5.3 СМАЗКА
Щековые дробилки серии «С» NORDBERG
5.3.1 Общие сведения
Обеспечение соответствующей смазки является крайне важным для вашей дробилки. Чтобы гарантировать постоянную соответствующую смазку вашей дробилки, внимательно выполняйте инструкции, приведенные в данной главе.
5.3.2 Характеристики смазки
Для точек смазки рекомендуется использовать многоцелевую смазку на литиевой основе со следующими характеристиками:
· NLGI класс 2
· Минимальная вязкость масла-основы должна быть 160 мм2/сек (СантиСтокс) при +400С/1040F а минимальный индекс вязкости 80.
· Должно годиться для использования при низких температурах (-30оС /-22оF) и при высоких температурах (температуры непрерывной работы +100оС/212оF).
· Хорошее сопротивление воде.
· Смазка не должна легко окисляться и должна содержать ЕР — добавки.
Ниже приведены некоторые из рекомендуемых марок смазок на основе лития. Также могут использоваться другие марки смазки с аналогичными характеристиками.
Марка | Тип |
CASTROL | APS 2 |
BP | Energrease LS-EP 2 |
ESSO | Beacon EP 2 |
GULF | Gulfcrown Grease EP 2 |
MOBIL | Mobilux EP 2 |
SHELL | Alvania Grease EP 2 |
SKF | LG EP 2 |
Таблица 5-2 Рекомендуемые марки смазки
ОПАСНОСТЬ! |
Не используйте сорта смазок, содержащих молибден или кальций, так как их твердые компоненты вызывают дополнительный износ в подшипниках и, таким образом, сокращают срок службы подшипников. |
ОПАСНОСТЬ! |
Дробилки серии С не рассчитаны на эксплуатацию при температурах ниже -30оС /-22оF. Если рабочие температуры должны быть ниже -30оС /-22оF, обращайтесь в Metso Minerals. |
Metso Minerals не рекомендует смешивать смазки различных марок. При возникновении затруднений обращайтесь в Metso Minerals.
5.3.3 Подшипники эксцентрикового вала
Смазка сферических роликовых подшипников щековой дробилки осуществляется с помощью ручного смазочного шприца или с помощью системы автоматической смазки, через четыре
Смазочных штуцера. Смотрите Рисунки 5.4 и 5.5.
Рисунок 5.3 Смазка сферических роликовых подшипников щековой дробилки с помощью смазочного шприца
Позиция | Позиция | Описание | |
1 | Узел насоса | 2 | Распределительное устройство |
Рисунок 5.4 Смазка сферических роликовых подшипников щековой дробилки с использованием автоматической смазочной системы
В процессе работы всегда имеет место небольшое вытекание смазки наружу через подшипники рамы и подвижной щеки и через смежные лабиринтные уплотнения. Выход смазки наружу из подшипников и налипание смазки с внешней стороны уплотнения защищает подшипники и уплотнения от попадания посторонних частиц. По наблюдениям вытекания смазки оператор легко сможет оценить объем и частоту смазки подшипников. Объем требуемой смазки,
И временные интервалы между смазками будут изменяться в зависимости от рабочих условий.
Перед смазкой подшипников, тщательно очистите место вокруг каждого смазочного штуцера, перед тем как снять с него защитный колпачок. Если используется метод ручной смазки с помощью нагнетательного шприца, добавляйте смазку сразу же после отключения дробилки, пока подшипники еще остаются теплыми. Смотрите Регламент смазки в Таблице 5-3.
Модель | Ручная смазка | Автоматическая смазка | |
Нормальные условия (каждые 80 часов) | Сильная запыленность (каждые 40 часов) | Любые условия (непрерывно) | |
Количество смазки/штуцер Грамм (унц.) | Количество смазки/штуцер Грамм (унц.) | Количество смазки/штуцер Гр/час (унц.,час) | |
C63 | 60 (2.1) | 30 (1.1) | |
C80 | 60 (2.1) | 30 (1.1) | 1.1 — 1.8 (.04 — .06) |
C95 | 125 (4.4) | 63 (2.2) | 2.0 — 3.4 (.07 — .11) |
C100 | 175 (6.1) | 88 (3.1) | 2.9 — 4.8 (.1 — .17) |
C105 | 125 (4.4) | 63 (2.2) | 2.0 — 3.4 (.07 — .11) |
C110 | 175 (6.1) | 88 (3.1) | 2.9 — 4.8 (.1 — .17) |
C125 | 250 (8.8) | 125 (4.4) | 3.9 — 6.5 (.14 — .23) |
C140 | 300 (10.5) | 150 (5.3) | 4.7 — 7.8 (.16 — .27) |
C145 | 300 (10.5) | 150 (5.3) | 4.7 — 7.8 (.16 — .27) |
C160 | 400 (14) | 200 (7) | 5.9 — 9.8 (.2 — .34) |
C200 | 500 (17.5) | 250 (8.8) | 7.7 — 12.9 (.27 — .45) |
C3055 | 175 6.1) | 88 (3.1) | 2.9 — 4.8 (.1-.17) |
Таблица 5-3. Регламент смазки подшипников эксцентрикового вала
ОПАСНОСТЬ! |
Избегайте использования слишком большого количества смазки, так как лишняя смазка приведет к перегреву и сокращению срока службы подшипников. |
5.3.4 Температура подшипников эксцентрикового вала
Необходимо производить регулярную проверку температуры подшипников, и при обнаружении ненормального повышения температуры немедленно прекратить процесс смазки. В процессе работы подшипники будут казаться на ощупь теплыми, но всегда необходимо задержать на них руку в течение нескольких секунд, без ощущения дискомфорта для руки. Нормальная рабочая температура подшипников составляет 40 – 70 оС (104 – 158 оF). Если температура повышается до 75 оС (167 оF), или при очень высокой окружающей температуре до 90 оС (194оF), необходимо выполнить проверку, для определения причины такого повышения. Необходимо также выполнить проверку, если температура одного из подшипников выше температуры других подшипников на 10-15оС (18-27оF)
ОПАСНОСТЬ! |
Дробилки серии С не рассчитаны на эксплуатацию при температурах ниже -30оС /-22оF. Если рабочие температуры должны быть ниже -30оС /-22оF, обращайтесь в Metso Minerals. |
ОПАСНОСТЬ! |
Если на дробилке не установлены температурные датчики, измерение температуры должно быть выполнено после остановке дробилки. |
5.3.5 Подшипники опорного вала
При использовании опорного вала его подшипники должны смазываться вручную с помощью нагнетательного шприца. Перед выполнением смазки подшипников тщательно очистите место вокруг каждого смазочного штуцера, перед тем как снять с него защитный колпачок.
Если используется метод смазки с помощью нагнетательного шприца, добавляйте смазку сразу же после отключения дробилки, пока подшипники еще остаются теплыми. Смотрите Регламент смазки в Таблице 5-4.
Рисунок 5.5 Смазка подшипников опорного вала
Модель | Нормальные условия (каждые 80 часов) | Сильная запыленность (каждые 40 часов) |
Количество смазки/штуцер | Количество смазки/штуцер Грамм (унц.) | |
C80 | 40 (1.4) | 20 (0.7) |
C95 | 40 (1.4) | 20 (0.7) |
C105 | 40 (1.4) | 20 (0.7) |
C110 | 70 (2.5) | 35 (1.2) |
C125 | 70 (2.5) | 35 (1.2) |
C140 | 70 (2.5) | 35 (1.2) |
C145 | 70 (2.5) | 35 (1.2) |
C160 | 80 (2.8) | 40 (1.4) |
C200 | 80 (2.8) | 40 (1.4) |
C3055 | 55 (2) | 28 (1) |
Таблица 5-4 Регламент смазки подшипников опорного вала
ОПАСНОСТЬ! |
Избегайте использования слишком большого количества смазки, так как лишняя смазка приведет к перегреву и сокращению срока службы подшипников. |
5.3.6 Температура подшипников опорного вала
Необходимо производить регулярную проверку температуры подшипников, и при обнаружении ненормального повышения температуры немедленно прекратить процесс смазки. В процессе работы подшипники будут казаться на ощупь теплыми, но всегда необходимо задержать на них руку в течение нескольких секунд, без ощущения дискомфорта для руки. Нормальная рабочая температура подшипников составляет 40 – 70 оС (104 – 158 оF). Если температура повышается до 75 оС (167 оF), или при очень высокой окружающей температуре до 90 оС (194оF), необходимо выполнить проверку, для определения причины такого повышения.
