Штамповка деталей из металла в Москве
Современный прогресс не стоит на месте и с каждым годом появляются как новые, так и модернизируются существующие методики обработки различных материалов. Штамповка деталей из металла – это далеко не новая операция, качество и точность выполнения которой напрямую зависит от применяемого оборудования и устройств. Именно инновационные методы и современные станки являются основой качественного и оперативного выполнения заказов любой сложности.
ОАО «ЭЛТЕЗА» предлагает профессиональное изготовление штампованных деталей из металлов. Высокотехнологичное оборудование и производственные мощности нашего предприятия обеспечивают возможность оперативного выполнения заказов любой сложности. Мы всегда будем рады обеспечить возможность быстрого выполнения работ и гарантировать качество каждой произведенной детали. Современная листовая штамповка – это один из передовых методов производства разнообразных деталей из листового металла, который позволяет максимально быстро и с минимальными затратами получить требуемый результат.
Технология производства штампованных деталей
Штамповка металлов предусматривает комплекс технологических этапов, результатом которого является требуемая деталь. Очень важным параметром при этом является согласованность работы оборудования и максимально точный контроль параметров, при выполнении каждого из процессов. Штамповка деталей может быть представлена в виде следующих операций:
- резка металла для обеспечения оптимального размера каждой из заготовок;
- гибка металла позволяет изменить форму заготовки в радиальной площади;
- процесс формовки предназначен для обеспечения нужной формы с сохранением основных контуров детали;
- обжим предусматривает применение штампов, призванных сузить отдельные части заготовки;
- вытяжка детали является обязательным элементом для достижения максимальной плоскости изделия;
- отбортовка деталей предполагает отжим метала по кругу, расширяя его диаметр. Особенно важен этот процесс, при изготовлении хомутов, сгонок и фланцев.
Таким образом, можно смело заявить, что листовая штамповка деталей – это сложный, многообразный процесс, который может потребовать большое количество разнообразного оборудования и персонала с высокой квалификацией.
Примечание: изготовление деталей по данной технологии требует проектирования и изготовления средств специального технологического оснащения производства
Преимущества изготовления деталей штамповкой
Современная штамповка деталей из листового металла имеет массу преимуществ перед аналогичными способами обработки материалов. К ним относятся:
- возможность обработки материалов и изготовления деталей минимальной массы, при повышенных требованиях к уровню жесткости;
- возможность получить деталь максимальной точности;
- выполнение всех процессов производится на автоматизированном оборудовании, что исключает возможность ошибки, вследствие человеческого фактора;
- возможность обеспечить высокую производительность и получения заказчиком больших партий товара в максимально короткие сроки.
Эти преимущества делают изготовление деталей с помощью штамповки, одним из самых выгодных и доступных решений для любых предприятий.
Профессиональные услуги штамповки деталей в Москве
ОАО «ЭЛТЕЗА» предлагает заказать штамповку металла на самых выгодных коммерческих условиях. Мы всегда готовы в точности воспроизвести требования каждого заказчика и гарантируем качество выполнения любой детали, независимо от сложности и размера партии. Наша штамповка деталей из листового металла в Москве пользуется спросом как у крупных компаний, так и у небольших организаций, а предложенные нами цены являются одними из самых доступных в регионе.
www.loetz.ru
Листовая штамповка деталей: технологии и особенности процесса
Серийное производство деталей, применяемых в сборке технических изделий и приборов, предусматривает воздействие экстремальных температур и прессования. Исходя из этих требований и подбираются оптимальные технологии обеспечения механической обработки. Например, в производствах объемных и плоских тонкостенных элементов распространено применение листовой штамповки. Данный метод позволяет с небольшими затратами справиться с выпуском большого количества деталей за одну рабочую смену с минимальной загрузкой по ресурсам. Кроме этого, операция листовой штамповки выгодна и по качеству конечного результата. Дело в том, что массовое изготовление технических элементов с использованием металла на высоких частотах редко характеризуется получением высококачественной продукции на выходе. В данном же случае особые условия изготовления обеспечивают и наделение материала оптимальными для будущей эксплуатации свойствами.
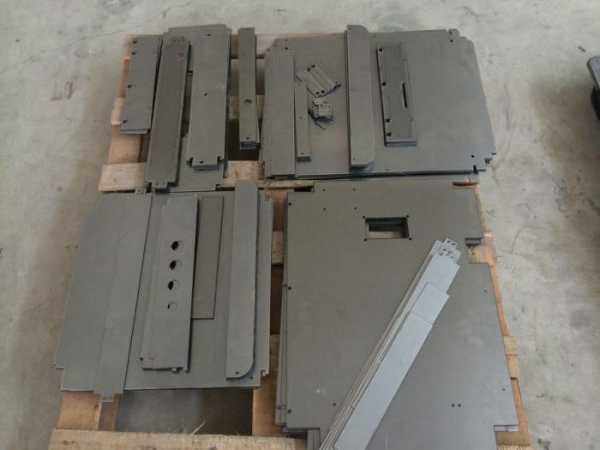
Общие сведения о процессе штампования
Для получения тонкостенных осесимметричных деталей применяются современные способы формообразования. В частности, такие методы позволяют работать с изделиями сужающейся и усеченной формы. Чаще всего эти способы подразумевают применение инструментов пластического деформирования тонкостенных заготовок в особых средах. Например, штамповка листового металла может выполняться в условиях всестороннего воздушного растяжения. То есть, помимо средств механического воздействия, технологи предусматривают и благотворные с точки зрения формования физико-химические процессы воздействия на исходный материал.
