В чем отличие резины от силикона?
ЧТО же ЛУЧШЕ: РЕЗИНА ИЛИ ПВХ?Вот хочешь ты купить резиновые сапоги. Покупаешь. А потом оказывается, что на самом деле они не из резины, а из ПВХ.
И ты не знаешь, хорошо это или плохо. А, может, разницы и нет? Давайте разбираться, что лучше резина или ПВХ?
ИСТОРИЯ ВОЗНИКНОВЕНИЯ РЕЗИНЫРезина (каучук) – это, можно сказать, прародитель современного ПВХ (PVC). По легенде, индейцы собирали сок с каучуконосных деревьев и делали из них мячи, посуду и первые резиновые сапоги. Правда, способ был не из приятных. Они обмазывали ноги каучуком и держали их над костром. В результате получалось непромокаемое покрытие. Кстати, перья индейцы клеили тоже каучуком. Об этом всем рассказал Колумб, когда вернулся в Европу, но его тогда почему-то не услышали.
Вторая попытка знакомства Европы с этим материалом состоялась в 1738 году. Тогда путешественник Ш. Кодамин, вернувшись из Америки, приехал в академию наук Франции и рассказал ученым про каучук. Даже показал, как его получить. Но каучук быстро высыхал и твердел. Что с этим делать никто не знал. Почти 85 лет он применялся только для изготовления ластика-стирашки.
В 1823 году химик из Шотландии Чарльз Макинтош придумал, как по-новому использовать каучук. Он растворил его в керосине. И полученным раствором пропитал плотную ткань. Она стала водонепроницаемой. Так появились первые макинтоши. А чуть позже и влагозащитные галоши. Но на холоде они твердели. А в жару становились мягкими, липкими, как смола, и к тому же издавали жуткий запах.
Еще немного и о резине забыли бы. И, может быть, даже навсегда. Но в дело вмешался молодой изобретатель Чарльз Гудиер. Он был настолько настойчив в своем желании дойти до самой сути, что даже, несмотря на крах своего некогда успешного бизнеса, не оставлял попыток. Он распродал имущество, чтобы расплатиться с кредиторами, отправил семью в пансион, а сам на чердаке с другом-аптекарем проводил бесконечные эксперименты.
Шли годы. В 1839 году он смешал каучук с серой, нагрел… И получил резину. Ключ к головоломке был найден.
С тех пор резина прочно вошла в нашу жизнь. Резиновые сапоги, галоши… Кто не помнит это чудо советской легкой промышленности? Но вот, спустя некоторое время, в конце 20 века весь прогрессивный мир перешел на ПВХ. И причин здесь несколько.
ТРИ КЛЮЧЕВЫХ ОТЛИЧИЯ ПВХ ОТ РЕЗИНЫ: 1. САПОГИ ИЗ ПВХ АБСОЛЮТНО ГЕРМЕТИЧНЫ.А вот сапоги из резины, как это ни странно, могут протекать. Их делают из кусков, которые сваривают между собой. Именно поэтому нежелательно покупать китайские резиновые сапоги, особенно для детей. Лучше выбрать ПВХ.
ПВХ производится несколько по другой технологии: жидкий материал заливают в специальную форму. Такие сапоги монолитные: не имеют швов и стыков. А значит, вероятность протечки равна нулю. При этом вполне реальны ситуации, когда после использования обуви из ПВХ ноги сырые. Но здесь причины в другом.
2. САПОГИ ИЗ ПВХ БОЛЕЕ ДОЛГОВЕЧНЫ И НАДЕЖНЫ.А вот сапоги из резины рассыхаются со временем, ломаются на сгибах, трескаются от перепада температур. Да и вообще, менее устойчивы к повреждениям.
И дело даже не в цене (оба варианта стоят не так дорого). И не в том, что сапоги придется менять чаще. Проблема в том, что их надо будет менять в самый неподходящий момент. Как раз тогда, когда они так необходимы. А необходимы они, как назло, именно сейчас.
3. САПОГИ ИЗ ПВХ ГОРАЗДО ЛЕГЧЕ.Казалось бы, разница не очень большая, но когда ты несколько километров пройдешь по лесу в тяжелых резиновых сапогах, эта разница станет более ощутимой.
Неужели у ПВХ нет недостатков? Есть. Один. ПВХ «боится» растительных и животных жиров. Но не настолько, чтобы одна капля разъела насквозь вашу любимую пару обуви. В конце концов, для работы в критичных условиях выпускают специальную рабочюю обувь из ПВХ, в составе которой имеются необходимые добавки. Благодаря им сапоги имеют допуски на масло и бензостойкость. В них даже можно ходить в 30% растворе соляной кислоты.
Но в повседневной жизни это, разумеется, ни к чему. Для прогулок по лужам, походов за грибами, поездок на рыбалку достаточно и обычных сапог из ПВХ. При правильном уходе они верой и правдой прослужат долгие годы.
zirochka.zakupka.com
Преимущества и преимущества силиконовой резины
В этой статье мы вводим много выгод и преимуществ силиконовой резины.
- Выдерживает высокие и низкие температуры гораздо лучше, чем органического каучука
- Хорошая термическая стабильность
- Отталкивает воду и формы жесткие уплотнения
- Отличная электрическая изоляция, не снижение производительности изоляции даже при погружении в воду, что делает его идеальным изоляционный материал
- Гибкий при низких температурах, напрягается вверх при более высоких температурах
- При обычном давлении, контакт с паром, как правило, мало или совсем не ухудшения
Почему силикона является идеальным материалом для экстремальных температур
Силиконовая резина выдерживает высокие и низкие температуры гораздо лучше, чем их органических резиновых аналогов.
- Возможность использовать при постоянной температуре 150 ° C (302 ° F) при практически полном отсутствии изменений в его свойствах.
- Некоторые силиконовые соединения выдерживают использовать даже при температуре 200 ° C (392 ° F) в течение 10000 часов или более.
