Дюралюминий сплав — состав, свойства, виды дюралюминия
В промышленности применяют множество конструкционных материалов и один из них дюралюминий. По сути — это собирательное название сплавов, изготовленных на базе алюминия и состава легирующих компонентов. Сплав получил своё название от слова Dural. Именно таково было название одного из первых сплавов, который подвергался термической обработке.
Немного истории
Дюралюминий разработан немецким ученым Вильмом в 1903-ем. Металлург попросту смешал алюминий, медь, кремний. С этого момента до начала серийного производства прошло всего 6 лет. В 1911 году дюралюминий стали применять строительства воздушных судов, в частности, дирижаблей и тяжелых бомбардировщиках. Малый вес конструкций при сопоставимой с прочностью стали позволил уменьшить массу летательных аппаратов в 2 — 3 раза. Это привело к резкому развитию авиационной промышленности.
Основные свойства этих сплавов
В базовый состав сплава входят следующие вещества:
- медь — до 0,5%;
- марганец до 0,5%;
- магний до 1,2%;
- кремний и многие другие.
Изменяя пропорции используемых веществ можно изменять и свойства дюралюминия.
Прочность дюралюминия достигает — до 500 МПа под действием временных нагрузок и 250 — 300 при стандартных нагружениях, (прочность чистого алюминия — 70-80 МПа). Этот параметр сделал дюрали материалом, используемым во многих областях промышленности в том числе и высокотехнологичных. Сплав алюминия с некоторыми элементами, в определенных пропорциях, изменяет полученного сплава.
Благодаря компонентам, применяемым в производстве дюралюминия он приобретает ниже приведенные свойства:
- прочность, которая сопоставима с определёнными марками стали;
- высокая стойкость к температурному воздействия. материал начинает плавиться при температуре 650 ºC.
- повышенная электропроводность. это происходит из-за наличия меди.
- дюраль хорошо переносит прокат как по горячей, так и по холодной технологии.
Высокие технологические свойства дюралюминия, привели к высокому спросу на него. В мире производят порядка 60 000 тысяч тонн, из которого почти половину (свыше 30 000 тысяч тонн) изготавливают на территории КНР. Россия занимает второе место об объёмам производства, металлургические заводы получают 3 580 тыс. тонн.
Особенности производства
Производства дюраля, как и большинства сплавов, сопряжено с рядом сложностей. Получение дюраля происходит последовательно. На первом этапе получают технический алюминий и только потом в него начинают вносить добавки, формирующие его свойства. На втором этапе, получений первичный дюраль проходит через термический отжиг, производимый при 500 ºC. Такой режим обработки обеспечивает гибкость и мягкость металла. Для повышения прочности дюраль проходит через операцию старения.
Отечественная и иностранная промышленность освоила выпуск следующих видов проката:
- листы и полосы разного типоразмера ГОСТ 21631-76;
- прутки круглые и многогранные по ГОСТ 21488-97;
- трубы разного диаметра и разной толщиной стенок ГОСТ 18475-82 и ГОСТ 18482-79;
- профили различной формы сечения.
Основные виды сплавов
Существует несколько видов сплавов, отличающихся своими характеристиками.
1. Алюминий + марганец или магний. Такой сплав называют «магналии». Материал отличает высокая стойкость к коррозии, хорошая сварка и пайка. Между тем — материал плохо поддаётся обработке на металлорежущем оборудовании. Кроме того при работе со сплавом магнолии никогда не используют промежуточную закалку.
Магнолии применяют для бензопроводных систем, радиаторов для автомобилей, ёмкостей различного назначения.
2. Сплав, состоящий из алюминия, магния и кремния, получил название — «авиаль». Сплав обладает такими свойствами как:
- Высокая стойкость к воздействию коррозии;
- Высокая прочность сварных и паянных швов.
Для получения данных технологических свойств авиаль проходит термообработку. Ее проводят при температуре, почти в 520 ºC. Последующее резкое охлаждение необходимо выполнить в воде, температура которой составляет 20 ºC.
После проведения такой обработки авиаль можно использовать для работы в условиях повышенной влажности, его широко применяют в самолетостроении. В последние годы, авиаль используют для замены стальных деталей из носимым устройств связи, например сотовых аппаратов и пр.
3. Еще один сплав — дюралюмин. В него, кроме алюминия входят медь и марганец. Пропорции компонентов изменяют, тем самым модифицируя качественные свойства сплава. Но несмотря ни на что, дюралюмин обладает не высокой стойкостью к коррозии. Поэтому на поверхность наносят слой чистого алюминия. Такая операция называется плакированием и с успехом предотвращает воздействие коррозии.
Дюралюмин применяют в транспортном машиностроении, в частности, детали из этого материала установлены в скоростном поезде «САПСАН».
Использование дюралюминия
Это семейство сплавов, по сути, базовый материал, применяемый в строительстве авиационной и космической техники. Это его использования началось в начале ХХ века при сооружении первых дирижаблей.
В наши дни на практике используется больше десяти марок этого сплава. При сооружении авиационной техники чаще используют материал под названием Д16т. В его состав состоит из девяти веществ — никель, титан, в качестве легирующих составляющих применяют медь, кремний и пр. Но при всем. Доля алюминия остаётся неизменной — 93%.
При выборе материала для деталей и узлов технолог должен помнить, что далеко не все дюрали хорошо свариваются или паяются. В таком случае для сборки деталей из него применяют заклепки. Такие операции широко распространения при сборке фюзеляжей и плоскостей при строительстве самолетов, водного транспорта всех типов. Так, небольшая лодка, применяемая для своих целей, может прослужить ее хозяину на 20 лет больше.
С другой стороны, некоторые марки дюралюминия хорошо свариваются при использовании аппаратов аргонной сварки.
Кстати, еще в ХХ веке велись опытные работы по использованию дюралей в автомобильной отрасли. Из него изготавливают кузова автобусов, некоторых марок легковых и спортивных автомобилей. Само собой дюрали применяют и в силовых узлах.
Некоторые марки этого сплава применяют для производства труб, которые устанавливают на судах, авиационной технике, автомобилях.
Свойства дюраля позволили его использовать и в пищевой промышленности, например, из дюралевой фольги производят фантики для конфет и шоколада.
Нельзя забывать и том, что многие домохозяйки применяют кухонную утварь, выполненную из этого материала.
Низкий вес дюраля позволяет его применение при выполнении буровых работ. Все дело в том, дюралюминий в 3 — 4 раза легче стали. Кроме этого трубы из дюралюминия проще переносят вибрацию, которая неизменно возникает при выполнении буровых работ.
Отдельного разговора требует применения дюраля в строительной отрасли. Его применяют для производства облицовочных материалов, различных ограждающих конструкций и пр.
