Сплавы меди с оловом — бронза оловянная. Сплавы меди с алюминием-бронза алюминиевая
Сплавы меди с такими элементами, как Sn, Al, Si, Be и некоторыми другими, называют бронзами с прилагательным, указывающим на второй компонент. Таким образом, сплавы с оловом называются оловянными бронзами.
Как и в предыдущей системе, при всей сложности диаграммы в целом, практический интерес представляют начальные области со стороны меди: область одного твердого раствора, обозначаемого буквой а, распространяющаяся до 16% Sn (линия насыщения BFF0), и лежащие за этой линией области с двумя фазами и превращениями, из которых наиболее важным является эвтектоидное, происходящее на линии FEG; здесь твердый Т-раствор распадается в эвтектоидную смесь по реакции
1 = a -f- 8.
эвтектоид
8-фаза соответствует содержанию ~32% Sn и по природе своей представляет химическое соединение Cu4Sn (или Cu31Sn8).
Ввиду того, что сплавы этой системы дают большое разнообразие состояний и структур в зависимости от условий (скорости) охлаждения, на фиг. 214 приведены\’ линии троякого рода .соответственно превращениям, происходящим в разных условиях:
1) сплошные линии (ABFF0, ACDHKM, FEG и др.) отвечают превращениям и границам областей, получающихся в условиях весьма медленного охлаждения или длительного, практически выполняемого отжига; эти линии представляют обычную диаграмму состояний, соответствующую равновесию сплавов, осуществляемому в практике;
2) линии, проведенные жирным пунктиром (Abff0, ЬВ, fF), отвечают превращениям и границам фаз, получаемых в обычных условиях отливки сплавов в холодные формы, т. е. при ускоренном охлаждении сплавов и получения их в неравновесном состоянии;
3) линии, проведенные тонким пунктиром (Fde, dmn), отвечают превращениям и границам, получаемым в условиях чрезвычайно длительных выдержек (отжига в течение тысяч часов) после обработки сплавов давлением; такие условия в практике обычно не осуществляются, и состояния и структуры, соответствующие этим превращениям, в обычных условиях использования сплавов не наблюдаются.
Учитывая сделанные замечания, рассмотрим состояния и структуры технических оловянных бронз в связи с диаграммой состояний, приведенной на фиг. 214.
Структура оловянных бронз, а-бронза должна иметь такой же -вид, как а-латунь, т. е. дендритную структуру твердого раствора в неравновесном состоянии (в литых необработанных образцах; см. фиг. 208) или зернистую (полиэдрическую) после отжига (см. фиг. 209). При этом здесь также после предварительной деформации и рекристаллизации (отжига) в зернах — полиэдрах наблюдаются двойники (см. фиг. 210).
Если же по составу бронза заходит за предел насыщения (>16% Sn), то в условиях равновесия (соответственно сплошным линиям диаграммы фиг. 214), кроме а-фазы должны наблюдаться участки эвтектоида (а + §) в большем или меньшем количестве, в зависимости от содержания Sn. В практических же условиях охлаждения отливок из бронзы легко могут получаться неравновесные состояния, и тогда структура сплавов будет согласовываться с диаграммой, показанной жирным пунктиром.
Здесь в сплавах, относящихся к области а уже при содержании Sn более 7-8% благодаря очень большой ликвации, последние порции жидкости (остаточного раствора) по концентрации переходят за предел насыщения bff0 и при относительно быстром затвердевании дают участки второй фазы р, переходящей при дальнейшем охлаждении в фазу Т; последняя же распадается, в свою очередь, в эвтектоид (а + 8) при 520°. Поэтому в структуре указанных бронз вместо одной а-фазы наблюдаются еще эвтектоидные участки.
На фиг. 215 показана подобная структура бронзы с 10% Sn; на фоне а-фазы с дендритной структурой ясно различаются островки пестрого эвтектоида (а + 8)- Поскольку участки эвтектоида в таких сплавах неравновесны, постольку они могут быть уничтожены или уменьшены путем диффузионного отжига (гомогенизации, см. § 91).
Свойства оловянных бронз. Свойства этих сплавов, в целом, определяются свойствами составляющих их фаз и дают картину изменений, аналогичную латуням: в области одной а-фазы наблюдается небольшое увеличение прочности и твердости; пластичность же растет до некоторого максимума (около 5% Sn) и далее быстро снижается. Только здесь влияние олова более интенсивно, чем цинка в латунях, и возрастание твердости и прочности с каждым процентом Sn значительнее.
Кроме того, благодаря отмеченной большой ликвации и легкому получению неравновесных эвтектоидных участков в а-сплавах замечается очень сильное падение пластичности уже начиная от 7-8% Sn, при одновременном сильном возрастании твердости и прочности. Поэтому отливки из таких бронз уже не подвергают прокатке, а используют как литейный материал.
Оловянная бронза раньше имела весьма широкое распространение благодаря высоким литейным качествам — жидкотекучести, малой усадке, а также благодаря прочности, твердости, стойкости против коррозии и красивому желтоватому цвету. Укажем на изготовление монет и медалей из обрабатываемой бронзы с 5% Sn, которая поэтому и называлась монетной или медальной. Далее, известна пушечная бронза, из которой раньше изготовлялись пушки. Она содержала около 10% Sn и относилась к литейному материалу, поскольку содержала обычно значительное количество эвтектоида.
В настоящее время можно встретить отливки с таким же или еще большим содержанием Sn, которые обычно называют машинной бронзой. В частности, подобную бронзу, содержащую даже до 14-16.% Sn, иногда .применяют как антифрикционную — подшипниковую. Но, вообще, вследствие дефицитности и дороговизны олова в технике стремятся заменять оловянную бронзы другими сплавами (см. ниже), поэтому не введены в стандарт машинные бронзы типа пушечной (марки БрОЮ)1 и др.
В стандарт введены марки сложных бронз, содержащих небольшие количества олова и ряд других элементов.
Например: марка БрОЦСН 3-7-5-1 — оловянно-цинково-свинцовая с никелем, содержащая всего 3% Sn. Эта марка может быть как обрабатываемой (пластичной), так и литейной, применяемой для художественного литья.
Существует довольно много марок подобного типа оловянных бронз, в которых добавки элементов, как Zn, Pb, Р и др., удешевляют сплав и придают улучшение главным образом его литейным свойствам.
Таким образом, оловянные бронзы в наших стандартах представляют собой преимущественно сложные (специальные) сплавы.
Сплавы меди с алюминием-бронза алюминиевая
Диаграмма состояний системы Си-А1 приведена на фиг. 216. Как и в рассмотренных раньше системах, практический интерес представляют начальные области, прилегающие к меди (а также к алюминию, которые рассмотрим дальше, § 166). Области, прилегающие к меди, отвечают сплавам, которые называются алюминиевыми бронзами.
Начальная область а-твердого раствора простирается до 9,8% А1 (предел насыщения — линия FF0).
Здесь а-бронзы являются однофазными.
За пределом насыщения а, т. е. свыше 9,8% А1, бронзы становятся двухфазными, причем вторая фаза — f (твердый раствор) при обыкновенной температуре включена в эвтектоид, получаемый при 535° (на линии FEG) в результате распада твердого раствора по реакции.
Таким образом, двухфазные алюминиевые бронзы при высоких температурах содержат наряду с а вторую р-фазу,1 а при низких температурах — эвтектоид (а + Т).
Структура а-бронз совершенно такая же, как а-латуней и оловянных бронз. Структура же двухфазной бронзы с 10% А1 приведена на фиг. 217. На фоне светлой «-составляющей видны участки эвтектоида, весьма схожего по виду с пластинчатым перлитом.
Свойства алюминиевых бронз по мере изменения состава (% А1) изменяются аналогично латуням и оловянным бронзам, но более резко. На фиг. 218 показаны кривые изменения их механических свойств соответственно диаграмме состояний.
Твердость (Яв), прочность (о-,) и пластичность (5) быстро растут, причем только однозначно растет по мере увеличения содержания А1; пластичность же достигает максимума при 5% А1, после чего быстро снижается и становится ничтожной при содержании А1 свыше 12%, когда преобладает хрупкая Т-фаза.
В связи с этим и ад растет и достигает максимума при содержании А1 около 10-11%, а затем снижается в силу возрастания хрупкости сплава. Поэтому в практике из двухфазных бронз применяют бронзы, содержащие не более 11 % А1, а из однофазных наиболее употребительными являются бронзы с 5% А1, наиболее пластичные, которые в практике можно также назвать монетной или медальной бронзой, заменяющей соответствующую оловянную.
Марка такой бронзы обозначается: БрА5. Она представляет пример обрабатываемой («нахолоду») алюминиевой бронзы. Двухфазная же бронза марки БрАЮ является примером литейного сплава, отличающегося повышенной твердостью (>Ю0 Яв), прочностью (~65 кг/мм2) и достаточной пластичностью (8 -15%). Механическая обработка давлением в нем применяется лишь горячая (>600°).
Следует также отметить, что механические свойства этой бронзы могут быть существенно изменены закалкой и отпуском аналогично изменениям, наблюдаемым при подобных операциях в стали, причем структура закаленного сплава здесь весьма сходна с игольчатой структурой мартенсита.
Конечно, и в алюминиевых бронзах широко используется легирование, т. е. добавка других элементов с образованием сложных бронз. Укажем, например, на такие марки:
БрНА14-3, называемая в практике «куниаль А» и идущая на фасонное литье ответственного назначения вместо оловянной бронзы;
БрАЖ9-4с9% А1 и 4% Fe, представляющая как литейный, так и обрабатываемый сплав.
Литейные свойства алюминиевой бронзы удовлетворительны, но все-таки усадка в ней более значительна, чем в оловянной бронзе и, кроме того, в ней часто получается сниженная жидкотекучесть вследствие загрязнений жидкого металла окислом алюминия.
www.inmetal.ru
Цинк и его сплавы. Структура и свойства чистого цинка. Сплавы цинка. Припои, страница 2. Цинк алюминий медь
Сплав ЦАМ — состав, свойства, применение
Как материал сплав ЦАМ был разработан почти 100 лет назад. Точное имя человека (или группы лиц), сделавшего это, неизвестно. Но мы знаем, что он был сотрудником американской компании the New Jersey Zinc Corporation. С каждым годом ЦАМ открывает для себя новые способы применения в производстве, вытесняя с рынка своих давних конкурентов: алюминий и латунь.
Состав сплава ЦАМ
Это разновидность цинкового сплава, основными легирующими элементами которого является алюминий и медь. Сама аббревиатура ЦАМ расшифровывается как цинк-алюминий-медь. Цифры, указанные после названия сплава, обозначают процентное содержание металлов. Так обозначение ЦАМ 4-1 говорит, что сплав включает в себя пр имерно 4% алюминия, 1% меди и 95% цинка. Также ЦАМ всегда содержат в своем составе небольшое количество (до 0,1%) магния.
Цинк представляет собой пластичный металл серебристого цвета и белого оттенка. Достаточно хрупок. Отличается пониженной температурой плавления, высокой жидкотекучестью и низкой стоимостью. Является основой для ЦАМ.
Алюминий сокращает растворимость железа в сплаве, что благоприятно воздействует на механические и литейные характеристики ЦАМа. Помимо этого, алюминий уменьшает влияние зональной ликвации. Способствует измельчению зерна.
Медь вводят в сплав с целью увеличения его прочностных характеристик. Один процент меди повышает значение твердости ЦАМ примерно на 7%. Обратной стороной данного легирования является ухудшение коррозионностойких и пластичных свойств сплава.
Магний – компонент, отвечающий за сдерживание ЦАМом зарождения очагов коррозии, включая самую худшую ее разновидность – мелкозернистую. Также он замедляет процессы старения в с
pellete.ru
Сплавы меди с алюминием — бронза алюминиевая
Реактив выявляет также микроструктуру меди, латуней и бронз. Бета-фаза в латунях темнеет, хорошо выделяется эвтектоид. В сплавах меди с алюминием, фосфором и бериллием а-фаза темнеет. Двойниковое строение обнаруживается слабо. Травление проводят в течение 0,5—3 мин и более. Образующуюся на шлифе пленку (например, на алюминиевой бронзе) удаляют погружением на несколько секунд в 10%-ный раствор соляной кислоты. Воду можно частично заменить спиртом. [c.27]Сплавы меди с оловом принято называть оловянистыми бронзами, сплавы меди с алюминием — алюминиевыми, а остальные сплавы на медной основе—специальными (например, свинцовыми, кремниевыми, марганцевыми, бериллиевыми, кадмиевыми — по главному, кроме меди, компоненту сплава). [c.89]
Сплавы меди с оловом, алюминием, бериллием, никелем, марганцем, кремнием, фосфором и др. элементами называются бронзами. Наименование бронзы получают в зависимости от главных легирующих элементов, например, бронзой оловянной называется сплав меди с оловом, бронзой алюминиевой — сплав меди с алюминием и т. д.. [c.41]
Сплавы меди с алюминием — бронза алюминиевая [c.349]
Бронзы представляют собой сплавы меди с оловом (оловянные бронзы), алюминием (алюминиевые), бериллием (бериллиевые) и с другими легирующими элементами. Марки бронз обозначаются буквами Бр (бронза), за которыми следуют буквы и цифры, показывающие, какие легирующие элементы и в каком количестве содержатся в данной бронзе (табл. 13).