- Некоторые из силиконовой резины продукты могут выдержать нагрев свыше 350 ° C (662 ° F) в течение коротких периодов.
Силиконовый каучук также обладает отличной устойчивостью к низким температурам.
- Точка охрупчивания для некоторых силиконовых частей составляет от -60 ° до -70 ° С, (-76 ° С до -94 ° F) (резины составляет от -20 ° до -30 ° C, (от -4 до -22 ° F)
- Некоторые силиконовые изделия способны выдерживать очень низкие температуры, сохраняя их эластичность при температуре от -100 ° C (-148 ° F) и ниже.
www.minchsilicone.com
О силиконе — Группа компаний Резинотехсервис
Силикон или кремнийорганическая (силиконовая) резина является современным материалом, обладающим уникальными свойствами, которые отличают его от простых органических резин. По внешнему виду силикон напоминает синтетическую или обычную натуральную резину. Однако вследствие своей особой химической структуры силикон отличается целым рядом свойств, которые позволяют ему занять особое место среди резиновых эластичных материалов.
Силиконовые изделия могут использоваться в ситуациях, при которых невозможно применение традиционных эластомеров. Так, например, уплотнительные кольца из силикона устойчивы к воздействию озона, морской и пресной воды (в том числе, кипящей), спиртов, минеральных масел и топлив, слабых растворов кислот, щелочей и перекиси водорода. Кроме того, силиконы устойчивы к механическим воздействиям, длительно сохраняют свои свойства, обладают способностью увеличивать или уменьшать адгезию, придавать гидрофобность, работать и сохранять свойства при повышенной влажности, биоинертны, экологичны. Изделия из силикона переносят перепады температур, сохраняя свои свойства от -60 °C до +200 °C, морозостойкие типы — от -100 °C, термостойкие — до +300 °C.
Важным фактором является то, что химическим путем можно изменять длину основной кремнийорганической цепи, боковые группы и перекрёстные связи для того, чтобы синтезировать силиконы с разными свойствами. Силикон может быть тонкой консистенции, высоко связным или жидким, в зависимости от плотности и производственного процесса. Все это обусловливает широкое применение силикона во многих отраслях промышленности.
Силиконы, в зависимости от химических свойств, делятся на силиконовые жидкости, силиконовые эластомеры и силиконовые смолы.
Силиконовые жидкости и их эмульсии широко применяются в качестве или в основе силиконовых антиадгезивных смазок для пресс-форм, масел, амортизационных жидкостей, теплоносителей и охлаждающих жидкостей, герметизирующих составов, пеногасителей.
Силиконовые эластомеры применяются в виде силиконовых каучуков, резин горячего отверждения, герметиков.
Герметики применяются для заделки и склеивания всех видов швов и стыков, когда нужна надежная изоляция от внешних воздействий, высокая влагостойкость, прочность и эластичность. Применяются высококачественные силиконы и в медицине.
www.rezina.biz
Как отличить силикон от ПВХ
В быту часто приходится использовать шланги. Их применяют в аквариумах для обогащения воды кислородом, для полива садовых и дачных участков, в пищевом производстве, например виноделии и самогоноварении. Такая продукция делится на две группы: силиконовый шланг и шланг из ПВХ. И если во многих ситуациях материал, из которого изготовлены трубки, не принципиален, то при изготовлении продуктов питания качество шланга имеет большое значение.
Особенности ПВХ-шланга
Трубки из поливинилхлорида довольно часто используют в бытовых и производственных целях. Их главным достоинством является невысокая стоимость. Однако в стремлении сэкономить потребитель часто забывает о свойствах этого материала.
Да, он устойчив к воздействию многих агрессивных сред, например бензина, соляной и азотной кислот, но только до тех пор, пока их температура не поднимается выше 60 градусов. При нагревании же ПВХ-шланг начинает гореть и выделять ядовитые для человека вещества – диоксиды.
Поэтому использование изделий из ПВХ допускается только в тех случаях, когда не предполагается их нагрев.
Преимущества силиконовых шлангов
Этот вид изделий легко переносит высокие температуры, не вступая в химическое взаимодействие с продуктами и средами, которые находятся внутри них. Среди достоинств продукции из силикона следует отметить такие особенности, как:
- Нетоксичность, полная безопасность для человека и животных. Пищевой силикон представляет собой соединение кислорода и кремния, что не несёт никакой опасности или угрозы здоровью.
- Повышенные прочностные и износостойкие характеристики.
- Устойчивость к любому механическому воздействию – сгибанию, сдавливанию, сжиманию. Принимая необходимую пользователю форму, материал сохраняет свои качества.
- Способность выдерживать низкие и высокие температуры (от -60 до +250 градусов) без потери свойств.
- Антиадгезия. Внутренние стенки не притягивают к себе продукты распада, благодаря чему не происходит сужения диаметра трубки.
- Удобство эксплуатации и хранения. Эти изделия легко скручиваются, занимая минимум места, хорошо растягиваются, принимая затем исходную форму.
- Долгий срок службы.
Единственным недостатком силикона является его более высокая цена. Поэтому, выбирая силиконовый шланг или ПВХ, потребитель может сам для себя расставить приоритеты, отдавая предпочтение экономии или качеству изделия.
Как отличить силикон от ПВХ
Довольно часто случается, что производитель обманывает потребителей, выдавая силикон за ПВХ. Поэтому прежде, чем отправляться за покупкой, следует знать, как отличить силиконовый шланг от ПВХ. Есть несколько способов сделать это:
- Возьмите трубку и помните её в руках. Силикон обладает более мягкой структурой, его легче растянуть. Однако этот способ не всегда оказывается эффективен, так как производители научились выпускать поливинилхлорид, по качеству максимально приближенный к силикону.
