесины и в тоже время не будет создавать в шпале раскалывающих усилий.
Для переводных брусьев пробки должны изготавливаться для заделки костыльных отверстий поперечным сечением 22×22 или 24×24 мм, а для заделки шурупных отверстий — втулки диаметром 25 и 27 мм.
Изготавливать пластинки-закрепители следует из здоровой древесины старогодных шпал.
Работы по содержанию и продлению срока службы лежащих в пути шпал и брусьев выполняются бригадами по текущему содержанию наравне с другими путевыми работами.
В состав работ по содержанию шпал и брусьев включаются:
— удаление изношенной древесины с зачисткой заусенцев и смазыванием антисептиком зачищенных мест;
— постановка во время перешивки пути пластинок-закрепителей костыльном скреплении и втулок при шурупном;
— установка П-образных скоб на верхней постели и на торце у верхней постели при незначительно развитых трещинах по торцу, если ранее не были установлены торцевыми пластинами.
После проведения работ по уходу за шпалами и брусьями:
— заусенцы у краев подкладок должны быть зачищены и смазаны антисептиком;
— в шпалах и брусьях с незначительно развитыми трещинами на торцах должны быть установлены П-образные.
Несоблюдение рекомендаций по эксплуатации шпал и брусьев, изложенных в настоящем разделе, приводят к случаям преждевременной порчи продукции ОАО «Борисовский шпалопропиточный завод», на которые гарантийные обязательства не распространяются!
Сколько весит шпала деревянная пропитанная тип 1, 2 – вес, размеры, срок службы с антисептическими средствами – креозотом, ултаном, с фото
Ключевая часть ж/д пути – это опорные элементы: их укладка должна проходить по всем нормам, жизненно важно правильно их выбрать, а для этого нужно знать их особенности. Поэтому сегодня расскажем о шпале деревянной пропитанной, тип 1, 2: ее размеры, ГОСТ, срок службы и другие технические характеристики будут рассмотрены подробнейшим образом. Зачем? Чтобы вы понимали, чем один вид отличается от другого, как эксплуатировать, чтобы они служили максимально долго, не требуя замены.
Содержание
- Классификация деревянных шпал по типам
- Применение и размеры шпалы деревянной пропитанной типа 1
- Размеры и применение шпалы деревянной пропитанной типа 2
- Технические условия
- Ремонт
- Методики обработки
- Фактор влажности
- Отклонения, которые допускаются
- Стандартизованные размеры
- Габариты брусьев для стрелочных переводов и критерии параметров их соответствия
- Мостовые брусья: специфика стандартизации
Сразу отметим, что такие конструкции до сих пор традиционно используются на дорогах, оставаясь актуальными даже несмотря на наличие более прочных железобетонных. Все дело в материале их исполнения: хвойные породы (сосна, кедр, лиственница, пихта, ель) и даже береза значительно легче бетонных аналогов, в результате чего различные элементы ВСП не расползаются под воздействием динамических нагрузок, а при необходимости их проще поменять. Колея сохраняет структуру, необходимую для безопасного движения транспорта. Кроме того, их цена ниже. А для предохранения от влияния осадков и разрушения насекомыми-короедами их покрывают специальными составами.
Они подразделяются на следующие группы, в зависимости от назначения:
Для рельсовых ж/д линий первого-второго класса; допустим и третий, если его годовая грузонапряженность больше 5 миллионов т/км и/или локомотивы едут по ним со скоростью выше 100 км/ч.
Для подъездных, приемоотправочных (станционных), сортировочных линий, а также для магистралей четвертого класса.
Для малодеятельных, маневрово-вывозных и прочих колей пятого класса.
Рассматриваемые нами опорные элементы используются в первом и во втором случае соответственно, а значит их геометрия и эксплуатационные характеристики должны быть строго стандартизированы.
Используется для укладки самых ответственных участков – главных Ж/Д-путей, испытывающих максимальные нагрузки, – и поэтому должна быть повышенной прочности, что отражается как на ее габаритах, так и на ее цене – она стоит дороже других вариантов, так как материала на ее изготовление уходит больше.
а) обрезная;
б) полуобрезная;
в) необрезная.
Плотность шпалы деревянной пропитанной (типа 1), размеры, вес
Ее масса составляет 85 кг, она на 5 кг тяжелее той, что 2 вида (которую мы подробно рассмотрим ниже). Эту разницу как раз и обеспечивает увеличенная на 2 см ширина. В результате повышенная нагрузка на грунтовую подушку не становится критичной, а вот избежать деформаций помогает.
Именно такая геометрия была проверена на практике и поэтому до сих пор указывается в качестве актуальной в межгосударственных стандартах.
Отдельного внимания заслуживают те параметры, которые не подпадают под стандартные ДхШхВ, но все равно являются достаточно важными. Это:
высота пропиленных боковых сторон – 150 мм;
толщина – от 180 до 185 мм.
Параметр | Показатель, мм | ||
Длина | 2750 ± 20 | ||
Ширина по пласти | |||
Нижняя | Верхняя | 250-255 | 180 и 210 |
Подъем | 180 |
Благодаря такому соотношению геометрии они и способны выдерживать серьезные воздействия в течение длительного времени, не испытывая деформаций.
Шпалы деревянные, пропитанные по ГОСТ 78-2004 и 78-89, являются настоящей классикой для Ж/Д-проектирования. Древесина для их производства – это преимущественно хвойные породы: уже упомянутая сосна, как самый распространенный и доступный по цене вариант, а также ель, пихта, реже лиственница, – но возможно исполнение из березового массива.
Могут быть как обрезными (полуобрезными), так и нет, но все три варианта укладываются на широких путях, преимущественно главных, на которых требования к качеству опорных конструкций самые высокие.
При должной прочности отличаются легкостью (по сравнению с ЖБ-элементами ВСП). Еще одно их практическое преимущество – универсальность: рассчитаны на все классы железных дорог, поэтому они актуальны вот уже 100 лет и не собираются сдавать своих позиций.
Так как шпалы, пропитанные креозотом, весом в 85 кг достаточно технологичны в эксплуатации, их удобно менять, а переделывание полотна не вызывает проблем, они продолжают быть задействованы на ответственных ж/д линиях. Свою роль здесь играет и упругость материала: сосна, ель или другая порода, из которой может быть выполнен брус, хорошо переносит динамические воздействия и не просаживается в областях стыка.
При ремонте для скрепления с рельсом требуется минимум элементов: пара подкладок и десяток костылей (в общем случае). Поэтому чинить поврежденные участки можно по шаблону – быстро и при этом качественно.
В числе минусов – сравнительно небольшой ресурс (в среднем 15 лет) и склонность к растрескиванию. Чтобы предотвратить появление дефектов, можно набивать по бокам специальные пластины.
Похожие новости
- Железнодорожные деревянные брусья для стрелочных переводов: назначение, ГОСТ, размеры, вес
- Брус железобетонный для стрелочных переводов (1/9, 1/11, 1/6)
- Размеры железнодорожной деревянной шпалы: длина ЖД опоры, описание, ГОСТы, ТУ
- Виды и размеры железобетонной шпалы: вес, длина и ширина ЖБ опоры на железной дороге
- Все о железнодорожных шпалах.
Используется для укладки на подъездных и станционных линиях, то есть на не самых ответственных объектах. Поэтому тоньше, если сравнивать ее с первым видом, следовательно, и стоит дешевле. Материал исполнения не влияет на конечную цену, так как в любом случае представляет собой одну из вышеназванных пород – ель, сосна, береза, пихта или лиственница – точно так же предварительно просушенную и покрытую тем же защитным составом от влаги и микроорганизмов.
а) обрезная;
б) полуобрезная;
в) необрезная.
Размеры и масса шпалы деревянной пропитанной типа 2
Ее вес равняется 80 кг, она на 5 кг легче той, что 1 вида – именно за счет уменьшенной на 2 см ширины, которая никак не снижает надежность или долговечность использования, а также не нагружает грунтовую подушку. Так как укладывается на линиях с не самой большой грузонапряженностью, не испытывает настолько серьезных нагрузок, чтобы возникали деформации. Проще говоря, таких габаритов хватает, что уже было доказано в течение десятилетий практики.
По аналогии с предыдущим вариантом отдельно приводим параметры, не подпадающие под соотношение ДхШхВ, но в значительной степени определяющие эксплуатационные свойства. Это, опять же:
высота пропиленных боковых сторон – 130 мм;
толщина – от 160 до 165 мм.
Параметр | Показатель, мм | ||
Длина | 2750 ± 20 | ||
Ширина по пласти | |||
Нижняя | Верхняя | 230-235 | 150 и 195 |
Подъем | 160 |
Геометрия опорных брусьев регламентирована межгосударственным стандартом 78-89.
Внимание, вес шпалы деревянной пропитанной Б/У будет несколько отличаться от новой – из-за износа, от степени которого и зависит разница (обычно она не превышает нескольких десятков грамм, поэтому не может считаться существенной).
Выпускается согласно требованиям межгосударственного стандарта 78-89 (78-2004) в одном из трех вариантов исполнения: бывает обрезной, полуобрезной, необрезной. Материал для изготовления – хвойные породы (массивы уже упомянутых сосны, ели, пихты или лиственницы), либо береза.
Находит самое активное применение в создании главных Ж/Д-колей третьего-четвертого класса.
Кроме того, шпалы железнодорожные деревянные пропитанные длиной 2750 мм и 230 мм шириной, становятся надежной основой при строительстве путей сортировки и приема-отправки на подъездных участках и станциях, если эти места отличаются достаточно интенсивным характером эксплуатации.
Согласно межгосударственному стандарту 78-2004:
Расположение нижней и верхней пластей – взаимно параллельное, с допусками строго в рамках заданных норм по ДхШ.
Пропилы торцов – только перпендикулярно продольной оси, со скосом, не превышающим 20 мм по толщине.
При производстве необходимо очистить обзольные места от луба и/или коры.
Закомелистость и сучки нужно срезать, не допуская зарубов и запилов по верхней стороне или делая их не шире 40 мм и не глубже 20 мм в других случаях.
Шпалы, пропитанные ултаном или другим средством по ГОСТам 20022.0 и 20022.5, должны быть предварительно защищены от растрескивания – способом, принятым у производителя и соответствующим общей инструкции по содержанию элементов ВСП.
Маркировка обязана быть явной и четкой и представлять собой клеймление или обозначение краской на торце.