Что касается непосредственно штампования, то данный процесс позволяет работать с металлами, обеспечивая на выходе различные формообразования в соответствии с задачами проекта. Собственно листовая штамповка является лишь разновидностью общей технологии пластической деформации. В отличие от оборудования для объемной обработки, данная методика предполагает работу с тонкостенными заготовками, что определяет и менее высокие трудозатраты в процессе обеспечения механического усилия. Впрочем, на этом особенности метода не заканчиваются.
Особенности листового штампования
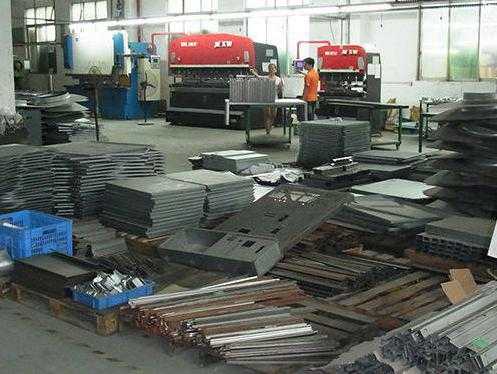
Поскольку технические средства, за счет которых обеспечивается процесс штампования такого типа, предполагают работу с тонкими листами заготовок, то основной упор делается на операции формования. То есть операторы выполняют работы по сгибу, скручиванию и зажиму материала, позволяя образовать на выходе изделие необходимой формы. С такими действиями не справится оснастка для объемной штамповки – или, по крайней мере, выполнит такую работу менее качественно. Есть и другая особенность, которой обладает листовая штамповка в традиционном понимании. Опять же, если объемная обработка делает акцент на силовое воздействие, то в данном случае оно не является главным. Этим объясняется и разнообразие материалов, с которыми работает метод листового штампования. Так, помимо металла, производители обрабатывают также картон, эбонит, пластики, кожу, резину, фибру и заготовки из другого сырья.
Технология холодного листового штампования
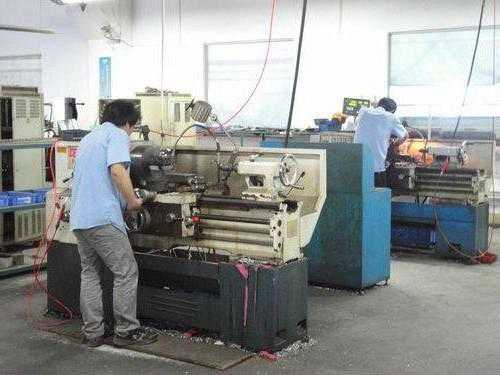
Практически все альтернативные способы штампования делятся на холодные и горячие методики. В случае с листовым штампованием подразумевается в основном холодная обработка. В качестве заготовки применяется металлопрокат в виде ленты или полосы, которая изначально может быть свернута в рулон. Далее через специальную подающую оснастку или без нее материал поступает на рабочую площадку, на которой производятся основные технологические процессы. Если речь идет о металле, то заготовка может подвергаться значительной пластической деформации. То есть желательно, чтобы исходный материал сам по себе располагал достаточными качествами пластичности. На выходе холодная штамповка листового металла позволяет формировать пространственные и плоские детали высокого качества. Готовая продукция такого рода используется во многих отраслях промышленности, среди которых приборостроение и электротехническое производство.
Операции листового штампования
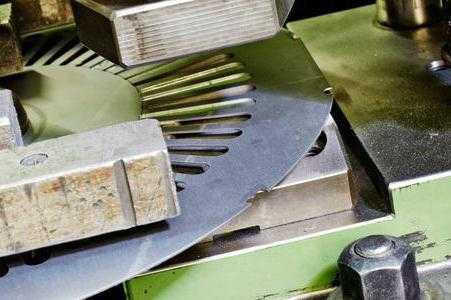
Несмотря на высокую эффективность выполнения формовочных действий, все же основу рабочего процесса на большинстве предприятий составляет механическая обработка посредством резки, пробивки и вырубки. В частности, распространено отделение части заготовки по кривой или прямой линии. Резка осуществляется различными видами ножничных установок. Данная техника позволяет обеспечивать раскрой металлических пластов с получением полос нужных размеров. Кстати, если объемная обработка дает возможность работы с твердыми и толстыми металлами, то листовая штамповка в плане механической резки отличается высокой точностью. На практике это означает получение изделий с параметрами, оптимально подходящими для использования в дальнейшей сборке. Это же относится к операциям рубки и пробивки.
Механизм процесса формовки
Метод изготовления осесимметричных элементов нередко предусматривает деформирование секционными разжимными пуансонами. При этом формируемые детали после процесса штампования по окружности могут иметь недопустимую с точки зрения дальнейшего использования продукции огранку. То есть при выполнении операций по сгибу, закручиванию и сжатию также стоит задача максимального исключения дополнительной доработки. Иными словами, готовая к конечному применению деталь должна выпускаться за один производственно-формовочный цикл. Добиться высокого качества в образовании деталей помогают штампы для листовой штамповки, параметры которых соответствуют требованиям проектного решения. Технически рабочий процесс выполняется с применением матрицы, активного пуансона, раздвижных секторов и вспомогательной оснастки, посредством которой осуществляется воздействие на заготовку.