- Подожгите край трубки и посмотрите на реакцию материала. Если при нагревании изделие начнёт плавиться и чернеть, образуется дым чёрного цвета с едким запахом, значит, перед вами ПВХ. Если под воздействием высокой температуры структура материала не изменится, а лишь появится небольшой светлый дым и пепел белого цвета, то вы держите силикон.
- Ещё один эффективный способ того, как проверить, силиконовый шланг или ПВХ вы приобрели, можно применить в домашних условиях. Положите изделие в морозильную камеру минут на 10. Силикон сохранит свои свойства мягкости и эластичности, а ПВХ станет твёрдым и плохо гнущимся.
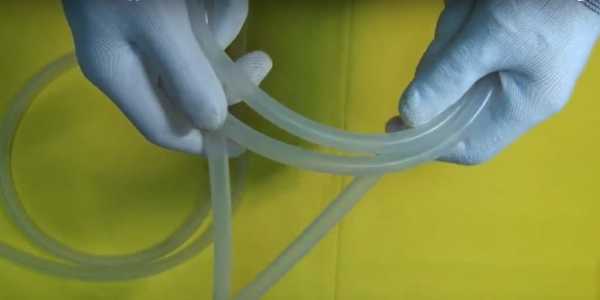
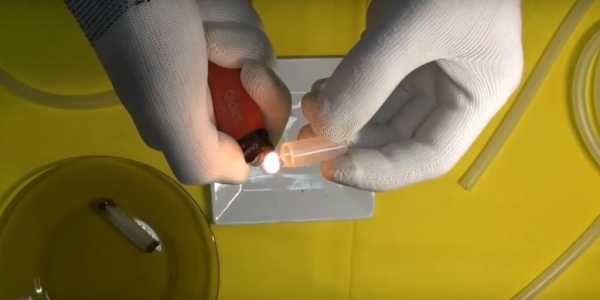
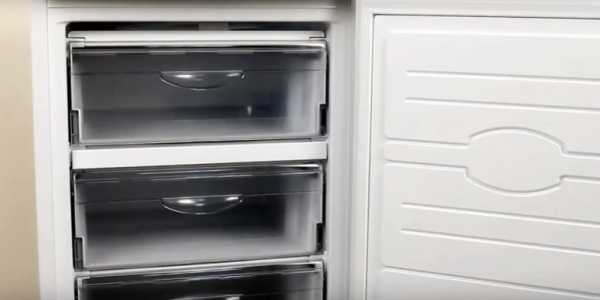
Эти приёмы позволят вам легко определить, что предлагает вам магазин – шланг ПВХ или силикон. А что выбирать – это уже личное дело каждого.
Если у Вас есть вопросы, звоните по бесплатному номеру в Екатеринбурге и Свердловской области 8-800-250-4337.
xn—-dtbegn3a5abh8i.xn--p1ai
Ответы@Mail.Ru: Подскажите Формулу Силикона
химическая формула [R2SiO]n, где R = органическая группа (метиловая, этиловая или фениловая). Т.е. к примеру SiO3(Ch4)6 <br>(замечание: цифры должны быть индексами)<br><br>тем, которые ниже написали, а где у вас про саму формулу? это можно и в интернете найти.<br>Тогда уж по-русски бы написали: Силиконы имеют строение в виде основной неорганической кремний-кислородной цепи (…-Si-O-Si-O-Si-O-…) с присоединенными к ней боковыми органическими группами, которые крепятся к атомам кремния (а не какими то вставками).<br>Да и еще одно: различными свойствами при разных температурах обладает не сам силикон:<br> Силиконовый каучук (силастик) обладает высокими электроизоляционными качествами и большой термостойкостью и морозостойкостью. Он сохраняет эластичность в интервале температур от -60 до +200 °C и широко применяется в современной технике (жароупорные прокладки, клапаны, мембраны, детали прожекторных установок, электроизоляционные материалы и др.). Многочисленные кремнийорганические полимеры используют для приготовления хладостойких (теплостойких) смазок, жидкостей, работающих при температурах от -100 до +250 °C. Применяют для гидрофобизации различных материалов, тканей, бумаги, стекла, керамики, строительных материалов, а также в производстве лаков и пластмасс.<br><br>
Основная структура силиконовой резины, в отличие от обычных видов резины, – это цепи из атомов кремния и кислорода с редкими поперечными сшивками. <a rel=»nofollow» href=»http://www.arsrti.ru/silikon.html» target=»_blank»>http://www.arsrti.ru/silikon.html</a>
Силиконовая резина или просто силикон – это эластичный материал, получаемый на базе высокомолекулярных кремнийорганических соединений и по внешнему виду напоминающий синтетическую или обычную натуральную резину. Однако вследствие своей особой химической структуры силикон отличается целым рядом свойств, которые позволяют ей занять особое место среди резиновых эластичных материалов. <br><br>Основная структура силиконовой резины, в отличие от обычных видов резины, – это цепи из атомов кремния и кислорода с редкими поперечными сшивками. Этим обстоятельством обуславливается присущий силикону, в некоторой степени, неорганический характер. Силиконовая резина сохраняет свои свойства практически неограниченное время при температурах от -50°С до +180°С.<br><br>Силикон можно использовать при температурах, близких к +250°С в течение нескольких сотен часов без появления хрупкости. Особо термостойкие типы силикона имеют достаточно долгий срок службы, при температуре выше +200°С. Точно также особые сорта применимы при температурах до -100°С.<br><br>Свойства силиконовой резины в отличие от натурального каучука не меняются под воздействием света и воздуха в нормальных температурных диапазонах. Дождь, снег, морская вода также практически не оказывают воздействия на силикон, поэтому её можно считать устойчивой к атмосферным воздействиям. Кроме того, силикон устойчив даже к озону, благодаря чему приобретает особенно важное значение для электротехнической промышленности, силиконовая резина устойчива к таким явлениям, как электрическая корона и дуга.<br><br>Из-за своих антиадгезионных свойств силикон с трудом совмещается с другими материалами. Для достижения достаточной прочности сцепления необходимо использовать специальные клеи. <br><br>На все уже ответили, можно только добавить, что силоксаны или по западному силиконы избретены в СССР в ВНИИСК им. акад. Лебедева (СПб).
touch.otvet.mail.ru
Чем силиконовые патрубки лучше резиновых? ― Компания РТИОПТ
Патрубки очень просты с виду. Но их роль – важна, от этого будет зависеть результат всей работающей системы. Поэтому автомобилисты и сотрудники СТО всегда с предельной тщательностью выбирают данный вид резинотехнических изделий, уделяя им не меньше времени, чем запчастям для мотора или подходящим в тормозную систему.