ОПАСНОСТЬ! |
Если на дробилке не установлены температурные датчики, измерение температуры должно быть выполнено при остановке дробилки. |
5.3.7 Упорные подшипники и подшипники глухой гайки
Это относится только к дробилкам, оборудованным механической регулировкой ширины разгрузочной щели. Смазку глухих вращающихся гаек и упорных подшипников необходимо производить вручную, в соответствии со следующим регламентом смазки (таблица 5-5).
Модель | Упорные подшипники | Глухие гайки |
|
Количество смазки/штуцер Грамм (унц.) | Количество смазки/штуцер Грамм (унц.) | ||
C63 | N/a | 20 (0.7) |
|
C80 | N/a | 20 (0.7) |
|
C95 | 20 (0.7) | 20 (0.7) |
|
C105 | 20 (0.7) | 20 (0.7) |
|
C110 | 20 (0.7) | 20 (0.7) |
|
C125 | 20 (0.7) | 20 (0.7) |
|
C140 | 20 (0.7) | 20 (0.7) |
|
C145 | 20 (0.7) | 20 (0.7) |
|
C160 | 20 (0.7) | 20 (0.7) |
|
C200 | 20 (0.7) | 20 (0.7) |
|
C3055 | 20 (0.7) | 20 (0.7) |
|
Таблица 5-5 Регламент смазки упорных подшипников
5.3.8 Приводной электродвигатель
Для получения соответствующих инструкций, смотрите документацию электродвигателя, которая поставляется вместе с дробилкой.
5.3.9 Распорная плита и вкладыши распорной плиты
ОПАСНОСТЬ! |
Не смазывайте вкладыши распорной плиты, распорную плиту или концы распорной плиты. Эта часть дробилки рассчитана на работу без смазки. |
Рисунок 5.6 Не смазывайте вкладыши распорной плиты, распорную плиту или концы распорной плиты.
5.3.10 Клинья регулировки ширины разгрузочной щели
ОПАСНОСТЬ! |
Не смазывайте клинья регулировки ширины разгрузочной щели. Данная часть дробилки рассчитана на работу без смазки. Необходимо оградить данную область дробилки от воды или брызг при подавлении пыли. |
Распорная плита и подшипники не ее обоих концах имеют твердую скользящую поверхность. Износ этих компонентов ускоряется после износа твердого покрытия. Заменяйте эти детали, когда их износ достигнет порядка 3 мм …
Заменяйте изношенные плиты, не допуская их полного износа.
Заменяйте защитную плиту, не допуская ее полного износа.
msd.com.ua
Централизованная система смазки дробилки
Централизованные системы смазки в промышленном производстве
Исторические предпосылки вопросаВ России, в силу исторических и географических предпосылок, всегда бурно развивалось промышленное производство. На смену старым предприятиям приходят новые, также активно модернизируются заводы советского наследия.
Один из важнейших аспектов обеспечения высокого КПД цеха, это профессиональная настройка конвейерных лент и вспомогательного оборудования.
Использование дорогостоящих материалов, технологичных механизмов и других современных инженерно-конструкторских решений, в обязательном порядке должно сопровождаться комплексом мер по сервисному обслуживанию.
К таким мероприятиям относят проверку и тестирование узлов трения, а также контроль и подачу смазочных материалов.
Традиционно существуют два подхода к вопросу смазки производственных механизмов:
— Ручная подводка
— Автоматическая подача
Отметим сильные и слабые стороны подходов:
— Смазка при участии механика:
Плюсы: 1. Экономия на автоматике. 2. Возможность визуального контроля узлов.
Издержки: 1. Необходимость остановки конвейера или машины. 2. Временной простой, риски ошибок оператора. 3. Утечки смазок. 4. Закрытые технологические агрегаты бывают недоступны без разбора. 5. Оплата работы механиков.
— Подача при помощи автоматики:
Плюсы: 1. Обеспечение бесперебойности линии. 2. Повышение выработки. 3. Страховка от поломок и утечек. 4. Соответствие современным стандартам. 5. Точная подача смазочных материалов к любым закрытым узлам.
Издержки: Необходимость первоначальных вложений для модернизации оборудования и обучения персонала.
Таким образом, очевидно, что автоматика значительно расширяет производственный потенциал.
По большому счету, это подметили уже дано. Еще в 19-ом веке, во времена технической революции, тенденция стала очевидной. Росло количество новых промышленных предприятий и для обслуживания сложных машин начали внедряться автоматические системы.
Примером служат мельницы, где часть металлических сочленений научились смазывать капельным путем без постоянного участия оператора. А в те времена мельницы представляли собой серьезные промышленные центы по переработке, фасовке, помолу и распилу.
Но, не смотря на историю вопроса и доказанную эффективность мероприятий автоматической смазки, сегодня множество фабрик не имеют данного оснащения в полной мере.
Частично это связано с кризисными явлениями прошлых периодов, а где-то задача по модернизации не ставилась из-за внутренних организационных причин.
Стоит отметить, что на стадии строительства фабрики и монтажа механизации конвейерной линии, вопрос установки централизованной системы смазки иногда опускают, для изначальной экономии и запуска предприятия. Ставка делается на персонал и ручную диагностику.
Но, при выходе на полную мощность, вопрос поднимают уже на актуальную повестку. Так как, речь идет о повышении безотказности и бесперебойности работы.
В современных реалиях установка машинного способа смазки это обязательное требование для успешного развития. В конечном итоге, предприятия с высокой автоматизацией более конкурентные, чем фабрики с ручным трудом.
Основные стимулы к установке машинной системы смазки:
— Сохранение локальных узлов производственной механизации
— Обеспечение надежности конвейера в целом
— Повышение точности производимых сервисных мероприятий
— Экономия времени на ТО
— Возможность выходить на новые циклы работы, и создать безостановочную линию
— Отсутствие утечек масла и адаптация к точной дозированной подаче смазки
— Обслуживание труднодоступных скрытых сочленений
— Значительное увеличение коэффициента полезного действия и выработки.
Применение современной автоматизации актуально практически для всей промышленной области.
Можно выделить направления по типу деятельности:
— Дробильные цеха
— Сборочные линии
— Распределительные конвейеры
— Фасовка материалов и продуктов различного назначения
К таким предприятиям относится широчайший список компаний.
Направления могут быть различными:
— Горная разведка и добыча
— Изготовление проката металла
— Литье
— Пищевая и химическая промышленность
— Заводы железобетонных изделий
— Гидроэлектростанции и дизельные генераторные установки с массивными альтернаторами
— Деревообработка и целлюлозное производство
— Переработка твердых бытовых отходов
— Железнодорожные перевозки и депо
— Судостроение, портовые работы
Стоит отметить, что наша компания сотрудничает с предприятиями, практически всех перечисленных областей. В частности, предлагаем вашему вниманию пример монтажа автоматики в цех конвейерного дробления.
Проект автоматизации смазки конвейера промышленной дробилки
Существует множество вариантов реализации системы централизованной смазки конвейера.По виду, различают проточную и циркуляционную технологию.
Циркуляция необходима для дополнительного отвода тепловой энергии. В остальном смысл остается одинаковый, а именно подать смазочное вещество к агрегатному сочленению.
В рамках представленного проекта, наша компания смонтировала проточную систему смазки на редукторы цепного привода дробилки.
Перед монтажом мы тщательно проанализировали зоны повышенной тепловой генерации. Выявили узлы с мощными роликовыми подшипниками и места подвода масла.
Анализ работы дробильной установки показал:
— Наличие открытых и закрытых узлов трения
— Повышенный уровень загрязненности механизмов мелкой фракцией отработки
— Работа в бесперебойном режиме
Пыль, оседая на цепь, ухудшает свойства масла, и появляется необходимость в чистке и подаче свежей смазки.