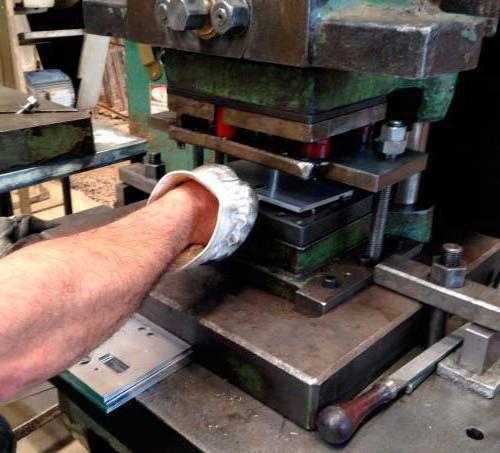
Применяемое оборудование
Чаще всего используются небольшие производственные комплексы, представляющие собой многофункциональные линии обработки листового металлопроката. Но даже рядовой частный мастер может организовать в небольшом помещении аналогичную линию из отдельных компонентов. Для рабочего процесса потребуется упомянутый штамп, выполненный из инструментальной стали. Важно именно применение оснастки из высокопрочных сталей, иначе она не прослужит долго. Основой для операционной функции выступит пресс, который обеспечит базовые операции резки, раскроя и формовки. Иногда в целях удешевления технической организации производства некоторые компоненты линии изготовления заменяются подручными приспособлениями. К примеру, процесс листовой штамповки можно выполнять и с применением контейнера с водой, который заменит собой базовую нишу пуансона.
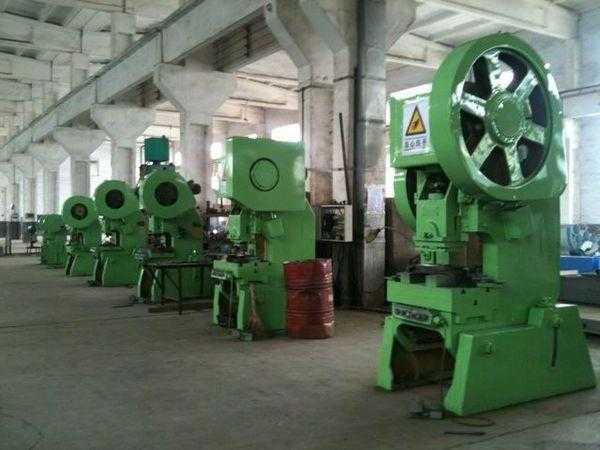
Характеристики получаемой продукции
Метод позволяет формировать изделия высокого качества, что выражается в точных размерах и ровных геометрических линиях. Специалисты отмечают, что только эта технология формирует плоские металлические детали, толщина которых практически не изменяется по сравнению с заготовками. Изделия, которые выпускает листовая штамповка, отличаются магнитной и электрической проводимостью. Это значит, что детали могут использоваться в электротехнической промышленности, выполняя и функции проводников тока. В зависимости от исходного материала производители могут наделять конечные детали высокой прочностью, оптимальными показателями вязкости и теплостойкостью.
Преимущества метода
Кроме выгодных технико-эксплуатационных качеств производимых данной методикой изделий, такой подход к обработке материалов целесообразно использовать по экономическим соображениям. Дело в том, что широкое разнообразие материалов, которые могут подвергаться такой обработке, обуславливает универсальность метода. Хотя есть очевидные ограничения по использованию твердотельных и объемных заготовок, спектр того же металлопроката довольно широк. Вместе с этим штамповка деталей из листового металла относится к традиционным средствам механической обработки, не требующей высоких вложений. Организовать мощный и производительный штамп не составит труда при наличии базовых навыков работы в сфере металлообрабатывающей отрасли.
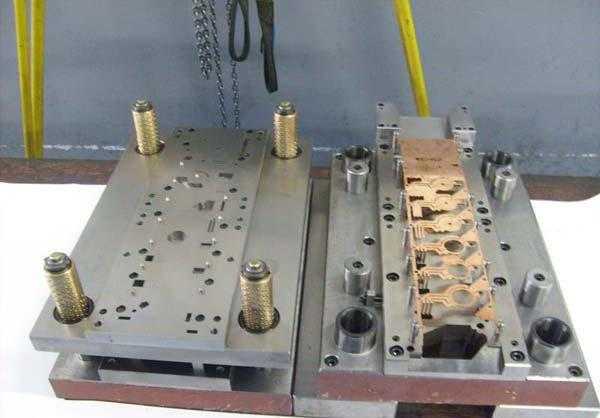
Заключение
При оценке эффективности того или иного метода обработки металлов показатели эксплуатационных качеств получаемой продукции все реже выходят на первый план. Это связано с тем, что плазменные, гидроабразивные и лазерные станки практически устранили все барьеры в достижении высокоточной резки. И понятно, что по качеству выпускаемой продукции им заметно уступает обычный металлообрабатывающий станок. Тем не менее листовая штамповка деталей существенно минимизирует этот разрыв, позволяя сохранить и достоинства традиционного оборудования. Эти преимущества во многих случаях имеют большое значение для предприятий, поскольку выражаются и в снижении финансовых затрат на обработку, и в упрощении самого процесса организации производства. Достаточно отметить, что штамповка в отличие от абразивной резки не нуждается в подаче расходных материалов в виде песка и воды.
fb.ru
Холодная штамповка деталей из листового металла
Листовая штамповка – вид обработки давлением, в котором заготовкой выступает отдельный лист металла, полоса, лента или рулон. Размер обрабатываемой детали может различаться в огромных пределах.