Основные отличия силиконовых и резиновых патрубков
Обычно автомобиль выпускается с резиновыми патрубками, которые выполняют свою функциональную нагрузку, но не являются лучшим решением, исходя из качества и долговечности. Практика показывает, что с целью обеспечения лучшего охлаждения, вентилируемости и отвода газов предпочтительнее устанавливать силиконовые патрубки. Они очень отличаются от резины. Последние ломаются и твердеют всего после нескольких лет эксплуатации. Силиконовые же напротив, износоустойчивы и имеют длительный эксплуатационный срок. По сравнению с резиновыми, их называют вечными. Во время повышения давления в трубе, повышаются показатели температуры выхлопа, а также охлаждающей жидкости.
Резина имеет свойство быстро устаревать. И ее применение в системе охлаждении мотора и картерных, турбонаддува и вентиляции выхлопных газов не является лучшим вариантом. Износ резины проявляется в ее растрескивании, поломках, отвердении. Резина не сможет выдерживать перепады температуры благодаря своему составу. Их необходимо меня достаточно часто, особенно зимой.
Особенно портят патрубки воздух и жидкость для охлаждения, циркулирующие в них. Причиной тому является давление. Это может привести к неполадкам и возникновениям трещин. Если они визуально видимы снаружи, это говорит о том, что замена патрубка нужна незамедлительно. Профилактический осмотр помогает выявить трещины внутри патрубков.
Чтобы правильно подобрать силиконовое изделие, следует выявить все параметры работы, от давления, которое будет проходить в них, до формы и используемых в системе хомутов. Если использовать армированные каркасы для силиконовых патрубков, это усилит показатели жесткости и прочности, что поможет уменьшить, например, турбояму в турбированных моторах.
Схожая форма силиконовых патрубков с оригинальными, резиновыми помогает обеспечить правильную работу любой системы. Если будут иметься отличия, тогда нарушатся параметры, указанные заводом-изготовителем при выпуске автомобиля. Ресурс силиконовой запчасти будет высоким, что окупит сторицей вложенные деньги за само резинотехническое изделие. Покупая силиконовые патрубки, можно существенно снизить расходы на эксплуатацию автомобиля.
Сравнивая эти 2 материала, современный водитель, не обращая внимания на ценовую политику (стоимость силиконовых патрубков всегда выше), выбирает профилактические результативные меры в противовес обрушившейся на голову катастрофе. Для безопасности и значительного облегчения жизни закупаются силиконовые изделия.
Особенности и роль силиконовых патрубков
Силиконовые патрубки являются резинотехническими изделиями, которые не расширяются под избыточным давлением и выдерживают даже высокие его показатели. Это помогает сглаживать турбоямы и турболаги. В итоге – само время до возникновения факта турбонаддува будет уменьшено тоже.
Применение соединительных элементов из силикона позволяет упрощать соединение пайп и различных автодеталей друг с другом. Универсальное применение патрубков в данном случае – неоспорима. Только благодаря им может быть обеспечена работа всей системы охлаждения средства передвижения на максимально эффективном уровне. Поэтому, подбирая патрубки из силикона правильно, основываясь на диаметр каналов как пайпинга, так и выходных, можно обеспечить высококачественную работу автомобиля, и при этом не волноваться за собственную безопасность.
Подбирая формы патрубков из силикона, следует обращать внимание на системные конфигурации. Чаще всего можно встретить изогнутые патрубки, угол наклона которых будет прямым. Универсальные внутренние диаметры позволяют применять их на разные транспортные средства. Это добавляет еще один «плюс» в копилку данных РТИ. Многослойный силикон, сорт которого будет только 1, поможет не пропускать высокую температуру и жидкость тоже. Но происходит это также благодаря следующим фактам: армированию и многослойности полиэфирного трикотажа. В итоге толстая трубка, отличающаяся эластичностью, будет предотвращать утечки охладительной жидкости и сопротивляться влиянию повышенной или пониженной температуры.
Особыми «плюсами» характеристики силиконовых патрубков являются:
- полное соответствие заявленных характеристик по отношению к тому, что происходит в реальности, особенно при смене температуры;
- высокие показатели долговечности резинотехнического изделия, что напрямую сказывается на низких расходах на эксплуатацию и частоту ремонтов;
- гибкость и мягкость материала изделия, что сказывается напрямую на высокие показатели сопротивляемости всем деформационным процессам в условиях сжатия;
- возможность их применения как основных элементов для соединения системы охлаждения автомобиля или как каналов распределения охлаждающей жидкости;
- применение в любом положении, лишь бы подходил диаметр изделия, например, как соединение между помпой и радиатором, термостатом и двигателем, чему способствует отсутствие влияние на них температуры, агрессивности окружающей среды, и состава разных веществ;
- компактность сбора разных механизмов при применении силиконовых патрубков, чему очень помогает наличие разных по длине и форме резинотехнических изделий (это помогает производить техосмотры быстро и качественно, не «захватывая» лишнюю площадь в автомобиле).
Бывают не только универсальные силиконовые патрубки, которые можно применить, исходя из их объема и диаметра, но и те, которые имеют определенную форму изгиба. И в первом, и во втором, лучше всего подбирать патрубок из силикона схожий с резиновым прототипом который стоял в системе изначально. Хотя, не следует забывать, что основные свойства силикона заключаются в долговечности, эластичности и гибкости материала.
