Литейные сплавы алюминий-кремний – aluminium-guide.com
Алюминиевые литейные сплавы отличаются от алюминиевых деформируемых сплавов в основном тем, что они содержат значительно большее количество кремния.
Алюминиевые литейные сплавы должны содержать в дополнение к упрочняющим элементам достаточное количество элементов, которые образуют эвтектику. Это необходимо для того, чтобы литейные сплавы имели высокую текучесть для подпитки и заполнения пор и трещин при усадке, которая неизбежно возникают во всех отливках, кроме, может быть, самых простейших.
Силумины – сплавы алюминий-кремний
Сплавы алюминий-кремний, которые не содержат добавок меди, применяют тогда, когда требуются хорошие литейные свойства и высокая коррозионная стойкость. Часто их называют силуминами. Металлографические структуры чистых компонентов, алюминия и кремния, а также нескольких промежуточных химических составов показаны на рисунке ниже. Промежуточные составы являются смесью алюминия, который содержит около 1 % растворенного кремния и частицы почти чистого кремния.
Рисунок – Фазовая диаграмма алюминий-кремний и литейные микроструктуры чистых алюминия и кремния, а также сплавов различного химического состава
Если требуется высокая прочность и твердость, то в эти сплавы добавляют магний, который делает их термически упрочняемыми. Сплавы с низким содержанием кремния, таким как 2 %, иногда применяют для отливок, но обычно содержание кремния в литейных сплавах составляет от 5 до 10 %.
Прочность и пластичность этих сплавов, особенно с высоким содержанием кремния, может быть значительно улучшены модификацией эвтектики алюминий-кремний.
Модифицирование доэвтектических сплавов (содержание кремния менее 12 %) особенно часто применяют при литье в песчаные формы. Это модифицирование достигается путем введения в расплав контролируемых добавок натрия или стронция, которые измельчают эвтектическую фазу.
Содержание кремния в пределах от 4 до 12 % снижает потери от брака литья, а также дает возможность отливать более сложные отливки с большой разницей по толщине, а также обеспечивает более высокое качество поверхности и внутреннее качество металла. Это происходит благодаря влиянию кремния на повышение жидкотекучести сплава, снижения растрескивания и улучшения наполняемости форм.
Оптимальная эвтектика алюминий-кремний
Требуемое количество эвтектики зависит также от особенностей процесса литья. Сплавы для литья в песчаные формы обычно имеют меньше эвтектики, чем те которые льют в металлические формы. Это связано с тем, что в «мягких» песчаных формах отливки меньше растрескиваются, чем в жестких металлических. Повышение сопротивления растрескиванию в ходе литья способствует небольшой интервал температуры затвердевания.
В сплавах алюминий-кремний без добавок других элементов при неравновесном условиях литья объемная доля эвтектики линейно увеличивается от 0 до 1 при возрастании содержания кремния от 1 до 12 %.
Источник: Aluminum and Aluminum Alloys, ASM International, 1996
Наиболее распространенные алюминиевые сплавы
Наиболее распространенные алюминиевые сплавы
Большинство алюминиевых предметов, на самом деле, изготовлены из алюминиевых сплавов. Механической прочности чистого алюминия, как правило, не хватает для решения даже самых простых бытовых и технических задач. Добавление легирующих элементов в алюминий существенно изменяет его свойства.

Дюралюминий | Основной химический состав, % | ||||
Cu | Mn | Mg | Si,не более | Fe,не более | |
Д1.![]() |
3,8-4,8 | 0,4-0,8 | 0,4-0,8 | 0,7 | 0,7 |
Д16….. | 0,3-0,9 | 1,2-1,8 | 0,5 | 0,5 | |
Д18….. | 2,2-3,0 | <0,2 | 0,2-0,5 | 0,5 | 0,5 |
Д19….. | 3,8-4,3 | 0,5-1,0 | 1,7-2,3 | 0,5 | 0,5 |
Д20.![]() |
6,0-7,0 | 0,4-0,8 | <0,05 | 0,3 | 0,3 |
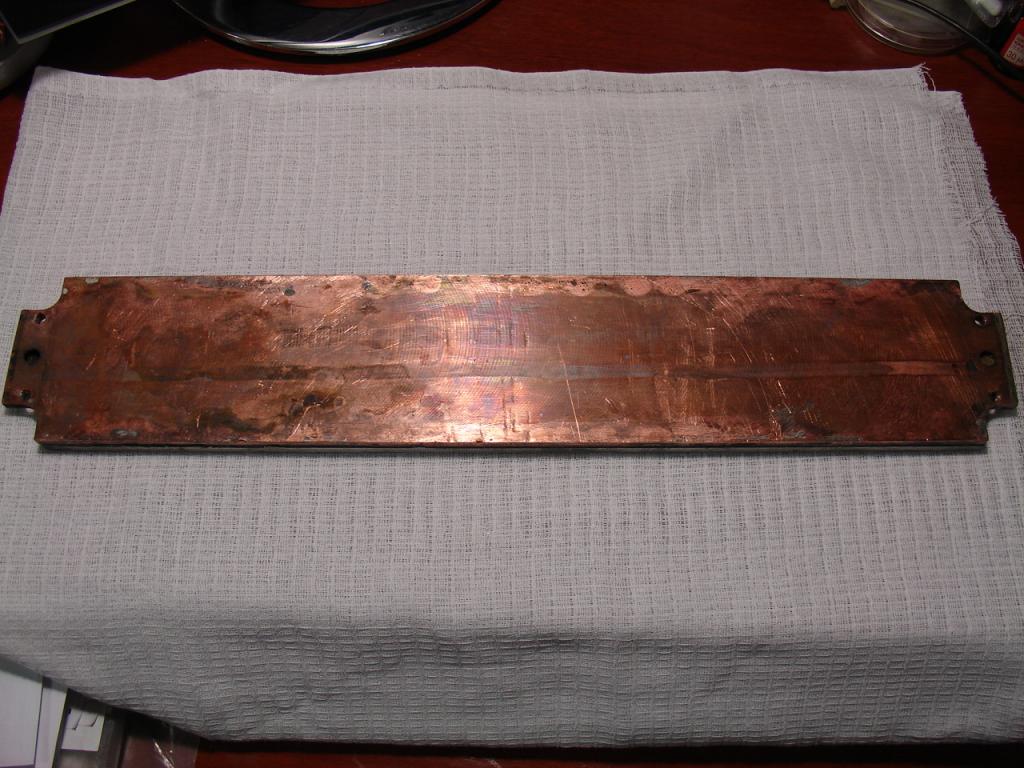

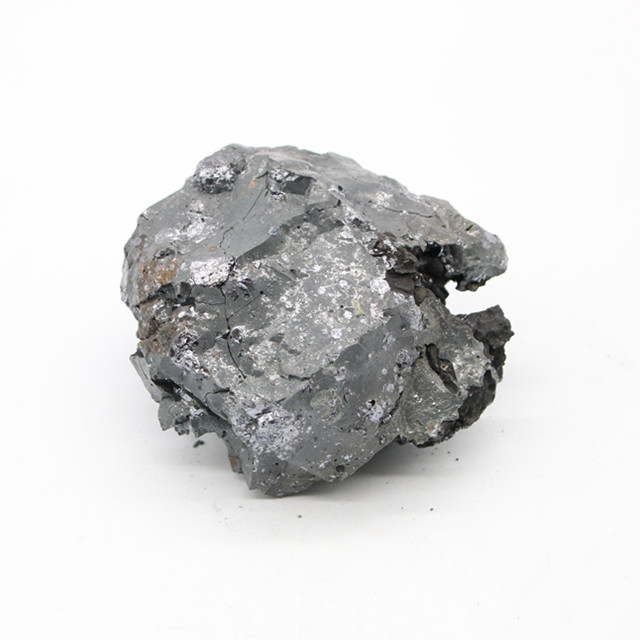
Обозначение марок | Химический состав в % | ||||||||||||||
Бук- вен- ное |
Циф- ро- вое |
ASTM | Al | Cu | Mg | Mn | Fe | Si | Zn | Ti | Примеси, не более | ||||
каж- дая в отд. ![]() |
сум- ма |
||||||||||||||
АДОО | 1010 | 1260 | 99,70 | 0,015 | 0,02 | 0,02 | 0,16 | 0,16 | 0,07 | 0,05 | 0,02 | 0,30 | |||
АДО | 1011 | 1145 | 99,50 | 0,02 | 0,03 | 0,025 | 0,30 | 0,30 | 0,07 | 0,1 | 0,03 | 0,50 | |||
АД1 | 1013 | 1230 | 99,30 | 0,05 | 0,05 | 0,025 | 0,30 | 0,30 | 0,1 | 0,15 | 0,05 | 0,70 | |||
АД | 1015 | 1100 | 98,80 | 0,1 | 0,1 | 0,1 | 0,50 | 0,50 | 0,1 | 0,15 | 0,05 | 1,20 | |||
ММ | 1511 | 3005 |
ос- но- ва |
0,2 |
0,2 — 0,5 |
1,0 — 1,4 |
0,6 | 1,0 | 0,1 | 0,1 | 0,05 | 0,2 | |||
АМц | 1400 | 3003 |
ос- но- ва |
0,1 | 0,2 |
1,0 — 1,6 |
0,7 | 0,6 | 0,1 | 0,2 | 0,5 | 0,1 | |||
АМцС | 1403 |
ос- но- ва |
0,1 | 0,05 |
1,0 — 1,4 |
0,25 — 0,45 |
0,15 — 0,35 |
0,1 | 0,1 | 0,05 | 0,1 | ||||
АМг2 | 1520 | 5052 |
ос- но- ва |
0,1 |
1,8 — 2,6 |
0,2 — 0,6 |
0,4 | 0,4 | 0,2 | 0,1 | Cr 0,05 | 0,05 | 0,1 | ||
АМг3 | 1530 | 5154 |
ос- но- ва |
0,1 |
3,2 — 3,8 |
0,3 — 0,6 |
0,5 |
0,5 — 0,8 |
0,2 | 0,1 |
Cr 0.![]() |
0.05 | 0.1 | ||
АМг4 | 1540 | 5086 |
ос- но- ва |
0,1 |
3,8 — 4,5 |
0,5 — 0,8 |
0,4 | 0,4 | 0,2 |
0,02 — 0,10 |
Cr 0.![]() — 0.25 |
Be 0.002 — 0.005 |
0.05 | 0.1 | |
АМг5 | 1550 | 5056 |
ос- но- ва |
0,1 |
4,8 — 5,8 |
0,3 — 0,8 |
0,5 | 0,5 | 0,2 |
0,02 — 0,10 |
Be 0.![]() |
0.05 | 0.1 | ||
АМг6 | 1560 | 5556 |
ос- но- ва |
0,1 |
5,8 — 6,8 |
0,5 — 0,8 |
0,4 | 0,4 | 0,2 |
0,02 — 0,10 |
Be 0.![]() — 0.005 |
0.05 | 0.1 | ||
АД31 | 1310 | 6063 |
ос- но- ва |
0,1 |
0,4 — 0,9 |
0,1 | 0,5 |
0,3 — 0,7 |
0,2 | 0,15 | 0,05 | 0,1 | |||
АД33 | 1330 | 6061 |
ос- но- ва |
0,15 — 0,40 |
0,8 — 1,2 |
0,15 | 0,7 |
0,4 — 0,8 |
0,25 | 0,15 |
Cr 0.![]() — 0.35 |
0.05 | 0.15 | ||
АД35 | 1350 | 6351 |
ос- но- ва |
0,1 |
0,8 — 1,4 |
0,5 — 0,9 |
0,5 |
0,8 — 1,2 |
0,2 | 0,15 | 0,05 | 0,1 | |||
АВ | 1341 | 6151 |
ос- но- ва |
0,1 — 0,5 |
0,45 — 0,90 |
0,15 — 0,35 |
0,5 |
0,5 — 1,2 |
0,2 | 0,15 |
Cr 0. ![]() |
0.05 | 0.1 | ||
АВч |
ос- но- ва |
0,05 |
0,06 — 1,0 |
0,05 | 0,12 |
0,35 — 0,55 |
0,05 | 0,05 | 0,1 | ||||||
Д1 | 1110 | 2017 |
ос- но- ва |
3,8 — 4,8 |
0,4 — 0,8 |
0,4 — 0,8 |
0,7 | 0,7 | 0,3 | 0,1 |
Ni 0.![]() |
0,6 — 1,0 |
0.05 | 0.1 | |
Д1ч |
ос- но- ва |
3,8 — 4,8 |
0,4 — 0,8 |
0,4 — 0,8 |
0,4 | 0,5 | 0,3 | 0,1 |
Ni 0.![]() |
Fe + Si 0.7 |
0.05 | 0.1 | |||
Д16 | 1160 | 2024 |
ос- но- ва |
3,8 — 4,9 |
1,2 — 1,8 |
0,3 — 0,9 |
0,5 | 0,5 | 0,3 | 0,1 | Ni 0.1 | 0.05 | 0.1 | ||
Д16ч | 2124 |
ос- но- ва |
3,8 — 4,9 |
1,2 — 1,8 |
0,3 — 0,9 |
0,3 | 0,2 | 0,1 | 0,1 | Ni 0.05 | 0.05 | 0.1 | |||
ВАД1 |
ос- но- ва |
3,8 — 4,5 |
2,3 — 2,7 |
0,35 — 0,8 |
0,3 | 0,2 | 0,1 |
0,03 — 0,10 |
Zc 0.07 — 0.2 |
Be 0.002 — 0.005 |
0.05 | 0.1 | |||
Д19 |
ос- но- ва |
3,8 -4 ,3 |
1,7 — 2,3 |
0,5 — 1,0 |
0,5 | 0,5 | 0,1 | 0,1 |
Be 0.002 — 0.005 |
0.05 | 0.1 | ||||
Д19Ч |
ос- но- ва |
3,8 — 4,3 |
1,7 — 2,3 |
0,4 — 0,9 |
0,3 | 0,2 | 0,1 | 0,1 |
Be 0.002 — 0.005 |
0.05 | 0.1 | ||||
1163 |
ос- но- ва |
3,8 — 4,5 |
1,2 — 1,6 |
0,4 — 0,8 |
0,15 | 0,1 | 0,1 |
0,01 — 0,07 |
Ni 0.05 | 0.05 | 0.1 | ||||
САВ1 |
ос- но- ва |
0,012 |
0,45 — 0,9 |
0,012 | 0,2 |
0,7 — 1,3 |
0,03 | 0,012 | Ni 0.03 | Cd 0.001 | Be 0.012 | 0.03 | 0.07 | ||
АК6 | 1360 |
ос- но- ва |
1,8 — 2,6 |
0,4 — 0,8 |
0,4 — 0,8 |
0,7 |
0,7 — 1,2 |
0,3 | 0,1 | Ni 0.1 | 0.05 | 0.1 | |||
АК8 | 1380 | 2014 |
ос- но- ва |
3,9 — 4,8 |
0,4 — 0,8 |
0,4 — 1,0 |
0,7 |
0,6 — 1,2 |
0,3 | 0,1 | Ni 0.1 | 0.05 | 0.1 | ||
АК4 | 1140 |
ос- но- ва |
1,9 — 2,5 |
1,4 — 1,8 |
0,2 |
0,8 — 1,3 |
0,5 — 1,2 |
0,3 | 0,1 |
Ni 0.8 — 1.3 |
0.05 | 0.1 | |||
АК4-1 | 1141 | 2618 |
ос- но- ва |
1,9 — 2,7 |
1,2 — 1,8 |
0,2 |
0,8 — 1,4 |
0,35 | 0,3 |
0,02 — 0,10 |
Ni 0.8 — 1.4 |
Cr 0.01 | 0.05 | 0.1 | |
АК4-1ч |
ос- но- ва |
2,0 — 2,6 |
1,2 — 1,8 |
0,1 |
0,9 — 1,4 |
0,1 — 0,25 |
0,1 |
0,05 — 0,1 |
Ni 0.9 — 1.4 |
Cr 0.1 | 0.05 | 0.1 | |||
Д20 | 1120 |
ос- но- ва |
6,0 — 7,0 |
0,05 |
0,4 — 0,8 |
0,3 | 0,3 | 0,1 |
0,1 — 0,2 |
Zc 0.2 | 0.05 | 0.1 | |||
1105 |
ос- но- ва |
2,0 — 5,0 |
0,4 — 2,0 |
0,3 — 1,0 |
1,5 | 3,0 | 1,0 |
Ti + Cr + Zc 0.2 |
Ni 0.2 | 0.05 | 0.2 |
Группа сплава | Сплавы | Основной химический состав,% | Перечень марок входящих в группу | ||||
Mg | Si | Cu | Zn | Ni | |||
1 | АЛ8 | 9,5-11,5 | — | — | — | — | АЛ13, АЛ22, АЛ23, АЛ27, АЛ28, АЛ29, |
2 | АЛ2 | — | 10-13 | — | — | — | АЛ4, АЛ9 |
3 | АЛ7 | — | — | 4-5 | — | — | АЛ19 |
4 | АЛ3 | 0,35-0,6 | 4,5-5,5 | 1,5-3,0 | — | — | АЛ5,АЛ6, АЛ10, АЛ14, АЛ15 |
5 | АЛ1 | 1,2-1,75 | — | 3,75-4,5 | — | 1,75-2,3 | АЛ16, АЛ17, АЛ18, |
АЛ11 | 0,1-0,3 | 6,0-8,0 | — | 7-12 | — | АЛ20, АЛ21, АЛ24, | |
АЛ26 | 0,4-0,7 | 20-22 | 1,5-2,5 | — | 1,0-2,0 | АЛ25, |
Группа I. Алюминий чистый (нелегированный). | Содержание алюминия не менее 99,0%. Примесей не более 1,0%, в том числе: кремния — 0,5%; меди — 0,05%; железа — 0,5%; цинка — 0,1%. | А999, А995, А99, А97, А95, А85, А8, А7, А7Е, А6, А5, А5Е, А0, АД0, АД1, АД00. |
Группа II. Сплавы алюминиевые деформируемые с низким содержанием магния (до 0,8%) | Содержание в сплаве не более: цинка — 0,3%; кремния — 0,7%; меди — 4,8%; железа — 0,7%. | Д1, В65, Д18, Д1П, АД31, АД. |
Группа III. Сплавы алюминиевые деформируемые с повышенным содержанием магния (до 1,8%) | Содержание в сплаве не более: цинка — 0,3%; кремния — 0,7%; меди — 4,9%; железа — 0,7%. | Д12, Д16, АМг1, Д16П. |
Группа IV. Сплавы алюминиевые литейные с низким содержанием меди (до 1,5%) | Содержание в сплаве не более: цинка — 0,5%; магния — 0,6%; кремния — 13,0%; железа — 1,5%. | АЛ5, АЛ32, АЛ2, АЛ4, АЛ4-1, АЛ9, АЛ9-1, АЛ34 (ВАЛ5), АК9 (АЛ4В), АК7 (АЛ9В), АЛ5-1. |
Группа V. Сплавы алюминиевые литейные с высоким содержанием меди | Содержание в сплаве не более: цинка — 0,6%; магния — 0,8%; кремния — 8,0%; железа — 1,6%. | АЛ3, АЛ6, АК5М2 (АЛ3В), АК7М2 (АЛ14В), АЛ7, АЛ19, АК5М7 (АЛ10В), АЛ33 (ВАЛ1). |
Группа Vа. Сплавы алюминиевые литейные с высоким содержанием кремния | Содержание в сплаве не более: меди — 6,0%, никеля — 3,6%, цинка — 0,5%; железа — 0,9%. | АЛ1, АЛ21, АЛ25, АЛ30, АК21М2,5Н2,5, АК18, КС-740. |
Группа VI. Сплавы алюминиевые деформируемые с высоким содержанием магния | Содержание в сплаве не более: меди — 0,2%, магния — 6,8%, цинка — 0,2%; железа — 0,5%; кремния — 0,8%. | АМг2, АМг3, АМг4, АМг5, АМг5п, АМг6. |
Группа VII. Сплавы алюминиевые литейные с высоким содержанием магния | Содержание в сплаве не более: меди — 0,3%, магния — 13,0%, цинка — 0,2%; железа — 1,5%; кремния — 1,3%. | АЛ8, АЛ27, АЛ27-1, АЛ13, АЛ22, АЛ23, АЛ23-1, АЛ28. |
Группа VIII. Сплавы алюминиевые деформируемые с высоким содержанием цинка | Содержание в сплаве не более: меди — 2,0%, магния — 2,8%, цинка — 7,0%; железа — 0,7%; кремния — 0,7%. | В95, 1915 и 1925. |
Группа IX. Сплавы алюминиевые литейные с высоким содержанием цинка | Содержание в сплаве не более: меди — 5,0%, магния — 0,3%, цинка — 12,0%; железа — 1,3%; кремния — 8,0%. | АЛ11, АК4М4, АК4М2Ц6. |
Новый способ получения сплавов алюминия с кремнием Текст научной статьи по специальности «Технологии материалов»
19/ тткмтшрпъ
Ifc I 3 (80), 2015-
УДК 669.094.25:669.715 Поступила 08.06.2015
НОВЫЙ СПОСОБ ПОЛУЧЕНИЯ СПЛАВОВ АЛЮМИНИЯ С КРЕМНИЕМ NEW METHOD OF PRODUCTION OF ALUNINUM — SILICON ALLOYS
В. К. АФАНАСЬЕВ, Сибирский государственный индустриальный университет, г. Новокузнецк, Россия,
Е. И. МАРУКОВИЧ, Институт технологии металлов НАН Беларуси, г. Могилев, Беларусь,
М. Н. ЧУРИК, Институт порошковой металлургии НАН Беларуси, г. Минск, Беларусь,
В. В. ГЕРЦЕН, А. В. ГОРШЕНИН, Сибирский государственный индустриальный университет,
г. Новокузнецк, Россия, А. А. САМОНЬ, ОАО «Информационные спутниковые системы
им. акад. М. Ф. Решетнева», Россия
V. K. AFANASIEV, Sibirian State Industrial University, Novokuznetsk, Russia,
E. I. MARUKOVICH, Institute of Technology of Metals ofNational Academy ofSciences of Belarus, Mogilev, Belarus, M. N. CHURIK, Powder Metallurgy Institute of National Academy of Sciences of Belarus, Minsk, Belarus, V. V. GERTSEN, A. V. GORSHENIN, Sibirian State Industrial University, Novokuznetsk, Russia, A. A. SAMON, OJSC «Information Satellite Systems named after acad. M. Reshetnev, Russia
Разработан новый подход к приготовлению алюминиево-кремниевых сплавов, базирующийся на представлении о ведущей роли водорода в формировании структуры и свойств сплавов и заключающийся в использовании в качестве шихтовых материалов диоксида кремния (кремнезема) и водорода взамен кристаллического кремния. Предложены первоначальные практические пути реализации нового способа на примере промышленных сплавов, приготовленных на шихтовом синтетическом сплаве. Показано, что применение предложенного способа позволяет повысить механические свойства и снизить коэффициент линейного расширения сплавов Al-Si. Изучено влияние термической обработки на механические свойства, плотность и тепловое расширение синтетических сплавов.