Размер обрабатываемой детали может различаться в огромных пределахВ качестве примера миниатюрной детали можно привести шестеренки наручных часов, а наибольшими деталями, получаемыми из листа, выступают корпуса самолетов и кораблей.
Особенности листовой штамповки
Листовая штамповка является наиболее распространенным видом обработки металлов с использованием давления. Причины её высокой популярности следующие:
- Возможность изготовления деталей сложной конфигурации;
- Возможность производства прочных и одновременно легких конструкций;
- Высокая точность изготовляемых деталей;
- Легкая переналадка оборудования;
- Отсутствие нагрева для обработки, что позволяет сохранить поверхность качественной;
- Возможность использования труда с низкой квалификацией без снижения качества продукции;
- Значительная производительность, особенно на специальных устройствах;
- Невысокие нагрузки во многих операциях;
- Значительные возможности по механизации и автоматизации;
- Низкая стоимость продукции в условиях массового производства.
Все эти достоинства приводят к тому, что объем деталей, полученных листовой штамповкой, составляет 60-95% в разных областях промышленности.
Оборудование и инструменты для листовой штамповки
Листовая штамповка выполняется на прессах. Наибольшее распространение получили кривошипно-шатунные и гидравлические пресса. Молота плохо подходят для штамповочных операций из-за крайне низкой точности и сильному износу инструмента.
В кривошипно-шатунных прессах рабочий орган приводится в движение электродвигателем. Перевод вращательного движения электродвигателя в поступательное происходит при помощи шатуна, который работает аналогично поршням в двигателе внутреннего сгорания. Также между двигателем и валом, на котором вращается верхняя часть шатуна, расположена ременная передача. Шкив, находящийся на валу электродвигателя, имеет небольшие размеры. Второй шкив обладает большими размерами и называется маховиком. Он выступает в качестве механического аккумулятора энергии.
Необходимость в маховике обусловлена разными режимами работы двигателя и рабочего инструмента – двигатель вращается постоянно, а инструмент нагружается периодически. Маховик позволяет аккумулировать механическую энергию и отдавать её в моменты нагрузки. Это дает возможность использовать двигатели меньшей мощности, чем в схеме пресса без маховика. Остальные известные схемы превращения вращательного движения двигателя в поступательное перемещение инструмента показывают меньшую эффективность, поэтому они не получили распространения.
Гидравлические пресса используются во всех видах обработки металлов давлением, и листовая штамповка не исключение. Данные пресса имеют все достоинства, важные для кузнечнопрессовых машин. Их размер может различаться в значительных пределах. На территории России работают два наибольших пресса в мире – усилием 750 МН. Они используются для штамповки цветнометаллических модулей.
Инструментом для листовой штамповки выступают штампы. Их строение может значительно различаться в зависимости от операции. Основными компонентами штампов выступают:
- Плиты, верхняя и нижняя. Выполняются массивными, на них опираются остальные элементы штампа. Верхняя крепится на ползуне пресса, а нижняя – к столу пресса. Некоторые штампы имеют дополнительную среднюю плиту.
- Колонны. Соединяют плиты, вдоль них происходит перемещение элементов штампов.
- Матрица и пуансон. Детали штампа, которые непосредственно выполняют штамповку.
- Съемники и выталкиватели. Требуются для того, чтобы деталь не застревала в штампе. Съемник удаляет заготовку с пуансона, а выталкиватель – из матрицы.
- Втулки, подкладки, держатели и т. д. Необходимы для закрепления компонентов штампа.
Операции листовой штамповки
Все операции, применяемые в листовой штамповке, можно выделить в 3 группы:
- Разделительные. Они характеризуются запланированным разрушением заготовки, то есть заготовка разделяется по заранее намеченному контуру. Особенность разделительных операций – небольшой ход инструмента, несколько больший, чем толщина заготовки. Поэтому для резки листового металла вдоль прямой линии используют специальные машины, предназначенные для этих операций. Резка вдоль сложного контура выполняется в штампах, в которых может одновременно выполняться несколько операций, например, получение множества отверстий.
- Формообразующие. На них заготовка меняет свою форму без разрушения. Позволяют превратить плоскую заготовку в пространственную деталь, иногда довольно сложной формы, например, кузов автомобиля.
- Сборочные. Предназначаются для соединения двух и более заготовок в одну деталь. Соединение может осуществляться разными способами: запрессовкой, вальцовкой, клепкой и т. д.
В условиях крупносерийного производства, когда на первое место выходит производительность, широко применяются комбинированные штампы, которые дают возможность выполнить две и более операции за один ход пресса. Такие штампы отличаются сложностью конструкции.
samara-metall.ru
Штамповка — это… Что такое Штамповка?
