Состав нержавеющей стали: какие типы антикоррозийных сплавов существуют
Сталь – высокопрочный и долговечный материал, способный выдерживать значительные нагрузки в течение многих лет. В его состав входят железо (50%) и углерод (не более 2,14%), последний значительно улучшает износоустойчивость сплава, его твердость.
Чтобы произвести нержавеющий сплав, требуется также хром. Из чего еще состоит нержавеющая сталь еще? Разбираемся.
Особенности сплавов, устойчивых к коррозии
Легирующим элементом нержавеющей стали является хром, а также вольфрам, никель, ниобий, молибден и т. д. С их помощью сталь обретает все необходимые антикоррозийные и физико-механические качества. Другие возможные примеси – кобальт и титан, процент которых в составе металла минимален.
Пластичность и хрупкость (твердость) – два физических свойства, определяющих качество стали. Первое из них показывает, насколько сильно может деформироваться изделие из нержавеющей стали без разрушения. Твердость металла – обратный показатель, означающий способность материала удлиняться в незначительной мере, без появления больших остаточных деформаций.
Чтобы отрегулировать эти свойства (изменить внутреннюю структуру сплава), проводится термическая обработка: закалка критически высокой температурой и охлаждение в несколько подходов.
В зависимости от физических свойств состав нержавеющей стали бывает трех типов:
- коррозиестойкий. Используется в быту и на производстве, в котором не требуется высокая защита металла от вредных сред;
- жаростойкий. Не деформируется и не меняет свойств, в том числе в условиях крайне высоких температур;
- жаропрочный. Сохраняет прочность в агрессивной среде, но может ржаветь.
Ассортимент сплавов отечественного рынка можно разделить на 2 группы: хромистые и хромоникелевые стали. Обе включают такие структурные классы:
- Аустенитный. Обладает хорошими антикоррозионными качествами. С повышением доли никеля и хрома в составе (до 20%) улучшает сопротивление к высокой температуре.
Такая сталь называется жаропрочной.
- Ферритные. Содержат малое количество хрома и углерода (до 17%).
- Дуплексные. Сочетают качества двух предыдущих типов. Никель в составе нержавеющей стали на уровне 4,5–8%, хром – до 28%.
- Мартенситные. Сплав с уменьшенным содержанием углерода, укрепляется методом закалки, благодаря чему долго не стареет.
Чаще всего используется химический состав нержавеющей стали аустенитного и ферритного типов в литом либо деформированном состоянии. Отдельная группа – хромомарганцевоникелевые сплавы, по структуре они сходны с хромоникелевыми.
Типы нержавеющих сплавов и их свойства
Как известно, для того чтобы железо стало коррозиеустойчивым, в него необходимо добавить какой-то цветной или благородный металл. В зависимости от того, какой состав металла нержавеющей стали, выделяют 3 его типа. Самая простая структура у марок 08X13 и 12X13, чаще всего используется в быту и промышленности, где нет высоких ударных нагрузок. Процент хрома в таких сплавах равен 13%. 8 и 12 в маркировке – это цифры, обозначающие процентное соотношение углерода.
Более высокое содержимое этого элемента (от 17%) делает нержавейку хорошо приспособленной к применению в самых агрессивных средах. Имеющаяся на поверхности металла оксидная пленка не позволяет образовываться окалине.
Химические свойства хромистых коррозиестойких сталей
Железо – основа любой стали – может обретать состояния, сопоставимые с периодами активности и покоя кристаллической решетки, которые являются определяющими для коррозионной выносливости. Более высокий показатель свидетельствует о большей пассивности металла.
Чаще всего встречаются сплавы высокой гибкости (образующиеся при закладке мартенситной структуры). Химически это чистый металл с насыщенным содержанием углерода в составе. Сюда относится быстрорежущая и пищевая нержавейка, из которой делают кухонную посуду и ножи. Такой металл отлично переносит контакт с веществами, оказывающими незначительное химическое воздействие.
Еще один тип – ферритные сплавы, магнитные. Кристаллическая решетка такого вещества имеет несколько иную структуру из-за наличия хрома. Такой состав пищевой нержавеющей стали также используется в производстве инструмента.
Что касается мартенситно-ферритных сплавов, то они сочетают качества двух предыдущих типов: прочны, устойчивы к деформации, имеют магнитный потенциал. Среди минусов – меньшая устойчивость к окислению.
Отличительные черты аустенитных сплавов
Так называемое γ-железо представляет собой прочный сплав с углеродом. Он подвергается коррозии даже при высоком содержании хрома (если в нем нет ниобия и титана). В таком случае проводится термообработка.
Другие свойства металла высокого уровня: прочность, технологичность, пластичность. Для производства кухонной утвари этот класс не пригоден из-за высокой аллергенности никеля.
Независимо от того, что входит в состав нержавеющей стали аустенитной, она всегда немагнитная. Однако при незначительном холодном изгибании магнитные свойства могут появиться, так как в этом случае аустенит трансформируется в феррит. Чтобы обеспечить прочность таких сплавов, уменьшается содержание углерода, но не более чем до 0,04%. В противном случае образуются карбиды. Нередко для улучшения прочности стали в состав добавляется связанный азот, образующий карбонитрид (например, марка Х17АГ14).
Другие составы имеют несколько иные параметры, например, аустенитно-мартенситные. Они менее устойчивы к коррозии, но более крепкие, тяжело поддаются температурной обработке. Преимущественно используются в производстве легких конструкций.
Аустенитно-ферритные сплавы содержат относительно небольшое количество никеля, благодаря чему их проще сваривать, выполняя швы высокого качества. Примером могут послужить марки 08Х22Н6Т или 12Х21Н5Т. Однако стоит заметить, что такие промежуточные составы менее пластичны и жаропрочны.
Сталь 3сп — Сталь конструкционная углеродистая обыкновенного качества
Сталь 3СП
Данная марка стали 3сп имеет распространенную маркировку в виде СТ3СП. Она относится к разряду углеродистых конструкционных сталей, имеющих обыкновенное качество. В основе данного сплава находится феррит, но по причине того, что данный материал недостаточно прочен и пластичен, в чистом виде он применятся не может. Именно поэтому проводится процедура насыщения его углеродом. Помимо всего прочего, в состав сплава стали 3сп добавлены сера, мышьяк, фосфор, медь, хром, марганец, никель и кремний. Именно количество фосфора и серы в составе сплава определяют его пластичность и уровень прочности. Это дает возможность утверждать о том, что точный состав сплава, а также технология его производства целиком и полностью определяются требованиями, выдвигаемыми к физическим и химическим свойствам полученной в результате стали 3сп.
Свойства марки стали 3СП
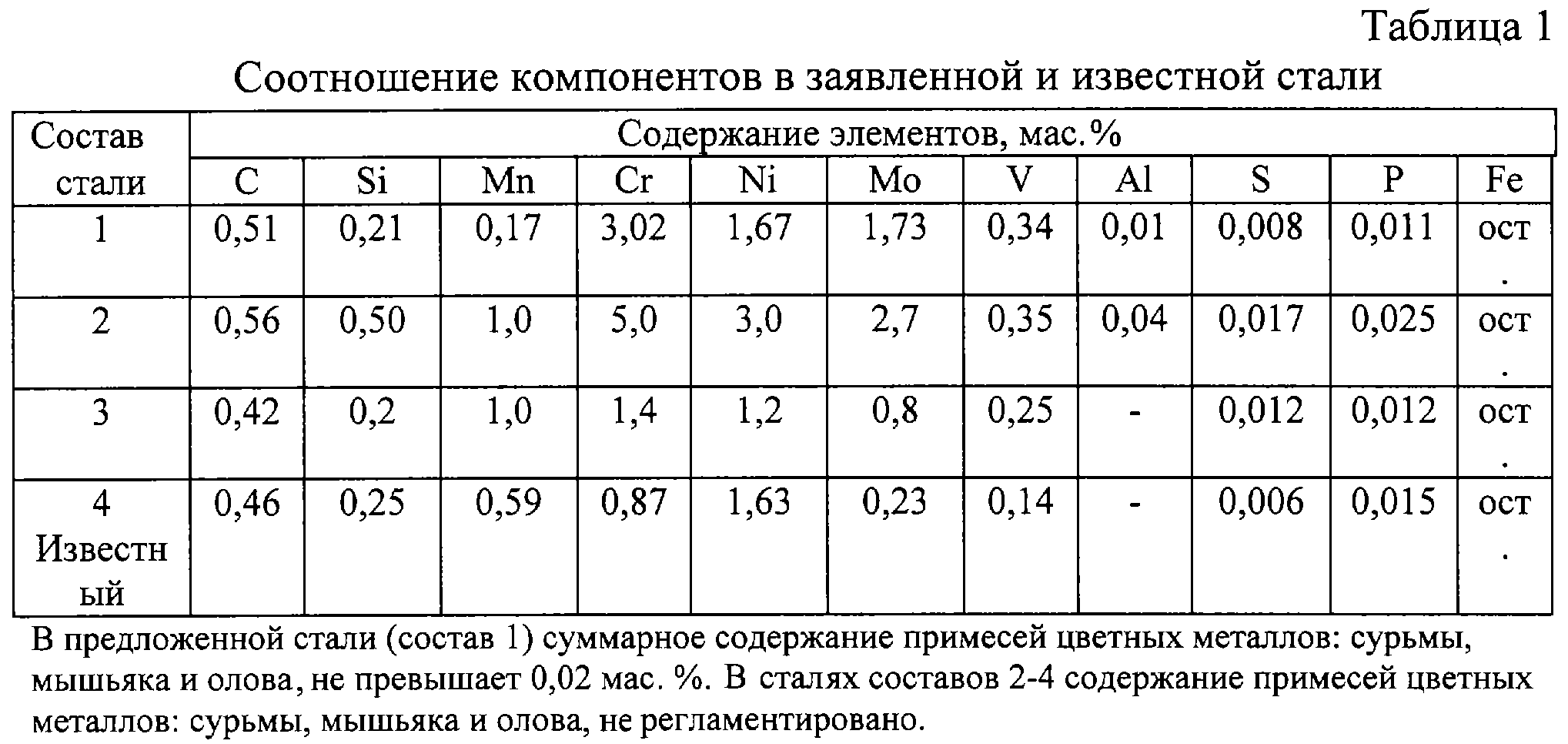
Для улучшения определенных свойств металла без изменения его химического состава, часто используют термическую обработку, во время которой металл подвергается сильнейшему нагреву, а после чего некоторое время охлаждается в жидкой среде с поддержанием низких температур. Проведение подобной процедуры позволяет в разы продлить эксплуатационный срок готового изделия, изменить общую массу или его габариты. Во время термической обработки происходит изменение механических свойств сплава, который в горячей форме может принять любую заданную форму.
Типы термообработки стали 3сп
На данный момент выделяют три основные разновидности термообработки для сталей – отпуск, закалка и отжиг. Последний применяется в тех случаях, когда необходимо получить у сплава равномерную структуру или уменьшить пластичность. Закалка используется в большинстве своем для придания материалу неравновесной структуры и нетипичных характеристик.
Процесс термической обработки наделяет сталь 3сп рядом качеств, которые позволяют использовать ее, как материал в основе несущих элементов множества конструкций. Помимо этого, данный сплав стали 3сп может быть использован при создании деталей, работа которых должна осуществляться исключительно при положительных температурах окружающей среды. Заметим также, что она используется в виде листового или фасонного проката с толщиной не более десяти миллиметров в качестве несущих элементов в конструкциях, созданных с помощью сваривания, которые могут функционировать в диапазоне температур: от -40 до +425 градусов Цельсия.