Постоянные обороты с преодолением мощного тягового сопротивления приводят к выгоранию масла в редукторе, и появляется необходимость подачи новых объемов.
В ходе разработки проектной документации были внесены следующие положения:
— Внедрить современное дополнительное оснащение цеха, отвечающие высоким стандартам качества и пригодное для эксплуатации в условиях фабрики
— Создать систему автоматического обслуживания редукторов сортировочной ленты
— Подобрать технологию подачи масла к открытым и скрытым элементам конвейера
— Разделить линии интенсивности подачи для каждой конкретной зоны
— Использовать объемный централизованный резервуар со смазочным веществом, для оптимизации процесса доливки
Для выдерживания ритмов интенсивной работы и соответствия требованиям проекта, было поставлено итальянское оборудование Ciaponi.
Аргументация выбора системы смазки Ciaponi
Ciaponi – итальянская компания по производству передовых систем автоматической подачи смазочных материалов и комплектующих для монтажа.Бренд широко востребован в Европе и достаточно популярен в России. Крупные холдинги вносят данное оборудование в техническое задание на модернизацию производства и используемой тяжелой техники.
Наша организация является официальным дистрибьютором марки в России.
Мы обладаем большим опытом в подборе оснастки и её установке.
Кратко можно выделить следующие достоинства:
— Возможность реализации широкого спектра технологических решений
— Объемная номенклатура расходных материалов, присутствующих в наличии
— Высокая надежность насосов, распределителей и блоков управления
— Детали рассчитаны на длительное многолетние функционирование
Положительный опыт работы с брендом, дает основание применять его для реализации самых серьезных и ответственных проектов.
Реализация монтажных работ установки комплектующих Ciaponi:
Произведена поставка:
1. Насос Ciaponi с объемным баком на 8 литров масла
2. Оригинальные итальянские прогрессивные распределители
3. Подводящие гибкие шланги, для подачи смазки в редукторы и на звенья цепи
4. Вспомогательные элементы для крепления и прокладки линий
Монтаж смазочного оборудования на конвейере
1. Временная остановка движения дробилки
2. Чистка зон креплений
3. Прокладка труб
3. Установка насоса и подключение к сети
4. Программирование циклов
5. Тестирование и ввод в эксплуатацию
Преимущества поршневого насоса Ciaponi
В централизованных системах смазки очень важно подобрать правильный тип насоса, чтобы он соответствовал техническим условиям проекта.Поршневой механизм является наиболее распространенным. Этот агрегат может взаимодействовать с различными видами приводов: электрический, пневматический, а также гидравлический.
Насос технологически адаптирован для дозированной подачи смазочных материалов, при этом, в тандеме с прогрессивными распределителями появляется возможность настраивать циклы для каждой точки обслуживания.
Поршневой принцип нагнетания хорошо встраивается в проточную систему смазки. Такты подачи синхронизируются с выработкой узла трения смазываемого сочленения.
Комплектующие Ciaponi позволяют тонко настроить данный вариант монтажа, что подтверждает верность решения внедрения итальянского оборудования на конвейерную ленту дробилки.
В дальнейшем наша компания осуществляет гарантийную поддержку. При необходимости заказать запасные части или дополнительные блоки мы оперативно проводим поставку.
Система микродозирования для смазки приводных элементов конвейера
В проекте модернизации дробильного цеха, кроме подачи на редукторы с подшипниками, предусмотрены линии капиллярной смазки приводных цепей. За счет использования технологии микродозирования, на цепь поступает смазочный материал в предельно малых объемах, но достаточных для эффективной смазки элемента привода.Таким образом, мы достигаем:
— Увеличение срока службы цепной передачи
— Уменьшение нагрева и шумового давления при работе
— Рационализацию расхода смазочных материалов
— Улучшенные показатели по выработки цеха
Технологию можно реализовать путем установки дозирующего лубрикатора. При этом допускается подключение, как к отдельному насосу, так и к основному. В зависимости от целей и масштабов объекта, инженерный состав принимает решение о типе привода.
Наша компания осуществляет данные расчеты и предлагает наиболее оптимальные варианты с точки зрения надежности и долговечности. Поэтому, если в рамках конкретного описания, у Вас возникают вопросы, мы можем внести ясность непосредственно по каждому аспекту проводимых мероприятий.
Требуемые компетенции для монтажа проектов автоматизированных систем смазки
Монтаж автоматики и подающих элементов должен осуществляться специалистами с широкой профильной базой.Во-первых, необходимо уметь читать проектную документацию. Во-вторых, владеть навыками инженерного мышления. В-третьих, обладать опытом монтажных мероприятий.
Вдобавок к этому, специалист должен разбираться в комплектующих и распределительных системах.
В нашей компании трудятся профессионалы высокого уровня подготовки. Мы ответственно подходим к вопросам кадров. Инженеры помимо теоретических изысканий, имеют опыт внушительной практической деятельности.
Также являемся сертифицированными представителями завода производителя Ciaponi, что дает возможность детально подходить к оснащению каждого проекта.
Опыт внедрения автоматизированных систем подачи масла на промышленных объектах
Наша компания зарекомендовала себя как надежный партнер в сфере проектирования и внедрения систем смазочной автоматики.Являясь дистрибьюторами, также реализуем практическую деятельность по установке импортной оснастки.
Активно сотрудничаем с крупными промышленными предприятиями по России.
Нас ценят за оперативность в поставках и высокий уровень подготовки в проектно-инженерных решениях.
За внушительный временной промежуток успешной работы, наша организация смогла модернизировать сотни единиц тяжелой техники, и большое количество линий механизации.
Адаптация производственных площадок, дополнительное оснащение конвейерных лент, промышленных установок различного назначения.
Глубоко понимая нюансы функционирования индустриальной механизации, нам удается находить эффективные пути конструктивных улучшений.
Если вы хотите выйти на новый уровень в производственной деятельности, мы готовы помочь и разработать уникальный проект централизованной системы смазки основных средств вашего предприятия.
www.gesem.ru
Щековая дробилка. Смазка узлов трения
25.07.2017Щековая дробилка — это тип дробилки, использующей для измельчения кусков горной породы сжатие щёк. Щёками называются рабочие детали дробилки, которые представляют собой стальные плиты, сжатие которых приводит к разрушению крупных кусков горной породы. На рисунке 1 показан внешний вид щековой дробилки традиционной конструкции. На рисунке 2 – рабочий орган дробилки. Принцип действия щековой дробилки напоминает действие механизма для раскалывания орехов. Можно сказать, что щековая дробилка — это гигантский «Щелкунчик».
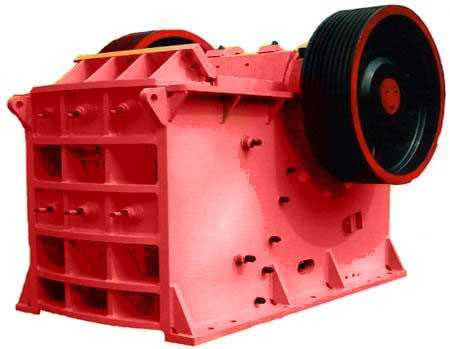
Щековый дробильный механизм имеет электромеханический или дизель-механический привод. В дробилках, установленных в цехах стационарно, используются электромоторы, в то время как в карьерных условиях могут использоваться дизельные двигатели. Механизм качания подвижной щеки представляет собой эксцентриковый или шатунный механизм. Нижний край подвижной щеки также имеет подвижное крепление, регулирующее зазор между щеками, определяющий размер фракции на выходе из дробилки.
Все узлы трения столь мощного агрегата построены на подшипниках, которые воспринимают и передают гигантские механические усилия. Огромные удельные давления, ударные нагрузки и вибрации, действующие в подшипниках дробилки, предполагают использование специализированных смазок с усиленными трибологическими свойствами. Однако сочетание повышенных скоростей и динамических нагрузок создают известную сложность в подборе смазок, удовлетворяющих этим противоречивым условиям работы. Частота вращения эксцентрикового вала 120-300 об/мин определяет вязкость базового масла в составе смазки в пределах 150-220 сСт. Ударные нагрузки и высокие удельные давления предполагают использование твёрдых смазочных добавок графита, дисульфида молибдена или других веществ слоистой кристаллической структуры, способной создать противозадирный эффект в условиях граничного трения.