Объёмная Ш. (или Ш. сортового металла) по сравнению с ковкой позволяет получать поковки более сложной конфигурации, требующие значительно меньшей обработки резанием для окончат. оформления детали. При объёмной Ш. течение металла ограничивается стенками полости штампа, что вызывает увеличение сопротивления деформированию тем в большей степени, чем сложнее конфигурация поковки. Нагрев заготовки позволяет примерно в 10—15 раз снизить сопротивление деформированию, а также повысить пластичность металла. Холодная Ш. сортового металла применяется для изготовления небольших деталей — массой менее 1
кг, горячая — для деталей массой 1,5―2 т; более тяжелые поковки изготовляются ковкой. Границы между этими процессами изменяются по мере совершенствования кузнечно-прессового оборудования и увеличения развиваемого ими усилия деформирования. Поскольку стоимость штампов наряду со стоимостью металла заготовки является основной составляющей себестоимости поковки, применение объёмной Ш. экономически выгодно при серийном производстве.Объёмная Ш. сопровождается потерями металла с удаляемым заусенцем (облоем). Меньшие отходы даёт Ш. в закрытых штампах, однако удельные нагрузки в них больше, чем в открытых, что приводит к уменьшению стойкости штампов. Снижение отходов при Ш. в открытых штампах достигается предварительной обработкой заготовки в заготовит. ручьях, ковочных вальцах, использованием заготовок, приближающихся по форме к поковке, а также выбором рациональной формы канавки для заусенца. При горячей Ш. поверхность заготовки окисляется, образуя слой окалины, что также ведёт к потерям металла; потери металла с окалиной сокращаются при безокислительной нагреве в пламенных печах (с защитной атмосферой) или скоростном нагреве в индукционных нагревательных установках. Применение высокоскоростной Ш. (скорость подвижных частей молота 10—25
При листовой Ш. заготовкой служит лист, полоса или лента. Применяется листовая Ш. для изготовления плоских и пространственных (в т. ч. сложных) деталей, у которых толщина значительно меньше др. размеров — обычно менее 10 мм. Заготовки большей толщины обычно штампуют с нагревом до ковочной температуры (горячая листовая Ш.). При листовой Ш. (особенно холодной) отделочная обработка деталей резанием, как правило, не требуется. Листовая Ш. рациональна в производствах с различной серийностью.
В мелкосерийном производстве применяются особые способы Ш.: Ш. эластичными средами (жидкостью, резиной, полиуретаном и т.п.), импульсная Ш., использующая энергию ударной волны в жидкости (взрывная и электрогидравлическая Ш.) или действие мощных быстроменяющихся магнитных полей (электромагнитная Ш.). С целью увеличения допустимого формоизменения заготовки иногда применяется Ш. с дифференцированным нагревом. В этом случае деформируемая часть заготовки нагревается за счёт контакта с нагретым инструментом или при прохождении через неё электрического тока. Рациональное распределение температур в заготовке и соответственно механических свойств металла значительно повышает допустимое формоизменение заготовки.
Для Ш. используются разнообразные машины: Молоты, кривошипные прессы (См. Кривошипный пресс), горизонтально-ковочные машины (См. Горизонтально-ковочная машина), гидравлические прессы (См. Гидравлический пресс), кузнечно-штамповочные автоматы (См. Кузнечно-штамповочный автомат) и др. В крупносерийном производстве для Ш. применяют автоматы и автоматизированные линии, а также всевозможные загрузочные и манипулирующие устройства (включая промышленных роботов), позволяющие существенно повысить производительность труда.Лит.: Малов А. Н., Технология холодной штамповки, 4 изд., М., 1969; Брюханов А. Н., Ковка и объёмная штамповка, 2 изд., М., 1975.
Е. А. Попов.
dic.academic.ru
Холодная штамповка – щадящий и эффективный метод производста
1 Что дает материалу холодная деформация?
Металловеды и люди, связанные с производством, знают, что такое штампование, но мы все-таки уделим немного внимания и расшифруем этот термин. Это процесс пластической деформации материала, в результате чего последний приобретает заданные размеры и формы. Если есть воздействие больших температур, то речь идет о горячем деформировании, но мы более подробно остановимся на холодной штамповке металла, которая проходит без термического влияния.
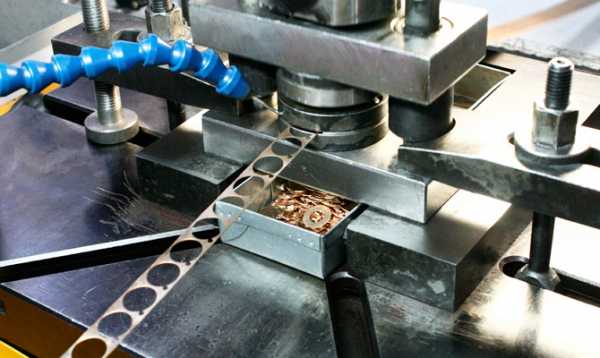
Фото холодной штамповки металла
Рекомендуем ознакомиться
Все операции в этом случае выполняются в специальных технологических оснастках (штампах) и обязательно сопровождаются упрочнением. Благодаря чему готовое изделие отличается повышенным значением этой характеристики. А вот его пластические свойства, напротив, ухудшаются. Однако повышение прочности имеет и некоторые побочные эффекты, например, материал становится более хрупким и т. д. Поэтому между операциями осуществляют рекристаллизационный отжиг. Детали отличаются повышенной точностью и прекрасным качеством.
2 Листовая и объемная штамповка – в чем разница?
Особенностью холодной объемной штамповки является температура заготовок, которая не должна превышать ковочную. Это способствует увеличению сопротивления металла, а, следовательно, его текучесть снижается. Этим методом изготавливают элементы повышенной точности. К достоинствам относится отсутствие различных дефектов, таких как царапины, горячие трещины, риски, усадка. Однако из-за повышенного сопротивления внутри материала изготовить деталь сложной формы не удастся, для этого нужно прибегнуть к горячей штамповке.