Может осуществляться без снятия опорных конструкций с пути, в этом случае:
Изношенные части удаляются, заусенцы зачищаются, после чего места обработки покрываются каменноугольным маслом (или другим подходящим составом).
На время перешивок устанавливаются втулки при шурупном стыке или пластины-закрепители – при костыльном.
Трещины и отверстия от элементов крепежа также защищаются от влаги и вредителей.
На торцах нижняя пласть армируется П-образными скобами (их нужно 6 штук или больше).
Шпалы железнодорожные деревянные пропитанные антисептическими средствами отработанные снимаются с колеи и заменяются. Непригодными к дальнейшей эксплуатации они считаются тогда, когда их повреждения превышают допуски и/или когда они лежат подряд в количестве от 3 штук. До их замены необходимо ограничить скорость движения по участку до минимально возможной.
Представляют собой несколько схем воздействия на конструкцию давлением (Д) и вакуумом (В). Актуальный сегодня вариант – Д-Д-В:
Для достижения нужной глубины проникновения порода предварительно накалывается.
Заготовки помещаются в камеру, из которой откачивают воздух.
Затем туда заливается маслянистый состав.
Средство пропитывает поры древесины.
Завершающим этапом становится просушка.
Чтобы предохранить массив от гнили, применяют следующие жидкие составы:
Креозотный – дистиллят каменного или древесного угля дегтярной смесью. Пропитка дешевая, однако крайне ядовитая. Дерево после нее чернеет.
Элемсепт – включает в себя оксидные соединения, содержащие в составе медные, хромовые и мышьяковые выключения. Менее ядовит, дает брусу светлый оттенок зеленого.
ЖТК – расшифровывается как жидкость термоконденсационная. Хотя и результат перегонки нефти, токсичных паров практически не выделяет. Точного состава в открытом доступе нет. Древесину практически не окрашивает.
Ултан – средство на водной основе. Хорошо проникает внутрь массива, придавая ему зеленый цвет. Губителен для вредителей, питающихся древесиной. Для человека и животных в целом безопасен.
По умолчанию шпала деревянная пропитанная типа I, II изготавливается из массива, содержащего до 22% влаги. Если же данный показатель выше, в габариты конструкции должны быть заложены припуски на усушку. Поэтому фактическая ДхШхВ готового изделия может несколько отличаться от указанной в нормативных документах.
Межгосударственные стандарты подразумевают возможность некоторых погрешностей при производстве – по следующим параметрам:
длина – ± 20 мм,
толщина – 5 мм,
подъем боковых сторон,
ширина пластей,
отступы между болтами,
отклонения от оси.
Геометрические характеристики опорных конструкций 1 и 2 типа мы привели в таблицах выше (а также рассмотрели, сколько весит шпала железнодорожная деревянная пропитанная – напоминаем, 85 и 80 кг). Поэтому сейчас давайте взглянем на третью категорию.
а) обрезная;
б) полуобрезная;
в) необрезная.
Параметр | Показатель, мм | ||
Длина | 2750 ± 20 | ||
Ширина по пласти | |||
Нижняя | Верхняя | 230 ± 5 | 140-190 |
Подъем | 160 |
В конструкции ВСП есть еще один важный элемент, который также должен отвечать ряду нормативов – предлагаем обратить на него внимание.
Отметим, что как и обычные опоры, они могут использоваться:
На главных (магистральных) линиях первой и второй категории, а также третьей, если скорость движения по таким колеям превышает 100 км/ч, а грузонапряженность больше 50 млн т/год.
На основных путях II-IV класса, на интенсивно эксплуатируемых подъездных, на точках сортировки и приемоотправки.
На малодеятельных, станционных, маневрово-вывозных колеях.
Показатель влажности идентичный: нормой признаны 22%, если же он выше, следует предусматривать допуск на усушку. Цифровые значения выпуска регламентированы межгосударственными стандартами 6782.1-75 и 6782.2-75.
Для наглядности сведем их в таблицу:
Параметр | Показатель, мм | ||
для I | для II | для III | |
Ширина | |||
По верхней пласти | 200 или 220 | 175 и 220 | 175 и 200 |
По нижней | 260 | 250 | 230 |
По частям без пропилов | 300 | 280 | 260 |
Толщина | 180 ± 5 | 160 ± 5 | |
Высота боковой стороны | 150 | 130 |
Если тот же вес одной шпалы железнодорожной деревянной пропитанной типа 1, 2, по ГОСТ 78-2004, отличался в зависимости от вида опорной конструкции, но был строго определен – либо 85, либо 80 кг, – то в данном случае есть не конкретная цифра, а их диапазон, причем достаточно широкий.
Варианты исполнения могут быть от 3 до 5,5 м, с шагом в 0,25 м и допуском в ± 0,02 м.
Изготавливаются из тех же пород, что и уже рассмотренные элементы, но должны быть прямоугольной формы, одного из следующих видов сечения:
или 220 х 240 мм;
или 220 х 260 мм.
Длина обоих одинакова и составляет 3250 мм, хотя критические отклонения уже могут различаться. По отдельной договоренности с клиентом производитель может выпустить опорные брусья 220 х 280 или 240 х 300 мм. Но допустимый уровень влажности у каждого по умолчанию 20%, а не 22%.
Альтернатива деревянным: эти конструкции предварительно напряженные и укладываются на магистральных линиях – для рельсов Р-50, Р-65, Р-75. Разделяются по нескольким показателям, в числе которых:
Итак, как же наша такая опора соединяется с направляющими? Возможны 3 варианта:
Ш1 – раздельно, с фиксацией подкладки болтами;
Ш2 – уже нераздельно;
Ш3 – без использования прокладки.
Чтобы было проще сравнивать, представлены в формате таблицы:
Значение | Показатель, мм | ||||||
Ш1 | Ш2 | Ш3 | |||||
Крайние точки между кромками | |||||||
Упорными | Концевыми | 2016 | 406 | 2016 | 406 | 1966 | 359 |
Подъем в сечении | |||||||
Подрельсовое | Среднее | 193 | 145 | 193 | 145 | 193 | 145 |
ДхШ при этом фиксированные – 2700 на 300 мм. Подобная геометрия обеспечивает приемлемую безопасность при прохождении транспорта даже на высокой скорости.
Совпадения, а также различия с железобетоннымиДля шпалы деревянной пропитанной, средний срок службы которой составляет 15 лет, при хорошем уходе и не особенно интенсивном использовании его можно продлить до 20 лет. У ЖБ-конструкций ресурс значительно выше и достигает 45-50 лет, при том, что за их состоянием не нужно столь пристально следить.
Выполненные из массива сосны, пихты, ели (и других пород) опорные элементы верхнего строения пути значительно легче – 80-85 кг против, как минимум, 270 кг. Они создают меньшую нагрузку на подушку и поэтому используются на слабых грунтах. Кроме того, они обходятся дешевле при производстве, а значит и стоят меньше. Плюс, их не так сложно утилизировать. Еще одно различие кроется во внешнем виде: вы можете посмотреть, как выглядят шпалы деревянные пропитанные новые (фото мы представляем ниже) и сравнить их с железобетонными.
В остальном же два этих вида опорных конструкций похожи. В частности, близки они по сферам применения: на некоторых линиях и участках они даже продолжают, заменяют, взаимно дополняют друг друга. И оба варианта остаются актуальными в условиях Ж/Д-проектирования и строительства, как у нас, в России, так и в Европе или Америке.
Мы постарались как можно более подробно рассмотреть данные элементы ВСП и дать вам представление об их особенностях. А если потребуется еще и купить их, обращайтесь в «ПромПутьСнабжение»: мы продаем их по доступным ценам, предъявляем сертификат на шпалы деревянные пропитанные, паспорт качества и другие необходимые документы, заботимся о быстроте доставки – у нас удобно заказывать.
Также смотрите видео.
___________________
Также на нашем сайте вы можете прочитать статью о пропитках ж/д опор, а также – более полный обзор на их железобетонные аналоги. Также можете почитать про виды железнодорожного крепежа, накладки и подкладки.
Время перемен – железобетонные шпалы вместо деревянных
Время перемен – железобетонные шпалы вместо деревянных
06 сентября 2014 г.
В ходе эксплуатации железобетонных шпал были в полной мере оценены все их достоинства, главное из которых долговечность. Если средний срок службы деревянных шпал на железных дорогах СССР не превышал 16 лет, то расчетный срок службы их железобетонных «собратьев» составлял 40–50 лет, то есть втрое больше.
Железобетонные шпалы имеют еще ряд существенных плюсов, например обеспечивают повышенную устойчивость колеи в отношении боковых сдвигов и выброса вверх, что особенно важно при использовании длинных рельсовых плетей, чувствительных к изменениям температуры. Именно это свойство железобетона способствовало внедрению на отечественных магистралях бесстыкового («бархатного») пути, придающего движению поездов замечательную плавность. Кроме того, шпалы из железобетона сохраняют однородность физического состояния на протяжении всего срока службы, что позволяет обеспечивать одинаковую упругость подрельсового основания.
Наконец, наращивание производства таких шпал позволяет значительно сократить расход древесины, снизив тем самым остроту экологических проблем. Ведь для изготовления шпал только на один километр пути вырубается до двух гектаров высококачественного леса из 80–100-летних деревьев. В свое время из-за истощения ресурсов места заготовки древесины в СССР были перемещены на северо-восток, где восстановление лесов длится намного дольше, а иногда вообще невозможно. Кроме того, массовые вырубки меняют климат целых регионов, уложенные в путь деревянные шпалы, пропитанные креозотом, отравляют почву, а те, что отслужили свой век, очень сложно поддаются утилизации.
Однако и у железобетонных шпал есть свои противники. В числе недостатков этой технологии называют ее относительную дороговизну. Поэтому, с одной стороны, всегда стояла задача удешевить производство верхнего строения пути, а с другой – использовать железобетон на самых грузонапряженных участках пути, чтобы ускорить его окупаемость. Другой недостаток – высокая жесткость пути приводит к повреждению рельсов в зоне стыков. Эту проблему старались нивелировать укладкой железобетонных шпал под бесстыковой путь. Сочетание железобетонной шпалы с бесстыковым путем в значительной мере компенсировало изъяны обоих элементов рельсошпальной решетки и было признано оптимальным.
В целом же плюсы всегда намного перевешивали минусы. А потому полигон использования железобетонных шпал рос буквально каждый год. Вот лишь несколько цифр. К 1967 году в СССР железобетонные шпалы были уложены более чем на 8 тыс. км путей (развернутая длина всех главных путей была тогда 171,2 тыс. км). А в 1977 году они эксплуатировались более чем на 45 тыс. км пути.