Нормативная база
В нашей стране существует несколько ГОСТ, которые нормируют требования к алюминию и его сплавов. Один из них — это ГОСТ 4784-97 Алюминий и сплавы алюминиевые деформируемые. Марки (с Изменениями N 1, 2, 3, с Поправками). Он распространяется на алюминий и сплавы из него, которые предназначены для получения полуфабрикатов различного типа и форм.
В частности, ГОСТ определяет соотношение алюминия и остальных компонентов. В этом же документе указаны требования.
Кстати, в этом же документе можно найти и наименование иностранных аналогов, например,
Д16 можно заменить на AlCu4Mg1, а Д16ч на сплав 2124.
В документах, которые предоставляет производитель, в обязательном порядке должны быть указаны не только марка готовой продукции но и ее химический состав.
Немного экономики
Изделия из дюралюминиевого сплава не составит труда приобрести. Его производство развёрнуто почти на всех предприятия цветной металлургии. Цена на продукцию образовываются в зависимости от состава, сортамента, размеров отгрузки и, конечно, удалённостью производителя до места реализации.
Немного слов в заключении
Про дюралюминий, можно смело сказать, что его появление обеспечило технологические прорывы в самолетостроении, космической промышленности и без своевременного появления мы бы летали на самолетах из дерева.
Оцените статью:Рейтинг: 0/5 — 0 голосов
состав, свойства, применение различных марок сплава
Для производства различных деталей и вещей может использоваться дюралюминий. Данный материал получил свое название от города, в котором он был создан. Отличия дюрали от алюминия заключаются в химическом составе, который оказывает влияние на основные эксплуатационные качества. Рассмотрим особенности данного сплава подробнее.
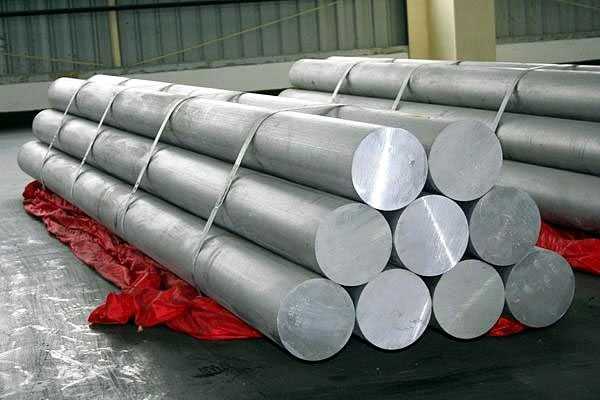
Дюралюминий
Химический состав
Появление дюралюминия связывают с немецкой компанией, которая расположена в городе Дюрен. Специалисты этой компании занимались разработкой нового сплава, и ошибочно провели смешивание ранее не используемых компонентов. После проведения предварительных тестов они были удивлены тем, какого смогли добиться результата, но изначально посчитали их ошибочными. Спустя некоторое время они повторили свой эксперимент и добились еще более высоких результатов.
Алюминий и дюралюмин, в первую очередь, отличаются друг от друга химическим составом. Дюралюминий обладает следующим составом:
- 4-5% меди;
- 93% алюминия;
- 2-3% других легирующих элементов, которые добавляются для придания сплаву особых качеств.
Состав различных марок дюрали
Долгое время дюралюмин изготавливался при обычных условиях, что определяло некачественное соединение элементов. Начавшаяся война сделала данный металл стратегически важным, что привело к поиску более эффективных методов соединения всех компонентов. Результатом данных исследований стали следующие технологические особенности процесса:
- Нагрев проводится при температуре до 500 градусов Цельсия.
- На разогрев уходит около 3-х часов.
- Проводится быстрое охлаждение водой или селитрой для повышения прочности.
Состав дюралюминия может существенно меняться — все зависит от особенностей применяемой технологии производства.
Наиболее распространенная марка Д16 имеет следующий химический состав:
- Основная часть дюралюминия во всех случая представлена алюминием, на который приходится 90-94% от общей массы.
- В состав добавляется достаточно большое количество меди (3,8-4,9%).
- Обязательным условием можно назвать добавление в равных частях кремния и железа, примерно по 0,5%.
- В состав входит цинк (не более 2,5%).
- Добавляется фиксированное значение магния — 1,8%.
Остальные компоненты представлены хромом, марганцем, титаном, которые берутся примерно по 1%.
Получаемый дюралюминий при подобном химическом составе обладает достаточно высоким показателем мягкости. Именно поэтому Д16 зачастую применяется в качестве полуфабрикатов при производстве штамповок.
Не только состав сплава дюрали оказывает влияние на основные технологические свойства. Вместе со специфической подборкой компонентов применяются технология искусственного старения, которая заключается в закалке.Для повышения прочности и твердости поверхности сплав подвергается термической обработке с охлаждением.
Технологические свойства дюрали
В зависимости от химического состава и применяемого метода изготовления технологические свойства дюрали могут существенно отличаться. ГОСТа именно для этого металла пока нет.
Сразу после появления дюралюминия его назвали самым подходящим материалом для строительства дирижаблей и самолетов.
Среди технологических свойств следует отметить нижеприведенные моменты:
- Низкая стоимость, которая обуславливается простой технологией производства. Тот момент, что компоненты не нужно разогревать до экстремально высоких температур определяет существенное удешевление материала. Также на стоимости благоприятно отражается возможность проведения производства в обычной среде.
- Небольшой вес. Рассматривая химический состав можно отметить, что большая часть состава представлена алюминием. Этот металл известен своей легкостью.
- Высокие показатели температуры плавления позволили использовать сплав дюраль при производстве различных элементов самолетов и другой техники. Температура плавления дюралюминия около 650 градусов Цельсия. При этом обычный алюминий плавится уже при более низких температурах, что приводит к изменению основных технологических качеств и деформации изделий.
- Плотность дюралюминия составляет 2,5 грамма на кубический сантиметр (у стали на каждый кубический сантиметр приходится 8 грамм). Именно этот показатель определяет существенно снижение веса изготавливаемых деталей. Данный показатель может варьироваться в относительно небольшом диапазоне, достигать значения 2,8 грамм на кубический сантиметр.
- Статическая прочность дюралюминия достаточно высока, что определяет устойчивость к разовой нагрузке. Именно поэтому сплав применяется при изготовлении различных ответственных деталей. Проведенные исследования указывают на то, что разрушить подобный материал довольно сложно.
Однако есть и один недостаток – относительно невысокая устойчивость к воздействию повышенной влажности. Разрушение сплава блокируют путем нанесения защитного покрытия, что несколько повышает стоимость сплава.