Вывод можно сделать такой, что силиконовые патрубки, в отличие от резиновых, являются уникальными и даже универсальными изделиями. Учитывая их износоустойчивые свойства, устойчивость к температурам, как повышенным, так и пониженным, гибкость и долговечность службы, не склонность к растрескиванию и механическим повреждениям, армирование и все вытекающие последствия, это позитивно отражается на жизни самого автомобилиста. Основной результат – это значительное облегчение задач, которые стоят по уходу за собственным автомобилем, особенно благодаря выпуску в разных или универсальных формах.
Устанавливая силиконовые патрубки в собственный автомобиль, владелец может не проверять треснутую или лопнувшую резину, потому что ее просто не будет во всех важных внутренних системах. Установив единожды РТИ из силикона, автомобилист на практике проверит, насколько гарантированным являются заявленные параметры силиконовых патрубков. Подбирая трубки, каждый поймет, что их многообразие настолько же комфортно для подбора под собственный автомобиль, как и универсальность применения, учитывая преимущества изделия. Быстрое проведение ремонтных работ и самостоятельной осмотр с заменой необходимых деталей значительно сэкономят ваше время, силы и финансы.
Каждый волен сам выбирать, на что и как тратить финансы, но принимая во внимание лозунг обеспеченных людей о том, что они «не столько богаты, чтобы тратить свои деньги на дешевые и некачественные вещи», мы и сами не можем позволить себе это.
rtiopt.com
ЧТО ТАКОЕ СИЛИКОНОВАЯ РЕЗИНА ГОРЯЧЕЙ ВУЛКАНИЗАЦИИ?
Силиконовая резина. – это эластичный материал, получаемый на базе высокомолекулярных кремнийорганических соединений и по внешнему виду напоминающий синтетическую или обычную натуральную резину. Однако вследствие своей особой химической структуры она отличается целым рядом свойств, которые позволяют ей занять особое место среди резиновых эластичных материалов.
Основная структура силиконовой резины, в отличие от обычных видов резины, – это цепи из атомов кремния и кислорода с редкими поперечными сшивками. Этим обстоятельством обуславливается присущий ей в некоторой степени неорганический характер.
СТРУКТУРА.
Силиконовая резина. – это эластичный материал, получаемый на базе высокомолекулярных кремнийорганических соединений и по внешнему виду напоминающий синтетическую или обычную натуральную резину. Однако вследствие своей особой химической структуры она отличается целым рядом свойств, которые позволяют ей занять особое место среди резиновых эластичных материалов.
Основная структура силиконовой резины, в отличие от обычных видов резины, – это цепи из атомов кремния и кислорода с редкими поперечными сшивками. Этим обстоятельством обуславливается присущий ей в некоторой степени неорганический характер.
Остальные связи кремния заняты органическими радикалами (R), в первую очередь метильными, чем объясняется сходство с обычными сортами резины.
Наряду с метильными группами полимерная цепь содержит небольшой процент алкиленовых групп, в первую очередь – винильных, что повышает реакционную способность при перекисном образовании сетчатых структур.
СВОЙСТВА.
- Устойчивость к экстремальным температурам.
- Силиконовая резина сохраняет свои свойства практически неограниченное время при температурах от -50 °С до +180 °С.
- Её можно использовать при температурах, близких к +250 °С в течение нескольких сотен часов без появления хрупкости.
- Особо термостойкие типы силиконовой резины имеют достаточно долгий срок службы при температуре выше +200 °С.
- Точно также особые сорта применимы при температурах до -100 °С.
- Учитывая её хорошие электроизоляционные свойства, силиконовую резину можно отнести к категории теплостойкости H.
Зависимость свойств от температуры.
Как и у всех силиконов, большинство свойств силиконовой резины зависят от температуры в меньшей степени, чем у органических материалов. Благодаря этому силиконовую резину можно с успехом использовать при более высоких и более низких температурах. К таким свойствам относятся, например, сохранение формы, эластичность, упругость, прочность, жёсткость и предельное удлинение. Среди электрических характеристик, которые также в меньшей степени зависят от температуры, следует назвать пробивную прочность, диэлектрические показатели, объёмное сопротивление.
Электрические свойства.
Силиконовая резина при комнатной температуре обладает отличными изоляционными свойствами. Как уже отмечалось, эти свойства зависят от температуры лишь в малой степени. Поэтому силиконовая резина при температурах выше +100°С превышает по своим изоляционным показателям все традиционные эластомеры.
Следует также отметить, что при хранении в воде отмечаются лишь ничтожные изменения электрических свойств.
При сгорании изоляции из силиконовой резины остаётся непроводящий слой SiO2, благодаря чему обеспечивается более высокая защита электрических приборов и установок при нежелательных перегрузках.
Химическая стойкость.
Силиконовая резина устойчива к растворам солей, кипящей воде, спиртам, фенолам, различным минеральным маслам, слабым кислотам и щелочам, а также к перекиси водорода. В определённых условиях при контакте с алифатическими углеводородами наблюдается сильное набухание силиконовой резины, но после их испарения к ней возвращаются первоначальные механические свойства, так как она не содержит экстрагируемых составных частей.
Физиологическое воздействие.
Силиконовая резина не токсична, если она обработана по всем правилам. Поэтому она является идеальным материалом для медицинской техники и пищевой промышленности. Однако некоторые вулканизирующие средства могут оказывать на неё неблагоприятное воздействие. Эти средства вулканизации и продукты их распада устраняются путём достаточно длительного воздействия высоких температур.
Устойчивость к атмосферным воздействиям и озону.
Свойства силиконовой резины в отличие от натурального каучука не меняются под воздействием света и воздуха в нормальных температурных диапазонах. Дождь, снег, морская вода также практически не оказывают воздействия на свойства силиконовой резины. Поэтому её можно считать устойчивой к атмосферным воздействиям.
