Шпиндели
×
Search Results
- <
- 1
- >
- станки
Вертикальные фрезерные станки- Вертикальные фрезерные станки
- Серия VF
- Универсальные станки
- Фрезерные станки Мини
- Формовочные машины
- Сверлильная/резьбонарезная/фрезерная серия
- Фрезерные станки серии «Toolroom»
- Компактные фрезерные станки
- Серия «Портал»
- Симулятор управления
- Автоматический загрузчик деталей для фрезерных станков
Токарные станки- Токарные станки
- Серия ST
- Двухшпиндельный
- Токарные станки «Toolroom»
- Патронный токарный станок
- Устройство подачи прутка
- Автоматический загрузчик деталей
Горизонтальные фрезерные станки- Горизонтальные фрезерные станки
- Конус ISO 50
- Конус ISO 40
Просмотрите изделия и устройства индексации- Просмотрите изделия и устройства индексации
www.haascnc.com
Шпиндели деревообрабатывающих станков — Деревообрабатывающие станки
Шпиндели деревообрабатывающих станков
Категория:
Деревообрабатывающие станки
Шпиндели деревообрабатывающих станков
Шпиндели служат для закрепления и вращения режущего инструмента в продольно-фрезерных, фрезерных, шипорезных, сверлильных, цепнодолбежных и некоторых других станках, предназначенных для обработки древесины методом фрезерования или сверления.
На рис. 1 показана конструкция шпинделя фрезерного станка. Шпиндель с помощью шариковых подшипников устанавливается в полом стакане суппорта станка. В верхней части шпинделя предусмотрено коническое гнездо для закрепления насадки с режущим инструментом. На нижней консольной части крепится на шпонке гайками шкив.
Суппорт вместе со шпинделем может перемещаться в вертикальном направлении. Для этого используется механизм подъема с неподвижно укрепленным на станине винтом, взаимодействующим с гайкой. Гайка связана с шестерней, которая входит в зацепление с другой шестерней (на рисунке не показана), сидящей на валу с маховичком. При поворачивании маховичка поворачивается гайка и перемещает суппорт со шпинделем. Перемещать шпиндель надо при настройке станка.
Шпиндельная насадка закрепляется в конусе шпинделя дифференциальной гайкой (рис. 2) с двумя резьбами — одной на участке а, второй на участке. Резьбы имеют различный шаг (отсюда и название гайки), но одно направление. При затягивании гайка одновременно перемещается относительно шпинделя и насадки. Так как шаг резьбы, соприкасающийся со шпинделем на участке, больше шага резьбы на участке а, то перемещение гайки относительно шпинделя при одном угле поворота несколько опережает ее осевое перемещение относительно насадки, и конус насадки с большой силой входит в коническое гнездо, обеспечивая надежное крепление насадки с режущим инструментом на шпинделе.
В станках, предназначенных для обработки деталей цилиндрической формы (круглопалочных и других), применяют полые шпиндели (рис. 3), внутри которых проходит заготовка. Обработанная резцами ножевой головки заготовка подается роликами церез шпиндель, который через шкив получает вращательное движение от привода. Иногда требуется, чтобы длина шпинделя изменялась. Для этого шпиндель делают составным из двух частей, одна из которых на шпонке или шлицевом соединении может скользить по другой части.
На рис. 4 показана схема составного шпинделя: верхняя его часть со шкивом установлена в шариковых подшипниках; подвижная часть закреплена в специальном стакане, который может скользить в направляющих под действием рычага с рукояткой.
Рис. 1. Шпиндель фрезерного станка в сборе
В деревообрабатывающих станках шпинделями часто служат удлиненные валы электрод вигателей. Режущий инструмент закрепляется непосредственно на валу или с помощью шпиндельной насадки. При нормальной частоте то ка 60 Гц шпиндели-валы электродвигателей могут делать около 3000 об/мин; однако для того чтобы обеспечить требуемое качество обработки и высокую производительность оборудования, шпиндели-валы совершают около 4500, 6000 об/мин и более.
Для этого в станках устанавливают преобразователи, повышающие частоту тока соответственно до 75; 100 Гц и выше.
Рабочие органы ленточкопильных станков (рис. 5) выполняют в виде двух шкивов. Нижний шкив приводной.