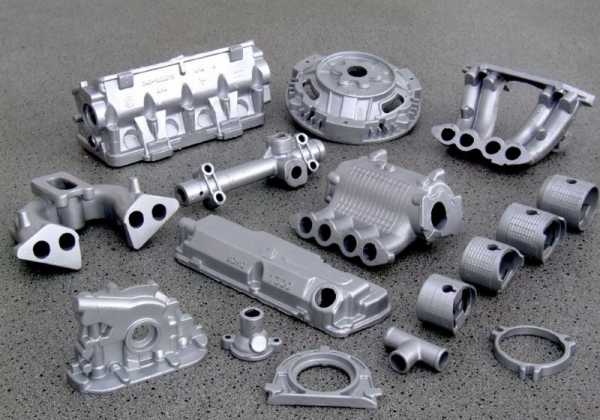
Детали из дюрали
Дюралюминий Д16 получил достаточно широкое распространение. Отличные эксплуатационные качества он демонстрирует при температуре не выше 250 градусов Цельсия. Стоит учитывать, что уже при температуре 80 градусов Цельсия появляются признаки образования межкристаллической коррозии.
В последнее время в чистом виде дюралюминий практически не применяется. Это связано не только с высокой вероятностью появления коррозии, но и другими недостатками алюминиевого сплава. Для повышения эксплуатационных качеств сегодня выполняют следующее улучшение:
- Закалку в естественных условиях. При маркировке указывается буква «Т».
- Выполняют процедуру искусственного старения, что также отражается на маркировке «Т1».
- Анодирование и покрытие поверхности специальными лаками (в маркировке указывают букву «А»).
Снижение коррозионной стойкости происходит не только по причине повышения температуры, но и механического воздействия. Именно поэтому уделяется внимание дополнительным процедурам увеличения эксплуатационных качеств.
Более высокими эксплуатационными качествами обладает сплав под названием ВД95. Кроме этого, данная разновидность сплава проходит процедуру старения, за счет чего существенно повышается потенциал этой разновидности дюралюминия.
Область применения
Тугоплавкость дуралюмина марки ВД95 определяет его широкое применение не только в сфере авиастроения, но и изготовления скоростных поездов, которые постепенно становятся самым распространенным транспортным средством в Европе и Азии. Это связано с тем, что при движении на большой скорости из-за возникающего трения поверхность может сильно нагреваться. Слишком высокая пластичность из-за перестроения кристаллической решетки становится причиной деформации поверхности при механическом воздействии. Также применение дюралюминия представлено производством прутков, заклепок, болтов и других крепежных материалов.
- Дюралюминий в авиастроении
- Дюралюминий в строительстве
Несмотря на тугоплавкость, есть возможность проводить сварочные работы с помощью аргона. Данный процесс настолько прост, что его можно провести в собственном гараже. В различных отраслях машиностроения дюралюминий применяется для получения изоляционных материалов. Примером можно назвать появление фольги толщиной около 0,2 миллиметров, которая применяется в качестве отражающего слоя при производстве изоляции.
В пищевой промышленности фольга из дюралюминия встречается довольно часто — ее используют для оборачивания конфет.
Сплав получил широкое применение и в буровой отрасли. Это связано с уникальным сочетанием нижеприведенных качеств:
- Легкость.
- Прочность.
- Стойкость к повышенным температурам и влажности.
Изготавливаемые буры из дюралюминия отлично справляются с гашением вибрации.
В заключение отметим, что широкая область применения определена особыми эксплуатационными качествами и относительно невысокой стоимостью материала. Кроме этого отметим, что сегодня алюминий в чистом виде стали использовать намного реже.
Если вы нашли ошибку, пожалуйста, выделите фрагмент текста и нажмите Ctrl+Enter.
stankiexpert.ru
Промышленные сплавы системы Al-Cu-MgКонструкционные дюралюминиевые сплавы (дюраль, дуралюмин) Д1, Д16, Д19, ВД17, 2024 и др. упрочняют термической обработкой, они обладают высокими характеристиками механических свойств. Упрочнение дуралюмина при термической обработке достигается в результате образования зон Гинье-Престона сложного состава или метастабильных фаз S’ и θ’. Дюралюминий получают легированием алюминия медью и магнием. Система легирования Al-Cu-Mg была открыта А. Вильмом, когда он получил сплав Д1. Дюралюмины остаются важнейшим сплавом для машиностроения и авиации. Самые значимые для промышленности сплавы в группе дюралюминов Д16 или 2024 и его модификации Д16ч и 1163 используют в термически упрочненном состоянии. Стадия старения после закалки проходит в естественных условиях при комнатной температуре (20°С) и обозначается буквой «Т» после марки сплава — Д16Т, Д16чТ, 1163Т по ГОСТ или «Т4» в импортной маркировке — 2024Т4. Такая термообработка создает хорошее сочетание характеристик вязкости разрушения, выносливости и скорости роста усталостной трещины. Дюралюминий Д16 уступает по прочности и коррозионной стойкости сплавам системы Al-Zn-Mg-Cu (В95, В95пч, В95оч), но превосходит по сопротивлению трещинообразованию при одинаковых относительно прочности напряжениях. Плотность Д16 равна 2,78 г/см3, что ниже плотности В95 — 2,85г/см3. Сплавы 1163 и Д16ч применяются для деталей, от которых требуется повышенная выносливость в условиях растягивающих напряжений. Сплавы типа дуралюмин упрочняются при термической обработке, состоящей из закалки с 490—525°С (в зависимости от состава сплава) и естественного (зонного) или искусственного (фазового) старения. В наиболее легированных сплавах (Д16, Д19, ВД17 и ВАД-1) содержание меди и магния превышает предельную растворимость этих элементов в твердом растворе или приближается к ней, что обусловливает гетерогенное состояние сплавов при температурах нагрева перед закалкой. Ограничение верхнего предела по содержанию легирующих элементов позволяет уменьшить количество растворимых избыточных фаз и повысить вязкость разрушения без снижения прочности. Различие естественного и искусственного состаренных сплавовТемпература эксплуатации сплавов Д16, Д16ч, 1163 в естественно состаренном состоянии ограничена 80°С из-за снижения коррозионной стойкости в случае нагревов при более высоких температурах. Эти сплавы в искусственно состаренном состоянии имеют улучшенную коррозионную стойкость, которая не снижается при нагревах, более высокие прочностные свойства, особенно предел текучести, однако более низкие значения относительного удлинения, вязкости разрушения, выносливости по сравнению с естественно состаренным состоянием. Существенное улучшение вязкости разрушения в искусственно состаренном состоянии достигается в результате снижения содержания железа, кремния, а также легирующих элементов. Поэтому для деталей в искусственно состаренном состоянии используются улучшенные модификации сплава Д16 — Д16ч и 1163. Эти сплавы в искусственно состаренном состоянии могут применяться в температурно-временных областях, в которых не рекомендуется применять сплавы в естественно состаренном состоянии: при эксплуатационных нагревах при температурах выше 80°С или технологических нагревах выше 125°С, а также при повышенной опасности коррозии под напряжением. При изготовлении деталей из сплавов Д16ч и 1163 в искусственно состаренном состоянии необходимо выбирать конструктивные формы с минимальной концентрацией напряжений, отрабатывать плавность переходов при изменении сечения деталей, уменьшать эксцентриситеты. Кроме того, ограничиваются допустимые деформации при формообразовании и правке в зависимости от состояния термообработки, величины зазора перед сборкой, не рекомендуется ударная клепка. Сплавы системы Аl-Сu-Mg превосходят по жаропрочности сплавы систем Аl-Mg, Аl-Mg-Si, Аl-Zn-Mg-Cu. Их преимущество перед высокопрочными алюминиевыми сплавами