A new approach to the preparation of aluminum-silicon alloys, based on the concept of the leading role of hydrogen in determining the structure and properties of alloys consists in using as charge materials of silicon dioxide (silica) and hydrogen instead of crystalline silicon was described. Practical ways to implement the new method were proposed on the example of industrial alloys prepared on charge synthetic alloy. It is shown that the application of the proposed method allows to improve the mechanical properties and reduce the coefficient of thermal expansion alloys, Al-Si. The effect of heat treatment on mechanical properties, density and thermal expansion of synthetic alloys was researched.
Ключевые слова. Синтетические сплавы алюминия с кремнием, водород, кремнезем, механические свойства, тепловое расширение.
Keywords. Synthetic alloys of aluminum and silicon, hydrogen, silica, mechanical properties, thermal expansion.
Современное машиностроение широко использует сплавы алюминия с кремнием для приготовления отливок ответственного назначения.
Для получения сплавов окончательного химического состава применяются шихтовый алюминий технической чистоты и дорогостоящий кристаллический кремний.
Для снижения себестоимости шихты и, в конечном итоге, стоимости конструкционных алюминиевых сплавов необходимо применение новых ресурсосберегающих технологий.Ю2 путем одновременного катодного соосаждения А1 и Si [2].
В настоящее время ни один из перечисленных методов не нашел широкого применения в промышленности, что можно объяснить следующим. Электротермические сплавы в силу специфики производства (высокотемпературное углетермическое восстановление оксидов Si и А1) загрязнены оксидными и карбидными включениями, удаление которых сопряжено с технологическими трудностями. В целом электротермическое производство силумина характеризуется высокой энергоемкостью, что с учетом дополнительных затрат на внепечную очистку от включений определяет высокую себестоимость продукции.
Снижение энергетических затрат достигается при металлотермическом получении сплавов за счет проведения его при пониженных температурах (700-900 °С), а если учесть, что получение и рафинирование сплавов осуществляются в одном и том же металлургическом агрегате, то этот способ обеспечивает минимальную себестоимость продукции. 2А12+,
а также необходимость нагрева «балластного» материала, являющегося электролитом.
Из рассмотренных способов приготовления сплавов, использующих кремнезем, наибольший практический интерес представляет способ, основанный на восстановлении SiO2 в среде расплавленного алюминия. Однако присущие ему недостатки не позволяют рекомендовать его для широкого внедрения в промышленности. С целью совершенствования металлотермического способа получения сплавов необходимо проведение исследований в двух основных направлениях:
1) интенсификация окислительно-восстановительных процессов, протекающих в системе Al-Mg-SiO2;
2) замена металлов-восстановителей другими более активными элементами, например водородом.
В настоящей работе проведено исследование возможностей интенсификации магниевотермического восстановления кремнезема и получения сплавов алюминиево-кремниевых с использованием алюминия технической чистоты и кремнезема.
Поскольку в алюминии и его сплавах всегда присутствует водород, было сделано предположение о возможном его участии в восстановлении кремнезема в расплавленном алюминии. Для доказательства этого предположения были проведены эксперименты на вторичном и первичном алюминии, предусматривающие предварительное наводороживание или дегазацию расплава (продувкой аргоном).
Исследования проводили в лабораторных условиях с выплавкой сплавов в шахтной печи сопротивления в интервале температур 750-1100 °С по следующей методике. Навеску алюминия А7 или сплава алюминия с магнием помещали в корундовый тигель и расплавляли. После достижения заданной температуры расплав наводороживали путем продувки водяным паром. Затем на поверхность расплава загружали кварцевый песок в количестве 5-10% от массы расплава. После перемешивания продолжали продувку водяным паром в течение 20-30 мин. Операции наводороживания, введения кремнезема и перемешивания составляют один цикл обработки._
/ 3 (80), 2815-
общим названием — цикл обработки. Общее время синтеза составило 180 мин, что соответствует шести циклам обработки.
Готовый сплав после удаления шлака разливали в алюминиевый кокиль, а полученные слитки взвешивали и использовали в дальнейшем для изготовления образцов для проведения комплексных исследований с привлечением механических испытаний, металлографического и дилатометрического анали-
На первом этапе исследования проводили на вторичном алюминии, содержащем 10% магния. Отличительная особенность этой методики проведения исследований заключалась в следующем: во-первых, температура ведения процесса 770-780 °С; во-вторых, разовая загрузка кварцевого песка, предварительно подогретого до 870 °С и взятого в количестве 25% от массы расплава; в-третьих, непрерывная продувка расплава водяным паром в течение 120-180 мин.
Результаты влияния времени обработки расплава водяным паром на содержание в нем магния и кремния приведены в табл. 1, 2. Для сравнения представлены также соответствующие данные по составу расплава, который перемешивался без водяного пара [1].
Т а б л и ц а 1. Влияние времени обработки расплава на содержание магния в сплаве
Вид обработки Содержание магния, мас.%
время, мин
60 90 120 150 180 240 270
Перемешивание 4,73 2,41 1,03 0,54 0,31 0,18 0,15
Перемешивание с одновременной продувкой водяным паром 4,06 1,65 0,68 0,27 0,16 — —
Т а б л и ц а 2. Влияние времени обработки расплава на содержание кремния в сплаве
Вид обработки Содержание кремния, мас. %
время, мин
60 90 120 150 180 240 270
Перемешивание 4,4 5,6 6,9 8,2 9,6 11,8 13,6
Перемешивание с одновременной продувкой водяным паром 5,3 7,6 9,4 11,7 13,0 — —
Из таблиц видно, что обработка расплава водяным паром позволяет в 1,5-1,6 раза сократить время процесса получения синтетических сплавов с содержанием кремния 11-13 мас.% из вторичного маг-нийсодержащего алюминия. Наблюдаемые кинетические закономерности окисления магния и восстановления кремнезема в системе Al-Mg-SiО2-h3О можно объяснить следующим образом.
При обработке расплава водяным паром наряду с реакцией (1) будут проходить следующие окислительно-восстановительные процессы:
^]+Н2О ^ MgO+2[Н], (2)
4[Н^Ю2 ^ ^]+2Н2О, (3)
3SiО2+4[А1] ^ 3^]+2А1203. (4)
Сопоставляя реакции (1)-(3), можно отметить, что на получение 1 г-атома кремния расходуется 2 г-атома магния, а кремнезем восстанавливается как продуктами распада молекул Н2О, так и непосредственно магнием и алюминием. При этом реакция (4) имеет место независимо от способа обработки расплава. Следовательно, интенсификация процесса получения сплавов и соответственно вывода магния из вторичного алюминия с использованием кремнезема достигается за счет реакций (2) и (3), протекающих при обработке расплава водяным паром, т.е. водород принимает активное участие в процессе восстановления SiO2.
Для дальнейшего подтверждения предположения об активной роли водорода в восстановительных процессах, протекающих в объеме расплава, были проведены исследования на первичном алюминии технической чистоты по той же методике. Поскольку восстановление кремнезема может проходить за
_/хггггг: г^штптг Лч
-3 (80),2015 / ШЧМ
счет реакции взаимодействия с алюминием (реакция (4)), то необходимо оценить ее вклад в суммарный процесс получения сплава. С этой целью были проведены опыты, в которых обработку расплава осуществляли продувкой аргоном, т.е. в условиях, предусматривающих частичное удаление водорода из расплава. Результаты этих опытов для сравнения, а также соответствующие данные, полученные при обработке расплава водяным паром, приведены в табл. 3.
Т а б л и ц а 3. Влияние обработки расплава на содержание кремния в синтетическом сплаве
(один цикл при 900 °С)
Характеристика газа Количество вносимого кремнезема, % от массы расплава Время продувки, мин Содержание кремния в сплаве, мас.%
Аргон 5 20 0,60
Аргон 8 25 0,90
Аргон 10 30 1,10
Водяной пар 5 20 3,90
Водяной пар 8 25 4,05
Водяной пар 10 30 4,68
Из таблицы следует, что относительный вклад реакции (4) довольно значителен и в процентном соотношении составляет величину, изменяющуюся в пределах 16-23, при этом относительный вклад возрастает с увеличением количества вносимого кварцевого песка при прочих равных условиях, что можно объяснить увеличением поверхности контакта алюминия с кремнеземом. Изменение температуры обработки в пределах 800-1100 °С незначительно влияет на величину относительного вклада реакции (4). Последнее косвенно свидетельствует о том, что ведущим механизмом взаимодействия является изоморфное замещение кремния алюминием в структуре кремнезема.
Результаты исследования влияния температуры и количества циклов обработки расплава водяным паром на содержание кремния в конечном сплаве, полученном в случае трех циклов синтеза и трех циклов обработки расплава, приведены в табл. 4. При этом в одном цикле синтеза в расплав вводили 8% SiO2 при 750, 800 °С и 11% SiO2 при 900, 1000 °С.
Т а б л и ц а 4. Влияние температуры и количества циклов обработки расплава водяным паром на содержание кремния в синтетическом сплаве
Температура, °С Содержание кремния, мас. %
число циклов
1 2 3 4 5 6
750 1,7 2,6 3,5 7,5 13,0 14,1
800 3,0 6,4 8,7 12,0 14,2 15,8
900 4,0 9,6 11,8 13,2 15,1 17,0
1000 5,0 12,0 13,5 15,9 17,7 18,4
1100 6,0 13,0 14,0 17,0 18,8 20,0
Из таблицы видно, что в изотермических условиях ведения процесса получения сплава содержание кремния закономерно возрастает с увеличением числа циклов обработки. При этом максимальная скорость накопления кремния наблюдается в случае получения сплавов доэвтектического и эвтектического состава, особенно при повышенных температурах.
Такой способ получения сплавов алюминия с кремнием повышает их механические свойства по сравнению с обычным приготовлением. Очень важно, что у заэвтектических сплавов повышаются и прочность, и пластичность одновременно (табл. 5).
Т а б л и ц а 5. Механические свойства сплавов
Содержание кремния, мас. % Обычного приготовления Синтетические
ств, МПа 8,% Нт, МПа ств, МПа 8,% Нт, МПа
6 134 10,2 189 139 8,8 326
8 138 8,7 279 143 4,5 472
11 141 3,4 303 160 2,7 671
13 148 2,0 340 167 2,6 761
15 147 1,4 386 179 1,7 823
20 120 0,3 430 140 0,9 920
■ и/ 3 (80), 2015-
Микротвердость эвтектики при увеличении содержания кремния увеличивается. Получение сплавов на кремнеземе резко усиливает это повышение. Возможно, это связано с тем, что при разложении SÍO2 в жидком алюминии освобождающийся кислород, кроме удаления в шлак, еще и легирует a-твердый раствор.
Для проверки влияния масштабного фактора на технологические показатели процесса получения сплавов были проведены исследования в условиях Новокузнецкого алюминиевого завода. Выплавку проводили в индукционной печи в графитовом тигле, причем масса загруженного первичного алюминия составляла 20 кг. Результаты этих опытов показали незначительное уменьшение содержания кремния в сплаве при соответствующих режимах ведения процесса в лабораторных условиях (см. табл. 4). Например, при 750 °С за 4 цикла обработки расплава был получен сплав, содержащий 7,2% кремния, а при 900 °С за такое же число циклов обработки содержание кремния составило 12,1%. Наблюдаемое относительное снижение содержания кремния в конечном сплаве (возрастающее с повышением температуры) можно отнести за счет увеличения теплоотдачи в окружающую среду в случае выплавки сплава в индукционной печи и соответственным снижением температуры поверхностного слоя расплава.
В результате восстановления кремнезема в среде расплавленного алюминия в присутствии водяных паров образуется шлак. Сплав, полученный в этом случае, назван авторами синтетическим для формального разделения от сплава, приготовленного на кристаллическом кремнии.
Таким образом, на основании представлений о ведущей роли водорода в получении металлических материалов, базирующихся на водородной платформе периодической системы элементов [3-5], показана принципиальная возможность получения новых сплавов Al-Si без применения дорогостоящего кристаллического кремния.
Практическая реализация разработанного способа
После установления принципиальной возможности получения сплавов Al-Si на SÍO2 с помощью водорода необходимо определить области их применения.
В ГОСТ 1583-93 приведено 25 сплавов систем Al-Si, Al-Si-Mg и Al-Si-Cu, поэтому, прежде всего, следует определить свойства промышленных сплавов, приготовленных на синтетическом шихтовом двойном сплаве Al-Si. Это послужит основанием для развития новой водородной металлургии алюми-ниево-кремниевых существующих и будущих новых сплавов с требуемыми структурно-технологическими свойствами.
Для приготовления сплавов АК7ч и АК9ч применяли алюминий А0 и АВ97 и синтетический сплав А1-11-13% Si.
Специально приготовленные промышленные сплавы содержали ГОСТовское и повышенное содержание железа (табл. 6).
Сплавы АК9ч и АК7ч приготавливали в лабораторных условиях в алундовых тиглях при 730°С и заливали в алюминиевый кокиль. Полученные слитки разрезали для изготовления образцов для металлографических исследований, механических испытаний и измерения плотности и определения коэффициента линейного расширения (КЛР). Приготовление образцов и их испытания проводили по стандартным методикам.
Сплав АК9ч
Микроструктура сплавов АК9ч с различным содержанием железа, приготовленных на синтетическом сплаве, по размерам и характеру распределения структурных составляющих (участков a-твердого раствора кремния в алюминии и в эвтектике) не отличается от сплавов такого типа, полученных на кристаллическом шихтовом кремнии.штгпп /17
-3 (80), 2015 /II
Рис. 1. Линейное расширение литого сплава АК9ч, приго- Рис. 2. Линейное расширение литого сплава АК7ч, приготовленного на синтетическом силумине *0 — сплав обычно- товленного на синтетическом силумине *0 — сплав обычного го приготовления: ◊ — 0; V — 1; х — 2; □ — 3; о — 4 приготовления: ◊ — 0; V — 5; х — 6; □ — 7; о — 8
ной техники. Установлено, что новое приготовление уменьшает КЛР сплава № 1 по ГОСТ во всем диапазоне температур испытания (50-450 °С). Увеличение содержания железа дополнительно резко снижает аномалию КЛР при ¿исп= 250-300 °С (рис. 1).
Сплав АК7ч
Микроструктура маложелезистых сплавов (составы приведены в табл. 6) характеризуется участками а-твердого раствора и модифицированной эвтектикой, а по характеру распределения и количественному соотношению между структурными составляющими подобна сплавам обычного приготовления.
Термическая обработка новых сплавов по режиму Т6 приводит к укрупнению участков а-твер-дого раствора, огрублению эвтектики и частичному растворению интерметаллической фазы.
Свойства исследованных сплавов в литом и тер-мообработанном состояниях приведены в табл. 8. Из таблицы видно, что приготовление на кремнеземе повышает механические свойства. Значения КЛР новых сплавов приведены на рис. 2. Из рисунка следует, что для этого типа сплавов увеличение содержания железа сопровождается уменьшением коэффициента линейного расширения в интервале температур 50-450 °С.
Рис. 3. Влияние условий приготовления и термической обработки на линейное расширение литого сплава АК7ч. Термическая обработка: 535 °С, 2 ч, вода +175 °С, 10 ч, воздух; ◊ — обычного приготовления; V — приготовление на синтетическом силумине; х — приготовление на синтетическом силумине + термическая обработка
Wl /хгг:г г г^7Шглтг:г_
/ 3 (80), 2015-
Новый сплав состава № 5 по ГОСТ имеет КЛР практически одинаковый со сплавом обычного приготовления. Очень важно, что термическая обработка его снижает КЛР во всем интервале испытания 450 °С и полностью устраняет аномалию при температуре испытания 300 °С (рис. 3), что очень важно для поршней двигателей внутреннего сгорания.
Приведенное наглядно убеждает, что новая водородная металлургия сплавов Al-Si перспективна и даст значительный экономический эффект.
Т а б л и ц а 6. Состав промышленных сплавов, приготовленных на синтетическом силумине
Номер сплава Сплав (ГОСТ 1583-93) Содержание основных компонентов, мас.%, А1 — остальное
Si Mg Mn Fe
i АК9ч 9,10 0,27 0,40 0,60
2 То же 9,70 0,25 0,41 1,80
3 » 9,20 0,23 0,43 2,32
4 » 9,50 0,25 0,41 3,07
5 АК7ч 7,81 0,37 — 0,65
6 То же 7,55 0,37 — 1,66
7 » 7,37 0,34 — 1,84
8 » 7,24 0,33 — 2,90
Т а б л и ц а 7. Влияние термической обработки на механические свойства и плотность сплава АК9ч,
приготовленного на синтетическом силумине
Номер сплава Состояние Временное сопротивление разрыву, ав, МПа Относительное удлинение 5, % Твердость НВ, МПа Плотность р, кг/м3
1 Литой 178 1,9 600 2680
Термообработанный 256 2,1 — —
2 Литой 157 1,5 630 2710
Термообработанный 225 1,8 — —
3 Литой 96 1,0 720 2720
Термообработанный 114 1,0 — —
Термообработка: 535 °С, 2 ч, вода + 175 °С, 10 ч, воздух.
Т а б л и ц а 8. Влияние термической обработки на механические свойства и плотность сплава АК7ч,
приготовленного на синтетическом силумине
Номер сплава Состояние Временное сопротивление разрыву ав, МПа Относительное удлинение 5, % Твердость НВ, МПа Плотность р, кг/м3
5 Литой 174 1,3 690 2680
Термообработанный 245 1,7 — —
6 Литой 168 1,3 670 2710
Термообработанный 193 1,5 — —
7 Литой 160 1,2 724 2710
Термообработанный 192 1,3 — —
8 Литой 60 0,4 710 2720
Термообработанный 106 0,5 — —
Термообработка: 535 °С, 2 ч, вода + 200 °С, 3 ч, воздух.штптг /10
-3 (80),2015 / IW
References
1. Patent USA, no 4097270, kl 75-68, publ 27.06.1978.
2. D e l i m a r s k i y Y u. K. Teoreticheskie osnovy elektroliza ionnykh rasplavov [Theoretical bases of electrolysis of ionic fusions]. Moscow, Metallurgiya Publ., 1968. 223 p.
3. A f a n a s i e v V. K. Vodorodnaya platforma periodicheskoy sistemy elementov [Hydrogen platform of the periodic system of elements]. Part I. Metallurgiya mashinostroeniya — Metallurgy of Engineering. 2011, no. 2, pp. 21-26.
4. A f a n a s i e v V. K. Vodorodnaya platforma periodicheskoy sistemy elementov [Hydrogen platform of the periodic system of elements]. Part II. Metallurgiya mashinostroeniya — Metallurgy of Engineering. 2012, no. 4, pp. 3-7.
Сведения об авторах
Афанасьев Владимир Константинович, д-р техн. наук, проф., заведующий кафедрой материаловедения и технологии новых материалов, Сибирский государственный индустриальный университет, Россия, 654080, г Новокузнецк, ул. Грдины, 26, кв. 16. E-mail: [email protected].
Марукович Евгений Игнатьевич, акад., д-р техн. наук, проф., Институт технологии металлов НАН Беларуси, Беларусь, 212030, г. Могилев, ул. Бялницкого-Бирули, 11. Тел.: +375 (222) 279-367. E-mail: [email protected].
Information about the authors
Afanasiev Vladimir, Doctor of Engineering, Professor, Chairman of the Department of new material technologies and material engineering, 26-16 Grdiny str., Novokuznetsk city, 654080, Russia, E-mail: [email protected].
Marukovich Evgeny, Academician of National Academy of Sciences of Belarus, Doctor of Engineering, Professor, Institute of Technology of Metals of National Academy of Sciences of Belarus. 11, Bialynitskogo-Biruli str., Mogilev, 212030 Belarus. E-mail: [email protected].