Бронзами называются сплавы меди с оловом, алюминием, марганцем, кремнием, свинцом и рядом других металлов. Название бронз обычно определяется вводимом добавкой, т. е. сплавы меди с оловом называются оловянистыми бронзами, сплавы меди с алюминием—алюминиевыми бронзами, сплавы с кремнием— кремнистыми и т. п. [c.143]
Бронзы. Сплав меди с оловом, алюминием, свинцом и другими элементами, среди которых цинк и никель не являются основными, называют бронзой. По основному легирующему элементу бронзы делятся на оловянные, алюминиевые, кремнистые, бериллиевые, свинцовые и др. Бронзы обладают хорошими литейными свойствами, хорошо обрабатываются давлением и резанием. Большинство бронз отличаются высокой коррозионной стойкостью и, кроме того, широко используются как антифрикционные сплавы. [c.201]
Как показывают длительные испытания, в морской агрессивной атмосфере легирование меди алюминием, цинком, никелем и оловом повышало их сопротивляемость коррозии и поэтому алюминиевые бронзы, томпак, сплавы меди с никелем и цинком, сплавы с никелем и оловом оказываются более стойкими, чем чистая медь. Алюминий оказывает благотворное влияние также в субтропической морской и в сельской атмосферах. Алюминиевые бронзы в этих условиях обнаружили более высокую стойкость. В других атмосферах, и в особенности в промышленных, легирование меди положительных эффектов не давало. Более того, оно часто приводило к понижению стойкости основного компонента сплава. Высокопрочные латуни, содержащие, кроме меди, цинк (20—24%), марганец (2,5—5,0%), алюминий (3—7%) и железо (2—4%), оказались во много раз менее стойкими по сравнению с чистой медью более подробно о коррозионных свойствах различных медных сплавов см. в гл. V).
Бронза — сплав меди с оловом, алюминием, кремнием и другими элементами. Бронзы различают а) по составу — простые и сложные б) по структуре — однофазные и двух-,или многофазные в) по способу изготовления деталей — литейные и деформируемые. Для химического оборудования широкое распространение получили алюминиевые бронзы, достаточно прочные и обладающие более высокой коррозионной стойкостью, особенно в кислотах, чем медь. Однако при длительной эксплуатации в растворах некоторых солей (сульфатов, хлорида натрия), а также едких щелочей наблюдается избирательная коррозия алюминиевых бронз, в результате которой постепенно снижается прочность и пластичность сплавов. При введении марганца коррозионная стойкость алюминиевых бронз повышается. [c.114]
Реактив окрашивает за 20—60 сек феррит в высококремнистых углеродистых сплавах. Применяется также для травления сплавов меди с оловом, цинком, алюминием и т. д. При этом а-фаза оранжевая, т)-фаза в алюминиевых бронзах черная, б-фаза коричневая [88]. [c.59]
При плавке алюминиевых бронз и кремнистых сплавов в результате взаимодействия окислов меди с алюминием и кремнием могут образоваться тугоплавкие окислы алюминия и кремния, выделяющиеся затем в отливках в виде плен и включений. С целью их избежания медь перед введением в неё алюминия или кремния должна быть раскислена фосфором. Фосфор вводится с расчётом получения его в сплаве в количестве не более 0,02 /о. [c.404]
Бронзы. Сплавы меди с оловом, алюминием, кремнием, марганцем, свинцом, бериллием называют бронзами. Раньше к бронзам относили сплавы только двойной системы медь — олово. С течением времени разработаны новые сплавы на медной основе, в которых олово частично или полностью заменено другими элементами. Однако название сплавов осталось прежним, так как они по многим физико-механическим свойствам и цвету не отличаются от медно-оловянистых сплавов. В зависимости от введенного элемента бронзы называют оловянистыми, алюминиевыми, кремнистыми, марганцовистыми и т. д.
Широкое распространение имеют бронзы — сплавы меди с оловом, кремнием, алюминием, свинцом, фосфором, марганцем и некоторыми другими компонентами. В зависимости от главных добавок к меди различают бронзы оловянистые, алюминиевые, свинцовистые и др. [c.10]
Бронзы — это сплавы меди с оловом, алюминием, кремнием, никелем и другими химическими элементами. Бронзы маркируются буквами Бр., после которых следует буква, обозначающая основной легирующий элемент О — оловянистые, А—алюминиевые и т. д., в остальном их маркировка аналогична латуням. Например, марка Бр.АЖН 10-4-4 обозначает алюминиевую бронзу, содержащую алюминия—10%, железа 4%, никеля 4%, остальное — медь. [c.164]
Сваривают изделия из меди, латуни (сплава меди с цинком), бронзы. Сварку широко применяют также для изделий из алюминия, силумина (сплава алюминия с кремнием), дюралюминия (сплава алюминия с. медью, магнием и марганцем). В последние годы сварные изделия изготовляются из алюминиево-марганцовых и алюминиево-магниевых сплавов. [c.208]
Сварка бронз. Сплавы меди с оловом, алюминием, бериллием и некоторыми другими элементами называют бронзами. Бронзы принято маркировать Бр с начальными буквами добавляемых элементов и целым числом их процентов. Например, марка Бр-ОЦСН-3-7-5-1 —оловянисто-цинково-свинцовая с никелем, содержащая олово 3%, цинка 7%, свинца 5%, никеля 1%. Сплавы меди с оловом называют оловянистыми или оловянными бронзами, с алюминием — алюминиевыми бронзами, с бериллием — бериллиевыми бронзами и т. д. [c.283]
Бронзами называют сплавы меди с оловом, алюминием, марганцем, кремнием и другими металлами. Наряду с оловянисты-ми бронзами, для которых требуется дорогое олово, широкое применение находят специальные бронзы— алюминиевые, марганцовистые, кремнемарганцовистые и др., которые по своим свойствам заменяют оловянистые бронзы. В зависимости от состава и свойств бронзы могут быть литейными и обрабатываемыми давлением.
Алюминиевые брснзы выделяются высокими механическими свойствами среди медных сплавов, в связи с чем их широко применяют в машиь острое-нии. В промышленности используют как двойные сплавы меди с алюминием (простые бронзы), так и более сложные по составу бронзы с добавками марганца, железа, никеля и других элементов. На поверхности алюминиевой и кремнистой бронз образуется окис-ная пленка, которая трудно удаляется с использованием обычных флюсов. Изделие перед пайкой необходимо обрабатывать во фтористс-водородпой или плавиковой кислоте. При пайке оловянно-свинцовыми припоями применяют активные флюсы с повышенным содержанием соляной кислоты. Рекомендуются предварительная очистка и флюсование поверхности алюминиевой бронзы смесью борной кислоты с хлористыми солями металлов. Марганцевые бронзы следует паять с использованием ортофосфорной кислоты. [c.253]
Титан в сплавах цветных металлов. Добавки титана к меди, медным и алюминиевым сплавам улучшают их физико-механические свойства и сопротивление коррозии. Для раскисления меди применяют купротитан —сплав меди с титаном, содержащий 6— 12% Т1. Для повышения прочности алюминиевой бронзы (сплав меди с алюминием) в бронзу вводят от 0,5 до 1,55% Т . Присадку добавляют в виде сплава алютита, содержащего 40% А1, 22—50% Л, 40% Си. [c.212]
Сплавы меди с алюминием, кремнием, бериллием и другими элементами также называются бронзами в отличие от оловя-ннстых их называют соответственно алюминиевыми, кремнистыми и т. д. Малой величиной усадки оловянистая бронза превосходит эти бронзы, но они в свою очередь превосходят оловя-нистую в других отношениях по механическим свойствам (алюминиевая, кремнистая бронза), но химической стойкости (алюминиевая бронза), по жидкотекучести (кремнецннковистая бронза). Олово — дефицитный элемент, поэтому эти бронзы, кроме, разумеется, бериллиевой, дешевле оловяннстой.
Специальнаябронза, т. е. сплавы меди с алюминием (алюминиевая бронза), с кремнием (кремни.тая бронза), с магнием, кадмием, марган.,ем, никелем, свинцом и лр. содержание меди не менее 78 / . Одновременно в сплаве находится до 3 видов присадочных металлов из числа указанных. [c.1135]
Практическое применение имеют сплавы меди с алюминием, содержащие до 10—11 % А1. Поэтому при изучении структуры алюминиевых бронз нужна только левая часть диаграммы состояния, т. е. области а и а+Т2- Сплавы, отвечающие по составу области а, — однофазные сплавы, термически не обрабатываемые, весьма пластичные структура их состоит из однородных зерен твердого раствора а. Сплавы, отвечающие по составу области а+Т2> — двухфазные сплавы, термически обрабатываемые, значительно менее пластичны, чем сплавы области а в структуре содержат эвтектоид а + у2- Вследствие больщой хрупкости фазы уг двухфазные алюминиевые бронзы при-меняют-ся только доэвтектоидные, т. е. с со- [c.253]
В настоящее время наряду с оловянистыми бронзами широко применяются алюминиевые бронзы, марганцовистые бронзы, кремнемарганцовистые бронзы и др. В связи с дефицитностью олова применение оловянистых бронз необходимо всемерно ограничивать. Сплавы меди с алюминием, железом и другими металлами по своим физико-механическим свойствам полностью заменяют оло-вянистые бронзы. [c.358]
Бронзами называют сплавы меди с алюминием, марганцем, кремнием, бериллием и другими элементами, кроме цинка. В зависимости от легирукяцего элемента бронзы носят названия алюминиевые, марганцовые, кремнистые, алюминиевомарганцовые, алюминиевожелезные и т, д. [c.66]
Кроме указанных сплавов, в качестве бронз применяют сплавы меди с алюминием (алюминиевые бронзы), с кремнием (кремнистые бронзы), с бериллием (бериллие-вые бронзы), с железом (железистые бронзы) и др. Бронзы делятся на оловянистые и безоловянистые. В бронзах может быть небольшое количество цинка, однако цинк в этом случае является не основным легирую-ш,им элементом и вводится в сплав в малых количествах. Широко применяются следующие бронзы БрОФ 6,5-0,25, БрАЖ-9-4, БрАЖМц 10-3-1,5, БрКМц —3-1, БрБ. [c.121]
Бронзами называются сплавы меди с оловом (оловянистые бронзы), алюминием (алюминиевые бронзы), марганцем (мар-ганцевистые бронзы) и другими ком-понентами. [c.52]
Бронзы — это сплавы меди с оловом (оло-Бяиистые бронзы), алюминием, кремнием и бериллием (алюминиевые, кремнистые и бсрил-лиевые бронзы). Состав и свойства некоторых оловянистых бронз приведены в табл. 8.38. [c.298]
Бронзы — сплавы меди с оловом, свинцом, алюминием, железом, кремнием, марганцем и другими металлами (кроме цинка), в соответствии с которыми бронзы получают название. Обозначение марки бронзы начинается с букв Бр, за которыми) следуют заглавные буквы легирующих элементов и их процентное содержание. Например, БрОФ 10-1 — бронза, содержащая 10 % олова, 1 % фосфора и остальное — медь. Бронзы обладают высокими антифрикционными, антикоррозионными и литейными свойствами и имеют хорошие механические характеристики. Наилучшие антифрикционные и механические свойства имеют оловянные бронзы Бр010Ц2 и БрОЮСЮ. Вследствие высокой стоимости и дефицитности оловянных бронз часто применяют безоловянные бронзы, выпускаемые в соответствии с ГОСТ 18175—78 . Из них наибольшее распространение получила алюминиево-железная бронза БрАЖ9-4 для венцов червячных колес, гаек ходовых и грузовых винтов и т. п. [c.32]
Бронзой называется сплав меди с оловом и другими элементами, кроме цинка. Различают простые (оловянистые) и специальные (безо-ловянистые) бронзы. Бронзы, в состав которых входит олово, являются оловянистыми. В специальных бронзах олово заменено свинцом, алюминием, железом, марганцем, кадмием, бериллием и другими элементами. В зависилюсти от химического состава такие бронзы называются свинцовистыми, алюминиевыми, марганцовистыми, беррнлиевыми и т. д. Как и латуни, бронзы делятся на литейные н деформируемые. [c.36]