К 1970-м годам ежегодные объемы укладки были доведены до 4,4–4,5 тыс. км, а в середине 1980-х они превысили 4,7 тыс. км. Для того чтобы
обеспечивать растущий спрос, по всей стране строились новые заводы. Впрочем, далеко не все они носили узкоспециализированный характер. Многиепредприятия производили не только шпалы, но и иную железобетонную продукцию, к примеру строительные плиты, трубы.
Однако конец XX века для многих предприятий отрасли стал настоящей проверкой на прочность. Проблемы в экономике страны нарастали как снежный ком. Строительные проекты какое-то время еще велись по инерции, но на рубеже 1980-х и 1990-х годов почти все остановились. Из-за резкого сокращения спроса производства, ориентировавшиеся на выпуск строительных конструкций, были поставлены на грань выживания.
Подобная участь постигла, к примеру, Лискинский завод «Спецжелезобетон». Обиднее всего, что это было почти новое предприятие: его пустили в строй лишь летом 1980 года. А уже в 1988-м Министерство промышленности строительных материалов СССР, в состав которого входил тогда завод, решило закрыть предприятие, посчитав его неэффективным. На базе производственных активов вполне в духе того времени был создан кооператив «Струна», который тоже просуществовал недолго. Таких историй было очень много, а производственные линии останавливались почти повсеместно. Для предприятий, выживших в те тяжелые годы, это оборачивалось прежде всего потерей квалифицированных кадров – предприятия были вынуждены сокращать штат.
Но даже если спрос на продукцию сохранялся, возникал вопрос: сможет ли покупатель рассчитаться? Популярным инструментом в 1990-е стал бартер: за железобетонные конструкции различной сложности платили консервами, сапогами, бытовой техникой, одеждой и даже сигаретами, то есть всем, что служило средством натурального обмена.
Впрочем, сложности были не только с покупателями, но и с поставщиками сырья и комплектующих. К примеру, на Челябинском заводе, который когда-то был пионером в деле выпуска железобетонных шпал, чтобы снизить зависимость от поставщиков, начали осваивать вспомогательные производства. Так, был построен цех, где изготавливались закладные шайбы и пилорама, на которой выпускались деревянные прокладки.
Одним из немногих надежных партнеров в те времена являлось Министерство путей сообщения, продолжавшее закупки железобетонных конструкций (в первую очередь шпал). Поэтому неудивительно, что заводы стремились расширять взаимодействие с железной дорогой. «1990-е – это были тяжелейшие времена. Задача была выстоять, ведь Министерство промышленности строительных материалов СССР, куда входил наш завод, ликвидировали. У нас было два пути – приватизация, как это сделал Муромский завод, после чего и закрылся, или вхождение в состав МПС, нашего основного заказчика. Это был правильный выбор. Мы выстояли», – вспоминает заместитель генерального директора Вяземского завода Олег Свиридов.
Стремясь к сотрудничеству с железной дорогой, некоторые предприятия спешно меняли вид деятельности. Например, расположенный в Энгельсе (Саратовская область) ЖБИ № 6 до распада СССР был крупным производителем сборного железобетона для мелиоративного строительства. В начале 1990-х государство прекратило финансировать это направление, выпускаемая заводом продукция оказалась никому не нужна. Зато на находящейся рядомПриволжской железной дороге ощущался острый дефицит шпал: привозить их издалека было невыгодно, а вблизи ни одного производителя не было. Энгельсский ЖБИ № 6 в сжатые сроки наладил выпуск шпал, а в дальнейшем вошел в состав данной железной дороги.
Коллектив Энгельсского завода неоднократно отмечался за производственные достижения. Так, например, в марте 1981 года предприятие было награждено орденом Трудового Красного Знамени. «Эта государственная награда не только стала венцом десятилетнего юбилея завода, но и подчеркнула его заслуженный статус лучшего железобетонного предприятия Советского Союза», – говорит председатель профкома Энгельсского филиала Александр Имкин. Он вспоминает, что уже в первые годы работы предприятие не только освоило выпуск простейших конструкций из железобетона, но и запустило в производство такие уникальные изделия, как крупногабаритные преднапряжные плиты облицовки каналов, напорные трубы с металлическим сердечником. «Талантливые, думающие специалисты, выросшие на предприятии, они брались за реализацию наиболее важных проектов для мелиорации и строительства», – говорит Александр Имкин
Надо сказать, что по такому пути в те годы пошли многие предприятия. Магистраль, в состав которой включалось предприятие, гарантированно получала материалы верхнего строения пути, а завод обеспечивался твердым заказом. Для многих такая схема оказалась единственным спасением. Например, после ликвидации производственного кооператива «Струна» все производственные мощности Лискинского завода вошли в состав Юго-Восточной железной дороги. Сначала ситуация была крайне тяжелой, но со временем картина выправилась. «В первый год зимой д ля обогрева в цехах разводили костры – центральное отопление попросту не работало. Но постепенно началось возрождение завода. Пошли заказы на шпалы, началось восстановление предприятия», – вспоминает тот период нынешний директор Лискинского филиала Александр Кадуков. Уже в 1990-х предприятие удалось модернизировать. А вскоре Лискинский завод расширил ассортимент своей продукции, приступив к производству бруса для стрелочных переводов.
Присоединение к Министерству путей сообщения сыграло важную роль также в истории Горновского завода – предприятия, являющегося теперь крупнейшим производителем за Уралом. Первую партию шпал и железобетонных труб, на тот период крайне важной и необходимой для развития народного хозяйства на востоке страны продукции, завод выпустил в 1974 году. Для своего времени это было очень прогрессивное по уровню оснащения предприятие. Важно и то, что оно «привязано» к весьма богатой местной сырьевой базе: расположенные рядом Буготакские сопки содержат запасы качественных диабазовых порфиритов и базальтов. Однако в 1990-х перед этим заводом, как и перед многими другими, встал вопрос выживания. Решением оказалась полная переориентация производства на выпуск железнодорожной продукции.
Вспоминает Иван Маложон, начальник Дирекции по ремонту пути Западно-Сибирской железной дороги:
– Из-за резкого уменьшения спроса на профильную продукцию – железобетонные трубы – Горновский завод оказался в 1990-х на грани остановки. Его руководство во главе с директором Валерием Александровичем Отмаховым наметило программу освоения видов продукции, пользующейся спросом у платежеспособных партнеров.
Так в круг интересов завода попала наша магистраль. Главной продукцией, изготовленной для железнодорожников, естественно, стали шпалы. Затем – склейка изолирующих стыков. Следующим этапом, который смело можно назвать революционным, было освоение технологии изготовления рельсовых скреплений, в которых дорога испытывала острую нужду. Их выпуск позволил избежать срыва планов ремонта пути.
К списку новостей
СОСТОЯНИЕ ВОПРОСА ПРОИЗВОДСТВА И ЭКСПЛУАТАЦИИ ЖЕЛЕЗНОДОРОЖНЫХ ШПАЛ ИЗ РАЗЛИЧНЫХ МАТЕРИАЛОВ |Лесотехнический журнал
Т.
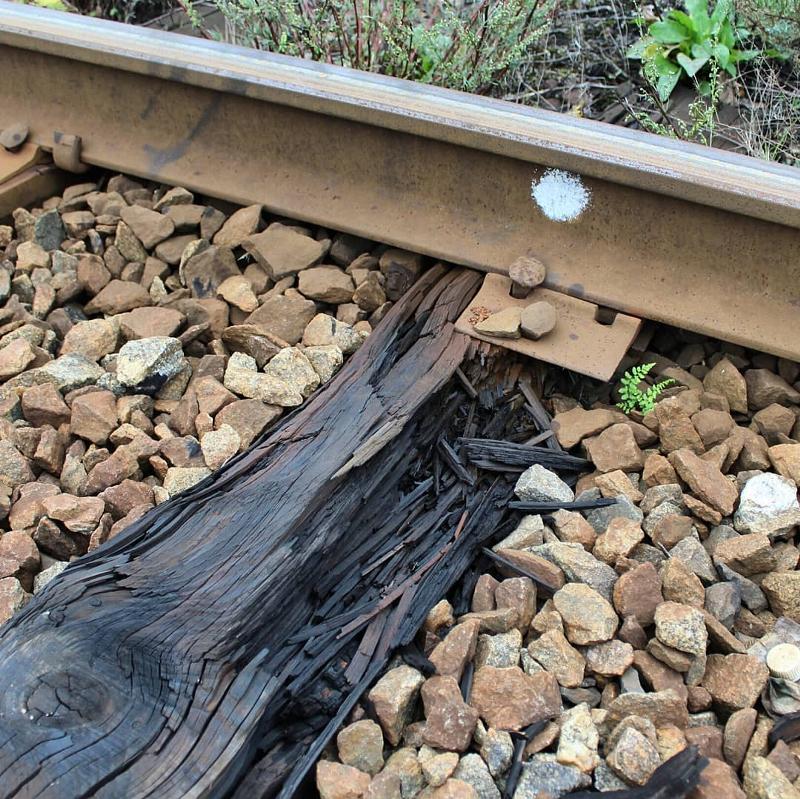
Скачать
№ 4 (28)
Деревопереработка. Химические технологии
Сведения об авторах
Курьянова Татьяна Казимировна – кандидат технических наук, доцент, доцент кафедры древесиноведения
ФГБОУ ВО «Воронежский государственный лесотехнический университет имени Г.Ф. Морозова», г. Воронеж, Российская Федерация
e-mail: [email protected]
Платонов Алексей Дмитриевич – доктор технических наук, доцент, заведующий кафедрой древесиноведения
ФГБОУ ВО «Воронежский государственный лесотехнический университет имени Г.Ф. Морозова», г. Воронеж, Российская Федерация
e-mail: [email protected]
Михеевская Марина Александровна – старший преподаватель кафедры технологии и машин лесозаготовок
ФГБОУ ВО «Ухтинский государственный технический университет», г. Ухта, Российская Федерация
e-mail: [email protected]
Паринов Дмитрий Александрович – младший научный сотрудник
ФГБОУ ВО «Воронежский государственный лесотехнический университет имени Г.Ф. Морозова», г. Воронеж, Российская Федерация; e-mail: [email protected]
Сафонов Андрей Олегович – доктор технических наук, профессор, декан лесопромышленного факультета
ФГБОУ ВО «Воронежский государственный лесотехнический университет имени Г.Ф. Морозова», г. Воронеж, Российская Федерация
e-mail: [email protected]
Мозговой Николай Васильевич – заведующий кафедрой промышленной экологии и безопасности жизнедеятельности
ФГБОУ ВО «Воронежский государственный технический университет», г. Воронеж, Российская Федерация
e-mail: [email protected]
Первакова Елена Анатольевна – преподаватель кафедры технологии и машин лесозаготовок
ФГБОУ ВО «Ухтинский государственный технический университет», г. Ухта, Российская Федерация
e-mail: lena. [email protected]
Аннотация:
Элементом верхнего строения железнодорожного пути являются шпалы. При выборе материала для изготовления шпал исходят из таких основных факторов, как стоимость в расчете на весь срок службы и эксплуатационные характеристики. При выборе материала для изготовления шпал исходят из их стоимости в расчете на весь срок службы и эксплуатационных характеристик. В связи с истощением запасов древесины в мире и малым сроком службы деревянных шпал в настоящее время интенсивно идет процесс использования шпал из железобетона, металла и пластика. Срок службы сосновой шпалы составляет не более 12-15 лет, железобетонных шпал – порядка 30-50 лет, пластиковых – до 40 лет, а металлических – 50-60 лет. Однако деревянные шпалы отличаются наименьшей стоимостью, практически не имеют ограничений по зонам укладки, а в некоторых случаях имеют явное преимущество перед другими материалами. Железобетонные, металлические и пластиковые шпалы дороже деревянных, имеют больший срок окупаемости, и их рекомендуется укладывать на путях с высокой грузонапряженностью, где они могут максимально быстро окупаться. Уменьшить недостатки шпал из натуральной древесины возможно, если для их изготовления использовать модифицированную древесину лиственных пород, которая за счет прессования будет по прочности превосходить шпалы из натуральной древесины, которая по своим физико-механическим показателям не уступает шпалам из натуральной хвойной древесины. Однако определенным недостатком модифицированной древесины является ее способность изменять размеры и форму при повышении влажности. Стабилизацию размеров и формы модифицированной древесины возможно повысить, пропитав ее составом антисептика со стабилизатором. Прогнозируемый срок службы шпал из модифицированной древесины может быть существенно выше, чем у деревянных шпал из натуральной хвойной древесины.