Ось верхнего ведомого шкива ленточно-пильного станка закрепляется на специальном суппорте, позволяющем изменять его положение относительно нижнего шкива, что необходимо для натяжения полотна пилы и регулирования его положения в процессе работы.
Рабочие органы шлифовальных станков выполняют в виде двух или трех шкивов, соединенных шлифовальной шкуркой, а также в виде диска или цилиндра. Лобовую плоскость диска или поверхность цилнндра обтягивают шлифовальной шкуркой. Шкурку натягивают на диск с помощью кольца (рис. 6). Под шкурку подкладывают фетр или войлок, что позволяет избежать обрыва шкурки и улучшить работу шлифовальных станков.
Рис. 2. Закрепление на шпинделе насадки с помощью дифференциальной гайки: 1 — шпиндель, 2 — насадка, 3 — дифференциальная гайка, 4 — кольца, 5 — гайка для крепления фрезы; а — резьба на насадке, б — резьба на шпинделе
Рис. 3. Полый шпиндель: 1 — задние подающие ролики, 2 — шкив шпинделя, 3 — корпус подшипников 4 — подшипник, 5 — шпиндель, 6 —ножевая головка, 7 — передние, подающие ролики, « — обрабатываемая заготовка
Рис. 4. Схема составного шпинделя: 1 — сверло, 2 — подвижная часть шпинделя, 3— стакан, 4 — шкив, 5, 7 — подшипники. 6 — закрепленная часть шпинделя, 8 — рукоятка рычага
Рис. 5. Схема рабочего органа ленточнопильного станка: 1 — ведущий шкив, 2 — полотно пилы, 3 — противовес, 4 — суппорт крепления верхнего шкива, 5 — ведомый шкив, 6— направляющее устройство, 7 — стол
Рис. 6. Схема рабочего органа шлифовального станка: 1 — шлифовальная шкурка, 2 — войлок, 3 — кольцо, 4 — диск, 5 — электродвигатель, б — станина
Реклама:
Читать далее:
Механизмы подачи деревообрабатывающих станков
Статьи по теме:
pereosnastka.ru
Шпиндели для фрезерных станков с чпу
Шпинделем называют движок с надетым на него патроном, который именуется «цанга». Шпиндель станка держит и вращает инструмент, например, сверло, гравер, резак. Это устройство условно можно подразделить на две категории: производственная и любительская. Рассмотрим, в чём их отличие.
- Производственный (промышленный) шпиндель фрезерного станка рассчитывается и проектируется для большой боковой нагрузки. У него усложнённая охлаждающая система и схема смазки.
- К любительским шпинделям можно отнести обычную дрель или маломощный фрезерный станок, чаще всего использующийся в быту. Заметим, что работа дрели предусматривает вертикальную нагрузку, производимую вдоль инструмента, у неё довольно слабые подшипники удержания вала.
Производственный шпиндель
Производственный шпиндель станка встроен в агрегат перпендикулярно получаемой нагрузке, поэтому без качественных подшипников давление будет для него непосильным. Устройство такого вида не нуждается в смазке, его не нужно чистить, вообще он требует минимум ухода в течение всего срока использования. Купить шпиндель станка производственного типа – значит избавить себя от проблем по уходу за ним и риска того, что устройство не выдержит нагрузку.
Благодаря цанговому зажиму, который присутствует в комплектации шпинделя, прочно и надёжно фиксируется рабочий инструмент. Устройство рассчитано на стандартный зажим инструмента с типовым хвостовиком. Наиболее популярны цанги ER11 и ER16. Они сочетаются с инструментом, имеющим хвостовик 2,5-3 и 3,2-8 мм соответственно. Размер цанги 25 на хвостовик 16 мм используется только для специфических операций по снятию толстых слоёв металла. Кроме того, направляющие не смогут полноценно взаимодействовать с инструментом такого диаметра хвостовика. Поэтому принцип: «больше — лучше» здесь не работает. Поставив такой инструмент, вы получите в итоге деформированные направляющие и сломанный агрегат. Максимально подходящая маркировка цанги ER11.