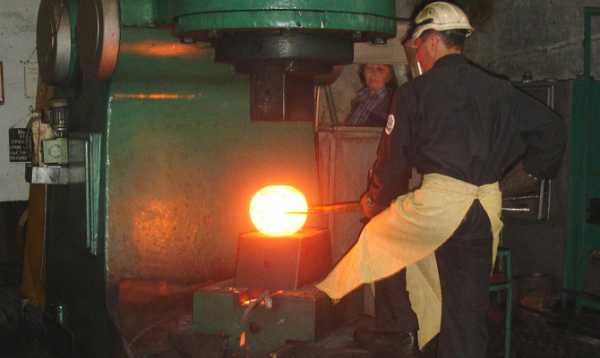
На фото — горячая штамповка
Следующий вид – листовая штамповка. Ее особенностью является форма заготовки – лист, лента, полоса. Этим методом можно получить самые разнообразные изделия массой от нескольких грамм до десятков килограмм. В основном толщина стенок получаемых деталей такая, как у исходного материла. Получить пространственные элементы можно только из достаточно пластических металлов.
3 Какой путь проделывает деталь?
Сегодня существует множество специальных программ проектирования штампов для холодной штамповки, однако они неавтономные и в основном неразрывно связаны со всей системой. Чертежи могут быть как двумерными, так и современными, выполненными в формате 3D. А сам процесс требует некоторых навыков, знания компьютера и выполняется в такой последовательности:
- нанесение эскиза;
- изучение схемы раскроя и ее проверка специальной программой;
- редактирование;
- повторная проверка размеров;
- нанесение рабочих отверстий.
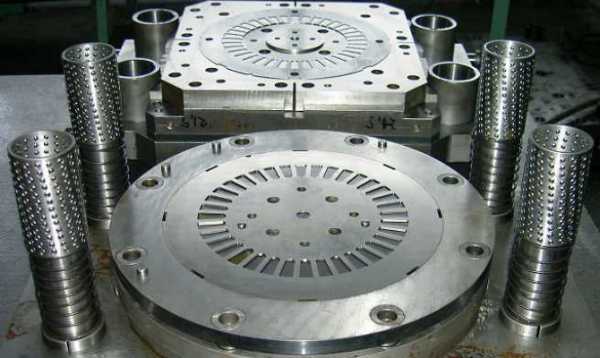
Фото штампов для холодной штамповки
Далее следует довольно тяжелый и ответственный процесс изготовления штампов холодной штамповки. После окончательной подготовки чертежа изделие разделяют на отдельные части, внимательно изучают их. Обязательно необходимо уделить особое внимание техническим требованиям, предъявляемым к готовой детали. Затем составляют для каждого элемента маршрутно-технологическую карту с учетом всех нюансов, начиная от времени, потраченного на изготовление, и заканчивая характеристиками. Следует заметить, что в этом процессе не может быть мелочей, так как любой, даже самый незначительный недочет приведет к дефектам. Имеет значение последовательность операций, правильное распределение материала, подбор оборудования и режимов.
К качеству штампов для холодной штамповки тоже предъявляются весьма серьезные требования. Ведь именно от них зависит размер, форма и чистота поверхности готового изделия.
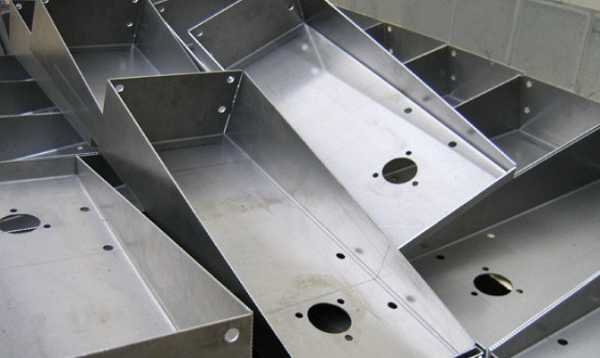
На фото — формирование элементов листовым способом
Формирование элементов листовым способом подразумевает ряд операций. Сначала материал поступает на стан, где вырезаются либо выдавливаются части детали. Затем следуют формоизменяющие операции. К ним относятся гибка, обжим, формовка и вытяжка. При этом не стоит недооценивать и роль вспомогательных процессов. Это отжиг и травление, благодаря которым задаются желаемые механические свойства. Еще можно повысить износостойкость с помощью дополнительных защитных покрытий. Кроме того, детали подвергают правке, очистке и смазке.
Технологический процесс объемной холодной штамповки делится на две основные схемы. Первая состоит из трех операций. Предварительно проводят термическую обработку металла с целью его разупрочнения. Затем подготавливают поверхность проката и осуществляют непосредственно штамповку. Но можно придерживаться и иной схемы, включающей в себя 4 этапа. В этом случае сначала подготавливают мерные заготовки, а потом уже проводят все операции аналогично первой схеме.