Отличные результаты в подшипниках щековых дробилок показала смазка Elit M EP2 от российской компании АРГО. Оптимальное сочетание минерального масла вязкостью 150 сСт с 3% содержанием дисульфида молибдена обеспечивают высокую защиту подшипников.
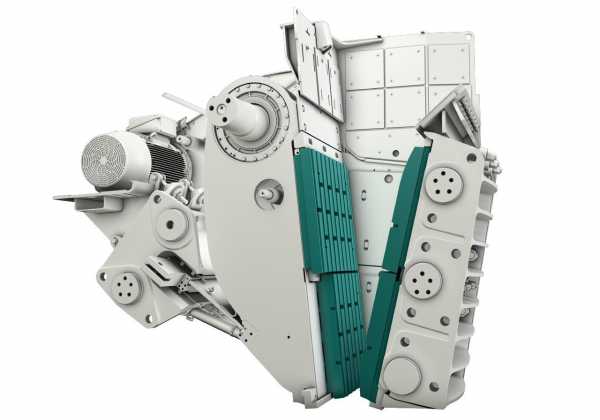
Вот характеристики АРГО Elit M:
Характеристика |
Метод |
АРГО Elit M EP2 |
Загуститель |
— |
Lithium |
Содержание MoS2, % |
|
3 |
Диапазон рабочих температур, ºС |
— |
-30..+130 |
Классификация смазок |
DIN 51502 |
KPF2K-30 |
Цвет смазки |
Визуально |
Темно-серый |
Класс консистенции NLGI |
DIN 51 818 |
2 |
Пенетрация 0,1 мм |
DIN ISO 2137 |
265-295 |
Вязкость базового масла при 40ºС, мм2/с |
DIN 51562-1 |
150 |
Температура каплепадения,ºС |
DIN ISO 2176 |
190 |
Нагрузка сваривания, Н |
DIN 51350 |
3920 |
Смазка АРГО Elit M представляет собой традиционное решение для подшипников дробилок, проверенное временем. Современные достижения в области производства пластичных смазок открывают новые возможности и снимают противоречие, связанное с необходимостью одновременно учитывать повышенные скорости и ударные нагрузки, характерные для работы дробильного оборудования. Смазки нового поколения на комплексе сульфоната кальция позволяют отказаться от использования твёрдых смазочных добавок, одновременно обеспечив максимальные трибологические свойства за счет особенностей этого загустителя.
О твёрдых смазочных добавках расскажу несколько подробнее. Сложность подбора смазок с дисульфидом молибдена или графитом для подшипников обусловлена тонкой гранью между гидродинамическим и эластогидродинамическим режимами трения с вероятным срывом к граничному трению. Уловить эту грань невозможно в условиях, когда машина работает одновременно при повышенных скоростях и с ударными нагрузками. Твёрдые смазочные добавки, надёжно защищая при граничном трении, создают обратный абразивный эффект при высоких скоростях. Смазки для дробильного оборудования это всегда компромисс. Разрешить противоречие можно только с помощью смазок, противозадирные свойства которых обеспечены свойствами неотъемлемого компонента пластичной смазки – загустителя. На настоящем этапе эволюции смазок этому требованию соответствуют только сульфонатно-кальциевые смазки, а также смазочные пасты, загущенные ультрадисперсным политетрафторэтиленом (PTFE) – фторопластом. Последние в силу весьма высокой стоимости в горно-обогатительном производстве не применяются.
Но о сульфонатно-кальциевых смазках с этого момента поговорим более обстоятельно.
В более ранних статьях мы подробно рассматривали особенности сульфонатно-кальциевых смазок, но считаю необходимым ещё раз подчеркнуть их уникальное сочетание свойств. На примере смазки TermoLub S 220 от российской компании АРГО вспомним о:
- непревзойдённых трибологических свойствах, обусловленных собственными противоизносными и противозадирными свойствами загустителя,
- отличной водостойкости,
- рекордных высокотемпературных свойствах,
- антикоррозионной защите металлов в условиях высокой влажности.
Вот подробная техническая характеристика TermoLub S 220:
Показатель |
Метод |
TermoLub S 220 ЕР2 |
Загуститель |
— |
Calcium Sulfonate Complex |
Диапазон рабочих температур, ºС |
— |
-25..+180 |
Классификация смазок |
DIN 51502 |
KP2R-25 |
Цвет смазки |
Визуально |
Янтарно-коричневый |
Класс консистенции NLGI |
DIN 51 818 |
2 |
Пенетрация 0,1 мм |
DIN 51818 |
265-295 |
Вязкость базового масла при 40ºС, мм2/с |
DIN 51562-1 |
220 |
Температура каплепадения,ºС |
DIN ISO 2176 |
>300 |
Нагрузка сваривания, H |
DIN 51350 |
3685 |
Пятно износа при нагрузке 60 кг., мм не более |
DIN 51350 |
0,7 |
Критическая нагрузка, Н |
DIN 51350 |
1098 |
Да, чуть не забыл о главных трудягах – двигателях и смазках для них. Дизельные ДВС здесь рассматривать не будем, ведь моторные масла — тема не нашего блога. Но о пластичных смазках для электродвигателей поговорим. Применительно к дробильному оборудованию, спешу порекомендовать два типа пластичных смазок для подшипников. Оба они предназначены для пожизненного использования. Выражение «пожизненная» смазка, конечно, условно, ведь ни чего вечного не бывает. Но ресурс смазок, соизмеримый с ресурсом труднообслуживаемых или малообслуживаемых агрегатов реален и актуален. Для обеспечения «долгоиграющих» свойств смазка должна содержать либо специальное базовое масло, либо поликарбамидный загуститель – полимочевину.
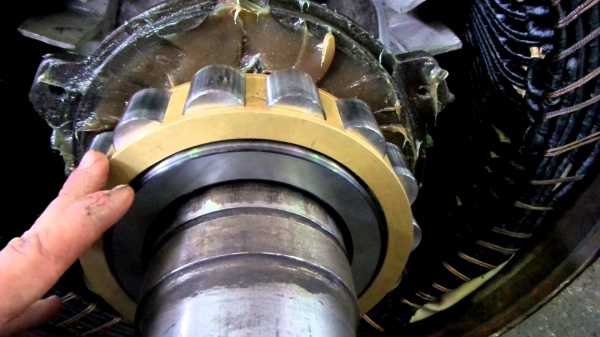
В качестве специального базового масла обычно используются полиальфаолефиновые (ПАО) синтетические масла с очень высокой термоокислительной стабильностью, позволяющей эксплуатировать смазки длительно при повышенных и высоких температурах. В качестве загустителя этих смазок традиционно используют комплексное литиевое мыло. Из западных продуктов с длительным ресурсом использования на российском рынке наиболее популярна смазка Mobilith SHC 100 от ExxonMobil, наглядно характеризующая данный тип смазок. Одним из наиболее успешных отечественных аналогов этого продукта, выступает смазка TermoSint 100 от российской компании АРГО. Вот её характеристики:
Характеристика |
Метод |
TermoSint 100 EP2 |
Загуститель |
— |
Li-Complex |
Диапазон рабочих температур, ºС |
— |
-40..+180 |
Классификация смазок |
DIN 51502 |
KPHC2R-40 |
Цвет смазки |
Визуально |
Красный |
Класс консистенции NLGI |
DIN 51818 |
2 |
Пенетрация 0,1 мм |
DIN ISO 2137 |
265-295 |
Вязкость базового масла при 40ºС, мм2/с |
DIN 51562-1 |
100 |
Температура каплепадения, ºС |
DIN ISO 2176 |
260 |
Нагрузка сваривания, Н |
DIN 51350 |
2607 |
Альтернативным принципом обеспечения ресурса смазки является использование в качестве загустителя поликарбамидного комплекса – полимочевины. В качестве базового масла в этом случае обычно используется минеральное масло. Защитный антиокислительный эффект создается загустителем. Примером «долгоиграющей» смазки на полимочевине является смазка Mobil Polyrex EM также от ExxonMobil, которую не менее успешно заменяет смазка TermoLux P 150 снова от АРГО. Вот и её технические показатели:
Показатель |
Метод |
TermoLux P 150 EP2 |
Загуститель |
— |
Polyurea |
Диапазон рабочих температур, ºС |
— |
-20..+150 |
Классификация смазок |
DIN 51502 |
KP2N-20 |
Цвет смазки |
Визуально |
Синий |
Класс консистенции NLGI |
DIN 51818 |
2 |
Пенетрация 0,1 мм |
DIN ISO 2137 |
265-295 |
Вязкость базового масла при 40ºС, мм2/с |
DIN 51562-1 |
145 |
Температура каплепадения, ºС |
DIN ISO 2176 |
260 |
Нагрузка сваривания, Н |
DIN 51350 |
4900 |
Тест на коррозию |
ASTM D 1743 |
Проходит |
Как видно из технических характеристик, пластичные смазки АРГО наиболее продвинуты технологически и успешны коммерчески. Не уступая лучшим зарубежным продуктам, смазки АРГО составляют достойную альтернативу для их импортозамещения.