Она устойчива даже к озону, благодаря чему приобретает особенно важное значение для электротехнической промышленности. Кроме того, силиконовая резина устойчива к таким явлениям, как электрическая корона и дуга.
Антиадгезионные свойства.
Большинство сортов силиконовой резины обладает плохой адгезией к поверхностям различных материалов. Поэтому их можно использовать как материалы для изготовления форм, покрытий для транспортёров, по которым перемещаются липкие детали, покрытий валов в текстильной промышленности и искусственных материалов. Из-за своих антиадгезионных свойств силиконовая резина с трудом совмещается с другими материалами. Для достижения достаточной прочности сцепления необходимо использовать специальные клеи.
Теплотехнические свойства.
- Теплопроводность силиконовой резины составляет ~4•10-4 кал/см.град.с (измерена при температуре +80 °С).
- Коэффициент линейного расширения составляет ~2•10-4 град.-1 в пределах температур от 0 до +150 °С.
Оба эти показателя зависят от типа и количества наполнителя.
Общие положения.
Обработка силиконового каучука горячей вулканизации требует применения смесительных вальцов, пластикатора, экструдера, каландров, вулканизационных прессов и отопительных каналов. Такое оборудование обычно имеется только на резинообрабатывающих заводах, поставляющих готовые изделия из силиконовой резины. Для снабжения таких заводов исходными материалами в удобной и универсальной форме предлагаются исходные смеси силиконовых каучуков. Подобные смеси состоят из силиконового каучука, активного наполнителя на базе кремниевой кислоты, полу- и неактивных наполнителей, как, например, инфузорная земля и вспомогательные материалы на силиконовой основе, служащие для упрощения процесса обработки. При добавлении соответствующих вулканизаторов при температурах более +100°С из них можно изготовить эластичные резиновые детали.
Путём развальцовывания других наполнителей в эти исходные смеси можно получить вулканизаты с требуемыми производными свойствами.
Очень важно помнить, что все машины по переработке силиконовой резины должны содержаться в полной чистоте. Даже самые малые количества серных катализаторов и антиоксидантов, которые обычно используются для органической резины, могут сделать силиконовую резину абсолютно непригодной. Поэтому для обработки силиконовой резины целесообразно использовать отдельные машины.
Хранение.
Исходные смеси, а также смеси силиконового каучука следует хранить в закрытых емкостях и защищать от воздействия солнечных лучей. Хранение должно производится отдельно от каучуков на органической основе. Хранение готовых к вулканизации смесей (содержащих перекиси) должно производиться при температурах не выше +30°С, в противном случае при обработке могут возникнуть определённые сложности. Срок хранения исходных смесей не менее 12 месяцев, а готовых к вулканизации смесей не менее 4 месяцев.
Пластификация.
При длительном хранении смеси силиконовых каучуков становятся хрупкими, поэтому перед обработкой их необходимо пластифицировать для того, чтобы изготовляемые из них изделия имели качественную поверхность.
Пластификация проводится на смесительных вальцах стандартной конструкции. Фрикционная передача обоих вальцов должна быть от 1:1,2 до 1:1,5 и должна иметь охлаждение. Смесь силиконового каучука подаётся в широкий зазор между вальцами и пропускается несколько раз. Если в результате длительного хранения она крошится и падает в ванну кусками, то е надо подавать на валки до тех пор, пока не образуется сплошная лента из материала. Проскакивающие вниз куски следует снова подавать на вальцы, так как если это сделать с запозданием, они не размягчатся, что может привести к образованию уплотнений. Подобные уплотнения значительно снижают характеристики и ухудшают внешний вид резины. Если каучуковая смесь проходит равномерно, то зазор между валками делается уже. Сначала смесь пропускают через вальцы с меньшей скоростью вращения, а затем переходят на более быстрые. За счёт интенсивной обработки смеси время пластификации можно значительно сократить. Не следует опасаться «мёртвого валка», хотя смесь при длительной обработке на валках иногда становится слишком клейкой. Поэтому целесообразно использовать обрезной нож, чтобы эти мягкие смеси можно было снимать с валков.
Пластифицированные смеси остаются готовыми к переработке в течение нескольких дней. Постепенно они снова застывают, поэтому репластификацию необходимо повторять.
Смешивание с наполнителями.
При достаточной пластичности исходной смеси на смесительные валки можно дополнительно подавать наполнители. Добавка наполнителей обеспечивает повышение прочности и во многих случаях удешевляет материал. Увеличение содержания наполнителя может упростить процесс напыления для различных смесей.
Для силиконовой резины наиболее часто используются следующие наполнители:
- Высокодисперсная пиролитическая кремниевая кислота с развитойповерхностью в 200 м²/г;
- Инфузорная земля;
- Карбид кремния тонкого помола;
- Оксид цинка;
- Оксид титана и т. д.
Оксид титана и некоторые оксиды железа способствуют повышению термостойкости (до +200-300 °С).
При дальнейшем увеличении количества наполнителя наблюдается, как правило, более или менее заметное ухудшение механических показателей, зависящее от использованного наполнителя и его количества. Не следует добавлять более 100 частей неактивного или полуактивного и 30 частей активного наполнителя.
Вулканизирующие средства.
Для вулканизации смеси силиконового каучука применяются различные органические перекиси, которые добавляются в исходную смесь, как правило, после наполнителей. После введения перекиси смесь необходимо основательно охладить во избежание её девулканизации.
Органические перекиси, как правило, представляют собой вещества, взрывающиеся от ударов и легковоспламеняющиеся. Вследствие этого они используются часто не в чистом виде, а в разбавленном, например, в виде паст. Эти пасты безопасны при обработке и легко смешиваются. Некоторые другие перекиси даже в чистой форме бывают настолько стабильными, что не реагируют на удар и трение, однако, следует помнить, что они вызывают раздражения кожи и, прежде всего глаз. Поэтому при работе с ними необходимо надеть перчатки и очки. Качество готовой силиконовой резины зависит не только от исходной смеси, но также в значительной мере от выбора перекиси и её количества.