Бронзы — сплав меди с оловом. Из-за дефицитности олова его теперь частично заменяют цинком, свинцом, фосфором. Имеются бронзы алюминиевые, свинцовые, кремнистые и др., совсем не содержащие олова. Применяются для изготовления шестерен, втулок, подшипников и т. п. Маркировка начинается с букв Бр. Например,. маркой БрА5 обозначается бронза с содержанием около 5% алюминия, маркой БрАЛ[c.23]
Сплавы цветных металлов довольно широко применяют в машиностроении наибольшее распространение нашли сплавы меди, баббиты и легкие сплавы. Медные сплавы подразделяют на бронзы (все медные сплавы, за исключением латуни) и латуни, в которых основным легирующим элементом является цинк. Бронзы разделяют по содержанию в них основного легирующего элемента на оловянные, свинцовые, алюминиевые и др. Бронзы обладают высокими антифрикционными и антикоррозионными свойствами и поэтому широко применяются в узлах трения (для изготовления вкладьппей подшипников скольжения, червячных и винтовых колес, гаек грузовых и ходовых винтов н т. п ) и в водяной, иаровой и масляной арматуре. Латуни разделяют на двойные (сплавы меди с цинком) и сложные, в которых кроме меди и цинка содержатся еще некоторые элементы, как, например, свинец, кремний, марганец, алюминий, железо, никель, олово. Латуни обладают хорошим сонроттюлением коррозии, антифрикционными свойствами, электропроводностью, хорошими технологическими свойствами и поэтому широко применяются для изготовления проволоки, гильз, арматуры деталей электрической аппаратуры, электрических машин и т. п. [c.19]
Сплавы меди с оловом, т. е. оловянистые бронзы, обычно именуются просто бронзами. Остальные сплавы на медной основе называют бронзами специальными, прибавляя к названию бронзы наименование легирующего элемента. Таким образом, специальная бронза, легированная алюминием, носит название алюминиевой бронзы. Та же бронза, содержащая, кроме алюминия, также добавки железа, носит название алюминиевожелезной бронзы и т. д. [c.357]
Бронза —сплав меди с оловом, алюминием, кремнием, марганцем и цинком. В зависимости от содержания этих добавок бронзы подразделяются на оловянные бронзы, содержащие 8— 10% олова, 2—4% цинка, остальное медь, и специальные бронзы, к которым относятся алюминиевые, железомарганцовые, марганцовые, кремнистые и др. [c.213]
Стыковой сваркой сваривают медь и ее сплавы (бронза — сплав — меди с оловом, латунь — сплав меди с цинком), алюминий и его сплавы. Медь и алюминий обладают значительно больщей теплопроводностью, чем сталь, вследствие чего требуют большего тепла для образования слоя расплавленного металла на торцах. Из-за больщой теплопроводности и низкого электросопротивления оплавление в целях концентрации тепла около торцов проводится с повышенными скоростями при повышенных плотностях тока. Сильное окисление с появлением тугоплавких пленок требует, наряду с интенсивным оплавлением, больших скоростей осадки с приложением значительного усилия, необходимого для удаления окислов из стыка. Перемещение плиты должно проводиться по графику, близкому к полукубической параболе. При оплавлении меди поддерживать на торцах слой расплавленного металла, а также прогреть металл на достаточную гл бину еще труднее, вследствие чего для получения соединения необходимого качества применяются большие усилия осадки (до 40 кг1мя1 ). Следует от.метить, что исходное состояние сплава (в особенности алюминиевого) существенно влияет на условия его сварки оплавлением и на качество получаемых соединений. Режимы сварки некоторых изделий из цветных металлов приведены в табл. 20. При сварке латуни наблюдается выгорание цинка (температура плавления которого 419° С) это может привести к изменению свойств лат ни. С целью уменьшения выгорания цинка необходимо процесс оплавления и осадки вести с большой скоростью. Сварка латуни затруднена также из-за ее быстрого окисления и небольшого интервала температур перехода из твердого состоя-иия в жидкое. В сгыках лат ни, соде,рлоднофазная структура а-латуни в этих случаях стык равнопрочен основно.му металлу. При содержании цинка более 40 Ь (например, Л59) в стыках наблюдается (а + -f ), латунь, закаливающаяся до твердости 170 кг/лш при твердости основного металла 125—130 кг1мм-. Отпуск при 600—650° С обеспечивает требуемую пластичность латуни. [c.155]
Бронзы. Сплавы меди с оловом, алюминием, кремнием, марганцем, свинцом, бериллием называют бронзами. В зависимости от введенного элементабронзы называют оловянными, алюминиевыми и т.д. [c.102]
Биметаллы успешно применяются во многих отраслях промышленности при решении конструктивных и технологических вопросов (гибка, сварка, отделка поверхности). Для изготовления емкостного оборудования используют биметалл углеродистая стальЧ-нержавеющая сталь . Весьма эффективно применение биметаллических конструкций из высокопрочных сталей с титаном. В этом случае удается получить высокую прочность и высокую коррозионную стойкость. Обычно такие биметаллические конструкции производят с применением взрывной технологии или диффузионной сваркой. В практике нашел широкое применение биметалл сталь-f медь , особенно для труб, подвергающихся высокому внутреннему давлению и действию коррозионной среды. Путем наплавки (иногда с последующей деформацией) производят биметаллические полуфабрикаты и изделия из биметалла сталь-f бронза . Большинство листов из алюминиевых сплавов производится с технологической планировкой чистым алюминием или сплавом алюминия с цинком, которая выполняет роль более коррозионностойкого слоя. [c.77]
Исследования показали, что полученный таким образом диффузионный сплав на основе меди соответствует по структуре литой алюминиевой бронзе с содержанием алюминия 9—11%. Сплав может быть отнесен к классу диснерсионно-твердеющих. Дальнейшее изменение его твердости может быть достигнуто закалкой в масле и старением при температуре 250—300° С в течение 1—2 ч. [c.187]
mash-xxl.info
Алюминий-медный сплав для литья
Алюминий-медный сплав для литья, содержащий по существу нерастворимые частицы, которые занимают междендритные области сплава, и свободный титан в количестве, достаточном для измельчения зернистой структуры в литейном сплаве. Сплав содержит, мас.%: Cu 3,0-6,0 , Mg 0,0-1,5, Ag 0,0-1,5, Mn 0,0-0,8, Fe 0,0-1,5, Si 0,0-1,5, Zn 0,0-4,0, Sb 0,0-0,5, Zr 0,0-0,5, Со 0,0-0,5, свободный титан >0,15-1,0, нерастворимые частицы 0,5-20, Al и неизбежные примеси — остальное. Нерастворимые частицы занимают междендритные области сплава и содержат частицы диборида титана. Алюминий-медный сплав обладает высокой пластичностью и прочностью на разрыв, а также усталостной долговечностью. 2 н. и 6 з.п. ф-лы, 7 ил.
Настоящее изобретение относится к алюминий-медным сплавам для отливки. Алюминий-медные сплавы имеют потенциально более высокую прочность, чем другие системы алюминиевого сплава для отливки, например алюминий-кремниевые сплавы. Однако использование алюминий-медных сплавов для высокопроизводительных областей применений ограничено вследствие их относительно плохих литейных качеств по сравнению с алюминий-кремниевыми сплавами.
Заявка на патент Великобритании 2334966А раскрывает алюминий-медный сплав, в котором по существу нерастворимые частицы, предпочтительно диборид титана или, возможно, другие соединения, такие как карбид кремния, оксид алюминия, диборид циркония, карбид бора или нитрид бора, занимают междендритные области сплава при литье. Предполагалось, что подобные частицы, которые обычно являются тяжелыми и хрупкими, приводят к неприемлемому снижению пластичности литейного сплава, но в действительности исследование показало, что хорошая пластичность сохраняется, поскольку частицы изменяют характеристики затвердевания сплава, устраняя макромасштабную неоднородность по составу и уменьшая усадочную пористость. Во время затвердевания сплава частицы TiB2 заполняют междендритные пространства, поскольку дендриты алюминия зарождаются и начинают расти, а наличие частиц TiB2 ограничивает передвижение оставшегося жидкого металла через междендритные каналы. Это способствует передвижению по направлению к подаче массы, что уменьшает возникновение внутренней и поверхностной усадочной пористости. Однако несмотря на то, что TiB2 является известной добавкой, измельчающей зерно, размер зерна остается очень большим (например, около 1 мм). Данная неизмельченная зернистая структура может привести к проблемам, связанным с образованием горячих трещин, особенно в отливках в песчаные формы, а также может привести к образованию усадочной пористости в больших медленно остывающих отливках, таких как отливки, производимые посредством литья по выплавляемым моделям или литья в песчаные формы.
JP 11199960 раскрывает алюминиевый сплав, подходящий для изготовления отливок для головок блоков цилиндров двигателей, который может содержать титан. Однако сплав представляет собой алюминий-кремниевый сплав: такие сплавы в основном обладают гораздо большей жидкотекучестью и литейными качествами, чем сплавы, содержащие незначительное количество или не содержащие кремний, и не подвергаются тому же уровню образования горячих трещин или усадочной пористости, как последние сплавы.
В соответствии с первым аспектом изобретения алюминий-медный сплав, содержащий по существу нерастворимые частицы, которые занимают междендритные области сплава, обеспечивается свободным титаном в таком размере, что в комбинации с нерастворимыми частицами это приводит к дополнительному измельчению зернистой структуры в литейном сплаве и способствует последующему улучшению его литейных качеств и физических свойств.
Сплав может содержать по меньшей мере 0,01% титана
Сплав может содержать вплоть до 1% титана
Сплав может содержать вплоть до 0,50% титана
Сплав может содержать вплоть до 0,15% титана (гипоперитектический)
Сплав может содержать больше чем 0,15% титана (гиперперитектический)
Сплав может содержать:
Cu (медь) | 3,0%-6,0% |
Mg (магний) | 0,0% — 1,5% |
Ag (серебро) | 0,0% — 1,5% |
Mn (марганец) | 0,0% — 0,8% |
Fe (железо) | 0,0% — максимум 1,5% |
Si (кремний) | 0,0% — максимум 1,5% |
Zn (цинк) | 0,0% — 4,0% |
Sb (сурьма) | 0,0% — 0,5% |
Zr (цирконий) | 0,0% — 0,5% |
Сo (кобальт) | 0,0% — 0,5% |
Ti (титан) | 0,01% — 1,0% |
Нерастворимые частицы | вплоть до 20% |
Al (алюминий) и неизбежные примеси | Баланс |
Нерастворимые частицы могут иметь размер частицы, составляющий 0,5 мкм или больше. Он может составлять вплоть до 25 мкм. Предпочтительно, размер частицы может составлять до 15 мкм или вплоть до 5 мкм. Наличие нерастворимых частиц может составлять по меньшей мере 0,5%, возможно вплоть до 20%.
Сплав может содержать:
Cu (медь) | 4,0% — 5,0% |
Mg (магний) | 0,2% — 0,5% |
Ад (серебро) | 0,0% — 0,5% |
Мп (марганец) | 0,0% — 0,6% |
Fe (железо) | 0,0% — 0,15% |
Si (кремний) | 0,0% — 0,15% |
Zn(цинк) | 0,0% — 1,8% |
Sb (сурьма) | 0,0% — 0,5% |
Zr (цирконий) | 0,0% — 0,5% |
Co (кобальт) | 0,0% — 0,5% |
Ti (титан) | 0,01% — 1,0% |
Нерастворимые частицы | до 10% |
Al (алюминий) и неизбежные примеси | Баланс |
Сплав может содержать:
Cu (медь) | 4,0% — 5,0% |
Mg (магний) | 0,2% — 0,5% |
Ag (серебро) | 0,4% — 1,0% |
Mn (марганец) | 0,0% — 0,6% |
Fe (железо) | 0,0% — 0,15% |
Si (кремний) | 0,0% — 0,15% |
Zn (цинк) | 0,0% — 1,8% |
Sb (сурьма) | 0,0% — 0,5% |
Zr (цирконий) | 0,0% — 0,5% |
Со (кобальт) | 0,0% — 0,5% |
Ti (титан) | 0,01% — 1,0% |
Нерастворимые частицы | вплоть до 10% |
Al (алюминий) и неизбежные примеси | Баланс |
Нерастворимые частицы могут присутствовать в пределах от 0,5%, до 10% или от 0,5% до 9%, или от 3% до 9% или от 4% до 9%.