Химический состав стали 3сп
C | Si | Mn | S | P | V | Cr | N | Cu | As | Fe |
0.58 — 0.67 | 0.22 — 0.45 | 0.5 — 0.9 | до 0.02 | до 0.03 | 0.08 — 0.15 | 0.08 — 0.15 | до 0,008 | до 0,3 | до 0,08 | ~97 |
Зарубежные аналоги маркм стали 3сп
США | A284Gr.![]() |
Германия | 1.0038, 1.0116, DC03, Fe360B, Fe360D1, RSt37-2, RSt37-3, S235J0, S235J2G3, S235JR, S235JRG2, St37-2, St37-3, St37-3G |
Япония | SS330, SS34, SS400 |
Франция | E24-2, E24-2NE, E24-3, E24-4, S235J0, S235J2G3, S235J2G4, S235JRG2 |
Англия | 1449-2723CR, 1449-3723CR, 3723HR, 40B, 40C, 40D, 4360-40B, 4360-40D, 4449-250, 722M24, Fe360BFU, Fe360D1FF, HFS3, HFS4, HFW3, HFW4, S235J2G3, S235JR, S235JRG2 |
Евросоюз | Fe37-3FN, Fe37-3FU, Fe37B1FN, Fe37B1FU, Fe37B3FN, Fe37B3FU, S235, S235J0, S235J2G3, S235JR, S235JRG2 |
Италия | Fe360B, Fe360BFN, Fe360C, Fe360CFN, Fe360D, Fe360DFF, Fe37-2, S235J0, S235J2G3, S235J2G4, S235JRG2 |
Бельгия | FE360BFN, FE360BFU, FED1FF |
Испания | AE235BFN, AE235BFU, AE235D, Fe360BFN, Fe360BFU, Fe360D1FF, S235J2G3, S235JRG2 |
Китай | Q235, Q235A, Q235A-B, Q235A-Z, Q235B, Q235B-Z, Q235C |
Швеция | 1312, 1313 |
Болгария | BSt3ps, BSt3sp, Ew-08AA, S235J2G3, S235JRG2, WSt3ps, WSt3sp |
Венгрия | Fe235BFN, Fe235D, S235J2G3, S235JRG2 |
Польша | St3S, St3SX, St3V, St3W |
Румыния | OL37.![]() |
Чехия | 11375, 11378 |
Финляндия | FORM300H, RACOLD03F, RACOLD215S |
Австрия | RSt360B |
Механические свойства стали 3сп
t испытания,°C | σ0,2, МПа | σB, МПа | δ5, % | ψ, % | KCU, Дж/м |
Горячекатаная заготовка размерами 140Х120 мм | |||||
20 | 220 | 445 | 33 | 59 | 154 |
300 | 205 | 199 | |||
500 | 180 | 285 | 34 | 80 | 119 |
Лист и фасонный прокат в горячекатаном состоянии толщиной до 30 мм | |||||
20 | 205-340 | 420-520 | 28-37 | 56-68 | |
200 | 215-285 | ||||
300 | 205-265 | ||||
400 | 155-255 | 275-490 | 34-43 | 60-73 | |
500 | 125-175 | 215-390 | 36-43 | 60-73 | |
Образец диаметром 6 мм, длиной 30 мм кованый и нормализованный.![]() | |||||
700 | 73 | 100 | 57 | 96 | |
800 | 51 | 63 | 95 | 95 | |
900 | 38 | 65 | 84 | 100 | |
1000 | 25 | 43 | 79 | 100 | |
1100 | 19 | 31 | 80 | 100 | |
1200 | 14 | 25 | 84 | 100 |
Технологические свойства стали 3сп
Температура ковки | Начала 1300, конца 750. Охлаждение на воздухе. |
Свариваемость | Сваривается без ограничений; способы сварки: РДС, АДС под флюсом и газовой защитой, ЭШС, КТС.![]() |
Обрабатываемость резанием | В горячекатаном состоянии при НВ 124 σB = 400МПа, Kυ тв.спл. = 1,8 и Kυ б.ст. = 1,6 |
Склонность к отпускной способности | Не склонна |
Флокеночувствительность | Не чувствительна |
404 Not Found | 404 Страница не найдена
Отдел продаж
По вопросам приобретения контрольно-измерительного оборудования Вы можете обратиться к сотрудникам отдела продаж посредством «Skype». Свяжитесь с нами в режиме онлайн!
Васюкова Юлия Павловна | Заместитель коммерческого директора | Вопросы по приобретению оборудования | |
Гавриков Андрей Юрьевич | Начальник отдела продаж №1 | Вопросы по приобретению оборудования | |
Гофман Анна Валерьевна | Начальник отдела продаж №2 | Вопросы по приобретению оборудования | |
Степанов Евгений Евгеньевич | Руководитель дилерской сети | Вопросы по работе с дилерской сетью |
Центральный федеральный округ
Разгуляев Вячеслав Валерьевич | Менеджер ОП №1 | Костромская область | |
Зырянова Лариса Владиславна | Менеджер ОП №1 | Москва и Московская область | |
Удалова Татьяна Александровна | Менеджер ОП №1 | Калужская, Смоленская, Тверская области | |
Иванова Екатерина Александровна | Менеджер ОП №1 | Брянская, Владимирская, Ивановская, Рязанская, Тульская, Ярославская области |
Северо-Западный федеральный округ
Удалова Татьяна Александровна | Менеджер ОП №1 | Санкт-Петербург, Калининградская, Ленинградская, Мурманская, Новгородская области, Карелия | |
Иванова Екатерина Александровна | Менеджер ОП №1 | Архангельская, Вологодская, Псковская области, Ненецкий АО | |
Бобырь Вера Сергеевна | Менеджер ОП №2 | Республика Коми |
Уральский федеральный округ
Разгуляев Вячеслав Валерьевич | Менеджер ОП №1 | Курганская, Свердловская области | |
Иванова Екатерина Александровна | Менеджер ОП №1 | ХМАО-Югра, Челябинская область | |
Удалова Татьяна Александровна | Менеджер ОП №1 | ЯНАО, Тюменская область |
Башкирия, Татарстан
Грищенко Юрий Евгеньевич | Менеджер ОП №2 | Республики Башкортостан и Татарстан |
Приволжский федеральный округ
Бобырь Вера Сергеевна | Менеджер ОП №2 | Нижегородская, Пензенская, Самарская, Кировская, Оренбургская, Саратовская, Ульяновская области; Чувашия, Марий Эл, Мордовия, Удмуртия | |
Пикунов Игорь Андреевич | Менеджер ОП №2 | Пермский край, Удмуртия |
Сибирский федеральный округ
Маркина Екатерина Андреевна | Менеджер ОП №2 | Иркутская, Кемеровская, Новосибирская, Томская области; Алтайский край, Красноярский край, Забайкальский край; Бурятия, Хакасия, Тыва, Алтай | |
Иванова Екатерина Александровна | Менеджер ОП №1 | Омская область |
Южный Федеральный округ
Разгуляев Вячеслав Валерьевич | Менеджер ОП №1 | Астраханская, Волгоградская, Ростовская области, Краснодарский край, Адыгея, Калмыкская Республика, Крым |
Северо-Кавказский федеральный округ
Разгуляев Вячеслав Валерьевич | Менеджер ОП № 1 | Дагестан, Ингушетия, Кабардино-Балкарская республика, Карачаево-Черкесская республика, Северная Осетия, Ставропольский край, Чеченская республика |
Дальневосточный Федеральный Округ
Маркина Екатерина Андреевна | Менеджер ОП №2 | Вопросы по приобретению оборудования |
Казахстан, Узбекистан, Киргизия, Таджикистан, Туркмения
Пикунов Игорь Андреевич | Менеджер ОП №2 | Вопросы по приобретению оборудования |
Иванова Екатерина Александровна | Менеджер ОП №1 | Вопросы по приобретению оборудования |
Грузия, Армения, Азербайджан
Разгуляев Вячеслав Валерьевич | Менеджер ОП №1 | Вопросы по приобретению оборудования |
Углеродистая и легированная сталь: классификация по химии
23 апреля 2021, 09:17Химический состав сталей:
- Углеродистая (нелегированная)
- Легированная
Углеродистая сталь
Углеродистая сталь — сплав железа с углеродом. Содержание углерода варьируется от 0,02 до 2,14%, дополнительные примеси: марганец Mn до 0,9%, кремний Si до 0,5%, сера S до 0,06%, фосфора P до 0,07%. Главной составляющей, определяющей свойства стали, является углерод.
Основа такого сплава — высокое содержание углерода. В зависимости от его процентного соотношения, сталь разделяют на виды:
- низкоуглеродистую = углерода до 0,25%
- среднеуглеродистую = углерода от 0,25 до 0,6%
- высокоуглеродистую = углерода от 0,6% до 2,0%
Зачем потребовалась дополнительное разделение по степени содержания углерода? Такой выбор обусловлен последующей технологической обработкой. Взаимодействие углерода с железом в составе стали определяет эксплуатационные и технологические свойства. Однако, если в сплаве содержание углерода меньше 0,05%, то такой сплав относят к технически чистому железу. Максимальное значение углерода теоретически может достигать 2%, а практически — редко встречается больше 1%.
Дополнительные элементы сплава называют легирующими добавками.Легированная сталь
Легированная сталь — углеродистый сплав, в состав которого введены дополнительные элементы и специальные добавки для придания определенных механических, физических, химических свойств.
Стоит отметить, что в основу состава легированной стали входят все элементы углеродистой стали с добавлением специальных добавок, таких как: азот, хром, ванадий, вольфрам, никель, кобальт и др. Выделяют соотношение влияния легирующих элементов на углерод и разделяют их на две группы: образующие с углеродом химические соединения – карбиды (хром, марганец, титан, ванадий, вольфрам, молибден и др.) и не образующие карбидов (никель, алюминий, кремний и др.). Легированные карбидообразующие сплавы имеют высокое сопротивление к износу.
В зависимости от легирующих элементов, входящих в легирующие сплавы, сталь подразделяют на виды:
- низколегированную = добавок не более 2,5%
- среднелегированную = добавки от 2,5% до 10%
- высоколегированную = добавок более 10%
Если суммарное количество легирующих элементов превысит 50%, то такой сплав нельзя отнести к сплаву с основой из железа и его нельзя назвать сталью. Добавки же менее 1%, как правило, не могут серьезно повлиять на состав сплава — такой вид не будет отнесен к легированным сталям. Присутствие некоторых элементов (бор, ниобий) в сотых, тысячных долях процента заметно меняет свойства стали. Такую сталь называют микролегированной. Легирующие добавки повышают прочность, коррозийную стойкость стали, снижают опасность хрупкого разрушения.
— Осколкова Анастасия, контент-менеджер «ОНИКС»
стали и сплавы — Fonderia Augusta
Предприятие регулярно производит следующие сплавы:
- Мартенситные нержавеющие стали
Аустенитные нержавеющие стали
- Дуплексные и супердуплексные нержавеющие стали
Углеродистые стали
Низколегированные стали
Сплавы на никелевой основе
Износостойкие чугуны
Стальное литье поставляется вместе с сертификатом химического состава и другими сертификатами качества согласно требованиям заказчика. Это неполный список наиболее востребованных марок стали, которые поставляются в соответствии со стандартами ASTM и европейскими нормами.
Если интересующий вас материал отсутствует в списке, свяжитесь с нами, указав ваши специфические требования.
Fonderia Augusta выпускает более 300 различных стальных сплавов.