АЛЮМИНИЕВЫЕ СПЛАВЫ • Большая российская энциклопедия
АЛЮМИ́НИЕВЫЕ СПЛА́ВЫ, сплавы на основе алюминия; обладают малой плотностью (до 3000 кг/м3), высокими электро- и теплопроводностью, коррозионной стойкостью и удельной прочностью. Первые А. с. – сплавы алюминия с кремнием, полученные в 50-х гг. 19 в., имели малую прочность и низкую коррозионную стойкость. Поворотным моментом в истории развития А. с. стали исследования А. Вильма (Германия, 1903–11), который обнаружил в закалённом А. с., содержащем медь и магний, повышение прочности в процессе вылёживания, т. н. эффект старения (см. Старение металлов). В 1921 А. Пач (США) модифицировал сплав Al – Si путём введения в него микроскопич. доз Na, что привело к значит. улучшению его свойств. Позже для получения А. с. с определёнными свойствами стали применять легирование разл. металлами (Cu, Mg, Mn, Si, Zn, Ni, Li, Be и др.). В России в 1930–40-х гг. разработку А. с. и внедрение их в произ-во осуществляли Ю. Г. Музалевский, С. М. Воронов, И. Н. Фридляндер и др.
До 1940-х гг. применялись гл. обр. сплавы на основе систем Al – Si (силумины), Al – Mg (магналии), Al – Cu – Mg (дуралюмины), Al – Mg – Si (авиали). Впоследствии также получили развитие высокопрочные (на основе систем Al – Zn – Mg, Al – Zn – Mg – Cu, Al – Mg – Si – Cu), жаропрочные (Al – Cu – Mn, Al – Mg – Li, Al – Cu – Mg – Fe – Ni), пониженной плотности (Al – Be – Mg, Al – Mg – Li, Al – Cu – Li) и др. А. с. В зависимости от способа произ-ва полуфабрикатов и изделий А. с. делят на деформируемые, используемые для изготовления листов, плит, профилей, труб, поковок, проволоки путём деформации (прокатки, ковки, штамповки и др.), и литейные – для изготовления фасонных изделий литьём. Состав и некоторые свойства наиболее распространённых А. с. приведены в таблицах 1, 2 (см. стр. 578).
Деформируемые сплавы по объёму произ-ва составляют ок. 80% всех А. с. Химич. и фазовый состав, режимы термич. обработки деформируемых А. с. определяются необходимостью получения оптим. комплекса эксплуатац. и технологич. свойств. Сплавы системы Al – Mg (магналии) имеют высокую коррозионную стойкость, хорошо свариваются, но не упрочняются термич. обработкой; для повышения прочности в эти сплавы вводят Sc. Сплавы Al – Zn – Mg обладают высокой прочностью, хорошо свариваются, но при значит. концентрации Zn и Mg склонны к замедленному коррозионному растрескиванию. Сплавы Al – Mg – Si (авиали) сочетают хорошую коррозионную стойкость с выраженным эффектом старения; хорошо поддаются анодированию. Сплавы Al – Mg – Si – Cu сильно упрочняются в результате старения, но отличаются пониженной коррозионной стойкостью. Сплавы Al – Cu – Mg (дуралюмины) имеют ср. прочность, но высокие пластичность и вязкость разрушения, малую скорость развития усталостных трещин. Сплавы Al – Zn – Mg – Cu характеризуются самыми высокими прочностью и пределом текучести. Сплавы Al – Mg – Li имеют такие же, как и у дуралюмина, механич. свойства, но пониженную (на 11%) плотность и больший модуль упругости. Сплавы Al – Be – Mg обладают высокими удельной прочностью и модулем упругости, хорошей коррозионной стойкостью, пластичностью, хорошо свариваются, но из-за токсичности их применение ограничено. Полуфабрикаты из деформированных А. с. для последующей обработки получают из слитков простой формы – круглых, плоских, полых.
Таблица 1. Химический состав и механические свойства некоторых деформируемых алюминиевых сплавов
Система | Марка сплава | Легирующие компоненты (% по массе) | Типичные механические свойства | |||||
---|---|---|---|---|---|---|---|---|
Cu | Mg | Mn | Si | Прочие | Предел прочности, МПа | Предел текучести, МПа | ||
Al – Mg (магналии) | АМг6 | < 0,1 | 5,8–6,8 | 0,5–0,8 | ≤ 0,4 | Zn < 0,2; Fe ≤ 0,4 | 340 | 170 |
1570 | < 0,1 | 5,3–6,3 | 0,2–0,6 | ≤ 0,2 | Zn < 0,1; Fe ≤ 0,3; Sc 0,25 | 410 | 310 | |
Al – Mg – Si (авиали) | АВ | 0,1–0,5 | 0,45–0,9 | 0,15–0,35 | 0,5–1,12 | Zn < 0,2; Fe ≤ 0,5; Ti <0,15 | 340 | 280 |
АДЗЗ | 0,15–0,4 | 0,8–1,2 | < 0,15 | 0,4–0,8 | Zn < 0,25; Fe ≤ 0,7 | 320 | 260 | |
Al – Mg – Si – Cu | АК6 | 1,8–2,6 | 0,4–0,8 | 0,4–0,8 | 0,7–1,2 | Zn < 0,3; Fe ≤ 0,7 | 390 | 300 |
АК8 | 3,9–4,8 | 0,4–0,8 | 0,4–1,0 | 0,6–1,2 | Zn < 0,3; Fe ≤ 0,7 | 470 | 380 | |
AI – Cu – Mg (дуралюмины) | Д1ч | 3,8–4,8 | 0,4–0,8 | 0,4–0,8 | <0,5 | Fe < 0,4 | 380 | 220 |
Д16ч | 3,8–4,9 | 1,2–1,8 | 0,3–0,9 | <0,2 | Fe< 0,3 | 440 | 300 | |
Al – Zn – Mg – Cu | В96Ц | 2,0–2,6 | 2,3–3,0 | – | <0,3 | Zn 3,0–8,0; Fe < 0,4; Zr 0,1–0,2 | 650 | 620 |
1933 | 0,8–1,2 | 1,6–2,2 | – | <0,1 | Zn 6,35–7,2; Fe 0,06–0,15; Zr 0,1–0,18 | 510 | 460 | |
Al – Cu – Mg – Fe – Ni | АК4–1 | 1,9–2,7 | 1,2–1,8 | ≤ 0,2 | «0,3 | Zn ≤ 0,3; Fe 0,8–1,4; Ni 0,8-1,4 | 420 | 350 |
Al – Cu – Mn | 1201 | 5,8–6,8 | < 0,02 | 0,2–0,4 | <0,2 | Zn <0,1; Fe ≤ 0,3 | 420 | 320 |
Al – Mg – Li | 1420 | < 0,05 | 4,5-6,0 | – | <0,15 | Fe ≤ 0,2; Li 1,8–2,3; Zr 0,08–0,15; Na < 0,03 | 430 | 290 |
1424 | – | 4,7–5,2 | 0,05–0,25 | ≤ 0,1 | Zn 0,4–0,8; Fe ≤ 0,1; Li 1,5–1,8 | 460 | 320 | |
Al – Be – Mg | АБМ–1 | – | 4,2–5,5 | 0,3 | 0,1 | Fe 0,2; Be 28-32; Ni 0,1 | 430–500 | 250-300 |
АБМ–3 | – | 1,5–2,5 | 0,2 | Fe 0,2; Be 67–72 | 550–620 | 380-480 | ||
Примечание. В ряд сплавов вводятся малые добавки Cr, Zr, Sc, Ti, Be, Ca. |
К деформируемым А. с. относят также спечённые сплавы (вместо слитка для формования изделий используют брикет, спечённый из порошков): спечённая алюминиевая пудра (САП) и спечённые алюминиевые сплавы (САС). САП, упрочнённая дисперсными частицами оксида алюминия, превосходит все А. с. по жаропрочности. САС, легированные Si, Fe, Ni, отличаются очень низким коэф. линейного расширения.
Таблица 2. Химический состав и механические свойства некоторых литейных алюминиевых сплавов
Легирующие компоненты (% по массе) | Типичные механические свойства | ||||||||
---|---|---|---|---|---|---|---|---|---|
Система | Марка сплава | Cu | Mg | Mn | Si | Прочие | Предел прочности, МПа | Предел текучести, МПа | |
Силумины | Al–Si | АК12 (АЛ2) | 0,6 | – | 0,5 | 13,0 | – | 200 | 110 |
Al–Si–Mg | АК9ч (АЛ4) | 0,3 | 0,17–0,3 | 0,2-0,5 | 8,0–10,5 | – | 260 | 200 | |
АК7ч (АЛ 9) | 0,2 | 0,2–0,4 | 0,5 | 6,0–8,0 | – | 230 | 130 | ||
Al–Si–Cu–Mg | АК5М (АЛ5) | 1,0–1,5 | 0,35–0,6 | 0,5 | 4,5–5,5 | – | 240 | 180 | |
АК8М3ч (ВАЛ8) | 2,5–3,5 | 0,2–0,45 | – | 7,0–8,5 | Zn 0,5–1,0; Ti 0,1–0,25; В 0,005–0,1; Be 0,05–0,25 | 345 | 290 | ||
Al–Мg | АМг10 (АЛ27) | – | 9,5–10,5 | – | – | Zr 0,05–0,20; Ti 0,05–0,15; Be 0,05–0,15 | 314 | 176 | |
АМг6л (АЛ23) | 0,15 | 6,0–7,0 | – | – | Zr 0,05–0,20; Ti 0,05–0,15; Be 0,02–0,1 | 225 | 127 | ||
Al–Cu | АМ5 (АЛ19) | 4,5–5,3 | 0,05 | 0,6–1,0 | 0,3 | Ti 0,15–0,35 | 370 | 260 | |
АМ4,5Кд (ВАЛ10) | 4,5–5,1 | 0,05 | 0,35–0,8 | – | Ti 0,15–0,35; Cd 0,07–0,25 | 420 | 300 |
Для литейных сплавов, особенно важны такие характеристики, как высокая жидкотекучесть, малая склонность к образованию усадочных и газовых пустот, трещин, раковин. Наиболее высокие характеристики достигаются при литье в металлич. формы (в кокиль, под давлением, при жидкой штамповке). Важнейшие литейные А. с. – силумины – содержат св. 4,5% Si, к ним относятся сплавы системы Al – Si и более сложных систем: Al – Si – Mg, Al – Si – Cu – Mg; обладают хорошими литейными свойствами, неплохой коррозионной стойкостью, ср. прочностью, в отливках не образуется усадочной пористости. Сплавы с содержанием Mg св. 5% (сплавы систем Al – Mg, Al – Mg – Si с добавкой Mn, Be и Ti) коррозионностойки, высокопрочны, высокопластичны и обладают пониженной плотностью. Длительные низкотемпературные (60–80 °C) нагревы приводят к ухудшению коррозионной стойкости литейных А. с. с высоким содержанием Mg. Технология изготовления этих сплавов сложна, изделия отливаются гл. обр. в земляные формы. Сплавы с содержанием Cu св. 4% (сплавы систем Al – Cu, Al – Cu – Mn с добавкой Ti, Cd) по жаропрочности превосходят другие литейные сплавы, но имеют пониженные коррозионную стойкость и литейные свойства. Литейные сплавы (кроме силуминов) в принципе аналогичны деформируемым сплавам соответствующих систем, но отличаются более высоким содержанием легирующих компонентов (Cu, Mg), добавок (Ni, Ti) и примесей (Fe).
На свойства литейных сплавов помимо способов литья также влияют входящие в их состав компоненты, которые для одних сплавов являются легирующими, но оказывают вредное влияние на другие: Si снижает прочность сплавов Al – Mg; примесь Zn ухудшает механич. свойства сплавов Al – Si и Al – Cu; Sn и Pb даже в десятых долях процента значительно понижают темп-ру плавления сплавов. Вредное влияние на силумины оказывает Fe, вызывающее образование хрупких включений, кристаллизующихся в виде пластин. Содержание Fe зависит от способа литья: оно максимально при литье под давлением и в кокиль и минимально при литье в землю. Качество фасонных отливок из А. с. существенно повышается при использовании чистой шихты (уменьшение количества вредных металлич. и неметаллич. примесей в сплавах), модифицировании сплавов (введение малых добавок Ti, Zr, Be), использовании прогрессивных методов рафинирования и термич. обработки.
А. с. относятся к важнейшим конструкц. материалам. По масштабам производства и потребления занимают 2-е место после стали; в пром-сти используют ок. 55 марок А. с. Благодаря уникальным эксплуатац. свойствам широко применяются: в авиа- и ракетостроении – шасси, лопасти воздушных винтов, силовые элементы летат. аппаратов (обшивка, фюзеляж, шпангоуты, лонжероны, нервюры, верхние и нижние плоскости крыльев), корпусы ракет, топливные и масляные баки; в судостроении – корпусы судов, палубные надстройки, разл. судовое оборудование; в автомобилестроении – детали двигателя (поршни, головки, блоки цилиндров), радиаторы охлаждения, отопители, кабины, салоны автобусов, цистерны для перевозки химич. и нефтехимич. продуктов, сыпучих грузов; в строительстве – строит. конструкции, оконные рамы и двери; в пищевой пром-сти – банки для пива, воды, пищевых продуктов, бытовая фольга и др.
Кремний в сплавах алюминиевы — Справочник химика 21
В последнее время для определения кремния в алюминиевых сплавах широко применяется фотометрический метод, основанный на образовании кремнемолибденовой сини. Этот метод позволяет определять кремний при его содержании в сплаве от [c.93]Из сплавов алюминия наиболее распространен дюралюминий, сокращенно дюраль ( дюр означает твердый ). Большую твердость дюралю по сравнению с чистым А1 придают добавки меди ( 4%), марганца (—0,57о), магния (- 1,5%), кремния и железа (доли %). Применение нашли также сплав А1 с Si — силумин (16% Si) — и алюминиевая бронза (89% Си). [c.56]
Сплавы алюминиевые литейные и деформируемые. Методы определения кремния [c.571]
Алюминиевые сплавы, содержащие менее 0,5% кремния, растворяют в 5 мл концентрированной соляной кислоты с добавлением по каплям перекиси водорода. При наличии более 0,5% кремния сплав растворяют в платиновой чашке в 10 мл воды при добавлении по каплям фтористоводородной кислоты до полного растворения. Затем добавляют еще 5 мл фтористоводородной кислоты, несколько капель концентрированной азотной кислоты и 2 мл концентрированной серной кислоты и нагревают до удаления НР. Остаток растворяют в 10 мл разбавленной (1 1) азотной кислоты. [c.253]
Порфирьев Н. А. Колориметрический метод определения кремния в алюминиевых сплавах. Уч. зап. Казанск. ун-та, 1948, 1С8, кн. 1, с. 85—91. 5286 [c.204]
В бронзах олово часто заменяют другими металлами, что приводит к изменению свойств сплавов. Алюминиевые бронзы (5—10 % по массе алюминия) обладают повышенной прочностью. Очень прочны, тверды и упруги бериллиевые бронзы, массовая доля бериллия в которых составляет 2 %. Широкое применение в народном хозяйстве нашли бронзы, содержащие свинец, марганец, сурьму, железо, никель и кремний. [c.251]
В отличие от самого алюминия его сплавы характеризуются высокой удельной прочностью, приближающейся к высокопрочным сталям. Основные другие достоинства всех сплавов алюминия — это их малая плотность (2,5—2,8 г/см ), удовлетворительная стойкость против атмосферной коррозии, сравнительная дешевизна и простота получения и обработки. Эти сплавы пластичнее сплавов магния и многих пластмасс, стабильны по свойствам. Основными легирующими элементами являются Си, Mg, 31, Мп, Хп, которые вводят в алюминий главным образом для повышения его прочности. Типичными представителями сплавов алюминия являются дуралюмины, относящиеся к сплавам системы Л1—Си—Mg. Высокопрочные сплавы алюминия относятся к системам Л1—7п—Mg—Си, содержащим добавки Мп, Сг, 2т. Из других сплавов широко известны силумины, в которых основной добавкой служит кремний, магналий (сплав алюминия с 9,5—11,5% магния). Алюминиевые сплавы применяются в ракетной технике, в авиа-, авто-, судо- и приборостроении, изготовлении строительных конструкций, заклепок, посуды и во многих других отраслях промышленности. [c.633]
При оиределении кремния в алюминиевом сплаве Д5 = 0 соответствовала концентрации g = l,70%, а для эталона с концентрацией i = 0,72% ASi = —0,48. [c.132]
Определить содержание кремния в алюминиевом сплаве, [c.146]
При определении кремния в алюминиевом сплаве для построения градуировочного графика были получены следующие результаты массовой доле = 1,70% соответствовала = О, массовой доле сОд = 0,72% соответствовала А8 = -0,48. Построить градуировочный график и определить массовую долю (%) [c.177]
ОПРЕДЕЛЕНИЕ КРЕМНИЯ В АЛЮМИНИЕВЫХ СПЛАВАХ [c.61]
Бронза— сплав меди с другими элементами, в основном с металлами. В зависимости от состава различают оловянную бронзу (состоит из меди и олова), алюминиевую бронзу (содержит до 5—11 % алюминия), свинцовую (до 33% свинца), кремниевую (до 4 % кремния) и др. Применяется для изготовления частей машин и для художественных отливок. [c.156]
Тихонова А. А. Определение молибдена в легированных сталях на фотоколориметре. Зав. лаб., 1949, 15, № 1, с. 107—108. 5825. Тихонова А. А. Определение хрома в алюминиевых сплавах на фотоколориметре. Зав. лаб., 1949, 15, № I, с. 108—109. 5826 Тихонова А. А. Определение кремния в алюминиевых сплавах фотоколориметрическим методом. [М.], Оборонгиз, 1949. 8 с. с илл. [c.223]
Принадлежность данного сплава к определенному типу дает возможность с большой степенью достоверности предвидеть примерный его состав. Так, например, алюминиевые сплавы содержат магний, железо, кремний, титан, медь, цинк, марганец, никель и др. медные сплавы — олово, цинк, СБ1 н ц, сурьму, висмут, железо, никель, кремний, фосфор и др. [c.453]
Метод определения титана и кремния 11 021.009.3—83 Сплавы алюминиевые для изделий электронной техники. [c.31]
Качество химического полирования зависит не только от состава ванны, но и от выбора сплава. Алюминиевые сплавы, содержащие цинк и медь, плохо полируются и анодируются. Особенно плохо полируются сплавы алюминия с высоким содержанием кремния. Наилучшие результаты получаются для алюминия высокой чистоты (99,99%). [c.25]
Определение кремния в алюминиевых сплавах [c.107]
Сущность метода. Для определения кремния в алюминиевых сплавах при его содержании от 16 до 30% используется реакция образования кремнемолибденовой гетерополикислоты с последующим ее восстановлением до молибденовой сини. [c.99]
Кремний, образуя химическое соединение с магнием, является легирующим элементом в алюминиевых сплавах. Его содержание в деформированных сплавах обычно достигает 0,5—1,2%. При большем количестве кремния в алюминиевых сплавах механические свойства их существенно не повышаются, но пластичность при этом заметно падает. [c.154]
Поэтому чистый алюминий используются только для формирования тонких (меньше 30 нм) зародышевых и смачивающих слоев, а для остальных целей применяются пленки сплавов алюминия, из которых особенно часто используются сплавы А1 — 1% Si — 0,5% Си = Al[Si, u] и Al — 0,5% Си = А1[Си] [12]. Добавка кремния в алюминиевый сплав препятствует процессам диффузии и растворения атомов кремния из /з-/2-переходов в алюминии при его осаждении в контактные окна ИМС, а добавка меди способствует повышению стойкости к процессу электромиграции. [c.172]
Установлено, что распределение этих соединений, например кремния, в алюминиевых сплавах оказывает влияние на величину [c.165]
В паяных алюминиевых конструкциях разделительные пластины покрываются припоем. Такая разделительная пластина может состоять из алюминиевой основы, плакированной очень тонким слоем, содержащим припой. Типичный плакирующий сплав состоит нз 92 % алюминия и 7,5% кремния [2], Кремний снижает точку плавления покрытия примерно на 50 °С ниже точки плавлеиия алюми- [c.305]
Алюминиевые сплавы в соответствии с основными ко.мпонента-ми (основой) получили следующие названия силумины (алюминий-кремний), дюралюмины (алюминий — медь — марганец), магналии (алюминий — марганец). В зависимости от назначения они подразделяются на литейные и деформируемые (до 80% от всех сплавов). [c.225]
Наиболее распространенные алюминиевые литейные сплавы — это силумины (сплавы алюминия с кремни- [c.52]
Наряду с железом и железными сплавами широкое применение в современной технике находят алюминий и его сплавы. Алюминиевые сплавы делят на две группы деформируемые и недеформируемые (или литейные). Наиболее распространены силумины и дюралюминий. Силумины содержат 10—13% кремния и небольшое количество магния и обладают хорошей коррозионной стойкостью из-за образования на их поверхности защитного слоя ЗЮа. Дюралюминий отличается высокими механическими свойствами наряду с легкостью. Изделия из этого сплава при равной прочности в два раза легче стальных. Коррозионная стойкость чистого алюминия во много раз выше, чем алюминиевых сплавов, в особенности сплавов, содержащих медь, железо и никель. Несмотря на то что алюминий имеет отрицательный потенциал (—1,67В), он является довольно коррозионностойким во многих средах в воде, в большинстве нейтральных сред и в сухой атмосфере. Такое поведение алюминия обусловлено его способностью к самопассивации. В зависимости от условий алюминий покрывается защитной пленкой разной толщины — от 150 до ЮООА, которая состоит из А12О3 или А12О3 [c.72]
Механические свойства литейных алюминиевых сплавов могут быть существенно улучшены модифицированием в жидком состоянии. Так, модифицирование силумина с содержанием 13% кремния приводит к повышению предела прочности от 140 до 180 МН/м и удлинения от 3 до 8%. При более высоких требованиях к прочностным свойствам применяют специальные силумины с добавками меди, марганца, магния, с термической обработкой закалкой с последующим старением. Однако механические свойства литых сплавов значительно уступают термически упрочняемым сплавам. Поэтому применение литых сплавов для нагруженных деталей целесообразно лишь в случае сложной формы изделия или выигрыша в весе, в остальных случаях предпочтительнее применение кованых, более прочных сплавов. [c.53]
При получении покрытия из расплава в ванну с расплавленным алюминием обычно добавляют кремний, чтобы затруднить образование слоя хрупкого сплава. Полученные из расплава покрытия используют для повышения устойчивости к окислению при умеренных температурах таких изделий, как отопительные устройства и выхлопные трубы автомобилей. Они стойки к действию температуры до 480 °С. При еще более высоких температурах покрытия становятся огнеупорными, но сохраняют защитные свойства вплоть до 680 °С [21]. Использование алюминиевых покрытий для защиты от атмосферной коррозии ограничено вследствие более высокой стоимости по сравнению с цинковыми, а также из-за непостоянства эксплуатационных характеристик. В мягкой воде потенциал алюминия положителен по отношению к стали, поэтому покрытие является коррозионностойким, В морской и некоторых видах пресной воды, особенно содержащих С1″ и SO4″, потенциал алюминия становится более отрицательным и может произойти перемена полярности пары алюминий—железо. В этих условиях алюминиевое покрытие является протекторным и катодно защищает сталь. Показано, что покрытие из сплава А1—Zn, состоящего из 44 % Zn, 1,5 % Si, остальное — Al, имеет очень высокую стойкость в морской и промышленной атмосферах. Оно защищает также от окисления при повышенных температурах. [c.242]