tutmet.ru
Штамповка деталей — Справочник химика 21
Обычно это неглубокие трещины, образующиеся, например, при накатке резьбы, изготовлении пружин. При холодной штамповке деталей могут появиться трещины в местах резких перегибов, особенно когда пластические свойства материала недостаточно высокие из-за дефектов структуры. [c.378]Пресс для штамповки деталей из размягченной массы стекла. Пресс (рис. 87) для штамповки стекла имеет сменные пуансоны и матрицы, изготовленные из стали. Нижняя часть — матрица — [c.174]
Технологические процессы производства аппаратуры охватывают почти все виды обработки металлов горячую и холодную обработку давлением (гибочные операции, штамповка деталей аппаратов), сварку металлов и сплавов, термическую и холодную резку (разделительную и поверхностную), термическую обработку (во многих ее разновидностях), механическую обработку, сборку и др. [c.3]
В последнее время термическую обработку и нагревание при ковке и штамповке проводят в атмосфере инертных газов (аргон, гелий), смеси азота с водородом и вакууме. При нагревании в перечисленных средах резко уменьшается глубина разрушения, что позволяет значительно снизить глубину механической обработки, существенно сократить расход ценного металла и обеспечить точную штамповку деталей. [c.88]
Кроме описанных способов получения точных деталей в комбинированных и простых штампах, в последние годы освоен новый способ штамповки деталей в универсальных штампах из отдельной заготовки, который приведен в книге В. М. Богданова и А. Г. Яковлева. [c.209]
Более толстые хроматные пленки на алюминии применяют в качестве защитно-декоративных и более дешевых, чем при анодировании. Хроматные пленки на алюминии (как и анодные) позволяют производить штамповку деталей из покрытой ленты без разрушения покрытия. Это значительно снижает трудоемкость. [c.111]
Пресс для штамповки деталей из размягченной массы стекла. [c.174]
Для штамповки деталей из алюминия, а также черных металлов и медных сплавов. [c.335]
Разработка специальных составов делает возможной горячую штамповку деталей из тонколистных материалов, таких, как титан, молибден, вольфрам. При этом тонкая (1 мм) листовая заготовка обмазывается слоем высококалорийного пиротехнического состава при его поджигании лист сразу по всей поверхности нагревается до нужной температуры. Из-за кратковременности нагрева металлы (молибден, вольфрам) не успевают окисляться на воздухе [60]. [c.287]
Имеются сведения о применении покрытия, состоящего из 85% РЬ и 15% 5п, с целью улучшения обрабатываемости листовой стали давлением [16]. Свинцовооловянное покрытие при операциях штамповки деталей выполняет роль смазки. [c.121]
Штампы для штамповки деталей из полосового материала. [c.110]
Горячая штамповка деталей средней сложности из легированных сталей 11 [c.121]
Эпоксидные литьевые смолы применяются в США для производства форм глубокой вакуумной вытяжки из термопластичных пленок. Для снижения усадки и повышения теплопроводности формы покрывают алюминиевым порошком. При изготовлении штампов для штамповки деталей из тонкого листа в эпоксидную смолу в качестве наполнителя добавляют окислы алюминия. При изготовлении шаблонов, гибочных штампов, калибров и другого штампового инструмента применяют эпоксидные смолы, усиленные стекловолокном. Поверхности перечисленных деталей покрывают эпоксидным лаком с окислами алюминия. Это усиливает сцепление стекловолокна с поверхностью формы. Поверхности больших моделей покрывают слоем замазки на основе эпоксидных смол. Эта замазка затвердевает в обычных условиях, повышает качество поверхности и увеличивает срок службы моделей [30]. [c.87]
При необходимости использования для штамповки деталей предварительно лакированного материала применяют матрицы, изготовленные из нейлона. Так, по зарубежным данным, для матриц, на которых производилась гибка закругленных уголков орнаментной рамки для крепления стекла в телевизорах, использовали нейлон. Матрица изготовлялась из листового нейлона толщиной 6—4 мм и прикреплялась винтами к стальной плите, что придавало ей необходимую жесткость и прочность. [c.87]
ТОЧНАЯ ШТАМПОВКА ДЕТАЛЕЙ ОПТИКО-МЕХАНИЧЕСКИХ ПРИБОРОВ [c.1]
Книга посвящена практике холодной штамповки деталей оптико-механических приборов. В ней описываются современные методы точной штамповки — комбинированная штамповка в совмещенных и последовательных штампах, штамповка в перфорированной полосе и объемная штамповка прессованием и выдавливанием. [c.2]
Отделение небольших излишков материала (припусков) после вырубки или объемной штамповки деталей с целью получения геометрически правильных и точных по размеру и чистых поверхностей среза [c.8]
При штамповке деталей сложной конфигурации следует при- менять наклонный, встречный (заход ряда в ряд), многорядный раскрой и раскрой с поворотом полосы. [c.64]
Из примеров видно, что наибольшую экономию материала дает раскрой без перемычек, который применяется лишь для штамповки деталей, имеющих малую точность размеров. [c.64]
На фиг. 6. 5 приведена более сложная и совершенная конструкция штампа совмещенного действия для штамповки деталей типа зубчатого колеса. В штампе совмещаются вырубка по контуру и пробивка центрального и фасонных отверстий. В качестве материа- [c.92]
При штамповке деталей оптико-механических приборов часто встречается обратная (реверсивная) вытяжка. Штамп, совмещающий вырубку, вытяжку и обратную вытяжку, приведен на фиг. 6. 34. Его действие понятно из чертежа. [c.120]
Сущность способа заключается в проведении множества шта.мпо-вочных операций и операций резания — фрезерование, сверление и др. — непосредственно в полосе, не отделяя от нее деталей, с постоянной базировкой на специальные пробиваемые в полосе технологические (перфорационные) отверстия, являющиеся базовыми (фиг. 8. 1). При изготовлении деталей по этому способу в зависимости от количества операций требуется соответствующее количество штампов, на которых производится выполнение каждой отдельной штамповочной операции, и станков для выполнения операций резания. Полоса по следовательно передается со штампа на штамп или на станок для выполнения очередной операции. Как и при штамповке деталей из штучных заготовок, при этом способе можно также соз- [c.169]
В целом гехнологич
www.chem21.info
станки и прессы для холодной штамповки
Один из самых востребованных способов металлообработки, позволяющий получить как плоские, так и объемные детали сложной конфигурации — штамповка металла.