проявляется при температурах выше 100°С и особенно при длительных выдержках. Сплавы Д1, Д16 склонны к образованию кристаллизационных трещин и поэтому относятся к категории несваривающихся плавлением сплавов. Cвариваемым сплавом является сплав ВАД-1. Возврат при старенииВ естественно состаренных сплавах типа дуралюмин при быстром и кратковременном (2 мин) нагреве до 250—300°С происходит снижение прочности до значений, свойственных свежезакаленному состоянию. Это явление называется возвратом при старении. Искусственное старение уменьшает явление возврата. Зависимость свойств дюралюминия от степени рекристаллизацииМеханические свойства горячедеформированных полуфабрикатов из сплавов типа дуралюмин сильно зависят от степени рекристаллизации в процессе нагрева при деформации и термической обработке. Разница в прочности закаленного и состаренного рекристаллизованного и нерекристаллизованного материалов достигает 200 МПа. Полуфабрикаты с нерекристаллизованной структурой по сравнению с рекристализованной при повышенных прочностных свойствах в долевом направлении имеют преимущество по вязкости разрушения, выносливости при одинаковом по абсолютной величине уровне напряжения, сопротивлению коррозии под напряжением, но обладают более низким относительным удлинением в долевом направлении; выигрыш по прочностным свойствам уменьшается на образце с отверстием. Листовой материал, изготовленный методом горячей и последующей холодной прокатки, а также проволока и трубы, изготовленные холодной прокаткой и волочением, в закаленном состоянии имеют полностью рекристаллизованную структуру. Профили и прутки, полученные горячим прессованием, после термической обработки могут иметь структуру от полностью нерекристаллизованной до полностью рекристаллизованной. Возможно получение преимущественно нерекристаллизованной структуры и в плитах. Сохранению нерекристаллизованной структуры способствует повышение температуры и уменьшение степени горячей деформации изделий, понижение температуры и времени выдержки при нагреве под закалку, увеличение содержания элементов (Мn, Cr, Zr и др.), повышающих температуру рекристаллизации. Химический состав по ГОСТ 4784–77 и ОСТ 190048–77Сплавы данной группы содержат от 2 до 5 % Cu, 0,15–2,7 % Mg, 0–1,0 % Mn, до 0,7 % Fe, до 0,7 % Si и небольшие количества цинка и титана в виде примесей. В сплавы с повышенным содержанием магния (Д19, ВАД-1, Д19П) вводят небольшие количества бериллия для понижения окисления в процессе плавки, литья и термической обработки.
Влияние примесей на механические свойстваКроме основных легирующих элементов, в дюралюминии присутствуют небольшие количества примесей. Некоторые из них (железо и кремний) имеются в исходном первичном алюминии, другие (цинк и никель) попадают в сплавы при переплаве отходов, третьи (бериллий, титан и цирконий) вводят в сплавы специально в качестве технологических добавок. В сплавах типа дуралюмин железо образует соединения, оказывающие охрупчивающее влияние. Железо соединяется с медью и уменьшает количество растворимой меди, которая упрочнеяет сплав при старении. Кремний в этих сплавах увеличивает склонность к трещинообразованию при сварке (ВАД-1) и литье, особенно крупных слитков из сплавов Д16, Д19, понижает пластичность заклепок из всех сплавов. Для нейтрализации вредного влияния кремния при литье и сварке содержание железа в сплавах должно в 1,1–1,5 раза превышать содержание кремния. Для получения высокой пластичности литого и деформированного материала, а также для повышения вязкости разрушения содержание железа и кремния должно быть минимальным. Никель образует нерастворимые фазы с медью и железом, уменьшает пластичность и прочность термически обрабатываемых сплавов, улучшает твердость и прочность при повышенных температурах и понижает коэффициент линейного расширения. Совместное присутствие железа и никеля в сплавах системы Al-Cu-Mg обеспечивает повышение механических свойств при комнатной и повышенных температурах по сравнению со сплавами, содержащими либо железо, либо только никель. Положительное влияние совместного содержания железа и никеля связано с образованием нерастворимой фазы FeNiAl9, в которой отсутствует медь. В дюралюминах Д1, Д16 и др, содержащих железо и кремний в виде примесей, при введении никеля фаза FeNiAl9 не образуется. Небольшие количества цинка (0,1—0,5 %) не влияют на механические свойства рассматриваемых сплавов при комнатной температуре и значительно понижают их жаропрочность. Примесь цинка в количестве 0,1—0,3 % увеличивает склонность к трещинообразованию при литье и сварке. Бериллий в небольших количествах (около 0,005 %) предохраняет сплавы с высоким содержанием магния (1,5 % и более) от окисления при литье и термической обработке, не оказывая влияния на механические свойства как при комнатной, так и при повышенных температурах. Бериллий входит в состав окисной пленки, состоящей в этих сплавах главным образом из окиси магния, способствует ее упрочнению и, следовательно, уменьшает дальнейшее окисление сплава. Более высокое содержание в сплавах бериллия (0,1— 0,5 %) требует особых мер предосторожности при плавке и литье из-за его токсичности. Литий увеличивает прочность при комнатной и повышенных температурах, понижает плотность и увеличивает модуль упругости, но снижает пластичность. Хром, как и марганец, повышает температуру рекристаллизации сплавов. Выделения частиц, содержащих хром, имеют игольчатую форму и в большей мере, чем марганцовистые, снижают характеристики разрушения. Хром в присутствии марганца, железа и титана может выпадать в виде грубых составляющих фазы СгAl7. В промышленные сплавы типа дуралюмин хром не добавляют. Титан, в алюминиевых сплавах применяется в основном для измельчения зерна литого металла. Природу способности титана измельчать литое зерно объясняют образованием в расплаве зародышей, служащих центрами кристаллизации. По данным одних авторов, эти зародыши — алюминид титана, по данным других авторов,— карбид титана. В присутствии бора такими зародышами будут частички борида титана. Цирконий в небольших количествах, так же как и титан, является модификатором. Добавка циркония практически не влияет на прочностные свойства холоднодеформированных полуфабрикатов из сплавов, содержащих марганец, и несколько повышает их у сплавов без марганца. Цирконий аналогично марганцу, но при значительно меньшем содержании повышает температуру рекристаллизации сплава, что способствует получению нерекристаллизованной структуры и высокой прочности горячепрессованных полуфабрикатов. Влияние циркония как антирекристаллизатора в сплаве Д16 при содержании менее 0,1 % незначительно. При концентрации циркония более 0,15 % отмечается появление первичных интерметаллидов с цирконием, увеличивается количество дефектов, выявляемых ультразвуковым контролем. Цирконий снижает сопротивление коррозии под напряжением. Небольшие количества бора (0,005—0,01 %) измельчают зерно алюминия и его сплавов. Эффект модифицирования увеличивается в присутствии небольших количеств титана (0,01 %). Эти два элемента образуют соединение TiB2.