Так, аргон используют в качестве защитной атмосферы (предохранение от окисления) при выплавке таких металлов, как уран, торий, германий, цирконий и гафний, а также при получении чистого кремния. На практике широко распространен способ электросварки (а также наплавки и резки) металлов в защитной атмосфере инертного газа —обычно аргона (аргонно-дуговая сварка титановых, алюминиевых, магниевых и др. сплавов, меди, вольфрама, нержавеющих сталей и т. д.). Чистые гелий и аргон—непревзойденные защитные газы при работе с химически малоустойчивыми веществами, легко поддающимися окислению. [c.544]
На очищенную поверхность алюминиевого сплава помещают 1-2 капли 15 %-ного раствора щелочи. По истечении 5 мин снимают жидкость фильтровальной бумагой. Оставшееся на поверхности металла темное пятно обрабатывают 1-2 каплями раствора Н N ( и) = 66 %), Через 3 мин снова снимают раствор фильтровальной бумагой. Образующееся при этом серое пятно свободного кремния служит признаком силумина. Дюралюминий этой реакции не дает. [c.120]
Малая плотность, пластичность и устойчивость к коррозии обеспечили алюминию применение в авиа- и автопромышленности. Он входит в состав легких сплавов дюралюмина (сплава алюминия, меди, магния и марганца), силумина (сплава алюминия и кремния) и некоторых других. Из алюминиевых сплавов изготовляют корпуса искусственных спутников Земли и космических кораблей. [c.315]
Носков М. М , Скорняков Г. П. и ЧукинаТ. П. Спектральный экспресс-анализ основных мартеновских шлаков с применением искрового режима дуги переменного тока. Зав. лаб., 1951, 17, № 4, с. 429—430. 4982 Носков Ф. Н. и Соколова В. М. Фотоколориметрическое определение кремния в алюминиевых сплавах. Зав. лаб., 1952, 18, № 2, с. 176. 4988 [c.194]
Одними из наиболее важных сплавов, имеющих промышленное значение, являются сплавы алюминия с кремнием. Сплавы, содержащие от 5 до 14% кремния, называются силуминами. Такие сплавы могут быть получены путем электролиза соответствующих ионных расплавов. В этом отношении значительный интерес представляет работа [38], в которой исследован электролиз расплавленной системы МадА1Рб — 5Юз — МаОд. Если во время электролиза применять жидкий алюминиевый катод, то возможна реакция взаимодействия алюминия с окисью кремния с образованием сплава Л1 —51. В растворе расплавленно- [c.132]
При плавке алюминиевых сплавов и алюминиевых бронз содержащийся в сплаве алюминий химически взаимодействует с футеровкой, при этом он активно восстанавливает кремний из кремнезема П1 лукислой или алюмосиликатной футер. вки, Он также может реаги-рогать с оксидами железа и хрома, обычно в небольших количествах присутствующих в футеровочных материалах [c.88]
Алюминиевые сплавы подразделяются на деформируемые и литейные. Деформируемые сплавы отличаются высокой пластичностью и механической прочностью, К таким сплавам относятся, например, дуралюмины, содержащие добааки меди, магния, марганца, кремния, железа упрочняющей фазой в них являются соединение АЬСи и другие интерметаллиды. Дуралюмины характеризуются, однако, сравнительно невысокой коррозионной стойкостью, поэтому их часто применяют в плакированном виде, т. е. [грокатанными вместе с покрывающим их листовым чистым алю-ми [ием. Литейные сплавы содержат легирующих добавок больше предельной растворимости. Из них готовят различные фасонные отливкн. К литейным сплавам относятся содержащие до 7% кремния (силумины) или до 10% магния последние отличаются высокой коррозионной стойкостью. Алюминиевые сплавы применяют в самолетостроении, судостроении, ракетостроении, транспортном машиностроении (вагоны, автомобили, тракторы и т. п.), промышленном и гражданском строительстве (подъемно-транспортные сооружения, мосты, сборные дома, трубы для нефтедобывающей промышленности), а так /ке для орошения и дождевания в сельском [c.258]
Основные элементы, которыми легируют деформируемые алюминиевые сплавы для обеспечения их упрочнения при термической обработке — медь, кремний, магний, цинк. В некоторые сплавы добавляют литий, церий, кадмий, цирконий, хром и другие элементы. К наиболее важным и распространенным сплавам, упрочняемым закалкой с последующим старением, относятся сплавы систем А1—Си—Mg типа дюралюминий, А1—Мд—51, ави-аль А1—2п—Mg—Си (высокопрочные сплавы Ов бОО— 700 МН/м ), А1—М —2п (самозакаливающиеся свари—ваемые сплавы, сгв=400—450 MH/м ), не требующие термической обработки после сварки, А1—Си—Сс1— (жаропрочные сплавы, Ов = 360—400 МН/м ) после 1000 ч выдержки при температуре 180°С. К высокопрочным сплавам относятся сплавы В93, В95, В96 системы А1—2п—Mg—Си, сплав ВАД23 системы А1—Си—Мп— С(1 и, частично, в зависимости от применяемой термической обработки и вида полуфабриката, сплавы. Д16, Д19, системы А1—Си—Mg, сплав АК8 системы А1—Си—Mg—51. Наибольшей прочностью при комнатной температуре обладают сплавы В93, В95, В96 и ВАД23. Сплавы Д16 и Д19 обладают меньщей прочностью при комнатной температуре, чем сплавы В93, В96, В95. Однако их преимущество заключается в большей жаропрочности и меньщей чувствительности к коррозии. Сплав ВАД23 сохраняет относительно высокие прочностные характеристики после длительных нагревов до 160— 180°С. Исходя из характеристик алюминиевых сплавов следует применять сплавы В93, В95, В96 для конструкций, работающих до температуры 100°С, при этом в конструкции должны отсутствовать концентраторы напряжений, расположенные в плоскости, перпендикулярной к действию силы. Для нагружения конструкций, работаю- [c.49]
Применение оловянистой бронзы ограничивается изготовлени ем деталей для отдельных узлов оборудования. В настоящее время оловянистые бронзы заменяются более экономичными и прочными алюминиевыми бронзами — сплавами меди с алюминием. Промышленность выпускает также специальные бронзы, в которых не содержится олово, но имеются добавки алюминия, марганца, кремния и др. [c.32]
Пример 2. При анализе алюминиевого сплава на кремний по методу одного эталона получили почернение (5) линий гомологической пары в спектрах эталона (5si=l,09 и iSai = 0,37 при si = 0,95%) и анализируемого образца (Ssi = 0,86 и Sai = 0,34). [c.128]
Кремний входит в состав многих железных, медных, алюминиевых и других сплавов. В небольших количествах (до .0 8%Ьп [c.93]
Во время электролиза образующийся металл перио. дически удаляется со дна электролизера, он содержит обычно 98,5—99,8% алюминия, механические примеси (электролит, окись алюминия, уголь, адсорбированные газы) и сплавы с элементами, которые встречаются в алюминиевых рудах (З), Ре). Механические примеси и адсорбированные газы обычно удаляют переплавкой алюминия-сырца, а железо, кремний удаляют последующим электролитическим рафинированием. После электролитического рафинирования получают алюминий [c.333]
Опыт 10. Идентификация алюминиевых сплавов. На очищенную поверхность образца нанесите каплю 15%-ного раствора NaOH. Выделение водорода через некоторое время указывает на то, что в сплаве содержится алюминий. Составьте уравнение реакции. Примерно через пять минут после нанесения щелочи снимите жидкость фильтровальной бумагой и нанесите на пятно, оставшееся на поверхности образца, 1—2 капли HNOg (d=l,4). В случае сплавов алюминия с кремнием остается серое пятно элементарного кремния. Поставив параллельно тот же опыт с образцом дюралюминия, можно убедиться, что в этом случае серого пятна не образуется . [c.201]
Некоторые металлы и неметаллы (Sn, Zn, Al, Si и др.) растворяются в щелочах, Поэтому при анализе некоторые сплавы (например, алюминиевые) растворяют в 25%-ном растворе NaOH. В раствор переходят алюминий, цинк, олово, кремний в осадке остаются железо, магний, марганец, медь и другие нерастворимые в щелочах компоненты исследуемых сплавов. [c.439]
Алюминиевые сплавы » Все о металлургии
23.04.2015
В качестве основных присадок в эти сплавы входят кремний и медь, а за последнее время также и магний.
Влияние кремния. Кремний является составляющей большинства алюминиевых сплавов, применяемых для литья под давлением. Он придает им большую пластичность при высоких температурах, что особенно важно при отливке полых деталей, когда металлические стержни, выполняющие полости, препятствуют свободной усадке сплава.
По данным акад. А.А. Бочвара, основным условием обеспечения хорошей сопротивляемости сплава усадочным напряжениям является наличие в сплаве достаточно большого количества эвтектики (от 15 до 25%) или другой составляющей, кристаллизующейся в последнюю очередь и при постоянной температуре. При той концентрации сплава, начиная с которой во время кристаллизации не наблюдается линейной усадки, происходит резкое возрастание сопротивляемости напряжениям.
При соответствующем количестве эвтектики уменьшается степень дендритности кристаллов и увеличивается контактная поверхность зерен. Эвтектическая жидкость кристаллизуется при постоянной температуре, т. е. без создания новых напряжений; она имеет способность свободно перемещаться между осями дендритов. Трещины, возникающие в эвтектических сплавах, благодаря этому сейчас же заполняются жидкостью и не развиваются до конца кристаллизации.
Кремний обладает способностью образовывать с алюминием твердый раствор с весьма ограниченной растворимостью кремния в алюминий. При 578° — температуре образования эвтектики — растворяется всего 1,65% Si. С охлаждением сплава до комнатной температуры растворимость кремния, значительно уменьшаясь, доходит в некоторых случаях почти до 0,2%.
При увеличении содержания кремния он образует эвтектику с твердым раствором кремния в алюминии. В сплавах, содержащих 11,7% Si, твердый раствор образует с кремнием эвтектическую смесь. В структуре заэвтектического сплава (при содержании кремния выше 11,7 %) появляются кристаллы свободного кремния, количество которых увеличивается по мере увеличения содержания кремния.
Кроме наличия эвтектики в литье под давлением, большое значение имеет пластичность сплава ниже температуры его затвердевания.
В табл. 35 приводятся механические свойства двух алюминиевых сплавов при высоких температурах. Они показывают, что удлинение сплавов алюминия с кремнием сильно возрастает с температурой.
Значение удлинения сплава Al+12% Si относится к модифицированному сплаву, отлитому в песчаную форму. При литье под давлением удлинение при низких температурах будет несколько меньшим.
Сочетание в алюминиевых сплавах с кремнием (типа силумин) большого количества эвтектики с высокой пластичностью при повышенной температуре делают эти сплавы нечувствительными к горячим и холодным трещинам.
Сплавы системы алюминий—кремний приобретают высокую пластичность в нагретом состоянии уже при содержании кремния 4,5%. Добавление кремния в количестве от 1 до 3,5% к сплавам типа алюминий—медь во всех случаях улучшает их пластичность. Кремний повышает литейные свойства алюминиевых сплавов., увеличивает их жидкотекучесть и уменьшает усадку.
Жидкотекучесть сплавов алюминий—кремний возрастает с повышением содержания в них кремния и достигает своего максимума вблизи эвтектической точки (11,7% Si).
При литье в песчаные формы сплавы алюминия с кремнием обычно приобретают грубокристаллическое игольчатое строение и обнаруживают сравнительно невысокие механические свойства вследствие выделения кремния, игольчатых кристаллов FeAl3 и твердого раствора R (Fe+Si), которые появляются в эвтектическом силумине уже при 0,9% Fe в виде первичных кристаллов.
Главным способом улучшения механических свойств сплава является его модифицирование, т. е. измельчение его структуры при помощи химических реагентов (натрия или фторидов щелочных металлов). В литье под давлением модифицирование не применяется, потому что вследствие долгого выдерживания металла в котле машины или в раздаточной печи модифицирование теряет свое действие — происходит демодифицирование; кроме того, при впуске металла в форму под давлением и быстром его охлаждении возникает большое количество центров кристаллизации и Si, FeAl3 и β (Fe—Si) не успевают вырасти до размера игл или пластинок; в результате силумин приобретает повышенную прочность и твердость.
Модифицирование, повышая прочность сплава, одновременно увеличивает и его удлинение; при литье под давлением удлинение обычно падает, находясь у силумина в пределах 1,5—3,0% (табл. 36).
Следует иметь в виду, что сплавы с высоким содержанием кремния вступают в реакцию с железом плавильных тиглей.
Влияние меди. Сплавы типа алюминий—медь, несмотря на свои высокие литейные свойства, мало пригодны для литья под давлением из-за своей склонности к образованию трещин.
Из этих сплавов отливают в металлических формах детали средней сложности, и не имеющие больших полостей, ни резких переходов от толстых сечений к тонким, ни местных скоплений металла.
В сплавах типа силумин с высоким содержанием кремния влияние меди (до 0,8%) сказывается увеличением предела упругости, прочности и твердости; при дальнейшем увеличении содержания меди значение предела прочности и упругости уменьшается. Удлинение при добавлении меди (уже при 0,4%) прогрессивно падает. В сплавах, содержащих до 7% Si, медь в количестве 1,0—2,0% улучшает чистоту поверхности отливок под давлением.
Добавление к силумину до 0,8% Cu практикуется при отливке деталей, предназначенных работать в условиях вибраций и при динамических нагрузках. Медь в силумине понижает его коррозионную устойчивость.
Влияние железа. Взаимодействие между алюминием и железом, происходящее в процессе литья под давлением, следует рассматривать с двух точек зрения.
Железо неизменно присутствует во всех алюминиевых сплавах и при небольшом его содержании (оно различно для разных типовых сплавов) является даже полезным. Например, сплавы системы Al—Cu при содержании железа не больше 1,4% имеют повышенные предел прочности и удлинение, в то же время они менее склонны к усадке и образованию трещин в горячем состоянии. В сплавах типа силумин—железо при содержании его не выше 0,6% также способствует увеличению прочности. В ряде алюминиевых сплавов умеренное содержание железа значительно улучшает их обрабатываемость резанием.
При значительном содержании железа в алюминиевых сплавах их литейные и механические свойства ухудшаются. Сплав делается менее жидкотекучим и требует для хорошего заполнения формы повышенной температуры перегрева. Кроме того, происходит ликвация сплава, т. е. разделение сплава в процессе кристаллизации на зоны с различной концентрацией железа. Это приводит к получению отливок с неоднородными механическими свойствами. Железо присутствует в виде химического соединения FeAl3, которое образует пластинки, выпадающие первыми, что вызывает образование крупных кристаллов и сопровождается резким снижением механических свойств сплава и появлением хрупкости.
Оптимальное содержание железа в различных алюминиевых сплавах зависит от способности того или иного сплава образовывать эвтектику с растворенным в нем железом. Из диаграммы затвердевания сплавов тройных систем Al—Si—Fe, Al— Cu—Fe и четверной системы Al—Cu—Si—Fe следует, что эвтектическое содержание железа в алюминиевых сплавах уменьшается с увеличением содержания меди или кремния. Это же показывают данные об эвтектическом содержании железа в некоторых алюминиевых сплавах, применяющихся на практике (табл. 37).
В литье под давлением вредное влияние избыточного железа частично парализуется огромной быстротой кристаллизации. Поэтому в сплавах допускаются более значительные количества железа, особенно для тонкостенного литья.
Алюминий и его сплавы обладают высокой способностью растворять в себе различные металлы, в частности, железо, что должно особенно учитываться при литье под давлением на машинах с горячими камерами прессования. Здесь металл постоянно находится в чугунных или стальных котлах, вмонтированных в машины, а так как это обстоятельство требует производства заливки при более высокой температуре, то, следовательно, растворение железа в алюминии будет происходить достаточно быстро. Поэтому при работе на машинах с горячими камерами прессования допускается содержание железа в сплавах до 2—2,5%.
При работе на машинах с холодными камерами металл содержится в отдельной раздаточно-подогревательной печи и соприкасается с камерой прессования и формой только в течение короткого периода, поэтому здесь содержание железа может находиться в пределах его эвтектической концентрации в сплаве.
Необходимо указать, что применение технически чистого сплава, т. е. сплава с очень малым содержанием железа (ниже 0,6%), тоже имеет недостатки; реакция такого сплава с железом формы идет особенно интенсивно; следовательно, интенсивнее будет износ формы и в больших размерах происходит налипание металла на форму.
Влияние цинка. Алюминиевые сплавы с присадкой цинка становятся красноломкими, поэтому цинк редко применяют для алюминиевых сплавов литья под давлением, где отливку приходится снимать с выступающих частей формы и стержней в горячем состоянии. Исключением является гидроналий, содержащий 0,15—0,25% Zn, а также сплав AЛ11, применяемый для некоторых отливок при особых требованиях к условиям резания и к чистоте поверхности.
Влияние никеля. Никель, увеличивая прочность и твердость отливки, не делает ее хрупкой. При наличии никеля прочность сплава мало уменьшается при повышении температуры примерно до 350°.
Никель способствует свариваемости металла (что весьма важно при отливке тонкостенных деталей) и ослабляет разъедающее действие расплавленного металла на стальные формы и стенки камеры прессования. Кроме того, под влиянием никеля (1,0—1,5%) отливка лучше воспринимает полирование и поверхность ее приобретает яркий блеск. Применение никеля ограничивается его дефицитностью.
Влияние магния. Растворимость магния в алюминии при температуре эвтектики достигает 12—15%; при комнатной температуре она составляет, по данным разных авторов, от 3 до 10%. Присадка магния к алюминию в количестве от 4 до 10% дает сплавы, отличающиеся высокой коррозионной стойкостью и пластичностью. Механические свойства сплавов улучшаются по мере увеличения содержания магния до 10%.
Введение магния в небольшом количестве (0,2—0,3%) в сплавы типа силумин способствует повышению их предела прочности и твердости, предела упругости и предела усталости при некотором снижении относительного удлинения. Благодаря этим свойствам магний находит применение в литье под давлением в тех случаях, когда требуется получить отливки высокой прочности.
Влияние марганца. Марганец смягчает влияние железа. В сплавах алюминия с кремнием допускается до 0,5% Mn. Марганец в количестве до 0,4% увеличивает удлинение сплава. В сплаве гидроналий (см. табл. 38) марганец в количестве — 0,5 % применяется для увеличения коррозионной стойкости и уменьшения вредного влияния железа.
Твердые включения в сплавах алюминия с кремнием. Сплавы типа алюминий—кремний ввиду их непревзойденных литейных свойств, высоких механических свойств, а также достаточно высокой коррозионной стойкости нашли преобладающее применение в литье под давлением среди других алюминиевых сплавов. Опыт применения вторичных сплавов для литья деталей из сплава алюминий—кремний показал, что посторонние металлические и неметаллические примеси, имеющие место в этом исходном материале не ухудшают литейных свойств, что создало ошибочное представление о целесообразности его применения в значительном ряде случаев. Производственный опыт и исследование последних десяти лет показывают, что чистота сплавов типа алюминий—кремний, получаемая в результате применения исходных материалов, лишенных примесей, а также в результате применения рациональных методов шихтовки и плавки, имеют решающее значение для обеспечения высоких механических свойств и коррозионной стойкости, а также для условий резания и получения при этом высокой чистоты поверхности деталей.
Вопрос о влиянии посторонних примесей на механические и коррозионные свойства сплавов освещен выше.
Изучение причин плохой обрабатываемости сплавов типа «силумин» показывает, что она хуже в больших сечениях, где кремний содержится в более крупных кристаллах в результате менее интенсивного охлаждения.
Плохая обрабатываемость объясняется также наличием твердых включений. Твердость различных структурных составляющих сплава, измеренная на приборе для определения микротвердости следующая:
Наличие Al2O3 и Si затрудняет обработку и приводит к быстрому затуплению инструмента. Наличие в структуре разнообразных по твердости составляющих препятствует получению чистой поверхности.