Ключевые слова:
шпала, модифицированная древесина, прессование, антисептик, влажность, стабилизатор, физико-механические свойства, анатомическая структура древесины
Литература:
1. ГОСТ 20022.5-93. Автоклавная пропитка маслянистыми защитными средствами. Введ. 1995-01-01 [Текст]. – Минск : Межгос. совет по стандартизации, метрологии и сертификации, 1994. – 5 с.
2. ГОСТ 78-2004. Шпалы деревянные для железных дорог широкой колеи. Введ. 2006-01-01 [Текст]. – М. : Межгос. совет по стандартизации, метрологии и сертификации, 2004. – 7 с.
3. Железнодорожный транспорт России: современное состояние, проблемы и перспективы развития [Электронный ресурс]. – Режим доступа: http://viperson.ru (дата обращения: 07.06.2017 г.).
4. Фадеева, Г. Д. Железнодорожные шпалы: настоящее и будущее [Текст] / Г. Д. Фадеева, К. С. Паршина, Е. В. Родина // Молодой ученый. – 2013. – № 6. – С. 161-163.
5. Хухрянский, П. Н. Прессование древесины [Текст] / П. Н. Хухрянский. – 2-е изд., испр. и доп. – М. : Лесн. пром-сть, 1964. – 361 с.
6. Шамаев, В. А. Модифицирование древесины [Текст] : моногр. / В. А. Шамаев, Н. С. Никулина, И. Н. Медведев. – М. : ФЛИНТА : Наука, 2013. – 448 с.
7. Navi, P. Combined densification and thermo-hydro-mechanical processing of wood [Text] / P. Navi, F. Heger // MRS Bull. – 2004. – No. 29. – P. 332-336.
8. Effect of oil impregnation on water repellency, dimensional stability and mold susceptibility of thermally modified European aspen and downy birch wood [Text] // A. A. Sheikh, T. Morén, M. Sehlstedt-Persson, Å. Blom // Journal of Wood Science. – 2017. – No. 63. – P. 74-82.
9. Solute diffusion into cell walls in solution-impregnated wood under conditioning process I: effect of relative humidity on solute diffusivity [Text] / S. Tanaka [et al.] // J. Wood Sci. – 2015. – No. 61. – P. 543-551.
10. Studies on pre-treatment by compression for wood drying I: effects of compression ratio, compression direction and compression speed on the reduction of moisture content in wood [Text] / Y. Zhao [et al.] // J. Wood Sci. – 2015. – No. 61. – P. 113-119.
Шпалы — статьи компании «Портал»
Поделиться
Советуем почитать
Соединения и пересечения железнодорожных путей
02 сентября’ 17
Интересное
Соединения и пересечения железнодорожных путей
Чем пропитывают деревянные железнодорожные шпалы
20 января’ 20
Интересное
Чем пропитывают деревянные железнодорожные шпалы
Неисправности стрелочного перевода: когда запрещается эксплуатация?
20 января’ 20
Интересное
Неисправности стрелочного перевода: когда запрещается эксплуатация?
Классификация дефектов рельсов
20 января’ 20
Интересное
Классификация дефектов рельсов
Какой должна быть подуклонка рельсов
20 января’ 20
Интересное
Какой должна быть подуклонка рельсов
Какие типы рельсов бывают?
20 января’ 20
Интересное
Какие типы рельсов бывают?
Виды стрелочных переводов
18 февраля’ 20
Интересное
Виды стрелочных переводов
Какую ручную лебедку выбрать
18 февраля’ 20
Интересное
Какую ручную лебедку выбрать
Назначение и виды ж/д противоугонов
18 февраля’ 20
Интересное
Назначение и виды ж/д противоугонов
Реечный домкрат: какой лучше выбрать
18 февраля’ 20
Интересное
Реечный домкрат: какой лучше выбрать
Типы рельсовых скреплений
18 февраля’ 20
Интересное
Типы рельсовых скреплений
Виды путевых работ на ж/д
05 марта’ 20
Интересное
Виды путевых работ на ж/д
Зачем нужен контррельс?
05 марта’ 20
Интересное
Зачем нужен контррельс?
Как работает реечный домкрат
05 марта’ 20
Интересное
Как работает реечный домкрат
Работа рельсовых стыков
05 марта’ 20
Интересное
Работа рельсовых стыков
Чем можно быстро распилить рельсы?
05 марта’ 20
Интересное
Чем можно быстро распилить рельсы?
Как быстро разрезать рельс
07 мая’ 20
Интересное
Как быстро разрезать рельс
Как меняют шпалы на железной дороге
07 мая’ 20
Интересное
Как меняют шпалы на железной дороге
Как работает контактный рельс
07 мая’ 20
Интересное
Как работает контактный рельс
Особенности работы автосцепного устройства вагона
07 мая’ 20
Интересное
Особенности работы автосцепного устройства вагона
Подбивка шпал
07 мая’ 20
Интересное
Подбивка шпал
Виды неисправностей автосцепного устройства вагонов
07 мая’ 20
Интересное
Виды неисправностей автосцепного устройства вагонов
Какие отрасли промышленности связаны с железнодорожным строительством
07 мая’ 20
Интересное
Какие отрасли промышленности связаны с железнодорожным строительством
Какие существуют материалы путевого строительства
07 мая’ 20
Интересное
Какие существуют материалы путевого строительства
Когда нужно проводить утилизацию железнодорожных шпал
07 мая’ 20
Интересное
Когда нужно проводить утилизацию железнодорожных шпал
Устройство тормозных колодок вагонов
07 мая’ 20
Интересное
Устройство тормозных колодок вагонов
Все статьи
Пиролиз – перспективный способ переработки деревянных шпал
Пиролиз – перспективный способ переработки деревянных шпал
За последние 25 лет экологические требования в европейских странах ужесточились и направлены на ограничение использования деревянных шпал, пропитанных креозотом . А в Нидерландах пропитанные креозотом деревянные шпалы уже запрещены по экологическим причинам. Это заставляет железные дороги искать новые экологически безопасные решения, такие как пиролиз.
Украинская железная дорога занимает шестое место в Европе и двенадцатое место в мире по общей протяженности путей – эксплуатационная длина основных участков составляет 22,3 тыс. км. Сегодня около 75% железнодорожного пути состоит из деревянных шпал, пропитанных креозотом для предотвращения гниения. Столь широкое использование деревянных шпал обусловлено рядом их преимуществ. Деревянные шпалы весом около 80 кг значительно легче железобетонных шпал, вес которых составляет 270 кг. Это позволяет производить прокладку и ремонтные работы бригадой рабочих без привлечения специальных грузоподъемных механизмов и инструментов.
Деревянные шпалы обладают необходимой жесткостью и упругостью для равномерного распределения нагрузок от колесных пар подвижного состава на рельсы. Кроме того, можно легко увеличить ширину колеи на поворотах малого радиуса (эта процедура необходима в некоторых случаях для предотвращения возможного схода вагонов с рельсов).
Шпалы из дерева являются хорошим диэлектриком, в отличие от железобетонных шпал, которые благодаря металлической арматуре хорошо проводят электрический ток.
Однако нормативный срок службы деревянных шпал, обработанных антисептиками, составляет 14-25 лет, но в зависимости от условий окружающей среды и в связи с интенсификацией транспортных потоков и увеличением нагрузок и скоростей срок службы может быть снижен до 8 лет. -10 лет и требуют регулярной замены изношенных шпал… Например, на железных дорогах Северной Америки ежегодно приходится заменять 14 миллионов из 700 миллионов деревянных шпал.
Шпалы, отслужившие свой срок, подлежат утилизации или захоронению на специальных полигонах промышленных отходов. Однако с каждым годом места на свалках становится все меньше и меньше, и в настоящее время из-за переполненности свалок или их отсутствия деревянные шпалы, бывшие в употреблении, зачастую складируются в не предназначенных для этого местах. Это оказывает негативное влияние на окружающую среду, поэтому проблема утилизации шпал имеет большое значение.