Пожалуй, на этом статью стоит завершить. Друзья, присылайте ваши вопросы на e-mail: [email protected].
Смазки из статьи:
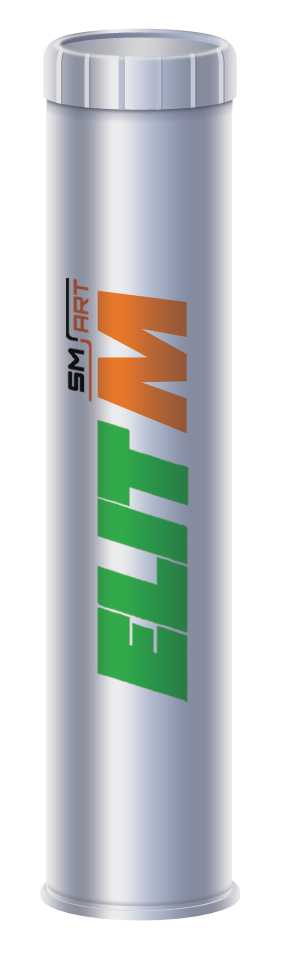
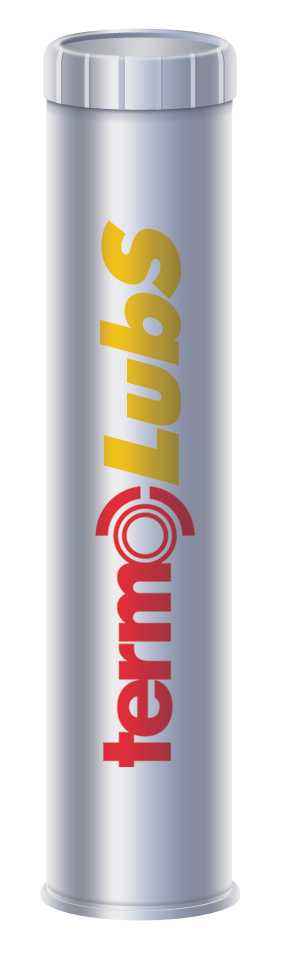
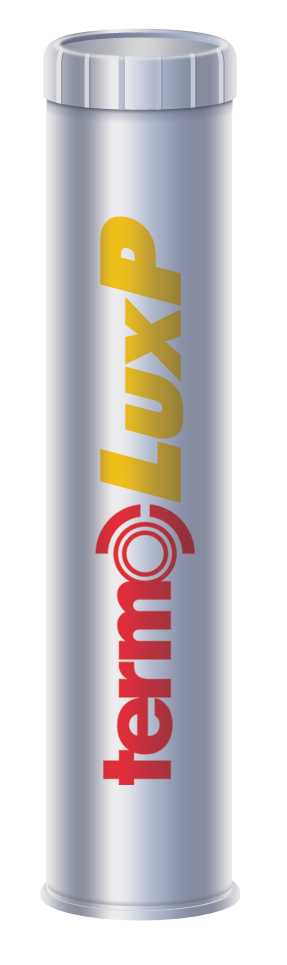
До новых встреч!
Павел Надежный
tpgargo.ru
Централизованные системы смазки для дробильно-измельчительного оборудования
А.И.Госман, менеджер по Восточной Европе компании LINCOLN Gmbh & Co. KG, Германия
Эффективность применения централизованных систем смазки (ЦСС) доказана опытом их использования на технологическом транспорте и мощном горно-добывающем оборудовании (журнал «Горная Промышленность», №3•2001, №6•2002 и «Специальный выпуск» 2004). При этом было показано, что за счет сокращения времени на проведение смазочных работ возрастает сменная производительность оборудования, сокращаются затраты на ремонт и обслуживание, на запасные части, на смазочные материалы. Кроме того, исключается необходимость в наличии различных смазочных материалов для смазки трущихся пар.
Положительный опыт применения ЦСС позволяет с равным успехом использовать их и на другом оборудовании горнодобывающих предприятий, в частности, на дробильно-измельчительных комплексах.
Фирма Lincoln является одним из основных поставщиков смазочнного оборудования для производителей всевозможного дробильного и измельчающего оборудования. Основными нашими заказчиками являются Q&К, Krupp Fördertechnik, IBAG GmbH, Hymbold-Weder AG, Gebr. Pfeifer AG, KHD AG и др. Как правило, дробильно-измельчительные установки оснащаются двухлинейными или прогрессивными системами смазки.
Использование смазочных систем на дробильном и измельчающем оборудовании может быть показано на примере применения ЦСС на дробилках типа КРД-700/100 А или КРД-700/75 прозводства «ОМЗ-Горное оборудование и технологии».
В качестве основных элементов ЦСС КРД применяются:
1. Блок управления работой смазочной станцией типа SA-E.380, FXYBU-2WX с логическим управлением, помещенный в металлический шкаф размером 600(600(210 SA-200.
2. Насосная станция типа Р-215-М 100-30 XYBU-2K6/1К7-380-420
3. Прогрессивные распределители смазки типа SSV 6-N и SSV8-N
4. Электромагнитный клапан (З/2-Wege-Magnetventil, 24V DC).
По заказу клиента ЦСС может комплектоваться насосом для автоматической заправки смазочной станции Р-215 из 200 литровой емкости.
Принцип работы централизованной системы смазки для дробилок
Смазочная станция типа P-215 в комплекте с контролем уровня смазки в 30 литровой емкости размещается в непосредственной близости от дробилки. Станция имеет три насосных элемента, которые имеют возможность непосредственной регулировки выхода смазки.
Прогрессивные распределители смазки типа SSV6-N и SSV8-N с электронным счетчиком количества ходов предназначены для подачи заданного количества смазки к парам трения. Электронный контроль на распределителях смазки предназначен для регистрации заданного количества сделаных циклов. Питатель SSV6-N предназначен для подачи смазки к подшипникам ведущего и ведомого валов дробилки (0.20 см3/ч и 0.40 см3/ч, соответственно). Один из восьми выходов питателя SSV8-N предназначен для подачи смазки к противопылевому уплотнению дробящего конуса с потребностью 3.2 см3/ч. Подача смазки к верхнему подвесу дробилки (41.6 см3/ч) осуществляется непосредственно от насосного элемента К 7.
После подачи заданного количества смазки к подшипникам ведущего и ведомого вала электромагнитный клапан по команде блока управления переключается на линию слива смазки в емкость станции P-215. При достижении заданного количества смазки на противопылевом уплотнении дробящего конуса блок управления подает команду на отключение насоса. В это время, согласно установленной дозировки и подбора насосного элемента, подшипник верхнего подвеса дробилки получит 41.6 см3/ч. По истечении времени паузы блок управления дает команду на включение насоса P-215 в работу. Согласно заданной потребности и периодичности подачи смазки к трущимся частям дробилки, согласованной с конструкторами «ОМЗ-Горное оборудование и технологии», был подобран следующий режим централизованной системы смазки: время паузы – 47 мин., время работы – 13 мин.
Выбранный режим работы централизованной системы обеспечивает постоянное поступление смазывающего вещества малыми порциями в пары трения во время работы дробилки. Это в свою очередь препятствует попаданию загрязнений в пару трения и, тем самым, увеличивает срок службы подшипника и узла в целом.