Сплав может содержать:
Cu (медь) | 4,2% — 5,0% |
Mg (магний) | 0,2% — 0,5% |
Ag (серебро) | 0,0% — 0,85% |
Mg (марганец) | 0,0% — 0,4% |
Fe (железо) | 0,0% — 0,15% |
Si (кремний) | 0,0% — 0,15% |
Zn (цинк) | 0,0% — 1,8% |
Sb (сурьма) | 0,0% — 0,5% |
Zr (цирконий) | 0,0% — 0,5% |
Со (кобальт) | 0,0% — 0,5% |
Ti (титан) | 0,01% — 1,0% |
Нерастворимые частицы | 1,5% — 9,0% |
Al (алюминий) и неизбежные примеси | Баланс |
Сплав может содержать:
Cu (медь) | 4,2% — 5,0% |
Mg (магний) | 0,2% — 0,5% |
Ag (серебро) | 0,0% — 0,85% |
Mg (марганец) | 0,0% — 0,4% |
Fe (железо) | 0,0% — 0,15% |
Si (кремний) | 0,0% — 0,15% |
Zn (цинк) | 0,0% — 1,8% |
Sb (сурьма) | 0,0% — 0,5% |
Zr (цирконий) | 0,0% — 0,5% |
Со (кобальт) | 0,0% — 0,5% |
Ti (титан) | 0,01% — 1,0% |
Нерастворимые частицы | 4,0% — 9,0% |
Al (алюминий) и неизбежные примеси | Баланс |
Сплав может содержать:
Cu (медь) | 4,2% — 5,0% |
Mg (магний) | 0,2% — 0,5% |
Ag (серебро) | 0,0% — 0,85% |
Mg (марганец) | 0,0% — 0,4% |
Fe (железо) | 0,0% — 0,15% |
Si (кремний) | 0,0% — 0,15% |
Zn (цинк) | 0,0% — 1,8% |
Sb (сурьма) | 0,0% — 0,5% |
Zr (цирконий) | 0,0% — 0,5% |
Со (кобальт) | 0,0% — 0,5% |
Ti (титан) | 0,01% — 1,0% |
Нерастворимые частицы | 1,5% — 9,0% |
Al (алюминий) и неизбежные примеси | Баланс |
Сплав может содержать:
Cu (медь) | 4,2% — 5,0% |
Mg (магний) | 0,2% — 0,5% |
Ag (серебро) | 0,0% — 0,85% |
Mg (марганец) | 0,0% — 0,4% |
Fe (железо) | 0,0% — 0,15% |
Si (кремний) | 0,0% — 0,15% |
Zn (цинк) | 0,0% — 1,8% |
Sb (сурьма) | 0,0% — 0,5% |
Zr (цирконий) | 0,0% — 0,5% |
Со (кобальт) | 0,0% — 0,5% |
Ti (титан) | 0,01% — 1,0% |
Нерастворимые частицы | 4,0% — 9,0% |
Al (алюминий) и неизбежные примеси | Баланс |
Нерастворимые частицы могут иметь размер, который, по меньшей мере, в области на порядок величины меньше, чем расстояние между осями дендритов/размером зерна твердого сплава и занимают междендритные/межзерновые области сплава.
Частицы могут содержать частицы диборида титана.
Сплав может содержать 0,5% — 20% частиц диборида титана.
Сплав может содержать 0,5% — 10% частиц диборида титана.
Сплав может содержать 3% — 7% частиц диборида титана.
Сплав может содержать 4% частиц диборида титана.
Сплав может содержать 7% частиц диборида титана.
Двумя основными аспектами, которые были определены как факторы, которые приводят к изменчивости механических свойств и структурной целостности в базовых алюминий-медных сплавах, являются сегрегация компонентов сплава и образование междендритной пористости, особенно поверхностной пористости.
Исследование в отношении алюминий-медных сплавов для отливки показало, что значимым фактором, влияющим на изменчивость свойств материала, такого как сплав, является течение растворенного обогащенного материала через поры между дендритными осями, образованными во время затвердевания.
С целью предупреждения или сокращения перечисленных возникающих явлений было произведено введение высокодисперсных практически нерастворимых частиц в соответствии с изобретением. Обычно предполагалось, что добавление таких частиц, которые обычно являются твердыми и хрупкими, приводит к неприемлемому снижению пластичности сплава. Однако проведенное исследование показало, что хорошая пластичность сохраняется, как будет показано в нижеприведенном примере.
Дисперсная междендритная пористость является характеристикой данных сплавов из-за проблем заполнения усадки при затвердевании через дендритные поры. Этот тип пористости также приводит к снижению механическю и усталостной долговечности.
Следует понимать, что в настоящем изобретении добавление высокодисперсных практически нерастворимых частиц изменяет характеристики затвердевания сплава, но они не применяются как непосредственный механизм его затвердевания. Дополнительное добавление титана при разных уровнях приводит к существенному уменьшению размера зерна и дополнительно изменяет данные механизмы кристаллизации нижеописанным способом.
В соответствии с еще одним аспектом настоящего изобретения, заявляется способ изготовления отливки, содержащий шаг плавления алюминий-медного сплава, содержащего:
Cu (медь) | 4,0% — 5,0% |
Mg (магний) | 0,2% — 0,5% |
Ag (серебро) | 0,0% — 1,0% |
Mn (марганец) | 0,0% — 0,6% |
Fe (железо) | 0,0% — 0,15% |
Si (кремний) | 0,0% — 0,15% |
Zn (цинк) | 0,0% — 1,8% |
Sb (сурьма) | 0,0% — 0,5% |
Zr (цирконий) | 0,0% — 0,5% |
Со (кобальт) | 0,0% — 0,5% |
Ti (титан) | 0,01% — 1,0% |
Al (алюминий) и неизбежные примеси | Баланс |
Содержание нерастворимых частиц | 0,5% — 10%, |
и заливку полученного сплава в форму.
В соответствии с другим аспектом изобретения, обеспечивается отливка, изготовленная из сплава или посредством процесса в соответствии с настоящим изобретением.
Ниже следует описание изобретения на примере со ссылкой на прилагаемые чертежи, где:
Фиг.1 представляет собой схематическое изображение формы для отливки тестовых образцов.
Фиг.2 представляет собой схематическое изображение полученной отливки.
Фиг.3 представляет собой схематическое изображение полученной отливки после секционирования для микроскопического исследования.
Фиг.4 а, b, с представляют собой макроскопические изображения, показывающие уменьшение размера зерна при увеличении уровней титана 0,02 весового %*, 0,15 весового %*, 0,44 весового %*.
Фиг.5 а, b, с представляют собой изображение оптического микроскопа, показывающее изменение в микроструктуре при увеличении весового процента титана 0,02 весового %*, 0,15 весового %*, 0,44 весового %*, соответственно.
Фиг.6 а, b, с соответственно изображают в увеличенном масштабе микроструктуру сплавов при увеличении количеств титана.
Фиг.7 a, b изображают влияние на микроструктуру, полученное посредством регулирования скорости остывания отливок.
Примечание* Все приведенные весовые проценты в данном разделе являются измеренными показателями и, следовательно, подвергаются среднеквадратической погрешности. Композиционный анализ проведен посредством оптической эмиссионной спектроскопии с индуктивно-связанной плазмой и подвергается среднеквадратической погрешности, составляющей ±2% от полученного показателя.
В соответствии с изобретением сплав, содержащий*:
Cu (медь) | 4,35% |
Mg (магний) | 0,42% |
Ag (серебро) | 0,70% |
Mn (марганец) | 0,01% |
Fe (железо) | 0,01% |
Si (кремний) | 0,07% |
Zn (цинк) | 0,01% |
Ti (титан) | 0,02% |
TiB2 | 4,80% |
Означенный сплав А
был отлит стандартным способом.
Сплав отлит в склеенную смолой песчаную форму; конфигурация формы подробно описывается на фигуре 1. Образец заливают непосредственно из ковша при температуре 850 градусов по Цельсию, и полученная отливка затвердевает на воздухе. Полученная отливка, фигура 2, секционировалась, как описано на фигуре 3, а поверхность сплава А, отмеченная на фигуре 3, шлифовалась при использовании карбидокремниевой наждачной бумаги 120-1200 грит и полировалась при использовании алмазного соединения и коллоидного кремнезема. Затем полученную поверхность протравливают при использовании реагента «Kellers» и получают изображение при использовании оптического макроскопа и микроскопа.
Сплавы похожего состава, содержащие*
Cu (медь) | 4,29% |
Mg (магний) | 0,49% |
Ag (серебро) | 0,75% |
Mn (марганец) | 0,0% |
Fe (железо) | 0,01% |
Si (кремний) | 0,05% |
Zn (цинк) | 0,01% |
Ti (титан) | 0,15% |
TiB2 | 4,89% |
Означенный сплав B
и
Cu (медь) | 4,42% |
Mg (магний) | 0,26% |
Ag (серебро) | 0,78% |
Mn (марганец) | 0,01% |
Fe (железо) | 0,01% |
Si (кремний) | 0,04% |
Zn (цинк) | 0,01% |
Ti (титан) | 0,44% |
TiB2 | 4,58% |
Означенный сплав С
приготовлены похожим способом и в соответствии с изобретением.
Как видно из вышеприведенных составов, данные сплавы в соответствии с изобретением содержат от 1% до 9% частиц диборида титана. Данные частицы имеют размер, находящийся в пределах от 0,5 до 15 микрон. В вышеприведенном примере установлено, что размер зерна сплава находится между 40 и 200 мкм, а размер частицы диборида титана находится в пределах от 0,5 до 15 мкм; таким образом, частицы были примерно на порядок величины меньше, чем размер зерна. При сравнении трех отливок в макромасштабе и микромасштабе отчетливо наблюдается относительное уменьшение размера зерна при увеличении уровня титана.
Фигура 4а показывает в макромасштабе зернистую структуру в отливке сплава А. Фигура 4b показывает в том же масштабе зернистую структуру отливки сплава В, а Фигура 4с показывает зернистую структуру в отливке сплава С. При увеличении уровня титана отчетливо видно относительное уменьшение размера зерна. Фигуры 5а, 5b и 5с изображают зернистую структуру, полученную в трех сплавах, в микромасштабе.
Сплав А, содержащий 0,02%* титана, демонстрирует относительно равноосную крупнозернистую дендритную структуру, на фигуре 5а.
Сплав В, содержащий 0,15%* титана, демонстрирует мелкозернистую структуру с по-прежнему видимыми некоторыми первичными дендритными осями, на фигуре 5b.
Сплав С, содержащий 0,44%* титана, демонстрирует полностью мелкозернистую гомогенную структуру, на фигуре 5с.
Данный эффект увеличения весового процента титана оказывает воздействие на механизмы кристаллизации и отвердевшую структуру сплава. Данные измененные механизмы кристаллизации возникают вследствие взаимодействия усиленного измельчения зерна (результат активированного TiB2 и или TiAl3) и неактивных «проталкиваемых» частиц TiB2. Данное взаимодействие приводит к значительно сниженной тенденции сплава к образованию горячих трещин, минимизированному воздействию скорости остывания на размер зерна и, следовательно, к более устойчивым механическим свойствам по всем сечениям разной толщины, улучшенной чистоте обработки поверхности, а также оно предусматривает значительное снижение уровня подачи металла, необходимого для получения плотной отливки.
Добавление свободного титана оказывает воздействие на сплав двумя способами в зависимости от количества добавленного титана.
Во-первых, добавления титана ниже 0,15 весового процента осуществляются в гипоперитектической области; это означает, что ниже данного уровня частицы TiAl3 не будут образовываться в алюминиевом расплаве. Однако теория зарождения зерна приводит к предположению, что на гипоперитектических уровнях атомный тонкий слой, похожий по структуре с TiAl3, образуется на поверхности частиц TiB2, и это способствует зарождению α-алюминия. Посредством данного механизма добавление TiB2 в алюминиевые расплавы приводит к измельчению зерна, поскольку частицы TiB2 выступают в качестве мест гетерогенного зарождения для α-алюминиевых зерен. Считается, что эффективность данных частиц составляет около 1-2%, таким образом, только относительно маленькое количество частиц фактически инициирует образование зерна; оставшиеся частицы проталкиваются к фронту затвердевания посредством растущих алюминиевых зерен.