Технологические свойства дюралиПлакированные листы отличаются высокой коррозионной стойкостью,
прессованные изделия, штамповки и поковки — пониженной стойкостью. Прессованные
изделия из дюралюминия Д1 и Д16 в закаленном и
естественно состаренном состоянии при эксплуатационных нагревах выше 100°С
склонны к межкристаллитной коррозии; искусственное старение повышает
сопротивление коррозии. Неплакированные детали из дуралюминов следует подвергать
анодированию и защищать лакокрасочными покрытиями. | Связанные страницы: |
www.metmk.com.ua
Дюраль
Состав, свойства и применение дюрали
Дюраль (дюралюмин) представляет собой группу важных промышленных сплавов, сыгравших большую роль в развитии самолётостроения и других областей техники. Современные дюралюмины — это многокомпонентные сплавы на основе системы А1-Cu-Mg с добавками марганца и других элементов.
Все дюралюмины, применяющиеся в настоящее время в промышленности, можно разделить на четыре подгруппы:
1. классический дюралюмин (Д1), состав которого практически не изменился с 1908 года;
2. дюраль повышенной прочности (Д16), отличается от сплава Д1 более высоким содержанием магния;
3. дюраль повышенной жаропрочности (Д19 и ВД17), главным отличием которых является увеличенное отношение Mg/Сu;
4. дюраль повышенной пластичности (Д18), отличается пониженным содержанием меди и магния.
Помимо меди и магния в дюрали всегда содержатся марганец и примеси железа и кремния.
Медь и магний — основные компоненты, обеспечивающие упрочнение сплавов. Марганец является обязательной присадкой, измельчающей структуру, повышающей прочность и коррозионную стойкость.
Железо и кремний — неизбежные примеси. Железо является вредной примесью, снижающей прочность и пластичность дюралюмина. Кремний до некоторой степени устраняет вредное влияние железа, связывая его в более легко разрушаемую при деформации фазу.
Наибольшее применение среди дюралюминов нашли сплавы Д1 и Д16, которые широко используют в авиационной промышленности. Из сплава Д1 изготовляют листы, профили, трубы, проволоку, штамповки и поковки. Такие же полуфабрикаты, кроме поковок и штамповок, получают из сплава Д16.
Дюралюмины повышенной пластичности (Д18) имеют узкое назначение — из них изготовляют заклёпки для авиастроения. Из сплавов ВД17 и Д19 можно получать различные деформированные полуфабрикаты, предназначенные для работы при повышенных температурах.
Сплав Д16 при комнатной температуре обладает наиболее высокой прочностью по сравнению с другими дюралюминами.
Упрочняемая термическая обработка дюралюминов
Для обеспечения высокой прочности дюраль подвергают закалке и естественному или искусственному старению. Чтобы уяснить причины упрочнения сплавов при термической обработке, рассмотрим фазовый состав и превращения в двухкомпонентном сплаве, состоящем из алюминия и 4% меди (рис1.).
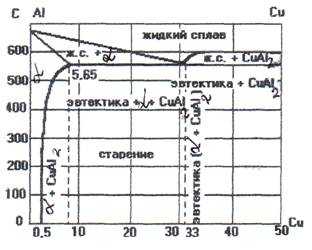
Рис. 1 .Часть диаграммы состояния Аl — Cu.
Равновесная структура сплава при комнатной температуре представляет собой — твёрдый раствор, содержащий около 0,5% меди, и включения интерметаллидов типа СuАl2, При такой структуре сплавы обладают низкой прочностью и хорошей пластичностью. Для максимального упрочнения сплавов термической обработкой необходимо решить две задачи:
1. Повысить прочность основной части структуры, т.е. кристаллов — твёрдого раствора;
2. Обеспечить образование вместо относительно крупных избыточных кристаллов интерметаллида СuАl2,большого количества мельчайших вторичных выделений, препятствующих движению дислокаций.
Известно, что напряжение, необходимое для «проталкивания» дислокации между частицами, разделёнными расстоянием L, равно:
, где
G — модуль сдвига, в — вектор Бюргерса дислокации.
Следовательно, чем мельче частицы, тем больше их количество, меньшее расстояние L между ними и большее напряжение «проталкивания». Отсюда, чем мельче частицы, тем больше их упрочняющее воздействие.
Первой упрочняющей операцией для дюралюмина является закалка. Возможность применения закалки основана на наличии переменной растворимости меди в алюминии. Её цель — получить в сплаве неравновесную структуру пересыщенного твёрдого раствора с максимальной концентрацией меди. Закалка заключается в нагреве сплава несколько выше линии переменной растворимости (но не выше солидуса) с последующим резким охлаждением в холодной воде.
При нагреве происходит полное растворение вторичных кристаллов Си Аl2, и сплав приобретает однофазную структуру — твёрдого раствора с высокой концентрацией меди (около 4%). В результате быстрого охлаждения распад высокотемпературного твёрдого раствора не успевает происходить, несмотря на понижение растворимости меди. Таким образом, при комнатной температуре удается зафиксировать пересыщенный твёрдый раствор меди в алюминии с сильно искажённой кристаллической решёткой. Это искажение решётки твёрдого раствора способствует торможению дислокаций и вызывает повышение прочности сплава.
Так, например, отожжённый дюралюмин Д16 имеет предел прочности 220 Мпа, а непосредственно после закалки около 300 Мпа. Однако наибольшее упрочнение происходит при последующем старении.
Старение представляет собой выдержку закалённого сплава при сравнительно невысоких температурах, при которых начинается распад пересыщенного твёрдого раствора или подготовительные процессы, предшествующие его распаду.
Сильная пересыщенность твёрдого раствора после закалки обуславливает его высокую свободную энергию. Распад твёрдого раствора приближает структуру к равновесной, а следовательно, ведёт к уменьшению свободной энергии системы, т.е. является самопроизвольным процессом.