Любительский фрезерный шпиндель
Представьте себе бытовую дрель, вмонтированную во фрезерный агрегат. Что из этого получается? Подшипники быстро выходят из строя, ведь они не выдерживают такой нагрузки, патрон будет вибрировать и биться, точность выполнения работ снизится. Кроме того, дрель быстро перегревается, а на агрегате работают не один час. Автоостанов дрели просто сработает в целях безопасности и ваш фрезер остановится, проработав час или два. Но ПО фрезерного станка с ЧПУ не знает, что такое бытовая дрель и каковы её параметры работы. Сам фрезер не остановится и продолжит работу. Результатом будет поломка оборудования.
Какая мощность должна быть у шпинделя
В данном случае справедливо правило «больше – лучше». Если предполагается выполнять сверление, гравировку, то оптимально подойдёт шпиндель, мощность которого 400 – 600 Вт. Резка на фрезерном станке ЧПУ металла, твёрдого дерева потребует шпиндель, чья мощность 1000 – 1500 Вт. Для более серьёзных воздействий на материал, нужен шпиндель мощностью 2000 Вт и более. Имеется ввиду твёрдость материала или глубина обработки.
Особенности шпинделя по мощности
Надо заметить, что фрезерование может быть силовым и скоростным. Здесь получается два варианта: в одном случае производится медленная подача фрезы при быстром вращении, во втором – быстро подаётся, но медленно вращается.
Производственный фрезерный станок использует силовой метод, так как он позволяет делать быструю выборку заготовки. На фрезерном станке устанавливают нужные параметры и режимы скорости для каждой фрезы: подачи, вращения, углубления. Так появляется оптимальное соответствие между возможностями станка и его отдачей. Отличная производительность без перегрева и перенапряжения со стороны оборудования. Регулировать базовую комплектацию не нужно. Разработчики оборудования уже позаботились от этом.
Усилие подачи – один из важных режимов агрегата. В случае невозможности станка развивать необходимое усилие подачи, то поможет максимальная раскрутка шпинделя. То есть шпиндель станка должен раскрутиться по максимуму и медленно двигать инструмент по материалу. Это скоростной тип фрезеровки.
Как подобрать шпиндель фрезерного станка по мощности
Итак, на основании вышесказанного, получается, что шпиндель фрезера должен быть выбран по скорости или по мощности. Целью является максимальная, но безопасная для оборудования раскрутка инструмента. Производственные шпиндели не нуждаются в подборе. Здесь «всё включено»: скоростные параметры – более 20000 оборотов, усилие подачи на фрезе – свыше 2000 Вт. То есть, фрезеровка будет производиться на скорости 8000 – 15000 оборотов.
Удобное соответствие, взятое производителем за эталон. Но не всегда такое вращение даёт нужный результат. К примеру, обработка древесины маленькими кусочками образует древесную пыль. Она забивает элементы фрезы и увеличивает трение, соответственно, нагрев деталей. В результате рабочие детали станка перегреваются. Это может привести к порче оборудования.
Важный нюанс: если рассматриваются шпиндели на 3 фазах, то у них имеются 3 провода питания плюс одно заземление. Их подключают на соответствующее количество проводов.
Комплектация и мощность скоростных шпинделей поставляемых в Россию
Поделиться:
frezeru.ru
Шпиндель станка KESSLER | Поворотные столы
Завод станочных узлов KESSLER (Германия) специализируется на производстве станочных шпинделей, приводов, поворотных столов, а так же иных компонентов для предприятий станкостроения.
Видео: KESSLER — обзор завода
*Для просмотра в HD-качестве нажмите «шестерёнку» в нижнем правом углу окна и выберите HD-разрешение.
KESSLER — завод станочных узлов: шпиндель станка, привод, поворотный стол.
Завод-производитель станочных узлов KESSLER гибко подходит к решению задач станкостроительной отрасли: обладая широкой линейкой стандартных станочных шпинделей и приводов, предприятие способно решать и индивидуальные, особые сложные задачи.
Шпиндель станка KESSLER
Специалисты компании KESSLER обладают опытом и возможностью разработки уникальных компонентов и могут разработать шпиндель станка по спецификациям заказчиков. Огромный опыт в разработке электродвигателей для станкостроительной промышленности позволил KESSLER нам стать лидером рынка шпинделей. Компанию KESSLER ценят за быстрое удовлетворение потребностей клиентов по самым высоким стандартам.