Таким образом, в сплаве в соответствии с изобретением добавление гипоперитектических уровней титана в расплав значительно активирует частицы TiB2, присутствующие в нем. Вместо использования одних частиц TiB2 для оказания воздействия на течение жидкого металла, они служат двойной цели измельчения зернистой структуры сплава, при этом также оказывая воздействие на течение жидкого металла и механизмы подачи. При добавлении чистого TiB2 в качестве добавки для измельчения зерна уровень добавления составляет до 0,004 весового процента, и даже при данных уровнях эффективность зарождения зерен составляет 1-2%. В сплаве в соответствии с изобретением уровни TiB2 могут быть более высокими, таким образом, имеется огромное количество частиц TiB2, которые остаются неактивными, и данные частицы проталкиваются растущими зернами в межгранулярные области во время затвердевания. Данное проталкивание частиц в сочетании с измельчением зерна, наблюдаемым в результате добавления гипоперитектических уровней титана, приводит к значимым преимуществам, как излагается ниже:
• Более мелкий размер зерна приводит к более маленьким более однородным индивидуальным ячейкам, и при кристаллизации это способствует передвижению к подаче массы, наблюдаемому в сплаве. Алюминиевые сплавы дают усадку при затвердевании; обычно этому способствует течение жидкого металла через междендритные области, а участки, в которые не поступает жидкий металл, при усадке образуют поры, называемые усадочными порами. Принцип подачи массы работает на основе того, что благодаря наличию частиц TiB2 в междендритных областях, оказывается достаточное сопротивление течению жидкого металла и сплав подталкивается к подаче посредством движения массы агломерации жидкость/ твердое тело/ частица. Это может произойти только в течение продолжительного периода времени, если распределение частиц является крайне гомогенным, что может обеспечиваться только в том случае, если размер зерна является маленьким и однородным.
• Данное двойное использование частиц TiB2 в качестве добавки, измельчающей зерно, и модификатора кристаллизации/подачи значительно улучшает сопротивление в отношении усадочной пористости и образования горячих трещин, а также обеспечивает большую гомогенность как литой структуры.
• Гомогенное распределение частиц TiB2 по всей отвердевшей структуре также предусматривает более устойчивые механические свойства и сохранение удлинения. Мелкозернистая структура предусматривает широкое и равномерное распределениеTiB2 по всей отвердевшей структуре, в противном случае частицы TiB2 будут скапливаться вместе и как хрупкая керамика будут способствовать росту трещин по сплаву, значительно снижая пластичность.
• Переход от дендритной подачи к массовой подаче имеет очень важные последствия в отношении разработки компонентов системы литья и подачи. Одна из самых больших проблем с ранее известным алюминий-медным сплавом заключается в том, что для получения плотной отливки в нее должно подаваться большое количество жидкого металла и, как следствие, выход материала является очень низким. Это сильно влияет на экономическую эффективность сплава, так как из больших количеств первичного металла, подлежащего плавлению, производятся относительно маленькие компоненты. Переход к подаче массы предусматривает значительное снижение требований к подаче, что улучшает эффективность в отношении использования материалов и затраты энергии на отливку.
Однако при данной концентрации титана измельчение зерна признано сильно зависящим от скорости остывания. Укрупнение зерна может возникнуть в медленно остывающих областях с ячеистой структурой, становящейся более глобулярной и дендритоподобной, что может отрицательно повлиять на сплав, делая его более подверженным таким проблемам, как образование горячих трещин, что сводит к нулю снижение требований к подаче металла. Следовательно, сплав в соответствии с изобретением с данным диапазоном Ti является наиболее подходящим для быстро остывающих систем, например для отливки, полученной литьем под давлением.
Со свободным титаном, превышающим 0,15 весового процента, сплав становится гиперперитектическим с учетом содержания титана. Частицы TiAl3 могут образовываться в алюминиевом расплаве выше данного уровня. Добавление гиперперитектических уровней титана в сплав приводит к дополнительному неожиданному уменьшению размера зерна и дополнительным крайне важным изменениям в поведении материала при затвердевании. Обычно добавление гиперперитектических уровней титана в сплав, уже содержащий 4-5 весовых процентов TiB2, предполагает оказание незначительного дополнительного воздействия на измельчение зерна, но в соответствии с изобретением было установлено, что объединенные эффекты TiB2 и TiAl3 не только уменьшают размер зерна, но также оказывают существенное воздействие на кристаллизацию и механизмы подачи, с получаемыми в результате улучшениями литейных качеств.
Добавление титана в данную гиперперитектическую область приводит к образованию частиц TiAl3, которые хорошо образуются в алюминиевом расплаве выше ликвидуса. TiAl3 оказался более сильной измельчающей зерно добавкой, чем TiB2, таким образом, в жидком металле до затвердевания находится огромное количество частиц TiAl3, суспендированных вместе с частицами TiB2. При затвердевании частицы TiAl3 быстро зарождают очень большое количество алюминиевых зерен, а рост зерна ингибируется посредством частиц TiB2, поскольку они проталкиваются к границам зерна. Как в случае с TiB2, не каждая частица TiAl3 будет зарождать зерно, однако в отличие от TiB2 частицы TiAl3 засасываются за счет ускоренного роста вперед, а не проталкиваются, что является критическим в сохранении пластичности сплава. Образование TiAl3 в расплаве приводит к дополнительному уменьшению размера зерна по сравнению с добавлением гипоперитектического титана и допускает образование очень мелких зерен при высоких скоростях остывания. Однако, что еще более важно, он допускает образование очень мелкозернистых структур даже в медленно остывающих участках. Измельчение зерна по-прежнему является функцией скорости остывания, но высокий уровень измельчения зерна означает, что даже при медленных скоростях остывания, размер зерна является достаточно мелким для возникновения подачи массы. Таким образом, с добавлением гиперперитектического титана зерна, наблюдаемые ранее в гипоперитектическом сплаве, можно не только переносить в технологии литья в песчаные формы, но и по выплавляемым моделям, поскольку они фактически способствуют дополнительной экономии подачи металла, приводящей к увеличению выхода материала и увеличению экономии материалов и энергии.
Вышеприведенные воздействия на зернистую структуру изображены на фигурах 5a, b и с, а также на фигуре 6. Фигура 6а иллюстрирует микроструктуру сплава при очень низком весовом проценте свободного титана, несмотря на то, что структура является равноосной и показывает некоторые доказательства измельчения зерна, уровень измельчения является очень низким. Фигура 6b показывает гипоперитектическую микроструктуру с содержанием свободного титана вплоть до 0,15 весового процента. На фигуре 6b TiB2 можно наблюдать присутствие в центре алюминиевых зерен и отсутствие алюминидных частиц, что указывает на то, что сплав находится ниже перитектического порога. Фиг.6с показывает, что при весовом проценте титана от 0,15 вплоть до весового процента титана 1,0, TiAL3 можно наблюдать в центре алюминиевых зерен, указывающих на то, что уровень титана находится выше перитектического порога, и алюминиды теперь выступают в качестве нуклеирующих частиц.
Добавление титана предусматривает широкий диапазон размеров зерна в состоянии литья, зависящий от скорости остывания. Фиг.7а и 7b, соответственно, демонстрируют, на фиг.7а, исключительно мелкозернистую структуру, которую можно получить при очень высокой скорости остывания, тогда как на фиг.7b изображается более крупнозернистая структура при более низкой скорости остывания; данные сплавы содержат гиперперитектические уровни титана.
В общем, как объяснено выше, количество свободного титана, необходимого для измельчения зернистой структуры в литейном сплаве и облегчения передвижения к подаче массы, относится к скорости остывания отливки, изготовленной из сплава. В общем, для отливок сравнимого размера, стандартная отливка в песчаную форму и отливка по выплавляемой модели, требуются уровни титана выше перитектического порога вследствие присущих им медленных скоростей остывания. Однако более высокая скорость остывания литейных обработок, например отливка, полученная литьем под давлением, и сильно охлаждаемая отливка в песчаной форме, могут быть мелкозернистыми при использовании гипоперитектических уровней свободного титана.
Усиление явления подачи массы, наблюдаемого в диапазоне гиперперитектического титана, позволяет значительно сократить подачу металла, необходимого для производства отливки в песчаной форме. Обычным алюминиевым сплавам необходимы большие емкости жидкого металла для обеспечения затвердевания и усадки отливки, если участок изолирован от подачи жидкого металла, и образуется пористость, чтобы компенсировать изменение объема, поскольку отливка отвердевает и дает усадку. Если структура это подача массы и отливка становится когерентной структурой на более раннем этапе в процессе кристаллизации и, если в ходе затвердевания отсутствует междендритное передвижение жидкого металла, то существует очень небольшая вероятность возникновения усадочной пористости.
Практический результат этого в производстве отливки заключается в том, что выход отливки или отливок из определенного количества металла значительно улучшается, то есть количество определенных компонентов, которые можно отлить из определенного количества металла, увеличивается. Это приводит к экономии затрат и энергии в производстве отливок и в обработке компонентов после отливки.
Более того, уменьшение размера зерна и преобразование из дендритной в ячеистую структуру приводит к уменьшению поверхностной и критической, внутренней, усадочной пористости. Это непосредственно оказывает воздействие на усталостную характеристику компонентов, отлитых из сплава, поскольку пористость является одним из факторов, угрожающих усталостной долговечности. Поры выступают в качестве точек инициирования в образцах для испытаний на усталость, а также оказывают воздействие на распространение трещин и окончательный разлом, выступая в качестве концентраторов напряжения и сокращая область восприятия нагрузки.
В данном описании: все составы выражаются в процентах по весу: под фразой «нерастворимые частицы», «нерастворимый» подразумеваются частицы, которые, по меньшей мере, по существу нерастворимы в сплаве; под «частицами» подразумеваются частицы металла или интерметаллическое соединение, или металлокерамический материал. Частицы могут содержать, например, диборид титана или карбид кремния, оксид алюминия, диборид циркония, карбид бора или нитрид бора: несмотря на то, что только один специальный состав сплава, осуществляющего изобретение, был описан выше на примере, другие составы сплава относятся к изобретению и к формуле изобретения в данном документе, а сплав, являющийся примером осуществления изобретения, может иметь состав сплава, состав частицы, размер частицы, содержание частицы и так далее, как описано в любой части данного описания.
Использованные в данном описании и формуле изобретения термины «содержит» и «содержащий» и их вариации означают, что упомянутые признаки, шаги или целые числа включены. Термины не должны интерпретироваться с целью исключения наличия других признаков, шагов или компонентов.
Признаки, раскрываемые в вышеприведенном описании или нижеследующей формуле изобретения, или на прилагаемых чертежах, выражены в своих специальных формах или касательно средств осуществления раскрытой функции, или способа, или процесса для получения раскрытого результата при необходимости могут отдельно или в любом сочетании таких признаков использоваться для реализации изобретения в его разных формах.
1. Алюминий-медный сплав для литья, содержащий, мас.%:
Cu (медь) | 3,0-6,0 |
Mg (магний) | 0,0-1,5 |
Ag (серебро) | 0,0-1,5 |
Mn (марганец) | 0,0-0,8 |
Fe (железо) | 0,0-1,5 |
Si (кремний) | 0,0-1,5 |
Zn (цинк) | 0,0-4,0 |
Sb (сурьма) | 0,0-0,5 |
Zr (цирконий) | 0,0-0,5 |
Со (кобальт) | 0,0-0,5 |
Свободный Ti (титан) | >0,15-1,0 |
Нерастворимые частицы | 0,5-20 |
Al (алюминий) и неизбежные примеси | Остальное, |
в котором нерастворимые частицы занимают междендритные области сплава и содержат частицы диборида титана, при этом алюминий-медный сплав содержит более чем 0,15 мас.% свободного титана для измельчения зернистой структуры в литейном сплаве.
2. Сплав по п. 1, в котором нерастворимые частицы имеют размер в диапазоне от 0,5 до 25 мкм.
3. Сплав по п. 2, в котором размер частицы находится в диапазоне от 0,5 до 15 мкм.
4. Сплав по п. 3, в котором размер частицы находится в диапазоне от 0,5 до 5 мкм.
5. Сплав по любому из пп.1-4, который содержит 3-7 мас.% частиц диборида титана.
6. Сплав по п. 5, содержащий 4 мас.% частиц диборида титана.