В закалённом дюралюмине подготовительные стадии распада проходят без специального нагрева, при вылёживании в естественных условиях в цехе, на складе или в другом помещении, где температура составляет от 0°С до 30°С. Такое вылёживание в естественных условиях приводит к некоторым изменениям структуры и сопровождается повышением твёрдости и прочности. Этот процесс длится около 5…7 суток и называется естественным старением. Процесс старения, происходящий при повышенных температурах 100…20 OC, называется искусственным старением.
При старении изменение структуры и свойств в зависимости от температуры и времени выдержки происходит в несколько этапов.
На первом этапе в решётке твёрдого раствора образуются субмикроскопические зоны с высокой концентрацией меди. Если в основном пересыщенном растворе содержится около 4% меди (в рассматриваемом сплаве Аl + 4% Cu), а в соединении CuАl2, которое должно выделиться в конечном счёте из раствора — 52% Cu, то в этих зонах концентрация меди промежуточная и возрастает по мере развития процесса. Эти зоны получили название зоны Гинье-Престона, или зон Г.П.. В сплавах типа дюралюмин они имеют пластинчатую форму, а их кристаллическая структура такая же, как и у твёрдого раствора, но с меньшим параметром решётки.
Сущность второго этапа процесса (деление на этапы весьма условно) заключается в некотором росте зон Г.П., обогащении их медью до концентрации, близкой к соединению СuAl2, и упорядочении их структуры.
Третий этап наблюдается при повышенных температурах старения (или при длительных выдержках), когда из пересыщенного раствора выделяются частицы промежуточной фазы . Этот этап является началом собственно распада пересыщенного твёрдого раствора. — фаза по составу соответствует стабильной фазе (CuAl2), но имеет свою особую кристаллическую решётку, отличающуюся от решётки твёрдого раствора и от решётки CuА12. Выделения — фазы не полностью отделены от твёрдого раствора, так как их кристаллические решётки когерентны и не отделены друг от друга поверхностью раздела.
Четвёртый этап характеризуется образованием стабильной фазы (CuAl2). Когерентность решёток твёрдого раствора и выделяющейся фазы полностью нарушается. В дальнейшем частицы CuAl2 коагулируют (укрупняются).
Рассмотренные выше этапы охватывают процесс распада пересыщенного раствора полностью, до получения равновесной структуры, соответствующей диаграмме состояния. При естественном старении обычно образуются зоны Г.П., при искусственном старении — фаза. Четвёртая стадия наблюдается лишь при отжиге, т.е. при нагреве до высоких температур 300… 400 OС.
Описанные выше превращения при старении закалённого дюралюмина сопровождаются изменением свойств. На рис.2. схематично показана типичная закономерность изменения твёрдости (прочности) закалённого сплава в зависимости от температуры нагрева при старении.
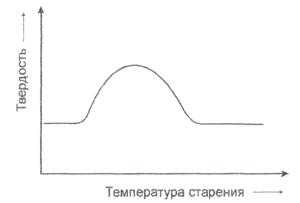
Рис.2 Изменение твёрдости закалённого дюралюмина в зависимости от температуры старения
Нагрев пересыщенного раствора первоначально сопровождается ростом твёрдости и прочности, а затем вызывает их снижение. Упрочнение связано с первыми этапами процесса распада, т.е. с образованием зон Г.П. или выделением промежуточных метастабильных фаз (-фазы). Последующие этапы, приводящие к образованию и коагуляции стабильной фазы CuAl2 (-фазы), обуславливают разупрочнение.
Значительное разупрочнение дирали при естественном и искусственном старении является результатом того, что зоны Г.П. и метастабильные промежуточные фазы служат препятствием для движения дислокаций. Скольжение дислокаций осуществляется путём проталкивания их между этими частицами. По мере того, как расстояние между частицами уменьшается, напряжение «проталкивания» дислокаций между препятствиями возрастает, что и приводит к упрочнению. Именно поэтому максимальный эффект упрочнения наблюдается при тех режимах старения, при которых образуются дисперсные, равномерно распределённые на небольших расстояниях одна от другой метастабильные промежуточные фазы. Укрупнение частиц приводит к уменьшению их количества, увеличивает расстояния между ними и способствует снижению прочности и твёрдости.
Режим упрочняющей обработки дюралюминов разных марок отличаются незначительно, но особенностью их термической обработки является необходимость жёсткого соблюдения рекомендованной температуры нагрева под закалку. Так, например, для Д16 температура закалки должна составлять 495…505 °С. Это требование объясняется тем, что указанные температуры весьма близки к температуре начала плавления. Превышение рекомендуемых температур вызывает оплавление границ зёрен и вызывает резкое снижение пластичности. Что касается режимов старения, то они могут быть разнообразными. Так при естественном старении сплава Д16 максимальная прочность достигается через 4 суток. Искусственное старение при температурах 120… 190°С значительно быстрее и, как правило, не превышает нескольких часов.
Дюралюмины способны обеспечивать высокие механические свойства (на уровне углеродистых сталей), обладая в то же время малым удельным весом. Это делает их очень ценным конструкционным материалом для многих областей техники.
К недостаткам дюралей следует отнести их пониженную по сравнению с алюминием коррозионную стойкость. Для них надо применять специальные средства защиты от коррозии. Наибольшее распространение получили плакирование (покрытие листов дюралюмина тонким слоем чистого алюминия) и электрохимическое оксидирование (анодирование).
Также по теме:
Расширение при нагреве. Дилатограммы. Расширение металла при увеличении температуры.
Закалка стали. Термообработка углеродистой стали для упрочнения и повышения твердости.
svarder.ru
Какими характеристиками обладает дюралюминий, и где применим этот материал
Дюралюминий был разработан более сотни лет назад, в 1903 году. Тогда Альфред Вильм, инженер-металлург, будучи сотрудником германского металлургического завода, установил некую закономерность. Оказалось, что сплав алюминия с четырьмя процентами меди после закалки при +500° C и резкого охлаждения, выдержав при комнатной температуре несколько дней (до 4–5), становится более прочным и твёрдым, но и не теряет при этом своей пластичности. Дальнейшие эксперименты привели к расширению количества входящих в состав элементов, что повысило прочность чистого алюминия (примерно 70–80 МПа) до 350–370 МПа.
История названия
Группа сплавов этого типа названа в честь немецкого города Дюрен. Здесь же и было начато их производство в промышленном масштабе в 1909 году, спустя шесть лет после открытия и изучения свойств. Кроме названия «дюралюминий» встречается также:
- англизированный вариант – «дюралюмин»;
- старая форма – «дуралюминий»;
- «дюраль», как общее название «семейства» алюминия этого типа.
В них же чувствуется аллюзия на латинское слово Durus, что означает жёсткий, твёрдый. Именно так характеризуются основные свойства этих металлов.