Резьба получается нечистая с рваными нитками, такая, что не обеспечивает плавности хода винтовых соединений в точных приборах.
Оптимальное для условий резания содержание кремния определяется в зависимости от количества включений, которое, с одной стороны, пропорционально содержанию кремния, а с другой стороны, зависит от других структурных составляющих сплава и прежде всего железа.
На фиг. 163 видна железосоставляющая в бедном силумине. На основном фоне светлых кристаллов α-раствора с небольшим участком эвтектики выделяется темная, резко очерченная железосоставляющая и в ней единичные белые иглы FeAl3 и черные включения шлака.
Присутствие железосоставляющей в сплаве указывает на высокое содержание в нем железа при достаточно большом количестве кремния и наличии меди. Такие составляющие имеются, например, в сплавах, содержащих 7.5% Si, 1,4% Cu и 1,6% Fe.
Кремний. Кремний вкрапливается в сплав в виде отдельных кристаллов голубоватого цвета, чаще всего в форме квадратов и треугольников, придавая блеск поверхности детали (фиг. 164). Наличие в сплавах кристаллов свободного кремния является следствием насыщенности алюминиевого раствора железом и медью, под влиянием которой сплав хуже удерживает кремний в твердом растворе, и длительного нагрева при повышенной температуре, вызывающего укрупнение кристаллов кремния.
Кристаллы свободного кремния чаще наблюдаются в силуминах, близких по составу к эвтектическому (11,7% Si).
Включения окиси алюминия. При работе на гидравлических поршневых машинах возникают условия для насыщения сплава окисью алюминия. Вследствие длительного нахождения расплавленного металла в тигле раздаточной печи его поверхность окисляется и образуется пленка окислов. Борьба с окисью алюминия требует очень тщательной заливки, так как вследствие перемешивания металла и постоянного черпания окислы в нем замешиваются, образуя твердые включения, взвешенные в металле, благодаря своему удельному весу, приближающемуся к весу сплава.
Включения окиси алюминия и свободного кремния, образующиеся при плавке и разливке, а также наличие железосоставляющей затрудняют механическую обработку отливок и пагубно действуют на резцы. Согласно последним исследованиям наилучшим условиям резания отвечают силумины с содержанием 8,0—9,5% Si. По своей структуре эти сплавы приближаются к силумину эвтектического состава.
Хорошо обрабатываются сплавы эвтектического состава только при полном отсутствии в них кристаллов свободного кремния. Так как в условиях литья под давлением не всегда возможно получить требуемую структуру и полностью устранить включения, следует иметь в виду, что практически лучшая обрабатываемость получается у силумина, содержащего 8—9% Si. При малом содержании в сплаве меди и железа (суммарно до 0,9%) наилучшей надо считать обрабатываемость, которая достигается при 10—10,5% Si.
В табл. 38 приводятся данные об алюминиевых сплавах для литья под давлением.
Стандартные алюминиевые сплавы, в которых основными легирующими элементами являются кремний и медь, не лишены недостатков, которые нередко затрудняют использование этих сплавов для литья ответственных деталей.
К таким недостаткам относятся:
1) невысокое удлинение;
2) невысокая коррозионная стойкость, особенно при наличии в силумине примесей меди и железа;
3) затрудненная механическая обрабатываемость сплава с высоким содержанием кремния.
Из сплавов, в значительной мере лишенных этих недостатков и одновременно обладающих свойствами, которые необходимы для литья под давлением, следует отметить алюминиевые сплавы, содержащие магний (сплав АЛ13 и гидроналий).
Сплавы алюминия с магнием превосходят по коррозионной стойкости и по пластичности в холодном состоянии все другие литейные алюминиевые сплавы, применяемые для литья под давлением, и очень хорошо обрабатываются резанием, давая гладкую блестящую поверхность.
Испытания гидроналия на открытом воздухе, во влажной атмосфере и в «тумане» морской воды во всех случаях показали высокую стойкость против коррозии.
Детали из гидроналия могут применяться без покрытий при эксплуатации внутри помещений. Блестящая поверхность, получаемая при полировании, сохраняется практически неограниченное время при незначительном уходе.
Гидроналий поддается анодному оксидированию, причем получаемый блестящий слой окиси отличается высокой твердостью и износоустойчивостью, а также повышенной коррозионной стойкостью.
Технология плавки и отливки этих сплавов более сложна, чем других алюминиевых сплавов. Сплавы алюминия с магнием обладают расширенным интервалом кристаллизации, что может явиться причиной повышенной пористости и требует упрочнения и подпитки при высоком давлении. Для этого необходимо применять литниковую систему с утолщенными впускными литниками, более значительные удельные давления и более длительную выдержку под давлением.
Уступая по своим литейным свойствам сплавам алюминия с кремнием, эти сплавы более чувствительны к напряжениям при затрудненной усадке на стержнях, но практически не принадлежат к красноломким сплавам и при соблюдении правильной технологии не дают трещин на глубоких стержнях.
Менее высокие литейные свойства вынуждают вести отливку при более высокой температуре формы (220—250°) и металла (700—750°).
Стержни необходимо нагревать сильнее, чтобы уменьшить влияние усадки. Охват металлом стержней более сильный, что требует быстрого удаления стержней (без резких толчков и ударов).
Несмотря на более сложную технологию, сплавы алюминия с магнием успешно внедряются в производство благодаря отмеченным выше преимуществам.
За последние два года советскими исследователями (А.А. Иванкин) проведены работы по улучшению литейных свойств алюминиево-магниевых сплавов и повышению их коррозионной стойкости.
Добавки до 1 % Si позволили повысить литейные свойства. Приготовление этих сплавов на чистом алюминии без добавок цинка, а также понижение содержания магния до 7% (±1) дали возможность получить высокие прочностные характеристики в сочетании с достаточно высокой пластичностью.
Для изготовления деталей средней сложности, подлежащих обработке, в частности, нарезке резьбы, за последнее время нашел широкое применение сплав АЛ11, отличающийся от сплавов системы Al—Si хорошими условиями резания и отсутствием дефектов поверхности, так называемый «мороз». Согласно ведомственным нормалям в целях улучшения условий обрабатываемости содержание цинка в этом сплаве понижено до 6—11%, а кремния — до 6-9%.
В табл. 39 приведены данные об алюминиевых сплавах применяемых для наиболее ответственных деталей. Эти сплавы благодаря высокой чистоте имеют несколько повышенные значения относительного удлинения и коррозионной стойкости.
Термическая обработка отливок из алюминиевых сплавов, полученных литьем под давлением
Алюминиевые (а также магниевые) сплавы, нагреваемые до температуры немного ниже солидуса, имеют склонность к образованию воздушных пузырей, поэтому долгое время термическая обработка отливок из алюминиевых сплавов с переводом компонентов в твердый раствор считалась невозможной в промышленных условиях.
Сплавы на алюминиевой основе теряют свою прочность при температуре выше 400° С и не могут сопротивляться расширению сжатого воздуха, находящегося в отливке в значительно сжатом состоянии.
Термическая обработка при более низких температурах, не превосходящих 400° С, не позволяет полностью переводить компоненты в твердый раствор, но способствует получению механических свойств сплавов, более высоких, чем до указанной термической обработки.
В этом направлении необходимо изучать вопрос о термической обработке алюминиевых сплавов, литых под давлением.
Так, например, применяемое на практике охлаждение отливок из гидроналия в воде непосредственно после их выталкивания из формы является подобием полузакалки, которая, несколько повышая предел прочности и твердость, улучшает обрабатываемость сплава.
Опыт термической обработки алюминиевых сплавов, отлитых при очень больших удельных давлениях (7000 кг/м2), с получением деталей без воздушных включений показал, что в результате такой обработки повышены механические свойства сплава гидроналий до следующих показателей: предел прочности 42—49 кг/мм2, удлинение до 15%.
Если будут созданы условия, при которых станет возможной термическая обработка литья из алюминиевых сплавов для повышения их низких пластических свойств и получения более устойчивых механических свойств, то область применения процесса для изготовления ответственных изделий будет значительно расширена.
Обработка зерна первичного кремния в заэвтектических сплавах
Требования к отливкам постоянно ужесточаются, и, как следствие, требования металлургического характера к сплаву также повышаются. По этой причине в настоящее время все чаще начинают применять сплавы, которые раньше имели очень ограниченный диапазон использования, например, литейные алюминиевые заэвтектические сплавы.
Введение
До сих пор литейные алюминиевые заэвтектические сплавы использовались главным образом в производстве поршней. Это связано с их малым коэффициентом термического расширения, что обуславливает такие свойства, как высокая твердость и износостойкость.
Как следствие этого в дальнейшем эти сплавы используются не только при литье в кокиль в поршневом производстве, но также и при литье в землю, например, для производства тормозных дисков. Процесс литья в землю подразумевает оборудование литейной части сложной системой воздушного охлаждения.
Медленная скорость кристаллизации при этом процессе литья требует очень тщательной обработки расплава, которая включает очистку расплава, а также измельчение зерна первичного кремния. По этой причине встает необходимость использования другого метода обработки расплава, нежели обычное введение медно-фосфорной лигатуры.
Обработка кремния в заэвтектическом силумине
В сплаве, содержащем 18% кремния, кристаллы формируются при охлаждении до температуры примерно 700 ° C. При уменьшении скорости кристаллизации при литье в землю или литье в кокиль (в сплавах с высоким содержанием алюминия), эти кристаллы имеют время для роста. В зависимости от интенсивности охлаждения они преобразуются в дендритную форму и образуют более или менее крупные кристаллы (рис. 2). После затвердевания кристаллов кремния крайне сложно получить сравнительно мягкую эвтектику. В принципе, это сочетание является идеальным для наличия абразивного эффекта, едва ли вредного для отливок. Однако это работает только, когда кристаллы небольшого размера и равномерно распределены на поверхности и внутри отливки (рис. 3). Кристаллы кремния обладают высоким сопротивлением и разрыв кристалла в любом случае не вредит отливке.
Это может быть достигнуто эффективной обработкой зерна кристаллов кремния
Измельчение зерна достигается при помощи кристаллизаторов. Это бориды титана для первичного алюминия в доэвтектических сплавах и фосфиды алюминия для первичного кремния в случае заэвтектических сплавов. Фосфид алюминия очень токсичен, который не должен быть использован при литье алюминия, так как он образует с влагой высокотоксичный фосфид водорода (Ph4).
Каким образом возможно внести фосфид алюминия, необходимый для обработки зерна, в расплав? Добавление красного фосфора в алюминиевый расплав для формирования фосфида алюминия оказалось не очень эффективным, так как фосфор сложно смешивается с алюминием и немедленно окисляется с выделением дыма. Применение медно-фосфорной лигатуры является общепринятой практикой. В этом случае сплав меди и фосфора должен применяться как медь, фосфор может быть замешан достаточно хорошо и форма эвтектики получается с 8% фосфора. Следовательно, медь работает в качестве «переносчика» фосфора.
Однако, этот метод имеет недостатки, так как лигатуры CuP растворяются только при очень высоких температурах (минимум 800 ° С) и только в этом случае фосфор может вступать в реакцию с алюминием с образованием AlP. Время реакции составляет около 40 минут.
Тем не менее, большую продолжительность реакции можно избежать, если добавлять в фосфор в алюминий непосредственно в виде лигатуры.
Лигатура с фосфидом алюминия
Для производства лигатуры с фосфидом алюминия должны быть использованы процессы порошковой металлургии. Для добавления в расплав фосфору нужен «переносчик». В этом плане оказалось эффективным соединение фосфора и железа. Железо и фосфор образуют фазу фосфор-железо (Fe2P) с 24% содержанием фосфора (рисунок 1). Это очень твердый порошкообразный материал смешивается с мягким порошком алюминия, прессуется в заготовки, а затем экструдируется в стержни.
Доля фосфида железа не может быть слишком высокой, потому что смесь должна быть экономична. На практике состав с менее чем 1 / 3 фосфида железа и соответствующей долей алюминия оказался экономичным и эффективным. В результате этого достигается лигатура с содержанием фосфора 6-8%. В ходе этого процесса фосфор диффундирует в алюминий и образует включения фосфида алюминия, являющимися цетрами кристаллизации.
В процессе выдавливания мягкий алюминий плакирует твердые частицы фосфида железа. Таким образом, алюминий покрывает твердые частицы и в этом случае возможен процесс диффузии.
Фосфор диффундирует в алюминий с образованием фосфида. Таким образом, лигатура содержит большое количество небольших кристаллизаторов фосфида алюминия и может быть очень эффективным при обработке расплава.
Согласно опытам, введение небольшого количества (примерно 40 ppm) фосфора приводит к необходимому качеству обработки первичного кремния (при введении 1 кг PROBAT FLUSS VLP-200 на 1000 кг расплава).
Доля железа в сплаве возрастает до 200 частей на миллион. В принципе, это увеличение может быть принято, так как оно находится в пределах зоны допуска для литейных сплавов.
Использование лигатуры для обработки расплава фосфором
Лигатура PROBAT FLUSS VLP-200, производства SCHÄFER Chemische Fabrik GmbH, изготовлена в форме стержней. Такой же вид лигатуры обычно используется для обработки зерна боридами титана или модифицирования стронцием.
Лигатура PROBAT FLUSS VLP-200 производится в виде мерного прутка длиной 1000 мм круглого сечения (рис. 4), благодаря чему они могут быть легко введены в расплав.
Перед обработкой расплав должен быть очищен от оксидных примесей при помощи импеллерной системы. При использовании импеллера так же должен быть добавлен препарат, не содержащий натрий, такой как PROBAT FLUSS AL 3125. Современные установки, такие как импеллер MBC 6000 в сочетании с дозировщиками флюса производства Fuco-Heg осуществляют эти операции автоматически. Такая установка повышает эффективность обработки расплава благодаря последовательному изменению направления вращения ротора.
В конце процесса очистки в расплав добавляют лигатуру в тот момент, когда импеллер еще вращается. Стержни растворяются очень быстро и освобождают кристаллизаторы. При этом они равномерно распределяются в расплаве. Согласно практике применения, температура не играет значительной роли в этом процессе. Обработка может быть выполнена при температуре ниже 700 ° C.
Сплав может разливаться без дополнительной выдержки, так как во время реакции кристаллизаторы уже сформированы. Это доказывает, что эффект сильнее, чем при добавлении медно-фосфорной лигатуры, из-за высокой дисперсности фосфида алюминия, который был сформирован в процессе диффузии. Таким образом, эффективная обработка моет быть достигнута уже при концентрации фосфора 40 ppm.
Эта лигатура может быть применена не только для заэвтектических сплавов. Зернистая структура эвтектики в доэвтектических сплавах также может быть достигнута с добавлением фосфора, например, в сплаве G-AISi8Cu3 (226).
Лигатура PROBAT FLUSS VLP-200 также используется в литье под давлением алюминиевых сплавов..
Выводы
Для получения мелких кристаллов кремния в заэвтектических сплавах необходима лигатура, которая содержит эффективные кристаллы фосфида алюминия (PROBAT FLUSS VLP-200 производства компании Schäfer Chemische Fabrik GmbH). Эта лигатура производится методом порошковой металлургии. В результате образуются эффективные кристаллизаторы (центры кристаллизации), которые добавляются в расплав при производстве литейных сплавов. Практика показала, что применение этого материала более эффективно, чем добавление медно-фосфорной лигатуры. Равномерное распределение первичных зерен кремния в расплаве может быть достигнуто с меньшим количеством фосфора.
Материал прост в применении, так как обработка расплава может осуществляться при низкой температуре с незначительным временем реакции. Эта лигатура может быть использована не только для заэвтектических сплавов, но и при обработке доэвтектических для достижения зернистой структуры эвтектики.
Описанная лигатура производится компанией SCHÄFER Chemische Fabrik GmbH под торговой маркой PROBAT FLUSS VLP-200. Материал был разработан автором этой статьи. Процесс производства запатентован.
— обзор
2.5.2 Микроструктура
В предыдущем разделе мы видели роль различных легирующих элементов. Кремний и другие вторые фазы, присутствующие в алюминиевой матрице, контролируют механические свойства, включая износостойкость сплавов алюминий-кремний. Часто роль микроструктуры в износе не до конца понятна из-за различных условий эксплуатации.
Есть сообщения, что утверждается, что кремний не влияет на износостойкость алюминиево-кремниевых сплавов, в то время как другие обнаружили явное преимущество использования эвтектического сплава с содержанием около 12.5 мас.% Кремния. Еще одна группа выступила за лучшую износостойкость заэвтектического сплава. Было высказано предположение, что причиной этой путаницы являются неконтролируемый состав и меняющиеся условия испытаний (Subramanian, 1989). Например, Ванделли (1968) обнаружил, что сплав алюминия с 17 мас.% Кремния имеет лучшую износостойкость, чем сплавы, содержащие 14,5 или 25 мас.% Кремния, но другие легирующие элементы, такие как медь и никель, не поддерживаются постоянными. Сплав, который имел более высокую износостойкость, имел более высокую твердость, предположительно из-за упрочнения твердого раствора присутствием меди.Прамила Бай и Бисвас (1986) не обнаружили изменений в скорости износа алюминиевых сплавов с различным содержанием кремния от 4 до 15 мас.%, За исключением того, что чистый алюминий изнашивается немного больше, чем сплавы алюминий-кремний. Они использовали коммерческие сплавы с небольшими количествами других элементов, таких как железо, марганец, титан и медь. Аналогичное наблюдение было также сделано Окабаяси и Кавамото (1968). Однако кремний играет роль в переходной нагрузке, то есть нагрузке, при которой механизм износа изменяется от мелких равноосных частиц до ламинарных.
Еще одно противоречие касается оптимального размера частиц кремния в износостойких алюминиевых сплавах. Алюминиево-кремниевые сплавы содержат эвтектический кремний плюс первичный алюминий (заэвтектический) или первичный кремний (заэвтектический). Размер частиц эвтектики и первичного кремния можно уменьшить, добавив модификатор (натрий или стронций <0,05 мас.%) И рафинер (фосфор <0,05 мас.%). Хорошо известно, что более мелкие частицы кремния приводят к улучшенным механическим свойствам.
Было обнаружено влияние таких улучшений микроструктуры на износостойкость алюминиевых сплавов. Сообщалось, что модификация эвтектического сплава алюминия и кремния увеличивает износостойкость сплава и его композитов (Subramanian and Kishore, 1986), что прямо противоречит результатам исследования (Pramila Bai et al. , 1983), где о каких-либо положительных эффектах не сообщалось. Было показано, что рафинирование первичного кремния в заэвтектических алюминиево-кремниевых сплавах улучшает износостойкость (Jaleel et al., 1984). Следует отметить, что во время процесса скольжения любой кремний в приповерхностной области будет фрагментирован и сферодизирован до размера 1–5 мкм, независимо от его первоначального размера (Antoniou and Borland, 1987).
Более недавнее исследование Elmadagli et al. (2007) о влиянии микроструктуры (массовый процент кремния, размер частиц, морфология и твердость сплава) на износостойкость алюминиево-кремниевых сплавов пришел к выводу, что увеличение содержания кремния увеличивает переходную нагрузку, но оказывает незначительное влияние на скорость износа.Аналогичный эффект отмечен для твердости сплава. С другой стороны, уменьшение аспектного отношения или размера частиц кремния увеличивало как износостойкость, так и переходную нагрузку.
Алюминиево-кремниевый сплав для автомобильной и оборонной промышленности
В сложных условиях, например в автомобильной и оборонной промышленности, требуются материалы с улучшенными механическими свойствами. Сплав AMC ® 4632 компании Materion представляет собой высококачественный алюмосиликатный материал, который производится методом порошковой металлургии, который улучшает микроструктуру, что приводит к уникальным свойствам.Использование этого сплава для замены существующих материалов может помочь снизить вес и улучшить стабильность при повышенных температурах. Сплав AMC 4632 может быть подвергнут механической обработке с высокой чистотой поверхности и допусками с использованием высокоскоростных технологий.
ТЕПЛОВОЕ УПРАВЛЕНИЕ ДЛЯ КОСМИЧЕСКИХ И ЗАЩИТНЫХ ПРИЛОЖЕНИЙ
Управление температурой в космической и оборонной электронике — постоянная проблема. По мере того, как мощность устройств увеличивается для поддержки более сложных технологий, увеличивается и потребность в дополнительном отводе тепла.Как правило, материалы, которые обладают идеальными характеристиками теплоотдачи, также очень плотные, что увеличивает их вес, что может снизить производительность в приложениях с ограниченным количеством топлива. Поэтому очень важно найти материал, который сочетает в себе необходимую теплопроводность и низкую плотность, избегая при этом термической усталости.
AMC 4632 — легкий жесткий материал с контролируемым расширением. В то время как другие алюминиевые решения, используемые в облегчении, имеют высокий коэффициент теплового расширения (CTE), AMC 4632 решает эту проблему, согласовывая CTE меди — обычного материала, который выбирают для печатных плат и разъемов, — при этом обеспечивая преимущества алюминия.
Узнайте больше об AMC 4632 как решении для управления температурным режимом.
ГИПЕРЕВТЕКТИЧЕСКИЙ СПЛАВ AMC 4632 ДЛЯ АВТОМОБИЛЯ
В автомобильных гоночных поршнях наш алюминиево-кремниевый сплав AMC 4632 может использоваться в качестве замены обычных алюминиевых сплавов, таких как AA4032 и AA2618. Это позволяет снизить вес и повысить стабильность, несмотря на высокие температуры, связанные с двигателями внутреннего сгорания. Хотя AMC 4632 представляет собой заэвтектический сплав и обрабатывает его аналогично, это превосходный материал, поскольку усовершенствованный процесс, который мы используем для его создания, делает концевой сплав более жестким и прочным, чем другие заэвтектические алюминиевые сплавы.