Данная технология позволяет производить изделия весом до 2 тонн, более крупные изделия изготавливаются методом ковки.
Принцип штамповки и технологические процессы при ней
Штамповка изделий и деталей из металла относится к металлообработке давлением, при этом возможности данной технологии достаточно широки. При помощи штамповочного оборудования выполняется резка заготовок по заданным размерам и конфигурации, изменение формы путем пластической деформации и другие преобразования исходного материала.
К основным штамповочным операциям относятся:
- Гибка — процесс позволяющий изменить форму заготовки по заданным радиусам.
- Формовка позволяет изменить форму отдельных участков детали при сохранении основных ее контуров.
- Обжим применяется для сужения частей полых объемных заготовок. Для этого применяется объемные штампы различной конфигурации, которые воздействуют на обрабатываемую деталь снаружи. От формы штампа и матрицы зависит будущая конфигурация изделия.
- При осуществлении вытяжки заготовки из листовой стали формируются в объемные плоские изделия. Данная операция позволяет получать цилиндрические, полусферические или конические детали.
- Отбортовка позволяет получить отогнутый край по контуру заготовки или вокруг пробитых в ней отверстий. Данный метод применяется для изготовления горловин, фланцев и других подобных узлов.
Штамповка изделий из металла предполагает выполнение и различных отрезных (разделительных) операций:
- Резка может выполняться как по прямой линии, так и по кривой различной конфигурации. Предназначена для получения заготовок с определенными параметрами из листа металла.
- Вырубка применяется для отделения заготовки, имеющей замкнутый контур.
- Пробивка используется для получения отверстий различного диаметра.
Виды штамповки
На сегодняшний день существует несколько разновидностей технологии штамповки, они отличаются источником энергии, создающим давление на штамп, температурным режимом и другими характеристиками.
На практике чаще всего используют следующие технологии:
- Холодная штамповка
Холодная штамповка изделий из металла применяется при обработке легированной или углеродистой стали, меди и алюминия, а также их сплавов. Выполнение этих работ не требует предварительного разогрева заготовок. Данная технология позволяет получать изделия с высокой точностью размеров, достигается это благодаря отсутствию термической усадки, которая характерна для других технологий, предполагающих предварительный разогрев заготовок.
При помощи холодной штамповки можно получать детали, имеющие минимальные размеры и массу. Применяемое оборудование и технологические линии позволяют организовать производство, как в серийном, так и в единичном масштабе. Оборудование достаточно просто перенастраивается для изготовления деталей с различными параметрами.
К недостатку технологии стоит отнести тот факт, что с ее помощью можно изготовить только сравнительно небольшие изделия, максимальная масса которых не превышает 1 тонны. Изготовление более крупных деталей требует приложения значительных усилий и является экономически нецелесообразным.
- Горячая штамповка
Горячая штамповка листового металла и профиля имеет большую сферу применения. Применяется данная технология для производства деталей из периодического проката, профилей различного сечения (квадрат, круг, прямоугольник). Заготовку после предварительного прогрева в электрических, индукционных или пламенных печах формуют при помощи штампа, имеющего полость, соответствующую форме будущего изделия. Нагрев заготовки позволяет выполнять обработку с приложением меньших усилий, поэтому данная технология позволяет получать изделия весом до 2 тонн.
Учитывая энергоемкость технологии (основная часть тратится именно на разогрев металла), ее применение целесообразно только при серийном производстве деталей различной конфигурации, единичная штамповка металла на заказ таким способом не выгодна.
- Валковая технология штамповки
Валковая технология штамповки применяется для работы с заготовками цилиндрического сечения. В процессе обработки происходит формовка изделия под воздействием перемещающегося пуансона и радиальный изгиб при помощи обкатки специальными валками.
К преимуществам данной технологии относятся низкая стоимость оборудования и оснастки, что делает экономически выгодным производство любых партий изделий. Качество и точность получаемых деталей достаточно высоко, как и чистота обрабатываемых поверхностей.
Применяемое оборудование
На производстве в промышленных масштабах применяется разнообразное оборудование для штамповки металла, обеспечивающее создание необходимого давления на обрабатываемые заготовки:
- Механические молоты.
- Различные по конструкции прессы (чаще всего применяют гидравлические или кривошипные модификации).
- Кузнечно-штамповочные автоматы.
- Горизонтально-ковочные машины.
Высокую производительность и максимально возможное качество продукции обеспечивают производственные линии с автоматизированным управлением. Обычный пресс для штамповки металла, управляемый непосредственно оператором, не способен обеспечить высокую интенсивность производство. Именно поэтому все современное оборудование развивается в направлении автоматизации и компьютеризации.
Станок для штамповки листового металла обычно создается на основе гидравлического пресса, характеристики которого идеально подходят для работы с толстым материалом. К преимуществам этого оборудование стоит отнести его устойчивость к возможным перегрузкам и достаточно простую конструкцию, которая значительно упрощает техническое обслуживание.
Для выполнения холодной штамповки чаще всего применяют кривошипный пресс, при этом его конструкция может содержать от одного до четырех кривошипных ползунов. Оборудование данного типа позволяет производить изделия сложной конфигурации, в том числе и ассиметричные.
Технология штамповки металла позволяет организовать изготовление различной продукции с минимальными потерями материала, благодаря чему при выпуске крупных серийных партий продукции достигается существенная экономия.
Именно низкая себестоимость производства и предопределило развитие данной технологии обработки металла давлением.
steelguide.ru