7. Сплав по п. 5, содержащий 7 мас.% частиц диборида титана.
8. Способ литья алюминий-медного сплава, включающий плавление сплава по любому из пп.1-7 и подачу полученного сплава в форму.
www.findpatent.ru
Как называется сплав алюминия с медью? Производство сплавов металлов на основе алюминия и меди — Radiodvor.com
Одним из самых распространенных металлов на Земле считается алюминий. Его еще называют «летающим металлом». Несмотря на то, что в природе он не встречается в чистом виде, его можно найти во многих минералах. А самый распространенный сплав, который используется для производства множества деталей и конструкций, – это дюралюминий (дюраль).
Одним из самых распространенных металлов на Земле считается алюминий. Его еще называют «летающим металлом». Несмотря на то, что в природе он не встречается в чистом виде, его можно найти во многих минералах. А самый распространенный сплав, который используется для производства множества деталей и конструкций, – это дюралюминий (дюраль). Его изобрел немецкий ученый Альфред Вильм, который работал на заводе Dürener Metallwerke AG (город Дюрен). Он определил, что сплав алюминия с медью обладает намного более лучшими характеристиками, чем сам металл в чистом виде.
Группа высокопрочных сплавов
На самом деле дюралюминий – это целая группа сплавов, в которых основным компонентом является алюминий, а его легирующими элементами – медь, цинк, марганец, магний. Но в целом их характеристика определяется не только составом, но и способом термообработки. В 1903 году впервые было обнаружено, что в процессе старения сплав алюминия с медью становится еще более прочным и твердым. Как выяснилось позже, это объясняется тем, что когда после закалки металл находится несколько дней при комнатной температуре, его перенасыщенный твердый раствор распадается, а это, в свою очередь, сопровождается упрочнением материала.
Процесс старения и возврат к предыдущему состоянию
Как уже было сказано ранее, старение металла – важный процесс, который обуславливается структурными превращениями, вызывающими изменения физических и механических свойств. Оно может быть естественным и искусственным. В первом случае сплав выдерживают несколько суток при комнатной температуре.
При искусственном старении время обработки сокращается, но при этом увеличивается температура. Для того чтобы вернуть сплав к предыдущему состоянию, его необходимо на несколько секунд нагреть до 270 градусов и затем быстро остудить.
Производство алюминия
Для того чтобы изготовить сплав алюминия с медью, необходимо высокотехнологичное оборудование и, конечно же, сам металл. Его добывают из бокситов. Это горная порода, которую необходимо измельчить, добавить в неё воду и обработать паром под большим давлением. Таким образом из глинозема отделяют кремний. Затем густую массу помещают в специальную ванну с расправленным криолитом. Содержимое нагревают до 950 °С и через него пропускают электрический ток в 400 кА. Это позволяет разорвать связь между атомами кислорода и алюминия. В результате последний оседает на дно в качестве жидкого металла. Так из жидкого алюминия делают отливки. Теперь металл полностью готов к механической обработке. Однако для того чтобы повысить его прочность, необходимо в него добавить легирующие элементы и таким образом получить высококачественный сплав алюминия с медью.
Производство дюрали
В общей сложности все алюминиевые сплавы делятся на две группы: литейные и деформированные. Процесс их производства зависит именно от того, какой вид должен получиться в конечном итоге. Кроме того, способ изготовления также зависит и от требуемых характеристик. Для производства дюраля алюминиевые слитки расплавляют в электрической печи. Интересно, что это один из немногих металлов, который можно переводить из твердого состояния в жидкое и наоборот множество раз. Это не повлияет на его характеристики. В расплавленный алюминий по очереди добавляют медь и другие легирующие элементы, такие как марганец, железо, магний. Очень важно соблюдать процентное соотношение: 93% алюминия, 5% меди, остальные 2% приходятся на другие легирующие элементы.
Закалка и отжиг дюраля
Обязательным для такого сплава является процесс закалки. Время выдержки для небольших деталей составляет всего несколько минут, а температура — около 500 °С. Сразу после процедуры дюраль получается мягким и вязким. Он легко поддается деформации и обработке. Спустя некоторое время сплав твердеет и его механические свойства повышаются. Если превысить порог температуры, происходит окисление и материал теряет свои характеристики. После закалки его необходимо медленно остудить в прохладной воде. Итак, вы уже знаете, как называется сплав алюминия с медью. Он нередко поддается деформации: холодному прокату, вытяжке, ковке. При этом возникает так называемая нагартовка. Это процесс, в ходе которого в структуре металла происходит передвижение и размножение дислокаций. В итоге сам сплав меняет свою структуру, становится более твердым и прочным. При этом снижается его пластичность и ударная вязкость. Для того чтобы деформации проходили более легко и нагартовка не разрушала металл, используют отжиг. Для этого сплав нагревают до 350 °С и затем остужают на воздухе.
Диаграмма состояния сплава (алюминий и медь)
Для того чтобы наиболее четко описать взаимодействие компонентов дюраля в твердом и жидком состоянии, а также объяснить характер изменения свойств сплава, используют диаграмму состояний.
Из неё видно, что наибольшая растворимость Cu в сплаве с алюминием наблюдается при температуре 548 °С и при этом она составляет 5,7 %. При повышении температуры она будет увеличиваться, а при понижении – уменьшаться. Минимальная растворимость (0,5 %) будет наблюдаться при комнатной температуре. Если же дюраль закалить выше 400 °С, он станет твердым однородным раствором – α. Во время данного процесса будет происходить распад твердого раствора. Очень необычно ведёт себя сплав алюминия и меди, формула которого — CuAl2. Процесс сопровождается выделением избыточной фазы А1. Такой распад протекает в течение длительного времени. Это и есть то естественное старение, о котором мы уже ранее упоминали.
Свойства сплава
Легирование металла теми или иными элементами позволяет повысить его характеристики. Вы запомнили, как называется сплав алюминия с медью? Какими же свойствами он обладает?
Сам по себе алюминий очень легкий, мягкий и совершенно непрочный. Он растворим в слабо концентрированных щелочах и кислотах. Добавив к алюминию медь и магний, можно получить уже достаточно прочный сплав. Его эксплуатационные параметры достаточно легко улучшить – просто нужно оставить его полежать при комнатной температуре. Так, эффект старения увеличивает прочность дюраля, о чём мы говорили выше. Сам по себе алюминий достаточно легкий. Незначительный процент меди не утяжеляет сплав. Еще одна положительная характеристика – это возможность многократно переплавлять сплав. При этом он не будет терять своих свойств. Единственное, что необходимо, так это после отливки дать ему «отдохнуть» пару суток. Недостатком дюралюминия является его низкая коррозионная стойкость. Поэтому чаще всего такой материал покрывают чистым слоем алюминия или же красят лаками и красками.
Алюминиевые сплавы и их применение
Впервые дюраль был использован для изготовления дирижаблей. Легкость и прочность этого материала позволила создать отличный летательный аппарат. Для этого применялась марка Д16т. В настоящее время сплавы с алюминием, цинком, медью и другими легирующими элементами широко используются в космонавтике, авиации и иных областях машиностроения.
Так, например, использование дюралюминия при изготовлении авто может значительно снизить его вес и стоимость, но при этом оно будет достаточно прочным. В общем, можно отметить, что ассортимент данного сплава достаточно широк: трубы, проволоки, листы, ленты, прутки и литые детали разных форм. Одной из самых востребованных и распространенных марок по-прежнему считается Д16т. Маленькая буква «т» в конце маркировки означает, что сплав закаленный и естественно состарился. Он используется: В конструкциях космических аппаратов, морских судов и самолетов. Для изготовления различных деталей для станков и машин. Для изготовления уличных табличек, дорожных знаков. Название сплава алюминия и меди должен знать каждый. Дюраль используется и в нефтяной промышленности. Так, специальные трубы, изготовленные из него, могут обеспечить эксплуатацию скважины в течение 6-7 лет.
Как называется сплав алюминия и меди, запомнить легко. Итак, мы рассказали, каким свойствами он обладает и где применяется. Он с легкостью может заменить стальной прокат, в особенности если необходимо сделать конструкцию маловесной.
radiodvor.com
никель сплавы алюминия сплавы меди
МЕДИ СПЛАВЫ — сплавы на основе меди, содержащие олово, цинк, алюминий, никель, железо, марганец, кремний, бериллий, хром, свинец, золото, серебро, фосфор и другие легирующие элементы. Добавки повышают прочность и твердость, стойкость против коррозии, улучшают антифрикционные свойства. М. с. делят на латуни, бронзы и медно-никелевые сплавы. Латуни — М. с., в которых главным легирующим элементом является цинк. Самыми распространенными латунями являются томпак (80 [c.156]Коррозионная активность диметилгидразина невелика, с ним нормально работают стали, чистый алюминий и его сплавы без окислов, титан, никель, монель-металл, сплавы меди применять не рекомендуется. В качестве прокладочного материала можно применять фторопласты, полиэтилен, каучук, асбест с фторопластом (фторасбесты). Допустимы эластомеры и бутилкаучуки, хлоропрены, плексиглас. Материалы, пригодные и проверенные при работе с гидразином, предпочтительнее применять с диметилгидразином, ограничения на материалы для гидразина относятся и к диметилгидразину. [c.142]
Ценные свойства проявляют медно-никелевые сплавы. Они имеют серебристо-белый цвет, несмотря на то что преобладающим компонентом в них является медь. Сплав мельхиор (массовая доля никеля 18—20%) имеет красивый внешний вид, из него изготавливают посуду и украшения, чеканят монеты. В сплав нейзильбер кроме никеля и меди входит цинк. Этот сплав используется для изготовления художественных изделий, медицинского инструмента. Медно-никелевые сплавы константан (40% никеля) и манганин (сплав меди, никеля и марганца) имеют высокое электрическое сопротивление. Их используют в производстве электроизмерительных приборов. Характерной особенностью всех медно-никелевых сплавов является их высокая стойкость к коррозии. Широкое применение в машиностроении, химической промышленности, в производстве бытовых товаров нашли латуни — сплавы меди с цинком (массовая доля цинка до 50%). Латуни — дешевые сплавы с хорошими механическими свойствами, легко обрабатываются. Для придания латуням особых свойств в них часто добавляют алюминий, никель, кремний, марганец и другие металлы. [c.251]
Из технических сплавов известны сплавы титана с железом, медью, алюминием, хромом, марганцем, кобальтом, никелем, молибденом, вольфрамом, ванадием и др. [c.86]
С. можно классифицировать 1) по числу компонентов — па двойные, тройные, четверные и т. д. 2) по структуре — на гомогенные (однофазные) системы и гетерогенные (смеси), состоящие из нескольких фаз последние могут быть стабильными (в равновесных С.) и метастабильными (в неравновесных С.) 3) по характеру металла, являющегося основой С., — на черные — сталь, чугун (см. Железа сплавы), цветные — на основе цветных металлов (см. Алюминия сплавы. Меди сплавы, Никеля сплавы и т. д.), С. редких металлов (см. Вольфрама сплавы, Молибдена сплавы. Ниобия сплавы, Циркония сплавы и др.), С. радиоактивных металлов — на основе урана и плутония 4) по характерным свойствам — на тугоплавкие, легкоплавкие, высокопрочные, жаропрочные,твердые, антифрикционные, коррозионноустойчивые, износостойкие, проводниковые, с высоким электросопротивлением, магнитные и др. 5) по технологич. признакам — на литейные (для изготовления деталей методом литья) и деформируемые (подвергаемые ковке, штамповке, прокатке, протяжке, прессованию и др. видам обработки давлением). [c.502]
Латуни. Латунями называют сплавы меди с цинком, содержащие от 10 до 50% 2п, иногда дополнительно легированные рядом других элементов (алюминием, оловом, кремнием, никелем и др.). В первом случае это так называемые простые латуни, во втором — специальные латуни. [c.252]