Мартенситные нержавеющие сталиCA6NM — спецификация ASTM | 1.4317 (GX4CrNi13-4) — спецификация EN 10283
CB7CU — спецификация ASTM | 1.4525 (GX5CrNiCu16-4) — спецификация EN 10283
CF8M — спецификация ASTM A743-A351 | 1.4408 (GX6CrNiMo18-10) — спецификация EN 10283
CF3M — спецификация ASTM A743-A351 | 1.4409 (GX2CrNiMo19-11-2) — спецификация EN 10283
CF3 — спецификация ASTM A743-A351 | 1.4309 (GX2CrNi19-11) — спецификация EN 10283
CF8 — спецификация ASTM A743-A351 | 1.4308 (GX6CrNi18-9) — спецификация EN 10283
1. 4584 (GX2NiCrMoCu 25-20-5) спецификация EN 10283 (AISI 904L-UNS N08904)
CK3MCUN (SMO 254) — спецификация ASTM A351 | 1.4557 (GX2CrNiMoCuN20-18-6) — спецификация EN 10283
CD6MN, Duplex Gr. 3A спецификация ASTM A995-A890 | 1.4460 — спецификация EN 10283
CD3MN, Duplex Gr. 4A — спецификация ASTM A995-A890 | 1.4470 (GX2CrNiMoN22-5-3) — спецификация EN 10283
CE3MN, Super duplex Gr. 5A — спецификация ASTM A995-A890 | 1.4469 (GX2CrNiMoN26-7) — спецификация EN 10283
CD3MWCuN, Gr. 6A — спецификация ASTM A995-A890 | 1.4417 (GX2CrNiMoN25-7-3) — спецификация EN 10283
CD4MCuN, Duplex Gr. 1B спецификация ASTM A995-A890 | 1.4593 (GX3CrNiMoCuN24-6-2-3)
1.4517 (GX2CrNiMoCuN25-6-3-3+AT) — спецификация EN 10283
WCB — спецификация ASTM A216 | 1.0619 (GP240GH) — спецификация EN 10213
WCC — спецификация ASTM A216 | 1.0625 (GP280GH) — спецификация EN 10213
LCB — спецификация ASTM A352 | LCC — спецификация ASTM A352 | 1. 6220 (G20Mn5) — спецификация EN 10293 | 1.1131 (G17Mn5) — спецификация EN 10293
39NiCrMo3 (38NCD4)
WC6 спецификация ASTM A217 | 1.7357 (G17CrMo5-5) — спецификация EN 10213/10293
WC9 спецификация ASTM A217 | 1.7379 (G17 CrMo9-10) — спецификация EN 10213/10293
CW6MC (INCONEL 625) — спецификация ASTM A494 | 2.4856 (NiCr22Mo9Nb)
CW12MW (HASTELLOY C) — спецификация ASTM A494 | 2.4686 (G-NiMo17Cr)
N12MV (HASTELLOY B) — спецификация ASTM A494
ASTM A532 Cl.2, Cl.3
Ni-Hard 4
Состав нержавеющей стали – какие типы сплавов существуют? + видео
Сегодня все большей популярностью пользуются легированные сплавы, особенно с добавлением хрома, который входит в состав нержавеющей стали, обладающей высокими антикоррозийными свойствами. Мы рассмотрим, какие бывают классы нержавейки.
1 Рассмотрим особенности коррозиеустойчивых сплавов
Стали с различными добавками, улучшающими физические свойства, называются легированными. К ним относятся и нержавеющая сталь, в состав которой обычно входит хром, как основной элемент, отвечающий за сопротивление коррозии. Для этой же цели используются в некоторых случаях никель, ванадий, марганец, медь и даже связанный азот. В гораздо меньшем процентном соотношении добавляются другие элементы, улучшающие качества металла: ниобий, кобальт и молибден, иногда – титан. И, конечно, не обойтись без вечных спутников железа – углерода, серы, фосфора, кремния. К слову, чем меньше их процентная доля в сплаве, тем выше качество стали.
Нержавеющая сталь
Нержавеющий сплав образуется в том случае, если химический состав имеет включение более 13 % хрома. Если же этот элемент добавить в количестве свыше 17 % от общего соединения компонентов, то сталь будет устойчива к коррозии даже в предельно агрессивных средах. Различают 3 типа нержавейки, которые определяются физическими свойствами. Так, обычный сплав называют просто коррозиестойким, он применяется в быту, а также повсеместно на производстве, где нет необходимости высокой степени защиты металла от агрессивных сред. Второй тип – жаростойкий, у него устойчивость к коррозии сохраняется при крайне высоких температурах. И, наконец, жаропрочный, у которого, как можно понять из названия, в той же агрессивной среде остается неизменной прочность, но коррозия нержавеющей стали у марок этого типа вполне возможна.
Итак, две основные группы нержавеющих сплавов – хромистые и хромоникелевые. Та и другая включают в себя несколько структурных классов. В первую входят мартенситные и ферритные стали, а также еще одна, являющаяся промежуточной и объединяющая в себе некоторые химические показатели двух первых – это мартенситно-ферритный сплав. Во второй группе насчитывается 4 класса: аустенитные, а также переходные аустенитно-ферритные, аустенитно-мартенситные и аустенитно-карбидные. Существует также группа хромомарганцевоникелевых сталей, которые, в целом, схожи по своей структуре с хромоникелевыми. Рассмотрим более подробно все вышеуказанные типы и классы.
2 Типы нержавеющих сплавов и их свойства
Как уже было сказано, коррозийную стойкость железо приобретает при добавлении в его расплав другого металла, как правило, благородного или любого цветного. При этом, в зависимости от химического состава сплава, сталь может получить свойства одного из 3 типов нержавейки. Самый простой структурой обладают обычные коррозиестойкие марки, такие как 08X13 и 12X13. Они пластичны и могут быть использованы как в быту в виде различных изделий, так и в промышленности, там, где от деталей и узлов требуется устойчивость к ударным нагрузкам. Как ясно из маркировки, содержание хрома в этих сплавах составляет 13 %. Первые же 2 цифры – это количество углерода, исчисляющееся в сотой доле процента.
Трубы из нержавеющей стали
Следующие 2 типа относятся к сплавам, которые должны сохранять коррозиестойкость при воздействии высоких температур. В жаростойких сталях добавление хрома (или кремния) в количестве от 28 % и более обеспечивает снижение интенсивности окисления вплоть до полного его прекращения даже при сильном нагреве. Иными словами, окалина практически не возникает по той причине, что на поверхности уже имеется оксидная пленка. В той же степени хром может изменить структуру сплава при выработке жаропрочных марок сталей, которые обладают высокой степенью прочности под большой нагрузкой в процессе сильного и длительного нагрева.
3 Химические свойства хромистых коррозиестойких сталей
Следует отметить, что железо, которое является основой любой стали, имеет несколько состояний, совпадающих с фазами активности и покоя кристаллической решетки, которые зависят от степени коррозийной стойкости. Чем она выше, тем более пассивным считается металл. Наиболее распространенными считаются сплавы с образующейся при закалке мартенситной структурой, обладающие достаточно высокой пластичностью. Согласно химическим характеристикам, это железо в α-фазе (чистый металл), содержащее насыщенный твердый раствор углерода. К таковым относятся пищевая и быстрорежущая нержавейка, из которой изготавливают изделия для использования в быту на кухне, например, всевозможные емкости и ножи. Мартенситные стали способны выдержать контакт со слабоагрессивными химическими веществами.
Хромистые коррозиестойкие стали
Другой тип – ферритные сплавы с достаточно высоким магнитным показателем. Разница у них по большей части в форме кристаллической решетки, она имеет кубическую структуру, в отличие от тетрагональной мартенситной. В целом же это средненасыщенный твердый раствор углерода в α-железе с добавлением легирующих элементов, таких как хром. Примечательно, что такие сплавы не подвергаются изменениям при нагреве до предельно возможных температур и не теряют свои свойства. Чаще всего таким изделиям находят применение в пищевой промышленности или для изготовления инструментов. Мартенситно-ферритные сплавы имеют свойства обоих перечисленных типов, то есть они механически устойчивы, обладают высокой прочностью и имеют магнитный потенциал. Но устойчивость к окислительной среде у таких сталей не очень высока, намного ниже, чем у обычных ферритных сплавов.
4 Отличительные черты аустенитных сплавов
В первую очередь рассмотрим аустенитные структуры сталей, которые определяются, как γ-железо (высокотемпературное изменение кристаллической решетки металла) в виде твердого раствора с углеродом. Проще говоря, такие сплавы могут подвергаться межкристаллической коррозии даже при высоком содержании хрома, если не имеют включения дополнительных элементов, таких как титан или ниобий. Во избежание их обязательно подвергают термообработке. В остальном это очень пластичные, прочные и технологичные стали, содержащие, помимо хрома еще и никель, которые относят к разряду конструкционных. Также из этих сплавов изготавливают инструменты, а вот в пищевой промышленности, равно как и для изготовления кухонной утвари, марки данного класса непригодны, поскольку никель весьма аллергенный.
Аустенитные сплавы
Межкристаллической коррозией называют внутреннее окисление металла, проходящее по границам отдельных зерен стали. По этой причине разрушение изделия остается незаметным, при сохранении характерного блеска узнать о коррозии можно только по звуку при ударах
Что примечательно, каким бы ни был химический состав аустенитных сплавов, они всегда немагнитные. Но при любой холодной деформации, например, под воздействием механических воздействий, они начинают приобретать небольшой магнитный потенциал. Это происходит по той причине, что при нарушении кристаллической решетки аустенит на некоторых участках превращается в феррит. Прочность таких сплавов достигается путем предельного уменьшения содержания углерода, впрочем, до определенного порога – не ниже 0,04 %, по причине присутствия в растворе никеля. В таких условиях легко образуются карбиды, то есть химическое соединение хрома с углеродом. Иногда в сплав добавляют связанный азот, благодаря которому возникают карбнитриды, также повышающие прочность стали. Примером может послужить марка нержавейки Х17АГ14.
Промежуточные сплавы имеют несколько иные характеристики, в частности, аустенитно-мартенситные. Они имеют более низкую коррозиестойкость, чем просто аустенитные структуры, но намного прочнее. При этом данный класс довольно тяжело поддается термообработке, вернее, воздействие на него высокими температурами связано с некоторыми сложностями. Зачастую такие сплавы со свойствами мартенситов требуют не только закалки, но также обработки холодом с последующим отпуском металла. Однако при такой технологии прочность нержавейки переходного класса повышается в несколько раз. В производстве элементов для тяжелых несущих конструкций стали, вроде марок 09X15Н8Ю или 20Х13Н4Г9, не используются, их применяют только для изготовления легких конструкций.
Особенность аустенитно-ферритных сплавов заключается в том, что они содержат сравнительно небольшое количество никеля в сравнении с другими промежуточными классами. За счет этого такие стали, как 12Х21Н5Т или 08Х22Н6Т, имеют гораздо лучшую свариваемость, швы при соединении металлопроката из них получаются очень качественные и прочные на деформацию. Обеспечивается это влиянием ферритной структуры, обеспечиваемой элементами Сr, Ti, Mo или Si. Однако следует отметить, что по той же причине, то есть из наличия ферритообразующих включений, в значительной степени ухудшается жаропрочность, равно как и пластичность. Высокой остается только механическая прочность.
В марках сталей обычно присутствуют буквы кириллицы, они тождественны латинским обозначениям, в частности Ю означает «ювенал» – алюминий, причем так он маркируется только в сталях. Другие элементы могут означаться также не по первым буквам, например кремний – С, от силициума, а марганец – Г, поскольку эта буква имеется в середине слова.
Ученые МИСиС разработали новый сплав стали, позволяющий продлить срок службы нефтепроводов / Интерфакс
«Ученые НИТУ «МИСиС» предложили инновационную технологию получения рулонного проката для производства коррозионностойких промысловых труб с улучшенными механическими характеристиками», — говорится в сообщении.
Отмечается, что новая марка стали позволит существенно снизить экологические риски и эксплуатационные затраты при добыче нефти, в том числе на труднодоступных месторождениях Западной Сибири, где ремонт и замена труб осложнены условиями их доставки, а состав углеводородного сырья обуславливает повышенный уровень коррозионного износа.
«Нашей основной задачей стала разработка новых схем легирования (добавления в состав материалов примесей для улучшения свойств основного материала), обеспечивающих необходимый структурно-фазовый состав стали при производстве рулонного и листового проката», — приводятся в сообщении слова одного из разработчиков проекта, научного сотрудника МИСиС Александра Комиссарова.
Ученые рассчитали условия комплексного микролегирования расплава стали такими элементами, как хром, медь и никель, чтобы получить необходимые свойства. Введение этих металлов в жидкую сталь позволяет регулировать состав коррозионно-активных неметаллических включений в стали, уменьшая их негативное влияние на ее свойства.
По словам А.Комиссарова, разработчики уже в этом году намерены получить международный патент, а в будущем планируют выдавать гарантию минимум на двукратное увеличение срока эксплуатации труб, полученных с использованием разработанной технологии.
Новый сплав разработан по заказу ПАО «Северсталь». На предприятиях компании уже проведена серия экспериментальных плавок и выплавка опытной партии, после чего образцы «Северкора» успешно прошли коррозионные испытания.
В настоящее время к запуску готовятся полномасштабные опытно-промысловые испытания трубопровода из новой стали на западносибирских нефтяных месторождениях компаний «Лукойл», «Газпромнефть», Иркутской нефтяной компании.