История
Завод KESSLER, обладая штатом в 700 человек и производственной площадью 23,000 квадратных метра, является крупнейшим в Европе предприятием-производителем комплектующих для станкостроения. Шпиндель станка KESSLER известен не только в Европе, но и далеко за её пределами.
Шпиндель станка KESSLER — будущее
KESSLER поставляет шпиндель станка, приводы и поворотные столы для станкостроительной промышленности по всему миру. Гибкость и опыт KESSLER в поиске решений для электродвигателей приводов, прямого привода поворотного шпинделя, наклонно-поворотных силовых столов, а также специальные индивидуальные решения компанию лидером рынка.
Шпиндели станков для всего мира
Шпиндель станка, поворотные столы, приводы и другие компоненты KESSLER установлены в станках по всему миру. Компания KESSLER обладает обслуживающей сетью по всему миру. Уже сегодня в России всегда на складе вы можете найти запасной шпиндель станка для машины, поставленной в страну. В случае аварии заменить шпиндель станка можно в беспрецедентно короткие сроки — не требуется время на доставку из Германии и таможенную очистку. KESSLER: наши дочерние службы всегда будет рядом с вами.
Узлы для станков
Корпоративная культура KESSLER основана на изготовлении лучших комплектующих для станкостроительной промышленности. KESSLER решает задачи потребителей любого объёма: возможны как единичные поставки, так и изготовление больших партий компонентов станков, от статоров электроприводов до собранных, готовы к установке агрегатов. Задача KESSLER всегда иметь на складе запасной шпиндель станка под станок, поставленный заказчику.
Сервис и ремонт шпинделей
Нередко бывает, что шпиндель станка в течении длительной эксплуатации теряют первоначальную точность, требуют ремонта и замены комплектующих. Так же встречаются аварии, когда шпиндель станка ударяется в заготовку. KESSLER может отремонтировать такой шпиндель станка, проведя входную диагностику. По завершению ремонтных работ шпиндель станка соответствует заводским нормам точности и ему присваивается гарантия. В 2013 году компания KESSLER открыла сервисный центр в России.
Шпиндель станка KESSLER
www.novator-grp.ru
3.7. Особенности обработки шпинделей прецизионных станков
Технологический процесс изготовления шпинделей прецизионных станков более сложный, так как к таким шпинделям предъявляются более высокие требования. Например, у шпинделя координатно-расточного станка 2А430 отклонения от конусности и овальности опорных шеек не должны превышать 0,002…0,001 мм, биение должно быть не более 0,003 мм, параметр шероховатости Ra = 0,04 мкм, биение конусного отверстия относительна оси вращения шпинделя должно быть не более 0,0015 мм у конца шпинделя.
Для устранения влияния остаточных напряжений, которые могут вызвать деформирование шпинделя не только в процессе его обработки, но и в период эксплуатации, шпиндели прецизионных станков неоднократно подвергают термической обработке.
Так как необходимы высокая точность, правильность формы и малая шероховатость поверхности опорных шеек и исполнительных поверхностей, обычно производят неоднократное шлифование и доводочные операции. При шлифовании особое внимание уделяется устранению динамической неуравновешенности абразивного круга, которая может возникнуть в процессе обработки и значительно ухудшает качество изделия. Доводочными операциями могут быть притирка, хонингование и суперфиниширование.
Для получения поверхности опорных шеек Ra < 0,15 мкм их подвергают суперфинишированию. Сущность этого метода заключается в том, что при определенных условиях мелкозернистыми абразивными брусочками с поверхности заготовки удаляют гребешки, оставшиеся после предыдущей операции, и поверхность доводят до зеркального вида.
Рабочими движениями при суперфинишировании наружных цилиндрических шеек являются вращение шпинделя, короткие возвратно-поступательные (осциллирующие) движения брусков и движение продольной подачи их вдоль оси обрабатываемого шпинделя при длинных шейках (примерно 0,1 мм/об).
Рекомендуемые режимы обработки: скорость колебательного движения брусков 8…15 м/мин; амплитуда колебаний брусков < 6 мм; линейная скорость вращения заготовки: а) для абразивных брусков в начале цикла 16…60 м/мин, а в конце цикла 64…230 м/мин; б) для эльборовых брусков линейная скорость вращения заготовки 300 м/мин, но не более 400 м/мин; давление брусков р = 3, МПа при максимальном давлении в начале цикла и при минимальном давлении в конце цикла.