Одним из наиболее распространенных способов утилизации деревянных шпал является сжигание. Огромным недостатком этого метода является большое количество токсичных веществ (фенолы, фенантрен, ацетон, бутанол). Эти вещества негативно влияют не только на окружающую среду, но и на здоровье человека, способствуя возникновению и развитию различных заболеваний, в том числе онкологических.
В связи с выделением ядовитых веществ также абсолютно недопустимо использование старых деревянных шпал для строительства различных казарм, подсобных помещений, настила, мостов и тому подобного. Кроме того, такие устройства пожароопасны – огонь быстро распространяется, помещение прогорает за 15-20 минут.
Перспективным способом утилизации шпал может быть пиролиз – термическое разложение без доступа воздуха отходов деревянных шпал от перегонки этого каменноугольного масла. Есть надежда, что использование пиролиза для утилизации шпал позволит не только предотвратить загрязнение окружающей среды, так как процесс осуществляется в герметичной среде, но и получить экономическую выгоду. При правильной организации технологического процесса этот способ утилизации позволит не только покрыть энергетические потребности процесса пиролиза, но и использовать образующееся избыточное тепло на технические или бытовые нужды.
Утилизация отработанных деревянных шпал в качестве топлива на основе технологии газификации позволяет решить все насущные проблемы, обеспечив:
- эффективное использование шпал в качестве топлива для производства тепла;
- обязательных экологических показателя;
- замена значительного количества природного газа и угольного топлива на возобновляемое топливо – отработанные железнодорожные шпалы.
Полученная тепловая энергия может быть использована для систем отопления как жилых, так и промышленных объектов. Все это позволит логически замкнуть жизненный цикл бывших в употреблении деревянных шпал, дав им возможность повторно эффективно работать на завершающем этапе своего существования.
Одним из перспективных решений замены деревянных шпал является использование пластиковых шпал. По сравнению с деревянными, пластиковые шпалы имеют ряд преимуществ – не гниют, не раскалываются, имеют гораздо больший срок службы (до 50 лет). Деревянные шпалы можно постепенно заменять пластиковыми и для этого используется то же оборудование, что и при установке деревянных шпал. Но самым главным преимуществом использования пластиковых шпал является возможность их вторичной переработки и повторного использования.
Железнодорожный журнал «Железнодорожное снабжение». на нашей странице Facebook , Twitter , LinkedIn , читайте журнал Railway Supply онлайн .
Разместите свою рекламу на портале и в журнале Railway Supply. Подробная информация в Набор средств массовой информации для снабжения железных дорог
Обзор материалов для железнодорожных шпал | Дерево, сталь, бетон, пластик
8 марта 2017 г.
Железнодорожная шпала — это часть железнодорожного пути, которая обычно прокладывается между двумя рельсами для сохранения правильного положения стального рельса. Железнодорожная шпала также известна как шпала или шпала. Рельсовая шпала в основном используется для передачи нагрузки локомотива на железнодорожное полотно. Обычно железнодорожные шпалы можно разделить на несколько типов в зависимости от материалов. Из чего сделана железнодорожная шпала? Железнодорожная шпала может быть изготовлена из дерево, железобетон и пластик и так далее. Различные типы железнодорожных шпал могут применяться в разных областях, например, деревянные шпалы в основном используются в США, а бетонные шпалы занимают самый большой рынок в Европе и Азии. Каждый вид железнодорожной шпалы имеет свои преимущества и недостатки.
Деревянная шпала
Деревянная шпала — это традиционный тип железнодорожной шпалы. На сегодняшний день деревянные шпалы по-прежнему занимают наибольшую долю рынка железнодорожных шпал. Особенно в Северной Америке деревянные галстуки занимают 93% железнодорожных шпал. В зависимости от типа древесины, деревянные шпалы можно разделить на шпалы из твердой древесины и шпалы из мягкой древесины . В частности, к шпалам из лиственных пород относятся железнодорожные шпалы из дуба, ярра, шпалы карри и т. Д. Пихта Дугласа является типичным видом древесины хвойных пород для изготовления шпал на железной дороге.
Преимущества деревянной шпалы
- Деревянная шпала настолько легкая, что ее легко транспортировать, устанавливать и обслуживать.
- Деревянная шпала имеет широкое применение на железнодорожном полотне, подходит для любого участка.
- Он имеет более низкую стоимость, чем другие виды железнодорожных шпал.
- Шпалу бывшую в употреблении можно использовать для садоводства или ландшафтного дизайна.
Недостаток деревянной шпалы
- Легко пострадать от влажности.
- Его трудно перерабатывать, что делает деревянную шпалу более дорогой.
- Срок службы деревянной шпалы короче.
Бетонная шпала
Бетонная шпала в основном изготавливается из предварительно напряженного бетона. Это метод создания внутреннего напряжения в шпале перед заливкой, что снижает повреждение от внешнего давления во время эксплуатации. Как правило, бетонные шпалы используются на высокоскоростных железных дорогах. Бетон может выдерживать большие нагрузки, что обеспечивает высокоскоростным железным дорогам возможность более высокой скорости. Бетонная шпала была впервые использована во Франции и стала обычным явлением после мировой войны Ⅱ. В настоящее время бетонные шпалы в основном применяются в Азии, Европе и Австралии. Но бетонная стяжка имеет меньшую долю рынка в США.
Преимущества бетонной шпалы
- Более длительный срок службы по сравнению с деревянной шпалой (40-50 лет).
- Большая устойчивость из-за того, что он тяжелее, чем другие типы рельсовых шпал.
- Это рентабельно в долгосрочной перспективе.
- Бетонные рельсовые шпалы требуют меньше обслуживания.
Недостатки бетонной шпалы
- Он настолько тяжелый, что с ним трудно справиться.
- Имеет ограничение в применении (не может применяться в мостах и переездах).
Стальная шпала
Железнодорожная шпала изготавливается из прессованной стали и имеет корытообразное сечение. К верхней части стальной шпалы приварен корпус системы рельсового крепления. Поскольку стальные железнодорожные шпалы прочнее дерева и дешевле бетона, они обычно считаются промежуточным звеном между деревянными и бетонными шпалами. Кажется, что стальная шпала является лучшим выбором, но стальные железные дороги применяются в некоторых областях, таких как второстепенные линии в Великобритании, гораздо реже, чем другие типы рельсовых шпал. Факты доказали, что стальные рельсы более подходят для некоторых специальных железнодорожных участков, например, Хиджазской железной дороги на Аравийском полуострове, стальные шпалы обеспечивают решение давней проблемы, связанной с тем, что местные жители крадут деревянные шпалы для костров.
Преимущества стальной шпалы
- Стальная шпала легко устанавливается на существующем балластном слое, что требует низкой стоимости.
- Стальные шпалы также легко укладывать из-за их легкого веса и формы.
- Имеет длительный срок службы (более 50 лет).
- Стальная шпала подлежит вторичной переработке.
Недостатки стальной шпалы
- Химическая коррозия является недостатком стальной шпалы.
- Более высокая стоимость обслуживания.
- На данный момент стальные шпалы можно использовать только в некоторых особых местах из-за проблем с изоляцией.
Пластиковая железнодорожная шпала
Пластиковая железнодорожная шпала, также называемая композитной шпалой, в основном относится к железнодорожной шпале, изготовленной из пластикового композита. Пластиковый композит – абсолютно современный материал для изготовления рельсовых шпал. Это смеси пластика и использованной или отработанной резины. Пластиковая шпала сочетает в себе податливость дерева и прочность бетона, при этом избегаются шортики других типов. Пластиковые шпалы впервые используются на железной дороге Японией, которая является лидером в производстве композитных материалов. После этого пластиковые композитные шпалы были установлены на пути моста Цолламт в Вене, Австрия.
Преимущества пластиковой шпалы
- Пластиковые шпалы лучше снижают вибрацию.
- Композитная шпала легко разрезается и легко монтируется и может применяться в любом сечении рельса, как и деревянная шпала.
- Он пригоден для вторичной переработки, что означает, что использованная композитная шпала может быть повторно использована в новых шпалах.
- Пластиковая шпала имеет более длительный срок службы (около 30-80 лет).
- Это также своего рода экологически чистая железнодорожная шпала.
Недостатки пластиковой шпалы
Стоимость пластиковых шпал ограничивает возможность их применения в больших масштабах.
В заключение, деревянные шпалы, бетонные шпалы, стальные шпалы и пластиковые шпалы важны для современного железнодорожного пути. Как профессиональный производитель железнодорожной продукции, AGICO Rail может предоставить различные виды необходимых вам железнодорожных шпал, например, 9Стальные шпалы серии 0003 UIC865 и стальные шпалы серии BS-500 , а также различные шпалы из твердой древесины и т. д. Доступна быстрая доставка по индивидуальному заказу. Узнайте больше о том, как укладывать железнодорожные шпалы.
Вам также могут понравиться:
- Сравнение железнодорожных шпал
- Что вы знаете о железнодорожных шпалах?
- Направляющая бетонной шпалы
- Что такое деревянный шпал?
- Где купить железнодорожные шпалы?
- Как построить фальшпол из железнодорожных шпал?
- Обзор типовых железнодорожных шпал — деревянные шпалы, шпалы из твердой древесины и шпалы из дуба
- Крепление железнодорожных костылей к железнодорожным шпалам
- Рельсовая шпала
КАТЕГОРИИ
- Рельсовые скрепления
- система крепления рельсов
- рельсовый зажим
- железнодорожный костыль
- Гусеничный болт
- рельсовые плечи
- рельсовый анкер
- рельсовый зажим
- соединительная пластина
- Рельсовая подушка
- рельсовый изолятор
- пластиковый дюбель для рельсов
- прочие рельсовые скрепления
- Железнодорожный переключатель
- Система крепления рельсов серии SKL
- Китайская стандартная рельсовая система крепления
- винтовые шипы
- Система крепления крановых рельсов
- Рельсовые соединения (накладки)
- рельсовые стыки
- рычажный болт
- Изолированный рельсовый стык
- Стальной рельс
- Рельсовый путь
- Термитная сварка рельсов
- Железнодорожная шпала
- Деревянная шпала
- Композитная шпала
- Бетонная шпала
Популярные продукты
система крепления рельсов рельсовый зажим рельсовые стыки
Брошюра о продукции
Брошюры о продукции, Мгновенная БЕСПЛАТНАЯ загрузка
Мы уважаем конфиденциальность вашей электронной почты, мы ненавидим спам так же сильно, как и вы!