Легированная сталь
: все, что вам нужно знать о легированных сталях и их роли в строительстве
Обзор «стали»Сталь — один из самых популярных материалов, используемых в строительной отрасли. По данным Всемирной ассоциации производителей стали, в 2018 году во всем мире было произведено около 1808 миллионов тонн нерафинированной стали, и около 50% этой продукции было использовано в строительной отрасли. Кроме того, они также заявляют, что существует до 3500 различных марок стали, и каждая марка обладает экологическими, химическими и физическими свойствами, уникальными для этой марки стали.Сталь претерпела значительные изменения с течением времени, и около 75% всех видов современной стали были разработаны за последние 20 лет. Интересно отметить, что если бы Эйфелева башня (построенная в 1887 году) была построена в наши дни, для нее потребовалась бы только треть стали, используемой тогда.
Виды стали
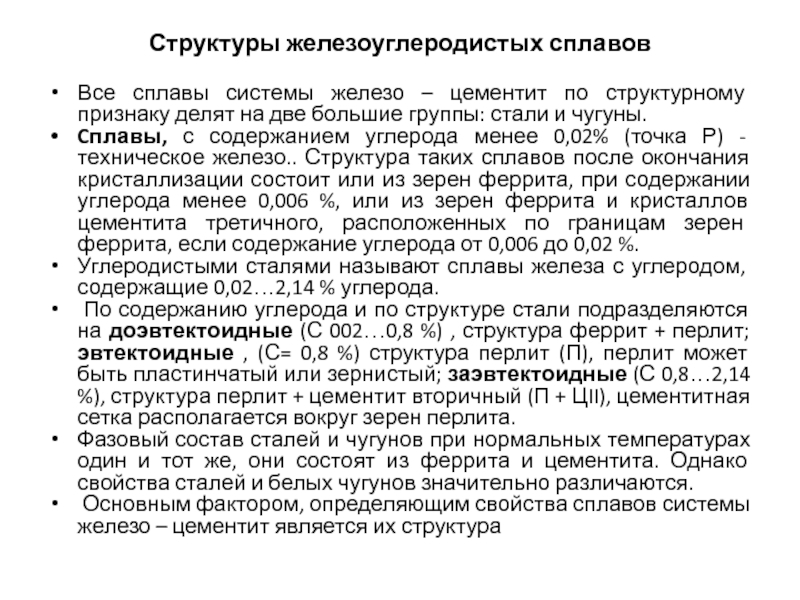
Легированная сталь
Когда к углеродистой стали добавляются другие элементы, содержащие металлы и неметаллы, образуется легированная сталь.Эти легированные стали обладают различными экологическими, химическими и физическими свойствами, которые могут варьироваться в зависимости от элементов, используемых для легирования. Здесь соотношение легирующих элементов может обеспечивать разные механические свойства.
Эффекты легирования
Легирующие элементы могут изменять углеродистую сталь несколькими способами. Легирование может повлиять на микроструктуру, условия термообработки и механические свойства. Современные технологии с использованием высокоскоростных компьютеров позволяют предвидеть свойства и микроструктуру стали при холодной штамповке, термообработке, горячей прокатке или легировании.Например, если для некоторых применений стали требуются такие свойства, как высокая прочность и свариваемость, тогда углеродистая сталь сама по себе не будет служить этой цели, поскольку присущая углероду хрупкость сделает сварной шов хрупким. Решение состоит в том, чтобы уменьшить углерод и добавить другие элементы, такие как марганец или никель. Это один из способов изготовления высокопрочной стали с требуемой свариваемостью.
Виды легированной стали
Существует два вида легированной стали — низколегированная и высоколегированная.Как упоминалось ранее, состав и пропорция легирующих элементов определяют различные свойства легированной стали. Низколегированные стали содержат до 8% легирующих элементов, тогда как высоколегированные стали содержат более 8% легирующих элементов.
Легирующие элементы
Существует около 20 легирующих элементов, которые можно добавлять в углеродистую сталь для производства различных марок легированной стали. Они предоставляют различные типы свойств. Некоторые из используемых элементов и их эффекты включают:
- Алюминий — очищает сталь от фосфора, серы и кислорода
- Хром — может повысить ударную вязкость, твердость и износостойкость
- Медь — может повысить коррозионную стойкость и жгут
- Марганец — может повысить жаропрочность, износостойкость, пластичность и прокаливаемость
- Никель — может повысить стойкость к коррозии, окислению и прочность
- Кремний — может увеличить магнетизм и прочность
- Вольфрам — может повысить прочность и твердость
- Ванадий — может повысить коррозионную стойкость, ударопрочность, прочность и ударную вязкость
Другие легирующие элементы, которые обеспечивают различные свойства, включают висмут, кобальт, молибден, титан, селен, теллур, свинец, бор, серу, азот, цирконий и ниобий.
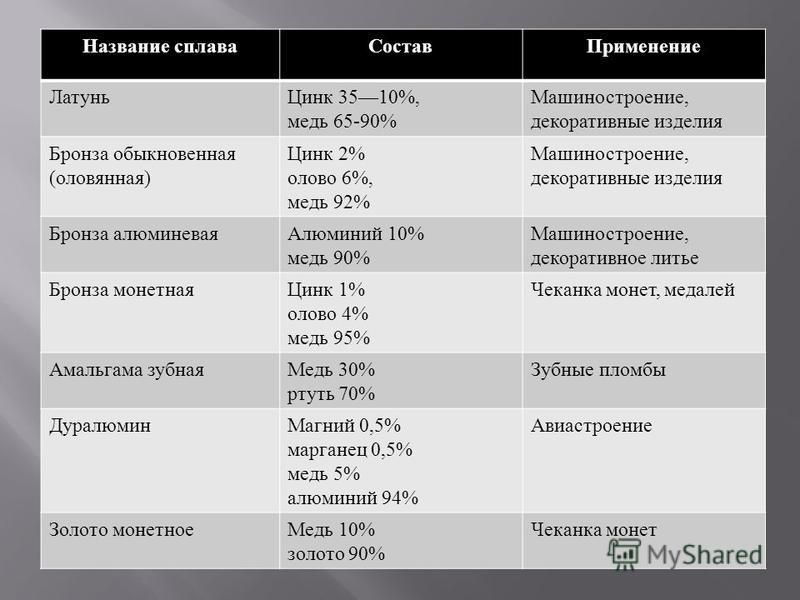
Свяжитесь с ближайшими к вам крупнейшими дилерами стали и получите бесплатные расценки
Изделия из легированной стали и области их применения
Существуют сотни продуктов, которые могут быть изготовлены из легированных сталей различного состава. Сюда входят трубы и трубки из легированной стали, пластины, листы и рулоны из легированной стали, прутки из легированной стали, прутки и проволока, кованые фитинги из легированной стали, стыковые фитинги из легированной стали, фланцы из легированной стали, крепежные детали и многое другое.Легированные стали находят широкое применение в различных отраслях промышленности, таких как автомобилестроение, горнодобывающая промышленность, машиностроение и оборудование, железные дороги, дорожное строительство, здания, бытовая техника и оффшорные приложения.
Применение в строительстве крупных сооружений
В строительстве легированные стали используются для изготовления очень больших современных конструкций, таких как аэропорты, мосты, небоскребы и стадионы в виде стального каркаса. Легированные стали обеспечивают необходимую высокую прочность для поддержки таких больших конструкций.Даже в бетонных конструкциях легированная сталь используется в качестве арматуры для увеличения прочности и снижения общего веса конструкций. В строительстве используются более мелкие изделия, такие как винты, гвозди и болты из легированных сталей.
Применения в строительстве мостов
В мостах используются специальные легированные стали, известные как погодостойкие. Они обеспечивают улучшенную защиту от коррозии из-за присутствия никеля, меди и хрома в качестве легирующих элементов. Погодостойкая сталь также находит применение в зданиях в качестве облицовочного материала для улучшения внешнего вида.Погодостойкая сталь предлагает несколько преимуществ, включая высокую безопасность, простоту и скорость строительства, эстетичный внешний вид, небольшую глубину конструкции, низкие эксплуатационные расходы и возможность внесения изменений в будущем. Из-за его естественной выветривания отделка не требует покраски, что позволяет избежать проблем с окружающей средой, вызванных красками. Погодостойкие стали в долгосрочной перспективе чрезвычайно рентабельны.
Плоский прокат из легированной стали
Из легированных сталей делают плоский прокат — листы и полосы.Таблички доступны в широком диапазоне сортов и размеров. Они используются в строительстве путем приваривания пластин к сборным секциям.
Лента и рулоны из легированной стали
Доступны полосы горячего и холодного проката и горячеоцинкованные рулоны. Оцинкованные методом горячего цинкования рулоны используются для изготовления строительных изделий, которые включают облицовку стен и крыш, боковые перила, прогоны крыши, легкие стальные рамы и перемычки.
Сортовой прокат из легированной стали Легированные стали
используются для производства сортового проката, используемого в строительной отрасли, такого как балки, конструкционные профили, стержни, рельсы, стержни и проволока.
Фланцы из легированной стали
Еще одним важным продуктом из легированных сталей являются фланцы. Они используются в трубопроводах из нержавеющей стали. Эти фланцы могут быть изготовлены для различных применений. Некоторые из них включают фланцы с приварной шейкой, которые имеют ту же толщину и фаску, что и труба, и могут хорошо работать в суровых условиях высокого давления, высокой температуры или минусовых температур. Фланцы с соединением внахлест представляют собой надвижные фланцы, подходящие для трубопроводов из легированной стали, которые требуют регулярного технического обслуживания и осмотра.
Трубы из легированной стали
Трубы из легированной стали являются важным материалом в строительстве из-за их эксплуатационных характеристик, таких как пластичность, простота крепления без термической обработки и высокая прочность. Они представляют собой сплав нержавеющей стали, хрома и никеля. Некоторые специальные типы труб из легированной стали включают сварные трубы большого диаметра, трубы, полученные электросваркой плавлением, сварные трубы и бесшовные трубы. Они чрезвычайно полезны для высокотемпературных или агрессивных сред, помимо сред с высоким давлением.
Цена легированной стали
Поскольку легированные стали обладают особыми свойствами, необходимыми для конкретных применений, цены сильно различаются в зависимости от марок, входящих в состав легирующих элементов, процесса производства и размера. Цены на легированные стали, доступные в Индии, обычно варьируются в диапазоне от 90 580 рупий (1294 доллара США) за тонну до 4 08 730 рупий (5839 долларов США) за тонну.
Как видно из вышеизложенного, легированные стали играют важную роль в строительстве и других отраслях промышленности.Легированные стали отличаются экономичностью, высокими эксплуатационными характеристиками, коррозионной стойкостью, долговечностью, высокой прочностью, высоким соотношением прочности и веса, высокими эксплуатационными характеристиками в суровых условиях и широким ассортиментом продукции для большинства областей применения.
Обратитесь к ближайшим к вам ближайшим дилерам стали и получите бесплатные расценки
Типы и применение легированной стали | Кованые детали сосуда
Для проектов по производству устьевых компонентовAPI иногда требуется сталь с особыми свойствами. В легированной стали углеродистая сталь сочетается с другими материалами, такими как алюминий, никель или медь, в соответствии со спецификациями проекта.Легированная сталь в первую очередь классифицируется по легируемому или процентному содержанию сплава.
Высоколегированная сталь
Высоколегированные стали отличаются высоким процентным содержанием легирующих элементов. Наиболее распространенной высоколегированной сталью является нержавеющая сталь, которая содержит не менее 12 процентов хрома. Нержавеющая сталь обычно делится на три основных типа: мартенситную, ферритную и аустенитную. Мартенситные стали содержат наименьшее количество хрома, обладают высокой способностью к закалке и обычно используются для изготовления столовых приборов. Ферритные стали содержат от 12 до 27 процентов хрома и часто используются в автомобилях и промышленном оборудовании. Аустенитные стали содержат большое количество никеля, углерода, марганца или азота и часто используются для хранения агрессивных жидкостей и горнодобывающего, химического или фармацевтического оборудования.