В случае включения в комплект ЦСС бочечного насоса для автоматической заправки емкости насоса P-215 не требуется дополнительное оборудование на режим автоматической заправки. По мере снижения уровня смазывающего вещества в емкости P-215 бочечный насос автоматически включается в работу и по мере достижения верхнего уровня автоматически отключается.
Опыт применения ЦСС на подобных установках позволяет утверждать, что потребное количество смазки может быть снижено не менее чем в два-три раза. При этом качество процесса смазки не ухудшается, а наоборот оптимизируется.
Преимущества применения централизованной системы смазки:
— надежное обеспечение всех пар трения заданным количеством смазки;
— постоянная готовность дробилки к работе;
— сокращение времени на обслуживание и ремонт;
— сокращение расхода смазочного материала;
— сокращение расхода на запасные части;
— отсутствие зависимости работы дробилки от человеческого фактора.
Централизованная система смазки для мельниц
В качестве основных элементов централизованной системы смазки применяются:
1. Насосная станция SAF.1 YL, с уровнем контроля смазки.
2. Блок управления работой смазочной станцией и возможным подключением нагревательного элемента и термостата для 200 литровой емкости, типа SA-Е.380, FXYBU-2WX, с логическим управлением, помещенный в металлический шкаф размером 600(600(210 SA-200.
3. Комплектная панель с форсунками распыливания густой смазки.
4. Термостат для 200 литровой емкости.
5. Нагревательный элемент для 200 литровой емкости.
6. По необходимости блок подготовки воздуха, трубопроводы и соединительные элементы.
Одним из энергоемких и металлоемких элементов как в материальном, так и в экономическом смысле, является зубчатый венец барабана мельницы. Ремонт и простой мельницы является очень чувствительным для потребителя. Для увеличения срока службы зубчатого венца и шестерни привода на шаровых мельницах фирма Lincoln имет ряд стандартных решений по их смазыванию. В качестве одного из типовых решений по смазке венцовой шестерни предлагается комплект смазочного оборудования, состоящий из насоса, панели с форсунками распыливания густой смазки, блока управления и, по необходимости, прилагается нагревательный элемент и термостат. Насоная станция может размещаться в удобном месте, а панель с форсунками непосредственно на кожухе шестерни привода. Система смазки распыливания смазывающего вещества с хорошей прилипаемостью разработана специально для нанесения его на поверхность приводной шестерни, которая переносит эту смазку на зубья венцовой шестерни. Применяемая смазка должна иметь консистенцию 0 или 00 согласно стандарта NLGI-Klasse.
В случае понижения температуры смазки доведение ее до нужной консистенции обеспечивается нагревательным элементом, устанавливаемым на наружнюю поверхность 200 литровой емкости. Нагревательный элемент включается автоматически через общий пульт управления.
Поддержание заданной температуры обеспечивается при помощи термостата. Форсунки распыливания смонтированы на одной панели с расстоянием друг от друга в 150 мм. Конроль за работой форсунок по смазке происходит при помощи электронного датчика, установленного на прогрессивном распределителе, который также смонтирован на этой панели. Контроль по воздуху происходит через реле давления, размещенного на панели подготовки воздуха.
Комплектная панель распыливания смазки монитруется на кожухе венцовой шестерни. Панель поготовки воздуха размещается вместе с бочечным насосом в удобном месте.
Все элементы электрического контроля системы смазки распыливания имеют выход на блок управления, который в автоматическом режиме включает насос в работу и после выдачи заданной порции смазки отключает его. Блок управления смонтирован в металлическом ящике системой контроля типа Siemens S7 и текстовым дисплеем TD 200. Питание на управление электромагнитных клапанов и реле давления – по желанию заказчика (24 В или 230 В).
Согласно заданному режиму работы блок управления дает команду на пуск насоса и одновременно на подачу воздуха к форсункам. Смазка поступает по трубопроводам к форсункам через прогрессивный распределитель. В форсунке воздух, смешиваясь со смазкой, наносится равномерным слоем на зуб шестерни привода или на зуб венцовой шестерни. Режим работы системы смазки подбирается таким образом, чтобы выдерживались следующие параметры:
— от 2.2 до 3.0 г/см в час поверхности (ширины) зуба;
— от 1.0 до 1,5 г/см в час для малых шестерен;
— на 0.3–0.6 г увеличение расхода при повышенной запыленности.
Традиционные смазки и битумные расходуются в количестве от 3.5 до 5.0 г/см в час.
Рекомендуемый расход смазки подобран на основании совместной работы с изготовителями мельниц и смазочного вещества.
Наиболее опитмальным и хорошо зарекомендовавшим себя смазочным веществом для смазывания венцовых шестерен может быть предложена смазка типа MALLEUS GL 95 фирмы Shell.
Преимущества применения централизованной системы смазки для шаровых мельниц:
— надежное обеспечение всех пар трения заданным количеством смазки;
— постоянная готовность дробилки к работе;
— сокращение времени на обслуживание и ремонт до 30–40 %;
— сокращение расхода смазочного материала до 50 %;
— при применении смазки MALLEUS GL 95 дает экономию до 70 %;
— сокращение расхода на запасные части до 30–50 %;
— отсутствие растворителя в смазке;
— высокие антикоррозийные и антизадирные свойства.
В случае возникновения воросов или встречных предложений обращаться непосредственно на фирму Lincoln или к нашим региональным представителям, координаты которых имеются на сайте
www.lincolnindustrial.de
Журнал «Горная Промышленность» №4 2004
mining-media.ru
Смазки для дробилок, масла для дробильного оборудования от Kluber Lubrication
Для этих видов применения крайне важно учитывать скоростной фактор подшипника. Именно по этой причине компания Klϋber Lubrication разработала альтернативные виды смазки для этих машин, которые отличаются широким диапазоном вязкости, что позволяет машинам справляться с различными скоростями и нагрузками.
Мы предлагаем широкий ассортимент высококачественной продукции для смазки стационарного оборудования.
- Дробильное оборудование: Мы знаем, насколько важно обеспечить соответствие стандартам производства и соответствие требованиям, предъявляемым к оборудованию данного типа, на котором подшипники вала испытывают особенно сильные механические напряжения под действием вибрации, соударений и возможного нарушения соосности – всех тех факторов, которые необходимо компенсировать посредством смазки.
- Электродвигатели: особые смазки могут внести значительный вклад в надлежащую работу подшипников, продление срока службы оборудования, увеличение надёжности и снижение уровня шума. Более того, они позволяют работать с более высокой скоростью и делают механизмы устойчивыми к внешним факторам воздействия.
Консистентные смазки для дробильного оборудования
Применение |
Продукт |
Состав |
Твёрдая смазка |
Характеристики |
Подшипники качения |
Klüberplex BEM 41-141 |
Литиевый комплекс, минеральное масло |
— |
Очень хорошая защита от износа и
|
Klüberlub BE 41-542 |
Специальное литиевое минеральное масло |
— |
Высокая несущая способность и защита Скоростной фактор 500 000 |
|
Klüberplex BE 31-502 |
Специальное кальциевое минеральное масло |
— |
Отличная защита от износа, коррозии, высоких температур и экстремальной Скоростной фактор 200 000 |
|
Klüberlub BE 41-1501 |
Специальное литиевое минеральное масло |
MoS2 + графит |
Отличная защита от износа и устойчивость к экстремальным нагрузкам и низким |
|
Klüberlub BE 41-1002 |
||||
Klüberlub BVH 71-461 |
Полиуретан, минеральное масло |
— |
Хорошая защита от износа, устойчивость Скоростной фактор 200 000 |
Масла для дробилок
Применение |
Продукт |
Базовое масло |
Рабочая температура |
Характеристики |
Зубчатые колеса, втулки, подшипники скольжения, валы, подшипники качения |
Klüberoil GEM 1N ISO VG 46 — 1000 |
Минеральное масло |
от −15 до 100 °C |
Минеральное масло, высокая степень нагрузки до задира, FZG ≥ 14, API GL4 — устойчивость к точечному выкрашиванию и средним температурам |
Klübersynth GEM 4N ISO VG 32 — 680 |
Синтетическое масло |
от −50 до 140 °C |
Синтетическое масло на основе ПАО, смешиваемое с минеральным маслом, высокая степень нагрузки до задира и устойчивость к низким температурам |
www.klueber.ru
5.3 СМАЗКА | Дробилки МСД
5.3.1 Общие сведения
Обеспечение соответствующей смазки является крайне важным для вашей дробилки. Чтобы гарантировать постоянную соответствующую смазку вашей дробилки, внимательно выполняйте инструкции, приведенные в данной главе.