Обработку ведут с применением СОЖ определенной вязкости.
Припуск фактически определяется высотой неровностей, остающихся на поверхности после предыдущей операции шлифования.
Для остальных заготовок обычная толщина снимаемого слоя присуперфинишировании не превышает 5…7 мкм, поэтому и припуск оставляется около 0,005 мм. Так как суперфиниширование уменьшает шероховатость поверхности и не исправляет макрогеометрию, то геометрическая форма обрабатываемых заготовок перед суперфинишированием должна отвечать техническим требованиям к параметрам готовой детали.
Зернистость абразивных брусков выбирают в зависимости от требуемой шероховатости. Применение литых брусков на керамической связке по сравнению с применением прессованных брусков уменьшает шероховатость обрабатываемой поверхности. После суперфиниширования параметр шероховатости поверхности шеек предварительно обработанных тонким шлифованием, достигает Rz = 0,1…0,05 мкм.
Обработка шеек под подшипники высокоточных станков производится также тонким шлифованием и доводкой (притиркой). Тонким шлифованием можно получить высокую точность формы (отклонение от круглости не более 0,5 мкм) и параметр шероховатости поверхности Ra = 0,16…0,04 мкм.
Доводку выполняют с помощью притиров из серого чугуна СЧ 18, СЧ 21, СЧ 24 с применением абразивной пасты (электрокорунда — 60 %, олеиновой кислоты — 28 %, стеарина — 12 %), а также алмазной пасты. При доводке частота вращения заготовки, установленной в центрах токарного станка, в начальный период 1,7…2,1 с-1, а при окончательной доводке 0,8 с. Операция эта трудоемкая и требующая высокой квалификации рабочего.
Шпиндели зубо-шлифовальных и резьбо-шлифовальных станков (рисунок 3.3.) высокой точности в условиях среднесерийного и мелкосерийного производства изготовляют по типовому регламенту.
Рисунок 3.3. – Эскиз шпинделя
1. Отрезка заготовки из стали 38Х2МЮА.
2. Кузнечная обработка.
3. Термическая обработка (отжиг).
4. Черновая обработка торцов и центровых отверстий на токарном станке.
5. Термическая обработка — закалка с высоким отпуском.
6. Обработка торцов и центровых отверстий.
7. Обработка точных наружных поверхностей, поверхностей под резьбу, под шлифование, обработка прочих поверхностей окончательно.
8. Обработка пазов, лысок.
9. Обработка образцов-свидетелей под шлифование.
10. Предварительное шлифование точных наружных поверхностей и торцов с припуском 0,25…0,35 мм на кругло-шлифовальных станках 3М151 при установке на центровых фасках.
11. Термическая обработка — стабилизирующий отпуск (вместе с образцами-свидетелями).
12. Шлифование центровых (базовых) фасок.
13. Предварительное шлифование точных наружных поверхностей и торцов с припуском 0,15 мм. Овальность и конусообразность обработанных базовых поверхностей не должны превышать 0,005 мм, Ra < 0,63 мкм.
14. Термическая обработка — отпуск стабилизирующий (вместе с образцами-свидетелями).
15. Шлифование центровых (базовых) фасок. Операции № 13, 14 и 15 предусматривают только для деталей средней и малой жесткости.
16. Шлифование наружных рабочих поверхностей и торцов под азотирование с припуском 0,05…0,08, Поверхность под резьбу не шлифовать. Овальность и конусообразность обработанных базовых поверхностей не должны превышать 0,0025 мм. Радиальное биение обработанных поверхностей относительно общей оси базовых поверхностей должно быть не более 0,008 мм. Параметр шероховатости обработанных поверхностей Ra < 0,63 мкм.
17. Термическая обработка — азотирование (вместе с образцами-свидетелями). Азотирование газовое в шахтных электропечах.
18. Шлифование центровых (базовых) фасок. Эту и последующие операции для шпинделей станков класса точности В, А, С рекомендуется выполнять в термоконстантном помещении.