Сталь низколегированная
Низколегированные стали имеют гораздо меньшее процентное содержание легирующих элементов, обычно от 1 до 5 процентов. Эти стали имеют разную прочность и применение в зависимости от выбранного сплава.Производители фланцев большого диаметра обычно выбирают сплавы по определенным механическим свойствам. Разнообразие потенциальных сплавов делает низколегированную сталь полезной для множества проектов, включая изготовление бесшовных катаных колец и изготовление выпускных отверстий для шпилек.
Тип по сплаву
Легированная стальчасто классифицируется по типу сплава и его концентрации. Вот несколько наиболее распространенных добавок к легированной стали:
- Алюминий удаляет кислород, серу и фосфор из стали.
- Висмут улучшает обрабатываемость.
- Хром увеличивает износостойкость, твердость и ударную вязкость.
- Кобальт увеличивает стабильность и способствует образованию свободного графита.
- Медь улучшает закалку и устойчивость к коррозии.
- Марганец повышает прокаливаемость, пластичность, износостойкость и жаропрочность.
- Молибден снижает концентрацию углерода и увеличивает прочность при комнатной температуре.
- Никель улучшает прочность, коррозионную стойкость и стойкость к окислению.
- Кремний увеличивает прочность и магнетизм.
- Титан улучшает твердость и прочность.
- Вольфрам улучшает твердость и прочность.
- Ванадий увеличивает ударную вязкость, прочность, коррозионную стойкость и ударопрочность.
Вам нужно производство форсунок для сосудов под давлением?
Если вам необходимо изготовление подводных соединений, ковка сопла с длинной приварной шейкой или выпускные отверстия под шпильки для промышленных фланцев, обратитесь в Forged Components, Inc.Cегодня. Позвоните нам по телефону (281) 441-4088 или свяжитесь с нами через Интернет.
Классификация углеродистых и низколегированных сталей
Американский институт чугуна и стали (AISI) определяет углеродистую сталь следующим образом: Сталь считается углеродистой сталью, если не указано или не требуется минимальное содержание хрома, кобальта, колумбия [ниобия], молибдена, никеля, титана, вольфрама, ванадия или цирконий или любой другой элемент, добавляемый для получения желаемого эффекта легирования; когда указанный минимум для меди не превышает 0.40 процентов; или когда максимальное содержание, указанное для любого из следующих элементов, не превышает указанных процентных значений: марганец 1,65, кремний 0,60, медь 0,60.
можно классифицировать по множеству различных систем в зависимости от:
- Состав, например углеродистая, низколегированная или нержавеющая сталь.
- Методы производства, такие как мартеновский, кислородный или электропечи.
- Метод чистовой обработки, такой как горячая или холодная прокатка
- Форма продукта, такая как прутковая плита, лист, полоса, трубка или структурная форма
- Практика раскисления, такая как сталь с убитым, полузабитым, укупорочным или окаймленным стальным покрытием
- Микроструктура, такая как ферритная, перлитная и мартенситная
- Требуемый уровень прочности, как указано в стандартах ASTM
- Термическая обработка, такая как отжиг, закалка и отпуск, а также термомеханическая обработка
- Дескрипторы качества, такие как качество поковки и товарное качество.
Углеродистые стали
Американский институт чугуна и стали (AISI) определяет углеродистую сталь следующим образом:
Сталь считается углеродистой сталью, если не указано или не требуется минимальное содержание хрома, кобальта, колумбия [ниобия], молибдена, никеля, титана, вольфрама, ванадия или циркония, или любого другого элемента, добавляемого для получения желаемого легирующего эффекта. ; когда указанный минимум для меди не превышает 0,40 процента; или когда максимальное содержание, указанное для любого из следующих элементов, не превышает указанных процентных соотношений: марганец 1.65, кремний 0,60, медь 0,60.
Углеродистая сталь может быть классифицирована в соответствии с различными методами раскисления как сталь с ободом, покрытая оболочкой, полузабитая или раскисленная сталь. Практика раскисления и процесс производства стали будут влиять на свойства стали. Однако изменения содержания углерода имеют наибольшее влияние на механические свойства, при этом увеличение содержания углерода приводит к увеличению твердости и прочности. Таким образом, углеродистые стали обычно классифицируются в соответствии с их содержанием углерода.Вообще говоря, углеродистые стали содержат до 2% общих легирующих элементов и могут быть подразделены на низкоуглеродистые, среднеуглеродистые, высокоуглеродистые и сверхвысокуглеродистые стали; каждое из этих обозначений обсуждается ниже.
В целом углеродистые стали являются наиболее часто используемыми сталями. Более 85% стали, производимой и поставляемой в США, составляет углеродистая сталь.
Низкоуглеродистая сталь содержит до 0,30% C. Самая большая категория стали этого класса — плоский прокат (лист или полоса), обычно в холоднокатаном и отожженном состоянии.Содержание углерода в этих сталях с высокой формуемостью очень низкое, менее 0,10% C и до 0,4% Mn. Типичное применение — панели кузова автомобилей, жесть и изделия из проволоки.
Для листового стального проката и профилей содержание углерода может быть увеличено примерно до 0,30%, а марганца — до 1,5%. Эти материалы могут быть использованы для штамповки, поковок, бесшовных труб и котельной плиты.
Среднеуглеродистые стали аналогичны низкоуглеродистым сталям, за исключением того, что содержание углерода колеблется от 0.От 30 до 0,60% и марганца от 0,60 до 1,65%. Увеличение содержания углерода примерно до 0,5% с сопутствующим увеличением марганца позволяет использовать среднеуглеродистые стали в закаленном и отпущенном состоянии. Использование среднеуглеродистых марганцевых сталей включает валы, оси, шестерни, коленчатые валы, муфты и поковки. Стали с содержанием углерода от 0,40 до 0,60% также используются для изготовления рельсов, железнодорожных колес и осей рельсов.
Высокоуглеродистые стали содержат от 0,60 до 1,00% C с содержанием марганца от 0.От 30 до 0,90%. Высокоуглеродистые стали используются для изготовления пружинных материалов и высокопрочной проволоки.
Сверхвысокоуглеродистая сталь представляет собой экспериментальные сплавы, содержащие от 1,25 до 2,0% C. Эти стали подвергаются термомеханической обработке для получения микроструктур, состоящих из сверхмелких, равноосных зерен сферических, прерывистых частиц доэвтектоидного карбида.
Стали высокопрочные низколегированные
Высокопрочные низколегированные (HSLA) стали или микролегированные стали предназначены для обеспечения лучших механических свойств и / или большей устойчивости к атмосферной коррозии, чем обычные углеродистые стали в обычном смысле, потому что они предназначены для удовлетворения определенных механических свойств, а не химический состав.
Стали HSLA имеют низкое содержание углерода (0,05–0,25% C) для обеспечения адекватной формуемости и свариваемости, а также содержание марганца в них до 2,0%. Небольшие количества хрома, никеля, молибдена, меди, азота, ванадия, ниобия, титана и циркония используются в различных комбинациях.
Классификация HSLA:
- Погодостойкая сталь , показывающая превосходную стойкость к атмосферной коррозии
- Контрольно-прокатные стали , горячекатаные в соответствии с заданным графиком прокатки, разработанные для развития сильно деформированной аустенитной структуры, которая при охлаждении преобразуется в очень мелкую равноосную ферритную структуру.
- Стали с пониженным перлитом , упрочненные очень мелкозернистым ферритом и дисперсионным упрочнением, но с низким содержанием углерода и, следовательно, с небольшим содержанием перлита в микроструктуре или без него
- Микролегированные стали с очень небольшими добавками таких элементов, как ниобий, ванадий и / или титан, для измельчения зерна и / или дисперсионного твердения
- Сталь с игольчатым ферритом , очень низкоуглеродистая сталь с достаточной способностью к закалке для превращения при охлаждении в очень мелкую высокопрочную структуру игольчатого феррита, а не в обычную структуру многоугольного феррита
- Двухфазная сталь , обработанная до микроструктуры феррита, содержащей небольшие равномерно распределенные области высокоуглеродистого мартенсита, в результате получается продукт с низким пределом текучести и высокой скоростью деформационного упрочнения, что обеспечивает получение высокопрочной стали. превосходной формуемости.
Различные типы сталей HSLA могут также иметь небольшие добавки кальция, редкоземельных элементов или циркония для контроля формы сульфидных включений.
Стали низколегированные
Низколегированные стали представляют собой категорию черных металлов, которые демонстрируют механические свойства, превосходящие простые углеродистые стали, благодаря добавкам легирующих элементов, таких как никель, хром и молибден. Общее содержание сплава может варьироваться от 2,07% до уровней чуть ниже, чем у нержавеющих сталей, которые содержат минимум 10% Cr .
Для многих низколегированных сталей основной функцией легирующих элементов является повышение прокаливаемости с целью оптимизации механических свойств и ударной вязкости после термообработки. Однако в некоторых случаях добавки сплава используются для уменьшения ухудшения состояния окружающей среды при определенных условиях эксплуатации.
Как и стали в целом, низколегированные стали можно классифицировать по:
- Химический состав , например никелевые стали, хромоникелевые, молибденовые, хромомолибденовые стали
- Термическая обработка , такая как закалка и отпуск, нормализация и отпуск, отжиг.
Из-за большого разнообразия возможных химических составов и того факта, что некоторые стали используются в более чем одном термически обработанном состоянии, существует некоторое совпадение между классификациями легированных сталей. В этой статье рассматриваются четыре основные группы легированных сталей: (1) низкоуглеродистые закаленные и отпущенные (QT) стали, (2) среднеуглеродистые сверхвысокопрочные стали, (3) подшипниковые стали и (4) жаропрочные стали. стойкие хромомолибденовые стали.
Низкоуглеродистая закаленная и отпущенная сталь сочетает в себе высокий предел текучести (от 350 до 1035 МПа) и высокую прочность на растяжение с хорошей ударной вязкостью, пластичностью, коррозионной стойкостью или свариваемостью.Различные стали имеют разные комбинации этих характеристик в зависимости от их предполагаемого применения. Однако некоторые стали, такие как HY-80 и HY-100, подпадают под военные спецификации. Перечисленные стали используются в основном в качестве листового металла. Некоторые из этих сталей, а также другие аналогичные стали производятся в виде поковок или отливок.
Среднеуглеродистые сверхвысокопрочные стали — это конструкционные стали с пределом текучести, который может превышать 1380 МПа. Многие из этих сталей имеют обозначения SAE / AISI или являются патентованными составами.Формы продукции включают заготовку, пруток, пруток, поковки, лист, трубы и сварочную проволоку.
Подшипниковые стали , используемые для шариковых и роликовых подшипников, состоят из низкоуглеродистой (от 0,10 до 0,20% C ) цементированной стали и высокоуглеродистой (-1,0% C) стали с сквозной закалкой. Многие из этих сталей имеют обозначения SAE / AISI.
Хромомолибденовые жаропрочные стали содержат от 0,5 до 9%, Cr, и от 0,5 до 1.0% Пн . Содержание углерода обычно ниже 0,2%. Хром обеспечивает улучшенную стойкость к окислению и коррозии, а молибден увеличивает прочность при повышенных температурах. Обычно они поставляются в нормализованном и отпущенном, закаленном и отпущенном состоянии или в отожженном состоянии. Хром-молибденовые стали широко используются в нефтяной и газовой промышленности, в ископаемом топливе и на атомных электростанциях.
Прочный, твердый и выносливый: самые разные никельсодержащие легированные стали обеспечивают
Легированные сталивключают широкий спектр материалов на основе железа.Содержание никеля колеблется от очень низкого, ~ 0,3% в некоторых легированных сталях, до 20% в мартенситностареющих сталях. Каждый сплав разработан для некоторого сочетания большей прочности, твердости, износостойкости или ударной вязкости, чем углеродистые стали. Обычно они используются в оборудовании, которое подает мощность, формирует и режет металл, или используются при низких температурах, когда углеродистые стали не обладают достаточной прочностью. Для простоты легированные стали можно разделить на несколько типов с особыми свойствами для конкретных конечных применений.Стали из никелевых сплавов необходимы для изготовления инструментов и оборудования, которые позволяют промышленности производить другие инструменты и оборудование.