Благодаря более низкому КТР, AMC 4632 обеспечивает более жесткие допуски в конструкции поршня, предлагая при этом высокий модуль упругости (примерно на 19% выше, чем у алюминиевого сплава AA4032), хорошую прочность и отличное сопротивление усталости при температуре окружающей среды и повышенных температурах. Кроме того, этот материал подходит для гонок, где использование композитов с металлической матрицей запрещено.
Загрузите техническое описание AMC 4632.
Чтобы узнать больше о наших гоночных решениях из композитных материалов с металлической матрицей, посетите нашу страницу о композитах SupremEX®.
Используйте приведенные ниже таблицы свойств, чтобы сравнить AMC 4632 с другими решениями из алюминиевых материалов.
СРАВНЕНИЕ СВОЙСТВ СПЛАВА И АЛЮМИНИЯ AMC® 4632 2618
Свойство | АМС 4632 | 2618 * | Разница |
Форма выпуска | Кованые | Кованые | |
Темперамент | Т6 | Т61 | |
0 руб.2 МПа | 380 (55) | 370 (54) | + 3% |
Rm МПа (тыс. Фунтов / кв. Дюйм) | 430 (62) | 440 (64) | -2% |
Модуль упругости, ГПа (msi) | 94 (13,6) | 75 (10,4) | + 25% |
Относительное удлинение% | 2 | 10 | -80% |
Плотность г / см³ (фунт / дюйм³) | 2.7 (0,097) | 2,75 (0,099) | -2 % |
Теплопроводность Вт / м / К | 127 | 146 | -13% |
Тепловое расширение ppm / K | 16,1 | 22 | -27% |
Твердость по Виккерсу Hv10 кг | 180 | 140 | + 29% |
* Алюминий 2618, данные из MatWeb
СРАВНЕНИЕ СВОЙСТВ AMC 4632 Сплав и АЛЮМИНИЙ 4032
Свойство | АМС 4632 | 4032 ** | Разница |
Форма выпуска | Кованые | Кованые | |
Темперамент | Т6 | Т6 | |
0 руб.2 МПа | 380 (55) | 315 (46) | + 21% |
Rm МПа (тыс. Фунтов / кв. Дюйм) | 430 (62) | 380 (55) | + 13% |
Модуль упругости, ГПа (msi) | 94 (13,6) | 77 (11,4) | + 19% |
Относительное удлинение% | 2 | 9 | -78% |
Плотность г / см³ (фунт / дюйм³) | 2.7 (0,097) | 2,68 (0,097) | + 1% |
Теплопроводность Вт / м / К | 127 | 138 | -13% |
Тепловое расширение ppm / K | 16,1 | 20,2 | -20% |
Твердость по Виккерсу Hv10 кг | 180 | 137 | + 31% |
** Алюминий 4032, данные из MatWeb
ПОДРОБНЕЕ О СПЛАВЕ AMC 4632 СПЛАВ
Поговорите с нашими инженерами, чтобы узнать, может ли алюминиево-кремниевый сплав AMC 4632 повысить прочность вашего приложения.
Алюминиево-кремниевые сплавы
Отливки — основное применение алюминиево-кремниевых сплавов, хотя некоторые листы или проволока изготовлены для сварки и пайки, а некоторые поршневые сплавы прессуются для ковки склад. Часто паяльный лист имеет только покрытие из алюминиево-кремниевого сплава и сердечник состоит из другого тугоплавкого сплава.
Сплавы без содержания меди используются для отливок низкой и средней прочности с хорошими характеристиками. устойчивость к коррозии; медный подшипник для отливок средней и высокой прочности, где коррозионная стойкость не критична.Благодаря отличной литейной способности это можно изготавливать надежные отливки даже сложной формы, в которых минимум механические свойства, полученные на плохо загруженных участках, выше, чем у отливок, изготовленных из более прочных, но менее литейных сплавов. Сплавы этой группы относятся к пределы состава:
Si | 5-25% | Mn, Cr, Co, Mo Ni, Be, Zr | до 3% |
Cu | 0-5% | Fe | до 3% |
Mg | 0–2% | Na, Sr | <0.02% |
Zn | 0–3% | п | <0,01% |
Кремний — основной легирующий элемент; придает высокую текучесть и низкую усадку, что приводит к хорошей литейной и свариваемости. Низкий коэффициент теплового расширения используется для поршней, высокая твердость частиц кремния для износа сопротивление. Максимальное количество кремния в литых сплавах порядка 22-24%. Si , но сплавы, полученные методом порошковой металлургии, могут достигать 40-50% Si .
Натрий или стронций образуют «модификацию» и зародыши фосфора. кремний, чтобы обеспечить тонкое распределение первичных кристаллов. Железо — это основная примесь, и в большинстве сплавов стараются сохранить ее на экономически низком уровне возможно из-за его вредного воздействия на пластичность и коррозионную стойкость. Для отливок в песчаные формы и неразъемных форм верхний предел обычно составляет 0,6-0,7%. Fe . В некоторые поршневые сплавы железо может добавляться намеренно и при литье под давлением. до 3% Fe допускается.
Кобальт, хром, марганец, молибден и никель иногда добавляют в качестве корректирующих веществ. для железа; их добавление также улучшает прочность при высоких температурах. Медь добавлена для повышения прочности и сопротивления усталости без потери литейных качеств, но при за счет коррозионной стойкости. Магний, особенно после термической обработки, существенно увеличивает прочность, но за счет пластичности.
Цинк — допустимая примесь во многих сплавах, часто до 1.5-2% Zn , потому что это не оказывает существенного влияния на свойства при комнатной температуре. Титан и бор являются иногда добавляются в качестве измельчителей зерна, хотя размер зерна в этих сплавах не слишком велик. важно, потому что свойства в основном контролируются количеством и структурой кремния в результате модификации, произведенной добавками натрия или добавки фосфора.
Иногда различие между растворенным и «графитовым» кремнием производится путем растворения сплава в кислотах, в которых растворенный кремний превращается в SiO 2 , тогда как графит остается несоединенным.Продолжительный или повторяющийся нагревание имеет тенденцию к сфероидизации кремния. Это сфероидизация быстрее в модифицированном сплавов и приводит к укрупнению кремния до размера, очень близкого к размеру немодифицированный материал. В отсутствие меди железо обычно находится в Al-FeSiAl 5 -Si эвтектика в виде тонких пластинок, вкрапленных с кремнием иглы или стержни. При содержании более 0,8% Fe , первичный FeSiAl 5 , появляются кристаллы.
Титан и бор обычно добавляют в количествах, лежащих в пределах их растворимости в твердом состоянии. и не образуют отдельной фазы.Железо снижает их растворимость, поэтому необходим для измельчения зерна; 0,1-0,2% V , как сообщается, улучшает FeMn соединения. Олово и свинец, если они присутствуют вместе с магнием, имеют тенденцию попадать в Mg 2 Si-фаза. Все образующиеся фазы имеют тенденцию концентрироваться в зерне. границы в виде сложных эвтектик, более или менее связанных.
Параметр решетки немного уменьшается из-за кремния в растворе и несколько уменьшается. еще медью; ни один из других элементов не влияет заметно.Таким образом параметр сплавов находится между a = 4,045 x 10 -10 м и a = 4,05 x 10 -10 м, в зависимости от состава и лечения.
Тепловое расширение существенно уменьшается за счет кремния и намного меньше заметно от всех других добавок, кроме магния, который имеет тенденцию к увеличению это слегка. Коэффициенты расширения при отрицательных температурах также составляют около 10-20%. ниже, чем у чистого алюминия. Снижение коэффициента расширения титаном и добавок циркония сообщается, но очень сомнительно, что это может быть заметно.Сплавы, полученные методом порошковой металлургии, содержащие до 50% Si , имеют еще более низкую коэффициенты расширения. Постоянное расширение сопровождает выпадение осадков из раствор кремния, магния и меди; сумма варьируется, но может быть такой же высокой как 0,15%.
Коэффициент теплопроводности составляет порядка 1,2-1,6 x 10 -2 Вт / м / К, более низкие значения для сплавов, литых в металлических формах или термообработанных до удерживают кремний, медь или магний в растворе.
Электропроводность в основном зависит от количества кремния в растворе; на него также влияют медь и магний. Значения порядка 35-40% МАКО для отожженных материалов и 22-35% IACS для сплавов, обработанных на твердый раствор. В жидкости государственное удельное сопротивление примерно в 10-15 раз больше удельного сопротивления при комнатной температуре. Марганец, хром, титан, цирконий также снижают проводимость, как и модификация.
Магнитная восприимчивость лишь незначительно уменьшается из-за кремния, меди и магний, но зависит в основном от содержания марганца.
Механические свойства. Сплавы, приготовленные из порошков, имеют несколько более высокую сильные стороны, особенно при повышенных температурах. В кованых изделиях предел прочности при растяжении достигаются прочности 200-400 МПа при относительном удлинении от 20 до 2-3% соответственно. Плохая технология литья может снизить свойства, хотя алюминиево-кремниевые сплавы являются одними из наименее чувствительных к таким переменным, как газосодержание, конструкция отливок, скорость охлаждения и кормления.Особая чистота находит, что специальные обработки могут дать свойства примерно на 10-20% лучше, чем в среднем, и, наоборот, вторичные сплавы, как правило, имеют более низкую пластичность, чем у первичных. Литье под давлением улучшает свойства по отношению к те из поковок.
Увеличение содержания кремния увеличивает прочность за счет пластичности, но это эффект не очень заметен. Модификация натрием дает ограниченное увеличение прочность, но увеличение пластичности значительно, особенно в отливках в песчаные формы.При более высоких скоростях охлаждения, обычных для отливок в металлических формах, кремний уже несколько доработан без модификации, а улучшение от модификации уменьшено. Влияние размера ячеек и расстояния между дендритными плечами на механические свойства сплавов с Si > 8% не очень заметно, но в сплавах с низким содержанием кремния, в которых преобладают дендриты алюминия, эффект в норме.
Железо может немного увеличить прочность, но резко снизить пластичность. особенно если выше 0.7% Fe и не исправлено марганцем, кобальтом и т. Д. Бериллий, марганец, хром, молибден, никель, кобальт и цирконий — все немного увеличить силу; марганец, кобальт, никель и молибден, если необходимо исправить для чугуна также может повысить пластичность; в противном случае они все уменьшают его. Сообщается также, что бериллий корректирует эффект железа. Медь и цинк увеличивают прочность за счет пластичности, но самый эффективный усилитель — магний, особенно после термической обработки, при условии, что количество и распределение магний правильные.
Улучшение зерна добавками титана, бора и циркония имеет только ограниченное влияние на механические свойства. Сообщается, что добавление серебра увеличивается удлинение. Сурьма, олово, свинец и кадмий снижают все свойства, а сурьма — в сочетании с магнием может снизить реакцию на термическую обработку. Кальций может увеличить прочность и уменьшить относительное удлинение в прямых алюминиево-кремниевых сплавах, но он оказывает вредное воздействие на сплавы поршней.
Прочность на сжатие выше, чем на разрыв примерно на 10-15%. Прочность на сдвиг составляет примерно 70% от прочности на разрыв.
Ударопрочность низкая, но такая же чувствительность к насечкам, как и следовало ожидать в сплавах, содержащих большое количество твердой, хрупкой второй фазы, часто с острыми углы. Ударопрочность улучшается за счет сфероидизации кремния.
Модуль упругости порядка 85-95 ГПа, меняется с температурой, как и прочность на разрыв.Сообщается об уменьшении демпфирующей способности при старении.
Свойства при криогенных температурах выше, чем при комнатной температуре; там незначительно или совсем не увеличивается до 170 К, но при 70 К сила становится некоторой На 20% выше, чем при комнатной температуре, с незначительным снижением пластичности или без него. Notch прочность существенно не меняется при криогенных температурах. Эффект легирующие элементы на криогенные свойства не слишком хорошо установлены, но, вероятно, это ничтожно мало.
При высокой температуре прочность снижается, а пластичность увеличивается. В спад является регулярным и более быстрым, чем для других алюминиевых сплавов, за исключением алюминий-цинк-магниевая группа. Незначительное увеличение силы, проявляемое теплом обрабатываемых сплавов, особенно если они состарены естественным путем, носит временный характер, если наступает стадия перезарядки, происходит резкое падение, а затем падение прочности с температурой становится регулярной. Ударопрочность увеличивается с увеличением температура.При более высоких температурах элементы с высокими температурами плавления (медь, железо, марганец, никель, кобальт, хром, вольфрам) в некоторой степени снижают снижение по силе, хотя их влияние незначительно. Бериллий тоже сообщается повысить жаропрочность. Несмотря на низкую жаропрочность и сопротивления усталости, алюминиево-кремниевые сплавы широко используются для поршней благодаря низкому коэффициенту расширения, хорошей износостойкости и хорошей литейной способности.Заэвтектические сплавы с добавками до 2-3% меди, никеля, железа, марганца, хром или магний предпочтительны, хотя также были получены хорошие характеристики с доэвтектическими сплавами и сплавами с низким содержанием тяжелых металлов. Уменьшение количества цинка, свинца и олова жаропрочность. Модифицированные сплавы имеют несколько более низкую высокотемпературную сила.
Сопротивление ползучести не очень хорошее. Кремний увеличивает ползучесть сопротивление алюминия намного меньше, чем у большинства других легирующих элементов.Медь, железо, марганец, никель, кобальт, хром и т. д. увеличивают его, как и следовало ожидать, и поэтому делаю магний и редкоземельные элементы.
Сопротивление усталости относительно низкое, особенно если силикон не модифицирован или сфероидизируется при термообработке. Кобальт и марганец снимают усталость сопротивление. Давление при замерзании увеличивает усталостную прочность и износостойкость; ее снижают дефекты поверхности и сложные нагрузки, особенно при высоких температурах.Усталость прочность плавно падает с температурой в прямом алюминий-кремний, но есть отсутствие перепадов температуры до 500 К в сплавах алюминий-медь-кремний. Сплавы подвержены термическая усталость из-за значительной разницы в коэффициенте расширения матрица и частицы кремния.
Износостойкость очень хорошая, особенно в заэвтектических сплавах, в которых твердые частицы кремния хорошо распределяются либо за счет зародышеобразования фосфора, либо за счет производство порошковой металлургии или сплавов с добавлением висмута.Носить стойкость высококремниевых сплавов (20-25% Si ) в 10 раз лучше, чем у гладкая сталь и сопоставима со сталью с поверхностной закалкой. Трение в парах стали по сравнению с алюминиево-кремниевыми сплавами уменьшается с улучшением поверхности и твердостью из стали; однако алюминиево-кремниевые сплавы для подшипников не принесли успеха. если они не содержат значительного количества олова.
Коррозионная стойкость. Алюминиево-кремниевые сплавы без меди имеют хорошую коррозию. устойчивость к большинству реагентов; только в щелочных растворах, которые также атакуют кремний как алюминий, их характеристики плохие.Медь значительно снижает коррозию сопротивление, как и железо, если не исправлено марганцем или хромом. Цинк до 2-3% не действует. Олово и кальций также оказывают вредное воздействие на коррозию. сопротивление. Пористость снижает коррозионную стойкость. Коррозия проточной водой быстрее, чем в стоячей воде, но того же типа. Алюминиево-кремниевые сплавы с железо и никель обладают особенно хорошей устойчивостью к воздействию высокотемпературной воды или пара. Во вторичных сплавах, где многие элементы присутствуют в небольших количествах, цинк и марганец компенсирует медь и никель, а коррозионная стойкость выражается как очень близко к первичным сплавам.Контактная коррозия особенно плохо сплавы алюминий-кремний-медь, но даже сплавы без меди в этом отношении хуже чем алюминий 99,8%.
Обрабатываемость плохая, потому что объединенная чрезвычайная твердость кремния из-за относительной мягкости матрицы инструмент очень быстро изнашивается. В заэвтектические сплавы с добавками фосфора, улучшающими распределение кремния улучшить обрабатываемость; но в доэвтектических сплавах фосфор имеет тенденцию его уменьшать, тогда как натрий улучшает его.Медь дополнительно снижает обрабатываемость тех же содержание кремния, особенно после термообработки, но такое же, как в медно-кремниевом сплавы с низким содержанием кремния могут иметь обрабатываемость, равную или лучше высокой, чем у сплавы с высоким содержанием кремния, не содержащие меди. Железо, марганец, никель, цинк, титан и др. не снижает обрабатываемость.
Алюминиево-кремниевый сплав | AMERICAN ELEMENTS ®
РАЗДЕЛ 1. ИДЕНТИФИКАЦИЯ
Название продукта: Алюминиево-кремниевый сплав
Номер продукта: Все применимые коды продуктов American Elements, например.г. AL-SI-01-P.50SI , АЛ-СИ-01-П.36СИ , АЛ-СИ-01-П.35СИ , АЛ-СИ-01-П.25СИ , АЛ-СИ-01-П.12СИ , АЛ-СИ-01-П.10СИ , АЛ-СИ-01-П.02СИ , AL-SI-01
Номер CAS: 11145-27-0
Соответствующие установленные области применения вещества: Научные исследования и разработки
Информация о поставщике:
American Elements
10884 Weyburn Ave.
Los Анхелес, Калифорния
Тел .: +1 310-208-0551
Факс: +1 310-208-0351
Телефон экстренной связи:
Внутренний, Северная Америка: +1 800-424-9300
Международный: +1 703-527-3887
РАЗДЕЛ 2.ИДЕНТИФИКАЦИЯ ОПАСНОСТИ
Классификация вещества или смеси в соответствии с 29 CFR 1910 (OSHA HCS)
Вещество не классифицируется в соответствии с Согласованной на глобальном уровне системой (GHS).
Опасности, не классифицированные иным образом
Информация отсутствует.
Элементы маркировки
Элементы маркировки GHS
Неприменимо
Пиктограммы опасности
Неприменимо
Сигнальное слово
Неприменимо
Формулировки опасности
Неприменимо
Классификация WHMIS
Не контролируется
Система классификации
Рейтинги HMIS (шкала 0-4)
(Опасные материалы) Система идентификации)
Здоровье (острые эффекты) = 0
Воспламеняемость = 0
Физическая опасность = 0
Другие опасности
Результаты оценки PBT и vPvB
PBT:
Не применимо.
vPvB:
Не применимо.
РАЗДЕЛ 3. СОСТАВ / ИНФОРМАЦИЯ ОБ ИНГРЕДИЕНТАХ
Химические характеристики: Вещества
№ CAS Описание:
7429-90-5 Алюминий
7440-21-3 Кремний
РАЗДЕЛ 4. МЕРЫ ПЕРВОЙ ПОМОЩИ
меры помощи
Общие сведения
Никаких специальных мер не требуется.
При вдыхании
В случае жалоб обратитесь за медицинской помощью.
При контакте с кожей
Обычно продукт не раздражает кожу.
При попадании в глаза
Промыть открытый глаз под проточной водой в течение нескольких минут. Если симптомы не исчезнут, обратитесь к врачу.
После проглатывания
Если симптомы не исчезнут, обратиться к врачу.
Информация для врача
Наиболее важные симптомы и воздействия, как острые, так и замедленные
Отсутствует какая-либо соответствующая информация.
Указание на необходимость немедленной медицинской помощи и специального лечения
Отсутствует какая-либо соответствующая информация.
РАЗДЕЛ 5. МЕРЫ ПОЖАРОТУШЕНИЯ
Средства пожаротушения
Подходящие средства тушения
Специальный порошок для металлических возгораний.Не используйте воду.
Средства пожаротушения, непригодные из соображений безопасности
Вода
Особые опасности, исходящие от вещества или смеси
При пожаре могут образоваться следующие вещества:
Дым оксида металла
Рекомендации для пожарных
Защитное снаряжение:
Нет специальных мер обязательный.
РАЗДЕЛ 6. МЕРЫ ПРИ СЛУЧАЙНОМ ВЫБРОСЕ
Меры личной безопасности, защитное снаряжение и порядок действий в чрезвычайной ситуации
Не требуется.
Меры по защите окружающей среды:
Не допускайте попадания материала в окружающую среду без соответствующих правительственных разрешений.
Методы и материал для локализации и очистки:
Собирать механически.
Предотвращение вторичных опасностей:
Никаких специальных мер не требуется.
Ссылка на другие разделы
См. Раздел 7 для получения информации о безопасном обращении.
См. Раздел 8 для получения информации о средствах индивидуальной защиты.
Информацию об утилизации см. В Разделе 13.
РАЗДЕЛ 7. ОБРАЩЕНИЕ И ХРАНЕНИЕ
Обращение
Меры предосторожности для безопасного обращения
Хранить контейнер плотно закрытым.
Хранить в сухом прохладном месте в плотно закрытой таре.
Информация о защите от взрывов и пожаров:
Никаких специальных мер не требуется.
Условия безопасного хранения с учетом несовместимости
Хранение
Требования, предъявляемые к складским помещениям и таре:
Нет особых требований.
Информация о хранении в одном общем хранилище:
Не хранить вместе с кислотами.
Хранить вдали от окислителей.
Дополнительная информация об условиях хранения:
Держать емкость плотно закрытой.
Хранить в прохладных, сухих условиях в хорошо закрытых емкостях.
Особые виды конечного использования
Отсутствует какая-либо соответствующая информация.