Состав сплавов алюминия: разные виды
- Системы Al-Mn, Al-Mg. Главная характеристика — высокая коррозийная стойкость (чуть меньше, чем у чистого алюминия). Кроме того, они хорошо поддаются сварке и пайке, но не резке. Эти сплавы не упрочняют при помощи термической обработки. Применяют для изготовления баков, маслопроводов, бензопроводов, радиаторов авто и тракторов, элементов посуды, в строительстве (в зависимости от конкретного вида и его характеристик).
- Семейство Al-Mg-Si — сплавы, которые называются коррозионно-стойкими. Упрочняют их при помощи термической обработки. Она заключается в закалке при температуре 515–525 градусов Цельсия с последующим охлаждением в холодной воде с естественным старением при 20 градусах около десяти суток. Основным свойством готовых материалов этой группы является высокая коррозионная стойкость в обычных условиях и в случаях эксплуатации под напряжением.
- Сплавы Al-Cu-Mg называются конструкционными, или же дюралюминиевыми. Их основа – алюминий, который легирован в разных пропорциях медью, магнием и марганцем. Исходя из них, получают разные виды со своими характеристиками, которые можно разделить на некоторое число групп, что будет рассмотрено далее.
Материалы группы дюраль обладают мощными механическими свойствами, но сильнее подвержены коррозии, чем второй рассмотренный вид семейства сплавов. С этим частично борется марганец, который дополнительно вводят в состав. Но при эксплуатации дюралюминия необходимо защищать его при помощи лакокрасочных покрытий или же подвергать анодированию. Если сплав применим для плакированных листов, то они и сами отличаются достаточной степенью стойкости к коррозии. То есть, она также во многом зависит от типа обработки.
Кроме вышеперечисленных систем сплавов, имеются также:
- жаропрочные;
- ковочные;
- жаропрочные ковочные;
- высокопрочные конструкционные сплавы.
Как видим, многие года изучения свойств материалов с основой алюминия позволило создать множество их различных видов и типов, которые обладают необходимыми в конкретной отрасли свойствами.
Сплавы типа дюралюминий
Всего имеется 4 сплава типа дюралюминий. Все они в разной пропорции содержат как основные компоненты (купрум, магний, марганец), так и другие (Fe, Si, Ti, Zn, Ni).
- Д1: купрум — 4,4 ±0,4%, магний — 0,6 ± 0,2%, марганец — от 0,6 ± 0,2%;
- Д16: купрум — от 3,8 до 4,9%, магний — 1,5 ±0,3%, марганец — 0,6 ±0,3%;
- Д19: купрум — от 3,8 до 4,3%, магний — 2,0 ±0,3%, марганец — от 0,5 до 1,0%;
- ВД17: купрум — 2,9 ±0,3%, магний — 2,2 ±0,2%, марганец — от 0,45 до 0,7%.
Остальные элементы присутствуют в материалах в общем размере не более двух процентов.
Для каждого типа дуралюмина также необходим свой режим термической обработки.
Сплав Д1 закаливается при температуре 495—510° C, а затем проходит стадию естественного старения при 20° C в течение 96 часов и более.
Для Д16 закалка проходит в двух режимах (зависимо от того, в каком виде будет представлен исходный материал). Если речь о листах из Д16, то для него нужна температура закалки 500 ± 5°C. Процесс старения можно произвести при 20 °C в течение четырёх суток и более, или при 188—193°C за гораздо меньшее количество часов — 11–13. Если же этот Д16 после используют для прессованных изделий, то предел температур закалки падает до 485–503° C. Старение тоже можно выполнить двумя путями:
- комнатная температура — в те же сроки;
- при температурах 185–195° C — в интервале 6–8 часов.
ВД17 закаляется в пределах 495–505° C, а старение выполняется только в принудительном порядке при 170 ± 5° C в течение 16 ±1 часов.
Д19, как и Д16, имеет разные условия закалки и старения материалов:
- для листов — t=505 ± 5° C, старение — при 20° C в течение 5–10 суток или при 185–195° C 13 ±1 часов;
- прессованныее изделия — t=500 ± 5°C, старение — аналогичное при комнатных условиях, или при 190 ± 5°C за 9 ±1 часов;
stanok.guru
Дюралюминий — это… Что такое Дюралюминий?
Дюралюми́ний — торговая марка одного из первых упрочняемых старением алюминиевых сплавов. Основными легирующими элементами являются медь (4,5 % массы), магний (1,6 %) и марганец (0,7 %). Типовое значение предела текучести составляет 450 МПа, однако зависит от состава и термообработки.
Названия
Фирменное название дюра́ль (Dural®) в русском языке стало по преимуществу разговорным и профессионально-жаргонным. Иногда встречаются также старая (основная до 1940-х) форма дуралюми́ний и англизированные варианты дуралюми́н, дюралюми́н, дюралеалюми́ний. Название происходит от немецкого города Дюрен, нем. Düren, где в 1909 году было начато его промышленное производство[1].
Дюралюминий разработан германским инженером-металлургом Альфредом Вильмом (Alfred Wilm), сотрудником металлургического завода Dürener Metallwerke AG. В 1903 году Вильм установил, что сплав алюминия с добавкой 4 % меди после резкого охлаждения (температура закалки 500 °C), находясь при комнатной температуре в течение 4—5 суток, постепенно становится более твердым и прочным, не теряя при этом пластичности. Дальнейшие эксперименты со сплавами этой системы привели к освоению в 1909 году заводом Dürener Metallwerke сплава дюралюминия. Обнаруженное Вильмом старение алюминиевых сплавов позволило повысить прочность дюралюминия до 350—370 МПа по сравнению с 70—80 МПа у чистого алюминия[2]. Распространённые в Европе (Швейцария и Великобритания) алюминиевые сплавы марок Avional и Hiduminium являются близкими по составу к дюралюминию сплавами других производителей.
Дуралюминами называют сплавы Al-Cu-Mg, в которые дополнительно вводят марганец. Типичным дуралюмином является сплав Д1, однако вследствие сравнительно низких механических свойств производство его заметно сокращается; сплав Д1 для листов и профилей заменяется сплавом Д16.
Свойства и применение
Дюралюминий — основной конструкционный материал в авиации и космонавтике, а также в других сферах с высокими требованиями к весовой отдаче.
Первое применение дюралюминия — изготовление каркаса дирижаблей жёсткой конструкции, с 1911 года — более широкое применение. Состав сплава и термообработка в годы Первой мировой войны были засекречены. Благодаря высокой удельной прочности дюралюминий начиная с 1920-х годов становится важнейшим конструкционным материалом в самолётостроении.
Плотность сплава 2500—2800 кг/м³, температура плавления около 650 °C. Сплав широко применяется в авиастроении, при производстве скоростных поездов (например поездов Синкансэн) и во многих других отраслях машиностроения (так как отличается существенно большей твёрдостью, чем чистый алюминий).