Применение. Важнейшая область применения алюминия— производство легких сплавов на его основе. Алюминий широко используют в качестве легирующих добавок в сплавах на основе меди, магния, титана, никеля, цинка и железа. В виде чистого металла алюминий используют для изготовления химической аппаратуры, электрических проводов. Алюминиевая фольга используется для изготовления конденсаторов. [c.282]
В качестве катализаторов гидрирования применяют никель, платиновую и палладиевую чернь. В последнее время используются сложные катализаторы, состояш,ие из смеси окислов хрома и некоторых других металлов (меди, цинка). Особенно активным катализатором является никель Ренея, который получается при обработке сплава никеля с алюминием (1 1) едким натром. Катализаторы применяются в мелкораздробленном состоянии, в большинстве случаев на носителе (активированный уголь, асбест) и при различных температурах. В присутствии никеля Ренея, платины и палладия гидрирование обычно проводят при комнатной температуре, а в присутствии никеля и меди — при нагревании. [c.147]
Различают пластичные ( НВ 100) подшипниковые сплавы. К пластичным материалам относятся баббиты, антифрикционные сплавы алюминия с медью, никелем и сурьмой, свинцовые бронзы. Их применяют в высокоскоростных опорах, рассчитанных на работу в режиме жидкостной смазки. Эти материалы не обладают высокой прочностью и их наносят наплавкой или заливкой тонким слоем на твердую и прочную основу — подложку из стали, чугуна или бронзы. Выпускают биметаллические вкладыши, трубы и ленту с антифрикционным покрытием из пластичных материалов. Толщина слоя заливки вкладышей составляет от десятых долей миллиметра до 2-3 мм. Пластичные подшипниковые материалы обладают высокими антифрикционными свойствами, хорошей прирабатываемостью и износостойкостью, удовлетворительно работают в режимах полужидкостного и даже полусухого трения. [c.99]
Фильтровальной бумагой просушивают пятно, полученное в результате обработки поверхности исследуемого объекта щелочью, наносят каплю азотной кислоты и перемешивают стеклянной палочкой. В случае сплава алюминия с медью, никелем и цинком пятно мгновенно обесцвечивается. В присутствии в сплаве кремния обесцвечивания не происходит. [c.181]
Большая часть алюминия применяется в виде его сплавов с магнием, медью, кремнием, цинком, никелем, железом и другими металлами. Наиболее важные — сплавы типа дюралюминия (я 94% А1, 4% Си, 5% Mg и 0,5% Мп), литейные сплавы — силумины ( — 12% 51) и сплавы с магнием ( 10% Mg). По своим ценным свойствам сплавы алюминия занимают второе место после сплавов железа, причем области применения их неуклонно расширяются. Особенно возросло их применение в транспорте и строительном деле. Благодаря таким свойствам, как малая плотность, [c.476]
Присутствие же в алюминии легирующих присадок резко сказывается на его способности растворять водород, особенно R жидком состоянии. Так, изучением растворимости водорода в алюминии в интервале температур 700—1000° было установлено. что медь, кремний и олово ее понижают, причем из сплавов алюминия с медью минимальной растворимостью водорода обладает сплав с 6% меди. Добавка к алюминию марганца, никеля, магния, железа, хрома, церия, тория и титана повышает растворимость в нем водорода, причем последние три металла увеличивают растворимость водорода в большем интервале температур, чем железо и хром. В присутствии 2,8 /о Мп или 6 /о Mg алюминий приобретает способность поглотать водород б твердом состоянии, при 600° в присутствии марганца и при 500° — в случае добавки магния [175]. [c.214]
Образование указанных фаз определяется природой легирующего элемента и способностью к растворению его в феррите или аустените. Например, никель, кремний, алюминий и медь образуют с а-железом твердые растворы — легированный феррит, а хром, молибден и вольфрам — преимущественно карбидную фазу. Образование фаз в большой степени зависит от количества в сплаве углерода и характера термообработки. [c.95]
Многие хлористые соединения — растворы хлористой меди, алюминия, кальция и других металлов — являются также сильными агрессивными средами. В таких растворах разрушаются алюминий, сплавы меди, серебро и сплавы никеля с [c.543]
Алюминий —одна из наиболее распространенных добавок в сплавах на основе меди, магния, титана, никеля, циика, железа. [c.637]
Значительно чаще применяют металлические сплавы на основе железа (сталь и чугун), алюминия, магния, меди (бронза и латунь), никеля, ниобия, титана, тантала, циркония и других металлов. [c.175]
Хорошо известная диаграмма равновесия системы железо— углерод исключительно сложна. Она позволяет судить о том, как широк диапазон режимов термообработки и закалки. Сплавы цветных металлов имеют несколько иную кристаллическую структуру, поэтому для них используют ограниченный диапазон режимов термической обработки. Некоторые сплавы меди, алюминия и никеля можно подвергать различным методам термообработки. [c.316]
Ингабитор предназначен для защиты сложных изделий (состоящих из различных металлических и неметаллических материалов) от атмосферной и биологической коррозии. Применяют для защиты изделий из стали, меди и её сплавов, алюминия и его сплавов, хрома, кадмия, никеля, олова, серебра и припоя, а также оксидированных, хромированных, кадмированных, никелированных поверхностей металлов, в том числе оксидированного магния. Ингабитор применяют на пористых носителях, содержащих 40-50 % (мае. доля) ингабитора. [c.377]
Извлечение щелочью алюминия и кремния из их сплавов с никелем, кобальтом, железом или медью применяется для приготовления ( скелетных ) катализаторов. [c.64]
Вообще говоря, в морской воде в качестве окислителя могут выступать ионы НзО или молекулы воды и растворенный кислород. Исследованию катодных процессов в хлоридсодержащих средах были посвящены работы Г. В. Акимова, Н. Д. Томашева, Г. Б. Кларк, И. Л. Розенфельда. Как показали исследования, коррозия магния и его сплавов протекает в основном за счет водородной деполяризации алюминий и его сплавы, коррозионностойкие и конструкционные стали, никель и никелевые сплавы, медь, медные сплавы подвергаются коррозии с кислородной деполяризацией. Растворимость кислорода в морской воде ограничена. При протекании коррозии с кислородной деполяризацией очень часто скорость катодного процесса определяется диффузией кислорода и поверхноети металла. В таких условиях перемешивание среды или перемещение поверхности металла относительно среды является важным фактором, который может оказать существенное влияние на характер коррозии. При перемешивании скорость катодного процесса будет уве-личиваться и металл из пассивного состояния может переходить в пробойное состояние (см. рис. 18). [c.43]
МОНЕЛЬ-МЕТАЛЛ — сплав на основе никеля, содержит до 30% меди, 2—3% железа, марганец, иногда алюминий. Очень устойчив против коррозии в морской и пресной водах, в щелочах, органических кислотах и красителях. Обладает хорошими механическими и термическими свойствами. М.-м. широко применяется в электротехнике, судостроительной, электровакуумной, текстильной, химической и других промышленностях, в медицине, а также в аппаратостроении. [c.164]
При определении в бронзах алюминия, железа, никеля и цинка медь обычно удаляют электролизом или тиосульфатом. В бронзах, содержащих одновременно бериллий, алюминий и желе-3 о, требуется много предварительных операций для их разделения. В сплавах медь — железо, содержащих до 50% железа, медь количественно выделить невозможно. В указанных случаях анализ может быть выполнен при помощи хроматографического ионообменного разделения. [c.147]
Титан губчатый. Технические условия Титан и сплавы титановые деформируемые. Марки Сплавы титановые. Методы определения алюминия Сплавы титановые. Методы определения ванадия Сплавы титановые. Метод определения хрома и ванадия Сплавы титановые. Методы определения вольфрама Сплавы титановые. Методы определения железа Сплавы титановые. Методы определения кремния Сплавы титановые. Методы определения марганца Сплавы титановые. Методы определения молибдена Сплавы титановые. Методы определения ниобия Сплавы титановые. Методы определения олова Сплавы титановые. Метод определения палладия Сплавы титановые. Методы определения хрома Сплавы титановые. Методы определения циркония Сплавы титановые. Методы определения меди Сплав титан-никель. Метод определения титана Сплав титан-никель. Метод определения никеля Титан губчатый. Методы отбора и поготовки проб Титан губчатый. Метод определения фракционного состава Сплавы титановые. Методы спектрального анализа Титан и сплавы титановые. Метод определения водорода Титан и титановые сплавы. Методы определения кислорода Титан губчатый. Метод определения твердости по Бринеллю Свинец, цинк, олово и их сплавы Олово. Технические условия [c.579]
Широкое применение при гидрировании кратных С==С-связей нашли сплавы меди с никелем, палладием, алюминием. В настоящее время считается признанным, что каталитическая и хемосорбционная активность в реакциях окислительновосстановительного типа связана с электронной конфигурацией переходных металлов, с незаполненностью их -уровней [291, 292]. При сплавлении переходных металлов с другими металлами, дающими твердые растворы, можно получить набор катализаторов, отличающихся электронной структурой. Например, медь и никель дают непрерывный ряд твердых растворов, в которых -зона никеля постепенно заполняется электронами меди, что должно изменять каталитическую активность. -Уровень никеля полностью заполняется при содержании меди 60%. В согласии с теорией Даудена можно ожидать, что при достижении этого критического состава активность сплава должна резко упасть. [c.98]
Методы испытаний необходимо разрабатавать и выбирать для каждой группы сплавов в отдельдости. Так, согласно ГОСТ 9020—74 магниевые сплавы испытывают во влажной камере или при полном погружении в 0,001- и 3 %-ные растворы хлористого натрия. Алюминиевые сплавы рекомендуется испытывать при полном погружении в 3 %-ный раствор хлористого натрия, содержащий 0,1 % Н2О2, при переменном погружении в 3%-ный раствор хлористого натрия, в камере соляного тумана или просто во Влажной камере при повышенной температуре и периодической конденсации влаги. Не может быть единого метода испытания для всех сплавов и тем более единых коэффициентов пересчета результатов лабораторных испытаний на длительную эксплуатацию, так как данные коррозионная среда и вид испытаний не в одинаковой степени ускоряют процесс коррозии различных металлов. Периодическая конденсация влаги увеличивает коррозию цинка и стали, а коррозию никеля ускоряет незначительно (если атмосфера не содержит промышленных загрязнений). Железо и его сплавы, как и сплавы алюминия с медью, весьма чувствительны к периодическому смачиванию электролитами, коррозия же кадмия и чистого алюминия при этом ускоряется в меньшей степени. [c.7]
Поэтому, например, сплавы АЛ4 и АЛ4В предназначаются для изготовления деталей, работающих в контакте с коррозион1 оактивными средами. Широко известны деформируемые сплавы алюминия с медью и небольшими добавками кремния, магния, марганца и никеля так называемый дюралюминий (Д1, Д16) и сплавы АМг и АМг-б — алюмомагниев1ые, с содержанием 1—6% магния. По коррозионной стойкости дюралюминий значительно уступает чистому алюминию, особенно после термической обработки. [c.112]
Медные сплавы — это сплавы меди с другими элементами при содержании ее более 50%. Медные сплавы получили в технике широкое распространение в машиностроении— латунь (медь с цинком) и бронза (медь с оловом, алюминием, свинцом, кремнием, марганцем, железом или бериллием), обладающие высокой прочностью и антифрикционностью в электротехнике— сплавы меди с никелем, цинком и марганцем, обладающие повышенным электросопротивлением. Медные сплавы находят широкое применение для изготовления корпусных и других деталей запорной и регулирующей арматуры. [c.32]
Из этих данных видно, что хлорид алюминия в порошкообразном или расплавленном виде, а также расплав хлоралюмината натрия при изученных температурах обладают высокой коррозионной активностью по отношению к ух леродистым, нержавеющим сталям, никелю и его сплаву ХН78Т, алюминию, меди. Скорость коррозии этих материалов колеблется в пределах от 3,5 до 18 мм/год. Более высокую коррозионную стойкость показали сплав молибдена Щ-10, а также молиб-денсодержащие никелевые сплавы. [c.114]