Типичный химический состав некоторых известных никельсодержащих легированных сталей
Сталь Тип | Класс (UNS) | К | Ni | Кр | Fe | Прочие | Приложения |
Закаливаемая | AISI 4340 | 0.4 | 1,8 | 0,8 | бал | Пн | Шестерни трансмиссии, валы и шасси самолета |
AISI 4320H | 0,2 | 1,8 | 0,5 | бал | Пн | Шестерни и шестерни с поверхностной закалкой для повышения износостойкости, но с прочным сердечником | |
AR450 | 0.26 | 0,70 | 1,0 | бал | Пн | Пластина износостойкая для желобов, футеровок, решеток, баллистических пластин | |
Инструментальная сталь — | A9 (T30109) | 0,5 | 1,5 | 5,0 | бал | Mo, V | Штампы для волочения и формовки, ножницы |
Инструментальная сталь — | P6 (T51606) | 0.1 | 3,5 | 1,5 | бал | Плашки для литья под давлением цинка и пластмассы | |
Высокопрочный | A588 Gr C | 0,1 | 0.35 | 0,5 | бал | Cr, Cu, V | Обеспечивает более высокое соотношение прочности и веса, чем обычная углеродистая сталь, и более высокую стойкость к атмосферной коррозии для использования в строительстве мостов. |
Никелевая сталь | 9% никелевая сталь (K81340) | 0,13 | 9,0 | – | бал | Криогенные применения, такие как хранилище СПГ | |
Мартенситностареющая сталь | Maraging 300 (K93120) | 0.03 | 18,5 | – | бал | Co, Mo, Al, Ti | Кожухи ракетных двигателей, планеры, приводные валы, шасси самолетов, пресс-формы, штампы |
Закаливаемая низколегированная сталь
Эти стали относятся к категории черных металлов, которые по своим механическим свойствам превосходят простые углеродистые стали.Это достигается добавлением легирующих элементов, таких как никель, хром и молибден, с последующей закалкой (быстрым охлаждением) и отпускной термообработкой. Эти элементы, растворенные в аустените перед закалкой, увеличивают прокаливаемость. Никель дополняет упрочняющий эффект хрома и молибдена и играет важную роль в обеспечении ударной вязкости твердо-мартенситной микроструктуре, которая возникает в результате термообработки с закалкой и отпуском.
Сравнение типичных механических характеристик для AISI 4340 в отожженном, закаленном и отпущенном состоянии с углеродистой сталью AISI 1045
Круглый пруток диаметром 75 мм (3 дюйма) | Предел текучести МПа (тыс. Фунтов на кв. Дюйм) | Предел прочности МПа (тыс. Фунтов на кв. Дюйм) | % |
AISI 4340 отожженный | 588 (86) | 752 (110) | 21 |
AISI 4340 ASTM A434 класс BD | 847 (124) | 963 (141) | 18 |
AISI 1045 нормализованное | 410 (60) | 629 (92) | 22 |
Инструментальная сталь
Инструментальная сталь — это термин, применяемый к множеству высокотвердых, устойчивых к истиранию сталей, используемых для таких применений, как штампы (штамповка или экструзия), резка или резка, изготовление пресс-форм или ударные инструменты, такие как молотки (личные или промышленные).Их термическая обработка аналогична закаливаемым низколегированным сталям.
Закаленные на воздухе инструментальные стали уменьшают деформацию, вызванную быстрой закалкой в воде, и обладают балансом износостойкости и вязкости.
Инструментальная сталь для пластмассовых форм — это низкоуглеродистые стали, которые формуют, а затем науглероживают, закаляют и затем отпускают до высокой твердости поверхности, что делает их идеальными для форм для литья под давлением и штампов для литья под давлением.
Высокопрочная низколегированная (погодостойкая сталь)
Более мелкозернистая структура этих сталей обеспечивает повышенную прочность по сравнению с обычными углеродистыми сталями.Это более мелкое зерно достигается за счет воздействия на температуру превращения, так что превращение аустенита в феррит и перлит происходит при более низкой температуре во время охлаждения на воздухе. При низком уровне углерода, типичном для сталей HSLA, такие элементы, как кремний, медь, никель и фосфор, особенно эффективны для получения мелкодисперсного перлита.
Добавление хрома, меди и никеля создает устойчивый слой ржавчины, который прилипает к основному металлу и является гораздо менее пористым, чем слой ржавчины, который образуется на обычной конструкционной стали.В результате скорость коррозии значительно снижается, что позволяет использовать эти стали без покрытия.
В таблице ниже показаны различия в механических свойствах углеродистой конструкционной стали ASTM A36 и высокопрочной низколегированной конструкционной стали ASTM A588 Grade C.
Разница в механических свойствах углеродистой конструкционной стали ASTM A36 и высокопрочной низколегированной конструкционной стали ASTM A588 класса C
Марка | Предел текучести МПа (тыс. Фунтов / кв. Дюйм) мин. | Предел прочности при растяжении МПа (тыс. Фунтов на кв. Дюйм) мин. | % Относительное удлинение мин |
ASTM A36 | 250 (36) | 400 (58) | 23 |
ASTM A588 Gr C | 345 (50) | 485 (70) | 21 |
Никелевая сталь
Ферритные стали с высоким содержанием никеля, обычно более 3%, находят широкое применение в областях, связанных с воздействием температур от 0 ° C до -196 ° C.К таким приложениям относятся резервуары для хранения сжиженных углеводородных газов, а также конструкции и оборудование, предназначенные для использования в холодных регионах. Эти стали используют эффект содержания никеля для снижения температуры ударного перехода, тем самым улучшая ударную вязкость при низких температурах.
В углеродистых и большинстве низколегированных сталей при понижении температуры ниже 24 ° C (75 ° F) прочность и твердость увеличиваются, а пластичность и вязкость при растяжении снижаются. Никель улучшает низкотемпературную ударную вязкость, о чем свидетельствуют результаты удара по Шарпи на рис. 1 .
Впервые примененная в резервуарах с жидким кислородом в 1952 году, 9% никелевая сталь с тех пор в основном используется для внутренней оболочки резервуаров для СПГ. Он выбран вместо аустенитных нержавеющих сталей из-за сочетания высокой прочности и надежной вязкости разрушения при очень низких температурах до -196 ° C.
Углеродистая стальи нержавеющая сталь
Все стали содержат углерод (фактически от 0,02% до 2,1%!), Так почему же одна разновидность стали называется углеродистой сталью? Как оказалось, термин углеродистая сталь на самом деле используется для описания двух различных типов стали: углеродистой стали и низколегированной стали.С другой стороны, нержавеющая сталь — это специализированная группа стальных сплавов, разработанных для защиты от коррозии. В этой статье мы сравниваем углеродистую сталь и нержавеющую сталь.
Запросите бесплатную металлическую деталь, напечатанную на 3D-принтере
Что на самом деле означает углеродистая сталь?
«Углеродистая сталь» имеет два значения — техническое определение и более общую классификацию. Техническое определение очень четкое: согласно Американскому институту чугуна и стали (AISI), сталь должна соответствовать следующим стандартам, чтобы соответствовать техническому определению углеродистой стали:
- Не указано и не требуется минимальное содержание хрома, кобальта, колумбий [ниобий], молибден, никель, титан, вольфрам, ванадий или цирконий или любой другой элемент, добавляемый для получения желаемого эффекта легирования
- Когда указанный минимум для меди не превышает 0.40 процентов
- Когда максимальное содержание, указанное для любого из следующих элементов, не превышает указанных процентов: марганец 1,65, кремний 0,60, медь 0,60.
Техническое определение, хотя и сложное, сводится к одному простому ограничению — настоящая углеродистая сталь должна почти не содержать легирующих элементов, что делает их в основном состоящими из двух материалов: железа и углерода. Количество углерода может варьироваться, и есть несколько приемлемых легирующих материалов, но эти стали простые.
В дополнение к точному определению термин углеродистая сталь также используется для обозначения широкой группы легированных сталей, которые не являются нержавеющими сталями. В отличие от углеродистых сталей, низколегированные стали могут содержать в небольших количествах широкий спектр легирующих элементов, что позволяет адаптировать их для более широкого круга применений. Эти стали, хотя и не удовлетворяют техническим требованиям к углеродистой стали, означают больший разрыв в стали: нержавеющая сталь по сравнению со всем остальным.
Углеродистая сталь (по определению)
Проще говоря, углеродистая сталь по определению чрезвычайно проста.Это железо с небольшим содержанием углерода и ограниченным количеством легирующих элементов. Кроме того, любая сталь, для которой требуются легирующие элементы (например, 4140 и 4340), является углеродистой сталью , а не . В рамках определения углеродистой стали материалы могут быть определены как низкоуглеродистая сталь или высокоуглеродистая сталь. Низкоуглеродистые стали чрезвычайно распространены, в то время как высокоуглеродистые стали используются только в высокопрочных, некоррозионных средах. Сталь 1020, низкоуглеродистая сталь, является одной из самых популярных сталей, производимых сегодня.
Прочитайте наше Руководство по проектированию Metal X
A36, разновидность углеродистой стали, часто используется для конструкционных балок, подобных этим двутавровым балкам. Источник: https://www.worldsteelgrades.com/astm-a36-steel/
Углеродистая сталь имеет различные механические свойства в зависимости от содержания углерода. Низкоуглеродистые стали слабее и мягче, но их легко обрабатывать и сваривать; в то время как высокоуглеродистая сталь прочнее, но значительно труднее в обработке. Все углеродистые стали подвержены ржавчине, что делает их непригодными для широкого спектра конечных применений.В целом углеродистая сталь отлично подходит, если вы ищете недорогой металл, но, как правило, не подходит для высококачественных или высокоточных производственных операций.
Низколегированные стали (иногда называемые углеродистыми сталями)
Низколегированные стали содержат один или несколько легирующих элементов (например, хром, кобальт, ниобий, молибден, никель, титан, вольфрам, ванадий или цирконий) для улучшения качества материала свойства традиционных углеродистых сталей. Часто они прочнее, жестче и немного более устойчивы к коррозии, чем традиционные углеродистые стали.
Легированные стали определяются по основным легирующим материалам (помимо углерода). 4140, одна из наиболее распространенных легированных сталей, представляет собой хромомолибденовую легированную сталь. Это означает, что основными легирующими элементами являются хром (повышающий коррозионную стойкость) и молибден (повышающий ударную вязкость). В результате 4140 используется в условиях сильного износа и повышенных температур.
Легированные стали сегодня являются одной из наиболее широко используемых сталей в промышленности. Они поддаются механической обработке, доступны по цене, легко доступны и обладают хорошими механическими свойствами. Если деталь не обязательно должна быть коррозионно-стойкой, низколегированная сталь дает лучший результат.
Свойства, которые делают легированную сталь выгодной для производства традиционными методами, делают ее менее ценной для 3D-печати.Поскольку металлическая 3D-печать легко обрабатывается и дешево приобретается, более высокая стоимость деталей делает ее экономически невыгодной для печати. Некоторые компании, занимающиеся печатью на металле, предлагают низколегированные стали, такие как 4140, но, как правило, они встречаются редко.
Нержавеющая сталь
Нержавеющие стали объединяет одно ключевое свойство материала: отличная коррозионная стойкость, связанная с высоким содержанием хрома (> 10,5% по массе) и низким содержанием углерода (<1,2% по массе). Помимо коррозионной стойкости, механические свойства этих сталей могут сильно различаться.
Аустенитная нержавеющая сталь является наиболее распространенным типом нержавеющей стали. Они устойчивы к коррозии, легко обрабатываются и свариваются, но не подвергаются термообработке. 303 и 304 являются наиболее распространенными типами аустенитных нержавеющих сталей, а 316L — вариантом, обеспечивающим максимальную коррозионную стойкость. Эти стали используются в самых разных операциях — поскольку они устойчивы к атмосферным воздействиям, они работают практически везде. Из-за более высокой стоимости металлическая 3D-печать может быть жизнеспособным методом изготовления этих деталей.
Нержавеющие стали, такие как 316L, часто используются для изготовления рабочих колес и других деталей, погружаемых в жидкость. Источник: https://gpmsurplus.com/product/tri-clover-c327-02a-316l-6-75-stronic-steel-semi-open-impeller/ Мартенситные нержавеющие стали обладают лучшими механическими свойствами по сравнению с аустенитными. стали ценой пластичности. В целом им не хватает универсальности аустенитных сталей, однако их высокопрочная твердость в сочетании с коррозионной стойкостью, намного превосходящей низколегированные стали, делает их пригодными для любых высокопрочных деталей, находящихся в окислительной среде.Кроме того, мартенситные стали можно подвергать термообработке для дальнейшего повышения твердости, прочности и жесткости.