После отжига (нагрева до температуры около 500 °C и охлаждения) становится мягким и гибким (как алюминий). После старения (естественного — при 20 °C — несколько суток, искусственного — при повышенной температуре — несколько часов) становится твёрдым и жёстким.
В настоящее время сплавы алюминий — медь — магний с добавками марганца — известны под общим названием дюралюмины. В их число входят сплавы следующих марок: Д1, Д16, Д18, В65, Д19, В17, ВАД1. Дюралюмины упрочняются термообработкой; подвергаются, как правило, закалке и естественному старению. Характеризуются сочетанием высокой статической прочности (до 450—500 МПа) при комнатной и повышенной (до 150—175 °C) температурах, высоких усталостной прочности и вязкости разрушения[3].
Недостаток дюралюминов — низкая коррозионная стойкость, изделия требуют тщательной защиты от коррозии. Листы дюралюминов, как правило, плакируют чистым алюминием.
Интересные факты
- В конце 1930-х годов правление фирмы Dürener Metallwerke AG и исследовательские лаборатории располагались в Берлине, район Борзигвальде. Здесь в начале 1940-х годов разрабатывались деформируемые высокопрочные сплавы системы Al-Zn-Mg, нашедшие применение в самолетостроении Германии в период до 1945 года, в частности сплав Hydronalium Hy43 (1940) состава Al — 4,5Zn — 3,5Mg — 0,3Mn — 0,4Cu разработки Института DVL, на который к 1944 г. Министерством авиации RLM выпущена спецификация Flw3.425.5.[4]
Ссылки
- ↑ Краткий словарь авиационных терминов. Под редакцией проф. В. А. Комарова. М.: Изд-во МАИ, 1992, с. 54
- ↑ A. Wilm, Physikalisch-metallurgische Untersuchungen über magnesiumhaltige Aluminiumlegierungen. Metallurgie, 1911, Bd. 8, N 7, 225-27
- ↑ Алюминиевые сплавы.- В кн.: Авиация: Энциклопедия / Гл. ред. Г. П. Свищев. — М.: Науч. изд-во «Большая рос. энцикл.» : Центр. аэрогидродинам. институт им. Н. Е. Жуковского, 1994. — 736 c.: ил. ISBN 5-85270-086-X
- ↑ Mühlenbruck A., Seeman H.J. Untersuchungen an Al-Zn-Mg-Knetlegierungen. Luftfahrtforsch., 1942, Bd. 19, N 9, s. 337—343
См. также
dic.academic.ru
Основные качества и компонентный состав дюралюминия
Дюраль представляет собой особый по своим параметрам дюралевый сплав особой марки. Материал разработан германским инженером-металлургом по имени Альфред Вильм. Это сотрудник металлургического завода, расположенного в Германии.
В начале 20 века Вильм в процессе работы установил, что алюминиевый качественно выполненный сплав особой марки, в котором присутствует определенное количество меди, после достаточно резкого и сильного охлаждения, находясь в помещении с комнатной температурой в течении примерно 5 суток, постепенно и верно становится очень прочным и очень твердым, так как дюралевый состав оптимален. При этом сплав совершенно не теряет свою пластичность.
Состав материала
На данном достижении эксперименты, которые проводились, не закончились. Обнаруженные специалистом строения металлов и сплавов позволили значительно повысить показатели уровня прочности такого основания, как дюралюминий, примерно до 350—370 МПа. Этому способствует особый состав и сплав качественных компонентов.
Дюраль имеет в своем составе такие элементы, как:
- медь 4,4%;
- марганец 0,5%;
- магний 1,5%;
- кремний 1,2%;
- железо примерно 0,1%;
- алюминий – все остальное.
Показатели прочности находятся на самом высоком уровне, именно по этой причине ему дали название «дюраль», который в переводе с латинского обозначается, как твердый состав.
к меню ↑Как получается материал
Данный сплав получается в процессе нагревания его до температуры не менее 500 градусов. После этого материал закаливается в нужной температуры воде или упрочняется посредством методов естественного или качественного искусственного строения. После данной процедуры дюралюминий обретает такие показатели, как гибкость и мягкость, а после придания сплаву старения становится он очень твердым и приобретает такое качество, как прочность. Сварка проводится на высоком качественном уровне, а состав его отличается идеальным качеством.
Процесс естественного старения осуществляется, как правило, в течение суток. При этом выдерживается температура примерно 20 градусов. Что касается искусственного старения, то оно обычно занимает не так много времени, но при этом требует применения более высоких температурных показателей. В результате проведенных работ металл в процессе изготовления получается очень прочным. Сплав дюралюминий в состоянии идеально противостоять всем механическим повреждениям и выдерживать серьезные нагрузки.
к меню ↑Применение материала
Дюралюминий на данный момент считается не таким распространенным, как обычный алюминий, несмотря на это в процессе строительства он просто незаменим, особенно при таком процессе, как сварка. Используют его, как правило, при возведении разнообразных жилых сооружений, а также в распространенных сферах автомобиле- и авиастроения. Подобная популярность основана на том, что дюраль обладает высокими показателями прочности, в отличие от самого алюминия.
Детали, которые производятся из качественного дюраля обладают показателями плотности от 2500 до 2700 килограмм на один метр кубический. Отмечаются также такие качество, как износоустойчивость. Технические свойства характеризуются, как уникальные и по достоинству оцениваются большим количеством специалистов. Они осуществляют с ним такие виды деятельности, как сварка и иные манипуляции.
к меню ↑Особенности соединения материала
Такой процесс, как сварка данного сплава должен осуществляться строго в среде защитных инертных газов. Как правило, для этой применяется аргон, но наиболее преимущественным является гелий или смесь гелия и аргона. Более высокий показатель теплопроводности гелия обычно определяет и более высокие температурные показатели у сварочной ванны. Это оказывается преимущественным в процессе сварки достаточно толстостенных конструкционных элементов. Если использовать смесь защитных газов, это будет способствовать более полному выведению газа. Тогда вероятность образования пор при осуществлении шва при таком деле, как сварка, значительно уменьшается.
В заключение стоит отметить, что дюралюминий, как высококачественный конструкционный сплав и материал, используется по причине его достаточно высоких механических качеств, а также относительно небольшого удельного веса. Внимания заслуживает тот факт, что сплав обладает относительно невысокой сопротивляемостью к разрушительной коррозии. Для повышения данного показателя дюралюминий в процессе производства покрывают чистым алюминием, слой которого с каждой стороны составляет примерно 5% от общей толщины сердцевины такого материала, как дюраль. Данный материал не рекомендуется подвергать достаточно серьезной и долговременной термической обработке. Это основано на том, что медь особым образом диффундирует в особый плакировочный слой, который при этом утрачивает все свои защитные свойства.
Похожие статьиgoodsvarka.ru