5.3.2 Характеристики смазки
Для точек смазки рекомендуется использовать многоцелевую смазку на литиевой основе со следующими характеристиками:
· NLGI класс 2
· Минимальная вязкость масла-основы должна быть 160 мм2/сек (СантиСтокс) при +400С/1040F а минимальный индекс вязкости 80.
· Должно годиться для использования при низких температурах (-30оС /-22оF) и при высоких температурах (температуры непрерывной работы +100оС/212оF).
· Хорошее сопротивление воде.
· Смазка не должна легко окисляться и должна содержать ЕР — добавки.
Ниже приведены некоторые из рекомендуемых марок смазок на основе лития. Также могут использоваться другие марки смазки с аналогичными характеристиками.
Марка | Тип |
CASTROL | APS 2 |
BP | Energrease LS-EP 2 |
ESSO | Beacon EP 2 |
GULF | Gulfcrown Grease EP 2 |
MOBIL | Mobilux EP 2 |
SHELL | Alvania Grease EP 2 |
SKF | LG EP 2 |
Таблица 5-2 Рекомендуемые марки смазки
ОПАСНОСТЬ! |
Не используйте сорта смазок, содержащих молибден или кальций, так как их твердые компоненты вызывают дополнительный износ в подшипниках и, таким образом, сокращают срок службы подшипников. |
ОПАСНОСТЬ! |
Дробилки серии С не рассчитаны на эксплуатацию при температурах ниже -30оС /-22оF. Если рабочие температуры должны быть ниже -30оС /-22оF, обращайтесь в Metso Minerals. |
Metso Minerals не рекомендует смешивать смазки различных марок. При возникновении затруднений обращайтесь в Metso Minerals.
5.3.3 Подшипники эксцентрикового вала
Смазка сферических роликовых подшипников щековой дробилки осуществляется с помощью ручного смазочного шприца или с помощью системы автоматической смазки, через четыре
Смазочных штуцера. Смотрите Рисунки 5.4 и 5.5.
Рисунок 5.3 Смазка сферических роликовых подшипников щековой дробилки с помощью смазочного шприца
Позиция | Описание | Позиция | Описание |
1 | Узел насоса | 2 | Распределительное устройство |
Рисунок 5.4 Смазка сферических роликовых подшипников щековой дробилки с использованием автоматической смазочной системы
В процессе работы всегда имеет место небольшое вытекание смазки наружу через подшипники рамы и подвижной щеки и через смежные лабиринтные уплотнения. Выход смазки наружу из подшипников и налипание смазки с внешней стороны уплотнения защищает подшипники и уплотнения от попадания посторонних частиц. По наблюдениям вытекания смазки оператор легко сможет оценить объем и частоту смазки подшипников. Объем требуемой смазки,
И временные интервалы между смазками будут изменяться в зависимости от рабочих условий.
Перед смазкой подшипников, тщательно очистите место вокруг каждого смазочного штуцера, перед тем как снять с него защитный колпачок. Если используется метод ручной смазки с помощью нагнетательного шприца, добавляйте смазку сразу же после отключения дробилки, пока подшипники еще остаются теплыми. Смотрите Регламент смазки в Таблице 5-3.
Модель | Ручная смазка | Автоматическая смазка | |
Нормальные условия (каждые 80 часов) | Сильная запыленность (каждые 40 часов) | Любые условия (непрерывно) | |
Количество смазки/штуцер Грамм (унц.) | Количество смазки/штуцер Грамм (унц.) | Количество смазки/штуцер Гр/час (унц.,час) | |
C63 | 60 (2.1) | 30 (1.1) | 1.1 — 1.8 (.04 — .06) |
C80 | 60 (2.1) | 30 (1.1) | 1.1 — 1.8 (.04 — .06) |
C95 | 125 (4.4) | 63 (2.2) | 2.0 — 3.4 (.07 — .11) |
C100 | 175 (6.1) | 88 (3.1) | 2.9 — 4.8 (.1 — .17) |
C105 | 125 (4.4) | 63 (2.2) | 2.0 — 3.4 (.07 — .11) |
C110 | 175 (6.1) | 88 (3.1) | 2.9 — 4.8 (.1 — .17) |
C125 | 250 (8.8) | 125 (4.4) | 3.9 — 6.5 (.14 — .23) |
C140 | 300 (10.5) | 150 (5.3) | 4.7 — 7.8 (.16 — .27) |
C145 | 300 (10.5) | 150 (5.3) | 4.7 — 7.8 (.16 — .27) |
C160 | 400 (14) | 200 (7) | 5.9 — 9.8 (.2 — .34) |
C200 | 500 (17.5) | 250 (8.8) | 7.7 — 12.9 (.27 — .45) |
C3055 | 175 6.1) | 88 (3.1) | 2.9 — 4.8 (.1-.17) |
Таблица 5-3. Регламент смазки подшипников эксцентрикового вала
ОПАСНОСТЬ! |
Избегайте использования слишком большого количества смазки, так как лишняя смазка приведет к перегреву и сокращению срока службы подшипников. |
5.3.4 Температура подшипников эксцентрикового вала
Необходимо производить регулярную проверку температуры подшипников, и при обнаружении ненормального повышения температуры немедленно прекратить процесс смазки. В процессе работы подшипники будут казаться на ощупь теплыми, но всегда необходимо задержать на них руку в течение нескольких секунд, без ощущения дискомфорта для руки. Нормальная рабочая температура подшипников составляет 40 – 70 оС (104 – 158 оF). Если температура повышается до 75 оС (167 оF), или при очень высокой окружающей температуре до 90 оС (194оF), необходимо выполнить проверку, для определения причины такого повышения. Необходимо также выполнить проверку, если температура одного из подшипников выше температуры других подшипников на 10-15оС (18-27оF)
ОПАСНОСТЬ! |
Дробилки серии С не рассчитаны на эксплуатацию при температурах ниже -30оС /-22оF. Если рабочие температуры должны быть ниже -30оС /-22оF, обращайтесь в Metso Minerals. |
ОПАСНОСТЬ! |
Если на дробилке не установлены температурные датчики, измерение температуры должно быть выполнено после остановке дробилки. |
5.3.5 Подшипники опорного вала
При использовании опорного вала его подшипники должны смазываться вручную с помощью нагнетательного шприца. Перед выполнением смазки подшипников тщательно очистите место вокруг каждого смазочного штуцера, перед тем как снять с него защитный колпачок.
Если используется метод смазки с помощью нагнетательного шприца, добавляйте смазку сразу же после отключения дробилки, пока подшипники еще остаются теплыми. Смотрите Регламент смазки в Таблице 5-4.
Рисунок 5.5 Смазка подшипников опорного вала
Модель | Нормальные условия (каждые 80 часов) | Сильная запыленность (каждые 40 часов) |
Количество смазки/штуцер Грамм (унц.) | Количество смазки/штуцер Грамм (унц.) | |
C80 | 40 (1.4) | 20 (0.7) |
C95 | 40 (1.4) | 20 (0.7) |
C105 | 40 (1.4) | 20 (0.7) |
C110 | 70 (2.5) | 35 (1.2) |
C125 | 70 (2.5) | 35 (1.2) |
C140 | 70 (2.5) | 35 (1.2) |
C145 | 70 (2.5) | 35 (1.2) |
C160 | 80 (2.8) | 40 (1.4) |
C200 | 80 (2.8) | 40 (1.4) |
C3055 | 55 (2) | 28 (1) |
Таблица 5-4 Регламент смазки подшипников опорного вала
ОПАСНОСТЬ! |
Избегайте использования слишком большого количества смазки, так как лишняя смазка приведет к перегреву и сокращению срока службы подшипников. |
5.3.6 Температура подшипников опорного вала
Необходимо производить регулярную проверку температуры подшипников, и при обнаружении ненормального повышения температуры немедленно прекратить процесс смазки. В процессе работы подшипники будут казаться на ощупь теплыми, но всегда необходимо задержать на них руку в течение нескольких секунд, без ощущения дискомфорта для руки. Нормальная рабочая температура подшипников составляет 40 – 70 оС (104 – 158 оF). Если температура повышается до 75 оС (167 оF), или при очень высокой окружающей температуре до 90 оС (194оF), необходимо выполнить проверку, для определения причины такого повышения.