Вот некоторые, самые популярные перекиси:
- Бис-(2,4-дихлорбензоил)пероксид (2,4-ДХБ, DCLBP). Используетсяисключительно для вулканизации без давления. Таким способомизготовляют шланги, кабели, профилированные детали. Вулканизацияпроисходит непрерывно под действием горячего воздуха. Дляускорения вулканизации необходимо поддерживать температуру впределах от +250 до +400 °С.
- 2,5-диметил-2,5-ди(тетрабутилперокси)гексан (DHBP). Придаётхорошие механические свойства. Вулканизация идёт при температуревыше +170 °С. Благодаря хорошей Scorch-характеристике он особеннопригоден для литья под давлением и литьевого прессования.
Пигменты.
Смеси силиконового каучука, как правило, хорошо окрашиваются, так как они непрозрачно-прозрачные или имеют бело-серую окраску. Для окрашивания используются неорганические термостабильные пигменты.
Если не требуется устойчивость к высоким температурам, то можно использовать органические красители:
- Белый — диоксид титана, оксид цинка;
- Красно-коричневый — оксид железа красный;
- Синий — кобальт синий;
- Чёрный — сажа.
Пигменты смешиваются в количестве до 1% с перекисью. Равномерность окраски говорит о равномерном распределении перекиси. Следует упомянуть, что особенно удобно применение красок в виде паст.
СПОСОБЫ ПЕРЕРАБОТКИ.
Формование и литьевая прессовка.
При формовании, а также литьевой прессовке смесь заливается или запрессовывается в форму и выдерживается под давлением определённое время. Температура при этом доводится до температуры вулканизации (в зависимости от перекиси). В качестве смазки пресс-форм используется разбавленный водой раствор моющих средств.
Давление, как правило, составляет от 40 до 80 кг/см². Продолжительность воздействия температуры и давления зависит, как правило, от толщины формы и определяется экспериментальным путём. При толщине изделия до 10 мм достаточно, как правило, 10-15 минут. Если в форму попадает воздух, то в вулканизате образуются коричневые плохо провулканизированные места. Поэтому при вальцовке смесей и при заполнении форм необходимо следить за тем, чтобы туда не проникал воздух.
Важно при закрытии форм обеспечить удаление воздуха. При загрузке заготовки в горячую форму надо помнить, что прессовка должна следовать немедленно. В противном случае смесь начинает вулканизировать и не растекается достаточно по форме.
Во многих случаях полезно оставить резину охлаждаться до +80°С под давлением. Если это невозможно, то следует проверить, не начнёт ли эта форма деформироваться.
Литье под давлением.
Обработка смесей силиконового каучука методом литья под давлением целесообразна при крупносерийном производстве. При такой технологии применяется значительно более высокие температуры, но время вулканизации здесь существенно короче.
Изготовленные методом литья под давлением формы мягче других примерно на 5-10 единиц А Шора. Это можно компенсировать при изготовлении смеси за счёт увеличения количества наполнителя.
Подача смеси осуществляется роликовым ленточным перегружателем. Этот перегружатель либо протягивается и сгружает смесь на каландр, либо устанавливается на литьевой машине.
Экструзия.
Этим методом на литьевых машинах, применяемых в резинообрабатывающей промышленности, изготавливают профильные детали, прутки, ленты, шланги и кабельные оболочки. Вулканизация осуществляется в канале с подачей горячего воздуха, но возможна также и вулканизация паром (вулканизация CV).
В качестве вулканизирующего средства может применяться только перекись с двумя перекисными группами (например, 6ис-(2,4-дихлор6ензоил)пероксид), которые требуются для вулканизации без давления.
Для вулканизации CV пригодны так же и другие перекиси, как, например, 2,5-диметил-2,5-ди (тетрабутилперокси)гексан. Для усовершенствования работы профильного пресса его целесообразно оснастить питающим валком. Литьевой цилиндр нагревать не следует. Вместо этого рекомендуется охлаждение выдувной головки и шнека. В качестве присыпки можно применять тальк и активную кремниевую кислоту.
Температура внутри вулканизационного канала устанавливается на +250-350°С. Чем выше температура, тем быстрее идёт процесс. При +350°С он продолжается лишь несколько секунд. Достаточно, чтобы деталь приобрела стабильную форму, так как за вулканизацией следует поствулканизация (отжиг).
Процесс отжига может быть либо прерывистым и проходить в печи с циркуляцией воздуха, либо непрерывным в специальном нагревательном канале. В последнем варианте необходимо обеспечить достаточную подачу воздуха.
Наслоение.
Смеси силиконовой резины можно наносить методом погружения, намазывания рекельным ножом и каландрирования. Способ погружения предусматривает прохождение полотна ткани с помощью специального приспособления в 10-35% эмульсию силиконового каучука в растворителе. Затем растворитель при температуре менее +80°С испаряется, а каучуковая смесь вулканизируется на полотне ткани в шахтах с нагревом до температуры +120-250°С.
Метод погружения обладает тем преимуществом, что эмульсия хорошо пропитывает ткань. Резина при этом хорошо закрепляется на поверхности ткани, что даёт возможность получать очень тонкие покрытия. Отрицательной стороной является относительно большой объем растворителя, требующийся при этой методике.
Способ погружения используется, как правило, для нанесения резиновых слоев на стеклоткань.
При методе нанесения эмульсия из силиконового каучука наносится на ткань с одной стороны при помощи рекельного ножа. Содержание плотного вещества должно составлять 40-60%. Затем следуют те же операции, как и при погружении.
По сравнению с методом погружения нанесение позволяет получать более толстые слои и используется в тех случаях, когда нанесение требуется только с одной стороны.