РАЗДЕЛ 8. КОНТРОЛЬ ВОЗДЕЙСТВИЯ / ИНДИВИДУАЛЬНАЯ ЗАЩИТА
Контроль воздействия
Средства индивидуальной защиты
Общие защитные и гигиенические меры
Следует соблюдать обычные меры предосторожности при обращении с химическими веществами.
Поддерживайте эргономичную рабочую среду.
Дыхательное оборудование:
Не требуется.
Защита рук:
Не требуется.
Время проницаемости материала перчаток (в минутах)
Не определено
Защита глаз:
Защитные очки
Защита тела:
Защитная рабочая одежда.
РАЗДЕЛ 9. ФИЗИЧЕСКИЕ И ХИМИЧЕСКИЕ СВОЙСТВА
Информация об основных физических и химических свойствах
Общая информация
Внешний вид:
Форма: Твердое вещество в различных формах
Запах: Без запаха
Порог запаха: Не определено.
Значение pH: Не применимо.
Изменение состояния
Точка плавления / интервал плавления: Не определено
Точка кипения / интервал кипения: Не определено
Температура сублимации / начало: Не определено
Воспламеняемость (твердое, газообразное)
Не определено.
Температура возгорания: Не определено.
Температура разложения: Не определено.
Самовоспламенение: Не определено.
Взрывоопасность: Не определено.
Пределы взрываемости:
Нижний: Не определено
Верхнее: Не определено
Давление пара: Не применимо.
Плотность при 20 ° C (68 ° F): Не определено.
Относительная плотность
Не определено.
Плотность пара
Не применимо.
Скорость испарения
Не применимо.
Растворимость в / Смешиваемость с водой: Не определено.
Коэффициент распределения (н-октанол / вода): Не определено.
Вязкость:
динамическая: Не применимо.
кинематическая: не применимо.
Другая информация
Отсутствует какая-либо соответствующая информация.
РАЗДЕЛ 10. СТАБИЛЬНОСТЬ И РЕАКЦИОННАЯ СПОСОБНОСТЬ
Реакционная способность
Информация отсутствует.
Химическая стабильность
Стабилен при соблюдении рекомендуемых условий хранения.
Термическое разложение / условия, которых следует избегать:
Разложение не происходит при использовании и хранении в соответствии со спецификациями.
Возможность опасных реакций
Реагирует с сильными окислителями
Условия, которых следует избегать
Отсутствует какая-либо соответствующая информация.
Несовместимые материалы:
Кислоты
Окислители
Опасные продукты разложения:
Пары оксидов металлов
РАЗДЕЛ 11.ТОКСИКОЛОГИЧЕСКАЯ ИНФОРМАЦИЯ
Информация о токсикологическом воздействии
Острая токсичность:
Эффекты неизвестны.
Значения LD / LC50, относящиеся к классификации:
Нет данных
Раздражение или разъедание кожи:
Может вызывать раздражение
Раздражение или разъедание глаз:
Может вызывать раздражение
Сенсибилизация:
Сенсибилизирующие эффекты неизвестны.
Мутагенность зародышевых клеток:
Эффекты неизвестны.
Канцерогенность:
ACGIH A4: Не классифицируется как канцероген для человека: Недостаточные данные для классификации агента с точки зрения его канцерогенности для людей и / или животных.
Репродуктивная токсичность:
Реестр токсических эффектов химических веществ (RTECS) содержит репродуктивные данные для этого вещества.
Специфическая системная токсичность, поражающая отдельные органы-мишени — многократное воздействие:
Эффекты неизвестны.
Специфическая системная токсичность, поражающая отдельные органы-мишени — однократное воздействие:
Эффекты неизвестны.
Опасность при вдыхании:
Воздействие неизвестно.
От подострой до хронической токсичности:
Реестр токсических эффектов химических веществ (RTECS) содержит данные о токсичности при множественных дозах этого вещества.
Дополнительная токсикологическая информация:
Насколько нам известно, острая и хроническая токсичность этого вещества полностью не изучена.
РАЗДЕЛ 12. ЭКОЛОГИЧЕСКАЯ ИНФОРМАЦИЯ
Токсичность
Водная токсичность:
Отсутствует какая-либо соответствующая информация.
Стойкость и способность к разложению
Отсутствует какая-либо соответствующая информация.
Способность к биоаккумуляции
Отсутствует какая-либо соответствующая информация.
Подвижность в почве
Отсутствует какая-либо соответствующая информация.
Дополнительная экологическая информация:
Общие примечания:
Не допускайте попадания материала в окружающую среду без соответствующих правительственных разрешений.
Избегать попадания в окружающую среду.
Результаты оценки PBT и vPvB
PBT:
Не применимо.
vPvB:
Не применимо.
Другие побочные эффекты
Отсутствует какая-либо соответствующая информация.
РАЗДЕЛ 13. УТИЛИЗАЦИЯ
Методы обработки отходов
Рекомендация
Проконсультируйтесь с государственными, местными или национальными правилами для обеспечения надлежащей утилизации.
Неочищенная тара:
Рекомендация:
Утилизация должна производиться в соответствии с официальными предписаниями.
РАЗДЕЛ 14. ИНФОРМАЦИЯ ПО ТРАНСПОРТИРОВКЕ
Номер ООН
DOT, ADN, IMDG, IATA
Неприменимо
Собственное транспортное наименование ООН
DOT, ADN, IMDG, IATA
Неприменимо
Класс (ы) опасности при транспортировке
DOT, ADR, ADN, IMDG, IATA
Класс
Неприменимо
Группа упаковки
DOT, IMDG, IATA
Неприменимо
Опасности для окружающей среды:
Неприменимо.
Особые меры предосторожности для пользователя
Не применимо.
Транспортировка наливом в соответствии с Приложением II MARPOL73 / 78 и Кодексом IBC
Не применимо.
Транспортировка / Дополнительная информация:
DOT
Морской загрязнитель (DOT):
№
РАЗДЕЛ 15. НОРМАТИВНАЯ ИНФОРМАЦИЯ
Нормы безопасности, здоровья и окружающей среды / законодательные нормы, относящиеся к веществу или смеси
Элементы маркировки GHS
Не применимо
Опасность пиктограммы
Неприменимо
Сигнальное слово
Неприменимо
Краткая характеристика опасности
Неприменимо
Национальные правила
Все компоненты этого продукта перечислены в U.S. Закон о контроле за токсичными веществами Агентства по охране окружающей среды Реестр химических веществ.
Все компоненты этого продукта занесены в Канадский список веществ, предназначенных для домашнего использования (DSL).
SARA Раздел 313 (списки конкретных токсичных химикатов)
7429-90-5 Алюминий
Предложение 65 Калифорнии
Предложение 65 — Химические вещества, вызывающие рак
Вещество не указано в списке.
Предложение 65 — Токсичность для развития
Вещество не указано.
Предложение 65 — Токсичность для развития, женщины
Вещество не указано.
Предложение 65 — Токсичность для развития, мужчины
Вещество не указано.
Информация об ограничении использования:
Для использования только технически квалифицированными специалистами.
Этот продукт подпадает под требования к отчетности раздела 313 Закона о чрезвычайном планировании и праве общества на информацию от 1986 года и 40CFR372.
Другие постановления, ограничения и запретительные постановления
Вещество, вызывающее особую озабоченность (SVHC) в соответствии с Регламентом REACH (EC) № 1907/2006.
Вещества нет в списке.
Должны соблюдаться условия ограничений согласно Статье 67 и Приложению XVII Регламента (ЕС) № 1907/2006 (REACH) для производства, размещения на рынке и использования.
Вещества нет в списке.
Приложение XIV Правил REACH (требуется разрешение на использование)
Вещество не указано.
Оценка химической безопасности:
Оценка химической безопасности не проводилась.
РАЗДЕЛ 16. ПРОЧАЯ ИНФОРМАЦИЯ
Паспорт безопасности в соответствии с Регламентом (ЕС) №1907/2006 (REACH). Вышеупомянутая информация считается правильной, но не претендует на исчерпывающий характер и должна использоваться только в качестве руководства. Информация в этом документе основана на текущем уровне наших знаний и применима к продукту с учетом соответствующих мер безопасности. Это не является гарантией свойств продукта. American Elements не несет ответственности за любой ущерб, возникший в результате обращения или контакта с вышеуказанным продуктом. Дополнительные условия продажи см. На обратной стороне счета-фактуры или упаковочного листа.АВТОРСКИЕ ПРАВА 1997-2021 AMERICAN ELEMENTS. ЛИЦЕНЗИОННЫМ ДАННЫМ РАЗРЕШЕНО ИЗГОТОВЛЕНИЕ НЕОГРАНИЧЕННЫХ КОПИЙ БУМАГИ ТОЛЬКО ДЛЯ ВНУТРЕННЕГО ИСПОЛЬЗОВАНИЯ.
% PDF-1.4 % 1346 0 объект > эндобдж xref 1346 111 0000000016 00000 н. 0000005298 00000 н. 0000005449 00000 п. 0000005993 00000 н. 0000006407 00000 н. 0000007072 00000 н. 0000007138 00000 н. 0000007556 00000 н. 0000007671 00000 н. 0000007784 00000 н. 0000007882 00000 н. 0000008556 00000 н. 0000009230 00000 н. 0000009611 00000 н. 0000010290 00000 п. 0000010976 00000 п. 0000011673 00000 п. 0000012364 00000 п. 0000013048 00000 н. 0000013730 00000 п. 0000014285 00000 п. 0000014375 00000 п. 0000014902 00000 п. 0000015497 00000 п. 0000016188 00000 п. 0000086262 00000 п. 0000086915 00000 п. 0000087147 00000 п. 0000087231 00000 п. 0000087288 00000 п. 0000092491 00000 п. 0000095297 00000 п. 0000098470 00000 п. 0000098893 00000 п. 0000099410 00000 н. 0000099872 00000 н. 0000104224 00000 н. 0000104344 00000 п. 0000104420 00000 н. 0000104519 00000 п. 0000104670 00000 п. 0000104784 00000 н. 0000105191 00000 п. 0000105537 00000 п. 0000105809 00000 н. 0000107087 00000 п. 0000107152 00000 п. 0000107272 00000 н. 0000107392 00000 н. 0000107461 00000 п. 0000107497 00000 н. 0000107831 00000 н. 0000107910 00000 п. 0000115174 00000 н. 0000115243 00000 н. 0000115279 00000 н. 0000115613 00000 н. 0000115692 00000 н. 0000121827 00000 н. 0000121906 00000 н. 0000122024 00000 н. 0000122103 00000 н. 0000122254 00000 н. 0000122353 00000 п. 0000122780 00000 н. 0000122859 00000 н. 0000163836 00000 н. 0000165693 00000 н. 0000165734 00000 н. 0000204392 00000 н. 0000204504 00000 н. 0000204653 00000 н. 0000204795 00000 н. 0000205208 00000 н. 0000205617 00000 н. 0000206025 00000 н. 0000206367 00000 н. 0000206765 00000 н. 0000208593 00000 н. 0000208995 00000 н. 0000209113 00000 н. 0000209231 00000 н. 0000209350 00000 н. 0000209468 00000 н. 0000209537 00000 н. 0000209561 00000 н. 0000210768 00000 н. 0000210847 00000 н. 0000210916 00000 п. 0000210952 00000 п. 0000211285 00000 н. 0000211364 00000 н. 0000218624 00000 н. 0000218681 00000 п. 0000218999 00000 н. 0000219078 00000 н. 0000219229 00000 п. 0000219328 00000 н. 0000219408 00000 п. 0000219465 00000 н. 0000219782 00000 н. 0000219861 00000 н. 0000219890 00000 н. 0000220616 00000 н. 0000238570 00000 н. 0000239296 00000 н. 0000256559 00000 н. 0000257285 00000 н. 0000274903 00000 н. 0000005093 00000 н. 0000002572 00000 н. трейлер ] / Назад 1613417 / XRefStm 5093 >> startxref 0 %% EOF 1456 0 объект > поток hV {PSW; # 7K ˊ ĀU4> {@ DJZuJ +: 2B-v ] m] huv3 $;}
Как и почему в алюминий добавляются легирующие элементы
Q — Мне сообщили, что чистый алюминий обычно не используется в конструкционных целях и что для производства алюминия с достаточной прочностью для изготовления элементов конструкции необходимо добавить к алюминию другие элементы.Какие элементы добавляются в эти алюминиевые сплавы? Как они влияют на характеристики материала? И в каких приложениях используются эти сплавы?A — Полученная вами информация в основном верна. Было бы очень необычно найти чистый алюминий (серия сплавов 1ххх), выбранный для изготовления конструкций из-за его прочностных характеристик. Хотя серия 1xxx представляет собой почти чистый алюминий, они будут реагировать на деформационное упрочнение, особенно если они содержат значительное количество примесей, таких как железо и кремний.Однако даже в состоянии деформационного упрочнения сплавы серии 1ххх имеют очень низкую прочность по сравнению с другими сериями алюминиевых сплавов. Когда сплавы серии 1xxx выбираются для применения в конструкции, их чаще всего выбирают из-за их превосходной коррозионной стойкости и / или их высокой электропроводности. Чаще всего сплавы серии 1xxx применяются в алюминиевой фольге, шинах электрических шин, металлизации проволоки, резервуарах для химикатов и системах трубопроводов.
Добавление легирующих элементов в алюминий является основным методом, используемым для производства ряда различных материалов, которые могут использоваться в широком диапазоне конструкционных применений.
Если мы рассмотрим семь обозначенных серий алюминиевых сплавов, используемых для деформируемых сплавов, мы можем сразу определить основные легирующие элементы, используемые для производства каждой из серий сплавов. Затем мы можем пойти дальше и изучить влияние каждого из этих элементов на алюминий. Я также добавил некоторые другие часто используемые элементы и их влияние на алюминий.
Серия Первичный легирующий элемент
1xxx Алюминий — 99.00% или больше
2xxx Медь
3xxx Марганец
4xxx Кремний
5xxx Магний
6xxx Магний и кремний
7xxx Цинк
Основные эффекты легирующих элементов в алюминии следующие:
Медь (Cu) 2xxx — Алюминиево-медные сплавы обычно содержат от 2 до 10% меди с небольшими добавками других элементов.Медь обеспечивает значительное увеличение прочности и способствует дисперсионному твердению. Введение меди в алюминий также может снизить пластичность и коррозионную стойкость. Повышена склонность к растрескиванию при затвердевании алюминиево-медных сплавов; следовательно, некоторые из этих сплавов могут быть наиболее сложными для сварки алюминиевыми сплавами. Эти сплавы включают одни из самых прочных, термически обрабатываемых алюминиевых сплавов. Чаще всего сплавы серии 2xxx применяются в аэрокосмической, военной технике и ракетных плавниках.
Марганец (Mn) 3xxx — Добавление марганца к алюминию несколько увеличивает прочность за счет упрочнения раствора и улучшает деформационное упрочнение, не снижая заметно пластичность или коррозионную стойкость. Это материалы средней прочности, не поддающиеся термической обработке, которые сохраняют прочность при повышенных температурах и редко используются в основных конструкционных приложениях. Чаще всего сплавы серии 3ххх применяются в кухонной утвари, радиаторах, конденсаторах систем кондиционирования, испарителях, теплообменниках и связанных с ними трубопроводных системах.
Кремний (Si) 4xxx — Добавление кремния к алюминию снижает температуру плавления и улучшает текучесть. Сам по себе кремний в алюминии дает сплав, не поддающийся термической обработке; однако в сочетании с магнием он дает дисперсионно-твердеющий термообрабатываемый сплав. Следовательно, в серии 4xxx есть как термически обрабатываемые, так и не подлежащие термической обработке сплавы. Добавки кремния к алюминию обычно используются для изготовления отливок. Чаще всего сплавы серии 4xxx применяются для присадочной проволоки для сварки плавлением и пайки алюминия.
Магний (Mg) 5xxx — Добавление магния к алюминию увеличивает прочность за счет упрочнения твердого раствора и улучшает их способность к деформационному упрочнению. Эти сплавы являются алюминиевыми сплавами наивысшей прочности, не поддающимися термической обработке, и поэтому широко используются в конструкциях. Сплавы серии 5ххх производятся в основном в виде листов и пластин и лишь иногда в виде прессованных изделий. Причина этого в том, что эти сплавы быстро затвердевают при деформации и, следовательно, их трудно и дорого подвергать экструзии.Некоторые распространенные области применения сплавов серии 5xxx — это кузова грузовиков и поездов, здания, бронетранспортеры, кораблестроение, танкеры-химовозы, сосуды под давлением и криогенные резервуары.
Магний и кремний (Mg 2 Si) 6xxx — Добавление магния и кремния к алюминию дает соединение силицид магния (Mg 2 Si). Образование этого соединения обеспечивает серию 6ххх их термообрабатываемость. Сплавы серии 6xxx легко и экономично экструдируются, и по этой причине их чаще всего можно найти в широком ассортименте экструдированных форм.Эти сплавы образуют важную дополнительную систему со сплавом серии 5ххх. Сплав серии 5ххх, используемый в форме пластины, и сплав 6ххх часто присоединяются к пластине в некоторой экструдированной форме. Некоторые из распространенных применений сплавов серии 6xxx — поручни, приводные валы, секции автомобильных рам, велосипедные рамы, трубчатая мебель для газонов, строительные леса, ребра жесткости и распорки, используемые на грузовиках, лодках и многих других конструкционных изделиях.
Цинк (Zn) 7xxx — Добавление цинка к алюминию (в сочетании с некоторыми другими элементами, в первую очередь магнием и / или медью) позволяет получать термически обрабатываемые алюминиевые сплавы высочайшей прочности.Цинк значительно увеличивает прочность и способствует дисперсионному твердению. Некоторые из этих сплавов могут быть подвержены коррозионному растрескиванию под напряжением и по этой причине обычно не свариваются плавлением. Другие сплавы этой серии часто свариваются плавлением с отличными результатами. Некоторые из распространенных применений сплавов серии 7xxx — аэрокосмическая промышленность, бронетехника, бейсбольные биты и велосипедные рамы.
Железо (Fe) — Железо является наиболее распространенной примесью алюминия и специально добавляется в некоторые чистые сплавы (серия 1ххх) для небольшого увеличения прочности.
Хром (Cr) — Хром добавляется в алюминий для контроля структуры зерен, предотвращения роста зерен в алюминиево-магниевых сплавах и предотвращения перекристаллизации в сплавах алюминий-магний-кремний или алюминий-магний-цинк во время термообработки. Хром также снижает подверженность коррозии под напряжением и улучшает ударную вязкость.
Никель (Ni) — Никель добавляется в сплавы алюминия с медью и алюминия с кремнием для повышения твердости и прочности при повышенных температурах и для снижения коэффициента расширения.
Титан (Ti) — Титан добавляется в алюминий в основном в качестве измельчителя зерна. Эффект измельчения зерна титана усиливается, если бор присутствует в расплаве или если он добавляется в виде лигатуры, содержащей бор в основном в виде TiB 2 . Титан — обычное дополнение к алюминиевой присадочной проволоке, поскольку он улучшает структуру сварного шва и помогает предотвратить растрескивание сварного шва.
Цирконий (Zr) — Цирконий добавляется к алюминию для образования мелкодисперсного осадка из интерматаллических частиц, препятствующих перекристаллизации.
Литий (Li) — Добавление лития к алюминию может существенно повысить прочность и, модуль Юнга, обеспечить дисперсионное твердение и снизить плотность.
Свинец (Pb) и висмут (Bi) — Свинец и висмут добавляются в алюминий для облегчения стружкообразования и улучшения обрабатываемости. Эти легко обрабатываемые сплавы часто не поддаются сварке, поскольку свинец и висмут образуют легкоплавкие компоненты и могут давать плохие механические свойства и / или высокую чувствительность к образованию трещин при затвердевании.
Резюме:
Сегодня в промышленности используется много алюминиевых сплавов — более 400 деформируемых сплавов и более 200 литейных сплавов в настоящее время зарегистрированы в Алюминиевой ассоциации. Безусловно, одним из наиболее важных факторов, которые необходимо учитывать при сварке алюминия, является определение типа свариваемого сплава на основе алюминия. Если тип основного материала свариваемого компонента недоступен из надежного источника, выбор подходящей процедуры сварки может быть затруднен.Есть несколько общих рекомендаций относительно наиболее вероятного типа алюминия, используемого в различных областях, таких как упомянутые выше. Однако очень важно знать, что неверные предположения относительно химического состава алюминиевого сплава могут привести к очень серьезным последствиям для характеристик сварного шва. Настоятельно рекомендуется произвести точную идентификацию типа алюминия, а также разработать и протестировать процедуры сварки для проверки характеристик сварного шва.