Марганец применяется главным образом в производстве легированных сталей. Марганцовистая сталь, содержащая до 15% Мп, обладает высокими твердостью и прочностью. Из нее изготовляют рабочие части дробильных машин, щаровых мельниц, железнодорожные рельсы. Кроме того, марганец входит в состав ряда сплавов на основе магния он повыщает их стойкость против коррозии. Сплав меди с марганцем и никелем — манганин (см. 200) обладает низким температурным коэффициентом электрического сопротивления. В небольших количествах марганец вводится во многие сплавы алюминия. [c.663]
При решении вопроса о допустимости контакта между металлами можно также рукоиодствоваться следующими данными. Все металлы разделены на пять групп первая группа магний вторая — п,и1гк, алюминий, кадмий третья — железо, углеродистые стали, свинец, олово четвертая — никель, хром, хромистые стали (Х17), хромоиикелевые стали (Х18Н9) пятая — медноникелевые сплавы, медь, серебро. [c.182]
Использование никеля в технике. Большое количество никеля используется для никелирования, т. е. обработки поверхностей из-де.чий из других мегаллов. Никель добавляют как легирующий материал в стали, придавал им особые свойства он является основой некоторых жаропрочных сплавов его сплавы с медью обладают ценными свойствами. Таковы константан и никелин, использую-Н1,исся в качестве материала для электропроводов, гейзильбер — иеокисляюшийся сплав, содержащий кроме никеля и меди также и цинк. Никель применяется также в сплавах с алюминием. [c.318]
Необходимо также отметить существование четвертого класса— дисперсионно-твердеющих нержавеющих сталей, которые приобретают высокую прочность и твердость в результате низкотемпературной термообработки, проводимой после закалки с вы—сокой температуры. Эти сплавы Сг—Ре содержат меньше никеля, чем это требуется для стабилизации аустенитной фазы (или вообще его не содержат). Зато они содержат такие легирующие элементы, как алюминий или медь, которые обеспечивают высокую твердость, приводя к образованию и выделению интерметаллических соединений вдоль плоскостей скольжения или границ зерен. Эти стали применяют в тех же случаях, что и коррозионностойкие никеле- [c.297]
Имеются доказательства, что при пластической деформации атомы цинка концентрируются преимущественно у границ зерен Различия в составе приводят к электрохимическому взаимодей ствию таких участков с зернами. По этой причине в ряде агрес сивных сред небольшая межкристаллитная коррозия может про исходить и без приложенного напряжения. Однако участки пла стической деформации при определенных значениях потенциала могут способствовать адсорбции комплексных ионов аммония, что в свою очередь приводит к быстрому образованию трещин. Аналогичный эффект может наблюдаться и вдоль линий скольжения (транскристаллитное растрескивание). По-видимому, выделение цинка на границах зерен является существенной причиной наблюдаемой межкристаллитной коррозии латуней в то же время наличие структурных дефектов в области границ зерен или линий скольжения играет большую роль в протекании КРН. Следовательно, разрушение медных сплавов в результате растрескивания наблюдается не только в сплавах меди с цинком, но также и со множеством других элементов, например кремнием, никелем, сурьмой, мышьяком, алюминием, фосфором [21 и бериллием [31]. [c.338]
Основная часть никеля (85—87%) расходуется для- производства сплавов с железом, хромом, медью и другими металлами. Эти сплавы отличаются высокими механическими, антикоррозионными, магнитными и электрическими свойствами. Сплавы никеля с алюминием (а также с магнием и кремнием) используются в качестве исходного вещества для получения никеля Ренея — никелевого катализатора скелетного типа, образующегося при действии щелочи на эти сплавы. [c.286]
Большинство химических элементов являются металлами (см. рис. 53). Многие из них в силу своей химической активности находятся в природе в связанном состоянии, и поэтому до XVIII в. были известны лишь металлы, встречающиеся в самородном состоянии или легко выплавляемые из руд, такие, как золото, серебро, медь, ртуть, свинец, олово, железо и висмут (причем висмут долгое время принимали за разновидность свинца, олова или сурьмы). Использование сплава меди с оловом сыграло важную роль в развитии производительных сил общества и открыло бронзовый век . Совершенствование плавильных печей позволило производить чугун и другие сплавы железа, появление которых явилось новой вехой в создании человеком материальных ценностей. Алюминий, никель, хром, марганец, магний и другие хорошо известные теперь металлы стали получать лишь в конце XIX — начале XX в., а титан — только в середине XX в. [c.390]
chem21.info
Медь и ее сплавы с оловом, цинком, алюминием, никелем, серебром, железом, свинцом
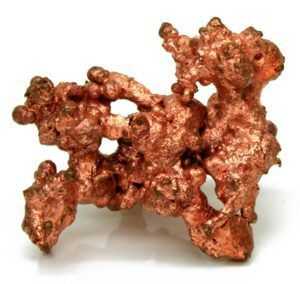
Минерал меди
Металл, имеющий розовато-красный цвет и температуру плавления – 1083 °С, называется медью. Для этого химического элемента не свойственно содержать полиморфные соединения. Его кристаллизация происходит в гранецентрированной решетке. Влага и углекислый газ оказывает медленное воздействие, вещество обретает зеленый цвет после покрытия пленкой. Этот налет служит в качестве защиты для меди от коррозии.
Где используется медь и ее сплавы? В технике при низких температурах медь и ее сплавы выступают в качестве традиционных материалов. Также, как и для серебра, химического элемента, существенно иметь высокие механические свойства и теплопроводность, обладать коррозийной стойкостью.
Механические и технологические свойства такого элемента, как сплавы на основе меди нарушаются под влиянием вредных примесей таких, как серы и кислорода, висмута и свинца.
Основные технологические процессы получения металла:
1. Для обогащения руды используют метод флотации, при помощи которой соединения меди и пустой породы проходят смачивание. Отдельно подготавливается суспензия с флотационным агентом и соединяется с размельченной рудой. В качестве флотационного агента можно использовать пихтовое масло, благодаря которому на поверхности рудных частичек образуется пленка. На поверхности руды собираются пузырьки, они появляются от продувки воздухом, затем образуется пена. На дно опускается пустая порода, не прошедшая смачивания маслом. До 30% меди находится в собранной и высушенной пене – концентрате.
Подробнее о методе флотации
2. Сернистый газ получается в результате обжига концентрата. Таким образом, получается обожженный медный концентрат и серная кислота, без содержания алюминия. Затем в отражательных печах получается медный штейн, ингредиент, в состав которого входит сульфид железа и медь.
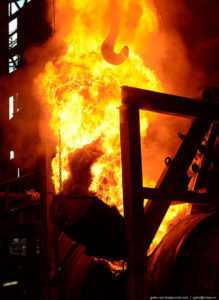
Заливка штейна в конвертер
3. Для продувки штейна предусмотрены конвертеры с кислородом, в них получается черновая медь. У такого ингредиента содержится 1,5% примеси без серебра и алюминия. Во время продувки участвует кварцевый песок, окись железа образуется благодаря переходящим сульфидам, после этого образуется шлак. Серная кислота получается благодаря поступлению сернистого газа.
4. Черновая медь очищается при помощи огневого или электролитического метода. Деревянные жерди используются при огневом способе, а затем происходит пропускание воздуха. Примеси выводятся благодаря окислению жердей кислородом воздуха. Электролитический метод включает в себя установление меди в качестве анода, а медные листы служат в виде катода. Анод начинается растворяться, когда проходит ток, при этом на дне происходит оседание меди на катоде. Изделия из меди и серебра, имеющие вес 60-90 кг можно получить в течение 10 дней. В это время дно ванны наполняется шламом – осадком примеси. Чаще всего шлам состоит из серебра – 35%, золота – 1% и селена – 6%, без железа и свинца, а вот алюминия здесь не обнаружено.
Сплавы химического элемента – меди
Латунь
На основе меди получается двойной или многокомпонентный сплав – латунь, мягче и легче стали. В ней легирует главный ингредиент – цинк. В отличие от меди у металла больше прочности, устойчивости перед коррозиями, а также лучшая обрабатываемость, как у железа и стали. Химический элемент, как алюминий с легкостью можно разрезать, или разлить. Цинк в латуни содержится до 45%, а вот серебра и железа нет. Чем больше металл находится в составе, тем становится менее прочным. Сплавы на основе меди не содержат легирующие ингредиенты больше 7-9%.
Технологический признак металла состоит из литейных и деформируемых веществ. Из этих элементов изготавливают фасонные отливки, они выглядят в форме чушки.
Изделия из латуни
Из деформируемых латуней делают простые элементы. Проволока, прутки, полосы, ленты, трубы, листы, и другие прокатные, а также прессованные изделия считаются полуфабрикатами латуни, напоминающие изделия из алюминия. В общем, и химическом машиностроении металл, так как и бронза широко используется.
Немного о бронзе
Бронза
Бронза — это сплав меди, в который добавляется олово, марганец, алюминий, свинец, кремний, бериллий, чего нет в стали. Бронза, наподобие серебра, она устойчивая перед коррозией, у нее высокие антифрикционные и хорошие литейные свойства, её легко можно обработать резанием. Чтобы улучшить механические характеристики, а также придать особые свойства металлу — бронза, для легирования используют никель, железо, цинк, титан, фосфор.
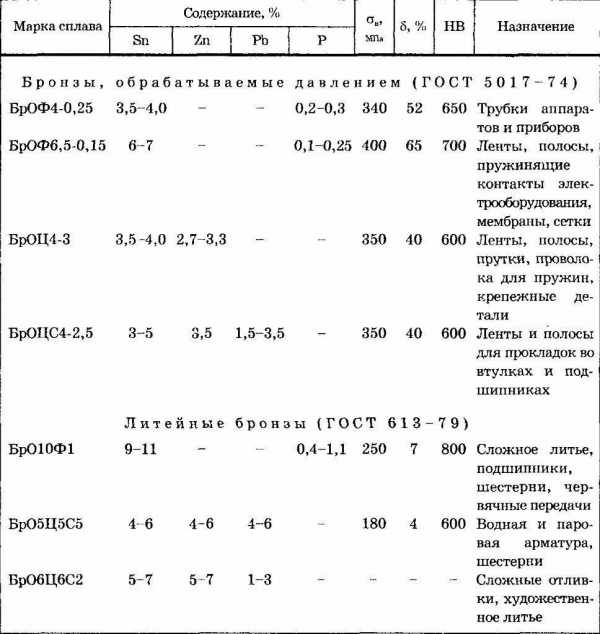
Химический состав и механические свойства некоторых бронз
Если к химическому элементу добавить марганец, у элемента появится устойчивость к коррозии, при добавлении никеля, бронза становится пластичней. Чтобы изделие сделать прочным, наподобие стали, рекомендуется добавить немного железа. Улучшит литейные свойства элемента цинк. С помощью свинца, бронза станет более обрабатываемая.
Сплав – никель и медь
Медноникелевым сплавом называется соединение, в котором основой является медь, а легирующий элемент – это никель, алюминия и свинца не обнаружено. В основном используют электротехническими и конструкционными сплавами.
Соединение, состоящее из меди, никеля и алюминия принято называть куниали. Его основными элементами является никель – 6-13%, немного алюминия – 1,5-3%, все остальное занимает медь. В отличие от серебра, это изделие проходит термическую обработку. Из металла изготавливают детали, имеющие повышенную прочность, к ним относятся электротехнические изделия, а также пружины, как изготавливают из стали.
Изделие, которое представляет собой сплав меди с цинком и никелем носит необычное название – нейзильбер. В его составе содержится никель – 15%, цинк – 20%, весь остальной состав принадлежит меди, и нет свинца. Металл, в отличие от стали, обладает приятным белым цветом, который приближен к окраске серебра. Химический элемент, как и бронза, хорошо выдерживает атмосферную коррозию, он служит неотъемлемой частью приборостроения, а также при производстве часов.
Нейзильбер часто используется как конструкционный материал
Металлы, содержащие медь с никелем в небольшом количестве и марганец, не превышающий 1%, называются мельхиорами. У этих изделий, как и у стали, повышена устойчивость перед коррозией, на них не оказывает влияние морская вода. Металлы чаще всего применяют при изготовлении теплообменных аппаратов, из них делают чеканные и штамповые изделия.
Для изготовления термопар пользуются специальным термоэлектродным сплавом, который называется – копелем. В состав химического элемента входит никель с медью и составляет 43%, а также марганец, в количестве 0,5%.
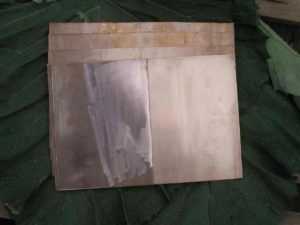
Марганцовистая бронза — манганин
Сплав, у которого есть высокое удельное электрическое сопротивление, носит название – манганин. Это изделие состоит из марганца, который составляет 12% и меди с никелем, на них отводится 3%, серебра и железа не обнаружено. При изготовлении электронагревательных приборов в отличие от алюминия и стали, медь и бронза используется чаще.
Важным преимуществом такого металла, как медь и бронза является то, что ее применяют в электротехнической промышленности. Металл широко используют при изготовлении электрических проводов. Чем чище химическое изделие, тем высоко его преимущество. Проводимость электричества упадет на 10%, если в меди будет обнаружено 0,02% алюминия.
В определенной области производства изделия из меди, стали и серебра считаются лучшим материалом. Механические детали производственного оборудования не могут быть изготовлены из другого металла, алюминия или железа. Кроме меди и стали в современном мире высоко ценится бронза. А вот сплав меди с оловом считается прочным металлом, в котором сохранена пластичность.
Видео: Добыча Меди
ecology-of.ru