ОПАСНОСТЬ! |
Если на дробилке не установлены температурные датчики, измерение температуры должно быть выполнено при остановке дробилки. |
5.3.7 Упорные подшипники и подшипники глухой гайки
Это относится только к дробилкам, оборудованным механической регулировко
drobilci.ru
Гидромаслостанции централизованной жидкой смазки для дробилок и горного оборудования.
Надежная, долговечная и экономичная работа дробильного оборудования невозможна без соответствующей работы станций смазки, подающих масло в тяжело нагруженные механизмы. Конструкторское бюро нашего предприятия разработало серию гидромаслостанций для системы централизованной смазки и для гидропривода регулирования выходной щели дробилки КСД(КМД)-1200 с разными эксплуатационными и ценовыми характеристиками.
Мы готовы удовлетворить как самого взыскательного заказчика с современными запросами к надежной работе станций в автоматическом режиме. Так и небольшие предприятия с отдельными дробильными комплексами, где не требуется особая ритмичность работы.
В первом случае для гидравлики применяются итальянские комплектующие, включая насос и реле давления. Во втором станция работает на российской гидравлике и в зависимости от требований заказчика может быть упрощена до минимально работоспособного варианта с соответствующей ценой.
На системе смазки применяется решение , которое исключает работу дробилки без масла. Контроль возврата масла в бак дублируется несколькими датчиками разных типов.
Для тех предприятий, которые привыкли не использовать гидравлику для откручивания — закручивания регулирующего кольца дробилки КСД(КМД)-1200, поставляется только смазочная станция , комплектация которой может быть также различной согласно условий эксплуатации и требований заказчика.
Срок отгрузки гидромаслостанции от 3 дней до полутора месяцев. Возможно заключение договора на диагностику, реконструкцию вашей старой гидравлической станции и ее восстановление. Срок исполнения любой из заявок определяется наличием комплектующих и сроком закупки недостающих.
Купить документацию купить смазочную станцию и комплектующие.
Краткое описание.
Централизованные смазочные станции циркуляционной жидкой смазки представляют собой насосные агрегаты, которые доставляют смазочную жидкость к узлам трения различных механизмов удаленных друг от друга на какое-то расстояние . Различаются по составу оборудования ,обьему бака , количеству и охвату функций контроля и автоматики. По желанию заказчика состав оборудования и технические характеристики насосных станций (смазочно-насосных, гидромаслостанций, блоков маслостанций, смазочных станций) могут быть скорректированы либо спроектированы заново по заданию заказчика.
Станции постоянно совершенствуются и поэтому на странице представлены только базовые варианты.
Модернизация действующей смазочной станции . Во время ревизии определяют неисправные блоки, и принимают решение о ремонте либо полной замене. Работа выполняется силами службы механика с выездом нашего шеф-инженера. Блоки насосных установок, блоки фильтров, датчики и указатели уровня, электроконтактные термометры, реле давления , реле протока, блоки манометров, блоки клапанов или отдельные аппараты, заливные фильтры и сапуны комплектуются под заявку.
Фильтры- один из главных элементов гидравлических устройств , отвечающий за экономичную, надежную и долговременную эксплуатацию любой гидросистемы .
Гидростанция С630-1200М для конусной дробилки
Совмещенная станция для централизованной смазки дробилки и работы гидропривода регулировки выходной щели. Бак разделен на две полости -для работы системы смазки 630 л, для работы гидропривода 200 л. Два шестеренных насоса(рабочий и резервный)расположены на крышке бака подача 56 л/мин. Для гидропривода -шестеренный насос с подачей 32л/мин. системы визуального и автоматического контроля уровня масла в баке , электроподогрев масла с визуальным и автоматическим контролем и поддержанием заданной температуры, фильтрация масла с контролем загрязнения и очисткой фильтров, система резервирования основных функций, визуальный и автоматический контроль давления и подачи масла.
Станция смазки для дробилки КСД-900
Бак с датчиком уровня, насос с электродвигателем , два фильтра -грубой и тонкой очистки, манометр и клапан настройки давления . На сливе контроль протекания масла и фильтр. Это минимальная комплектация , которая может быть усилена согласно технического требования заказчика.
Станция смазочная СС70/05-01 -характеристики
Два шестеренных насоса(рабочий и резервный)расположены внутри бака, подача 70 л/мин, обьем масла в баке 2 м3, системы визуального и автоматического контроля уровня масла в баке , пароподогрев и электроподогрев масла с визуальным и автоматическим контролем и поддержанием заданной температуры, фильтрация масла с контролем загрязнения и очисткой фильтров, система резервирования основных функций, визуальный и автоматический контроль давления и подачи масла. СС70/0,5 комплектуется теплообменником. Полный перечень технических характеристик и состав оборудования в паспорте маслостанции.
Станция смазочная 0,8СС56-01 и 0,8СС75-01
Два шестеренных насоса(рабочий и резервный)расположены на крышке бака подача 56 л/мин либо 75л/мин, обьем масла в баке 0,8 м3, системы визуального и автоматического контроля уровня масла в баке , электроподогрев масла с визуальным и автоматическим контролем и поддержанием заданной температуры, фильтрация масла с контролем загрязнения и очисткой фильтров, система резервирования основных функций, визуальный и автоматический контроль давления и подачи масла. 0,8СС56-01 комплектуется теплообменником. Полный перечень технических характеристик и состав оборудования в паспорте смазочной станции.
Станция смазочная 1,4СС70-01
Два шестеренных насоса(рабочий и резервный) расположены на боковой стенке бака, подача 70 л/мин, обьем масла в баке 1,4 м3, системы визуального и автоматического контроля уровня масла в баке , электроподогрев масла с визуальным и автоматическим контролем и поддержанием заданной температуры, фильтрация масла с контролем загрязнения фильтров, система резервирования основных функций, визуальный и автоматический контроль давления и подачи масла. 1,4СС70 комплектуется теплообменником. Полный перечень технических характеристик и состав оборудования в паспорте смазочной станции.
Установка насосная УС-63 Два шестеренных насоса(рабочий и резервный) расположены на боковой стенке бака, подача 63 л/мин, обьем масла в баке 1,25 м3, системы визуального и автоматического контроля уровня масла в баке , электроподогрев масла с визуальным и автоматическим контролем и поддержанием заданной температуры, фильтрация масла с контролем загрязнения фильтров и очисткой фильтров, система резервирования основных функций, визуальный и автоматический контроль давления и подачи масла, комплектуется теплообменником. Полный перечень технических характеристик и состав оборудования в паспорте смазочной станции.
Для комплектации смазочных станций применяются насосные установки,блоки насосных установок, визуальные указатели уровня, датчики уровня, фильтры, приборы контроля и регулировки давления. Для ремонта уже работающего оборудования или самостоятельного изготовления смазочных станций перечисленные позиции моможно заказать у нас
Насосная станция фильтрации и охлаждения масла
Для улучшения эксплуатационных характеристик станций централизованной смазки предлагаются насосные станции , которые осуществляют дополнительную фильтрацию и охлаждение рабочей жидкости. Фильтры на этой станции устанавливаются с электрическим приводом для автоматического очищениия от загрязнений. Теплообменники на этих станциях устанавливаются в зависимости от температурного режима работы и дополнительных пожеланий заказчика. Насосная станция также может быть использована для быстрой откачки и закачки масла при замене рабочей жидкости в основном баке.
Более детальная информация о работе системы смазки конусных дробилок находится в следующем разделе:Смазка дробилки.
www.dso55.ru