Разработка доэвтектических алюминиево-кремниевых сплавов для трехмерной печати на основе GMAW с использованием клиновых отливок
L.E. Мурр, Э. Мартинес, К. Амато, С. Гайтан, Х. Эрнандес, Д.А. Рамирес, Р. Б. Уикер, Изготовление компонентов из металлов и сплавов с помощью аддитивного производства: примеры 3D материаловедения. J. Mater. Res. Technol. 1 (1), 42–54 (2012)
Статья Google Scholar
T. Wohlers, T. Caffrey, Wohlers Report 2014 Годовой отчет о мировом прогрессе за 2014 год (Wohlers Associates, Inc., Fort Collins, CO, 2014)
Google Scholar
W.E. Фрейзер, Аддитивное производство металлов: обзор. J. Mater. Англ. Выполнять. 23 (6), 1917–1928 (2014)
Артикул Google Scholar
T.J. Хорн, О. Гарриссон, Обзор современных технологий аддитивного производства и избранных приложений. Sci. Прог. 95 (3), 255–282 (2012)
Артикул Google Scholar
Т.Wohlers, T. Caffrey, Wohlers Report 2015 Annual Worldwide Progress Report (Wohlers Associates, Inc., Fort Collins, CO, 2015)
Google Scholar
L.E. Мурр, С. Гайтан, Д.А. Рамирес, Э. Мартинес, Х. Эрнандес, К. Амато, Р. Б. Уикер, Производство металлов путем аддитивного производства с использованием технологий лазерной и электронно-лучевой плавки. J. Mater. Sci. Technol. 28 (1), 1–14 (2012)
Статья Google Scholar
К. М. Б. Тамингер, Р. А. Хафли, Изготовление электронно-лучевой формы произвольной формы: процесс быстрого осаждения металла, в г. Представлено на 3-й ежегодной конференции по автомобильным композитам , Трой, Мичиган: Общество инженеров по пластмассам, Inc (2003)
JP Kruth, Производство материалов в прессе методами быстрого прототипирования. CIRP Ann. Manuf. Technol. 40 (2), 603–614 (1991)
Артикул Google Scholar
Дж. Пилс, 3D-печать металлом: от лаборатории к фабрике. Внутри 3DP, (2014 г.), www.inside3dp.com/metal-3d-pinting-lab-fab/. Последний доступ 22 марта 2016 г.
G.C. Анзалоне, Ч. Чжан, Б. Вейнен, П.Г. Сандерс, Дж. М. Пирс, Недорогой металлический трехмерный принтер с открытым исходным кодом. IEEE Access 1 , 803–810 (2013)
Статья Google Scholar
A. Pinar, B. Wijnen, G.C. Анзалоне, Т. Хэвенс, П. Сандерс, Дж. М. Пирс, Недорогой монитор напряжения и тока с открытым исходным кодом для 3D-печати газовой дуговой сваркой.J. Sens. 876714 , 2015 (2015). DOI: 10.1155 / 2015/876714
Google Scholar
Я. Нильсиам, А. Хазельхун, Б. Вайнен, П. Сандерс, Дж. М. Пирс, Интегрированный вольт-амперный мониторинг и управление магнитным шарнирным 3-мерным принтером с открытым исходным кодом для дуговой сварки в газовой среде. Машины 3 (4), 339–351 (2015)
Артикул Google Scholar
B. Wijnen, G.C. Анзалоне, А.С. Haselhuhn, P.G. Сандерс, Дж. М. Пирс, Бесплатное программное обеспечение с открытым исходным кодом для управления трехмерным движением и обработкой. J. Open Res. Софтв. 4 (1), 4: e2 (2016). DOI: 10,5334 / jors.78
Google Scholar
Sciaky, Inc. Преимущества проволоки AM по сравнению с порошковой AM, (2016), http://www.sciaky.com/additive-manufacturing/wire-am-vs-powder-am. Последний доступ 22 марта 2016 г.
A. Ujiie, Патент США № 3665143. (Опубликовано 23 мая 1972 г.). Вашингтон, округ Колумбия: Бюро по патентам и товарным знакам США (1972)
H.T. Brandi, H. Luckow, патент США № 3 985 995 (опубликован 12 октября 1976 г.). Вашингтон, округ Колумбия: Бюро по патентам и товарным знакам США (1976)
Д. Динг, З. Пан, Д. Цуйури, Х. Ли, Многогранная модель перекрытия для роботизированной проволоки и аддитивного производства дуги (WAAM) . Робот. Comput. Интегр. Manuf. 31 , 101–110 (2015)
Статья Google Scholar
Дж. Ф. Ланкастер, Металлургия сварки (Chapman & Hall, Лондон, 1993)
Google Scholar
A.S. Haselhuhn, E.J. Гудинг, А.Г. Гловер, Г.С. Анзалоне, Б. Вейнен, П.Г. Сандерс, Дж. М. Пирс, Механизмы высвобождения подложки для газовой сварки металлическим электродом в газовой среде, 3D печать на металле алюминия. 3D печать. Addit. Manuf. 1 (4), 204–209 (2014)
Статья Google Scholar
A.S. Haselhuhn, B. Wijnen, G.C. Анзалоне, П. Сандерс, Дж. М. Пирс, Формирование на месте механизмов освобождения подложки для трехмерной печати металла сварного шва в газовой среде. J. Mater. Процесс. Technol. 226 , 50–59 (2015)
Статья Google Scholar
A.S. Haselhuhn, M.W. Buhr, B. Wijnen, P.G. Сандерс, Дж. М. Пирс, Взаимосвязь между структурой и свойствами обычных алюминиевых сварочных сплавов, используемых в качестве сырья для трехмерной печати на основе GMAW.Матер. Sci. Англ. A 673 , 511–523 (2016)
Артикул Google Scholar
А.К. Дале, К. Ногита, С.Д. Макдональд, К. Диннис, Л. Лу, Эвтектическая модификация и развитие микроструктуры в сплавах Al – Si. Матер. Sci. Англ. A 413–414 , 243–248 (2005)
Артикул Google Scholar
A. Pacz, Патент США № 1387900A. (Опубликовано 16 августа 1921 г.).Вашингтон, округ Колумбия: Бюро по патентам и товарным знакам США (1920)
S.C. Flood, J.D. Hunt, Модификация эвтектических сплавов Al – Si с помощью Na. Встретил. Sci. 15 (7), 287–294 (1981)
Артикул Google Scholar
C.E. Cross, D.L. Олсон, Модификация микроструктуры металла эвтектического шва. Сварка. J. 61 , 381с – 387с (1982)
Google Scholar
С.-З. Лу, А. Хеллавелл, Механизм модификации кремния в сплавах алюминий – кремний: двойникование, индуцированное примесью. Металл. Пер. A 18 (10), 1721–1733 (1987)
Артикул Google Scholar
Лю Циян, Ли Цинчунь, Лю Цифу, Модификация сплавов Al – Si натрием. Acta Metall. Матер. 39 (11), 2497–2502 (1991)
Артикул Google Scholar
С.-З. Лу, А. Хеллавелл, Модификация сплавов Al – Si: микроструктура, термический анализ и механизмы. JOM 47 (2), 38–40 (1995)
Статья Google Scholar
Х. Ляо, Г. Донг, Г. Сан, Исследование влияния натриевой или стронциевой модификации на коррозионную стойкость сплава Al – 11,7% Si. J. Mater. Sci. 42 (13), 5175–5181 (2007)
Артикул Google Scholar
Л. Лу, К. Ногита, А.К. Дале, Объединение добавок Sr и Na в доэвтектических литейных сплавах Al – Si. Матер. Sci. Англ. A 399 (1–2), 244–253 (2005)
Артикул Google Scholar
Н.С. Тидже, Дж. Тейлор, М.А.Истон, Подача и распределение пористости в литых сплавах Al – Si в зависимости от состава и модификации сплава. Металл. Матер. Пер. A 43 (12), 4846–4858 (2012)
Артикул Google Scholar
С.-С. Шин, Э.-С. Ким, Г.-Ю. Йом, Ж.-К. Ли, Модифицирующий эффект Sr на микроструктуру и механические свойства переработанного сплава Al – 10,5Si – 2,0Cu для литья под давлением. Матер. Sci. Англ. A 532 , 151–157 (2012)
Артикул Google Scholar
C.M. Диннис, А. Дале, Дж. А. Тейлор, М. Отте, Влияние стронция на формирование пористости в сплавах Al – Si. Металл. Матер. Пер. A. 35 (11), 3531–3541 (2004)
Статья Google Scholar
П. Шрирангам, М.Дж. Крамер, С. Шанкар, Влияние стронция на жидкую структуру доэвтектических сплавов Al – Si с использованием дифракции рентгеновских лучей высоких энергий. Acta Mater. 59 (2), 503–513 (2011)
Статья Google Scholar
П. Шрирангам, С. Чаттопадхьяй, А. Бхаттачарья, С. Наг, Дж. Кадук, С. Шанкар, Т. Шибата, Исследование локальной атомной структуры сплавов Al-Si, модифицированных Sr. Acta Mater. 65 , 185–193 (2014)
Артикул Google Scholar
D.L. Чжан, Б. Кантор, Гетерогенное зарождение затвердевания Si твердым AI в доэвтектическом сплаве Al-Si. Металл. Пер. A 24 (5), 1195–1204 (1993)
Артикул Google Scholar
Н. Фатахалла, М. Хафиз, М. Абдулхалек, Влияние микроструктуры на механические свойства и разрушение промышленного доэвтектического сплава Al – Si, модифицированного Na, Sb и Sr. J. Mater. Sci. 34 (14), 3555–3564 (1999)
Артикул Google Scholar
М. Зариф, Б. Маккей, Дж. Ли, П. Шумахер, Исследование влияния стронция (Sr) на зародышеобразование эвтектического кремния (Si) в доэвтектических сплавах Al – 5Si высокой чистоты. BHM Berg-Huettenmaenn. Монатш. 155 (11), 506–511 (2010)
Статья Google Scholar
М. Зариф, Б. Маккей, П. Шумахер, Исследование гетерогенного зародышеобразования эвтектики Si в сплавах Al – Si высокой чистоты с добавкой Sr. Металл. Матер. Пер.A 42 (6), 1684–1691 (2011)
Артикул Google Scholar
Лю, А.М. Самуэль, Ф.Х. Самуэль, Х.В. Доти, С. Вальтиерра, Характеристики α-дендритных и эвтектических структур в литейных сплавах Al – Si, обработанных Sr. J. Mater. Sci. 39 (1), 215–224 (2004)
Статья Google Scholar
С. Нафиси, Р. Гомащи, Х. Вали, Эвтектическое зародышеобразование в доэвтектических сплавах Al – Si.Матер. Charact. 59 (10), 1466–1473 (2008)
Артикул Google Scholar
Г. Хейберг, Л. Арнберг, Исследование микроструктуры эвтектики Al – Si в бинарных сплавах алюминий – кремний 7 мас.% Методом дифракции обратного рассеяния электронов (EBSD). J. Light Met. 1 (1), 43–49 (2001)
Статья Google Scholar
S.S. Sreeja Kumari, R.М. Пиллаи, T.P.D. Раджан, Б. Пай, Влияние индивидуальных и комбинированных добавок Be, Mn, Ca и Sr на поведение затвердевания, структуру и механические свойства сплава Al – 7Si – 0.3Mg – 0.8Fe. Матер. Sci. Англ. A 460–461 , 561–573 (2007)
Артикул Google Scholar
S.S.S. Шриджа Кумари, Р. Пиллаи, Б. Пай, Структура и свойства обработанного кальцием и стронцием сплава Al – 7Si – 0.3Mg: сравнение.J. Alloys Compd. 460 (1–2), 472–477 (2008)
Статья Google Scholar
Г. Хейберг, К. Ногита, А.К. Дале, Л. Арнберг, Переход от столбчатого к равноосному эвтектике в доэвтектических алюминиево-кремниевых сплавах. Acta Mater. 50 (10), 2537–2546 (2002)
Артикул Google Scholar
C.M. Диннис, А. Дале, Дж. А. Тейлор, Трехмерный анализ эвтектических зерен в доэвтектических сплавах Al – Si.Матер. Sci. Англ. A 392 (1–2), 440–448 (2005)
Артикул Google Scholar
С.Г. Шабестари, М. Кешаварц, М.М. Хиджази, Влияние стронция на кинетику образования и сегрегацию интерметаллических соединений в алюминиевом сплаве А380. J. Alloys Compd. 477 (1–2), 892–899 (2009)
Статья Google Scholar
L. Heusler, W.Шнайдер, Влияние легирующих элементов на результаты термического анализа литейных сплавов Al – Si. J. Light Met. 2 (1), 17–26 (2002)
Статья Google Scholar
Б. Кулунк, Д.Дж. Зулиани, Применение стронциевой обработки деформируемых и литых под давлением Al. JOM 48 (10), 60–63 (1996)
Артикул Google Scholar
S.D.Макдональд, А.К. Дале, Дж. А. Тейлор, Д.Х. Сент-Джон, Эвтектические зерна в немодифицированных и модифицированных стронцием доэвтектических алюминиево-кремниевых сплавах. Металл. Матер. Пер. A 35 (6), 1829–1837 (2004)
Артикул Google Scholar
М. Тимпель, Н. Вандерка, Р. Шлезигер, Т. Ямамото, Н. Лазарев, Д. Исхейм, Дж. Банхарт, Роль стронция в модификации алюминиево-кремниевых сплавов. Acta Mater. 60 (9), 3920–3928 (2012)
Артикул Google Scholar
К. Ногита, Х. Ясуда, К. Ёсида, К. Уэсуги, А. Такеучи, Ю. Судзуки, А.К. Дале, Определение сегрегации стронция в модифицированном доэвтектическом сплаве Al – Si с помощью микрорентгенфлуоресцентного анализа. Scr. Матер. 55 (9), 787–790 (2006)
Артикул Google Scholar
A.K. Дале, К. Ногита, С.Д. Макдональд, Дж. Зиндель, Л.М. Хоган, Зарождение и рост эвтектики в доэвтектических сплавах Al – Si при различных уровнях стронция.Металл. Матер. Пер. A. 32 (4), 949–960 (2001)
Статья Google Scholar
Y.H. Чо, Х.-К. Ли, К. Ой, А.К. Дале, Влияние стронция и фосфора на зарождение эвтектики Al – Si и образование β-Al5FeSi в доэвтектических литейных сплавах Al – Si. Металл. Матер. Пер. A. 39 (10), 2435–2448 (2008)
Статья Google Scholar
S.D. Макдональд, А.К. Дале, Дж. А. Тейлор, Д.Х. Сент-Джон, Образование пористости в доэвтектических сплавах алюминия с кремнием, связанное с модификациями. Металл. Матер. Пер. B. 35 (6), 1097–1106 (2004)
Статья Google Scholar
S.D. Макдональд, К. Ногита, А.К. Дале, Размер зерна эвтектики и концентрация стронция в доэвтектических алюминиево-кремниевых сплавах. J. Alloys Compd. 422 (1–2), 184–191 (2006)
Статья Google Scholar
Х. Ляо, Ю. Сан, Г. Сан, Корреляция между механическими свойствами и количеством дендритной фазы α-Al в литых почти эвтектических сплавах Al – 11,6% Si, модифицированных стронцием. Матер. Sci. Англ. A 335 (1–2), 62–66 (2002)
Артикул Google Scholar
М.М. Хак, М.А.Малек, Влияние переменных процесса на структуру и свойства алюминиево-кремниевого поршневого сплава. J. Mater. Процесс. Technol. 77 (1–3), 122–128 (1998)
Статья Google Scholar
М. Истон, Д. Сент-Джон, Улучшение зерен алюминиевых сплавов: часть I. Парадигмы зародышеобразователя и растворенного вещества — обзор литературы. Металл. Матер. Пер. A 30 (6), 1613–1623 (1999)
Артикул Google Scholar
М. Истон, Д. Сент-Джон, Улучшение зерна алюминиевых сплавов: часть II. Подтверждение и механизм парадигмы растворенных веществ. Металл. Матер. Пер. A 30 (6), 1625–1633 (1999)
Артикул Google Scholar
Л. Лу, А.К. Дале, Эффекты комбинированных добавок измельчителей Sr и AlTiB в доэвтектических литейных сплавах Al – Si. Матер. Sci. Англ. A 435–436 , 288–296 (2006)
Артикул Google Scholar
D.G. Маллапур, С.А.Кори, К.Р. Удупа, Влияние Ti, B и Sr на микроструктуру и механические свойства сплава А356. J. Mater. Sci. 46 (6), 1622–1627 (2010)
Статья Google Scholar
B.S. Мурти, С.А. Кори, М. Чакраборти, Улучшение зерна алюминия и его сплавов путем гетерогенного зародышеобразования и легирования. Int. Матер. Ред. 47 (1), 3–29 (2002)
Статья Google Scholar
Y.C. Ли, А. Дале, Д.Х. Сент-Джон, Д.Е.С. Хатт, Влияние измельчения зерна и содержания кремния на формирование зерна в доэвтектических сплавах Al – Si. Матер. Sci. Англ. A 259 (1), 43–52 (1999)
Артикул Google Scholar
Мартуканиц Р.П. Выбор и свариваемость термически обрабатываемых алюминиевых сплавов. ASM Handb. 6 , 528–536 (1993)
Google Scholar
P.B. Дикерсон, Сварка алюминиевых сплавов. ASM Handb. 6 , 722–739 (1993)
Google Scholar
M.J. Caton, J.W. Джонс, Дж. М. Буало, Дж. Э. Эллисон, Влияние скорости затвердевания на рост малых усталостных трещин в литом алюминиевом сплаве типа 319.Металл. Матер. Пер. A. 30 (12), 3055–3068 (1999)
Статья Google Scholar
Буало Дж., Эллисон Дж. Э. Влияние времени затвердевания и термообработки на усталостные свойства литого алюминиевого сплава 319. Металл. Матер. Пер. A. 34 (9), 1807–1820 (2003)
Статья Google Scholar
I.C. Стоун, Х. Джонс, Влияние скорости охлаждения и скорости фронта на выбор микроструктуры затвердевания в Al – 3.Сплавы от 5 мас.% Fe – 0 до 8,5 мас.% Si. Матер. Sci. Англ. A 226 , 33–37 (1997)
Артикул Google Scholar
М.Ф. Урфали, И. Тодд, Х. Джонс, Влияние скорости охлаждения при затвердевании на морфологию и количество первичных частиц Mg2Si в единице объема в заэвтектическом сплаве Al – Mg – Si. Металл. Матер. Пер. A. 36 (5), 1368–1372 (2005)
Статья Google Scholar
Дж. Чжан, З. Фань, Y.Q. Ван, Б. Чжоу, Влияние скорости охлаждения на микроструктуру заэвтектических сплавов Al-Mg2Si. J. Mater. Sci. Lett. 19 (20), 1825–1828 (2000)
Артикул Google Scholar
J.A. Хуарес-Ислас, Д.Х. Уоррингтон, Х. Джонс, Образование стабильных и метастабильных фаз в сплавах Al – Mn с использованием технологии литья под давлением с охлаждением. J. Mater. Sci. 24 (6), 2076–2080 (1989)
Артикул Google Scholar
А. Хоксворт, W.M. Рейнфорт, Х. Джонс, Выбор микроструктуры затвердевания в системах Al-La, Al-Ce и Al-Nd с высоким содержанием алюминия. J. Cryst. Рост 197 (1), 286–296 (1999)
Статья Google Scholar
J.H. Перепезко, К. Хилдал, Анализ микроструктур затвердевания при литье клина. Филос. Mag. 86 (24), 3681–3701 (2006)
Артикул Google Scholar
A.F. Norman, P.B. Прангнелл, Р. МакИвен, Поведение при затвердевании разбавленных сплавов алюминия и скандия. Acta Mater. 46 (16), 5715–5732 (1998)
Артикул Google Scholar
A.F. Norman, K. Hyde, F. Costello, S. Thompson, S. Birley, P.B. Прангнелл, Исследование влияния Sc на алюминиевые отливки серий 2000 и 7000: для улучшения сварки плавлением. Матер. Sci. Англ. A 354 (1–2), 188–198 (2003)
Артикул Google Scholar
W. S. Rasband, Image J., Национальные институты здравоохранения США, Бетсесда, Мэриленд, США, http://imagej.nih.gov/ig/, 1997–2014 гг.
D. Bouchard, J.S. Киркалди, Прогнозирование расстояний между ветвями дендритов при нестационарном и установившемся тепловом потоке однонаправленно отвержденных бинарных сплавов. Металл. Матер. Пер. B 28 (4), 651–663 (1997)
Артикул Google Scholar
С. Су, Х. Лян, А. Моран, Э.Дж. Лаверниа, Поведение сплава Al – 6Si при затвердевании во время распыления и осаждения. Int. J. Rapid Solidif. 8 (3), 161–177 (1994)
Google Scholar
D.W. Херд, С. Брофи, М. Брочу, Изготовление твердой формы из компонентов Al – Si произвольной формы с помощью процесса CSC-MIG. Может. Металл. Q. 51 (3), 302–312 (2012)
Статья Google Scholar
ASTM B557-02. Стандартные методы испытаний на растяжение деформируемых и литых изделий из алюминиевых и магниевых сплавов. ASTM International, West Conshohocken, PA, 2013, www.astm.org
Q.G. Ван, микроструктурные эффекты на растяжение и разрушение алюминиевых литейных сплавов A356 / 357. Металл. Матер. Пер. A. 34 , 2887–2899 (2003)
Статья Google Scholar
Q.G. Ван, К.Дж. Дэвидсон, Поведение литейных сплавов Al – Si – Mg при затвердевании и выделении. J. Mater. Sci. 36 (3), 739–750 (2001)
Артикул Google Scholar
S. Kou, Welding Metallurgy (Wiley, New York, 1987)
Google Scholar
М. Тирякиоглу, Дж.Т. Стейли, Металлургия и влияние легирующих добавок в алюминиевые сплавы, в справочнике по алюминию , вып.1, изд. автор: G.E. Тоттен, Д.С. Маккензи (Marcel Dekker Inc, Нью-Йорк, 2003), стр. 81–209
Google Scholar
Q.G. Ван, Ч. Касерес, Дж. Р. Гриффитс, Повреждение из-за эвтектического растрескивания частиц в алюминиевых литейных сплавах A356 / 357. Металл. Матер. Пер. A 34 , 2901–2912 (2003)
Артикул Google Scholar
М. Друзи, С. Якоб, М.