19. Окончательное шлифование прочих наружных поверхностей и поверхностей под резьбу при установке на центровых фасках до получения заданных параметров шероховатости и точности согласно техническим требованиям чертежа.
20. Шлифование (нарезание) метрической резьбы на станках высокой точности 5К832В или токарно-винторезных станках 16К20П с установкой заготовки на центровых фасках.
21. Окончательное шлифование наружных рабочих (опорных) поверхностей и торцов с установкой на центровых фасках до получения заданных параметров шероховатости (Ra < 0,15 мкм) и точности согласно техническим требованиям чертежа. Предпочтительнее шлифование производить кругами из эльбора. Для опорных шеек с Ra < 0,15 мкм можно рекомендовать суперфиниширование, которое производится на станках 3Д871 и других при установке заготовки на центровых фасках.
Операции окончательного шлифования производят на станках повышенной точности ЗМ151В. При обработке заготовка обычно базируется на неподвижных центрах станка, поэтому поверхность центрового отверстия должна быть высокой точности. Центровые отверстия целесообразно шлифовать на центровально-шлифовальном станке MB-119 или 3922Р с планетарным и осциллирующим движениями режущего инструмента в плоскости, наклоненной под углом 30° к оси конуса.
Эти станки обеспечивают необходимые геометрические параметры и соосность центровых фасок.
Допускается замена шлифования центровых фасок притиркой, осуществляемой обычно на токарных станках с помощью специальных притиров с углом конуса 60°±3′. В качестве притирочного материала можно применять смесь веретенного масла № 3, олеиновой кислоты и микропорошка М7-М5 в жидкой консистенции.
Обработку шпинделя, начиная с операции № 17 следует про-изводить в термоконстантном помещении.
studfiles.net
Технологический процесс изготовления шпинделя токарного станка
Министерство образования Российской Федерации
Факультет Машиностроительный
Кафедра «Технология машиностроения»
Дипломный проект
На тему:
Технологический процесс изготовления Шпинделя токарного станка
Тольятти 200 г.
ВВЕДЕНИЕ
Научно-технический прогресс в машиностроение в значительной степени определяет развитие и совершенствование всех остальных отраслей. Важнейшими условиями ускорения научно-технического процесса являются рост производительности труда, повышение конкурентоспособности и улучшению качества.
Совершенствование технологических методов изготовления машин имеет при этом первостепенное значение. Качество машины, надежность, долговечность и экономичность в эксплуатации зависят не только от совершенства ее конструкции, но и от технологии производства. Применение прогрессивных высокопроизводительных методов обработки, обеспечивающих высокую точность и качество поверхностей деталей машины, методов упрочнения рабочих поверхностей, повышающих ресурс работы деталей и машины в целом — все это направлено на решение главных задач: повышения эффективности производства, конкурентоспособности и качества продукции.
Целью дипломного проекта является: разработка технологического процесса обработки детали “Шпиндель” в условиях среднесерийного производства.
1.АНАЛИЗ СОСТОЯНИЯ ВОПРОСА
1.1 Анализ служебного назначения детали
Деталь – шпиндель входит в состав шпиндельного узла токарного станка Афток 10Д.
Основное служебное назначение шпинделя токарного станка Афток 10Д – сообщать обрабатываемой заготовке вращательное движение с определенной угловой скоростью или крутящим моментом.
На рисунке 1.1 представлен фрагмент шпиндельного узла токарного станка. На шпиндель 1 напрессованы подшипники качения 2, которые в свою очередь, запрессованы в переднюю бабку 3. Натяг подшипников осуществляется стопорными гайками 4 и 5. С помощью шпонки 6 и стопорной гайки 7 на конце шпинделя 1 устанавливается шкив 8.
В процессе работы со шкива 8 на шпиндель 1 ,через шпонку 6, передается вращательное движение, которое получает заготовка, закрепляемая в патроне. Патрон устанавливается на шпиндель спереди, базируясь по наружному конусу.