Срок службы деревянных шпал в Индонезии | Джарванто
Срок службы деревянных шпал в Индонезии
Djarwanto Djarwanto, Sihati Suprapti, Sri Rulliaty
Abstract
Древесина обладает огромными естественными преимуществами, такими как эластичность, гибкость и устойчивость к сжатию, а также к ударной нагрузке. Таким образом, древесина является удивительно лучшим материалом для железнодорожных шпал, чем бетон. Несмотря на преимущества древесного материала, он подвержен воздействию организмов. В этой статье рассматривается срок службы деревянных шпал на острове Ява, Индонезия. Древесные шпалы наблюдались визуально с наземной железнодорожной системы, провинция Бантен включает макроскопическую идентификацию древесных пород и атаку организмов. Результаты показывают, что стойкость шпал к естественной древесине относительно высока, поэтому прогнозируется, что шпалы прослужат долго. Порода древесины шпал – тик ( Tectona grandis ), балау ( Hopea sp.), мербау ( Intsia bijuga ) и улин ( Eusideroxylon zwageri ). Шпалы также были поражены грибком за пять месяцев. Наблюдаемые разлагающиеся грибы: Dacriopinax sp. , D. spathularia, Lentinus sp ., Panus sp ., Pycnoporus sp. , P. sanguineus, Polyporus spp., Schizophyllum commune и Trametes сп.
Ключевые слова
срок службы; деревянная шпала; дереворазрушающие организмы; грибы.
Полный текст:
PDFСсылки
Amemiya, S.; С. Мацуока. 1979. Долговечность тропических лесов. ЯРЬЯ9 13(4): 256-262. Япония: Центр исследований тропического сельского хозяйства.
Брюс А.; Б. Кинг. 1983. Биологический контроль гниения древесины с помощью Lentinus lepideus (Fr.), Произведенного остатками Scytalidium и Trichoderma. Материал и органы 18. Группа 1983 Heft 3, Duncker & Humblot – Берлин.
с.: 171-181.
Брюс А.; Б. Кинг. 1986. Биологический контроль разложения обработанных креозотом распределительных столбов. Material und Organismen 21. Band 1986 Heft 1, Duncker & Humblot — Берлин. стр.: 1-13.
БСН. 2013. Национальный национальный стандарт Индонезии: SNI 0197:2013. Банталан Каю Рел Керета Апи. Джакарта: Badan Standardisasi National (BSN).
Де Гроот, Р.К. 1992. Испытательные сборки для мониторинга гниения древесины, выставленной над землей. Международная биодеградация и биодеградация 29: 151-175.
Джарванто; С. Абдуррохим. 2000. Технологии обработки древесины для увеличения срока ее службы. Бюллетень Кехутанан дан Перкебунан 1 (2): 159-172.
Джарванто; С. Супрапти. 2004. Устойчивость трех пород древесины железнодорожной шпалы к дереворазрушающим грибам в лабораторном эксперименте. Журнал Penelitian Hasil Hutan 22(4): 215-221.
Джарванто; С. Супрапти. 2008а. Технология Pengawetan Kayu Untuk Bantalan Rel Kereta Api. Исследовательский отчет. Центр исследований и разработок технологий лесных товаров. Богор-Индонезия (неопубликованный отчет).
Джарванто; С. Супрапти. 2008б. Влияние коррозии металла на разложение четырех пород дерева, происходящих из Сукабуми. Журнал Ilmu dan Teknologi Hasil Hutan 1(2): 55-59.
Джарванто; С. Супрапти; У. Сударджи. 2007. Керусакан Каю Банталан Рел Керета Апи. Предварительный национальный семинар IX MAPEKI tanggal 11–13 августа 2006 г., Банджарбару, с. 573-579. Факультет лесного хозяйства Университета Ламбунг Мангкурат, Банджар-Бару, Южный Калимантан.
Джубер, САС. 1977. Пеманфаатан Потенси Каю Банталан. Кехутанан Индонезия III: 11-15. Дункан, К.Г. 1960. Мягкая гниль в древесине и исследования токсичности грибков-возбудителей. American Wood-preservers Organisms.p. 1-8.
Дункан, К.Г.; Ф.Ф. Ломбард. 1965. Грибы, связанные с основным разложением изделий из дерева в Соединенных Штатах. Исследовательский документ Лесной службы США WO-4. Министерство сельского хозяйства Вашингтона, округ Колумбия.
ФАО. 1957. Отчет Рабочей группы ECAFE/FAO по железнодорожным (деревянным) шпалам. Экономический и Социальный Совет ООН. E/CN.11/TRANS/Sub.1/47. 28р.
ФОРПРИДКОМ. 1971. Деревянные железнодорожные шпалы: их преимущества перед стальными и бетонными. Техническая записка 105. Филиппины: Комиссия по исследованию лесных товаров и развитию промышленности.
ФОРПРИДКОМ. 1974. Качество некоторых филиппинских лесов, удерживающих железнодорожные шипы. Техническая записка 138. Филиппины: Комиссия по исследованиям в области лесных товаров и развитию промышленности.
Martawijaya, A. 1961. Некоторые результаты эксплуатационных испытаний обработанных шпал. Связь ЦНИИ лесного хозяйства Богор-Индонезия №74.
Мартавиджая, А. 1965а. Влияние возраста дерева на долговечность тика (Tectona grandis L.f.). Отчет № 98. Научно-исследовательский институт лесных товаров. Богор.
Мартавиджая, А. 1965б. Естественная долговечность некоторых индонезийских хвойных пород древесины. Отчет № 99. Научно-исследовательский институт лесных товаров. Богор.
Martawijaya, A. 1983. Keawetan Beberapa Jenis Kayu Dipterocarpaceae. Происходит Пертемуан Ильмия Пенгаветан Каю. п. 157-169. Джакарта, 12–13 октября 1983 года. Центр исследований и разработок лесных товаров. Богор.
Мартавиджая, А. 1989. Кеаветан Каю янг Берасал дари Хутан Алам дан Хутан Танаман. Слушания Diskusi Sifat dan Kegunaan Jenis Kayu HTI, 23 марта 1989 г., Джакарта. п. 280-288. Агентство исследований и развития лесного хозяйства. Джакарта.
Кип Н., Ван Вин Дж.А. 2015. Двойственная роль микробов в коррозии. Журнал ISME 9: 542-551.
Ноэцли, К.П.; А. Б. Б. Фрей; Ф. Граф; Т. С. О. Холденридер. 2007. Высвобождение железа из скрепляющих гвоздей в плотинах для контроля потока и его влияние на разложение древесины Fomitopsis pinicola. Wood Research 52(4): 47-60.
Oey, DS 1990. Удельный вес индонезийского леса и его значение для практического использования. Номер связи 3. Центр исследований и разработок лесных товаров. Богор.
Перусахан Джаватан Керета Апи. 1986. Perencanaan Konstruksi Jalan Rel (Peraturan Dinas No.10), С.К. Кепала Перусахан Джаватан Керета Апи Танггал 2 апреля 1986 г. № KA/JB/18798/SK/86.
Suprapti, S. 2010. Устойчивость к гниению 84 индонезийских пород древесины против грибков. Журнал науки о тропических лесах 22(1): 81-87.
Suprapti, S. 2013. Pengelolaan Jamur Perusak Kayu untuk Mendukung Pelestarian dan Pemanfaatan Sumber Daya Hutan. Химпунан Бунга Рампай: Ораси Ильмиах Ахли Пенелити Утама (ВСУ) Пусат Пенелитиан и Пенгембанган Кетекникан Кехутанан и Пенголахан Хасил Хутан. ISBN 978-979-3132-44-0.
Супрапти, С.; Джарванто. 2001. Использование древесного бревна в качестве среды для грибов Pleurotus sajor-caju. В Правирохатмоджо, С.; С.Н. Марсоэм; AH Soetjipto (ред.). Охрана окружающей среды за счет эффективного использования лесной биомассы. стр: 333-340. Джокьякарта: ДЕБЮТ Press.
Супрапти, С.; Джарванто. 2002. Устойчивость двенадцати пород древесины к шести дереворазрушающим грибам. Материалы Четвертого международного симпозиума по науке о древесине, 2–5 сентября, Серпонг. п. 164-189. Исследовательский центр физики, ЛИПИ. Индонезия.
Супрапти, С.; Джарванто. 2015. Испытания на гниение пяти пород древесины, скрепленных металлическим шурупом. Журнал Penelitian Hasil Hutan 33 (4): 365-376.
DOI: https://doi.org/10.51850/wrj.2015.6.1.1-7
Рефбеки
- В настоящее время нет рефбеков.
Copyright (c) Журнал исследований древесины, 2018 г.
Indexed by:
Copyright © Wood Research Journal
ISSN : 2087-3840, EISSN : 2774-9320
This work is licensed под международной лицензией Creative Commons Attribution-ShareAlike 4.0.
Шпалы для железнодорожных и подкрановых путей
Шпалы, также известные как шпалы или путевые балки, являются частью верхнего строения пути подкрановых и железных дорог. Шпалы поддерживают рельсы и, таким образом, системы, которые проходят по ним. Важно, чтобы рельсы были и оставались устойчивыми, чтобы кран или поезд не сошли с рельсов и не вызвали ненужной вибрации и шума. Шпалы не уменьшают шум или вибрацию, но могут доставлять массу неудобств, если они отклоняются.
Типы шпал
Помимо шпал для подкрановых путей (из бетона, пластмассы или дерева) Bemo Rail также поставляет стандартные рельсовые шпалы.
Уникальными являются наши бетонные шпалы для подкрановых путей, рассчитанные на стандартную колесную нагрузку до 450 кН. Они очень подходят для мест, где фундаментные бетонные конструкции недостаточны из-за осадки грунта. Эти усиленные шпалы подкранового пути были специально разработаны для кранов RMG (ARMG) компаниями Konecranes, ZPMC, Gottwald, Kuenz, Liebherr и Kalmar, среди прочих. Они часто используются в контейнерных терминалах с «мягкой» поверхностью.
Инновации
В Bemo Rail мы считаем, что качество и долговечность очень важны. Вот почему мы постоянно внедряем инновации, ищем лучшие приложения и материалы. Таким образом, в дополнение к нашим стандартным материалам также можно выбрать один из наших инновационных продуктов. Мы также предлагаем бамбуковые шпалы и шпалы из серобетона.
Бамбук: бамбук поглощает в 5 раз больше CO2 и производит на 35% больше кислорода, чем эквивалентный кусок леса с деревьями. Кроме того, он вырастает до 1 метра в день, не разрушая бамбуковый лес. Бамбук расщеплен на полоски, а свободные волокна спрессованы с помощью экологически чистой смолы, в результате чего получается очень прочный и надежный материал, идеально подходящий для шпал.