17-4 PH — это особенно полезный тип мартенситной нержавеющей стали, которая может подвергаться термообработке для соответствия различным свойствам материала. Из-за его высокой твердости и чрезвычайно низкой обрабатываемости 3D-печать зачастую дешевле, чем кропотливая обработка на станке. Если вы хотите узнать больше о 3D-печати металлических деталей, ознакомьтесь с Markforged Metal X.
Запросите расценки на Metal X
Углеродистая сталь против нержавеющей стали: окончательный вердикт
немного сложнее, чем первоначально предполагалось, поскольку углеродистая сталь может относиться к двум различным типам стали: традиционной углеродистой стали и низколегированной стали.
По сравнению с низкоуглеродистой сталью нержавеющая сталь предлагает значительное повышение прочности, твердости и, что наиболее важно, коррозионной стойкости. По прочности высокоуглеродистая сталь не уступает, а иногда и превосходит нержавеющую сталь, но в основном это нишевый материал в мире производства. В отличие от любой углеродистой стали, нержавеющая сталь может выжить и процветать без окисления в агрессивных или влажных средах. При этом углеродистая сталь намного дешевле нержавеющей стали и лучше подходит для крупных конструктивных элементов, таких как трубы, балки и листовой прокат.
Низколегированная сталь во многих отношениях превосходит углеродистую, но все же не обладает коррозионной стойкостью. Он может эффективно соответствовать свойствам материала нержавеющей стали — в результате сплавы, такие как 4140 и 4340, часто обрабатываются и используются во многих областях, в которых небольшое окисление не повредит. Нержавеющая сталь — это материал более высокого качества, который лучше использовать в промышленных операциях, где качество деталей не может быть снижено.
Производство литой стали | Блог по литью металла
Испытания и осмотр в литейном цехе
Литая сталь — это сплав черных металлов с максимальным содержанием углерода около 0.75%. Стальные отливки — это твердые металлические предметы, полученные путем заполнения пустоты в кристаллизаторе жидкой сталью. Они доступны во многих из тех же углеродистых и легированных сталей, которые могут производиться как деформируемые металлы. Механические свойства литой стали обычно ниже, чем у деформируемой стали, но с тем же химическим составом. Литая сталь компенсирует этот недостаток своей способностью формировать сложные формы за меньшее количество шагов.
Стальные отливки — это твердые металлические предметы, полученные путем заполнения пустоты в кристаллизаторе жидкой сталью.Свойства литой стали
Литые стали могут производиться с широким диапазоном свойств. Физические свойства литой стали существенно меняются в зависимости от химического состава и термической обработки. Они выбираются в соответствии с требованиями к производительности предполагаемого приложения.
- Твердость
Способность материала противостоять истиранию. Содержание углерода определяет максимальную твердость стали или ее прокаливаемость.
- Прочность
Величина силы, необходимая для деформации материала.Более высокое содержание углерода и твердость делают сталь более прочной.
- Пластичность
Способность металла деформироваться под действием растягивающего напряжения. Более низкое содержание углерода и меньшая твердость приводят к более высокой пластичности стали.
- Прочность
Способность выдерживать нагрузки. Повышенная пластичность обычно связана с лучшей ударной вязкостью. Вязкость можно регулировать добавлением легирующих металлов и термообработки.
- Износостойкость
Сопротивление материала трению и износу. Литая сталь обладает такой же износостойкостью, что и деформируемые стали аналогичного состава. Добавление легирующих элементов, таких как молибден и хром, может повысить износостойкость.
- Коррозионная стойкость
Устойчивость материала к окислению и ржавчине. Литая сталь обладает такой же коррозионной стойкостью, что и деформируемая сталь.Высоколегированные стали с повышенным содержанием хрома и никеля обладают высокой стойкостью к окислению.
- Обрабатываемость
Легкость, с которой стальная отливка может изменять форму за счет удаления материала путем механической обработки (резки, шлифования или сверления). Обрабатываемость зависит от твердости, прочности, теплопроводности и теплового расширения.
- Свариваемость
Способность стальной отливки свариваться без дефектов. Свариваемость в первую очередь зависит от химического состава стальной отливки и термической обработки.
- Высокотемпературные свойства
Стали, работающие при температурах выше температуры окружающей среды, подвержены ухудшению механических свойств и преждевременному выходу из строя из-за окисления, водородного повреждения, сульфитных отложений и нестабильности карбидов.
- Низкотемпературные свойства
Вязкость литой стали значительно снижается при низких температурах. Легирование и специальная термообработка могут улучшить способность отливки выдерживать нагрузки и напряжения.
Химический состав литой стали
Химический состав литой стали оказывает большое влияние на эксплуатационные свойства и часто используется для классификации стали или присвоения стандартных обозначений. Литые стали можно разделить на две большие категории — углеродистые литые стали и легированные литые стали.
Углеродистая сталь
Как и деформируемые стали, углеродистые литые стали можно классифицировать по содержанию углерода. Литая низкоуглеродистая сталь (0,2% углерода) относительно мягкая и не поддается термической обработке.Среднеуглеродистая литая сталь (0,2–0,5% углерода) несколько тверже и поддается упрочнению термической обработкой. Высокоуглеродистая литая сталь (0,5% углерода) используется, когда требуется максимальная твердость и износостойкость.
Сталь легированная литая
Легированная литая сталь подразделяется на низколегированные и высоколегированные. Низколегированная литая сталь (содержание сплава ≤ 8%) ведет себя так же, как обычная углеродистая сталь, но имеет более высокую прокаливаемость. Высоколегированная литая сталь (содержание сплава> 8%) предназначена для обеспечения определенных свойств, таких как коррозионная стойкость, жаропрочность или износостойкость.
Обычные высоколегированные стали включают нержавеющую сталь (> 10,5% хрома) и марганцевую сталь Хэдфилда (11–15% марганца). Добавление хрома, который образует пассивирующий слой оксида хрома при воздействии кислорода, придает нержавеющей стали превосходную коррозионную стойкость. Содержание марганца в стали Хэдфилда обеспечивает высокую прочность и устойчивость к истиранию при тяжелых работах.
ASTM | Требования к химическим веществам | Требования к растяжению | |||||||
---|---|---|---|---|---|---|---|---|---|
МАРКА СТАЛИ | Углерод | Марганец | Кремний | сера | фосфор | Предел прочности | Предел текучести | Относительное удлинение 2 дюйма | Уменьшение площади |
Макс.% / Диапазон | мин. тыс. фунтов / кв. дюйм [МПа] / диапазон | мин. % | |||||||
ASTM A27 / A27M | |||||||||
ASTM A27, класс N-1 | 0,25 | 0,75 | 0,80 | 0,06 | 0,05 | НЕТ | НЕТ | НЕТ | НЕТ |
ASTM A27, марка N-2 | 0,35 | 0,60 | 0,80 | 0.06 | 0,05 | НЕТ | НЕТ | НЕТ | НЕТ |
ASTM A27, класс U60-30 | 0,25 | 0,75 | 0,80 | 0,06 | 0,05 | 60 [415] | 30 [205] | 22 | 30 |
ASTM A27, класс 60-30 | 0,30 | 0,60 | 0,80 | 0,06 | 0,05 | 60 [415] | 30 [205] | 24 | 35 |
ASTM A27, класс 65-35 | 0.30 | 0,70 | 0,80 | 0,06 | 0,05 | 65 [450] | 35 [240] | 24 | 35 |
ASTM A27, класс 70-36 | 0,35 | 0,70 | 0,80 | 0,06 | 0,05 | 70 [485] | 36 [250] | 22 | 30 |
ASTM A27, класс 70-40 | 0,25 | 1,20 | 0,80 | 0.06 | 0,05 | 70 [485] | 40 [275] | 22 | 30 |
ASTM A148 / A148M | |||||||||
ASTM A148, класс 80-40 | НЕТ | НЕТ | НЕТ | 0,06 | 0,05 | 80 [550] | 40 [275] | 18 | 30 |
ASTM A148, класс 80-50 | НЕТ | НЕТ | НЕТ | 0,06 | 0.05 | 80 [550] | 50 [345] | 22 | 35 |
ASTM A148, класс 90-60 | НЕТ | НЕТ | НЕТ | 0,06 | 0,05 | 90 [620] | 60 [415] | 20 | 40 |
ASTM A216 / A216M | |||||||||
ASTM A216, класс WCA | 0,25 | 0,70 | 0,60 | 0,045 | 0,04 | 60-85 [415-585] | 30 [205] | 24 | 35 |
ASTM A216, класс WCB | 0.30 | 1,00 | 0,60 | 0,045 | 0,04 | 70-95 [485-655] | 36 [250] | 22 | 35 |
ASTM A216, класс WCC | 0,25 | 1,20 | 0,60 | 0,045 | 0,04 | 70-95 [485-655] | 40 [275] | 22 | 35 |
Марки стали литые
Сорта сталибыли созданы организациями по стандартизации, такими как ASTM International, Американский институт железа и стали и Общество автомобильных инженеров, для классификации сталей с определенным химическим составом и соответствующими физическими свойствами.Литейные заводы могут разрабатывать собственные марки стали для внутреннего использования, чтобы удовлетворить потребности пользователей в определенных свойствах или стандартизировать определенные марки продукции.
Спецификации деформируемых сталей часто использовались для классификации различных литых сплавов по их основным легирующим элементам. Однако литые стали не обязательно соответствуют составу деформируемой стали. Содержание кремния и марганца в литых сталях часто выше, чем в их деформируемых эквивалентах. В дополнение к преимущественно более высокому содержанию кремния и марганца в легированных литых сталях для раскисления в процессе литья используются алюминий, титан и цирконий.Алюминий преимущественно используется в качестве раскислителя из-за его эффективности и относительно низкой стоимости.
Производство стального литья
Практика литья стали восходит к концу 1750-х годов, намного позже, чем литье других металлов. Высокая температура плавления стали и отсутствие технологий для плавки и обработки металлов задержали развитие индустрии стального литья. Эти проблемы были преодолены благодаря достижениям в технологии печей.
Печи — это сосуды с огнеупорной футеровкой, которые содержат «шихту», которая представляет собой плавящийся материал, и обеспечивают энергию для плавления.В современном сталелитейном производстве используются печи двух типов: дуговые и индукционные.
Электродуговая печь
Электродуговая печь плавит партии металла, называемые «плавками», с помощью электрической дуги между графитовыми электродами. Заряд проходит непосредственно между электродами, подвергая его воздействию тепловой энергии продолжающегося электрического разряда.
Электродуговая печь плавит партии металла с использованием графитовых электродов; заряд проходит непосредственно между электродами, подвергая его воздействию тепловой энергии.Электродуговые печи работают по циклу от выпуска к выпуску:
- Загрузка печи
Загрузка стального лома и сплавов добавляется в печь.
- Плавка
Сталь плавится путем подачи энергии внутрь печи. Электроэнергия подается через графитовые электроды и обычно вносит наибольший вклад в операции по плавке стали. Химическая энергия подается через кислородные горелки и кислородные фурмы.
- Очистка
Кислород вводится для удаления примесей и других растворенных газов в процессе плавления.
- Удаление шлака
Избыточный шлак, который часто содержит нежелательные примеси, удаляется из ванны перед выпуском. Удаление шлака также может происходить внутри ковша перед разливкой.
- Выпуск (или выпуск)
Металл удаляется из печи путем наклона печи и заливки металла в передаточную емкость, например ковш.
- Оборот печи
Выпуск и подготовка завершены для следующего цикла загрузки печи.
На различных стадиях этого процесса часто предпринимаются непрерывные дополнительные операции для дальнейшего раскисления стали и удаления шлака с металла перед разливкой. Возможно, потребуется скорректировать химический состав стали, чтобы учесть истощение сплава во время длительного выпуска.