Для обоих названных способов пригодны только те смеси силиконового каучука, которые легко растворяются. В качестве растворителей используются: толуол, ксилол, тест-бензин, бутилацетат, декалин, перхлорэтилен и т.д. Эмульсии готовятся в аппарате с быстро вращающейся мешалкой (волчковые смесители). Целесообразно начинать готовить эмульсию при соотношении 1:1 и лишь затем добавить остаток растворителя.
Каландрирование является третьим способом нанесения. При этом смесь силиконового каучука, готовая к вулканизации (без растворителя), наносится с помощью каландра на полосу ткани. Покрытая этой смесью ткань пропускается через гидравлический пресс, канал с подогретым воздухом или вулканизируется в вулканизирующей машине непрерывного действия. При способе каландрирования сцепление между резиной и тканью не такое прочное, как в двух предыдущих методах. С другой стороны, здесь можно использовать смеси, как правило, плохо диспергирующиеся, но позволяющие добиться высоких характеристик по прочности. Методом каландрирования можно наносить толстые слои как с одной стороны поверхности, так и с двух.
Дополнительная вулканизация.
Силиконовая резина, вулканизированная на прессе или в канале с разогретым воздухом, обладает, как правило, хорошими показателями по прочности на растяжение, однако, другие качества, например остаточная деформация сжатия, оставляют желать лучшего. Поэтому в большинстве случаев требуется дополнительная вулканизация (отжиг). Отжиг рекомендуется проводить в печи с циркуляцией воздуха. При этом необходимо следить за тем, чтобы детали не касались друг друга и воздух проходил беспрепятственно. Для большинства изделий из силиконовой резины достаточна обработка в течение 2-6 часов при температуре +200°С, но, например, для изделий медтехники необходим более длительный отжиг при более высоких температурах. Для непрерывного отжига применяются более высокие температуры (до +350°С) с целью сокращения его продолжительности до 0,5-3 минут.
Показателем, который существенно улучшается после отжига, является остаточная деформация сжатия (остающееся изменение формы после обработки под давлением). Её величина должна быть по возможности минимальной в тех случаях, когда резиновые детали работают под давлением, т.е. в первую очередь прокладки.
Необходимое время отжига существенно зависит от толщины вулканизатов. Для деталей толщиной менее 5 мм достаточно лишь несколько часов, в то время как для деталей толщиной более 20 мм требуется постепенный отжиг и более длительная обработка при необходимой температуре, с тем, чтобы все летучие компоненты испарились.
Детали из силиконовой резины, особенно после отжига, дают усадку, которая зависит от продолжительности и температуры отжига, от типа и размера деталей. Усадка составляет 2-5% и при изготовлении форм её необходимо учитывать.
Склеивание силиконовой резины.
Силиконовая резина, обладая антиадгезионными свойствами, трудно склеивается сама с собой и с другими материалами. Обычные клеи для этого не пригодны. Поэтому были разработаны специальные грунтовки и клеи на силиконовой основе, которые обеспечивают достаточный склеивающий эффект.
Склеивание возможно двумя принципиально различными способами :
- использование вулканизирующего средства, обладающего адгезионными свойствами;
- склеивание вулканизированных деталей между собой и с другими материалами с использованием клея.
ПРИМЕНЕНИЕ.
Возможности применения силиконовой резины чрезвычайно разнообразны и охватывают все отрасли промышленности.
В электротехнике её используют как изоляционный материал, особенно при высоких температурах, а также в тех случаях, которые связаны с воздействием влаги и озона. Из силиконовой резины делают оболочку для кабеля и проводов. В других случаях из неё изготовляют изоляционные трубы, либо без укрепляющих добавок, либо совместно со стеклонаполнителем. Ленты, изготовленные из стеклонитей или полиэфирного волокна и покрытые силиконовой резиной, в вулканизированной форме, служат как изоляционный материал, который накручивается внахлёст на электрический провод. Силиконовая резина используется в качестве замазки для нагревательных элементов, устанавливаемых для подпольного отопления террас, передающих установок, наружных лестниц. Следует отметить также токопроводящие силиконовые резиновые смеси, используемые для изготовления специальных кабелей, например, в автомобилестроении, а также клавишных переключателей в электронных усилителях, использующих изменение сопротивления от давления, высокие токи включения в которых могут создавать акустические помехи.
Наконец, силиконовая резина играет большую роль в области электротехнического машиностроения, например, там, где действуют высокие температуры: в рольгангах, в тяговых электродвигателях, в крановых электродвигателях. Кроме того, из силиконовой резины можно изготовлять покрытия с подогревом, при этом провод сопротивления вводится в резину.
Особую роль силиконовая резина играет в самолёто- и судостроении. Именно в этих отраслях требуется её работоспособность при высоких и низких температурах. Поэтому силиконовой резине здесь отдаётся предпочтение при изготовлении уплотнителей и изоляции.
В машиностроении силиконовая резина играет большую роль как уплотнительный материал. Широкое распространение нашли мембранные вентили и диафрагмы из силиконовой резины. Большое значение имеют, прежде всего, воздуходувки (шланги) горячего воздуха с тканевыми фильтрами и без них.
Транспортёры покрывают силиконовой резиной в тех случаях, когда они транспортируют горячие или липкие изделия. Для текстильной промышленности незаменимое значение приобрели термостойкие и антиадгезионные покрытия из силиконовой резины для валов. Силиконовые резины используются для раскатки клеевых слоев. В стекольной промышленности по роликам из силиконовой резины осуществляется транспортировка горячих стеклянных заготовок.
Благоприятные физиологические свойства силиконовой резины используются в медицине и пищевой промышленности. Для медицины огромным преимуществом является то, что силиконовую резину можно стерилизовать горячим воздухом и водяным паром (до +135 °С). В медицине нашли применение пробки для флаконов с лекарствами, дренажные трубки, катетеры и зонды из силиконовой резины.
iter.org.ua