Серобетон: Серобетон на 100% состоит из кругов, имеет низкий уровень выбросов CO2 и не теряет качества. Продукт похож на обычный бетон, в котором цемент и вода заменены серой.
Свяжитесь с нами, чтобы узнать о возможностях.
Бетонные шпалы
Бетонные шпалы
Бетонные шпалы кранового пути тяжелее деревянных или пластиковых шпал и поэтому идеально подходят для транспортных средств с большей нагрузкой на колеса. Дополнительным преимуществом бетона является его долгий срок службы не менее 40 лет и низкие эксплуатационные расходы.
Благодаря длительному сроку службы бетонная шпала более экологична, чем деревянная шпала. Бетон также поглощает CO2 в течение своего срока службы, что обеспечивает низкий след CO2. Благодаря способу изготовления бетонной перекладины гарантируется размерная стабильность (в пределах установленных допусков).
Бетонные шпалы подкрановых путей:
- Изготовлены из предварительно напряженного бетона очень высокого качества.
- Подходит для максимальной нагрузки на колесо 450 кН; выше возможно по запросу.
- Минимальный срок службы ок. 40 лет.
- Относительно низкая стоимость строительства.
- Низкое давление C02 на ногу.
- Легко корректируется после урегулирования.
- Легко снимается или перемещается после использования.
Бетонные железнодорожные шпалы:
- Изготовлены из очень высококачественного предварительно напряженного бетона C 50/60.
- Ширина гусеницы 1435 мм.
- Наклон опорной поверхности: 1:40.
- Нагрузка на ось: 225 кН или более для максимальной скорости.
- Подходит для различных типов рельсов.
- Минимальный срок службы ок. 40 лет.
- Относительно низкая стоимость строительства.
- Низкое давление C02 на ногу.
- Легко корректируется после урегулирования.
Деревянные шпалы
Деревянные шпалы
Деревянные шпалы для крановых путей особенно подходят для низких колесных нагрузок до 450 кН.
Деревянные шпалы для крановых путей:
- В основном изготавливаются из лиственных пород азобе или дуба.
- Подходит для максимальной нагрузки на колесо 450 кН.
- Минимальный срок службы ок. 20 лет.
- Относительно низкая стоимость строительства.
- Доставка со знаком FCA (желательно Bemo Rail).
- Легко корректируется после урегулирования.
Деревянные железнодорожные шпалы:
- В основном изготавливается из твердой древесины азобе или дуба. Возможны другие породы дерева.
- Номинальная ширина колеи 1435 мм. Другая ширина колеи по запросу.
- Применяется для различных задних (наклонных) плит.
- Нагрузка на ось: 225 кН или более для максимальной скорости.
- Подходит для различных типов рельсов.
- Срок службы ок. 20 лет.
- Относительно низкая стоимость строительства.
- Легко корректируется после урегулирования.
- Доступен как новый, так и бывший в употреблении.
Синтетические шпалы подкрановых путей
Синтетические шпалы для подкрановых путей
Синтетические шпалы для подкрановых путей изготовлены из переработанного пластика, это прочный продукт с длительным сроком службы ок. 50 лет. Пластик используется для изготовления мостов во всем мире уже много лет. Кроме того, он также используется для стрелочных переводов, железнодорожных путей, метро, компаний GVB и в промышленных целях. Преимуществом является высокая производительность; Продукт прочный, долговечный, легкий, легко и быстро собирается и полностью пригоден для вторичной переработки.
Характеристики синтетических шпал подкрановых путей
- Ожидаемый срок службы ок. 50 лет.
- Полностью переработанный и пригодный для повторного использования материал.
- Высокая емкость 100 000 единиц и возможность масштабирования.
- Используется во всем мире.
- Стойкий к формованию под действием давления.
- Прочность, пластик поглощает энергию при нагрузке.
Мы также поставляем синтетические железнодорожные шпалы.
Сопутствующие товары
Запросить предложение
Мы можем вам чем-нибудь помочь? Хотите узнать больше о наших продуктах или услугах?
Позвоните в наш офис по телефону
+31 (0) 226 — 42 53 00.
Вы также можете заполнить нашу контактную форму, и мы свяжемся с вами как можно скорее.
Шпалы на железной дороге | Бетон Гражданское строительство
Железнодорожные шпалы традиционно изготавливаются из дерева, но в настоящее время также широко используется предварительно напряженный бетон, особенно в Европе и Азии. Стальные шпалы распространены на второстепенных линиях в Великобритании; пластиковые композитные шпалы также используются, хотя и гораздо реже, чем деревянные или бетонные. По состоянию на январь 2008 г. приблизительная доля рынка традиционных и деревянных шпал в Северной Америке составляла 91,5 %, остальное — бетон, сталь, азобе (красное железное дерево) и пластиковый композит. Приблизительно 3520 деревянных шпал используются на милю магистральных железнодорожных путей в США (расстояние между шпалами номинально составляет 18 дюймов, включая одну шпалу и колыбель), 2640 на милю (30 на 60-футовый рельс) на магистральных линиях в Великобритании. Рельсы в США могут быть прикреплены к шпалам с помощью железнодорожных костылей; опорные плиты из железа и стали, привинченные к стяжке и прикрепленные к рельсу с помощью запатентованной системы крепления, такой как Vossloh или Pandrol, широко используются в Европе.
.
Типы шпал
1. Деревянные шпалы
Обычно они имеют ширину 254 мм, толщину 127 мм в поперечном сечении и длину 2600 мм. Шпалы сначала выдерживают (сушка до 12 месяцев, чтобы удалить сок/сок) и обрабатывают консервантом. Креозот – это масло, обычно используемое/распыляемое на поверхность. Они бывают из твердой или мягкой древесины. Деревянные шпалы — идеальный тип спального места. Поэтому они используются повсеместно. Полезность деревянных шпал не уменьшилась с течением времени.
Преимущества деревянных шпал
- Они дешевы и просты в изготовлении
- С ними легко обращаться, они не повреждаются
- Больше подходят для всех типов балласта
- Они поглощают удары и вибрации лучше, чем шпалы других типов.
- Идеально подходит для участков с рельсовой цепью
- Фитинги немногочисленны и просты по конструкции
- Хорошая устойчивость
- Простота обращения
- Адаптируемость к нестандартной ситуации
- Электрическая изоляция
Недостатки деревянных шпал
- Они легко подвержены нападению паразитов и непогоды
- Они восприимчивы к огню
- В случае деревянных шпал трудно поддерживать ширину колеи
- Стоимость брака незначительна
- Срок их полезного использования невелик и составляет от 12 до 15 лет.
2. Стальные шпалы
- Стальные шпалы используются там, где древесина или бетон не подходят, например, в туннелях с ограниченным дорожным просветом
- Они также используются при большой кривизне, склонной к расширению калибра.
- Этот тип стальных стяжек может вызвать проблемы с системой управления сигналами
- Также возникли некоторые проблемы усталостного растрескивания.
- В связи с возрастающим дефицитом древесины в стране и другими экономическими факторами, на железных дорогах стали использовать стальные и железобетонные шпалы.
Преимущества стальных шпал
- Более долговечны. Его жизнь составляет около 35 лет
- Небольшие повреждения при обращении и транспортировке
- Не подвержен атаке паразитов
- Невосприимчив к огню
- Цена лома очень хорошая
Недостатки стальных шпал
- Подвержен коррозии.
- Не подходит для рельсовой цепи
- Может использоваться только для рельсов, для которых он изготовлен
- В процессе эксплуатации появляются трещины в посадочных местах рельсов.
- Требуемые фитинги больше в количестве
3. Чугунные железнодорожные шпалы
Они далее делятся на две категории:
- Чугунные шпалы чашеобразного типа
- Чугунные плоские шпалы
Преимущества чугунных шпал
- Очень долгий срок службы
- Менее подвержен коррозии
- Образуют хорошую колею для легкого транспорта со скоростью до 110 км/ч, так как образуют жесткую колею, подверженную вибрации под действием движущихся грузов без какого-либо демпфирования
- Высокая стоимость брака
Недостатки чугунных шпал
- Обслуживание манометра затруднено, так как стяжки изгибаются
- Не подходит для замкнутого пути
- Требуется большое количество фитингов
- Подходит только для каменного щебня
- Интенсивное движение и высокие скорости (>110 км/ч) могут привести к расшатыванию ключей и развитию сильного ползучести
4.

Расчетный срок службы до 40 лет. Им можно легко придать необходимую/проектную форму, чтобы выдерживать нагрузки, вызванные быстрым и интенсивным движением. Шпалы из железобетона и предварительно напряженного бетона теперь заменяют другие типы шпал, за исключением некоторых особых обстоятельств, таких как мосты и т. д., где используются деревянные шпалы. Бетонные шпалы могут быть двух типов:
- Моноблочные бетонные шпалы
- TWIN BLOCK Бетонные шпалы
Преимущества бетонных шпал
- Более долговечны, имеют больший срок службы (до 50 лет)
- Экономичен по сравнению с деревом и сталью.
- Простота изготовления.
- Не подвержен атаке паразитов
- Невосприимчив к огню
- Подходит для участков с рельсовыми цепями
Недостатки бетонных шпал
- Он хрупкий и без предупреждения трескается.
- Не подлежит ремонту и требует замены.
- Количество требуемых фитингов больше.
- Нет стоимости брака
Отказы железобетонных шпал в течение срока службы
Джаббар-Али Закери , Фаршад Хашеми Резвани
Школа железнодорожного машиностроения, Иранский университет науки и технологий, Тегеран, Нармак, почтовый ящик 16846 – 13114, Иран
Адрес для переписки: Джаббар-Али Закери, Школа инженеров железнодорожного транспорта, Иранский университет науки и технологии, Тегеран, Нармак, почтовый ящик 16846 – 13114, Иран.
Электронная почта: |
Copyright © 2012 Научное и академическое издательство. Все права защищены.