Шпиндельный узел токарного станка Афток 10Д
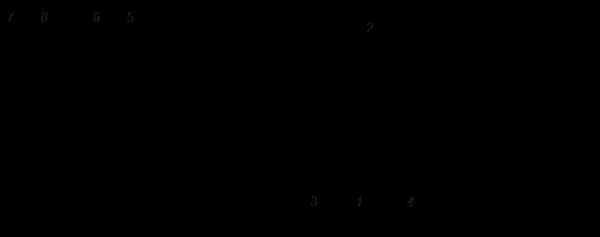
Шпиндель изготовляется из легированной конструкционной стали 12ХН3А ГОСТ 4543-71. Область применения стали 12ХН3А: сильно нагружаемые детали с высокой поверхностной твердостью, износоустойчивостью и вязкой сердцевиной, работающие при больших скоростях и ударных нагрузках – шпиндели, валы в подшипниках качения, шестерни сложной конфигурации и т.д.
Химический состав и механические свойства стали 12ХН3А представлены в табл. 1.1.
Таблица 1.1.
Химический состав и механические свойства стали12ХН3А
На рисунках 1.2. и 1.3. представлена схема кодировки поверхностей и размеров детали, а в табл. 1.2. – классификация поверхностей по служебному назначению. Обоснование технических требований к поверхностям шпинделя,
исходя из его служебного назначения сведено в таблицу 1.3.
Таблица 1.2
Классификация поверхностей по служебному назначению
Таблица 1.3.
Обоснование технических требований к поверхностям шпинделя, исходя из их служебного назначения
1.2 Анализ технологичности детали
К не технологичности детали – шпиндель можно отнести следующие элементы:
— достаточно большая длина детали L/D > 8, что снижает жесткость и повышает возможность коробления шпинделя во время механической и термической обработки;
— глубокое отверстие, требует при изготовлении шпинделя применение специального инструмента;
— закрытые шпоночный паз и пазы под стопорные многолапчатые шайбы;
— наличие точных конусных поверхностей;
— близко расположенные резьбовые отверстия на фланце шпинделя;
— наличие маслоотводных канавок требует применение специального инструмента – фасонного резца;
В целом конструкцию можно считать технологичной и доступной для обработки.
Кодировка поверхностей детали
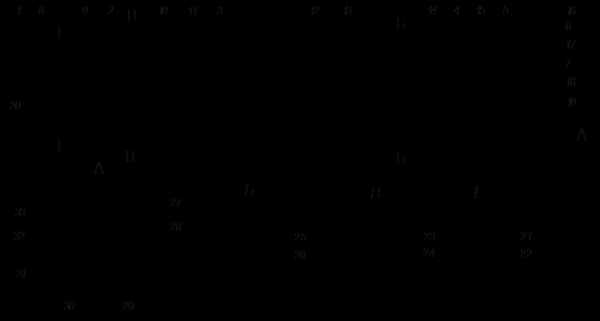
Рис. 1.2.
Кодировка размеров детали
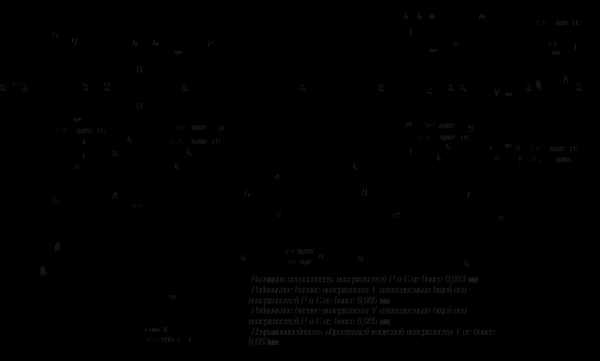
Рис. 1.3.
1.3 Определение типа производства и стратегия разработки
технологического процесса
Выбор типа производства проводим исходя из массы детали и ее годового объема выпуска по [2, с.24, табл.3.1].
Масса детали 16,8 кг, годовой объем выпуска – 10 тысяч штук, следовательно, тип производства – среднесерийный.
На основании выбранного типа производства разрабатываем стратегию технологического процесса и сводим ее в табл. 1.4.
Таблица 1.4.
Стратегия ТП для изготовления детали в условиях среднесерийного производства.
1.4 Анализ базового технологического процесса
Данная деталь – шпиндель по базовому ТП изготовляется в единичном производстве. Используемое оборудование и оснастка – универсальное. Заготовка на обработку поступает в виде проката, это увеличивает время обработки и отхода металла в стружку.
Базовый технологический процесс приведен в табл. 1.5.
Таблица 1.5.
mirznanii.com