Индукционная печь
Индукционная печь — это электрическая печь, в которой тепловая энергия передается за счет индукции. Медная катушка окружает непроводящий зарядный контейнер, и переменный ток пропускается через катушку, чтобы создать электромагнитную индукцию внутри заряда.
Индукционные печи способны плавить большинство металлов и могут работать с минимальными потерями расплава. Недостаток в том, что возможно небольшое рафинирование металла. В отличие от электродуговой печи сталь не подвергается переработке.
Индукционная печь — это электрическая печь, в которой тепловая энергия передается за счет индукции и может работать с минимальными потерями расплава.Современные сталелитейные заводы часто используют переработанный стальной лом, чтобы снизить затраты и снизить воздействие на окружающую среду при производстве отливок.Устаревшие автомобили, механические компоненты и подобные предметы разделяются, калибруются и отправляются на литейные заводы в качестве металлолома. Он объединяется с внутренним ломом, образующимся в процессе литья, и в сочетании с различными легирующими элементами для загрузки в плавильную печь.
Термическая обработка
После затвердевания отливки, извлечения из формы и очистки физические свойства литой стали развиваются за счет надлежащей термической обработки.
- Отжиг
Нагрев стальных отливок до определенной температуры, выдержка в течение определенного периода времени и затем медленное охлаждение.
- Нормализация
Аналогично отжигу, но стальные отливки охлаждаются на открытом воздухе, иногда с помощью вентиляторов. Это помогает отливкам достичь более высокой прочности.
- Закалка
Подобно нормализации, но охлаждение происходит в гораздо более быстром темпе с использованием принудительной подачи воздуха. В качестве закалочной среды используются вода или масла.
- Закалка (или снятие напряжений)
Метод, используемый для снятия внутренних напряжений внутри отливок.Эти напряжения могут возникать в процессе литья или во время упрочняющих или упрочняющих термообработок, таких как нормализация или закалка. Снятие напряжений включает нагрев отливок до температуры значительно ниже температуры отжига, выдержку при этой температуре и затем медленное охлаждение.
Контроль стального литья
Стальные отливкичасто подвергаются инспекциям для проверки конкретных физических свойств, таких как точность размеров, чистота поверхности отливки и внутренняя прочность.Кроме того, необходимо проверить химический состав. На химический состав существенно влияют добавленные в материал второстепенные легирующие элементы. Литые стальные сплавы подвержены изменениям своего химического состава, поэтому перед литьем требуется химический анализ для проверки точного химического состава. Небольшую пробу расплавленного металла выливают в форму и анализируют.
Точность размеров
Контроль размеров проводится для того, чтобы убедиться, что производимые отливки соответствуют требованиям заказчика к размерам и допускам, включая припуски на механическую обработку.Иногда может потребоваться разрушить образцы отливок для измерения внутренних размеров.
Состояние поверхности
Контроль качества поверхности отливок используется для изучения эстетического вида отливок. Они ищут недостатки на поверхности и под поверхностью отливок, которые могут быть не заметны визуально. На чистоту поверхности стальной отливки может влиять тип рисунка, формовочный песок и покрытие формы, а также вес отливки и методы очистки.
Контроль качества поверхности позволяет выявить дефекты на поверхности и подповерхности стальных отливок.Внутренняя прочность
Все отливки имеют некоторый уровень дефектов, и спецификация надежности определяет допустимый порог дефекта. Превышение максимально допустимого уровня дефектов приведет к более высокому проценту брака и более высоким затратам на литье. Занижение максимально допустимого уровня дефекта может привести к отказу.
Три общих внутренних дефекта, которые встречаются в стальных отливках:
- Пористость
Пустоты в стальной отливке, которые характеризуются гладкими блестящими внутренними стенками.Пористость обычно является результатом газовыделения или улавливания газа в процессе литья.
- Включения
Кусочки постороннего материала в отливке. Включение может быть металлическим, интерметаллическим или неметаллическим. Включения могут поступать изнутри формы (мусор, песок или материалы стержня) или могут попадать в форму во время заливки отливки.
- Усадка
Вакансия или область с низкой плотностью, как правило, внутри отливки.Это происходит из-за того, что расплавленный островок материала не имеет достаточного количества исходного металла для его подачи в процессе затвердевания. Полости усадки характеризуются шероховатой кристаллической внутренней поверхностью.
Химический анализ
Химический анализ литых сталей обычно выполняется методами влажного химического анализа или спектрохимическими методами. Влажный химический анализ чаще всего используется для определения состава небольших образцов или для проверки анализа продукта после производства.Напротив, анализ с помощью спектрометра хорошо подходит для рутинного и быстрого определения химического состава более крупных образцов в условиях загруженного производственного литейного производства. Литейные предприятия могут проводить химический анализ как на уровне нагрева, так и на уровне продукта.
Тепловой анализ
Во время теплового анализа из печи выливается небольшой образец жидкой литой стали, дается возможность затвердеть, а затем анализируется химический состав с помощью спектрохимического анализа. Если состав легирующих элементов неправильный, перед разливкой можно произвести быструю регулировку в печи или ковше.После того, как все сделано правильно, тепловой анализ обычно считается точным представлением состава всей плавкости металла. Однако ожидается изменение химического состава из-за сегрегации легирующих элементов и времени, необходимого для отвода тепла от стали. В процессе заливки может происходить окисление некоторых элементов.
Во время теплового анализа образец жидкой литой стали выливают из печи, дают ему затвердеть, а затем анализируют химический состав с помощью спектрохимического анализа.Анализ продукта
Анализ продукта выполняется для проверки конкретного химического анализа, поскольку состав отдельных отливок может не полностью соответствовать применимым спецификациям. Это может произойти, даже если продукт был разлит из плавки стали, и анализ плавки был правильным. Отраслевые практики и стандарты допускают некоторые различия между анализом нагрева и анализом продукта.
Испытания стального литья
Различных механических свойств отливок из углеродистой и легированной стали можно добиться путем изменения состава и термообработки литых сталей.Литейные производства используют специализированные методы испытаний для проверки механических свойств перед завершением производства продукта.
Что касается испытания стального литья, в промышленности используются два типа испытаний: разрушающий и неразрушающий. Разрушающее испытание требует разрушения тестовой отливки для визуального определения внутренней прочности детали. Этот метод дает только информацию о состоянии тестируемого изделия и не гарантирует, что другие изделия будут исправными. Неразрушающий контроль используется для проверки внутренней и внешней прочности отливки без повреждения самой отливки. После прохождения испытаний отливка может использоваться по назначению.
Прочность на растяжение
Свойства стального литья на растяжение являются показателем способности отливки выдерживать нагрузки в условиях медленной нагрузки. Свойства при растяжении измеряются с использованием репрезентативного литого образца, который подвергается контролируемой растягивающей нагрузке — тяговым усилиям, действующим на любой конец растягивающего стержня — до разрушения.После разрушения исследуются свойства при растяжении.
СВОЙСТВА НА РАЗРЫВ
Напряжение, необходимое для разрушения отливки при растяжении или растягивающей нагрузке.
Точка, в которой отливка начинает податливаться или растягиваться и демонстрировать пластическую деформацию при растяжении.
Мера пластичности или способности отливки пластически деформироваться.
Вторичный показатель пластичности отливки.
Демонстрирует разницу между первоначальной площадью поперечного сечения натяжного стержня и площадью наименьшего поперечного сечения после разрушения при растяжении.
Свойства изгиба
Свойства изгиба определяют пластичность отливки с помощью прямоугольного репрезентативного образца, согнутого вокруг штифта под определенным углом. Полученный в результате изогнутый стержень проверяется на предмет нежелательного растрескивания.
Ударные свойства
Ударные свойства — это мера вязкости, полученная в результате испытания энергии, необходимой для разрушения стандартного образца с надрезом. Чем больше энергии требуется для разрушения образца, тем прочнее литой материал.
Твердость
Твердость — это мера устойчивости отливки к проникновению с помощью испытаний на вдавливание.Это свойство указывает на износостойкость и стойкость литых сталей к истиранию. Испытания на твердость также могут обеспечить простой рутинный метод проверки показателей прочности на разрыв в производственных условиях. Результат испытания по шкале твердости обычно тесно коррелирует с характеристиками прочности на разрыв.
Услуги кастомного литья
Reliance Foundry работает совместно с клиентами, чтобы определить лучшие физические и химические свойства, термическую обработку и методы испытаний для каждой индивидуальной отливки.Запросите расценки, чтобы получить дополнительную информацию о том, как наша служба кастинга может соответствовать требованиям вашего проекта.
Поковки из легированной стали| Производитель кованой легированной стали
Кованая легированная сталь — это сталь, к общему содержанию которой добавлено небольшое количество одного или нескольких легирующих элементов, кроме углерода. Эти добавленные элементы могут включать марганец, кремний, никель, титан, медь, хром, алюминий и другие.Эти добавленные элементы придают поковкам особые свойства, которых нет в поковках из обычной углеродистой стали. Кроме того, легированные стали становятся все более популярными из-за их доступности, более низкой экономической стоимости, отличных механических свойств и простоты обработки.
Если у вас есть какие-либо вопросы о ковке из легированной стали, свяжитесь с нами или запросите предложение для подробного анализа цен.
Применение кованой легированной стали и отрасли промышленности
- Коленчатые валы
- Детали машин
- Крепежные изделия
- Зубчатая передача
Варианты и характеристики поковок из легированной стали
В зависимости от потребностей вашего проекта существует широкий спектр доступных вариантов, когда речь идет о марках легированной стали.Как производитель поковок из легированной стали, наши легированные стали могут подвергаться термообработке для улучшения их обрабатываемости, прочности и пластичности. Добавляя определенные элементы к своей стали, вы получите широкий спектр различных результатов, в том числе следующие:
- Никель и медь — Повышает коррозионную стойкость, одновременно повышая прочность.
- Хром, ванадий, молибден и вольфрам — Эти элементы повышают прочность за счет образования карбидов второй фазы.
- Марганец, кремний, никель и медь — Добавление этих элементов увеличивает прочность за счет образования твердых растворов в феррите, который идеально подходит для экстремального теплового воздействия.
- Молибден — Когда молибден добавляется сам по себе, он помогает стали сопротивляться охрупчиванию.
- Кобальт, хром и никель — Эти добавленные элементы улучшают сохранение прочности и пластичности при более высоких температурах эксплуатации.
- Кремний и никель — Сохранение пластичности и ударной вязкости улучшается при низких рабочих температурах за счет добавления этих элементов.
Отрасль, в которой используется кованая легированная сталь, и ее предполагаемое применение будут определять необходимый тип ковки из легированной стали.
Легированная сталь марки
- 4130
- 4140
- 4150
- 4340
- 4340AQ
- A105
- Нитрол 135MOD
Дополнительные марки стали и спецификации высылаются по запросу.
Кованая легированная сталь без открытого штампа
В процессе ковки легированной стали в открытой матрице к стальным заготовкам или слиткам прикладывается тепловая и механическая энергия, которая затем изменяет форму сплава в твердом состоянии.Кованые изделия из легированной стали прочнее и надежнее, чем отливки, поскольку ковка включает изменение потока зерна, имитирующего форму детали. Термический цикл и процесс деформации приводят к измельчению зерна и рекристаллизации, что в конечном итоге приводит к упрочнению полученного стального продукта.
Кроме того, как производитель поковок из легированной стали с открытой матрицей, наши спецификации включают: AISI, ASTM, AMS, API, SAE, ASME, AWS, JIS и GB. Наши поковки доступны во многих нестандартных формах и условиях термообработки для достижения критических физических свойств, таких как растяжение, текучесть, удлинение и уменьшение площади для желаемого конечного использования, как указано покупателем.
Кованая легированная сталь Преимущества
Поковки из легированной стали обладают рядом преимуществ. В Great Lakes Forge мы понимаем ценность создания поковок из легированной стали улучшенного качества для нужд вашего проекта. Некоторые из основных преимуществ кованой легированной стали включают следующее:
- Кованые сплавы исключают возникновение усадки, пористости, пустот, которые обычно встречаются в отливках.
- Зернистая структура кованых сплавов обеспечивает высокую износостойкость.
- Кованая легированная сталь прочнее и прочнее литой стали
- Кованые легированные стали Высокая прочность усилена за счет добавленных элементов, которые были введены в углеродистую сталь.