Аннотация
Шпалы, после рельсов, являются наиболее важным компонентом верхнего строения пути на обычных путях. Сохранение геометрии пути, несущие нагрузки, действующие от рельса, и передача на балласт являются основной обязанностью шпалы. Условия их качества оказывают существенное влияние на качество геометрии. Более того, расходы на техническое обслуживание треков зависят от этого элемента из-за их большего количества. Для этого, чтобы уменьшить объем эксплуатации и технического обслуживания и, с другой стороны, для большего признания шпал B70, используемых на иранских железных дорогах, были проведены некоторые исследования и полевые исследования бетонных шпал, и их результаты были выражены в виде классификации отказов бетонных шпал. В статье оцениваются действующие факторы и причины их возникновения при рассмотрении отказов и условных дефектов в процессе эксплуатации шпал (включая стадии производства, транспортировки, строительства и эксплуатации), а также предлагаются пути их снижения.
Ключевые слова: Строительство бетонных шпал, дефекты шпал, разрушение шпал
Структура статьи
- 1.
Введение
- 2. Методика исследования
- 3. Выявленные дефекты
- 3.1. Повреждения при изготовлении и соединении (панель)
- 3.2. Дефекты при транспортировке и установке
- 3.3. Ухудшение или дефекты во время операции
- 4. Методы уменьшения дефектов спящих
- 5. Выводы
1. ВВЕДЕНИЕ
- . Наряду с распределением давления и передачей нагрузки на нижележащие слои железнодорожные шпалы должны поддерживать ширину колеи, обеспечивать поперечную устойчивость пути и способствовать улучшению геометрических условий пути [4,10]. На рельсовые шпалы действуют вертикальные, боковые и осевые силы. Эти усилия должны передаваться нижележащему балластному слою в пределах допустимого диапазона напряжений с минимальным нарушением качества пути и остаточной деформацией. Фактически не существует комплексного подхода к давлению шпал и механизму передачи нагрузки путевой конструкции [2, 12].
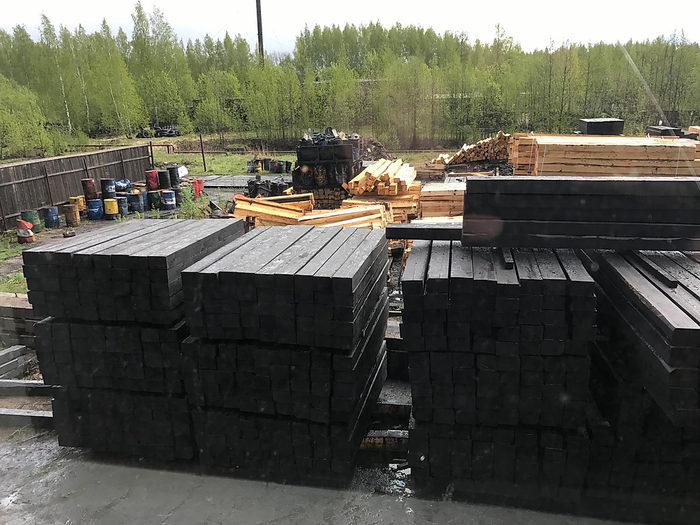
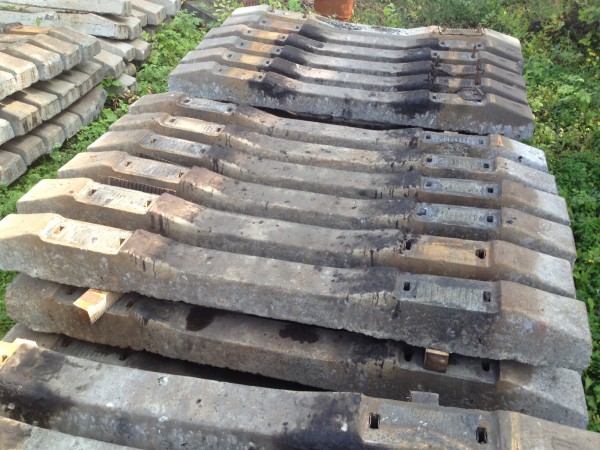
2. Методология исследования
- B70 и B58 с креплениями типа Vossloh и Pandrol являются типами железобетонных шпал, используемых на иранских железных дорогах. Шпалы B70 используются с рельсами UIC 60 и шпалы B58 с рельсами U33 (только с зажимами Vossloh). Для выявления основных дефектов бетонных шпал, дефекты жизненного цикла шпал были в первую очередь классифицированы следующим образом [3]: 1. Износ в процессе производства и муфта (рельсовая обшивка) 2. Износ при транспортировке и монтаже 3. Ухудшение качества при использовании. Сбор данных об износе в процессе производства и соединения (обшивки) путем оптического контроля с заводов по производству железобетонных шпал в Карадже и Андимешке и анализ отчетов контроля качества, запрос мнения специалистов производства.
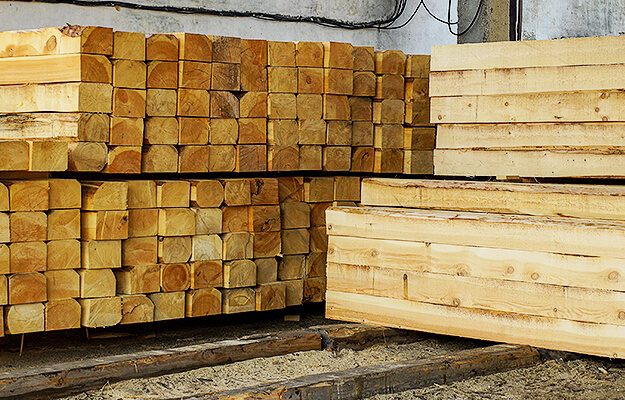
3. Обнаруженные дефекты
3.1. Повреждения при изготовлении и соединении (панели)
- Среди причин износа при изготовлении и соединении неисправности и дефекты, связанные с первичным материалом, бетоном, обработкой и выгрузкой (вакуумированием) из формы, структурные дефекты и дефекты, такие как прокатный налет можно отметить наклон, избыток валкового покрытия, проникновение бетонного сока и/или другого избыточного материала внутрь валкового налета, проникновение воды внутрь валкового налета и его замерзание в холодную зиму и/или наличие внешнего материала внутри валкового налета.
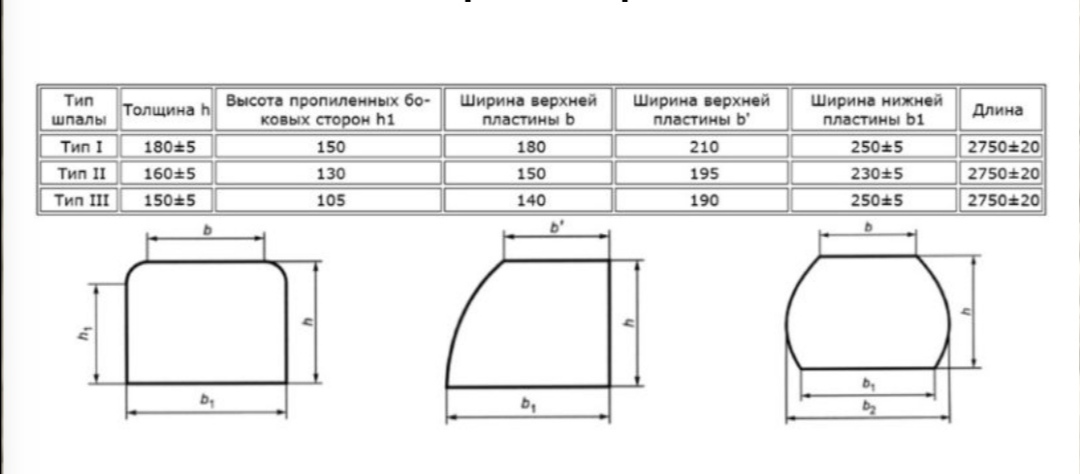
3.2. Дефекты при транспортировке и монтаже
- Монтаж шпалы или панели (сцепки) осуществляется различными способами. Использование крана Plattow и установка методом укладки панелей являются обычными для иранских железных дорог. В этом способе правильное распределение первого слоя балласта является одним из факторов, препятствующих возникновению дефектов железобетонных шпал. Кроме того, из других причин дефектов падение крышки заглушки, неправильное складирование, неточность при загрузке и разгрузке панели, а также неправильная упаковка, неразборная укладка панели первого балластного слоя со скоплением балласта в центре шпалы, поломка шпалы из-за можно отметить неправильную первичную загрузку, разгрузку и неправильную укладку пути.

Рисунок 1 . Схемы распределения напряжения |
Рис. Продольная трещина в бетонной шпале |
|
Рис. Поломка шпалы в результате схода с рельсов |
3.3. Износ или дефекты во время эксплуатации
- Состояние пути в надлежащем состоянии играет значительную роль в износе пути и его компонентов. Для этого управление техническим обслуживанием пути, определение циклов осмотров, циклических осмотров, выявление дефектов, своевременный ремонт имеют существенное влияние на увеличение срока службы пути, а также на снижение затрат на жизненный цикл пути.


4. Методы уменьшения дефектов шпал
- В соответствии с исследованиями, проведенными в рамках данного исследования и выявлением причин дефектов, также изучаются эффективные методы уменьшения этих последствий на этапах производства, монтажа и эксплуатации. Эти методы рекомендуются для иранских железных дорог, и ожидается, что за счет внедрения соответствующей системы контроля качества и контроля элементов, описанных в этой главе, будет значительно снижена стоимость жизненного цикла, особенно железобетонных шпал. Статистический анализ дефектов шпал на Иранских железных дорогах показывает, что наибольшее количество дефектов возникает на стадии эксплуатации. Некоторые из этих дефектов могут быть предотвращены работами на стадии производства. После стадии производства большинство дефектов являются производственными дефектами. Среди исследуемого статистического общества 1,2 % изготовленных шпал имели брак, из них 0,3 % используются на второстепенных путях, а остальные (0,9 %) выбраковываются.

|

|
5. Conclusions
- В соответствии с важностью шпал и их ролью в железнодорожной надстройке выявление дефектов шпал является первым шагом к повышению эффективности пути и снижению затрат на техническое обслуживание. После выявления дефектов вторым важным этапом является обследование с целью выяснения причин этого дефекта. В этом исследовании, в зависимости от типа шпал, используемых на Иранской железной дороге (бетонная шпала B70), основные дефекты жизненного цикла этих шпал подразделяются на три группы: 1. Дефекты при изготовлении. 2. Дефекты при транспортировке и установке. 3. Дефекты при эксплуатации или техническом обслуживании. Статистический анализ показывает, что большинство дефектов возникает на стадии эксплуатации. После этапа эксплуатации большинство дефектов возникает во время производства и обслуживания.
